pumpindustry
Non-return valves:
more than meets the eye
Scaling new heights
Your predictions for the year ahead
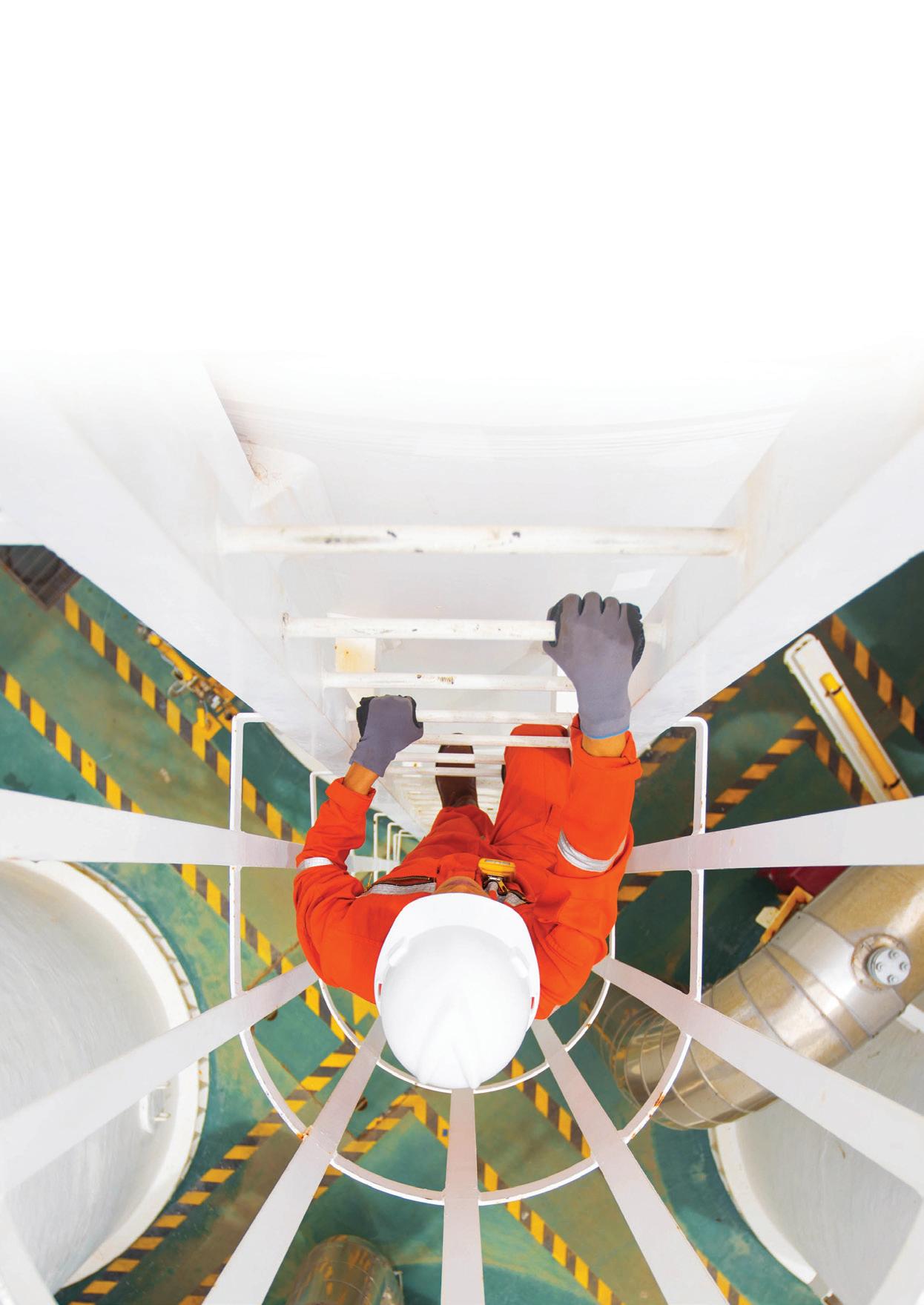
Cost-saving opportunities for
Non-return valves:
more than meets the eye
Cost-saving opportunities for
The key to successful, hassle free sump pumping is to eliminate priming issues.
Which is exactly how our ‘V’ Series Vertical shaft column pump works. Unlike a surface mounted unit, the ‘V’ Series is always primed as it’s submerged in the liquid, avoiding the need and expense of a suction line or foot valve and the NPSH restrictions associated with surface mounted pumps.
Its space saving design minimizes or eliminates floor space required for installation with the motor out of the liquid for easy maintenance and monitoring.
With the ability to pump water, suspended solids or semi viscous products and be used in high temperature applications and explosive atmospheres, the ‘V’ Series is also very versatile. Save time, money and space up top, with an ASM ‘V’ Series pump down below. For more information contact ASM Pumps on (03) 9793 7577 or visit asmpumps.com.au
Pump Industry Australia Incorporated
PO Box 55, Stuarts Point NSW 2441 Australia
Ph/Fax: (02) 6569 0160
pumpsaustralia@bigpond.com
PIA Executive Council 2018
Dave Alexander - President KSB Australia
John Inkster - Vice President Brown Brothers Engineers
Kevin Wilson - Treasurer/Secretary Executive Officer
Keith Sanders - Councillor Executive Officer - Marketing & Statistics Life Member
Alan Rowan - Councillor Executive Officer - Publications & Training Life Member
Ken Kugler Executive OfficerStandards Life Member
Ron Astall - Councillor Astech Technology
Mike Bauer - Councillor Dynapumps
Andrew Black - Councillor Envirotech Water
Malcolm Eyre -Councillor Franklin Electric
Ashley White - Councillor Davey Products
It is hard to believe it is a new year already. Where did 2017 go?
It feels like only yesterday that I took over the reins of President from Ron Astall during the 2016 AGM.
Ron certainly left big shoes, and at times he keeps us all sane with his choice of jokes and stories.
Being the President does have its challenges, and as re-elected PIA President for 2018, I do hope to make further progress on 2017’s achievements, as well as previous achievements by Ron and the PIA team, to ensure members gain maximum benefit from their important key industry body.
In addition to the various Council meetings held throughout 2017 both in Perth and via Conference calls, your PIA committee had another year of action with many programs run over the course of the year. These included:
• 21 and 22 February - Technical meeting, and Installation and Commissioning Course at Hydro Innovations in Sydney. The program included “Introduction to Life Cycle costs” presented by Keith Sanders, and Vertical Gear – Motor Drives for large pumping applications, presented by David Goodchild and Prasanna Santhanum from ABB Australia
• 27 April - How to get the best out of your pumps seminar held in Melbourne
• 9 May - Technical meeting in Brisbane where Keith Sanders provided an update of the IBIS Pump market in Australia, and Alex Sohler, Managing Director of TECO Australia, presented on the impact of stray currents on inverter driven electric motors
• 24 May - Installation and Commissioning Course held at Link Pumps in Williamstown
• 12 July - Breakfast meeting at The Boathouse in Melbourne where Brett Dundules provided an outline of Fire Protection Association Australia (FPAA) activities in the fire protection sector
In addition to these meetings, with the latter correlating to the following comments, our Executive Officers Keith Sanders and Ken Kugler have been working on the Fire pump checklist (the latter has been supported extensively by Grundfos/BKB, which PIA appreciates), AS 2941-2013 standard for fire pumps to be adopted by ABCB as a reference for fire pump installations in the Australian domestic market.
Also Keith Sanders is continuing to liaise with Energy Action, who is a consultant for ABCB to review the requirements of Section J of the NCC, which covers the maximum power levels for pumps used in HVAC installations.
And it was a pleasure to work with Irrigation Australia (IAL) to come to a formal agreement where both PIA & IAL can work closer together.
I would also use this time to make you aware of the 2018 business plan which includes the key objectives to:
• Drive up memberships
• A minimum of four general / technical meetings annually
• Two Breakfast meetings
• Three Installation and Commissioning Courses
In addition to these actions, myself as the President and the PIA Council team, we would welcome your comments for improvement and particular areas you would like the Council to focus on.
I am always contactable on 0438 100 227.
I would like to take this opportunity to thank the PIA team, for all the work they have done throughout the year. It is predominantly voluntary, and does take time and effort.
A big thank you to John Inkster, Ashley White, Malcolm Eyre, Peter Passalacqua, Mike Bauer and our three Executive Officers, Ken Kugler, Keith Sanders and Alan Rohan.
Thank you to the companies they represent: Brown Brothers, Franklin, Grundfos, Dyna Pumps, and Davey.
And of course thank you to our Secretary Kevin Wilson.
Bring on 2018…. Here’s to pumping…
Yours in pumping, Dave Alexander
Cover image highlights the State of the Industry feature which looks at your predictions for the year ahead.
Published by Monkey Media Enterprises
ABN: 36 426 734 954
PO Box 1763
Preston South VIC 3072
P: (03) 9988 4950
F: (03) 8456 6720
monkeymedia.com.au
info@monkeymedia.com.au
pumpindustry.com.au
magazine@pumpindustry.com.au
Publisher: Chris Bland
Editor: Lauren Cella
Senior Associate Editor: Jessica Dickers
Journalists: Elisa Iannunzio, Nicole Valicek, Kirsty Hutton
Marketing Director: Amanda Kennedy
Marketing Associate: Sam Penny
Marketing Assistants: Rima Munafo, Katie Chancellor
Production and Customer Service:
Titian Bartlau
Senior Designer: Alejandro Molano
Designer: Jacqui Abela
ISSN: 2201-0270
This magazine is published by Monkey Media in cooperation with the Pump Industry Australia Inc. (PIA). The views contained herein are not necessarily the views of either the publisher or the PIA. Neither the publisher nor the PIA takes responsibility for any claims made by advertisers. All communication should be directed to the publisher.
The publisher welcomes contributions to the magazine. All contributions must comply with the publisher’s editorial policy which follows. By providing content to the publisher, you authorise the publisher to reproduce that content either in its original form, or edited, or combined with other content in any of its publications and in any format at the publisher's discretion.
more to non-return valves than meets the eye..............................................................
applying positive displacement pumps
Lauren Cella has been appointed the new Editor of Pump Industry Magazine.
Lauren has been with the Monkey Media team since 2016, working across the Pump Industry magazine, website and newsletter. She has also worked across Monkey Media’s other magazines including Infrastructure and Utility
Before joining Pump Industry, Lauren worked in a variety of journalism roles including Australian Geographic magazine, country newspapers, online news sites and community radio station Radio Adelaide.
During her time with Pump Industry Lauren has worked closely with pump suppliers and manufacturers to create tailored content for their websites, representing the magazine at PIA events where she has met a lot of readers and contributors, and has continued to build up her pump knowledge.
“I have loved writing about Australia’s pump industry, from our technical content to profiles of Pump Pioneers. I find the industry and the wide variety of pump applications really interesting – there’s always something new to talk about.
“In my new role as Editor I look forward to getting to know the pump community better, as well as growing the print and online audience among all pump users, suppliers and manufacturers by continuing to provide them with high-quality and engaging content,” Lauren said.
Former Editor Chris Bland will remain as Publisher.
Work has started in Blessington, Tasmania, on the $30 million North Esk Irrigation Scheme, following the award of the design and construction tender in November 2017.
Gradco will build the dam, and Shaw Contracting (Australia) will build the pump stations and pipeline network.
The tender process and the applications for Development Approval lodged with the Launceston and Northern Midland Councils were the final steps before construction could begin.
The 468ML scheme proposes to take water from the North Esk River at Watery Plains in Blessington during winter and transfer it to a storage facility at White Hills, that is yet to be constructed.
The 5,200ML “Dalness Dam” will be used to store scheme water for delivery during a 120-day irrigation season nominally from November through March each year.
Two pump stations are proposed for the scheme: The North Esk Watery Plains transfer pump station, and a boost pump at the Rocklands Dam to service the White Hills and Logan Road areas.
The majority of the scheme’s water (85 per cent) will be distributed via gravity.
Some 63km of pipelines are proposed varying in size from 710mm down to 160mm.
These pipes are all proposed to be of High Density Polyethylene (HDPE) and will be installed with a minimum of 700mm of cover from the top of the pipe.
Assistant Federal Minister for Agriculture and Water Resources, Anne Ruston, said, “Areas of the Northern
Midlands and around Launceston support a variety of agricultural enterprises, and the main impediment to expansion of irrigation in the region is the limited supply of water and associated lack of reliable water.
“The North Esk Irrigation Scheme will help overcome that by providing 4685ML of high security irrigation water to the Northern Midlands and increase the irrigation footprint in the region by a substantial area.”
Tasmanian Deputy Premier and Minister for Primary Industries and Water, Jeremy Rockliff, said as many as 30 full-time equivalent jobs are expected to be created.
“The statewide irrigation program is a key part of the Hodgman Government’s Sustainable Agri-Food Plan to grow the value of agriculture to $10 billion by 2050,” Mr Rockliff said.
“This North Esk Irrigation Scheme will deliver a reliable water source and allow for the expansion of horticulture, viticulture, mixed cropping and intensive livestock grazing.
“Importantly farmers are genuine partners investing with government in the capital works as well as the additional on-farm infrastructure like dams, pipes and centre-pivots or drippers.”
Almost $19 million for the North Esk Irrigation Scheme comes from the Federal Government, with the State Government contributing $4.5 million and irrigators a further $7 million.
Water Corporation has finished work on Exmouth’s southern borefield in WA which includes the installation of 10 new solar powered bores.
The $2.1 million project will enable 10 additional water supply bores to be brought online to supply the growing popular tourist town and help meet peak demand periods.
The installation of solar panels and the additional bores will increase the capacity of the borefield to produce an additional 500,000 litres of water each day.
Solar power will be used to pump water from the borefield to a five million litre water storage tank, which then supplies water to the Exmouth community.
Minister for Water, Dave Kelly, said the project was a great example of how renewable energy can be used to reduce the operating costs of supplying water to the town.
“The solar panels will generate around 144,000 kilowatt hours annually, which is the equivalent energy to power 25 average households for a year,” Mr Kelly said.
“This is an example of the Water Corporation’s work to reduce its environmental footprint while continuing to maintain a sustainable and secure water supply for the Exmouth community.”
Construction on the project started in June 2016 and was completed at the end of September 2017.
Perth-based company EMC Solar Construction completed the work for the Water Corporation, with about 15 Western Australian workers on site throughout the project, including local subcontractors.
Engineers from the Georgia Institute of Technology, Stanford, and Purdue University have developed a ceramic-based mechanical pump able to operate at record temperatures of more than 1,400°C and can transfer high temperature liquids such as molten tin, enabling a new generation of energy conversion and storage systems.
The new pump could facilitate high efficiency, low-cost thermal storage, providing a new way to store renewable energy generated by wind and solar power, and facilitate an improved process for generating hydrogen directly from fuels such as methane – without producing carbon dioxide. Use of ceramic components, normally considered too brittle for mechanical systems, was made possible by precision machining and seals made from another high-temperature material, graphite.
The research was supported by the Advanced Research Projects Agency – Energy (ARPA-E) and reported in the 12 October 2017 issue of the journal Nature
An assistant professor in Georgia Tech’s Woodruff School of Mechanical Engineering Asegun Henry said that until now, the pump industry had a ceiling for the highest temperatures at which heat could be moved and stored.
“The hotter we can operate, the more efficiently we can store and utilise thermal energy. This work will provide a step change in the infrastructure because now we can use some of the highest temperature materials to transfer heat. These materials are also the hardest materials on Earth,” Mr Henry said.
