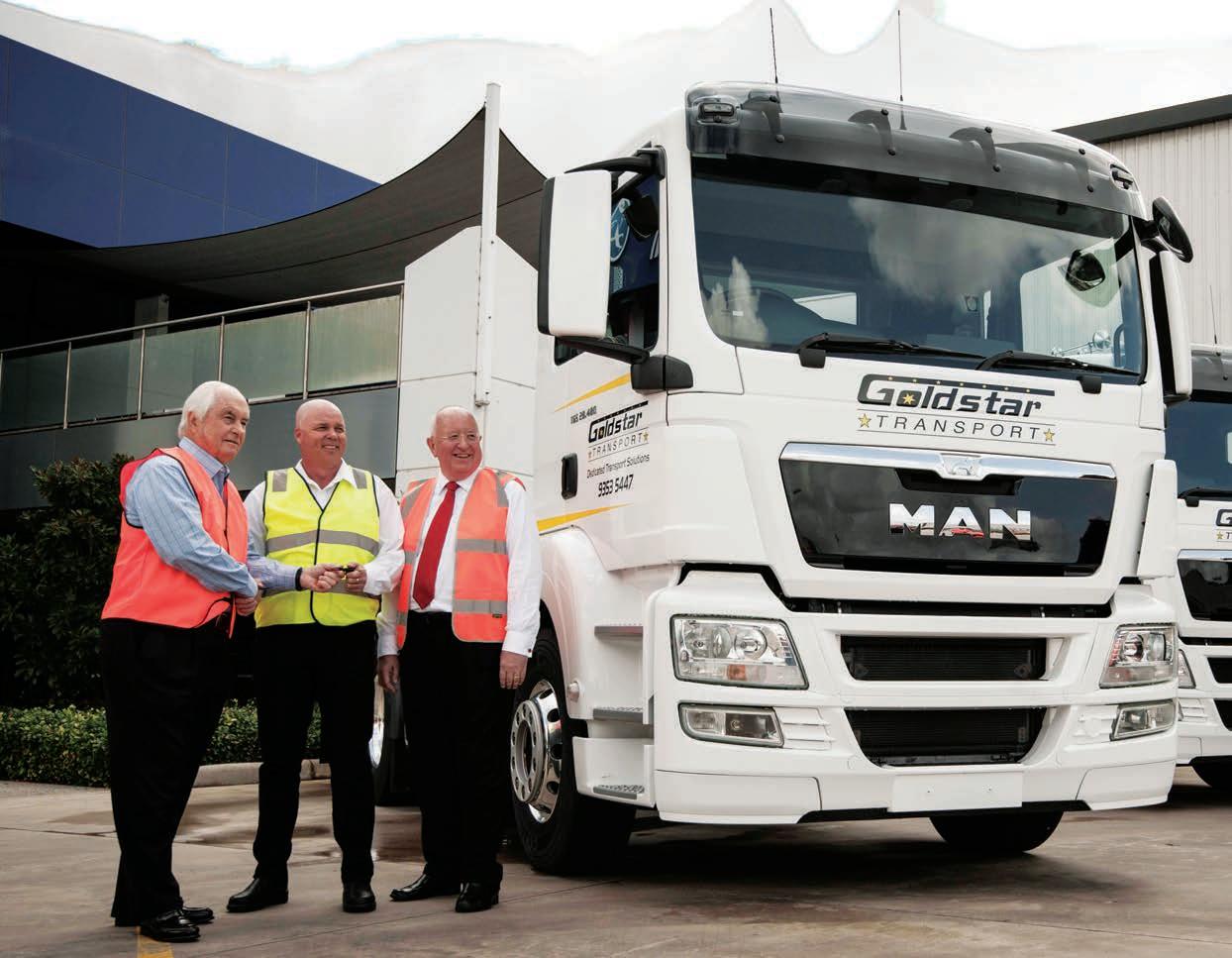
9 minute read
Rear Window
by Prime Group
REAR
At a casual glance it can be difficult to pick the difference between 6x2 and 6x4 (and 8x2 and 8x4) trucks. While both have tandem or bogie rear axles that externally look much the same, a quick check underneath reveals either two drive axles connected by an inter-axle drive shaft (bogie-drive) if it’s a 6x4; or if it’s a 6x2 in Australia, the forward rear axle is usually the drive axle, paired with a beam axle similar to those found on trailers. This type of 6x2 is called a ‘tag’ axle arrangement. Another iteration of the 6x2 scenario, known as a ‘pusher’ axle setup, sees the drive axle at the rear and the lazy in front, with the ‘pusher’ terminology stemming from the ‘pushing’ position of the rear drive axle behind the lazy axle. This style of truck is popular in Europe where electronically controlled air suspension enables the lazy axle to be lifted clear of the road when travelling unladen, thus further reducing tyre wear and fuel use. Tailoring the spec to the application is key to every successful trucking venture. For metropolitan pickup and delivery, 6x2 and 8x2 units can be a compelling choice.
