
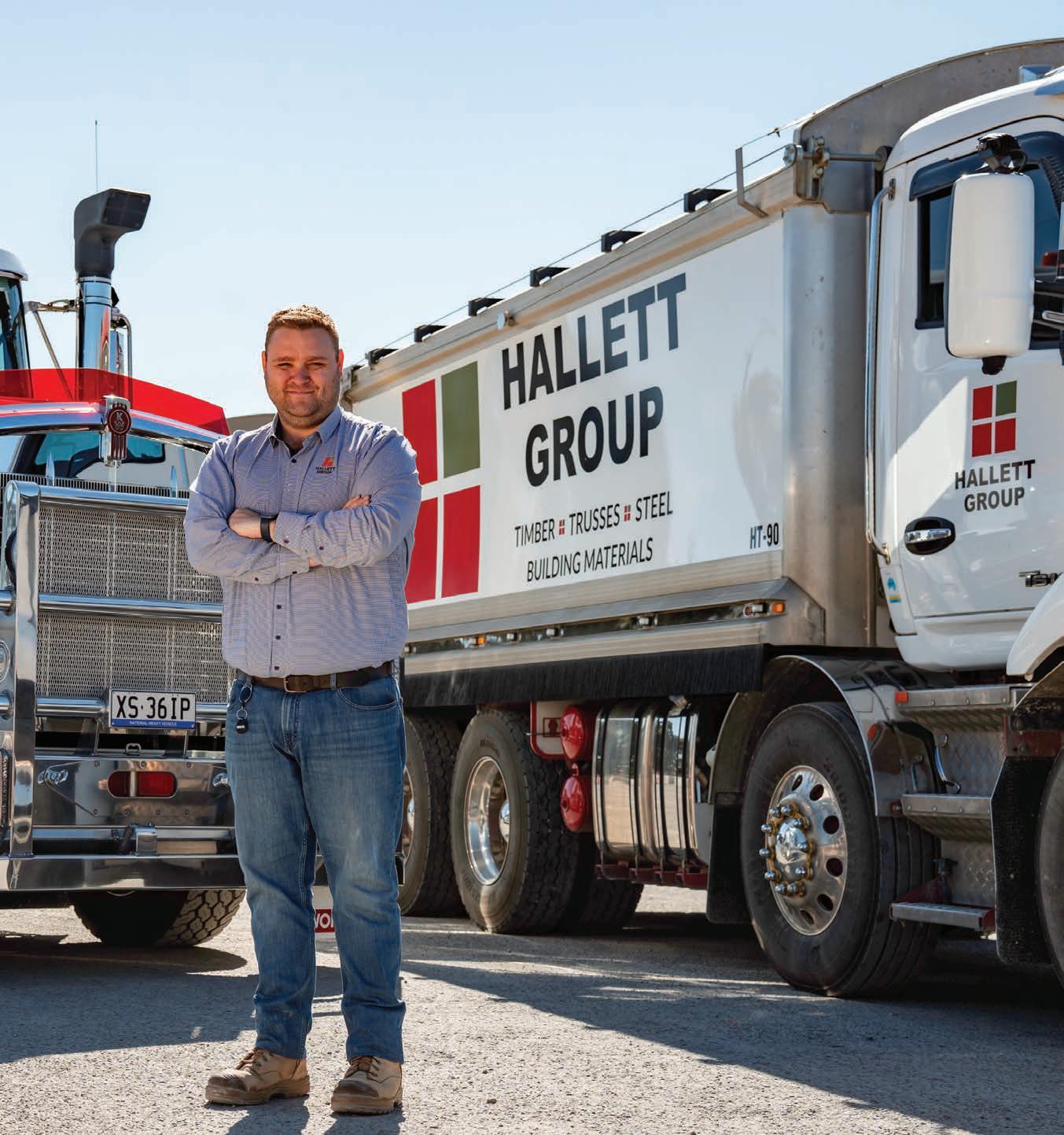
INDUSTRY
Carrier: D&G Logistics
Special Report: Driver Recruitment
Personality Profile: Bianca Slack-Smith
INNOVATION
Fleet: Active Tree Services
Windscreens: BORAFLOAT 33
Spotlight: Tug Fifth Wheels Test Drive: Volvo FH16 780
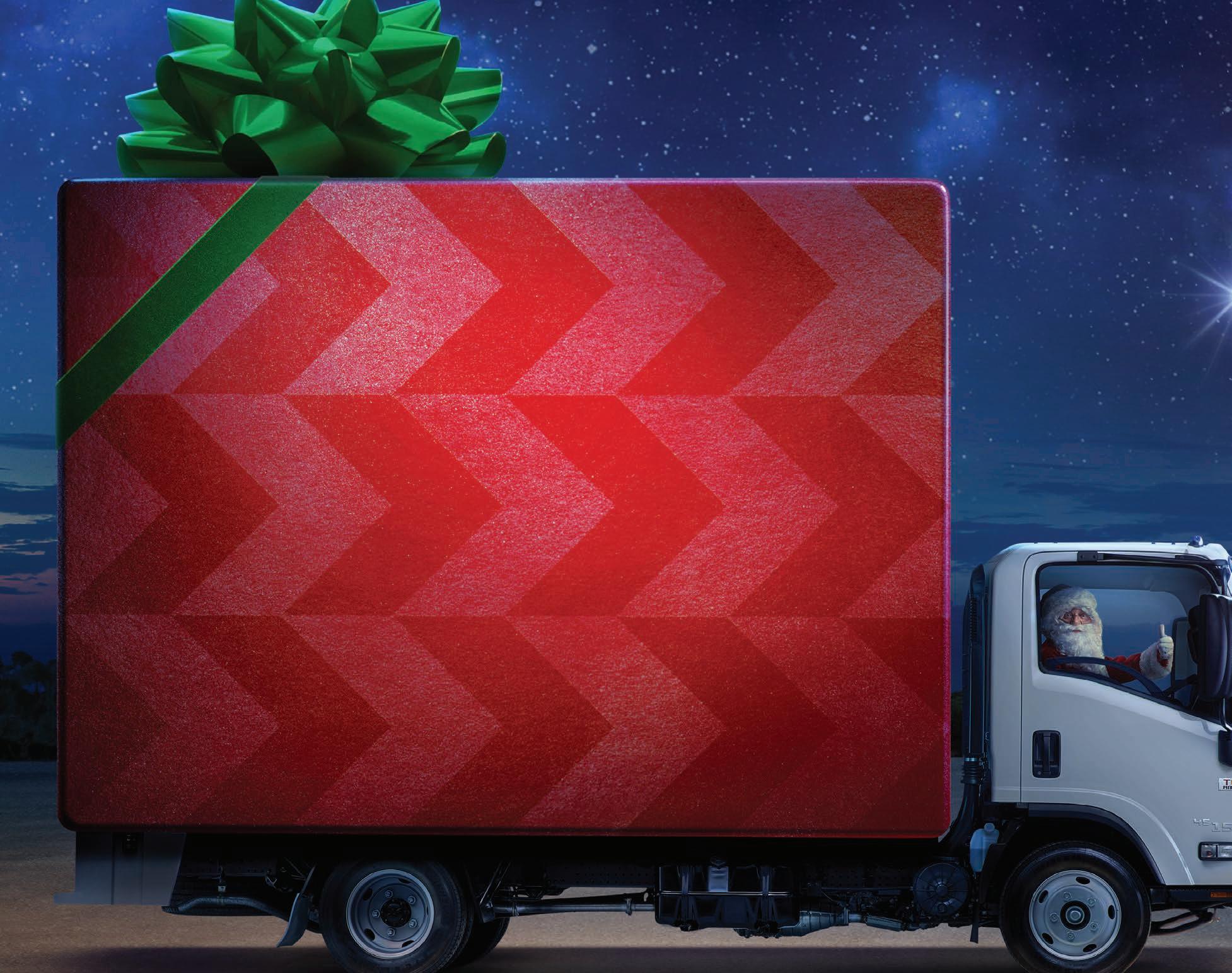
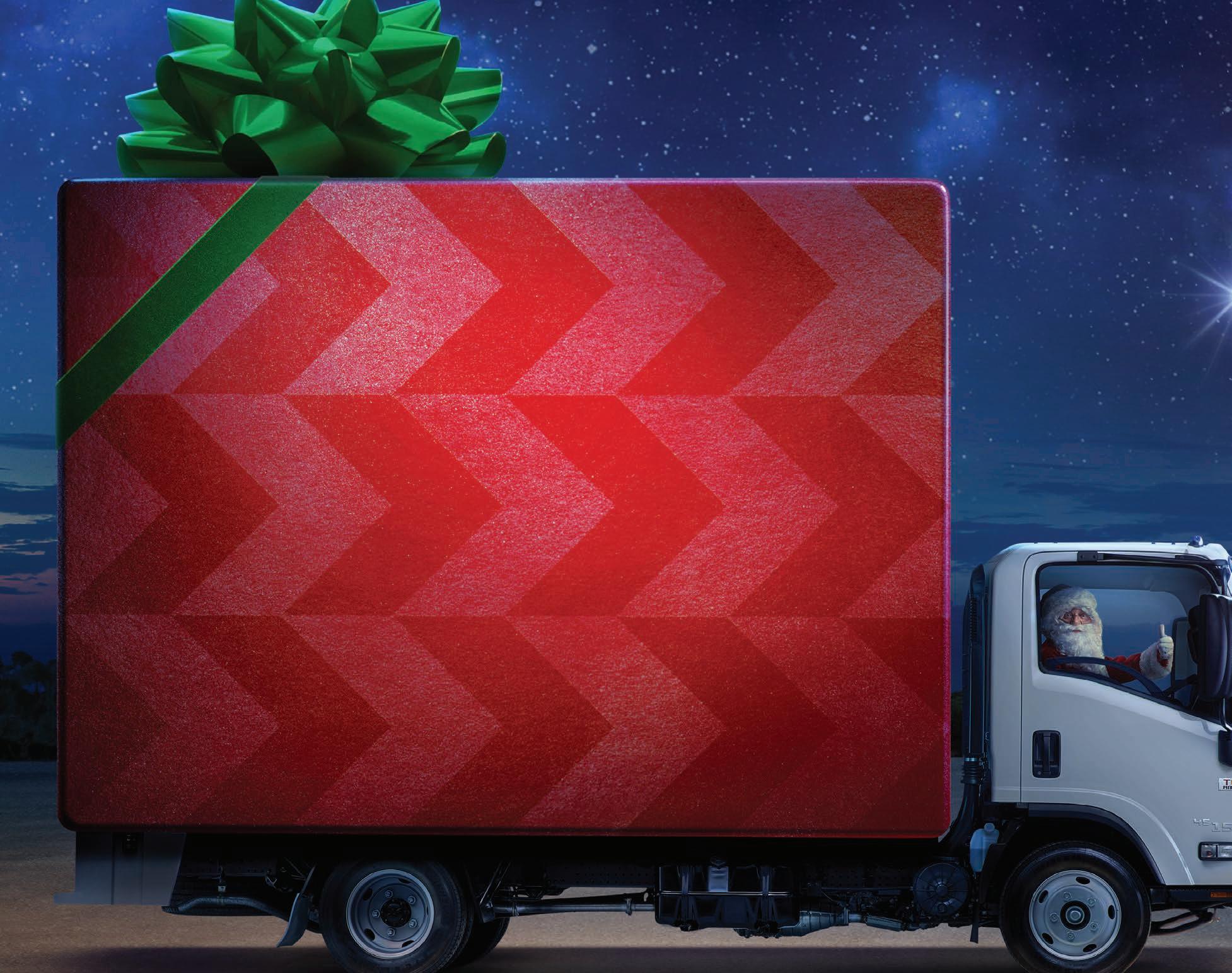

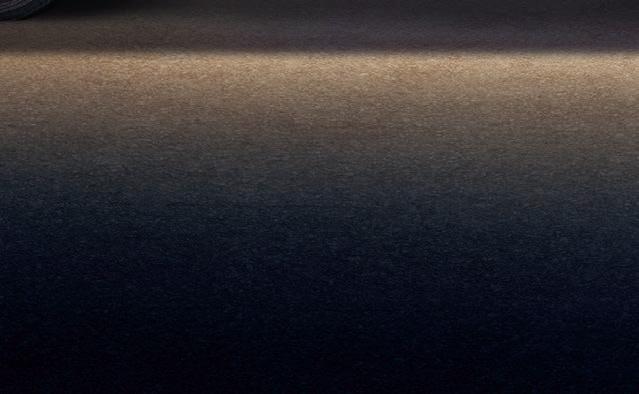
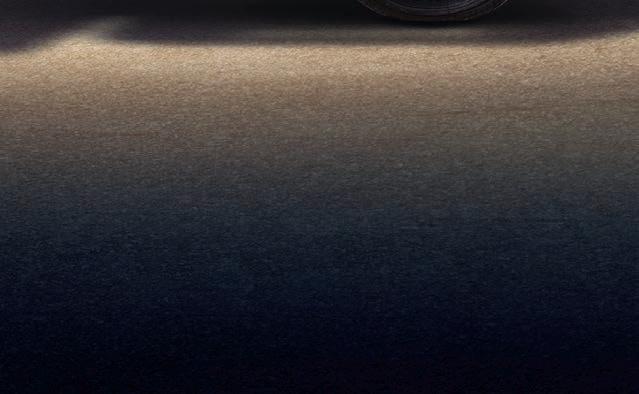
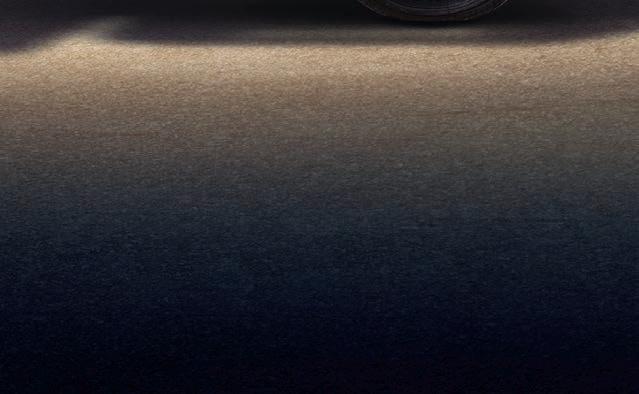

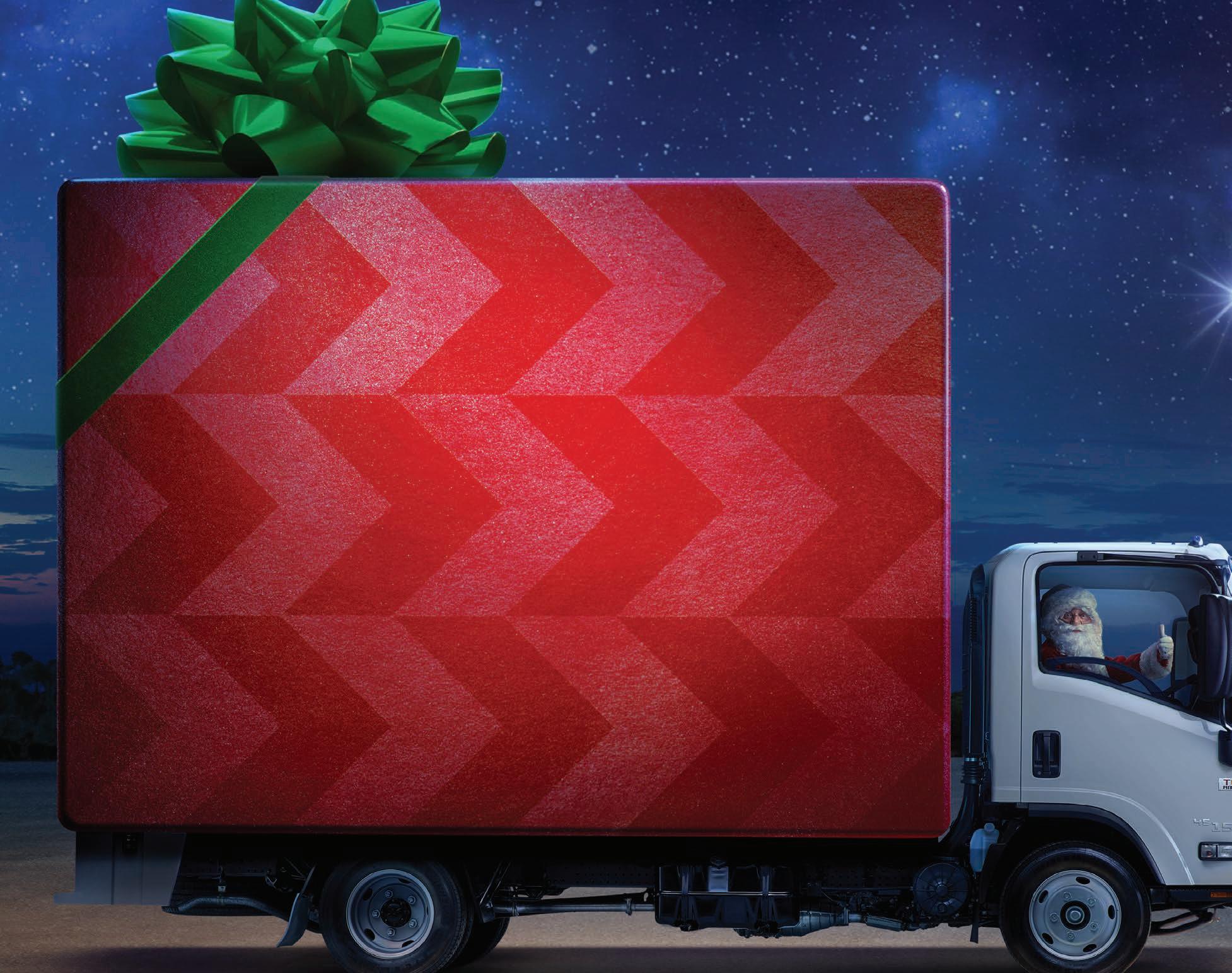
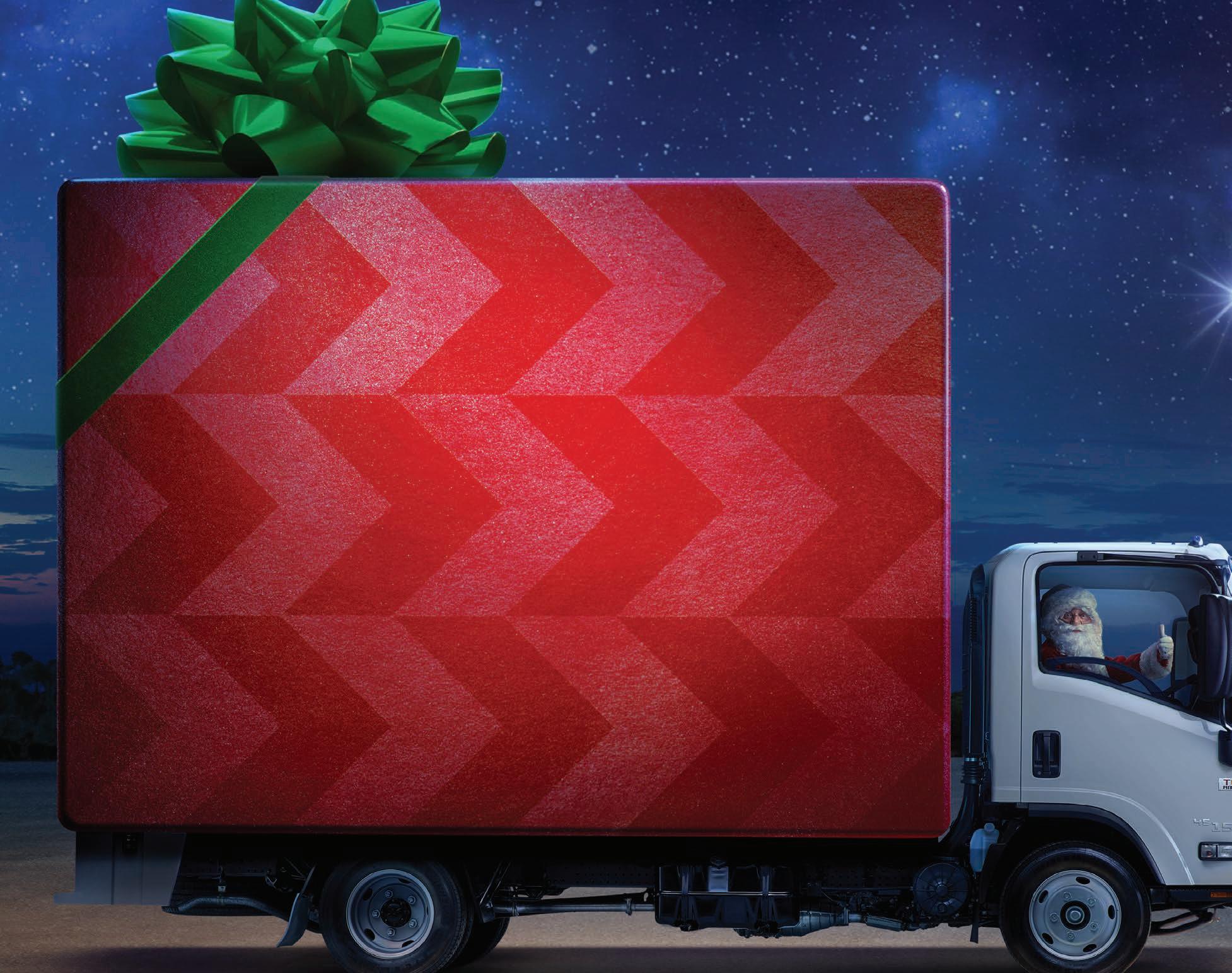
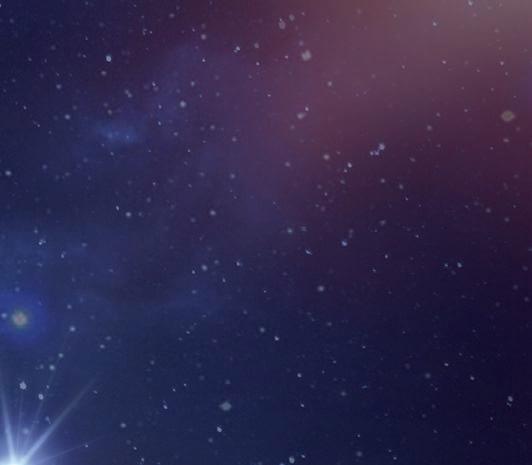
INDUSTRY
Carrier: D&G Logistics
Special Report: Driver Recruitment
Personality Profile: Bianca Slack-Smith
INNOVATION
Fleet: Active Tree Services
Windscreens: BORAFLOAT 33
Spotlight: Tug Fifth Wheels Test Drive: Volvo FH16 780
We’re proud to provide the full offer for your workshop; a growing national network providing with widest product range, next level customer service, technical and product knowledge and 24/7 ordering through NAPA ProLink. YOUR PROFESSIONAL ADVANTAGE.
