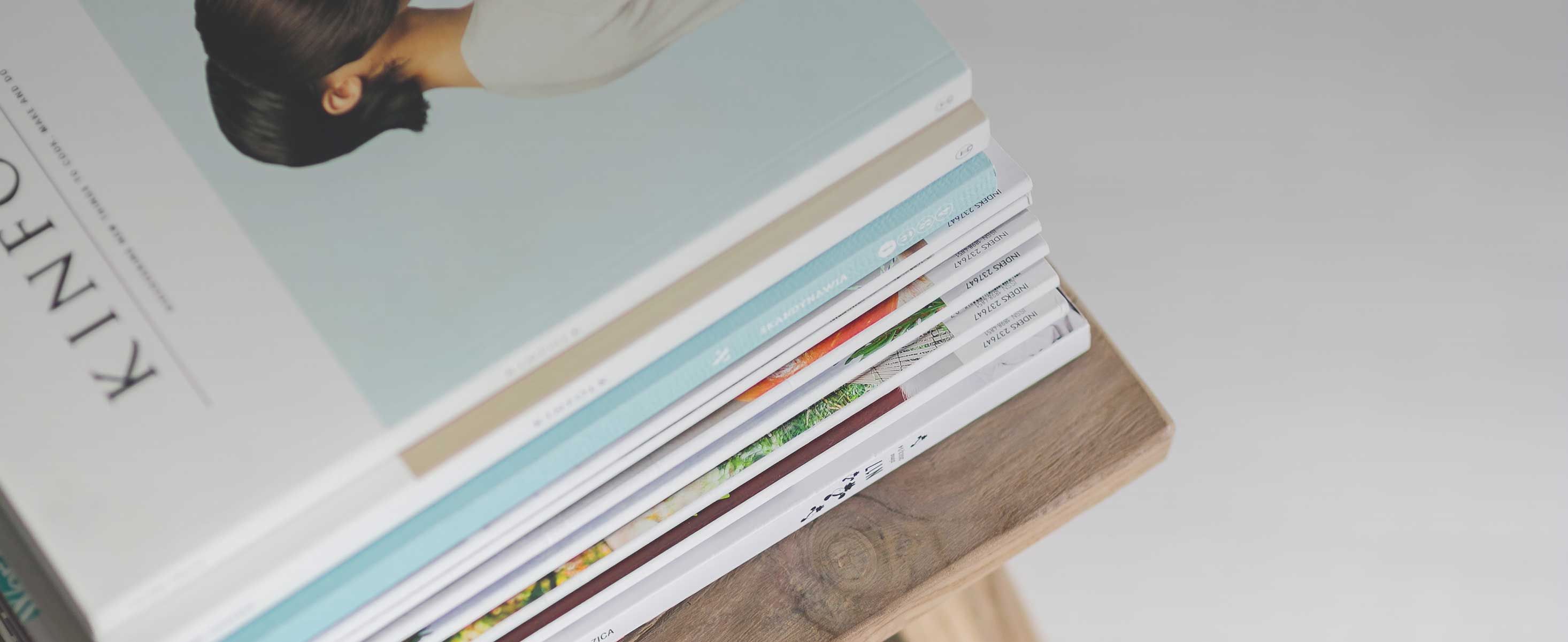
7 minute read
IN QUAD WE TRUST
Three years ago, Angelo Lamattina had an idea. He was determined to find a more efficient linehaul solution for transporting, by truck, carrots from farm to market. Having noticed several 26 to 33-pallet trailer combinations out on the road helped him to eventually find it.
