pumpindustry
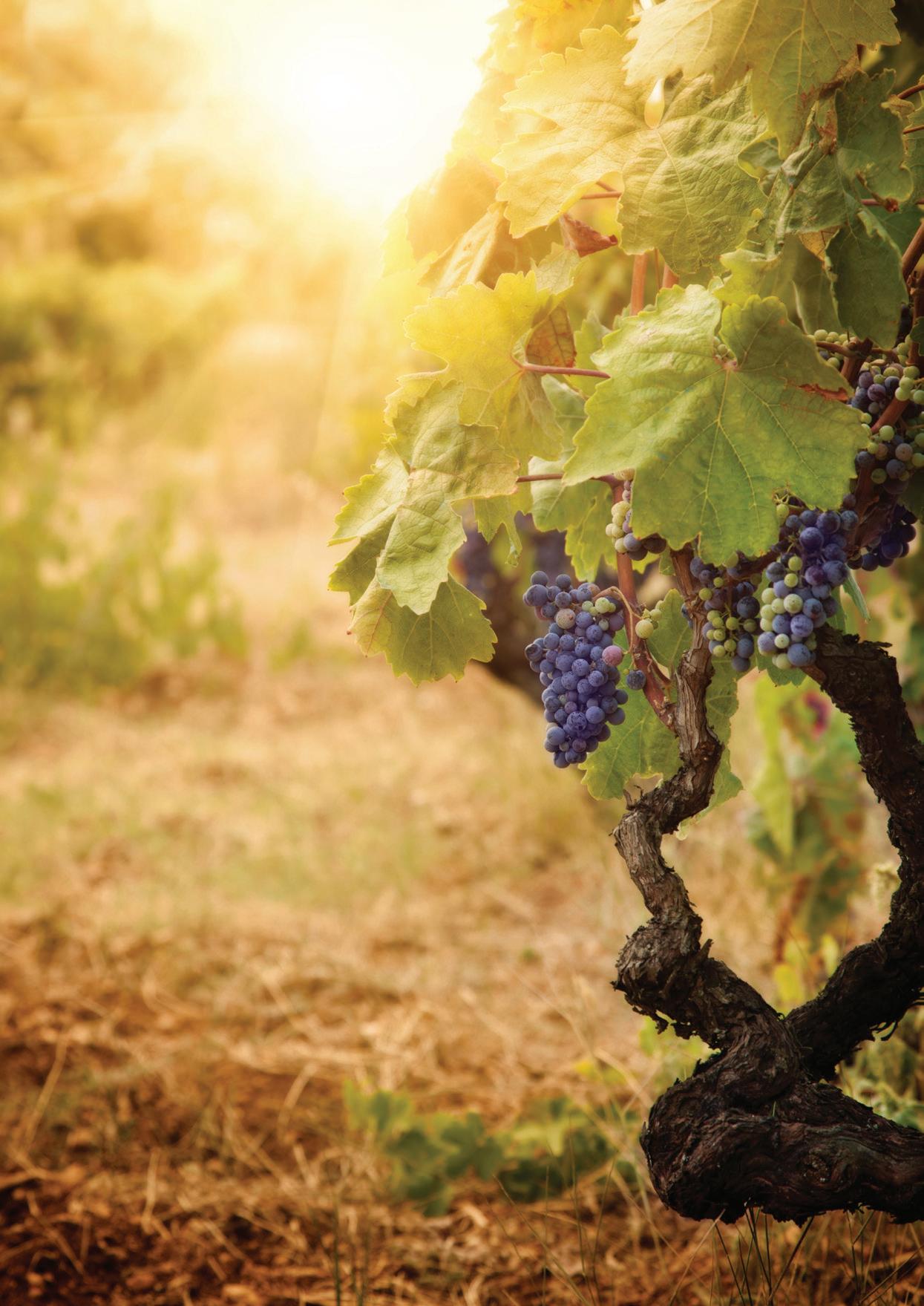
Innovative, efficient and compliant. That sums up the WEG W22 Ex series of hazardous motors.
From small Low Voltage motors through to large High Voltage machines, our comprehensive ranges of Ex-d, Ex-nA, Ex-tb, Ex-tc and Ex-p motors comply to all the relevant IEC standards and are designed with reliability, efficiency and overall performance in mind.
For more information, please contact your local Sales Representative. www.weg.net/au
Pump Industry Australia Incorporated
PO Box 55, Stuarts Point NSW 2441 Australia
Ph/Fax: (02) 6569 0160 pumpsaustralia@bigpond.com
Ron Astall – President United Pumps Australia & Astech Consulting Services
John Inkster – Vice President Brown Brothers Engineers
Kevin Wilson – Treasurer/Secretary Executive Officer
Keith Sanders – Councillor Executive Officer – Marketing & Statistics Life Member
Alan Rowan – Councillor Executive Officer Publications & Training Life Member
Ken Kugler Executive Officer – Standards Life Member
Ashley White – Councillor Davey Pumps
Frankie Camilleri – Councillor John Crane
David Brooks – Councillor Flowserve FSD
Dave Alexander – Councillor KSB
Jamie Dixon – Councillor White International
How do you know whether you got what you paid for? This can be difficult for pumping systems.
I was recently asked for an opinion from a large pump user on a noisy pump. This was a quite large unit with a 1,200kW electric motor driver and the noise was thought to be cavitation. I even visited the installation, and yes, the pump was noisy indeed. The point at issue was whether the noise problem was due to the pump being “dodgy”, or whether it was an installation problem. The pump vendor had performed a works test and declared that the pump was fine on test and that the problem must be due to deficiencies in the installation. Of course, the customer had an opposing point of view. The customer believed that their installation was fine and that this was a problem inherent to the pump. It is not appropriate for me to detail my conclusions here – perhaps later when the dust has settled!
So why mention it at all? The first question I asked the customer was: “Was the pump noisy when undergoing works testing?” It turned out that the customer had not bothered to attend the official works test, and no-one had bothered to record noise levels. How simple would it have been if the works test had been witnessed by the
customer? Noise levels could have been confirmed and, if necessary, resolved before the pump had been delivered. For the saving of an extremely small percentage of the initial capital cost, the purchaser had elected not to witness the pump test. Even for much smaller pumping systems, the cost of witness testing is very small compared to the total cost of ownership. Witnessed pump testing protects both the manufacturer and the purchaser.
Aside from detecting and resolving any mechanical and general performance issues, witness testing is really the only way to ensure that the quoted energy efficiency has been achieved. Pumping systems are often extreme energy consumers, and the total cost of ownership can be massive over the life of an installation.
I encourage all pump purchasers to seriously consider witnessed performance testing for all their significant pump purchases. A small upfront cost, but excellent long-term assurance that you are actually getting what you paid for.
Ron Astall President, Pump Industry Australia3,345
ABN: 36 426 734 954
PO Box 3121
Ivanhoe North VIC 3079
P: (03) 9440 5721
F: (03) 8456 6720
monkeymedia.com.au
info@monkeymedia.com.au
pumpindustry.com.au
magazine@pumpindustry.com.au
Publisher and Editor: Chris Bland
Managing Editor: Laura Harvey
Marketing Director: Amanda Kennedy
Marketing Consultant: Aaron White
Associate Editor: Michelle Goldsmith
Associate Editor: Emily Thomas
Journalist: Jessica Dickers
Designer: Alejandro Molano
Designer: Jacqueline Buckmaster
Creative Director: Sandy Noke
ISSN: 2201-0270
This magazine is
All communication should be
The publisher welcomes
ater is our most precious resource, and an essential part of Australia’s agricultural industry, which is worth $44 billion to our economy every year.
Without irrigation there would be no agricultural industry and in turn, without pumps, there would be no irrigation.
The Federal Government, having recently pledged a further $12.5 million for irrigation infrastructure upgrades in the Murray-Darling Basin, as well as $120 million for projects in Tasmania, has plans for further investment across the nation including North West WA, Darwin, NSW and Victoria.
In this issue we’ve covered irrigation schemes around the Murray and in Tasmania; and we’ve also taken a closer look at some innovative new technologies that have allowed farmers to pump higher volumes of irrigated water further than ever.
We’re excited to be a media partner at the Irrigation Australia Expo in Melbourne in May and look forward to talking to our readers there.
As well as preserving our precious water resources, pumps play a key role in saving energy.
In this issue, we also take a look at pumps in the HVAC space, and particularly the role they play in improving efficiency and driving down costs, whether in the commercial or residential sectors.
We are also a media partner at the ARBS show, also in Melbourne in May and look forward to seeing some of you there. In fact, we’ll almost be living at the Melbourne Convention Centre in May with a booth first at Ozwater, followed by these two events.
So if you’re exhibiting or visiting any of these, then please stop by and take the chance to learn a little bit more about what we do. Monkey Media does more for the pump industry than publish this magazine; we also act as a marketing agency for a number of companies active in the industry, creating content and managing custom newsletter and social media campaigns.
I’m looking forward to catching up with as many of you as possible at these events.
Chris Bland Publisher and EditorAuthorised Australian Distributor for
Head Office: 88 Wedgewood Road, Hallam VIC 3803, Australia Phone: (03) 9796 5001 Fax: (03) 9796 3499
RECESSED IMPELLER RECESSED IMPELLER
SUBMERSIBLE SCREW CENTRIFUGAL SUBMERSIBLE SCREW CENTRIFUGAL
TOP ENTRY SIDE ENTRY & PORTABLE MIXERS TOP ENTRY SIDE ENTRY & PORTABLE MIXERS
Large internal passages for handling solids up to 200 mm.
Replaceable wear element, extra-thick castings and hard metal construction for abrasion resistance.
Foot mounted casing provides true back pull-out.
Available in horizontal, vertical dry pit, vertical bearing, vertical cantilever and submersible designs.
Gentle, low shear pumping action minimizes product damage and prevents emulsification.
Single channel open impeller for solids up to 178 mm diameter
High efficiency reduces power costs.
High flow/low head hydraulic characteristics.
Low NPSH.
Available in horizontal, vertical dry pit & submersible designs
Simultaneously chops and pumps solids. Eliminates the need for grinders.
External and internal cutting actions.
Patented high efficiency, anti-fouling impeller
Available in horizontal, vertical dry pit, vertical bearing, vertical cantilever and submersible designs.
Economical solution for general duty in industrial sumps
Reliable self-priming independent of pit depth. Optional sealed columns for harsh environments. Standard designs for pit depths up to 14 feet, custom versions to 20 feet+.
Recessed impeller, chopper and process pump wet-ends available.
For submerged operation in tanks or sumps. Chopper, recessed impeller, and screw centrifugal designs available.
Capacities up to 910 m3/hr
Heads up to 61 metres
Temperatures up to 150°C
Solids up to 200 mm diameter
Capacities up to 2730 m3/hr
Heads up to 60 metres
Temperatures up to 150°C
Solids up to 178 mm diameter
Capacities up to 1408.4 m3/hr
Heads up to 40 metres
Temperatures up to 150°C
Capacities to 681.36 m3/hr
Heads to 91.4 metres
Temperatures up to 204°C with jacketing
Three drive sizes cover this series which feature a third lower output bearing which helps isolate hydraulic loads from the gearbox.
Wide range of rugged direct and gear driven mixers available in clamp and fixed mounting arrangements with a variety of sealing systems for closed tanks.
Capacities up to 2730 m3/hr
Heads up to 60 metres
Temperatures to 110°C
152 mm diameter maximum solids size
0.19 to 373 kW
Typical volume range: 0.09 to 3785.4 m3
the future for our pump
turn the pump
Bill Aitken was making cannons for the Second World War before he discovered a love of pumps and has never looked back. Bill reflects on his life in the pump industry and shares his thoughts on what the future holds for the industry.
NSW irrigators can apply for a share of $111 million in funding to upgrade their farm water infrastructure through Round Seven of the Sustaining the Basin Irrigated Farm Modernisation program.
Deputy Prime Minister and Minister for Agriculture and Water Resources, Barnaby Joyce, and NSW Minister for Primary Industries, Niall Blair, said the program would help irrigators modernise their on-farm infrastructure and improve their water use efficiency.
“Under this program, irrigators are able to implement infrastructure improvements that deliver real benefits at the farmgate like greater flexibility in crop choice, increased yields and the ability to produce a larger crop from lower water allocations,” Mr Joyce said.
“More than $9.5 million was invested in projects under Round Six of the program, including works to upgrade
and reconfigure water storages and install new infrastructure such as pump stations and lateral move irrigation systems.
“These projects are expected to generate more than 2,960ML in water savings — of which more than 700ML will be retained by irrigators, and the remainder used to support positive environmental outcomes in the Basin.
Mr Joyce said building better infrastructure is at the core of a productive and healthy Murray-Darling Basin, and the government is making an average of $2.5 million available each day for infrastructure upgrades to support agricultural productivity and profitability, strong communities and healthy ecosystems across the Basin.
Minister Blair said Round Seven of the program would focus on the NSW Border River, Lower Namoi and BarwonDarling catchments.
“We’ve listened to feedback from irrigators in these catchments and under this round of the program we will be releasing indicative prices for entitlements, so irrigators can have greater confidence in planning and costing their project proposals,” Mr Blair said.
“We have also responded to requests from irrigators for greater flexibility when it comes to their project contribution and participants will now have the option of offering water entitlements instead of cash as their contribution to the project — although there will be no obligation to do so.
“Irrigators can also apply for up to $2,000 to use towards an Irrigated Farm Water Use Efficiency Assessment to help them identify areas of inefficiency and bring lost water back into productive use.”
Construction has begun on MidCoast Water’s $1.2 million water recycling project which includes modifications to the Gloucester Sewage Treatment Plant.
The project is designed to meet conditions imposed by the Environmental Protection Agency (EPA) and will see approximately 98 million litres of treated recycled water used for agricultural recycling each year.
As well as the sewage treatment plant modifications, the project will also include the installation of an irrigation system on a nearby agricultural area.
Once operational, which is expected to occur by September, the recycling scheme will reduce the amount of treated water released to the Gloucester River.
MidCoast Water is also working on an upgrade to the Gloucester Water Treatment Plant, with more than half a million dollars to be invested in the facility.
The work will deliver an automated modern treatment facility for the residents of Gloucester and Barrington.
Improvements to be undertaken as part of the $800,000 upgrade include
the replacement or renewal of aged and failing mechanical equipment, installation of automatic online water quality analysers and replacement of some electrical equipment.
Work is currently focusing on upgrading the plant’s chemical dosing systems and several building modifications to improve work health and safety outcomes.
MidCoast Water General Manager, Ken Gouldthorp, said “The Gloucester water treatment plant was originally built back in the late 1930s/early 1940s and was last upgraded in the 1980s.
“As a result, the infrastructure in the scheme is ageing and experiencing issues and this can impact on the levels of service we can provide to our Gloucester and Barrington customers.”
Mr Gouldthorp said over the last few months a number of improvements have been made at the plant, including the completion of a new pump station and access platform and repairs to a number of operational areas of the plant.
“The upgrade will improve the service Gloucester customers receive, and importantly, automating the process
will increase our ability to monitor water quality and initiate alarms and shutdown procedures when required.”
The project is expected to be completed by mid-August 2016.
TransGrid has awarded a contract for the replacement of its Metrogrid tunnel pump and rising main.
NSW company Prime Water Australia has been named the contractor for TransGrid’s tunnel rising main and pump replacement project.
The project will be completed by June 2016 and the estimated value is $328,000.
Two water authorities are working together to connect more than 370 properties to a new reticulated pressure sewer system, with the 200th in-ground pressure sewer pump unit having just been installed.
South East Water has teamed up with South Gippsland Water for the Poowong, Loch and Nyora Sewer Scheme, which will benefit properties across the three South Gippsland townships.
The project aims to tackle the growing public health and environmental problems caused by failing septic systems.
Under the partnership, South Gippsland Water is responsible for the overall funding, as well as defining the scope and project requirements, and managing community and customer engagement.
to its customers ahead of time and at significantly less cost than a traditional gravity sewer network.
The sewer scheme involves the installation of a pressure sewer pump in a small storage tank at each house, which connects to a reticulated network.
Central to the design is a remote control telemetry system, called OneBox, which is designed and developed by South East Water.
OneBox manages property connections on a real time basis, regulating flows of waste into the network to optimise capacity.
Its ability to smooth peak flows means that pipes across the network can be much smaller, and aided by horizontal directional drilling, the need for expensive and large-scale excavation is eliminated.
pumps are one of the dynamic leaders in pump technology, built in Australia and sold across the globe. Heavy duty multistage Turbine Pumps for deep well applications are available in cast iron or cast stainless steel in sizes up to 750mm diameter.
The Flo-Max range also includes single stage split case or end suction centrifugal pumps.
Dynapumps can engineer a dynamic pump solution to meet every requirement. Our tailored pump packages can be found in all types of bores, dams and rivers. specialise in all aspects of Irrigation and SUBMERSIBLE
In the Winter 2016 issue of Pump Industry, we’ll be including a wall chart which outlines key pump types used in verticals across the country.
