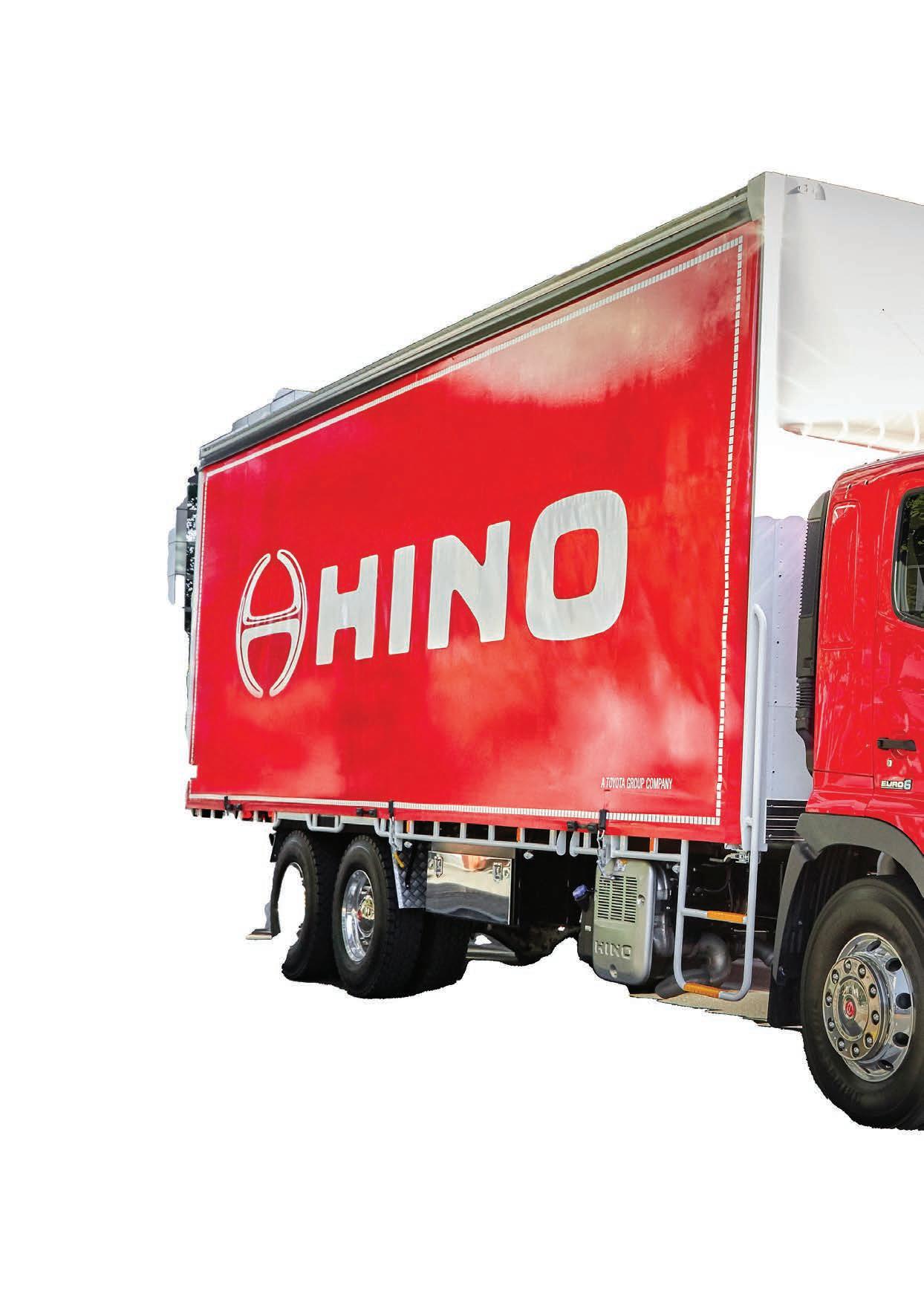
23 minute read
A GENUINE HEAVY DUTY CHALLENGER FROM HINO
A GENUINE HEAVY DUTY
The complete renewal of the Hino truck range reaches its conclusion with the introduction of the new 700 Series models and sees a genuine heavy duty challenger from Hino coming on to the Australian truck market.
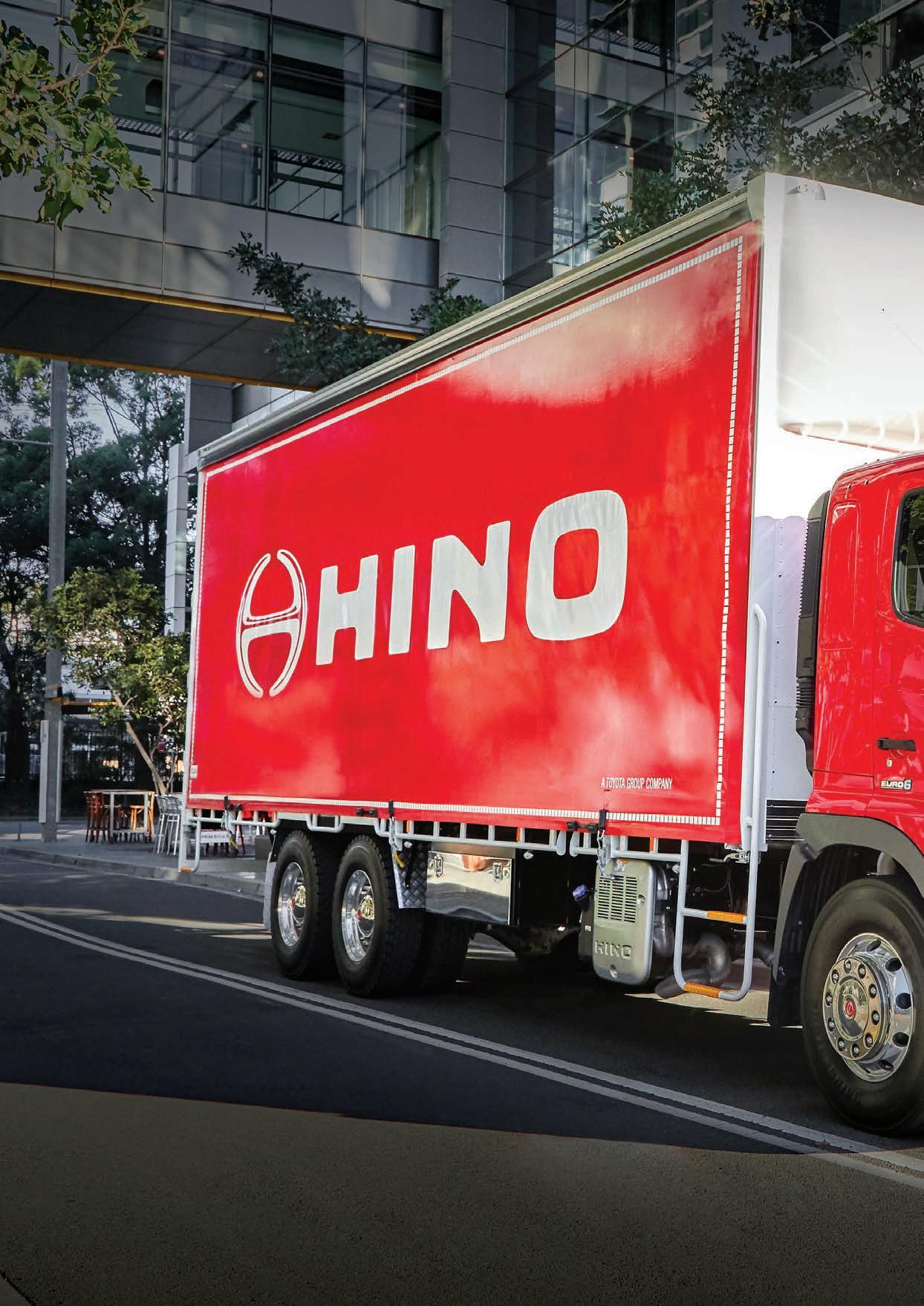
A GENUINE HEAVY DUTY CHALLENGER FROM HINO
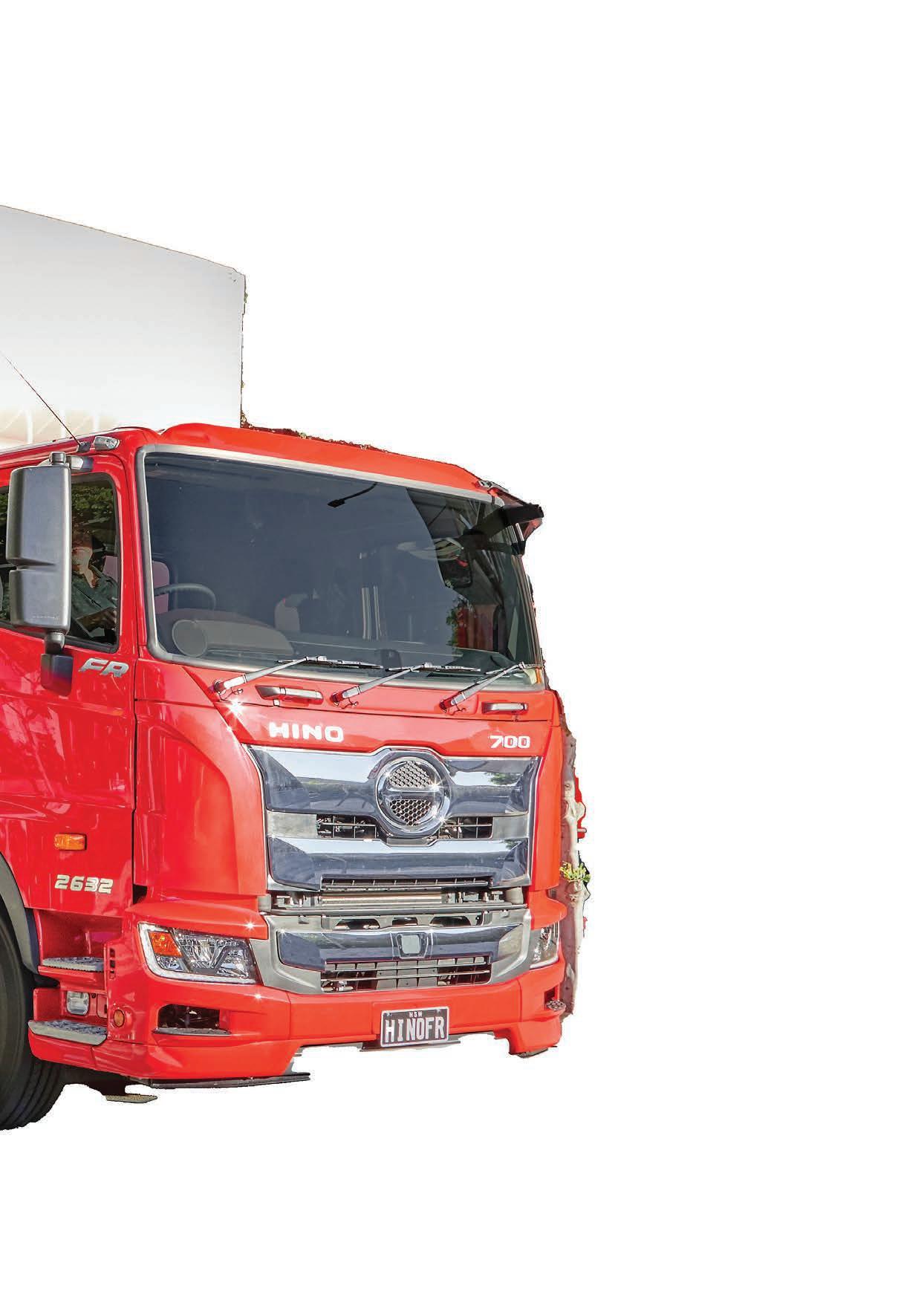
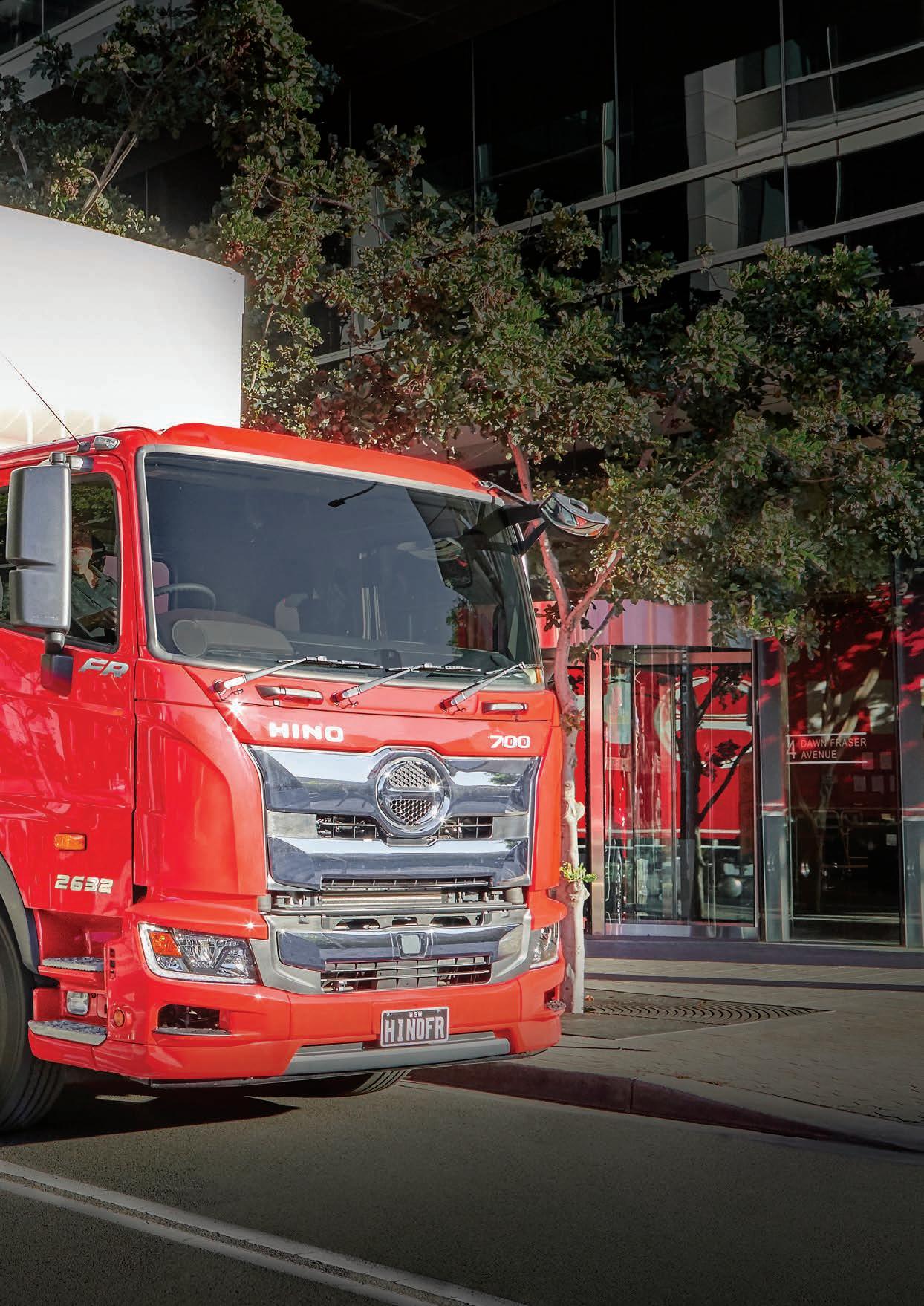
Over the last few years, Hino has completely upgraded all of the trucks it offers to the Australian truck market. It started with the new 500 Series, was then followed by the new 300 Series, and now we see the arrival of the new 700 Series heavy duty truck range from the Japanese manufacturer.