Thermal energy, fundamental to power generation and many industrial processes, is most valuable at high temperatures because entropy – which makes thermal
energy unavailable for conversion – declines at higher temperatures. Liquid metals such as molten tin and molten silicon could be useful in thermal storage and transfer, but until now, engineers didn’t have pumps and pipes that could withstand such extreme temperatures.
“The hotter you can operate, the more you can convert thermal energy to mechanical energy or electrical energy,” Mr Henry said.
“But when containment materials like metals get hot, they become soft and that limits the whole infrastructure.”
Ceramic materials can withstand the heat, but they are brittle, and many researchers felt they couldn’t be used in mechanical applications like pumps. But Mr Henry and graduate student Caleb Amy decided to challenge that assumption by trying to make a ceramic pump.
“We weren’t certain that it wouldn’t work, and for the first four times, it didn’t,” Mr Henry said.
The researchers used an external gear pump, which uses rotating gear teeth to suck in the liquid tin and push it out of an outlet. That technology differs from centrifugal and other pump technologies, but they chose it for its simplicity and ability to operate at relatively low speeds. The gears were custom-manufactured by a commercial supplier and modified in the Carbon Neutral Energy Solutions (CNES) Laboratory at Georgia Tech.
“What is new in the past few decades is our ability to fabricate different ceramic materials into large chunks of material that can be machined,” Mr Henry said.
“The material is still brittle and you have to be careful with the engineering, but we’ve now shown that it can work.”
Addressing another challenge, the researchers used another high-temperature material – graphite – to form the seals in the pump, piping and joints. Seals are normally made from flexible polymers, but they cannot withstand high temperatures. The team used the special properties of graphite – flexibility and strength – to make the seals. The pump operates in a nitrogen environment to prevent oxidation at the extreme temperatures.
The pump operated for 72 hours continuously at a few hundred revolutions per minute at an average temperature of 1,473 Kelvin – with brief operation up to 1,773 Kelvin in other experimental runs. Because the researchers used a relatively soft ceramic known as Shapal for ease of machining, the pump sustained wear. But Mr Henry said other ceramics with greater hardness will overcome that issue, and the team is already working on a new pump made with silicon carbide.
Among the most interesting applications for the high-temperature pump would be low-cost grid storage for surplus energy produced by renewables – one of the greatest challenges to the penetration of renewables on the grid. Electricity produced by solar or wind sources could be used to heat molten silicon, creating thermal storage that could be used when needed to produce electricity.
“It appears likely that storing energy in the form of heat could be cheaper than any other form of energy storage that exists,” Mr Henry said.
“This would allow us to create a new type of battery. You would put electricity in when you have an excess, and get electricity back out when you need it.”
The Georgia Tech researchers are also looking at their molten metal pump as part of a system to produce hydrogen from methane without generating carbon dioxide. Because liquid tin doesn’t react with hydrocarbons, bubbling methane into liquid tin would crack the molecule to produce hydrogen and solid carbon, without generating carbon dioxide, a greenhouse gas.
The pump could also be used to allow higher temperature operation in concentrated solar power applications, where molten salts are now used. The combination of liquid tin and ceramics would have an advantage in being able to operate at higher temperatures without corrosion, enabling higher efficiency and lower cost.
The ceramic pump uses gears just 36mm in diameter, but Mr Henry said scaling it up for industrial processing wouldn’t require dramatically larger components. For example, by increasing the pump dimensions by only four or five times, and operating the pump near its maximum rated speed, the total heat that could be transferred would increase by a factor of a thousand, from 10kW to 100MW, which would be consistent with utility-scale power plants.
Mr Henry said for storage, molten silicon – with still higher temperatures – may be more useful because of its lower cost. The pump could operate at much higher temperatures than those demonstrated so far, even past 2,000°C.
• Flows to 7,500 L/Sec
• Heads to 500 m
• Power to 1000+ kW
• Temperatures to 150°C
• Bowls Diameter up to 45 inch
Design Advantages
• Exceptional engineering quality
• Highly efficient hydraulic design
• Heavy duty component castings
• Cast discharge heads
• In-built thrust bearing with anti-rotation arrangement
• Standard IEC electric motors
• Superior quality column assemblies
• Materials of construction options
• Shaft sealing options
• Engine drive options
Applications
• Irrigation
• Water Supply
• Process water
• Geothermal
• Cooling towers
• Fire protection
• Marine
• Water treatment
• De-watering
Layne Bowler vertical turbine pumps have a proven record under the most demanding and toughest of conditions.
A Sydney pump station has been recognised for its national engineering heritage by Engineers Australia at an Engineering Heritage National Marker ceremony.
The iconic Ryde Water Pumping Station and its surrounding site host the original steam-powered Ryde Pumping Station No.1 operated from 1891 to 1930.
To increase capacity for the increasing water demands of a growing northern Sydney, pumping station No. 2 was commissioned on 15 September 1921, which was also steam-powered and built on the same site as pumping station No. 1.
Sydney Division President of Engineers Australia, Julie Mikhail, said the pumping station was recognised for its vital role in supplying water to the Northern Suburbs of Sydney, and for its technical, historical and aesthetic heritage significance.
“The site has a remarkable history and reflects a series of world-class engineering feats and innovation in its design and construction,” Ms Mikhail said.
President of World Federation of Engineering Organisations, Dr Marlene Kanga, said it is a wonderful opportunity to acknowledge and remember the outstanding contribution of early engineers, who would have to develop their drawings without the use of computers and sophisticated software,
but with a compass and slide rule.
Minister for Energy and Utilities, Don Harwin, said that today, many Sydneysiders are not aware of the early struggles the city experienced to secure a safe and regular supply of water to communities.
“The Ryde Water Pumping Station is an important part of this incredible story, signifying engineering achievements and innovation in the water industry.
“Before the opening of the Ryde Water Pumping Station No. 2 in 1921, Sydney was not only in continual drought, but water was particularly scarce north of the harbour. This station was instrumental in providing water supply to the northern suburbs of Sydney,” Mr Harwin said.
When plans for the new water pumping station No. 2 were initiated in 1915, they were hampered by WWI which prevented the delivery of boilers and steam turbines ordered from Great Britain.
At this time, not only were there difficulties with accessing machinery, but all financial transactions had to be reviewed under war-time regulations and this created many challenges for the expansion of the plant.
On 15 September 1921, the second Ryde Water Pumping Station was commissioned as the largest water pumping station in Australia, and was a key factor in the growth of the Northern Suburbs of Sydney.
Managing Director of Sydney Water, Kevin Young, said locals are lucky enough to live in a city which supplies safe and high-quality drinking water to communities every single day, and this is much to the credit of early forward-thinking planners, designers and engineers.
“The Ryde Pumping Station, almost 100 years on, continues to be an integral part of Sydney’s water supply. It continues to serve around one million residents every day and remains the largest water supply pumping station in Sydney,” Mr Young said.
“This station has played a vital role in keeping Sydney a liveable city and will continue to do so into the future. It is interesting to look back on the early challenges which our predecessors experienced, as we look ahead and plan for our city to secure water supply for an even greater increase in population – eight million people in Sydney by 2050.”
More than 90 years young
• Pump repairs onsite mechanical repairs and upgrades.
• Repair bands, gibaults, filters/screens, media tanks, saddles, foot valves.
• Filtration systems, manifolds and more.
• Standard sizes in stock or made to order.
• Aluminium, stainless and steel fabrication.
• Plasma cutting, pipe work manufacture and install.
CERTIFIED UNDER AS/NZS ISO 9001
KSB Australia offers realtime pump monitoring with the precise and robust PumpMeter
Achieve transparency in system operation and gain deeper insight to your pump’s operating characteristics - in realtime.
Simplify your system and save time, energy and money with the intelligence to optimise efficiency measures. Talk to KSB Australia about modernising your existing systems, or starting a new energy-efficient project.
The Western Australian Government is providing $15 million towards a new water treatment plant in Glen Iris.
Construction of the plant will start in the first half of 2018 and will support local jobs over a two-year construction period.
The plant will secure a sustainable water supply for Aqwest’s 35,000 customers and is capable of producing 10 megalitres of drinking water per day – equivalent to four Olympic swimming pools.
WA Premier, Mark McGowan, said the project will secure the future drinking supplies of the Greater Bunbury region.
“Importantly, it will also support local jobs for people in Bunbury during construction, as well as ongoing operational jobs,” Mr McGowan said.
Water for the Bunbury area is currently drawn from several bores along the coast where, due to the impacts of climate change, the risk of increasing salinity levels threatens water quality.
Minister for Water, Dave Kelly, said the southwest of Western Australia is one of three places in the world most impacted by climate change.
“This project will help protect water quality in the Bunbury area by safeguarding against seawater intrusion
caused by climate change,” Mr Kelly said.
“The new treatment plant will improve water quality in the area and reduce Aqwest’s water treatment costs, which will be of benefit to customers.”
The new water treatment plant will extract water from a higher quality in-land groundwater bore, creating greater water production cost efficiencies and delivering benefits to customers.
Bunbury MLA, Don Punch, said, “The project will be an example of the McGowan Government’s commitment to local projects supporting local jobs and will contribute to employment in the construction sector.
“This is exactly the type of project we need for Bunbury, one that improves our local infrastructure, supports the growth of our city and delivers on local jobs.”
Aqwest operates an integrated treatment and distribution system comprising 12 bores, six water treatment plants, four reservoirs, one water tower and about 380km of water mains providing water to approximately 17,000 water services.
SERVICING ALL MAKES AND MODELS OF PUMPS AND CONTROL CIRCUITS
• Pumping problems resolved from 0.5kW up to 500kW
• Written report provided
• Service and repair of any pump product in-house
• Programmed service and maintenance calls
• Service vehicles carry extensive range of stock
• Workmanship guarantee
KELAIR SERVICE CAN PROVIDE
• Breakdown service
• Routine preventative maintenance
• Reverse engineering manufacture
• Engineering / Spare parts / Machining
• Commissioning and installations
A major upgrade to the heating, ventilation and air conditioning system at the Canberra Museum and Gallery located at the North Building in Civic will reduce ACT greenhouse gas emissions by 263 tonnes.
ACT Minister for Climate Change and Sustainability, Shane Rattenbury, said the upgrade replaces a gas-fired system with a new electric system, and will also reduce costs by more than $120,000 per year.
“The upgrade to the North Building, which faces the ACT Legislative Assembly, is part of the ACT Government’s efforts to improve the energy efficiency and reduce the carbon footprint of its buildings,” Mr Rattenbury said.
“The large, multi-purpose facility houses offices, arts facilities including a museum, art gallery, cafe and multicultural centre, and operates 24/7 to maintain archival quality air for the Canberra Museum and Gallery.
“The move to air rather than water cooled chillers provides additional maintenance savings and negates the need for cooling tower maintenance and water treatment, registration and ongoing risk assessment costs.
“This is fairly new technology and the ACT Government will be actively monitoring this low-carbon innovative project, with the view to demonstrate that the technology is viable in the ACT climate,” Mr Rattenbury said.
In 2016 the project received a $650,000 loan under the ACT Government’s Carbon Neutral
Government Fund to enable it to transition away from gas-fired power.
The Carbon Neutral Government Fund provides loans for agencies to implement energy and fuel saving projects.
“The fund has now supported 25 projects with a total of $13.6 million in loans provided across ACT Government which will provide around $2 million in annual cost savings,” Mr Rattenbury said.
“Many of these projects are implemented in public buildings, such as libraries and schools, providing a direct community benefit from the government’s investment.”
Long-time pump professional, and Life Member of the PIA, Ken Willcock passed away in late September 2017.
Over the course of his career in pumps, Ken worked for Pomona Pumps, Kelly & Lewis, and GAAM Engineering.
He was also a member of the Australian Pump Manufacturers Association (APMA) - the forerunner of the PIA - from its inception, was a member of the APMA council since 1975, and took on the role of President from 1980-1982.
A long career in pumps
Ken’s career in pumps started after a visit to the Snowy Hydro Mountains Scheme, which spurred him to complete a Certificate of Civil Engineering. It was during the course of his studies that he met his mentor Bob Moore and began working as a spotter for Pomona deep well pumps (a product line of FN Bethune). He stayed with Bethune until the company was acquired by Clyde Engineering.
Following his time with Bethune, he worked for Harland Engineering as Sales Engineer until 1962 when he began working for Kelly & Lewis (K&L) where he was later appointed Sales Manager (Standard Products). In 1970 K&L opened a sales and engineering office in Singapore and Ken took on the role of South East Asian Manager. This involved moving to Singapore where Ken stayed with his family until 1975 when he took on the role as General Sales Manager of K&L. He was also appointed to K&L’s Board as Commercial Director in 1978.
In 1976, Wormald International took over K&L’s parent company Mather and Platt, however the relationship was not a happy one. So Ken accepted the position of General Manager at a small Australian pump company called GAAM Engineering - a subsidy company of UK company SPP. A few years later Ken was appointed Managing Director of GAAM, following the company’s takeover by Canadian company Wajax Limited. Ken retired from GAAM in 1995.
After this, Ken did some consulting work for GAAM and Weir Engineering in Vietnam and the Philippines respectively.
Ken’s passion for pumps was evident throughout his career and he was held in high regard by his colleagues and the industry.
During his time with the APMA Ken worked as an industry lobbyist, using his contacts with government to deal with issues such as terms and conditions, tariffs and state preferential purchasing. These were all issues that impacted significantly on APMA members.
“He was a very good leader and formed many friendships across the industry, and he used these friendships to further the interest of the APMA and encourage participation... He remained a friend and continued his interest in the industry association becoming a Life Member and participating in AGM’s and annual dinners,” Kevin Wilson, PIA Treasurer/ Secretary and Executive Officer said.
Outside of pumps, Ken had a love for classical music which began as a boy when he learnt piano. He was a keen sailor and joined a group of friends each weekend to race a Diamond Class yacht on Port Phillip Bay. He also loved skiing and would take winter holidays to follow his pastime of cross country skiing. Following his retirement he decided to learn the trumpet and played with Melbourne’s Stonnington City Brass before moving to Tasmania to be closer to his son. He also enjoyed playing bowls.
Ken is survived by his wife Cherie and his two children Stewart and Kerry.
Last November, the PIA council and its members gathered for the association's 14th annual general meeting and dinner. Attendees heard about the activities and achievements of the association over the last 12 months and celebrated members’ contributions to the industry.
The PIA reported that it successfully held three Installation and Commissioning courses in 2017 in Sydney, Melbourne and Brisbane, as well as two technical seminars in Brisbane and Melbourne.
Melbourne also hosted a successful Breakfast Meeting in July where attendees were updated on the PIA’s cooperation with the Fire Protection Association Australia (FPAA) to promote better standards in the fire protection market.
The PIA council also discussed its continuing liaison with industry organisations and government departments to promote cooperation between industries, and improve standards.
Activities included:
• FP008 Fire Pump Committee worked on AS2304 Fire water tanks which is now completed and was expected to be published by the end of the 2017
• Reviewed DR AS2419.1 Hydrant Code and submitted strong commentary in respect of boosting by the Fire Brigade through the pump
• AS2118.1 'Sprinkler' standard has finally been published and the NCC/BCA has accepted this new code thus allowing fire pump duty requirements to be more clearly specified
• AS2417 – 2001 Pump test code has slowly worked its way through Standards Australia. The revised standard will be known as AS ISO 9906 – 2017 (or 2018 if publication is delayed further)
AS2941 Check List activities are still ongoing with a proposal submitted to the NCC to have the standard written directly into the NCC/BCA codes, however this was rejected and will remain as a 'secondary' standard in the sprinkler and hydrant codes
The PIA council reported it is continuing to liaise with Energy Action, who are consultants for ABCB, to review the requirements of Section J of the NCC which covers the maximum power levels for pumps used in HVAC installations.
