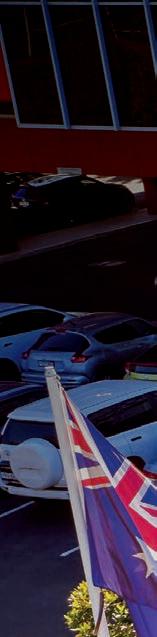
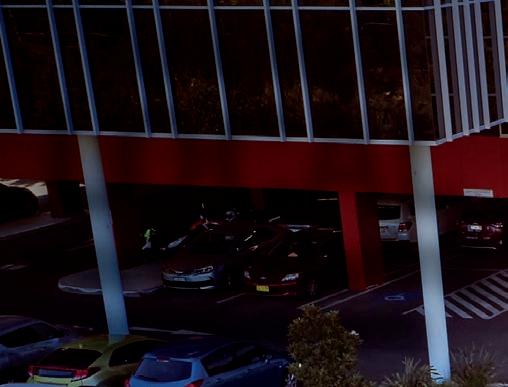
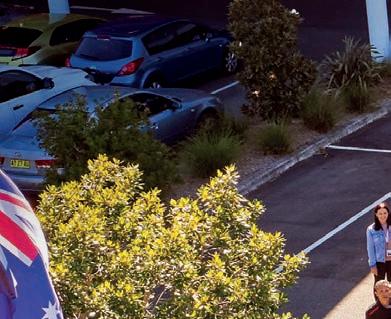
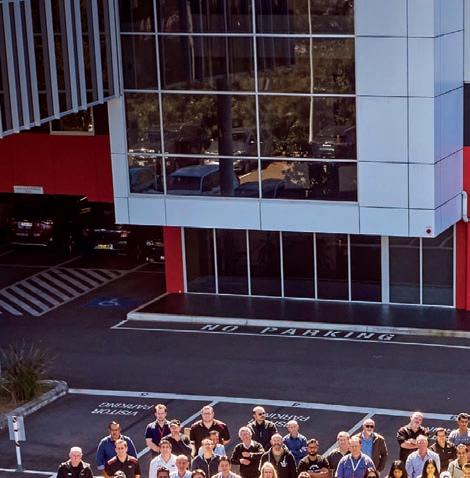
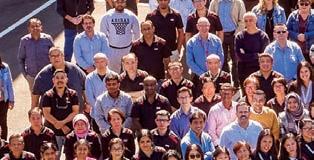
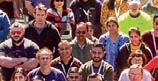
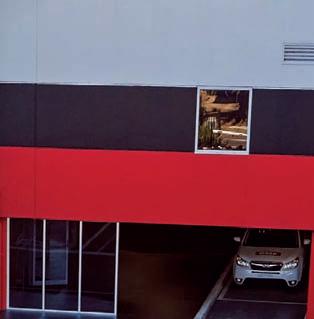


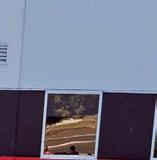


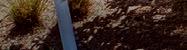


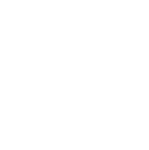
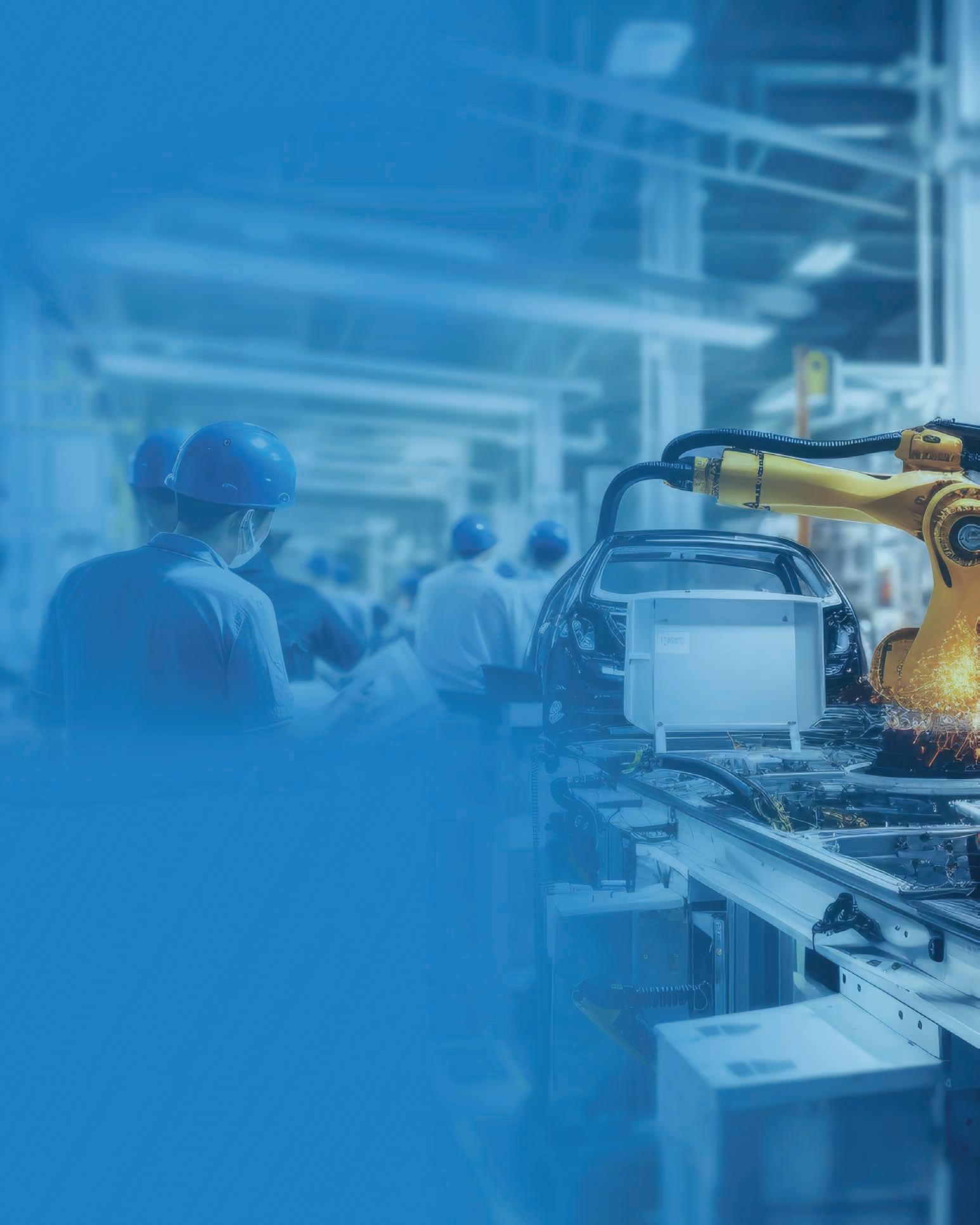
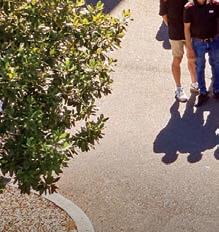



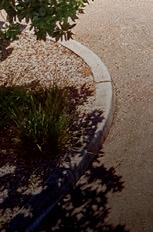


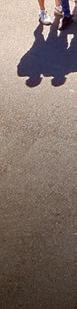


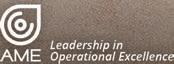
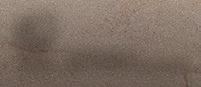
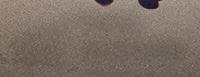
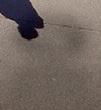


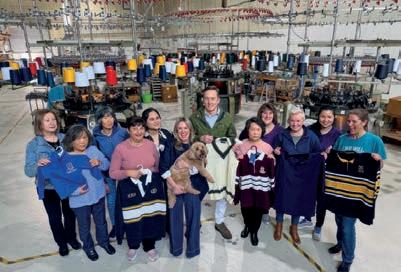
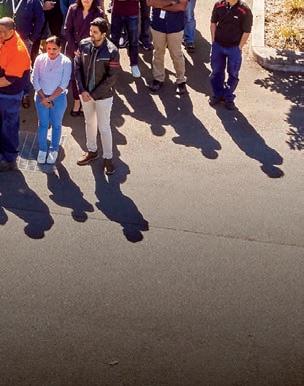


CEO: John Murphy
Chief Operating Officer: Christine Clancy
Managing Editor: Mike Wheeler
Assistant Editor: Jack Lloyd jack.lloyd@primecreative.com.au
Journalist: Mannat Chawla mannat.chawla@primecreative.com.au
Head of Design: Blake Storey
Design: Alejandro Molano
Sales/Advertising: Emily Gorgievska Ph: 0432 083 392 emily.gorgievska@primecreative.com.au
Subscriptions
Published 11 times a year
Subscriptions $140.00 per annum (inc GST)
Overseas prices apply
Ph: (03) 9690 8766
Copyright
Manufacturers’ Monthly is owned by Prime Creative Media and published by John Murphy.
All material in Manufacturers’ Monthly is copyright and no part may be reproduced or copied in any form or by any means (graphic, electronic or mechanical including information and retrieval systems) without written permission of the publisher. The Editor welcomes contributions but reserves the right to accept or reject any material. While every effort has been made to ensure the accuracy of information, Prime Creative Media will not accept responsibility for errors or omissions or for any consequences arising from reliance on information published. The opinions expressed in Manufacturers’ Monthly are not necessarily the opinions of, or endorsed by the publisher unless otherwise stated.
© Copyright Prime Creative Media, 2024
Articles
All articles submitted for publication become the property of the publisher. The Editor reserves the right to adjust any article to conform with the magazine format.
Head Office
379 Docklands Drive
Docklands VIC 3008
P: +61 3 9690 8766
enquiries@primecreative.com.au www.primecreative.com.au
Sydney Office Suite 11.01, 201 Miller St, North Sydney, NSW 2060
Printed by: The Precision Group 83-89 Freight Drive. Somerton
3062 Ph: (03) 9794 8337 manmonthly.com.au
Welcome to the December edition of Manufacturers’ Monthly.
In this issue’s Manufacturing Focus, we spotlight the local production and innovation of Australia’s only manufacturer of UHF CB radios and emergency beacon products, GME. Next, we explore Capral Aluminium’s successful partnership with renowned defence shipbuilder, Austal.
This edition also includes an in-depth look at Australia’s sovereign textile manufacturing industry, featuring a case study on one of Australia’s last three knitting mills.
To round out the issue, we present expert commentary from CSIRO on flexible solar technologies and insights from SEMMA addressing the state of Victorian manufacturing.
As we hit the final month of 2024, Australia’s manufacturing industry continues to excel in different sectors such as defence, maritime, renewables and transport. In this edition, we examine the rapidly evolving landscape of an industry embracing sustainability, digital transformation, and advanced technologies.
Recently, new developments have emerged that are poised to shape the industry’s future trajectory.
The local build of Volgren’s first hydrogenpowered bus was one of these developments, as it presents another example of Australian manufacturing shifting towards a cleaner future. Developed in partnership with Wrightbus, the vehicle is the latest addition to Volgren’s Zero Emission Bus portfolio, which now features over 150 battery-electric and fuel-cell buses.
This surge in renewable energy manufacturing was also marked by the signing of a memorandum of understanding (MoU) between SunDrive Solar and Trinasolar. The majority Australian-owned joint venture is set to combine SunDrive’s solar technology with Trinasolar’s manufacturing expertise to further establish local production capabilities.
Shifting to another burgeoning industry, maritime manufacturing has seen numerous developments lately. This includes a landmark acquisition that will see Civmec gain all assets, employees, and licences of Luerssen Australia. The buyout has strong defence implications, as Luerssen Australia’s sole responsibility is the build of six Arafura Class Offshore Patrol vessels for the Royal Australian Navy.
And talking of building water vessels, developments in defence shipbuilding continue as the Federal Government has announced plans to establish a Defence Precinct at Henderson
shipyard in Western Australia. This will see the build of new infrastructure that is set to support the build of Army landing craft, Navy frigates, and the maintenance of nuclear-poweredsubmarines.
Finally, the critical minerals sector has also remained in the spotlight, as NSW Government’s Critical Minerals and High-Tech Metals Strategy continues to grow.
The latest development of the strategy was its $250 million royalty deferral initiative that prioritises the reduction of initial investment barriers for critical minerals projects surrounding specific minerals used in solar and battery manufacturing.
As the industry reflects on a year marked by strong partnerships, growth, innovation, and investment, it stands ready to embrace 2025 with renewed momentum, driving towards a future proudly made in Australia.
CEO, WELD AUSTRALIA
Australia’s welding industry continues to grapple with a severe skills shortage, with a projected shortfall of more than 70,000 welders by 2030.
We have reached a juncture that poses a threat to our national economic growth and productivity – with major infrastructure projects already at risk of delays due to a lack of skilled workers.
Welders are more in demand than ever, due to large-scale initiatives like AUKUS, South Australia’s $9.9 billion Torrens to Darlington (T2D) project and the renewables revolution, as well as metropolitan infrastructure projects such as the $12 billion Sydney Metro and the $5 billion Melbourne Airport Rail Link. While larger firms absorb as much available talent as possible, small to medium businesses across the general manufacturing sector are left unable to access the workforce they need to continue operations.
These conditions make it imperative for construction and manufacturing businesses, industry bodies, and government agencies to work together, adopting a multi-pronged approach that includes investment into both training and technology.
Even before the global pandemic, the number of welding trade workers in Australia was in steady decline – falling by 8 per cent in five years, from 75,800 in 2014 to 69,600 in 2019. Completion rates of welding apprenticeships are also dropping, as much as 23 per cent each year.
The impact of COVID-19 only exacerbated the issue, as the closure of international borders to migrants and short-term workers had the effect of further shrinking the labour pool. Welding job vacancies have increased in recent years, by 87 per cent in Queensland and 80 per cent in Western Australia – the two most impacted states.
Another factor is Australia’s changing demographics: an ageing workforce means that around 30 per cent of welders are now aged over 45 years. As the industry faces a wave of retirements in the decade ahead, with fewer younger people entering the profession, welding
positions will simply become impossible to fill.
