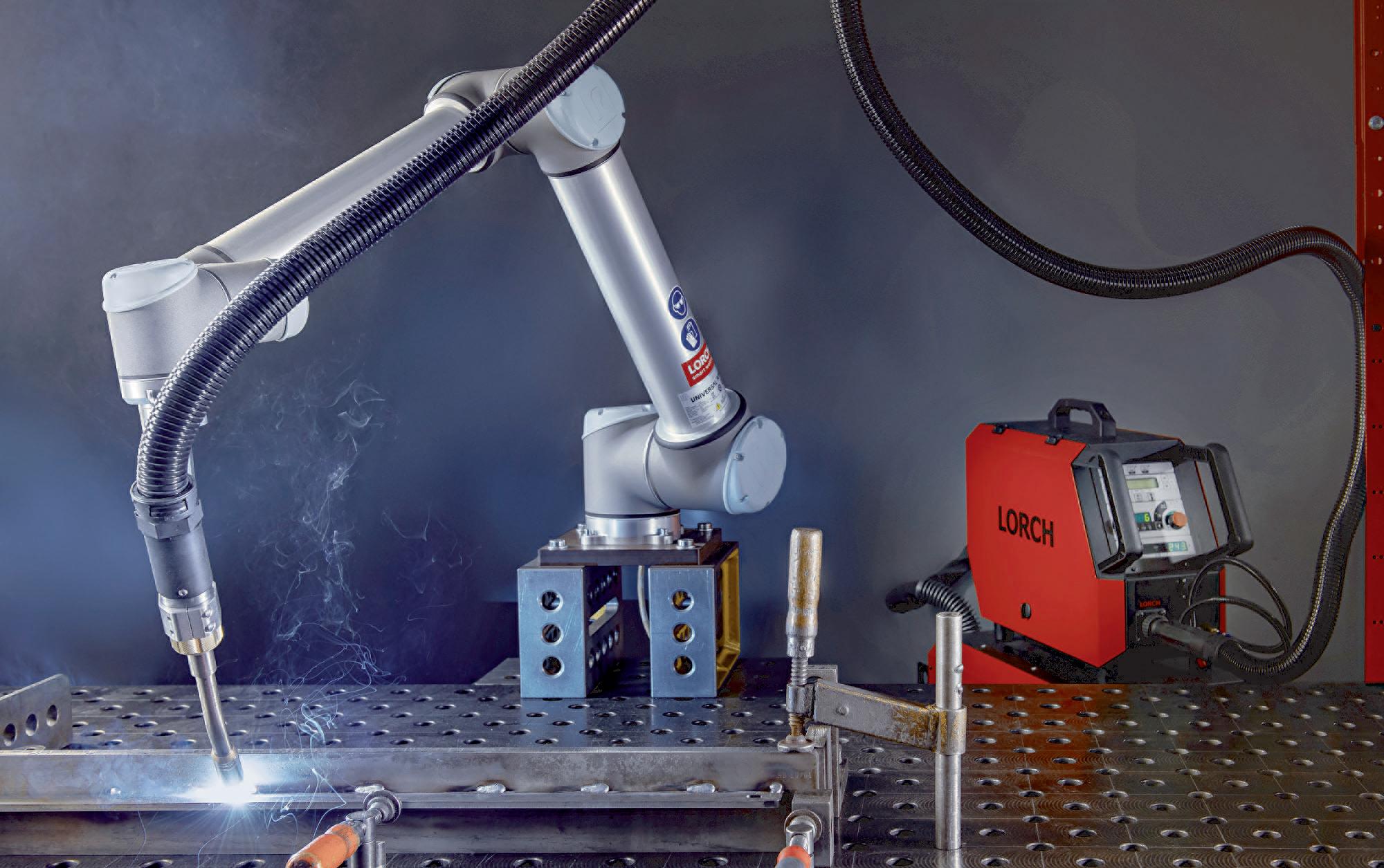
6 minute read
Welding
Cobots: An automated welding solution
David Wilton, managing director of Lorch South-Pacific, speaks with Manufacturers’ Monthly on how the company is developing smarter solutions for tomorrow’s industrial challenges, such as the Lorch Cobot Welding system – a collaborative robot designed to take welding to the next level.
WITH the demand far exceeding the supply of skilled welders in the market, smarter solutions where welding processes can be automated are needed. In the 2021 October edition of Manufacturer’s Monthly, managing director of Lorch SouthPacific, David Wilton, had shared with us about bringing together the art of high-level welding and cobot technology. Here, he gets down to the nitty gritty.
