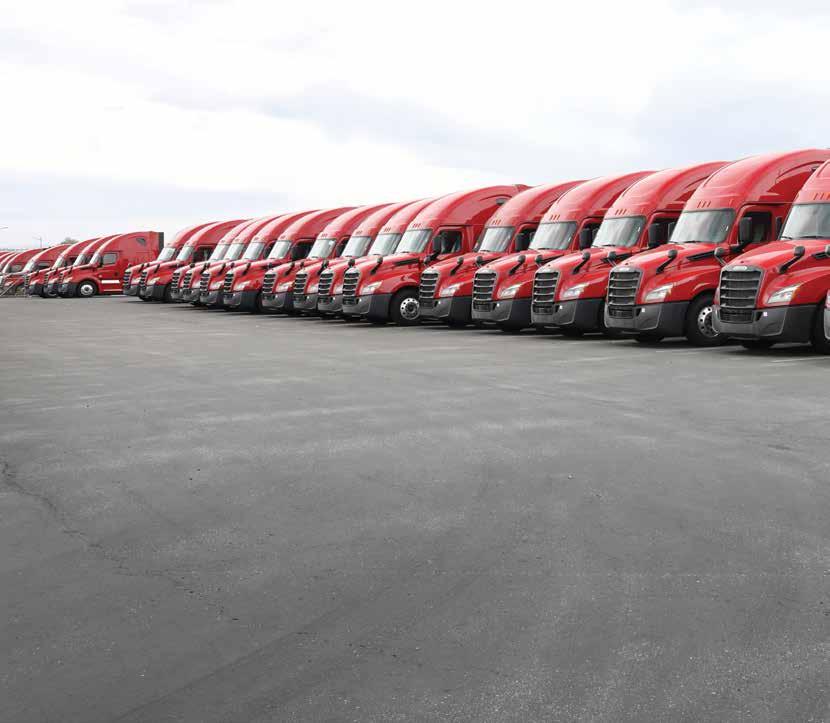
34 minute read
Keeping Cool Coast to Coast
THE CR ENGLAND TRUCKING OPERATION WAS FOUNDED IN 1920 BY CHESTER RODNEY ENGLAND WITH A 1920 FORD MODEL T TRUCK OFFERING FARM TO MARKET TRANSPORT FOR FARMERS IN THE AREA AROUND PLAIN CITY, UTAH. WITHIN A FEW WEEKS HIS FLEDGLING BUSINESS HAD GROWN ENOUGH TO REQUIRE A BIGGER TRUCK. TO CALL IT A MAJOR OPERATOR IN NORTH AMERICA NOW WOULD BE AN UNDERSTATEMENT.
Currently overseen by the fourth generation of England family and based in Salt Lake City, Utah, CR England advances towards its century next year, with its fleet having expanded to more than 4,700 trucks to make it one of the largest refrigerated transport companies in the world with an annual turnover of $2 billion USD. A major change occurred in 1959 when CR England offered its 72 hour coast-tocoast freight promise at a time when there was no true national highway system. More growth was made possible due to industry deregulation in 1980 through the Motor Carrier Act which removed restrictions on trucking between some of the states. Ron Hall is the Vice President of Equipment and Fuel and has been with the company for 29 years. Ron’s responsibilities extend to the purchase of vehicles, fuel, tyres and management systems such as telematics and the costs of these factors have a direct effect upon the profitability. “Driver wages are typically slightly more than 25 per cent of the company’s total expenses and fuel is typically slightly less than 25 per cent,” says Ron. “Prime mover leasing, maintenance and safety costs vary between five and ten per cent each.” The company purchased its first new Freightliner prime mover in 1985 and has purchased more than 22,000 examples of the brand since. Many of the purchase decisions back then are just as relevant now due to the current Freightliner Cascadia’s generous internal cab space and the trucks’ overall fuel efficiency. A strong relationship which extends far beyond being client and supplier has developed between the company and its Freightliner dealerships as well as with Freightliner’s head office in Portland, Oregon. This has delivered benefits for both. When CR England became aware that crosswinds would have a detrimental effect on fuel economy, yet with little empirical data available from which to devise a solution, it took up the matter with the Portland office of Freightliner where a turntable was developed so full sized trucks could be tested for the effects of crosswinds using the wind tunnel at the Daimler Trucks North America head office. CR England’s capacity to move freight is the major component of its offering to clients. At the end of July 2019 the company fleet had 4,437 Freightliners near evenly split between day cabs and sleepers (or ‘condos’) plus 334 nonFreightliners. As a result one brand now dominates with 93 per cent of the current total. Those trucks pull 5,300 refrigerated trailers and 1,000 dry van trailers with an additional 150 flat-bed trailers on specific applications. The ‘dedicated’ division has 2,100 truck and trailer combinations hauling freight for single clients including Walmart and Hershey Chocolates.