These are concerns, given how critical welding will be to the success of our renewable energy revolution. However, the problem is not unique to Australia, with Europe, the UK and North America all experiencing massive welding shortages.
Weld Australia has developed an innovative solution: a micro-credentialling program that is designed to produce job-ready, certified welders within four to 12 weeks. This rapid training will complement existing apprenticeship models, while accelerating the process of getting welders onto sites to fill the growing skills gap.
This program offers an immediate solution by providing students with targeted procedure training aligned with the ISO 9606 standard. Graduates are certified to perform specific welding procedures so they can start contributing to the workforce sooner. At the same time, they can continue their long-
term apprenticeship pathway to become qualified. In fact, students who complete the ISO 9606 micro-credential are better positioned to complete further training, equipped with hands-on industry experience and practicalskills.
A key objective of the micro-credential program is to create rapid pathways for marginalised groups, tapping into a pool of potential workers who have traditionally been underrepresented in skilled trades. After Weld Australia’s success with prison welding programs in Victoria, there are plans to extend the program to school leavers, indigenous communities, women in welding initiatives, and the long-term unemployed. Providing participants with the skills they need to enter the workforce will not only fill the talent gap but improve employment outcomes for these groups – helping them secure stable, high-paying careers in welding.
This program is not intended to replace existing apprenticeship models but rather to complement them, providing a full spectrum of short-, medium-, and long-term solutions to the growing skills gap. The new approach offers flexibility for both individuals and employers, accelerating the process of getting welders onto job sites while still supporting the long-term training pathways of apprenticeships.
Rather than competing with traditional apprenticeship programs, our micro-credential approach fills the gaps and enhances the offering. It allows students to start contributing to the workforce quickly, while keeping the door open for further, long-term training. This way, we have a comprehensive approach to addressing the weldingshortage.
Weld Australia is currently working to establish welding academies and build partnerships with industry stakeholders to deliver the microcredential program where it’s most needed, ensuring a steady pipeline of workers to regions facing the highest demand.
In the construction sector, lack of productivity is one of the major barriers to project completion – resulting in only 50 per cent of project owners meeting delivery deadlines, according to KPMG’s Global Construction Survey. While the number of construction workers has increased in the past decade, output per worker has reduced. The average person now works two hours less per year, and yet their output is around 25 per cent lower. For businesses that are already grappling with skills shortages, greater productivity is the key to raising worker output. This will be crucial to the sector’s ability to deliver on the Federal Government’s pipeline of $120 billion infrastructure spend and $800 billion investment in renewable projects by 2050. Improvements to the industry’s
productivity performance is also a boon for the Australian economy, saving an estimated $47 billion annually.
Weld Australia’s 2024 Member Survey revealed that half of Australia’s welding workshops are operating at 80 per cent capacity or below, largely because of a lack of skilled workers. More than 42 per cent of welders are spending eight hours or less on site every day, and one quarter spend less than two hours of their shift doing actual welding. Businesses that maximise their efficiencies benefit from cost savings and better use of resources, with productivity gains leading to faster completion times.
Advanced technologies, including automation, robots and collaborative robots (also known as cobots), play an essential role in driving efficiencies and improving productivity. Automation has the power to accelerate processes and eliminate workflow delays, errors, and bottlenecks, while delivering superior quality outcomes with higher repeatability.
A report commissioned by Google noted that automation could deliver a $1.2 trillion boost to the Australian economy by 2030 through productivity gains. Increases in productivity also enable manufacturers to adapt quickly to changing customer needs and maintain a sustainable competitive advantage in domestic and export markets.
Cobots are robotic arms that are designed to work alongside human beings – being smaller, lightweight, more versatile, and easier to program than industrial robots. By taking on mundane and repetitive tasks, they don’t replace workers but rather free up their time and energy to focus on high-value activities that require critical thinking and creativity. Cobots are also capable of collecting enormous volumes of data that can be leveraged in areas such as predictive maintenance.
Importantly, the use of robots and cobots actually improves safety for welders and other manufacturing workers, by reducing dangerous and physically demanding work and removing welders from exposure to potential hazards, toxic fumes, UV radiation, heat and sparks. As a result, workplace injuries are predicted to fall by 11 per cent and unburden the average Australian of two hours of the most tedious and manual work each week, creating a safer and more satisfying working environment.
Despite the clear benefits – from improved productivity and quality to worker safety and satisfaction – Australia tends to lag in digital adoption, and the welding industry is no exception. Advanced technologies are becoming a crucial factor in the success of a welding business,
but uptake of cobots and robots remains low in comparison to other advanced economies. Australia recently dropped from 18th to 35th (out of 37) globally for industrial robot application.
With advancements in robotics and automation technology, and the likelihood of increased industry uptake, the issue of employment rates is inevitablyraised.
Media outlets frequently report that the more automated the manufacturing industry becomes, the less jobs there are available. This is simply untrue. Robotics and automation technology make manufacturing processes more efficient and increase productivity and competitiveness. This is important for small-to-medium businesses which, in Australia, account for over 90 per cent of the manufacturing industry.
This increased productivity and competitiveness can increase demand, creating new job opportunities, particularly for highly skilled workers, and have a positive impact on wages.
Robots substitute labour activities but do not replace jobs. According to the International Federation of Robotics, less than 10 per cent of jobs are automatable. Increasingly, robots are used to complement and augment labour activities; the net impact on jobs and the quality of work is positive.
Technological innovations allow businesses to make better use of human skill and innovation, with machines taking over mundane tasks so that employees can focus on critical thinking, quality and creativity. This opens new opportunities for businesses to improve and optimise their operations.
In light of this, Weld Australia is currently partnering with two of the world’s largest not-forprofit welding organisations: EWI in the United States and CWB in Canada. This partnership will pave the way for cutting-edge international manufacturing expertise to flow into Australia. Weld Australia members, and the broader manufacturing industry, will be able to access the latest research and innovations in welding, advanced technology, materials science and more.
To secure Australia’s manufacturing future, we must urgently address the welding skills shortage. By fostering the right training programs, embracing advanced technology, and breaking down barriers to skilled employment, we can build a robust workforce capable of driving productivity and innovation.
This isn’t just about bridging a skills gap – it’s about positioning Australia’s welding sector for sustainable growth, ensuring our ability to deliver on ambitious infrastructure projects and compete on a global scale. With a multi-faceted approach, the welding industry is poised to overcome its challenges and thrive – powering Australia’s industrial growth for generations to come.
Australian-Singaporean engineering group, Civmec, has entered into a non-binding Heads of Agreement with Naval Vessels Lürssen (NVL) to acquire Luerssen Australia.
Upon completion of the transaction, NVL will transfer all its shareholding in Luerssen Australia to Civmec, including all assets, employees, and licences.
Luerssen Australia’s sole focus is the build of six Arafura Class Offshore Patrol vessels for the Royal Australian Navy.
“The acquisition of Luerssen Australia is a natural step for Civmec as a sovereign Australian shipbuilder with world-class shipbuilding facilities and an experienced shipbuilding workforce,” said Civmec’s executive chairman, Jim Fitzgerald.
“Having worked on the project since 2018 we’re confident in our ability to execute the remaining work scope and ensure a smooth transition for all stakeholders.”
The transfer is set to ensure the uninterrupted design and build of both companies’ operations at the Osborne South shipyard in South Australia and the facility in Henderson, Western Australia.
The proposed change is subject to Commonwealth Government consent. To obtain such consent, both companies will begin engaging with the
Commonwealth in the required administrative approval process.
Both parties are working towards a target date of 31 December 2024, with the non-binding Heads of Agreement subject to satisfactory due diligence and meeting Conditions Precedent.
In parallel with the Commonwealth consent
process, an Effective Date in the coming months will allow the parties to conduct necessary due diligence and detailed planning.
The priority is to agree on a framework for the interim period in which Luerssen Australia and Civmec will closely cooperate in managing the SEA1180 project.
Australia’s largest bus body manufacturer, Volgren, has announced the local construction of its first hydrogen-powered bus, in collaboration with Wrightbus.
Volgren’s first hydrogen fuel cell electric buses to operate in Australia represent a step in the transition to cleaner public transport.
“This project demonstrates the strength of Australia’s local manufacturing sector and the value of collaboration,” said CEO of Volgren, Thiago Deiro. This model, alongside a second hydrogen bus to be delivered in the coming months, are an addition to Volgren’s Zero Emission Bus portfolio.
This portfolio now includes more than 150 zeroemission buses across six battery-electric and fuel-cell variants.
The company has also collaborated with a firm that specialises in zero-emission bus technology, Wrightbus. This collaboration has enabled the integration of hydrogen fuel cell expertise into locally manufactured buses.
While Wrightbus pioneered the world’s first
hydrogen-powered double-decker bus, Volgren ensures that this technology can meet the needs of the Australian market.
Wrightbus supplied the hydrogen fuel cell chassis
technology for the buses, marking the first time its powertrain technology has been used in Australia. This partnership allows for Volgren to bring advanced global technology to Australia.
The Gas Appliance Manufacturers Association of Australia (GAMAA) welcomed the commencement of construction on the $65.46 million Murray Valley Hydrogen Park near Wodonga, Victoria. The project is led by the Australian Gas Infrastructure Group (AGIG) with Longi Hydrogen, Energy Australia, Powernet, Valmec, GPA Engineering.
It is also supported by the Federal Government’s
According to Jamieson, gas is the favoured energy source for more than 60 per cent of
Australian Renewable Energy Agency (ARENA) and the Victorian Department of Energy Environment and Climate Change.
“This project shows how industry and government can work together to make renewable hydrogen on an industrial scale a reality by the end of this decade,” said GAMAA president, Ross Jamieson.
A 10-megawatt LONGi Hydrogen electrolyser is set to enable Hydrogen Park Murray Valley to generate
around 500 tonnes of renewable hydrogen and avoid around 3,000 tonnes of emissions each year.
The renewable hydrogen will then be blended into the existing natural gas distribution network. This will then be delivered to around 40,000 AlburyWodonga homes and businesses and won’t require any changes to the appliances already in use.
“This is an important first step in the transition to 100 per cent renewable gas,” said Jamieson.
“Australian gas appliance manufacturers and their workforces are ready today to support the clean energy transition. We already have the equipment, the skills and the experience to create a thriving and competitive renewable gas appliance manufacturing base.”
Jamieson said the project will save consumers money allowing them to continue to use gas for cooking, heating and hot water.
“The Murray Valley project underlines the importance of maintaining a viable hydrogen ready distributed gas network which, together with new high efficiency gas appliances will significantly decarbonise gas supply to households and small businesses,” he said.
More than 60 per cent of gas appliances sold in Australia are designed and made in Australia, for Australian conditions.
Solar and battery manufacturers are set to benefit from the NSW Government’s $250 million royalty deferral initiative, which is the first action of the NSW Government’s new Critical Minerals and High-Tech Metals Strategy.
This development represents a shift to combat high initial investment costs for critical minerals projects that have been a barrier for the industry.
Currently there are 12 critical minerals, mining and processing projects in NSW that are ready for investment. They need around $7.6 billion in capital investment value and are expected to generate about 4,600 jobs during construction and 2,700 ongoing jobs.
The royalty deferral scheme will assist in easing financial pressures and attracting investment for new projects in the early stages of development.
The Critical Minerals and High-Tech Metals Strategy identifies priority minerals and metals in NSW that have uses in the manufacturing of clean energy products like solar panels and batteries. The minerals and metals include rare earths,
scandium, cobalt, copper and silver.
“Our vision for NSW is to be a global leader in critical minerals and high-tech metals, generating economic prosperity through exploration, mining, processing and advanced manufacturing,” said Minister for Natural Resources, Courtney Houssos.
“The new strategy sets out a clear vision for NSW to be a leader in critical minerals and high-tech metals, generating economic prosperity through responsible exploration, mining, processing, recycling and advanced manufacturing.”
The strategy focuses on the role of critical minerals in supporting broader government priorities, including the clean energy transition and driving domestic manufacturing.
Examples of this in the strategy include investigating opportunities to pilot common-user refineries and supporting investment in domestic manufacturing.
Fully realising the opportunity of the state’s critical minerals and high-tech metals deposits means moving further down the supply chain and beyond only extracting and exporting resources.
critical minerals has the potential to cut costs for business and also significantly reduce environmental waste,” said Husic.
A $2.4 million grant was awarded to WaveX to work on the development of its anchors for offshore wind and wave energy.
“We want Australia to be a renewable superpower that’s why we’ll continue to back companies like WaveX,” said Husic.
efficiently, with great potential for exports and local jobs,” said Husic.
Round 16 of the Cooperative Research Centres Projects (CRC-P) is awarding 23 grants in total to successful companies. These other companies include:
• Nonocube Health in Victoria who received $3 million to drive development of technology for early detection and treatment of pancreatic cancer.
• Miniprobes in South Australia who was granted $1.5 million to deliver an AI-enabled optical scanner to rapidly assess beef quality.
The CRC Program grants for industry innovation were announced in Perth by the Federal Minister for Industry and Science, Ed Husic.
“West Australian smarts are showing the rest of the world how to get things smarter, more
Nearly $3 million was awarded to CPC Engineering to develop a new technology to separate iron, aluminium and other metals. Using membrane technology to separate the minerals has the potential to reduce waste while also cutting costs for mineral processors.
“CPC Engineering’s pioneering work filtering
• Emesent who was funded $2.4 million to pioneer an innovative autonomous mining platform to collect and merge data from field robots and sensors.
Since its inception in 1990, the CRC Program has helped to fund the commercialisation of technologies, products and services across a range of sectors and industries including manufacturing.
Australian solar innovator, SunDrive Solar, and global solar manufacturer, Trinasolar, have signed a Memorandum of Understanding (MoU).
The MoU forms a majority Australian-owned
joint venture (JV) aimed at establishing solar manufacturing capabilities in the nation.
With SunDrive’s solar technology innovation, and Trinasolar’s global manufacturing expertise and
technology, the collaboration is set to enhance Australia’s ability to competitively produce highquality solar products locally.
This collaboration is set to help Australia’s energy security and renewable energy goals and could position the nation as a global leader in solar technology.
