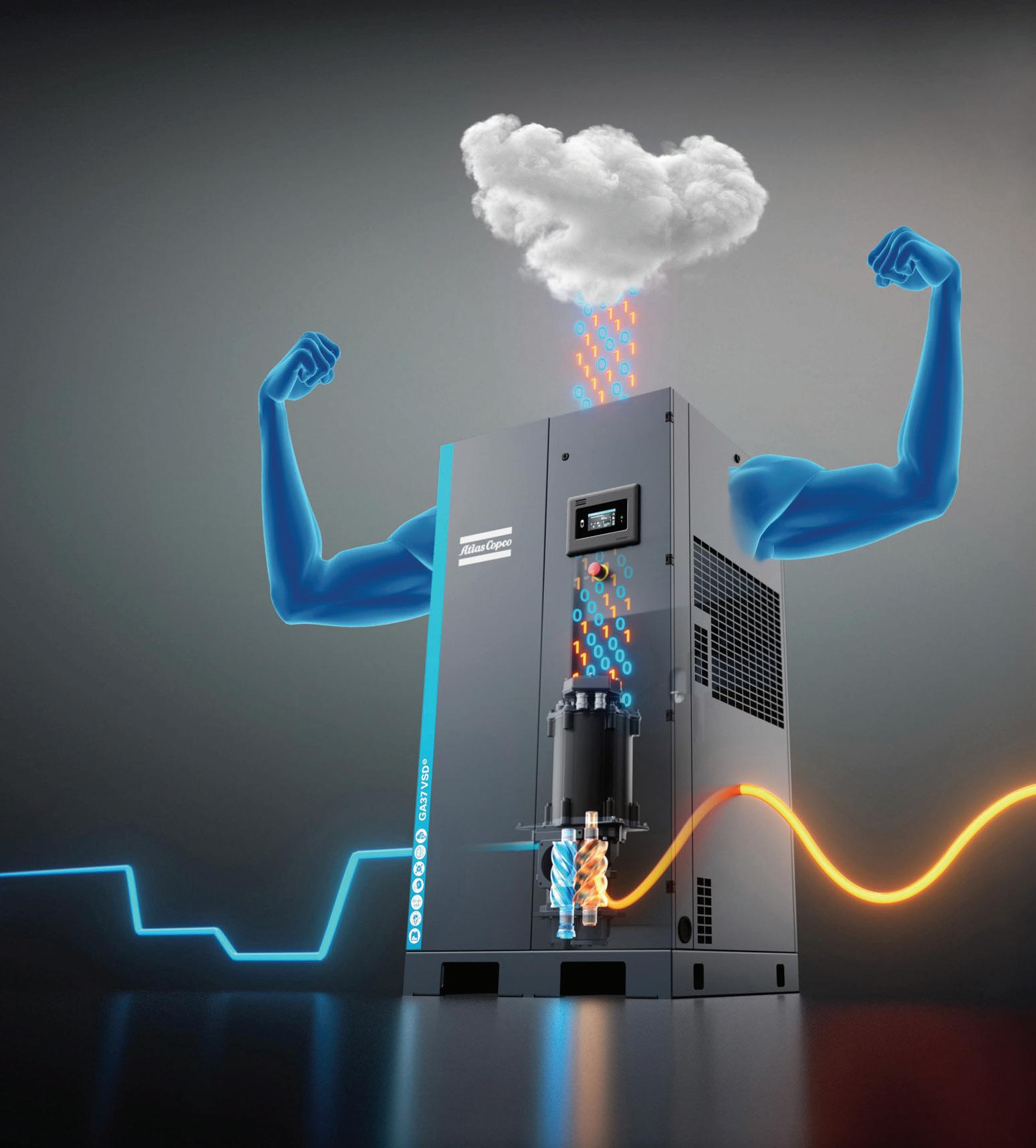

Atlas Copco’s GA FLX is a new dualspeed rotary screw compressor designed for significant energy savings and optimal air delivery at any pressure.
Its advanced engineering and connectivity ensure superior performance and flexibility, making a real difference to your operations and bottom line. Featuring:
Re-engineered drivetrain
Market leading Neos Next inverter
Advanced dual speed control
Elektronikon Touch controller
Remote & mobile monitoring
Temperature sensing fan control
Atlas Copco premium filtration
Integrated refrigerant air dryer
No-loss electronic drains
Nationally certified service network
www.atlascopco.com
Dozens of Australia’s leading manufacturers
CEO: John Murphy
Chief Operating Officer: Christine Clancy
Managing Editor: Mike Wheeler
Assistant Editor: Phillip Hazell
phillip.hazell@primecreative.com.au
Journalist: Jack Lloyd jack.lloyd@primecreative.com.au
Head of Design: Blake Storey
Design: Cat Zappia
Sales/Advertising: Emily Gorgievska Ph: 0432 083 392 emily.gorgievska@primecreative.com.au
Subscriptions
Published 11 times a year
Subscriptions $140.00 per annum (inc GST)
Overseas prices apply
Ph: (03) 9690 8766
Copyright Manufacturers’ Monthly is owned by Prime Creative Media and published by John Murphy. All material in Manufacturers’ Monthly is copyright and no part may be reproduced or copied in any form or by any means (graphic, electronic or mechanical including information and retrieval systems) without written permission of the publisher. The Editor welcomes contributions but reserves the right to accept or reject any material. While every effort has been made to ensure the accuracy of information, Prime Creative Media will not accept responsibility for errors or omissions or for any consequences arising from reliance on information published. The opinions expressed in Manufacturers’ Monthly are not necessarily the opinions of, or endorsed by the publisher unless otherwise stated.
© Copyright Prime Creative Media, 2024
Articles
All articles submitted for publication become the property of the publisher. The Editor reserves the right to adjust any article to conform with the magazine format.
Head Office
379 Docklands Drive
Docklands VIC 3008
P: +61 3 9690 8766
enquiries@primecreative.com.au www.primecreative.com.au
Sydney Office Suite 11.01, 201 Miller St, North Sydney, NSW
Welcome to the October edition of Manufacturers’ Monthly. Our cover story takes an in-depth look at Atlas Copco’s GA FLX compressor, showcasing its dual-speed functionality and energy-saving potential, a vital innovation for manufacturers. Additionally, we present the much-anticipated IBISWorld Top 100 Manufacturers List, spotlighting key industry trends and insights for 2024. Finally, we have a sneak-peak of this year’s Endeavour Awards, which honours excellence in Australian manufacturing. Happy reading!
Welcome to the October edition of Manufacturers’ Monthly. A highlight of our editorial calendar is the return of the popular Top 100 Manufacturers List.
Put together by IBISWorld, this list is a guide to the top-tier manufacturers in Australia. The accompanying article gives a great overview of where the Australian manufacturing sector is at in terms of turnover, profit and how it stacks up against other industries.
As we delve into the achievements of these top companies, we also spotlight stories that exemplify the dynamic growth and strategic investments shaping the future of Australian manufacturing.
From Hanwha Defence Australia’s new Armoured Vehicle Centre of Excellence (H-ACE) in Geelong to Pfizer Australia’s upgrade in Melbourne, these initiatives are laying the groundwork for Australia’s industrial future.
Hanwha’s H-ACE facility stands as a beacon of advanced defence manufacturing, promising to bolster the capabilities of the Australian Army while creating thousands of well-paying jobs.
This state-of-the-art facility is more than just a production site; it represents a commitment to sovereign capability and local economic growth, demonstrating the vital role of Australian manufacturing in national defence.
On the pharmaceutical front, Pfizer’s $150 million investment in its Melbourne site addresses one of the most pressing global health challenges – antimicrobial resistance.
By upgrading this facility with cutting-edge technology and embracing AI, Pfizer is not only enhancing its production capabilities, but also positioning Australia at the forefront of global efforts to combat this silent pandemic.
The Queensland Train Manufacturing Program (QTMP) is another testament to the power
of collaboration and innovation in Australian manufacturing.
By engaging with the disability sector and local communities, the QTMP is setting new standards in accessibility and inclusivity for public transport, ensuring that the benefits of advanced manufacturing reach all Australians.
Finally, regional manufacturers like Apollo Fabrication remind us of the critical role that small and medium enterprises play in the national landscape.
With strategic government support, Apollo is expanding its operations, creating jobs, and contributing to many infrastructure projects across the country.
As we celebrate the top 100 manufacturers, let us also acknowledge the broader spectrum of industry players – big and small – who are driving Australia’s manufacturing renaissance. This edition is a tribute to their hard work, vision, and dedication to excellence.
Gateway by ICN is Australia’s most comprehensive supply chain solution, connecting the most capable verified suppliers in the regions with projects, big or small.
2023-24 HIGHLIGHTS
8, 42 8
$258B+
VALUE OF NEW PROJECTS
$5.07B+ CONTRACTS AWARDED
VALUE OF AWARDED CONTRACTS
2,796 NEW WORK PACKAGES
Save time and money with Gateway and easily promote upcoming procurement and contracting opportunities to local suppliers. Think of it as your essential connection to the best local suppliers, whatever your industry.
123
NEW PROJECTS LISTED
Unlock your potential with Gateway by ICN – Your Gateway to Australian and New Zealand projects!
In an increasingly competitive market, Gateway by ICN opens up new opportunities for your business. You can search for projects online and register your interest directly.
All backed by the experts at Industry Capability Network. Powerful procurement and supply chain tools. Expert advice and support.
Weld Australia’s 2024 survey highlights chronic work shortages and rising costs. Local content policies are needed to boost manufacturing capacity, technology investment, and global competitiveness.
Weld Australia has released the results of its 2024 Member Survey. The findings demonstrate that Australia’s welding and fabrication industry is facing chronic work shortages, along with cost challenges amid rising prices of energy, materials and labour.
The Federal and state governments must commit to building sovereign manufacturing capability by legislating local content policy.
This will create a capacity mechanism that generates a clear, long-term signal for in the necessary technology, workforce, and equipment. With long-term demand a reality, local manufacturers will have the confidence to improve production efficiencies and global competitiveness.
Weld Australia’s 2024 Member Survey has
revealed the key challenges facing Australian welding businesses. Distributed annually, the survey was completed by members across the country, which includes major players in the defence, power generation, mining, rail and infrastructure sectors.
The results show that half of welding workshops are currently operating at 80 per cent capacity or below. Almost 7 in 10 Weld Australia members say they have capacity for additional work or that their pipeline is drying up—overwhelmingly citing a lack of work (75 per cent). When asked what their main concern is right now, 21 per cent of business owners stated that a lack of work is what keeps them awake at night.
It’s no secret that Australian manufacturing has been suffering a slow decline for decades. Today,
manufacturing is responsible for just 5 per cent of our GDP and only 5.4 per cent of total employment, despite its vital role in the Australian economy. For comparison, Canada – a similar economy to ours – has 1.7 million manufacturing workers where Australia has 47,500.
While this demise can be partially attributed to market forces, offshoring of manufacturing work that could be handled by the local industry is to blame. However, recent government initiatives present a once-in-a-generation opportunity to reinvigorate Australia’s manufacturing industry while supporting the national transition to a net zero economy.
The renewable energy revolution is Australia’s chance to undo some of the damage done over the past 60 years – both to the environment and to the
Australian manufacturing industry.
Australia is at a pivotal moment in its energy transformation journey. With the Federal Government’s commitment to reducing emissions by 43 per cent by 2030 and achieving net zero by 2050, the transition to renewable energy is not just a goal—it’s an urgent necessity. The scale of this transformation is unprecedented, demanding an increase in renewable energy generation from 64GW to over 218GW by 2050.
This shift presents both immense opportunities and significant challenges for the Australian manufacturing sector, particularly in the production of wind towers and transmission infrastructure. The domestic demand for wind towers over coming decades is huge. Based on AEMO scenarios, the market could range from $20 billion anywhere up to $80 billion.
To turn this vision into reality, a focused and actionable plan is essential. Specific, enforceable local content requirements must be implemented to ensure that Australia’s renewable energy projects are driven by domestic manufacturing. These local content mechanisms must be attached to government procurement, particularly initiatives like the Capacity Investment Scheme and the Future Made in Australia program.
Weld Australia strongly recommends that a significantly favourable merit weighting be given to tenderers who guarantee local content of Australian fabricated steel as follows:
• Onshore Wind Towers >50 per cent
• Offshore Wind Towers >40 per cent
• Solar Farms > 60 per cent
• Monopole Transmission Towers > 60 per cent
• Lattice Transmission Towers > 60 per cent
The contracts awarded must then be drafted with sufficient power to be readily enforceable by the Federal and state governments.
Weld Australia’s 2024 Member Survey also revealed that inflation is key concern for the welding industry. When it comes to the factors most likely to inhibit business growth over the next 12 months, 64 per cent of business owners cited the rising cost of energy, 61 per cent cited the rising cost of materials, and 50 per cent cited rising labour costs.
Members rated themselves as highly-productive: two-thirds of business indicated that the productivity of their welding staff as good or excellent.
However, out of the total labour hours per shift, 25 per cent of survey respondents indicated that they spend less than two hours of their shift doing actual welding (with the arc switched on); 58 per cent spend less than four hours. This is compared with fi ve hours per welder per day in countries like
the United States and Germany (that have similar Workplace Health and Safety Standards).
