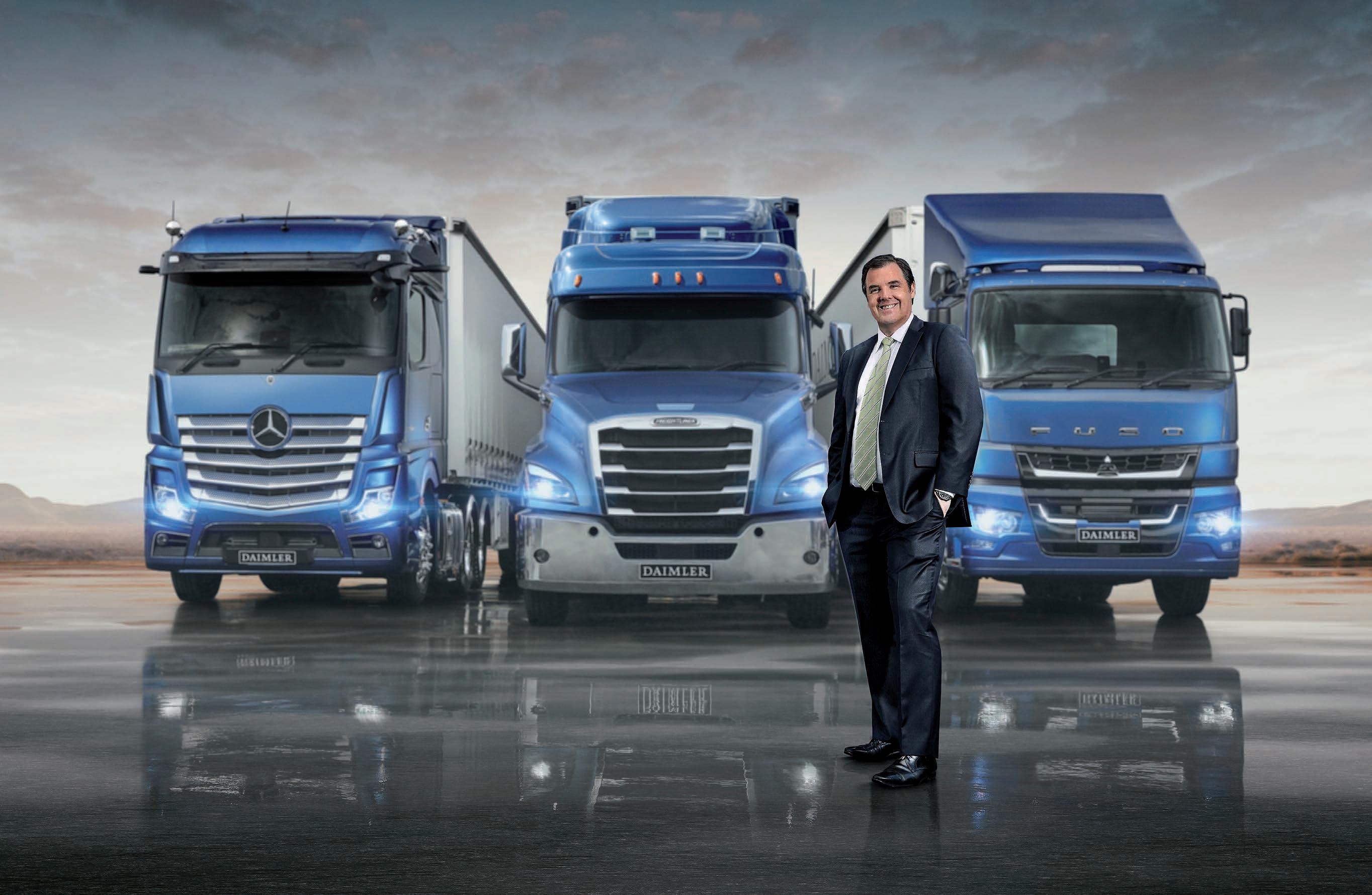
63 minute read
Mindset
by Prime Group
SUPERANNUATION MINDSET OEM MINDSET
Daniel Whitehead
Daniel Whitehead is the President and CEO of Daimler Truck and Bus Australia Pacific, which represents the MercedesBenz Trucks, Freightliner and Fuso brands.
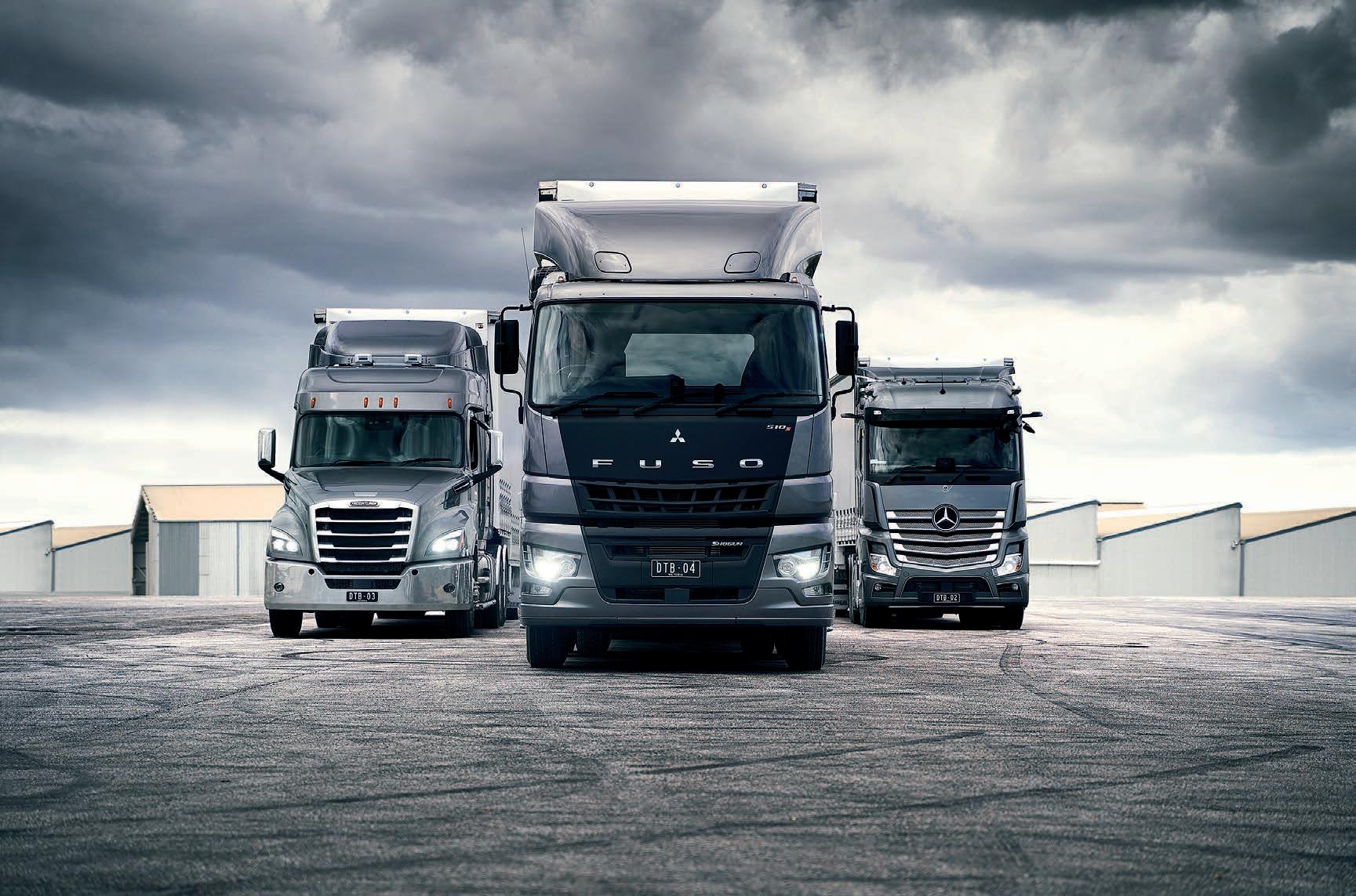
OPPORTUNITY KNOCKS
The future is bright for the Australian trucking industry.
That much was clear at the recent Australian Trucking Association Trucking Australia conference on the Gold Coast, especially during the Daimler Truck Future Leaders presentation. A joint initiative between Daimler Truck and the ATA since 2018, the development program has helped nurture some wonderfully talented young people who will help our industry navigate the challenges of the future. Daimler Truck sees massive potential in embracing new ideas and empowering our next generation. We are also proud to back Transport Women Australia Limited and are the only truck manufacturer to be accredited by the Workplace Gender Equality Agency, demonstrating a genuine willingness to make Australian road freight a destination industry for the best and brightest, regardless of gender. In an industry traditionally dominated by men, often older, we celebrate new perspectives and fresh ideas. We believe the future of Australian trucking will benefit greatly from investment in people as well as the continued innovation of products and services. As the world’s leading truck manufacturer, Daimler Truck has always been prepared to invest in order to deliver the most advanced technology to help our customers save fuel, boost safety and improve driver comfort across our Mercedes-Benz Trucks, Freightliner and Fuso brands. Our track-record shows leadership with the introduction of Euro 6, seamless fully-automated transmissions, integrated Advanced Emergency Braking Systems (AEBS), airbags in conventional trucks, high-resolution tablet screens, electric trucks and guaranteed buyback finance programs. While some of our rivals had to be dragged kicking and complaining to recently introduce Euro 6 as an option by progressive customers who demanded it be offered, Daimler Truck set the standard with the first complete range of heavy trucks to feature Euro 6 engines when the new generation Mercedes-Benz Trucks Actros was launched locally back in 2016. Some critics thought we went too early, but operators soon discovered that our advanced technology enabled them to reduce emissions and save on operational costs at the same time. Mercedes-Benz Trucks first introduced this AEBS autonomous emergency braking technology here all the way back in 2010, Freightliner introduced it first as standard on conventional trucks in 2019 and Fuso became the first manufacturer to offer it as standard on a complete range (light, medium and heavy) as well as light bus, last year. We have had several customers mention a dramatic reduction in incidents involving their AEBS trucks, with some even reporting no crashes since we introduced the technology. Indeed, a large US fleet, which switched to AEBS-equipped Freightliner Cascadias saw incident repair costs
SPONSORED BY
for its trucks ‘drop off a cliff,’ thanks to the feature. Saving lives and money. Now, that’s a great outcome. Regulators recently announced AEBS will be mandated in stages between November 2023 and February 2025, but it is clear to us that customers shouldn’t wait until then to choose models with this brilliant technology. Recently, we launched Australia’s first Level 2 automated truck, a MercedesBenz Actros that can effectively steer itself (although the driver must have their hands on the wheel). You have to get behind the wheel to experience this amazing optional technology, which really does help reduce the fatigue of drivers and free them up to concentrate on driving. The proactive system basically keeps the truck centred in its lane, in order to prevent drivers from drifting out, while the electric assistance makes life easier for the driver both on the highway and in the yard. There can be some default resistance to these kinds of technology, but most drivers come around once they experience the benefits for themselves. Of course, the biggest benefit is avoiding fatigue-related incidents that occur on our highways, often in the early hours that can tragically
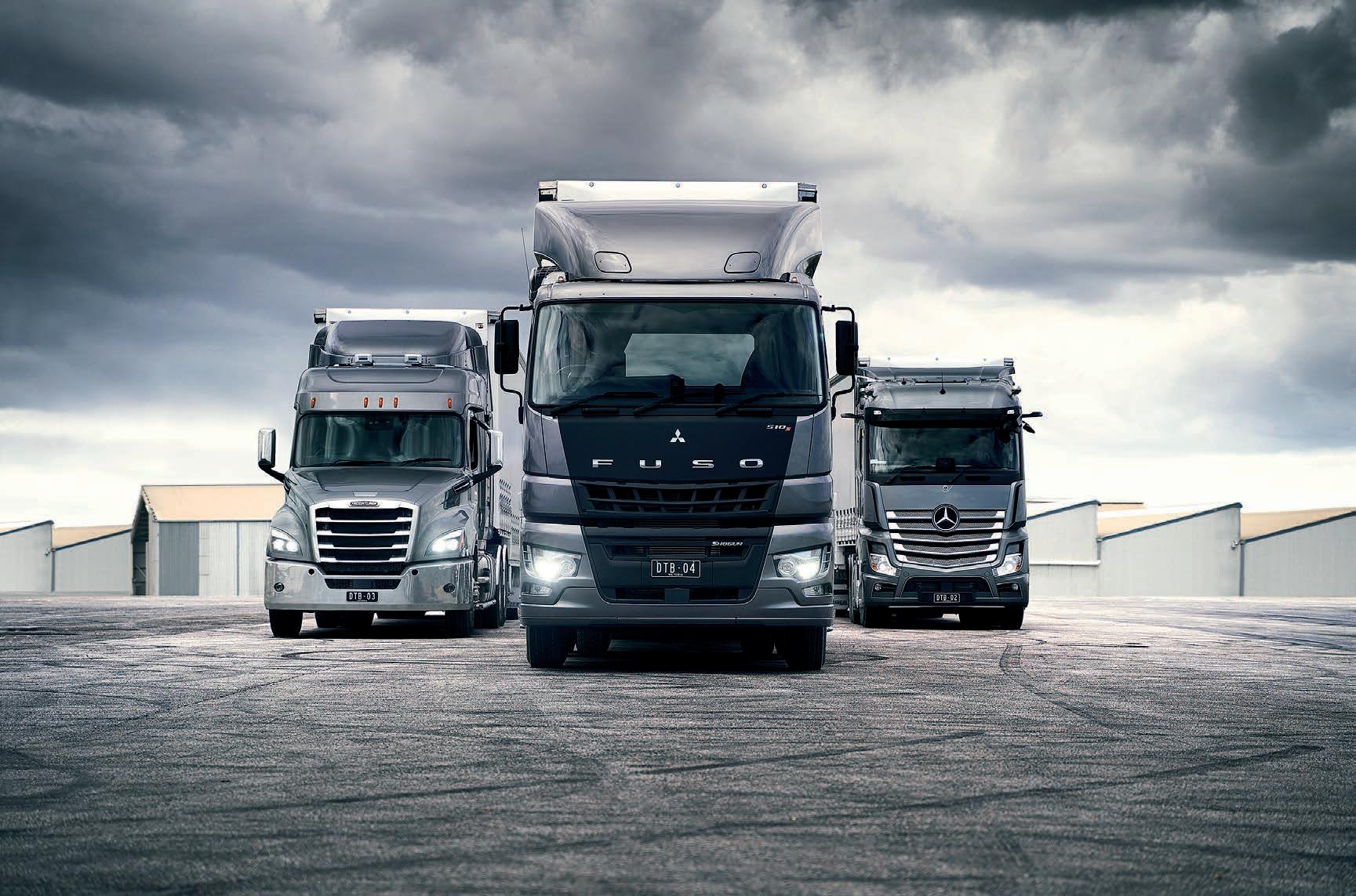
Daimler’s three truck brands.
change or even end a life. Daimler Truck was also the first Original Equipment Manufacturer to launch an electric truck with the Fuso eCanter last year with more exciting zero emission solutions hitting Australia in the very near future. These will start with battery electric for shorter haul operations while hydrogen fuel cell technology shows great promise for long haul zero emission work. Embracing these various innovations will lead to a better, cleaner, safety and more profitable road freight industry in Australia. The future is full of exciting opportunity; let’s make the most of it.
COVER STORY
DIESEL & DUST
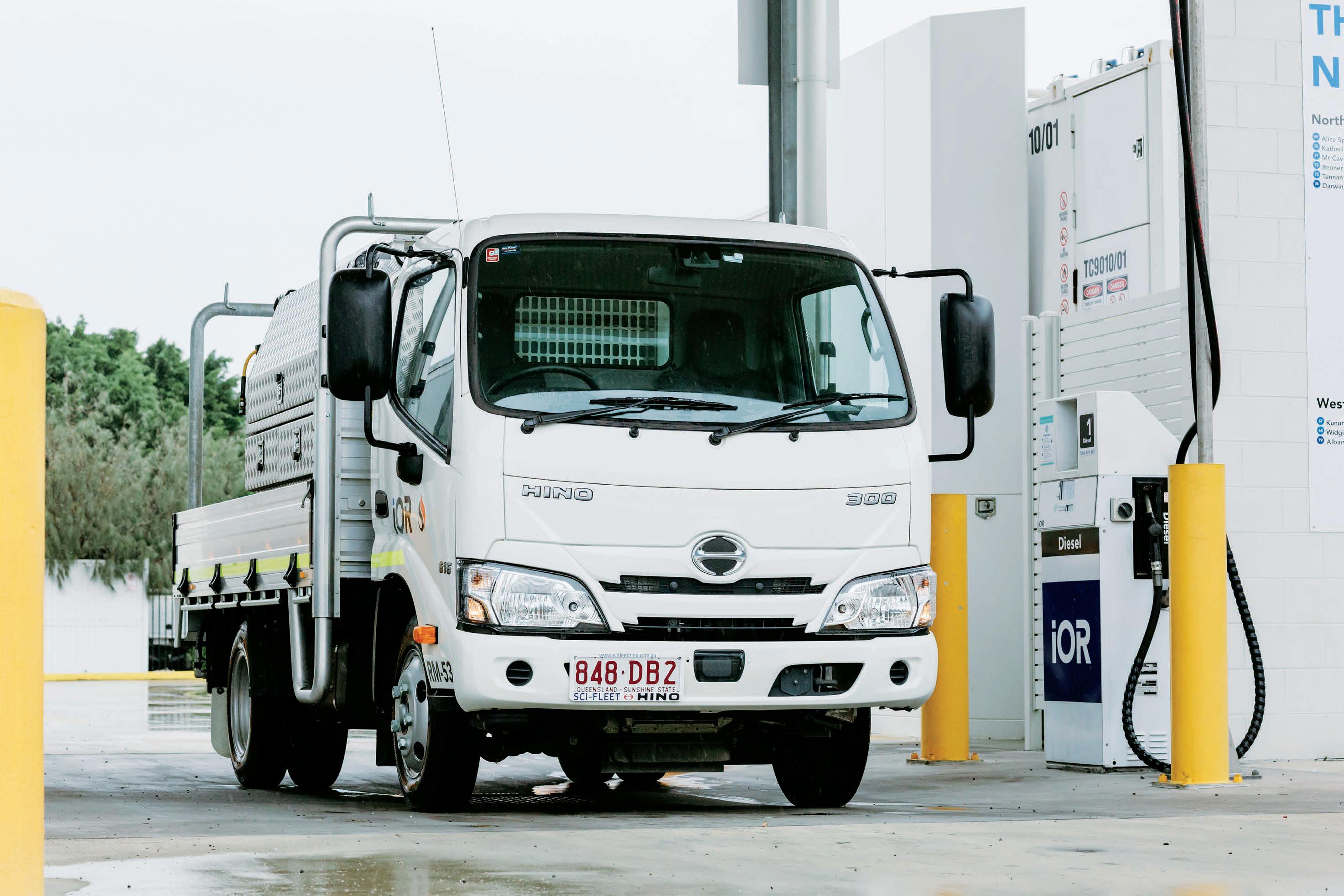
DIESEL & DUST
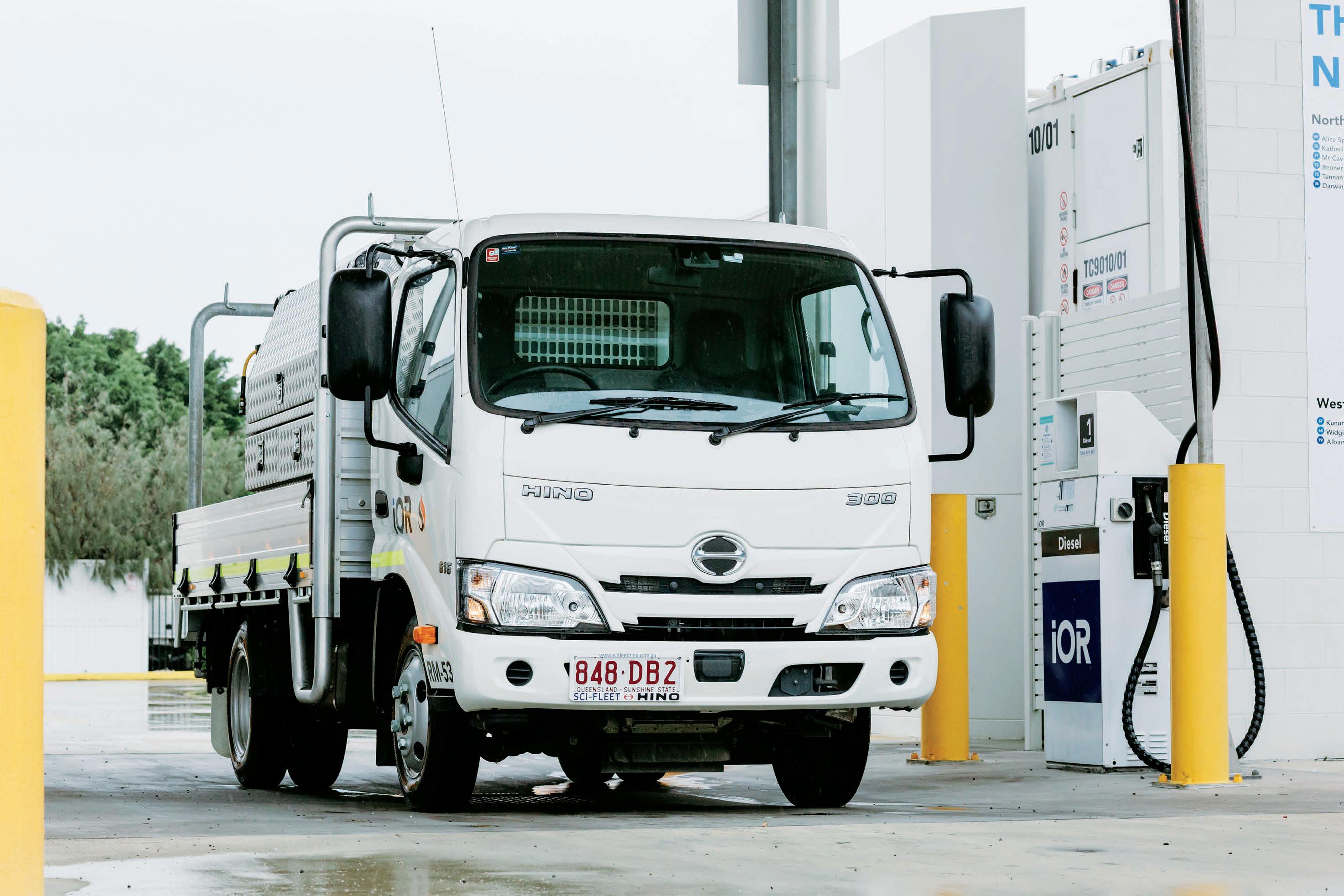
A major player in national fuel infrastructure, IOR meets the needs of Australia’s long haul transport industry with an expanding national network of diesel stops amid a significant profile of mounting and ambitious projects.
