
10 minute read
Manufacturer Focus
Cast-in ferrule connection placement on a robotic mould for a lightweight curved panel.
Advancing the manufacture of curved concrete
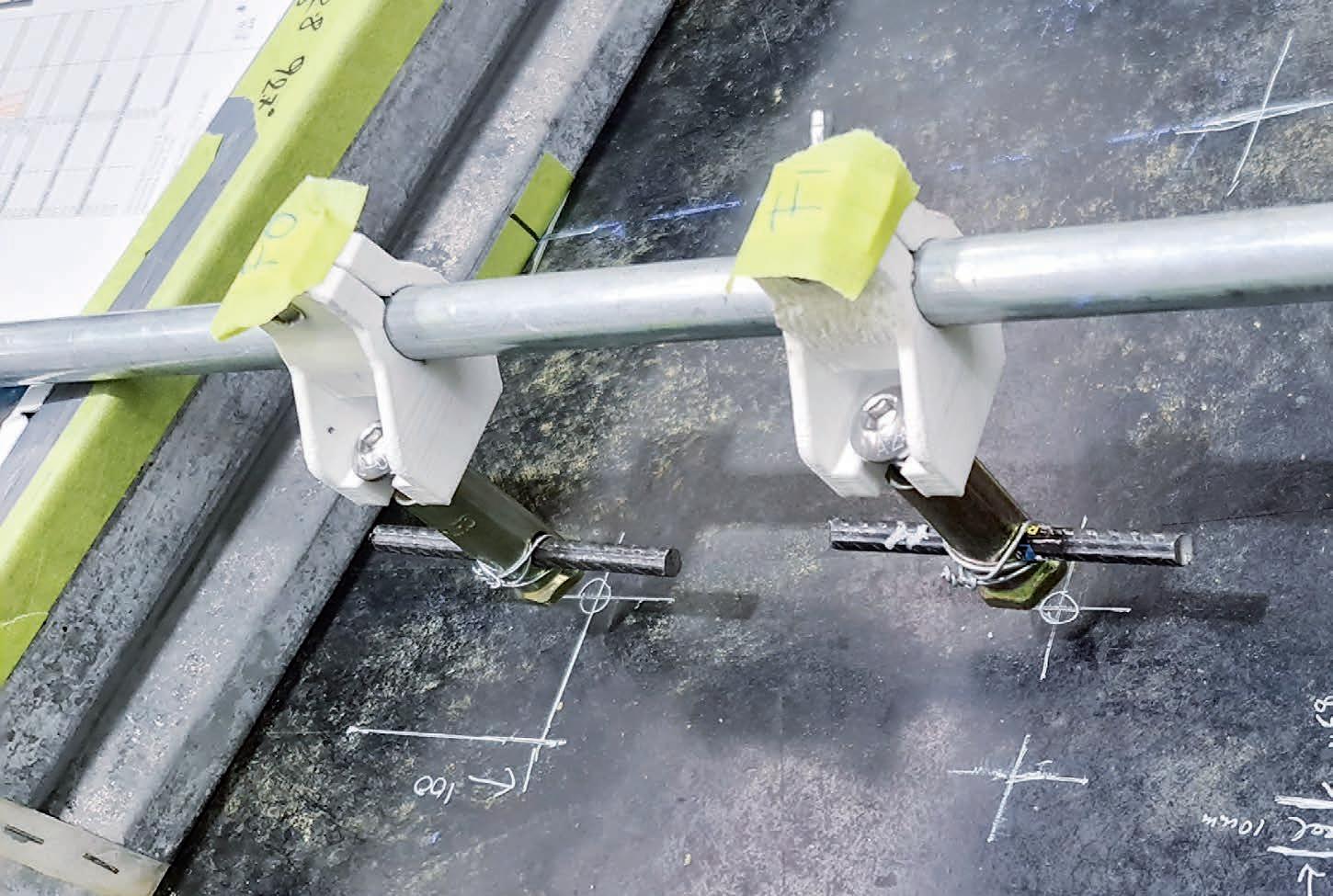
Alexandra Cooper speaks to Daniel Prohasky, co-founder and CEO of Curvecrete, about the new company’s bespoke, sustainable, curved concrete manufactured in Melbourne using advanced manufacturing.
ONE of the main advantages of utilising industrial advanced robotic systems in the manufacturing industry lies in the improved security of the supply chain at large, according to The Action Plan for Critical Technologies report from the Australian Critical Technologies Policy Coordination Office (CTPCO). With the amplified demand for implementing advanced robotics within the manufacturing process in many businesses, this has become increasingly evident.
