New wastewater infrastructure to cater for a growing SEQ
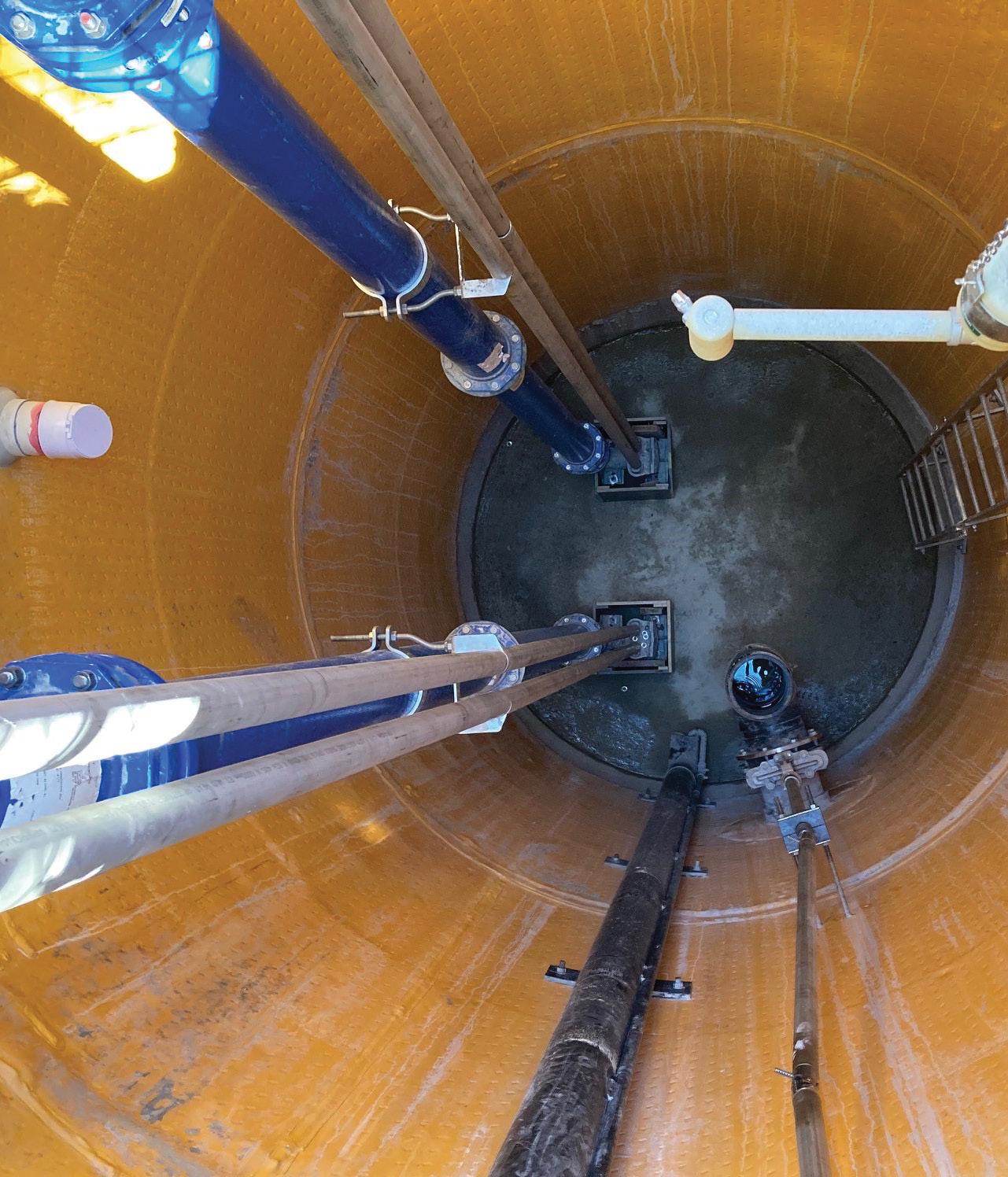
Rethinking the NPSH matrix
New wastewater infrastructure to cater for a growing SEQ
Rethinking the NPSH matrix
2022 anticipating better times ahead
Climate
population growth, and water scarcity are creating new challenges, and desalination is becoming an important alternative to traditional freshwater resources.
Hello all and welcome to the Summer Edition of Pump Industry Magazine. On Wednesday 10 November, PIA held its 18th AGM via a Zoom meeting hosted once again by Laura Harvey, Managing Editor at Monkey Media. As you know, Monkey Media is the publisher of the PIA’s official magazine. Hopefully as Laura said we will be able to meet face to face in 2022, but as I stated in my President’s address, we cannot say the end is in sight and as I write this editorial, we are learning of yet another variant – Omicron – which has been found around the world and in Australia; the level of severity of the new variant will take some weeks to determine.
Drainage Act 2018 (PD Act 2018). The QBCC petitioned the Services Trade Council (STC), an instrument of the QBCC, on our behalf. The matter was tabled with the STC on 6 October where it remains; we understand the matter remains under consideration and we await a formal response.
Pump Industry Australia Incorporated C/-340, Stuarts Point Road
Yarrahapinni NSW 2441 Australia Ph/Fax: (02) 6569 0160 pumpsaustralia@bigpond.com www.pumps.org.au
PIA Executive Council 2022
John Inkster - President Brown Brothers Engineers
James Blannin - Vice President Stevco Pumps & Seals
Kevin Wilson - Treasurer/Secretary Executive Officer
Alan Rowan - Councillor Executive Officer - Publications and Training, Life Member
Ken Kugler Executive Officer - Standards, Life Member
Michael Woolley - Councillor Tsurumi Australia
Geoff Harvey - Councillor Irrigation Australia Limited
Billie Tan - Councillor Regent Pumps
Steve Bosner - Councillor Pioneer Pumps
Joel Neideck - Councillor TDA Pumps
Matt Arnett - Councillor Ebara Pumps Australia
Jamie Oliver - Councillor Grundfos Pumps
We had 56 registrations at the AGM, representing some 40 member organisations, so a pleasing turnout; this reflects the growing Membership of PIA which now stands at over 90. A highlight of the AGM was guest speaker Jason Cunningham, accountant and owner of business advisory firm The Practice. Jason is a born entertainer and enjoys sharing his business insights and experience with fellow owners looking to grow their business. His theme for the night was “Beginning with the end in mind – Build a business ready for sale”. Jason has both an engaging and energising manner which enables him to communicate in a way everyone can relate to. We received many positive comments about his presentation.
At our AGM, James Blannin was reelected VP, Kevin Wilson was re-elected as Secretary/Treasurer. Our Standards Officer Ken Kugler was re-elected, as was Alan Rowan our Publications and Training Officer. All other Councillors were re-elected except for Anant Yuvarajah who did not stand for re-election. I take this opportunity to thank Anant for his contribution to Council and at the same time welcome Jamie Oliver from Grundfos Pumps. We welcome Grundfos Pumps back into the PIA as it is important to have a good cross section of industry representing all our Members.
So, what were the highlights of 2021; unfortunately COVID greatly restricted face-to-face activities, but we were able to hold the second of our Pumps & Systems Training Course in Melbourne in March and then a very well-attended meeting in Perth in April hosted by Tsurumi Australia. After that, COVID regulations and the uncertainty of border closures hindered any further attempts.
During the year we initiated dialogue with the Queensland Building and Construction Commission (QBCC) on behalf of those Members who conduct work covered by the Plumbing and
Meanwhile, we have learnt that the Department of Energy and Public Works, on behalf of the QLD Government, will be carrying out an independent review of the QBCC governance arrangements. The review will look at the QBCC’s structure, governance arrangements, roles and responsibilities, providing recommendations about legislative or administrative changes that might improve operations of the QBCC. Fire Pumps Australia (FPA) has also been notified of this.
How this might impact our discussions is unknown at the present time. This is an extremely important matter to many of our QLD Members, some of whom have experienced firsthand the QBCC regulations. To date I am not aware of any Members who have been fined for non compliance under the PD Act but I know some have been questioned. As more information comes to light, PIA will keep you informed.
In an endeavour to hold more online Seminars in 2022, Council consulted with Rob Welke of Tallemenco. Rob has been involved in pumping and hydraulics for over 50 years and is a well-known independent consultant and educator. We successfully held our first Seminar on the “Energy Efficiency of Pipelines” on 24 November, attracting 71 registrations which was great for our first effort. The Seminar was heavily subsidised by PIA as an inducement to Members to attend.
PIA is planning to run another Seminar with Rob hopefully mid-February on “Flow metering for on-site pump tests”. Malcolm Robertson of Robertson Technology in WA has also offered to do a Seminar on “Condition monitoring”, and I am sure Ron Astall would be like-minded.
As always, I extend a hand out to the larger pump organisations to participate more fully in PIA activities; we would benefit greatly from your experience and knowledge as we endeavour to act as the peak body representing all the pump industry.
I take this opportunity to thank all the Executive and Executive Officers for their assistance during the year and extend a warm welcome to Jamie Oliver in joining Council. Special thanks to our hard-working Secretary Kevin Wilson for his good work.
I wish you all a COVID-safe and prosperous 2022
John Inkster - President
Polymaster’s unique Enclosed IBC Bund solves many of the problems associated with IBC storage and chemical/fluid decanting in a weather resistant, purpose-built enclosure.
Æ Full weather protection – stops rain entering the enclosure
Æ Easy forklift loading with wide forklift access from both side and back
Æ 250ltr day tank
Æ Lockable cabinet to keep system secure
Æ Venting by two sides
Æ Viewing windows incorporated into the doors
Æ 110% bund capacity complies with AS3780
Æ Sight tube and low-level alarm available
Æ Chemical resistant – high grade polyethylene construction
Published by
ABN: 36 426 734 954
C/- The Commons, 36-38 Gipps St, Collingwood VIC 3066
P: (03) 9988 4950
F: (03) 8456 6720
monkeymedia.com.au info@monkeymedia.com.au pumpindustry.com.au magazine@pumpindustry.com.au
Editor: Lauren Cella
Contributing Editor: Michelle Goldsmith
Journalists: Annabelle Powell, Christopher Allan
Business Development Manager: Rima Munafo, Jacob Trad
Design Manager: Alejandro Molano
Designers: Jacqueline Buckmaster, Danielle Harris, Luke Martin
Publisher: Chris Bland
Managing Editor: Laura Harvey
ISSN: 2201-0270
BCI Minerals Limited (BCI) has awarded a $16 million contract for a main seawater pump structure at the Mardie Salt and Potash Project, also announcing that the project’s northern embankment trial is nearly completed and construction of its southern trial pond is beginning.
The contract for the main seawater pump structure is fully funded from BCI’s existing cash balance of $110 million as of July 2021, and has been awarded to Western Australian company, Ertech’s Geomarine business.
Ertech’s Geomarine specialises in designing and constructing nearshore marine infrastructure for the resources, infrastructure and defence sectors.
When the project is fully operational, the primary seawater pump station will pump 160GL of water into the evaporation ponds each year, equivalent to approximately 70,000 Olympic swimming pools.
The Mardie Salt and Potash Project’s investigative works are an essential precursor to main construction, to provide confidence about key assumptions, including materials availability, construction methodology, pond wall settlement, pumping rates, pond floor water retention, and cost and schedule assumptions.
Construction of the northern embankment trial was nearing completion in September and the southern trial pond will incorporate construction methodology, materials and equipment learnings from the northern embankment trial.
Construction of the civil works will form part of a broader contract awarded to WBHO Infrastructure in March 2021,
which includes the northern embankment trial, southern trial pond, and after full regulatory and access approvals, Pond 1 and Pond 2.
The work involves the design, procurement, construction and commissioning of all the detailed earthworks, piling, structural steel, concrete, mechanical and electrical installations required to accommodate and operate six 3,000L per second pumps within the pump structure.
Main construction of the project can only commence when BCI has received approval from the Western Australian Minister for Environment, as well as associated secondary approvals, including when final tenure and funding have been secured.
BCI anticipated all these to be in place by late 2021.
WELCOME TO THE BIG END OF TOWN.
VERTICAL TURBINE PUMPS
Layne Bowler vertical turbine pumps have a proven record under the most demanding and toughest of conditions.
• Flows to 7,500 L/Sec
• Heads to 500 m
• Power to 1000+ kW
• Temperatures to 150°C
• Bowls Diameter up to 45 inch
When high head and high flows are required look no further than this quality Italian made range.
• Flows to 5000m³/h
• Head to 220m
• Pumps that exceed EN733 (DIN 24255 standard)
Designed for long life and maintenancefree service in the harshest environments. This market leading hose is tough and durable with exceptional resistance to abrasion and cutting.
A heavy reinforced fluid transfer hose made from a blend of nitrile rubber and PVC, with added UV barrier to prevent damage from UV radiation.
INTERNATIONAL DRINKING WATER CERTIFICATION
AUSTRALIA AS-NZS4020-2005 APPROVED UK WRAS APPROVAL to BS6920 USA NSF61 LISTED GERMANY KTW-DVGW APPROVED POLAND PZH APPROVED
The Tasmanian Government has launched the Preferred Option Design for the Sassafras Wesley Vale Irrigation Scheme Augmentation, which includes 95km of new and refurbished pipeline and five pump stations.
This Tranche Three irrigation project is expected to double the amount of high-surety irrigation water delivered to farmers in the productive North West Tasmanian region. It is also expected to create an estimated 120 jobs and underpin $28.3 million in on-farm investment.
The Tasmanian Government has committed $18.34 million, the Australian Government $30.57 million and landowners $13.81 million to refurbish existing infrastructure and construct additional pipelines and pump stations to increase the capacity of the scheme from 5,660 to 13,686 megalitres.
Expected to be operational for the 2025/26 irrigation season, this water will enable farmers to invest,
diversify, expand and value add, as well as provide muchneeded guarantees for crop contracts and on-farm investment leverage.
The Preferred Option Design follows a similar alignment to the existing scheme and includes 95km of new and refurbished pipeline, five pump stations and the replacement of 70 property outlets.
Water will be sourced at the Great Bend Pump Station on the Mersey River and backed up by releases from Parangana Dam.
This project is one of ten Tranche Three irrigation schemes being developed by Tasmanian Irrigation to assist the Tasmanian Government in reaching its target of increasing the farm gate value of the state’s agricultural sector to $10 billion a year by 2050.
Kelair Pumps Building & Fire Division is one of the most technically-competent suppliers in Australia. We can provide a complete range of fire sprinkler pumpsets for all applications, fully compliant to technical specificiations.
Benefits of containerised fire pump units:
- Purpose built to individual requirements
- Compact, pre-fabricated, complete packaged solution
- Simple to mobilise and transport
- Fully tested to AS2941/ISO9906 and pre-commissioned
- Wall insulation keeps operational noise to a minimum
- Turnkey installation saves time and labour costs
We know the importance of choosing the right equipment to match your process. With our extensive range of pumps, first class customer service and ongoing comprehensive support, Kelair Pumps are second to none when it comes to your pumping requirements.
Acquiring Galbraith’s gives Brown Brothers NZ access to Oceania and strengthens the fire pump position, while solidifying the Group’s market leadership.
Galbraith Engineering – a family-owned business – is recognised as New Zealand’s leading fire pump specialists, designing and manufacturing diesel and electric fire pumps under the Firewater brand. In addition to this, Galbraith also builds pump sets for irrigation, snow-making and frost fighting. They also supply consultancy and system design, pump commissioning, pump performance testing, pipe fabrication, and maintenance and repair. Galbraith has 14 employees with headquarters in Christchurch and a service base in Auckland.
“We have been in the business for 28 years, and we’ve come to the point where we were looking for a strategic partner that could take us to the next level. We have known Brown Brothers New Zealand for many years now and we see them as a like-minded organisation with an eye for future growth,” said Steve Galbraith, General Manager and part-owner of Galbraith Engineers.