COVER STORY
Among the innovations taking place in the essential fuel industry sectors, IOR Group, an Australian-owned business established in 1984, leads the way through an adoption of new technology, sound investments and rapid expansion. On the back of an oil refinery in Eromanga, a little-known town in outback southwest Queensland where IOR originates, owners Stewart Morland and Ross Mackenzie have been steadfast in realising a shared vision — a vision to scale up the 24-hour company-owned Diesel Stops that service remote areas of Australia. The business, in accordance with the pursuit of that vision, has grown exponentially with over 90 of these Diesel Stops now in effect all over the country while bolstering infrastructure and diversifying its customer portfolio for good measure. One of the company’s core aims is to serve more customers in more places. It’s a unique model. Many of its regional depots are operated by local community members. Bulk fuel is then distributed to surrounding communities and regionally based industries, such as long-distance transport, farming, local councils, mining and oil and gas. As it offers fully integrated fuel management services, IOR handles most of its operations inhouse. “We have infrastructure, capability and people across the entire Australian fuel supply chain” says Drew Leishman, IOR Head of Infrastructure. “IOR tries to do everything, within reason, ourselves. That’s the most important thing. We secure our own supply chain and COVID has taught us that’s more important now than ever.” As a service provider to the remainder of the business, Drew’s role is to look after all assets. That encompasses everything that goes with physical infrastructure including property from its construction to operation, service, maintenance, and keeping the multitude of fuel assets pumping every day. Workshops also come under this portfolio. In this day
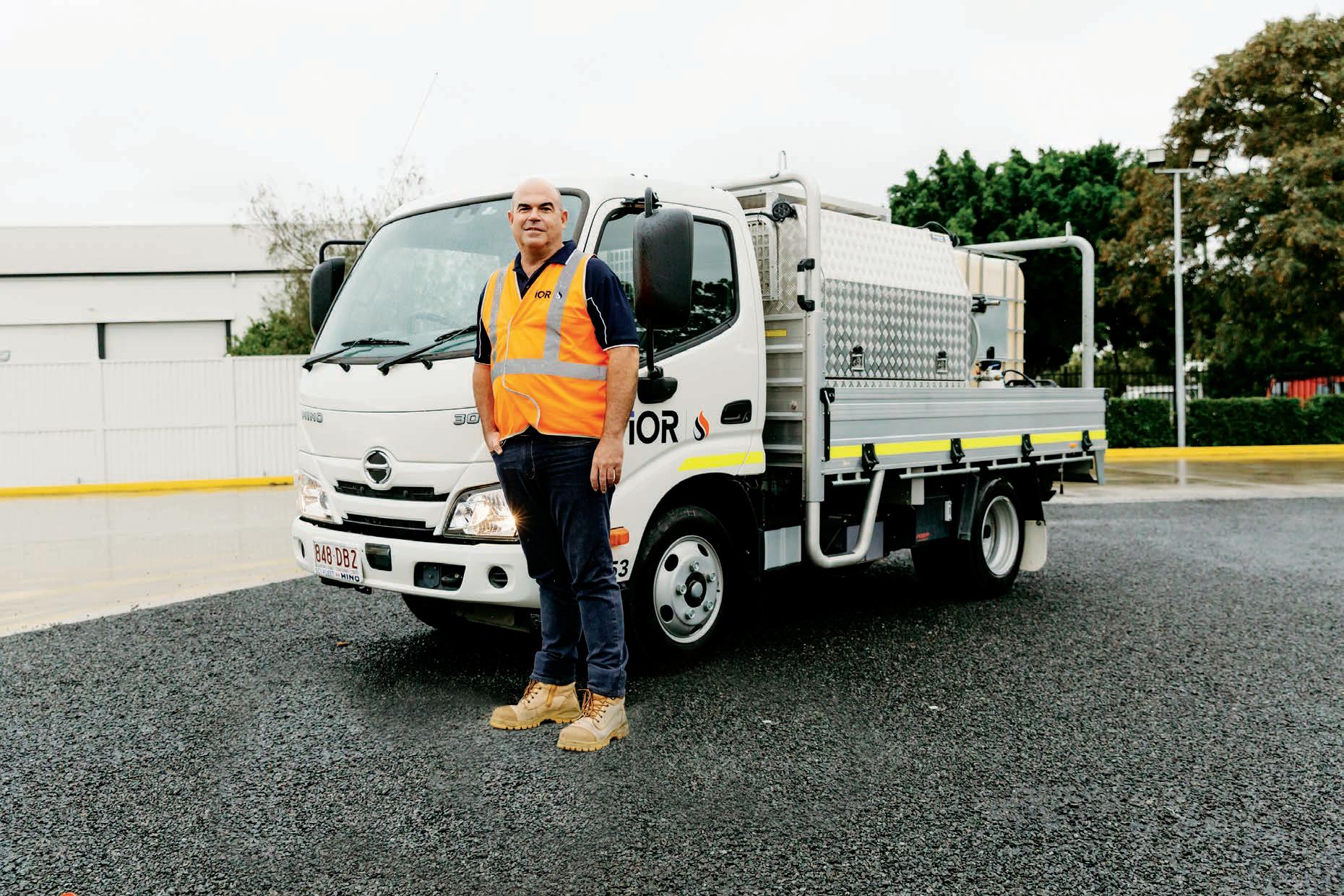
Colin Quinn.
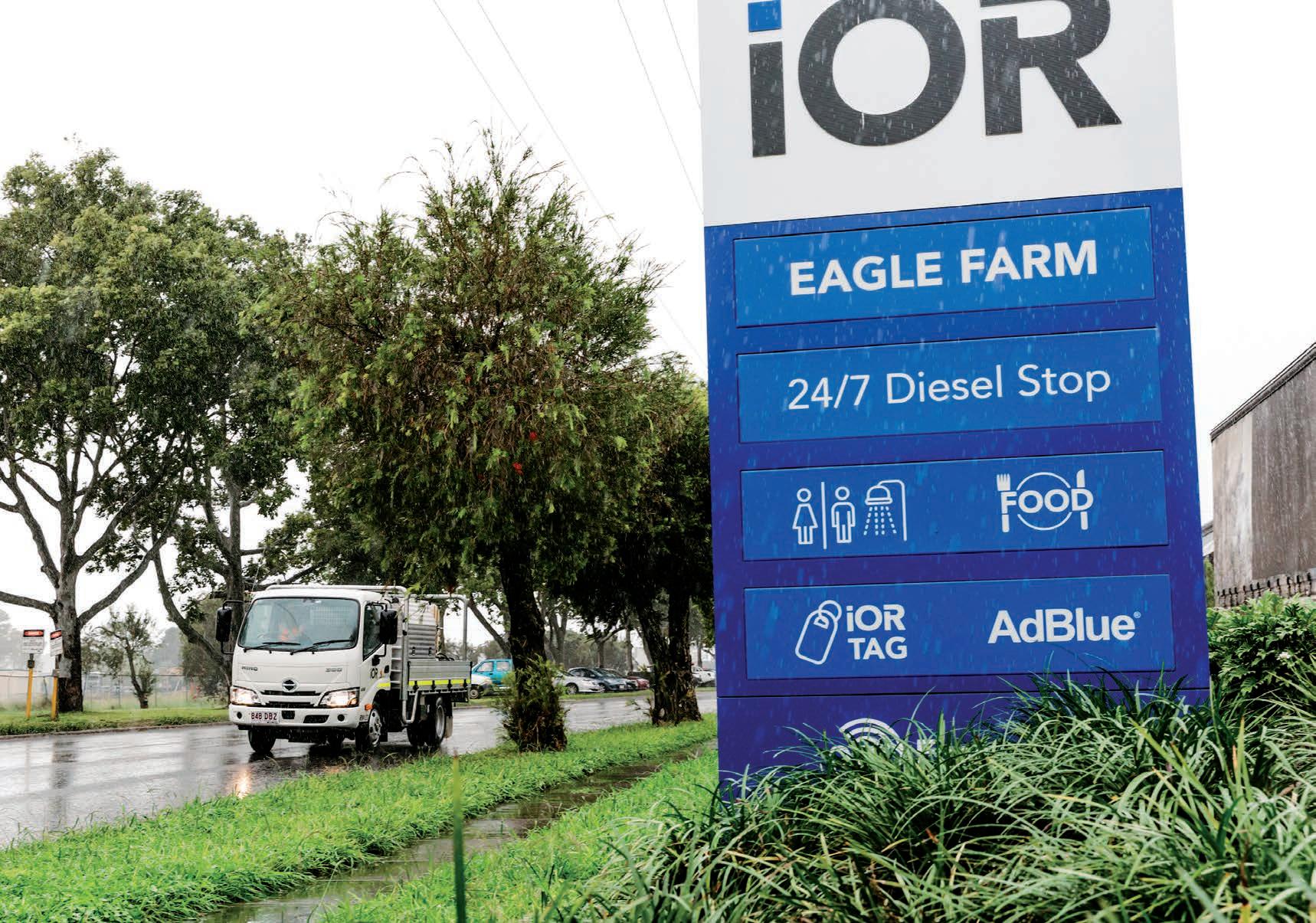
IOR’s Eagle Farm Diesel Stop.
and age it’s a formidable business that foregoes the need to outsource any of its operational inputs to third parties. “We take a hands-on approach to our site development, including planning, legal, engineering and construction all being executed in-house,” says Drew. Fuel tank manufacturing takes place at IOR’s infrastructure hub in Eagle Farm. IOR runs a fleet of around 110 trucks and 300 trailers as part of its transport operations, a business unit to itself. Several new Hino trucks have been acquired of late as service vehicles to help with remote sites which, like everything, require maintenance. On a normal preventative maintenance run, attendance of these new Hino 300 Series vehicles can involve minor tasks such as the replacement of parts and metre calibrations to major internal and external cleans. The trucks are commonly fitted with a tray-back upon delivery. After that point, the pump fit-outs, tanks and hydraulic-driven equipment is all installed in the IOR workshop. Breakdown maintenance might require the changing of hoses, nozzles and pumps, as well as different types of mechanical and electrical components. IOR technicians, according to Drew, must be multi-skilled. In addition to breakdown and preventative maintenance they will participate in site builds, installations of underground and aboveground tanks and be asked to perform welding and electrical work — usually in remote Australia. “They might even paint tanks and change stickers and decals,” he says. “These trucks have a couple of IBC containers in the back with hose reels and tools. They will have pipe racks on the roof and are driven thousands of kilometres or more to either fix something or build something.” Drew’s team also runs a 24-hour hotline. Faults on sites are detected through a cloud-based telemetry system IOR has built. In fact, that’s the project that brought Drew to the company ten years
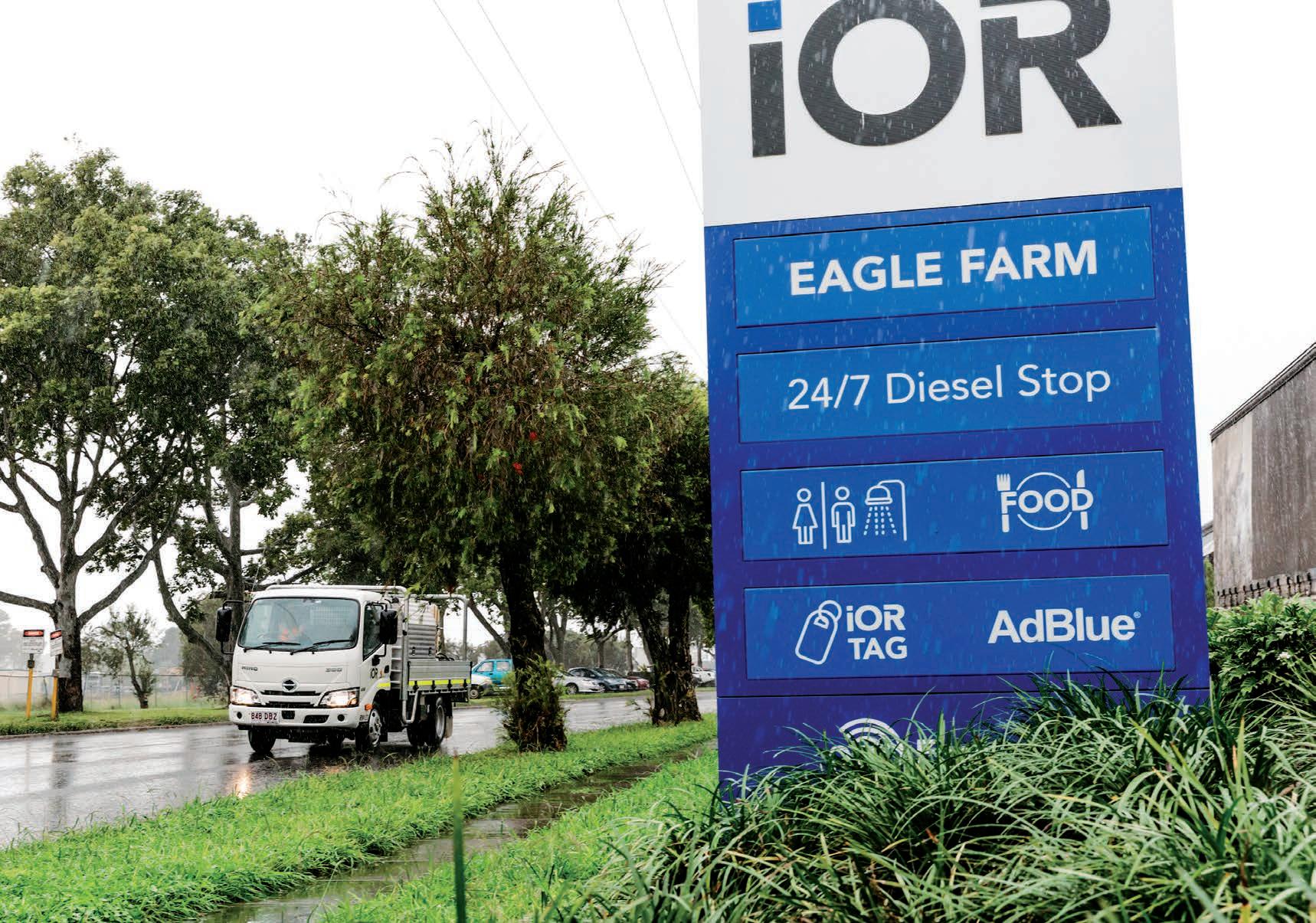
Drew Leishman IOR Head of Infrastructure
COVER STORY
ago. The online system, known as HyDip fuel management, runs the entire IOR network. Fuel tank levels at all sites can be monitored online via HyDip in realtime. It also provides notifications for faults on hoses and dispensers. “We have eyes through the cloud on every single facility and that’s what feeds into our maintenance plans and sending people all over the country,”
explains Drew. “That, if anything, sets us apart in the industry. We have got leading technology that has enabled us to establish remote unattended refuelling sites around the country, which wouldn’t have been possible without HyDip and this is why we have invested so heavily in it.” IOR will have an engineer or technician onboard ready to assist customers should they call up with an issue on site. “When a customer, no matter where they are, calls up for a fix on fuel tags or pin numbers or a reset they are talking to someone who actually goes out and fixes the tanks,” Drew says. “That’s pretty unique at any hour of the day.” Unlike the company’s fuel service trucks, that are rented to third parties, the maintenance vehicles are not 4x4. The fuel service trucks, however, are fitted with 5000 litres of diesel storage, some AdBlue, grease and air and are rented for use on large mine or construction sites before they are returned and refurbished by IOR for another project. “I’m a fan of Hino and Toyota,” says Colin Quinn, IOR Infrastructure Fabrication Manager. “I find them robust and easier to service. The insides are always quite flash, it’s all buttons — like driving a car. They’re practical and good to run. When the rental vehicles come back to us, we’re only replacing mudguards and broken taillights. Nothing is rattled. They’re unshakeable in that sense.” The relationship with Hino is relatively recent. Along with John Fraser who runs the Transport Division, Drew decided
it was time for a change of OEM and a conversation with Sci Fleet Hino’s Nathan Murdoch proved fortuitous for both parties. “To be quite honest he’s been awesome to deal with and he’s looked after us really well,” says Drew. “So, we have kept going back for more. Any time we’ve wanted any factory extras, like PTOs or different guards or trays and fit-outs, they’ve always been accommodating.” Partnering with Hino resonates on another level. It enables the service and manufacturing team to continue in its mission to bring new refuelling services to regional and remote communities, in places like Quambone, or on King Island Airport, that might never have had fuel infrastructure beforehand. “That’s what we do. We just continue to roll these facilities out,” says Drew. “Our roots as a company are in the bush. That’s where we come from. Our business has always been about challenging ourselves and going out to remote and regional places, establishing new fuel and energy infrastructure, enabling remote communities with access to fuel, 24/7, and giving back by supporting organisations that save lives and improve people’s wellbeing. For years, IOR has been a major supporter of RACQ LifeFlight Rescue, Heart of Australia, It’s a Bloke Thing, Outback Futures, and the Westpac Lifesaver Rescue Helicopter Service Queensland.” Self-bunded fuel tanks are a major part of the rental business. These range from 1000-litre tanks up to 100,000-litre tanks. There are more than 50 other small mobile fuel assets to rent which provide capacity for 2000-litre trailers and go up to 24,000-litre trailers for towaround projects. Agricultural customers, particularly in time for harvest, take the 24,000-litre self-bunded quad dog trailers according to Drew. “They can be towed around the farm to fill up equipment. This way of bringing fuel to equipment in the field reduces downtime and enables massive productivity improvements at a critical time of the year,” he explains. “The smaller stuff is hired out by oil and gas groups and solar farms and civil construction projects, rail projects.” The company continues to invest heavily in research and development to provide integrated fuel access, storage and management solutions to meet the specific needs of its customers. In Yaraka, 220 kilometres south of Longreach, to give an indication of its isolation, the only option to refuel in the district was, previously, a 100-kilometre trip to Isisford before IOR developed a 24/7 refuelling site. That required farmers and residents to make costly return journeys to purchase fuel. Bedourie in the Simpson Desert is another new location in the IOR network. The refuelling site here will support connectivity and access to fuel for transporters from northern Queensland into South Australia. “We’re building sites in the locations our customers need us most,” says Drew. “The more we connect the dots, the more the network grows, the further our customers will be able to go.” Joining the refuelling sites with major highways is critical to this expansion strategy and sees the company growing its presence in metro areas. Aviation fuels were added to the business in 2017
Drew Leishman IOR Head of Infrastructure
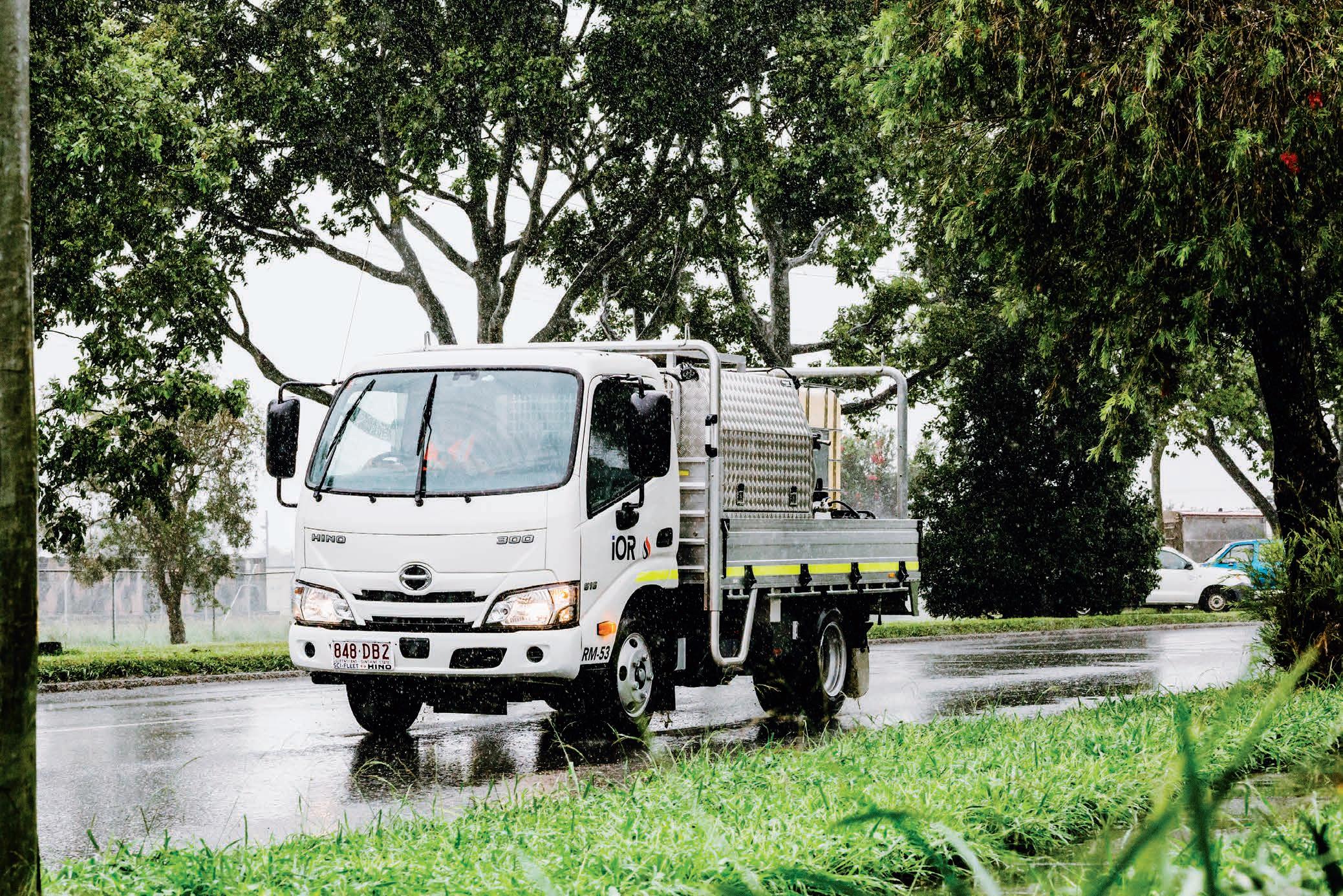
to expand and strengthen its services to remote and regional areas. It follows the diesel network model, combining HyDip with aviation grade fuel tanks which it uses at regional airports. IOR plans to further increase the number of airports it services in the coming year. Back in February it was announced that IOR had secured a $15 million loan from the Queensland Government’s Building Acceleration Fund to help expedite the development of a new diesel import terminal at IOR’s site in the Port of Brisbane. Operated as a Crude Oil Terminal until last year, the Lytton Terminal facility was constructed in 1984 and was acquired by IOR in 2008. The planned upgrades will be critical for Southeast Queensland’s fuel security, introducing new fuel importing and storage infrastructure. Upon completion, the Terminal will provide Brisbane with 110 million litres of new domestic diesel storage. IOR is commissioning an estimated $50 million of works. For perspective on the scale of the project, the site’s existing 50ML tank is being repurposed for diesel storage, two new tanks are being erected for extra diesel capacity and one new tank for biodiesel additive. Various upgrades have also been greenlit including improvements to the containment bund, electrical infrastructure as well as delivery of new diesel loading pumps and loading bays, and construction of a 4km pipeline to the nearby wharf complete with new marine loading arms. The project will support over 260 construction and eight operational jobs. “IOR’s core business is the on-road refuelling sites and bulk fuel. But each business unit including lubricants, aviation and tank rentals are essential to IOR and our customers in their own rights,” says Drew. “Together it just creates a great proposition and capability that can do a lot of things for a lot of people. If someone calls us for support on their project, in most cases, we can solve nearly all of their problems in one hit.” Cohesion across the business is therefore vital. The two directors Stewart Morland and Ross Mackenzie, according to Drew, are still both in the office every day. “They are heavily focused on getting the terminal up and running in Brisbane and keep on investing in the business,” he says, “It’s exciting. That’s why I’ve stayed as long as I have and will continue to. It’s such a good place to work. There’s never a dull moment.” Despite ongoing scarcities in global markets that continue to ripple across the world, it’s reassuring to see dedicated energy, ambition and Australian knowhow are not, at least where IOR is concerned, resources in short supply.