Established in 2019 through the support of the University of Melbourne and Swinburne University of Technology, the curved concrete and robotics manufacturing company, Curvecrete, was founded by CEO Daniel Prohasky and CFO Warren Rudd. Prohasky’s love for the idea of creating exciting architecture, to construct high quality buildings using low carbon, and less wasteful materials drove the creation of the new advanced manufacturing company.
The robotic concrete moulding technique was originally invented by Paul Loh, David Legget, and Prohasky at the University of Melbourne. It produced bespoke curved concrete panels – making a simpler, faster, zero waste production process.
“I was doing my PhD at RMIT for Aerospace Engineering and was getting very involved with the digital fabrication space and trying to realise ways that we could build better by integrating architecture and engineering,” Prohasky said. “Collaborating with researchers at the University of Melbourne eventuated in the core technology that we use at Curvecrete. We started from a passion of trying to build higher quality buildings and even more so now with a strong focus on sustainable processes, Curvecrete is on a mission to accelerate the use of low carbon materials in construction. Advanced manufacturing is an enabler of that.”
After negotiating a licensing agreement with the University of Melbourne, the founders then set off down the commercialisation route. In October 2021, Curvecrete won an Accelerating Commercialisation
ManufacturerFocus
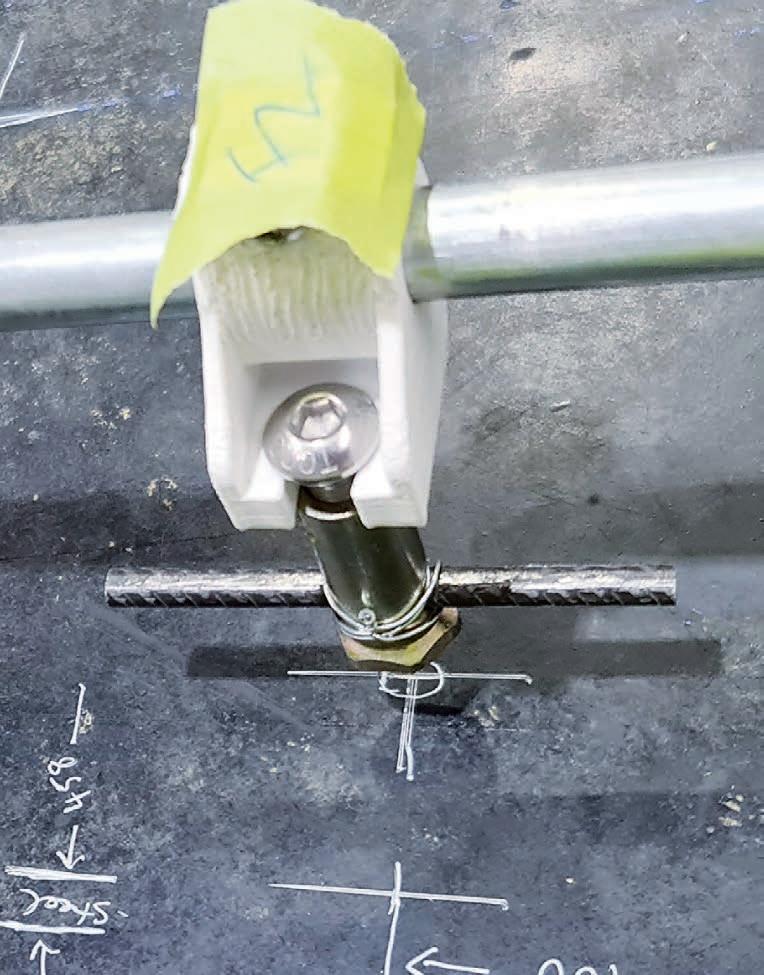
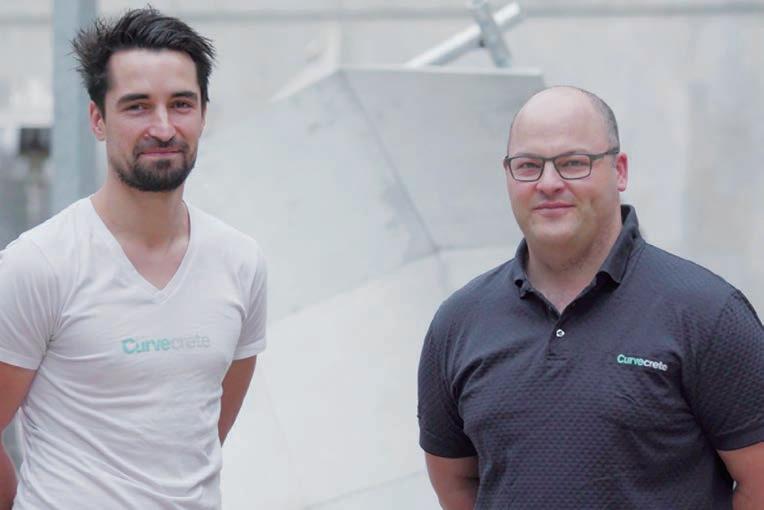
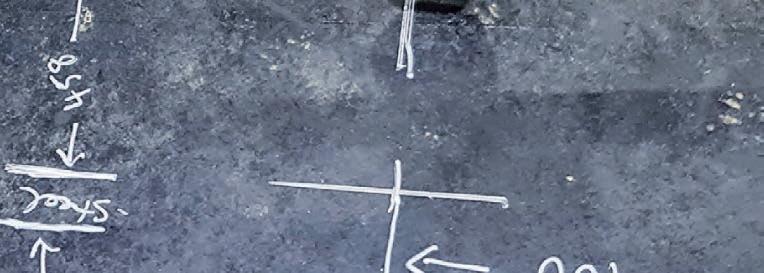
Compared with the traditional manufacturing process of curved concrete and all of the waste associated with the formwork, by eradicating this formwork we save 35 per cent for nonstructural panels and up to 75 per cent for structural panels.
Grant from the federal government worth $325,158 to develop a pilot advanced manufacturing facility in Melbourne. This facility is enabling the scaled manufacture of low carbon construction materials, and using Curvecrete’s signature fit-for-purpose robotic systems to help deliver on new projects cost effectively and with high precision.
The manufacturing business’ pilot project, delivered as part of the Accelerating Commercialisation Grant, was the first step in proving the technology in the commercial space.
“For our first project, we created an extension of the fire escape for a multi-residential building in Melbourne,” Prohasky said. “It’s an existing 14-storey building, and we designed an access stairway to the rooftop and a curved concrete canopy to enclose that spiral staircase, for the residents to have access to the rooftop.”
This is just one example of a typical application for this new curved concrete moulding technique.