With a growing range of over 15,000 SKUs per branch, covering automotive electrical, air conditioning, mechanical servicing and repairs, workshop consumables, tools and equipment, we go out of our way to make sure you’ve got what you need, when you need it. We stock the leading brands you trust and rely on every day, and offer greater choice
Australia’s leading truck magazine, Prime Mover, continues to invest more in its products and showcases a deep pool of editorial talent with a unique mix of experience and knowledge.
Christine Clancy | COO
With more than two decades of experience as a media professional, Christine has worked in newsrooms across Canada, Vietnam and Australia. She joined the Prime Creative Media team 12 years ago, and today oversees more than 43 titles, including a dozen print and digital transportation titles. She continues to lead a team that focuses on continuous improvement to deliver quality insights that helps the commercial road transport industry grow.
William Craske | Editor
Over the past two decades William has published widely on transport, logistics, politics, agriculture, cinema, music and sports. He has held senior positions in marketing and publicity for multinational businesses in the entertainment industry and is the author of two plays and a book on Australian lm history. Like many based in Melbourne he is in a prolonged transition of either returning or leaving.
Peter Shields | Senior Feature Writer
A seasoned transport industry professional, Peter has spent more than a decade in the media industry. Starting out as a heavy vehicle mechanic, he managed a fuel tanker eet and held a range of senior marketing and management positions in the oil and chemicals industry before becoming a nationally acclaimed transport journalist.
Peter White | Journalist
Since completing a Bachelor of Media and Communication degree at La Trobe University in 2021, Peter has obtained valuable newsroom experience, supplemented by direct industry exposure at Prime Creative Media. As the Editor of Trailer, Peter brings a fresh perspective to Prime Mover. He has a strong interest in commercial road transport and in furthering the magazine’s goal of growing the industry.
Sean Gustini | Journalist
Having completed a Bachelor of Arts majoring in Media and Communications at the University of Melbourne in 2024, Sean looks forward to bringing his passion for writing and journalism to the road freight and transport industries. He previously lived in the Philippines, Vietnam, Indonesia and Malaysia. In his downtime he enjoys playing the guitar and running.
Ashley Blachford | Business Development Manager
Handling placements for Prime Mover magazine, Ashley has a unique perspective on the world of truck building both domestically and internationally. Focused on delivering the best results for advertisers, Ashley works closely with the editorial team to ensure the best integration of brand messaging across both print and digital platforms.
CEO John Murphy john.murphy@primecreative.com.au
Editor William Craske william.craske@primecreative.com.au
Managing Editor, Luke Applebee Transport Group luke.applebee@primecreative.com.au
Senior Feature Peter Shields Writer peter.shields@primecreative.com.au
Business Ashley Blachford Development ashley.blachford@primecreative.com.au Manager 0425 699 819
Art Director Blake Storey blake.storey@primecreative.com.au
Design Blake Storey
Contributors Sean Gustini sean.gustini@primecreative.com.au
Peter White peter.white@primecreative.com.au
Client Success Salma Kennedy Manager salma.kennedy@primecreative.com.au
Head Of ce 379 Docklands Drive, Docklands VIC 3008 enquiries@primecreative.com.au
Subscriptions
03 9690 8766 subscriptions@primecreative.com.au
Prime Mover magazine is available by subscription from the publisher. The right of refusal is reserved by the publisher. Annual rates: AUS $110.00 (inc GST). For overseas subscriptions, airmail postage should be added to the subscription rate.
Articles
All articles submitted for publication become the property of the publisher. The Editor reserves the right to adjust any article to conform with the magazine format.
Copyright PRIME MOVER magazine is owned and published by Prime Creative Media. All material in PRIME MOVER magazine is copyright and no part may be reproduced or copied in any form or by any means (graphic, electronic or mechanical including information and retrieval systems) without written permission of the publisher. The Editor welcomes contributions but reserves the right to accept or reject any material.
While every effort has been made to ensure the accuracy of information Prime Creative Media will not accept responsibility for errors or omissions or for any consequences arising from reliance on information published. The opinions expressed in PRIME MOVER magazine are not necessarily the opinions of, or endorsed by the publisher unless otherwise stated.
”Hallett has in recent years increased the average unit carrying capacity of its heavy fleet by over 40 per cent to now boast the highest capacity and most efficient construction materials fleet in South Australia.”
FLEET FOCUS
26 New Colossus
As one of South Australia’s biggest vertically integrated family businesses, Hallett Group is accustomed to pushing the envelope when it comes to cutting edge ideas. It’s recent launch of an A-triple roadtrain embodies these innovations with a vengeance.
32 When the Lion Roars
One of the first new generation 640 horsepower MAN TGXs into the country has landed at Sydney traffic and network repair specialist T&S Roadworks.
36 Going to Any Length
Maintaining vegetation growth and keeping it clear from power lines is a specialised service requiring specialised vehicles.
& TECH
44 Meet the Resistance Glass specialist SCHOTT asks what difference an impactresistant windshield would make to the bottom line of Australian linehaul fleets.
48 Expanding Horizons
Refrigerated truck and fleet company Scully RSV has developed a strong presence in nearly every state and territory over the last 30 years with a new Adelaide site recently opened.
58 In Bloom Volvo’s new 17-litre Euro VI engine, now available with up to 780 horsepower, is taken for a drive as an AB-triple pulling over 100 tonnes in rural Western Australia..
William Craske Editor
In ation in the 1970s ran at nearly triple the rate of the previous two decades. By as early as 1972 the adverse effects of the cost of living were being felt across industry in the United States. The previous year, under the Tehran Price Agreement of 1971, the posted price of oil spiked and, due to a decline in the value of the US dollar relative to gold, certain anti-in ationary measures were enacted. On 15 August President Nixon, issued an Executive Order effectively making the dollar convertible only to gold directly on the open market. As the dollar started to oat free of the old link to gold, oil producers who priced their product in dollars, began seeing major reductions in income.
In September 1971, OPEC issued a joint communiqué stating that from then on, they would price oil in terms of a xed amount of gold. The glacial pace at which OPEC readjusted their prices to re ect the depreciation, however, did little to alleviate mounting pressures on transport businesses especially edgling independents.
In March of the previous year, Congress had given itself a huge 41 per cent pay rise but only 5.4 per cent for postal
workers. In New York City, where letter carriers walked off the job, the largest wildcat strike in US history ensued lasting eight days. Not even a month later, Teamster drivers, outraged over the meagre pay raise their union leadership had negotiated, walked off the job in 16 cities across the Midwest. In Cleveland, strikers devised a patrol system that would stop trucks carrying cargo outside of essentials food, pharmaceuticals and, yes, beer.
All this mattered increasingly to the little guy on the ground, who was getting squeezed by discretionary spending at both ends.
Federal Express, established in 1971, was one of these. Founder and Executive Chairman Fred Smith, who had raised nearly $90 million in venture capital from investors like Allstate and Newport Securities, was soon haemorrhaging costs mainly on fuel two years later. Down to his last $5,000, Smith, out of sheer desperation, pitched General Dynamics for a lifeline. But it refused. Staring down oblivion, he did what any self-respecting executive would have done before the Securities and Exchange Commission got its teeth. He hit the blackjack tables in Las Vegas — and gambled the lot. In that moment of bravery or recklessness, depending
on where you sit on the scales, Smith turned the $5,000 into $27,000. Having been able to take care of the fuel bill with his winnings, more importantly, it bought him some time. He soon raised another $11 million and by 1976, FedEx’s revenue was valued at $75 million. All this after running at a loss for 2.5 years before it would break even. According to its current market cap, FedEx Corp is valued in the top 300 companies in the world.
Smith once said he learned more in three years as a serviceman in the Marine Corps where he was awarded two Purple Hearts and a Silver Star for active duty in Vietnam than his entire time at Yale Business School.
In the movie The Card Counter, a skill the military more than likely also taught Smith, Oscar Isaac notes “what separates blackjack from other games is that it’s based on dependent events, meaning past affects the probability in the future.”
It’s a life lesson that never loses relevance. Now if someone would inform the blokes in charge of the printer spewing out our at currency.
Qube has welcomed a new Volvo FH16 prime mover to its fleet as part of an extended partnership with Pilbara Minerals.
The new FH16 will operate 24 hours a day in support of Pilbara Minerals’ Pilgangoora Operation.
It replaces a Qube vehicle that has been hauling for the Western Australian fleet since first production in 2018 with over two million kilometres.
The Yindyamarra-wrapped truck is part of a Qube fleet dedicated to Pilbara Minerals, and has been specifically designed to transport spodumene concentrate from the Pilgangoora Operation to Port Hedland for storage and shipping.
It features artwork by Wiradjuri and Sydney-based artist Darren
Charlwood, commissioned as part of Qube’s 2023 Reconciliation Action Plan.
Qube Pilbara Logistics Manager, Byron Messer, said Qube was pleased to dedicate one of its wrapped trucks to Pilbara Minerals to mark the extended partnership.
“Qube truly values the opportunity to continue managing the haulage, stockpile, storage facilities and vessel loading for Pilbara Minerals,” he said.
“We are excited to support Pilbara Minerals’ growth and expansion projects into the future, as the world’s largest, independent hard-rock lithium operation, and are pleased to dedicate this fantastic truck to its Pilgangoora Operation, given what it represents for us.”
Pilbara Minerals Executive General Manager Operations, Brett McFadgen, said the extension to the haulage services agreement with Qube followed an extensive evaluation process.
“As a valued partner of Pilbara Minerals since 2018, Qube has been part of our growth journey and is an integral part of the concentrate and logistics supply chain, ensuring our product safely gets from our mine site to Port Hedland,” he said. “They handle our concentrate product on site, transport it to Port Hedland, manage our storage facility and load our vessels.
“The special edition truck was a welcome addition to site and it’s been great to see the artwork on the truck as it’s travelling around our operation.”
ACFS Port Logistics is operating a Mercedes-Benz eActros as part of an all-electric container delivery pilot program in Sydney.
The logistics provider is the first company to run the eActros prime mover in Australia as part of the ‘ACFS Better Way”’program, which represents the company’s commitment to sustainability and innovation in the logistics industry.
The eActros features an e-axle, which integrates electric motors into the drive axle of the truck and replaces a traditional driveshaft.
Daimler Truck Australia Pacific President and CEO, Daniel Whitehead, said the ACFS pilot program is demonstrating the benefits of running an electric truck in Sydney.
“ACFS has a proven track record of striving to reduce its emissions in any way it can, including purchasing Daimler Truck vehicles that meet Euro 6 or equivalent emissions levels
such as the Mercedes-Benz Actros and Fuso Shogun,” said Whitehead.
“The all-electric eActros goes a step further and delivers huge benefits in built up areas, producing zero driving emissions and operating near silently. It is a sustainability pioneer, but is also a true workhorse, which the ACFS team is finding out in its daily operations.”
ACFS Port Logistics Chief Executive Officer and Managing Director, Arthur Tzaneros, said the pilot program represents an important milestone for the company.
“We are proud to introduce the Mercedes eActros to our fleet and be at the forefront of clean Transport solutions,” he said in a statement. “This continuing focus to lead and innovate by piloting the heavy vehicle electric technology not only reflects our commitment to sustainability, but also enhances the service we provide to our customers.”
ACFS is looking to the future,
according to Tzaneros, by integrating trucks such as the eActros.
“As we embrace innovative solutions, we are also taking significant steps toward reducing our carbon footprint and supporting the communities we serve. We believe this initiative will pave the way for further advancements and investment in our operations and contribute to a greener future for all,” he said.
Daimler Truck Australia Pacific Sales and Marketing Vice President, Andrew Assimo, said the company is ready to help customers achieve their sustainability goals.
“Daimler Truck offers our customers a complete sustainable truck solution, whether it be low emission diesel or battery electric,” he said. “As part of that commitment, when it comes to our amazing electric trucks from Mercedes-Benz and Fuso, we can help with everything from selecting the correct specification and route planning to charging infrastructure advice. Each truck comes with a complimentary servicing package and there is a raft of financing packages including guaranteed buyback options,” added Assimo.
The eActros features three lithium-ion battery packs with a total capacity of 336kWh.
Running with a single trailer, it can operate at total Gross Combination Mass (GCM) of 36-tonnes.
It features a five-stage recuperation braking system that works like an engine brake to both spare the service brakes and recoup significant amounts of electricity, which is fed into the batteries.
Daimler Trucks Brisbane and Gold Coast General Manager, Aaron Camilleri, said ACFS has been a valued client since 2019 and has always been very clear that decarbonation is a key priority.
“It’s great to see ACFS’ continued commitment to their emissions reduction strategy,” said Camilleri.