The factors most likely to impact on the productivity of welding staff are time spent on tasks like materials handling (42 per cent) and joint preparation and fit up (21 per cent).
A clear pathway to productivity is through the use of technology. When companies are focused on improving their processes, they naturally innovate—implementing the latest technologies in a bid to streamline operations. However, Australian companies generally lag their global competitors in digital adoption and unfortunately the welding sector is no exception. Uptake of advanced welding technology remains relatively slow, and this lack of tech adoption is impeding our ability to navigate the current challenges facing the industry.
The survey revealed that most businesses have not planned any investment in technology for the coming 12 months. Tech investment has not risen substantially since 2023, and in some areas has actually dropped. The types of technology that the welding industry has planned, in progress or completed include: Industry 4.0 (42 per cent); robots (37.5 per cent); and cobots (25 per centdown from 35 per cent in 2023).
By leveraging the benefits of advanced technology and automation, businesses can increase their productivity and reduce labour costs, while improving the quality of their welds. Given that the major barriers to productivity are materials handling and a lack of skilled staff, there is a significant opportunity for welding businesses to harness the capabilities of advanced welding technologies to overcome these issues.
Business owners are caught in a difficult position, juggling rising costs and a lack of work with the imperative to innovate and remain competitive. The reality is that without a guaranteed supply of work, particularly from government-backed projects, many welding businesses will find it difficult—if not impossible—to justify the necessary investments in advanced technologies.
The survey results highlight sustainability as a continued area of focus for the welding industry. A vast majority of Weld Australia members (69 per cent) support the Federal Government’s Climate Change Bill. However, almost as many respondents (66 per cent) say they would like to see Australian governments do more to help industry transition to net zero by the target date.
Welding businesses are doing what they can on their own to ramp up investment into sustainability initiatives. Most have already planned, started or completed the implementation of LED and sensor lighting (74 per cent), waste reduction programs
(76 per cent), recycling programs (70 per cent), digital transformation (64 per cent), water use reduction (65 per cent), and the installation of solar panels (53 per cent).
While these numbers represent an enormous increase from 2022, it’s worth noting that all have fallen slightly since last year’s survey—which may indicate a shift in focus to the more pressing issue of rising operating costs. And with over half of welding businesses yet to initiate a net carbon plan, the need for Federal and state government support for industry decarbonisation—coupled with a long-term pipeline of work secured via local content requirements—is evident.
Similarly, in the area of corporate responsibility, all figures are down slightly from 2023—potentially due to a change in priorities amid cost challenges. But encouragingly, many welding businesses are still investing in a range of corporate responsibility initiatives including:
• Employee wellbeing programs (76 per cent)
• Opportunities for women (76 per cent)
• Mental health and fitness programs (75 per cent)
• Opportunities for apprentices and trainees (71 per cent)
• Diversity and inclusion initiatives (69 per cent)
• Modern Slavery Act initiatives (59 per cent)
• Implementing a Reconciliation Action Plan (48 per cent)
Despite the lack of work and cost challenges, sentiment across the welding industry remains fairly positive. 68 per cent of respondents rated the prospects of their business as strong or very strong.
However, this is a significant decline from 88 per cent in last year’s survey. And while 83 per cent are confident that their business will be in operation in 12 months’ time, this is also down from 90 per cent in 2023.
Despite recent government investment in infrastructure projects and a rising preference for locally manufactured goods, it’s evident that these efforts alone are insufficient.
The implementation of specific, enforceable local content requirements is crucial.
For business owners and senior managers, these mandates provide the long-term certainty needed to confidently invest in initiatives like advanced technologies, workforce skills, sustainability and corporate responsibility. Such investments are vital to boosting productivity and mitigating the escalating costs of energy, materials, and labour.
Without these guarantees, the industry risks stagnation, unable to keep pace with global competitors or capitalise on emerging opportunities like those in Australia’s renewable energy revolution.
Unlock flexibility and energy savings with Atlas Copco’s GA FLX dual-speed compressor.
Adopting the latest technology is essential for the seamless operation of any manufacturing business. The new GA FLX dual-speed compressor from Atlas Copco represents a leap forward, offering efficiency and flexibility.
Compressed air is vital across various industries, from inflating balloons and tyres to food processing, pharmaceuticals, and even the production of electronic devices. The right compressor can have a good impact on your operational efficiency and energy costs.
Compressed air is often considered the fourth utility in the industry, following water, electricity, and gas. It’s used in numerous applications, making the selection of the right compressor crucial. Factors like flow (l/s), pressure (bar), and usage (duty cycle) play a significant role in this decision.
Screw compressors are popular in industries of all sizes due to their efficiency over traditional piston technology. Atlas Copco offers both fixed-speed and variable-speed options.
Fixed-speed compressors are reliable and easy to use, while variable-speed compressors provide energy efficiency and good control functionalities.
Imagine having the benefits of both fixed and variable-speed compressors in one unit. The GA FLX is a dual-speed, oil-injected screw compressor that operates at two speeds –Speed 1 for maximum capacity and Speed 2 to reduce energy consumption during unload.
This innovative design reduces transient and blow-off losses and can start under pressure, offering flexible pressure settings without loss of flow. These features can lead to up to 20 per cent energy savings compared to traditional fixed-speed compressors.
One of the standout features of the GA FLX is its ability to convert into a variable-speed drive (VSD) compressor with the click of a button. This can achieve up to 50-60 per cent energy savings. After 1000 hours of operation, the GA FLX provides an energy consumption evaluation, helping users calculate the ROI of switching to the VSD option.
With its patented screw element, IE5 efficient motor, and electronic gearbox, the GA FLX offers top-tier performance. Available in the 1130kW range, it comes with various options and ancillaries to meet a user’s specific needs.
The compressed air industry is moving towards energy efficiency, efficient production, and carbon emissions reduction. The GA FLX is a flexible and reliable solution that can adapt to a company’s current and future compressed air requirements.
Choose the GA FLX for a smarter, more efficient, and sustainable approach to air compressor needs.
Want to see what the GA FLX looks like in your facility? We can give you an Augmented Reality sneak peek. Just scan the QR code with your mobile device and take a look.
Pharmaceuticals, foodstuff, healthcare, chemicals and other specialised manufacturing applications have especially high demands when it comes to compressed air quality.
For these sensitive processes, KAESER Australia has released the latest class 0 oil-free compressor. Newly launched in Australia, the new CSG.1 rotary screw compressors have air flow rates ranging from 4 to 15 m³/min and pressures up to 11 bar. Customers are offered the choice of air- or water-cooling and can select an optional integrated refrigeration dryer or an i.HOC (heat of compression) dryer.
The CSG.1 can be specified as a fixed speed, fixed flow rated machine or, for applications with fluctuating compressed air demand, variable speed controlled “SFC” versions are available with IE5 Ultra-Premium Efficiency synchronous reluctance motors.
Australian customers can be assured they will receive a premium, factory-backed sales and service experience. Recently, KAESER Australia welcomed Oil-Free Product Specialists from the company’s headquarters in Coburg, Germany. Service technicians and sales engineers from across Australia gathered for in-depth training on the CSG.1 at the national head office in Melbourne.
The state-of-the-art training centre (part of KAESER Australia’s $15 million facility upgrade) saw participants receive practical training that equips them with the knowledge and skills to maximise the CSG.1’s potential for customers nation-wide.
Certified assurance
The risk of potential product contamination by oil from the rotary screw compressor is evaluated and minimised by means of an HACCP (Hazard Analysis Critical Control Point) analysis. Process validation is made easier for the customer, as KAESER’s diligence is confirmed by the TÜV Rheinland in
the form of a residual oil class 0 certificate in accordance with ISO 8573-1.
The CSG.1 has also been certified according to ISO 22000:2018, which covers the manufacture of food and beverage equipment. To further formalise the supply chain’s integrity, customers can also option the CSG.1 with Pharmaceutical, Food or Engineering Industry Certification Packages. Additionally, customers can request certification that the machine is free of silicone contamination, as per VW PV 3.10.7.
KAESER’s patented, energy-efficient Sigma Profile rotors now feature an innovative, wear-resistant PEEK coating, which results in an air end that will exhibit no air flow loss during its lifetime.
Developed in-house, the special coating has three layers; nanoceramic, PEEK basecoat and topcoat. This coating is biocompatible, FDA-certified and compliant with European requirement VO 1935 for food contact materials, making it ideal for use in the food and pharmaceutical industries.
Efficiency maximised, running costs minimised
The highest resource consumption in compressed air technology occurs over long-term operation. Accordingly, the compressed air supply must be as energy-saving as possible. For KAESER, even improving efficiency in increments of only 1 per cent is seen as a worthy development. Each increment serves to create a whole which is greater than the sum of the parts.
The search for sustainability involves state-of-theart simulation and calculation tools, together with the validation of prototypes, provide the basis for a highly efficient, dependable and resource-friendly compressed air supply.
These and other optimisation measures have enabled efficiencies to be honed even further.
The updated CSG.1 series can deliver 16 per cent higher flow rates from the same power-rated motor as previous.
The latest iteration of the integrated Sigma Control 2 (SC2) controller not only provides dependable and energy-efficient control of the compressor operation, but also enables connection to any master compressed air management system.
Furthermore, the SC2 continually monitors several sensors throughout the CSG.1 (including motor bearing temperature, winding temperatures and airend vibration) to ensure the compressor is operating within its optimal conditions at all times.
A further aim of the range’s refinement was to improve the compressor heat recovery systems. This allows the heat generated by compression to be easily incorporated into other aspects of the business, such as space or process heating, thus allowing maximum reduction in the CO² footprint.
Whether for the semiconductor, food or automotive industries, Kaeser’s two-stage dryrunning compressors tirelessly prove that processappropriate purity and cost-effectiveness can go hand in hand – even under adverse conditions.
The updated CSG.1 series sees service intervals for the compressor as well as gear oil changes extended by 50 per cent. This reduces service costs and means less materials are consumed. Many of the materials used in the manufacture of the machines are recyclable. And the product’s exceptional durability means they can serve a company for long periods of time, reducing costs and environmental impact.
Proud Sponsor of the 2024 Endeavour Awards
Our extensive range of products and services ensures we deliver quality solutions for a wide variety of motion applications.
Industries include but not limited to:
• Food and Beverage
• Manufacturing
• Logistics
• Wastewater
• Agricultural
• Mining
Products and Services include:
• Gearmotors and Gear Units
• Motors
• Decentralised
• Mechanical Variable Speed Drives
• Heavy Industrial Solutions
• Product Life Cycle Services
• Online Support
• Custom Engineered Drive Solutions
• ...and many more!
AMADA’s metal fabrication equipment is known for its safety and product range, but the inadequate enforcement of existing safety regulations for cheaper alternatives underscores the urgent need for stricter oversight and proper education.
In the world of metal fabrication, safety standards can sometimes vary.
While some manufacturers adhere to rigorous safety protocols, others offer cheaper alternatives that lack the same level of safety.
This disparity poses a risk to operators. AMADA is at the forefront for stricter safety measures and enforcement. The company provides advanced sheet metal and structural steel equipment.
AMADA offers a range of machinery, including lasers, turret punches, press brakes, robotic bending systems, welding equipment and automation solutions.
Known for its emphasis on safety and technological innovation, AMADA serves diverse industries with high-quality equipment designed for efficiency and precision.
Manufacturers’ Monthly spoke with AMADA’s national sales manager, Jan Halfar, to delve into its product range and address safety issues linked to fibre laser welding technology especially with cheaper alternative products.
“Safety is our top priority. We are committed to ensuring that no one is harmed while using our
equipment, which is a key consideration in the design of all our products,” said Halfar.
AMADA’s laser welding machines are designed to meet a range of manufacturing requirements, optimising processing efficiency and minimising production costs.
However, Halfar explained that due to the inherent risks associated with fibre laser welding machines, it’s essential for manufacturers to source machines from reputable sources and for operators to ensure their safety and safety of people around them.
“Fibre laser technology utilises a laser beam of a specific wavelength, which offers significant benefits for its applications,” he said.
“However, it also poses serious risks as exposure to this laser beam can cause irreversible retinal damage, leading to blindness among other things.
“Unlike lasers of other wavelengths, such as CO2 laser, the fibre lasers typically emit light in the near-infrared spectrum, with common wavelengths being 1064 nm (nanometres) for ytterbium-doped fibre lasers.”
Halfar said that exposure to fibre laser light can
pose many risks to the eyes, specifically, with retina damage.
“The eye’s cornea (lens) can focus this light onto the retina, potentially causing retinal burns or photochemical damage,” he said.
“Retinal damage can result in permanent vision loss or permanent blind spots. Most importantly this damage can be caused not only by a direct ‘hit’ but also by scattered reflection of the beam off another surface.”
Halfar continued to explain that there are additional risks, including potential burns to the skin and body due to the laser’s active nature.
Despite the serious health risks associated with operating fibre laser welding machines, AMADA has reported no accidents resulting in injury from its equipment.
Halfar attributes the absence of injuries to the solutions implemented by AMADA and the company’s commitment to safety.
“If an incident occurs, we are required to write a report and send it to our head office in Japan.”
“All data is collected and reported up the chain to ensure thorough documentation and review.
