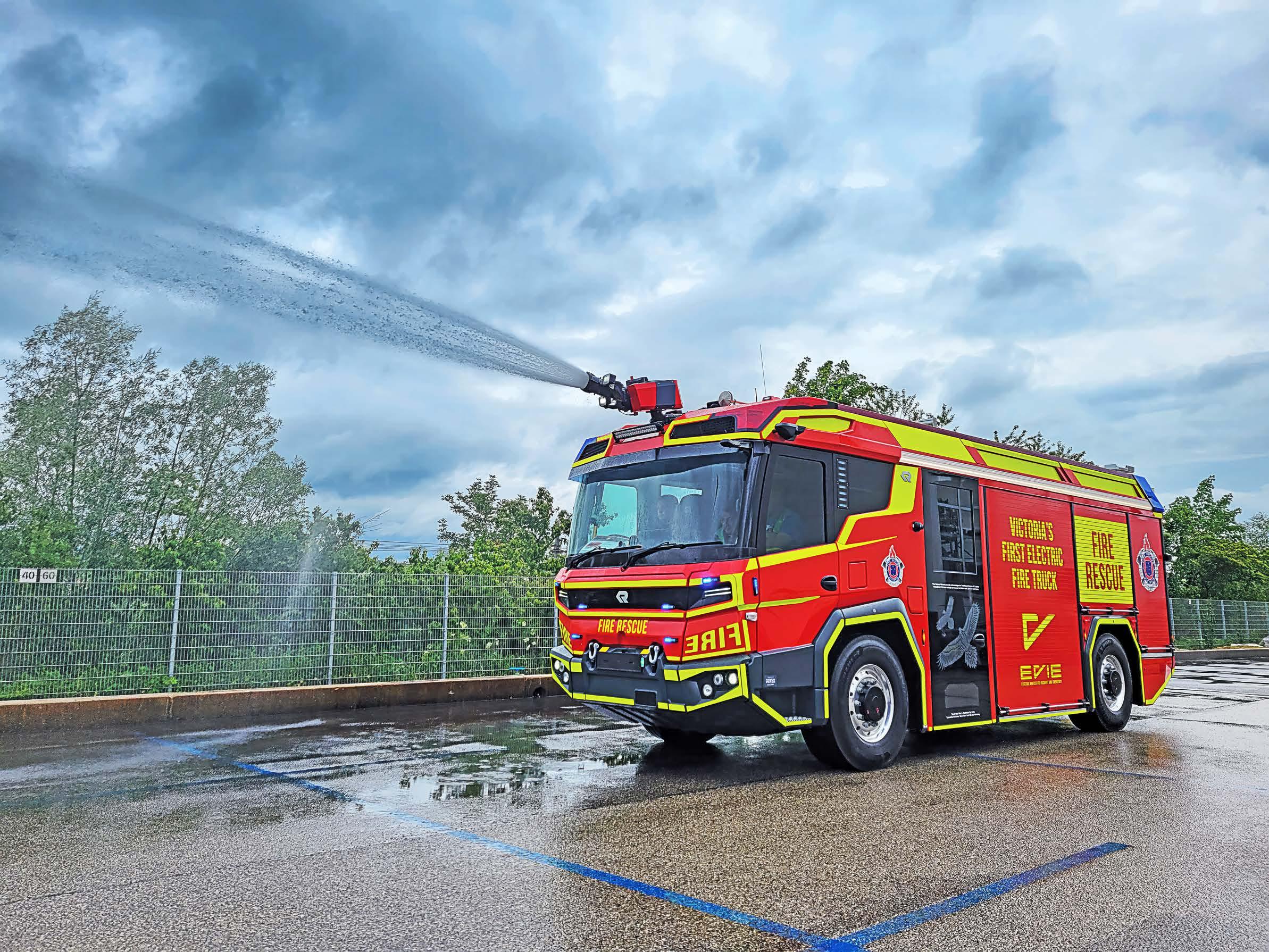
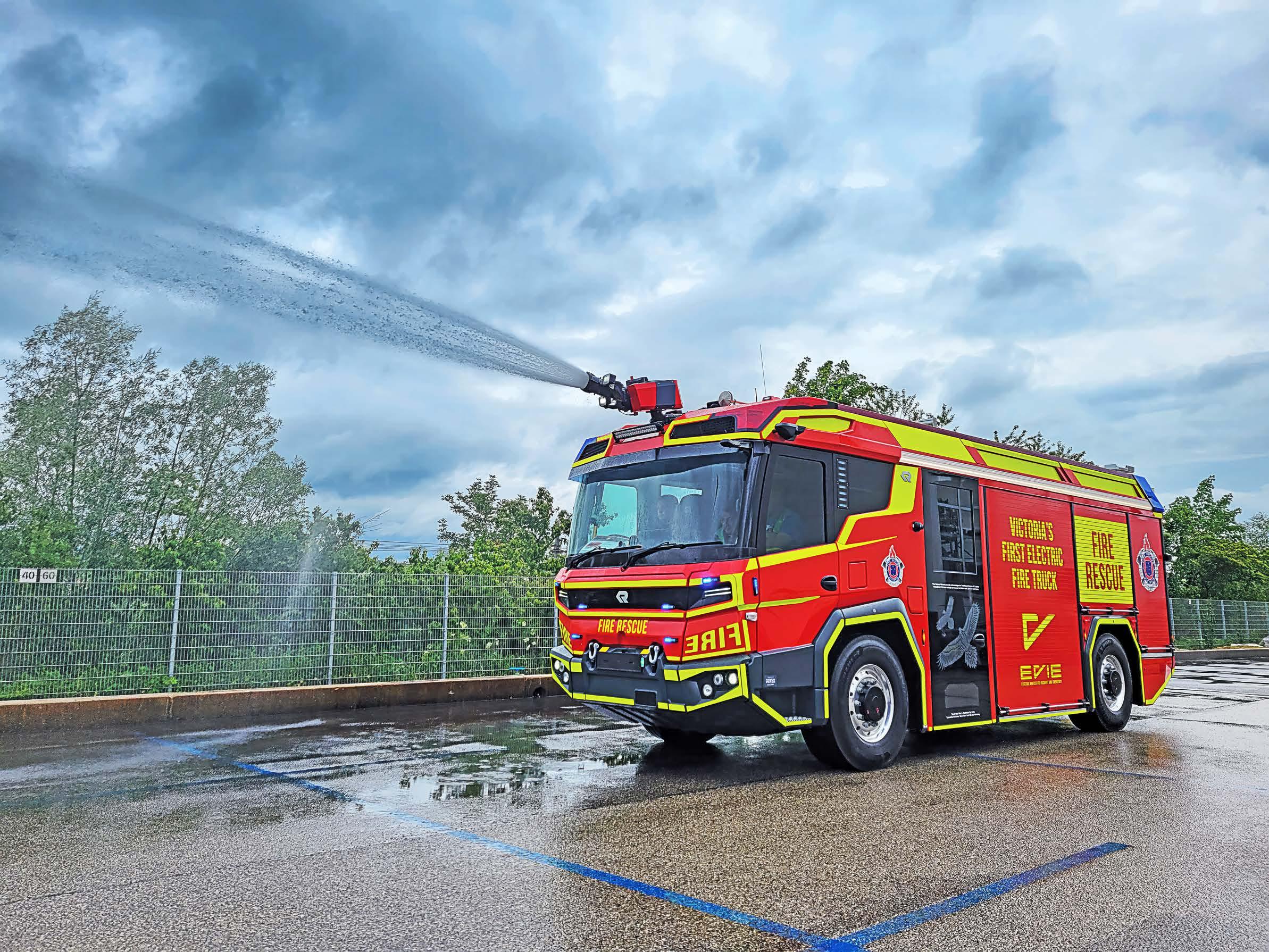
Electrifying NEW TECHNOLOGY

Powerful Partnership
Robust, fuel-efficient industrial diesel engines
Engines that keep running even in the toughest conditions. Easy to install, operate and maintain. A powerful partnership you can trust all the way from the drawing board throughout the operational life of your engine. Competitively priced complete power-pack units ready for delivery Australia wide with a local support team on hand 24/7.
To find your nearest dealer visit volvopenta.com/industrial
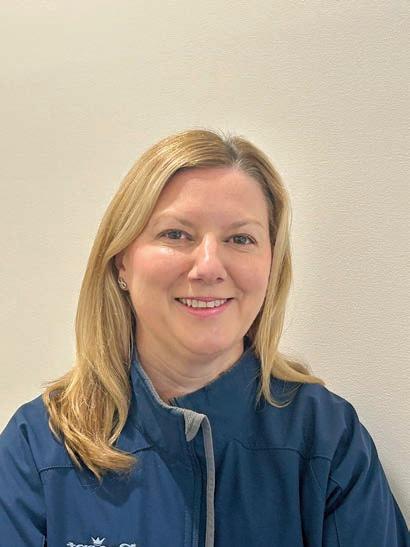
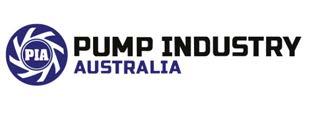
Pump Industry Australia Incorporated
PO Box 527
YARRAWONGA VIC 3730
Phone: +61 493 975 931 secretary@pumps.org.au www.pumps.org.au
PIA Executive Council 2025
Kylie Kinsella - President Regent Pumps
Joel Neideck – Vice President TDA Pumps
Tracey Guida – Treasurer/Secretary
Alan Rowan – Councillor Executive Officer – Publications and Training, Life Member
Ken Kugler
Executive Officer – Standards, Life Member
Steve Bosnar – Councillor Franklin Electric/Pioneer Pumps
Michael Woolley – Councillor Tsurumi Pumps
Luke Biermann – Councillor Mechanical Seal Engineering
Tim Yakup – Councillor Regent Pumps
Alex Calodoukas – Councillor Pump Strategy
Keith Bowen – Councillor Xtron Pumps Australia
President’s welcome
Welcome to the summer edition
Pump Industry. The simplicity of sunshine and warmer weather fosters optimism about the upcoming months. For all our PIA members and industry colleagues, it is also time to celebrate the 60th Anniversary of the pump industry of Australia.
As we reflect on the beginnings of our association, we recognise the early pioneers and life members of the PIA: Dr Bruce Sharp, quoted as the ‘father’ of the association, and George Snow, a founding member. Dr Sharp travelled overseas and completed a technical survey of African export markets; and his findings, combined with his industry experience, encouraged the Australian government to recognise the potential of our export markets, leading to the formation of the Australian Pump Manufacturing Association (APMA). This collaboration among the manufacturers in the APMA created new ideas and a collective force to drive export markets in Australia.
Over the last 60 years, contributors to our industry association have included PIA life members Bill Aitken, Geoff Daniels, Lex Torr, Bill Coulter, Alan Rowan, Ken Kugler, David Macpherson, Bruce Ellis, Robert Moore, Arthur Feiner, Antony Grage, Ken Willcock, Bob Hancock, Keith Sanders, John Link and Les Boeklckey.
Congratulations to Kevin Wilson and John Inkster on being inducted this year as new life members of the PIA. I had the honour of presenting them with life membership at our annual PIA AGM and Dinner, which was held in Melbourne in November.
Kevin’s career in the pump industry lasted over 50 years. Despite retiring in 2003, he maintained contact with the industry, managing the operations of the APMA and then serving as the secretary of PIA until 2023.
John retired this year after 38 years at AX Flow, Kelair Pumps and Brown Brothers. He was a committee member,
Vice President and then President of the PIA.
Kevin and John’s recent generosity in leading the association as PIA committee members in various roles indicates their continued passion for the industry and the people involved.
I would like to thank the 2023/2024 committee members, especially our Vice President, Joel Neideck, for leading the PIA during the year.
As we now look to our future, it is essential that, as members and industry colleagues, we look to the next 60 years.
The pump manufacturing industry now employs approximately 3,600 people and has 180 businesses Australia-wide. These numbers do not include pump agents, distributors, and other businesses that supply products and services to the pump market.
We have evolved as an association from solely supporting the manufacturing companies to now recognising a diverse range of service and supply companies that form the Australian pump industry.
The newly elected committee for 2024/2025 will work hard to promote diversity and drive initiatives this coming year. We ask that you attend our events and activities as they are promoted throughout the year.
As the new President of the PIA, I would like to thank all of you for your ongoing support and dedication to Pump Industry Australia. If you are an industry colleague who is not currently a member, please consider joining the association so we can grow as an industry and contribute to its future. I look forward to meeting and talking to our members and industry colleagues at our events over the coming year and hearing how we, the PIA committee, can support your business and the changing face of our industry in the future.
To all of you, Merry Christmas and Happy New Year.
Kylie Kinsella PIA, President
Scan to subscribe to Pump Industry’s weekly newsletter –delivered to your inbox every Thursday afternoon.
Cover image: Fire Rescue Victoria’s new electric fire truck.
Published by
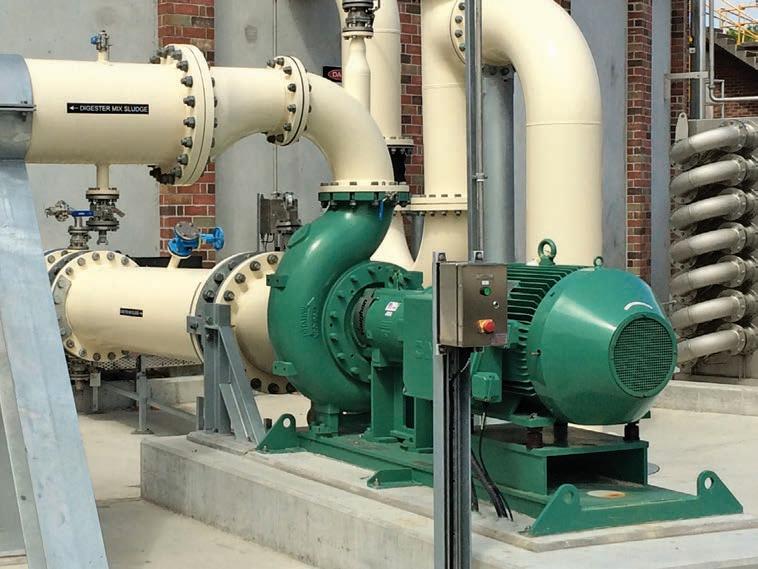

Contents
COVER AND FEATURE STORY
6 Electrifying fire rescue
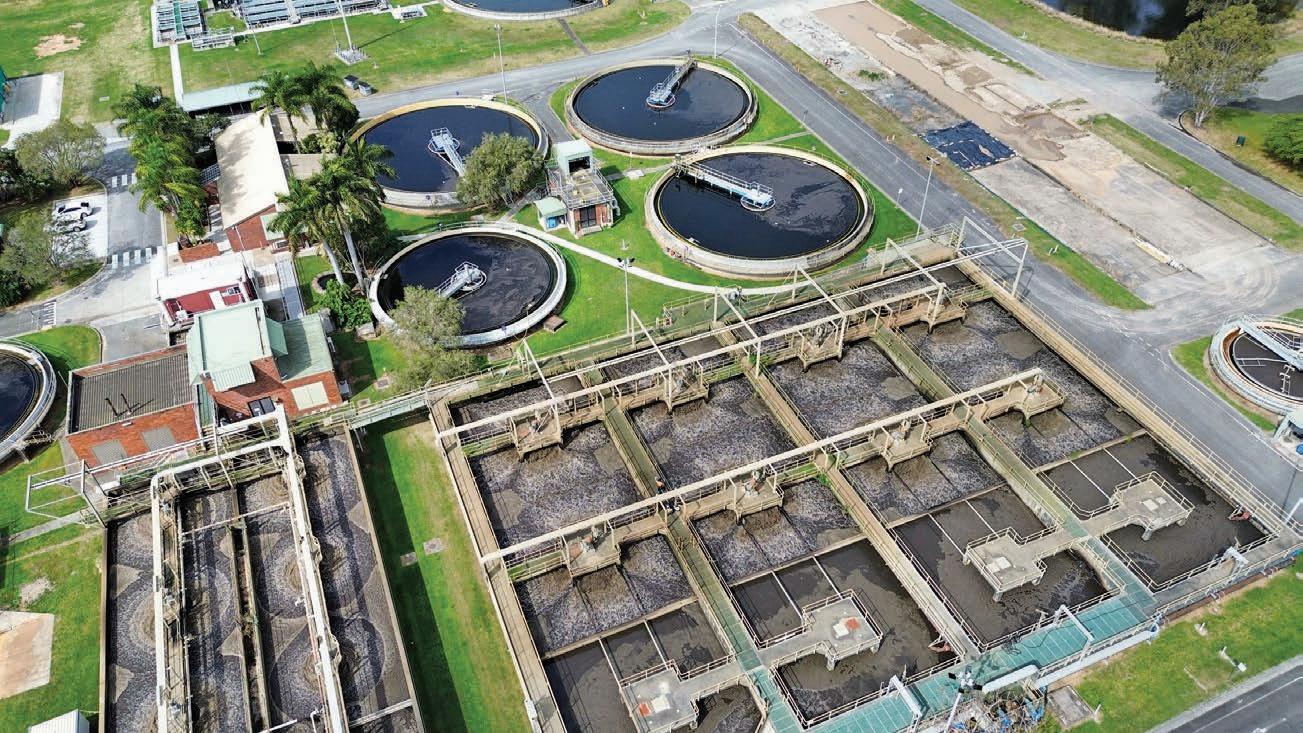
Prime Creative Media
ABN: 51 127 239 212
379 Docklands Drive
Melbourne VIC 3008 Australia P: (03) 9690 8766
www.primecreativemedia.com.au enquiries@primecreative.com.au
Editor: Chris Edwards
Journalists: Kody Cook, Tess Macallan
Business Development Manager: Rima Munafo
Art Director: Alejandro Molano
Designer: Jacqueline Buckmaster
Marketing Manager: Radhika Sud
Marketing Associate: Bella Predika
Digital Marketing Assistant: Emily Gray
Publisher: Sarah Baker
Managing Editor: Laura Pearsall
ISSN: 2201-0270
This document has been produced to international environmental management standard ISO14001 by a certified green printing company.
8 Future trends in wastewater pumping
PIA MEMBER NEWS
12 PIA celebrates 60 years
14 When the process gets tough, just pump it up!
16 New inverter optimises solar pumping applications
18 Leading the way in pump technology
20 Smarter pumping for industrial efficiency
22 Seal solutions for longevity
24 Driving innovation in pump solutions
26 Minimising downtime and maximising efficiency
Regulars
PIA WELCOME
3 President’s welcome
PUMP SCHOOL
50 How to control a hose pump
28 Sludge handling gets a makeover
30 Submersible pumps made in Melbourne
32 Professional engineers registration
WASTEWATER
34 Pioneering sustainable wastewater treatment
36 Dosing precision through advanced metering
38 Chopping, cutting and grinding
STATE OF THE INDUSTRY
41 State of the Industry report
EVENTS
48 AIMEX moves to Adelaide
PUMP HANDBOOK
52 Pump installation
PUMP CURVES
56 Seals under pressure: Part 2
This magazine is published by Prime Creative Media in cooperation with the Pump Industry Australia Inc. (PIA). The views contained herein are not necessarily the views of either the publisher or the PIA. Neither the publisher nor the PIA takes responsibility for any claims made by advertisers. All communication should be directed to the publisher.
The publisher welcomes contributions to the magazine. All contributions must comply with the publisher’s editorial policy which follows. By providing content to the publisher, you authorise the publisher to reproduce that content either in its original form, or edited, or combined with other content in any of its publications and in any format at the publisher's discretion.
Pumps Industry acknowledges Aboriginal Traditional Owners of Country throughout Australia and pays respect to their cultures and Elders past, present and emerging.

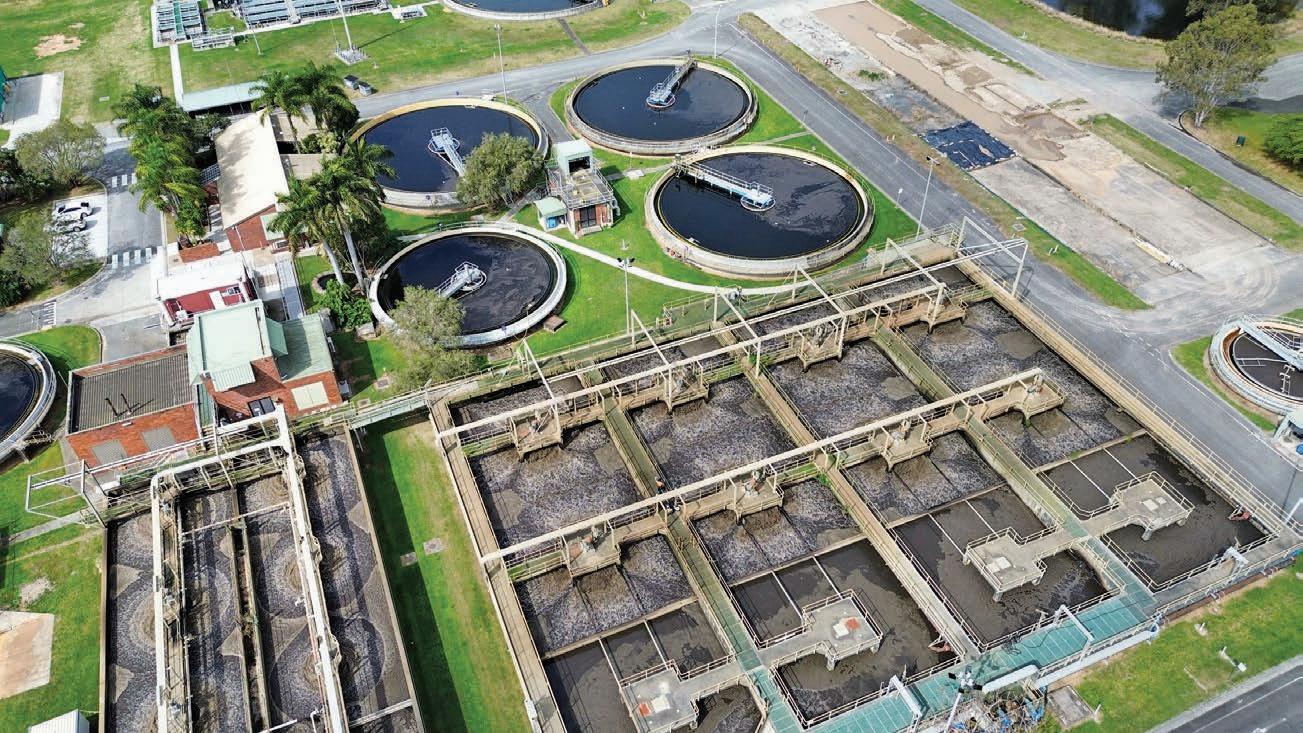
INTELLIGENT WASTEWATER POWERTRAIN SOLUTIONS
Purposefully designed gear motors from Bauer for fully submersible applications in wastewater treatment and other water or sludge type applications.
• German Engineered IP68 gearmotors that incorporate the latest in epoxy coatings, seal design, electrical connection and stainless-steel shafting
• Power classes from 0.37 to 11kW
• Submersible to 5m
• Application specific seals available
• Epoxy Coating to 400um
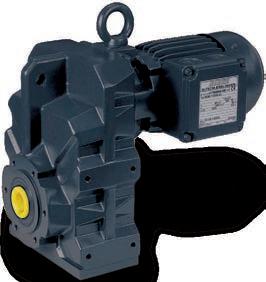

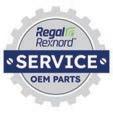
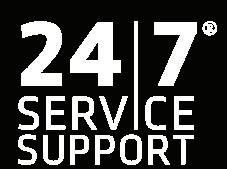
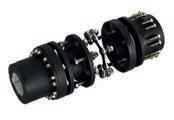


Epoxy Coated to 400um and Stainless Steel shafting to ensure complete corrosion protection, even when fully submerged
outcomes and maneuverability.

Electrifying fire rescue
Witnessing the consequences of climate change has seen this emergency management body fast-track its pilot of an electric fire truck.
EVIE has a larger tank on a smaller frame, improving
Image: Fire Rescue Victoria