WINDOW
Goldstar Transport uses MAN TGS 26480 6x2s on a grocery contract.
Put simply, both 6x2 and 8x2 configured trucks have two rear axles, one driven and one lazy, while the 8x2 has the benefit of an extra steer axle which allows 11 tonnes to be carried by the twin steer axle group provided load-sharing suspension (such as that used on the 8x2 Scania) is fitted. Non load-sharing front suspension twin-steers are limited to 10 tonnes, while single steer trucks are limited to 6.5 tonnes on the steer axle. For quite a number of years in this country the 6x2 body truck has been the standard horse for many local pickup and delivery (PUD) roles that don’t involve off-tarmac operation. Leading the charge with sales of this type of vehicle is Australia’s overall truck market leader, Isuzu Australia Limited (IAL). The company has significantly developed and refined its 6x2 offerings over the last two decades, with its most popular 6x2 model in recent years being the FVL 240-300, the Auto model in particular. “I believe we have the right formula for the Australian market, and especially the “bread and butter” choice of body for this spec: a 14-pallet curtainsider, with or without a hydraulic tail-lift,” says Simon Humphries, Chief Engineer, Product Strategy at Isuzu Australia Limited. “This is the key reason we deemed it essential to include the FVL Auto in our FreightPack Ready-To-Work range last year.” According to Simon, the Isuzu FVL formula for success is spearheaded by Isuzu’s renowned reliability and performance, with the FVL’s 6HK1 engine rated at 300hp (221kW) accompanied by 981Nm of torque. “Both of these outputs are at the head of the pack compared with the next three volume competitors with a similar price point,” Simon explains, adding that there are higher power and torque 6x2 models on sale, including Isuzu’s FXL 240-350, but they are all significantly more expensive. He also describes the Allison MD3500 six-speed automatic as “bulletproof and matched beautifully with the 6HK1 engine to produce effortless performance, even when fully laden.” Simon also makes mention of Isuzu’s cab design and low interior noise levels, citing superior visibility, strength and driver