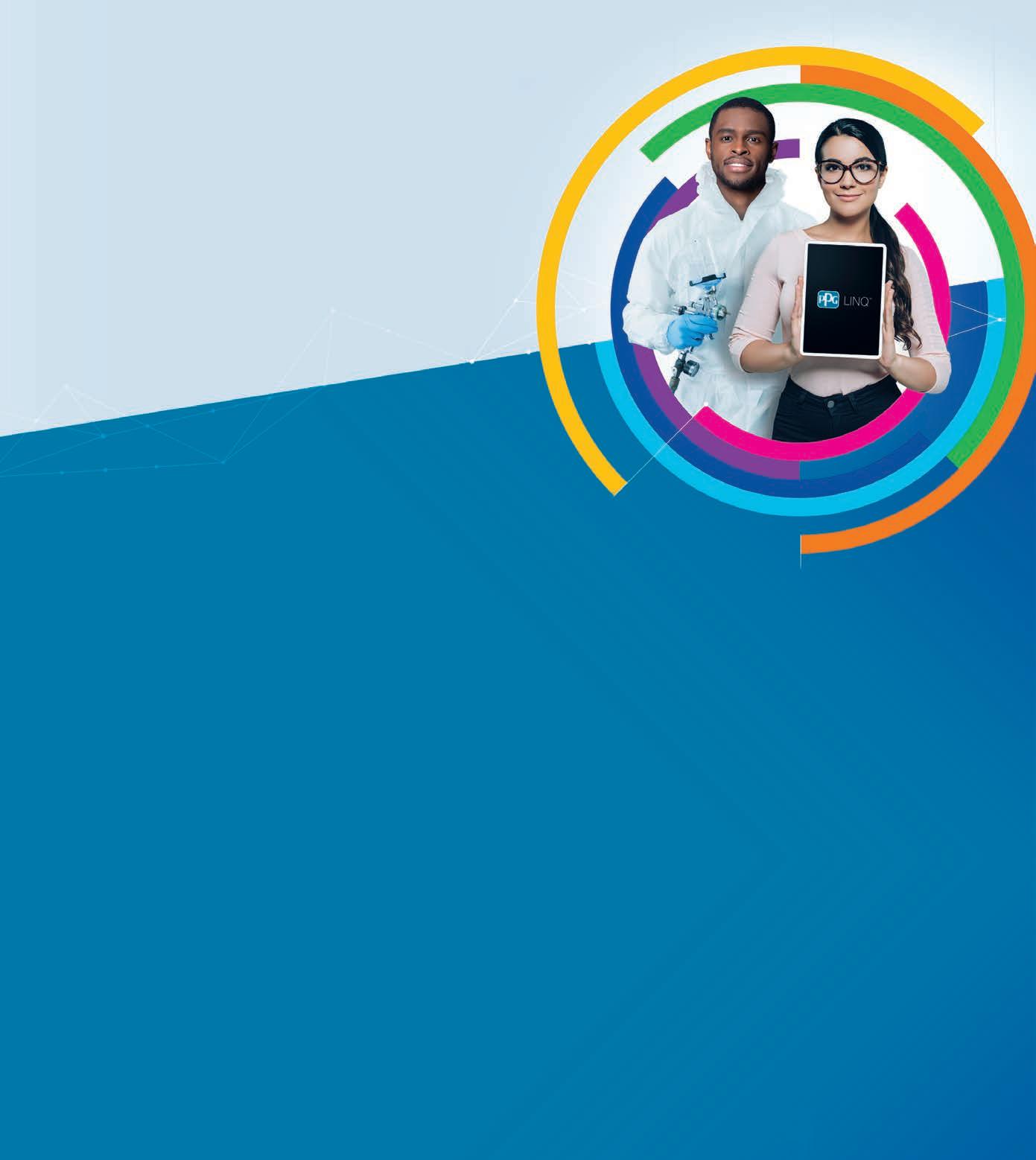
ACKNOWLEDGED

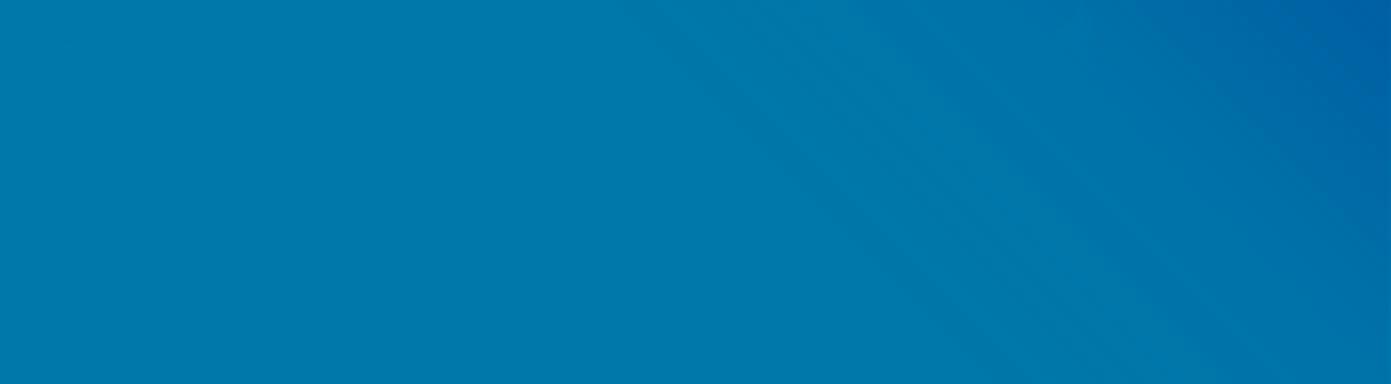

ACKNOWLEDGED
With the Jollift 1330 Fast Repair Bench you can now equip each work bay with a quality Italian manufactured car bench.
The flexibility of the modular design means that multiple benches can share one pull post, one set of clamps and one set of wheel stands, which makes it totally affordable for each work bay to have its own repair bench.
• 100mm lowered height
• 1300mm lift height
• 3000kg lift capacity
The Jollift Flat Line NM65 is a cutting-edge vehicle lift redefining industry standards. Crafted with precision in Italy, this powerhouse boasts a lift capacity of 3000kg, effortlessly handling various vehicle types.
With a sleek lowered height of just 65mm, it offers unparalleled accessibility for low-profile vehicles.
The National Collision Repairer doesn’t like to shy away from looking at the issues faced by the industry. Almost two thirds of the way through 2024 and many of these challenges don’t appear to have got much easier. Whether it is grappling with tightening margins, staring down the barrel of advancing technology or tackling the long, slow quest to get skilled sta , there appears to be no easy fi x.
But with each of these problems it is important to remember workshops are not alone. Professional business services, associations and groups, even the shop down the road, all have a surprising number of resources to help willing businesses take on these problems and thrive.
At NCR we have always felt that these pages are a mirror to the industry and can also portray some of its successes and achievements. Not least of these are the stories of the many people who encounter these challenges, often on a daily basis, but with a combination of innovation, commitment and energy, fi nd ways to overcome them. These too can be of assistance. The celebration of role models is fi tting in an industry that is too often overlooked for its vital role in keeping things moving. In addition, these stories can also form a salutary example that inspires others to try new ideas or new approaches.
The many networks and groups repairers belong to can often serve the same inspiring purpose. There may be much to complain about but there is also much worth celebrating.
In this edition, we sit down with retiring Capricorn CEO David
Fraser. His story is a good example of someone who refl ects the culture of an organisation whose fundamental aim is helping its members. If ‘Stronger Together’ is a catchy slogan, its real weight lies in how e ectively the cooperative can make that motto real in the everyday working lives of its members. And Capricorn has been doing this for some time; ever since a few Golden Fleece service stations got together back in 1974.
Now in 2024, 50 years and almost 30,000 members strong, the cooperative gives an indication of just how many automotive businesses have embraced the concept of strength in a collective. As Fraser’s insight shows, this is about a lot more than a buying group.
For instance, Capricorn’s yearly State of the Nation report is open-eyed about examining and facing up to the problems confronted by the repair and wider automotive industry, but it is also increasingly o ering advice, examples and resources on how members could potentially overcome some of these problems. This underscores the truth that cooperatively the industry can achieve so much more in tackling industry-wide issues like the skills shortage.
Innumerable small shops competing for the same dwindling pool of talent is a recipe for disappointment. But with the help of organisations like the Australian Collision Industry Alliance, the Australian Automotive Aftermarket Association, the MTAs and other active bodies, there is the potential to collectively change policy, promote the industry and increase the pool of talent. The workshops, big and small can add their voice to these collectives and reciprocally benefi t from the advice and experience to make their workshops the employer of choice.
Together, everyone is better o .
Eugene Du y Editor
The National Collision Repairer
Needing integrated and e cient, yet visually pleasing products and systems for your busy workshop? Look no further than Car-O-Liner’s Workshop Solutions series.
An organised inventory of control solutions such as tool boards, wall sections and separators allow workshops to configure their own unique work bays. Car-O-Liner’s WorkShop Solutions specialises in meeting collision repair workshops’ space requirements. Ensure your workshop is well equipped and well planned out with parts silhouettes on your tool board. This quick and streamlined approach will save you time on the job as tools and equipment always return to their correct place.
One piece of equipment on the Workshop Solutions series is CarO-Liner’s EVO System. This system provides workshops with a flexible and universal clamp that will e ortlessly integrate with workshop flow and Car-OLiner products.
The EVO System
A flexible product that can fit unique repair requirements, the EVO™ System has three separate fittings for universal anchoring, holding and fixturing.
The EVO System 1, 2 and 3 is made of an optimal number of components, allowing the products to be used
alone, or combined with one another.
For optimal workshop e ciency, the anchoring, holding and fixturing EVO System works for every vehicle year, make and model. This swiftly eliminates the traditional fixture costs.
Fully integrated with Car-O-Liner® data and software, the EVO System is modular and upgradeable.
Benefits of Caro-O-Liner’s Workshop Solutions
The Workshop Solutions series comes with many features and benefits that will elevate your workshop experience.
Creating a workshop that has e cient inventory control ensures tools are returned to the proper location.
The ergonomic factor also enables workshop technicians to complete repairs faster.
Creating a workshop environment that is organised is more attractive to customers as it increases confidence and trust in the repair team.
The high-quality clamps hold multiple parts and gives a long-life cycle with low maintenance costs.
The flexible product design range matches multiple car manufacturers’ parts design, creating a seamless process for integrating Car-O-Liner products into your workshop.
For more information, visit, https://car-o-liner.com/
To celebrate our 50-year milestone, we are offering unbelievable ‘Special 50-year Promotion Deals’ on all Car-O-Liner Benches and Car-O-Tronic Measuring Equipment ... and you also receive our normal ‘Trade-in Deal’ which is still available. This Special Offer is 50-years in
Great restorations take e ort, attention to detail and passion, but doing a job right takes time.
Over 1,000 hours and more than 12 years in the case of Anthony Cappelluti’s 1967 Austin-Healey 3000 Mark III BJ8 sports convertible.
The Austin-Healey 3000 represents the end of an era. Assembled on 25 June 1967, in Abingdon UK, it was one of the last before production of the 3000 ceased and Austin-Healey merged with Jaguar.
Cappelluti’s 3000 was imported to Australia, changed hands a couple
of times before ending up in “The Healey Factory” in Melbourne (a classic sportscars specialist business), where Cappelluti found it.
“We went to The Healey Factory with a mate to look over it for him, intending for us to restore it. But once we pulled it apart and after abrasive blasting, we realised it would be a huge and costly project. I o ered to buy it o him.”
As owner of CAPPA Motor Bodies in Naracoorte, SA, Cappelluti has been repairing and restoring vehicles for more than 30 years, and was determined to give the car a faithful,
high-end restoration. But with family and a business to run, the project took a back seat.
“It sat in the shed for 10 years. I wanted it finished for our daughter’s graduation, then our son’s wedding, then our daughter’s wedding… We did work when we could.”
The car had previous but incomplete restoration work, a lot of further work was still needed, including the chassis. The 3000 is unique for its welded interior construction and aluminium body over steel chassis. A full ‘body o ’ restoration required cutting sections and precision rewelding.
The panel restoration also needed special jigs, so Cappelluti relied on the experts at The Healey Factory while undertaking the bulk of the restoration back at CAPPA Motor Bodies.
“After it had been abrasive blasted, we used the RAPTOR 2K Epoxy Primer, which is a great base for applying filler over the top,” says Cappelluti.
“Restoration cars often sit around for a while, so they need something to stop moisture corrosion. The RAPTOR Epoxy is perfect, providing a good base for filler and nothing gets through to the steel.”
The CAPPA team opted for U-pol’s Dolphin Glaze Fine Filler.
“It would be a disservice to all that e ort to not use the highest quality
refinish products,” says Hayden Bennier, who worked on the car at CAPPA.
“Having the right products makes all the di erence. U-pol’s Dolphin Premium was the only choice. It adheres great, it sands easily and smooth. We use it every day, have done for years now. It’s a no brainer for us.”
Cappelluti and the team finished the car with a classic Healey Blue over Ivory White two tone paint job and tan interiors.
As the best known of the ‘Big Healeys’ the 3000 Mark III BJ8 is highly sought after by collectors - Jerry Seinfeld has one in his famous collection. Restored 3000s can sell for over $100,000 in Australia. But Cappelluti is not about to sell.
“You’re never going to go into a restoration thinking you’ll make money out of it,” he says.
Instead, for Cappelluti, it’s about sharing the hard work and dedication that went into this meticulous restoration.
As a registered historic vehicle, Cappelluti has driven his 3000 in the Bay to Birdwood, one of Australia’s premiere vintage car rallies, as well as
photoshoots for the occasional wedding.
“It’s great taking people for drives with the top down and watching them enjoy a classic car that really doesn’t have any modern features.”
But mostly, Cappelluti enjoys spending time driving with his wife Sarah to wineries and enjoying the countryside, weather permitting. “It’s a car for nice weather, it’s a holiday car. A good time car.”
For further information on the products Cappelluti used contact the U-pol (Australia) technical support team on (02) 4731 2655 or visit the website www.u-pol.com.au
Ease of use, adding to workshop e ciency by reducing repair steps and enhancing sustainability are just some of the benefits all contained in a new aerosol primer Axalta has released.
Standox, a global refinish coating brand from Axalta, has introduced a new 1K-Allround Primer Surfacer U3080S as an aerosol, which shortens the repair process considerably. During preparation, small sand-throughs are common and these must be primed or sealed before top-coating. Available in grey and designed to maximise e ciency and sustainability, the innovative 1K-Allround Primer Surfacer U3080S allows fast processing as it provides excellent filling power and good adhesion on both metal and plastic substrates.
Axalta Product and Technical Manager for Australia and New Zealand Jim Iliopoulos, says the 1K-Allround Primer brings multiple benefits to the workshop.
“Thanks to the 1K-Allround Primer Surfacer’s simple and universal application and its fast-drying
performance, bodyshops can be more e cient, profitable and sustainable,” he says.
1K-Allround Primer Surfacer U3080S is suitable for use on bare metal providing very good corrosion protection, and on all common plastic substrates with required flexibility.
Application is very easy with good sprayability and flow, thanks to SprayMax technology.
“1K-Allround Primer Surfacer U3080S delivers high filling power with easy sanding. It can be re-coated after sanding with waterborne basecoats as well as with solvent-borne basecoats or topcoats.” Iliopoulos says.
1K-Allround Primer Surfacer U3080S Aerosol in grey is available now from your local Standox distributor.
Additional colours – black and white – will be available in due course.
For more information, contact your local Standox distributor or visit standox.au
At a time when energy costs continue to climb, repairers need to choose the best solutions for their workshops ensuring lower overheads and better environmental outcomes.
Coatings giant PPG has developed its Sustainability CO₂NCEPT system as a practical service aimed towards longterm profitability and sustainability.