“We take proactive measures to address potential issues, educate customers and engineers, and ensure safety standards are maintained.
“The welding torch itself also has a sensor that ensures it must be in contact with the material before it can fire. It will also detect back reflection or incorrect beam output and again prevent the torch from firing.”
This setup prevents accidental firing, such as pointing the torch at someone’s body. Additionally, the full-size welding helmet rated for the fiber wavelength offers higher protection than laser safety glasses, according to Halfar.
“Commonly, alternative sources lack such safety mechanisms and could potentially fire if pointed inappropriately, our system ensures a higher level of safety,” he said.
Halfar explained that while the government safety regulations are mostly in place, the enforcement and pro-active oversight from the government body for workplace safety is somewhat lacking.
“Hearing stories of door knocking salesmen going around industrial parks throughout the country and offering fiber laser welder demonstrations in the middle of an office environment is preposterous,” he said.
“Many types of equipment on the market have long adhered to standardised safety requirements established over decades.
“There are some constraints and broader factors to consider, but it’s evident that this is a significant concern that requires immediate attention.”
Halfar highlighted that the absence of oversight allows some manufacturers and distributors to produce and sell equipment without ensuring thorough safety.
The authorities simply drop the liability on the operators instead of the importers.
AMADA’s clients have consistently expressed satisfaction with the safety features integrated into their products.
The company’s focus on enhancing safety has led to a range of technologies designed to protect operators and improve operational reliability.
Panelprint, an Australian-owned family business established in 1983, offers a range of services including laser-cutting, CNC punching, sheet metal fabrication, welding, powder coating, and printing.
Renowned for delivering high-quality products, the company has consistently
expanded over 40 years through investments in staff, training, and automation.
Panelprint also utilises machines supplied by AMADA.
“We chose the AMADA FLW 1500 MT Fibre Welding cell for two reasons; safety and local support,” Matt Jones, operations manager, at Panelprint.
“The interlocked cell, helmet and torch system offers a level of safety not offered by others, and the safety of our team wasn’t something we were willing to compromise on.
“Production results have exceeded our expectations, and local AMADA support is prompt as always.”
Cybersecurity expert Dawn Cappelli returns from retirement to lead Dragos’ OT-CERT initiative, poised to empower manufacturers with critical OT/ICS security resources and guidance.
Dragos is a cybersecurity company focused on safeguarding critical industrial infrastructure, particularly operational technology (OT) systems.
Dragos provides the most effective OT cybersecurity technology for industrial and critical infrastructure to deliver on our global mission: to safeguard civilisation.
With real-world experience handling landmark OT attacks, Dragos understands the complexity of industrial operations.
The Dragos Platform provides visibility and monitoring of OT environments for asset identification, vulnerability management, and threat detection with continuous insights generated by the industry’s most experienced OT threat intelligence and services team.
It discovers and monitors OT, IT, IoT, and IIoT assets within the OT environment and integrates with IT security infrastructure.
Founded by experts who have handled cyberattacks, Dragos offers threat intelligence, security platforms, and professional services to protect industries like manufacturing, oil and gas, and electric grid operations.
Dawn Cappelli, director of OT-CERT (Operational Technology – Cyber Emergency Readiness Team) at Dragos, returned from retirement to help with
that mission, and is heading to Australia to spread awareness about some of Dragos’ latest programs.
“Our mission is to safeguard civilisation, and some might say that sounds a bit corny, but we take it very seriously,” said Cappelli.
“We also recognise that small and medium organisations often lack the resources, funding, or expertise to secure their industrial infrastructure.
“Yet, these organisations are essential for our livelihoods, well-being, and the stability of our civilisation.”
Dragos offers the OT-CERT (Operational Technology Cyber Emergency Readiness Team) program, which provides free resources to help small- and medium-sized organisations build and improve OT cybersecurity programs.
“I believe there are so many organisations, especially in Australia, that could benefit from these free resources but simply aren’t aware of them,” said Cappelli.
The program includes over 50 resources, such as toolkits, templates, demonstration videos, and tabletop exercises for OT ransomware.
Cappelli, who previously worked as the chief information security officer at Rockwell
Automation, explained that Dragos approached her with the idea of creating OT-CERT, and the rest was history.
“I actually came out of retirement for this,” she said.
“After retiring from Rockwell in February 2022, Dragos approached me with the idea of creating OT-CERT, and I couldn’t resist.”
Cappelli said that these resources are sectoragnostic, allowing organisations from various industries to benefit from them.
OT-CERT is aimed at helping organisations secure their industrial environments, especially those that lack the resources, money, or expertise.
Despite targeting smaller organisations, large companies also find the resources valuable.
Dragos’ goal is to equip organisations with practical guidance on how to protect themselves from various cyber threats, such as ransomware and state-sponsored attacks.
The program reflects Dragos’ mission of “safeguarding civilisation” by supporting critical infrastructure across the globe.
“Our platform is specifically designed for industrial environments, tailored to their unique protocols,” said Cappelli.
“We know exactly what to look for in those settings.”
The cybersecurity landscape has been reshaped in recent years by escalating geopolitical conflicts and evolving cyber threats.
Increasing global tensions, exemplified by the Ukraine-Russia conflict and the Israel-Hamas war, have led to a surge in cyberattacks.
“This increased volatility has led to a growing number of attacks on critical infrastructure sectors, such as water, heating, gas, and power,” said Cappelli.
Once known for relatively simple attacks, hacktivist groups have partnered with state actors to execute more sophisticated and damaging operations.
“Previously, state actors were cautious about impacting critical infrastructure, but this line has increasingly been crossed,” said Cappelli.
“We now see both state actors and hacktivist groups targeting these vital systems.
“For instance, the CyberAveng3rs, linked to the Iranian government, and the Cyber Army of Russia Reborn, affiliated with Russia, are now executing more sophisticated attacks on water utilities.”
Ransomware attacks are also on the rise, with industrial organisations becoming prime targets.
The complexity and disruption caused by these attacks make such organisations more likely to pay ransoms, further fuelling the growth of ransomware activity.
“Industrial organisations are particularly vulnerable due to their complex recovery processes, making them more likely to pay ransoms,” said Cappelli.
In this heightened threat environment, Dragos’ Platform, services, and threat intelligence, as well as the OT-CERT program can be a vital resource among manufacturers.
Cappelli explained that as the threat landscape continues to evolve, understanding and addressing these risks is more critical than ever.
“To confront these escalating threats, Dragos delivers OT-CERT resources that offer essential, sector-agnostic tools for safeguarding any organisation,” she said.
The interconnected global supply chain amplifies cybersecurity risks, as a single compromised component can affect numerous devices and systems across various manufacturers.
The latest Dragos Year in Review highlights a nearly 50 per cent increase in ransomware attacks on the manufacturing sector in 2023, underscoring the financial and operational impacts.
The report stresses the need for strict network segmentation, improved security protocols, and a collaborative approach to cybersecurity to
address these evolving threats.
The Boston Beer Company, renowned for its iconic brands like Samuel Adams and Angry Orchard, has modernised its cybersecurity strategy with the help of Dragos.
In response to rising cyber threats and the need for robust protection of its four US breweries, Boston Beer embarked on an IT and OT cybersecurity upgrade led by CISO Brandon Catalan.
“We’re not just a beer company, we’re a manufacturing company. If we lose the ability to brew, bottle, and can, then we’re out of business,” said Catalan.
The company chose Dragos for its superior OT-native cybersecurity platform, praised for its comprehensive features, including asset visibility, vulnerability management, and intelligencedriven threat detection.
“The executive leadership team asked me what I needed. I pointed at Dragos and said, ‘I need this’,” said Catalan.
“When you really want to make a difference and you’re not willing to gamble, you go with the Cadillac. That is Dragos.”
This platform has since helped Boston Beer manage and secure its OT systems against sophisticated cyber threats, which in-turn, has given the company operational security.
Specifically, the platform automates the identification, management, and monitoring of all OT, IT, IoT, and IIoT assets using data from over 600 protocols, network data, and logs for enhanced security and operational efficiency.
It provides unique, enriched, and prioritised guidance for managing vulnerabilities throughout their lifecycle, focusing on high-priority issues to reduce risk, minimise downtime, and efficiently allocate resources.
“The platform categorises vulnerabilities based on their criticality. Vulnerabilities categorised as ‘Now’ in the Platform are actively exploited and need urgent attention,” said Cappelli.
“‘Next’ vulnerabilities are serious but can be addressed during scheduled maintenance.
‘Never’ vulnerabilities are rarely exploited and pose minimal risk.
“This categorisation helps users focus on the most critical issues, saving time and reducing headaches.”
Additionally, the program can detect and analyse malicious activity in ICS/OT networks with precision.
“We know what the behavioural patterns of various threats look like, including how different threat actors infiltrate and compromise industrial environments,” said Cappelli.
“We incorporate this knowledge into our platform to detect such threats and notify our customers.”
The platform ultimately assists in pinpointing the root causes of operational problems, managing assets with up-to-date network schematics, and resolving operational challenges.
“When we acquired breweries, we integrated their legacy networks into our legacy network, and we had very little documentation of asset inventories and network designs,” said Catalan.
“Once we got the Dragos Platform up and running, we got a better picture of what our networks actually looked like.
“Our 30,000-foot view came into focus, and we could see where we needed to make changes. Before Dragos, it was guessing at best.”
Eventually, Boston Beer successfully aligned IT and OT teams, leadership, and the board on the critical need for securing OT environments.
The company achieved a 15 per cent yearover-year reduction in cybersecurity insurance premiums and realised a 100 per cent return on investment within the first year of a five-year commitment.
As cyber threats continue to evolve, Dragos’ OT-CERT program offers manufacturers resources and guidance to enhance their cybersecurity.
The program has demonstrated effectiveness in real-world applications, such as with the Boston Beer Company, showcasing its potential to strengthen operational security.
By providing tools and expertise tailored to industrial environments, Dragos aims to support organisations in addressing their cybersecurity needs.
Manufacturers’ Monthly delves into how the Kito EQ electric chain hoist redefines manufacturing standards, with its features driving improvements in efficiency, safety, and productivity.
In today’s fast-paced manufacturing environment, reliable, efficient, and safe lifting solutions are essential. The Kito EQ electric chain hoist offered by Kito Crosby Australia offers features that enhance operational efficiency, ensure safety, and boost productivity. This editorial delves into the key attributes and benefits of the Kito EQ electric chain hoist, providing a comprehensive understanding of its capabilities and practical applications.
Advanced features of the Kito EQ Electric Chain Hoist
The chain hoist is engineered to meet the demands of modern manufacturing. Key features include:
1. Inverter control system – this ensures smooth and precise load handling with variable speed control, reducing load bounce and enhancing positioning accuracy. The inverter also optimises motor performance, contributing to energy efficiency and lowering operational costs, allowing the adjustment of the lifting speed to suit the application.
2. Lightweight and compact design, which facilitates easy installation and reduces the strain on supporting structures, allowing for greater flexibility in tight spaces.
3. High-duty cycle motor, which is designed for heavy-duty operation. It can withstand demanding work environments, ensuring reliable performance over extended periods with reduced maintenance needs.
4. Its dual-speed operation provides the flexibility to choose between fast and slow lifting speeds, and is ideal for handling delicate or sensitive loads. Speeds can be altered to match job requirement.
5. Triple safety mechanisms that are equipped with an electronic overload limiter, friction clutch, and upper/lower limit switches to prevent accidents and protect both the operator and the equipment.
6. Enhanced operator comfort and efficiency. The ergonomic push-button pendant allows for easy one-handed operation, is IP65 rated for dust and water resistance, and features an emergency stop button for added safety.
Enhancing efficiency in production
Efficiency is paramount in manufacturing, and the Kito EQ hoist’s inverter control system is designed to enhance production processes.
With adjustable dual lifting speeds, operators can choose the optimal speed for each task, ensuring both precision and efficiency.
The system’s overload protection features further safeguards equipment and loads, minimising interruptions and improving workplace safety.
The “No-load high-speed” function accelerates operations by allowing the hoist to run at 130 per cent speed when carrying less than 30 per cent of its rated load. Coupled with the CH meter (counter/hour meter), which enables precise maintenance planning, these features reduce the risk of unexpected breakdowns and ensure that maintenance occurs only when necessary. This combination optimises workflow, minimises downtime, and keeps the hoist operating at peak performance.
Additionally, the lightweight and compact design of the Kito EQ allows for quick and easy installation, integrating smoothly into existing production lines with minimal disruption.
Glenn Morgan, Kito Crosby Australia’s national hoist specialist, highlighted the importance of these features.
“The dual-speed operation allows for fast and precise load handling, significantly increasing throughput and minimising downtime,” he said.
Safety is paramount in manufacturing. This hoist incorporates several features that enhance operational safety and protect personnel and equipment. The emergency stop button provides immediate halting of operations in case of an emergency, while the overload limiter prevents the hoist from lifting loads beyond its rated capacity.
The upper and lower limit switches ensure that the hoist operates within safe limits, preventing the load from being lifted too high or lowered
too far. These switches protect the hoist’s components and prevent accidents caused by overtravel. Additionally, the smooth and precise load handling facilitated by the inverter control system reduces the risk of load bounce, which can cause injuries and damage to materials.