This renewal across the brand has seen the introduction of state-of-the-art safety systems and modern electronics throughout the range. The Hino brand has been uncompromising in its mission to bring the latest technology into the Japanese segment of the truck market.
In the past, Japanese truck manufacturers have always been a couple of steps behind competitors from Europe, in terms of technological sophistication, but this series of truck releases has seen the Hino brand closely match Europeans in terms of technology toe-to-toe.
Ostensibly, this release is to introduce the latest low exhaust emissions engines onto the market. However, it does not stop at Euro 6, there is also a suite of electronic safety features which brings the complete offering from Hino bang up to date.
Each time PowerTorque reports on the latest release from Hino, it inevitably leads to a long list of three- and four-letter abbreviations for all of the systems which are now included. Overall, the package is called Hino SmartSafe and now includes Driver Monitor (DM), the Pre-Collision System (PCS), Autonomous Emergency Braking (AEB), Pedestrian Detection (PD), Lane Departure Warning system (LDWS), Vehicle Stability Control (VSC), Reverse Camera, plus more features which do not have simple abbreviations.
The Pre-Collision system uses a radar and video feed which constantly monitors the road in front of the truck. The
This new model sees the introduction of a new driver monitoring system, a first for Hino in Australia.
combination of the two systems will work out what any object in front of the truck is and how fast, and in what direction, it is travelling.
Based on this information, it will react if it calculates there is danger of a collision. Depending on the urgency of the situation it can slow the truck, it can introduce some braking or, in the most dangerous circumstances, apply 100 per cent braking immediately and bring the vehicle to a halt before any collision.