The New South Wales Rural Fire Service has taken the Volvo FM Electric for an extended test drive in an effort to understand how low emissions vehicles can be integrated into emergency services fleets in the future. With an RFS water tanker in tow, the electric prime mover tackled the 550-kilometre route from the services’ Glendenning NSW logistics headquarters to the border city of Albury, arriving to be displayed at the NSW RFS Championships in the suburb of Thurgoona. The driving team, consisting of Inspector Brendan Doyle, RFS Logistics Manager and Peter Duff RFS Logistics & Transport Supervisor shared driving duties over the route to asses the performance and driveability of the vehicles as well as the heavy vehicle charging experience.
“This drive presented a great opportunity for us to touch, feel and experience an electric prime mover on public roads,” said Doyle. “It also allows us to consider where a vehicle like this could fill roles within our logistics fleet
in the future.”
Over the course of the trip, the truck averaged 88.7 km/h with an energy consumption of 1.24kWh/km.
Required charging time was 120 minutes to complete the 6.2 hour trip with stops made at Goulburn and Tarcutta. The driving experience was sensational according to Duff.
“One of the key takeaways for me was that you could take anyone familiar with an existing Volvo truck and they’d
be able to drive this without additional training at all,” he said.
Volvo Group Australia Vice President, Governmental Sales, Cameron Bettany says that there has been a lot of interest in battery electric trucks from fire and emergency services around the country.
“Fire and emergency services are on the front line when it comes the impact of climate change on our local environment,” said Bettany.
A refreshed NSW Heavy Vehicle Access Policy roadmap will reportedly deliver a fit-for-purpose road freight network. Announced by NSW Minister Jo Haylen at NatRoad Connect in Coffs Harbour, the policy outlines a new and updated strategic approach to heavy vehicle access in NSW for state, regional and local roads.
Under the roadmap, access for the safest, most sustainable and productive heavy vehicles is optimised while data and technology support greater efficiencies in the freight and supply chain system.
The Policy will support an efficient road freight network that is connected to local NSW communities and commercial hubs, and is integrated with railways, intermodal terminals, ports and airports.
Since the Policy’s original release in 2018, significant improvements
in heavy vehicle access have been achieved.
This includes key freight routes being unlocked and greater access for higher productivity vehicles.
The Heavy Vehicle Access Policy was refreshed in 2024 to ensure Transport remains responsive to the needs of NSW’s growing population; the impacts of climate change and net zero emission targets; shifting global trends including the rise of e-commerce increase in innovation, technology and data available for heavy vehicles.
The Policy sets out a five-year roadmap and actions to optimise access for the safest, and most sustainable and productive heavy vehicles on NSW state roads.
The Policy, according to Transport for NSW, was developed based on extensive research and consultation with freight operators and industry,
academia, and all parts of government. The updated Policy is one of the immediate actions recommended by the NSW Freight Policy Reform Panel in its recently released Interim Directions Paper.
“This Policy is our new strategic approach to managing heavy vehicle access on our roads, ensuring the goods we need can move through the state in the safest, most sustainable and productive manner,” said Bianca Slack-Smith, Director Policy and Regulatory Reform Transport for NSW.
“The Policy outlines our five-year action roadmap to streamline access for the highest performing heavy vehicles on the network.
“The launch of the updated Policy is one of the immediate actions recommended by the NSW Freight Policy Reform Panel in its recently released Interim Directions Paper.”
FREIGHTLINER IS SERIOUS ABOUT SAFETY.
Every Cascadia comes with a complete suite of fully integrated active safety features and connected technology that helps you get on with your work.
With Active Brake Assist, which can even detect moving pedestrians, Side Guard Assist, a driver airbag, and forward-facing camera footage that can be sent on-the-go for immediate incident reports, the Cascadia sets a new standard for practical safety.
A record crowd attended the Australian Freight Industry Awards where Lindsay Fox was recognised as the Personality of the Year. The prestigious blacktie Gala Presentation, the 34th in its history, was hosted at Melbourne’s Palladium Room at Crown, celebrating excellence across the freight and logistics industry on 7 September. Judges evaluated a record-breaking number of applications across a range of categories.
The winners of the 34th AFIAs were: Lindsay Fox, Personality of the Year Award; Namrita Anchan of Linfox Australia, Women’s Leadership Award; Sean Draffin of Xtreme Freight, Emerging Leader Award; Qube Bulk, Green Star Award; Secon Freight Logistics, Application of Technology Award; Freight Cyber, Best Practice
Safety Award; Alex Fraser Recycling, Investment in People Award; Australian Paper Recovery, Waste & Recycling Business of the Year Award.
“After what has been another challenging year, it was fantastic to take a moment to reflect on and celebrate our industry and those that keep pushing for greatness and embracing innovation to keep our country moving,” said VTA CEO, Peter Anderson. “The AFIA Committee extends its sincere congratulations to every winner and finalist and thanks those who lodged an entry and shared their stories. We look forward to building on the success of this outstanding event for many years to come.”
The Application of Technology Award highlights innovation in utilising
technology to solve problems, enhance productivity, and improve efficiency. The win for Secon Freight Logistics was attributed to the successful installation of its 25kg automatic debagging machine in May, which has since revolutionised its operations.
“A huge thank you to everyone who contributed to this achievement – we’re proud to celebrate this recognition and look forward to continuing to push boundaries in the industry,” the company said in a statement.
Guests at the event were treated to entertainment courtesy of Master of Ceremonies, Lizzy Hoo, and the musical stylings of the Matt Hetherington Band and the Zandra Trio.
500-600 HORSEPOWER
,850-2
1,850-2 ,050
lb-ft @ 975RPM
Extreme duty and heavy hauling for your biggest jobs
Detroit’s most powerful truck engine ever, the DD16 boasts up to 600 horsepower and 2,050 lb-ft of torque. The big bore workhorse provides efficient and dependable power and performance without compromise.
Advanced combustion and aftertreatment technology exceed future emissions requirements whilst retaining exceptional fuel efficiency and uptime.
This power, performance, and efficiency are backed by the most comprehensive warranty and extended coverage packages, ensuring the highest level of support for our customers.
When you buy a Detroit product, you’re buying billions of miles of engineering excellence. Tried and true, Detroit engines are built to ride the roughest roads.
With Detroit, there’s no compromise. @ 1,800 RPM
Wickham Freight Lines has taken delivery of the 18,000th truck ever sold by Brown and Hurley. It’s part of a long-term arrangement in which the Warwick-based carrier purchases every 1000 unit brought on line by the truck and trailer dealer.
The Kenworth T659 will be working in the interstate fleet handling refrigerated goods between Melbourne, Adelaide and Sydney.
It marks the 35th new unit handed over to the business just this year with near identical numbers on the waitlist for next year Thomasin Roberts, Wickham’s Managing Partner told Prime Mover “We have just over 200 prime movers in the fleet now, it’s quite funny to look back on, we often joke that we thought we were busy with 70,” she said.“There’s a lot of moving parts in our business, and our people and partners enable us to move forward. We’re very thankful and appreciate everyone’s time and effort.”
It also epitomises the longevity of the ongoing partnership.
Jim Hurley, Brown and Hurley Director, attended in person for the milestone handover, the 18th time Wickham Freight Lines have accepted a new 1000th truck sold by Brown and Hurley.
“Jim has handed over and taken orders to four generations of our family and my son Rhett is lined up to place the next order, into Jim’s infamous ‘order book’,” said Roberts. “Having five generations of orders is pretty special, we appreciate the relationship with Jim and the team at Brown and Hurley. As you can see, it extends generations.”
Powered by a 600hp rated Cummins X15 engine, the new Kenworth T659 features the numerals 18000th on the exhaust stacks and at the rear of the cabin.
It also comes with a large 50” bunk. The driver is also very happy with it according to Roberts.
“We’re all pretty impressed with the new
Leading freight carrier, Cahill Transport, has appointed a new Chief Executive Officer. The company’s recent General Manager of Operations, Nathan Perrott, was promoted internally within
the organisation.
In an online statement issued last month the company said the appointment reflected Perrott’s extensive experience and his significant contributions to
650s, the comfortability and reliability is hard to match,” she said. “The 650s are one of our fleet favourites.”.
Wickham Freight Lines is celebrating their 30th year in business in 2024, a major milestone that is equally exciting for the business and family.
“It’s a great time to reflect on the hard work and dedication of our people and the commitment of our partners, we’re very proud of all our achievements so far,” said Roberts.
She added that they were well on their way to purchasing 400 Kenworth trucks.
Wickham Freight Lines received their 350th truck in September last year.
“We are moving in to more automatic transmissions and we’re in love with the K220 product so more of those are coming soon,” she said.
“We are also celebrating the arrival of our 300th FTE van. This is another milestone the business and family are proud of, which we’ll have celebrations for in October.”
the business since he joined in November 2023.
“With decades of executive experience in the transport industry, Nathan’s leadership will ensure we continue delivering exceptional service to our valued customers,” the company said. Since crossing over from Toll Group, where he served in various leadership roles for 23 years, Nathan Perrott has had an ascendant rise at Cahill Transport joining initially as Victorian State Manager.
The key change to its organisational structure is reportedly designed to better serve its customers.
A major move last year into the temperature-controlled sector was predominantly driven by current customer requirements within the market.
In January former CEO Chris Ellis moved into a part-time Chairman role after nearly fours years at the helm.
Unlike a standard wash bay, We are able to setup a temporary washbay onsite! This cuts costs and time down considerably by eliminating lengthy trips to offsite washbays. We also utilise a road legal Yard Tug, This allows our team to move trailers around your yard without setting foot on the ground!
With multiple collection methods to suit most situations, We are able to collect and remove all truck wash water from the premise to be disposed of safely. All of this is done at no additional cost!
As Australia’s leading mobile washing supplier, We are in position to service fleets sizes from 15 to 15,000! Wash It Australia is proudly the preffered supplier for Australia’s largest transport company & Australia’s largest supply chain solutions
> MGM BULK welcomes milestone Kenworth to fleet
MGM Bulk has recently announced the addition of its 200th Kenworth. The bulk haulage titan represents a significant presence in Australia’s transport and mining industries. It’s quad roadtrains in the Pilbara region are known internationally. The business manages the logistics of mineral sands, iron ore, lithium, salt, copper concentrate, timber, gravel, limestone and sand.
Operating out of Perth, the 200th Kenworth is a brand-new K220 10 x 6, part of MGM’s 32-metre PBS combination fleet. It will be transporting lithium approximately 1000 kilometres a day into MGM’s Bulk Storage Sheds in Bunbury. The fleet’s new K220 is equipped with the MGM Safety Package, containing technologies which ensure a high quality of driver assistance
The team at MGM Bulk following the delivery of its 200th Kenworth truck.
and protection. In announcing the milestone, MGM paid tribute to its long serving partners—CJD Equipment,
PACCAR Australia, and Bruce Rock Engineering—for their contributions to the efficiency of MGM’s transport.
Regulations setting mass limits under the Heavy Vehicle National Law have now been amended to allow heavy vehicles to meet the latest international standards. From 1 November 2024, a 500kg increase in general access mass limits will apply to trucks in Australia that comply with Euro VI or equivalent noxious emissions standards.
Minister for Infrastructure, Transport, Regional Development & Local Government, Catherine King described
it as a boost to trucking productivity. “This will improve safety and emissions reduction outcomes in our heavy vehicle fleet and follows the Government’s recent announcement of tighter noxious emissions standards for new trucks and buses, which must be met from 1 November 2024 onwards,” she said in a statement. “The mass limit amendments have been made under the Heavy Vehicle National Law, which is based in Queensland and
adopted by participating states and territories.
“The increase in heavy vehicle mass limits is an important step towards improving productivity and safety in the heavy vehicle sector, while reducing emissions.
“I thank State and Territory colleagues, the National Transport Commission and the National Heavy Vehicle Regulator for working together to achieve this important change.”
Followmont Transport has acquired five new Kenworth K220s, bringing the fleet’s total number of Kenworth prime movers on the road to 52.
The latest models, powered by Cummins X15 Euro V engines and fitted with Endurant XD Pro automated transmissions, are specifically designed to handle Australia’s toughest conditions.
They will operate across interstate routes hauling general freight from Brisbane to Far North Queensland, and returning with produce down to Sydney and Melbourne.
In these operations the trucks are expected to cover an impressive 240,000 kilometres annually, reinforcing Followmont’s commitment to reliable and efficient transport solutions.
Followmont Transport Managing
Director, Mark Tobin, commented on the role that the Kenworth additions play as part of the company’s ongoing fleet renewal strategy.
“Kenworth trucks have been a cornerstone of our fleet for years because they are built to endure,” he said. “We choose Kenworth consistently because we know they are a valuable asset to our business.
“We believe the toughness of the Kenworth K220s makes them an ideal fit for our operations.
“Their capability allows us to confidently tackle the long hauls and heavy loads that are part of our everyday business.”
Additionally, the trucks have reportedly been well-received by drivers.
“The K220s are up to the task of hauling heavy loads day in and day out, keeping our promise of service
excellence to our customers,” Tobin said. “We’re fortunate to have an outstanding partnership with Brown and Hurley, who always ensure they meet our expectations, making this investment even more seamless.”
Followmont Transport COO, Ross Longmire, further emphasised the importance of maintaining a strong fleet.
“By investing in the latest Kenworth K220s, we’re ensuring that we stay at the forefront of the industry,” he said.
“These trucks are replacing older units, allowing us to maintain a high level of service while supporting our drivers with the best equipment, improving our fuel efficiency and lowering our emissions.
“We trust Kenworth’s ability to deliver performance, durability and reliability, and we know our drivers love them.”
GTS Freight Management has taken delivery of six Mercedes-Benz Actros trucks at its Mildura headquarters. The privately-owned company, which loads 500 trailers each day and covers 3 million kilometres every month, chose the 580hp Euro 6 rated Actros 2658.
Daimler Truck Australia Pacific President and CEO, Daniel Whitehead, handed over the keys to GTS Freight Services Managing Director, Damien Matthews, at its Mildura headquarters.
“We are thrilled to see the Actros in GTS black,” Whitehead said. “GTS is achieving great things and is actually growing its business in a challenging economic environment, which shows it is really delivering for its customers. The fact that GTS will be using six MercedesBenz Actros support these customers is something we are very proud of.”
Matthews said the Actros trucks, which were delivered by Daimler Trucks Mildura, are a welcome addition to the GTS Freight Services fleet.
“We know from previous experience
that the Actros is great on fuel and the drivers have already told me, after the first trip, how comfortable and quiet these new trucks are,” he said.“The high level of active safety features that Mercedes-Benz prides itself on is also really welcome because safety underpins everything we do at GTS.”
Importantly, the Mercedes-Benz Actros comes standard with engines that meet Euro 6 emissions ratings, which are stricter than existing Australian trucks emission standards.
Matthews was also attracted by the complimentary servicing offer that was part of the package.
Daimler Truck Australia Pacific Head of Retail Fleet Sales, Barry Smith, worked closely with Matthews ahead of the delivery.
The chosen truck runs the OM 473 15.6-litre six-cylinder that pumps out 580hp and 2800Nm of torque and is linked to a 12-speed PowerShift Automated Manual Transmission (AMT). It features Predictive Powertrain Control (PPC) which uses topographic map data and GPS to help the truck anticipate terrain and select the optimum shift pattern and engine response for maximum fuel economy including coasting when safe.
> MaxiTRANS announces comprehensive rebranding, launches Freez-R product line
Victorian-based trailer builder, MaxiTRANS has officially rebranded at a major launch event.
Unveiling a new logo and visual identity last month, the company will now be known as Freighter Group.
At an event held over two days in Ballarat where key suppliers, partners, industry representatives, media and stakeholders were in attendance
Executive Chairman Greg L’Estrange made several major announcements for the group which marks a significant milestone in the company history.
The MaxiTRANS trailer business was purchased by a group of local private investors in September 2021.
Since then the focus of the business including a $50 million advanced manufacturing upgrade to its Ballarat facility has been on long-term sustainability.
“We set about embarking on a significant transformation journey when we purchased the trailer business, with the aim of creating a new era for the future of the company and the trailer manufacturing industry in Australia,” said L’Estrange.
“The journey started with a $50 million investment into our Ballarat site. This investment has seen the introduction of a range of state-ofthe-art equipment and an expansion of the overall footprint of the facility, transforming it into a modern manufacturing environment.
“The completion of the upgrade puts the business in a position to be able to continue to evolve with the changing needs of our customers long into the future.”
Several Tier 1 fleets were present including representatives from Ron Finemore Transport, Lindsay Australia, KS Easter, Hentschke Loxton and Wettenhalls among others. The name change to Freighter Group reflected the new era the company was entering into while recognising its past legacy. The Freighter brand dates back to 1946.
“The Freighter Group name not only connects our rich heritage but importantly it connects our vision of ‘freight it for life’, which is our total commitment to supporting our customers for the life of our product,” said L’Estrange. “We are excited to take the business forward under the Freighter name and continue to deliver product solutions through our wide range of industry leading brands.”
One of which will be Freez-R, a new refrigerated trailer offering. Launched in collaboration with partners Schmitz Cargobull, Freez-R is constructed from Ferroplast technology and will be the first of Freighter Group’s trailers to come with TrailerConnect telematics as standard.
“Through our partnership with Schmitz Cargobull, collaboration with customers and our industry experience, we have been able to design and create a product with the exacting needs of the Australian market,” said L’Estrange.
Freighter Group will offer spare parts for all of its OEM products manufactured under the new name given the agreement with MaxiPARTS to supply parts has formally
concluded. Customers will be able to contact their local Freighter Group dealer for their spare parts needs. With that Freighter Group introduced Hitcher Parts as its new spare parts brand.
“Hitcher Parts will consist of an expansive range of quality trailer parts that are designed to go the distance,” said L’Estrange. “The Hitcher Parts range continues to expand and will soon be available on our product, as well as available in the aftermarket.”
In addition, Freighter Group announced it had developed a preengineered product offering — the Ready Range of trailers. Designed for a wide range of applications, the Ready Range will be competitively priced and further streamline the ordering process by assisting in delivering shorter manufacturing lead times.
