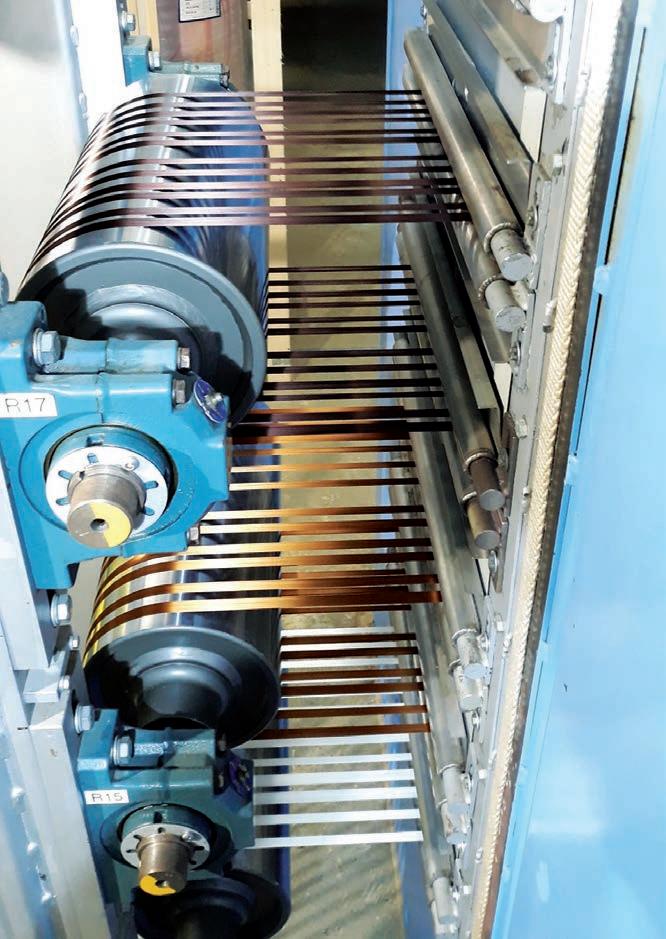
6 minute read
Engineering Focus
Defence contractor Thales Australia has entered into a collaboration with Deakin University and the Innovative Manufacturing Cooperative Research Centre to develop a lightweight composite overwrap for gun barrels. Manufacturers’ Monthly speaks to the people behind the project.
AFTER establishing the Commonwealth in 1901, the Australian government faced responsibility for the country’s defence for the first time. To be free of complete dependence of British munitions and armament supplies, the decision was made to build a factory to manufacture small arms in the New South Wales town of Lithgow.
In July 1914 – despite the centre only being in operation for two years – The Lithgow Small Arms Factory had to rise to a mighty challenge. During the first world war, over 1500 men worked at the facility, enduring cold winters and terrible living conditions to make almost 100,000 Short Magazine Lee-Enfield rifles and accessories over the next five years.
Graham Evenden, Thales Australia’s director integrated weapons & sensors, said from manufacturing the .303 and SLR to today’s Austeyr SA2 and the EF88, Lithgow has a unique heritage.
“The factory was designed specifically with steam powered, belt driven machines,” he said. “They were able to manufacture that rifle in less than half the time of the same rifle which was being manufactured back in England.”
Today, the facility designs new Australian weapons for military and civilian markets. Thales Australia recently invested $6.5 million in the first step to transform the factory into a modern manufacturing and integration hub for the design, development and precision manufacture of next generation weapons systems.
At the forefront of this push is an exciting new six-month, $234,000 research and development (R&D) project to deliver a carbon fibre overwrap that will reduce the thickness of the gun barrel, resulting in a lighter product with increased precision.
The research collaboration is a part of a wider R&D program for Thales and is in collaboration with Deakin University and the Innovative Manufacturing Cooperative Research Centre (IMCRC), based around two fundamental factors: taking an in-demand product to market and securing an onshore supply of the raw material.
“Weight reduction is critical,” Evenden said. “One of the key
The carbon fibre project hopes to advance in-country composite manufacturing capabilities.
contributing subsystems for any rifle is the barrel which is usually a fairly large chunk of steel. The lightweight carbon overwrap seems like an obvious solution for that.”