Introducing an electric fire truck for use by Fire Rescue Victoria (FRV) represents a watershed moment in emergency response technology.
Dubbed EVIE (Electric Vehicle for Incident and Emergency), this new addition to FRV’s fleet merges sustainability with cutting-edge functionality, offering benefits that extend far beyond the environmental realm.
EVIE showcases advancements in pumping capabilities and exemplifies a broader move towards innovationdriven efficiency in emergency services.
Reimagining pumping power
EVIE is designed with a groundbreaking independent “pump-and-roll” feature that allows for simultaneous driving and pumping. This is a significant advancement over traditional pumpers that rely on the vehicle’s engine.
Craig Brownlie, Assistant Chief Fire Officer at FRV, describes it as a “game changer in terms of efficiencies in getting water, ultimately, on the fire”.
EVIE’s separate electric drive motors allow it to begin pumping before firefighters exit the cab, reducing response times and enabling faster, more effective firefighting. This innovation is particularly vital in high-stakes situations where every second counts. With the ability to pump water on the move, EVIE meets one of the industry’s long-standing challenges: delivering powerful water flow while maintaining vehicle mobility. Designed with a highperformance NH 55 pump, EVIE provides a remarkable flow rate of 6,000 litres per minute, significantly exceeding the 4,000 litres per minute achieved by the current fleet. This ensures the truck can tackle larger urban fires with ease.
Adding further versatility, EVIE’s integrated foam proportioning system simplifies the application of Class B foam, which is essential for certain types of fires. This combination of high flow rate and foam capability allows FRV to respond to fires more efficiently, enhancing EVIE’s value as a multi-functional, all-electric emergency vehicle.
A sustainable approach
In a proactive response to the urgent need for climate action, FRV has integrated EVIE into its fleet as a cornerstone of its decarbonisation strategy. EVIE runs entirely on electric power 98 per cent of the time, relying on a diesel generator only in extended emergency scenarios where continuous
pumping is required. This is a step towards FRV’s long-term goal of becoming the world’s first net-zero emission fire service. This vision aligns with FRV’s heritage of embracing innovation, from its early adoption of motorised fire engines to today’s advancements in electrification.
“Climate change is a real issue,” said Assistant Chief Fire Officer Brownlie. “We are contributors to environmental carbon via our fleet, but we also see the consequences of climate change with increased operational activity.”
With rising instances of intense fires and storm events, the impact of climate change on emergency response has become increasingly evident. EVIE’s emissions-reducing design also addresses another pressing health concern: diesel particulates, a known carcinogen that has long plagued fire stations. By reducing these pollutants, EVIE contributes to a cleaner, safer environment for firefighters and the communities they serve. The electric pumper is setting a precedent for emergency response vehicles across the industry.
Prioritising firefighter health and safety
The electric pumper goes beyond just reducing emissions – it’s also engineered with firefighter health and safety in mind. Traditional fire trucks require firefighters to jump from ladders or high steps, often resulting in musculoskeletal injuries. EVIE, however, incorporates a stair-like entry and exit system designed to reduce injuries to knees, backs and ankles.
Inside the truck, the seating layout has been reimagined. Instead of the forward-facing layout typical of fire trucks, EVIE’s crew seating faces sideways, allowing for clearer invehicle communication.
“It’s much quieter, with no diesel engine running underfoot, which gives us a better communication environment,” Assistant Chief Fire Officer Brownlie said. “The enhanced layout allows the officer to brief the crew effectively enroute to a call, ensuring everyone is prepared and aligned before arriving at the scene.”
Moreover, EVIE features an airscrubbing system that circulates 3,000 litres of air per minute within the cab, continuously removing harmful contaminants.
“As firefighters, we go into areas where we’re exposed to smoke and
other hazardous products,” Assistant Chief Fire Officer Brownlie said. “Once we’re back in the cab, this system cleans and scrubs those chemicals out, keeping the environment as safe as possible for our firefighters.”
Tailored for urban and peri-urban environments
Though primarily designed for urban areas, EVIE can handle off-road situations in peri-urban environments. With adjustable ground clearance and all-wheel drive, the electric truck can navigate rugged terrain, allowing firefighters to access difficult-to-reach areas during emergencies.
Assistant Chief Fire Officer Brownlie has extensive experience in both urban and rural firefighting. “EVIE has better ground clearance than most fire service heavy tankers in its highest capacity,” he said. “This makes it well-suited to the rural-urban interface and enables FRV to respond effectively to fires on back fences or rural properties.”
Looking to the future
For FRV, EVIE is not merely an innovation – it’s a glimpse into the future of firefighting. Assistant Chief Fire Officer Brownlie said, “We aim to lead by example and demonstrate that we can decarbonise our fleet.”
Beyond immediate local impact, FRV’s decarbonisation efforts are part of a global initiative to promote sustainable firefighting. Through Zeon (Zero Emissions Operational Network), an FRV-led collaboration with fire services in Berlin, Vancouver, and Los Angeles, FRV shares valuable insights and best practices on electrification. This network serves as a resource for other fire services interested in adopting low-emission solutions, providing them with guidance on implementation and overcoming potential challenges.
By integrating advanced pumping systems and sustainable powertrains, EVIE is reshaping what it means to be a high-performance and eco-conscious emergency vehicle. For pump industry stakeholders, the electric pumper reflects a broader shift toward solutions that don’t compromise performance or safety for environmental goals. EVIE’s arrival is a testament to FRV’s mission of aligning emergency response with the demands of a changing world, setting a new benchmark for what can be achieved in firefighting and pump technology.
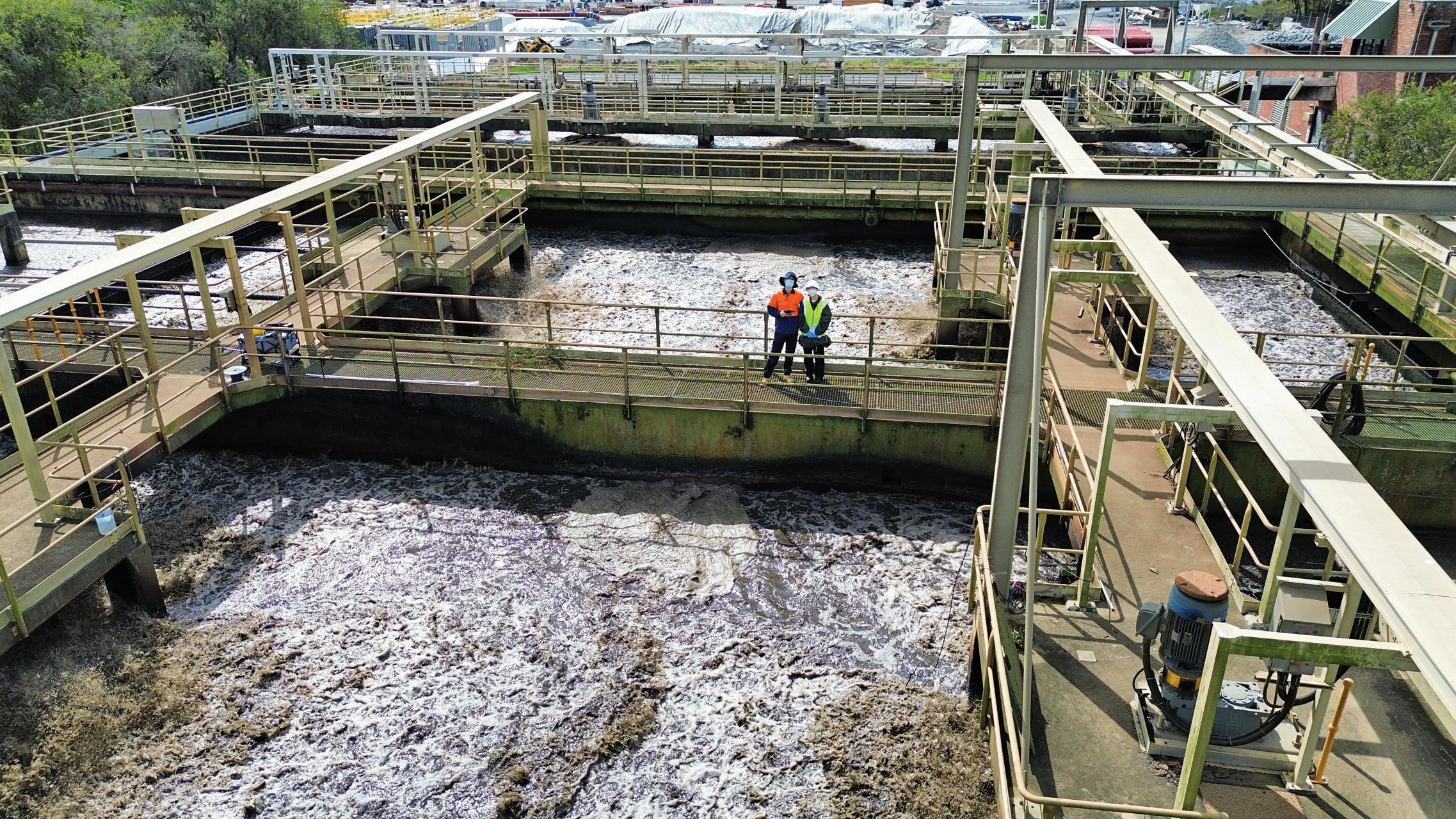
Future trends in wastewater pumping
One researcher is delivering a vision for smarter, energypositive pumps in wastewater treatment, advancing sustainability and global growth opportunities for the industry.
“I love the environment, and I love water,” University of New South Wales (UNSW) senior lecturer Haoran Duan said. “I like to see dirty water turning into clean water. That’s a natural driving force for me to study environmental engineering and my love for nature.”
Dr Duan is originally from China and has a PhD from the University of Queensland. His passion for wastewater treatment has carried him to a leading role at UNSW Sydney. Dr Duan is at the forefront of innovative wastewater treatment technologies that minimise environmental impact.
Dr Duan’s work goes beyond clean water, encompassing solutions to complex challenges in emission reduction, nutrient recovery, and sustainability in urban water management. His research combines environmental engineering fundamentals with advanced data science tools like deep learning to model and manage greenhouse gas emissions in wastewater systems. This area is of growing interest for industries that rely on extensive water handling and purification processes, including those in the pump sector.
Pumping a sustainable future
Achieving global carbon reduction targets requires a transformation in wastewater treatment, an energyintensive process that contributes to greenhouse gas emissions yet plays a critical role in sustainable water management.
“While current technologies are widely adopted, they are far from optimised for today’s climate goals,” Dr Duan said. “Wastewater treatment itself is energy-intensive.”
His work focuses on reducing the energy footprint of these processes, making them more profitable and environmentally sustainable without relying solely on regulatory pressure.
Dr Duan’s approach aims to make wastewater treatment self-sustaining and “not just driven by policy”.
Advanced pumps and other energy-efficient technologies that drive wastewater processes toward a net-zero, energy-positive future are vital to this transition. Pumps, essential components in moving and treating large volumes of water, offer significant potential for improvement. Optimising pump efficiency directly reduces energy consumption, while
innovations in recovery technologies allow facilities to harvest biogas and other resources from the wastewater itself, transforming treatment plants from energy consumers into resource recovery hubs.
Challenges for pumps in wastewater Pumps are essential workhorses in the wastewater industry. They move wastewater from households and enterprises to treatment plants and circulate it through various treatment stages. Pumps are everywhere in wastewater management, from transporting wastewater to providing the essential aeration that drives natural biological processes within treatment systems. The evolving demands for net-zero emissions and energy efficiency present new challenges and opportunities for pump technology in this sector, mainly as wastewater utilities increasingly aim to achieve ambitious sustainability goals.
Wastewater treatment relies on aerobic and anaerobic biological processes to clean and purify water. Pumps facilitate these processes by delivering the necessary flow, mixing, and aeration levels.
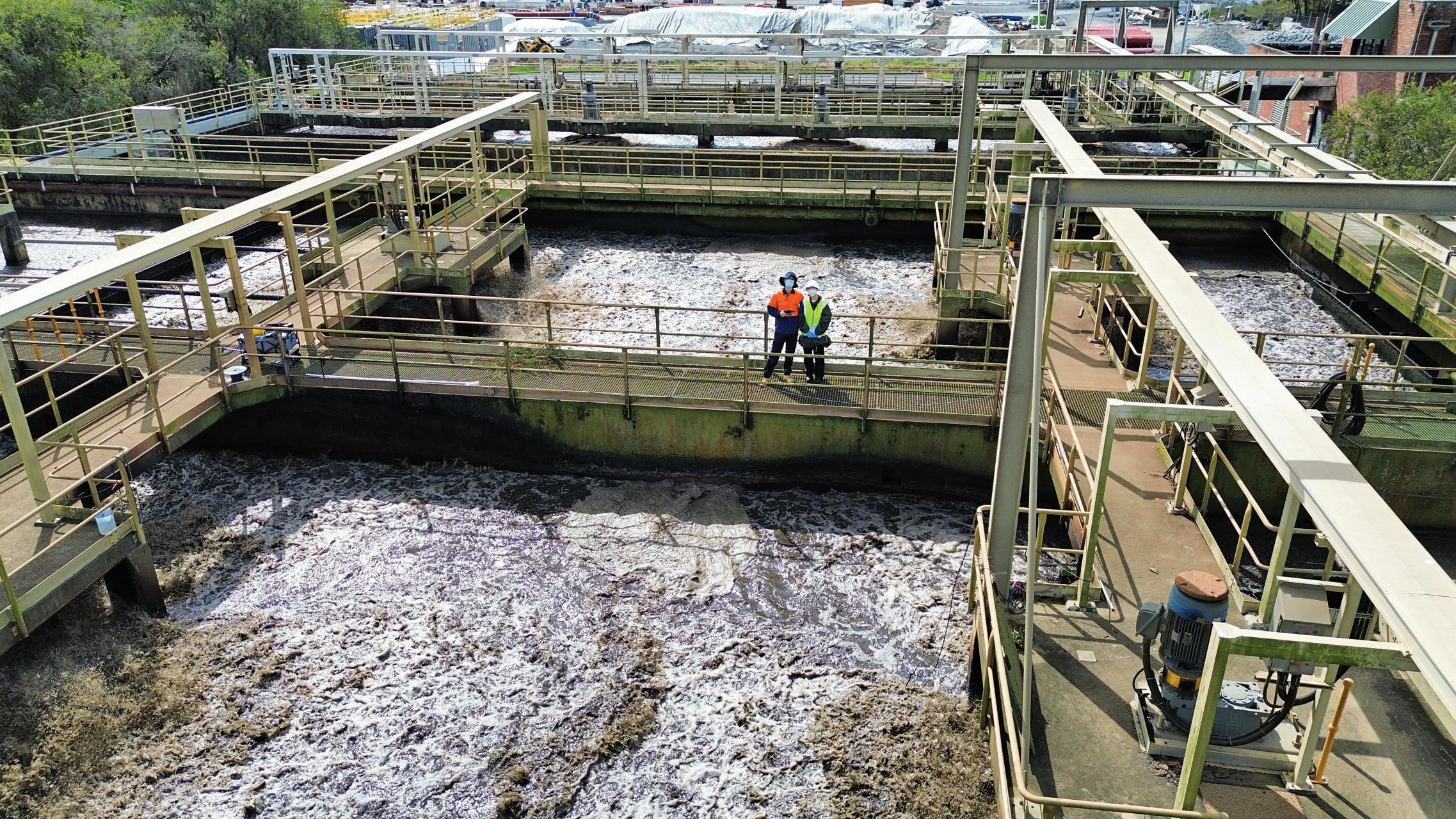
“Essentially, the wastewater treatment process is just an engineered solution of natural processes,” Dr Duan said. “We are using engineered approaches to facilitate the aerobic process, to facilitate the anaerobic process. Aeration, for example, is particularly energy-intensive, and maintaining the right levels is key to both treatment efficacy and controlling greenhouse gas emissions.”
With the rise of climate commitments, utilities in Australia and worldwide are increasingly pledging to reach net-zero emissions within the coming decade. This goal adds pressure to optimise pump performance and integrate more intelligent control systems. Many Australian utilities, for instance, aim to achieve net-zero emissions as early as 2025, requiring better energy management and sophisticated process controls to reduce emissions and improve energy recovery. The challenge is to ensure that pumps are not merely passively controlled by existing supervisory control and data acquisition (SCADA) systems but actively integrated as intelligent components in the treatment process.
“Pumps are controlling many parameters such as hydraulic retention time, sludge retention time, and dissolved oxygen levels,” Dr Duan said.
Smarter pumps
This push for smarter pumps has implications for the entire wastewater treatment infrastructure. Beyond their traditional roles, next-generation pumps could interact directly with process models, sensors, and data systems, enabling real-time adjustments that optimise energy efficiency and emissions reduction.
Dr Duan and his colleague Professor Bruce Bing-Jie Ni are exploring mathematical models that enhance process control, and their results are promising. One previous collaborative study between the University of Queensland and SA Water reduced greenhouse gas emissions by controlling the air pump. The changes to the air pump looked specifically at dissolved oxygen levels, showing how precise pump control can contribute to emission mitigation efforts.
However, this evolution toward “smart” pumping requires pumps to respond to complex wastewater
treatment processes’ complex variables.
Dr Duan envisions a future where pumps become actively engaged in wastewater control, adjusting automatically based on real-time data rather than passively executing preset commands.
“The pump industry or pump itself should be more actively engaged in such control,” he said. “Future pumps might dynamically regulate flow and aeration in response to changing conditions within the treatment process.”
Managing nitrous oxide emissions
Nitrous oxide (N₂O) emissions pose a significant challenge for the wastewater treatment industry due to their potent impact on climate change. Although nitrous oxide makes up only about five per cent of global greenhouse gas emissions, it can account for as much as 50-80 per cent of a wastewater treatment plant’s carbon footprint due to its high global warming potential. Through advanced control and integration, pumps can substantially reduce nitrous oxide emissions. By adjusting flow rates, mixing intensities, and dissolved oxygen levels, smart pumps can help optimise the aeration process, potentially lowering N₂O emissions.
Dr Haoran Duan and PhD student Ms Shuting Wang working at a wastewater treatment plant on the Gold Coast.
Images: Dr Haoran Duan
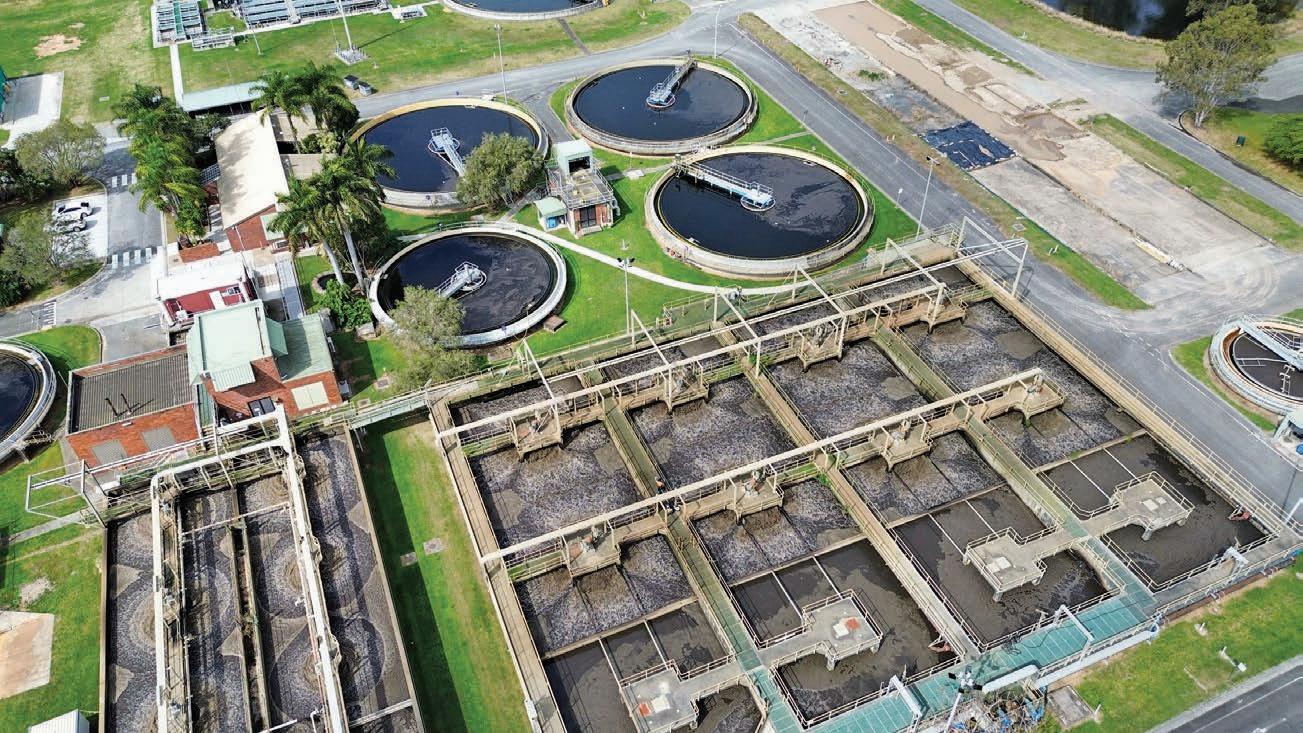
“Advanced control is needed to reduce nitrous oxide,” Dr Duan said. “The gas’s emission pathway is difficult to manage, and the challenge lies in finding control strategies that limit its release without compromising treatment efficiency.”
One promising approach is to integrate pumps with real-time monitoring systems and intelligent process controls that adjust operations based on the microbial activity influencing N₂O production. By modulating aeration based on real-time data, pumps can help maintain oxygen levels that minimise the specific microbial pathways known to produce N₂O. This type of control is more feasible now due to recent advancements in digital technology and data-driven solutions that enable pumps to respond dynamically to changing treatment conditions.
Smart pumps can enable better control over hydraulic retention time (HRT) and sludge retention time (SRT) in treatment plants. By optimising these variables, plants can improve the efficiency of nitrogen removal processes and potentially reduce conditions that lead to higher N₂O emissions.
While traditional pumps execute commands based on set parameters, next-generation smart pumps can adjust operations continuously to minimise
energy use and emissions, making the entire wastewater treatment process more sustainable and cost-effective.
Opportunities for the pump industry
Dr Duan sees many exciting opportunities for the pump industry in Australia, particularly in taking a leading role in addressing international needs. He recently participated in a research trip to Indonesia thanks to the University of Technology Sydney (UTS).
“There’s a lot of potential for pump manufacturers to enter a range of emerging markets, such as Indonesia,” he said. “During the trip, I discovered that only around 20 per cent of Indonesia’s population is connected to sewer infrastructure. They have a bold plan of increasing that portion to a significantly higher level in the next decades, and pumps could be central to this transformation.”
Australia’s established role in providing equipment and expertise to Indonesian treatment facilities makes the opportunity for the Australian pump industry clear.
“What can the Australian pump industry do there?” he said “There is enormous potential for Australian pump manufacturers to adapt their designs to meet local climate and economic conditions.”
Other countries in the region, such as the Pacific Island nations, represent an underserved market for reliable wastewater management technology. These areas often lack centralised treatment systems, leading to sanitation and public health challenges. For Dr Duan, this is where Australian pump expertise could make a meaningful impact.
“A lot of meaningful work needs to be done in these regions, where many systems are either poorly, unsafely managed or are treated on-site in ways that lack rigorous safety standards,” he said. “By creating adaptable, cost-effective pump solutions, the industry could expand the application to those emerging markets, addressing essential needs while building new business opportunities.”
Within Australia, the focus shifts to developing the “next generation” of pumps that integrate more sophisticated control systems and improve energy efficiency. Dr Duan believes there is potential in incorporating the pumps into the control or making the pump more energy efficient. This aligns with the increasing demand for intelligent systems in wastewater treatment, which can reduce energy consumption, adapt to real-time data, and contribute to the
Investigating the greenhouse gas emissions from wastewater treatment on the Gold Coast.
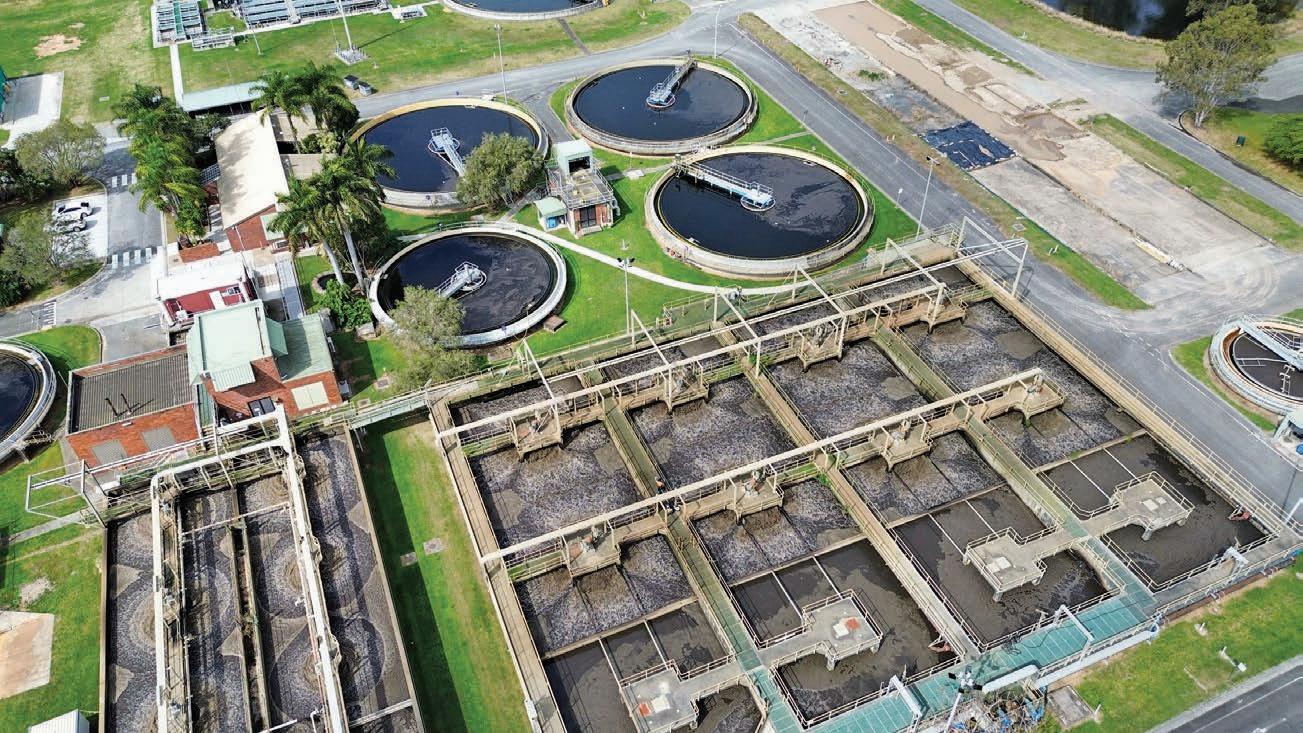
sector’s net-zero goals. By investing in advanced technology, Australian manufacturers can continue to lead the market and offer high-value solutions domestically and abroad.
An energy-positive future
Dr Duan emphasises the importance of shifting from an energy-intensive model to an energy-positive and environmentally sustainable one in envisioning a sustainable future for the wastewater industry.
“Wastewater treatment is really like a foundational pillar of modern society,” he said. “Despite its essential role, the industry still carries a significant carbon footprint and relies heavily on energy. This dependence strains the grid and contributes to ongoing environmental issues. I believe in a future where wastewater treatment minimises its energy consumption and produces more energy than it uses.”
According to Dr Duan, the key lies in harnessing the chemical energy embedded within wastewater.
“This energy is often overlooked, but it offers a powerful opportunity for transformation,” Dr Duan said. “By optimising treatment processes, wastewater facilities can convert organic materials into energy, turning the plants into energy-positive assets for their managers.”
Dr Duan and his team at the University of Queensland have already demonstrated that this vision is achievable. They have proven that wastewater treatment can generate surplus energy when efficiently managed.
He was recently involved in a global research project that sought to find new pathways for advanced resource recovery from waste. The team found that there are many emerging technologies for transforming waste into high-value commodities, including the recovery of cellulose, biopolymers, and proteins from waste. By properly utilising the right pump technology, these materials could be extracted downstream to create value for wastewater facilities, thereby increasing economic sustainability.
Beyond energy positivity, Dr Duan also stresses the importance of achieving net-zero carbon emissions. This dual goal – minimising energy consumption and offsetting unavoidable emissions – represents the next frontier in sustainable wastewater management. To reach this objective, the industry must reduce its emissions and explore solutions like carbon
sequestration, which captures and stores carbon, offsetting the impact of necessary operations.
Dr Duan believes an energy-positive, net-zero wastewater treatment industry would be transformative. This would make these facilities
By achieving this vision, wastewater plants could support broader societal goals for sustainability, contributing to climate change mitigation and resource efficiency.
“The future I see for wastewater treatment is not just to reduce energy
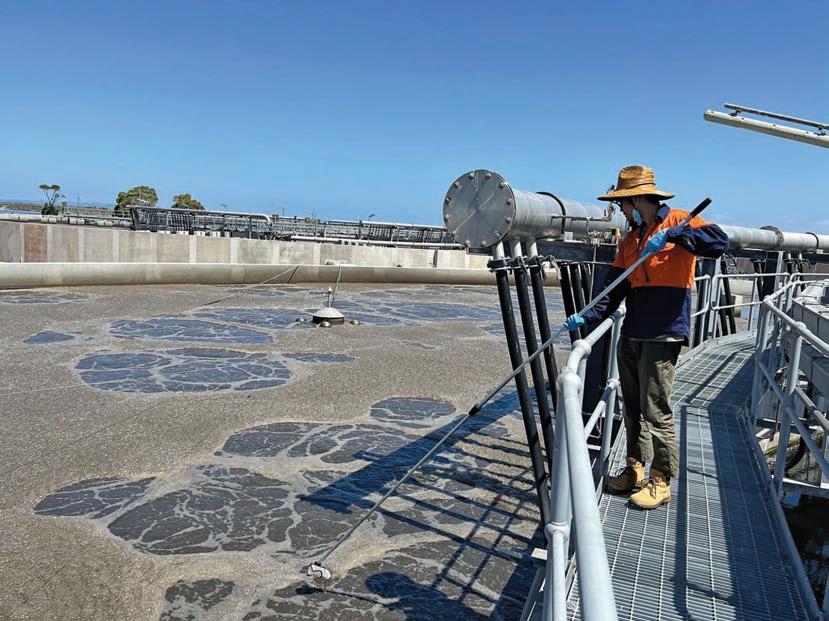
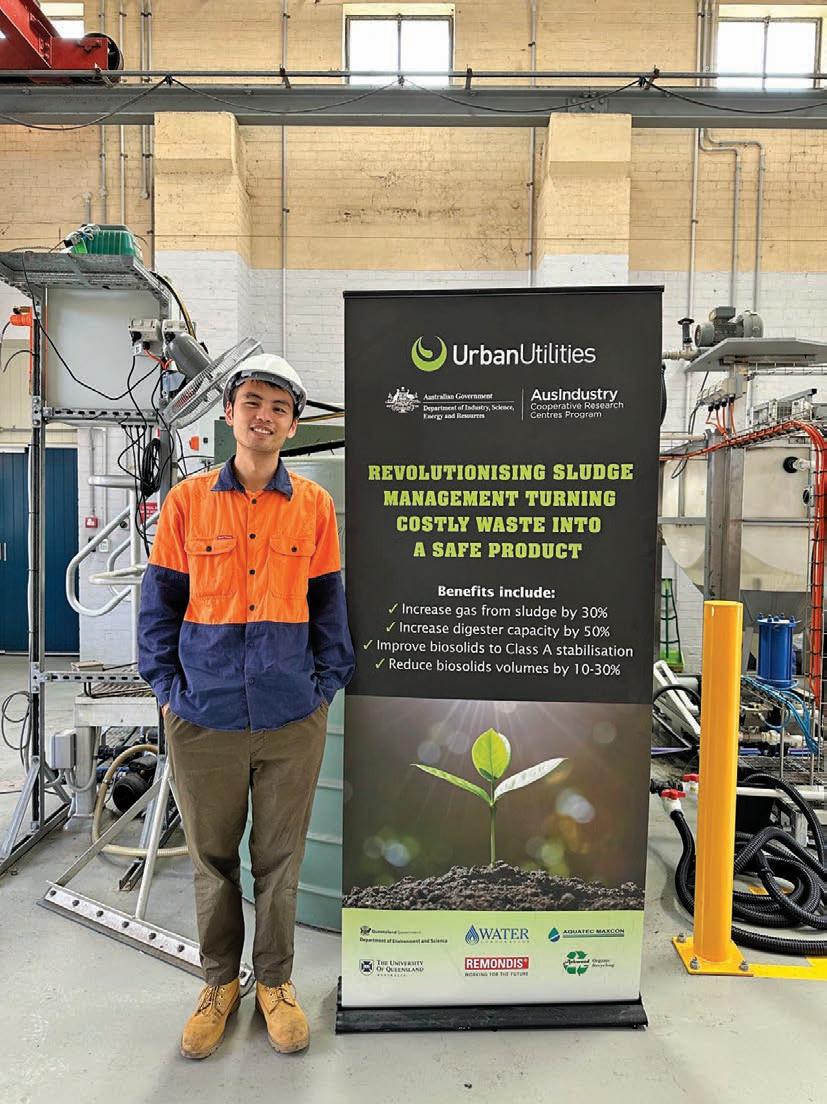
Working at a wastewater treatment plant in Melbourne.
Dr Duan has worked with multiple water utilities to improve the reuse of wastewater and sludge.
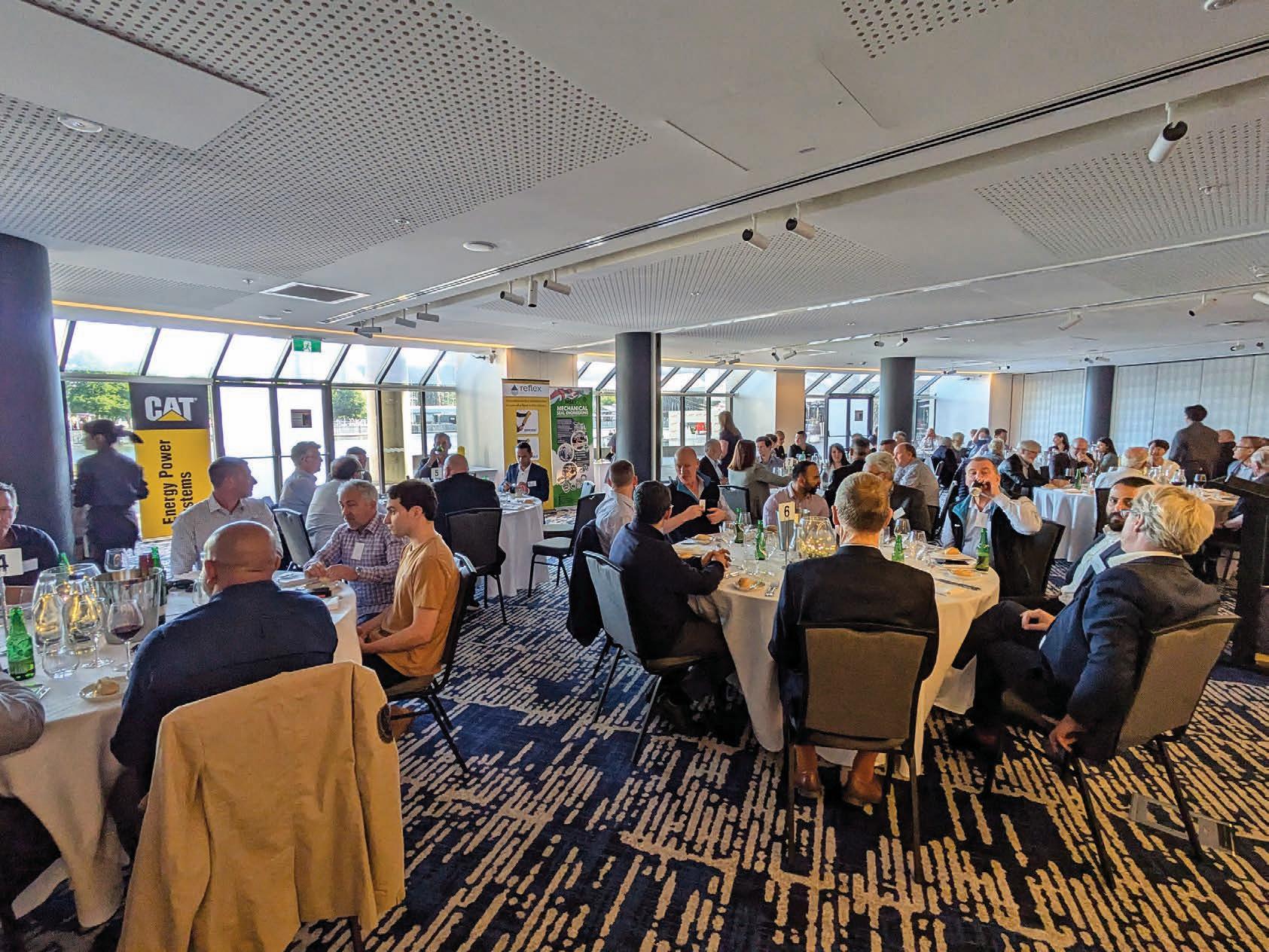
60 years of pump excellence
With a new lease on life, Pump Industry Australia brought together over 100 members to celebrate a milestone anniversary.
At the Crowne Plaza in Melbourne’s Docklands district, Pump Industry Australia (PIA) members celebrated 60 years of advocacy and support for pump engineers, manufacturers, and suppliers nationwide. The Annual General Meeting (AGM) was an opportunity to reflect on the previous year, providing unique insights into what it had been up to.
Over 100 people attended the Annual General Meeting (AGM) and Dinner, and Councillor Luke Biermann was an excellent host for both events. Several members tuned into the live stream of the AGM to engage from their offices.
First female president elected
For the first time in its 60-year history, a woman has been elected president of the PIA. Kylie Kinsella, the Managing Director of the Regent Holdings Group, was elected unopposed. Joel Neideck, the Managing Director of TDA Pumps, will serve as vice president.
At the dinner, Ms Kinsella discussed the opportunities that will arise for the PIA in the coming years as a younger cohort of council members joins her. It will be a year of growth and increased engagement with the broader pump industry to reassert itself as the peak body for the Australian pump industry. Other councillors elected were:
• Michael Woolley (Tsurumi Australia)
• Alan Rowan (Life Member)
• Alex Calodoukas (Pump Strategy)
• Tim Yakup (Regent Pumps)
• Steve Bosnar (Pioneer Pumps)
• Keith Bowen (XTron Pumps)
• Luke Biermann (Mechanical Seals Engineering)
One committee spot remained vacant.
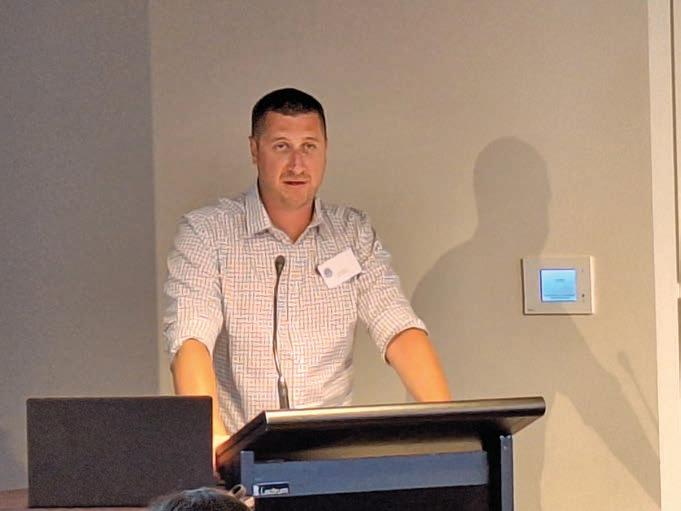
of the last 12 months, Mr Neideck took the opportunity to assess the PIA’s activities.
“Congratulations to the new president, Kylie, and Tracey as Secretary and Treasurer,” he said. “Also, congratulations to new and existing life members and our new councillors.”
Mr Neideck reiterated the importance of having everyone in the industry as a member of the PIA.
“We are out there campaigning for the industry and its members all the time,” Mr Neideck said. “We want to grow and increase representation, and to do that, we need to expand throughout Australia and potentially into New Zealand.”
The PIA seeks to be Australia’s leading authority on pumps and pumping systems. It also aims to advance collective thinking and become a nation that recognises the importance of and invests more in its capital infrastructure.
with an energised council and a renewed outlook,” Mr Neideck said. “Under the leadership of the new president, Kylie, whose impressive credentials and natural aptitude make her a perfect fit for the role, we are excited to build a more connected and supportive industry network.”
The PIA’s focus for the coming year is to deepen its engagement with members, emphasising support and clear communication. This includes launching new events to foster networking, share industry knowledge, and build camaraderie across the pump community. These initiatives aim to create meaningful connections, enhance expertise, and ultimately reinforce the shared commitment to the pump industry.
“With Kylie’s leadership and the council’s dedication, we look forward to a vibrant, collaborative year ahead for Pump Industry Australia,” Mr Neideck said.
Vice President Joel Neideck addressed the PIA Annual General Meeting.
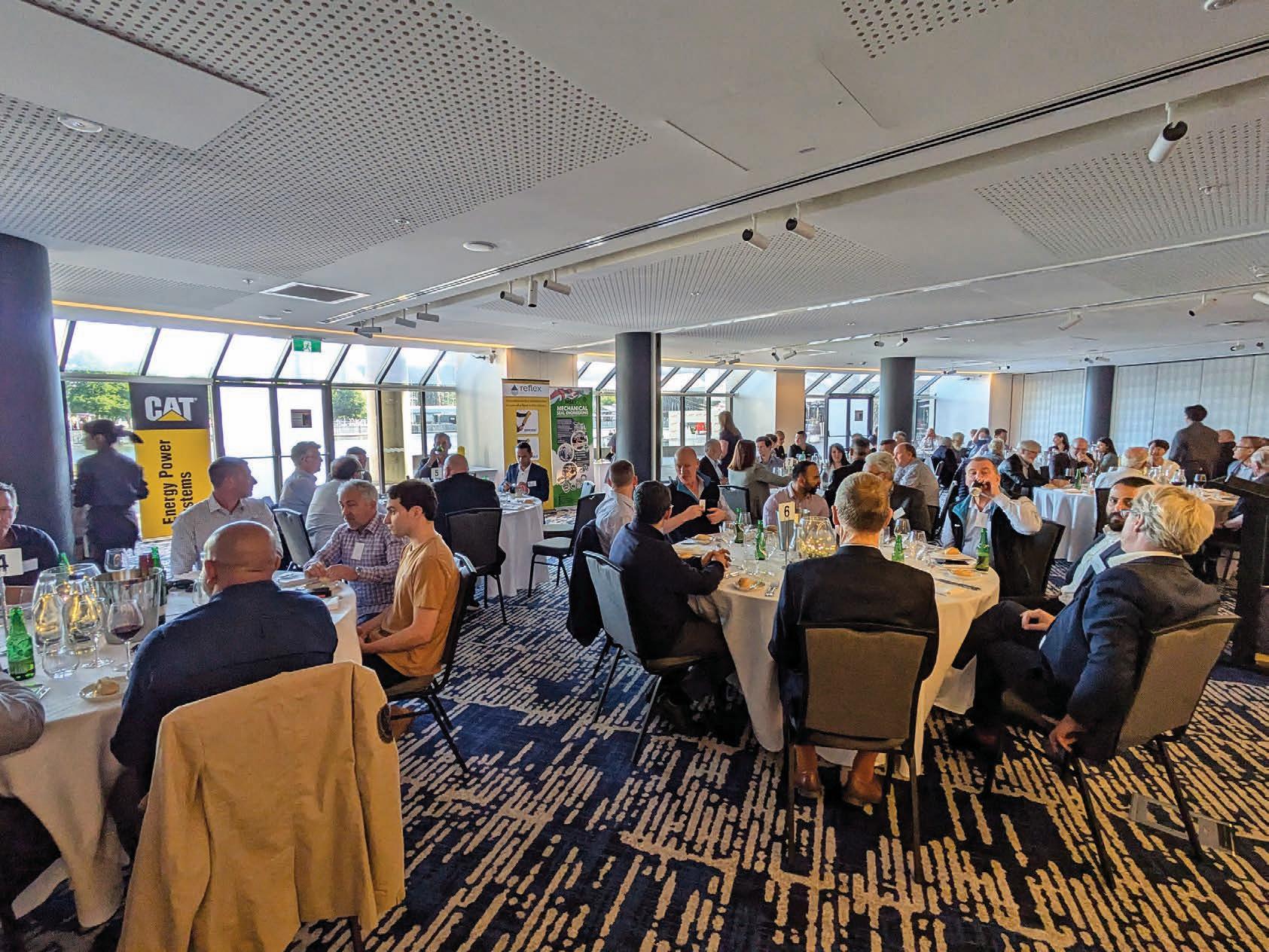
Standards and handbooks
Life member and councillor Alan Rowan addressed the AGM to discuss his achievements as an executive officer. He focused primarily on Australian standards, specifically pump pipe friction. His articles in Pump Industry are among the most popular online articles, with hundreds of people reading them weekly.
One thing that amused the attendees was Mr Rowan’s story about someone who examined a particular standard and wanted to know what it meant. These questions normally come in from the technical email address.
“Someone called up, saying that they don’t understand what is in the tables, as it relates to poly pipe,” Mr Rowan said. “He said that you call series ten pumps in this table, but all the manufacturers call them PN10 pipes. I looked at the most recent edition and could not see what he was referring to. I reviewed previous editions and could not find the reference. The gentleman sent through one of the pages, and we found what he was looking at. When we checked it on the Standards Australia website, that had ceased to be the standard in about 1986, which meant his version of the friction handbook was a first edition.”
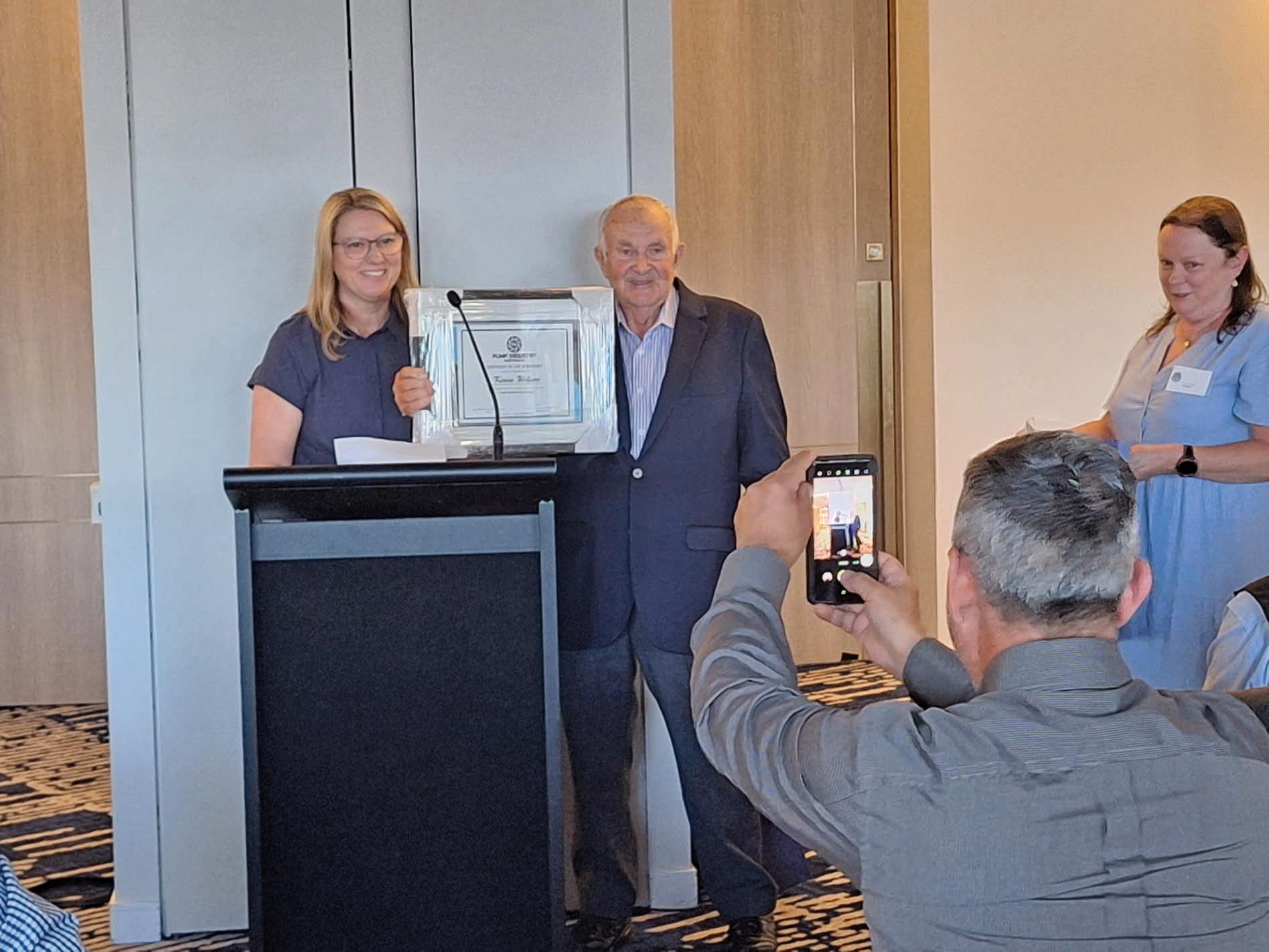
Fellow life member Ken Kugler spoke about his work with Standards Australia. He discussed the difference between aged, withdrawn, and renewed standards for those who are getting older.
“We’ve been working with Standards Australia on a range of standards and requesting feedback wherever possible,” Mr Kugler said. “It can be pretty hard to get feedback from the industry, but we do what we can.”
has had a long and successful career in the Australian pump industry. Since joining FN Bethune at 20, he has worked at Kelly & Lewis, BTR Australia, and the Weir Group. He also served as the Secretary of the PIA and has worked for a wide range of companies.
Former president John Inkster joined Mr Wilson as a new life member of the PIA. Mr Inkster retired from Kelair Pumps earlier in 2024, and this nomination reflects his commitment to the industry, having
Kelair Pumps and Brown Brothers Engineers evolved from a family-owned enterprise to a thriving member of the AxFlow Group with a diverse portfolio of successful companies.
The attendees enjoyed a few drinks, some excellent food, and canapés between the formalities. It was an excellent opportunity to reflect on the year that was for the PIA. Collectively, the energy of the room was one of youthful endeavour and spirit, with everyone gathered together and looking forward to an exciting future.
Over 100 attendees enjoyed the Images: Prime Creative Media
Kylie Kinsella (left) from Regent Pumps is the PIA’s first female president, here with new Life Member Kevin Wilson.
When the process gets tough, just pump it up!
GSOF pumps excel in heavy-duty jobs and are ideal for cooling steel or mixing molasses, ensuring smooth operations across industries.
After successfully introducing the GSO ISO2858/5199 process pumps into the industrial product range in 2023, EBARA PUMPS AUSTRALIA has launched a new range called the GSOF pumps.
GSOF pumps, with their open impeller design, comply with ISO 2858/5199. They allow the transfer of slurry-containing chemical liquids, such as organic materials (such as PVC, plastic, sugar, and starch) and inorganic materials (like metal and drainage sand), in industrial processes.
Following on with EBARA PUMPS AUSTRALIA and its history of excellence, the GSOF range has been crafted from stainless steel alloys designed for long-term use. EBARA PUMPS AUSTRALIA also offers duplex and super duplex stainless steel wetted parts. These wetted parts are commonly found in valves, pumps, and other equipment in many industries, including oil and gas, chemical processing, and marine. These alloys are known for their strength, ductility, and corrosion resistance and are often used in environments where corrosion is a concern.
EBARA PUMPS AUSTRALIA also offers double ball bearings, oil lubrication, and single and double mechanical seal combinations by providing mechanical seal piping plans. These plans improve the environmental conditions around seals, extend their capabilities, and allow operators to monitor seal performance. Adjusting the impeller clearance through a set screw on the bearing cover is designed to be simple for any experienced pump operator.
The GSOF pumps can be used in a wide range of industries and liquids, with a liquid temperature range of -30-150 °C. These industries include chemical, pharmaceutical, food and beverage, steel, pulp and paper, automotive, water treatment, wastewater treatment, and mining.

The pumps were designed by engineers from EBARA Corporation, Japan. They are manufactured at one of EBARA’s owned and operated factories overseas, under strict EBARA Japanese QA standards and management policies.
About EBARA
EBARA Corporation was founded in Japan in 1912 as a manufacturer of industrial pumps. Today, the group comprises over 100 companies across six continents, with a workforce exceeding 19,000. EBARA Corporation manufactures out of company-owned, Japanese-managed factories in ten countries and four continents.
EBARA is constantly committed to researching, developing, and designing new products. It manufactures its
inventory using modern technology, which matches the considerable scale of production and distribution. EBARA products have gained a worldwide reputation for their technology and quality.
For over 40 years, EBARA pumps have been sold and used in Australia, satisfying many customers and building a reputation for their quality and reliability. EBARA PUMPS AUSTRALIA was established in 2000 to better service the market with an increasing range of quality products. A strong network of nationwide dealers has been developed to support the sales and service of our extensive range of products.
For more information, visit ebara.com.au
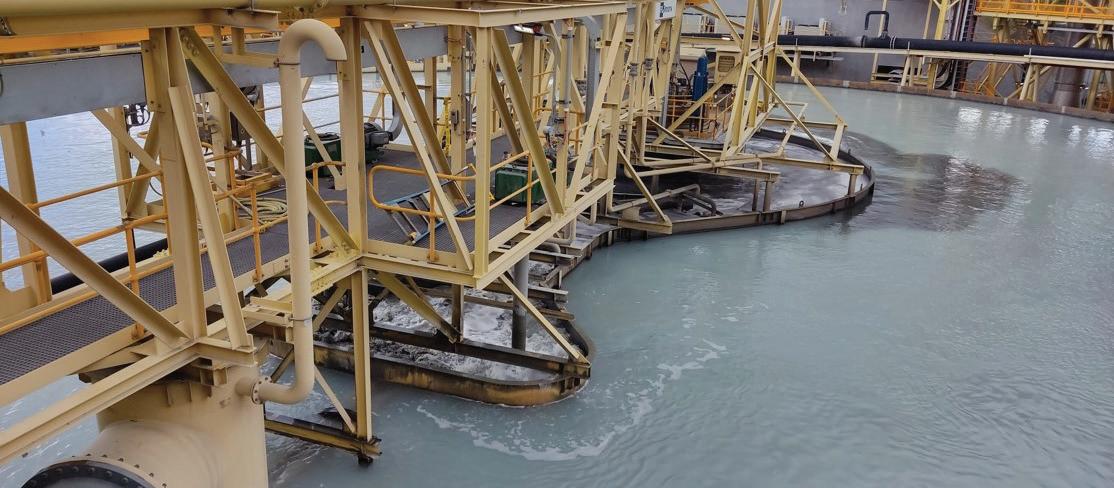
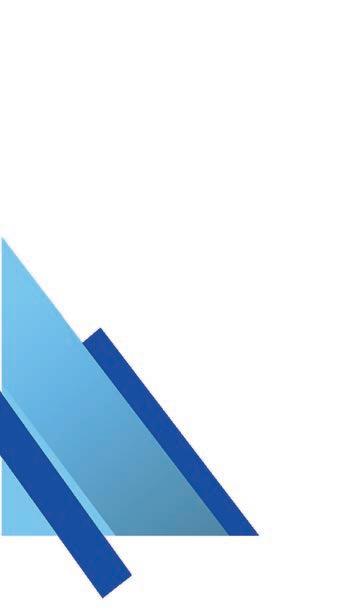
The GSOF pumps from EBARA PUMPS AUSTRALIA represent high-quality and excellent performance. Image: EBARA PUMPS AUSTRALIA
Model GSOF
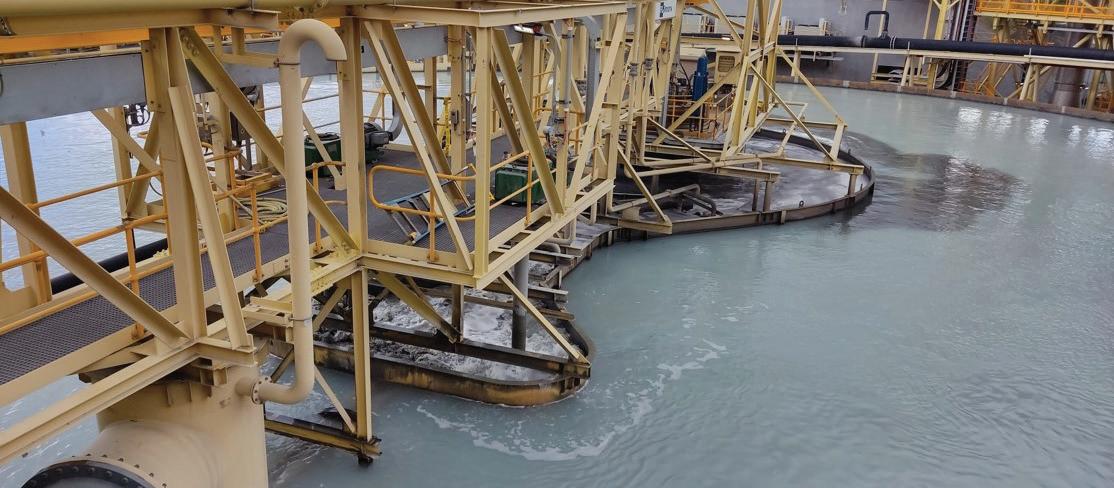
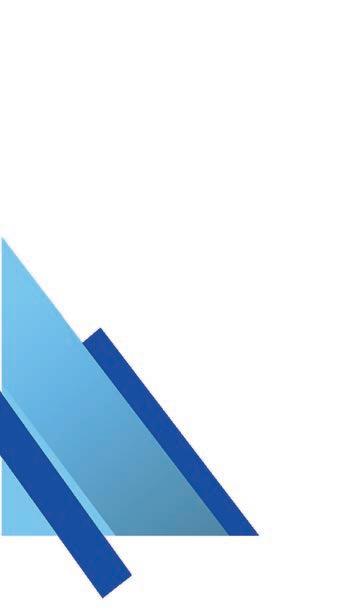
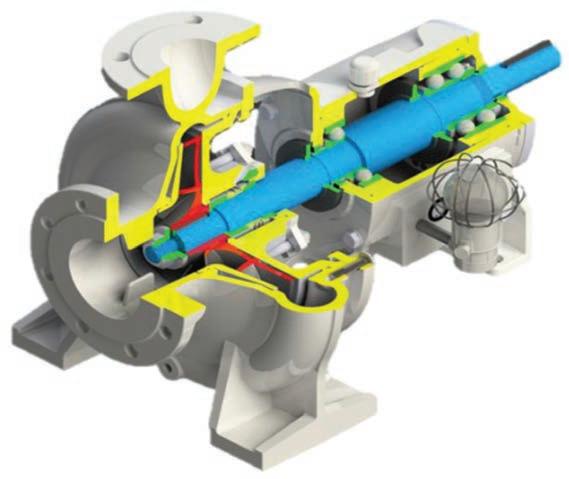
• Discharge sizes : up to Φ65 mm
• Flows : up to 210 m³/h
• Heads : up to 105 m
• Maximum working pressure : 16 bar
• Liquid temperature range : - 30 to +150°C


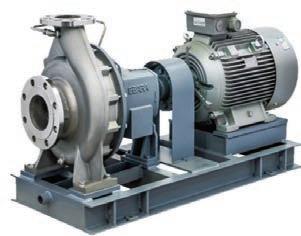
Standard designations
Stainless steel solutions 304,316,316L, Duplex & Super duplex stainless steel wetted parts
Innovative hydraulic solutions Semi open impeller for slurry contained chemical liquid
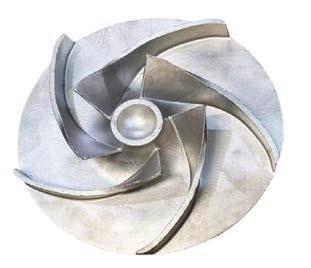
New inverter optimises solar pumping applications
The significant reduction in the pricing of photovoltaic panels, together with the upward trend in the cost of fossil fields and grid electricity, has led to a boom in profitable solar pumping systems.
Developed using WEG’s expertise in industrial drive technology and extensive experience in solar and pump applications via photovoltaic (PV) panels, the ADV200-SP solar pump drive converts energy received via a PV array into electrical power capable of operating a standard three-phase electric pump.
At the heart of this innovation is the MPPT dynamic search algorithm. This algorithm ensures that the ADV200-SP Drive continuously adapts to varying irradiation and temperature conditions, maximising system load at maximum output power. This adaptability maximises efficiency and performance under real-world conditions.
The ADV200-SP Drive offers remarkable versatility for various plant configurations. It effortlessly adjusts to isolated systems powered only by a PV array or dual supply systems that switch automatically between solar energy and an additional AC source, such as a grid connection or generator. This adaptability can eliminate the expensive requirement of installing a grid connection in remote locations or reduce the dependence on fossil fuel-powered generators.
If operation must be guaranteed even under low irradiance conditions, then the ability to have a dual supply, including a backup power source such as a grid supply or a genset, adds a level of redundancy and allows for longer operating times under low irradiance conditions. The ADV200-SP has the intelligence to supervise both supplies, ensuring a seamless transition from one source to the other. The Solar Pump drive can even operate from the PV array and the backup source simultaneously, always preferring to harness the free power of the sun, minimising the costs associated with the import of electricity or fuel for local generation.
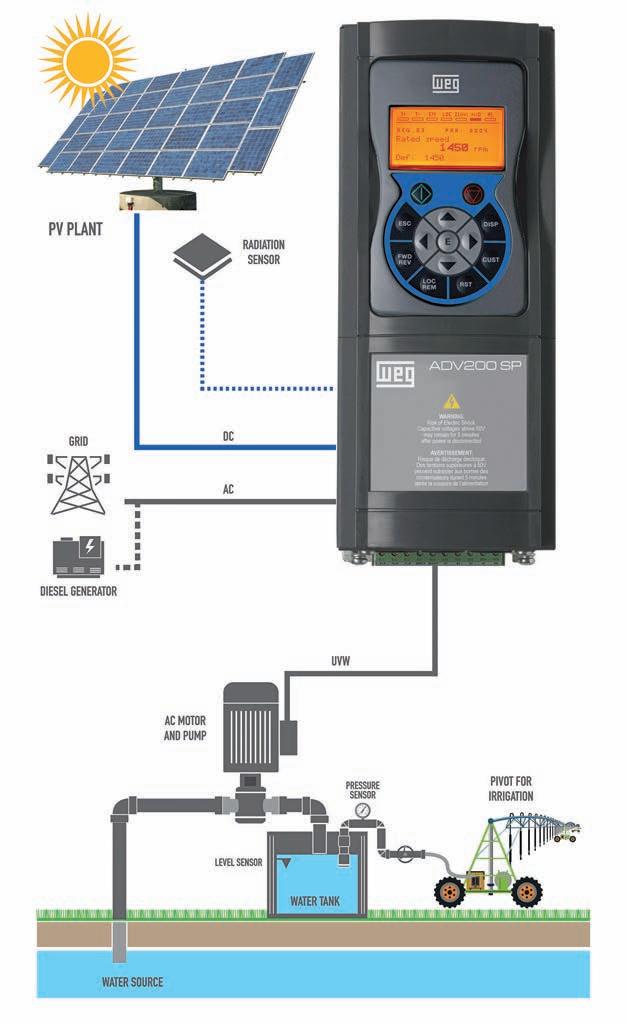
The solar pump drive boasts an extensive power range from 1.5 to 400 kilowatts (kW), making it suitable for a wide array of applications. In fact, the ADV200-SP allows the parallel connection of power modules, increasing the maximum conceivable power limit to 1.8 megawatts (MW). With control features such as dual PID loops for pressure, flow, or tank level control, and a real-time clock for auto start and stop, the ADV200-SP can run independently or equally well at home, being integrated into other control platforms.
The ADV200-SP also offers the convenience of advanced pump protection features, such as dry pump protection, burst pipe protection, and de-ragging. These features aim to maximise plant uptime while harnessing the maximum potential energy from the sun. The ADV200-SP can handle applications such as flood irrigation, pivot irrigation, remote water supply, cattle drinking fountains, water treatment, and fish farming.
The ADV200-SP, together with the power of the sun, is the ultimate energy-efficient pump solution.
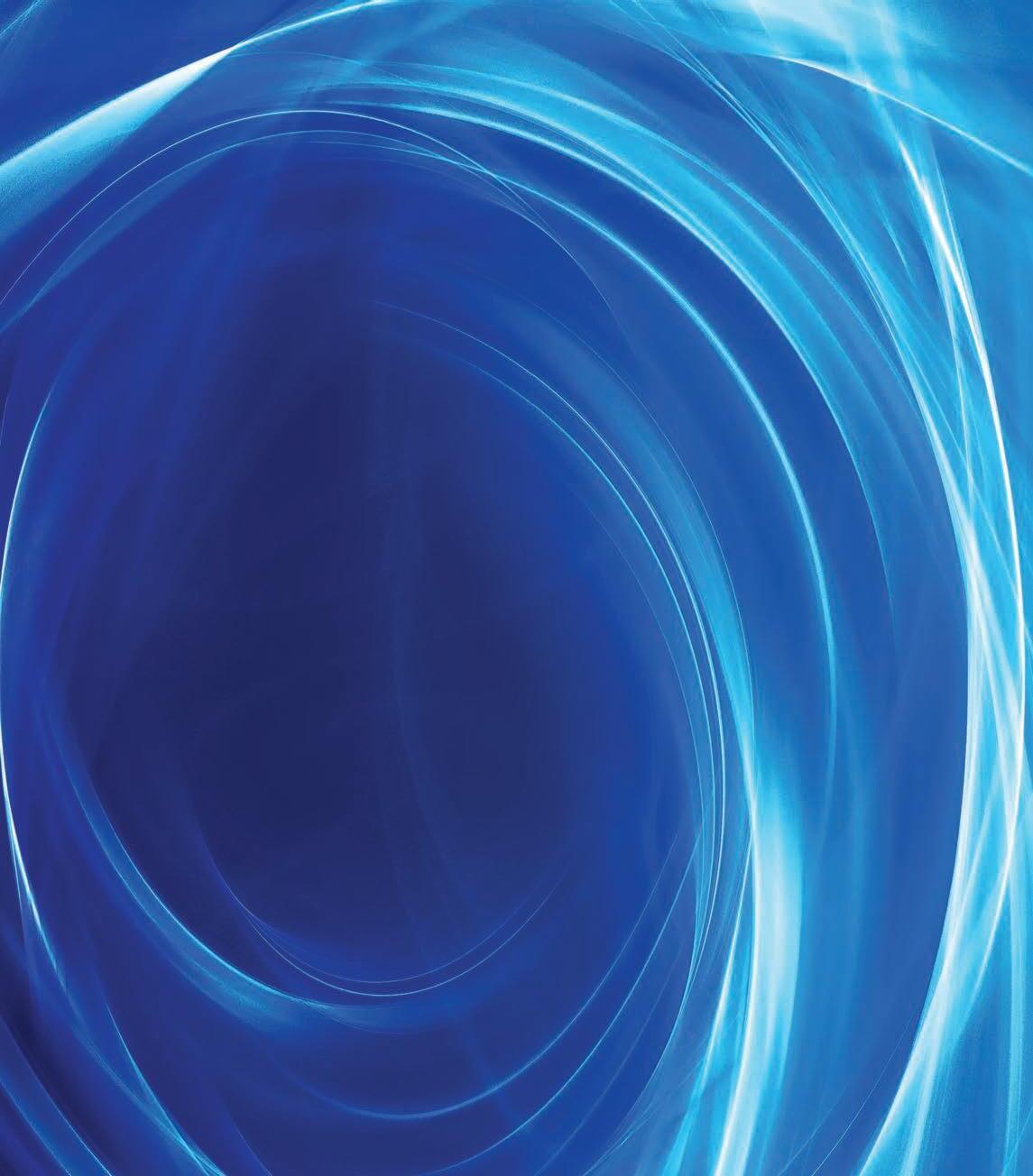
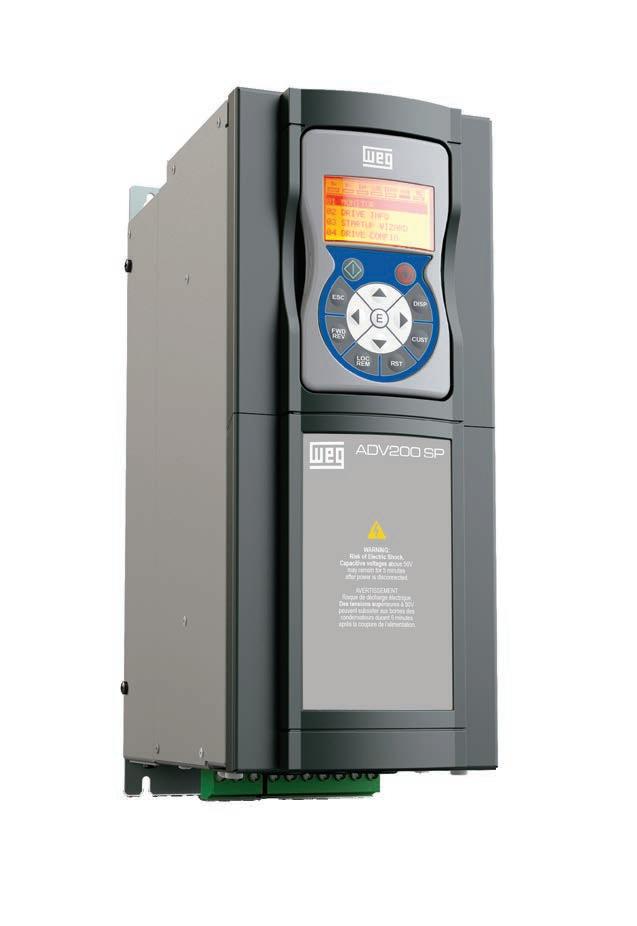
This new inverter can better harness the power of the sun. Image: WEG
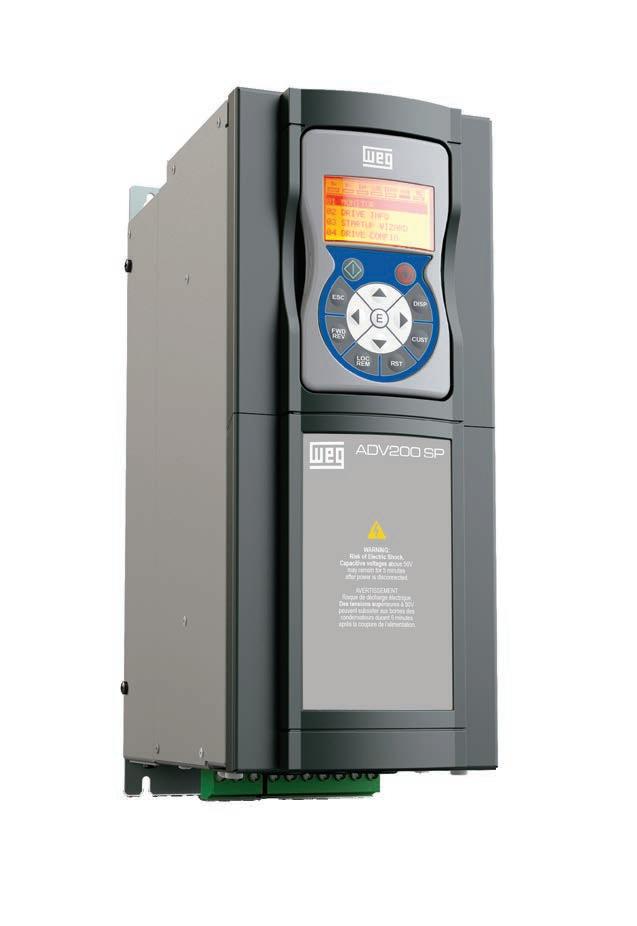
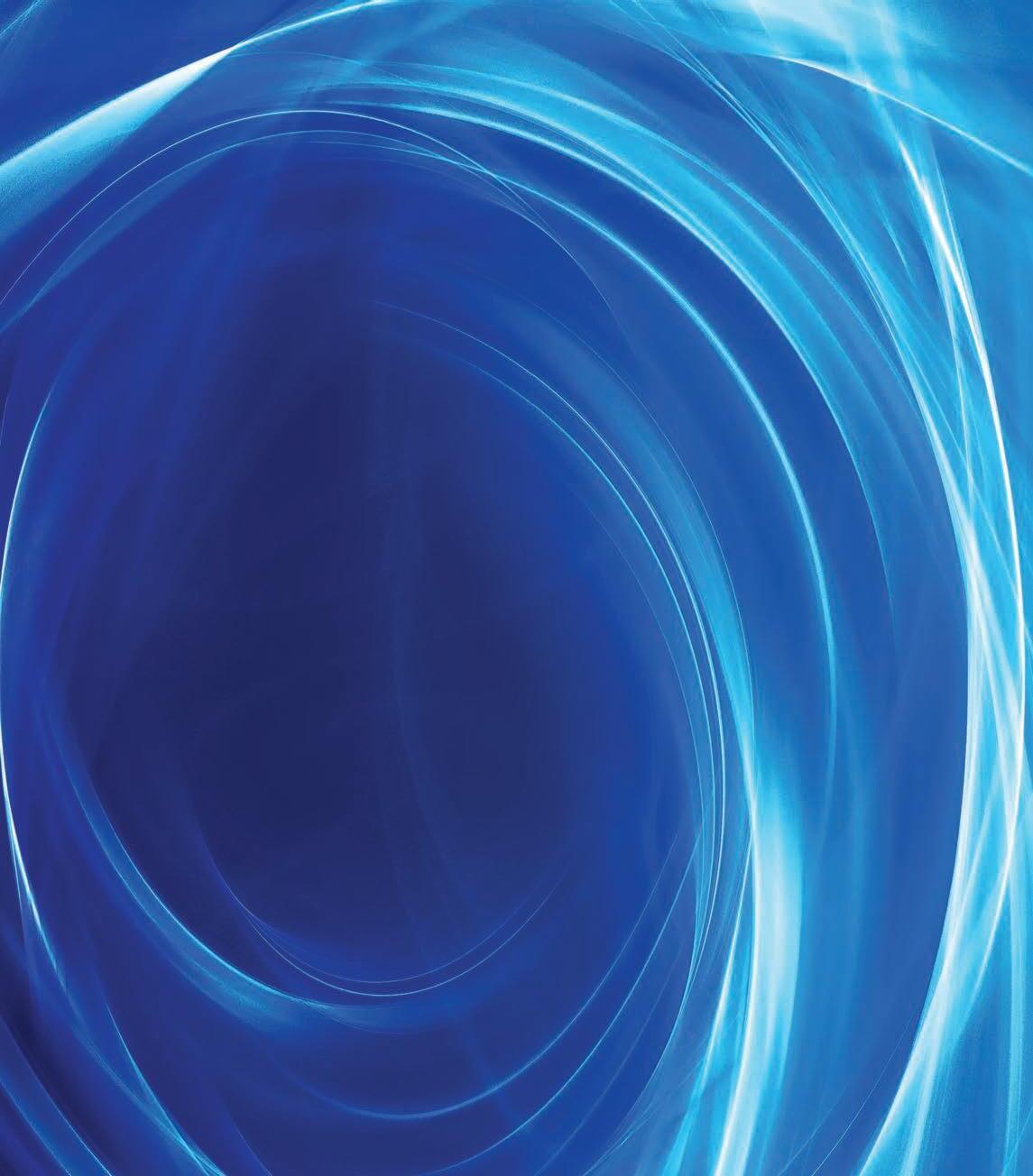
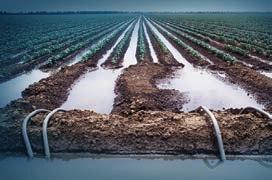
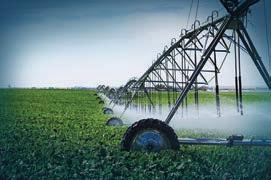