comfort as key components that help minimise fatigue over a hard day’s work. “Interior noise levels of the Isuzu fullsize FV cab are significantly lower than its Japanese competitors, as measured by calibrated sound meters under equivalent conditions,” he says. “While the standard air-suspended ISRI 6860 driver’s seat with integrated seatbelt is the best on the market.” Other noteworthy standard features of the FVL 6x2 are driver and passenger airbag, Michelin tyres, Meritor axles with Stemco oil-filled hubs on both the steer and lazy axles, and Meritor Q-Plus drum brakes with ABS on all axles. “This axle and brake package is common to many heavy trucks, and their light weight also contributes to a very handy payload advantage when compared to other equivalent Japanese and European brands,” Simon says. Victorian-based operator Glen Cameron Group runs a large fleet of 6x2 trucks and according to Shane Coates, Glen Cameron Group’s Asset Manager, the 6x2 configuration is ideal for the majority of the company’s PUD work. There are, however, some specific contracts where the 6x2 is not entirely suitable, and the solution for Shane has been to recruit Scania 8x2 units. The main issue that arises with 6x2 body trucks running close to their maximum gross weight is keeping the steer axle weight legal at all times. This can prove quite a challenge in multi-drop and pickup applications where the truck is either leaving fully loaded from the depot and being unloaded incrementally at a number of locations, or conversely, being loaded from empty with heavy pallets from different locations in a multiple pickup operation. The problem arises when heavy pallets (weighing between 750-1,000kg) are located at the front of the body with
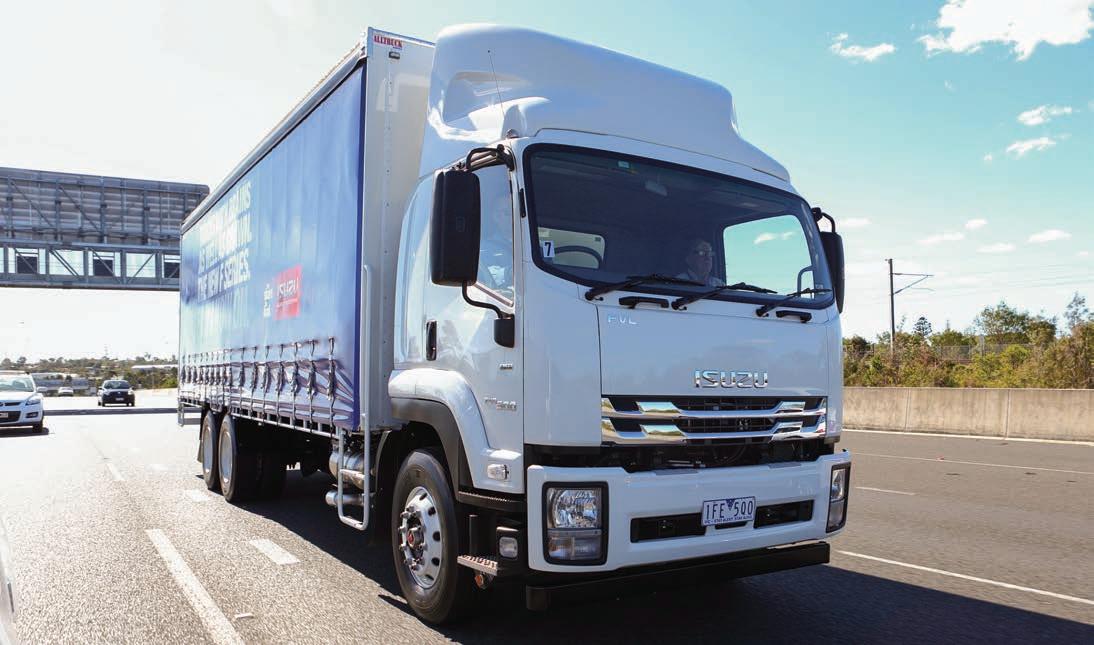
Isuzu has helped pioneer and popularise the 6x2 through its FVL range.
no weight behind the rear axles to counterbalance the load. This inevitably throws too much weight onto the steer axle, causing it to exceed the 6.5 tonne limit. Ever mindful of its obligations to run legally and safely at all times, Glen Cameron Group turned to Scania, which is currently the only truck maker offering the 8x2 spec in Australia.