The Curvecrete panels can be used in: • Non-structural cladding applications such as curved sculptures, facades, rain screens, and non-combustible cladding replacement; • Structural applications such as modular curved homes, urban artwork, seating, and balustrading; and • Infrastructure including curved pedestrian bridges, highway sound barriers, and pylons.
Curvecrete co-founders, CEO Daniel Prohasky and CFO Warren Rudd.
A robotic, sustainable process
The robotic concrete moulding technique works by using a parallel robotic system with several actuators. As a completely fit-for-purpose actuated system, it is specifically designed as an adaptable mould that can manipulate its shape to form the curved concrete panel in a variety of different shapes, Prohasky explained.
“It’s got very minimal actuation, there’s only three actuators, but there’s a lot of different moving parts that work in unison. We also developed some joinery that is like a triaxial joint,” he said. “The idea is that minimising the number of actuators significantly lowers the cost, time to manufacture, and reduces maintenance of the system; the next equivalent system is an order of magnitude more expensive, that uses an array of actuators. The output forms a series of curved concrete panels in a rapidly reusable process. Just today, we produced two panels on the same robotic mould with our rapid setting low-carbon concrete.”
The advantage of this is that it removes all the labour and waste material associated with the traditional manual forming process. As a reusable system it produces zero waste in comparison to a traditional formwork process, whereby for every tonne of precast concrete that is made, 10-15 per cent of the material would be wasted.
Prohasky likens the unsustainable traditional formwork process to building a boat, then disposing of said boat on arriving at its destination.
Curvecrete’s robotic approach has also proven to be more cost-effective.
“Compared with the traditional manufacturing process of curved concrete and all of the waste associated with the formwork, by
Manufacturer Focus
eradicating this formwork we save 35 per cent for non-structural panels and up to 75 per cent for structural panels,” Prohasky said.
The raw materials that Curvecrete use are concrete waste by-products from coal power and the steel manufacturing industry.
“The material itself uses waste by-products, and we use a proportion greater than 50 per cent within our material,” Prohasky said. “So, we’re only using slightly less than 50 per cent raw material for aggregates, as opposed to reused, and we’re going to be pushing even further to use recycled aggregates in the future as well. The mission really is to become negative waste, so we actually consume more waste than we use in raw material.”
