
7 minute read
REAL WORLD COUPLING TESTING PROGRAM
from PowerTorque May 2022
by Prime Group
Australian Multiple Combinations test truck components to their limits, and a new initiative is setting up a real world coupling testing program, to assess the forces exerted on the connections between road train elements.
Currently, the Australian Design Rules covering heavy vehicle do not offer any guidance for truck and trailer manufacturers beyond a truck GCM of 125 tonnes. At the same time, overall GCM ratings at higher tonnages are increasing and the Performance Based Standards Scheme (PBS) needs precise data on each articulation point, both fifth wheel and pin type, to design and assess possible configurations for submission to the scheme.
Measuring the forces at play between elements of a road train uses what is called the D-value, measured in kilonewtons (kN) and representing the theoretical horizontal force between towing vehicle and trailer, and between trailers.
Needless to say, this is a complicated calculation and one which is left to the engineers developing truck and trailer combinations around the world. However, Australia is one of the few places where the combinations on the road go outside of the normal parameters used globally. As a result, the development of ever heavier road trains has taken those engineering outside of the normal envelope of understanding and created an issue for those developing large combinations.
The project is an initiative of the ARTSA Institute as lead, alongside the Australian Trucking Association (ATA), Truck Industry Council (TIC) and Heavy Vehicle Industry Australia (HVIA) and is funded by the Commonwealth Government through the National Heavy Vehicle Regulator’s (NHVR) Heavy Vehicle Safety Initiative.
The team behind the project is chaired by Martin Toomey (ARTSA-i) and supported by a Steering Group made up of Chris Loose from the Truck Industry Council, Bob Woodward from the Australian trucking Association, plus ASRTSA-i members Greg Rowe, Rob Smedley and Wayne Baker. there will be three working groups, On Road Testing, Laboratory Testing and Communications. Each of the working groups will have industry representation as well, from suppliers like Jost, BPW, SAF Holland and V.Orlandi.
Project Manager and mechanical engineer Wayne Baker explains the background “We are aware that as a heavy vehicle combination gets heavier and longer, the forces that the couplings are subject to are lower than what a theoretical calculation shows. It is this phenomena that we are hoping to understand and quantify.”
LOOKING AT D-VALUES “Currently, the D-value formula on larger combinations, under the rules, caps out at 125 tonnes GCM,” says Rob Smedley, Director and Senior Engineer, Smedley Engineers. “When the calculation is used in larger combinations it can come out so high that manufacturers don’t even make couplings that meet that D-Value.
“However, those same couplings that don’t meet that D-value are being used successfully on our roads. At the moment there’s a black hole, where operators and trailer makers aren’t covered because, technically, they are
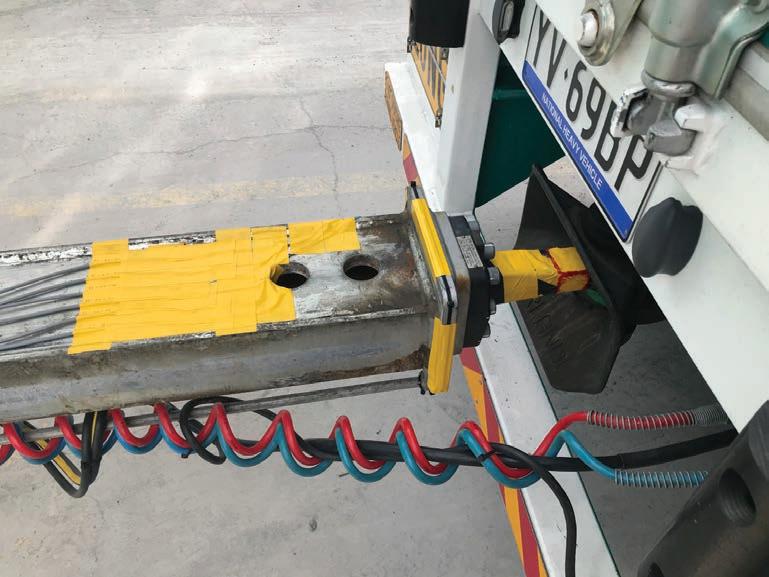
using couplings which don’t meet the standard, but the standard was not developed in consideration of these kinds of combinations.”
Another complicating factor is that none of the normally used couplings are made here in Australia.