“We are excited about the significant transformation the Freighter Group business has been going through,” said L’Estrange. “Our whole team has been dedicated to our vision and I can’t thank them enough for the hard work and dedication they have shown through this transition.”
Karin Rådström has been appointed the new Chief Executive Officer of Daimler Truck AG effective October 1, 2024.
Appointed in this function until January 31, 2029, she will succeed Martin Daum who will simultaneously resign as CEO paving the way for the next chapter of the company’s transformation according to a statement issued in September by the Supervisory Board. Martin Daum will remain as full member of the Board of Management until December 31, 2024, to support a smooth handover.
The Chairman of the Supervisory Board of Daimler Truck Holding AG, Joe Kaeser, thanked Daum for his outstanding achievements and commitment in his nearly four decades long career at Daimler.
“Personally, and on behalf of the entire Supervisory Board, I would like to thank Martin Daum for his commitment and outstanding results,” he said. “He has been leading Daimler Truck’s transition from a conglomerate division into a successful DAX-listed company in a convincing manner. Thus, he led it through one of its most eventful times in recent history and has been the key architect of Daimler Truck’s economic success and international reputation.
“His dedication to the company, its customers and employees is remarkable. He is a ‘trucker’ with heart and soul. Martin Daum hands over a successful company which is well prepared for the challenges ahead.”
Starting his career at Daimler-Benz AG in 1987, Daum has been instrumental in shaping Daimler Truck’s global success.
As CEO of Daimler Trucks North America, he played a key role in growing the local business.
Today, the segment North America is one of Daimler Truck’s powerhouses. Since assuming the role as member of the Board of Management of the former Daimler AG for Trucks and Buses in 2017, Daum and his leadership team have significantly increased revenues while strongly enhancing margins, thereby providing greater flexibility for
Under his leadership, Daimler Truck has spearheaded the technological transformation with both battery electric and hydrogen-based drivetrains. His successor, Karin Rådström, joined Daimler Truck’s Board of Management in 2021 and since then has been responsible for Mercedes-Benz Trucks. Within a short period of time, Rådström, a trained engineer, has successfully reshaped the segment profitability and advanced its transformation towards sustainability.
With foresight and entrepreneurial spirit, she has introduced a range of new battery electric trucks while driving customer focus together with her team, leading to an enhanced service offering and an increased customer satisfaction. Before joining Daimler Truck, she oversaw Sales & Marketing as a member of the Executive Board at Scania.
At her former employer, she previously also held the position of Senior Vice President, Head of Buses & Coaches.
“We are delighted to win Karin Rådström with her outstanding industry knowledge and leadership skills as the new CEO of Daimler Truck Holding AG,” said Kaeser. “She has proven that she is able to successfully advance the transformation of a brand while navigating a challenging external environment. As a true leader, Karin Rådström has been instrumental in
establishing a new performance culture and fostering empowerment, diversity and customer focus.
“These principles are essential for Daimler Truck to master the transformation of mobility successfully and be our customers’ first choice. We wish her and her team great success and we are very much looking forward to continuing our collaboration.”
Michael Brecht, Vice Chairman of the Supervisory Board of Daimler Truck Holding AG and Chairman of the General Works Council said as labour representatives, they had enjoyed a trusting relationship with Karin Radström in the recent years.
“It is important to us that Daimler Truck under her leadership remains a successful and future-proof company,” said Brecht. “Thereby, the interests of employees and shareholders must be taken into account equally. This is a prerequisite for secure and good jobs.
“Our explicit thanks and greatest respect go to Martin Daum, who has successfully positioned Daimler Truck globally with great care. He has achieved outstanding accomplishments, led Daimler Truck to independence and always listened to the interests of the workforce.”
Karin Rådström will, for the time being, remain responsible for Mercedes-Benz Trucks until her succession is decided.
Find out More https://www.schott.com/en-gr/ expertise/applications/borofloat-borosilicate-glass-for-windshields
As one of South Australia’s biggest vertically integrated family businesses, Hallett Group is accustomed to pushing the envelope when it comes to cutting edge ideas. It’s recent launch of an A-triple roadtrain embodies these innovations with a vengeance.
Over the last four decades Hallett Group has built a reputation as the largest integrated supplier of building, construction and mining materials in South Australia. The Hallett stable houses dedicated divisions in Resources, Concrete, Transport, Building Supplies and Timber & Truss in addition to recent horizontal and market extension acquisitions such as DK Quarries and Daecon Trusses, to name but a few. Total staff hovers around 500 in South Australia with two operations, Major Timber and Daecon Trusses, based in Victoria. For the record, Hallett’s preceding entity MSP Group was established in 1980. The name was changed to Hallett Group in 2022. Much of these non-competing revenue streams rely on road transport.
In early September a delivery ful lled by CMV Truck Centre Adelaide of ve new Kenworth T659 prime movers made it clear that the eet was preparing for a major shakeup. The trucks have been gradually brought online as the trailers for each unit become available contingent to the many necessary approvals from the National Heavy Vehicle Regulator. These ve Kenworth trucks ultimately will be responsible for three different tasks.
Three of the ve units will be devoted to an end-tipper application running primarily from quarries Hallett owns in Kulpara, Truro and a sandpit at Clinton to its Dry Creek concrete plant and the BHP Prominent Hill Mine.
Final approval for network access to the BHP mine at Prominent Hill is also underway where Hallett and one of its customers both maintain plants.
Hallett Group actively situates its operational footprint at the forefront of technology and innovation, often pursuing strategies that make it the fastest and most adaptive to identify, realise and seize new opportunities. Sustainable transportation, increasingly as a strategic vision means being able to survive into the low emissions age through the recourse of PBSapproved higher productivity roadtrain
combinations. A mammoth new A-triple is the epitome of said vision.
The project commenced two years ago in partnership with heavy vehicle engineering and design specialty rm Tiger Spider.
“We wanted to start working on what we could do to increase our capability and reduce trucks on the road,” says Rhylie Ayres, Hallett Group Operations Manager – Transport. “It would obviously reduce our emissions but also allow us to deliver increased payloads to our internal and external customers.”
Over the gestation and build period, Hallett Group begun the task of phasing out some of its double roadtrains in anticipation of the bigger units.
The rst of three A-triples is now operational. It carts concrete aggregates such as 10ml and 20ml stone, quarry dust and construction sand.
“PBS regulations have improved in South Australia enabling eets to operate much bigger combinations closer to the city,” says Rhylie. “Though a metro area, Dry Creek is on the northern side of Adelaide where roadtrains are common. You’re seeing AB-triples and some eets are getting approval for 53.5-metre-long combinations.”
The Hallett A-triple is 44.9 metres in length. With a GVM of 141.5 tonnes, it’s approved to decamp at that weight directly from the Dry Creek facility. No trailers during operation need to be separated. From the yard it runs empty to Kulpara, loads up to a 96-tonne payload and returns to Dry Creek where drive-over grids with ramps are used. This affords the operator to tip off directly into each grid so that the combination can remain intact. Tipping off takes about 20 minutes before the unit is out of the yard and heading north again.
Powered by a Euro 4 600hp Cummins X15, the engine runs through an 18-speed Eaton RoadRanger gearbox, which is speci ed according to Rhylie, so that drivers can have more control. MTData is the preferred telematics provider across the entire transport eet. Front dash and side wing cameras
are tted to manage operator fatigue on every prime mover in the road transport eet.
“Having the tri-drive prime mover matched with tri-axle trailers and dollies enables substantial increases in payload compared to our normal bogie prime mover running an A-double roadtrain,” explains Rhylie. “With the tri-drive and the triple trailers we will get 96 tonnes, an additional 36 tonnes payload compared to the double roadtrains.” Turntables on the dollies had to be modi ed to ensure the correct weight distribution – 22.5 tonnes to be precise – was arranged for each of the axle spacings. Hallett Group, moreover, uses weighbridges at dispatch to ensure compliance with axle weights and mass management requirements “Those checks and balances help to ensure we’re always compliant on the road and meeting our compliance requirements,” says Rhylie.
Tiger Spider and Bulk Transport Equipment (BTE) helped partner on all the engineering details including the design approval from the NHVR and the South Australia Department of Transport before the units went into production.
“Once everything was out of the factory and in here, we did the nal PBS approval through the NHVR and it was all signed off very easily,” says Rhylie.
Being at a Level 4 weight Hallett will need to apply for route speci c permits to make certain it meets bridge assessments.
“We’ve got a route permit from Dry Creek directly to Kulpara quarry and back loaded both ways and we stick to that route as it’s not on a network at Level 4,” says Rhylie.
This particular shift sees the A-triple travel nearly 700 kilometres. The leg to Prominent Hill, where it will run ve days a week, increases the distance each time by a further 700 kilometres.
The Kenworths are tted with Barry Stoodley bullbars, hydraulics for end and side tippers, conveyer guards, chassis walkways, Clare Valley Auto electrical and a Truck Art Icepack.
Custom Air supplied the sleeper interior components, including microwaves and dual fridges.
The Kenworth eet is entirely acquired via lease packages put together by PACCAR Australia. It provides the exibility to turn over the prime movers every 42 months according to Rhylie.
“We want to make sure we are getting a full use of the trucks,” he explains. “As it stands, we get a lot more kilometres out of our tippers being mostly double shifted compared to our cement powder tanker trucks which we own.”
There are 160 trucks in the Hallett Group eet which comprises prime movers, concrete agitators, pneumatic tanker trucks, tipper trucks, at bed rigids and crane trucks.
In South Australia the eet has pioneered the six-axle truck and dog unit. It now has eleven of these.
Plans are underway already for an A-triple tanker set and two triples with side-tippers that have already entered into production. The side-tippers have been assigned to the company’s Green Cement Transformation Project launching next year in Port Augusta. It involves decarbonating the concrete being produced by using the byproducts used to make slag and y ash.
According to Kane Salisbury, Hallett Group Chief Executive Of cer, the Green Cement Transformation Project is the company’s proudest achievement to date.
“Hallett is creating new sources of low carbon cementitious materials from local industrial byproducts for the South Australian market and beyond,” he says. “By adding these new sources to
the global pool of low carbon cement alternatives we truly impact global CO2 emissions.”
The trucks for this project will run to Port Pirie before returning to Hallett’s Port Augusta Hub. Rhylie anticipates these units will have even greater carrying capacity given the product is a lot lighter per cubic metre.
“We’ll probably get upwards of 100 tonnes of payload over these trailers because of how the pro le of freight actually sits,” he says.
Rhylie has been with Hallett for just over 12 months having come across from Toll Group where he was employed for ve years.
“With Toll being a worldwide company it was a great experience looking after oil and gas general freight linehaul,” he recalls. “Having that knowledge base has been good and it’s been bene cial coming here and bringing that previous experience into the Hallett
Group. There’s a bit of crossover with some customers I used to deal with previously.”
In the last 18 months, Hallett has intensi ed its focus on enhancing its operational network to enable the use of high-performance vehicles like these new A-triples.
“Hallett has in recent years increased the average unit carrying capacity of its heavy eet by over 40 per cent to now boast the highest capacity and most ef cient construction materials eet in South Australia,” says Kane. “This enhanced carrying capacity when combined with great prime movers and trailers drives greatly improved emissions performance.”
Hallett is now planning for the next evolution of alternative fuels transport and is particularly excited by its potential to trial a variety of future technologies from its new Port Augusta hub.
One of the rst new generation 640 horsepower MAN TGXs into the country has landed at Sydney tra c and network repair specialist T&S Roadworks.
Athird generation family concern in Sydney, T&S Roadworks certainly lives up to its name even if the operational footprint is perhaps more divergent than what the brand confers. Not only does it specialise in road maintenance, but it also provides emergency response for accidents and incident cleanups in the aftermath of natural disasters.
Concrete and asphalt resurfacing and repairs within the Sydney metropolitan region is the bread and butter of the business. While it manages ongoing works with many Tier 1 partners, their biggest account is with Transport for NSW, who awards contracts for three zones across its extensive 12,368.2km² Sydney road network.
Here T&S Roadworks is now a major presence with projects underway on various major arterial roads where they are completing road repairs in addition to conducting routine maintenance of concrete national pavements on the likes of Picton Road, M1 Freeway and Sydney Harbour Bridge. Endowed with a growing arsenal of sophisticated tools including a weighty Wirtgen cold milling machine, and a PBS trailer tasked with carrying it, T&S Roadworks uses and owns an array of different heavy equipment. Excavators are one of the predominant assets in the business. They also own and regularly deploy backhoes and skid steer loaders. The road milling machine features a rotating drum with a cutting width of 1.5 metres.
weights, especially with the milling machine just on its own weighing nearly 30 tonnes you need some grunt behind it.”
To haul this imposing 22-metre unit T&S Roadworks have purchased a brand-new MAN TGX 26.640. It’s the fth MAN the business has purchased since it formed a relationship with the OEM back in 1994 and the fourth MAN currently active in the truck eet, which is now up to eight units in total.
The trailer that it is coupled to is an FWR quad axle twin-rear-steer low loader oat. While its main purpose is to haul the milling machine around it also transports excavators and has the capability to
at all hours of the day or night, holidays, Christmas breaks, whenever an incident happens, we’ve got to be there.”
The majority of shifts unsurprisingly take place at night, but this is variable. Recent heavy rains have dictated the movements of various crews during the day as they perform urgent cleanups.
Having an emergency response division has helped protect the business from lapses in work. In fact, the opposite, according to Peter, is true.
“Because there’s been a lot of rainfall, the road network is slowly becoming worse,” he says. “We’re all hands-on deck especially with ood recovery as well. We’ve been there on many occasions to help reopen bridges and causeways and to allow ferries to operate.”
T&S Roadworks Operations Manager Peter Argyropoulos.
conduct wide load transportation with a deck opening width of up to 3.5 metres. The milling machine was purchased speci cally for the company’s asphalt division.
“It basically rips up the old asphalt or any damaged asphalt pavement to allow new asphalt to be laid in that area,” explains Operations Manager Peter Argyropoulos. “Obviously when you’re up to those
“The main purpose of the machine was to expand our eet and our expertise and also to have the peace of mind that we’ve got our own equipment to do the tasks that we need to do and now clients have a higher regard of that because we’re pretty much a one stop shop within our industry,” says Peter. “We needed equipment so that we could provide emergency responses
A few years ago, a landslide on Putty Road in which a section above the road gave way required attendance from T&S Roadworks who were tasked with removing the over ow of soil so that specialty contractors could stabilise the mountain and the adjacent rockface and the road could be opened to traf c at the quickest possible convenience.
“Our main task is to get the job done safely and to secondly perform our job to a quality standard and thirdly to be ef cient in doing so,” says Peter. “They’re our three values in business — safety, quality and ef ciency. In our line of work, we need to be ef cient and open the traf c back to the general public as quickly as possible. You can imagine if major arterials are blocked for roadworks during the day, it would be an absolute nightmare.”
The company recently moved its headquarters over to Moorebank where a bigger facility is now located. They were previously based in Bankstown.
“Given our growth it wasn’t feasible to stay there as a property,” says Peter. “We just didn’t have the room.”
Peter’s grandfather, his namesake, rst migrated to Sydney from Greece in 1970. His father Tony and grandfather had a business together for a number of years before the retirement of the latter compelled the son to go out on his own. He started off with one backhoe, one excavator and a truck. Peter and his brothers Michael and Stan are now the company directors. The business currently employs 25 staff.
Back in the 1990s they ran a transfer station. The road maintenance commenced in the early 2000s before it eventually became the main focus. Around this time, they invested in several new second generation MAN TGS 26.480s.
The latest TGX 26.640, the most powerful MAN available, has no problems lugging around the milling machine.
“I believe it’s the best product on the
market,” says Peter. “I’ve driven other European trucks and personally for me I like the way MAN trucks are designed, how they’re built, their build quality and their maintenance.”
Peter need not rely on second hand accounts from drivers and dealers. He’s very familiar with the unit having driven the truck on several occasions including interstate.
“I was gobsmacked by the amount of torque and the gearing of it,” he says.
“They’ve developed a good product as a whole. As a drivetrain assembly it just works wonders. Especially, as I said, when you’ve got heavy weights behind you and you’re up and down hills and in and around city areas.”
The three operator modes available via the ick of a switch are major advantages in this particular line of work.
“You’ve got Manoeuvre for tight operations and Ef ciency for day in and day out driving, and you’ve got Performance,”
explains Peter. “When you’re in Performance and you’ve got a bit of weight behind you, you can de nitely feel the difference. To give you an understanding, our truck and trailer is 22 metres long. It’s under a special permit class as a quad axle oat. The truck gives the driver the ease and con dence that he can get into those tight places. The vision out of the truck increases the safety as well.”
Having been to Germany a few times including the recent IAA Transportation 2024 fair in Hannover, Peter has seen how the MAN trucks are built in Munich and the technology that goes into the product. He saw what he describes as the “meticulous” way each truck is built.
“The robots within the factory are very minimal,” he says. “It’s still built by hand, by quality tradesman. Each truck is off the line. It’s checked and it’s double checked. It’s just phenomenal,” he says. “The truck as a whole for the pricing of it, with the engine, the various functions and safety
features, I don’t think you can compare it. That was the main reason we purchased the truck. The service intervals are great for us, the cost of ownership is minimal within our industry. That helped us make our choice.”
So too did the brand’s reliability. It’s vital, when taking emergency callouts at any time day or night, to have a prime mover that is always ready to go, even on short notice. “For a business of our nature it means a lot to an operator when you can just start a truck up in the morning and you haven’t got any headaches,” adds Peter. “When that happens day in and day out it’s crucial. The last thing we need, with our work, is a truck that doesn’t start or is not reliable.”
For the previous MAN TGS trucks they serviced them once a year given the vehicles rarely amassed signi cant kilometres working within the Sydney metro area. The new truck, however, is a noticeable step up compared to the previous truck platform. The safety features have come a long way
according to Peter.
