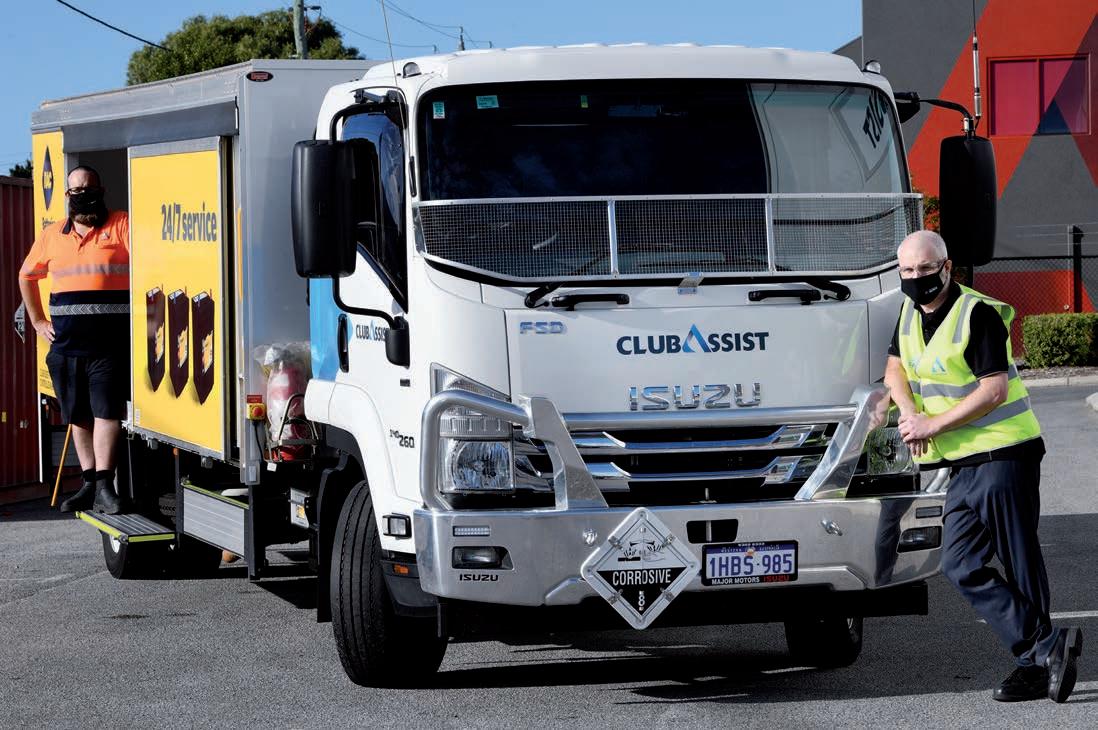
28 minute read
Taking Charge
by Prime Group
TAKING
Celebrating 30 years in business this year, Club Assist offers a comprehensive car battery replacement service for customers across Australia. For its most rigourous operation in Western Australia, the company relies on a new Isuzu FSD 140-260, which travels up to 3,000km per week delivering batteries to outlying regions where rough roads and searing summer temperatures take their toll.
Club Assist was founded in 1991 in Dandenong, Victoria. Realising that roadside battery replacement services were not offered by any of the automobile clubs in Australia, and sensing an enormous opportunity, the business undertook an 18-month study, researching data on roadside emergency calls from auto club members in Victoria. The study revealed dead batteries were the most common reason for roadside assistance calls and in response they came up with a revolutionary solution that would redefine roadside assistance by providing battery replacement at the roadside. That started a partnership with the automotive clubs and by 2000, Club Assist’s fully integrated roadside service solution had expanded to include
Driver of the Isuzu FSD 140-260, Clayton Trezise with Steve Williams.
CHARGE
partnerships with other motoring clubs across Australia and in New Zealand. Club Assist expanded across the world in 2001 to North America and Canada. Today, Club Assist supports its motoring club partners in serving more than 66 million members worldwide. In North America, Club Assist is proud to have been the Preferred Supplier for the AAA/ CAA Mobile Battery Service Program for 20 years. “Club Assist is primarily a business-tobusiness automotive battery supplier,” says Adrian Smith, Executive General Manager at Club Assist. “We also operate roadside service vehicles on a contract basis for the automobile clubs in Victoria, New South Wales, Queensland and the Northern Territory.” Adrian explains that while the main focus has been on supplying batteries to automobile clubs in all states and territories of Australia as well as in New Zealand through a joint venture, the company recently started supplying batteries to other automotive outlets including Pedders Suspension & Brakes, JAX Tyres & Auto and Penske Trucks. With the introduction of new national key accounts and growing volumes with the Motoring Club often requiring larger consignments of batteries, the company was prompted to purchase a new Isuzu FSD 140-260 for its Perthbased operation. “We’ve been using Isuzu trucks for a long time and about 12 months ago we embarked on an extensive fleet renewal program which involved acquiring a number of new Isuzus,” Adrian says. “Our number one priority when selecting vehicles is a three-element approach to safety – safety for our drivers, pedestrians and the load. After extensive study we found that Isuzu vehicles were ideally placed to meet these criteria.” After safety, the other important aspects, Adrian notes, are efficiency and functionality. “We are very happy with the safety features of the Isuzu vehicles from a driver’s perspective and also in terms of the pedestrian warnings,” he says. “In the case of the new FSD, we’ve also gained worthwhile improvements in efficiency and driver convenience due to its larger fuel and payload capacities – important factors due to the vast distances it travels in WA.” These features, according to Adrian, enable the driver to cover more distance in a day and be less fatigued at the end of the day. Furthermore, the design of the body has been modified to reduce manual handling for the driver. “We designed the body so as to reduce a significant amount of manual handling – both loading and unloading – which further helps in reducing fatigue,” he says. “The feedback from the driver has been very positive. He feels safer while driving and fresher at the end of the day thanks to features such as the air suspended seat with improved damping, rear air suspension and cruise control.” Adrian says the vehicle covers regional areas of WA radiating out from Perth