PPG created the Sustainability CO₂NCEPT, consisting of a suite of products, processes, digital tools and consulting services, it o ers unique opportunities to embrace sustainability and reduced energy consumption as a pathway to long term profitability.
Using the app-based Sustainability CO₂NCEPT Calculator, a PPG representative can work with individual collision repairers to input a variety of the business’ parameters. This includes the current gas and electricity price, estimated gas usage per booth cycle, booth airflow, estimated electricity draw for lights, motors, etc, average ambient temperature for the area and product bake times.
Using these parameters, the Calculator generates an estimate of the current energy e ciency and carbon emissions. As well as providing a handy starting point, it’s also a springboard to exciting improvements in both sustainability and profitability.
Although it was created by the PPG Europe team, the Sustainability CO₂NCEPT Calculator available to local repairers has been thoroughly tuned to this market using local data and information.
Rather than going through the hassle of actually introducing a new product or process into the workshop and then monitoring it to check its impact, the Sustainability CO₂NCEPT Calculator o ers a quick, simple alternative.
By using simulations, it’s easy to do instant virtual changes to any of the many di erent product or process options that are on o er to PPG customers, including things like UV cured technology, air dry primer and clearcoat technologies and shorter bake cycle clearcoats.
With immediate results on hand, it’s very straightforward to see the impact any changes would have on cycletime, energy usage, waste and the collision centre’s carbon footprint. That makes the Sustainability CO₂NCEPT an extremely powerful tool that can be used to rein in electricity and gas costs, as well as meet any sustainability targets.
Whichever options you choose, PPG support is available right along the journey, such as training to bring your team quickly up to speed and guidance from your MVP Business Solutions Manager to give you peace-of-mind that you are making the most of any opportunities.
For more information about the PPG Sustainability CO₂NCEPT, speak to your MVP Business Solutions Manager, your PPG Territory Manager or the PPG Customer Service Hotline 13 24 24 (Aust) or 0800 320 320 (NZ).
As it looks forward to its next 50 years, Capricorn is going from strength to strength as a cooperative. Recently it has enjoyed unprecedented growth and is fast nearing 30,000 members. The secret is in its culture of service to its members, exemplified by the passion and belief of outgoing Group CEO David Fraser.
After 18 years at Capricorn, five as its head, and over twice that in the automotive industry David Fraser has many illuminating memories. One he recalls, with a lesson about growth, was a time some years ago when talk at the cooperative was, they would reach a limit at 15,000 members.
“And I remember thinking perhaps we’ve set the bar too low,” Fraser says. “We really need to be thinking a lot more holistically and believe that we had something special.
The something special was the wide range of services and support they could o er members and the collective strength a large member-based organisation could have in improving the automotive aftermarket industry. This became the catalyst for more growth, but always returning to those basic principles.
“It took us 30 odd years to get to that first billion in sales and took another 10 to get to the second billion. We will be near $4 billion this time next year on the back of some of that strategic work that we did.”
But proud as he is of the growth of the cooperative, Fraser believes it is the importance of keeping the culture vibrant and living up to its ‘stronger with’ promise and the service this plays for the wider automotive industry that he considers the real achievement of his time at Capricorn.
“We are the collective of those 29,000+ small businesses, and their success is our success, and our success is their success. And for me, it’s really important that we continue to grow
As
celebrates its 50th
the membership because it’s a great opportunity for those small business owners to have a stronger and more sustainable future in what’s going to be a decade of change, with regards to the vehicle car parc changing to meet its future Net Zero targets.”
“We are very much a purpose driven business. Every time we make a decision, whatever that decision is, we will always look to do the right thing for our members. If those decisions were based purely on the commercial viability
or the commercial perspective, you wouldn’t always do it, but sometimes it’s the right thing to do because it helps them as a small business owner, to be stronger, be sustainable and maintain a position of competitiveness.”
The collective strength for Fraser goes back to 1974 when a group of WA service stations formed the first buying group.
“The whole reason Capricorn was formed or founded in the first instance was the fact that you had these like-
minded business owners who thought that if they collaborated and cooperated together, they would be able to be stronger than by standing alone.”
In times of change.
Capricorn’s success as a cooperative with a wide range of Preferred Suppliers and its rewards programs for members are well known, but it also believes strongly in extending the help to service and support.
Investing in market research is one way Capricorn has been able to help members both by giving them more insight into the challenges facing the industry and where solutions lie. Last year their annual State of the Nation report, which takes a comprehensive look at the automotive aftermarket sector, focussed specifically on the skills shortage and made some striking findings. Fraser says it was part of a theme that has come through from members for three or more years and so the specific focus was stepping up to that need.
“We’re not going to be the silver bullet that fixes that problem, but we want
to be part of the solution the industry needs to find by working together to help address it.
“We’re all feeling the pain of the problem, whether you’re small, medium or large business, whether you see it in the supply chain or the value chain, it’s a common problem for everybody and we want to be part of helping find the solution.
“For us, it’s using that information, looking at what more Capricorn can do to help drive better outcomes. Whether that’s opportunities for us to work directly with members, or whether its working with other industry associations or trade associations or working a little bit more closely with advocates to help and drive government decision making.”
What was di erent about the depth of the State of The Nation: Special Report on the Skills Shortage in 2023, is it looked comprehensively at all the sectors within automotive including collision repair and o ered a dedicated website with resources, case studies and ideas on how workshops could overcome some of the issues of recruitment and retention of sta .
New technology, new ideas
Fraser says the surveys and research also help in shaping better decisions on how the cooperative can help its members on other key issues such as meeting the advance of automotive technology.
“This is about us stepping up and wanting to be part of shaping a future market. And by being really clear about the direction our industry is heading.”
This included an intense study tour for a small group, comprising of Executives and Directors, to understand where new drivetrains like EVs were heading and their potential impact on Australia.
“We visited Norway, Sweden and the UK, because those markets are more advanced than the Australian marketplace, to try and understand the impact of the changes that had already occurred in some of those Nordic countries. It was also about understanding what the downstream impact was at the at the workshop level.
“That intelligence now helps us be part of shaping the future of our industry, and specifically helping our members understand some of the things that they
want to or should be aware of.”
Fraser says information they can o er can help a workshop understand whether they should be preparing to adapt or should be becoming proficient and equipping immediately.
“Our members will say one of the most significant marketing tools is word of mouth, contributing to more than 50 per cent of their new business. My message is; if you start turning away vehicles because you’re not ready for them, you risk losing, not just the customer you’ve turned away, you risk losing other future customers.”
Fraser says other learnings from visiting advanced workshops can also be shared with members such as how EV uptake a ects workflow for maintenance and repair.
“A workshop of that kind in the future would be reliant on higher volumes and therefore, you’re going to need more cars in and out on a daily basis. Then you’ve got to think about trying to help the customer understand not to come back at the end of the day, for instance, but come back by lunchtime because otherwise you need to find some way to store that car.”
Lights, cameras, action
Fraser explains that one of Capricorn’s strengths is having the breadth to investigate future technology to see how it will serve members needs and help them meet these future demands. Their joint venture with remote technician service providers Repairify, who have established a global reputation before their launch in Australia in 2023, was an example of bringing the leading technology into the Australian marketplace.
“We saw that as a growing opportunity, a growing need for the market as more people invest in that sort of service and repair perspective.”
He said Capricorn was vigilant to the increasingly prevalent ADAS technology and the recognition that cameras, radar and in the future, LIDAR sensors were inescapable elements in new car comfort and safety.
“It doesn’t really matter whether it’s
an electric vehicle, or whatever mode of drive train, the reality is ADAS is the future,” he says.
“I think vehicle connectivity is another way of the future. Telematics has been around for a long time but clearly vehicle connectivity is going to be a key future driver. As Capricorn’s business evolves over the coming decade, we will look to help our members and have a bigger part of that.”
Another example of Capricorn’s growth lies in the uptake of other services including loans and risk protection (an alternative to insurance).
“I look at our loan book as a barometer as to the health of the industry,” Fraser says.
“If people are prepared to reinvest in their businesses, through the need to buy more capital equipment then I see that as a positive. It’s another example of us helping out. We’ll always be looking for new pillars of growth to help support not just our growth but our members growth.”
This ethos and a brand loyalty to Capricorn have also helped with their insurance products which have enjoyed
a 98 per cent renewal rate.
“Capricorn Mutual is a discretionary mutual and unlike an insurance company, operates as a non-profit entity solely for the benefit of its members. That is something we promote as a benefit.”
The industry specific application of risk protection also helps members because of the increased focus and knowledge of automotive businesses, their particular risks and liabilities.
“It’s very tailored to our members’ businesses. Our risk account managers can visit the members’ workshops, they can do a proper risk assessment in the business and help the member understand what might have changed because they sometimes overlook things themselves. We can help them understand their protection needs.”
He says the dedicated sales force means they can advise with preventative measures whether it is helping prevent fires in a spray booth by ensuring service is up to date or taking precautions with Lithium-Ion batteries, both in EVs and the multiple applications they have in tools in the workshop.
But growth often comes with the risk of dilution and the challenge of keeping a culture alive. During his years at Capricorn, Fraser was determined to avoid this.
“We needed to grow the membership, but we also needed to be able to support a growing membership, and make sure that we were having good quality conversations each time we visited the workshops.
“The last thing I wanted to do was to grow the membership to a point where our sales force were only focused on new member acquisition and therefore weren’t able to spend quality time with those members who had joined.
“For me it was about really repositioning Capricorn in the marketplace. Certainly, grow the membership, because a growing membership would help grow our business, but I also genuinely believe that it would make our industry stronger. What was driving me was wanting a
stronger, independent aftermarket industry.”
Fraser is a firm believer a culture must be the foundation for successful growth.
“You can have the best dressed strategy in the world but if you haven’t got the culture to support it, then you won’t be successful. That’s been an important part of what we’ve tried to build. My goal was to really work hard on developing our culture and that’s something that you should never stop working on.”
Stepping away from Capricorn later this year, he will leave the helm in the hands of current CEO of Automotive Brad Gannon. Fraser will look toward more board activity where he believes he still has a lot to o er. He believes it is a passion for the industry that he will take with him, after it has been one of his formative characteristics over the decades.
But looking back, Fraser says, his greatest satisfaction has come on a more basic level, with the direct contact
with the members, talking to them about their businesses and how Capricorn can help.
“They are salt of the earth people. And I’ve really enjoyed trying to understand what their pain points are and by listening to them, work out how we can foster a better Capricorn,” he says.
“You’ve got to be a good listener and you’ve got to encourage people to have those kinds of honest conversations. I’ve always been one that says, ‘don’t be defensive, be curious.’”
His parting thoughts return to an optimism about the industry and his belief in strength that grows out of unity.
“You can achieve more by working together than you can by standing alone,” Fraser says.
“When I consider the numerous challenges our industry is currently facing or will encounter as it evolves over the next decade, it’s clear that many of these issues are shared. By collaborating, we can work together to find solutions to these common problems.”
Leading the way with a revolutionary way of work for Australian businesses, Iain Kippen from Bissell’s Paint and Panel has cracked the code for creating a healthy and sustainable balance between personal life and work.
A four day working week and year round sunshine sounds pretty idyllic.
For Bissell’s Paint and Panel in Noosaville, Queensland, this dream lifestyle is fast becoming a reality.
Having been nominated and awarded three best bodyshop of the year awards since 2021, there is something that Bissell’s Paint and Panel is doing that is working in their favour.
Spearheaded by businessman Iain Kippen, Bissell’s Paint and Panel is a workshop embracing a new way of both working and living.
National Collision Repairer sat down with Iain Kippen to discuss how workplace productivity has risen since going to a four-day work week, and
how he promotes and maintains a happy, and balanced community of sta .
Hailing from the United Kingdom, Kippen and his family relocated to Noosa from England for a change of scenery in 2001.
The Bissell’s Paint and Panel business had already been in operation for over two decades before Kippen took over in 2010.
Coming out of retirement after nine years, Kippen bought the panel shop for his son who had experience in the automotive industry.
Despite not having experience in the
technical side of automotive, Kippen had a keen interest in collecting cars. In the early 2000’s, Kippen would take his cars to the former owners of Bissell’s who had a niche for restoring old cars.
“When they o ered to sell the business to me, I initially had no plans of going back to work. As a family we took the challenge on, and built it up to what it is now,” Kippen says.
In 2010, the shop was relatively small, but it already had a solid reputation locally.
“As a family, we decided to build a purpose-built workshop. We are now a medium to large sized workshop. My son is now at the helm of the business, and my daughter is also the business accountant,” Kippen says.
A businessman with a good eye for opportunity, Kippen brought his British expertise to Australian shores to create a well-respected workshop where sta are treated as the main priority.
Before Bissell’s, Kippen had no prior experience in the automotive industry, but that has not stopped him from creating an e cient and streamlined business that is always looking for areas of improvement and sta
satisfaction. Kippen identified how the Australian automotive scene in 2010 was starkly di erent from the UK.
“It was quite a shock to begin with, there was no real regulation. After a few years, and a few workshops uniting to initiate change, we were among the first onboard to welcome and embrace the new ways of operating,” Kippen says. “I come from a business background, not a panel background, so I view change quite di erently. I have been very fortunate to have also had great sta who have embraced the change as well.”
Embracing change has helped Kippen to propel his business into new territory on how a business can potentially operate in Australia.
What makes Bissell’s Paint and Panel stand out from other businesses and repair shops, is their revolutionary fourday work week; e ectively covering the full allotment of working hours with one less day on the roster for sta .
Kippen cites the COVID-19 pandemic as the major instigator for the four-day change. Bissell’s was still operational during the COVID lockdowns, and it was during this time that the idea
was planted in Kippen’s mind to really consider a major dynamic shift in the workplace.
“The pandemic was life changing, and it changed everyone in some way. Our business certainly changed after COVID,” Kippen says.
“It was during a smoko break, around the time when the Queen passed away, and the guys were talking and joking about how great it would be to have a four-day work week every week.”
Kippen’s business mind quickly clicked into gear, and he began thinking of the logistical side of implementing such a change.
“If you run a workshop correctly, you are only billing hours, not selling days or weeks. You have X amount of hours you can use. So, I told the guys if they wanted to work four days, go for it, it shouldn’t make much di erence,” Kippen says.
After consulting his family, and discussing the potential side e ects, they decided to run with the idea. However, with twenty-two sta members under Kippen’s leadership, the change didn’t come without precautionary measures.
“I put out a survey for everyone to fill out. I had to make sure that everyone
was happy to have a four-day work week to start with,” Kippen says.
Addressing the advantages and the pit falls was also part of the process in changing the work structure.
“With a go ahead with the survey results, and through increasing the hours each day slightly, we were able to make it work,” Kippen says.
Kippen outlined how his sta have 20 per cent less travel time each day, and the equivalent of nine extra weeks at home.
“By reducing our work week from five to four days, our turnover went up by 20 per cent. Everyone got a wage rise, so everyone was happy. I also found that there was less downtime, as everyone wanted to complete the work,” Kippen says.
After the three-month trial Kippen had a meeting with each sta member individually to discuss the four day work week.
“The emotion in the guy’s faces was unbelievable. They were happy to come to work,” Kippen says.
“I had one guy say that for the first time ever, he was able to pick up his children from school. I had another guy, who was a surfer and he loved surfing on Friday when nobody else was on
the waves. The benefits are fantastic,” Kippen says. “The four-day work week works. It absolutely works.”
Creating a community in a workplace is one of Kippen’s strengths. Listening to sta and implementing their feedback on work/life balance was the driving force for Kippen’s decision to move to a four-day work week.
“Over the last three years, I have really focussed on the mental state of everyone who works with me. I ensure it is a positive place to work. We put work happiness and satisfaction over a profit,” Kippen says.
Constantly analysing e ciency standards and processes is Kippen’s speciality. Working one week on-site in the workshop in Noosa, and three weeks remotely from his home in
Victoria’s High Country, Kippen has the luxury to be that one step removed from physically working in the business.
“Any business needs to run e ciently, with streamlined processes, with very little waste. It needs to be easy,” Kippen says.
