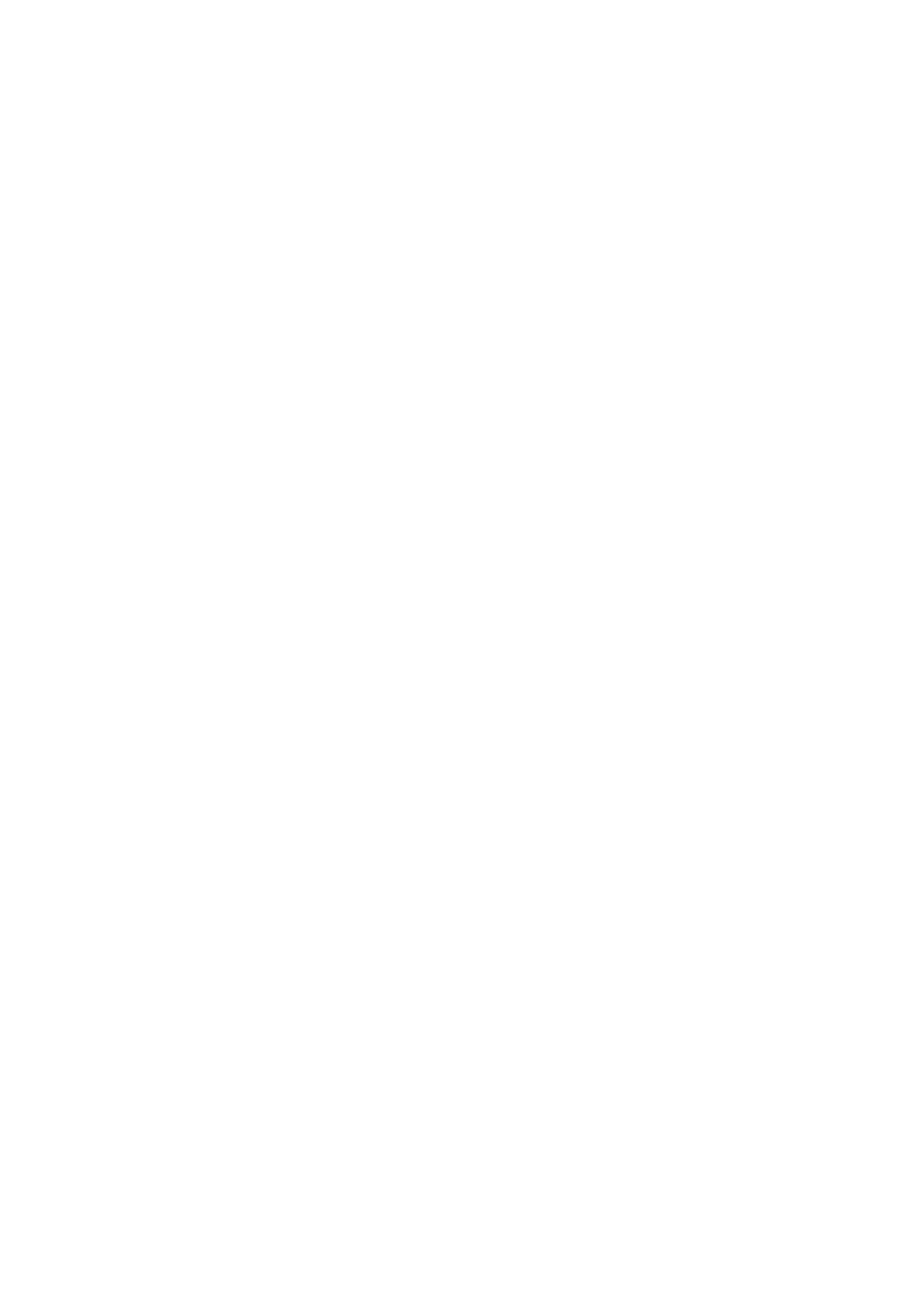
15 minute read
Coming Clean
COMING CLE
As a niche essential business, Container Fumigation Services in Melbourne is dependent on quality commercial vehicles. The challenges of a tough 2020 have been counterweighed, in part, by an informed recent investment in four new MAN trucks.