Morgan emphasised the importance of these safety features.
“Safety is our top priority. The built-in safety mechanisms in the Kito EQ hoist are designed to protect operators and equipment, ensuring a safe working environment” he said.
Productivity is the cornerstone of successful manufacturing operations, and the Kito EQ electric chain hoist plays a pivotal role in boosting productivity. The dual-speed operation allows for faster lifting speeds when handling fewer delicate loads, reducing cycle times and increasing output. The precise load handling enabled by the inverter control system minimises the need for manual adjustments, streamlining operations and reducing the time spent on each task.
The hoist’s high-duty cycle motor is designed to handle demanding production schedules, ensuring reliable performance with minimal interruptions. This durability leads to a more consistent workflow, while the reduced maintenance requirements and extended service life further enhance productivity by minimising downtime for repairs and upkeep.
In an era prioritising sustainability, this chain hoist offers an economically sustainable solution, delivering substantial long-term returns for manufacturers.
1. Energy efficiency: The inverter control system optimises motor performance, reducing energy consumption. Lower energy use decreases operational costs and environmental impact, aligning with sustainability goals and regulations.
2. Durability and reduced maintenance. The Kito EQ’s high-duty cycle motor and robust construction mean fewer breakdowns and less frequent maintenance. This durability lowers maintenance costs and reduces downtime, ensuring heavy-duty productivity.
3. Reduced replacement frequency. The extended lifespan of the Kito EQ reduces the need for frequent replacements, saving on capital expenditure. Investing in durable equipment allows manufacturers to allocate resources to other critical areas, fostering innovation and growth.
4. Minimised downtime. With its reliable performance and lower maintenance needs, the Kito EQ ensures minimal operational interruptions. Long-term operation without frequent halts for repairs or maintenance enhances overall productivity and efficiency, translating to higher output and profitability. Morgan highlighted the economic advantages.
“Our hoists are built to the highest standards, resulting in minimal breakdowns and repairs, which translates to significant cost savings over time. This reliability makes a substantial difference in the long run.”
The versatility of the chain hoist makes it suitable for a range of applications in the manufacturing sector. Its compact design and lightweight construction allow it to be used in various settings, from large-scale industrial plants to smaller workshops. The precise load handling and variable speed control make it suitable for tasks that require delicate or sensitive lifting, such as handling electronic components or assembly line work.
In heavy-duty applications, the high-duty cycle motor and robust construction of the Kito EQ ensure reliable performance. The hoist can handle heavy-duty operations in demanding environments, such as metal fabrication, automotive manufacturing, and heavy machinery production. The enhanced safety features make it a trusted choice for operations where safety is a critical concern, such as chemical processing plants and pharmaceutical manufacturing.
“From an end-user point of view, quality and durability are paramount,” said Morgan.
“End users should specify Kito hoists because they offer lower runtime costs and increased productivity.”
Investing in the Kito EQ streamlines operations, protects personnel and equipment, and boosts productivity.
In a competitive industry, the Kito EQ meets efficiency, safety, and sustainability needs. Its energy efficiency, durability, and reduced maintenance make it a smart investment. Manufacturers benefit from long-term cost savings, increased reliability, minimised downtime, and staying ahead in a changing industry.
“We have always insisted on making highquality products designed to last and maximise safety,” Morgan concluded,
“Kito Crosby is dedicated to creating the safest possible products for the industry, and I believe we are the best at doing this.”
For sales and service support contact your nearest BOGE partner
Manufacturers’ Monthly spoke with ELGi Equipments, a leader in air compressors renowned for its innovative, technologically advanced systems that maximise customer productivity while minimising ownership costs.
Air compressor manufacturers ELGi offers a portfolio of more than 400 products and accessories, including a range of compressors tailored to meet the diverse needs of various sectors within the manufacturing industry.
The company has built a strong brand through strategic partnerships with global leaders, product innovation driven by in-house research and engineering, and a customer-centric approach.
“ELGi has always had ambitious aspirations, which are deeply embedded in our company ethos,” said Mark Hollingsworth, managing director at ELGi Australia.
“Our philosophy is centred around delivering superior value, which aligns with our commitment to our customers.
“We focus on developing products with the best lifecycle costs, ensuring that our customers experience the lowest total cost of ownership.”
Founded in 1960 as a producer of air compressors and garage equipment, ELGi has expanded its product range and adapted to shifting market demands.
“We made a strategic decision in 2011 to establish direct presence and grow our footprint in the Australian market.
For 50 years since we’ve been focusing on providing an array of advanced and compressed air
systems to our customers,” said Hollingsworth.
“We set up operations in Sydney and have since expanded through key partnerships with dealers and distributors,” explained Hollingsworth.
“Since our direct entry into the market, we acquired a company early on to strengthen our East Coast coverage and have continuously grown our distribution network.
“Many of our distributors have been with us for 13 years, reflecting the quality and market demand for our products.
“We have thousands of satisfied customers and continue to build on that success.”
The company is committed to delivering highvalue, high-quality products that meet the needs of its customers.
With more than 400 products in its range, ELGi ensures that there’s always a solution available, no matter the context.
The company does not follow a one-size-fits-all approach; instead, it provides specific products tailored to customer needs, whether it’s a standard fixed-speed compressor or an energy-saving variable frequency drive machine.
ELGi places emphasis on understanding customer requirements, dedicating time to sales training
to ensure the right products are selected to meet those demands effectively.
“Our distributors cover a wide range of industries, from manufacturing to food and beverage, and some specialise in sectors like resources, healthcare, and pharmaceuticals,” explained Hollingsworth.
“We’re particularly growing in the pharmaceutical and medical sectors, especially with our oil-free product range, which is crucial for these industries.
“While some distributors focus more strongly on certain sectors, ours are equipped to handle all industries.”
Hollingsworth expressed pride in the satisfaction of many ELGi customers with the quality of their products.
“From my visits to customers, it’s clear that they are very satisfied with our products. Initially, some customers felt they were taking a bit of a risk with us, but we’ve always stood by our products,” said Hollingsworth.
“We ensure that spare parts are readily available through our dealers and head office locations, which reassures our customers.
“Once they’ve invested in our compressors, we often see them returning to upgrade or purchase additional units, especially on larger sites.”
Hollingsworth explained that one of the points of
difference that ELGi has, is its ability to predict the needs of its customers and look to the future.
“We’re always looking ahead, understanding that the market’s future needs might differ from today’s requirements,” he said.
“We’re not just focused on what customers need now, but also on anticipating what they’ll need in the future, even if they don’t realise it yet.
“That’s why we’re continually developing products that challenge the status quo.”
In 2019, ELGi won the prestigious Deming Prize for its commitment to quality and Total Quality Management (TQM) excellence.
“Quality is at the heart of everything we do, driving the reliability of our product offerings and ensuring we meet the needs of our customers – both for today and for the future,” said Hollingsworth.
ELGi is on a growth trajectory, continually expanding its global presence and offering a product range that offers innovation and performance.
The company’s products are designed to meet the needs of customers today and anticipate their future requirements – often before customers even realise them.
ELGi is always looking ahead to identify the next solutions that will be essential for its customers.
“People recognise that by offering an industry leading warranty and long-term support for products signals high quality and justifies the investment,” said Hollingsworth.
“ELGi’s commitment to support includes having products and spare parts readily available, as well
as providing technician training.
“Both globally and locally, ELGi strives to be ‘always better,’ reflecting its dedication to excellence in the market because when reliability matters most ELGi compressors have
Manufacturing in Australia has undergone significant transformation over the years, which has reshaped the industry’s landscape, driven by the need for efficiency, quality, and innovation.
Understanding Manufacturing in Australia
From traditional methods to advanced technologies, the manufacturing sector continues to evolve, reflecting the dynamic nature of the global economy.
Manufacturing is a cornerstone of the Australian economy, contributing significantly to GDP, employment, and exports.
It supports a diverse range of industries, from food and beverages to advanced machinery and pharmaceuticals.
The sector’s role in providing high-quality jobs and reducing reliance on imports underscores its economic importance.
By investing in manufacturing, Australia can enhance local production capabilities and strengthen its position in the global market.
Louis Quintal, the new head of manufacturing at RSM, explained that investing in manufacturing in Australia can prove beneficial for the country.
“By investing in manufacturing, Australia can reduce its reliance on imports, boost local production, and create high-quality jobs,” he said.
“Manufacturing today is not just about producing goods. It encompasses a wide range of activities, including research and development, design, production, distribution, and after-sales services.
“Modern manufacturing leverages cuttingedge technologies and lean manufacturing such as automation and artificial intelligence to enhance efficiency and innovation.”
Quintal continued to explain that this holistic approach to manufacturing ensures that the sector remains competitive and sustainable in the global market.
The concept of lean manufacturing emerged in the mid-20th century, particularly with the Toyota Production System (TPS), which aimed to eliminate waste and optimise processes.
“Lean manufacturing focuses on creating more value for customers with fewer resources by identifying and eliminating non-value-adding activities,” said Quintal.
Understanding what the customer values and focusing efforts on enhancing these aspects:
• Analysing the flow of materials and information to identify and eliminate waste.
• Ensuring that production processes flow smoothly without interruptions.
• Producing only what is needed, when it is needed, to reduce inventory costs.
• Encouraging a culture of ongoing improvement at all levels of the organisation.
Implementing lean manufacturing has led to significant improvements in efficiency, quality, and customer satisfaction.
“Companies that have successfully adopted lean principles report reduced lead times, lower costs, and higher employee engagement,” said Quintal.
Lean manufacturing is increasingly becoming a key focus point and requirement for manufactures because of the pressures regards cost of living, higher labour and energy costs in Australia when compared to their neighbouring countries in the region.
Technology has played a pivotal role in modern manufacturing, with advancements such as automation, robotics, and digitalisation driving significant changes.
These technologies have improved planning, scheduling, and shop floor operations, leading to increased productivity and reduced costs.
However, the integration of technology has also raised concerns about cybersecurity and the potential displacement of human workers.
“Technology has been a game-changer in the manufacturing sector, driving advancements in automation, data analytics, and connectivity,” explained Quintal.
Quintal explained that there are several different aspects of technology innovation that is used and currently been developed which the Australian manufactures are making use of some of these include:
• Automated systems and robots have revolutionised production lines, increased speed, precision, and safety while reducing labour costs.
• Internet of Things devices enable real-time monitoring and control of manufacturing processes, leading to improved efficiency and predictive maintenance.
• Artificial Intelligence machine learning algorithms optimise production schedules, quality control, and supply chain management.
• Predictive analytics by creation of digital twins of physical assets, enabling simulation and analysis to optimise performance and predict failures.
“These technological innovations are transforming Australian manufacturing by enhancing efficiency, precision, and safety,” said Quintal.
Quintal explained that there are leading companies in various manufacturing sectors have set industry benchmarks through their innovative practices and strategic approaches.
He highlighted key lessons from these companies:
• Embrace continuous improvement: The commitment to ongoing, incremental enhancements can result in substantial long-term gains.
• Invest in technology: Adopting and integrating advanced digital technologies is crucial for maintaining a competitive edge.
• Focus on quality: Prioritising rigorous quality control and precision engineering underscores the importance of delivering reliable and high-quality products.
• Sustainability matters: Incorporating sustainability into manufacturing processes can drive innovation and attract environmentally conscious consumers.
• Employee engagement: Fostering a culture of engagement and empowerment among employees at all levels promotes innovation and accountability.
These technologies are not only enhancing productivity but also driving innovation and sustainability in the manufacturing sector.
“Manufacturing giants have provided valuable lessons in innovation, growth, resilience, and operational excellence,” said Quintal.
“Some have shown the importance of continuous improvement and risk management. However, they can also demonstrate the consequences of complacency and a lack of adaptability.
“The manufacturing process has evolved through various stages, each marked by its own set of challenges and opportunities.”
Quintal explained that implementing lean manufacturing principles, harnessing the power of technology, and learning from the experiences of manufacturing giants are crucial for achieving sustainable success in this ever-evolving industry.
Continuous improvement, a focus on innovation, and a commitment to operational excellence remain the cornerstones of a robust manufacturing sector in Australia.
“To remain competitive, we must embrace automation, AI, and predictive analytics in our production processes,” said Quintal.
“These tools provide the data and insights needed to identify where and when to make improvements, whether in automated systems or manual operations.
“Predictive analytics is crucial—it empowers us to make informed decisions and drive meaningful changes.”
Over the past year, Lightforce Group has cemented its status as a premier designer, innovator, and manufacturer of military and law enforcement solutions, showcasing our dedication to South Australia’s manufacturing goals.
Join us at the 2024 LandForces International Land Defence Exposition! Visit Site A069 to discover our groundbreaking solutions and engage in impactful discussions.
FIN Windows & Doors partners with Capral Aluminium to source Australian-made components, ensuring high-quality custom windows and doors for Newcastle, Central Coast, and Hunter Valley customers.
Based in Newcastle, FIN Windows & Doors (FIN) has been at the forefront of custommade aluminium windows and doors since 1968.
Serving the Newcastle, Central Coast, and Hunter Valley regions, it prides itself on delivering highquality, bespoke solutions tailored to the unique needs of its residential and commercial clients in the area.
Vital to its success is a partnership with Capral Aluminium, ensuring the premium Australian-made components that define its products.