“That provides us driver assurance and it gives us, as company owners or as principals, more con dence that we have equipment on hand that will prevent an incident from happening,” he says. “For us it’s more about having a truck that is stress free.”
In the new MAN range, there’s a camera switch on the dash which does away with having to buy an auxiliary screen and mount it in the cabin. As the new media infotainment system allows two cameras to run through the main 12-inch screen itself, T&S Roadworks has wired up a truck and trailer camera so that the driver can ick between the two views depending on whether he’s hooking up to the trailer from the prime mover or if he’s reversing both units, he can defer to the trailer vision.
“Being able to do stuff like that is cost effective,” says Peter. “You buy the harness, and you wire it up, and you don’t require screens all over the place. Nine times out
of ten if you add another screen, it will affect your vision coming out of your front windscreen one way or another.”
The new MAN TGX 26.640 also features detailed airbrush art with the words the “Lion King” above the image of a noble looking male lion on the side and rear of the cab. Peter drove the truck up to Brisbane recently to have a few spots in the paintwork touched up. On the return leg he ran out of hours giving him the chance to sleep in the truck for the night. When he turned in something fell between the driver’s seat and the bunk.
“So, I went to grab it and I discovered there was a European socket there,” he recalls. “It actually has an inverter within the truck. I didn’t specify it. I said to myself this is a $2000 inverter that is within the price of the truck that allows you to run a laptop or a printer. It’s little things like that for me that makes a difference.”
He adds, “MAN thinks outside the square.”
Maintaining vegetation growth and keeping it clear from power lines is a specialised service requiring specialised vehicles.
Irrespective of how it is generated, electricity is the dominant power source for Australia and the reliable and safe transmission of energy through overhead wires requires continuous maintenance to ensure vegetation growth does not interfere with the poles and wires and to reduce the likelihood of bush res starting in electricity transmission corridors. Active Tree Services will celebrate 50 years of operation in 2025, having been founded by Mark Willcox in 1975, and today the operation has grown to be one of the most successful of its type in Australia with a nationwide footprint and 1,000 full time employees.
Throughout its history Active Tree Services has invested signi cantly in technology and innovation to address its requirements for the equipment which suits its often, unique applications. Active Tree Services currently has more than 900 pieces of mechanical equipment including a eet of more than 270 specialised trucks, with around half of these currently based on various Hino cab-chassis models. Active Tree Services was one of the rst in Australia to use truck-mounted insulated elevated work platforms (EWPs) to facilitate the safe operation of removing vegetation without the risks associated with working close to live wires. Nationally, Active Tree Services has approximately 170 of these specialised vehicles which are actually produced in-house by Aerial Access, which is a division of Active Tree Services established in 1992 dedicated to the development, manufacture and maintenance of these key pieces of equipment.
Over almost 50 years Active Tree Services itself has fostered longstanding working relationships with a wide range of clients, spreading across large power companies and electrical authorities, local government bodies, Tier 1 construction
companies and smaller businesses in the arboriculture and vegetation management industries. Most of the Hino orders are through CMI Hino in Melbourne which is able to deliver the trucks completed by Aerial Access as a ‘turnkey’ deal to external customers.
Aerial Access supports its parent Active Tree Services with specialised eet management and maintenance. This now also extends to servicing the growing number of external customers who are purchasing trucks and equipment through Aerial Access across a variety of industries such as power utilities and local councils which are using the equipment to perform their own vegetation
management tasks.
The Active truck eet also includes more than 80 tippers that transport the removed vegetation and are frequently towing wood chippers. Mark Willcox happened to be one of the rst private companies
to import a petrol-powered chipper to Australia.
“Our industry is tough on gear for a few reasons,” says Fleet Manager Luke Hounslow. “Wherever they run the power lines, in order to maintain growth of the
vegetation under it, we’ve got to access it.”
The result is therefore a requirement to travel frequently on rough tracks, often with steep inclines and poor traction.
“Our typical working environment involves tough conditions, and our cutting crews
work off-road continuously following the electrical powerlines and infrastructure to maintain vegetation growth to prevent bush res,” says Jason Gaskin, the Manager of Builds and Sales at Aerial Access. “We ask a lot of the trucks and therefore we need reliability foremost.”
Reliability is just one factor which assists the business case for Hino to stack up. Options such as larger diameter wheels to increase ground clearance are also important and automatic transmissions are favoured and have eliminated any diff or gearbox problems which might have happened in the past. The type of work being performed can also involve extensive periods of engine idling to operate the PTO driven hydraulic cutting equipment, which can be hard on engines.
“We like the Hino because it’s Japanese and it’s good quality, it’s not the most expensive but it’s also not giving us problems,” says Jason.
“For the larger 50- to 60-foot reach towers we go for the 4x4 Hino GT1528. It’s unmatched in that category and there’s
nothing else in its GVM range.”
The eet, according to Luke, opts often for a Hino 4x2 with a 40-foot platform which they will take into the scrub on jobs.
“They do a bloody good job for us,” he says.
Meanwhile, a trio of Hino 700 Series prime movers is utilised to transport various pieces of heavier equipment in the Active arsenal.
Safety is a crucial factor in the overall operations, and particularly in relation to the elevated work platforms due to having people working at heights with chainsaws near high voltage power lines, sometimes in poor weather conditions. The maintenance scheduling for this type of equipment is rigorous. The insulated towers are heavily regulated pieces of plant and are inspected every three months, plus an annual inspection every 12 months.
The typical service life of ten years can be extended after an even higher-level major inspection.
“Innovation is a big part of Aerial Access and Active Tree Services and we are
constantly trialling and developing what we call the ‘smart’ things to improve safety and ef ciencies with our trucks and equipment. One of the good things about Active is it’s not afraid to be innovative and to invest in developments,” says Jason. “An example is the ‘smart’ or electric PTO. At present we’re trialling one out of the US which is designed for the insulated tower and truck mounted EWP markets. It’s good for inner urban work because the diesel engine doesn’t have to be running so it’s a much quieter operation combined with a fuel saving. We can show a council how much emissions are being avoided. It’s a hybrid set up and the engine powered PTO is still available if required. It needs to return to base to recharge the battery pack so it’s not suitable for rural areas where the truck may not return to base every day.”
The Aerial Access team have created in-house some very unique plant and equipment, typically based on the back of Hino cab-chassis products. One such unit has an air-conditioned operator’s cab located at the rear which can slew
from side to side. The operator controls a 70-foot telescopic insulated boom with large hydraulically driven cutting head that can easily cut through vegetation including quite thick branches. This unit eliminates the requirement for anyone to be working at heights in close proximity to live power lines.
Aerial Access is the Dealer for the Versalift brand of EWP from Texas in the United States.
“Versalift is well known as the rugged heavy market leader with vegetation management operators,” says Jason. “Pair a Versalift platform tower with a Hino truck product and you’ve ticked two pretty
important boxes straightaway. You know it will go the distance.”
The designs for tipper bodies tted to Hino’s have been re ned over the years and now include a tipper with a rear mounted chipper and the ‘combo’ which features a tipper bin, a truck mounted chipper and an elevated work platform.
“Hino trucks have been a great support in this area over many years and understand our business and have worked closely with us to help perfect the various designs,” says Jason. “Many of the rigid trucks come in a variety of wheelbase dimensions which match our EWP and tipper builds, negating the need for chassis modi cations.”
‘Keeping our communities safe and green’ is the stated purpose at Active according to Jason.
“That drives everything we do,” he says. “Whether it’s delivering world class vegetation management services to help ensure public safety through bush re prevention and tree safety management, or urban greening through tree planting and watering.”
D&G Logistics isn’t letting a di cult market get in the way of its rapid expansion.
Established in 2016, the freight carrier, D&G Logistics has largely own under the radar over the past eight years despite accruing major accounts as a contractor for the likes of Toll, Team Global Express and Linfox.
The bulk of new work it has been furnished is in refrigerated transport, a growing sector it has no doubt hitched some future ambitions to.
The company currently runs a eet of 60
prime movers. Pantechs, however, are becoming more prominent at dispatch despite nearly 90 per cent of their mobile assets being operated in a standard B-double mezzanine application.
“Everyone is facing challenging times with costs going through the roof,” says D&G Logistics General Manager Ray Spiteri. “In response to the current economic climate, we’re trying to do things a bit differently.”
The business is now running B-triples,
roadtrains and quads as an outcome of this stagnating in ationary environment. That means adding new lanes, upping payload capacity and capitalising on the innovations of high performance freight units when investing in new eet.
“We’re nding the margin is getting smaller and smaller in regard to earnings,” says Ray. “Our onus is in trying to get customers direct because it makes it a bit more feasible. Running quads and triples that will increase our pro t and
we can leverage off that and then pass on some of those savings to the customer.”
Part of that is providing a juxtaposition for the customer when it comes to the price of a B-double versus a B-triple.
D&G Logistics will reduce that space it carries so the customer has to commit to loading extra.
“So instead of having to load two trailers you have to load three trailers and then there’s a discount in the rate,” explains Ray. “We’re having a lot of success in regard to selling that because the proof is in the $50 or $60 a space difference in
price which is helping us to kick a lot of goals at the moment.”
In maximising the capacity of the goods each truck is assigned, greater opportunities to discount or reduce costs for customers, are being found on these bigger combinations.
“Instead of us using two prime movers we’re using one prime mover and we’re moving instead of say, 34 spaces we’re moving 46 to 60 spaces,” notes Ray. “It’s a cost-saving to the customer and it’s a lot more ef cient for us with less prime movers on the road as well.”
A recently launched ABB-quad roadtrain is now running between Brisbane and Darwin. At present they anticipate approval soon for a permit to operate a B-triple from Melbourne into Brisbane, the biggest corridor for the business, currently.
“We’ve been really successful from Brisbane and heading towards North Queensland,” says Ray. “We’re looking at opening depots in Cairns, Townsville, Mackay and Rockhampton. It’s quite funny. You could say we’re an interstate company but most of the work that
we’re winning is ex Brisbane which is ne for us. It just shows us how much opportunity there is out there in every state.”
Of late the company has undergone several exciting changes including investments in new safety systems, new tracking systems, the gradual rollout of new dashcams and installation of Guardian driver fatigue technology in every truck.
“We’re getting extra cameras put on the side of the trucks to help with the drivers,” explains Ray. “It’s really positive stuff for the business.”
D&G Logistics earlier this year received its HACCP Certi cation to cart refrigerated goods and in addition to this the business will move into warehousing
out of Melbourne.
Ray Spiteri and Business Development Manager Marcus Franco are based in Melbourne where a new depot is being established to go with the one in Brisbane. Plans are already in place to secure their own location, a third, in the Sydney area.
Ray and Marcus joined the company seven months ago. When the company was founded by its owner, Gurpreet Dhillon Singh, the business model was initially anchored around use of rigid vehicles. This soon led to adoption of semis and then B-doubles. A high percentage of the work is still in grocery supply with a strategic shift, of late, into the express freight sector.
“We’ve been very strong in the express
section and we’re now doing triples and quads,” says Ray, who is the brother of Danni Spiteri, SGGS Victorian Branch Manager. “Refrigeration is now just booming for us. And we’ve got an order for another ten or 12 B-double pantech trailers on the way with more mezzanine units also coming in. We’ve got major expansion plans.”
There’s also a high demand for the business to establish a permanent presence in Sydney.
“As all of our operations must be done through our customers it becomes a challenging point, not having anything in Sydney already,” says Ray.
The city can be daunting to outsiders particularly from the perspective of initial nancial outlay. The price of entry is
exorbitant. Rental properties for those who haven’t originated or long ago established a footprint in Sydney can be intimidating.
“The dif culty is it’s really expensive compared to other major cities. Rental properties are through the roof,” says Ray. “We’re nding that a lot of companies share with each other only because it is so expensive.”
Even so, they’re prepared to start out small while leveraging off warehousing to cover costs.
“We’ll store freight and that will help us out and we’re looking at that model in Sydney because we sort of need to in regard to entering the market.”
At their 20,000m2 Brisbane site, D&G Logistics has opened up its own workshop with plans to replicate something similar in Melbourne as the business will take on its own repairs, another costly byproduct of the post-COVID economy.
“When you get a maintenance plan for a brand-new truck, any big issue whether it be a clutch or a turbo, it’s covered,” says Ray.
“We don’t have to worry about any of that. In saying that, you’ve got to ensure you’re not paying more on truck repayments month-by-month. Whereas some see it as taking the headache out of things.”
The mixed eet is dominated by Mercedes-Benz Actros units with a sprinkling of Volvos and Kenworths. The new AAB-quad is being pulled by a Volvo FH700 Globetrotter with an XXL cab. Vawdrey have built the trailers. The combination grosses at 119 tonnes.
“With the quads we weren’t heavily reliant on any one customer to load all of the trailers because we’ve got a few customers who don’t really like mixing and matching,” says Ray. “For customers, 98 per cent of the time it’s either a B-double or a single. So having to get a customer to technically load two B-doubles at once is challenging.”
They have found, however, the further the end point of the freight lane is, the easier it is to allocate loads.
A quad naturally brings with it different considerations. There’s obviously a lot more tyres involved should there be a breakdown.
“The thing is we’re not running 50 a week, we’re only doing one a week at this stage,” says Ray. “Same guy, same truck, same trailers. In regard to heading over to Darwin there’s no issues. It’s quite easily done.”
On an NHVR gazetted route, D&G Logistics runs its B-doubles out to Gatton where they will hook up additional trailers before advancing into Darwin. The trip takes in total four days.
“We try and leave Friday morning to be over there by Monday,” says Ray. “The thing with Darwin is everyone is pretty good in terms of transit times. We tell the customers ve days express, six days general freight. But we get it there within four. We always allow that little bit extra in case there’s an issue. We’re now eight consecutive weeks running it. Originally it was launched as an ad hoc request if, say, a customer wanted to load all four of the trailers. This is the third month that we have consistently launched it every Friday to be there Monday. It’s gaining momentum.”
By going digital with your fatigue management, you can reduce risk, eliminate guesswork and improve scheduling. With Teletrac Navman’s NHVR-approved EWD, you can exceed expectations with a solution designed to help drivers safely get on with their day without the worrying of rest breaks and available hours. Benefit from realtime fatigue status information at all times.
Are broken windscreens a constant in your eet? Glass specialist SCHOTT asks what di erence would an impact-resistant windscreen make to your business?
The rugged task of carrying freight by road in Australia is a punishing one. Trucks encounter, often over vast distances, some of the harshest conditions on the planet. Windscreen damage and impairment can cost road transport eets signi cant overages every month. More often than not the entire windscreen, when chipped or scratched, needs to be replaced. In the age of integrated electronics, cameras, sensors and safety feature requirements can make windscreen exchanges even more expensive. The subsequent downtime alone can represent costly disruptions to asset utilisation and delays to pressing duty cycles.
There is a new solution at hand from SCHOTT. The German glass specialist is providing BOROFLOAT 33 for innovative impact-resistant windscreens as the outer ply giving them superior stone impact resistance as well as a better abrasion resistance in comparison to conventional windscreens.Conventional windscreens, typically made of soda-lime glass, are particularly susceptible to damage. They have a high probability of chipping and tend to suffer from extensive damage patterns after stone impacts. This fragility leads to frequent replacements and greater overall maintenance, not to mention nearmandatory equipment add-ons such as mesh stoneguards.
Select mechanical tests in which soda lime glass is directly compared to specialty glass BOROFLOAT 33 will leave no doubt as to the superior performance and durability of the latter product.
In the Vickers indentation test a diamond tip is pushed onto the glass surface [see picture below]. Afterwards the imprint is investigated under a microscope. For the soda lime glass at a load of 2 Newton, four cracks have occurred around the imprint, whereas BOROFLOAT 33, even at 4 Newton, does not crack.
In sum, the load applied to initiate a crack needs to be much higher in the specialty glass in comparison to standard soda lime glass.
“There are much fewer cracks, less necessary repairs and your truck can keep moving,” says Dr Juliane BrandtSlowik, Manager Business Development & Sales – Doctor of Engineering –
Material Scientist at SCHOTT.
“The bene t is an increase in reliability and durability.”
In the stone impact test (DIN EN ISO 20567-1) gravel is shot onto the surface
with a certain pressure. The damaged surface area at 1 bar is 10.7 per cent for soda lime glass, while it is only 2.5 per cent for BOROFLOAT 33. At 2 bar the damaged surface area is 19.2 per cent for soda lime
glass, while it is between 5.5 and 10.7 per cent for soda lime glass. The stone impact resistance therefore is much higher for BOROFLOAT 33 in comparison to soda lime glass.
Windscreens that do not have to be regularly replaced because of superior scratch resistance will continue to provide good long-term vantages for the human eye, sensors and cameras especially in dusty environments like the outback and deserts. The results of a typical abrasion test, which has its origin in the porcelain industry, the PEI (porcelain enamel institute) test is illustrative. Here loose grain is rotated above the materials surface. The microscopy pictures show minor defects for the BOROFLOAT 33 surface, whereas the soda lime glass surface shows defects, which are longer, deeper and more pronounced. BOROFLOAT 33 is particularly abrasion resistant.
Illustrated here in a simpli ed way are the glass structures of the two glass types. On the left soda lime glass; on the right BOROFLOAT 33.
One reason for the better performance is the special structure of the glass according to Juliane.
“Because of the high packing density and low network connectivity, the soda lime glass has a higher density and does have a higher elastic modulus, which does mean it is as brittle as normal glass is,” she says.
Stone impact test comparison.
“Because of the high packing density and low network connectivity, the soda lime glass has a higher density and does have a higher elastic modulus, which does mean it is as brittle as normal glass is.”
Dr Juliane Brandt-Slowik Manager Business Development & Sales – Doctor of Engineering – Material Scientist at SCHOTT
“Whereas because of the low packing density and the high network connectivity of the BOROFLOAT 33 glass, the density as well as the elastic modulus are low, which does mean that the glass behaves relatively elastic.”