“This collaboration demonstrates SunDrive and Trinasolar’s mutual belief that Australia’s engine of solar innovation can drive a global solar manufacturing powerhouse, producing the future of clean energy from right here at home,” said SunDrive CEO, Natalie Malligan.
As a part of the MoU, a new facility is set to create over 300 skilled jobs of the future.
In addition, by building a robust and diverse local supply chain for solar products, the JV will also create a resilient and sustainable domestic energy system.
SunDrive will lead an application for funding under ARENA’s Solar Sunshot program, which is crucial to advancing the JV.
Vast Renewables and its consortium partner, Mabanaft, have awarded international engineering group Fichtner and German e-fuels leader bse Methanol contracts to commence pre-front-end engineering and design (FEED) work on the green
methanol plant, SM1.
SM1 is a first-of-its-kind project that can demonstrate the potential and catalyse Australia’s green fuels industry and a global pipeline of projects.
CEO of Vast, Craig Wood, said that the pre-FEED commencement is a milestone to progress the plant, which itself has the potential to make a difference in the hard-to-abate transport sector.
“We’re looking forward to building on Fichtner and bse Methanol’s strong platform of work to date to deliver SM1,” said Wood.
Part of the Port Augusta Green Energy Hub in South Australia, SM1 will have the capacity to produce 7,500 tonnes of green methanol each year. Methanol is a versatile hydrogen derivative and, if produced using clean energy, has the potential to decarbonise shipping and aviation fuels.
SM1 will be supplied with base load clean and renewable heat from Vast’s 30 MW/240 MWh concentrated solar thermal power (CSP) plant. This milestone comes after Vast and Mabanaft signed a joint development agreement in June 2024.
The project has secured funding agreements for up to $19.48 million from the Australian Renewable Energy Agency (ARENA) and up to €12.4 million from Projektträger Jülich (PtJ) on behalf of the German government.
Construction of Australia’s first five-star river cruise, the PS Australian Star, is picking up steam.
The Federal Government has invested $2.25 million through the Regional Tourism Investment Fund to build the paddle steamer, which is being delivered by local company Murray River Paddlesteamers.
“I’m so excited to see this iconic local tourism project coming to life – giving visitors yet another reason to visit the Murray region, with those benefits flowing to local businesses and the community,” said the Victorian Minister for Tourism, Sport and Major Events Steve Dimopoulos.
Later this year, a refurbished 1907 wood-fired steam engine is set to be installed, and the main deck will also be constructed.
The vessel will operate from the Port of Echuca and will be able to carry 38 people eachtrip.
Featuring 19 ensuite cabins, a fine dining restaurant, function space, a guest lounge and bars, the PS Australian Star adds to regional Victoria’s tourism offering.
The vessel also will include accessible cabins, with elevator access to all levels.
Construction of the vessel has created 13 local jobs and will create a further 16 ongoing jobs when it beginscruising.
“The PS Australian Star is powering towards completion and will deliver another unique and
exciting tourism experience in regional Victoria –while supporting local jobs in the process,” said Minister for Regional Development, Gayle Tierney.
Almost 5.9 million people visited the Murray region in the year ending September 2023, contributing almost $2 billion to the state economy.
GME manufactures UHF CB radios and emergency beacon products, exemplifying its commitment to local production and innovation in the Australian manufacturing industry.
In an initiative to stimulate local economies and support job creation, the New South Wales Government is set to implement new measures aimed at enhancing the role of businesses in government procurement processes.
The NSW government aims to prioritise local suppliers and drive regional economic growth. This transformative approach aligns with the government’s commitment to fostering a robust manufacturing sector, ultimately benefiting communities across NSW.
An example of this commitment to local manufacturing is GME, a family-owned company and Australia’s sole manufacturer of UHF CB radios and emergency beacon products.
Founded by Edward Dunn in 1959 and based in Winston Hills, NSW, GME has championed local production, ensuring that more than 85
per cent of its revenue comes from Australianmade products. By investing in manufacturing facilities and fostering community partnerships, GME exemplifies the positive impact of local procurement.
The company’s emphasis on quality, innovation, and workforce development not only strengthens its market position but also supports the broader objectives of the NSW Government to create jobs and invigorate local industries. As the government shifts its focus, GME stands ready to leverage these changes, further solidifying its role in the future of NSW manufacturing.
Initially focused on repairing television tuners, GME has achieved some world firsts, including producing Australia’s first EPIRB (Emergency
Position Indicating Radio Beacon) in 1979 and the world’s first VHF Sea Phone in 1989.
“By the year 2000, we were producing a wide range of products, from EPIRBs to UHF and VHF radios,” said Tony Crooke, group marketing manager, GME.
“As our business has grown, we’ve diversified into new markets while remaining proudly Australianowned, with most manufacturing still in Sydney. For 65 years, we’ve led the RF communications industry in Australia, and we take great pride in that legacy.”
GME’s primary markets now encompass 4WDs, agriculture, heavy vehicles, and marine and outdoor recreation. Its offerings cater to essential industries, including boating, fishing, and offroading, with a strong emphasis on safety through its EPIRBs and personal location beacons (PLBs).
One of GME’s core values is maintaining Australian manufacturing. With more than 230 staff, GME operates a facility that consolidates research and development, engineering, quality control, manufacturing, and technical services, all under one roof.
“We operate several Surface Mount Technology (SMT) lines for local PCB production and have a fully integrated lean manufacturing facility and national warehousing on-site,” added Crooke.
“This centralisation allows us to provide a true end-to-end Australian manufacturing solution. Additionally, we’ve recently invested in a dedicated Zone 4 manufacturing facility for secure electronics production, enabling us to deliver high-assurance equipment to Australian Defence customers.”
This strategy aligns with recent initiatives from the New South Wales government aimed at reducing dependency on global supply chains, particularly in the wake of challenges posed by the COVID-19 pandemic.
“We’ve seen a sustained increase in demand for Australian-made products, leading to heightened manufacturing output at our New South Wales facility,” said Crooke.
“This surge, coupled with investments in additional engineering resources to accelerate our product development cycles, has resulted in a substantial workforce increase of around 30 per cent.”
“With more than $7 million invested in additional manufacturing infrastructure over the last few years, we are ready to meet growing demand and support local job creation,” explained Crooke.
With the capability to produce over 500,000 units per year, GME’s manufacturing facility is designed for end-to-end production, allowing GME to maintain quality control throughout the manufacturing process.
It maintains an ISO 9001-certified Quality Management System (QMS) to ensure its products are built to endure harsh environmental conditions. Its testing process combines advanced environmental testing equipment with realworld assessments.
The on-site environmental test facility features a range of specialised equipment, including a salt fog chamber, accelerated UV chamber, vibration and shock testing apparatus, antenna whipping machines, and Ingress Protection chambers.
“While controlled tests are crucial, we prioritise real-world testing to ensure our products meet the demands of the environments customers encounter, guaranteeing reliability and durability over time,” said Crooke.
GME offers advanced electronics manufacturing, including build-to-print services, secure production at its Zone 4 facility, PCB design, and surfacemount technology, providing an end-to-end manufacturing solution.
The Sydney facility is complemented by an offshore site for some sub-assemblies and strategic subcontracting. The company actively engages with other local Australian manufacturers producing electronics in New South Wales.
This commitment to sustainability is reinforced by maintaining an ISO 14,001-certified environmental
management system and aiming to reduce environmental impact.
“Our employees receive training on environmental responsibility as part of our Environmental Management System, and we partner with regulated waste management contractors to ensure hazardous materials generated during manufacturing are handled offsite according to best practices,” added Crooke. GME’s efforts in sustainability not only benefit the environment but also enhance its appeal to customers who prioritise eco-friendly practices.
To ensure the future of local manufacturing, GME engages with educational institutions, from secondary schools to universities. The company maintains scholarship programs, particularly through partnerships with the University of
Technology Sydney, aimed at nurturing young engineering talent.
These initiatives are designed to attract, engage, and develop the next generation of engineers, providing them with valuable hands-on experience in a thriving manufacturing environment.
By investing in workforce development, GME not only secures its future but also contributes to the broader manufacturing landscape in Australia. The company’s commitment to training and education is crucial for addressing the skills gap in the industry, ensuring that future workers are equipped to meet the challenges of an evolving market.
While GME has successfully established itself as a prominent local manufacturer, it does face challenges. The higher labour costs associated
with it can be a barrier compared to countries with cheaper labour.
However, GME offsets these costs by producing higher-quality products that boast lower failure rates, thereby gaining a competitive advantage.
The company has also experienced the same global supply chain issues that many manufacturers have faced, particularly regarding semiconductor shortages.
As GME relies on several components sourced from countries such as China, Taiwan, and Malaysia, the volatility of these supply chains necessitates strategic planning and flexibility. GME continues to work towards building resilience within its supply chain by strengthening relationships with local suppliers and investing in domestic capabilities.
Looking ahead, GME is focused on further enhancing its local operations through continued capital investment in advanced manufacturing technologies, including automation and robotics.
“We aim to expand our product lines and accelerate development cycles to meet the demands of both existing and emerging markets,” added Crooke.
“In addition, GME is dedicated to strengthening its partnerships with local suppliers, which is essential for promoting a robust local manufacturing ecosystem that supports the community and drives economic growth in New South Wales.”
For manufacturing executives, safeguarding operational technology (OT) is not just a priority—it's a necessity. This comprehensiveExecutive Guide on OT Cybersecurity summarises the unique challengesof securing manufacturing environments and offers actionable stepsto improve your security posture. Scan to Download Now →
Good relationships are key to building a successful manufacturing enterprise. Manufacturers’ Monthly looks at the bond between Austal and Capral.
Founded by John Rothwell in 1988, Austal has taken Australian shipbuilding to the global stage, building a diverse portfolio of vessels.
“It started out as building fishing vessels and has grown from there into building fast ferries, and then into the defence market,” said head of supply chain at Austal, Brent Carey.
Originally an entrepreneurial venture by Rothwell, Austal’s manufacturing capacity has evolved to meet a demanding market.
“We’re up to about 360 vessels for about 60 countries,” said sales operations manager at Austal, Matthew Klingberg.
From starting in Australia 36 years ago, Austal has since expanded its manufacturing to the United States, Philippines and Vietnam.
Austal designs, constructs and supports vessels for a diverse range of global customers, including the Australian Defence Force.
“We build ferries and commercial vessels in our yards in the Philippines and Vietnam, but predominantly in Australia we concentrate on defence vessels,” said Klingberg.
Klingberg, who himself has been with Austal for 19 years, said the company’s ability to produce vessels for different markets stems from a well-resourced and experienced team.
“We’ve got 3,000 years of collective ship building experience here within the Austal precinct in Henderson,” said Klingberg.
“I think what we do differently is we don’t have
a product that we try and fit customers into. We provide customised solutions. If you have requirements, then we’ll have a solution for you. That shows in the vast number of ships for different customers that we’ve built all around the world.”
These capabilities are based around two facilities in Western Australia. One is located within the Henderson Defence Precinct, a hub for the development of naval vessels. Austal manufactures the Evolved Cape-class Patrol Boats at the yard, using aluminium.
“It’s lightweight so it allows us to add lighter engines and components to the vessel. It’s less likely to corrode and it’s more resilient,” said Carey.
“It provides a greater level of efficiency over steel and allows us to put some different types of equipment on the vessel, meaning it can meet the functional performancespecifications.”
To ensure the successful build of these aluminium vessels, Carey said that Henderson shipyard has now perfected a seamless production line.
“We start out with raw sheets of aluminium, and we start to bring that through into the various assembly bays. And within each of those bays we have people who do fabrication and welding, fit out and electrical,” he said.
“It’s a really quite a broad range of skills that we have.”
When a vessel’s structural integrity and a supply chain’s success is dependent on a material, having a reliable supplier becomes paramount. Austal recognises this necessity, demonstrated by its 25-year partnership with Capral, an Australian supplier and distributor of aluminium products.
“Capral quality is world class. All the products could be benchmarked against anything around the world,” said Klingberg.
“From Capral, we get a lot of aluminium plate and extrusions, and some of those extrusions are quite intricate, detailed and high quality. The products are also DNV certified, which provides us with peace of mind,” said Carey.
Klingberg further highlighted the importance of Capral’s DNV-certificated products.
“The ships are built to classification society requirements and a part of that is we need aluminium that’s certified,” he said.
Additionally, Klingberg emphasised that Austal not only benefits from the quality of Capral’s products, but also enjoys the advantage of a productive, collaborative relationship.
“Relationships with your clients and your suppliers are key to being successful. That’s why we engage companies like Capral,” he said.
“They’re reliable, so we know what we’re going to get. It’s going to be on time. I think we’ll be continuing to use them for a long time into the future.”
Carey agreed with the sentiment and noted that the trust between the two companies was a catalyst in their continuous, strategic alignment.
“One of the great things about our relationship with Capral is our strategic alignment. It’s nice to have a supplier that shares a vision and values, and that understands our needs,” he said.
In addition to a strong partnership, Capral’s Australian origins play a crucial role in supporting Austal’s shipbuilding operations.
“It’s important that they’re an Australian supplier. They respond quickly to our needs, are highly adaptable and are just around the corner,” he said.
“From cutting a piece of raw aluminium to completing a finished ship in around 15 months is an amazing timeline. Not many people in the world can achieve those sorts of timeframes; there’s a lot that goes into these boats.
“Something like 50,000 individual objects that will go into an Evolved Cape-class Patrol Boat. The team here is managing a lot of moving pieces.”
Months of hard work at Austal culminate in the launch of boats, on average, twice a year.
“You get to see it evolve from a sheet of aluminium into a finished product and then ultimately launched into the water,” said Carey.
“Every time we deliver a boat, we have a ceremony with the ship staff along with our team and our key suppliers.”
Carey said that while his time at Austal has sometimes been challenging and complex, there have been many rewarding experiences, too.
“I enjoy working with people, collaborating with our team here on site, and collaborating with all of our suppliers,” said Carey.
Klingberg feels equally as privileged within his role at Austal, which has allowed him to travel the world and fulfill his dream of building world class boats.
“I guess when you are living your dream of what you wanted to do, you feel very privileged,” he said.
In reflection, Klingberg noted that Austal’s success is more satisfying considering that the team is largely homegrown.