The PIA was also happy to report it has come to a formal agreement with Irrigation Australia (IA), and will work closely together on a range of activities.
The council also awarded the PIA Industry Innovation Award 2017 to Hydro Innovations for its test loop systems. To find out more about the award, go to page 18.
Concluding the evening, the council encouraged members to be actively involved in the PIA if they want to get the most benefit from the association, and to recommend fellow companies to join.
At the PIA annual general meeting last November, the association was excited to announce a new Life Member, Les Boelckey, for his significant contribution to the association and the industry.
During his early career Mr Boelckey worked in the steelweld fabrications and pressure vessel manufacture divisions at the Lance Reichstein’s Indeng Group in Australia, where he held positions as both contracts and general manager.
At the time, the group manufactured Licenses for United Centrifugal Pumps (UCP) in San Jose, California.
UCP were eager to continue a presence in Australia so negotiated a new joint venture with United Pumps Australia (UPA), in November 1984.
Due to his success at UCP, Mr Boelckey was chosen as the first general manager of a newly formed UPA.
The company started with six employees, but with Mr Boelckey at the helm it soon grew to be a respected market leader in Australia in the specialist area of API 610 Process Pumps for oil and gas.
Among his many achievements, Mr Boelckey has served as a former PIA President from the mid to early 90s, and was a long serving councillor of the Board.
At the PIA annual general meeting last November, the association presented the 2017 Industry Innovation Award.
The PIA launched the Industry Innovation Award in 2016 to recognise and encourage new products and techniques that the Australian pump industry will need to use in the future to stay on top of the global pump industry.
The winner of the 2017 PIA Industry Innovation Award was presented to New South Wales-based company Hydro Innovations for the development of its test loop system that is being used to train operators in pump hydraulics, troubleshooting and maintenance.
Hydro Innovations is the exclusive distributor of Gorman-Rupp pumps in Australia, which is well known as a world leaders in self-priming centrifugal wastewater pump technology.
The test loop system is part of the company’s training centre, known as the Hydro Innovations Pump Institute, and is used to show engineers how self-priming pumps can deliver benefits to their projects.
The innovative system, which is one of the many training aids offered at the centre, was developed with input from Gorman-Rupp, other Gorman-Rupp distributors and internal input, to demonstrate the priming and re-priming capability of Gorman-Rupp wastewater pumps.
“The test loop system was developed to train our customers in the application of self-priming pumps, and the benefit in safety and lifecycle cost savings that Gorman-Rupp self-priming wastewater pumps can deliver to asset owners,” General Manager of Hydro Innovations, Garry Grant said.
It also demonstrates the accuracy of the liquid level control system and the value of the developed mode of
operation in clearing all of the solids contents within wastewater wet wells with each and every pump cycle, and reducing energy consumption.
Mr Grant said it was an honor to be selected as the winner of the innovation award by the peak body in the Australian pump industry.
“The award is a vindication that the time and effort put into building the centre was worthwhile,” Mr Grant said.
The Institute covers two floors and houses a variety of training assets. It focuses on self-priming pumps, but the curricula also includes training on standard centrifugal and other types of pumps.
Hydro Innovations was nominated for the award by a number of workers in the pump industry who attended training sessions at the facility and said providing the necessary training in pump hydraulics would benefit their expertise and knowledge in the industry.
Applications for the Industry Innovation Award is open to full members of PIA who can demonstrate that they have made a significant contribution in Australia to the design and development of a product, pumping system or project and that this innovation has resulted in dramatic improvement in environmental outcomes.
Kubota’s Power Packs are pre-assembled industrial engines and make choosing the right engine for your equipment easy. Simply hook it up to your pump and it’s good to go when you are.
All base Power Packs come complete with radiator and guarding, coolant tank, muffler, fuel filter, air cleaner, temperature switch and engine feet. Electric Power Packs also include an electric lift pump and Deep Sea engine control unit with a weather proof harness, which makes for easy operation.
Built with Kubota’s renowned quality and world-class components, each Power Pack is further supported by an extensive Australia-wide service support network and a 2-year/2000HR factory warranty.
Call now for low finance rates & your nearest dealer. AUSTRALIA WIDE 1300 582 582.
Pump Industry Australia’s (PIA) next technical meeting, hosted by Kelair Pumps, will include presentations about pumping solutions and capabilities.
Kelair Pumps will host the technical meeting at its head office in Arndell Park in Western Sydney on Tuesday 20th February from 4.30 – 6.30pm.
The presentations will be followed by a forum on HVAC pumps based on the submission PIA has made to the Australian Building Codes Board (ABCB) and Energy Action for amendments to the National Construction Code (NCC) scheduled for 2019.
The NCC is an initiative of the Council of Australian Governments developed to incorporate all on-site building and plumbing requirements into a single code. The NCC sets the minimum requirements for the design, construction and performance of buildings throughout Australia.
These presentations give the opportunity for the ACBC and Energy
Action to outline the proposed changes to Section J of the NCC 2019, which covers the maximum power levels for pumps used in HVAC installations, and engage in discussion with members on the PIA’s suggestions for amendments to NCC 2019 with respect to pumps for HVAC systems.
The meeting will also be open to non–members who have an interest in the presentations, as either a user or specifier of pumping equipment, and aims to create stimulating discussion of key issues in the industry, as well as provide an opportunity for PIA members in New South Wales to network with local pump people.
The meeting will be followed by light refreshments and guests are required to register with PIA Secretary, Kevin Wilson at pumpsaustralia@ bigpond.com if they wish to attend.
DATE
Tuesday 20th February 2017
ADDRESS
Kelair Pumps 211-215 Walters Road
Arndell Park
NSW 2148
TIME 4.30 – 6.30pm
Note: Parking available on-site
Venturi Aeration systems are now available in Australia through Hydro Innovations, and are ideal for a variety of applications, including odour control, sludge digestion, wastewater aeration, lake destratification, septage treatment and many more.
The Venturi Aerator is a static device that is installed immediately downstream of a pump. The pumped fluid is forced into the Venturi Aerator, where a specially designed and machined nozzle produces a venturi effect, enabling atmospheric air to be drawn into the system and mixed with the pumped fluid. The aerated fluid is then pumped back into the lagoon or basin the water was drawn from.
When used with self-priming pumps, the system can be mounted on the banks of lagoons, making them safer, cheaper and easier to maintain than other systems. Hydro Innovations is in the unique situation of being able to supply the Venturi Aerator packaged with Gorman-Rupp self-priming pumps, as the authorised Australian distributor of both US manufacturers.
Hydro Innovations claim that by using a Venturi Aerator with a Gorman-Rupp pump, asset owners can transfer oxygen at a cheaper rate per kW employed than other forms of aeration.
Other forms of aerator are mounted on pontoons and are tethered to banks via cables, whereas the Venturi Aerator system is mounted on lagoon banks, not in them.
This makes this style of system safer, easier and more cost effective for operators to maintain. Operators don’t have to drag floating units into banks or row out to them.
Venturi Aerators are available in 50mm, 75mm, 100mm and 150mm sizes, with fluid transfer rates from five L/s through to 80 L/s with a single unit.
…Gorman-Rupp Pumps – no worries…
Ebara is known worldwide as one of the largest and most diverse manufacturers of custom, industrial and general purpose pumps. Since its beginnings in Japan over 100 years ago, the Ebara Corporation has been a major supplier of pumping equipment to Japanese industry, and over the last 50 years expanded to all industrial markets worldwide.
Ebara has factories and sales offices in six continents and has recently undertaken a major globalisation of its standard industrial product range. This includes the introduction of a new range of EN733 end suction pumps, and a redesigned and economical vertical multistage pump.
In Australia, the Ebara name has been renowned for its quality and reliability. The Ebara Pumps Australia standard product line has been sold and supported in Australia for over 30 years.
Ebara continues to supply world-leading pumps.
Two recent examples are shown below:
Ebara has supplied some of the world’s largest boiler feed pumps to supercritical power plants in China. These were the first single pumps capable of supplying boiler feed water to an entire 1,000MW power plant.
Discharge: 500mm (20") Power: 37,000 kW (37 MW)
Duty: 3,200t/hr @ 3,800m.hd.
Many Ebara custom pumps have also been installed in Australian and New Zealand power stations and in industry for over 40 years with trouble free operation.
The new products have been designed to global standards to suit the world market, and are manufactured at Ebara owned and managed factories in Europe and South East Asia. This is building on the 100 years of Japanese technology and engineering expertise obtained in the manufacturing of high-end custom pumps.
Ebara has recently manufactured its largest submersible pump in terms of length and motor power. This will be installed at Lake Mead to supply water to Las Vegas, US.
Diameter: 900mm Motor Power: 2,500kW
Duty: 79m3/min @ 132m.hd. Length*: 130m
Length*: The pump is assembled with 24 x 5.2m column pipes
Ebara have been supplying pumps into Australia for over 30 years and have gained a reputation for their quality and reliability.
Single stage end suction centrifugal pumps
Börger rotary lobe pumps have conveyed highly viscous, chemically aggressive media or media containing solids for more than 30 years. The pumps can be used as stationary, mobile or submerged versions due to the compact design.
At the heart of the ONIXline pump are the rotors. They were developed by using the most advanced flow simulation technology. The special geometry of the rotors with exactly calculated windings ensures gentle, practically pulsation-free pumping with maximised efficiency.
In order to fully benefit from the advantages of the new rotors, Börger has adapted the pump casing to the rotors with optimal flow properties. A very robust carrier and timing gear makes sure that the clearance between the rotors and the pump casing is very small.
When combining this with the precise rotors in a flow-optimised pump casing, excellent efficiency is achieved even with high pressures.
Different sealing systems can be used due to the large sealing area and the porting integrated in the pump casing for a sealing circulation system.
The application options of Börger rotary lobe pumps have also expanded with the ONIXline pump. With the BLUEline and ONIXline pump, Börger offers its customers 25 pump sizes with flow rates between one and 1,500 m³/h, and a pressure stability of up to 16 bar.
Using a modular principle, all components of the rotary lobe pump are individually selected for each purpose of the pump.
All Börger pump units can be manufactured according to the European ATEX guidelines (94/9/EG) intended for use in potentially explosive atmospheres. In addition, an API 676 compliant design is possible.
The Dodge Vertical Gearmotor provides an alternative to common vertical pump drive technologies and offers significant benefits when compared to other systems. The Vertical Gearmotor is built on a standard low pole count motor platform utilizing proven Dodge planetary gear technology. This results in a smaller, lighter, more cost-effective and highly efficient package. www.abb.com/mechanicalpowertransmission
Tsurumi Pump is widely regarded as a leader in submersible pump technology. Distributed for the last seven years by Australian Pump Industries, the Japanese company and its product range has seen a complete rebirth in Australia.
The Tsurumi philosophy
Tsurumi is still run by the family of its founders, the Tsugimoto family, who take intense pride in providing customers worldwide with the best possible product, quality and performance. They match that with a production efficiency level that enables the company to offer significantly better products at highly competitive prices.
Subs for all reasons
Tsurumi’s products in the single phase sector range from heavy duty agitator pumps for slurry handling to cutter pumps and solids handling pumps for sewage or wastewater.
ACMA certified
The Australian Communications and Media Authority (ACMA) endorses products as being suitable for sale within Australia for applications that aren’t regarded as a permanent industrial chore.
The testing parameters are extensive and hence why many low-quality, poorly made products don’t qualify.
Users can check the approvals on the ACMA database. Failures generated by non-ACMA listed pumps, such as property damage, electric fires or personal injury, can lead to recovery claims against the supplier or even the manufacturer.
Horses for courses
Tsurumi’s LB series is regarded as the world’s most popular, hire and construction single phase pump. Designed specifically for these markets, these lightweight, high performance single phase pumps are narrow enough to fit down a nine inch bore or piling on construction sites.
For basic dewatering, Tsurumi follows a design principle that is simple and combines low cost with the ability to move sand and gravel. Called the HS series, these pumps have a bottom discharge port with the automatic version using conventional float systems.
The new NK and HSD series single phase pumps are market leaders, providing higher head and greater flow. The HSD features an integrated agitator that will move solid laden liquid from rest into slurry without issues.
Tsurumi’s TM series with titanium and poly carbon materials is ideal for dewatering corrosive liquids such as seawater or chemical-laden sewage.
Sewage pumps
UT series cast iron pumps with vortex impellers are designed for handling compressible solids in suspension.
These epoxy coated sewage pumps in solid cast iron feature vortex impellers in specially compounded resin.
For larger flow sewage applications, the PU series in stainless steel and poly carbon, come into their own. These single phase pumps are lighter than conventional cast iron sewage pumps, and offer excellent performance in both flow and head. These pumps can easily interchange with other brands.
Rental and plumbing industries are catered for by Tsurumi’s LB series and the unique ‘Puddle Sucker’ which are able to lift water from one millimetre depths. This provides the ability to clean up spills in factories or even mop up after floods and heavy rains.
All Tsurumi pumps come with unique features that justify the three year warranty.
Tsurumi’s unique cable entry system prevents water wicking down a damaged cable and reaching the motor. Double silicon carbide seals effectively eliminate water entry from the pump chamber.
Tsurumi’s patented oil lifter is also unique to the company. Other features include thermal cut-outs on all single phase pumps that automatically stop the pump in the event of dry running before the motor overheats.
Australian Pump Industries wholeheartedly supports and is committed to Tsurumi’s product range in Australia, educating customers on the value and benefits of buying better quality single phase pumps.
Programmable controllers come in many form factors and levels of hardware options and software capabilities Productivity controllers combine compact, modular, rack-based or stack able hardware with advanced tag name -based programming. Multiple built-in communications por ts, OLED/LCD displays and a secure web ser ver are valuable features of the Productivity series
Brick PLCs contain the processing, memor y and I/O inter face needed in an automated control system A wide variety of low- cost, practical CLICK PLC units are available with different combinations of built-in discrete inputs/outputs, analog inputs/outputs and communication por ts Plus FREE software...
NEW! C-more - HMI
C-more 10-inch widescreen and 15-inch base model HMI touch panels
The new C-more 10-inch full featured EA9-T10WCL widescreen color TFT touch panel ($1290.00) has three serial por ts, an Ethernet 10/100BaseT por t, two USB 2 0 por ts, one SD memor y card slot and audio line out Screen resolution is 1024 x 600 pixel WSVGA in 64k colors. The Cmore 15-inch base model EA9-T15CL-R color TFT touch panel is $2450 00 and includes one Ethernet 10/100BaseT por t, one serial por t, two USB por ts and two SD memor y card slots. Screen resolution is 1024 x 768 pixel XGA in 64k colors. Both touch panels are 12-24 VDC powered and an optional attachable AC power adapter is available The panels are NEMA 4/4X and IP65 rated (for indoor use only) and are programmed using the EA9-PGMSW programming software, priced at $179.00. C-more HMI touch panels are UL, cUL & CE approved
Don’t waste time with Dollars-and-Cents.
Download Produc tivity Suite today and tr y it out. No license fees or registration keys are needed and it’s the full package - no restric tions - no limitations.
