
9 minute read
Personality
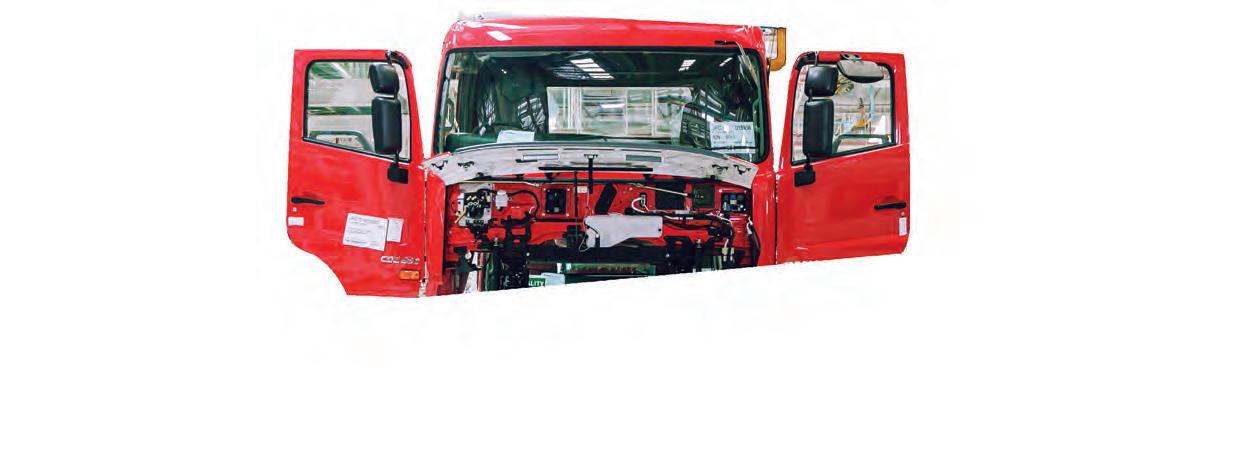
QUALITY The UD plant is located in Samutprakarn outside Bangkok.
SCHEMES
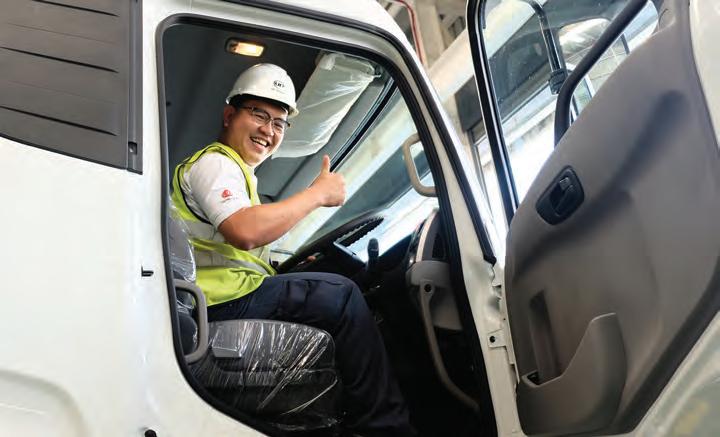
Helen Savmyr has a background in chemical engineering. She joined the Volvo Group in 2000 and has been in charge of the Thai-Swedish Assembly (TSA) operation for the past three years. In what was once a Volvo and then Ford passenger vehicle plant, Helen oversees a complex operation which involves multiple checking points, and an adherence to high quality standards which, for example, sees UD vehicles receiving the same paint procedures as the Volvo units, and every completed vehicle being dyno tested and laser wheel aligned prior to despatch. PM: Why does Volvo build many of its UD trucks in Thailand? HS: I believe that the main reason that Thailand was sought out by the Japanese UD management was the very good quality and good competence linked to the Thai automotive industry. I think the adherence to quality schemes is better in Thailand. It’s quite easy to get good quality here. The component supply chain is good here due to there being so many manufacturers. Some readers may be interested to learn that the UD Trucks Croner range which will be available in Australia over the next few months is actually manufactured at a modern plant located at Samutprakarn just outside of Bangkok in Thailand. The automotive industry in Thailand manufactures more than two million vehicles each year, as wide ranging as UD Croner and Quester trucks and Volvo buses, and pick-up trucks such as the Ford Rangers and Toyota HiLux utes which are currently so popular in Australia.