COAST TO COAST

CR England is one of the few intermodal operators in the US and has terminals in centres such Chicago, Los Angeles and Stratton in Pennsylvania where trucks using skel trailers take containerised freight from the clients to the rail heads where they are double stacked on rail cars and run across the country via train. CR England trucks then collect at the other end and deliver to the final destination. Currently this service accounts for 250 trucks and 1,650 containers. The ‘over the road’ division has around 54 per cent of its trucks operating with two-up drivers. Trucks dedicated to single clients, however, operate with around 86 per cent single drivers and are chiefly designated as ‘one truck – one driver’ operations. Trucks are traded at 500,000 miles (800,000 km) at an average age of 37 months. Vehicle maintenance is performed by company workshops (22 per cent), Truck Stops (16 per cent), dealerships (14 per cent) and outside vendors (48 per cent). At the sprawling Salt Lake City facility Freightliner dealer technicians perform pre-delivery, pre-trade and warranty work on-site, such is the size of the CR England enterprise. “Testing has shown that with the oils we use the engines could be stretched out to 100,000 miles (160,000 km), but the grease is only good for 70,000 miles,” says Doug Kading who has been the Vice President- Maintenance since 2014. “We currently use Mobil Delvac 10w30 and change it at 70,000 miles (112,000 km) in our own facilities but drop that to 50,000 miles (80,000 km) when using third party facilities where we don’t get to specify the oil.” Fuel purchases are aligned with two truck stop chains, Loves and TA/Petro. These have a combined footprint of almost 700 locations and have sufficient truck parking facilities to enable driver sleep breaks. The company has its own parking yard facilities in ten metropolitan areas where drivers can park overnight. Every truck has Bluetooth hands free capability and drivers use smartphone mobile apps to locate available parking in other locations. The drivers’ facilities at the Salt Lake City head office extend to include a full size convenience store. The company has 1,200 ‘non-driving’ staff and more than 6,400 drivers with 200 graduates from its internal driver academies every week, making it the largest driver trainer of refrigerated trucks
CR England operates more than 4,700 commercial vehicles.
in North America. The training fleet itself has 150 trucks and 200 trailers making it larger than most trucking companies. Similar to many operators in the US and Australia, CR England faces a serious driver shortage and a high rate of turnover of up to 160 per cent per year bringing it in step with the industry average. In 2018 the company began to implement a number of initiatives with the intention of building a reputation for being the best place to work in the industry. “We benchmarked our pay against other carriers, and in response, adopted the largest driver pay increase in company history,” says Ron. Other factors that influenced driver retention were also addressed including set runs that improved driver home time, shortening of the time drivers wait for a truck assignment and establishing a recognition program for high performing drivers that takes into account such factors as safety, service and fuel efficiency. The driver rankings are published weekly within the company. “There’s not much compensation attached to it but you’d be amazed how competitive our drivers become when it comes to the areas that they can control,” says Ron. “Being in the top ten per cent means a
Doug Kading, Vice President Maintenance and Ron Hall Vice President Equipment and Fuel.
lot, but being in the bottom ten per cent means way more than a lot, so there is a lot of emphasis on that program.” Technology and training have narrowed the range between lower performing drivers and good ones. To gain a Commercial Driver’s Licence (CDL) it costs around $5-6,000 USD ($7,500 – $8,900 AUD). The company will recompense that amount for any new drivers who stay for more than eight months. “To be an executive at CR England you must hold a CDL and we all do exactly what we say – get out on the road,” says Ron. During his 90th year Gene England, one of the sons of the founder Chester, was approached by one of his own sons about retiring from doing the occasional truck drive. “He said ‘Dad, we think you ought to hang it up, and I said that my CDL is good for another year or two and I want to run it out,” says Gene. Unfortunately the attorneys and insurers had other ideas so Gene retired from truck driving. A decade later Gene, who turned 100 on 24 October this year, still comes into the office on most days. The United States regulations limit drivers to 11 hours of driving each day, with a maximum of 14 hours combination of driving and other on-duty activities including 15 minutes for pre-trip inspections for each drive sector, and
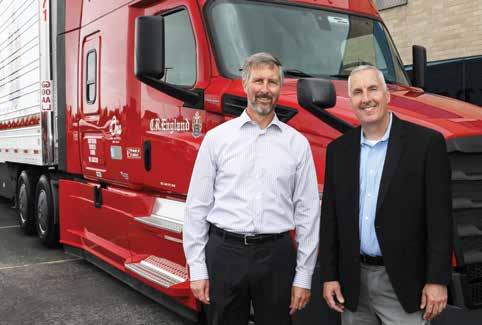
30 minutes of rest/meal break for every eight hours on duty. CR England is quite aggressive in its auditing and counselling of its drivers to maintain compliance to the regulations and drivers are also encouraged to avoid driving between the hours of 1.00am and 4.00am to avoid fatigue-related incidents. Fuel for the linehaul divisions requires five to six million US gallons (18.9 to 22.5 million litres) of diesel per month for CR England’s own trucks, with additional fuel being used by carrier partners (‘subbies’). Consequently, fuel efficiency plays an important role in truck and trailer specifications, maintenance and driver behaviour. The average miles per gallon metric across the fleet in 2005 was 5.78 (2.05 kilometres per litre) and due to significant efforts this has improved to 8.02 (2.84 kilometres per litre) in 2019. Aerodynamics have played a role in improving fuel efficiency and numerous innovations have been trialled to complement the slippery shape of the Cascadia. The gap between the truck and trailer has been shortened to 42 inches (1067mm) which is sufficient to prevent damage between the two main components and unquestionably helps with the fuel efficiency. The trucks are programmed to minimise idling time and the automated DT12 transmissions have no manual mode and can only select the ‘crawler’ low speed for reverse gear. The Detroit Assurance collision avoidance and lane departure systems are used throughout the Freightliner fleet. The speed limiters are set at the 65mph (104.6 km/h) when operating on the cruise control with only 63mph (101.4 km/h) available in manual mode as a way of encouraging drivers to engage the more fuel efficient cruise control. The specification of the trucks has been changed to increase power from 400hp to 455hp. Revised specifications like these have been proven to work well with the 2.16:1 final drive ratio and an average load of 42,000lbs. Perforated mudflaps have been trilled on 100 trucks over the period of a year, with an average fuel saving of 0.25 of a per cent. Low rolling resistance tyres are employed throughout the fleet. The company has trialled super singles which have a weight advantage but were found to be susceptible to damage from road shoulders and any fuel saving was negated by the loss of re-treading case credits so duals continue to be the standard, helped by the fitment of aerodynamic discs on the drive wheels. As an organisation CR England is a strong supporter of a national program that assists in feeding hungry children and the aim of providing for one meal for every load has resulted in more than two million meals to date. Allowing the drivers to determine where the meals are available retains a community focus. Always looking to the future the company has been testing some hybrid vehicles and is in ongoing discussions with Tesla, Nikola and Daimler, with two executives including Ron Hall participating on Daimler’s Electric Vehicle Council. Twenty build slots for the Tesla Semi prime mover have been purchased but that particular project is running well behind its originally projected timetable. Ron Hall also has an interest in the development of the Nikola hydrogen cell truck. “Within five years it will be commonplace to see electric tractors,” says Ron. “I think we are going to see a platform change particularly in day cab applications.”