“There is a continuous demand for fire pumps in the commercial world of warehousing, fuel terminals, oil and gas, and a wide range of industrial sectors. Having Galbraith
Engineers in the Group will allow us to consolidate the fire business in Oceania region and partner with Kelair Pumps for high-end applications,” said John Inkster, Managing Director of Brown Brothers Engineers Group.
“As one large Group, we will be well-positioned to continuously take market shares in Oceania while strengthening our strong supplier relationships and attract the best talents.”
KEY APPLICATIONS Fair Pricing Policy For Pumps And Other Brand Spares Trusted Helical Rotor Pump Manufacturer For Over 20 Years In Australia
Primary, Secondary & Tertiary Clarification Process | Sludge Thickening Process | Digestion Process | Dewatering and Sludge Incineration Process | Polymer Dosing
The Townsville City Council contracted local business CivilPlus Constructions to replace two 120kg pumps that supply raw water to the Giru Water Treatment Plant, ensuring steady water supply for the coastal regions of Cungulla and Giru.
Townsville Council Water and Waste Committee Chairperson, Russ Cook, said the pump renewal project was about ensuring Cungulla, in the Townsville local government area, and Giru, in the Burdekin Shire, had a reliable water source for decades to come.
“Townsville City Council is committed to ensuring our community has a safe and reliable water supply now and into the future, and this $500,000 investment is about delivering on that commitment for our communities like Cungulla and Giru,” Mr Cook said.
“This project is part of the Council’s $177 million investment in water infrastructure and services this financial year.
“Besides the installation of the new pumps, the works will involve installing new structural steel beams, which will be lifted into place by helicopter, as well as some electrical works on the bridge to accommodate for the two 120kg pumps.
“While the pumps are being replaced, potable water will be trucked to the Giru Water Treatment Plant and the Cungulla Reservoir to minimise the impact to residents.”
Burdekin Shire Council Mayor, Lyn McLaughlin, said the pump renewal would provide peace of mind for Giru and Cungulla residents.
“I want to thank Townsville City Council for recognising the importance of water infrastructure upgrades across their network, and thank Giru and Cungulla residents for their patience as pump renewals are completed,” Ms McLaughlin said.
Works were expected to be finalised by the end of October 2021.
The Maxijet Polyethylene Pump Wells are typically used for stormwater and sewage applications for domestic, commercial, and industrial applications. Compatible with any submersible Pedrollo, Zenox or Hyjet Pumps.
These Polyethylene Pump Wells can be pre-plumbed with single or dual pumps and are supplied with barrel unions, valves, non-return valves and outlets all with interconnecting pipework.
To meet local standards and codes for underground soil loading requirements, the MPPS Series are engineered in compliance to meet Australian Standards.
Sizes available: 100L-5000L, larger sizes in fibreglass available on demand.
The HMV Series are variable speed drive stainless steel vertical multistage pumps. Designed for pumping non-loaded fluids for pressurising systems; irrigation; drinking and glycol water; water treatment; heating and air conditioning; washing systems suitable for both commercial and domestic projects throughout Australia.
The HMV Series are at the pinnacle of quality and innovation, Maximum efficiency - low power consumption and cost efficient.
Driven by the E1-E318 Variable Speed Drives, and Manufactured in Italy. Systems built to size and applications.
The first tender for Stage 2 of the Haughton Pipeline was released by the Queensland Government and Townsville Council in November, signalling the start of construction.
Detailed design work for the pipeline and pump station is now set to be finalised with delivery partners.
The tender for long lead items was expected to be released by the end of 2021 and tender for construction of the pipeline will be released in early 2022.
Queensland Premier, Annastacia Palaszczuk, said her government was providing up to $195 million in funding for the project.
“Stage 2 of the Haughton Pipeline project will go a long way in ensuring Townsville water security for decades to come,” Ms Palaszczuk said.
“My government knows how important this project is for Townsville’s future and that’s why we are providing $195 million in funding.
“This project will also support hundreds of jobs during construction, boosting North Queensland’s economic recovery.”
Queensland Minister for Resources and Member for Townsville, Scott Stewart, said the project would provide a substantial economic boost for the city.
Townsville City Council has formally signed off on a detailed roadmap for the project, including approving increasing the budget to $274 million, which includes an appropriate contingency allowance.
Townsville Mayor, Jenny Hill, said a considerable amount of planning had been undertaken by Council officers and specialist consultants in the past 12 months.
“Completing the second stage of the Haughton Pipeline will give Townsville the water security it needs as it grows over the next 50 years,” Ms Hill said.
“It realises the recommendation made by the Townsville Water Security Taskforce’s final report of November 2018 that a pipeline be constructed between the Ross River Dam and the Burdekin River near Clare, to enable the dam level to be managed to best deliver water to the city.
“I thank the Premier and her ministers for their willingness to work with Council to deliver this game-changing infrastructure for our city.”
Ms Hill said Council would fund all costs above the $195 million provided by the State Government.
“The Council is committed to securing Townsville’s water security and this project will do that,” Ms Hill said.
“It will mean that Council will need to provide up to $79 million to fund this vital investment in our city’s longterm future.
“We will manage the risks in this project closely to put downward pressure on costs, but we are not going to cut corners. This piece of infrastructure will provide water security for the next 50-80 years and we will do it right.”
“Stage 2 of the Haughton Pipeline will deliver water security, but it will also deliver jobs,” Mr Stewart said.
“The project is expected to support hundreds of jobs in the region. This couldn’t come at a better time as Townsville and North Queensland continue to recover from COVID-19 global pandemic.”
Member for Thuringowa, Aaron Harper, said the Queensland Government had stepped up when the Federal Government failed to deliver on its commitment to fund the project.
“Investing in Townsville’s water security is a priority of the Palaszczuk Government – that’s why we stepped in and committed $195 million to the project,” Mr Harper said.
“This project will secure Townsville’s future.”
Mr Walker said, “The Palaszczuk Government is committed to working with Mayor Jenny Hill and Townsville City Council to get this vital infrastructure built.
“Water infrastructure projects like this one are a key part of Queensland’s plan for economic recovery.”
Townsville Water and Waste Committee chairperson, Russ Cook, said Townsville City councillors were recently briefed on the project.
“Anyone who has built major infrastructure like this knows it simply doesn’t happen overnight, and this stage of the project has presented a variety of different challenges compared to the Stage 1,” Mr Cook said.
“Construction of the pipeline and pump station is expected to be complete by the end of 2024 with testing and commissioning to be finalised by March 2025.”
AGL Loy Yang has completed $98 million maintenance works on the power station, including a major turbine and generator overhaul.
Loy Yang Power Station’s Unit 3 and the mine’s Dredger 15 were successfully returned to service following upgrades and maintenance completed by more than 1,000 contractors over approximately eight weeks.
AGL Chief Operating Officer, Markus Brokhof, said the maintenance works were crucial in ensuring energy reliability ahead of summer.
“The teams have faced some unique and challenging circumstances, with the Latrobe Valley experiencing some of the most severe weather it has seen in decades while also managing the ongoing impacts of the pandemic,” Mr Brokhof said.
“Given the challenges, we’re pleased that we have been able to employ hundreds of contractors from our local community,
bringing a much-needed boost to the region after the last 18 months.
“Everyone involved has done an excellent job at managing the obstacles which will allow for efficient and reliable operations into the future.”
AGL Loy Yang General Manager, Christo van Niekerk, said the works included inspections and maintenance works on a boiler, gas pass, cooling water and electrical plants.
“We also utilised new, innovative technology called ‘HoloLens’ to conduct critical technical works under remote supervision,” Mr van Niekerk said.
“This new technology saved time and reduced the safety risk that faces our people every day.
“I want to thank all our employees and contractors who have ensured safety remained the number one priority throughout the outage.”
A$14 million upgrade to Tasmania’s Greater Meander Irrigation Scheme Augmentation – including pump upgrades – is expected to deliver reduced costs to irrigators and farmers.
The upgrades will produce more than 11,000ML of additional, high-surety irrigation water to the 28,800ML Greater Meander Scheme.
The Federal Government will provide $5 million for the scheme as part of the $108 million National Water Grid Connections funding pathway.
Assistant Minister for Industry Development and Senator for Tasmania, Jonno Duniam, said the National Water Grid Connections is about delivering short-term economic stimulus through small-scale projects.
“This important project will convert open supply channels to new and extended pipelines,” Mr Duniam said.
“This will help to provide an additional 11,000ML of water for irrigators in the area, which will deliver huge benefits for agriculture in this region.
“It is part of a $20 million federal commitment under this funding pathway for Tasmanian projects to improve water reliability and efficiency across the state.”
The Tasmanian Government has allocated $2 million toward the upgrade of the Meander mini-hydro power station along with an additional $3.5 million for solar upgrades across a number of other schemes.
A further $7 million will be contributed from the sale of new water entitlements.
Tasmanian Primary Industries and Water Minister, Guy Barnett, said the Tasmanian Government welcomes federal funding for water projects in Tasmania under the National Water Grid Connections funding pathway initiative.
“The Tasmanian Government is on track to deliver our ambitious target to grow the farm gate value of agriculture
to ten billion by 2050 and irrigation is an integral part of that strategy,” Mr Barnett said.
“The Greater Meander Scheme is a great example of the Tasmanian and Australian Governments partnering with farmers to deliver water at a reduced cost by generating renewable energy, giving great water surety to farmers and also contributing to better river health.”
The works, including pipeline extensions, converting riparian flow to piped water, intake screen and pump upgrades and the installation of solar power plants to pump stations, will result in an additional high-surety irrigation water being delivered to farmers and reduced costs to irrigators.
EXCELLENCE – MADE TO LAST
Mobile, stationary or submerged – Börger configures and builds each rotary lobe pump in line with the requirements of the specific application.
The application options of Börger pumps have expanded with the new B BLUEline Nova rotary lobe pump. The BLUEline Nova pump ensures the best efficiency even with high pressures. Börger pumps are available in 25 pump sizes with flow rates between 1 – 1,440 m³/h.
Further to this, Börger also offers three different macerators - providing efficient chopping operations and capabilities, ensuring downstream machines and pumps to perform smoothly.
The 2021 PIA AGM took place online in early November, allowing Members to attend from across the country from their offices or at home, no matter what restrictions were in place in their state or territory. While the year did not go as planned, attendees were able to hear about some of the successes and activities that did happen, and plans to resume to more in-person meetings and training in 2022.
The PIA reported that while COVID-19 continued to have an impact on some activities over the course of 2021, it has continued to successfully liaise with government and other organisations on items of interest to the industry, and membership has continued to grow, putting the Association in a good position for 2022.
Industry engagement
Due to ongoing restrictions making it difficult to organise in-person events for most of the year, the PIA was only able to hold one Technical Meeting and one Pumps and Systems training course.
The Pumps and Systems training course took place in Melbourne in late March, with 21 people to date having completed the course. As there are a number of competing training courses across the country, the PIA will look at ways to increase interest in the nationally-recognised course in 2022.
In April, a Technical Meeting was held in Perth at Tsurumi Australia with over 30 people in attendance. Attendees heard from PIA President, John Inkster, and Tsurumi Australia Managing Director, Michael Woolley, before hearing a presentation about Tsurumi Australia and taking a factory tour.
At the time of the AGM, there was an online seminar scheduled for late November on Energy Efficiency of Pipelines. The seminar was taken by Rob Welke, Managing Director at Tallemenco, and looked at energy optimisation of pipelines and pipeline performance degradation. A second online seminar is planned for Q1 on flow metering for onsite pump testing.
The PIA has also been busy undertaking other activities to engage the industry, and provide support and assistance where needed. A key engagement has been with the Queensland Building and Construction Commission (QBCC), following a request made for more clarity on works being
undertaken that are covered by the Plumbing and Drainage Act 2018 so companies could ensure compliance and avoid fines. Discussions with the QBCC were initiated in July regarding the licensing of PIA Members for work covered by the Act. The case was tabled in early October with the Services Trade Council (an instrument of the QBCC) and was under consideration in November with the PIA awaiting a formal response. The PIA aims to get a better understanding as to what needs to be done so that regulations aren’t broken by the many small to large companies that are based or do work in Queensland.
The PIA continued to engage with Australian and international standards organisations, and government departments to review and provide expert comment on related standards.
It was on three Standards Australia committees in 2021:
• FP-008 Fire Pump Committee
The only notable work to take place on this Committee over the year was the review of AS2419.1 Fire hydrant installations, Part 1: System design and installation. This standard has been under review for a number of years and PIA submitted a number of comments, with a majority of them accepted. The revised standard has now been published
• ME-030 Pump Committee
ISO 21630:2007 (vers. 3) Pumps - Testing - Submersible mixers for wastewater and similar applications came up for review
• EL-58 Energy Efficiency for Swimming Pool Pumps Committee
PIA was asked for input on Draft AS 5352 Swimming pool and spa heat pump systems. The Association submitted substantial reviews of the standard to sort out some issues and to try to clear up if pumps were included in the energy efficiency calculations or not. The draft standard was expected to be released for public soon at the time of the AGM
Other important work and changes included the review of draft changes to the NCC 2022, as well as aged standards; and support was provided to ensure the PIA’s Pump Technical Handbook was up to date with the most current standards in preparation for a new edition to be released in 2022. Two items of note were ISO 50001 Energy management systems – Requirements with guidance for use will become Australian Standard AS/NZS ISO 50001:2021; and Europump announcing it is now pushing legislators in Europe to implement the extended product approach on behalf of pump manufacturers to have any energy calculations also include the pump, motor, drive and controller.
With training taking a backseat again in 2021, a major focus of the year was updating the Pump Technical Handbook. It has taken many hours and the help of volunteers to complete, with the aim to release the new version in Q1. The PIA would like to thank all those who took the time to lend their expertise to review the Handbook.
The PIA reported that with the effects of the pandemic expected to continue into 2022 and the uncertainty of how it will play out, it is difficult to formalise a business plan for the year. However, provided the situation allows it, the Association intends to hold a number of Breakfast Meetings, Technical Meetings and online seminars over the year.
The PIA also hopes to continue to grow its membership in 2022 to more effectively represent all businesses, with the incoming council encouraged to reach out to the larger pump organisations in particular for their support and experience.
The AGM ended with a presentation by Jason Cunningham, Co-founder and Director, Head of Business Advisory at The Practice, about the key ingredients to business success based on his book Have Your Cake And Sell It Too – the 7 Key Ingredients of Business Success.
Jason provided an informative and entertaining presentation, with attendees hearing about some of the ingredients they need to grow their business asset for tomorrow, while enjoying the profit and lifestyle rewards now, and securing their future.
The virtual PIA AGM was facilitated by Pump Industry magazine publisher Monkey Media and hosted by Monkey Media Managing Editor, Laura Harvey.
Thanks to their construction, the FK Series – DAB’s professional submersible wastewater pumps – can guarantee reliability, efficiency and ease of maintenance, all of which are important values for installers and maintenance engineers.
Suitable for the transfer of wastewater in public buildings, industries, subways and parking lots, the FK range has been designed for pumping wastewater with varying solids, from the drainage of surface water, up to residential wastewater, from wastewater with high fibre content up to industrial wastewater.
Conveniently, the FK range is available with either a vortex or single channel impeller depending on the application.
Why is the FK Series reliable?
New non-clogging vortex impeller
The guarantee of operation comes before efficiency. A new design of the vortex impellers and the total solid handling are respectively the two guarantees to have no-clogging issues.
Moisture sensor
Supplied as a standard option, it allows the prevention of any engine failures due to possible water infiltration in the oil chamber seals.
Bi-component coating
Unlike conventional water-based paints, the bi-component coating is more suitable in aggressive environments such as wastewater. It prevents oxidation and the consequent wear of the pump.
IECex and ATEX Compliant
The FK Series is IECex and ATEX compliant when required for sensitive projects.
New auto coupling DA-V
The seal mounted on the new auto coupling ensures a tight contact, which optimises pumping efficiency while minimising operating costs.
Why is the FK Series efficient?
