
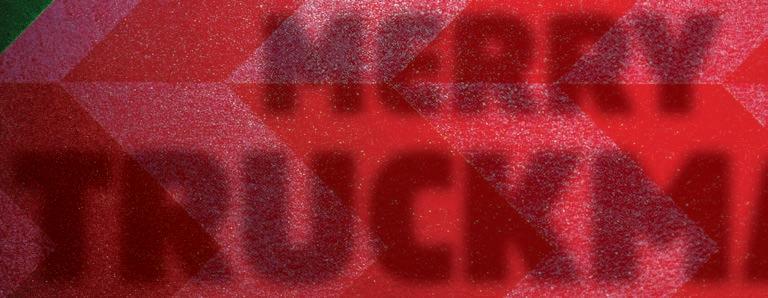

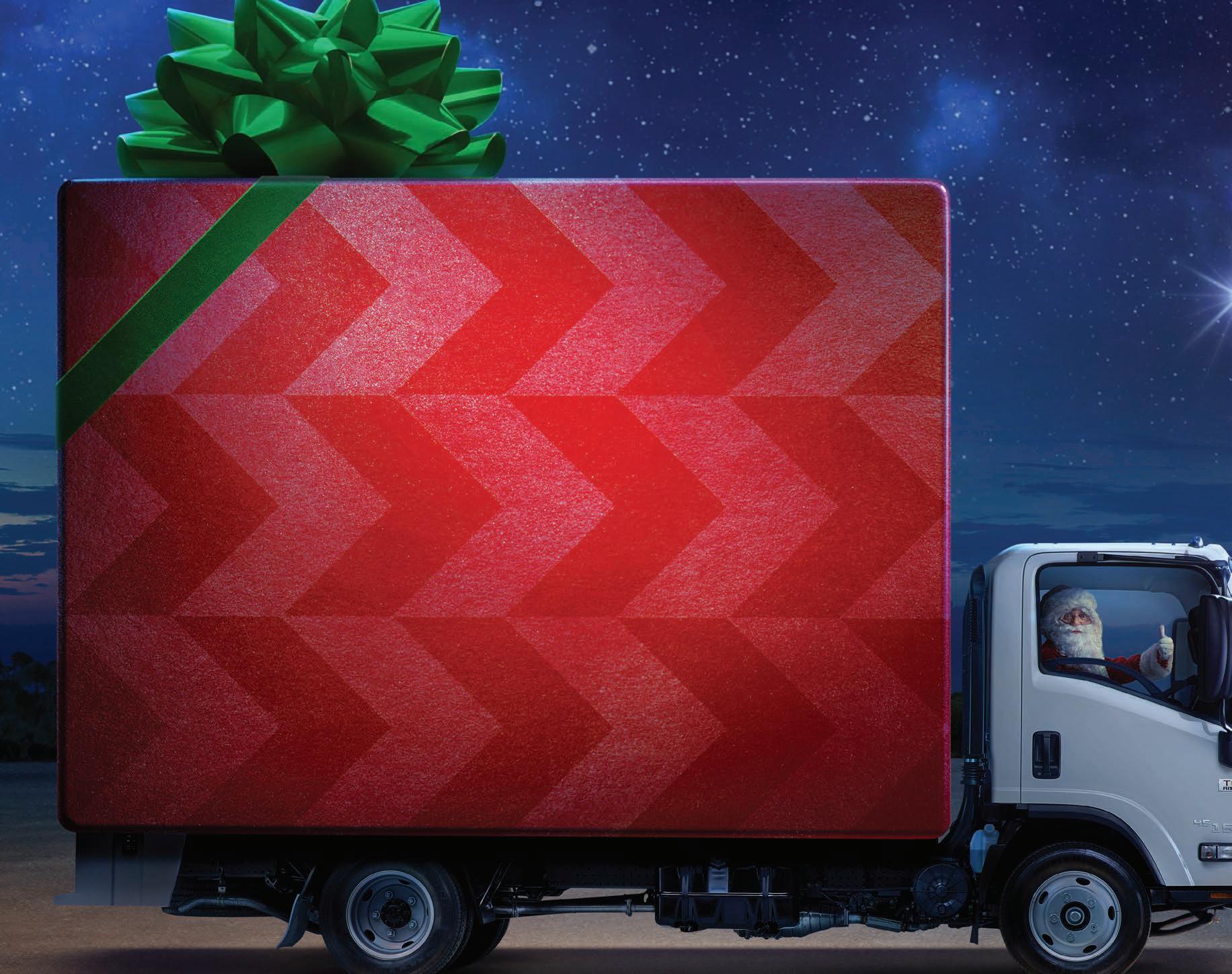
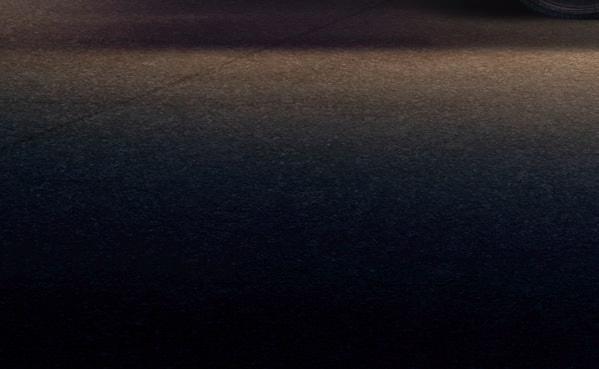

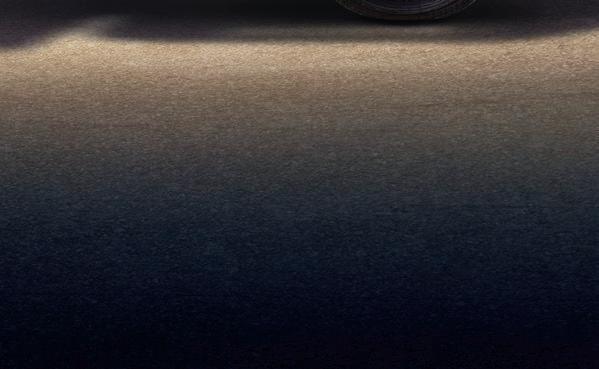
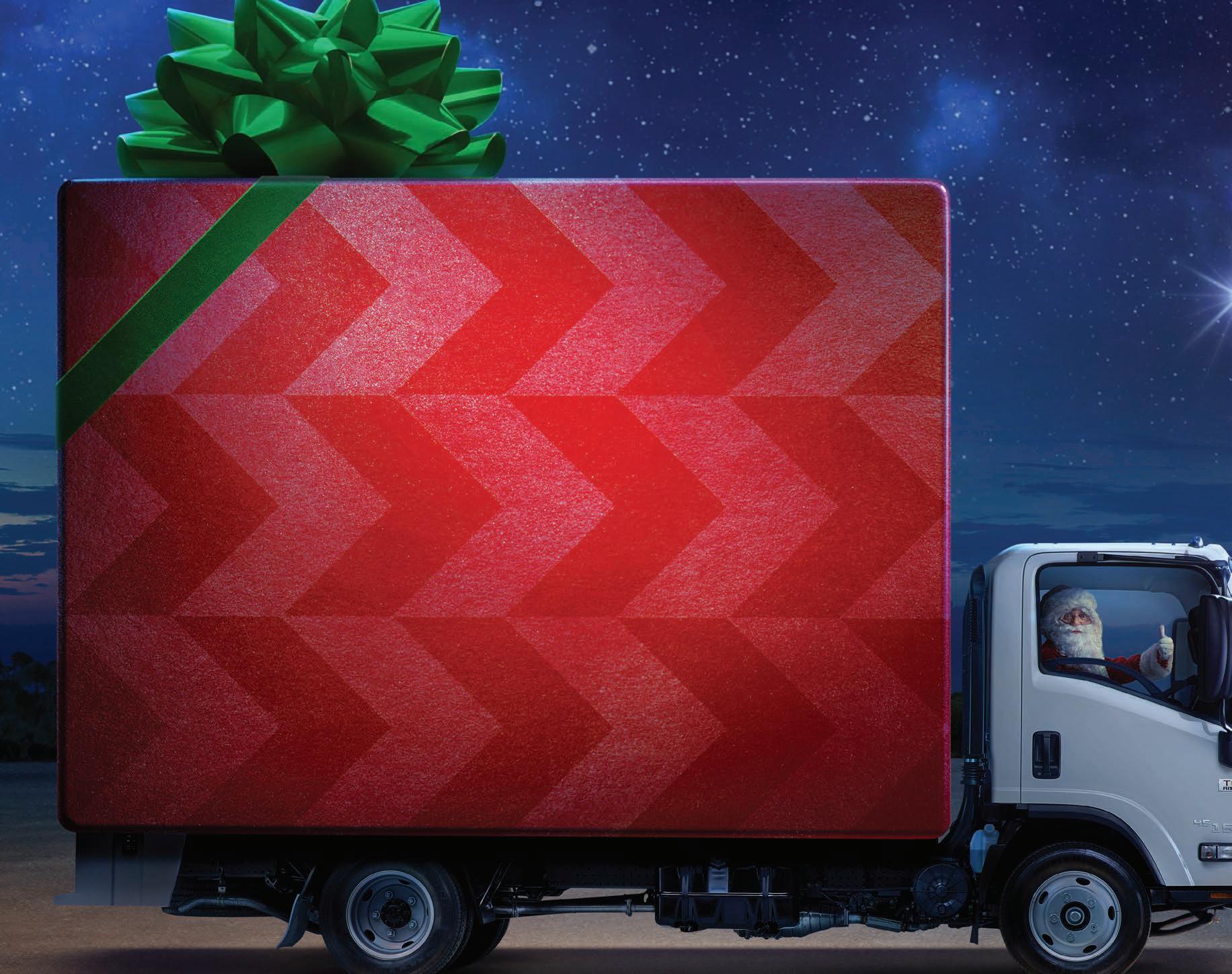
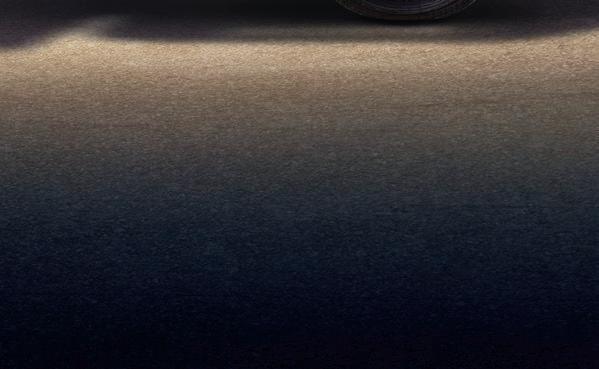
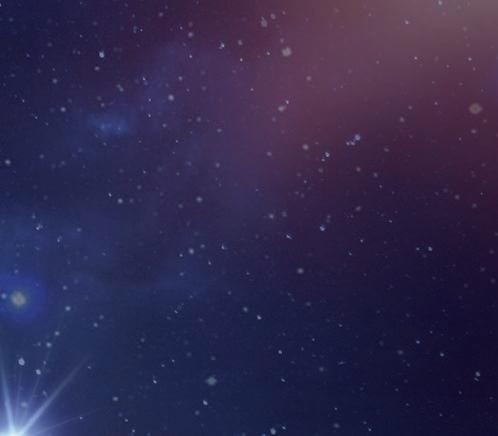
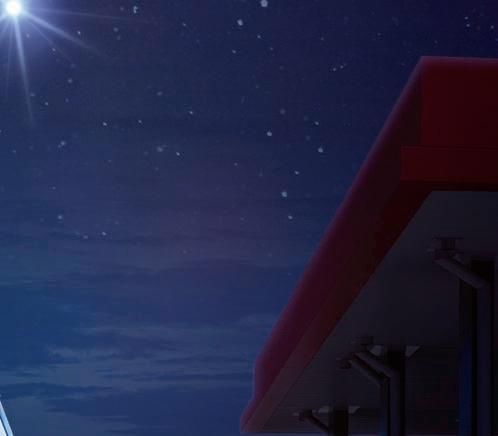
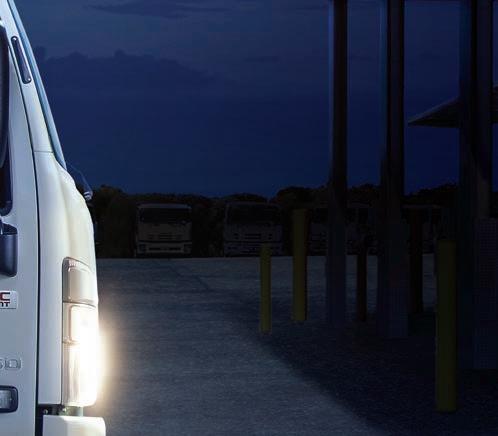
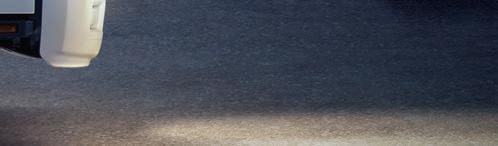
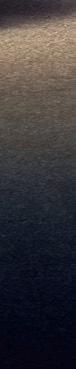

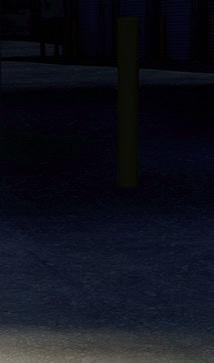
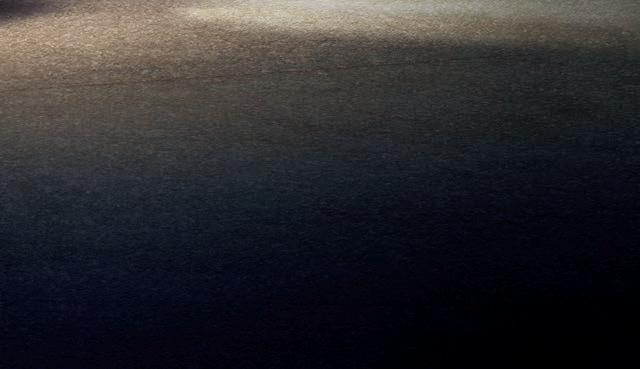

his is my last editors note in PowerTorque, as I move on into semi-retirement, which means that it’s not farewell, it’s au revoir. I will be continuing to contribute feature articles to the magazine without continuing with the task of organising and running a publication.
It is at this point that I have an opportunity to reflect upon my career involved with the trucking industry. It all began back in 1977 with a chance encounter with a truck owner while hitchhiking. He needed someone to drive his truck because he had to spend more time at his depot. The deal was done and I started work the following week.
I have fond memories of that 1967 Ford D series, though at the time I didn’t have experience with a newer truck in good condition. However, it didn’t take long for me to realise that the grass was greener elsewhere and I moved on to better operations with better gear.
At that time, it seemed normal to move from job to job at regular intervals. I did not work full-time for any operation for more than two years. Transport companies would come and go, distribution contracts would come and go, the price of the commodity would drop through the floor and make transport less profitable.
However, I was up for the ride and was not giving up on the trucking industry, working for a series of operators varying from those with just the one or two trucks up to the large national fleets, gaining experience all of the way.
Of course there are times when you become disillusioned with the industry as a whole. For me it was the period when I had young children at home, a
large mortgage and a job which was not consistently reliable.
After trying a few alternative career paths, all of which proved to be equally unreliable, the lure of the culture in trucking, and the lifestyle where you are on the road, seeing new places, meeting new people and having plenty of banter with fellow truckies, brought me back. This was the career which had chosen me.
I ended up driving refrigerated semis all over Europe, before getting the opportunity to drive trucks here in Australia. The job with a national bakery was to be the longest duration of a truck driving job in my career.
When that ended abruptly with retrenchment, I got lucky and fell into a job as Technical Editor at ATN Magazine. This was an amazing transformation of a career for me and it ticked all of the boxes. I still got to test drive trucks all around Australia. I still got to listen to and tell stories with other truck drivers and operators, at the same time as writing about the industry I love.
Prime Creative Media Pty Ltd
ABN 51 127 239 212
379 Docklands Drive, Docklands VIC 3008 Australia
Telephone: 03 9690 8766
Email: enquiries@primecreative.com.au
Chief Operating Officer: Christine Clancy
Managing Editor: Geoff Crockett
Editor: Tim Giles
Assistant Editor: Alex Catalano
Contributor: Bob Woodward
Correspondent: Will Shiers (UK)
Advertising Manager: Trevor Herkess: 0411 411 352, trevor.herkess@primecreative com.au
Client Success Manager: Salma Kennedy, salma.kennedy@primecreative.com.au
Circulation & Subscriptions Manager: Frank Rapone
Head of Design: Blake Storey
Designers: Danielle Harris, Jacqueline Buckmaster
Official Media Partners:
REGISTERED BY Australia Post - ISSN 1445-1158
SUBSCRIPTION
03 9690 8766
This last stage of my career, writing for Prime Mover, Diesel and then PowerTorque magazine has been a great deal of fun. I have worked with a very large number of great people, across the trucking operators and drivers, the truck manufacturers, the associations and the regulators, and had a great time. Way too many to mention here.
I am just taking this opportunity to thank them all for all of the help and guidance, which has enabled me to do my job. I am also grateful for all of the great friendships I have made with trucking folk, friendships which will continue, as a I dial back my duties to a more relaxed lifestyle.
EDITOR
subscriptions@primecreative.com.au PowerTorque Magazine is available by subscription from the publisher. The right of refusal is reserved by the publisher.
Annual rates: AUS $60.00 (inc GST). For overseas subscriptions, airmail postage should be added to the subscription rate.
PowerTorque Magazine is owned and published by Prime Creative Media.
All material in PowerTorque Magazine is copyright and no part may be reproduced or copied in any form or by any means (graphic, electronic or mechanical including information and retrieval systems) without written permission of the publisher.
The Editor welcomes contributions but reserves the right to accept or reject any material.
While every effort has been made to ensure the accuracy of information, Prime Creative Media will not accept responsibility for errors or omissions or for any consequences arising from reliance on information published.
The opinions expressed in PowerTorque Magazine are not necessarily the opinions of, or endorsed by the publisher unless otherwise stated.