The second, and for Evenden, most exciting reason behind the project is the opportunity to advance in-country composite manufacturing capabilities.
“Currently, the intermediate modulus carbon fibres suited to the overwrap are only available from overseas supply chains that face frequent disruptions. By developing these fibres on Australian soil, Thales is establishing an innovative capability that can be applied to other small arms products across civil and defence sectors,” he noted. “In these times, localising material is so important.”
Dr. Sarah Sharp heads Thales Australia’s integrated weapons and sensors business’ technology and engineering team, having been involved in the development and taking-to-market of new Australian products for many years. As part of Thales’ military rifle R&D program, Sharp has been looking for the right partners, which Deakin University fit perfectly.
“Deakin is our materials research and development partner and the industrialisation of the product is where we’ll be taking the lead,” Evenden said. “They play an absolutely critical role from a materials perspective and how the material is presented will influence the design of the product. We will work hand in glove with Deakin to upskill staff at our Lithgow Arms facility to work with composites, further contributing to sustainable growth within Australia’s manufacturing sector.”
The Carbon Nexus Centre in Victoria’s south.
EngineeringFocus
Thales’ mechanical design engineers will be leaning on the company’s experience in working on lightweight carbon systems for aircraft and the defence industry. Evenden is immediately turning his attention on planning how to execute the design into a tangible manufactured product.
“At the beginning of the design phase our industrial team will be involved because at some point, we have to manufacture the product,” he added. “Quality engineering will also be involved from the start, so we can design a quality plan for testing and qualification. It’s important to embed those quality control assurance aspects from the beginning.”
The passion for engineering at the Lithgow factory stems from its rich history. Thales has a number of exmilitary staff, but Evenden explained the devotion to providing for the defence industry goes way beyond personal experience.
“Some employees are the fourth generation working at the facility since it opened in 1912,” he said. “There are family with brothers, sisters and fathers working at the factory who carry the passion for manufacturing, so the team really cares about what goes out the door.”
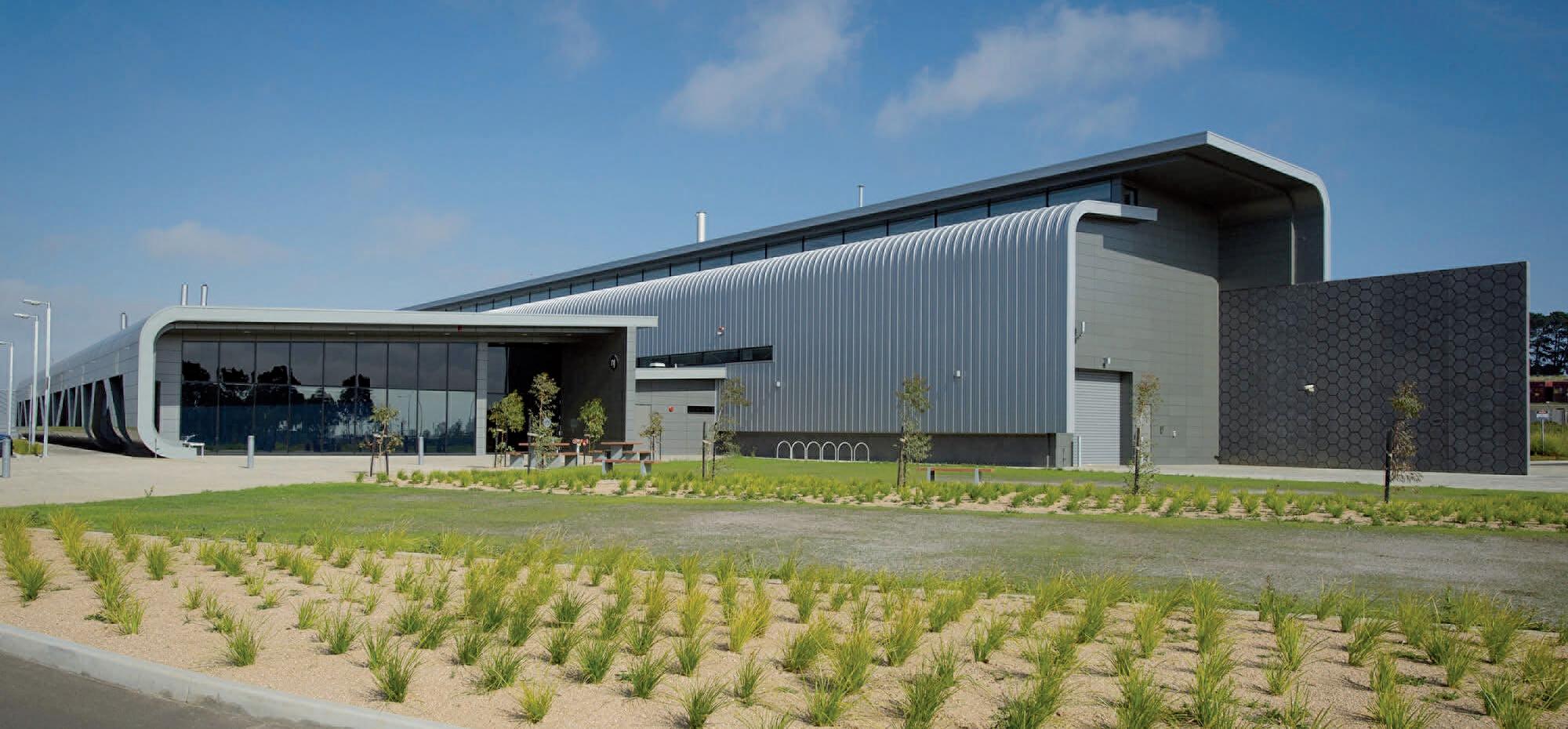
Carbon Nexus
Prof Russell Varley, professor of composite materials at Deakin University, said the IMCRC activate collaboration will draw on local knowledge and expertise to meet the growing global demand for lightweight, high-performance components.
