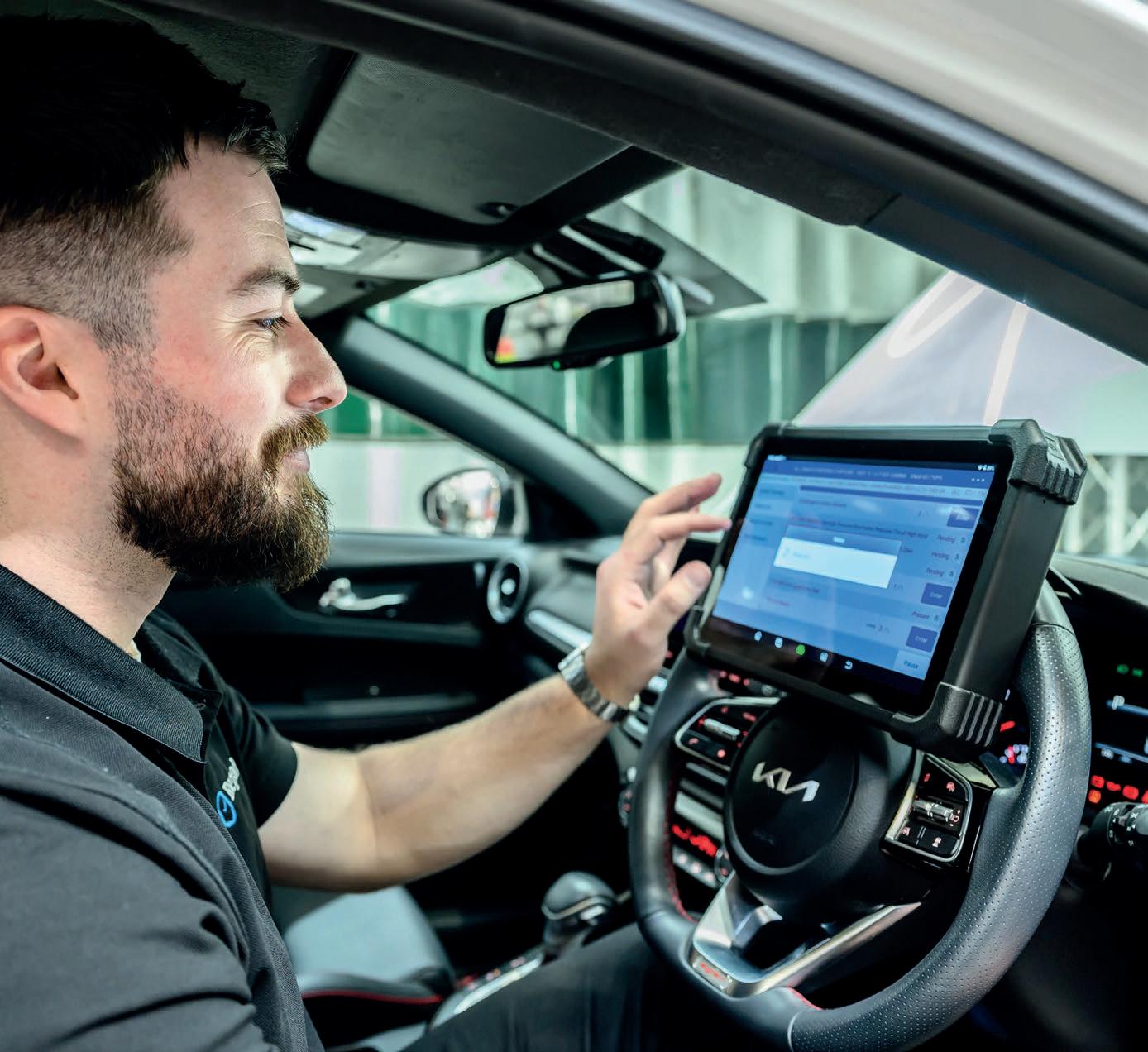
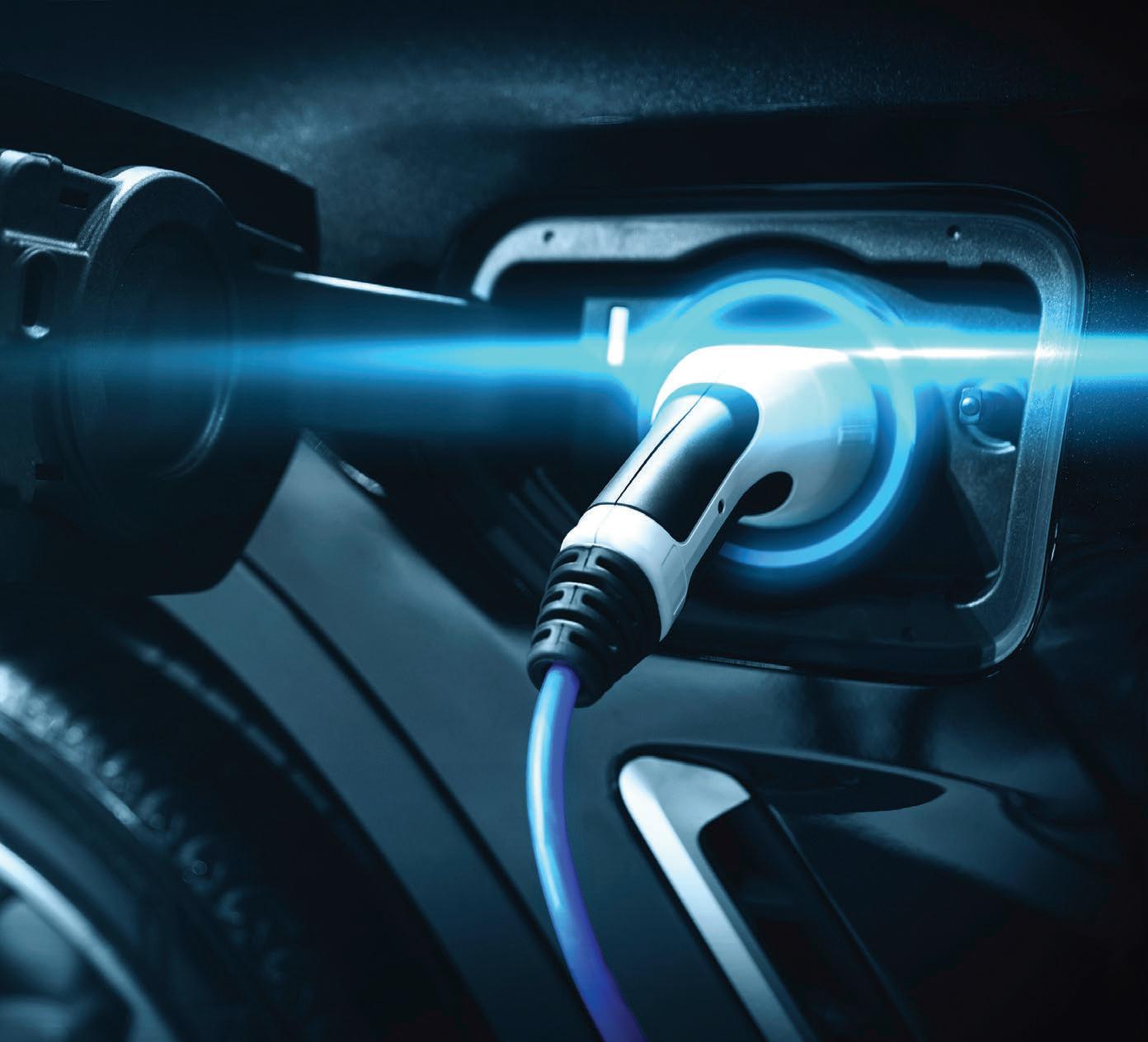
Fix Auto is Charged for the Future with Fully Trained Network
3M™ Cubitron™ 3 Cut-Off Wheels with their fast cutting andlong-lasting performance improve productivity and efficiencyin various body shop cutting processes.
These Cut-Off Wheels are built with the 3M™ Cubitron™ 3 Precision Shaped Grains –designed with sharp, angularstructures that continuously fracture to form fresh, sharppoints that allow the discs to slice faster, and last longer. They will cut through most materials, including high strength steels, stainless and mild steel.
bradley.buchanan@primecreative. com.au 0413 672 403
eugene.du y@primecreative.com.au 0412 821 706
The collision repair sector is an industry renowned for getting the job done.
Everyday thousands more cars are delivered back into the hands of eager customers who just want to get behind the wheel of their own vehicle again. However big the job or however long this takes, businesses are motivated by three guiding principles: safety e ciency and quality.
However, one of the biggest impediments of recent years for the industry to bring those jobs to completion has simply been having the people to get the work done.
Skills shortages in the automotive sector are not a surprise to anyone. If they have dragged on for many years in collision repair and look set to persist through 2025, it is also unfortunate that any comprehensive and lasting solution is going to take some time.
But there is some silver lining in his cloud; 2024, as a year, did end with a few positive points on the skills front. Capricorn’s State of the Nation snapshot survey showed, despite still ranking high as an issue, there was a slight improvement. Those saying they are still struggling to get skilled sta dropped from a high of 43 per cent to 39 per cent in automotive. Paint and panel remains the worst a ected aftermarket fi eld with almost three quarters responding that they have a resourcing issue of some kind.
But these businesses are also doing something about it; with more than four in fi ve employing apprentices and interns. Every collision repair employer knows this is a long pipeline to the skills needed but it is a proven pathway to get some outstanding quality workers down the track. This is why the continuing work of the Australian Collision Industry Alliance in conjunction with its partners is so important. To ensure that pipeline continues to be fed with talent and that collision repair apprenticeships should be seen as equally attractive, skilled and rewarding as other industries.
Another piece of news to end the year which bodes well,
was the announcement by the federal government that it would include panel beaters and spray painters on the Core Skills Occupation List.
While it is a major credit to the MTAs and the AAAA for their long advocacy to get this recognition from the top level of government and hopefully simplify and broaden the skilled migration system, it is also realistic to say signifi cant barriers remain to it being a solution for every workshop. The cost alone to sponsor a skilled worker to fi ll a role remains very high, the paperwork is intense and lengthy and, as our special report in this edition highlights, can take a minimum of 12 months before businesses have a worker on the tools. The skilled migration solution also has a long pipeline and the advice of the migration agents that NCR spoke with is if you are considering it then start on the process now.
There is yet another solution to help ease the skills crisis, and it may even have the advantage of a faster turnaround. It involves upskilling the existing workforce.
Business owners know the value of the team they have and making the investment and taking the time out to train many of these dependable workers could be one of the best solutions of all.
Increased expertise in technology, e ciency and safety of the team may be the accelerator a business is looking for to take on more work. It also has the lasting advantage of consolidating the careers of those already in the workforce. Added skills and training not only opens up new personal potential and career enrichment but gives confi rmation of the value of these workers, strengthening retention and loyalty.
As I-CAR’s successful Gold Class accreditation training program has shown, this can be a career a rming exercise for the whole team, benefi tting the business as well as enriching and empowering each individual.
The skills shortage is widespread and can even appear daunting, but 2025 could be a good year to wrest back control with one of these solutions.
Eugene Du y Editor The National Collision Repairer
To celebrate our 50-year milestone, we are offering unbelievable on all Car-O-Liner Welders, Benches and Measuring Equipment ... and you also receive our normal ‘Trade-in Deal’ which is still available. This Special Offer is 50-years in the making.
The new ‘jet X’ flagship model rolls 100 years of SATA experience and knowledge into an advanced spray gun that is designed to bring out the very best in every painter.
The release of a new SATA flagship spray gun is an occasion well worth celebrating – especially for painters. The new jet X model is all about supporting painters via advanced technology that helps them produce the best possible finish with the minimal e ort. With its innovative nozzle technology, advanced digital functions, cutting edge ergonomics and unique detailed solutions, the jet X truly is the gun that ‘works for you’.
Labyrinth airflow system
Building on SATA’s proven X-Nozzle system, the innovative ‘labyrinth airflow system’ sets a new benchmark for atomisation and transfer e ciency. Via precision designed internal passageways, air is guided to the nozzle
in such a way that it exits each orifice at exactly the same pressure, as well as being free of turbulence and pulsations. The result is exceptionally fine and consistent atomisation. The reward for painters is unprecedented control and ease of use thanks to optimised material distribution and an even spray pattern with clearly defined fade-out zones. There is the choice of HVLP or RP technology in SATA’s ‘I’ (‘control’) nozzle system which features a longer spray pattern with an even material distribution. Regardless of the nozzle, the fan dimension remains constant across the full spectrum of nozzle sizes.
The most digital SATA ever
The jet X model will come with more digital capabilities than ever before thanks to the choice of not one but two digital options. On these models the new digital display screen faces back towards the painter, making the information very easy to read. With a simple 90-degree swivel, the digital unit can be easily removed when cleaning. Functionally is a key feature on both units which gives painters more valuable information and options to help achieve standardised, repeatable results. The adam X digital unit, fitted to the jet X DIGITAL, displays a spread of useful information, including dynamic inlet pressure, ambient temperature, elapsed operating time and battery status. The jet X DIGITAL Pro features a more advanced adam X Pro unit which steps up the depth of information. It’s divided into two level with the main screen o ering a clearly organised display that includes current actual pressure, previously set target pressure, the dynamic pressure that was applied when the trigger was last pulled, deviations between the actual and target pressure in a graphical visualisation and a handy alarm symbol if the actual and target pressure di er by more than 0.2 bar (3 psi).
Ergonomically tuned to you
Ergonomics have always been a SATA strong-suit and the jet X continues the trend with a fresh, sophisticated design that sits comfortably in the hand and is finely balanced so that it doesn’t become top-heavy, even with a large, full cup. The fact that the new jet X is a substantial 50 grams lighter than its predecessor, the SATAjet X 5500, helps make it a pleasure to move around the job and get into tight spaces. In addition, there are thoughtful design elements everywhere you look, such as the air micrometre adjustment being moved to a more natural and convenient location at the bottom of the handle. For ease of cleaning and maintenance, the trigger can now be removed in one easy step, without tools or snap rings. It’s made from a technical polymer material and has a handy tool moulded into it which is ideal for loosening or tightening the fluid tip.
Once you purchase your jet X, simply registering it on the SATA website will extend the warranty out to three years of coverage. The jet X is backed up by a full set of spare parts and maintenance items to keep it in tip top condition for many years to come.
The jet X is set to arrive at ANZ SATA distributors early in 2025 so keep your eyes peeled for details on how to be one of the first to get your hands on one.
Car-O-Liner have introduced a new work bench, the BenchRack™ Versa, to their impressive range of repair workshop equipment.
A versatile and flexible solution for various collision repair needs, the BenchRack™ Versa is a seamless and accessible piece of equipment.
Regardless of vehicle shape and size, the BenchRack™ Versa maximises repair e ciency.
The bench provides a full 360° vehicle access to attach the Draw Aligner, allowing technicians to perform complex repairs with exceptional accuracy. The 10-ton Draw Aligner pulls from almost any angle, 360º around the vehicle. A second Draw Aligner can also be added for double the pulling power.
Car-O-Liner aims to produce workshop equipment that focuses on ergonomic work posture. The BenchRack™ Versa aims to minimise work-related strain injuries.
The bench is purpose-built for inground installations. This latest lifting innovation from Car-O-Liner, allows for valuable time to be saved in the daily operations of a workshop. By saving essential floor space, the in-ground installation of the bench allows for maximum productivity and e ciency.
The BenchRack™ Versa is designed to revitalise your workshop by providing strong lifting capabilities, enhanced ergonomics and compliance with OEM requirements.
Whether you’re working on lowprofile sports cars, SUVs, or light delivery vans, the BenchRack™ Versa o ers the versatility and performance you need to handle any repair job with ease and precision.
Elevate your shop’s capabilities
• Extended Lifting Capability. The BenchRack™ Versa o ers an increased lifting capability of up to 1.450 mm (58”). This significantly enhances the ergonomic working height and provides greater comfort and e ciency for technicians.
• Extended Pillar Jacks. The new reinforced pillar jacks have extensions to compensate for pit depth and a reduced weight to provide a more ergonomic experience for technicians.
The new short ramps facilitate lifting by the wheels, allowing for a fast and secure process to position the vehicle at an optimal working height. The ramps are made of high-strength steel
and aluminium to minimise weight and improve ergonomics.
Additionally, these ramps are strategically positioned higher on the frame, enabling quick diagnostic measurements while the vehicle remains on the ramps, enhancing both e ciency and safety. The low-profile, lightweight ramps ensure compliance with OEM requirements, particularly for EVs.