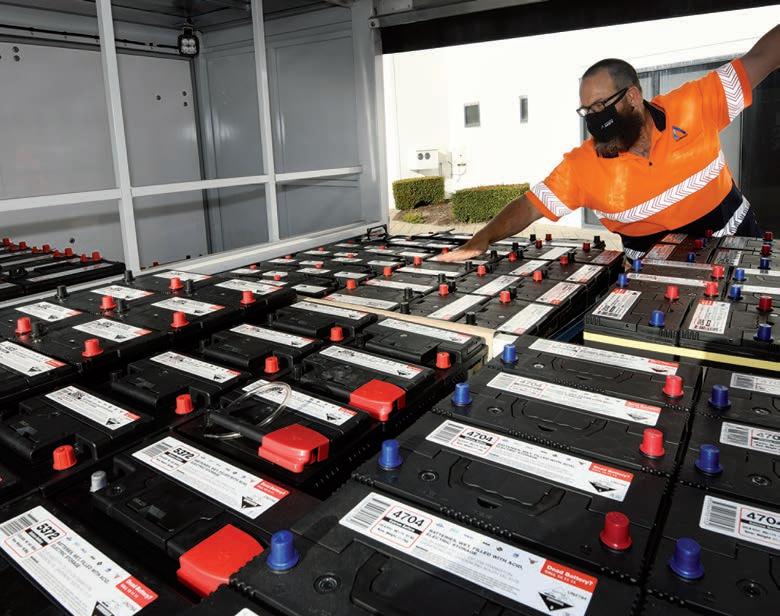
Clayton inspects the battery stock carried by the Isuzu FSD 140-260.
– travelling up to 3,000km per week – and is right at home in the harsher environment of country driving. “In terms of safety and functionality it fits the bill and has been very reliable so far,” he says. The FSD 140-260 has respective gross vehicle and gross combination (GVM/GCM) figures of 14,000kg and 20,000kg. This allows Club Assist a payload capacity of 7,500kg which equates to around 500 batteries. Respective power and torque outputs of 256hp (191kW) at 2,400rpm and 761Nm (561lb/ft) between 1,450 and 2,400rpm are delivered by the 7.8-litre six-cylinder diesel engine which features common-rail injection, an electronically controlled variable nozzle turbo and air-to-air intercooler. Euro 5 emissions standards are achieved using cooled Exhaust Gas Recirculation (EGR) and a Diesel Oxidation Catalyst (DOC). Transmitting torque to the rear wheels is an Allison LCT2500 six-speed torque converter automatic with double overdrive ratios of 0.74 fifth and 0.64 sixth. The full-floating Banjo style differential has a ratio of 5.125:1 and is saddled with Hendrickson HAS200 air suspension with a 9,000kg capacity. Brakes are ABS mastered dual circuit airover-hydraulic drums on both axles. On the safety front, the FSD 140-260 has driver and passenger airbags and seatbelt pretensioners, an ECE-R29 (cab strength) compliant cab, Antilock Braking System (ABS), front stabiliser bar and cornering lamps. Cab comfort and convenience features include an ISRI 6860 air suspension driver’s seat with pneumatic lumbar support and automatic weight adjustment, electric mirrors, cruise control and a satellite navigation (GPS) system. Optional equipment comprises a telematics system integrated with the multimedia unit, up to four camera inputs including a rear microphone, reversing sensors, tyre pressure monitoring system, airbag compatible bullbar and a roofmounted air deflector. The custom designed body fitted to the vehicle, Adrian explains, was specifically designed to reduce manual handling by a massive 75 per cent compared with the vehicle it replaced. “The body is designed to be accessed from both sides as well as the rear whereas the unit it replaced was only able to be accessed from one side,” Adrian says. “That significantly reduced manual handling because we were not having to push the batteries through the full width of the body.” It was also designed for better efficiency in servicing the company’s regional WA clients which are typically smaller workshops and approved repairers that require limited quantities of batteries delivered just-in-time. “The previous vehicle had to be fully manually loaded and unloaded while this one has provision for both forklift and manual loading,” Adrian explains. “Therefore, we now use pallet loading and unloading wherever possible which saves the driver a lot of time and effort. We’re really ecstatic with the fact that he is so happy with the new truck because his safety and comfort are our prime priorities.” Running hot on the heels of these priorities, Adrian says, was the company’s need for solid dealer support and it was here that Perth Isuzu dealer Major Motors didn’t disappoint. “We really can’t fault the servicing and support we receive from Major Motors; this was certainly a big factor in us choosing to go with Isuzu in our WA operation,” Adrian says. When it’s all boiled down, the FSD 140-260 with its custom-built body is a vehicle that’s suitably tailored to the task and backed by a dealer network that ensures it will remain reliably and efficiently traversing the WA outback for years to come. Add to the equation a very happy driver, who feels safe and comfortable behind the wheel for his 3,000km each week, and it’s all boxes ticked for Club Assist.
Steve Williams, Sales and Operations Manager.