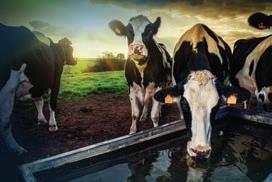
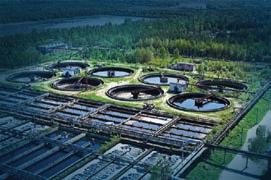
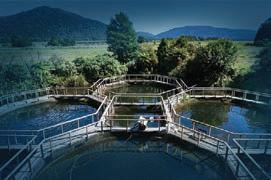
Leading the way in pump technology
By combining cutting-edge engineering with reliability, this industry leader has swiftly earned trust across Australia and Southeast Asia.
Pioneer Pumps Australia, a division of Franklin Electric, has been making waves in the pump industry since its establishment in 2013. Focusing on innovation, performance, and reliability, Pioneer Pumps has quickly become a trusted name in the Australian and Southeast Asian markets.
One key factor behind Pioneer Pumps’ success is its commitment to cutting-edge hydraulic engineering. The company’s centrifugal pumps are designed to provide better flow, higher head, greater efficiency and unparalleled service, meeting the unique challenges of various industries, including agriculture, mining, construction, defence, municipal, oil and gas, and industrial sectors. This dedication to performance through innovation has earned Pioneer Pumps a reputation for delivering high-quality products that withstand the toughest conditions.
Pioneer Pumps Australia operates from its manufacturing, parts and service facility in Melbourne, ensuring fast support for the entire region. The Pioneer Prime range offers high flows of up to 4,250 m³/h and heads of over 700 feet (210 m) with vacuum-assisted dry priming and run-dry capability, providing the highest outputs of any company in the self-priming pump market. It is built to deliver performance and reliability in demanding environments such as mines, flood response, dewatering and land reclamation. This focus on quality and reliability has made Pioneer Pumps a go-to choice for many businesses in need of robust pumping solutions.
Another aspect that sets Pioneer Pumps Australia apart is its extensive network of dealers and distributors. By partnering with specialised dealers, the company ensures that its products are readily available and supported across Australia and New Zealand. This network also allows Pioneer Pumps to provide personalised solutions tailored to the specific needs of its customers, further enhancing its reputation for exceptional service.
Taking a future-oriented approach
Pioneer Pumps’ journey began in 1998 in Canby, Oregon, USA, and it has since expanded its reach globally. The
It’s important to have a contingency plan for any pumping situation. Images: Franklin Electric
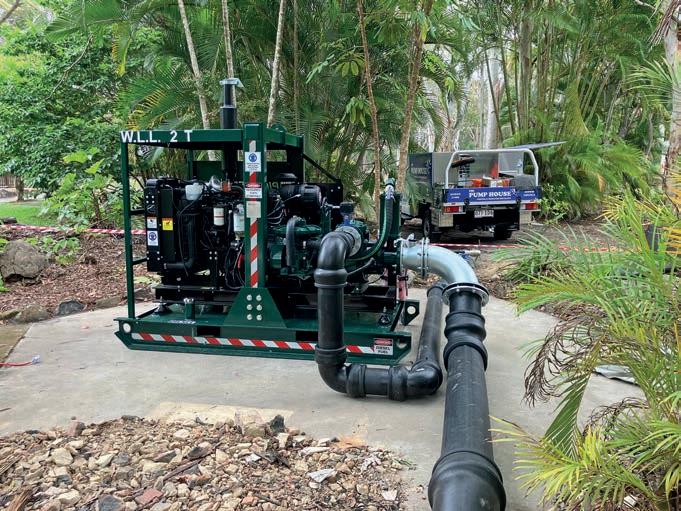
company’s entry into the Australian market in 2013 marked a significant milestone, bringing Pioneer Pumps’ expertise in hydraulic engineering to a new region. Since then, the company has continued to grow, leveraging its extensive knowledge and experience to meet the unique demands of the Australian market.
In 2020, Franklin Electric consolidated its global water business group under one company, Franklin Electric Australia New Zealand Pty Ltd, with Pioneer Pumps Australia joining this larger entity. This consolidation has allowed Pioneer Pumps to benefit from Franklin
Electric’s extensive resources and expertise, further enhancing its ability to deliver high-quality pumping solutions.
As Pioneer Pumps Australia continues to expand its presence in the Southeast Asian market, the company remains committed to its core values of innovation, performance, and reliability. Focusing on delivering exceptional products and services, Pioneer Pumps is well-positioned to lead the pump industry for years to come.
For more information, visit global. pioneerpump.com/se-ß-pacific
Pioneer Pumps is a division of Franklin Electric, and its pumps are well-regarded across the industry.
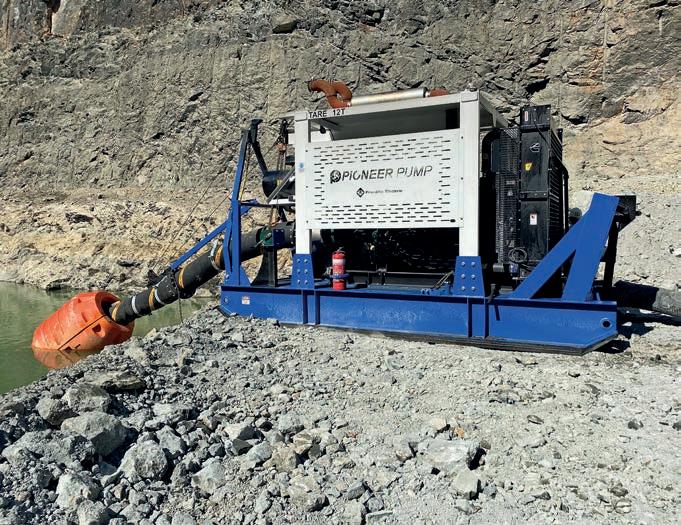
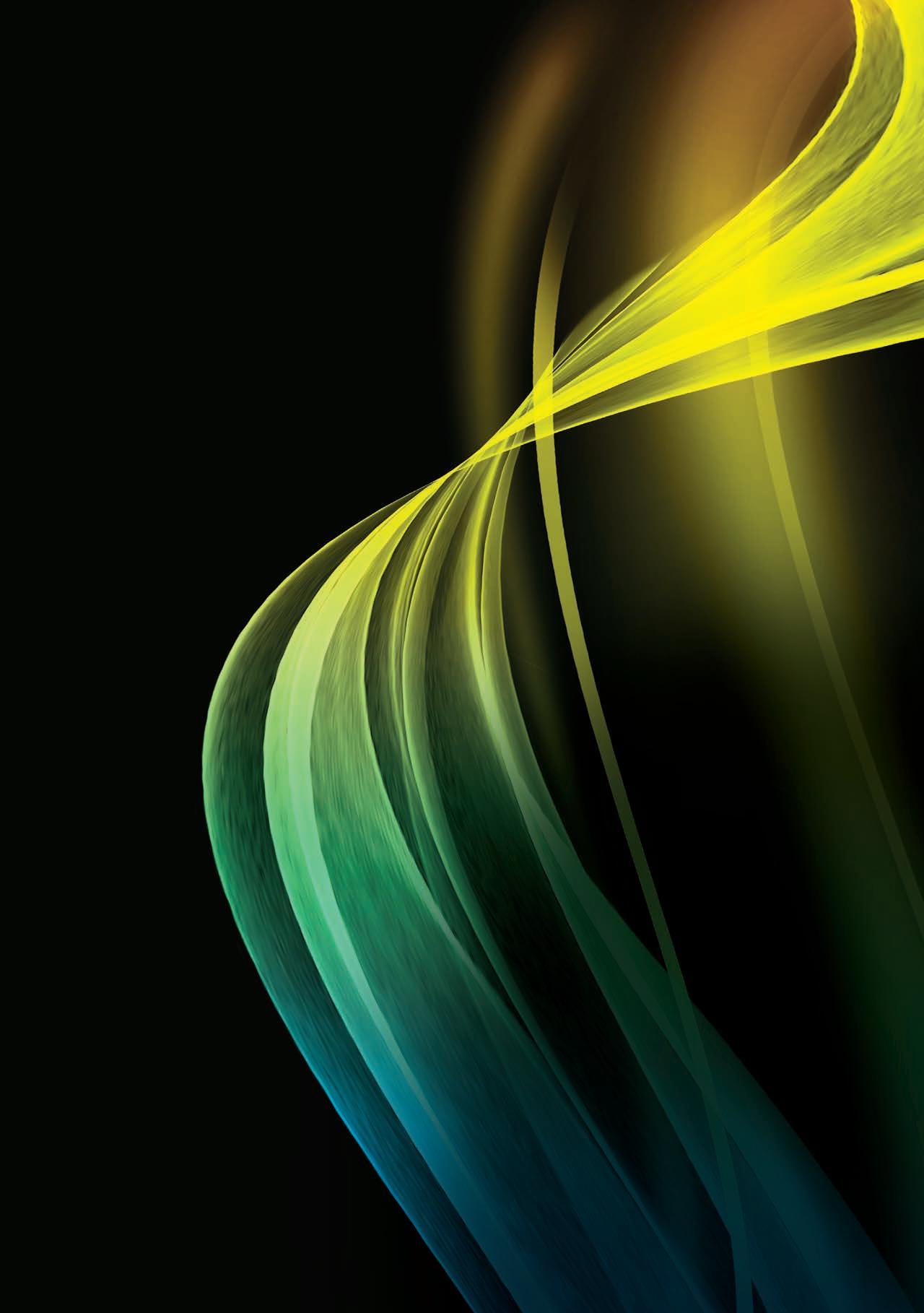
Simplicity + Reliability.
It’s the Chesterton® standard.
The Chesterton 1510 represents over 40 years of engineering excellence in our most streamlined mechanical seal yet.
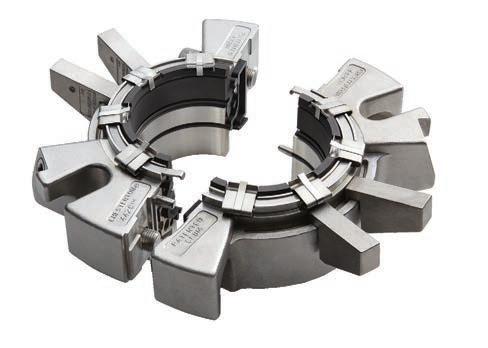



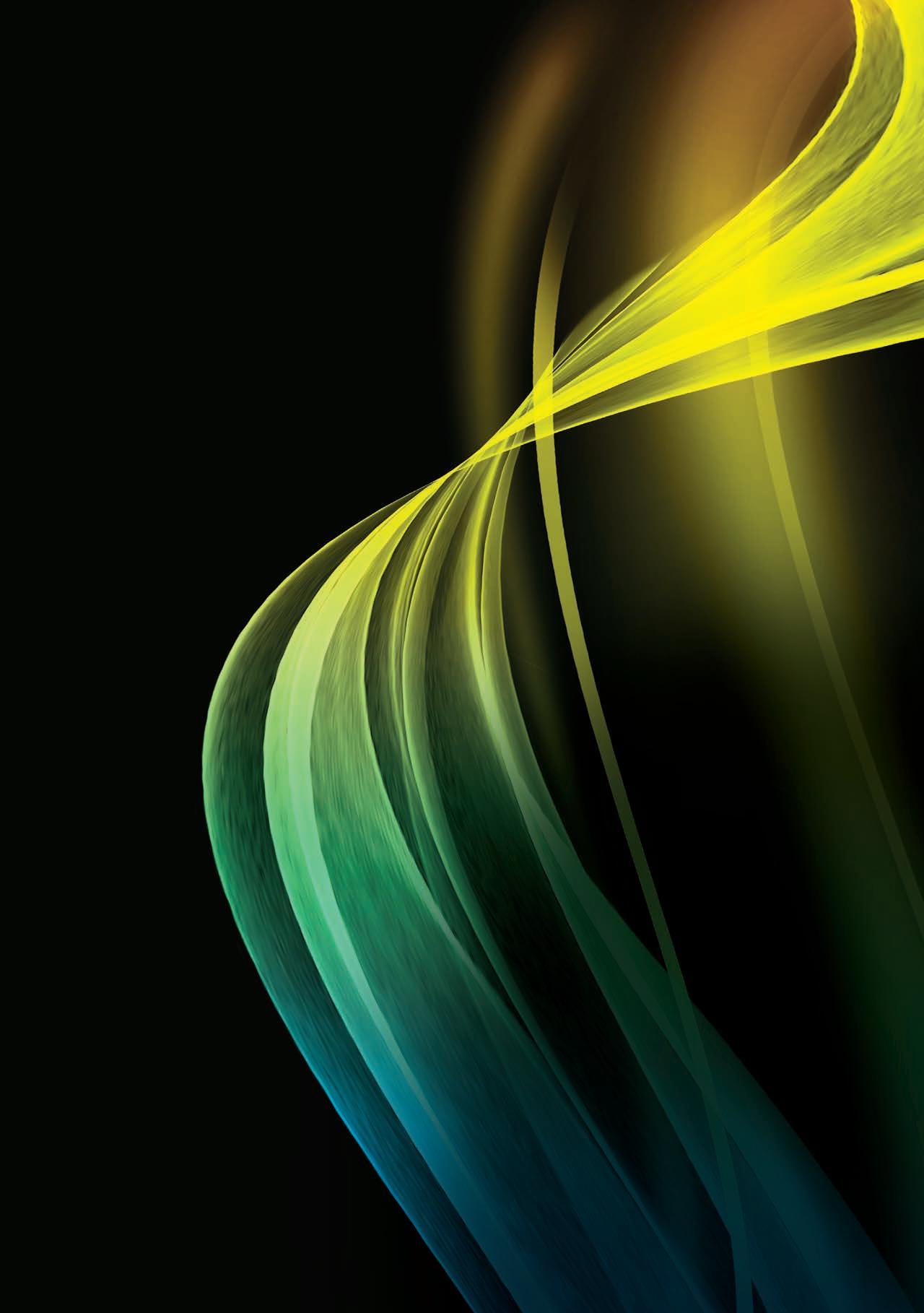
Maximize maintenance efficiency and increase plant productivity with the 1510 Single Cartridge Seal.
Designed to fit process equipment plant-wide by incorporating Chesterton T.A.B.S. (Tapered Adjustable Bolting System), the compact profile makes seal installation easy.
Advantages
n Reliable through temperature cycling and intermittent process with monolithic seal faces
n In service impeller adjustment is possible with the unique centering strap
n Prevents damage to your equipment and internal components via true non-fretting design

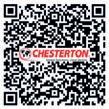
Download Our FREE E-Book: “Taking the Mystery Out of Mechanical Seals”
Grundfos supplies compact and reliable pumps for a range of specialist wash and clean applications. Images: Grundfos
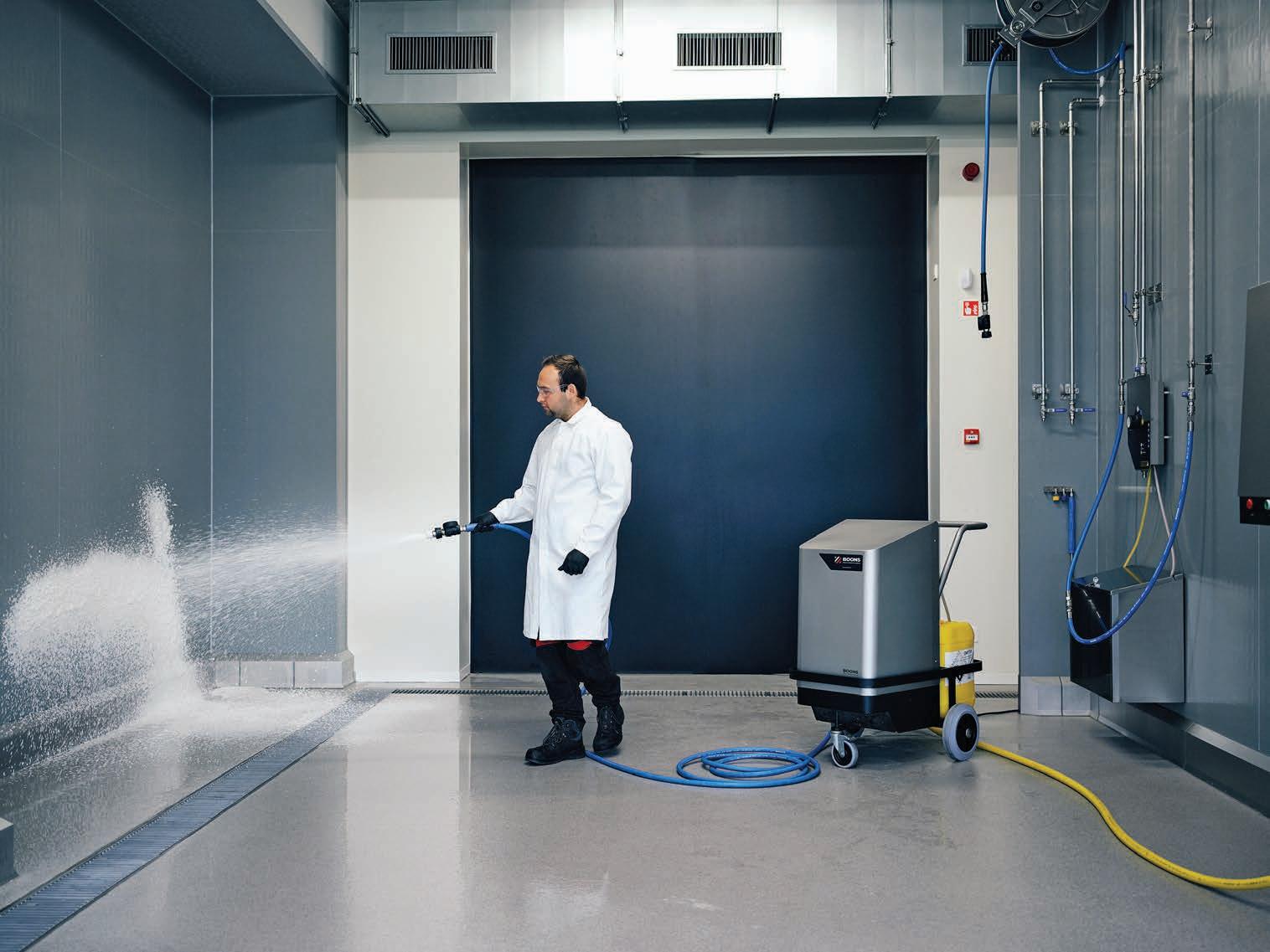
Smarter pumping for industrial efficiency
Advanced pump systems lower energy costs and streamline operations in high-pressure industrial applications.
From food processing to pulp and paper, industrial applications rely on high-pressure pumps to handle demanding washing and cleaning needs. While functional, traditional pump setups often have significant drawbacks: high maintenance, frequent downtime and mounting operational costs. Emerging technologies offer smarter, costeffective solutions that address these challenges with precision and efficiency.
Advanced solutions
One of the most promising new solutions is Grundfos’ Hydro HP technology. This technology combines intelligent features designed to streamline high-pressure pumping systems. At its core, Hydro HP includes CR/CRN vertical multi-stage pumps, known for their reliability and ease of maintenance. These pumps can handle high- and low-flow needs, reducing energy consumption while delivering consistent performance.
“The system’s versatility also allows it to cater to varying industry demands,” a spokesperson said. “Our Hydro HP system is designed to accommodate different industrial pressures and flows without compromising energy efficiency or reliability. With this adaptability, it’s the answer to diverse and complex industrial needs.”
The ability to integrate variablefrequency drives (VFDs) into the
system further boosts efficiency by automatically adjusting motor speed to meet specific flow requirements. This feature lowers energy consumption and reduces system stress, minimising the need for frequent maintenance.
Grundfos has developed the control system for Hydro HP to be centred around the CU 352 multi-pump controller. With seamless integration to plant SCADA systems, operations staff can monitor and manage the pumps’ performance in real time, streamlining maintenance and troubleshooting processes.
Facilities can set optimal operating conditions and observe valuable data points, such as system pressure, flow, and operational status.
Reducing operational expenditures
The cost of ownership of a pump system goes beyond its initial purchase price, representing only around 10 percent of the asset’s life. Traditional high-pressure systems often require expensive maintenance, especially in demanding industrial environments such as wastewater treatment.
The Hydro HP system is built with wear-resistant materials and easyto-replace components, significantly reducing the time and cost required for routine servicing.
The CR/CRN pumps within the Hydro HP are equipped with
Grundfos-engineered cartridge seals, which enable fast, on-site replacement in under 30 minutes. By simplifying maintenance, these pumps help facilities save on parts and labour.
“Our goal is to minimise disruptions by designing a system that can be maintained in-house,” the spokesperson said. “Our cartridge seals and stack kits allow quick replacements, reducing downtime and lowering operational costs.”
The system offers energy-saving features that reduce energy consumption by 20 to 50 per cent compared to fixed-speed pumps, leading to long-term cost savings. Hydro HP uses variable frequency drives (VFDs) that automatically adjust motor speed, conserving energy and lowering overall costs. According to Grundfos, enhancing energy efficiency and simplifying maintenance can result in a positive return on investment within the first few years of operation.
The packaged approach
In addition to addressing operational pain points, the Hydro HP system integrates pumps, controls, and customisation options within a single, fully-engineered package. With its flexible configuration, the system can be tailored to meet specific operational demands or expanded for future growth while maintaining a compact footprint.
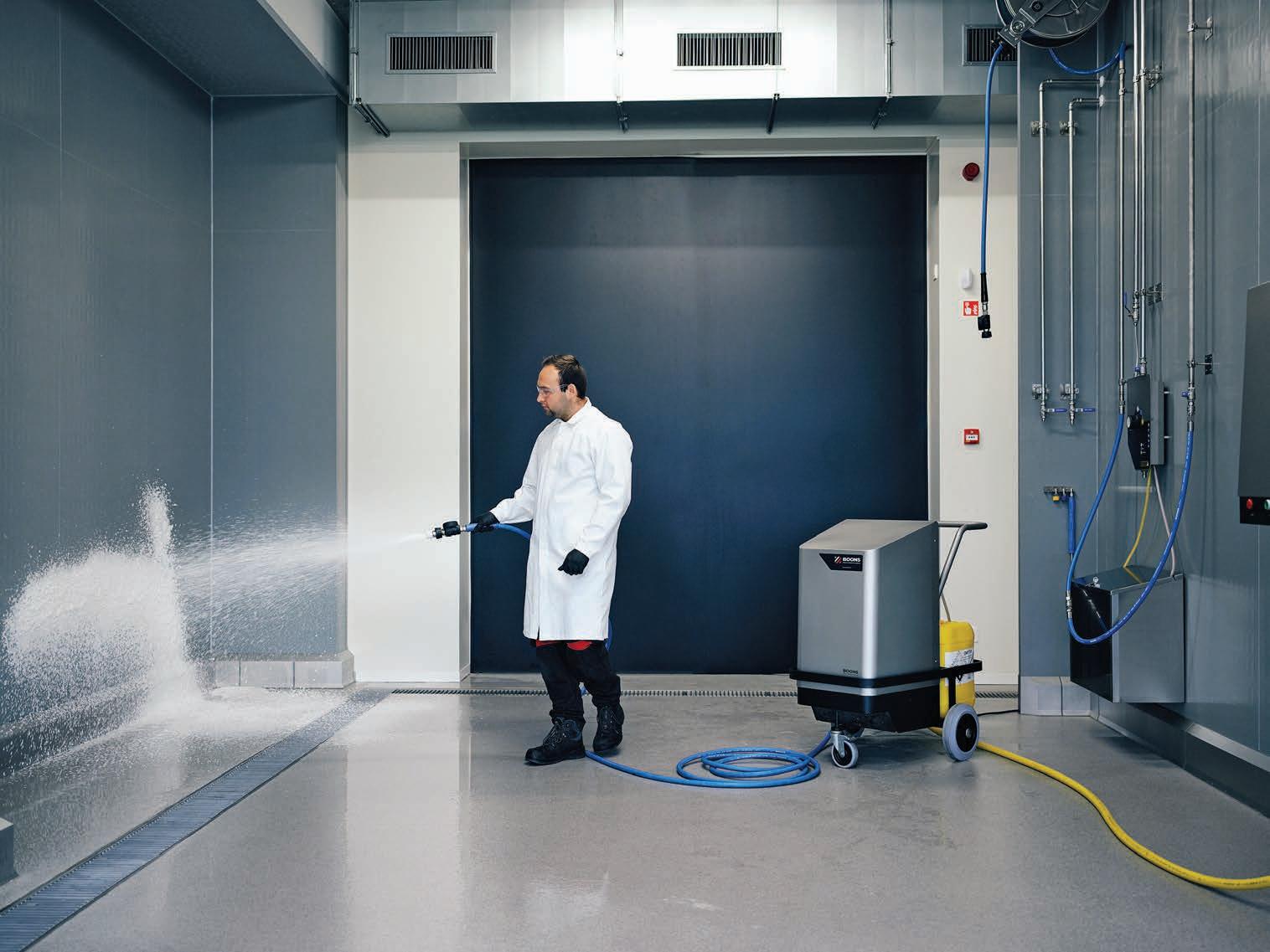
It is factory-tested and has a two-year warranty, ensuring reliability and a streamlined installation process.
“We’re seeing an increased demand for systems that combine performance with ease of installation and support,” the spokesperson said. “Hydro HP meets this demand by delivering an integrated solution, providing facilities with dependable performance and the added security of comprehensive support.”
Hydro HP’s packaged pumping solution from Grundfos is a forwardthinking choice for facilities looking to boost efficiency and minimise long-term costs. Enhanced monitoring, efficient energy use, and low-cost maintenance provide a sustainable solution to modern industry demands.
About Grundfos
Grundfos is the largest pump manufacturer in the world. Based in Denmark, it employs more than 19,000 people worldwide. It is the first water solutions company to set validated, science-based targets to achieve netzero emissions and maintain rigorous standards to continually improve our social impact and inclusion.
Visit product-selection.grundfos. com/au/industries
Grundfos supplies compact and reliable pumps for a range of specialist wash and clean applications.

MINE DEWATERING EXPERTS

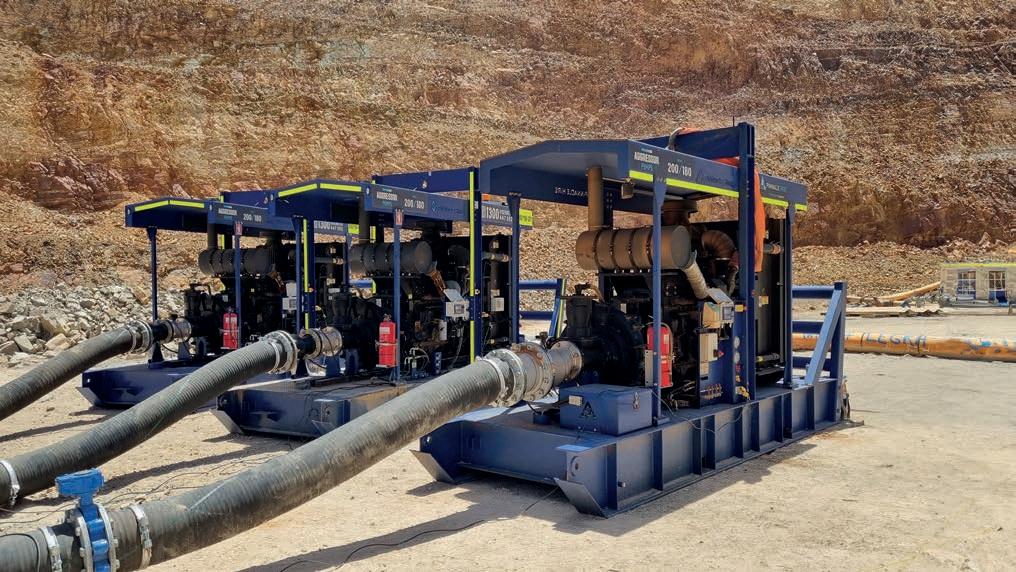
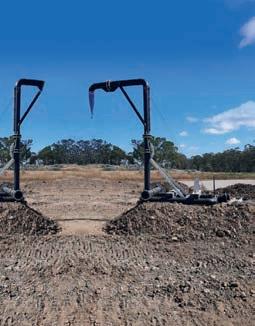
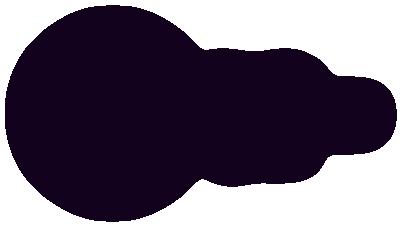
The quality of seals from Chesterton is designed for the many different industries that treat water and wastewater, among other areas. Image: sirisakboakaew/stock.adobe.com
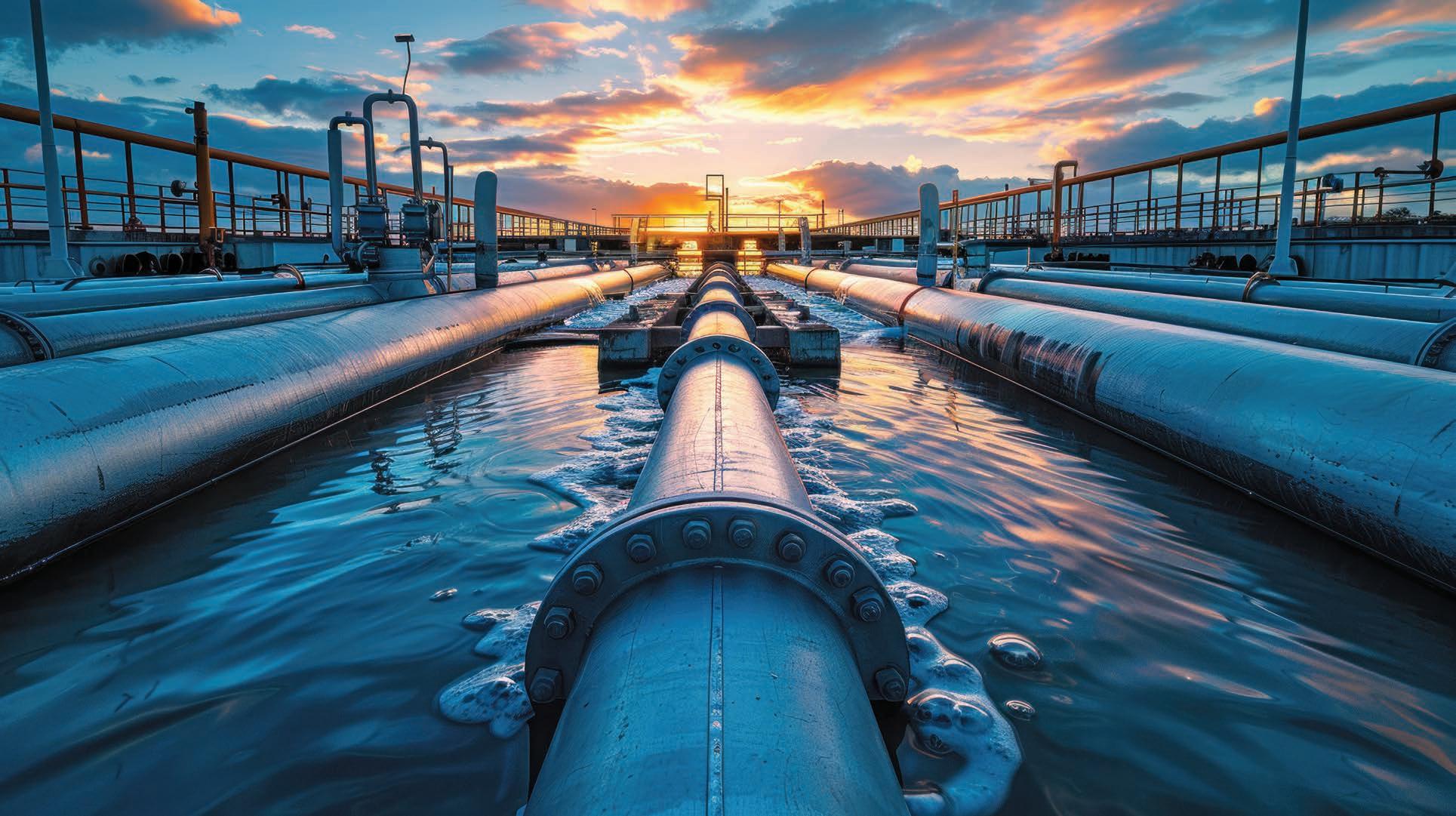
Seal solutions for longevity
Seal away pump worries with innovative technology that boosts reliability and makes downtime nearly disappear.
Pump installation and maintenance in the water and wastewater industry present many challenges. Seal fatigue and breakdown inevitably lead to pump downtime and substantial labour and maintenance costs.
Technological advances have brought proven solutions that can dramatically reduce seal installation time, pump maintenance, and the likelihood of asset failure.
Advanced seal technology and configuration solutions
While mechanical seals only represent a small proportion of a pump’s overall acquisition cost, their failure can amount to significant expenditure. The key to reliability lies in maximising pump life, which can be effectively achieved with two simple yet highly effective solutions.
Split seals and active throat bushing technology considerably improve overall equipment reliability. Together, they enhance the seal environment with minimal or no flush water requirements
and dramatically decrease the efforts (and costs) spent on pump maintenance.
Split seal technology
As the name suggests, split seals are split into at least two elements. They perform the same role as standard mechanical seals and can be utilised in the same locations (on rotating equipment). However, the most significant advantage offered is that no equipment disassembly is required to fit a split seal, and no additional expertise is needed.
Other advantages include the provision of a leak-free or virtually leak-free seal that will last for years. It can eliminate excessive shaft or sleeve wear while minimising the corrosion of essential assets. By providing solids handling capabilities, systems benefit from fewer clean-ups and fewer issues surrounding the disposal of products through the seal.
This further decreases the volume of water used to flush the system, as well as reducing a range of associated
costs with maintaining pump systems. As a result, the return on investment increases significantly, providing better financial outcomes for shareholders.
Active throat bushing technology
The environment around the seal directly impacts its lifespan and reliability. The two most significant issues are contamination and heat. The traditional approach is an external flush – generally water – with the hope that this provides cooling, prevents abrasives from degrading the seal, and reduces the build-up of solids.
Despite such efforts, it’s common for seals to fail, mainly due to ineffective cooling and poor lubrication.
Active throat bushing is a cuttingedge technology that addresses heat and contaminant issues in one straightforward solution. It removes particulate contamination from the stuffing box and away from the seal, allows air to escape the stuffing box upon flooding and creates adequate
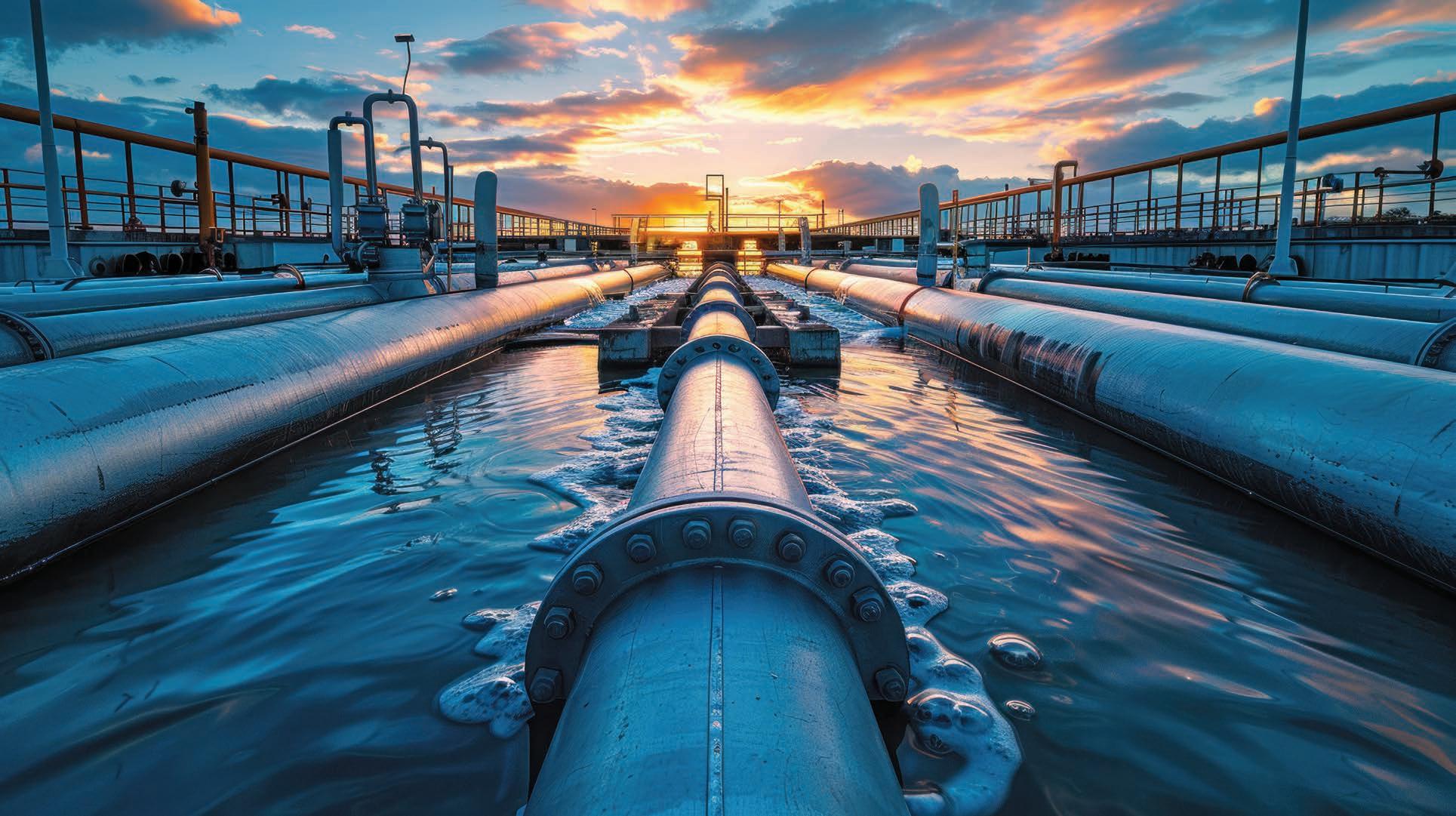
circulation around the seal to minimise
This technology has far-reaching simplifies operations, saves money by reducing the need for constant seal replacements, and promotes environmentally responsible practices.
The advantages of these dual technologies for water and wastewater processing are remarkable. Both are proven and in use globally, offering substantial savings on energy, running
Chesterton ensure that the seals they install are designed to provide maximum durability and longevity.
Image: Chesterton
chestertoncustomseal.com.au
This article is an excerpt from Chesterton’s e-book on how advanced sealing technologies can help maximise the life of your pumps and other rotating equipment in water and wastewater plants. To learn more, scan the QR code to download the free e-book in full.
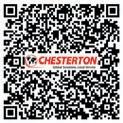

Driving the world
When quality and innovation combine
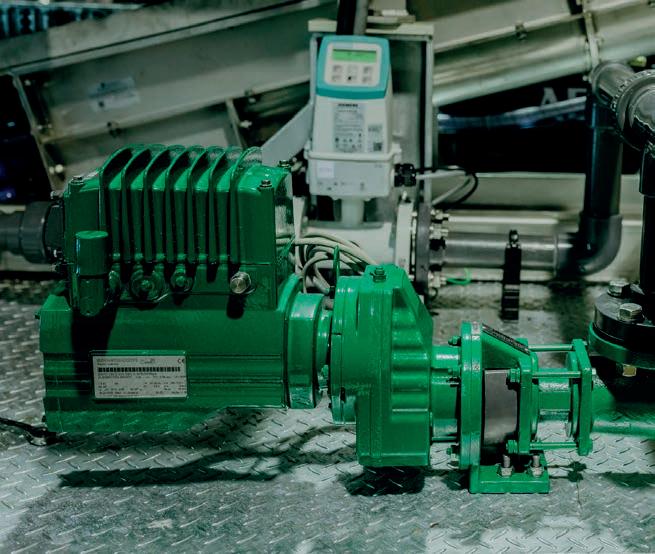
How can we help you achieve your KPIs?
At SEW-EURODRIVE, we understand the operational needs and demands that pump a pplications require. We provide efficient and sustainable solutions using the latest in drive system technology from our vast range of products.
Worrying about failure rates and operational costs is a thing of the past; it’s time to shift your focus to exceeding productivity and sustainability.
Want to learn more about how we can support you? Get in touch today! Scan QR code to view our website