The green trucks of Fred’s Interstate Transport have been a familiar sight across Australia’s east coast for the past 40 years.
20 MERCEDES-BENZ’S FIRST ELECTRIC PRIME MOVER
In this test drive, Tim Giles goes for a spin in the first electric prime mover from Mercedes Benz to be released in Australia.
26
Wightman Transport Managing Director, Peter Starke, spoke to us at the handover of the first of several batches of MAN prime movers, from Penske Rental.
34 LIVESTOCK ISSUES AT THE FOREFRONT
Members and delegates from the rural transport industry had the chance to speak their mind on the issues affecting their work at this year’s LRTAV Conference.
46
Due to government subsidisation, the process of electrification is well advanced in North America when compared to Australia.
The future of truck telematics was at our doorstep, as Alex Catalano got the chance to take a look at the latest advancements in technology.
74
The introduction of an increase of mass limits is a welcomed one, but how it will actually affect industry? Technical Editor Bob Woodward explores the issue.
With its introduction of a suite of new technologies and leaving behind some of the older ideas about tr ucks, Western Star is changing the narrative about truck development.
38 MIND YOUR PEES AND POOS
The ALRTA wants to remind everyone within the livestock supply chain to stay on top of best practices when it comes to the Effluent Code.
42 MANAGE YOUR ROLLOVER PLAN
Truck rollovers can be deadly, especially when carrying livestock. The LBRCA has put together a program to make sure all truckies have all the tools they need to stay safe.
52 CHECK YOUR TRUCK’S HEIGHT
As we approach the busy holiday season, we must address an ongoing issue that impacts our roads: over-height trucks, particularly in New South Wales.
64 NEW AGITATOR AS GOOD AS GOLD
Local Ballarat business Eureka Concrete is enjoying the work of a new Isuzu agitator, which has quickly become a key part of the fleet.
66 CLEAN TECH FOR TOP TIER NZ FLEET
Tranzliquid Logistics is one of New Zealand’s top tier fleets, a company that has forged a reputation for its immaculate equipment, exemplary safety record and great team culture.
77 CELEBRATING A YEAR OF COLD CHAIN GROWTH
In the fast-paced world of cold chain logistics, the right partnership can be the driving force behind transformative growth and success.
The federal government has set new mass limits for heavy vehicles under the Heavy Vehicle National Law (HVNL), after it was amended to allow Australia’s heavy vehicles to meet the latest international standards.
From November 1, 2024, general access mass limits will increase by 500kg for trucks in Australia that comply with Euro VI or equivalent noxious emissions standards.
“This will improve safety and emissions reduction outcomes in our heavy vehicle fleet and follows the government’s recent
announcement of tighter noxious emissions standards for new trucks and buses,” Federal Transport Minister Catherine King says.
“The increase in heavy vehicle mass limits is an important step towards improving productivity and safety in the heavy vehicle sector, while reducing emissions.”
It follows the government’s recent announcement of the introduction of tighter noxious emissions standards for new trucks and buses, which must also be met from November 1, 2024.
NatRoad has called on both the NSW and federal governments to reject all proposals for a carbon tax on trucks.
NatRoad’s message follows the recent NSW Freight Policy Reform: Interim Directions report recommending consideration for vehicle charges based on carbon emissions, creating what would essentially be a carbon tax on trucking in Australia.
The proposal for an MC licence split is progressing after Australian Trucking Association (ATA) CEO Mat Munro spoke to a transport roundtable at Parliament House earlier this year.
Convened by Senator Glenn Sterle, who has been a key delegate to the transport industry, the roundtable included Prime Minister Anthony Albanese.
The roundtable was briefed on the ATA’s plans for driver licencing, training, road safety and how to attract new workers to the industry.
“One of our most important proposals is to split the MC licence class in two. The new
MC2 class we are proposing would require additional training, assessment and experience, to reflect the skill required to drive large combinations,” Mat says.
“We are proposing that the MC class be split at 37 metres of combination length.
“This would mean that A-doubles, B-doubles and B-triples would be in the MC1 licence class. Longer combinations would require the MC2 licence.
“Existing MC licence holders with more than six months of experience would be automatically designated as MC2 under our plan.”
is a recommendation from an independent panel, not current government policy. However, we believe it is vital that all governments immediately rule out this proposal,” NatRoad CEO Warren Clark says.
carbon tax on trucks would be devastating to small and medium trucking businesses that are already struggling with rising costs.”
NatRoad CEO says that imposing a carbon tax on trucks wouldn’t help with reducing emissions, but would instead add unnecessary financial strain on truck businesses.
“This tax would delay the ability of small and family-owned businesses to invest in lower-emission vehicles,” he says.
“It’s a blunt tool that targets the wrong people, particularly regional and long-distance operators, where low-emission alternatives like electric trucks are not yet viable.”
Outgoing PowerTorque editor
Tim Giles was recognised for his outstanding service to the trucking industry at NatRoad’s awards in September.
Our editor was awarded the Ted Pickering Memorial Award, recognising his 47-year career in the trucking industry both on the road in Europe and Australia, and as a journalist and test driver.
NatRoad says these awards “highlight the dedication, professionalism, and commitment of individuals who have set new standards of excellence in road transport”.
The industry association recognised Tim’s “dedication to informing and uplifting the industry, as well as his
ongoing passion for technology and preparing the industry for the future”.
Jade Harney from Followmont
Transport was awarded the Sam Sali National Young Driver of the Year, named in honour of the late industry veteran.
The Professional Driver of the Year was won by James Ellison of Ditton Bulk Haulage, recognising his impeccable safety record and dedication to mentoring and uplifting those around him.
“These awards reflect the hard work and passion of individuals who have excelled in their roles, and gone above and beyond to have a significant positive impact on the broader industry,” NatRoad CEO Warren Clark said.
The work of the federal government’s Steering Committee has been extended, working on the Heavy Vehicle Rest Area (HVRA) initiative until at least June 30, 2025.
The committee works to improve safety and facilities for truckies across Australia, focusing on facilities such as parking, toilets, showers, drinking water and shelter at rest areas.
Pure Hydrogen has officially registered Australia’s first hydrogen-powered prime mover, with the truck set to be handed over to PepsiCo in the coming weeks.
The registering of the vehicle is the latest event in the partnership between Pure Hydrogen and PepsiCo, which initially commenced in 2022. Now, PepsiCo will trial the vehicle for the next six months.
Pure Hydrogen managing director Scott Brown says the real-world trial of the prime mover is the next step in the long partnership between the two companies.
“The completion of the prime mover
registration follows an extensive period of collaboration between Pure Hydrogen and PepsiCo,” he says.
“This marks the latest step in our development strategy for hydrogenpowered vehicles in Australia.
“Pure Hydrogen continues to pioneer the use of hydrogen fuel cells and is establishing itself as an emerging leader in the Australian hydrogen and energy space.
“The six-month trial will allow Pure Hydrogen to demonstrate the hydrogen fuel cell prime mover’s potential to a broader range of potential local and international customers.”
“I welcome the news that the work of the government’s Heavy Vehicle Rest Area Steering Committee will continue following the extension of the committee’s terms of reference,” says Senator Glenn Sterle.
“This group was established to ensure that those who have the steering wheel in their hands or who know the challenges drivers face have a seat at the table when making important decisions about where funding is directed to support vital rest area projects.
“I am extremely proud of the current committee and look forward to continuing to work with them as we work to deliver more rest areas for our essential truckies to help with them manage their fatigue.
“I encourage truck drivers to engage with the committee as well as local and state governments so we can continue to identify priority locations for rest area projects which could be funded through this program.”
The National Heavy Vehicle Regulator (NHVR) has announced that Main Roads Western Australia’s 25 transport inspectors will now carry real-time heavy vehicle analytics on site that use national technology.
This means that heavy vehicle inspections in the state will connect with the national enforcement database through the NHVR’s Regulatory Compliance Mobility Solution (RCMS) app.
The app allows Main Roads WA to target high risk offenders by giving inspectors access to a central database with driver and vehicle information so that they can administer digital notices during a heavy vehicle intercept.
NHVR CEO Sal Petroccitto says the app provides a single central system that stores and analyses compliance and enforcement data in real time.
“Camera sightings from over 115 fixed cameras across Australia alerts RCMS users if an approaching heavy vehicle is unregistered, has current defect notices, compliance breaches or recently failed to enter an inspection station,” he says.
“The NHVR and Main Roads WA are addressing key safety risks quickly and accurately to deliver an efficient
Long-time owner driver and transport industry great Don McGlinchie has passed away at age 88.
Heralded as the ‘ultimate professional’, he spent decades as both a truck mechanic and ownerdriver, driving east-west across the Nullarbor from Sydney to Perth.
He was a loyal driver of Internationals from his early days behind the wheel, but he also spent time toiling in a B-model Mack amongst other trucks.
Don took a break from the world of trucking in 1974, but the call of the road was too hard to resist. By 1976 he was back behind the wheel doing what he loved again.
He became largely known in trucking circles over the decades following after he became the test driver for Truck & Bus Transportation magazine, one of the first big Australian trucking publications.
Don spent the better part of the last 20 years delivering new trucks all over the country for dealers, still not fully out of the trucking game even in his older age.
He was inducted into the National Road Transport Museum’s Shell Rimula Wall of Fame at Reunion 2008.
Don is survived by his wife Bronwyn, his two daughters, two sons and his grandchildren.
The Victorian government is trialing greater livestock truck access to Melbourne’s major tunnels, partnering with Transurban and the freight industry to allow the heavy vehicles to enter Citylink tunnels for a 12-month trial in 2025.
Livestock trucks had previously been banned from the Burnley and Domain tunnels due to low-clearance infrastructure, but recent upgrades to raise it to a safe height mean the trucks can enter the tunnels with no risk to animals on-board.
The trial is expected to remove 600 trucks from city streets each week, with City Road, Power Street, Olympic Boulevard and Hoddle Street
likely to see the biggest benefits.
“The trial is a win-win for our city and our freight industry,” Minister for Roads and Road Safety Melissa Horne says.
“By taking livestock trucks off innercity streets and into the tunnels we’re improving road safety while also keeping our freight sector moving.”
Additional signage and road markings will be added to arterial roads to support the trial.
This trial is the latest in a string of moves by the state government to reduce the number of trucks on Melbourne’s roads, including the recent addition of 29 hectares of land to the Port of Melbourne’s lease.
Six new projects have been announced under the Heavy Vehicle Rest Area (HVRA) project.
The over $6.85 million committed to the six new projects has been funded through the third round of the HVRA. $5.48 million of this latest round of funding is being provided by the federal government, with the remainder coming from state, territory and local governments.
Overall, the value of the HVRA is $140 million over 10 years.
The newly funded projects, which include the construction of new rest areas with facilities including
toilets, resurfacing, line-marking and bitumen sealing are:
• Wollondilly Shire Council – Ted ‘Greendog’ Stevens truck parking bay renewal (NSW).
• Walcha Council – New Pindari Tops rest area on Thunderbolts Way (NSW).
• Bourke Shire Council – new heavy vehicle rest area on the Bourke to Milparinka Road at Goonary (NSW).
• Shire of Mukinbudin – heavy vehicle rest area (WA).
• Shire of Coolgardie – Asphalt surfacing of road train/truck stop
area at intersection of Bayley Street/Great Eastern Highway and Ladyloch Road in Coolgardie (WA).
• Norther n Territory – five heavy vehicle rest areas on Buntine Highway to be upgraded.
Senator Glenn Sterle says the upgrades will continue to improve road safety and outcomes for Australia’s truckies.
“These projects are another example of the Australian government’s Heavy Vehicle Rest Area initiative boosting heavy vehicle user safety and productivity through new and upgraded rest areas.”
Mitsubishi Fuso is demonstrating battery swapping capabilities for its electric trucks with the start of a trial on public roads in Kyoto, Japan.
Selected electric light duty eCanter models have been equipped with new energy solution company Ample’s swappable battery modules as a part of the trial.
The eCanter’s batteries will be swapped at Ample’s battery swapping stations deployed in Kyoto City in collaboration with ENEOS Holdings Inc. Yamato Transport Co. will be trialling the battery-swapped eCanter for local
collection and delivery operations.
When the eCanter enters the Ample fully-automated swapping station, robots automatically exchange batteries within the target time of five minutes, which Mitsubishi Fuso demonstrated at the Japan Mobility Show in 2023.
This trial will determine the viability and benefits of the battery swapping process, and whether it is scalable for use in Japan and other markets globally.
“This joint demonstration is an important step towards Mitsubishi Fuso’s ambition to drive EV truck expansion,” Mitsubishi Fuso says in the statement.
Penske Australia and New Zealand has presented Jason Gavin and Frederich Pfuhl the 2024 Penske Guild Master Technician awards for on-highway and off-highway, respectively.
Penske Guild members from around Australia and New Zealand competed in qualification rounds prior to the final, vying for the title of Master Technician.
Including general procedural tasks and advanced diagnostics scenarios, the 12 finalists competed against each other and the stopwatch.
Based in Penske’s Perth branch,
Jason has expertise across the full range of Western Star, MAN, and Detroit product portfolios, particularly Western Star, having worked with the brand for 14 years.
Penske Australia and New Zealand Training Manager Russell Koch says Jason humbly credited his win to the supportive culture and the training investment made in him by the organisation.
“The on-highway battle was fierce. Demonstrating his competitive spirit and commitment to excellence, Jason is a worthy winner,” he says.
The top apprentice mechanics and service technicians across the country have been recognised with the 2024 Cummins Scholarships. The 2024 recipients are:
• Joshua Troeth – Tatiara Truck & Trailers, Bordertown, SA
• L achlan Evans – Divall’s Earthmoving and Bulk Haulage, Goulburn, NSW
• Samuel Della – Frasers Livestock Transport, Warwick, QLD
• Z ethaniah Copland – McColls Transport, South Geelong, VIC
The winners will experience a pre-conference tour of the Cummins
The Australian Trucking Association (ATA) has called on the federal government to ensure that heavy vehicles and truck drivers are included in its planned road safety campaign.
$10.8 million has been pledged for a oneyear National Road Safety Education and awareness campaign through the 2024-25 Budget, but the ATA fears that truck drivers will be overlooked.
While the trucking industry’s safety had improved markedly over the decades, the National Truck Accident Research Centre’s 2024 major incidents report, released this week, raised concerns according to ATA Chair Mark Parry.
“Our industry is much safer than it used to be. For example, there were 56 fewer fatal crashes involving articulated trucks in 2023 than in 2003,” he says.
“The increase in safety is even more marked when you consider that the number of articulated trucks on the road almost doubled from 2003 to 2023.
“But the NTARC 2.0 report highlights issues we must address. The report found that driver inattention or distraction incidents have increased since 2022. Incidents due to inappropriate speed have increased, as have incidents involving tailgating.”
ATA’s Technology and Maintenance Conference as part of the conference opening on October 22, and will be paired with an experienced industry mentor to help make the most of their conference experience,” ATA chair
Support, Scott Alexander says.
“Today’s apprentices are the future of our industry, and this program is crucial in supporting the professional growth of people entering the industry’s workshops.”
Transport Workers Union NSW/ QLD State Secretary Richard Olsen has been appointed as one of the heads of the new Road Transport Advisory Group, which helps to inform the Fair Work Commission Expert Panel.
It will lead consultation with workers, employers and industry groups on the standards that the FWC will enforce through the new Closing the Loopholes bill.
Olsen will lead the RTAG alongside ARTIO Secretary and VTA CEO Peter Anderson, with the pair ratified into their roles by Federal Workplace Relations Minister Murray Watt.
“Our fundamental mission is to
represent the voices of transport workers and push for fairer conditions across the industry,” Richard says.
“The power of this legislation is the industry consultation through the RTAG that will advise the expert panel on standards to ensure transport is not only safe and sustainable but also equitable for all road transport workers and businesses.
“Road transport reform is about creating a fairer, more sustainable industry, with safe, secure jobs at its heart. The subcommittees, composed of key industry representatives, will tackle critical issues like gig economy
exploitation and payment fairness throughout supply chains, ensuring that justice is delivered to all.”
Electric vehicle expert Joe Di Santo has been appointed as the new General Manager of Sustainable Vehicle Solutions.
SVS provides sales and servicing of one of the world’s pre-eminent zeroemission vehicle brands, Foton Trucks, to Victorian and South Australian customers, and is a division of CMV Group.
Executive Director Jonathan Crawford says CMV is excited to have appointed someone of Joe’s pedigree to the role.
“We are thrilled to welcome Joe Di Santo to our Sustainable Vehicle Solutions business,” he says.
“His expertise and vision for the future of EV align perfectly with our mission to provide sustainable transportation
solutions for our customers.”
“I am excited to join Sustainable Vehicle Solutions and work with a team that is so passionate about shaping the future of transportation,” Joe said of his appointment.
“Together we will empower businesses to make informed decisions for future planning and deliver exceptional value to our customers.”
The green trucks of Fred’s Interstate Transport have been a familiar sight across Australia’s east coast for the past 40 years. Alex Catalano got to know a bit more about the family-owned operator.
Fred’s Interstate Transport is now into its third generation as a family-run trucking operator, and is rolling on stronger than ever.
The Shepparton-based business is almost instantly recognisable by its fleet of green Kenworths, which run between Melbourne, Sydney and Brisbane direct to customer delivering goods like paper, soft drinks, building materials and everything inbetween.
Running around 60 B-doubles, they have been a staple of what is one of Victoria’s richest transport hubs, still on the same land since the business was started in 1978.
Founded by its namesake, Fred Borg, it hasn’t always been the powerhouse it is now today. Like many transport businesses, Fred’s came from humble beginnings, as PowerTorque learned from now CEO Danny Borg.
Fred’s son, Danny has been working in the family business since the early days, jumping into the operations side of Fred’s more than 35 years ago.
But the story begins with Danny’s parents, who founded the business more than 45 years ago after they worked on one of the local orchards for most of his childhood.
“We grew up out there as kids, my brother and I,” Danny says.
“Mum would pack fruit, and the old boy was running the cooler stores there.