Containers arriving in Australia from overseas ports are subject to biosecurity requirements and procedures to ensure the threat of exotic pests and diseases are eliminated during their clearance. This also applies to the goods they carry by federal law. Container Fumigation Services (CFS) based out of Spotswood in Melbourne, has been immersed in this segment since it was founded by Greg Ross, a Director of the company, on 6 March, 1996. In essence the company is taking containers off the wharf as allocated, cleaning them before readying each for approval through quarantine. The company was started on the strength of a tip Greg received that quarantine laws regarding port operators would be extended outside of the five kilometre perimeter. On the premise that customers he had unloaded for previously would bring him containers, Greg set about securing a depot. With that the business purchased a secondhand Mack from an auction — the company’s first. Mobile equipment was acquired under this model for the first few years as they built up business which went from good to better. Over the ensuing years CFS has put together an impressive client base that now includes the likes of ACFS Port Logistics, Seacom, SunRice, John Deere and QANTAS. However, hire trucks required to satisfy the urgent tasks that were going unfulfilled by incidents of broken-down secondhand vehicles were fast proving costly. “We got sick of putting mounds of money into bloody repairs, hire trucks and having them parked up at great expense,” Greg says. “It was decided with my business partner that it was time to buy a new truck. I went around to every manufacturer and got the rundown on all of them.” It resulted in a month’s worth of data and engineering specifications to calculate. The criteria for evaluating the best truck for their needs started at price. As that
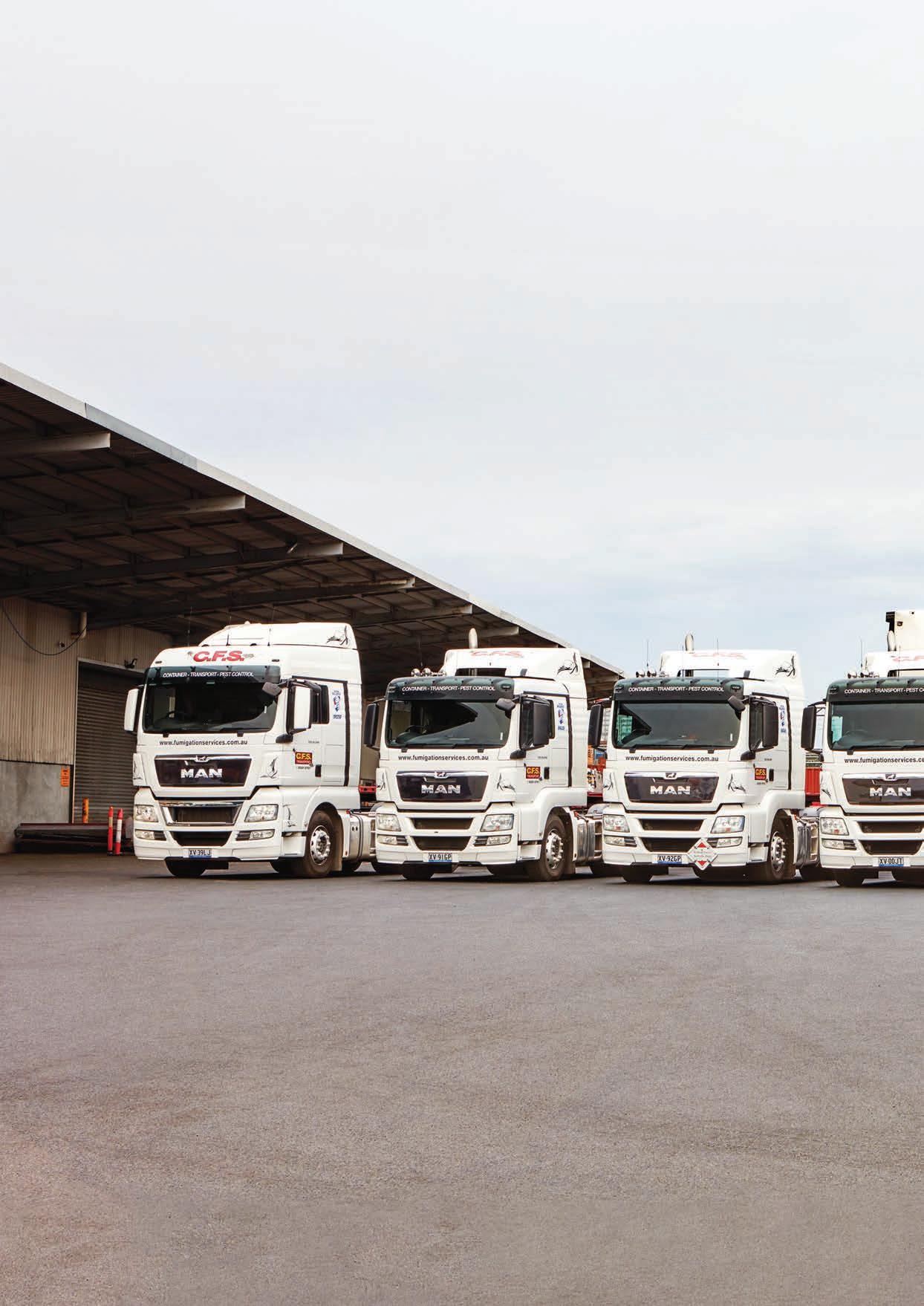
AN
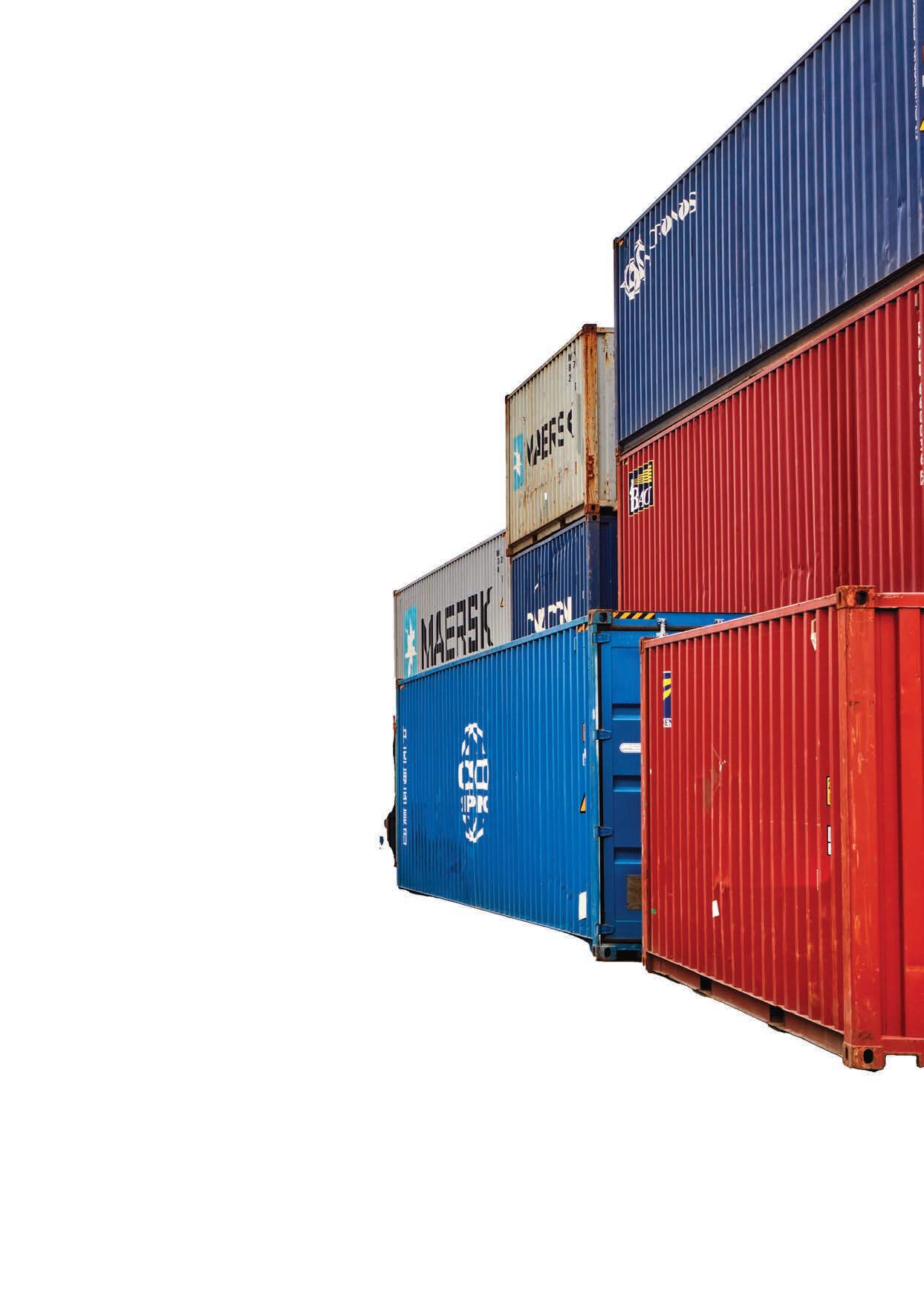
