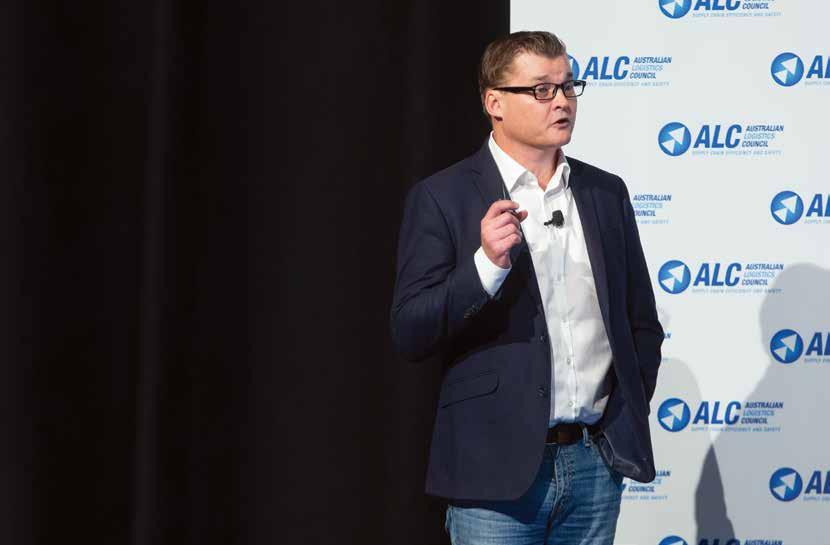
10 minute read
Personality
SAFETY MANAGEMENT:
THE PARADOX VIEW
At a standing room only presentation at the 2019 ALC/ATA Safety Summit held in Sydney, Greg expressed his fervent concern about organisations committing significant resources into systems of safety management which can increase legal risks and threaten, rather than improve, actual safety outcomes. Greg also spoke with Prime Mover magazine with the understanding that his comments are general in nature and not to be construed as legal advice. PM: You use the term ‘safety paradox’. How is it that safety administration can be a threat to safety rather than a solution? GS: The great majority of what we do in the name of health and safety is about the collection of evidence based on activity and has nothing to do with safety. Most reports are merely a measure of activity and I would suggest tell absolutely nothing about whether the health and safety of the business is being adequately managed. In the case law that I’ve worked on for the last thirty-odd years there is not one example where a company has presented their monthly health and safety report as evidence that their systems are safe. When we look at a large number of safety initiatives, not only do they not create a safety benefit, but in many cases they actively undermine the things we want to achieve in health and safety. PM: The amendments to the Chain of Responsibility legislation in October last year have put more focus on contracts. Should transport operators be concerned? GS: The relationship between legal A LAWYER WITH WAYLAND LEGAL WHO SPECIALISES IN THE LEGAL ASPECTS OF HEALTH AND SAFETY MANAGEMENT, GREG SMITH IS THE AUTHOR OF A NUMBER OF BOOKS INCLUDING CONTRACTOR SAFETY MANAGEMENT WHICH WON THE 2014 EDUCATIONAL AWARD FROM THE WORLD SAFETY ORGANISATION.
risk management and safety risk management translates into a lot of what we do in the name of health and safety in the contractor area and can actually increase our legal risk. You have a lot of well-intentioned amateurs trying to tell experts how to do their job and when they do what you tell them, it means you have just taken control. If an electrician comes to your home, you show him where the fuse box is and then leave him to do their thing, yet in the workplace, all of a sudden, we become the experts in what contractors should do.
PM: Can you comment on the current trend towards multiple compliance regimes and audits? GS: My great fear for the health and safety management industry is that we are being exposed to more pressure to create more nonsense supposedly in the name of legal defence but I think that direction is going to make workplaces less safe. You have to weigh up what is the actual safety benefit because a lot of what we do in the name of health and safety management does (a) absolutely nothing to improve safety outcomes and (b) despite your best intentions with the mountains of checks you are developing, it does absolutely nothing to mitigate legal risk. In fact, often, you are actually increasing it. The only people who read most of your policies and procedures are lawyers and regulators after accidents. I think there is a significant body of evidence which tells us that the way we approach safety management at the moment actually makes workplaces less safe because what we are doing distracts the organisation away from the true risks.