“Like most orchards they ran their own trucks to move produce. In those days, it was 14, 18 Benzs, UDs, in a time pre-Kenworth and North American products really.”
It was in these very early days where Fred picked up his first ever customers, and gained experience managing a fleet of trucks. Working as the manager, he would take those lessons forward into his own venture.
Fred’s was almost born from chance, as the orchardist went out of business and needed their last bits of stock moved out. Luckily, Fred Borg was up for the task for the next nine months with the help from another local operator.
“After that, dad went out and bought his first Kenworth,” Danny says.
“That was really the start of Fred’s as you know it today. Some of those
accounts we still do today, and some of them have been through about five ownership changes.
“There’s a lot of people we’ve worked with through the journey, which was how the business ran for a long time.”
Those early days came with their significant challenges, with new legislation allowing for the introduction of B-doubles to Australian trucking fleets.
This meant significant purchasing of new trailers, as well as the expansion of the land Fred’s stands on in order to fit them all.
“Before this depot the old boy had a yard around the corner, with three or four trucks,” Danny says.
“We built the house out the front and it’s only expanded as the fleet has gotten bigger. We’ve continued to buy land off the farm behind us.”
This was where Danny first came into the business, helping brother Grant and dad Fred with the massive logistical task of converting the fleet from bogie drive to B-double.
It came at a good time, as Fred’s moved to what is now its iconic fleet of Kenworths.
“From day one it’s always been Kenworth,” Danny says. At least, when Fred’s started getting them into the fleet 10 years into their operation in 1988.
Before that there were models from
Mack, Iveco, a significant number of short-bonneted Western Stars with Stratosphere cabs, and a handful of Dennis Eagles.
But looking at the fleet now, it is dominated by Kenworths, which Danny says is for good reason, including securing the long-term interest of the business.
“We went Kenworth for a number of reasons,” he explains.
“Our view here has always been you enjoy a bit better resale value. You’re paying for that to a degree. That has changed a bit today too.
“If you look at a new product, Volvo or Western Star, they’re all in line with each other. Those three, the ones that we look at, are certainly priced very similar.
“The resale end as I say is where it’s not relative. You’ll see that difference and they’ll only continue to get more expensive.”
In terms of engines, the Fred’s fleet are almost entirely running Cummins, with Meritor on the drivelines.
That was another adjustment though from the early days of the ’80s or ‘90s, when they had to shift towards where the market was leaning.
“Early ‘90s to mid ‘90s we ran a lot of Caterpillar stuff alongside the Cummins product,” Danny says.
“Those engines in singles back then were an awesome product, the best engine I’ve ever run in terms of longevity, fuel and drivability. C15 and C16 was in B-doubles.”
The workshop is equipped with all the little fiddly bits that it takes to keep the fleet on the road.
Bringing in the Kenworths was the first big challenge for the Fred’s fleet. The next was refreshing it decades later.
Danny’s son even did his mechanical apprenticeship within the four walls, before setting off to cut his teeth outside of the family business.
“We’re currently in the hunt for property for a new one,” Danny says.
Danny had dozens of new trucks to purchase, get delivered and then get moving across a period of only a few years. It only worked as well as did due in big part to how organised the Fred’s workshop and front office is.
“We bought something like 65 new prime movers, all Kenworth, a combination of K200, 610 SARs in small and big cabs, T909 in 36 and 50 inch, and some specific customer stuff,” Danny explains.
“There’s a bit of PBS stuff in the fleet too, our blue and white 909s and the rest in our traditional all-green colours.
“They’re all decked out, fridges, TVs, microwaves, air conditioning when the engine is off. We want them to be the home away from home for our drivers.”
One of the benefits Fred’s has is the ability to maintain and prepare its fleet, both trucks and trailers, completely in-house.
This is so much so that Danny reckons that some of the oldest trailers they’ve got look like they were delivered yesterday.
This is thanks to the extensive workshop, where the Fred’s mechanics are working on at least a handful of bits of equipment every day.
“We refurbished the trailer fleet ourselves here,” Danny says.
“They were stripped, refurbished, resprayed, mechanical, electrical, new lights. The facility always has a trailer getting refurbished. It’s all designed to be able to do it in house.
“It gets very time-consuming when you’re running them around for outside work. It was built with that process in mind.
“We’re into a strong pattern of turning equipment over. The trailer fleet we’ll just continue to maintain. The next cycle becomes the maintenance turnover.
“The last six years have seen a lot of work done, but that’s behind us now.”
While Fred’s has always been traditionally run out of Shepparton, more and more of the business has continued to run through Brisbane.
Line haul trucking has always been the main focus of their work, but gradually more of their drivers and their clients have become Queensland based.
Fred’s does have a Brisbane facility, which it has owned since the ‘90s, but it has been recently sold off.
“We used to be in Chipping Norton in Sydney but we closed that down. It was only an office, we had one in Penrith too which we also closed.
“Everything we do is direct to customer. We don’t cross, stock, store or distribute, so we don’t really require depots other than to park vehicles, like we do here.
“A lot of the fleet is based in Brisbane now, hence why we’ve been looking for something up there.”
As the transport game changes, and Fred’s fleet and business grows, being able to operate just out of Shepparton is no longer as viable as it was in the early days.
Having a proper depot in Queensland would allow more flexibility, giving the Fred’s drivers the ability to run out of a separate facility and not have to drive all the way from Shepparton first.
“It’s always been Brisbane, Sydney, Melbourne, but now we have more drivers and equipment up there than we have in the past,” Danny says.
“Early days everything was based in Shepparton, it’s a big transport area. There’s more short haul than line haul now. There were operators like Sali’s and Mathieson’s.
“But the need to have something
Over the radio or the counter, at the rest stop or the table, at the pick-up or at your final destination, connections are made. It’s in the nod of your head, the wave of your hand, or the tilt of your hat. Only those who do it understand what it’s about.
It’s heritage. It’s a legacy.
kenworth.com.au/legacy
in Brisbane is there. We’ve got a lot of customers up there. We used to do Adelaide but cut it out and fine-tuned the operation.
“Ideally we would be replicating something similar in terms of our workshop in Brisbane going forward. It would be designed with similar operational practices, being able to maintain the fleet.
“That would be the next major project should we choose to go down that path. Right now it’s about setting up the new facility.”
Danny, as CEO, and brother Grant as CFO represent the second generation of the Borg family working at Fred’s, taking over the business in the stead of Fred, who passed away two years ago.
Reflecting on his time with the family business, it was never really going to be anywhere else for Danny, with some of his earliest memories in the trucking game.
While he admits he needed a break after the past six years of organising the logistics of basically buying a whole new fleet of trucks and trailers, it has been what he has known as his career for more than 30 years.
“I’ve always been here,” Danny says.
“I would have taken off and done my mechanic apprenticeship, but that would have been cars, not trucks. I always spent time here after school, I was drawn to the mechanical side and the truck side of it.
“My work was workshop stuff early days, then operations, fleet maintenance, warranty, purchasing, sales, a bit of everything. Every facet of the business really.”
While Danny now primarily spends a lot of time in the office, handling operations and logistics, he also made the most of getting his hands dirty when he could.
“I was rebuilding engines in the workshop, a little bit of driving,” he says.
“Really later on I was running the workshop and the maintenance and purchasing side of new equipment. That for me started in earnest in the late ‘80s, early ‘90s.
“1993-94 in particular, I was speccing the B-double fleet to change
it over. I still do it now. At the same time I was also heavily involved in operations, running the maintenance side of it.
“I’m just not quite as involved as I was once was, but I have been for the past six years, sanding trailers like an idiot.
“I had that bit of a breather afterwards for 12 months and freshened up. We’re into third generation Borgs now on my brother’s side.”
Jye Borg is one of those thirdgeneration workers, the son of Danny’s brother Grant. He’s now the Operations Manager for Victoria and SA for Fred’s.
His path into the transport world wasn’t quite as crystal clear, tipping his toes in the world of real estate but eventually returning to the family business.
“I was a year younger when I finished Year 12, and I didn’t know what I wanted to do with myself when I graduated,” Jye says.
“Dad told me to go learn somewhere else new first. I did that, got my real estate agent licence but then came back here.
“I worked through the office, did accounts receivable/payable then did some work with clients, and then operations now for seven or eight years.
“I enjoy it, every day is different. I found paperwork a bit repetitive. It’s
legends of the transport world in Victoria.
The mural is on Fred’s 150th Kenworth, marking a special milestone, the 150th Kenworth. It just so happened
“Our signwriter got a connection to come up here and get it done in nine hours. It’s come up really nicely now.”
In this test drive, Tim Giles goes for a whirl in the first electric prime mover from Mercedes-Benz to be released in Australia.
The step-by-step transition across to zero emission vehicles has taken another leap forward here in Australia with the introduction of an electric prime mover fitted with an e-axle. This is opposed to motive power in the prime mover coming from an electric motor placed in front of the current model’s transmission in the engine bay, as is the case with the Volvo prime movers released last year.
Mercedes-Benz seem to be one step ahead of Volvo in the development of their electric truck offering, but this is not an unusual situation for Volvo to find itself in, as it tends to be more conservative in its technology decisions, taking its time to get things right. However, there is an e-axle from Volvo in the future program for Australia.
The Mercedes-Benz eActros truck tested in this particular road test is the 4x2 prime mover. Development of the eActros with tandem drives is still ongoing, and Daimler is not willing to predict a date for its arrival, just yet. Here is where the more conservative attitude from Volvo comes into play, as
This 4x2 eActros is aimed at the prime market sector which is likely to be interested in this kind of product. The truck is ideal for freight tasks, which are not at top weights, such as supermarket distribution from DC to supermarket as well as other metropolitan distribution tasks, warehouse to warehouse or warehouse to shop type applications. There is also interest from container and car haulers for this kind of truck.
The back to base nature of the work and the opportunity to recharge trucks parked on a loading bay makes these trucks a viable option. Also, the near silent running of the trucks makes them more attractive in busy urban environments. There is also the publicity aspect to these sorts of truck purchases – the city dwellers driving on busy streets around the city see them every day, plastered with signage touting the corporate customer’s green credentials.
“We think the eActros prime mover is perfect for certain applications where full-electric operation is really important,” says Andrew Assimo, Vice President Sales & Marketing,
and bridges with ease means the drivers will enjoy it as well. This is a great example of how operators can achieve their sustainability goals and still get the job done.
“Don’t forget that it is in the big cities, where there are so many people, that zero emission operation of trucks like the eActros and the eEconic makes the most difference. Our customers are after a fully-integrated solution, with the latest technology, and we are thrilled to be able to offer this eActros as either a rigid or prime mover and also the eEconic as a more specific waste-focussed vehicle.
“This is the only truck in its class with an e-axle and we know it is the best technology for efficiency. The customers also know that it is a Daimler Truck product that is the result of massive research and development and supported by an experienced and well-trained dealership network.”
Walking up to the truck for the first time, it has a familiar shape, using the narrower metro cab. The light
The other feature that needs to be noted is one that doesn’t stick out like a sore thumb, the MirrorCam system, which is now an optional replacement for the rear view mirrors. These did not get a particularly warm reception first time around, but have been redesigned, with shorter stalks and smarter cameras. In what can be seen as a bold move, these second generation MirrorCams are standard on the eActros with their two in-cab A-pillar mounted 15-inch monitors.
Climbing up into the cabin is a familiar process and the dash and layout have come straight out of the diesel powered model it is based on. However, there is one new very obvious feature and that is a orange coloured emergency battery-kill control near the driver’s left knee. This is one of the safety systems which is essential in these electric trucks where the batteries and the 600V electric power system can create some safety concerns.
This emergency cut-off for the electric power is one of several safety devices specifically made for the eActros. Another of them is the smoke detection system along the top of the batteries, which includes smoke detectors which can sniff out any hint of smoke coming out of the cells. It will immediately cut off the electricity supply to avoid problems with runaway fires. These have been known to occur with lithium batteries in vehicles, as was evidenced by the runaway truck fire on the approach to the West Gate Bridge in Melbourne earlier in 2024.
According to Mercedes Benz the truck in this configuration, currently, would have a range up to 200km, taking into account the fact that in this sort of work around half the mileage can be with an unladen truck. On the model driven, during this test, the current GCM available is around 35 tonnes, giving the combination tested a payload ability of around 16.5 tonne. The axle mass on the steer was right up to 6.5 tonnes, with 10 tonnes on the drive.
The innovation which arrives in Australia for the first time in a prime mover is the e-axle which uses two integrated liquid cooled electric motors and an inbuilt two speed
transmission. This axle is capable of putting out 536hp (400kW) as its peak performance or 443hp (330kW) of continuous output. This model is fitted with three lithium-ion battery packs which adds up to 336kWh capacity. The e-axle used is exactly the same as the one on the rigid eActros, driven and reported on in the May/June 2024 edition of PowerTorque
There is a five-stage retardation system included which charges the batteries as the trucks slow, using the electric motors as regenerative chargers reclaiming energy, as this
power is fed into the batteries. There is an additional function available – the truck has a high power brake resistor (HBR) system that allows the electric drive axle to retain its retardation capacity. HBR will take the energy created by the rolling wheels and dissipate it by converting it into heat, to retain the retardation capability, even when the batteries are fully charged. In this way, the truck can always decelerate using a combination of the drive axle and either the battery or the HBR retardation system.
The Mercedes-Benz Pure Actros.
With a 3-year loan term and Guaranteed Buy Back option*, the Mercedes-Benz Pure Actros means business. Packed with all the pioneering innovation and economy you’d expect from a Mercedes-Benz, and backed by an 800,000km warranty.
MAKE YOUR MOVE.
*Finance restricted to approved business customers (excluding fleet, government, or rental buyers) of Daimler Truck Financial Services Pty Ltd ABN 23651056825 and subject to standard credit assessment, lending criteria and fees of up to $1,440 may apply. Guaranteed Buy Back (GBB) only available on Asset or Hire Purchase Loans (excluding leasing products) and is subject to vehicle eligibility and excess kilometre charges calculated at $0.15/kilometre in excess of the agree annual allowance. Fair wear and tear return conditions apply.
Jumping into the cabin is simple –put the key in the ignition, turn the truck on, wait for it to go through its initiation process, release the handbrake and press the go pedal. It is at this point that the first strong impression, which this kind of truck gives us, comes into play.
It is surprising just how quiet it is in the cabin as the truck is heading off down the road. This does make for very relaxing driving, and also reduces any vibration. The loudest noise the truck makes is the sound of the tyres against the bitumen.
Of course, this is a MercedesBenz, and therefore, as a new truck, it is fitted with all of the latest safety devices which come as a package along with the truck. These include the active brake assist, stability control, lane keeping, attention assist, stability control, rollover prevention, and can also include tyre pressure monitoring.
The camera systems, which are associated with the safety systems, also look out for vehicles ahead and for pedestrians on the road in front of the truck. Because of the relative silence of the truck, there could be a problem for those pedestrians. However, if the truck is traveling 20km/h or under it makes a warning sound, in order to give any pedestrians around the vehicle an audible alert that there is a truck traveling in their vicinity.
In the event of a pedestrian alert set off by the cameras, the truck will activate the autonomous emergency braking system as soon as it detects any danger of a collision between truck and pedestrian.
This driver was not game enough to actually test this system out in the real world, but we are already used to the autonomous emergency braking coming into play, if a vehicle (or any obstacle) in front of the truck is being approached at an excessive speed.
According to Mercedes-Benz, it is possible to charge the batteries from 20 per cent to 80 per cent in one hour and 15 minutes using a 150 kilowatt charger. This 20/80 rule is often mentioned by electric truck developers. Below 20 per cent, there is a risk of running out of charge before
Unlike past power buying decisions, the choice of electric motor used in a truck is not a major talking point. Electric motors are now quite generic. With this kind of tech, things like the axle housing, wheel ends and other components are the differentiation items, and in this case they are all identical to those in the diesel Actros.
All of the internal electrics in the cabin are also the same as the standard 24 volt system in the internal combustion engine (ICE). This reduces complexity for the servicing of the trucks, because of the parts’ interchangeability and diagnostics.
As the transition across to zero emission running continues, the intention is to maintain one electrical infrastructure across the range, whether it is diesel, some other kind of ICE, electric or fuel cell. There will be
Any development in truck design is now specified to be agnostic about how the power is supplied to the drive tyres, so a large proportion of developments being made in trucks are the same no matter the power source.
With the wheelbase on this particular model, the eActros has room to fit three batteries. With the current battery chemistry the storage capacity of this array is a claimed 336kWh. Increased range should be possible as new battery chemistry is developed for this truck.
Looking back at the development of Daimler’s first electric truck, the Fuso eCanter, the storage capacity from the fitted batteries doubled in the transition from the first eCanters in the
battery electric and fuel cell trucks.
It’s the same story with the truck’s electronics. The designers are no longer developing electronic equipment to run a particular system. They are now building the CANbus systems to be capable of being utilised by numerous iterations of software and other systems for several generations of trucks, as we move towards what is becoming known as ‘software defined vehicles’.
This level of sophistication comes at a high price and Daimler has entered another joint venture/alliance with Volvo Trucks to work together on the development of software. Because this part of the design process is currently a quite dynamic space, the research and development cost can escalate swiftly on an exponential development path. Therefore, even these massive global players have to collaborate
result.
The two truck giants have also collaborated on the CellCentric project to produce a viable fuel cell technology to take them forward into zero emissions technology.
Driving this virtually silent electric prime mover (we might start complaining about intrusive tyre noise in the future), shows us how this transition is likely to play out over time. The technology is being developed and does work.
configuration may have a few years to wait, because 4x2 prime movers predominate in Europe and get the initial funding. However, 6x4 is coming and as this technology matures we should see more efficient batteries, giving us more range. The introduction of a fuel cell would simply introduce the same truck with a fuel cell and hydrogen tanks instead of batteries. This is our first experience of this kind of truck, but it won’t be our last.
Wightman Transport Managing Director, Peter Starke, spoke to Tim Giles at the handover of the first of several batches of MAN prime movers, from Penske Rental, which have been sourced to handle a major part of the Coles freight task, both in and out of the Coles facility in the Northern Adelaide suburb of Edinburgh.