One of the new Hino 300 Series deployed in IOR’s maintenance fleet.
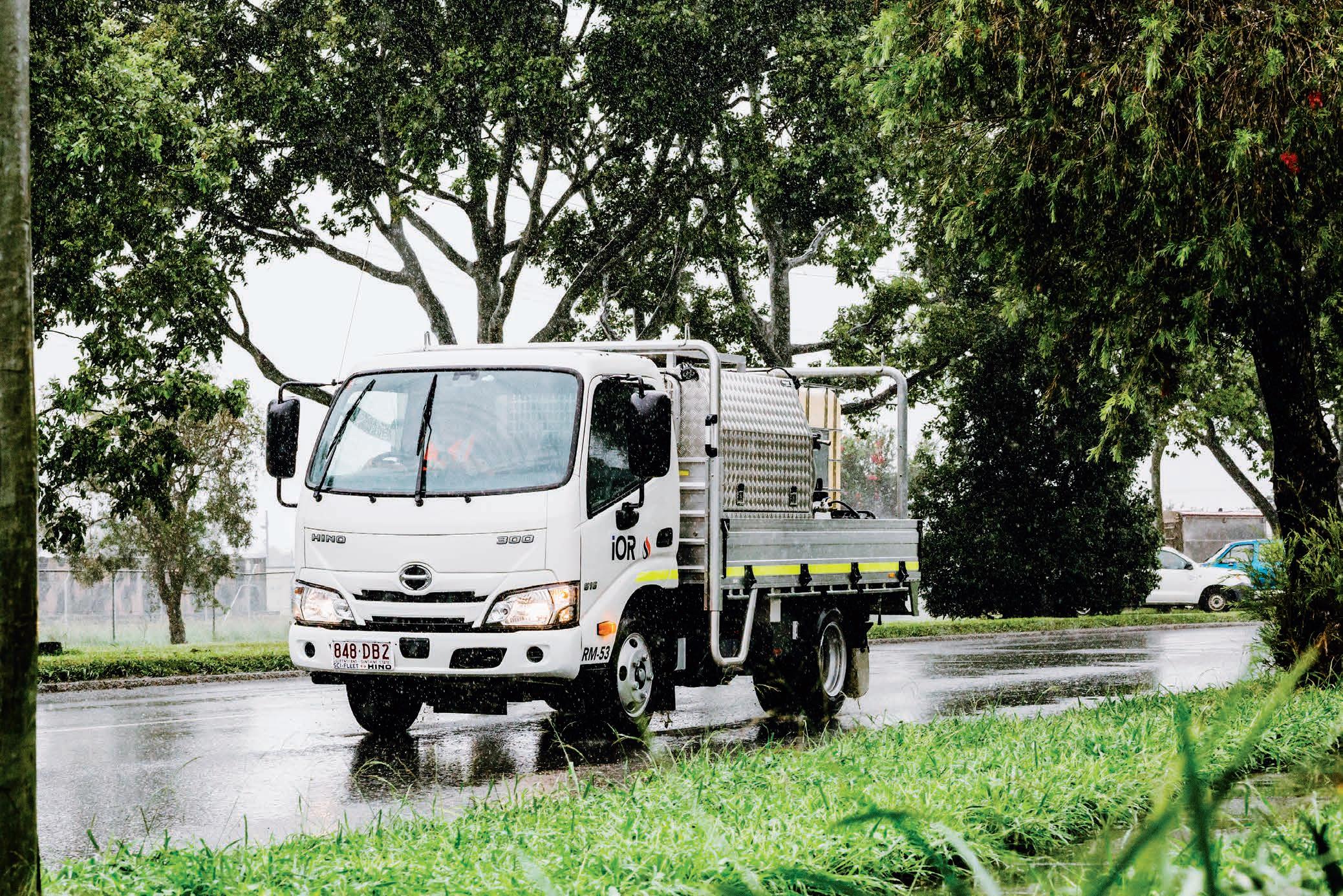
FLEET FOCUS
Isuzu FVZ 260-300.
HERE TO
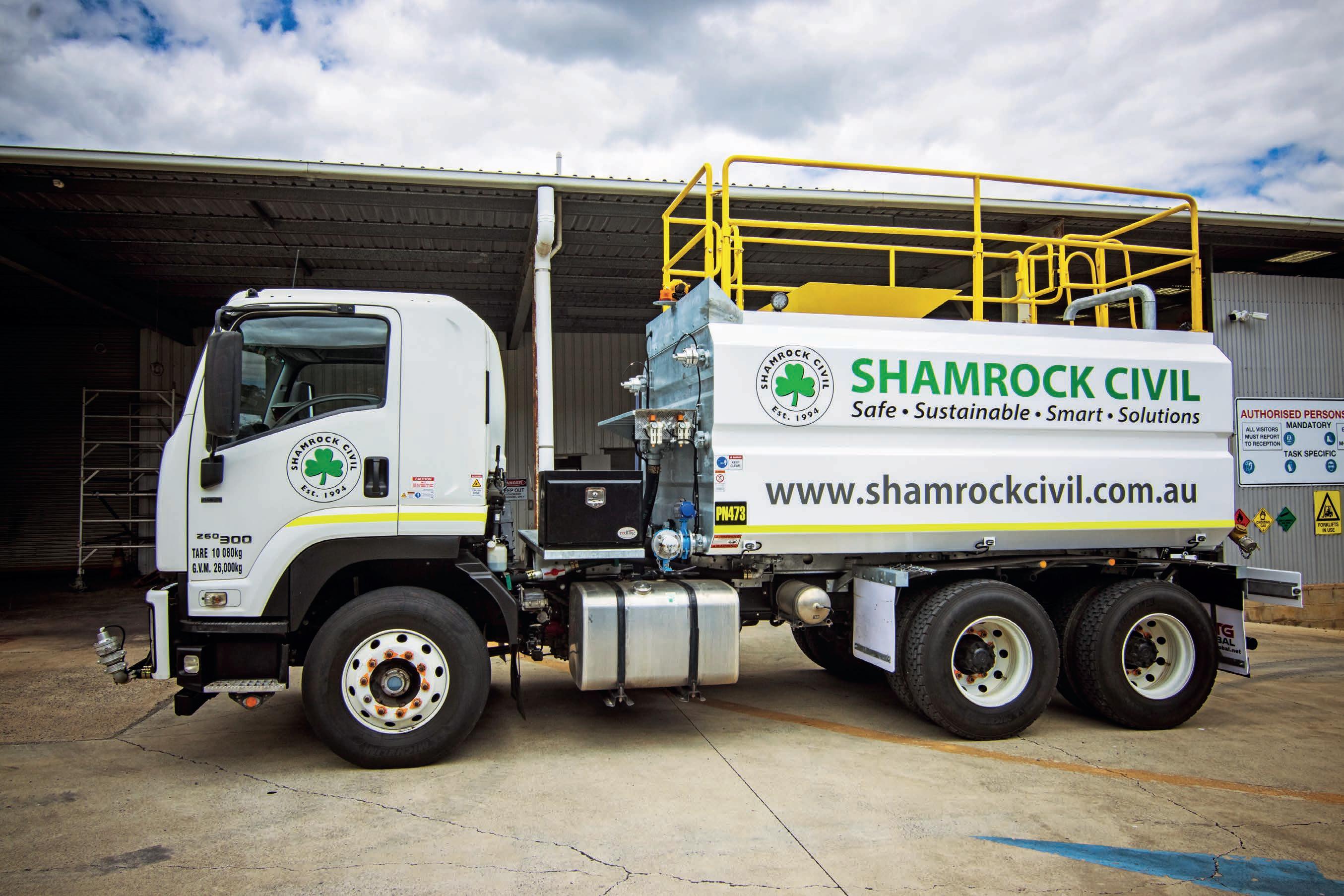
TO HELP
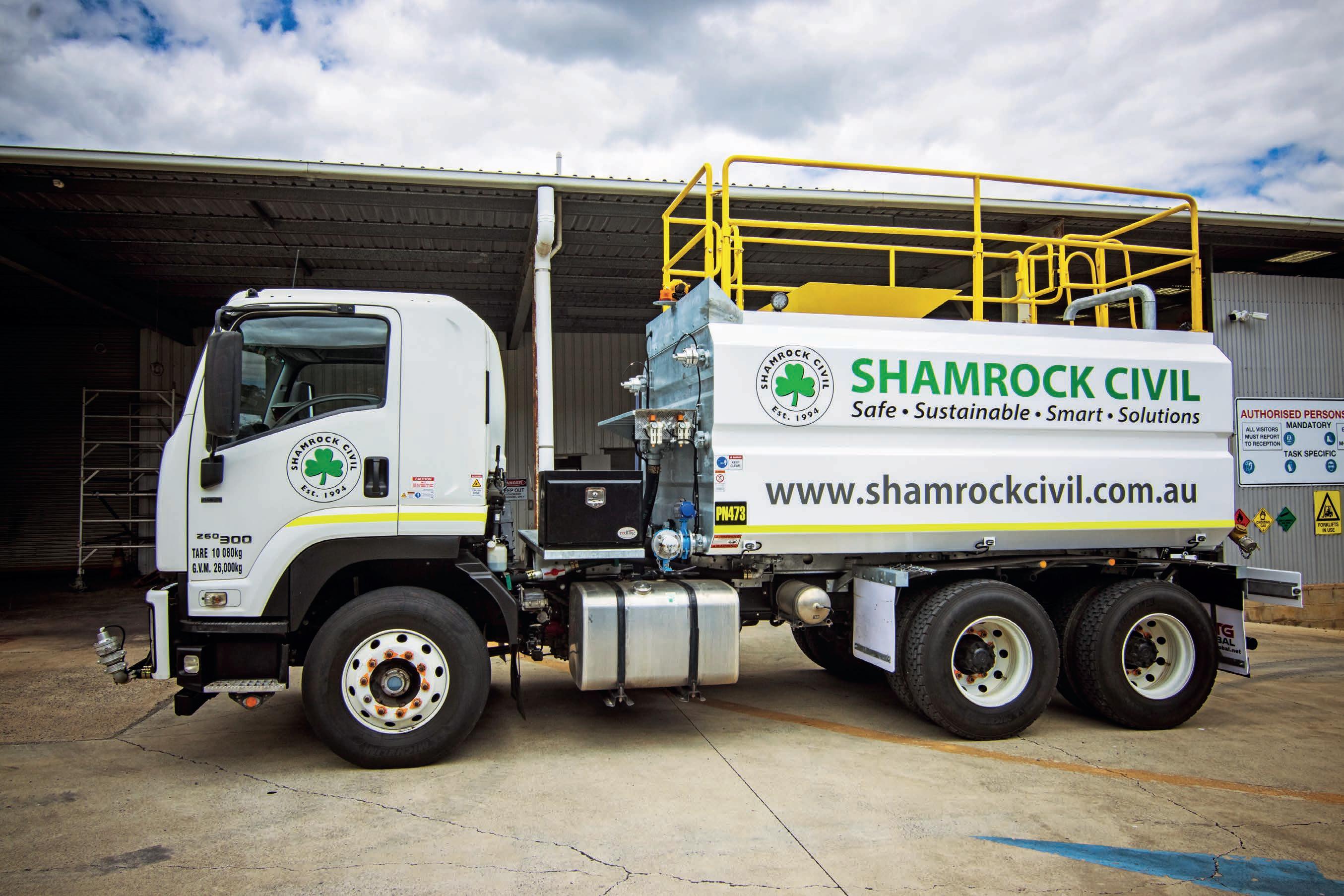
Established in Brisbane in 1994 Shamrock Civil Engineering has been steadily expanding its operational footprint from Southeast Queensland into central and north Queensland, South Australia, Northern Territory and Victoria.
FLEET FOCUS
Widely known throughout the industries in which it operates as simply ‘Shamrock Civil’, the company is involved in a variety of construction and environmental projects in both remote and metropolitan locations, with works including concrete, roads, pipelines, and major earth works. Shamrock Civil’s team provide expertise for a diverse range of construction projects delivering services to gas and mining, transport infrastructure, commercial, defence and government development sectors. They have had a hand in constructing gas fields, defence facilities, major shopping centres and even concrete bridges such as the Chardon Bridge in Logan City, south of Brisbane. An area of increasing activity for the Shamrock Civil organisation is the preparation of refuse waste dump sites for clients such as, local councils and major contractors such as Cleanaway. This sector can encompass the initial earthworks and the ‘capping’ procedures necessary as the refuse landfill cells reach their capacities. Rehabilitation of mine site areas is yet another sector where Shamrock Civil’s experience, expertise and equipment are put to good use. “The one area that we don’t get into is residential sub-division work,” explains Shamrock Civil Director, Leslie Zeeman. “A couple of years ago we decided to become more geared up towards the management of bigger jobs, with bringing in sub-contractors and equipment to complement our own if we needed to.” Shamrock Civil has grown to employ around 150 full time employees including managers, engineers, quantity surveyors and safety advisors. The company comfortably contracts for projects totalling around $150 million per year. Currently there is at least $150million of future work on the books. “There are very good conditions at the moment and we have to be prepared on how to get through all of it,” says Leslie. The core fleet of equipment includes more than 120 items ranging from bulldozers, graders and excavators with up to 50 tonne capacity, dump trucks with up to 40 tonne capacity, skid steer loaders, as well as small and large tippers with up to 40 tonne capacity. They also
A water truck on site in Whyalla, South Australia. own 20 water trucks ranging from 8,000 to 40,000 litre capacities. “We’ve gone through a big capital expenditure program over the last couple of years and have spent about $5.5 million on plant and equipment, with an additional $3 million over the next six months,” says Leslie. The fleet includes many items other than vehicles and earthmoving equipment such as generators, pumps, portable site offices and a series of attachments. “The basic intention is to use companyowned assets as the mainstay, especially in the work being done for defence and our larger contracts for Cleanaway doing rehabilitation of refuse sites as well as our current work with premium companies such as Santos and Arrow Energy,” says Leslie. “We’ve always stuck with Toyota as our main fleet vehicle, but last year we decided we needed to diversify so we could keep up with the supply and demand. After we did a bit of investigating, we decided on supplementing our fleet with the Isuzu D-Max.” In addition to the water tankers, the Isuzu brand appears on tippers and

Shamrock’s Plant Operator, Jonathan Skinn with a 15,000-litre water truck.
service vehicles for maintenance of the various pieces of earthmoving equipment. A dedicated team of diesel fitters perform scheduled servicing and maintenance on the plant and equipment, which reduces the risk of down time and ensures the fleet is utilised to its maximum capacity. John Delaney, Plant Manager for Shamrock Equipment, is proud that the company’s Isuzu FVZ 260-300 water truck was a finalist in the Isuzu Truck of the Year awards. “We love our Isuzu water truck, it’s the perfect addition to our fleet,” he says. Consequently, three similar Isuzu 15,000 litre water truck units are on order from Isuzu. The FVZ 260-300 is a 6x4 configuration with a GVM of 26,000kg and a GCM of 36,000kg. It is powered by the 8.0-litre Isuzu six-cylinder engine which meets Euro 5 emission regulations without the use of a Supplementary Catalytic Reduction (SCR) system and its associated requirement for AdBlue liquid. The engine develops 221kW of power and delivers 981Nm of torque and the truck rides on Isuzu’s six rod multi-leaf rear suspension. In similarity to operators around the world, a challenge for Shamrock Civil is more about being able to get the equipment. “We have ten Isuzu D-max utes on order,” says Chief Financial Officer Shamrock Equipment and Shamrock Site Services, James Moore, who looks after the company’s assets. “We were hoping we would get them by January, but the world of COVID has pushed that back so we’re probably talking about mid this year.” Shamrock Civil has been in the vanguard of corporate and community responses to recent and past incidences of flooding in Brisbane. “In 2011, we saw some of the worst floods Brisbane had ever dealt with, that’s when we first got involved with the Brisbane City Council,” says Leslie. “They even used our premises to fill sandbags and deliver them to affected areas. We got involved again in the 2022 flood events and this time made machinery available to repair roads and help with the wide scale clean up. We often do silent charity work because that’s just the way we are and we like helping where we can. If people need us and we can help, we most certainly will.” Flood clean-ups and equipment delays aside, the future for Shamrock Civil looks very positive. The construction industry in Australia has not been as badly affected through the COVID pandemic as others. Achieving $160 million this year represents a 60 per cent increase and is an indication of the greatly increased level of activities in which Shamrock Civil is involved. “We’re thinking positive, and we are having a good run, but we have our ups and downs just like any business,” says Leslie. “At the moment we are doing well.” Shamrock Civil has a strong commitment to understanding, meeting and continuously evolving its approach and responsibilities to the environment. They have developed, and rigorously apply their own environmental management system to reduce the impact their operations have on all aspects of the environment, including native flora and fauna, air and water quality, soil conditions and cultural heritage. Shamrock Civil also has a strong commitment to ensuring they provide a healthy and safe work environment for their employees, subcontractors and project partners. The company approaches its 30th year in 2024 and in an industry sector like road transport, one of the biggest challenges is recruitment and retention of qualified people. Shamrock Civil commits significant time and resources to retain its reputation as an employer of choice and a core group of employees has been extremely loyal to the business over the past couple of decades. The very first employee appointed by Shamrock Civil is still with the company today. “I’ve been here for two years, and I’ve never worked in a company where so many of the people have been here ten plus years,” says James. Shamrock Civil also aims to make a positive impact on the local communities in which they operate, which includes employing local people and supporting local businesses wherever possible. Shamrock Civil also has a strong history of providing indigenous employment opportunities and developing cultural understanding.
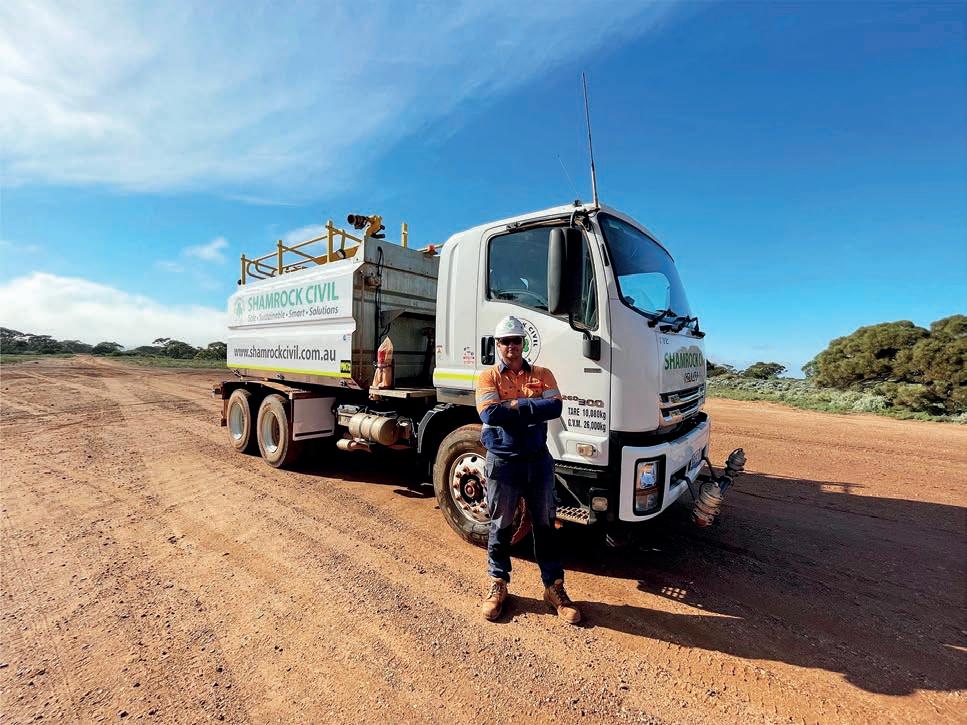
FLEET FOCUS
CLEANING
As the swing towards environmentally friendly solutions continues to gather momentum, Cummins is shifting gears to stay ahead of the curve. As a result, forward thinking companies like Energy Logistix are availing of the red engine maker’s offering of Euro 6 versions of its heavy-duty X15 powerplant to help them in their ‘clean ‘n’ green’ quests.
