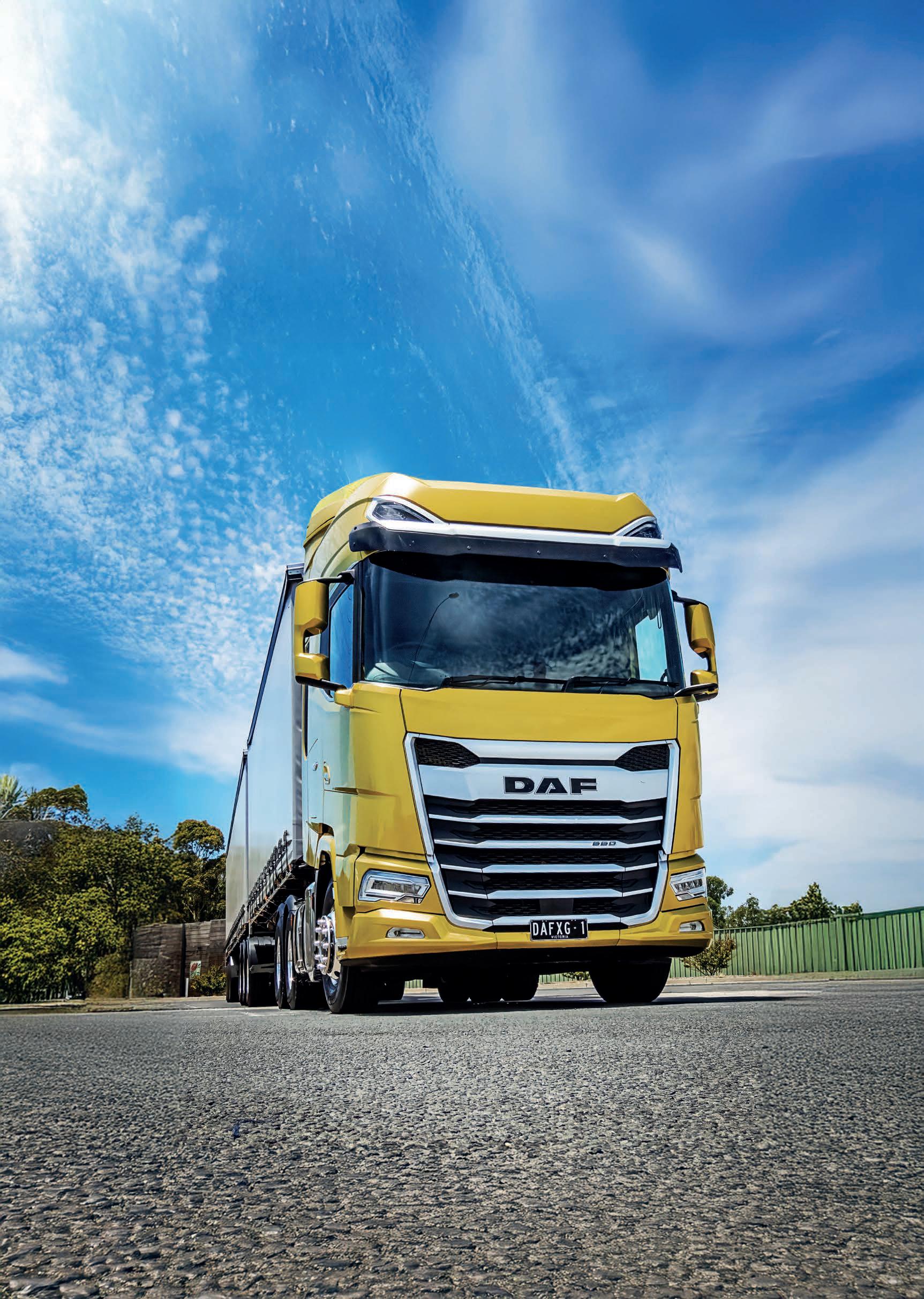
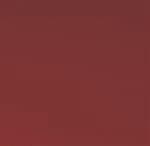
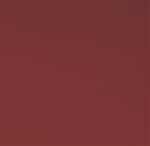
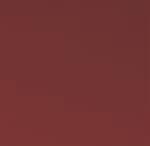
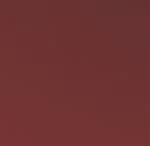
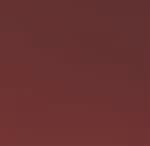
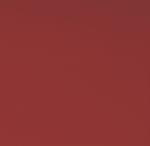
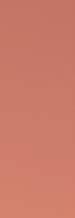
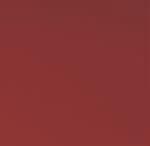
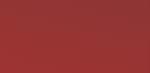


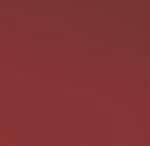
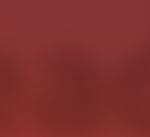

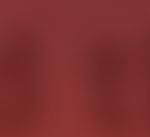
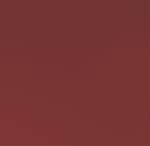
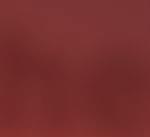

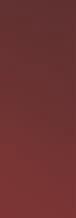
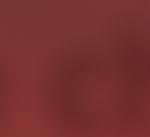


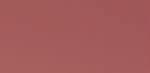

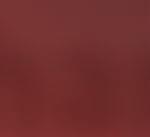

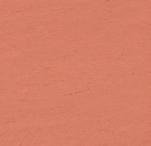

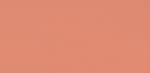
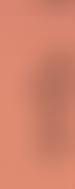




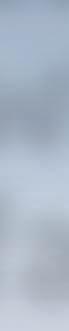

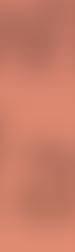
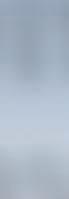
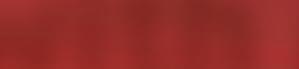
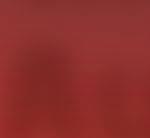
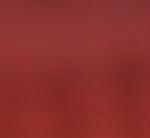
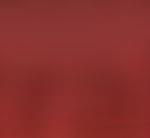
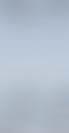

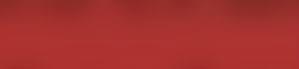
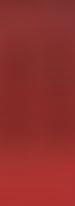
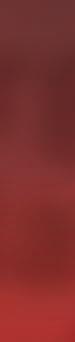
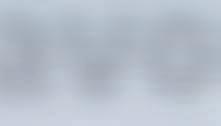
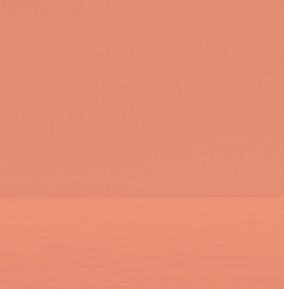
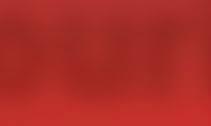
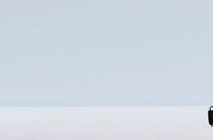
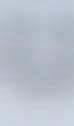
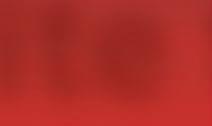

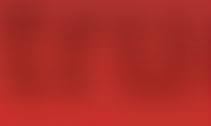
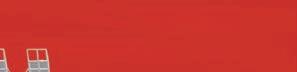
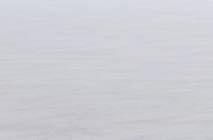
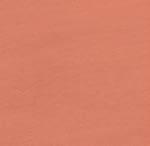
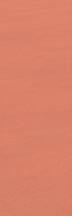

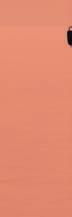

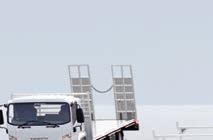
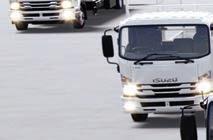
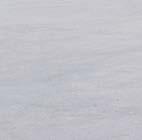


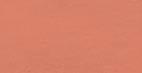
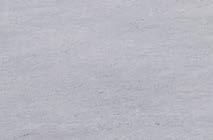
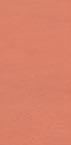
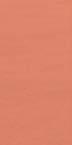
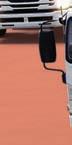
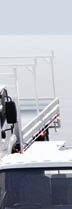
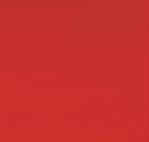



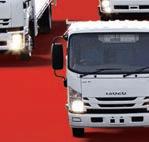


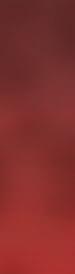
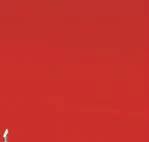
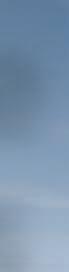
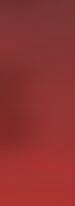
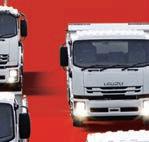
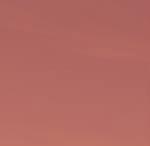



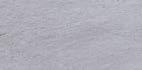

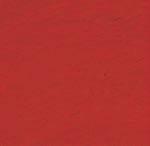
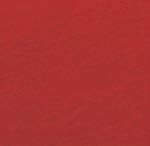
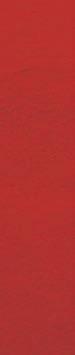
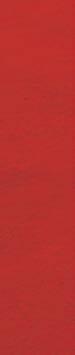
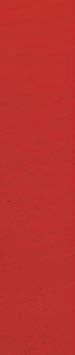

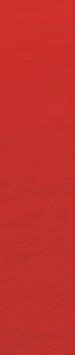
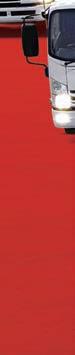
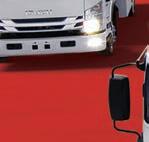
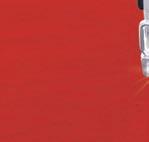
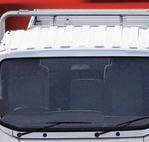
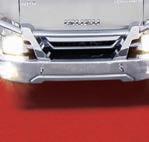
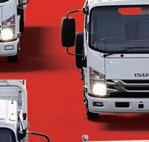
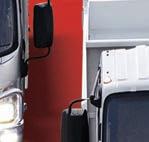
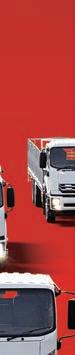
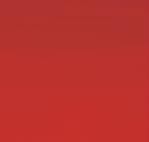
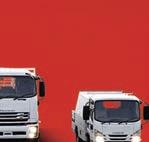
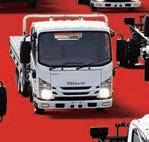
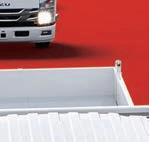
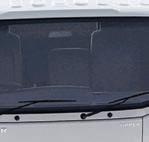
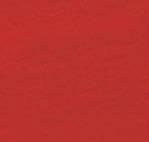
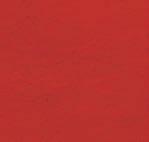
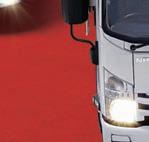
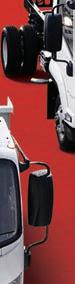
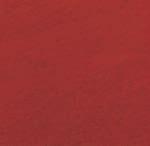

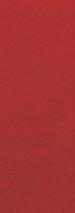
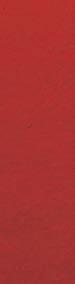
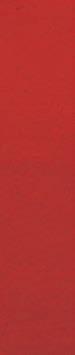
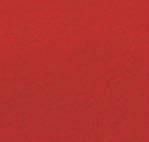
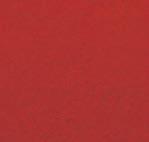

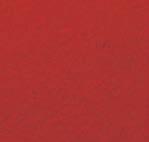

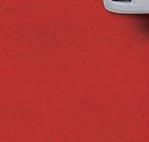
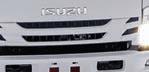



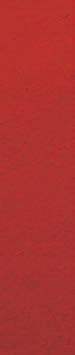
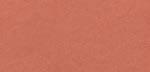


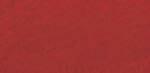

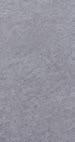

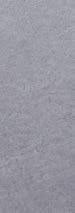
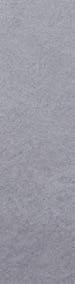
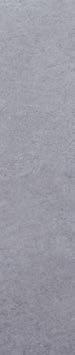
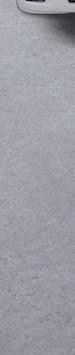

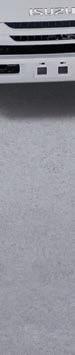
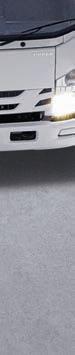


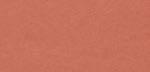
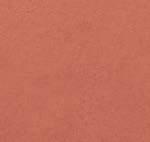
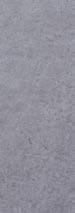






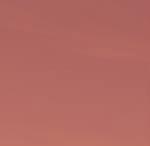
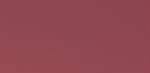
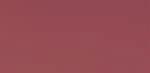


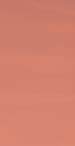
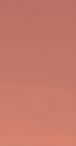
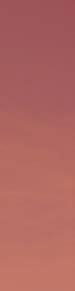
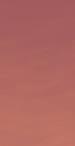

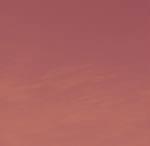
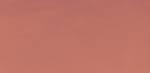
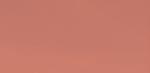

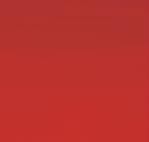
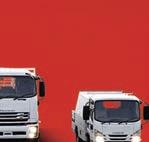
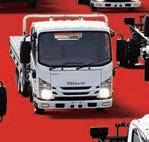
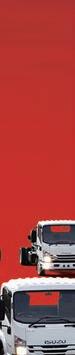


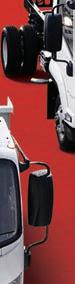

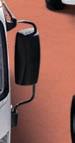

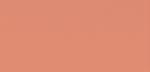
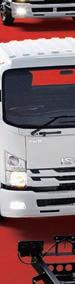

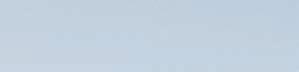
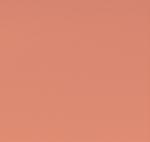
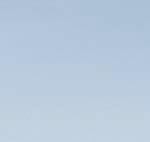

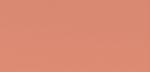
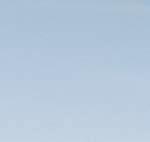
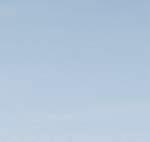
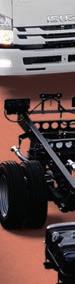
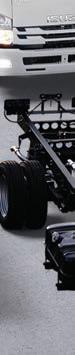
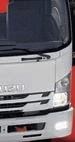

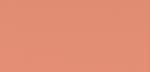

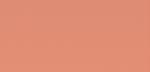
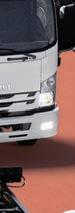
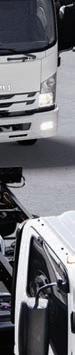
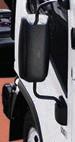
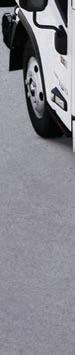
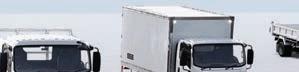
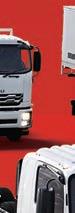
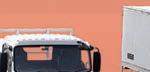

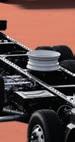
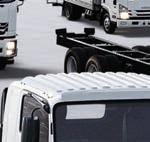
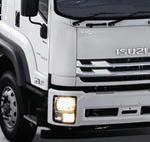
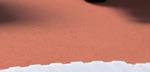
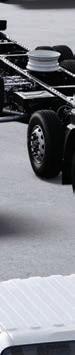
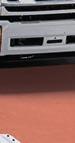
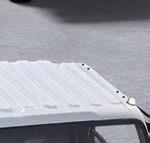
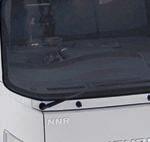

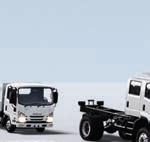
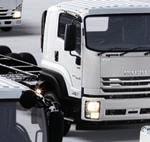



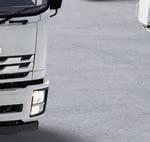

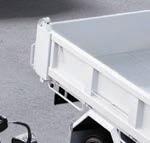
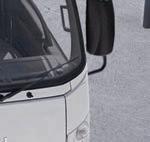
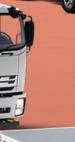
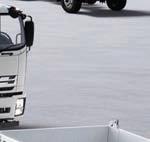

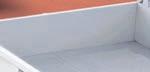

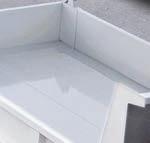
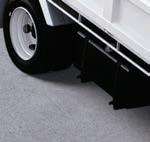

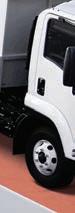
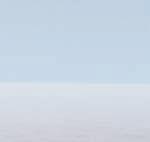
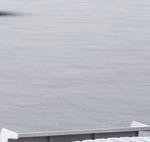
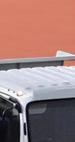
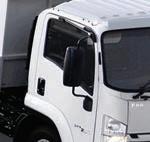
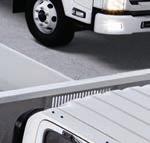
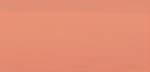
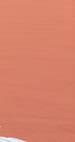
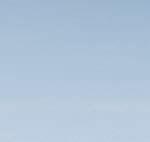
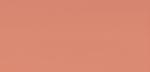
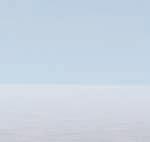
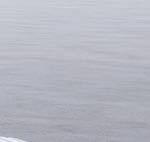
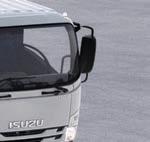
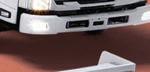
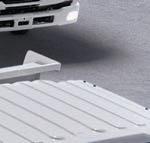

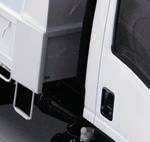

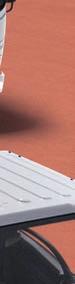



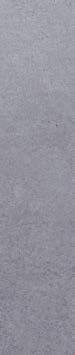

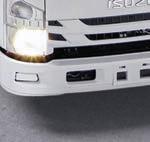


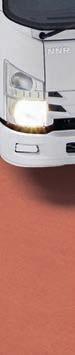
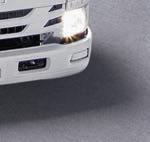
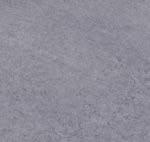
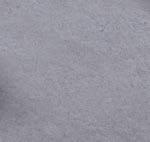
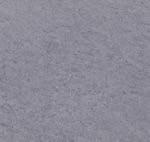
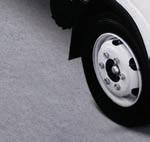
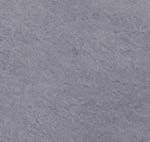
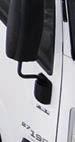