Wightman Transport has come a long way from humble beginnings 60 years ago. Starting as a produce carrier from the Adelaide Hills region into the city, the business now embraces the latest in modern technology and truck procurement to fulfil its latest contract handling distribution for Coles.
Wightman has been in business 60 years, started by Peter’s father-in-law back in 1964. Peter had married into the family and his parents were friends of the operation’s founder, Doug Wightman. Doug had a property at Ashton, in the Adelaide Hills, where he grew produce and would haul it down out of the mountains to Coles’ facility in Adelaide.
After a few years, Coles suggested he should also take loads out of their distribution centre after delivering there. At this time, Coles owned their own fleet and were looking for subcontractors. This arrangement lasted for a few months, before Coles asked Doug if he wanted to take over all of their transport, at that time using just seven trucks.
“I had only just turned 18 when I started, it was a 10 pallet petrol Bedford truck, and then it just grew on from there,” says Peter. “Then Coles got to the point where they had to expand and moved, firstly out to Gepps Cross. Then many years later in 2007, Coles built the massive distribution centre out at Edinburgh Park, which housed all the chiller, freezer, fruit and veg; the whole kit and caboodle.
“Prior to that, we only ever did the grocery lines, so when we got into there, it was a different kettle of fish.
Then we had to look at refrigerated gear. Our fleet expanded very, very quickly. We currently run close to 150 units. We do a lot of work for Coles and inbound freight for Coles Collect, running from Adelaide to Melbourne and back.”
Currently, the operation runs eight to 12 B-doubles a day out of Melbourne into Adelaide. The company had the contract with Coles for 55 years, but lost it in 2019 only to win it back again
taken over the contract struggled to handle the task.
The fleet covers regional areas as well, servicing the likes of the Riverland, Berri and Mildura. Heading north out of Adelaide the trucks go out to Port Pirie, Port Augusta, Port Lincoln, to the east to Mount Gambier as well as Broken Hill and Swan Hill. This is alongside servicing the 45 stores in the local Adelaide area.
For over 50 years, Penske has kept fleets and businesses moving forward. From uptown to across the continent and any direction you need, our truck leasing and commercial rental solutions have you covered. Because when your business is on the line, you have everything to lose but even more to gain.
The return of the Coles contract to Wightman was somewhat rushed, leaving the back office with the headache of getting hold of enough rolling stock to fulfil the task, at relatively short notice. The long waiting lists which ramped up so quickly around the pandemic are starting to shorten, but the wait for a new truck can still be substantial.
Peter’s experience with Penske Rental in the past, as he coped with the ups and downs of demand for Wightman’s services, led him to approach them for vehicles to cover the recently reacquired Coles contract.
Working with Coles Collect means the contractor must do the freight with their own trucks – the work can’t be subbied out to other operators. This meant the fleet had to expand swiftly to haul the new trailers bought in to handle the task.
This is where Penske Truck Rental came into the picture. They were able to supply the right number of prime movers on a leasing basis to ensure the work would get done. There was
a requirement to only use Euro 6 compliant engines and, it so happens, they were only available at 400hp.
“We were given a demo and after we’d driven it, we liked it,” says Peter. “My lad said it was a little bit doughy off the mark, but once you got going, they were not a drama. I mean, we’re not pulling triple road trains. As we go to Murray Bridge, we’ve got 7km of a hill, then it’s up and down, then it’s flat. We’re very happy with the size of it, and there’s good space in the cab.
“Coles are going to like it, we explained it all to them. They wanted to know everything that that we were purchasing, to make sure it was the right spec. They questioned the horsepower, and we told them about the higher torque and that satisfied them.
“Leasing the trucks takes a lot of pressure off us, especially with Penske based two minutes away from the Coles DC. We’ve got brand new units, fully maintained. All we’re paying for is tyres. If there’s an issue, it’s a matter of just bringing them straight
in, changing them out with another truck, and we go on, so we’ve always got that back up. We’ve had a good rapport dealing with Penske Rental since 2015.”
Adrian Beach, General Manager of Penske Truck Leasing also values the relationship.
“Peter was our very first customer when we opened the Adelaide branch back in 2015 and has been one of our most loyal customers ever since.
“Their support has been critical to our success in Adelaide. We’re very grateful for the relationship and proud of the confidence he showed in us by placing this substantial order. In turn, we are highly committed to their success. We hired a technician just for this task and bought a few extra Euro 6 rental trucks to be used as dedicated substitutes for any servicing or repair. Our goal is to give Peter and his team 100 per cent uptime and I think the reliability of the new TGS 26.400 combined with the support from Penske and MAN will help get us there.”
The Winner of HVIA’s Safety Innovation Award for 2023 is now available as an option on steer axles in addition to drive axles, delivering dynamic pressure-control and balanced-load sharing across the entirety of a prime mover. Suspension that features Base Air™ actively operates as dual and single-circuit systems as required. With our national network of accredited installation partners, it is now easier than ever to reduce driver fatigue, improve traction and braking, and Level the Road.
AVAILABLE FOR HEAVY & LIGHT-DUTY VEHICLES WITH PNEUMATIC HCV SUSPENSION VIA AUTHORISED INSTALLERS ONLY
Call (07) 3382 7747 or visit baseair.com to find your nearest authorised installer
With its introduction of a suite of new technologies and leaving behind some of the older ideas about trucks, Western Star is changing the narrative about truck development with the introduction of the X Series.
The Western Star X Series truck range first appeared some time ago, but global supply chain issues have meant there has been a considerable period that has elapsed between the initial unveiling of the new range and numbers of the trucks getting out into the trucking industry.
North American style bonneted truck, which references a look and a style which has been a preferred option for people working in the Australian trucking industry for some time.
The fact of the matter is that in developing the X Series, Western Star in Australia has completely transformed its entire range, taking it from a traditional truck with a design which was beginning to show its age, to a thoroughly modern truck, but one with a genuine Aussie sensibility, connecting to the preferences and likes of the typical Australian truckie.
It looks the part and the casual observer is left in no doubt that this is a
Under the skin of this new range there is a lot of sophisticated technology and a capacity within the vehicle to keep up with the changing regulations and changing preferences of trucking operators into the future.
As with most things, ‘the proof of the pudding is in the eating’ and the reception the new models have received is an indication of how well the transition across to a more modern design has worked for the Western Star brand.
The fact of the matter is that safety regulations along with changing exhaust gas emission regulations mean that it was important to make the
move to the latest version of the Detroit DD 13 and DD 16 engines to remain complaint. This has been coupled with the integration of these new Detroit engines with the latest version of the Detroit DT 12 transmission, which arrives with the X Series in its latest iteration.
At the same time, safety regulations around the trucking industry and the requirements necessary to comply with the requirements of the higher productivity vehicle schemes now developing on our roads mean that it is necessary to have all of the latest software on board to meet the criteria.
“What we’re seeing from the initial launch of X Series is a completely opposite change from the legacy product, with the driveline integration of the DT 12 with the DD engines,” says
– Tim Dardania, managing director of Dardania Logistics
MAN’s truck generation boasts excellent driver fit, great efficiency and economy features, optimised uptime, and makes for a strong business partner. Ready to elevate your fleet? Contact us today to discover how MAN can drive your business forward.
Kurt Dein, Head of Western Star Trucks for Penske Australia. “We’re seeing a huge percentage increase growth in our AMT transmission. We are also going back to speak to customers that were sold trucks six or eight years ago, where driveline, ergonomics and so forth come into play for us.
“We’re now opening up new markets and we are making transactions with operations like Toll and some key accounts. We’re breaking into those national fleets, and with X Series we speak about the ambitious plans for market share growth that we have.
“The development and cost involved in the X Series coming to market was to get the runs on the board and get the product back up the ladder. We’re definitely seeing, 18 months after launch, north of 200 trucks on the road
today, and over the next 90 days we’ve got a huge volume going onto the road. We’ve certainly got stock and the supply chain is definitely freeing up now.”
The kind of feedback coming from the market is about the smoothness of the driveline and the integration of the AMT. This is quite a break, going from a standard 18-speed to a majority of the trucks being sold with an automated transmission. It would seem that although the 18 speed crash box will always have its place, more and more operations are biting the bullet and specifying an AMT and also finding the results to be satisfactory.
“We’re seeing a net result gain in fuel economy and trip times overall,” says Kurt. “We’re putting a more compliant emission engine with the horsepower out there and seeing a favourable fuel economy improvement to help with the
total cost of ownership. It’s definitely been a very pleasing 12 months of supplying product to market, which we launched 18 months ago.
“We were very conscious when we brought X Series in that we still played with manual transmission, drum brakes and optional safety systems. The customer acceptance to go into AMT with a full safety suite and disc brakes has really not surprised us, but it’s good to see the customers are really backing that drive around the cost of ownership and an efficiency model.
“The fleets are definitely driving AEB, but also the owner operators are definitely embracing that safety functionality within their trucks. But it’s probably a bit of a surprise in the size of, and how strong a foothold it’s gained, to be honest.”
The introduction of the mandate to fit
autonomous emergency braking (AEB) in 2025 will mean the safety suite will become standard.
“Certainly, from my point of view, I think the it’s absolutely logical that the B-double fleet trucks, the ones where we’re in competition with a wider market, they’ve absolutely got to be using an automated driveline and full safety system because that’s what the market expects,” says Bob Gowans, Detroit Business Manager at Penske Australia. “What surprised me the most with the DT12 is how it’s been accepted into what would traditionally have been a manual application at the heavier end, the road train market, and how just how well received its been, by some of the customers that have taken it.
“With a lot of the bigs runs for the B-double East Coast operators, you can
argue it’s because of driver availability. With a lot of the road train customers you start to hear from people that it’s not necessarily because they can’t get a driver who can handle a manual. People are starting to realise that yes, I’m perfectly capable of driving the manual, but I don’t need to anymore.
“We’ve got to the point where the transmission is now capable of driving almost as well as the best drivers currently do, rather than in the previous period where, when you get to particularly extreme weights, you had a choice. You could either drive it properly or you could have an automated box to make your life easy, but we’ve now got to a point where the DT12 means that the truck can drive itself properly in those sorts of applications.”
Western Star customers were, in the
past, particularly conservative. The acceptance shown towards the X Series is an indication that the shift which has been in play for over twenty years, as trucks move across from manual and analog, to automated and electronic is now spread all of the way through the Australian new truck market.
“If you look at costs of business today and profitability and where you can really get bottom line resolved, they’re really embracing the new systems, there are driver shortages across the board,” says Kurt. “They’re definitely coming across and absolutely buying the new X Series. We’re seeing customers that have owned manual trucks, but their auto demo works so well, they are turning around and saying, ‘I probably should have a look at this’. Multiple customers are buying them.”
Transport legends of Shepparton and surrounds are honoured within the MOVE Museum.
Members and delegates from the rural transport industry had the chance to speak their mind on the issues affecting their work at this year’s LRTAV Conference, as Alex Catalano found out.
This year’s Livestock and Rural Transporters Association of Victoria conference, held in Shepparton, was an important one for several major issues affecting drivers, farmers and operators across regional Victoria.
As the peak body for rural transport in the state, members flocked from all over Victoria, while representatives from the Australian Livestock and Rural Transporters Association, NTI, NHVR and more were in attendance.
Top billing was misgivings from
many members surrounding the state’s road network, and the application of high productivity vehicles.
A panel was assembled including industry leaders on the subject, giving members an opportunity to highlight what they see out on the roads on a daily basis.
“We want to be able to explain what we’re doing inside the association on high productivity livestock vehicles and PBS going forward,” said LRTAV President Russell Borchard.
Operator Anthony Boyle of Boyle’s
Livestock Transport runs a fleet of more than 20 trucks out of Allansford along the Great Ocean Road, servicing livestock markets across the state.
He detailed his struggle with making his fleet meet PBS standards, particularly facing the financial challenges of the endeavour.
“It cost me about $300,000 to get vehicles approved,” Anthony says.
“It gave me access from Mount Gambier in South Australia, to Warrnambool down the Princes Highway, back to Melbourne, through
FREIGHTLINER IS SERIOUS ABOUT SAFETY.
Every Cascadia comes with a complete suite of fully integrated active safety features and connected technology that helps you get on with your work.
With Active Brake Assist, which can even detect moving pedestrians, Side Guard Assist, a driver airbag, and forward-facing camera footage that can be sent on-the-go for immediate incident reports, the Cascadia sets a new standard for practical safety.
Scan for video demo
approval for existing equipment instead of going for new designs was tedious and very long.
“Just when you’ve got it all approved, another bridge would pop up and you’re shelling out for another bridge assessment.”
The push to ‘Keep the Sheep’ was also touched on, as the advent of new legislation threatens to make a significant dent to the work of sheep transporters.
from livestock transporters and farmers across the country. LRTAWA VicePresident Ben Sutherland is one of the voices behind the movement.
He travelled to Canberra before the LRTAV Conference as a part of the Keep the Sheep delegation, telling Parliament the importance of the live sheep export trade in Australia.
“Keep the Sheep’s a grassroots campaign which came about from us saying no,” Ben said at the conference.
“At the moment we’ve got 83,500 signatures. We’ve just amassed $475,000 for our warchest to give the federal government a kick.
“This thing is not just a WA problem. It’s an Australia-wide problem.
Agriculture keeps getting kicked in the teeth, and we’re agriculture are we not?
“We need to make that decision and have a crack at it. When it first came out, it was 30 per cent of my business being taken away.
“All the money that we’re putting in is for people like you. Help us keep the sheep.”
The conference also featured a number of technical talks, including from Air Brake Systems’ Shane Pendergast.
Shane earned the prestigious Craig Roseneder Award for Technical and Maintenance Excellence last year, as
recognition for the work he’s done both industry around electronic braking and
educational opportunity for operators who may not be monitoring or maintaining their braking systems as closely as they should be.
He worked at Cootes for 16 years as a workshop manager, where he perfected his craft as one of the industry’s technical and mechanical experts.
It was when he was there that he witnessed an accident that would change safety regulation in trucks to the modern day.
“The Pebbly Beach rollover was responsible for the implementation of modern day rollover stability control,” Shane said.
“I was in the Port Botany workshop at Cootes. This was a horrific accident. It closed the South Coast Road for nearly a week. The trailer was fitted with standard ABS only.
“That accident could have been avoided if it had been fitted with a rollover stability control system.”
While the process of testing and diagnosing these systems can be long and painful, Shane has the benefit of advanced data systems on his side.
It is vitally important to ensure your truck and trailers are braking how they should.
“There’s never been a more important time to have stability control
function and braking systems in your trailers,” he said.
“I have no issue with high productivity vehicles – we have a lack of drivers, so that’s where we need to be. How lucky are we that we make the best trailers in the world.
“But if you’ve ever driven an A-double or a B-double that’s not set up correctly, it’s not fun at all. Braking systems need to be harmonised. We need to be doing onset testing.
“Brakes have always been a problem. If you’re not harmonising your braking systems, you’re completely wearing down your brakes.
“If you’re not doing brake rollover testing, you may never know the deficiencies in your systems.”
The LRTAV capped off the conference with a number of awards, honouring long-serving and upcoming members of the association.
Running over two days, the Young Driver of the Year Award was awarded to Caleb Baldock from Mibis Transport during Friday’s night proceedings, recognising him as an up and comer in the industry.
At 28 years old, his work includes carting livestock all the way through to oversize work. He was commended for his positive attitude and the responsibility he takes on in the workplace.
Following this, the LRTAV held its Gala Dinner on Saturday night, where a new LRTAV life member was inducted and the Shane Knight Memorial Award was presented.
Delegate and committee member Kevin Keenan had the honour of inducting past president Graham Howell as the newest LRTAV life member.
“Whatever he has to say is genuine and from the heart,” Kevin said.
“He’s a good thinker. He’s been in the industry since the early 80s. He’s stepped up to executive roles whenever it’s been required. A lot of people could look up to this fella as a genuine leader of our industry.
“Last year it was my turn, and it was a great honour to be recognised by your peers.”
Graham accepted the award
graciously, thanking his fellow association members for the opportunities he’s had since becoming a member nearly 25 years ago.
“Becoming a life member is something you don’t expect, and it’s the second shock I got this afternoon,” he laughed.
“My wife turned up at 4:30 and I thought something was wrong. Now I realised what’s going on.
“It’s been a privilege to be part of the LRTAV. I’ve seen people trying to make good of the industry, so you give a bit back to the industry that’s been good to you.
“I came to my first conference and got involved in Shepparton in 2000. I stepped in as a delegate and it went from there. I want to thank all the friends I’ve made in the industry. We don’t do it for accolades, but it’s a certain privilege to receive one.”
The Shane Knight Memorial Award is one of the association’s top honours, recognising outstanding work in making the rural transport and livestock industry safer.
It is named in honour of the late Shane Knight, who was a long-standing member of the LRTAV and was a key driver of developing the Guide for Safe Design of Livestock Loading Ramps and Forcing Yards.
“This award was introduced back in 2017 to recognise people who have made a significant contribution to safety in the transport and livestock sector,” said LRTAV representative Mick Debenham.
“Moving forward as an industry, safety around crates needs to be a priority. We all know there’s a lot of
Shane’s wife Jeanine was given the honour of presenting the award to Cannon Trailers.
“As a family we all turned up to Shane’s induction as a life member of the LRTAV, and surrounded by all his friends, it was a real surprise to him,” she said.
“He had his last conference with you all eight years ago. He was very honoured to receive his early induction into the Transport Hall of Fame and catch up with all of you legends. It was a night I’ll never forget.
“Tonight allows us to acknowledge all the work Shane did with a band of helpers who were all instrumental in making loading ramps in saleyards safer for one and all.
“He liked being called on the phone for his advice and thought nothing of jumping in that blue ute to go anywhere and everywhere to assist. He didn’t do it for himself or any accolade, he did it because he loved his association.
“I’m privileged to stand up here with his mate Mick and see our son Mark in the crowd. He was a proud dad and grandpa.
“Times are busy for us all, and it all goes by too quickly, but when I speak with people what strikes me as most important is we all want safety in our proud work environments. All the people in the room who run a business put people into their trucks to drive them knowing their safety is important.
