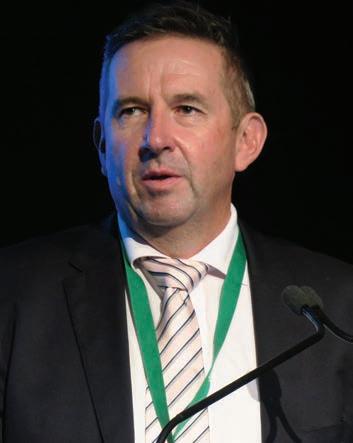
20 minute read
NEWS AND VIEWS
NATROAD REALIGNS WITH POWER TORQUE
“NatRoad is working hard to provide the industry with a voice, and we invite feedback from Power Torque readers on the issues they are facing,” said Warren Clark, NatRoad CEO, after reaffirming the strong relationship between his organisation and PowerTorque Magazine.
“NatRoad looks forward to providing Power Torque readers with up-to-date, relevant industry information to help keep them on the road. Our team regularly meets with key decisions makers and regulators in the industry to improve the operating environment for all. Therefore, NatRoad looks forward to working with Power Torque to keep operators informed on changes that affect their business.”
First cab off the rank is NatRoads campaign to improve payment terms and stop owner-operators being used as ‘Cheap Finance’.
The NSW Small Business Commissioner has recently released the Small Business Shorter Payment Terms Policy, which requires companies entering into contracts with the NSW Government to pay their subcontractors within 20 business days following the receipt of invoice. This applies to contracts from July 1 2021 with a value of $7.5 million or more.
Although this is a welcome change, it only applies to a small number of owneroperators, with large numbers of operators struggling to pay their own bills.
Delayed payments or non-payments are the major contributors to business closure. Large companies are effectively using sub-contractors as a way to finance their operations by not paying them on time.
NatRoad said it continues to lobby the federal government to make 30-day payments a maximum time within which payment to a small business must be made. A national law to that effect would help end the uncertainty and inconsistency of payment times for transport small businesses.
Many companies are using COVID-19 as an excuse to push payment times out further than 30 days. In the face of this trend, it is hoped that the changes in NSW point to a trend that can help reduce the uncertainty and inconsistency of payment times for small transport owner-operators. But more needs to be done and similar changes should be introduced nationally and made law rather than form part of a government code.
Better support and protection are needed for road transport operators to keep them on the road during these turbulent times.
Warren Clark, NatRoad CEO
TRUCK CRASHES WENT DOWN DURING THE PANDEMIC
It is common knowledge in the trucking industry, but the the latest accident research has confirmed that the number of truck crashes went down during the pandemic.
NTI’s National Truck Accident Research Centre (NTARC) today published its 10th, and now annual, national report into the cause of major crashes involving heavy vehicles, has found that during COVID Australia’s roads were the safest they’ve been in years, with the number of multi-vehicle crashes involving heavy vehicles down more than 16 percent.
NTARC author, Adam Gibson, of NTI, said the positive findings came despite more trucks and freight being on Australian roads, particularly during the pandemic.
“The industry should be congratulated for keeping Australia moving and for keeping supermarket shelves stocked especially during COVID lockdowns,” said Adam.
The report found evidence road safety messaging is working, with fatiguerelated crashes involving heavy vehicles down from 27 per cent in 2005 to eight per cent last year.
“There’s been a massive reduction in multi-vehicle crashes involving trucks and the lowest number of fatiguerelated crashes since NTI began keeping records 18 years ago,” said Adam. “It is a credit to the industry, truck drivers and all road users.”
Technology and smart trucks are key to further driving down the road toll. The report found one in eight truck crashes were due to inappropriate speed for the conditions, however this did not mean the vehicles were exceeding the speed limit.
“Speed cameras, radar traps and increased speed enforcement help deter high speed offences, but data shows technology and smart braking systems on trucks are key to reducing singlevehicle rollover crashes,” said Adam.
NTI is working with the National Heavy Vehicle Regulator (NHVR) to use data from the NTARC report to develop new education initiatives to further improve road safety.