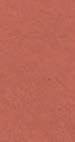
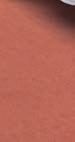
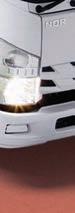
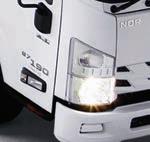
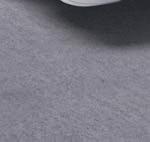


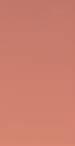
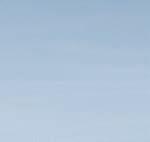


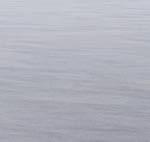
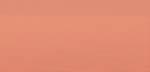
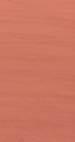
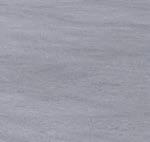

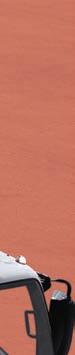
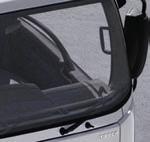
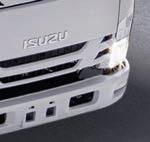
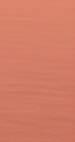

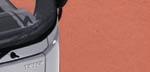
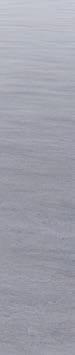

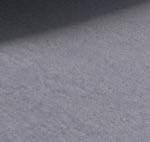


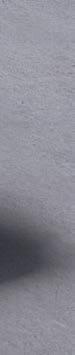



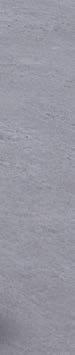
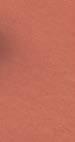




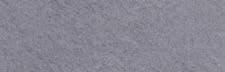
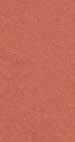



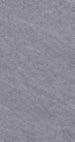
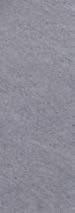