Angelo, the Director of Rocky Lamattina & Sons, of which he is one, has, after three years of global challenges, finally made the dream a reality on a new twinsteer Kenworth K200 prime mover with an 18.2 metre fridge van split quad. It carries 30 pallets between Wemen to the markets in Melbourne and Sydney. To meet the objective of increasing the carrying capacity while incorporating the wheelbase of a twin-steer which is customarily around 500mm longer bullbar to turntable, Kenworth engineers were engaged to make some key customisations to the design. The first of note affected the position of the AdBlue tank which was moved between the steer axles on the passenger’s side. The fuel tanks were sculpted, as a consequence, to miss the front leaf spring hangers therefore bringing the bullbar to turntable back to the single steer K200 length already in use on the usual applications. Here an additional flexibility has ensued, given the prime mover can be hooked up to a B-double without it being over length.
Calculations were also made in order to maximise the pallet capacity. A particular vehicle mass for a payload of 37.4 tonne had to be achieved incorporating both weight distribution and swept path.
“This was a process motivated by the gains we were looking for within a feasible framework,” explains Angelo. “It involved going through all the relevant criteria to ensure we ticked all the right boxes for the NHVR.”
Independent engineer Phil Ramfos was instrumental here when it came to the PBS design requirements.
The trailer build was assigned to longterm partner Southern Cross Trailers, where Engineering Manager Remo Centifanti, who was heavily involved in the whole concept, made a major contribution.
“We’ve been dealing with them for 30 years,” says Angelo. “It was an obvious choice to collaborate with them again to build the trailer.”
Another key supplier was SAF-Holland.
Angelo initially approached Managing Director Mario Colosimo, who has an engineering background, to explain his concept and to discuss proposed axle configurations. There was some early talk about having a single axle out front of a tri-axle.
“We decided against that ultimately, as having an axle isolated on its own made it vulnerable, at least in theory, to the possibility of being overloaded,” says Angelo. “When you’re on airbag suspension all the airbags are equal. There’s an expectation that you get 9 tonnes on one axle and 7 3/4 tonne on the other axles. Unless you use different size airbags and pressure regulators it’s already getting more complicated and potentially problematic in the future.” The better way to do it was to put two groups of axles together to mitigate against any unknown failures. It made everyone more comfortable in the decision-making process.
“By doing what we did together gave us peace of mind we weren’t going to put the product beyond its capabilities,” recalls Angelo. “That was pretty important.”
Split quads in themselves are not new. They’ve been used on low loaders for many years.
“I’ve had some experience many years ago with belly axles on semis which were fitted over in Western Australia. They worked well. No issues. We’ve also seen belly axles overseas in Canada so it’s not unheard of,” says Mario. “But it is obviously new for us in the sense that this Lamattina semi-trailer has got to go very long distances. Especially with refrigerated units, there is an advantage in going to one semi rather than having a B-double to cart your freight. In particular, because you’ve only got one fridge unit and insulating property.”
A light weight SAF-Holland INTRA fabricated trailing arm, rigidly connected to the axle, was chosen for the non-steer axles. The shock absorber is protected due to its position in the functional suspension arm and the extremely robust design makes it ideal for PerformanceBased Standard applications. For the steer axles Angelo opted for the well proven Mobil suspension.
“The actual running gear is proven technology which has been around for a long time,” says Mario. “With a quad we’ve gone with the bigger airbags because it will pump up faster which is what you need. With a quad axle you need more air than in a tri-axle.”
As there’s particular convex and concave curves the vehicle needs to sit on, having insured all axles can put pressure on the ground equally under these circumstances justified some tweaks to the design. According to Mario this resulted in ensuring there was enough stroke in the suspension to avoid having the front axle bottom out while the middle axles are flat on the ground surface.
“The wider the spread of your axle combination, the worse off you’re going to be,” he says. “This was mentioned early and the suspension was specified accordingly.”
SAF offered Lamattina some longer shockers to deliver what Angelo describes as a “bit more travel” that also helped with meeting one of the requirements that are part of the procedure of getting these vehicles approved with the National Heavy Vehicle Regulator. All high productivity freight vehicles, more or less, undergo an intricate process of concept-design-build-approval. No matter the design, once somebody has proof of concept and it works for one truck it will work, at least in theory, according to Angelo, for all trucks. “When you build something a little bit different which is what we’ve done we have to be the ones who do that groundwork to achieve that which is good in one way,” he says. “The negative is you have to do it yourself but the positive is you fully understand how much work is involved in the vehicle. People probably think a truck is running up and down the road with no science behind it, but there is some engineering there that gets done to meet certain standards for the safety of the Australian community.”
