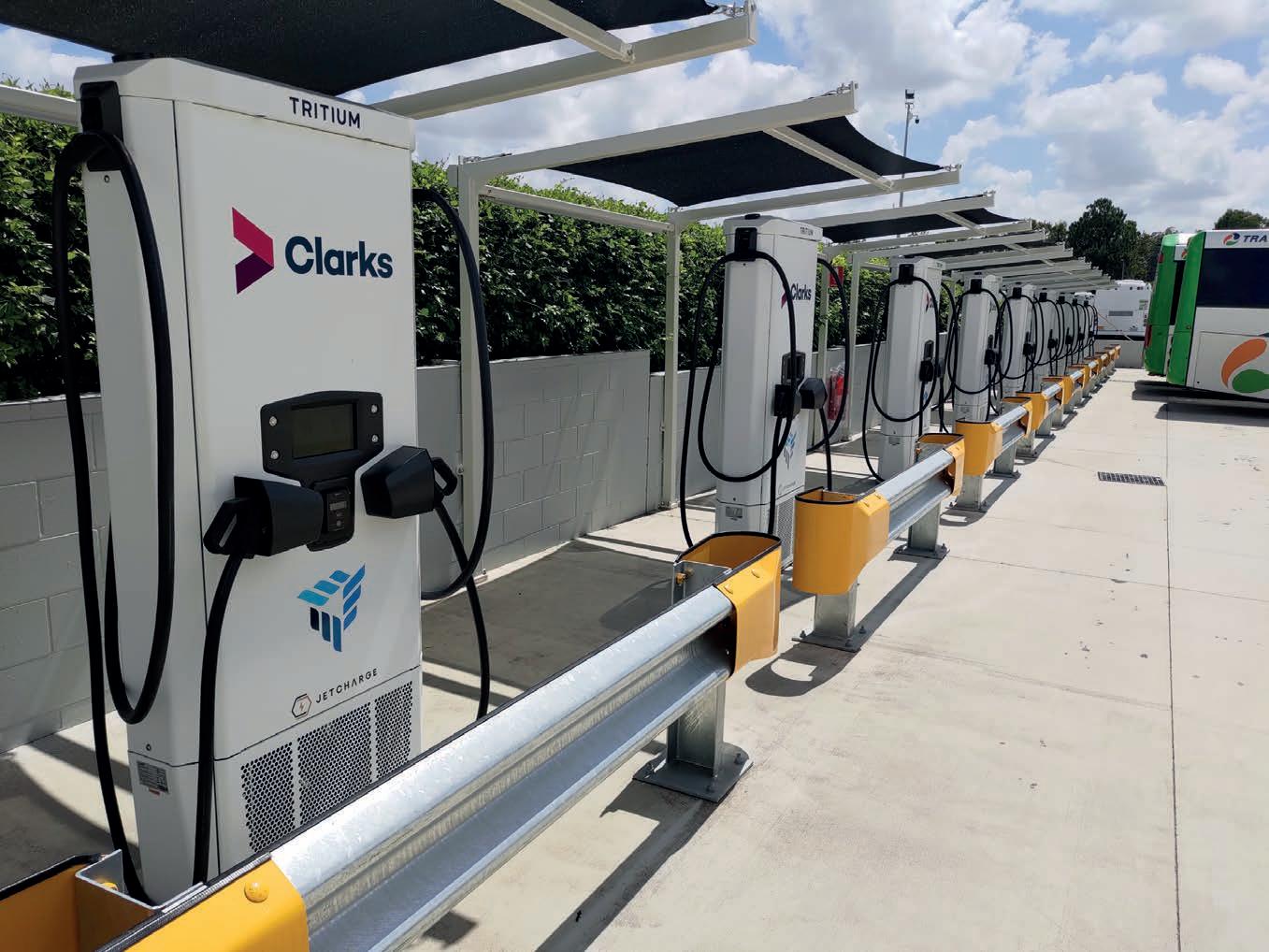
9 minute read
ELECTRIC TRUCK CHARGING FAQS
from PowerTorque May 2022
by Prime Group
Many trucking operators know that in years to come they will need to be setting up a charging station for their trucks, so PowerTorque asked JET Charge about some of the electric truck charging FAQs which the company comes across.
Whether we like it or not there are some major changes in the future for the trucking industry. The reality of climate change is dawning across Australia, and this will, one day, introduce an increasing drive towards zero emission trucks. Exactly what that day will look like and when that day will come is uncertain, but that day is becoming inevitable.