This new model sees the introduction of a new driver monitoring system, a first for Hino in Australia. The Driver Monitor system has a camera monitoring driver behaviour and distraction fitted to the A
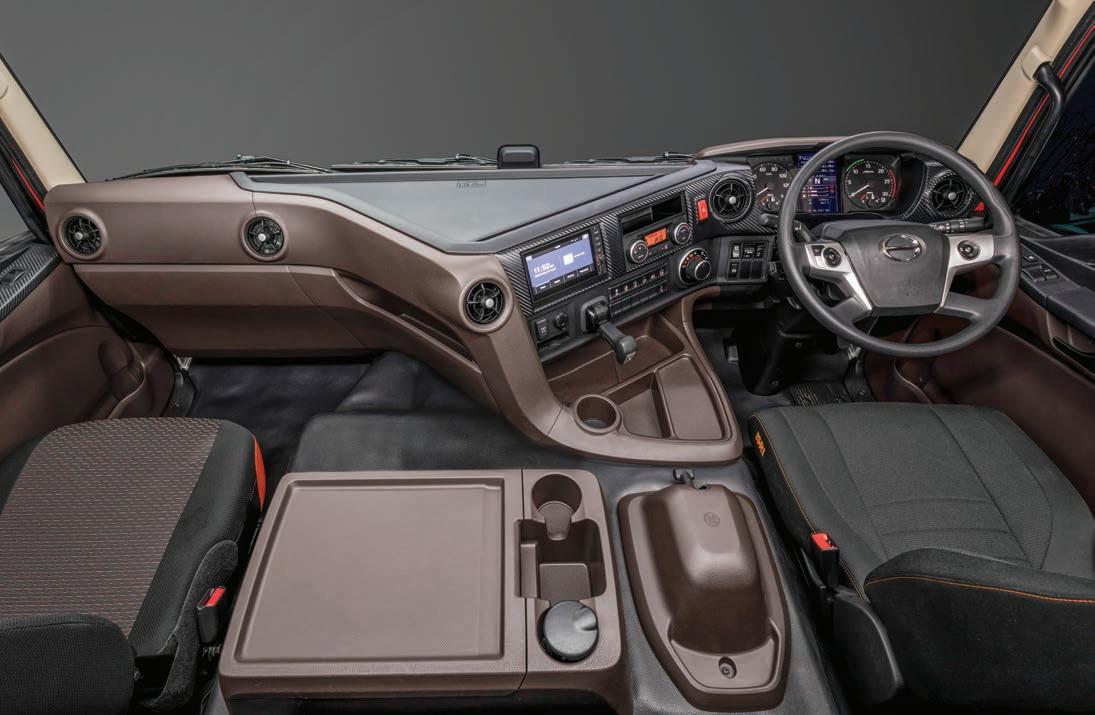
pillar. This will set off an alarm if serious fatigue or inattention is detected. The camera is monitoring the drivers posture, where they are looking and eyelid movement, it then interprets this data to decide whether it needs to alert the driver. There is a small infrared camera which is embedded in the A-pillar. The SmartSafe system is available in most models as the new 700 Series rolls out, with the twin steer 8x4 models joining the SmartSafe party in 2022.
BROADENING THE RANGE Another major feature of this new 700 Series range is a broadening of the models available. The 700 Series now includes a nine-litre engine option, which opens these models up to a number of new market segments which have not been able to access the 700 Series before.
The 700 Series range goes from the 10 models of the previous iteration to 19 models in the new range. Engines, previously only available as options in the 500 Series have now got some extra horsepower and are available in a 700 Series chassis.
This first of the two new nine litre engines, the A09C-VP, is rated at 320hp (235kW) and produces 1275Nm (940 ft lb) of torque, which is available from 1100 rpm all the way up to 1600 rpm. This engine is available with the Allison 3200 six speed automatic transmission.
There is also a more powerful 360hp (265kW) 9-litre available, the A09C-BN, which puts out 1569 Nm (1157 ft lb) of torque. With this engine the Allison 4440 auto is included in the driveline. This higher horsepower engine will be powering the new 8x4 models and using this heavier automatic gives the truck a deeper first gear, improving startability, enabling it to be used up to 42.5 tonnes GCM.
The nine-litre engine is an upgrade on the current nine-litre sold in the top end of the 500 Series trucks at the moment. This latest version, the Euro 6 model, uses the same engine block as has been used before, but in virtually every other system there have been upgrades on this latest engine.
The new engine at the lower power rating will be available on the 4x2, 6x2 and 6x4 models, and the larger more powerful engine will be available on the 8x4 models, which Hino offers, for the first time, with a load sharing suspension. In tare weight terms of the nine litre offers a reduction in overall weight of around 500 kg, when comparing models like for like. This is particularly apparent, and relevant, in the 8x4 model.
This development sees Hino finally coming to the Australian 8x4 party and should enable them to start to compete in market segments like concrete agitators, where it has been unable to genuinely compete in the past.
This latest launch and these new models sees the Hino brand finally competing strongly in a segment of the market which has become highly competitive in the last few years, with just about every truck brand improving its offer into the highly specialised twin steer segment and the fiercely fought heavy rigid market.
The differential ratios on offer have been altered for these new models and now the engine rpm sits at around 1700, when the truck is doing 100 km/h.
Trucks fitted with the nine litre engines have a cabin which sits about 120 mm lower than those fitted with the 13-litre engine. This is possible because the truck is fitted with an adapted version of the cooling package fitted in the lower 500 Series when using the nine-litre engine.
“The new 700 Series is a massive deal for the Hino brand,” says Daniel Petrovski, Manager of Product Strategy for Hino Australia.”It puts a comma on the product renewal across our range, it’s stage one of what will be a multi stage 700 Series introduction. It will begin with an expanded model range.”
“It is a new truck, I think the only thing that remains from the old model is the chassis rails. All of the chassis packaging and accessories around the chassis rails have been updated. Plus, we now add in the nine litre engine.”
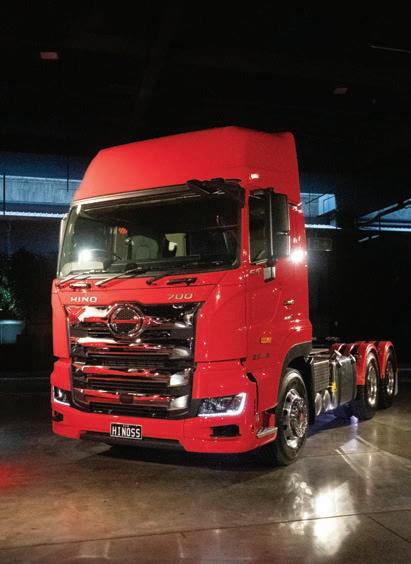
HIGHER POWER The 13 litre engine fitted in the new 700 Series from Hino also sees an upgrade, the SH 1845 4x2 prime mover models will feature the E13C-BL engine with 450hp (331kW) and 2157 Nm (1591 ft lb)of torque on taap. Meanwhile, the 2848 6x4 prime mover, FS 2848 6x4 rigid and FY 3248 8x4 rigid models will get the E13C-BK engine with a horsepower rating of 480hp (353kW) but still with 2157Nm (1591 ft lb) of torque available. Maximum torque is now available in the 13 litre engines from between 1000 to 1500rpm. These updated 13 litre engines are paired with the ZF 16-speed AMT, the TraXon TX 2441TO.
All of these engines, both 9 and 13 litre options also have a Jacobs engine brake included, to further enhance the driving experience. On the 13 litre engines this retardation is further enhanced by the inclusion of a ZF Intarder in the driveline, with a maximum of 684 kW of retardation available on the more powerful option.