Car-O-Liner Australia’s reputation is built on the complete line of collision repair solutions, including alignment, and straightening systems, joining, and heating equipment, measuring systems and workshop solutions.
Car-O-Liner provides continual sales, service, and technical support. Their extensive range of OEM approvals means that our customers can continue to rely on Car-O-Liner as the car manufacturers accelerate their influence on the industry.
Find out more at https://www.car-o-liner.com.au/
Despite the influx of imitators, RAPTOR remains the original and best in the market. Its proven track record, continuous innovation, and unwavering commitment to quality have solidified its position as the market leader and the brand of choice.
RAPTOR Coatings has set the standard for tough, reliable, and versatile protective coatings. Its journey from industrial origins to becoming a staple in the 4WD community and beyond is a testament to its exceptional performance and enduring appeal.
RAPTOR has firmly established itself as one of the bestselling 2K polyurethane tough and textured coatings in Australia. And for good reason – high performance.
Renowned for its durability and versatility, RAPTOR has become the go-to product for those seeking reliable protection for their vehicles and equipment. Its widespread popularity is a testament to its superior performance, ease of application, and the trust it has earned among users.
Originally developed as an industrial coating, RAPTOR quickly found a niche among ute owners and 4WD enthusiasts.
The texture and durability of RAPTOR resonated with the rugged o -road image of 4WD and has become embedded in the must-do list for vehicle makeovers and upgrades.
Beyond 4WD, car restoration experts, such as Perfection Body Worx in Sydney, use RAPTOR as an underbody coating, protecting vehicles from rust and damage.
As owner Scott McGuire put it:
“In car restoration, detail is everything. Why go to all that e ort and forget about the most vulnerable part of the vehicle? We use RAPTOR because it’s a 2-pack paint that provides high film build that resists stone chipping. RAPTOR provides bottom-up protection.”
RAPTOR’s versatility extends beyond 4WD vehicles and is now widely used in various applications, including caravan and trailer manufacturing.
Returning to its industrial roots, RAPTOR is being used as a protective coating for equipment and machinery. Commodore Electrical, based in Shepparton, Victoria, designs, builds, and installs o -grid solar and pumping solutions for agricultural and industrial customers.
Drew Lythgo, design consultant from Commodore Electrical, explains:
“We ensure our solutions fit our customers’ needs. Whether for a small farmhouse or a large mining site with significant dust and UV exposure, we use the right components and paint from start to finish.”
One of their projects, a solar pump skid, features an IP55-rated cabinet for remote monitoring. The entire build is designed to handle robust conditions, including the paint.
Commodore Electrical chose RAPTOR coating for its UV resistance, anticorrosive properties, and scratch-proof durability.
“It perfectly suits our long-term o -grid solar solutions. RAPTOR’s coating has been very easy for the team to apply at the final stage.”
What makes RAPTOR so tough? The answer lies in its chemistry.
U-POL, based in the UK, boasts a rich heritage in industrial chemistry that spans over 70 years, developing highperformance fillers, coatings, aerosols, adhesives, and paint-related products.
RAPTOR is a 2K polyurethane. Its two components chemically react to form a highly durable and resilient coating
resistant to UV rays, solvents, and physical abrasion. The result is a tough, long-lasting protective layer ready for Australia’s brutal conditions, whether oroad, on a farm, at work in transport, or underground in mines.
RAPTOR was originally designed as a new industrial coating to replace traditional tough protective coatings that required labour-intensive preparation, technical ability, and other complications to achieve full strength and durability.
For testing the chemical resistance of industrial coatings, horse urine is top of the list.
As any owner of a horse float will confirm, horse urine is corrosive stu and will eventually eat through an aluminium or steel floor—but not if it has been coated with RAPTOR.
ASTM is an internationally recognised technical standard for testing a wide range of materials, including industrial coatings.
RAPTOR Coating has been independently tested (and passed) the ASTM standards for salt spray resistance, water immersion, abrasion resistance, hardness, adhesion, chip resistance, impact resistance, anti-slip, UV resistance, and a range of chemicals and solvents, including xylene, sodium hydroxide, hydraulic oil, Petrol, diesel, water, ethylene glycol, motor oil, and, of course, horse urine.
For industrial applications, being able to produce ASTM certifications and Standard Operating Procedures for paint preparation and application is mandatory for manufacturing quality control and meeting the stringent requirements of large industrial users
such as mining, oil, and gas companies. This is another factor that sets RAPTOR apart from its imitators and instills confidence you are protecting the asset with the right product.
Imitators fall short
In the field, it’s di cult to compare two coatings objectively because factors like surface preparation, application film thickness, and curing times produce variations. In the laboratory, however, ASTM specifies standardised testing regimes resulting in objective testing across the full spectrum of qualities. These results are graphically represented using a radar chart comparing RAPTOR with yet another recently launched imitator. While able to match RAPTOR on a few characteristics, the imitator fell short in key areas of adhesion, hardness, ease of application, and appearance. RAPTOR has been
20 years in development and has a considerable head start.
RAPTOR continues to innovate and expand its product range. The RAPTOR family now includes high-temperature aerosols, which can withstand heat up to 1,000°C, making them ideal for applications like engine manifolds, exhaust systems, brake callipers, and even pot-belly stove exhaust flues. Additionally, new products such as RAPTOR 1K Tough Undercoating,
Adhesion Primer, and 1K RAPTOR for household use have been introduced, further enhancing the versatility and application range of RAPTOR coatings. Further exciting innovations are in development. Whether you’re protecting a ute, a caravan, or industrial equipment, RAPTOR is trusted for unparalleled protection and durability.
For more details, visit raptorcoatings.com.au.
Axalta has released a new product from refinish coating brand Spies Hecker that is o ering a host of sought after qualities to help speed up spot repairs.
The new Permasolid UV-TEC Primer Surfacer 9003 is designed to o er fast drying and curing, superior adhesion, and enhanced corrosion protection, making it the ideal addition to any bodyshop looking for the latest in spot repair solutions. It replaces the existing Permasolid 1K UV Starlight Primer Surfacer 9002.
Axalta ANZ Product and Technical Manager, Jim Iliopoulos, says the benefits of 1K UV primer surfacer will be great for existing cosmetic repairers or those thinking of introducing the service.
“The speed and performance of
At Premium Diagnostic Equipment, we don’t just supply top-of-the-line scan tools – we empower you to get the most out of them with our dedicated, expert technical support.
Why do our customers love the Phoenix Max?
- Fast & Accurate Diagnostics
Quickly identifies and resolves vehicle issues with OE-level coverage.
Essential for modern vehicles with complex systems post-collision.
- ADAS Calibration Ready
Seamlessly integrates with ADAS calibration tools for safety feature realignment after repairs.
- Compatible with 12/24V systems
Perfect for workshops handling both passenger and commercial vehicles.
9003 make it the ideal option for bodyshops that provide smart and small repair services. And for those bodyshops planning to extend their portfolio with a cosmetic o ering, this primer surfacer is the perfect first step for them,” he says.
“Thanks to a curing time of just one minute, waiting times for both bodyshops and customers are cut down. This leads to higher productivity, faster throughput, and is beneficial for cosmetic repairs.”
Permasolid UV-TEC Primer Surfacer 9003 doesn’t need any activator or thinner, so can be used right away. Based on 1K UV technology, it also means minimal cleaning and there are no time or process restrictions, so you won’t need to worry about pot life.
Superb adhesion properties ensure that paint is both easy to apply and lasts
longer, leading to excellent corrosion protection. It also generates minimal waste and, because it requires no baking, it cuts your energy requirements too. Its semi-transparent grey colour ensures easy application, making it easier to see where you have applied it and prevents heavy application.
“There is a growing demand for solutions that drive an increase in e ciency but are also sustainable. With fewer process steps and products used, a simple universal application technique, and rapid-drying performance, the new Permasolid UV-TEC Primer Surfacer 9003 is a must-have for bodyshops looking for reliable results coupled with an uncomplicated repair process,” concluded Jim.
Upgrade Your Workshop Today! Contact Premium Diagnostic Equipment for Exclusive Deals on the Topdon Phoenix Max.
Comprehensive Support: With Premium Diagnostic Equipment, you’re not just getting a product; you’re gaining a partner. Our expert technicians are here to answer questions, provide troubleshooting tips, and help you master new features and updates.
If there is one thing Premium Diagnostics does well, it is their ability to provide top-notch car diagnostic tools and workshop gear at unbeatable prices.
Born from a lack of clarity surrounding diagnostic tools for di erent tasks and vehicles in Australia, Premium Diagnostics aims to simplify and lead automotive businesses and mechanics towards easier, streamlined solutions.
Backed by solid aftersales support, Premium Diagnostics aims to be with technicians every step of the way.
Keeping in touch with clients, and creating a trusted relationship, is one of Premium Diagnostics’ many strengths. This is showcased through their loyal customer base.
The Topdon Phoenix Max Professional Diagnostic Scan Tool is the latest automotive diagnostic scan tool. It is also one of the most popular pieces of equipment at Premium Diagnostics.
“The Phoenix Max has been the best investment for my workshop,” business owner Ben Townsend says.
“I am no longer having to turn away work or sublet jobs because I can do it all in-house. The service from the team at Premium Diagnostics is also great. It’s been a game changer for us.”
Another customer branded the Phoenix Max as an ‘impressive tool’.
“Once again, top-notch customer service from the team. Very happy we went with the Topdon Phoenix Max,” Reece Aderman says.
With a 13.3” screen, the all-in-one tool o ers a wide array of functionalities that will expand any technician’s capacity to complete every job.
The Phoenix Max includes a 4-channel oscilloscope for in depth electrical testing, ADAS calibration compatibility, and Topology Mapping that shows all car systems in one view. The Phoenix Max has a wide vehicle coverage and is compatible with 12V and 24V systems and software for vehicles, trucks and machinery.
The scan tool o ers advanced features at a more a ordable price
compared to competitors, making it ideal for workshops looking to expand services without breaking the budget.
The advanced ECU programming and coding enables online programming for 15 di erent vehicle brands, creating a reliable and ‘one stop’ solution.
It’s updated VCI includes J2534, CanFD, DoIP, D-PDU, and RP1210 protocols, allowing professionals to perform more complex repairs on a variety of automotive and heavy-duty vehicles.
For the Phoenix Max, Premium Diagnostics o ers free shipping, aftersales technical support, a 12-month warranty, and 2 years of free updates.
Premium Diagnostics believe in their products and provide a 30-day moneyback guarantee.
The Topdon Phoenix Max Professional Diagnostic Scan Tool 12/24 V is available on Premium Diagnostics website, with an array of other automotive scan tool equipment.
Learn more at /premium-diagnostics.com.au
Change is a constant in the automotive industry and 2025 looks no di erent. But as the Fix Network shows with the rise of specialised repairs and its recent move to be EV ready, it is a future worth tackling head on.
The collision repair sector is ever evolving. While there are many trends we expect to see continue, such as increasing vehicle complexity, growth in the adoption of EV and high voltage vehicles, and a shift to more e cient and eco-friendly repair process, 2025 is certain to present some previously unanticipated challenges. The rising costs of parts, labour shortages, and supply chain disruptions will see the industry moving towards more robust resourcing strategies and turning its attention to recruiting and upskilling technicians to handle more advanced technology, more e ciently than ever before.
The team behind Fix Auto in Australia views these challenges as opportunities and have turned their focus towards testing new and innovative ways to stay competitive while o ering customers the same best-in-class services and experience. As the automotive landscape continues to change, one thing remains the same - a committed to the growth and development of people will be the key to success in a rapidly changing industry.
Fix Auto recently announced its designation as an authorised repairer for EV/Hybrid vehicles. Just one example of how it has prioritized the development of a highly skilled workforce, equipping its team with specialised expertise in handling new technologies and repair techniques. Through ongoing training and investment in upskilling its already skilled team of technicians, it will continue deliver on the industry’s changing demands and exceed customer expectations.
Human capitol is the key to success
No business in the collision repair industry is immune to the impacts of the ongoing labour shortage. Like many businesses across the industry, Fix Auto has experienced the challenged that the increasing complexity of modern vehicles has had, requiring a highly
specialised skillset. Paired with a legacy workforce that is preparing to retire, the industry is in the midst of a transition that has left it with fewer trained technicians available to manage the increasing volume of complex repairs.
To address this, Fix Auto has prioritized upskilling it’s shop teams while leveraging its global network of shops, training centres, and technicians to test and adopt new technologies and more e cient processes. Additionally, a continued focus on enhancing workplace culture supports in retaining team members but also ensures the company is prepared to face these industry shifts head on.
Fix Auto’s parent company, Fix Network, has been monitoring and analysing the impact of increasing complexity of vehicle technology, in particular the rapid growth of more sophisticated Advanced Driver Assistance Systems (ADAS) and the adoption of hybrid and electric vehicles (EVs), and is actively preparing for the increasing demand for technology readiness, recognizing its critical role in the future of collision repair. With ADAS becoming a standard feature in modern vehicles, Fix Network knows it’s approach to repair and calibration must evolve just as rapidly. To do that, it has focussed on fortifying
its capabilities in-house to ensure its shops and technicians are equipped to perform ADAS calibrations accurately and e ciently. This is not just about meeting customer expectations—by o ering in-house calibration services, Fix Auto is confident it will improve turnaround times, reduce costs, and enhance the overall quality of repairs. As these systems become more complex, Fix Auto is dedicated to ensuring that its sta stays up to date with the latest technologies and best practices. The key to keeping up with the challenges ADAS calibration brings, is in viewing it not only as a service, but as a way to di erentiate the company in the market. Ultimately, this is about future-proofing the business and industry, while ensuring it continues to provide safe, high-quality repairs for its customers as vehicle technology continues to advance.
In the same vein, the rise of hybrid and electrified vehicles is poised to present a unique challenge because of their distinct mechanical and electrical systems, such as highvoltage batteries and lightweight materials like aluminium. To manage these repairs safely and e ciently, it is essential for collision repair businesses to invest in specialised training for technicians, seek out the right tools and equipment for shops, and prioritize ongoing education to test new and innovative repair techniques.
AI and automation will also play a crucial role in streamlining operating processes. AI is helping Fix Auto to assess damage, and process claims more e ciently and accurately, giving it the edge in turnaround times and overall service quality. On top of that, modern vehicles generate a lot of data through telematics systems. By leveraging this data, Fix Auto can diagnose issues more precisely, plan repairs more e ectively, and ultimately deliver better results for its customers.
The shift toward advanced technologies is a challenge, but it’s also an exciting opportunity for the collision industry in Australia to evolve and lead the charge in the future of repair with more accuracy, safety, and e ciency.
2025 will be a formative year for many collision repair businesses as they confront several ongoing and some new problems. Tackling them and thriving is all about getting the right support.
2025 could be a crunch year for some small repair businesses according to Fix Network Head of Business Scott Croaker but equally it could also o er an opportunity to make the choices to ensure they have a vibrant future.
“I think 2025 is one of those years that is going to start to demonstrate some of the challenges and stresses on the industry a little bit more,” he says.
“There’s an ageing network, an increase in technologies and there are increased compliance and expectations from the insurance companies around privacy, security, and ESG that is ever more challenging for the individual independent businesses to meet.
“The typical independent mum-anddad shops often don’t have the facilities to be able to provide this and respond to these expectations. Potentially, they won’t meet the compliance requirements and might not get the work because of this, whereas the MSOs and bigger infrastructures often can.”
He says MSOs are often expanding or acquiring in certain areas of high value and can potentially threaten the work allocation of independents from insurers. While some independent businesses will see this challenge as an opportunity to sell or retire, Croaker says there is also many small businesses where their loyalty and commitment is unwavering, and they are looking for the best way forward to retain the elements of ownership and remain viable. This is where Fix Network can o er another path, utilising a franchise model.
“We provide the back-end support and corporate infrastructure to enable
franchisees to compete against the MSOs from a compliance point of view,” he says.
“We o er the business training and skills. We provide support for privacy, security and legislation and are focused on our ESG o ering in terms of the corporate compliance requirements from an insurer. And we continue to develop our processes and strategies to support those on a global scale.
“We also have the high-level relationships with insurers, so that our family of franchisees are treated similarly to an MSO, even though we are a network of independently owned businesses. We get a seat at the table and get greater consideration when it comes to the work provision and allocation.”
One of the most valuable forms of support in the network he says, is providing individually based business reviews, insight and support that allows the workshop to meet these challenges and grow their capacity.