There can be no denying that fossil fuel burning engines are steadily on the way out the back door, with a range of electric options steadily spooling up to take their place. However, while this snail’s pace shift in reliance on new power sources plays out over the next few decades, the interim measure is to ensure the ongoing diesel donks are developed to the pinnacle of possibility in terms of fuel efficiency and minimal emissions. For its part, Cummins South Pacific has been evaluating Euro 6 engines in Australia for the past four years. Over that time, X15 Euro 6 engines have chalked up millions of kilometres in a wide range of applications and environments, hauling a range of combinations including single trailer, B-double and roadtrain. Importantly, Cummins has been able to meet the stringent Euro 6 standards without the need for exhaust gas recirculation (EGR), which the company
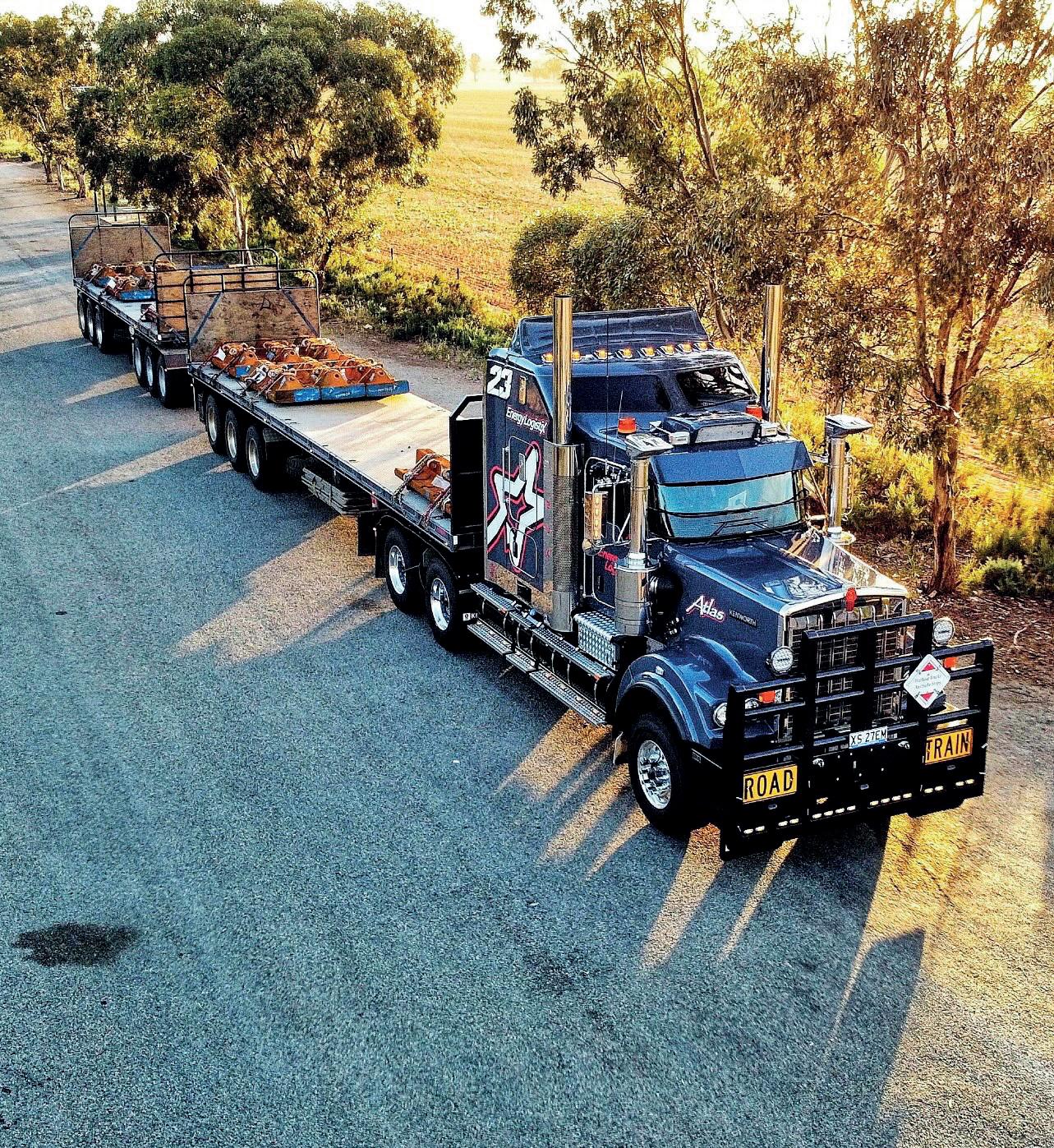
One of the Kenworth roadtrains Energy Logistix operates.
CLEANING
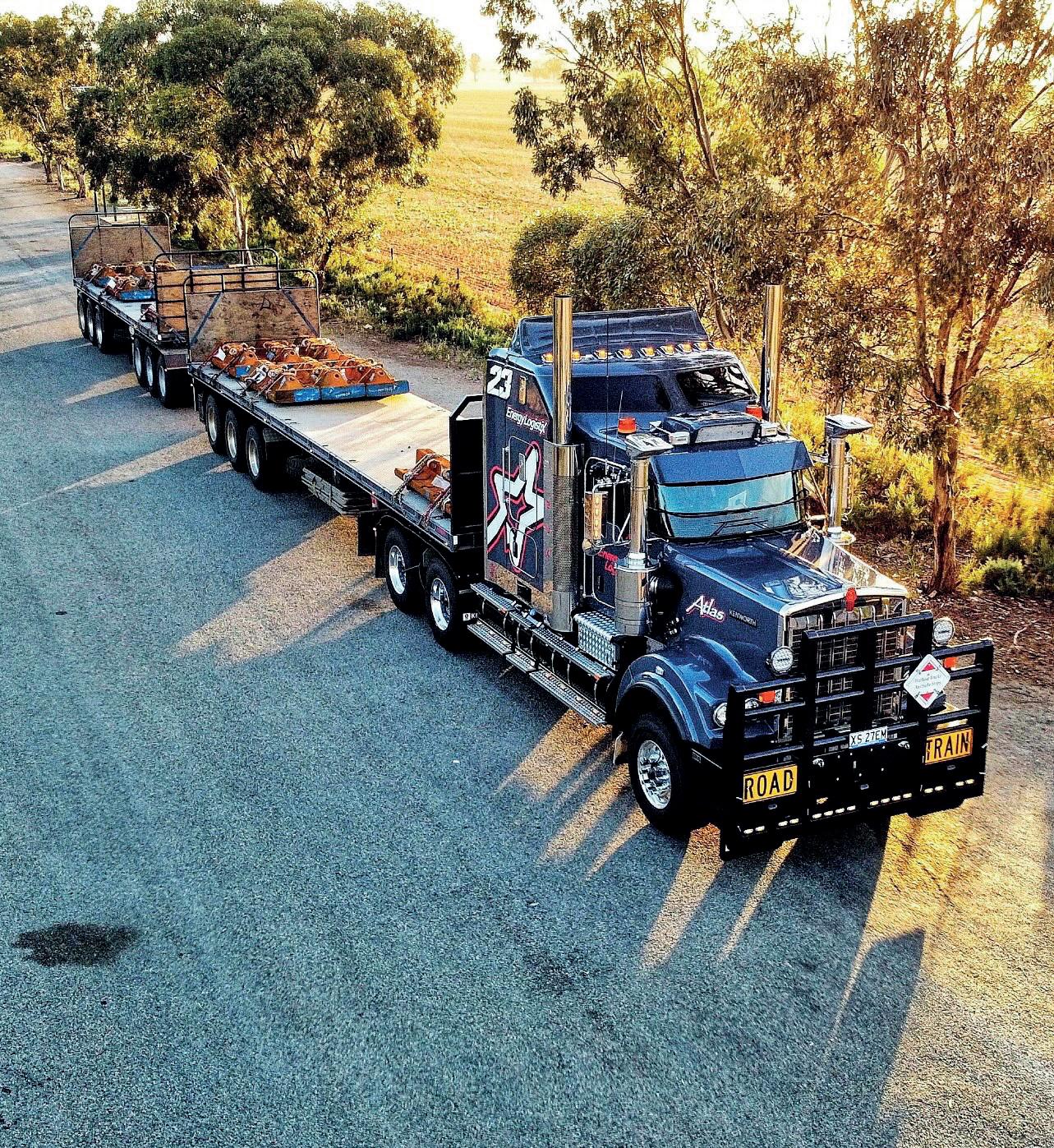
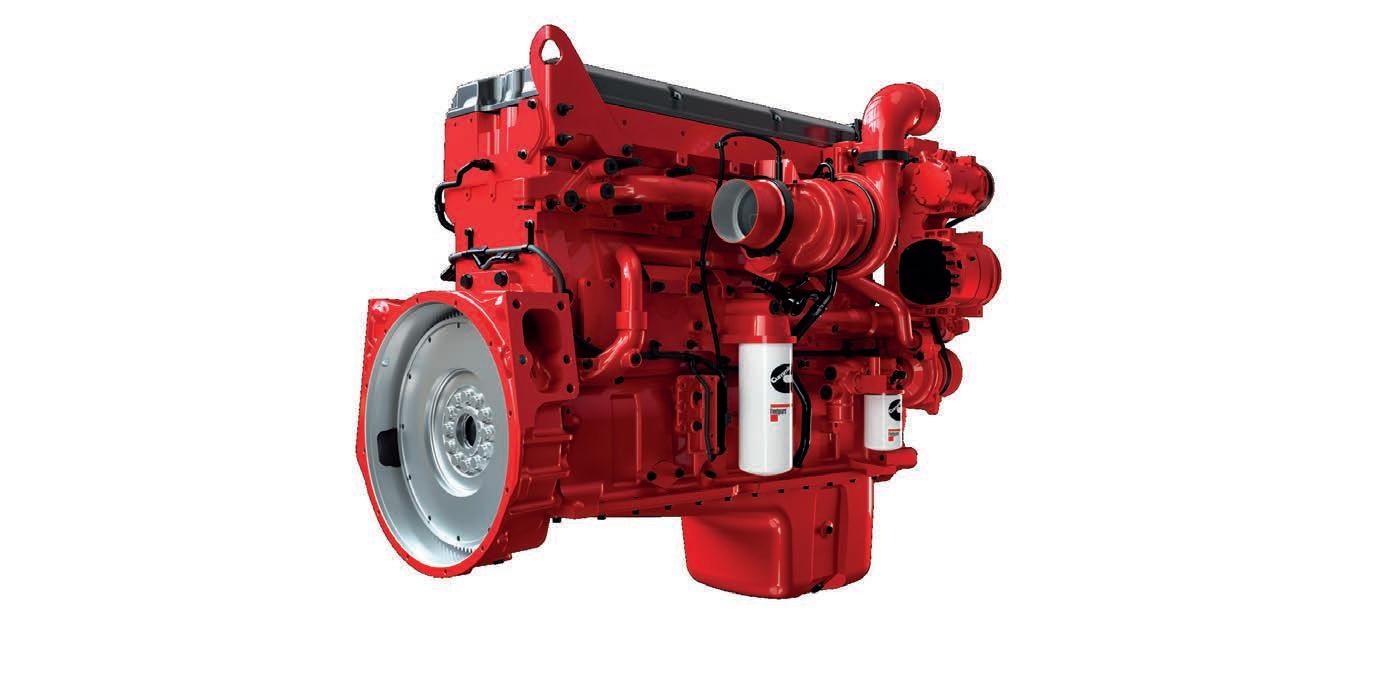
was keen to avoid due the issues it caused in the past. Reduced emissions start with Cummins’ Extreme Pressure Injection (XPI) system that is claimed to reduce noise and improve combustion efficiency and fuel economy; while a relatively simple wastegate turbocharger is also used rather than the complex and potentially problematic variable geometry turbo (VGT). It also utilises selective catalytic reduction (SCR) and a diesel particulate filter (DPF) combined in a single housing known as Single Module Technology, which is said to be more compact, lighter and stronger than separate module designs. The Cummins X15 Euro 6 is available in two variants known as Performance Series and Efficiency Series. The differences between the two comprise altered hardware including intake air management and compression ratios along with tailored computer software. The Performance Series has ratings ranging from 525 to 625hp, with peak torque of 1,850 to 2,050lb-ft, while the Efficiency Series features ratings ranging from 460 to 550hp, with peak torque between 1,650 and 2,050lb-ft. The top Efficiency Series rating of 550hp accompanied by 1,850 to 2,050lb-ft of torque was previously the preserve of the 600hp class. According to Cummins, this rating is ideal for B-double prime movers with down-sped (lower 100km/h cruising RPM) drivelines, to promote fuel efficiency without compromising performance and trip times. This variant is intended for mating with Eaton’s UltraShift Plus 18-speed automated manual transmission (AMT), while the Performance Series, which is intended for vocational and heavy haulage roles, is best suited to the Eaton 18-speed manual ‘box. One of the early adopters of Cummins X15 Euro 6 technology is Energy LogistiX (ELX), a multi-million dollar transport and logistics company founded by Co-Directors Jo Williamson and her son, Shaun, just over ten years ago. Jo worked with her father at his transport company and also worked for some other large trucking companies before starting her own business, with Shaun joining her soon after. “At the time I was working on oil and gas rigs and I suggested to mum that she should focus her efforts in the resources space because I’d identified a gap in the market at that time,” Shaun says. “Not long after I came onboard as a partner in the business, and the rest, as they say,
Energy Logistix is running with the Cummins X15 Performance engine.
FLEET FOCUS
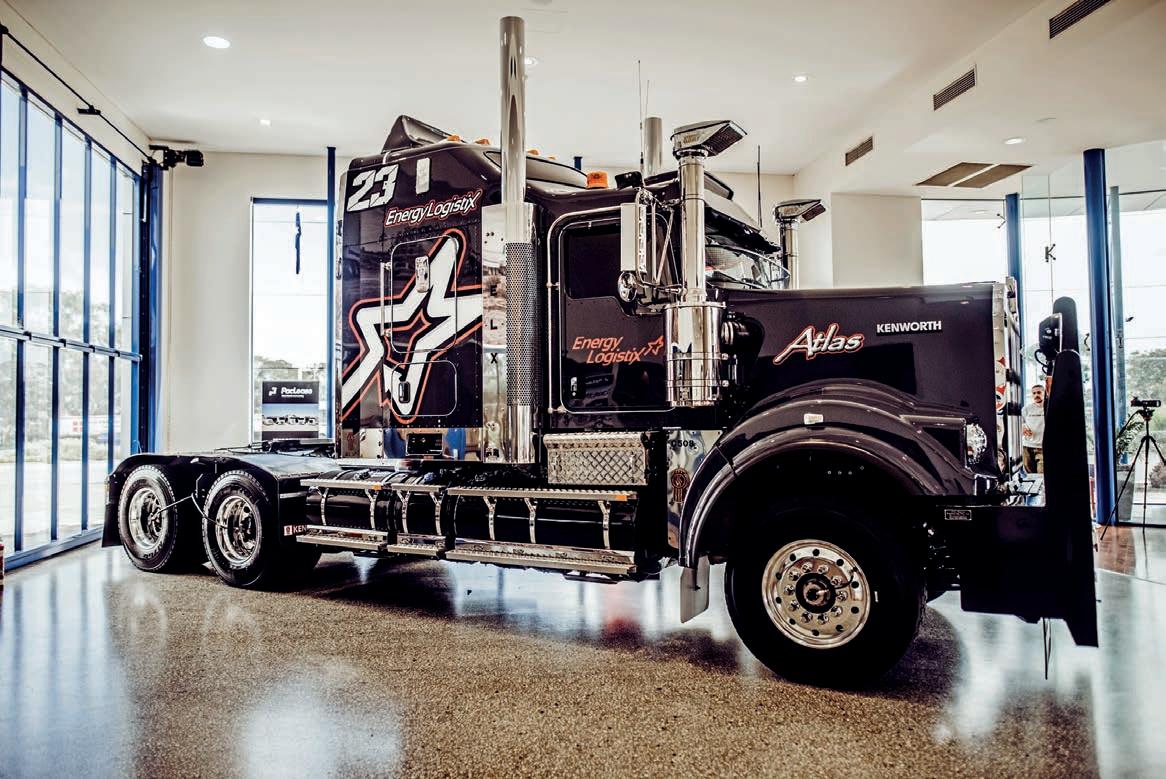
New Kenworth C509 specified for roadtrain application.
is history.” According to Shaun, the growth of the business has been phenomenal – in the vicinity of 20 to 30 per cent, year-on-year. Today the company runs a fleet of prime movers and has a subcontractor base of roughly equal size. The company fleet comprises a couple of Western Stars and the same amount of a European brand, with the majority being Kenworths. “Our fleet of double and triple roadtrain prime movers is primarily Kenworth with Cummins engines and we have a very strong relationship with our local dealer CMV in Adelaide,” Shaun says. As for the reasoning behind choosing to purchase Euro 6 compliant prime movers well before the introduction of equivalent Australian legislation, Shaun says it’s all about going on the front foot and leading by example. “My mum is nearing retirement age and she wanted to take a step back so early last year we sat down together to work out a direction for the business,” Shaun explains. “I have two young kids and the vision we had as a family was to build a sustainable generational business, so we needed to work out how the next five to ten years in our industry would look and where we would fit in.” Shaun says that’s when the issues of sustainability and reducing emissions came into sharp focus, including increasing technological innovation and efficiencies in the company’s truck combinations and other areas of the business. “One of the imperatives that came out of this was that any new trucks we purchase from now on will be Euro 6 compliant at a minimum,” he says. Kenworth was quick to come onboard with the idea and in turn got Cummins involved. “All the parties including Kenworth, Cummins and CMV got involved and found out what we needed, with the
Energy Logistix prefers to invest in Australian- made products.
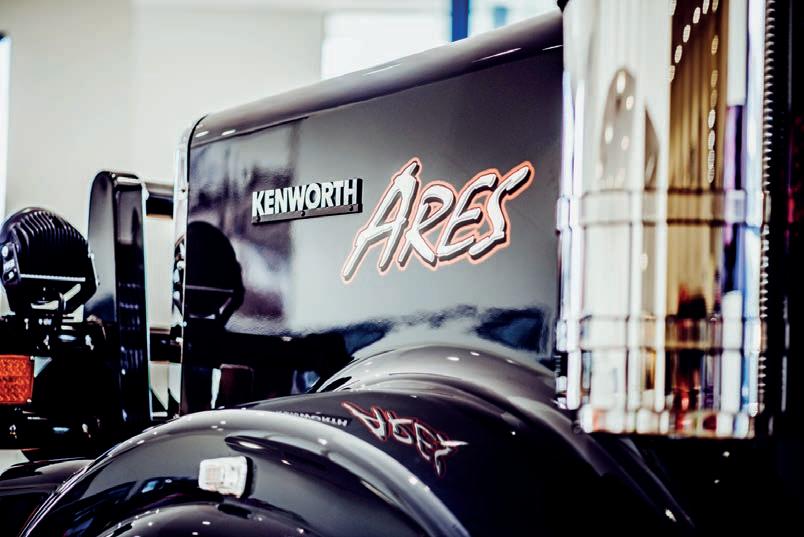
Shaun Williamson Co-Director, Energy Logistix (ELX)
end result being that we were able to take delivery of two new Kenworth C509 roadtrain prime movers fitted with X15 Euro 6 engines,” Shaun recalls. “We’re one of the few companies in Australia that has adopted these new Euro 6 engines for the heavier end of the load capacity – which is a 130-tonne payload.” Shaun mentions that the company does a lot of carrying to remote mine sites across Australia which demands ultimate reliability. He says that one of its key customers is right behind the push to develop a sustainable transport business and industry, adding impetus to ELX’s efforts. “They backed the idea of us trialling one of these trucks in our operations which enabled us to move forward with the concept,” Shaun says. Perhaps going some way to explaining why not every transport operator is keen to jump aboard the Euro 6 bandwagon just yet, Shaun mentions that from a financial perspective he believes there is no tangible benefit from using Euro 6 compared to Euro 5 compliant engines. “From our experience the new Euro 6 engines are using a fair bit more AdBlue than our Euro 5 Cummins engines which essentially means the Euro 6 engines are running cooler, and of course, there are less emissions coming out,” Shaun says. “From a fuel usage perspective, to be honest, we haven’t seen any noticeable benefits yet but they are still breaking in with about 80,000km on the clocks, so we are hoping to see a small improvement in fuel economy once they are fully run in.” Nevertheless, Shaun says that he feels the benefits of running cleaner engines will play out over the longer term and that he is proud to be an early adopter of the Euro 6 technology. “I’m young and an innovative thinker and my goal is to push this space forward, whereas generally the industry isn’t quite so proactive in this area,” he says. “There are a lot of bigger companies these days and many of the medium-sized private enterprises like ours don’t exist anymore, while those that are still operating generally have older people running them who tend to not want to change the way they do things unless it provides a cost reduction for the business.” Then there are the big multinationals who are investing in European trucks in the Euro 6 space in Australia. “But for us,” Shaun continues, “we’ve always tried to invest in Australian-made products where possible, and for us that’s the Kenworth product.” For the moment, it’s trailblazing companies like ELX that are paving the way for the Euro 6 equivalent emissions standards this country will have in the near future. The advantage for companies such as Cummins, the world’s largest independent powertrain manufacturer, is that having forward thinking companies willing to bite the bullet with the Euro 6 engines means the technology will have many runs on the board when it comes time for the mainstream rollout.
Part of Energy Logistix’s formidable Kenworth fleet.
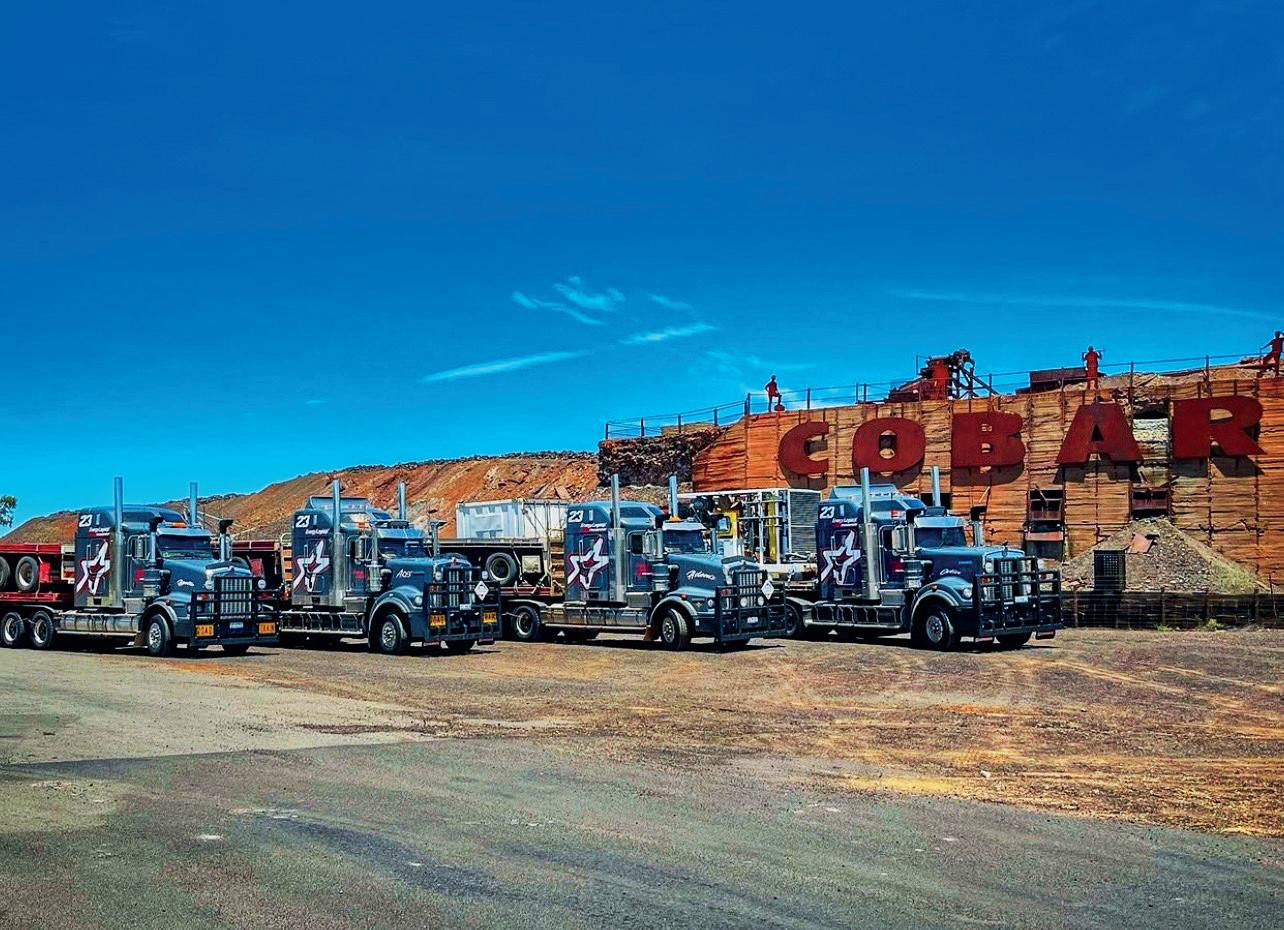
TRUCK & TECH
MERCURY REVS
Operating from the Pilbara Region of Western Australia, the AK Evans Group utilises such brands as Kenworth and Dana to handle the demands its vehicles are required to meet.