“Thank you to all the people who make life easier for transport operators. To everyone that does their best for their business, I thank you.”
Trucking operators usually have to learn the hard way about managing an emergency incident. Speakers at the Australian Livestock and Rural Transporters Association conference tried to bring those in attendance up to speed on the subject.
There is no doubt that running a trucking operation is a dangerous business. Sending large moving vehicles at masses up to and over 90 tonnes on public roads, through towns and cities, and into workplaces is inherently, and literally, an accident waiting to happen.
No matter how safety smart the operation and the vehicle is, no matter how well the truck driver has been trained, there are myriad actions or incidents which can lead to an accident, and sometimes to a catastrophe.
The larger corporate operators can have a department in the organisation whose duty is to handle major problems and manage the way the issues around an incident need to be framed. For the smaller operator, there is no such luxury. Incidents can come out of the blue and the management will have little experience in handling the bad media attention which may follow, if the incident is particularly severe.
After spending more than 30 years as a journalist working for Channel Nine, Channel 10 and Channel Seven’s Current Affair, Leisa Goddard founded
and is now Managing Director of Adoni Media. No longer chasing wrong-doers down the street to get an answer, she now provides PR services, reviews training and crisis communication support. Insurance supplier NTI, as part of their policies, is now automatically covering policy holders with crisis communication support, in conjunction with Adoni.
Operators may well have that worst possible day where there is an incident, some form of accident, and find their reputation is at risk. They may have media knocking on the door, or worse still a journalist like Leisa chasing them down the street. Adoni now try to work in the backroom behind the scenes helping operators manage that worst of all possible days.
Looking at that scenario, a crisis communications professional advising operators and their respective governing bodies will try and help get some positive information out there. This often seems to get lost when an incident gets picked up and and pushed through the media or to the broader community through social media.
“A lot of it is about transparency, and transparency helps build trust,”
said Leisa. “I’m a huge advocate of that. When we’re dealing with a crisis. I don’t believe you should be a ‘no comment’, put your hand up and refuse to answer calls. I think the very worst thing you could do in a crisis is have the media report that you weren’t available for comment or said no comment. Too many people think that no comment is the answer.
“Looking at your social media, if something does go bad, then you really have to monitor it closely. You might be thinking you’re clever and trying to dodge the media, but what is happening on your social media profile is effectively quotes that the media will use.
“The very first place that we go to is social media. We go there, and it sounds awful, but if it’s a fatality, this is the first place the media will go to find the photograph. It may not necessarily be the company’s page, it might be the driver’s page. One of our first jobs is to alert the companies and the associations, or the drivers families, to look at what’s on social media.
“Comments online which people may think is a humorous post or talks about alcohol, it may be a comment on something related to road safety
that may be a bit off-point. These sorts of comments can get used.”
One of the first places any operator should go is to triage their social media. The flip side of that is it can be used to educate, to promote the brand, act as a showcase of the great drivers that have been working in the industry for years, or decades, doing great things on the road, because it’s all about building the positive brand. If something bad does happen, this data is already there, in the bank, something which is proof of what a responsible safe company they are.
“I feel really sorry for small and medium sized operators, because a lot of them have not put into place any sort of crisis plan,” said Leisa. “They’ve never thought about the day when something may go wrong and the media may be calling. I would suggest that operators put some time and thought into having a policy, even if it’s just something jotted down that you’ve spoken to your drivers and your team about.
“When you pick up the phone and, for example, it’s a newspaper journalist, the moment you say something, that’s a quote. When we step into the fray, I’ve had situations where I’ve had a transport operator who has tried to block the view of television crews who are, legally, on the footpath of their property.
“As reporters, we know exactly where we can go and where we can’t. In this case, they were filming and what they filmed was the company trying to block the vision of the TV crews, of the truck that had been damaged. That’s not a good look.
“It’s about being smart about how you’re going to approach the media, how the drivers are informed about what they can say or can’t say, if they’re approached by media. What’s your front reception going to say? Have you even thought about what that protocol is? Alarmingly, there are a lot of big companies who might have crisis plans in place or media policies in place, but they’re out of date, or they haven’t bothered to run a workshop or a scenario where they can test them.
“I had an example about a year and a half ago, and this was a large company. The new company secretary said to me, that’s been on my list and I just haven’t got to it. It was a big incident, and it had blanket national media coverage. We were pretty much working from scratch behind the scenes with my team together to do the work to protect their reputation as best we could.”
There is always something those involved can say or do, which is not no comment. It is important for a trucking operator to publicly reiterate its commitment to safety. By talking, it may be possible to humanise the drivers involved. The fact that a driver has been working with the industry for more than 40 years, for example, emphasising that the driver was doing the right thing. Choosing the language used carefully and repeating information like 40 years experience in the industry and a clean safety record can be useful, to show you are not being argumentative.
“The first rule of crisis communications is empathy, action, update, keep it simple,” said Leisa. “There are people involved, there may be livestock involved and you’ve got animal welfare activists who are potentially going to arc up at a big incident. You need to have a strategy there and hopefully, you never have to use it. But if the day comes when you do, you can at least manage a
situation until we can get involved, and then we’re not starting from behind the eight ball.”
Now that the National Heavy Vehicle Regulator covers all of the eastern and southern states, it is able to get closer to the real picture of what is happening on our roads, and how it involves the trucking industry.
“It’s terrible every time a driver or someone else involved loses their life,” said Paul Salvati, COO at the NHVR. “There are appalling suicide rates, and that’s a symptom of modern age, it’s really has a massive impact on drivers when a member the public self harms in front of them. But, in terms of what we’re seeing across the country, the long term trend we’re seeing is one of improvement.
“We’re seeing heavy vehicle operators and drivers get better, we’re seeing less fatigue incidents leading to fewer fatalities. We’re seeing less mechanical issues and fatalities over the long term. Since COVID, we have seen an upwards trend in fatalities in the state of Queensland. It used to be New South Wales, but now Queensland is number one, and this is a real challenge for us.
“If I break it down, what we’re seeing is that speed is always a big one. There’s issues around stopping distances and light vehicles not always understanding how to drive around heavy vehicles. We’ve had a whole media campaign to educate light vehicles around driving safely. We’re seeing fatigue, even though it’s less of an issue.
“Driver training is the newest one resulting from the driver shortage. There are more drivers coming onto the road who haven’t got the training to operate the vehicle they are behind the wheel of. That leads to some pretty unsafe operations.”
The NHVR is looking to all operators to make sure their drivers understand how to operate the vehicle and they’re driving safely. This includes things like load restraint, how to load properly, as well as understanding fatigue and the need for rest breaks.
Truck rollovers can be deadly, especially when carrying livestock. The LBRCA has put together a program to make sure all truckies have all the tools they need to stay safe.
The Livestock, Bulk and Rural Carriers Association (LBRCA) has announced the official launch of the Heavy Vehicle Rollover Awareness Program (HVRAP), a groundbreaking initiative aimed at reducing heavy vehicle rollovers and crashes and preventing the loss of life or serious injury in the Australian road freight industry.
HVRAP is a comprehensive program developed by LBRCA to provide the industry with the necessary tools and resources to foster a culture of safety.
Funded by the National Heavy Vehicle Regulator’s (NHVR) Heavy Vehicle Safety Initiative (HVSI) and supported by the federal government, the program allows individuals to learn from the real-life experiences of professional drivers at their own pace, in their own time, and on their own terms.
Key features of the Heavy Vehicle Rollover Awareness Program include:
Learning Modules:
• Understanding Heavy Vehicle Rollovers
• Understanding the Forces
• The Contributing Factors
• Tackling the Issue
Additionally, load-specific modules such as grain, cotton, and fertiliser are included, addressing the unique challenges associated with various cargo types.
Learning Videos:
Each module is accompanied by informative learning videos, providing a dynamic and engaging educational experience for participants.
HVRAP Toolbox:
The program’s website houses the HVRAP Toolbox, a comprehensive resource centre containing links, tools, and other valuable information to support individuals and organisations in their commitment to safety.
HVRAP empowers the road freight industry to create a culture of safety, recognising that a culture of safety is synonymous with success. By providing accessible and flexible learning opportunities, LBRCA aims to significantly reduce the incidence of heavy vehicle rollovers and crashes, enhancing the overall safety of Australia’s road freight network.
“The Heavy Vehicle Rollover Awareness Program is a testament to our commitment to the safety and wellbeing of our industry professionals,”
says LBRCA Chief Operating Officer Bec Coleman.
“We believe that by equipping individuals with the knowledge and tools to prevent rollovers, we can create a safer working environment and save lives.”
“An enormous amount of support and participation from the industry has gone into developing the program,” says Alan Pincott from Australian Trucking Safety Services & Solutions.
“It makes us all proud that their efforts have gone into a program that is available to everybody and is free to all users.”
“Through the HVSI, the NHVR is able to invest in crucial projects like HVRAP, that deliver tangible improvements to heavy vehicle safety,” says NHVR CEO Sal Petroccitto.
“This innovative initiative will support drivers by providing them with the resources they need to make informed decisions on the road about their safety.
“I’m pleased to see LBRCA paving the way for a safer future on our roads with this exciting new program.”
Association members had the chance reflect on recent events at the NatRoad Conference. It was a time to examine the implications of some significant changes to the industry which have happened in the last year.
It’s been a big year, and we’ve been working very hard,” said NatRoad Chair, Paul Fellows, at the opening of this year’s NatRoad Conference, held in Coffs Harbour. “NatRoad has been at the forefront of some really significant changes to the industry, we’ve been in and out of ministerial meetings, industry round tables and knocking on departmental doors in federal and state governments.
“We’ve been very vocal about the Heavy Vehicle National Law and the farce it’s become, but we’re working towards getting those heavy vehicle rules changed. On tolls, we’ve worked very hard. Our hard working CEO, Warren Clark, has gone hard on trying to get these tolls dropped or not increased.
“We’ve been working very heavily with a sensible approach to PBS access. From my own experience, it’s enough to drive you insane, but we’ve been working very hard to try and get that sped up. We’ve been working on improving bridge assessments. Every time you get a bridge assessment, it’s seven grand. I get mine this week, and someone else will get theirs done next week. That’s a clip of the ticket all the way through, and we think there may be some light in the tunnel with that.”
The last year has seen the passing of the Closing Loopholes Fair Work legislation and NatRoad was working representing the interests of the employers. Another major initiative for the organisation this year was joining the International Road Transport Union, which, as the voice of more than 3.5 million companies operating mobility and logistics services in over 100 countries, says it ‘leads solutions to help the world move freight better’.
An online presentation to the conference from Natalia
Corchado, Strategic Planning and Business Specialist at the IRU, saw her provide some data about the global nature of the driver shortage. She was able to give the conference a picture of the size of the issue in 2024. She presented a snapshot of the truck driver population and a forecast for the coming years.
“Why did we start this study?”, asked Natalia. “Because our members, our operators, were facing a huge shortage and there were no figures to prove that this was a reality, or at least not at a supranational level. We decided to carry out this study, an online survey that is disseminated to transport operators through our members, our national associations.
“There were 21 countries that were surveyed, and we collected more than 4000 answers. I would like to really thank NatRoad and their members for making this initiative possible for the first time in Australia.
“We have a benchmark to put Australia in the global context. The share of companies surveyed that were facing severe or very severe difficulties was close to 50 per cent. In Europe, it was even higher, 70 per cent.”
“Over 26,000 drivers are needed to fill the current gaps in the trucking sector, with big fleet operators the most impacted. There is a need for around 180,000 drivers for an effective road transport sector, so this represents a 14.4 per cent shortfall, well over the current national job vacancy rate of between five and six per cent.”
There is also a large portion of drivers nearing retirement age. The survey found almost 50 per cent of all drivers were over the age of 55, with an average age of 49. The participation of young people and women in the industry is very low, with 5.2 per cent of drivers under 25 and just 6.5 per cent women.
Warren Clark, NatRoad CEO took a look forward towards where NatRoad expects to go in the future, with freight expected to grow by about 57 per cent by the year 2040. Warren examined the issues which are likely to arise.
“The problem with it is, that we’re still facing the same issues that we faced decades ago; rising costs, staff shortages, red tape,” said Warren. “Now, we’ve got the issues of decarbonisation, and we’ve got technology advancements. For many in the industry, these things are overwhelming, and that’s why you join an association like NatRoad.
“We have the staff, we have the resources and take up the fight for the industry. To get any decisions made, you need to be very united. We’ve got the ear of the politicians at the federal and state level. We’ve got it on both sides of the house, and it’s taken a lot of work, but we believe that they’re starting to listen to us.
“We’re there to take up the rights and future of your business, and we don’t stop until we start to get some sort of hearing. It was only a week ago (in September) that we had a major roundtable in Parliament House. We struggled to get some ministers on board, but at this particular meeting, we had the ear of the prime minister, who actually stopped in for about 15 minutes.”
Australian trucking has to deal with regulations and rules that are decades old, and any change is hard to achieve. The trucking industry is not taken seriously in Parliament House. The importance of the industry was illustrated during the global pandemic to the public, the decision makers and the policy makers, to see it as an essential service.
“One of the big changes, is the change in the industrial relations legislation, the Closing Loopholes Bill. We do need change in this industry, there’s no doubt about it, but we don’t know what that’s going to look like. It’s being handled through the Fair Work Commission and, traditionally, that’s been a bit of a battleground for the industry. But we’re pooling our resources with others and we’re at the table, we’re there.
“We’re going to be fighting for industry in the way of efficiency gains and safety gains. This year there’s been an increase in major incidents by 27 per cent so really, what it’s showing is that we actually need to do something about it. It’s across all sectors in the industry, large, small and medium, it’s not just segregated to any one particular group.
“A major focus of our organisation is going to be safety and sustainability. The other problem that we talk about is driver shortage. Without drivers, the industry can’t grow. We risk long term disruptions to the supply chain. The thing that’s frustrating is we don’t do enough to promote our careers in this industry – things like flexible working hours, self employment opportunities. You can come to this industry, earn a good wage, own your own business, and guess what? You can actually do it for your whole entire life, if you’re successful.”
Due to government subsidisation, the process of electrification is well advanced in North America. PowerTorque’s European Correspondent, Will Shiers headed to the United States to talk to a fleet getting smart about transitioning across to electric power.
Located next to Los Angeles’ LAX Airport, Griley Air Freight is a fourth generation, family-run trucking company specialising in air freight.
“My great-grandfather started trucking in our family in 1949, and this was his first ever job,” says Griley CEO, Katie Griley, who took over the day-to-day running of the company from her father, Tom Griley, two years ago. She’s pointing to a giant invoice printed on the Griley Air Freight boardroom wall. It was to move 360 Firestone tyres to car manufacturer Studebaker, and paid $14.42.
These days the company moves far higher value products, working for some of the big worldwide freight-forwarding companies, and transporting both Apple and Microsoft products.
Freight is collected from and delivered to Los Angeles International Airport (LAX). Most product is stored in its secure 3,000 m3 facility, prior to distribution to customers in the Los Angeles region, whereas other loads are shipped directly to customers’ warehouses.
Although airports aren’t considered, what is referred to in the US as drayage, short distance freight like containers, Katie knows that it’s only a matter of time before regulations relating to the use of electric trucks at LAX will be introduced.
With this in mind, two years ago she decided to get some valuable experience with the vehicles, and added a Volvo VNR Electric to the company’s 90-strong mainly Freightliner fleet. The truck has been leased from Zeem Solutions (see box),
which also takes care of the charging.
“Volvo approached us, and we never even looked at anyone else,” explains Katie. “We run a lot of Freightliners, but the eCascadia didn’t come out until after we had acquired the Volvo. Anyway, we are very happy with Volvo.”
So happy in fact, that last year it took delivery of another VNR Electric. Unlike the first truck, which only had four batteries and a 150-mile (240km) range, this one had two additional batteries on the external cab wall, increasing the range considerably.
While this second truck was purchased outright, Griley Air Freight still chose to partner with Zeem Solutions for charging. “They offer parking and charging at their location just down the street,” Katie says. “It’s been seamless. The drivers drop them
Griley Air Freight puts considerable thought into which of its drivers it wanted to put in the electric trucks.
“We intentionally chose drivers that might be more receptive to them,” explains Katie. “For instance, one of them drives a Tesla.”
The drivers in question are Sam Mauro and Mario Benavides, and although both admit to having had some reservations to start with, they are now thrilled with the Volvos.
“I didn’t know if it would have the power,” admits Mauro, “but it does, and I love it. I wouldn’t go back to diesel now, as they’re too shaky. When I have a full load on it feels good - nice and smooth.”
These are sentiments echoed by Benavides, who reckons some of the other drivers are jealous. “On the hill to Ontario I was loaded with 19 pallets, and thought I’d be stuck in the inside lane with my flashers on. But instead I was passing diesels.”
off, and go home in their personal cars, which have been left there during the day. Zeem then charges the trucks overnight, and takes care of everything.”
While one is leased and the other purchased outright, both trucks have been part-funded by grants. Katy describes the process of applying for funding as ‘tough’, but believes it needs to be that way to ensure that the money goes to deserving companies.
“If those grants weren’t in place, this would never have happened,” admits Tom, who is shocked to learn how small grants are elsewhere in the world, in comparison.
The trucks, which are coupled to tandem-axle semi-trailers, wrapped in customers’ liveries, do between two and four runs to the airport per day. They pick up international customs freight orders, and deliver them to
customers or to the Griley Air Freight warehouse.
Loaded to 40,000lb (18 tonnes) the older truck does about 100 miles (160km) per day, whereas the sixbattery-pack VNR Electric can manage 200 miles (320km) or more, at full payload, allowing it to be doubleshifted.
The electric trucks have been well received by the public. Katie explains that as part of the infrastructure grant subsidy requirements, Griley Air Freight was required to seek support from the local community.
“People appreciated what we were trying to do, and we received a lot of letters of support,” she says.
They weren’t the only ones to appreciate the initiative, the trucks receiving full support from customers too. Consequently, Griley Air Freight has been able to pass on the increased
costs associated with running electric trucks by charging customers a higher freight rate.
“Of course, we might not be lucky enough to be able to do that in the future,” admits Katie, referring to a time when rivals also operate electric trucks. “But for now, we have something to offer that our competitors don’t, and we have even gained two new clients as a direct result.”