“Australia’s trucking industry is set for an information boom over the next decade, which will help improve safety and increase productivity,” said Sal Petroccitto, NHVR CEO. “The NHVR is committed to ongoing fatigue detection programs and support, together with delivering safety campaigns such as We Need Space, aimed at reminding light vehicle drivers about the importance of driving safely around truck drivers on the road.
“We want every driver to travel safely and arrive safely at their destination and ensure these NTARC report figures continue to improve.”
Since 2003, when the first NTARC report was released, the number of freight movements and heavy vehicles has increased by 50 per cent.
COMPREHENSIVE ELECTRIC CHARGING SYSTEM FOR TRUCKS
Three of the big four global truck manufacturers have come together to sign an agreement to develop a comprehensive electric charging system, initially in Europe, but one in North America is also on the cards.
Between them Daimler Truck, the Traton Group and Volvo Group represent a majority proportion of the trucks manufactured across the globe. These three have signed a non-binding agreement to install and operate a highperformance public charging network for battery electric heavy-duty long-haul trucks and coaches across Europe.
The group are planning to start operations in 2022, investing 500 million Euros ($790 million) to install and operate at least 1,700 high-performance green energy charging points close to highways as well as at logistic and destination points, within five years from the establishment of the JV.
The three players are also heavily involved in the US truck market, since Traton finalised its takeover of International Trucks earlier this month. Reports suggest a similar JV in North America will be announced relatively soon.
The number of charging points is with time intended to be increased significantly by seeking additional partners as well as public funding. According to the three major players, this joint action addresses the urgent need for a high-performance charging network to support truck operators with their transition to CO2neutral transport solutions, especially in heavy-duty long-distance trucking.
A recent industry report called for up to 15,000 high-performance public and destination charging points no later than 2025, and up to 50,000 highperformance charging points no later than 2030. According to the joint venture partners, their kick-start is a call for action to all other industry players, as well as governments and regulators, to work together for a rapid expansion of the necessary charging network to be able to contribute to reaching the climate targets. As a clear signal towards all stakeholders, the charging network of the three parties will be open and accessible to all commercial vehicles in Europe, regardless of brand.
“For the Traton Group, it is clear that the future of transport is electric,” said Matthias Gründler, CEO Traton Group. “This requires the rapid development of publicly accessible charging points, especially for long-distance heavy-duty transport. We are now moving forward together with our partners Daimler Truck and Volvo Group to make this high-performance network a reality as quickly as possible. We now make the first step to accelerate the transition towards sustainable, fossil free transport. The second step should be a strong engagement of the EU for the full scale-up of a charging network across Europe.”
Volvo Group, Daimler Truck and the Traton Group will own equal shares in the planned JV, but continue to be competitors in all other areas. The creation of the JV is subject to regulatory and other approvals. The signing of a JV agreement can be expected by the end of 2021
“We are laying the necessary foundation in making a break-through for our customers to make the transformation to electrification by creating a European charging network leader, said Martin Lundstedt, President and CEO Volvo Group. “We have powerful electromobility technologies, and now, with Daimler Truck, the Traton Group and thanks to the European Green Deal, also an industrywide understanding as well as a political environment to make fundamental progress towards sustainable transport and infrastructure solutions.”
