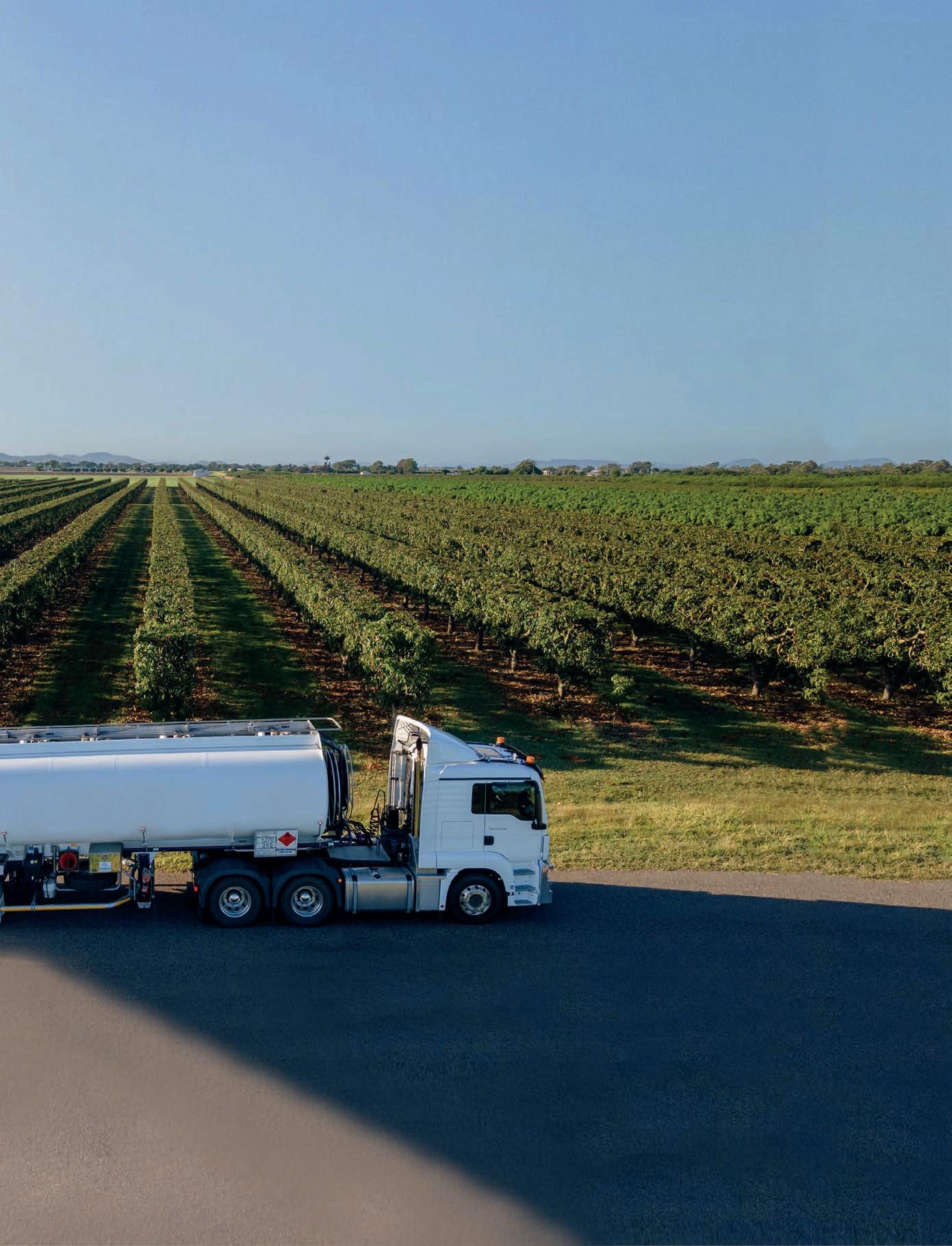

INDUSTRY
Fleet: Josie’s Transport Group
Feature: Foodbank WA
Livestock: Multiquip
Personality Profile: Cameron Bettany
INNOVATION
Carrier: Metropolitan Express
Spotlight: Garden City Plastics
Roadtrains: Land Transport
Test Drive: Mercedes-Benz eActros 600
At Isuzu, we’ve always taken great care of our customers.
At Isuzu, we’ve always taken great care of our customers.
We’re Australia’s number one truck… an honour we’ve held for over three decades.
We’re Australia’s number one truck… an honour we’ve held for over three decades.
It’s part of our DNA.
It’s part of our DNA.
That means more businesses put their trust in us than any other truck brand. We understand that reputations are riding on us and that’s why Isuzu Care is more than just an aftersales service package.
That means more businesses put their trust in us than any other truck brand. We understand that reputations are riding on us and that’s why Isuzu Care is more than just an aftersales service package.
From day one, we support customers and demonstrate that reliability is everything. We pride ourselves on being proactive and always going the extra mile.
From day one, we support customers and demonstrate that reliability is everything. We pride ourselves on being proactive and always going the extra mile.
Isuzu Care is what sets us apart. Always has, always will.
Isuzu Care is what sets us apart. Always has, always will.
And as we look to new frontiers, we’re finding new ways to help our customers exceed their goals.
And as we look to new frontiers, we’re finding new ways to help our customers exceed their goals.
Australia’s leading truck magazine, Prime Mover, continues to invest more in its products and showcases a deep pool of editorial talent with a unique mix of experience and knowledge.
Christine Clancy | COO
With more than two decades of experience as a media professional, Christine has worked in newsrooms across Canada, Vietnam and Australia. She joined the Prime Creative Media team 12 years ago, and today oversees more than 43 titles, including a dozen print and digital transportation titles. She continues to lead a team that focuses on continuous improvement to deliver quality insights that helps the commercial road transport industry grow.
William Craske | Editor
Over the past two decades William has published widely on transport, logistics, politics, agriculture, cinema, music and sports. He has held senior positions in marketing and publicity for multinational businesses in the entertainment industry and is the author of two plays and a book on Australian lm history. Like many based in Melbourne he is in a prolonged transition of either returning or leaving.
Peter Shields | Senior Feature Writer
A seasoned transport industry professional, Peter has spent more than a decade in the media industry. Starting out as a heavy vehicle mechanic, he managed a fuel tanker eet and held a range of senior marketing and management positions in the oil and chemicals industry before becoming a nationally acclaimed transport journalist.
Peter White | Journalist
Since completing a Bachelor of Media and Communication degree at La Trobe University in 2021, Peter has obtained valuable newsroom experience, supplemented by direct industry exposure at Prime Creative Media. As the Editor of Trailer, Peter brings a fresh perspective to Prime Mover. He has a strong interest in commercial road transport and in furthering the magazine’s goal of growing the industry.
Sean Gustini | Journalist
Having completed a Bachelor of Arts majoring in Media and Communications at the University of Melbourne in 2024, Sean looks forward to bringing his passion for writing and journalism to the road freight and transport industries. He previously lived in the Philippines, Vietnam, Indonesia and Malaysia. In his downtime he enjoys playing the guitar and running.
Ashley Blachford | Business
Development Manager
Handling placements for Prime Mover magazine, Ashley has a unique perspective on the world of truck building both domestically and internationally. Focused on delivering the best results for advertisers, Ashley works closely with the editorial team to ensure the best integration of brand messaging across both print and digital platforms.
CEO John Murphy john.murphy@primecreative.com.au
Editor William Craske william.craske@primecreative.com.au
Managing Editor, Luke Applebee Transport Group luke.applebee@primecreative.com.au
Senior Feature Peter Shields Writer peter.shields@primecreative.com.au
Business Ashley Blachford Development ashley.blachford@primecreative.com.au Manager 0425 699 819
Art Director Blake Storey blake.storey@primecreative.com.au
Design Blake Storey
Contributors Sean Gustini sean.gustini@primecreative.com.au
Peter White peter.white@primecreative.com.au
Client Success Salma Kennedy Manager salma.kennedy@primecreative.com.au
Head Of ce 379 Docklands Drive, Docklands VIC 3008 enquiries@primecreative.com.au
Subscriptions
03 9690 8766 subscriptions@primecreative.com.au
Prime Mover magazine is available by subscription from the publisher. The right of refusal is reserved by the publisher. Annual rates: AUS $110.00 (inc GST). For overseas subscriptions, airmail postage should be added to the subscription rate.
Articles
All articles submitted for publication become the property of the publisher. The Editor reserves the right to adjust any article to conform with the magazine format.
Copyright PRIME MOVER magazine is owned and published by Prime Creative Media. All material in PRIME MOVER magazine is copyright and no part may be reproduced or copied in any form or by any means (graphic, electronic or mechanical including information and retrieval systems) without written permission of the publisher. The Editor welcomes contributions but reserves the right to accept or reject any material.
While every effort has been made to ensure the accuracy of information Prime Creative Media will not accept responsibility for errors or omissions or for any consequences arising from reliance on information published. The opinions expressed in PRIME MOVER magazine are not necessarily the opinions of, or endorsed by the publisher unless otherwise stated.
“It’s fantastic to see the number of hybrid vehicles coming to market, and BMD is focused on incorporating hybrid options across our fleet to align with the government’s New Vehicle Efficiency Standard.”
FLEET FOCUS
24 Urban Legend
The BMD Group is a leader in the construction industry as Australia’s largest privately-owned civil contractor and has a unique approach to the management of its vehicle fleet.
30 Good to Go
The experienced ownership team at Josie’s Transport Group are taking the established business to another level as a specialised regional carrier.
34 Perfect Partners
Precast concrete components have revolutionised the construction industry. Delivering the heavy pieces to site requires a specialised approach to transport.
TRUCK & TECH
46 Take it to the Bank
Demand for Foodbank WA’s essential services has doubled over the past five years. To maintain optimal, reliable service levels, the organisation has invested in new Isuzu trucks.
50 In the Realm of the Sensor
JOST, a longtime supplier for Multiquip, has provided the poultry and transport company with a new Loc-Light fifth wheel sensor to trial.
William Craske Editor
The rst strikes in response to Houthi operations in the Red Sea were coordinated by the United States and Great Britain on 11 January, barely a week into the new working year. But by March three people on a commercial ship had been killed by another Houthi rocket attack in the Gulf of Aden with another four critically injured. The use of anti-ship ballistic missiles against commercial shipping vessels was a new development legacy supply chains and US intelligence had not previously encountered. Asymmetrical tactical warfare had made it, nally, onto the audit trail.
That these weapons can be launched at distances of 480 kilometres makes oil tankers and car carrying ships, like the Galaxy Leader, all but defenceless. What’s more, from well beyond the horizon.
In November the Japanese-chartered ship, with 25 crew on board, was seized by the Houthi. Ships that belong to Israel or its Western allies, they have claimed, are those foremost being targeted.
The Houthis, a Zaydi Shiite militia from Yemen, also have inexpensive Iranian-
designed attack drones in their arsenal, like the 15-foot wide Samad, which has a range of up to 1,770 kilometres. Economic disadvantages have brought with them other capabilities that are effective enough to reduce maritime traf c in the region to a chokepoint. Despite being considered the poorest country in the Middle East, Yemen shares over 1,900 kilometres of coastline in and out of the Suez Canal, a trilliondollar global trade route linking Europe and Asia. With 15 per cent of the global economy reliant on passage via the Red Sea, controlling the waterways here remains of vital importance.
Even after months of intense naval operations, a coalition of military superpowers have, however, failed to secure the area where attacks and hijackings are now so commonplace the world’s largest container ship companies Maersk, Hapag Lloyd, and MSC, among them, have opted to avoid the Suez Canal where 30 per cent of global container traf c had until recently owed. Last December many of these companies decided instead to circumnavigate the Cape of Good Hope in Africa at no small inconvenience. Shipping times and fuel costs soon blew out. Not to mention insurance premiums.
High-frequency transit estimates indicate that the volume of trade that passed through the Suez Canal dropped by 42 per cent compared to its peak in the rst two months of 2024, while the volume of trade transiting around the Cape of Good Hope surged by an estimated 74
per cent above last year’s level.
The Suez Canal is located at the northern end of the Red Sea. At the southern point is the 32-kilometrewide strait known in Arabic as the Bab el-Mandeb or in English as the Gate of Grief. Until recently it accommodated an estimated 25,000 ships and nearly 2 billion barrels of oil.
More recently, a salvage operation to recover a Greek-registered oil tanker stranded ablaze in the Red Sea after an attack by Houthi militants was necessary to avert a potential spill that was set to become the largest ever from a ship in recorded history. The Sounion, which the Houthis and maritime sources have said has been rigged with explosives, is laden with about 1 million barrels of crude oil. This is not a movie. Since last year, the Houthis have launched more than 100 attacks and the US Navy claims to have shot down more than 150 drones and missiles red by the militia that controls one-third of Yemen, including the capital Sanaa. With no sign of the crisis ending, mounting pressure in the region to recapture Hodeidah province and its ports from the Houthis, if order is to be restored to international shipping lanes by this time next year, is likely to test the willingness of nation states whose appetite for unilateral coercive measures to control the global supply of crude oil is not apparently what it once was.
DAF is versatile and an all-rounder with the perfect combination of superior comfort and luxury for the driver and maximum vehicle efficiency for the operator. So, you need a prime mover with superior robustness and high payload? There’s a DAF for that!
Whether your needs are long-distance haulage, city distribution, construction transportation, bulk or tank transport, the versatility of DAF keeps you moving, and that’s good for business. DAF.COM.AU
> ERH adds three new K220 roadtrains to Kenworth fleet
Melbourne-based cold carrier, ERH Refrigerated Transport, has deployed three new Kenworth K220s with another two on the way.
The 97-tonne Gross Combination Mass (GCM) rated units are specified for pulling roadtrains along the eastern seaboard between Melbourne, Brisbane and Sydney for ERH’s temperature sensitive freight tasks.
The K220s are powered by 550hp Cummins X15 Euro 5 engines and Eaton Endurant XD Pro automatic transmissions with Meritor RT46160 axles.
They were specified to ERH’s particular needs by Hallam Truck Centre in Melbourne.
Exterior bling kits include Barup bullbars, drop visor tank trims, extra grille bars, additional roof and mirror lights, two 650-litre rectangular fuel tanks and a
column-mounted transmission control.
Inside the 2.3m aerodynamic roof sleeper cabs are custom-made storage shelves and a bunk cooler with auxiliary lithium batteries.
“We’re an 80 per cent Kenworth fleet, that’s what we do,” ERH Refrigerated Transport Director, Rupert Smith, told Prime Mover. “We have some standing orders with Kenworth every year based on a fleet replacement program for growth, and when we got the opportunity to move to the K220s we jumped on it.”
Following their early operations, Smith said the feedback has been positive all-round.
“The initial feedback has been fantastic,” he said. “Everyone has been super impressed with the ergonomics of the new cab. They think it will keep the heat out in the summer.”
The ride quality, spacious cab and transmission and engine combination are also highlights for ERH’s drivers.
“They’ve performed well,” Smith said.
“It’s hard to comment on something when they’re so new, but the fuel is comparable and they’re certainly handling the roadtrain job very well — as you’d expect for a Kenworth.”
ERH’s new K220s join a fleet of 65 Kenworths, including T610s, SARs, K200s, K220s and a Legend 900, which have all served the business extremely well.
“It speaks for itself that their marque makes up the majority of the fleet,” Smith said.
“We run our own workshop and maintain them all in-house, which is helpful for minimising downtime as well. Looking ahead, I’m completely positive they will be a good thing.”
We are embracing our path to zero emissions. The ADR80/04 rating will bring Australia’s emissions standards in line with Euro VI.
• The power of versatility
• 525 - 625 hp
• 1850 - 2050 lb-ft
• Peak torque at 1000RPM
• Ultimate flexibility suitable for both maunal and automated transmissions
• EGR-free design meeting Euro VI emission standards
Scan here to learn more about our Euro VI offerings
The resilience of Qube’s business and growth prospects have contributed to its strong financial performance.
The latest results – for the 12 months ended 30 June 2024 – show how Qube has mitigated cost inflation and continued with its acquisition strategy to diversify earnings.
Statutory revenue was $3,357.2 million (+16.6 per cent) and underlying revenue was $3,503.6 million (+17.2 per cent). Statutory net profit after tax was $221.9 million (+32.2 per cent), while underlying net profit after tax was $258 million (+14.8 per cent).
The key markets that Qube engages in includes containers, agriculture, automotive, forestry, resources, energy as well as other commodities, services and products.
In addition to being well diversified across Australia’s states and territories and abroad, it delivered growth in every region. Acquisitions added revenue to Queensland and South Australia (Kalari), Western Australia (Stevenson Logistics)
and New Zealand (Pinnacle). Weaker agriculture volumes in New South Wales and Queensland were largely offset by increased grain trading revenue in New South Wales.