“We want to pride ourselves on being very good at manufacturing windows and manufacturing to the highest standard,” said Jeff Picton, general manager at FIN Windows & Doors.
Founded in 1968 by the Drinkwater family, FIN is known for being ‘First in Newcastle.’
Picton noted that the company’s primary clients –SMEs and homeowners – value FIN’s service highly. With more than 55 years of experience, the FIN team prides itself in providing reliable service and quality products.
The team also takes pride in offering a tailored approach for each project, addressing the unique
needs of every customer.
“We like to be individual and treat everyone differently – in that way they’re treated, the way they need to be treated, and get the product that they need for their home,” Picton said.
“When someone comes in with questions, we make sure to take the time to understand their specific needs and requirements for their home. We focus on helping them achieve their goals.”
The company also offers an onsite delivery and installation service for its clients. While it doesn’t handle installation directly, the company partners with skilled carpenters to ensure windows are installed by professionals.
The company produces all of its products in-house, using advanced machinery such as CNC routers and up-cut saws, ensuring precision and consistency.
One example of FIN’s successful projects is its ongoing relationship with Candor Homes, an Australian builder located in Greater Newcastle area of NSW.
Candor Homes is a family-owned Australian builder
offering personalised, high-quality new homes, knockdown rebuilds, as well as house and land packages.
“They have developed properties across the Hunter region, from Huntlee to Newcastle and Lake Macquarie, including multi-developments,” said Picton.
Since 2018, FIN has supplied Candor with highquality aluminium products, contributing to various developments across the Hunter region.
This collaboration underscores the trust and quality associated with FIN’s offerings.
“We’ve supplied them from day one, and that relationship has been great,” said Picton.
Capral Aluminium’s support and contributions
To uphold its high standards and meet the diverse needs of its clients, FIN has recognised the importance of partnering with key industry leaders.
To ensure the highest quality in their custom aluminium solutions, FIN has forged a strategic partnership with Capral Aluminium.
The product range fostered by this relationship includes AmpliMesh security screens, windows, doors, and flyscreens.
In addition to its commitment to Australianmade products, FIN is dedicated to advancing its environmental goals.
Capral Aluminium has been instrumental in supporting these objectives by providing LocAl Aluminium, which aligns with FIN’s sustainability efforts.
“We aim to keep costs low and minimise our environmental footprint. Working with Capral and their low carbon aluminium, we’re all making a conscious effort to improve our products sustainably,” said Picton.
“We didn’t sign up separately for low carbon aluminium because Capral includes it as part of their standard range.
“All products in our Urban, Urban Plus, and AmpliMesh ranges use low carbon aluminium. Not only is it locally sourced, but it also helps us reduce our carbon footprint in production.”
FIN initially collaborated with Capral Aluminium on the Genesis range of architectural windows, contributing to both the manufacturing and development processes.
This partnership enabled the distribution of the product across key regions, including Sydney and the Hunter Valley.
“We’ve been with Capral for about 16 years, and they’ve been fantastic with their support. We get deliveries from them almost every day.”
This support has been crucial for multi-unit developments, with Capral playing a key role in their successful execution.
“We’ve got windows supplied by Capral that’s all to the standards that we need to achieve to be able to supply these multi-reses, as we call them,” said Picton.
As Picton highlights, Capral’s support extends beyond supplying high-quality materials. Its consulting services have proven invaluable, particularly when FIN undertook the task of designing a new showroom.
“Ian Burnett, or Rocky, as we like to call him – he’s our rep,” said Picton
“He’s very helpful any time we need anything from Capral.
“Ian’s always there and available to us to assist in things if there’s something damaged or if we’ve cut something incorrectly.”
Going above and beyond FIN was assigned the task of constructing a showroom. However, as Picton noted, the company had limited experience in this area.
This is one example where the company utilised the support of Capral.
“We needed to set up a new showroom and inquired if they could assist with its design, as we had very little experience or knowledge in showroom design,” said Picton.
“The showroom design options provided by Capral included one that was ultimately chosen from two proposals.
“Capral’s design was crucial in creating an impressive showroom that effectively displays the product and accurately represents what customers will receive, and their support throughout the process has been greatly appreciated.”
Additionally, most tools utilised in FIN’s manufacturing facility is sourced directly from Capral.
This has enabled FIN to produce products of which the company is proud.
“Capral has supplied the tooling throughout our factory, which is fantastic. The tooling is of high
quality – very accurate and user-friendly,” said Picton.
“We are producing windows more efficiently now.
“They’re quality products that we can put out the door and be proud of.”
Apart from its custom aluminium windows and doors catalogue, Capral also offers a range of standard and custom powder-coated colours.
Capral’s new powder-coating facility in Sydney has offered many benefits to FIN.
“Capral’s new powder-coating line in Sydney has been a tremendous asset for us. It has significantly reduced our lead times, allowing us to complete jobs more quickly,” said Picton.
“This improvement means our customers are much happier, which is our ultimate goal. It all starts with Capral’s excellent organisation and their ability to supply what we need promptly.
“The new powder-coating line is impressive and has greatly enhanced our efficiency and customer satisfaction.”
Ultimately, the long-standing partnership between FIN and Capral has contributed to the company’s success.
By using Capral’s high-quality aluminium and low-carbon products, FIN ensures top-notch custom solutions for its clients while staying true to their environmental commitments.
This collaboration continues to drive the company’s ability to deliver exceptional products and services across their service areas.
If you’re interested learning more about how Capral enables FIN, please scan the QR code below to see the latest addition in the ‘Crafted with Capral’ series.
Exclusive insights into the top manufacturers in Australia.
IBISWorld’s Top 100 Manufacturers list, based on these companies’ financial performance in 2023, identifies key players in the sector and their strategies during recent economic volatility.
IBISWorld has unveiled its Top 100 Manufacturers List for 2024, comprising companies that together generated $357.0 billion in revenue, up from $345.2 billion the previous year. Representing 62 different industries – ranging from food and beverage, wood and metal, building and chemical products, to transport equipment – this list captures the breadth of Australia’s manufacturing sector.
The Pharmaceutical Product Manufacturing industry is the most represented by the number of companies, with six making the list, including CSL Limited, which ranks 5th overall. However, in terms of revenue, the Petroleum Refining Fuel Manufacturing industry dominates, generating $57.9 billion during the year. This list reflects the diversity and economic impact of Australia’s top manufacturers.
• Manufacturers dealt with headwinds like fluctuating commodity prices, supply chain disruptions and rising operational costs.
• Revenue changes for many top manufacturers are closely tied to price fluctuations for key inputs like milk, sugar, crude oil and gold.
• Railway transport manufacturer and maintenance provider Alstom Transport Australia recorded the strongest growth, benefiting from an acquisition of one its major rivals as well as a number of large-scale transport contracts.
Alstom Transport Australia Holdings recorded the strongest growth among Australian manufacturers, with its revenue surging 81.5 per cent to $1.2 billion in the year to March 2023. This performance is primarily due to Alstom’s involvement in several major transport projects.
The company’s participation in the Queensland New Generation Rollingstock project has boosted its revenue.
Contracts for Electric Multiple Unit trains and rail cars in Perth and Adelaide and VLocity Diesel Multiple Units in Melbourne also elevated its
revenue. These large-scale contracts have raised demand for Alstom’s manufacturing and repair services for trains, trams and light rail vehicles.
By securing contracts for these critical transport initiatives, Alstom has positioned itself as a key player in modernising Australia’s transportation network.
This has ensured a steady stream of revenue for the company and has solidified Alstom’s position as an industry leader.
The start of the Russia-Ukraine war in 2022 caused a surge in crude oil prices. Despite remaining volatile throughout 2023, crude oil prices fell from the high recorded in 2022. These lower prices weighed on the performance of petroleum refiners Ampol Limited and BP Australia Investments Pty Ltd. Revenue for Ampol, the largest manufacturer in the country, only fell slightly due to a drop in refined petroleum prices and a decline in demand from its convenience channel.
Refined petroleum prices in Australia fell 11.3 per cent over the 2023 calendar year, according to data from the ABS. At the same time, Ampol’s sales volumes in Australia rose 11.0 per cent.
It was a different story for BP Australia, as both volume and price declines caused the company’s revenue to fall 18.9 per cent in the year to December 2023.
Although falling petroleum prices weakened revenue for these manufacturers, gold performed well.
The price for the precious metal, which is generally seen as a safe haven asset, escalated amid growing investor uncertainty.
The combined impact of persistent, high global inflation, a weakening US dollar and rising geopolitical tensions in Europe and Asia contributed to a boost in demand for gold. In addition, central banks in various countries increased their gold reserves, further driving up prices. These trends supported revenue rises for Gold Corporation (trading as The Perth Mint) and Pallion Group, the second and tenth largest manufacturers on the list, respectively.
Food and beverage manufacturers account for just over 20.0 per cent of revenue on the list. Revenue from these companies collectively grew 9.0 per cent in 2022-23, almost triple the combined revenue growth of all companies on the list of 3.3 per cent. Sharp increases in major food commodity prices can largely explain this contrast.
A near three-decade low in raw milk supply drove a 31.3 per cent surge in farmgate milk prices, which reached a record high of 74.8 cents per litre in 2022-23. Falling raw milk production weakened dairy product volumes, but processors passed the higher farmgate prices on to customers. That’s why the three dairy product manufacturers in the Top 100 – Bega Cheese Limited (23rd), A.C.N. 166 119 133 Pty Ltd (trading as Saputo Dairy Australia)
(28th) and Lactalis Australia Pty Ltd (37th) – saw revenue increases of 12.7 per cent, 8.1 per cent and 12.8 per cent respectively.
Poultry meat is the number one consumed meat in Australia. The three largest poultry processors in the country all feature on the list of Top 100 manufacturers in Australia: Inghams Group Limited sits at number 27, Baiada Poultry Pty Limited at number 45 and Turosi Pty Ltd at number 76. Australian poultry production only edged up 1.1 per cent in 2022-23. However, sharply rising costs for farmers – especially for feed, utilities and employment – saw poultry processors ramp up the prices they charged wholesalers and retailers. Despite the strong price rises, per capita poultry meat consumption remained relatively stable, boosting processors’ revenue. Revenue for Inghams rose 12.4 per cent, while Baiada Poultry’s climbed 4.2 per cent and Turosi’s lifted 10.7 per cent.
Sugar also experienced price increases. Weak production in India and Thailand, which together account for one-quarter of global sugar output, led world sugar prices to skyrocket 27.0 per cent in the 2023 calendar year. Two sugar manufacturers, Wilmar Sugar Australia Limited and Queensland Sugar Limited, come in at number 32 and 60 on the list, respectively, both having benefited from the global price increases. Wilmar Sugar’s revenue grew 18.1 per cent, even though its raw sugar production remained stable at around 2.1 million tonnes. Queensland Sugar’s revenue jumped 34.7 per cent over the 2022-23 financial year. The company’s rising raw sugar sales volumes, which leapt 21.4 per cent from 1.4 million tonnes to 1.7 million tonnes, as well as increased prices in the second half its reporting period, supported its revenue growth.
The Grain Mill and Cereal Product Manufacturing industry is represented by six companies on the list this year, which all recorded double-digit percentage revenue growth. Similarly to sugar manufacturers, rising global prices and increased production aided these manufacturers’ revenue. Australian wheat and coarse grain harvests reached record or near-record levels in 2022-23, and while this would typically place downwards pressure on prices, tight global supplies due to the Russia-Ukraine war hiked prices during the year. Manufacturers passed these higher costs on to their customers, thereby lifting revenue. For example, flour and grain mill manufacturer Cajosa Pty Ltd (trading as Manildra Group) (38th), which derives around half its revenue from international markets like the United States and Japan, saw its revenue rise 21.7 per cent. PFG TopCo1 Pty Ltd (trading as Allied Pinnacle) (84th), a major premixed bakery product manufacturer, had revenue growth of 14.3 per cent.
Rising energy prices have hiked costs for manufacturers, including manufacturers of building construction products like concrete and cement. In addition to rising energy expenses, these manufacturers faced higher costs from labour shortages, which they passed on to their customers.
Cement and lime prices rose 11.7 per cent in 2022-23, while concrete prices rose 15.5 per cent, and rising demand throughout the year also had a two-fold effect on revenue. Strong demand from non-residential building construction – largely from government infrastructure projects like the West Gate Tunnel Project in Victoria, WestConnex in New South Wales and the Tonkin Gap project in Western Australia – outpaced declining demand from the residential construction market. Furthermore,
increasing demand from these projects put pressure on supply throughout the year, lifting prices.
Building material manufacturers feature throughout the list. These include concrete, aggregate and cement manufacturers like James Hardie Industries Public Limited Company (16th), Boral Limited (21st), Hanson Australia (Holdings) Proprietary Limited (36th), Holcim Participants (Australia) Pty Ltd (41st) and ADBRI Limited (47th). These companies’ combined revenue rose 10.5 per cent, to $15.7 billion. Holcim Participants (Australia) and Boral recorded the strongest revenue rises of these companies, up 18.8 per cent and 17.8 per cent, respectively. Boral reported revenue growth across all its product segments, including 20.0 per cent growth in concrete, where the company reported 6.0 per cent volume growth and 12.0 per cent growth in prices. Holcim Australia’s acquisition of ready-mix concrete manufacturer Vic Mix Pty Ltd in September 2023 bolstered its revenue.