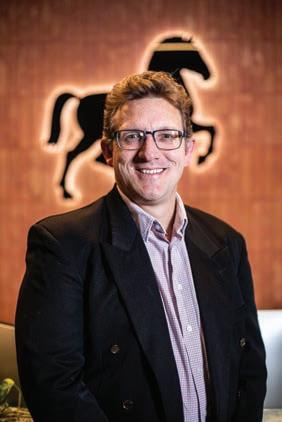
As this edition of Powertorque magazine heads off to the printers hundreds of roads are still blocked in North Queensland in the wake of a major floods around Townsville.
Residents and townships have been without power for nearly 10 days, and trucks have been backing up on the Bruce Highway, unable to get past the Ollera Creek Bridge between Ingham and Townsville — because half of the bridge fell into the creek.
Thankfully the Army is on site putting together a temporary bridge that will allow emergency services and some vital supplies through.
It is in these tough times that the transport industry truly steps up, and the broader community starts to realise just how important those trucks rolling up and down the highway all day, every day, really are.
It has been heartening to see the Queensland Trucking Association on the front foot advocating for transport operators in the region, and transport companies lining up to have supplies ready to roll as soon as possible to re-stock the shelves and help the people of North Queensland to get back on their feet.
Any disaster relief funding that comes through for this latest episode should include some support for the businesses along the supply chains, from the transport
operators to the wholesalers and retailers brought to a standstill by the weather.
It is also imperative that any rebuilding takes note of the water levels achieved in this latest episode and ensures roads and bridges are upgraded to withstand the pressure of a Queensland wet season.
Building for a safer, more productive, future is a key element of the stories in this edition of the magazine.
On the new truck side, Tim Giles shares his findings on the latest DAF being built at Bayswater, complete with all the safety gear and a low emission engine.
We also take a look at the role hydrogen power may have for certain trucking tasks, and how the ARENA funding roll out is attempting to fast track the move to greener transport alternatives.
PUBLISHED BY
Prime Creative Media Pty Ltd
ABN 51 127 239 212
379 Docklands Drive, Docklands VIC 3008 Australia
Telephone: 03 9690 8766
Email: enquiries@primecreative.com.au
Chief Operating Officer: Christine Clancy
Editor: Geoff Crockett: 0421 299 963 geoff.crockett@primecreative.com.au
Assistant Editor: Alex Catalano
Technical Editor: Tim Giles
Contributor: Bob Woodward
Correspondent: Will Shiers (UK)
Advertising Manager: Peter Hockings: 0410 334 371 peter.hockings@primecreative com.au
Client Success Manager: Isabella Fulford, isabella.fulford@primecreative.com.au
Circulation & Subscriptions Manager: Frank Rapone
Head of Design: Blake Storey
Designers: Danielle Harris, Jacqueline Buckmaster
Outgoing NHVR CEO Sal Petroccitto reflects on 10 years in the hot seat and we talked to a range of operators including Russell Transport who celebrate 100 years in the game in 2025.
Closer to the workshop, Cummins, Atmus and Hendricksen have news to share on their products, while Geotab reflect on the eight big areas they see telematics impacting in 2025.
I hope you enjoy the read, and encourage you to get in touch if there’s an issue or story you would love to see tackled in a future edition of PowerTorque magazine.
Official Media Partners: REGISTERED BY Australia Post - ISSN 1445-1158
SUBSCRIPTION
03 9690 8766
subscriptions@primecreative.com.au PowerTorque Magazine is available by subscription from the publisher. The right of refusal is reserved by the publisher.
Annual rates: AUS $60.00 (inc GST). For overseas subscriptions, airmail postage should be added to the subscription rate.
DISCLAIMER
PowerTorque Magazine is owned and published by Prime Creative Media.
All material in PowerTorque Magazine is copyright and no part may be reproduced or copied in any form or by any means (graphic, electronic or mechanical including information and retrieval systems) without written permission of the publisher.
The Editor welcomes contributions but reserves the right to accept or reject any material.
While every effort has been made to ensure the accuracy of information, Prime Creative Media will not accept responsibility for errors or omissions or for any consequences arising from reliance on information published.
The opinions expressed in PowerTorque Magazine are not necessarily the opinions of, or endorsed by the publisher unless otherwise stated.
Sometimes, sticking to what you know is the best way to handle change. At least, that’s what worked best for Queensland-based The Careful Carriers.
The issue facing the engineers at Paccar Australia designing the DAF XG+ for the Australian truck market was just how to bring together both European and North American technology.
Dairy producers Lactalis Australia rely on their fleet of MAN trucks, hired through Penske Leasing, to get their milk and cheese onto supermarket shelves.
After over 10 years in the role as CEO at the National Heavy Vehicle Regulator, Sal Petroccitto is moving on. Tim Giles sat down with him for an in-depth chat.
Storied trucking operator Marley’s Transport has found a unique way to get a massive combination on the road, with help from Eaton.
Gas trucks are growing in popularity in the UK, and Will Shiers gets behind the wheel of a potential game-changer, a BioCNGpowered Scania R460 6X2*4.
Getting to 100 years in business is a milestone, but how Russell Transport has achieved their longevity comes down to making all the right moves.
The launch of TruckSafe in New Zealand will be a huge milestone for the Australian Trucking Association, writes TruckSafe Chair Paul Fellows.
42 THE CASE FOR SLASHING ACCESS PERMITS
NatRoad CEO Warren Clark believes that removing the majority of heavy vehicle access permits will save time and money for operators and governments alike.
HYDROGEN FINDING A HOME
While hydrogen-powered trucks are still at their genesis in Australia, they may be finding a niche in the market.
NEW LOOK COMING TO NHVR PORTAL
One of the National Heavy Vehicle Regulator’s most important services,the NHVR Portal, is set for a new look.
POWERTRAIN INTEGRATION HAILED AS WIN Cummins will be showcasing its new integrated powertrain for the first time at the upcoming Brisbane
PREDICTIONS FOR AI INSIGHTS
From AI-powered insights to smarter infrastructure, Geotab is anticipating how a number of trends are going to shape connected transportation in Australia across the next 12 months.
ALIGNMENT POINTERS
Conducting wheel alignments might not be the end of solving issues with your tyres or suspension.
• Supporting drivers for more than 50 years
• Seating – on a higher level
The Roe 8 and 9 Perth Freight Link project has officially come to a close after the finalisation of an amendment to the Metropolitan Region Scheme.
Construction on the road could no longer go ahead after the WA government removed the Primary Regional Roads reservation form the MRS, with high environmental and heritage significance areas now reserved for parks and recreation. It was originally planned as a freight route for trucks travelling to Fremantle Port, but the current WA government
saw the $450 million price tag as too high a cost.
“This amendment marks a significant milestone in the WA government’s 2017 election commitment to scrap the destructive Perth Freight Link project,” says state planning minister John Carey.
“The road reservation has long been a barrier to planning for the Fremantle/ Cockburn area, and the finalisation of this amendment provides certainty to all stakeholders and the community that this road can no longer go ahead.”
The National Heavy Vehicle Regulator and South Australian state and local governments have collaborated to deliver key heavy vehicle productivity initiatives.
As of January 23, the NHVR is introducing three Oversize Overmass (OSOM) trial notices which will replace the need for operators and drivers to apply for permits on key freight routes.
“Streamlining heavy vehicle access by transitioning permits
to notices will allow operators to travel more efficiently, and I thank the NHVR for their enthusiastic response to improve access to routes subject to multiple heavy vehicle access permits,” says state transport minister Tom Koutsantonis said.
“This announcement is part one of a multi-stage plan to drastically reduce the need for thousands of heavy vehicle permits in South Australia.”
Image:
Adwo/stock.adobe.com
Image:
Simon/stock.adobe.com
Kenworth DAF Melbourne has appointed Paul Wiffrie as its new General Manager.
He will oversee the day-to-day operations of the dealership –including TRP Geelong – and started his career with PACCAR in 2007 in a number of training positions culminating in a stint as its Learning and Development Manager.
Following this he transitioned to PACCAR Parts as its Materials and Quality Manager before he took on the role of Dealer Development Manager in 2019.
PACCAR Australia Managing Director Damian Smethurst says Paul is exceptionally qualified to lead Kenworth DAF Melbourne into its next chapter.
am thrilled to welcome Paul to this pivotal role at Kenworth DAF Melbourne,” Damien says. expertise and leadership will be invaluable as we continue to enhance our service offerings and
This year’s annual NatRoad Conference, NatRoad Connect 25, is set to be held in Shepparton across two days in September, from the 11th to the
More detailed information will be released regarding the conference in the coming months.
The “must attend” event will connect industry representatives, operators, NatRoad members and partners with practical operational
information and advice. Last year’s conference featured discussions, presentations and events surrounding a wide variety of industry-relevant subjects including the creation of mentally healthy workplaces by Healthy Heads in Trucks and Sheds, unfair contract terms from Bristow Legal’s Gillian Bristow, and navigating the road to compliance from Director of TPRS Management Vlad Dugandzic.
The fourth round of the Heavy Vehicle Rest Area initiative will see six new rest area projects funded by the federal government as a part of a $17.4 million investment from the federal and state and territory governments.
These include the construction of two new heavy vehicle rest areas and widespread upgrades at existing areas across the country.
Overall, the initiative provides $140 million in federal government funding over 10 years for the construction of new and upgraded heavy vehicle rest areas.
The New South Wales government is using its $5 million Smarter Highways program to tackle driver safety across the state’s highways.
Regional NSW highways will utilise low-cost technology trials in an attempt to prompt safer driver behaviour, specifically focused on behavioural issues that can lead to crashes, on these roads across 2025. Each trial will utilise
different kinds of technology to detect issues in the network and warn drivers about hazards, including:
• Smarter Highway Activated Vehicle and Environmental Systems (SHAVES)
• Permanent traffic counters
– Road Pod Vehicle Magnetometer (VM)
• Rural Intersection Activated Warning System (RIAWS)
The NSW government hopes that these solutions will lead to safer rural roads across the state.
The projects included through the fourth round of funding include:
• Maranoa Shire Council, Queensland –Asphalt surfacing of the existing heavy vehicle truck stop area at the Roma Truck Stop precinct.
• Queensland – Design and construction of a new heavy vehicle rest area at Homestead West on Flinders Highway.
• Nar romine Shire Council, NSW – Upgrade to the heavy vehicle rest area at Tomingley.
• New South Wales – Upgrade to Ravensworth Eastbound and Westbound rest areas on Sturt Hwy, Maude.
• Yarriambiack Shire Council, Victoria –Upgrade to nine existing truck parking locations in the Yarriambiack Shire.
• South Australia – Stuart Highway Rest Area Upgrade at Arcoona and a new heavy vehicle rest area at Pimba.
In Australia’s busy bushfire seasons, the performance of emergency vehicles can have a considerable impact in saving lives and keeping people safe.
There is an estimated over 10,000 emergency vehicles currently in service across the country, many of which are using Allison transmissions. Their fully automatic
transmissions offer greater control of these vehicles, allowing workers to focus as fully as possible on emergency response.
“Approximately 90 per cent of all metro fire fleets and 80 per cent
“We’ve been supplying the country’s fire services since the 1970s alongside a range of OEM partners including Isuzu, Hino, Scania, Iveco, Freightliner, Mercedes Benz and Volvo. We cover a range
A new report has shown that job seekers are increasingly looking to truck driving as their next career.
The latest Work Watch report from not-for-profit employment services provider Workskil Australia suggests jobs for truck drivers rose 30 per cent in the September quarter of last year, making truck drivers one of the most in demand roles in the employment market.
“The good, the bad and the ugly in the employment market is clearly on show,” Workskil Australia CEO Nicole Dwyer says.
“The overall rise in job placements is very pleasing to
see but it doesn’t hide the reality that it’s increasingly harder for disadvantaged Australians to find a home, pay their bills and hold down a job.
“Often, homelessness goes
unreported because many job seekers do not consider couch surfing to be a form of homelessness. However, it’s difficult to sustain employment when the most basic necessities are unmet.”
Data released by the Truck Industry Council has shown Australia’s heavy vehicle market has continued to go from strength-to-strength, as it recorded a third-straight year of record truck sales across the country.
51,277 units were sold across the country in data released on January 3, 2025, an increase of 3520 units – or 7.4 per cent – over the previously record-breaking 2023 mark of 47,757.
The 7.4 per cent increase was bolstered by the decision for LDV and Peugeot to share data with the Truck Industry Council for the first time in 2024, however excluding the extra 3010 additional sales registered by the two new brands, 2024 would still have been a recordbreaking year.
Significant continued growth in the van sale market laid the foundation for the overall growth
Industry association NatRoad says it is encouraged by the action taken by the Interim Directions Paper of the NSW Freight Reform Program when it comes to fixing the state’s roads.
These directions lay out a new standard for roads in the state, working towards making an automated system for the categorisation of roads. This will provide an easier way to identify problems in the road network.
“Roads are often a thorny issue for government. That’s why it’s
refreshing to see encouraging signs of positive action in the Interim Directions Paper of the NSW Freight Reform Program,” says NatRoad CEO Warren Clark.
“The proposal to implement service level standards on our road network would be a strong step towards better roads. The standards would shine a light on parts of the road network which fall short on road quality, safety and rest areas. Standards must be backed, with governments prioritising funding to fixing the gaps in the network.”
The first Australian-built Volvo FH16 780 XXL prime mover has rolled off of Volvo Group Australia’s Wacol production line and is set to be delivered to NSW company SRH Milk Haulage.
The vehicle features the most powerful truck engine in Australia, the D17 780, and new features including a Crawler Gear equipped with new generation I-Shift transmission and Volvo Dynamic Steering with Pilot Assist.
It will be put to work pulling an A-Double tanker combination between sites on the NSW Central and Northern Coasts.
SRH’s Scott, Regina and Mitchell Harvey were on site at the Wacol production facility to mark the completion of construction.
“Our company has had a long history with Volvo Trucks,” Scott says. “Knowing these trucks have been engineered and built locally for Australian conditions really makes a difference to us.”
Penske Australia and New Zealand has made two new Brisbane-based executive appointments to begin the year.
Gary Bone has joined the business as General Manager of Eastern Operations, while Derek Smits
has taken on the role of General Manager of Truck Supply Chain.
Gary will oversee Penske’s retail branch operations in Wacol, Lytton and Yatala in South East Queensland and Sydney, while Derek will lead
operations teams as well as the vehicle processing centre.
Gary most recently held senior leadership roles with Mack Trucks and Volvo Trucks, and Derek with Diverseco and Hendrickson Asia
The Western Australian and federal governments will conduct the next steps of the $1 billion Tonkin Highway Extension with a contract now awarded for the project.
Along with the Thomas Road Upgrade, the projects will see the transformation of the south-east of Perth, delivering a 14-kilometre extension of Tonkin Highway as well as major upgrades to Thomas Road. The contract to deliver the project has been awarded to the Tonkin Extension Alliance consortium which includes BMD, Civcon Civil and Project Management, Georgiou Group, BG&E, and GHD.
The extension of Tonkin Highway will include a four-lane dual
carriageway from Thomas Road all the way to South Western Highway, including a number of grade-separated interchanges, underpasses and roundabouts.
“The federal government is proud to partner with the Western Australian government to deliver this transformative project, which will significantly enhance Perth’s south-east by reducing traffic pressure and improving connectivity,” says federal transport minister Catherine King.
“This project will deliver significant benefits to Western Australia’s freight and logistics network, by creating a highstandard north-south transport
link, improving road safety, freight efficiency, and connectivity for residents, businesses, and commuters.”
The federal and Western Australian governments are jointly funding a $700 million upgrade for the Kwinana Freeway to greatly increase the state’s freight capacity.
These upgrades will support WA’s Westport project, with the widening of the freeway adding around 50 per cent capacity to the upgraded sections to improve freight efficiency on a road that carries 100,000 vehicles per day.
The new funding builds on the previous $67 million joint commitment towards the planning
and scoping of landside enabling infrastructure for the Westport project.
“Western Australia is an economic powerhouse,” says Prime Minister Anthony Albanese.
“We want to make sure we are investing in future job creating projects like Westport, while still delivering immediate congestion benefits for commuters now.
“This project will support jobs, improve safety and ease congestion for the 100,000 commuters who use the Kwinana Freeway each day.”
The Australian Trucking Association and Daimler Truck Asia Pacific have announced the 10 new Daimler Truck Future Leaders for 2025.
The event is an award-winning leadership program aimed at giving promising young professionals added tools, knowledge and training they need to become strong and effective industry advocates.
Participants in this year’s Future Leaders’ Forum were selected by the ATA’s member associations and Daimler Truck Asia Pacific.
This year’s Future Leaders participants are:
• Jo Tomaszewksi (Road Freight NSW)
• Thomas Morton (Victorian Transport Association)
• Drew Hipwood (Queensland Trucking Association)
• James Upton (Tasmanian Transport Association)
• Sam Jago (Northern Territory Road Transport Association)
• Jonathon Sassella (NatRoad)
• Har rison Gill (Australian Furniture Removers’ Association)
• Sarah Woodruff (Australian Livestock and Rural Transporters Association)
• Ainsleigh Thomas (Transport Women Australia Ltd)
• Monique Robertson (Daimler Truck Asia Pacific)
The Hume City Council in Melbourne’s north-west is proposing a truck ban on sections of its major roads in an effort to ‘improve quality of life’ for people living along them.
It has called for a truck ban to be imposed on sections of Konagederra Road, Wildwood Road, Gellies Road and Bardwell Drive.
Between February and April 2022, the intersection of Mickleham Road and Craigieburn Road was closed by Major Road Projects Victoria so that part of the Craigieburn Road could be upgraded.
Traffic was redirected onto surrounding roads, with council monitoring this increase in traffic and have continued to do so.
Since the intersection reopened, traffic data shows that higher volumes of heavy vehicle traffic have been using local roads like Bardwell Drive, Konagaderra Road, Gellies Road and Wildwood Road (North and South). The council says nearby arterial roads, which are designed for this kind of traffic, have capacity.
Sometimes, sticking to what you know is the best way to handle change. At least, that’s what worked best for Queensland-based The Careful Carriers
Seventy years on the road is no mean feat. For Brisbanebased transport operator The Careful Carriers, it’s a badge of pride they wear with honour.
A family business, the story started in 1954 when Sid Smith bought with his very first truck, which, like many operators post-World War II, was an old Bedford. A loyal man, Sid stuck with his first ever customer, who he hauled paper products for around south-east Queensland, and The Careful Carriers continued with them for 65 years.
Things look a little bit different now, with Sid’s grandson Zacc at the helm of the business. While Sid was delivering single cartons in his Bedford, this continued to evolve with the decades, to semi-trailers, and now four Hinos, which make up the current fleet.
Zacc is the third generation of Smiths running The Careful Carriers, taking over from his father Kenneth 20 years ago and continuing to grow the
business ever since. “Being a family business, it was a big part of our life growing up,” Zacc says.
“I remember every time dad bought a new truck, he’d bring it home so he could show it to us.
“That was some of my earliest memories. I’ve got a picture with my grandfather with one of his old Commers.
“When I first started, we had an old Bedford and two Internationals, an ACCO C and ACCO D.”
Zacc has been a Hino customer for more than 30 years, even going for his truck licence in a Hino GD before he joined The Careful Carriers.
While he doesn’t have to do much driving, leaving that to his fleet of experienced drivers, it comes in handy more often than he anticipated.
“I like taking the trucks for a service or to get washed,” he says.
“Driving is something I do when I can, I still love it, but there’s no need for me to do it as much anymore.”
While he now handles the
operations side of the business, Zacc first started driving for his dad, giving him a wider view of what it takes to make a transport business tick.
He was driving an SBR Isuzu flat top hauling toilet paper, which he says gave him the opportunity to “earn his stripes”.
“Every load needed to be tarped heavily – I really started from the ground up,” Zacc says.
“I certainly didn’t jump to management straight away. It took me quite a few years to go anywhere near that. When I first started, I was given the older civil trucks. But I was never pushed into the business.
“That was one thing my father was very big on. It was my own decision. I went away to backpack through Europe for six months, and came back and truly decided that’s the way I wanted to go.
“So I had to learn Brisbane and body trucks first up. We would do a lot of hospital deliveries and very tight little places. Then I moved into
semi-trailers and was doing a lot of grocery runs.”
The past 30 years as a Hino customer has given Zacc zero reason to look anywhere else when it comes to purchasing new trucks.
fleet are two 700 Series SS2848s, a GH 500 and a GH 1728. Reliability and optimisation for the task has kept The Careful Carriers going back to Hino for the past three decades, and Zacc says that’s unlikely to change.
“The biggest thing for us to continue with Hino is one word, and
“Our Hinos are comfortable, they’re reliable vehicles and they just keep going. I’ve never been one to look for flashiness first and foremost. We ran single prime movers for many years.
“We do less than 20,000km in them a year, being a local transporter. We have different challenges to the line haul drivers. They have problems with distance related maintenance, whereas we have to focus more on starter motors and batteries.
“Our vehicles are starting 100 times a day, and our tyres are getting wear because we’re spinning around in yards. Hino have been great with the servicing side of it and addressing our specific issues.
“The 700 Series are barely a year old. We’re out of the body truck era, and we’ve just got the prime movers now.”
Matching the fleet, The Careful Carriers use the Hino-Connect telematics platform to help manage their operations across various areas.
Zacc says the data and compliance
insights it can offer have been extremely helpful to the efficiency of the fleet, offering a strong link to the communication with drivers.
“The Hino-Connect telematics have been really good for the compliance side of things,” he says.
“It can track your over-speeds, over-idles, and a lot of compliance. You can manage all of your compliance KPIs through that, which has been really good for us.”
Streamlining communication with drivers by being able to monitor where trucks are has saved Zacc plenty of headaches and has made working with them easier too.
“Hino-Connect has stopped us from needing to have a lot of unnecessary communication with our drivers.
“There’s no longer the need to pick up the phone and say ‘hey, how far off are you? Where are you?’
“We know where they are. I just look it up on the app, and I can see where they are. We use it on our phones a lot.
“It also takes a lot of stress off the drivers, because whether you’re conscious of it or not, ringing a driver and asking them where they are puts a lot of pressure on them. This allows them to focus on the road and the job.
“No one wants to be
micromanaged. If they can go about their job without that, it decreases the stress of the managers too. We’ve loved that the telematics have solved this for us.”
While the fleet stands at only four trucks, for the demands of The Careful Carriers’ contracts, the current Hinos are more than enough to do the job.
In combination with their skilled fleet of drivers and streamlined operations, they can constantly assess whether the fleet needs expansion.
“We’re more of an integrated transport solution, so our work tends to rise and fall,” Zacc says.
“So we increase our fleet as required by the customer. We take a lot of that from the customer themselves, what their requirements are and make sure we’re fulfilling those.”
Zacc and the team say they’re in the best hands to purchase through Hino, with Sci-Fleet Hino, who also act as their service dealership.
Like any transport business, there’s been plenty of changes along the way for The Careful Carriers. Even more so when you’ve been in business for 70 years.
Even across Zacc’s time alone, trends have changed, compliance has evolved, and the trucks have grown bigger and more expensive.
But as the saying goes, and there’s a good reason it’s still a saying, you don’t fix what isn’t broken. It’s a motto that seems to drive the operations to this day.
Zacc says this was laid out by his father and grandfather before him, and it’s something he carries forward into 2025 and beyond.
“We were always very process orientated,” he says.
“My father was set on that, and he had the systems that he would use in place. The biggest change I’ve seen is compliance related. We are TruckSafe and NHVAS Maintenance managed.
“That compliance, when I first started, was nearly non-existent. But with dad’s process, the movement across to accreditation was not that a
big a leap from most of what we were doing anyway.”
While increases in the breadth of compliance have in ways made running the business more challenging, Zacc says it has also offered him a reprieve in certain areas.
Especially when it comes to running a smaller business, there can be a lot required in a single role, but having the oversight of independent auditors has made some aspects of meeting compliance easier.