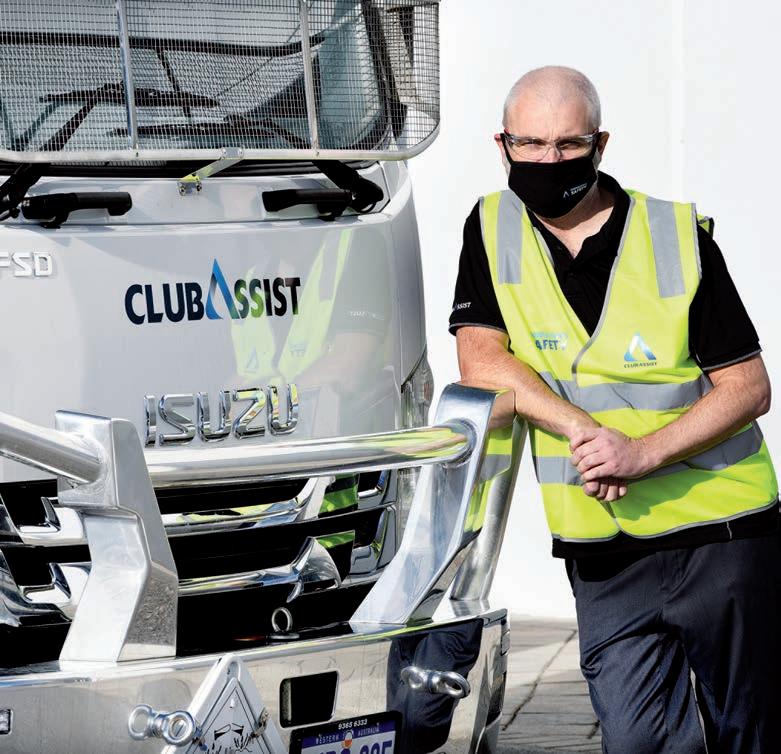
The unveiling of the new Mack Super-Liner 100 anniversary edition.
ACTIONMACK IN
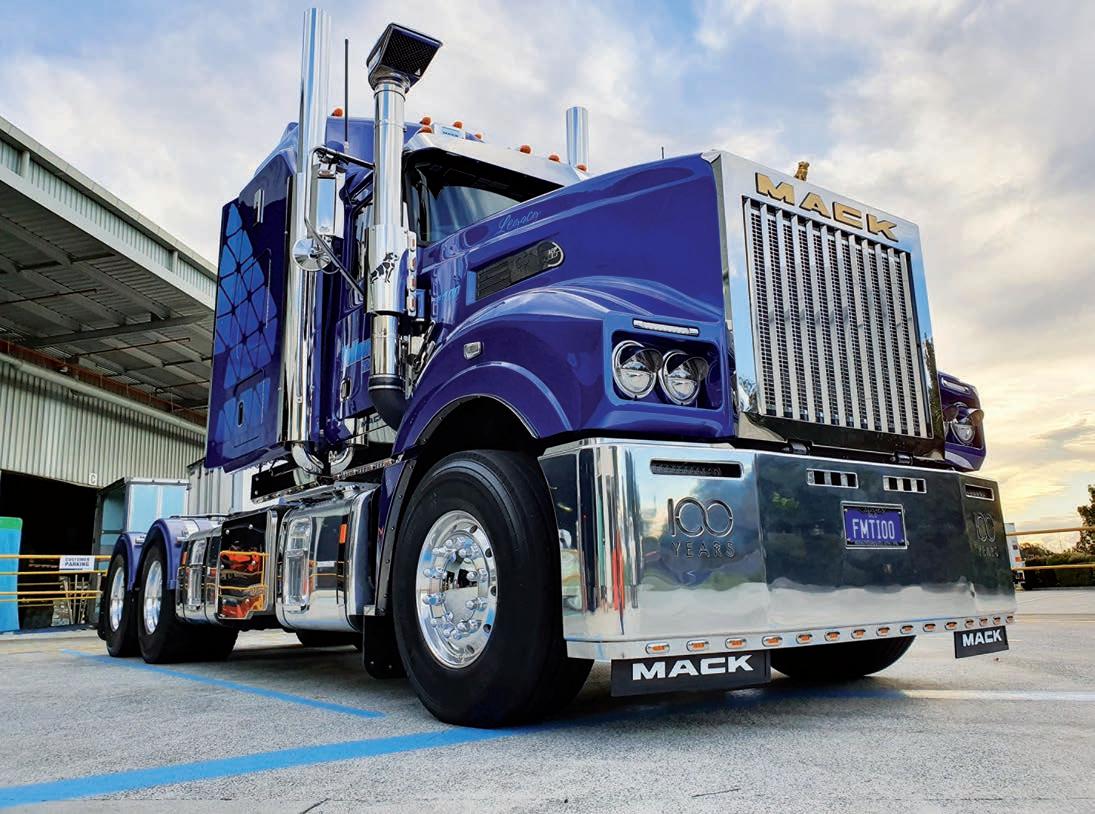
Followmont Transport celebrates its history with new commemorative limited edition Mack Super-Liner.