“We have our Business Excellence program, where we conduct a quarterly review of their business, look at their high-level key performance indicators (KPIs), throughout and then drill down on any areas of concern. It’s both a desktop review and an on-site review in terms of workflow processes; What’s driving those performances? What are the bottlenecks?
“And we get the shops engagement in terms of, what are the changes that need to happen to improve the results, and how do we do it?”
“It is a continuous improvement program, that essentially looks at operational KPIs, financial KPIs
and customer sentiment, the three key pillars that we feel drive the performance and represent the health of the business. We use them to review and understand, to improve how they operate and to get the best result.”
Fix Network’s focus is all about this potential to grow capacity and e ciency. Their more than twenty member businesses across Australia have shown significant success in meeting these changes.
“Over the last couple of years, we’ve got a number of our shops that have extended and expanded, or for example bought the factory next door to accommodate more work or leased a lot down the road to house the cars and manage capacity and workflow issues, so that the shops themselves are as e cient as possible.”
The strength of the network also enables them to o er support to franchisees on several other pressing issues collision repair businesses are facing.
For the long-running issue of recruitment, for instance, Fix Network has been able to tackle some of these problems collectively. A recent recruitment drive to utilise skilled migration from the Philippines has filled positions at multiple businesses.
Similarly, the increasing demands of technology on workshops is an area where Fix Network can utilise existing strategic partnerships with specialised providers in areas such as ADAS equipment and calibration services. Whether outsourcing services
or investing to bring them in house and take up the revenue opportunity, these are also a business assessment they can help workshops with. The network also has the advantage of incorporating NOVUS Glass and its experience in dealing with the demands of windscreen cameras.
Fix Network’s ongoing focus on ESG will continue into 2025 with specific plans to look at energy consumption and the footprint of the business both at a global and local level. But this will also serve in practical areas, such as energy consumption and costs and passing those benefits on to their businesses.
“We’ll be exploring how to scale the network to secure greater value for our Franchisees across the country, combining both the Fix Auto and NOVUS Glass networks of franchisees. Our goal is to increase value for energy suppliers and maximize benefits for the entire network.”
These are just a few instances of the leverage a network can o er.
“We’re growing in terms of our scale and growing our relevance and importance to the work providers, he says. “We’re strengthening our position within the industry through our network, and reinforcing relationships and supply partnerships, so that we can grow that way.”
In all these areas of support, Croaker
stresses it is tailored to the individual needs of each member, and this follows from a culture that promotes the familial elements of each business.
“What happens on the ground is a lot more nuanced and subtle, but independent to the individual shops. The support we o er through our field team is that we treat the businesses, and they treat us, like family. With the team that have been in the business and in the franchise for a long time, it is almost like family. They’re treated with all the care and respect of a family member.”
“One of the biggest things that has been a challenge for us, from a franchising point of view, is just the lack of understanding of what franchising is and the value it can provide. So, we’re looking at adapting our approach and strategy,” he says.
“Because for us, the franchise model has the best mix you get - the investment from the owner operators. It’s probably one of the things that, anecdotally, we see missing from an MSO. There may be great capacity, great volume, but there can be a lack of investment and ‘skin in the game’ from the operators. We get that extra edge in the owner-operator. From this point of view, owner operators are more invested in the success and reputation
of their business, it is their livelihood after all.”
Croakers says it is vital to retain this for the long-term health and sustainability of the industry.
“We see ourselves as the guardians of the independent network, and certainly we provide that support and infrastructure for them to compete at a higher level than they would if they stayed independent. We broaden their scope; their contact and we also increase visibility of these businesses by elevating them from where they would typically sit.”
Croaker remains highly optimistic about Fix Network’s growth plans but also the ongoing ability for a diverse industry to meet its challenges and through high-quality work, keep Australia moving forward.
“I think for us, it’s not growth for growth’s sake, it’s that we want to support these shops. We want to a establish a network that services and meets insurers expectations from a location, capacity, quality, relationship point of view.
“We’re looking for the right people to support that, and at the same time looking at supporting the independent industry in terms of sustainability, growth and value, to ensure that there is an independent network in five, 10- or 15-years time.”
Training. We know it’s important, but who do you turn to? This suite from 3M may have the answers.
Technicians, estimators even assessors alike need to have expert level knowledge and skills which, in a perfect world, would be refreshed at regular intervals to ensure high quality repairs and maximized productivity. But where do you turn when you have a requirement for training or you need to keep up with advances in the industry? Whether you’re an apprentice starting their automotive career or a smash repairer looking for points to achieve I-CAR certification and everyone inbetween, 3M have training solutions for all designed to keep industry professionals up to date and upskilled.
The first part of the 3M Training suite is the expertise employed to design, deliver and tailor training that is as individual as it is informative. 3M has had technical departments for as long as most can remember, engineers and scientists who know the intricate details of products and processes and locally George Di Scala is the Application Engineer who is on hand to assist with, and carry out, product and process trials and evaluations ensuring that shops remain as productive as possible. Recently 3M has identified the importance of training within our industry and in line with this have added James Lawson as Collision Repair Specialist Trainer to their team to develop and oversee industry training. James has spent over 16 years working in collision repair and restoration shops
as a dual trade technician both in England and more recently Sydney. As a senior ATA accredited Panel and Paint technician and with approvals for VW/Audi group and JLR cars James obviously has the right expertise and now with a newly acquired Cert 4 in Training and Assessment he is perfectly placed to o er specific training options to anyone working in our industry. Add to this, a sales team who constantly undergo training and development, all of whom can o er product-based training meaning 3M have personnel to o er training in all regions of ANZ.
To assist with delivering training 3M have their regional training centre in Sydney, a facility fully equipped with 2 classrooms, workshops for industrial training, welding training facilities and of course their Lowbake Alpha Spray booth, Prep bay and mixing room. This state-of-the-art facility allows 3M to o er training for all aspects of the collision repair process from structural panel bond repairs, plastic repairs right the way through to paint finishing and polishing training.
For shops and technicians that require refresher training or less formal training 3M has recently launched a free to use online training resource, the 3M Collision Repair Academy can be accessed on most devices and currently has a total of 21 di erent modules o ering self-paced
learning in bite sized chunks. Added to this are the regular online Webinars where 3M Technical and Training sta discuss products and processes and allow for live Q&A sessions meaning no matter where you are you can have your questions answered directly.
Once training has been completed though, how can shops ensure that skills learned can be implemented in daily operations? Well to assist 3M can o er a complete catalogue of SOP’s or Process Charts to refer to which ensures each step of the process can be followed. Training delivered is always backed up by specific SOP sheets to take back or as leave behind resources and where necessary SOP’s can be tailored to shops specific requirements depending on factors such as paint system used.
For repairers looking to either gain or retain I-Car accreditation 3M currently o er a range of courses which allow technicians to gain I-Car points and learn process steps or repair procedures, these courses can be held at local training facilities, the 3M Training Centre or at a suitable repair facility.
To access the 3M Collision Repair Academy simply visit learn.3m.com/ pages/3m-academy-en-au-nz-collisionrepair for all other training enquiries call 0435 233 347 or contact your local 3M sales representative
2025 is shaping up to be a key year for upskilling existing workshop sta , as businesses strive to stay up-to date and e cient in a changing market. To keep abreast of changes, leading industry training provider I-CAR Australia has highlighted five courses not to be missed for any competitive business this year.
Finding time to stay across ever-evolving automotive technology and repair techniques remains one of a repair businesses greatest challenges and 2025 looks like being no exception. The continued transition of the Australian car parc to include more electric and hybrid vehicles, the prevalence of ADAS systems incorporating cameras and sensors along with the increased use of new materials in automotive technology are just a few of the changes workshops will encounter as repairs role in the door. Having all the skills needed on the floor can also be di cult for an already busy workshop. This is where I-CAR’s combination of online, hands-on and remote training modules can o er enormous flexibility to the weekly workflow of a business.
Top considerations for any workshops should be ensuring sta have the minimum skill levels to deal with new technology and techniques and ensure work can be completed safely but also to the high standards the business requires. Here are five key areas, no technician should be left behind on.
This is the essential starting point for all technicians hoping to work safely on or with new electric or hybrid vehicles. The short online course o ers an introduction to high voltage safety and explains the elements of electricity and the relationship between voltage, current and resistance with high voltage systems. With a strong focus on safety in the workplace, it details the potential e ects of electricity on the body and highlights the required personal protection equipment needed when working around high voltage.
As an introduction to EVs, it also identifies the major parts of an electric vehicle’s high voltage (HV) system, HV safety measures in a vehicle design and methods to reduce shock risks.
This course requires no prior qualifications and is highly recommended for all sta in the business that are considering taking on repairs for the increasing fleet of cars that use electricity as a primary or supplementary power
source for their powertrain. Essential skills for the future industry.
Welding is a fundamental skill for major repairs, but the materials used by manufacturers and the techniques needed to correctly and safely repair them are continually evolving. Aluminium, for instance, is often used for its lightness in vehicle design but is also prone to porosity with incorrect welds. Welds are often the repair outcomes a customer cannot see, but poor welds or overheated welds can lead to part failure and compromise safety for the passengers in a vehicle.
Introduction to Welding Basics is a course designed to help already skilled welders to improve weld quality and equipment. It is an intensive 16-hour course including 12 hours of hands-on training, working with basic zinc coated automotive steel. The course includes instruction in meeting visual standards and destructive testing for defects in the weld.
and techniques
This is not a certification program but is a valuable pathway to other welding qualifications and is recommended for structural technicians and 3rd & 4th year apprentice non-structural technicians. The training program is also a great opportunity for technicians to learn to correctly set the new Inverter Synergic welding equipment being recommended by a growing number of OEMs. manufacturers.
This online course is specifically designed to keep sta up to date with vehicle trends and techology to stay ahead in collision repair and act as a supplement to other skills and knowledge on the workshop floor. It will examine what’s new in the automotive industry for 2025 and look at the latest vehicles, technologies, and innovations from major manufacturers.
The course begins with a exploration of global industry-wide trends including battery technology and wireless EV charging, along with the rise of hydrogen powered vehicles. It also looks at the critical areas of advancements in ADAS and nighttime emergency braking, autonomous vehicle identification, and changes to braking systems and paint.
Then it moves on to dedicated modules covering each of the major car making markets with separate examinations of features, updates, and industry trends across American, Asian, and European brands. This will incude new models from major OEMs, including Ford, GM, Stellantis, Toyota,
and Honda, along with models from Kia, mini, BMW, and Mercedes Benz.
Rivet bonding is increasingly being used by OEMS as they incorporate innovative materials and design in vehicles. The advantages of riveted bonding over conventional welding for aluminium welding, for instance, is that heat poses a problem with thinner sections of aluminium such as doors and panels. High temperatures can pose issues such as warping, distortion and burnthrough due to aluminium’s relatively low melting point.
This process also allows for the joining of di erent materials that are used in modern vehicle construction methods.
Rivet bonding also o ers increased corrosion resistance of the repair joints through the adhesive bond, ideal when joining dissimilar materials as the adhesive provides a barrier between the two metals avoiding galvanic corrosion.
Riveted bonding also has better overall mechanical properties than with riveting alone; providing less noise, vibration and dampening. Given these advantages workshops can expect to see more rivet bonding in new vehicle design, making skilled understanding of how to repair the joins essential.
This four-hour, hands-on course instructs technicians how to properly perform rivet bonding procedures, how to properly remove and install various types of rivets such as blind and solid rivets. It also o er training in the setup of SPR installation equipment and the need for a well-planned and organised approach to ensure the rivets are installed before the adhesive sets.
The course is recommended for steel and aluminium structural technicians
and non-structural technicians giving the skills to complete higher quality repairs with rivet binding. Faster repairs on these modern techniques with less touch time also means improved productivity for the workshop. It o ers valuable skills for the workshop committed to high quality repairs and safe outcomes with the most up to date techniques.
5 Incorporating ADAS in your business
The advance and uptake of ADAS systems on modern vehicles means few repairs are fully complete without calibrations. The know-how is now a vital part of e cient and safe repairs for any repair business tackling this technology but also looking for the business opportunity o ered by keeping the service in-house .
Incorporating ADAS in Your Business is a short online course suitable for a wide range of technicians including estimators and assessors and helping them to understand the importance of preparing the business for ADAS repairs. This course identifies the di erent options available for ADAS calibrations and what is required to develop an inshop ADAS calibration facility.
From March 2025, Automatic Emergency Braking systems will be mandatory in new vehicles in Australia, just one ADAS system repair shops are certain to see more of in the future. This year poses a great opportunity to improve understanding and skills in a soon to be standard part of the automotive future.
Full course information, including course times and qualifications are available at i-car.com.au/wp-content/uploads
Global trends, including advancing automotive technology, combined with other pressure on workshops, look set to continue in 2025 but as Repairify Managing Director – International Phil Peace explains, there are ways businesses can prepare and adapt.
Technological trends may change but a workshop’s objective remains the same; getting the repaired vehicles back on the road e ciently and safely. One of the fundamentals to make this happen is for technicians to get the vehicle information they need for repairs, when and where they need it.
Phil Peace explains that while OEM secure gateways and proprietorial protections of their systems are not new, they can still potentially complicate access for workshops causing delays and added costs. He says in this regard 2025 will be an interesting year to watch.
In a recent development, a landmark case in the European Court won by Belron, a major automotive glass service, has set precedents in what is permissible with secure gateways.
“There’s no definitive outcome at this stage, but there’s lots of conversations going on in Europe about what the future looks like in terms of accessing vehicles,” Peace says.
“The question lies in what the OEMs put behind the wall today and in the future. And obviously it’s important that access to vehicles is controlled, particularly security related items and to a degree, safety related items in the autonomous world.”
But even with the cooperation of the OEMs, there are issues related to the volume of the material workshops need to access and whether it comes in a uniform format from multiple and diverse car makers. This in turn Peace says, can a ect the e ciency of workshops doing diagnostic work or calibration on vehicles and may have outcomes for their turnover and profitability.
“I think there’ll always be a situation where the aftermarket is behind the OEMs in terms of engineering and the tools,” he says.
The wide range of cars can make it di cult for any workshop to have the specific diagnostic tools available. This is where a subscription service like Repairify, that has a strong global relationship with nearly all the major vehicle manufacturers, can open
up gateways and e ciently access information. Repairify o ers its All-InOne Diagnostic Tool as the solution to this advancing complexity and this is backed up with its remote diagnostics service.
“Another aspect is expertise; you’ve got technicians in your body shop, they’re panel beaters or painters, but they don’t always have the skills set in programming and that’s where we come in. We can step into that environment; our teams have got the skill set to help them through. Workshops connect through to us, and we’ll talk them through the whole process.”
Peace says Repairify’s Remote Services can help speed up diagnostics and the increasingly important calibrations on many vehicles.
“In many cases, what we’re doing is at the end of the repair process. If for instance it’s a radar calibration, the car’s been put back together and we are the last point. But if the workshop can’t calibrate it, they can’t get it back on the road, they can’t invoice it and return it to a satisfied customer. So, for us, that’s such an important process, we’ve got to do everything we can to help that shop get that car back on the road.”
Experts on your doorstep
Regional bodyshop repairers without the in-house expertise face even longer delays and costly transport costs trying to overcome these barriers.
“This is why this expertise is so valuable In the Australian market because you’ve got such huge distances,” he says.
But overcoming delays can be
a critical business advantage for workshop e ciency and key-to-key times even if calibration or other services are nearby.
“Basically, it brings the OEM tool to your doorstep. It makes the vehicle think the OEM tool is in the car.”
While many Australian repairs have fixed costs, the delays and additional costs are invariably reflected in the premiums the customer pays, so Peace says this e ciency is a win all round for the customer, insurer and industry. The use of higher labour rates for faster keyto-key times in the UK is an example of how the industry is creating incentives to increase this objective.
Peace says even the OEMs benefit from the faster turnaround times. He notes that statistics indicted a major proportion of vehicle owners change vehicles within 12 months of a collision,
so it is in the OEM’s best interest to preserve its brand reputation.
“From a manufacturer’s point of view as well, it’s actually in their interest to get that vehicle repaired as quickly as possible,” he says.
“What we find as well is the dealerships don’t really want the vehicle. If they have to delay it a week or so, it doesn’t really work in the repair process and is a bad experience for the customer. This service actually helps that process, speeds it all up, and helps the customer get the car back on the road.”
European and US precedents indicate ADAS systems could eventually become almost ubiquitous in vehicles presenting to the workshop. Australia has already started on that path.
Automatic Emergency Braking systems will become mandatory for new vehicles in March. But overseas markets indicate these systems are also multiplying and becoming a major selling point for OEMs and an ongoing demand for workshops to fit into their processes.