The full-colour wall chart will be an indispensable reference tool for pump end users, outlining pump types, their key capabilities and applications, and the considerations users need to take into account when choosing a pump type. The chart will also feature highquality images and illustrations of the pump types featured.
The Pump Industry pump guide wall chart will be displayed on the walls of end users across Australia, and will
become the industry’s easy reference for pump selection. Pump categories to be featured include:
• Dewatering
• Irrigation
• Water
• Wastewater
• Minerals processing
• Hydrocarbon processing
• HVAC
• Industrial/manufacturing
The pump guide wall chart will also
feature a limited number of advertising spaces for interested parties. Whether you’re a manufacturer, importer, supplier, or someone who provides services to pump end users, the wall chart is a prime opportunity to get yourself in front of your customers, day in, day out. Associating yourself with this high quality reference tool shows your customers you’re someone they can rely on.
If you’re interested in booking a space on the wall chart, contact the team at Pump Industry on 03 9440 5721.
Irrigation Australia has appointed its new CEO to lead the organisation and enhance its value and effectiveness, on behalf of its members.
After an extensive recruitment process, Bryan Ward was appointed CEO and commenced in the role on March 14.
For the past nine years Mr Ward has been the General Manager of Think Water, a franchised network of irrigation and pumping businesses across Australia and New Zealand.
Prior to Think Water, Mr Ward has had a long career in the meat and dairy industries in roles at GM and CEO level.
Mr Ward also has experience with industry associations, including the Australian Dairy Corporation, the Tasmanian Dairy Industry Authority and the New Zealand Meat Industry Association.
Australia has had its own pump test code since 1931, which has helped to guide the industry for almost a century. However the future of the code – which hasn’t been updated since 2001 – is somewhat uncertain.
Australia’s pump test code originated as ASCB9 and the first AS2417 code was published in 1980. This 1980s edition, in three parts, was based on the British code ruling at the time. Our current 2001 edition of AS2417 is actually a direct text adoption of the ISO Standard ISO 9906:1999
At the time of writing, Standards Australia has advised on their website that all standards older than ten years have been listed, with a view to deleting them. AS2417-2001 obviously fits this category and thus has a very high possibility of being deleted, especially as it’s not a statute requirement of the National Construction Code.
In Australia, AS2417-2001 has been and still is the prominent pump test code for clients purchasing pumps for most water supply, water treatment works, fire protection pumps and similar applications where a guaranteed performance is critical.
The major importance of a pump test Standard for a user is the guarantee that a pump performance will be within a particular tolerance range for their requirement. Performance parameters are flow rate, generated head, speed, and the power required for a specified flow rate and head. Finally, the pump efficiency is a calculated value from the power absorbed.
A manufacturer’s published pump performance indicates all the parameters, and in most cases, includes a note advising the particular standard that the pump is guaranteed to meet.
For the pump industry, the test tolerances of a pump’s performance are the major issue that purchasers and suppliers concern themselves with.
Currently AS2417-2001 (ISO9906-1999) provides the following test tolerances for a pump:
Acceptance
Grade Grade 1 Grade 2 Series
Annex A
Flow Rate +/-4.5% +/-8% +/-9%
Head +/-3% +/-5% +/-7%
Power
Absorbed – –+9%
Efficiency -3% -5% -7%
Purchasers should be aware that most pump suppliers guarantee their standard general purpose pumps to meet the tolerance “Series or as per Annex A”.
To illustrate this, a manufacturer supplying a pump to provide a flow rate of 100L/s at 100m head will guarantee to supply a pump that will have a minimum flow rate of 91L/s at 100m or up to 109L/s at 100m. Alternatively, the pump may deliver a minimum head of 93m at 100L/s or a maximum head of 107m at a flow rate of 100L/s.
Unfortunately, many specifiers do not realise that just because the pump has a guaranteed performance, it still may not meet their minimum performance criteria because of the allowable tolerance.
It is logical that as the current AS2417 is a complete take up of the ISO9906-1999 edition, then perhaps Standards should update to the current ISO9906-2012 edition.
ISO9906-2012
Examination of the table:
1. Three tolerance grades remain in each standard, although the previous “Annex A” is now designated as “Grade 3”.
2. All tolerance values are identical apart from the Grade 1 flow rate that has been increased from +/- 4.5% to +/-5%.
3. An additional “Acceptance Grade” now provides a “Unilateral” acceptance grade.
4. Guarantee requirements are now clearly indicated as “Mandatory” or “Optional”. This was not as clearly indicated in AS2417-2001.
The Unilateral Acceptance Grades are a very interesting development. Essentially, these grades require that for a specified pump (a very important point) to meet 1U or 2U tolerances, it must meet the specified performance without a negative tolerance being applied. Only a positive tolerance is acceptable.
A negative side of this is that the power now has a very large positive tolerance. It will be interesting to see how purchasers and pump suppliers will address this issue, as the cost of the driving electric motor or diesel engine is a major cost item, both from a capital and operating point of view. I suspect the clever purchaser will nominate an efficiency to be achieved rather than power.
ISO is essentially a European and British standard. However, Australian industries, based on American technology or American-owned companies, have tended to nominate American-based test codes as their Standard here in Australia. The oil and gas industry is a typical user of American pump standards.
So what is the current American standard? The Standard is known as ANSI/HI 14.6-2011 Rotodynamic Pumps for Hydraulic Performance Tests.
The major point of interest of this standard is its foreword which states “It is in harmony with revised ISO9906…this means that users in all parts of the world…when specifying a pump hydraulic performance acceptance test, will be working with identical technical requirements and acceptance grades.” Further investigation confirms that ISO9906-2012 and ANSI/ HI 14.6-2011 are virtually identical in their content.
The Australian pump industry, its suppliers and its consumers need to take action to ensure they are not being left behind, or indeed more confused with the requirements in the future.
SERVICING ALL MAKES AND MODELS OF PUMPS AND CONTROL CIRCUITS
• Pumping problems resolved from 0.5kW up to 500kW
• Written report provided
• Service and repair of any pump product in-house
• Programmed service and maintenance calls
• Service vehicles carry extensive range of stock
• Workmanship guarantee
KELAIR SERVICE CAN PROVIDE
• Breakdown service
• Routine preventative maintenance
• Reverse engineering manufacture
• Engineering / Spare parts / Machining
• Commissioning and installations
The ever-present tension between price and quality is currently well and truly at the forefront of daily negotiations and thought processes, and the whole idea of achieving the best value proposition has never been more complex.
For such an old and simple technology, the induction motor can still be the basis of difficulties and confusion when making the best choice for any given application or project.
In simple terms, the issues relating to electric motors can be listed under four subgroups: electrical, mechanical, environmental, and certification and compliance, and within each of these categories, there are plenty of traps to fall victim to.
For a device that is commonly designed to operate for 15 to 20 years, and in many cases lasts much longer, the initial purchase decision can have significant cost consequences – both good and bad – for the end user.
Good choices for “future-proofing” a product with such a long service life are not only important for total-costof-ownership calculations impacted by reliability and efficiency levels, but are also critical for one of the most overlooked aspects not often considered: asset value.
Asset value, to be measured at any future moment in time through contemporary metrics, is something that management boards (and owners) are certainly aware of and are critically interested in. A typical demand from board level is: “We want all our operating
assets to be high quality, contemporary, efficient, and reliable.” But how is this playing out in current market conditions?
The term future-proof refers to the ability of an item to continue to be of value into the distant future, and not become obsolete. In a time when industrial design, environmental, and workplace health and safety trends are so dynamic, it’s not hard to envisage the many traps that await anyone who doesn’t put some serious thought into the purchasing of products that are generally expected to have such a long operational life.
A motor’s running costs over a three to six month period can easily equate to its purchase price. Imagine if your car had those running cost proportions! You would certainly be taking some time to think about the critical performance features of that car you were buying, and yet that is the exact situation in regards to electric motors.
We all know the adage “you get what you paid for,” and while there may be some doubts as to whether this really does apply to motors these days, the fact remains: staying at the leading edge of design, manufacturing, and compliance, on all aspects of electrical and mechanical features, requires investment which does show through
on the finished product, and its installed performance and reliability.
In today’s economic climate where the focus and pressure is on all “Capex” and “Opex,” the temptation is to forego all those sales features and simply look at that bottom line price. But at what long-term cost to the client?
Without consideration, many companies are simply driving price down to the lowest possible level, and taking their eye off the longer-term consequences.
With new efficiency standards proposed just around the corner (2018) and those inherent qualities that produce long-term reliability appearing to be easily and quickly undervalued, just what asset value will many of these end users end up with in a few years time?
The comparable cost between having a high efficiency, quiet, and highly reliable motor, compared to the cheapest available, is not that great, and the difference is easily made up through either energy running costs or a few hours of maintenance during repair, or early replacement.
Asset value, running costs, and longterm peace of mind – I suggest they’re the points that should be discussed with all your customers as you promote your brand and unique value proposition.
Multiphase DAF pumps provide asset owners with a simple and easy-to-use system which can replace a range of existing equipment, leading to significant savings in maintenance costs and increased energy efficiency.
A single dissolved air floatation (DAF) pump is able to replace the entire air bubble system on DAF plants, according to authorised distributor Hydro Innovations. Their EDUR® multiphase pumps draw in air through a snorkel in the suction line, shear the air, then feed it into the DAF plant, producing a discharge stream into the tank that is saturated with 30 to 50 micron air bubbles.
Conventional DAF systems normally consist of a wastewater tank, compressor, air saturation vessel and effluent pump. The effluent pump draws effluent from the tank and pumps it into the air saturation vessel. A compressor pumps air into this same vessel. The air/water mixture is saturated under pressure, then released back into the wastewater tank at atmospheric pressure, where tiny bubbles form and adhere to the suspended matter (fats, oils and other small wastewater particles). The bubbles (with their attached suspended matter) float to the surface of the tank, where floatables can be skimmed off the surface.
By using EDUR multiphase pump technology, asset owners can replace the compressor, air saturation (pressure) vessel, control system and multistage pump with a single pump that can replicate or improve the performance of the conventional system. The EDUR pump is set up the same as a conventional pump, to draw liquid from the clean side of the DAF tank, but it also draws atmospheric air into its suction line instead of using a compressor for this task. Standard pumps are not capable of handling air this way. The air is mixed with the water as it moves through the pump, and the air goes into solution as it is saturated under pressure.
The EDUR multiphase DAF pump greatly simplifies the system, and
because of this, capital costs and maintenance costs can be greatly reduced. No compressor to maintain and no pressure vessel to maintain and certify. There is also an energy saving, because there is no longer a running compressor.
EDUR multiphase pumps can deliver flows from 1l/s (for smaller DAF plants) to 15l/s (which cater for wastewater inflows of up to 150l/s with a single pump, or use multiple pumps if flows are higher) and produce pressures to 12Bar. A variety
More
of materials and seal arrangements enable EDUR pumps to operate in a very wide range of applications. Available materials include ductile iron, gunmetal bronze, stainless steel and super duplex. Mechanical seals are available as balanced, double and tandem.
When Australian Pump Industries was appointed as exclusive distributor for Tsurumi Pumps, their first job was to build up stock within the territory. Improving availability is just as fundamental as sensible pricing.
The company invested heavily but even now, four years later, Australian Pump Industries (also known as Aussie Pumps) has trouble keeping up with the surge.
“One of the issues we face is the complexity of the product range and the wide scope of applications for Tsurumi products,” said Australian Pumps’ Product Manager Neil Bennett. “Just when we think we’ve got a market covered, we find that the accelerating demand wipes us out of stock.”
Lead times for Tsurumi’s factories are typical of any well-organised Japanese manufacturing operation. Three to four months is not unusual, with the company carefully planning its production to make sure that both quality and economies of scale are observed.
“We’ve air-freighted big LH pumps for mining applications. We understand that this is just another investment that has to be made in building Tsurumi’s market share in Australia,” Mr Bennett said.
Australian Pumps buys its single phase Tsurumi pumps in 40ft high cube containers. That equates to around 1,400 pumps per shipment, across a range of top quality Tsurumi equipment for septic tanks, dewatering, drainage and residue pumping.
Tsurumi’s range of dewatering pumps is possibly the biggest in the world.
The products include the threephase heavy duty cast iron KTZ series, some models of which now come with automatic level control electrodes fitted as standard equipment.
There are 22 KTZ series dewatering pumps in the product range, from 1.5kW all the way through to 11kW. Their performance makes them suitable for virtually any dewatering, tunnelling or drainage well application.
4 pole super heavy duty
Tsurumi’s 4 pole KRS series of high flow pumps extend from 3 inch submersibles up to 8 inch pumps with flows of up to 12,000 litres per minute. All feature Tsurumi’s anti-wicking cable entry, thermal motor protector and double silicone mechanical seal in oil chamber.
Tsurumi NKZ series, heavy duty sand pumps, and GPN pumps, extreme duty sand pumps, add another two ranges of product. The GSZ series, 4 and 6 pole motor driven pumps, are designed for draining sand laden water, slurry in cement plants, quarries or mines or heavy duty wastewater treatment plant applications.
“You can understand the dilemma. With such a huge product range, despite a willingness to invest, we still aren’t covering all the market,” said Mr Bennett. “Sewage pumps, cutter pumps, grinders and the huge range of Tsurumi aerators and water treatment equipment make it even more complex.
“Yes, we are following the 80/20 rule,
but frankly, the rule keeps changing as the market learns more about Tsurumi and we learn more about the market.”
Pump Bank to the rescue
Australian Pumps has established master distributors around the country with excellent stocks of fast moving Tsurumi models, suitable for immediate shipment.
“Spreading product around the country has certainly alleviated the load,” said Mr Bennett. “But we still needed more help.”
Understanding the challenge of having to carry such a huge product range while the market is being built, Tsurumi elected to take the unprecedented and unorthodox step of backing up Australian Pumps with a Japanese-based and organised “Pump Bank”.
The Pump Bank carries thousands of pumps, including up to 2,000 or more KTZ series dewatering pumps, huge sand and slurry pumps and even 8 inch 110kW dewatering pumps.
Wastewater pumps are also covered with up to 1,000 B series channel impeller pumps, and hundreds of Tsurumi’s hugely successful cutter pump range.
Australian Pump feels that the pressure is still on to carry big stocks locally. Sea-freighting from Japan takes up to four weeks so the Pump Bank
acts as a kind of buffer stock. Australian Pumps works on a long lead time, forward order program, but can draw on the Pump Bank for top up stocks where needed.
“The Pump Bank started six months ago and has saved our bacon on a number of occasions,” said Mr Bennett. “One of the downsides is that it is ‘first come first served’ so what’s in stock today may not necessarily be there in one or two days’ time.”
Tsurumi’s Pump Bank isn’t just available to Australian Pump Industries. It’s become a hugely successful investment in providing distributors around the world with a unique advantage.
“Working with Tsurumi is a great privilege,” said Mr Bennett. “They’ve made the evolution from manufacturer to international submersible pump leader,” he said.
The attitude of being prepared to invest to support the market is symbolic of Tsurumi’s commitment to its customers throughout the world. In
Tsurumi’s GPN series are serious 4 pole extreme duty sand pumps with hi chrome wearing parts.
the South Pacific, Australian Pump has made huge inroads into a wide range of markets by pushing Tsurumi’s quality, performance and value for money. The big challenge has been availability. With Tsurumi’s Pump Bank, the way forward is clear.
For further information, including copies of the brand new Tsurumi Selection Guide, contact Tess Sheslow at Australian Pump Industries or visit www.aussiepumps.com.au.
Supreme features coupled with excellent performance have resulted in Shakti solar pumps making a distinctive mark in the pump market around the world.
Available in the range of 0.37-75kW, Shakti solar pumps offer 40 per cent more discharge as compared to other pumps. This makes Shakti Pumps a leader in the solar pump market.
Shakti Pumps has always been a pioneer in state-of-arttechnology, and has designed its solar pump sets based on its signature fabricated technology for the best discharge and value for money.
This technology is independent of electricity and diesel, so people at remote locations can enjoy the benefit of a Shakti solar pump. Agricultural users can enhance their cropping area with regular water supply through these pumps.
Being solar powered, users are able to avoid the downtime that can be associated with load sharing and interrupted supply. Solar pumps are also free from problems like feeder damage, supply cuts and rate hikes.
It has been noted that as a result of voltage fluctuations, some motors can get burnt out, requiring costly and timely repairs. With solar pumps this is not the case; and Shakti solar pumps are able to generate constant, high quality energy which can enhance the life of pumps by up to 25 years.
Shakti has aimed to create the best quality products,
utilising the latest technology at an affordable price, so that customers with a range of different budgets can enjoy the performance of Shakti products.
Shakti solar pumps are specially designed with the latest technology, lowering the risk of damage and protecting them from unfavourable conditions. Shakti solar panels are made of tempered glass, which is extremely durable – a crack in tempered glass will not impede the solar cells from working properly.