Legacy is often the means to value people and traditions. It’s an inheritance from which to remember and learn. Indeed, legacy served as one of the main themes of a recent Followmont Transport Leadership Conference which gathered together over 50 senior managers from across Queensland and NSW where the past and the present helped shape discussion of future directions and set the table for a major reveal. Followmont Transport legacy itself begins 36 years ago when it was co-founded by Bernard Tobin and Alan Salpietro. For 25 years they guided and built the company on an ethos of hard work and strong customer service. More than ten years ago, the four shareholders of the company which includes Managing Director and CEO Mark Tobin, realised the importance of healthy leadership, the significance of having a roadmap and agreed to a goal of working smarter rather than harder. That was a watershed moment for the business which from that point underwent a seismic change. While the foundation of the business remains service, its legacy now revolves around its people having a real sense of belonging to a family business including the values that come with it. “Our business has transitioned, as has our legacy,” says Mark. “Our legacy today, whilst the foundation is still service, is around our people having a sense of belonging to a family business and our people feeling empowered, educated and inspired by leadership as opposed to having it demanded by leadership.” Underpinning this is the notion of care — caring at once for one and other and customers while acknowledging everyone is only as good as their last delivery and therefore, last interaction. The Leadership Conference included a special reveal of the 100th anniversary Legacy Mack Super-Liner. Mack, as part of customising each of the commemorative trucks, made available a year from every one of its last 100. Followmont selected 2016, the same year Mark purchased Followmont thus preventing it from being sold to Toll. “Where we are now we can be seen as one of the top transport businesses in Australia,” he says. “That is why we celebrate with the newest addition to the fleet family, the 100 Year Mack – Legacy.” With so many of the Followmont Transport team having a close association with the Mack over the years it is considered a fitting addition to the everexpanding fleet. The 11-tonne special edition Mack SuperLiner is spec’d for B-double operations. At about 8 metres long it will carry all forms
of freight. Based out of Brisbane it is likely to travel up and down the whole of the eastern seaboard. Belair Spray Painting were authorised to carry out finishing flow and clear coatings by Mack Trucks Australia on all 100th anniversary Limited Edition trucks. Followmont and VCV Brisbane then commissioned Belair to air brush the custom Followmont branding. The design concept was put together from another print piece with a view of creating something bold that would include the emblem as well as the gradient concept. This was carried out prior to the final clear coats to preserve the artworks for the life of the truck. It’s the third truck that Brand Manager Meg Ellis has been entrusted in to project manage. King Bars also created a one-off custom Texas Bumper for Followmont based off the original 100th anniversary bumper design. Blingman HQ carried out a few custom stainless and LED lighting creations to further enhance the vision in creating this tribute to the Legacy of the Tobin family within the Followmont team. The Followmont and Mack Trucks relationship has been built on the back of the 30-plus year history between Followmont and UD Trucks.|When Volvo Group Australia took control of the UD brand a number of years ago it gave them the opportunity to showcase their other products in the business. This saw both Mack and Volvo commercial vehicles ingratiated into operations. VCV Brisbane North has since built a very strong relationship between the whole Followmont family, with sales, service and parts supplies only a few minutes away. Today, as a result of this partnership, there are approximately 45 Mack, 25 Volvo and around 180 UD Trucks in the Followmont fleet with additional units from each brand on order currently. Mack Trucks, VGA and VCV Brisbane North were all invited by Mark to be involved in the project. Given the legacy of Mack Trucks Australia in the Australian road transport industry, the limited edition Mack Super-Liner was considered a great fit to play a small part in the Followmont Legacy project. Family values have been carried through the business generationally from Bernie, Mark and now Ben Tobin. This is inherent in the company legacy as are its people with many longstanding staff members having been employed between 15 and 25 years. The values the Tobin Family live by echo through the business according to Chris Fasone, Followmont Transport Regional Manager South QLD, who started in 1988 having had to take on a second job sorting magazines to support his new family after the birth of their first child. “It didn’t take me long to be tempted in making Followmont my primary role with the opportunities available to me back then and the care shown by Bernie Tobin who took me under his wing and shared his wealth of experience with me,” he says. “I don’t know if I can ever voice enough in gratitude to thank the Tobin Family and Followmont for the opportunities and life lessons they have afforded me over the years. I have never met a family that is so generous with their time.” Since then Chris has been provided with many opportunities in various positions including Forklift and PUD operator, supervisor, customer service representative, depot manager and regional manager. “In every position I have received their full support and assistance and in every instance it has made me better personally and operationally,” he says. “Not only have they made me feel part of the family, they also have employed Jason, my first born who has been provided with the same opportunities as have many others. Followmont has become part of me over the years and I treat it as my lifeline and will be forever grateful to Bernie, Mark and Ben for the experience I have gained.”
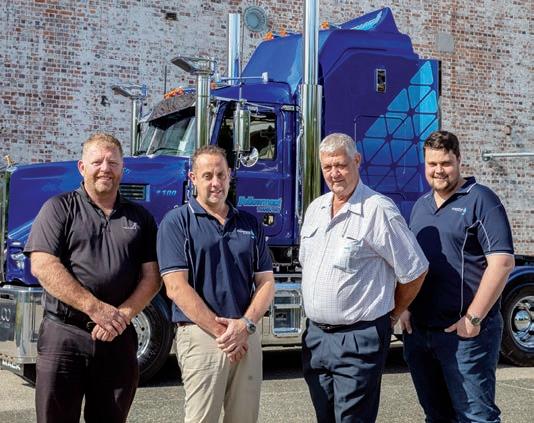

FIT FOR PURPOSE
Fatigue is recogised as a major cause of accidents involving heavy vehicles.

Digital platform, Fatiguefit, helps ensure operator fitness so transport managers and their business are in a scientifically and legally defensible position for fatigue risk management.