The Logistics and Infrastructure business unit reported high volumes across most containerised activities including transport, empty container parks and warehouses.
The MLP IMEX Terminal commenced normal automated operations in late FY24. Qube handled around 24,000 TEU through this terminal July last year which was under the annualised target of 300,000-350,000. However, monthly volumes are expected to build during FY25. An empty container park adjacent to MLP IMEX has also commenced operations.
Ports and Bulk saw strong growth particularly with higher volumes of motor vehicles, fertiliser and bulk commodities.
In FY24 Qube acquired the remaining 50 per cent stake in Pinnacle, completed
Port of Melbourne will lease approximately 29 hectares of the former Melbourne Markets site to 2066. The announcement made in late August falls in line with its existing 50-year port privatisation lease and represents its largest expansion since it was granted a long-term lease in 2016.
Victoria’s supply chain efficiency and resilience is likely to be bolstered considerably following the Port of Melbourne securing crucial access to an additional parcel of land. Based on current planning, Port of Melbourne expects to invest more than $200 million into the development of the site.
Considered a strategic transformation of the Port precinct, the development will play a critical role in preserving Port of Melbourne as the key trade gateway for southeastern Australia, while reducing congestion and minimising impact to surrounding communities.
“This is a great deal for Victoria — we’re getting more trucks off local roads, increasing the amount of freight the Port of Melbourne can handle, boosting trade and the economy, while strengthening Victoria’s supply chains,” said Minister for Ports and Freight Melissa Horne.
Significantly, the future-focused
its integration of Narrabri Property and Infrastructure and is still in the process of integrating Stevenson Logistics. For FY25, Qube will continue to undertake value accretive bolt-on acquisitions. The acquisition of Melbourne International RoRo & Automotive Terminal (MIRRAT) is expected to complete by H1 FY25, subject to ACCC and Port of Melbourne approval.
Qube also acquired Colemans on 21 August 2024. The integrated transport, logistics and storage business has a specialised licensed infrastructure which supports the Security Sensitive Ammonium Nitrate (SSAN) supply chain in Western Australia.
Qube acquired more than $90 million of assets including high security storage sheds in the mining centres of Kalgoorlie, Port Hedland and Wyndham in Western Australia as well as in Kwinana. This acquisition will serve as a platform for Qube to enter Western Australia’s SSAN supply market.
integration of the site into the Port precinct supports a $36-billion freight sector that employs 260,000 Victorians.
“With container volumes at Port of Melbourne expected to double by 2050, access to additional land at the former Melbourne Markets site unlocks opportunities that are critical to the future needs of Victoria,” said Saul Cannon Port of Melbourne CEO.
“Port of Melbourne is proud to invest in developing the site to support forecast growth and demands.”
Consistent with the Victorian Government’s 2018 Victorian Freight Plan, Port of Melbourne will invest in developing the site for a range of uses, including truck parking facilities and container storage. The establishment of port functions at this site will reportedly improve traffic movement in the area, complementing the West Gate Tunnel when it opens.
Interstate transport company, SGGS Transport, has unveiled its first B-triple with CTI Logistics. The B-triple combination is servicing CTI depots between Sydney and Perth each week, a round trip of approximately 8000km. Built to specifications supplied by CTI, the Performance-Based Standards approved high performance vehicle was, up until its maiden run, an aroundthe-clock project for Nigel Pretyman CTI NSW Business Manager and Dannii Spiteri SGGS Victorian Branch Manager. “This has taken us approximately eight months, with Nigel’s knowledge and additional help from Tiger Spider for the route and permit and Royans for their prompt and quality work on the livery on the trailers,” said Spiteri.
Project milestones included the required PBS certification requirements for both the unit and Kenworth K200 prime mover to achieving the permit to run directly out of CTI’s site in Sydney to having the Vawdrey trailers painted up until the launch day in the first week of July. There were few engineering or design challenges according to Spiteri.
“By partnering with quality providers in Vawdrey, Kenworth, Tiger Spider and Royans, we were able to achieve this in a less stressful time and manner, running to over and above General Mass Limits to Concessional Mass Limits, giving us greater weight carrying capabilities to CTI’s varying customer requirements,” she told Prime Mover
The B-triple combination is already providing improved efficiencies by carrying more cargo per trip than a B-double combination, reducing the number of trips required to move CTI’s express and premium express LTL Freight from Sydney to Perth.
Powered by Euro 5 X15 Cummins engine, the Kenworth K200 is one of 16 it purchased earlier in the year.
Spiteri said the B-triple further strengthened the current and ongoing partnership between the two companies.
“By utilising the B-triple combination, this has provided decreased traffic congestion, less trucks on the road running east-west and has helped reduce operational costs and increase
profitability in a tough and softening market,” she said. “By doing this, it has enabled CTI to continue to provide a cost effective express and premium express service offering to their customers.
“In addition to this, it has also assisted SGGS in lowering fuel costs, bring down maintenance requirements and reduces the number of trips required over B-double combinations.”
According to Spiteri, SGGS is committed also to providing marketing exposure for its customers by ensuring branding, in this case on the trailer curtains, is vivid and distinctive. The collaborative project has thus far proven a winning combination for both parties.
“CTI has enjoyed working with SGGS. The partnership continues to grow and evolve,” said Pretyman. “SGGS is now one of our major linehaul providers, and we look forward to building on our partnership in the future. The communication, technology and quality of equipment provided is best in class and what CTI requires from a partner.”
The flexible specialist
The flexible truck, ready for any assignment. Body builder-friendly to be tailored for your business.
>
Queensland-based transport company, Jarratt Transport Solutions, has taken delivery of four new Kenworth T610SAR prime movers for B-triple roadtrain applications.
The new trucks join a fleet of eight Kenworth T610SARs, all in identical spec, which travel from Far North Queensland to central South Australia carting cotton, citrus, wind and solar farms freight and power and infrastructure goods.
Jarratt Transport Solutions Managing Director, Phil Jarratt, told Prime Mover the new units have been performing faultlessly in their operations so far. “I couldn’t be happier with them,” he said. “They fit the job perfectly – they have great tare weights, they run nicely and the drivers are satisfied with them. “They’re the perfect truck for the work and jobs that we do, and in the terrains that we work in. As far as we’re concerned, they’re awesome for us.”
The Kenworths are all powered by 615hp Cummins X15 Euro V engines and 18-speed manual Eaton RoadRanger gearboxes with 1,850 lb-ft
of torque.
They feature microwaves, inverters, fridges, Icepacks, Teletrac Navman Electronic Work Diaries (EWD) and onboard electronic scales, among other standard commodities.
“They’re all spec’d identical,” Jarratt said. “The only difference from one to the other is the registration number. Everything else is exactly the same.”
The four new T610SARs also arrived with four new O’Phee B-double roadtrain sets, two roadtrain leads and two roadtrain dollies from The Drake Group. “We only have O’Phee,” Jarratt said. “If I can’t buy a trailer with Mick O’Phee, I don’t have one.”
They too join an identical O’Phee fleet
of 11 B-double sets, six roadtrain leads and six roadtrain dollies, plus one B-double drop deck for the odd occasion where the fleet needs one.
“The idea behind having the six roadtrain trailers was that they would allow us to operate six roadtrains and six B-triples out of the 12 vehicles,” Jarratt said.
“They’re all interchangeable. So, any of the roadtrain trailers can be connected to any of the roadtrain dollies, and any of the dollies can be put in front of the B-double sets.”
In terms of the Kenworths, Jarratt said durability, quality of service and his relationship with the dealer, Brown and Hurley, were all contributing factors to the ongoing purchases.
Driver satisfaction and the “overall fit-for-purpose” of the first eight T610SARs, he said, were also standout aspects.
That being said, Jarratt is planning for further Kenworth additions in the near future.
“There will be others,” he said.
“There will be a big order placed at some point in the next 12 months or so.”
Nowra business, SCCCR Quarries, in September unveiled a new Kenworth T610SAR.
Running as a truck and dog combination, the prime mover is powered by a Euro 5 Cummins X15 delivering 550hp at 1,850lb-ft through an 18-speed Eaton RoadRanger. Suttons Kenworth & DAF sales consultant Shane Boag oversaw the delivery.
The second-generation business operates 20 units in its mixed fleet having recently moved to Kenworth as a key supplier.
“We’ve gone for a bit of a changeup which has taken us down the Kenworth path,” said Owner Bud Green.
“Essentially I was looking for reliability, durability and the ability to withstand
the day-to-day rigours of heavy transport in the quarry field.”
The new Kenworth is expected to travel just under 300,000 kilometres in a year, mainly dedicated to short haul runs for the regionalised quarry work it conducts mainly across the south coast of New South Wales. SCCCR vehicles transport a mix of raw and recycled construction materials.
Headquarters are situated at a hard rock quarry that produces up to 500,000 tonnes per year of natural and recycled materials.
Sloanebuilt delivered the body and trailers on the combination which achieves a payload just under 37.5 tonnes.
“We’re really happy with the build quality and the payloads that we are
achieving,” said Green.
The company was founded in the mid1980s by Green’s father John Green.
“We’ve gone through various phases of expansion and contraction over the years depending on the interchanging workplace,” said Green.
“Our remit has been to provide consistent service to our clients and maintain repeat business and generate new work as or when there’s opportunities available.”
SCCCR Quarries, an abbreviation of South Coast Concrete Cushing & Recycling, is also transitioning into a third-generation family business with Green’s son Seth and daughter Ariel very much involved in operations.
Earlier in the year SCCCR Quarries took delivery of a Kenworth K200 with a flat roof, its first from the brand.
Martins Stock Haulage have unveiled a unique wrap design on its latest Mack Super-Liner to support blue collar mental health group TIACS. The truck aims to raise awareness of TIACS (This is a Conversation Starter), a professional mental health counselling service for tradies, truck drivers, farmers and blue collar workers.
Founded by TradeMutt, renowned for their range of eye-catching workwear, TIACS aims to get people talking about mental health.
Jason Martin, CEO of Martins Stock Haulage is a big supporter of TIACS, having already bought into TradeMutt’s Funky Friday shirts, and when he met the co-founders at the Dalby Stock Show, something special happened.
“We were the charity beneficiary of one of the horses that had been sold,” said Ed Ross of TIACS and TradeMutt. “We were having a beer to celebrate when we were introduced to Jason. He was telling us about the pink Mack Martins did last year, and he asked us if we’d be interested in doing something similar. Were we interested? We jumped at it.”
And so a conversation over a beer set in motion a sequence of events that resulted in one of the more interesting looking trucks to be found on Australia’s roads.
Ross showed Martin the TradeMutt design catalogue and he chose the Razzle-Dazzle print. From there a whole team was involved in getting the truck on the road.
“Tom Chapman, the current VP of Mack at the time got right behind it,” said Adam Ross, General Manager of Martins Stock Haulage. “Ben Dare of Western Truck Group was superb co-ordinating everything.”
The truck was wrapped in the print by Bailey Print Group, who hadn’t handled anything on that scale before.
“Bailey’s have wrapped all our Mazdas, but this was the first time they’d been asked to wrap a truck, and they did a brilliant job,” said Ed Ross. With finishing touches added by The
Bling Man, the Mack Super-Liner certainly makes a statement, and with a 58-inch sleeper cab fitted behind the driver, the aim is to have it working all over Australia.
“She’ll be doing B-double, B-triple and triple roadtrain work hauling cattle wherever she’s needed in Australia,” said Adam Ross. “We want to get this truck out in front of as many people as possible, after all, the whole idea is to start a conversation and we reckon this truck will do the job.”
The new Super-Liner follows on from the pink Mack Martins launched last year to acknowledge women in the workforce.
“We’re a family owned and run company,
and all our staff are part of that extended family,” said Adam Ross. “A lot of men have difficulty talking about things that are going on in their lives, and this is particularly true of drivers, who are often away from home for long periods and spend a lot of time alone in the cab.
“Jason’s seen a lot of this over his career, and we want to make sure we look after our people. Mental health’s a big part of that.”
Martins Stock Haulage now have four Titans and eight Super-Liners in the fleet, with two of them making bold statements for causes that the Martins team believe in.
The most-tested Western Star ever, the X-Series is seriously tough. Boasting our legendary Star durability, the X-Series features a powerful integrated driveline, advanced safety
systems, and superior comfort - even in the most rugged of applications. But talk is cheap. Experience it for yourself.
CONTACT US TODAY
Ballarat Isuzu has opened a newly built facility in Mitchell Park, Ballarat. The all-new Dealership has expanded on Ballarat Isuzu’s previous offering, covering 15,000m² with a large open plan truck showroom and modern workshop space.
Mitchell Park also offers more turnaround space for vehicles with capacity for a larger volume of on-hand stock.
Providing an expansive product line-up of Isuzu Trucks model variants — reportedly the largest of any truck manufacturer in Australia — and Isuzu Power Solutions products, Ballarat Isuzu has been focused on delivering exceptional service and value for customers over decades.
“Along with Isuzu Trucks we have been supporting Ballarat businesses for nearly 50 years,” said Dealer Principal, Ian Deacon. “We believe Isuzu resonates with the transport community here, keeping them moving and their trucks on the road for the long-term.
“One of the real drivers of growth for our business has been an ongoing commitment from the staff to our customers, which has led to us breaking ground on this exciting, brandnew facility.”
Full-length service bays fitted with best-in-class equipment will offer
faster turnarounds for truck servicing and boost internal efficiency for the dealership.
The ability to offer timely maintenance is backed by ready availability of genuine parts and stock from Isuzu Australia’s National Parts Distribution Centre, which is situated just over an hour’s drive from Ballarat on the Western Freeway on the outskirts of Melbourne.
“In a regional setting such as ours, having the technical capacity to get vehicles back on the road as quickly as we can—with parts in stock—is one of the most important aspects of our business,” continued Deacon. “We’re hoping that the new facilities will maintain our excellent staff team and existing technicians and also help to attract more talent to the dealership in future.”
Takeo Shindo, Managing Director and Chief Executive Officer of Isuzu Australia Limited (IAL) recently joined key IAL head office staff and customers on site for the opening of the new facility.
“It is a fitting home for one of our best performing Isuzu Dealerships,” he said. “Ian and the team’s focus on their customers and the local community has delivered success, which is reflected in the opening of this model Dealership within our network—they should all be very proud.”
On a larger scale, the significant investment of Ballarat Isuzu in its new facility demonstrates the widespread confidence that Isuzu’s Dealer Network has in the prosperity of Isuzu Power Solutions and Isuzu Trucks brands — the latter of which is currently in its 35th consecutive year as Australian market leader.
At a local level, Ballarat Isuzu’s confidence to invest in their own future is well-assured, with the Dealership recognised as a perennial top performer for Isuzu.
They have taken out the prestigious title of Isuzu Dealer of the Year over multiple years, among other awards.
IAL Head of Network Development, Nathan Ton, said outcomes for Isuzu customers in the Ballarat region would only continue to improve with the opening of the new facility.
“The team at Ballarat Isuzu and Dealer Principal Ian Deacon have greatly impressed everyone at IAL with their dedication to improving their own operation and the outcomes that they can achieve for their customers,” he said.
“To sum it up, if you purchase an Isuzu truck or power solution product from Ballarat Isuzu, you can be sure that you will be fully supported by the Dealership for many years to come.”
The US Department of Transportation has announced it will fund an electric truck freight corridor on the West Coast of the United States to tune of $USD102 million. Managed by the California Department of Transportation, the West Coast Truck Charging and Fueling Corridor Project will deploy charging and hydrogen fuelling stations for mediumand heavy-duty electric trucks along 2,500 miles (or 4000kms) of freight corridors in California, Oregon and Washington.
The project will allow “emissions-free movement of goods” along the corridor and will connect major ports, freight centres and agricultural regions between the US borders with Mexico and Canada per the grant application.
Construction of the charging stations is expected to start in 2026.
“Decarbonising the transportation and goods movement sectors is essential for
fighting the climate crisis and protecting public health in communities along busy corridors,” said California Senator Alex Padilla. “To successfully meet California’s critical climate goals, we need to scale up our charging and fuelling infrastructure up and down the state through transformative projects like the West Coast Truck Charging and Fueling Corridor Project.”
The Department of Transport announced 51 electric vehicle charging projects totalling $521 million earlier in the week across 29 states and the District of Columbia.
The move follows criticism that the current government had made good on only 11 EV charging stations as part of bloated bipartisan infrastructure bill with little to show for it with an election only a few months away in November.
Congress at the urging of the Biden Administration agreed in 2021 to spend
$7.5 billion to build tens of thousands of electric vehicle chargers across the country.