When we visited Griley Air Freight earlier this year, news had just reached the team that Korean Airlines is to start giving loading/unloading priority to zero-tailpipe-emission trucks. With waits of two to four hours common place at LAX, this was welcome news indeed.
“This is something we weren’t expecting, and it could save us $100 per trip to the airport,” reckons Tom. “And if more airlines follow suit, then
Superior construction and performance; now with intelligent control.
Unlock your Ultima light bar’s full potential with a revolutionary new Ultima Connect+ Controller.* Featuring 3 customisable driving modes, boost mode and the ability to connect multiple lights, Connect+ gives you total beam control.
Ultima High Performance Light Bars are the first in Narva’s innovative Ultima Connect+ range.
BRAWN: Ultima Light Bars
• Market-leading beam performance
• 2 beam pattern options available
• Unprecedented 10-year warranty
BRAINS: Connect+ Controller
• Adjustable brightness
• Boost mode – 15% more power for 30 seconds
• Single unit to control all Connect+ enabled products
*Sold separately
Although she comes from a long line of hauliers, Katie says it was never assumed that she would follow her father into the family business. “After college I asked my dad for a job because I wanted to discover what we did,” she tells us. “You see, he never really spoke about it much when he came home from work.”
Her first job was dispatching at one of Griley Air Freight’s larger key accounts at the time, DHL Forwarding. After a couple of years of dispatching she was managing the account and overseeing 250-plus local pickups and deliveries per day, holding driver meetings and creating relationships with clients.
“Since then I have been aggressive ever since, working my way up to the top. And Tom has been incredibly supportive,” she says.
this will be a big cost-saving for us,” adds Katie.
Griley Air Freight will ramp up its electric fleet in the coming years, in line with the legislation. According to the US’s Advanced Clean Truck (ACT) rule, 10 per cent of its fleet will need to be electric by 2027. With this in mind, a third battery-powered truck will be added to the fleet later this year, with more to follow.
Although happy with its partnership with Zeem, as the fleet expands so it will take the charging in-house. It has had infrastructure grant money approved, and will install six dual-port chargers at its depot in the next couple of years.
“We have had to learn a lot very quickly, but we are eager to be a part of the sustainability movement,” concludes Katie. “And we plan to keep on trucking.”
Founded by Paul Gioupis in 2017 with the aim of making EVs affordable to commercial fleets, Zeem Solutions, based in Los Angeles, is going from strength to strength. In addition to leasing an array of different electric vans and trucks, it also provides a full charging service.
“Some companies get challenged building their own infrastructure,” explains Gioupis. “They discover that it takes a couple of years to set up charging, and that they may have to do it multiple times. So instead they may decide to come to Zeem, and allow us to take care of everything for them.
“It [running electric trucks] is a different way of doing business, and often fleets want to see if it works for them. They are used to starting off at their HQ, so using Zeem is a bit of a change for them. So we make it as easy as possible, and optimally locate close to the warehouses and airports.”
Zeem currently operates two sites in Southern California, with four additional ones in the planning. We called in on its two-acre LAX facility, where Griley Air Freight charges its trucks. The site has a 7MWh capacity, which according to Gioupis is the equivalent of seven Walmart stores. This feeds 56 dispensers on 28 dual-port DC fast chargers, and 18 slower chargers. In addition to servicing airport car rental businesses, it takes care of 11 truck fleets here. It’s open 24 hours a day, 365 days a year.
• The speed rewind control system on all models ensures that the hose retracts at a safe & steady speed
• The stop-at-any-point latching mechanism secures the hose at the desired length every time
• Sliding guide system ensures that the hose returns neatly & evenly onto the barrel assembly
• Gen3 hose assemblies offering ultimate flexibility are kink-free under pressure
AIR HOSE REEL - 20M X 12MM ID
As we approach the busy holiday season, we must address an ongoing issue that impacts our roads: over-height trucks (OHT) in New South Wales, writes NHVR COO Paul Salvati.
OHT incidents are significant contributors to infrastructure damage, particularly to tunnels, and they lead to considerable traffic congestion, causing major disruptions for drivers.
In August 2024 alone, seven new OHT detections were recorded, bringing the year’s total to 38. The Sydney Harbour Tunnel remained the most problematic location, accounting for half of these incidents.
Following closely was the M5 East Tunnel with 10.5 per cent of occurrences, and the Domain, Eastern Distributor, and GHD Airport Tunnels, each contributing 7.9 per cent. The Lane Cove Tunnel had the next most, with 5.3 per cent of total incidents.
Despite this, we have seen encouraging progress in reducing OHT incidents. Between January and August 2024, NSW experienced a 54.8 per cent decrease in detections compared to the same period last year, resulting in 46 fewer incidents.
This reduction is a direct result of targeted measures implemented by the National Heavy Vehicle Regulator (NHVR), NSW Police and Transport for NSW (TfNSW).
Stricter penalties have been enforced, including fines of up to $5,500 for OHTs that ignore lowclearance signage, along with 12 demerit points for drivers.
TfNSW may also suspend a driver’s licence for up to six months and issue a registration suspension for trucks for the same duration.
Recognising the need for education,
TfNSW have launched campaigns aimed at reaching drivers and operators. At the NHVR, we have enhanced our educational efforts through advertising on social media, radio, and online platforms.
We also developed a brochure translated into Arabic, Hindi, and Chinese to inform drivers about the steps they can take to avoid incidents. However, every incident, no matter how small, can still cause serious disruption. This progress relies not only on regulatory measures but also on the collective responsibility of everyone involved. Loaders and operators play a crucial role in preventing incidents.
It is important that they measure loads accurately before departure and ensure that trucks are within legal height limits.
By doing their part, they help maintain safe roads for all users and protect our state’s infrastructure.
With more tunnels and bridges with low clearances of less than 4.6 metres than any other state in Australia, NSW remains particularly vulnerable to OHT accidents.
Roads leading to tunnels and bridges which may be of concern are equipped with an array of sensors, median strips, and signage to warn drivers of what is ahead.
When measuring your load, check the height of your load using a height stick, measuring tape, laser technology, or an electronic measuring device.
In NSW, heavy vehicles higher than 4.3 metres have restricted travel
conditions and must use approved road networks. If your vehicle exceeds this height, ensure compliance with the required National or State notice or access permit from the NHVR.
Before departure, check and make sure your vehicle has the capacity to accommodate the load type and size and the load is secured so it is unlikely to fall or be dislodged during your journey.
Ensure the load is restrained using an appropriate method. Loose or incorrectly restrained loads can be life-threatening to others and can cause damage to property or hazards. The load restraint must be equipment in serviceable condition and appropriately rated for the task. Ensure the position of the load on the vehicle maintains adequate stability, steering, and braking.
When in transit, check your load for movement at regular intervals throughout the journey, as it can shift, pull into rest areas when needed, and ensure you are aware of tunnel or bridge height clearances.
Over the past 12 months, industry members have played an important role in our progress, and we thank them for their dedication to training drivers and effectively managing routes.
Every incident involving overheight trucks can lead to significant traffic congestion, potential damage to infrastructure, and serious risks for heavy vehicle drivers and other motorists. Therefore, complacency is not an option.
As we look ahead to the busy holiday season, the stakes are even higher.
The Australian Trucking Association is firm on its stance that truck driver licensing is in desperate need of review.
Australia’s governments must take a new approach to truck driver licensing to increase safety and encourage more people to join the industry, says ATA Chair Mark Parry.
The association is releasing its plan for truck driver licensing, which was developed with the advice of a Workforce and Driver Training Summit held in June.
Mark says the current licensing arrangements for truck drivers were inadequate.
“The problems became apparent to all in February 2016, when the crew of a B-double proved unable to reverse their overheight truck out of the entrance to a Sydney tunnel,” he says.
“The association of government transport agencies, Austroads, has done an extended review of driver licensing, but governments now need to act.
“Many driving training organisations do a great job. Others train to a price or a time. Driver trainers must be assessed more rigorously, by experienced auditors who understand driver training and competencies.
“There should be minimum behind the wheel training times, with the driver training experts at our summit proposing longer training times for discussion than the ones put forward by Austroads.
“At present, truck drivers progress through the licensing classes on a time basis. For example, once you have a medium or heavy rigid truck licence, you must wait a year before you can get a heavy combination (HC) licence.
“You are not required to use your licence and build up your driving skills and experience.
“Austroads has proposed that drivers should also be able to advance through the licence classes based on their driving hours, with accelerated progression for drivers who are supervised. There would still be training and assessment requirements.
“We support these new pathways, but the existing time-based option should be removed. There is no connection between the passage of time and driving skill.”
Mark says the current MC class should be split into two classes, to reflect the extra skills required to drive combinations such as triple road trains, quads and quins.
“Drivers with existing MC licences would be automatically assigned to the higher MC2 class.”
The ATA believes driver medicals should be part of the licensing process and should be done before training gets underway.
“Our summit participants told us about job applicants who had gone to the time and effort of getting a licence and then being offered a job, only to discover during their employer induction that they did not meet the driver medical standards.”
Mark says that strengthening driver licensing and training would encourage more people to join the industry.
“Truck driving is highly skilled, but the issues with the licensing system mean that many drivers end up having to learn critical safety skills and
A Low Carbon Fuel Standard is necessary for the transport industry to reach its net zero goals, writes NatRoad CEO Warren Clark.
As we face the challenge of reducing carbon emissions, it’s crucial that we consider the future of the internal combustion engine (ICE), which remains a vital part of Australia’s heavy transport landscape.
A key solution for maintaining the efficiency of our supply chains while working towards a low-emissions future is the introduction of a Low Carbon Fuel Standard (LCFS).
An LCFS would provide a pathway for ICE vehicles to continue contributing to the economy as an essential part of the national supply chain while we work to help meet the government’s carbon reduction goals.
Gradually decreasing the carbon intensity of the fuels we use, rather than relying solely on the rapid transition to technologies not yet ready for use in all specific freight tasks, like electric or hydrogen-powered trucks, is a realistic and cost-effective way for the road freight sector to help achieve net zero.
It’s true that achieving net zero for road freight will ultimately require a mix of technologies. Electric vehicles are increasingly suitable for urban-based freight tasks, where the distances are short and the infrastructure easier to develop.
Hydrogen holds potential for heavier freight tasks, which also need more vehicle range. However, for Australia’s longer-distance, remote, and heaviest freight tasks, the internal combustion engine will continue to play a critical role for many years to come. We need a solution that recognises this reality.
An LCFS allows us to do just that. An LCFS creates a stable investment environment by setting a carbon intensity reduction target for fuel suppliers that increases over time.
This motivates fuel suppliers to introduce solutions such as biodiesel and renewable diesel to the market – an opportunity to reduce emissions without the need for immediate, largescale infrastructure changes.
One of the key benefits of an LCFS is that it allows the market to find the most cost-effective solutions.
Rather than governments dictating specific technologies or fuels, the LCFS would provide a framework that can innovate and deliver more choice for individual businesses. This is particularly important in the road freight industry, where flexibility and cost-effectiveness are essential.
The gradual introduction of an LCFS is also important. We wouldn’t see a sudden shift to 100 per cent renewable diesel overnight. Instead, renewable diesel could be blended with regular diesel, increasing over time, allowing the industry to scale up gradually and avoid price shocks at the pump.
the fuel would drop, helping the entire industry move towards a lower emissions future.
This would ensure a smooth transition for operators, and provide certainty to fuel suppliers, enabling long-term planning and investment.
Renewable diesel isn’t a silver bullet. The feedstocks used to produce it are not unlimited, and we will still need a mix of solutions, including electrification and hydrogen.
But an LCFS would ensure the internal combustion engine continues to have a place in the freight sector, particularly for tasks where ICE vehicles remain essential.
The introduction of an LCFS offers a practical transition pathway for every trucking business in Australia. Operators would be able to reduce their carbon emissions, without needing to make major changes to their vehicles or operations.
The benefits of an LCFS also extends beyond environmental gains. By starting gradually, we can allow the renewable diesel industry to mature, ultimately driving down the cost of low-carbon fuels. This would provide much-needed relief to operators who are already managing a challenging economic environment.
In a sector as critical as road freight, where the cost of fuel can make or break a business, we need a balanced, flexible, and cost-effective approach to reducing emissions.
We want policymakers to recognise the vital role the internal combustion engine will continue to play in Australia’s freight landscape and to put in place a framework that secures its future in a low-emissions economy.
A Low Carbon Fuel Standard provides that solution, allowing us to continue powering Australia’s economy while contributing to a more sustainable future.
We are embracing our path to zero emissions. The ADR80/04 rating will bring Australia’s emissions standards in line with Euro VI.
• The power of versatility
• 525 - 625 hp
• 1850 - 2050 lb-ft
• Peak torque at 1000RPM
• Ultimate flexibility suitable for both maunal and automated transmissions
• EGR-free design meeting Euro VI emission standards
Does anyone else harbour a deep mistrust when it comes to car manufacturers’ fuel economy figures? You know that the only way you’ll ever come close to the official L/100km number is if you’re coasting downhill with a tailwind.
Lately, I’ve started feeling the same way about truck manufacturers and the range claims for their new electric vehicles. I recently read a press release about a battery-powered prime mover, and the quoted range didn’t even account for towing a trailer!
When Mercedes-Benz Trucks CEO, Karin Rådström, confidently proclaimed to the world’s press last year that the new eActros 600 could cover 500km on a single charge while hauling 40 tonnes, I took her claim with more than a pinch of salt. My scepticism only deepened when I discovered that the eActros 600 has 621kWh of installed battery capacity, nearly identical to the Scania 45 R/S, which quotes an official range of just 350km. Sure, the new eActros is
highly aerodynamic, but I can’t shake the feeling that someone’s telling porky pies!
So, when I was invited to France this summer to take the wheel of an eActros 600 for a stage of its 15,000km European Testing Tour 2024, I jumped at the opportunity. After all, this was my chance to prove Mercedes wrong, and that’s exactly what I aimed to do…
Mercedes certainly can’t be accused of rushing the eActros 600 to market. The company has been teasing its zerotailpipe-emission long-haul truck for at least two years, and despite already securing 1,000 confirmed orders, fullscale production won’t begin until the end of 2024.
When it comes to developing an electric truck, there are two main approaches. The easier route is to convert an existing diesel model. The more challenging, expensive, and timeconsuming option is to design an electric truck from the ground up, and that’s exactly the path Mercedes has taken.
A key example of this is the truck’s 13-tonne electric axle (E-axle), which integrates twin motors and a four-speed transmission. The E-axle eliminates the need for a prop shaft, freeing up valuable chassis space. This area, located between the two chassis rails, houses three Chinese-sourced lithium iron phosphate 207kWh LFP battery packs, all mounted perpendicular to the direction of travel.
The new aerodynamic ProCabin takes centre stage with its sleek design, extending 80mm beyond the current model and featuring smooth, curved surfaces that enhance airflow by nine per cent. This improvement results in a two to three per cent boost in fuel efficiency. The ProCabin, available in StreamSpace, BigSpace, and GigaSpace variants, will soon be featured on diesel-powered Actros L models with 2.5m wide cabs and level floors.
My test truck, equipped with a StreamSpace cab, was a late prototype. It would be joined on this journey by another test vehicle, operated by two Mercedes-Benz Trucks engineers. This
Mercedes-Benz reckons its eActros 600 electric truck will do 500km on a single charge, but PowerTorque’s European Correspondent, Will Shiers has his doubts.
second one featured an aerodynamic package, with 315/70R 22.5 tyres, plastic wheel infills, and the absence of a sun visor. Along with new side skirts on 4x2 prime movers, these features further improve fuel economy by a claimed two to three per cent.
Behind the wheel, the eActros 600 offers a familiar driving experience with its streamlined dashboard, digital instrument cluster, and large information screen, just like the conventional Actros. The main distinction lies in the right dial, which provides detailed information on battery charge and clearly indicates whether you’re in propulsion or regenerative mode.
Between the two dials, a kWh per 100km figure is displayed, serving as the electric truck’s equivalent to the traditional L/100km measurement.
On average, a 40-tonne electric truck consumes around 120kWh per 100km (1.20kWh/km). Mercedes allows access to 95 per cent of the truck’s 612kWh battery, translating to 600kWh, hence the truck’s name. Dividing 600
by 1.20 gives 500, which explains the claimed 500km range.
The truck features three distinct performance modes: Power, Economy, and Range. In Power mode, you access 100 per cent of the available power, though it limits the full 860hp to extend tyre life. Economy mode delivers 85 per cent of the power, striking a balance between performance and efficiency. Range mode, designed to maximise distance when the battery is low, provides 70 per cent power. Additionally, a boost mode offers a quick surge of extra power when needed, akin to a kick-down. I reset the trip computer, selected Economy mode, and set off onto the motorway.
ON
Mercedes was blessed with ideal conditions for the 400km drive. The temperature was a warm 32°C, and traffic was minimal. What’s more, there were no trucks on the road since it was a Saturday, French regulations mandating that they’re parked-up on weekends. I had special dispensation as
I wasn’t operating for hire and reward.
The eActros automatically detected that I was on a French motorway and displayed a 90km/h speed limit sign on the dashboard. But I set the adaptive cruise control to 85km/h, matching the speed of the second truck to ensure a realistic comparison by the end of the route.
At this point, a quick glance at the dial revealed an average consumption of 144kWh/100km (1.44kWh/km), indicating a range of approximately 416km by my calculations. Although this was in line with my expectations, it was frustrating to see the figure gradually improve over time.
During the drive, I encountered some steep inclines that caused the truck to shift from fourth to third gear. The transition was remarkably smooth; if not for the display, I might not have even noticed it. On one particularly steep grade, my speed dropped to 50km/h, which felt much slower than it actually was, likely due to the absence of a roaring combustion engine beneath me.
At that moment, I spotted the ‘boost ready’ indicator on the dashboard, which reminded me of the racing game I used to play on my Commodore 64 in the mid-1980s. Without hesitation, I pressed the button, and the display instantly lit up like an erupting volcano.
reference: if it fits through a gap, the camera arm will too.