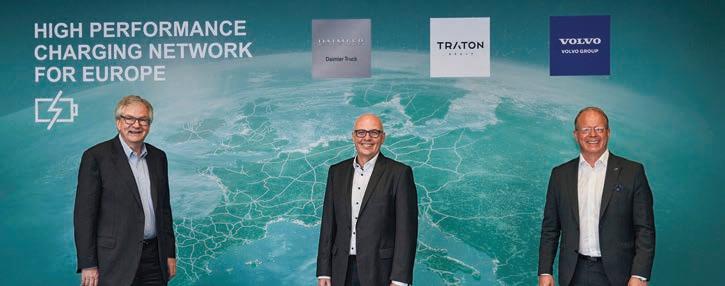
Martin Daum, CEO Daimler Truck, Matthias Gründler, CEO Traton Group and Martin Lundstedt, President and CEO Volvo Group
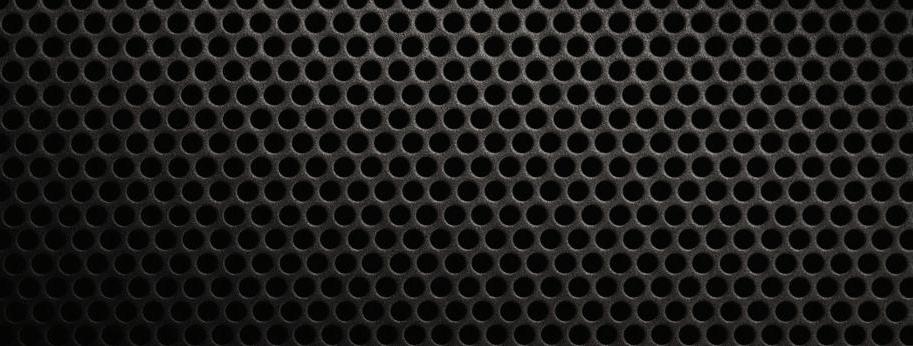
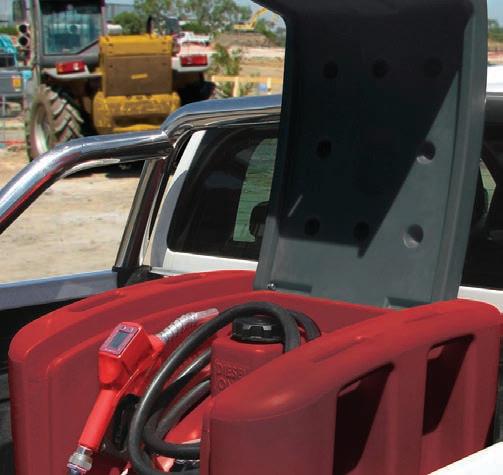
ENGINE REMAPPING CLAMP DOWN
An initiative from the National Heavy Vehicle Regulator is educating all road users on the environmental issues and safety issues as part of an engine remapping clamp down.
The NHVR education campaign will highlight the health and safety risks caused by illegal engine remapping. The campaign will focus on educating the heavy vehicle industry and public on the harmful effects that engine remapping can have on heavy vehicle drivers and logistics workers, as well as communities and the environment.
NHVR CEO Sal Petroccitto said the campaign was an opportunity for the NHVR to work collaboratively with the heavy vehicle industry to remove engine remapping and improve safety.
“The NHVR’s highest priority is safety and we’ll continue to focus on compliance while delivering education and awareness through information like the engine remapping campaign,” said Sal. “By and large, our industry does the right thing, but occasionally we see unsafe practices occurring and it’s our job as a regulator to lead change.
“Whether you’re an owner, driver, mechanic, part of the supply chain or a light vehicle driver, engine remapping puts everyone at risk.”
The campaign will be delivered in two phases, with an initial focus on the exposure that toxic diesel emissions can have due to engine remapping. Research indicates that remapped engines can release up to 60 times more pollutants* into the atmosphere, which can cause damage to the health and safety of workplaces, communities and the environment.
The second stage of the campaign will focus on remapped engines that disable speed limiter controls. With recent compliance checks indicating up to 10 per cent of all heavy vehicles are operating with illegally remapped engines**, the danger is significant and can cause serious injury. * Australian Bureau of Statistics January 2017 Motor Vehicle Census ** Transport for New South Wales heavy vehicle compliance checks 2019 - 2021
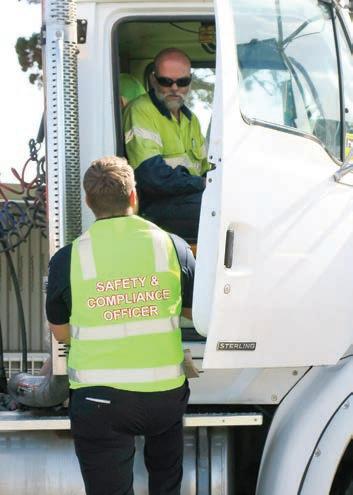
In terms of the assessment of fitness to drive, medical standards for truck drivers need to improve. The point has been made by the Australian Trucking Association in its submission to the National Transport Commission’s review of Assessing Fitness to Drive
Backed by sound legal advice, the ATA submission recommends improving the AFTD commercial standards.