PM: Does the vehicle build quality here have to be at least equal to that in Japan? HS: It has to be comparable for sure. We don’t produce Croner in Japan, only
here, as well as the (heavy duty) Quester. The Quon is produced in Japan. Quester and Croner are very much linked to this type of market of developing countries including Thailand and Vietnam. Of course, it’s a combination of how to secure a good footprint from a manufacturing perspective, and then you have to secure good quality wherever you are. That’s why the Volvo production system is really important for us to ensure that every operation is following certain standards. When it comes to quality we have a Global Quality Audit manual which all Volvo plants worldwide follow. We have seen that we are very competitive when it comes to our quality standards.
PM: The Bangkok plant has ISO 9001/14001 accreditation and also achieved gold standard on the Volvo production quality scale. What is the significance of that? HS: When we started with this assessment process we said that the minimum standard globally should be gold. Then we know we have a very good standard globally and every plant should come to the gold level. The ones ahead can support the others with benchmarks. We are all assessed globally and we get external people coming here to interview and observe us.
PM: Is gold the top of the quality scale and, if not, do you intend going for a higher level? HS: The Ageo facility in Japan is platinum, and ladies like diamonds….
PM: What are you main goals here? HS: My mission of course is to ensure that we achieve good performance. My second mission is to develop the organisation and to develop the leadership and to ensure that we have a sustainable performance and improvement. We might not always have a (Swedish) ex-pat in charge. We are going the extra mile in our world class operation for our customers’ success. It is our customers who tell us we produce and deliver trucks that exceed their expectations.
PM: Walking through your plant we can’t help but notice how happy and engaged the workers seem. Is that part of the strategy? HS: Behind everything we do it is people and it is our aspiration to be one of the most attractive employers in the Thai automotive business. We try to engage our colleagues as much as possible. We have recognition programs relating to quality. We also have yearly health checks and random drug testing. We have our own soccer field which employees use for training and to play soccer. Our annual sports day pits employees against management in friendly competition. We also have a spirit house shrine and garden which is important for good spirits and peace on our site.
PM: Is getting good staff a problem in Thailand? HS: We have a mix of permanent and temporary employees in order to be flexible. So far we have not experienced any difficulty in attracting industrial
Helen Savmyr.

workers. Of course, we are training them so we put in a lot of effort which I would say is a bit different from Europe. I think we have better training centres here. For white collar employees it is attractive to work here. Volvo people are seen as good people. Volvo has a reputation for a culture of good work/ life balance.
PM: What is the capacity of the facility? HS: We can currently produce up to 20 Complete Build Up UD trucks per shift, plus 10 Volvo trucks per shift from kits. We also produce the FM, FH and FMX cabs for export to Volvo in Australia.
PM: The Thai government provides some duty concessions via the Regional Value Content scheme which requires a minimum of 40 per cent ‘local content’. Is it a challenge to achieve this? HS: We have set the goal to never go below 45 per cent and we are actually quite higher in the range of 50 to 60 per cent. It’s quite easy for us as suppliers to come much closer. A Ford logistics manager once told me manufacturing is only the disruption in the flow of components.
OWN WAY GO YOUR
The Ross Transport fleet in 1975 comprised a single prime mover. Today, the fleet has more than 60 prime movers and 110 trailers. It specialises in moving dangerous goods and over-dimensional loads as well as intrastate and interstate transportation. True Ross, whose grandmother, Frances Ross, and father, Alan Ross, have been running Ross Transport since 1975 has been involved in the industry as long as she can remember. “I grew up in and around the transport industry, spending school holidays and many Saturdays at the workplace with Dad,” she says. “When I finished school, I started working for the business part time and one thing led to another and I now spend half of my life here.” A standard day for True Ross is a busy one as she directs her own transport company that she started in 2016 in addition to managing the day-to-day operations ofRoss Transport. “I manage the compliance and work health and safety for the companies as well as oversee all roles at Ross Transport,” she says. “My job is very chaotic, I am the go-to person, but that’s exactly how I like it. I do anything that passes my desk. Each day is filled with meetings as well as keeping the business in check and ensuring everything is being completed the way it should be.” This impressive balancing act did not go unnoticed by the industry at large. In May 2019, True Ross joined the Transport Women Australia Limited (TWAL) Board of Directors. According to True it was her first real opportunity to help make a difference for women in the industry. “When I was appointed to the TWAL Board the feeling was absolutely incredible,” she says. “There is no other community like ours, especially where I live in the Illawarra. The transport industry is such a challenge which sometimes has a positive and negative impact, however, overall, I couldn’t think of a different industry that I would want to be in. I like the challenge and I hate Ross Transport is a family owned and operated business that has served New South Wales for 45 years. In her role as manager, True Ross is committed to improving operator safety and making the industry more accessible for the next generation.