“The ZF Intarder is going to represent around 90 per cent of all of our customers’ auxiliary braking,” says Daniel. “with our brake blending button on the dashboard, the system calculates how much brake you are asking for, from how the brake pedal is pressed. It will use engine braking to bring the vehicle to stop, before it will introduce the service brakes.
“There are no manual transmissions available in these trucks. A number of years ago we made the decision that manual transitions were on the decline and with this range it was designed around automatic and AMT transmissions. This has been backed up by the fact that we haven’t sold a truck with a manual transmission in the last two years.”
Hino has moved to a rotary dial controller on the dashboard for the AMT, similar in design to that used on DAF and MAN trucks. This new controller is a major
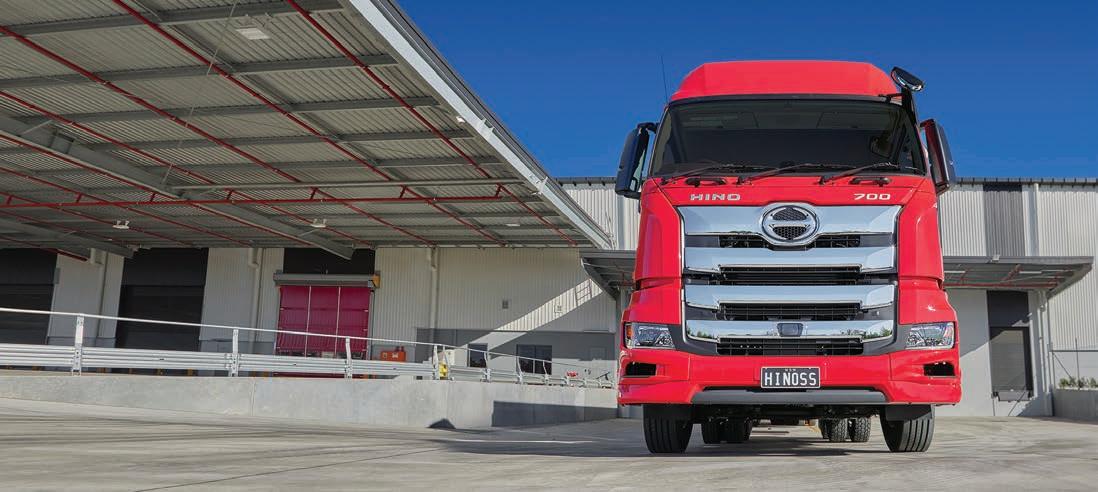
improvement on the previous large stick controller, which was situated in the former gearstick position. Flicking from auto into manual and intervening by the driver, to either go up a gear or down a gear, can now be done on a steering column stalk. This new controller means cross cabin access is much improved and more driver-friendly on this model.
On both of the new engines, the point at which maximum torque is reached has been brought down the rpm range. This means that fuel consumption will be decreased, when compared to the previous engines in the Hino 700. These new engines also use the, more slippery, dimpled cylinder liners, first introduced with the 500 Series, which further enhance the efficiency of the engine.
MOVING ACROSS TO EBS Electronic braking systems are now available all of the way across the 700 Series range of trucks. This brings the brand up to date in terms of braking technology. The combination of EBS with features like stability control and integration with EBS fitted trailers further enhances safety in this model.
Over the last few years Hino have been improving their cabin interior design, as they move away from the very predictable grey Japanese truck interior we have become used to. With the introduction of the new 700, the cabin interior has a quality look and is probably feels more European than Japanese, in terms of first impressions.
The dashboard has been carefully thought out, looks good and is definitely much more modern than some of this truck’s direct competitors. However, this is still a Japanese track and it does have those features which reflect the conservative nature of the domestic Japanese truck market, which expects those features which we see in every Japanese truck like the high engine cover, relatively small bunk and clunky handbrake mounted on the engine cover.
The electronic dashboard directly in front of the driver has a neat feature, when the driver is driving normally it has a blue background colour, but when the driver takes more care and is driving more economically, the background turns to green. The display also includes driver reminders to avoid behaviours which are detrimental to the overall fuel consumption. It will tell the driver when they have been over speeding or over revving and a reminder pops up to ask them to take it easy.
FULL REFRESH OF THE MODEL LINE-UP The new 700 Series from Hino is the last part of the puzzle for the new look from the Japanese brand. All models now have the new large grille, with clear branding. There is also now stability group control across the range, apart from the twin steer models, but this will be arriving next year. There is also the availability, across the brand, of a comprehensive safety suite, which is one of those features which is becoming more and more important for trucking operators in Australia and around the world.
The introduction of the nine-litre engine into the 700 Series allows Hino to also offer a wider range of wheelbases, to suit various applications, many of which are very different to those needed by the buyers of the larger 13 litre powered trucks. For example, a longer 4.5 metre wheelbase will enable Victorian tipper operators to now meet the bridge formula length requirements in that state, enabling them to run at higher masses.
This latest launch also means that the entire range of Hino models, from the 4.5 tonne 300 to the 70 plus tonne 700 all come with Euro 6 compliant engine.
According to Daniel, the 8x4 model comes in at a tare weight which is in that useful, just over eight tonne, range, which means it may come into consideration by the concrete companies as an agitator. One of the advantages it may have is the fact that it is fitted with a heavier duty Allison transmission, than some of its direct competitors in what remains a very tight market.
At the new 700 Series launch, there was a hint that there may be a model coming onto the Australian market from Hino with a power rating over 500 hp. However, over the years PowerTorque has learned to take these kinds of hints with a pinch of salt.
There is also a hybrid version of the 700 in the pipeline for the Japanese truck market and Hino are indicating it will eventually flow through into the Australian market but unwilling to put a date on any introduction.