Rising geopolitical tensions in the Asia-Pacific region, as well as the ongoing war in Ukraine, have supported revenue growth for defence manufacturers in Australia. These tensions have fuelled demand for military equipment, technologies and services, enabling local manufacturers to secure substantial financial gains. The emphasis on strengthening defence capabilities has also spurred international collaborations, like AUKUS, further enhancing
revenue streams for Australia’s Defence industry. Consequently, the Australian Government has ramped up defence spending, leading to lucrative contracts for Australian defence firms.
Companies like BAE Systems Australia Holdings Limited (48th) and ASC Pty Limited (89th), which are major shipbuilders in Australia, benefit from long-term, often multibillion-dollar projects. Heightened tensions in the South China Sea in recent years have increased the need for naval fleet upgrades, which helped support rising revenue for these companies in 2022-23.
Leveraging the capabilities of Australia’s manufacturing and mining sectors will be essential in the transition to net zero greenhouse gas emissions by 2050. Australia is a leading producer of copper, zinc and lead, and these metals are crucial to the renewable energy transition.
The Copper, Silver, Lead and Zinc Smelting and Refining industry was worth $4.5 billion in 202223, and two companies – Sun Metals Holdings Limited (69th) and Nyrstar Australia Pty Ltd (87th) – have made it on IBISWorld’s list of the Top 100 Manufacturers. These companies run Australia’s only two zinc refining plants, and zinc is essential for protecting solar panels and wind turbines from corrosion and for reducing carbon emissions in battery production.
Sun Metals’ revenue grew 6.9 per cent over the year to December 2023, to reach $1.0 billion*. Nyrstar Australia experienced similar growth of 5.1 per cent over the 12 months through September 2023. Although zinc prices declined over both of these companies’ reporting periods, strong demand for zinc –especially in overseas markets like the United States, China and other countries in the AsiaPacific region – bolstered revenue growth. Nyrstar Australia also refines lead, a key input in battery manufacturing.
Australia’s Top 100 manufacturers span a diverse range of industries. Rising input prices, which were passed on to customers, drove revenue shifts. For instance, elevated milk and sugar prices fuelled strong gains for processors like Bega Group and Queensland Sugar, while gold producers like Pallion and concrete giants like Boral also saw revenue boosted from price hikes. On the flip side, falling refined petroleum prices led to a steep revenue drop for BP Australia.
However, price fluctuations aren’t the only factor at play. The biggest mover, Alstom Transport Australia Holdings, surged thanks to its acquisition of rival Bombardier Transportation Australia Pty Ltd and ongoing state government contracts. Additionally, manufacturers like Sun Metals and Nyrstar Australia have thrived amid the green energy transition, as their zinc products have been in high demand for solar panels, wind turbines and batteries.
*Sun Metals reports in US dollars, but this figure represents the Australian dollar amount.
The Industry Capability Network connects local suppliers with projects via its Gateway by ICN platform, promoting Australian manufacturing and supporting the Future Made in Australia Act to boost economic growth and sustainability.
Industry Capability Network (ICN) is an independent organisation aimed at connecting local suppliers with projects across Australia and New Zealand.
The principal objective of the ICN is to promote and facilitate the participation of Australian and New Zealand industries in supplying products and services for projects that offer economic benefits.
ICN achieves this by acting as an intermediary, addressing market failures in buyer-seller transactions.
This role includes helping local suppliers gain fair opportunities to compete for public and private projects and assisting purchasers in finding suitable suppliers.
ICN also supports government initiatives by ensuring local participation in infrastructure, defence, and resource projects.
Through its online platform, Gateway, ICN enables businesses to register capabilities and search for relevant projects.
On the project side, Gateway helps project managers to find suppliers that meet their needs while encouraging local companies to expand
their networks and enhance their business prospects.
“Our primary role is to support local industries by facilitating fair and reasonable access to projects and opportunities, ultimately fostering economic prosperity and local jobs,” explained ICN general manager, Louise Wakefield.
By fostering partnerships between government bodies, industry leaders, and local suppliers, ICN plays a vital role in boosting domestic manufacturing capabilities and ensuring Australian businesses are competitive in global markets.
Earlier this year, Prime Minister Anthony Albanese introduced the Future Made in Australia Act, a new legislative framework aimed at enhancing local manufacturing and driving economic growth.
Wakefield explained that ICN can play a crucial role as a delivery partner for the Future Made in Australia Act by leveraging its network and expertise to support the Act’s objectives.
“Our role within Future Made in Australia is to serve as a gateway for local businesses, providing
access to vital information and opportunities driven by government policy,” she said.
“With over 40 years of experience, we are wellpositioned to take on this responsibility.
“ICN is ideally positioned to help businesses identify complementary capabilities or direct supply opportunities for specific projects.”
Unveiled at the Queensland Media Club earlier this year, the Act includes a $22.7 billion investment over the next decade into key areas such as renewable hydrogen, green metals, critical minerals processing, and clean energy manufacturing.
The strategy features a National Interest Framework to guide public investment, focusing on net zero transformation and economic resilience.
Throughout its history, ICN has facilitated more than $53 billion worth of projects for Australian and New Zealand companies.
“This success is largely attributed to our core platform, Gateway by ICN, and our Industry Specialists, who assists project proponents in breaking down large-scale initiatives into smaller,
manageable work packages,” said Wakefield.
Wakefield explained that this approach enables small businesses to bid on and secure these packages, ensuring fair distribution of opportunities.
“Building on this, we are ready to be a key delivery partner for the Future Made in Australia policy by focusing on maximising local content and strengthening supply chains in key priority areas,” she said.
“We are also committed to reducing Australia’s reliance on overseas products and services.”
Aligning with the Act’s goal of boosting domestic green manufacturing, ICN can help companies integrate and align with these sustainability objectives.
“Additionally, we play a significant role in the net zero transition. With a dedicated climate team, we help businesses prepare for and thrive through this transition,” said Wakefield.
“This includes supporting their understanding of Scope 3 emissions, now mandatory for reporting, and assisting major project owners in identifying supply chain participants who are already taking steps towards net zero, as well as those who need support to get started.
“We’ve already seen great traction in this area – our upcoming webinar on the subject attracted 650 businesses almost immediately.”
ICN utilises several key databases to support local businesses and projects effectively.
The company’s database is a resource featuring around 100,000 companies. It plays a crucial role in connecting local suppliers with relevant project opportunities.
As the database continually grows, it serves as a tool for both businesses seeking new contracts and government bodies requiring detailed information to support their economic development strategies.
ICN’s new initiative, the Climate Readiness Database focuses on mapping Australian supply chains based on their preparedness for climate action.
It identifies businesses that are already engaging in climate initiatives or can begin, thereby aiding the transition towards net zero emissions.
This resource is instrumental in helping businesses align with sustainability goals and informing project owners about the climate readiness of potential supply chain participants.
“This capability allows us to map Australian supply chains in terms of their climate readiness, providing valuable insights,” said Wakefield.
“Additionally, our ESG and climate specialists are available to support these activities, ensuring businesses are well-equipped for the transition to
sustainability.”
Gateway by ICN lists major projects and enables smaller enterprises to bid on specific work packages.
This database ensures that smaller businesses have a fair opportunity to participate in big projects, fostering an inclusive and competitive environment.
Together, these databases support efficient project delivery, enhance local business opportunities, and contribute to the overall economic development and sustainability goals of the region.
“Ideally, these databases exist to support local industries by facilitating access to projects, ensuring they have full, fair, and reasonable opportunities,” said Wakefield.
Ultimately, ICN plays a crucial role in advancing Australian manufacturing and economic growth by connecting local suppliers with major projects and facilitating access to opportunities aligned with national priorities.
Through its network and platforms, ICN has contributed to project facilitation and has supported local industries in becoming competitive and resilient.
This supports the goals of the Future Made in Australia Act, driving economic progress and industry innovation.
Our breakthrough new range of pallet wrappers deliver real cost reduction per pallet and an extra level of performance.
• Intelligent technology to get the best load containment whilst reducing your wrap usage.
• Unusually shaped loads, unstable or light loads, sharp edges, and loads in cold or hygiene zones – we’ve got it covered.
• Full range of performance wrap and pallet consumables - specified by process technicians not stationary suppliers.
• Fully installed and serviced.
Ask us about paper wrapping options too.
Ceccato’s ECOntrol+ system optimises compressor room performance, boosting efficiency while reducing energy consumption and environmental impact.
As well as being a monitoring tool ECOntrol+ is the brain of a compressor room. Capable of connecting to 10 compressors, ECOntrol+ ensures seamless operation by reducing the pressure band and minimising unloaded running hours.
This synchronisation leads to energy savings, a critical factor considering that energy consumption accounts for 80 per cent of a compressor’s total cost of ownership.
One of the features of ECOntrol+ is its ability to guarantee a continuous air supply, even in the event of a breakdown.
By equalising equipment running hours, the system not only saves on maintenance costs, but also minimises downtime.
This flexibility is crucial for managing complex air demand profiles, ensuring that operations run smoothly and efficiently.
Aurora Process Solutions, a company that provides end-of-line packaging systems, has unveiled its latest pallet wrapping system range.
Aurora Process Solutions’ (Aurora) latest packaging systems are designed to meet the diverse packaging needs of its clients.
Aurora focuses on automating and optimising packaging processes to enhance efficiency and safety in various industries.
Its solutions cover everything from design and installation to ongoing support, emphasising strong client engagement.
Aurora is introducing its latest range of pallet wrapping systems supplied by Robopac – an Italian packaging equipment manufacturer – which includes the Technoplat, Rototech (a rotary arm wrapper), and Genesis (a ring wrapper).
“Aurora Process Solutions specialises in both distribution and integration of packaging systems, offering semi-automatic pallet wrappers and fully automated solutions,” said Braden Goddin, sales and marketing manager at Aurora.
“We integrate these systems into conveying and end-of-line packaging setups, providing comprehensive services including automation, controls, installation, commissioning, staff training, and ongoing optimisation.”
One of the main features of Aurora’s latest pallet wrapping systems is its focus on reducing the cost per wrap.
Traditionally, pallet wrappers were specified by stationers and simply put in place to wrap loads, with little consideration for film optimisation.
However, Aurora’s new systems are designed with advanced software and intelligent mechanical components that reduce film consumption without compromising load containment.
This is advantageous for medium to large users of stretch wrap, where the savings can quickly accumulate.
“There’s a significant difference between a wrapper chosen by a local stationery supplier and one selected by a process technician who understands how to optimise load containment, film application, and overall efficiency to achieve cost savings,” explained Goddin.
Additionally, Aurora’s collaboration with Robopac has played an important role in these innovations. The technology in Robopac’s machines allows for
up to 400 per cent pre-stretch, meaning that each roll of polyethylene wrap can cover more pallets than conventional methods. This not only reduces material costs but also minimises the environmental impact of plastic waste.
“It achieves this through a pre-stretch mechanism, which is quite substantial,” said Goddin.
Sustainability is a key concern for manufacturers worldwide, and Aurora’s latest developments are addressing this head-on.
In partnership with Robopac, Aurora has introduced equipment capable of wrapping pallets with engineered paper instead of polyethylene.
This paper, designed with substantial stretchability and strength, provides up to 40 per cent better pallet stability in some applications compared to traditional plastic wrap, according to Goddin.
“Regarding paper wrapping, one key advantage is that it uses larger rolls of consumable material,
Advanced Robopac technology allows up to 400 per cent pre-stretch, cutting material costs and lessening environmental impact.
reducing the frequency of roll changes and increasing automation,” said Goddin.
While paper wrapping is best suited for dry logistics chains, its advantages are significant. The ability to print directly onto the paper offers a marketing opportunity, reducing the need for additional labels, and the fact that the paper is recyclable makes it an environmentally friendly alternative.
This innovation is timely, as Goddin explained, because companies are increasingly looking for ways to reduce their carbon footprint.
“Reducing the carbon footprint is crucial for companies not only to meet regulatory requirements but also to enhance their sustainability profile and appeal to environmentally conscious consumers,” he said.
“Studies indicate that using paper instead of plastic film can reduce the carbon footprint by up to 62 per cent.”
The new pallet wrapping systems are not just about cost
savings and sustainability, they also offer versatility.
The range includes semi-automatic machines for smaller operations, as well as automated systems capable of handling heavy industrial environments, low-temperature freezer applications, and even corrosive environments such as fertiliser or salt processing.
In terms of capacity, Aurora’s systems can handle a variety of pallet types and sizes, with some machines capable of wrapping up to 160 pallets per hour –more than the industry standard of 30 pallets per hour.
“There’s a wide variety of wrappers available, including turntables, rotary wrappers, rotary arms, and ring wrappers,” Goddin.
“For impressive performance, consider the Genesis model, which offers a maximum output capacity of up to 160 pallets per hour – exceptionally fast for its category.
“A typical throughput is around 30 units.”
This increased throughput is made possible by Robopac’s advanced wrapping methods, including rotary arm and ring wrappers, which are gaining popularity in Australasia due to their efficiency and effectiveness.