Shakti solar pumps:
• Are India’s largest manufacturer and exporter of solar pumps
• Feature proven motor, pump and motor control and solar PV maximum power point technology for reliable and fail safe operation
• Offer supply, installation and commissioning turnkey capability for solar pumps, either directly or through channel partners
• Are easy to operate, simple to install, require no maintenance, and offer value for money and attractive paybacks.
AllightSykes introduces a new, whisper-quiet range of pumps designed for urban and other project sites where noise can be a problem.
The new range of Sykes Quiet Solution (QSM) pumps has been designed to comply with the stringent noise output regulations governing work sites and urban areas.
The QSM range has a noise level output of 67dBA at 7m and features impact resistant polyethylene panels, roof, vents and doors.
The steel bunded chassis features a single point lift eye, fork tynes and houses the 345 litre polyethylene fuel tank.
Group Product Manager Chris O’Brien said “The QSM range incorporates both the strength of the QS Steel canopies, and the new-age look of the Yakka polyethylene non-corrosive panels.”
The QSM can be easily bolted to a galvanised skid or a road registerable dual axle trailer, and incorporates suction hose storage racks and a layflat discharge hose storage bin.
Key features include:
• Impact resistant polyethylene panels, roof, vents and doors
• Panels easily removed for maintenance
• 67dBA at 7m
• Single point lift frame
• Steel bunded chassis
• Fork tynes
• 345 litre polyethylene fuel tank
• Emergency stops on each side
• Lockable door handles
• Vertical or underslung discharge
• Lightweight
• Custom colours available for multiple orders (more than five).
The QSM is designed to accept the following Sykes Pump models:
• CP100i
• CP150iC
• CP150i
• CP220i
• CP250i
• MH130i
• MH150i
• HH80
• WD100i Wellpoint Pump
• WD150iC Wellpoint Pump.
Our continuous exposure to a wide range of problems and Industrial applications across numerous markets, has ensured we have the know how to handle pump repairs of all sizes and complexities, including re-engineering, testing, laser alignment and condition monitoring.
With each repair job we implement a thorough inspection process and follow strong control and stringent acceptance criteria carried out by a team dedicated to keeping your pump working at optimal performance.
Hire
Link Pumps has been servicing the needs of Australian Industry with pump hire solutions for over 50 years, and as such has built a reputation for being able to solve complex engineering problems and additionally undertake complex setups with complete reliability notwithstanding working to the exacting standards of environmental and occupational health and safety expected by that of our customers and regulatory authorities.
For all your Pump Hire and Repair needs you can’t go past Link Pumps, so call us now…. We perform, Anytime, Anywhere
Techtop Australia is proud to introduce you to the Varvel range of gearmotors. It is a strategic partnership which extends the global alliance of the two brands.
Techtop Australia is proud to introduce you to the Varvel range of gearmotors. It is a strategic partnership which extends the global alliance of the two brands.
Techtop Australia is proud to introduce you to the Varvel range of gearmotors. It is a strategic partnership which extends the global alliance of the two brands.
Techtop Australia is proud to introduce you to the Varvel range of gearmotors. It is a strategic partnership which extends the global alliance of the two
With Techtop motors and Varvel gearboxes working together on product lines, you can be sure there is the right pairing for your particular requirements.
With Techtop motors and Varvel gearboxes working together on product lines, you can be sure there is the right pairing for your particular
With Techtop motors and Varvel gearboxes working together on product lines, you can be sure there is the right pairing for your particular requirements.
With Techtop motors and Varvel gearboxes working together on product lines, you can be sure there is the right pairing for your particular
Gaine
Dandenong Sth VIC 3175 Australia
+61 (0) 3 9753 2222
+61 (0) 3 8692 6670
(0) 7
(0) 7
The pump industry relies on expertise from a large and varied range of specialists, from experts in particular pump types to those with an intimate understanding of pump reliability; and from researchers who delve into the particulars of pump curves to experts in pump efficiency. To draw upon the wealth of expert knowledge the Australian pump industry has to offer, Pump Industry has established a panel of experts to answer all your pumping questions.
Our progressive cavity pump expert is Peter Vila, Managing Director of SEEPEX Australia. Peter has been involved with pumps for 35 years. He spent the first five years repairing them and the subsequent 30 years directly in technical sales, and for the past 15 years he has been predominately involved with SEEPEX progressive cavity pumps.
We often hear that progressive cavity pumps are of the positive displacement variety. Does this mean they are well-suited to dosing and metering applications?
Most certainly yes. Progressive cavity style metering pumps have highly repeatable accuracy. They can be used in virtually all industries for metering and dosing precise quantities. They are particularly good for minimal pulsation conveying of thin to high viscosity fluids, as well as corrosive media containing solids, all with minimal pulsation and to the exact drop.
Progressive cavity metering pumps can be used for applications in agriculture, automotive assembly, bakeries, building products, ceramics, chemical and biochemical processing, coating kitchens, stock preparation and de-inking in paper mills, confectioneries, dairies, distilleries, dye and ink plants, fruit and vegetable processing, pharmaceuticals, cosmetics and personal care products, poultry, meat and fish processing, oil, gas and petrochemicals, shipbuilding, sewage sludge dewatering, wastewater treatment, water purification, wineries, wood treatment and fabrication.
Typical progressive cavity metering pump
Popular features:
• Simple interchangeability due to modular construction
• Infinite turndown
• Minimal pulsation, no pulsation dampers required
• Constant flow, independent of pressure
• Low shear characteristics
• High metering accuracy
• Valveless flow control
• No check valves, no gas locking or blocking by solids
• Drive options and control systems available that allow user-friendly metering applications.
Performance range:
• Conveying capacity: 0.06 l/h–1,000 l/h (0.016–264 USGPH)
• Pressure: up to 24bar (360psi)
Progressive cavity metering pump with an integrated programmable drive
Common applications:
Filler Feeding
Volumetric fillers such as those used in the food industry to fill bottles, cans or cups have tanks above piston-actuated filling devices. The levels in the tank need to be maintained and are usually measured with capacitance probes that output a 4-20 mA signal. In combination with a programmable integrated drive, PC pumps can be used to maintain a proper level in the supply tank, without requiring a separate controller or electrical panel.
Sodium hypochlorite (NaOCl) can be reliably injected into the discharge of a vertical turbine pump, in a water well, to increase the chlorine contact time for more positive disinfection. PC pumps with a programmable integrated drive can follow the signal from a flow meter, on the discharge of the centrifugal pump, to maintain the proper dosage in ppm of chlorine.
Liquid injection into extruders.
Extruders are commonly used to form a variety of shapes in the manufacturing of breakfast cereals, dry pet food and certain snack products. PC pumps with a programmable integrated drive can be used in conjunction with a PLC to inject liquids or dyes and change the colour of these products continuously, without a system shutdown. They can also be used to inject vitamins, oils, syrups or other liquids.
Extruder injection.
By using two PC pumps with an integrated programmable drive, the pH of a process or waste stream can be controlled. A standard program is used and the pumps are controlled by a PLC that defines one pump handling alkaline to increase its speed as the pH drops, or the other pump handling an acid to increase its speed as the pH climbs. By using PC pumps with an integrated programmable drive, users can significantly reduce the installation time and cost because they do not need remote panels.
pH control.
Other applications:
• Boundary layer injection
• Multiple component blending
• Extruder injection of colours, vitamins or minerals
• Release agents, creping agents, colours and other paper chemicals
• High fructose corn syrup
• Alpha and beta amylase in corn processing
• Any enzyme
• Liquid fertilisers or herbicides into a centre pivot irrigation system
• Scents and flavours into any food product, even tobacco
• Filter aids like diatomaceous earth for cold filtered beer
• Polymer flocculants and ferric chloride
• Water treatment chemicals of any type
• Spray applications like spray dryers or flavoured coatings for snack foods because of the non-pulsating flow.
When Yarra Valley Water needed a solution to continue supplying water to homes while they upgraded their pipeline infrastructure, they found an innovative partner in Crusader Hose.
Yarra Valley Water (YVW) is engaged in a steady program of regular maintenance works for the water distribution pipelines that supply the residents in their catchment areas. Some of these pipes are over 100 years old and are cracked and leaking.
When the utility identifies water mains that need servicing or relining, it is important that the works are carried out efficiently and effectively. For YVW, it’s also important that their customers are not inconvenienced by being left without water while maintenance works are underway.
YVW teamed up with Crusader Hose to develop a solution to the challenge of continuing potable water supply into homes during upgrades. The solution involves using Crusader’s range of flexible hose, Waterlord, to connect residents to their water source.
YVW were looking for a better way to provide customers continuous access to potable water while mains upgrades were being carried out. Previously, the utility would disconnect affected homes in the morning and reconnect them in the evening, causing inconvenience to customers, who were left without water for a significant portion of each day.
For the utility itself, it was also an inefficient use of staff time, with hours spent each day suspending refurbishment works in order to reconnect homes. As a result, only short sections could be undertaken and costly diggings were carried out daily. These maintenance works were taking longer and longer to complete.
When YVW approached Crusader Hose, they were looking for a solution which would save them man hours
SEEPEX Smart Conveying Technology extends the life of your stator. Adjustment of the retaining segments takes just 2 minutes and restores 100% pump performance.
Tests have shown up to 3x stator life compared to conventional progressive cavity pump design Join the smart revolution and test our innovation “Smart Conveying Technology”.
SEEPEX Australia Pty. Ltd. Tel +61.2.4355 4500 pvila@seepex.com www.seepex.com
The Pureline system uses Waterlord 300 series hose to create a temporary water bypass.
plus result in improved outcomes for customers.
Together, YVW and Crusader Hose developed the Pureline system, using the Waterlord 300 series hose to create a temporary water bypass. Customers along the street for up to 2km, are connected to a potable bypass hose so that works can proceed on the damaged pipeline in question without interrupting household supply.
“This bypass system incorporates T fittings at 9m intervals so that there is a point from which to feed into each household,” said Crusader Hose Managing Director Francois Steverlynck.
Once set up and connected, the innovative system can provide residents with an uninterrupted potable water supply for weeks at a time. In turn, this
allows maintenance works to proceed without the interruption or downtime required to disconnect and reconnect residential supplies at the beginning and end of each day.
The Pureline system is compact and easy to handle and install, giving YVW contractors the ability to set up within hours.
Thanks to the practical Pureline solution, customers are happy, and the utility is saving time and money win-win across the board.
Choosing the size of a pump discharge pipe can be a complicated process, with a range of factors to consider. Ray Hardee shares his insights into how choosing the right size discharge pipe can reduce operating time and costs.
Iwas teaching a Piping System Fundamentals course at an open pit copper mine and mill in the south-western United States. During my introduction I stressed the importance of understanding how the individual items of a piping system work together. I then went around the room asking each attendee what they did at the facility and what they hoped to get out of the course. Each attendee had a specific topic of interest and I remember the dewatering engineer saying his goal was to improve the operation of the dewatering pumps.
Being that the mine was in the desert, I asked him how big the pumps were. He mentioned they were mounted on a semitrailer so they could be moved around the mine, along with a second semi for the diesel electric power supply. Even though they were in the desert, all the rainfall would run off the ground resulting in flash floods that could quickly collect in the mine causing a disruption in production.
During the course of the training, when I discussed system static head, I made a point that the static head of the dewatering system amounted to the difference in elevation between the water level at the bottom of the mine, to the elevation of the end of the discharge piping.
When we covered the material on pipeline sizing, the dewatering engineer asked why we needed to perform this calculation. He said his rule of thumb was to size the discharge pipe to that of the pump’s discharge flange. For example, if the pump’s discharge nozzle was 150mm, he would use a 150mm nominal size pipe for his discharge header. In this article we’ll discuss why his rule of thumb may be costly.
A piping system is made of three elements: the pump elements, adding all the fluid energy; the process elements, making the product or providing the service; and the control elements, improving the product quality. Figure 1 shows the system details.
In this example system the pump is an end suction design with a manufacturer’s identifier of 8x6-11, operating at 3,000rpm. The pump curve used in this example can be found in Figure 2. Based on the manufacturer’s information, the pump suction flange is eight inches in diameter (200mm) and the pump discharge flange is six inches in diameter (150mm), with the eleven inch (279mm) indicating the pump’s maximum impeller diameter.
The process elements consist of the supply tank, with a liquid level of zero metres above the common datum. The destination tank has a liquid level of 62m above the common datum. A short 350mm diameter pipeline serves as the pump’s suction line with insignificant head loss. The discharge pipe is
1,200m in length made of steel schedule 40 pipe. We will vary the pipe diameter to demonstrate how a change in the pipe diameter affects the flow rate through the system.
Finally, the control elements of the system consist simply of an on/off control for the pump. When the supply tank is pumped down, the pump shuts down to prevent the pump from running dry; when the supply tank is full the pump is turned on. As a result, all the energy supplied by the pump is used to move the fluid through the process elements.
Now that we have the three elements defined, let’s see how a change in the pipe diameter effects the flow rate through the system.
First we will look at the system with a 150mm nominal size discharge pipe. This is the same diameter as the discharge flange on our pump. The resulting flow rate through the system is 171.9m3/h, resulting in a head loss of 41.97m of fluid in the discharge pipeline. Adding the head loss of the pipeline with the system’s static head of 62m results in a head of 103.97m for the process and control. To check this result, we can see from the pump curve that a flow rate of 171.9m3/h through the pump results in a head of 104m. As we can see, the balanced flow rate through the system is such that the head produced by the pump is equal to the head consumed by the process and control elements.
Next we’ll calculate the power cost needed to pump 1,000m3 of water at 15°C through a 150mm pipe using Formula 1.
Where:
H = pump head in metres of fluid
ρ = fluid density in kg/m3 (999)
ηM = motor efficiency (.94)
ηP = pump efficiency (.48)
$/kWh = power cost per kWh (.20)
Table 1. How the system operates with various pipe diameters, along with the resulting cost in Australian dollars per 1,000m3 pumped.
From the table, you can see interaction between the various elements found in a fluid piping system. As you can see, as the pipe diameter increases, the head loss in the pipeline decreases along with the fluid velocity. With lower pipeline head loss in the larger pipe diameter, more of the pump’s energy can be used to move the fluid.
As the flow rate increases in the pump, the head produced by the pump decreases as demonstrated on the pump curve (Figure 2). We also notice changing the flow rate through the pump varies the pump efficiency.
Graph 1 shows how changing the nominal pipe diameter affects the pumping costs. As you can see from this graph, sizing the discharge pipeline to match the pumps discharge flange is not the most economical choice. The other item to point out is that the pumping cost per 1,000gpm decreases rapidly but the savings decrease with increasing pipe diameters.
Increasing the pipe diameter increases the construction cost of the pipeline. As a result, accurately optimising the system would require the calculation of both the construction costs and operating cost for each available nominal pipe size. This can become a tedious calculation and is best performed by specialised computer software.
Rather than performing a detailed cost optimisation for sizing pipelines, companies have developed piping specifications based on the process fluid being handled. These specifications have been developed over time, based upon the company’s needs and experiences. A chemical process plant will typically have many pipe specifications to handle the various process fluid they have, where an industrial plant may have a few specifications for the cooling fluids and
> Easily programmable to suit all pumping and irrigation applications
> Simple, intuitive controls mean you always know how your pump is performing
> Easy speed control of mechanical or electronic engines
> Remote monitoring and alarms from your smart phone or tablet
> Quickly disable failed sensors to ensure continued water supply to stock or crops
Graph 1. The pumping cost per 1,000m3 for pumped fluid for various nominal pipe diameters.
transporting fluids needed for the process.
The Crane Technical Paper 410, Flow of Fluids Through Valves, Fittings, and Pipe, provides recommended fluid velocities for general service applications, pump suctions, and municipal applications. The pipe fluid velocity range for general service applications is between 1.2 to 3m/s.
How do pump manufacturers arrive at a flange diameter?
After all this, you may ask why the pump manufacture doesn’t size the pump discharge flange for the recommended pipe diameter. There are a variety of reasons for this:
1. The larger the discharge flange, the greater the pump footprint. Since one of the major costs of the pump is the
pump case, a larger flange size would increase the size and cost of the pump.
2. The distance the fluid travels from the impeller tips to the discharge flange is short compared to the discharge piping. As a result, higher fluid velocities within the pump can be used because of the limited head loss due to the moving fluid and the stationary pump.
3. To minimise the number of castings required to meet their customers’ pumping needs, a manufacturer may trim the impeller, or design the pump to operate at various synchronous speeds. For example, the manufacturer supplying the pump in the system makes it available with impellers ranging from 229-279mm. In addition, the pump is available with both 1,500 and 1,000rpm drives. The variation in the pump impeller diameter and synchronous speed affect the flow rate through the pump.
Conclusion
As shown in this article, it is not the recommended practice to choose the pump discharge pipe based on the pump discharge flange size. As we saw in this application, sizing the pipe diameter to match pump discharge diameter resulted in a greater unit cost for pumping the process fluid. In addition, for this system, the smaller pipe diameter resulted in lower flow rates through the system.