New IE3 motors
The new IE3 premium efficiency motors drastically reduce energy operating costs. Given its low running temperatures, it guarantees operation up to 40°C, as well as thermal protection being standard.
New single channel hydraulics
The new high efficiency single-channel hydraulic has been designed especially for continuous wastewater operations with high flow demand and low fibre content.
Why is the FK Series easy to maintain?
One cable to the pump
A single standard cable that encloses power and signal inputs together, drastically reduces the possibility of problems due to cuts or leaks.
Single-unit cartridge seal
A single-unit cartridge seal is a great advantage for maintenance of the pump as it allows the removal and insertion of the seals in less time. It is an exclusive DAB patent: a double mechanical seal Sic-Sic with opposite faces, independent from the rotational direction of the shaft.
ENERGY EFFICIENCY
NEW IE3 MOTORS
The new IE3 high efficiency motors drastically reduce operation energy costs. Due to the low overheating temperatures, their operation is guaranteed for temperatures up 40 °C. Thermal protection is standard.
IECex approved version available.
The cartridge is a great advantage during maintenance of the pump, as it enables removing and replacing the seals in less time, with full reassurance that the operation has been carried out correctly. This is an exclusive DAB patent, with double Sic/Sic seal with opposite faces independent from the direction of rotation, with Viton elastometers and Corteco.
The reliability comes even before efficiency. A new design of Vortex impellers, and the guarantee of always having a total free passage, are two of the most important functionalities of the new FK. In compliance with European Standard EN 12050-1
NEW SINGLE-CHANNEL HYDRAULICS
New high efficiency singlechannel hydraulics for applications requiring continuous high flow rate operation with loaded water with low fibre content. In compliance with European Standard EN 12050-1
Ebara has rethought the hydraulic design used in multistage pumps. Utilising the latest in computational fluid dynamics and design, followed by rigorous testing, Ebara has developed a unique impeller design that offers solutions and value to the customer – the Shurricane.
The imbalance of forces acting on the front and rear shrouds of a conventional impeller results in axial thrust. This thrust load is compounding in multistage pumps, and has to be allowed for in the pump design.
For pumps with conventional impellers, the existing solutions include having a thrust bearing built in the pump, or to use a special motor fitted with a larger thrust bearing. Both are costly and can be complicated. Another solution has been to simply have a smaller diameter back shroud to reduce the thrust.
Ebara has rethought the hydraulic design used in multistage pumps. Utilising the latest in computational fluid dynamics and design, followed by rigorous testing, Ebara has developed a unique impeller design that offers solutions and value to the customer.
The optimised shape of the Shurricane maintains high efficiencies and very significantly reduces the axial thrust – meaning that any standard IEC motor can be used and bearing life is improved.
Built like a Katana
A Katana is a traditional Japanese product manufactured with care and precision. Only years of experience can give the necessary capacity to build a masterpiece.
This is what Ebara does with its pumps. The result of over 100 years of Japanese experience in pump manufacturing, its pumps offer highquality performance, reliability and cutting-edge technology.
Ebara’s Shurricane vertical multistage pumps are manufactured to the highest standards of quality, and achieve reliable operating performance by means of strict technical evaluation criteria and control programs that involve the whole manufacturing process.
Shurricane pumps are suitable for a wide range of applications, in the industrial, commercial and agricultural fields. They can be used at water treatment plants (for reverse osmosis and filtration), for the pumping of hot or cold water for HVAC systems, for the pumping or boosting of water in general, and in boiler feed, irrigation and fire fighting systems.
The Ebara Shurricane pump utilises cutting-edge technology, designed in Japan and manufactured in Italy.
The pumps can be coupled with any motor, anywhere. Optional materials are part of the unique hydraulic design, and there are optional connections for customers to consider.
Innovative hydraulic solutions
• Commercial motors can be fitted to all of the pump models without any modifications thanks to low pump axial thrust load
• Long life of the motor bearing
• High pump efficiency classified in MEI > 0.7 as the most efficient models
• Patent Application
Energy saving
• High pump efficiency with MEI (minimum efficiency index) > 0.7
• E2 motors fitted as standard with E3 available as an option
• Suitable for use with variable frequency drives for further energy savings
Piping connection options
• The various pipe connections are available depending on the application requirements
• The external dimensions can be adjusted to the replacement of the existing pump in the wide majority
Easy maintenance
• The cartridge shaft seal enables the plug in replacement of the shaft seal without disassembling the motor bracket
• The spacer coupling allows easy maintenance without having to remove heavy motors 5.5kW and above
Smart plug solutions
• Air ventilation plug
• Water filling and sensor plug
• Commercial sensor fitting
• Measurements for suction and discharge pressure/drain
The optimised shape of the new Shurricane impeller maintains high efficiencies and very significantly reduces the axial thrust – meaning that any standard IEC motor can be used, and bearing life is improved.
The disruption of the global supply chain is causing havoc for many businesses. Time delays, exorbitant increases in shipping costs, strikes and threats of more strikes have all caused a reshuffle of priorities in many a boardroom. Crusader Hose, also affected by these worldwide events, has been working tirelessly to help support its customers during these unprecedented times.
The worldwide pandemic has illustrated the vulnerability of the global supply chain and has forced many businesses to review their supply chain strategies. Analysts writing for Harvard Business Review encourage businesses to examine their Tier 1, Tier 2 and other level suppliers. Relying heavily on importers is no longer seen as a viable business model. Sourcing from local manufacturers for goods is being encouraged to reduce risks associated with supply chain disruptions.
As an essential service provider and Australia’s local manufacturer of industrial layflat hose, Crusader Hose has been able to keep its doors open and continue to service the mining, industrial, agricultural and firefighting sectors. It has delivered well over 550,000m of hose since the first major lockdown.
Crusader Hose, an Australian-owned company, has been manufacturing layflat hose for over 35 years and has grown from a small, family-run business to a medium-sized business with more than 40 employees. In its early years, the volume of imported hose on the streets had put significant pressure on the company. However, with its culture of continuous improvement, its many investments and machine upgrades have been producing world-class hoses. Crusader Hose has forged many strong partnerships throughout Australia and is the name many companies trust.
Working closely with industry, Crusader Hose has been designing, manufacturing and supplying the pumping sector with layflat hose for water logistics and bore water pumping. During these challenging times, the Melbourne-based factory has been working around the clock to support resellers in meeting the demands of their customers.
Flexibore® flexible rising main is the ideal solution for the installation of submersible pumps. Manufactured with a TPU-extruded textile reinforcement of high-tensile polyester, Flexibore® can withstand the weight of the pump and the weight of the column of water without a safety cable. The flexible nature inherent to the hose makes handling Flexibore® easy and simple compared to rigid pipes; its swelling feature of up to ten per cent makes it extremely efficient in reducing pumping costs and friction loss. By dilating under pressure, no internal build-up of iron bacteria occurs, as seen with rigid pipe use such as steel or fibreglass.
Flexibore® is compact, requiring less trucks for transportation and a smaller workforce and machinery for installation. The Flexibore® systems are designed to handle the small pumps often used with shallow bores to the very large pumps, which handle the ultra-deep bores to 400m. Installation rollers and lifting clamps are available to suit the different systems.
Waterlord®, their heavy-duty layflat hose, is ideal for moving large volumes of water. Manufactured in large diameters of up to 12”, Waterlord® moves water in quickly and safely, assisting in keeping projects efficient and on time. The high-pressure reliability of Waterlord® comes from the world’s-best manufacturing process of the TPU (thermoplastic polyurethane) thru-the-weave extrusion encasing a robust textile reinforcement. It is manufactured in one continuous length of up to 250m and can handle high-working pressures; its tough exterior can withstand all types of terrain – urban and regional. Both flanges and couplings are available, which can easily connect to existing pipelines.
Its progressive engineering department has designed and manufactured turntables and reeling systems to safely and efficiently deploy and retrieve multiple lengths of hoses. Although a smaller workforce suffices when unrolling shorter lengths of hose, turntables and hose reel systems are ideal for pipelines. Interchangeable spools make it quick and easy to handle multiple lengths. Many operators are asking for the Waterlord® layflat hose reeling system because of its inbuilt properties: keeping multiple lengths compact, and making layflat hose easy to handle and deploy.
“We have seen the importance of supporting local manufacturers in the preservation of the supply chain for successful business,” said Francois Steverlynck, Managing Director of Crusader Hose.
“Buying from an Australian producer gives you peace of mind regarding backup, quality, quick turnaround and excellent customer service. We stand by our products so your needs will be looked after.”
Local manufacturing is critical in these times of uncertainty. Let Crusader Hose be part of your business success for the timely delivery of the products you need.
Waterlord® reeling system: fast, compact and easy to use for rapid dewatering.
it with hydrolysis-resistant polyurethane.
Proudly manufactured in Australia by Crusader Hose, Flexibore® 250 is made to suit most bore water pumping applications and is manufactured in a large range of diameters from 40 mm to 152 mm, in continuous lengths of up to 250 m.
With a high burst pressure for deep bore water pumping, the Flexibore® 250 can handle the weight of the pump plus water up to 250 m without a safety cable.
Quality you can trust
Deep ground water pumping up to 250 m
Ultra-high tensile strength for large submersible pumps
Flexible, so easy to install & retrieve
Swells up to 15%, avoiding internal build-up
Rigorously tested
Secure couplings
Lower pumping costs and friction loss
Contact us today on +61 3 9720 1100 or email sales@crusaderhose.com.au to learn more or request a quote!
WEG has a complete range of medium voltage motor control products and the expertise to offer optimised solutions for any application. Contact WEG Australia to discuss the options available for single and multi-pump applications.
WEG Drive and Soft-starters
• WEG MVW01 medium voltage drive
• WEG MVW3000 medium voltage drive
• WEG SSW7000 medium voltage soft-starter
All WEG medium voltage drive panels incorporate the following user benefits:
• Fully withdrawable power cells. The power cells are rack-in and rack-out for ease of use and safety
• Key interlock system that ensures mechanical and electrical interlocking for safe panel access
• Long-life plastic film capacitors, extending both the product lifespan as well as the maintenance cycle. This technology eliminates the need for reforming the capacitors after storage, even after prolonged storage
WEG MVW01 High Efficiency Drive System
WEG MVW01 medium voltage variable speed drive uses state-of the-art high voltage IGBT technology and consequently boasts industryleading drive efficiency of over 98.5 per cent. The MVW01 drive also offers the flexibility of either integral dry-type transformer or separate outdoor oil-type transformer, which equates to extraordinary reduction in heat loss and footprint in the substation room.
MVW01 highlights:
• Transformer integral dry-type, or outdoor oil type
• High efficiency of >98.5 per cent
• 300kW up to 24MW
• 3.3kV, 4.16kV, 6.6kV
• VSD panel dimension:
» 2316 x 1000 x 980 (h x w x d in mm) – up to 850kW
» 2190 x 2600 x 960 (h x w x d in mm) – up to 2800kW
WEG MVW3000 Multi-Level H-Bridge Drive System
WEG MVW3000 medium voltage variable speed drive range offers plug and play 3-cables-in and 3-cables-out design. It comprises integral transformer, optional integral switchgear, and modular power cells providing motorfriendly multi-level sinusoidal output voltage. Perfect for standard motors, it can be applied to both new and retrofit installations without concern for the motor insulation system. It is also beneficial for applications of long cable lengths.
MVW3000 highlights:
• Integral solution – plug and play
• Sinusoidal motor-friendly output waveform
• 300kW up to 12MW
• 3.3kV up to 13.8kV
WEG SSW7000 Medium Voltage Soft-starter
WEG SSW7000 soft-starter boasts state-of-the art motor control and protection. It has multiple starting control mode options, including a special algorithm for pump starting and stopping designed to eliminate pressure overshoots and water hammer. The SSW7000 incorporates built-in automatic bypass function as a standard feature and can also be programmed for DOL starting in the event of a thyristor failure.
SSW7000 product highlights:
• Built-in automatic bypass
• Application specific starting control such as Pump Torque Control
• Starting option for DOL can be selected to allow starting even in the event of a thyristor fault
• 300kW up to 10MW
• 3.3kV up to 13.8kV
Customised Solutions
WEG medium voltage variable speed drives have proprietary PLC functionality available as an optional accessory. This allows customised programming of customer specific application requirements. One such application is multi-pump starting using one VSD. In this scheme, one VSD is able to start a pump and then bypass that motor to the grid using its synchronous bypass functionality. In this way the VSD can be used to start multiple pumps in a system, and speed control can be applied to one selected unit to allow for flow control.
Starting scheme for multi-pump using one VSD with synchronous bypass functionality.
Are you ready to dive into every aspect of Caprari’s product range? Discover our selection of webinars, your professional training resource available anytime, anywhere.
Listen to our webinars to get to know all of our products’ characteristics and applicable sectors, as well as exclusive Caprari patents, presented by our very own Product Manager.
Visit Digital House, where, as always, you will find a wide array of product videos, reference projects and free-to-download information catalogues.
Need more info?
Thanks to Digital House, you can now ask our Product Manager or Sales Department directly via a live meeting.
Step into the digital world of Caprari.
Thanks to their reliability, top performance and versatility of use, Caprari’s PM horizontal pumps series – built to withstand high pressures – have long stood as a reference point in the market, representing the best that current technology has to offer.
These pumps can be used in the water industry, the drinking water sector, reverse osmosis snowmaking and marine applications. They are specially designed to be consistently durable and to function in such a way that the need to replace wearable parts is kept to a minimum.
Their robust structure is resistant to mechanical stress, thanks to specially designed dimensions which allow for especially high performance and operation stability up to 100 bar of pressure.
High efficiency at the BEP, ensured by optimised geometry in the blade profiles of the impellers and diffusers, is one of the series’ biggest strengths. Furthermore, wear is reduced to a minimum as the hydraulics are equipped with an axial thrust compensation system.
The sizes of the hydraulics which make up the PM Series cover a wide range of flow rates and are available in cast iron, stainless steel and duplex.
It is exactly these PM machines, built for high pressures up to 100 bar, which benefit from the new size 65 hydraulic models. Depending on how the pump is going to be used, either a packing seal or a mechanical seal can be selected. The mechanical seal guarantees perfect regulation and protection against leakage, while the packing seal boasts superior ease of assembly and maintenance, reducing the risk of machine downtime.
The H version PM65 with 4 poles is the configuration that allows for use with superheated water at temperatures of up to 120°C – though it is necessary to carry out checks on the 2 poles depending on the conditions the pump
will be used in. The materials selected here guarantee durability even in such thermally heavy duty operating conditions. Vibration propagation is minimised in a great deal of operating conditions. As a result, barely any noise is created, which is a vital benefit especially when placing several machines at the same site.
Such reliability, top performance and versatility are the fruits of a great many years of experience in engineering, construction and application in the most diverse fields of use.
• Up to 100 bar of delivery pressure
• Metallurgy construction to guarantee high performance
• Reliability and low costs with regards to both operation and maintenance
• High hydraulic efficiency
• Wide flow rate capacity
The Speck Group, with its headquarters in Roth in Germany, is a family-run enterprise in the mechanical engineering sector that manufactures high-quality pumps and compressors for industrial applications.
Speck has been active in this market for over 100 years and supplies its products to original equipment manufacturers and systems manufacturers in over 80 countries. Manufacturing is usually order-based. A strong customer focus, high levels of expertise and the development of customised solutions are the main factors which set Speck apart in these activities.
Speck Industries is a subsidiary of Speck Pumps of Roth, Germany. Servicing the ever-growing needs of OEMs and distributors in the region, Speck Industries offers a convenient local hub for Speck pump sales, distribution and technical support.
Speck offers fast delivery throughout Australia and New Zealand with our tailored transport arrangements. With our hub situated in Perth, we’re well located to deal with suppliers in Europe and customers in east Australia and New Zealand all within the working day.