Bissell’s Paint and Panel’s streamlined processes include low cycle time, high quality repairs and equipment and quality service to the customer and work provider.
“Getting your car repaired isn’t a nice thing to do. So, we try and make sure that the experience is as comfortable as possible,” Kippen says.
For Kippen, refining the booking systems and progress reports allows for a streamlined structure that benefits not only the flow in the workplace, but the clients as well.
“If the car isn’t being touched, it
shouldn’t be in the workshop. Having everything in check and operating well allows smooth and e cient sailing throughout a work day,” Kippen says.
Creating an atmosphere where the sta are happy to work and challenge themselves is also part of Kippen’s streamlined e ciency ethos.
“After implementing the four-day work week, our business was more streamlined because our sta were happier. Everyone wanted to be there, everyone cruised through their work,” Kippen says.
Sta meetings once a month allow Kippen to touch base with his sta and ensure everything is on track.
“When I am up in Noosa we have a training day after work. But it is really just a chance for everyone to catch up and have a chat,” Kippen says.
“It is the sta that make a business, you have to listen to them.”
Identifying weaknesses within the business structure is also a strength of Kippen’s, and acknowledging the limitations in the chain is something Kippen embraces.
“For a panel shop, repairing 40 to 50 vehicles a week is optimum, and the most e cient profit per vehicle. We have the capacity to repair more, but we ensure quality is our main target,” Kippen says.
With one successful shop with happy sta and a system that works well, Kippen is not too interested in expansion at the present time. However, fine tuning the existing structures will always be a priority.
Bissell’s Paint and Panel have embraced the new technologies of the future. With I-CAR Gold Class Collision Status under their belt, they are constantly upskilling and training their sta for the new developments on the horizon.
“We always stay up to date with the latest technologies and trainings. You can fall behind really easily, so it is important for us to remain ahead of the game,” Kippen says.
Working on EVs has broadened Bissell’s Paint and Panel clientele,
but the EV landscape hasn’t taken over ICE vehicles just yet.
“I’m still not convinced that the volume of electric vehicles will overtake petrol cars in the expected time frame,” Kippen says.
“But there will still be a good percentage of EVs coming through our workshop, but it is not the 30 per cent we expected. Yet, you still need to be able to handle that.”
“We focus on keeping ahead of the game through upskilling our sta and equipment. We need to stay aligned with the evolution of the industry.”
Even with each workshop member either an I-CAR Gold Class or Platinum member, there is always something new to learn in the next wave of automotive developments.
“There is always something to keep up with, whether that is the di erent metals being used, or the carbon fibres, there is always something to keep up with. EVs and ADAS are the latest and biggest thing,” Kippen says.
Since implementing a few key changes, including the four-day work week, Bissell’s Paint and Panel has not had any trouble retaining or finding sta .
“People want to come and work here. We are lucky to have loyal workers as well,” Kippen says.
Bissell’s Paint and Panel has four apprentices who stayed on after their training. They are now fully qualified panel technicians and they are still working in the shop.
“We are fortunate to have good sta , including our apprentices. We have really focused on creating a community where people want to stay,” Kippen says.
“We don’t give our sta any reason for them to go elsewhere.”
Extreme weather events including hailstorms are having an increasing impact on the auto-insurance and collision repair industries.
2023 may have been a calmer year for insurance claims but one extreme weather event still cost the nation $1.6 billion in losses, including about $170 million in motor losses.
The latest damage estimates of the Christmas storms across the eastern states comes at a time of increased focus on extreme weather events under climate change across the globe and their impact on the repair and insurance industries.
Perils, an independent Zurich-based organisation providing industry-wide catastrophe insurance data, released its third loss estimate for the Australia Christmas Storms which a ected Victoria, New South Wales, and Queensland from 23 to 29 December last year.
The updated industry loss figure is of $1,563m and is based on detailed loss data by postcode and property and motor hull lines of business that Perils collects from the majority of the Australian insurance market.
While the majority of the figure, 72 per cent, relates to property losses
from the private sector, eleven per cent has been attributed to motor losses including damage caused by extreme elements such as large hail shattering windscreens and damaging panels.
Almost three quarters of the claims were made in Queensland, a quarter in NSW and five percent Victoria.
Perils Head of Asia Pacific Darryl Pidcock says the damage came amidst a relatively benign period of major natural catastrophes in 2023 compared to previous years.
“Notwithstanding, it highlights the increasing risk not only of severe convective storms along coastal regions but, as we observed in this case, the potential for competing air pressure systems prolonging storm activity over an extended period,” he says.
“Combined with PERILS Industry Exposure data it enables further insights to be obtained especially regarding vulnerabilities of the di erent lines of business by linking physical intensities with insurance losses.”
In the US, the CCC Intelligent Solution Q2 Crash Course Report has a
specific focus on hurricanes and convective storms in the US with a specified aim to help the industry to navigate the 2024 extreme weather season.
While hurricanes in the US wreak the largest amount of damage, it is hailstorms that account for the largest amount of automotive damage with a 17 per cent increase in the number of storms unleashing hailstones three cm or larger. This resulted in an increase of comprehensive claims to 11.8 per cent for all claims in 2023 from nine percent in 2020.
But they are also 21 per cent more costly than a comparable comprehensive claim and while they often include dented panels and broken windscreens, they can also include costly damage to sensors and cameras.
As recently as May 2024 hail shattered windscreens in Texas and in June reports of hails as large as pineapples were made in the same state, possibly the largest ever recorded.
Some scientists like, Associate
Professor of Atmospheric Science, University at Albany, New York, Brian Tang believe the atmospheric conditions that produce very large hail have increased in the US.
The CC report also noted higher frequency of this damage with severe weather events occurring in states where they were once less likely and with larger populations there a ected.
The report has interesting lessons for Australia where extreme weather events are also of concern to the insurance industry, most frequently from floods and bushfires but also from other extreme weather.
The Insurance Council of Australia has highlighted the growing protection gap of many Australian households as risk and premiums increase.
It lists extreme events like the 2023 Christmas’s deluge a ecting three states and two major hailstorms in Queensland in 2020 that caused $2.5 billion of damage, as examples of the damaging conditions this weather can produce.
An Insurance Council of Australia (ICA) spokesperson outlined why vehicle insurance premiums are increasing, “Each insurer calculates its motor vehicle insurance premiums according to their own underwriting (insuring) criteria and will use these criteria to determine the risk of individual policies,” the ICA spokesperson said.
“Currently motor vehicle premium prices are rising because of the increasing value of motor vehicles making them more costly to replace, inflation and supply chain issues driving up repair labour costs and price of motor parts, and the increasing cost of capital for insurers driven by ongoing extreme weather events.”
According to the ICA, motor
insurance claims costs rose by 43 per cent between 2017 and 2023, which is double the rate of inflation for the same period.
“Cars are now more complex and sophisticated - a small ding that might have once sent drivers to the panel beaters for a straight-forward repair now requires fixing and testing the complex sensors that are used for navigation and safety systems,” the spokesperson said.
The latest Crash Course report from the US cited the Colorado State University as also predicting 11 hurricanes for the US this 2024 season with five categorised as major events.
The CCC industry analysts and experts provide an insight into historical claims and repair data, while also evaluating geographical and migration trends, as well as non-peak perils, such as hail.
“Extreme weather events are increasing in severity, becoming major disruptors in the auto claims and repair industry,” said Crash Course co-author and CCC Industry Analytics Director Kyle Krumlauf.
“Our Q2 report delivers critical insights, showing that the frequency and severity of storms are not just a seasonal issue but a persistent challenge that demands strategic planning and swift adaptation from industry players.”
The report’s insights and data allow repairers to validate their current strategies, make informed adjustments, and enhance their preparedness. It also recommends:
Utilise claim management technologies. Claim management technologies can
help reduce the need for carriers to put personnel physically on the ground and streamline repeatable processes. This approach can vastly improve the employee experience while also ensuring storm-related claims are settled accurately and e ciently.
Prepare for downstream impacts. As economic challenges persist for consumers, the potential for vehicle damage to go unrepaired continues to rise, especially as motor vehicle costs rise. As of April, the consumer price index for motor vehicle insurance was plus 22.6 per cent year-over-year and plus 41.7 per cent since April of 2022.
Assess repair inventory. Hurricanes and other severe storms may impact supply chains, potentially halting or delaying parts deliveries to shops, which can impact productivity. While the unpredictable nature of weather events can make planning ahead di cult, there are two ways shops can prepare for this possibility. One, is to review current parts inventory, assess stock levels and identify critical components that are likely to be in high demand. Two, is to maintain strong relationships with suppliers to secure priority access to parts when supply chains are disrupted.
Communicate clearly and regularly. Given the unpredictability of storms, it’s important for carriers to engage with policyholders by maintaining open and transparent communication. Providing timely updates on storm forecasts, evacuation orders, and claims procedures will help mitigate losses and get people out of harm’s way. Repair shops can leverage social media and online communication tools to update repair timelines, operation hours, and rental car availability.
‘Work
smarter not harder’ is the adage and, according to PPG’s business experts, there has never been a better or more important time to look closely at workshop e ciency.
Repair industry veteran Greg Tunks has visited hundreds of shops in his capacity as a business advisor and manager for PPG’s MVP Business Solutions and he is forthright when it comes to the challenges they will continue to face.
Maximising volumes, skills shortages, insurer negotiations, the pressure from MSOs and new technology are all pressures adding to the everyday grind facing workshops, he says.
But Tunks says this is why an outsider’s objective view can be the first step in helping small to medium businesses find solutions to some of these issues.
“I think a lot of body shop owners and managers don’t get out and see what is going on down the road, while we have the luxury of visiting hundreds of body shops right across the country and seeing what works and what maybe doesn’t work in a wide variety of places. Having an open mind and thinking about how they can do things a little bit di erently from a shop owner perspective, and listening to outside suggestions can be a big help for them.”
Best of all, he explains, these incremental improvements can be made without any compromise to quality but have demonstrable benefits to turnover and profitability.
“They need to look at how they can become more e cient by changing the way they process the vehicle through the shop, to enable some of those businesses to do the volumes without sacrificing the quality.”
“A common misconception is people say ‘I’m working flat out; I physically can’t do any more.’ A part of our business solutions program is going in
and looking at businesses and seeing where they can eliminate the waste. A lot of people don’t really have an understanding of lean methodology, or lean training. Where you can eliminate the waste out of the business, you can produce more without working any harder. But until you actually take a step back and have an outsider come into your business, and physically stand back and look at what you’re doing you may not discover these elements. The numbers tell us one thing from a financial perspective, but the shop floor experience comes into play as well.”
One example Tunks cites is the possibility expensive equipment can be underutilised, such as not harnessing the full potential of spray booths.
“One spray booth should be able to do 25 cars a week comfortably, and yet, we have shops with two spray booths, and they’re still only doing 20 to 30 a week. By utilising your spray booths better, as an example, we can produce more work”.
He says the expert consultants from MVP Business Solutions can look at the workshop process to ensure each stage of a repair helps this e ciency and volume.
“You don’t spend $150,000 on a spray booth to mask a car,” he advises. “You spend it to spray, flash and bake a car. You don’t buy one to mask a car. You don’t buy one to prep solid in.”
Tunks says some large MSOs have a target turnover time for their booths of 45 minutes and if he sees a booth cycle time in a shop of 2-3 hours, he identifies how much more capacity they have.
“If you look at how equipment is
utilised, you can pick up how some of that wasteful time can be put into producing more cars, putting more work through a shop without increasing your overheads.”
He said they also look at the layout and design of a workshop and how it can a ect this e ciency.
“Go back to the 80’s and the spray booth was down the far back corner of a workshop and if it is like that now it’s totally in the wrong place. Existing shops can change things by just moving some stu around and changing the layout.”
He says workflows and tra c management plans are other areas where the advice from outside experts can have a significant e ect on e ciency.
“With Business Solutions it is about having a structured business from front to back, not just in reading numbers and facts and figures, but looking at processes and everything else that goes on the workshop floor.”
The holistic approach to the workshop can then look at the other elements a ected by the increase in cars numbers whether it is check-in, estimating or fitting.
No matter where the business is, the starting point for Tunks and his team of six consultants at MVP Business Solutions is listening. The individual qualities of each business and the issues they face are important to hear and study, so they can enrol their expertise into a range of tailored suggestions that form part of the consultation.
Listening is what the MVP team are good at, and they are also hearing from shop owners about industry wide issues like the skills shortage, Tunks says. While they don’t consult specifically on sta solutions like recruiting or utilising skilled migration to fill the gaps, they can advise on
elements in the existing business that may ease some of the sta pressures.
“Sta are the backbone of your business, and you cannot survive without them. We aim to make a better workplace for all the sta that are involved, so they actually enjoy coming to work. By providing an organised work environment, it makes it better to work for those business owners.
“We’ve made shops more e cient and the sta more e cient. They don’t physically work any harder, they just work easier by removing the hurdles they have to jump over all the time in the workshop. They become better, more e cient and generally happier.”
Tunks explains that this has an enduring impact on sta retention because people remain in jobs where they are happy, but it can even help attract new recruits considering desirable workplaces.
“Having an organised, clean work environment counts for a lot. If you’ve
got a well-organised, well stocked workshop and you’ve got decent equipment, you’re halfway there.”
He said elements like investing in dust extraction in a panel beating workshop are a practical step that can change the work environment and bring it up to date, similar in the way paint shops evolved with protective equipment for spray painters.
Tunks’ experience has also given him insight into advising on how businesses can meet the challenges of advancing technology such as ADAS calibration. His understanding of workflows, the space available in the workshop and the equipment needed can be helpful in assisting business owners in deciding whether to invest in the business opportunity.
Whatever decision they make, Tunks advises a passive “wait and see” attitude can mean potentially losing business. This alertness and “staying on the front foot” are critical as competition increases and he cites the example of traditional hardware stores which declined as they failed to change.
“If you keep doing the same thing and the same way that you’ve always done, you will become extinct. The world is going to move on by, and you know you need to do something di erent to survive.”
But if businesses have the willingness to change and thrive, he says, this is where MVP Business Solutions’ perspective and expertise can be a great advantage to ensure a business’s health and profitability into the future. The way they study each business is not as a list of problems but as opportunities for improvement. The consultation also comes free to PPG supplied businesses.
“It costs you nothing to try and you’ve got nothing to lose.”
PPG’s MVP Business Solutions program is available as part of PPG’s comprehensive support package. Enquire at mvp.anz@ppg.com or call PPG customer service on 13 24 24 (Aus) 0800 320 320 (NZ).
The Sheen Community Fund has a long history of philanthropy but one practical and inestimable reward is the smiles it brings to young people’s faces.
With a well-known culture of generosity and philanthropy, Sheen Panel Service is focussed on building strong relationships within the community and workshops.
Sheen Panel Service created The Sheen Community Fund to help streamline their community work. The Sheen Community Fund is a dedicated charity fund helping families and children in need.
In July, The Sheen Community Fund
focussed their e orts on partnering with a true and trusted children’s charity, Variety, to deliver bikes for underprivileged children for the Bikes for Kids Foundation.
Head of Operations at Variety, Kellee Ireland, spoke about the work the charity does to help improve the lives of disadvantaged children.
“At Variety we really focus on helping children and families who come from low socio-economic backgrounds, and
children with disabilities. We recognise the stress that families are under, and we want to help in any way we can,” Ireland says.
“We are grateful that Sheen partner with us to deliver such a great day for the kids who really need it the most.”
The day kicked o with members of the Sheen Panel Service Sunshine building the bikes in their pristine workshop. In under two hours, members of the Sunshine Workshop built twelve bikes of all sizes for twelve lucky children.
Sheen Panel Service Sunshine manager, David Farrugia highlighted the importance of the day for the community.
“All the guys jumped on board to help put this day together. No one had to come in on their Saturday, but everyone was happy to help,” Farrugia says.
“It’s a great day, everyone enjoys it. It’s priceless seeing the families and children come in and see their bikes.”