“In Australasia, we primarily use turnatable wrappers, with rotary arm and ring wrappers more popular in other parts of the world,” said Goddin.
“We’re eager to introduce this technology here because it offers significant benefits. For instance, these wrappers rotate the film rather than the pallet, which is ideal for unstable or light loads.
“This approach speeds up the wrapping process and helps maintain the integrity of the load.”
Aurora doesn’t just supply wrapping machines – it provides a service package that includes integration into existing packaging lines, automation, and ongoing support to ensure machines continue to operate at peak efficiency throughout their lifecycle.
“At our company, we handle the entire process: from automation and control installation to commissioning, staff training, and optimisation,” said Goddin.
“A key aspect of our service is providing ongoing support to ensure the machine remains optimised throughout its lifecycle.”
Ultimately, Aurora distinguishes itself with a strong focus on service and optimisation, offering support throughout the lifecycle of its machinery.
“The true test of our service begins after installation, when the dust has settled, and clients need ongoing support. We don’t just install a unit and walk away; we understand that continuous support is crucial,” said Goddin.
“We provide training, optimise settings, and ensure film consumption is maintained. We also retrain existing staff as needed.
“Our commitment extends for the long haul, particularly for rural-based clients who value this level of support.”
This commitment includes automation, control installation, commissioning, staff training, and ongoing maintenance, ensuring sustained performance and value.
As the packaging industry evolves, Aurora remains at the forefront with solutions that address current needs while anticipating future challenges.
By prioritising cost efficiency, sustainability, and advanced technology, Aurora aids businesses in enhancing packaging processes, reducing environmental impact, and improving financial outcomes.
“It’s an exciting time for the industry. There’s significant pressure to reduce plastic consumption, which is driving innovation,” said Goddin.
“Our role is to assess and introduce these innovations from around the world to Australia and New Zealand.
“We aim to be a trusted advisor in pallet load containment, including both equipment and consumables.”
Efficient and continuous operation are key elements in manufacturing, so it is important to have a compressor solution that does both.
CAPS Australia is all about delivering rotary screw air compressor solutions that drive productivity and improve profitability. It does this by offering energy-efficient and precisionengineered solutions that are built to last.
A specialist provider of compressed air and power generation solutions across Australia, CAPS has a portfolio of products and brands that are suited to Australian operating requirements.
Founded in Western Australia in 1980, CAPS joined the Ingersoll Rand family early in 2024 expanding its access to the Ingersoll Rand’s global offering of mission-critical air, fluid, energy and medical technologies.
CAPS Compressed air product manager, Paolo Lazzari, said compressed air systems to support the varied demands of manufacturing industries,
generally requires specifically designed systems that are configured to each application.
“Our name highlights our commitment to delivering the complete air and power solutions (CAPS) that our customers need,” he said.
“We have the ability to select the correct equipment for certain applications to ensure it meets our customer’s key requirements such as reliability, durability and energy efficiency.”
This is why CAPS delivers complete solution designs, developed by its in-house engineering team and supported through its Australian ISO9001 accredited manufacturing facility. These custom-built systems are matched to clients’ requirements.
Since it started, CAPS has been supplying Ingersoll Rand equipment and the RS & RM-Series oil-flooded screw air compressors leverage an advanced compressor core to achieve exceptional performance and reliability standards, which are ideal for manufacturing applications.
The optimised rotor profile and standard premium efficiency motor provides efficiency gains resulting in lower energy costs and reduced operational spend.
The compressor includes an intelligent controller that monitors key operations and adjusts system parameters to maximise uptime and minimise energy consumption meeting IE5 energy-efficiency standards using a variable speed custom Hybrid Reluctance Motor.
With 10 branches nationwide, its dedicated team delivers service, expert advice, support, and spare parts.
With a 24/7 maintenance and breakdown service, they ensure customers’ operations run smoothly.
“CAPS gives our customers access to interact directly with product managers who have years of expertise, to ensure we understand their requirements, something that other OEMs struggle to
provide because they are overseas,” Lazzari said.
“We operate in the same time zones and can be with our customer through the entire process, ensuring we understand their requirements, offering suggestions, providing advice and ultimately delivering the solutions they need.”
CAPS now provides Ingersoll Rand PackageCARE plans, giving clients value for managing their assets by transferring operational risk to Ingersoll Rand.
Scheduled air compressor maintenance, as well as using predictive analytics and analytical tools, can help prevent unexpected interruptions in production.
With more flexibility than an extended warranty, PackageCARE maximises equipment uptime.
CAPS delivers competitively priced, turnkey solutions that keep operations running smoothly all year round.
The company also offers short and long-term rental of compressors and generators at good rates across Australia, making them suitable for projects, seasonal peak demands and breakdown requirements, with the flexibility to suit various needs.
With experience in renting equipment, CAPS maintains a large fleet of units ready for immediate
performance and lower operational costs.
dispatch from their local hubs.
This fleet satisfies a range of applications while ensuring top-quality equipment and a high standard of customer service.
Whether it is an industrial air compressor, a portable diesel air compressor, a back-up power
generator, air blower, gas generator or air treatment equipment, the air and power solution is provided by CAPS, utilising quality products with proven reliability to ensure they work where and when they are needed.
Get in touch with the CAPS team on 1800 800 878 or check out www.caps.com.au
ECI Solutions’ M1 ERP transforms supply chain management by fostering collaboration, streamlining operations, improving efficiency, and unlocking cost savings.
The balance between dependable suppliers and cost-effective materials seems to have reached its end for discrete manufacturers. As production is disrupted and profit margins decrease due to late deliveries and widespread inflation, the urgency for creative and cost-effective solutions has never been greater. ECI Solutions has been working with manufacturers for over 30 years, providing industry-specific ERP software The industry has seen rapid changes during this time with many manufacturers realising that effective supply chain management holds the key to financial prosperity in this volatile manufacturing market.
Current conditions are worsening
Amid turbulent economic conditions characterised by rising inflation and disruptions in the supply chain, the traditional adversarial relationship between manufacturers and suppliers has evolved into a dangerous dance. The absence of trust and open communication fosters an environment where blame precedes problem-solving, impeding joint efforts to navigate volatile markets. The escalation of prices introduces a ‘knock-on’ effect, with each supplier passing on the burden to the next, ultimately squeezing the already struggling margins of manufacturers. Inflexible contracts and a lack of adaptable collaboration further restrict agility, leaving both parties susceptible to disruptions and missed opportunities for cost-saving and efficiency improvements. This outdated model, founded on suspicion and short-term gains, threatens both sides, necessitating a transformative shift towards a collaborative, data-driven approach that prioritises mutual resilience and success.
The supply chain arena is filled with the victims of obsolete strategies. Escalating expenses, fragmented communication, and fragile vendor partnerships leave manufacturers and suppliers wounded and exhausted. Supply chain management is a game-changing approach transforming the supplier landscape from a battleground into a flourishing ecosystem of cooperation and collective triumph. This is where a manufacturing specific ERP software like ECI Solutions’ M1 ERP can help businesses connect their suppliers with
their business demands for better supply chain management.
The pains of poor vendor relationships: the price squeeze
Imagine paying an excessive premium for a vital component, only to witness its arrival date fluctuate like the stock market. Each delay pushes back production, inflating overhead costs—leaving you caught between shrinking margins and inflated demands.
Poor communication with suppliers is not only frustrating but also a logistical minefield. Every missed deadline, vague response, and shipment shrouded in secrecy throws your production schedule into chaos. You find yourself scrambling to adapt, appease customers, and navigate through the fog of uncertainty armed with nothing but empty promises.
Picture receiving a delivery of components only to uncover a box of inconsistencies. Inconsistent quality from unreliable suppliers is not merely inconvenient, but it sets the stage for delays, rework, and, ultimately, a tarnished reputation. Every flawed product that slips through your gates erodes customer trust, compelling you to allocate precious resources to remediation and replacements.
Surplus stock or stock-outs are often a direct result of the lack of collaboration and visibility with your vendors. The consequence? Warehouses become chaotic and aren’t aligned with production needs. This impacts the bottom line, forcing you to squeeze margins with price discounts to clear stagnant stock or spend crippling amounts to get expedited stock in time for a job.
The traditional “vendor-buyer” relationships, characterised by transactional interactions, are now considered outdated. In today’s dynamic market, adopting a strategic shift that replaces adversarial barriers with collaborative connections
is essential. By embracing a “partners-in-success” approach, you align your interests with your suppliers, transforming them from vendors into collaborative allies.
Cost reduction: By sharing data analytics and implementing transparent pricing strategies, you can uncover hidden cost drivers and identify opportunities for joint savings.
On-time deliveries: Instead of relying on guesswork, real-time inventory visibility and joint forecasting enable precise planning. Proactive risk management and shared logistics planning ensure that components are delivered promptly to the correct location, maintaining smooth production lines and ensuring customer satisfaction.
Quality improvement: Through continuous datadriven monitoring and joint quality control initiatives, inconsistencies and defects can be identified and resolved before they disrupt operations.
This strategic transformation would not have been achievable without the use of Supply Chain Management (SCM) software. M1 ERP provides the dedicated solution for this. It serves as the digital conduit, facilitating:
Exchange of information: Real-time data regarding inventory levels, production schedules, and market trends seamlessly flows between departments, promoting transparency and collaborative decisionmaking.
Joint planning: Collaborative forecasting tools and integrated planning modules enable the synchronisation of production schedules, optimisation of logistics, and anticipation of future challenges.
Coordinated operations: Real-time dashboards, alerts, and automation ensure that all stakeholders are on the same page, allowing for swift responses to disruptions and proactive adjustments to ensure smooth operations.
With M1 ERP as your guiding force, you can embrace a future where your suppliers aren’t just vendors but valuable partners.
Diving into the details and enhancing efficiency and visibility
Automated purchase orders: Simplify your ordering process by implementing automated generation and
approval workflows, minimising errors, and saving valuable time.
Supplier performance dashboards: Gain immediate access to supplier performance metrics, including on-time delivery, quality, and cost.
Risk management tools: Take proactive measures to mitigate disruptions with scenario planning, early warning systems, and supplier contingency management tools. Identify and resolve potential bottlenecks in your supply chain before they impact your operations.
Collaborative planning modules: Foster collaborative planning and forecasting with your suppliers. Optimise logistics, inventory levels, and production schedules through shared data and integrated workflows.
Advanced analytics: Uncover valuable insights, understand demand patterns, identify cost drivers, and optimise sourcing strategies for better pricing and quality.
Predictive disruption management: Use data-driven algorithms to anticipate potential disruptions and proactively adjust your operations.
Scenario planning and optimisation: Test supply
Trust through transparency
Shared data hub: Establish a centralised and reliable source of supply chain data.
Process visibility: Track orders, shipments, and production progress in real-time.
Collaborative performance tracking: Jointly monitor performance and address areas for improvement
Taking the first step M1 ERP has Supply Chain Management functionality, along with inventory, purchasing, production, job costing, and every other manufacturer operation. If you want to unlock the financial power in your manufacturing business take advantage of a free demonstration of M1
Manufacturers’ Monthly recently sat down and spoke with APS Industrial, the national distributor for Rittal, to discuss enclosures for manufacturing sites.
As the national distributor of Rittal products, APS Industrial offers bespoke and customisable enclosure solutions to a wide range of industrial applications across Australia, and manufacturing is no exception.
What are enclosures?
An enclosure is a protective housing designed to shield electrical components from environmental hazards and accidental contact.
Enclosures come in various forms, including different types of metal and plastic, and are commonplace across all industrial applications, from indoor manufacturing plants to outdoor mining sites.
Essentially, if there is critical equipment for the smooth operation of a plant or site, enclosures are used.
“An enclosure serves as a protective housing for electrical components, safeguarding them from environmental factors such as wind, rain, and dust, while also preventing unauthorised access to electrical equipment,” said Lenard Scott, Rittal and Weidmuller product manager at APS Industrial.
How are they different?
Thanks to APS Industrial’s partnership with Rittal, the company offers many different enclosure variations, each suited for specific applications with unique strengths.
For indoor use in industries like food and beverage and processing, standard metal enclosures are commonly used.
When it comes to stainless steel enclosures, which are particularly beneficial in foodprocessing and washdown environments, these traditionally required opening the box and manually wiping the seals to ensure cleanliness.
“In food and beverage areas, stainless-steel 304 enclosures are typically used. For wash-down applications, 304 stainless-steel with a hygienic seal is preferred and the Rittal HD range is market leading in this field,” explained Scott.
Enclosures with an IP69K rating can withstand high-pressure wash-downs at temperatures up to 80°C. This is crucial in manufacturing plants where equipment is exposed to harsh cleaning processes.
Ultimately, the ability to maintain a sealed
environment under these conditions ensures that the electrical components inside are protected, reducing the risk of malfunctions and extending the lifespan of the equipment.
Manufacturing environments often require highly customised setups to accommodate various equipment and processes.
Enclosures that offer modular designs, such as bayable systems that can extend over 20 metres and can house both data cabinets and control gear, provide the flexibility needed to optimise space and functionality.
The partnership between APS Industrial and Rittal again offers advantages for local manufacturers as they can facilitate bespoke modifications to enclosures before they are shipped.
Custom cutouts for switches, cable entries,
and HMIs can be pre-installed, simplifying the assembly process and reducing installation time.