“You’ve got forward facing cameras, you’ve got radar in some vehicles, you’ve got LiDAR, and then you’ve got 360 degree cameras. They all do various di erent things, but they’re supporting more and more features on a vehicle. The anti-collision braking, for example, lane-assist, automatic cruise control and you’ve got all of the parking functions that come from the 360 camera. And then there is Tra c Sign Recognition which is a new one. We’re seeing more and more features that are derived from the ADAS equipment.
Some of those are critical safety features and are therefore required to be calibrated and be accurate, because, if they’re slightly out for any reason, it can have serious consequences that can be at worst, fatal.”
Peace says there is some hesitation over fully autonomous technology but it shows the movement in the industry the repair industry must be ready for.
“I think we’re a little way away from the fully autonomous but the benefit of the manufacturers working to autonomous is the volume and function of the safety related elements that they’re putting into the vehicles.”
One of the big industry questions is whether this technology will reduce the number of crashes. Peace says exact data on the reductions in number of collisions has not yet been calculated but it could pose a future challenge for the industry. He says current challenges in the EU also include higher excess insurance payments prompting people to opt out of claims and a higher level of write o s. These issues and an overall subdued market in the EU and
UK are some of the factors pressuring workshops that sometimes have resulted in business consolidation.
Given these challenges, Peace says the competitive advantage for smaller workshops in the Australian market being able to o er a full suite of technological solutions and deliver results quickly and e ciently gives them a commercial edge. This is where Repairify becomes a valuable partner to businesses.
“It means they’re not having to invest in all of that technology, but they’re able to access the latest technology to solve issues with a vehicle,” he says.
Peace says the challenges of running a repair business in Europe, many of which are mirrored in Australia, like the skills shortage, make an adaptive and innovative approach to technology even more important for business success.
“We’re in a challenging situation for shops at the moment, they can’t get the sta they want, along with other aspects of repair, the cost of materials and components for repair is high. The wait times on materials is high.
“The changing technology means
you’ve got to invest in training and development so it’s sort of evolving into a very technical industry, and that is a challenge, but there are ways around it.
“And Repairify is definitely one of those ways around it, in that you don’t have to invest in the OEM technology. We can support you remotely by providing access to the tools, equipment and the technicians with the skill set to help you.”
Peace has some final advice for repairers for the year to come.
“ Embrace the technology, “ Peace says. “Talk to organisations like us. We’re here to help and we’ve got products and services that can definitely help. It’s a case of looking and understanding how we can fit into your shop’s business model.
“We’re evolving with the marketplace and the legislation. We’ve got relationships with, the AAAA with AASRA, we’re represented at the highest level in Australia and we’re here to support people, support shops, and help them through change and developing technology.”
Through growing a business from a one man show to a team of eight a decade later, Matt Bruce from MJB Bodyworks has learnt many lessons. One of the most important is learning how to build a trusted team.
Growing a business through quality craftmanship and a genuine passion for automotive are healthy indicators of a successful collision repair workshop, but fostering a great team can be the key to cementing its reputation in the community.
MJB Bodyworks, run by Matt Bruce in Maroochydore, Queensland has been nominated for a string of awards for being a well-run and respected workshop.
From being a one man show, repairing only four vehicles a week in 2011, to expanding the workshop and team size in 2024, MJB Bodyworks now employs eight people and repairs 25 vehicles a week. However, it is not the numbers that Matt focuses on. Instead, he has turned his attention to fostering
a healthy environment in the workshop where ‘no job is beneath anyone’.
“I ran the business on my own for five years before I took on sta ,” Matt says. “My main focus now is on the growth and function of the business.”
“I also enjoy working in the workshop with my team and helping out on the paint and panel side of things when needed.”
The workshop began in 2011 as a collision repair shop and a 4WD fabrication business in a 150suare metre workshop.
“I have always had a foot in smash repair work ever since I started my apprenticeship, but I wanted to mix it up a bit with doing my welding for 4WD fabrication,” Matt says.
“But with an expanding family and rapidly growing business it was time to focus on what my business needed to continue to grow and function, which was to focus on smash repairs.”
By 2024, the workshop expanded to 330 square metres and the team at MJB Bodyworks have never looked back.
After growing up around cars, boats and trucks, Matt has always had a keen interest in automotive.
However, it wasn’t until he bought his first car at age 16, that the interest in repair and remodelling began.
“My interest really started to kick o when I got to start tinkering away at bits and pieces of my own car,” Matt says.
After initially planning on going into the RAAF after high school, Matt leant into
his interest in automotive and decided on a spray-painting apprenticeship instead.
“Luckily enough my boss at the time convinced me to also become a panel beater and I learnt spray painting later,” Matt says.
For Matt, defining a successful workshop is all about the people who you surround yourself with.
“Working with a group of people that genuinely enjoy working together enables us to function as a team, produce great results for the customer, and be satisfied with our job at the end of the day,” Matt says.
Having a team that enjoys their work, and is happy to be in the workplace greatly benefits the customer and their wellbeing.
Matt highlights customer care as the main strength at MJB Bodyworks.
“Our consistent customer care is something we are really proud of,” Matt says.
“We aim to treat all our customers as people and not as numbers. Our growth and success has been a result of our word-of-mouth referrals.”
“Knowing that a previous customer has referred someone to our business is a rewarding feeling as we know we are on the right track.”
The momentum from positive feedback and a growing business has resulted in a few memorable moments.
“My proudest moments are knowing that all the hard work I was putting in was paying o ,” Matt says.
“Watching the installation of my first Full Down Draft Booth in August 2015, and then my second Draft Booth in 2021, were moments of great reflection.”
Since 2011, MJB Bodyworks has grown at a steady pace. One of the main lessons Matt has learnt along the way, is to lead by example.
“We have a team of people that enjoy working together,” Matt says.
“We can have a laugh together, yet knuckle down and get the job done. No job is beneath anyone including myself; leading by example is key.”
Every Monday morning the team at MJB Bodyworks has a ‘toolbox’ meeting where they discuss what everyone got up to on the weekend. Every morning they also have a meeting to discuss the days work requirements to ensure everyone is on the same page and aware of what is going on.
“I make sure there is always banter and good humour to start the day on a
positive and enjoyable note. It isn’t all business and work talk,” Matt says.
Ensuring that there are facilities in the workplace to provide an opportunity for people to sit and chat has also been a key reason for a harmonious workplace.
“All sta get together at the same time for a lunch break in our kitchen/ meeting area. We find it to be an organic way for people to communicate about work and their personal lives too,” Matt says.
“We also have a few social functions throughout the year where sta bring their partners.”
As the team has more than quadrupled since 2011, so has Matt’s leadership and people management skills.
“I have now learnt to acknowledge that my team members all have the ability to do their jobs at a great level,” Matt says.
“However hard it seemed in the early years, I had to ‘let go’ and let them do their job and not micro-manage.”
“I have an open door policy and I aim to be approachable. I want my sta to know they can raise any issue or suggestion they have.”
Carefully building his team together has resulted in having trusted employees that Matt looks upon with competence and satisfaction.
“I know that I can step back and the business can function without me being on the workshop floor every day,” Matt says.
“I can focus on the business’ growth,
and I can even go away on holiday. I know that the business is in great hands and the day-to-day function will continue.”
Collision repair workshops are often run by panel technicians who have been in the industry for decades. With decades of experience working on cars, Matt o ers some advice for people looking to open a repair workshop of their own.
“Ensure you have a thorough understanding and knowledge of estimating,” Matt says.
Matt outlines how identifying your strengths and weaknesses is an asset to your business.
“You can be the best tradesperson and do a fantastic job but that doesn’t matter unless you’re getting paid correctly for the job.”
The issue of sta and labour shortages has put a strain on the collision repair industry.
Promoting the industry as a viable option for the next generation and people looking to switch careers is an area that is gaining attention and development. Even so, with the average apprenticeships turnaround about four years, filling roles will take time.
In the meantime, skilled migration has been proposed as one solution to the multifaceted labour shortage problem.
The core issues that workshops have encountered when trying to recruit skilled migrants have been the timely process, the cost, and the red tape.
Alison Turnbull from Al’s Panel Shop in Darwin spoke to NCR about the challenges of sponsoring skilled migrants in their workshop
“The visa process has changed dramatically over the years since we have been sponsoring people. The amount of paperwork, proof and the cost of sponsoring employees is huge,” Alison says.
“At the end of the day there is no guarantee that you will get a worthy employee, but I guess the same can be said of hiring an apprentice.”
“Unfortunately, we don’t have a large pool of trades people or even young people interested in this trade
in Darwin, which makes importing workers an easier option, even as lengthy as it is.”
The Australian Government announced the release of the Core Skills Occupation List (CSOL) in December 2024. The CSOL includes panel beaters and spray painters (vehicle painters) in its list of 456 occupations. It was hailed at the time as a step forward for repairers to find a way through the red tape of skilled migration.
It also includes motor mechanics and automotive electricians among nine essential automotive trades as part of the occupations eligible under the new Skills in Demand visa and the Direct Entry stream of the Employer Nomination Scheme (subclass 186) visa.
There has been praise for the new CSOL from industry advocate groups that outline the inclusion as a step in the right direction.
MTAA CEO Matt Hobbs said it was a “major victory” for the automotive sector across Australia and a credit to the united advocacy of several key groups.
“Our comprehensive submission, backed by extensive economic research from Deloitte Access
Economics, clearly demonstrated the critical necessity of including these automotive trades in the CSOL,” Hobbs says.
“This successful outcome validates MTAA’s evidence-based approach, which included detailed wage analysis and industry data highlighting the severe skills shortages facing the sector.”
Outgoing VACC CEO Geo Gwilym corroborated this position and the importance of the advocacy to ensure the government was listening to industry issues.
“The inclusion of these critical automotive occupations acknowledges the severe skills shortages facing our sector and provides a clear pathway for addressing workforce challenges,” Gwilym says.
The CSOL however, does not address some other core issues of skilled migration; the cost, the ine cient process, and lengths of time it takes to employ, and prepare a skilled migrant. Ash Jardine from Bodyshop Recruit, and Fred Molloy, the director of migration agency, Konnecting are two experts in the field who feel significant barriers remain for repairers.
With close to 40 years of experience in the repair industry, Ash Jardine is well equipped to discuss the ins and outs of the skilled migration process.
“The only major di erence with the CSOL is that they are now allowing spray painters into all areas of Australia,” Jardine says.
“The process for repairers is still extremely di cult. It’s a 12-month process, and repairers need people now.”
“We find that a lot of the repairers don’t want to wait that long. The cost is also a large factor.”
Fred Molloy is a registered migration agent who specialises in the Automotive aftersales and collision industries running several businesses including Konnecting Migration, AutoRecruiter and AutoPersonnel.
“It’s been almost a two year process since the former Minister for Home A airs Clare O’Neill announced the migration strategy review on April 26, 2023,” Molloy says.
“The strategic approach should give both employers and potential migrants more confidence in the new occupation shortage lists under the Skills in Demand Visa (SID) which replaced the Temporary Skill Shortage (TSS) Visa from December 7, 2024.”
Molloy cites the major change of the CSOL for repairers, is for vehicle spray painters, as the occupation can now be nominated in metro areas of Sydney, Melbourne and Brisbane.
“A useful point of note is that a skills assessment is not required for these three occupations whereas is required for most of the others if the applicants are coming from China, Fiji, India, Philippines, South Africa, Zimbabwe, Thailand and Vietnam,” Molloy says.
“The changes should help attract these candidates globally to fill the shortages that cannot be completed by the local candidates.”
“The streamlined process with a single consolidated list replacing multiple complex lists, the new system is based on evidence of genuine
skills shortages and the list will be reviewed regularly based on labour market needs.”
The CSOL demonstrates the government’s acknowledgment and recognition of the skills shortages issue in the industry. However, more needs to be done to alleviate the costs associated with bringing a skilled migrant into Australia, advocates say.
“It is upwards of $20,000 per person. There are no guarantees either. The person may not arrive, or they may not pass the qualifications,” Jardine says.
“There is a fee for the applicant as well, and nearly all the applicants can’t a ord to pay it.”
“In most cases, employers loan them the money to be able to pay for their skills assessment costs.”
Jardine highlighted how the main hurdle for panel beaters and mechanics is going through the ACTS skills assessment.
“It is a certificate three, so it takes upwards of six months to complete,” Jardine says.
“Not a lot of them fail the course, but some do. The main problem is that the course is quite intense. The guys who usually fail only do because of the English barrier, when the assessor is asking questions.”
Jardine emphasises the challenge for skilled migrants to complete the skills assessment in their home countries.
“The skills assessment is about $6,500. Most of the workers that come out of the Philippines earn around $120 a week. So, they don’t have the money to pay for that kind of thing,” Jardine says.
“Repairers are in charge of finding somewhere for the migrants to live, which is di cult with the housing shortages as well.”
Molloy outlines the changes that will help repairers gain further insight into skilled migration with the di erent visas and schemes that are currently in place.
1. Work Experience: For the new Skills in Demand Visa, the post qualification
work experience has been reduced from 2 years to 1 year.
2. Employee Mobility: From July 1st 2024 a major change under Migration Exploitation Regulations allows sponsored 482 visa holders with mobility to change employer and work for anther employer for up to 6 months without the need to transfer the original visa;
3. Permanent Employer Sponsored Employer Nomination Scheme (ENS) visa: A subtle change now permits visa holders to use their combined work experience in their occupation across multiple employers to meet the 2 years’ work experience requirement under the ENS transitional stream. Previously these 2 years needed to be with same employer in the same position nominating for PR.
4. Direct Entry ENS: The inclusion of Vehicle Spray Painter, Vehicle
Trimmer and Vehicle Body Builder in the CSOL also give a Direct Entry employer pathway to Permanent Residence previously unavailable before the change. A skills assessment in the occupation and 3 years post qualification work experience with any employer is required and other criteria such as English level and age still apply.
5. Training Visa (Subclass 407): With the addition of Spray Painter on the CSOL, it’s now possible to utilise the Training Visa in metro areas.
6. Other Visa Options: There are still other options for sponsorship outside the CSOL by way of some regional visas, and separately negotiated Labour Agreements.
With no clear pathway in sight for repairers on the issue of labour shortages, Jardine urges workshops to act now.
“The skills shortage will get worse before it gets better,” Jardine says.
“Even though it will take upwards of 12 months, you have to start now and have someone in the pipeline ready to come when they get approved.”
“We get so many repairers who come back after 12 months saying they wish they had started a year ago.”
If, or when a workshop is considering skilled migrants, Jardine suggests getting at least two new employees.
“We recommend getting two tradesmen, so they have someone to talk to. We have had some workshops get around ten people at once,” Jardine says.
‘We are here to help the repairer through the process. It’s a minefield, it’s not ideal. But there aren’t many ways around the labour shortages issues.”
The demand for automotive tradespeople has been exacerbated in the post-pandemic period.
Molloy highlighted the competitive process, and encourages employers who plan to embark on sponsoring overseas sta to be prepared.
“For example, setting up as a Standard Business Sponsor (SBS), undertake local Labour Market Testing, and ensure their business can meet other visa criteria such a paying market salaries rates above the Temporary Skills Migration Income Threshold (TSMIT),” Molloy says.
“Each state and territory also have di erent licencing requirements and depending on where the applicant is coming from, and which trade, will also determine if the applicant will require a skills assessment before lodging a visa application.”
“It’s important for the employer to understand the requirements and if required seek professional advice of a registered migration agent/lawyer.”
As rising energy costs threaten to blow out bodyshop overheads, PPG says its low energy cure solutions provide readymade tools that drive sustainability, along with profitability.
When was the last time you looked at your collision centre’s energy bills?
The relentless rise in the price of both gas and electricity has made it a key industry talking point. However, although repairers can readily see the increase in cost, most are unsure of how that impacts the businesses bottom line, says PPG Sales Director Australia John Hristias,.
“The way energy prices have spiralled upwards can come as a real shock but it’s di cult for individual repairers to get a clear understanding of how that actually translates to cost per job. To get the answers, PPG’s MVP Business Solutions team conducted a comprehensive study across the local industry.
In it, they analysed over 50,000 individual repair jobs and found that the energy cost per job came out at about $31.00 per job. As those costs continue to rise, their mounting impact on business overheads is making energy usage an increasingly important factor in the repair process.”
PPG’s relentless focus on its own, inhouse, global Environmental, Social and Governance (ESG) program has actually influenced product development within the company Hristias says.