SMOOTH SOPHISTICATION
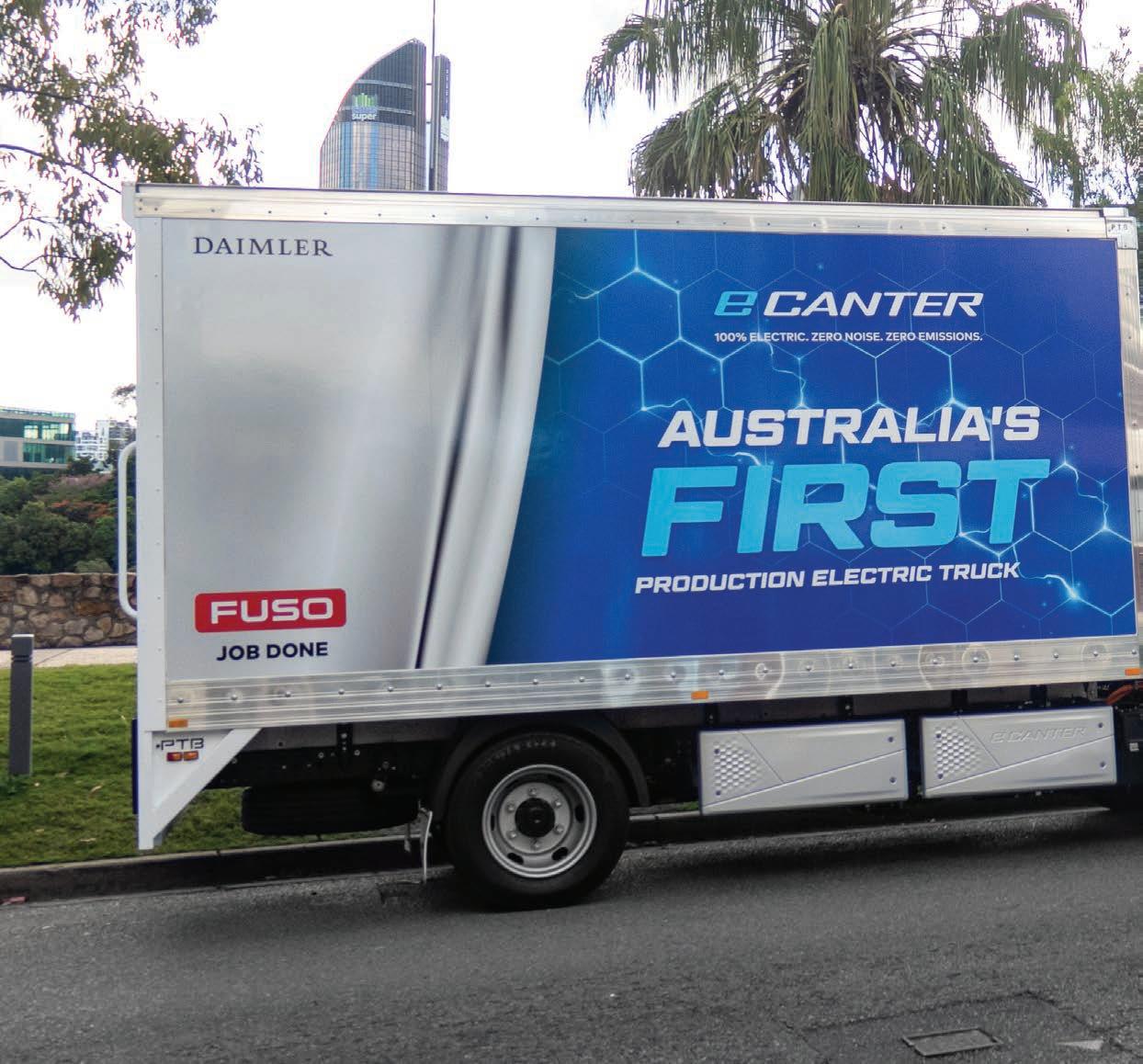
FROM AN ELECTRIC TRUCK
The actual driving experience is not something people normally expect from a truck test drive, but it is possible to get smooth sophistication from an electric truck, reckons Tim Giles after driving the Fuso eCanter.
There is no doubt about it, electric trucks are flavour of the month, or more precisely, flavour of the decade. On the evidence of the Brisbane Truck Show this year not only are there new electric trucks coming onto the market but there is also a lot of interest on the part of truck buyers in the new technology and its potential.
Fuso is the first major global truck manufacturer to release an electric truck in the Australian market. Fuso have long been a leader in this field of technology, having shown prototypes at major truck shows around the world regularly over the last 10 years.
PowerTorque was able to test drive an early prototype model back in 2019, but now the company has released a vehicle onto the Australian market. All of these electric drivelines can be expected to follow a similar course from most of the major manufacturers.
The first vehicles to enter the market will be those in the light duty segment, where the benefits of an electric
driveline are the most obvious and easiest to achieve. Later developments going up the weight range become more problematic as the need for more and heavier batteries comes into the equation and compromises payload.
This eCanter has been in production since 2017 and can be seen working in places like Japan and Europe, where government subsidies encourage operators to opt for the nearest technology to zero emissions available.
The truck tested by PowerTorque was the one displayed on the Daimler stand at the 2021 Brisbane Truck Show and comes in a typical Fuso guise. This is a light duty truck, a typical around the town delivery vehicle. Of course, this particular model has a large artwork on the truck and body proclaiming its electric power technology. It is a show truck after all.
On the trucks which will be offered for sale, from the outside there is very little difference between the look of this truck and its diesel engine equivalent. The giveaway is the blue flashes on the vehicle name and the model designation. However, anyone paying the hefty premium which comes along with electric power, at the moment, would be crazy not to proclaim the truck’s green credentials in large letters on the truck.
