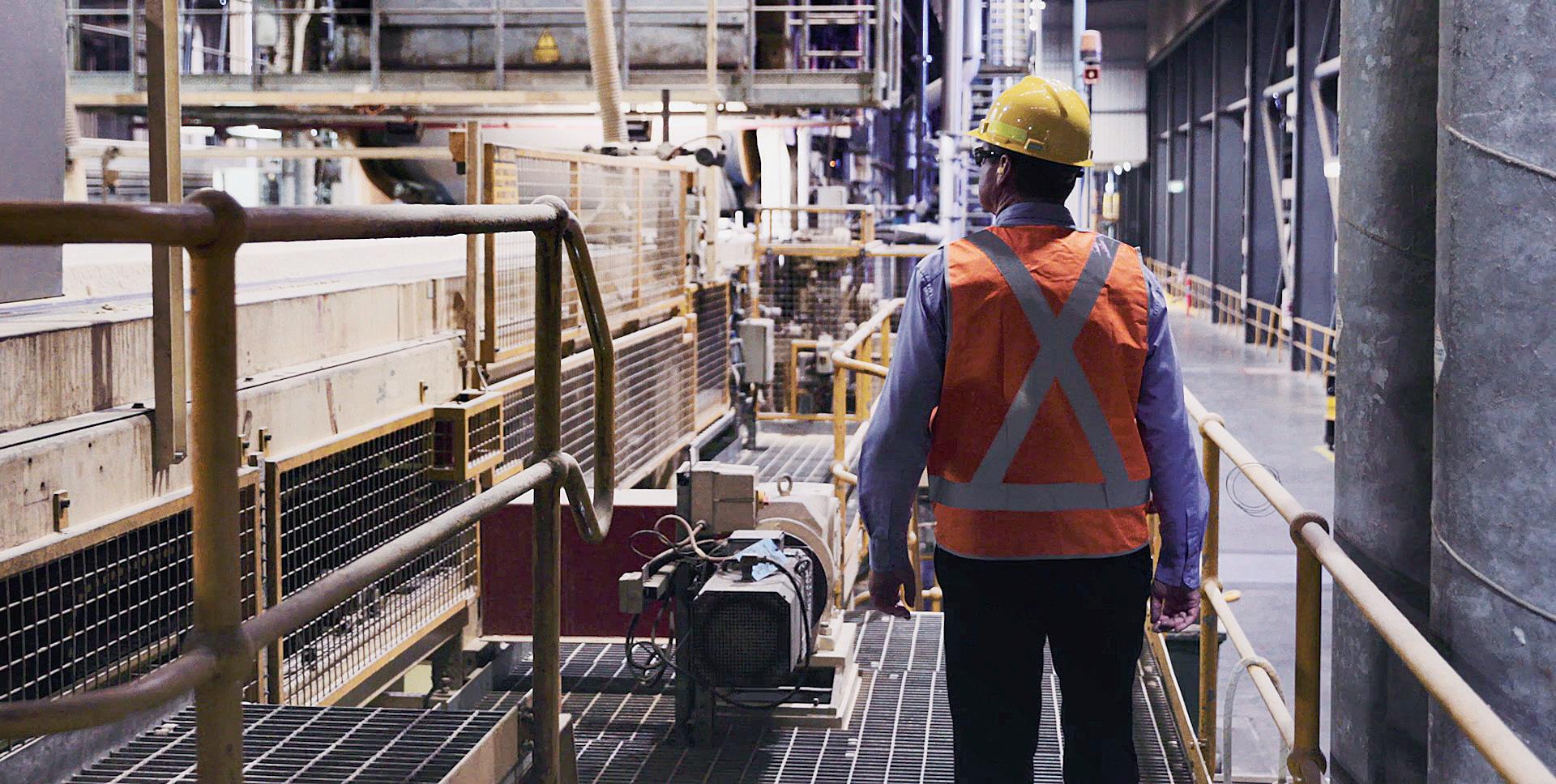
4 minute read
Manufacturing Excellence
Laminex Australia brings local manufacturing back
Manufacturers’ Monthly throws a spotlight on Laminex Australia’s very first manufacturing plant and how it made a monumental change to secure future success for the company, in a chat with its general manager of Operations, Graham Andrew.
SPANNING 85 years of history, Laminex Australia is a manufacturer of highpressure laminate, compact laminate and wet-area panelling, decorated MDF used for cabinetry doors, raw particleboard and MDF. With multiple manufacturing plants across Australia, the company’s original manufacturing plant was located in Cheltenham, about 18km south of the Melbourne CBD. It was here that Laminex Australia became the only producer of thin high pressure and compact laminates in Australia and New Zealand – which is still true today.