There is plenty of debate about exactly how Australia will get to a lower carbon trucking industry. There is also an ongoing debate about electric power, hydrogen and other forms of gas power. One thing seems increasingly certain, there will be a lot of electric trucks on our roads around our cities, handling the short to medium haul work.
If this is the case in the future, the implication for road transport is that it needs to think about how it is going to move over to this power source, whether it is in five, ten, fifteen or twenty years time. If an expanding trucking operation is developing a new depot, they may need to think about putting in a fuel bowser, but they definitely need to be prepared to make sure the basics are in place for any future electric vehicle charging system.
PowerTorque sat down with Alex Bowler, who is the Business Development Sector Manager for bus and truck at JET Charge, currently concentrating on the bus industry. Some bus operators are already well down the road to electrification, years ahead of the trucking industry, but our industry can learn a lot from how the project is developing.
JET Charge was created in 2013 to supply and install electric vehicle chargers beginning with installing EV Chargers for Tesla owners in Victoria. The company has grown to be a supplier of the full range of EV charging needs. JET Charge provide services across the EV charging industry, all the way from selling the accessories an EV owner needs in their garage, to setting up full blown charging infrastructure for large fleets.
“We are already doing a lot of work with logistics fleets, and we are also doing more and more work with bus depots,” says Alex. “The size of the jobs we do can vary greatly depending on the size of the fleet that is being transitioned at each site. For operators with one or two vehicles, job requirements are very different in comparison to a fleet with hundreds of trucks. The fundamental design principals are similar, but the size, scale and cost of the infrastructure increases with the fleet size.
“Every site is going to need the basics, like a connection to the grid or power source which runs through some sort of low voltage distribution on the site to connect up to the chargers. For bus and truck charging, you’re going to need a 3-phase connection to get enough power to the vehicles.
“There are two different types of chargers you’ll need to consider, alternating current (AC) and direct current (DC). All vehicle batteries are ultimately fed with DC electricity. The conversion or rectification
from AC to DC happens either via the on-board charger in the vehicle if using an AC charger, or in the charger itself which then feeds DC power to the vehicle. The conversion requires some heavy and expensive equipment which needs to sit either in your vehicle or in the charger.
“Most of the AC chargers we see at the moment cap out at 22kW based on the on-board charger or rectifier size in the vehicle, although there are some buses and trucks coming to market which support around 40kW to 80kW AC charging. It will be interesting to see if the new electric trucks coming to market in the next few years are going to push the requirement for AC charges higher. JET Charge has a prototype 40kW and 80kW charger we’re looking to test. Having said that, we have seen a strong trend towards DC only charging in the bus space.”
A lot of smaller trucks, those involved in pick-up and delivery tasks, will be able to get by using these AC chargers. If they have batteries sizes up to 100 kWh, they can be charged up in around five hours or overnight. If you can get away with an AC charger for a transport task, there is an advantage, they are a substantially cheaper to buy and install than the more powerful DC chargers. If a 22kW AC charger costs $2,000 - $3,500 a 22kW DC charger will cost closer to $20,000.
AC/DC CHARGING As vehicles get bigger, the batteries get bigger and the operator needs higher power levels which can be provided by DC Charging systems. These DC chargers start at around 20kW, but can go as large as you need. There are 600kW DC chargers available in the Australian market if you need them.
“The current standard charging plug is called Combined Charging System 2 (CCS2), and it can handle around 350kW, so you could buy massive chargers, but you are still limited by the capacity of the plug,” says Alex. “In many instances, the vehicles have a maximum charge rate anywhere between 100kW to 250kW to protect the batteries, so you are still looking at a two or three hour charge time on some large batteries around 450 kWh. This is a long time if you don’t have a lot of downtime in your duties, but its more than enough for most of the bus operators we work with.”
Most DC chargers do not have batteries included in their design, they are converting the AC power from the grid into the direct current needed to recharge the battery. However, some specialist models do have integrated batteries, which are constantly being topped up from the grid, and can discharge quickly. These are useful when you have a limited electrical capacity, but still need to charge at high powers.
“The charge rate is dependent on a lot of different elements and can be constrained at a number of different points in the charging system,” says Alex. “The vehicle can constrain the charge rate to protect the batteries, or the size of the cable you are using can limit the total current. When using a high power charger, charge rates are generally constrained by the voltage of the battery system in the truck and the amount of current you can get through the cable between the charger and the battery. This is why its important to consider how your vehicle and charger will work together before you buy them and bring them to your depot.