PM: What about the basics such as pretrip checks? GS: We should get rid of the zero harm logos off our shirts and put ‘tick and flick’ on there instead. ‘Tick and flick’ positively undermines safety because it disengages the people who are doing the job and it creates an illusion of safety. Check lists have very little evidentiary value other than to show you that you weren’t doing what you’d said you’d do.
PM: Do ‘lost time due to injury’ rates provide a valid metric? GS: Almost every major accident enquiry that I’ve dealt with over the past 30 years has said words to the effect that injury rate data is just pointless. At least two major enquiries have said that reliance on injury rate data distracted the organisation from the critical risks in the business and was a causal factor in the incident which was being investigated. And yet it is still the primary measure. It’s just nonsense that doesn’t tell us anything about anything that matters. Find me a single case or enquiry where the defence has said ‘here is our injury rate for the last four years and that is evidence that we have a safe system of work’.
PM: Is there any value in how the changes to CoR have ushered in
Greg Smith.
additional compliance burdens for many transport operators? GS: For too long the safety tail has wagged the dog around commercial arrangements and it results in a really bad disconnect. It would be better if on a case by case basis you enter into your commercial arrangements first, understand how you want to manage your contract and how you want this thing to physically work, and then all the health and safety person needs to say is if that is the way in which you want the contract to operate these are the safety consequences of operating that way.
PM: Do you have any final thoughts? GS: If I could just leave you with one thought, it is the safety paradox methodology. Look at what you are doing for safety. Is it achieving the outcomes you want or is it undermining the outcomes you want to achieve?
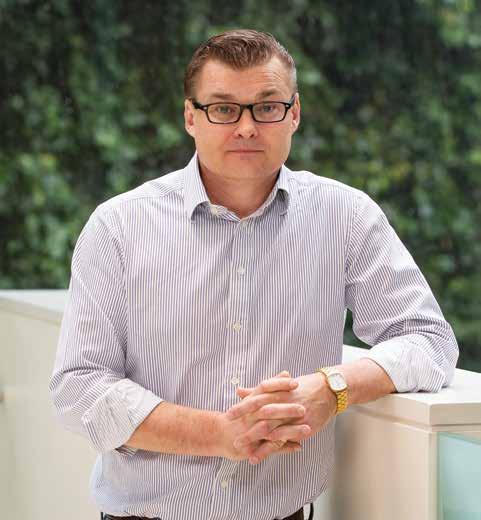
KNOCKS OPPOR
EMMA THOMPSON WORKS FOR NEWCASTLE-BASED LIQUIP DISTRIBUTOR AND TANKER BUILDER, DURHAM FABRICATIONS. AT THE TIME SHE JOINED THE BUSINESS, IT WAS A COMPLETELY NEW CAREER PATH AND ONE THAT HAS SINCE TAKEN HER ON AN EXCITING LEARNING CURVE IN THE TRADITIONALLY MALE-DOMINATED TRANSPORT INDUSTRY.
The trucking industry is not historically frequented by female participants. For Emma Thompson It must have taken a good deal of courage and conviction to step out of a comfortable and familiar career into one that was completely foreign. This meant, 16 years ago, leaving an account administration background and prior to that a career managing a hairdressing salon after completing a hairdressing apprenticeship. Having since risen through the ranks at Durham Fabrications, she now occupies the role of Operations Manager, a position she has held for the past three years. “I was looking for a career change and wanted to be involved in something different from what I had done before – a career that would keep me motivated and provide me with the opportunity to grow and continue to learn new skills,” Emma explains. “As such, when the opportunity came up for me to join Durham Fabrications, I grabbed it with both hands. I knew it would not be easy and I would have a lot to learn, but I also knew that I was more than up for the challenge.” She has not regretted the move having seized upon the challenge to better herself in the role. Over the years she
Emma Thompson.