was negligible in range when applied to most other brands being considered, the evaluation entered the next set of criteria as Greg and his transport operations manager, Neil Ryan, deliberated on the significant indicators of performance, service and backup. “There’s only ever a tuppence between most of the commercial vehicles you are considering in this sort of purchase process,” says Greg. “Once you start to settle on certain factors like servicing and backup things come into sharper focus.” The first service of 70,000 kilometres at MAN soon got their attention while the parameters around backup, in which a hire truck was also provided by Penske Truck Rental, along with the impression made by MAN dealer Jarrod Bennetts of Westar Truck Centre, who was easy to get along with according to Greg, eventually won them over. Knowing they would have had to service their vehicles at least three times before hitting 70,000 kilometres and accessing a hire truck at no charge to keep the business running without suffering in any way, imbued the prospective buyers with a newfound confidence they had made the right choice. “If any of these new trucks go in for a scheduled service our fleet can complete the same numbers asked of it,” Greg says. “For mine, the MANs come out on top in every facet. Jarrod was great to deal with and that made the decision easier. The deal we got, well, I can’t complain. If I had to buy another one I would go straight back to him.” And he did — three more times. Container
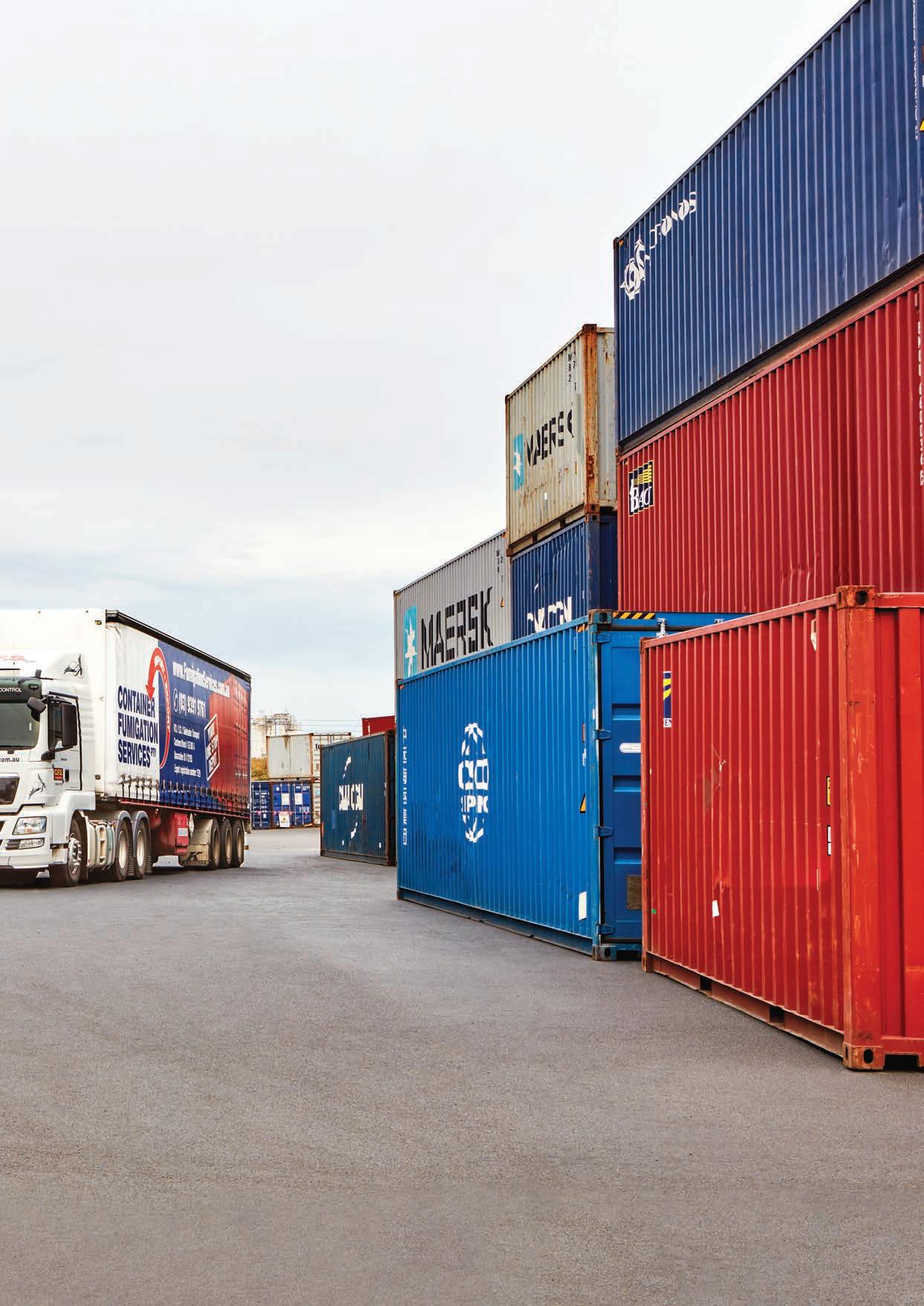
Fumigation Services now operates three MAN TGS26.540s and one TGX26.540 XLX cab. All the vehicles are rated to 70 tonnes gross combination mass for B-double application. They are moving both 20- and 40-foot containers in a cabover design, comfortable for the drivers with superior vision, manoeuvrability and safety. As it foregoes an engine tunnel in the cab for more space, the TGX is slightly raised, making the vehicle a foot taller in height than the TGS. The flexible TGS, more commonly seen in interstate linehaul, is a smaller presence on the road, making it less daunting a container carrier, for other road users. The Electronic Stability Control, a standard feature on the MAN trucks, is a musthave for relaying containers, each of which weighs around 24 tonnes, in and around the crowded port precinct. The key considerations for CFS to invest in these trucks, according to Jarrod, were the obvious safety