“PPG is currently running an award winning ESG program across the company and that is also influencing the product development pathway. It means that our company values are driving product direction and it seems that is also in sink with what our customers’ needs. It highlights the
fact that rising energy costs is now a significant aspect in many global markets, such as Europe, as well as locally. It’s about taking sustainability seriously which empowered our R&D teams to come up with e ective, easy to use product solutions that really deliver by helping repairers lower there carbon footprint while, as the same time, working faster and more profitably.
“By tapping into these up-to-theminute global PPG formulations, we can keep the local refinish market on the cutting edge of refinish technology. This has allowed us to launch a complete range of low energy cure solutions, as a part of the region’s most popular refinish system, ENVIROBASE® High Performance. Together, they mark a real step change in the paint shop that goes all the way from primer to the final finish. Each of these easy to use products can make a positive impact on a collision centre’s energy usage and, subsequently, the cost of running the business.
“And what has really blown people’s minds is that, other than choosing to use the actual low energy cure products, there is no equipment investment required – you can use your conventional spray equipment and application area. And while in the past these types of products typically came with certain downsides, these latest PPG product innovations are totally robust so they deliver their performance without weaknesses. For me, the big positive kicker is that
this complete low energy cure range can easily be taken advantage of by a collision centre doing one car a day, right through to a large business turning out 20 or 30 cars per day.”
According to Hristias, the Envirobase High Performance paint system is already well known for its speed, colour strike and advanced colour matching tools but the introduction of
a low energy cure range has added yet another string to its bow.
“The single biggest feature which has really made people sit up and take notice is the air-drying capabilities –we are talking minutes to cure, not hours with no reliance on factors such as humidity. At the same time, it gives repairers complete flexibility – you can run in air-dry mode to save on energy usage and, if a job needs to be pushed through quickly, simple choose the bake mode that suits your cycle-time/ energy consumption requirements.
“The new low energy cure range comprises LVP565 Air-Dry Primer, along with LVC-177 Rapid Performance Clearcoat and LVC-131 UHS Clearcoat. With LVP565 you have a primer that can air-dry in just 30 minutes at 20°C and it’s not dependant on humidity. It’s fast, too, with a single visit application mode where absolutely no flash-o is required, as well as excellent filmbuild and a super smooth lay down that makes it extremely easy to sand. When it comes to clearcoat, LVC-177 also o ers a game-changing air-dry mode where it’s dust free and ready to handle in just 20 minutes at 20°C. Alternatively, you can choose from the
low temperature or high temperature bake cycle to suit your needs. It also features single visit application mode to help boost process speed.
“For all round performance, LVC131 o ers multipurpose application from a single panel to a full respray, di erent bake options and a fast, one visit application mode. Apart from the ability to make significant savings on energy, the air-dry options o er another big advantage. With the overwhelming trend towards plug-in hybrids and full electric vehicles, the ability to use air-dry mode gives repairers an instant option to deal with these vehicles. By avoiding a bake cycle, it minimises the potential for heat to impact the battery cells.
“This trio of PPG low energy cure products slip neatly into the modern refinish process and immediately raise the game. Whether a collision centre is looking to reduce its carbon footprint to enhance its green credentials or whether it’s all about minimising their energy costs (or both!), this new range of options have really made repairers sit up and take notice. It has gotten people very excited about the possibilities. In fact, we had
customers putting orders in for these products before they even left the launch events and that has gotten them o and running and enjoying the benefits already.”
For more information about PPG low energy cure products and the entire Envirobase High Performance range, speak to your PPG Territory Manager or call the PPG Customer Service Hotline on 13 24 24 (Aust) or 0800 320 320 (NZ).
For support to calculate your own energy cost per job, contact Greg Tunks, MVP Business Solutions Manager ANZ, on 0411 288 451
For businesses trying to keep up with ever changing technology and repair procedures, having a friendly sales rep who knows what he is talking about can be a godsend. Few industry veterans come with as much experience as Car-O-Liner’s Vic/NT sales manager Lindsay Batten.
The journey began for Lindsay in 1979 at a time back when the suburb of Richmond, in inner Melbourne, was not only more industrial but had some special pockets dedicated to automotive repair. Lindsay did his apprenticeship as a panel beater at one of the leading shops of that era, Parkes Body Works, renowned for a culture of turning out the highest quality repairs.
“They were fanatical about what they did,” he says. “They were called the surgeons of steel, that was their logo, and they lived by it.”
“And Trevor Parkes he’s a good guy. He was demanding back in the day. But you know, it turned everybody who worked there into good people. It made a di erence.”
Twenty years as a panel beater at various shops, including running his own business, LMS Panel Service in Frankston, has given Lindsay a world of experience and insight beyond the average sales representative and many shops will turn to him for advice.
In the 26 years working for Car O-Liner he has also taken on responsibility for supporting customers in Northern Territory and last year added Tasmania to his care. But, in many ways, there is part of Lindsay that still identifies with the skilled tradies on the tools.
“When I first started, I was in a panel shop, wearing a nice blue collared shirt, trying to look all informal and be the sales rep. I put the bench in and I was training the guys on it, teaching them how the stu works. And one of the panel managers actually said to me, ‘What would you know, you’re just a sales rep?’ And I said, ‘I tell you what,
let’s repair this car, you and me. I’ll show you how it works. I’ll square the car. And, when we finish, you can then ask me that question again.’”
The panel manager ended up learning a thing or two that day, and Lindsay has continued to believe over the years that knowing the gear and how technicians can best work with it, is how to win their respect.
“When you’re in a shop, people will stop and listen to what you’re talking about, because you’re not just a sales rep, you’re actually there as a panel beater. You know the work and know what you’re talking about. You understand the industry, and that makes a big di erence.”
If it is all about knowing the industry from the inside, for Lindsay, it is also about an ongoing cultivation of the relationships across the industry and acting wherever possible as a conduit of important repair information.
“The workshops, they’re trying to keep up with it all,” he says.
“We’re happy to pass on information, especially with the latest and greatest equipment because the people in the shops sometimes they can’t get the access to all the information they need.
“They’re all trying to get it right. They’re all trying to do get repair procedures and make sure they’re doing it correctly, so that it’s not going to come back, or the insurance company aren’t going to send it somewhere else, and they get this rectification bill.”
Lindsay takes this educational role seriously and part of this is staying upto date with Car-O-Liner products and the innovation in the industry. Repeated
international trips to the Car-O-Liner factory in Sweden and Germany, its training centre in Thailand and the SEMA aftermarket show in Las Vegas have been invaluable in helping him keep ahead of developments. He says this knowledge helps him detail how Car-O-Liner’s innovation can translate into greater e ciency, quality and throughput for repair businesses.
“Car-O-Liner sells itself,” he says. “It’s such a good product and such a wellknown product.”
“Some people say, ‘Why do you need three Car-O-Liners? And I can explain, with three guys repairing three cars at the same time, you’re not waiting, it’s not wrapping up the shop.
“John Barry at Flagsta is a perfect example. He’s a pretty smart operator. He’s worked out the correct number of cars in and out of the shop. He says his perfect number is 68 cars per week. Anything more than that, it doesn’t work, anything less than that is not enough, the guys are standing around scratching themselves. And he’s got four Car-O-Liner benches and three measuring systems. He’s really got the system working.”
Another example he cites is Chelsea Autobody where Lindsay first helped the owner install two new Car-O -Liner benches.
“Then John rang me and said, ‘I’ve got some bad news. You’re going to hate me for this but I need you to move these benches - I’ve just bought a bigger factory!’ So I said, ‘That’s all right, no problem we’ll just do it.’ We came and moved him and he then buys three more speed benches.”
Watching businesses expand successfully has been one of the added satisfactions for Lindsay.
“Huss from Carllision Body Works is another business owner who has been so great for me and Car-O-Liner,” Lindsay says. “We have built a great relationship in the industry, and like all of my customers I consider we all have special relationships.”
“I have good relationships with all the body shop owners, and I like to see them doing well,” he says. “I have a lot of
time for people. I enjoy training, I enjoy passing on information, that’s all part of the support. There is so much new information, so pass it on if you can.”
In all this 26-year journey with CarO-Liner, Lindsay also has a special word for his boss, industry veteran and Lifetime Achievement Award recipient Julie Thomas.
“I have to say how great it is to have a boss like Julie that has been easy to work with and so understanding whether they are great or trying times.”
“Without a boss like that I may not have lasted this long,” he says. “And all the people in the Car-O-Liner family. That’s what it’s like, a big family and support network.”
Lindsay has also witnessed the strain of skills recruitment felt in the many workshops he visits and believes nurturing a next generation of technicians and business owners is something the whole industry can play a part in.
He says Car-O-Liner’s long relationship with TAFEs are important, particularly in training on the latest equipment that can send a strong message to young people about the high standards of the trade.
“There is a lot of good people in this trade, especially apprentices that we deal with. We look after WorldSkills as well, as a preferred partner and supply equipment for WorldSkills
in Queensland. There’s lots of opportunities for apprentices, which is great. To see an apprentice in a shop, and to say in five - or 10-years’ time, he could own his own shop and to know you’ve sort of planted that seed.”
He says young people need to know it is a career with a future and multiple career pathways that can open for those with dedication and skill.
If Lindsay is an example of how repair careers can give back to the industry with new roles, he is not alone. His own son Michael, having qualified and worked as a panel beater then moved into construction but has now returned and also works for Car-O-Liner.
Despite challenges around recruitment and ensuring the high levels of skilled repair work are su ciently remunerated by insurance companies, Lindsay says he is optimistic about the industry’s future.
“I’ve seen a lot and a lot of di erent stu but I don’t think it’s going backwards at all. I think it’s growing. There’s a lot more MSOs and the industry will continue,” he says.
“It’s an amazing group of people. And they are the people that have been in this field for a long time and there is definitely some characters out there in this industry. It’s not a dying race, that’s for sure.”
2025 will be a big year for ADAS and a big year for the collision repair industry as it embraces a new proposed code of review to help make ADAS compliance a part of everyday processes.
The year ahead holds plenty of milestones in the ever-advancing journey of automotive technology. The NVES is likely to see an even greater diversity in the car parc and the March 2025 mandate for Automatic Emergency Braking will further add to the complexity of new vehicles.
To meet these challenges, a technical working group was set up in late 2024 from six members of the aftermarket’s key repair body Automotive Repairers Council of Australia (ARCA) to help develop a voluntary ADAS industry framework to help the repair industry meet this future.
One of the key objectives of the proposed code is to give repairers a clear set of guidelines, specifically as to when and how ADAS systems should be included in the repair process.
Australian Automotive Aftermarket Association Director of Government Relations and Advocacy Lesley Yates says one of the key strengths and benefits for businesses of the proposed code of service will be clarity in the often-complex world of automotive technology.
Yates is quick to point out that there has been some contradictory advice
which may have confused some workshops, from the extremes that every time you touch a vehicle it needs calibration, to myths that it is never needed because ADAS systems are self-calibrating.
“Neither of which are true, “ she says. “Any work that you do to the body of the vehicle, to the bumpers, to the lights, there are a number of activities that you’ll do with the vehicle which will require you then to send the vehicle o or do an in-house calibration.”
The purpose of the proposed guidelines will be to guide repairers through the middle ground of when
calibration is necessary and dispel some erroneous conceptions of their sensitivity.
“The systems are quite robust,” Yates says. “A good example is some nonsense that modified vehicles can’t be calibrated, that as soon as you lift them they won’t focus on the target. That’s not true. We have done testing and if you legally lift the vehicle, a proper 50 mm lift, you need to do proper testing and evaluation, but you will be able to calibrate it.”
The code aims to set the groundwork for repair workers to assess the degree of calibration that is needed and how it will be done.
The ARCA working group hopes to bring the best of international models, such as the six-point code developed by the Thatcham Institute for UK repairers, but it also wants it to be a more practical guide.
While it is still developing a check list, one of the key first steps for repairers Yates says, will be ensuring an environmental scan of any vehicle is done.
“When the vehicle comes in, before
we open up the bonnet or are even quoting the job, the environmental scan should be ascertaining what ADAS systems are on this vehicle,” Yates says.
“What model is this? What does it have and how does it do it? Because we know that the camera placement is di erent on every vehicle. Whether it’s got one forward facing camera or more. Are there parking sensors in the back that do more than just parking sensors?”
“Do an environmental scan, put the scan tool in and find those answers; what features, and how it measures distance, how this vehicle takes in information from around the vehicle.”
The role of the working group is to ensure the repair industry has a uniform set of standards and guidelines. Supported by the various sectors of the repair community, once this is established it has the foundations on which it can then tackle some of the evolving issues
“The other issue here is ADAS is not just another automotive technology like ESC or EFI,” Yates says. “It’s challenging our whole business model for a couple of reasons, and one is, there’s a blurring
between mechanical repair and collision.
“For example, you bump a sensor out by hitting your bin on the way out of your driveway. You may not have an insurance claim, you may not have a major panel issue, but you will take it to your mechanic because you’ve got a sensor warning light.”
“We’re doing a lot more ADAS calibration in collision but it is well and truly migrating its way into mechanical services.”
A code of service puts the industry in a better place to tackle other crucial issues like getting the buy-in of both insurers and customers, she says.
Part of this will be managing consumer expectations; customers who expect safety systems to work to purpose for instance.
“My technician might say to me, for example, ‘We’ve replaced your headlights, there’s cameras in them and we want to calibrate it. This is the cost.’ You need the consumer to say, ‘Yes, please, I want all of my systems to work, and my safety is reliant upon these systems working well, so I authorise that work.’”
“Who will pay for it is a great question, so getting sign-on from both the
consumers and insurance companies is important.”
Having established this benchmark set of standards for the industry, it is then Yates believes governments may have a role in assisting support the level of training and equipment that workshops could need, along with a role in public education about these expectations.
“We expect to be having conversations with government about what meaningful role they can play to assist us to skill up, and increase consumer awareness, because that’s probably the key to insurance companies accepting that most cars in the future are going to require a calibration if it’s going through collision repair,”
Yates returns to the imminent mandating of AEB systems in all new vehicles from March 2025 and notes that while governments can legislate from a manufacturing and importing point of view based on the safety outcomes, they needed to better understand how the laws relate to the ongoing life of the vehicle, especially after service and repair.
“If your vehicle has AEB as part of the Australian Design Rules, it becomes a component of road worthy. Your vehicle must continue to meet the ADRs that
were applicable to that vehicle when it goes back to a customer.”
Yates firmly believes the industry is best positioned to self-regulate when it comes to training and standards.
“We are the ones who know what the industry needs,” she says.
“Our workshops don’t need to be dragged kicking and screaming into this. They will want to make sure that the chain of accountability is sound. That’s what we do, and we’ve always done. It’s no di erence between that and ensuring a vehicles brakes are working properly.”
Yates says government accreditation would be problematic and potentially cumbersome, and consumers would be better served by protections under existing Australian Consumer Law and the completion standards already established by levels like road worthiness certification.
“The Australian Consumer Law dictates that it is illegal to be o ering a service that you’re not qualified to o er. There are laws in place to ensure that you don’t o er a service you’re not able to o er or that you’re not misleading as to that service.”
The working group aims to have a draft version completed by March with consultation then open to a wide range of players in the repair space to ensure it is as relevant as possible to both collision
and mechanical repair sectors . It will then look to developing launching a final version at Autocare 2025 in June.
For small businesses, the working group’s draft not only aims to add clarity but help them better evaluate their business opportunities and seek out the services and skills that will help them prepare for the future.
“We want to be able to reduce the fear factor,” Yates says.
“We don’t want people saying, ‘We don’t work on cars with ADAS’. We’re going through technological change, but the industry has always gone through technological change; electronic fuel injection, electronic stability control. This is not our first rodeo. We know how to learn the new technology and adapt.
“If you don’t want to be doing ADAS calibrations in house, whether that’s because there are issues about how flat your floor is or how much space you’ve got, then team up with a facility that can help.”
The ARCA ADAS Technical Working Group is comprised of representatives from mechanical repair (including Bridgestone, mycar), collision repair technical training, windscreen replacement, and ADAS equipment experts and the group is chaired by ARCA Chair Mr Craig Baills (Highfield Mechanical).
Years in the making, a new code to govern insurers and repairers was always going to be crucial, so getting it right for all parties was critical, advocates have argued.
The collision repair industry’s critical Motor Vehicle Insurance and Repair Industry Code of Conduct should be released later this month for industry consultation.
Delays in late 2024, from an earlier schedule, were caused by ongoing negotiations that took place after more than a dozen meetings of the Code Administrative Committee (CAC).
The draft document has undergone a number of amendments as the automotive sector and insurance council members who make up the Code Administrative Committee thrashed out a consensus in 2024.