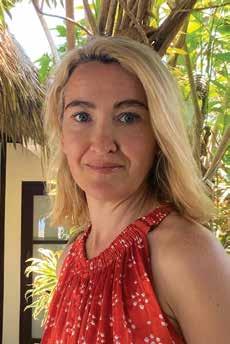
has relished the ability to increase her knowledge and understanding of the Liquip product range and the bulk road tanker repair and servicing procedures offered by Durham Fabrications. Emma is married and has two young boys, so juggling a full-time career with her family commitments is a constant challenge. Yet, to this end, she says she is very grateful to have a flexible working arrangement with her employer. “I start and finish work later than the team which gives me the opportunity to drop my children at school,” she says. “It is important to me that I maintain a good work-life balance. While I don’t usually get to see the children until late most evenings, it is nice for me to be at home of a morning making sure they are equipped for their school day.” As Operations Manager, Emma says her number one priority is customer service. She has her finger on the pulse across the entire enterprise. This includes visiting clients to make sure they are happy with the services the company is providing them. “I am across all aspects of running the business including making sure we keep the fuel terminals loading the tankers and the tankers on the roads,” she says. “The thing I love most is that every day is different. Someone may need a part that has suddenly failed, and someone else may need some extra advice on a technical enquiry or an urgent repair. If our workshop personnel are flat strap and I can answer a question or help a client, then I most certainly will.” One of the benefits of her flexible working hours is that at the end of the day, after the workshop and admin employees go home, Emma has the chance for some quiet time and to get things done without distractions, although more often than not, she adds
TUNITY
As Operations Manager Emma’s number one priority is customer service.
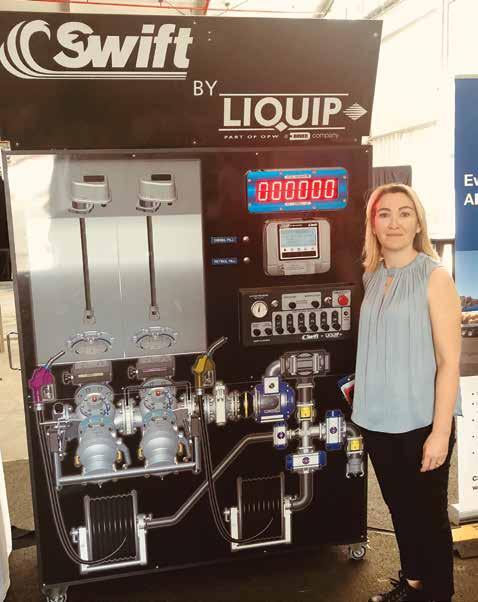
with a laugh, the phone keeps ringing. “To me that’s a great indication that at Durham Fabrications we are doing things right and providing our customers with the expertise and services they value,” Emma says. Her motivation to develop new skills is still strong while the chance of accomplishing additional feats in the job continues to inspire enthusiasm even as she recalls some of the early highlights of her career. “I could never have imagined that my career path would lead me to supply metering and pumping equipment to a company on one of the Australian islands for their farm fuel upgrade, or measuring and supplying a loading arm to one of the bulk fuel terminals in Newcastle,” she says. The opportunity to provide and promote the latest products and services,
according to Emma, in which the company specialises, is an ongoing cause for excitement. She recalls with fondness when she worked with a client and the workshop team to deliver the company’s first 25,000 litre fuel tanker built to dangerous goods specifications last year. “There’s nothing better than getting a call from the client at the end of a build telling you how happy they are,” she says. Among the many elements she finds most enjoyable in working within the transport industry she cites the many different people she gets to come across. As Durham Fabrications is centrally based in the Newcastle suburb of Cardiff in New South Wales, clients come from far and wide to avail it of its services. “There is always someone new to talk to or meet,” she says. “There may be a new fleet maintenance manager or I might get to chat with a tanker driver that I have known for 16 years. For me it’s the people themselves that make it the great industry it is and they each have a unique story to tell.” Emma adds, “I particularly love the fact that I am part of a company that contributes to the way products make their way to the consumer.”