“The biggest change for us was the audits, where we’re now having to have a second set of eyes come in and have a look over and make sure
But to have someone come in and look over at what you’re doing with the compliance, and offer suggestions on what could change or what other companies have been doing, has been really helpful.”
Even outside of what happens inside the office, the operations on the road and out on the floor look significantly different than they did in The Careful Carriers’ early days, though these are most certainly changes for the better.
“Back in the day, there was no high vis or steel caps,” Zacc laughs.
“You see someone without a high vis now, and ironically they stand out so much!”
drivers that have made the deliveries possible.
With what has been a traditionally small fleet, everything tends to be more personal for The Careful Carriers management. Less people to manage means the ability to have more of a hands-on involvement with every person that makes the magic happen.
As such, Zacc says that most of the drivers they’ve had over the years have continued to stick around for a long time.
“We keep guys around long term,” he says.
“I’ve found that if we look after them, they look after us. We’ve got
maintenance.” Using tautliners helps their drivers reduce the risk of back injuries through lowering the requirement for heavy lifting, and keeps the loading and unloading process as fast and efficient as possible.
Any little thing to keep drivers around and happy on the job is important to consider for every part of The Careful Carriers’ operations.
Ironically, while it is one of their biggest strengths, the aging driver workforce is also one of their primary challenges. It’s a sentiment that many trucking businesses can relate to.
The average age of truck drivers and transport workers only continues to get older. There’s not too many coming through like Zacc who started his transport life at an early age.
“It’s probably not an industry that many people come out of school and think, ‘I’m going to go straight into driving’,” he says.
“Back in the day, people used to go out with their parents and drive, but nowadays that doesn’t happen anywhere near as much. Personnel is probably the biggest struggle that
the industry as a whole is dealing with right now.”
Zacc believes that the quality of training and development that is available to drivers isn’t necessarily helping getting skilled workers into the industry.
There have been calls in the past to develop truck driving into an apprenticeship, like most popular trades. It’s a task that the industry is still trying to work on its approach to.
“I think there’s a lot of people trying to figure out we need, because we need to increase the quality of drivers coming through,” Zacc says.
“That’s the challenge the industry is facing, and it’s a long-term challenge. It isn’t something that’s going to be fixed very quickly or easily. But it’s happening in a lot of industries at the moment, isn’t it?
“If you try to go and find a plumber, or an electrician, that’s difficult too. I think drivers in many cases need to be as trained as those other professions.
“You’re running around in heavy vehicles and sharing the road with families. You really need to know what you’re doing.”
As The Careful Carriers has been
passed down through generations of the Smith family, each one has left their lasting mark on it which will always be remembered.
Starting the operation was one thing, but keeping it going throughout eras where so much changed from decade to decade, and then eventually year to year, is certainly no mean feat.
Seven decades in, and they show no signs of slowing down. What all started as a one contract job has been carried on through professionalism and a strong dedication to doing the best job every time.
While the trucks and people may look different, Zacc believes that what each person has left behind has helped keep The Careful Carriers doing what they do best.
“My grandfather, father and I all have our own legacy,” he says.
“My grandfather, Sid’s, legacy was starting the business. My father’s legacy was building it into a bigger operation.
“Then my legacy and the biggest change I’ve seen in my time has been compliance.”
It’s safe to say that The Careful Carriers’ legacy will continue on.
The Winner of HVIA’s Safety Innovation Award for 2023 is now available as an option on steer axles in addition to drive axles, delivering dynamic pressure-control and balanced-load sharing across the entirety of a prime mover. Suspension that features Base Air™ actively operates as dual and single-circuit systems as required. With our national network of accredited installation partners, it is now easier than ever to reduce driver fatigue, improve traction and braking, and Level the Road.
AVAILABLE FOR HEAVY & LIGHT-DUTY VEHICLES WITH PNEUMATIC HCV SUSPENSION VIA AUTHORISED INSTALLERS ONLY
Call (07) 3382 7747 or visit baseair.com to find your nearest authorised installer
The issue facing the engineers at Paccar Australia designing the DAF XG+ for the Australian truck market was just how to bring together both European and North American technology, while at the same time getting the cocktail mix just right. Tim Giles reckons the recipe seems to be working
The latest new truck on the Australian truck market harks back to a previous generation of trucks, in some ways, but in another way demonstrates a set of interesting and exciting future possibilities for trucks not only in Australia but also elsewhere in the world.
The truck we’re talking about is the DAF XG+ which has been designed by Paccar and is now being built at the Bayswater plant in Melbourne, Australia.
The most exciting element of this variant is the fact it is powered with a Paccar PX15 engine. This engine is, in essence, the Cummins X15D, which is part of the agnostic engine platform which Cummins unveiled back in 2022. It is a common engine block with different cylinder heads to enable it to be fuelled by diesel, hydrogen or gas combustion. The new Cummins engine is also lighter than the current X15 by over 200kg.
What this model represents is something which could well be the Australian truck drivers’ dream solution, a comfortable, spacious and well-designed European cabover prime mover, but with a North
American designed engine with all of the caché of big North American iron.
The question on my mind, when climbing up into the cabin of the XG+ for a test drive out of Melbourne, heading west to Nhill, before returning to the Victorian capital, was not whether this new truck would be any good. The DAF brand does not design bad trucks, Cummins do not make bad engines and the Paccar organisation in Australia has a long history of integrating various elements of a truck from different sources, over decades.
This is just the latest challenge for the engineers at Bayswater, and yet again they have come up trumps with something which does have all of that European comfort drivers like, plus it has that famous Cummins’ torque rise available under the driver’s right foot. It even sounds right –– there is not the distant murmur of a diesel engine in the cabin that one would expect from a top of the range European prime mover. The engine tone is not obtrusive, but it does make enough noise for you to hear that familiar engine note which we expect from a Cummins engine.
of elements available to them, as a company, and turn it into something which the Australian truck market has been seeking for some time — that is, the ideal combination of both European and North American technology in one vehicle as a complete whole.
There have been attempts at this in the past which have had mixed results, the Iveco Powerstar being one of the most obvious examples, where the truck was designed to create a European cabin with a conventional bonnet and a choice of European or North American drive line. It didn’t last long.
With the DAF XG+, designers have done a much better job of combining elements from the different trucking philosophies and come up with a design which not only does the job, but actually adds a little extra to the mix. The aspect of the design which surprised me the most was the fact that Paccar chose an engine out of the North American tradition and coupled it with a transmission straight out of the heart of the European trucking tradition, the ZF Traxon. Also in the mix is the Meritor back end.
interface between the engine and the transmission. Instead of using the Cummins engine’s own ECU, the team developed their own ECU to directly control the engine from the truck’s CANbus.
It was interesting to climb up into the cabin and experience just what this melding of philosophies can bring to a truck. Can the two world views actually exist side-by-side? Can DAF replicate the kind of fully-integrated system normal in the European truck, while introducing an engine from a different continent’s trucking philosophy? The essential answer to this question is, of course, yes. The
DAF engineering teams based both in Bayswater and at DAF HQ in Eindhoven in the Netherlands have managed to come up with a solution which is both practical and effective.
The big question for me when driving the truck out on the road was probably something along the lines of, ‘is it a real Cummins?”. The familiar rapid torque rise in the Cummins range is the element which creates the excitement drivers feel when driving a Cummins powered truck. In European engined trucks the torque is not quite so rapid and acceleration is extremely smooth and unfussy. What would this engine feel like?
The answer is somewhere in between. Pushing down on the
accelerator does stir it into action immediately. The engine note rises in the cabin and the truck picks up speed, in a controlled manner. This is not like some European set-ups where the driveline can feel a bit doughy, after driving something with an X15 under the bonnet. The ZF transmission can clearly handle the torque coming through and has been tuned to give the driver that ‘just right’ feeling, halfway between a sluggish and a racing truck. This engine does pass that test. It does sound American enough and the acceleration is also American enough, but comfortably mixed in with a stateof-the-art European-style feel and response.
North American engines pick up torque quickly and make more noise when compared to a European engine, but the ZF AMT has been designed to suit all those European engines. Has this engine been designed with a bit of a smoother torque rise?
“DAF have noted what you’re asking about and have been challenged by it, but not in a serious way,” explains Ross Cureton, Paccar Australia Director of Product Planning. “It’s just different and because you’re in complete control of the engine, you can modulate that to suit.
The impression when climbing up into the cabin of the XG+ is deceiving. It actually looks like quite a big cab but in reality there are only three steps up to the driver’s seat, where most large European prime movers have four.
After settling into the driver’s seat, the next impression is how good the visibility around the truck is from this position. The cab is relatively high,
but the windscreen does sit very low and has been designed this way to maximise the amount the driver can see in the immediate vicinity of the truck. This impression is further enhanced by the side view system, which is on a display high up on the passenger side A-pillar. This shows an image from around the front of the truck, but also down the side by the passenger door. It can be a little confusing at first, but once the driver sits and watches a pedestrian walking around the truck or sees people standing on a pavement near the truck it becomes apparent this single screen gives the driver a clear idea of everything which is going on, in that blindspot on the passenger side.
The instrument panel is at once both familiar and also brand-new. The layout is one which would be familiar to anyone who has driven any DAF or any other European truck. The dashboard display directly in front of the driver is the same basic design as in the Kenworth K220.
First impressions are important when jumping into something completely new like this XG+. It is surprising how a few extra centimetres of width, height and depth can achieve such a strong sense of space. This feels like a roomy cabin and it’s very easy to move about inside. The steering wheel folds up and next to the windscreen, making ingress
possible to hear that distinctive Cummins engine note, something which will be comforting to the North American engine fans, who may be a little suspicious of this European import. Releasing the electronic park brake and setting off sees the ZF Traxon transmission running as smoothly as one would expect. The changes are effortless and quick with that familiar engine note rising and falling to make the driver feel a little more comfortable.
The truck has a number of nice little touches, like a switch which can be flicked to turn off the reversing buzzer and replace it with flashing hazard lights, useful in a situation when unloading late at night in a populated area.
The electronic park brake will
brake will automatically activate if the driver opens the door. There is also a tug test button to test the trailer brakes or straighten up a combination, when required.
When a driver activates ‘urge to move’ on the righthand stalk, the clutch and brake control is changed, so that when the driver takes their foot off the brake, the truck will move forward up to four km/h. There are more little elements to the design for the driver to discover and utilise, too many to get familiar with on a two-day test run.
There is a rigorous internal process
with the new engine were concerned about the level of turbo whistle the new engine was producing. The team in Australia had to explain to their colleagues that Australian truckies would expect to hear that familiar sound in their truck.
“DAF have got a truck over there, in Eindhoven and they test it over there, then we do it here. We compare notes, we agree to disagree or agree to an action to change it,” says Brad May, Paccar Australia Chief Engineer. “It’s just been unbelievable, a lot of meetings, a lot of discussions, but it’s been fantastic.”
The Paccar assembly plant in
Bayswater was already building DAF CF models, so was equipped to deal with the chassis. There is now a different cab lifting arrangement because the XG is bigger than the CF. The first one down the line was built in the normal sequence and the plant had built more than 60 of them by the end of 2024.
The current CF kit comes into the country almost complete, but for the XG there are a lot more locally sourced components, moving the process closer to full truck manufacturing than simple kit assembly. The vehicles come down the production line alongside the Kenworths.
Paccar in Australia had been wanting a 15 litre engine inside a DAF, as the 13 litre limited opportunities in the very large heavy GCM segment. According to Paccar, it was always going to be a Cummins engine.
The other major plus for the truck was its aerodynamic performance. In fact, the key difference is the radius on the front corners of the cabin. It is much larger than normal, and then tapers out, only getting to full width behind the door. The most efficient design uses digital mirrors, but there are also traditional mirrors as well. It seems the digital versions are a step too far for Australia, just now.
“We saw an opportunity for a 15 litre, but the key was, could we get the kind of fuel efficiency improvement DAF had got with the 13 litre, or would it undo all their good work?” says Ross. “The objective with this XG was to not be any heavier than the XF, even though it’s 500mm longer. At its highest spec, the larger XG+ is just 20kg heavier, when compared to the XF models.
“We saw this opportunity, this great new DAF that looks terrific, but we needed a 15 litre and at the same time, were having conversations with Cummins about a newly developed engine. You wouldn’t normally do that, but the outcome was going to be so much better that it was worth embarking on this huge validation program to make sure the new cab and new engine were both going to work, so that’s what we did.
“The European 15 litre market in Australia is not going away. If
anything, it’s growing. So we see a real opportunity there. We knew that DAF had the most dominant long haul prime movers in Europe already, and they were going to do better still. It stood to reason, it was going to be very competitive product.”
The XG+ also brings something else to the Paccar party, and that is a future solution for a problem which has been hanging over the Paccar Australia organisation for some time.
The dilemma it has faced is the fact that the existing Kenworth cabover sold by the company, the K220, is probably the last iteration of the famed
series which has been with us in the Australian market since 1971.
The Paccar organisation needs a ready alternative to be waiting in the wings, if or when production of the K220 eventually ends, at some point in the future.
The XG+ is the kind of truck which is likely to be able to fill that gap in truck showrooms around Australia. It may be difficult for European truck enthusiasts to understand just how important North American iron is within the trucking industry in Australia. Truck buyers are constantly tossing up between driver acceptance and the need to have the latest technology on board in their trucks.
One of the elements which may well benefit the XG in the Australian truck market is the kind of fuel economy being achieved. This has been a strong selling point for other European brands in recent years.
For the new DAF achieving similar outcomes to those found in the other European brands, added to the fact that this is a North American style engine, may well be a strong selling factor.
Currently the XG will only be available as a 6x4 prime mover, but the team at Paccar are not ruling out an 8x4 model in the future, which would certainly be attractive to New Zealand trucking operators.
Dairy producers Lactalis Australia rely on their fleet of MAN trucks, hired through Penske Leasing, to get their milk and cheese onto supermarket shelves
Do you ever wonder just where exactly your milk and dairy products come from? While it might not be quite as convenient as glass bottles being dropped at our doorsteps anymore, chances are most of your cheese and yoghurt comes directly from Lactalis Australia.
They manufacture dairy products across some of the biggest brands in the country, including Pauls, Vaalia
Probiotics, Ice Break, Oak, Breaka, Lemnos, President and Galbani.
Lactalis was first founded as Pauls nearly a century ago, and only became known as Lactalis after a series of acquisitions from Parmalat and eventually the French head company of Lactalis across the ‘90s and 2000s.
The business has only continued to grow in Australia, with factories across the country which create the products that end up on supermarket shelves.
But none of it would get to those shelves without the fleet of trucks that Daniel Cooksley is responsible for. Managing outbound logistics for Lactalis’ Victorian operations, he makes sure that all the trucks end up in the right place at the right time.
“We produce milk, flavoured milk, yoghurts, cheese, desserts, any type of dairy products you can think of,” Daniel explains.
“Our factories are right around
Image: Adobe/Doublelee/stock.adobe.com
Australia, every major capital city, every state and territory. They’re all localised products made locally and sold locally. In Victoria, our main factory site is in Rowville, with our two main production facilities in Rowville and Bendigo, then we’ve got a number of smaller factories, Dandenong, Campbellfield and several across regional Victoria. Then we distribute through a distributor network.
“There’s not many hours of the week
where the wheels aren’t turning, from midnight Monday morning through to midnight on Sunday night. That’s the demand of reliability.”
While all of the factories have trucks delivering their products across their respective states, most use third party logistics and contract carters in their operations.
The Victorian Lactalis factories have the advantage of having their own 20-strong fleet, which is all run in-house through Daniel and their drivers. The majority of this fleet is made up of leased Penske trucks, all MAN models, run mostly as B-doubles with refrigerated trailers.
“It’s our own logistics department essentially,” Daniel says.
“We’ve got our own drivers as our company drivers, and our prime movers through Penske. Our trailers are through Scully RSV.
“Those 20 prime movers are running across the Rowville and Bendigo sites, and we’ve got about 50 trailers. Given we dominantly run B-double combinations all our drivers are required to be multi-combination licenced.
“We don’t run them interstate. We’ll move milk from state to state and across the different plants through our third-party logistics providers from other companies, but the Victorian fleet will stay just in Victoria.”
With the model of hiring much of their fleet through Penske Leasing, Daniel believes this gives Lactalis a significant advantage in Victoria, not only through lowering operating costs, but providing the flexibility needed to stay on top.
The leasing arrangement has been one that Lactalis has found easy to manage after trialling several different approaches to fleshing out their fleet of trucks.
It’s only a recent change in their Victorian factories, having been working with Penske Leasing for the past two and a half years. While they use leasing in Victoria and third-party logistics elsewhere in Australia, they had looked to different approaches before ultimately settling on working with Penske Leasing.
“We’ve gone through various iterations and brands in my time here,” Daniel says.
“Lactalis had previously been running Volvos, and then we had bought our own MAN truck, and now we’ve moved over to the lease model. With those leased trucks comes scheduled servicing, breakdown support and afterhours support.
“It’s all very important to an operation where we’re running pretty much 24/7. The guys on the MAN side
and the Penske side, nothing’s ever too hard for them. They’re always contactable in the rare case that we do have a breakdown or an issue.
“But in the case that we do, the wheels are put in motion to rectify the situation and get us back on the road.”
Lactalis recently took delivery of five brand new Euro 6 compliant MAN TG3 models, a truck which Penske Leasing has recently seen a significant uptake of.
As the need to meet approaching emissions goals continues to get closer in Australia, having access to the most up-to-date low emissions vehicles is becoming more important than ever.
The new models give Lactalis the chance to lower their emissions on top of leasing reliable trucks that are up to the job.
“The Corporate Social Responsibility piece within Lactalis is huge globally,” Daniel says.
“We need to hit both local targets and targets set by the company and corporate globally. The Euro 6 efficiency of the trucks has really helped us drive down our fuel usage.
“It’s not just about meeting targets, it also helps in cost of operation. You burn less, you spend less. We find that we’ve been able to do more with less. We can burn less fuel and emit less carbon dragging a 70-ton B-double across town than we ever have before.”
Taking on any new truck comes with the process of number crunching and comparing, while also making sure they right for the task.
Cost and efficiency always come out as the biggest factors to consider, but going through Penske Leasing, Daniel says that the little things have made them keep to the leasing model with their MANs.
“We do predominantly highway running, and we’ve compared all the models out there, any brand you can think of,” he says.
“Looking at the comparative numbers, the MANs, in terms of fuel economy, reliability, service network, availability of parts and servicing have come out on top. As a company and operation, we’ve been brand agnostic in the past, and we’ve found that this is the best deal there is.
“Being in a post-COVID world, it was hard to get back stock of trucks coming into the country. While that’s improved, using a leasing model gives us a bit more flexibility.
“We do have peaks throughout the year and demands in different areas of the business, so we can go up and down under a lease as required. It gives us that aftersales support too. It’s all inclusive.
“It can be difficult to capture capital for a fleet of vehicles. By spreading the cost for a lease agreement, it makes it more appealing to a larger organisation.”
As a company in the dairy business, it’s no surprise that there are extra considerations Lactalis must make in moving their products.
Most of the trailers within the fleet are refrigerated, keeping the various milks, cheeses and yoghurts fresh until
they hit the supermarket stockrooms, and then the shelves.
Maintenance and upkeep of the trailer fleet is just as important for Lactalis, especially when it is going on 50 strong, and vitally important to their transport work.
“I’d say that 90 per cent of our fleet is refrigerated. Everything is loaded straight out of the coolroom,” Daniel says.
“At different times of the year we have different challenges. In the middle of summer heatwaves that we’ve just had in Victoria, reliability is important, as is your fuel economy and your cold chain.
“It’s basically a 24-hour battle against the weather. At other times of year, when it’s colder in the middle of winter, it can be colder outside of the trailer than in it.
“Reliability and servicing are the two main challenges if we do get a breakdown or have an issue, as well as monitoring.”
The monitoring side of managing temperatures is done through the telematics in the trailer, where Daniel can make sure they are staying as cool as they need to be.
This is also important to meeting cold chain compliance to maintain the safety and quality of all of their dairy products, from farm all the way to the supermarket.
“When it comes to cold chain
compliance and remote monitoring, we can see where all our trucks and trailers are at any one time,” Daniel explains.
“We can see what their operating temperature is, and we can display any potential breaches for culture. From a Penske point of view, the telematics on the trucks is just as important. You don’t want to be taking a large load from here to Bendigo and have a breakdown on the side of the road.
“If you don’t have reliable equipment, it makes the job a lot harder.”
While Lactalis’ Victorian operations use their own fleet to deliver products from the plants to supermarkets, the delivery of the milk itself is provided by third party logistics providers to the factories across Australia.
The cold chain functions like a well-oiled machine, with each part of the chain taking care of steps along the way to get products onto shelves, and ultimately into our fridges.
But it all starts with the farmers,
hold in extremely
Many of their supply arrangements with farms across the country have been running for more than 20 years. Recognition and maintainance of strong relationships with dairy farmers is always the first steps in ensuring the best products get out there.
“Lactalis relies very, very highly on the supply from our farmers,” Daniel says.
“We don’t really interact with the
farm pickup side of the operation within our fleet. It requires specialised tankers and other bits of equipment.
“We pride ourselves on the finished goods and the finished products, and getting it back into the market in a safe, saleable, cold condition.
“Obviously everybody drinks milk and puts it on their Weetbix! It’s a bit of a circular economy, it comes off the farm to us, and then it goes back out to market. That’s a very important chain to get right.”
Impressive 8.5 tonne lifting capacity per column for trucks and trailers’
Versatility for your workshop with variable configurations using 4 to 16 columns to suit your set up