benefits, not to mention the accurate forecasting of whole of life costs in addition to the service they would receive from the Westar dealership. “For Greg and his team the MAN was the obvious choice. The vehicle is setup perfectly for running around the tight streets of Melbourne yet is not claustrophobic,” says Jarrod. “The package that we have setup through the dealership means that Greg can forecast the costs for this truck for five years accurately. The only expenses are fuel, drivers and tyres. This is a big change from the second-hand gear that they were running that would not only cost them in repairs and maintenance it would also cost in the silent money drainer, downtime.” Hours supplant kilometres as the better metric in which to measure vehicle use. Even so, one scheduled service per year, as it works out, means CFS are off the road for only one day at a time. The backing of a rental vehicle inside the warranty importantly ensures they can work, if need be, 365 days a year — as suits their current operational framework. For Greg’s part he starts most mornings at 3am. For the majority of weeks he is required to work six days and seven days every five weeks. In 2018-19 the Port of Melbourne reported passing 3.02 million TEUs, an increase of 3.1 per cent on the previous year. Last year’s COVID-19 disruptions notwithstanding, the ongoing work is unabated. Greg often works a Saturday for no extra charge to his clients. The busiest times of year is the period leading into Christmas and, what is now widely referred to in shipping circles, as Stink bug season. That starts 30 September and runs to 31 May. Upon the onset of cold weather in the Northern Hemisphere, the Brown marmorated stink bug seeks shelter to spend the winter in a dormant phase known as diapause — a period of suspended development in some insects. Regulatory requirements primarily target importers of goods and cover their responsibility to ensure that certain types of cargoes are properly treated and certified prior to arriving in Australia. The process of fumigation takes 12 hours according to
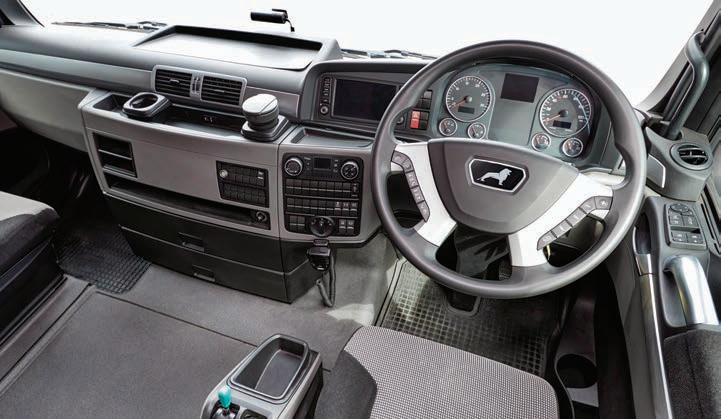
Electronic Stability Control comes standard and is a must in port cartage.