The business is also trying to source their materials within Australia, where possible.
“We use fly ash and slag – the fly ash is sourced in Australia and the slag is currently imported,” Prohasky said. “We’re trying to source slag locally before we consume high volumes, so we’re looking for slag suppliers locally. With the robotic systems, we manufacture everything locally that we can, but we do source a few components for the actuators from China. The rest is sourced locally and manufactured locally.”
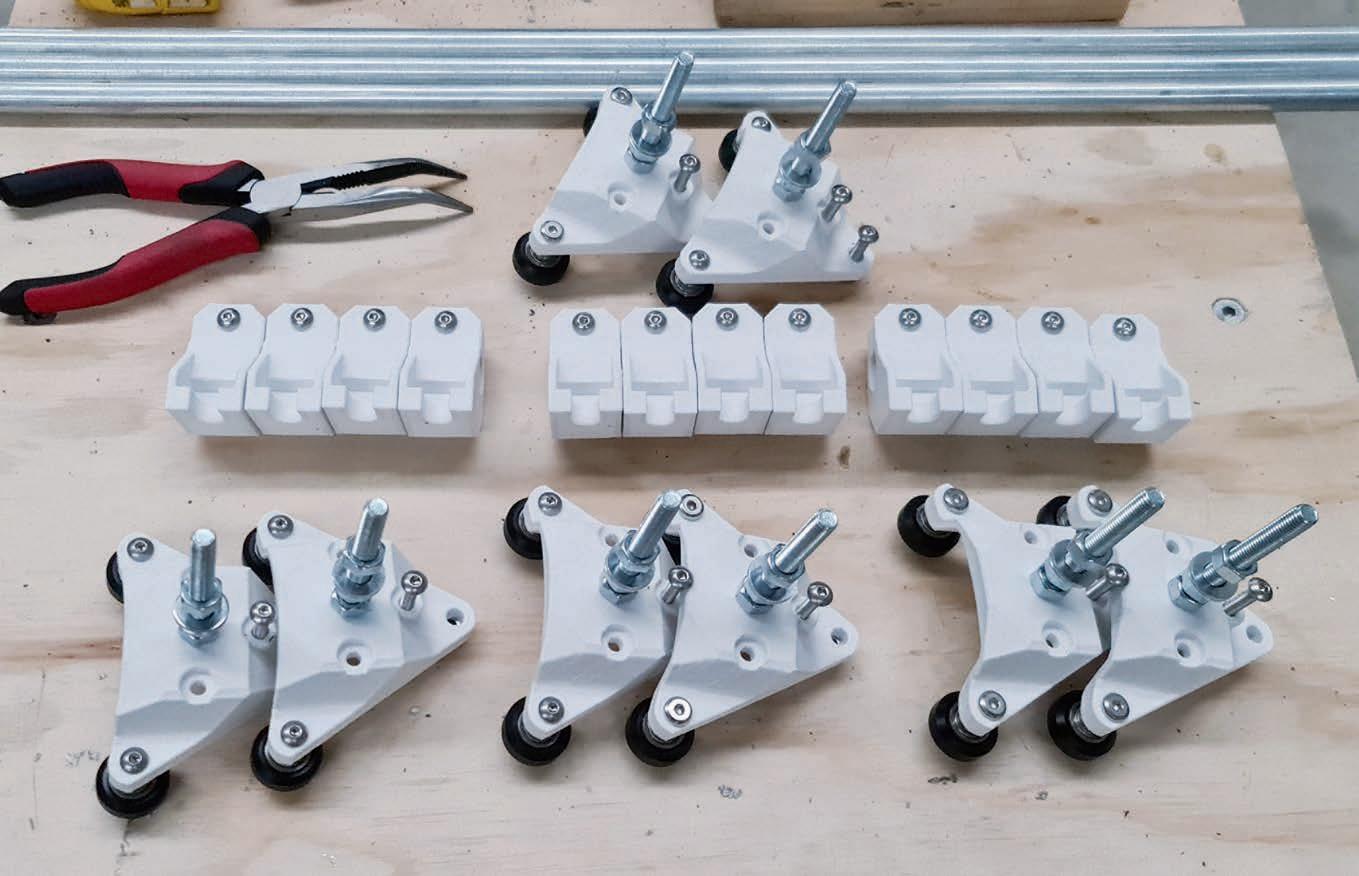
Overcoming challenges
There were several challenges that have confronted Curvecrete both as a manufacturer and as a business. The first sizeable hurdle was translating the research from the university into setting the business up for success. There have been some recent improvements on remedying this, including the federal government’s $5.8 million University Research Commercialisation Scheme that was introduced in the 2020-21 Budget and their $242.7 million Trailblazer Universities initiative, introduced in November 2021. However, Prohasky feels that a lot more still needs to be done in facilitating research translation.