DRIVE HEAD NEW AUSTRALIAN





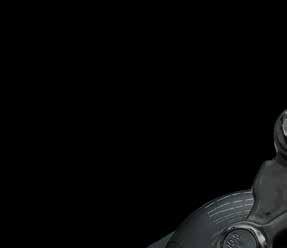
FORCE-FED LUBRICATION



TOUGH OPERATION CONDITIONS
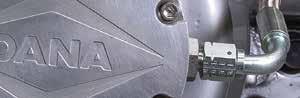


INCREASE LIFE-TO-OVERHAUL
MADE IN AUSTRALIA



For more information contact Dana on 1300 00 DANA or visit us at www.Dana.com.au
GAS IT’S A
THE ANTICIPATED IMPOSITION OF EVER MORE STRINGENT VEHICLE EMISSION REGULATIONS IN NEAR FUTURE HAS OPENED UP OPPORTUNITIES NOT JUST FOR ALTERNATIVE ENGINE FUELS, BUT AS WELL FOR REVOLUTIONARY PROPULSION SYSTEMS. THE COLLABORATION OF AN ADVANCED LEADER IN THE DISRUPTIVE TECHNOLOGIES WITH A GLOBAL LEADER IN ALTERNATIVE FUEL ENGINES SEEMS LIKELY TO DELIVER THE FUTURE MUCH SOONER THAN THOUGHT EVEN A YEAR OR SO AGO.
CNH Industrial (CNHi), owner of numerous vehicle and equipment manufacturers including IVECO trucks and light commercials, was the source of a couple of significant announcements made at the New York Stock Exchange in early September. The first announcement was that it will be separating it’s ‘on-highway’ divisions, including IVECO, from its ‘offhighway’ activities such as agricultural and construction equipment manufacturing. The restructuring is expected to be completed by the end of 2022. The ‘Transform 2 Win’ plan follows a review of the on-highway and off-highway (mainly New Holland agricultural and Case construction equipment) businesses that have identified their diverging regulatory and customer requirements are impacted differently by changing industry
Gerrit Marx, IVECO President Commercial and Specialty Vehicles.
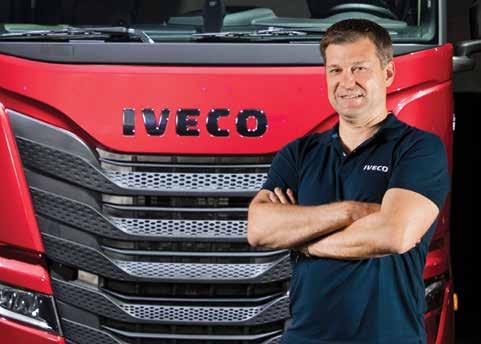
trends including automation, emissions, and digitalisation. The second significant announcement by the CEO of CNH Industrial, Hubertus Mühlhäuler, was the $USD 250 million investment into a partnership with Nikola Corporation to accelerate the development of the Nikola ONE and TWO prime movers and the Nikola TRE heavy duty cab-over truck. IVECO has been a leader in the development of liquefied natural gas (LNG) engines for the past 20 years and has produced some 50,000 natural gas powered engines to date including 28,000 trucks and buses. IVECO and CHNi’s powertrain division FPT Industrial has been largely instrumental in the expansion of the natural gas refuelling network in Europe and the fuel-cell technology which Nikola has been working on is regarded as the next logical step. On display for the Wall Street announcement was the latest IVECO concept truck, the centre-steered Z-Way powered by a liquefied natural gas engine the company claims has a range of 2,200 kilometres. However, rather than using the futuristic Z-Way, much of the focus of the initial phases of Nikola’s joint project will be on the much more contemporary S-Way prime mover which was released in Spain in July and will form the ‘bones’ of the new range of trucks. “The recognition that there needs to be fundamental reductions in automotive emissions is driving our industry to rapidly seek advanced technological solutions,” said Mühlhäuser. “Nikola’s choice of IVECO as its strategic partner is testament to our internationally recognised excellence in heavy duty trucks and alternative powertrain technologies. Nikola has the technology but needs a partner with a European network to achieve success in a timely manner.” Gerrit Marx, President of IVECO Commercial and Specialty Vehicles added, “While today LNG delivers significantly lower well-to-wheel emissions, in the medium to long term, fuel cell and Battery Electric Vehicle (BEV) will deliver the ultimate goal of zero-emission trucking.” Led by its visionary CEO Trevor Milton and based in Phoenix, Arizona, Nikola Corporation designs and manufactures hydrogen-electric vehicles, electric vehicle drivetrains, vehicle components, energy storage systems, and hydrogen refuelling stations. Nikola holds in excess of 14,000 pre-orders for its own Nikola ONE (bonneted sleeper), Nikola TWO