By midday, red, fluorescent pink,
and rainbow coloured bikes lined the workshop walls waiting for their new owners to take them home and enjoy them.
As the families arrived with eager anticipation, the children inspected the bikes as they patiently waited for the presentation.
While the finishing touches were being made on the bikes, the families and team members enjoyed a BBQ and co ee van.
Once the bike building was completed and each bike was given all clear by a safety technician, the families listened to a speech from Variety CEO Mandy Burns. Each child was then called up to receive their bike, with a goody bag and chocolates from Sheen Panel Service.
One parent kept the day as a surprise for her two sons, who did not realise they were going to be gifted a bike each.
“They were a bit confused when we arrived, but now they’re so happy and cannot stop smiling,” the parent says.
“They can ride the bikes to school, to their friend’s houses, it will be great.”
The strong community spirit on the day was underpinned by Sheen Panel Service and the team members at Variety who went the extra mile to make the day an inclusive experience for everyone involved.
“We’ve addressed a specific need, and everyone gets a bike. We bring
the family in under the Sheen banner, and everyone’s had a great, heartfelt day,” a Sheen Panel Service spokesperson says.
The vision of Variety – the Children’s Charity is for all children to reach their full potential regardless of background or ability.
With a network of 40 o ces across 14 countries, Variety is dedicated to supporting children who are living with illness, disability or experiencing disadvantage through the lack of the provision of grants, scholarships, programs and events.
Variety’s work helps children to achieve freedom and mobility, access
their community, communicate and achieve independence and increase self-esteem.
In Victoria, Variety holds numerous events every year to help. disadvantaged children.
“Every year we have an event for 5,000 children across Victoria. We all come together, and everyone gets a gift. For some children who attend, it will be their only present for the entire year,” Ireland says.
“For Sheen to facilitate a day like this, it makes all the di erence.”
Sheen Panel Service ensure that their fundraising e orts flow into some of
Victoria’s much needed charities.
Sheen Panel Service has a prominent history in Victoria’s repair industry. Their philanthropic history spans more than 30 years, and the culture they have crafted brings a sense of community.
The Sheen Community Fund is expected to raise more than $300,000 in 2024 through donations.
Whichever causes are the beneficiaries, the fund’s principle remains the same; a conscious determination to change people’s lives for the better.
The flexibility of the Sheen Community Fund was again on display in April for the Good Friday Appeal.
In April, the fund, supported by Sheen Panel Service, donated $35,000 to the Royal Children’s Hospital – Good Friday Appeal. Sheen partnered with 3AW and the Sheen team members
joined the Climb for The Kids event. Sheen committed the event’s largest contribution.
Sheen Panel Service has a long history of supporting the Good Friday Appeal.
“The shops contribute to the fund every year on a corporate level, so all our businesses pay their way and contribute to the community fund. That’s built into the way our business operates,” a Sheen spokesperson says.
The funds raised went towards research and equipment at the Royal Children’s Hospital to treat critically ill children. The fund’s contribution helped the Good Friday Appeal raise an incredible $20 million in 2024.
These positive results of making a di erence then flows onto the 27 Sheen Panel Service workshops that contribute to the Community Fund.
Shining a spotlight on the Apple Isle, this month’s Future Leader is award winning Jack West from southern Tasmania.
NCR spoke with Jack about his most recent award win, and on his experiences and learnings so far in the automotive repair industry.
The Tasmanian Automotive Chamber of Commerce (TACC) and the Victorian Automotive Chamber of Commerce (VACC) held their annual President’s Gala Dinner at the Palladium at Crown on the 29th of June.
An array of awards were presented on the night, including apprenticeship and automotive excellence awards. Jack took home the TACC Apprentice of the Year Award under his apprenticeship workplace, European Technology Bodyworks, Bocchino Pty Ltd.
Jack says he was thrilled by the
recognition of his e orts with the award.
“I am very happy to have won and I thoroughly enjoyed my time at the presentation night,” Jack says.
Growing up in Hobart, Tasmania, Jack’s first dabblings in the industry was through work experience while completing his Year 10 studies.
Now, five years later, Jack has completed his certificate 3 in Automotive Body Repair Technology at TasTAFE, and is working full time at European Technology Bodyworks, Bocchino Pty Ltd.
“I am currently working on small to large jobs on all types of vehicles. It is great to reflect on how far I have come,” Jack says.
Navigating the automotive repair industry is a challenging career path, with the constant changes and training, and Jack has done well to adapt and continues to work hard at learning.
Jack’s favourite part of the job is seeing the end result.
“Seeing the final product of my hard work is my main motivation,” Jack says.
Jack identified the key traits and attributes that he has observed in his career so far that have made a good leader.
“Problem solving and communication are two areas that I would highlight. Both traits have been essential in my learning and apprenticeship so far,” Jack says.
NCR recognises the ongoing support of IAG for the Future Leader’s series, along with the continued support of I-CAR in developing industry skills.
Jack’s colleagues at Bocchino Pty Ltd have encouraged him each step of the way, and celebrated his Apprentice of the Year award with him at the President’s Gala.
The General Manager at Bocchino Pty Ltd, Angelo Bocchino, praised Jack for his growth and integration into their team.
“Since joining our team, Jack has shown remarkable growth and development. Initially quite shy, he has developed into a confident and integral part of our team,” Bocchino says.
“His hard work and diligent focus on
every task have been exemplary. He consistently collaborates e ectively with his colleagues, always willing to go the extra mile to ensure his work is flawless.”
“His respectful and honest demeanour has garnered him the trust and admiration of both his peers and clients.
“Furthermore, his readiness and proactiveness in assisting others whenever needed highlights his commitment to the success of our team and to the workshop as a whole.”
Next in line for Jack is to further
develop his training and development through upskilling in his new area of interest.
“I would like to start a spray painting apprenticeship in the future. I am always thinking of ways to improve and learn new skills,” Jack says.
With five years in the industry, and an apprentice of the year award to his name, Jack is well placed to share some advice for young people entering the automotive repair industry.
“My main advice would be not to be afraid to ask for help,” Jack says.
“We all have to start somewhere.”
EV training and compliance are a matter of urgency for the collision repair industry and Australia’s leading aftermarket association is turning up the pressure on governments to ensure businesses get the support they need.
Sometimes it comes down to a di erence between the idea and the reality.
Legislation for a New Vehicle Emissions Standard has passed parliament but the details of how this will look as the Australian car parc transitions to EVs and how they operate successfully, is not so clear.
The Australian Automotive Aftermarket Association (AAAA) is pushing for the whole life cycle of vehicles, particularly repair, to be properly looked at by government, along with industry readiness to meet the change.
“We need to ensure that there’s the expertise out there to work on these vehicles safely and e ciently, and that just isn’t being prioritised by governments, and it will mean that people have poor ownership experiences,” CEO Stuart Charity says.
“It potentially increases the cost of insurance, and if cars are having to be written o because the industry doesn’t have the skill sets or the ability to repair them e ectively, the public will lose confidence in the technology.”
Charity has been a voice of warning that the best intentions of a push towards a zero-emission fleet could be undermined if the whole of the lifecycle experience is not considered, including e cient and widespread charging infrastructure and the ability to meet the repair needs of the new vehicles.
“A holistic EV transition approach needs to be implemented to ensure that someone’s first EV purchase is not their last.”
Already the US market, that has a higher uptake of EVs, is encountering repair problems and leaving EV owners with a bad experience to the point where
some are turning back to ICE vehicles, To avoid these future issues of unwanted vehicles stockpiling and lowering targets, Charity says governments need to act now.
The AAAA has also highlighted the willingness of the repair industry to play its part in supporting a new low-emissions car parc with one in ten shops ready for EVs and a further 24 per cent planning to do so within the next two years. This takes on a heightened urgency for the collision repair industry.
“For repair and maintenance, newer cars need less and traditionally they go to the dealers for a while under warranty. So, the general mechanical repair community has a bit more time to prepare but the collision repair industry doesn’t. These vehicles can potentially be involved in a collision, which can happen in week one of a car’s life.”
Charity says all levels of government need to have a more realistic and broader focus to ensure the transition to low emissions vehicles is a lasting success.
“They are still a small percentage of the overall car parc but we’ve seen a massive lift in the number of EVs sold, and we will continue to see a strong growth over the coming years, particularly with the new vehicle emission standard, along with the FBT benefits if you lease a car, and states also have incentives. But they’re all designed to get cars into the pipeline and that’s only one side of the equation. Governments can’t then just wipe their hands of everything else that happens from that point on in the life of a vehicle.”
“The whole ownership experience is really important. We hear from the federal government that we need more electric cars on the road, but very little in terms of policy and focus around that whole infrastructure to support this rollout.”
One of the key areas where governments can make a di erence is ensuring there is an adequate workforce to meet the demand and ensure owning an EV doesn’t turn into a repair nightmare of delays and limited options.
Charity commends the changes the Federal Government made in May by widening the criteria of the New Energy Program for apprentices, a subsidy of $10,000 for working with EVs. This was a change the AAAA and the MTAA had lobbied hard for. Now Charity says governments need to look at upskilling the existing workforce.
“There literally is not enough registered training organisations and TAFEs and other training institutes that have the expertise or the capacity to train. The issue here is we’ve got
an existing workforce of somewhere above 70,000 technicians that need upskilling and training in this area.”
Access and cost are becoming key barriers to adequate training, he says.
“One issue is the availability and the accessibility of training. Even if you want to do the training, it’s very di cult to access, and that gets magnified when you’re in rural and regional areas because the training infrastructure there is even less. It often means that technicians have to go into metropolitan centres to do that training.
“The other problem is the cost to train a technician fully, beyond the basic safety training. If you want full competency in EV repair, it’s a sixmodule training course that can cost up to $20,000 per technician.
“Then you’ve got time out of the workshop to do the training. Workshops have to invest in insulated tools and other equipment to work on EVs and set up dedicated EV bays.
“It’s a big financial commitment and many of our businesses are familyowned operations, and there is not the
business case at the moment to invest in this because they’re not seeing the government support. Without support, if you did it on commercial reasons now, based on the number of cars on the road, it doesn’t stack up.”
The AAAA would like to see governments, at both state and federal level, focus on increasing the capacity of the training organisations to be able to deliver this training and potentially subsidise it, to make it more a ordable for all businesses. The AAAA is also looking for support, whether through tax incentives or other programs, to help businesses with the capital equipment purchases, to encourage workshops to invest in this capability.
“The government wants something like 80 per cent of all new cars sold by 2030 to be electrified, if we want to achieve that, we need to be investing in the infrastructure now to be able to support it.”
Charity says there have been positive steps so far in training, including
grants for EV training undertaken by the MTA NSW and MTA SA and some private industry players. The Australian Automotive Service and Repair Authority has also seen strong interest, with around 700 industry participants signing up for the EV accreditation to access the OEM information AASRA can open up to technicians. But he stresses this is only a starting point.
Charity says compliance with the basic EV safety module will also have serious implications for the risk assessment of a business and occupational safety of workers across the industry, so governments have a responsibility to support these developments.
“As a bare minimum, particularly collision repair workshops if they’re taking in electric or even hybrid vehicles, they should have all their sta trained in that basic safety procedure to be able to depower and make a vehicle safe. We should have Australian standards around an EV bay set up and personal protection equipment etc.”
Charity also stresses that dedicated and supported training will also be crucial in shaping a future generation of workers.
“The challenge with the apprentice scheme is they’re going to take four years before they’re fully qualified,” he says. “But that is a good start and will help attract talent into the industry. Electric vehicles and new-vehicle technology will help attract the sort of calibre of young talent into the industry that we need to take us forward. That’s a positive.”
The next step in the journey will be the release of the parliamentary committee’s report into the transition. Whatever that reveals, it is certain the AAAA and other industry advocates will be keeping a close eye on its results and taking the arguments to the key players in government.
“We’re talking to all those ministers regularly about these issues, creating a bit of awareness about this and hopefully we can get focus from government on helping the industry to transition.”
As car manufacturers gear up to deliver automated driving technology, Australian regulations surrounding crash responsibility could shift to insurers and automotive manufacturers.
As car manufacturers like MercedesBenz deliver their Level 3 autonomous driving technology, the Australian Government is working towards establishing a safe deployment of automated vehicles.
Mercedes-Benz has begun rolling out Level 3 autonomous driving technology on a market-by-market basis through its Drive Pilot software.
The Drive Pilot software was first introduced in Germany as an optional extra on certain models from May 2022. The US states of California and Nevada followed suit in 2023.
In media reports Mercedes also said for crashes using autonomous settings of level 3 or upwards, responsibility could lie with insurance providers, software developers, and automotive manufacturers rather than the driver.
Mercedes-Benz’s autonomous driving program head Jochen Haab, told website Drive that while the approach was still only theoretical as they had had no accidents yet with those applications, they could take financial responsibility for the crash under certain circumstances.
Australia currently allows Society of Automotive Engineers (SAE) Level 2 standard of automated driving.
Level 2 is categorised as partial driving automation. These features provide a combination of steering and brake/ acceleration support to the driver.
Level 3 means conditional automation under certain conditions – the car can be in control of up to 60km/h, but only on a freeway and the driver must be able to take back control within 10 seconds.
Mercedes is hoping to increase the speed permitted to 90 km/h later this year, and 130km/h by the end of the decade.
From Level 3 upwards, instead of drivers being held to blame in the event of a crash, the responsibility can be put in the hands of insurance providers, software developers, and automotive manufacturers – when the car is operating under autonomous settings.
Current Australian laws do not allow for the use of automated vehicles on public roads. Australia is in the process of updating regulatory frameworks for vehicles to ensure the safe operation and use of automated vehicles on public roads.
Infrastructure and transport ministers, through the Infrastructure and Transport Ministers’ Meeting, have agreed on a national approach to regulating automated vehicles. The department is working with the National Transport Commission and state and territory governments to implement this national approach.
A new law called the Automated Vehicle Safety Law (AVSL) will be an important part of this framework. The AVSL is being developed by the department in line with the National inservice safety framework for automated vehicles developed by the National Transport Commission.
The AVSL will place the responsibility for the safety of an automated driving system on a corporation and not the human driver. This corporation will need to have the right skills, capacity and capabilities to look after the automated driving system over its operational lifetime. The corporation will be known as the Automated Driving System Entity.
The new Automated Vehicle Safety Law will be supported by
complementary changes to state and territory legislation and to existing Commonwealth legislation such as the Road Vehicle Standards Act 2018. Together these laws will form the end-to-end regulatory framework. This includes:
• making sure an automated vehicle is safe when it is first supplied in Australia, including that it meets any relevant technical standards for an automated driving system
• ensuring that there is a corporation (the Automated Driving System Entity) with the right skills and capabilities to take responsibility for the safety of the automated driving system for its on-road life
• keeping the automated driving system safe when it is operating on the road by placing clear safety duties and other obligations on the Automated Driving System Entity
• ensuring that people that use and interact with an automated vehicle understand what their roles and responsibilities are
• These laws will create the regulatory arrangements to enable safe operation of automated vehicles on our roads and should help Australia to gain the potential benefits of automated vehicles.
Crash damage caused when the driver is not even in the car are the among most common form of insurance claims according to a new report.
The Royal Automobile Association data highlights that vehicle damage caused while it is parked is the most common reason for making a car insurance claim – accounting for more than 10,000 claims every year.
The South Australian insurance provider and motoring association highlighted the top 10 most reasons for a car insurance claim and with ‘damaged while parked’ was the highest at 18 per cent of all motor claims.
This cause was followed by hit fixed object, (17 per cent), windscreen damage (16 per cent) and rear end collision (12 per cent).
PPG has found new fertile ground for its coatings expertise by bringing insurers up to speed with complexities of vehicle paint.
PPG has utilised its training network to develop a specialised, national training
Head of Claims at RAA Insurance
Jess Lyons said the RAA received more than a thousand car insurance claims every week.
“In the 2022-23 financial year we paid out more than $250 million in car insurance claims,” Lyons says.