As a result, by sizing the pipeline correctly, you can reduce not only your operating costs but also the time the pump needs to operate. In our mine dewatering example this would pump the mine out faster allowing the mine operation to return to normal quicker.
• Construction of Buildings, Dams & Harbour walls
• Long distance pumping applications (up to 4 km)
GOODWIN SUBMERSIBLE P UMPS INTRODUCE THE REVOLUTIONARY DIRTY
For further information
Call +61 (0)7 3205 7860 www.goodwinaustralia.com.au
• Agriculture - Irrigation / Centre Pivots, Dam Feeding
• Emergency and Environmental control
The Goodwin DWHH pump benefits from many of the Submersible Slurry Pumps unique advantages, making it one of the most versatile pumps in the world.
• Max solid content - 5%
• Max particle size - 10mm
• Max head - 130m
• Max submergence depth - 28m
SUBMERSIBLE SLURRY PUMPS FOR THE MOST DEMANDING ENVIRONMENTS
If you talk to any wastewater or sewerage field worker, they will tell you one of the most frustrating tasks they have to perform is retrieving submerged pumps from wells.
But a brand new device called the Platycat Snatcher Lifting Bell is giving wastewater workers a safer, quicker and simpler way to solve that messy problem – and that means big savings in time and money, but most importantly, big safety improvements for operators.
Traditionally, to retrieve a submerged pump, a worker had to manually guide a hook on a winch wire to attempt to hook it up to a non-standardised eye or loop on top of the pump. Depending on the situation, this could vary from an eye-bolt to a chain link, or even a simple piece of poly rope. Working at depth, the operator had to make the connection with the eye and hope the hook-up held while the pump was raised.
While each authority has its own safety regulations in place, in practice it is difficult to use a latched hook to lower the pump back to its pedestal, because of the difficulty of releasing the hook.
Enter the Platycat Snatcher Lifting Bell, an innovative solution to an old problem. It is in fact a two-part device; firstly, the bell-shaped lifting unit, and secondly, a custom-made tongue which is attached to the pump. The Platycat Snatcher Lifting Bell features a unique design which allows it to align itself to the custom-made tongue. So, no more peering down a dark hole, twisting and twirling a wire and hoping to make a
secure hook-up. The unique, patented design of the Platycat Snatcher Lifting Bell uses simple gravity to ensure that it hooks up every time.
The latching release mechanism has also been designed with safety in mind. When there is a load on the mechanism, it cannot be released. The only time the mechanism can be released is when the load is placed on a firm surface and the weight comes off the hook. This also applies when lowering the pump back down to its pedestal. The operator gives the wire a shake to ensure the seals are seated in and the job is done.
The Platycat Snatcher Lifting Bell has a solid industry-based background, invented by an Aussie wastewater worker who had enough of doing the ‘sewer well shuffle’. Knowing there had to be a better way, Joe Kearney toiled away in his back shed until he had a working prototype design.
Now, with further research and development, the Platycat Snatcher Lifting Bell is the latest in clever, innovative design, inspired by a need and realised through dedicated attention to detail.
The Platycat Snatcher Lifting Bell offers the triple bottom line for water and wastewater authorities; it offers a solution to an old problem which saves time and effort, thus saving costs. But most importantly, the
Platycat Snatcher Lifting Bell offers a significant improvement in safety for field operators, through less time near open wells, less chance of injury through a dropped pump and reduced risk of hand or finger injury. For example, a dropped pump could mean costly delays in getting compliant operators into a confined space, adding to the risk of workplace injury.
The Platycat Snatcher Lifting Bell is a below-hook accessory that can connect to any standard crane hook, so there is virtually no need to change existing operating procedures. It can be used with almost any type of crane, fixed or mobile, including winch trucks, hoists and lifting arms.
The Platycat Snatcher Lifting Bell was originally conceived for use in the wastewater industry but its unique design means it has applications across a wide range of industries. It is especially useful in confined and hazardous spaces, in dirty, dangerous or toxic situations, or any hostile environment that represents a risk of injury to workers.
The Platycat Snatcher Lifting Bell is precision-engineered, using industrial quality materials, and fully tested to meet A/NZ standards. It is important that buyers are not fooled by cheap imitations; Platycat Snatcher Lifting Bell needs no messy guide wires to operate.
For more information about the Platycat Snatcher Lifting Bell, head to www.futureinlifting.com or call 0455 941 419.
Previously unconnected parts of regional Victoria are being connected to Victoria’s water grid to provide water security to rural communities for the first time ever.
Victorian Premier Daniel Andrews joined Minister for Environment, Climate Change and Water Lisa Neville and Agriculture Minister Jaala Pulford in the Wedderburn district to announce that approximately 1,300km of pipelines will be built to link the West Waranga Channel with the Wimmera Mallee Pipeline.
Rural communities in south-west Loddon Shire are largely dependent on rainfall for their water supply, and after three years of drought conditions, many rural residents have been forced to cart water for stock and domestic purposes.
Under stage two of the South West Loddon Rural Water Supply Project, more than 260 farm businesses and 370 other rural properties will be connected to the grid, creating 134 jobs during and beyond construction.
The pipelines will deliver about 780 million litres of water to local
landholders and hydrants, and standpipes will be installed at strategic locations to improve water access for emergency services and residents.
The project is expected to cost about $80 million, which includes $40 million from the Labor Government and a $20 million contribution from Grampians Wimmera Mallee Water and landholders. The Commonwealth Government will also be asked to contribute.
Stage one of the South West Loddon Rural Water Supply Project was announced in November and includes building 40km of trunk pipelines and associated infrastructure such as hydrants and pump stations around Korong Vale, Wychitella, Buckrabanyule and Woosang.
In addition to these connections, the Coonooer Bridge peripheral pipeline extension project will connect properties in and around Coonooer
Bridge for the first time, including the township’s CFA station and community centre.
The $245,000 project will be jointly funded by the Labor Government and Grampians Wimmera Mallee Water, and will build around 8km of stock and domestic pipeline off the Wimmera Mallee Pipeline.
“The sheer number and complexity of the many pipelines that cart water around this state is mind-boggling,” said Daniel Andrews.
“By extending the Wimmera Mallee Pipeline, it will be able to reach more than 300,000 hectares currently left off the grid. That’s an area four times the size of Singapore.
“We will build an array of pipelines that – laid end to end – would almost be as long as New Zealand.
“Water is an asset - our whole state deserves to share it.”
According to Mr Andrews, communities around Loddon Shire have been doing it tough without reliable and secure access to water.
Stage two of this project will connect hundreds of properties in south-west Loddon Shire to the water grid for the first time ever, significantly increasing the region’s water security and helping local farming. For local families forced to cart water during dry conditions, this will save time and money.
According to Minister for Environment, Climate Change and Water Lisa Neville, stage two of the project will significantly lessen the impact of dry seasons on farm businesses and other rural properties.
“Connecting the West Waranga Channel and Wimmera Mallee Pipeline will mean a previously isolated water system will now give customers greater water security whilst still using existing water entitlements,” said Ms Neville.
Minister for Agriculture Jaala Pulford said “We are proud to deliver this project that will connect southwest Loddon Shire to Victoria’s water grid – it will benefit farmers, businesses and communities.”
Visit Sulzer at Ozwater’16, stand K11, Melbourne Convention and Exhibition Centre. Be eligible for a product trial to save energy and enter a draw to win a Sulzer pump handbook.
As the rags and solids in wastewater increase, you need innovation that keeps pumping stations problemfree. The submersible sewage pump type ABS XFP from Sulzer, with its versatile range of Contrablock Plus impellers, is insurance against downtime that’s easy to acquire.
The impellers’ superior rag handling and minimum free solids passage of 75 mm mean you spend far less time on troublesome pumping stations. Switching from an existing pump is easy, and you save energy immediately with the XFP’s premium-efficiency IE3 submersible motor – which Sulzer pioneered and provides as standard. Sulzer
Farmers in Moree, NSW, are able to run their irrigation bore pumps 24/7 while reducing their diesel usage, thanks to an innovative new off-grid solar–diesel hybrid power plant.
The solar-diesel hybrid power plant has been commissioned on a cotton farm in Moree. This power plant allows the cotton grower to pump high volumes of irrigation bore water, while reducing diesel consumption by up to 60 per cent.
Designed and built by YellowDot Energy (YDE), this hybrid solar-diesel power plant allows 24/7 operation of the irrigation bore pump with daily volumes of up to 4ML and an annual yield of 890ML. Innovative use of variable frequency drive (VFD) technology combines electricity from a diesel generator and solar PV. Over the course of a year, this site is projected to displace 60 per cent of the diesel consumption from the previous diesel engine direct drive pump.
The Moree power plant is designed around a proprietary electronic control system that includes a range of sensors, remote telematics and backup battery power. The grower can choose to operate seasonally between hybrid and a solar-only mode and can monitor and control the system remotely via an internet connection.
According to Glenn Clark, YDE Director, during growing season, farmers need to operate their bore pumps 24/7 – resulting in considerable expense. Many pumps will be dieselpowered, and the annual bill for diesel on a farm can be upwards of $1million.
“Pumps are a huge user of energy for farmers, especially those who need to pump bore water,” said Mr Clark.
“This translates into a significant cost for farmers. Often these pumps are powered by diesel engines, and during the peak cotton growing season between October and February, bore pumps are typically operating 24/7.”
After identifying the opportunity to provide farmers with considerable energy savings through a hybrid diesel-solar power source, YDE set about developing a prototype model. The process from idea to the recent deployment of the first model in Moree has taken about six years, but for Mr Clark and the farmers benefiting from the system, the wait has been worth it.
“The technology and commercial model has steadily evolved over the last six years. It has been a process of perfecting the design and providing the
best possible benefit to farmers.”
While solar-diesel hybrid power systems have been on the market for a while, they’ve traditionally been complicated and expensive, due to the large number of inverters required by the system.
The key difference YDE’s model offers is that it utilises a variable frequency drive (VFD), eliminating the need for solar inverters – significantly reducing the upfront capital cost for owners.
In the YDE model, power is injected directly into the VFD, a critical element for 24/7 pump systems.
Typically, the pump is powered by solar during the day and diesel overnight. The system is remotely monitored and controlled so users can change settings based on their own preferences – the system can quickly move to diesel power if it becomes too cloudy to operate on solar alone, allowing farmers to keep the water pumping with no downtime.
The system also features an advanced telemetry system, allowing users to keep up to date with the pump’s performance and to change the operation remotely. “Farmers are used to having telemetry with most of their modern equipment so we needed to be able to offer this feature,” noted Mr Clark.
According to Mr Clark, the process of retrofitting existing pumps to the solar-diesel hybrid model is relatively straightforward.
“We can retrofit almost any pump so that it’s powered by our new system, from line shaft to submersible pumps.”
And it’s not just farmers and irrigators who can benefit from this new system. YDE believes the solar-diesel hybrid system could be utilised in municipal
works, such as at wastewater treatment plants, and in the pumping of mains water.
“We believe we have developed an innovative technology that has multiple applications. When water is pumped there’s usually considerable expense – but also considerable opportunity for efficiency savings. Our solar/diesel power system has the potential to play an important role in helping to make pumping a more efficient process.”
According to Rob Mailler, YDE Chief Engineer, Australian farmers have a history of adopting new and innovative farm practices – a history which the new pump system responds to.
“We have developed a way to reduce production costs associated with diesel and engine maintenance. In addition, the system results in lower diesel consumption, which results in a lower extraction cost per ML of water. This lower cost allows an irrigator to expand their planting choices to crops that would not have been economically viable with diesel only pumping.”
KEY FEATURES
• Integrates power from solar PV and a diesel generator via a high capacity variable frequency drive
• Capable of operating 24/7 in hybrid mode or during daylight hours in solar-only mode
• Electronic control system manages the generator, PV, drive output and the hybrid integration
• DC optimised PV modules provide power control from the solar array
• Multiple sensors and modem communications provide monitoring and remote systems control
• Submersible three-phase electric pump.
PROJECTED OUTCOMES
• 890ML pumped per year – up to 4ML per day during peak season (hybrid) and up to 1.6ML per day off season (solar only)
• Annual diesel saving 40,760L which is a 60 per cent reduction on original diesel engine
• Operating 6am to 6pm has yielded actual results averaging under 15L of diesel per ML pumped
• Reduced annual maintenance costs.
Melbourne Convention Centre
May 10th-12th, 2016 Booth G23
Electric actuators for the water industry
Reliable, powerful, effi cient. AUMA offer a large portfolio of actuator and gearbox type ranges.
■ Automating all types of industrial valves
■ Integration into all commonly used control systems
■ High corrosion protection
■ Service worldwide
In North Queensland, an innovative farmer has teamed up with a group of suppliers to install the East Coast’s first megalitre per day false bore pump, powered entirely by the sun.
The story began in early 2015, when a property owner in North Queensland began investigating the possibility of solar electricity powering the residence and workers’ accommodation on his farm, which up until then was being fed by a single-wire earth return (SWER) powerline.
SWER powerlines are common in outback and regional areas of Queensland; but they have power limitations due to the single-wire return configuration.
The property owner arranged an initial site visit with Atlas Solar at his property outside Collinsville. The owner enquired about either solar powering an irrigation pump, which at that time was being powered by the SWER line, or using a mobile diesel-powered pump.
Both of these applications (as most owners will tell you) require lots of maintenance and lots of money to run.
“Solar power and solar pumps have been around for a long time, but mainly in small configurations for supplying water for stock, so it came as a bit of a shock when the owner said he wanted to pump 1.2 megalitres of water per day from a riverbed, up a 30 metre rise and then 1km to the holding dam,” said Matthew Beech of Atlas Solar.
“At first we didn’t know if it could be done,” said Mr Beech. “But we knew we could build any size solar system to meet any demand, and with the support from Supply Partners in Brisbane and ABB in Sydney, we came up with the perfect combination.
“Everything we did, from panel selection to power cable, was overengineered for this project. These systems will be built in extreme conditions and they need to last, this one was no exception. We have built this to last the owner twenty or more years,” said Mr Beech.
Working in partnership with CSWS Irrigation and Pumping in Toowoomba, who had a man on the ground in North Queensland and from the first site visit,
the team worked together towards the ambitious goal of building the first megalitre per day false bore pump, on the East Coast, powered entirely by the sun.
Many man hours went into engineering the components. The installation took about a week and was commissioned in early November 2015. Some fine tuning was required on the solar side, which now gives the owner up to ten hours of run time on clear days and four to five hours on cloudy days.
“It was an amazing feeling when the ABB pump drive was powered up for the first time and beautiful clear water was seen exiting the pipe nearly one kilometre away,” said Mr Beech.
“We believe that with the successful installation of this groundbreaking solar pump, we can offer irrigators the opportunity to power their operations efficiently and, more importantly, without another fuel bill.”
According to Mr Beech, the client for this project put in a monumental effort to assist in the completion of it. Sadly, the owner’s father, who was involved in the construction of the project, passed away shortly after the project was completed. The owner told Mr Beech that all his father wanted was to see the pump work. “He got his wish, and we thank him for it,” said Mr Beech.
Ef ficiency Impr ovement
Reconditioning
Restor e Clear ances
Re- Engineering
P f T ti erfor mance Testing.
Services available include:
• Inspection and trouble-shooting
• Case build up and re-machining
• Aillitfid bi Axial split case facing and reboring
• Axial thrust balancing
• Shaft and bearing API 610 upgrades
• Mechanical Seal upgrades to API 682
• Bearing housing & back cover retrofit
• Lube system upgrades
• Composite Wear Parts
• Tighter clearances
• Hydraulic Re-Rating
• Ridtti Rapid prototyping
• Driver upgrades (MEPS compliance)
• Baseplateadaptors and rebuilding
• Custom Spare Parts
• Rotating Element balancing
• ASME & AS1210 qualified Welding
• Hydrostatic Testing
• Performance Testing
• FFT Vibration analysis
Stage 3 of the South East Irrigation Scheme in Sorell, Tasmania, has recently commenced operation, and is set to increase much needed water capacity for agricultural land by 6,000ML. Pump Industry spoke with Paul Ellery, Senior Project Manager at Tasmanian Irrigation, to take a closer look at how the scheme was developed and exactly how it will benefit farmers and the community at large.
Floating the 950m section of pipe into place across the River Derwent.
During the 1980s, the push for a reliable water supply within the low rainfall rural districts north of Hobart brought the Sorell Irrigation Scheme into being. The area was favourable to the production of cool temperature crops such as lettuces and fruits, and lay within close proximity to population centres. A reliable water supply would allow the region to become an agricultural gold mine, providing a boost to the state’s economy.
The scheme has since been carried out in three stages, with the third and recently completed South East Stage 3,
increasing capacity to 6,000ML over two delivery periods.
Stage 1
The first stage of the scheme began in 1985 with the construction of the Craigbourne Dam, located on the Coal River. The dam was built to release 5,400ML per annum into the river, to make 3,500ML of water available to be pumped onto farms within the district.
