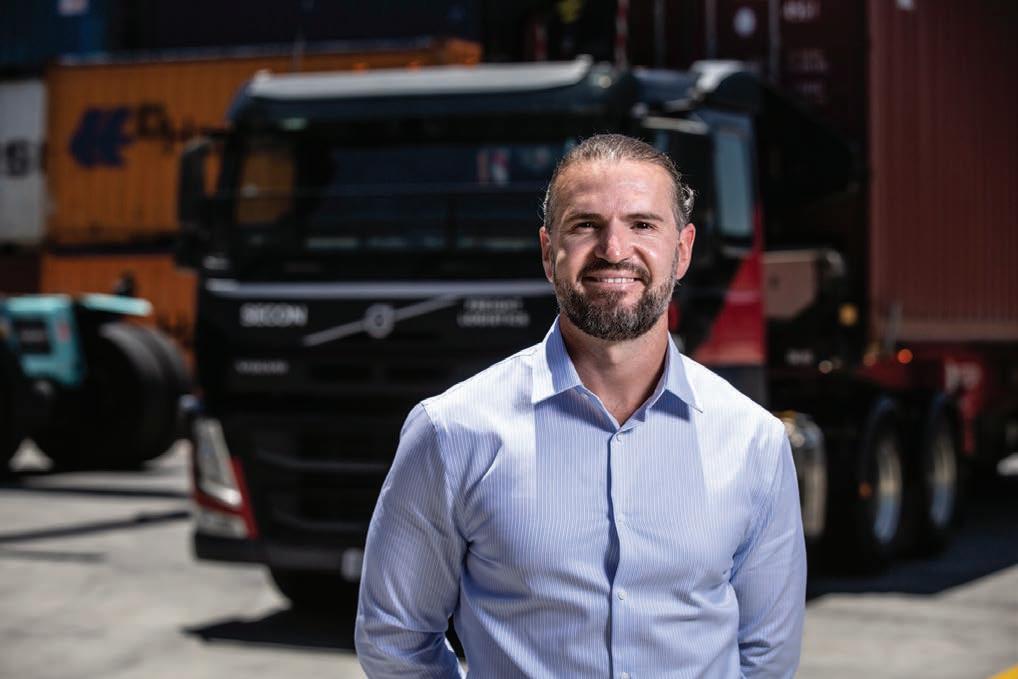
5 minute read
ARRY
Gardens Hotel, in which Maurie Considine, who was working for NZ Wool Trading Company, happened to be sitting next to heavy vehicle operator Jim Seide, led to a partnership where roles and the division of labour were suitably aligned for what has subsequently proven a successful strategy. When Maurie first suggested they go into business together, Jim was working, at the time, as a subcontractor moving wool in break bulk to the wharf on a flat top truck. Here the bails would be craned off the wharf for shipment overseas.
“If you look after the trucks I’ll get the customers,” Maurie had said. That was late in 1968.
Container hauling in Australia began in earnest the following year. This served as the platform that would catapult his connections at NZ Wool Trading Company, Maurie had put together a strong network. Many of these acquaintances were “most anxious to get people to pack their own containers,” Maurie recalled in an interview in 2016. Some of that work, invariably, soon fell to Maurie and Jim. a sideloader, one of the first in use in Victoria. It was acquired for $80,000. The gamble soon paid off. Maurie by now had been inducted as a life member at the Hawthorn Football Club where he had played 37 games and more significantly had been an assistant coach under AFL hall-of-fame member John Kennedy.
In 1978, Maurie’s son, Vincent, who had been training as a motor mechanic, changed career tack and under Jim’s tutelage joined the company. In 1981, Maurie’s sons Terry and Brendon also joined the business consolidating what was a family affair in operations. After they gained experience in driving forklifts and manual labour both sons were inducted into operational “slots” where they have left an indelible impression on the expansion of the business. Today Brendon serves as Managing Director. Paul Considine joined in 1983 followed by Matthew Considine in 1988.
In 2012, Secon moved to a facility in Sunshine on the recommendation of Terry. It proved a masterstroke in terms of productivity returns and the accelerated growth of the business, which continues today. The move to Truganina, an area west of Melbourne where much commercial development and expansion has taken place in the last five years, has required the company to redesign their commercial structure and customer profile. As part of these developments, it now has its own 26,000m2 yard where container dispatch is now staged. The site container yard to the loading of loose freight on vehicles.
The wharf fleet, which is predominantly Volvo vehicles with a few UD trucks, operates 24 hours, five days a week and weekends, as required. It underwent the first stage of an upgrade in 2019 as Secon, in keeping with changes in heavy vehicle technology, invested in safer, more fuel-efficient trucks under the guidance of its drivers. Trucks, by and large, originate from the CMV Truck & Bus network and are Euro V and Euro VI emissions compliant. The systematic fleet refreshment has subsequently seen many of its older trucks phased out.
Advancements in integrated electrical systems and computerised diagnosis of vehicle faults, according to Chief Executive Officer, Daniel Considine, have been expressed in a different approach to repair and maintenance.
“It became too complex for a general diesel mechanic who once upon a time would have lifted up the hood to get to the root of any problem,” he says. “We had to strategically align ourselves to a single supplier and we chose Volvo Group to streamline our R&M. The fleet consequently has a uniform approach to serviceability.”