The lower density of the BOROFLOAT 33 glass also enables it to produce lighter glazing solutions, which helps to save money and to reduce CO2 footprint, two other major considerations for the modern Australian eet.
With a 3-year loan term and Guaranteed Buy Back option,* the Mercedes-Benz Pure Actros means business. Packed with all the pioneering innovation and economy you’d expect from a Mercedes-Benz, and backed by an 800,000km warranty.
*Finance restricted to approved business customers (excluding fleet, government, or rental buyers) of Daimler Truck Financial Services Pty Ltd ABN 23651056825 and subject to standard credit assessment, lending criteria and fees of up to $1,440 may apply. Guaranteed Buy Back (GBB) only
Refrigerated truck and eet company Scully RSV has developed a strong presence in nearly every state and territory over the last 30 years with a new Adelaide site recently opened.
Breaking onto the scene in 1993, Scully RSV was a breath of fresh air for Australia’s cold chain logistics industry. There was a large market waiting to be tapped into and provided for, as consumers across the country needed a means to store various products in a temperaturecontrolled environment.
Scully RSV saw this, acted, and the rest
is history. Back then, Scully RSV was a modest business which looked to service clients however they could and took pride in their tight-knit community of staff members. Today, CEO Andrew McKenzie and the company still think this way.
“We’re not a large corporation,” he says.
“We’re a nimble, agile, small Australianrun business that loves what we do.”
But the current numbers paint a different picture. While their modesty may still be intact, Scully RSV has seen incredible success in the industry since its inception, quickly becoming one of Australia’s leading manufacturers and servicers for refrigerated transport. In 2024, this success has culminated in the major expansion of the company’s operations across the country. Scully RSV
is strengthening its presence through the upgrades of existing sites but has also opened a brand-new facility in South Australia.
Having opened in early October, the new site — located in Wing eld, Adelaide and helmed by Asmara Thompson— is a mighty testament to the company’s growth in terms of size and capacity.
The facility is approximately 8,000m2 big, built to accommodate Scully RSV’s massive scale of operations which has grown to service increasing customer demand.
Hosting a truck, van and trailer eet which will consist of anywhere between 30 and 40 vehicles at any given time and feature particular multi-temp and roadtrain truck models, the site was speci cally designed as more of an operational hub when compared to other Scully RSV sites around the country, as, according to Andrew, the concentration of South Australia’s population in Adelaide demanded that the Wing eld site be fully stocked up with equipment and eet power.
Additionally, the site’s location is imperative to Scully RSV’s revenue, as it consolidates the company’s business efforts which are spread out across Australia.
“The Adelaide market is incredibly interesting,” he says. “It signi cantly punches above its weight from a transport and freight task perspective. It acts as a key corridor for business running from the east to the west, and from the north to the south. It’s really important for Scully RSV to integrate into this area.”
Despite its essence to Scully RSV’s continued success, the opening of the Wing eld site was quite straightforward for the company, which has constantly re ned its expansion and rollout plans in its three decades of practice. According to Andrew, Scully RSV runs like a well-oiled machine.
“We have a great understanding of our market, what our consumers and opportunities look like, and how that ows,” he says. “The opening of this site is the evolution of that understanding. We have a good roadmap for how we execute our plans to open a site: from looking at land, negotiations, all the way to nalising the purchase itself.”
Scully RSV’s brand is now stretched all around Australia, but this has not stopped Andrew from ensuring continuity in the customer experience at any given outlet. The company’s Wing eld site guarantees the same
experience as any other Scully RSV facility.
Andrew credits Scully RSV’s extreme growth to its sense of community and values-driven ethos. The company’s unwavering commitment to both the needs of individual consumers and the needs of company employees at every site is essential to its brand and is re ected in their immense success. Every expansion opportunity that Scully RSV undertakes is approached on the condition that the company can maintain these core values across all of its sites.
“It is critical for Scully RSV that the experience we provide to everyone, customers and employees, is the same
at any of our locations,” he says. “We always strive to capture the heart and minds of the people that have been with us for a while, and the people that are joining us, especially now as a relatively sizable organisation. We believe it is achievable to promote the same values at every outlet. Every site is a Scully site.”
On top of working as a powerhouse for Scully RSV’s country-wide operations, the Wing eld site will continue to uphold the company’s communityoriented values, which manifest in a wide range of engagement efforts across the many areas that Scully manufacturing and servicing sites operate in. The company supports many grassroots organisations and social
groups which bring locals together in positive ways, from local sporting clubs to schools, and even develops career pathway programs for children interested in the industry.
“When you can afford to give back, you do,” Andrew says. “We really are about entrenching ourselves into the areas and communities we operate in. We’re a proud Australian business, and we’d like to think we’re punching above our weight in a lot of respects, and we certainly do that by being user-friendly.”
The opening of the Wing eld site remains a major milestone for Scully RSV, a company expertly balancing its big ambitions with its small-company values.
As a global leader in IoT and connected transportation, Geotab processes and analyses data from over 4 million connected vehicles, generating over 75 billion data points per day. It’s a huge amount of data, and it is most powerful when we have the right tools to securely and efficiently manage it. That’s why we have partnered with Google to leverage Google Cloud’s data analytics and machine learning solutions.
Geotab has been awarded two Google Cloud Customer Awards for its achievements in the transportation sector. Recognition in both the Cross Industry and Sustainability categories underscore Geotab’s successful use of Google Cloud’s analytics to innovate and drive sustainable practices in fleet management.
Kirsten Kliphouse, the President of Google Cloud Americas says that the Awards are an opportunity to recognise the most innovative, technically advanced, and transformative cloud deployments across industries globally built on their platform.
In her congratulatory message to Geotab, she acknowledged Geotab’s role in “serving as an innovator for the industry”, which also highlights Geotab’s innovative integration of data to revolutionise the transportation sector, leading to transformative impacts across organisations and customers around the world.
As the world’s premier EV telematics provider, Geotab has demonstrated its commitment to reducing emissions through its Electric Vehicle Self-Assessment (EVSA) tool, which won Google Cloud’s Award for Sustainability.
The tool provides tailored EV recommendations to support businesses and governments in transitioning to electrified fleets.
For two consecutive years, Geotab was also identified as a Cross-Industry winner impactful transformation facilitated by Google Cloud. The award also acknowledges the launch of the Intelligent Transportation Systems (ITS) and its flagship transportation analytics platform Altitude.
Altitude has been pivotal in supporting government agencies by offering actionable, privacyconscious data insights for city planning and transportation network enhancements.
Strong synergy of Geotab and Google Cloud show great potential
As a valued partner in the Google Cloud Ready - Sustainability validation program, Geotab plays a crucial role in accelerating sustainability programs and informing strategic decisions for future developments.
Geotab’s collaboration with Google Cloud delivers significant benefits, including real-time improvements in driver safety and behavior, advancement of sustainability goals, enhanced productivity and significant cost savings.
This partnership not only redefines fleet management standards but also illustrates the impactful role of technology in fostering a more sustainable and efficient transportation industry.
An industry-leading solution
Geotab’s partnership with Google demonstrates the company is at the forefront of leveraging data analytics and machine learning to enhance fleet management, drive sustainability and create safer transportation systems worldwide.
By integrating Google Cloud’s advanced analytics with its telematics expertise, Geotab is confident of continuing its lead in the development of sustainable transportation solutions, demonstrating the profound impact that innovative technology can have on the transportation system today.
SAF-Holland manufactures a variety of products for the trucking industry. The company’s ‘TUG’ fth wheel is a small but crucial addition to an expanding portfolio.
SAF-Holland was born from the merging of two mature heavyweights in the manufacturing space. Otto Sauer Achsenfabrik (SAF) was founded in 1881, the venture of a German blacksmith family which produced the rst steel axles for agricultural vehicles. Meanwhile, Holland was established in 1910 as the Safety Release Clevis Company in the USA, specialising in safety couplings between horses and ploughs.
Over time, these two entities outgrew their initial value propositions, turning
into manufacturing powerhouses for their respective markets. Both parties acquired various rms and product lines under their respective belts, before joining forces as SAF-Holland in 2006. Together, SAF-Holland is responsible for the supply and manufacturing of countless trailer and chassis components, providing equipment solutions to a wide array of customers.
Among the prized products the company’s manufacturing repertoire offers is the fth wheel, which is now synonymous in a range of heavy
commercial applications.
Over 50 years ago, SAF-Holland developed the rst fth wheel for terminal tractors. The company over the intervening decades has re ned this product, creating designs which have included a myriad of features and capabilities for the right customers. The ‘TUG’ fth wheel is built for the use of specialty vehicles – TUGs – which are responsible for the towing of large trailers around lots. TUG fth wheels with air cylinders are now being utilised by many eets including Woolworths and Linfox
to move trailers around their own yards. These devices integrate classic equipment designs with new additions that cater directly to customer feedback, according to Nemanja Militec, Product, Engineering and Technical Manager of SAF-Holland Australia.
“Holland ‘TUG’ fth wheels are an old design and have been proven in service for many years,” he says. “They have been a standard spec for some manufacturers for decades. However, based on customers’ feedback, there is always room for improvement.”
This process of improvement, involving clear communications with the company’s engineering team, reworking and rigorous testing, ensures that the product is of top quality and all customers are satis ed. These same needs of customers have helped prompt SAF-Holland to vary its TUG fth wheel designs, some of which are built with the intention of broad use. For example, one of SAF-Holland’s TUG fth wheel models, the XA351TT1, is built as a universal tug wheel for all vehicles.
It is the biggest seller in the product line, used by various large truck eets. Meanwhile, some are built for more exacting purposes. The FW3510TR model, for instance, is used for speci c Terberg vehicles exclusive to Australia.
These are just some of the many TUG fth wheel models in SAFHolland’s extensive product line, with the newest iteration being the XA351TT1.
As the most recent model, this fth wheel has been built with a new range of features which enable it to carry much larger loads.
“The XA351TT1 includes a higher strength from its improved top plate design,” Nemanja says.
“The updated top plate also includes a higher strength steel alloy compared to its predecessor. Also, the yoke shaft spring has a retainer for easier and quicker replacement — the yoke does not ‘stick out’ anymore.”
The XA351TT1’s capabilities extend beyond these. Built with a weight capacity of 36 tonnes, a strategically enhanced rib structure and an integrated
automatic secondary lock – as well as many other features – this TUG fth wheel is built to combine safety with ef ciency when towing trailers.
“The crucial functions for this TUG fth wheel are safety, reliability, durability and easy maintenance,” Nemanja says. “Its new and improved air cylinder design also dramatically increases the service life to ensure a safe and reliable coupling process.”
According to Nemanja, drivers using the XA351TT1 fth wheel appreciate its robustness, reliability, and the simplicity of coupling and uncoupling.
The device’s jaws are built to allow for anywhere between 100 and 200 opening and closings for multiple trailer movements daily.
Though it is one of many devices manufactured by SAF-Holland, the XA351TT1, and its TUG fth wheel predecessors, remain vital products to the transport industry, enabling the safe and smooth movement of trailers in their own lots so that they can take on the roads in the best possible shape.
A Daysworth tug in a CEVA Logistics yard.
Australia’s trucking labour shortage is now reaching critical levels. Calls for major legislative reform in the industry from individuals, companies and organisations have often fallen on deaf ears. But is it about to change?
The trucking industry is the backbone of Australia’s economy. Regarded as the largest in the Southern Hemisphere and 13th largest in the world, it constantly transports a plethora of goods and services to producers and consumers across the country, tirelessly maintaining its intricate ow. And as the country’s freight task is expected to increase 57 per cent by the year 2040, the sector, as it fast becoming evident, will only become more important. But despite this essential role in delivering a high quality of life to Australians around the country, the trucking industry faces an extreme and ongoing labour shortage that threatens Australia’s supply chain.
The National Road Transport Association (NatRoad) has attempted to engage with the government in the hopes of inciting positive change. NatRoad’s 2024 Call to the National Cabinet revealed alarming statistics from its industry
survey, completed in collaboration with the International Road Transport Union (IRU). This survey found that in July of this year, there were over 26,000 vacant truck driving positions across Australia, with the number to increase should the industry fail to act.
As the issue reaches a boiling point, it has been simmering for a long time. Warren Clark has been the CEO of NatRoad since 2015, and during his tenure the labour shortage now confronting Australian trucking has only intensi ed. Helming the association that is desperately trying to spark change for the industry, he has recognised the problem has now reached critical levels.
“I think this shortage has been an issue for a number of years,” he says. “It had crystallised after COVID and is continuing to get worse. Now we’ve reached a crucial level where if we, as an industry, as a government and as the public, don’t start to x some of these issues, we will have severe problems.
This is something that needs addressing immediately.”
Confronting the issue though may not be as straightforward as it seems. It is now largely understood that the trucking labour shortage is the result of many intersecting issues within the industry, which are hindering the process of attracting new workers.
The trucking industry is experiencing large skill gaps in hired drivers that can diminish safety standards that can add to negative public perceptions, another challenge the sector has done much good in overcoming in recent years.
There is also an extravagant demographic problem: the NatRoad and IRU July report found that nearly 50 per cent of all drivers in the industry were over the age of 55 and close to retirement. Additionally, it is older men that dominate the eld; the population of women drivers was reportedly only 6.5 per cent, and a staggering 5.2 per cent of drivers were considered ‘young people’.
“This shortage is the result of a mixture of these symptoms, 100 per cent,” Warren says.
The lack of a strong governmentmandated national training program for truck drivers, and reforms around the licencing system, serve as large contributors to the national truck shortage; different states, territories and even trucking companies instead instill their own training systems onto young drivers, which can sometimes lead to inexperienced drivers taking jobs from other individuals and driving dangerously on roads.
Tony Armstrong of Armstrong’s Driving Education in Victoria has recognised this lack of uniform training in the trucking industry for years.
“I’ve been trying to drive reform in the industry since the early 2000s,” he says.
“There’s de nitely a driver shortage, but it’s a quality driver shortage. We need to train people to drive at low risk. We need to train them so they’re not
only employable but are protecting the community. Experience is irrelevant if you don’t have the right foundation to build that experience on.”
Australia’s truck licencing system places importance on the age of the driver and the time they’ve held the licence for, as opposed to the driving practice and experience they have accrued. Warren is pushing for reforms which will target this system, enabling younger drivers with proven experience to start driving sooner, and to curb the industry’s ageing workforce.
“Provide competency-based training, remove age barriers, and ensure that all new drivers are totally prepared,” he says.
“The only way that truck companies can do it is by taking training into their own hands and providing decent facilities themselves. Some large companies do that already, but if you’re a small company, you can’t afford to do that. There’s a safety issue present here.” Truck companies big enough to
implement their own training programs are doing their best to cure the industry’s shortage symptoms, but it doesn’t seem to be enough.
Take Followmont, for example — a large Queensland-based truck company, whose eet of over 1,000 trucks makes daily journeys around the state and interstate, transporting a wide range of products and equipment. Amid the labour shortage, CEO and Managing Director Mark Tobin is frustrated with the Queensland Government’s lack of initiative and has sought to take driver training into his own hands.
“I believe the government has nowhere near supported the labour gap through training or development of Cert III programs,” Mark says. “We’re not getting it off the ground. The government in Queensland is just not waking up to what’s going on in the industry. At the end of the day, in a cost-of-living crisis, unfortunately, the consumer is going to have to pay.”
In addition to the lack of a developed training course for drivers in the state, Mark also believes Queensland’s infrastructure conditions are exacerbating the issue, discouraging workers from joining the industry. Sending his own drivers on these roads, Mark is nothing short of impressed by the work they can do despite the challenges they face.
“What the transport industry in Queensland achieves every day is outstanding if you look at the infrastructure we’re dealing with,” Mark says. “The road network across Queensland isn’t suf cient to handle the country’s freight task. I don’t know how many people have to die on the Bruce Highway before the government wakes up. It’s appalling. And with all of this while trying to attract drivers — why would anyone want to go and drive a truck from Brisbane to Cairns?”
Followmont’s own training programs are an attempt to combat the dangerous combination of inexperienced drivers and poor infrastructure, working to give quality attention to the company’s staff and aiming to attract more workers.
For Mark and Followmont, this effort is imperative to labour retention, as it communicates to the workers that the company cares.
“We put a lot of time and effort into our recruitment,” Mark says. “We develop career pathway programs for employees wanting to become drivers. You can’t just throw people in trucks; you need to train them, support their education. You’ve got to actually put back into the business to show people what the task is, rather than throwing them in a truck and telling them to go to work.”
A substantial aspect of Followmont’s training and driver education aims to advertise the bene ts of working in the industry, ghting against the public’s negative perception of trucking which is impacting the labour shortage. According to Mark, there are many advantages to working in trucking that consumers don’t understand, even though they rely on the industry so heavily.
Warren Clark has gained valuable insight into the upsides of the trucking industry
while running NatRoad, and also believes the greater public needs greater awareness.
“Most people don’t understand the rewards, the job security and the potential future of our industry,” he says. “We need to better market the bene ts and careers in trucking, increase the interest and potential candidacy. You’ve got exible work hours, high renumeration, and not too far down the track, self-employment. If you go into the industry, you basically have a job for life. People aren’t even aware of that sort of thing.”
Doing his part to dispel negative trucking clichés, Mark is vocal about the positive treatment of his workers, painting a much more attering and sophisticated picture of truck drivers compared to the ones in the minds of many Australians.
“Transport is not a rogue industry like we’re portrayed,” Mark says. “We get all this bad press from the media, but people just don’t understand what goes into this industry. We treat our drivers like pilots. All our linehaul vehicles where drivers will need to sleep in cabs, are tted with TVs, microwaves and air conditioning units. At all major changeover points we have built dedicated drivers’ quarters and will often put drivers up in hotels if required. We’re doing everything we
possibly can to support them.”
Followmont is also working a great deal to attract many women drivers in light of labour scarcity and a lack of diversity in the industry. “We run a campaign every year around promoting the career paths available for females in the industry,” Mark says. “We invest a lot into promoting the positive image of our industry, and we invest in training and development — it doesn’t matter who you are.”