The submission begins, though, by recounting Nathan’s story. In February 2010, Nathan passed away after a B-double collided with his ute on the Pacific Highway. The B-Double driver had been examined under the medical standards just three months before the crash, but the exam had failed to reveal that he had severe sleep apnoea. The B-double driver had fallen asleep at the wheel.
“The AFTD commercial standards are simply not fit for purpose,” said Andrew McKellar, ATA CEO. He said cardiovascular disease, sleep apnoea and diabetes were significant issues for the trucking industry, with truck drivers recording a higher rate of these medical conditions compared to the Australian population.
“Despite these findings, the current AFTD screenings are subjective, unsuitable and out of date. They are unable to properly recognise medical issues that would affect a driver’s fitness to drive,” said Andrew.
The ATA submission highlights an example of this with the AFTD patient questionnaire and its use of the Epworth Sleepiness Scale, a tool that is proven to be unsuitable for determining if commercial drivers have sleep apnoea.
The NTC has proposed creating a separate, additional standard for drivers working for certified businesses, but Mr McKellar said that the AFTD commercial standards should instead be improved to include objective medical screening tests.
“The rail medical standards include an objective screening matrix for sleep apnoea, a diabetes screening test and an objective cardiac risk assessment using the Australian absolute cardiovascular disease calculator,” Mr McKellar said.
To support its submission, the ATA sought legal advice from national law firm Holding Redlich. The advice concluded that no jurisdiction’s legislation would prevent AFTD from mandating specific examination procedures similar to the rail worker medical standards.
“The NTC has argued these objective tests are beyond the scope of what they can do, but as outlined in our submission, there is no legal reason why objective screening like this cannot be included in driver medicals,” he said.
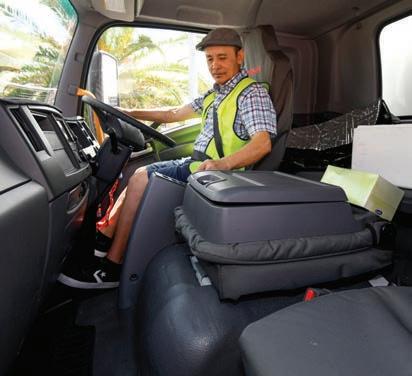
SAFETY-CRITICAL REPLACEMENT PARTS
The ARTSA Institute (ARTSA-i) has unveiled a Good Practice Guide, which aims to raise awareness of suppliers, purchasers and installers of safety-critical replacement parts about supply practices.
The Guide describes actions that suppliers should take to ensure parts are suitably certified, that records are kept and installation information is provided. The Guide does not favour original equipment parts over after-market parts. Nor does it favour bricks and mortar retailers over online suppliers. It provides common-sense actions that all part suppliers should take, but often don’t.
“We aim to reduce the risk of workshops fitting poor quality or inadequately rated safety-critical parts as well as providing an understanding of the different types of replacement parts available in the market,” said Dr Peter Hart, Executive Member at ARSTA-i and a certified vehicle engineer.
“Operators should purchase good-value parts for heavy vehicles that will provide safe, reliable, and legal performance. The Guide defines acceptable supply practice and advises purchasers what to expect from suppliers. The use of poor-quality parts leaves the operator vulnerable to expensive breakdowns and reworks, enforcement attention and loss of insurance cover. For this latter reason alone every vehicle operator is urged to ensure that their in-house technicians or third-party workshops and suppliers fit parts that are suitable for the job.
“We want to reduce the risk of in-service failure of all replacement parts, to avoid the vehicle crashing, or simply breaking down on the highway where they may be vulnerable to impact by other road users, potentially causing death, injury, loss or damage. We believe these risks can be mitigated if replacement parts suppliers implement the quality-assurance activities specified in this new Guide.”
The Guide recognises four risk levels which are: 1. Safety Critical 2. Safety and Compliant Relevant 3. Minor Safety Relevance and 4. No Safety and Compliance Concerns.
