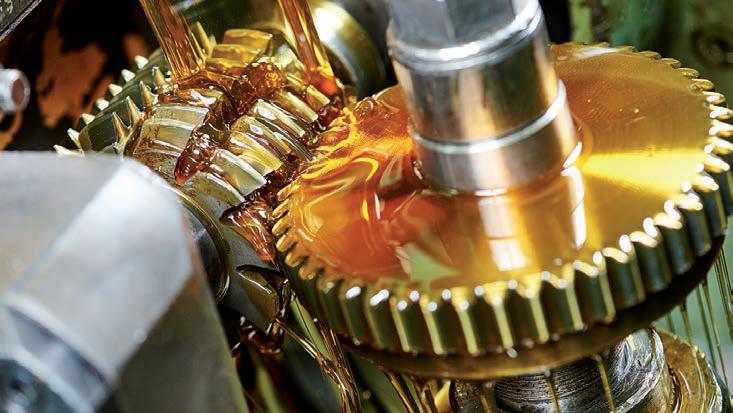
3 minute read
Lubrication
Engineering lubrication systems to work with equipment
Manufacturers’ Monthly speaks with the John Sample Group about the importance of pairing the most suitable lubrication system – and lubricating while equipment is running – with different industrial environments.
Optimum lubrication happens when the equipment is still running.
JSG Industrial Systems (JSGIS) – a John Sample Group business – enter technical partnerships with manufacturing businesses, delivering lubrication systems engineered to specifically meet a customer’s requirements.
This specificity, according to National Sales Manager Italo Marcantonio, is only possible with access to a diverse range of products.
This luxury, or rather necessity, is afforded to JSGIS as the distributor for SKF’s Lincoln lubrication systems since 1961, and SKF’s largest lubrication system partner globally.
“Problems occur for businesses when they work with people trying to shoehorn solutions into areas they aren’t absolutely suited to,” Marcantonio said. “Our broad range covers the simplest to the most complex lubrication system covering the full range of lubricants available.”
JSGIS became strongly linked with SKF when they acquired the Lincoln Group in 2010. JSGIS has been involved in the delivery of highquality lubrication systems to various markets for more than 50 years.
One of the key causes of machine failure occurs when incorrect quantities and type of lubricant make its way into a machine. Italo says it can be a daunting process for businesses without help who don’t know how to solve such a problem.
“Businesses shouldn’t be intimidated by the process of specifying a lubrication system,” Marcantonio noted. “It’s quite a simple process once clearly explained, which is why we place an emphasis on educating the customer because there is sometimes a lack of industry knowledge. We can provide the initial assessment right through to the design and implementation, but it’s critical for the customer to understand what the products and systems do.”
JSGIS works with the customer to determine the required lubricant – whether that’s fluid grease, oil or standard manufacturing grease – and the number of lubrication points and where those points are located on the equipment.
Lubrication systems can range from basic single point lubricators through to fully integrated 80100 point systems, which can cost hundreds of thousands of dollars by the time they’re installed.
SFK’s progressive lubrication system helps to bridge the gap of this cost, being easy to install and simple to engineer for industrial environments.
The SKF ProFlex and Lincoln Quicklub, can be used on small- to medium sized machines with dispersed lubrication points requiring varying lubrication quantities. The system has a pump connected to at least one primary metering device. If needed, second level metering devices can be connected to the outlets of the primary metering device to increase the number of lubrication points.
Italo pointed to the progressive lubrication system’s flexibility to explain its popularity in manufacturing and industrial environments.
“Its design capabilities are able to cover the bulk of the small to medium range applications,” he said. “You’re able to do 40-100 lubrication points in confined spaces, so the system is more than capable of delivering grease to all points within say a 20 metre radius. Where we see systems get challenged is when they must deliver heavy greases over very long distances, which increases the cost of the system. But in manufacturing typically, the bulk of the applications that we see, particularly in food and beverage is relatively self-contained, easy to pump and you can design around the equipment.”
SKF and JSGIS strive to educate its customers about the importance of good lubrication. SKF has conducted studies for as long as it has manufactured bearings to investigate the causes of premature bearing failure, which show contamination of the lubricant, over and under lubrication, incorrect storage of lubricants, incorrect handling of lubricants and any cause of cross contamination as major factors.
Italo says over the last ten years, businesses are becoming more aware of the importance of good lubrication.
“Businesses find out the most effective lubrication system delivers lubricant while the system is running,” he said. “That’s when you get the best coverage and protection. People are beginning to understand it’s not just about pumping equipment full of grease with a grease gun at the end of a shift. That gives you some protection, but using much smaller volumes of lubricant more frequently optimises machine performance.”
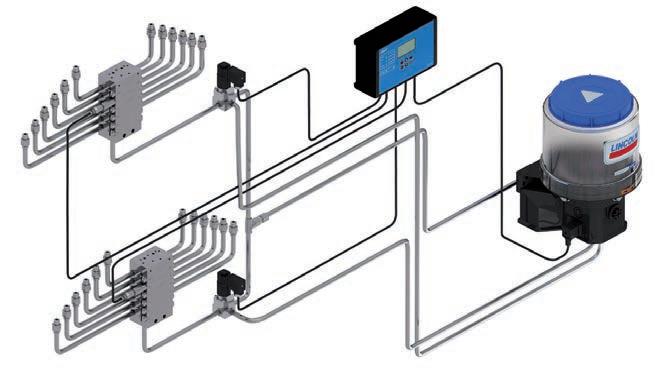