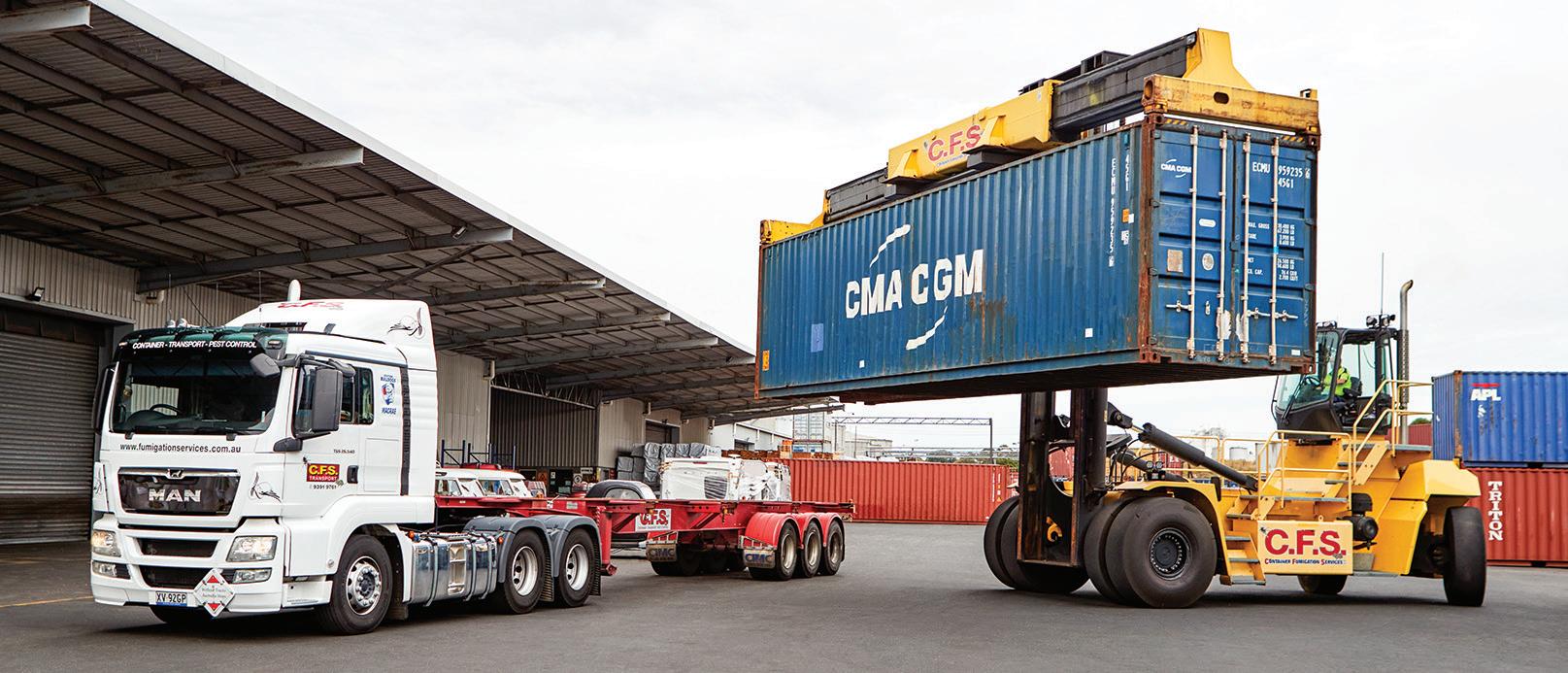
Greg, who uses a Threshold Limit Valve or TLV to carry out the work. In the afternoon the boxes, once they are unpacked for day proof, are released. Container Fumigation Services organises to have the container moved the next morning. All up it’s a 24-hour turnaround. The paperwork is then sent to quarantine who, often working two or three days in arears, will release the box. This clears the pads so restacking containers can resume in an area certified for fumigation. It’s not uncommon for Greg to get a late call from a client who will have a container on hold in customs for up to ten days. His job is to arrange to get it off the wharf on the day by coordinating with one of his drivers to pick it up. Drivers, at present, account for four of the company’s 35 staff although casuals are put on to meet peak demand. The CFS facility in Spotswood, which looks out over where many of the vessels come in, houses eight trucks and 15 forklifts. As a customs, quarantine and bond yard, containers can be packed and unpacked for export or goods can be stored for longer periods in a warehouse prior to being transported. CFS also has a second depot in Portland, Victoria to service the logging industry. Fumigation operations have been suspended of late after China placed bans on Australian timber exports in November. While 2020 proved to be a challenging year for most businesses associated with international shipping, Greg has helped to future proof his operations with high performance commercial vehicles on a service package that allows him to budget better with costs. Particularly in regards to maintenance with a service warranty that goes beyond spare parts and repairs. What’s more, the MAN vehicles have proven popular among the drivers since the first TGS26.540 was introduced into the fleet in April, 2019. “I’ve spoken to all the drivers about the trucks. They tell me the MAN is like driving a Fairmont,” he says. “It’s decked out with a fridge and all the modern conveniences. You can sit back in comfort. They absolutely love them. I have not had one complaint out of the drivers.”
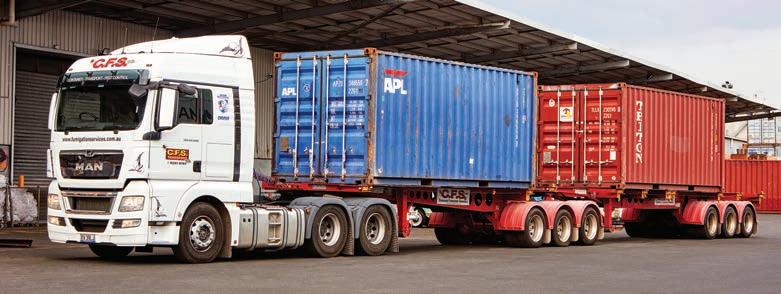
CFS spec’d MAN vehicles are rated to 70 tonnes gross combination mass for B-double application.