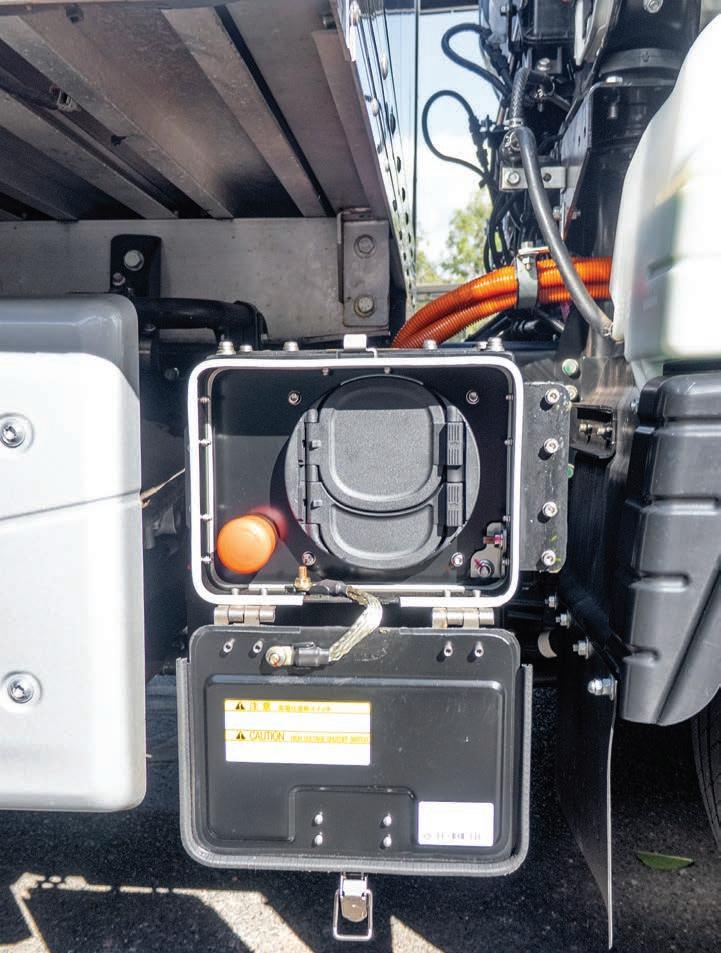
FIRST IMPRESSIONS Stepping up into the cabin of this truck, it’s just the same as it is in any other truck. As the driver sits in the driving seat, they are presented with a layout which is very similar to the one which they are used to on a day-to-day basis.
The controls are pretty much the same as they are on the standard Canter truck. However, some of the controls perform different functions than they would in the diesel alternative.
It is difficult to guess what the electric truck ignition switch should be called, as of course, there is no actual ignition taking place. In this truck the way you get things going is using a large insertable ‘key’ which slots in to a socket on the dashboard. There is a start button next to it and this driver decided to have the driver’s door window wound down when pressing this button to hear the system start-up behind the cabin.
Charging the vehicle up is a simple operation. Just behind the cabin, fixed to the side of the chassis is a large socket.
There is a clearly discernible whirring sound which indicates that the cooling and other systems have commenced operation. In fact, the truck still requires a 12 V battery to commence operation.
Next, it’s a matter of selecting a gear, except that the ‘gearstick’ is in fact simply a switch to turn the system on to drive or reverse. Next, the driver simply releases the parking brake and presses the accelerator.
Acceleration inside eCanter sounds pretty much like a tram taking off from a tram stop, without the metallic clanking of the wheels and rails. In fact, from the driving seat, the whole experience is eerily quiet.
Apart from the lack of noise the basic driving experience is very similar to driving this truck with a diesel engine and an automatic transmission. There will be little need for comprehensive training for a driver taking over a truck like this, the basic driving skills required are the same.
The factor which differentiates this truck from other electric trucks, including the prototype eCanter, which PowerTorque experienced a couple of years ago, is how well the vehicle’s main computer modulates the truck’s performance to keep the behaviour within acceptable parameters.
This is where the sophistication does come in. Simple electric trucks will tend to be able to accelerate very swiftly away from traffic lights and can require extra braking when slowing down for a red light. This is because the electric motor has full torque available from zero rpm and there is none of the inertia, which we experience in a diesel engine, when slowing down.
These two issues are overcome by programming the truck’s computer to only give the driver the kind of power required to accelerate smoothly and not too fast, plus enabling it to bring in regenerative braking in a controlled and reactive way to slow the truck up smoothly and effectively. In fact, the regenerative braking not only charges the battery, but replicates the kind of deceleration a normal diesel engine brake can provide.
The overall impression for the driver is one of a very smooth experience, in setting off, in cruising along the road, and in decelerating when required. However, there are occasions in traffic where just a little bit more acceleration maybe required to stay away from a sticky situation or to get across into a gap in traffic.
When travelling at a normal road speed, a quick kick down on the accelerator will provide that burst of
The computer modulation of the motor power will go along way to ensuring good energy economy.
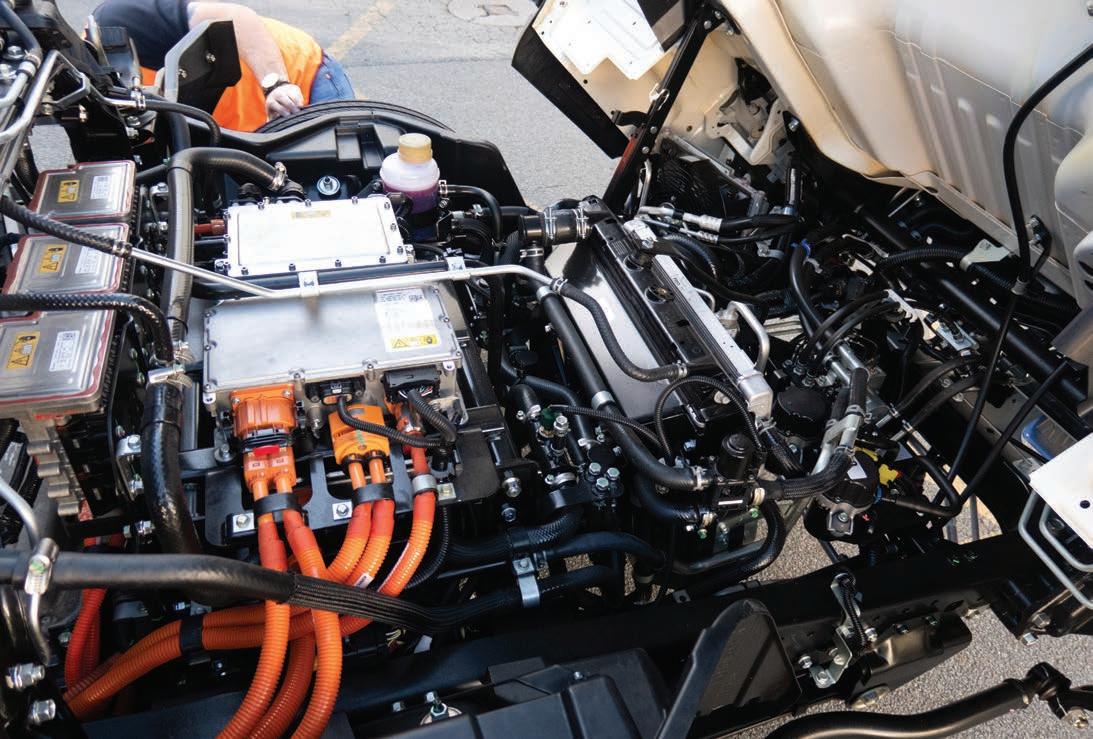
increased speed required to make such a manoeuvre. There is absolutely nothing sluggish about this vehicle, even when loaded, as it was on this road test.