Money for the latest round of grants including the West Coast truck corridor comes from the CFI grant program, established by the 2021 Bipartisan Infrastructure Law.
The program provides $2.5 billion over five years to fund EV charging and alternative-fuelling infrastructure to help meet the Biden administration’s goal of reducing carbon dioxide emissions from cars and trucks.
“The Biden-Harris Administration has taken action to ensure that America leads the EV revolution, and the historic infrastructure package includes resources to support a nationwide EV charger network so that all drivers have an accessible, reliable, and convenient way to charge their vehicles,” said Transportation Secretary Pete Buttigieg.
Global logistics company, DSV, has signed an agreement with Volvo Trucks to support decarbonisation of road freight. DSV plans to deploy 300 electric trucks from Volvo for its European operations. The deal includes 500 Volvo trucks with fuelefficient diesel and gas drivelines.
The heavy vehicles are expected to be delivered between 2024 and 2026.
“I’m very proud to deepen the partnership we have with DSV,” said Volvo Trucks President Roger Alm. “Collaboration and a strong commitment to really make a difference is essential for making sustainable transport and big CO2 reductions a reality.
“This order is proof of their trust in our company and shows that zero-emissions transport is a viable solution here and now.”
DSV Road CEO Søren Schmidt said close collaboration across sectors provides an opportunity for the fleet to be a key enabler for decarbonisation in the industry.
“We are happy to extend our partnership with Volvo in our joint effort to reduce emissions in the transport industry,” said Schmidt.
“As a global leader in logistics, we strive to stay at the forefront of the green transition and this agreement is a fantastic example of how new technologies can be brought to
market at scale to make them more accessible for our customers.
“The deal with Volvo is an important step towards enabling a more sustainable future in trucking.”
The trucks being supplied to DSV will include the new Volvo FH Aero Electric, which has improved aerodynamics, making it even more energy efficient.
DSV is the largest transporter of goods for the Volvo Group, and its electric trucks are already used on lanes in Sweden and Denmark where DSV has established charging infrastructure using electricity from solar panels at its distribution centres in Landskrona and Horsens.
The BMD Group is a leader in the construction industry as Australia’s largest privatelyowned civil contractor and has a specialised approach to the management of its vehicle eet.
The M in the BMD acronym stands for Founder and Group Board Chairman Mick Power AM. The B is for his sister Beverley and her husband Bevin who were both originally partners in the business, and the D for Mick’s wife Denise.
Now considered Australia’s leading integrated engineering, construction and urban development business, BMD, over its 45-year-history has grown to become a $2 billion operation that now shares its expertise internationally in the Philippines and the United Kingdom. Nigel Scott is the National Fleet Manager
based at BMD’s of ce in Brisbane and looks after the company’s vehicles in every state and territory including just under 1,000 light commercial utes. The changes in the Australian commercial vehicle landscape are emphasised by the fact that when Nigel commenced at BMD, some three years ago, the total vehicle count was around 1,100 units, of which approximately 900 were Holden Colorado utes. The withdrawal of the Holden brand means there are no longer any Colorados in the eet which currently totals just over 1,500 vehicles, showing a growth of around ten per cent year-on-year.
This also translates to the arrival of approximately 30 new vehicles every month and a corresponding 30 being replaced.
A principle of BMD’s eet management is that the organisation sources and disposes of its various vehicles internally, with long-term partnerships built with Brisbane dealerships such as Sci-Fleet for its Toyota and Hino requirements, and Barton’s for the Hyundai, Nissan and Mitsubishi brands.
Sci-Fleet delivered BMD its 100th Hino in 2024, demonstrating the enduring relationship built over 35 years of being in business together. BMD’s eet currently includes around 75 Hino 300 Series factory tippers, most of which are car licence rated 616 models. There are a couple of 716 models which have slightly higher GVMs and require a Light Rigid licence, plus a Hino 500 Series
water truck. One Hino is equipped with a truck-mounted crane and used to deliver steel reinforcing mesh.
Other than the water truck, there are no heavy vehicles in the eet. If one of BMD’s 50-tonne excavators requires relocating, a low loader operator is contracted. Similarly, if a portable site of ce needs to be moved, a tilt tray from a tow truck company is engaged.
BMD did consider obtaining its own car carrier at one point, but with cars and light commercials being despatched to various locations right across Australia, several would have been needed which didn’t re ect BMD’s focus on its core activities of construction and development.
The Hino 300 Series has proved to be a good t for the overall operation.
“Most of our people are construction workers, not truck drivers, and we can
basically switch a driver out of a Toyota ute and put them straight into a Hino,” explains Nigel, who has a preference for fully automatic transmissions over automated manual transmissions (AMT) citing a higher level of driver familiarity with torque converter transmissions which also deliver an advantage on slippery building sites.
“A 4x4 version would be good sometimes depending upon what site they are on. Dependent on the weather and ultimately the conditions of the site, they do get stuck occasionally,” Nigel says.
“We utilise crew cabs which can be handy on site to move team members from A to B.”
All Hino servicing is carried out by SciFleet on an as-needed basis rather than on a maintenance contract.
“Everything is electronic now with requirements for actions such as software
updates so we don’t do our own servicing on the Hino trucks,” says Nigel.
BMD actually has its own licenced motor dealership, Better Motor Deals (another BMD), which specialises in the sale of the BMD Group’s ex-company vehicles.
BMD also has a half share in East Coast Commercials, located in Acacia Ridge, which also facilitates passing ex-company vehicles onto their next owners. The majority of vehicles on sale, including Hino trucks, are three to ve years old and have certi ed service history logbooks which makes them an attractive proposition for the buying public.
“We set the residual and we know what these units are going to be worth at the end of their initial working life,” adds Nigel.
The COVID pandemic created challenges in vehicle supply across the world and to address this BMD extended the leases on
“Most of our people are construction workers, not truck drivers, and we can basically switch a driver out of a Toyota ute and put them straight into a Hino”
Nigel Scott BMD National Fleet Manager
many of its then-current vehicles for an additional year. Following the pandemic, the decision was made to turn them over but due to the continuing extended delivery times, models such as Nissan Navara, Toyota Hilux and Isuzu Utes were sourced from dealers who were able to supply from their stock.
By late 2024 the eet is now back to its regular replacement cycles where the main replacement criteria is vehicle condition.
“We do look at the kilometres but
condition can be a big factor with small tippers because they do get knocked around working on sites,” notes Nigel. The current replacement cycle generally sees management vehicles changed at three years, utes at four years and the Hino trucks are typically changed over at ve years. A Hino tipper in good condition may even be held for an additional two years because they spend most of their time idling on construction sites rather than travelling.
“I’ve had some of the Hino trucks
handed back in after seven years and they might have only done 50,000 kilometres,” says Nigel. “A challenge can be just maintenance due to the way they can be based on site so servicing can be sometimes overlooked.”
This is a part of the reason all trucks are equipped with GPS trackers which also track the hours of operation to ensure servicing can be scheduled accordingly. “But compared with our vehicles doing high kilometres we don’t see many issues,” Nigel adds.
BMD has a concentrated focus on growth and sustainability, recognising its responsibility to minimise environmental impact while maximising the positive contributions and enduring legacies it can make to communities.
BMD works closely with clients and supply chain partners to reduce carbon
emissions and has introduced the use of electric vehicles and charging stations to many of its site operations.
BMD has trialled some Electric Vehicle (EV) trucks from SEA Electric which were based on Hino 300 Series cab chassis but at around three times the price of a diesel equivalent the sums just don’t add up at the moment.
The Hino Series 300 Electric Hybrid is being considered but as it is not yet available as a factory tipper, the extended time currently required to have a local body built and installed is a barrier. The nature of the typical BMD application essentially precludes a full EV as the trucks spend most of their working life on construction sites where the electricity grid doesn’t become generally available until towards the very end of the project. “It’s fantastic to see the number of
hybrid vehicles coming to market, and BMD is focused on incorporating hybrid options across our eet to align with the government’s New Vehicle Ef ciency Standard (NVES),” says Nigel.
“I’m hoping a hybrid light commercial ute comes out soon in addition to the current EV options.”
The hybrids, according to Nigel, would be great as a tipper option. “The ability to use fuel is vital for our vehicles which can operate on remote site locations,” he says. “We are always looking into what’s coming up so that we can continue to integrate sustainable options which is a core to our business strategy.”
The BMD Group is recognised for its innovative approach to construction and development and the same can be said about the management of its everexpanding in-house vehicle eet.
The experienced ownership team at Josie’s Transport Group are taking the established business to another level as a specialised regional carrier.
Josie’s Transport Group has a proud history in the Geelong region. When new ownership took over in 2020, they were determined to honour the legacy of the original Runia family by protecting its roots while taking the business into the next stage of expansion. When the business, based at Lara, was purchased the existing site was demolished and new of ces and a warehouse were erected. The location is in close proximity to major freight routes with direct access to Melbourne and regional southwest Victoria, a traditional stronghold. The eet is a mixture of company-owned vehicles and subcontractors. There is about 20 late model Isuzu units, and two IVECO S-Ways augmented by use of over 85 subbies which brings allocation of the total vehicle pool consistently well over 100 trucks. Daily runs include Geelong, Colac, Hamilton, Portland, Horsham, Warrnambool, Ballarat, Bendigo and Metropolitan Melbourne. Service is same day or generally next day explains Aaron Cole, Josie’s Transport Group Chief
Executive Of cer.
“Unlike the Melbourne based services there’s no time critical stuff where drivers don’t get paid very well,” he says. “Our drivers get paid well so they stay with us.
That’s really important for us to make sure we have good quality drivers. In a lot of regional areas our drivers are forward facing. Good quality driver means good customer service.”
Trucks dispatched to Geelong typically don’t run fully loaded as that would preclude the pickups scheduled for the afternoon. The cycle is dictated, rstly, by how many pallets are initially assigned the vehicle. Those deliveries will be completed by as early as 1pm at which time the allocators will have transmitted the pickups to bring the vehicle back.
“They will load plan the regional eet,” says Aaron. “By 3- or 4pm they know what’s coming in tomorrow. It’s already in our system generally by 4pm.”
At night, up to 15 trucks will get loaded and the allocators will stage four or ve based on the load plan. The rst semi-
trailers arrive at 4am for Melbourne. Much of the work involves onboarding where that is eventually broken down into pallets or mixed pallets.
“We don’t have to have the trucks here or even the freight here to do that,” says Aaron. “As long as we know it’s already in the system.”
Horsham is, at present, the furthermost point a Josie’s truck will venture. Along with Hamilton and Warrnambool, these destinations are loaded rst so that the freight gets out rst.
Trips, as a result, are staggered.
“You can’t get down too early because nothing will be open,” says Aaron. “So, they will probably leave between ve and six in the morning. The last one will leave around 7- or 7.30. There’s also pickups to do.”
Ballarat is usually loaded last because it can be recovered the same day.
“If we have an issue with a Warrnambool load you can’t actually get down there and back in time,” says Aaron. “Ballarat and also Geelong are close enough. We don’t classify those as regionals.”
Josie’s have a particularly big presence in western Victoria. When new ownership acquired the business, it had two or three vehicles going regionally. Now there’s well over 20.
The company eet is responsible for the regional work as it wants to be able to control that task. Subcontractors, at the minute, take care of most of the Melbourne deliveries.
The rigid eet was recently upgraded, and presently consists of 14-pallet Isuzu FVL 240-300s with automated manual transmissions (AMT). Josie’s invests heavily in this area. The average age of the company-owned vehicles is about 2.5 years old.
The new warehouse covers an area of 2100m². Previously it was 750m² before the rebuild. At the old facility they would have to tarp the freight if it was raining outside and play “Tetris”, as Aaron likens it, when loading.
“When you had to tarp everything, you couldn’t get throughput. Now we can get the volume through,” says Aaron. “It’s rare now trucks are held up. The only
way you can do it is to invest back into the business.”
The new warehouse capacity, being triple in size, was settled on after acquiring KDs Transport.
“We looked at their volumes and we thought we’ll only need double what we had because we’ve got all the hardstand here that we can use and we can use the awning,” says Aaron. “From that perspective we forecast what our work would look like over a period of time.”
There’s also another big area out back that they can grow into if needed down the track. The provision for expansion is now embedded in the business model.
As part of its robust future planning, Josie’s purchased Lightning Transport in 2022. That integration is currently being completed. Until very recently the two eets were being operated separately.
“There’s probably 25 vehicles that we call on from time to time,” explains Aaron. “We probably do more for them than they do for us.”
While Josie’s is known as a Geelong business, Lightning maintains a strong presence in Melbourne Metro, upping the eet presence for its urban customers.
“The reason behind the integration piece is we’re looking at Gippsland early next year,” says Aaron. “The move into Gippsland was the catalyst for that integration piece. We’re looking at sites at the moment around Pakenham. We were looking to commence that later this year, but I just want to make sure that our customers are happy and that our drivers are happy and that there’s no churn from a driver perspective when they assimilate into the new world.”
It’s important that Josie’s handle the last mile. Aaron doesn’t want to on-forward any freight. Ultimately, that remains a strong point of difference for the business. “There’s a lot of transport companies out there that are servicing Victoria but they’re using agents to do the last mile,” he says. “I want to ensure we’re doing the last mile whether it’s our own vehicles or own subcontractors.”
The expansion into Gippsland is further proof the current model is not only successful but t for replication. The second site intended for Gippsland would also service Melbourne.
“I think there’s a real opportunity to disrupt the Melbourne market,” says Aaron. “People are more organised these
days. I’ve been in the game a long time. Fifteen years ago, you’d be taking orders at 4 o’clock in the afternoon. These days it’s all nished by around 1pm because of that improved organisation.”
Offering a next day service into Melbourne, by that token, disrupts the market for the time critical and urgent deliveries. Josie’s is already picking up from South Dandenong in the afternoon and servicing the markets in western Melbourne the next day which is disrupting that time critical task. Having a site in Pakenham would enable Josie’s, essentially, to do all of Melbourne. Once the move happens Aaron and his team, which includes Rhys Rutland Transport Manager, will closely consider procurement of the next vehicles which will be based in the southeast.
“When we started, we only did Warrnambool and Ballarat. Since then, we’ve opened up Bendigo, Shepparton, Castlemaine, Echuca, Albury, Wangaratta,” says Aaron. “This opened up partly on the back of a customer who underpinned that additional work for us. We began going there twice a week and then three times a week. Now we’ve got multiple vehicles. Again, it’s about farming your
customer base and saying this is what we offer. So you pick up ratio and you grow in both lanes.”
Chief Financial Of cer Mark Muscat is overseeing the Lightning Integration and move into Gippsland.
Aaron Cole and Co-Owner Scott Peacock were previously at Kings Transport for nearly 18 years. Aaron started there in 1997. They cut their teeth in the time critical, local Melbourne transport sector before migrating to contract logistics and permanent vehicles. They helped take that business all around Australia and also into New Zealand through both organic and inquisitive growth. After going their separate ways for a few years they were keen to get back together when the opportunity to purchase Josie’s arose.
“We see the regional transport industry as a solution not a commodity,” says Aaron. “In Melbourne you’re a bit of a commodity. Where here you’re a solution. If you can service a number of different regional destinations, you can provide EI, you’ve got all the sign on glass and new gear and discrepancy reporting and KPIs you provide the customers. If you can pick up out of Melbourne and deliver to Albury
the next morning, or wherever it might be, you’re actually a solution. There’s a lot of people in the Me2 game in Melbourne. We don’t want to be in the Me2 game. So that’s why the regional space attracts us.”
Josie’s Transport Group invoices 750 customers a month. There’s room, according to Aaron for further growth and they have already, as a business, spoken to their customers who will support them should they need them to.
Two B-double rated IVECO S-Ways perform linehaul duties though both are actually being used as 22-pallet single trailers. The prime movers were purchased with a 700,000km warranty over four years. They’re a custom build.
“We do a Blood Bank for the Red Cross and we needed speci c orientation of our turntables which IVECO were more than happy to work with us and get all that tted for us,” says Rhys. “When we picked up the vehicles, they were pretty much good to go.”
The standard tting of the turntable is between both rear axles. These units are bogie drive. Generally speaking, the adjustable turntable sits centre and then the orientation will slide back around
300 millimetres.
“With these the orientation had to be situated over the rear axle but still have that capacity to go over forward between both axles and then further back as well,” explains Rhys. “Just the way the trailers are built for the Red Cross. That was a customcustom build.”
The Red Cross mobile units are stationed in Traralgon where people can donate their blood.
“One of the prime movers does linehaul in and out of Melbourne over the course of the day,” says Rhys. “It can go regionally, and the other one will either mirror that as well or it will go regionally just where it is required.”
While a lot of regional carriers have umbilical cords attached to other transport companies, Josie’s is not one of them. That’s a major advantage.