Reduce paperwork, save time and money with an NHVR approved EWD solution
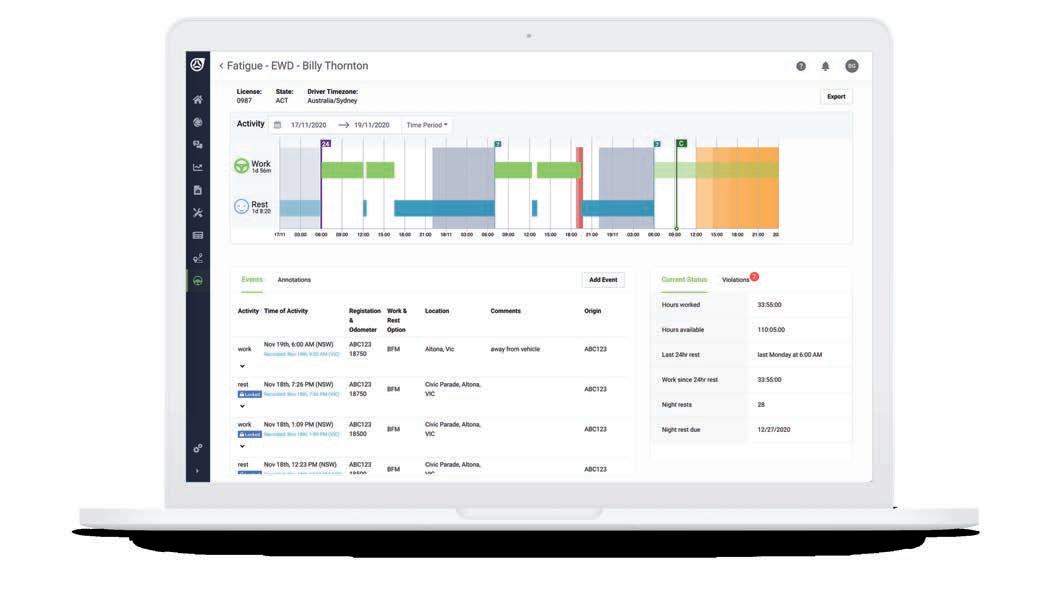
1300 111 477
SUNS
A faster than expected push to online retail due to distancing measures and a renewed focus on local manufacturing and production will invite growth opportunities according to a report released by Isuzu Australia Limited.
The release last December of the Isuzu Future of Trucking Report, the first by the leading commercial vehicle manufacturer, helped to outline the case for continued growth in last mile demand which was providing significant opportunities for fleets of all sizes despite recent unprecedented challenges. The report, conducted by independent research firm ACA Research, presents the findings of more than 1,000 road transport survey respondents bringing together a broad mix of industry and vocational voices. With insights pulled from both the distribution and freight, logistics perspectives, accounting for in total 60 per cent of all respondents, the remaining 40 per cent of respondents hailed from a range of other service provision industries, including government as well as primary production industries such as agriculture and mining. The decision by IAL to conduct the largest ever road transport survey in Australian history, was to acknowledge what it calls the rapid pace of change besetting the broader transport sector at present. Nearly half of larger operators (46 per cent) had shown they have clear and comprehensive strategies in place to address evolving industry changes. The large, more diverse fleets, however, remained best placed to deliver the bulk of the linehaul business across broad geographic areas. Reflecting their more complex operating environments, larger fleets are also most likely to recognise the pace of change currently facing the industry — pre and post-COVID according to the report. The confidence that large fleets have in their strategy for the future suggests a strong understanding of the markets in which they operate, greatly assisting their response to the ongoing COVID operating environment. Underpinning this is the effective use of data to inform business operation, with large fleets clearly differentiated in their ability to capture and utilise data. Large fleets are more likely, under the specter of what amount to more routine considerations for them, to have recognised the value of effective data capture, investing in fleet management technologies that can help them address fleet utilisation. This existing investment in new technologies is a key input to helping them sustain and increase business
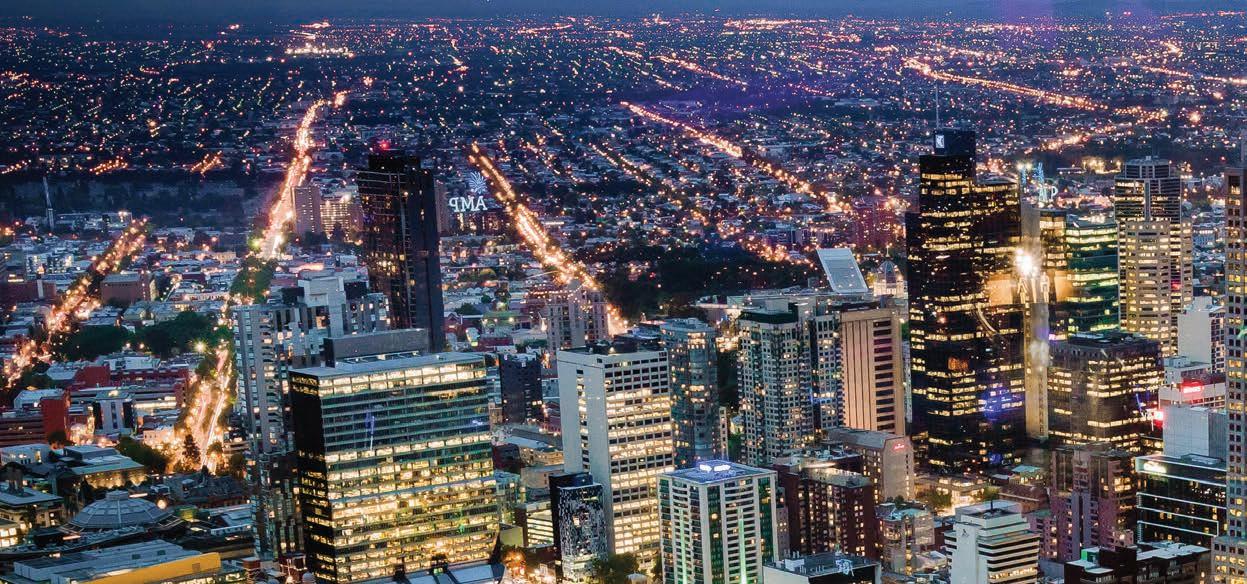
ETLIMITED
productivity in today’s increasingly challenging environment. Survey work informing this report was conducted towards the conclusion of 2019, with subsequent, followup survey work conducted in mid-2020, following the onset of the COVID-19 global pandemic. IAL acknowledged that the report’s authors have taken into account the ramifications of such unprecedented circumstances on the economy this year. The finalisation of the report, ultimately factored in these considerations. “Any survey