Manufacturers’ Monthly (MM): Cobots are great for replacing standard welding tasks. Where and how much of the human element is still a factor in the entire welding process, and why? David: Let me break this down into a few parts. Any Automation is great for welding large amounts of repetitive parts, in the sense of never taking a break and working around the clock. Whether it be cobot, industrial robot or fixed automation, will achieve this. The fundamental difference with a cobot is its simplicity, speed of setup, flexibility to weld small batch quantities and ability to work in the general work environment closely with humans. So yes, a cobot can do large volumes of repetitive work, but also is highly flexible in performing very high-quality welding on a single part or small to medium batches of subassembly parts, like 20 to 40 parts.
Let’s be clear, no automated welding solution is going to take the place and skill of a highly trained, certified welding professional with the knowledge and experience for all welding applications. The problem is, we don’t have enough of these people – so why not use some of their skills in conjunction with cobot technology? The best welders in a shop can still be welding, but they can also support a number of cobots to perform many of the mundane simple welding tasks. Taking this approach broadens our capabilities, drives productivity, improves welding quality and shop floor efficiencies. Overall, makes the team stronger!
The Cobot can be used to offset the shortage in skilled labour.
MM: How would a manufacturer or fabricator decide if a collaborative robot is right for the welding application? David: Lorch Cobot Welding was released several years ago in Germany and now all across Europe, today growing at an exponential rate. Lorch Cobot Welding is new for Australia and New Zealand, but not for more progressive countries like Germany that have a very high level of welding automation. Cobot welding has proven its place as a very good solution for small to medium enterprises that are looking for simplicity, flexibility, and a fast return on their investment (ROI).