Transport operators concerned about fatigue risk management have typically had to engage with consultants for an assessment and solutions. Given the nature of the service and the expertise involved the recommendations sought through this process come with a significant price premium making the cost involved prohibitive for many organisations. With Workplace Health and Safety Legislation imputing governance responsibilities right up and down the supply chain this looms as a major stumbling block for many in the industry. Legislation, under chain of responsibility, has evolved past the point of penalising truck drivers for driving with undue care. Now the people responsible for the culture that allowed the poor decision-making at a company will also be personally and criminally liable. More than ever it’s vital that directors and board members are across what’s happening from a broader workplace and health perspective, many of whom lack visibility on where they fail to properly meet their fatigue risk management compliance. Fatiguefit has emerged in response to the need to have a fast, easy to use and cost-effective fatigue risk management solution for carriers who might be exposed. Developed by Sleepfit Solutions, an Australian digital health company in partnership with Professor Drew Dawson, a leading expert in fatigue risk management, Fatiguefit consists of an online assessment and report which allows businesses both large and small, to determine if they are complying with their fatigue risk management legal requirements. At present, there is a misunderstanding among many industry people that the enterprise bargaining agreement is actually their fatigue management policy. While it does indicate acceptable working time arrangements it’s not actually a safety document. It is estimated that 85 per cent of companies who should be doing something about fatigue risk, like those in road transport, energy, logistics and
mining, aren’t necessarily. Fatiguefit has automated the process so operators don’t have to spend a fortune to hire consultants. The initial aim, according to Steven Perlen, Fatiguefit Chief Operating Officer, was to create a ‘consultant in a box’ that was scalable, accessible, cheap and within reach of any organisation. “By putting information, tools and training in the hands of the businesses that need it, Fatiguefit not only keeps people safe, but it keeps the business safe as well,” he says. “It allows people to maintain control and gives them risk management choices, rather than having an expert dictate what they need to do.” As an online digital platform Fatiguefit allows businesses of any size to undertake their own fatigue risk management compliance assessment in around 15 minutes and only costs $99. It’s evidence based and provides the operator with a legally and scientifically defensible position. Fatiguefit then provides a set of tools and templates to close any compliance gaps, covering policy, training and risk identification and mitigation. Importantly, operators using Fatiguefit can pick and choose the solutions they use to cover those gaps and implement them in their own time. In short, they can integrate their fatigue risk management with their other operational demands and existing safety systems, including fatigue detection technologies. That way they take control of the process and can do it in a very cost-effective way. “The Assessment and Report provides clear understanding of where the compliance gaps are for fatigue risk management,” says Steven. “It gives businesses visibility of where their exposure lies so people can make informed decisions about managing their risk.” Recognising that different organisations are going to want to manage their compliance differently, the Fatiguefit team can also provide additional expert support for businesses that are looking for a little more guidance. Professor Drew Dawson, the Australian expert who helped create Fatiguefit, notes fatigue risk is hard to assess. “This is because the person is the actual hazard rather than a third party such as a chemical spill or a saw without a blade cover,” he says. “With a people risk like fatigue, the hazard is somewhat invisible.” While Fatiguefit has been created to minimise fatigue risk, it also features tools to help minimise fatigue itself. Sleepfit, for instance, allows individuals to determine the likelihood that they have a treatable sleep disorder such as insomnia or sleep apnoea, prevalent issues amongst the driver community, and then get treatment. “Better sleep quality means improved rest and recovery which equates to greater productivity and reduced fatigue risk,” says Steven. Fatiguefit isn’t however, as Steven points out, about eliminating fatigue. “That’s unreasonable — it’s about ensuring people can continue to work safely whilst fatigued,” he says. Fatiguefit has been designed to help businesses of all sizes. Smaller firms will do one assessment and then decide who in their team are the highest priority for the risk management activities. Bigger companies may run separate assessments across multiple depots to get visibility across their entire operation. This will guide their decisions on where to focus the implementation of the Fatiguefit solutions. And for Tier 1 companies that already have confidence in the procedures they have in place to manage their own employees, Fatiguefit can be used as a platform to work with their subbies to ensure that they are meeting their COR obligations. “Whether your business has six trucks or 6000 trucks you can use the Fatiguefit platform in different ways to achieve that scientifically and legally defensible position for your fatigue risk management.” says Steven.
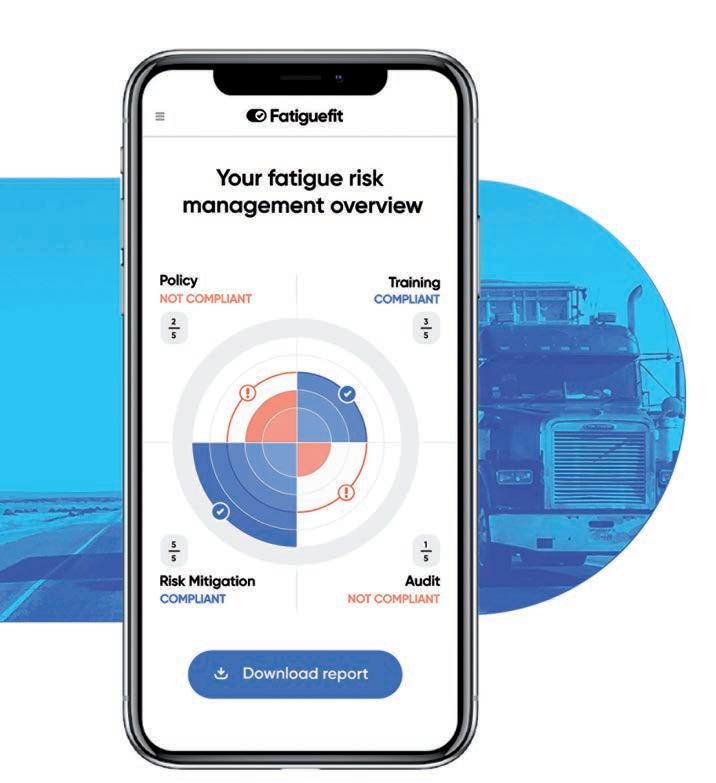
SOLVING
THE ENERGY CRISIS
R&R Corporate Health offers fatigue management training and well-being services ideal for handling the pressures of commercial road transport and enhancing company culture.