Create a safe and organised workspace with wireless controls linked to intuitive LCD touch screen control panel
After over 10 years in the role as CEO at the National Heavy Vehicle Regulator, Sal Petroccitto has moved on. Before he left the building, he sat down for a chat with Tim Giles about his time at the regulator and what had been achieved in the last decade
Historically, the relationship between the trucking industry and its regulators has been fraught with hostility. This issue was exacerbated by the fact that, before the NHVR, each state had a different set of rules and regulations for the trucking industry, and the variations in rules between the states were considerable and petty, leading to vehicles being compliant in some states and non-compliant in others.
The NHVR was created to improve the situation out on the road, but its first few months of existence were chaotic at best.
The CEO at the time resigned, the trucking industry was in uproar, the permit systems around Australia failed and the situation was much worse than it had been under the previous set of regimes.
The man who was called in to try and clean up the mess was Sal Petroccitto, who had been involved in the development of the NHVR when he was working for Transport and Main Roads in Queensland. Sal faced a daunting task, as the project looked to be failing and an extremely angry trucking industry was struggling to cope with the pushback. This is not the sort of situation anyone would choose to face on their first day in the job, but that is the scene which Petrocitto faced on May 19, 2014.
10 years later, as Sal was facing his last days in the job, he recalled advice from the first NHVR Chairman he worked with, Bruce Baird: ‘Sal’, he said, ‘if you’re ever going to go, you go on a high’.
“An OAM last year, three consecutive customer service awards, transition program awards, an industry that now respects us, I think we are doing a pretty good job,” says Sal.
“I can remember my first couple of conferences where I went to make presentations and people were just standing there going bang, bang, bang with issues. Compare that to now, where I think we have clearly made a difference.”
The trucking industry’s calls for consistent rules and enforcement across the country had a long history. Each state authority with responsibility for the trucking industry took a slightly different take on the rules.
B-doubles able to drive around in Queensland would get pinged when crossing into New South Wales for being over length because of the different parameters the roadside enforcement teams used to measure
travelled from state to state. This was a long and drawn out process which eventually led to the decision to create the National Heavy Vehicle Regulator, which would enforce a Heavy Vehicle National Law on which all of the states should agree.
There followed a complicated
process whereby the new HVNL was developed and passed into law in the Queensland State Parliament. At that point, both the Northern Territory and Western Australia decided that the process was not for them and stepped back from passing the law.
The remaining states did pass laws, using that basic Queensland law as a template, but several of them also added in their own sub-clauses, conditions and variations to the regulations in their particular state.
At the same time as this process was happening, the project of creating an agency, which would eventually be the NHVR, began. It was decided that the first part of the process for the agency would be taking over the permit system.
Once the NHVR went live in February 2014, the issues immediately began, with massive delays and mistakes in the issuing of permits. Complaints came in from around the country and the problem gained national news attention.
The causes of the issues were varied, depending on the speaker’s point of view. Some laid the blame at the feet of the state bureaucracy, sabotaging a process they did not want to happen. A Nick Cater opinion piece in The Australian painted the NHVR development process as a disaster waiting to happen, with the state governments around Australia unable to stop it from happening.
While wanting to negotiate about the details, there was never any hesitation on the part of trucking in supporting the idea of the NHVR, but the permit chaos caused uproar. Blame was allocated on the basis of your point of view. Many claimed the state authorities were sabotaging the process after the loss of their functions.
“With the NHVR coming into existence, who is threatened?” asked a PowerTorque opinion piece. “The comfortable bureaucratic fiefdoms of the State Road Authorities, who have made the truckie’s life difficult for so many years, that’s who. These state authorities are also the people who know how to help any potential national regulator get the permitting system right from the word go.”
“The launch and the operation of the NHVR was always only going to be as good as the support that it received,” said Chris Melham, then CEO of NatRoad.
“Did the NHVR get the support it needs from jurisdictions during the planning phase? Was the volume of permit applications received by the NHVR in line with the projected workload expected?”
At that point, the principle of a single national law for road transport was at stake. Richard Hancock, who was the CEO during the process of building the NHVR, resigned under the pressure of the issues in May 2014. During this fraught period, Sal
Petroccitto was looking on from his position in Queensland’s Transport and Main Roads.
As the dysfunction played out, Queensland, then New South Wales, Victoria and South Australia took their permit functions back, but Tasmania stuck with the NHVR. After this, the first CEO had moved on. Sal was recruited as his replacement and started work on May 19.
“I’ve still got a couple of staff here that were there from the start,” says Sal. “They remember just how shaky it was, the death threats and all that. It was pretty serious for them, but we’ve come a long way.
“I remember when I walked in, we had about 110 people, and we were losing them, rather than keeping them. I told them what we needed to do was stabilise, and get industry back on deck. We knew that there were going to be challenges, but we had to make sure that we got that relationship with the industry, because if we didn’t, we wouldn’t exist.
“At the time I said, ‘there won’t be another CEO if we don’t fix it’. The Commonwealth’s desire to establish a regulator by getting them to focus on an access system as its priority probably wasn’t the smartest thing to do. In hindsight, what the Commonwealth should have done is focus on getting all the jurisdictions
to agree that we’re establishing an NHVR and these are the functions they were going to let go.
“I said to my team, ‘if we continue to stay in our Fortitude Valley office, we’re never going to survive. You need to be out there, and you’re going to cop some really difficult discussions. But if you don’t, you’re not going to understand what’s really hurting. You’re also not going to build the trust with them to say, you keep turning up, you keep coming back, so you’re genuine’.”
Those dark days in early 2014 are now well behind us, as the NHVR has established its place in the trucking world. The work continues and the agency is still building. The process led by Sal has been a careful stepby-step one, creating a workable permit system, which will function for the industry involving working in an environment where NHVR doesn’t have the ultimate say. That stayed with the state road agencies, and this is where many of the ongoing issues still lie.
“The permit system will be, in my view, an ongoing conundrum for this industry,” reckons Sal. “I think we’ve done a really good job in fixing the front end and actually starting to work really well with industry. There are jurisdictions that are now starting to really understand their networks.
“However, I’m seeing other jurisdictions that I think are going to tighten up. I am worried about what, ultimately, the whole access framework for this country looks like.
“We’re doing some really good work with South Australia. At the moment, the minister’s really focused on trying to get out of permits. He has a particular view, that if a particular road has had multiple requests for a permit, why isn’t it a notice?
“The work we’ve been doing with Victoria on really understanding how they can get out of permits into notices is good. It will be an ongoing issue while you’ve got a regulatory framework that says the NHVR is not the ultimate decision maker, it’s what we’re given.”
In a job like NHVR CEO it can
why do jurisdictions continue to fight it? It’s sort of like defending your home turf and keeping your ivory tower intact, totally. But isn’t it the role of the leaders to actually step in and tell the staff, ‘actually this decision has been made by our minister, we’re going to let go, we’re going to trust them, we’re going to work with them’?
“I think we’ve started to see some really big wins, we’ve built that relationship of trust, where we’re now working collaboratively. We’ve always understood that there’d be a healthy tension, because we’re technically an independent regulatory body that’s been asked to do something under a
colourful operator, the staff knew him,”
with you, lets us have a discussion’.
“We’re slowly moving it, we’re getting much more confidence among the drivers to actually engage with our staff. The approach that we kicked off a few years ago, around that whole educate, inform and enforce has really made a difference. I think that’s probably one of the proudest things we have achieved in that regulatory space. When I see 5,000 hours of education, well that’s potentially 5,000 blisters that might have been issued. It is making a difference, and we’re building that respect.”
There are, of course, unfulfilled hopes. Sal has worked hard to get
Western Australia and the Northern Territory to come on board with the NHVR. It has been a conciliatory approach to the issue, emphasising the positives, rather that the negatives, the NHVR is learning from effective systems in WA. There are now coordinated initiatives and data sharing but no talk of integration into a single regulator, just yet.
“Do not attack my people who are trying to do a job in a really difficult environment, in a framework that we inherited,” says Sal. “If you’ve got a gripe, have the gripe at the system, because that’s what’s failing. Not the organisation that is busting their arse
to try and make it better.
“We’re the only regulatory body that has a productivity remit, and I think it’s the biggest success factor from the way the law was structured, giving the regulator the ability to pursue productivity as well as the enforcement of compliance and safety.
“We’ve been able to show industry that through a safety lens, productivity can be delivered, that a productive operator is a safe operator. I’m pro common sense. If I can give an operator an outcome that actually allows them to be productive, I know that they’re going to invest in better safety.
“The win there is two fold. You have a win because you’ve got a safer
operator, they’re probably treating your infrastructure better. I have a win because I’ve got an operator that’s now wanting to be more compliant. Isn’t that the measure of success? They’re also making more money, which means that they might then look at the next truck and the next safety feature.”
Chain of Responsibility is a complex issue and the NHVR have been unable to get one of those impactful CoR prosecutions which would really make the big freight customers sit up and take more notice of their effect on safety in the trucking industry.
Sal also hopes the NHVR Portal will continue to deliver great functionality for industry.
“We’ve got defects in the portal, we’ve got the compliance module in the portal, and it is now becoming a real industry focused hub,” says Sal. “I think it’ll start to see value, and the operators will see value. So that’s working through. I think for us, that’s how we start to progress.
“The next iteration will be around the discussions we have had around chain of responsibility, around where the primary duties go, where the focus needs to be, and it needs to move away from the driver to the chain, and that’s a trajectory that we wanted to focus on.”
When Sal first came to the post of CEO, a well-known Victorian livestock transport personality walked in and told Sal, ‘don’t worry about your superannuation, you’re not going to be here long enough to cash it in’. Sal took it on the chin, but does remind his critic, when he sees him, that his super is looking pretty good right now.
“If industry is definitely trying to do the right thing, we’ll acknowledge that, but we’ve also got a job to do if there’s a safety risk, and I think everyone would expect us to do that,” says Sal.
“We can collectively work together to deliver a better outcome for industry. Whether they like me for it or not, I don’t know, but I think it’s the right thing to do.”
The search is on for a successor, with big boots to fill.
The launch of TruckSafe in New Zealand will be a huge milestone for the Australian Trucking Association, writes TruckSafe Chair Paul Fellows
TruckSafe is the Australian Trucking Association’s industry focused chain of responsibility (CoR) safety management system (SMS) that is aimed at improving the safety and professionalism of trucking operators across Australia, and soon also in New Zealand.
Trucksafe was set up in 1996 in response to government concerns over what the road transport industry was doing to improve safety. Now almost 30 years on, the program is recognised by a growing list of well-known consignors and prime contractors.
I signed my business up to TruckSafe back in 2001 and have not looked back. In fact, I joined the TruckSafe board many years ago and was privileged to be voted in as Chair in 2021.
Together we developed and released the first and only industry-led comprehensive safety management system (SMS) in 2024. We also introduced an owner-driver SMS, specifically designed for the one person businesses that comprise close to 60 per cent of industry operators.
system allows a business to break away from a restrictive, reactivebased compliance approach and adopt a flexible and proactive riskbased approach which can be tailored to its size and risks.
For me, the new TruckSafe SMS is a game changer. Not only are TruckSafe members using best practice methods for the identification and management of CoR, but they also have the flexibility to create and use policies, procedures, and processes that suit their business activities rather than the one size fits all approach used by traditional compliance-based schemes.
I believe that the TruckSafe SMS is world class when it comes to assisting businesses with meeting their CoR obligations.
Our members attain certification based on satisfying a set of core components and their associated elements to assist their business to operate safely and responsibly.
Certification is achieved and maintained through independent audits and adherence to the TruckSafe Codes of Conduct.
The TruckSafe board and I are excited about the introduction of TruckSafe in New Zealand. Working alongside the Australian Trucking Association and the New Zealand Trucking Association, we have a longstanding collaboration on TruckSafe and safety within the road transport industry in both countries.
Currently, New Zealand’s road freight sector lacks an industry-wide system driving compliance with transport rules and regulations. While overall compliance is high in NZ, it is mainly driven by operator goodwill and an enforcement model targeting
There is no widely adopted heavy vehicle safety accreditation or
certification scheme in New Zealand that incentivises safety, ensures compliance, and recognises good practice.
The impending release of TruckSafe’s SMS in New Zealand will enhance performance and safety outcomes for the entire industry. Certification to this system will not only improve safety and professionalism but will also provide business owners with the peace of mind that they are safeguarding their people, clients, and operations by meeting the highest standards.
There is a growing list of companies eager to join TruckSafe, and the highly skilled TruckSafe Industry Council comprising experienced industry operators will ensure the program in New Zealand is robust, practical and fit for purpose.
TruckSafe will be open to New Zealand members in the first half of 2025 with the website already accepting expressions of interest at trucksafe.net.nz. Companies that register will be amongst the first to know when the program officially launches.
Meanwhile, the alignment of the SMS documents and supporting templates with New Zealand’s legislative and regulatory framework is taking place along with the creation of a highly trained independent auditor network.
If you’d like to learn more about TruckSafe, I’d encourage you to visit trucksafe.com.au in Australia or trucksafe.net.nz in New Zealand.
Take your fleet operations to the next level with Geotab, the industry leader in telematics. Our advanced solution combines real-time vehicle data, powerful analytics and intuitive dashboards, empowering you to make smarter, faster decisions that keep your fleet on the road.
DEPARTURE
9:10 AM
Visit www.geotab.com/au/ to learn how our telematics solutions can
The Australian and New Zealand Trucking Associations have come together to form an innovative new safety system
The introduction of adaptive and versatile safety standards into the transport industry marked a turning point for the trucking world.
TruckSafe, first launched by the Australian Trucking Association in 1996, has continued to grow and evolve, even going international.
A partnership between the ATA and the New Zealand Trucking Association, or NTA, will see a version of the system launched for our friends across the ditch. This is set to be introduced across 2025 in the pioneering collaboration between the two associations.
Through the launch of the SMS, the NTA says it wants to ‘elevate safety, well-being, and operational standards across the transport and logistics sector, fostering a culture of compliance, safety, and professionalism on New Zealand roads’.
“This initiative is more than just compliance — it’s about embedding safety at every level of operation,” David Boyce, CEO of the NTA said at the time of the announcement last year.
“As public and regulatory expectations evolve, TruckSafe New Zealand will help companies stay ahead while promoting a culture of excellence.”
We spoke to the NTA at the time of the announcement to gain some insight into how the need for a development of an NZ TruckSafe system came to be.
The process began with the acknowledgement that legislation protecting truck drivers and transport workers in New Zealand wasn’t as comprehensive as it needed to be. Unlike Australia, New Zealand doesn’t regulate the industry through
Chain of Responsibility laws, instead relying on Health and Safety at Work Act 2015.
While this Act offered transport workers protections under the law, it wasn’t specifically geared towards them, which the CoR aims to address, being tailored towards every level in the chain.
This led to the establishment of the NZ TruckSafe Council, who would begin engaging with the ATA to figure out what could be taken from the Australian TruckSafe, and what would need to be changed.
The opportunity arose in tandem with the ATA developing the newest version of TruckSafe, and became the start of the partnership between the two associations.
“We commenced putting together the latest TruckSafe SMS back in 2022. Once we started on that, we got
the guys in New Zealand expressing their interest,” says Kevin Walsh, manager of the ATA’s TruckSafe program.
“They didn’t have anything remotely similar, and were looking for a solution over there. We had a chat with them, and they turned that into a collaboration with us. We signed an agreement for them to be able to use TruckSafe in New Zealand. We’ve been collaborating with them ever since.
“They had a hand in peer reviewing the SMS when we were doing it here. They had some input into what would be relevant in the SMS, and they’ve been involved in every step of the process the whole way.
“We created the SMS and then they’re now localising it to suit their conditions.
“With their Work Health and Safety, there is some legislation in there that to a degree covers the equivalent of CoR here. We’ve been providing some assistance with that process as well.”
The NTA says that a big part of the process of getting TruckSafe set up will be reviewing the Health and Safety Act, to make sure that it does help to offer transport workers added protections to then guide the NZ TruckSafe.
They are however confident that most New Zealand trucking businesses should already meet the requirements of TruckSafe. Rather than creating sweeping change, it will offer easier guidance for operators and businesses.
Kevin says that going through the process of the introduction of TruckSafe in New Zealand has also offered a chance to reflect on how the ATA’s own system can work better for industry.
“It has opened us to change in that New Zealand has similar businesses in type and size,” he says.
“The bulk of the transport industry is made up of small operators, be that mum and dad operators or single truck operators. There was nothing really there that suited them. The SMS technically suits them because it’s so flexible. Then it’s about the degree of things you put in place to suit your risk.
“In talking to the NTA, we’ve
developed the owner-driver version. There’s two versions of the SMS, full-size and owner-driver. They will be heavily using the owner-driver version.”
The recent developments from the ATA and NTA saw the 2024 TruckSafe Owner-Driver Safety Management System released last year.
From feedback from the transport industry, the ATA acknowledged that small operators needed an SMS that suits them, and couldn’t make do with a system that was primarily designed with larger fleets in mind.
With continuing awareness of developments in safety, with new mandates already coming into place for new truck models at the start of 2025, Kevin says it’s never been more important to stay up-to-date.
“Safety has been pushed to the front of everyone’s minds,” he says.
“The CoR legislation was created and orientated around safety management. It was initially going to be an SMS style of legislation. They didn’t make it like that because they thought it would be too complicated, so it’s become the way that it is now.
“Now that everyone is used to it, we’ve taken it to the next step. We’ve created the SMS that links to the CoR very closely.
“The beauty of having it is that if the legislation changes in the future, the SMS is much more flexible and can be adapted easier than having standards like the NHVAS.
“When our members moved from the 2015 standards to 2019, that was a big jump. A lot of them found it difficult, and we totally understood that. We moved to the SMS as a much simpler approach.”
Kevin says continuing to offer the industry flexibility will give businesses more options to manage their compliance and safety.
“The new SMS lets businesses use what they’ve got, and then modifying or ensuring that it covers their risk.
“That’s the approach that we’re taking now rather than having a prescriptive set of standards that are inflexible or everyone has to apply regardless of whether they’re a one truck or 100 truck operator.”
• 30 + years in the market place
• Clean, grease-free fifth wheel
• More cost effective
• Easy to fit
• Consistent steering characteristics
• Environmentally friendly
• Australian designed & manufactured
• Used by some of the most highly respected companies since 1990
WE STOCK AFTER-MARKET REPLACEMENT KITS TO SUIT MOST GREASELESS OR LOW-LUBE FIFTH WHEELS.
NatRoad CEO Warren Clark believes that removing the majority of heavy vehicle access permits save time and money for operators and governments alike
In four short years heavy vehicle access permits could largely become a thing of the past.
NatRoad has proposed slashing 90 per cent of heavy vehicle access permits by 2028 in a submission to the National Heavy Vehicle Regulator (NHVR) Productivity Plan 2024–2029 and our response to the review of the Heavy Vehicle National Law (HVNL).
It seems obvious to us that the current access system needs a major shake up. It’s clearly not working and just puts even more roadblocks in front of trucking operators. These operators are already struggling with the rising cost of living, escalating fuel costs and the driver shortage. The last thing they need is more red tape.
If we can improve access for heavy vehicles, we can move more freight in fewer trips, leading to lower costs, improved safety, and reduced emissions.
In my view, NatRoad’s recommendations to fix access are just common sense.
If we can make heavy vehicle access easier, it would reduce the number of individual trips and of course this would lower costs, improve safety and reduce emissions.
Central to our recommendations is replacing the current unworkable permit process with network-based access, the National Automated Access System (NAAS). Tasmania has shown this approach works through its Heavy Vehicle Access Management System. The proposed NAAS builds on the success of HVAMS and would see a transition from permits to network-based access.
The benefits of such a system are clear. For heavy vehicle operators, automated access reduces red tape, saving time and money. For governments, it lightens
administrative burdens, enabling resources to be better allocated elsewhere. For consumers, the knock-on effect of improved freight efficiency is ultimately savings.
Of course, automation isn’t the answer to everything. There’s a danger it could just be a Band-Aid if we layer it over the top of an already dysfunctional system.
What we really need is a new approach to network-based access that slashes red tape for industry and removes administrative burdens for governments.
The government must avoid reform just for reform’s sake without any real results.
We’ve seen the government take initial steps towards automated access but to be frank, those steps aren’t enough. We need more commitment from government to make automated access a reality.
We can’t risk this issue just becoming another talk fest.
Governments must step up and show leadership and commitment. Either they embrace meaningful reform and unlock the productivity gains of a modern freight system or risk dragging their feet while costs and inefficiencies pile up.
We’ve said far too often that nearly everything in Australia is delivered on the back of a truck, and it’s true. Heavy vehicles underpin our supply chains. This means the issues generated by the inefficient access permit system ripple through nearly every sector of the economy.
The public may not understand the intricacies of the outdated permit system, but they certainly understand when there’s no bread on the supermarket shelves.
A government that ignores this issue does so at its peril. This is not an industry issue, it’s an Australian issue. Voters expect their leaders to make bold choices and it’s time for action.
For over 50 years, Penske has kept fleets and businesses moving forward. From uptown to across the continent and any direction you need, our truck leasing and commercial rental solutions have you covered. Because when your business is on the line, you have everything to lose but even more to gain.
One of the National Heavy Vehicle Regulator’s most important services, the NHVR Portal, is set for a new look, writes Executive Director Michelle Tayler
One of the most important services the National Heavy Vehicle Regulator (NHVR) offers our customers is the NHVR Portal.
The Portal is the digital platform that transforms the way we deliver our services to support our stakeholders, their outcomes and community needs. It provides a single gateway to access a wide variety of tools, services and systems for operators and road managers to help meet their safety, productivity, sustainability, and regulatory needs.