“Fortunately, our customer base isn’t exposed to the vertical,” says Aaron. “Our top ten represents only 30 per cent of our business. Of course, you don’t want to lose your top ten, but we can and we’d be ne because we’re across multiple industries. For a regional carrier that is underpinned by Border Express, StarTrack or Mainfreight, one change in that business and they’re exposed.”
It’s also crucial for the owners of the business to maintain and strengthen the ties to the Geelong area and local communities. That includes sponsoring different organisations and charities in the local area.
“Josie herself was really strong on community engagement, sponsorships and events,” says Aaron. “I want to continue that and be very respectful of their past and the legacy of Josie and the family because we wouldn’t be here without them.”
One of the main allocators at the business Phil Runia, is Josie’s son. Grandsons of Josie have been driving for the eet. It’s still by and large a family business.
“We wanted to keep the feel of that and hopefully, when people enter, they see it’s a calm and a welcoming place,” adds Aaron. “Even though we’re getting fairly big we want to keep that which is really important for the Josie business and Josie’s people.”
Precast concrete components have revolutionised the construction industry. Delivering the heavy pieces to site requires a specialised approach to transport.
When driving around the Melbourne metropolitan area chances are you’ve been supported by bridge and overpass beams produced by Westkon, which also supplies other precast concrete components including traf c barriers, architectural columns and panels, noise reducing walls as well as precast concrete slabs and walls for industrial and commercial buildings.
Westkon has extensive manufacturing facilities in the Melbourne suburbs of Melton and Sunshine and has grown to become Victoria’s largest manufacturer of precast concrete components. Transporting those precast components to site can’t be considered as an afterthought and requires a specialised and experienced approach. Safety is the key priority across the entire operation and for the past ve years Westkon’s component
transport function has been handled by Metropolitan Express.
“Safety is a massive obligation for us all,” says Camille Zeiback, Westkon’s Business Operations Manager. “Safety is in everything we talk about, not just in the transport sense, but in every other way we operate.”
The same non-compromising approach is applied by Metropolitan Express’s Sam Pantou.
“Some people we deal with must think we are obsessed with safety,” says Sam. “I’d rather go on and on about safety than not, because it only takes that one incident to occur and all the great leadership we’ve done over the years gets undone and we get remembered for that one incident which created havoc because a concrete panel or a concrete beam has fallen onto the road.”
Handling precast concrete components
is much different from moving more conventional palletised freight as the operators have to deal with products that are of different shapes, lengths and weights.
Until a few years ago Westkon handled the deliveries of precast components in-house using its own trucks supplemented by sub-contractors.
Camille has an extensive background in transport from a time previous to him joining Westkon and he has recognised the advantages of retaining the trailers while looking at the transport market to provide a better contract logistics solution, which is where Metropolitan Express came on board.
“When Metropolitan joined with us, we already had an established operation, so it wasn’t as if we all started from scratch,” recalls Camille. “We had the basis of how we already operated ready for them to take on and to understand and then further evolve from. We continue to own the trailers and they operate the prime movers. Probably the key parts of the relationship has been greater supervision and safety auditing which have increased signi cantly over the years and most recently under the watch of Metropolitan. We wouldn’t go back to our own setup like it was because the balance we have at the moment works well.”
The trucks are based at Westkon’s facilities along with three dedicated members of Metropolitan’s management staff who oversee the transport
operations. Typically, deliveries are mainly within the greater Melbourne metropolitan area with some regional trips and even a very occasional interstate run. Due to Westkon being frequently involved in supplying components for massive infrastructure projects such as freeways and sporting stadiums, sometimes it can be around the clock night work delivering to construction sites that can sometimes also be challenging to access. The latest information technology is used to support the on-road activities including detailed route planning and having alerts in the trucks and back at head of ce if a driver goes off-route. But the combined operation relies upon more than geo-fencing mapping.
“The fundamentals don’t change,” says Camille. “You’ve got to load it well, restrain it well and deliver it well, otherwise you’ll have problems, and all the bells and whistles of IT won’t really mean much.”
Sam agrees. Operational vigilance is the sine qua non of the game.
“There’s no time for any blasé approaches in this business,” he says.
“You only need to have one incident and it tarnishes your whole reputation.”
Over the last 20 years Metropolitan Express has become renowned for bringing a lot of innovative work practices into its diverse transportation business, and not only talking about safety, but putting safety practices into action to become part of the DNA
of the organisation. In addition to the dedicated activities performed with Westkon, Metropolitan Express continues to provide a diverse service offering to other clients including eets of courier vehicles performing pick-ups and deliveries throughout Victoria, and
crane trucks servicing the construction industry. Metropolitan Express also provides warehousing and 3PL operations from its locations located in Dandenong and Albury. Indeed, Metropolitan Express’s dedication to best practice is re ected throughout
every division of the company’s operations.
The variables in the range of Westkon’s concrete products presents a challenge in the design of the trailer equipment and experience has shown that no individual trailer can meet all purposes, and it has been important not to invest in equipment and then for it to be only used for one project.
The combined experience and knowledge of Westkon’s management and logistics team and Metropolitan’s supervisors is drawn upon to provide the driver’s with a high degree of detailed instructions in relation to the loading, securing and transporting of the components. The induction process for new drivers is broad based and vigorous. As part of its dedication to workplace health and safety Metropolitan Express has also invested time, energy and nances into the development of its unique fall prevention safety system which continues to be re ned.
The approach to recruitment, induction
and supervision of operators shares common goals for both businesses.
“The new wave of drivers entering the market are a lot greener than they have ever been, so we invest more in the training, the trucks, the auditing and the overall safety,” says Camille. “The greatest risk in getting it all wrong is that these drivers aren’t educated enough.”
Metropolitan Express has earned a good reputation for its extensive eet of modern vehicles across its various categories and for the Westkon application the Mercedes-Benz Actros is the prime mover of choice for Sam.
“Both companies are all about safety and the Mercedes-Benz brand is synonymous with safety,” says Sam. “We haven’t had any problems with the Mercedes-Benz vehicles.”
The Mercedes-Benz Actros prime movers are equipped with the latest comprehensive suite of safety features and carry livery for both companies where presentation is important as both companies place a high level of pride in the appearance of the vehicles which is also re ected in the drivers’ positive attitudes and morale. The drivers are recognised for representing the front-line image of both companies and are respected accordingly.
“It’s hard to make concrete look sexy,” says Camille. “We have a focus on how we present at Westkon and I know that Sam is very similar to me in that sense and we’re both very much aligned in what we expect of the entire transport function.
There’s a balance to strike because there is a cost to doing business well and there is a cost to doing business poorly.”
In the highly competitive Australian transport market understanding the requirements of a major customer such as Westkon by an operator like Metropolitan Express has been a major factor in the ongoing success of the business relationship between the two companies.
“Camille knows what he wants, and he is not afraid of asking for it and I like the fact he keeps our guys on their toes,” says Sam.
For nearly 50 years, Garden City Plastics has supplied horticulture products and services far across the country. Since 2021, their partnership with DAF Trucks has further sustained this outreach.
Founded by Lenny and Austral Wilson in 1975 in regional Victoria, and currently managed by their son, Graeme, Garden City Plastics (GCP) has evolved into Australia’s leading manufacturer and distributor of horticulture goods, offering a wide variety of industry stock to clients.
Following steady success under Lenny’s leadership, GCP outgrew its humble beginnings and sought to expand company operations, moving to a twohectare warehouse in Monbulk in 1992. Over time, history repeated itself, and GCP moved again, to Dandenong South in 2016. There, the company purchased an old General Motors-Holden factory, and completely refurbished it into the ultimate facility for horticulturaloriented production and distribution. Fast forward eight years, and GCP employs over 400 staff, with two manufacturing and ve distribution
sites in the country. Operations around Australia are non-stop, according to GCP General Manager, Geoff Allison.
“To accommodate the market, we’ve had to grow,” he says. “We run 24 hours a day.”
The behemoth Dandenong South site is the headquarters of GCP’s panAustralian force, decked out with the necessary equipment to facilitate frequent demand. The site features ten injection-moulding machines, an engine room, a massive machine shop, and employs a multitude of electricians, plumbers, and other workers, stretching for 35 acres.
“Yeah, it’s certainly a large operation,” Geoff says.
From this nucleus of production, contracted B-double trucks embark on long drives to distribute products to customers across Queensland, New South Wales, South Australia and Western Australia.
Geoff attests that GCP’s widespread presence in the country is what gives the company its de nitive edge over competitors in the horticulture, gardening and nursing industry.
“We have warehouses in each state that are full of stock, all the time,” he says.
“We have a system in our warehousing where our stock between locations can be replenished, so it’s kept full at all times.”
GCP’s engagement with growers is, in addition to its large-scale distribution network, also handled by specialised sales representatives and product managers who go out to meet growers face-to-face and assess their product needs.
GCP also maintains its force in the nursing and gardening industry by attending all its trade shows, and even running its own shows, in which it invites the company’s major suppliers to provide technical advice to existing and
prospective clients.
GCP’s undeniable outreach across Australia, providing clients with large orders and highly demanded products, would not be possible without a reliable vehicle eet to make these crucial journeys. GCP’s eet has been sustained by known truck manufacturer, DAF, who shares a close professional relationship with the company.
Since partnering in 2021, DAF has provided GCP with ve trucks out of the company’s current 17-vehicle eet, and more DAF trucks are expected to be added with time. The majority of these trucks are housed in the company’s Victoria site, though one was purchased for GCP’s New South Wales branch in 2023.
“As the older trucks drop off, we’ll be adding some more DAFs,” Geoff says. Muzammil Syed better known under the sobriquet ‘Muza’, is their DAF Consultant at the Hallam Truck Centre.
GCP’s eet has engaged in previous partnerships, collaborating with a Japanese brand for a period, as well as another prominent European cabover OEM, a few of whose trucks are sparingly represented in the company’s current eet.
The ve DAF trucks have quickly proven their worth to the GCP eet and its operations across Australia, strengthening the company’s ability to distribute products on a national scale. The DAF trucks, coming in two models, are each designed to carry out speci c distribution tasks.
The DAF LF290s operate in a 14-pallet application. These have been assigned to distribute many basic products and equipment to customers. GCP has primarily been a manufacturer of plastic plant pots throughout its history, the size of which can vary anywhere from 50-700 millimetres, but the LF290s have also been able to support GCP’s ambitious growing range of product offerings.
GCP now supplies its own aligned products like fertilisers, various plantsupporting hardwares, bamboo stakes to encourage vertical plant growth, chemicals like herbicides and pesticides
to control unwanted plant life, and more. GCP’s truck eet has enabled them to expand their value proposition and cater to more consumer needs.
“We try and give clients a one-stop show to go to,” Geoff says. “Anything to do with trying to grow a plant, we can provide.”
The other DAF model in the GCP range is the CF530. Built with DAF’s highest horsepower capability, running on the PACCAR MX-13 powerplant that
delivers maximum torque of up to 2,600 Nm, the trucks are paired with trailer attachments, designed to carry heavy cargo.
GCP has speci cally been using the Euro 6 DAF CF530s to distribute low-density plastic powder to create hollow plastic hardware. This powder weighs between 20 and 22 tonnes, requiring the CF530s sturdy chassis to support the heavy cargo on interstate trips. The plastic powder is produced by Micropellets, a
subsidiary of GCP established in 2005. Customers apply this powder to the rotational moulding process to create various water storage tanks for their horticultural needs.
DAF’s partnership with GCP has allowed the horticulture manufacturer to continue servicing clients across the country for many nursing and gardening needs, but it has also brought many bene ts to the company’s own drivers. DAF has delivered a high standard
of care and engineering which GCP’s drivers have actively praised, passing on their thoughts regarding the quality of the manufacturer’s workmanship and attentiveness to Geoff.
“The DAF trucks have been fantastic additions to the current eet. The professionalism from the DAF team during the transition to the new trucks, and the service on our existing DAF trucks, has been incredible,” Geoff says, speaking on behalf of the company
drivers. “The comfort of the trucks helps me with long trips. And they’re very good with fuel ef ciency.”
Having grown its presence into every corner of the country, the company’s current priority is to maintain its operational capacity across Australia. Only a few years into a fruitful partnership, the continued integration of DAF vehicles into GCP’s powerful eet can only tighten the company’s rm grip on the nursery and gardening market.
help,” adds Robert who has overseen the introduction of two new units from the Western Star X-Series both 49Xs. The rst of which entered operations in propitious circumstances. It coincided with a 40th anniversary celebration the company held over Easter at its home base in Toowoomba where 200 guests connected to the family, business associates, key suppliers and customers were in attendance. Local dealership Pengelly Trucks & Trailers had the vehicle, painted especially for the occasion, ready in time for the event.
“We had it painted red, white and blue in the same colour scheme as our rst two Western Stars back in 1994,” says Robert. “The truck was very much a tribute for both the business and Scott Pengelly, given those inaugural Western Stars in our business were also two of the rst trucks he sold.”
Robert’s father Barry, Director of Land Transport, was only aware of a new truck purchase. After all he was paying for it. But his sons had kept the details secret. The throwback heritage design made for a nice surprise.
The second Western Star 49X arrived in late July. It too was delivered by Pengelly’s in Toowoomba.
Land Transport provides a regional roadtrain service all over Australia. Western Star trucks form a cornerstone of the family business.
The fusion of camera and radar technology employed on the Active Brake Assist 5 function, a feature of the new Western Star 49X, detects distance and speed to moving and stationary objects in its path. What this does is help determine if braking is necessary. Working down as low as 8km/h, it’s the only system on the market capable of doing so at that speed. Robert Land, National Manager Land Transport is certainly partial to it.
“I always like new tech that comes out,” he says. “It’s always evolving and that’s a good thing. I’ve found the radar on
the truck picks up stuff on its approach really well.”
Active Brake Assist 5, in which the driver initially receives a simultaneous visual dash alert and pulsating warning tone before it escalates to a warning with partial braking and eventually engages in full braking and solid warning tone, should there be no subsequent input from the driver, is one of a host of cutting-edge features that make the new X-Series the most technologically advanced Western Star truck platform yet.
“Any new tech nowadays is a massive
Drivers have so far raved in their appraisal of the vehicles. They’re particularly pleased with the roomy 72-inch cabin — it being the biggest on offer in the market at present.
“There’s plenty of space and comfort is very much a premium for an interstate roadtrain driver,” says Robert. “They ride beautifully with the longer wheelbase as well. The drivers realistically haven’t had anything to complain about. To be honest, it’s all been praise.”
Drivers are unlikely to fault the eld of vision with the surface area 28 per cent larger than the previous Western Star product, making it one of the largest windshields in its class. It comes with 24-inch wiper blades that cross over the centre glass for 37 per cent improved wiper zone.
Pulling roadtrains all over Australia, these Western Stars have no xed route. They are hauling, in the main part,
general freight across three trailers depending on the consignment which changes by the day.
Payload on these combinations runs to 66 tonnes. The new trucks are powered by the latest Detroit DD16 600hp engine. Land Transport has opted for a manual transmission in each truck.
“The new Detroit driveline seems to be great so far. We haven’t had any dramas,” says Robert. “Our fuel burn gures are a little bit better at the moment. The truck is still very new. It’s dependent on the loads of course. The varied loads we roll with makes it hard for us to get constant fuel numbers.
But for what we’re doing the numbers are pretty good in comparison to the legacy model.”
Land Transport runs 24 Western Stars in a eet that currently features 110 prime movers and 320 trailers in total. Operations are augmented by an
new Western Star X-Series trucks for the Penske Australia aligned dealerships. “Western Star is a quality truck,” says Robert. “They haven’t done us wrong since the brand rst entered into our business in 1994. We’ve stuck with it since then.”
These new Western Stars will, at a minimum, be pushed to an estimated 250,000 kilometres on a typical annual duty cycle.
“Most times we’re keeping trucks to 1.2 million to 1.5 million kilometres,” adds Robert. “That’s usually when we will start to consider trading them in.”
Barry and Raewyn Land “took the plunge” back in 1984 when they purchased their rst truck, a Ford Louisville LMT. The Toowoomba head of ce is in the same location four decades later. The company now has 13 depots spread nationwide and it employs approximately 290 staff.
“Being consistent keeps the business rolling through. Especially for our current crop of customers. When we grow, they grow as well, which is always a good thing.”
Robert Land Land Transport National Manager
additional 74 rigid trucks. All up there’s some 600 bits of registered equipment.
Western Star remains one of the company’s preferred partners for spearheading long haul multicombination units. As a primary contractor, Land Transport secures and looks after its own freight consignments which include contracts with global businesses that are ongoing.