Driving innovation in pump solutions
Regent Pumps delivers reliable, Australianmade centrifugal pumps and services, setting benchmarks for quality, longevity and industry leadership.
For over 70 years, Regent Pumps has been a cornerstone of Australia’s pump industry, supplying robust centrifugal pumps and tailored services to domestic and international markets. As a wholly Australian-owned manufacturer, Regent Pumps remains committed to blending tradition with innovation, consistently delivering reliable, high-quality products to meet the evolving needs of the industry.
One of Regent’s standout strengths lies in its dedication to dimensional compatibility. This ensures that replacement pumps seamlessly fit into existing systems without requiring costly rework. With an extensive database of over 600 obsolete pump models, Regent excels at providing modern alternatives that match the original footprint and flange-to-flange dimensions. This approach minimises downtime, eliminates expensive piping modifications, and reassures customers that today’s solutions will remain serviceable for decades. The durability of Regent’s products is a testament to this commitment, with pumps manufactured in the 1950s and 1960s still operating in the field today.
Regent Pumps’ product range is equally impressive. The company offers a comprehensive lineup designed to meet diverse industrial applications, from DIN and ISO centrifugal pumps to fire-fighting, self-priming, vortex, and submersible pumps. Each product is manufactured with the highest possible Australian content, reinforcing the company’s support for local industries while ensuring superior quality and reliability.
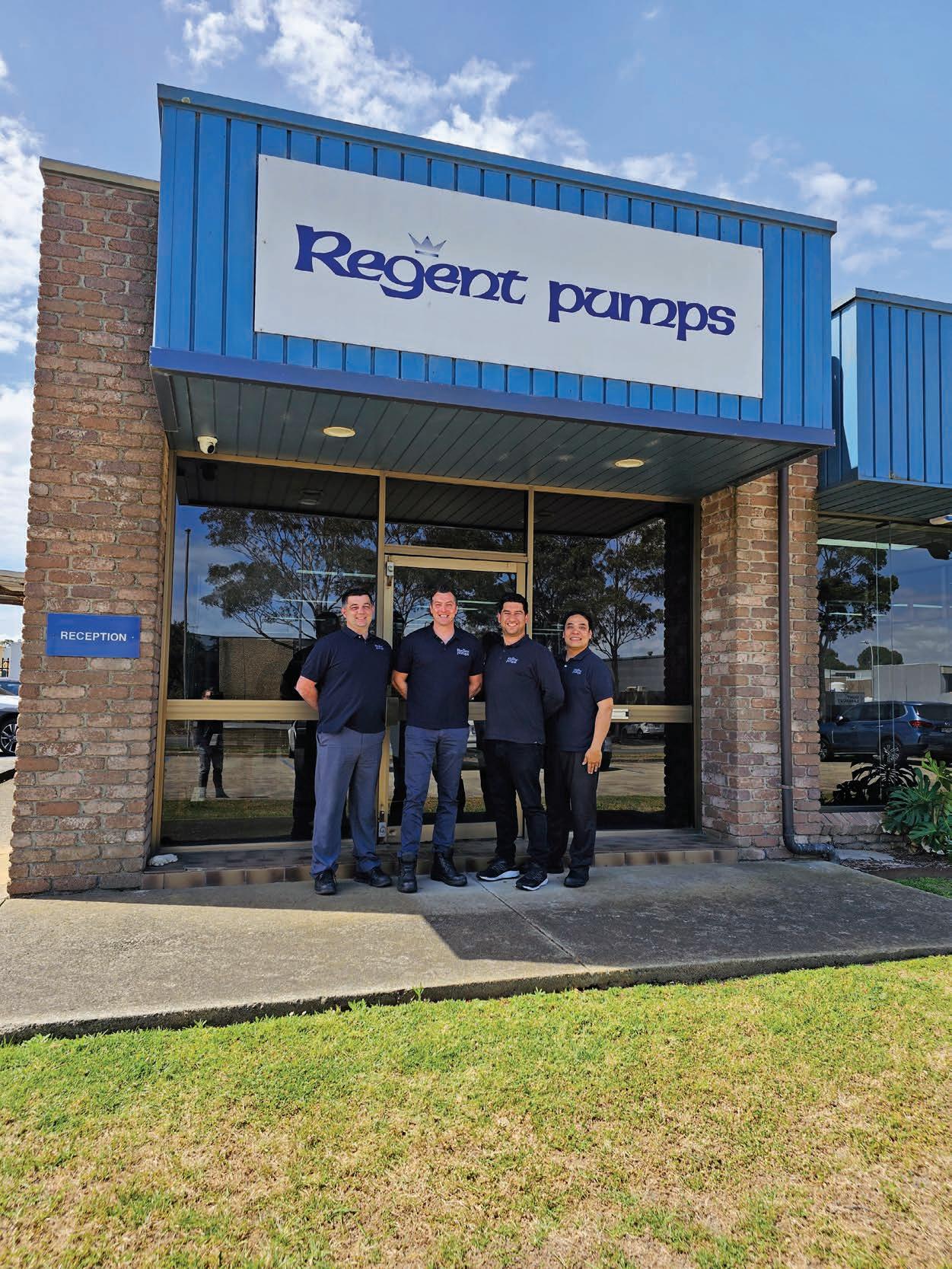
A leadership team that blends extensive experience with fresh perspectives is driving this success. Conor McDonagh, recently appointed Operations Manager, brings innovative ideas to propel Regent into an exciting new chapter of growth and modernisation. Conor is supported by Kylie Kinsella, Regent’s Managing Director and the newly elected President of the Pump Industry Association (PIA). With over 25 years of experience, Kylie is a respected figure in the industry, known for her expertise and leadership.
Kylie and Conor are joined by National Sales Manager Tim Yakup, Engineering Manager Elvin Khoo, and Procurement Manager Nick Hogan. Each has more than 15 years of experience in the pump industry, contributing to a management
team that combines deep industry knowledge with a clear vision for the future.
Regent Pumps’ commitment to quality manufacturing extends to the lifetime availability of spare parts, ensuring that customers can maintain their pumps without interruption for decades. This philosophy aligns with Regent’s broader mission: to deliver solutions that are not only reliable but also sustainable over the long term.
As the pump industry evolves, Regent Pumps remains steadfast in its pursuit of excellence. Whether replacing obsolete models or delivering cutting-edge solutions, Regent continues to lead with confidence, reliability, and a deep commitment to the Australian market.
Regent Pumps continues to showcase a spirit of excellence through all its products. Image: Regent Pumps
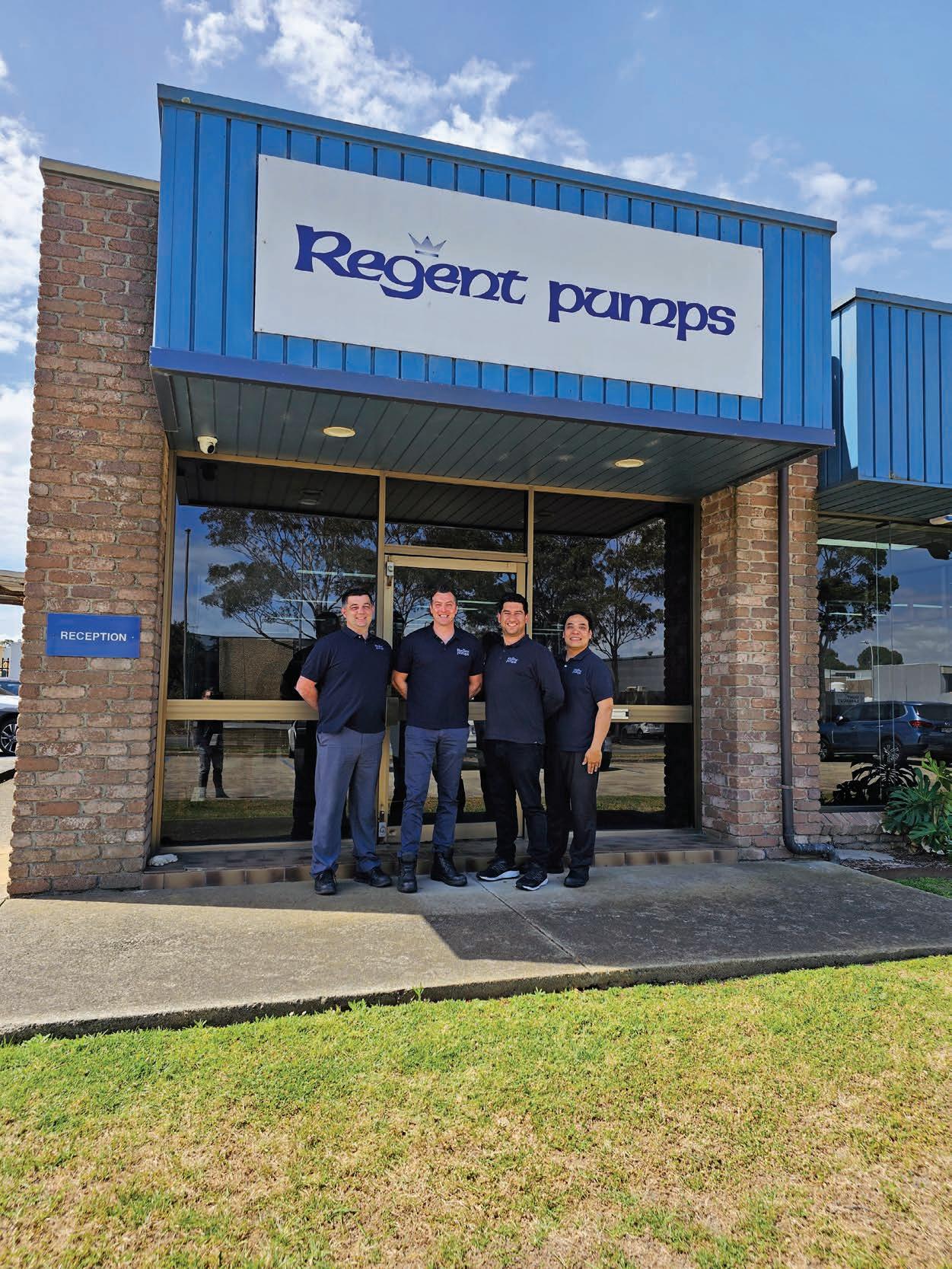

Steel construction.A single Carbon/ Ceramic Mechanical Seal is standard, other seals available on request or designed for application.
APPLICATIONS
Air Conditioning, Water Pressure Boosting, Heating and Cooling, Liquid transfer, Water Treatment and Supply, Effluent, Irrigation and Drainage, Petroleum Products, General Industry
PERFORMANCE
Flow rates up to 1500 litres per minute with pressures up to 150 Meters.
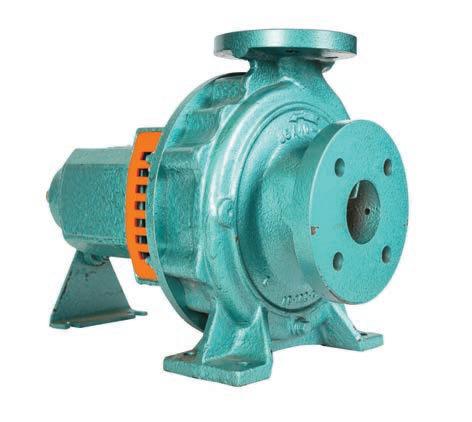
Minimising downtime and maximising efficiency
Keeping the flow going shouldn’t drain your time or wallet. Maintenance-in-place technology ensures smooth operations without the usual pump and circumstance.
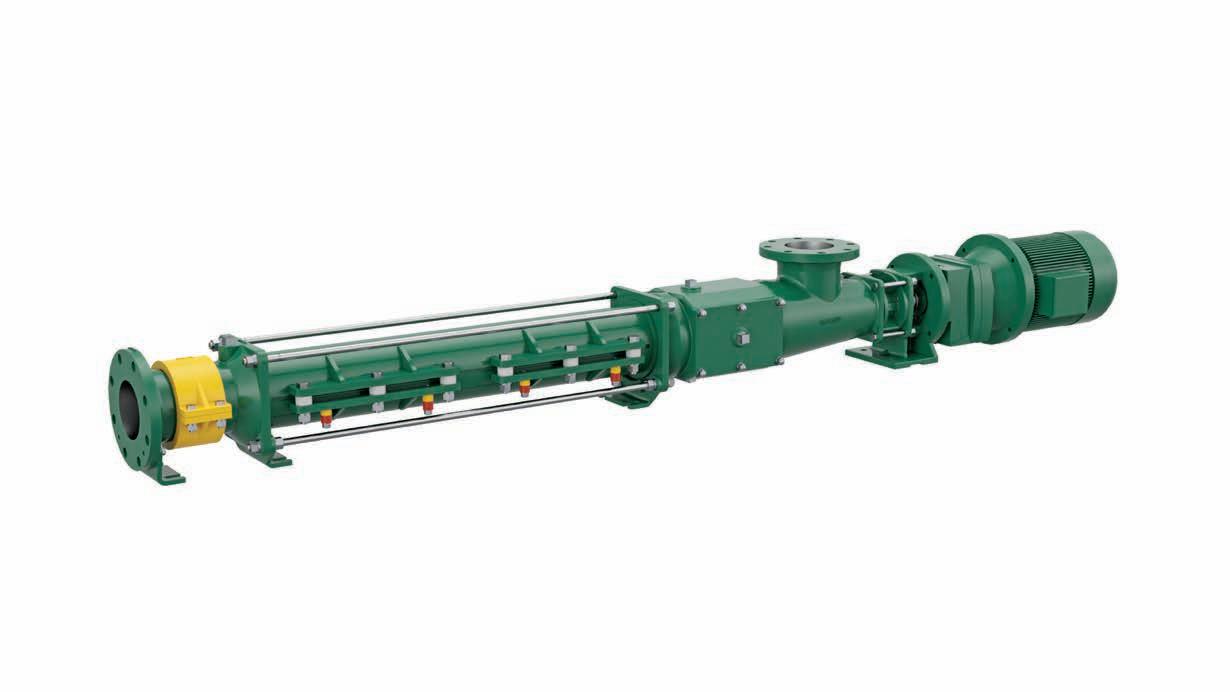
The Roto KWIK Pump addresses the problems of downtime and unscheduled maintenance. Images: ROTO PUMPS
Operational efficiency is key in high-demand industries such as wastewater treatment, oil and gas and mining. However, it is often jeopardised by common issues with pump maintenance. Progressive cavity pumps, known for handling abrasive, viscous, and high-solid-content fluids are essential in these sectors. However, they are prone to challenges such as frequent wear and tear, difficult maintenance procedures and costly downtimes.
Traditional pump maintenance is labour-intensive and time-consuming. It typically requires complete system shutdowns and complex disassembly to access internal parts. This process impacts productivity and leads to higher operational costs, as additional labour, replacement parts, and extensive downtime accumulate. For facilities relying on continuous operation, these issues can significantly affect profitability and process efficiency.
Roto KWIK pump
The Roto KWIK Pump is a groundbreaking solution crafted to tackle these challenges. Featuring maintenance-in-place (MIP) technology and a wear compensation stator, the Roto KWIK Pump provides a novel method for reducing maintenance downtime while enhancing operational efficiency.
In contrast to conventional pumps, the Roto KWIK allows for rapid and hassle-free on-site maintenance,
eliminating the necessity to detach from the pipeline system. This distinctive design enables operators to facilitate smoother and more efficient processes with little disruption.
Distinctive features
A specialised quick-release clamp enables the rotor and stator to be removed quickly, saving significant time during maintenance. The dual inspection windows allow easy access to the coupling rod and make it convenient to check for blockages or wear without dismantling the machine.
A split coupling rod allows maintenance staff to safely and swiftly access the pump’s internal rotating components. Similarly, the one-piece stator reduces the risk of media leakage, unlike the split stator design. Additionally, the enhanced universal cardan joint can manage high axial loads and guarantee smooth transmission, further increasing the pump’s reliability.
These features collectively enable rapid maintenance, reduce labour requirements, and eliminate the space needed for disassembly, making the Roto KWIK an ideal choice for industries that require frequent maintenance.
Importance of the wear compensation stator
The optional wear compensation stator is a stand out feature of the Roto KWIK Pump. Over time, pump components are subject to wear and tear, which can compromise efficiency by causing reduced flow and pressure.
The wear compensation stator tackles this issue proactively, using spacers of predefined lengths to regulate adjustments and maintain optimal interference between the rotor and stator, even as the parts experience wear.
Maximising efficiency
The Roto KWIK pump features maintenance-in-place technology and wear compensation stabilisers, showcasing Roto’s dedication to innovation and efficiency. By minimising downtime and maintenance costs while providing consistent performance, Roto KWIK Pumps enable industries to enhance their operational efficiency and reduce maintenance disruptions. In industries where uninterrupted operation is critical, Roto KWIK Pumps serve as a revolutionary solution, delivering unparalleled reliability and simplified maintenance.
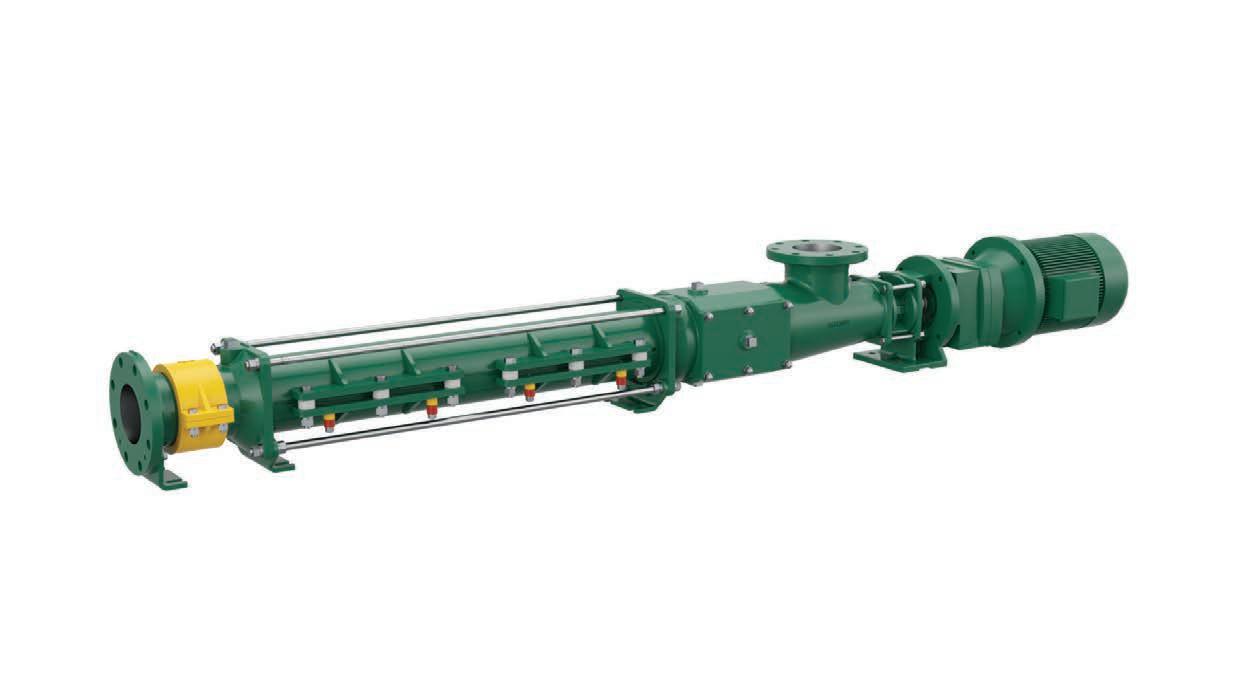
The Wear Compensation Stator tackles wear and tear to regulate adjustments and maintain optimal interference.

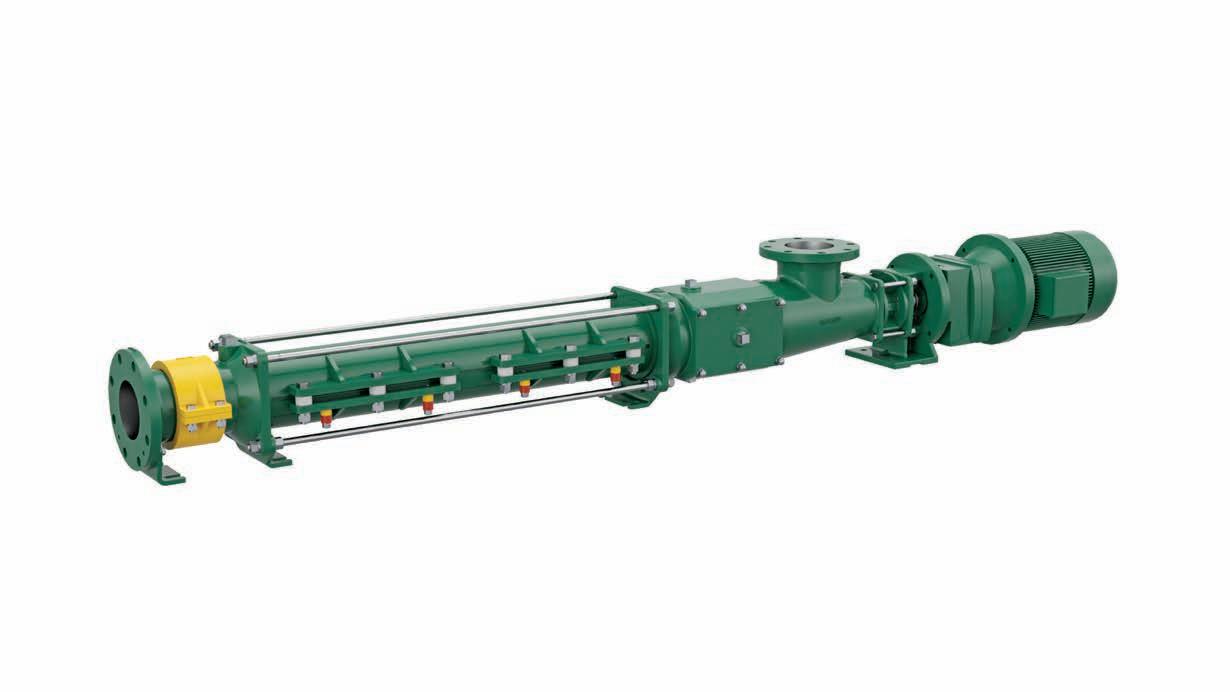
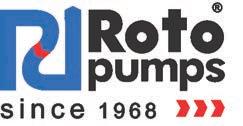

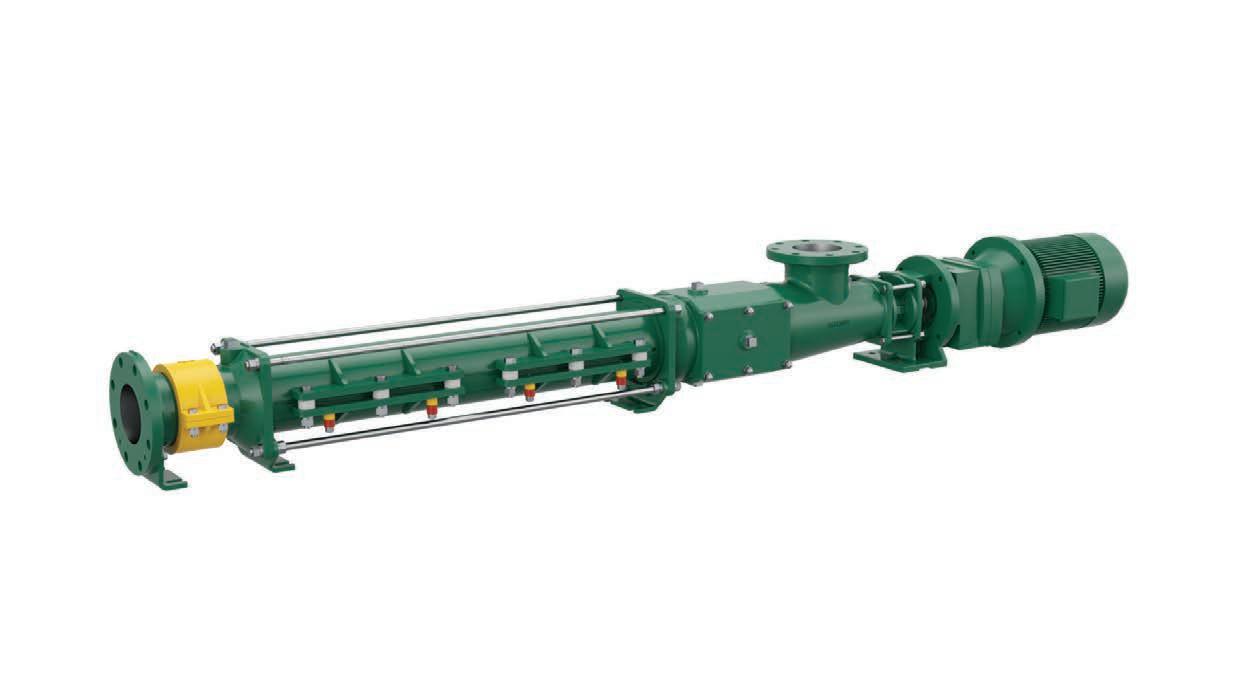
•Built
•Equipped

Sludge handling gets a makeover
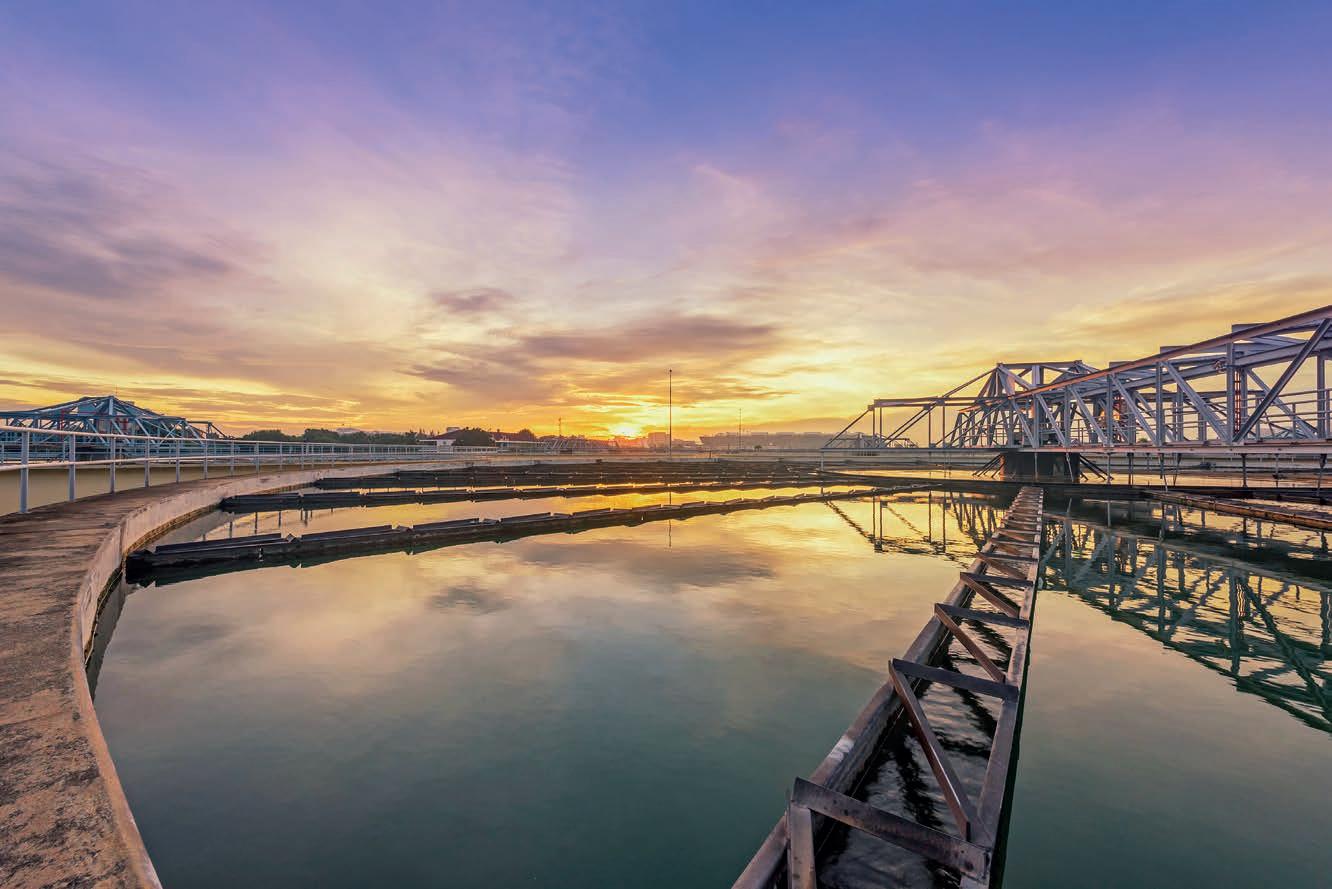
The Australian wastewater industry has long relied on traditional mechanical conveyors and belt systems to transport dewatered sludge. However, SEEPEX’s Smart Air Injection (SAI) is changing the game. Offering significant cost savings over conventional systems, SAI provides an innovative, energy-efficient solution for transporting thick, dewatered sludge and biosolids.
What is unique about SAI?
The SAI system is a precisely engineered sludge handling solution developed by SEEPEX, a global leader in progressive cavity pump technology. SAI combines progressive cavity pumping with dense-phase pneumatic conveying to transport highly dewatered sludge exceptionally efficiently.
Unlike traditional methods that use belt or screw conveyors, SAI moves dewatered sludge in short, dense plugs through a pipeline using compressed air pulses. This process minimises friction and energy losses, as the air interacts only with these dense plugs rather than the entire pipeline. Enhancing efficiency further, SAI injects a minimal yet effective amount of polymer, keeping usage low while ensuring efficient sludge transport. This costeffective approach quickly pays for itself.
With a low-pressure pump, accessible maintenance features and PN10 piping, the system is energy-efficient but also maintenance-friendly and gentle on its components. SAI can transport sludge up to 1,000 metres, making it versatile and suitable for a variety of installations, including wastewater treatment plants and industrial facilities.
Advantages over conventional conveyors
SAI stands out for its energy efficiency, offering significant savings over traditional conveyor systems. Belt and screw conveyors often require multiple mechanical components and motors due to continuous resistance along the entire length of the conveyor, resulting in higher energy requirements. In contrast, the SAI system minimises
friction losses within the pipeline, further reducing energy consumption.
In addition to energy savings, SAI reduces both operational and maintenance costs. The low pressure minimises wear and tear on the entire system, extending the lifespan of components like pumps, pipelines, and valves. This is in stark contrast to conveyor systems, which incur higher maintenance costs due to the constant mechanical movement and friction they endure.
SAI offers maintain in place features with smart conveying technology, which allows rotor and stator replacements in less than an hour with minimal space requirements. In contrast, conventional conveyor systems, with their numerous moving parts, such as belts, pulleys, and bearings, demand regular maintenance and frequent replacements. This complexity leads to more downtime during servicing and makes traditional systems less reliable over time.
SAI provides operational flexibility, especially in constrained environments or brownfield sites where space is limited. The system can be retrofitted into existing infrastructure without significant modifications. Traditional conveyor systems, on the other hand, often require substantial structural support and space, making them less suitable for retrofitting into tight or vertically constrained spaces. The compact, mobile nature of the SAI system allows it to fit seamlessly into existing layouts with little to no disruption to operations. This flexibility is particularly valuable in the wastewater and by-product management sectors, where continuous operation is critical.
The SAI system operates in a sealed pipeline, reducing the risk of odour release or emissions, which are common issues with traditional belt conveyors. This enclosed system improves safety and working conditions and improves environmental compliance. This is particularly true in urban or residential areas where odour control is crucial. Additionally, SAI eliminates the risk of
material spillage or leakage, further enhancing its environmental credentials. In contrast, with their open design, traditional conveyors often require extra odour extraction systems and are prone to biosolids falling off the belt during transport.
SAI’s streamlined design significantly reduces the physical footprint required for sludge conveyance. Traditional belt conveyor systems are bulky, requiring multiple stages of mechanical transportation, including vertical lifts and additional supporting structures. This complexity can lead to higher construction and operational costs, particularly in retrofitting scenarios. SAI, on the other hand, uses a single pipeline to transport dewatered sludge directly to the destination, whether it is a silo, truck, or incinerator. This complexity reduction saves space, shortens construction time, and lowers associated costs.
Proven global success
SEEPEX’s SAI system has been successfully deployed in over eighty facilities worldwide, proving its effectiveness in municipal and industrial contexts. At the Hetlingen wastewater treatment plant in Germany, the installation of SAI resulted in energy savings of 20-25 per cent and a significant reduction in maintenance costs. The plant handles approximately 46,000 tonnes of sludge annually, and the switch to SAI has proven to be a cost-effective, low-maintenance solution.
SEEPEX’s Smart Air Injection is a transformative innovation in dewatered sludge transport. With advantages such as energy efficiency, cost savings and environmental and operational improvements, it is a compelling choice for wastewater resource recovery facilities in Australia. As more installations showcase its benefits, SAI aims to become an industry standard, providing a sustainable, efficient, and cost-effective solution for sludge conveyance.
For more information, visit seepex.com
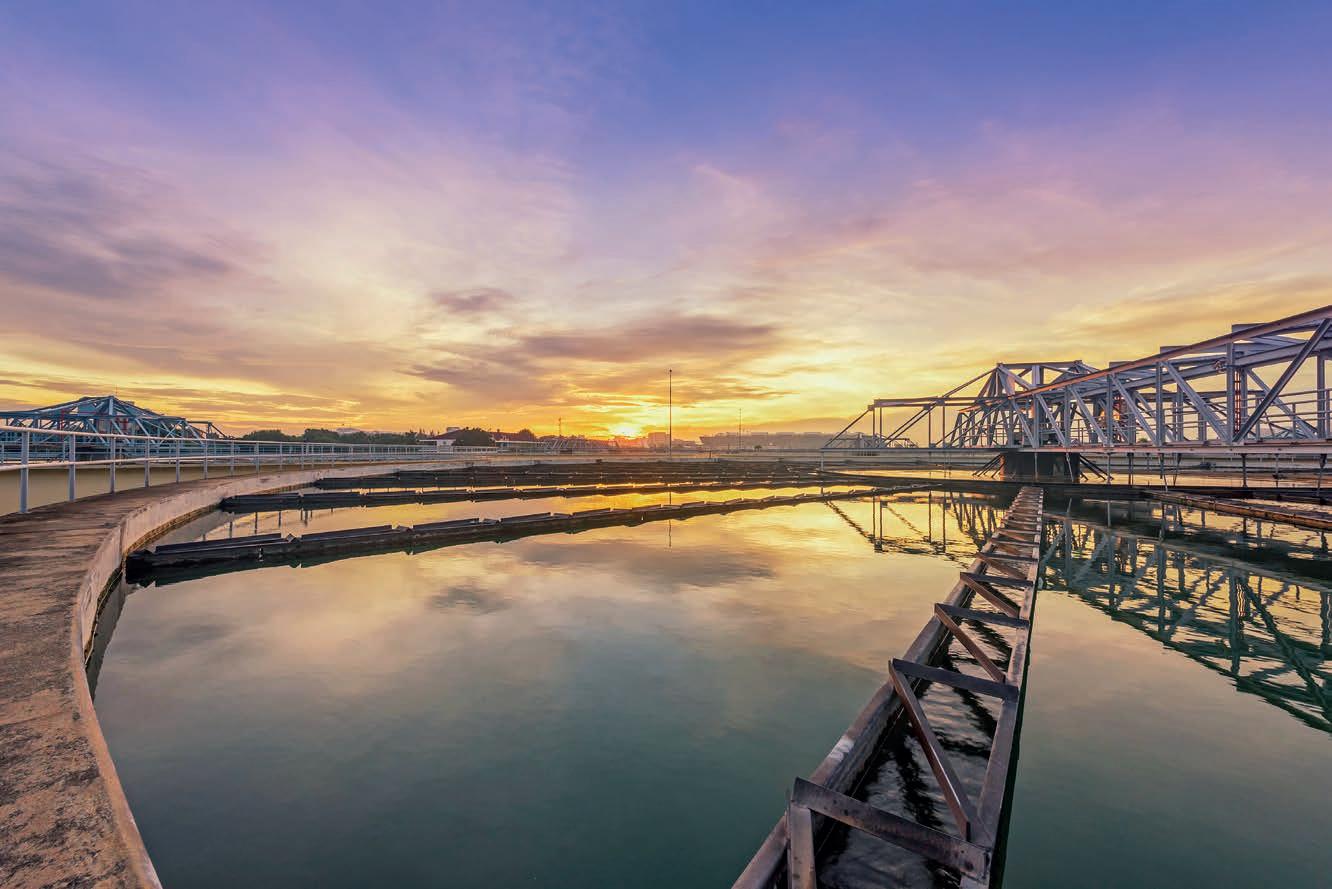
DEWATERED SLUDGE OVER LONG DISTANCES SMART AIR INJECTION
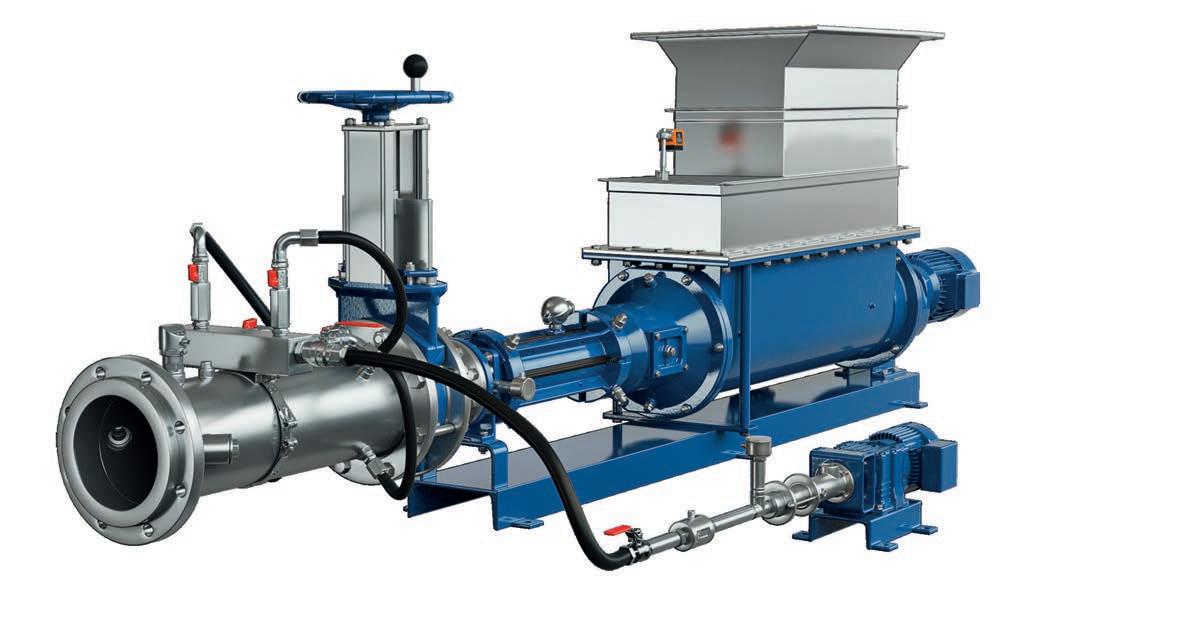
Your complete, customized system for pumping sludge long distances.
In the field of progressive cavity pumps, Smart Air Injection (SAI) is the efficient solution for pumping dewatered sludge with a dry solids content of 20-40% over long distances: effortlessly, with low pressure and up to 1,000 m.
YOUR BENEFITS WITH SAI
y Low investment costs and reduced operating costs
y Long lifetime due to low pressure level
y Closed system solution with a small footprint
y Simple integration into existing automation and control systems
y Energy efficient due to Smart Conveying Technology
SEEPEX Australia Pty. Ltd. info.au@seepex.com www.seepex.com

Submersible pumps made in Melbourne
Built for Australian conditions, these submersible pumps deliver performance across demanding and diverse applications.
Sterling Pumps has been designing and manufacturing submersible pumps in Australia, using its heritage brands for over 40 years. This rich history of manufacturing locally has allowed Sterling to develop technology that is directly suited to Australian conditions.
In 2020, Sterling acquired United Pumps Australia (UPA), which has Australian manufacturing experience dating back to the 1940s. UPA started as a service-oriented company focused on refurbishing and improving existing pump technologies. Over the years, the company has leveraged its expertise in designing and manufacturing customengineered pumping solutions, gaining a reputation for durability and efficiency.
The two companies’ combined manufacturing and engineering strengths allow them to expand their reach and capabilities. With an impressive engineering design and R&D team, Sterling has developed over 50 unique submersible pump hydraulics with bowl diameters between 100 and 915 millimetres (mm). These pumps are rigorously tested in their 2,500 kilowatt (kW) or 1000kW test rooms. From design to casting, machining to testing, Sterling is committed to Australianmade products.
Development
Sterling developed its own submersible pump and motor combination, which means that units are matched from
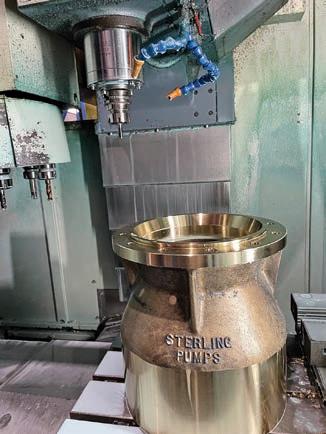
design to perform as one unit. For high-head applications, pumps are hydraulically balanced, significantly reducing the load on the motor thrust bearing. In recent years, Sterling has redeveloped its range of six to 12-inch submersible pumps to include investment cast impellers and diffusers. This improves the surface finish of these components, increasing pump efficiency.
The Sterling submersible pump range now covers flows of up to 3,600 cubic metres per hour (m³/hr) and heads of over 550 metres. Construction is either a traditional submersible motor mounted below the pump or a ballast design with the submersible motor mounted above the pump for shallow applications.
Wear rings and bearings are made of bronze, stainless steel or tungsten carbide. These hard-wearing materials maintain running clearances for longer, allowing the pump to maintain its efficiency for longer. Specific material selections are made for each application. Irrigation, mining, municipal, seawater lift, and DNVcertified pumps each have specific requirements that our application engineers meet.
Local support
Sterling engineers, manufacturing and testing are all based in Melbourne and all staff are Melbourne-based. This ensures that Sterling’s customers can receive full support without referring to an offshore engineering team.
The Sunshine and Pakenham teams welcome product inspections, pump and system testing. With support from its project engineering team, Sterling can supply fully engineered and documented projects to the highest standards, such as API 610.
As a global WPIL International Group member, Sterling Pumps remains committed to excellence and providing custom solutions for its clients. By sharing designs, patents, and information across the group, Sterling Pumps and other members of the WPIL International Group can continue to be trusted leaders in the design and manufacture of industry-specific products and pumps.

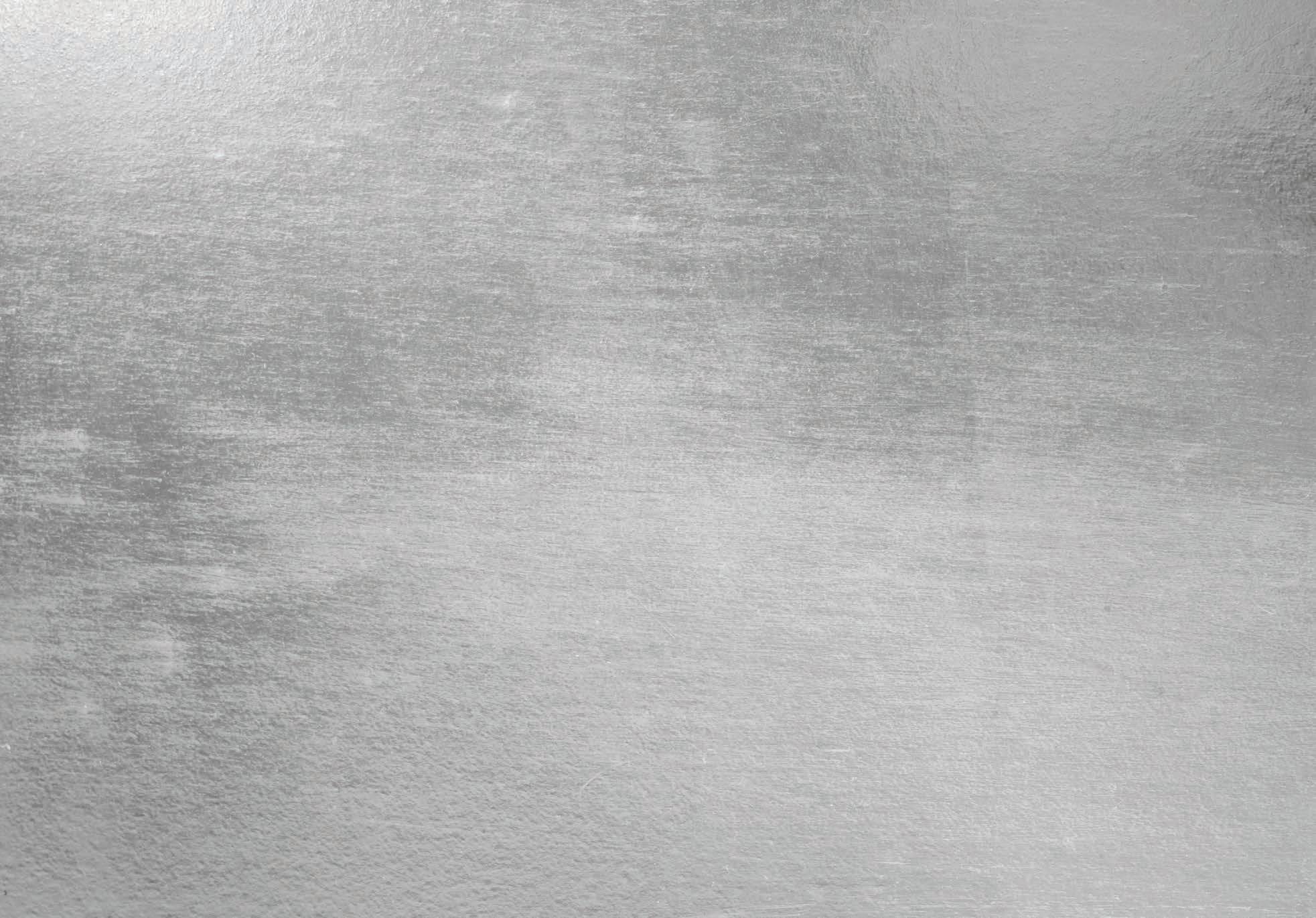
The test bay at the workshop in Sunshine, western Melbourne, is testing a 230kW duplex submersible pump. Images: Sterling Pumps
Machining of a 12-inch nickelaluminium-bronze pump.
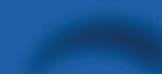



Proven Reliability
Oil & Gas, Industrial, Defence, Power, Municipal, Irrigation & Mining. Engineered and Manufactured in Melbourne



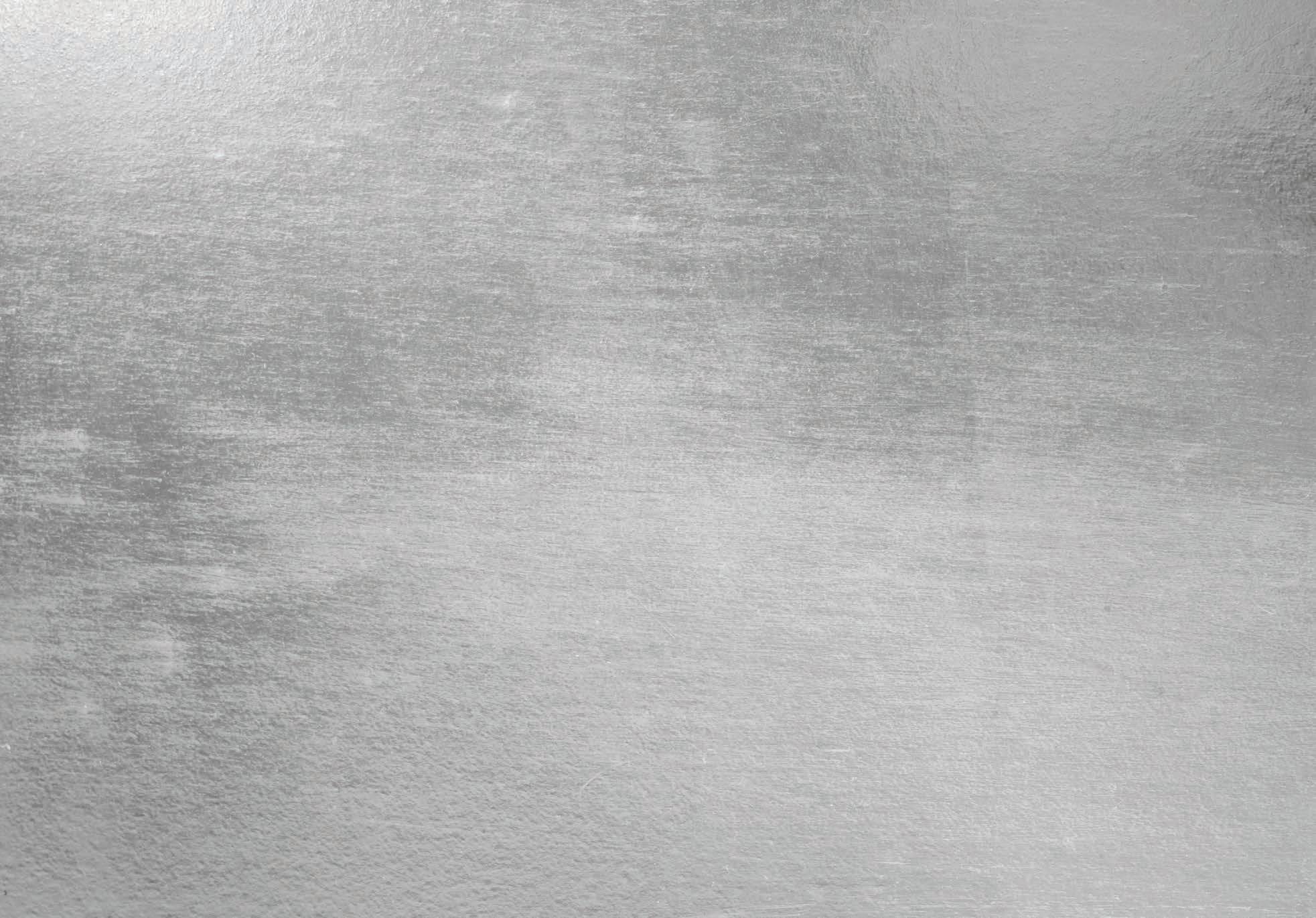
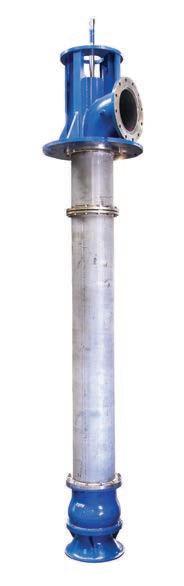
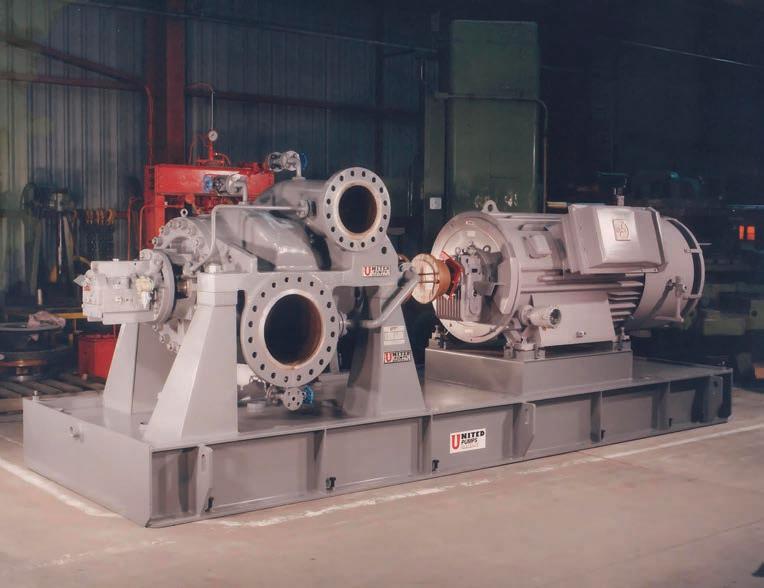
Submersible Pumps and Motors, Ballast pumps, Vertical Turbine Pumps API610 Pumps – Extensive Reference Lists Repairs, Design Upgrades, OEM spare parts and 2.5mw test facility
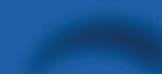