Our local branch stocks a range of pumps, such as side channel, boiler feed, liquid ring vacuum, positive displacement and more to cover a wide range of industries from plastics manufacture, food and beverage, industrial heating and cooling, chemical and pharmaceutical plus a wide range of others.
Our experts on hand will help you determine the best solution for your specific flow requirements.
Our specialised products are principally used in medical technology, the chemical and pharmaceutical industries, cooling and tempering appliances and in the plastics industry. Speck is very export-oriented and employs over 575 staff members worldwide.
Products from Speck are characterised by a wide range of available variants which is specially tailored to the customer’s needs. Our staff in the Technical Department are constantly working on new solutions and further developments to our existing products that help our customers move forward – day in, day out.
Over time, pumps and associated components are subject to wear, corrosion and cavitation damage in service, resulting in downtime, reduced efficiency and service life, increased costs, and in some applications, safety hazards. As this deterioration occurs on the surfaces of the components, having a high-quality protective coating installed by an experienced company can preserve assets, extend their service life, and improve safety.
The Belzona Polymeric range of metal, rubber and concrete repair and protection materials – distributed in Australia solely by Rezitech – allow the rebuilding and protection of damaged machinery and equipment, ensuring they will stand up to chemical attack, constant immersion in liquids and other industrial environments.
The Belzona range reduces labour time and costs by eliminating the need for disassembly, welding, and postweld heat treatment; decreases costs by increasing asset availability; and enhances safety by allowing in-situ cold work with solvent-free materials.
Belzona fixes common problems associated with industrial equipment by:
• Extending service life and delaying replacement – the products provide a superior layer of protection for damaged equipment
• Simplifying maintenance procedures and reducing costs – the polymers are resistant to abrasion, erosion, chemical attack, corrosion, and are relatively easier to clean than bare surfaces
• Improving operational efficiency – polymer surfaces are easier to work on compared to bare surfaces, resulting in less to worry about during operations
• Minimising downtime – damaged industrial equipment can disrupt operations. Polymeric solutions minimise downtime and don’t get in the way of production
Belzona protective coatings feature:
• WRAS approval
• AS/NZS 4020 approval for drinking water use
• High adhesion
• Low surface tension
• High mechanical strength
• No shrinkage
• Electrical insulator
• Smooth surface
• Long working life
• Chemical and impact resistance
• Safe for constant immersion
• Safe for cold application
• Environmentally friendly
In 2010, a major Australian water utility was undertaking scheduled routine maintenance on a pump and was extremely happy to find that the Belzona coatings that had been applied 19 years previous were still intact and evident, and there was no additional repair or coating of the internal casing/cover required. Furthermore, an independent test by the water authority confirmed efficiency gains in flow capacity were accomplished between 4-7 per cent.
In 2012, Belzona was installed on cones in a cyclone wash infiltration plant in a limestone quarry in England. As the
cones were suffering heavy levels of abrasion, the mean time between failure was unacceptable, with unprotected clones failing within one month and rubber-coated cones only lasting for six months. The downtime and replacement costs were costly for the client.
Belzona was used for a trial application to increase the working life of the cones, and resulted in the cones lasting 18 months – a lifespan increase of 12 months. As well as reducing the cost of replacement, the largest cost saving for the plant was the reduced downtime. After the successful trial, Belzona was made the standard solution for all abrasion areas within the plant.
Your trusted and experienced Australian distributor for Belzona
Rezitech is an 100 per cent Australian-owned company and the sole distributor of Belzona in Australia.
It has been involved with major plant upgrades and expansions projects for many major companies servicing a wide range of industries. Its team of experienced industry professionals are able to diagnose a problem and recommend a solution, as well as apply Belzona coatings either on-site or at its dedicated workshop.
Rezitech can also provide on-site supervision, NACE qualified coating inspectors, and in-plant seminars and on-site training.
Rezitech combines the wide range of Belzona materials with its application expertise to provide high-quality, longlasting repairs for all types of equipment and structures.
• Unique Australian design
• 100% Australian Manufactured
• Unique durable plastic liquid ring vacuum pump
• More resistant than stainless steel
• Added protection against chemical attack
• For all your liquid ring vacuum pump supply and repairs
• Flowtech and Robuschi liquid ring vacuum pumps available in a multitude of materials
• Flowtech conical cone design has a fully shrouded rotor for added strength and protection against failure due to harmful carryover. This pump also has detachable bearing housings for easy and quick change over of impeller shaft bearings
• On-site volumetric testing on liquid ring vacuum pumps with after test report provided
• Dedicated application engineer to support you in pump selection or pump package design
• Internal coating capabilities with Belzona polymer coatings
• Extended life cycle of pumps through internal coating of components with superior wear resistant Belzona coatings
• Resistant to rusting and seizing when used on priming pump applications where pumps are left standing without operation for long periods of time
• Sewerage waste extraction
• Decades of experience in repairing pumps
• New pump warranty on all pump repairs
• Liquid vacuum pump repairs
• Repairs to split case, multistage, submersible, slurry, volute and multitude of other pump configurations
• Rezitech’s workshop bring you superior engineering capabilities in the area of repair to a multitude of rotary equipment componentry ie pump components, induction fans, screw augers, roller shaft repairs
Now in its eighth year, Pump Industry’s State of the Industry explores how the industry fared in 2021, how this compared to expectations, and the challenges and opportunities 2022 is expected to bring. This year’s survey uncovered a renewed optimism and reduced uncertainty as the industry begins to emerge from the shadow of the pandemic, provided a meter of sector performance over 2021, and provided insight into the key factors expected to shape the industry over 2022.
On the whole, survey respondents were anticipating improved performance in 2022 and growth in work volumes in key sectors. And while COVID-19 undoubtedly affected the industry in 2021, the majority of respondents reported a decent year and expected things to keep improving.
Despite the vicissitudes of the past few years, many within the pump industry are looking to 2022 with a renewed sense of optimism and reduced uncertainty, with 84.07 per cent of respondents reporting a positive outlook for their company for the year ahead. This represents a significant increase in positivity compared to 2020 and 2021 surveys, when positive outlooks stood at 68.25 and 69.56 per cent respectively. In fact, more respondents reported a positive outlook for their company than in any of the previous eight years the State of the Industry survey was undertaken.
Of the remaining responses, 14.16 per cent had a neutral outlook for 2022, a slight reduction on the previous year’s 20.29 per cent, and the lowest number in the last four years, by a tiny margin. Only 0.88 per cent of this year’s respondents had a negative outlook, the same proportion as those who were uncertain what 2022 might bring. Compared to the survey for 2021, where 7.25 per cent had negative expectations and 2.90 per cent said they didn’t know, negative outlooks and uncertainty noticeably decreased.
When it comes to the effects of the COVID-19 pandemic, it appears that many respondents can finally see the light at the end of the tunnel, as the vaccine rollout continues and restrictions ease in those states where outbreaks occurred in 2021. Some contributing factors to the increased morale within the industry could include a sense that the worst of the pandemic is over, and those whose businesses survived feeling more confident in their ability to withstand any future
challenges that may arise. It’s also possible that some of those who’ve had a tough few years, yet are still active within the industry, may feel that things can only get better. There is also the possibility that some businesses that were already struggling before the pandemic have closed since previous surveys, reducing the responses from those with negative company outlooks. Respondents may also hope to reap extra business resulting from federal and state governments seeking to stimulate economic recovery through funding infrastructure projects. Some companies may already be seeing increased business as a result, or have such work lined up.
The confidence the majority of survey respondents feel about 2022 could well be influenced by the performance of their businesses over the past year. Although 2021 was a ‘pandemic year’ with disrupted international supply chains, travel restrictions and lockdowns in response to virus outbreaks in New South Wales and Victoria, respondents largely reported that their companies performed as well or better than expected.
Overall, 57.52 per cent of respondents stated that their company’s performance in 2021 met expectations, compared to 32.61 percent in 2020. Meanwhile, 28.32 per cent reported that their business exceeded expectations, compared to 24.64 per cent in 2020. The proportion of companies underperforming against expectations reduced to 14.16 per cent for 2021, from 2020’s 42.75 per cent. These results may be partly attributed to companies being able to consider the pandemic into their 2021 expectations, whereas nobody could have anticipated its impact in 2020. One respondent explained that they’d been “unsure of what would happen due to various COVID influences, but it was not as terrible as predicted for us”. Another respondent said, “We were able to keep serving our customers with few problems due to the COVID outbreak.”
Some businesses found they were able to adapt in 2021 and make changes to keep overall performance steady throughout the pandemic. “Our structure changed to meet the shifting requirements of our customers and this ensured we retained and met our goals through trying times,” said one respondent. For some, 2021 saw a shift in demand for different product and service offerings. “Some markets fell, others grew. Met overall budgets, but with different products and services than traditionally expected,” one respondent said. Whether 2021 performance met, exceeded, or fell short of expectations also varied by a company’s sectors and services, as well as its dependence on imports and exports. For instance, some respondents with a significant involvement in consulting, pump asset services and aftermarket needs found that work volume continued as expected, as essential pump systems still needed to be maintained and optimised. One respondent noted that there were still “many problems in
my field due to misunderstandings about pumps by the water/ installation engineers”.
Factors that enabled companies to exceed expectations included a skilled workforce, growth in certain sectors, projects proceeding, and being able to provide services and products that others couldn’t throughout the pandemic. “We had fantastic growth on PY in the retail domestic and farming sector,” said one respondent, while another noted that the steel company for which they provide pump services and after sales support made a “huge profit”. “Vertical integration gave us the ability to deliver when others were hampered by supply chain issues,” said another respondent.
The influence of supply chains on 2021 performance was reinforced by other responses, such as one respondent who largely attributed their company’s success to “industry growth and local manufacture and supply”.
Some respondents who found business fell short of expectations indicated that they had underestimated the longevity of the pandemic and its impact. “We expected normality to return early in 2021…” explained one respondent.
Disrupted global supply chains and project postponement were key factors for many companies, with respondents citing “delayed or cancelled projects” and “international supply and freight issues”. Others found the pandemic and travel restrictions affected their operations, especially when it came to seeing clients face-to-face. Other ongoing issues for the industry, such as export constraints and Australia’s tense relationship with China, were also cited as reducing performance for respondents over 2021, as were staffing issues.
While many respondents were optimistic about the year ahead for their own companies, there remained more uncertainty when it came to the outlook of the industry as a whole for 2022.
This uncertainty is reflected in the 19.47 per cent of respondents who were unsure about how they expected the industry to perform, similar to the 20.29 per cent last year. Still, a 62.83 per cent majority of respondents reported a positive outlook for the industry, an increase on 52.17 per cent in the previous survey. Meanwhile, 16.81 per cent of respondents saw a neutral industry outlook for 2022, somewhat less than in the last four years. Negative outlooks for the industry dropped to 0.88 per cent, compared to 4.35 per cent last year, and represented a historic low for the survey.
The year that was: 2021 industry performance by vertical
Key to understanding the current state of the industry is evaluating sector performance over the last 12 months. Once again, we asked respondents about the volume of work experienced over key verticals throughout the year, then compared these responses to data about how each sector was expected to perform in 2021 from the last time the survey was completed.
It is important to note that the expectations from the previous year were based on the assumption that the COVID-19 situation at the end of 2020 (low to no community transmission and most state borders open to each other) would be maintained, which did not turn out to be the case. This may explain why none of the verticals performed as well as expected through 2021.
According to respondents, water and wastewater, mining, irrigation, and chemicals and pharmaceuticals sectors performed the best in 2021. As depicted in Figure 6, the frontrunners were water and wastewater, followed by mining, which respondents predicted. The worst performing sectors were pulp and paper, manufacturing, and food and beverage, where work volumes slightly decreased overall, contrary to the previous year’s expectations. Meanwhile, work in the power generation sector neither increased nor decreased. The sectors that experienced growth throughout 2021 were largely those that were considered essential services, reducing the impact of the pandemic and resulting mitigation
Expected vs. reported growth across industry sectors for 2021
measures on their operations. On the other hand, the sectors where work volumes shrunk, such as food and beverage, were those that may have been more heavily affected by various pandemic-related factors such as work-from-home orders, reduced retail spending, supply disruptions, and the shutdown of the hospitality and retail industries in states experiencing outbreaks. Some of the general trends in sector performance over recent years can be seen in Figure 7.
Continuing the more optimistic theme of 2020’s survey results, respondents expect some magnitude of growth in almost all sectors over 2022. The one exception was plastics and rubber, where they expect work volumes to neither increase nor decrease. The verticals expected to perform the best throughout the year are once again water and wastewater, mining and irrigation. Chemicals and pharmaceuticals is also
expected to experience similar growth to that of 2021. Oil and gas, pulp and paper, manufacturing, power generation, building services and HVAC, and food and beverage are expected to perform significantly better than they did in 2021.
survey. Nevertheless, 60.27 per cent of respondents agreed that the pandemic would continue to have significant lingering negative effects on the industry throughout 2022.
Some of the main impacts the pandemic had on respondents throughout 2021 included project postponement or cancellation, freight and supply chain difficulties, staffing issues, and difficulties accessing work sites. According to one respondent, “COVID has meant that a lot of food and beverage, and water sector clients are restricting access to their sites, so projects are being deferred”. Another stated that over 2021 “delays in oil and gas projects due to COVID had the biggest negative impact” on their business. “Global supply chain disruption has had an effect on both supply and pricing,” said one respondent. Another respondent described the “significant impact caused by global supply chain disruption, basically longer lead times for all goods”.
A smaller number of respondents had a more positive spin on the pandemic’s effects, citing that their businesses had benefited from factors such as “delays in deliveries from competitors,” such as manufacturers based in China.
shaping the industry?
A multitude of different global and national factors play into the performance of Australia’s pump industry at any time. The State of the Industry survey asked respondents about some of the key factors that affected industry performance throughout 2021, and those expected to play the biggest role in shaping the industry in 2022. Due to the diverse sectors and businesses within the pump industry, various events or trends affect different industry participants differently. As a result, opinions varied as to which factors respondents considered the most significant, and in some cases, what some respondents saw as a positive was a negative for others. The bumpy road back from COVID-19
The COVID-19 pandemic continued to affect all facets of industry throughout 2021, both locally and globally. The level of restrictions pump industry participants had to contend with locally varied considerably by the outbreak status of the states and territories in which they operated, supply chains were disrupted globally, and international travel remained largely off the cards. With Australia’s vaccine rollout now progressing and restrictions easing within Victoria and New South Wales, respondents were generally more hopeful than in the previous
As 2021 drew to a close, respondents noted that COVID-19 was “tending to have less impact on day-to-day operations,” but certain impacts were likely to remain key issues for the industry for some time. In particular, respondents expected the supply chain, freight and pricing effects to linger. “The impact will continue in 2022, probably throughout the entire year. Increases in raw materials pricing, shipping cost increases, and material supply will be big issues in 2022,” said one respondent. Another said, “I believe that this will continue in the short term but will level out over the next 18 months as the world gets back to normal business”. However, as one response stated, an awareness of the likely longevity of some pandemic impacts will enable industry participants to “be better prepared” to meet the challenges they pose.
With Australia gradually opening back up, respondents were generally feeling positive about the prospects of increased work driven by postponed projects getting back underway, and new projects beginning over 2022. As one respondent summarised, “Projects are starting to move now and should open up in 2022.” Overall, 67.12 per cent of respondents believed that the amount of major projects underway and being approved would be one of the biggest positives of 2022.
The mining and natural resources sectors have been key drivers of industry growth over recent years. In 2020 the pandemic hit the mining industry with significant pricing volatility and associated cash flow and liquidity issues, and these continued throughout 2021. Despite this, it remained one of the best performing sectors for the year and is expected to rebound and continue to drive significant growth in 2022.
Of the survey respondents involved in the mining sector, 45 per cent reported that work volumes remained steady over 2021, 22.5 per cent said they somewhat increased, and 17.50 per cent reported that they increased significantly. Only five per cent of respondents found a significant decrease in work in this sector, and ten per cent found they somewhat decreased.