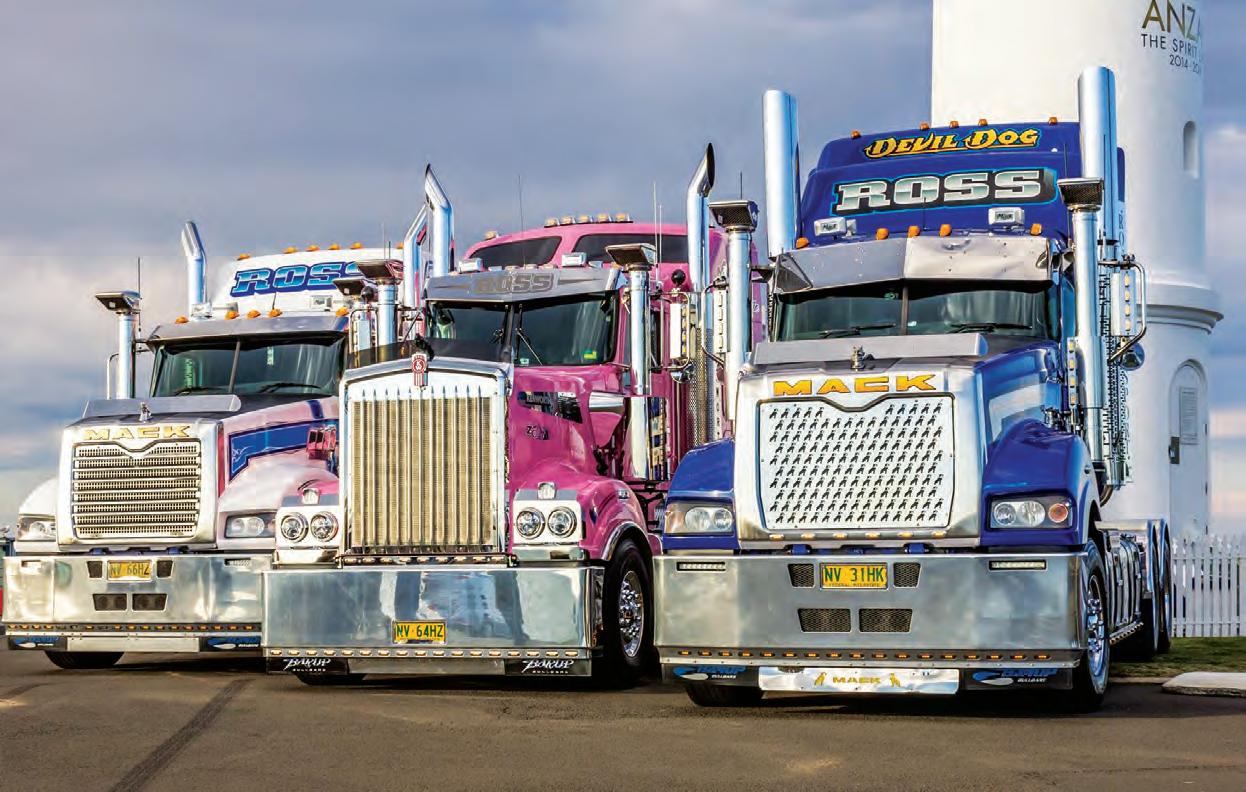
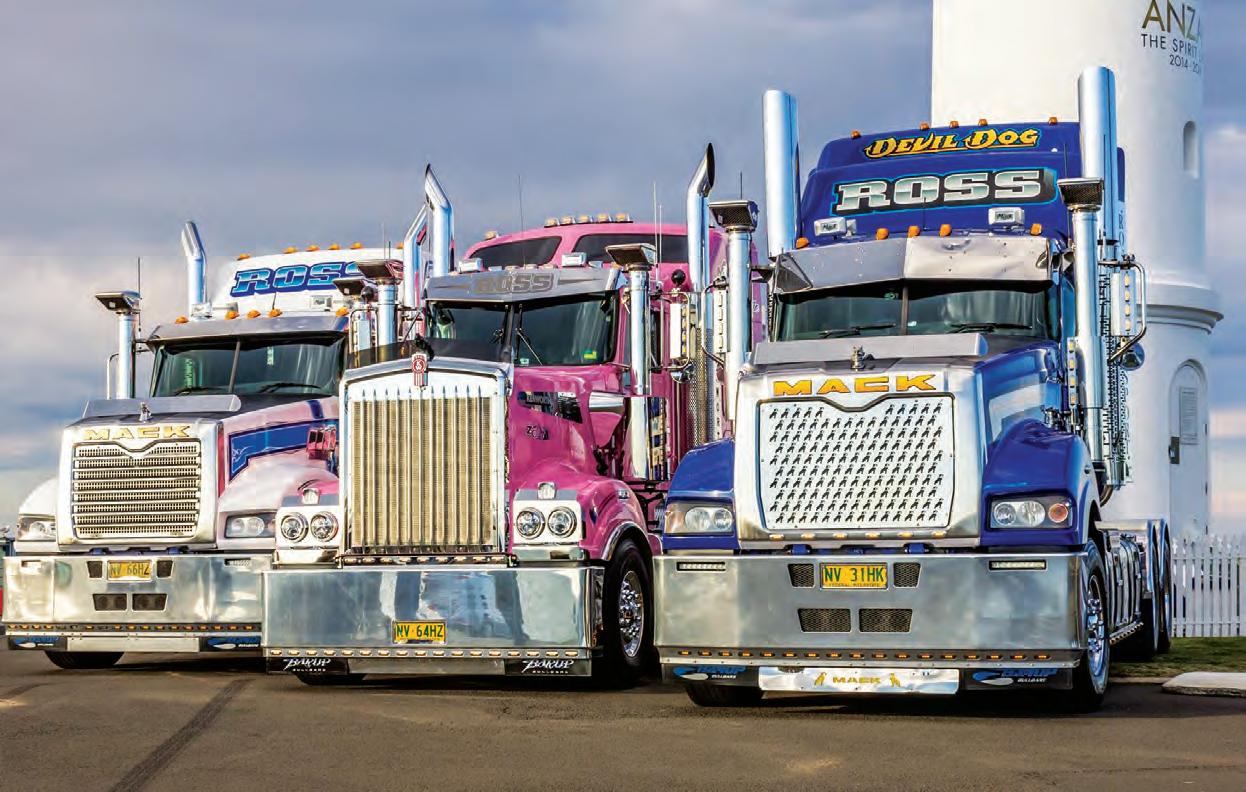
Ross Transport runs 60 prime movers from its base in NSW.
Truely Fantastic is a specially commissioned Kenworth.

True Ross.
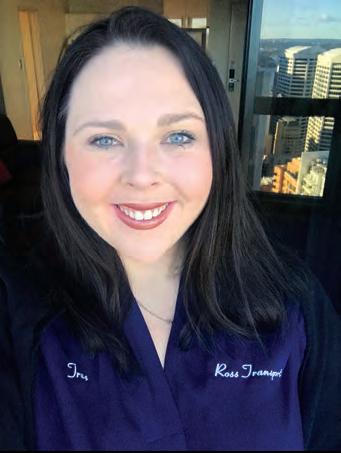
life being dull, which in transport it never is.” Female representation in the commercial road transport industry is critical, according to True Ross, but it is important that both genders are appreciated and recognised for the work they do. “Female-driven events are so important to recognise how far women in transport and women in general have come, but also to recognise that there is still an array of issues that women are still facing in the workplace and climbing the career ladder,” she says. “Both genders have a lot to offer and show different perspectives. We need to have female-driven events to empower and encourage our curre nt, future and aspiring women leaders from all roles across road transport. Having these events can assist women in ways to overcome obstacles in their career progression, juggle personal and professional responsibilities and build better relationships. These events are also equally as important for men to attend so they have a better understanding of the challenges women are still facing and how they can help in assisting women overcome these obstacles.” True Ross says it is important for people and companies to openly address transport as a career choice for women. In advertising positions within the industry, for instance, she would like to see more appealing propositions for female workers with inclusions such as flexible working hours or an exclusionary statement encouraging women to apply for roles. “If the company can afford it, advertise to upgrade licences and conduct a training program for women, so that they have an opportunity to enter the industry,” she says. “I just want to express that both women and men have skills and perspectives to bring to the table. We do need to keep continuing to support women’s contribution and continue to encourage women into transport whether it be as a driver, a logistics manager, in health and safety roles or an administration role. “The transport industry can be very hard and costly to get involved in. If there are more accessible ways to enter, it will make the industry more at tractive.”
FAST FACT True Ross and her father, Alan, commissioned the design of a pink truck dubbed ‘Truely Frantastic’. The moniker is a blend of Frances (True’s grandmother) and True’s names. The business is proud of this truck and how it recognises the contribution of women in industry.