Get the Productivity-PLCs with powerful, FREE software... FREE feature-packed PLC software With Productivity Pro, you always get dependable, full-featured hardware with FREE feature-packed software. Our Productivity Suite programming software was developed in-house with customer satisfaction as a primary objective The result was programming software that is power ful, efficient and easy to use
Just check out what FREE will get you:
• Flexible tag name programming
• Convenient, fill-in-the -blank function blocks
• Time -saving hardware auto-discover y feature
• Built-in Web ser ver and mobile connectivity for remote access
• Power ful Task Manager for increased efficiency
• Automatic tag creation with predefi ned tag structures
• Detailed Data view and histogram functionality
• Recently added: Custom Ethernet communication protocols and ProNET (peer-to-peer) networking options for better communication
H2 CPU- 205 PLCs
The Do-more H2 series PLC combines a high-per formance CPU with our DirectLOGIC DL205 hardware to provide a dependable, power ful PLC with over 65,000 possible I/O points Do-more Designer is the full-featured programming software for Do-more H2 Series PLCs Plus FREE software...
C-more -HMI
C-more industrial touch screens are designed to give you the best cost of ownership, considering initial price, features, ease of use, reliability and free award-winning technical support More and more people have found that C-more touch panels have what it takes to meet most of their HMI application needs
From the smallest pipes to the most powerful motors, protecting your fixed pipework against the effects of vibration, even in the most demanding operating environments, is a critical factor in any project’s design phase.
If overlooked, excessive vibration can cause serious damage to equipment, leading to a potential safety hazard for those in the near vicinity as well as having adverse environmental effects.
It is important for an engineer to identify how vibration is controlled in order to mitigate risk, damage or wear to a system. It is a common mistake to assume that adding pipe mounts or fixing the pipework to other ‘solid’
objects to prevent the pipe from moving will solve the issue. This may help in some cases but more often than not, the vibration and the problem is shifted to another position in the system.
Flexible expansion joints are the most effective tools that can be used to combat the potential devastation caused by uncontrolled or unrestricted vibration. Expansion joints that will make you feel those good vibrations.
Maximising throughput
Whether for tank trucks or power stations, flexible bellows have a lasting impact on a system’s performance and can restrict a system’s output. Choosing the right expansion joint that will go the distance will reduce the need for continual maintenance.
When you get to the bulk end of the scale, having access to an expansion joint for almost every industry and every application is important. With sizes from DN25 to DN4200, our expansion joints can handle the most demanding operating environments, from freezing arctic climates to power station engine rooms. The ERV-GS HNBR has the ability to constantly work up to +100°C and is fire resistant up to 30 minutes at +800°C.
ELAFLEX expansion joints cover a wide variety of fluids with global experience in industries such as wastewater, power generation, petrochemical, aviation, LPG, marine, food, dairy pharmaceutical and many more.
Rubber has a limited resistance to heat and flame, Flame Protection covers, made of glass fiber fabric, with a cover silicone-Aluminium-glass fabric (certified acc. MED A1/3.13), reliably shields the expansion joint against heat and direct flames up to +800 °C for 30 minutes.
ERV-BR : Rubber Expansion Joint for abrasive Media
ELAFLEX PACIFIC, a daughter company of ELAFLEX Hamburg in Germany, is the supplier of the Elaflex product range: ZVA nozzles, rubber hoses, couplings and ERV expansion joints along with MannTek Dry Disconnect Couplings in the Pacific region, including Australia, New Zealand and the Pacific Islands.
The ELAFLEX ERV-BR, rubber expansion joint has been created specifically for abrasive media and is perfectly suited to the aggressive nature of sludge dewatering, mineral processing and the transfer of many types of slurries. Our online configurator is the perfect tool to get a fast and efficient overview of the product you require. Try it at
http://ervconfigurator.elaflex.com.au/
Caprari's ongoing research is centred on the creation of eco-friendly products that both protect the environment and optimise energy efficiency and savings during operation.
With its usual care to customer needs, the company has set itself the objective of making its products competitive both in the value of the initial investment, and the operational and maintenance costs.
In recent years Caprari has developed a comprehensive range of electric pumps produced with special materials, suitable for use in heavy duty conditions with brackish, aggressive, sandy and marine waters: the ENDURANCE series.
These products are made using a precision stainless steel casting technique, which is capable of ensuring a high efficiency when combined with Caprari's sophisticated design systems, above all thanks to the optimisation of the hydraulic profiles.
The high thickness of the stainless steel and the elimination of any welding give the ENDURANCE series extreme resistance to wear from sand and abrasion.
From design to manufacture, every aspect of these machines – materials, thickness, innovation and patents – is designed to make them the best performing, most reliable and most durable on the market.
With a high head per stage, this series offers a smaller size, more reliability and greater savings compared to top competitors.
Precision casting technology makes it possible to produce very thick components. The absence of welds guarantees continuous hydraulic profiles without friction and turbulence for greater durability and reliability compared to welded and moulded steel sheet solutions.
It is also possible to achieve performance curves centred on the duty point with specific impeller trimming.
All components are made of AISI 316 stainless steel, which guarantees high corrosion resistance (40,000 parts per million of TDS – Total Dissolved Solids).
In addition, for maximum reliability even in highly aggressive environments, the shaft and joint are made of duplex. The feather key seat on the shaft end has been eliminated, increasing the component resistance thanks to the transmission through splines.
The ENDURANCE electric pumps are designed to withstand galvanic corrosion thanks to the exclusive DEFENDER® system, an intelligent passivation device designed and patented by Caprari that protects the machine from the very first moments after installation.
ENDURANCE electric pumps are suitable for applications with solid content up to 150g/m3. They feature bearings with anti-recirculation lip protected against the introduction of sand.
The special PROTECTOR® device, installed in Nema couplings between the wet-end and motor, perfectly seals the area, protecting the coupling and preserving the motor mechanical seal against solid substances.
Therefore Caprari represents an innovative approach, aiming at carrying out an ongoing improvement of the combination of products and services, while remaining focused on the needs of customers, for whom Caprari represents not only a supplier, but an authoritative, reliable and attentive partner.
For more information, contact Caprari Pumps Australia on (08) 8240 0767 or visit www.caprari.com
Designing the future with highly appreciated and advanced solutions for Industrial Applications
Pumps and electric pumps able to raise primary process water and waste water.
ENERGY | METAL INDUSTRY | PAPER INDUSTRY | FOOD & BEVERAGE
www.caprari.com |
The fifth annual Pump Industry State of the Industry survey conducted recently showed a positive shift in expectations for the year ahead. Despite reporting a rise in overseas competition and increasingly demanding customers, the outlook is good for the Australian pump industry. With the challenges of 2016 and 2017 now behind us, optimism seems to be increasing for growth and opportunity.
There’s no doubt that there have been a couple of tough years for the pump industry, with unstable commodity prices, a weak Australian dollar and a downturn in the mining industry all impacting the industry.
The Pump Industry survey this year produced some interesting insights around business and consumer behaviour in the industry. Respondents reported that during 2017 their customers have become more internet savvy, increasingly willing to shop online for imported goods and have become far more price driven.
However, despite recent challenges for the pump industry, optimism remains high. Although almost 30 per cent of survey respondents said the performance of their company in 2017 fell short of their expectations, 43.6 per cent said it met expectations and 27.2 per cent reporting that it exceeded expectations. These results can be seen in Figure 1.
This positivity is also reflected in company outlook for 2018 with almost 80 per cent reporting a positive outlook, and only 21.82 per cent reporting a neutral outlook. No one
reported a negative outlook for 2018. These results are more optimistic than those of 2017 where only 70.4 per cent had a positive outlook, 21.2 per cent were neutral and 5.6 per cent had a negative outlook. This change could be due to industry uncertainty decreasing in some sectors such as mining as the downturn experienced in the last few years comes to an end.
Figure 2 shows the increasing optimism at a company level over the last three years.
Comparing the results of questions two and three of this year’s survey suggests that respondents were more positive about their company’s outlook for 2018 than the industry as a whole. The results can be seen in Figure 3, with only 45.5 per cent of respondents having a positive outlook for 2018, 38.1 per cent neutral and 1.8 per cent negative.
However, compared to previous years there is a trend of increasing optimism for the industry with 2018’s outlook up from 41.1 per cent for 2017 and just 22 per cent for 2016 (Figure 4).
Key to understanding the current state of the pump industry is to examine which particular verticals performed the best and worst for businesses during 2017, and to identify how key sectors are expected to fare in 2018. We asked our respondents how the volume of work across key verticals had changed for their businesses during 2017, and how they expected them to change in 2018.
Figure 5 illustrates the actual reported performance of various verticals for our respondents during 2016 and 2017, and their anticipated performance in 2018.
According to respondents, the best performing verticals were water and wastewater, mining, and power generation. On the other hand, the vertical that performed the worst was oil and gas which is making a comeback from a largely negative reported result in 2016.
Overall, most verticals experienced increases in volume of work compared to 2016.
Similar to respondent expectations for 2017, the water and wastewater, and mining industries are expected to be the best performing verticals in 2018. Most respondents thought the volume of work in these areas will increase in 2018, and no respondents thought they will decrease. Significantly more work is also expected in oil and gas than in 2016 and 2017.
Figure 6 shows the areas of growth reported and predicted across the industry. Interestingly, water and wastewater growth was not as robust as predicted in 2017, with 28.21 per cent of respondents reporting the volume of work from this sector increased somewhat, and 10.26 per cent reporting a significant increase. A third of respondents said their volume of work in this sector had not changed. This is compared to reported expectations at the end of 2016, where 60.78 per cent of respondents expected a slight increase in volume of work and 13.73 per cent were expecting a significant increase. Predictions for growth in 2018 are in line with what we saw in 2017 with almost 54 per cent reporting that ‘major projects approved and/or underway’ would have a positive impact on their business in 2018.
The lower-than-predicted growth cannot easily be explained, but is likely
Figure 1: Did your company’s performance in 2017 meet, exceed or fall short of expectations? Figure 2: Despite difficult conditions over the past few years, company confidence is increasing. Figure 3:Water and wastewater is expected to be a continued area of growth in 2018.
impacted by a number of factors, including simple over-optimism around the state of the market heading into 2017. This could also be due to delays in projects starting as reported by some respondents, so we may see some of the expected growth to occur over 2018 as these projects start moving forward again. Respondents also noted that changes in government impacted on their business with one stating the merger of shires created confusion and delays.
Growth from the irrigation sector was also lower than expected in 2017, with 41.18 per cent of respondents predicting the volume of work to increase somewhat, compared to only 15.38 per cent reporting this growth. Significant growth was predicted by 15.69 per cent of respondents at the end of 2016, but only 7.69 per cent actually reported this significant growth over 2017. Predictions for growth in 2018 sit between these two sets of results.
Mother Nature seems to have had a big impact on the volume of work in the irrigation sector, with a number of respondents commenting that the weather had impacted their business. Interestingly, we had differing reports around whether business had been positively or negatively impacted by these conditions.
Some of our respondents reported that dry conditions have prompted farmers to take action. One respondent reported that “Lack of rain in the winter months propelled our business earlier than expected, as we normally have a slump over winter.” This has also had a positive effect on solar pump manufacturers and sellers with respondents reporting that drought along with high energy costs had prompted more customers to change to
solar pumps in order to decrease costs.
However, others reported this has directly impacted the capital expenditure budget of their customers, at times putting further investment in infrastructure out of reach.
The 2016-17 financial year was a great year for farmers, with favourable weather conditions contributing to a record high of $63 billion for Australia’s farm production value, according to the Australian Bureau of Agricultural and Resource Economics and Sciences (ABARES). This financial year has not been so kind, dry conditions in graingrowing regions has resulted in an expected seven per cent decline in Australia’s farm production value.
It could be that with the record results in 2016-17, increased spending on irrigation seemed unnecessary to some farmers, despite possibly having some extra spending money. With no foreseeable decline in demand for agricultural products, some farmers are looking for safeguards for their crops, and here is where we may see some growth in the irrigation sector.
Interestingly, mining is one of the major expected areas of growth for the pump industry in 2018. After a five-year investment slump in the mining sector,
the Mining in Australia 2017 to 2032 report from forecasters at BIS Oxford Economics predicts the current financial year to see mining production to grow by 5.5 per cent. This is good news for our survey respondents, with 48.72 per cent listing the performance of the mining industry as one of the factors expected to have a positive impact on
their business in 2018.
One big indication that faith in the mining industry was returning is that none of our respondents reported an expectation that the volume of work in that sector would decrease in 2018, and a majority (56.41 per cent) expect the volume of work from this sector to increase.
This more positive outlook comes
on the back of almost 36 per cent of respondents reporting an increase in the volume of work for their business from the mining sector in 2017. This is in stark contrast to the reported actual results for 2016, where 45 per cent of respondents reported a decrease in work from this sector (Figure 7).
One respondent taking advantage of repairs and maintenance work noted that mines are now paying more attention to the overall cost of equipment, stating, “Mining houses are looking for total cost of life savings. This opens the door for us.”
However, the mining turnaround has not yet impacted all survey respondents. Depending on where businesses sat in the industry, the increased activity has not necessarily translated into increased business. Capital sales were an opportunity in the initial turnaround and expansion of the industry, but those who missed out on those opportunities know it will be some time before major repairs or upgrade sales will occur.
While the general feeling is that the mining downturn has halted, a number of respondents reported concerns about the stability of the mining sector
due to the fluctuation of commodity prices, the value of the Australian dollar, and Australia’s ability to compete with Asian mines.
A recurring theme in the responses for 2018 was a report of customers having a reduced capital expenditure budget, resulting in an upturn for repair and spare parts suppliers in the industry,
but a challenge for sales.
This may also be driving the increased interest in importing cheaper products. Some respondents noted that this was the feeling they got from clients in both government and the private sector.
Many respondents commented on the difficulty of competing with internet sales. At the end of 2016, our respondents were already reporting an
increase in cheaper imported products impacting the market, and this trend looks set to continue. One respondent said, “Australia is being saturated by imported pumps and there is very little control on the quality coming in.” Another agreed that customers were becoming more inclined to choose price ahead of a trusted local brand.
While still relatively new, so far the China-Australia Free Trade Agreement (ChAFTA) has had little impact on most respondents. Those who use Chinese suppliers are looking forward to continually reduced costs, but others are concerned that this will lead to a further out-pricing of local products.
In fact, the competition linked to “cheap imports” is a concern raised by many of our respondents. This coupled with the belief that customers are focusing on price over quality more than ever before is likely to impact those manufacturing and supplying equipment currently sourced from within Australia.
Those already in trade agreements with Chinese manufacturers will see a reduction in the cost of importing goods over the coming years which has been reported on positively. Some respondents are expecting the increased use of imported parts and products will lead to an increased need for maintenance and repairs. This potentially opens the door for more players and opportunities for work in this area of the industry.
Adapting to a tougher market
With many respondents accepting the inevitability of increased competition from around the globe, particularly from Asia and India, some saw this as a positive and the push
they needed to improve their own operations.
One respondent noted that their approach would be to target industry sectors still willing to look and pay for solid, reliable performance ahead of cheaper, lower quality work.
Another survey respondent commented that they had already revamped their business and revised their product portfolio in order to compete, and were now in a strong position for the new market conditions.
The change in customer behaviour over the last 12 months also hints at the financial challenges they have faced. Respondents noted that customers are more price driven than ever before and have become more accepting of non-original equipment manufacturer (non-OEM) parts. Perhaps for the first time in the industry, for many customers the cost of goods and services seems to significantly outweigh quality concerns.
With the willingness to use the internet for supply and research also comes an interest in smarter technology, which some respondents expect will have a positive impact on the industry in the coming years.