“We have great apprenticeship, trainee and graduate programs that attract and recruit many
people every year, but we also have a lot of people across the business who have been here for a very long time as well,” said Klingberg.
“They’re highly skilled and very dedicated to Austal. I think you could almost say they’d bleed Austal.”
This continuity of work gives Klingberg confidence in Australia’s shipbuilding industry, especially as Austal works towards becoming the Commonwealth of Australia’s Strategic Shipbuilder in Western Australia, announced in November 2023.
“An apprentice could start this week and spend his whole career here now,” said Klingberg.
With a commitment to strong partnerships, innovation and expansion, Austal continues to reinforce Australia’s reputation as a leader in advanced maritime solutions.
Our inline plasterboard measurement system comprises two high-precision laser profile scanners, offering both online and motorised offline caliper systems for measurement of edge angle, edge width, recess width, depth and board thickness. Place this system anywhere on the forming belt and you can monitor the profile from anywhere.
Contact our engineers or visit www.bestech.com.au for more information.
Email: enquiry@bestech.com.au
Goulburn Mulwaree Council fosters manufacturing innovation with the region’s prime location, strong infrastructure, and dedicated business initiatives.
The Goulburn Mulwaree region is situated in the Southern Tablelands of New South Wales.
Encompassing the city of Goulburn along with the villages of Marulan, Tarago, Towrang, and several others, the council operates over an expansive land area of 3,223 square kilometres, and is home to a diverse population of more than 32,000 residents.
This region’s strategic location – an hour’s drive from Canberra and two hours from Sydney –facilitates connectivity via road and rail, enhancing its appeal as a growing hub for economic activity and attractingbusinesses.
Goulburn Mulwaree Council (GMC) not only oversees local governance, but also drives community development while ensuring essential services and infrastructure meet the needs of residents and the business community.
Goulburn’s proximity to metropolitan areas like Canberra and Sydney positions it as an attractive site for manufacturing and other industries.
The region has a robust infrastructure network that includes a direct connection to the newly constructed Western Sydney Airport and an efficient route to Port Kembla.
“Our strategic location on the main freight route from Queensland to Victoria, along with proximity to Wollongong and Port Kembla, makes our location ideal for sourcing local goods, but also importing and exporting,” said Danae Vitnell, economic development manager, Goulburn MulwareeCouncil.
“Our location plays a key role in our manufacturing growth, which has outpaced the rest of New South Wales. Almost all transport routes converge in Goulburn, allowing easy access to key markets without the traffic constraints of larger cities like Sydney and Melbourne.”
This accessibility is an advantage, as it fosters growth in manufacturing. Currently, there are 108 registered manufacturing businesses within the GMC local government area, employing more than 1,200 individuals and contributing $154 million to the local economy.
Tribe Breweries, originally from South Western Sydney, moved to Goulburn to take advantage of the
area’s reliable water supply and strategic location near the Hume Highway. As a contract brewer, it produces beers for major retailers like Coles and Woolworths, while marketing its own labels under Stockade Brew Co.
Beginning production in late 2013, Tribe has become integral to the local economy. Its offerings include Ducks Lane Lager and various ready-todrink beverages, with annual production capabilities of 30 to 40 million litres. The brewery also features a unique brewing system found in only three locations in Australia.
“Tribe Breweries chose Goulburn primarily because it has a secure water source, which is
crucial since the majority component of beer is water,” said Geoff Kettle, government relations and community engagement, Tribe Breweries.
“Additionally, we aim to employ local people – more than 95 per cent of our staff are from Goulburn, contributing to the area’s growth and development.”
With more than 2,800 registered businesses in the region – a number that has consistently grown since 2014 – the council collaborates with two chambers of commerce and industry, as well as other stakeholders, including Regional Development Australia Southern NSW and ACT and The Department of Primary Industries and Regional Development, to foster a supportive business environment.
“In my role within the economic development team, we provide a concierge service for new and existing businesses, streamlining the process of accessing support and grants to facilitate business growth and investment,” said Vitnell.
“Dealing with council can be frustrating – there are 400 staff members with many different roles. You go in with an idea, but you’re unsure who to talk to and may have to meet with many departments. We’ve streamlined that process. Now, businesses can come to me directly, simplifying the development and investment phase for them.”
Through the Employment and Rural Lands Strategy, GMC aims to manage land use effectively and avoid future conflicts that could arise from uncoordinateddevelopment.
“Unlike larger cities, where industrial areas might be surrounded by residential developments, we’re planning now to ensure our industrial lands remain viable. This proactive approach is an advantage for businesses looking to establish themselves here,” said Vitnell.
The council plays a key role in facilitating services in the region, including the management of water, sewer, and waste systems, while also supporting the maintenance of road networks.
It is dedicated to executing a capital works program, which encompasses a variety of projects aimed at enhancing the liveability of Goulburn. Initiatives include the recent upgrades to the Goulburn Aquatic & Leisure Centre and the development of a new Goulburn Performing Arts Centre, both designed to enrich community life and provide cultural enrichment.
The council has also made investments in expanding walking and cycling paths, including the scenic river walk, which promotes an active lifestyle among residents. These projects reflect a comprehensive approach to urban planning, balancing development with community needs.
“Goulburn offers a forward-thinking and businessfriendly council and affordable real estate. With great healthcare, education options, and a strong community, Goulburn is poised for stable growth and is an ideal place for businesses to thrive,” added Kettle.
“Our council manages water and wastewater services and is currently undertaking major upgrades to ensure a reliable water source for the community,” explained Vitnell.
The council has invested in capital projects that are in various stages of development to futureproof water infrastructure. The council’s waste team regularly engage with businesses to review services and ensure everything operates smoothly.
“The growth of the Goulburn economy will expand the talent pool available for hiring,” said Michael Leahy, managing director ANZ, Aviagen.
“Goulburn’s proximity to transport routes, access to Sydney International Airport, and relatively low level of poultry production make it an excellent location for producing breeding stock and delivering to our Australian and international customers.”
Aviagen’s role as a global supplier of chicken meat breeding stock is essential for a city’s overall growth. Over decades, investments in facilities and skilled personnel have enabled the production of efficient, healthy chickens.
This commitment not only creates jobs but also attracts further investment and enhances the city’s reputation in agriculture.
“We want to protect local businesses and provide clarity on where they can expand. Our goal is to balance economic development with community needs, ensuring that we attract industry, create jobs, and provide sufficient housing for everyone. It’s all part of that bigger picture,” said Vitnell.
“Council’s Economic Development team has three main priorities. The first is investment attraction, promoting Goulburn and its strengths. With over 100 manufacturing businesses employing more than 1,200 people, manufacturing is vital to our community.
Second, we prioritise community development through projects like the new Aquatic & Leisure Centre and Performing Arts Centre, enhancing liveability and making Goulburn an appealing place for businesses and their employees. Finally, we aim to sustain a vibrant local economy that fosters innovation and job creation while preserving our unique character.”
“Camcast moved to Goulburn to expand because there’s much more room here – twice the land we had in Sydney, and I see great opportunities in Goulburn, especially as a manufacturer outside of metropolitan Sydney,” said Troy Rath, director, camcast.
Camcast is a non-ferrous foundry specialising in the casting of metal alloys. The company primarily serves the petroleum industry, producing components for fuel tanker handling systems and the electrical sector, supplying high-conductivity copper parts for power lines and substations.
“The council here is a major support; they actively reach out to me and seek my input on manufacturing,” added Rath.
Goulburn offers a place for manufacturers to find their footing and grow. Its strategic location and reliable infrastructure create a solid foundation for business operations.
As the community continues to develop, Goulburn Mulwaree Council stands ready to support those seeking to establish or expand and ensure that resources are available for success.
As ransomware threats continue to evolve, investing in Operational Technology (OT) cybersecurity solutions is vital for manufacturers.
Ransomware has evolved from simple extortion software into complex cybercrime operations that threaten businesses and critical infrastructure worldwide.
Unlike regionally or sector-focused cybercriminals, groups operating under the Ransomware-as-aService (RaaS) model have elevated these operations to the next level. These groups adapt and innovate to maximise extortion efficacy, impacting organisations across all industries. These industries include those where operational downtime is highly disruptive or intolerable, particularly in industrial and critical infrastructure sectors.
Financially motivated and opportunistic, these ransomware groups often collaborate with other cybercriminal entities, such as Initial Access Brokers (IABs), who provide them with preliminary access to victims’ environments. Cybercriminals’ ecosystem of collaboration accelerates ransomware deployment and amplifies the risk, making RaaS operations a challenge for global cybersecurity.
Dragos monitors the activities of ransomware groups, which disrupts operations within Industrial Control Systems (ICS) and Operational Technology (OT) environments.
Ransomware incidents impacting industrial sectors nearly doubled between Q1 and Q2 2024. The manufacturing sector even accounted for 66 per cent of all attacks on industrial organisations globally. These incidents highlight the increasing overlap between operational technology (OT) and IT systems, where breaches in IT can disrupt OT
operations, leading to shutdowns and cascading supply chain disruptions.
Ransomware incidents nearly doubled from 169 in the first quarter of 2024 to 312 in the second quarter. The increase in incidents and their impact is notable, considering significant law enforcement operations involving ALPHV (BlackCat) and Lockbit 3.0 in previous quarters. These ransomware groups quickly adapted and recalibrated their strategies, increasing incidents in Q2 of 2024. Necessity drives innovation, and ransomware groups frequently adjust their strategy and tactics to avoid exposure and achieve their goals. The resilience and adaptability of ransomware groups make them an ongoing and growing risk to industrial sectors.
The manufacturing sector was the most affected, with 316 observed incidents across the first two quarters of 2024. The second most affected sector was developers and manufacturers of Industrial Control Systems (ICS) equipment and software, with 68 incidents.
In the Asia-Pacific region, which includes Australia, several key manufacturing sectors – such as automotive and food and beverage – reported disruptions as ransomware incidents targeted IT systems, indirectly impacting production operations. In the second quarter, indirect impacts of ransomware attacks on OT included system shutdowns, OT disruption, and access to SCADA system data, which had the potential to halt production and disrupt services.
Although ransomware groups have not yet directly
attacked OT systems, the interconnectedness of OT and IT environments means that IT breaches can paralyse OT functions.
For example, ERP systems that manage supply chains or production scheduling often share infrastructure with OT systems, allowing ransomware to propagate quickly through both environments.
A ransomware incident in manufacturing can quickly spiral into financial losses.
Globally, production delays due to ransomware cost manufacturers an excess of $1 million per day, with downtime in Australia further compounded by its reliance on just-in-time supply chains. In some cases, manufacturers also face penalties for missed contracts or regulatory non-compliance.
A ransomware incident 2023 involving the Brunswick Corporation cost the company an estimated US$85 million due to production disruptions. A similar incident in Australia could result in comparable losses and cascading effects across domestic and international markets.
Ransomware typically starts by compromising IT systems through phishing emails, weak or stolen credentials, or vulnerabilities in remote access software.
Once inside a network, adversaries often pivot toward OT systems due to poor network segmentation or shared authentication systems. This scenario is dangerous for manufacturers, where compromised OT systems can disrupt automated production lines, damage machinery, and jeopardise worker safety.
A notable example is the ransomware attack on an Australian automotive parts manufacturer in the second quarter of 2024. The attack started with the compromise of IT systems, but the lack of network isolation allowed it to spread into OT systems, forcing a week-long production halt. Such disruptions underscore the need for OT-native defences to isolate critical systems and detect intrusions early.
Manufacturers need OT-specific cybersecurity solutions to address the unique risks of industrial environments. Traditional IT security tools often lack the visibility and control to protect OT systems. Additionally, OT systems may run on legacy hardware or software, making them harder to patch and secure without disrupting operations.
OT-native solutions can make a difference within: Network Segmentation: Implementing segmentation between IT and OT environments
limits the movement of ransomware across systems, containing breaches before they escalate to impact business-critical physical operations.
Advanced Threat Detection: OT-specific monitoring tools can detect abnormal behaviours, such as unauthorised access to SCADA systems before ransomware takes hold.
Integrated Investigation and Response Playbooks: Incident response plans with OT considerations enable fast recovery with minimal downtime, reducing an attack’s financial and operational impact.
Automated Recovery Systems: In OT environments, real-time recovery systems ensure critical operations can resume without extended manual intervention.
Investing in OT cybersecurity is not just a technical upgrade – it provides measurable business benefits. These include reducing ransomware recovery times, minimising downtime, and avoiding the need to pay ransoms. Furthermore, these solutions help manufacturers avoid fines for regulatory non-compliance and maintain strong relationships with suppliers and customers by ensuring production continuity.
The systems also help manufacturers in reducing downtime, which even by one day could save millions. It also can help businesses in maintaining uninterrupted production to avoid fines from delayed deliveries, which can run into millions for large-scale manufacturers.
With ransomware attacks expected to continue rising, Australian manufacturers must act now. OT-native cybersecurity solutions are no longer a luxury but a necessity. Manufacturers must adopt a proactive, layered defence strategy as ransomware groups evolve tactics, targeting IT systems with OT consequences. Executives should assess their organisations’ cybersecurity posture today and invest in OT-native solutions to ensure operational resilience.
Ransomware presents a growing threat to Australia’s manufacturing sector, with disruptions increasingly affecting IT and OT environments. Investing in OT-specific cybersecurity solutions offers manufacturers the best chance to contain attacks, minimise downtime, and protect business continuity. The lessons from recent ransomware incidents are clear: A failure to secure OT systems is not just a cybersecurity risk – it’s a business risk. With the proper defences, Australian manufacturers can safeguard their operations, protect their bottom line, and stay resilient in the face of evolving threats.
Researchers
Agroup of eight researchers from the University of Melbourne, CSIRO and the Florey Institute of Neuroscience and Mental Health are developing new diagnostic technology that could transform how iron deficiency is detected.
Iron deficiency can lead to fatigue, poor concentration, a weakened immune system, reduced sports performance, pregnancy complications, and, if left untreated, lifethreatening anaemia.
“Inaccurate iron testing has the potential to cause major health consequences, for women in particular,” said Gawain McColl, FeBI founder and project lead, Florey associate professor.