The Guide’s advice is graduated according to these levels.
By implementing the Guide’s suggestions suppliers will identify appropriate technical standards, hold validation test reports, keep supply records, review failure reports, and provide installation information.
The Guide is applicable to replacement parts which are used to replace an original part, and for parts that are used to modify a vehicle.
This Guide identifies good practices that will support suppliers, purchasers, operators, and others involved in the servicing or modification of heavy vehicles, to enhance the safety and reputation of the road transport sector. Additionally, the purchaser and fitter of these parts will have peace-of-mind that they have completed satisfactorily their role in the chain of responsibility.
NET ZERO COMMITMENT FROM FUSO
Japanese truck maker Fuso will be following the Daimler Truck target of CO2neutrality in production sites, with the net zero commitment from Fuso aiming to shift all plants to CO2-neutrality by 2039.
Operations at Fsuo’s European in Portugal will becomeCO2-neutral during 2022. Other plants in Japan will follow to achieve CO2-neutrality by 2039 at the latest, with the Kawasaki and Nakatsu Plants having reduced CO2 emissions by 17 per cent since 2015.
The Japanese government recently stated that it would ‘aim to become carbon neutral [in the automotive industry, including the entire supply chain’ in its action plan for the Green Growth Strategy, which was approved by the Japanese cabinet in June 2021.
The Tramagal Plant in Portugal is the leader in the drive to zero emissions. This is the plant where the eCanter model, shown at the Brisbane Truck Show, and now on sale in Australia, is being built.
The plant is increasingly using green electricity, increasing on-site solar power production and switching to selfconsumption, The entire internal logistics and warehouse fleet is being converted to electric vehicles. The plant is currently exploring the possibilities of green hydrogen production with the support of solar panels, to gradually replace natural gas consumption.
Daimler says it is also committed to sustainability in other aspects of the value chain, with all European Daimler Trucks and Buses plants will have a CO2-neutral energy supply by 2022.
At the Kawasaki Plant, where the Fuso Canter sold in Australia is currently made, and the Nakatsu Plant, where transmissions are manufactured, Fuso is implementing a five-year plan to decrease CO2 emissions by 17 per cent compared to 2015 levels. It has created a new roadmap to decarbonise the Kawasaki Plant by 2039.
The Kawasaki Plant, where the Fuso Canter sold in Australia is made
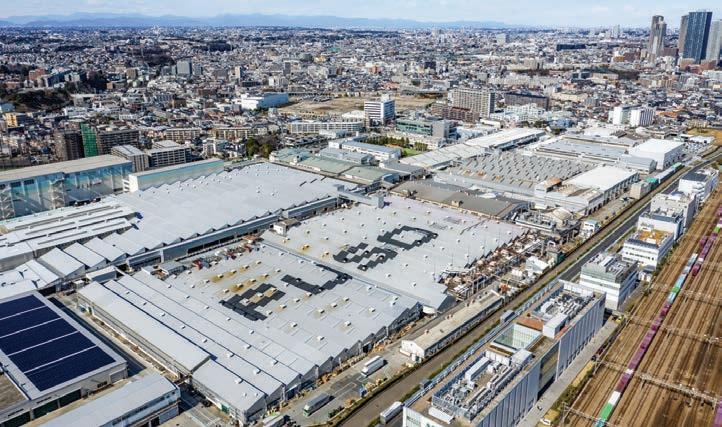
A LONG HISTORY IN THE TRAILER BUILDING BUSINESS
One of the key people in the MaxiTRANS organisation is Kevin Manfield, who has a long history in the trailer building business. Nowadays, Kevin is the General Manager of Sales for MaxiTRANS.
Based in Queensland, Kevin Manfield has moved into the General Manager position from his previous role as General Manager of Products and Markets.
On a day-to-day basis, Kevin assists and supports individual sales people and management in putting together deals, including pricing, structure and specifications. When required, he assists with customer support and contact.
“Look, to be honest with you, I’m actually a tradie,” says Kevin. “I did a trade, worked on the shop floor and I worked my way into engineering. Then I moved through engineering and into manufacturing.”