EXHIBITION SPACE NOW ON SALE
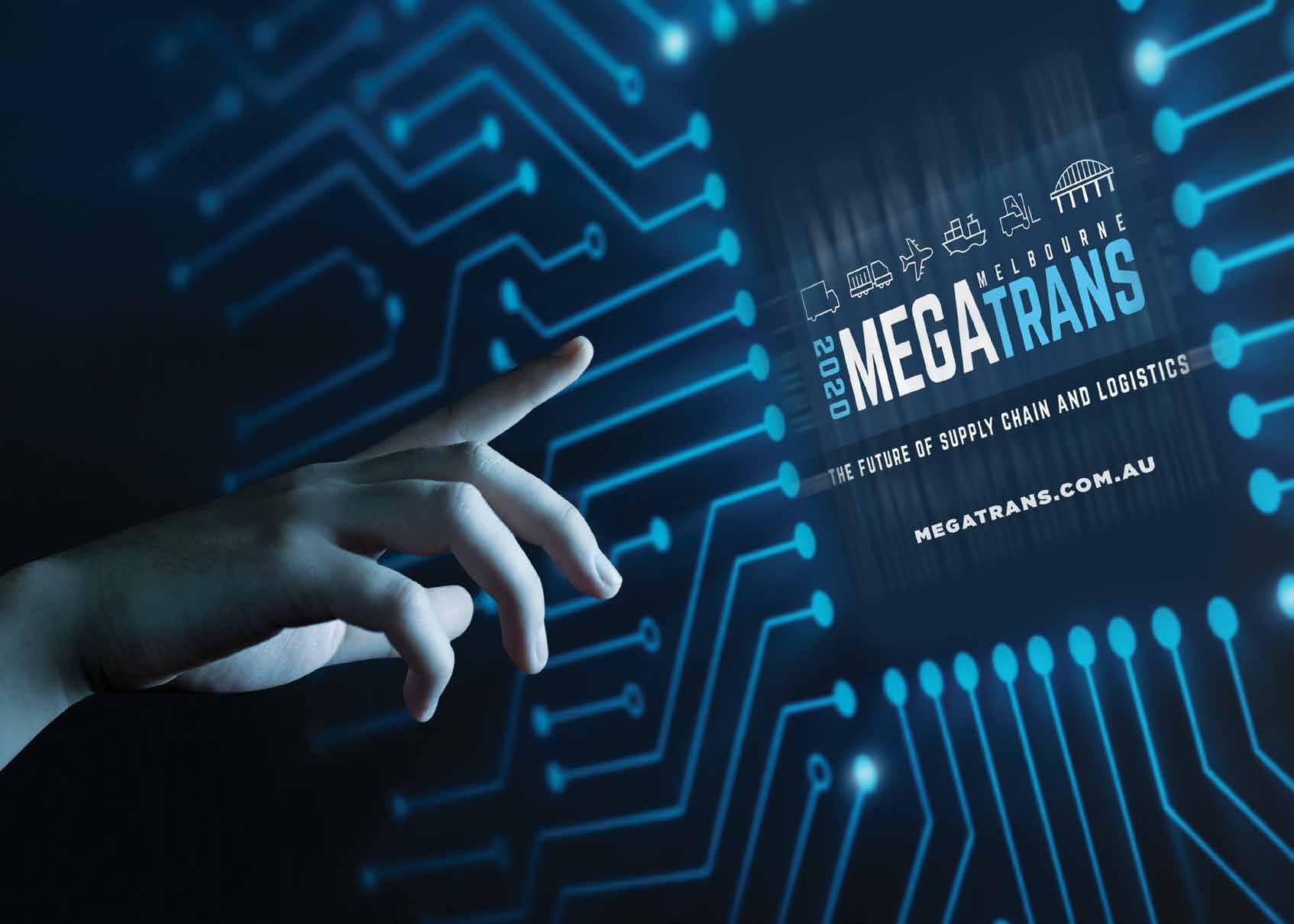
1ST - 3RD APRIL 2020 MELBOURNE CONVENTION & EXHIBITION CENTRE