(bonneted day cab) and Nikola TRE (a European-style cab over sleeper). The intention of the Nikola/IVECO partnership is to accelerate industry transformation towards emission neutrality of Class 8/Heavy Duty trucks in North America and Europe through the adoption of fuel cell technology. Nikola’s zeroemission Heavy Duty trucks are powered by a proprietary hydrogen fuel cell and battery technology. Nikola’s disruptive business model foresees an industryfirst ‘all-in’ lease rate, which includes all vehicle, service, maintenance and fuel costs, providing long-term total cost of ownership certainty and is expected to be at or below costs of equivalent diesel powered trucks. The CNH Industrial strategic stake in Nikola comprises of $100 million USD cash and $150 million USD in services, such as product development, manufacturing engineering, and other technical assistance, as well as the supply of certain key components to accelerate the production timeline of the Nikola TWO and Nikola TRE. As part of the exchange Nikola will contribute technologies for a European Joint Venture with CNH Industrial that will include fuel-cell expertise, electric drive axles, inverters, independent suspensions, on-board hydrogen fuel storage, overthe-air software update functionality, infotainment, vehicle controls, vehicle-tostation communication protocols, power electronics, and access to a hydrogen fuelling network. “The time has come to finally provide a zero-emission solution to the heavy duty truck market,” says Nikola’s Trevor Milton. “While other OEMs believe zero
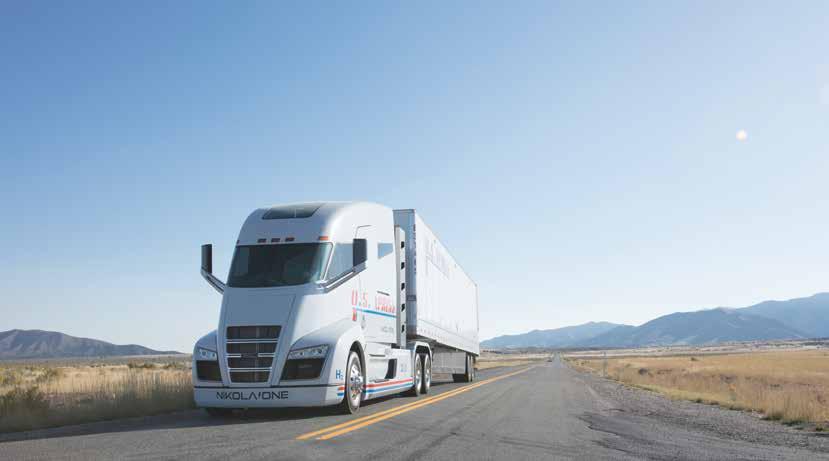
emission solutions cannot happen in the time frame regulators have mandated, Nikola, FPT Industrial and IVECO are proving that these timelines are not unreasonable. Nikola has the technology but needs a partner with a European network to achieve it in a timely manner. With CNH Industrial’s investment and partnership, we can now bring zeroemission trucks to Europe. By bringing CNH Industrial on board, we now have access to manufacturing know-how, purchasing power, validated truck parts, plant engineering and much more. Few will doubt our ability to commercialise a truck now.” Nikola’s development of commercial vehicles has also already attracted a number of mainstream component suppliers including Bosch which in September committed more than $100 million USD to Nikola. Bosch has been an instrumental partner for Nikola in the development of its state-of-the-art heavy
Nikola One has a range of 1,280 - 1,920 kilometres.
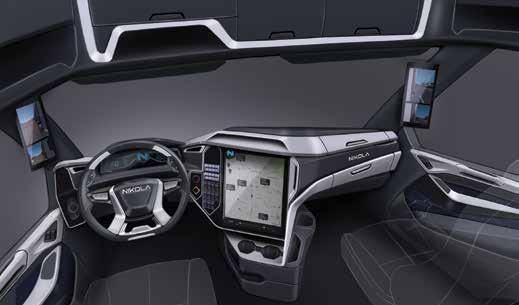
duty vehicle fuel cell system and battery technology. The Nikola fully electric drivetrain is powered by high-density lithium batteries. Energy is supplied on-the-go by a hydrogen fuel cell giving the Nikola One a range of 800 - 1,200 miles (1,280 -1,920 kilometres) while delivering over 1,000 horsepower and 2,000 ft. lbs. of torque, almost double that of a typical prime mover. The best-in-class fuel efficiency and significantly improved performance over its diesel competition are delivered with zero-emissions. Nikola is rolling out an ‘ecosystem’ of hydrogen re-fuelling stations across North America and Europe. In keeping with the commitment to the philosophy of 100 per cent clean and renewable energy, solar panels will be employed in generating the clean electricity that is critical to the production of renewable hydrogen at a price that meets or beats the economics offossil fuels.