Kevin came into the ancestry of MaxiTRANS four decades ago when he joined Maxi-CUBE. His introduction to Maxi-CUBE came when, working for a previous employer, he was involved with a joint-venture building insulated railway containers. Maxi-CUBE had the contract to build the panels.
“I was helping manage the project, doing a lot of design drafting,” he says.
Following the contractual involvement with Maxi-CUBE, the company approached him and offered a position at Maxi-CUBE’s Coopers Plains, Brisbane, facility. And so, in 1981 Kevin Manfield commenced working out of the Brisbane facility in a design and drafting role.
Established in that position, he was offered a promotion.
“I was asked if I would be interested in moving down to Melbourne,” says Kevin.
Accepting the offer, Kevin and his wife relocated to Melbourne and he began working in the Maxi-CUBE engineering department. Another offer, another promotion and acceptance, and Kevin moved back to Queensland as State Manager for Maxi-CUBE. In this position, he ran the Queensland wing of the company including operations and the service department. And in what was becoming a geographical game of tennis, Kevin again relocated. This time back to Melbourne as General Manager of Manufacturing at Hallam.
“At that stage we were in the process of acquiring Fruehauf Trailers,” says Kevin. “So we took on Fruehauf and the manufacture of these trailers was transitioned to our Hallam plant.”
The company went public at this stage before Maxi-CUBE acquired Freighter Trailers, and soon after MaxiTRANS was established. At this time, Kevin moved into a National Sales position. In a restructure of the company after being listed on the Stock Exchange, Kevin took up the role as the Maxi-CUBE Product Manager. Yet another corporate restructure saw Kevin Manfield move into the position of General Manager of Products and Markets for MaxiTRANS.
“I would have all the products under the brand reporting back to me. I did that for a number of years.”
And then Kevin moved into his current position as General Manager of Sales.
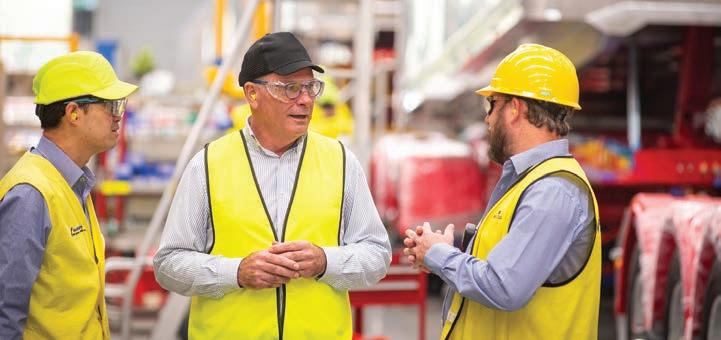
Centre, Kevin Manfield, MaxiTrans General Manager
APPROVED THE OPERATOR’S OWN EXCLUSIVE OBM
By signing off on McColl’s Integrated Mass Management System (MIMMS), Transport Certification Australia has approved the operator’s own exclusive OBM.
McColl’s Transport Operations Pty Ltd is Australia’s largest independent bulk liquid carrier of milk, food and bulk chemicals and the MIMMS system was developed exclusively for use by the operation.
MIMMS uses an innovative combination of technologies, systems and processes to meet the performance requirements of the OBM System Functional and Technical Specification.
This approval comes as part of the National Telematics Framework which is intended to provide transport operators with the opportunity to have their own technologies and systems recognised by TCA.
“We are very pleased to have received TCA approval for MIMMS,” said Simon Thornton, McColl CEO. “This comes after two years of hard work for our team to deliver this new capability to us. Safety is at the top of our values list and this system will be another asset to help us to keep our drivers and other road users safe.
“MIMMs will allow us to be sure that we are always operating within the gross vehicle mass limits for the roads that we are driving on. Our federal, state and local governments make big investments to provide Australians with first class road infrastructure.
“Managing and reporting our mass in real time is part of our commitment to keeping that infrastructure in top working order. We have a particular interest in regional and rural roads as we collect milk from farms and the infrastructure on these smaller roads is particularly vulnerable to over-weight vehicles.