marks a point in time, and our Isuzu Future of Trucking Report is no different,” IAL remarked of the report. “The project was commenced in late 2019 and the bulk of the findings represent the sentiment of industry participants before the onset of COVID-19. The authors of the report had since saw it pertinent to revisit the market to gain an understanding of how the changed social and economic landscape had affected attitudes and opinions of those who participated in it,” the company said. “The current and ongoing impact of COVID-19 is a significant challenge for the world,” declared the ACA authors. “That said, the findings in this report are important, as they combine underlying industry changes with the current COVID operating environment.” Although broad reaching in its scope, the report’s findings can be separated into five key areas of interest: The Freight Task & Business Recovery; Changing Customer Preferences; Total Cost of Ownership; Technology and Innovation; and Chain of Responsibility. The results in terms of Business Recovery
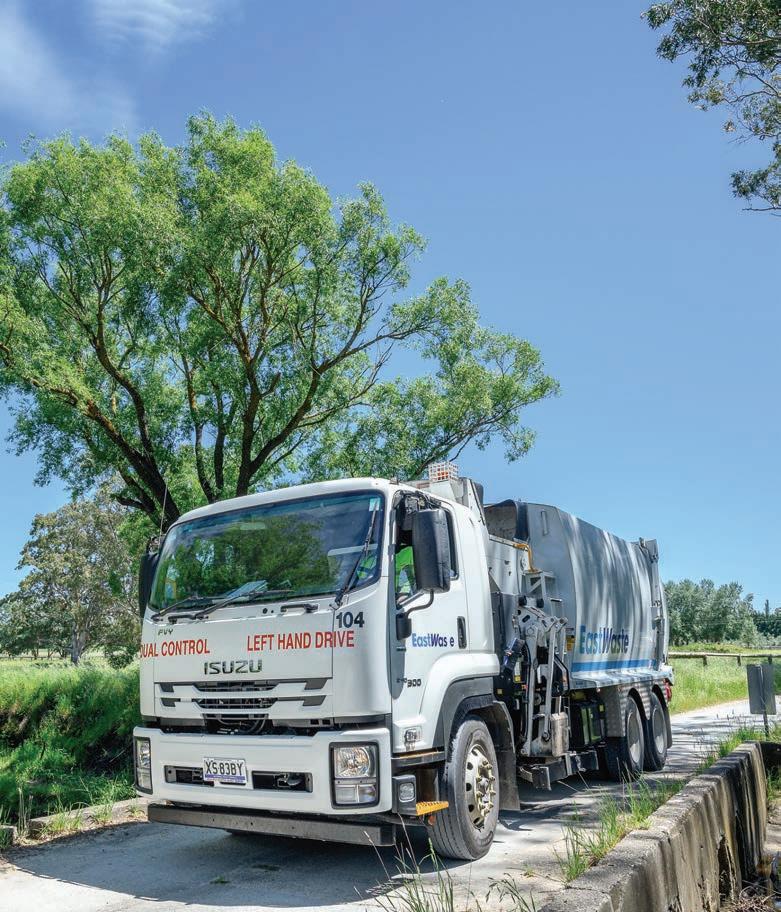
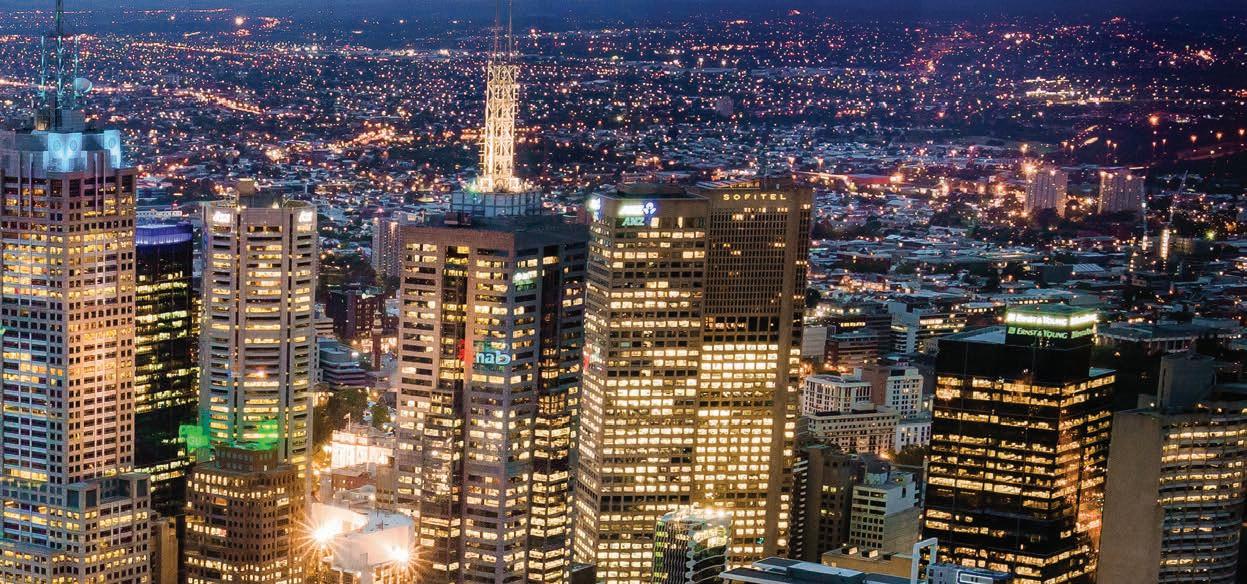
were predominantly positive across multiple segments and vocations according to IAL, with the effects of COVID, insofar as they had gravely impacted some industries, not altogether dampening spirits for most operators who were seeing strong demand for their services into the future. Similarly, government forecasts predicting growth in the road freight task to 2030 gave further rise to this confidence. Of those that participated in the survey 58 per cent operate in Australia’s metropolitan areas, typically with sub-100 kilometre, back to base ranges. Another 14 per cent fell into the long haul category, representing a far greater route range and interstate movements. Australian truck fleets, it was revealed, expect freight volumes to increase significantly by 8.2 per cent in the next two years. Key among Changing Customer Preferences was the trending demand for immediacy and availability of turnkey, fit-for-purpose products with broad driver appeal. Within the labour market, the persistent challenge of driver and skills shortages continues to concern operators. The findings demonstrate, however, that beyond just awareness, employers are and have been active in their efforts to review driver recruitment. In terms of Total Operating Costs, the ongoing cost of operating and maintaining an ageing Australian truck also remained a concern for respondents. Meanwhile, the pace of technological change dictates two key areas of focus for Australian trucking operations with the role of technology as it relates to driver safety of major interest and also the introduction and uptake of alternate drivetrain technology such as hybrid and electric options. The report considers both functions of road transport technology are critical markers in the future operational nature of Australian road transport. Findings for Chain of Responsibility legislation awareness were less encouraging the report noted, especially in regard to operators of small to medium fleets. Larger fleets, at the other end of the scale, displayed