Followmont’s current staff is made up of 79 per cent men and 21 per cent women, and the company has been taking great strides to lower the barriers of entry for more women in the industry. Earlier this year, Followmont’s own 24-year-old Jade Harney won the National Young Driver of the Year award. These efforts undoubtedly help to diversify the industry in a time where workers are more essential than ever, but not everyone agrees with this method of achieving diversity.
Jacquelene Brotherton has spent over 50 years in the trucking industry, both behind the wheel and in many management positions. Today, she sits as the Chair for Transport Women Australia and is somewhat resistant to some of the tactics that truck companies and organisations have implemented
to involve underrepresented groups in the industry.
“The idea of an equal-opportunity employer does not work as a marketing strategy,” Jacquelene says. “The industry has focused so long on women and the youth to solve our shortage problem, but there aren’t enough of them interested. It’s a great industry for women where the sky’s the limit, but we need to be selling the job, not the diversity points.”
According to Jacquelene, she has been observing the ongoing labour shortage for at least the last decade and is also acutely aware of the industry’s negative perception, but believes that the reputation of trucking must be xed before trucking organisations can pander to underrepresented groups for labour.
“Trucking does not promote itself in the right way,” Jacquelene says. “People think the industry and its jobs are low-tech and low-skilled, when it’s really the opposite. Trucks are decked out with modern equipment, and young people don’t realise that they don’t have to be big and tough to drive.”
Jacquelene’s own experiences working her way up in the trucking industry as a woman have been overwhelmingly positive. According to her, she never faced issues in workplaces due to her gender, was embraced by the companies and groups she worked for and found immense success as a result. She doesn’t believe in quotas ensuring proper representation and seems pragmatic about the make-up of the industry’s labour.
Deciding that women and the youth will not be galvanised into joining the industry based on the attempts of its many companies, Jacquelene is encouraging the industry to turn to a seemingly untapped labour market to give Australian trucking the support it needs.
“We need to look to migrant workers and make them welcome,” she says. “There are many skilled workers outside of the country’s borders who want these opportunities, and we need the help.”
This is yet another potential labour shortage solution that rests in the Federal
Government’s hands. Warren Clarke has attempted to pass this message on, as he also sees migrant workers as a valuable source of labour to help keep Australian trucking a oat.
“We want immigrants to come into our country,” Warren says. “For this, we want immigration laws to be changed so that trucking is seen as suffering from an essential skill shortage. But if we’re going to have foreign drivers come into Australia, they’ve got to be evaluated for competency and trained properly, and they must have an Australian licence when they’re driving a vehicle 4.5 tonnes and over. At the present time, not all of them need to do that.”
Australia’s trucking labour shortage is a multi-faceted issue that has been putting industry titans into a panic for years. Now reaching new heights — an incohesive national truck licencing program, dangerous stateroad infrastructure and a strong lack of domestic workforce interest in trucking — change must come and it must come rst at a federal level.
Volvo’s new 17-litre Euro VI engine, now available with up to 780 horsepower, is taken for a drive as an AB-triple pulling over 100 tonnes in rural Western Australia.
Truck manufacturers are implementing a variety of solutions on their journeys towards lower emissions and Volvo is demonstrating there is still a lot of potential in internal combustion engines. Volvo Trucks is resolute in its commitment to deliver net zero emissions by 2050 and has indicated that it will only be supplying
net zero emission vehicles from 2040 to enable the global Volvo eet to be replaced during the following decade.
The popular solution to achieve low or zero emission levels is electri cation, including battery electric and fuel cell electric, with internal combustion engines (ICE) still playing a role using different fuel sources such as LNG, biogas, biodiesel,
Hydro-treated Vegetable Oil (HVO) and hydrogen as a fuel. As Volvo plans for what will ultimately be a non-ICE future, it has also embarked on parallel development of a new diesel engine for the Volvo FH and the result is the Euro VI D17 which can be optioned in a number of power specs starting at 600hp/3,000Nm through to a 780hp/3800Nm version, currently the most powerful production engine available anywhere.
The 17-litre engine has a bore size 5mm larger than the 16-litre engine it replaces with the other main difference being the tment of a single variable geometry
turbocharger which, as well as improving engine response and power, contributes to an over-all reduction of engine weight by 70kgs. Despite the larger displacement 17-litre engine, the FH16 nomenclature for the truck remains, as Volvo consider this to be model branding rather than a description of what’s under the cab between the chassis rails.
The 17-litre engine carries over many of the components found in the 16-litre such as the crankshaft and connecting rods and features low friction cylinder liners encasing wave top pistons. The revised fuel system enables the truck to operate on
biofuels including HVO. Prime Mover had a brief drive of a 17-litre FH earlier in 2024 during winter conditions in Sweden when we took the wheel of what was close to an Australian A-double con guration grossing 64 tonnes. A more extensive drive under Australian conditions and at Australian weights seems to be a good idea, especially if performed in roadtrain country in Western Australia. Our test combination is known in WA as a “C-train”, which is an AB-triple con guration common in grain and ore hauling applications with-load sharing twin-steer front axles on the prime mover. This particular Volvo is rated at 150 tonnes GVM but as the prime mover is a demonstrator and doesn’t have a current HML permit we’re restricted to a gross combination weight of 107.5 tonnes.
After the initial load at the grain handling facility at Geraldton port our rst pass across the scales showed us to be a tad heavy, so looping around and dumping a few bushels gives us a nal gross of 106.98 tonnes, so it’s time to head out along Route 123 towards Mt Magnet via remote settlements such as Mullewa. Our co-pilot for this trip is the incomparable Heather Jones of Pilbara Heavy Haulage Girls fame who also happens to own the trailer set we are using.
Volvo FH models rated up to 150 tonnes GVM, like this one, have conventional drive axles while super heavy haulage spec trucks above 150 tonnes GVM have reduction hub rear ends.
Spring is a great time to be out in the west with masses of vibrantly coloured wild owers bordering the roadside combined with the green and gold colours of the wheat and canola elds, providing a uniquely patriotic Australian landscape. The rainfall has arrived in the right amount and at precisely the right time to deliver
the promise of an excellent harvest season which will require many trucks like this one to deliver the grain.
The Volvo Globetrotter cab has a big bed tted with a 213cm mattress and access to the cab is made safer due to the redesigned non-slip steps which have no ridge to catch the soles of work boots.
The contemporary dash features a multifunction screen angled towards driver, a proximity fob key and start/stop button plus some USB2 charging ports.
The electronic parking brake is released when a gear is selected in the I-Shift transmission and the driver pushes the accelerator pedal. In addition, there is a Brake Hold button which, obviously, holds the service brakes on but without dumping air. This is a terri c feature which reduces driver fatigue and saves time and to prevent it being incorrectly used as the parking brake, if left on for more than a few minutes it will activate the maxis automatically.
There is the extensive array of Volvo safety features such as the driver and passenger airbags, and the Electronic Braking System (EBS) provides the overarching control for the Anti-lock Brakes (ABS) and the electronic stability control (ESC).Other
active safety features include Adaptive Cruise Control (ACC) and Hill Descent Control which allows the driver to set a maximum downhill speed and the truck will hold it using a combination of engine and exhaust braking and the service brakes.
The Volvo I-Shift transmission has been revised to handle the power and torque of the 17-litre engines with features such as polished gears which reduce internal friction losses to save fuel and also to deliver quicker shifts. The oil change interval for the gearbox has been taken from 450,000 kilometres out to 800,000 kilometres.
The redesigned transmission controller ts neatly into the driver’s hand and operates the gear selection across three transmission modes as well as giving the option of manually shifting gears. We keep in mostly in the ‘Power’ mode as with 780hp that’s pretty much the whole point of this exercise.
Although speed limited to 90km/h we are content to mostly roll along at a little less than that but keeping an eye on the mirrors, so we don’t slow any of the many other roadtrains sharing the road with us. At the end of the trip the
107-tonne combination registered a fuel consumption rate of 1.3km/litre, which can rightfully be expected to improve with a more experienced driver and the freeingup of the engine. In order to receive the full power and torque experience provided by the 780hp/3,800Nm, we drive a lot of the trip ‘on the pedal’ rather than engaging the cruise control. This behaviour will also have adversely affected the consumption gures but we’re making no apologies. There are few big hills out here, unlike the 12 per cent gradient we easily took the 17-litre up in Sweden. The astounding level of torque available from the 17-litre results in top (twelfth) gear being used during the majority of the trip towards Mt Magnet with just the very occasional downshift to eleventh when tackling a ‘jump up’. On one occasion we manually click back to tenth and then switch back to auto and the Volvo actually upshifts itself to eleventh as we drive up the rise.
The maximum 3,800Nm of torque is available between 1000 and 1,200rpm and at 1,400rpm there’s still 3600Nm available and at 1,700rpm the maximum 780hp is developed with 3400Nm of torque at that point. The best fuel economy results can be achieved by keeping the engine between 900 and 1300rpm.
The FH has lane keeping assistance which helps make steering this 100+ tonne triple combination straightforward and the stability afforded by the twin-steer front axles makes it easy keeping the rig aligned with the ‘fog line’ on the left side of the bitumen.
The FH is equipped with a driver monitor feature which uses a camera mounted on the A-pillar to ensure the driver keeps their eyes on the road and is effective even if dark glasses are being worn. Spend too much time looking at the dash or even at the kerbside mirror and it will remonstrate you with a loud warning.
The Volvo FH has been in production for 30 years and more than 1.4 million examples of the iconic model have been sold around the world. It has now been reinvigorated with its new 17-litre engine which, due to its ability to ef ciently operate on non-fossil fuels, has extended the future of internal combustion.
Tickford Racing trusts Castrol fluids in its supercars and transporters. When performance matters, trust Castrol in your trucks.
Transport for New South Wales (TfNSW) is the lead agency for various forms of transport in the state and performs a central role in planning for the future of road freight.
Bianca Slack-Smith is the Director of Policy and Regulatory Reform at TfNSW, and has been closely involved in what is essentially a ve-year road map intended to improve access for high productivity road transport vehicles, in addition to providing a state government’s perspective on other important industry issues.
Prime Mover: What sort of challenges face the planning for the future of freight?
Bianca Slack-Smith: Traditionally freight has increased in line with the population, but more recently freight volumes are increasing at a higher rate than the population growth which is re ecting our higher standards of living and our changing lifestyles and consumption patterns. We also know that climate change and the drive towards decarbonisation and emerging technologies are driving changes to freight demand and the way freight moves along the logistics chain.
PM: What sort of growth numbers are we looking at here?
BS-S: Without going into too much detail, it’s known that the freight task will continue to grow 34 per cent across New South Wales by 2061 with a 56 per cent increase in Greater Sydney. We are already seeing in just one year a 60 per cent growth in metropolitan deliveries and a 51 per cent growth in regional deliveries. So there is impetus to have an ef cient, effective, integrated and connected freight network
PM: Where does freight t into the overall planning strategy for New South Wales?
BS-S: In terms of strategic planning, we want freight to be recognised as a vital service, similar to other utilities like water and power. We see it as an important direction to ensure that there is adequate planning for, and delivery of, industrial land for freight purposes. A key recommendation is progressing the necessary business cases and planning for a dedicated Western Sydney rail freight line and appropriate intermodal terminal facilities.
PM: In addition to infrastructure planning, can an agency such as TfNSW assist with the chronic operator shortages?
BS-S: We can assist by supporting the industry to address immediate workforce shortages and focus on truck and freight train drivers in the rst instance, including a commitment to deliver the heavy vehicle ‘driver experience’ pathway which will fall under the model proposed in the Austroads review of the licencing framework. We recognise we need to expedite that and just start getting on with it.
PM: Should the states be involved in reforms to road use charging?
BS-S: It is proposed that we [TfNSW] work with the other jurisdictions and the Commonwealth to progress a model of distance-based charging for zero emission vehicles rst, and develop the model and prove it. Then it can be expanded across
all heavy vehicles and potentially across other vehicles. We know industry needs transparency around charging when considering these long-term investments and we know that long-term fuel excise revenue is diminishing.
PM: ‘Access’ is a continual subject of discussion within the road freight sector. How is this being addressed?
BS-S: The Heavy Vehicle Access Policy recently launched by the Minister was developed with extensive and multiple rounds of industry consultation. I thank everyone who took the time to provide feedback and ensure we got this right.
In New South Wales we do think we’re reasonably progressive in terms of how we manage access to the network, but the Access Policy rmly recognises there is so much more we can be doing. The objective is to optimise the use of the network to achieve overall improvements in terms of the outcomes – safety, sustainability and productivity – of freight movements. This can involve increasing the certainty of access to encourage the investment in safer and more innovative high productivity vehicles and technologies, and making it easier for the safest, most sustainable and most productive vehicles to access the network, which is the inverse of how the system seems to currently operate. Evidenced-based changes to accommodate new and emerging vehicles, service models and disruptive innovations, and cooperating with industry and local councils to improve end-to-end access across the network will enhance ef ciencies in the supply chain.
PM: At a state level, what is being done around the move to zero emissions?
BS-S: Almost a year ago we launched the Towards Zero Net Emissions Freight Policy. This policy recognises the freight sector is going to be one of the hardest to abate and we need to take steps to reduce emissions in the current environment while we work together to support transition to new technologies aimed at net zero. I want to highlight the two-year access trial which came with the policy which is allowing access for zero emission vehicles up to
eight tonnes on a single steer axle, up to 18.5 tonnes on the drive to a total combination of 26 tonnes. It is available under Notice but if people are looking for additional access for zero emission vehicles please reach out to us as we are really keen to get vehicles moving. I also encourage people to check the Online Tool we have developed which provides information in a Knowledge Hub around the types of technologies that are available to reduce emissions. It also performs as a comparison tool which enables industry to compare zero emission alternatives to their current eet and freight task. We are keen to continue to work with industry to support the reduction in emissions and transition to net zero.
PM: How important in formulating these types of plans is accurate data and other information?
BS-S: Quality data deepens our understanding of present and future freight infrastructure needs, offering insights that can guide how we can directly address those needs and invest cost-effectively. It enables all participants in the freight logistics chain, including governments and industry alike, to ef ciently plan, manage and optimise freight movements.
An independent expert panel chaired by Dr Kerry Schott is making key recommendations to advance freight in New South Wales. These recommendations, including immediate actions and proposed longer term directions, have been highlighted in an Interim Directions Paper. In the paper, the panel discusses nine key focus areas, including the importance of improving information and data to achieve better freight outcomes. It points out the necessity of identifying existing data sources and recognising any gaps that need to be addressed. Importantly, the paper highlights the need to work with industry and others to establish better data sharing. Improvements in data and information will be of bene t to governments, freight logistics operators and end consumers alike, driving greater safety and productivity that result in a more resilient, sustainable and responsive supply chain.
PM: Is the plan to make these interactions more collaborative?
BS-S: We believe the Heavy Vehicle Access Policy and the outcomes of the Freight Policy Reform Program are going to be transformative and we want to work with industry to make that a reality.
The NHVR continues to evolve and communicating its messages is vital for the road transport industry
Michelle Tayler joined the NHVR in January 2022 to lead the Corporate Affairs Division, which includes government affairs, corporate and digital communications, media, industry engagement and customer experience. Michelle is a quali ed journalist with almost 20 years’ experience working in media, communications, engagement and corporate affairs across the private and public sectors. Michelle began her career as a cadet journalist at a regional daily newspaper and then worked extensively in the energy and mining sectors before moving to the Queensland Government, where she held Executive Director level roles with Queensland Fire and Emergency Services and the Queensland Police Service. Michelle presented at the NatRoad Connect 2024 conference where she spoke of the industry bene tting from a consistent heavy vehicle regulatory service now the entire eastern seaboard and Tasmania is overseen by the Regulator.
The NHVR has been operating for a decade and in April 2024 the state of Queensland transitioned responsibility for delivering heavy vehicle regulatory services, including on-road compliance and enforcement and prosecutions, and programmed heavy vehicle inspections,
from Transport and Main Roads (TMR) to the NHVR, with a new head of ce located in Townsville which opened in June.
Queensland was the nal participating jurisdiction to switch to the NHVR (Western Australia and Northern Territory continue to be stand alones) and Queensland is now the NHVR’s Northern Region under the management of Director Kelli Ready, who herself has extensive experience in leading and delivering regulatory compliance programs across various Queensland Government agencies including Queensland Police, Environmental Protection Authority, and TMR.
As part of the transition 160 new employees joined the NHVR, with 110 of them transferring from TMR. The NHVR currently has 14 regional home base locations across Queensland, and a satellite of ce in Mt Isa, with staff working roadside across the state including in the far north and western areas.
“Now the work really begins in bringing consistency across the Heavy Vehicle sector,” Michelle says. “This is the opportunity to expand our reach and work together on harmonisation. We are encouraging voluntary compliance through education and our approach
around ‘inform, educate and enforce’ will continue as the keys to our compliance strategy and we are making sure the training within our team is consistent in the implementation of that. Education is the key – you don’t know what you don’t know.”
Improvements to facilities and technology are on the NHVR’s agenda including improved separation of intercept areas from live traf c lanes.
“Other key elements to enhance productivity and safety we are focusing on include infrastructure upgrades for weigh-in-motion and weighbridge facilities to reduce time required for a heavy vehicle to be stationary,” says Michelle.
The NHVR will expand its use of technology to initiate risk-based intercepts and look at vehicles of interest rather than random engagements.
“This helps identify those we need to pay attention to and those that are doing the right thing. We try to avoid intercepting them where we can,” adds Michelle.
The inclusion of Queensland under the NHVR regime should lead to bene ts for operators in other states.
“From an operational outlook, one thing we are focusing on, now we’ve got all the participating jurisdictions
on board, is borderless operations,” says Michelle. “You can be sure that when crossing the border within those participating jurisdictions you are given the same experience and treated the same when you are interacting with our staff. We’re doing what we can to make sure we are working with the states to get that seamless approach.”