The code has now gone back to the lawyers, responsible for the rewrite, and is expected to be released shortly.
The updated code, drafted by MST Lawyers in response to Dr Michael Schaper’s independent review of the code completed in 2023, will seek industry feedback on the draft, with accompanying questions from the CAC.
CAC Chair George Manos said the opportunity for broader industry consultation would be the next key step in a building a crucial document.
“We have recognised the importance of carefully working through each element of the code to closer align both sides,” Manos says.
“This process of negotiation has taken time and ensures that the consultation draft is both workable and takes steps to address industry’s concerns.”
“The CAC has met regularly since receiving the first draft of the updated Code from MST Lawyers, which included an agreement to seek input from the Australian Motor Body Repairers Association (AMBRA).”
The process also included review and input from the Insurance Council
Association of Australia
MTAA CEO Matt Hobbs has reiterated the importance of the Code of Conduct and said the process reflected that it was a substantial rewrite, not a minor tweaking of the old code.
“I cannot stress enough how crucial it is that the MVIRI code is shaped through extensive whole-of-industry consultation,” Hobbs says.
“At its core, the MVIRI code is an agreement between repairers and insurers—a document that balances the needs of both sides while improving service delivery, industry transparency, and operational e ciency.”
“This is a negotiated outcome with the intention we create a code that benefits the industry as a whole,” he says.
“This code is not just a technical tool, but a shared commitment to creating a better, more e cient industry for all.”
“The redevelopment of the MVIRI Code represents a pivotal moment for the sector. As the industry continues to evolve, getting the revision right will create a critical
framework for improving practices, enhancing transparency, and fostering collaboration between insurers, and repairers.
“Most importantly, it is an opportunity to speed up the resolution of disputes and reduce associated costs—an issue that has been long overdue for reform,” Hobbs says.
He says this balanced approach would be extended to how the code was implemented.
“Importantly, an independent chair of the CAC will provide impartial oversight, ensuring that decisions reflect the interests of all stakeholders and are not influenced by any one party.
Dr Michael Schaper’s review outlined key weaknesses in the code and made 15 recommendations to help make it more relevant and e ective.
The reviews principal criticisms were that it was not su ciently known or utilised by the repair industry or insurers. It noted that for a sector which represented 45 per cent of Australia’s 3.9 million insurance claims, “the number of parties using the code appears to have declined significantly”.
Big day of ideas, big night of celebration
On a special day in May 2025, the repair industry’s most prestigious awards will return, and the celebratory gala night will also be accompanied by a feast of ideas for all things collision repair.
NCR’s Symposium 25, featuring leading industry experts, issues and practical solutions will be held in Melbourne on Wednesday, May 7 2025. To cap o this informative day, the peak of collision repair will be celebrated at a gala dinner held to recognise the 2025 Lifetime Achievements Awards.
It is also your chance to shine a light on those who deserve applause for their contributions to the industry with nominations now open for all categories.
Join us at a special venue, The Glasshouse on Olympic Boulevard in the Sports and Events Precinct, Melbourne for this very special day for the industry in 2025.
Held annually, the recipients of The National Collision Repairer’s Lifetime Achievement Awards are inducted and honoured for their outstanding service to the collision repair industry.
The awards evening also sees further prestigious awards presented on the night: The Next Generation Leader of the Year Award; and The Woman in Automotive Award.
In 2025, these prestigious awards will be joined by special awards dedicated to sustainability and safety in the collision repair industry.
The Excellence in Sustainability Award aims to identify and reward businesses that are passionate and innovative in optimising e ciencies that also help look after the environment. The award is looking for ideas and actions that have made a demonstrable di erence in the sustainability of the industry.
The Safety Champion Award is a new award that recognises individuals and businesses who have made strong inroads in workplace well-being.
Without any limitations on the size of the business or the number of employees, this new award highlights those dedicated to making sure everyone gets home safely.
One way to be part of this unmissable event is to nominate someone from the industry you think is worthy of any of the five great awards that showcase the
night; the Lifetime achievement Award, the Woman in Automotive and the Next Generation Leader, Excellence in Sustainability or Safety Champion.
It’s time to celebrate one of the industry’s greatest assets, its people and you can play a part just by nominating someone you think is worthy.
The National Collision Repairer Lifetime Achievement Awards began in 2007 and was created to acknowledge the dedication and commitment of the men and women who have contributed to the collision repair industry over and above their “day job”.
The criteria for induction are a minimum of 20 years in the collision repair industry, contributions to the industry beyond the scope of their local area, contributions to the industry beyond the scope of their direct employment and nomination from within the industry.
The gathering each year represents a who’s who of the repair industry, including sponsors, collision repairers, suppliers, insurers, and previous inductees who gather to celebrate the people that make the industry strong, innovative and supportive.
The honour roll includes those who have not only contributed to the
development of the industry but also left an indelible mark on the Australian collision repair landscape and recognises the recipients’ perseverance, contributions and experience.
A fun and glamourous night that “honours the past” and now, recognises the industry’s bright future. Importantly, we continue to attract sponsors that are the leaders in the collision repair industry, many of whom have been with us since the inaugural awards.
Mark the date, May 7, in your calendar for a not-to-be-missed event in 2025 for the collision repair industry.
To get involved and support the Lifetime Achievement Awards visit ncrlifetimeawards.com.au or contact Michael Ingram at michael.ingram@ primecreative.com.au
Richard Nathan 2007
David Weatherall 2007
Terry Flanagan OAM 2008
Marshall Duncan 2008
Graham Winter 2008
Je Hendler (Int) 2008
Max Chanter 2009
John Howes 2009
Robert Renwick (Int) 2009
David Newton-Ross 2009
Wayne Phipps 2010
Richard Pratt 2010
Bob Rees 2010
Lance Weiss 2011
Mark Brady 2011
Don Wait OAM 2011
Tony Farrugia 2012
Bob Christie 2012
John Zulian 2012
Tom Vukelic 2013
Robin Taylor 2013
Ray McMartin 2013
Colin Edwards 2013 Ian Wilkinson 2014
Julie Thomas 2014
Brian Johnson 2014
Terry Feehan 2014
Owen Webb OAM 2015
Phil Nixon 2015
Trevor Parkes 2015 Tony Warrener OAM 2016
Brenton Abbott 2016
Michael Killen 2017
Carl Tinsley 2017
Per Madsen (Int) 2017
Rex Crowther (Int) 2017
Garry Clear 2018
Cec Simpson 2018
Michael Wilkinson 2018
Mark Czvitkovits 2019
Martin Stone AM 2019
Julie Wadley 2019
Walter Zuber (Int) 2019
Brad Franklin 2020
Jim Vais 2020 Je Williams 2020
Steve Economidis 2021 Garry Maher 2021
Peter McMahon 2021
Rob Mildenhall 2021
Cafasso 2022 Michelle Morgan 2022
Peter Ruggeri 2022 Darren Wales 2022 Ben Chesterfield 2023
Scott Donnelly 2023
Morry Corvasce 2023
Craig Carey 2024
Collisions are fundamentally a negative experience for the vehicle owner, ensuring the first touchpoints in the repair journey are a friendly and positive reception are important. For Chantel Griezans it is all about staying people focussed.
Business owners know it is often the customer service sta that keep the flow of operations ticking over, not to mention the critical first point of call for customers. It makes employees like Chantel Griezans invaluable.
Chantel approaches her customer service role in the repair industry with enthusiasm and a drive to learn as much as she can about automotive technology.
Stumbling upon the repair industry completely by chance, Chantel found her passion in an unconventional setting.
Originally from England, Chantel found the repair industry while travelling around Australia on a working holiday visa in 2017. She was given the opportunity to work as an administrator for Action Smart Group to help with the remaining claims at the end of the hailstorm season.
“I thrive in working in a fast-paced environment and was fascinated by the buzz of working in the hail industry,” Chantel says.
After returning to England, Chantel missed the Australian lifestyle and decided to move back in 2019.
“I returned to the hail world where I was fortunate to chase the hail for 5 years while also getting to see new parts of Australia,” Chantel says.
Chantel now works at ADAS Solutions as an ADAS Specialist in Brisbane. Her role includes answering emails from repairers, adding bookings and determining if further information is needed.
Chantel is responsible for ensuring that their clients across Australia receive accurate and timely invoices, all while remaining committed to
delivering quality and trusted customer service.
She has thorough knowledge of ADAS calibrations, and is often on calls from the Queensland area assisting with repairs that involve calibration, coding, or diagnostic repairs.
“My role is crucial in ensuring that repairers’ technical needs are accurately identified and addressed promptly,” Chantel says.
Customer service
Chantel has always pursued customer service roles, from working in retail as a sales assistant, to managing calls and complaints as a senior advisor.
“I feel extremely passionate about always trying to provide the highest level of customer service,” Chantel says.
“I aim to treat people and their vehicles how you would wish to be treated and how you would want your car to be treated.”
Taking advantage of the COVID lockdowns, Chantel took the opportunity to upskill and further her understanding of the dynamics of business. Goal oriented, Chantel shifted her focus to enhancing her skills.
“I completed a Diploma and an Advanced Diploma in Business to help strengthen my career, and I am so glad that I did it,” Chantel says.
For Chantel, the repair industry is centred around people, and she highlights that is where the focus should always be.
“It is definitely my favourite
part of the industry,” Chantel says.
“I’ve met some remarkable people over the years, colleagues as well as customers.”
Creating a personable relationship with clients and customers has been an area that Chantel has excelled in.
“I have absolutely loved being in a customer facing job, building relationships and being on their repair journey with clients from start to finish,” Chantel says.
Chantel goes the extra mile for her clients, and often keeps in touch with customers, even after their cars have been collected.
“I have always cared a lot about my customers and wanting to ensure I can give them the best service that they deserve.”
The care and passion for her clients also extends towards the community of colleagues in the repair industry. Working in a predominantly male industry, Chantel has found she has been treated well and met with respect and appreciation.
“I’ve found that I’ve not only made friends in the industry, but also found what feels like a second family,” Chantel says.
“I have so much love for every team that I’ve worked with, many of them will always hold a special place in my heart.”
Her hard work, and caring approach has not gone unnoticed or unrecognised. A standout moment in her five-year career was winning the admin/customer service award at the Women in Collision industry night. With numerous people nominating her for the award, it was well deserved.
“I find it di cult to put into words how I felt accepting the award as I’ve only ever felt like I’ve just done my job,” Chantel says.
“In saying that, I am extremely grateful for the award and everyone who put my name forward.”
Outside of her work life, Chantel describes herself as a ‘wannabe Aussie’, who loves the beach and a Great Northern Super Crisp (or two).
“Living in Australia has definitely made me appreciate the finer things in life and I regularly have “pinch me” moments and realise how lucky I am to be here,” Chantel says.
Being outside and enjoying the Queensland sun has also meant Chantel is a member of her local CrossFit club.
“I have met some of the most inspiring individuals at the club who motivate me every day,” Chantel says.
“The camaraderie and support within the community push me to reach my fitness goals, but it also encourages personal growth and resilience too.”
For anyone wanting to start a customer service job, remaining resilient and embracing the challenges are all part of the role, according to Chantel.
“My main advice would be to stay positive, support your peers and keep smiling,” Chantel says.
Chantel is committed to further expanding her knowledge with ADAS Solutions and the rapidly evolving field of automotive technology.
“I am really enjoying my journey so far,” Chantel says.
“My approach to my profession is built on two pillars: continuous learning and self-improvement. I have found both in this industry.”
Despite some testing times and challenges working in customer service, Chantel’s passion and care for the clients and her colleagues fuels her motivation.
“There has been blood sweat and tears at times, but I honestly feel so grateful to have met the people that I have in such a short period of time,” Chantel says.
“I know countless of them will continue to be a big part of my life for years to come.”
Starting a new career at age 48 would be a daunting endeavour for anybody. But for Nikola Radulovic, who had already escape his worn-torn country in 1991 and adapted to Australia, his determination and resilience trumped any initial hesitations.
The collision repair industry often focuses on recruiting the next generation. But accommodating for people of all ages who are willing to re-skill can lead to dedicated new members of a knowledgeable team.
A long way away from the seaside city of Rijeka in Croatia, Nikola Radulovic has called Australia home for the last 33 years.
Originally born in Australia, Nikola was six years old when he and his family moved back to Croatia. When the Yugoslavia War began in 1991, Nikola escaped the conflict and decided at age 19, to leave his family behind and live in Australia.
“I had just finished high school when everything changed,” Nikola says. “Overnight the civil war began in Croatia.
“I had to flee.”
After working hard to establish and build a life for himself in Australia, Nikola’s parents and brother joined him in Sydney a few years later.
“It was hard to begin with. Not only
was there the language barrier, but trying to find a job was challenging,” Nikola says.
Nikola worked in hospitality for 28 years, but the COVID lockdowns prompted a change in career.
With a lifelong interest in the automotive space, Nikola had often bought damaged cars from the auctions and restored them, ready to sell again.
“I already knew I enjoyed restoring cars,” Nikola says. “I had a lightbulb moment and decided to pursue it full time.”
After completing his apprenticeship, and spray painting and panel beating course at TAFE NSW, Nikola is now fully qualified at the age of 52. He is now working full time at W Parks Smash Repairs in Sydney.
“If I can finish it and follow it through, so can the young ones,” Nikola says.
“Being born here is such an advantage. You don’t have the language barrier, and everything is already familiar. You can really achieve anything you want.”
As Nikola delved deeper into the industry over the past 4.5 years, his passion for paint and colours only grew.
“I love the di erent colours. My favourite is candy red,” Nikola says.
Learning how to apply colours and clears has been a welcome challenge for Nikola.
“Technique is a big thing. Learning how to mix paint and chemicals correctly and then apply it to the car for repair has been a test for me,” Nikola says.
“It’s not just the technique you have to learn, but all the di erent products and how and when to use them. There is a lot to learn but it’s been worth it.”
Nikola often reaches out to his TAFE teachers, Carl Tinsley and Dat Bui for some extra assistance.
“I still ring up both Carl and Dat when I need some extra help. They are always happy to help, even now when I’m no longer a student,” Nikola says.
“Carl’s knowledge of colours and products is very impressive.”
Nikola also reaches out to his panel technician teacher, Dat for guidance.
“Dat is always up for a chat. He has been very helpful over the four years I have known him,” Nikola says.
“I was actually older than Dat in the class. I sometimes played that card in class which we both still joke about.”
Learning how to repair a vehicle, and learning how to repair it well are sometimes entirely di erent pursuits. Nikola prides himself on his attention to detail and commitment to ensuring quality craftsmanship.
“There are so many shonky jobs out there,” Nikola says.
“We often do repairs not only on a vehicle’s original damage but also the previous repairer’s damage as well. It’s crazy how unsafe it can be.”
Treating each vehicle with the same level of care and attention is a key
focus for Nikola. He cites European cars as being more time consuming and harder to fix than Japanese models.
“A couple of weeks ago we had an Audi R8 come into the workshop. My job was to take the rear bar o , and it took me three days to do it. It was a very complicated job.”
In his spare time, Nikola enjoys going to car shows and restoring old vehicles to pristine condition.
“I restored my brother’s Chevrolet Camaro 69 which was old and totally wrecked. It took me 1.5 years to finish it,” Nikola says.
“He takes his car to car shows and gets awards for best bodywork and paint job. I am happy to see him with his trophies and I am proud of my work.”
With a strong push from electric vehicle (EVs) advocate groups, and governments to purchase an EV, many
repairers have found the repairing of EVs to be a challenging task.
One of the issues Nikola has encountered is the possibility these cars will be written o by the insurer because of potential damage to the large batteries that make up a big portion of the base of the vehicle.
“One EV we repaired had a damaged side skirt, and we couldn’t do any welding there because it was housing the battery,” Nikola says.
“I think the car manufacturers are still playing with the designs on how to build an EV that can be easily repaired.”
Despite the multiple hurdles Nikola has overcome to be a spray painter and panel technician, he remains thankful and grateful for his TAFE teachers and his boss, Van Bien Doan for continuing to encourage and support him.
“Van has been very fair to me, he’s been a good boss. He has shown compassion in teaching me the job,” Nikola says.
“I’m really enjoying my current workplace, it is a good environment.”
Enjoying his career, Nikola encourages others to consider a career in a trade.
“If I can do it at 52, so can young people too,” Nikola says.
“When I was at TAFE, there were a lot of 18 and 19 year olds who gave up and didn’t finish the course.”
“I think if you start something you need to finish it o and follow it through.”
Upon reflecting on his time in Australia since leaving Croatia, it is his determination that Nikola is the proudest of. Growing up quickly and escaping a worn torn country, Nikola learnt early on that you have to work hard for the things you want in life.