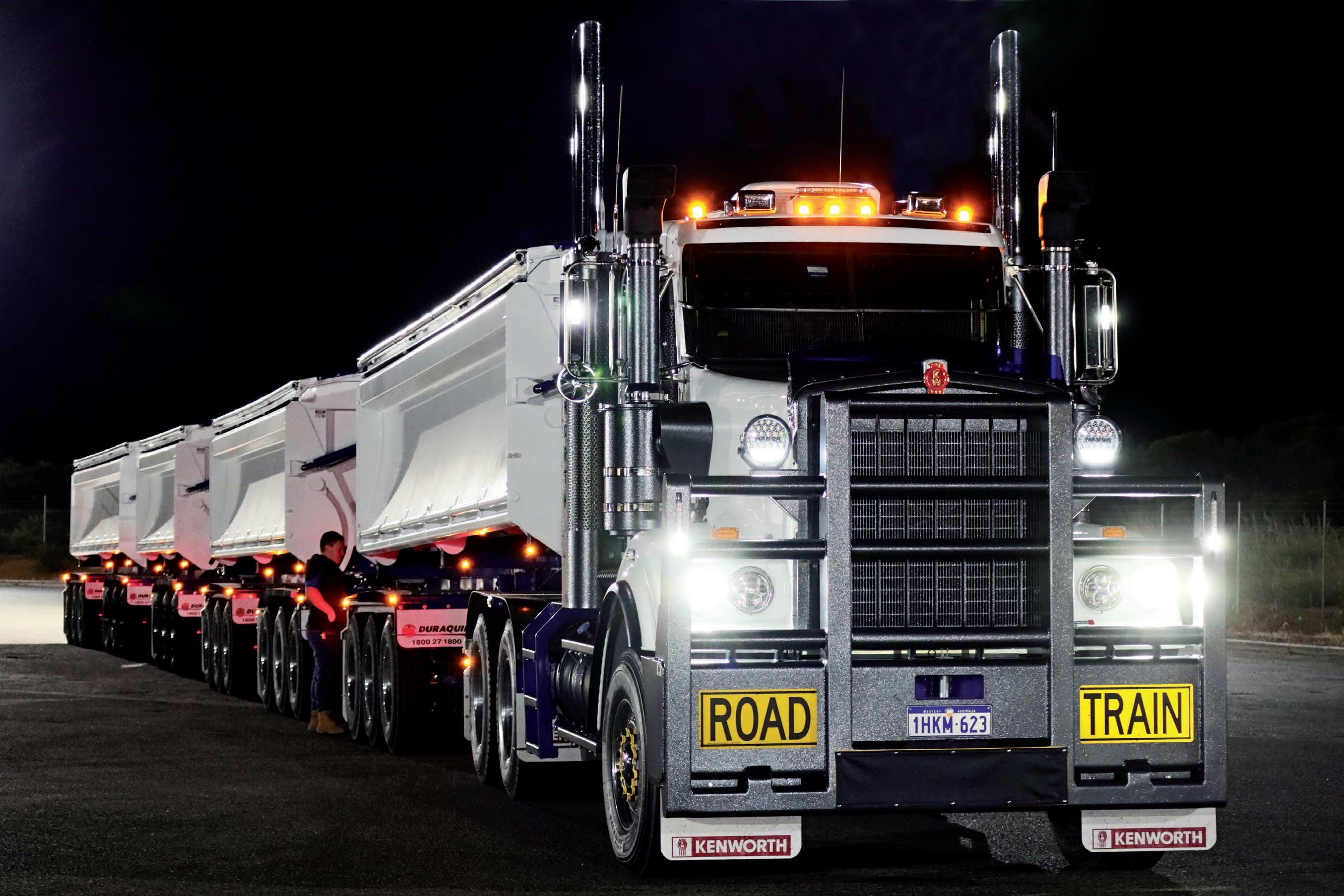
Kenworth C509 triple roadtrain.
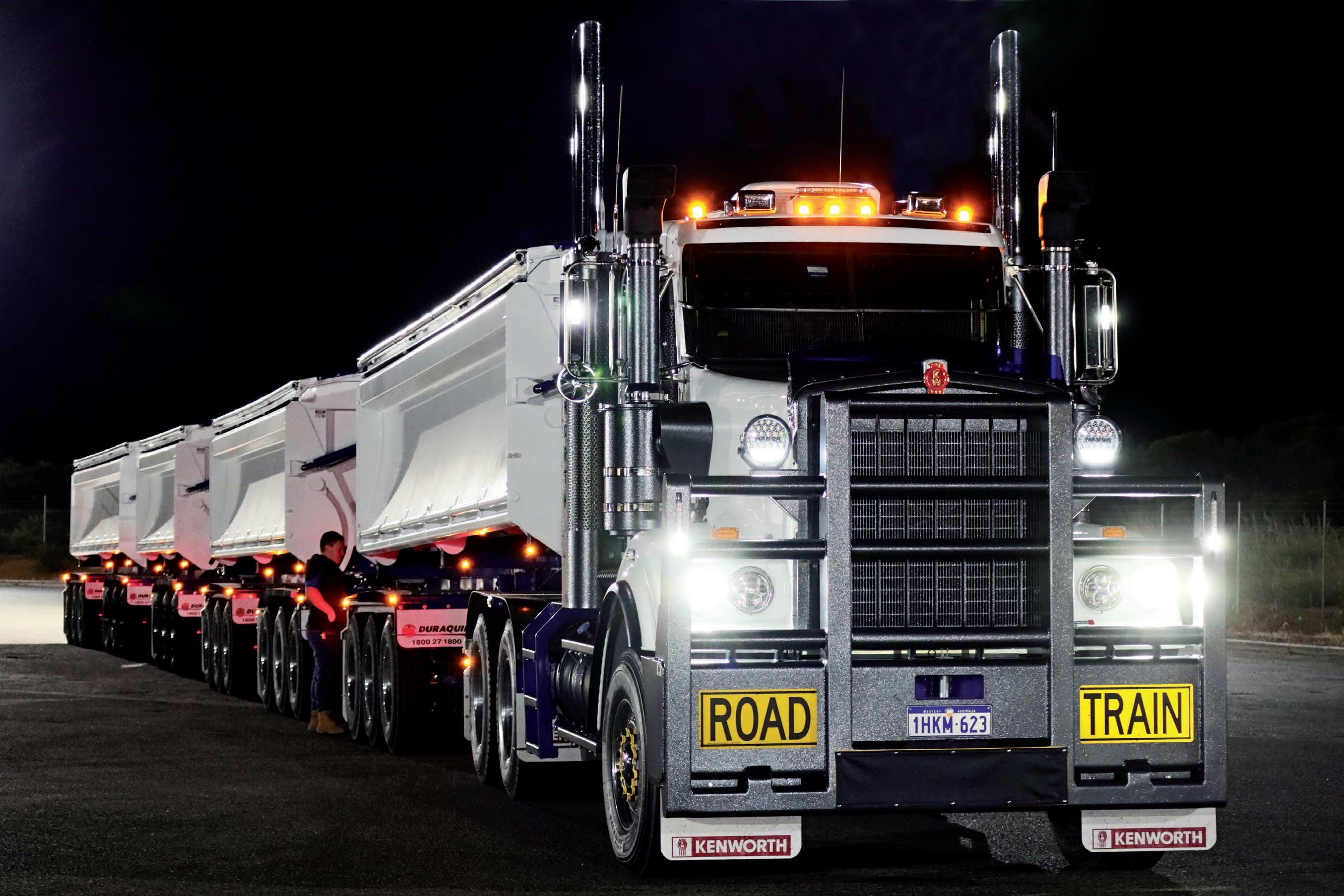
TRUCK & TECH
The mention of the Pilbara region in Western Australia’s northwest usually evokes two distinct images: red dirt and big trucks. Since it was established in 2006, the AK Evans Group has amassed considerable experience in both of these. AK Evans has progressed from specialising in the hire of earthmoving plant and equipment, to a rapidly growing bulk haulage division and an increasing involvement in the construction of renewable energy facilities. Access to the mines requires roads which can be used in all weather conditions and the construction and maintenance of those vital supply lines requires a spectrum of earthmoving equipment. Those big yellow pieces of machinery also require transport to and from their hirers’ sites and AK Evans has an extensive selection of floats of up to 100 tonnes complemented by ramp-equipped drop deck trailers and conventional flat top trailers. Hauling, the often, high levels of mass is a fleet of Kenworth C509 prime movers, many equipped with tri-drive axles supplied by Dana. In fact, Dana components are specified in bogie drive configurations as well, along with Dana steer axles on single- and twinsteer trucks. Traditionally AK Evans was a plant and equipment hire company with a few prime movers designated for transporting their own pieces of equipment. Early in 2021 the company began its involvement with bulk commodities including moving ore. Initially, this was intended to improve the utilisation of trucks and trailers which were often parked and not doing a lot of work between shifting equipment. AK Evans already had some side tippers which were used mainly in construction work in double trailer configurations. The first triple was put to work after they moved into bulk ore transport and the winning of a sizable contract, subsequent to that, resulted in the need for ten quad trailer combinations. “There was a quite a challenge for the business going to triples, and then we won a contract hauling manganese ore for Element 25 and we needed ten quads,” says AK Evans Managing Director, Michael Still. “We decided that we were going to do it properly and buy brand new Kenworth C509s and new quad side tipper sets. I’m a big believer that a poor man pays twice, so when we were successful in securing our first long term contract we went and secured brand new equipment for it.” While other prime movers may have been up to the task, the decision to choose Kenworth has led to an unintended consequence in the area of driver recruitment and retention. “When we spec the trucks we don’t skimp on anything and they really do look the part,” says Michael. “The Kenworths are also one of the reasons people want to work for us. Good drivers attract more good drivers and by providing new gear morale is good, the staff are happier, and the potential justifies the investment. With what we have committed to, by mid-2023 we’ll have 60 prime movers in our fleet.” The expansion of the AK Evans operation has been made possible in part due to a focus on the company culture both as a group and from an individual employee’s perspective and the need to care about the well-being of people such as truck drivers. “We’ve taken some hard looks at ourselves and the leaders we employ, and in our industry getting people who actually ‘like’ people can be challenging,” says Michael. “Fortunately, we’ve got a very good group of leaders who want to see other people be successful.” One of the challenges Michael gives to the leadership group as individuals is for
Aerial view of the rugged Pilbara region.
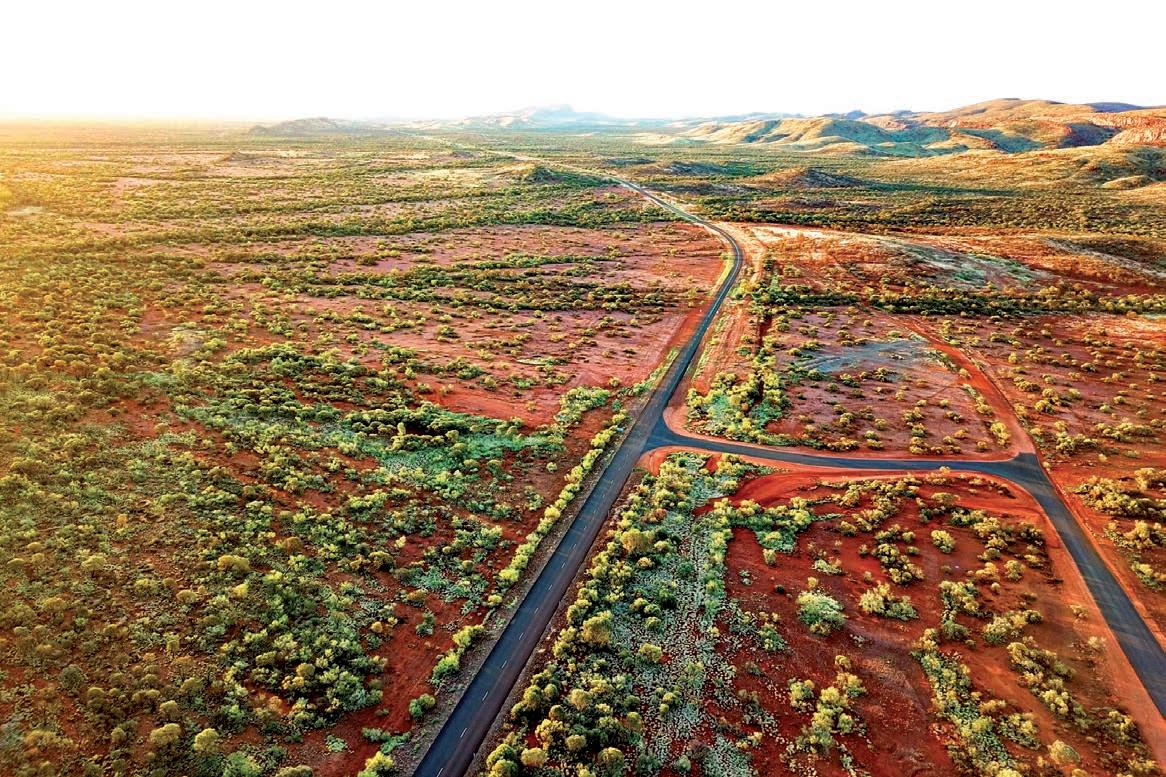
them to employ people with the potential to take over their own jobs, which can be quite daunting sometimes. “They might ask: ‘What if they do take my job?’ Well, that’s great because it means the business is growing and you can grow within the business. We probably have a different outlook and perhaps that’s why we haven’t had any trouble attracting people, including drivers.” Another attraction for professional drivers is the roster system which is possibly unique in the industry. The drivers work 12 days on and then they have nine days off, instead of the more common two weeks on and one week off. “It fits within fatigue management and rather than working them for fourteen days with an RDO in the middle of those 14 days up at a work or mine site, we work to where they can still be within allowable hours working 12 days straight and have their RDO at home with their families,” Michael explains. MTData and Guardian driver fatigue systems are being rolled out to all of the trucks to ensure the best safety measures are in place. AK Evans may have grown by being a hire company, but it has also increasingly been asked by clients to be a solutions business. A key factor of that is running some projects with its own people including operators, supervisors and engineers. The expertise embodied in the AK Evans team is available to properly manage projects for better efficiencies and in the project management capacity, the company will oversee onsite operations, procurement, subcontractor management and resourcing, which contributes to streamlining the overall construction process. Future-proofing the business has been secured by making a commitment to the renewable energy sector across Australia and AK Evans has, in the past few years, built recognised capabilities in solar and wind farm civil construction projects. Renewables has become one of the three core parts of the business joining the equipment hire and haulage divisions. One of the initial projects in the renewables sector has been to build a 10Mw solar farm for Aggreko Energy with Goldfields Mining as the end user. “That project opened up our eyes to the fact that there are very few mining contractors that had experience in building solar farms, or solar farm contractors that understand mining,” recalls Michael. “Being in the Pilbara we understand the requirements of working in mine sites and that’s probably why we see a massive future for our business in building renewables. Plus, we are trying to do the right thing and reduce the impact our industry has had on the planet.” Another successful renewable-focused
Michael Still AK Evans Managing Director
project has been the Christmas Creek solar farm, which at the time of its construction was the largest off-grid solar farm in the country. A project on the eastern side of the country has been the 120Mw solar farm at Nevertire, in NSW, which provides electricity to the nearby city of Dubbo as well as to the NSW energy grid. “We have good partnerships with people who need us on the east coast and the benefits of having our own trucks and having our own mobile workshops and some of our 150-plus staff already based on the east coast, it’s not a far stretch for us to mobilise to even quite remote sites to set up shop,” Michael explains. “It is something we can do really easily and with flexibility. There is plenty of work in WA but through those partnerships moving forward we will be involved in more projects in NSW and Victoria.” The Kenworth C509s are powered by Cummins engines with Eaton Road Ranger manual transmissions delivering the power to tandem or tri-drive Dana rear axles, some of which are equipped with reduction hubs. All are fitted with Dana’s Australian-designed lubrication pumps that contributes to extending the life of the lubricant and reducing internal component wear. The pump circulates the lubricant to ensure components, which are subjected to the high loads experienced in AK Evans applications, such as power dividers and ring and pinion gears, receive adequate lubrication with the additional benefit of reduced temperatures throughout the entire axle assemblies. In conditions combining high ambient temperatures with high gross
mass loads the Dana drive axles have a distinct advantage provided by the oil pumps over conventional ‘splash feed’ lubrication methods. “We’re very happy with the service we get out of Kenworth and the CJD dealership. All of our new gear is Dana-equipped and manufactured in Melbourne which also gives us confidence in the product,” says Michael. “Jock Pickford, one of Dana’s key truck sales support people, actually flew up to the Pilbara to meet with some of our customers to see firsthand the challenges we have up north. We have no Dana-related issues with our trucks and Dana have been really reliable truck components for us.” Michael has been closely watching the local development of battery electric trucks such as those from Australian company Janus, which uses Dana electric motors/inverters and he looks forward to performing some trials with the concept. “We are in contact with Janus already because I believe personally that there is a really great future for our business as well,” he says.
TRUCK & TECH
COMING
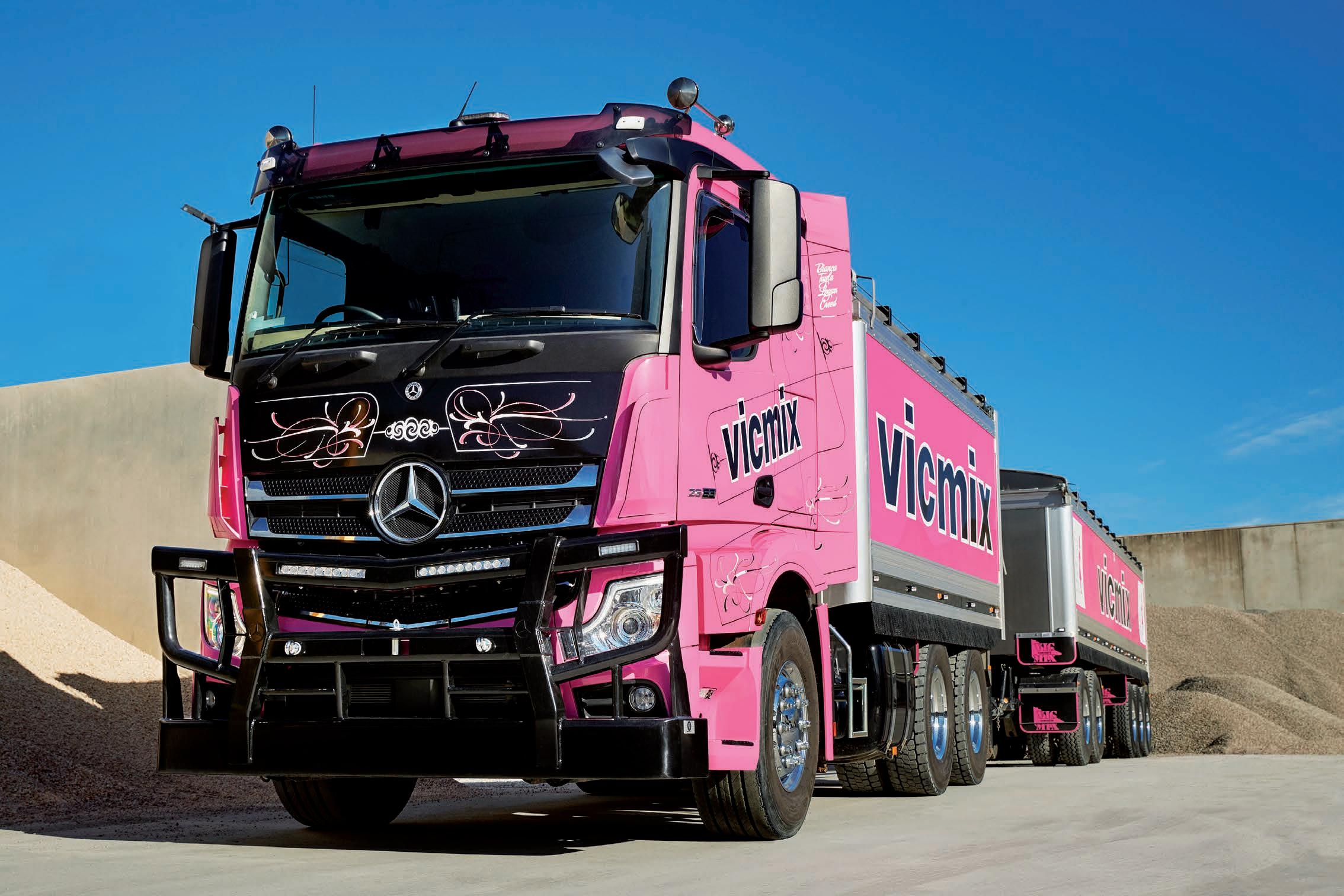
OF AGE
Mercedes-Benz Actros 2663. Vic Mix, a Melbourne-based concrete supplier, runs a fleet of hard-to-miss pink heavy vehicles across its operations. An eyecatching new 630hp Mercedes-Benz Actros is the latest addition.