“The list of most common claim types makes for interesting reading – with the most common cause being vehicles damaged while they’re stationary.
“Having your vehicle hit while parked is unfortunate and often out of your control – so you probably don’t want to be footing the repair bill yourself.
“In this instance, we always recommend getting the details of the driver who hit you if you can, so your insurer can help you investigate potentially having your excess waived if you weren’t at fault.
“If you’re the one who hits a parked car, you must stop and provide your details or report the incident to the police.
“We also receive a lot of claims for damaged windscreens, which can be a real safety hazard, so we recommend getting these repaired as soon as possible.”
program with specialist transport and logistics insurance provider, NTI.
The NTI training program will reach about 45 people from the NTIS’s repair management team conducted at PPG Training Centres in Brisbane, Sydney, Adelaide, Perth and Melbourne
Fabian Gaida, PPG Market
Development Manager says PPG was requested if it could provide a targeted training program to help expand the paint knowledge of the repair management team.
“NTI and PPG have worked closely together on a number of projects over the years, so we have a very good relationship.,” Gaida says.
“When NTI requested some support with training, we were happy to help out. We developed a comprehensive paint training program to suit NTI’s needs and, although it covered some quite technical aspects, it was delivered in an easily understood format. During
the one-day session we explain the di erent OEM vehicle paint layers (for both cars and heavy vehicles) and the expected film builds for each layer. From there we look at how to maintain good paintwork and some of the common defects they might come across, as well as repair methods for accident damaged paintwork.
“After lunch each group finishes with a hands-on, practical session where they learn various, best practice paint rectification methods. As we have rolled out the national training program, the feedback has given it a huge thumbs up. All the participants leave with a much better understanding of the technical aspects of modern vehicle paint.”
For more information on the extensive training opportunities through PPG, contact your PPG Representative or call PPG’s Customer Service Hotline 13 24 24 (Aust) or 0800 320 320 (NZ).
Hybrids have continued their market surge in the sale of new vehicles which, with EVs, now make up almost one in four new car sales.
The June figures from the Federal Chamber of Automotive Industries show hybrids have risen to 14.4 per cent of all new vehicles sales almost double last year’s June figure while EVs dropped slightly to 8.0 per cent (from 8.8 per cent in May this year).
But total sales for EVs so far in 2024 are 16.5 per cent up on 2023 with 50,219 new EVs on Australian roads.
Hybrid sales are partly driven by the Toyota RAV4 SUV, part of Toyota’s strategic hybrid push, at number three on the best-selling list, while the Tesla Model Y is the top selling EV at number five.
RAV4’s sales in 2024 have risen almost 88 per cent to 25,404 vehicles of which 23,934 or 94.2 per cent are hybrids. Toyota has become the first auto maker to sell more than 100,00 hybrids in 12 months.
The Ford Ranger held onto top spot for new vehicles, 6,289 in June, ahead of the Toyota HiLux (5,630), Toyota RAV4 (3,907), Mitsubishi Outlander (3,045) and Tesla Model Y (2,906).
Total sales for the first six months of 2024 were 632,412 vehicles, a year-todate increase of 8.7 per cent on last year and surpassing the previous record of 605,522 in 2018.
June was however slightly lower than June 2023 as monthly sales declined by 4.2 per cent compared to last year.
FCAI Chief Executive Tony Weber
said the yearly sales were encouraging considering the ongoing economic challenges.
“The end of the financial year has traditionally been a strong month for vehicle sales and achieving 632,412 sales in just six months is a testament to the resilience of the market.
“We hope to break the significant milestone of 100,000 EV sales in 2024,” Mr Weber says.
“As customers increasingly turn to electric vehicles, it is critical that governments focus on the delivery of widespread recharging capability across Australia.”
Toyota was the market leader with sales of 20,903 in June, followed by Ford (9,493), Mazda (9,483), Kia (8,225) and Mitsubishi (7,723).
The NSW State Budget has revealed extensive funding and support for the commitment to the future of electric vehicles and the required infrastructure to support them.
The Federal Chamber of Automotive Industries (FCAI) welcomes the NSW Government’s commitment to EVs.
FCAI CEO, Tony Weber, outlined how the budget measures will play a pivotal role in transforming the automotive landscape in NSW.
“The NSW Government’s significant investment in electric vehicle infrastructure is a decisive step towards wide-spread adoption of the zeroemissions technology,” Weber says.
“By supporting the development of fast chargers, local government and business fleets, and EV infrastructure in key areas, this budget addresses crucial barriers to EV adoption.”
“The FCAI acknowledges the approach taken to ensure that both
metropolitan and regional areas benefit from enhanced EV infrastructure. This balanced investment is essential for ensuring that all NSW communities can benefit.”
“We look forward to working with the NSW Government to support the successful implementation of these initiatives and to continue advocating for policies that promote cleaner, and low and zero-emission options for all Australians. The measures announced today are an important step towards the ambitious 50 per cent target of all new car sales being electric by 2030.”
The NSW Government’s commitment to electric vehicles includes a funding package aimed at expanding EV infrastructure across the state:
• $149.0 million to co-fund EV fast chargers, reducing the time needed to recharge batteries.
• $105.0 million to support businesses and local government fleets
in procuring EVs and installing necessary charging infrastructure.
• $20.0 million to co-fund EV destination chargers at regional tourist spots, promoting sustainable tourism.
• $10.0 million to co-fund EV kerbside chargers in metropolitan areas, aiding EV drivers without o -street parking access.
• $10.0 million to co-fund retrofitting of EV infrastructure in apartment buildings.
The NSW Government has dedicated a further $263.5 million to advance the rollout of the updated NSW EV Strategy.
Suncorp aims to be a dedicated insurer following the last approval for the sale of its banking arm.
Late in June Federal Treasurer Jim Chalmers approved the sale of Suncorp’s banking business to ANZ for a reported figure of $4.9 billion.
The sale has been a long time coming, initially announced in July 2022, but the Australian Competition and Consumer Commission then moved to block the deal last August.
The Australian Competition Tribunal’s decision in February however gave the acquisition the green light, leaving only the conditions required by Queensland legislative amendments and the Federal government’s approval to move ahead.
Dr Chalmers says the decision was made after “careful consideration” into the impact the acquisition would have.
“I also took into account the unique features of this proposal, including the fact that Suncorp is one of the few remaining combined bank and insurance companies in Australia,” Chalmers says.
“The proposal will allow Suncorp to focus on its insurance businesses at a time when the sector faces a range of specific challenges, including access and a ordability.”
Suncorp Group CEO Steve Johnston says approval now frees the company up to pursue its plans of becoming a dedicated trans-Tasman insurer.
“Following completion, Suncorp will focus on meeting the evolving needs of insurance customers and addressing increasingly complex challenges such as climate change and a ordability,” Johnston says.
“This decision also brings us
another step closer to the delivery of the jobs and investment package Suncorp agreed with the Queensland government as part of the sale process, with benefits not only for Queensland but across Australia and New Zealand more broadly.”
Some of the conditions the federal government has stipulated include no changes to the number of Suncorp bank branches in Queensland and no net job losses for three years because of the transaction at Suncorp bank and ANZ scheduled for August 1.
“The conditions I have imposed,” Chalmers says. “Are legally binding and ensure Australians continue to have access to vital banking services, employees aren’t left behind, and Queensland and Australia benefit from the transaction.”
The future of South Australia’s collision repair industry looks brighter than ever as a record of more than 500 guests celebrated the Motor Trade Association’s (MTA SA NT) 2024 Automotive Awards and Graduation Ceremony.
The strength of collision repair was on display, with apprentice and industry representation across seven of the 16 award winners.
MTA SA/NT CEO Darrell Jacobs praised the graduates and award winners, noting the importance of trade skills and continuous learning to keep pace with industry changes.
“The rapid growth of EVs and hybrids, which now make up a quarter of new car sales, shows the need for skilled apprentices. By equipping apprentices to work with the latest technology, skills and knowledge, we prepare them to become leaders in the industry,” Jacobs says.
“As the only training provider for collision repair apprenticeships in South
Australia, the MTA is proud to see this vital sector flourishing.”
South Australian Minister for Education, Training, and Skills, Blair Boyer joined the ceremony to award graduate certificates.
“The work that the MTA does and the jobs that are available in automotive are a fantastic example for young people,” Boyer says.
MTA Body Repair Division Chair Dario
Tonon reflected on the importance of the industry addressing skill shortages through apprenticeship opportunities.
“It’s always great to see a young person come into the workplace with curiosity and enthuse people around them,” Tonon says.
“I’d love it if every person in my position had the same enthusiasm for young people because they are the next generation of the workforce.”
Crash data from the states and territories will now be linked to Federal Government funding, following a 10 per cent rise in the number of deaths on Australian roads over the last year.
Figures published by the Bureau of Infrastructure and Transport Research Economics for the 12 months up to 31 May this year show 1303 people died on our roads, a 10.4 per cent rise compared to 1180 the year prior.
The latest numbers include increased fatalities in NSW (32.9 per cent) and the Northern Territory (72.4 per cent), as well as rises in Victoria (5.1 per cent), Queensland (5.1 per cent), and South Australia (2.1 per cent). The numbers also come after a long but successful campaign by the Australian Automobile
Association to ensure states are sharing their crash and safety data.
AAA managing director, Michael Bradley, said the figures showed why federal and state transport ministers must agree to data transparency reforms as part of their next five-year road funding deal.
“The best way to understand what is going wrong on our roads is to look at data about the causes of crashes, the state of our roads and the e ectiveness of police tra c enforcement,” Bradley says.
“State and territory governments hold this data but keep it secret. At a time when current policies are failing and more than 100 people are dying on the roads each month, the secrecy must end.”
In May, the federal government announced $21 million into a crash data hub in a move that will also tie road funding to the states into a transparent return of crash and road safety data aimed at lowering the road toll.
Bradley highlighted that the federal transport minister Catherine King had called on states and territories to agree to release this data as part of the next federal funding agreement, that took e ect from 1 July.
For the first time, the federal government will seek to include a provision in its five-year funding deal with the states and territories that requires them to provide a nationally consistent data set.
One in twenty learner drivers are involved in a crash while training and of these more than half are at fault, a new look at the safety of beginners has found.
The survey from Budget Direct found training log times were exaggerated and assisting trainers needed refreshers, among other recommendations to help reduce the rate of collisions.
The Budget Direct Car Insurance Learner Driver Survey recorded responses from 968 Aussie drivers on a variety of topics, from falsifying learner log books, to involvement in tra c accidents.
Almost half of Australian motorists aged 18 to 27 are exaggerating the number of hours recorded in their learner driver’s logbook, survey data reveals.
Of the 968 Aussies to take part in the nearly 40 per cent of 18- to 27-yearolds admitted to falsifying the entries in their logbook.
While driving as a learner, three per cent of Australians surveyed were
involved in an accident and also found at fault. An additional 1.45 per cent of learners were not found at fault in accidents. According to the survey, nearly five per cent of 18–27-year-olds were found at fault when they were involved in an accident as a learner.
Nearly six per cent of South Australian drivers surveyed were involved in an accident as learners and found at fault.
Survey data revealed that about 23 per cent of 18- to 27-year-old motorists failed to look over their shoulder during their practical driving exam. A further nine per cent admitting to failing to indicate/signal.
From an insurers perspective the gaps in training and the rate of accidents, confirmed the position that 18–25-yearolds remain potentially high-risk drivers.
But the survey also found that there is a consciousness of these shortfalls and respondents outlined a range of actions they think could help reduce risk and the number of crashes.
When it came to sentiment around safety, more than 40 per cent of
respondents believed that recording mandatory logbook hours in di erent weather conditions similar to existing mandatory hours for night driving, was helpful in improving the learner driver process. Almost half of respondents 43.7 per cent advised this as a safety step.
Other options considered include o ering refresher courses for nonprofessional supervisors, such as a parent, (31 per cent), improving the quality of driving instructors, (32 per cent) and increasing the minimum age of learner drivers 25 per cent and overall logbook hours, 18 per cent.
The AMA Group has taken the next step in its new look leadership group with a new top financial o cer and changes to its key executive line-up.
It announced Domenic Romanelli was appointed Group Chief Financial O cer to replace Geo Trumbull, who will resign in August.
In other major moves at Australia’s largest repair group, Stuart Faid will take over as Executive General Manager for the AMA Collision Division.
Industry veteran Faid took over the Specialist Business in April and has been overseeing projects like the TechRight advance into in-house ADAS calibrations.
Faid described the appointment at the largest network of collision repair facilities in Australia on social media as a 30-year career highlight.
Another industry veteran, Darren Wales announced he would be retiring from the AMA Group’s heavy repairs division at the end of July to spend more time with family, after 38 years in the sector.
“I would like to thank our exceptional
team at Wales and the AMA Group, who have made this journey with me,” Wales wrote on social media. “I cannot thank you enough for your support, professionalism and friendship over the years. It has been the number one reason for our success.”
“Our wonderful and loyal customer base, our supportive supplier network have all been a part of what makes the Wales team tick, in delivering the highest quality repair services available to the industry.
“I leave with the comfort that Wales Heavy Motor, is in the very capable hands of my replacement Jim Lynch EGM of Wales and Specialist Business. “
The AMA Group also saw an overhaul of its board in June with four new board members and Brian Austin becoming the new chair. It also announced a proposed sale of its parts division, ACM Parts.
Romanelli is an experienced listed company senior executive and CFO and joins AMA Group from Pro-Pac Packaging Limited where he was CFO from November 2022.
In a statement to the ASX, Romanelli was listed with over 25 years of experience in large and internationally located companies across the industrial and resources sectors including Gale Pacific Limited, Orica Limited, Smorgon Steel Group and BHP Limited.
“He has substantial transaction experience including debt, equity, acquisitions, and divestments, as well as significant experience managing finance teams and functions,” the release noted.
Romanelli will join AMA Group on 26 August 2024, and Geo Trumbull will remain with AMA Group through the transition period.
AMA Group Chief Executive O cer Mathew Cooper said, “This is an exciting time for AMA Group, as we continue to see positive business performance and strong momentum.
“I welcome Domenic to the team and look forward to the benefit of his extensive experience as a listed company executive and CFO as we continue to capitalise on the opportunities available to us.”
One of the National Collision Repairer’s entrepreneurial women and future leaders of the industry, has added another award to her resume.
Welder, and fabricator, Bonnie Inkster, has taken out one of the two Apprentice of the Year awards at the 2024 Chisholm Education Awards.
Bonnie completed a mechanical automotive apprenticeship, followed by a Certificate III Engineering Fabrication MEM31922, to pursue her dream of working in the traditionally maledominated motor sports industry.
Having also won the Empowering Women in Trades Award this year, Bonnie now travels nationwide
with her racing team at Walkinshaw Andretti United.
From bartending to working on supercars, Bonnie Inkster is a shining example of what happens when you drown out background noise and pursue your dreams.
Building on fundamental welding skills, she shows how apprentices, given the right support and training, can help shape a future industry.
In a male dominated industry, Bonnie Inkster has done well to make a name for herself. With seven years of welding experience under her belt, her desire to become a role model for the younger generation in the automotive industry is
proving inspirational to many.
After also winning the EWIT Apprentice of the Year Award in February Inkster has even more motivation to develop her skills.
with Barry Edney
In the second part of his interview with Evolution Repair Group founder Anthony Heard, Barry Edney looks at the pace of change in the UK.
It’s been an interesting few weeks, here in the UK. Since the first part of my interview with Anthony Heard went to print. We’ve had a general election and a new government installed with a massive majority, promising a raft of employment reforms including increasing minimum wage and employer costs. Most in our industry are waiting to find out what that will really mean for their businesses and their costs line. All of these concerns really highlight Anthony’s views about understanding and managing costs as the key to being successful or even surviving.
Also in the news is the recent announcement by Steer Group, one of the bigger UK consolidators, that they are acquiring Gemini ARC. All of this confirms Anthony’s view that the consolidators will only get bigger, and independents must work together to survive.