Fatigue, for Matthew Beechey, Director of R&R Corporate Health, is not unlike dealing with mental health — early intervention is crucial. The company, which specialises in health and safety with Human Resources departments to develop their well-being brand, offers deep dive solutions into fatigue management with two decades of experience working within the logistics and road transport sectors. In 2018 Monash released findings from a study correlating driver fatigue and road accidents. Based on the presence of factors such as extended driving hours, falling asleep at the wheel,
Matthew Beechey. distractions, driving right of centre and night-time driving, the study estimated fatigue contributed to 19.9 per cent of accidents. According to a NTARC Report released in 2019, fatigue was underlying cause of crashes 34.8 per cent of the time in which truck drivers died with inattention/distraction representing another 30.4 per cent of these tragic incidents. Most definitions of fatigue include the concept of a deterioration with extended effort in work output, physiological well-being or feelings. In a logistics world where long hours and shift work are par for the course fatigue is commonplace even when guidelines of fatigue management compliance are in place. “Managing stress effectively is a big part of it both personally and professionally,” says Matthew. “It’s doable but not without management. Sometimes in fatigue management that word management is the bit we don’t take seriously enough.” People who start the training course, which teaches sustainable behaviour and lifestyle changes, often don’t have a true understanding of what fatigue is, mistaking it, for the most part, with tiredness. Many different factors can lead to fatigue such as problematic relationships, an unwell child, and even dehydration. It’s important to recognise the signs of fatigue according to Matthew, no matter if you’re a forklift driver, big rig operator or using heavy machinery. “Too many people are working in Australia in close to a fatigue state,” he says. “So much so that it eventually becomes the norm.” In these circumstances our energy battery is inordinately depleted. Most people wouldn’t buy a mobile phone under these terms let alone drive a car. “It happens so slowly and we’re not actually sure that’s where we’re at,” says Matthew. “But we work on an empty battery, topping it up intermittently to keep it going.” Often this is how a dependency begins on high sugar foods and high sugar drinks. Someone working long hours and sleeping poorly or unable to resolve issues at home will do their best to chase energy. A bad diet is a consequence of this. Given shift work involves long hours it
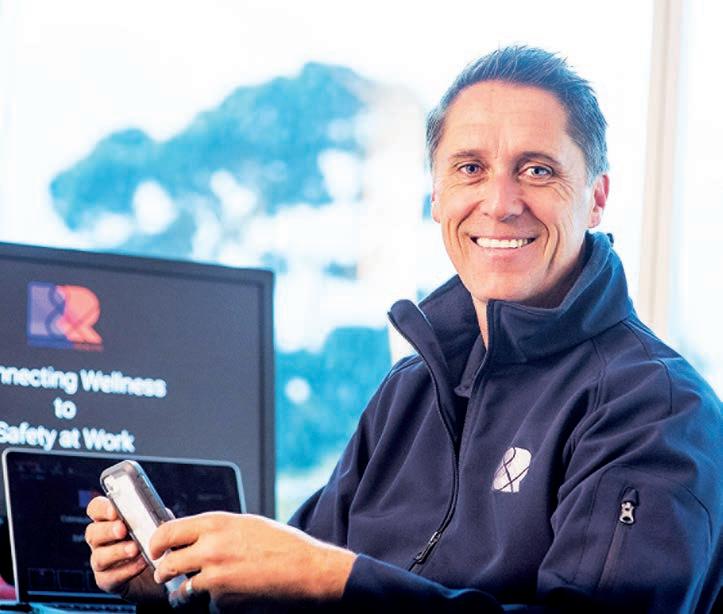
Early intervention is important in identifying fatigue and managing it.
will push our body to its limit especially if we don’t get right what Matthew calls the ‘one percenters’ — solid sleep, diet, exercising and stretching. Indeed these one percenters help to maintain a solid energy base which in turn enables greater wellbeing. But if we’re having to go searching for energy constantly than there’s a problem according to Matthew, who points to night shift workers and overnight truck drivers being more susceptible to fatigue incidents. “We shouldn’t have to be consciously trying to stay awake. Our energy should be vital and not a conscious process,” he says. “We typically wait for a crisis before we take action.” As part of managing fatigue R&R incorporates what Matthew refers to as the ‘Three As’ — Aware, Accept and Act. Awareness is often the easy part; acceptance, however, can prove a challenge. Most people are not willing to accept where they are at and should they be able to they’re often unwilling to accept that they need to do something about it. Matthew says there are a range of factors that influence why this next step proves so hard for some people. Pride, for one example, intervenes in us sharing our feelings or reaching out to tell someone we are struggling. Fear also plays a part in this as people worry that they might lose their job or be considered difficult or unfit for employment. “A significant near-miss or an incident will motivate us as human beings to acknowledge we need to do something about it,” Matthew says. “Why do we let it get to the point we have hit a rumble strip for the third time in a night before we pullover?” Unfortunately, it often takes for something to go wrong before we reach the acceptance stage of the Three As of Fatigue. By then, if it’s not too late, it’s about accepting that we need to make drastic changes. It’s doable, of course, but not without management. R&R takes a holistic approach in delivering education outcomes in managing fatigue, energy and wellbeing. The 3 As of Fatigue have given businesses a common language for managing fatigue according to Matthew. A former registered nurse who moved into massage therapy in 1999 to work with heavy vehicle operators, Matthew got to understand firsthand how the toll of working long hours with a bad diet impaired their sleep and importantly affected their desire to do something about it. At the core of Matthew’s ambition is to help look after heavy vehicle operators, given they are in one of the most dangerous occupations in Australia. In 2008 he authored The Healthy Road Warrior, a book for truck drivers and between that year and 2014 he estimates he trained nearly 7,000 drivers. At the time the concept of wellbeing was considered fluffy and feel good. Even now current fatigue management compliance doesn’t necessarily factor in the whole spectrum of issues when it comes to instilling preventative measures for exhaustion and fatigue and ultimately injury. Inspired by these Aussie Road Warriors, R&R is looking to create a culture around it. “In order to work to those schedules a person really does need to be eating well, drinking lots of water and getting as much good sleep as is possible,” he says. “These are a solid base in which to work from when it comes to managing stressors in their lives whether they be personal or professional as one invariably impacts the other.” Despite COVID-19 making personal engagements with businesses difficult last year, through necessity Matthew was forced to create an online course package with rich media online training. It is a blended learning model of online and face-to-face interaction. “Any business working in fatigue management needs incredibly consistent message,” he says. “Online helps facilitate this through learning a truly common language.” R&R Corporate Health will have an exhibit at MEGATRANS2021 in September.