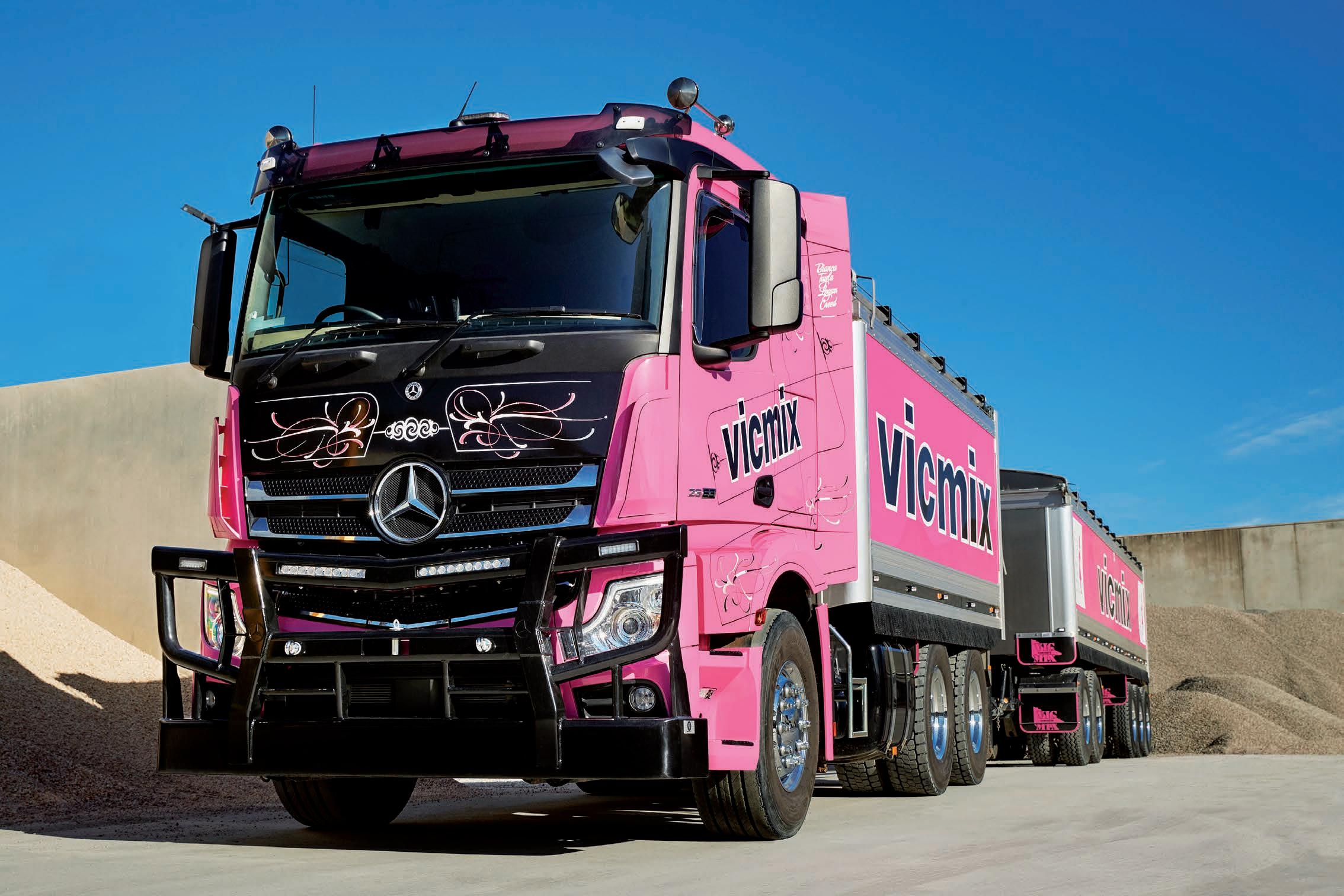
Vic Mix takes transportation of its core products - namely cement, sand and rock — very seriously. The Victorian business, which specialises in pre-mixed concrete for decorative, industrial and domestic use, considers itself a transport company first and a concrete company second. The fleet at current is made up of a range of different trucks to suit all projects, with revenue bifurcated between commercial and residential streams. These include 8x4 agitators, tankers and truck and dog applications that ferry materials depotto-depot and between quarries. A new Mercedes-Benz Actros 2663 was introduced into the fleet of pink trucks some weeks back for the latter task. Its owner-driver, Daniel Venditti, fits into this broader picture as a long-time subcontractor who has been working for Vic Mix or one of its subsidiaries, for the better part of 30 years, having started out at the age of 19. That amounts to a lot of hours in the saddle, especially when appointed to do so, more often than not, six days a week. “I’ve driven Kenworths, Sterling and International trucks,” he says. “I’ve been in a truck for most of my adult life.” The human body over that time can take a battering. To the point his last truck, an Actros 2658, provided him noticeable relief at once as a working environment and on overheads. Fuel consumption being a major one. In the 2658 Daniel soon discovered remarkably low noise levels. Up until that point he had been making gradual upgrades through a range of ageing trucks hunkered over a clutch pedal. There were a few factors that helped convince Daniel to ultimately try out an automated transmission, Mitchell Hynd, Whitehorse Truck Centre, Sales Manager, was one of them. “Quite often veteran drivers have to be talked into driving an automatic as was the case with me,” says Daniel. “Once you make that change you wonder why you didn’t do it earlier. I’ll never go back.” Last April, after four and a half years of gallant service and over 600,000 kilometres, Daniel traded in the Actros 2658. “There were no issues with the truck so his servicing was essentially paid for,” says Mitchell. “Knowing Daniel was chasing 63 tonnes in the application, the Actros MP5 can provide him with the extra power he needs now that he has upgraded.” The new Actros 2663 features the Euro 6 rated OM 473 630 hp engine capable of 3000 Nm maximum torque. Coupled with the Mercedes PowerShift 3, it enables fast shifting from forward to reverse and highratio reverse gears for easy manoeuvring. On that front, the Actros is particularly suited for the access requirements of the sites hence the five-axle dog trailer which accords with this consideration. A six-axle dog might provide an increase in payload, but it won’t get drivers into the concrete plants, the most common destination for Daniel, who is in and out of these facilities, not to mention traffic, throughout the day. “Cabovers, to compare, are much easier to
TRUCK & TECH
manoeuvre than a bonneted truck in this line of work,” Daniel says. “This has also got the pulling power I need.” Traffic delays are commonplace for heavy vehicle operators and with Vic Mix’s four operation plants spread throughout metro Melbourne — head office is in Dandenong — the agitation caused by congestion is lessened considerably by his ability to adjust to conditions promptly. “I’m in and out of traffic for the best part of my time,” says Daniel. “In that sense the automatic makes it more like driving a car.” Moving off is noticeably more comfortable by virtue of the crawler mode, which allows the vehicle to creep forwards automatically when the service brake is released and to roll along at idle speed when the accelerator pedal is not depressed. After creeping forwards, the vehicle will continue to roll at idle speed until the vehicle is stopped with the service brake or the crawler mode is deactivated. Creeping forwards and rolling at idle speed take place in all permissible start-off gears so that when in traffic jams, rolling speed can be adjusted to the traffic. It’s not all urban navigation, however. Notwithstanding the plants, Daniel often finds himself on the open road attending quarries, contingent on the job allocation he receives the night prior. He finds himself as far east as Bairnsdale, southwest in Moriac, as far north as Glenrowan and on the outer edge of Western Port Bay at Grantville in the southeast. Fuel economy sits around 2.3 to 2.4 km/l fully loaded. The new Actros 2663 averages around 3000 kilometres a week, roughly between 500 to 600 kilometres a day. As the Actros 2663 truck and dog combination has been approved for 106 tonnes GCM, it’s crucial that Daniel can monitor trailer and drive axle weights. He retains full visibility on payload from the dash cluster. Predictive Powertrain Control optimises the vehicle’s kinetic energy to avoid unnecessary acceleration, shifting or braking. Cruise control, consequently, is made available in more situations. The benefits are many for the driver, assisting, for example, in the enhancement of a fuel-efficient driving style. On the longer highway stretches Daniel is likely to
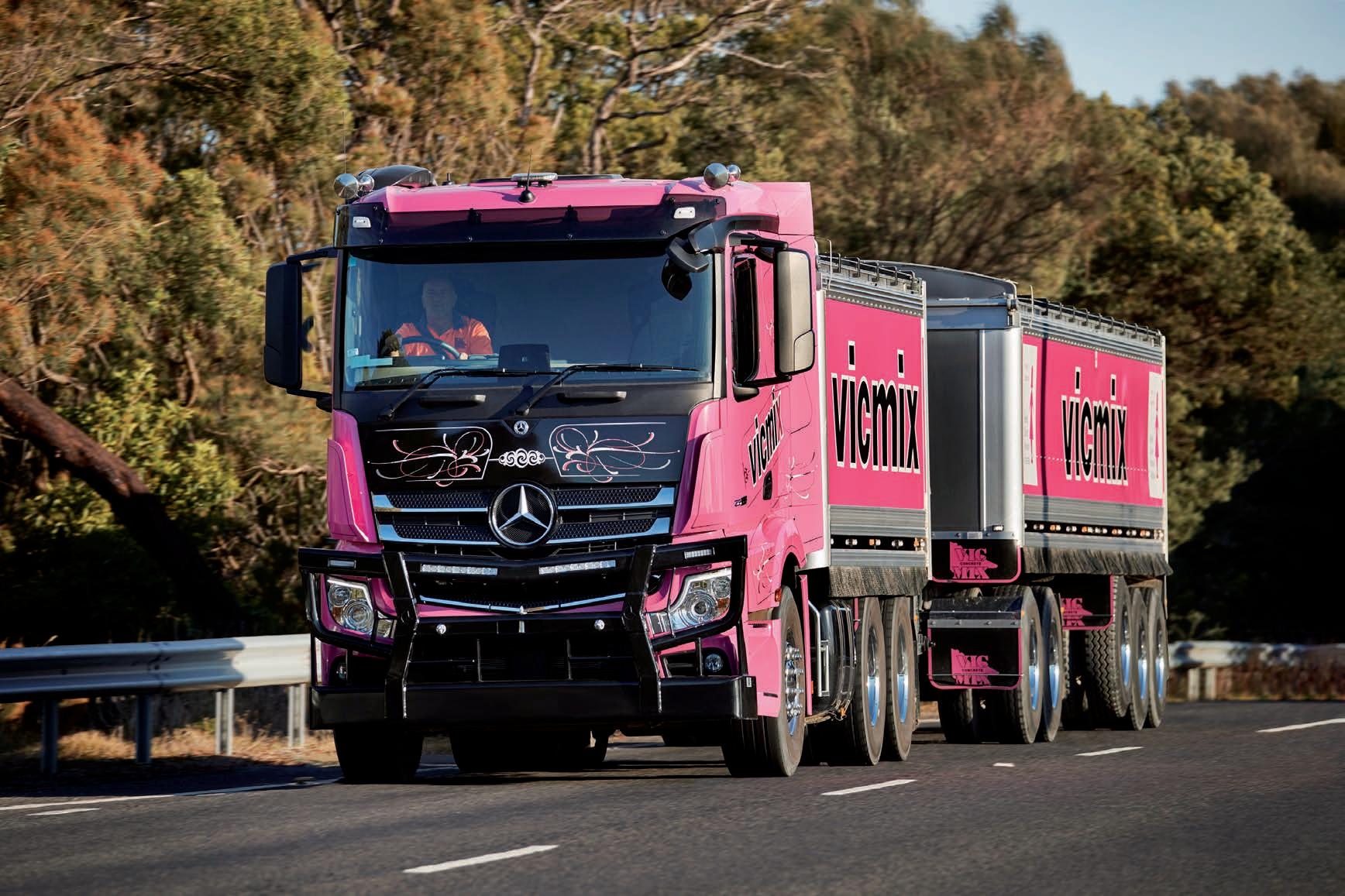
Daniel Venditti. The new pink Actros as truck and five-axle dog in Melbourne.
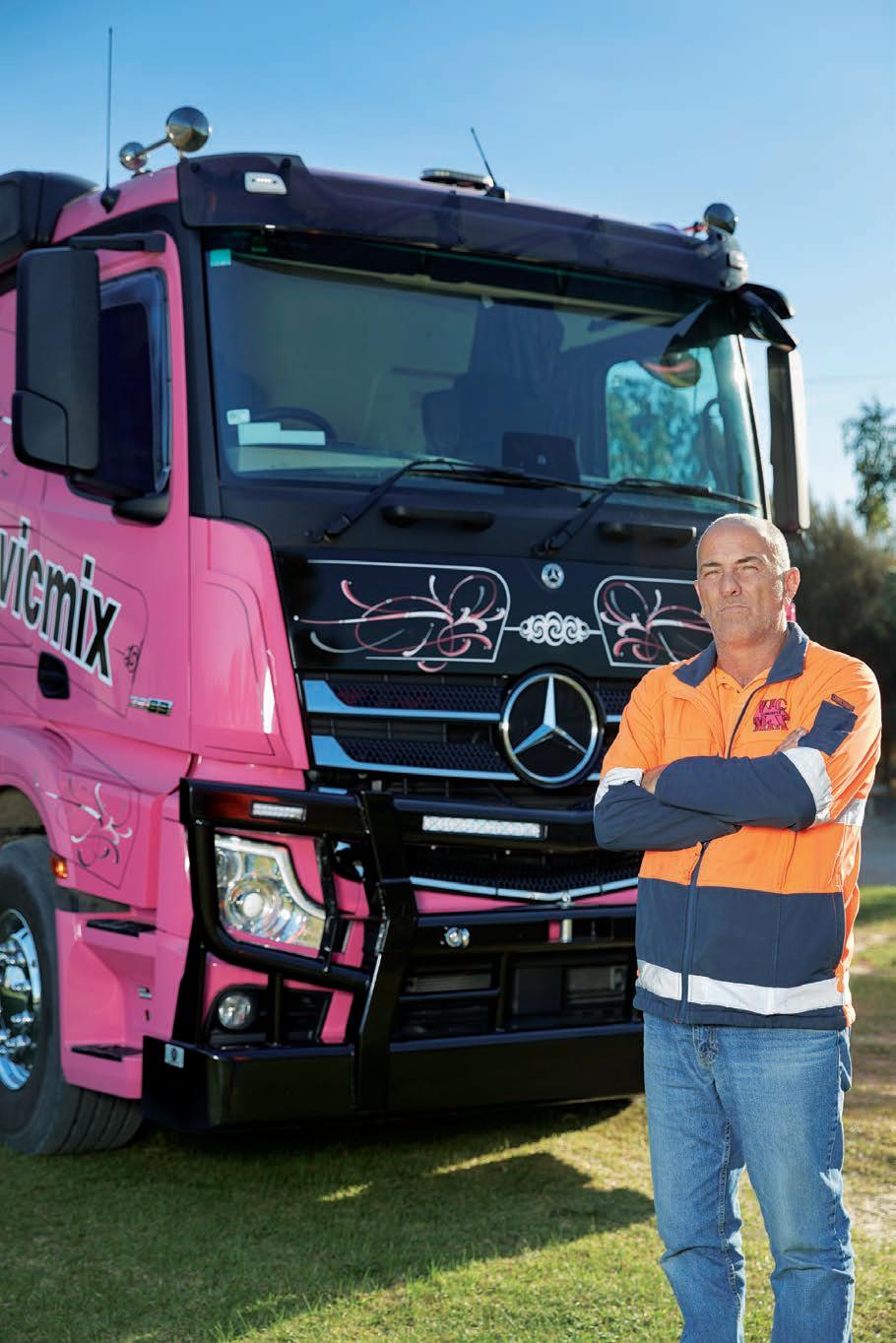
encounter en route to a regional quarry, the vehicle, through this function, can be put to even greater use. Bulk Transport Equipment have provided the tipper and dog trailer bodies. As the vehicle is nearly identical to his last Actros, on hand diagrams allowed BTE to commence body building work before Daniel had possession of the truck. As a result they turned around the build quickly in under three months. The recent boom in the new housing market can be felt, without question, in the surging demand for materials and the resultant movement of tippers and dog trailers on the road is appreciable. Exposed aggregate is proving popular, again, for residential driveways and also for footpaths in areas with aging populations. After placement of the concrete, the top few millimetres of concrete paste are removed from the surface in order to reveal the stone called aggregate embedded within. A sealer is then applied to enhance and protect the finished product. Aside from a myriad of colourful designs it also grips better under foot. “On the Mornington Peninsula exposed aggregate is preferred by councils where older residents might have less confidence walking on wet surfaces,” Daniel says. “That’s something I’ve noticed when I’ve got time to notice. To be honest it’s been that busy — the busiest time in the years I’ve been driving.” An ability to efficiently and reliably manufacture load after load of concrete has become for Vic Mix, inextricably linked to the capabilities of its trucks with their memorable signage — signage that’s hard to miss. In addition to a shrewd branding strategy, the fleet of pink trucks help raise awareness for breast cancer with Cancer Council stickers also a prevalent part of the livery. On the new Actros, Daniel has opted for an ‘old school’ paint detail, a personal preference over the current trend of vinyl wraps. The pink with black trim matched with black bullbar certainly make for a striking presentation. The spry appearance of the truck would, at first glance, suggest its occupant might be a much younger driver. “The Actros has got a level of comfort that should appeal to older, experienced drivers,” he says. “I like to keep things fresh — myself included.”
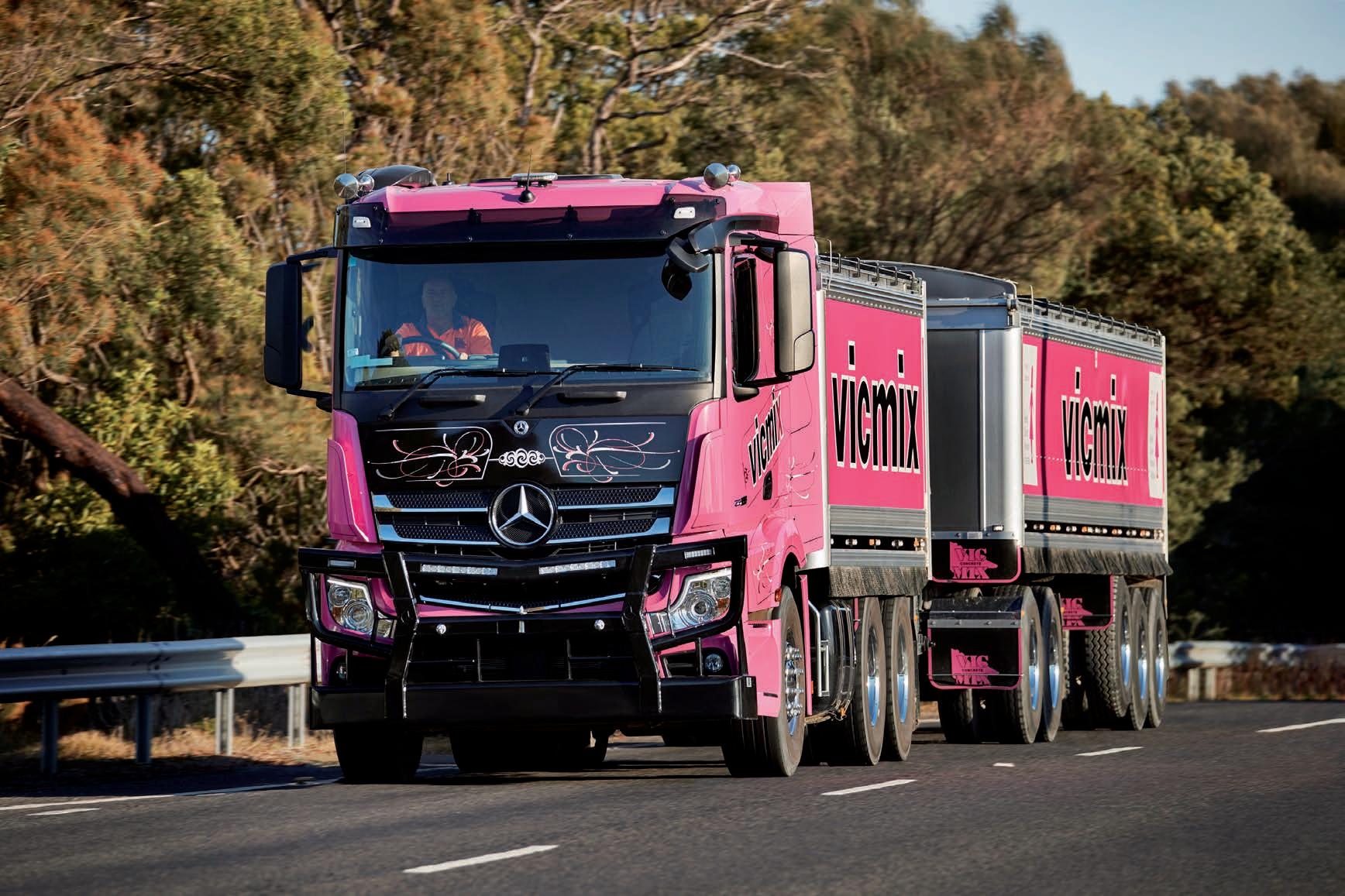
TRUCK & TECH
REQUIEM FOR A HEAVY WEIGHT
Multi-drop loads, with their constantly changing weight distribution can easily catch drivers out leaving them at risk of an axle overload. Transport & Waste Solutions and Axtec provide real-time information to the drivers of thousands of vehicles from 3.5t van-based derivatives through to 26t and 32t rigids.
Since commencing operation in 2009, Sydney company Transport & Waste Solutions has built a strong reputation for providing and installing NMI approved weighing systems — systems that have been tested and passed to meet predetermined standards to ensure upmost accuracy, to the waste sector and other industries. In 2018, continuing with its loadmanagement focus, TWS formed a strategic partnership with UK axle weighing specialist, Axtec. Forming a partnership with Axtec, according to TWS Founder and Managing Director, Chris Coleman, just made sense. “It allowed us to continue to help our customers maximise their payloads whilst operating within the law,” he says. “By achieving this, our customers improve their efficiencies, resulting in greater profits, whilst reducing their environmental impact.” Put simply, Axtec OnBoard axle load indicators allow drivers and fleet managers to ensure appropriate placement of loads and avoid overloading vehicles.
A DAF prime mover approaches an Axtec dynamic axle weighbridge.

Here green indicates that the vehicle has safe loads over each of its axles.