“Deakin, through its Carbon Nexus research centre, is excited to support Thales in the development of new carbon fibre materials which, will be used to produce a composite demonstrator at Thales Australia’s Lithgow manufacturing facility,” he said.
The Carbon Nexus research centre is a purpose-built carbon fibre research facility committed to supporting the Australian composite industry and creating Australian carbon fibre. This project provides the ideal platform to do this, by growing our manufacturing and research capability, while creating jobs for Australia.
Prof Russell Varley said that Carbon Nexus is proud to be at the nexus of industry, research and teaching for the global carbon fibre community.
Almost 20 years ago, Australia was falling behind in new manufacturing opportunities amid increasing demand for lightweight, low-cost and energy efficient carbon fibre.
With the closure of iconic factories and large-scale employers in manufacturing in Geelong, such as the Ford Australia plant and Alcoa’s Point Henry smelter, the region embraced the opportunity to support local manufacturing.
Carbon Nexus has worked with some of the world’s largest and most important companies such as Vestas, Boeing, Ford and PETRONAS to name a few, whilst collaborating with many Australian companies looking to utilise more carbon fibre in their manufacture. Carbon Nexus provides research and development services across the entire carbon fibre value chain, from precursor and carbon fibre development to composite manufacturing delivered by a team of globally recognised, advanced materials experts. The centre continues to innovate, leveraging off its recent commercial success.
The pilot scale facility at Carbon Nexus, provides a unique advantage over other similar facilities, allowing technology developments to be scaled up in readiness for commercial exploitation.
“At a manufacturing capability of between 50 and 100 tonnes of carbon fibre per year,” he added. “any new technology, whether developed by or with an industry partner is able to take the next step towards the marketplace. .”
Prof Russell Varley believes that the Thales and Deakin’s R&D partnership will act as a testbed for future developments of Australian manufactured bespoke carbon fibres.
“We would love to see this really kick-start the nascent Australian carbon fibre industry,” he said. “And Carbon Nexus is the seed to do that given the difficulty of suppliers in sourcing the carbon fibre they need at the right price.”
Dr Matthew Young, manufacturing innovation manager at IMCRC echoes this sentiment.
“This collaboration will develop a niche, high-quality product with significant export opportunities. By partnering with an Australian worldclass research facility on composite materials, this project will directly support growth within a key national manufacturing priority area,” he said.
“It’s a prime example of the role shorter-term R&D collaborations can play in strengthening the future of defence manufacturing within Australia.”