Stage 2
Stage 2 involved extending the scheme, by pumping water from Richmond to Cambridge through underground pipes. Stage 2 was
completed in 1991 and supplemented in 2000-01 by the construction of the Daisy Banks Dam. This dam enabled water provided by Hobart Water to be linked into Stage 2.
According to Mr Ellery, reliability of supply was the focus for Stage 1. Stage 2 enabled farmers to grow a wider variety of agricultural produce.
“The region is low rainfall at around 500 to 600 millimetres per year, so before the scheme began, the area could only be used for sheep and cattle. Stage 2 allowed for the production of more intensive crops, and today
there are apricots, cherries and many vineyards within the area.
“A major player within the region is a lettuce growing company called Houston’s Farm, which is one of the largest agricultural producers in Tasmania. Without irrigation water, no fruit or vegetable production would have been possible.”
South East Stage 3 was commissioned in May 2015 and commenced operations in October 2015. The district now services agricultural, horticultural and viticultural enterprises around the townships of Tea Tree, Campania, Orielton, Pawleena, Penna, Sorell and Forcett. Water is sourced from the River Derwent at TasWater’s water treatment plant at Bryn Estyn, and transported by TasWater via the Box Hill Head Tanks and West Derwent Main to an off-take on the western side of the river near Granton.
From Granton, water is transported to the eastern side of the River Derwent via an underwater crossing, and transported to the irrigation district via a 630mm supply line. Delivery throughout the district is via a pipeline distribution network, with water
pressurised at the Tea Tree Road Pump Station and boost pumps at Shrub End Road and Table Hill.
Hazell Bros was the head contractor for the project, and Netco Pumps were contracted for the supply of pumps and pumping equipment.
According to Mr Ellery, the decision to go ahead with Stage 3 of the scheme was due to water supply falling short of demand, and farmers being keen to pay a premium for a reliable source of water. “We only build based on demand, and in each case demand has exceeded what can be supplied.”
According to Mr Ellery, this irrigation scheme is just one of ten that have been built in Tasmania over the past five years. All have had the financial support from the Tasmanian and Federal Governments, as well as farmers within the area.
“We’ve put in lots of pumps and pipelines over the years and are currently working on another five schemes. It’s quite a big undertaking for a relatively small area. With the government and local farmer support, it is a public/private partnership,” said Mr Ellery.
There are three pump stations located within the South East Scheme, at Tea Tree, Pawleena and Forcett.
Netco Pumps have supplied the pumps and materials, which include centrifugal end suction style pumps manufactured by KSB at Tea Tree, and Grundfos vertical multistage pumps at Pawleena and Forcett. These have been sold and serviced locally by Netco Pumps in Derwent Park.
According to Nathan Cruickshank, Manager at Netco, “The pumps at Tea Tree are ISO 150x125-315 mounted in a long coupled configuration on a common heavy-duty baseplate, complete with 132 kW CMG motors. The Grundfos vertical multistage pumps at the other stations are close coupled in vertical configuration with common manifolds.
“The Tea Tree pump manifolds are DN600 hot dipped galvanised steel and AVK valves were used throughout the pump station, including isolation valves, check valves and air release valves.
“A DN600 strainer is also mounted on the inlet pipework to protect the pumps from any debris that may be resident in the pipework from the construction stage, as the water is from
OVER 90,000 installations worldwide
Flexible Rising Main
Wellmaster Approvals:
a potable source it is not anticipated that water quality will be changing or be troublesome as far as the scheme goes.”
According to Mr Ellery, the Pawleena and Forcett stations are the smaller boost pump stations that pump water up to two separate high points in the scheme where farmers require water to be delivered.
“The pump at Tea Tree is the largest, delivering 3,000ML of water over the summer period, with a delivery requirement of 16.7ML a day. There is also a large dam that can be used as backup storage located a few kilometres away from Tea Tree Road pump station. It’s somewhat like a holding dam, where if we have an issue and we can’t get water supply for a period of time, we can still use the holding dam to release water. The pumps are capable of putting through 28ML a day, so we can still deliver the 16.7ML to the farmers and
another 11.3ML into the holding dam at the same time,” said Mr Ellery.
According to Mr Cruickshank, the pumps were of a standard type and construction, however, the biggest challenges were the large range of pump head conditions required at Tea Tree, and the endless pump duties that may be experienced depending on actual water distribution at any given time.
“The Tea Tree station was designed with two pumping solutions, one involving pressurisation of the distribution line for flows in excess of 130L/s, and the other involving a back-up holding dam if the potable supply happened to be restricted at any time.
“A solution for this application required a design that could provide for flows from 130L/s at 0 metres head, right through to 324L/s at 70 metres head,” said Mr Cruickshank.
High efficiencies were also a requirement, as each scheme had a kWh/ML target in order to give stakeholders the best value for money water. This was a difficult range of duties to meet, said Mr Cruickshank, and compromises had to be made.
A large number of pump sizes and configurations were examined before three end suction centrifugal pumps were chosen for installation at Tea Tree, the Pawleena and Forcett Stations were much more straightforward.
Together, they have the ability to provide up to 324L/s flow with a high point control that provides a minimum of 7 metres head at any given flow.
“The median range of flows expected were identified to be in the vicinity of 1,500-1,650rpm for the pump motors,” said Mr Cruickshank. “For these particular pumps with speeds as low as 700rpm and as high as 2,150rpm, to eliminate
efficiency loss, it was decided that it was better to overspeed 4 pole motors than run 2 pole motors at such low speeds.
According to Mr Ellery, coordination and cooperation with landowners before and during the construction of the scheme was critical to the successful outcome of the project.
“We held a lot of public meetings and sent out newsletters to keep people updated on how the scheme
was progressing. We also engaged with landowners when completing studies along the construction footprint. These could be flora, fauna and Aboriginal heritage studies.
“For the South East Scheme, there were 150 separate landowner agreements to be made across the 84km of pipeline. That’s a lot for a single job, so we had Hazell Bros working full time to manage the landowner liaison and so did we.”
Mr Ellery has said that the scheme will not only service the area with a reliable water source, but also has the potential to lead to a significant economic boost to the region.
“It’s looking like a couple of hundred jobs relating to horticulture will arise due to the increase in water availability. Also, Sorell is becoming a bit of a commuter town due to its proximity to Hobart, so there is some fantastic agricultural land which has been going under sub-division,” said Mr Ellery.
Thanks to the scheme, the future for agricultural production within the region looks more positive than ever before.
“A reliable water source for the region is now a game changer for agricultural production and farming.
“Especially during these time of significant drought, everyone is really noticing a great difference. It’s safe to say that because of the scheme, the future of Sorell is looking bright,” said Mr Ellery.
The $265 million Federal Government-funded South Australian River Murray Sustainability (SARMS) program has been designed to achieve the industrydriven outcomes first sought by the Water Industry Alliance through the original River Murray Improvement Program, and is now being delivered on behalf of the Government of South Australia by Primary Industries and Regions SA (PIRSA).
In August 2013, a National Partnership Agreement between the South Australian and Australian governments was signed, which allocated a total of $265 million to SARMS, with the commitment to return 40GL in South Australian River Murray water entitlements to the Murray Darling river system over a six-year period.
Since then, 33GL is ready for return back into the river system. Funding opportunities for local irrigators are being awarded under the $240million SARMS Irrigation Industry Improvement Program (3IP), and $25million for regional development is being provided via the SARMS Regional Economic Development (RED) program.
On the provision that entitlements of water are returned to the River Murray, 3IP funding is giving local growers the
ability to adopt innovative systems to improve their water and production efficiencies. A spin-off effect from the funding has also been noted in the form of a significant economic boost to the state.
According to Andy Roberts, CEO of the Water Industry Alliance, “When organising the 3IP program, the key principle was to support irrigators that were going to stay in the industry; those that were going to be a part of the future of the irrigation industry and the future of the region.
“The requirement to give back water was something that needed to be done for the MDB plan, but it was seen as an opportunity rather than a risk. We explored ways to encourage irrigators to operate as businesses, rather than just as irrigators, and to explore what they could do to maximise their businesses and maximise what they could do for the state,” says Mr Roberts.
3IP is designed to deliver maximum and lasting benefit from the funding dollar to river communities through a competitive application process.
This will be achieved by encouraging optimised irrigation practices from South Australian River Murray Water Access Entitlement holders to return much needed water to the MurrayDarling river system.
Record levels of government funding are providing local growers along South Australia’s River Murray with the opportunity to remain at the forefront of irrigation practice, while returning much needed water to the Murray-Darling Basin (MDB) river system.
The $240 million in 3IP funding is allocated through three investment streams:
• Stream One – Irrigation Efficiency – supporting water efficiency improvements. All projects under Investment Stream One are required to return at least 50 per cent of the proposed water savings, with a minimum of 10ML of technically feasible water savings to be provided under 3IP.
• Stream Two – Water Returns – to acquire water through direct purchase.
• Stream Three – Irrigation Industry Assistance – accessible to improve farm productivity only when the applicant is returning water through Streams One and/or Two.
The remaining $25 million has been used to support a Regional Economic Development (RED) program to deliver significant outcomes in regional research and economic development through:
• $12.5 million Regional Development and Innovation Fund
• $5 million Industry-led Research Sub-Program (IRSP)
• $7.5 million redevelopment of the Loxton Research Centre.
The following two case studies are
from major contributors to the South Australian agricultural industry. Each has successfully implemented 3IP funding to develop their irrigation infrastructure, and are already reaping the rewards of more efficient and practical systems.
Jubilee Almonds, located at Overland Corner near Waikerie, SA, recently completed major pump and irrigation system upgrades across their orchards after receiving $5.6million of funding from streams one, two and three of the 3IP program.
Canopy low-throw sprinklers were upgraded to a dual micro-sprinkler/drip system during replanting, and according to Jubilee Almonds CEO Brendan Sidhu, the benefits of the upgrade have been nothing short of impressive.
“As the ground at the orchard is very sandy and conducive to drift, initially our plantings were irrigated via low-throw sprinklers. With the advancement of drip, we decided to replace the low throws with a dual drip and microsprinkler system.
“By introducing a dual system of both micro-sprinkler and dripper, the benefit is twofold. The micro-sprinklers enable us to establish cover crop to hold the soil between each tree, as well as helping to control frost during winter. With cover crop in place, the drip system is then able to be used to irrigate the trees as well as distribute fertiliser.”
According to Mr Sidhu, the orchard’s original system did not provide the orchard with a high level of water security. “We originally had two 500kW electric pumps down at the river and a diesel booster pump installed at the orchard to boost water flow and pressure. Each of the pumps had to be started manually, and if one of the
pumps failed, we would lose 50 per cent of our pumping capacity. If there was a power outage, we simply had no backup to keep the pumps running.
“The new system now involves four 280kW turbine pumps, meaning we would only lose 25 per cent of capacity if one was to fail. They are now also controlled by variable speed drives, giving us the capacity to run them at anywhere between 40L per second to up to 650L per second.
“The new system has enabled us to eliminate the diesel pump altogether and has provided us with a fantastic level of flexibility for different demands of water across the orchard.
“Mature plantings require far more water than young plantings, so this new system allows us to change the amounts of water delivered depending on our needs, and providing us with real water savings. As it is now fully automated, we can program everything from the orchard without having to go to the pumps. We also were able to install a plug-and-play generator if required.
“Overall, we have been able to increase efficiencies and we now have a system that is a lot more reliable,” said Mr Sidhu.
According to Mr Sidhu, he is proud of the program and was very happy to have been able to participate. “SARMS funding is a great model and has been great for South Australia. It has not only benefited our almond production and water efficiency, but has also provided a boost for our local contractors.”
Byrne Brothers operates a dynamic trio of vineyards, incorporating an impressive acreage of wetlands and agricultural farmland dotted across the SA Murray-Darling Basin region.
Major irrigation infrastructure upgrades were recently carried out at the Byrne Lone Oak Farm, which neighbours the company’s Glen Devlin Vineyard at Devlins Pound near Waikerie. These upgrades were initiated to allow for the production of new and diverse crops such as 800 hectares of Lucerne.
According to Rob Byrne, a partner in the Byrne Brothers family business, contracts to receive the 3IP funding were signed in 2014 with pump infrastructure undergoing installation in mid-2015.
“There were a number of different upgrades completed across the Lone Oak property. These included the installation of diversion pumps from the River Murray, installation of an upgraded rising main as well as a re-lift
booster pump station and associated distribution mains with connections for centre irrigation pivots.
“Two 400mm vertical turbine pumps with vertical hollow shaft motors were installed alongside an original pump at the river.
“Four booster pumps, centrifugal in design and coupled with 75kW electric motors were then installed within our booster station located close to our main South Australian Power Networks (SAPN) connection. The 5km main distribution line was then upgraded including a part 450mm diameter pipeline with 200mm PVC underground ring mains.
According to Mr Byrne, the upgrades have resulted in large water efficiencies and an increase in pumping capacity.
“Pumping efficiency increased by eight per cent, from 78 to 86 per cent following the upgrades. Capacity was also increased via the 450mm main line, which transports the pumped water to the farmland,” says Mr Byrne.
Further benefits of the upgrades include the increase in production of other crops via shared farming agreements.
“The new upgrades have allowed for an increase in shared farming for potato production. Farmers avoid growing potato on the same land from year to year. Instead, they grow potatoes in rotations of three or more years, alternating with other ground cover crops.
“It is during the three-year cycle, that we will be able to use the land to also plant Lucerne.
“Our centre pivot irrigation system on site is now also being fed via the upgraded infrastructure, and specialised software communicates between the sites.
“Our system is innovative in itself,
with its design allowing for it to be moved from a circle to another circle area within two hours. This means we can irrigate up to three circles of Lucerne or other crops with one centre pivot.”
According to Mr Byrne, the upgrades have reached further than the farm and have provided tangible benefits for the community at large.
“With the support of SARMS 3IP program, we have been able to employ more people and improve their skill base by adopting new technologies.
“The funding has given us the freedom to be highly innovative in designing systems, and working with suppliers has led to greater conversations and activation of irrigation best practices.
Covering 14 per cent of the total landmass of Australia, the Murray Darling Basin (MDB) is Australia’s main source of food production and agricultural farmland. Known as Australia’s “food bowl”, the MDB generates 39 per cent of the national income derived from agricultural production.
The MDB is defined by its water, involving 23 rivers and their catchments, yet less than 15 per cent of the area of the basin contributes to runoff – except in times of flood. High evaporation rates, expansive floodplains and significant water diversions for towns and agriculture mean that much of the surface water in the basin does not reach the ocean.
As three quarters of Australia’s irrigated crops and pastures are grown within the basin, numerous programs have been put in place by government and authorities to help secure the future of Australia’s most precious water system.
“Although 3IP is a government recovery of water entitlements, the program seeks out best practice to bring sustainable agriculture to farming communities that improve crops and output,” says Mr Byrne.
The benefits of 3IP so far
According to Ben Fee, PIRSA Agribusiness Manager, the benefits of 3IP funding are widespread and have already resulted in impressive innovation measures and significant water returns.
“SARMS 3IP has provided the opportunity for long-term water delivery infrastructure changes that deliver ongoing benefits to multiple end users, based along the River Murray,” said Mr Fee.
“Just one example is the energy savings generated through the installation of the latest industryleading pump technologies within the SARMS 3IP funded Irrigation projects, which will provide productivity benefits to around 200 irrigators. Many of the funded projects have also factored in future technology advancements in the area of solar power, which they are now able to easily introduce without further significant capital expenditure as a result of their SARMS 3IP project.
“The program is unique in that the water returns look after the environment, the irrigation and production efficiencies look after the farmers, and the mix of regional development opportunities look after the region’s communities.
PLC control for the irrigation system.
“The SARMS National Partnership Agreement seeks the final water returns to be made by March 2017, with the program well on target to meet this goal.”
The River Murray is the lifeblood of the Murraylands and Riverland regions of South Australia. With the area home to 70,000 South Australians and $840million worth of irrigated agriculture, the River Murray supports industries such as vegetables, grains and livestock in the Murraylands, and irrigated horticulture (fruit, nuts and grapes) in the Riverland.
Water returns will aid in keeping the Murray Mouth open and flush salt from the system, while meeting salinity and water quality targets to protect the Coorong, Lower Lakes and the river channel, and provide environmental flows to River Murray wetlands and floodplains.
Bill McNally shares his expertise on selecting the correct type of mechanical seal, installing proper environmental controls, choosing the right materials for your application, and installing seals correctly.
Let me mention here at the beginning that mechanical seals fail for only two reasons:
• One of the seal materials becomes damaged
• The lapped seal faces open and allow the product to leak.
Please keep that information in mind as you read this article.