For those of you who missed the first part of my in-depth interview with Anthony Heard, Anthony is the founder of Evolution Repair Group, a group of independent repairers working under a single banner to leverage their combined scale.
Barry Edney: In past articles for NCR I’ve reported on the ups and downs in workload across the UK. I also read recently that claims are down by 30
per cent. What’s driving this?
Anthony Heard: The main driver seems to be the cost of living. Insurance premiums in the UK have increased by an average of 61 per cent. As a result, people are raising their excess to lower their premiums, making them less likely to claim for smaller damages. For example, two years ago, someone might have had a £250 excess, making it cheaper to claim for a £750 dent. Now, with a £750 excess, they opt to pay out of pocket or simply not repair it.
BE: That makes sense. Are there any other factors contributing to this downturn?
AH: 2023/24 was the mildest winter for years. Normally, December is hectic due to winter conditions, and that carries through to March. But this year, December was mild, so there was less damage. Consequently, January and February, which are typically slow due to post-Christmas recovery, were even quieter. By March, instead of picking up, we were still down by 30 per cent because fewer people were claiming.
BE: How are the big groups responding to this downturn?
AH: The large groups are pressuring their work providers to send them all available repairs, arguing that with such large sta numbers, they can’t a ord the drop in work. This leaves
the independents, who usually rely on overflow from the big shops, struggling. Now, independents are down by 30 per cent and losing substantial amounts of money each month.
BE: What does this mean for the future of independent body shops?
AH: Unfortunately, many independents will likely go under. They’re unable to compete with the big groups’ buying power and processes. As a result, I’ve seen body shops sell for a fraction of their previous value because they’re desperate to sell. For example, shops that were worth a million pounds six months ago are now available for next to nothing because they’re losing £50,000 to £60,000 a month.
BE: How has your business managed to stay profitable in this climate?
AH: Despite the downturn, my six body shops are still profitable because we have higher average repair costs. While others are estimating at £2000, we’re at £4000. Even with a 30 per cent decrease in work, we’re still making money. It’s crucial to know your numbers. Many body shops don’t understand their financials well enough and end up as busy fools, chasing volume without profitability.
BE: Are you seeing any changes in the behaviour of repairers in the current market?
AH: Yes, work providers in the UK report receiving 50 to 60 calls a day from repairers begging for work, even o ering to increase discounts. This is a dangerous strategy as it doesn’t ensure survival, just busyness without profitability.
BE: What does this mean for the future landscape of the industry?
AH: In the next six months, I expect to see many independent body shops closing. While this might seem advantageous for larger groups like ours, it’s disheartening. I don’t want to see anyone go bust. This situation underscores the importance of collaboration and understanding every penny going in and out of your business.
BE: Shifting gears a bit, many shops complain about a skill shortage in the industry. Do you agree?
AH: Yes and no. While it’s true that fewer young people are entering the industry, we also aren’t doing enough to attract them. For example, when Chris Weeks visited a college, students had outdated perceptions of the motor trade. Once he explained the modern technology involved, like using computers for diagnostics, many students showed interest. We need to do a better job of educating potential newcomers about the advanced skills required in today’s auto repair industry.
BE: So, the problem isn’t just a lack of interest from young people?
AH: Exactly. The industry itself is partly to blame for not showcasing the technological and skilled aspects of the
work. Additionally, many shops have the wrong people in the wrong roles, which exacerbates the perceived skill shortage.
BE: Can you elaborate on that?
AH: Sure. For instance, when I bought Manchester Accident, we had four panel beaters. Two left for higher-paying jobs, and the owner panicked, thinking we needed more panel beaters. However, by analysing their e ciency, we discovered they were only 60 per cent e cient. By reallocating tasks, such as like having a dedicated strip and re-fit person, we improved e ciency without needing to hire more panel beaters.
BE: So, smart task allocation can address some of these issues?
AH: Absolutely. It’s about having the right people doing the right jobs. This ensures e ciency and maintains skill levels. For example, we avoid having panel beaters handle tasks like door replacements, which can be done by
strip-and-fit personnel. That allows panel beaters to focus on complex repairs.
BE: How do you manage recruitment for your shops?
AH: We’ve started our own recruitment company, Motor Match Recruitment, to handle sta ng for the entire Evolution group. This approach allows us to control costs and ensure we get the right people. We o er a fixed recruitment fee, which is significantly cheaper than other recruiters in the UK.
BE: That sounds e cient. Do you think other body shops could benefit from your model?
AH: Definitely. By reducing recruitment costs and improving task allocation, we help body shops operate more e ciently. We want to support the industry as a whole, not just our own group.
BE: You mentioned the importance of maintaining skills through appropriate task allocation. Can you expand on that?
AH: In the past, there was a push to replace rather than repair for speed and profit, which led to a decline in repair skills. We focus on balancing e ciency with skill maintenance. For instance, a new door replacement is often more e cient and results in a perfect finish, unlike a complex repair which might not meet quality standards.
BE: Have you considered expanding your expertise internationally, particularly in markets like Australia?
AH: Yes, Australia’s market is quite similar to the UK, and there’s a lot
we can learn from each other. I’m interested in visiting and possibly attending industry seminars there to share our experiences and gain new insights. This could be beneficial for our brand and help further our impact on the global auto repair industry.
BE: How do you stay informed about global industry practices?
AH: Through networking and staying connected with industry experts worldwide. For instance, a former colleague, who is now based in Australia, recently shared how their body shop showed some of my
LinkedIn posts to their sta to highlight what we do. Such exchanges highlight the global relevance of our practices.
BE: Do you have any plans to visit Australia?
AH: I’m considering it. Attending a seminar or conducting a study tour in Australia would be beneficial for both our brand and the industry. I’ll be looking into opportunities to make this happen. Hopefully I can work with NCR on this. Watch this space!
BE: Thank you, Anthony. This has been incredibly insightful.
AH: Thank you. It’s been a pleasure
to share our ideas and good to know there is an interest in what we do.
BE: As we wrap up our discussion, how would you summarise your key to success?
AH: Knowing your numbers is the key to survival in this industry. Everyone can repair cars, but managing your finances e ectively is what makes the di erence. This downturn has highlighted the need for financial acumen alongside technical skills in the body shop industry.
BE: Many thanks for your time. I really do appreciate you sharing your insights. Any final thoughts to wrap up?
AH: The auto repair industry is evolving, and by adopting e cient practices and focusing on skill development, we can overcome challenges like skill shortages and improve overall service quality. It’s an exciting time to be part of this transformation.
I couldn’t put it better myself. I have always been amazed how our industry continues to adapt and rise to the never-ending number of challenges that come our way. We always find a way. We’re a tenacious bunch in the collision industry!
The pace of consolidation continues in the UK as one of its leading repairers, Steer Automotive Group expands with new acquisitions and capabilities.
Gemini Accident Repair Centres was integrated integration into the Steer Automotive Group in July adding all 37 Gemini sites, plus Gemini’s Head O ce, to Steer’s extensive network.
The Steer group has integrated sta and management from the acquisitions with Managing Director Dave Sargeant and Finance Director Phil Coleman continuing to oversee operations and controls. CEO and founder Tim Hopkins has handed over control and left the business.
“These are exciting times as we enter a new era, and I am proud of this alliance,” Gemini Accident Repairs managing director Dave Sargeant says.
“This transaction unites two leading businesses, enhancing our repair capabilities across the UK. It significantly broadens Steer’s presence, and I look forward to working with Richard Steer and the team. I thank Tim for an incredibly successful 15 years, during which we grew the business from a single site to 37. We at Gemini wish him all the best.”
Founded in 2008 by Tim Hopkins, Gemini grew from a single-site operation to a semi-national network.
Steer Automotive Group CEO Richard Steer says Gemini is renowned for its dedicated customer relationships, innovative training and apprentice programs and with high levels of service that have established an outstanding and successful business model.
“Their repair process will further enhance our mutual client relationships and performance, developing and improving client experience delivery across the UK.
“We are proud to welcome Gemini’s exceptional team into the Steer family,” Steer says.
“Gemini’s innovative repair proposition and steadfast dedication to outstanding service have set an industry benchmark. Their business model, which consistently delivers top-tier service to their valued clients, will greatly enhance our operational capabilities. This acquisition strengthens our commitment to service excellence across the UK, ensuring that we remain at the forefront of the automotive repair sector and continue to meet the evolving needs of our customers.”
The Steer network now stretches the length of the UK from Edinburgh to Cornwall. Gemini Accident Repairs will maintain its brand under the name, Gemini Accident Repairs, part of the Steer Automotive Group.
Just prior to the Gemini acquisition Steer also took over Chartwell and M&A Coachworks, two prestige repairers.
“This strategic move significantly bolsters our capabilities in the luxury vehicle repair sector, expanding our luxury repair footprint and increasing capacity to e ectively support the world’s leading OEM factory recommendations, approvals and
its highly valued dealership retailer partners,” Steer said in a statement.
Chartwell, established in 1966, and M&A Coachworks was established in 1971 and the two collective organisations hold recommendation and approval for iconic luxury brands such as Porsche, Aston Martin, Bentley, Lamborghini, McLaren and Maserati.
Chris Brightmore, Managing Director of Chartwell, remained operationally responsible for the Chartwell business, while at M&A Coachworks, George Dionisiou stepped down as chairman. Dean Dionisiou, Sales Director and other family members remained in the business with Danny Rota as Managing Director.
“These iconic brands represent the pinnacle of the luxury repair market. We are dedicated to preserving the heritage of these esteemed businesses, which are strongly associated with the world’s premier supercar brands.” Steer says.
The move into luxury brands follows the expansion in March with the acquisition of six Innovative Repair Group sites, established in 1999. The acquired sites are in Wales (Whitland, Swansea, and Pontypridd) and England (Bristol, Birmingham, and Wolverhampton).
The March acquisition opened a new geographical catchment area for Steer in South Wales, and the addition of sites in Wolverhampton and Birmingham introduced a hub model to their operations.
with John Yoswick
The di culty in attracting and retaining technicians in a workshop are as acute in the US as they are in Australia. Several business owners share their ideas on what has worked for them.
Aaron Flett, owner of Kent Collision in Washington state, says when he opened his shop 10 years ago and considered what he needed to do to attract and retain employees, he thought about the di erences he’d seen and heard about big-box national retailers, one of which had closed its stores in his region, while the other is successful across the US.
“One of the big things that we learned about the di erence is just a work-life balance [for employees],” Flett says, during a panel discussion at recent industry event. “We’ve all had techs who want to work 10- or 12-hour days. We don’t really allow that. We want to make sure they get their eight hours in and go home, to enjoy their family, be healthy, have longevity in life and longevity in the industry. We want fair compensation plans that make them want to not have to work 12-hour days.”
Another Washington state shop owner on the panel, Micah Strom of Modern Collision, says his company took a di erent approach to providing that work-life balance.
“We switched to four 10-hour workdays, which is a little unusual in our industry, but has been very well accepted by our team,” Strom says. “It’s a great attraction for new talent coming in. We get three days a week to spend with our family at home. Some of them do have things going like daycare or getting kids o to school, so we have flexible hours. I think it’s important to accommodate because everybody has di erent things going on in life.”
Another panelist, Kevin House of Center Collision in Tacoma, Washington, says he’s placed an emphasis on employee retention by focusing on building camaraderie and culture within
his 30-year-old business.
“We look for opportunities for our employees to interact not just at work, but outside of work,” House says, pointing to recent paintball contest his employees had against employees of a nearby tyre shop. “My employees just had a great time. That’s part of our culture, making it not just about work, but about a little bit of a life experience. Does anybody know what national holiday was last Friday? It was national grilled cheese day. There’s a holiday for every day of the year. You can Google it to create opportunities. We grilled cheese sandwiches for the whole sta . We shut down for an hour and all have lunch together every Friday. We take the whole crew out boating every year. We just look for opportunities to build a team, to create that culture and make it more than just going to a job.”
The panel agreed that improved
benefits have become as important as wages in terms of attracting and retaining employees.
“One thing that I’ve found surprising, that’s changed since I was a tech in the industry, is that it seems like people coming in want a better benefits package,” Flett says. “When I was in my twenties as a prepper or a painter, I just wanted a paycheck. Give me more money, fewer benefits. But now they definitely know the importance of having good benefits. We’ve recently added a [retirement savings plan], we pay for everybody’s vision and dental insurance 100 per cent, and we’ve increased our contribution to the actual medical portion of the health insurance as well. That helps us compete with the MSOs that also have a pretty good benefit package based on their size.” Strom agreed.
“We have the dental, vision and life insurance,” he says. “We’ve had a really
good healthcare plan, and a [retirement savings plan]. We also just started [giving new hires] one week’s vacation after six months. So they’re not working a whole year without having any paid time o . Times have changed. This younger generation needs something di erent. It’s about adapting and working with it, not against it. If you want to sit there and stay the same, you’re going to end up being behind.”
Strom also says it’s important for the industry to be involved in their local schools, saying his shop tries at least once a year to bring an intern in for job shadowing.
“I’d have to say probably at least six of them we actually hired on afterwards,” he says. “If we aren’t involved with the schools, there’s so many other trades out there that are. Probably a lot of us growing up, your dad worked on cars, or your uncle or your grandpa. Nowadays, the kids don’t have that opportunity. The parents take their car to a shop. That’s all they know. So it’s our job to get out there, to talk to the kids, to get involved in the schools, and show them this a rewarding career and it’s a lot of fun.”
Andrew Riggs, a collision repair instructor at Bellingham Technical College in Washington state says his program made a change to help keep
students engaged: They eliminated classroom time.
“We don’t sit our students down anymore and make them listen to us lecture,” Riggs says. “We moved that online. They can do that at home on their own time. And then when they come to the college, it’s all lab. So all the time we get to spend with our students is handson lab activities, and that’s made a huge di erence.”
He says one of the primary challenges that programs such as his face is the public misperception about the industry.
“The biggest thing that we fight is the stigma of this industry from the parents,” he says.
“They think you’re just going to grab a hammer and beat on metal in a dark, dirty shop, and that it’s a go-nowhere job,” Riggs says. “So we have a ‘Try a Trade’ event where we get to set up resistance welders, we get to set up our virtual painter, stu like that. So the high schoolers come in with their parents and they get to see this equipment and understand that this is not easy. This is a complicated career. There’s a lot that goes into it. We’re electricians, we’re plumbers, we’re artists. It really does change the parents’ perspective, and that has helped a lot.”
To help perspective students and
their parents see the opportunities available in the industry, Riggs sometimes asked successful graduates to share their income tax returns. He removes their personal information from the paperwork, and sets them out so students and parent can see what they’re earning.
“They don’t have to be worried about their son or their daughter going into a dead-end job,” Riggs says. “You can make a good living doing this.”
He says students in his program finish with a three-month internship in a shop, usually paid.
“If that opens the door, if that shop is happy enough with them for that three months, then it turns into full-time work after that,” he says.
Beyond wages and benefits, he says, the young people in his program are very much interested in a good work-life balance.
“They want some freedom, whether it be 4-day workweeks, or the ability to build their own schedule a little bit,” Riggs says. “Maybe they can’t be in at 8 o’clock every morning because they have to get their kids o to school. From what I understand, they have no problem staying later if they can start a little later, so they can still have a family and spend some time with them.”
The Insurance Institute for Highway Safety and the Highway Loss Data Institute Crash have studied records and insurance data over several years and found little evidence that partial automation systems are preventing collisions.
“Everything we’re seeing tells us that partial automation is a convenience feature like power windows or heated seats rather than a safety technology,” IIHS President David Harkey says.
The clearest evidence so far comes from studies of BMW and Nissan vehicles that have been on the road for a number of years. HLDI studied these vehicles in 2021. Now a new study of the same vehicles from IIHS confirms that partial automation in these vehicles doesn’t confer additional safety benefits beyond those of crash avoidance features like front automatic emergency braking (AEB).