The additional 15 per cent power made all the difference, and when I crested the hill, I was back in top gear. Despite the climb, average consumption was now 120kWh/100km (1.2kWh/km), and it was about to improve further. What goes up must come down, and thanks to recuperation, consumption dropped to 112kWh/100km (1.12kWh/km) by the time I reached the bottom of the hill.
During the drive, I encountered several toll booths, offering a chance to test the five-stage electric motor brake. This system provides continuous braking power of 400kW, with a peak of 600kW, and the display shows energy being recaptured and returned to the batteries. Even with some enthusiastic acceleration after each toll, consumption remained steady at 108kWh/100km (1.08kWh/km) for several kilometres.
Four hours into the journey, I realised I hadn’t given MirrorCam a second thought. This might be a controversial statement, but the mirror replacement system felt completely natural to use. The second-generation system, with its smaller camera arms, protrudes less, reducing the risk of being knocked by overhanging trees or toll booths. You can use the passenger door blindspot mirror as a
The shorter arms have significantly improved the view on the screen. Previously, the trailer occupied about 30 per cent of the image; now, it’s down to roughly 10 per cent. This change provides less vehicle reference and more visibility of the surroundings. It works well, and when I stopped for my 45-minute break, I found that it also makes reversing easier.
The consumption figure had dropped to 105kWh/100km (1.05kWh/ km) by now, and as I set off for the last hour it continued to improve. I had even left the air conditioning on during my break, but that only consumed 4kWh of energy.
My journey concluded at a new truck charging station on the outskirts of Rouen. This station is operated by Milence, a joint venture among Daimler Truck, TRATON, and the Volvo Group. Milence plans to establish and manage 1,700 public charging points across Europe by 2027, and this is one of the first.
The secure charging site was next to a truck stop, which, unfortunately, was closed on weekends. This left me without any facilities, not even a toilet. If drivers are expected to charge during their mandatory breaks, addressing this lack of amenities will be essential.
All Milence sites currently charge €0.39 per kWh (AUD 0.64 per kWh) and deliver power at a rate of up to 400kW (350kW in this instance).
With no option for a coffee, I settled in the cab and calculated the consumption figures while the truck recharged. Remarkably, the 40-tonne truck had covered 406km with 36 per cent battery remaining, averaging just 98.9kWh/100km (0.989 kWh/km).
The following truck, equipped with the aerodynamic kit, performed even better, with an average consumption of 93.4kWh/100 km (0.934kWh/km). These figures suggest potential ranges of 606km and 642km, respectively.
It’s important to note that these results were achieved under optimal conditions. Even considering adverse weather, traffic congestion, and a heavier foot on the pedal, it’s reasonable to expect that the eActros 600 can comfortably exceed 500km on a single charge.
So, in a way, I did prove Mercedes’ figures to be wrong after all, I just didn’t realise it had grossly underestimated instead of overestimated them, a refreshing change indeed.
Model: Mercedes-Benz eActros 600 4x2 prime mover
Cab: ProCabin StreamSpace Range: 500km
Power output: 400kW continuous (600kW peak)
Battery chemistry: LFP
Installed battery capacity per pack: 207kWh
Installed battery capacity: 621kWh
Battery packs: 3
E-axle: Two integrated motors
Length: 2,300mm
Width: 2,500mm
Wheelbase: 4,000mm
GCM: 42 tonnes
Charging time CCS: 20 per cent to 80 per cent in one hour at 400kW
Charging time MCS: 20 per cent to 80 per cent in 30 mins at 1MgW
Start of production: End of 2024
Tickford Racing trusts Castrol fluids in its supercars and transporters. When performance matters, trust Castrol in your trucks.
The holiday season is often a time to hit the brakes, celebrate success, and enjoy a little festive cheer.
For employers, managing workplace events like end of year parties comes with added responsibilities. Here’s how you can manage the risks associated to keep your business, and your employees, in the clear.
Even at a festive gathering, employers must remember that Australian laws regarding misconduct, harassment, bullying, and discrimination still apply — even when the tinsel is up and drinks are flowing. As such, employers must ensure the party remains an extension of the professional environment and that team members know this.
A key pit stop here is ensuring policies are in place before the party starts. Clear communication about what behaviour is expected is essential. You wouldn’t send a driver out without a map, so don’t let your employees head into a work event without guidance!
You should provide employees with a reminder before the event, highlighting key points around expected behaviour, limits on alcohol consumption, responsibilities around safe transportation and a reminder of the business’ code of conduct policy and stance on harassment, bullying and social media posts.
This can be communicated through a memo or email beforehand and should be in writing so you can rely on it later, if needed.
One of the biggest risks at any work event is alcohol. While a few drinks can liven up the atmosphere, too much
alcohol can lead to bad decisions, risky behaviour, and potential legal issues.
Ensure that you limit the amount of alcohol available, provide nonalcoholic options and plenty of food. Also consider using a venue with professional bartenders who are trained to monitor consumption and cut people off before they hit the brakes too late and implement a strict ‘responsible drinking’ policy for the event.
To avoid employees driving home under the influence and minimise your liability, you should organise safe transport options for employees after the event.
This could include providing taxi vouchers or ride-share credits, hiring a shuttle bus, or organising designated drivers.
In the age of social media, what happens at the work event doesn’t always stay at the work event. Photos or videos featuring inappropriate behaviour can quickly become public, affecting both individual reputations and the business’ image.
Before the party, remind employees about your social media policy and direct them to think before they post.
Employers can face liability if something goes wrong at a work event, even outside regular work hours. Issues like harassment, bullying, or injury can lead to legal claims.
A key part of managing this risk is ensuring staff know what to do if they
witness or experience inappropriate behaviour. Establishing a clear reporting process can help mitigate these risks and keep your business’ reputation on track.
Remember, if the party runs late and employees decide to kick on elsewhere, make it clear that those extra festivities are no longer part of the work event. Letting them know when the business’ responsibility ends is critical.
If something goes wrong, don’t let it gather dust like a forgotten load at the depot. Act swiftly and take it seriously. Ensure you have a clear procedure for handling complaints, then investigate any complaints with the same diligence you’d apply to a workplace incident. This shows your commitment to creating a safe and professional work culture, regardless of whether the incident happened behind the wheel or at the bar, and will assist in the event you need to dispute a claim against your business. If you’re not comfortable investigating a complaint, get professional advice to ensure you get it right.
Just like a well-maintained truck, a well-organised work event will help avoid costly breakdowns. So go ahead, plan that festive gathering, but just remember — set expectations early because employment relations doesn’t take a holiday.
Prefer to leave it to the experts? Would you like some more guidance or a free copy of our memo regarding workplace events? Reach out to advice@clear-er.com.au
With a huge range of exciting new product including Ultima MK3 driving lights, 70/80 Series Rear Lighting, MicroLux work lamps and much more, the new Narva catalogue is better than ever. Scan the code below to view online or get a hardcopy.
Local Ballarat business Eureka Concrete is enjoying the work of a new Isuzu agitator, which has quickly become a key part of the fleet.
There is nothing better than putting the keys into the ignition of a brand-new truck.
Eureka Concrete in Ballarat is doubling down on that golden feeling, having recently collected a bright yellow FYJ 300-350 Auto concrete agitator to add to their growing Isuzu fleet.
The business has been providing concreting services in Ballarat, Ballan, Beaufort and Maryborough in Victoria for over 50 years. Alongside their four concrete plants, the family-owned and operated business also runs a quarry in Amphitheatre.
“Back when our dad, Graeme Beaston first started the business 52 years ago, he had two concrete trucks and a front-end loader,” explains Eureka Concrete Manager, Troy Beaston.
“I’ve been here for over 30 years with my three brothers also working for the business. We now run around 45 concrete trucks plus a few tippers.”
While Eureka Concrete can be found delivering concrete for government and commercial projects, they also provide product for domestic builds, industrial sites, windfarms and local mining operations.
Their range of eye-catching washed pebble finishes and coloured concretes that utilise pigments when blending offers a striking rainbow of options to satisfy any customers’ designer dreams.
Trucks in Eureka’s fleet, such as their new FYJ Auto Agitator, will take on five to six loads per day on average,
with some days jumping up to as many as 10 loads. This is prevalent on “the sunny days which are always busy,” according to Troy.
Eureka’s new FYJ Agitator would probably travel up to 200 or 300 kilometres a day and be in operation for up to 10 hours.
As one of the largest trucks in Isuzu’s model range, sitting at a GVM of 30,000 kg, the FYJ Agitator is underpinned by a 6UZ1-TCC turbocharged engine, producing 257 kW of power @ 2,000 rpm and 1,422 Nm of torque @ 1,400 rpm.
With this kind of power under the hood, the truck can haul a whole lot of concrete, with no worries about lasting the distance for Eureka’s job roster.
Power assisted recirculating ball steering combined with heavy-duty
Allison 4430 automatic transmission makes handling loads that much easier. Despite its hefty size, the FYJ has a reasonably tight 17.9-metre kerbto-kerb turning circle.
“We decided to go with the Isuzu FYJ because of its high horsepower and its manoeuvrability,” Troy says.
“We appreciate that they are such a well-presented vehicle as we put a high value on presentation of product along with quality.”
The in-cab control panel of the FYJ Agitator features Isuzu’s kerb-andchannel functionality in both forward and reverse gears as a standard inclusion.
Improved operational safety comes with the kerb-and-channel system disabling should the driver remove their foot from the brake pedal and power divider and cross-locks protection – eliminating the risk of a driver engaging locks when the truck’s wheels are spinning.
For ease of operation, the Allison 4430 automatic transmission programming has been enhanced by Isuzu for the FYJ Agitator, improving overall control and reducing service brake wear. This includes industry-
Ensuring that trucks well-maintained and smartly replaced when needed keeps the business operating as efficiently as possible.
Importantly, any new Isuzu FYJ 300-350 Auto Agitator cab chassis is supported with a three-year (or 300,000 km) ‘harsh application’ standard new vehicle warranty (no hours stipulation), which includes three years of 24/7 roadside assistance and Isuzu Care only a phone call away.
“The industry is keeping us pretty busy; it’s been pretty much growth right from the word go,” Troy says.
for the build
dealership in Mitchell Park this year.
For Eureka Concrete, expanding service outside of Ballarat could be in the pipeline, but with such strong community ties right at home, increasing product output for existing clients is their primary focus.
“Because our Isuzu truck is going really well for the business, we are planning to update older vehicles over time with Ballarat Isuzu so we can have Isuzu trucks all throughout our fleet,” Troy says.
The foundations for the working relationship between Ballarat’s biggest concrete supplier and one of
The new dealership premises is geared to support growth, extending the service and product support that customers such as Eureka Concrete have come to rely on.
“We have a connection with the team at Ballarat Isuzu – we’ve known them for a long time and we’re glad to do business with them,” Troy notes.
“We enjoy looking after the local community and businesses in Ballarat.”
Dealer Principal Ian Deacon said the dealership was delighted to hand over the keys of the new agitator to a local customer, noting the mutual trust between Eureka and Ballarat Isuzu.
milestone that their FYJ Agitator could
Tranzliquid Logistics is one of New Zealand’s top tier fleets, a company that has forged a reputation for its immaculate equipment, exemplary safety record and great team culture.
Tranzliquid has been operating the sole Euro 6 Cummins X15 engine in New Zealand since 2021 which, at the time of writing in September, had just exceeded 600,000 km.
Importantly, it has Greg Pert’s stamp of approval as more stringent emission regulations loom on the horizon.
In Australia, around 350 Euro 6 Cummins X15 engines are running in the lead up to the introduction of Euro 6 – or ADR80/4 – from November 1, 2025.
Greg founded Tranzliquid in Mt Maunganui in 2000 with partner Jackie Carroll following a career as a driver and independent operator in the tanker industry, transporting non-hazardous and dangerous goods products throughout New Zealand. His formative years in the trucking industry were with Freightways Bulk Services where he started as a driver in 1977 at the age of 18 and went on to become an independent operator with the company, hauling a vast array of liquid products from chocolate to fruit juice, to molasses, to petroleum.
Today, Tranzliquid has 50 Cummins X15-powered Kenworths – mainly T610s and K200s – which operate throughout the North Island and South Island, hauling fuel and liquid bitumen for blue chip customers, while a small number of trucks also do container deliveries.
The Euro 6 Cummins is available in two series, Efficiency and Performance, and both are EGR-free and have a standard wastegate turbocharger. Single module aftertreatment
technology integrates both the diesel particulate filter (DPF) and AdBlue SCR system.
Tranzliquid’s Euro 6 engine – the flagship Performance version rated at 625 hp with peak torque of 2050 lb ft – is installed in a T610 Kenworth and stirred by Eaton’s 18-speed RTLO20918 box.
With the Meritor rear axle ratio of 4.10, the 15-litre Cummins is downsped to optimise fuel economy, turning over at 1410 rpm at the 90 km/h speed limit in New Zealand. At this point in the rpm range, peak torque of 2050 lb ft is on tap, all the way back to 1000 rpm, providing the grunt to meet both driver and trip time expectations.
“Southpac Trucks (New Zealand’s Kenworth dealer) asked us if we wanted to be part of a Euro 6 trial and we thought it would be a good idea to be involved due to the benefits that would play out over the longer term,” Greg says.
“After 600,000 kilometres we now have a good working knowledge of the Euro 6 Cummins which will be beneficial as the technology becomes more widely adopted and emission requirements are tightened.”
Performance and fuel efficiency of the Euro 6 X15 are in line with expectations at Tranzliquid which is regularly double-shifting the two-trailer combination seven days a week.
A recent ECM download showed overall fuel consumption at 2.01 km/ litre while time spent in top gear was 45 per cent.
“We’re operating in some tough terrain in the North Island which eats into the fuel economy,” Greg says.
“Our fully loaded running is generally around the 70 to 80 per cent mark.”
The download also showed AdBlue being injected into the exhaust flow at a rate of eight per cent of fuel burn.
Apart from a couple of minor sensor issues, the Euro 6 engine has basically been trouble-free. The DPF was changed out at 600,000 km in line with Cummins’ recommended maintenance schedule.
Cummins’ support is a key factor in keeping the Tranzliquid fleet running
at the required utilisation levels.
“We get very good support from Jade Whiteman and the team at Cummins,” Greg says. “We don’t have to ask for support, we’re offered support. Cummins understands our needs.”
Greg is showing keen interest in Cummins’ industry-first fuel agnostic platform of advanced diesel, hydrogen and natural gas internal combustion engines.
“The diesel internal combustion engine will be around for a long time yet for heavy haulage, as confirmed by Cummins, but the hydrogen combustion engine could definitely be of interest to us for specific applications in the future,” he says.
“One of our customers, Waitomo Group, is establishing a green hydrogen refuelling network for heavy vehicles and has already opened three sites in the North Island.”
Greg says that the lack of recognition for the road transport industry’s contribution to reduced environmental impact has been a concern of his.
“We are moving much bigger tonnages today while using less fuel and significantly reducing atmospheric pollutants,” he says.
Not surprisingly, risk management is a critical factor in the safety record of the Tranzliquid fleet.
“We give our drivers all the tools to help them do their job efficiently and safely,” Greg says.
Both trailers behind the Euro 6 prime mover are disc-braked while all Tranzliquid Kenworths have the full suite of electronic/active safety features such as electronic stability control, adaptive cruise control with engine braking, collision mitigation system with autonomous emergency braking and lane departure warning.
There’s great emphasis at Tranzliquid on team culture which revolves around core values such as accountability, delivering on promise, having the right attitude and treating people with dignity and respect.
Greg says they’re constantly looking at ways to improve the way they do business.
“Tranzliquid prefers to be a leader in the industry, not a follower.”
While the advent of auto brake adjusters has helped the function of braking systems, maintaining them is just as important to allowing them to run smoothly.
Brake adjusters play a crucial role in maintaining proper brake function on heavy vehicles. Regular inspection of these components is essential for safe vehicle operation.
Auto brake adjusters have greatly improved the reliable function of these braking systems. However, there are important things that a technician needs to be aware of to ensure they continue operating effectively.
Let’s look at a few tips that will ensure reliable and durable brake adjuster operation.
The most important piece of advice, that is often ignored, is do not adjust an auto brake adjuster other than on installation or brake reline.
Some technicians, often ones that have been in the industry for years, will tighten and back off the brake adjuster every service, just as they have been doing with manual brake adjusters.
However, regularly adjusting an automatic brake adjuster can cause premature wear on internal components and could lead to the adjuster becoming inoperable.
On the other hand, if an auto brake adjuster is out of adjustment, then the cause needs to be investigated and repaired. There are many issues that can cause an auto brake adjuster not to operate correctly. Manually adjusting the auto brake adjuster will not correct any of these.
The most basic check is that of brake adjuster free stroke, which is an indication of necessary brake shoe clearance. Hendrickson uses the Haldex S-ABA automatic brake adjuster that uses free stroke clearance as a basis for self-adjusting. When free stroke becomes greater than a certain amount it will move the adjustment up.
To check free stroke, add a brake check gauge or mark to the brake chamber rod. Use a bar or lever to move the brake adjuster from the full retracted position until the shoes contact the drum. Measure this movement to determine the free stroke. If this measurement is between 10 and 16 mm, then the basic adjustment is correct, and the brake adjuster is doing its job.
If there is excessive free stroke, inspect the adjuster for installation issues, the adjuster anchor grommet for excessive wear and verify that the adjuster anchor is properly secured and correctly installed.
With this basic check carried out, the technician can move onto checking the brake applied stroke, inspecting foundation brakes, friction lining material, drum surface and wear limits, brake chamber mounting, and other brake components for wear or damage.
Another item that is easily neglected is that of lubrication. Different manufacturers have different grease and greasing intervals. Avoid using
moly (molybdenum disulfide) grease in Haldex brake adjusters, as it can potentially interfere with operation of the internal friction clutches and compromise the automatic adjustment’s reliability. It is important to follow the lubrication specifications for the specific brake adjuster installed on the vehicle.
By regularly inspecting the free stroke without adjusting the auto brake adjusters, technicians can ensure that the braking system operates reliably and efficiently.
Appropriate maintenance of brake adjusters not only enhances vehicle safety but also extends the life of the brake components, ultimately reducing maintenance costs and downtime.