According to Trevor Hart, Global Mining Leader at KPMG, while the pandemic increased risks associated with supply instability and economic downturns, it has also prompted enormous stimulus spending in most major economies.
“We’ve seen not just a spike in prices for iron ore but more broadly government stimulus and supply interruptions caused by COVID-19 has been driving up prices for commodities,” said Mr Hart. “Volatility in global markets has also seen investors flock to safe havens, driving strong precious metal prices, such as gold. This is not just a commodities story. COVID-19 also seems to have accelerated the focus on climate change and efforts to decarbonise.”
According to the September 2021 Resources and Energy Quarterly published by the Department of Industry, Science, Energy and Resources, export earnings reached a record $310 billion during the 2020-2021 financial year. Iron ore export earnings reached a record $153 billion over this period, thanks to a strong demand from China and restricted market supply from Brazil due to COVID-19-related workplace issues. However, in the second half of 2021, prices declined from the highs of over US$230 a tonne seen in May. This can largely be attributed to falling domestic demand for steel in China and the Chinese government’s efforts to limit the country’s 2021 steel output to 2020 levels, and ramping up of a number of key government policies to limit energy use and emissions. A rebound occurred in late-November to early-December as steel output restrictions were somewhat relaxed and production in China’s steel mills increased.
Likewise, steel prices experienced a number of significant surges and declines over 2021, due to factors including changes in Chinese domestic demand for construction projects and production restrictions being tightened or loosened.
Coal exports were impacted by import restrictions as a result of tensions with China, although there was growing optimism about resuming trading towards the end of the year, after data reported that small amounts of Australian coal had cleared borders in October. However, a volatile relationship with China is likely to continue to impact trading opportunities in an array of industries, with words exchanged between governments as 2021 drew to a close.
The Department of Industry, Science, Energy and Resources states that the outlook for Australia’s mineral exports remains
strong. As the world economy rebounds, prices across a number of resource and energy commodities remain high, and the Australian dollar has slightly weakened from recent peaks. The department states that some moderation and reduced volatility in prices is likely in 2022, as supply rises and demand growth moderates. Overall, export earnings are forecast to rise in 2021-22 to $349 billion, before falling back to around $300 billion in 2022-23. More moderate growth in steel exports is forecast for 2022 and 2023. Australian iron ore export volumes are expected to grow steadily, from 868 million tonnes in 202021 to 939 million tonnes by 2022-23. The department also expects Australia’s coal export values to reverse most of their recent pandemic-induced decline. Likewise, uranium export values are forecast to increase from a low of $465 million in 2021-22, to reach $551 million by 2022-23. Australia’s gold exports are forecast to reach a record $29 billion over what remains of the 2021-2022 financial year.
Meanwhile, the total value of Australian exports of aluminium, alumina and bauxite is forecast to increase at an annual average rate of 5.8 per cent between 2021-22 and 2022-23. Copper prices surged in 2021, and are expected to retain most of this gain. Australia’s nickel export earnings are expected to rise on the back of growing export volumes and higher prices, and zinc export earnings to increase from $3.3 billion over the 2020-21 financial year, to around $4.1 billion in 2021-22 and $3.9 billion in 2022-23. Rising prices for lithium are supporting the recovery of Australian producers with two refineries under construction and Australia’s lithium export earnings are forecast to increase from $1.1 billion in 2020-21 to $3.8 billion in 2022-23.
“In addition to boosting domestic consumption, globally, government stimulus measures are being directed into energy transition and infrastructure building projects,” said KPMG’s Trevor Hart. He believes that this will continue to drive significant demand for raw materials, such as copper and nickel, over the years ahead, as will the rising demand for battery minerals and rare earths, although some sectors, such as coal, will continue to face growing headwinds.
Survey results indicate that pump industry participants operating in the mining sector were overwhelmingly optimistic about its outlook for 2022, with 64.29 per cent expecting somewhat of an increase in work volumes, 9.52 per cent anticipating a significant increase, and 21.43 per cent expecting volumes to remain steady. The remaining 4.76 per cent expected a slight decrease, and no respondents expected a significant decrease. 49.32 per cent of respondents identified the performance of the mining industry as a key positive for 2022, while 17.81 per cent thought that it would have negative effects.
“Green minerals and the EV sector creating a drive to develop lithium, nickel, copper, graphite will affect our business in a positive manner,” explained one respondent.
Respondents involved in the oil and gas sector had mixed results over 2021, despite a rebound in oil and gas prices. For 30 per cent of respondents work volumes remained the same over the year, while 26.67 per cent reported that they increased somewhat, and ten per cent that they increased
Despite significant pricing volatility and associated cash flow and liquidity issues, the mining sector remained one of the best performing in 2021.
significantly. In contrast, 26.67 per cent said work in the sector had decreased somewhat, and 6.67 per cent decreased significantly. According to one respondent, work had “been stable to a degree throughout 2021 except for oil and gas”.
When it came to 2022, respondents were largely optimistic. 42.42 per cent of respondents expected oil and gas work volumes to remain steady, 39.39 per cent anticipated somewhat of an increase, and 12.12 per cent a significant increase. Only 3.03 per cent anticipated a slight decrease and 3.03 per cent a significant decrease.
The impacts of commodities prices and the Aussie dollar
While trends in commodities prices could be drivers of growth in some sectors serviced by the pump industry, such as mining, they also have potential ripple effects that could have positive or negative consequences over 2022. For instance, extremely strong export earnings forecasts can have downsides including a potential spike in global inflation, and a resulting rise in interest rates. Additionally, increased investment in certain sectors can potentially result in decreased investment in others, creating a strong split in opinions. For instance, one respondent cited the increasing oil price as a key upcoming challenge for their company, as it may result in a reduced focus on renewable energy projects. However, participants working in the oil and gas sector viewed price increases as a strong positive.
At the time of the survey, 23.29 per cent of respondents considered trends in commodities prices as a considerable positive for 2022, while 31.51 per cent saw them as a significant challenge. “Reduction in the iron ore price will affect future projects,” said one respondent. When it came to the global oil price, 15.07 per cent of respondents viewed it favourably, while 34.25 per cent viewed it negatively.
Larger economic trends such as the performance of the Australian dollar were also divisive, and could be positive or negative for respondents, depending on whether they relied more heavily on imports or exports. While 32.88 per cent of respondents believed the performance of the Aussie dollar would have a positive impact on the industry in 2022, 36.99 per cent expected it to have a negative effect. “The exchange rate has positive impacts,” said one respondent. Meanwhile another respondent cited a “rise in AUD, which will affect us exporters” as a key challenge for the year ahead. Similarly, 16.44 per cent of respondents were positive about forecast interest rates in 2022, while 19.18 per cent considered them negatively.
As the drive to decarbonise world economies proceeds, many pump industry participants are hopeful of picking up work from an increasing number of renewable energy projects. The growing global hydrogen market, especially demand for hydrogen from renewable sources, was also cited as an area likely to fuel growth. Pump industry participants largely viewed the transition to renewable energy as an opportunity, with 43.84 per cent identifying renewable energy projects as a key positive for 2022. A much smaller 4.11 per cent were less enthused, largely due to the possibility of losing business from fossil fuels. “Declining investment on fossil fuel technology will still impact our business in 2022,” said one respondent. Another respondent identified hydrogen projects as a key opportunity.
The water and wastewater sector is generally one of the best performing sectors for the Australian pump industry, and survey respondents have largely reported work volumes remaining steady or increasing in this area over
the years. This was again the case over 2021, with 37.70 per cent of respondents in the sector reporting somewhat of an increase in work volumes, 19.67 per cent saying they increased significantly, and 34.43 per cent reporting they remained the same. They decreased slightly for 4.92 per cent, and significantly for 3.28 per cent. “We are in entry level wastewater,” said one respondent, “Seems quite stable off the back of a big 2020/21”. “The demand from the water and wastewater sector is an unending business with positive growth with increase in population,” another respondent put it.
The 2021-2022 Federal Budget announced funding for a variety of water initiatives, including an extension of the On-farm Emergency Water Infrastructure Rebate Scheme for 12 months until June 2022, and up to a further $258.0 million from the $3.5 billion National Water Grid Fund towards the construction of new and augmented water infrastructure projects, including up to $160 million through the National Water Grid Connections pathway.
Respondents operating within the sector were overwhelmingly positive about its 2022 outlook, with 61.29 per cent expecting work volumes to increase somewhat, and 11.29 per cent expecting them to increase significantly. Just over a quarter (25.81 per cent) of respondents expected similar performance to 2021, and 1.61 per cent of respondents expected somewhat of a decrease. No respondents expected a significant decrease.
Some respondents identified new water and wastewater opportunities as a key positive for their companies for 2022, citing “approval of municipal and aquatic projects, which dominate our overall turnover”.
Agriculture and irrigation grows
Agriculture was another strong performer over 2021, and similar is expected for 2022, with the sector also benefiting from the 2021-2022 Federal Budget.
Over 2021, work volumes in this area remained steady for 41.18 per cent of respondents in the sector, while 31.37 per cent saw somewhat of an increase, and 9.80 per cent a significant increase. For 11.76 per cent of respondents work volumes declined somewhat, and they declined significantly for 5.88 per cent.
“We operate predominantly in the irrigation sector and have found that there is definitely an increase in demand for our services and the agricultural industry is still growing at great pace,” said one respondent. “However, since we operate in four states we found COVID-19 border restrictions extremely challenging, which definitely restricted the growth of our business.”
Another respondent said that “retail and farming pump sales were up considerably”. For one respondent “increased activity in major irrigation/agricultural projects” was a key factor that drove business over 2021. However, one respondent said that due to “the wetter seasons, irrigation has remained the same or dropped back”.
The influence of weather or climate-related factors on the irrigation sector was summarised by one respondent. “Dropping municipal dam levels creating water restrictions, public sentiment on water usage, and long-term wet weather also affects the sale of irrigation.”
Looking towards 2022, 40.38 per cent of respondents in the sector expected work levels to remain steady, while 48.08 per cent expected them to increase somewhat, 5.77 per cent expected a significant increase. Another 5.77 per cent expected somewhat of a decrease, yet no respondents expected a significant decrease. 7.95 per cent of respondents identified the agriculture industry as likely to be a key positive for business in 2022, while only 5.48 per cent were negative about prospects in that area.
When it came to climatic conditions more generally, 34.25 per cent expected climatic conditions to have positive effects on the industry in 2022, while 21.92 per cent expected them to have significant negative effects.
Ongoing issues with competition and skilled labour
Increasing competition in a globalised market, as well as staffing difficulties, have been issues within the pump industry throughout recent times, and this was no different in 2021. One respondent stated that “unskilled opposition entering our markets” was one of the biggest challenges of 2021, and expected that they would “continue to provide pricing pressure” in the future. Another respondent cited “staying ahead of your competition, as everyone is chasing the same opportunities” as a significant challenge in the industry. For 2022, 39.73 per cent of respondents thought online competition was an important factor that would affect the industry negatively, while 5.48 per cent saw it in a positive light.
Staff availability and finding adequately skilled personnel remains an issue for many. A “shortage of workforce” and “smaller number of apprentices – expected to remain the same if nothing changes in the training sector,” were challenges for many respondents. One respondent identified “competition for skilled labour” to be “probably the biggest issue” for the industry in 2022. Current trends in unemployment rates, which impact labour supply, were expected to be a key challenge for the year ahead by 28.77 per cent of respondents, while 6.85 per cent thought they would be a positive.
The fraught relationship between Australia and China has undoubtedly had far-reaching effects on Australian industry, the pump industry included, with 2021 seeing no thawing in relations. Bans and increased tariffs on Australian imports to China remain in place, after coming into being after the rapid deterioration of the relationship between the two governments over 2020, following a push by the Australian Government for further investigation into the origins of COVID-19. Nearing the close of 2021, tensions again escalated between the countries’ governments over Taiwan.
China is Australia’s foremost trading partner for both imports and exports, meaning the volatile relationship has significant consequences for many industry sectors and the Australian economy in general. Colin Heseltine, senior adviser to Asialink at University of Melbourne, states that when it comes to the economy as a whole, overall “the impact of China’s trade sanctions has been less serious than first feared (though damaging to individual companies),” noting that “with the benefit of exports of iron ore, which are essential to China and therefore not subject to sanctions, and a very high iron ore price until recently, the value of Australia’s goods exports to China actually hit a record in the first half of 2021”. China has
announced its intention to break its dependency on Australian iron ore imports by ramping up domestic production, increasing investments in overseas mines, and strengthening scrap steel recycling. However, many commentators and investors remain sceptical about the viability of this plan. Nevertheless, taking iron ore out of the equation, the effects of a fractious relationship on Australian imports has hit some industries hard. The Australia-China Relations Institute reported that from January to September 2021, the value of 12 disrupted goods fell by $US12.6 billion ($17.3 billion), compared with 2019.
As a result, many survey respondents reported tensions between Australia and China as having significant impacts on performance over 2021, and expected this to continue in 2022. Negative impacts reported by survey respondents included “raw materials costs increasing significantly” or “skyrocketing”. “Tariffs affecting prices and longer lead times are the most noticeable effects,” said one respondent. Other respondents said that “China has influenced local spending in mining” or that the issue had a “major effect on client confidence”.
“Almost all industries and markets have been affected negatively due to our failed relations with China,” said one respondent. “We have definitely noticed a negative impact particularly with our wine producing customers,” said another. “These customers have lost between eight per cent and in some cases up to 90 per cent of their business due to the breakdown in the relationship with China.”
Other respondents, particularly those involved in domestic manufacturing, saw upsides to the conflict. “More manufacturing is coming back to Australia and exporters are finding new markets outside China,” said one respondent. Another reported that they had seen “a lot less cheap product on sale.”
Nevertheless, over half of respondents (58.90 per cent) expected relations with China to be a key challenge for the industry in 2022, while a smaller number (10.96 per cent) anticipated positive effects. Opinion was divided as to how affairs between countries would develop into the future. For instance, one respondent was “hoping for improvements” as a result of a developing “two-way investment relationship,” while another said, “things will get worse.”
“I believe we need to either do something to improve our relationship with China (without compromising our sovereignty),” said one respondent. “Or if that's not possible then I think that the Federal Government needs to make significant investment into promoting our products overseas and provide accessible funding to companies for technological advances and export potential.”
In accordance with the industry’s generally optimistic outlook for 2022, survey respondents identified a number of growing areas of opportunity. Many of these related to the aforementioned expected growth in key sectors for the pump industry.
Seizing opportunity in post-COVID economic recovery
Government investment to spur economic recovery through infrastructure projects and other funding offers substantial opportunities to those who can secure the contacts. In particular, respondents mentioned spending on power generation, agriculture and water industries. “Building and construction boom inputs” were also seen as potential drivers of business.
As restrictions ease around Australia, a general uptick in business was also anticipated by some. “Sales and services should increase due to the backlog created by the pandemic,” said one respondent.
In recent years, many end users have focused increasingly on maintenance, with capital being allocated towards asset services and aftermarket needs rather than replacing equipment. This trend was exacerbated during the pandemic and shows no sign of abating. Pump industry participants who can pivot their businesses to meet these changing needs will be able to enhance customer relationships and unlock additional revenue and service offerings, giving them a competitive edge. Additionally, while they may not be able to compete purely on price, those who manufacture and sell pumps and associated products within Australia can offer enhanced aftermarket services, giving them an advantage over overseas competitors.
As renewable energy continues to gain traction within Australia, and coal declines as a result of emissions targets and reduced profitability, opportunities can be found in this arena.
Various renewable energy projects announced, underway or proposed have roles for pumps to play, the most well-known involving pumped hydro. Meanwhile, hydrogen, carbon capture and storage offer additional opportunities.
Solar pumps are increasing in use in irrigation, with one respondent saying that “solar pumping is our main growth area”. Renewable-powered heat pumps are also receiving increasing attention.