United Pumps support our heritage product Harland Pumps, Indeng, Johnston Pumps

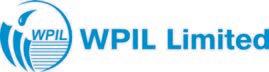
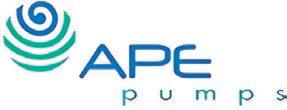

Professional engineers registration: an update
Pump industry legends Ron Astall and Alan Rowan have come together to explain the importance of registration and how to register in each jurisdiction of Australia.
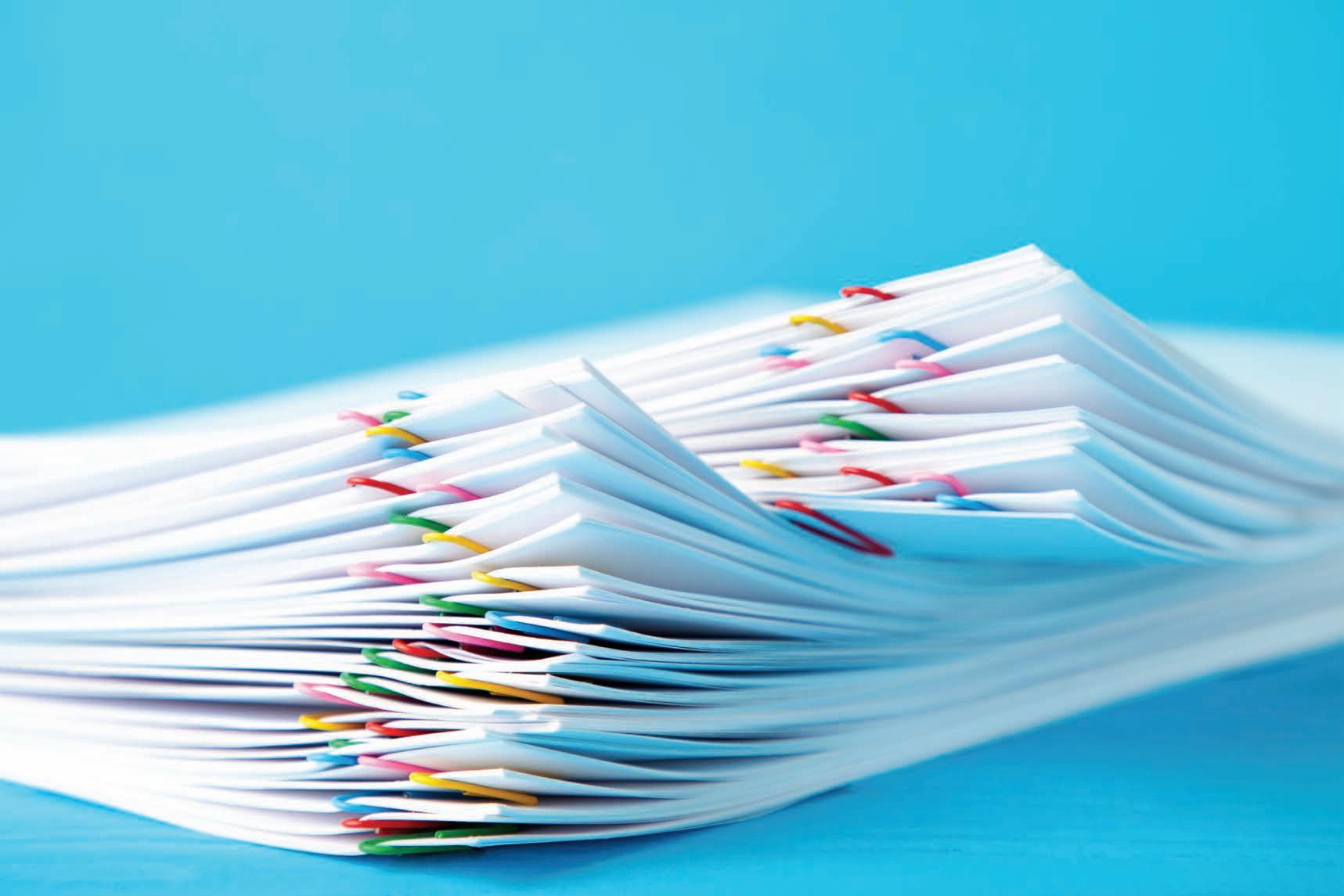
In the article in the Spring edition featuring Ron Astall and an open letter from the Victorian Business Licensing Authority, engineers can provide engineering services without registration, provided that a registered engineer supervises the work.
It should also be noted that this applies not only to engineers in Victoria providing the services but also to engineers working on projects in Victoria who are outside the state, whether in other states or overseas.
The current situation
As it currently stands, Queensland, along with Victoria, also requires engineers to be registered. Some other states also require some sort of registration, but to a lesser degree. The following details the registration process and where states other than Victoria stand with professional engineer registration.
The starting point for registration is to be assessed and accepted onto the National Engineers Register (NER), which is overseen by Engineers Australia. You do not need to be an EA
While the amount of paperwork has increased, it’s essential to understand what needs to be done in which jurisdiction. Image: Mouse family/stock.adobe.com
member to be evaluated; however, if you are a chartered engineer, you are automatically on the NER. In addition to compiling a record of experience and proof of qualifications, you must nominate two suitably qualified referees.
The link outlining the entire process is listed on the Engineers Australia website under Credentials – Registration.
Being on the NER confers no registration status in the individual states. It just confirms that you have met the eligibility requirements to be registered, with Engineers Australia providing a report and letter confirming that you have met the assessment requirements. The process first involved making an application online with Engineers Australia and uploading documents to demonstrate your experience and expertise. Members do not need to provide proof of educational qualifications.
The fee for an NER assessment is $365. For non-Engineers Australia members, it is $610.
Armed with the EA letter, you can then apply separately to the relevant state body to register and pay additional fees.
They require formal ID confirmation and a police check.
It is important to note that ongoing Continuing Professional Development (CPD) requirements exist to maintain your status.
Current state and territory registration requirements
Queensland has the most comprehensive registration requirements, followed by Victoria and, recently, the ACT. Most other jurisdictions are currently only focusing on building engineering.
Engineers Australia has provided the following information:
Victoria
Those wishing to investigate Victoria’s registration should visit the Victorian Consumer Affairs website. The initial registration fee for three years is currently $542.40.
In Victoria, all engineers providing “professional engineering services” in the following five prescribed areas of engineering need to be registered under the Act:
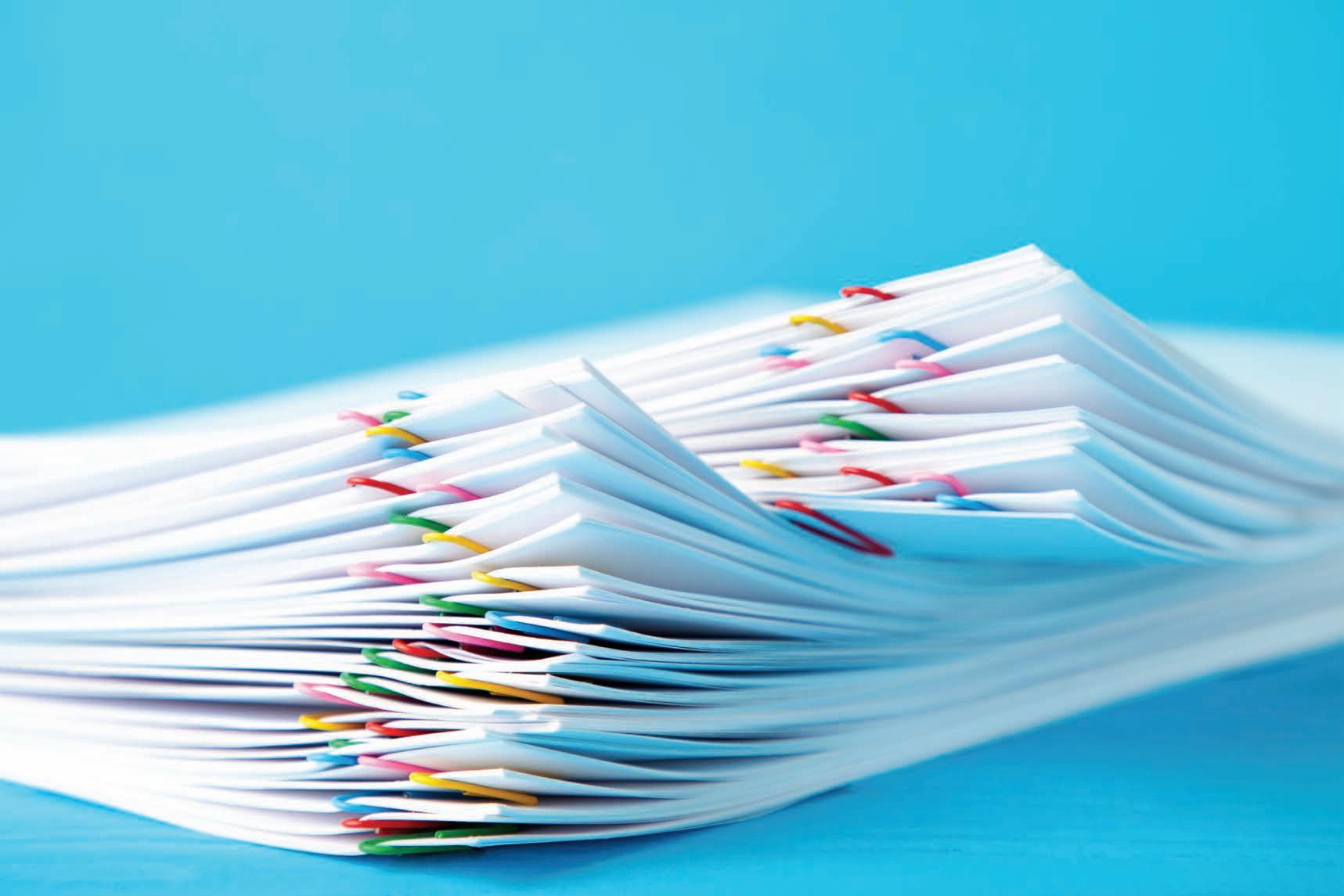
• Fire safety engineering
• Civil engineering
• Structural engineering
• Electrical engineering
• Mechanical engineering
• Building industry (separ registration)
Queensland
Queensland requires registration of a broader range of areas of practice. For full details, refer to the Board of Professional Engineers Queensland (BPEQ). The application fee is around $70, and the annual fee is $255.
Tasmania
In Tasmania, the Consumer, Building and Occupational Services (CBOS) registers engineers. Registration is only required for the building industry and certain engineering areas. For more information, visit the CBOS website.
Western Australia
New laws requiring building engineers to be registered by the Building Services Board to carry out building engineering work in Western Australia or contract with consumers to carry out building engineering work went into effect on 1 July 2024.
Registration will be implemented in a two-year transition period:
1. From 1 July 2024 to 30 June 2026 –structural, fire safety and fire systems engineers
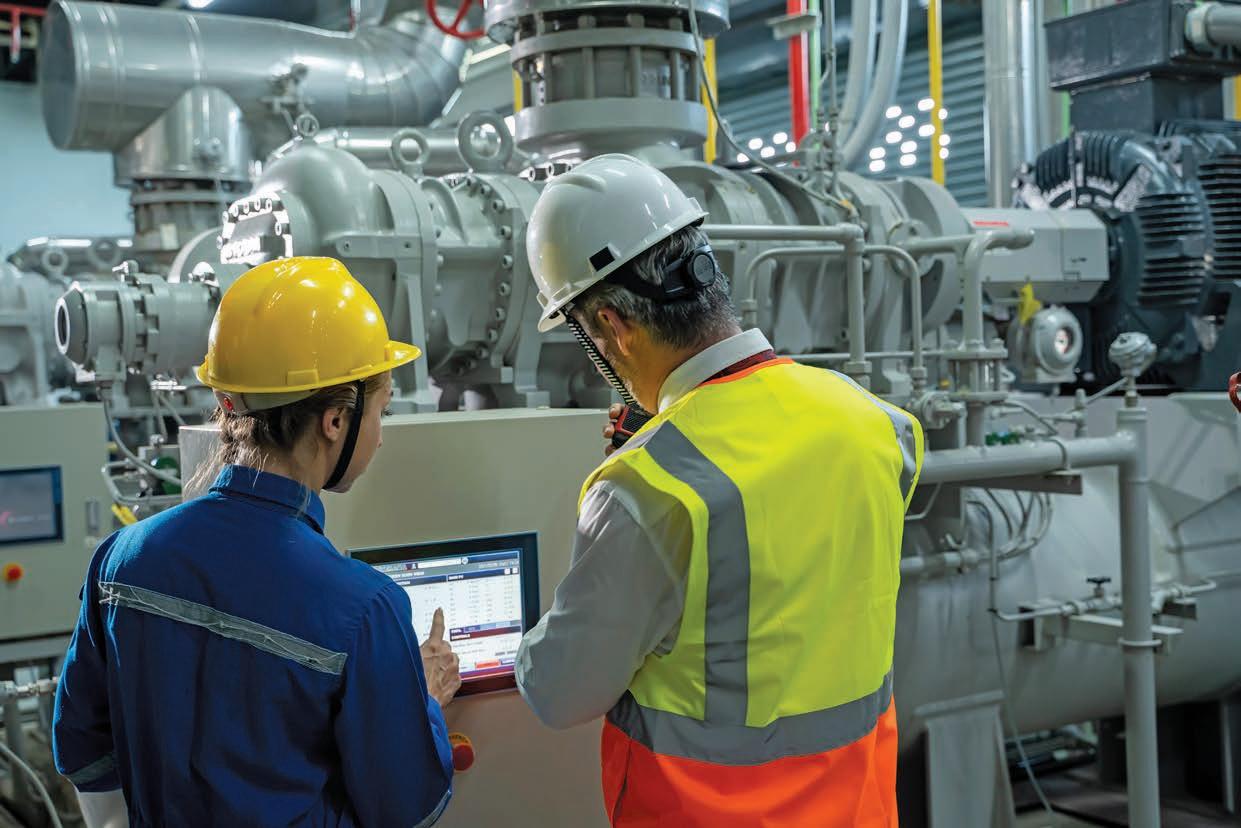
2. From 1 July 2025 to 30 June 2027 – civil and mechanical building engineers
ACT
Engineer registration commenced in the ACT on 6 March 2024, and all those practising civil, structural, mechanical, electrical, and fire safety engineering must register.
The scheme will be implemented in three phases:
• Phase 1 – 6 March 2024 for Civil and Structural Engineers
• Phase 2 – 24 July 2024 for Mechanical Engineers
• Phase 3 – 11 September 2024 for Electrical and Fire Safety Engineers
From 6 March 2025, all professional engineers providing professional engineering services in these areas of engineering must be registered.
NSW
In NSW, not all engineers need to be registered. However, if you’re a professional engineer working on class 2 buildings or buildings with a class 2 part, class 3, or class 9c, you may need to register. Fair Trading registers professional engineers and design
The regulations aim to ensure that everyone working on pumps and within the engineering industry has the proper qualifications. Image: visoot/stock.adobe.com
practitioners under the Design and Building Practitioners Act 2020. Visit NSW Fair Trading to find out if you need to register.
NT
In the Northern Territory, the Building Practitioners Board registers engineers. Registration is only required for the building industry and specific engineering areas. Visit the NT Building Practitioners Board for more information.
South Australia
At the time of writing, South Australia has no statewide regulations that require the registration of engineers.
Geographical region of practice
It does not matter where you reside or where your office is – the criteria for registration is where a project is located. If, for example, you live and work in Hawaii and you are undertaking professional engineering work for a project in Brisbane, you need to be registered in Queensland – or have a suitably qualified Queensland registered engineer check and sign off on your work.
Mutual recognition
Professional engineers must register in each jurisdiction that requires registration if they plan to practise there. However, under the Mutual Recognition Act 1992, if you’re registered as an engineer in one Australian jurisdiction, you can be registered as an engineer in another. Suppose you’re already registered in Queensland. In that case, you’d still need to apply for registration in Victoria. Still, mutual recognition means you may only need to complete the competency assessment for registration once to cover both jurisdictions and provide a report and a letter confirming that you have met the assessment requirements. The process through Engineers Australia first involved making an online application and uploading documents to demonstrate your experience and expertise.
Summary
We hope that the above will help pump engineers ensure that they can comply with the needs of various states when they provide professional engineering services.
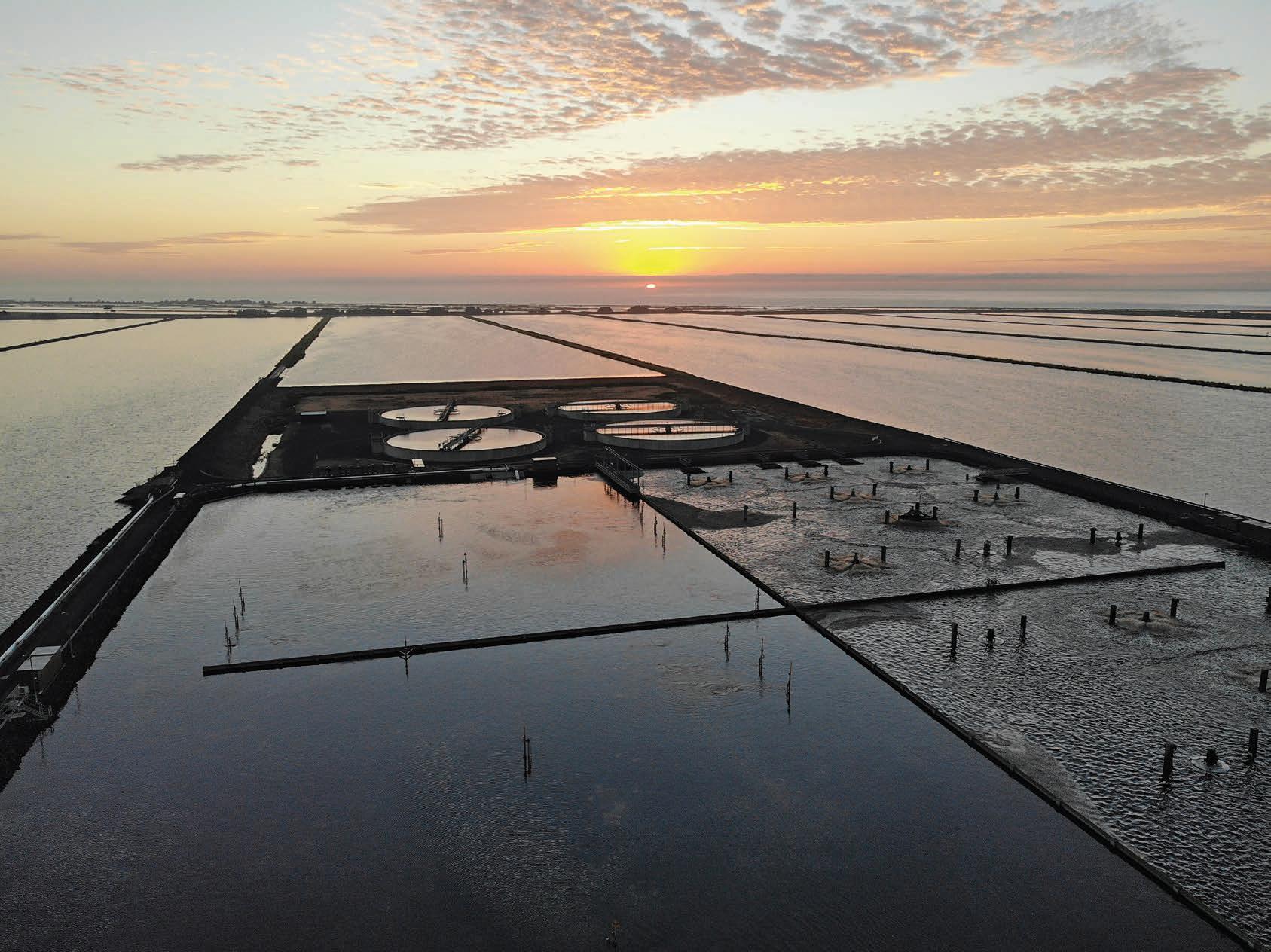
Pioneering sustainable wastewater treatment
An innovative wastewater treatment plant from Melbourne Water is supporting Victoria’s circular economy and ecosystem resilience.
T(WTP) in Werribee, Victoria is more than just a facility for treating wastewater. As one of Australia’s largest and most environmentally progressive treatment plants, the WTP is pioneering sustainable practices that place it at the forefront of the wastewater industry. With over a century of history, the site’s contribution to Melbourne’s infrastructure, environment and biodiversity has evolved significantly since its establishment in 1898. Today, the WTP is a leader in sustainable sewage management, resource recovery, and environmental conservation.
“Our Western Treatment Plant is unlike any other in Australia and is widely regarded as a world leader in environmentally-friendly sewage treatment,” said Kris Coventry, Head
Sewerage Transfer at Melbourne Water. Through resource recovery and energy production innovations, the WTP manages Melbourne’s wastewater and contributes significantly to the State’s circular economy.
A legacy of transformation
The origins of WTP date back to a public health crisis in the late 1800s, when Melbourne’s inadequate sewage infrastructure earned it the unflattering nickname “Smellbourne”. Rapid population growth, fuelled by the Gold Rush, had overwhelmed the city’s waste management capacity, leading to alarming rates of diseases like diphtheria and typhoid. The situation led to an 1888 Royal Commission and ultimately the establishment of the Werribee Sewage Farm – now known as the Western Treatment Plant – to combat the spread
The site initially included the township of Cocoroc, which housed sewage farm workers and their families until the 1970s. Parts of Cocoroc remain today, preserved alongside Melbourne Water’s operations and educational facilities, adding to the plant’s rich historical significance. In 2021, the WTP was added to the Victorian Heritage Register, acknowledging its pivotal role in Melbourne’s development.
Environmental stewardship and biodiversity Conservation
The WTP site is vast, stretching nearly 20 kilometres from end to end. Its size is only part of what makes it unique; the plant is also home to one of Australia’s most significant wetlands, recognised under the RAMSAR Convention for its ecological importance. The man-made sewage treatment lagoons at WTP
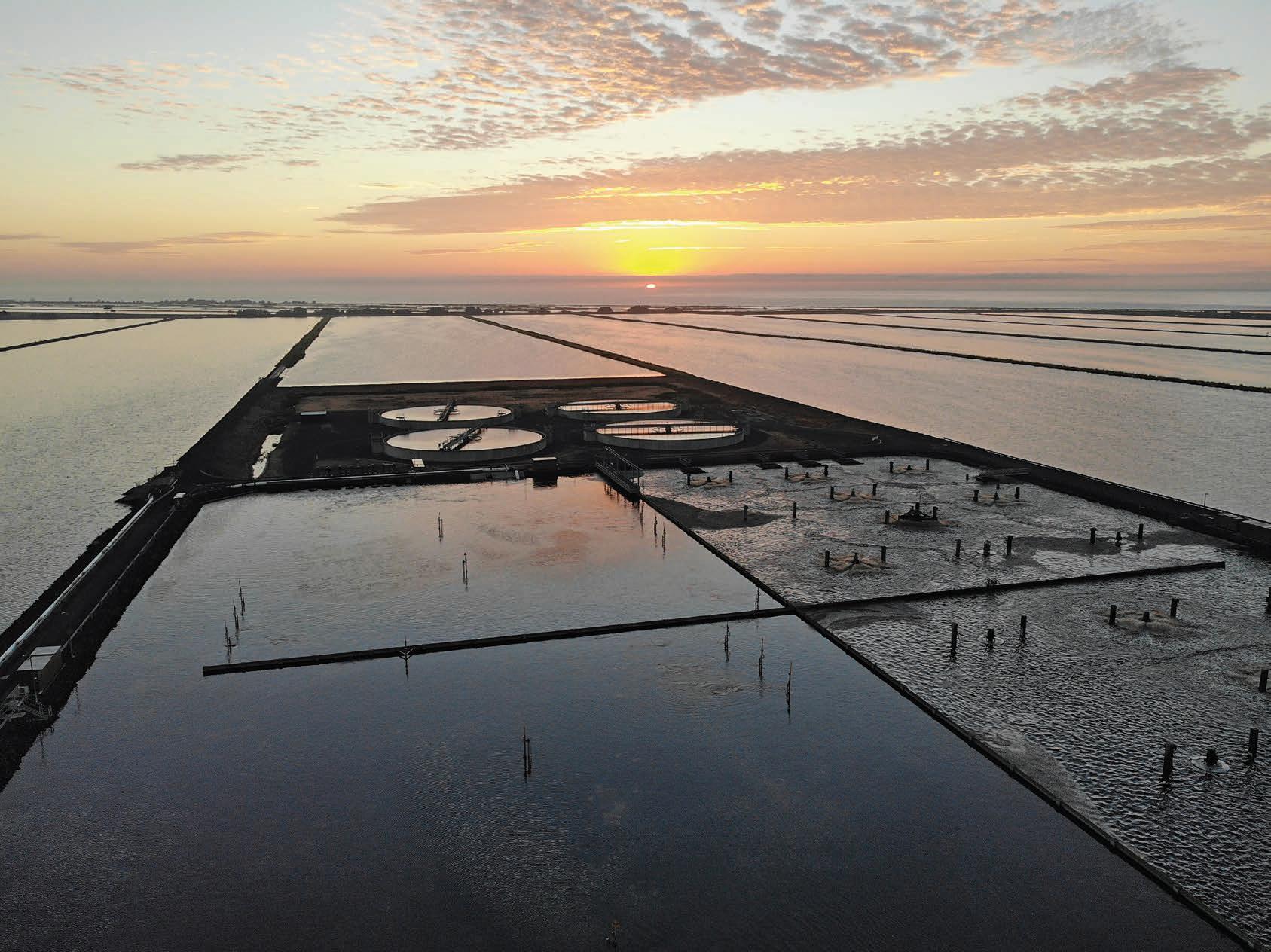
The Western Treatment Plant is also a RAMSAR-protected wetland.
Images: Melbourne Water
attract diverse wildlife, providing water and nutrients to support over 280 bird species, including migratory shorebirds that journey from Siberia every year. Threatened species, such as the Growling Grass Frog and the Orange-bellied Parrot, also inhabit this critical habitat.
“It’s very special that we have such a large, intact habitat so close to a city,” Mr Coventry said. “Without the WTP, these species potentially wouldn’t have sufficient habitat to survive in this part of the world.” Melbourne Water actively manages the ponds and wetlands to maintain this biodiversity, ensuring that migratory and local species thrive. This balance of industrial use and ecological stewardship is central to the WTP’s mission.
Demand and climate challenges
With Melbourne’s population projected
to nearly double by 2050, WTP’s role in treating the city’s sewage – about 200 billion litres annually – will become increasingly vital. “Melbourne is facing multiple future challenges, including projected population growth and a hotter, drier climate,” said Mr Coventry. “We’re investing in ways to reduce the environmental footprint of WTP while ensuring we can meet future population demands.”
In line with these goals, Melbourne Water has embarked on a comprehensive 50-year Sewerage Strategy. This strategic plan addresses the dual challenges of climate change and population growth by maximising circular economy opportunities at the WTP while preserving the environment. One of the most ambitious projects in this strategy is the Resource Recovery and Re-Use Complex, a new $711 million facility designed to transform how the WTP treats and recycles sewage.
Resource Recovery and Re-Use Initiated in early 2024, the Resource Recovery and Re-Use Complex will enhance resilience in Melbourne’s wastewater management system and advance resource recovery. “Our contribution to Victoria’s circular economy is significant,” Mr Coventry said. “We’re investing in a new state-ofthe-art facility at WTP that will further reduce greenhouse emissions and cater to Melbourne’s growing sewage needs.”
The complex, set for completion in 2029, consists of four major projects to modernise the treatment processes at WTP. These include new preliminary and primary treatment processes to divert raw sewage from overloaded anaerobic lagoons, reducing the frequency of odour-intensive maintenance works. Additionally, improved solids handling and anaerobic digestion processes will divert sludge from the aerated ponds, capturing carbon and enhancing safety.
A new receiving facility is being introduced to manage tankered waste and ensure Melbourne Water meets its obligations under the Environmental Protection Act. A fourth feature – a liquid food waste facility – will accept waste from industrial customers, producing renewable energy through co-digestion. Together, these improvements will enable WTP to operate more sustainably, enhance its role in Victoria’s circular economy, and support Melbourne Water’s path to net-zero emissions.
Sustainable agriculture and water management
Agriculture remains integral to WTP’s operations, with grazing lands dating back to the early 20th century. Pastures irrigated with treated wastewater are used for sheep and cattle grazing, providing a “green break” between urban development and ecologically significant sites. This approach enhances biodiversity and synergises treatment processes, as water resources are effectively recycled and managed.
Renewable Energy and Circular Economy Contributions
One of the WTP’s notable achievements in recent years is its on-site biogas facility, which captures methane from treatment processes to generate renewable energy. This biogas production meets all of the WTP’s energy needs, with excess power fed back into the grid. Such innovations in renewable energy production are pivotal to reducing the WTP’s environmental footprint and supporting Victoria’s circular economy.
A model of environmental and industrial balance
The WTP is more than just a wastewater treatment facility; it’s an ecosystem and an energy source, serving Melbourne’s needs while conserving precious resources and habitats. As it continues to innovate and adapt, the WTP exemplifies a vision of industrial facilities working harmoniously with the environment.
Mr Coventry reflected on what has been achieved by looking into the future. He said, “The Western Treatment Plant needs to address multiple challenges now and in the future. Our primary role of receiving and safely treating the sewage from half the population of Melbourne will continue to be a key focus for the plant. But alongside this are responsibilities to preserve and enhance the environment, generate renewable resources and contribute to a sustainable future.”
Through its historical legacy, ecological significance and forward-thinking strategies, the WTP is setting a new standard for the wastewater industry. As Melbourne Water leads with projects like the Resource Recovery and Re-Use Complex, the Western Treatment Plant will remain a model of environmental and industrial innovation, guiding the future of sustainable wastewater management in Australia and beyond.
These devices are simple to use in any wastewater situation, ensuring the provision of high-quality treated wastewater.
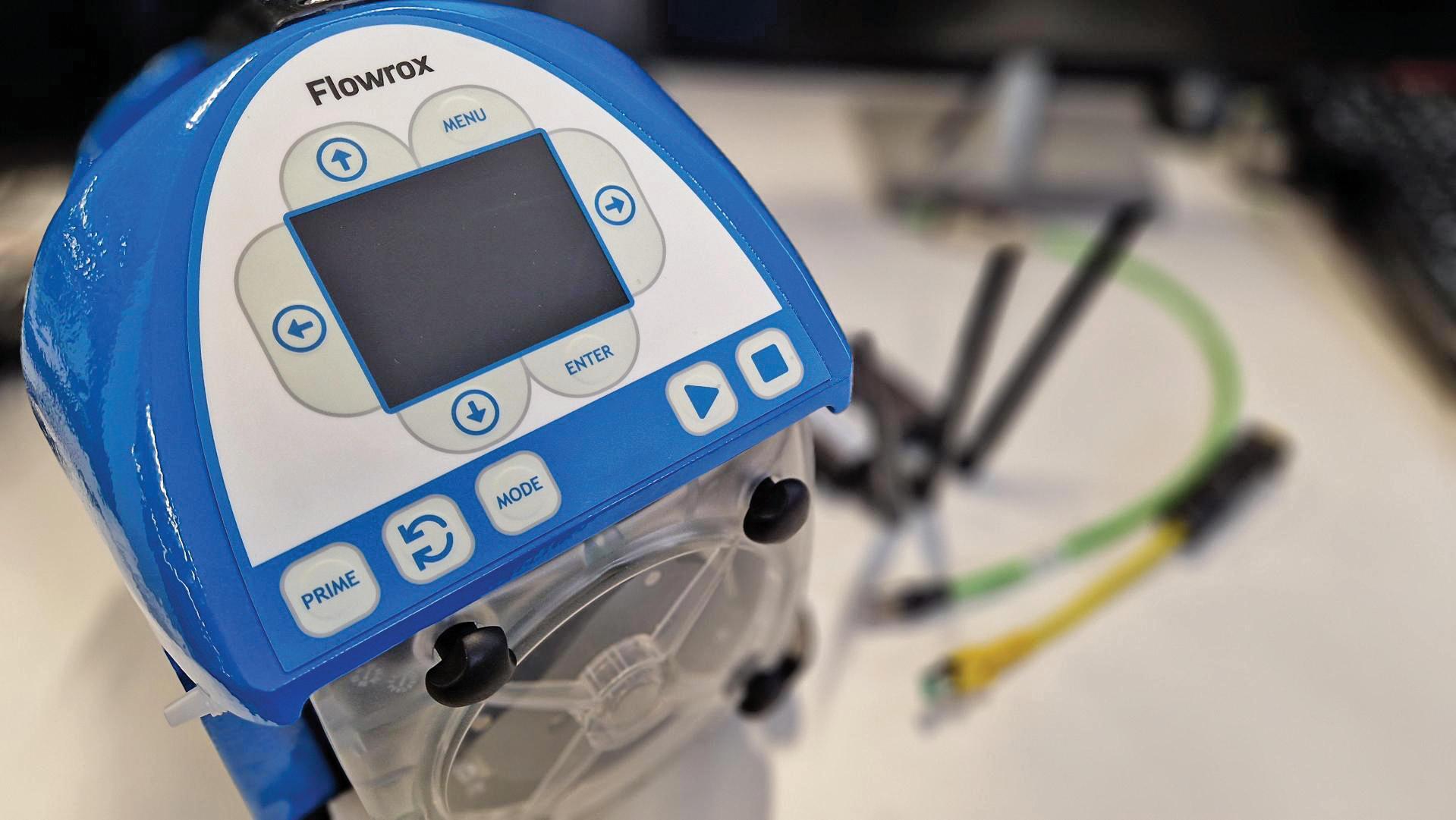
Dosing precision through advanced metering
Precision pumps provide efficient wastewater treatment through advanced digital integration and safety features.
In today’s wastewater treatment facilities, precise chemical dosing is paramount for achieving efficiency and compliance. Advanced metering pumps are essential tools for controlling chemical dosing with accuracy and reliability, and the latest innovations are pushing the boundaries of what is possible in the industry.
Valmet’s Flowrox FXM metering pumps are at the forefront of precision chemical dosing in the wastewater industry. Their robust design and advanced features make them an essential component of any modern wastewater treatment facility.
Cutting-edge connectivity
One of the most significant advancements in modern metering pumps is the integration of fieldbus connectivity. The industry is shifting from analogue signals like 4-20 milliamps (mA) to advanced digital protocols. These digital communication systems – including Ethernet/IP, Modbus, PROFINET, and PROFIBUS – provide real-time data transfer, reduce the need for extensive wiring, and simplify complex installations.
With a single network connecting multiple devices, operators can easily monitor and control pumps remotely, achieving a seamless, integrated system. This connectivity upgrade allows wastewater treatment plants to utilise data-driven insights to optimise chemical dosing, saving time and resources.
By streamlining communication between devices, the plants can adopt more sophisticated control algorithms, improving chemical dosing precision and overall treatment efficiency.
Enhanced dosing flexibility for varied applications
Modern metering pumps offer multiple control options beyond fieldbus. This flexibility enables integration into various systems across diverse wastewater treatment applications. Such versatility is critical in a sector where different processes and site requirements demand adaptable solutions.
Advanced metering pumps like the FXM metering pumps are designed to handle both dispensing and
proportional dosing. In dispensing mode, the pump can release a fixed volume of chemicals on demand, which is ideal for batch dosing requirements. In proportional dosing, the pump automatically adjusts the chemical flow rate to suit the treated fluid’s flow rate. This dynamic response is invaluable in facilities where flow rates fluctuate, ensuring a consistent and precise dosing process that matches real-time operational demands.
Exceptional turndown ratio
Accurate dosing requires a pump with a wide range of control. The latest models from the FXM pumps achieve a 5,000:1 turndown ratio, enabling them to dose accurately across a wide range of flow rates. This precision is crucial in wastewater treatment, where over- or under-dosing can lead to process inefficiencies and regulatory compliance issues. A high turndown ratio ensures that the pump can be set to the exact requirements of each application, whether it is handling high or low volumes.
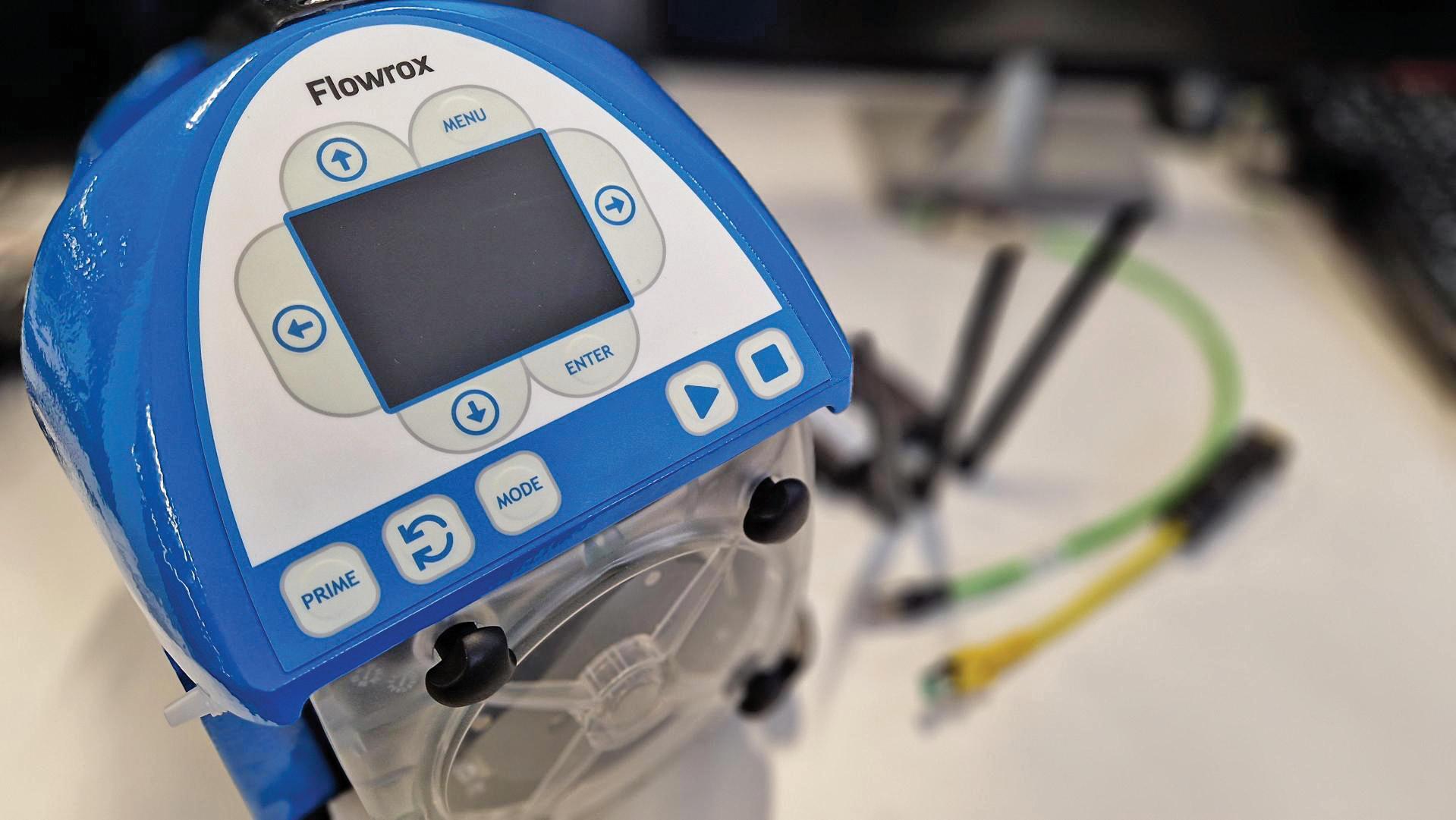
Durability and compatibility
The FXM pumps feature a rugged design suited to the often harsh conditions of wastewater treatment facilities. Their IP66/NEMA 4X enclosure protects them from dust and water ingress, making them reliable in outdoor or highmoisture environments.
Various tube materials are available to handle diverse chemicals, ensuring chemical compatibility across applications. Additionally, the pumps feature dry run capability, allowing them to operate without damage even if the fluid source is temporarily interrupted.
Driving efficiency and reliability
Precise chemical dosing directly impacts the effectiveness of wastewater treatment. The FXM advanced metering pumps are optimised to meet this industry’s rigorous demands. From enhanced connectivity options and adaptable dosing modes to robust safety features and user-friendly controls, these pumps are designed to improve the efficiency and reliability of wastewater treatment processes.
Wastewater treatment facilities adopting advanced metering pumps are seeing tangible improvements in their operations, translating to cost savings and higher-quality effluent output. These technological advancements mark a significant step forward for the pumping industry, setting new standards for precision, safety, and operational efficiency.