“Our freight is varied. We move machinery, seed, chemicals, food. Whatever we can get put on the back of a trailer — we will take it,” explains Robert. “We go where the money takes us.”
Put another way, they will traipse all over the country in every type of condition. The tougher the truck the better.
They also move vehicles including all the
into the model very early on.
“The business kicked off carting machinery and then bringing whatever we could back home,” says Robert.
“It’s evolved since then. With the varied freight model it limits our vulnerability say, should the construction industry become dicey at a certain time we’re fortunate enough that another area will pick up. It might pelt down with rain so next thing we’re busy with is the chemicals we transport. We’ve always got different sectors to lean back on to keep us busy.”
The business has maintained a cluster of depots across northern NSW, a stronghold in terms of moving its regional freight.
“That’s because a lot of transport companies haven’t wanted to extend lead times on the freight task,” says Robert. “They prefer to get to Melbourne in two days whereas if it takes us three sometimes, well that’s ne. But along the way we’re picking up and dropping off freight through all those regional towns anyway at our own depots and eventually we end up in Melbourne at some point or Adelaide.”
Naturally, Land Transport has got freight coming back out of those regional areas, too.
It’s a family affair. Barry is the Company Director. Robert’s brothers Nathan and Ben both work at Land Transport. Nathan manages the Toowoomba depots while Ben manages the one in Melbourne.
The key drivers of growth for the business over the last decade can be attributed primarily to the service it provides according to Robert.
“Being consistent keeps the business rolling through,” he says. “Especially for our current crop of customers. When we grow, they grow as well, which is always a good thing.”
Because they need exibility on their trailers to mix and match the loads, Land Transport uses several different trailer builders. Vawdrey, Freighter, O’Phee and Tuff Trailers are among the key suppliers. Revenue diversi cation was embedded
“If we rip off half a load somewhere there will always be another half a load to whack straight back on it to keep you going where you’re headed to,” says Robert. “One thing we’ve always liked, again working in the regionals, sometimes you’ve got to use on-forwarders as well and that might be a mum and dad out ts running one rigid on a 100-kilometre radius around Dubbo or somewhere and we’ll get them, on some occasions, to take it to the nal destination on our behalf. A lot of those smaller companies have grown as we’ve grown.”
In that way Land Transport helps smaller independent businesses stay a oat on the same business model of which it, too, is reliant.
“That’s one of the things we’re proud of,” says Robert. “Again, when the town prospers, we prosper at the same time.”
Demand for Foodbank WA’s essential services has doubled over the past ve years. To maintain optimal, reliable service levels and support families in need, the organisation has invested in new Isuzu trucks.
Foodbank WA is a food relief charity group dedicated to providing essential food and meals to people in need across Western Australia. A combination of full-time support staff and volunteers works tirelessly to ensure that food gets to where it is needed.
Senior Infrastructure & Logistics Manager Mike McLaren oversees the important distribution of food across the state via truck transport, but that is not all that the organisation does.
“At Foodbank WA, we feed, we advocate, and we educate,” Mike says. “We’re constantly out shouting from the rooftops, trying to get more government support out there to help feed people.
“We also have a whole team of nutritionists educating people on how to eat healthily and cook healthily as well.”
Foodbank WA has seen tremendous growth over the years. Five years ago, it provided about 400 families with access to healthy food and meals. Today, the organisation has extended its capability to provide for 700-800 families. This signi cant increase in outreach requires a lot of work and commitment, but many of WA’s humanitarians are more than happy to help.
“In WA, we’ve got about 85 people fulltime,” Mike says, “and we’ve got 2,300 volunteers actively working with us as well. Some are 60, 70 [years old].”
“We’re not short of volunteers. It’s a great social network for them. A lot of them are retirees who are just giving back to the community.”
The organisation shows no signs of slowing
down, particularly as new challenges affect the Australian people. As a result of the country’s current cost of living crisis, the average change in prices for food and non-alcoholic beverages has jumped by 3.8 per cent from June 2023 to June 2024, according to the Australian Bureau of Statistics.
Amid this crisis, as an increasing number of people struggle to afford necessities
like groceries, Mike and Foodbank WA are more determined to help than ever.
“Everyone is needing money for rent, bills, fuel, kids, clothing, everything,” Mike says. “All those costs have gone up. Foodbank can help reduce those costs. If they come and shop here for $30-40, rather than going to Coles where it’s $300400, that money there can be put into clothing, shoes, fuel, rent, whatever. We’re
just helping people meet those cost-ofliving increases.”
Foodbank WA engages in various partnerships to meet its growing demand across the state, ranging from large food grocers to different transport manufacturers. Much of the food that the organisation receives from these grocers is fresh and healthy produce which would alternatively be wasted.
“We work with all the big supermarkets,” Mike says, “Coles, Woolworths, Metcash, Bega, Harvey Fresh, Ingham’s. There’s plenty of organisations we work with where we can actually rescue food that would otherwise go to land ll.”
In a valiant effort to consolidate Foodbank
WA’s distribution capabilities, Mike has recently upgraded the organisation’s 18-truck eet to include the Isuzu NLR 45-150 AMT.
This model is an essential asset to Foodbank WA’s eet. Equipped with refrigerated van bodies to keep food fresh, these vehicles allow the organisation to make journeys all around the state to provide vital food relief for a greater number of people.
“In the metro area, we’ve got about 30 locations that we go to in our Mobile Foodbank,” Mike says. “Some of the regional towns, they’ve got Mobile Foodbanks as well.”
Foodbank WA’s direct provision of food,
thanks to its reliable truck eet, is what distinguishes the organisation from its counterparts in most other states and territories.
Unlike the rest of the organisation’s States, which exclusively supply numerous charities, Foodbank WA and SA/NT have physical branches for end users who can receive the food they need immediately on a referral basis and have a greater capability to deliver food over large distances.
“We’re mainly 85-90 per cent individuals,” Mike says. “In order to actually come and shop at Foodbank, you phone up charities. If you talk to them about food stress, they’ll send you to us with a referral. We’ll then accept that referral. We don’t judge
Foodbank WA has a fleet of 18 trucks.
who comes through our front door, that’s not our job. We’ll then give them a card that will enable them to shop here for the next six months. It’ll give them up to 75 kilos of produce a week.”
Additionally, Foodbank WA does engage in partnerships with 300 charities in the state, massively contributing to the organisation’s long reach. The Isuzu NLR 45-150 AMT maintains this by distributing food and set meals to those charities, which can provide the goods to more remote communities.
“Those charities spread down to Esperance,” Mike says. “If there’s a charity that is after food, we’re happy to provide them with hampers and that sort of thing.”
Many of Foodbank WA’s own volunteers and staff drive the NLR Isuzu 45150 trucks to branches and charities, which informed Mike’s choice for the trucks to be equipped with automatic manual transmissions (AMTs), to make any long delivery drives as easy and straightforward as possible across long stretches of country roads.
“I’d rather keep the eet all the same, so the volunteers aren’t jumping from one make of vehicle into another,” Mike says. “We’re just trying to keep people familiar with one vehicle as it were. Having an auto
is another thing that will enable them to just focus on the road and what they’re doing as well.”
For Mike, partnering with Isuzu was a nobrainer, citing reliability, cost of servicing and value for money as key factors considered in the decision-making process for acquiring the new heavy vehicles. He said these qualities are deeply embedded in the Isuzu brand.
Isuzu is one of a few major transport collaborators on Foodbank WA. The organisation also works with Major Motors for all eet repairs, and Budget, which provides essential vehicle care to Foodbank WA’s eet after accumulating hundreds of kilometres on food drives.
“We’ve got Major Motors literally two
doors down from us here,” Mike says.
“They’ve got night servicing. Our Mobile Foodbank trucks are out on the road every single day of the week, and we don’t want to let people down. We’ll nish a shift at 2 or 3 o’clock, we’ll go drop the vehicle off, and it’ll get serviced that evening, and then it’s back on the road the next day. To me, that’s a huge positive.”
Armed with a reliable eet of trucks, dedicated staff and enthusiastic volunteers, Foodbank WA’s goal for the remainder of 2024 is the same as it has been since the organisation’s inception.
Mike is committed to continuing Foodbank’s mission of helping those in need and making sure there is enough produce and groceries to feed them.
Australia’s construction industry is facing a labour crunch and supply chain issues, which means builders need to be more cost conscious than ever before. Your vehicles are an obvious place to start. Geotab’s innovative open platform for fleet management helps project managers track assets, increase equipment uptime and lower operating costs seamlessly. Here are three reasons why Geotab’s telematics technology might be the right fit for your construction project:
Track and locate equipment, while ensuring maximum utilization
It’s hard to control costs without visibility over your equipment. There’s a lot going on at a construction site at any one time, but devices such as our GO9 RUGGED can collect data from any vehicle. From fuel consumption to engine hours, our telematics technology connects directly to the vehicle’s computer and efficiently tracks every piece of equipment to ensure it is well-utilised and costed for. And by tracking it, you will always know where it is, which means you won’t have to lease additional equipment because you can’t find it when you need it. Moreover, our real-time equipment tracking can switch between cellular and satellite networks, meaning that costs are tracked and nothing gets lost, even on remote work sites.
Enjoy Fuel Tax Credit Rebates with our data automation
Fuel Tax Credit Rebates can offer substantial savings for construction businesses, especially if they use a lot of fuel. But those savings could be far less if an accountant has to spend valuable hours collecting and untangling the data in order to get the payment processed. Geotab’s solutions can make the process much easier. Our telematics technology can accurately measure on and off-road usage, which is essential data used to claim fuel tax credit rebates. Calculating usage is a different process for construction sites, as it focuses on engine hours instead of distance travelled. GO9 RUGGED can track data on fuel usage and economy, and can also track fuel usage while trucks (such as a cement truck) are stationary and idling.
Access everything seamlessly on our single platform
Geotab offers the greatest possible flexibility for construction projects. Our devices can be attached easily to any vehicle – regardless of manufacturer – and they can send the data to the same platform. Installation is simple, which means it is possible to attach a device to contractor and subcontractor vehicles, giving you visibility over the whole project, and enabling you to track fuel efficiency, fuel burn, RPM, battery oil, engine health and other key indicators. Furthermore, through the multi-streaming function, subcontractors can be granted access to a database for a fixed duration. When the contract ends, their visibility to the site will cease, and the contractor can reassign it to someone else.
Our devices are built tough, to withstand conditions on work sites. Our GO9 RUGGED device is ideal for heavy equipment, construction, utilities, powered assets and trucks. It’s also IP68 and IP69K rated with impact, water and humidity resistant housing.
Begin your journey with Geotab today, into a future where every trip is safe, and every operation is efficient. With our GO9 RUGGED, you can track valuable assets, increase equipment uptime and lower operating costs.
JOST, a longtime supplier for Multiquip, has provided the poultry and transport company with a new Loc-Light fth wheel sensor to trial.
Over the last four decades Multiquip has grown exponentially, becoming a national presence across four states and operating large eets of hundreds of trucks and trailers which are essential to the distribution of poultry farming and the transportation of other goods.
Despite the company’s large size and scale of operations, Multiquip is rst and foremost a family business. Born from Steve and Lucy Mikosic’s purchase of a chicken farm in 1981, and of cially formed as Multiquip Pty Ltd in 1983, the Mikosics and their four children have remained at the helm of the company through its many stages of constant development, remaining essential to its operations. This family structure and in uence seems to have strongly informed the company’s values, with safety Multiquip’s critical priority. This priority is emphasised by Daniel Mikosic, Workshop Manager at Multiquip. “We really want to promote a high safety culture,” Daniel says. “For all our drivers, our staff, everyone in general and also to be able to provide the best customer service that we can for our customers.”
Multiquip’s rapid growth has partly been sustained by the partnerships that have helped add to its operational capacity. The company’s steadfast commitment to safety, on that front, has necessitated it aligns with other organisations that hold similar values.
“We have roughly 300 Scanias which range from the G500 Scania up to the R770. We roughly have about 500 trailers in the eet,” Daniel says. “The majority of the trailers we have would be Muscat trailers, so all the tippers that we have are all Muscats.”
These vehicles take Multiquip’s products and services all over the country, and across a variety of terrain. In addition to product distribution in metropolitan areas, the company’s trucks and trailers travel to and from chicken farms in regional areas along rural roads. Multiquip’s own commercial hatchery is based in Picton, in regional New South Wales, where it hatches roughly
2 million birds a week. Due to these long and potentially hazardous drives, the vehicles in the eet must offer various safety features for drivers.
The Scania trucks, for example, are tted with electronic parking brakes. These brakes automatically engage when the truck’s door is opened and can only be taken off through gear selection when the truck driver’s seatbelt is buckled.
“We’ve worked with Scania to get this in all our vehicles.” Daniel says.
“This spec comes as a standard in a Multiquip vehicle.”
Other essential equipment pieces included in Multiquip’s Scania prime movers, like fth wheels, landing legs and turntables, are supplied by heavy vehicle equipment specialist JOST. In fact, Multiquip has partnered with JOST for much of its lifetime.
“We’ve been using JOST for a number of years,” Daniel says. “From before I even started. It’s been a very long-standing relationship. JOST always supplied us with really good aftersales service, really good quality parts, and the availability of parts has always been very good. They understand what our core values are, and how our business works.”
Under this partnership, the various pieces of equipment JOST supplies to Multiquip has been integral to bolstering the safety, quality, and ef ciency of the company’s truck and trailers. Most recently, JOST has supplied its latest safety provision device for Multiquip to trial: the Loc-Light.
The Loc-Light is a sensor for JOST’s own manufactured fth wheels, implemented to ensure that coupling is correctly completed, and to save time in the transport process as a result. The sensor noti es drivers of unsuccessful coupling via the ‘Go/No-Go’ indicator, displayed as an LED light. A green light will indicate a successful coupling, while a red light, equipped with an audible sounder indicates an unsuccessful coupling. Insecure or unsuccessful couplings have had disastrous consequences for
commercial vehicle eets, as large and valuable payloads can be lost, damaged and pose hazards to other drivers when disconnecting. The vehicles in Multiquip’s large eet undergo hundreds of deployments daily, so the need for correct coupling, it goes without saying, is of paramount concern.
“These trucks and trailers can be unhooked up to ten times in one night,” Daniel says. “So, there are a lot of times for the drivers to have to hook, unhook, and make sure everything is done correctly.”
Since receiving the Loc-Light in early
August, Multiquip has applied it to one of their A-trailers for testing. This A-trailer is part of the company’s live bird eet, picking them up from farms and transporting them to processing plants. In this short period, Mulitquip has been very pleased with the device.
“We have received positive feedback from the drivers.” Daniel says. “It is easier for them to check the coupling, they feel more comfortable with having the extra feature, and knowing when it is 100 per cent hooked up properly.”
Multiquip has found the Loc-Light
particularly useful in mitigating the serious risk associated with night-time coupling and during low visibility days. The Loclight sensors, helpfully illuminates the connection between both vehicles in otherwise dif cult conditions.
“The work that is done, the majority of the time, is done at night.” Daniel says.
“The advantage that we’re nding with the Loc-Light system is that you can easily see where the driver is supposed to hook things up, because of the green light. But then another advantage is that there’s a light underneath where the driver can see the jaw and kingpin of the turntable, and they can make sure it is 100 per cent hooked up.”
Drivers are usually arriving at chicken farms during nighttime hours when there is no external light such as streetlamps or lights from the factory according to Daniel.
“You rely mainly on a phone light or a head torch or something equivalent,” he says.
The Loc-Light has allowed Multiquip to make further progress towards running its operations in the safest way possible, and upholding the company’s key tenet. As yet another successful collaboration in a long partnership, Daniel Mikosic and Multiquip couldn’t be clearer on how they feel about JOST and the product.
“We’re really happy with what they are providing,” Daniel says.
Tickford Racing trusts Castrol fluids in its supercars and transporters. When performance matters, trust Castrol in your trucks.
In commercial road transport, size, contrary to the oft-cited cliché, does matter.
In the road transport industry, maximum payload every trip means the difference between a pro t or a loss. For operators and eets, ensuring payloads are optimised is not only bene cial for increased ef ciencies but help to achieve improvements in productivity across the board. In this area, accurate on-board weighing systems or weighbridges are advantageous.
Tramanco, a family-owned Brisbanebased business established in 1975, manufactures a range of Static and OnBoard Mass (OBM) weighing systems and specialises in this eld precisely. Its agship electronic weighing and data logging systems, particularly CHEKWAY and KWIK-CHEK, are engineered to allow operators to weigh any type of vehicle regardless of their make, model or size.
“Tramanco’s systems are internally monitored for accuracy, damage and
tampering every 30 seconds and any discrepancies are reported in real-time with GPS location and speed,” says Tramanco owner, Roger Sack. “So, they allow the driver to con dently load to maximum payload every trip by relying on the displayed weights they are seeing.”