Many Rittal enclosures are designed to be modular, enabling users to add or modify components as needed.
With that in mind, APS provides a configuration software that lets clients design their enclosures online, including custom cutouts and attachments.
Once the design is finalised, the specifications are sent to a Perforex machine for precise cuts, and the complete enclosure is shipped ready for use.
“Rittal has been using one of these machines for nearly 15 years,” explained Scott.
“We have recently installed a Perforex unit of our own at the APS Industrial Manufacturing Centre and we’re delighted to be able to offer this important service to our customers”.
This automated system ensures consistent
and accurate cuts, with a wide work-piece holder capable of accommodating fully welded enclosures.
The service includes versatile capabilities such as precise hole drilling, thread tapping for secure fastening, and custom cut-outs tailored to specific requirements.
Additionally, Rittal provides load testing and documentation for its enclosures.
“Every component, from rails to doors, undergoes rigorous load testing. For instance, if you have a specific enclosure, you can be confident that the door can support up to 15 kilograms because it’s been tested,” said Scott.
“The mounting plate is also tested for load capacity, with larger enclosures capable of holding up to 1,500 kilograms internally.
“When combining multiple enclosures, they provide precise load-bearing details, such as the middle unit supporting 1,500 kilograms while the adjacent units can each handle 700 kilograms.”
Rittal products can also be customised by CAD (Computer-aided design).
“Online, you can select the product and go to the downloads section, where you’ll find CAD files for every drawing package,” explained Scott.
“It’s not just about the quality of the
enclosures but also the support service. If you need a specific drawing, it’s readily available.
“While you might find a more cost-effective enclosure elsewhere, you’d then have to search for CAD files, load ratings, and certifications for shipping, mining, and hazardous areas. Rittal has already completed all that testing.”
These CAD drawings, complete with load ratings, ensure that the enclosures precisely meet the specific operational requirements of each client.
“With E-pocket, you can generate a QR code that links directly to all your documentation, securely stored in the cloud,” said Scott.
“This cutting-edge solution, developed in collaboration with Rittal’s Eplan software, transforms how you manage and retrieve crucial information, making it effortlessly accessible from anywhere.”
Traditionally, documentation for an enclosure, such as wiring plans and control system details, is stored in a physical pocket attached to the back of the enclosure door.
This method requires manually retrieving and managing physical paperwork.
With the new E-pocket system, Rittal offers a modern solution where all documentation is
stored digitally in the cloud.
As Scott explained, by generating a QR code, users can easily access and download all relevant documents from a secure online server.
“It’s a streamlined way to retrieve files directly on your tablet or laptop, without the need for physical paperwork,” said Scott.
Rittal enclosures are used in precasting facilities that are producing up to 44,000 concrete segments for the 6.5 km North East Link Tunnels.
The North East Link represents the largest investment ever made in Melbourne’s northeast, which is set to transform how people navigate the city.
As a key component of Victoria’s Big Build, this initiative includes three major road projects.
The 6.5 km North East Link tunnels, stretching from Watsonia to Bulleen, will complete a crucial gap in Melbourne’s freeway network, reducing local truck traffic by 15,000 vehicles per day and cutting travel times by up to 35 minutes. By safeguarding vital electrical components in harsh construction environments, Rittal enclosures are ensuring the reliability and efficiency of operations at the heart of this transformative infrastructure project.
Manufacturers’ Monthly Magazine’s Endeavour Awards are the premier accolade in the Australian manufacturing industry, celebrating excellence and innovation across the sector.
Recognising the achievements of manufacturers who set the benchmark for success, the Endeavour Awards span a range of categories that highlight leadership, sustainability, innovation, and growth within the industry.
As the 21st annual Endeavour Awards approaches, we are actively seeking expressions of interest for sponsorship opportunities. Sponsoring these awards is an opportunity to position your brand as a leader in the manufacturing sector.
With exposure to a targeted audience and the ability to align with a category that reflects your company’s values and direction, it’s the perfect platform to enhance your reputation and drive future growth.
Not only can you gain exposure within sector, but you can also stand shoulder to shoulder with other giants within the industry.
The sponsors for the upcoming Endeavour Awards represent a diverse range of industries, each bringing a unique contribution to the event.
Weld Australia, a not-for-profit organisation dedicated to supporting the Australian welding industry, is sponsoring the Safety Solution of the Year.
“As advocates for excellence and innovation within the manufacturing sector, Weld Australia is proud to sponsor the Safety Solution of the Year category at the 2024 Manufacturers’ Monthly Endeavour Awards,” said Geoff Crittenden, CEO, Weld Australia.
“Our commitment to enhancing industry standards and promoting safety aligns perfectly with the goals of these awards. “
Weld’s mission is to ensure the welding profession remains competitive on both local and global stages by providing members access to research, education, and industry connections.
“Sponsorship of this event not only underscores our dedication to driving advancements in manufacturing safety but also reflects our ongoing efforts to support meaningful and impactful industry achievements,” said Crittenden.
“By celebrating these innovations, we are not just recognising outstanding contributions but also encouraging a culture of safety and excellence that resonates throughout the sector.”
Bestech Australia, the sponsor for Manufacturer
of the Year, supplies state-of-the-art sensors, instrumentation, and teaching equipment for sectors like manufacturing, military, mining, and research laboratories.
It is known for delivering quality products and customer service across a range of industries.
SEW-EURODRIVE, a specialist in mechanical power transmission equipment, is sponsoring the Most Innovative Manufacturing Company Award.
With expertise in systems like geared motors and electronic frequency inverters, it offers integrated solutions that drive industrial efficiency.
BDO Australia, the sponsor for Excellence in Growth, provides accountancy, tax, and advisory services. Known for its deep sector expertise, BDO assists manufacturers in improving performance and leveraging Industry 4.0 advancements.
BlueRock, the sponsor for Outstanding Startup, is a purpose-led advisory firm supporting business owners with innovative strategies and financial planning. With a focus on manufacturing, it provides expert, tailored advice to help businesses grow and succeed.
If you represent a company that would be interested in recognising excellence within the manufacturing industry, please find the details below.
Whether you’re an industry veteran or an emerging talent, the Endeavour Awards provide a unique platform to showcase your achievements and receive recognition for your contributions to the sector.
Nominations are now open across 10 categories, offering the perfect opportunity to celebrate the outstanding work within the industry and inspire others.
You can nominate yourself, a colleague, or anyone whose exceptional efforts and accomplishments deserve national recognition.
The nomination process is free and must be completed online by 11:59 pm on Friday, September 20, 2024.
The Endeavour Awards 2024 will celebrate outstanding accomplishments across a range of categories, including:
• Technology Application.
• Environmental Solutions.
• Outstanding Start-Ups, Safety Solutions.
• Manufacturing Skills Development.
• Leader of the Year.
• Most Innovative Manufacturing Company.
• E xcellence in Growth.
• Project of the Year.
This prestigious event celebrates advancements and recognises leaders who drive innovation and excellence in the manufacturing industry.
Noteworthy highlights include awards for sustainability, safety, and growth, with categories designed to honour both established companies and emerging stars.
The awards are a testament to the dynamic and evolving landscape of Australian manufacturing.
If your company is interested in celebrating excellence or standing among the giants of the manufacturing industry, please reach out to our Business Development Manager: Emily Gorgievska
Email: emily.gorgievska@primecreative.com.au
Phone: +61 432 083 392
To nominate yourself, a peer, or to learn more about the process for the upcoming Endeavour Awards, visit our website: https://endeavourawards.com.au/ nominations/
Alternatively, you can contact our Events Conference Producer: Alicia Gomez
Email: alicia.gomez@primecreative.com.au
Phone: +61 409 138 604
From consultation to design, manufacture and installation to on-going service support, at KAESER we always aim to give you the most compressed air, for the least expenditure of energy.
The completely re-designed range of CSG oil-free rotary screw compressors is made in Germany to exacting standards and will save you energy and money, meaning it’s good for the planet as well as your bottom line.
Our factory-trained sales engineers can visit your site and advise you on the best system for your application. Book an appointment on 1800 640 611. au.kaeser.com
With over 110 years of experience, BOGE understands the challenges its customers face. As a leading compressed air specialist, we engineer, install, and upkeep premium systems trusted by over 100,000 users globally, adapting to diverse ambient conditions. We focus on optimising efficiency and cutting energy costs. With a focus on energy efficiency, optimised air compression processes, reduced operational costs BOGE compressed air sustainable solutions cater to various industrial needs, such as manufacturing, automotive, Laser-cutting and pharmaceuticals, Medical, Dentistry, Brewing, Fish farming enhancing productivity.
Compact BOGE oil lubricated screw compressors
C series have been known in the industry for their reliability in the generation of compressed air for many years. Whether frequency-controlled, beltdriven or directly coupled – these sturdy machines form the backbone of industry. BOGE Compressors
Australia keeps most of the models and configurations 7, 10, 13 and15bar in Standalone compressor, compressor with integrated dryer or full feature receiver mounted units in stock.
Most important characteristics:
Boge compact module
The optimised rotor profile of the BOGE compact compressor with oil-injection cooling guarantees optimal operation and high energy efficiency thanks to its components. The intelligent design of the overall unit results in extremely low internal pressure losses and particularly smooth running.
Innovative cooling air and soundproofing concept
All models benefit from the standard soundhood, which successfully minimises operating noise and vibrations. Furthermore, the targeted flow of cooling air through the soundhood, combined with the compressed air aftercooler, ensures minimum compressed air outlet temperatures, as well as optimum cooling of all built-in components.
Integrated frequency control with direct drive
Integrated frequency control pays off, particularly when the demand for compressed air fluctuates. This allows the compressor speed and delivery rates to be easily adjusted to the relevant requirement.
Maintenance friendly by principle
To ensure the most user-friendly maintenance possible, all the components have been arranged to allow quick access. For this, all sound-insulation panels can be effortlessly removed, and filters can be changed with minimal downtime.
Main advantages:
• Compact Design
• Unmatched
• Reliability
• Energy Efficiency
• Long lasting Performance
• Versatility and Quiet operation
• High Productivity24/7
• Maintenance Friendly
• Suitable for diverse industrial applications
BOGE Australia import and distribute BOGE high-quality German machines, spare parts and all ancillary equipment through a comprehensive network of fully trained sales and service Premium partners throughout Australia, New Zealand, Papua New Guinea and Fiji.
Company: BOGE Compressors
Phone: (03) 5940 5913
Website: www.boge.com/en-au/
Understand how to easily apply and implement the quality requirements defined in the ASME B31.3 Code with Weld Australia’s three-day course in December 2024.
Facilitated by US expert, Jim E. Meyer, a new course is being presented that will provide an introduction to the ASME B31.3 Process Piping Code. It covers the requirements of B31.3 for design, analysis, materials, fabrication, testing and inspection of process piping systems. It explores the rules for various components including fittings, connections, bends, valves and specialty components
Other topics include dimensions and ratings of components, fluid service requirements for joints, piping flexibility and support, welding, heat treatment, bending and forming, brazing and soldering, assembly, erection, examination and inspection.
This course is designed for engineers, managers and quality personnel who are involved in the design, manufacturing, fabrication and examination of process piping that is being built to the requirements of US Codes and Standards.
The course will cover:
• Introduction to B31.3
• B 31.3 Scope and Definitions
• D esign Considerations and Criteria
• Pressure Design of Piping Components
• D esign:
• Fluid Service Requirements and Standards for Piping Components Standards
• Fluid Service Requirements for Piping Joints
• Flexibility and Support
• Systems
• B ellows Expansion Joints
• Materials
• Fabrication, Assembly and Erection
• Inspection, Examination and Testing
Subhead: About the Presenter: Jim E. Meyer
Jim E. Meyer has more than 45 years of experience in refining petrochemical, chemical, power generation, and industrial facilities. He is a principal engineer at CDM Smith, a full-service engineering and architectural firm, located in Wadsworth Ohio. Meyer is experienced in
overall project coordination and management, pressure equipment, piping design, analysis, specifications, support design, mechanical system requirements, and documentation requirements. His technical competence includes ASME piping and pressure vessel codes, stress analysis, field troubleshooting piping system support, vibration, and expansion problems.
Meyer is a member of ASME and has been involved in the ASME B31.1 and ASME B31.3
Section committees for more than 40 years. Most recently, he co-authored chapters in the ASME Boiler and Pressure Vessel Companion Guide (5th Edition), covering the ASME B31.1 Power Piping Code and the B31.3 Process Piping Code. Past projects and work experience have involved oil refineries, petrochemical plants, fossil, nuclear, solar, and alternative energy generation, as well as cryogenic and vacuum test facilities.
For more information and to register, visit: https://weldaustralia.com.au/asme-b31-3process-piping-code/
Sydney Head Office and Technical Centre Unit 7/16 Lexington Dr, Bella Vista NSW 2153
Perth Service Centre Butler, WA 6036
Melbourne Office and Technical Centre Unit 1/3-4 Anzed Ct, Mulgrave VIC 3170
Brisbane Service Centre Stafford Heights, QLD 4053
Auckland Office and Technical Centre Unit 2/67 Business Parade South, East Tamaki, Auckland 2013
Adelaide Service Centre Lockleys, SA 5032