SUSTAINABILITY | AUTOMATION INDUSTRY 4.0 | E-COMMERCE
SUPPORTING SPONSORS
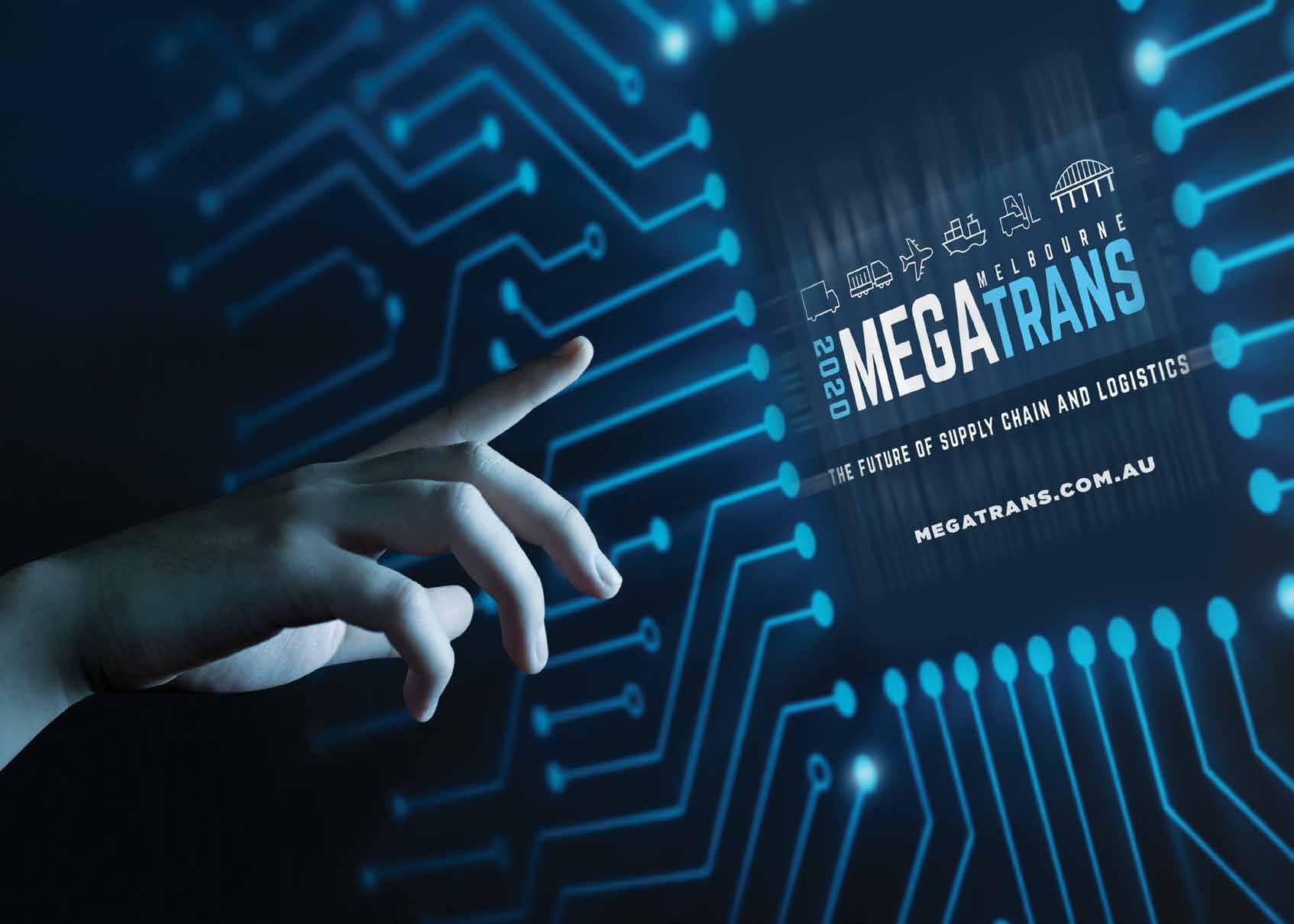
ASSOCIATION PARTNERS CONFERENCE SPONSORS