Both systems share common components and can be used with load cells, air and hydraulic pressure transducers, bending beam transducers and de ection or movement transducers of any type.
Tramanco prides itself for having quality Australian products which, from day one, were designed for Australian roads, loads and conditions. It also writes its own software and, in addition, has several extra programs for a variety of operations such as load/deliver to monitor different products as they are being loaded and then unloaded. Tramanco also provides 100 per cent
spare parts back-up, as well as immediate service reports for mass quality records which are unique to CHEK-WAY.
“This means the operator can be assured that our scales are accurate, and a problem can be diagnosed in real time and then scheduled for repairs,” Roger says.
Without a reliable OBM system or weighbridge to count on, operators are often left guessing what their loads are. What do you do, then, if you are overloaded on one trailer or worse, underloaded on both?
“Remember, only six tonnes of the total load is your pro t if you are fully loaded to 60 tonnes,” Roger says. “What happens if you are down say, three tonnes? Do you just go and hope you don’t get pulled over and weighed, or do you tip another two or three tonnes off the overloaded trailer so that you are just running for the experience?”
The same applies to small trucks such as
a 4.5-tonne 4x2 as well says Roger. “It’s just the size of the loss which is involved in the transaction,” he says. Size, as Roger notes, does matter. To ensure that your payload on any size vehicle remains legal, constant and
pro table on every trip, the solution is to invest in quality weighing systems like the ones available from Tramanco.
“Accuracy, longevity, and quality are never accidents, they are the results of intelligent effort,” he says. “Quality is
that inde nable element which can never be inserted into a product once it has been made, or into a service once it has been given. Nor can it be removed. So always buy quality as it is the only thing that lasts.”
Recent technology advances by Mercedes-Benz have resulted in ever more practical low and zero emission trucks.
The rapid advancement of technology can leave us slightly complacent at times. The iPod revolutionised how we stored and listened to music in 2001, the Blackberry revolutionised mobile phones in 2002, and Steve Jobs turned everything on its head when he presented the iPhone in 2007. Consumers have since enthusiastically adopted such technologies which now play an increasing role in society’s everyday activities.
Electric Vehicles (EVs) have also progressed remarkably in the past few years and only a couple of weeks prior to a recent visit to Germany we were driving around Melbourne in a Mercedes Benz eActros 300 4x2 prime mover with a tri-axle semi attached and were impressed by the truck’s performance and range capability of 300 kilometres. Mere days later in Germany we take the wheel of the next generation eActros 600 semi-trailer combination grossing 40 tonnes.
Mercedes-Benz refer to the small eet of test trucks made available to the media as “near-production” which is engineer-speak for saying there may be still a few minor tweaks to make, but these examples are very close to what will be going to market. The test units are distinguished by their wraps and trailer curtains.
The futuristic-looking Mercedes-Benz ProCabin has a distinctive design which is all about aerodynamic ef ciency and minimisation of energy consumption. Mercedes-Benz has also listened to drivers and incorporated some upgraded comforts including an improved slat style bed with a thicker mattress, as well as a second fridge. Commencing our test drive from the Mercedes-Benz customer centre located at the sprawling Würth factory we travel a 72-kilometre circuit which includes some city and suburban driving, some narrow secondary roads out in the countryside and then the autobahn which, for the uninitiated, can be a real eye-opener. As a road, the autobahn doesn’t appear to be much different from our own multi-lane freeways, yet the ‘fast’ lane (on the left
A High Power Brake Resistor system converts excess electricity into heat when batteries are fully charged.
in Europe, closest to the central median strip) has no set speed limit for most of the autobahn network and a “recommended” 130km/h over much of the other sections. Despite cars travelling at such speeds driver behaviour is the key and slower traf c (including our eActros which has to adhere to the 80 km/hr truck limit) does not even contemplate moving into the fast lane, unlike the lane hogs in Australia who frustratingly seem to get away with inappropriate speeds and create dangerous situations for themselves and others by being in the wrong lane.
The drive for the eActros 600 is through an 800-volt eAxle with two electric motors combined with a four-speed transmission. This delivers a continuous output of 400kW (536hp) with a peak availability of 600kW (an impressive 804hp). The fourspeed transmission also contributes to the effectiveness of the regenerative braking by overdriving the motors when they are switched to regenerator mode. At 40 tonnes gross the acceleration is remarkable and cruising at 80 km/h seems effortless as the truck just glides along. At 60 km/h with the radio volume subdued, the only noises to be heard in the cab are the air compressor and the HVAC fan. Move a little faster and some wind and tyre noise does creep into the cab, but it is minimal in comparison even with the current crop of diesel trucks.
The eActros 600 has three battery packs,
each rated at 207 kWh, resulting in a total installed capacity of 621 kWh. The batteries are based on lithium iron phosphate cell technology and are engineered and managed to provide a long service life. In addition to CCS charging with up to 400kW, the vehicle is also capable of megawatt charging (MCS) with the batteries charged from 20 to 80 per cent in approximately 30 minutes at a charging station with a charging power of around one megawatt. Developments in charging capabilities are also rapidly advancing and Mercedes-Benz engineers report they have successfully charged the eActros 600 to 1,000 kilowatts in an internal test.
The eActros 600 is equipped with a High Power Brake Resistor (HBPR) system which converts excess electricity produced during regeneration braking into heat if the batteries are already fully charged. On the eActros 300 models we drove in Australia a couple of heat exchangers are mounted on the back of the cab. On the eActros 600 we drive in Germany the HPBR is integral, and the heat is dissipated underneath the truck. The HPBR is required to comply with the latest European regulations which require all trucks including EVs to have a secondary braking system, such as a diesel’s engine brake, in addition to service brakes. The driver can select from ve different regenerative braking levels via the operation of the control stalk on the steering column.
Mercedes-Benz’s Predictive Powertrain
Control (PPC) is as effective in this EV as it is in trucks powered by internal combustion engines and promotes the most ef cient operation of the truck with the additional EV-speci c bene ts of minimising battery drain and maximising regenerative braking. These are achieved in part by taking advantage of the truck’s kinetic energy and harnessing downhill momentum to assist in subsequent uphill gradients, and all the while still maintaining acceptable point to point operational times. PPC recognises the upcoming topography of the road via its three -dimensional mapping function and uses route information from the navigation system to minimise unnecessary braking, acceleration and gearshifts, and to use the battery energy as ef ciently as possible. The actual energy consumption and the resulting range depends on multiple factors such as weight, tyre rolling resistance, temperature, weather conditions, traf c volume, topography, driving mode and, the big in uencer, driving style. Energy consumption also depends on which of the three drive programs is selected. “Range” mode restricts motor output to 70 per cent and road speed to 82 km/h, “Economy” mode permits 85 per cent of power and 85 km/h, and “Boost” mode delivers 100 per cent power and a maximum of 90 km/h.
We mainly keep driving in “Range” mode and a check of the calculations at the completion of our circuit shows the eActros’s energy consumption to be around 111kWh per 100 kilometres, in this instance
delivering a theoretical range of about 540 kilometres, which certainly is impressive for this type and weight of truck.
The Interactive 2 multimedia cockpit provides continuous information on the state of charge of the batteries, the anticipated remaining range, and the current and average energy consumption in kWh per 100 kilometres.
Driving on the ‘wrong’ side of the road in the northern hemisphere can be a bit daunting as spatial awareness can be compromised and is not helped by Europe’s penchant for roundabouts and the involvement of a mobile camera crew seemingly intent upon straying into the danger zone and getting very close to the truck while chasing good images. One way of ensuring we keep to our lane is to keep an eye on the eActros’s MirrorCam screens and judge the truck’s overall position on the road by where the trailer appears to be tracking. This is helped further by the second-generation Sideguard Assist 2 which now monitors the traf c on the driver’s side as well as the front passenger’s side. In addition, the system has an intelligent lane change warning, depending on the truck’s position in the lane, and can support drivers on both sides when changing lanes.
The inherent safety of the eActros 600 is built around a new electronics platform using advanced sensor fusion to merge radar and camera data and thus enable an even wider-area view to the front and sides. The electronics platform offers a 20 times higher data processing capacity than previously, and the total of six installed
sensors can now cover an angle of 270 degrees around the vehicle. The ‘600’ is equipped with the sixth generation Active Brake Assist 6 which is capable of performing automated full stop braking for pedestrians and cyclists at speeds of up to 60 km/h. A further bene t of the system is multi-lane monitoring at a distance of up to 180 metres to the front for detection of hazards including slower vehicles. Other systems to bene t from the 270-degree fusion technology are incorporated, such as Active Drive Assist 3 for partially automated driving (SAE Level 2), Front Guard Assist for monitoring the traf c space directly in front of the vehicle, and Traf c Sign Assist for real-time traf c sign recognition. In addition, the eActros 600 is equipped with an EU-compliant external Acoustic Vehicle Alerting System (AVAS) so that pedestrians or cyclists can be made aware of the low-noise electric truck in their vicinities.
The start of series production of the eActros 600 is planned for the end of 2024 and construction material giant Holcim has already placed an order for 1,000 of them. Meantime the eActros 300 rigid and eActros 300 prime mover are arguably the most advanced electric trucks in their respective classes in Australia and are available here right now.
“The remarkable eActros 600 provides a vision of what can be achieved in the future of electric trucking and moves the focus of our electric offering further out from the city-focused eActros 300 models,” says Daimler Trucks Australia’s Vice President Andrew Assimo. “We are currently looking at the role the exciting eActros 600, or a version of it, can play in Australia and will be conducting a local evaluation program next year.”
Travel a few hundred kilometres in Europe and you could be crossing several countries and the eActros 600’s range of around 500 kilometres or more, without any intermediate charging, mightn’t yet manage the entire run of the Hume or the Bruce, but it certainly provides enough juice for practical applications such as multiple trips to the container docks or from DCs to regional centres on Australia’s east coast.
Harness the power of the stars with the Antares 9-inch driving light, designed to illuminate your path even in Australia’s harshest conditions. With Antares, you’ll navigate any road safely and confidently, ensuring you reach your destination safe and secure.
SAFETY & VISIBILITY DAY & NIGHT
• Daytime Running Lamps provide visibility during daylight to alert oncoming traffic
• Unique look position lamps increase visibility in urban environments
TOUGH DRL INTEGRATED COVERS
• Provides stylish protection against sand, dust, mud and bugs.
• Includes distinctive Antares edgelight design
COVER DETECTION
• Switches off main beam when cover applied for greater operating efficiency
• Easily adjust between high and low output for optimal driver comfort
DIECAST ALUMINUM HOUSING & BRACKET
TOUGH CONSTRUCTION
• IP69K dust & waterproof, suits harsh Australian conditions
• Hard-coated UV stable polycarbonate lens
COMPOSITE LIGHTING DESIGN
• 3x projector spot beams exceed 800m distance
• 9x diamond glow position lamp with unique umbrella reflector technology
• 8x wide beam 10W LED clusters for even wider light dispersal (80m)
• With H4 & HB3 adaptors for easy DIY install
The new Antares LED driving lamps from HELLA are set to shine a new light on safety for Australian drivers.
Every aspect of the Antares, a new nine-inch (229mm) driving lamp kit launched by HELLA, is engineered and designed for Australia. An initiative embarked upon by global automotive supplier, HELLA, for the local Australian market, Antares takes careful consideration of the unique driving conditions faced by Australian road users, and includes, importantly, heavy vehicle drivers. Re ecting the brilliance of its namesake, Antares - one of the brightest stars in the night skythese driving lights are designed to keep drivers safe and guided whether on rural and outback highways, winding coastal roads or intricate suburban streets. Plus, these lights boast a sleek and stylish appearance for that added touch of sophistication.
At nighttime or in darker conditions, when the reaction times of the driver are often further reduced, having light that extends visibility both in distance
and width is a must have. The Antares is designed with these needs in mind, incorporating unique lighting features such ‘wide beam cluster LEDs’ and cutouts on the periphery of the light housing, designed to amplify the light thrown even further.
“This is a way for us to put a lot of power out to the sides to get that bigger picture,” says Gregory Foot, HELLA Australia Product Manager. “That sort of technology is important because we have a speci c requirement for it, and not just for spotting road hazards, but also for truck drivers as well.”
Any impact can result in a truck being run off the road with major damages to the vehicle and also the valuable products it is carrying so naturally the more visibility for a driver the better.
“These lights extend up to 80-metres in width out past 150-metres distance, maintaining a width of 45-metres even at 700-metre distance, which is really
impressive. And the main beam can give over 800-metres in forward distance” Gregory explains. “Not only is this great for overall visibility but it signi cantly reduces eye strain and fatigue that comes with driving in low light conditions.”
Depending on the application, truck drivers are not always on straight at pieces of road. Having a driving light that works like a traditional spot light but also with the volume of light should prove highly effective in forestry applications where steep inclines and low visibility are par for the course.
Indeed, drivers don’t necessarily need to be in a regional location to reap the safety bene ts. Industrial estates can be poorly lit after dark whereby other vehicles can appear, with minimal notice, in side streets.
“For truck drivers, it’s about spotting your turn off, illuminating those dark cul-de-sacs and side streets, all the common potential blind spots a driver
might encounter at night,” says Gregory. “When you’re turning in, you want to know what to expect. The same applies to coastal roads, mountainous roads, those environments where having light concentrated in front of you is sometimes less useful.”
In addition, these driving lights play an important role in daylight conditions as well. Daytime Running Lights (DRLs) are now considered a major safety component not just in automotive technology but for applications involving heavy vehicles. As one of the early pioneers of the technology, HELLA understands the many bene ts DRLs provide road users including the crucial role they play in mitigating impacts from oncoming vehicles. Especially in regional areas where overtaking is often necessary and frequent on single lane roads night or day.
“Even on straight road where you think it’s clear and you pull out and someone comes out of the shadows of a high bank of trees or after being hidden behind a heat haze,” says Gregory. “Having a lamp
that is playing a safety role, not just at high beam, but also a working DRL adds an additional layer of safety.”
What’s more, the Antares Position (PO) light represents a major advancement in technology. There’s actually over 50 LEDs in each lamp, many of which provides the glow intensity for backlighting. These can be wired up in line with existing position lights or low beam (check local traf c regulations and ADR 13/00) so that when the lights are activated, they automatically come on and increase the visibility of the vehicle because of the bigger surface area that has been created. Position lights, after all, are about giving the operator more visibility according to Gregory.
“It’s a bit like a lighthouse. It’s not really about projecting light but there to be seen,” he says. “It doesn’t hurt that these POs enhance the curb appeal quite a lot. Everything’s been designed to bend and scatter the light.”
There’s also little domes on the umbrella re ector, which changes the way the light itself looks giving it a distinct glowing presence.
“It’s drawing on our senses to alert other motorists that you are there,” adds Gregory. ”You know, a truck with the Antares looks really gorgeous when they’re running. The shape and style of the light gives it that sense of opulence — it’s functional, visually appealing and ADR compliant as well.”
The Antares can be tted to any truck that has a standardised spot for nineinch (229mm) lamps. It combines three separate beam technologies into one — a combined beam, a broad beam, and a focused beam.
In the interests of making Antares plug in and play, HELLA added a two-position switch to ick between DRL and position light that works on manual operation. It’s completely separate to the main switch according to Gregory.
So with their expert design and powerful performance, these sleek lights, according to Gregory, don’t just turn heads — they rede ne safety on the road.
“The Antares LED driving lamps from HELLA are where innovation and style meets safety,” he says.
Construction of the hydrogen refuelling station at the Viva Energy Hub is underway. Prime Mover was recently privy to an exclusive update on the role hydrogen will play in its planning and infrastructure by the project stakeholder.
Since construction began in early April, progress on the hydrogen refuelling station has been steady. One of a suite of projects in the Geelong Re nery precinct, the site is set to feature both traditional and emerging technologies such as diesel, hydrogen refuelling and EV charging. Scheduled to be commissioned by year’s end, the hydrogen refuelling station has four major partners in non-competing elds already attached. These are Toll, Cleanaway, Barwon Water and local bus eet ComfortDelGro Corporation (CDC).
Hydrogen refuelling is projected to play a major role in the broader energy transition pursued by transport operators actively looking to reduce their Scope 1 emissions. From a business standpoint Viva Energy is a technology agnostic according to Rhys Moore, Commercial Lead - Hydrogen and EV.
“Our priority is to help our customers in any way we can be that EV, biofuels, renewable diesel and hydrogen of course,”
he says. “We see them all playing a role in the broader energy mix. But we think hydrogen has got some great potential in that really dif cult to decarbonise sector of the transport market where heavy payloads and long distances are required for travel.”