We will begin with the type of seal you should be using. Seals fall into many categories:
Hydraulically balanced seals are the primary type to use because they generate less heat and they can handle a wide range of pressure, as well as a reasonable vacuum. If the pump suction pressure (not discharge) exceeds 400psi (28bar) you might have to go to a special version of a balanced seal. Likewise, if a vacuum on the suction side of the pump measures less than one “torr”, you will have to go to a seal with no elastomers, because elastomers “out gas” and shrink as the air is pulled out of the compound. This shrinking will cause the elastomers to leak and the vacuum can be destroyed.
The stationary version of the seal is the best design, because it will compensate for misalignment between the pump and its driver, as well as the stuffing box not being square or perpendicular to the rotating shaft. This type of seal also has some real advantages if you are converting a packed pump to a mechanical seal or running at greater than electric motor speeds.
Metal bellows seals should be selected if the product temperature is in excess of 400°F (200°C) and no cooling of the stuffing box is allowed. Metal bellows seals are also a good choice for cryogenic (cold) service. Remember that petroleum products have to be cooled because they will “coke or carbonise”, open the seal faces, and clog up seal components. Metal bellows seals are also a logical choice if no elastomers are allowed in the system.
Dual seals are becoming very important because of fugitive emissions laws. They can also act as a spare seal if you cannot afford an unexpected shutdown. Dual seals should always be designed with a “two way” hydraulic balance.
Non-metallic seals should be selected if the pump wetted parts are manufactured from non-metallic material such as carbon, Teflon, plastic, etc. These seals are normally mounted as outside seals and have no metal parts exposed to the fluid you are sealing.
Do not depend upon a flush into the stuffing box to protect the seal materials against corrosion, and do not try to second guess the application engineer that selected a non-metallic pump for this application. Stick with a non-metallic seal design in all non-metallic pumps unless you are a corrosion expert and willing to select the correct metal for the application.
Cartridge seals are necessary for ease of installation and to make pump impeller adjustments without changing the seal face loading,
but some of them have problems. Cartridge seals also allow you to compensate for thermal growth of the shaft. Be aware that there are special precautions you must understand if you are going to use cartridge mounted stationary seals.
Split seals can be used in most applications today, especially the larger shaft sizes. In most cases you can solve the packing conversion or seal leakage problem without taking the pump apart and getting involved in a lot of downtime. Split seals are the only real alternative to cartridge seal designs. Today, they are available in both rotating and stationary versions.
Most products contain solids so the seal should have built in slurry features. With the exception of most finished products, accept the fact that you are pumping a slurry.
Be sure that the brand of seal you select will not frett or damage the pump shaft. This will allow you to use solid shafts instead of the inferior sleeved version with its high L3/D4.
After choosing the seal type, we must select the seal materials. Most of the time you will be choosing three different materials.
You are concerned only about the parts that get wet in the fluid, unless the pump is in a very corrosive atmosphere. The wetted parts include the pump volute, impeller, shaft or sleeve, mechanical seal, stuffing box, etc.
The different grades of carbon/ graphite
Carbon/graphite manufacturers supply a carbon/graphite chart that will give you the details of any particular grade they manufacture. With few exceptions an unfilled carbon such as Pure grade 658 RC is always a safe choice if any grade of carbon is acceptable in your fluid.
The hard face
There are many to choose from, but self sintered silicon carbide will probably be your first choice. Reaction bonded silicon carbide is also popular, but can be attacked by many high pH fluids. The common cleaner “caustic” is a fluid that will attack reaction bonded silicon carbide.
The rubber parts (elastomers) that are exposed to the fluid
The dynamic O-ring (the one that flexes and rolls) is the most critical.
Most chemicals and chemical combinations can be sealed with either a good grade of Viton® or a good grade of ethylene propylene. Most solvents and a few other chemical combinations require something a little better. The super elastomers have just about replaced Teflon® in those applications, but they cannot be used everywhere.
It’s important to always choose the right seal for the job!
Remember also that all elastomers have an upper and lower temperature limit that must not be exceeded.
You must choose seal materials that are chemically compatible with all the fluids that might be passing through the equipment, and that includes any cleaners or solvents that might flush through the lines. This is especially critical with the choice of elastomer (O-ring). The metal parts and face combination are usually compatible with most cleaners and solvents.
The next step is to place your chemical into the proper sealing categories. Keep in mind that most chemicals fall into several sealing categories at the same time.
After you have placed your fluid in the proper sealing categories, selecting the correct environmental control comes next. If the equipment is going to operate 24/7, without shutdown, you have a simple sealing problem. But if you are on batch or intermittent service, or if a standby pump is run occasionally, then an environmental control will become critical. You need to know about the three most important environmental controls:
You can raise the temperature, lower it or keep it within certain limits that will be dictated by the seal design and product characteristics. Temperature control is most important when the pump is shut down and the pumping fluid either cools down or heats up because of ambient temperature.
There are many occasions where you will want to control stuffing box pressure to stop a fluid from vaporising, flashing or evaporating. We seldom have to lower stuffing box pressure, but if it is too high for a conventional balanced seal you will be better off going to a special high pressure design.
Clean products are easier to seal. Flushing is only one of your options, there are more.
Any of these environmental controls will work better if you have installed an
oversized stuffing box on your pump. The seal needs lots of radial room to allow centrifugal force to throw solids away from the lapped seal faces and to lessen the generation of heat in the stuffing box. Heat is a major cause of problems with both centrifugal pumps and mechanical seals. Anything you do that will help to remove heat from the stuffing box will add to the life of your seal and pump bearings.
If you have done all of the above, all that remains is to install the seal correctly, adjust the pump impeller (if it is an open, or semi-open design) and hook up the environmental control you chose to keep the seal functioning.
With a little luck, you should now get good seal life - in fact, with a few modifications, your seals might never run out.
Sealing Solutions is a privately owned and operated Australian company that specialises in the supply and refurbishment of sealing products to a wide range of industries. It is our commitment to provide the best service available across Australia.
Sealing Solutions provides:
Dimensional replacements for all seals makes. Seal refurbishment of all makes. Supply of replacement parts where required.
Quick turnaround for seal refurbishment.
Staff members with several lifetimes worth of experience in the sealing industry.
Australian distributor for Vulcan™ Engineering Ltd., the world’s leading single spring seal manufacturer. Our fully equipped sales and service centre has been in operation since 1995.
To one degree or another, we’ve all done it. We’ve found ourselves so far into the trees, that we can’t find the forest. In other words, we get too close the problem to identify a logical solution. It’s an easy trap for a pump engineer to fall into - here, we review the fundamentals of pump system reliability to help retain the big picture view.
On one occasion, I overheard a discussion on the merits of having a new pump supplied with a stainless steel bearing housing. The logic offered was that an acid was leaking from a valve above the proposed location of the pump. The leak would land directly on the pump bearing housing and cause considerable corrosion damage. This discussion ranged back and forth for quite a while before someone enquired, “Why don’t we stop the leak at the valve?”
In a similar vein, a group of pump people in a discussion group at the Pump Symposium in Houston a few years ago were heavily into a discussion of how to alleviate the pump problems being caused by the strain from a misaligned piping system. Once again, this discussion went on for some time before someone suggested the very practical solution of correcting the misalignment.
Some time ago, three highly placed engineers spent their valuable time writing an article for a magazine to offer the pumping community their expertise
in a new approach to pump reliability. Their premise was that too much time and trouble had been spent on mechanical and operational methods of reducing pump failure. They suggested a hydraulic design approach that would be more effective. At the end of a very well researched and well-presented discussion, the conclusion was twofold:
1. Operate the pump closer to its best efficiency point (BEP)
2. Operate the pump at a slower speed.
Quite apart from the fact that these two conclusions both seem like operational factors to me, anyone who has been around pumps in the field for any length of time is fully aware of the practical benefits of operating close to the BEP, and at slow speeds. We did not need a new way of considering pump reliability to tell us this. Nor did we need a new model to support it.
If a valve is leaking, fix it! Don’t focus on the damage the leak is doing. Correct the problem, not the symptom.
If piping is misaligned and causing
pump failure, realign the piping and the pump failure will stop.
When a pump is operated close to it’s best efficiency point, there are fewer energy losses in the pump. That’s what high efficiency means! The pump will run in a more stable condition and therefore will use less energy and also waste less energy.
There is also an inverse relationship between the rotational speed of a pump and the life of the bearings. When bearings fail less frequently, the pump is more reliable!
While theoretical models are essential to the continued development of the pump business, we cannot afford to lose sight of the practical situations. Most of the time, pump problems are caused by poor installation, clumsy operation, or unthinking maintenance.
One major challenge in pump reliability is created when a problem has been tolerated for so long that it becomes a “normal” condition, and no one even thinks about the fact that it may be unusual and could be improved.
A typical example is the pump in a high temperature acidic service, where the seals and bearings fail every five weeks, but the engineer wouldn’t even consider a new pump/seal combination because the twelve month guarantee offered was too far beyond his comprehension and belief for that service.
Then there is the fertiliser plant where they start every pump and let it run for five or ten minutes before they open the discharge valve, “Just to let it warm up before we put it online”...!
On the other extreme, there is the paper mill where every pump is dismantled and overhauled, with the seals and bearings changed every six months, as a method of preventive maintenance. Effective, but expensive.
Part of the problem is that most pump users assume that their pump suppliers are the fount of all knowledge and wisdom, and know everything
necessary to enable the pump to operate in that service. I really wish that were the case.
Many years ago I moved from the supply side of the pump business, to the user side. On reflection, it was more a slow change in attitude and approach than a change of environment and employer. I simply stopped looking at the pump as an isolated piece of machinery, and started to view it as part of a production system.
From my earlier position as a supplier, the pump was very much complete within itself. The only thing someone else had to do was to install it properly and run it correctly, and the pump was able to provide exactly the head and capacity for which it was purchased. Of course, if it wasn’t operated at the design condition, that was not the supplier’s fault and one could not reasonably expect the pump to perform reliably under different conditions.
My current perspective is neither better nor worse than my old viewpoint. It is simply different. In my earlier days as a pump salesman, the client supplied the anticipated operating conditions of a pump and I accepted them without question (even if questions had been tolerated!). I then proceeded to select a pump from a group of characteristic pump performance curves that most closely reflected the required conditions. When the sale was made, and the pump was manufactured, tested, shipped and accepted, the file was closed. In other words, when the pump supplier’s job was finished, the end user’s job was just beginning.
Please do not assume that the brevity with which I describe this transaction implies any careless or frivolous attitude towards the whole process on the part of the pump suppliers. Nothing could be further from the truth. The point is, that the function of the pump supplier is to supply a pump that pumps “x” gallons a minute at a total head of “y” feet of a specific liquid at a certain temperature.
When it has been established, either by site or shop tests, that this has been accomplished, their job is complete.
Now the pump user takes over.
The good news is that the vast majority of pumps are installed and run well for a reasonable period of time without any unacceptable incident. However, the true quality of a supplier should not be judged when things are going well, it’s when things start to go wrong that we test their true mettle. This is true whether we’re discussing a pump, a car, or a vacuum cleaner.
When the supplier hears about a pump that keeps failing, he has a problem pump on his hands, and probably an unhappy customer.
When an end user is faced with a pump that keeps failing, he is not just faced with a problem pump, he may have a complete system that is no longer operational, resulting in a loss of revenue caused by a reduced output of a profitable product. In addition, the end user is acutely aware that every dollar that is spent on maintaining this pump is being deducted directly from the bottom line profitability.
The question is, are we so wrapped up in our own area of responsibility that we are neither aware of (or possibly even concerned about) the ramifications that our decisions and actions may have on others in the loop?
Are we so wrapped up in bearing housing corrosion that we ignore the valve leakage?
Are we so concerned about pump failure that we forget about the reason it’s failing?
Do we get so wrapped up in theoretical models that we are unaware of existing field practices?
Let’s not get so far into the trees that we can’t find a forest. The easy decision may not always be the right one in the long term. By taking one step back from the problem and considering the bigger picture, the real solution is frequently easier to identify.
Three times longer life for pump components significantly lowers production costs.
High fluid velocity means wear, erosion and corrosion at high impact points like pump impellers, valve seats and stems, and bends and elbows in pipe work systems. A worn component means inefficiency and delays. We work with both pump OEMs and end-users to produce cost-efficient long-wearing solutions to high wear components. Our unique surface engineering technologies - developed to increase resistance to wear and corrosion – optimise component and system performance so they work better, last longer and cost you less.
Contact
Production equipment and components surfaceengineered by Laserbond® will operate in-situ for longer and perform more efficiently. An extended operating life increases the cycle time for regular maintenance and decreases maintenance costs.
Pump impellors, pump shafts, housings and seal areas are returned to original specification with laser cladding and machining. LaserBond® surface engineering improves and maintains operating efficiency, improves the overall process, and cuts production loss.
Find out more at laserbond.com.au/fluid_handling
Laurence Dinham, Machinery Group Lead at ExxonMobil, leads a group of machinery engineers onsite at the Mobil Altona refinery. The Altona refinery is amongst the safest and most reliable refineries, not just in Australia, but in ExxonMobil’s portfolio of refineries worldwide. In this article, we discuss pump reliability and the factors that contribute to achieving improvement.
Mobil’s Altona refinery currently has 580 pumps across the site. This is enough to keep Laurence and his trio of pump engineers busy monitoring, troubleshooting, optimising and upgrading, as well as procuring and installing pumps when required.
“Most of my time is spent troubleshooting and identifying opportunities for improvement, working closely with the process engineers, operators and technicians. We’ve upgraded a number of motors in the last few months, and also got some new pumps onsite. In the environment of changing feed stocks and export products, there is always opportunities to improve flow rates and efficiency.
“Our entire refinery (including the pumps) operates flexibly, with continual changes that allow us to optimise production based on feedstock and desired finished products. We really don’t ever sit still. The goal posts are almost always moving,” said Mr Dinham.
Choosing
When choosing a new pump, the system and design must fit from a process perspective. Mr Dinham must
first identify the desired flow rate and pressure, to ensure that hydraulically, the process conditions are met. Once this has been achieved, the design and materials used in the pump have to be taken into consideration.
“When choosing a pump, we have to be careful to select a material that is suitable for the chemical and environmental conditions in which it will be used,” said Mr Dinham.
Another design factor is the selection of appropriate seals, depending on aspects including the process stream and the risk of potential emissions.
“Reliability of the pump is a major consideration for us. Our goal is to maximise the safety and longevity of the pump while balancing the cost,” said Mr Dinham.
Throughout the process of pump design and selection, there are local and national standards to consider, as well as company design practices.
“All of our pumps must firstly adhere to the current American Petroleum Institute standards. We then have our own standards on top of those which add additional design requirements,” said Mr Dinham.
Procurement of a new pump can take many months to a year, as everything that is to be changed on site must be carefully reviewed and documented. This is to ensure that the refinery continues to run safely, smoothly and efficiently, with safety always being the number one priority.
“When procuring, installing or making changes to an existing pump, there is a management of change procedure,” said Mr Dinham. “There are many different departments that must approve any change, so this involves a lot of teamwork. Ultimately, the viability of a change in terms of cost versus benefit will be the deciding factor in whether it is supported.”
“Optimisation and changes to the pumps at the Altona refinery involves a huge amount of collaboration,” said Mr Dinham.
“It really is a big team effort, and I am always bowled over with how important this is. I used to work at a large refinery in Texas. I remember walking through the gates and looking
• Self priming
• Dry running
• High suction lift
• Extremely low maintenance
• Solids handling
• Reversible flow
• Shear Sensitive
• Large viscosity range
• Temperatures up to 280°C
• Low vibration
• Low noise
• Various material options
• High efficiency.
“We are very happy with the hollow disk pump which Pump Power Australia supplied. We have tried three other pumps on our service trucks over the years and this is the only one that has stood up to our challenging waste oil dispensing requirements, and it’s low maintenance too.” – Matt Kelly, Bard
at this incredibly large and complicated plant, wondering how it could all possibly work so smoothly. Although smaller, it’s the same here at the Altona refinery, the secret is teamwork.
“Everybody has an area of responsibility and accountability. There are process engineers, chemical, instrument, electrical and piping engineers. We all get together when we’ve identified any opportunity for
change or improvement. Everyone is focused on the same goal, keeping Altona refinery running safely, reliably and efficiently.
Usually reliability and profitability go hand in hand, said Mr Dinham, but there is a point where investment gives a diminishing return on reliability. Getting the balance right in terms of
the hardware and the maintenance activities is important.
“Pump reliability at the Altona refinery is now amongst the highest anywhere in world, as is our safety record. The high reliability has been achieved not by changing out all the pumps, but by increasing the focus on the way we operate and maintain the pumps.
“When I first started as a machinery engineer 25 years ago in the UK, we’d think it was good to have a pump run reliably for two or three years. I have since learned, that if we design it right, operate it right and maintain it right, a pump can run a great deal longer.
“Altona refinery now has an average run length of the pumps of around 14 years. How we have achieved this is by closely examining pump issues to understand the root cause - not just looking for opportunities in hardware design, but also applying learnings in the way we operated or maintained the pumps.