An estimated 1 in 5 women and 1 in 20 men in Australia suffer from iron deficiency, yet many remain unaware due to outdated and inaccurate blood tests.
The FeBI (Ferritin Bound Iron) project has demonstrated the potential of using diamondbased quantum sensors to measure iron levels more accurately than traditional blood tests.
Quantum sensors are advanced measurement devices that use principles of quantum mechanics to achieve extremely high levels of sensitivity and accuracy.
They leverage the unique properties of quantum systems—such as superposition and entanglement—to measure physical quantities with greater precision than classical sensors.
Currently, the standard method for diagnosing iron deficiency is the serum ferritin test, which measures the protein that stores iron in the body.
However, these tests can be unreliable for patients with conditions like inflammation, diabetes, or obesity, which can artificially inflate ferritin levels and lead to incorrect diagnoses.
“These conditions can cause ferritin concentrations to be very high, which can mask the true iron status,” said McColl.
McColl explained that these sensors address these issues by directly measuring iron content within ferritin molecules.
“What we’re trying to develop is a test that doesn’t measure the protein concentration of ferritin, but rather the actual iron load stored within it, avoiding the confusion caused by inflammation,” said Gawain McColl.
“The problem with current testing is that common health conditions such as diabetes or obesity elevate people’s ferritin but not their iron.
“Because blood tests detect all ferritin, regardless of whether it is iron-laden or iron-empty, they fail to diagnose many iron-deficient people because they have underlying health conditions.”
McColl explained that this technology has the potential to be particularly valuable for individuals with complex health conditions, ensuring they receive accurate diagnoses and appropriate treatment.
“All of these extra treatments and diagnostic tests are a burden on the Government’s health budget,” he said.
“Our quantum sensing technology provides a unique opportunity to develop world-leading medical technology.
“We are working hard to deploy a prototype into pathology laboratories to assess clinical samples. It will mean better outcomes for patients and healthcare systems.”
Ultimately, these tests can potentially improve diagnostic pathways for patients suffering with iron-deficiency.
McColl explained that this project ultimately stemmed from a conversation he had with colleagues.
However, the necessary tools to create it only became available recently.
“The project began from a combination of factors, but the idea originated from initial discussions between physicists and myself,” said McColl.
“Practically, the maturation of quantum-based sensors, which are now advanced enough to measure previously unmeasurable properties, and the collaborative environment at the University of Melbourne in Parkville, which helped to catalyse the project.”
McColl explained that this technology allows the team to measure iron levels in blood by examining differences in magnetism associated with ferritin.
“We haven’t had the required sensitivity until now,” he said.
“The diamond-based sensors detect the magnetic fields generated by the iron core in ferritin.
“The more iron present in the ferritin, the stronger the magnetic field it produces compared to ferritin with less iron.”
The technology is currently in the proof-of-concept phase, where it has been developed to the point that clinical sample testing can commence.
A proof-of-concept is a demonstration or trial used to validate whether an idea, concept, or technology is feasible and practical.
This phase validates the core technology and its potential before scaling up to broader clinical testing and eventual deployment in healthcare settings.
Researchers have already experimentally determined that they can measure the iron load in purified ferritin.
This marks the initial step toward transitioning the technology to measure serum samples from patients, which represents the next phase of development.
“Once we can measure serum samples, we will investigate how the sensors could have impacted the clinical journey for different patient groups,” said McColl.
“We aim to understand whether having such technology available would have changed their diagnostic pathways.
“This will ultimately serve as the real litmus test for the effectiveness of our technology in a clinical setting.”
McColl explained that researchers are looking to develop these endpoints within the next 24 months.
McColl explained that the FeBI project team is drawn to Victoria because of its substantial expertise in quantum sensing.
They aim to have a meaningful impact on Australian healthcare and value the importance of sovereign manufacturing capabilities.
While they plan to share the technology globally if it proves viable, their initial focus is on establishing a strong foundation in Victoria.
“We’re very interested in developing this technology in Victoria and establishing manufacturing capabilities there,” he said.
“That’s our long-term goal.”
McColl explained that, if proven effective, manufacturing this technology would involve two key aspects.
First, there’s the instrumentation-based manufacturing, which includes the box that performs the assay using optical readout technology.
Second, there will be a production of sensors,
which are based on nano-diamond technology.
Nano-diamonds are extremely small diamonds, typically with diameters ranging from a few nanometres to a few hundred nanometres.
McColl explained that the team will be seeking to source most materials locally, however, some specialised materials may require foreign suppliers.
“While some of the raw materials may be sourced from overseas specialist suppliers, everything else has the potential to be manufactured locally,” he said.
The FeBI project team have collaborative agreements with Victorian hospitals and are currently examining patient serum, though specific data is not yet available.
As McColl explained, their technology development is advancing on multiple fronts, including engineering and design improvements to enhance instrument sensitivity, as well as refining the nano-diamond sensors.
This involves optimising the presentation of serum samples to the sensors for the most accurate readout.
“For us, the goal is to build a deployable prototype that can be moved into a clinic or a public hospital pathology lab,” said McColl.
“This will allow us to conduct on-site clinical testing of patient samples and benchmark our readout against current tests.
“That is what we are now working towards.”
Manufacturers’ Monthly sat down with Professor Neeraj Sharma from UNSW Science to discuss research into a sustainable lithium-ion battery component that utilises food-based acids.
Despite lithium-ion batteries having applications across most household battery energy storage, vehicles and electronics, the current technology has limitations due to its graphite anodes.
Graphite has a relatively low storage capacity, and when sourced and processed, it becomes expensive and detrimental to the environment.
In response to these limitations, professor Neeraj Sharma from UNSW is co-conducting the development of an electrode component that is more efficient, affordable, and sustainable.
The component utilises food-based acids found in foods like sherbet and winemaking.
“We’ve developed an electrode that can significantly increase the energy storage capability of lithium-ion batteries by replacing graphite with compounds derived from food acids,” said Sharma.
need for innovation
Sharma currently leads the Solid State and Materials Chemistry group, which works with government and industry to improve battery designs now and into the future.
“Our research ranges from synthesising new materials, characterising new and commonly used materials and devices, to recycling and end-of-life challenges,” said Sharma.
Sharma’s team is just one response to what is an urgent need for novel battery solutions, which has recently increased due to renewable energy infrastructure.
It was this demand for performance and sustainability improvement of battery solutions that led Sharma to explore the graphite anodes of lithiumion batteries – commonly referred to as the negative side of a battery.
The graphite used in these anodes has a relatively low energy capacity and is associated with significant environmental impacts due to the sourcing, purification, and processing of the material.
“Graphite is not very environmentally friendly. It’s quite complex to mine and you have to use hydrofluoric acid and high temperatures to process it and get it to battery grade,” said Sharma.
“You lose anywhere from 30 to 60 per cent of what you mined to get battery-grade graphite.”
Given these challenges, Sharma’s team sought to address these issues by exploring alternative materials.
To explore these alternative materials, Sharma began co-developing a groundbreaking battery component with PhD candidate, Matthew Teusner.
“We leveraged his expertise and his background and looked where we could go with that,” said Sharma.
“I just provided the foundational framework; all the credit should go to him.”
Teusner’s lab experimentation would reach a milestone when he reported inconsistencies in the reaction between food acid and the metal surface of a battery component.
“A metal plus an acid gives you salt and hydrogen. And it’s that salt that gives you excellent performance,” said Sharma.
Sharma said that this reaction resulted in a material that showed potential to improve upon the graphite anode’s performance and cost.
“We found that we can replace graphite with this material. It’s a food acid plus a transition metal –iron, zinc, manganese – it’s that reaction and the resulting product,” he said.
“Using food acids to produce water-soluble metal
dicarboxylates presents a competitive alternative to graphite. We’ve demonstrated better battery performance, renewability and cost to better support battery demand.
“What’s nice about the energy storage density is that it is twice as much as graphite.”
The compound also showed improvements in sustainability. Where graphite is harmful to the environment in terms of sourcing, processing and manufacturing, the new material is not.
These findings were valuable in a battery manufacturing space that Sharma said is all about ways to move toward sustainability.
“How do we make batteries more sustainable? Everything from recycling all the way to processing materials itself and components,” he said.
This sustainability is initially seen in the sourcing of materials – the food acids that are utilised, as well as the tartaric and malic acids, which are easily sourced off the shelf as they are found typically in fruits, wine extracts, and even sherbet.
“At the moment, we’re buying the acids off the shelf from chemical manufacturers. We’re using quite pure feedstocks,” said Sharma.
One of Sharma’s next steps is to take this sustainability angle further and experiment with a potential future that could see food waste being utilised as a source of food acids.
“By using waste produced at scale for battery components, the industry can diversify their inputs while addressing both environmental and sustainability concerns,” said Sharma.
Food waste can be detrimental to the environment, contributing to three per cent of annual Australian greenhouse emissions according to the Department of Climate Change, Energy, the Environment and Water. This is a challenge that Sharma expects to address.
“We have to work out how to access these acids from food waste,” he said.
Alongside the sourcing of materials, the manufacturing processes are less environmentally intensive.
“They are processed with water instead of N-methyl-2-pyrrolidone (NMP), which is a toxic organic compound. The resulting performance using water-based processing is much higher than in NMP, which is fantastic. This is a benefit for sustainability by using a less environmentally intensive liquid,” said Sharma.
“We’ve got sustainable material, sustainable processing, which is a win, win scenario.”
After successfully identifying the sustainability advantages of this reaction, Sharma’s team saw the potential for a practical application.
This led to the development of a prototype
electrode, designed to replace graphite anodes with the new compound.
The prototype, a single-layer pouch cell, is a smaller version of what could one day be used in a range of devices.
“Everything from your mobile phones, electric vehicles and power tools, to grid scale and household storage. We envision its design to be a drop in solution,” said Sharma.
Overcoming past and future challenges
Sharma said the process wasn’t without its challenges. Within the early stages of fabricating the electrodes, the two materials were refusing to form a uniform layer.
“One of the biggest challenges was when you fabricate these electrodes, you want a nice uniform layer. But what we were finding for a long time was that the material was just peeling off. Imagine you do some painting, and you leave out in the sun, what happens over time, it cracks and peels off,” he said.
“We worked for a long time, and then we figured it out. We adjusted the formulation, and we were able to make really smooth electrodes.”
Going forward, another challenge stems from the team’s current use of coin cells for experimentation.
“These are cells about the size of a small coin. The idea is to do as much testing as possible on them,” he said.
“We optimise and manipulate the loading of the material, and undertake performance evaluation for
capacity, lifetime, and different charge discharge rates. We can do a lot of those tests in half cell format, and we can pull that up into a full cell within the same geometry – coin cells.”
Despite the testing freedom these coin cells provide, the team’s current challenge is exploring ways to upscale the technology to large pouch cell capability.
“We are working on how we can access the infrastructure so we can do that,” said Sharma.
He also foresees challenges in the scaling up and commercialisation of the technology, but insists that he is confident in the framework in place.
“Whether these materials make it commercially, well there’s a few steps there we would have to take. I would love to see it go from lab scale to commercial scale,” he said
“There could be issues in scale up, reformulation and in cell validation. However, I think we’ve got a good framework.”
Still new to the start-up game, Sharma said that a next step is the search for partners and investors to help take the technology from a prototype to a reality.
“This whole scale up idea is quite new to me. This is why I’m looking for partners. We’re looking for people who’ve done this sort of stuff before,” he said.
“We’ve got some interest from potential partners. Now we just have to see whether people are willing to invest.”
The team will also demonstrate industry viability and performance of the technology by running use/re-charge cycles at different temperatures and testing the technology’s applicability toward sodium-ion batteries, a cheaper, greener alternative to lithium-ion.
Collaborating now and into the future
Sharma said that collaboration on this technology is imperative in its development stage and moving forward.
“Matthew was the driver of this, and he’s amazing. We had a co-supervisor from the Australian Nuclear and Science Technology Organisation, Dr. Jitendra Mata, and we have used a whole bunch of different facilities at UNSW,” said Sharma.
“The business development managers have been fantastic. IP Lawyers also have answered all our questions. We’ve also worked with the folks at the Australian Synchrotron in Melbourne.”
In conclusion, Sharma expressed his satisfaction in what was, and is a team effort involving close collaboration with partners.
“It’s been quite an adventure,” he said.
As the demand for sustainable energy solutions grows, Sharma and his team are paving the way for a new generation of efficient and environmentally friendly batteries.
With the world shifting towards cleaner energy technologies, collaborations like these are set to be vital in driving change.
The Federal and State Governments have announced a dedicated Defence Precinct at Henderson Shipyard to enhance Western Australia’s shipbuilding and maintenance capabilities.
One of this year’s largest defence developments saw government officials come together to announce a consolidated, Commonwealth-owned defence precinct at Western Australia’s Hendersonshipyard.
“The spot on which we are standing right now will be part of the future Henderson Defence Precinct,” said deputy prime minister, the Hon Richard Marles MP.
“The Government’s commitments represent the most consequential defence investment in Western Australia in nearly four decades.”
The precinct builds upon a previously announced
strategic partnership between Defence and Austal Limited at Henderson. It is a next step in delivering continuous naval shipbuilding in Western Australia.
“The investment of tens of billions of dollars will turn Western Australia into a defence powerhouse,” said WA minister for Defence Industry, Paul Papalia.
Within the planned Henderson Defence Precinct is an array of facilities and capabilities, including:
•A naval shipbuilding and sustainment facility.
•A sustainment facility for Collins Classsubmarines.
•Contingency maintenance docking capabilities.
•A waterfront production facility.
•Depot level maintenance docking capabilities.
Marles said of these capabilities, a priority for the precinct is to support the build of both landing craft for the Australian Army and general-purpose frigates for the Navy.
“It is on this spot that we will be building our future general-purpose frigate. It’s on this spot that we will be building our future LOSVs,” he said.
As a state being dominated by minerals, resources and agriculture, Minister for Veterans’ Affairs and Defence Personnel, Matt Keogh, said this development will be especially prosperous for manufacturers.
“This is about high-end construction work. This is about manufacturing. This is about creating that complexity in our economy, diversifying the economy for generations to come,” he said.