As it looks to inhabit an active role in Australia’s broader energy transition, Viva Energy understands there are several business challenges that must be overcome on the decarbonisation front.
“Concurrent to that we have a large customer base that faces similar decarbonisation challenges,” says Rhys. “Large and small transport and anything in between are a big part of our transport fuels and lubricants portfolio.” Increasingly, these customers across the transport, marine and aviation segments are coming to Viva Energy to discuss how it can help in their energy transition plans. Commonly this revolves around the provision of a technology or a suite of technologies that can be made available to help them achieve their emission
reduction goals. Nominally these are Scope 1 emissions whereas for Viva Energy they represent a Scope 3 challenge.
The hydrogen refuelling station at the Viva Energy Hub is a rst of its kind in the Australian market. While its intended purpose is to look, act and feel like a regular service station, it will be unmanned with full public access 24/7. That sets it apart from other hydrogen refuelling depots currently in the market which are found typically in industrial precincts and require security access. Another unique feature of the hydrogen refuelling station is that hydrogen production will happen
on site. Viva Energy will generate hydrogen using a 2.5-megawatt electrolyser and recycled water supplied by Barwon Water. According to Rhys, having 2.5 megawatts of capacity will enable Viva Energy to generate a thousand kilograms of hydrogen per day.
“Really the cornerstone of the project is to be able to replicate as closely as possible today’s diesel’s refuelling pro le,” he says. “While the speeds aren’t exactly like refuelling a truck from a diesel perspective, they’re getting pretty close.”
On average the site is aiming to deliver a 30-kilogram hydrogen truck- ll in 8-10 minutes. Even more uniquely, the system will have the ability to refuel multiple vehicles back-to-back. Over the course of a two-hour period up to ten trucks on an average of 30 kilograms of hydrogen can fuel up.
“That’s right at the edge of where the technology is currently,” says Rhys. “As far as speeds goes, the hydrogen station does have the capacity to do both 350bar refuelling and 700bar refuelling.”
The site was initially designed only for 350bar, the pressure rating at which the hydrogen is discharged into a vehicle. That’s the optimal rating to capture a broad range of back-to-base hydrogen vehicles, such as busses, waste trucks and smaller prime movers. When Viva Energy saw there were some heavy vehicle suppliers potentially moving into the market that required 700bar, they pivoted the project scope to support a greater offering within the market.
“We made the decision to tailor to both options so it gives our customers full exibility when they’re selecting a vehicle, they know that they can come and get it either at 350bar or 700bar,” says Rhys. “We didn’t want to seem prohibitive to anyone participating in hydrogen fuel cell vehicle deployment.”
On that front, the Toyota Mirai and Hyundai Nexo both require 700bar as a standard fuel cell refuelling capability in addition to some of the latest hydrogen fuel cell trucks.
Construction is progressing well. The canopy is now up on site as well as critical infrastructure like the 2.5-megawatt
proton exchange membrane (PEM), the Air Liquide refuelling equipment, the compression equipment and storage equipment required to make the refuelling happen.
“That’s been pretty signi cant itself because to bring those items into the country there’s quite a long lead time,” says Rhys. “We got on the front foot very early and placed those orders with our suppliers for those pieces of equipment.”
Ahead of the of cial commissioning event, a date likely to happen by the end of Q1 2025, Viva Energy will work closely with its project partners when the vehicles are available to come in and test the system. From there, it’s about ensuring that everything is in order before the ribbon is cut and the site is opened up to the broader public. The greater goal is to make the site as user-friendly as possible for the heavy vehicle market.
At present, Toll plans on operating two hydrogen-powered prime movers from the site. Cleanway will match that with two hydrogen-powered waste trucks. CDC will operate two hydrogen powered busses in the local community and Barwon Water are also deploying a hydrogen prime mover for biosolids waste transportation in the local area. Viva Energy expects to announce additional partners down the track.
Located on the Princes Highway, the hydrogen refuelling station at the has 22,000m² of operational footprint that
includes not only the electrolyser, switch rooms, the refuelling canopy, swept paths for egress and ingress in addition to 350kw EV side-by-side fast chargers that are located further along on the forecourt. There will also be an amenities block. “Busses, trucks, and cars for that matter, can pull up like they would at a petrol bowser and refuel their vehicle with hydrogen,” says Rhys. “From a broader hydrogen market perspective, we have the capacity to sell bulk hydrogen from the facility.”
A bulk hydrogen gantry will be used to service tube trailers. For transport operators interested in having hydrogen at their depot in Melbourne, they will be able to pick it up from the hydrogen refuelling station and deploy hydrogen for direct use from their own location.
It’s a positive development, according to Rhys, that Viva Energy has the capacity to be able to service passenger vehicles as well. That in itself represents an opportunity to further explore once they’ve gone live with the project and people can see, touch and feel it.
“We’ve been focused on this being a really pleasing experience for our customers in the heavy transport market,” says Rhys. “We want this to be a showcase for hydrogen and the possibilities it can unlock in the Australian market and that’s where we’ve been focusing all of our attention.”
Reinvesting in the bottom line: value-added solutions for trucking industry managers.
For most businesses, managing costs and reinvesting is key to successful operations. Within the transport industry, Fuel Tax Credits (FTC) are a great way for trucking companies to reinvest the savings made back into the business, but the claims process is too easy to procrastinate on.
Australian fuel tax is added at the pump but can be refunded in the form of FTC for fuel used in business operations in vehicles, equipment, or machinery,
provided certain criteria are met. Despite the potential savings, the claims process is often complex, time-consuming, and prone to inaccuracies, leading many to either leave money unclaimed or overclaim, risking audits and penalties.
“Without technology, an accurate fuel tax credit claim takes a lot of time to process and can often rely on estimations,” says Teletrac Navman Chief Product Of cer, Andrew Rossington. “Automating fuel tax requirements with digital eet
management solutions can signi cantly reduce the time spent managing FTC claims and tax risks, resulting in a more accurate return to invest in other business areas.”
In the face of our cost-of-living crisis, many Australian trucking operators need more hours in the day and money in their accounts. Retaining the money spent on fuel tax is a welcome windfall. With a digital solution like Teletrac Navman’s FTC Manager, a four-year retrospective fuel tax refund review is possible, even if a claim has already been made. It can enable businesses to enjoy a quick in ux of cash and an ongoing solution to managing fuel tax.
For example, Porthaul, a bulk transport business based in Portland, started with a four-year retrospective review of its FTC claims and received a six- gure refund for previously unclaimed fuel tax rebates. “Managing fuel tax is an integral part of our business, so it only made sense to implement a solution that makes it so much easier,” says James Williamson, Porthaul Operations Manager.
This approach reduces the liability and risks involved with claims and empowers businesses across various industries –such as transport, construction, mining, gas, government, and agriculture – to fully bene t from Fuel Tax Credits for heavy vehicles on an ongoing basis by allowing businesses to reclaim a portion, or sometimes all, of the tax included in fuel prices.
Establishing a reliable system for tracking and calculating fuel use and understanding
eligible credits based on the eet’s fuel consumption leads to more accurate FTC returns according to Andrew.
“Many businesses underclaim their FTC entitlements by failing to accurately apportion fuel usage between on- and off-road activities,” he says. “Off-road activities, including travel, idling, and even the use of auxiliary equipment, qualify for a higher FTC rate than on-road activities.”
Businesses may also have incorrect FTC rates in work papers because FTC rates typically change twice a year, in February and August, in line with the Consumer Price Index, and possibly at the end of the nancial year as well.
Another common mistake is applying the road transport FTC rate to fuel used in offroad machinery such as tractors, graders, and loaders rather than the higher off-road FTC rate.
“By addressing these errors, you can maximise your ongoing FTC claims and even recover refunds for fuel used during the past four years,” says Andrew.
What’s needed, therefore, is an accurate Fuel Tax Credit solution.
Teletrac Navman’s FTC Manager is an automated solution that gathers information from telematics installed in vehicles and equipment using real-time, high-de nition GPS data to calculate off-road travel and auxiliary fuel use. This reliance on actual data from each vehicle, rather than average eet percentages, enhances accuracy.
Using high-de nition second-by-second waypoints instead of algorithms to connect the dots between timed position records is in nitely more accurate. FTC Manager, according to Andrew, has the road network mapped out, meaning the system can automatically allocate on and off-road use that you can easily authenticate.
“What’s important beyond GPS position records is accurate apportioning,” he says. “Rather than relying on a single percentage for your entire eet, you can have the correct percentage for each vehicle for every claim period, allowing you to get the
maximum possible refund.”
The added ability to connect up to six items of auxiliary equipment for an operator’s eet, distance travelled, and time idled on road construction and maintenance projects is also managed through FTC Manager, allowing decision-makers to manage FTC across all business areas.
FTC Manager, fortunately, is also backed by fuel tax experts.
“We’ve partnered with Fuel Tax Advisers to provide a unique service that supplies the data to support accurate FTC calculations and completes the complex calculations for you, especially considering the solution is supported by ATO’s product and class rulings,” adds Andrew. “FTC Manager simpli es and streamlines the claim preparation process to help you focus and improve ef ciency.”
No matter whether travelling off the public road network or using fuel for auxiliary equipment, transport businesses won’t miss out on their full fuel tax entitlement.
If you need one or 100 trucks moved, Australia’s leading truck mover will get the job done without fuss. Truck dealers, fleet managers and others in the truck trade rely on Truck Moves Australia every single day to move their trucks across the city, state and country. Since 1988 our national network of experienced drivers has moved more than 500,000 trucks efficiently and safely.
Our comprehensive service includes truck delivery, registration and storage, and we protect your business and reputation with the highest standards of safety, compliance and driver pay and conditions in the industry. When you need a truck moved, we can often pick it up same day and get it moving immediately. We’re standing by to help drive your success.
Call us for a free quote. 1300 885 799 www.truckmoves.com.au
Cameron Bettany has served apprenticeships boat building, and coach and body building where much of the work was manufacturing special vehicle bodies including re trucks. Getting away from the tools, he moved into business development and ultimately specialised in the public sector market.
Prime Mover: Does your role involve more than just selling trucks?
Cameron Bettany: I would say the selling of the truck is almost in the infancy of the overall process, almost a by-product but in a positive way. The rst task for me is to build the brand equity with organisations such as re services and the defence force and get to understand what their needs are now, and also going forward into the future and what is the technology road map for them and how does our product play a role in that. A lot of it is working really closely in partnership with the departments so they understand what we can bring to the table and that we understand what challenges they might face and how we can help solve them.
PM: Is it a long game?
CB: Very much so. We have to be prepared to play the long game in this
role. If you get your kicks out of really quick wins and instant grati cation, you won’t last too long in this sector. You’ve got to have a lot of patience and just constantly think about the long-term sustainable growth you can achieve.
PM: Is the Australia-made aspect of Volvo and Mack Trucks a commercial advantage?
CB: It’s two-fold. The rst factor is obviously the ability to customise the trucks at a local level here and to understand the market well. We work with a brilliant team of engineers, and they understand what we need to build, and also how we need to build it for our region. That’s a real strength. Secondly, government money is taxpayer money and spending that money with an Australian manufacturer translates into jobs. It’s a good economic story any government entity can tell when they award a contract to an Australian manufacturer such as Volvo Group. They de nitely have the public’s support and the support of those end users in these segments when they see the Australianmade badge on the truck.
PM: Are lower and zero emissions emerging factors when dealing with governments?
CB: I think government departments
will be among the rst movers in this technology because they have to be seen to do something, and they’re essentially mandated to do so by the Ministers. They can’t turn a blind eye to it and they have to work emission technology into their eet replacement roadmaps and their capabilities. It also helps to bring the emissions technologies to the overall commercial market.
PM: Are there any speci c examples you can discuss?
CB: We’ve had some success with Queensland Fire with a Volvo FMX electric prime mover as well as another FMX Euro VI 13-litre that’s running on HVO (Hydrotreated Vegetable Oil) fuel. Those two trucks will undertake some testing with Queensland Fire on how they can implement those technologies in the northern region of the state. One is based in Townsville and one out of Caloundra and they’ll do logistics runs for them taking supplies from base to base.
PM: Any other current zero emission projects?
CB: We’ve had a good long-term relationship and an ongoing project with the ACT emergency services agency in Canberra around decarbonising their eet. We’re operating closely with their
working groups to de ne the capabilities and how the technologies which we have t in and then ultimately bring that project together and get vehicles on the road.
PM: What about Defence contracting? What length of life cycle for trucks do you look at?
CB: Mostly they’ll keep those assets in service for 15 or 20 years before they start to look at the next replacement program. The challenge we’ll always have is there will probably be two or three governments within that product cycle as well, so the way of thinking could change dramatically. A focus for us at the moment is the defence force bolstering a lot of its commercial eetoften referred to as the ‘white’ eet - and that’s where we can implement some of the more conventional truck models we have. At the same time, we can look at new technologies such as battery electric or HVO powering Euro VI models.
PM: Is it important to put forth a broad offering to governments?
CB: The global Volvo organisation is quite vast and being the defence and government segments we’re quite lucky that we can look at our complete portfolio. For instance, looking for a total solution for defence is not only about Volvo Trucks but we also look at Volvo construction equipment, Volvo Penta for power generating systems as well as for marine applications. From a Volvo defence perspective, we do have quite an extensive ‘toy basket’ we can choose from to assist in gaining that business.
PM: What features in your personal background assist when dealing with the very competitive re and rescue vehicle market?
CB: My father was a Queensland re ghter for 38 years. Although I never joined, I was on the periphery working very closely with the re service on
vehicle projects. Fire ghters are very well respected within the community and a good bunch of people. Many have trade backgrounds and are quite practical people which lends itself to establishing relationships when you’re dealing with vehicles and speciality chassis. They can be a very discerning bunch and are not afraid to tell you what they think of something. Even if they don’t like it, they’ll tell you that, which is really good to help re ne things and get the feedback from them, but you need to get them on board when you’re introducing something new. There’s no point going to the executive or the commissioner at a re service and say “hey, buy this”. You’ve always got to make sure you’ve got the end user on board, the ‘ ries’ on the ground, because they need to be the ultimate acceptors of the product and the performance of the product, because at the end of the day they’re going to be using it to save someone’s life.
A Churchill Fellowship has provided an Australian transport industry communications specialist with a unique overview of the future of lower and zero emission transport.
The Churchill Fellowship is operated by the Churchill Trust with the aim to provide the opportunity to Australians to travel internationally to conduct research in their chosen eld. Kylie Johnson is the recipient of a 2023 Churchill Fellowship which involved her attending a number of important international events focusing on the bene ts and challenges of low and zero emission heavy vehicles and their potential contributions to the slowing of manmade anthropocenic
changes to climate.
During her career in the Australian media, Kylie has worked as an executive producer, presenter, newsreader and researcher for a number of television and radio broadcasters. In 2006, Kylie saw the emergence of digital media as an opportunity rather than a threat and went on to create the CSIRO’s rst podcast, which became Australia’s number one science podcast at the time.
Kylie for a time managed the communications of the Australian
Trucking Association and was intrigued by what she felt was an important issue for trucking as it dealt with factors relevant to prevailing decarbonisation issues and she could see the parallels which came with the advent of digital media.
“The transport industry had been told to get on board with zero emission vehicles without any guidance about how that was going to happen,” Kyle recalls. “I’m not what people expect when they talk about trucking, and I embrace that, and I was fascinated by what was happening overseas. The Churchill Fellowship provided me the opportunity to travel and to bring the knowledge back to Australia.”
Kylie attended COP28, the 28th annual United Nations climate meeting held in Dubai UAE where world governments discussed how to limit and prepare for what was reported as future climate change challenges.
“I wanted to put the trucking industry on a different stage,” says Kylie. “I’d worked within the industry, and I realised there were a lot of myths around trucking in the general community and I felt this trip might help correct some of that. There was so much happening internationally, compared to here, and I also wanted to spread a bit of Australia internationally.”
Kylie also wanted to help the local industry but was disappointed that things, in her opinion, were so slow to move in Australia. She felt that as an industrial nation Australia had fallen behind when it could have been in front.
“A major reason has been funding being stripped from scienti c organisations and government inaction has been disappointing,” says Kylie. “We are
nally seeing action now, but we are going to have to speed it up if we want to even reach what we have agreed to in the Paris Agreement”.
Kylie was fortunate enough to be in the Blue Zone at COP28, which is where, according to her, the “real decisions” are made.
“I believe I was the only representative of Australian trucking in the Blue Zone and it was such a privilege,” she recalls. “It was incredible to see people from across the world travel to have their say. I heard from their mouths how climate change is affecting them and it was sobering. I think I’ve been in denial about the reality of climate change but when I was at COP28 I realised we simply can’t mess around. We have to get on with this.”