One respondent told us that the difficult economic times will force some changes within their business and the industry as a whole. “Companies will need to evolve their business models, simply selling pumps is no longer sufficient, you will need other products and services. If you are just selling pumps you will end up in a margin game which is continually decreasing.”
Far from seeing the competition as something that will push them out of the
market, many respondents are actively looking for ways to set themselves apart from the others in the industry.
Despite an increasing concern in upfront costs, there is some interest in intelligent or smart pumps, which are traditionally more expensive upfront but can lead to savings down the track. The old way of selecting a pump that can meet the highest flow rate that will be demanded results in a significant amount of unnecessary energy wastage over the lifetime of the pump.
Intelligent features of newer pumps such as variable frequency drives and embedded sensors to detect flow rate allow pumps to operate at the level required for that moment in time, rather than operating at full capacity as a default position. This technology reduces the energy consumption of the pump, which has both a running cost and environmental benefit.
Increasing awareness and trust in this technology, along with customers doing their own research online, will help to drive this area of the pump industry.
Early adopters of smart pumps have been building services and HVAC, where energy efficiency impacts the Green Star rating of a building. Farmers across a variety of areas, including crops and animal farming, have also been increasingly adopting features such as variable speed drives to improve efficiency and productivity of their operations to reduce fuel and maintenance costs.
As understanding and trust in the technology increases, our respondents expect the application of smart pumps to expand.
As the world continues to focus on renewable energy, the pump industry has seen growth from the power generation sector, with 36 per cent of respondents reporting that business in this area had increased either somewhat or significantly in 2017. Respondents also predict the growth rate in this area to remain steady for 2018.
An exciting development for the pump industry is the government’s recent interest in exploring pumped hydro storage options. According to researchers at the Australian National University (ANU), there are at least 22,000 suitable locations nationwide for construction of pumped hydro storage plants. Used in conjunction with wind or solar power, pumped hydro could contribute to Australia using 100 per cent renewable power within two decades.
Set up costs are expensive, however, and it is unlikely at this stage that many private companies will enter this market, meaning the only hope for projects to go ahead is with government funding.
The government has already shown an interest in hydro storage forming part of the solution to Australia’s renewable energy goals, which is a positive sign for the pump industry.
Our respondents recognise that renewable energy will remain a topic of interest and are moving to take advantage of this. Where possible, some of our respondents stated their intention to diversify into servicing the solar panel industry as well, with another respondent commenting on the importance of consolidating company knowledge and potentially working alongside others in the industry.
Capital sales may have slowed, but maintenance and repairs usually increase in this situation. Those involved in repairs and maintenance looked towards the positive of cheaper imports and reduced capital expenditure budgets, seeing an opportunity for their own business growth in the fall out. A number of our respondents said future opportunities for their business would include an “increase in repair work” and “fixing up the mess left by others”.
One respondent pointed out that short-term savings are not necessarily a wise business decision: “Maintenance programs have been scaled back which will lead to greater failures in pumps, increasing replacements and spare part spending.”
Whether customers running their products to breaking point is a positive for respondents was directly linked to what area of the pump industry their business was in. Respondents in the direct sales areas seem to have accepted that customers may continue to be more difficult to sell to. Those servicing pumps are aware of the opportunities that may eventuate.
What the future holds
After surviving the last few tough years in the industry, it’s no surprise that many of our respondents mentioned hard work as a factor in their success. They talked about the importance of offering top quality service to their customers and expanding on what they could offer.
There was a definite optimism around controlling the things they could, such as attracting and training great staff and being smarter with buying options, and ensuring their own knowledge about the industry was first-rate.
The improvements in the mining sector is definitely contributing to the collective sigh of relief the industry breathed in 2017. Increased competition naturally adds stress, but most of our respondents are heading into 2018 with a positive outlook and the desire to do what it takes to succeed.
When installed and operated correctly, general purpose steam turbines are reliable. However, there are opportunities available to further improve reliability, reduce the risk of failures and save money by upgrading to advanced bearing housing protector seals. In this first of a two part series, Heinz P. Bloch and Richard Smith look at cost-saving opportunities for general purpose steam turbines.
It is not unusual for large oil refineries to have 160 general purpose (GP) steam turbines installed at a major site. As long as these machines are connected to a steam supply, preventing the often steam-inundated environment (see Figure 1) from entering the bearing housing is of great importance to reliability-focused refineries, fertiliser producers and petrochemical plants. Steam intrusion often occurs simply because the steam gland and bearing housing are adjacent to each other (Figure 2).
Fortunately, modern bearing protector seals are readily available for GP steam turbines. If well designed, these protector seals can virtually eliminate premature bearing failure. Upgrading to an advanced bearing housing seal retrofit arrangement (Figure 3) is, therefore, well worth considering.
Thoroughly engineered bearing housing protector seals achieve effective contaminant and vapor exclusion by incorporating an axially-moving O-ring. They are easily cost-justified and greatly contribute to run-length extension. Return-on-investment and projected payback
Return-on-investment (ROI) studies and related cost assessments indicate that major refineries may have opportunities to capture steam turbine-related corporate-wide maintenance savings in excess of $3,000,000 annually. These experience-backed savings projections can be examined more closely and deserve to be compared to what it costs to maintain small steam turbines with their 'as originally supplied' components.
Major refineries may have opportunities to capture steam turbine-related corporate-wide maintenance savings in excess of $3 million annually.
If available, readers can draw on their own in-plant experience and cost data; alternatively, they are encouraged to study and use our projected savings. Note that we have occasionally been asked where oil refineries have published their failure details and related maintenance cost records.
History provides the answer; it shows that entities that perform below par will not broadcast their poor performance to the rest of the world. Similarly, the few who stand out and excel will claim Competitive Advantage and are thus equally reluctant to communicate useful details on how they became Best-of-Class (BoC) performers. This is why we are ready to offer our own experience-backed numbers.
Where savings come from Maintenance savings and steam turbine run-length extension are in great part attributable to advanced bearing housing protection components (Figure 3). We have simplified our study results by expressing savings in different ways. Among these are time elapsed for benefits to equal investment, often called 'payback'. Another study examines the benefit-tocost ratio for advanced bearing protector components that can be fitted to new and also to existing steam turbines.
In particular, plants will find it easy to pursue such retrofitting as part of a structured plant-wide maintenance cost reduction and equipment availability improvement program. Working with a reasonably accurate total investment of $1,500 per GP steam turbine (which includes installing protective seals at the three locations identified in Figure 3), we often obtain breakeven or payback within less than six months.
We found that, although usually aimed at preventing bearing distress, upgrading to advanced bearing housing protector seals also captures safety benefits. Steam turbine fires can result from steam leaking into the bearing housing. As the steam then condenses, some of the oil is forced out as leakage. Because the upgrade prevents steam leaking into the bearing housing, the imputed value of fire avoidance is a cost saving that deserves to be included in cost justification calculations.
Some closely-guarded 'company confidential', albeit pessimistic, reports assume one $3,000,000 fire per 200 repair interventions on small steam turbines in low-performing oil refineries. True optimists assume one fire per 2,000 distress or repair events — the number we will actually use later.
A large corporation with 10 or 12 oil refineries may have a fleet of 1,600 small steam turbines installed. For an individual facility with 160 small steam turbines, 16 repair interventions per year would represent an MTBF of 160/16 = 10 years, which is a slightly above industry-average mean-time-between-failure.
Before discussing cost savings achieved with advanced bearing protection in GP steam turbines, recall that bearing failure avoidance through the conscientious implementation of precautionary maintenance routines is possible, but will cost money. 'Saving' such monetary outlays by doing nothing will be even more risky. 'Doing nothing' causes frequent failures; it incurs high repair expenditures, reduces equipment unavailability and causes safety incidents. We can be certain that 'doing nothing' neither enhances employee morale nor company image.
Not unexpectedly, a few facilities that report high steam turbine reliability have achieved low failure rates by spending more money for preventive maintenance. Recall that lubricating oil is contaminated by steam blowing past the carbon rings in the shaft glands (Figure 2). The contaminated oil requires periodic discarding and must be replaced by fresh, clean oil. As a precautionary activity, water must be drained off in an effort to extend bearing life and machine reliability.
However, by the time free water collects and is visible in a sampling line or sight glass, dissolved water will exist and often cause additives depletion through a process called partitioning. The additives partition themselves between the oil and water phase in proportions that largely depend on their relative solubilities. When free water is
removed from the oil by gravity, coalescing or centrifuging, these additives are lost. The loss deprives the oil of the protection normally given by anti-rust and anti-oxidant inhibitors. Moreover, water will combine with airborne dust to form sludge1
It follows that scenarios whereby free water is periodically removed manually are technically inferior; merely draining off free water is not found among the practices of reliability-focused Best-of-Class facilities. Sound water removal strategies involve mechanical equipment and include vacuum dehydration, coalescing and air sparging. All of these strategies cost more money than preventing water intrusion through the use of modern bearing housing protector seals.
Taking into account the above, some facilities schedule and carry out monthly precautionary lubrication interventions. As a result, labour costs are incurred to visit the machine for regular oil sampling, oil replacement, and waste oil disposal. Corrective action work orders are then required for the work activities to be initiated and carried out. Disposal costs of $4.00 (or more) are generally associated with each gallon of contaminated oil. Writing and processing a work order is typically assumed to cost $400.
It goes without saying that high reliability is also essential for machines in hot standby service, or serving as 'cold' (blocked-in, fully installed) spares. In all cases, steam turbine repairs can consume considerable workshop man-hours and associated money outlays. To restate the obvious: by simply doing nothing is a risky alternative to precautionary intervention; the 'do nothing' alternative is, therefore, never considered by reliabilityfocused and responsible Best-ofClass (BoC) users.
Reliability-focused users are thus left with either a precautionary intervention option that costs money over the life of the plant, or upgrade steps that are limited to the one-time cost of bearing housing protector seals with a demonstrated life that averages in excess of 10 years.
That said, BoCs take note that the component technology in
Taking chances by simply doing nothing is a risky alternative to precautionary intervention.
current use has changed little in 100 years2. But a measure of uniformity and reliability upgrading exist in certain industry standards. The machines at issue are almost always purchased by invoking the provisions of API-611, the American Petroleum Institute’s Standard for General Purpose Steam Turbines in the Petroleum, Chemical and Gas Industries3. In this instance, clauses that apply to bearing housing seals are of interest to us.
The applicable API-611 standard states:
6.10.4.2.1 Bearing housings shall be equipped with replaceable labyrinth-style end seals and deflectors where the shaft passes through the housing; lip-type seals shall not be used. The seals and deflectors shall be made of non-sparking materials. The design of the seals and deflectors shall effectively retain oil in the housing and prevent entry of steam, condensation and foreign material into the housing.
6.10.4.2.1 (Option) If specified, bearing isolation seals providing a positive tight seal to prevent the ingress of atmospheric contaminants shall be supplied.
1. Bloch, Heinz P. and Kenneth Bannister, 'Practical Lubrication for Industrial Facilities,' 2017, (3rd Edition); The Fairmont Press, Lilburn, GA, pp. 436, 437; ISBN 0-88173-761-5
2. Martin Harold M, ‘Labyrinth Packings’, Engineering, vol 85, 1908
3. API-611 General Purpose Steam Turbines for Petroleum, Chemical and Gas Industries, May 2008 (5th Edition), American Petroleum Institute, Washington DC
In the next part of this series Heinz P. Bloch and Richard Smith discuss the advantages of upgrading to new technologies, and the paybacks and expected performance for different upgrade situations.
Heinz P. Bloch resides in Westminster, Colorado. His professional career commenced in 1962 and included long-term assignments as Exxcon Chemical’s Regional Machinery Specialist for the US.
He has authored or co-written close to 700 publications, among them 20 comprehensive books on practical machinery management, failure analysis, failure avoidance, compressors, steam turbines, pumps, oil mist lubrication and practical lubrication for industry.
Mr Bloch holds B.S. and M.S. degrees (cum laude) in Mechanical Engineering. He is an ASME Life Fellow and was awarded lifetime registration as a Professional Engineer in New Jersey.
Richard Smith served as a Product and Services Manager with international responsibilities for AESSEAL, Inc, located in Rotherham, UK, and Rockford, TN.
His 35-year experience is largely concentrated in the development of advanced sealing products for fluid machinery in the petrochemical and petroleum refining industries.
Easy and quick
Light and compact
Absorbs vibrations, expansion and contraction
No hot work permit or heavy equipment required
Pipeline installation, modification and repair
Designed and fully manufactured in The Netherlands
High quality European value
Trusted applications
Unsurpassed product
Unrivalled specialist technical expertise
Personal and responsive service
Australian owned
3 9728
The Pump Genius is a customizable feature of WEG drives that enables your standard VSD to become dedicated for pumping systems. It ensures accurate pressure / flow control throughout the processing cycle, starting with raw water and its usage, ending on wastewater treatment.
With an easy-to-use programming wizard, Pump Genius helps you to minimize downtime and maximize energy savings Everything you need is available through selecting one of the three options that best fits to your application.
The Simplex software adds ideal features to the VSD for single pump control.
g Pipe Charging Mode
g Sleep & Wake-Up Modes
g Dry Pump Protection
g Broken Pipe or Leakage Detection
g Pump Cavitation Monitoring
Multipump is the best choice when a pumping system needs to be integrated with a costeffective solution. It enables one single VSD to control up to 5 pumps via DOL, soft-starter or other starting methods.
Multiplex software is the most complete solution to accurately control flow and pressure with high reliability.
The VSDs control, monitor and manage the entire system on their own. There is no need for additional PLC, HMI or any external devices thus installation costs can be optimized.
In this ongoing series of interviews, we talk in-depth with the end users of pumps across a range of industries and applications. In this edition, Neil Paton, Team Leader Mechanical Services Systems Operations at Wannon Water, discusses the importance of scheduled routine pump maintenance and what he believes to be the big issue facing the pump industry today.
Mr Paton has worked in the water industry as a fitter for 30 years, maintaining all types of pumps associated with sewer and potable water services.
In his current role at Wannon Water, he leads a team four fitters, scheduling preventative and reactive works, as well as assisting with new project design and fault finding issues within the Corporation.
Wannon Water is Victoria's second largest regional urban water corporation by service area, and extends over approximately 23,500 square kilometres, supplying water and sewerage services to a permanent population of more than 83,000 people. Mr Paton said completing routine maintenance is a key aspect of keeping costs down and ensuring reliable services.
“It is very important to have a proper maintenance schedule to ensure that the asset is kept to a high operating standard because normally a lot of money has been invested into the project,” Mr Paton said.
“Down time due to lack of maintenance is not acceptable in my view.
“Annually all pumps in our system are inspected, this could be as simple as listening to it running and greasing, to full service check involving ensuring that the base plate is tensioned down to plinth,
pump and motor tensioned to base, coupling alignment, thermal imaging, vibration analysis, bearing change, wear ring change or impeller balancing. All of this information is recorded in the Corporation's asset management system.”
Mr Paton said efficiency is the most important factor when selecting a pump but reliability, serviceability and cost also need to be taken into account.
“I believe efficiency is the most important factor in deciding on pump type and make for both ensuring that the company has minimal running cost associated with the pump, and also from an environmental side to reduce greenhouse gases and energy usage.”
Mr Patson said regular communication also plays an important role in the selection process to ensure the best results between client, consultant and supplier are achieved.
“Hold regular update meetings with all stockholders but keep them short and to the point with open conversation highlighting who is responsible for what actions.”