“People say, ‘I just don’t want to do FIFO anymore’. Well, you can drive in and out to work at Henderson, you can sleep in your bed every night and you get to do high paid, high end, advanced manufacturing work.”
Aside from shipbuilding efforts, the precinct is also set to contribute to the sustainment of Australia’s future conventionally armed, nuclearpowered submarines. Marles described the precinct’s importance to the AUKUS agreement and a sovereign fleet of nuclear-powered submarines as “critical.”
“Today we are also announcing that the sustainment and the maintenance of our future nuclear-powered submarines will happen right here in Western Australia,” he said.
These maintenance efforts will also extend to Australia’s surface fleet that includes the largest ship in the Australian Navy, HMASStirling.
“There’ll be a necessity to establish dry docks here in order to be able to maintain both our future submarines and our future surface fleet,” he said.
Western Australian premier Roger Cook said these capabilities will help in the creation of approximately 10,000 total jobs in manufacturing, construction and maintenance.
“That includes around 3,500 jobs across the water at HMAS Stirling, around 1,000 construction jobs here at Henderson, plus 3,000 jobs for depot-level maintenance at Henderson, around 1,200 for surface fleet jobs and around 1,100 jobs working on landing craft,” he said.
Minister for Defence Industry and Capability Delivery, Pat Conroy, said the investment in the precinct will ensure that locals are a centre piece to ensuring a ‘Future Made in Australia’.
“Successful consolidation of the Henderson precinct will secure decades of continuous shipbuilding in Western Australia, providing generational benefits for locals who play a vital role in keeping Australia safe,” he said.
Marles echoed this sentiment, confirming the nation’s defence and a ‘Future Made in Australia’ are top priorities of the precinct.
“The Government is committed to investing in the growth of a productive and resilient defence industry and workforce to keep our nation safe and deliver a future made in Australia – which is exactly what the Defence Precinct will deliver,” said Marles.
After speaking to the precincts capabilities, Marles took a moment to express his gratitude to various defence industry players for their contributions.
“I also want to thank Civmec and Austal who, through their MoU, opened the door for the ability for us to announce that the consolidation of the Henderson precinct would happen here at the southern end of the strip,” he said.
Delivering defence capabilities
After the announcement, the Federal and State governments signed a Cooperation Agreement to ensure the proper delivery of the ambitious Henderson Defence Precinct.
“It is a win-win for Western Australia and the nation,” said Cook.
The agreement sets out a foundation for the parties involved to deliver the precinct upon multiple levels. This includes the development of a joint forum to deliver the required workforce, the establishment of necessary infrastructure, and the active engagement across Federal, State and Local governments and communities.
As a part of these joint commitments, the Federal Government has already gotten the ball rolling and will make an initial investment of $127 million over three years to plan, consult and design the new precinct.
ABI research director Eric Abbruzzese spoke to Manufacturers Monthly about the rising adoption of Extended Reality (XR) technology among manufacturers.
Described as an all-encompassing term for Augmented Reality (AR) and Virtual Reality (VR), XR technologies are becoming a source of value among many manufacturers.
Implementing XR technologies in manufacturing would utilise AR smart glasses, which overlay digital information onto the real world, and VR headsets which fully immerse users in a virtual environment.
“Augmented Reality uses transparent screens to overlay digital data, maintaining user vision. Virtual reality fully obscures user vision with displays, using cameras to pass through a live video feed into the device,” said research director with ABI Research, Eric Abbruzzese.
“The value of XR to organisations has been known for years, in training, remote workforce enablement, and collaboration.”
Aligned with XR’s potential value, the Industrial and Manufacturing Survey 1H 2024: Extended Reality (XR) Report explores the increasing number of manufacturers beginning to evaluate product suppliers.
The survey, from ABI Research, found that 30 per cent of global respondents are deploying XR technologies, with two per cent already completing integration.
Working closely with the survey, Abbruzzese
said aside from those implementing, there is a larger number of manufacturers considering XR technologies.
“If most [manufacturers considering XR technologies] is simply over 50 per cent, it can be argued most already are considering it,” said Abbruzzese.
Similar to other digitally transformative technologies, XR is also rapidly rising within the Asian-Pacific (APAC) region.
“We expect 4.5 million smart glasses, and 1 million VR headsets shipped in manufacturing in the APAC Region in 2030,” said Abbruzzese.
The rising popularity of these XR technologies is due to their potential to improve upon a different array of manufacturing processes.
“Workflow instruction, training, virtual collaboration, and 3D data visualisation are common and proven use cases for XR,” said Abbruzzese.
“Things like IoT (Internet of Things), PLM (Product Lifecycle Management), ERP (Enterprise Resource Planning), digital twins, and simulation solutions are integrated and used as data sources for XR devices to visualise.”
These benefits vary depending on the device selected, with AR smart glasses and VR headsets excelling in different areas.
“AR smart glasses excel in hands-free workflow assistance. This can include step-by-step guidance, step verification, training hands free, and voice access for notes and hands-free service calls, with a live point of view camera feed available to a remote user,” said Abbruzzese.
“VR excels in data visualisation and content interaction, which is beneficial in training, design, and virtual collaboration.”
In addition, XR can utilise machine learning to help create an accurate and automated quality control system.
“You can also use machine vision with the point of view camera to automate, or assist in, quality control/verification steps. Logging data hands free is also valuable here,” he said.
Above quality control and workplace processes, the systems also offer sustainability enhancements through reduced scrapped material and worker travel.
“Reducing downtime often reduces scrap rates as they are correlated. Reduced planned and unplanned downtime does have that sustainability knock on effect,” said Abbruzzese.
“By leveraging remote expertise and virtual training, a company can reduce the number of flights in a given period.”
Despite XR technology’s applicability in many manufacturing contexts, Abbruzzese said the products can be beneficial in complex industries.
“Those with complex processes and access to operational data often recognise XR value most easily. Downtime reduction is a key performance indicator for XR solutions, and both automotive and aerospace have incredibly high downtime costs,” he said.
Despite potential advantages to manufacturing processes and workflow, there are still numerous well-known barriers.
“Device cost, integration concerns, and confusion around offerings are the most common barriers,” said Abbruzzese.
The report detailed that among these, people and process barriers are most common.
“The XR market has seen plenty of ups and downs over the past decade, which has hindered trust and understanding in the market despite proven value. A lack of clarity among available
platforms and paths to market holds back potential adoption,” said Abbruzzese.
“The biggest challenges XR faces are around user knowledge and awareness, device selection, and tolerance for new technology investment.”
While not extensive, Abbruzzese said that training must be undertaken prior to the implementation of these systems. The necessary training depends on the complexity of a situation.
“When a solution is properly integrated, such as with proper enterprise sign-on, security and privacy settings, device usage should be as streamlined,” said Abbruzzese.
“Depending on the complexity of the application or environment, anywhere from a few hours to a few days is common.”
While barriers exist, Abbruzzese remains optimistic on a future where they can be overcome. He said that these barriers at small to mid-scale are already starting to fall.
“Within the past few years, the level of complexity for integration and content creation has come down considerably,” he said.
“As public knowledge increases for XR hardware
and what it is capable of, by default enterprises become more knowledgeable and confident ininvesting.”
Abbruzzese insisted that the usability and cost of these devices should improve for businesses going forward, with exceptions.
“Large companies are getting much better in the user experience department, with an expectation for easy use out of the box. This isn’t universally true specifically in enterprise, but it is also getting better,” he said.
“Cost comes down over time, although it’s of course more complex than that. New device launches will add features, capability, and price compared to earlier generations. With high-end AR smart glasses, however, expect even new devices to cost less on average than older ones.”
Abbruzzese envisions a future where manufacturing businesses will see XR products improving exponentially as they keep utilising digitally transformative technologies.
“Over time, a more holistic view of visual workforce enablement will take hold, rather than a focus on individual technologies, and XR will be an increasing portion of that offering,” he said.
Silver Fleece’s recovery marks a turning point for Australian textiles, underscoring the need for unified support from consumers, brands, and the government.
In a victory for the Australian fashion manufacturing industry, Silver Fleece has been rescued from the brink of liquidation.
This pivotal turn of events has ignited renewed interest in the future of local textile production, a sector that has faced declining support for decades. With only a handful of knitting mills remaining in Australia, the survival of Silver Fleece signifies an opportunity for industry stakeholders and government bodies to prioritise domestic production amidst the challenges posed by increasing globalisation.
News of Silver Fleece’s struggle first emerged when reports indicated that the South Australian mill was set to close, prompting action from various fashion brands and industry organisations.
The urgency surrounding the mill’s fate was palpable: if Silver Fleece were to go under, it would mean not only the loss of an institution but also a further decline in the landscape of local textile manufacturing.
The Rise and Fall of Silver Fleece
Founded in South Australia in 1951, Silver Fleece has been a cornerstone of the local knitting industry. Known for its quality knitwear and ties to the community, the mill has supplied fabrics for everything from school uniforms to the vests for the Australian cricket teams.
Over the decades, it became synonymous with high-quality production and local craftsmanship, employing 20 skilled staff and technicians who are dedicated to preserving the artisan craft of knitting.
However, as the global trend leaned toward cheaper, overseas production, Silver Fleece found itself struggling to maintain operations. The mill’s previous owner faced years of declining orders and increasing competition from international markets, leading to a challenging transition and, ultimately, the threat of liquidation.
Dean and Melanie Flintoft, co-founders of the fashion brand Sunset Lover, recognised the potential of Silver Fleece and acted swiftly to acquire themill.
“We had looked at Silver Fleece in the past, and while it didn’t progress then, we kept an eye on it,” said Dean Flintoft.
“When we heard about the liquidation, we realised it aligned perfectly with our goals. Knitwear has always been a key part of our brands, so we reached out to the administrator and previous owner to understand the situation. We felt that if we didn’t save this, nobody else would.”
With backing from designers and brands committed to Australian-made products, funds were raised to secure Silver Fleece’s future. This acquisition symbolises a potential revitalisation of
local manufacturing, indicating that there is still a viable market for homegrown textiles.
With only a handful of knitting factories left in the country, and Silver Fleece, there are growing concerns about the future of local manufacturing.
“If Silver Fleece didn’t survive, the industry would shrink even further,” Flintoft added.
“The previous owner bought it during a decline
as brands moved to China, making it increasingly difficult tosustain.”
This reality has prompted calls for government action to prioritise and invest in local manufacturing, particularly within the fashion sector.
Recent research commissioned by the Australian Fashion Council (AFC), in partnership with Epson Australia, has underscored the critical importance of local manufacturing in the industry.
The study highlights that Australian-made garments bolster local economies and align with growing consumer preferences for ethical and transparent production. Key findings show that local manufacturing not only contributes to job creation but also has the potential to create thousands of new roles as brands shift production closer to home. This transition can mitigate supply chain disruptions, as seen during recent global crises, and ensure quicker
response times to market demands.
Moreover, the report emphasises the environmental benefits of local production, including reduced carbon footprints associated with transportation and more stringent compliance with local labour and environmental regulations. However, challenges such as higher production costs and limited scalability persist. To overcome these barriers, the report advocates for increased government support and incentives for brands committed to local manufacturing.
The need for government support
As Silver Fleece looks to solidify its future, collaboration with government entities becomes increasingly essential.
“We’re working with the government to secure orders for police and fire department uniforms to stabilise our business,” said Flintoft.
“This will allow us to expand into fashion brands and other products.”
Silver Fleece is equipped with 15 knitting machines, including circulars that produce rolls of fabric and flatbeds that knit garments, allowing the mill to create high-quality products. However, challenges in sales and marketing have hindered growth in recent years.
The decline of textile manufacturing in Australia has not gone unnoticed. Stakeholders are increasingly vocal about the importance of ‘Made in Australia’ initiatives. This ongoing dialogue stresses that buying locally is a sustainable choice that can help reduce carbon footprints associated with overseas shipping and production.
“After 30 to 40 years in the fashion industry, I’ve seen various production methods, but knitting stands out as one of the most sustainable,” said Melanie Flintoft.
“It’s akin to 3D printing, generating next to zero waste – there’s just a tiny bit from the in-between threads. Overall, it’s an incredibly eco-friendly manufacturing process.”
“When knitting with natural fibres like wool, cotton, or hemp, the process can be very sustainable and even compostable at the end of its life,” Dean added.
“This makes it a healthier choice for the planet and the economy. Additionally, while it requires a smaller workforce, our machines can operate 24 hours a day, allowing us to scale efficiently.”
The call to action is crucial as many local manufacturers are poised to take on more diverse production, from high-quality fashion items to essential uniforms for public services. With advanced machinery and skilled labour, local mills can meet demand while ensuring sustainable practices that resonate with today’s eco-consciousconsumers.
The Australian Fashion Council (AFC) serves as a national peak body dedicated to supporting and advancing the Australian fashion industry, including companies like Silver Fleece. Acting as a strategic advocate, the AFC promotes sustainability, innovation, and growth within the sector.
Silver Fleece’s collaboration with the AFC has been beneficial. The council effectively promoted the company’s acquisition through social media and its website, with the CEO providing daily updates to reach the right audience.
“The media campaign not only raised funds but also increased brand awareness among potential customers,” said Flintoft.
“As a result, we’ve had many people reaching out to explore opportunities to work with us, which has been fantastic.”
As the new owners of Silver Fleece prepare to integrate their fashion brand, Sunset Lover, with the knitting mill, it aims to create a synergy that not only boosts both brands but also sets a precedent for others to follow.
“We have plans that will allow the two brands to complement each other,” said Flintoft.
“Raising awareness for local manufacturing with Sunset Lover is a win for both, as their audience expects products made in Australia. With Sunset Lover’s strong, sustainable following, there’s great crossover potential.”
The Flintofts also emphasised the opportunities available to local manufacturers, noting that while many are skilled, they often lack visibility and marketing presence. It is essential to raise awareness of these manufacturers’ capabilities and encourage collaboration to share orders among local businesses, said Flintoft.
“To truly support local manufacturers, the government must invest its uniform spending domestically,” Dean added.
“With millions spent on uniforms across departments, keeping that money in the local economy could create a multiplier effect. This investment would enhance business viability, allowing us to spread overhead costs, lower prices, and invest in new machinery.”