“If we find a design opportunity, it can take months and years to modify and then see a return on reliability, but if we can find ways to improve the way we operate or maintain our pumps, those learnings can be applied very quickly and across the whole site. I don’t yet know what the ceiling is for high pump reliability, but I do know that month on month, we continue to see opportunities to improve the way we operate and maintain them.
“I have learned that the processes
“When I first started as a machinery engineer 25 years ago in the UK, we’d think it was good to have a pump run reliably for two or three years. I have since learned, that if we design it right, operate it right and maintain it right, a pump can run a great deal longer.”
Laurence Dinham, Machinery Group Lead at ExxonMobil
for achieving high reliability and safety are very similar. Treat every incident as avoidable, look for the learnings, and don’t just look for opportunities in hardware upgrades and technical innovation - the biggest opportunity is more often in people and their behaviours.
Beginning his career in UK, and working with ExxonMobil in the US, Mr Dinham has seen and worked with an immense range of pumps and equipment. Most excitingly, Mr Dinham said he is impressed with the quality and degree of service that Australian pump manufacturers offer.
“I’m a strong supporter of Australian pumps. There are some excellent manufacturers out there, offering excellent service. For low cost opportunities, ExxonMobil has the ability to use a number of international brands. However, for more critical oil and gas pumps we usually use Australian, European or American brands that are well known to the company.
“This can be costly, but brands like United Pumps and Flowserve are excellent. We actually have a Kelly and Lewis pump on site that has been running smoothly for 30 years – it’s a brand I’ve never seen outside of Australia.
The future of pumps, according to Mr Dinham, will see tighter emissions standards for seals, lower noise requirements, improved materials handling a wider range of fluids and temperatures, with an increasing need for instrumentation and monitoring to move more into predictive maintenance and away from costly planned maintenance activities with ever increasing reliability expectations. Each will challenge the way the industry designs and maintains pumps, as well as the way new manufacturing techniques allow suppliers to build pumps.
“Pumps being made in low cost countries while maintaining high reliability is a new opportunity for the industry. Moving to lower emissions and selection of mechanical seals and the associated instrumentation will be an increasing challenge for us in pump design.”
Over the last five years, smarter controls have greatly contributed to the overall efficiency of HVAC (heating, ventilation and air conditioning). Energy Action’s Projects and Advisory Services Division Director, Dr Paul Bannister, shares his insights into maximising HVAC energy efficiency and the key role that pumps can play in doing so.
The energy use of HVAC systems is typically around 40 per cent of total building consumption, across many building types. HVAC energy also constitutes around 70 per cent of the energy considered for the NABERS (National Australian Built Environment Rating System) Base Building ratings for offices and shopping centres. NABERS is a national rating system that measures the environmental performance of a range of building types in Australia and New Zealand.
Control is important in HVAC systems because the systems often consist of many components that all need to work correctly – in concert – to be effective.
“Failure to do so can result in different components working in contradiction of each other – with the most obvious example of this being simultaneous heating and cooling,” said Dr Bannister. “A poorly controlled HVAC system can use between 50-90 per cent more
energy than a well-controlled system.
“For pumped systems, control is needed to turn the flow down as far as possible during periods of low load. This can play a significant role in the achievement of overall HVAC savings.”
How climate affects efficiency
It’s important to be careful when talking about the effects climate can have on efficiency, because climate’s primary impact is actually not on efficiency, but on the nature and scale of the task itself.
Dr Bannister noted “In spite of that, temperate climates do have a particularly challenging job because the systems are designed for a reasonably tough cooling load (and a small but positive heating load) which is many times higher than the load the system runs at on an average day.
“So if the system fails to turn down to meet this minimal load, the effect on efficiency can be dramatic.”
By contrast, systems located in parts of Australia with a hot climate will have a high or very high cooling load.
For example, in a tropical climate like Darwin, there is no heating system and the buildings are typically simpler, so control is less important, while the raw efficiency of individual plant items actually becomes more important.
Enhancing control over HVAC systems
The key problems that create excessive energy consumption in HVAC systems relate to the time of use, turndown, conflicting uses and the robustness of the controls.
Dr Bannister said that ways to counteract these problems and enhance HVAC controls and energy effectiveness include:
• Time of use: don’t run a plant when it doesn’t actually need to run.
• Turndown: try slowing pumps and fans down to match the load, using variable speed drives (VSD). VSDs are critical to turn down, as a pump or fan with a VSD will use far less energy when run at lower speed than by any other means of capacity limitation.
• Conflict: try to prevent the simultaneous running of both heating and cooling or other forms of conflict within the system.
• Robustness: set up the controls so they are not thrown out by the first minor mechanical failure in the system.
How pumps can help
The effective control of pumps can help improve the energy efficiency of HVAC applications due to their significance in the systems. Pumps make up 10-15 per cent of HVAC consumption, their role only secondary to fans.
“Pumps are generally more difficult to control, due to the presence of static head and a condition known as “low delta-T syndrome” which tends to mean that flow demand reduces less than the load,” Dr Bannister says.
“However, by adding a VSD to a pump, it will almost always generate savings, provided the control and commissioning are done well.” Controls, however, work best when pumps are correctly sized. Dr Bannister notes, “One of the factors that compromises energy savings is when the pumps are selected based on over-inflated head pressures. Even with a VSD, it can be hard to get a useful reduction in energy use if the pump is on the flat section of the pump curve. Poor selection is pretty common, unfortunately.
“Design for a realistic load and, if necessary, use multiple pumps to serve highly diverse loads rather than just hoping that a single pump can be turned down across the whole range.”
Victorians have had a love affair with gas ducted heating systems every winter for many decades. But researchers from the Melbourne Energy Institute have found that heat pump technology could displace gas heating as the tool of choice for residents seeking to warm their homes in the cooler months.
The Melbourne Energy Institute recently conducted a study into declining gas demand in Australia, identifying a range of key factors which are influencing users to turn away from gas.
One of the key factors they found was the fact that in the buildings sector, gas faces increased competition from efficient-electrical appliances that utilise heat pumps.
In eastern Australia, there are potentially 500,000 to 1,000,000 homes where residents are unaware that they can immediately start to save hundreds of dollars per year on their space heating bill. To do this, they need to turn on their existing reverse-cycle air conditioner (RCAC) heat pumps and turn off their gas.
Economic fuel switching is the concept where gas consumers switch to using electrical appliances for their space heating, water heating, cooking, and possibly other heating needs.
Residential fuel switching from gas to renewables-based electricity, in concert with energy-efficiency measures, was proposed by Beyond Zero Emissions in 2013 as a way for homeowners and commercial building managers to reduce greenhouse gas emissions and move to 100 per cent renewable energy. In 2014, ClimateWorks likewise suggested fuel switching from gas to renewablesbased electricity was key to a deep decarbonisation scenario.
Refrigerators and most home air conditioners are heat pumps that use a refrigeration cycle to move
heat “uphill”, in a sense, from a cold location to a warmer location. An RCAC, known simply as a heat pump in some parts, is a device that can shift heat from inside of a building to outside (usually in summer) and from outside of a building to inside (usually in winter).
An RCAC operating in heating mode is essentially recovering free renewable ambient heat (a form of solar energy) from the air outside of the building, raising the temperature of that heat, and shifting it to inside the building. In so doing, RCACs, with efficiencies of over 500 per cent for top-of-the-line models, are far more efficient and have lower operating costs than simple electric-resistive heating devices (fan heaters, oil column heaters, panel heaters, etc.) that achieve efficiencies of only 100 per cent, and also have superior efficiency to gas-fired heaters that are limited to efficiencies of less than 90 per cent and perhaps as low as 50 per cent or less.
Heat pump water heaters (essentially RCACs that heat water) are eligible for renewable energy credits in Australia. RCAC space heaters are eligible for renewable energy credits in the UK but not in Australia.
In 2014, the Grattan Institute found that following an increase in wholesale gas prices of $5 per gigajoule, typical Melbourne, Sydney, and Adelaide homes can save $1,024, $628, and $517 respectively on the combined running-costs of space heating, water heating and cooking if they switch from gas to efficient-electric appliances.
can start saving immediately
A study conducted by the Alternative Technology Association (ATA) looked into the savings householders around Australia would see by shifting from gas heating appliances to RCACs. The largest savings identified apply to a large house in Canberra ($1,733 per year). A large home in Melbourne might save $658 per year. In every case, heating with an RCAC involved lower running costs. In no region or home type was gas heating found to be the cheapest option.
With respect to current space heating practices in eastern Australia, MEI have identified that there may be between 500,000 and 1,000,000 homes (particularly in Victoria) where RCACs have already been installed, but the householder is not aware that using the RCAC in winter can be the cheapest way to heat their home (i.e. instead of using their gas heating).
Were the householder to be informed of the possibility of savings, he/she might opt to switch off their gas heating, switch on their RCAC, and start saving money immediately.
For many householders, this will be news. This is because gas heating has traditionally been seen as the cheaper option in Victoria. As described by the ATA, homeowners lack the knowledge that the economics of space heating have changed. Gas appliance marketing can often mislead consumers. The ATA recommends that it is necessary to “strengthen the regulatory oversight of the marketing of gas as cheaper and more efficient than electricity”.
We need to look at more efficient ways of heating homes - heat pumps are one option.
Across eastern Australia, the amount of money that householders can save by using RCACs for heating instead of gas may be very large. For example, were 500,000 Victorian households able to save $500 per year, this adds up to a savings of $250 million dollars per year. These new space-heating economics have come about because of:
• Rising gas prices
• Falling electricity prices (energyonly costs, excluding fixed supply charges), especially for householders with access to rooftop-solar PV
• The emergence of efficient RCACs
• The recognition of the poor performance of, in particular, ducted-gas heating.
Heating cost savings achieved by using an RCAC instead of gas will depend on the effectiveness of the gas and electrical appliances being compared in delivering heat to where it is needed, the electricity and gas prices that consumers are able to negotiate with their suppliers, as well as comfort and convenience preferences.
Ducted gas space heating is the practice of using one central gas-combustion heater fitted with an air blower and a network of ducts (either under-floor or in the attic space) to carry warm air to the majority of rooms within a house. Around 40 per cent of homes in Victoria and the ACT use ducted gas space heating, whereas in no other eastern Australia state does its prevalence exceed 4 per cent.
As with any gas heating system, some of the energy contained within the purchased gas is lost in the hot flue gases. Additional heat is lost from the ducts by the mechanisms of conduction, convection, radiation and air leakage. Under-floor ducts often go uninspected for decades and yet can suffer damage from animals, children, or under-floor maintenance or renovation activities.
Blowing air around the house and through the ducting system can increase the leakage of warm air out of the house and the ingress of cold air. These losses can be exacerbated if internal doors block the flow of air back to the heater air intake. Lastly,
ducted systems may direct heat to rooms where heat is not needed. The practice of closing a limited number of hot air registers in unused rooms is often recommended, but this has the side effect of over-pressuring the ducts upstream of the closed registers which then increases warm air leakage.
The efficiency of ducted gas space heating systems in Australian homes can be as poor as 50 per cent or less. In other words, in some homes half or more of the gas purchased for space heating is, in a sense, immediately wasted and not used to effectively warm people in their homes.
Modern reverse cycle air conditioners are efficient
Contrasting with the potentially poor performance of ducted gas, some non-ducted RCACs achieve efficiencies of more than 500 per cent when they capture up to 4.8 units of free, renewable ambient heat from the outside air for every one unit of electricity applied. If the RCAC wall unit is located in the room directly where heat is needed, energy losses are minimal.
• Increased mechanical performances
and
• High external radial capacity and mechanical strength
• Reduction ratios between 1.3 and 280
• Specific reinforced seals, taper roller bearings and thrustbearings available
• Torque control, smooth start and stop modes to avoid water hammering
• Dedicated software for pump control systems
• Programmable timers with real time clock
• Early warnings and safety stops
• Optimized monitoring for energy saving
• Control of up to 7 pumps
• IP20/21 and IP54 rating
www.fcrmotion.com
(03) 9362 6800
Reverse cycle air conditioners, when used as heating devices, can save homeowners considerably.
Read the full
RCACs are a disruptive technology and are already very significant harvesters of renewable energy in Australia, exceeding rooftop solar photovoltaic (PV) panels in their energy recovery/production. In 2014, the renewable energy recovered by RCACs exceeded that of rooftop solar PV. In the coming years, RCAC-recovered renewable energy has the potential to double, as more buildings in Australia (and in particular in Victoria, as described above) adopt this method of space heating.
All of this provides a huge opportunity to the pump industry, and to the HVAC sector in particular. The challenge will be educating consumers about the benefits that are available to them – but it’s one that the industry shouldn’t shy away from. RCACs as residential heating devices is a new concept, particularly in Victoria, but it is a concept that ties into desires for reduced bills and enhanced energy efficiency. It’s time to encourage users to embrace the opportunities.
A recent industry study has found that the trend for connecting products to the internet – better known as “the internet of things” – is going to have a profound impact on the pump industry in years to come.
The decline in oil prices in the beginning of 2015, in particular, forced consolidation and a shift to innovative operational procedures as end users focused on value buying and energy efficiency. The state of global oil prices remains uncertain; but they are expected to remain low and have an ongoing impact on a range of sectors in the short to medium term.
The pump industry is one of those sectors being impacted by current oil prices; and this, along with developments in subsea and shale gas around the world, is opening up immense opportunities for pumps companies.
“The advent of the Internet of Things (IoT) is shaking things up in the global pumps industry,” said Frost & Sullivan Industrial Automation and Process
Control Research Analyst Shilpa Mathur Ramachandran. “The deployment of IoT and Industry 4.0 will increase operational efficiency by nearly 45 per cent, escalate return on investment for manufacturers and widen application scope.”
While turbulent global economic conditions are likely to cause price wars and dampen sales, the demand for costeffective, easy-to-install centrifugal pumps will balance out any fall in overall uptake.
Moreover, opportunities are ripe in Asia and Africa. Frost & Sullivan have identified Asia-Pacific as the next hotspot for greenfield and brownfield investments in the pump industry. The improving manufacturing competitiveness in Asian countries is spurring replacement opportunities for
advanced pumps.
Meanwhile, rising investments in the oil and gas, petrochemical, and food and beverage sectors are strengthening market prospects in emerging Latin American countries as well.
“As pump manufacturers look to tap this potential through sustained focus on innovation, the era of remote monitoring and proactive maintenance will unfold,” stated Ramachandran.
“With changes in the end user landscape causing a shift from transactional relationships to partnerships, suppliers will employ new business models such as analytics-asa-service and pump-as-a-service to remain relevant in the global pumps market.”
The PIA’s Australian Pump Technical Handbook is a cornerstone text for the Australian pump industry and, in our opinion, a must have for anyone who deals with pumps on a regular basis. In this ongoing series, we feature abridged chapters from the classic book to showcase the various areas covered and to reacquaint readers with the technical aspects of pumps. In this issue, we explore the various factors that should be considered when selecting a centrifugal pump for your specific application.
In order to operate effectively and reliably, a centrifugal pump should be matched to the pumping system and application both hydraulically and mechanically. Installing a mismatched pump can result in ongoing issues throughout the life of the system.
A number of factors should be taken into account in order to select a pump that matches the system and application’s hydraulic requirements. These include:
• System design,
• Quantity – flow rate
• System resistance
• System curve – duty point (rated flow at differential head).
System design – Oversizing or undersizing the pump for the given system should be avoided as it may result in the pump operating outside its allowable operating range. This can cause problems such as circulation
issues, vibration, cavitation and loud operation.
Flow rate – The flow rate achieved in a pumping system is the result of the head created by the pump.
System resistance – The system resistance head is the head necessary to overcome the static head and the friction head in the system. The duty point of the pump in a system is the flow at which the head created by the pump is equal to the system resistance head.
Duty point – The key to successful pump selection is to accurately specify the required duty point.
Net positive suction head available
Net positive suction head (NPSH) is the total absolute head at the pump suction minus the vapour head of the pumped fluid. Determining the NPSH made available by a pump is important for selecting a pump that will operate satisfactorily in your given application. This relates to the fact that one of the most significant causes of poor pump performance and high maintenance
requirements is cavitation. To prevent cavitation, the system net positive suction head available (NPSHA) must be greater than the pump net positive suction head required (NPSHR), preferably with an appropriate safety margin. (Equations for and sample calculations of these values are available in the Australian Pump Technical Handbook).
Suction lift
If your system is handling cold, clean water, calculations can be simplified using the concept of suction lift. Pump manufacturers sometimes publish performance curves depicting the suction lift performance of a pump for clear, cold water. However, as with NPSH, allowing a safety margin is recommended.
Matching the pump to these requirements
Having determined the flow rate, total dynamic head to be generated by the pump and the suction lift or NPSHA, you can then select a pump with a performance curve that satisfies all three of these requirements.
Pump manufacturers may present the performance curves of their pumps in a number of different ways:
• Performance presented at a constant speed with different head–quantity curves corresponding to different impeller diameters
• Performance presented at varying speeds with a constant impeller diameter.