When asked about challenges currently facing the pump industry, Mr Paton believes the most important issue is in sourcing spare parts.
“Most companies tend to stock minimal parts and I’m finding that it’s becoming a throw away industry due to cheaper quality imports,” Mr Paton said.
Mr Paton recently undertook the pump fundamental training at Link Pumps and highlighted the importance of regular training to keep up to date with changes in the industry.
“It is important to participate in training so that you can familiarise yourself with new ideas and products. Also to enhance your knowledge and skills already learnt,” Mr Paton said.
“I found the training to be relevant to the needs of pump installation and maintenance.”
With pump installations becoming a lot more sophisticated these days, chances are that you are installing more non-return valves.
Non-return valves (check valves) are mechanical valves that permit gases or liquids to flow in only one direction, preventing flow from reversing down the line. They are classified as one-way directional valves. Fluid flow in the desired direction opens the valve, while backflow forces the check valve to close.
Most check valves contain a flat disc that is slightly larger in diameter than that of the port. Flow indicators on the side of the body indicate the direction of the flow for correct installation.
‘Non-return valve’ is a generic term in that they are available in many different versions, such as spring or swing, and are also available in a wide variety of materials, such as brass, bronze and stainless steel, and with numerous end connections, such as threaded or flanged.
Spring check valves
Spring check valves have a disc held in place by a spring, which means they can operate in either a vertical or horizontal mounting position because they do not rely on flow pressure or direction to function. The advantage of the spring check is that they have a soft seat which allows for a perfect seal. Seats are available in a variety of materials such as Nylon and FKM. This means that they can be used in a variety of applications such as hot water.
Swing check valves
Swing check valves have a disc which swings into position, and can operate in either horizontal or vertical (upward flow) positions. Movement through the line automatically swings the disc open to allow full flow, so swing check valves must be installed with normal flow opening the disc.
Should reverse flow occur, the reversed pressure and the weight of the disc closes the disc back against the seat and back-flow is immediately stopped. This type of check valve offers minimal flow restriction allowing full flow to be achieved through the valve. It is important to note that the sealing is often metal to metal so a perfect seal is not always guaranteed.
Direction of ow
Swing check valve
Horizontal Lift check valves
Lift check valves work automatically with line pressure in a horizontal position only, as the bonnet is positioned vertically above the valve.
Like a globe valve, with its indirect line of flow, lift check valves are flow-restricting, and so are generally used as a companion to globe valves. Line pressure lifts the disc, and flow is allowed to occur. When flow reverses, the disc falls back onto its seat and immediately cuts off the flow, preventing backflow from occurring. This makes lift check valves ideal for high temperature applications.
Due to the fact that WaterMarking of pump sets and other installations has become mandatory, it is important to note that all of the valves discussed in this article are available in a WaterMarked version. This ensures that all components comply with the relevant Australian Standard. The applicable Australian Standard is AS 1628, Water supply—Metallic gate, globe and non-return valves.
Zetco’s prior written permission.
Represented in Queensland, New South Wales, Western Australia, Northern Territory, South Australia, Tasmania, Victoria and ACT.
In this article, we will define waterhammer and take a look at the events that lead to its occurrence. We will also try to gain some perspective on the additional pressure that it generates.
Waterhammer (also water hammer) is a pressure surge that can arise in any pumping system that undergoes an abrupt change in its rate of flow, and usually results from pump starts and stops, the opening and closing of valves, or water column separation and closure.
These abrupt changes can cause all or part of the flowing water column to undergo a change in its momentum. This change can produce a shock wave that travels back and forth between the barrier that created it and some secondary barrier.
If the intensity of the shock wave is high, physical damage to the system can occur. Oddly enough, it can be more of a concern in low pressure applications. Waterhammer is yet another example of conservation of energy and results from the conversion of velocity energy into pressure energy. Since liquids have a very low compressibility, the resulting pressure energy tends to be very high.
Perhaps the best way to visualise this action is to start with a hypothetical example. Figure 1 shows a pump that is pumping water into a pipe that was empty when the pump started. The valves, located at the pump discharge and the far end of the pipe, are fully open and both have the ability to close instantaneously.
What events occur as the column strikes the closed, downstream valve and why does water continue to enter the pipe even though the valve is closed?
Well, if this moving column was a column of metal instead of water (did I mention that this is a hypothetical example?), a couple of things could occur.
Depending upon its coefficient of restitution (its ability to avoid permanent damage) the kinetic energy due to flow (motion) could be transformed into mechanical energy as the leading edge of the metal column is crushed against the closed valve.
If this occurred, the column would come to rest and remain motionless at the valve. If its restitution is high enough to prevent crushing, that same kinetic energy could be used to reverse its direction in the form of a bounce.
Regardless of the outcome, the “entire” metal column would either come to rest or bounce in the opposite direction. Neither of these events occur when water is involved.
Water is a “nearly non compressible” liquid, but the flip side of that statement would indicate that it is “slightly compressible”. At ambient temperature one PSI will decrease its volume by about 0.0000034 per cent. That seems pretty small but the larger the volume, the easier it is to see the effect.
For example, if water did not compress, sea level would be roughly one hundred feet higher than its current level. At very high pressures, say 40,000 PSI, its compressibility is increased to about 10 per cent.
But, most water is not just water - it also contains air which is primarily nitrogen (78 per cent) and oxygen (21 per cent). If this were not the case, there would be no fish. Dissolved air composes about two per cent of a given volume of unprocessed water and adds, substantially, to its compressibility.
The pipe, valves and other fittings are entirely inelastic and no volume change can occur regardless of the pressure. Also, the column of water flowing through the pipe has a leading edge that is perfectly flat and matches that of the cross sectional ID of the pipe.
Just as the leading edge of the water column reaches the downstream valve, it closes at nearly the speed of light and entraps no air ahead of the water column. Even though the leading edge has struck the closed valve, flow into the pipe continues for the next few milliseconds. Just as flow ceases, the upstream valve closes (this time at the true speed of light) and the water column is completely isolated between the two valves.
It is water’s (and that of the dissolved air) compressibility that causes it to act differently than the column of metal. Were it not compressible, its leading edge would be permanently crushed or the entire column would bounce backwards. When the leading edge of a water column strikes the closed valve it comes to a halt, but the water behind it is still in motion so it begins to compress.
This compression along the entire length of the column allows a small amount of water to continue to flow into the pipe even though the leading edge has halted. When flow ceases, all of its kinetic energy of motion and that due to compression will have been transformed into pressure energy.
Compression begins at the leading edge of the water column, and since the additional energy it produces cannot continue on past the closed valve, a pressure or shock wave is generated and travels along the path of least resistance which, in this example, is back upstream. Its inception is very similar to the “echo” that is produced when a sound wave, travelling through air, strikes a similar barrier.
When the wave hits the upstream valve it is reflected back downstream but with a diminished intensity. This back and forth motion continues until friction and reflection losses cause the wave to disappear. The speed at which a wave travels and the energy it loses during travel depends upon the density and compressibility of the medium in which it is travelling. It turns out that the density and compressibility of water make it a very good medium for shock wave generation and transmission.
The pressure waves created by hydraulic shock have characteristics similar to those of sound waves and travel at a similar velocity. The time required for a waterhammer pressure wave to negotiate a length of pipe is simply the pipe length divided by the speed of sound in water (approximately 4860 ft/sec).
In waterhammer analysis, a time constant that is often used describes the progression of the wave from its inception to the secondary barrier and then back again. It takes the form of Tc = 2L/a (where “L” is the pipe length and “a” is the velocity of the wave (speed of sound)). For a 1000 foot length of pipe it would require less than one half second for the wave to make a complete round trip.
The pressure created by this shock wave is directly proportional to both the wave velocity and the velocity
of the water flowing in the pipe. Although the equation below does not take into account the effect of pipe diameter and elasticity, it will provide some insight as to the additional pressure that is created by a waterhammer pressure wave.
P(additional) = aV / 2.31g
“P” is the additional pressure created by the shock wave, “a” is wave velocity, “V” is the velocity of the flowing water in the pipe in feet per second, “g” is the universal gravitational constant @ 32 ft/sec2 , and 2.31 is the pressure conversion constant.
At a pipeline velocity of five ft/sec the additional pressure created by the shock wave is approximately 328 PSI. Increase that velocity to 10 ft/sec, and the additional pressure increases to about 657 PSI. Obviously, systems that are not designed to accommodate such an increased pressure are often damaged or even destroyed.
In the next part of this series we will take a look at the three major causes of waterhammer and the factors that contribute to the magnitude of the shock wave it generates. We will also see why waterhammer can be more damaging in low pressure systems.
Joe Evans has been in the pumps industry since 1986 and is passionate about the sharing of knowledge within the industry. To read more of his insights into the world of pumping, visit www.pumped101.com
01
EXPECT SOLUTIONS, NOT JUST PRODUCTS
IT TO BE EFFECTIVE AND EASY 02 03 04 07 08 05 06
EXPECT PROMPT RESPONSE
EXPECT A LONG-TERM PARTNERSHIP
EXPECT GLOBAL LEADERSHIP AND LOCAL COMMITMENT EXPECT QUALITY IN EVERY STEP
LASTING INNOVATIONS
TOTAL SAVINGS
When a power station using large coal-fired boilers needed to increase a system flow, one solution put forward was to duplicate the outflow line. While this might be a good idea to meet a need, Ray Beebe shows that a simple duplication would have problems and puts forward an alternative solution.
The power station of this story has large coalfired boilers. During combustion, ash falls into the furnace hearth, along with ash deposits cleaned off much of the furnace waterwall area using water-sootblowers. Ash on the convection pass tubes and dust collected in the electrostatic precipitators joins the hearth ash to be sluiced by jets from a sluice pump into the ash sump. Two identical single-stage ash disposal pumps are installed, with one normally in service to pump the dirty water over two kilometres away to the disposal pond.
Every few months, the power station coal-fired boilers have to be washed off-line with water to fully clear the ash deposits from the furnace walls. The outside of the boiler is also washed. All the dirty water falls into the furnace hearth and overflows the ash sump, ending up over the floor, making not only a mess but proving hazardous to the workers.
The Maintenance Engineer proposed that both pumps be run together. When little change in flow was evident, it was proposed that the outflow pipeline be duplicated. Fortunately, before this measure was taken the performance aspects were checked.
Figure 1 sketches the Head-Power-Flow performance of one ash disposal pump operating to the initial system. Head-Flow tests had given the operating point, and knowing the system Static Head of 20m, the system curve was found and superimposed on the pump curve, as shown. At the operating point, the pump flow was 120L/s at a head of 84m, with power of 115kW drawn. The motor rating of 132kW allowed a sufficient margin for normal operation.
When the curve for both pumps operating in parallel is drawn, as shown in Figure 2, the operating point shows that about 130L/s flow would be achieved – very little extra due to the relative steepness of the system curve and the flatness of the pump Head-Flow curve.
If the pipeline was duplicated, the combined system curve would be flatter, as shown in Figure 3. The total flow with both pumps running would be doubled to 240L/s, with each pump providing the same flow as before.
Flow L/s
However, when starting up the system, there would be a problem. If one pump was started with both systems open to flow, the power drawn would exceed the rating of the motor and it would trip on overload protection: see Figure 4
The solution: with one system only open to service, start one pump, then the second one. Only then, open up the second system to obtain the desired increased flow.
However, the system as designed had no isolating valves, so to enable the solution a suitable valve would need to be installed in the new line. After due consideration, the system was left unchanged.
What happens when a fire hydrant system is left unmaintained and unserviced? When subjected to a routine hydrostatic test, they can sometimes fail.
Fire hydrant systems are required to be hydrostatically tested by AS 1851-2012 every five years. Hydrostatic testing involves subjecting the system — including pipes, valves and connections — to the required amount of pressure to determine its reliability. If the system passes the test, it should reliably operate at the design working pressure, and the fire brigade should be able to use it in a real fire scenario effectively.
Fire Protection Association
Australia (FPA Australia) Senior Technical Officer, Brett Dundules, said, “Fire protection routine service providers are often contracted on up to three-year contracts and often owners don’t know, understand or detail that the required five-yearly
Unfortunately, some building and asset managers roll the dice with inspection and testing of these essential fire protection and lifesafety systems, hoping they will just work when needed the most. But ignorance is not bliss.
hydrostatic test needs to be conducted every half decade.
“As the fire protection service provider’s contract is for three years and the hydrostatic test is required every five, it’s not uncommon for it to be overlooked or ignored. The building owner should have awareness of this and liaise with their routine service provider to ensure the hydrostatic test is carried out when it’s due.”
Lengthy periods (beyond five years) between hydrostatic tests increase the risk of system failure. This could result in the uncontrolled release of water, which can damage property beyond the need to repair the hydrant system. Damage as a result of failures — demonstrated via hydrostatic tests — is often erroneously levelled at the fire protection service contractor engaged to test the system.
In reality, by undertaking the test, the fire protection service contractor often simply demonstrates that the system may have been neglected for a long time, and would not have functioned as expected in a fire. As a result, firefighters and occupants would be exposed to a higher fire risk.
So what should be done to reduce the risk and potential exposure faced by the service contractor when conducting routine tests?
According to Alan Wilson of Alan Wilson Insurance Brokers, who has managed many claims because of this issue, many fire protection industry members mistakenly proceed with the
hydrostatic pressure test without informing their clients of the potential risks and issues.
“Some systems will not have been properly tested for more than five years and it may look okay from the outside,” Mr Wilson said.
“[But] over time, the insides of pipes deteriorate—sometimes very severely and relatively quickly.
“Without testing, it’s likely that this potentially catastrophic situation will remain unknown until there is a fire and the system is used by the fire brigade, who should be able to rely on system performance to assist them to undertake their role.”
Testing requires the pressure in the system to be gradually increased to 1.5 times the design working
pressure of the approved design. This allows for some redundancy to account for the additional pressure caused by water hammer, and the variable operation of fire brigade pumping appliances that might be boosting the system during a fire.
Mr Wilson said that in his experience, most owners, clients, building managers, facility managers and their insurance companies automatically blame the routine service contractor for bursting the pipes.
“If the system was routinely serviced and tested properly, then the likelihood of bursting would be minimised. However, this is at a cost to the client.”
To reduce legal liability, Mr Wilson advises that routine service contractors preparing to undertake hydrostatic tests on hydrant systems should:
• Advise their client about the risks
• Clearly explain what they will be doing and why
• Have their client sign a waiver stating they understand the risks and therefore do not hold the contractor responsible if the causal issue is system failures that the hydrostatic test is intended to identify, including corroded pipes or fittings, poor connections or lack of routine servicing
“This is a real issue,” Mr Wilson said.
“Why should a contractor be responsible for their clients’ rotten pipes, especially if they got that way through neglect?”
Of course, if a pipe bursts through the contractor’s error — such as putting too much pressure in the system when testing — then their public liability or professional indemnity insurance will cover this.
Mr Wilson recommends that all contractors carrying out hydrostatic tests should use a hydrant and sprinkler testing information form, similar to the type he provides his customers.
“It is basically a waiver form. It states the issues and the results and the client must sign it off. If the client refuses to sign the waiver, we tell our insured customer not to do the testing,” Mr Wilson said.
“But the golden rules are: communicate with your customer, ask questions, keep them informed and don’t assume they know that keeping records is their job too.”
Let’s look at how simulating a large heat transfer system balance – found in many industrial plants – can be used to streamline plant operations. The system balancing ensures each heat exchanger is receiving the proper flow rate and pressure needed for the system to operate properly.