“I was determined to start a new career, but I was also determined to finish the course and my apprenticeship,” Nikola says.
“It’s been an achievement to show my child that no matter your age, you can still go after the things you want.”
The growth in electric/petrol hybrids and plug-in hybrids remained the big story of 2024 for new vehicle sales as they shape Australia’s future car parc.
The Federal Chamber of Automotive Industries sales figures show the upward trend for hybrids and the downward trend for straight EVs continued.
Overall, in 2024 EV sales have dropped to 74,612 vehicles, a decline of 14.5 per cent compared to 2023, however these FCAI figures do not include some makes such as Tesla.
By contrast, hybrid sales continued to surge with overall sales now at 172,696 for the year, a jump of 72 per cent since 2023.
Consumer appetite for alternative power trains, but without the range issues of straight EVs, was also reflected in the plug-in hybrid market that has doubled in a year from a low base to reach 23,163 new vehicles in 2024.
The Electric Vehicle Council has also released figures and is claiming sales are at an all-time high, incorporating
battery electric vehicles and plug-in hybrid electric vehicles into its total of the 114,000 vehicles sold in 2024, up from 98,000 in 2023.
Its figures show approximately 91,000 BEVs and about 23,000 PHEVs, indicating the two categories now make up nearly one in ten new car sales (9.65 per cent).
FCAI figures also show petrol vehicle sales are down a similar amount, about 10 per cent since 2023, in a sign the market is shifting with the advent of the NVES in 2025.
In December, Toyota’s RAV4, predominately hybrids, was Australia’s top selling vehicle with sales of 5,119 followed by the Ford Ranger on 4,493.
After several months leading the figures, this gave Toyota’s RAV4 the most popular position for the year with sales of 58,718 up 133 per cent on 2023 and eclipsing the Ford Ranger 4X4 with sales of 57,960, a drop of 42 percent on the previous year.
FCAI Chief Executive Tony Weber
wants money from the NVES scheme’s penalties to help boost the transition to new powertrains including better EV charging infrastructure.
“The industry is responding to NVES by increasing the range of zero and low emission vehicles on o er. However, a continuation of current customer buying preferences will inevitably lead to the accrual of substantial penalties under the government’s new scheme, which will create price inflation within the new vehicle market.
“Governments around the world have set regulations that are ahead of available zero emissions technologies and this is impacting both car makers and consumers,” he says.
“Manufacturers in the UK, Europe and the USA are under pressure because they have made huge investments to manufacture EVs, but customers are not buying them in the numbers needed to meet emission targets and to provide a return on investment.”
EV repairers have finally won their own classification after a long campaign to have the advanced skills recognised as the automotive industry transitions to low emissions future.
EV Technicians will receive their own classification (code 351434) under the new Occupation Standard Classification for Australia (OSCA) from 6 December 2024. This means the Australian Bureau of Statistics and other government departments will formally recognise the occupation separately from other automotive occupations and collect data and build policy accordingly. Automotive Electricians, for instance, are categorised in a separate occupation.
The ABS definition describes the roles as one that maintains, tests and repairs electric and hybrid vehicles systems
and components, including energy storage systems, traction motors and safety interlocks.
VACC CEO Geo Gwilym, said the classification is a win for both the industry and motorists.
“This new classification ensures our state’s automotive businesses are properly equipped to meet growing consumer demand,” Gwilym says.
He says the classification is particularly significant for Victorian workshops that are at the forefront of servicing the growing electric vehicle fleet.
“This is about future-proofing Victoria’s automotive industry,” Gwilym says.
“With government targets aiming for 50 per cent of new vehicles to be electric by 2030, this classification provides Victorian businesses with the framework
EV technicians will now be categorised separately. Image: milkywy/stockadobe.com
they need to confidently invest in their EV capabilities.”
“This recognition demonstrates how our industry is keeping pace with technological advancement,” Gwilym says. “It formally acknowledges the specialised skills required in the EV sector and shows that our industry is evolving alongside automotive innovation.”
New research from Suncorp insurer
AAMI reveals each state’s worst car park prang hotspot and when they are more likely to occur.
Analysis of more than 22,000 car park insurance claims across Australia from October 2023 to September 2024 has revealed December is the worst month for shopping centre car park collisions (2,659), closely followed by November (2,323).
There were about one third (36 per cent) more car park crashes in December than the monthly average for the 12 months to 30 September 2024 with Melbourne’s Doncaster again taking out Australia’s worst hotspot for car park collisions.
AAMI Motor Claims Manager Leah James said the data reflected shopping behaviour of Australians.
“A busy time for shopping means a busy time for car parks, and this is reflected in a spike in collisions over the festive season,” James says.
According to the research, Saturday has become the worst day to go shopping, with car park prangs spiking (3,703), closely followed by Friday (3,662) and then Thursday (3,514). Sunday is the best day to shop if you want to avoid a car park ding.
The afternoon (between 1-4:30pm) is by far the worst time of day to find yourself in a shopping centre car park, followed by mornings between (6-9:30am), and then peak evening shopping hours (between 4:30-8pm).
Aussie drivers are quick to acknowledge others for bad behaviour behind the wheel, with two thirds (60 per cent) having seen others driving too fast, and more than three in five Aussies (64 per cent) seeing another driver double-park or take up two spaces.
Drivers are less likely to confess to these issues with only one in five
admitting they’ve driven too fast, and one in ten (11 per cent) say they’ve double-parked or taken up two spaces.
“Every year we see a similar story unfold, making it even more important to do what you can to stay calm and cautious,” James says.
“Shopping on the quieter days, driving just that little bit slower and staying extra vigilant could be the di erence between a smooth ride and a prang.”
Australian insurer, IAG, is leading a global research project to create a best practice guide for the safe use and storage of lithium-ion batteries.
The research seeks to debunk misconceptions about battery fires and establish clear, practical safety guidelines for everyday use.
The insurer is teaming up with experts from QUT, EV FireSafe, Standards Australia, iMOVE Co-operative Research Centre, and other global specialists to explore how lithium-ion batteries are managed in electric vehicles (EVs) and micromobility devices such as e-scooters and e-bikes, both in Australia and around the world.
IAG Research Centre Head, Shawn Ticehurst says that as Australia’s EV and lithium-ion battery market accelerates, the development of safety standards, regulations, and the data needed to understand the risks associated with
batteries has struggled to keep pace.
“This year, the sales of EVs, including plug-in hybrids made up nearly 10 per cent of all new car sales in Australia,” Ticehurst says.
“This research will provide critical insights on how to safely store, handle and dispose of the increasing number of lithium-ion batteries as they reach the end of their life, helping to prevent incidents that pose a risk to life and property safety.”
According to IAG’s research, battery fires in electric vehicles remain rare, but there has been an increase in fires caused by lithium-ion batteries in e-bikes and e-scooters.
“There are many knowledge gaps we’ll be exploring through global collaboration, which will be key in developing e ective best practice strategies,” Ticehurst says.
“Among those are understanding how stored EV battery packs can fail following extended exposure to weather, methods
for containment of burnt or damaged packs, and exploring whether there’s a correlation between EV age and fire risk.”
EV FireSafe, specialises in EV battery fires and emergency responses, has established the world’s only verified database for EV fires, covering incidents in electric cars, buses, trucks, and specialist vehicles.
EV FireSafe Director Emma Sutcli e highlighted the importance of the research.
“The findings will be key to developing safety standards to help Australians use and store batteries safely,” Sutcli e says.
“Additionally, by addressing misconceptions around battery fires, we can enhance the safety of both emergency responders and everyone using and working around EVs and lithiumion batteries.”
The research findings are expected to be published in 2026.
with John Yoswick
Industry legend Mike Anderson is striving to get bodyshops and parts vendors to understand each other’s perspectives.
Mike Anderson of Collision Advice, a US-based training and consulting firm, has recently conducted more than a dozen meetings around that country, bringing shops together with the regional wholesale parts managers for a particular automaker.
“There has been one goal in my mind for these meetings: To better understand each other’s perspective, and to share information with one another that would give all of the participants a better understanding of how the parts processes work between the various stakeholders,” Anderson says.
He says the meetings helped him realise that the one voice often missing in industry gatherings are these dealership parts managers. So shops (and insurers) aren’t always aware of their perceptions and views – just as the parts vendors may not understand all the dynamics in the industry and how they can help.
Anderson says at each meeting, for example, he posed a scenario to shop representatives attending the meetings.
“Imagine you had a car you are repairing as part of a direct repair claim for Insurer ABC,” Anderson says he told the shops. “Your parts wholesale dealer doesn’t have the part but could get it from another dealership – they just can’t do so and give you the same discount they do on parts generally.”
At meeting after meeting, Anderson says, shop representatives generally say they’d almost always buy the part even if at a lower discount.
“‘I need it fast, regardless of money,’” Anderson quotes one shop owner.
“At the end of the day, cycle time often trumps discount. This can be true in many circumstances, but in some shop-insurer agreements, if a shop
doesn’t meet cycle time and customer satisfaction metrics, the shop has to give the insurer a designated percentage rebate over a specific period of time. So a single long delay even for a single part could skew the shop’s average and cost them a significant amount of money.”
This is one reason why honest communication between shops and parts vendors is so important, he says, particularly about parts availability. Based on what a shop is told about parts availability, they are making decisions about which vehicles to bring in for repairs and when. They are making decisions about which vehicles to disassemble. They are making decisions about promised completion dates to customers.
“If a parts vendor gives them bad information and they make a decision on that, it could possibly cost them tens of thousands of dollars,” Anderson says.
Anderson says he also conveyed at
the meetings another experience he heard about that highlights the need for good communication between shops and parts vendors.
“I was in a dealership bodyshop in Florida that had recently told a customer that a part for their vehicle was on backorder,” Anderson says.
“But that vehicle owner actually found the part at another dealership. He called the shop and said, ‘You told me this part was on backorder, but this other dealership says they have it.’
“So, the bodyshop called that other dealership, but that dealership wouldn’t sell them the part. That’s a hard conversation to have with a customer. They don’t understand why the shop can’t get that part from another dealership – often because they want to have that part on hand for their regular shop customers. But that hurts the OEM brand, and it makes the body shop look bad. So dealerships need to learn to
play nice in the sandbox together. They need to help each other.
“If there’s added costs to a wholesale dealer getting that part from another dealer – the time and money involved in physically going to pick that part up, for example – talk to the shop customer about that, Anderson says he advises parts vendors.
“The shop may be willing to pay a delivery fee added to the invoice for that,” he says. “Again, it comes down to good communication.”
At each meeting, Anderson asked shops for what they are looking for in a best-in-class parts vendor. While “a good discount” always made that list, it was not the first expectation mentioned by shops at any of the meetings, he says.
“It was usually the fifth, sixth or seventh thing that made it to the list,” Anderson says. “Parts order accuracy
and quality service were always ranked higher. The best discount in the world doesn’t matter, for example, if the part is wrong or it takes forever to get the part.”
Likewise, the wholesale parts managers at the meetings shared what sets some shops apart in terms of being among their best customers. They want customer that submit accurate and preferably complete parts orders. They want to work with shops that aren’t regularly hitting them up with last-minute orders. They want to work with shops with a low return percentage. Anderson says he advises the shops he consults with that they should be able have a return rate of less than four per cent, excluding any core charges.
“I believe any shop returning more than four per cent has an issue,” Anderson says. “They’re not doing complete disassembly, they’re pre-
ordering parts on potential total losses, they’ve got some process problems, or they’re ordering just what they only think they need.”
Not surprisingly, he says, parts vendors want shop customers that pay their bills on time.
One of the key take-aways from the meetings that shops and insurers need to know, Anderson says, is that parts vendors are under tremendous pressure on their margins, with the increase of delivery driver wages, having to subscribe to multiple software electronic ordering platforms, etc.
“It’s important we all understand: If we do not listen to their voice, you may see dealerships getting out of the wholesale business if it no longer pencils out,” Anderson says.
“This is not good for any stakeholder in our industry. This should be a wakeup call to the industry.”
A leading business analyst predicts the shift away from traditional petrol and diesel engines to electric and other sources will continue across the Asia Pacific region.
GlobalData’s report indicate the petrol engines market is expected to contract at 5.8 per cent in the Asia-Pacific (APAC) region over 2024-29.
The diesel engines market is also expected to record a negative compound annual growth rate of 2.0 per cent over the next five years.
Against this backdrop, the EV systems market is expected to record a growth rate of 9.1 per cent over 2024-29, according to GlobalData.
The report finds many Asian countries have demonstrated a proactive approach in implementing policies that foster the growth of the electric vehicle (EV) market, aimed at environmental sustainability and enhanced competitiveness in the global automotive manufacturing and export sectors.
GlobalData’s report, “Global Sector Overview & Forecast: xEV Systems Q3
2024” reveals that the xEV systems market is estimated at 194.6 million units in 2024 and is forecast to increase to 301.5 million units by 2029 in the APAC region.
The petrol engines market, estimated at 26.8 million units in 2024, is forecast to decrease to 19.9 million units by 2029.
At the same time another report from GlobalData reveals that the diesel engines market, estimated at 4.6 million units in 2024 will shrink to 4.2 million units by 2029 in the APAC region.
According to GlobalData, both the passenger and commercial vehicle segments are currently experiencing a trend toward electrification, but diesel engines are expected to demonstrate a slower rate of decline in comparison to petrol engines.
This transition is particularly significant in the context of the commercial vehicle segment, where the electrification process presents considerable economic challenges for fleet owners, it says.
Automotive Analyst at GlobalData, Madhuchhanda Palit, says China has
Global coatings giant Axalta has drawn its inspiration from the legendary British racing team for its 2025 Global Automotive Colour of the Year.
The colour called Evergreen Sprint, is Axalta’s 11th year at naming the colour as a harbinger of emerging automotive trends.
“Evergreen Sprint is a rich, deep forest green that pays homage to the legendary British racing green,” it noted in a statement. “A shade that has graced the finest racing machines and symbolises speed and performance. While capturing the thrill of motorsport, Axalta’s latest automotive colour of the year also brings a touch of sophistication to sedans and SUVs.”
Axalta Global Colour Marketing Director Dan Benton described it as a striking hue.
firmly established itself as a frontrunner in the global EV market.
“Other Asian countries are also making noteworthy advancements in the field of electrification,” Palit says.
“However, despite government initiatives to promote EVs, consumer reluctance to shift still exists due to several factors, including the high cost of EVs.”
“The adoption rate of EVs in the APAC region is increasing significantly; however, several challenges must be addressed to sustain this growth,” he says.
“Key issues include the necessity for a comprehensive charging infrastructure, advancements in technology to enhance adoption for both personal and commercial use, and the enhancement of consumer awareness regarding the benefits of electric vehicles and sustainability concerns.”
“To e ectively tackle these challenges, substantial public and private investments, along with suitable government policies, are essential.”
“Evergreen Sprint stands out on the road and evokes the spirit of performance, competition and adventure. The dynamic colour is sure to attract the attention of passionate drivers.”
According to Axalta’s Global
Automotive 2023 Colour Popularity Report, green is found on approximately two percent of vehicles worldwide.
For more information visit axalta.com/color.
A new study by a leading safety regulator suggests high-vis clothing that helps pedestrians stand out to drivers may make them invisible to automated crash prevention systems.
The Insurance Institute for Highway Safety (IIHS) study in the US comes as Australia prepares to require all vehicles on sale to be fitted with automatic emergency braking systems.
IIHS President David Harkey highlighted how the results suggest that some automakers need to tweak their pedestrian automatic emergency braking systems.
“It’s untenable that the clothes that pedestrians, cyclists and roadway workers wear to be safe may make them harder for crash avoidance technology to recognise,” Harkey says.
Automakers are already working to address the issue in response to IIHS ratings that now emphasise night time performance, but in the real world a host of factors come into play.
The new study investigated the e ects of conspicuous clothing and increased roadway lighting on the performance of the pedestrian AEB systems installed in three 2023 models — a Honda CR-V,
Mazda CX-5 and Subaru Forester.
For the current study, researchers conducted multiple trials with an adultsized dummy clothed in a black sweatshirt and pants, a retroreflective jacket with black sweatpants, the black sweatshirt and sweatpants with retroreflective strips added on the dummy’s limbs and joints, and a white sweatshirt and pants.
The tests were run at 25 mph (40km/h) with no roadway lighting, with 10 lux of illumination on the crossing or with the federally recommended 20 lux of illumination on the crossing.