Kylie sees numerous information campaigns in the northern hemisphere acknowledging that lower emissions are a good idea but perhaps industry isn’t yet ready for it.
“As a communications professional I found that situation really interesting,” she says. “It sounds like a great conspiracy theory but actually it’s not, but trying to get a practical EV (electric vehicle) message out to everyday Americans is now almost impossible.”
Kylie discovered numerous positives while in the United States where the Advanced Clean Transportation Expo in Las Vegas was another event she attended.
“It literally took my breath away,” she says. “The Biden administration’s In ation Reduction Act has unleashed a gold rush and private enterprise has come to the party. Predictably, there are some y-by-nighters but there were also some really impressive companies.”
During her travels Kylie was able to investigate the current and emerging emission-reduction technologies.
“Initially, I was wondering which side I fell on, but I don’t need to take sides,” she explains. “One of the most profound things I learned is it’s not one solution or another. Sure, it’s a race like any other race and we are used to that, but it’s not ‘either/or’. It’s hydrogen and electric and also renewable diesel and it’s biofuels and it’s also technologies we haven’t even thought about yet.”
At COP28 there was a lot of talk and those types of speeches Kylie had been previously familiar with having in the past I’ve written a lot of them.
“I know the political swordsmanship and the stunts for the cameras, but I also met people who had travelled from the four corners of the globe to be part of the event,” she says. “People from Sierra Leone who travelled literally on backs of donkeys, on trains, trucks and buses, and three plane trips to get there, but were so determined to get to say what was going on in their country.”
Her newfound knowledge also brought with it some challenges.
“I wrestled a lot at COP28 about how
I was going to convince the Australian trucking industry that climate change is real,” says Kylie. “It doesn’t matter if the industry believes in climate change or not, because the regulations are going to come in regardless and industry is going to have to accept it. That’s not saying that the trucking industry are a lot of Luddites and don’t believe in any of this, because they see effects of climate change every day through their windscreens.”
Kylie’s overall intention was to learn what was happening overseas and what changes were coming for Australia, and to look at what industry needs to do now, and into the future.
“I want to make sure we’re actually protected as an industry because the livelihoods of people are on the line here,” she says. “I want to keep working with industry and make it as straightforward as I can and ensure industry is as ready as possible.”
Kylie, however, is still trying to nd a central source of information in Australia where people can access everything.
“The California Air Research Board (CARB) has a brilliant platform but nothing similar exists here and we know there is a need for it,” she says.
“I’ve worked with scientists, politicians and academics for almost my entire career and did a lot of media training with them to help them communicate very dif cult and complicated things to ordinary people. I’d like to set up a group who communicate this to the general public so they can actually grasp and understand it, and make it simple, not because people are stupid, but because they’re busy and they’re confused.”
Kylie adds, “I think if we come together and determine a solution, we can make this work for trucking as well as the climate.”
(public) statistics do not split the prime movers into these two categories. The two factors involved here are the number of motor vehicles by type on the roads and the distance travelled by those motor vehicles. There are more rigid trucks than prime movers. But the prime movers probably travel a lot further per trip. The number of crashes involving each type is about the same.
There are two important ideas in this article. Firstly, Australia needs an Of ce of Heavy Vehicle Safety probably within the NHVR, or associated with it. The purpose of the Of ce would be to propose actions by government and industry that could substantially reduce the level of harm experienced. This would cover both road trauma and industrial accidents. Secondly, much can be learned by using statistics from different data sources and by adding vehicle knowledge into the safety considerations.
This article presents a sample of data from multiple sources in graphical form to show how additional insights into the HV road safety challenge can be gained from merged data sources. The statistics for Australian road trauma were recently released by the BITRE (Canberra). Figure 1 shows the road trauma involving a heavy vehicle type in the 12 months up to June 2024.
Figure 2 shows the HV-involved fatal crashes according to state population. The standout jurisdictions are the Northern Territory and South Australia. Why? They are neighbours.
Figure 3 shows the number of fatal crashes involving a heavy vehicle in each state divided by the number of that type of heavy vehicle registered in that state. The smaller the bar the better. The state of registration of the trucks involved is not (publicly) reported by
- June 2023 to June 2024 (BITRE)
BITRE. Heavy vehicles can be involved in an incident outside the state of registration – they are mobile. The high bars in Figure 3 identify performance that needs explanation.
ARTSA-Institute could play a positive
role supporting an Of ce of HV safety. However, it needs to be established by government.
Peter Hart, ARTSA-I Chair
Businesses across the road transport industry are under pressure. Driver shortages, an ageing workforce, tightening margins, and increased fees and nes are threatening the sustainability of the industry and, by extension, our national supply chain. In this environment the demand to get more drivers behind the wheel, to keep trucks moving, and keep businesses a oat, is growing. When poor regulation adds to this pressure, real dangers emerge.
Time-based licensing models that focus on duration over competence, the rapid provision of multi-combination (MC) licences, and accepting overseas licences without relevant experience are just a few examples.
While these methods might help ll the immediate need for drivers, they also bring signi cant risks. The rush to ll driver shortages should not come at the expense of safety, but unfortunately this is already happening. Drivers are nding themselves in charge of larger and larger vehicles without adequate preparation or experience. We need a more thoughtful, deliberate approach to licencing that ensures every driver on our roads is equipped with the knowledge and experience required to handle the realities of the job.
Time-based licencing is one area that needs reform. Just because a driver has held a licence for a set period doesn’t mean they’re capable of handling
the complexities of a large truck on Australian roads. The industry needs to move towards a competency-based approach, where drivers are tested on their ability to handle a vehicle in different conditions, not just how long they’ve held their licence. Similarly, overseas licences cannot be assumed to be suf cient in the Australian context, where road conditions, vehicle sizes, and local regulations could be very different to the country the licence was obtained in. That’s why we need a system that ensures all overseas drivers undergo testing, as well as additional training before they’re allowed to operate here.
The number of licence categories and the speed with which drivers can obtain an MC licence is also cause for concern.
It shouldn’t be possible to jump from operating a smaller vehicle to a fully loaded roadtrain in a matter of months without demonstrating the competencies needed to safely operate these vehicles.
The process needs to ensure that drivers are gaining the right experience before moving up to larger vehicles.
What we need is a nationally recognised system of training and licencing that prioritises demonstrated practical experience. This will give businesses con dence that drivers are truly ready to take on the job. The risk of unsafe practices can be signi cantly reduced through an education system that equips drivers with the knowledge they need to
stay safe on the roads.
Our licencing system must also be adaptable. As technology evolves and vehicle designs change, licencing processes need to allow for these advancements, ensuring that drivers are always operating with the most up-todate knowledge and skills. Career pathways also need to be established to encourage new entrants into the industry. With an ageing workforce, the industry is in desperate need of young drivers who see truck driving as a viable and rewarding career. Building clear pathways from training to employment will help attract the next generation of drivers while ensuring that they’re properly prepared for the demands of the job.
The bottom line is that licencing reform is not just a nice-to-have – it’s essential for the long-term viability of the trucking industry and the safety of road users. By ensuring that drivers are properly trained, licenced, and supported, we can maintain the safety, reliability, and sustainability of our national supply chain.
Unfortunately, the pace of change has been slow, and the industry is feeling the impacts now. But change is possible, and NatRoad is working hard to advocate for the necessary reforms.
Warren Clark National Road Transport Association CEO
TONY MCMULLAN
During the course of this year, in this Prime Mover column, I have touched on the challenges that the Australian heavy vehicle road transport sector faces in its quest to decarbonise. I have detailed that many applications within the sector have no current technical, or economically, viable decarbonisation solution, hence making them hard to abate segments. Further, I have detailed that there will be no one ‘silver bullet’ to solve this issue, nor will the heavy vehicle road transport sector decarbonise ‘overnight’. Rather, a raft of technologies and solutions will need to be deployed, over a period of time, in order for the sector to meet our government’s international commitments to reach net zero by 2050.
In my August column, I outlined a number of pathways that should be targeted by the heavy vehicle road transport industry and supported by appropriate government incentives to further the already started decarbonisation journey. These are:
• Freight consolidation. Moving more freight to higher productivity vehicles.
• Low carbon fuels. A R20 diesel fuel (20 per cent renewable diesel blend) run across the entire truck eet would result in an approximate 18 per cent reduction in CO2 emissions.
• Accelerated uptake of low emission (hybrid) and zero emission (battery
electric) trucks.
• Intermodal shift. Diverting more container movements from seaports to distribution hubs via rail and not truck, would reduce not only CO2 emissions, but ease traf c congestion and have improved road safety outcomes.
• Social change. An awareness campaign detailing how consumers could reduce their CO2 emissions
The issue of sustainable, or renewable, or low carbon, fuels is gaining attention, however there is also a degree of misinformation being populated about these fuels. To start with, the term low carbon fuel is not technically correct, as these fuels have about the same carbon content as mineral diesel, that is where the energy of the fuel is derived. Sustainable, or renewable fuel, is a more appropriate term, as these fuels are typically derived from plants that have captured CO2 from the atmosphere while growing and that CO2 is released again when the fuel is burnt in an internal combustion engine (ICE). The net result is no net gain in CO2 released into the atmosphere. There are some caveats that need to be applied to this process. Energy will be required to grow, harvest, transport and process the plant crops to produce sustainable fuels and depending on how ‘green’ these processes are, will determine the level of CO2 intensity of the fuel. There are international carbon accounting measures that are used to calculate how sustainable any speci c batch of fuel manufactured by this process is. Currently, R100 (100 per cent renewable diesel) being used for truck and machinery trials in Australia, supplied from Singapore, offsets just over 90 per cent of CO2 emissions when compared with conventional mineral diesel. Hence justifying the comment above that a R20 diesel blend
in Australia could provide 18 per cent CO2 abatement.
Another issue that gets raised in sustainable fuel discussions is that of land use, food versus fuel crops, etc. Currently Australia exports approximately 60 per cent of its canola crop to Europe and Asia for sustainable fuel production, while the majority of our used cooking oil is exported to the USA for their sustainable fuel manufacturing. Were Australia to keep and process those feedstocks here in Australia, we would go close to providing enough renewable diesel to run our truck eet on a R20 renewable diesel blend, without land use change, nor effecting the canola supply for food products. Renewable diesel is not the only sustainable fuel that could be used to power trucks in Australia, bio-diesel, biomethane and green hydrogen are other examples of sustainable transport fuels. All these fuels can be used in internal combustion engines (ICE), however only biodiesel and renewable diesel can be used in conventional diesel engines and there are limits on the percentage of these fuels, particularly biodiesel, that a conventional diesel engine can operate on without some modi cation. However, renewable diesel is chemically the same as mineral diesel and can be used across existing, storage, transport and refuelling infrastructure and trucks, making it the most viable sustainable fuel option at present.
Sustainable fuels are not the sole pathway to decarbonising trucks in Australia, however they can provide signi cant CO2 abatement in the short- to midterm, allowing time for other low and zero emission technologies to evolve to become practical and commercial realities for road transport operators.
Tony McMullan CEO, Truck Industry Council
The introduction of the Closing the Loopholes legislation, which took effect on 26 August, marks a signi cant turning point for Australia’s transport industry. As the CEO of the Victorian Transport Association (VTA), as well as National Secretary For the Australian Road Transport Industrial Organisation which advocated for the legislation, I wholeheartedly support these new laws, and believe they will bring substantial bene ts to transport operators and their workers.
The transport industry is the backbone of Australia’s economy, facilitating the movement of goods and services across vast distances. However, for too long, our industry has grappled with challenges that stem from outdated regulations and exploitative practices. The Closing the Loopholes legislation addresses these issues head-on, creating a fairer and more sustainable environment for all stakeholders.
One of the most critical aspects of this legislation is its focus on closing the gaps in existing laws that have allowed for unfair practices to persist. The transport industry, particularly in sectors like road freight and logistics, has been plagued by the exploitation of workers, especially those in vulnerable positions. Casual and contract workers, who make up a signi cant portion of our workforce, have often been subjected to insecure employment conditions, inadequate pay,
and a lack of access to essential bene ts. The Closing the Loopholes legislation introduces measures to ensure that these workers are treated fairly and with the respect they deserve. By tightening regulations around casual employment and contract work, the legislation will help prevent the exploitation of workers who have long been denied the stability and security they need. This is not just a win for the workers themselves but also for transport operators who strive to maintain ethical and sustainable business practices.
Safety has always been a paramount concern in the transport industry. However, the loopholes in current legislation have sometimes led to practices that compromise the safety and wellbeing of workers. For example, some operators have taken advantage of ambiguities in the law to push drivers into working excessive hours, leading to fatigue and increased accident risks. The new legislation addresses these concerns by implementing stricter regulations on working hours and conditions. This will not only protect workers from being overworked but also ensure that our roads are safer for everyone. A well-rested driver is a safer driver, and by promoting better working conditions, we can reduce the number of accidents and incidents on our roads. Moreover, the legislation will require transport operators to take greater responsibility for the wellbeing of their workers. This includes providing appropriate training, access to mental health resources, and ensuring that workers have the support they need to perform their jobs safely and effectively. In an industry where stress and long
hours are common, these provisions are crucial for maintaining a healthy and productive workforce.
For ethical operators who already adhere to best practices, the Closing the Loopholes legislation is a welcome development. By leveling the playing eld, the legislation will help ensure that businesses that prioritise fair treatment and safety are not undercut by competitors who exploit loopholes to cut costs. This is particularly important in an industry where margins are often tight, and the pressure to reduce costs can lead to unethical practices.
With the new regulations in place, ethical operators can compete on a fairer basis, knowing that their commitment to doing the right thing is recognised and supported by the law. This will foster a more sustainable industry, where businesses can thrive without compromising on the principles that matter most.
The Closing the Loopholes legislation represents a signi cant step forward for Australia’s transport industry. By addressing the gaps in current laws, the legislation will create a fairer, safer, and more sustainable environment for both operators and workers. As we move forward, it is essential that we continue to support and advocate for policies that promote fairness, safety, and wellbeing in our industry. The VTA is committed to working with all stakeholders to ensure that the bene ts of this legislation are realised and that the transport industry can continue to thrive in a fair and equitable manner.
Peter Anderson CEO, VTA
At Isuzu, we’ve always taken great care of our customers.
will have to be taken into account at some point and the market snapshot may have to be measured in other ways such as dollars rather than just raw units.
We’re Australia’s number one truck… an honour we’ve held for over
That means more businesses put their trust in us than any other truck brand.
The Truck Industry Council statistics for new truck sales in Australia during August totalled 3,155 prime movers and cab chassis, 135 units more than in the previous month of July (+4.5 per cent) and 229 less than during August of 2023 (-6.8 per cent). The year-todate (YTD) truck total of 26,144 units, shows 1,453 less than at the end of July but maintaining the same difference of -5.3 per cent when compared to the same period in 2023.
We understand that reputations are riding on us and that’s why Isuzu Care is more than just an aftersales service package.
It’s part of our DNA.
From day one, we support customers and demonstrate that reliability is everything. We pride ourselves on being proactive and always going the extra mile.
The Heavy Duty category clicked up 1,308 new units for the month, which was 101 less than during August last year (-7.7 per cent) and the YTD total of 11,328 was just 72 units less than for the rst eight months of 2023 (-6.4 per cent).
And as we look to new frontiers, we’re finding new ways to help our customers exceed their goals.
Isuzu Care is what sets us apart.
Always has, always will.
Medium Duty trucks showed 657 new units for August, taking the YTD accrual to 5,316. The month-on-month difference from August 2023 was just 36 less trucks (-5.2 per cent) and the YTD reached 5,316 which was 89 less than at the same point in 2023, leaving the category only 1.7 per cent behind the progressive accrual rate of last year’s record result.
The Light Duty category achieved 1,190 new trucks during August, which was 82 less than in August 2013 (-6.4 per cent) and the YTD total of 9,500 at the end of the month indicated the category is unlikely to be setting any records for the full year of 2024, being already 1,614 units down (-14.5 per cent) with just four months of the year left.
The large Van market had another strong month, bolstered, of course, by the inclusion during the past couple of months of the results from Chinese manufacturer LDV and French OEM Peugeot, helping take the month’s total to 959 vans. The addition of the orders of these two manufacturers may have skewed the total results in a positive way when compared with 2023, but the category was already running around 30 to 40 per cent more during the rst half of this year when compared with 2023. Vans YTD for the end of August of 3,664 shows a year-on-year growth of 93.9 per cent, but it was already running at +43.3 per cent at the end of June before the LDV and Peugeot numbers were added. It will be some time before the slowly increasing number of electric trucks coming to the Australian market will start to have an effect on overall sales. The additional investment required, not only for the vehicles themselves but for the required charging infrastructure,