Nikola One undergoing an on-highway evaluation.
A L I T T L E S O M E T H I N G EXTRA
It’s the last week in the office for Glen Stephan, the National Fleet Manager at Scott’s Refrigerated
Freightways in New South Wales where he has worked the last 11 years. He’s leaving behind a major operation that involves several of the businesses that fit under his purview and the AHG Refrigeration umbrella. These include JAT Transport, Rand Refrigerated Logistics and Harris. Based out of Prestons in Sydney, Glen is retiring after 53 years in the industry having started as an apprentice diesel mechanic in Brisbane, where he grew up. With commercial vehicles running around the clock, it’s a major role coordinating critical metrics on service intervals, maintenance, tyres and fuel usage across several businesses. There’s 50 Tautliners in operation and around 200 skels. On top of this the business owns another 250 pieces of equipment that are non-refrigerated. With over 500 B-doubles in transit at any one time, the vehicles are covering more than 500,000 kilometres daily. “If you calculate that it’s 12 and a half times around the circumference of the globe per day,” says Glen. “That’s a lot of ground we cover.” It’s also a lot of fuel. Across the group the combined fleet consumes an estimated 320,000 litres of fuel daily. The units, in large part, are running up and down the Eastern Seaboard and the routes extend essentially from Cairns to Perth. B-doubles operate continuously between Sydney and Adelaide direct on one of the longest of the daily runs. In regional areas the company might augment its operations with seasonal loads. In the main part the emphasis is on freighting produce, meat, processed refrigerated goods and frozen food. In 2011 Scott’s Refrigerated Freightways, already a long time Shell customer, were offered to trial Shell Diesel Extra. At the time Glen was searching for a premium fuel solution from his suppliers. Now, having found it, he says it’s been integrated across all of its sites. “Shell Diesel Extra is working behind the scenes at all times for us,” he says. “When we compare our results with other competitors, who are using the same equipment, we are seeing twice the kilometres before we have the same type of failures.” As a direct consequence there is no longer a need to replace the injectors on their engines according to Glen. This is achieved in part though the diesel fuel’s lubricity which is maintained and monitored to help prevent wear and fuel system corrosion. As it also reduces foaming when refuelling Shell Diesel Extra is ideal for operators chasing prudent fuel economy. Scott’s Refrigerated Freightways became the very first user of the product in road transport in Australia. The next big test for Glen, who knew it was a winner, as he recalls it, was to prove to his people that they wouldn’t have to pay for more fuel. Given fuel savings vary on the age and condition of the truck engine and fuel burn evaluations can take months to benchmark, he also tested it on smaller equipment and saw immediate results. Running the Shell Diesel Extra in a four-cylinder Holden Colorado ute soon confirmed the benefits. A tank fuel was yielding approximately 80 kilometres on a 60-litre tank. Shell Diesel Extra is designed to avoid rising fuel consumption over the lifetime of the vehicle by helping to keep the engine running in accordance with manufacturer’s specifications. The proof was evidenced, according to Glen, in the clean injectors. Meanwhile he was reporting a better fuel burn across the fleet. “We don’t have any issues with low AFTER IT SET OUT TO FIND A PREMIUM FUEL TO HELP IT MEET THE DEMANDS OF ITS NATIONWIDE FREIGHT TASK, SCOTT’S REFRIGERATED FREIGHTWAYS DISCOVERED SHELL DIESEL EXTRA. IT HAS BEEN A DEVOTEE EVER SINCE.

A L I T T L E S O M E T H I N G

Fuel injector failures ceased after Scott’s adopted Shell Diesel Extra.
power and that makes a difference depending on what you’ve got on the road and what you don’t,” Glen says. “We’ve got engines here that have done 2.5 million kilometres and never had an injector replaced.” The fleet runs a mix of makes with the bonneted trucks split between Kenworth and Freightliner. Hino, Isuzu and Fuso are operating in the lighter duty area with over 100 rigids on intrastate duties. Every vehicle is running on the same Shell Diesel Extra product. Every depot of bulk fuel is filled with it and 80 per cent of their fuel is taken out of their bulk tanks. Some of the engines have clocked 80,000 hours in a refrigeration application that have never been stripped down once they were on Shell Diesel Extra. Multiplying that over 62 units makes for a very good average according to Glen. He says the water retaining capabilities, moreover, are impressive as it actually prevents water going through the engine. Glen recalls a fuel tank full of water on a common rail engine stopping. It wasn’t a problem once they had it cleaned out, filtered and pressurised it through with fresh Shell Diesel Extra, and then, ran the engine on it for a while. “It started up and ran perfectly. That’s how good it is. We haven’t had a failure at all,” he says. “It’s astronomical to consider the kilometres you would have done if it was a car.” Seeing as it has stopped injector failures and reduced fuel contamination incidents, Glen refers to it as an unseen friend that looks after everything, keeping the trucks on the road and out of the workshop. Fuel pump servicing on the refrigeration units are also seldom. That’s a major cost benefit when there’s 1500 of those currently in operation on a daily basis. “In my experience Shell Diesel Extra relieves you from having to do major service items because you don’t have the failures,” Glen says. “Going on what we’re having to do behind the scenes it alleviates a considerable amount of the maintenance that you would nominally have to do.” After 53 years in trucking, solving problems, working long hours and reporting to multiple stakeholders, now that he’s retiring what’s he going to do with himself? “I’m just going home,” Glen says. “We’ve had a fair play.”