The workshop crew, of which there are six, have been upskilled and have their own computers now to perform diagnostic checks. While most of the R&M is now performed through a fully maintained service contract through Volvo, the technicians take care of trailer maintenance including stainless steel welding and manufacturing.
“All of the advancements and modifications of the trailers we do inhouse,” says Daniel. “There’s also an engineer in the workshop.”
In 2009, Secon Freight Logistics purchased specialised tipper transporters Bulk Carriers Australia, as both companies shared some of the same directors.
The business they inherited moves plastic resin extruded and pumped into tall storage silos. Specialised auxiliary equipment such as pneumatic tippers are used for unloading. This arm of the business generally services larger contracts nationally. There’s 18 of these customised trailers with suppliers Barker and Vawdrey building the chassis inhouse and retrofitting the pump. Secon recently appointed their own bulk manager for solutions to that industry.
Secon Freight Logistics operates 50 vehicles in total with Volvo FMs and UD Quons doing the bulk of the heavy lifting. New UD Croners are the preferred vehicle for Secon’s loose freight distribution division, while Isuzu rigids are tasked with jobs confined mainly to the yards.
“It’s important that we get the best value truck. It’s one of the prerequisites when it comes to replenishing the fleet which is low range and high usage,” says Daniel. “The biggest issue to date has been sourcing parts for vehicles given supply chain disruptions experienced worldwide earlier in the year and that’s ongoing.”
Three high productivity vehicles, originally deployed in 2020, are pair of A-doubles on purchase order through Vawdrey. Meritor, no less, is trialling axles on the Vawdrey trailer sets. More than a few million dollars of equipment, Daniel confirms, is scheduled to arrive mid-2023 to close out what is the most recent round of a formidable capital expenditure program. The UD Quons, readily available earlier in the year, were introduced to satisfy demand.
“Drivers like the Quon. It’s a comfortable vehicle to drive,” says Daniel. “We like that it’s also light in weight and can take more on.”
The company has worked hard on reverse engineering the traditional ship to shelf model by planning around the crucial end point. Depending on vessel availability, the process has been refined lulls for its customers. To make it work, Secon use map time slotting, all of it palletised. For this, there are 60 forklifts operational across two shifts, the latest ending at 2am. Significant investments have been made in the property next door at Truganina. It’s a nine-hectare extension at a $4 million investment which will increase container capacity, making Secon one of the largest container yards in Victoria able to handle full containers. Post tension concrete, which is deeper and reinforced during the curing process when the reo mesh in it is tightened, will allow operations to stack up to 120 tonne containers.
Delays in supply chain following the peak period in early 2022 brought disorder to the industry as businesses shipping schedules. Secon’s yard can handle up to 1500 TEUs efficiently. It was over 100 per cent capacity for a long time according to Daniel, who is a trained Occupational Therapist, but has been working in a business development role the last eight years since his uncle, Terry Considine, who has sadly since passed, seconded him to the company.
“We knew our competitors were struggling for space,” he says. “All the warehouses were filling up and for a while there was a lot of angst between us and customers. The crucial part of that was communication and managing expectations.”
In the past, a business, under these circumstances, might have been able to rely on labour hire as a pressure take a proactive solution and that was to give customers options so that they felt they had a choice. There were cost up around April. COVID lockdowns, however, were crippling given the company had lease arrangements for its old facilities that sat empty. They paid double rent for a while. Although costs went up, none of it ultimately impacted revenue.
Management had to incentivise its customers to move their containers as quickly as possible.
“We still needed arms and legs to do the work,” Daniel recalls. “Foremost, we protected our people during that time. It was all about our staff and empowering them post-COVID.”
With a payroll of over 200 staff, a major focus, naturally, is on its people but also the wider community.
“Adding the safest trucks to our fleet is an investment in our drivers,” says Daniel. “It’s also so the community can feel safe every time they pass a Secon truck on the road.”
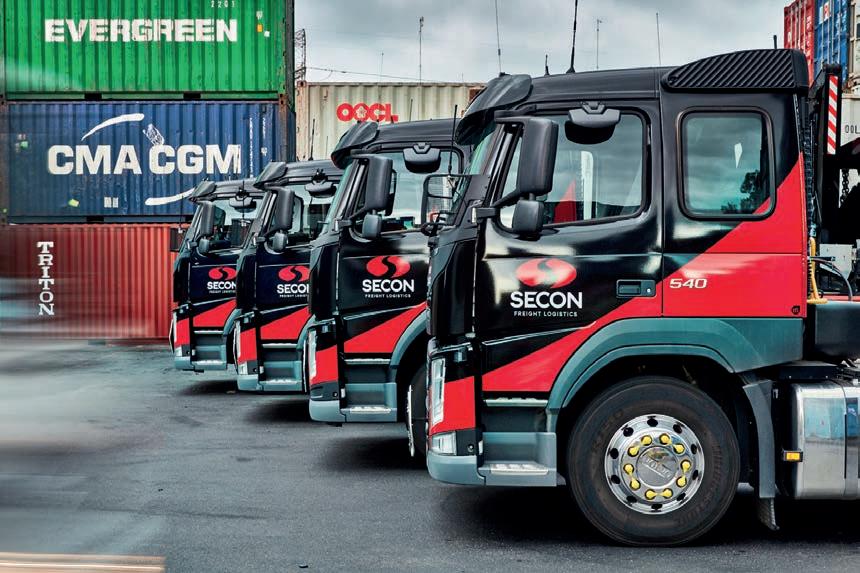