The 70,000th Kenworth produced in Australia.
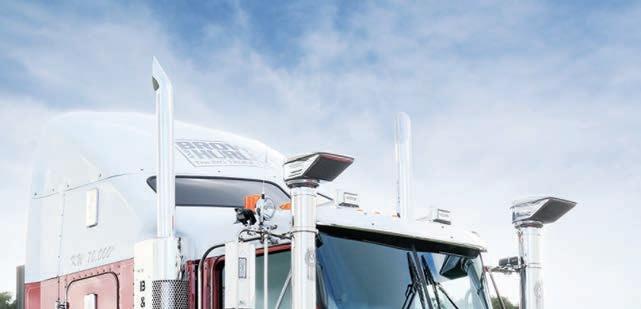
HISTORY
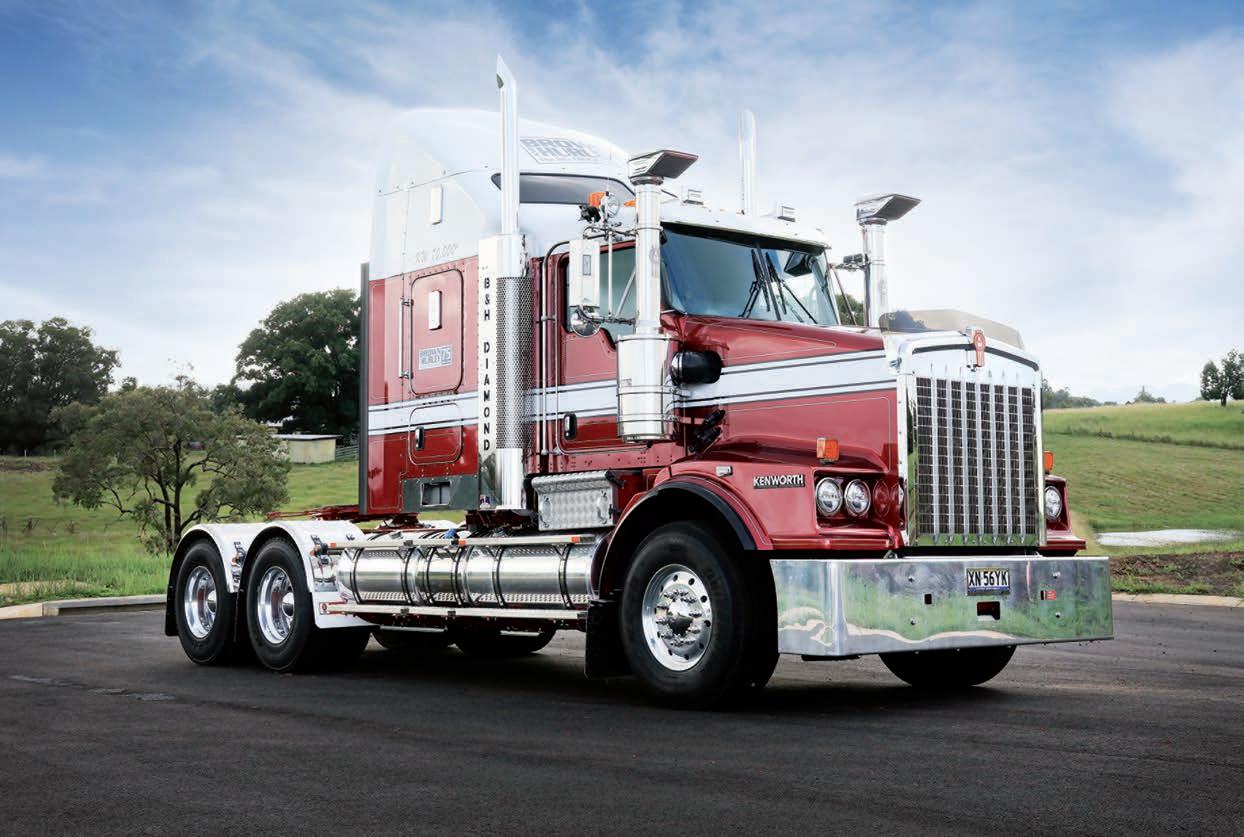
IN THE MAKING
One of Australia’s leading Kenworth and DAF dealerships, Brown and Hurley, celebrates 75 years in operation this June. Prime Mover speaks with Jim and Paul Hurley, son and grandson of co-founder Jack Hurley OAM, about the remarkable rise to prominence of this successful Australian family business.