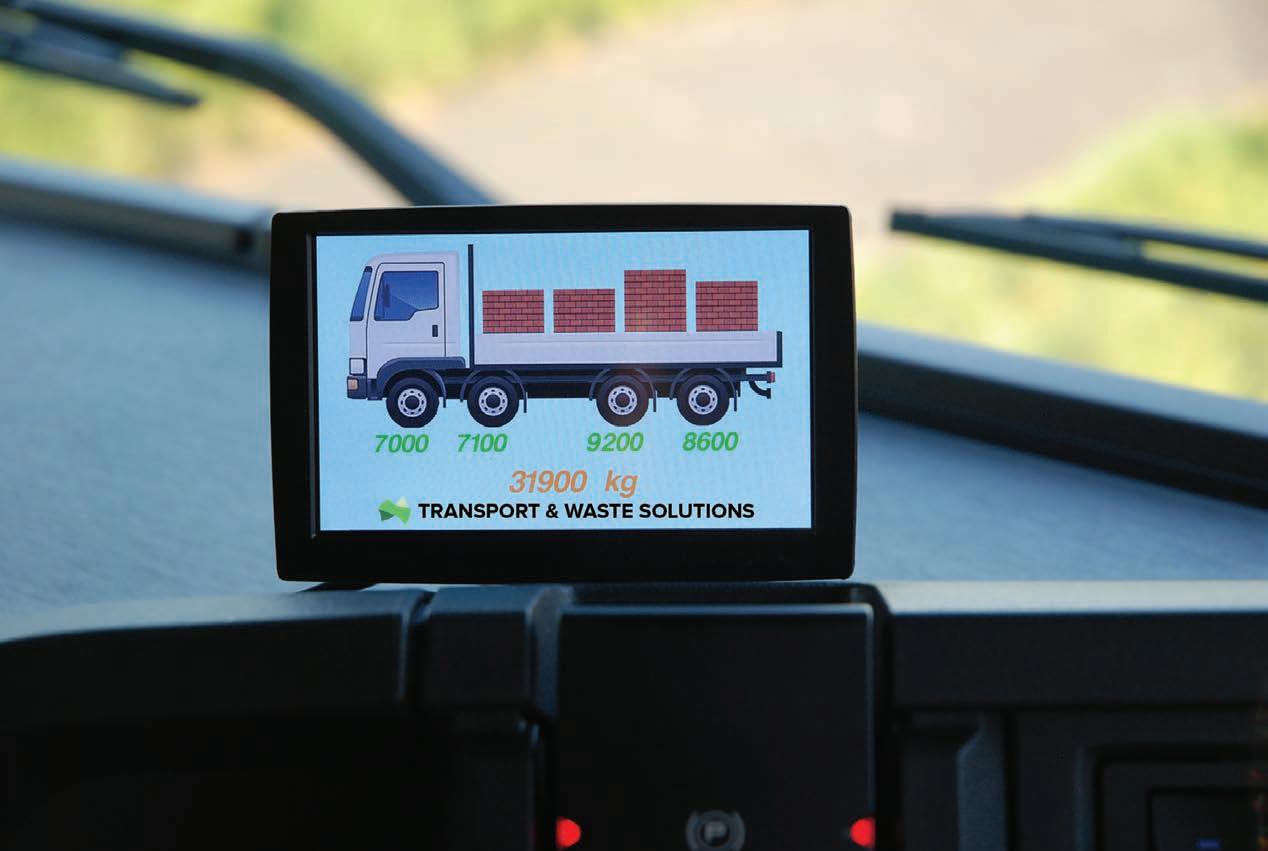
They can be applied to rigid vehicles from 3.5 tonne vans up to multi-axle 32 tonners with accuracy of up to 2.5 per cent margin of error. OnBoard connects to GPS and telematics devices and up to six cameras to help make the vehicle safer for the driver, other road users and pedestrians. It constantly displays the individual axle and gross vehicle weights to the driver via a clear colour coded graphical display and warns of overload via audible and visual prompts. Since becoming a strategic partner, Transport & Waste Solutions has gone on to install around 1000 units for Axtec nationwide. Axtec products are currently being utilised by several state utility companies which helps them meet Chain of Responsibility (CoR) obligations by providing accurate and reliable vehicle load information in real-time as vehicles perform their daily operations. The introduction of CoR legislation, as part of Australia’s National Road Transport Reform (Compliance and Enforcement) Act 2003, followed by the introduction of the Heavy Vehicle National Law, in which “anyone who has influence over the transport activity is responsible for safety on the road” has changed, among many other transport sectors, the waste and refuse industry. Under the legislation, those responsible for consigning, packing, loading or receiving goods in a business, regardless of whom is driving the truck, may be held legally responsible for breaches of the Heavy Vehicle National Law. Moreover, corporate entities, directors, partners and managers are not immune to the legislation. The law now requires all parties, who have a duty of care on the supply chain, to exercise due diligence to ensure safety across all transport activities. No less important for this very reason, axle load indicators help to ensure waste and recycle transfer businesses are complying with the legislation while out on the road. Weighbridges will confirm the gross mass of a vehicle, and whether load limits specified in the Heavy Vehicle National Regulation are exceeded, but they miss one vital statistic. To satisfy the regulations, loads must be placed in a way that ensures the vehicle remains stable and safe. In other words, loads need to be distributed so as not to overload axles; a common problem that until now has been often overlooked, and largely because of the difficulty in monitoring load distribution. Axtec offers what it calls dynamic, static, portable and on-board weighing systems. This includes the Axtec OnBoard Axle Load Indicator. The Axtec OnBoard Axle Load Indicator provides drivers with realtime information on axle and gross vehicle loads via a simple, easy to read, colour coded bar graph display. “Due to the simplicity of the screen, the driver doesn’t have to interact or scroll through menus,” says Chris. “Everything he needs to see is clearly presented for him. Further, from each display we can transmit RS232 protocol and what the driver sees on the display in the cab is what will be seen on the screen depending on the provider of the telematics.” He adds, “What we do is give the customer the RS232 protocol and then the telematics converts that into the language the customer wants to see it in.” The RS232 is user-friendly meaning a programmer can extract whatever information from it they want to see. Transport & Waste Solutions currently has two customers trialling a couple of units, using their own back-to-base system according to Chris. “Even if a customer doesn’t have the RS232 capability, if they can spare a fivevolt input into their tracking system, we can give them an in-load limit output,” he says. “But we don’t supply back to base information. There’s lots of people out there who can do that.”

TRUCK & TECH
Visual and audible warnings can prompt the driver when overloads are present, while load data can be simultaneously written to the built-in logger and transmitted to a tracker system. A colour touch screen automatically displays images from rearview or side-mounted cameras. It can also be set to dim when the vehicle is in motion. Imagine a traffic light with its red, amber and green lights. Green in this instance represents go, amber represents 80 per cent axle load capacity and red signifies the vehicle is overloaded. A warning light outside the cab can prompt the driver to check which axle is overloaded and adjust the load accordingly while they are still loading. “That’s what many of our clients are using it for,” says Chris. “You can be legal on the front axle, and you can be legal on the rear, but the combined two masses can put the truck over the general mass limits.” Operators in the waste sector are driven, Chris points out, to ensure that they get a premium load on the truck without breaching any overload requirements. “The waste industry is using the equipment to get maximum productivity without risking overloads, but they’ve got no way of measuring their weight while they are picking up bins because everyone has different volumes in their bins,” he says. “But if you’re on long haul or short haul and you’re up in Kempsey or down in the boondocks and you have loaded it up with a forklift and the public weighbridge is not working, you have a load indicator there to ensure that you are distributing your mass correctly.” Trucks found overloaded on the weighbridge are penalised according to how much weight they exceed on the limit. It’s not uncommon for a truck to be impounded depending on the severity of the breach. “That’s true of any weighbridge in NSW that is wired into the State Government,” says Chris. “If you go over that weighbridge overloaded it automatically sends a message to the RMS alerting them to the breach. Straight away that vehicle cops a fine. It doesn’t take much to go overloaded.” A commercial vehicle can over-tip in excess by as much as half a tonne over the front axle limit. An onboard system in this instance ensures that they get a maximum load over the rear axle especially when one or two additional bins will put them over the threshold. Because weights are variable during a trip it puts even more onus on operators to have real-time insights into their axle loads. Aside from assisting waste companies meet compliance and reducing possible fines and downtime from having the truck penalised, the Axtec system improves productivity. Transport & Waste Solutions uses a Swedish NMI approved weighing system. When used in conjunction with the onboard axle indicator, it enables the customer to charge their client a premium price for moving the waste, especially when working in a regional area. “They can monitor their axle loads to ensure the truck is economical to be run on the road for a long duration without going overloaded,” Chris explains. “They can use the NMI on their light bins. They can do multiple pickups at the same time ensuring that their axle limits are not exceeding the load limits.” Transport & Waste Solutions also installs the Axtec Load Indicator on prime movers, low loaders and drop deck trailers. “A customer of ours recently found that they have been going overloaded on their prime movers and they had no control over the weight on the drop deck,” Chris says. “We have done four drop decks now using the Axtec load indicator, and it’s working out fine. While you’re loading the vehicle you can either move the load towards the front or towards the rear to ensure you don’t exceed the load limit. The display can be used to pack the load on your trailer or tray of your truck. If you’re using a forklift, for instance, you can add a tonne here and a tonne there and pop up into the cab to observe how the weight distribution is going over the axles.” Transport & Waste Solutions also installs axle load indicators in the vacuum truck sector. Because they have got a 10,000-litre tank, many operators are under the impression that they can carry 10,000 litres of water. “They forget that they’ve got two blokes whose combined weight is 150 kilos plus their lunch box, half a tonne of shovels, picks and equipment, all of their PPE gear and at the end of the day they realise they can only carry 7,000 litres of water,” he explains. Infringements to loading and mass compliance are most common in the industry and so easily missed by loaders, load managers, drivers and operators. In this way the Axtec Onboard Load Indicator provides reassurance to drivers that they are complying with Mass Load limits while being able to distribute their loads safely and, it must be noted, legally at all times. “Everyone is pretty happy so far with the accuracy,” says Chris. “Not only because the accuracy is consistent but it’s repeatable. That’s the selling point.”
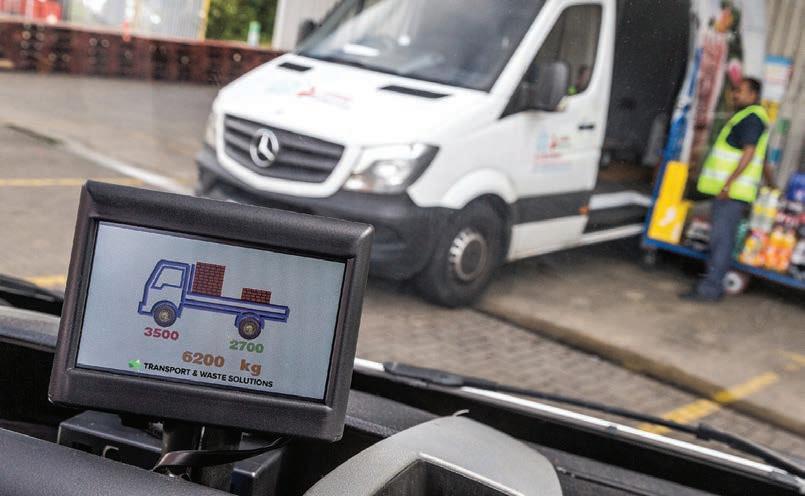
A colour touch screen automatically displays images.
TRUCK & TECH
Automated digital tracking solutions makes predictive maintenance easier.
CHEAP TRICKS
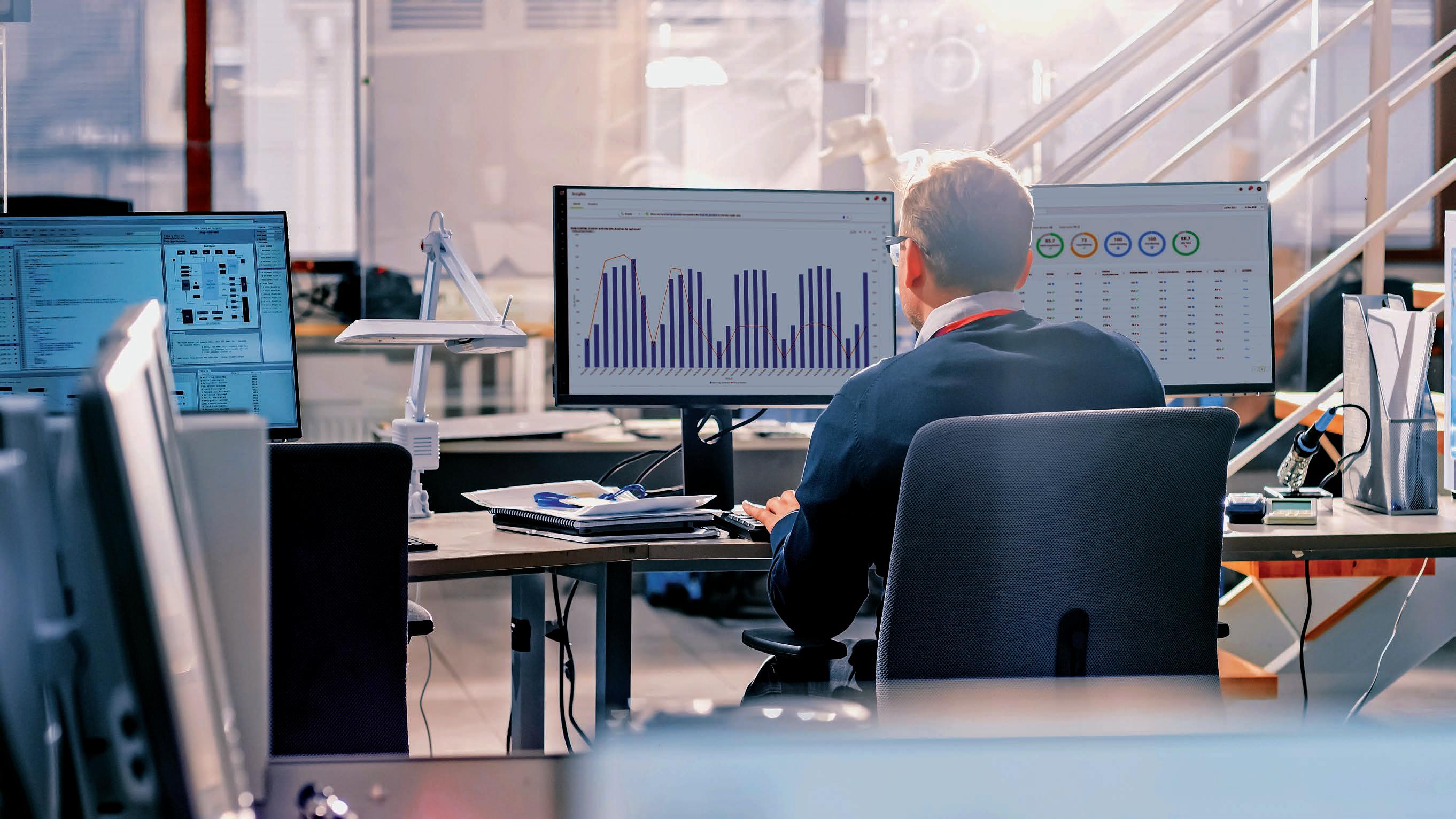
Fleet management technology can improve long-term fuel efficiency. Here’s how according to Teletrac Navman.
After wages, fuel is the second biggest direct expense for transport companies, accounting for around a third of all business costs. Given this, it’s no surprise that the recent rise in fuel costs is having a sizeable impact on the trucking industry. The 22.1 cent cut to the fuel excise has resulted in a mere 4.3 cent per litre reduction for truck drivers after factoring in the road user charge and the loss of Fuel Tax Credit. Without adequate government relief, the industry will continue to bear the brunt, with consumers eventually taking on the cost. However, the current situation offers a unique opportunity for operators to take control of fuel costs to ensure long-term success, rather than just weathering the fuel storm. By exploring the causes of fuel inefficiencies and embracing the opportunities that telematics technology and fleet management solutions can bring to the table, drivers can stay on the move now and well into the future. Here’s how technology, such as smart route mapping, can improve long-term fuel efficiency and reduce the impact of fuel costs. Reducing unnecessary kilometres to save on fuel costs is the first, easy step truck drivers can take to improve long-term fuel efficiency according to Andrew Rossington, Teletrac Navman Chief Product Officer. “At its most basic level, GPS fleet tracking gives businesses instant visibility to allocate fleets more efficiently and enhance fleet accountability,” he says. “Beyond this, AI-powered telematics technology also measures everything from driver locations to time spent at a job and travelling time.” The telematics platform allows for optimised route planning that shaves off unnecessary kilometres from trips. The application considers scheduled stops for jobs and waypoints vehicle operators must pass through for compliance. The prepared journey is then available in real-time to select through the driver’s invehicle device. “If you’ve deviated from your set path, you’re notified and immediately directed back to the defined route via the safest roads,” says Andrew. “Back-office staff are also alerted, helping managers identify consistent problems and overcome inefficiencies — simultaneously saving on fuel and protecting assets while increasing driver safety and compliance.” Predictive maintenance is an essential tool in a transport business’s belt. Proactively maintaining assets and keeping them at the top of their game ensures they operate smoothly,
TRICKS
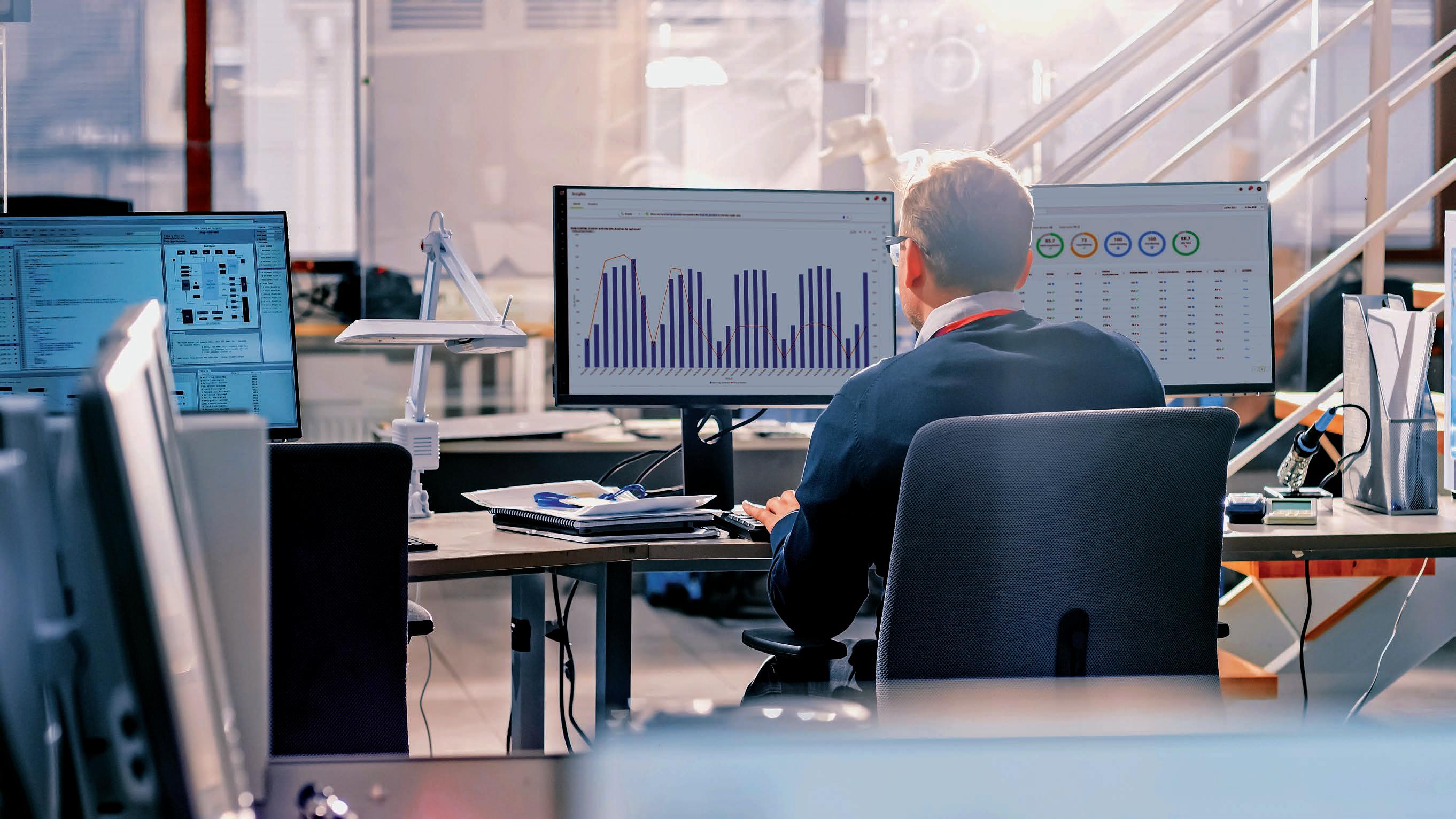
improving fuel efficiency. Equipment management solutions use historical data to identify and alert fleet managers of what equipment needs maintenance and when. Digitised systems fully automate maintenance routines with custom schedules and real-time access to equipment diagnostics and inspection reports. Key vehicle parts to keep in peak shape include tyres, motor oil, engine fans, sensors and battery cables. Ensuring these are well-maintained can have significant benefits for fuel efficiency. For example, reduced tyre pressure, misaligned wheels, and bad spark plugs can increase resistance, reducing fuel efficiency by up to 30 per cent, which equates to an added cost of 11–33 cents per litre. “Using automated digital tracking solutions makes predictive maintenance an easy task for businesses and helps to avoid costly breakdowns,” says Andrew. “It also greatly reduces manual labour on paper-based processes — increasing efficiency and savings both on and off road.” Driving performance and its improvement is another key indicator. Of course driving performance can drastically impact fuel efficiency. Driving faster than necessary, aggressive acceleration, harsh braking, and idling can all burn through excessive fuel. Reducing a truck’s average speed from 113 km per hour to 105, for example, can reduce fuel consumption by up to six per cent. Equipping your vehicle with a Smart Dashcam, which combines the power of AI technology with telematics data and advanced onboard sensors, provides insight into these metrics and identifies training opportunities. The camera provides alerts in realtime to reduce inefficient driving habits instantly. Smart Dashcams, as Andrew points out, also come equipped with built-in scorecard and coaching features to create long-term, fuel-efficient driving habits. “The live dashboard displays fleet and individual driver metrics meaning you’ll have complete insight into your performance,” he says. “You can see how you compare with your colleagues to foster healthy competition and encourage improvement. You’ll be alerted when there’s a significant change in metrics, either positive or negative. The system provides tips and feedback to help you set measurable goals and improve your driving habits and fuel efficiency over time.“ Long-term thinking is also a key part of improving fuel efficiencies. Weathering the soaring cost of fuel requires more than just a band-aid approach according to Andrew. “Instead, you should focus on identifying and tackling the root causes of fuel inefficiencies and adopting integrated fleet management solutions to create a solid foundation for long-term growth,” he explains. “Fuel costs may continue to rise, but with smart systems in place, you’ll give your business the best chance at a successful, fuel-efficient future.”