The likely effects of climate change on water security are also fuelling investment. Many respondents identified “wastewater, water scarcity and climate change” as longterm drivers of growth for the industry, as well as “increasing awareness of water value and the efficient use of it”, and saw opportunities in “irrigation water savings”, “water recovery” and “recycling and reuse”.
La Nina and current weather patterns were also noted as important factors. “Increased flows to the Murray Darling system due to higher-than-average rainfall will provide opportunities in the agricultural sector,” said one respondent.
Industry growth driven by increases in global demand and prices for specific resources offer significant volumes of work for pump industry participants involved in relevant sectors.
“I believe that as the commodities prices continue to
increase the mining sector will provide strong opportunities for the pump industry,” said one respondent. Rising oil and gas prices were also cited as likely to bring additional projects and work, as were “green minerals” and proposed hydrogen projects.
Energy efficiency improvements and smarter pump technologies were also key areas of opportunity identified by survey respondents. End user interest is growing not only in regard to new pumps, but also in the rental arena, and when it comes to upgrading and retrofitting older systems to enhance performance.
“Energy efficiency gains will always provide opportunities for suppliers in the pump industry,” said one respondent. “We have moved into an era and mindset in the pump industry now where energy efficiency is very important to end users and customers will definitely spend money to increase efficiency wherever possible.” Respondents noted that “energy efficient or low-lifecycle-cost products have a bright future” and anticipated “increased use of VSDs as the expected norm”.
Many saw future opportunities in “working with smarter, more energy efficient equipment and new technologies for operating and monitoring pump performance”, “further developments on environmental issues and reliability”, advancements in IoT, and the continued “development of new and innovative products”.
Overall, the majority of respondents expected new technologies and innovations to have positive impacts on the industry in 2022, with 52.05 per cent identifying this as one of the key positives for the year ahead, and only 4.11 per cent anticipating negative effects. Digitisation and IIoT were anticipated as positives for 19.18 per cent of respondents, while 8.22 per cent were wary of potential problems as a result.
While much about the next 12 months remains uncertain, and the COVID-19 pandemic has demonstrated the potential for unexpected events to throw a spanner in the works of even the best-laid plans, there is much to be optimistic about for 2022. Participants within the Australian pump industry are well positioned to grasp the opportunities provided by economic recovery and larger economic trends and set a path to greater things.
The environmental remediation of contaminated sites is a complex operation that requires multiple technological solutions. The solutions deployed for the removal and treatment of contaminants vary from site to site, with strict environmental regulations necessitating the need for flexibility in equipment. With over a decade of experience designing and engineering tanks for on-site wastewater and liquid treatment, SCF’s tanks and bunded containers have been utilised in multiple wastewater and remediation projects across the country. SCF recently collaborated with contamination environmental remediation specialists, Sarjaro, to supply a range of Bulk Liquid Storage Tanks, ISO Tanks and Dangerous Goods Containers, as part of a major wastewater remediation project north of Brisbane.
Following the acquisition of the 200-hectare Petrie Paper Mill Site in 2015 by the Moreton Bay Regional Council, Sarjaro was engaged by Orora to design, manufacture, install, commission, operate and maintain a bespoke multi-barrier water treatment plant (WTP) to remediate soil, groundwater, surface water and other sediments. The safe removal of 60 pollutants including multiple Per and Polyfluoroalkyl Substances (PFAS), metals and hydrocarbons, whilst adhering to strict regulatory limits, will allow discharge into the North Pine River and adjacent Moreton Bay Marine Park.
Building on a strong existing relationship with SCF, Sarjaro approached the company to supply
multiple tank and chemical storage container solutions for the Petrie Mill site. With limited space available, SCF was able to provide a range of equipment, which minimised the WTP footprint. It is expected the operation will process and treat up to 300 Megalitres of water over the next two years utilising the following SCF equipment:
• 25ft 37,000L Bulk Liquid Storage Tanks
• 45ft 77,000L Baffled Flow Back Tanks
• 20ft 24,000L Stainless Steel ISO Tanks
• 20ft Bolsters (Platforms)
• 20ft Single Side Opening Dangerous Goods Containers
• 20ft Site Offices
Andrew Reardon, Sarjaro Founder and Managing Director, said SCF was selected as the supply partner due to the company’s ability to provide modular equipment design, easier and more cost-effective transport and set-up when compared with conventional round polyethylene tanks, which take up twice the surface area of rectangular tanks, and are more expensive to handle.
“By using SCF Bulk Liquid Storage rectangular tanks, we can fit in the same water treatment plant, with the same capacity in half the surface area than if you use poly tanks,” Andrew said.
“SCF also has tight quality controls with the design of their equipment, and there are features that other tanks don't have, like baffles and weirs – systems that keep things in suspension – and there's certain mechanisms within the tanks that allow us to pump and recirculate the water. This keeps adsorption media within suspension, which is critical for water treatment.”
It is these features that has made SCF a popular choice for use in many environmental remediation and wastewater projects across Australia, for some of the nation’s largest resources, construction, and environmental management companies.
Jamie Driscoll, General Manager Tanks at SCF, said his tanks are designed and engineered in Australia to withstand harsh environmental conditions –which are exacerbated at remote locations – and to meet the strictest regulatory standards.
With a team of tank specialists located across the country, SCF can
provide custom-built tank and container solutions, or hire options, for equipment from their expansive product range. “Each customer’s project is unique, so each solution is tailored for site specific requirements. Our collective expertise in water remediation means the customer benefits from SCF’s years of experience in the field”.
SCF has a range of Bulk Liquid Storage tank types and sizes that are available to meet customers’ specific storage capacity and liquid mixing requirements. The product range benefits include:
• Portability – When the tanks are empty they can be quickly moved or transported to the next site, once a project is complete
• Transportability – The tanks are skid mounted, which means they are transportable and certified for rail and road
• Scalability – ‘Tank farm’ configurations allow tanks to be joined, then added or reduced to match the storage capacity requirements of the site
• Stackability – As the tanks are stackable, they are suitable for space constrained sites or where a smaller site footprint is desired
• Flexibility – Tanks can be hired for the duration of a project, allowing for them to be dehired once it has been completed
Jamie also highlighted the cost saving benefit of using Bulk Liquid Storage tanks as part of onsite WTPs, when compared to the cost of using water tankers to take fluids off-site for treatment.
Multiple media filtration vessels and pumps within a bunded SCF Dangerous Goods Container for safe and secure operation
SCF 45ft Baffled Flowback Tank with handrails erected for added safety when treating wastewater
“Storing and treating wastewater on site is more efficient than waiting around for water tankers, particularly if the remediated fluids are to be discharged back to the surrounding environment.”
“As well as eliminating the need to cart water offsite, SCF tanks can also mitigate the need for permanent tank structures, and as they are modular, they reduce site footprint”.
The smaller site footprint was a deciding factor for Sarjaro, who required a solution for multiple stages of wastewater at the project.
Throughout the WTP, a diverse range of pumps are housed in modified SCF containers including:
• Two Lowara Multistage Vertical Centrifugal Pumps, including integrated Hydrovar microprocessor variable frequency drives
• Two Ebara Horizontal Centre Line Discharge Centrifugal Pumps, including integrated Omron variable frequency drives
• Two Regent Horizontal Centre Line Discharge Centrifugal Pumps,
including integrated WEG variable frequency drives
• Two Ultraflow Submersible Pumps and four Grundfos Diaphragm Dosing Pumps, for pH control chemical transfer and dosing
• Eight IFM Flowmeters, Programmable Logic Controllers, Graphic User Interface, Telemetry and Instrumentation throughout All the various pumps are located throughout the WTP to transfer water in between each of the treatment stages, including the associated SCF tanks and containers.
“I have had the privilege of working with SCF for over a decade. In that time they have always provided impeccable customer service, with a focus on delivering quality equipment, on time, and at good value for money. SCF has been instrumental in providing Sarjaro adequate support to enable the completion of many high profile environmentally, politically and community sensitive projects throughout Australia,” Andrew said.
For more information, visit www.scf.com.au/water-remediation/
To cater for growth and development in one of the fastest growing cities in Australia, Urban Utilities has completed a major upgrade of the Bundamba Wastewater Treatment Plant in Ipswich. The utility has also installed a new belowground wet weather pump station in Hawthorne to service the area and enhance environmental outcomes in the popular Brisbane suburb.
Bundamba Wastewater Treatment Plant Upgrade Project
Urban Utilities, alongside project partner Ventia, has completed a $30 million upgrade to Ipswich’s largest wastewater treatment plant. The Bundamba plant receives and treats the wastewater from more than 93,000 people every day. The project to upgrade the site involved a range of works to renew and upgrade major
components of the plant, including the construction of new inlet works, a new septage and sludge receival facility, and a new electrical switchroom, as well as improvements in the dewatering, chemical receival bunding, service water, the final settling tank and sitewide control system improvements.
Urban Utilities delivery manager Vedran Maric said the investment in the plant, which has the capacity to service
133,000 people, would help future-proof the fast-growing region. He said a key part of the project also involved raising all critical equipment at the plant above the 2011 flood level to protect against future flooding.
“A new 50 tonne switchroom, which houses new switchboards and control system equipment, was raised above the flood level,” he said. “The new inlet works also has numerous flood
mitigation measures for critical process equipment, including service water boosters, located on mezzanine levels. Diesel storage tanks for the backup generators and site blowers were also raised as part of the project.”
Mr Maric said Urban Utilities and Ventia used a collaborative, innovative approach to complete the important project.
“To make the process as safe and efficient as possible we built the prefabricated switchroom off site and moved it into position with a 350-tonne crane,” he said. “We also took a collaborative approach to the procurement process for pumps and other essential equipment as part of the upgrade,” Mr Maric said.
“We worked with the contractor and designer in the final selection of many of the pumps, with the governing criteria subject to the application. For example, on a septage receival station, we opted for a Flygt Concertor for the integrated functionality and high torque. For the new service water pump sets, we went with Xylem’s package set, complete with drive-mounted integrated variable speed drive (VSD) and controller. For the inlet works pump station, we trialled an integrated package wet well and pump set from Aquatec. Performance requirements and capital, operational and maintenance costs were also considered as part of the procurement process.”
Mr Maric said the upgrade involved several planned shutdowns in the wastewater network and precise traffic management.
“Around 16 million litres – more than six Olympic swimming pools – of wastewater is treated at our Bundamba plant every day so it took a lot of careful planning to ensure the plant remained operational while we completed the upgrade,” he said.
“On-site traffic management during construction was challenging due to the old septage receival facility being located inside the plant. This meant that there were 10-15 trucks per day driving through the site to use the facility. The construction team implemented a traffic management plan and worked collaboratively with the on-site operations team to ensure there were minimal disruptions to the septage receival customers.”
Mr Maric said the larger planned shutdowns were undertaken at night when the flow into the plant was low.
pump stations needed to be isolated in the network and flows tankered to other treatment plants,” he said.
“Where possible, concurrent works were undertaken to minimise the impact to the plant operation. Safety, innovation and collaboration were essential to completing this project and I’m proud of what our teams have achieved.”
Urban Utilities and project partner Fulton Hogan Utilities have constructed a new belowground wet weather wastewater pump station at Hawthorne Park in Brisbane’s East. The project involved the construction of the wet weather pump station as well as the installation of new wastewater pipes to help manage wet weather overflows and improve environmental outcomes in the area.
Urban Utilities Project Manager, Stephen Harding, said the new pump station will operate during wet weather events to divert flows from the local wastewater network to a larger nearby trunk sewer.
Mr Harding said the majority of the infrastructure was built belowground to complement the bustling park’s aesthetics.
he said. “To keep the park open and accessible, the new pump station was built at the edge of Hawthorne Park, near the existing toilet facility.”
Mr Harding said most of the pump station’s infrastructure is underground, including a 7.4-metre-deep wet well, valve pits and pumps, with a ventilation pole and electrical switchboard sitting at ground level. “As part of the project we used two Xylem Flygt 13.5kW submersible pumps in a duty standby configuration,” he said.
To add some colour to the project and engage the local community, Fulton Hogan had the creative idea to cover the switchboard with a vinyl wrap artwork
Pump Station.
blending the structure into the park.
“Fulton Hogan’s Stakeholder Communications Manager, Gail Harris, encouraged the community to choose their preferred design and they selected an artwork with trees that matched the surrounding environment,” Mr Harding said. “Fulton Hogan also installed a community table and bench setting, which was welcomed by park users.”
“Significant planning went into those longer planned shutdowns as several
“Hawthorne is a leafy, welcoming suburb in Brisbane and we wanted to ensure we maintained the integrity of the green space at the popular park,”
Mr Harding said the popularity and central location of the park meant community consultation was at the forefront of the project.
“The park is widely used by the community from yoga and fitness groups, to the Morningside Australian Football Club. The construction site was also adjacent to commercial buildings such as the Hawthorne cinema which required additional community consultation to minimise disturbance,” he said.
“The project is a testimony to the good work of Fulton Hogan Utilities who were able to construct the pump station in a very busy location with minimal impact to the local community.”
United Pumps designs and manufactures pumps, our extensive Melbourne testing facility is utilized for product development, new pump test and customer pump testing. 2.5Mw capacity with NPSHr capability.
United have made a commitment to API610 pump manufacture in Australia. With decades of experience, we can provide you with the finest engineered equipment and support
Our extensive range of process and water pumps are available in materials to suit your application. With all design and manufacture carried out in Australia we can offer a true Sovereign solution.
Proven track record in municipal water applications over a wide range of the highest quality pumping equipment. Horizontal Split Case, Vertical Turbine, End Suction and Sewage.
Gippsland Water’s new Sale Outfall Sewer Pump Station is now operational, a $13.5 million project that will service the communities of Sale, Wurruk, and Fulham for the next 50 years. Pump Industry spoke with Gippsland Water’s Manager Asset Delivery, Paul Henderson, to learn how key planning and design decisions have delivered both successful asset performance, as well as positive amenity outcomes for the community like improved odour control.
Sewerage infrastructure in the Sale region is now more resilient and has a more amenable future, with Gippsland Water’s successful commissioning of the new Sale Outfall Sewer Pump Station last year.
The $13.5 million project, which will service the networks of Sale, Wurruk and Fulham for the next 50 years, was first identified as a top ten capital project in Gippsland Water’s 2018-2023 Price Submission to the Essential Services Commission.
Paul Henderson, Manager Asset Delivery at Gippsland Water, reveals that it was more cost-effective and beneficial to the Sale community to build a new pump station, with greater resilience and amenable design.
Key benefits delivered by the new station include greater capacity when compared to the old station, the inclusion of odour mitigation technology, and improved resilience of the asset under wet weather scenarios.
From design and procurement through to construction and operation, the new Outfall Sewer Pump Station has been
optimised for both performance and resilience for the next 50 years, from capacity improvements to better resistance to wet weather events.
“The old SPS was at capacity and could no longer contain flows to our containment standard, which is to contain flows from an 18.1 per cent annual exceedance probability (AEP) rainfall event,” Mr Henderson said.
“The pump station now services 7,586 existing connections – households and businesses – and is designed to cater for a further 2,000 connections.”
The likelihood of spills into Flooding Creek has also been addressed, by constructing a one megalitre storage tank that will be invaluable in managing wet weather events.
While the new pump station’s discharge capacity remains comparable to that of the old station, inflow capacity has been boosted significantly – also thanks to the station’s storage tank.
The new pump station caters for a peak dry weather flow of 346 litres per second (L/s) and peak wet weather flow of 628L/s.
Regarding the procurement process, Mr Henderson revealed that the new pump station was “primarily procured under two AS4000 civil construct contracts” along with a mechanical and electrical contract, and smaller equipment supply and installation contracts.
The two civil contracts were both awarded to local contractors in the Sale region.
Pump specification
Key pump specification decisions for the new station were made to best coordinate with the downstream Longford Booster Pump Station across different operation scenarios and sewage inflow rates.
“The pump station was designed with three Flygt NP 3231/735 3~ 480 pumps; duty, assist and standby, each VSD driven with 170kW rated motors,” Mr Henderson said.