an acute awareness and a practical application of management strategies to meet their obligations. Of the businsses using data to manage fleets more effectively 61 per cent had, at their disposal, upwards of 20 commercial vehicles. Of the 20 per cent who affirmed they were in the process or planning to invest in fleet management technologies, those businesses operating fleets over more than 20 trucks represented half of the sample (50 per cent). Some key takeaways from the report include: half of truck fleets saw no impact or increased business. This rises to two thirds for those fleets working in distribution; one in three saw 30 per cent plus decline in operating revenues, making them eligible for JobKeeper; construction saw declines in growth projections, but was largely insulated, with most respondents reporting they were likely to have a decline of less than 30 per cent; Retail & Hospitality was the hardest hit sector, with almost three in four down by more than 30 per cent on revenue projections. Growth projections in the road transport sector were varied significantly by industry type in the wake of government and media response to COVID-19. IAL Director and Chief Operating Officer, Andrew Harbison, acknowledges the Future of Trucking report was an opportunity for Isuzu Trucks to contribute to bettering the shared knowledge of the industry. “The Future of Trucking report was undertaken with some broad objectives in mind. Importantly, it has been a chance for Isuzu Trucks to further enhance and develop our own understanding of the industry we are operating in, but to also benefit every stakeholder in Australian road transport,” he says. “It’s been a challenging time for the nation and every industry sector has endured trials as a result of COVID-19. It remains the hope of IAL that some of the insights gathered as a part of this project can be utilised by industry participants in their daily operations.” While it was no secret the commercial road transport sector was going through a period of change, despite this transitional period Harbison was buoyed to see that the fleets surveyed were confident about the future of the industry and anticipated continued demand for their services in the years ahead. “With or without a global pandemic, the freight task continues to grow and now is the time to build on foundations, to reaffirm industry relationships and ensure an efficient supply chain as we work collaboratively through this next phase,” Harbison says. In a statement IAL recognised it had enjoyed an exceptional period of success over the last three decades, and insomuch as it was extremely proud of this achievement, it was concurrently viewed as a genuine privilege. Noting that the Australian transport sector was an extremely strong, inventive and resilient entity and that Isuzu took its role seriously as the truck market leader. “More than that, the company believes it has,” IAL notes, “an obligation to commit its own time and resources to the betterment of the collective.”
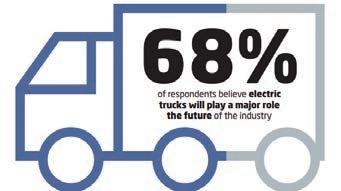
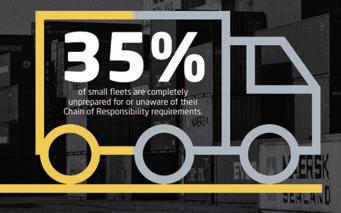
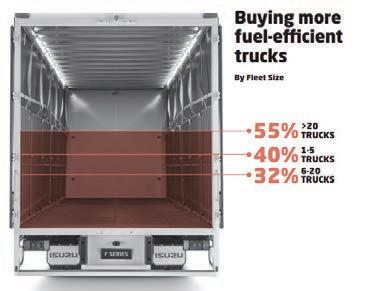