TEST DRIVE
CLIMBING THE RISE
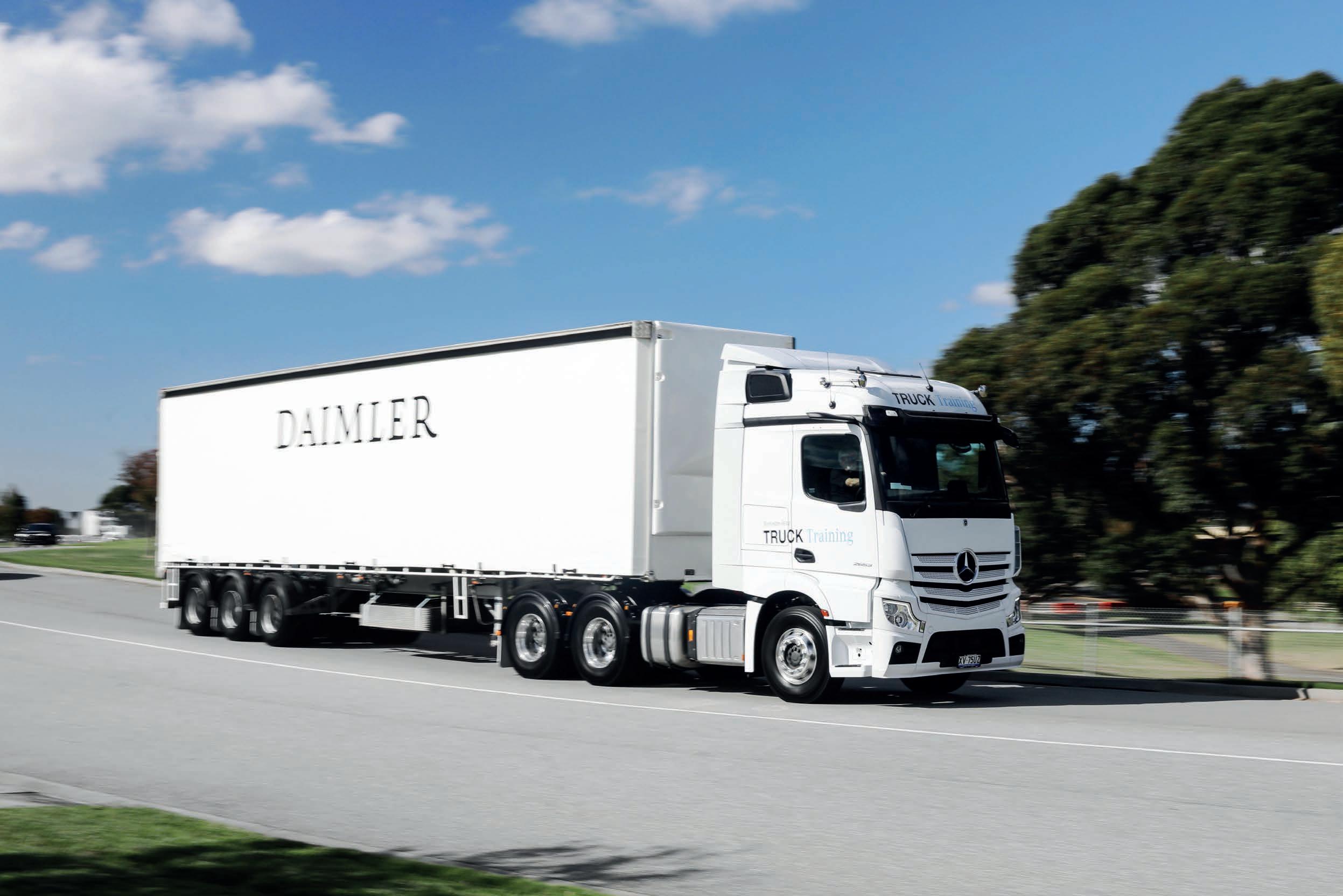
The evolution of advanced driver systems has been having a positive impact on vehicle performance and safety as more features are becoming integrated into vehicles such as the Mercedes-Benz Actros.
Development of autonomous vehicles over the past decade or so has not contributed to the demise of Western civilisation, as some early detractors may have preached, but instead has resulted in the progressive adoption of a number of key systems which offer to significantly improve the safety and efficiency of modern commercial vehicles. In many cases, what were futuristic concepts just a few years ago are now the new realities available in current generation trucks. The Mercedes-Benz Actros is enjoying considerable success across many world markets including Australia and is available with an expanding range of autonomous-related functions. The introduction of the Active Drive Assist (ADA) system by Daimler Trucks in Europe in 2018 made the Actros the first series production truck to be capable of partially automated driving (SAE Level 2). ADA is another step forward in terms of safety and delivers much more than the adaptive cruise control systems which are becoming more commonly available across a number of manufacturers. Under certain preconditions ADA actively supports the driver in the longitudinal and lateral guidance of the truck and can automatically maintain the distance to the vehicle ahead, accelerate and also steer if the necessary system conditions, such as adequate curve radius or clearly visible road markings, are met. The adaptive cruise control function integrated into the ADA means if the driver gets too close to a vehicle in front, the ADA can automatically brake the
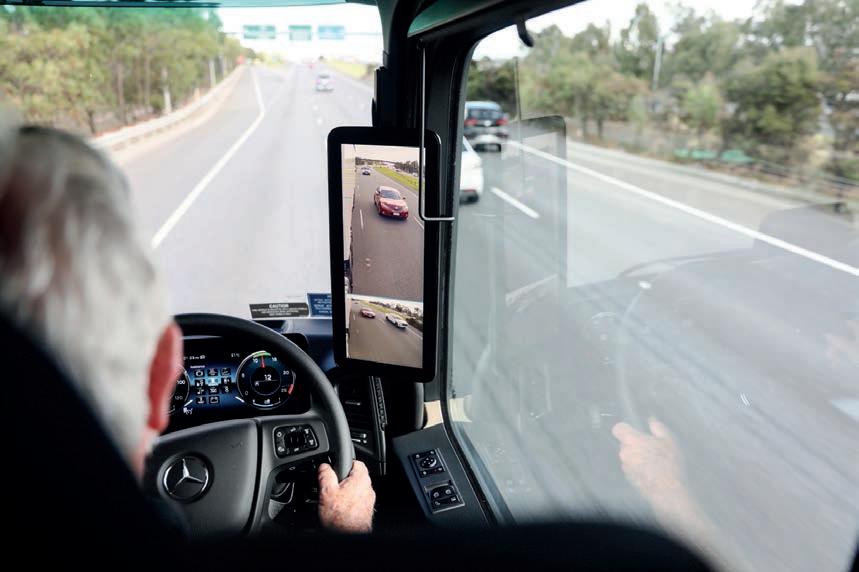
Mercedes-Benz Actros 2653 with Active Drive Assist.
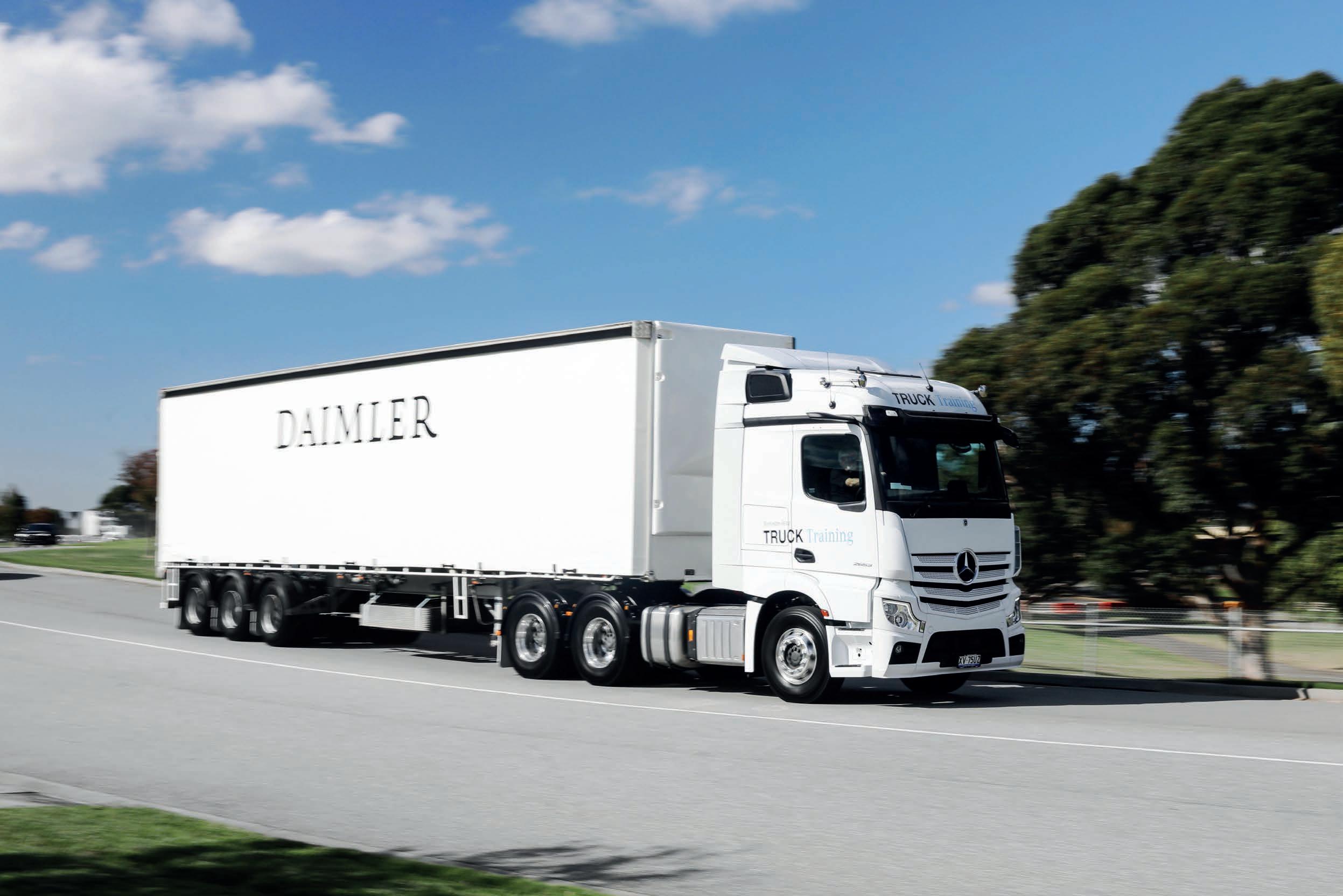
truck until the pre-determined minimum distance has been re-established. Once that is the case, the system can then re-accelerate the truck up to the predetermined set speed. The newest generation of ADA can do even more and the system is capable of initiating an emergency stop if it recognises that the driver has not been actively involved in the driving process for a certain period of time, which could be related to fatigue, inattention or medical issues. Initially the system requests the driver via visual and acoustic signals to place their hands on the steering wheel. If, even after multiple warnings, there is no response in the actions of braking, steering, accelerating or operating the vehicle systems via the buttons on the steering wheel, within its limits the ADA system can brake until the truck safely comes to a complete standstill while
MirrorCam view with panoramic mode on the new Actros.
staying within its lane and warning the following vehicles by automatically initiating the hazard lights. As the truck comes to a standstill, the system can automatically engage the electronic parking brake. In addition, the doors are unlocked so that paramedics and other first responders can directly reach the driver in the case of a medical emergency. Thankfully, we don’t have to resort to feigning a heart attack to test the ADA system, although it does demonstrate its effectiveness during our test drive when a passenger vehicle travelling in front decides, too late, to take an off ramp and leaves its rear bodywork partially in the lane in which we are following. We are far enough away to take evasive action if it becomes necessary and it is reassuring to feel the Actros’s brakes applied automatically. The only function missing from the scenario is an autonomous blast of the air horns directed at the fool who risked getting jammed between a semi and a guardrail. Previously we’ve had opportunities to assess Mercedes-Benz Actros trucks which have been equipped with the MirrorCam system and on other occasions the Predictive Powertrain Management system. However, this Actros 2653 is the first time we have been able to experience those two systems in the one truck, plus we are able to experience both in conjunction with the Active Driver Assistance system. The benefits of MirrorCam are numerous and the familiarity with the screens mounted on the A pillars quickly becomes intuitive and again we ask ourselves why wasn’t this available years ago. The effectiveness of MirrorCam is further highlighted when negotiating tight turns and reversing due to the automatic switching to panoramic mode providing an increased field of vision to the driver as the panning function delivers the situation, where the displayed image follows the trailer(s) according to input from the steering wheel angle. When overtaking on the highway the driver no longer needs to receive a headlight flash from the vehicle being passed thanks to the bar markings on the screens which show when it is safe to merge back into the left lane. The MirrorCam system is easily and quickly adjustable to suit various lengths of trailers and makes most drivers look like experts by delivering the ability to park within 20mm of a dock, which saves time and damage costs. The Predictive Powertrain Control once set and left alone will unobtrusively use its smarts to maintain momentum and maximise fuel efficiency by harnessing information from within the Global Positioning System using
TEST DRIVE
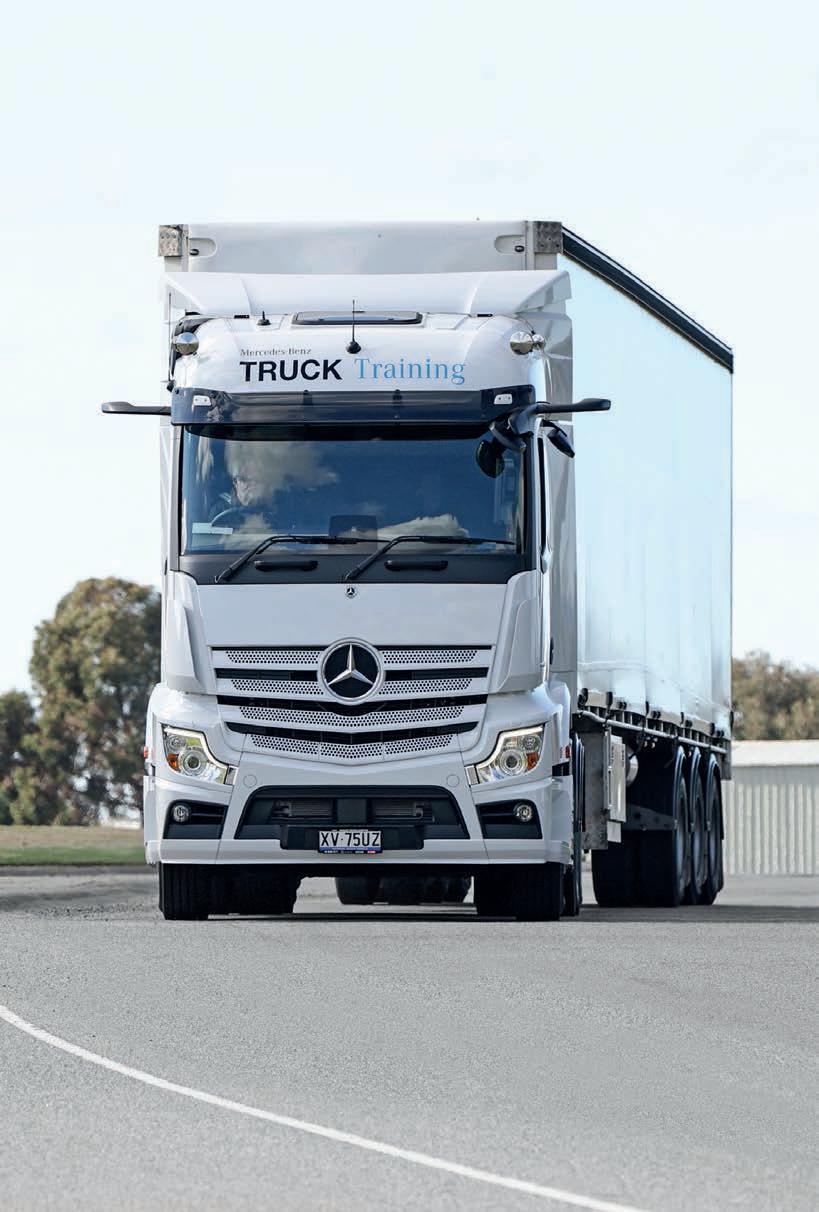
three dimensional topographic mapping combined with history from previous trips to provide the truck with the details of the road ahead for up to two kilometres. The system will continue to learn and plan from data collected on routes which haven’t been travelled previously. Data from the on-board weighing system is also constantly utilised to calculate loads, throttle and brake applications as well as gear selections. This has the potential for enormous benefits in fuel efficiency and trip times. For instance, when climbing a steep hill where the inclinometer in the prime mover senses that the top of the hill has been reached, yet the trailer(s) are still subject to gravitational pull due to still travelling on the upwards gradient, the Actros remains under power until the right time to ease the accelerator and upshift as the trailers pass the apex of the rise. We’ve been in other trucks equipped with conventional cruise control where the power was decreased and an upshift attempted at precisely the wrong point which required intervention from the driver to prevent a massive loss of momentum. Another situation in which the PPC makes its presence known is when travelling along an undulating road. Where possible it will ‘eco-roll’ in neutral and when driving down into a dip because the Actros knows what’s up ahead it will accelerate slightly approaching the bottom of the dip and then apply more power as needed to climb the other side. This can create the situation where the truck is travelling ten or so kilometres faster at the base of a climb than it would be if using a conventional form of cruise control or relying upon the driver’s knowledge and skill to apply the power at just the right instant to maximise the efficiency of climbing the rise, and at the same time avoiding inadvertent over-speeds. The Active Steering function, however, takes just a little time to get used to. Initially we found we were continually pushing slightly against the additional force used by the truck to keep in the selected position within the lane. The
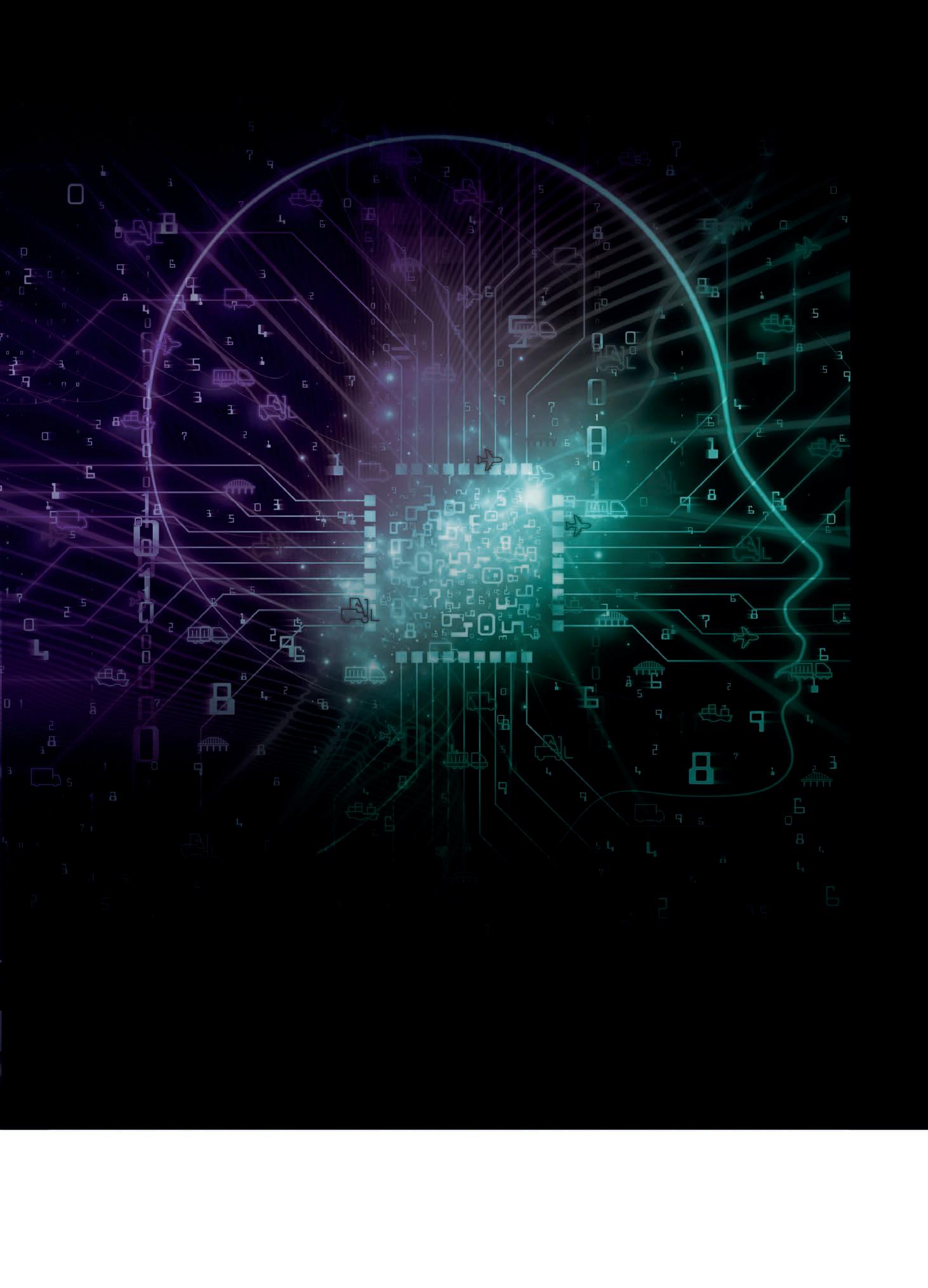
It’s the first time Prime Mover has experienced both Predictive Powertrain Control in conjunction with MirrorCam.
realisation that this driver’s natural lane positioning is slightly to the left of centre is the impetus to electronically realign the truck by making a small adjustment in the appropriate app via the centre touch screen which results in the truck shifting ever so slightly to the left and maintaining that position within its lane without any input from the driver. The same adjustment process can also be used to locate the truck closer to the right-hand side of the lane if that is the preference of the driver. When no longer pushing against the resistance delivered by the electronic-controlled steering the driver’s task is relaxed significantly. The highlights of the Actros’s interactive multimedia cockpit are the two screens with one positioned in front of driver (dashboard) which is adjustable from the controls on the steering wheel with the main displays being speedo, tacho and air pressure gauges as well as the complement of driver support readouts such as fuel burn, and adaptive cruise control settings. The multimedia display located on the dash to the left of the driver has components familiar to those fitted to the latest Mercedes-Benz passenger cars and is a leap forward in the connectivity between the trucks and their drivers and operators. The centre touch screen has the capability to be programmed to incorporate more than 200 ‘soft’ switches to operate components such as power take offs. The screen responds to operator’s input by making an on-screen switch available, which is not dissimilar to using an app on a smartphone. Reliability and durability are extended significantly as there is no longer reliance upon physical contact-making and -breaking switches. Daimler Trucks recognised early-on that autonomous trucking has enormous potential to fundamentally change the road transport industry. Crucially, Daimler also recognised it will take time to do it right with safety being the priority. The path to increased levels of autonomous trucking, to that end, is a marathon and not a sprint.