THE MACHINE THE MACHINE BEHIND


In essence, Scania’s Connected Uptime Solutions (CUS) is an intelligent service and maintenance program that uses operational data gained via an onboard telematics system called Communicator. This data is used to determine optimum service intervals and preventive maintenance schedules to ensure maximum vehicle uptime. According to Scania’s Aftersales Services Product Manager, Richard Bain, from late 2015 all new Scanias have been equipped with the Communicator 2G as standard. The unit was subsequently upgraded to 3G then 4G over the ensuing years. “We now have over 400,000 connected vehicles globally, 5,000 of which are operating in Australia,” he says. A value-add for customers, according to Richard, the vehicle communicates with the customer and Scania, informing both parties on ideal service intervals. “We use this information to ascertain optimum service intervals for each customer based on the individual operating conditions of each unit,” he explains. “Having access to this information means we can contact customers and book them in for servicing which saves them time and effort, while also helping us maintain peak workshop efficiency – it’s a win-win for everyone.” FOR CUSTOMERS OPERATING EXAMPLES OF ITS TECHNOLOGICALLY ADVANCED RANGE OF TRUCKS, SCANIA IS KEEN TO PROMOTE AN EXTRA DIMENSION IN AFTERSALES SERVICE CALLED CONNECTED UPTIME SOLUTIONS.
Scania’s Communicator is connected to 5,000 vehicles in Australia.
In regard to the flexible maintenance benefits of Communicator, Richard says it has allowed Scania to move away from the traditional small, medium and large services at set intervals, instead relying solely on the operating information gleaned by Communicator. “This means we are not over- or underservicing vehicles which enables us to price our repair and maintenance agreements more competitively and gives customers increased uptime due to less time spent in the workshop. We focus on uptime to ensure our customers don’t fail their customers,” he says. The Communicator, as part of the enhancements it’s facilitating, fits with Scania’s move to preventative maintenance where predicting when a component needs to be changed before it fails is imperative for minimising unscheduled downtime. According to Richard, each time the vehicle comes into the workshop it receives a combination of preventive maintenance and regular service procedures in what he describes as an holistic approach. “With the more sophisticated electronic systems in the new trucks we are able to determine if various parts are wearing out quicker than they should and take preventative action before they actually fail,” he says. “It’s pretty impressive technology. We log into a system and it tells us the percentage of life left in components based on prior experience and the vehicle operating hours and road conditions.” In the unlikely event of a breakdown, the Communicator is an invaluable tool in that it enables the problem to be diagnosed and the correct parts taken to the stranded vehicle by the technician. “If there’s a breakdown we can remotely access the fault codes which ensures the technician goes out with the right parts to fix the vehicle – this saves a lot of time,” Richard explains. Scania’s commitment to its customers can be viewed in part through the maximised uptime of their trucks as it ultimately determines the success of their businesses. Many original equipment manufacturers speak about customer uptime and how they can achieve the best results. Scania,
Preventative maintenance is a big part of Scania’s holistic approach.

according to Richard, is more committed to customer uptime than ever before. “We have the right foundations in place with our infrastructure in terms of our scheduling teams, our branches and the platform for communications with the vehicles. And the vehicles in the fleets are now smarter compared to the previous generation as we are moving ahead with supplying an increasing number of NTG Scanias to Australian businesses,” he says. “The vehicle itself, thanks to its advanced design and technology, gives customers better uptime but also with our new structures for communication we’re seeing an average 14 per cent increase in customer uptime.” He suggests Scania has a few more exciting initiatives in the repair and maintenance space that are expected to be rolled out in 2020. These are anticipated to further increase customer uptime to unprecedented levels. “We’re pretty excited about these new developments that will help us increase our captive and non-captive network,” he says. “This will mean employing more technicians to handle the increased workload, among an array of activities that will further improve customer uptime.” As a whole, Scania product must have a point of difference with a strong focus on service and the fuel efficiency of its trucks. “In particular we want to dispel the perception within the industry that our aftersales products and services are expensive,” Richard says. “We have worked hard to ensure there is competitive pricing on all our services and we believe the benefits well outweigh the cost, particularly considering some of the benefits aren’t immediately obvious.” Safety is one of these factors. Having vehicles on a repair and maintenance agreement gives the owner full access to the telematics package that will, according to Richard, provide information including whether or not the driver is using their seatbelt. “Anything the driver sees on the dash the owner can see via the portal, which provides a level of accountability on the part of the driver and also peace of mind for the owner,” he says. Lowering the transport industry’s environmental footprint is another benefit Richard explains. “There’s less wastage on over-servicing and customers’ time and mileage when taking the truck to be serviced,” he says. “And our Euro 6 vehicles are also at the highest order in terms of fuel efficiency and minimal emissions.” In sum, Scania’s stated intention is to continually ensure the ultimate in aftersales service for its customers. Having the in-built technology in the trucks to ensure optimum service and repair schedules throughout the life of the vehicle is a vital part of this philosophy.