“Mains power supply was extended to a new on-site 500kVA ring-main kiosk substation transformer for the new pump station.”
One major factor determining pump selection at the new station was ensuring that design discharge pressure in the rising main – downstream of the new pump station – is never greater than the maximum operating pressure experienced with the old pump station.
“This limited the head to around 44m and corresponding design discharge of 128L/s under the critical operating scenario – which is when the Longford Booster Pump Station is not operating and the new pump station pumps all the way to Dutson Downs,” Mr Henderson said.
The future-focused design of the new station is also reflected in the 5.5m diameter of the wet well, which is large enough to accommodate larger, 375kW pumps in the future.
This could be an important design decision should the new station’s connection with the Longford Booster Pump Station change via upgrade or decommissioning scenarios, in combination with upgrades to the rising main between Sale and Longford.
Improving asset amenity: from odour control to a positive visual impact
Gippsland Water’s commitment to asset amenity is reflected in many of the decisions made across site
selection, landscaping and design, as well as the inclusion of a comprehensive odour control system.
According to Mr Henderson, removal of the old pump station already improves views from the Port of Sale precinct, and much thought was put into the best location for the new pump station.
The selected project site on Foster Street in Sale was chosen for many reasons including proximity to existing infrastructure, adequate site size, height above the flood level, and vehicle access for operational maintenance.
A key design decision that improved the overall amenity of the asset was the inclusion of an odour control system, to reduce odours escaping from the site.
Potential odour sources identified included the inlet works, the wet well and the emergency storage tank.
A large fan draws air through a vacuum into the odour facility, a two-stage system comprising a bio-filter and an activated carbon polishing unit.
“This should remove all the odour, so that the clean air is discharged through the vent stack, so we don’t get odour leaving the site,” Mr Henderson said.
“Within the control cubicles for the odour system we have continuous hydrogen sulphide monitoring of before and after, to ensure that the air being discharged is clean.
“This also ensures compliance with the EPA regulations.”
Gippsland Water also managed the amenity of the new pump station by considering the asset’s visual impact.
“A key early stage of the project involved working closely with Wellington Shire Council, the community of Sale, and a landscape architect to create a facade for the new sewer pump station that complements the amenity of the area,” Mr Henderson said.
Landscaping efforts of the project include a planting scheme that incorporates native evergreen trees as well as indigenous plants laid out in organic shapes, with further planting to assist with screening the asset at its southern and eastern boundaries.
The site also features timber fencing as a reference to both the historic port of Sale and the local timber industry.
By Annabelle Powell, Journalist, Pump Industry Magazine
Pump systems are critical to keeping our world in motion. When selecting a wastewater pump, there are key factors to consider to ensure maximum efficiency and longevity, and to reduce long-term costs.
Wastewater pumps are used in the collection of sewage, effluent, drainage and seepage water. When selecting a wastewater pump, whether for a new system or replacing an old one, there are selection criteria to consider that can make big differences in performance, reliability and cost-saving energy efficiencies. This checklist includes liquid, flow rate, temperature, altitude and lifecycle costs.
Industrial applications come with many demands, such as resisting corrosive chemicals and handling high temperatures. Considering such demands as well as the application environment is crucial when selecting the most suitable pump for your application.
Determining these factors and selecting the right wastewater pump result in less maintenance, higher efficiency and long-term cost savings.
Different types of pumps
There are two main types pumps used for wastewater:
• Conventional wastewater pumps: These are also known as non-clog, solids handling or dry-well pumps. Their main purpose is to pump liquids that contain soft solids and other stringy material. They don’t require frequent servicing and cleaning, and operate without plugging. They can either be installed with horizontal or vertical mounting.
• Submersible pumps: These are non-clog pumps that are immersed in the wastewater for operation. They come equipped with powerful motors and are installed directly in the wet well. This means wastewater pumping stations that use submersible pumps don’t require a dry well. The pumping system construction above the ground is minimal, and all that’s visible above the surface is a concrete slab and a small housing construction for the control centre.
Pump capacity
A good first step when selecting a wastewater pump is to examine the application’s hydraulic characteristics. In choosing the right pump it’s key to accurately estimate the capacity that is required.
Reviewing the required flow rate and pipe size determination will make it a simple matter to estimate and graphically display these characteristics with a system curve specific for the application.
In order to create the system curve, two basic elements are required: static head and friction loss. Once the system curve is known, it is easier to determine the best pump for that application.
Fluid characteristics
The type of material in the fluid is a key consideration when selecting a wastewater pump. Fluid streams in wastewater
treatment plants are characterised by their properties – such as large solids, grit, sludge, scum and flocculated materials, or a mix – as these will create different considerations that need to be addressed when selecting a pump for the intended service.
Wastewater pumps are generally required to handle solids such as personal wipes, towels, and cleaning cloths, which have recently become more prevalent in wastewater flows. Selecting a pump that is capable of dealing with these solids is important, as these materials can bind together to create a large mass that can lead to clogging issues in the pump and associated piping. There are rotodynamic pumps on the market that are specifically designed to deal with solids and minimise clogging are referred to as solids-handling pumps.
Additional pump considerations include accounting for sludge, which can contain a significant volume of entrained gases, such as hydrogen sulfide, due to organic bacterial action. The pumps should address these characteristics and minimise the potential for clogging and gas binding.
Pumps also need to be able to handle flocculated materials. Pumps that transfer flocculated materials need to keep the material in the flocculated state and not shear it.
Fouling, corrosion, and erosion of pumps and pipes over time can be attributed to biological, chemical, and abrasive factors, so understanding fluid properties can be critical to avoid failure or the need for continuous and costly maintenance.
When considering altitude, it is important to know that the site evaluation for the pump installation can affect its operation as, generally, the higher the elevation of the installation, the less suction lift there is available for the pump.
For pumping systems with atmospheric suction pressure, the net positive suction head available (NPSHa) calculation should be checked to include the actual atmospheric pressure at the application site.
Altitude will also affect the selection of the pump driver and, when applicable, the variable frequency drive (VFD) because higher altitudes will result in the air providing less cooling, therefore potentially requiring the driver and VFD to be derated.
Heat can significantly impact a multitude of motor components, create deterioration and negatively impact pump performance. Consequently, temperature is a critical consideration when selecting a wastewater pump.
Many pump companies offer pumps with high-temperature winding options to address the maximum water temperature that can be pumped and the duration.
If high-temperature liquids are not properly accounted for when selecting a pump system, the pump may cavitate, which can reduce performance, and cause physical damage to the pump components and increased vibration.
A pump needs to be able to generate fluid flow, the output of which is represented in litres per minute (L/min). Flow rates are influenced by distance to the access points, pipework and elevation. ‘Maximum’ and ‘rated’ flow rates are helpful to understanding whether a pump is adequate for the function it needs to perform.
• Maximum flow rate: The maximum flow represents the number of litres that a pump can pressure immediately from itself without any need to travel up and through pipework
• Rated and normal flow rate: Rated flow is the operating condition that the pump is designed for. Another commonly
used term is ‘normal flow’, which represents the conditions the pump is expected to operate at most of the time.
Obviously, the pump flow rate must be greater than, or equal to, the maximum expected effluent flow. In wastewater piping and pumping systems in particular, the flow rate needs to exceed certain limits in order to ensure troublefree operation and avoid solid settling and sedimentation. Conversely, the flow rate should also not exceed certain limits to avoid potential wear and tear from erosion and abrasion.
It’s a good idea to consult the pump manufacturer if you are concerned about the operational flow rates expected, to avoid ending up with a pump that doesn’t perform its required function.
Pump manufacturers often provide a line graph displaying the expected maximum flow rates. Taking this into consideration when selecting a wastewater pump often requires some understanding of where your pump will be located and the network of pipes it will be attached to.
Rotational speed can be quantified as the number of revolutions a rotating system makes within a defined period of time.
Current wastewater pump design technology allows reliable operation of pumps with values of suction specific speed (Nss) through approximately 250 for metric units, depending on eye peripheral velocity, materials of construction, range of operation, pumped liquid properties, and other factors.
Higher Nss values result in pumps designed with lower NPSH requirements at the same or higher operating speeds. The maximum speed for a pump (n) due to NPSHa can be calculated from the Nss formula by expressing the rotative speed as a function of NPSHa, pump rate of flow (Q), and Nss.
The selection of pump rotational speed is closely related to the characteristics of the pump hydraulic system (circumferential speed, impeller, specific speed), as the overall strength and economic efficiency of the pump and drive system need to be taken into account.
When investing in a pumping system, focusing on the initial capital investment gives an inaccurate depiction of the true costs of the pump over its life. One way to avoid this mistake and get a more realistic picture of the true cost is to use a Lifecycle Cost (LCC) calculation.
The purchase price for pumps is typically less than ten per cent of the total lifecycle cost, so an LCC calculation assists in gaining a better understanding of the total cost over the pump’s life.
The Hydraulic Institute has defined the following LCC formula for pumping systems, which has become the industry standard:
Cic = Initial costs
Cin = Installation and commissioning costs
Ce = Energy costs
Co = Operational costs
Cm = Maintenance and repair costs
Cs = Downtime costs
Cenv = Environmental costs
Cd = Decommissioning costs
For small stations pumping raw sewage, maintenance can be a major component in the total LCC calculation. This is especially true if the pump is poorly matched to the pump system’s maintenance requirements.
In mid-September, Coliban Water completed works to install two huge 900mm valves on a water main in Golden Square, Bendigo. The valves are the biggest of their kind in the region and are part of the groundwork taking place to cater to the future population growth and providing greater flexibility to operate the pipeline.
Coliban Water’s Executive General Manager Service Delivery, Danny McLean, said the major project on Aspinall Street, which runs between Kangaroo Flat and Golden Square, will play a significant role in allowing for future growth to the west of Bendigo.
“The water main currently services more than 25,000 residents in Bendigo, including the Bendigo Hospital and St John of God Hospital, so it’s a major piece of infrastructure we’re working on to enable further growth,” Mr McLean said.
The water main runs from the Bendigo Water Treatment Plant at Kangaroo Flat to the Specimen Hill Reservoir in Golden Square. It then supplies numerous areas of Bendigo including Maiden Gully and Marong.
The installation of the new valves provide Coliban Water’s partner Veolia with greater flexibility to operate the pipeline under the terms of the AQUA BOOT (Build, Own, Operate, Transfer) contract.
A major part of the project was to install a new connection point or ‘T’, which is the beginning of a new trunk water main from Golden Square to Maiden Gully.
Procuring and installing the valves
Veolia led the planning process and consulted with Coliban Water and Lendlease for the design of the new works. Installation logistics was also a key consideration so that the utility could maintain services to customers and minimise risks.
Veolia was also involved in the procurement process for the works; and Bendigo-based contractor S & R Engineering and Construction was selected to carry out the works.
In order to undertake the works, the pipeline was shut down for a number of days and alternative arrangements were put in place to ensure an uninterrupted delivery of drinking water and that customers were not affected.
“We were pleased that installation went according to plan and there were no unplanned issues of any significance,” Mr McLean said.
“One minor challenge which the team worked to overcome was working with limited space for deep excavation. This involved having a geotechnical engineer inspect the site and ensure the excavation was safe.
“The location of works on Aspinall St also meant that it was a busy local road and urban bus route. This was dealt with by Traffic Management approved by the City of Greater Bendigo.”
The installation of the valves form part of the groundwork for the new trunk water main.
Construction on the new main is expected to start in mid2022, and take around eight months to build.
“This is a major step in progressing pressure improvement projects to the west of Bendigo, including suburbs like Marong and Maiden Gully,” Mr McLean said.
“There is huge growth in this part of the region, and it’s crucial we’re putting in the infrastructure now to support these communities into the future.”
As well as the valves and new main, Coliban Water is also looking at other projects that will provide the infrastructure needed to support the region in the future.
Another project currently underway to support growth in this area is the Marong Tank Project, with a new three megalitre tank and booster pump station to be installed.
“Most of the concrete walls of the tank are already completed on the project, which is designed to improve efficiency and create a more robust network in Marong,” Mr McLean said.
The tank project was expected to be completed before the summer of 2021 to ensure customers in the region have access to a strong, secure supply in the warmer weather.
Source: Hydrostor.
Large-scale and long duration energy storage will play a critical role in Australia to create a flexible and reliable energy system, support the increasing deployment of variable renewable energy sources, and to help manage the gradual retirement of conventional generation. There are a number of technologies that have been deployed to achieve this, with compressed air energy storage (CAES) one of the technologies looking to be established in the country to provide large-scale synchronous capacity. Here, we break down the technology and what equipment is involved, and explore the proposed 200MW utility-scale Advanced-Compressed Air Energy Storage (A-CAES) facility for Broken Hill, New South Wales.
What is CAES?
CAES is a method to store generated energy, allowing it to be used at a later time. At utility scale, this means that energy that is generated during off-peak (low demand) periods can be released at peak load (high demand) periods.
The technology is over 40 years old, and was seriously investigated in the 1970s for the nuclear power industry as a way to provide load to meet peak demand and following it, while also maintaining constant capacity factor. Since then, it has become commercially available, offering potential for both small-scale, on-site energy storage, and largescale installations to provide larger energy reserves for the electricity grid.
How does CAES work?
CAES plants have similar applications as pumped hydro storage, but instead of pumping water from a lower pond to an upper pond when there is surplus energy, ambient air or another gas is compressed and stored under pressure in an underground cavern (typically 500-800m deep) or container until it is needed at which point the pressurised air is heated and expanded in an expansion turbine to drive a generator to produce power.
Throughout the process, the air heats up during compression from atmospheric temperature to a storage pressure around 70-100 bar depending on the depth. Standard multistage air compressors using intercoolers and aftercoolers
are needed to reduce the discharge temperature to 149/177°C and the cavern injection temperature down to 43/49°C. This heat loss is then compensated for when the pressurised air is expanded in the turbine power generator phase by heating it in combustors using natural gas or by using the heat from a combustion gas turbine exhaust in a recuperator before the expansion cycle. This process is known as the diabetic method. Alternatively, the heat from compression can also be thermally stored before entering the underground cavern to be used for adiabatic expansion where the heat from compression is retained and then reused during expansion. This is known as the adiabatic method.
The major components of a conventional CAES plant include:
• A motor/generator with clutches on both ends (to engage/ disengage it to/from the compressor train, the expander train, or both)
• Multistage air compressors with intercoolers to reduce the power requirements needed during the compression cycle, and with an aftercooler to reduce the storage volume requirements
• An expander train consisting of high- and low-pressure turboexpanders with combustors between stages
• Control system (to regulate and control the off-peak energy storage and peak power supply, to switch from the compressed air storage mode to the electric power generation mode, or to operate the plant as a synchronous condenser to regulate VARS on the grid)
• Auxiliary equipment (fuel storage and handling, cooling system, mechanical systems, electrical systems, heat exchangers)
• Underground or aboveground compressed air storage, including piping and fittings
Compressors and expanders are two components that play a key role in a CAES system. Compressors are designed or selected based on the application and designed storage pressure of the air. Multistage reciprocating compressors are typically selected as the air pressure in a vehicle cylinder can reach 20MPa of storage pressure for higher energy storage density in a limited volume. For a large-scale CEAS system, the pressure is about 8MPa, so multistage compressors are used and normally combined with axial flow compressors and centrifugal compressors. Steam and gas turbines can be used for expansion. For example, a CAES plant in Huntorf, Germany, uses a steam turbine for first-stage expansion from 4.6MPa
Source: Hydrostor.
to 1.1MPa, and a gas turbine for second-level expansion from 1.1MPa to atmospheric pressure.