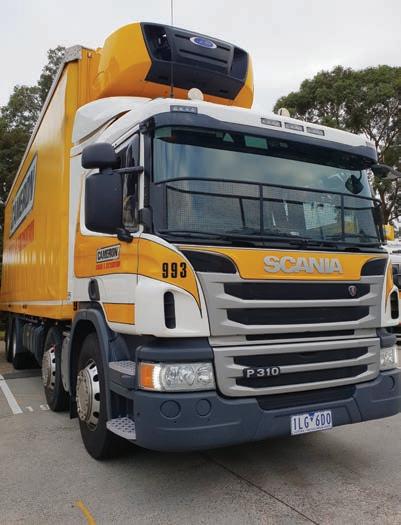
The company has a rigid truck fleet numbering around 200, with the majority of these having 6x2 axle configurations and either 12 or 14 pallet bodies. “For most of our applications the 6x2 configuration is fine but there are a number of instances where it doesn’t suit,” Shane says. “The first is when you want to carry a lot more payload than 12 tonnes and the second is where you have multi-drop/ multi-pickup runs where the truck will be travelling with a number of heavy pallets in the front half of the body during its operation cycle. Thirdly, with temperature-controlled applications such as our Cadbury Mondelez contract, where the 500kg weight of the refrigeration unit mounted on the front of the body bears directly on the front axles of the 8x2 trucks.” While some operators remain sceptical of the 6x2 and 8x2 rigid configurations due to perceived traction issues, Shane says that for the type of work Cameron’s does there have been no concerns whatsoever. “Most of our trucks are in and out of distribution centres where the lazy axle configuration works fine, which means we gain the benefits of a lower initial purchase cost, lower tare weight and lower fuel consumption compared to equivalent 6x4 and 8x4 units,” he says, adding that the issue of diminishing loads during the day was what prompted the company to first consider the Scania 8x2 several years back. “With the 8x2, we can have a fully loaded truck where we can pull six pallets off the back and still be legal on the steer axles,” he says. “This is usually not possible with a 6x2 truck.” While the 8x2 carries a significant price premium over an equivalent 6x2 unit according to Shane, the company considers it a necessary investment to ensure compliant operations across the fleet. “It was a big investment, but for us this was imperative to ensure compliance with our diminishing load rigid truck operations typified by our Cadbury Mondelez contract,” he says. While Shane is content with the 6x2 and 8x2 configured rigid trucks, he is ‘less than enamoured’ with 6x2 prime movers. Having trialled and evaluated some 6x2 prime movers side-by-side with 6x4 units, he has come to the conclusion that any benefits the 6x2 prime movers offer are outweighed by the negatives.
“We trialled a few 6x2 prime movers but the driver feedback wasn’t positive, particularly in terms of traction issues on wet roads and over gutters and the like,” says Shane. “We also didn’t find a measurable difference in fuel economy of the 6x2 prime movers compared to equivalent 6x4 units.” Perhaps the biggest drawback though, according to Shane, was the considerably lower resale value of 6x2 units over 6x4 prime movers. “They were a bit cheaper to buy but we found that they negatively impacted our exit position because they weren’t very popular in the second-hand marketplace,” he says. “The residual value at the end of ownership is an important consideration for us and in this respect we found that the 6x2 prime mover just didn’t stack up.” Overall, Shane believes the benefits of the lazy axle concept are clearly demonstrated in 6x2 and 8x2 rigid applications, which is why Glen Cameron Group opts for these configurations for the majority of its distribution centre PUD operations. Meanwhile, on the other side of the country, Goldstar Transport based in the Perth suburb of Kewdale has a positive story to tell about its four MAN TGS 26480 6x2 prime movers used for Woolworths grocery distribution work around Perth. In fact, Goldstar Transport Asset Manager, David Pedrotti, says the company couldn’t be happier with its four units, the initial two of which were put into service in 2017. “They’re faultless, we haven’t touched them,” he says. “The fuel economy is great – I really can’t speak highly enough of them. It’s a pleasure to have them in the fleet.” David notes the trucks which are used for single trailer grocery distribution around the Perth metro area are averaging around 2.3km/litre (6.5mpg). The units are at times called upon to haul B-double combinations, a task which they also

handle with relative ease, he adds. The MAN 6x2 prime movers are also highly regarded by the drivers who are especially impressed with the cab comfort and power. He says they have had no traction issues that he is aware of with the 6x2 configuration in the grocery operation. “Having 480hp to pull a single trailer is probably overkill but the fuel economy they are getting is outstanding,” David says. “I’d be happy to have a fleet of MAN trucks on our Coca Cola delivery contract.” The use of 6x2 and 8x2 trucks for specific applications is now considered a progressive step by a number of operators. Technology like traction control and airbag rear suspension, where the pressure can be varied to exert more weight on the drive axle, means the old bugbear of loss of traction is largely a thing of the past. All things considered, in the modern trucking environment where efficiency is everything, 6x2 and 8x2 trucks in suitable applications can make a tangible difference to the bottom line.