In terms of welding, the purposebuilt, fully integrated Lorch cobot welding system has all the latest and most advanced “Masters of Speed” welding processes with hundreds of wire/gas and process combinations that are suitable for the vast majority of welding tasks in any position with solid, flux cored and metal cored wires on all types of materials including steel, stainless steel and aluminium. If it is not already standard, Lorch can develop specialised synergic lines with any wire/gas combinations if required. MM: Could you share more about the ideal applications of using collaborative robots in a welding workspace and some advantages? David: We have set up our Australian website at www.lorch.com.au, with testimonials and case studies featuring real customers that have invested in one or more cobots, where you can see the advantages that cobot welding can bring to the table.
MM: How do you save overall bottom-line costs in implementing an automated welding system, like the Lorch Cobot Welding System, on the factory floor? (e.g. manual worker redeployment, longer production hours for menial welding tasks) David: This is difficult – it really depends on the individual company
Welding
and the welding applications they are seeking to automate. I would add, cobots are not always the right choice; some applications will be more suited to an industrial robot if there is a highly repetitive production.
Our Lorch cobot partners are available for all enquiries and anyone who wants to see the Lorch cobot in action and then to look at their individual applications to really validate if cobots are the best choice and can deliver an acceptable ROI. Then, with our partners, codevelop suitable plans for finance, installation and training.
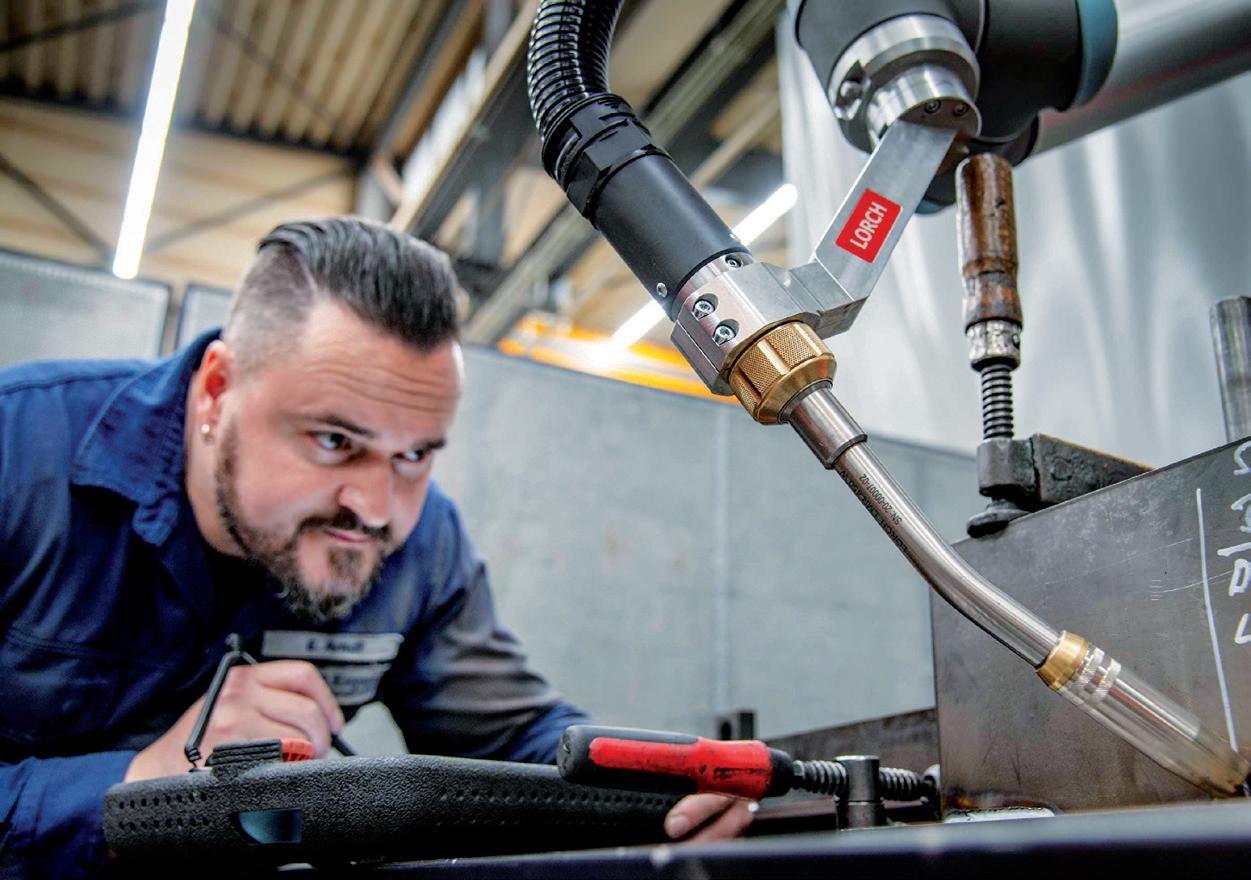
MM: In terms of ergonomics, how easy is it to deploy an automated welding system like the Lorch Cobot Welding system on the factory floor – sometimes there might be a need to move around machinery from time to time, especially in smaller businesses as they grow in size? David: The cobot itself only weighs 30kg. Normally you would mount the cobot on a suitable steel tool table that allows for simple jigs and fixtures. The table can be on wheels, highly manoeuvrable around a shop, while others will prefer a system more permanent, and the work can come to the cobot. This way, it is a bit easier to manage fume extraction.