In my early career, I worked as a startup and test engineer at Millstone Power Station Unit 2 for Northeast Utilities. Millstone 2 was a Combustion Engineering 870 MWe nuclear power plant, and was much larger than the plants that I had worked on in the Navy.
One of the first preoperational tests was balancing the component cooling water system (CCW) for Millstone Unit 2. The system had a normal operating mode in which cooling water was supplied to various heat generating equipment in the reactor compartment and auxiliary machinery spaces. The system had NRC licensing requirements to be operational when the reactor was producing power and when it was shut down. In addition, the system was designed to automatically provide cooling water to specific equipment during an off normal (post-accident) condition.
Once all the equipment in the CCW system was tested, the entire system was placed in operation and then balanced so that each heat exchanger received the design flow rate and pressure required for proper system operation. The system also had to be balanced for off-normal operation in the event of an accident.
The size of the CCW system was large with multiple pumps, heat exchangers, control valves and pipelines covering most of the plant. Since this was a safety related system, the CCW balancing had to be completed prior to the NRC issuing an operating license, which would allow the loading of radioactive fuel. The test was planned to
take approximately 10 days, with the actual plant testing to occur during the swing shift and midnight shifts. The testing required most of the operational staff to operate the equipment, and a group of test engineers to set the balancing valves to their prescribed positions. After all the balancing valves were set to the prescribed positions, plant test data was collected for further analysis.
The results of the nightly tests were compiled and sent to Bechtel Power in Gaithersburg Maryland which was the A&E firm for Unit 2. Their engineers reviewed the results to determine the flow rates through each of the CCW heat loads. Based upon the test results, they would generate a new table with the adjusted valve positions for each balancing valve to achieve the designed flow rate.
The CCW system was a network of looped loads, changing the position of any of the balancing valves affected the flow rates to all the loads. Each night we would adjust the balancing valves in the CCW system to the new valves and then rerun the test, compile the results, and submit them to the engineers in Bechtel.
The above process was continued until the system was balanced and the flow rate through each heat exchanger was at its designed value. This test took approximately eight days to complete with the many different iterations. Since it needed to be complete prior to the issuance of the plant’s operating license by the NRC, it received the highest level of interest and scrutiny from the management team.
Fast forward
After 10 years of starting up and testing power plants for EBASCO Services I decided to try something new. I became a co-founder of Engineered Software in 1982. PIPE-FLO was our first program to help simulate the operation of fluid piping systems. As time went on, more features were added to the program to allow for the simulation of larger fluid piping systems.
During a support call one of our customers at a nuclear plant mentioned they were modelling their plants CCW system with our piping simulation program. They needed to meet the needs of a NRC mandated study of the plant’s cooling water system. After a few months I followed up with our customer at the nuclear power plant and asked about their CCW study. They mentioned that they modelled their entire CCW system, and using the software they could effectively communicate the results of their system to the NRC.
A few years later I was conducting a training class on the use of our simulation software. One of the course attendees was a test engineer that I worked with from my Millstone days. For 10 years he was employed by Combustion Engineering, and had been involved with balancing CCW systems for numerous nuclear plants. He was currently working as the lead engineer for an operating nuclear power plant.
During the class, one of the attendees asked what the maximum number of pipelines the simulation
software could accommodate. I stated there were no program limits and asked the attendees to comment on the largest system they had modelled.
My friend from Millstone mentioned that he had created a model of their entire CCW system to help balance the system. After sharing our mutual experience with balancing the Millstone CCW system, he mentioned that he used the model to balance his current plants CCW system. After entering data for the piping system model, he was able to set the flow rates through each heat exchanger by using a throttling valve. The simulation then calculated the differential pressure across each throttle valve in the CCW system to achieve the design flow rate. Using the information
provided by the supplier of the balancing valves, he was able to calculate the valve position of each balancing valve.
I then asked how well that worked out? He commented that by setting the balancing valves for each loop to the calculated position they were able to balance the entire system with just one change. This resulted in completion of the entire system to a single day.
Most industrial processes have multiple piping systems to remove excess heat from operating equipment, provide chilled water and hydronic heating for HVAC systems, or using heat tracing to warm up fluids to operating conditions. Each of these systems
needs to be balanced so each load meets its designed flow rate. If the system is balanced by hand, then multiple iterations must be performed to balance the system to the design values. Often the system will operate with throttling valves open further than required to balance the system. This reduces the need to balance the system, but it requires a greater flow rate than needed which increases the system's energy cost and reduces the future capacity of the system.
By employing a simulation of a piping system, the position of the systems balancing valves can be calculated for the first pass greatly streamlining the balancing process.
Ray T Hardee, PE, is the Chief Engineer and a principle founder of Engineered Software Inc., creators of PIPE-FLO® and PUMP-FLO® software. The PIPE-FLO product line helps some of the largest companies across a variety of industries find hidden profit in the design and operation of their fluid piping systems through simulation software, modelling services, and training opportunities. Hardee is a member of the Hydraulics Institute, ASME Energy Assessment for Pumping Systems standards committee and ISO Pumping System Energy Assessment committee. Hardee’s publications include Piping System Fundamentals and contributions to HI’s Pump Life Cycle Cost and Optimizing Piping Systems. He can be reached at SimGuyRay@eng-software.com
Alignment in the pump business means that the centerline of the pump is aligned with the centerline of the driver. While this alignment was always a consideration with packed gland pumps, it is critical with mechanically sealed pumps, especially if you are using rotating seal designs where the springs or bellows rotate with the shaft.
A little misalignment at the power end of the pump results in a lot of misalignment at the wet end, and unfortunately that is where the seal is located (in most pump applications).
Problems caused by misalignment:
• It can cause rotating mechanical seals to move back and forth axially two times per revolution. The more the seals move the more opportunity for the lapped faces to open
• Packing could support a misaligned shaft. A mechanical seal cannot
• Misalignment will cause severe shaft or sleeve fretting if a spring loaded Teflon as a secondary seal is used in the mechanical seal design
• The pump bearings can become overloaded
• The misalignment could be severe enough to cause contact between stationary and rotating seal components
• The wear rings can touch and rub
• The shaft can come into contact with the restriction bushing (often found at the end of the stuffing box)
• The shaft or sleeve can contact the stationary face of the mechanical seal.
• The shaft can contact the disaster bushing in an API (American Petroleum Institute) gland
• The impeller could contact the volute or back plate
You must start with a pump and driver in good repair, irrespective of the alignment method you select. A thoroughly aligned piece of garbage is still a piece of garbage.
The following checks should also be made:
• A straight shaft that has been dynamically balanced
• Good wear rings with the proper clearance
• The correct impeller to volute, or backplate clearance
• The elimination of "soft foot"
• Eliminate all pipe strain
• Good bearings installed on a shaft with the proper finish and tolerances
• A good mechanical seal set at the proper face load. The closer the seal is to the pump bearings the better off you are going to be
The pump industry relies on expertise from a large and varied range of specialists, from experts in particular pump types to those with an intimate understanding of pump reliability; and from researchers who delve into the particulars of pump curves to experts in pump efficiency. To draw upon the wealth of expert knowledge the Australian pump industry has to offer, Pump Industry has established a panel of experts to answer all your pumping questions.
This edition of Ask an expert will look at why progressive cavity pumps are useful tools for the oil and gas industry.
Q: Do progressive cavity (PC) pumps really support the wide range of applications from upstream to downstream production?
A: Drilling waste management, produced water treatment, fraccing, LACT, multiphase boosting and crude oil transfer, MEG reclamation, sump/caisson emptying, FPSO and refinery wastewater: all these applications and more are easily handled with PC pumps.
PC pumps have many characteristics that make them suitable for oil and gas: flexible installation, pumping of non-flowable products and media with suspended solids, low NPSH, no gas locking, reduced space requirements, accurate linear flow and minimal shear.
In addition, their variable flow rate ensures optimum feeding of separation and processing equipment without the need for flow meters, which are prone to clogging. Flow rates can also be regulated via simple speed control which eliminates the need for control valves and spill back lines as used with other pump types. PC systems are delivered to be tolerant to changing flow requirements and prolonged gas slugging.
Manufacturers offer a wide range of pumps for this industry, from dosing and open hopper pumps to fully-submersible pumps or package solutions that allow for automatic control.
Q: Even a unique product has to fit within global standards and the customers’ engineering specifications. How do progressive cavity pumps hold up against the American Petroleum Institute (API) standards along with other specifications?
A: Progressive cavity pumps can generally conform to the following standards:
• API 676 rotary positive displacement pumps
• API 682 mechanical seals
• NORSOK M-650
• NACE MR-01- 75
• ATEX Directive 94 / 9 / EC
The fully API 682 compliant mechanical seals can also be upgraded with optimised seal plans. ASTM materials, full traceability, compliance with NACE MR0175 and a design for gas hazardous areas are additional supported features.
Additionally, PC pumps for dosing of corrosion inhibitors and general chemicals can achieve an accurate and repeatable flow rate that complies with API 675.
Applying PC pump technology is crucial for reliable in-service performance and cost savings for you, the customer. Contact an expert today, to receive a customised and intelligent design which will meet your stringent requirements.
Peter Vila, Managing Director of SEEPEX Australia, is a progressive cavity pump expert. He has been involved with pumps for over 35 years. Peter spent the first five years repairing pumps and the following 30 years in technical sales, 15 of which have been with SEEPEX progressive cavity pumps.
For more information on progressive cavity pumps, please contact SEEPEX Australia on (02) 4355 4500 or at info.au@seepex.com
The new BNA pump ensures compliance with API 676 and API 682 while reducing costs in petrochemical applications.
YOUR BENEFITS
API 676 and API 682 compliant
Extremely robust design
High containment pressure and corrosion resistance
Simple integration into piping systems
Non-welded casing means reduced documentation and fewer inspections
Shorter lead time
High operational safety Act now to experience the benefits of this API pump for yourself.
The PIA’s Australian Pump Technical Handbook is a cornerstone text for the Australian pump industry and, in our opinion, a must have for anyone who deals with pumps on a regular basis. In this ongoing series, we feature abridged chapters from the classic book to showcase the various areas covered and to reacquaint readers with the technical aspects of pumps. In this issue, we explore the defining characteristics of positive displacement pumps.
Progressive cavity pumps are also known as single screw or helical pumps. They consist of a resilient stator in the form of a double internal helix and a single helical rotor, with later designs consisting of a triple internal helix and a double helix rotor. The pump is helically shaped and follows a helical path from suction to discharge as the pump rotates.
The rotor, usually a sliding interface fit in the stator, maintains a constant seal across the stator and the seal travels continuously through the pump giving uniform positive displacement. The single helical rotor rolls in the stator with an eccentric motion so that a universally jointed drive shaft, or equivalent, is required to drive the motor.
A pump with a single pitch stator is called “single stage” and is usually
designed for a maximum rated pumping pressure of 6 bar, where a pump that uses a two pitch stator is called “two stage” and is designed for 12 bar. Similarly an eight pitch stator is 8 stage and designed for 48 bar.
Progressive cavity pump rotors use a coupling rod or flexible drive shaft to transmit the rotary drive whilst allowing the rotor to orbit within the pump stator. The coupling rod uses simple single pin universal joints, two pin universal joints, or gear joints which operate within the pumped fluid and are usually lubricated and sealed with flexible boots to prevent contamination of the lubricant by the pumped fluid, or vice versa.
Flexible drive shafts do not have joints that require lubrication, and are significantly longer than coupling rods. The coupling rod is driven by
a drive shaft that is supported by a separate foot mounted bearing house, or is fitted directly to a gearbox output shaft. The most unusual drive arrangements are electric motors either flexibly coupled, or flanged, to a gearbox. However, many other drives arrangements are also used.
Progressive cavity pumps come in a variety of sizes, ranging from small chemical dosing pumps suitable for flows as low as 20 l/h and pressures to 12 bar, to medium capacity, medium pressure (100 m3/h and 72 bar), and to high capacity, low pressure (420 m3/h and 6 bar) (300, discharge pipe size).
Wide or open throat variations are available with large rectangular inlet connections for very high viscosity liquids, and liquids containing very high solids content.
Some key points in selecting progressive cavity pumps are:
• Elastomer material - Progressive cavity pumps are available in a wide range of elastomers for the resilient stator and the universal joint boots. Selection of stator material is important and should take into account chemical and abrasion resistance, as well as strength. Chemical resistance is important as swelling of the elastomeric stator may cause an increase in interference between the rotor and stator, a loss of efficiency, and starting problems due to an increase in starting torque
• Self-priming - Provided piping is designed to ensure some liquid is trapped in the pump after shutdown and before initial start, the self-priming capability of these pumps is very good
• Rubbing velocity - A conservative approach should be taken when selecting the rubbing velocity between the rotor and stator, to ensure that an economical life can be
The interference fit between the hard rotor and soft resilient stator results in low slippage, good volume efficiency and very good self-priming. Since small abrasive solids are enveloped in the stator as the rotor passes them, abrasive wear is relatively low and subsequently the range of suitable applications is large. Non pulsing flow, low shear pumping action, and bidirectional flow possibility also increase the pump versatility.
The elastomeric stator should be selected for good chemical compatibility and temperature capability. Clean in place (CIP) can be used provided the pump selection takes into account cleaning fluid chemical compatibility and temperature.
Progressive cavity pumps should not be run dry. If the process and piping system cannot be designed to avoid this possibility, some type of dry running shutdown should be considered. Dry running warning or shutdown systems often use flow sensors, but the most popular system uses a temperature sensor embedded in the pump stator to detect frictional heating of the stator prior to high temperature damaging the stator.
achieved, even when pumping fluids with abrasive solids. Pump specifications frequently specify a maximum rotation speed (rpm) to avoid excessive rubbing velocity (m.s). However, since different size pumps have different rotor diameters and eccentricities, a maximum rubbing speed velocity should be specified instead of rotation speed. The most common progressive cavity pump geometries are designed for maximum rubbing velocity of 3.0 m/s. This usually provides a good life on clean water, but speed derating to 1.5 m/s or less is often desirable for liquids containing abrasive solids and/or high viscosity liquids
• The pump starting torque can be relatively highThe drive should be selected with an adequate starting torque factor for safety. This is particularly important when variable speed drives are used for either speed control or to reduce starting currents
Common applications for progressive cavity pumps include, but are not limited to:
• Sauces, confectionary, yogurt, and shortening in the food industry
• Chicken offal, meat purees, potato waste, thick nonflowing pastes
• Domestic and industrial sewage, primary and secondary sludges, dewatered sludge cake
• Shampoo, cosmetics, light creams
• Lime, bentonite and clay slurries
• Dosing of flocculants and various chemicals
• Wine must (grape juice with stalks and skins) using rectangular inlet versions
• High head mine dewatering usually containing abrasive rock particles and dust
• Shaft and submersible motor drive borehole pumps
• Low flow, high head, agricultural water pumping, particularly where long suction lines are required
Crescent internal gear pumps have an outer or rotor gear that is generally used to drive the inner or idler gear.
The idler gear is smaller than the rotor gear, and rotates on a stationary pin and operates inside the rotor gear. The gears create cavities as they come out of mesh and liquid flows into the pump. As the gears come back into mesh, the cavity volumes are reduced and liquid is forced out of the discharge port. Liquid can enter the expanding cavities through the rotor teeth or recessed areas on the head, alongside the teeth. The stationary crescent is integral with the pump head, and prevents liquids from flowing to the suction port from the discharge port.