The NHVR is committed to soon providing all regulatory services through the Portal and has been working to transform it into our ‘heavy vehicle business centre’.
In 2025, the Portal is taking an exciting new step by rebranding as ‘NHVR Go’.
NHVR Go is the heavy vehicle hub driving you forward. While it will offer the same tools and services as the Portal, the new name, look and feel reflects our commitment to gearing up for the future.
Australia’s trucking industry has undergone a significant digital transformation over the past few years. Both industry and government have sought to implement emerging technologies, with a goal of improving efficiency, safety, and sustainability through new and exciting means.
Technologies are being transformed across a range of areas, including telematics and fleet management systems, electronic work diaries, predictive analytics, infrastructure, training and support, and of course, the trucks and heavy vehicles themselves.
The NHVR’s online services hub is no different, and we too are working to adopt more modern technologies and systems for our customers. By
embracing a more progressive and smart approach to regulation, we can better support an adaptive, forwardthinking and fast-growing heavy vehicle industry.
NHVR Go’s new name, supported by a new look and feel across the entire site, illustrates our goal of providing a single, digital service point for industry and road managers to access all the tools they need. Our new look includes a refreshed colour palette, imagery and information to help you get the most out of our services.
Through NHVR Go, industry will be able to access the same tools and services as before, including route planning, access information, compliance and more. Operators will still use NHVR Go to apply for and track permit applications, NHVAS accreditation, Performance-Based Standards and Vehicle Standards.
The change to NHVR Go will align the Portal with more modern expectations of simplicity, efficiency and mobility. With a refreshed name and identity, NHVR Go embodies our commitment to innovation, accessibility, and user-centric design.
In 2024, the NHVR completed our National Services Transition program by assuming responsibility for heavy vehicle regulatory services in Queensland. As the final participating jurisdiction to transition, this was a huge achievement and a step forward for industry, with the NHVR now offering a single reference for consistent application of the Heavy Vehicle National Law. The transition has allowed us to accelerate regulatory compliance harmonisation across state borders and work towards a safer freight network.
Our vision for NHVR Go is an intuitive and reliable companion for heavy vehicle operators, paving the
way for greater efficiency and safety in the sector.
NHVR Go will become visible across the Portal from mid-March onwards, with distinctive colours and a new logo visible to all site users. Customers will also see the new name begin to appear in full use across our NHVR website and all affiliated resources.
For industry, it is important to remember the tools and services accessible through the Portal are not changing, but simply the look and feel of the system you use to access them. However, keep an eye out throughout 2025 as more features are added and improved across our entire technological offerings.
We look forward to having you join us at NHVR Go and continuing to support your heavy vehicle and regulatory needs. This next chapter will lead us to a better customer experience, and we are excited and ready to help you get Going.
ANPR cameras are improving heavy vehicle safety in South Australia, Tasmania, Victoria and Queensland. Operating in New South Wales in 2025.
The NHVR is boosting heavy vehicle safety across Australia’s freight network with the use of mobile Automatic Number Plate Recognition (ANPR) cameras.
Roadside trailers and vehicle mounted cameras automatically detect the number plates of passing heavy vehicles, allowing Safety and Compliance Officers to better detect and interrupt potentially high-risk behaviour and unsafe practices.
For more information visit nhvr.gov.au/anpr
Storied trucking operator Marley’s Transport has found a unique way to get a massive combination on the road, with help from Eaton
In nearly 60 years of operation, trucking operator Marley’s Transport has seen nearly everything there is to see in the transport industry.
The company was founded in 1969 by Frank Marley in the tiny Western Australian country town of Nangeenan, which to this day houses less than 100 people.
The Marley’s story starts with Frank’s very first truck — an old Commer which he couldn’t even drive yet, on account of being too young to earn a truck licence.
Having to bide his time, Frank took on the farmhand work that his father Tom had been doing, while Tom drove the Commer.
This is just one example of how the team at Marley’s finds solutions to their problems — something they’ve been doing since the company’s inception.
business and one of the staples of the transport industry in WA.
It’s a long jump from just one truck
of operations to allow the business to continue offering the most reliable and efficient transport services possible to their customers.
The core business remains primarily in agricultural work, delivering bulk commodities including grain, fertiliser and lime. Livestock and pelletised feed transport has also become a significant part of their business, which sees Marley’s deliver to some of the biggest intensive farms in the state.
While they service several large corporate entities, they still continue to work with smaller customers alongside the farms of the Wheatbelt and other small rural businesses.
Like any transport business, Marley’s takes great pride in its ever-growing fleet. It is predominantly companyowned, allowing for maximum flexibility in allocating vehicles to their various jobs.
This also comes with the advantage
of being able to standardise the maintenance process and implementing consistent quality control systems across staff and equipment company-wide.
The need to move bulk agricultural commodities comes with the need for power and performance to be able to handle some of the biggest jobs that Marley’s takes on. This is where the star of the fleet, a Kenworth K220 comes in.
Featuring a Cummins X15 fleet engine with 450hp and 1650Nm of torque as well as an Eaton Endurant XD Pro 18 speed transmission, it offers a unique solution to the challenges that hauling road trains provides.
Eaton’s Endurant XD Pro 18 speed automated transmission is engineered to provide enhanced low speed manoeuvrability and optimised performance throughout the gear range. The Endurant features an overall gear ratio of 20.5:1 which provides Marley’s Transport the versatility and reliability required to meet the needs of bulk grain operations.
Pulling a tipper road train, the relatively smaller horsepower engine needed to be carefully matched to the transmission to be able to handle its tough and varied jobs.
Marley’s engaged Kenworth and Eaton in order to tackle the task within the limited time window between production and delivery.
Eaton Engineering developed a bespoke testing regime to fine tune the
powertrain combination, optimised for the specific road train tipper trailers under both on and off highway conditions.
Once approved and completed, Eaton worked with the local Kenworth dealer during the delivery of the truck to Marley’s to see the calibration solution in action on the K220’s transmission. Feedback was immediate and strong from the Marley’s team, with the new truck a major success and now an important part of the fleet.
“Marley’s are experiencing similar or better fuel economy already compared to the current fleet,” says Marley’s owner Russell Marley.
“Drivers are loving the way the gearbox works and are basically saying that they rarely need to switch to manual.
“Feedback is that the drivers are actually feeling less fatigued on long runs and the trip times have slightly improved.”
While what’s under the hood is important to the performance of their trucks, keeping the fleet in good shape continues to help the longevity of Marley’s equipment.
The average age of the Marley’s fleet is approximately 10 years, which isn’t too out of the ordinary for a large trucking business. All trucks in the fleet are put through the workshop at least every 10 days in an effort to maintain reliability on the road and to reduce downtime.
Marley’s says the level of investment into fleet maintenance and the
Marley’s has been operating for nearly 60 years.
to continually take advantage of new technology.
It’s a perfect fit with the introduction of Eaton’s Endurant XD Pro advanced electronic technology and extended lubricant drain intervals, which retains the efficient transmission maintenance schedule. The technology improvements provide the maintenance efficiency and safety to be at the forefront of quality fleet maintenance.
Safety has always been a key value of Marley’s. In 1998, the business took on a Quality System Project and was officially Truck Safe Accredited as a result. They are also WA Heavy Vehicle Accredited, as well as holding accreditation from the Cooperative Bulk Handling Group as an approved supplier.
This also led to Marley’s winning the TruckSafe John Kelly Memorial Award in 2024, one of the industry’s most prestigious honours.
In his time at the helm of the business, Frank was also passionate about transport legislation, working to make the industry safer and make sure ‘all transport get a fair go and equal opportunity to compete’.
Inducted into the National Road Transport Museum’s Wall of Fame in 2002, Frank’s efforts have been recognised industry-wide. His strenuous work saw regulations lessened on road transport in WA, with the effects still being felt to this day.
Frank’s tireless work ethic has helped pave the way for the third generation to carry on his legacy that he has built over the last 55 years.
While hydrogen-powered trucks are still at their genesis in Australia, they may be finding a niche in the market
The interest and engagement in hydrogen-powered heavy vehicles is growing, as we learned at a recent industry open day.
Hosted by waste management business Solo Resource Recovery in partnership with Pure Hydrogen, the two companies showed off a recently delivered hydrogen waste truck, which is set to join Solo’s rubbish collection fleet.
As many as 80 interested parties turned out to the Clayton South location in Melbourne’s south-east to check out the truck and speak to representatives from both companies, including PowerTorque
Many were from local Melbourne councils, no doubt interested in what hydrogen solutions can offer their own waste management fleets.
Solo Resource Recovery’s Victorian state manager Adrien Scott spoke on the advancements that they have enjoyed throughout their history, with the move to hydrogen marking the next step.
“We want to recognise the innovation that Solo has done over the last 92 years,” he says.
“Throughout the 70s, 80s and 90s we pioneered the introduction of the side arm on our waste trucks. The next step is fuels, from a commercial point of view and an environmental point of view.
“The obligations for all the councils that are here by 2050 are a pretty steep mark to get to. We’d like to be a part of that journey and a part of that process.
“Our trucks include a true hydrogen truck, a battery electric truck, and all the others are Euro 6 or going to Euro 6. They offer us the best emissions outcomes.”
We were able to get a good look in and around the hydrogen waste truck, which cut a strong image with its bright green splashes on the back loader.
It features a 110kW Ballard hydrogen fuel cell, Hendrickson air suspension, hydraulic power steering and an ABS braking system. The body is a low cab, with electronic rear-view mirrors.
The cabin isn’t overly spacious, but for local driving doing waste collection work, it has all the necessities to make the drive as comfortable as possible.
Moving to hydrogen is a big step for Solo, but Adrien says they are hoping to be at the forefront of the next
“In 2007 and 2008 I was involved in the LPG conversion of diesel trucks for interstate transport to and from Sydney.
“All these things test the boundaries of what the transport sector is about. In South Australia we’ve tried the injection of hydrogen into the engine bay to burn off more carbon and reduce more emissions.
“We’re quietly confident that hydrogen is the way to go. Diesel is not going to go anywhere in a short timeframe, however. It’s just going to
become more expensive.
“I know it sounds awful, but the reality is we’re bound to the kilometres travelled when it comes to how much fuel we use.”
The TG23-H110 boasts an estimated range of 250km. While this obviously isn’t anything impressive for anything that has to do any sort of interstate driving, for a rubbish truck, this is more than enough.
General consensus amongst the councils present at the open day was one of positivity – with approaching new fuels, ‘someone has to be the first’.
Adrien says that the process of working with HDrive to get the truck delivered was an encouraging one, and has them optimistic about their partnership into the future.
“We’ve had a great collaborative approach with Pure Hydrogen and HDrive with the supply of the truck. We’re looking forward to 2025 and 2026.
“If all goes well, by the end of this year we’ll have the first side arm built for purpose on a hydrogen cab chassis. To date, hydrogen has always been an accessory, not built into the cab chassis.
“Hopefully by late this year or early next year, that will be coming to Victoria.”
HDrive CEO Ben Kiddle was also present at the open day, speaking to interested parties about what hydrogen can offer their operations.
He believes that waste management is an application that will fit hydrogen
well, with where their range and infrastructure is at the moment.
“Solo as a partner is something that we’ve dreamed of,” Ben says.
“It’s been six or seven years of product development and working with partners over in China. We’ve put a lot of effort into making sure our vehicles are fit for purpose in Australian conditions.
“We’ve got some of our first Australian-approved vehicles now coming to the country now, 70-ton hydrogen prime movers. We’ll also have some battery electric options.”
The prime movers have already received plenty of attention, receiving an order from national logistics provider Toll Group for two Taurus hydrogen fuel cell models.
In fact, 2025 is looking to be the biggest year for hydrogen in Australia yet, with more trucks on the road than ever before.
“We are excited to collaborate with Toll, a forward-thinking company embracing cleaner, greener transport solutions,” says Pure Hydrogen managing director Scott Brown.
“This partnership is an additional validation of the market responding to Pure’s high quality zero emission products. Orders and our sales pipeline are now accelerating as we witness strong interest from both government and corporate customers, including from Asia, Europe and North America.
“The deployment of the Taurus prime movers exemplifies our mission to deliver high-performance, reliable, and sustainable transport solutions to meet the demands of modern logistics. Furthermore, it underlines the growing traction that Pure Hydrogen and HDrive are establishing in the market for our leading range of commercial transport vehicles.
“We look forward to providing more updates on our vehicle sales pipeline in the months ahead, as we build momentum in our stated strategy to transition from vehicle development and testing to sales and revenue growth.”
HDrive recently delivered one of its Taurus prime movers to PepsiCo in Queensland, while also selling a handful of electric buses in 2024.
$12.8 million was committed to electrifying 112 zero-emission trucks for freight and logistics provider ANC.
There’s more funding than ever available for trucking businesses looking to make the move to electric vehicles
The Australian Renewable Energy Agency, also known as ARENA, is the federal government’s response to the lack of infrastructure and investment into the future of electric heavy vehicles in the country.
Since its founding in 2012, it has invested nearly $10 billion across the Australian renewable energy industry, with a direct $2.25 billion in grants funding for projects related to electric trucks and infrastructure.
It’s not just transport that ARENA focuses on – in 2024 alone it has also provided funding to projects in aviation, mining, consumer energy, food manufacturing, robotics, wastewater, buses and more.
In November it announced that $100 million in funding was available under its ‘Driving the Nation’ program dating back to 2022, which tackles three focus areas in transitioning heavy vehicles in fleets across the nation to electric.
Major operators including Linfox ($19.6 million) and Toll ($9 million) are set to benefit from this investment,
but smaller transport businesses have also been reaping the rewards across various sectors of the transport industry.
Now, 2025 is now set to be one of the biggest years for the funding of electric projects through ARENA, and could set the scene for major change in how Australian fleets look.
“We’re going to have $100 million in funding to support other recipients over the next year or year and a half,” says ARENA knowledge sharing manager Adrian Salinas.
“There’s currently about 20 projects in different stages of completion. Some of them have already been announced, with people working and completing milestones.”
Several projects in Western Australia have been completed over the past few years, which Adrian says they are particularly proud of.
Operators Patrick Terminals and Centurion have both previously received funding to transition their fleets and upgrade their infrastructure to support a higher volume of
working electric trucks. This funding is removing one of the biggest roadblocks for those interested in moving to electric, being the cost, which has continually been referenced as one of the major challenges in making the switch.
Patrick was awarded $2.5 million in an effort to reduce its emissions at what is WA’s largest container port in Fremantle, which sees a massive volume of both freight and vehicles moving through it.
That money allowed them to deploy nine battery electric terminal trucks and set up fast chargers in a first for the port.
“Patrick takes all these small trucks that move cargo containers in the port, uses them to take the containers from the ship and put them in the trailers themselves,” Adrian says.
“So now all of their operations inside of the port happen with zero emission vehicles. Those are heavy trucks that are moving containers inside of the port.”
The funding for Centurion’s project
was another major one, providing them with both a massive addition of electric trucks to their fleet and the infrastructure to go with it.
A grant of $15.8 million from ARENA was put towards 30 battery electric trucks and 15 dual port chargers to not only cut emissions, but increase their capacity to operate their new trucks.
“Centurion’s issue that they had was there’s not enough electricity on the grid to power their trucks,” Adrian says.
“What they did was utilise land that they had next door, and they installed a solar farm to power the trucks. That was a big project for Western Australia.”
While ARENA is continuing to grow the amount of transport projects that it is funding, it wasn’t initially a focus area.
But as ARENA’s team talked to industries across the country, transport continued to come up. Initially they had looked into light vehicles, including commercial vehicle fleets, but the heavy sector needs greater investment to impact the path to decarbonisation.
“We’ve looked at a number of different jurisdictions, in Queensland, New South Wales and Victoria, and they’re all talking about heavy transport,” Adrian says.
“Going back, transport wasn’t part of the plan to start with, but the opportunity came when looking at renewables in the future, and the largest user of electricity will be transport.
“We started in the light passenger sector to begin with, but in 2022 we decided to undertake projects in heavy transport for two reasons.
“The main one is that transport operators are really keen to decarbonise because all they think about is total cost of ownership. They’re not running trucks across the country for fun, they’re a business.
“In terms of emissions, the heavy transport sector is one disproportionately representing the amount of emissions with transport. We need to start taking care of that sector if we really want to decarbonise transport as a whole.”
One of the funding areas that ARENA announced under the Driving the Nation program in 2023 was a focus on electric vehicle charging solutions and infrastructure, with $70 million committed.
While this particular funding round was focused on public charging and innovation in the management of charging, they have since looked to privatised infrastructure.
ARENA funded a project to the tune of $8.5 million for fleet electrification specialist Zenobē (find more details in the previous edition of PowerTorque), which is incorporating off-site charging as one solution for electric fleets that lack the necessary infrastructure.
This is being put towards establishing an ‘electric charging hub’ in Mascot, Sydney to be used by Woolworths to charge its electric vehicles.
It will contain 22 dual-port chargers all equipped with smart charging software to optimise energy use while also using stationary battery storage made from repurposed batteries from old electric vehicles.
The site will support a fleet of 60 electric trucks leased to Woolworths and will also have the capacity to expand, creating a multi-user charging facility.
This particular hub is servicing trucks that are doing local deliveries – all on the smaller end of the scale at predominantly 4.5 tonnes.
While they won’t travel far from South Sydney, they still require a full day’s worth of charge to operate their routes.
With the hub being leased to Woolworths, this opens the door for other companies to lease out the space to charge their trucks in the future.
This could be a solution to provide charging infrastructure across a number of fleets without needing as much space that would be required for companies operating a full fleet of electric trucks.
“Let’s say I wanted to put a charging hub next door to a trucking company, the main thing I need is access to the land, and the second is connection to the grid,” Adrian says.
“We’re talking years back and forth to negotiate your lease agreement for the land and your connection agreement. What Zenobē did very cleverly is they partnered with Ausgrid, so the land belongs to the electricity company.
“Having the approval to connect and the access to the land is not an issue. From day one they are a couple of years ahead of someone that might have a good plot of land, but then has to start a lengthy conversation with an electricity company.
“The charging hub in this case is not installed on your premises or your depot, only servicing you. It’s like a petrol station of the future for heavy transport.
“The Zenobē project is one step
closer in the right direction, with land close to the airport and Woolworths as an anchor customer.”
The process of progressing the decarbonisation of the transport industry has been addressing the widespread concerns that many have when it comes to making the move to electric vehicles.
With other options becoming more viable like hydrogen and renewable fuels, businesses big and small have a choice to make about which path they are going to follow.
And with that choice comes a significant financial investment which for many could make or break their futures within the industry.
Helping operators and businesses to understand where the advantages in electric lie has been another focus of ARENA’s.
“Part of putting the business case forward for this new funding round was spending time with the transport operators themselves,” Adrian says.
“We went to all the conferences throughout 2024.
“We were everywhere, and what we hear from transport operators is ‘I’m ready, I want to do it, but I don’t know which door is for me’.
“And while the market is still looking at three doors at the moment, people are still not necessarily sure which technology fits the most to their operations and also when that
technology is going to be available.”
Attending industry events, conferences and forums has given ARENA a solid picture of what businesses and operators are thinking and the challenges they’re facing on the ground.
They attended an industry forum with more than 150 stakeholders from the heavy transport sector late in 2024, which provided valuable feedback.
“We use opportunities like these to get industry experts communicating to us as a group,” Adrian says.
“We can lay out the benefits of working with hydrogen, the benefits of
working with electricity, the benefits of working in the future with low carbon liquid fuels.
“There’s one technology out of these three that you can invest in today, which is electric trucks and electric chargers.
“If you were on the hydrogen path, that might be more of a 2030 scenario, and by 2035 we’re going to have solutions on the low carbon liquid fuels.
“So right now the funding that is available is for electricity, but we also have plans in the future in invest in these other technologies when and if the time is right.”
Wyndham Steel Solutions’ brand new Isuzu crane truck has been a big helping hand with the business’ construction jobs
n the heart of Werribee, Victoria, a family-run business is shaping the skyline of Greater Melbourne, one steel beam at a time.
Wyndham Steel Solutions isn’t just about steel, though; it’s about helping clients design and construct their dream homes and buildings.
With a fleet of Isuzu crane trucks carrying the weight of every project, the small but dedicated team is transforming how homes and commercial buildings rise from the ground up.
With clients ranging from small builders, high-end architectural firms and Tier 1 high-volume builders, Wyndham Steel Solutions is tackling everything from residential and commercial steel packages to complex architectural installations. They’re taking steel design, fabrication, installation — and their trucks — further than ever before.
“At Wyndham Steel Solutions, we pride ourselves on impeccable service and product quality, ensuring that
all project deadlines are met to the highest of standards,” says General Manager Noah Piggott.
Helping to deliver this premium service is a brand-new crane truck, an Isuzu FRR 110-240 AMT with a long wheelbase and an F.lli Ferrari crane installed onto the custom tray, built by LVTC Transport Equipment. This new rig joins a FVL 240-300 Auto crane truck and a classic NPR 300 already in the fleet.
The new FRR 110-240 is underpinned by an Isuzu 4HK1-TCH 16-valve engine, which provides a power punch of 177 kW (240 PS) @ 2,400 rpm and 765 Nm of torque @ 1,600 rpm.
With a generous GVM of 11,000 kg, the FRR 110-240 AMT has ample payload for both the crane and the required load of steel. This is supported by a long wheelbase of 4.99 metres, which provides plenty of room to move their products.
Graphic designer Rickie Arnott created the stylish look for the FRR with the wrap installed by locals Brand FX.
“We selected the FRR 110-240 because of its ability to carry structural beams and brick steel lintels, its manoeuvrability no matter the job site, and because it’s economically friendly with its fuel consumption,” says Noah.
“The F.lli Ferrari crane was handpicked due to the length we required at full capacity, and for length-toweight ratio, we found the FRR is the perfect match to get the crane on site.
“We can then use the crane to lift steel lintels off the truck and stabilise the weight of T-Bars, which are lifted into place over structures such as garages.”