The Brown and Hurley story started in the early 1940s during the Second World War when Alan Brown and Jack Hurley, who were both in the army at the time, met and became great mates. Due to their excellent mechanical skill set, rather than being sent into battle the dynamic duo was enlisted to train the soldiers in the service and repair of trucks and machinery used during the war. In 1946, after the war had ended, they decided to go into business together at Kyogle. With limited funds they started doing mechanical repairs in a shed behind a bike shop situated on a property owned by the Catholic church. The business, according to Jim, struggled to make money doing mechanical repairs over the following year or so, however, a turning point came in 1947 when the first new machinery sales were made. “A fellow came in and wanted a crawler tractor so they got him an Oliver Cletrac and then another fellow wanted a new White truck which they also managed to supply,” says Jim. “From those two sales they made 150 pounds commission, which convinced them that selling new equipment was the way they needed to go.” In the early 1950s the Catholic church decided to build a new church on the site, which prompted Jack and Alan to buy a block of land a couple of doors up and build their first dealership which was opened in 1953. Brown and Hurley subsequently became a White truck distributor and sold 154 units. They also sold 548 Leyland trucks between 1957 and 1968, along with a large number of Volvo trucks between 1968 and 1999. Also sold in the early years were significant quantities of Allis-Chalmers and David Brown tractors along with Blue Streak Two Man and One Man chainsaws (and later McCulloch chainsaws) which were tools of choice in the thriving logging industry in northern NSW at the time. A watershed moment came in 1964 with the appointment of Brown and Hurley as Australia’s first Kenworth dealership – an event that set up the company for ongoing success that continues unabated as the 75year milestone is passed. “We’ve been a truck dealer with various franchises for most of the 75 years,”
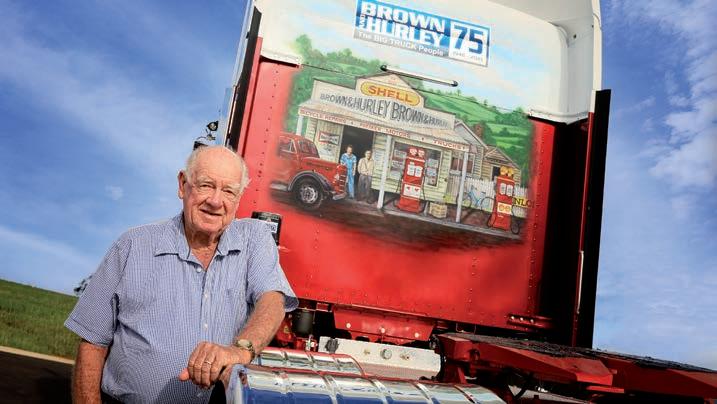
says Paul Hurley. “Becoming Australia’s first Kenworth dealer in 1964 and selling our first Kenworth in 1965 are certainly two of our biggest milestones. “Another was being given the opportunity by PACCAR to buy the 70,000th Kenworth produced in Australia, which was delivered to us in April this year.” Paul agrees that the successes of both PACCAR Australia and Brown and Hurley are intrinsically linked, with both businesses enabled to flourish due to the symbiotic relationship. “There’s no doubt that without the Kenworth products we wouldn’t have been able to achieve what we have and I’d like to think that we’ve played a part in helping PACCAR achieve its considerable success in this country,” Paul says. “Both companies have similar aspirations in that we have always strived to serve the end users who buy the trucks by supplying them with products tailored to suit their individual circumstances.” Paul explains that as a proudly Australian family-owned company Brown and Hurley has achieved this goal by continually investing in its people and facilities, including spare parts and service, to ensure excellence across the board. He also highlights the careful succession planning that has seen a third generation step up to guide the business through its next phase. “Both families have a long-term commitment to the company that has enabled continued investment in our brands. This, in turn, enables us to better serve our many loyal customers, without whom we wouldn’t have a business,” he says. Today, with a staff numbering 468, Brown and Hurley has a parts inventory of $24million and across all of its nine branches supplies around 97 per cent of Kenworth parts off the shelf. Historically, the company has sold between 27 and 30 per cent of Australianbuilt Kenworths and between 30 and 35 per cent of DAFs sold in Australia. Jim says the prowess of its sales people along with having its own technician training centre are big factors in the company’s success, particularly with selling DAFs. “Being able to support the product is key,” he says. “We have a head trainer who attended a course at DAF headquarters in Holland so he could come back and train our technicians, ensuring they’re right up to date with all the latest technology.” As part of its 75-year celebrations, Brown and Hurley recently released 75 Diamond Edition trucks which were all snapped up within 24 hours. A number of these were displayed at the recent Brisbane Truck Show. Celebrations continue throughout June with open days at the company’s nine branches scattered across northern New South Wales and Queensland. The first will be at the Kyogle headquarters on Saturday 5 June which will be opened by Federal Member Kevin Hogan MP at 11am. The event will include a new truck display and pallet sale auctioning goods donated by various parts and accessories manufacturers. The proceeds of this will go to the daughter of a staff member who is bravely battling leukaemia and has three young children. Also being launched that day is a book titled How a great oak from a little acorn grew, originally written by Jack Hurley OAM, detailing the first 60 years of the company’s history and recently expanded with the last 15 years of history by his son Jim. The Coffs Harbour branch also has its open day and pallet sale on 5 June, followed by the Yatala branch on 10 and 11 June and Toowoomba branch on 12 June. Rockhampton and Caboolture open days will occur on 19 June, while Townsville and Darra branches have their turn on 26 June. Kyogle, Toowoomba, Rockhampton, Caboolture and Darra branch open days will also play host to Show ‘n’ Shine events enabling truck enthusiasts to display their pride and joy for the general public to admire. The grand finale will be the open day at the Tamworth branch on 3 July which will also be a celebration of the official branch opening. All up, it’s a fitting celebration for the diamond anniversary of a great Australian company that started from little more than a shared vision of two talented men and has grown to become a pivotal part of this country’s vast and varied road transport industry. As the book title so aptly depicts, from a tiny acorn a mighty oak tree has grown.
Jim Hurley. An artist impression of the first Brown and Hurley outlet in Kyogle, NSW.
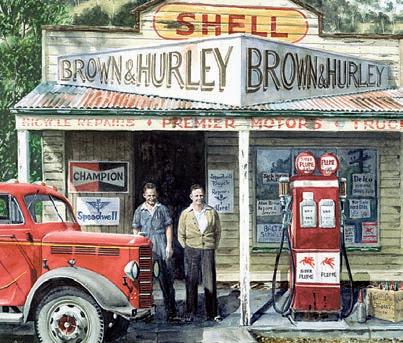