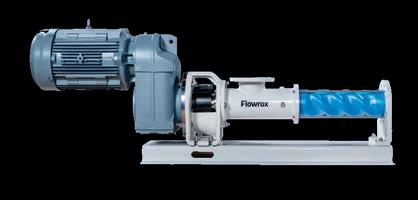
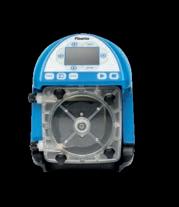

The Flowrox FXM Pumps from Valmet are designed for precise chemical dosing. Images: Valmet
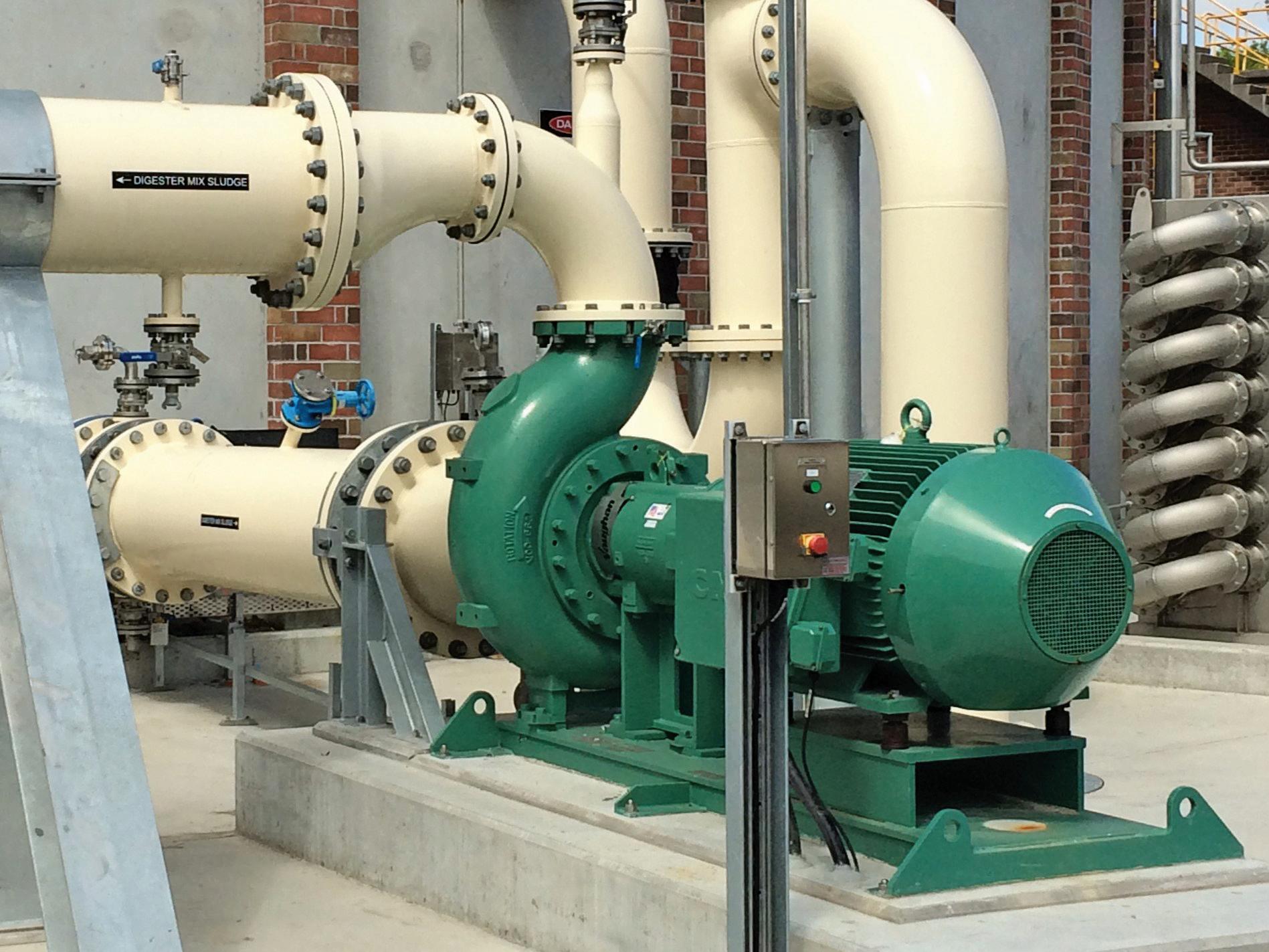
The range of chopper pumps from Pump Systems are designed to handle a range of different situations for any wastewater facility. Images: Pump Systems
Chopping, cutting and grinding
Understanding pump types can reduce downtime and improve efficiency in solids-laden applications. Eric Lawson from Vaughan Co. has some insights.
Pumps are arguably the most important and prevalent piece of equipment for any facility. The ability to transport fluids reliably and efficiently is critical to the modern world. However, we hardly ever have the luxury of transporting a pure liquid like clean water.
Pumping reliability is not solely based on mechanical performance but also on solids-handling performance. Clogging and binding represent system downtime, while plugging upstream piping and fittings can be even more troublesome. Given this reality, the need for solids-handling pumps becomes clear. So, why not design pumps to reliably pass solids?
Unsurprisingly, Vaughan Company does. Non-clog centrifugal and positive displacement pumps are extensively used in solids handling applications, generally with a specified maximum solids size, or ‘ball pass’, that can reliably pass through the pump. This may work for applications with larger pumps and smaller solids sizes, but this is rarely the case. Wastewater pumping commonly experiences unpredictable and/or large solids sizes, which may require active solids handling technology that does not just passively allow solids to pass through the pump but actively reduces and conditions them.
Pump types
There are three main types of active solids handling pumps: chopper pumps, cutter pumps, and grinder pumps. Unfortunately, the industry can be confused by the lack of a universal definition and manufacturers’ hybridisation. So, Vaughan would like to propose definitions that are simple to apply and provide a meaningful distinction. In a chopper pump, the hydraulic surfaces are integral to the solids handling, directly ‘chopping’ the solids using the impeller.
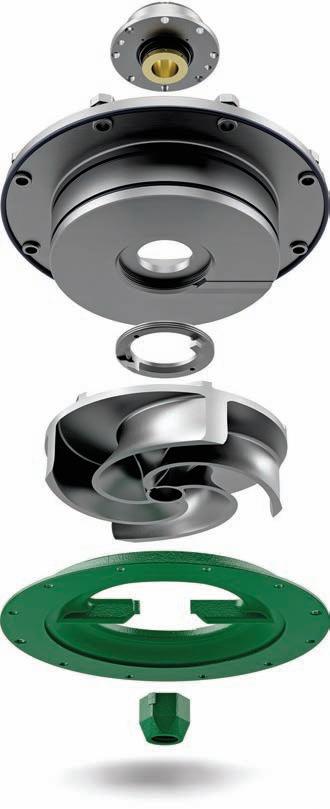
Each part of a chopper pump plays an important role in its overall operations.
Cutter pumps use stationary and rotating elements to handle solids. The core concept of a chopper pump is that it is impossible to separate the chopping from the pumping, whereas, with a cutter pump, the cutting feature is distinct. This allows cutter pumps to utilise various non-clog impeller types, but the added features increase power requirements.
A more specialised version of a cutter pump is a grinder pump, which integrates a grinding mechanism into the pump’s suction. This can significantly increase power consumption and reduce pump capacity but provides the most controlled discharge solids size. Grinder pumps are well suited for septic systems, where smaller piping and dependability are more important than efficiency. However, grinder pumps will rarely be seen in highercapacity pumping applications due to their poor efficiency.
Pump terms
In practice, manufacturers use the terms chopper pump and cutter pump interchangeably, while the term grinder pump is used rather consistently. However, most contemporary chopper and cutter pumps are hybridized variants of the two styles. For example, Vaughan Chopper pumps use the impeller to cut against a stationary cutter bar. This provides the chopping action, but several cutters are also integrated into the pump.
There is an external cutter that cuts fibres and prevents items from bridging the suction, an upper cutter behind the impeller that prevents fibres from wrapping around the mechanical seal and shaft, and an insert cutter in the backplate that keeps the pump-out vanes on the back of the impeller from binding. So, while it is marketed as a chopper pump, it does have cutters, which, without the chopping impeller, would make it a cutter pump.
Alternatively, a manufacturer’s pump might not feature a chopping impeller, or it might be a secondary feature to a primary cutter system and marketed as a cutter pump.
Regardless of labelling, the decision to use which type of pump should be based on the application’s needs.
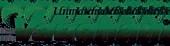
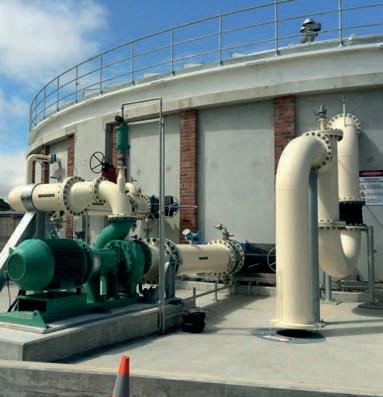

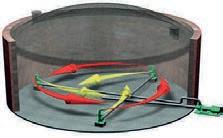
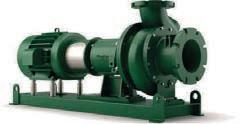

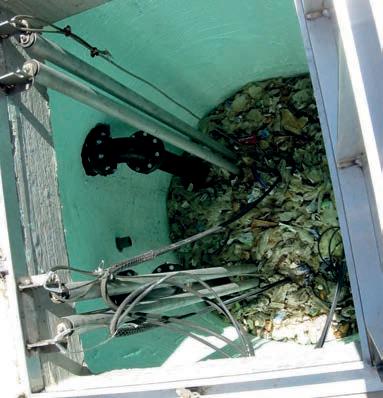
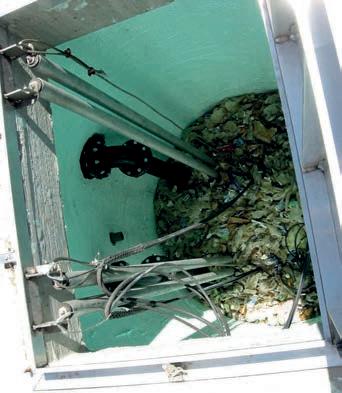
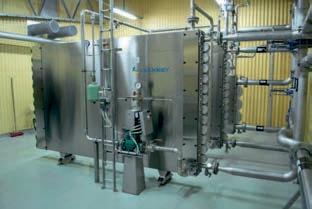

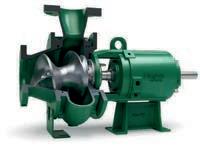
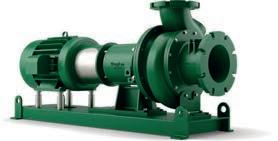
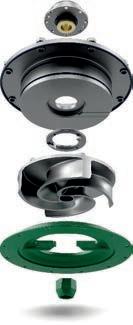
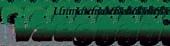




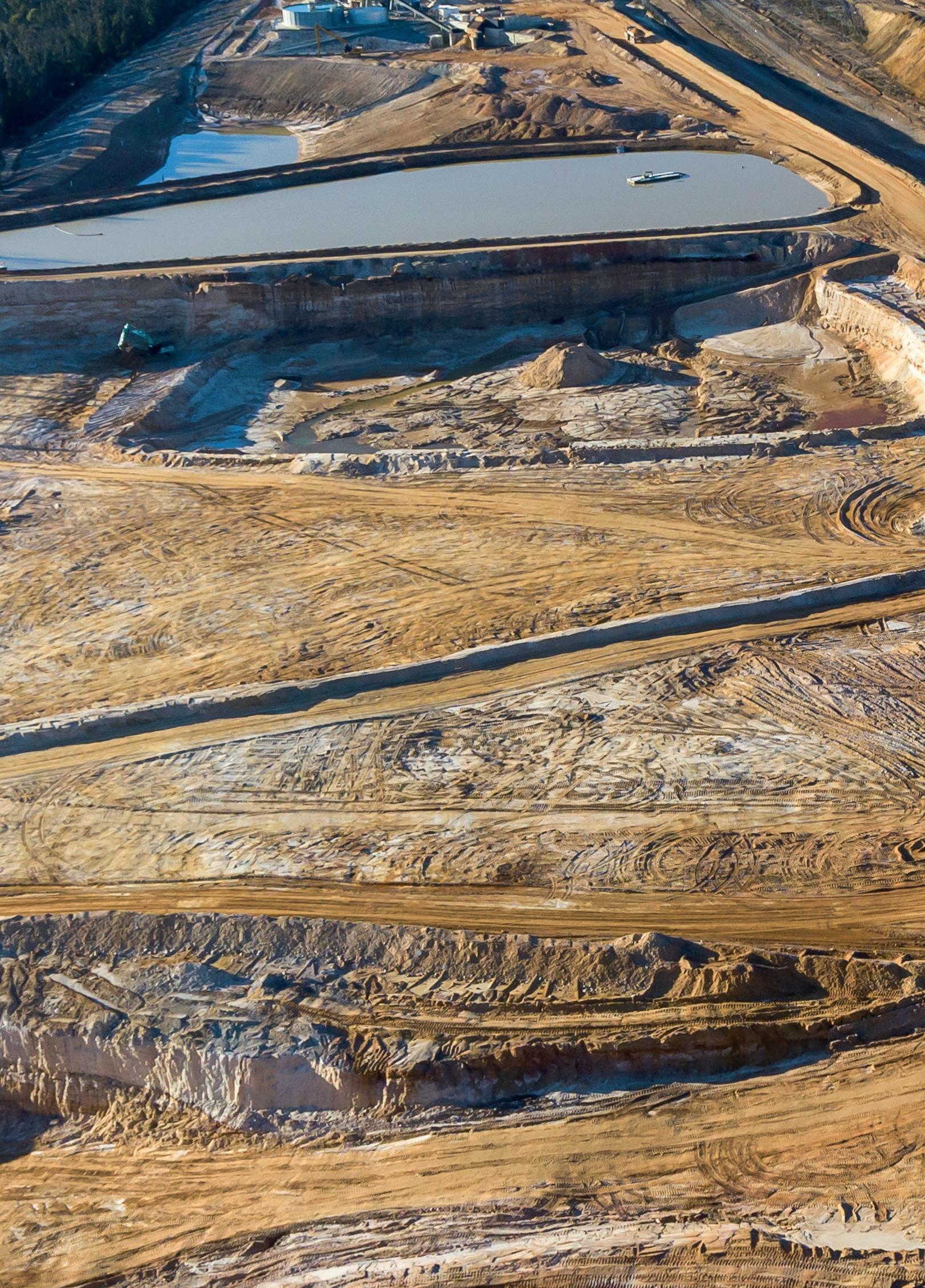
ASIA-PACIFIC’S INTERNATIONAL MINING EXHIBITION IS MOVING!
As Australia’s longest running mining show, Asia-Pacific’s International Mining Exhibition (AIMEX) has a long, established history of showcasing and supporting the latest trends and developments in the industry.
AIMEX is relocating and will call South Australia home for the next 10 years, following market feedback and strong support from the local government and key mining players.
The move marks an exciting new chapter for the event and the region’s resource sector, with the state leading the way in future-focused mining.
AIMEX offers unparalleled opportunities to connect with Australia’s largest community of mining suppliers and professionals in an environment that stimulates innovation and collaboration.
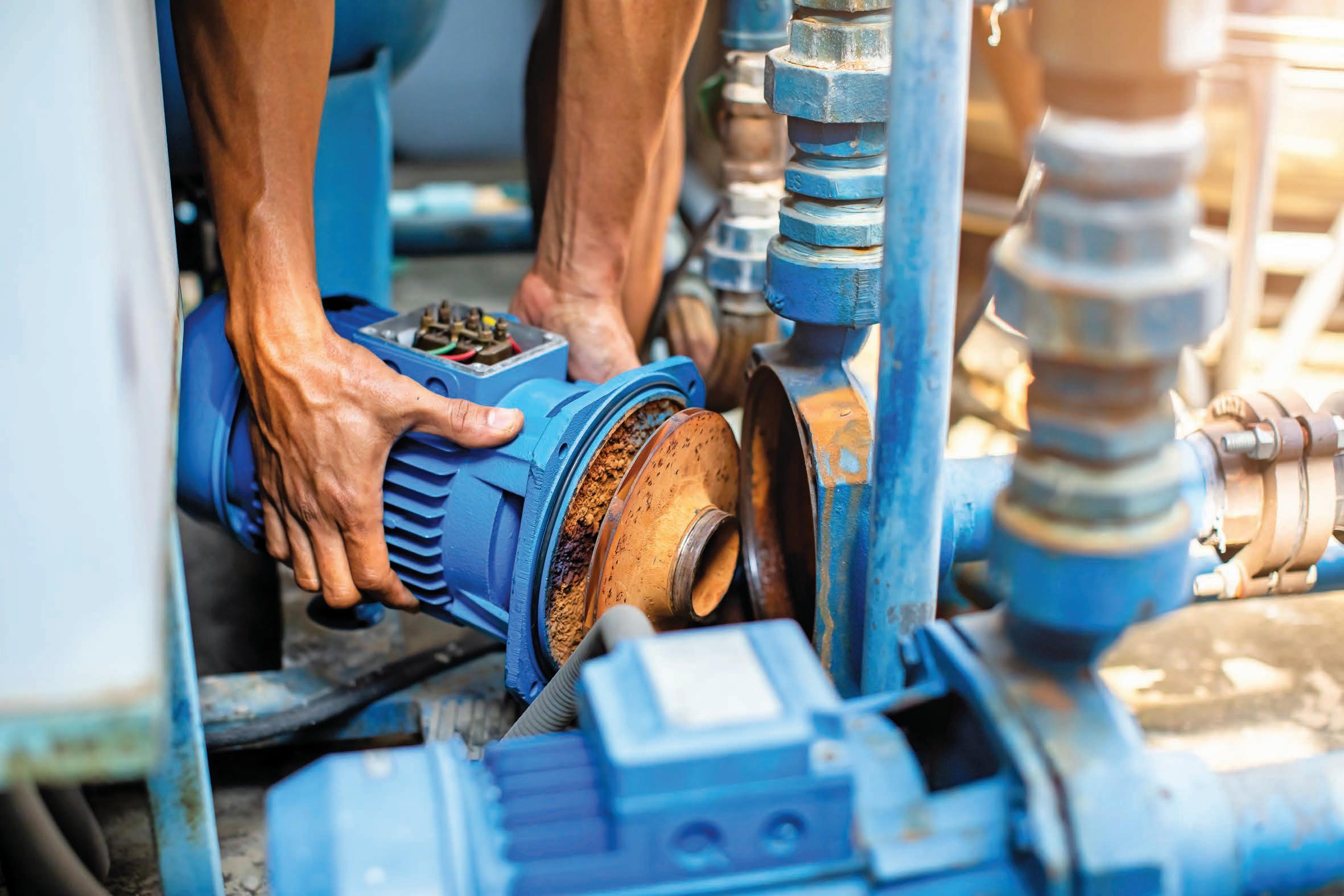
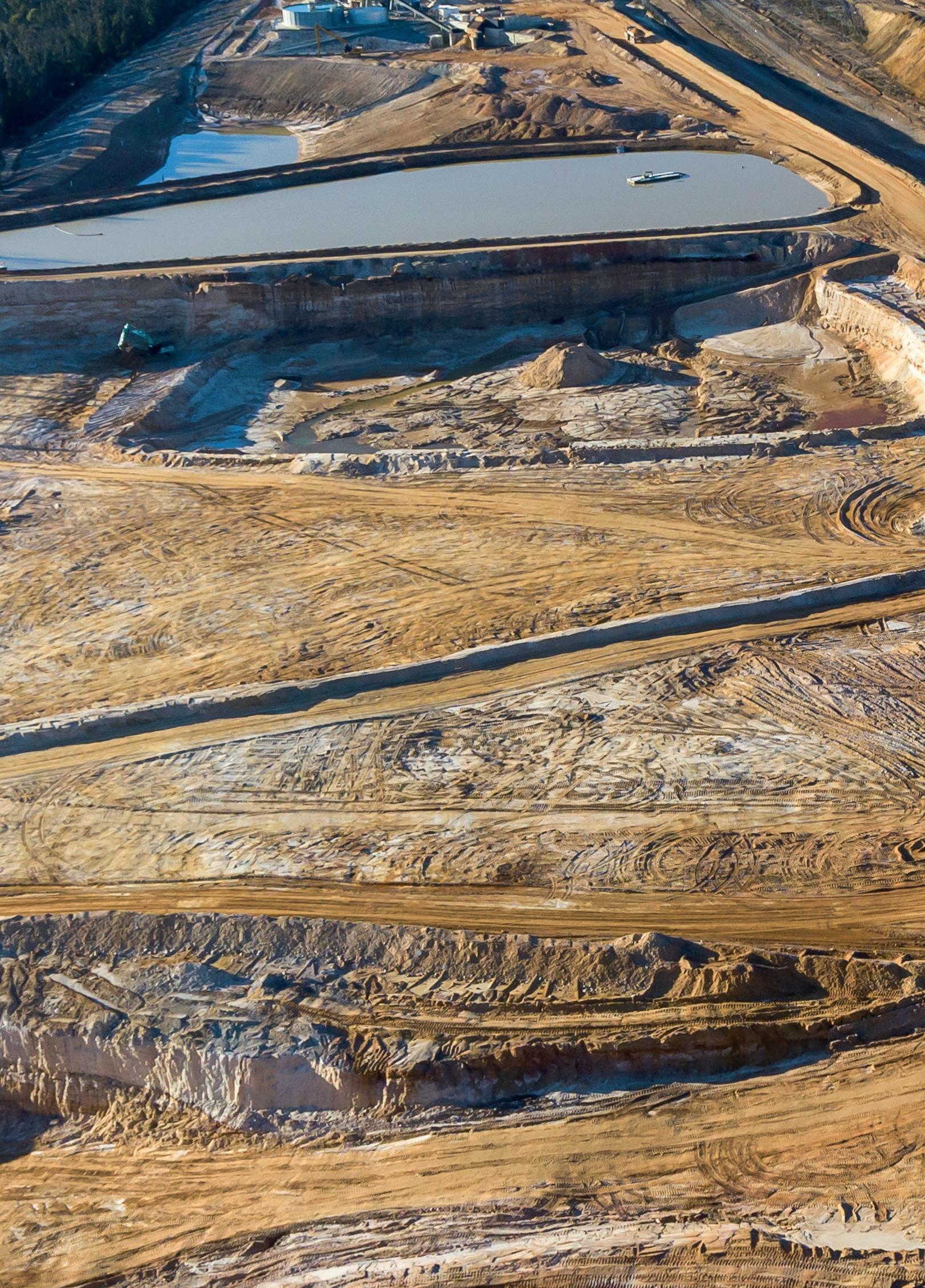
Now in its 12th year, the annual State of the Industry report examines how the sector fared in 2024 and looks ahead with continued optimism for 2025.
With ongoing challenges and a sea of new opportunities, our survey results suggest that 2024 was a mixed bag for the pump industry.
Soaring interest rates and supply chain shortages continued to cause trouble over the last 12 months, but increased investment in new infrastructure, particularly in the water and wastewater space, has had a positive impact on the industry.
As Australia’s climate continues to change, the Federal Government is pouring billions into new clean energy projects via its Future Made in Australia bill – and the race to net zero has seen an increase in demand for energy efficient pumping solutions.
Interest and inflation rates also started to level out in the last half of the year, which shows potential for economic relief in 2025.
Despite these challenges, The State of the Industry 2025 report offers a positive outlook for the future and shows exciting opportunities for growth across multiple sectors
State of the industry responses 2025
The forecast for 2025 remains overwhelmingly positive, and as seen in Figure 1, 61 per cent of respondents predicted a positive year ahead for the industry. While the results do show a slight downward trend compared to 64 per cent in 2024, last year had the highest positive response on record and it’s encouraging to see this optimism is continued in 2025.
Negative outlook responses have climbed to 4.3 per cent up from last year’s 2.27 per cent, and neutral responses are also trending upwards at 22.2 per cent compared to 18.18 per cent in 2024. However, when plotted alongside responses from previous years the results consistently show a very positive outlook for the pump industry.
There is a growing contingent of uncertainty as the world continues to experience changes in key areas like economic stability, global supply chain and technological shifts. However, only a very small percentage of respondents feel that the industry outlook is negative – a good sign for the year ahead.
Similar to the 2024 survey, the difference in positive outlook for the
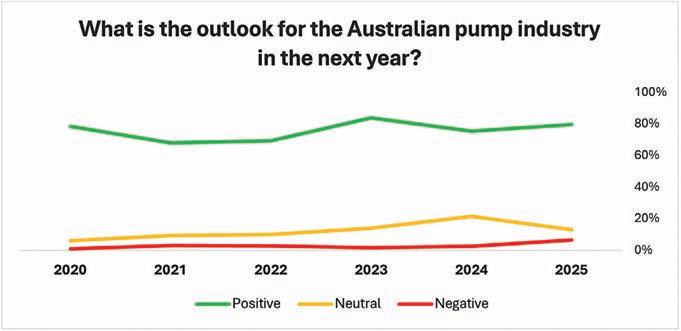


Figure 1. Tracking the outlook of the Australian pump industry from 2020 has shown that the industry remains broadly positive.
Figure 2. What is the outlook for the Australian pump industry in the next year?
Figure 3. What is your company’s outlook for 2025?
pump industry as a whole was lower than individual company expectations, with 80 per cent of respondents reporting a positive outlook for their own company in the year ahead.
While this is just a very slight increase from 79.5 per cent in 2024, this consistent proclivity for positive responses paints a picture of steadfast optimism in the industry.
Although 2024 may have seen a decline in negative responses with just 3.41 per cent, respondents to this year’s survey were a little more cautious, and 6.7 per cent reported a negative outlook for 2025. On the other hand, the number of neutral responses has dipped, with 13.3 per cent saying they felt neutral about their business’ outlook – as opposed to 2024 where neutral responses totalled 14.77 per cent.
It’s likely that these feelings of concern are reflective of Australia’s broader economic challenges, with rising cost of living, and worker and supply chain shortages creating uncertainty for the industry. However, with positive and neutral votes combining to make up 93.3 per cent of responses, the outlook for businesses is still trending towards being positive and secure.
Evaluating company performance in 2024
The rising cost of living has had an impact on not just the pump industry, but every industry in Australia. As interest rates, fuel prices and the costs of labour and materials skyrocket, it comes as no surprise that an increased number of respondents said their 2024 performance fell short of expectations.
Although there has been an increase in shortfalls, the number of respondents who said they had exceeded expectations has also shot up to 47 per cent compared to 30.6 per cent in 2024. Fewer respondents (33.3 per cent) said that they met expectations in 2024 compared to 51.4 per cent in 2023, but the results indicate this can largely be attributed to more companies achieving better results than they had predicted. Many companies attributed their success to sales being up and markets expanding. Several responders also noted internal operations as having a direct impact on whether expectations were met.
One company said that having a “closer interaction with its customer base” provided an opportunity to offer personalised solutions and improve its financial outcomes.
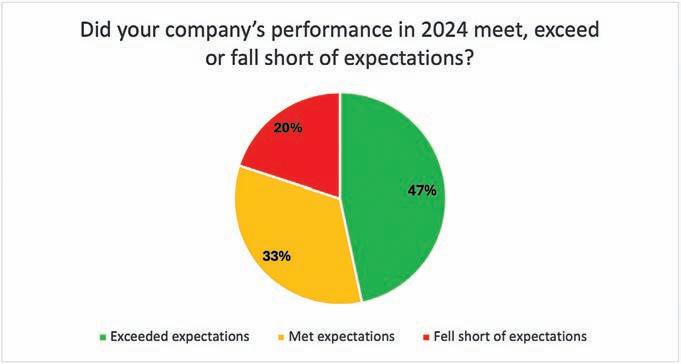

Another respondent said they had exceeded their sales budget, while others pointed to successful entrance into new market segments.
Conversely, respondents noted that broader economic issues impacted performance, including global supply chain challenges, skill shortages and increased cost of living.
Continuing this trend towards optimism, more than half of respondents said they expect their businesses to perform better in 2025 than in 2024.
One factor that could contribute to this positive outlook is the surge in
new water and energy infrastructure projects, which could provide an abundance of new opportunities for the Australian pump industry.
What industries does your company operate in?
When we look at the industries that respondents operate in (Figure 6), water and wastewater was the clear frontrunner, with 73.3 per cent of respondents reporting working in this sector.
Manufacturing, irrigation, filtration, mining, oil and gas, food and beverage and power generation were also
Figure 5. Do you expect your company to perform better in 2025 compared to 2024?
Figure 4. Did your company’s performance in 2024 meet, exceed or fall short of expectations?
primary sectors with around half of all respondents reporting working in these sectors. When looking at these figures in relation to positive outlooks for pump businesses, we can get a clearer picture of what sectors opportunities are likely to be found in.
Expected and reported sector growth
Expected versus reported growth, broken down by sector, provides a thorough snapshot of the key factors impacting the pump industry and sheds some light on why companies may or may not have met the expected growth projections from the previous year.
Survey respondents were asked to provide details about the volume of work experienced in critical sectors – including mining, water and wastewater, and irrigation – over the past 12 months. We then compared these responses to the growth expectations reported in last year’s State of the Industry survey to see how they compared.
As seen in Figure 7, a side-by-side comparison of expected versus reported growth shows all sectors struggled to meet their growth expectations, according to respondents.
It’s important to note, that in 2023 almost every industry reported unprecedented growth, and well exceeded all predictions, and it’s possible that these great result set unusually high expectations for 2024.
When compared to reported growth from previous years, we can clearly see that the water and wastewater sector continues to leading the charge, with respondents once again reporting more growth in this industry in 2024 than any other. Mining, irrigation, power generation, food and beverage and plastics and rubber also have a strong foothold, with demand in these sectors consistently increasing year-on-year.
We can also see a continued decline for the pulp and paper industry over time and fewer than 34 per cent of businesses reported working in this sector, which could highlight how this industry itself is shrinking.
The net zero reported growth in the building services and HVAC industry could connect to the existing problems in the construction sector. In the past few years, builders have grappled with significant challenges, from material shortages and soaring costs to the added complexity of uncertain skilled labour availability, impacting their on-site work scheduling.
At the same time, the Federal Government has pledged to create 1.2 million new homes over five years, the Victorian government plans to build 2.5 million homes by 2051, and the Queensland government aims to build one million quality homes by 2026. These targets are in addition to smaller targets from other governments across the country, ultimately squeezing the construction industry in both directions.
6. What industries does your business operate in?
Sector growth predictions
Despite not meeting expectations in 2024, the predictions for 2025 remain optimistic. Continuing the trends of previous years, the water and wastewater industry is predicted to experience the highest growth in 2025. Several respondents attributed this to a rise in funding for water and wastewater infrastructure, largely driven by heightened government investment in these initiatives.
Respondents also forecast strong growth in the mining and irrigation sectors, which could be attributed to national decarbonisation efforts and the need for more energy efficient pumping solutions. Critical minerals will play a key role in Australia’s transition to renewables and an increase in demand for these resources creates new opportunities for the pump industry.
Many respondents also noted that clean energy projects were likely to present opportunities for Australian pump companies in 2025, however project delays and slowed progress in the green hydrogen space are preventing the pump industry from fully reaping the rewards of the energy transition.
At the same time, the oil and gas industry is expected to shrink, with more than one-third of respondents saying they expect their involvement in this sector to decrease somewhat.

Figure
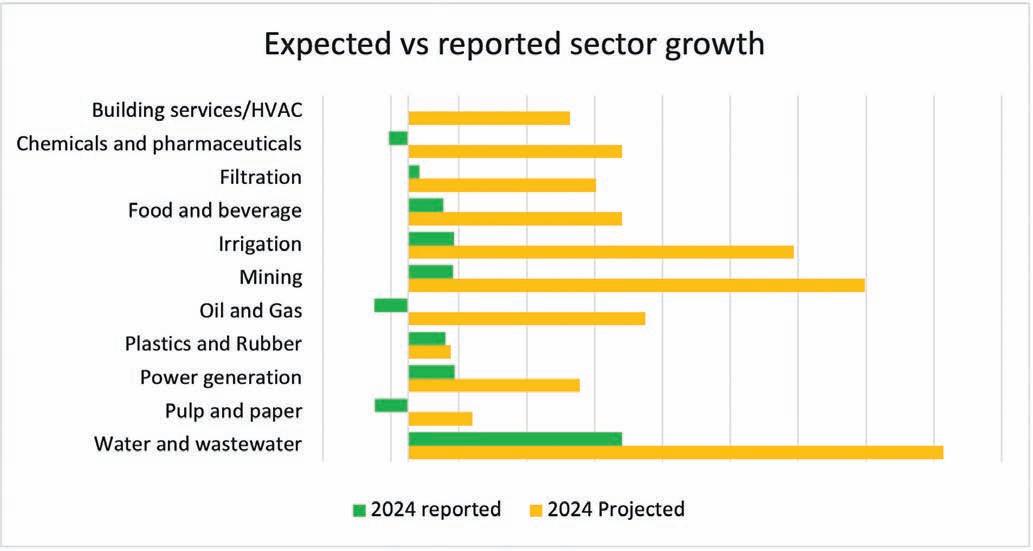
Analysing predicted impact of potential factors
The demand for critical minerals and the performance of the mining industry
The rise of various smart technologies and energy storage solutions has driven a significant increase in global demand for essential minerals like lithium, nickel, and rare earth elements.
According to Australia’s Critical Minerals Strategy 2023–2030, the country could see an additional
$71.2 billion boost in gross domestic product and create 115,100 full-time equivalent jobs.
This creates numerous opportunities for the pump industry to assist in mining these resources, and one respondent noted that there has been a considerable increase in requests to purchase Australian-manufactured products, which is in line with government policies encouraging such procurement activities.
Agricultural industry
Australia’s agricultural sector greatly influences the pump industry, stemming from the sector’s heavy reliance on irrigation.
The University of Western Australia Institute of Agriculture highlights that while irrigated agriculture is crucial for food production, there is an increasing necessity to yield more with less water. This competition and the reality of water scarcity are significant
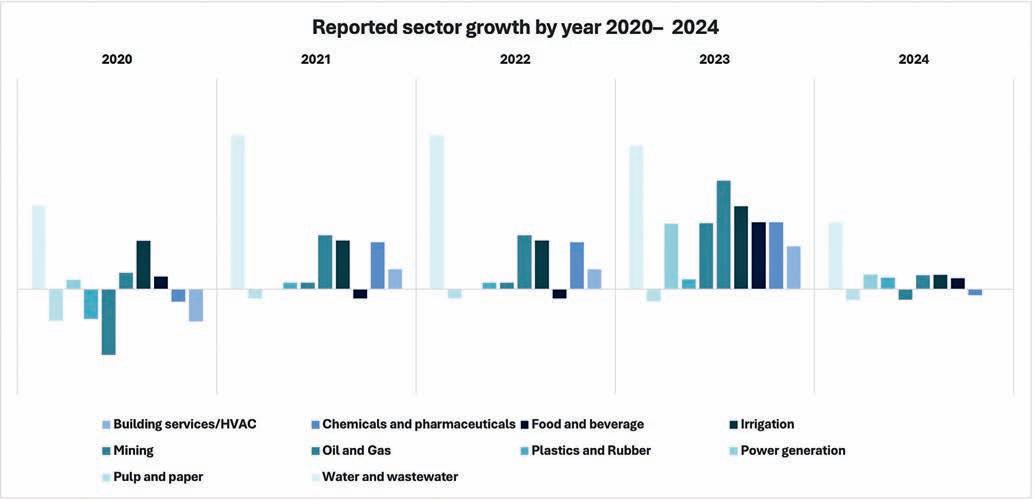
Figure 8. Reported sector growth by year 2020-2024.
Figure 7. Expected vs reported sector growth.
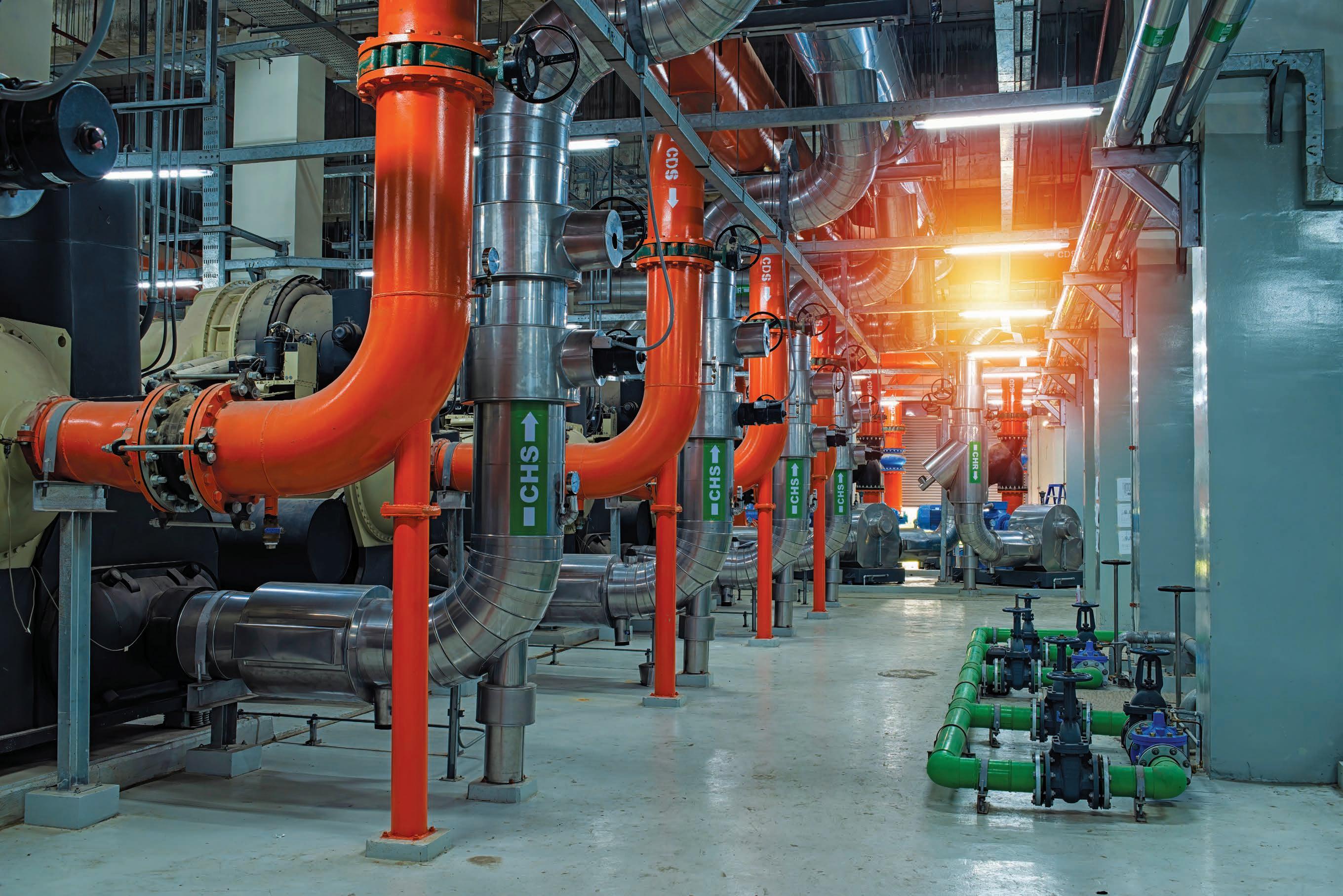
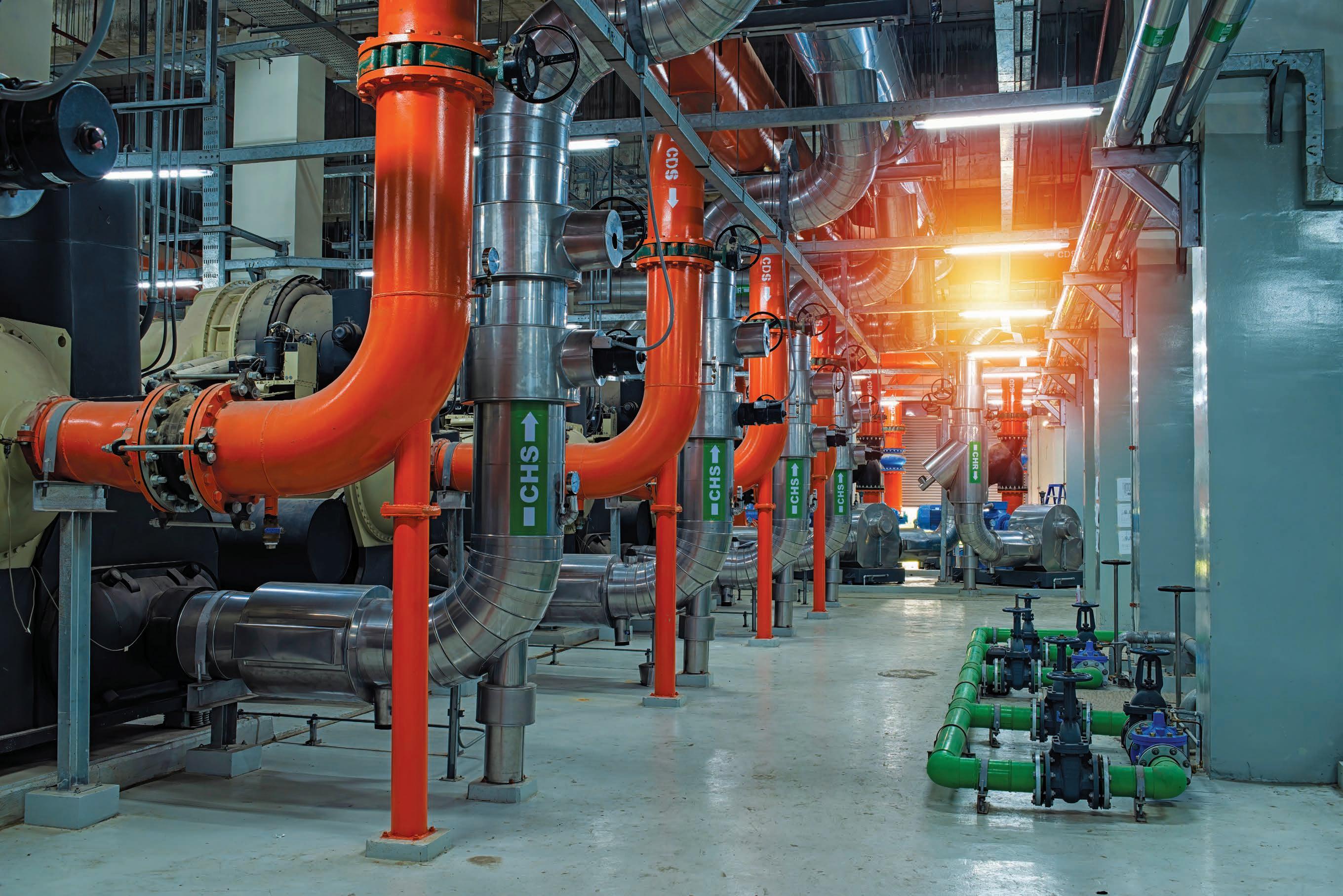
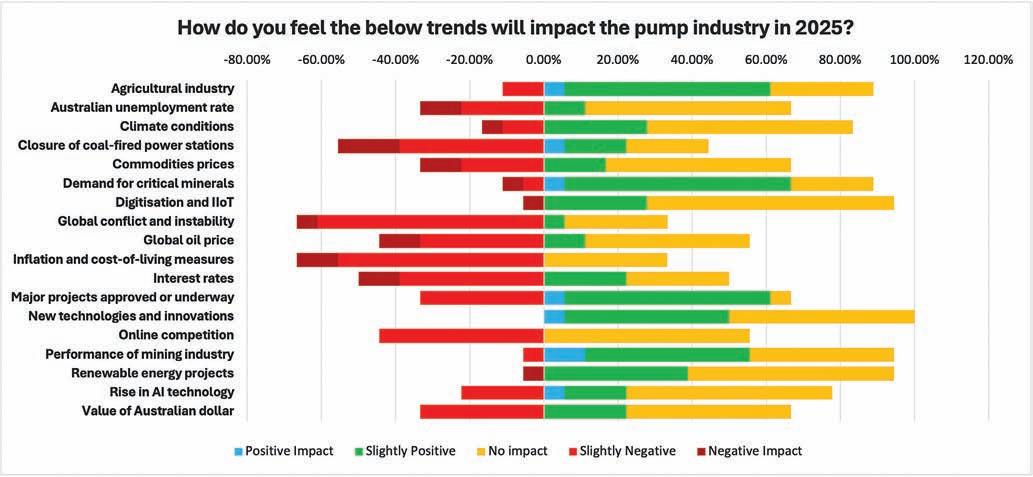
motivators for enhancing water efficiency in agriculture.
While the changing climate can significantly impact the agricultural industry, one respondent pointed out that where there are challenges, there are opportunities. As pumps are needed to move flood water from one place to another, this climate variability provides opportunities for innovation to meet these shifting requirements.
Major projects
Major construction projects are expected to continue to be a positive for the sector in 2025. To assess which projects could support the pump industry, the 2024–25 Federal Budget is an excellent place to start.
The Federal Government’s $22.7 billion Future Made in Australia package is set to drive growth and fast-track key renewable energy project. The package includes spending of:
• $134.2 million to streamline approvals for renewable energy projects deemed nationally significant and to facilitate quicker decisions regarding environmental, cultural heritage and planning permits.
• Invest $20.7 million to enhance outreach to communities affected by the energy transition and expedite the execution of essential energy initiatives.
• Assign $15.7 million to bolster oversight on high-risk foreign investment proposals, improve monitoring and enforcement efforts, and enable swifter decision-making.
• $17.3 million to mobilise private sector investment in sustainable activities, including extending Australia’s sustainable finance taxonomy to the agriculture sector.
• Establishing the $1.7 billion Future Made in Australia Innovation Fund and extending funding to the Australian Renewable Energy Agency for ten years. It also funds the $44.4 million Energy Industry Jobs Plan and $134.2 million for skills and employment support in key regions.
• $32.2 million to fast-track the initial phase of the Guarantee of Origin scheme, focused on renewable hydrogen, and bring forward the scheme’s expansion to accredit the emissions content of green metals and low carbon liquid fuels.
• Committing $1.5 billion to manufacturing clean energy technologies, including the $1 billion Solar Sunshot and $523.2 million Battery Breakthrough Initiative.
• Investing $8.8 billion over a ten-year period to add value to Australia’s resources and strengthen critical minerals supply chains.
T he 2024-25 Budget also sought to improve resilience in the face of a changing climate. With this knowledge, programs were put in place, including:
• Funding for the National Emergency Management Agency to supply communities with vital goods, equipment, and temporary accommodation during an emergency, aerial firefighting capability, and mental health support. This is
in addition to the $11.4 billion previously committed for Disaster Recovery Funding Arrangements for the states and territories.
• Provides $174.6 million from the National Water Grid Fund to deliver new water infrastructure projects that will enhance water security, boost agricultural production and help drought-proof regional communities.
• Provide $519.1 million from its Future Drought Fund to help farmers and rural communities manage the impacts of climate change and prepare for future droughts.
Looking ahead
Despite cost-of-living pressures, labour shortages and supply chain struggles, all indications show that businesses across the pump industry came out on top in 2024 – and the overwhelmingly positive outlook for the year ahead is a testament to the industry’s tenacity and importance in the Australian economy.
Although there are challenges likely to be faced in the coming year, there are also a lot of positives to look forward to –increased investment in critical minerals mining, renewable energy infrastructure and irrigation is likely to present some great business opportunities across the industry.
While there are clear challenges for our industry, there are opportunities also, and the survey data suggests that 2025 will be another good one for the pump industry.
Figure 9. How do you feel the below trends will impact the pump industry in 2025?
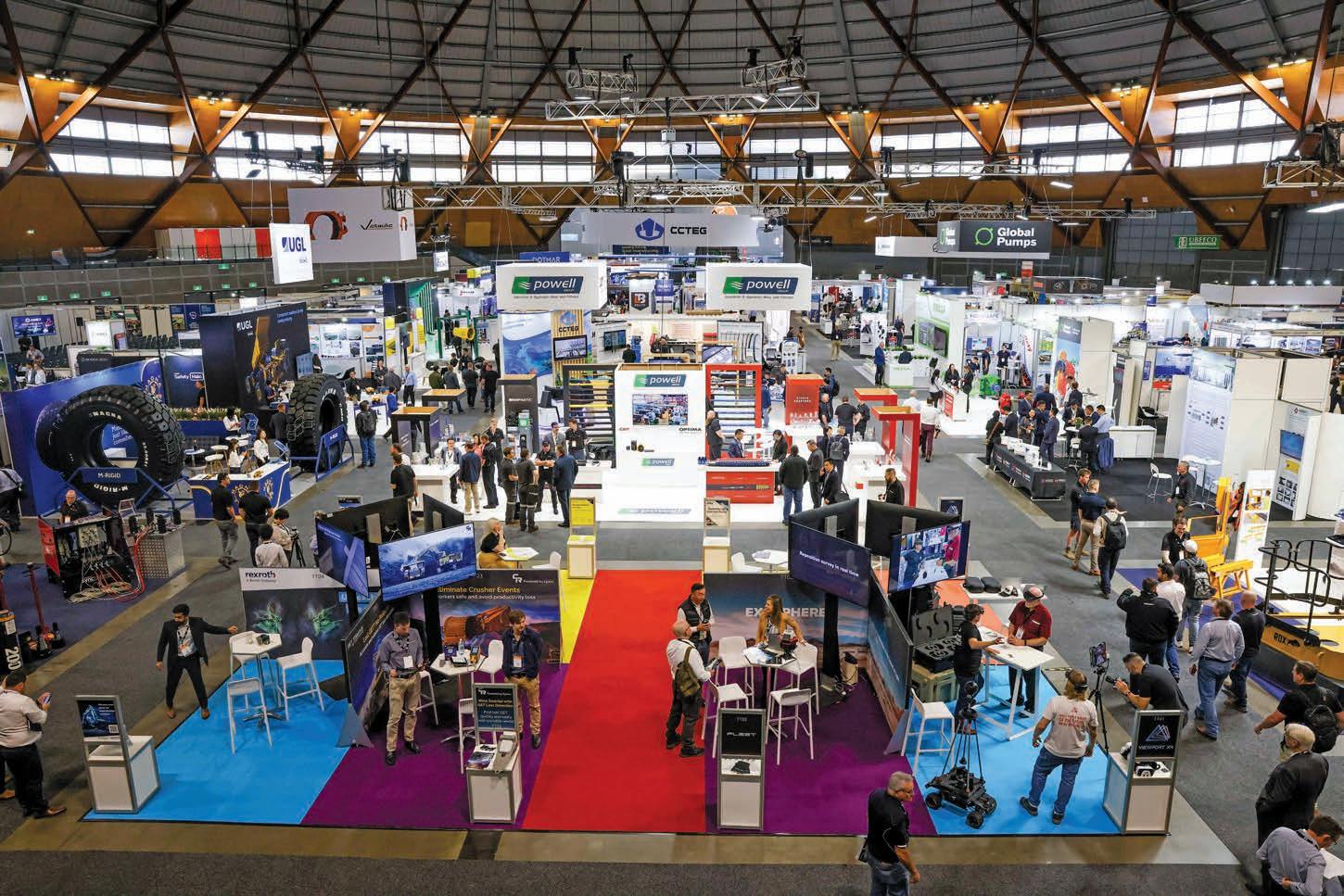
AIMEX moves to Adelaide
Adelaide will become the hub for Asia-Pacific’s mining future, driving innovation in critical minerals and sustainable energy solutions.
Following a strong bid from the South Australian Government and key mining stakeholders, AsiaPacific’s International Mining Exhibition (AIMEX) will move to Adelaide in 2025. The agreement will see AIMEX reside in Adelaide for the next ten years, strengthening South Australia as Asia-Pacific’s fastest-growing modern mining market.
Prime Creative Media acquired AIMEX in May 2024. As Australia’s longest-running mining show, AIMEX has a history of supporting the latest industry trends and developments. This move to South Australia represents the next phase in the regional resources sector. The state has been leading the charge in responsible exploration to unlock minerals. It has also been driving the investigation of solutions for global decarbonised steel making, efforts that are critical to the future of infrastructure development.
“We’re working to keep AIMEX’s reputation as a key event for the AsiaPacific region,” Prime Creative Media
General Manager of Events Siobhan Rocks said. “We knew we needed to do something significant to attract key players in the industry. When the mining industry asked us to come to Adelaide, we believed this change of location was the best way to serve this crucial sector.”
“With our natural advantages and ingenuity, South Australia has the potential to lead the world in decarbonising critical minerals, including green steel and copper,” South Australian Premier Peter Malinauskas said. “We have a compelling story to tell, and AIMEX being hosted in Adelaide for the next decade provides a strong platform to do just that.
“This exhibition will attract thousands of mining delegates from around Australia and the world to Adelaide every two years, significantly boosting South Australia’s visitor economy.”
According to Business Events
Adelaide Chief Executive Officer Damien Kitto, AIMEX is “a significant win for Adelaide” that will generate more than
$250 million for the state economy over the next decade.
“We are proud to be entrusted with this long-running business event, demonstrating that Adelaide is increasingly viewed as a modern powerhouse in sustainable energy generation,” he said. “Business Events Adelaide shares Prime Creative Media’s ambition of making AIMEX the world’s largest mining event.”
The South Australian mining industry is rapidly making a name for itself as a toptier jurisdiction for the critical minerals essential to the world’s energy transition, including copper, uranium, zircon, and zinc. With its extensive renewable energy network and significant investment in hydrogen projects to power green steel and future energy solutions, South Australia’s pioneering objectives distinguish it from other markets.
Prime Creative Media CEO John Murphy said that relocating the event to South Australia was an obvious strategic choice, given the significant developments and growth of the South
Cutting edge technology will provide numerous opportunities for investment.
Images: Prime Creative Media
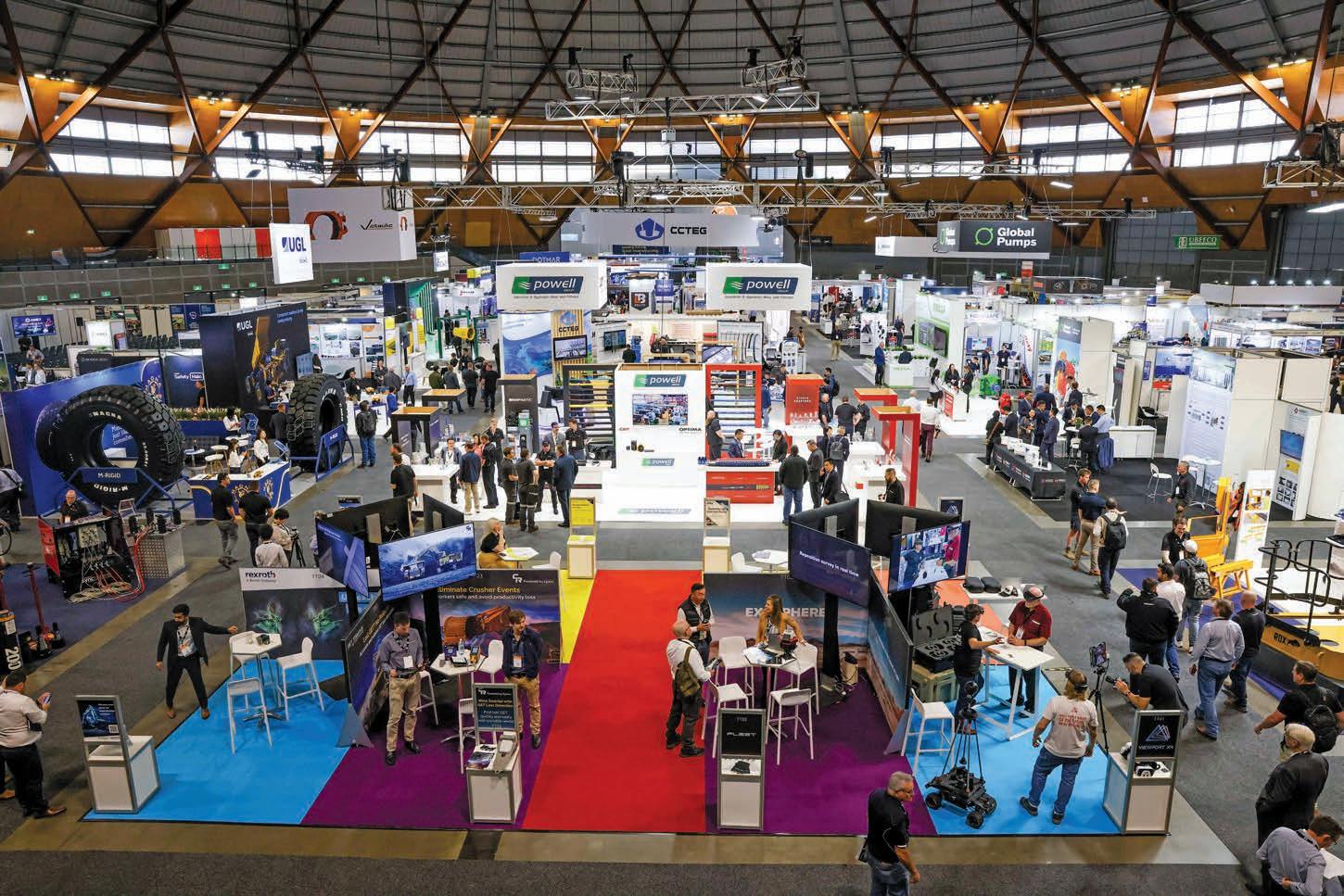
Australian resources industry, as well as the ramp-up in decarbonisation and sustainable supply chains.
“This is a critical time for the industry, and South Australia is emerging as a frontrunner in responsible mining and production of the future’s minerals, metals, and fuels,” Mr Murphy said. “It aligns with our purpose to deliver a forward-focused mining event for the next generation of Australian mining.
“There’s no denying the link between the mining industry and renewable energy. South Australia is a world leader in renewables and the global transformation economy. We’re proud to partner with the state to showcase the world-class change that the resources sector drives.”
AIMEX will allow delegates to gain future-focused insights from internationally renowned industry experts. The show also provides unparalleled opportunities to connect with Australia’s largest mining suppliers and professional community in an environment that stimulates innovation and collaboration.
To get involved in 2025 Asia-Pacific’s International Mining Exhibition, visit aimex.com.au
half page ad 2025.pdf 1 11/6/2024 8:59:33 AM
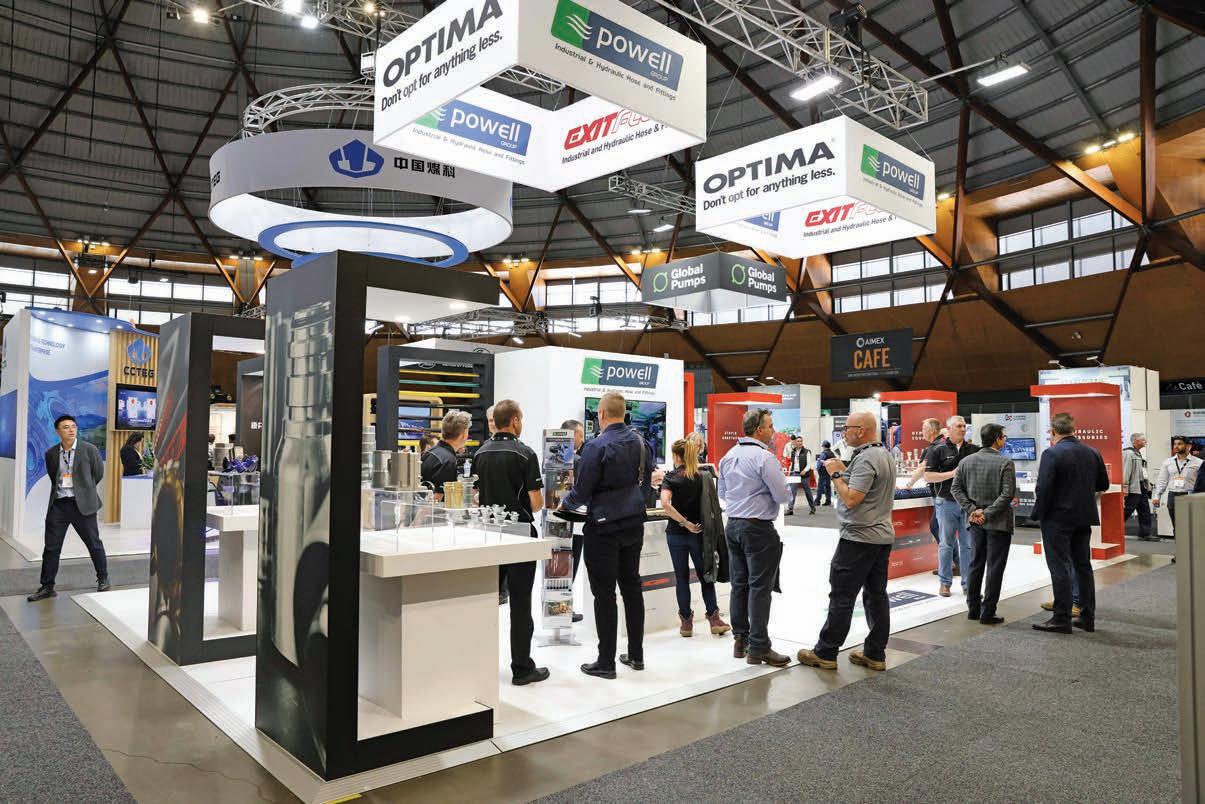