The performance of this truck does make the driver feel very comfortable. With the vehicle loaded to 6.5 tonnes it feels well balanced and sits nicely on the road.
Added security comes from the fact that this truck is fitted with all of the latest high-tech safety features which are becoming standard on truck ranges these days. All of the way from simple things like hill start aid to active cruise control, and onto advanced emergency braking are available to the driver.
The computer modulation of the power system also comes into play when the driver activates reverse. The truck takes off very steadily in reverse and allows for smooth well controlled low speed manoeuvring in reverse. This is also aided by smooth and very positive steering on this model, probably a product of being so well balanced.
FUELLING UP There is a nice touch on the dashboard, directly in front of the driver. In the position where we would normally see the fuel gauge indicating empty or full, we find an image which, at first glance, looks like a typical fuel bowser. In fact, the end of the wire, coming out of the bowser, is shaped like a plug, just to remind us it uses electric power.
Charging the vehicle up is a simple operation. Just behind the cabin, fixed to the side of the chassis is a large socket. The driver simply lifts the flap and plugs into the power source with which to recharge the batteries.
Fuso are quite conservative when talking about things like the range available to the operator with a fully charged set of batteries. By stating that this truck has a range of 100 km on one charge, Fuso are not taking any risks. Like any energy consumption on a truck, a lot depends upon driver behaviour and the way the vehicle is managed.
The computer modulation of the motor power will go along way to ensuring good energy economy from this vehicle.
Clearly, when fleets finally do get access to these vehicles they will do so on a trial basis in order to get a better handle on what sort of range these vehicles are capable of. Simply based on the experience of this test, PowerTorque is of the opinion that a smart driver will be able to get much more than 100 km out of a truck like this on one charge, especially if there is plenty of acceleration and deceleration in the day’s task.
All in all, at the end of the day this driver came away with the impression of a vehicle which really is smooth and sophisticated. Fuso have clearly done a lot of work on getting the driver experience just right in these vehicles. Not only are they great for the environment, but also a lot of fun to drive. Alongside this, is the fact that driving a shift in a truck like this with such a peaceful cabin can be a very pleasant experience.

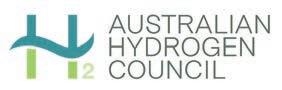
HYDROGEN
IS ON ITS WAY
The search for alternative power for trucks in Australia is definitely on its way and the Australian Hydrogen Council points out that in other parts of the world it is already a reality.
Hydrogen powered vehicles aren’t just the future – in parts of the world they’re the present. In other places they’re actually back in favour after having an initial run some time ago. Spend a bit of time digging about YouTube and you can find 1978 news footage of actor Jack Nicholson getting about in a hydrogen powered Chevy Impala.
More recently, and closer to home, the Western Australian government ran a hydrogen powered bus trial on a number of routes in Perth. These types of examples demonstrated that hydrogen could work, but technical and economic limitations stood in the way of their widespread adoption.
So, you see, the idea of using hydrogen to power transport is not new and despite a history going back quite a while, the true age of hydrogen is, well, if not now, then very, very soon.
Fuel cell vehicles are travelling highways around the world right now. As reported in PowerTorque Jan/Feb 2021, Hyundai is delivering 50 of its Xcient fuel cell vehicles to clients in Switzerland. Daimler and Volvo are also working together to develop fuel cells to be incorporated into their vehicles. Iveco has entered contractual arrangements to gain access to fuel cell technology for its trucks and PACCAR, manufacturer of Kenworth, Peterbilt and DAF rigs has partnered with Toyota to incorporate fuel cells into a number of Kenworths in the United States.
While there are some new names including US based Nikola (whose owners are engaged in an entertaining feud with Elon Musk after he tweeted “Fuel Cells = Fool Cells”), Hyzon (who have recently announced a deal to deliver five trucks to Ark Energy in Queensland) and Aussie based H2X threatening to change road transport forever, the active involvement of established names indicates that a change really is coming.
The actual number of hydrogen vehicles currently on the road is still pretty small however, it is almost certain that it will continue to grow. Governments around the world are showing a commitment to hydrogen to power not just their transport sector, but their manufacturing industries and to support their existing gas and electricity networks.
In Europe, Germany is seen as a leader, while in our region Japan and South Korea are looking to Australia to potentially supply the hydrogen (and hydrogen products such as ammonia) that they need. To this end, Australia has set itself a target of being a top three exporter of hydrogen around the world.
Even though not all of the hydrogen demanded by these countries will be used in fuel cell vehicles, it will hopefully spur the development of a hydrogen production industry which will get to scale and deliver the hydrogen to power our cars, trucks and buses (and trains, ships, aircraft) more cheaply.
In fact, the Australian government’s Clean Energy Finance Corporation has recently released a report which indicates that green hydrogen (that’s hydrogen produced using renewable electricity) is currently at cost parity with diesel for a range of applications including line-haul vehicles and back to base vehicles and is forecast to reduce cost further.
When you consider reductions in the price of hydrogen vehicles and refuelling infrastructure over time, this will lead to significant decreases in the lifetime cost of operating a heavy vehicle.
There are still challenges to be addressed before hydrogen powered trucks are an everyday sight on our roads. We don’t currently have the necessary refuelling infrastructure and the vehicles are pretty expensive right now. We also will need to build electrolysers to produce large quantities of hydrogen and we will need to make sure that we have a workforce trained to maintain and service hydrogen vehicles. Just as importantly, we need to make sure that people are comfortable with the idea that hydrogen is a safe and effective alternative to the way we currently do things.
We’ll look at how Australian can tackle these issues in the final part of this series, but in the meantime, if you still don’t think that the hydrogen revolution is coming, well, in the words of a long time hydrogen fan, “You can’t handle the truth”.
Submitted by Joe Kremzer, General Manager Policy at the Australian Hydrogen Council. For more information contact him at: jkremzer@h2council.com.au