Lorch’s type of welding automation leaves the welder in full control.
MM: For large industrial scale robots, maintenance can be difficult with downtime taking weeks due to the availability of parts. What is the maintenance of cobots like and what kind of after care service can customers expect with Lorch and its Cobot Welding System? David: With the Lorch Cobot system, the cobot is an Australian delivered Universal Robot (UR) that is warranted and fully supported in Australia. The welding system made by Lorch in Germany has a 3-year warranty and is fully supported with trained and accredited service locations across Australia and New Zealand. Also, spare parts are stocked in volume in Australia and shipped anywhere in the South Pacific within 24 hours.
MM: Despite being easy to use, there needs to be a certain level of training involved with automated welding. How much training does Lorch provide for its customers with the Lorch Cobot Welding system? David: When a system is purchased, part of the cost includes full installation and training program over two days. Additional training is available if needed, but two days is really all you need – the rest is practice.
In 2019 this internationally renowned event attracted:

INTERNATIONAL CONVENTION CENTRE SYDNEY, AUSTRALIA

The region’s largest international civil and defence maritime exposition, incorporating the Royal Australian Navy’s Sea Power Conference and the International Maritime Conference.
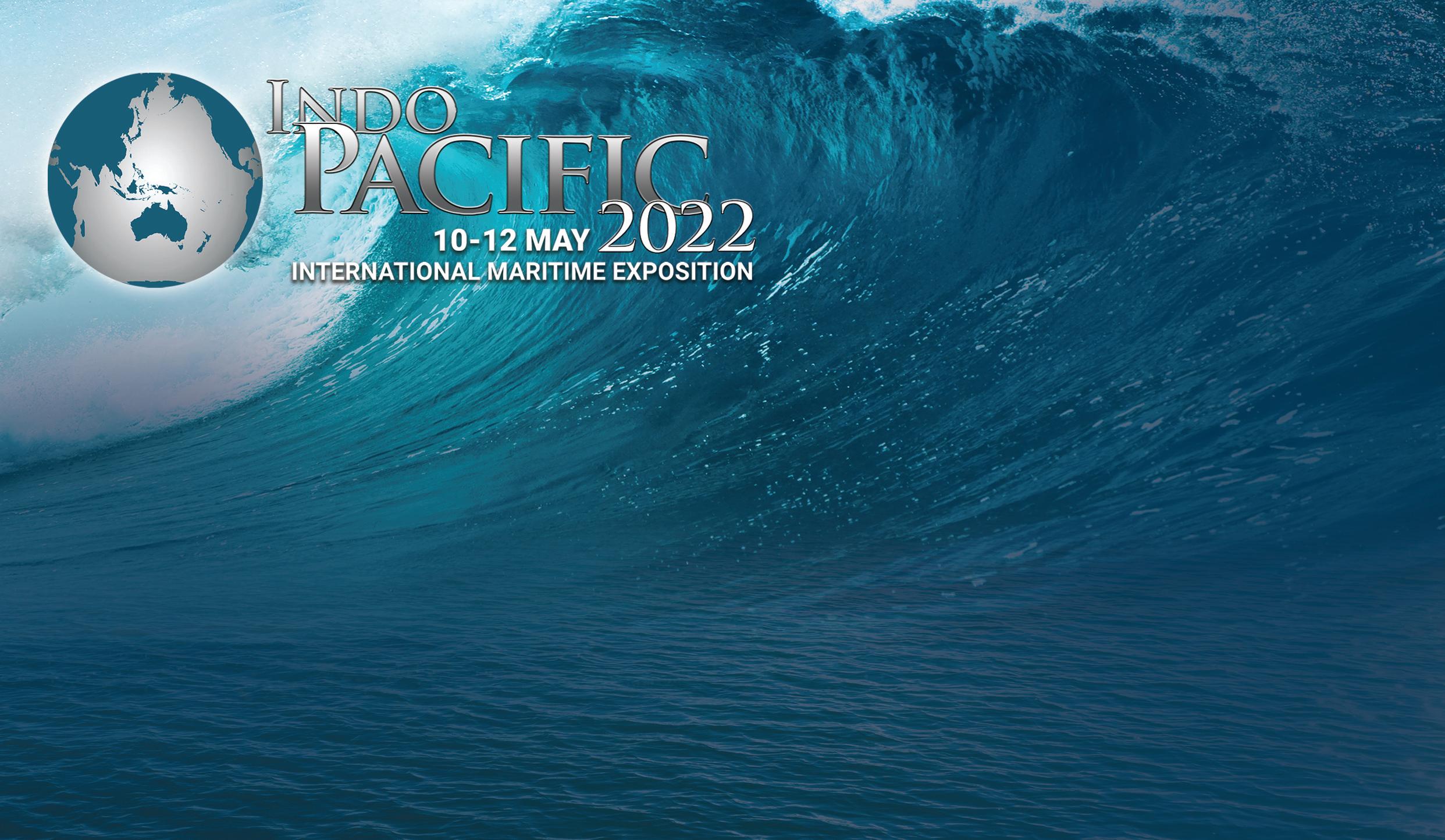
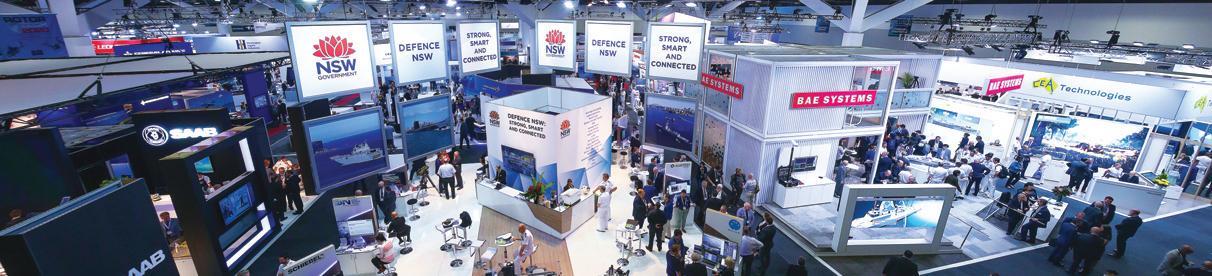
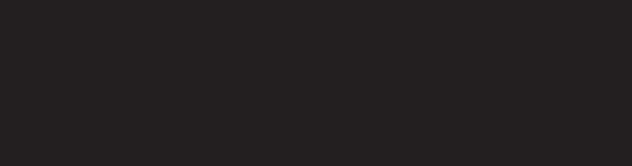
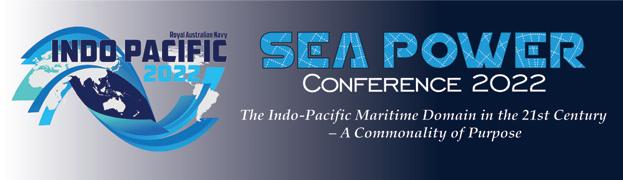
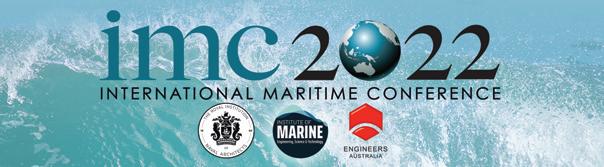
657 participating exhibitor companies from 22 nations 21,241 attendances across three days
182 industry, government, defence and scientic delegations from 48 nations 48 major conferences, symposia and forums
indopacificexpo.com.au
For further information contact the INDO PACIFIC 2022 Sales Team T: + 61 (0) 3 5282 0500 E: expo@amda.com.au