Internal gear pumps are often used in food manufacturing
The rotor gear is driven by a shaft supported by journal or anti-friction bearings. The idler gear contains a journal bearing rotating on a stationary pin in the pumped liquid. Depending on shaft sealing arrangements, the rotor shaft support bearings may run in pumped liquid, which is an important consideration when handling abrasive liquid as it can wear out a support bearing.
Typically these pumps are made in a range of sizes, from one to 10 inches, flows to 360 m3/h, pressures to 14 bar, and temperatures to 230°C.
Gear pump type and size are usually chosen from selection charts and then performance is found from individual performance curves. Individual curves are produced for a range of viscosities, and the curve for the viscosity nearest to that to be pumped is used. Performance can be checked by reference to the manufacturer or distributor.
Internal gear pumps are exceptionally versatile. While they are often used on thin liquids such as solvents and fuel oil, they excel at efficiently pumping highly viscous liquids such as asphalt, chocolate, and adhesives. The useful viscosity range of an internal gear pump is from 1cPs to over 1,000,000cPs.
In addition to their wide viscosity range, internal gear pumps also have a wide temperature range, handling liquids up to 250°C and in some cases, 400°C. This is due to the single point of end clearance (the distance between the ends of the rotor gear teeth and the head of the pump). This clearance is adjustable to accommodate high temperatures, maximize efficiency for handling high viscosity liquids, and to accommodate for wear.
Internal gear pumps are non-pulsing, have some self-priming capability, and can run dry for short periods. They’re also usually bi-rotational, meaning that the same pump can be used to load and unload
vessels. Because internal gear pumps have only two moving parts, they are reliable, simple to operate, and easy to maintain.
Common applications for internal gear pumps include, but are not limited to:
• All varieties of fuel oil and lube oil
• Resins and polymers
• Alcohols and solvents
• Asphalt, bitumen and tar
• Polyurethane foam (isocyanate and polyol)
• Food products such as corn syrup, chocolate and peanut butter
• Paint, ink and pigments
• Soaps and surfactants
• Glyco
External gear pumps come in single or double (two sets of gears) pump configurations with spur, helical and herringbone gears. Helical and herringbone gears typically offer a smoother flow than spur gears, although all gear types are relatively smooth. Large capacity external gear pumps typically use helical or herringbone gears. Small external gear pumps usually operate at speeds up to 3000 rpm and larger models operate at speeds of up to 640 rpm.
External gear pumps have close tolerances and shaft support on both sides of the gears, allowing them to run to pressures in order of 150 to 200 bar, making them well suited for use in hydraulics. With four bearings in the liquid and tight tolerances, they are not well suited to handling abrasive or extreme high temperature applications.
Tighter internal clearances provide for a more reliable measure of liquid passing through a pump and for greater flow control, making them popular for precise transfer and metering applications involving polymers, fuels and chemical additives.
Typically the pumps are made with a size range from ⅜ to four inches, flows to 45 m3/h, pressures to 150 or 200 bar, and temperatures to 230°C.
Characteristics of external gear pumps
The design of external gear pumps allows them to be made to closer
tolerances than internal gear pumps. The pump is not very forgiving of particulate in the pumped liquid. Since there are clearances at both ends of the gears, there is no end clearance adjustment for wear. When an external gear pump wears, it must be rebuilt or replaced.
External gear pumps handle viscous and watery-type liquids, but speed must be properly set for thick liquids. Gear teeth come out of mesh a short time, and viscous liquids need time to fill the spaces between the gear teeth. As a result, pump speed must be slowed down considerably when pumping viscous liquids.
The pump does not perform well under critical suction conditions.
Volatile liquids tend to vaporise locally as gear teeth spaces expand rapidly. When the viscosity of pumped liquids rises, torque requirements also rise, and pump shaft strength may not be adequate. Pump manufacturers supply torque limit information when it is a factor.
External gear pumps are popular style and are often used as lubrication pumps in machine tools, in fluid power transfer units, and as oil pumps in engines.
Common applications for external gear pumps include, but are not limited to:
• Lubrication pumps in machine tools, in fluid transfer units, and as oil pumps in engines
• Various fuel oils and lube oils
• Chemical additive and polymer metering
• Chemical mixing and blending (double pump)
• Industrial and mobile hydraulic applications (log splitters, lifts, etc)
• Acids and caustic (stainless steel or composite construction)
• Low volume transfer or application
Further information and detailed diagrams, equations and schematics can be found in the Australian Pump Technical Handbook, available from the PIA website. In the next edition of Pump Industry, we continue our explorations into the selection and application of different types of positive displacement pumps.
Arthur Connor has had a long and successful career as an engineer, from working as a draughtsman at Kelly & Lewis Pumps to assisting in the building of Melbourne’s trains and trams. His efforts and significant contributions to the pump industry have also been recognised by the Institution of Engineers, Australia. Here, Arthur shares his story of his time in the pump industry and the big role it has had in his life.
Having successfully completed a Technical Certificate course at Swinburne in 1949, and having finished first in engineering and second to the Dux of the school, it was time to get a job. Throughout the final year of my course I often looked out at the Kelly & Lewis (K&L) plant near the Springvale Station. I knew nothing about the company or what they did, but I was fortunate to be introduced by one of my Swinburne teachers for an interview.
I started at K&L as an apprentice turner and fitter on the understanding I could transfer to the Drawing Office after three years to complete the apprenticeship. However, three weeks after starting I was transferred to the Standard Pump Section of the Drawing Office, and as fate and luck determined, this held the opportunity for me to learn and specialise in a career involved with centrifugal pumps. This ultimately took me around the world and helped play a part in K&L’s strategic development in the pump business over the years ahead.
In 1952, I was transferred to the Design and Development office, known as Central Administration
(CA), based in the KL Electric Motors building on Springvale Road. My job as a draughtsman was to assist in drawing the future range of K&L Model 50 mass produced standard pumps. The model went to market as the “yellow” pump with replaceable bearing and shaft cartridge, developed for improved maintenance on farms, irrigation and industrial use. It was the first mass produced range made in Australia using the latest in German automatic drum control machines.
The experience with the yellow pump inspired me to begin a Mechanical Engineering Diploma course at Caulfield Technical College which took eleven years of part time study to complete.
In the design group at K&L there was one person in particular, Andy Gasiunas, a Lithuanian immigrant, who became a key lifetime mentor and went on to inspire me to study hydraulics and hydrodynamics. Through him I had an opportunity to learn the theory behind his designs and appreciate his foresight, which later enabled me to apply that knowledge to decide the best application of pumps and
draught them into manufacturing drawings.
The next six years were ones of dynamic advancement and inspiration for me. As well as continuing my studies, I was able to learn much about hydraulic and mechanical design of pumps from Andy. These were the most important formative years in my career involving pump design.
After the completion of my Engineering Diploma I became restless, and in January 1961 I applied for a sales position at the Shell Company of Australia and began my three month training course.
A few months later I was appointed as the Bitumen Representative seeking bulk bitumen and emulsion sales from councils and contractors, and in charge of the company Road Spraying Team for Victoria and Southern NSW right up to Hay.
The Shell sales experience proved valuable in “selling for Shell” and learning to deal with customers. I enjoyed the role and was somewhat reluctant to go back to K&L.
My return to K&L in 1962 arose due to Andy Gasiunas being appointed Technical Director of the Mather & Platt (M&P) Power Division based in Manchester, and I was to takeover his role as Chief Hydraulic Design Engineer at Springvale.
This was an exciting responsibility for me to undertake, especially my promotion within the Engineering Department and Drawing Office where I grew up and learned under some wonderful colleagues over the previous 12 years.
A winning design for a sewerage pumping station
One very memorable experience was a meeting with George Hauser, the Melbourne and Metropolitan Board of Works (MMBW) Engineerin-Chief, and Geoff Archer at the MMBW offices just after release of the tender documents for the South Eastern Purification Plant (SEPP) to be built at Carrum in the south-east of Melbourne.
Geoff Archer, the Superintendent of the Brooklyn Sewerage Pumping Station built by K&L over the late 1950’s, knew all about the pumping operations and experiences with that plant and had previously talked about overcoming certain maintenance issues for the proposed SEPP Carrum pumps, but did not specify the preferred features of the new pumps, leaving that to tenderers.
As a result, during the meeting in George Hauser’s office at the MMBW, I asked what they most wanted with the new pumps and Geoff Archer nominated the most important issues as:
• Pumps to be capable of continuous start up at closed valve and to minimise wear to impeller sealing rings
• To reduce internal corrosion of pump parts caused by electrolytic effects arising from the sewerage
• The highest pump efficiency consistent with non-clog ability, but high non-clog performance was an over-riding priority in serviceability
So, armed with this, I went back to Springvale and decided on a new design incorporating a double volute casing to balance out radial forces on the rotating element and a stainless steel impeller to eliminate electrolytic effects on the pump internals.
K&L won the contract and achieved all the desired benefits on test and subsequent installation, of which the MMBW was duly pleased.
In 1972 word reached us that Andy Gasiunas had passed away suddenly after catching a flu virus. He was solely responsible for introducing advanced hydraulic and mechanical design technology from the prewar age to the rapidly developing postwar age across the world. In consequence he helped lift K&L Springvale and later M&P in the UK to global competitive standards. Andy was my key mentor and engineering design inspiration during my working life.
Plant test bay examining the test performance results of a Kelly & Lewis new design 900/1050mm
Then came my 40th birthday, the 29th April 1973, a Friday. First thing on arriving in my office, I was invited to Harry Smith’s office in what was called “mahogany row”.
“How would you like to go to England?” Harry asked me.
I asked, “What do you want me to do?”
He said, “Go to live there to be the Technical Director of the Power Division of Mather & Platt in Manchester and head up Research and Development, and Engineering to continue the work started by Andy Gasiunas”.
The task was a move up for me in taking up such a role covering the R&D work and supervising the current production of oil field applications covering transfer, tanker loading and high pressure seawater injection pumps. This included electric motor contracts in the North Sea oil fields and similar applications of high speed oil pipeline pumps in the Middle East.
I accepted the position and reported at Park Works plant in Manchester on 31 July 1973.
I spent much of the first year dealing with the test bay backlog which involved engineering staff in the workshop and understanding who in the Technical Department ‘made a difference’ in getting results. As well as my role in Manchester, I was responsible for liaison with the company’s plants in Johannesburg, South Africa, and India over product issues and application advice for new major enquiries.
At the end of 1976, my family and I returned to Australia and set up in the managerial offices at K&L Springvale in the role of Group Engineering Director of the M&P global operations. At which time Wormald International, based in Sydney, acquired the worldwide operations of M&P which included K&L.
As the early 1980s progressed in Australia, industrial disruptions increased in the metal industries, in particular, over Union claims for a 35 hour week, along with ambit claims for an earlier retirement age.
At the same time, the Australian dollar was rising in value and imported engineered products started to flow in to Australia and our once loyal independent State Distributor warehouses turned to importing many lines.
Then the Arbitration Commission ruled on a union push to have over award payments paid by manufacturing industries absorbed into the award rate of pay, meaning that overtime would be at higher rate driving up wage costs.
This had a devastating affect on the foundry industry, as most needed overtime capacity and not enough work to do to make double shifts viable. The decision brought forward inevitable rationalisation and closures of some Machinery Group foundries.
Changing economic conditions, currency variations and globalisation of business since 1970 had brought big change to the ownership and success of the manufacturing industry in Australia and worldwide. It became clear to me, much more would evolve over the years ahead, especially in Australia, bringing unexpected change.
At the time I was on the committee of the Metal Trades Industry Association (MTIA) in Victoria and was invited to discuss issues with the Government in Cabinet with Malcolm Fraser and his ministers.
I was later invited to join the HEMA Committee in 1982, after being nominated by Jack Keegan, MD of Jaques, and commenced attending their regular meetings of key industry executives in Canberra. I went on to become Chairman of HEMA for two years over 1984 – 85 and was invited to sit on the Metals and Manufacturing Council within the Labor Government’s Industry Council set up by Senator Button.
As an outcome of declining economic circumstances, Wormald embarked in a sell off of all Machinery businesses in Australia and around the world to fund their New York Stock Exchange listing and global expansion in fire protection and security businesses. That, however, never eventuated, as Wormald themselves became the hunted and target of Asian investors and lost control of their worldwide company.
The M&P Manchester, K&L Springvale and Ballarat John Valve plants were all reduced to bare sites within three years.
The start of a new era
In March 1987, nearly three months after leaving K&L, I received a
call at home in Kalorama asking if I would be interested in attending an interview for the position of General Manager at the rolling stock plant of ANI Comeng (formerly Commonwealth Engineering) in Dandenong.
The company had large contracts building Melbourne’s trains and trams, and was at the early stages of design to build Australia’s first large export contract for Light Rail Vehicles (LRVs/Trams) for a project in the New Territories of Hong Kong.
I was told the Dandenong facility was “The Jewel in the Crown”; I soon discovered that the company was “No Jewel in the Crown” and that I had jumped from the Wormald frying pan into the Comeng furnace.
After an upsetting year throughout 1989 opening our doors to all and sundry, including all Australian competitors, and throwing our books open, we were forced to cut staff everywhere possible to reduce overheads. The morale amongst the employees hit rock bottom; including mine. Totally exasperated, I handed in my resignation in November 1989.
After treatment where the sewage and resulting clean water was separated the water was pumped from the plant
I was drained emotionally and affected especially by the forced dismissal of many very good and long-term staff.
I was advised of a deal that the Swedish company ABB was near signing a deal to purchase the Dandenong Rolling Stock plant. I was offered a three year contract to stay on, at the end of which I resigned in May 1993. Some months later, my wife, Marie who supported me so well, and I moved to Queensland to enjoy life on the Sunshine Coast.
Following my retirement in 1993, I was elected a Fellow of the Institution of Engineers, Australia. This was great honour and one of which I am very proud.
I hope the many aspects of my life’s working experience, and that of the many brilliant colleagues and exceptional engineers and commercial staff I worked with in Australia, the UK, South Africa, and especially at the Pune plant in southern India, where I was thought of as their guru, was of interest. I took great pride in helping them and they were very grateful. Any difference I made would not have been achieved without them and I remain very thankful.
The first pump of its type in Australia to have unique double volute balanced hydraulic design casings to greatly reduce seal ring wear when starting at closed valve
1951-52 Wellington Dam – Kalgoorlie Pipeline project
1952-1955 Development of the Model 50 Standard End Suction Range for general and agricultural duties
1956 The Model 60 range “back pull out” concept originates with an order for a 7/8 inch vertical pedestal mounted Pond Pump with parameters set by AAG and drawn up by RD in the latter days of CA Administration at K&L Electric
1956-1957 Contract received from MMBW VIC for the supply of 8 x 36/42 Vertical Solid Case Raw Sewerage Pumps and plant equipment for the deep well pumping station feeding the Werribee Treatment Plant
1958 4 x 48 inch Axial Flow Pumps for First Mildura Irrigation Trust – Psyche Bend
1958 72 inch Axial Flow Pumps and Flap Valves for AIS Wollongong
1959 Hunter District Water Board – Balickera Flood Control Pumping Station
1961 Development of 1 and 2 Stage Sabre Thrust Jet Propulsion Unit for Pleasure Craft
1966 Liddell Power Station High Pressure River Pumps
1969 Mannum Pumping Station – Pipeline to Myponga and South Para Reservoirs in Adelaide
1973 E&WS Murray Bridge to Onkaparinga Pipeline Pumping Project servicing Adelaide’s Water Supply
1985-1986 Brisbane City Council 2 x 72 inch x 1 Stage MFD Pumps