“Current bus systems have around 600 to 700 volt battery architectures, and we are starting to see cars coming out with 800 volt or higher battery architectures. As the voltage goes up, you can get more power into the battery for a given current.”
New charging standards are being developed, like the megawatt charging standard, but at the moment they are all in the research and development stage. When these appear, the charging systems will be able to get much bigger and charge at faster rates.
GOING TO HIGHER POWER SYSTEMS Although it may be desirable, there are some disadvantages to moving to higher power systems, in particular, the electrical infrastructure the operator needs to have in place to deliver the AC current to the chargers.
“As you step back from the interface between the vehicle battery and the charger, you start to look at the rest of the system and how it needs to develop,” says Alex. “The charger needs to be fed power from a distribution board, or the sites main switchboard (MSB). Many small commercial sites or depots will have an MSB and grid connection sized between 250 and 1000 amps (A)
“A 200 kW charger uses around 320 amps, so if you want to charge one truck, you are either almost using up your entire electrical capacity, or you might be able to charge two or three trucks at the same time. Because you can be constrained by power, you need to have a good idea of when and how much you’ll need to charge. We have also developed systems which control the charge rates and make sure you never exceed your capacity. This means you can plug in all your fleet, and let the computer
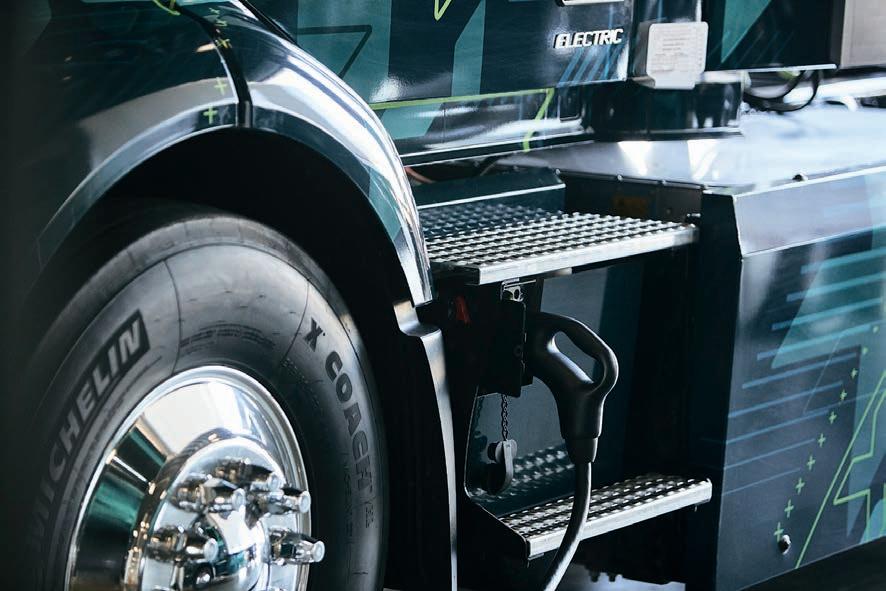
balance the charge rate and keep the total demand underneath a threshold.
“So when you start to scale up to high power charging across more of your fleet, it’s often the case that your current distribution and capacity is not big enough. Then you will need to put a new connection in and new switchboards which can really increase your infrastructure costs.
It does cost quite a lot, but in the total cost of ownership analysis we have done it’s still cheaper than diesel to upgrade the site, finance it, and have a lower operating cost through fuel savings. Also, once you’re at this scale, the cost per charging bay is marginal.”
There are some big changes in store for transport and logistics depot sites across the country. Its important to know that the infrastructure requirements are standard fare for the electrical industry. It is all a known quantity. The technology available today will be capable of keeping a fully electrified pick up and delivery local truck fleet on the road. Overnight and opportunity charging with current technology is available now.