One aspect of compliance enforcement which is being addressed involves the differences sometimes experienced by operators between police of cers and NHVR on-road of cers.
“This will see the NHVR training police in terms of how to enforce the HVNL [Heavy Vehicle National Law] and this is all about achieving consistent contact,” says Michelle. “We understand there are inconsistencies in the way in which it is currently applied, and we’re really keen to work with the police agencies to try and push the educational element as well by moving away from a heavy handed approach where it’s not needed and trying to uplift the industry through education.”
Heavy Vehicle inspection programs will be subject to review.
“Each state has a different inspection scheme in place which is obviously complex,” says Michelle. “We are trying to work with the states to harmonise that into a national scheme and there is a lot of work happening around that to provide national consistency for inspection requirements. We have been working on the rst phase of what
that could potentially look like. We’ve gone out and consulted with industry and are now looking at the second design phase.”
The revised program will be intended to provide savings in time and bureaucracy engagement for operators who demonstrate consistent approaches to safety and compliance.
“The result will be risk-based using intelligence and collected data so an example of what this could look like is operators classi ed as high risk may require two inspections per year, medium to high risk operators once per year, medium to low risk operators every two years and low risk could be every three to ve years,” says Michelle.
“We’re looking at things which reduce the burdens on those who are doing the right thing, but keeping our nger on the pulse for those who probably need a little more focus and work. We’re hoping to have a discussion paper to ministers in 2025, followed by implementation in 2026-27.”
Michelle acknowledges a frequent industry question about how owners learn if their vehicles have been intercepted and referred to a new data sharing program being launched at the end of 2024 which will be accessed via the NHVR portal which logs all intercepts.
“This will provide better oversight for owners when it comes to intercept outcomes for their vehicles but it doesn’t log driver info, just the registration details,” she says.
The NHVR has also developed strategies and resources to support the industry’s requirement for better access, particularly for PBS-style vehicles.
“It’s important that the industry sees what we are doing to work with road managers to enhance productivity and improve turn-around times for access approval,” says Michelle. “The Freight Task Tool provides road managers the tools to simply look at various vehicle combinations and what that means to them. It also gives industry the opportunity in rst instance to see if a particular vehicle was something that would pass the parameters road managers look at.”
We all bene t from increasingly long and heavy roadtrain combinations. With less fuel burned per tonne of payload, there is less environmental damage and less costs that must ultimately be passed on to consumers. However, it is important that there is no trade-off with safety. Professional drivers and the community quite rightly expect that heavier trucking eets are just as safe. Automatic Pin and fth wheel couplings must handle more load on quad roadtrains — yet these forces have never been investigated.
ARTSA Institute led a world- rst research project to work out the forces and determine what the future of heavy roadtrain couplings will look like in Australia.
The project was funded by the National Heavy Vehicle Regulator’s (NHVR) Heavy Vehicle Safety Initiative (HVSI) that is supported by the Australian Government.
For roadtrains, there are no redundant mechanical systems such as safety chains. Community safety relies primarily on the structural integrity of the coupling. The potentially ugly secondary safety measure is that a runaway trailer’s brakes come on automatically when the trailer’s airline connection breaks.
Australian Standards provide engineering formulae to work out
the minimum coupling rating. These formulae, which can be found in AS 2213 and AS/NZS 4968, are based on testing that took place in outback South Australia in the 1980s by the ARRB (now NTRO). At the time, triple-trailer roadtrains up to 125 tonne were tested on remote roads, and strain gauges were used to measure coupling forces. In short, the 1980s triple roadtrain tests showed that the forces through roadtrain couplings were about 40 per cent lower than as predicted using the formulas that apply to single trailer trucks. This was good news. Based upon these results, Australian and European Standards were updated, which allowed the use of regular couplings on heavy roadtrains.
Moving forward to the present day, quad roadtrains in use on Australian roads weigh in at around 160 tonnes, and there are prospects to increase combination weights towards 200 tonne. Questions linger. Do the 1980s formulas hold up? Can conventional couplings continue to be used on increasingly large roadtrains? If not, eets would need to t a new suite of couplings that are bigger, heavier, more expensive, and not interchangeable with the regular trucking eet when roadtrains are separated.
The project involved measurement of the coupling forces on quad-trailer 160 tonne roadtrains during routine daily journeys of hundreds of kilometres while underway in the Northern Territory, with part of the route on secondary roads.
ARTSA-i led an industry-wide working group bringing in key personnel from HVIA, ATA, and TIC. Engineers from the various coupling manufactures in
Australia and Europe also contributed their expertise, including Ringfeder/ VBG engineers who brought their Swedish coupling integrity testing experience. The research team pulled together industry support from all corners of the country. A purpose-built dolly manufactured in Perth by Howard Porter was tted with a custom drawbar in Melbourne by CIMC. The dolly was tted with specially designed hardware and measurement sensors by Smedley’s Engineers, before being transported to Direct Haul’s facility near Darwin. Both the automatic pin and fth wheel couplings recorded an array of force, speed, GPS, accelerometer, and road topography data in real time collecting orders of magnitude more data than the 1980s testing program that preceded it. The challenging eldwork, then the painstaking task of post-processing, was undertaken by Smedley’s Engineers, with mechanical engineer Dion Simms wrangling the mountains of collected data.
Three separate testing journeys took place. The instrumented hinged drawbar dolly was moved to the front, middle and rear positions in the quad combination for each respective journey, allowing the research team to compare coupling forces at the different locations.
When the data was pulled apart a number of signi cant ndings were revealed, including a few surprises: • The forces experienced by the couplings were similar whether the dolly was at the front, middle or rear locations within the roadtrain. This was due to dynamic forces and impacts as the roadtrain snakes along
the road, including whiplash and shunting. This result was contrary to conventional understanding as re ected in the current Australian Standards, which anticipates lower forces for couplings further from the centre of the train.
• The worst-case peak forces were reasonably well predicted by the existing formulae in the Australian Standards, with forces increasing in proportion to the weight.
• By far the most common occurrence of very high forces was not when the roadtrain was underway at speed, but instead when slow or coming to a stop: braking, shunting, and manoeuvring.
• The highest peak forces were measured while underway at speed over oodways. These peaks corresponded with a sudden pitch of the hinged drawbar dolly.
• Shunting within the coupling connection when braking at any speed resulted in high coupling forces, due to the delay in air braking signal between the front and rear trailers.
• Measured forces were input to proprietary simulation software to calibrate a roadtrain computer model. It was found that even the most advanced simulation software
available was severely limited when considering the complexities of the roadtrain combination being driven down a real-life road. Nothing replaces actual eld measurement to observe and learn from the complex dynamic phenomena that occurs.
A number of strategies may be considered to minimise the forces through roadtrain couplings without having to make a step-up in coupling size and spec:
1. Electric brake systems, which coordinate brake application for all trailers at once, should be mandated for all roadtrains over a certain mass.
2. Maximum wear tolerances are needed for roadtrain couplings over a certain mass. This may be a lower wear limit than that allowed by coupling manufacturers.
3. Consideration of rigid drawbar dollies to reduce the peak forces due to the pitch – and – shunt forces over undulating terrain.
4. Given that peak forces were similar at all dolly locations, couplings spec should be based on the worst case coupling within the entire roadtrain.
a. Taking this to the theoretical limit based on the formulae within existing standards, the maths reduces to the following simple formula:
COUPLING D-VALUE (in kN) = 1.5 X GCM (in tonne).
b. For example, a 160-tonne roadtrain would require a minimum D-Value of 240kN for all couplings. Put another way, a 240kN coupling would be 160-tonne ‘roadtrain’ rated.
c. Standardising connections throughout the roadtrain has interchangeability bene ts, and makes it easier for drivers, eets and regulators to check the component specs.
5. An important rst step will be to do the work to better understand the damaging peak loads during braking and lower speed manoeuvres.
It is hoped that strategies such as these will enable roadtrain drivers and operators to safely utilise regular coupling sizes on heavy roadtrain eets into the future.
Wayne Baker
Wayne is a chartered professional mechanical engineer, an executive director of ARTSA Institute, and was engaged as the Engineering Manager for this research project.
*ARTSA-I Change & Innovation Conference, Melbourne, 14 November.
TONY MCMULLAN
Compared to most other developed nations, it has to be said that Australia has been dragging its feet in relation to policy, infrastructure and incentives, both regulatory (for example, additional axle mass, vehicle access, etc) and nancial (for example, upfront government rebates to purchase a new low or zero-emission truck). China, Europe and the USA have put in place substantial government measures to encourage the uptake of commercial vehicles that offer signi cant carbon abatement in the heavy vehicle road transport sector. So where does that leave Australia and how are we fairing in the global truck decarbonisation race? Well not as bad as the lack of government assistance might suggest.
In September 2024 BloombergNEF released a signi cant report that looks at the global uptake of zero-emission commercial vehicles. The report titled Zero-Emission Commercial Vehicles –The Time is Now, was commissioned by the Dutch Ministry of Infrastructure and Water Management, in partnership with Smart Freight Centre of the Netherlands. The Bloomberg report detailed that zeroemission truck sales were close to 38,000 units globally in the rst half of 2024 and are set to be just over 1.5 per cent of total sales in 2024. At the end of June 2024, the Truck Industry Council’s (TIC) T-Mark new truck sales data showed that low and zero-emission truck and heavy
van sales in Australia were tracking at 1.0 per cent, up 61 per cent over sales to the same point in 2023.
Those global average and Australian sales look modest when compared to the 2024 zero-emission commercial vehicle sales in China, with Bloomberg reporting those Chinese sales account for more than 80 per cent of global volume, with new commercial vehicle adoption approaching 5.5 per cent in the rst half of 2024. In Europe, sales are concentrated in a handful of countries, particularly, Norway, Switzerland, Denmark, Sweden, Netherlands and Germany. While the US market shows only limited market growth, with zero-emission truck sales amounting to just 0.22 per cent of total sales in the rst two quarters of 2024. The European Union (EU) currently has the toughest CO2 emissions reduction limits for medium-and heavy-duty trucks. The EU regulations set progressively lower targets for the output of new commercial vehicles sold in the European Union countries, built on 2019 baseline emission levels. To meet these targets truck manufacturers in Europe will need to ensure approximately one third of their new vehicle sales will be zeroemission by 2030, increasing to over 85 per cent of sales if they are to meet the current European targets set for 2040. Signi cant, per vehicle, nancial penalties are set to apply to those manufacturers who fall short of these mandated abatement limits. Currently these CO2 emission targets are set as tailpipe emissions, however the European Union is planning a review in 2027 of both these emission limits and whether lifecycle emissions regulations should be considered in the future.
By comparison the USA, whilst having a
national target of 15-53 per cent lower tailpipe emissions from 2027 to 2032, has a more fragmented approach, that is largely state based.
Unsurprisingly, California has set the most ambitious abatement targets, setting minimum zero-emission sales percentages, rather than speci c CO2 emissions reduction limits. A 55-75 per cent zero-emission sales share for commercial vehicle manufactures by 2035. With some eet segments, for example school busses, needing to attain 100 per cent zero-emission sales.
TIC notes that in the absence of CO2 emissions reduction mandates, current Australian low and zero-emission truck and heavy van sales trail only slightly the global average. TIC also notes that this is occurring largely in the absence of Australian government emission reduction incentives for the road freight transport sector. In the global markets of China, Europe and the USA, substantial government incentives are currently on offer, and this will aid the transition to the abatement targets that those regions have set. The Australian road freight sector cannot be expected to deliver similar CO2 abatement, as those countries detailed above, without equivalent governmental assistance. The Truck Industry Council calls upon all levels of Australian government to reduce the regulatory barriers that currently exist (for example, the lack of axle mass compensation for low and zeroemission trucks) and deliver nancial incentives to offset the cost of purchasing a new low and zero-emission heavy commercial vehicle.
Tony McMullan CEO, Truck Industry Council
As CEO of the Victorian Transport Association (VTA), I have the privilege of advocating for one of Australia’s most vital industries – freight and logistics – at a time of transformative change. The need to decarbonise, driven by environmental imperatives and government mandates, is reshaping how we think about transport, and this change is especially profound in freight and logistics. As the industry begins its transition from fossil fuels to hybrid and alternative energy sources like hydrogen and battery electric vehicles, it is critical that Australian governments step up to support this change.
The journey toward decarbonisation is not one that can be taken lightly. While the long-term bene ts of moving away from fossil fuels are clear – reduced emissions, improved air quality, and the mitigation of climate change –the short-term challenges must not be underestimated. For operators in the freight and logistics sector, which underpins the national economy, the shift to alternative fuels represents a complex logistical and nancial challenge. Trucks and heavy vehicles that rely on diesel have long been the backbone of this industry, and moving to hydrogen and battery electric vehicles (BEVs) is no simple task. It requires not just the purchase of new eets but also the development of an entirely new
infrastructure to support these vehicles, such as charging stations and hydrogen refuelling sites.
This is where government intervention becomes crucial. Without adequate nancial and policy support from federal and state governments, the transition to alternative fuels will be slower, more expensive, and less effective. Governments must provide incentives, grants, and subsidies to assist operators in upgrading their eets and infrastructure. Additionally, policies that promote research and development into hydrogen and electric technologies will ensure Australia remains at the forefront of innovation in this space.
Furthermore, governments must take a leadership role in setting the regulatory framework that will guide this transition. The logistics and freight industries operate under stringent regulations concerning vehicle weight, emissions standards, and driver safety. With new fuel technologies come new challenges in ensuring compliance with these regulations while maintaining operational ef ciency. Policymakers need to be proactive in establishing clear, realistic guidelines that allow the freight industry to decarbonise in a way that is environmentally and economically sustainable.
At the VTA, we have long recognised the importance of leading the conversation on alternative fuels, which is why I am pleased to announce our upcoming Alternative Fuel Summit on Tuesday, 19 November in Melbourne. Now in its third year, the Summit will be a valuable forum for stakeholders across the freight and logistics industry to come together
and discuss the commercial realities of decarbonisation.
The Summit provides an opportunity to hear from a diverse range of experts – policymakers, regulators, original equipment manufacturers (OEMs), and suppliers – who are directly involved in shaping the future of transport. We are especially fortunate to have representatives from the Victorian Government and Opposition joining us to discuss the role of public policy in facilitating this transition. Their insights, alongside contributions from industry leaders, will provide a balanced and informed view of what lies ahead for freight operators as they make the shift to hydrogen and battery electric fuel sources.
The Summit will offer an opportunity to explore the latest innovations in alternative fuel technologies, discuss the practical challenges facing operators, and, most importantly, chart a responsible and achievable course toward a zero-carbon future. For further information and to register please visit www.vta.com.au
As our industry continues this historic transition, it is vital that state and federal governments recognise the importance of supporting the freight and logistics industry. With their backing, we can ensure that the shift to hydrogen and electric vehicles is not only achievable but also bene cial for the economy, the environment, and the many Australians whose livelihoods depend on this essential industry.
Peter Anderson CEO, VTA
The OECD’s latest economic outlook report forecasts that Australia will record GDP growth of 1.8 per cent in 2025, up from the forecast for 2024 of 1.1 per cent. Global GDP growth is forecast to be stable at 3.2 per cent in 2024 and 2025 with China’s growth forecast to be 4.5 per cent while the size of the USA’s economy is expected to increase by 1.6 per cent during 2025.
The Truck Industry Council’s statistics show a September new truck sales result of 3,566 new trucks, the local market’s best monthly result since June when 4,212 new units were delivered. September’s total was 221 higher than September 2023 (+6.6 per cent) and the accrued total for the rst three quarters of 2024 is 1,232 units less than for the same period of last year (-4.0 per cent), which should be regarded as an improvement because the TYD accrual was -6.4 per cent at the end of August.
of its haulage vehicle trucks and excavators to electric power, a move which is expected to cost more than four billion Australian dollars.
ON A 3-YEAR SERVICE AGREEMENT* WITH ANY NEW TRUCK.
The Heavy Duty sector had a very strong September with 1,530 new units, 134 more than in the same month of 2023 (+9.6 per cent) and kept the YTD total ahead of last year with 12,858 units by the end of the month (+1.6 per cent). Medium duty trucks also had a good month with 709 new units, 63 more than during September 2023 (+9.7 per cent). The YTD total of 6,025 units shows an additional 152 units over the rst nine months of this year compared to the same period last year (+2.6 per cent).
The Light Duty sector had a marginally better month compared with last year with 1,327 units during September, up just 24 on the same month of 2023 (+1.8 per cent) and the YTD remains substantially behind 2023’s record results with 10,827 units compared with 12,417 at the same point last year (-2,130 units or -17.1 per cent).
The results for the Heavy Van sector continue to surge with 980 new units during September, taking the YTD total to 8,545, which, thanks to the inclusion now of the LDV and Peugeot brands, is an 89.9 per cent increase over the same period last year. Taking those two brands out of the results still shows that the category is up 39.2 per cent on last year due to the muchimproved results of most other brands.
Isuzu Truckmas is the gift that keeps on giving. Buy a new Isuzu truck before 31 December and you’ll get $1,000 o a 3-Year Service Agreement*, giving you peace of mind that lasts and lasts. Find out more at isuzu.com.au or see your nearest Isuzu Truck Dealer.
Not expected to appear in the TIC statistics is the commitment by Fortescue Mining’s Andrew “Twiggy” Forest to signi cantly decarbonise its Pilbara operations by converting a large section
With a growing range of over 15,000 SKUs per branch, covering automotive electrical, air conditioning, mechanical servicing and repairs, workshop consumables, tools and equipment, we go out of our way to make sure you’ve got what you need, when you need it. We stock the leading brands you trust and rely on every day, and offer greater choice and value through our quality own brands.
We’re proud to provide the full offer for your workshop; a growing national network providing with widest product range, next level customer service, technical and product knowledge and 24/7 ordering through NAPA ProLink.