“Research translation is really hard. The licence negotiation process was really strung out because it took us 20 months for us to negotiate that deal. It’s so hard to focus on actually succeeding as a company before it has even begun,” Prohasky said.
“There’s been a lot of good work that has happened to improve that process and streamline it, but there’s still a lot of work that needs to happen within Australia to really create a clear process across the board that every university in Australia can operate under, that has a reliable and known low equity stake for the university. For collaborations to occur across universities easily, a broad-brush approach is needed across all Australian universities; meaning the exact same benchmarked deal for every university in Australia matching or surpassing the most innovative countries in the world. Then everyone can collaborate, and everyone knows the terms, so that they can commercialise really great research without being clouded by an unknown outcome during the research translation process.”
Upon embarking on the path to commercialising Curvecrete’s technology, the founders’ next challenge was upscaling the development of the product in a cost-effective way.
“The technology is quite
Curvecrete’s custom robotics components developed using FDM 3D printing.
ManufacturerFocus
sophisticated, so the challenge was reaching scale cost effectively and making sure quality control is tight and that everything for the new product complied with the construction industry to sign off as structural, and fire engineering compliance requirements” Prohasky said.
“We’ve got our non-combustibility AS1530.1 compliance for material and we’ve just received our certificate of compliance for structural engineering for our first job. It was difficult, because we were effectively bringing the product to market, speeding up production, and delivering on a project at the same time. But, we did it!”
What’s next for Curvecrete?
In the aftermath of their first project, Curvecrete is aiming to further streamline their production process and implement more robust systems.
“From a systems and engineering approach, we’ve got the overall production, design and compliance system in place, but now it’s just about optimising the nodes within that system and making incremental improvements to the system on particular things in terms of efficiency, productivity rates and production yields. All to achieve really high valued beautiful sculptural architecture with zero waste!” Prohasky said.
In addition, the business is searching for further collaborations with other Australian manufacturers and suppliers in terms of implementing different products to deliver an effective internal development process. This would aid Curvecrete in reaching their short- and long-term goals.
“We have a goal to reach a 95 per cent success rate for our panels by achieving zero tolerance on our machines. We want to bring in at least over $1 million in revenue in 2022, or even in the first half of the year. I think we have the capability to do that, too. We’re looking for more opportunities to explore what’s possible with our technology. We are looking to be challenged!”
For the long term, the manufacturer’s overarching mission is to accelerate the construction industry towards a low carbon future, through their innovative robotic concrete moulding technology and low carbon material use.

“We want to further enable the use of low carbon materials through efficient, elegant robotic systems that will enable that, and further implement those at scale,” Prohasky said. “We also aim to collaborate with pre-casters and other robotics manufacturers who are interested in collaborating to develop robotic systems for construction. We’ve got a lot of knowledge in the space to share.”
Beyond these goals, Curvecrete has the potential to package their advanced manufactured technology
as a more comprehensive, futureforward system to be used remotely – perhaps even in space.
“The goal is to create an automatic casting system – a robotic system which can manipulate itself based on backend database panels and churn out panel after panel
The technology is quite sophisticated, so the challenge was reaching scale cost effectively and making sure quality control is tight and that everything for the new product complied with the construction industry to sign off as structural, and fire engineering compliance requirements.
and include automated mixing, cleaning and setup,” Prohasky said. “We could package it up into a shipping container and then put it onsite in remote locations and then manufacture panels remotely. The next step beyond that might be even to develop robotic systems that could build on other worlds as well, like on the Moon or on Mars.”
With such an increased availability for federal government funding and commercialisation opportunities around manufacturing technologies that are suitable for use in a space environment – such as the relevant streams that fall under the federal government’s $1.5 billion Modern Manufacturing Strategy – this aspiration is well within the realm of future possibility for Curvecrete.
“We’re always looking for new projects,” Prohasky said. “Anyone who wants to build something exciting with precision and high quality finishes, your next solution to do that can be curved, using a sustainable zero waste method. Get in touch through the Curvecrete website.”