The Cheltenham plant has been in operation for almost 70 years, according to general manager for Operations, Graham Andrew.
“The plant at Cheltenham was built just after the second World War in the late 1940s, early 50s,” he said. “The equipment has been upgraded over the years but it is at the centre of the history of the company. Laminex started with the product that’s made at that plant, so it really was the height and founding location of the company.”
“And since then, the origins of the company have become part of our big growth story.”
Overcoming adversity
But several years ago, in 2019, the Cheltenham manufacturing plant was placed in the black. Operating on a limited three and a half days of production each week with 60 employees working across two shifts, the volume of their production was dropping fast.
“If you roll the tape forward a few years, there was a very high possibility that the plant would have to close,” Andrew said. “It would’ve been 60 jobs lost in Melbourne. So, we had to make a conscious decision to turn that around.”
This started with insourcing a product that was being made in China and imported. This was compact laminate, a 13mm thick and heavy product that’s often a material used for toilet partitions in spaces like hotels and airports.
“To get the plant up to 3 shifts and get some capacity and get some momentum going, we decided to make that product locally,” Andrew said. “We did a whole lot of product development work, and made certain we could do it, then included a $5 million investment into a finishing line, which basically trims the product and gets it looking good and ready to be dispatched to customers.”
This new investment was in a trimming machine which has the ability to finish the compact laminate after being pressed, creating a more presentable product for Laminex Australia’s customers.
Once that investment had been made, the volume was brought back into Australia and the shifts were able to increase. This created 20 new jobs at the Cheltenham manufacturing plant. The demand for the products then grew slightly more, which created more employment opportunities.
“In August last year we put a fourth shift on and another 18 people were hired,” Andrew said. “Overall, that’s about 38 extra
Laminex Australia’s original manufacturing plant has become key to its growth.
Manufacturing Excellence
people that we’ve hired now in that plant, compared to when it was going in the other direction a few years ago.”
Sustained success
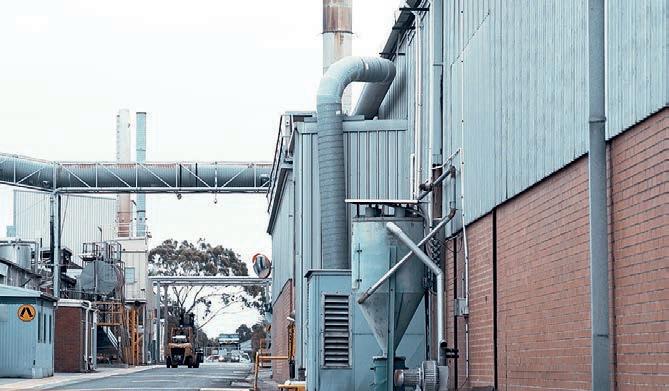
The success of the plant continued to rise from there – from a plant that was destined to be closed to becoming the foundation for fresh and sustained growth for the company in the future.
“We’ve also invested another $1 million since then and the plant actually shut in March for a big upgrade on one of the vessels we had to install there, which is a $2 million project,” Andrew said. “Overall, it’s about $8 million from where we started in 2019 from a combination of insourcing products instead of getting them from China, and also introducing new products we’re developing. We hope to launch the products on the market and load up the plant even more in the back end of this year.”
In embarking in more product development for the company, the Cheltenham plant has been working on several different avenues to boost the capabilities and aesthetics of their existing lines. One of these is introducing different types of décor for both the thin laminate and the thicker compact laminate.
“We use press plates to impart a new finish on the product, whether it be a grain finish, a stipple finish, or a smooth, glossy finish,” Andrew said. “With some of the new products, we’ve changed both the décors including the colours, patterns and designs that we have available, as well as the finish on the product.”
Another new option the plant explored was considering other functions and applications for their products. This kind of innovative product development could be the next step in generating further success for Laminex Australia. More information on this will become available soon.
Laminex Australia’s Cheltenham plant.
Future plans
For the near future of the Laminex Australia Cheltenham plant, Andrew says there will be an increased focus on upping the demand to support the extensive product development they are now undertaking. In doing this, the company hopes to employ more skilled employees.
“For the next two to three years, we want to fully load the fourth shift,” he said. “We made a big decision to put that fourth shift on, knowing that we don’t have all the demand and customers for those products yet – but we are committed to growth. So, we plan to work very closely with our technical team, as well as with our sales and marketing teams, to launch these new products and increase the demand so that we can fully load the fourth shift. That’s where we’re at for the future of the plant.”
PROCESSING + PACKAGING
One all encompassing show
Owned and presented by