More than half the new models for sale in 2023 were available with partial automation systems as an optional or standard feature, despite mounting concern over a series of high-profile crashes that occurred while drivers were using the technology. Using cameras and other sensors, these systems can keep your car moving down the road in the centre of the lane, navigating curves,
Two key US safety bodies have studied the rate of collisions and discovered partial automation is not necessarily preventing crashes.
slowing down to avoid other vehicles and then accelerating again when the way is clear.
“Vehicles equipped with these systems are far from self-driving,” Harkey says. “They can’t manage many routine roadway features and tra c situations, so drivers have to pay close attention to what’s happening on the road and be ready to take over at any time. That’s a big challenge because the technology can encourage a false sense of security and induce boredom, causing drivers to tune out.”
The report found there were key di erence between partial automation systems and the crash avoidance features that are sometimes sold separately.
“Crash avoidance features like AEB, blind spot warning and lane departure prevention only come into play when a potential danger arises — slamming on the brakes to avoid rear-ending another vehicle, for example. Because they’re unobtrusive under normal circumstances, most drivers who use them leave these features switched on all the time.”
A partial automation system works to keep the vehicle in the desired position on the road and is intended for use on highways and other limited-access roads.
These systems must be switched on whenever the driver wants to use them
HLDI has conducted multiple investigations into the potential safety benefits of crash avoidance features using insurance claims data.
The studies have all shown that features that warn or intervene in an emergency reduce the frequency of insurance claims, and the reductions increase incrementally as one feature is stacked on another.
Partial automation could also theoretically help prevent crashes. One of its component features, adaptive cruise control (ACC), keeps the vehicle traveling at a driver-selected speed when the road is clear and slows and accelerates to maintain a set distance from vehicles ahead.
“It is associated with longer following distances, less tailgating and fewer lane changes — positive driving behaviours that could reduce risk. The other main component of partial automation, lane centring, could potentially do a better job in preventing sideswipe and run-o -road crashes than lane departure prevention, since lane centring theoretically would pre-empt such departures rather than intervening as they occur.”
HLDI found that property damage
liability claims — which are for damage to other vehicles hit by the insured driver — were eight per cent lower for 2017-19 Nissan Rogues equipped with forward collision warning and AEB.
“However, there was no additional benefit associated with ACC or Nissan’s ProPILOT Assist partial automation system, which adds lane centring on top of ACC. Changes in claim rates under collision coverage — which is for damage to the insured driver’s own vehicle — were small for all the technologies.
“Forward collision warning and AEB were associated with a seven per cent reduction in collision claim rates and a 13 per cent reduction in property damage liability claim rates for 2013-17 BMW and Mini vehicles. BMWs and Minis that were also equipped with ACC showed a larger, 25 per cent reduction in property damage claims and no greater change in collision claims. As with the Nissan vehicles, there were no additional statistically significant reductions associated with BMW’s Driving Assistant Plus partial automation system.
The investigation also found HLDI’s claims data, collected from insurers representing 85 per cent of the private passenger vehicles in the US, don’t show whether the partial automation system was switched on during a crash, nor do they include the type of road where the insurance claims occurred.
“That means any potential benefits from partial automation, which is generally designed to be used on highspeed roads, would be diluted by the large volume of insurance claims for lowspeed fender benders.”
HIS senior vice president for research Jessica Cicchino says they also tried to determine if such safety benefits might be hiding in the HLDI data.
Cicchino compared police-reported crash rates for the same BMW and Nissan vehicles that HLDI studied in 17 US states during 2013-22.
She says she also had no way of knowing whether the features were switched on at the time of the crash but was able to restrict her study to the front-to-rear and lane departure crashes that partial automation could potentially prevent.
She looked at crashes on limitedaccess interstates, freeways and expressways and then looked separately at crashes on other roads and found substantial reductions in crash rates associated with crash avoidance features.
Front-to-rear crash rates were 49 per cent lower for Rogues with forward collision warning and AEB and 54 per cent lower for Rogues with forward collision warning, AEB and ACC than for vehicles with no crash avoidance features. There was no significant e ect on lane departure crash rates from lane departure prevention.
But Cicchino says she also found larger reductions associated with partial automation. Front-to-rear crash rates were 62 per cent lower for Rogues with ProPILOT Assist than for vehicles without any crash avoidance systems. Lane departure crash rates were 44 per cent lower for Rogues with ProPILOT Assist and lane departure prevention than for unequipped vehicles.
However, she found that the apparent benefits from ProPILOT Assist were the same on high-speed roads where IIHS research shows partial automation is most likely to be switched on and low-speed roads where the added convenience it provides is minimal at best. Below 37 mph, in fact, ProPILOT Assist’s lane-centring feature only works if you are following another vehicle.
“That suggests that other characteristics of the equipped vehicles or their drivers were responsible for the reduction.”
One such characteristic may be the vehicles’ headlights. Noting that Rogues of that vintage were equipped with
poor-rated headlights unless the buyer opted for a premium package, the study discovered that the rate di erences were greatest in the dark.
From Nissan marketing materials, she also ascertained that the 2018 and 2019 Rogues with ProPILOT Assist were more likely than unequipped vehicles to have acceptable-rated headlights. Acceptablerated headlights themselves reduce single-vehicle nighttime crashes by about 15%, compared with poor-rated ones, other IIHS research has shown.
For the BMW vehicles, Cicchino examined only lane departure crashes, because the vehicles with partial automation came with a more advanced front crash prevention system than those without partial automation, making it impossible to isolate the e ect of the partial automation system on front-torear crashes. She found that neither lane departure prevention alone nor the same feature combined with partial automation had a significant e ect on crash rates, either on limited-access highways or on roads with lower speed limits.
The vehicles in these studies range from five to 11 years old, and it’s possible that newer partial automation systems are more e ective from a safety perspective, she says.
“With no clear evidence that partial automation is preventing crashes, users and regulators alike should not confuse it for a safety feature,” Cicchino says.
“At a minimum, safeguards like those IIHS promotes through its rating program are essential to reduce the risks that drivers will zone out or engage in other distracting activities while partial automation is switched on.”
A new J.D Power study highlights the issues that repairers see with EVs in US workshops and reveals the most reliable car for overall product quality.
The 2024 J.D Power US Initial Quality Study (IQS) claims to be the auto industry standard for benchmarking new vehicle quality.
According to J.D. Power’s most recent IQS, there are 195 problems per 100 (PP100) on average for 2024 model year vehicles within franchise dealership repair visits.
There are even more issues with premium brands including electric vehicles (EVs).
J.D. Power found that repair data on EVs and plug-in hybrid electric vehicles (PHEVs) require more repairs than petrol or diesel-powered vehicles in all repair categories.
J.D Power senior director of auto benchmarking, Frank Hanley,
highlighted how owners of EVs and PHEVs are experiencing serious issues.
“Owners are experiencing problems that are of a severity level high enough for them to take their new vehicle into the dealership at a rate three times higher than that of gas-powered vehicle owners,” Hanley says.
The main issues in EVs are everyday functions such as windshield wipers, rear-view mirrors and the operation of OEM smartphone applications.
Repairs in this category are more than 30 per cent higher in EVs than in ICE-powered vehicles. The issue is exacerbated by Tesla’s recent switch to steering wheel-mounted buttons for horn and turn signal functions.
According to the J.D Power study, Ram is the highest-ranking brand overall in initial quality with a score of 149 PP100. Among mass-market
brands, Chevrolet ranks second, and Hyundai ranks third.
Among premium brands, Porsche ranks highest with a score of 172 PP100. Lexus ranks second and Genesis ranks third.
The study examines 227 problems, which are organised into nine categories:
• Climate
• Driving Assistance
• Driving Experience
• Exterior
• Features/Controls/Displays (FCD)
• Infotainment
• Interior
• Powertrain
• Seats
Vehicle repair visits are integrated into the scoring to provide a more comprehensive picture of product quality.
BASF Coatings Division has been honoured with the Red Dot Award in Product Design at one of the most prestigious design competitions in the world.
The colour, “Zenomenon”, designed by BASF was the only automotive paint to be honoured at this year’s awards.
The innovative technology and the special aesthetics of the coating have impressed the experts on the Red Dot jury in the
“Materials and Surfaces” category.
Zenomenon’s coating formulation is based on polymer structures developed by the cooperation partner Cypris Materials from California.
Instead of classic pigments, special polymer structures with a high proportion of renewable materials are used.
The formulation allows the colour to represent a more sustainable alternative in the area of surface aesthetics for automotive coatings.
The result is a unique colour e ect that arises from self-assembled layered structures, reflecting light in the visible spectrum with a flop e ect.
This gives the surface of the paint layer a shimmering, strikingly iridescent shine. With a view to future mobility, these polymers are also suitable for LIDAR or radar sensor systems.
Global head of Automotive Colour Design at BASF, Mark Gutjahr, highlights the significance of the award.
“Being awarded a Red Dot in product design is a very special honour for us – especially as a chemical company. The award underlines our design and technology expertise – and the trust in innovative solutions that our customers in the automotive industry place in us,” Gutjahr says.
At the Red Dot Design Award, all submissions are assessed based on the four basic principles of good design: the quality of function, the quality of seduction, the quality of use and the quality of responsibility.
“The development of Zenomenon is remarkably future-oriented. In particular, the interplay of aesthetics, sustainability and functionality is fascinating”, the independent Red Dot jury says.
All award-winning products will be on display until May 2025 as part of the winners’ exhibition at the Red Dot Design Museum at the UNESCO World Heritage Site Zollverein in Essen, Germany.
Leading Global repair trainer, I-CAR has celebrated its commitment to training workshops in an annual report that highlights the critical need for upskilling for a high-tech future.
I-CAR USA has released an Impact Report that covers its core achievements, initiative and reinvestments in the last year.
President and CEO, John Van Alstyne outlined how the report reflects industry needs and feedback.
Van Alstyne emphasised the key takeaways for automotive repairers.
“We’ve also evolved our training program to be really focused in on these more complex skills, especially in the structural repair area. There is more training required. And as the industry told us, we had to increase that level of training to more people within the shop,” Van Alstyne says.
“The total cost to train is up, but it’s up in the same relationship that cost to repair is up because the cost to repair a vehicle is greater than it was five, 10 years ago. You have ADAS today, you’ve got mixed materials today, you’ve got a lot more technical content in vehicles today than we had just a few years ago.”
Other key highlights from the report include:
• 97,419 unique students trained in 2023, up 17.5 per cent from the prior year
• 12,121 total shops trained, a 6.5 per cent annual increase
• 9,240 Gold Class repair facilities, a
4.4 per cent annual increase, and 33 OEM and insurance network program partners relying on I-CAR training
• 36,119 Platinum technicians, achieved through ProLevel 3 completion and ongoing annual training
• 632 career technical schools using I-CAR’s education-sector curriculum bringing in USD$1.5 million in revenue
• 57 Sustaining Partner program members helping to support and o set the cost of industry training.
The report noted the more technologically complex a vehicle is, the more the cost to repairs will increase. Equipping sta with the skills to fix EVs and high-tech vehicles is also critical as the Australian and international car parc evolves.
“Our instructors today are focused on going into shops and delivering skills training, like welding, MIG brazing, spot welding, and rivet bonding. We’ve had to kind of morph our instructor mix to instructors that are skilled in those areas as opposed to the more general instructors that could handle our training of the past,” Van Alstyne says.
Europeans will soon be forced to adhere to the speed limit, as all new cars sold from July will be equipped with speed limiters.
The new European Union Mandate will use a system known as Intelligent Speed Adaptation (ISA), that restricts the speed of a vehicle automatically.
The European Transport Safety Council has claimed that vehicles using the ISA technology will reduce tra c collisions by 30 per cent and road casualties by 20 per cent.
The technology is not currently enforced on new vehicles sold in Australia.
Although this law will not apply in Britain, it is likely that most new cars will be a ected by the
introduction of the technology.
RAC road safety spokesperson Rod Dennis outlined how UK drivers need to familiarise themselves with ISA as cars manufacturers won’t exclude the feature from the models they sell in the UK.
“Anyone getting a new vehicle would be well advised to familiarise themselves with ISA and how it works. In practice, if a driver exceeds the speed limit, an audible warning is sounded and then the car’s speed is automatically reduced. But a driver can still press hard on the accelerator to override it momentarily, for instance to negotiate a hazard in the road ahead,” Dennis says.
ISA uses a combination of GPS tracking data, satellite navigation, and
information on speed limits of that roads that the vehicle is currently on.
If the driver is travelling over the speed limit, the system can reduce engine power until the speed drops to the limit of the road. This means that no one can speed on any roads in Europe using new vehicles.
The 2019/2044 ISA regulation was written by the European Commission following years of research into improving safety for drivers and other road users.
It features in the EU’s plan to achieve zero road deaths by 2050.
Major car manufacturers, such as Ford, Renault, Volvo and Honda already include a limiter in their range of vehicles.
In positive news for electric vehicle buyers and manufacturers, new research on EV batteries suggests that the cost of battery replacement is declining.
The main barriers to purchasing an EV is often underpinned by uncertainty of cost, infrastructure, and trust in the new technology. However, as technology develops, and Government incentives increase, the cost of purchase and repair is expected to decline.
Government policies, like the New Vehicle E ciency Standard (NVES), aim to solidify the future of EVs on Australian roads by supporting the transition.
Recurrent Auto’s research into the lifespan of EV battery explores the declining cost of replacing an EV battery.
EV battery replacement cost
Electric car battery replacement costs outside of warranty can range from USD $6,500 to $20,000, depending on the size and manufacturer, but these out-of-pocket repairs are extremely rare.
This is partly due to EV batteries lasting longer than many people expected. While the overall rate of replacement in the Recurrent community is only 2.5 per cent, the highest rate of battery replacements come from the very first generation of EVs on the road. These cars are now 14 years old.
Are replacement costs going up or down?
The cost of batteries fluctuate - going up some months and down others - but the overall cost trend is declining.
As battery prices continue to decline, the price you would pay today is di erent than the price you would pay next year or in five years. In 2019, the Mack Institute for Innovation Management at the Wharton School for Business aggregated data found across academia, news,
search engines, experts within the industry, and public statements by manufacturers.
They found a 16 per cent decline in battery pack cost between 2007 and 2019. The authors estimated in 2019 that the average cost of battery packs was USD $161/kWh. With that estimate, in 2019, the cost of an out-of-warranty 100 kWh battery, as is common in Tesla long range vehicles, would be at least USD$16,100 before labour and taxes. If the trend in battery price reduction stays constant, then by 2025 the price in 2019 should be USD $56/kWh, or $5,600 to replace a 100-kWh battery.
That’s a big change in how much an EV battery costs to replace.
However, it’s worth noting that the overall downward market trend in the price of lithium faltered in 2021 - 2022 and the price of battery components actually began to rise a bit.
As of March 2023, the price is coming back down, though, and has fallen nearly 20 per cent since the beginning of the year. High demand for old lithium-ion batteries will keep
prices for battery replacements stable for at least another year.
How are battery replacement costs determined?
The cost of an electric car battery can be up to half the value of the car, depending on the type of vehicle (luxury vs economy) and battery size. A bigger battery has more minerals and costs more to produce.
According to an April 2019 report by the International Council on Clean Transportation (ICCT), the projected cost by 2025 should be USD $120/ kWh to $135/kWh. This is less generous than the Wharton analysis, suggesting by 2025 a 100-kWh battery replacement out of warranty may cost up to USD $13,500.
The ICCT report does note that battery cost forecasting has consistently under-predicted actual battery cost reduction. They provide a caveat that if a slightly rosier analysis is performed, battery pack-level costs could be USD $89/kWh by 2025 and $56/kWh by 2030.
The demand for new connectivity features in cars in the Asia-Pacific (APAC) region is expected to grow as a result of the proliferation of internet connectivity and deployment of 5G cellular technology.
According to GlobalData, the APAC connected vehicle technologies market is projected to grow at a compound annual growth rate (CAGR) of more than four per cent during 2023-2028.