The telematics market is one that continues to grow nationwide as the demands required of data and technology in our fleets increase.
This was never clearer than at WHG’s TechDrive Roadshow event, where industry leaders got to show off what they’ve been working on in response to these developing needs.
Held in Melbourne by the team behind the telematics company, WHG is continuing to expand its reach and partnerships in the tech space.
Director of Operations Dylan Hartley kicked off proceedings by detailing what has been happening in the past 12 months.
“After our first TechDrive, we wanted to be more active in the Australian space. I can say now we’ve done that,” he said.
“Our partnerships are a really important part of being able to do what we do.
“We have over 65 competitors in the telematics space. In the last 12 months we’ve seen a consolidation of providers, which is a positive move. There’s some restructuring happening in our market around major suppliers.
“It’s critical to highlight that we
need to get around our approved providers, which there are only nine of. That approval should give you peace of mind.”
Dylan believes the adoption of telematics at a higher rate than ever before is providing both benefits and
challenges for the industry.
While the technology is adapting to the change, that comes with legislation that regulates it, like every other part of the industry.
A trial in Western Australia is currently utilising telematics data through PBS vehicles, making it more specific and targeted.
The growing age of Australia’s truck fleet has also proven to be another factor that must be considered when implementing new technology.
“Our market is becoming more accepting of telematics,” Dylan said.
“The key factors driving growth in our industry are the chain of responsibility, regulatory telematics and harmonisation, performance and predictive maintenance and proactive response and behaviour. The market is moving and advancing in a positive way.
“We have to keep looking at how we engage young people to join our industry. For some of them it’s about making their roles interactive.
“From a regulatory perspective, there’s a massive shift coming. Being able to use that as an operator will bring a number of benefits.
“I used to say the average age of a truck in Australia is 14 years. It’s now 15.8 years, and a new vehicle is now in a fleet for an average of six years.
“It’s increasing the adoption of this technology in older vehicles.”
One of the next steps in the advancement of telematics is seeing how different solutions providers carve out niches within the industry.
They aren’t all entirely about tracking trucks and providing driving data and navigation – they can be used across nearly any aspect of the trucks in a fleet.
RPM Group is one of those companies finding their speciality, particularly in the realm of tyres.
CEO and Executive Director Guy Nicholls spoke on the recent partnership they have forged with WHG, looking at how they can leverage data on truck tyres to help lower costs and keep maintenance to as low a level as possible.
“80 per cent of our business is commercial fleets, so we live and
breathe trucks,” Guy said.
“From a fleet point of view, we understand that tyres are an important decision. It’s the third largest purchase you make behind fuel and vehicles.
“It’s not just about the cost, but how long they last, the downtime, and how safe they’re going to be. Those metrics are a place for us to make sure the trucks are still on the road.”
Guy believes that the next evolution in tyres will be around self-sealing tyres, as well as airless models.
With the advent of electric vehicles in fleets across Australia, low noise or noiseless tyres may also start to appear as the next innovation.
“All tyre brands are trying to innovate and stay ahead of each other,” Guy says.
“The great thing we think with tyres and electric vehicles is weight. We know the batteries are heavy, and the lack of torque is ripping tyres apart.”
WHG and RPM have been working together to create digital tyre pressure monitoring through telematics technology.
They’re aiming to take the manual challenges out of keeping tyres fresh, particularly in extreme cases that can
be seen around the nation.
Using Bluetooth systems, their solution can manage 80 tyres, keeping track through scanning and tyre depth detection and measurement.
“The connection between trailers and prime movers for instance on an AB quad in Queensland, 70 metres long, becomes quite challenging,” Dylan says.
“Your biggest cost in terms of your fleet is labour, fuel and tyres. It’s an investment worth focusing on.”
RPM sees used tyres as a big issue within fleets, with very few easy ways to recycle them.
This is also an unnecessary cost that can be removed, as they look towards how they can make an impact on the recycling of tyres.
“We understand buying tyres is a choice you make depending on brand and price,” Guy says.
“The problem we all face is what to do with all tyres. They are a burden. We have to pay to get rid of them ourselves.
“What we’re doing is launching a recycling station is Campbellfield. From a solutions point of view we want to help keep vehicles on the road while also solving the problem of waste tyres as well.”
The latest product catalogue from Narva contains more than ever before.
The latest edition of Narva’s product catalogue is here, and it’s larger than ever showcasing 790 new lighting and electrical products with 470 never before released products.
Designed for the trade, the 19th edition of the catalogue features more information than ever and introduces a curated new format that was implemented following extensive industry consultation.
The included new releases cover almost every product category, with extra attention paid to key categories including driving lights, work lamps, warning lights and LED truck and trailer lighting.
A notable inclusion in the catalogue is Narva’s new EX2 LED driving lights and light bars, which combine model choice and overall lighting performance with wide colour customisation options for owners thanks to interchangeable trims.
Also featuring prominently is the Ultima MK3 LED driving light and light bar range which can be linked to the clever Connect+ Controller, letting owners connect their Ultima lights and adjust performance parameters to suit conditions.
The latest catalogue debuts the new Microlux Work Lamp range; they are models that blend superior output and compact beam patterns in a package not previously available in Australasian markets.
There’s also more warning lamps with four new strobe ranges introduced, including the brand new Eurotech II and the market changing Optimax Beacons. All have been designed, engineered and tested by Narva to suit the unique ANZ market.
The lights (including rotating patterns) meet SAE Class 1 requirements, a performance measure
that’s unique to Narva. Also making a debut in the catalogue are two all-new light box ranges.
Additionally, the continued development of Self Contained/ Perimeter Warning Lights also introduces new options in this category. The latest offering showcases Narva’s new smoked lens variants and versatile flexible warning lights with all silicone optics for increased durability and snug fitment over vehicle contours.
And finally within this category, the Utility/Mine Bar range has been updated to include new beacons, strobes and light boxes as well as an ADR approved combination front position and forward facing indicator as a standard.
Another major highlight is Narva’s growing range of LED Truck and Trailer Lighting, with nine new models added, providing lighting solutions for everything from box and boat trailers to cattle trucks and road train trailers.
Standouts include the new 80 Series which is designed for the toughest commercial applications, and the stylish 70 Series with signature taillight function and first to market combination stop/ reflector.
Industry consultation has shaped the format and layout of the latest Narva catalogue, making it more functional and easier to use than ever – the latest edition is the ideal quick reference, countertop guide.
The new Narva catalogue introduces revised image placement to the leading edge of the left-hand page, letting users more easily see the images on both sides of the page when flicking through, making products easier to find.
New graphic icons have been introduced as well, allowing more information to be communicated in fewer words.
There are now also more line drawings included and they’re more detailed than previously. Where applicable, they include information covering distance between bolt holes (centre to centre) and PCD (pitch circle diameter) for round products. This means installers can be sure their chosen product will fit within the required space.
The number of QR codes in the new catalogue has grown as well, allowing trade professionals to quickly access product videos, application guides, tech tips and more. In the case of the new LED Truck and Trailer lighting range, QR codes link to surface CAD.
The catalogue also features three additional application guides covering Work Lamp, Emergency Lighting and LED Truck and Trailer Lighting – all are easily identifiable by their colour coded tables.
MZ34-168GP / RZ78-188G / RZ78-388G
• Precision-forged differential gears for more durability and strength
• Hypoid-Generoid gearing provides long life, exceptional strength and quiet operation
• Optional driver-controlled differential lock (DCDL) on most models, offering maximum traction and spin-out protection under slippery conditions
• Standard pressurised, filtered lube system protects against spin-out damage
• Available in drum or disc brake configuration
• Engineered to suit Australian conditions
The introduction of an increase of mass limits is a welcomed one, but how it will actually affect industry? Technical Editor Bob Woodward explores the issue.
Iremember well the discussions when industry was pressing to progress HML, and the road and infrastructure managers promoted how all these bridges would fail.
This someone developed into a monster called IAP and then suddenly, somehow, these structures got stronger!
Similarly with a need to increase steer axle weights with the introduction of Euro 4 in about 2006, according to road managers, the extra half tonne steer mass was going to result in extensive structure failures.
One industry association proposed a concept that considered a progression of steer axle mass limits from 6.0 tonnes to 6.5 tonnes; then onto to 6.7 tonnes; and 7.0 tonnes.
However, some sectors were so hellbent on a quick fix and getting prime movers legal, so the focus was on a short-term fix. Steer axle mass was progressed from six tonnes to 6.5 tonnes and the failures didn’t eventuate.
All the while some jurisdictions had already recognised a need for seven tonne steer axles (road train) and introduced permit schemes.
The journey to more stringent emission standards and the advent of electric heavy vehicles has brought yet another set of challenges, namely increases in prime mover and truck tare weight.
However, before focusing too much on electric vehicles, it is interesting to note that several of the major passenger automotive manufacturers are stepping back from electric vehicles, exploring
hydrogen, bio diesel and even ammonia.
Whilst electric alternatives may find significant application in urban short haul deliveries, I doubt it will be a significant player in long distance heavy freight transport. One supplier has recognised the disbenefits of recharging heavy electric vehicles supplying hydrogen buses to Tasmania and South Australia.
The recently announced amending of regulation that will allow an additional 0.5 tonnes for ‘complying’ Euro 6 single-steer and twin-steer axle vehicles, which move to seven tonnes and 11.5 tonnes respectively, with conditions, is welcomed.
Like so many other limitations, Euro 6 prime movers and trucks have been commonly available for more than 10 years. Whilst these steer axle mass issues are now being addressed, many operators have had Euro 6 complying vehicles for several years, some on their third rotation of Euro 6 prime movers, and suffered the tare weight penalty with a corresponding reduction in payload – a productivity disbenefit.
Whilst the requirement for a minimum 315mm section width will be seen by some as a hurdle, at least the maximum width of 2.55 metres does provide some scope for retreads; 315mm section width in dual configurations can at least be used on these prime movers.
Some road trains are permitted up to 7.1 tonnes steer axle mass, but these are required to have a minimum tyre section width of 375 mm and there is little scope for secondary retread use. The current selection of steer tyres with a section width ≥ 375 mm is limited.
The issue going forward now is what is next in the steer axle mass increase required to accommodate electric, hybrid and other low/ zero emission technology in heavy prime movers? There has been some discussion regarding a need for 7.5 tonnes and beyond being necessary on single steer axle for some zero emission prime movers.
Whilst some electric vehicles currently enjoy a mass concession at both the steer and rear axle groups, these are limited to restricted routes. These concessions are not available to other vehicles; what conditions including minimum steer axle tyre section width are being applied to these vehicles?
The debate regarding higher mass limits for wide based single tyres (super singles) has been in discussion for several decades.
Recent research suggests that the pavement impact of super single is not as bad as road managers have
promoted, something that industry has questioned all along.
Then there is the known improved fuel efficiency that super singles provide and the benefits in lowering carbon footprint. I doubt even the most adventurous gambler would be prepared to place bets on the timeframe for this recent finding to be introduced to legislation.
There are multiple issues with infrastructure managers, but they don’t own the infrastructure, the taxpayers own it. The infrastructure managers are there to manage, but by the state of the roads they are not doing such a good job.
It’s been more than 30 years waiting for an outcome on HML for super singles – better not proceed too hastily!
There will be alternative
technologies to electric in the zero emissions race in the future and therefore concessions must not be limited by vehicle type but should be available to all vehicles that meet a publicly specified performance criteria, for example zero emissions.
If its reasonably known now that electric vehicles may require a steer axle mass of 7.5 tonnes and beyond, then preparation better start now.
The bridge or culvert or pavement won’t know if it’s electric, hydrogen or bio diesel powered, so the bureaucrats need to listen today and then get on with the task of informing the politicians of what needs to be done so they can introduce pass policy and have the bureaucrats get on with the task of being technology ready – before the technology gets here.
SINGLE QUICK COUPLING MOTOR CAN BE USED WITH MULTIPLE QUICK COUPLING PUMPTUBES
Alemlube’s Tyre Inflator Gun offers a precise and reliable way
Winflation, precision and durability are important features for any workshop environment.
The Alemlube 51118 Tyre Inflator Gun with Digital Gauge, designed and manufactured in Italy sets a new standard with its exceptional performance and European engineering.
This tyre inflator not only provides precise inflation but also delivers accuracy with a digital number readout that enhances its versatility across various applications.
Crafted from impact-resistant aluminium alloy, the Alemlube 51118 Tyre Inflator Gun with Digital Gauge is built to withstand the rigours of demanding workshop conditions. Its robust housing containing a backlit digital display is shielded by an oil-resistant rubber casing, making it resilient to both physical impact and
This ensures that the tyre inflator remains reliable and functional even in the harshest of conditions.
Whether you are working in automotive, transport, construction or mining environments, the 51118 will be your digital tyre inflator of choice.
One of the standout features of the Alemlube 51118 Tyre Inflator Gun with Digital Gauge is its dual-function handle, designed with both inflation and deflation settings.
This ergonomic handle, coupled with internal brass fittings and a stainless-steel spring, guarantees consistent performance and accuracy with each use.
The inflator’s digital read-out is powered by two AAA batteries, providing clear and precise measurements with an accuracy of ± 1.6 per cent, which is critical for achieving optimal tyre pressure.
Gun with Digital Gauge supports a maximum pressure of 175 psi (12 bar) and operates effectively within a temperature range from -20°C to +60°C.
These specifications make it a versatile tool for various tyre inflation and deflation tasks. Additionally, its overpressure protection feature safeguards against potential damage, adding an extra layer of reliability and safety for the operator.
Whether you are managing a bustling vehicle workshop or operating in more demanding environments, the Alemlube 51118 Tyre Inflator Gun with Digital Gauge stands out for a high standard in engineering and performance. Find out more through the Alemlube website:
In the fast-paced world of cold chain logistics, the right partnership can be the driving force behind transformative growth and success.
Australian refrigerated transport solutions business
Eurocold prides itself on its ability to form long-term relationships with its clients, tailoring its fleet solutions to best drive business growth.
One of the standout examples of this is its recent partnership with Knighton, a cold storage and transport company that has seen significant expansion over the past year.
Knighton has extended its reach from the Central Coast to Greater New South Wales, fueled by the opening of a new 2,500-square metre cold storage facility.
This facility, which holds as much as 2,500 pallets of goods, has allowed Knighton to offer full pallet delivery services with a focus on serving food wholesalers across NSW.
Supporting this rapid expansion has been Eurocold’s fleet solutions, enabling Knighton to grow their services without compromising on efficiency or quality.
“Eurocold has been a game-changer for us,” says Knighton Operations Manager Ashley Knighton.
“Their trucks have been instrumental in allowing us to expand our operations and offer more services to our clients. Without Eurocold, we simply wouldn’t have been able to scale up as quickly and efficiently as we have.”
A key element of the partnership between Eurocold and Knighton is the quality and reliability of Eurocold’s fleet.
While advanced temperature control and tracking technology are standard features, it’s the trucks’ overall performance and dependability that have made the biggest impact.
Eurocold delivers trucks that are not only reliable but also adaptable, helping clients like Knighton manage their evolving needs and business growth with confidence.
For Knighton, Eurocold’s trucks have improved service quality by offering consistent, efficient performance, allowing them to meet tight delivery schedules and comply with strict food safety standards.
“The trucks Eurocold provides are top-notch,” Ashley says.
“Our drivers have commented on how comfortable and reliable they are, which is crucial when you’re handling delicate, time-sensitive deliveries.”
However, what Ashley values most in the partnership is Eurocold’s full service and repair offerings, which ensures smooth operations without the stress of unexpected downtime.
“The comprehensive service and repair support that Eurocold provides is truly invaluable. It’s a critical aspect of our partnership because it allows us to operate without disruption.
“Knowing that if an issue arises, Eurocold will resolve it promptly gives me the confidence to focus on growing our business.”
In addition to providing high-quality trucks, Eurocold’s flexibility and quick response times have been essential in supporting Knighton’s continued growth, ensuring their fleet needs are met as their operations expand.
What distinguishes Eurocold is its commitment to providing personalised, hands-on service.
Ernesto, Eurocold’s Development Manager for NSW, has been pivotal in ensuring that Knighton’s fleet needs are met consistently. His dedication and involvement have been crucial in helping Knighton manage its fleet expansion smoothly and efficiently.
“Ernesto has been an incredible asset to our business,” Ashley says.
“He understands what we need and is always there to make sure we get the trucks and the support
we need, exactly when we need it. Having that kind of personal touch is rare, and it’s made a huge difference in how smoothly we’ve been able to grow.”
Looking ahead, Ashley emphasised that the long-term relationship between Knighton and Eurocold will continue to play a crucial role in their success.
“We’re looking at even more growth in the future, and having Eurocold by our side is going to be key.
“The relationship we’ve built with them isn’t just about the trucks – it’s about trust, reliability, and knowing that we have a partner who’s just as invested in our success as we are.”
As Knighton continues to expand, Eurocold remains a critical partner, providing the fleet solutions and support needed to help the company achieve its long-term goals.
From reliable, custom-built trucks to expert fleet management, Eurocold’s commitment to Knighton’s success is clear.
For businesses seeking a reliable partner in refrigerated transport, the collaboration between Eurocold and Knighton is a powerful example of how strategic partnerships can drive growth and efficiency.
“We couldn’t have achieved the success we have without Eurocold,” Ashley says.
“And I’m confident that our partnership will be just as essential to our future as it has been to our past.”
UP TO 20%* FUEL SAVINGS WITH THE SELF-CHARGING HINO HYBRID ELECTRIC.
Change is inevitable, by embracing it with the Hino 300 Series Hybrid Electric, you can gain a genuine competitive advantage. Make real savings from your fuel and maintenance costs, reduce your operating costs and more. With superior technology at work, the Hino Hybrid Electric will deliver up to 20%* reduction in both fuel use and emissions, compared to a traditional diesel truck. As there is no starter motor, the regenerative braking system charges the batteries which means increased on-road time with no recharge requirements, and a 16% annual maintenance cost reduction due to less wear and tear on the brakes. That’s the power of change, that’s the Hino Hybrid Electric. Visit hino.com.au
*Actual