The combination, which is dedicated to carting crates and boxes, now achieves 1246kg per pallet space. An initial evaluation period of around four weeks took place before it was booked in for sign-writing at YBIFX, a Bendigo-based company that has provided the wrap used on the new trailer.
“Overall it seems to be doing exactly what he wants it to do,” says Mario. “The manoeuvrability is fine. He’s not getting a tyre scrub. The main thing for Angelo was to find someone who could make the side panels the right length in one hit. So there was quite a bit of homework from his side to get that exactly the way he wanted it.”
Angelo is at once a lateral but very practical thinker as Mario observes.
“He’s not going to do stuff just for the fun of it,” he says. “On this project he had been working on it for some time.”
Lamattina Farms runs 17 prime movers in total. Four of these are Kenworth T909s, three of which are twin-steers. The remainder are standard K200s. The operation also deploys B-quads farmto- farm with five trucks on those duties. While the predominant application is B-doubles, a B-triple occasionally runs to Queensland.
“One thing about Angelo is he’s definitely a forward thinker and definitely trying to think outside the box to try and get the best possible result for his business,” says Mario. “PBS is ideal for someone like him.”
The inconvenience of rising floodwaters in regional areas has detoured the new combination from the usual routes it would be expected to travel. Interestingly, that has involved the truck covering much further terrain than it would customarily be required to do, and given the team at Lamattina & Sons a good opportunity to look at its initial performance numbers in greater detail. The driver, according to Angelo, has noted that so far the Kenworth K200 split quad is using less fuel than he is accustomed to despite covering more ground.
“We’ve been pleased with what we’ve seen so far on fuel,” says Angelo. Embarking on such a project or any project reliant on heavy equipment engineering nous during recent years subject to border closures, supply chain turmoil and social distancing policy has proven a challenge. Parts and labour were one of the big obstacles in getting equipment turned around in time according to Angelo.
“Material and labour shortages blew out the schedule we had proposed,” he says. “Getting the appropriate parts took a lot longer than what we had anticipated.”
Part of that process is also explaining the concept for approvals and access. The PBS unit, which has a GVM of 62 tonnes, is operating on a Level 2 access permit. “It’s been a matter of convincing others, for much of the project, of what we’re trying to achieve,” says Angelo. “There’s a process you go through with PBS. We’ve been doing it the way it should be done. It’s more time consuming at the outset, but it gives you ultimately a faster result.” In the past, operators would often get their new truck combination designed and built before applying for the permit. This process would take too long according to Angelo, resulting in vehicles often being parked up for months. “What we do is what they call ‘in principle’ applications,” he explains. “So we say ‘if we build this vehicle and we apply for a permit to do this, this and this would you give it to me yes or no?’ That’s how we’ve always approached it.” In time the system has evolved to work increasingly that way. It suits Angelo. “We come up with our plan and people say ‘yes’ or ‘no’ and you argue and fight and explain it to them and get all that done and once that’s done, we receive an in principal agreement before you go and get the vehicle built and receive all the vehicle approvals,” says Angelo. “Last step is you apply for the permit because you have the in principal agreement, and within around two weeks you get the permit.”
The Kenworth split-quad is already in the process of being replicated. By the end of Q1 next year Angelo expects to have three more of these out on the road with additional units deployed in time for Christmas 2023.
“On a 32-pallet trailer previously I was only able to get 30 pallets for the weight,” he said. Now he can get full capacity and has converted, more conveniently, to one truck, one trailer and one fridge motor. “The beauty about it too is the combination makes life easier for the drivers. Not having to connect and disconnect, not having to back up two trailers and only having one,” he says. “It’s much more efficient and better for the environment.”