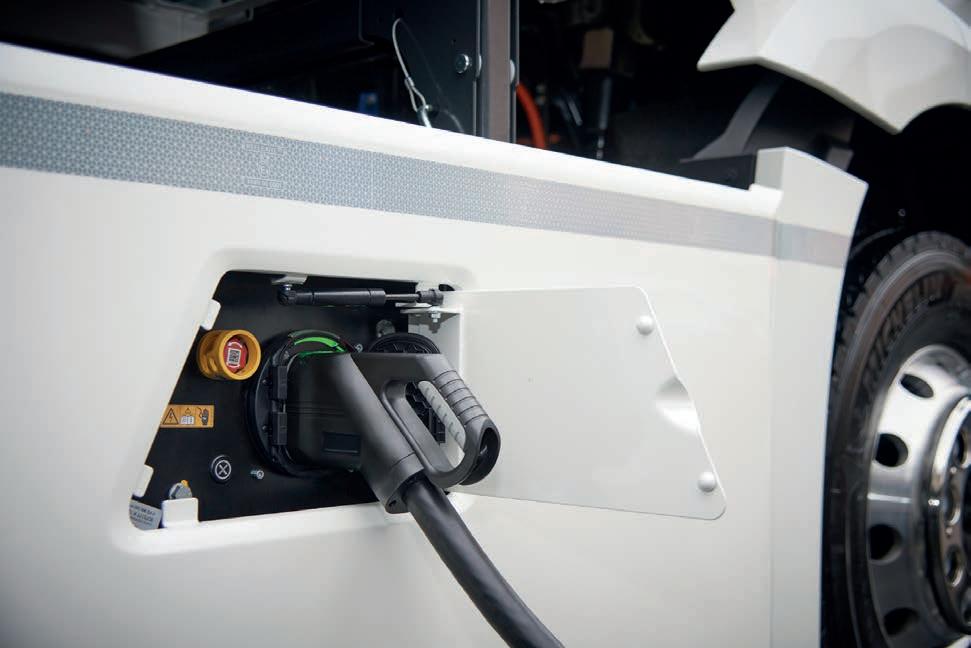
GETTING READY FOR ELECTRIFICATION JET Charge do have customers who go the whole hog in one go and get the infrastructure changed and fit all the charging facility at the same time. However, others will do it in stages, a long term plan is set up and each stage increases the company’s electrification capacity, spreading the cost out over a number of years. A step by step process from no electric trucks to a final goal of full electrification over a number of years is usually broken down to suit vehicle life cycles or planned fleet replacement.
The other infrastructure concern for truck operators will be in the positioning of chargers. Trucks are not going to be heading to bowsers and then parking up. Instead they will be charging at their overnight parking location.
This means rows of chargers along the end of the parking bays is likely to be the ideal location. Simply park the truck up at the end of shift and plug in the charger.
The analysis of Total Cost of Ownership calculations are going to be critical for many operators. There is a need to examine the current fleet and plan the replacement program, balancing the extra cost of the truck itself to the cost savings which accrue from using electricity as a power source.
The timing can be critical to ensure a smooth transition from diesel to electricity. Infrastructure preparation is going to be critical to a successful transformation.
“Infrastructure concerns are not the hard part, we know how to do that right now,” say Alex. “The main challenges are the commercial up front costs and political factors which are affecting decisions. For smaller operators, who do not have the knowledge to chew through this big transition, there are ways to implement the infrastructure without totally blowing the bank. We try and utilise as much of the existing infrastructure as we can, before breaking out the check book for lots of new stuff.”
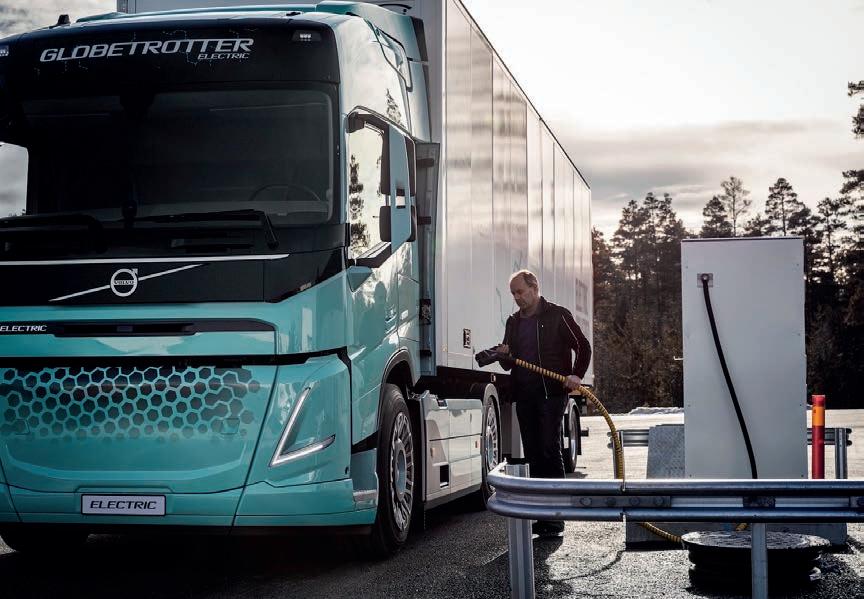