Major countries, such as China, India, South Korea, and Japan are expected to drive the demand.
Advancements in technology are being utilised to enhance passenger safety and boost the vehicles’ security features. Many startups have developed specialised chipsets that enable fast communication via 5G and decentralised networks.
GlobalData’s latest report, “Global Sector Overview & Forecast: Connected Vehicle Technologies - March 2024,” reveals that APAC held a significant share of the global automotive connected technologies market in 2023, with Asian countries leading in the adoption of OE smartphone and embedded connectivity units.
The APAC market is set to grow from 28.5 million units in 2023 to 34.6 million units in 2028.
Repairify’s director of innovation Martin Brown, emphasises the importance for the automotive industry to prepare itself for the future changes.
“Being prepared and equipped with the right resources for the new technology is essential,” Brown says. Brown emphasised the importance for workshops to identify the challenges and new technology in the automotive industry will bring.
“Now’s the time to get in on this because if you’re going to invest now, then you are in a good place to take on the work, perhaps also for other collision centres around you and make sure that you recoup the investment relatively quickly,” Brown says.
GlobalData Automotive, associate project manager, Gorantala Sravan Kumar, highlights the proliferation of new connectivity technologies in the Asia Pacific region.
“Consumers, especially younger generations, are hooked onto their smartphones and gadgets and want to be connected all the time. Their reliance
Chinese car manufacturers have responded to the European Union’s tari s on Chinese electric vehicles, as negotiations between government o cials continue.
The tari of up to 37.6 per cent on imported electric vehicles to Europe is in addition to the existing 10 per cent import duty. The European Union imposed the tax on vehicles from China in response to a flood of cheap electric cars manufactured with subsidies provided by the Chinese government.
The additional import tax is currently being treated as provisional for a four-month period while negotiations between government o cials and stakeholders continue.
Car manufacturers, like Tesla, spoke with Reuters about the impact of the tari s on the pricing of their vehicles.
Tesla is the largest importer of electric cars from China to Europe, and according to Reuters, Tesla will be forced to increase the price of the Model 3 due to the new tari . SAIC Motor – the Chinese state-owned parent company of nine car brands – says it will request a hearing with the European Commission. According to Reuters, the SAIC Motor claims the government body “overlooked some of the information and counterarguments submitted by SAIC during the investigation.”
On top of the current 10 per cent import duty, BYD will be hit with an
on the Internet and gadgets also seeped into their vehicles and want to stay connected even on the road.”
The middle and a uent classes are growing rapidly across various Asian countries, leading to an increased demand for smart and connected vehicle, Kumar says.
“Consumers are now seeking features such as in-car infotainment, connected services, and advanced driving assistance systems. Asia-Pacific nations have made significant investments in upgrading their digital infrastructure, including the deployment of 5G networks. These high-speed networks are crucial in providing reliable and fast communication between vehicles and the surrounding infrastructure.”
additional 17.4 per cent tari . However, BYD has plans to build a factory in Hungary, with a second plant reportedly planned in Turkey.
BMW, which manufactures its electric Mini in China, and is facing a 20.8 per cent tari , has come out against the import tax.
BMW CEO Oliver Zipse argued that the tari s do not strengthen the competitiveness of European manufacturers.
“On the contrary; it not only harms the business model of globally active companies, but it also limits the supply of electric cars to European customers and can therefore even slow down decarbonisation in the transport sector.”
Reacting quickly to market demand wasn’t always Holden’s strongest point, but the long history of providing more upmarket versions has produced some Australian classics.
IN 1948 when Holden launched Australia’s Own Car into a post-War world, any product that was basic in all respects was admired for its austerity.
People who wanted something more luxurious from their GM-H dealer could spend extra on a Vauxhall, or lash out on an imported Pontiac, and not until the 1960s did that attitude change.
Swelling the EJ range in 1962 was Holden’s Premier sedan, with metallic paint, a heater/demister and automatic
transmission all standard. The front seats were separated by a console and the interior trimmed in leather. Whitewall tyres and flashy wheel covers completed the package, but nothing could be done to improve Holden’s awful old Grey engine.
Eighteen months later came the EH Premier with a brand-new Red motor and power to match its presence. Next came the HK range with its V8 engine option, spawning an elongated Brougham with trim lifted straight
out of a Cadillac. The ploy bought Holden the time needed to design its Statesman; e ectively a Cadillac in miniature.
Prestige versions of once common Holdens have become scarce and often expensive. Quality and presentation are more significant (usually) than a car’s age. The provenance of one owner is impossible to truly value, except to say that the best car to buy is one that can document its journey from Day One.
NOT THE first Holden to wear the Premier badge, but way more marketable and popular than the underpowered EJ. Like the original, this Premier stuck with genuine leather trim and a central console. It then added a 179 cubic inch (2.9-litre) 86kW engine with manual or automatic transmission.
For families needing more space plus interior opulence there was an EH Premier wagon. Also the colour range available to Premier buyers was expanded to include not just metallics but Ivory and Black as well. Despite the powerful new engine there were no disc front brakes, and Holden’s reluctance would inspire individual owners to fit discs from later models, especially when they were adding carburettors to wring more performance from the 179 motor.
Modifications that don’t detract from the character of these cars don’t diminish their values and can sometimes even see a ‘hot’ Premier gain in value over a stock car in similar condition. However, leaving your Prem in stock condition is recommended.
Some years ago, a prominent Holden collector o ered for sale some of the country’s best Holdens and set an extraordinary $100,000 for an EH Premier wagon in rare specification. Values more recently have remained below that level, with excellent cars.
Value Range: FAIR: $25,000 GOOD: $52,000 EXCELLENT: $65,000
THIS ONE is HSV badged, but under the skin it is pure Holden and shares engineering basics with the VQ-VP Statesman. Central to the way these big Holdens ride and handle is the independent rear suspension pioneered by Holden’s VQ range.
When new, the Senator at $45,450 wasn’t the most expensive model on HSV’s list of o erings. However, with 217 cars produced from April-June 1992 they are easier to find than the more expensive 5000i. Senators delivered 180kW from the standard HSV V8, with automatic or five-speed manual transmission. Sports seats were trimmed in partial or full leather, and standard features include climate control air-con, a trip computer, and electric windows and mirrors. A multi-stack CD system was optional at undisclosed cost.
Despite scarcity, the VP Senator isn’t particularly expensive and typically cheaper than the less opulent VP GTS. Senators that have travelled just 8000 kilometres annually but need some attention to paint and trim, sell at $30-35,000.
Outstanding examples have been advertised at more than $60,000, but nailing down buyers at that level can prove di cult.
Value range:
FAIR: $15,000 GOOD: $35,000 EXCELLENT: $55,000
WHOEVER decides the relative values of interesting older cars really has their sums wrong when it comes to pricing the WB Caprice. The same goes for Statesman-based cars made by HDT; the Magnum which is ultra rare and still ridiculously cheap.
Benefitting from Holden’s Radial Tuned Suspension, the Caprice is a big car that handles like a smaller one. Body roll, providing the shock absorbers remain in good condition, is well-controlled, the all-coil ride is excellent and standard alloy wheels with their ER60 tyres adequately support 1800kg.
Seat trim in a Caprice can be leather or velour and the dash is liberally decorated with simulated veneer. Cars hoping to achieve the Condition 1 prices need to have the interior in close to mint condition.
Current Caprice values are inexplicably low and look set to remain that way until the numbers of cars in the market dwindles considerably. Lower priced examples will struggle as trim deteriorates and paint fades to justify their survival, but with some owners not especially bothered by appearance, these robust cars might go on almost indefinitely.
Value Range: FAIR: $14,000 GOOD: $27,500 EXCELLENT: $38,000
IN 1986 as the VL Commodore was launched, fears were rife that this could be Holden’s last Australian sourced car.
The company was out of money and almost out of ways to freshen a Commodore that had survived largely unchanged for eight years. However, Holden’s stylists knew people in the USA who had been playing for decades with hidden headlamps and happily shared plans for a mechanism that would partly conceal the lights on the Calais for a bit of added mystique.
What started out as a ploy became a fad as people walking past a parked VL would begin humming the Kim Carnes’ hit Bette Davis Eyes.
VL Calais sedans and the very rare wagon came standard with the Nissan six, but also Holden’s reincarnated 4.9-litre V8 that had learned to drink the new unleaded brew, or the 150kW turbo six.
Today, when scanning the classifieds for a decent Calais V8, discard any that might have been significantly modified. They are less likely to appreciate more than cars in stock condition and might in decades ahead, even have their use restricted as more stringent rules are applied to Historic vehicles with modifications.
Value Range:
FAIR: $24,000 GOOD: $52,000 EXCELLENT: $72,000
EVERYONE PANIC! Certainly everyone at Holden did when Ford shocked the market with its USA-sourced ZA Fairlane; a car to which Holden in 1967 had absolutely no reply.
A year later when the HK range emerged, GM-H had craftily extended the rear mudguards to produce a Fairlane rival, however, the market was having none of it.
The Brougham, produced in HK, HT and HG series, had a 5.0-litre V8, elaborate seat trim plus a decently sized boot. What it didn’t o er was the Fairlane’s longer wheelbase with extra rear legroom or cabin width and wouldn’t, until replaced in 1971 by the Statesman.
People buying a Brougham needed to spend $3855 against the $3453 for an HK V8 Premier. What they got for their money was that extra bit of boot space, a vinyl roof as standard and seat trim which Holden’s brochure writers described as ‘opulent, nylon blend brocade’.
Broughams in excellent condition generally cost $55-65,000 or somewhat less than a V8 Premier. Just how much less is often determined by how well that trim has resisted wear during its lifetime. Trimming in correct materials is expensive.
Value Range: FAIR: $14,000 GOOD: $45,000 EXCELLENT: $62,500
Toyota Australia’s hybrid strategy has not only consolidated its position as the most popular manufacturer in Australia but has helped deliver a record after-tax profi t of $342 million for the financial year ended 31 March 2024.
The company reported the results were helped by a turnaround in supply, with Toyota and Lexus achieving 246,389 vehicles – a 11.3 per cent increase.
Toyota delivered 230,560 new vehicles, with Lexus establishing its own record of 15,829 luxury vehicles.
Their joint hybrid tally of 94,744 vehicles accounted for 38.5 per cent of combined sales. Toyota also
launched its first BEV during the financial year, the bZ4X SUV.
TMCA President and CEO
Matthew Callachor says the latest financial results reflected the local company’s close collaboration with global production teams to achieve significantly higher vehicle allocation for Australia.
“The turnaround in supply was made possible by a strong team e ort over an extended period with our factories overcoming substantial challenges, supported by the dedication and support of TMCA employees, dealers and suppliers,” Callachor says.
“Importantly, our dealers played
a vital role in managing sometimes di cult conversations with customers as we addressed issues outside our control over the past 2-3 years, successfully returning many of our vehicles to an acceptable delivery period,” he says.
“We are extremely grateful to the loyalty and patience exhibited by our customers and thank them for their continued trust in our vehicles and in our brands.
“We can assure all dealers and customers that our plans, here and in Japan, are focused on continued strong supply, enabling us to deliver cars as quickly as possible and further reduce wait times.”
Australian roads will soon be home to a new brand of electric vehicles that could rival the best-selling Tesla Model Y.
The Xpeng G6 electric SUV has just gone on pre-sale in Australia, with deliveries to begin in late 2024.
The announcement comes after the United States and European Union’s tari s on Chinese-made electric vehicles.
Pre-orders for the 2025 Xpeng G6
electric SUV have opened, signifying the launch of the latest brand to enter the Australian new-car market.
O ering near-identical dimensions, Xpeng has clearly targeted the Tesla Model Y when designing the G6.
Representatives from the Chinese company’s Australian arm recently claimed the G6 was more on par with the likes of the Porsche Macan or Mercedes-Benz EQE SUV.
Buyers can register their interest on the Xpeng website, with two variants to choose from – the G6 Standard, and the G6 Long.
The G6 Standard comes with 66kWh lithium-ion battery o ering up to 435 kilometres of rated driving range (WLTP standard), with a single electric motor sending 190kW and 440Nm to the rear wheels.
The G6 Long, and the 87.5kWh battery increases the driving range rating to 570km (WLTP).
While it’s not clear whether the model will be o ered in the future, for the moment Australia misses out on the G6 Performance.
Though final specifications of the G6 will be announced closer to the car’s local launch in the latter part of 2024, it’s expected the electric vehicle (EV) will be o ered with a version of Xpeng’s Xpilot advanced driver assistance technology.
Only a little more than a year after relaunching in Australia, Chery has hit two milestones, reaching 10,000 sales in Australia with 1,000 monthly sales for the first time in June.
Chery is one of the largest Chinese exporters of vehicles across the globe and now has a presence as one of the fastest-growing auto brands in the Australian automotive market.
It pulled out of the Australian market in 2015 after four years, after some of its vehicles received lower safety ratings by ANCAP. Previous o erings - the Chery J11 (2 stars) and Chery J1 (3 stars) - achieved ANCAP safety ratings well below the expected standard when rated back in 2011.
But after relaunching in March 2023, it received a fi ve-star rating for its Omoda 5 from ANCAP and sales have climbed. Since then, the company has
moved from outsider to a position of strength in the Australian car parc.
Chery Australia CEO, Lewis Lu says they remain committed to delivering high-quality vehicles and exceptional customer experiences.
“We are excited about the future and look forward to introducing new models and technologies to our Australian customers,” says Lu. “Our goal is to continue growing our market share and enhancing our brand’s reputation and awareness in Australia. As a growth market for us globally, we are incredibly proud to reach these milestones in Australia so soon after celebrating our first anniversary.”
“Achieving 10,000 sales is a testament to the hard work and dedication of our local team, dealership network, and the ongoing support of our customers. Reaching
1,000 sales in a single month for the first time demonstrates the increasing demand for our vehicles and the strong market acceptance of Chery in Australia.”
Over the past year, Chery has introduced three new models: the crossover-style SUV OMODA 5, the medium-sized TIGGO 7 Pro, and the seven-seater TIGGO 8 Pro Max.
Chery plans to launch its first electric vehicle, the OMODA E5, later this year.
Toyota is bidding a farewell to its V8 LandCruiser 70 Series while shifting its focus for the popular workhorse by introducing a fi ve-speed manual gearbox for four-cylinder variants.
Paused ordering for the 1VD-FTV 4.5-litre turbo-diesel engine, which has been paused for almost two years, will not be reopened.
Final production of the V8 Wagon, Troop Carrier, and WorkMate and GX pick-ups will take place in September with delivery expected late 2024 or early next year.
Production of the bent-eight is scheduled to continue into next year, providing 79 Series GXL single and double cabs through to the final quarter of 2025.
The new fi ve-speed gearbox, which is engineered for higher torque than its V8 sibling, will be available from October production on all body styles
and grades, except for single cabs and Workmate Wagon.
Toyota Australia Vice President Sales, Marketing & Franchise Operations Sean Hanley says the decision to bring down the curtain on the V8 had been inevitable due to changing regulations and community expectations.
“Bidding farewell to the V8 marks
the end of one chapter and the start of another for the go-anywhere 70 Series – a vehicle that’s renowned for its ruggedness, reliability and simply getting the job done,” Hanley says.
“We continue to work closely with our production team to receive the maximum possible V8 allocation so that we can fulfil as many local customer V8 orders as possible.”
With the Jollift 1330 Fast Repair Bench you can now equip each work bay with a quality Italian manufactured car bench.
The flexibility of the modular design means that multiple benches can share one pull post, one set of clamps and one set of wheel stands, which makes it totally affordable for each work bay to have its own repair bench.
• 100mm lowered height
• 1300mm lift height
• 3000kg lift capacity
The Jollift Flat Line NM65 is a cutting-edge vehicle lift redefining industry standards. Crafted with precision in Italy, this powerhouse boasts a lift capacity of 3000kg, effortlessly handling various vehicle types.
With a sleek lowered height of just 65mm, it offers unparalleled accessibility for low-profile vehicles.