While state governments discuss this, securing those orders remains a challenge. If they mandated that a portion of uniforms be produced domestically, it would greatly benefit localbusinesses.
“We started in local manufacturing in South Australia over 20 years ago, supporting other manufacturers. Now, we’ve come full circle, returning to local manufacturing with Silver Fleece. We’re proud of our beautiful knitwear and see a lot of potential ahead,” said Flintoft.
Honorary senior research fellow at University of Sydney, Professor Phil Toner, spoke to Manufacturers’ Monthly to discuss the benefits of an Australian wind tower and turbine manufacturing industry.
Arecent report titled An Industrial Strategy for Domestic Manufacturing of Onshore and Offshore Wind Energy Towers and Equipment details the advantages of having a sovereign wind tower and turbine manufacturing industry.
“Manufacturing wind power equipment represents an enormous opportunity for Australia to attain a more balanced industrial structure and create wellpaid jobs,” said report author and honorary senior research fellow at University of Sydney, Professor Phil Toner.
The report from the Centre for Future Work contrasts these potential benefits with Australia’s current landscape, where all installed wind towers are sourced internationally.
“Whilst there is some flow-on to regional economies in terms of construction and some maintenance jobs, these benefits are temporary and often muted by the use of fly-in fly-out labour,” said Toner.
The research showed that establishing an Australian wind manufacturing industry would lead to an output of over 800 towers per year and over $15 billion cumulative value over the next 17 years. The sovereign industry would also bypass 2.6 million tonnes of CO2 emissions through a reduction in sea freight.
Additionally, Toner noted that the industry could create 4,350 direct and ongoing jobs across diverse skill sets, along with thousands more in indirect sectors.
“Designing and customising wind towers requires engineers, especially mechanical and structural,” he said.
“Many tradespeople will also be needed, especially welders experienced in operating automated and semi-automated welding gear; other metal tradespeople for CNC steel plate cutting, rolling and edge bevelling and painting tradespeople.
“A variety of semi-skilled jobs will be required for materials handling and despatching.”
The job spark would see regional Australia rewarded, where traditionally, it has only received damaged roads and congestion from renewables investment.
“It would benefit regions where manufacturing
Image: Michael
Evans/stock.adobe.com
jobs are scarce and especially those regions which have seen intensive renewable energy generation investment but have not benefited very strongly,” said Toner.
Beyond job creation, emissions reductions, and increased production, the industry could also serve as a source of demand for other manufacturing sectors. A beneficiary of this potential sovereign wind tower manufacturing is the local steel industry.
According to the report, the towers could create the demand for up to 700,000 tonnes of Australianmade steel per year.
“Based on Australian Energy Market Operator (AEMO) projections, if these land-based wind towers were produced locally, this would absorb more than Australia’s current production of plate steel. This is currently around 400,000 tonnes per year,” said Toner.
The demand could have further flow on effects for the steel industry by allowing plants to recapitalise with carbon-free technologies.
“Domestic production of wind towers would
contribute substantially to generating a level of output for local steel production to justify steel producers’ investment in ‘green steel’ technologies,” said Toner.
Other industries could also benefit from increased demand, which would lead to expanded production capacity.
“Other beneficiaries would be for example specialist flange makers, as each wind tower uses several bolted flanges to connect tower sections together and for connecting the tower to foundations and the nacelle,” said Toner.
“Wind tower production would also significantly increase demand for specialist non-corrosive coatings and large diameter bolts and fittings.”
Despite advantages for Australian industry, Toner noted hurdles that exist in establishing this local manufacturing sector. The initial challenge that he foresees is pushback from overseas wind tower suppliers.
“Overseas wind tower suppliers and developers will argue that local production will increase costs,” he said.
Aside from international struggles, Toner said a lack of government subsidisation for these wind towers and turbines could present a problem.
“Most other industrial countries are investing aggressively in manufacturing the new equipment and products that will be in demand as the energy transition continues. Australia needs similar policy activism,” he said
To address issues, Toner made a case for the Federal Government to employ its policy tools in its Future Made in Australia (FMiA) manufacturing strategy.
“Policy can offset initial cost differentials by subsidising capital investment or having a production subsidy for each tower produced,” he said.
“Wind tower production fits squarely within the remit of Federal Government programs such as the Future Made in Australia (FMiA) program.”
Toner said that wind tower manufacturing is closely linked to the FMiA program beyond its obvious sovereign renewable energy equipment production.
“Wind towers are within Australia current technological capacity, they meet the ‘feasibility’ criteria of FMiA,” he said.
“There are also strong supply chain links to existing industries, notably steel production, anticorrosion paint and flange manufacturers.”
“Finally, tower production holds the strong possibility of entering related and more advanced manufacturing activity entailed in wind turbine production such as blades, gearboxes and electrical control equipment.”
Aside from government investment, Toner said that ensuring the co-ordination of private sector investment across different industries is vital.
This would see production levels and amounts of skilled workers following the demand made by the new industry.
“The most obvious is the requirement for plate steel production to ramp up to satisfy the large increase in demand from wind towers. Without this, steel inputs will be imported. The same issue applies to skilled labour requirements,” said Toner.
Toner suggested that collaboration between multiple parties is also essential for proper implementation of these strategies.
“Collaboration will be essential to ensure coordination both in terms of scale and type of local industrial inputs and labour required for a successful wind tower manufacturing strategy,” he said.
This collaboration extends to joint ventures with large overseas manufacturers.
“This would allow easier access to the latest technologies and would reduce the level of resistance of international turbine suppliers to being required to ‘buy local’ if they had a direct commercial interest in the success of the local manufacturing plant,” he said.
Moving forward, the report also highlights the necessity for early and coordinated planning that involves all stakeholders. The report suggests that the Federal and state governments, along with industry, conduct a study to assess the feasibility of establishing wind tower manufacturing. This study would scope out the optimal location, plant size, plant layout, advanced production equipment, and minimum scale of output required.
“A relatively large site is required, given the size of the towers and for inventory storage. To be competitive, the production equipment, materials handling, and production site scheduling and layout, would have to be of world-leading efficiency,” said Toner.
On top of these policy and partnership requirements, there are also costs that the government will have to prioritise. Toner said that these costs would originate from manufacturing equipment and could end up totalling around $50 million.
“The major costs are materials handling equipment, especially large steel plate and rolled and welded tower sections; plate cutting, tube forming and rolling equipment; automated welding; and a large sandblasting and paint shop where corrosion-resistant coatings are applied,” he said.
If these recommendations were to be overlooked, Toner noted that Australia may again become just a raw resource supplier for other countries.
“These countries will purchase Australian resources at the going global rate, transform them into innovative and expensive products, and then sell them back to us at premium prices,” he said.
If they are considered, based on AEMO projections, Toner said that this will result in a large amount of expenditure, value and thus demand.
“Assuming all towers are made domestically this translates to more than $1 billion per year in the value of towers,” he said.
“This generates a level of demand for wind towers that can support a world-efficient scale of production across a number of local wind tower plants.”
Establishing a sovereign Australian wind tower and turbine manufacturing industry presents an opportunity for economic growth, job creation, and emissions reduction. However, to overcome existing barriers, Toner believes strategic collaboration and government support must be prioritised.
The 2024 Endeavour Awards highlighted innovation in Australian manufacturing, celebrating companies driving the future with technology, sustainability, and leadership across diverse sectors.
The 21st annual Endeavour Awards, held on November 7, 2024, in Melbourne, celebrated excellence in the manufacturing industry.
Hosted by Prime Creative Media, the event recognised outstanding achievements in leadership, sustainability, innovation, and growth, highlighting the industry’s top performers.
The awards showcased manufacturers who set benchmarks for success, emphasising their contributions to driving the industry forward through cutting-edge technologies, sustainable practices, and operational excellence.
The gala also featured insightful discussions and keynote addresses.
It focused on the future of manufacturing in Australia, covering topics such as digital transformation, smart manufacturing, and sustainable practices.
It underscored the vital role of the sector in the nation’s economy, with manufacturers demonstrating their ability to adapt and thrive in an ever-evolving global market.
“The Endeavour Awards were created to highlight and celebrate excellence within the Australian manufacturing industry,” said show director, Lauren Chartres.
“As the longest-running and most prestigious awards in Australian manufacturing, the Endeavour Awards continue to recognise outstanding contributors to our domestic manufacturing sector.”
The sponsors for the Endeavour Awards showcased a rich tapestry of industries, each contributing to the event’s success.
Weld Australia, a not-for-profit organisation committed to supporting the Australian welding industry, proudly sponsored the Technology
Application Award.
“As advocates for excellence and innovation within the manufacturing sector, Weld Australia is proud to sponsor the ‘Technology Application’ Award at the 2024 Manufacturers’ Monthly Endeavour Awards,” said CEO of Weld Australia, Geoff Crittenden.
“Our commitment to enhancing industry standards and promoting safety aligns perfectly with the goals of these awards.”
Bestech Australia, renowned for supplying sensors, instrumentation, and teaching equipment for sectors such as manufacturing, military, mining, and research laboratories, sponsored the Manufacturer of the Year award.
SEW-EURODRIVE, a specialist in mechanical power transmission, sponsored the ‘Most Innovative Manufacturing Company’ Award, while BDO
Australia, known for its sector expertise, backed the ‘Project of the Year’ category.
“As a long-time sponsor of the Endeavour Awards, SEW-EURODRIVE sees the value in inspiring and recognising those in the industry who have made advances in their field,” said marketing coordinator, SEW- EURODRIVE, Katrina Dalgleish.
“As a market leader in drive technology used across the manufacturing sector, big or small, SEWEURODRIVE sees our involvement in the awards as paramount in building and maintaining important relationships that foster growth and ingenuity throughout the sector.
“The Endeavour Awards offer many different award categories – particularly the one that we sponsor for the most innovative manufacturing company –bringing to light the nominees who have proven their
resourcefulness and innovative advancement have an impact. If these advancements continue to be celebrated and appreciated, progress will persist for the sector.”
BlueRock, a purpose-driven advisory firm, sponsored the ‘Outstanding Start-Up’ award, demonstrating its commitment to supporting emerging talent in manufacturing.
The Endeavour Awards provided a platform for industry veterans and emerging talents alike to showcase their achievements. Nominations opened across several categories, allowing individuals to celebrate the exceptional work that inspires theindustry.
The evening culminated in the announcement of the prestigious ‘Manufacturer of the Year’ award, which was won by data solutions developer MEQ. Not only did MEQ take home this award, but the company also won the ‘Technology Application’ award for its MEQ Live solution that provides real-time data solutions for feedlots and producers.
“We were a startup that was the genesis of a couple of PhD programs,” said Jordan Yeomans, chief technical officer MEQ.
“And since then, we’ve built our team from one person to 35 people now.”
The ‘Leader of the Year’ award went to Geoff Crittenden, for the pioneering work he has undertaken in his role as CEO of Weld Australia.
“When I was 19, I joined the Royal Military Academy,” said Crittenden.
“Over the last 50 years, I’ve learned one crucial lesson: it’s not about you; it’s about the people who work with you.
“I want to take this opportunity to thank my team at Weld Australia. They are absolutely fantastic, and without them, leadership means nothing.”
Shifting to the constantly evolving reality of the industry, Advanced manufacturer, AMIGA Engineering won the 2024 award for the ‘Most Innovative Manufacturing Company.’
“It’s been amazing to be recognised for innovation over the past few years,” said managing director at AMIGA Engineering, Michael Bourchier.
“This achievement is truly a result of the incredible efforts of our team, who consistently bring creativity and innovative thinking to ourbusiness.
“They continue to come up with remarkable ideas that drive us forward.”
Keeping with the theme of innovation, start-ups that are powering the future direction of Australian manufacturing were also recognised, as germicidal light manufacturer, Lindo Tube took home the prize for ‘Outstanding Start-up.’
Lido Tube has developed an endotracheal tube with antimicrobial blue light to reduce ventilatorassociated pneumonia in ICUs.
“We are excited to partner with Mayo Clinic to produce a proof of concept here in Australia,” said founder and director at Lindo, Robert Gangi.
“If my wife was here not looking after my wonderful children, I couldn’t thank her enough. She’s been an amazing, great support. So, thank you, everybody. I’m really excited.”
A project that took centre stage at one of this year’s largest events was also honoured, as CST Composites won ‘Project of the Year’.
The company saw its “Towreg” masts used on around half the boats competing in the 2024 Paris
Olympics, an incredible feat.
The event was more than just an awards ceremony; it was a celebration of the dynamic and evolving landscape of Australian manufacturing. By recognising both established leaders and emerging talents, the Endeavour Awards reinforced a culture of excellence and innovation that will continue to inspire future progress.
It was a night that not only honoured the achievements of today but also set the stage for the continued growth and success of Australia’s manufacturing industry.
Group Leader of Renewable Energy Systems at CSIRO, Dr Anthony Chesman, highlights a new facility dedicated to the development of printed solar cells, the organisation’s latest innovation.
At CSIRO, we’re driven to find innovative solutions that will accelerate the transition to a clean energy future. For over a decade, the incredible team at our Flexible Electronics Laboratories has been exploring the potential of printed solar cells – a technology that could revolutionise how we generate and use solar energy.
What exactly is printed flexible solar? It’s a developing technology that uses special inks printed onto thin, flexible plastic films using highthroughput processes similar to those used to print newspapers. This allows us to create ultra-thin, lightweight solar cells that can be applied to almost any surface, from curved structures and tents to backpacks and electronics, opening up exciting new possibilities for powering devices in ways we couldn’t previously have envisioned.
Unlike traditional rigid solar panels, these energygenerating solar cells are incredibly versatile. In the future, they could be seamlessly integrated into building facades, powering facilities in greenhouses or even supporting space missions.
To help make this a reality, we recently opened the CSIRO Printed Photovoltaics Facility at our Clayton site in Melbourne. This state-of-the-art facility, with cutting-edge printing and testing equipment, was officially opened by the Hon Ed Husic MP, Minister for Industry and Science on 30 October 2024.
This $6.8 million facility, co-funded by CSIRO and ARENA via the Australian Centre for Advanced Photovoltaics (ACAP), is a real game-changer. It houses equipment for roll-to-roll printing and encapsulation of solar cells, along with an automated system capable of producing thousands of test cells daily. This allows the team to rapidly optimise and scale up production, paving the way for commercialisation and widespreadadoption.