“Importantly, McColl’s milk trucks can now leverage the new High Productivity Freight Vehicle (HPFV) arrangements in Victoria that broaden access, deliver easier first-and-last-kilometre approval and reduce the need for permits, which provides greater protection for Victoria’s roads and bridges.”
COMPILING USEABLE STRATEGIC FREIGHT DATA
In an innovation demonstrating the value of the convergence of data, the Transport Certification Australia (TCA) has released details on how it contributed to the heavy vehicle movement insights provided through the National Freight Data Hub prototype website.
The new website went live as part of the Australian Government announcement. As part of this new initiative, the National Freight Data Hub prototype website provides a source of strategic freight data for industry, government and other technology users to help improve the efficiency, safety and resilience of the freight sector.
The prototype website features interactive truck telematics maps that provide insights into travel patterns, congestion and the use of rest areas by heavy vehicles.
These visualisations draw substantially from data derived from the ional Telematics Framework (NTF). This framework is the a nationally agreed digital platform linking technology providers with technology users.
Leveraging the NTF’s data protection mechanisms and privacy-by-design principles, TCA provided the National Freight Data Hub with aggregated, de-identified data extracts from applications of the NTF.
Heavy vehicle operators use NTF applications that include the Intelligent Access Program (IAP), the Telematics Monitoring Application (TMA) and the Road Infrastructure Management (RIM) application.
Standardised approaches to data collection and transfer, which underpin all NTF applications, offered the National Freight Data Hub an efficient way to access data from 6,500 vehicles operating across the country. The data is from transport operators who use Application Service Providers operating in the NTF.
Standardised data consent arrangements that TCA has in place with transport operators overcame challenges routinely
associated in obtaining data from heavy vehicle fleets. “The National Freight Data Hub prototype website showcases the availability of aggregated and de-identified telematics data in cutting-edge geo-spatial interactive insights,” said Matt Stockwell, National Freight Data Hub Assistant Director. “Working with TCA, the Hub team has visualised insights on congestion, rest areas and truck counts which enable industry and governments to get a national picture of freight movements. “The data helps answer our enduring freight questions such as where and when freight is moving on our roads and how we can improve the efficiency and safety of the freight task.” As more vehicles are enrolling in the NTF, and driven by the use of new productivity and safety reforms in use by road managers and regulators, future versions of the interactive maps on the Hub Power Torque Ad 3-Final2.pdf 3 26-Jul-21 3:26:04 PM will benefit from more data from a diverse range of vehicles.
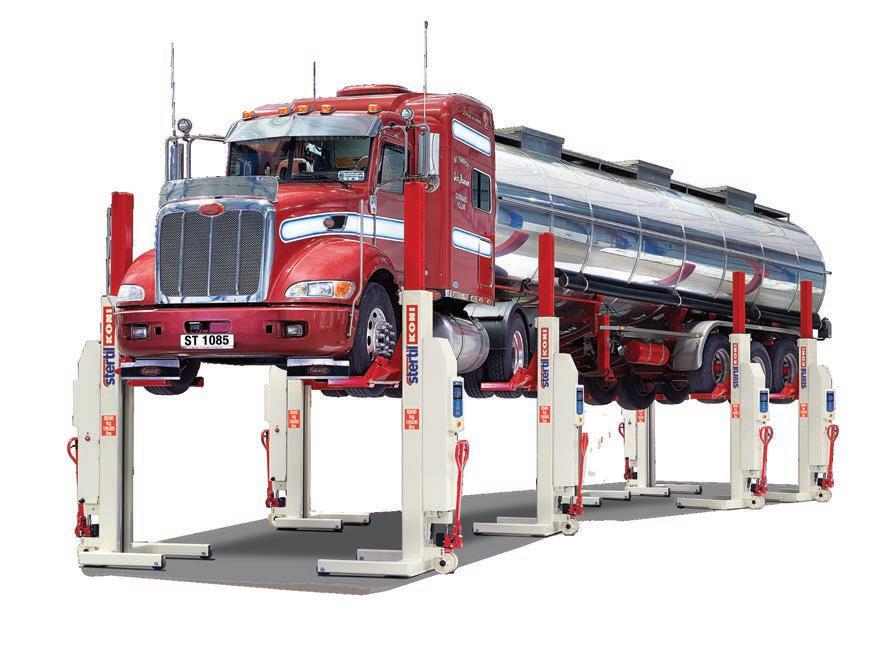
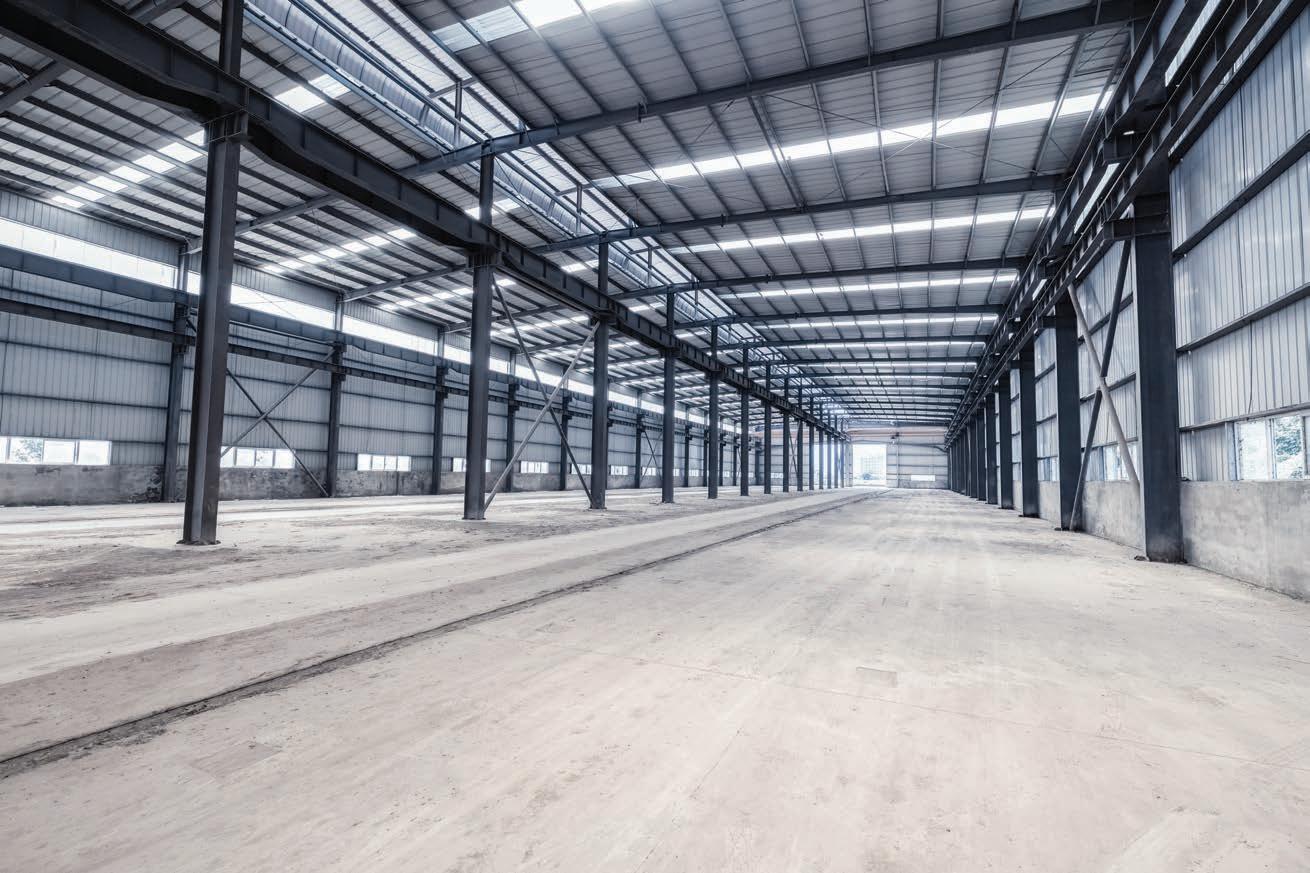