The CR-V and CX-5 hit the dummy in 84 per cent and 88 per cent of the test runs, respectively, while the Forester avoided a collision in all but one trial. Neither the CR-V nor CX-5 slowed at all when the dummy was wearing clothing with reflective strips that articulated its limbs
When the dummy was dressed in black, both vehicles slowed substantially when using their high beams — a test that was only conducted with no roadway illumination. Using their low beams in those same conditions, the CR-V failed to slow at all and the CX-5 reduced its speed by less than a third. Both vehicles did much better with 20 lux of additional light.
Global coatings giant PPG continues to gain recognition for its push into sustainable practices.
PPG was named in Newsweek magazine’s America’s Most Responsible Companies for the fifth consecutive year along with making Newsweek’s America’s Greenest Companies list for 2025
To create the 2025 ranking, the focus was placed on a holistic view of corporate responsibility that considers environment, social and governance factors.
Companies in the 2025 list were selected based on a review of publicly available data and a survey of 26,000
US residents about their perceptions of companies related to corporate social responsibility.
Out of 600 companies on the list, PPG ranked no. 110 overall and no. 8 in the Materials and Chemicals industry category.
The Newsweek magazine’s America’s Greenest Companies list recognises the top 500 private and public US companies that are committed to reducing their environmental impact in key areas, including greenhouse gas emissions, water management, and waste reduction
PPG Vice President Global Sustainability
Peter Votruba-Drzal highlighted
The test found a significant variation in how AEB systems responded to what a pedestrian was wearing.
For all the other types of clothing, the vehicles were only tested using their low beams.
When the dummy was dressed in the reflective jacket, the CR-V didn’t slow in any of the trials, regardless of additional roadway lighting. In contrast, with no roadway illumination and with 10 lux of added light, the CX-5 slowed much more than it did when the dummy was clad in black. But with 20 lux of added light, it performed worse with the dummy in the reflective jacket than when it was wearing the black outfit.
In contrast to the two other vehicles, the Subaru came to a complete stop without hitting the pedestrian dummy in every trial except one run in which the dummy was wearing clothing with reflective strips and the roadway was illuminated to 10 lux.
PPG’s commitment to sustainability.
“This recognition reflects our commitment to leveraging sustainability and corporate social responsibility as a means to serve our customers’ evolving needs and drive operational excellence,” Votruba-Drzal says.
“As part of our growth strategy, we focus on new product and process innovations that serve our customers and enable e ciency in the value chain.”
PPG was also recognised on the list of the ‘Best Places to Work in Information Technology (IT) in 2025’ by Foundry’s Computerworld.
The concept that new high-tech solar coatings could power vehicles is just one of the advanced experiments being explored by Mercedes Benz.
Mercedes Benz VISION EQXX technology programme is researching new technologies aimed at shaping mobility in an electrified future and includes a host of radical and innovative R&D concepts that could solve future problems.
These include new braking systems, augmented reality systems for drivers, robo -taxis and drone based logistic deliveries aimed at rethinking transport in three key cities, London, Los Angeles and Shenzen beyond 2040.
Mercedes Benz says the developments in the solar paint area could generate enough electricity for more than 12,000 km per year.
These coatings are five micrometres thick, significantly thinner than a human hair, weigh just 50 grams per square metre and are packed full of energy, it says in a statement.
Mercedes-Benz is researching a new type of solar module that could be seamlessly applied to the bodywork of electric vehicles – like a wafer-thin layer of paste. The active photovoltaic
surface can be applied to any substrate. The solar cells have a high e ciency of 20 per cent. An area of 11 square metres or equivalent to the surface of a mid-size SUV, could produce energy for up to 12,000 kilometres a year under ideal conditions, it says.
The energy generated by the solar cells is used for driving or fed directly into the high-voltage battery. The photovoltaic system is permanently active and also generates energy when the vehicle is switched o . In future, this could be a highly e ective solution for increased electric range and fewer charging stops.
considerably cheaper to produce than conventional solar modules.
The experiments have looked at di erent scenarios depending on levels of shade, the intensity of the sun and geographical location.
Their examples indicate a MercedesBenz driver in Stuttgart, Germany covering an average 52 kilometres a day, would have 62 per cent of its travel covered using solar energy while in Los Angeles, the driver could cover 100 per cent of their driving distance.
Mercedes says the solar paint contains no rare earths and no silicon, only non-toxic and readily available raw materials. It is easy to recycle and
After a patchy start for some imported brands in the early 2010’s, the latest batch of Chinese EV models are ranking among the best, with ANCAP awarding them five-star safety ratings.
Three of the latest electric cars from new Chinese brands have been awarded five-star safety ratings, as the first cars roll into Australian showrooms.
The Leapmotor C10, Zeekr X and XPeng G6 have earned top marks from ANCAP, based on testing conducted
in Europe to the latest criteria.
• The C10 was awarded category scores of 89 per cent for adult occupant protection, 87 per cent for child occupant protection, 77 per cent for vulnerable road user (pedestrian and cyclist) protection, and 77 per cent for safety assist technology.
• The Zeekr earned the highest adult occupant protection score of the trio, at 91 per cent, plus 87 per cent
Mercedes-Benz Group AG, Chief Technology O cer, Development & Procurement and Board Member Markus Schäfer says this was just one of the innovations being explored by a company that has been at the forefront for shaping the future of mobility for over a century.
“Innovative strength was and is among the most important driving forces of Mercedes-Benz,” Schäfer says.
“Our brand has been shaping automotive progress for almost 140 years with pioneering technologies. For us, innovation only makes sense if it o ers our customers real added value. Their perfect composition is what makes a Mercedes a Mercedes.”
for child occupant protection, 84 per cent for vulnerable road user protection, and 84 per cent for safety assist technology.
• The XPeng G6, with scores of 88 per cent, 86 per cent, 81 per cent and 80 per cent respectively across the four categories, was noted with “minor head contact” between front occupants in the passenger-side impact crash test, and lost points accordingly.
China is the new country of origin Australian repair shops are likely to see more of and 2024 proved no exception.
Amidst an international war of words over tari s and protection policies, Australia is a relatively benign market for the growing auto maker, and new brands are making their mark.
China remained behind Thailand and Japan as the top three countries of origin and missed hitting the 200,000 new vehicle sales mark partly due to the fall in growth of Tesla sales in 2024.
The advent of the NVES introduced this year has led to a proliferation of new Chinese brands, many launched in 2023, while established names have reported some significant growth.
MG is the top selling brand, in seventh position with sales of 50, 592 vehicles, a market share increase of about half a per cent.
Pure EV maker, Tesla that still sells about 40 per cent of all battery electric
vehicles, however, saw a slowing of sales in line with a slowing growth in pure EVs as consumers turned to hybrids.
According to data from the FCAI and the EV council, Tesla is still the top seller of electric cars – with 38,347 vehicles, or 42 per cent of the total –but it is down 17 per cent or about 8000 vehicles from 2023.
Great Wall Motors finished 2024 with its own record sales and secured a position in the top 10 of the Australian automotive market.
GWM sold 42,782 vehicles in 2024, the largest year-on-year growth among the top 10 manufacturers, with a 17.5 per cent increase in sales for 2024.
VFACTS national sales data showed it December alone it sold 4,073 units — a 5.5 per cent increase compared to December 2023 —a record monthly market share of 4.2 per cent.
Its leading vehicle was the Haval Jolion, which sold 1,691 units in
Axalta a leading global coatings company has been named as a recommended refinish supplier for BMW Group.
Axalta will be the recommended supplier when BMW private paint label, ColorSystem, is not present.
The news comes after Axalta’s positive results in 2024. According to Axalta, third quarter 2024 net sales increased 0.8 per cent year over year to a third quarter company record of $1.32 billion.
The new agreement, e ective from January 2025, is valid for several years and includes BMW Group’s network of dealerships and collision repair shops in over 50 countries worldwide.
In Australia, BMW rea rmed its
position as the top-selling premium automotive brand for the second consecutive year, recording 26,341 new vehicle registrations in 2024, according to FCAI figures.
BMW Group has also extended Axalta’s agreement as supplier for ColorSystem in the US and in China. Axalta has already been chosen as exclusive ColorSystem supplier in Europe and South Africa for several years.
BMW Group’s ColorSystem is engineered to be one of the world’s most technologically advanced paint systems.
Sales Vice President for Axalta Refinish in Europe, Fabien Boschetti, highlighted the high standards of the BMW Group.
December, capturing 14.8 per cent share of the small SUV market.
GWM also sold 11,980 hybrid vehicles in 2024, representing a 61 per cent increase and accounting for 28 per cent of GWM’s total volume mix.
BYD, another Chinese brand that has declared its ambitions in the Australian market, also saw strong growth with 20,538 new vehicles sold in 2024 an increase of 38 per cent over the previous year.
Other brands like Chery recorded sales of 12,603, an increase of 158 per cent year-on-year.
Worldwide Chery is also boasting of its status as one of the largest exporters on the planet, with a record full-year result of 2,603, 916 vehicles for 2024, a 38.4 per cent increase year-on-year.
Chery has now been the top Chinese passenger car exporter globally for 22 consecutive years with its EVs alone selling 583,569 vehicles.
The paint partnership will apply to Axalta when ColorSystem is not available. Image: littlewolf1989/stock.adobe.com
“Through the diligent multiple tender processes, Axalta has unequivocally met BMW Group’s high standards of quality, e ciency and sustainability,” Boschetti says.
“We will continue to support BMW Group’s dealerships and collision repair shops worldwide with our innovation and operational excellence.”
”Axalta will supply its patented Fast Cure Low Energy technology paint system, which delivers benefits including reduced carbon equivalent emissions and energy consumption, as well as best-in-class training support.”
with Cli Chambers
Much-loved performance cars were always something of a specialty on the Australian market. While not all of them were as successful as hoped, the public interest never abated, and they could never be labelled as boring.
Australians for longer than a lot of us have been alive, have loved locally-built performance cars.
It started with S4 Holdens, GT500 Cortinas and twin-tank Mini Coopers before moving in to a brawl for race circuit supremacy between Holden and Ford. Chrysler had a go as well, with a two-door Charger, but Holden was the brand that would take six-
cylinder honours with its XU-1.
From the mid-1970s Australian carmakers tried to back away from unfettered performance, but the public wouldn’t let them. After a short pause, we went back to producing some astounding performance cars, which were rarely raced and now cost far less than those that were.
Welcome then, to a diverse
group of local performance cars, spread across the four decades during which this country built some of the most interesting motor vehicles in the world.
Some models from the same era have gone on to be worth (literally) the price of a house, but these fi ve cars o er great driving experiences for a fraction of that cost.
People who have enjoyed the brilliant handling and braking capabilities of Nissan Special Vehicles Skyline GTS probably wondered as well why Fred Gibson’s team didn’t push harder to have the car powered by the company’s 3.0-litre turbo engine.
Holden had it in their VL and, if installed in the GTS, the 150kW straight-six would have transformed the Nissan into an almost perfect performance car. As it was, the Skyline with 130kW could cover ground with ease and at surprising pace.
The 55 profile, ZR rated rubber on 16-inch rims was more tyre than the car needed, and getting a GTS Skyline so out of shape that the tyres would squeal required a race track.
Just 200 of each version were made, with the original all white Series 1 car selling from June-December 1988 at a list price of $33,950. Series 2 cars in red that appeared late in 1989 and were based on the Ti, so were better equipped and with fourspeed automatic as the default transmission.
Finding surviving examples of either version won’t be easy, but not expensive either. A manual Series 2 car in excellent condition was o ered recently by a specialist dealer for $50,000 but very good Series 1 and 2 cars have in the past sold 30 percent below that.
Ford, when launching the XR8 Sprint, obviously didn’t want a marketing debacle to match the one created by the EB Falcon GT, so launched its performance derivative of the ED with minimal fuss. The Sprint used a 192kW version of the 5.0-litre GT V8, but looked so similar to a basic XR8 that hardly anyone noticed. Wheels that were di erent in style from XR8 rims were the biggest external giveaway, and inside, the Sprint owner got to enjoy tailored leather sports seats, standard air-conditioning and cruise control.
The exhaust was less intrusive than the GT system, but ED Sprints would still generate a purposeful howl as the 5000rpm power peak approached. Scarcity will plague anyone attempting to track down a Sprint. Ford only built 356 of them and 56 of those were exported to New Zealand.
Values a decade ago sat below $20,000 and only began to spark once the last new Falcon had been sold in Australia. One or two cars can be expected to reach the used market annually, making the process of tracking values quite di cult. Only recently have they reappeared in Value Charts, with excellent cars continuing to hover just below $50,000.
Having spent seven years under the spell of my own P76 V8 fourspeed, its inclusion might be seen as a Captain’s Pick, to which my response would be ‘go and drive a good one’.
Whether Leyland was spooked by political reaction to Ford’s GT-HO Phase IV isn’t known, but the all-alloy, 4.4-litre V8 came to market in seriously detuned form. The two-barrel carburettor was tiny and the single-pipe exhaust ensured performance petered out once the engine reached 4000rpm, with output a miserable 144kW.
Even so, when optioned with the same BorgWarner four-speed transmission as used in performance versions of the Chrysler Charger, a P76 V8 would run 0-97km/h in under nine seconds and overtake rapidly with an 80-110km/h time of 5.4 seconds.
Tweaking the inlet and exhaust tracts to let the alloy engine breathe made an instant di erence and delivered a reliable 180- 190kW, Thanks to active Owners Clubs, P76 V8 manuals survive in significant numbers, but don’t be surprised by how few still look the same as when they left Leyland’s production line.
Despite a super-scarce Force 7 coupe being o ered recently at $250,000, quality V8 sedans aren’t as yet expensive and most will change hands for less than $30,000. (Force 7 Coupe pictured)
Australia has produced some extraordinary muscle cars and this is among our best. During an era when 220kW was seen as power aplenty, HSV went to see its North American friends and came back with a motor from Callaway’s C4B programme which saw a prodigious 300kW extracted from 5.7-litre Chevrolet engines.
The version supplied to Holden was potent but tractable, unless provoked. Maximum power didn’t arrive until 6000rpm and a lot of owners would upshift well before the performance peaked.
With a 0-400m time of 12.6 seconds, the manual VTII version was the fastest four-door car in the country and not overwhelmed until the 7.0-litre W427 came along.
The bang for your buck comparison with other HSVs, and even the legendary Falcon GT-HO Phase III, is also just ridiculous.
At auction in late August 2024, a low-kilometre VX SV300, one of only 134 built and showing 117,000km, sold for a premium inclusive $48,355. An hour later at the same venue, an HSV VN GTS Group A, #187/302 and showing 125,000km brought more than three times the price of the SV300.
If you can’t see the logic in those numbers either, it might be time to give any SV300 that appears in the market a very serious second look.
According to the owner of an E48 Charger featured by Unique Cars some years back, this was arguably the most enjoyable and tractable of all the tripleWeber Chargers.
Where the race-spec E49 produced 225kW from its version of the in-line 4.3-litre engine, the E48 produced a still useful 210kW.
To generate its extra grunt the E49 employed a more aggressive cam profile, which manifested in to a rougher idle. Torque from the E48 at 431Nm, was almost identical to the E49’s 433Nm but was developed 500rpm lower. The E48 was an easier car to juggle on the clutch in tra c, could be upshifted sooner and, although nobody seems to have run fuel consumption figures on an E48, likely to have been better on fuel in suburban running than the E49’s 18 to 22 litres/100km. All three levels of VJ Charger could be specified with the E48 engine and drivetrain, but few buyers bothered. Only 122 basic Chargers are said to have been built as E48s, plus 16 each of the XL and 770. A specialist dealer in Sydney some years ago had in stock a 770-spec E48 in showroom condition showing just 11,560km.
Had it been an E49 with that odometer reading the asking price would have exceeded $250,000, however, the most this exceptional example of an E48 Charger could manage was $135,000.
3M™ Cubitron™ 3 Cut-Off Wheels with their fast cutting andlong-lasting performance improve productivity and efficiencyin various body shop cutting processes.
These Cut-Off Wheels are built with the 3M™ Cubitron™ 3 Precision Shaped Grains –designed with sharp, angularstructures that continuously fracture to form fresh, sharppoints that allow the discs to slice faster, and last longer. They will cut through most materials, including high strength steels, stainless and mild steel.
more life than our previous generation of Cubitron™ II Cut-Off Wheels Remove up to 40% more material thanCubitron™ II Cut-Off Wheels
With Remote Services, you can access expert diagnostics and support whenever you need it, with a wide range of OEM tools available to complete the most complex of repairs. You will be working faster with more accuracy on every job, making your customers happier and boosting your bottom line. Scan the QR and bring your workshop into the future.