The Minister’s visit highlights the national importance of this work. It’s not just about advancing solar technology, but about boosting Australian manufacturing and securing our place as a leader in renewable energy innovation. This
underscores the significance of the team’s efforts and reinforces our determination to continue pushing the boundaries of what’spossible.
Interestingly, flexible printed solar technology shares a lineage with another CSIRO innovation: polymer banknotes. Back in the 1960s, we embarked on a journey to create a more durable and secure currency, which culminated in the release of the first polymer banknote in 1988. This led us to develop unique expertise in printing and processing complex polymer materials. That know-how, honed over years of research and development, laid the foundation for our current advancements in printed solar. We essentially
took many of the lessons learned from printing banknotes and applied them to printing solar cells onto flexible plastic films. It’s a testament to the power of cross-disciplinary collaboration and the unexpected ways that scientific breakthroughs can emerge.
While we’ve experimented with various materials, our primary focus has been on perovskites – a class of materials with incredible potential for efficient and cost-effective solar cells. However, the team’s research extends beyond perovskites, exploring a landscape of organic and non-organic inks to uncover new possibilities and push the boundaries of printed solar technology. This facility is equipped to handle a range of materials, ensuring that we remain at the forefront of this rapidly evolving field.
This facility is more than just cutting-edge equipment; it’s a testament to the incredible team that has poured its expertise and passion into this technology for years. Its diverse skills – from chemistry to processing and engineering – have been instrumental in achieving remarkable outcomes. This includes a world record earlier this year for fully roll-to-roll printed perovskite solar cell efficiency. This breakthrough, published in the Nature Communications journal, highlights the importance of continued investment in this area. With this new facility, Australia is well-positioned to lead the global race to commercialise printed solar.
While I’ve had the privilege of helping develop this technology, my role is less hands-on now, focusing more on industry collaboration and advocacy. Credit for this technology belongs to the
The facility will accelerate our progress even faster and open up new opportunities. It will serve as a hub for innovation and collaboration where we can translate research breakthroughs into real-world applications. We see it as a launchpad for groundbreaking applications of printed flexible solar technology, with the potential to transform industries where lightweight, adaptable solar solutions are critical. Looking ahead, I envision this facility becoming a thriving hub of innovation, where industry and research converge to create truly groundbreaking applications for printed solar. This technology has the potential to transform industries. In five years’ time, I see us working with a diverse range of partners, developing customised solutions for niche markets and pushing the boundaries of what’s possible. In less than ten years, I believe
future and solidifying our nation’s position as a global leader in renewable energy technology. We are eager to collaborate with partners who share our vision of bringing flexible solar power to industries and applications for positive impact. This isn’t just about accessing our technology; it’s about partnering with CSIRO and leveraging our unique capabilities. We’ll work with you to research, develop and customise solutions tailored to your specific needs and push the boundaries of printed solar technology. Whether your mission is to enhance national security, rapidly deploy emergency power, construct off-grid infrastructure or pioneer new frontiers in space exploration – we want to hear from you.
We believe that printed solar has a vital role to play in the future of energy generation, complementing existing silicon technologies and expanding the reach of solar power into new and exciting domains. With the opening of this facility, we’re ready to embrace the next chapter in this exciting story, and we invite you to be a part of it.
In a recent collaboration with CSIRO’s Agriculture and Food team, we installed semi-transparent solar films on greenhouses at the University of Queensland’s St Lucia site to explore their impact on crop growth and energy generation. This project highlights the exciting possibilities of agrivoltaics, where solar technology is integrated into agricultural practices to enhance productivity and sustainability.
Of our economic challenges, our productivity performance of recent years is arguably the most pernicious.
Australia has worryingly seen low growth in labour productivity over the five years since the pandemic. As productivity is the foundation of national wealth, we cannot hope to achieve any of our economic or social goals if this pattern is allowed to continue.
Increasing our levels of technology investment is viewed as a key step needed to right the productivity ship. It allows businesses to innovate their products and processes, more efficiently deploy their workforces, and compete more effectively in local and global markets.
But the proof of the pudding is in the eating. While the national discussion often focuses on making new technologies – be they for automation, artificial intelligence or net zero – the real productivity gains only come when these are deployed at scale across industry.
How is Australian industry approaching the question of technology investment and deployment in today’s straitened economic conditions?
New Ai Group research shows there is considerable optimism among business leaders, but more work to be done to fix workforce and regulatory gaps.
The good news from our report, Technology Adoption in Australian Industry: Commercial, Workforce and Regulatory Drivers, is that business leaders are clearly committed to technology investment.
Of the 182 businesses we surveyed, 84 per cent reported that they are actively adopting new technologies in some way. Most of these firms, across all sizes and industry verticals, report active adoption, showing it is mainstream across the business community.
The reason is productivity. 88 per cent of business
leaders tell us improving efficiency is their leading objective when investing in technology, with financial returns and market positioning also high ranked.
The survey group, which employs 27,271 people, said managing workforce challenges is a central concern. With Australia’s labour market being at its tightest level since the 1970s, and skills shortages widespread, tech investments are viewed as a means of multiplying the productivity and potential of a constrained workforce.
Equally pleasingly, around half of business leaders, with $14 billion in revenue, tell us they are adopting artificial intelligence (AI) or net zero transition technologies.
AI adoption is viewed in similar terms to general technology – a means to augment workforce capability and drive productivity improvements. Net zero investment instead targets regulatory requirements and/or market pressures to reduce carbon emissions in industrial sectors.
This data suggests there is much to cheer in our tech investment – and ultimately productivity –outlook. But despite the optimism, there are also major fetters holding our performance back.
Workforce capability is the most significant, with
54 per cent of business leaders reporting technology skills constraints. The issue is whether existing staff can effectively utilise new technologies, and whether broader business processes can be adjusted around its implementation.
This finding reaffirms a well-established proposition: that the uptake of technology is as much about people as it is about the technology itself. Developing new technology in Australia can only go so far if we can’t organise and skill our workplaces to put it to best use.
It also shows that improving investment will require positive reform to our skills and industrial relations systems. Training systems need to be designed around the technology landscape of the future, not the past. Inflexibilities in our workplaces – which are unfortunately compounded by recent changes to the IR system – will have a chilling effect on technology adoption as well.
Regulatory factors were also a major inhibitor, but not in the way you might expect.
Take AI for example, where business leaders report healthy doses of both optimism and caution. They recognise that without appropriate controls and precautions, AI adoption could pose risks for both the business and society at large. Yet a lack of regulatory guidelines mean they are unsure of how to deploy AI safely and responsibly.
Clear and consistent AI regulation would go a long way to enabling businesses to move from experimenting to investing with confidence.
Similar regulatory factors inhibit investment in net zero technologies. Business leaders report uncertain returns and financing challenges as the proximate barriers to investment, but underlying these is the problem of policy certainty. With energy policy settings at the federal and state levels changing so rapidly, it becomes impossible to properly cost and commit to investment decisions.
In the words of one of our members: “Our business has a huge opportunity to develop decarbonisation products for industry, but investment is being destabilised by policy uncertainty.”
The enthusiasm for technology investment from Australian industry is welcome and is one of the keys to turning around our poor productivity performance.
One of the best ways to drive productivity outcomes will be to address the workforce constraints and regulatory gaps holding our technological progress back.
Read Ai Group’s Technology Adoption in Australian Industry: Commercial workforce and regulatory drivers here: https://go.aigroup.com. au/techadoption
As the advocacy voice for manufacturers in the south-east of Melbourne, The South Melbourne Manufacturers Alliance (SEMMA) is pushing for land and tax reform for manufacturers.
SEMMA has been working with a range of education and training organisations to ensure that manufacturing is at the table for important discussions on skills.
The Alliance has also been leading new supply chain opportunities for manufacturers in defence, infrastructure and the new renewables sector.
While SEMMA has met with the Victorian treasurer and a range of ministers, its requests have not been attended to. Because of Victoria’s debt of $178
billion, the government must look at what levers to pull in order to raise money.
For manufacturers, a base tax rate would be a huge incentive to invest and to stay in Victoria.
In the past 12 months, we’ve seen the cost of doing business in Victoria rise. These things are all relevant when you are trying to do business, grow and innovate. They are also relevant when you want to hire apprentices, or even keep your current staff.
If we don’t develop better policies to support the
engine room of the economy (manufacturing), we could have less SMEs, reduced competition and be stuck with higher prices for longer. How long can we sustain this cycle?
According to the Australian Securities and Investments Commission (ASIC), a number of Australian businesses entered insolvency last financial year, with firms in the construction and hospitality sectors most heavily impacted. While manufacturers have some buffer, the trickle-down effect is only a matter of time, as we are in a percapitarecession.
We need new policies to support manufacturers and the entire supply chain. We need to enhance our local capabilities and make sure our local content is more tightly regulated. We need to enforce our antidumping laws.
We need to be more strategic about our skilled migration policies and we need to cut red tape so we can bring in the skilled migrants that we need –engineers, mechanics, welders. We’ve done it before, like Snowy Hydro. Why not now?
And we need to encourage more women into these roles. We need to embrace the culture of change now or we risk stagnating for even longer. We need to be open to flexibility in our workplaces.
We also need a suitable mindset to rebuild our country after COVID-19. Victoria has been the slowest state to rebound. And that’s because we are the highest taxed state in Australia and it’s because we have overspent on infrastructure projects, while other states are working hard offering incentives to attract our best and brightest (companies and individuals) across the borders.
Our energy supply is another issue that keeps manufacturers awake at night. We need a consistent, uninterrupted base load. This is policy malaise. The National Reconstruction Fund has to do more for more SMEs in manufacturing if we are going to meet the needs of the new renewables sector, defence, housing and infrastructure.
SEMMA will be releasing its Manufacturing BLUEPRINT in 2025. In it, we will provide policymakers with our vision for not just Victoria –but Australia’s manufacturing future. We know what manufacturers need and want – therefore it’s up to us to guide our policymakers towards the future of manufacturing.
Backplane Systems Technology has released VECOW’s RCX-3750 PEG. The Vecow RCX-3750 PEG is an expandable GPU-accelerated system, built to handle demanding AI, edge computing, and industrial tasks. It is powered by Intel Core i9/i7/ i5/i3 processors from the 14th generation (RPL-S Refresh/RPL-S/ADL-S), offering scalability and performance suited for AI inferencing and highspeed industrial applications.
The unit supports up to seven PCIe slots, allowing for the integration of dual 900W NVIDIA or AMD 2-slot full-length graphics cards. This gives the system a maximum power budget of 1800W, making it suitable for AI workloads and inferencing processes that require significant GPU power. Its I/O includes two GigE LAN ports with TSN, four USB
3.2 Gen 2 ports, four COM ports, and 32 isolated DIO, ensuring a range of connectivity options. Additionally, the system offers four SATA trays for 2.5-inch SSD/HDD, two front-access M.2 SSD trays, and three SIM card sockets for enhanced data storage and network capabilities. It operates in industrial environments with temperatures ranging from -25°C to 45°C and features flexible power input options ranging from DC 16V to 50V and AC 90V to 220V.
It is also designed for use in 3D mapping, highspeed AOI, and industrial edgecomputing.
Key features:
•Workstation-grade platform: Intel Core i9/i7/i5/i3 processor (14th gen, codename: RPL-S Refresh/
RPL-S/ADL-S) running with Intel R680E PCH supports max 65W TDP CPU.
•Max 1800W power budget supports dual 900W NVIDIA or AMD 2-slot full-length graphics card.
•Flexible power input design with software ignition control: DC 16V to 50V.
•Up to seven slot PCIe expansions with PCIe 4.0 x8 and PCIe x4signals.
•Two front-access M.2 and 2 2.5-inch SSD Tray, multiple 5G/WiFi/4G/LTE/GPRS/UMTS.
Company: Backplane Systems Technology
Phone: 02 9457 6400
Website: https://www.backplane.com.au/
ICP DAS DLW-1120. The ICP DAS DLW-1120 is a compact, yet powerful mini weather station designed for real-time measurement of weather conditions and air quality. This robust device can monitor wind speed, wind direction, pressure, humidity, temperature, precipitation, and sea level, making it ideal for outdoor weather monitoring in various industries.
In addition, the DLW-1120 measures particulate matter (PM1, PM2.5, PM10) and hazardous gases, ensuring air quality assessment. With its IP54-rated protection and replaceable filter patches, this weather station is built to withstand harsh environmental conditions.
The DLW-1120 supports RS-485 and Ethernet (PoE) communication interfaces and
protocols, allowing for seamless integration with existing IoT networks. It can be paired with the WISE controller for remote monitoring and alarm notifications, ensuring users are always informed of critical changes in environmental conditions.
The device’s compact design makes installation easy, and it is suitable for smart agriculture, industrial air quality monitoring, and even marine and port applications. The ICP DAS DLW-1120 offers a reliable and flexible solution for organisations seeking accurate and real-time data on weather and air quality, helping optimise operations and maintain regulatory compliance.
Key features:
•Real-time measurement of outdoor weather information and hazardous gas detection.
straight/ horizontal rod body, easy to install.
•Provide RS-485 and Ethernet (PoE) communication interfaces.
•Support Modbus RTU/TCP, MQTT communication protocols.
•Can be integrated with the WISE controller to set alarm notifications to keep you informed.
•Combined with the ExoWISE, simple logic control settings.
Company: ICP Electronics Australia
Phone: (02) 9457 6011
Website: icp-australia.com.au
Investing in professional development isn’t just about enhancing skills; it’s a step toward securing a future where your expertise is in high demand.
With Weld Australia’s 2025 course offerings, industry professionals can kick-start the new year equipped with the knowledge and credentials that make a difference.
From mastering welding inspection techniques to obtaining globally recognised IIW certifications, each program is designed to elevate your career and give you a competitiveedge.
Weld Australia is Australia’s premier welder training organisation. Its comprehensive range of training, qualification and certification services are designed to help Australian welders, fabrication and manufacturing, and the industrial sector at large, achieve and maintain a competitive advantage.
Its experienced team delivers a range of face-