SAVINGS LIFE

Campbell Transport provides a diverse range of transport and freight services in Western Australia. These include general freight, bulk haulage and stock transport services, as well as warehouse facilities. The company has been operating for over 20 years, resulting in the accumulation of extensive knowledge and expertise in what’s required of equipment operating in the harsh north of Western Australia, where high loads and sweltering summer temperatures place enormous demands on trucks and their driveline components. Traditionally, mine haulage prime movers pulling super quad-trailer roadtrains up to 60 metres long have been fitted with heavy-duty hub-reduction tandem or tridem driveheads which provide the required final drive ratio and component integrity to manage the task. Dana, on the other hand, has taken a different approach to heavy-duty axle design. Instead of using hub reduction, Dana’s T78-590P Tri-Drive units feature double reduction pinion gears in the differentials. In the Campbell Transport fleet, the Dana TriDrives running a 5.19:1 final drive ratio are installed in six Cummins-powered Kenworth T909s. These have been supplied by Perth-based Kenworth and DAF dealer CJD Equipment for the past two and a half years. With the Tri-Drive assembly riding on Neway ADZ air suspension, the units feature a mammoth gross combination mass (GCM) rating of 220 tonnes. According to CJD Equipment Regional Sales Manager, Kurt Smith, the Dana TriDrives offer a number of advantages for combined off- and on-road applications over equivalent hub reduction units. “The hub reduction axles have more moving parts than the Dana Tri-Drives, which leads to additional heat build-up and higher fuel consumption in on-road applications due to the added friction and inertia of the extra gears turning at higher speeds,” Kurt explains. “In contrast, the Dana Tri-Drive comprises conventional driveheads with the addition of simpler DANA’S ULTRA-HEAVY-DUTY T78-590P TRI-DRIVE REAR AXLE ASSEMBLIES HAVE FOUND FAVOUR WITH WESTERN AUSTRALIAN COMPANY CAMPBELL TRANSPORT IN ITS HIGH GROSS COMBINATION MASS ROADTRAIN MINE HAULAGE OPERATION. THE COMPANY IS USING DANA TRIDEM-EQUIPPED KENWORTH T909 PRIME MOVERS HAULING SUPER-QUAD SIDE TIPPERS WITH GROSS WEIGHTS OVER 200 TONNES.
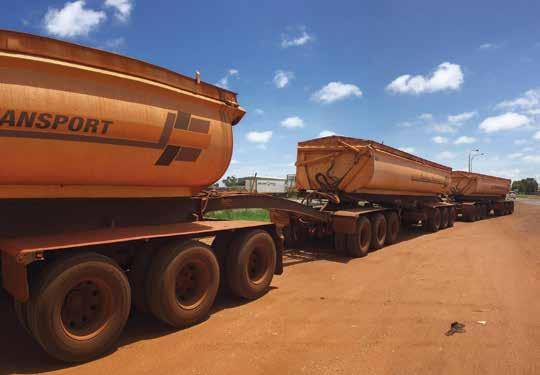
double reduction pinion gears in lieu of hub reduction components. Long distance heavy haulage applications at 80 to 90km/h average speeds are not ideal operating conditions for hub reduction axles.” There’s no need for the additional pumps, hoses or external oil coolers that hub reduction axles normally require of the fierce WA conditions, making for yet another major advantage of the Dana Tri-Drive units while promoting simple maintenance without compromising operating temperatures. Another advantage of the Dana Tri-Drive units over hub reduction axles, according to Kurt, is a dramatic increase in service intervals which means significant savings over the life of the truck. Oil change intervals on hub reduction axles are commonly scheduled for 250 operating hours, whereas the equivalent Dana Tri-Drive units can be operated for 1,000 hours between oil changes. The T78-590P Tri-Drive can be specified with a broad spectrum of ratios ranging from 4.75:1 to 10.9:1 and has a number of design features that bode well for a long service life under the harshest operational conditions. For instance, the crown wheel is supported by high-capacity bearings and has an extra wide face with helical-cut gear teeth which
Dana Super-Duty SD350 driveshafts meet the 220 tonne task in WA.