As an outfit that relies heavily on its fleet to deliver a full-package service, Wyndham Steel Solutions is looking to its transport partner to provide infallible backup support as the business expands and trucks that will last the distance under heavy duties.
It’s not all about steel, but it is a big part of Wyndham
The FRR 110-240’s six-year standard warranty (or 300,000 km) and six years of roadside assistance, which is available 24/7, are helpful in this regard.
They say never to mix family with business, but Wyndham Steel Solutions is proving an exception to the rule.
First opening the factory doors in 2021, the business was founded by father and son duo Dean and Logan Piggott, who put their considerable experience in the steel and construction industries to work for the family business. Noah (the younger brother) joined the team in 2023, bringing a background in Insurance Building, focusing on compliance and business management.
Starting out of a small factory in Melbourne, they provided a personal touch for their early clients, from handdrawn blueprints and hand-painted finishes on the steel to fabricating everything from the factory. They
focused on installing one residential project weekly while building up their client lists.
Four years on, the tightly run operation is still keen to keep all services under one roof: from drawings executed on AutoCAD and Tekla programs to fabricating steel products and working a painting station to streamline the production process. The in-house team also completes all installations of structural steel projects.
“Keeping everything in-house has allowed our business to grow our capacity, allowing us to install roughly two jobs a day, keeping a constant flow of work on our books,” says Noah.
“We have recently ventured into the brick steel lintel market and offer services for delivery and lifting of all lintels required for construction projects, with all projects installed with our Isuzu crane trucks.
“We are currently about to break ground with a new purpose-built factory, warehouse and office space. This will be our biggest in-house project to date, and we are excited to see the build come to life.
“This new space will be approximately three times the size of what we have now, so between the new factory and our new Isuzu, our capacity for jobs is set to triple in size.”
Gas trucks are growing in popularity in the UK, and Will Shiers gets behind the wheel of a potential game-changer, a BioCNG-powered Scania R460 6X2*4
With a population of 70 million, the UK generates a significant amount of waste. Turning that waste into biomethane to power trucks, rather than allowing it to escape into the atmosphere, is undoubtedly a positive step.
From a personal perspective, I reckon biomethane makes more sense than electrification for longhaul operations. While it’s not a zerotailpipe-emission solution, it offers a well-to-wheel CO2 reduction of up to 90 per cent compared with fossil fuels. What’s more, unlike electrification, biomethane benefits from an established and expanding refuelling infrastructure in the UK. The fuel is also cheaper than diesel, providing an additional incentive for hauliers. At
the time of writing, it costs 85p per kg (AUD 1.70), which equates to a 30 per cent cost saving when compared with diesel.
A growing number of UK operators are going down this route, with sales of gas-powered trucks steadily increasing, especially in northwest England, where the refuelling network is most mature. Iveco, Scania, and Volvo are all competing in this space. Iveco offers a locally converted 6x2 tractor for the all-important 44-tonne GVW artic sector, but until now, Scania and Volvo have only supplied 4x2 options, which are restricted to 40 tonnes. That’s about to change, though, with Scania launching a 6x2 tractor.
“Customers have been asking us for a 6x2 CNG vehicle for a long time, but we were adamant that we wouldn’t
build one until we could answer all the questions,” Scania UK pre-sales technical manager Phil Rootham told me. “I didn’t want to put one on the market that didn’t have the range — it would have set us up for failure.”
When Rootham talks about “answering all the questions,” the primary hurdle was achieving a practical range. Scania’s 4x2 CNGpowered extended-range tractor already delivers around 600km on a full tank, but the 6x2 configuration introduced new challenges, particularly with restricted chassis space.
The breakthrough was enabled by the European Union’s (EU’s) updated masses and dimensions regulations — the same changes that spurred the creation of longer, more aerodynamic
cabs such as the DAF XG, Volvo FH Aero, and Mercedes-Benz ProCabin. These revisions permit manufacturers to extend wheelbases and go beyond the long-standing 16.5m European length restriction, provided that safety and aerodynamic performance are enhanced.
Scania met the regulations by incorporating its Integrated Vehicle Functions (IVF) bumper — a discreet lip that enhances both aerodynamics and safety. This small adjustment allowed Scania to stretch the wheelbase by 500mm compared with a standard 6x2 tag-axle tractor. The extra space enabled the installation of four 95-litre gas tanks on either side of the chassis and two 232-litre tanks on the rear wall of the cab, delivering a total capacity of 1,224 litres. This matches the 600km range of the 4x2 version.
Another obstacle was ensuring compliance with current turning circle regulations. Scania addressed this by designing the truck as a 6x2*4 rearsteer tag. Using the drive axle as the
pivot point, the configuration meets these standards.
Although the demonstrator featured here is a bespoke build completed at Scania’s Laxå plant in Sweden, which concentrates on special vehicles, future 6x2 CNG trucks will be produced on Scania’s main factory line.
From the outside, it’s hard to tell this isn’t a standard diesel-powered R460. Only the extended wheelbase visible in the side profile hints at something different beneath the surface.
The CNG tanks are cleverly integrated. Four smaller tanks are hidden behind the side skirts, while two larger ones are mounted at the rear of the cab, partially concealed by the side fairings. These cab-mounted tanks, like the others, are designed and installed by Scania and are positioned exclusively on the lower section of the cab’s rear wall. Scania currently has no plans to extend the truck’s range by adding an extra tank.
What’s hidden from view is the updated driveline. It includes a re-engineered 12.7-litre spark-ignition engine built specifically for methane, delivering 460hp — a significant step up from the previous 410hp and one likely to appeal to drivers. For the first time, Scania has paired this gas engine with key elements of its Super diesel driveline. This includes the latest G25 Opticruise 12-speed gearbox and a new rear axle. Scania claims this pairing boosts fuel efficiency by 5 per cent, enhances performance, and retains the same service intervals.
The new R460 gas truck is equipped with Scania’s latest Smart Dash digital dashboard. Launched earlier this year to meet the EU General Safety Regulations, it features a configurable Driver Display directly in front of the driver, as well as a touchscreen Centre Information Display located to the left.
The Driver Display can be tailored to individual preferences and offers
clear, easy-to-read information. On the other hand, the Centre Information Display, which is compatible with Apple CarPlay, simplifies operations by removing the need for intricate menu navigation for straightforward tasks. While touchscreen interfaces are not to everyone’s liking, Scania has kept physical buttons for essential functions, ensuring ease of use is not sacrificed.
That said, Scania acknowledges that the Smart Dash isn’t without teething issues. For instance, as I made my way onto the motorway, the system erroneously displayed a 70mph (113km/h) speed limit sign. This is the maximum speed for cars on the UK motorway network, while trucks are limited to 90km/h.
Lately, it seems like almost every vehicle I drive is battery-powered, but the Scania R460 CNG surprises with a similarly quiet experience, particularly at a steady 90km/h. It’s an almost unnerving quiet, especially when you’d expect the typical sounds of a combustion engine straining against an incline. However, there’s no noticeable change in pitch or effort — just smooth, silent acceleration. A quick check of the dashboard reassures me the truck is maintaining its speed effortlessly.
This seamless performance persists throughout the journey. There are no inclines steep enough to push the truck’s limits. Only when I accidentally engage adaptive cruise control and get caught behind slower traffic does the vehicle lose any speed.
On the downhill stretches, the truck’s performance remains consistent. Setting the overrun speed to 95km/h, it holds that speed perfectly without any deviation. Sparkignition engines, unlike diesel ones, rely on retarders for braking rather than engine brakes. In this case, the retarder operates smoothly and efficiently, providing strong, controlled deceleration.
I’m particularly impressed by Scania’s new G25 gearbox, which works flawlessly in this truck. The gear shifts are precise, quick, and smooth, ensuring the 460hp engine and 2,300Nm of torque deliver performance comparable to a diesel equivalent.
Driving a truck with traditional mirrors feels like a bit of a novelty these days. Having grown used to various camera and screen systems, this truck reminds me that there’s still nothing quite like the clarity of good old-fashioned glass mirrors. While Scania has been working on mirrorless technology, having showcased a concept during the Super driveline launch over two years ago, it’s clear that the company hasn’t fully embraced it just yet. For now, mirrors remain the standard, as Scania continues refining its mirrorless systems.
After completing a 250km drive,
while running at 40 tonnes, the digital gauge indicates that 35 per cent of the fuel has been used. At this rate, the truck shows a potential range of 690km. This suggests that Scania’s projected range of 600km at 44 tonnes is not only attainable but comfortably within reach.
Some may argue that biogas is just a stepping stone towards full electrification, and while there’s some truth to this, the transition is likely to be a lengthy one. The significant investments from companies like CNG Fuels (see ‘filling up’) and Scania in biogas refuelling infrastructure and new vehicle development
demonstrate their confidence in its long-term potential.
In my opinion, biomethane is here to stay, providing a practical and sustainable option for operators looking to reduce their carbon footprint. With the arrival of the Scania R460 6x2, I believe more UK hauliers will make the switch to this fuel.
Before hitting the road, I made a stop at CNG Fuels’ facility in Warrington, located in northwest England, to refuel the tanks.
If you are of the opinion that refuelling with CNG involves complex safety training and multiple layers of personal protective equipment (PPE),
Getting to 100 years in business is a milestone, but how Russell Transport has achieved their longevity comes down to making all the right moves
An old saying goes like this: the first generation builds a business, the second generation grows it, and the third generation kills it. But they’re just sayings for a reason, and Russell Transport doesn’t particularly believe in this one.
The Queensland-based transport operator is celebrating 2025 with an extremely rare milestone: 100 years in business. Safe to say a fair bit has changed since Roy and Beryl Russell undertook what was then a tiny operation transporting motor spirit for the Commonwealth Oil Refinery in Brisbane.
Between Roy jumping in his first truck, and speaking to now-director Ken Russell (Roy’s grandson), we’ve landed on the moon, fought another world war, invented colour TV and the smartphone, and even made some slightly better trucks. Though that one might depend who you ask — some of us still swear by the old stuff.
But there’s nothing outdated about Russell Transport though, with the third generation in Ken, Julie and Michael leading the business into bigger and better things every year.
PowerTorque sat down to speak to
Ken and Julie alongside Phil Russell, part of the Russell Transport’s third and second generation respectively.
While the milestone is a massive one, they’re not making too much out of it.
“We really do live in it every day when you break down it down, we’re going through the same processes every single day,” Ken says.
“Is it different to 90 years or 80 years? Obviously, but everyone celebrates differently. I saw a business that’s 20 years old putting a big combination on the road. Everyone has different ways of celebrating.
“As you go along, each milestone means different things. It’s hard to put a finger on just what 100 means. It’s been asked heaps of times!
“Ultimately it’s been a lot of hard work from those before us to get here.”
From those early days of a husband, a wife and their truck, Russell Transport has grown to 270 employees, but with the same values and ethos that
made them strong from the start.
“The business has made 100 years in three generations in the single bloodline,” Ken says.
“There’s been challenges along the way, but the transport business has maintained throughout that time. The equipment we put on the road is very modest. But there is a lot of pride there.
“It’s not an easy industry. Anything that involves people involves pressure. The feeling of making it happen for 100 years makes me acknowledge that every day has been worth it. One of my goals when I became a director was to make it to 100 years.”
Nearly the whole Russell clan has experience being around the business from a young age, as many do in family businesses.
While kids aren’t exactly jumping in the passenger seat anymore for delivery runs, the business has been a staple of the lives of everyone in the family.
Looking back, Julie recalls some of her earliest memories being around her dad’s work.
“In the back of my mind I remember the layout of our site and how it used to be,” she says.
“There was a dirt yard at the back. There were Christmas parties with hay bales at the back of the trailers and you’d go for a drive back there. Over time that’s changed to concrete and there’s not so many snakes!
“I can remember being amongst the celebrations at the end of the year every year. I remember coming in on weekends when dad would come in to do some work. I remember him building us a cubby house out the back, trying to put it together.
“He was welding, and I was standing in the middle of an A frame
and it all fell down around me!”
Many of the memories Ken holds of his early days around the business were often spent out with the drivers.
Being long-time employees, they were always around the family. It was nearly impossible to not build familiarity.
It was those early experiences that led him to stay around the family business into his adult life.
“One of the drivers worked for grandad and dad, and I always went out with him in the truck when I was eight or nine,” Ken recalls.
“There was another gentleman who still works with us, Phil Thompson, who’s just turned 80. Still has the envy of the work ethic. When I was 14 through to 19 that’s who I would be sent with.
“I remember one time where we
went out to the Amberley Air Force base, and they were unloading aviation fuel. I went into the hangar and over to the platform where they practiced parachute jumps from. I dare say no child would be allowed onto that base now!
“When your family has a lot of equipment, you play around on it. We would jump from trailer to trailer in the yard.
“Dad taught us to be jacks-ofall-trades. We were electricians, plumbers, roofers, anything that needed to be done.”
Julie hasn’t spent quite as much time with Russell Transport as Ken, but has well and truly established herself as a trailblazer of the transport sector.
She was named National Trucking Industry Woman of the Year in 2015
and was awarded a Medal of the Order of Australia in 2023 for her services to the road transport industry.
She spent time working away from the Russell clan for a number of years, before being brought back into the fold as a Director in 2007.
The time away gave her the perspective and knowledge to continue adding to the legacy of Russell Transport’s 100 years.
Even though she enjoyed her time elsewhere, she says there’s nothing quite like family.
“To get to three generations, it’s special thanks to the people around us, some of which have spent their whole careers with us,” Julie says.
“That almost extends the family network.
“You’ve got solid support structures
around you, that have your back like family does.
“Each generation has had really strong support from the people in the business.”
“Julie and I had a dedication to the business from looking at the dedication and drive of my father and grandmother,” Ken adds.
Of the current day Russells, Phil has been the longest-serving, taking over from father Roy in 1970 and working 45 years in the director role.
He became well-known in the Brisbane community, and oversaw the growth of Russell Transport has become today.
Phil vividly recalls the days of his father delivering four gallon tins out of the back of a single storage shed at the oil refineries with his Dodge.
“He slowly built it up in the five years after he started to three trucks,” he says.
“Now that I look back over dad’s 45 years running the business, and he kept working until his 80th birthday, I’ve got a lot of respect for what he did it and how he did it and the effort he put in.
“As I look forward, I can see that I’m fortunate to have another
Traditionally, Russell Transport has been a general haulage and heavy haulage business, with their iconic ‘tan and white’ fleet. That had always been the backbone of the company, but it has continued to expand into other areas.
The diversification of the business has included a liquor business which involves the delivery of palletised goods to the Sunshine Coast and Gold Coast.
Russell Transport has also dipped into third party logistics, delivering products under the banner of other companies around Brisbane.
Continuing to expand the business in this way means that it is everevolving, allowing for a diverse portfolio under the Russell name.
“We have different eggs across different baskets,” Julie says.
“It’s not all the same type of cartage that we do for everything. When one industry’s up, another one might be down.
“We’ve got a balance to be able to spread our workforce around depending on the ebbs and flows of those industries. That’s where I’ve seen the change in our profile.”
This looks fairly different to how Russell Transport was operating 25 to 30 years ago, with the general freight haulage work built from Roy’s early days founding the business.
It has a separation of the business into different areas, hence the need for
expansion to closer to 300 employees, the biggest Russell Transport has ever been.
The 1990s and 2000s saw the start of that change, as Phil and Ken identified the need for growth.
“Grandad had a history with fuel and wool, and typical cartage. Dad had a history with fuel, heavy haulage and general cartage, and he got us into our first contract distribution role,” Ken says.
“In the late ‘90s and early 2000s was the paradigm shift in the business. There were some good decisions made, with the purchase of Caloundra General Transport and leveraging some of that business’ skills to get likeminded contracts.”
With that purchase came the splitting of the business into two, and eventually three, sections.
Now it operates as Russell Transport, Metro-Lift Cranes and Caloundra General Transport, all fulfilling different jobs.
This allows for synergies. Having Russell Transport’s heavy haulage division and Metro-Lift Cranes means the two companies are often working together to facilitate the loading and unloading of over-dimensional and over-mass freight.
Contract distribution has been one of the big sources of continuous growth for the businesses. From beverages, alcohol, groceries and even to steel, it all pulls from the same knowledge and experience in their operations.
“Our main history still sits in our
industrial resource services,” Ken says.
“But the business has been able to diversify and offer external services that are complementary to transport services.
“We have the base fleet, the freight terminal, our specialised transport, our heavy haulage, our container services, our lift and shift. There’s the crane hire business, the lifting operation.
“But then we still say we’re a small business! It’s a big operation, but we’re very diverse. That enables us to put together end-to-end solutions and show our customers we have the capability to either deliver a single package or move your entire manufacturing facility.
“We’ve been taking the opportunities that make sense to the core ethics of the business.”
The truck fleet is now pushing 200 strong to match the demands of the work Russell Transport undertakes. This isn’t even to mention the cranes, forklifts and other gear that are required for the numerous jobs.
They don’t stick strongly to any one brand, but the heavy haulage side of the business is entirely Kenworths.
In the fleet business, there’s a mix of Mack, Kenworth, DAF and Isuzus in the prime movers. But for body trucks, it is 100 per cent Isuzu models.
Ken says that figuring out the best truck for each task is more valuable than sticking solidly to one brand due to the diversity of the jobs required of them.
“That’s one thing I can say that dad had to teach me, is getting the specification of the vehicle for the application right,” he says.
“There’s no point over-specifying it, because then no one will pay you for it.
“But if we stuff it up and under-spec it, it’ll cost us a fortune to run.
“Sometimes we’ve got it right, and sometimes we’ve gotten it wrong.
“We have premium vehicles that are for high hours and arduous applications. If it’s on the highway doing 50,000km a year we’ll run a Hendrickson HAS suspension. We’re trying to match the cost profile that our customer is prepared to pay for the right piece of equipment for the task.”
With a large fleet of trucks also comes a large fleet of trailers. This is
Phil even has a trailer that he’s held onto for much longer than you would typically think wise in a 200-plus fleet of trucks.
“We still have a trailer that we bought
“Imagine a clown juggling when it comes to me trying to work out what equipment to buy,” Ken says.
“It’s honestly a moving target. I place the order when I can — either I have a
when they came in for instance.
“I believe we were built off International, having that modest approach, I grew up around that. We had the Kenworths, but they were our
Cummins will be showcasing its new integrated powertrain for the first time at the upcoming Brisbane Truck Show
The remarkable transformation of Cummins in recent years to become a genuine powertrain supplier – from engine to transmission to axles and brakes – will be in evidence for the first time in Australia at the Brisbane Truck Show in May.
A world-first display showing the integration of Cummins X15 engine, Eaton Cummins 18-speed Endurant speed transmission, and Meritor driveline and axles – will be in the spotlight at Brisbane.
Cummins’ acquisition of Meritor in 2022 was the critical piece for Cummins in being able to rollout a completely integrated powertrain.
In fact, the Brisbane show will be the first time the combined forces of Cummins and Meritor are displayed together at a truck show in Australia.
While the Meritor business now operates under the banner of Cummins Drivetrain and Braking Systems (CDBS), the Meritor brand is
retained for axles and brakes.
“The Brisbane show will be a great opportunity to see the result of the Cummins-Meritor integration and the benefits it offers customers as we bring together complementary power technologies to seamlessly enhance efficiency, performance and lower emissions across the powertrain system,” says David Cole, Managing Director of CDBS Australia.
“For customers this means lower total cost of ownership and having confidence in system dependability, backed by comprehensive Cummins support across the powertrain.”
Cummins’ fuel agnostic HELM capability with its X15 engine platform will also be showcased at the Brisbane show.
“HELM – higher efficiency, lower emissions, multiple fuels – highlights the innovation that is powering us forward,” says Sean McLean, Director
and General Manager of On-Highway Business for Cummins Asia Pacific.
The HELM engines are an important element of Cummins’ Destination Zero strategy to go further and faster to reduce the greenhouse gas (GHG) and air quality impacts of its products.
The industry-first HELM platform basically comprises one block and three-cylinder head options – a compression ignition head for diesel, and spark ignition heads for natural gas and hydrogen (a zero carbon fuel at the tailpipe).
This will be the 15-litre platform for future diesel development and will be released in OEM (original equipment manufacturer) applications for the Australian market in coming years.
The natural gas version of the X15 – the X15N – is now in full production, at Cummins’ Jamestown engine plant in the US, while the hydrogen version – the X15H – is expected to become
available later in the decade.
The X15N, the first natural gas engine to be designed specifically for heavy-duty truck applications, is offered with maximum outputs of 500 hp and 1850 lb ft of torque. The X15H will have higher peak outputs of 530 hp and 1900 lb ft of torque.
Cummins’ new HELM X10 engine will also be displayed at the show.
The X10 is a brand new 10-litre platform to be launched in North America and Europe in 2026 and other global markets at a later stage.
While the X10 has fuel agnostic capability and is able to run on hydrogen and natural gas, the diesel version will be available first, compliant with the ultra-low U.S. EPA 2027 and Euro 7 emission regulations.
Diesel will remain a critical technology for the on-highway market for years to come, and Cummins will continue to support it.
“We are committed to advancing diesel technology while our markets and our customers need it to run their businesses,” says Sean McLean.
The diesel X10 will be available with ratings up to 450 hp and peak torque of 1650 lb ft, outputs that will suit short haul and regional trucking operations as well as bus and coach applications.
CUMMINS X15 SPECS
Horsepower: 525-565 hp, 391-421 kW
Torque: 2508-2279 Nm
Governed speed: 1900 RPM
Cylinders: Six
System weight: 1430kg
Engine weight: 1343kg
Ensuring the health of your engine can be the key to both saving money in your operations and avoiding downtime
Staying on top of engine maintenance is key to your truck’s performance. Performing predictive and preventative engine maintenance then can ensure the health of your fleet, and minimise downtime, which leads to lost time and revenue.
This isn’t even to mention the costs that can come with emergency maintenance, running through diagnostics of major issues which could have been caught before they got out of control.
This is where the FleetguardMAP program comes in.
It is estimated that a significant 40 per cent of problems in heavy-duty diesel engines arise from insufficient maintenance of the cooling system.
Knowing then how to best manage your coolant, especially when it comes to maintaining a fleet of trucks, can provide a major advantage over your competition.
The FleetguardMAP coolant analysis program aims to work alongside your existing predictive and preventative maintenance platform to both complement and add to it.
The tests in the program can be used to identify early signs of overheating and corrosion, changes in the coolant chemistry (protection), coolant/additive dilution,
contamination by fuel/oil or hard water (calcium/magnesium), radiator fluxes, chlorides, and sulphate.
Each piece of equipment which is tested will have its fluid analysis history and recommendations retained for future reference.
The program functions through interaction between the customer and Fleetguard.