People from across the Asia-Pacific will flood into Adelaide for AIMEX.
How to control a hose pump
Learn the essentials of controlling peristaltic pumps to optimise flow rate, direction and remote operation for peak performance.
Controlling a peristaltic pump involves managing its operational parameters, such as flow rate, direction, and in some cases pressure. The method of control depends on the specific type and model of the peristaltic pump, as different pumps may have varying control mechanisms.
To effectively control a peristaltic pump, consider the following:
Understand your pump’s capabilities before attempting to control the pump, be sure you understand its specific capabilities, such as maximum and minimum flow rates, pressure limits, and the types of fluids it can handle.
Review the control interface
Hose pumps can have different control interfaces, ranging from simple manual dials to sophisticated digital keypads with programmable logic controllers (PLCs). Familiarise yourself with your pump’s interface.
Set the flow rate
The flow rate in peristaltic pumps is typically controlled by adjusting the rotor’s speed. This can be done manually via a dial or knob. Alternatively, the flow rate can be set digitally through a keypad or a connected computer system.
Step-by-step flow rate adjustment
Turn on the pump and access the control interface. Select the flow rate setting mode if it’s a digital pump. Adjust the speed of the rotor to your desired flow rate. This can involve turning a knob or inputting a value.
Determine the direction of flow
Most hose pumps allow you to control the direction of flow simply by reversing the motor’s rotation.
Direction control steps
Locate the direction control on the
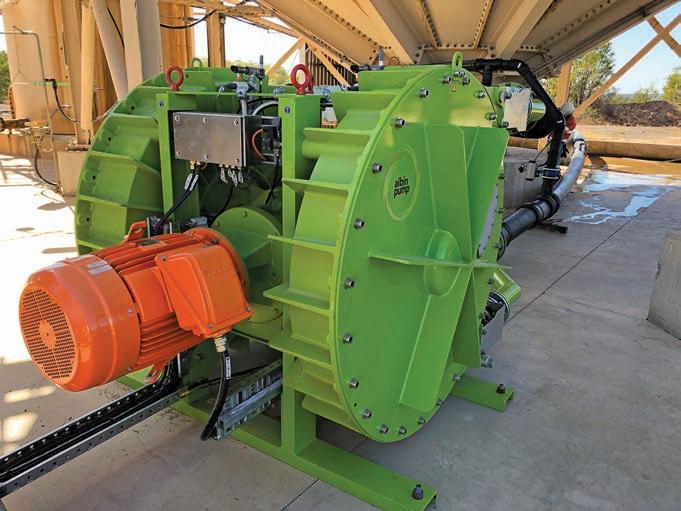
interface. Choose the desired direction, ensuring the tubing layout corresponds to the intended flow path. Use external control (if applicable).
Remote control implementation
Connect the pump to the control system using the appropriate cables. Program the control system to send the desired commands to the pump.
Programming operations
Access the programming mode on the pump’s interface. Enter the schedule, volume, or duration parameters as required. Save the program and ensure it has been properly activated.
Monitor pump operation
Continuously or periodically monitor the pump’s performance to ensure it operates as intended. This may involve observing the flow rate, checking for leaks, listening for unusual noises and utilising feedback loops.
Feedback loop setup
Install the necessary sensors (e.g., flow, pressure or temperature sensors) in
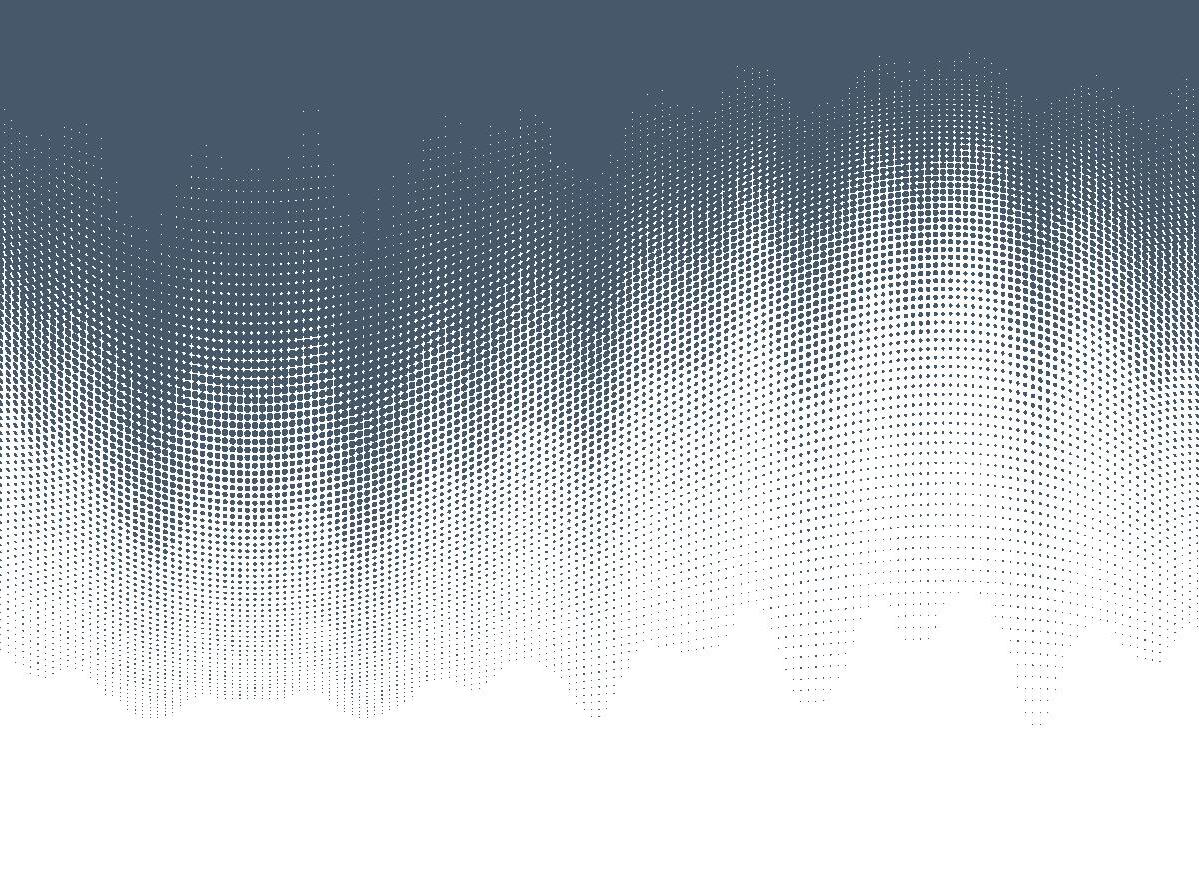
your system. Connect these sensors to the pump controller. Program the controller to adjust pump parameters based on sensor input.
Follow safety and operational protocols
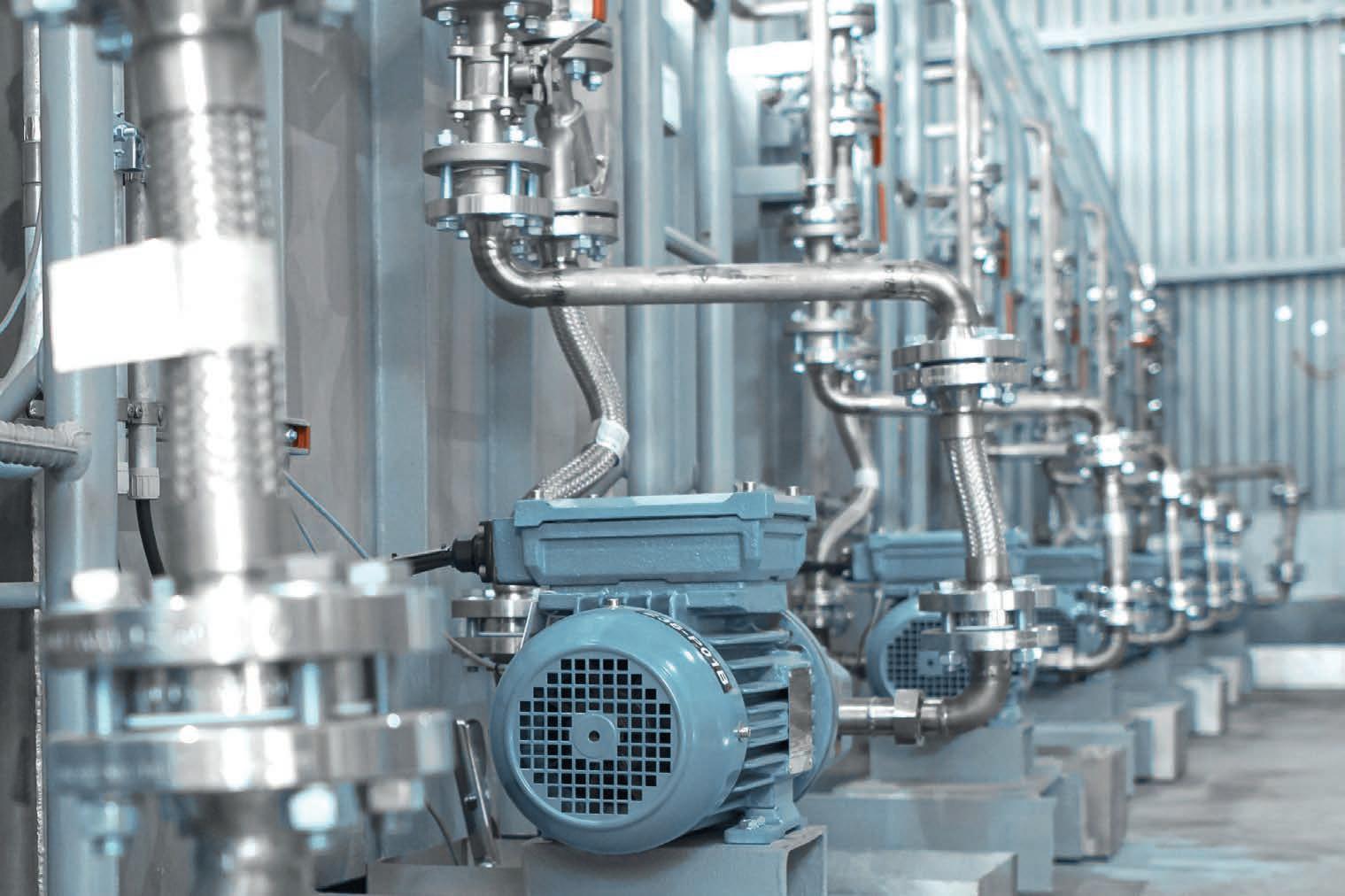
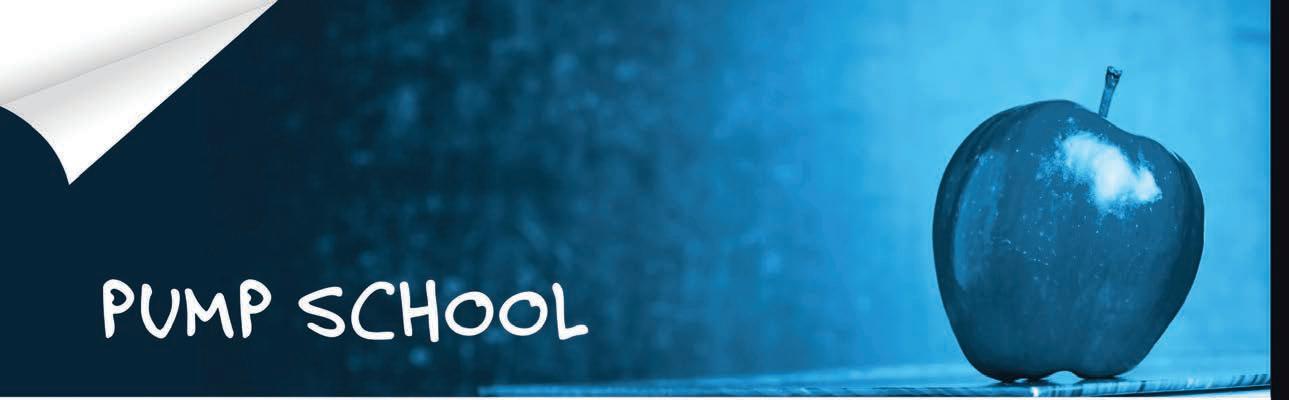
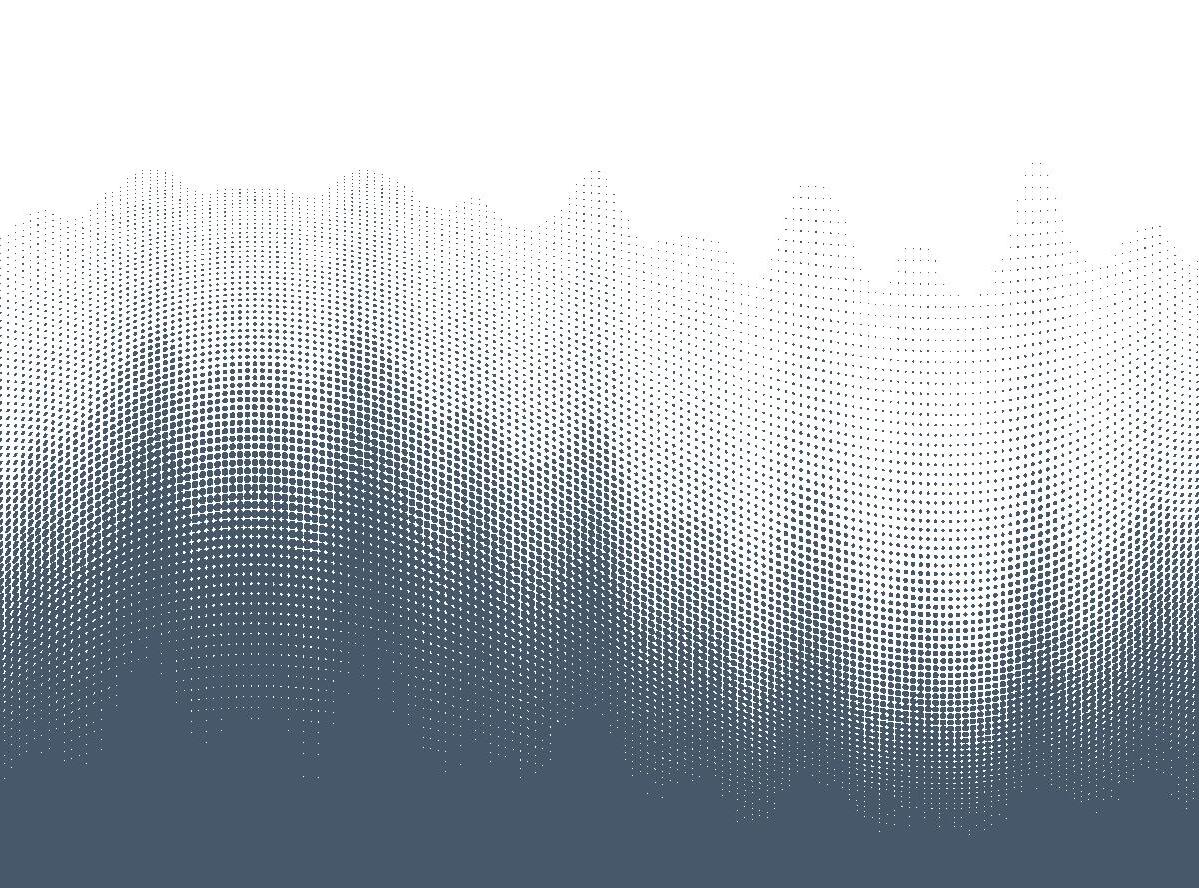
Follow the manufacturer’s instructions and safety guidelines when operating the pump. Be cautious of fluid compatibility with the pump tubing and wear personal protective equipment (PPE) when handling hazardous materials. Ensure the pump is operated within its specified operating conditions and take precautions to prevent overloading or damaging it.
Ensuring you have the right pump for the right application involves a thorough set of considerations. Consult a knowledgeable pump supplier, such as Kelair Pumps, to discuss your pumping requirements.
For more information, visit kelairpumps.com.au
An Albin Hose Pump – recently installed by Kelair Pumps at an Australian mine. Image: Kelair Pumps
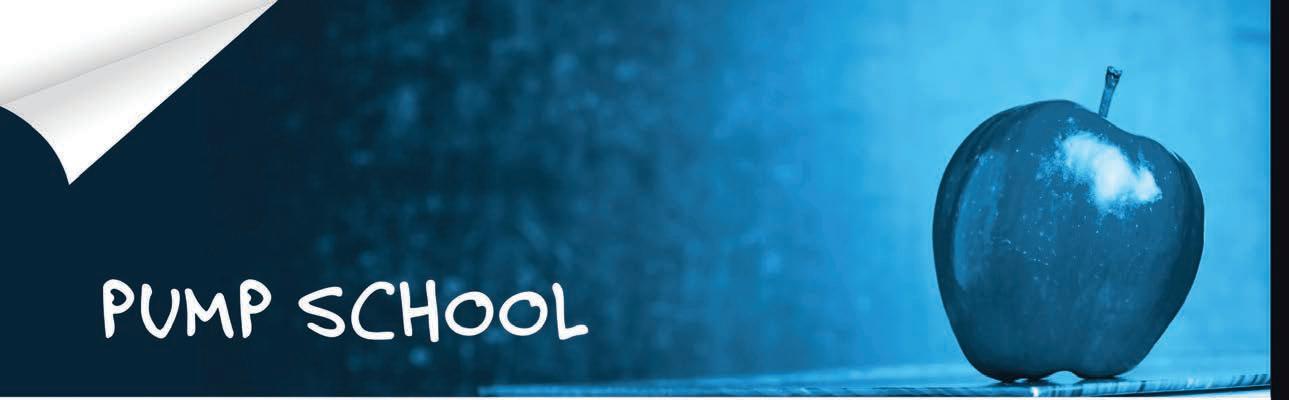
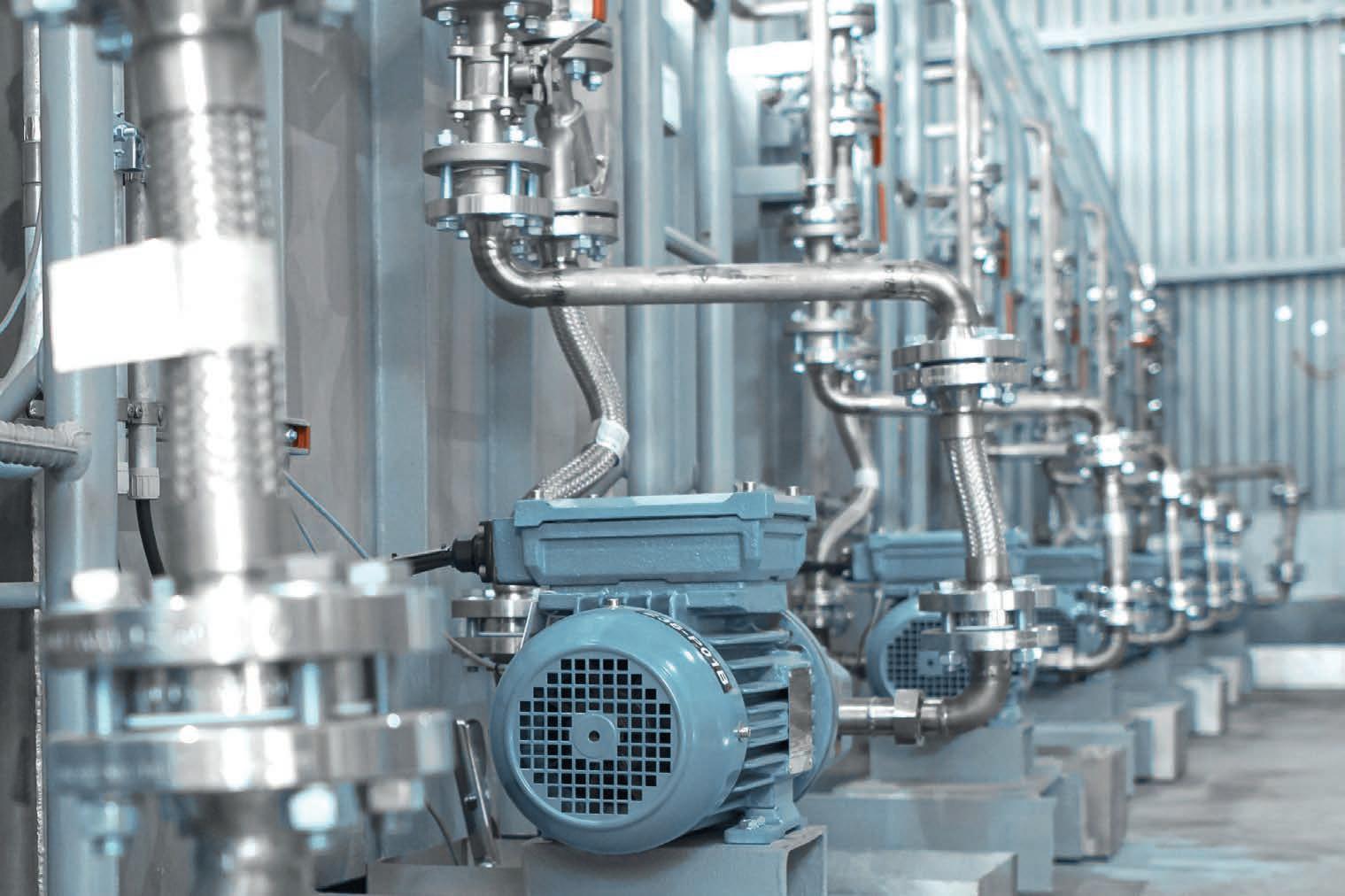
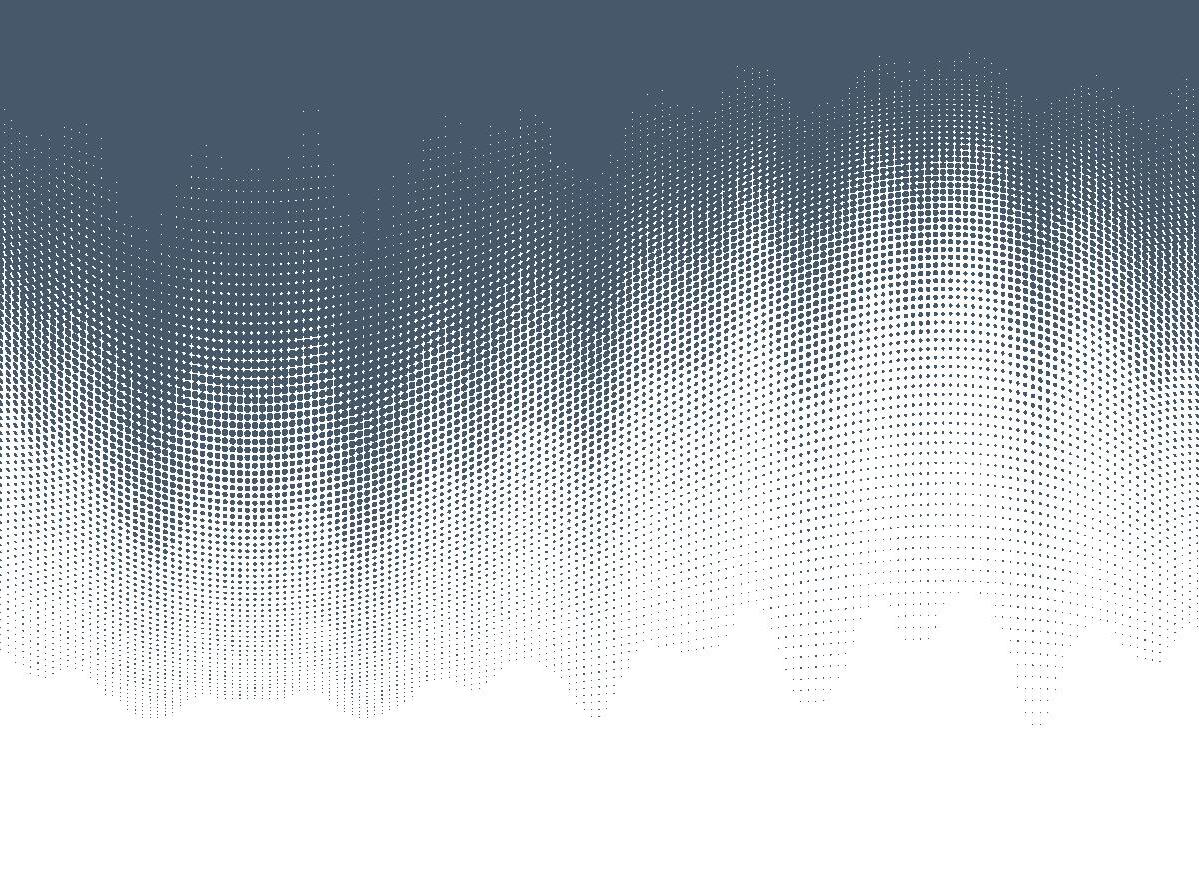
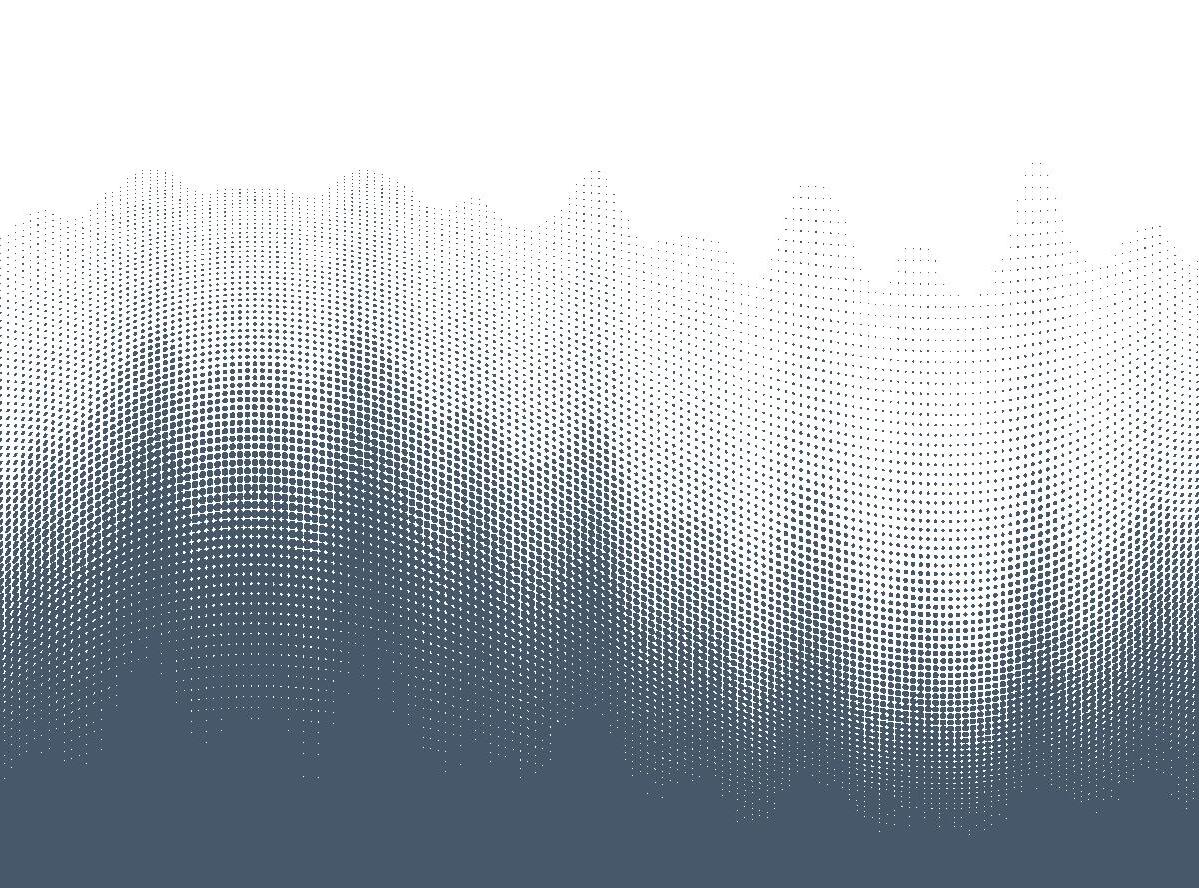
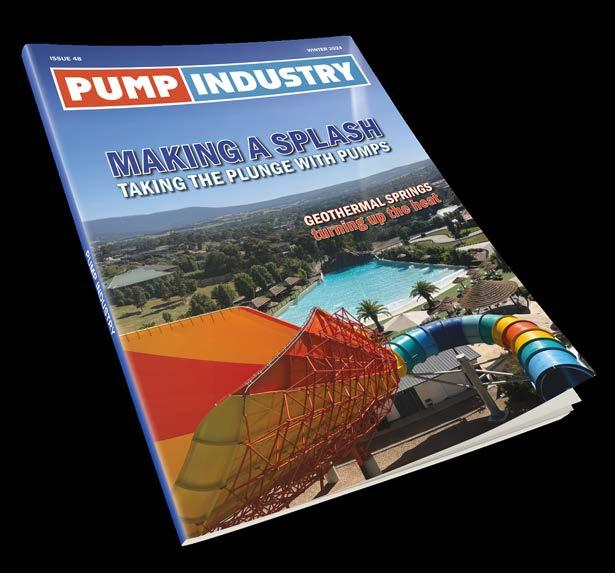
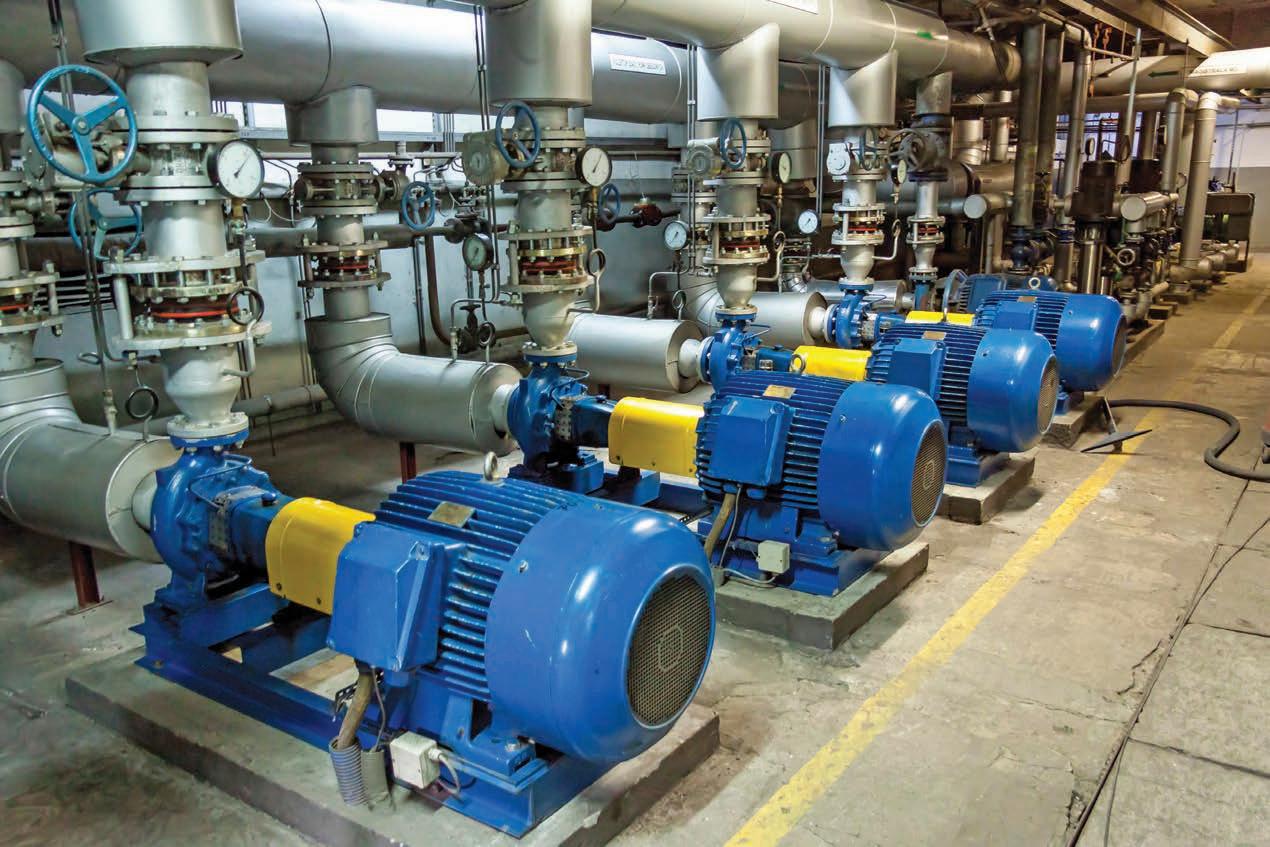
Installing pumps: the how, what and why
This is the start of a series of articles on the correct installation of a pump set and its associated pipework which is important for the ongoing operation of the pump system to ensure a long a trouble-free working life.
To complete the installation of a pump set the following safety equipment should be available and used where and when appropriate:
a. Work overalls
b. Hard hat
c. Work gloves
d. Eye protection
e. Face mask
f. Hearing protection
Note, the use of the some or all of the above safety equipment will also be required when commissioning a pump set as outlined in the next series of articles.
Some or all of the above will be required for the following operations which are described in this chapter:
a. Mixing grout
b. Drilling and cleaning holding down bolt holes
c. Grouting
d. Installation of pipework
e. Coupling alignment
Foundations
The pump set should be supported on a firm foundation or plinth preferably a rectangular concrete block with a mass equivalent to the weight of the complete pump set. The concrete plinth commonly has a height of 150mm above floor level and is generally about 300mm greater in length and width than the pump base.
A framework for the concrete block should be built and reinforcing steel used to make the block structurally strong. The framework should allow for the appropriate number of holes for the foundation bolts required to hold down the baseplate. These holes should be 4 times the foundation bolt diameter to allow for final positioning before grouting.
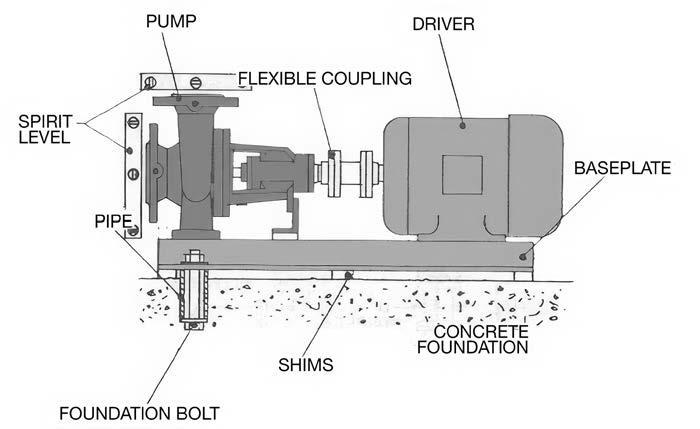
Grout allowance – set the top of the foundation 20 to 40mm below the bottom of the base level and the top surface of the block should be rough to provide a key for the grout. Note, before g routing the foundation block must be clean and wet to prevent excessive moisture loss from the grout face.
Allow the foundation to cure until it has adequate strength, before mounting the pump set on the foundation.
Erection
When pumps and their drivers are mounted on baseplates at the suppliers works, they are correctly aligned, i.e., the couplings are concentric and t he faces are parallel in both axis, care should be taken to minimise misalignment. It is absolutely essential t hat this alignment be checked and corrected after installation at site and prior to starting the pump set.
Care should be taken in the erection process to minimise any possibility of misaligning the pump set.
Insert steel wedges or packers and shims between the top of the foundation block and the bottom of the baseplate adjacent to and on each side of the foundation bolts. If the baseplate is
supplied with jacking bolts these can be used to level the baseplate instead of wedges or packers and shims. It is n ecessary, however, to maintain the horizontal centreline or horizontal fl ange f ace, whichever is applicable, at the correct RL.
When the pump or pump set is lifted into position it must be lifted with the appropriate lifting tackle and correctly slung by a qualified rigger.
Levelling
The pump set can now be levelled on the foundations using a straight edge and spirit level.
If the baseplate is installed separately without the pump and driver, an engineers’ level must be used to ensure both the pump and motor mounting pads are level in both directions. Again, t he correct RL must be maintained.
For baseplates with machined pump and motor pads, the pump and motor pads must be parallel to each other in both the length and width directions. If the pump set has been subject to maltreatment during transport, it may be necessary to adjust the position of the driver or the pump or both on the baseplate which will require the coupling
Figure 1.

alignment be checked at the end of the installation p rocess.
A degree of level of 0.1mm per 1,000mm of length of baseplate is generally acceptable. It should be noted t hat the accuracy of level can vary according to the preference of the end user or contractor. This accuracy can v ary between 0.05 to 1.5 mm/meter, however, the pump bearing type and its lubrication should be considered as these have a major impact on the level of accuracy required. Oil lubricated sleeve bearings on pump and/or motor (common in the oil industry) will require the highest degree of accuracy.
For the majority of pump sets which do not have machined pads a level accuracy of 1.5 mm/meter will be acceptable.
To obtain the levels outlined above it will be necessary to adjust the packers or levelling screws under or on the baseplate.
Remember when an adjustment is made the level in another direction will change.
During the grouting in of the pump set and its final alignment it is necessary t hat the pump set level be rechecked.
Grouting
If the unit is to be installed between fixed limits of suction and discharge piping, it is advisable to temporarily connect the piping to the pump before the pump set is grouted in. The pump set can then, if n ecessary, be moved slightly to suit the layout of the piping.
Grouting is carried out in two stages:
1. Grout and fix the foundation bolts before the pump set is installed on the plinth
2. The baseplate is grouted in after the pump set has been installed, levelled and the pipes connected
Traditionally, grout is made from
one part Portland cement and two parts sand (no aggregate). Mix with as little water as possible to minimise shrinkage. This grout can be used for both the grouting the foundation bolts and the baseplate.
Alternatively, a commercial non shrink grout material can be used, mixed and used according to the makers’ instructions.
Grout foundation bolts
Traditional method
For this method we use the holes for the foundation bolts cast in the plinth. 1. Mix the cement or commercial grout 2. With the bolts in place in each hole, fill with grout to within 25mm of the top to allow a key for final grouting
Modern method
For this method it is not necessary to cast holes in the plinth with epoxy adhesive being used instead of grout mix.
The following is a general description on how this is done, however when fixing with epoxy adhesive refer to the manufacturers’ instructions for t he a dhesive being used:
Step 1 – Measure and mark the position of the foundation bolts on the concrete block. For some baseplate designs it is possible to locate the pump set on the foundation and drill directly through the baseplate mounting lugs.
Step 2 – Drill a hole to take the foundation bolt which should typically be no larger than 6mm wider than the bolt diameter. For good quality concrete, the depth of the hole should be generally 10-15 times the bolt diameter, see Figure 3.
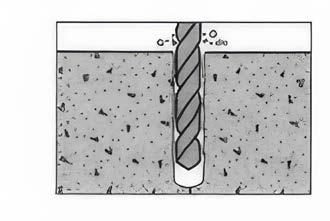
Step 3 – Scrub the hole with a stiff bristle brush to remove all drilling debris that will inhibit bonding, see Figure 4.

Step 4 – Blow hole clean with oil free compressed air, brush and blow clean again. All holes should be clean and sound, see Figure 5.
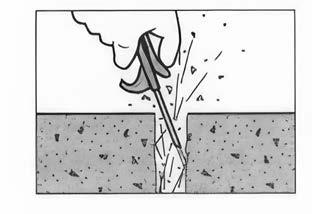
Step 5 – Prepare the epoxy mix in accordance with manufacturers’ instructions ready to fix in the foundation bolt.
Figure 2.
Figure 3.
Figure 4.
Figure 5.

Step 6 – Fill the prepared hole with the mix to approximately half the hole depth, see Figure 6.