“In contrast, the Dana tridem comprises conventional driveheads with the addition of simpler double reduction pinion gears in lieu of hub reduction components.” Kurt Smith CJD Equipment Regional Sales Manager
maximise the contact area with the pinion teeth for optimum strength and capacity. There’s also an integrated ring gear and wheel differential mounting system that eliminates bolted joints, large wheel differential gearing and an integral pinion cage and carrier that eliminates a potential leak path. The heat-treated steel differential cases feature heavy-wall construction for strength and durability. In addition, there are a number of Danapatented exclusive elements including a threaded input adjuster that precisely sets end play in the power divider without the use of shims. An on-demand integrated lube pump is claimed to reduce operating temperatures by as much as 10 per cent, helping extend lubricant life and reduce internal friction and wear. There are also threaded differential bearings with integrated adjusters that maximise component life by providing continuous adjustments and allowing precise settings of gear backlash and tooth contact patterns. Options include driver-controlled wheel differential or cross locks for maximum traction over slippery, loose or uneven surfaces. These can be retrofitted even after the vehicle is built or in use. There are also the options of wide-track axles for improved stability, and carrier integrated retarder mounting which Dana says provides more drivetrain options with increased strength, brake performance and reduced complexity. Another integral feature of the Campbell Transport Kenworths is the Super-Duty SD350 driveshafts that feature serrated interlocking flange mounting of the driveshafts to the differentials, ensuring ultimate reliability in this demanding application. The SD350 has been engineered to handle up to 35000Nmof torque which enables the Campbells fleet to meet the 220 tonne haul . This high capacity is thanks to a tube wall thickness of 6.0mm and the use of large journal diameter universal joints said to be the highest torque-rated of their kind in the industry. Other design features that enhance durability and minimise maintenance in high torque applications such as this are a service-free slip joint, the splines of which are treated with Dana’s patented GlideCote process. This is a permanent blue coloured surface coating that minimises friction between the moving parts. As with the universal joints, the slip joint is lubricated and sealed for life with synthetic grease at assembly. Given the earliest example of Dana’s T78- 590P Tri-Drive in the Campbell Transport fleet has recently clocked one-million trouble-free kilometres, the signs are extremely positive that these units are an ideal solution for this arduous application. The innovative design providing the necessary double reduction gearing within the differential rather than the wheel hubs is proving its worth in reducing operating costs.
IN SECONDS A UHF RADIO THAT INSTALLS
GME HAS INTRODUCED A NEW SUPER-COMPACT HIDEAWAY 80-CHANNEL UHF CB RADIO. THE INNOVATIVE XRS-330CP PORTABLE PACK UNIT, WHICH CAN BE QUICKLY AND EASILY INTERCHANGED BETWEEN VEHICLES, FEATURES A MAGNETIC-BASE ANTENNA AND PLUGS INTO A CIGARETTE LIGHTER OR ACCESSORY POWER SOCKET.
For those who regularly hire or drive a number of different vehicles, or only use a UHF radio occasionally, GME’s XRS-330CP is an ideal choice. The XRS family is a new Australianmade radio platform designed to be smart, adaptable and rugged. Enabled by Bluetooth® wireless technology, GME says its XRSTM range is the first of a new generation of connected UHF radios with unique features never before seen in this type of equipment. Much like a smart device, the XRS family is software upgradable via the app, keeping customers up to date with the latest features and technology. GME’s new open platform allows any customer to develop a customised app to control the functions of the radio. XRS Connect radios are equipped with ScanSuite which enables virtual private group communications. GME says that ScanSuite can now scan 25 per cent faster than previous generations and up to four times faster than competitor radios. The XRS Connect app provides access to more than 20,000 registered analogue frequencies. Operators can select frequencies based on the state in which they live, frequency type, or even their smart device’s current location. The XRS Connect app enables the radio to be software upgraded using the paired smart device internet connection. Notifications of new features and upgrades are available via the app. This app is free to download and, according to GME, includes features not

EverShine
previously available for a UHF CB radio. It is said to be compatible with Android 5.0 or iOS 9.0 models or later, as well as most smart phones and tablets. These devices can also be used as a secondary radio screen. The XRS-330CP Portable Pack unit possesses the traditional GME qualities of robust construction and longevity while providing the portability to be kept in a small case on the shelf when not in use. Importantly, it requires no drilling of holes, cutting or soldering in the vehicle, ensuring hassle-free do-it-yourself installation that takes less than a minute. The unit features a suction cup mount and a compact magnetic-base antenna with ample cable length for external attachment to the roof of the vehicle. The handpiece has a 2.0-Watt speaker microphone that has been designed for noisy environments. Powered by unique ClearSound DSP architecture GME claims it can produce clearer and more robust sound. According to GME, the XRS Connect speaker microphone has been uniquely designed to incorporate customisable buttons and an industry-first high-contrast OLED screen which provides a crystal-clear anti-glare display. The all-new XRSTM Portable Pack is ideal for casual users and owners of high-end vehicles who do not wish to permanently install a UHF radio in their vehicle. The XRS-330CP comes complete with everything needed including the premium XRS-330C UHF CB radio, suction cup mount, 12V accessory power lead, 2.1dBi magnetic antenna and mounting hardware. All components are contained within a handy carry case for convenient storage when the radio is not in use. XRS radios are claimed to be uniquely designed, engineered and built in Australia to withstand the harsh Australian conditions. The new XRS microphone, according to GME, is tested to over 1,000,000 PTT cycles and the professional grade strain relief and OLED screen make the microphone as durable as possible. The units are covered by GME’s five-year warranty. Customers who download and register the new XRS Connect App will also receive a one-year additional warranty.
The XRS comes with a high contrast anti-glare OLED screen.

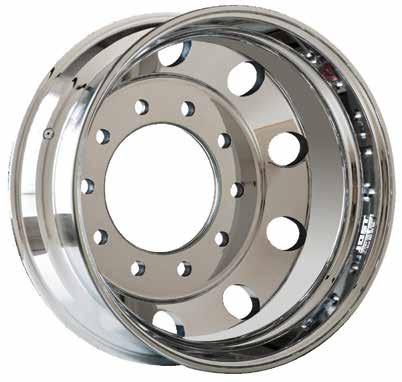
FAST FACT With its ultimate portability and exceptionally fast installation time, GME’s XRS-330CP Super Compact Hideaway 80-channel UHF CB radio is ideal for occasional use and for those who regularly change vehicles.