In setting up this testing project, no one is questioning the integrity of the couplings, or suggesting it is irresponsible of trailer makers to use them on these heavier combinations. There is also no suggestion that larger stronger couplings are needed.
The testing program is designed to quantify exactly what is going on at the point where one trailer is connected to the next, and tying up loose ends in the standards which were not designed to cope at these higher masses.
“We need to fully understand the forces that are in these larger combinations,” says Rob. “We are trying to make compliance work for everyone as these combinations continue to get bigger. Nothing like this has been done since back in the eighties. There just weren’t combinations like that on the road, at that time.”
PBS assessors are required to make these calculations on heavier combinations and the lack of real world data available to them does mean that there is not a clearly delineated set of calculations which can demonstrate that a particular configuration will be suitable and able to cope in all conditions.
The whole process should provide engineers, road users and managers with confidence to design increasingly innovative combinations.
The vehicles will be fitted with an array of instrumentation to make a series of measurements.
Currently, the calculation method is coming out with D-values up around the 600kN mark but fifth wheels which are rated at 350 kN are doing the job with little problem. This tells us that there is something not quite right about the way we calculate it.
“This work isn’t being done because of coupling failures,” says Rob.
The project is designed to increase knowledge about couplings in combinations running at these higher GCMs, with the aim of reducing the risk factors for those designing, building and operating combinations running at these very high masses.
The ultimate aim will be to make updates to the Australian Standard for this equipment, which reflect the findings of the investigation. Globally, the organisation behind ISO Standards will also use the data to inform its requirements.
The project will be doing field testing on quad combinations, in the Northern Territory. The vehicles will be fitted with an array of instrumentation to make a series of measurements. Most of the equipment will be concentrated around the dolly and its connections the fifth wheel and the pin coupling.
Strain gauges and accelerometers will quantify the forces at play between vehicle units and in the couplings. The road on which the combination is travelling will also be modelled. This will enable the team to see what input the roads surface and features end up creating as forces in the couplings as the combination travels the route. Undulations in the road, cattle grids, etc will be on the route, so that the instrumentation will collect data on the forces exerted within the combination, on a normal working truck.
“We are going to model that road and combination, virtually, within a program called MSC Adams Multibody Dynamics,” says Rob. “Then, we are able to virtually reconfigure the combination that was tested, and calibrate that model to the on road values we have measured. From there, we will be able to rearrange that


virtual vehicle into a number of different combinations, such as AB-triples, quins and other types of combinations.
“From this data we will develop a new formula, which can be used to determine coupling forces in all sorts of different combinations.”
Parallel to the on road testing the team will also be setting up a couple of projects in which laboratory testing of components, emulating the kind of forces at play on the road, are carried out in more controlled conditions. This will further validate the field testing results.
The D-value is simply a shorthand coupling specification that relates to the dynamic force between the vehicles in a combination. The value increases with higher the masses are either side of any connection.
The D-value requirement between the prime mover and the first trailer in a quad set-up, at the fifth wheel, is relatively low because the prime mover is a lot lighter than the trailers behind. The connection that requires the highest D-value is the one in the middle, with high masses in the trailers in front of it and behind. This is the coupling which appears to be undergoing forces higher than the notional design limits of the couplings.
“The vehicle we have selected for the project, we believe is going to be the worst case,” says Rob. “We are going to model other combinations to confirm it is the worst case, when we have calibrated it. Then we will be able to do many more combinations, even down to singles and doubles, to make sure we aren’t overestimating the forces.
“We should come up with a formula, which will be able to be used for all combination designers come up with. That’s the goal.”
The formula may not be one single calculation for all combinations. it may well turn out there is a different formula for each distinct configuration. The initial results of this research should be available in around 18 month’s time.
The next stage will be to incorporate the findings in the Australian Standard for these couplings. Once it is in the standards, that will feed back through the system, via relevant ADRs and the National Heavy Vehicle Standards.
The process of updating the Australian Standard is expected to be a relatively simple process, for this kind of change, because the decision-makers in this field are looking for a sound evidence base to provide clarity for the standard.
The whole process should provide engineers, road users and managers with confidence to design increasingly innovative combinations, with the benefit of a more precise knowledge of the forces being exerted on couplings within Australia’s heaviest combinations.
The ultimate aim will be to make updates to the Australian Standard for this equipment.