Fleetguard customers send coolant samples to inhouse FleetguardMAP experts who perform quality control tests on these samples to provide a comprehensive and easy to interpret report in a timely manner, usually indicated within 3-4 business days.
The report will indicate the condition and the quality of the coolant sample and highlight key issues and indicate recommendations.
Reporting on information such as whether the coolant is over diluted, cavitation protection is near lower limits or hardwater contamination is detected will be crucial for future maintenance.
The report is emailed to the customer and held securely in the cloud so that data can be reviewed and measured remotely for each engine over time.
For the greatest benefits when it comes to reducing total cost of ownership for your vehicles, use
Fleetguard’s engine coolants, PG Platinum and PGPlus.
PG Platinum coolant is a popular choice among HD engine owners because it is silicone-safe. This means that it doesn’t contain 2-ethylhexanoic acid (2-EH), which can cause silicone hoses, seals and gaskets to lose their flexibility and elasticity, ultimately leading to coolant leaks.
PG Platinum is a propylene glycolbased premixed coolant that uses organic additive technology (OAT), specially formulated to provide advanced, long-lasting protection against corrosion and liner pitting (also known as cavitation), which can pose significant issues in your engine.
It’s compatible with different elastomeric seals, gaskets, plastics and metal alloys used by OEM heavy-duty engine manufacturers.
Additionally, it is also fully supported by the Fleetguard Global Warranty.
From AI-powered insights to smarter infrastructure, Geotab is anticipating how a number of trends are going to shape connected transportation in Australia across the next 12 months
If you’ve heard it once, you’ve heard it a million times – artificial intelligence, or AI, is going to change the landscape of industries across the nation. For some, it already has.
Not all of it is going to be talking holograms and super-computational algorithms. Much of what AI can offer will be ways to streamline workloads and offer integrated solutions to make day-to-day tasks easier.
In the transport world, this often takes the form of being tied in with telematics, using data gathered to generate reports or run insights on how trucks are running. The benefits to this are obvious, but AI continues to evolve, with the capability to do so much more.
2024 was a transformative year for Australia’s fleet and heavy transport
industries, according to Geotab Associate VP APAC, David Brown.
From the 3G shutdown to the rise of the NVES and emerging Chinese vehicle manufacturers, the sector has experienced significant shifts.
As we start 2025, there is a huge opportunity for the industry to embrace transformative trends in AI, data privacy, and fleet sustainability, which will help tackle evolving demands in safety, cost management, and operational efficiency.
David and Geotab outlined the eight biggest predictions for 2025, with the eye towards the advancements to come in AI use and the benefits you can take away from it.
As the use of AI in telematics continues to grow, David sees customised telematics trending
towards becoming mainstream.
Telematics is the standard for fleet success, and in 2025, it will shift towards customised insights to meet unique needs to stay competitive and efficient. He says 2025 will be about quality data insights, open platforms and ecosystem partners adding specialised solutions for better outcomes. In Australia, this shift will be driven by the increasing demand for tailored solutions that address fleet-specific challenges, such as managing compliance with Chain of Responsibility (CoR) laws and improving fleet safety on regional and remote roads. 2025 will be about quality data insights, open platforms, and ecosystem partners adding specialised solutions for better outcomes. Local fleet operators are also likely to prioritise sustainable
practices, leveraging telematics to optimise routes and reduce emissions in line with Australia’s decarbonisation targets.
David also sees vehicles and telematics becoming more integrated than they ever have before.
This year will see the continuance of taking big data sets and making them digestible for fleet managers through the integration of OEM telematics data into the Geotab ecosystem, giving Geotab the ability to collect data from lots and lots of different vehicle types.
“In Australia, where fleets often include a mix of light commercial vehicles, heavy trucks, and specialised equipment for industries like mining and agriculture, this enhanced integration will be crucial,” David says, “and it will also help Australian fleet managers navigate the unique challenges of managing vehicle performance in harsh environmental conditions and over vast distances, making operations more efficient and cost-effective."
He predicts automated workflows will improve productivity with the biggest opportunity for the heavy transport industry in 2025 being to integrate workflows within their business, between their siloed software solutions, to allow for efficiencies through integration as fleet managers can see more data from a greater range of systems.
“Industry collaborations like our partnership with Logmaster will make work for everyone in the industry easier, whether they are drivers, fleet managers or bookkeepers.”
Through the use of AI, fleets can unlock greater savings through tax credits and rebates.
Some of the best savings’ opportunities for the industry come from unlocking government support through credits or rebates, such as Fuel Tax Credits. Many organisations just aren’t taking advantage of these initiatives because of the stringent record-keeping requirements needed to claim them.
“Using telematics and making the most of quality partners like KPMG, as
well as the many options found on our marketplace can make a fundamental difference with organisations and their confidence to move forward with a tax claim,” David says.
As AI advances, operations will also continue to grow more streamlined as more solutions become available. David believes that efficiency will shift the focus of sustainability.
In 2025, sustainability will look different for every fleet, but the common thread is efficiency. More focus will be on optimising operations — whether through electrification, smarter routing, or reducing idle time — to save both resources and costs. These factors are particularly important for Australian fleets, with a fledgling but rapidly expanding EV charging network providing greater opportunities for fleets to decarbonise.
With the ability to automate and collect more information on driver performance, David says transport businesses will be able to pay more attention to advancing driver wellbeing. In 2025, fleets will focus on proactive training, in-cab tech, and near-real-time feedback to enhance driving skills. Rewarding good driving behaviour will boost engagement and retention, helping fleets attract and keep top talent in a competitive market. Truckies make up the
backbone of Australia’s economy and ensures goods get to where they need to be when they need to be. Ensuring they can do so safely is critical to any fleets’ operations and keeps companies at their most efficient.
And lastly, the latest major shifts in technology will drive innovation.
The 3G shutdown has happened, but there’s still many fleets out there who haven’t transitioned yet or haven’t actually got telematics. For those still on 3G-enabled technology, the jump to the next generation of telematics means better functionality and integration with the most modern software integrations.
“This technology opens the door to many possibilities in improving a fleet’s operations, so it’s our job to let them know what telematics is, and how it can help their business.”
As we begin 2025, the fleet and heavy transport industries in Australia are poised for transformative growth. Advances in telematics, automation, and sustainability will not only drive operational efficiency but also ensure safety and compliance in an everchanging regulatory environment. By embracing customised solutions, deeper data integration, and innovative practices, fleet operators can unlock significant opportunities for cost savings, environmental impact reduction, and workforce wellbeing.
Conducting wheel alignments might not be the end of solving issues with your tyres or suspension
Sometimes, a vehicle may experience tyre wear, suspension issues, or drivability problems even after a recent wheel alignment, leaving technicians puzzled. If this happens it is important to take a step back and review the basics.
Here are a few things that need to be checked:
Carry out an “eyelignment” (visual alignment inspection) after a wheel alignment to ensure that it was carried out correctly. Are all the wheels and axles in line? Are they evenly spaced in the wheel arches? Occasionally we see trucks and trailers that have not had the suspension hangers installed correctly, leaving one side in a different position from the other.
Check to see if the wheels are parallel by running a straight edge across the tyres on both sides. A length of angle iron would be an appropriate straight edge. If one edge of a tyre is touching but the other side has a gap then you have a substantial alignment issue. Likewise, if an axle is not mounted centrally to the chassis, then the tyres will stick out on one side and then be recessed on the other. You can use a tape measure to check this.
Have a look at the position of the suspension pivot adjustment. On a Hendrickson suspension, the square alignment hole should be close to the 12 o’clock position. The maximum permitted adjustment angle is 45°. (Refer to Pivot Adjustment Range image.) If both collars are angled forward or rearward, the axle may not be centred in the wheel arch, potentially causing tyres rubbing on jounce or other damage. If the adjustment collars are at greater than 45° from 12 o’clock then you need to look at what is causing this issue. (Refer Pivot Adjustment Past 45° image.) Is it due to an alignment error, worn components, an incorrectly mounted hanger or
Ensure that your wheels and axles are all in line and evenly spaced.
damaged components/chassis?
Tyre pressures are often overlooked during wheel alignment. Incorrect tyre pressures can influence alignment, but worse still are uneven pressures between dual tyres, which causes patchy irregular wear patterns. You also need to check to ensure that the same type of tyres and rims are mounted on each axle. Tyres must be matched within 6mm of their diameter otherwise the vehicle may exhibit tracking and accelerated wear issues.
Ride height can greatly affect alignment, particularly on steer and steerable axles. Suspension height changes the caster angle and can impact camber, depending on the suspension design. These angles will affect drivability and impact tyre wear. Therefore, the ride height must be set correctly and the vehicle must be at this ride height when carrying out the alignment. An important related point is to ensure that the suspension is at ride height when fully torquing the pivot fasteners to avoid shortening the life of the pivot bush. By checking tyre pressures, ride height, and suspension alignment, you can ensure maximum tyre life and optimal vehicle drivability.
Our writer, Bob Woodward finds Australia has become a sea of red tape, severely impacting on road transport productivity
Red tape isn’t just affecting road transport — recently there was a news article about licenses, permits and registrations to open a café. In the NT, it was the least at 22, Victoria the worst, at 30.
Having been a part of the road transport productivity boom with safer vehicles, including the B-double with a standard trailer to the rear (tandem/tri - 1988); the Stinger Car carrier (1989); and the 19 metre B-double (1996) — it is hard to see it happening in today’s world.
The 19 metre B-double was a great example of pushing the boundaries — as a fuel tanker it was designed and built before access was approved. The unusual axle spacing (now accepted as normal) was necessary to comply with the B-double axle spacing mass schedule and to achieve weight distribution. But much of that productivity boom would not now be history without the unwavering support and commitment from many industry icons, and advice from a superior, ‘Don’t tell me it can’t be done, tell me what needs to be changed so that it can be done.’
The bureaucrats need to change and adopt this same approach.
More than 30 years back an application B-double (logging) access
in northeast Victoria was initially rejected on the basis that a bridge (at that time recently constructed) was unsuitable for eight-axle B-doubles at 59 tonnes. The issue was raised with a bridge engineer who was involved in the design of the bridge, and suddenly the bridge was suitable and access approved.
About 15 years back when triaxle converter dollies were new to NSW, industry was advised that many bridges in NSW were unconditionally unsuitable for Type 1 road trains with 12 axles. A crisis meeting with bridge engineers and subsequent review resulted in all of the referenced bridges being suitable with a conditional requirement of a minimum dimension (real world vehicles) from the first drive group axle to the last axle of the rear trailer.
When the project that has become PBS was first proposed and endorsed by the states, operators were excited at the prospect of a future with hope for a pathway to productivity. But what wasn’t considered was the limitations that could imposed by the states in regard to access.
Access is supposedly based on technically prescribed performance requirements, length, height, tracking ability, etc. Sounds simple, however the stumbling hurdle is bridge
assessment. The NHVR initiated through the Heavy Vehicle Safety Initiative (HVSI), the Strategic Local Government Asset Assessment Project (SLGAAP). SLGAAP is a government funded initiative to optimise heavy vehicle access on the local road networks across Australia to support local government in their role as road managers with bridge capacity and access decision making.
In the early stages this provided confidence that bridge assessment for HPFV access might be a new and technically based track for decision making.
Unfortunately, that hasn’t been the case with other assets (some state managed assets on major freight routes).
How can a HML route in a LGA suddenly be limited to GML by changing the “engineer in charge”. Surely the same technical standards with the same factors of safety should have been applied in the assessment? Obviously not.
Access advice — if you want access on a new route, survey the route yourself, before you apply. Endeavour to identify limitations, and whilst you may not be able to technically assess any bridges, the route survey will identify specifics and may save you an unnecessary application fee cost.
Following is a broad overview of comments from operators who were canvassed.
• The regulator doesn’t have jurisdiction over road access and they are a lame duck on the issue. It’s all about the road manager, and none of this will be fixed under the seven year long HVNL review.
• When application is made to the NHVR, frequently the regulator tells me to contact the local road manager. So now, I contact the local road manager before I make application to NHVR. That way if the local road manager says no, at least I don’t waste my application fee. So much for a one stop shop!
• The local government registry of infrastructure is often inaccurate or non-existent. An access application was rejected because of the “bridge” being unsuitable for A-double because of the bridge spans — it was actually four (4) box culverts.
• Road managers know well that the vehicles requiring access approvals under PBS are safer and better for the environment; however, they also know that they can’t easily put new rules in place for the general access fleet. So, the “compliance and oversight” ladened hopes
and inconsistent dreams of road managers are applied to the only cohort they have a right to inflict them upon, those vehicles requiring access approvals. These road managers would rather an unassessed and unaudited, general access vehicle on its network than an assessed and audited, purposebuilt vehicle with less than 10 per cent more weight.
• The cost of having to apply for multiple permits for different convertor dollies and then have them merged into one permit, A-doubles (livestock) road train combination up to 12 axles.
• There is disconnect between state and local government road managers, and the NHVR has failed to provide the single contact point vs industry’s needs and equipment investment for productivity.
• Bridge assessments are costing from $500 through to a quoted $10,000 plus and are almost always followed up with a request for an extension for time.
• At Trucking Australia in 2022, the then CEO of the NHVR, in the access session, stated that the fee paid for permit applications didn’t cover the costs incurred by the NHVR. The NHVR budget is included in the heavy vehicle cost base, which
helps to determine heavy vehicle road user charge, so regardless, industry still pays.
• Triaxle dollies continue to be an issue — tandem axle group mass and a tare weight penalty.
• Rail crossings — Intersection stacking continues to be a road block, with rail management deliberately impeding road transport.
• One operator spent more than $100K, for 1200 plus applications — with just over 500 access requests being granted (42 per cent).
• On a positive, the NHVR access portal function is good, but the content process is very slow and the resolution very poor especially on smaller mobile devices.
NHVR personnel are quick to claim credit for progress but are much quicker to point blame of access barriers on the States. The NHVR HVPP includes initiatives to accelerate the uptake of PBS vehicles, the fleet of the future — on our roads! This is unlikely to happen unless there is a quantum change in the approach to access.
Operators regularly state that the cost of PBS certification is a continued operational burden. The migration of PBS vehicles to prescriptive “deemed to comply” status is progressing at slower than snail pace.
The first obstacle to addressing the access problems is for road managers and the NHVR to acknowledge that the current access arrangements are a mess. By sharing open, respectful and evidence-based discussions, we can create positive change and amplify the benefits for industry and the country.
Road managers continue to be reluctant to engage in technical debate.
A bridge doesn’t know if the freight is drought relief HML or the increase in steer axle load is due to Euro 6 or electric. Newton’s laws don’t change, but some bridge engineers believe otherwise. It is difficult to accept that a change in engineer at local government changes the performance of a bridge — that what was once HML, suddenly becomes GML.
There are many tools available to manage mass and axle group loading. With mass management accreditation and available tools overloads should be a rarity.
Having participated in road trials where representatives of the road manager agreed, at-site, that the trial proved a vehicle performance suitable to the road infrastructure, then to go on and submit a report to the contrary — how can industry respect assertions that a 20mm difference in the spacing of axles within a group is critical to the longevity of infrastructure when road managers won’t share the engineering assessments? The work that I have seen shows minimal variation in stresses cause by the
vehicle, excluding the self-support stresses of the structure columns and support beams. Then there are the many times in government discussions having been advised that the assessment procedure is ‘policy’ but when requested, this muted policy never seems to be available.
The concept of access for vehicles with demonstrated performance (now PBS) was initially proposed in 1992.
It took some 15 years for that resolve to produce a vehicle assessment criterion and then, when PBS was first introduced, the states were to provide published PBS level networks within two years — it was another project fail. The rate of development of high productivity freight vehicles far exceeded establishment of approved network levels, and many applications and approval-in-principle has just been another process that hasn’t always guaranteed immediate access when the vehicle is PBS certified.
Access is a mess, compounded by bureaucratic red-tape. It can be fixed, but there has to be a change in the bureaucratic mindset. Industry needs to promote HPFV’s by giving operators 100 per cent confidence that when they invest access will be assured.
So as an industry we need to get started on the hard work. Don’t tell me it can’t be done, tell me what needs to be changed so it can be done.
The issues for each vehicle combination is how does it perform when compared to criteria?
Dimensions – linear and simple:
• L ength – intersection and rail
crossing stacking
• Height – structure clearances
• Width – all routes should be assessed on the basis of 2.6 metres width (international standard)
On-road Performance:
• Lane keeping
• Swept path
Structures – bridges:
• Axle spacing mass schedule
• GML
• CML
• HML
• Concessions (Emission/ technologies)
COMBINATION PREFERENCES
Many assessment practitioners promote roll coupled vehicle units to the rear of the combination. If this is fact, then is:
• An AB-triple (semi-trailer + converter dolly + B-double) a better performer than a BA-triple (B-double + converter dolly + dog trailer using the same individual vehicle units)?
• If typically, the BA-triple is a lesser performer, then should a PBS assessment (not certification) be carried in the vehicle operation documentation?
• Is an ABB- quad (semi-trailer + converter dolly + B-triple) better than BAB-quad (B-double + converter dolly + B-double)?
Multiple road train drivers promote the ABB-quad.
Routes:
• L ength (consider increasing prime mover length – future cabin aerodynamics’ and steer axle mass)
• Height (4.3 m-4.6 m) highlight restrictions
• Width – all routes should be assessed for an overall width of 2.6 metres, where deemed unsuitable the limitations need to be logged for future road works.
• Bridges and axle spacinggrouping (3L+12.5; 1.5L+29.5: or complies with another performance criteria) but it must be within the general scope of Australian Bridge Standards, for concessional mass limits and higher mass limits.
• L ane keeping ability
• Swept path (assess primarily on basis of PBS levels, however additional references are required.)
• Basic general access network – 20 metres OAL (Maybe 20.3m –some allowance for future aero); 4.3metres OAH; 45 tonnes: Example: if the operator has a modular AB-triple with an overall length of 42.5 metres:
Network
• L ength ≤ 42.5 metres √
• Height ≤ 4.3 metres √
• Swept path ≤ 11.2 metres √
• L ane keeping Level 3B √
• ASMS meets criteria √
The route A-B-C-D may be shorted but would be limited to GML and 4.3 metres height; whereas the route A-ED, would allow a HML operation with trailer up to 4.6 metres height.
It is acknowledged that there would need to be operational controls. These might include accredited operator requirements to participate in access self-
assessed access: ie: accredited to TruckSafe or NHVAS module (to be developed). Failure to comply may include temporary or permanent suspension of access module accreditation.
Freight movements and the nation has benefitted in the granting of access to the network such as the Sheahan Bridge at Gundagai, and the Hume Highway. The controls for trucks include lefthand lane only and 60 km/h speed limit, enforced by camera technology. This has allowed extended access to the Hume Highway for many HPFV vehicles. The restriction applies to about 1.5 kilometres, where the resulting travel time difference for that section between 100 and 60 km/h is less than 40 seconds.
The Gundagai bridge is an excellent example of a solution to an infrastructure limitation. However, when a network or specific access
is approved by permit, that access should generally be considered as a “proof of concept”. When the functionality and suitability of that access is proven over a period (not multiple years), it should then be migrated (with operational restrictions if required, such as speed) to the multi-tier approved network no longer requiring a permit.
Let 2025 be the year of change. NatRoad policy has a target — in that 90 per cent of permits should be eliminated by 2028, so it’s time to hold the bureaucracy accountable to clear and measurable outcomes.
The NHVR claim new initiatives that accelerate the update of PBS, and should also include Modular HPFV combinations in pursuit of pursuit of world-class safety and productivity outcomes. There is an urgent need to create positive change.
For reliable and safe column lifts, look no further than Alemlube’s new model
Working on heavy-duty vehicles requires column lifts that deliver on both strength and safety. For technicians to work comfortably and efficiently while running vehicle diagnostics, clear access to the undercarriage is essential. Alemlube have released new Heavy Duty Mobile Wireless Column Lifts able to safely and securely lift trucks, buses and other large commercial vehicles for unobstructed access during inspection, maintenance or repairs.
The new Alemlube AA Premium AAPMC85T Heavy Duty Mobile Wireless Column Lifts have an impressive lifting capacity of 8.5 tonne per columns for trucks and trailers. With versatile configurations possible, you can be confident that the weight of your heaviest vehicle is managed with ease.
Safely balance varying sizes of commercial vehicle by configuring four to 16 columns to manage the lifting capacity and even weight distribution. Each column lift is equipped with its own motor and lifting
mechanism which is wirelessly linked to the intuitive LCD colour touch screen control panel.
This modern system ensures synchronised lifting across your configuration, with each column lifting evenly and remaining stable during operation. Additionally, the wireless design eliminates the clutter of leads or cables, promoting a safer and more organised workspace. A safe environment is a productive one.
Moving and positioning these column lifts is a breeze with their built-in hydraulic wheel kit and forklift points. Instead of manoeuvring large vehicles around the workshop, technicians can easily move the lifts to the vehicle and set them up in the optimal position.
This reduces setup time, enabling technicians to focus on the vehicle repairs, and increasing their overall productivity. This mobility also allows columns lifts to be easily moved for storage when not in use, freeing up valuable workshop floor space.
Alemlube is your partner for maximising workshop efficiency. Focused on ensuring you optimise your
environment, the expert team can work with you to scope your workspace, and then commission and install the column lifts, providing an extended 30-month warranty. With ongoing service support, you have peace of mind your workshop will operate smoothly for years for come.
Strong, safe and versatile – the new AAPMC85T Heavy Duty Mobile Wireless Column Lifts redefine what it means to work safely and productively. Alemlube continues to deliver leading workshop solutions.
ADAPT TO ANY TASK WITH THE VERSATILE HINO HYBRID ELECTRIC. Australia’s only Hybrid Electric truck range has an extensive model line-up from car-licenced 4.5 tonne GVM all the way to medium-rigid licenced 8 tonne GVM. Unleash the power of versatility with the range now expanded to include Built to Go models, or customise a body to meet the unique needs of your business Delivering up to 20% * in fuel savings and emissions reductions, the Hino Hybrid Electric is ready to deliver from day one. That’s the power of change, that’s the Hino Hybrid Electric. Visit hino.com.au
*Actual results will vary depending on the application of the v ehicle and how it is driven