Step 7 – Insert the foundation bolt slowly in a twisting motion into the hole forcing it to the bottom until the adhesive flows to the top. Twist the bolt to ensure firm contact and a bond is established, see Figure 7.
For both above methods of grouting and fixing the foundation bolts, the g rout and adhesive should be allowed to cure. For the grout, 72 hours, for t he adhesive as recommended by the manufacturer.
Grouting the baseplate
Why grout a baseplate? Grouting makes up for any discrepancy in the elevation
and flatness of the concrete, it also fills a ny voids to provide a precise and level bearing for the baseplate.
When the foundation bolts are set, recheck the levels of the machined pads on the baseplate with a straight edge and spirit level.
To obtain these levels, it may be necessary to adjust the packing under the baseplate and tighten certain foundation bolt nuts to pull the baseplate down at certain points. It is for this reason that foundation bolts are grouted in first. It should be remembered that when an adjustment is made the level in another direction will change.
When levelling is completed and all foundation bolts are pulled down tightly, the preparation for grouting the baseplate can take place.
A dam should be erected around the baseplate just above the lower flange of t he channel as shown in Figure 8.
The grout should be from Portland cement and sand as discussed in the grout section above.
The grout should be well rammed under the baseplate with a wooden stick.
A s an alternative to the above, a commercial non shrink grouting
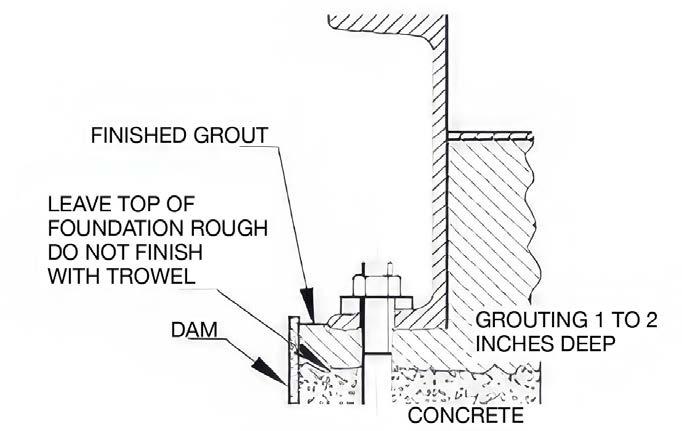
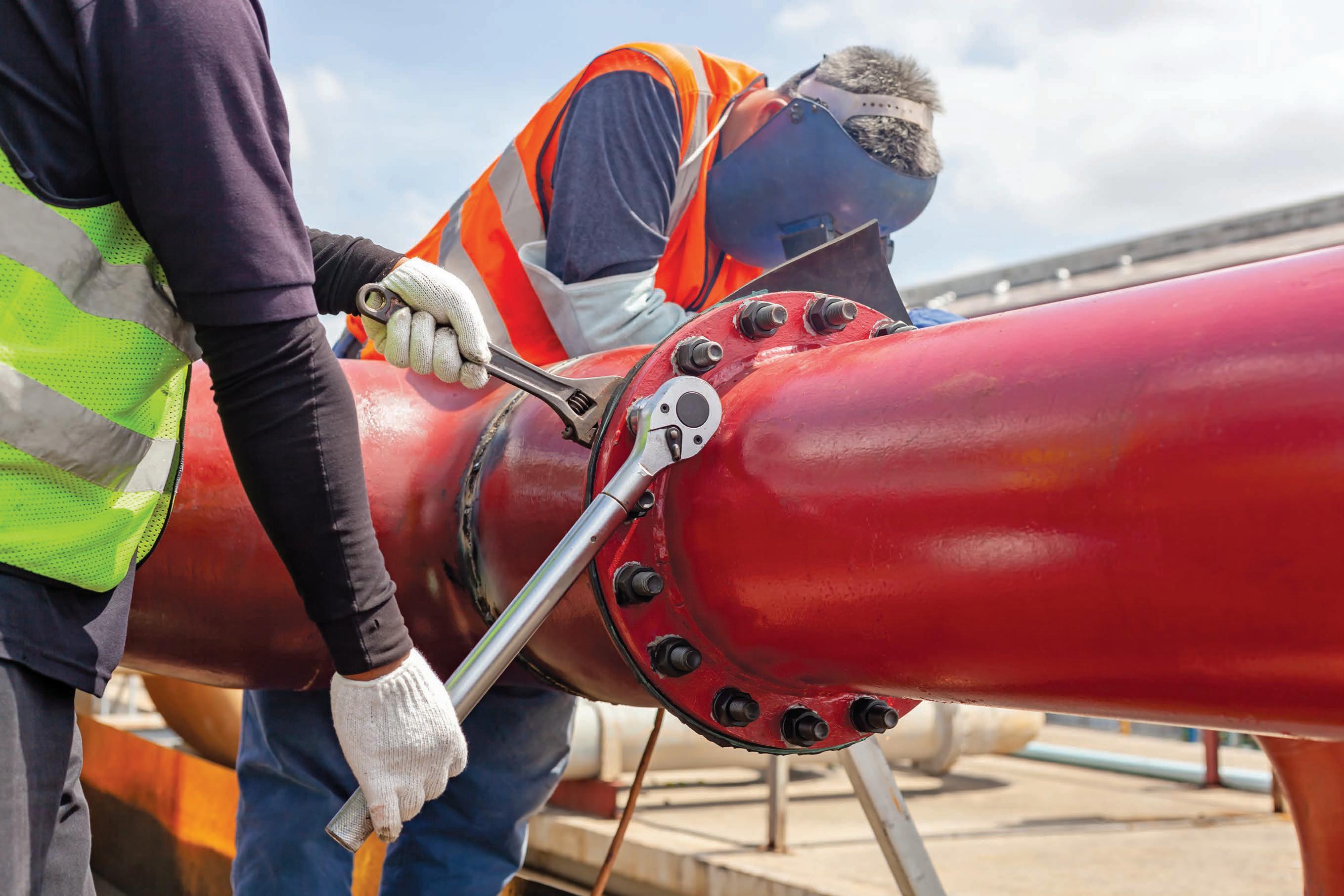
material can be bought, mixed and used strictly in accordance with the manufacturers’ directions.
Note: it is important that the grout fills all the cavities between the lower fl anges and the foundation and must not shrink after curing.
W hen the baseplate has a drip tray with air vents the grout must be filled to the top of all the air vents and fully penetrate every corner under the drip tray leaving no voids under the tray, because of the nature of this type of baseplate the grout is a critical part of the baseplate integrity and voids can lead to higher vibration when the pump is r unning.
When the grout is set (normally after 48 hours) the dam should be removed, a nd a smooth finish given to the grout a nd foundation surfaces. Uniformly re-tighten all foundation bolts and check the pump set alignment.
The next step is to align the driver with the pump if the driver has been supplied separately. It is important to note that the flexible coupling p ermits axial movement of both pump and driver shafts and compensates for thermal expansion. It is to be emphasised that since pin and bush type couplings are designed to reduce the transmission of shock to the bearings etc., and do not compensate for misalignment, they must be aligned to the same accuracy a rigid coupling.
Coupling alignment is fully explained in a later part of this series.
Summary
This article outlines the essential steps for correctly installing a pumpset to the point where the associated pipework is installed including the occupational and safety requirements. Future articles wil l cover the remainder of the installation process including pipe installation coupling alignment and installing b elt dr iven pumps.
Figure 6.
Figure 8.
Figure 7.
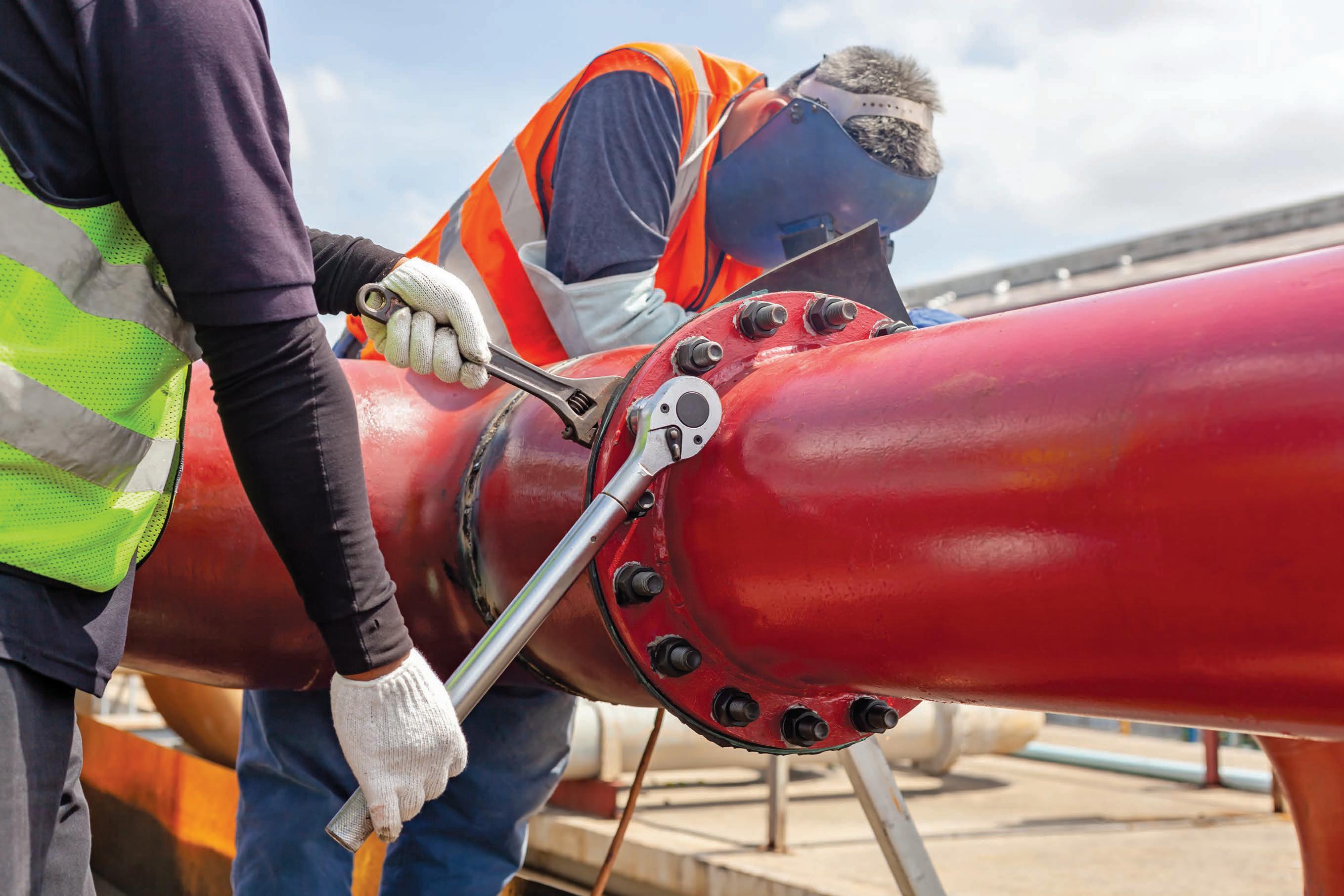
Properly installing a pump requires implementing the right processes and ensuring that you have prepared appropriately. Image: tong2530/stock.adobe.com
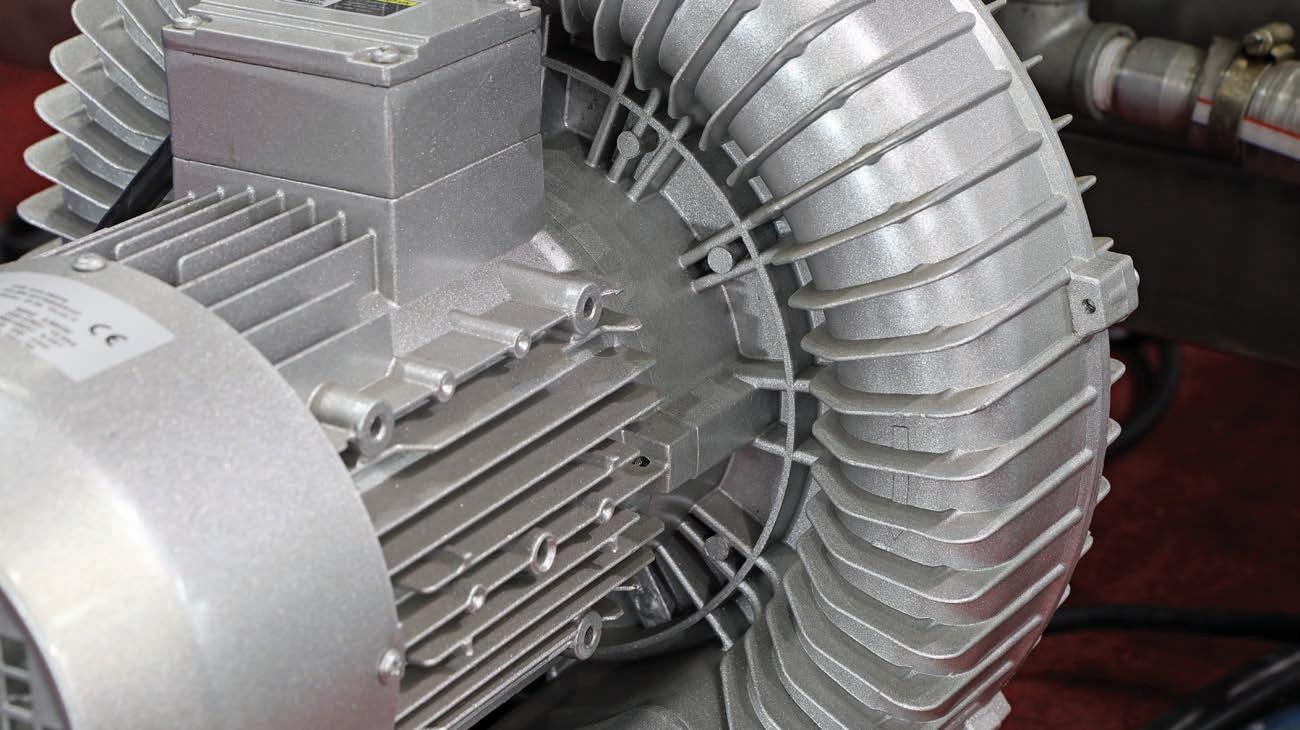
Under seal chamber pressures: part 2
Ron Astall of United Pumps Australia dives back into the world of pump curves to explain how understanding seal chamber pressures could leave you flush with success.
Often, seal and pump personnel are unclear about each other’s expectations. In the previous article, I looked at the pressures inside pumps and how these pressures affect seals. We also covered basic principles, examining pump internal construction and discussing how the pressure is distributed within the pump casing. The focus was on single-stage end-suction pumps, but the logic extrapolates to other configurations. Most single-stage conventional pumps will have front rings, back rings and balance holes. For these, the seal chamber will be at or slightly above suction pressure. For smaller pumps, there may not be back rings, and the seal chamber will be closer to discharge pressure.
In that previous piece, we asked, “Will flush piping change the pressure in the seal chamber?” The short answer is that it may. Seal piping systems are usually classified as either primary or secondary. Primary seal piping affects the seal chamber conditions inboard of the mechanical seal (or gland packing). Secondary systems are for dual seals and regions outboard of the seals. For now, we will only discuss what we call primary seal piping. That’s because this directly affects the seal chamber conditions, which dictate the rating and type of seal selected.
A flush creates flow
Fundamentally, a seal chamber flush creates a flow of liquid. A flush may also alter the seal chamber pressure, but only if the flow is restricted.
A tight clearance or an orifice in the flush circuit will create a change in pressure, depending on whether you are upstream or downstream of the restriction.
Why have a seal flush?
API 681 / ISO10349 standards define standardised piping plan layouts, which are useful across all pump types and
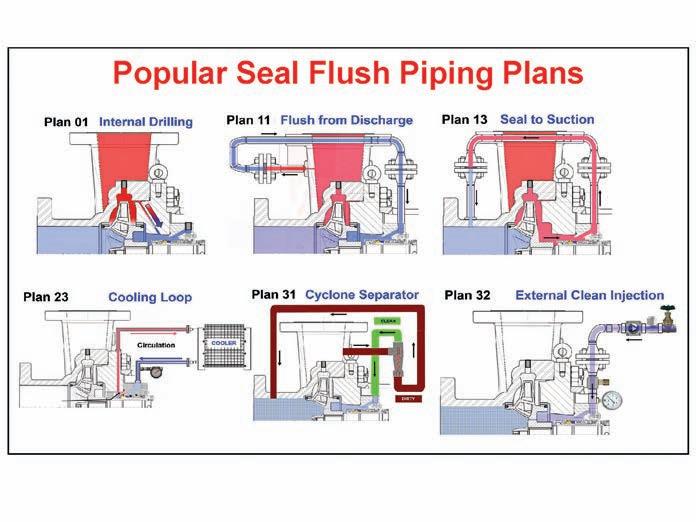
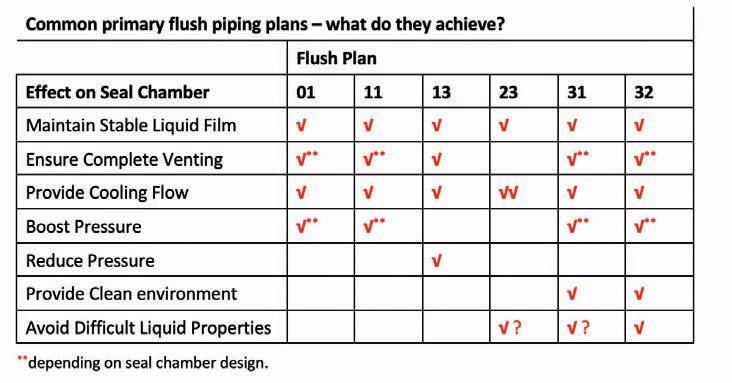
applications. A selection of common primary piping plans and their expected impact on seal chamber conditions is shown above.
Let’s look at several of these flush plans in more detail.
Plan 01 and Plan11
Plan 01 and Plan 11 are the most common flush plans. For many people, they are interchangeable as they create
a flow from a high-pressure region to the seal chamber. Usually, the highpressure region is the pump discharge; for multistage pumps, it may be from an intermediate stage. Plan 01 (Figure 1) uses internal passages in the pump casing, and the flow does not enter through the seal plate. For this reason, Plan 01 is not as flexible as Plan 11 (Figures 2 and 3) in controlling pressure and heat removal.
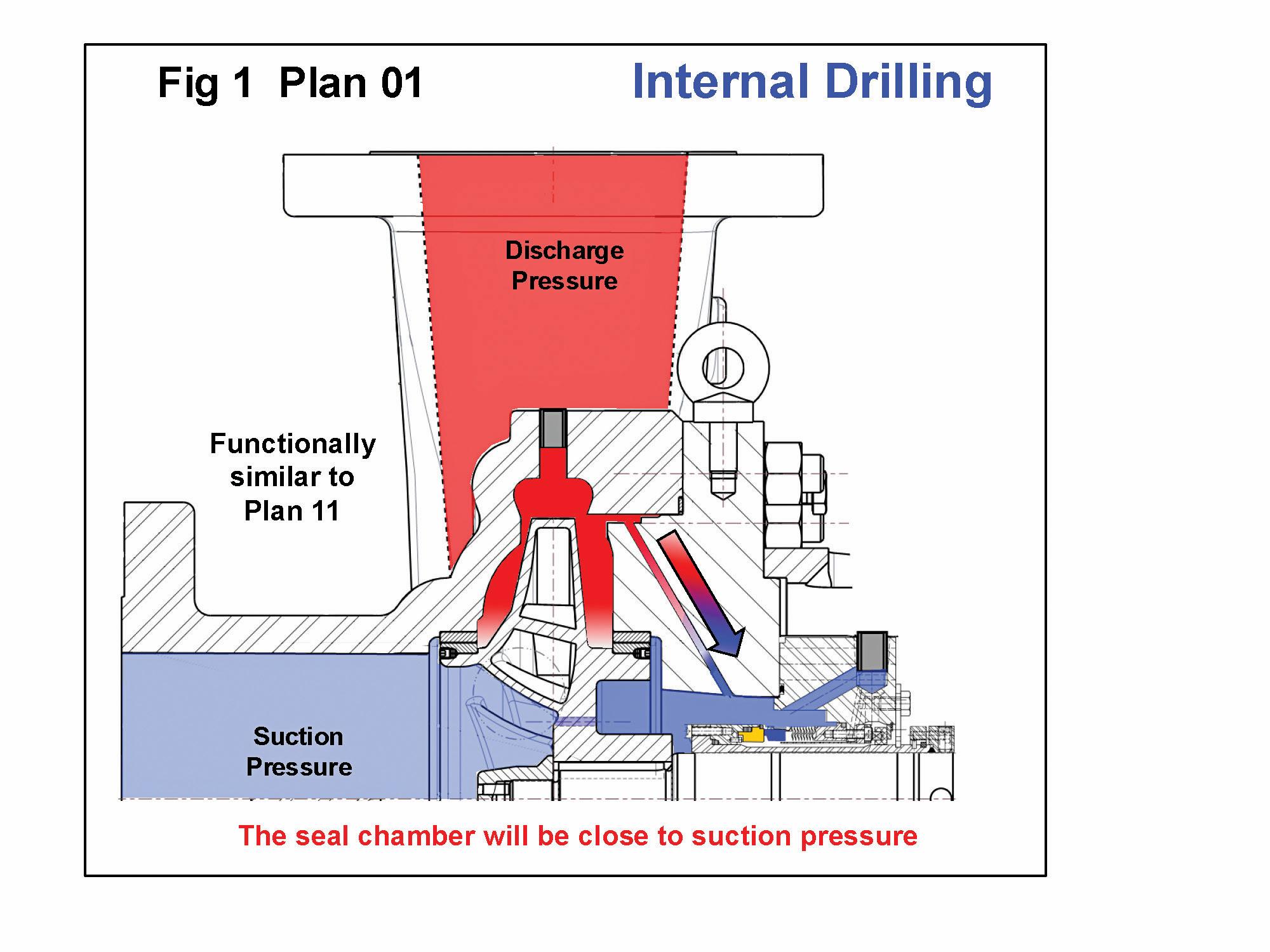
allows the use of an orifice to control flow. The flush past the seal faces limits local heat build-up but does not provide additional cooling. Because of the direct connection through the seal plate, the flush can also be directed more accurately to the seal faces.
When used in conjunction with a Throat Bush, Plan 11 can also increase seal chamber pressure (Figure 3).
Plan 13
Generally used for vertical pumps, Plan 13 (Figure 4) has the primary advantage of ensuring positive venting of the seal chamber. As with Plan 11, flow past the seal faces limits heat buildup but does not provide additional cooling. Flow is from the seal chamber back to pump suction, which means that the seal chamber needs to be above suction pressure to ensure adequate flow.

As with Plan 11, an orifice is usually installed to control the flow. This arrangement is often used when the pump does not have back rings and balance holes, particularly when the seal vendor wants a pressure higher than pump suction pressure in the chamber for vapour suppression purposes. When a throat bush is installed in the seal chamber, the Plan 13 bleed back to suction can, conversely, be used to reduce seal chamber pressure.
Why have a seal flush?
A flush is often indicated to improve the environment for the mechanical seal. We need a stable liquid film at the seal faces. An appropriate seal flush plan can ensure venting, cooling flow, and pressure control.
This article has only briefly scratched the surface showing several simple primary flush plans for single seals. We have also seen how a throat bush in the seal chamber can assist with pressure management.
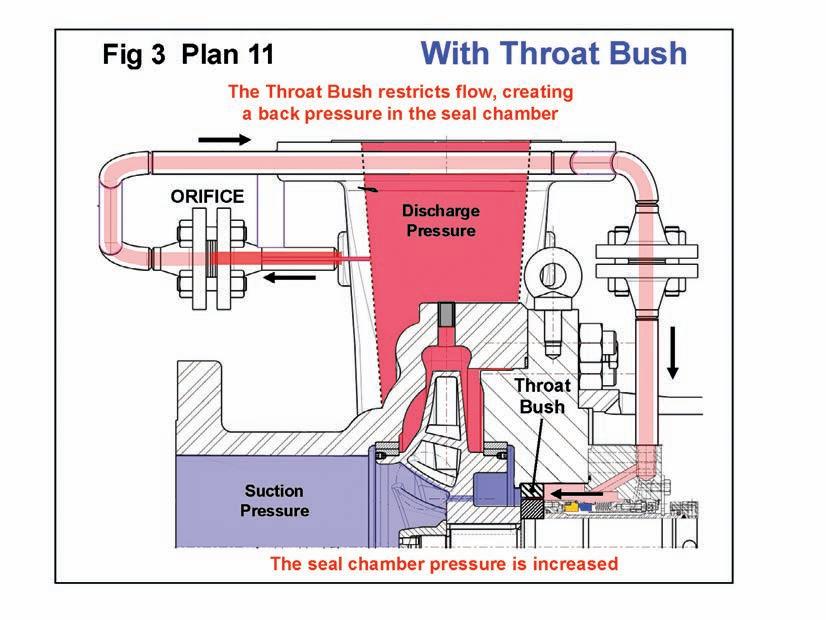
In the next instalment, we will discuss more of these plans and how to more positively manage liquid properties at the seal through cooling, solids removal, and clean injection.
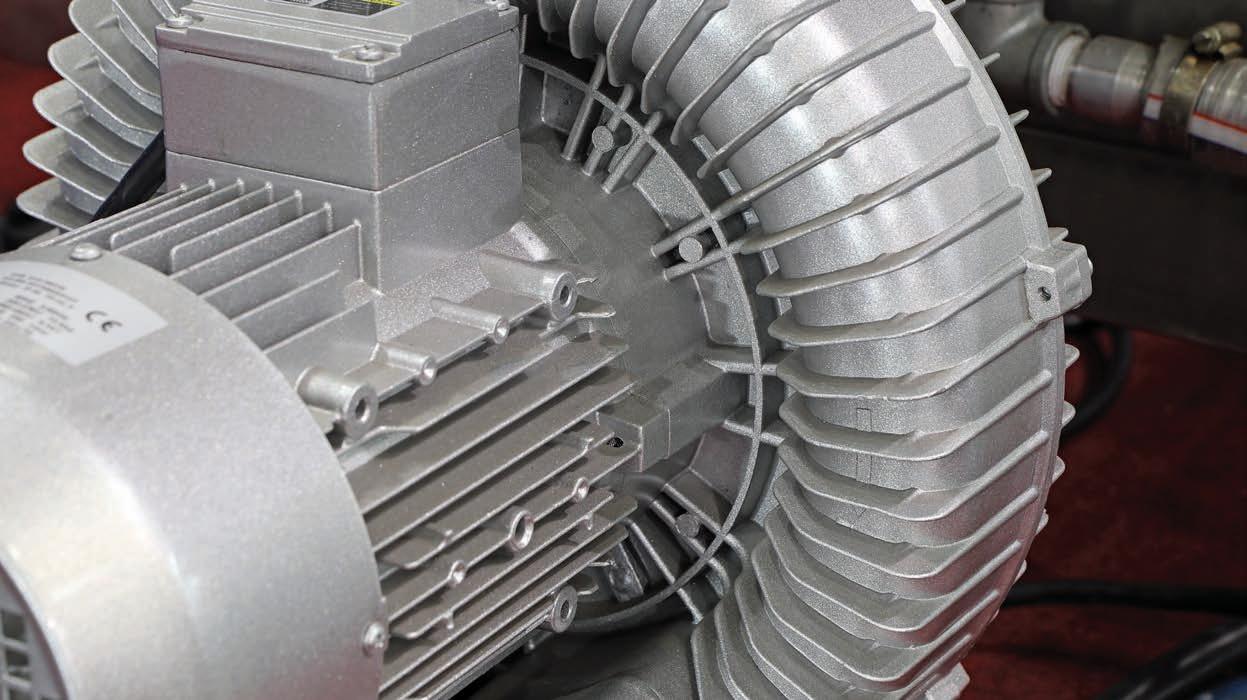

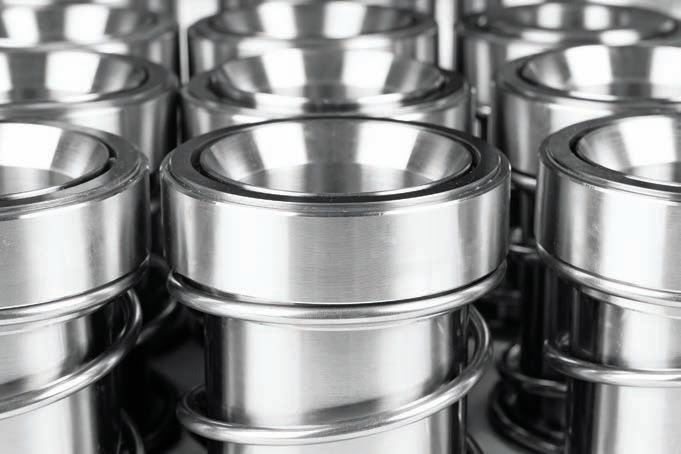
iSOLUTIONS
TAKE FULL CONTROL AND OPTIMISE COST SAVINGS
In almost every industrial cooling application, there are significant process optimisation potentials to be realised. With Grundfos iSOLUTIONS and E-pumps, you can achieve substantial savings in energy, water and other operational costs, while gaining greater system overview and control. So, if your daily operations includes a pump system for industrial cooling, Grundfos iSOLUTIONS can help you connect to higher cooling efficiency and control.
Read more about the benefits of Grundfos iSOLUTIONS and the cases to prove them at grundfos.com/au
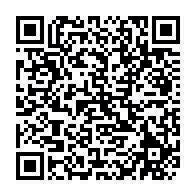
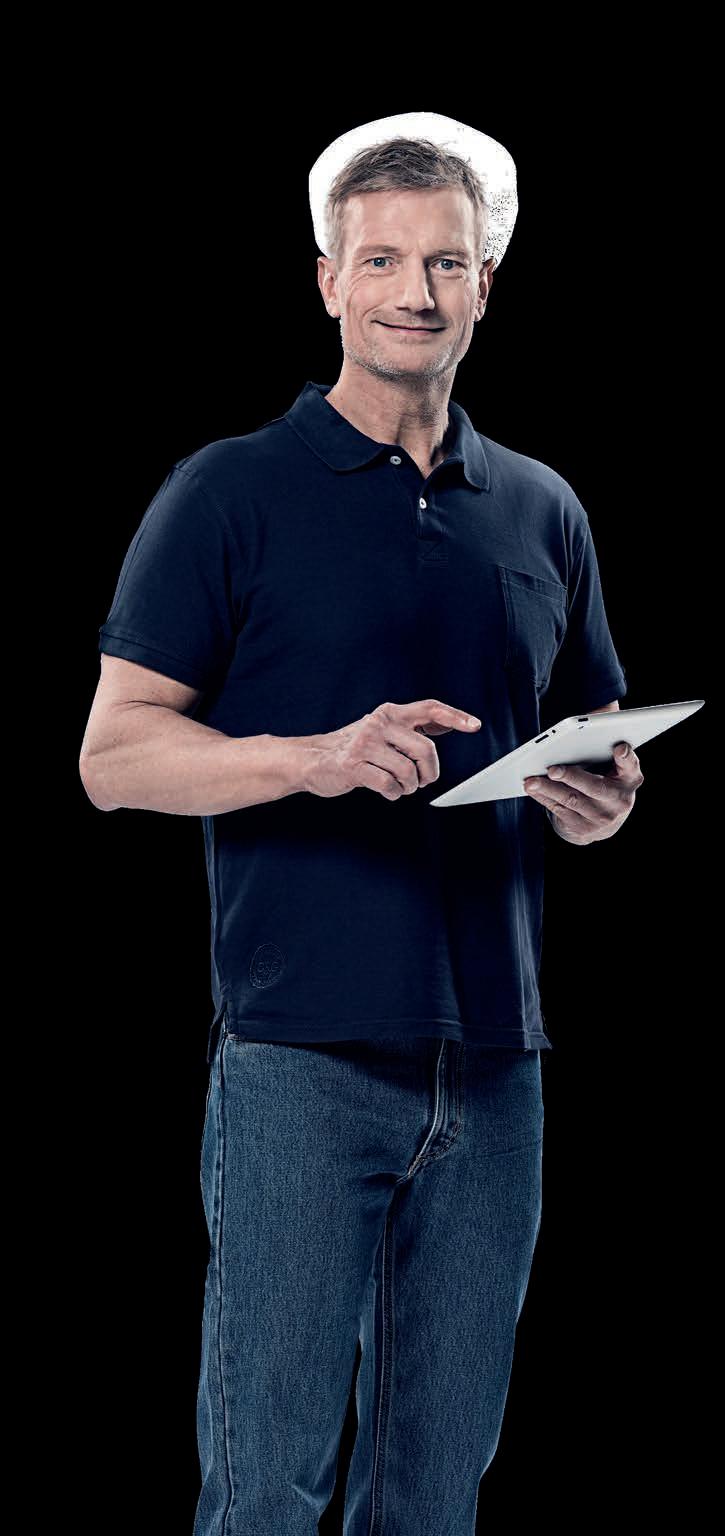


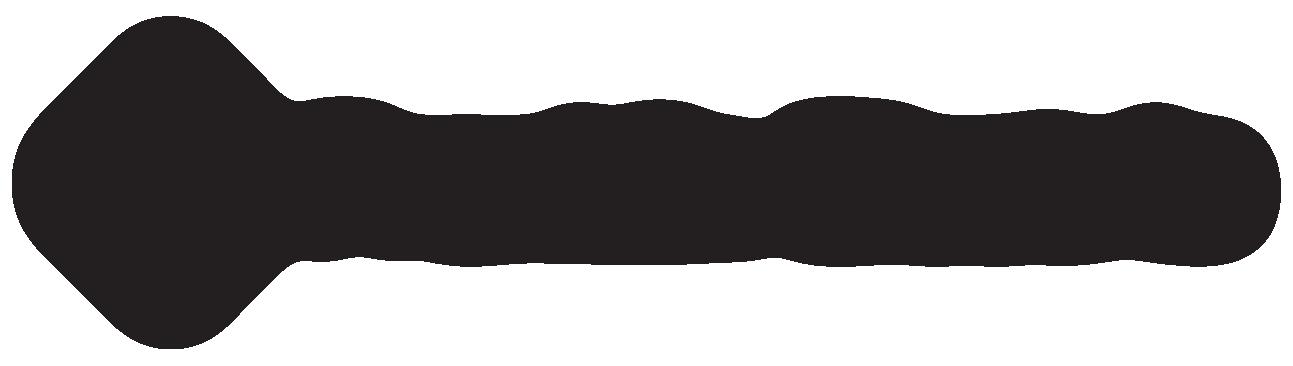

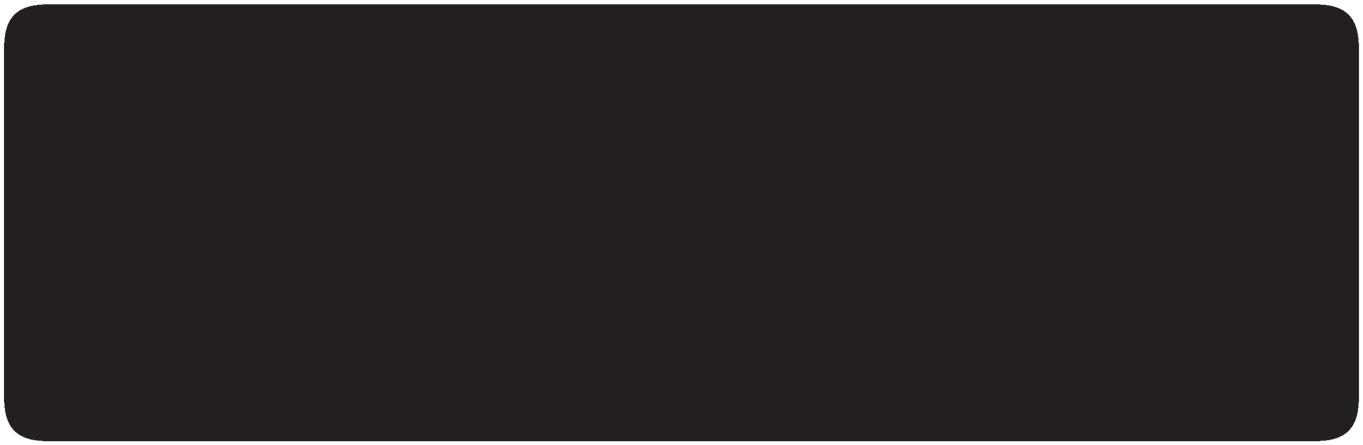

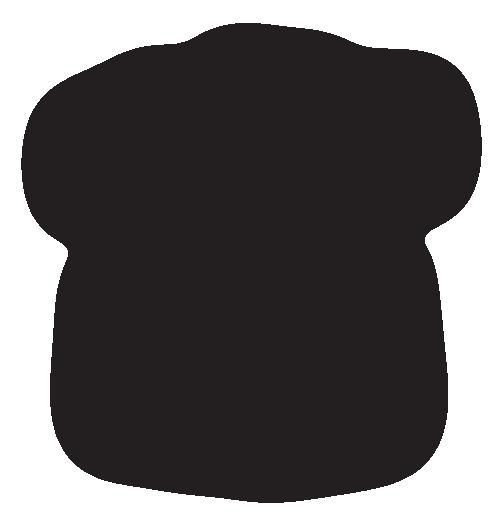
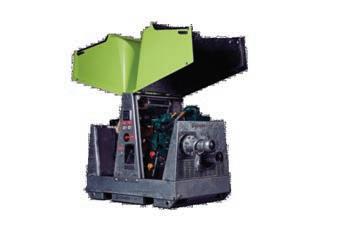
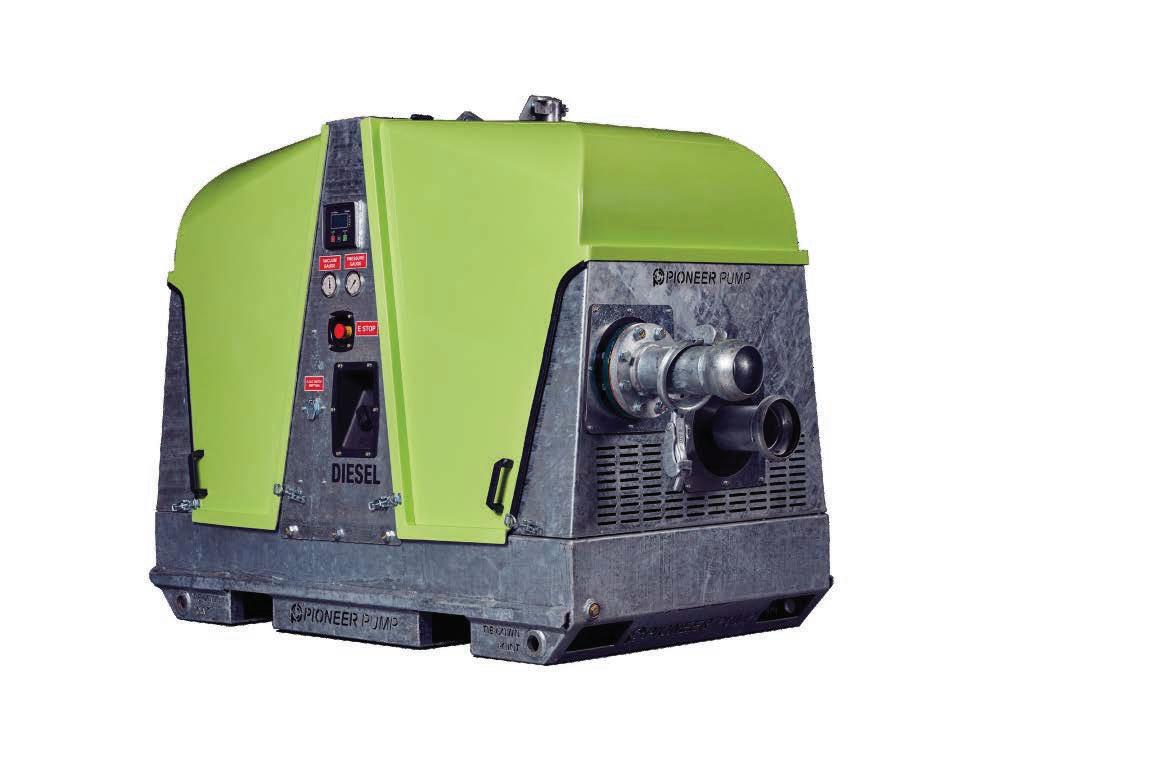

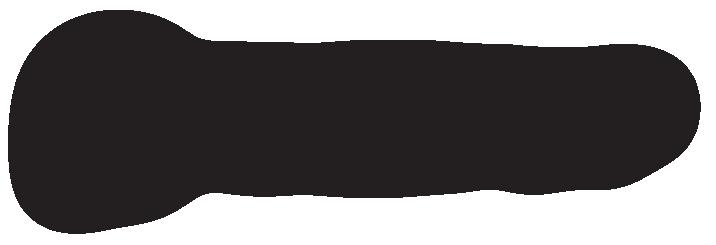
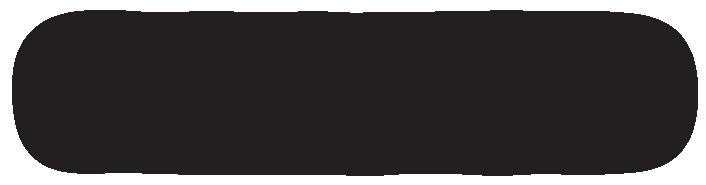

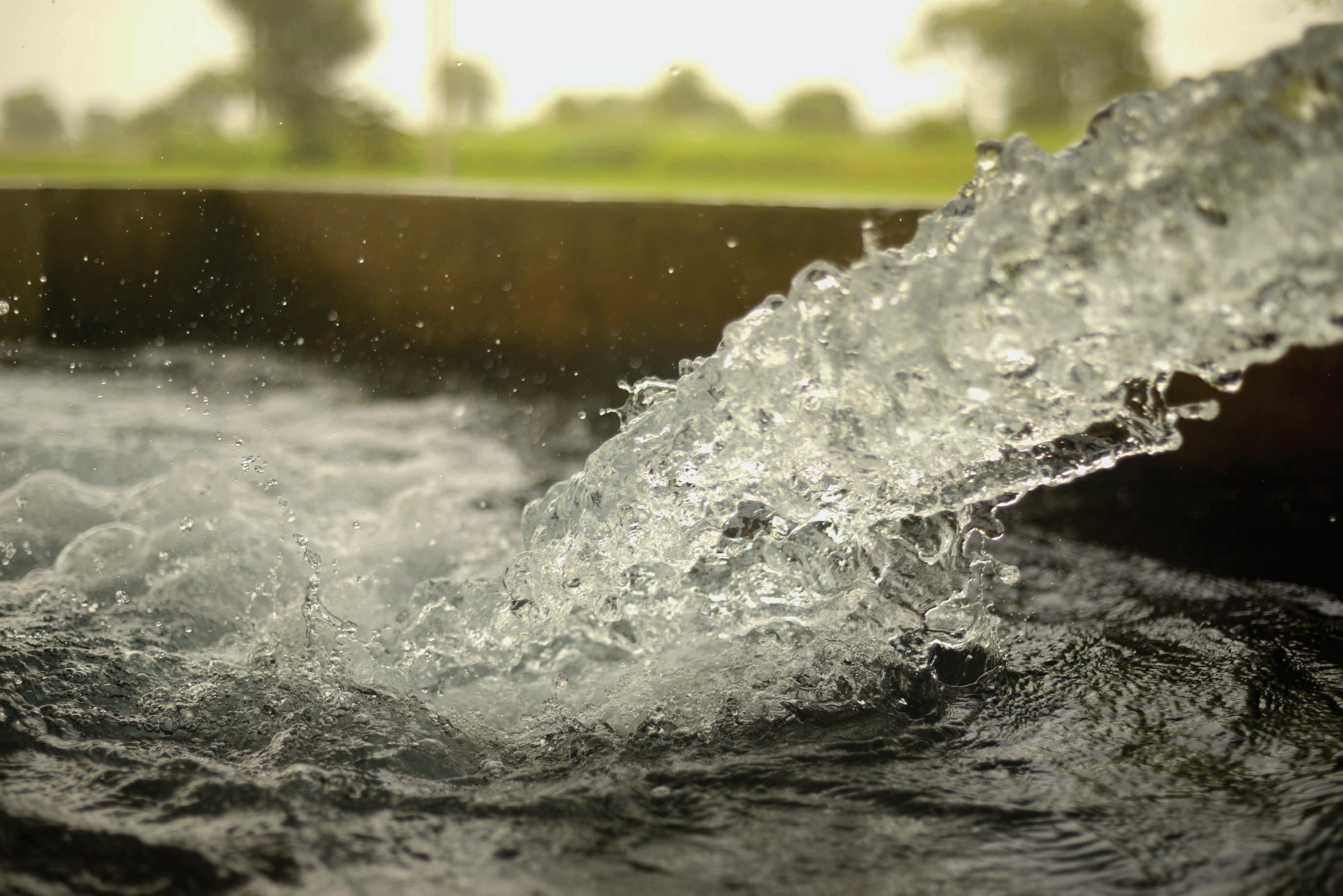

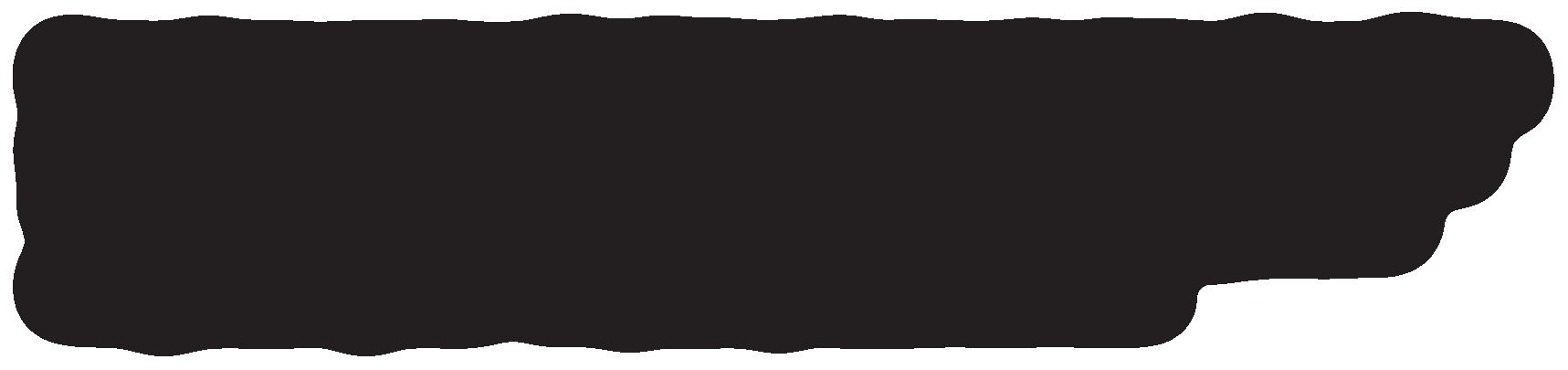
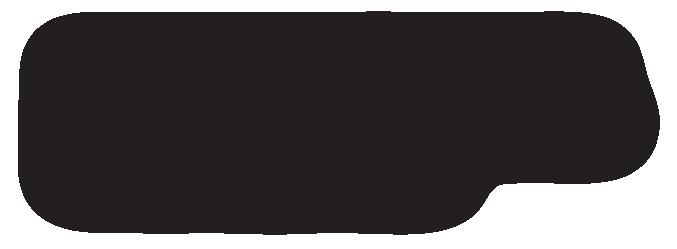

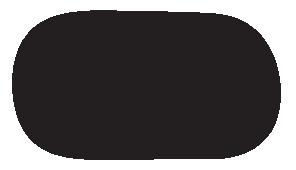
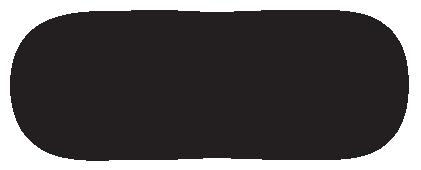
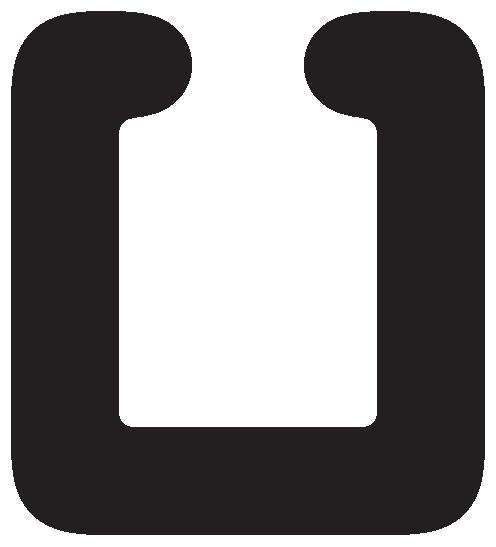
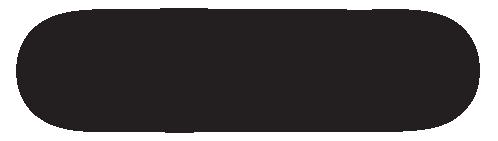