Either way, they will also indicate pump efficiency, power use, and the suction lift or NPSH required for the pump’s flow range. The speed (rpm) and input power (kW) required can then be determined by plotting the required flow, total head and suction lift on the performance curves.
However, keep in mind that the input power will usually be given for clear, cold water. Therefore, if the fluid to be pumped is heavier or lighter than water, pumping it will require comparatively more or less power.
Hydraulic selection – moving from ideal to real
The ideal pump for a system would be a pump running at best efficiency point (BEP) and with NPSHA greater than NPSHR by an adequate margin.
In this ideal case, the impeller and volute are operating at pump design conditions and the flow through the pump unit is smooth. Shock, vibration, energy dissipation, and bearing loading are at a minimum and the pump should have a long, problem-free operating life.
However, this ideal situation is not always possible in reality and a compromise must often be made. This is due to a number of factors:
• A finite number of available pumps – a perfect match for your hydraulic requirements is not always possible because it is simply not economically feasible for pump manufacturers to create a specially designed pump for every possible application. A pump will usually be chosen from the range of commercially available units.
• Specific speed limitations – if the specified duty point is one of high head and low flow rate, impeller geometry limitations may affect the pump selection. This may result in operation near pump minimum continuous flow.
• Net positive suction head – if the NPSHA is limited, the available pump selections and running speeds may be restricted.
• Variable duty requirements – a number of disparate operating conditions may have to be met, precluding an ideal selection.
• Mechanical simplicity/cost/ reliability – the ideal selection may be expensive or complicated. Pump selection is often a trade off between efficiency, cost and reliability.
A pump selection is normally considered acceptable if the duty point falls within the rate of 50 to 110 per cent of best efficiency flow rate. Also a selection to the left of BEP is normally preferred to one slightly beyond the BEP. This allows a greater margin for error in the event that the system designer has overestimated the actual system resistance curve. In many cases, centrifugal pumps can be successfully operated outside the above recommendations in circumstances where alternative selections are not available or economic. The pump manufacturer’s advice should be sought in these instances. Nevertheless, it is always preferable to operate a centrifugal pump as close as possible to its BEP.
HYDROVAR®, the modern variable speed pump drive taking pumping to a new level of flexibility and efficiency.
• Motor or wall mountable
• Fully programmable on site
• Software specifically designed for pump operation, control and protection
• High level hardware design
• More flexibility and cost savings
• Energy savings up to 70%
• Simple mounting “clip and work”
• Multi-pump capability up to 8 pumps
Ph: 1300 4 BBENG
Operating a pump left of BEP can result in problems such as low efficiency, noise and vibration, increased radial loads on bearings due to unbalanced volute pressures, and temperature rise due to dissipated energy created by low efficiency. On the other hand, operating a pump beyond BEP can result in low efficiency, increased power, noise and vibration, poor suction performance (high NPSHR) and increased radial loads on bearings.
Mechanical factors are also important in the selection of pumps. Many of the different mechanical configurations for pumps have been covered in the articles covering previous chapters of the Australian Pump Technical Handbook However, for optimum pump selection, it is useful to briefly examine the effects of system conditions on pump mechanical configuration.
The pump geometry to suit a particular application and its unique set of pumping conditions will depend on the chosen speed and number of stages.
For example, consider the following alternative pump selections for a duty point of 50L/s at a total dynamic head of 150m.
1. Single stage, 1450 rpm. Ns = 239, expected efficiency: 45 per cent, approximate pump outlet size: 100mm, approximate impeller diameter: 720mm. This is not a practical pump selection due to the large impeller diameter
required relative to pump size.
2. Single stage, 2950 rpm. Ns = 486, expected efficiency: 68 per cent, approximate pump outlet size: 100mm, approximate impeller diameter: 360mm. This is a reasonable selection with moderate efficiency.
3. Two stage, 2950 rpm. Ns = 818, expected efficiency: 74 per cent, approximate pump outlet size: 100mm, approximate impeller diameter: 260mm. Better efficiency but more complex and expensive.
This example illustrates the way that pump selection is often a trade off between practical design, simplicity, cost and efficiency.
There are three basic types of sealing which are used to seal the pumps where the shaft passes through the pump casing. These are packed gland seals, mechanical seals and centrifugal seals. Seal-less pumps are also becoming more common, particularly in applications where dangerous toxic or corrosive materials are being pumped and leakage cannot be allowed. The type of seal appropriate will depend on your system and application.
Greater mechanical complexity may result from attempts to create a more efficient pumping system. In some cases, a well selected multistage pump may also be more reliable than a poorly matched single stage pump. However, an increase in the number of stages and greater complexity generally provides greater potential for failure.
Aspects of pump construction that affect reliability include:
• Reduced complexity/number of stages (assuming good hydraulic selection),
• Sensible (larger) running clearances,
• Short shaft spans.
It is also worth noting that sometimes components designed for easier maintenance may reduce reliability. For example easy access to seals and bearings may require a larger shaft span than desirable for reliability considerations.
Apart from the purely hydraulic considerations of flow rate and total dynamic head, mechanical construction may be influenced by the effects of static pressure, liquid temperature, suction lift and normal operating point.
High-pressure conditions create the requirement for an adequately designed pressure retaining casing. Additionally, they can also cause pressure induced axial thrust on the pump shaft, which can lead to rapid bearing failure. Any pump with a single shaft entry can be affected in this way.
Measures to alleviate this problem include:
• Use of a hydraulically unbalanced impeller producing an opposing thrust.
• Reduced impeller back sealing ring diameter which produces an opposing thrust.
• Oversized thrust bearings.
• Use of double entry between bearings style of pump.
High temperatures
When selecting a pump for operation in high temperature conditions a number of factors must be considered. These may include:
• Construction materials that can withstand the temperatures they are exposed to.
• Centreline support of pump casing – this allows equal thermal expansion above and below the shaft axis, retaining shaft/coupling alignment, and is recommended at temperatures above 180°C.
• Increased running clearances to avoid internal contact due to differential expansion.
• Shaft sealing methods, such as high temperature mechanical seals.
• Auxiliary coolant requirements for bearings and seals.
• Extremely high temperatures and pressures may require the use of special gasketing and radially split casings only.
Low suction pressure/high suction lift Operation with suction pressures below atmospheric pressure may result in the ingress of air at the shaft seal(s). Measures to prevent this include:
• Routing a high-pressure flush connection to the stuffing box , thus maintaining pressure above atmospheric at the seal/packing
• Use of a suitable mechanical seal
• Use of a suction inducer.
When a single volute pump is operated at flow rates other than BEP, the pressure distribution around the impeller is no longer uniform, producing a radial load on the impeller and shaft which may result in bearing failure and shaft breakage in extreme cases.
If regular reduced flow operation cannot be avoided, consideration should be given to the following:
• Use of a double volute or diffuser style casing.
• Use of a stiffer/stronger shaft assembly.
• Employing a minimum flow bypass line around the pump.
• Use of a variable speed drive to allow reduced flow operations.
Further information and detailed diagrams, equations and schematics can be found in the Australian Pump Technical Handbook, available from the PIA website (pumps.asn.au/publications). In the next edition of Pump Industry, we go beyond selection, to look at the application of centrifugal pumps in a pumping system.
A WHISPER QUIET RANGE OF PUMPS DESIGNED FOR NOISE SENSITIVE APPLICATIONS.
The new range of Sykes Quiet Solution (QSM) pumps have been designed to comply with the noise output regulations governing work sites and urban areas.
The QSM has a noise level output of 67 dBA at 7m and features impact resistant polyethylene panels, roof, vents and doors.
The Steel bunded chassis features a single point lift eye, fork tynes and houses the 345 litre polyethylene fuel tank.
For more information on the full range of Sykes pumps visit us at www.allightsykes.com or freecall 1300 255 444 to speak with one of our sales and project efficiency experts
Bill Aitken was making cannons for the Second World War before he discovered a love of pumps and has never looked back. While the majority of his career has seen him work at Harland Engineering, Bill has also travelled around Australia and worked with several other Victorian pump companies over his 50-year career. Here, Bill reflects on his life in the pump industry and shares his thoughts on what the future holds for the industry.
In 1943, I left Preston Technical School and got a job at Harland Engineering. For about 18 months to two years, Harland was making 20 millimetre cannons for the war but switched to pumps when the weapons were no longer needed.
The factory was cleared out of all the machinery used to make the cannons and was converted into a place that could make pumps. Our factory was an offshoot of Harland Pumps in Scotland, so we got the pump designs from them and started producing pumps in 1945.
From then on, we sold pumps to a variety of different places, from power stations to water utilities. Working at Harland, I had the opportunity to get into the nitty-gritty of pumps and this appealed to me. Since then I never looked back, I just always had to be working in pumps.
At Harland I was a junior craftsman and when we started producing pumps, I discovered that I really liked it. This was because we weren’t just producing hundreds of the same item, there was lots of variation because we were making particular pumps that did certain things. This is what got me.
The other thing that I liked about the industry was that you got to meet lots of different people and I had the opportunity talk to the people who were actually using the pumps. Some of these pump users I got to know really
well, such as people who worked for the Melbourne and Metropolitan Board of Works.
At Harland, we sold pumps to people all over Australia so I also got to move around the country. This was quite interesting and I found that I really liked travelling.
I stayed at Harland Engineering, my first place of employment, for around 30 years, before moving on to work with other pump manufacturers.
After Harland, an opportunity came up to go to Ingersoll Rand in Dandenong and I jumped at the chance. I worked there for quite a few years, before moving to a manufacturer in Moorabbin. Then I got a phone call from Ken Wilcock asking me to go and work with him at GAAM Pumps. We had a meeting and I decided that the opportunity sounded pretty good, so I moved there and that’s where I worked until retirement.
That’s the thing about all the jobs I’ve had – I always received offers from people to go work for them, so I never really had to officially apply. They all sort of knew me or knew someone that referenced me and thought that I would be good for their business.
Throughout my professional life, I worked at designing and adapting pumps for specific functions. I spent time troubleshooting at various locations around Australia and I travelled to Scotland and America for consultations and to learn and sharing expertise.
I retired in 1997, when I was at GAAM Pumps, after more than 50 years in the pump industry.
I think the pump industry has changed tremendously. When I first started out at Harland, we only handled pumps that could pump water, and there were only about three of four different types of pumps. They progressively got more advanced over the years.
First there was the single stage pumps, which were driven by 10-15 horsepower motors, before multi stage pumps became more common and started being used in power stations and for pumping hot water.
I don’t think the variation of pumps has changed necessarily, but there is a difference in the things that now require pumping. It can be expensive to completely change the way you manufacture a pump, but if you change the material, the impeller or the casing, you can extend the life of the pump.
You might make them in a different metal, or material, which is how pumps have progressed to be able to pump all the fluids that are now available. Basically, you had to change what you were trying to do, to suit the people who were using the pumps.
After the war, when the factory at Harland was converted to make pumps, a gentleman called Harry Tippett joined the company and taught me everything I know about pumps. Harry knew a lot
MICK BUFFIER
Chairman World Coal Association
CHARLES MEINTJES
President – Australia Peabody Energy
ANDREW BARGER
Director Economic and Infrastructure Policy Queensland Resources Council
See the latest processes and technologies live in action
Hear from expert speakers sharing the newest industry information and insights
NETWORKING EVENTS
Connecting with like–minded industry professionals in an informal environment
about pumps and how they worked, so when he started working at Harland, it was the best thing that ever happened as far as I was concerned. He showed me all the differences between the types of pumps, how they worked, and how to cope with them if there are any problems.
Harry retired while I was still at Harland and I only saw him a few times before he passed away, but he was a great help to me when I started out. I remember initially we got a lot of pump drawings from Harland in Scotland which outlined the sort of pumps they wanted us to make, and Harry knew what type of pumps they were just by looking at them. He made me understand certain things about pumps and the industry that I hadn’t come across before.
Harry was a mentor to me, but another pump personality I worked with was Arthur Feiner, who moved from Harland in Scotland, and began working at Harland in Melbourne. I used to do the drawings of the pumps, and at one point Arthur and I decided to change a few things on the drawings and show the bosses what we did. I remember changing a few things to get the patents made differently, and the factory bosses thought it was pretty good.
The most significant development I’ve witnessed is the use of mechanical seals. Everyone might use them now, but they weren’t common when I first started. These seals stop leakage and in this industry, when you’re pumping things like oil and petrol, you really can’t afford any leakage because it could be dangerous. So people came up with these seals that could be made to suit whatever you needed, and could withstand a long duration. A mechanical seal eliminated the use of stuffing boxes, and you got no leakage at all from them.
I think the future will be very different for pumps than it is now, because there might not be as big of a demand for certain pumps. The biggest change will also be the increasing use of solar and batteries in energy production. Energy will come from the sun and batteries; so you won’t need to have generators. Pumps, and the production of pumps, will be reduced.
Of course, there will always be a need to pump something somewhere such as water, but the power to drive it will come from the sun, not a power station. They’re probably going to scrub coal power stations in the next ten or 15 years as well, due to climate change.
If you are passionate about pumps and want to work in them, by all means
do so, as working with pumps over the last 50 years has made for a very satisfying and fulfilling career. Just keep in mind, the industry is changing and will be very different from what it once was.
I retired from GAAM Engineering in 1997, when I was 70 years old, and was made a Pump Industry Australia Life Member in 2004.
When my wife died a few years ago, I moved into a retirement village which is quite pleasant, as I’ve got a two-bedroom house where I have people stay over. I’m getting a bit old for it now, but I like playing golf and I’ve told my daughter that I would teach her to play golf, and we’ll just get a buggy for me to get around in.
I have three daughters and a son who I see mostly every week. One of my daughters visits from Bairnsdale and helps me in the garden, and my other three children live around Melbourne. My son is the Managing Director of a business that designs computer software packages for other businesses, which is doing very well, another daughter is a school teacher and my youngest daughter has a business walking dogs.
Working with pumps over the last 50 years has provided me with a fulfilling career and many long lasting friendships in the industry.
How do I predict changes in pump performance with variations in speed?
Answer
There are fundamental laws which can be used to predict changes in pump performance with variations in speed. It is important in pump applications to be able to develop performance curves corresponding to various speeds from standard performance curves. The mathematical relationships between flow rate, head, power and speed which enable this are known as the Affinity Laws.
For variation in speed with constant impeller diameter, the following laws apply:
a) Pump flow rate (Q) varies directly with the speed (N)
Ti.e. Q1/Q2 = N1/N2
How do I predict changes in pump performance with variations in speed?
b) Pump head (H) varies with the square of the speed (N)
i.e. H1/H2 = (N1/N2)²
c) Power absorbed varies with the cube of the speed (N)
here are fundamental laws which can be used to predict changes in pump performance with variations in speed. It is important in pump applications to be able to develop performance curves corresponding to various speeds from standard performance curves. The mathematical relationships between flow rate, head, power and speed which enable this are known as the Affinity Laws.
For variation in speed with constant impeller diameter, the following laws apply:
a) Pump flow rate (Q) varies directly with the speed (N)
i.e. Q1/Q2 = N1/N2
b) Pump head (H) varies with the square of the speed (N)
i.e. H1/H2 = (N1/N2)²
i.e. P1/P2 = (N1/N2)³
c) Power absorbed varies with the cube of the speed (N)
i.e. P1/P2 = (N1/N2)³
In using the above formulae, it is assumed that efficiency remains constant. In practice, the efficiency is slightly less at lower speeds since friction and drag constitute a larger proportion of hydraulic power. It is important to note that these laws do not apply to NPSH.
In using the above formulae, it is assumed that efficiency remains constant. In practice, the efficiency is slightly less at lower speeds since friction and drag constitute a larger proportion of hydraulic power. It is important to note that these laws do not apply to NPSH.
Speed change example
If the pump speed is 1,450RPM and duty is 200L/sec at 30m head; power = 120kW. What would be the pump duty and duty power if the pump speed is increased to 1,600RPM?
If the pump speed is 1,450rpm and duty is 200L/sec at 30m head; power = 120kW. What would be the pump duty and duty power if the pump speed is increased to 1,600rpm?
Q1 = 200l/s, H1= 30m, N1=1,450RPM, P1=120kW
Q1 = 200l/s, H1= 30m, N1=1,450RPM, P1=120kW N2=1600RPM
N2=1600RPM
Using Q1/Q2 = N1/N2 Using H1/H2 = (N1/N2)² Using P1/P2 = (N1/N2)³
Q2 = 1,600 x 200
H2 = (1,600/1,450)2 x 30 P2 = 120 x (1,600/1450)3
1,450 = 36.53m = 161.23kW = 227.69 l/s
Duty at 1,600rpm is 220.69l/s at 36.53m head. Duty power equals 161.23kW
Duty at 1,600RPM is 220.69l/s at 36.53m head. Duty power equals 161.23kW
* Article courtesy of Kelair Pumps Australia “When Pump Knowledge Matters” Phone: 1300 789 466 www.kelairpumps.com.au