The selected thermodynamic cycle applied to a CAES plant can impact on plant costs, selection of components and overall operating/performance characteristics: Conventional (diabatic) cycle
The conventional (diabatic) cycle consists of the intercooled compressor train, reheat expander train, motor/generator, control system, and the air storage along with auxiliary equipment (fuel storage and handling, heat exchangers, mechanical systems, and electrical systems). In this cycle, the stored air is expanded through the reheat turboexpander train where it is heated (via combustion of fuel) sequentially in the high pressure and low pressure combustors before it enters the corresponding high pressure and low pressure expansion turbines. Plants designed with this cycle are characterised by relatively high heat rate (approximately 5,500Btu/kWh) compared to more recent designs, and are best suited for peaking and spinning reserve duty applications.
There are two major benefits of the conventional cycle. The first is that it can generate three times the output for the natural gas input as the compression of the combustion air is separated from and independent of the gas turbine process. This is because the compression stage typically uses about two thirds of the turbine capacity, and by separating this from the gas turbine process, the turbine has additional output. This has environmental benefits as well, as the specific gas consumption is reduced and CO2 emissions can be abated by about 40-60 per cent depending on whether waste heat is used to increase the air temperature in a recuperator, with this providing around 55 per cent efficiency compared to powerto-power at around 42 per cent.
Furthermore, as the air is not compressed using gas, lower cost excess energy can be used during off-peak periods.
Plants utilising this method, use sing-shaft machines with the compressor-motor/generator-gas turbine both located on the same shaft and coupled via a gear box. There are conceptual designs where the motor-compressor and generator-gas turbine will be mechanically coupled, making it possible to expand the plant modularly.
The main components of a conventional cycle plant are:
• Compressor train with intercooler and aftercooler
• Expander train
• Generator/motor
• A fuel/gas combustion system to preheat the released air
Source: Hydrostor.
The recuperated cycle is the conventional CAES thermal cycle with the addition of a recuperator which recovers the low pressure turbine waste heat to preheat the stored air before it goes to the high pressure combustor. This allows a reduction of fuel consumption by about 25 per cent compared to a conventional cycle plant. This cycle was designed for primary operation as a source of peak power and as a load management storage plant.
The main components of a recuperated cycle plant are:
• Compressor train with intercooler and aftercooler
• High and low pressure expansion turbines
• Generator/motor
• A fuel/gas combustion system to preheat the released air
• Recuperator
The combined cycle includes the addition of a heat recovery steam generator (HRSG) and a steam turbine. The HRSG recovers the exhaust heat from the low pressure expander to produce steam, which is used to drive a steam turbine and provide extra power. The additional power generated reaches full capacity around one hour after plant start up due to the thermodynamic inertia of the bottoming cycle equipment, therefore making this cycle appropriate for applications that need additional peak power for continuous long-term operations. This cycle has a reduced specific storage volume per kWh produced than the conventional cycle.
The main components of a combined cycle plant are:
• Compressors with intercooler and aftercooler
• Steam turbine
• Generator/motor
• A fuel/gas combustion system to preheat the released air
• Expansion turbine
• HRSG
• Boiler feed pump
• Condenser
The steam injection cycle is a conventional CAES cycle that has been adapted to use the HRSG to recover waste heat for steam production. The steam is added to the airflow from the storage cavern to increase mass air flow through the expansion turbine, increasing the plant’s output power level. The mass of air to be stored per unit of power output is greatly reduced due to steam injection with the corresponding reduction of the storage volume and costs. Like combined cycle plants, the additional power from the steam injection lags the power almost instantly produced by the air expansion turbine.
The main components of a steam injection cycle plant are:
• Compressors with intercooler and aftercooler
• Turbines
• Generator/motor
• A fuel/gas combustion system to preheat the released air
• Expansion turbine
• HRSG
• Boiler feed pump
Compressed air storage with humidification
The compressed air storage with humidification (CASH) cycle involves the stored air being humidified in an air saturator before being injected into the combustion turbine. Due to the humidification, the mass of air needed to be stored per unit of power output is reduced, therefore the storage cavern can be smaller than for other CAES cycle designs.
The main components of a CASH cycle plant are:
• Compressors with intercooler and aftercooler
• Turbines
• Generator/motor
• A fuel/gas combustion system to preheat the released air
• Expansion turbine
• HRSG
• Boiler feed pump
Adiabatic cycle
Plants using the adiabatic cycle are still conceptual, with major experimental projects and commercial ventures so
Basic functioning of a CAES facility. Source: Scientific American.
far failing to yield a viable prototype. The appeal of this type of CAES plant is that it has the potential to offer low-cost, large-scale operation without reliance on fossil fuels or rare materials.
This cycle can achieve higher efficiencies of up to 70 per cent by recovering the heat produced during compression and using it to reheat the compressed air during turbine operations. The main benefit of this is that gas is no longer needed to heat the decompressed air.
The main components of the adiabatic cycle are:
• Compressors
• Expansion turbine
• Generator/motor
• TES system
While the Broken Hill A-CAES Project is not the first CAES plant to be proposed to be built in Australia, it is the first largescale, long-duration energy storage project to be selected as a preferred solution in the first stage of a regulatory transmission planning process by a major utility, and if completed, it will be the first facility of its type in the country.
The Broken Hill Project is a proposed 200MW utility-scale A-CAES facility that is being jointly developed by Hydrostor and Energy Estate. It will be located at a local decommissioned mine and is designed to provide up to eight hours of electricity discharge at a time (i.e. up to 1,600MWh). The feasibility stage development work for the project is supported with funding from the NSW Government’s Emerging Energy Program. It will provide critical backup generation to ensure reliability of the electricity supply to the Broken Hill community and will solve significant congestion issues being experienced by existing renewable projects in the region.
The Broken Hill A-CAES project will allow the region to sustainably unlock the full economic potential of its traditional and renewable natural resources and our goals include working with existing and new resource companies to provide them with a low cost sustainable energy solution.
Broken Hill A-CAES Project details:
Size: 200MW/up to 1,600MWh (eight hours duration)
Owner: Hydrostor, Energy Estate
Location: Broken Hill, NSW
Application: renewables integration, non-network transmission reliability solution
Economic: Up to 750 full-time equivalent job years during construction, AU$550 million of expenditure will take place in NSW, of which 40 per cent (or AU$240+ million) will be in the local Broken Hill community (Third Party Report: ACIL Allen)
Project design life: 50+ years
In-service: 2025
The facility will use off-peak or surplus electricity from the grid or a renewable source to run a compressor, producing heated compressed air. Heat is extracted from the air stream and stored inside a proprietary thermal store, preserving the energy for later use. This adiabatic process will increase overall efficiency and eliminate the need for fossil fuels during operation. The compressed air will be stored in a decommissioned mine. Hydrostatic pressure forces air to the surface where it is recombined with the stored heat and expanded through a turbine to generate.
If the facility is approved for construction, Hydrostor will work with tier one OEM suppliers to deliver the equipment, including its turbomachinery and thermal management systems. The above-ground facility will be constructed by best-in-class EPC firms, which have multi-decade experience delivering directly analogous systems on-time and on-budget, while the subsurface component is delivered by world-class cavern construction specialists, who deliver identical caverns for more rigorous applications.
*The article below is extracted and based on the Hydraulics Institute White Paper for Understanding the Effects of Selecting a Pump Performance Test Acceptance Grade.
The introduction of AS ISO9906:2018 has opened the Australian pump industry to a wider range of pump test acceptance tolerances. Whereas the previous pump test standard offered only three acceptance tolerances, this latest standard now allows for the client and the pump supplier to negotiate one of six different acceptance tolerances.
Unlike the previous edition of the standard which allowed for positive and negative tolerances on flow and head, known as bilateral tolerances, it also now provides acceptance grades with unilateral or positive only tolerances. Table 1 below from HI ANSI14.6 is essentially identical to AS ISO9906. The two international standards are harmonised and will provide the same pump test outcomes.
Simply, in the past, the AS test standard only offered the 1B, 2B and 3B acceptance grades, that is, pump tests with a negative and positive tolerance on the guaranteed flow and head. Water suppliers and similar high energy consuming companies generally request pumps to be tested to the more accurate 1B while general and irrigation industries would request tests to Grade 2B. Pumps purchased “off the shelf” without a pump test would generally be guaranteed to perform within the tolerance bands of Grade 3.
One of the more common – and in fact a most important reason to have a manufacturer test a pump – is to have baseline data for diagnostic purposes in the future. For this reason alone almost any acceptance grade would suffice. But there are many other reasons why a purchaser may request a pump test and feel the need to select a tighter tolerance.
It is important for the client to have a full understanding of the acceptance grades and the implications that a tighter test tolerance may have on his application and on the pump cost and its delivery. In many cases a tighter tolerance
may adversely affect the delivery lead time and the cost of the testing.
No doubt, many pump purchasers would see the new 1U, 2U unilateral tolerance, a positive tolerance only on the performance requirement as an additional guarantee on their systems operation. As an example, the fire pump industry standard AS2941 (specifying fire pump requirements) has been requiring no negative tolerances on flow and head since 2013.
Let’s look at a tested pump curve together with its Grade 2B tolerance band. For example, if a pump was marketed for sale in an application where the acceptable performance Grade 2B is the market standard, shown in Figure 1 as the solid blue curve, will likely represent an average of the historical performance of similar units. The dashed curves above and below the blue curve characterise the pump’s performance that would meet the 2B criteria.
A manufacturer generating a submittal/quotation curve for an application requiring a 1U tolerance pump, that is a positive only outcome for the flow and head, will likely make adjustment to that general market curve, initially intended to have a 2B tolerance.
The orange dashed curve on Figure 2 below would bring the anticipated performance variation above a requested guarantee point.
In the process of raising the tolerance band on basic hydraulic performance, the power required would potentially increase due to the increase in expected rate of flow and head to be within the tolerance band of the requested performance. It will probably be necessary for the manufacturer to quote an increase in the pump power required to guarantee the performance, see Figure 3. Worst case, when allowing for a safety margin it may even mean that the maximum absorbed power would require the next size of electric motor to be supplied.
The table of tolerance grades specifies the allowable tolerance that the manufacturer must comply with on his quoted values. It is easy to perceive that a manufacturer guaranteeing a U tolerance would find it necessary to increase the guarantee value of the power absorbed to achieve the guaranteed flow and head.
Specifying a manufacturer’s test without any clear specification may mean that only the flow and head are guaranteed. It should not be taken as granted that the power or efficiency will be guaranteed. The standards, both ANSI and ISO, clearly indicate that these parameters are optional, and either power or efficiency will be guaranteed only when specified.
The most energy conscious tolerance is the 1E acceptance grade which will have its appeal to many users. Whilst the acceptable tolerances on the flow and head are the same as for 1U there is no negative tolerance allowable on efficiency.
As initially advised this brief article is extracted from the Hydraulics Institute White Paper for Understanding the Effects of Selecting a Pump Performance Test Acceptance Grade. The paper and a webinar are available online at no cost. Its 17 pages are much more explanatory on many other issues including crossing steep or shallow system curves, the interactions or trade-offs between each Acceptance Grade, the intended operating system, possible cost and delivery implications.
It is recommended that engineers specifying and requiring manufacturer tested pumps take the time to read and understand the benefits and possible implications of nominating a particular Acceptance Grade.
The White Paper may be found on the Pump Industry Australia website: https://pumps.org.au/product-category/publications/
Pumping and irrigation systems can account for a large proportion of farm energy use. Pumps are driven by electric or diesel motors to deliver water to the field for irrigating crops and stock, so operating them and the systems efficiently is important. Moving water is energy-intensive so effective irrigation will require less energy per unit of production: the energy water nexus.
Many irrigation systems have evolved with the farm over generations: the dependable pump and pipes may have lasted for several generations with changes in crops, block sizes and irrigation types.
The key is to ensure that a system continues to deliver the right amount of water at the right time and then supply it through the most efficient system.
The Spring 2021 Edition summarised the top eight ways to improve energy efficiency in pumps such as choosing a suitably sized pump, optimising piping, maintaining systems and using variable speed drives. This story illustrates those improvements with the results of some on-farm energy audits.
The Energy Savers programs have delivered over 300 energy assessments and audits in most agricultural sectors throughout Queensland, focusing on electric systems.
The most recent phase of the program, the Energy Savers Plus Program Extension (ESPPE) audits have identified annual savings of 7.5 million kWh, which would save an estimated $3 million and 6,000 tonnes of carbon emissions. If farms implemented all recommendations in the audits they would reduce energy consumption by around 40 per cent in the areas monitored. The most recent 180 audits included 670 recommendations with 270 relating to pumps and irrigation systems.
Irrigation efficiency opportunities in energy audits have identified an average of 16 per cent reduction in energy consumption with cost savings of around 34 per cent on the systems audited. The assessments have considered the water requirements and system configuration as well as the pump and motor. They include pipe upgrades, pump upgrades, pressure reduction and the addition of variable speed drives.
After implementation, some measurement and verification has been occurring and as well as quantifying actual savings, farmers have reported other benefits from irrigation upgrades such as improved crop consistency and time savings.
Energy Savers program in action
In a Whole of Systems review1 on Burnett fodder farm, the auditor identified that 15 per cent of energy use was due to static head caused by narrow pipe and a number of elbow fittings. The auditor recommended upgrading 130 metres of
100mm PVC pipeline to 150mm PVC to reduce annual pumping energy by 17,429kWh and cut annual costs by over $4,500. Three bore pump upgrades were also recommended. The farm is going ahead with the upgrade to three bore pumps.
One of the bore pumps will be replaced with a new pump and motor of approximately the same size, but as a new, high efficiency model, will deliver an additional five litres of water per second, reducing the pumping hours by 20 per cent and energy consumption by 30 per cent.
A Lockyer Valley fruit farm2 implemented all of their energy audit recommendations, which included lighting, refrigeration and irrigation. The 15kW irrigation pump is used every day to irrigate a number of different sized blocks on an undulating farm. The energy auditor contacted the original pump installer who advised that there were different blocks and duty points on the farm when the pump was originally installed. Although the pump has a variable speed drive, which was added some time ago, the assessment found the motor itself was worn and no longer suitable for the duty points. The new motor will be the same capacity, but the new, efficient model is predicted to increase productivity by around 10-20 per cent because of the increased irrigation flow, with irrigation efficiency improving from 4.36kWh/ML/m to 3kWh/ML/m. The farm has reduced annual costs by around $9,500 and will increase revenue due to the productivity improvement.
An Atherton Tablelands farm3 replaced a 55kW pump with a 45kW pump, adding a variable speed drive and moving the pump closer to the creek to reduce suction head. The farm has a centre pivot and lateral irrigator which are both different sizes and operate on a sloping part of the farm so the variable speed drive allows the pump to operate near its best efficiency point for both irrigators. A telemetry system has been installed so that the farmer can switch the pump remotely, saving a lot of trips to the pump at all hours of the day.
The farmer has also installed a 39kW Solar PV system with a 30kW inverter to power the pump.
Measurement and Verification (M&V) has found that irrigation system efficiency improved from 400kWh/ML to 251kWh/ML with a resulting cost saving of $34.80 per
megalitre pumped. The lower electricity consumption, combined with the addition of a solar system, has reduced the farms consumption from 130MWh to 70MWh per year, meaning it will be classified as a small customer. In conducting the M&V, the auditor found that the farm had not yet adapted to operating the irrigation mostly during the day when it could be powered by the solar and was still operating a larger period of time at night. Accordingly, higher savings are anticipated from a change to daytime pumping. With these and some efficiency savings to the farm shed, the farm will reduce energy consumption by 46 per cent and reduce carbon emissions by 48 tonnes per annum.
A Mackay cane farmer4 is replacing three Star Delta Starters with variable speed drives on centrifugal pumps ranging in size from 30kW to 45kW. Star Delta Starters have been commonly installed to reduce start up current. The pumps are being throttled to manage pressure to the irrigator as the pumps are oversized. The variable speed drives will manage the pressure efficiently by slowing the motor speed as well as reducing pressure to the irrigators without using valves. The auditor also recommended a number of other initiatives including installing a 10kW solar pump. All of the above projects will save the farm over 52,000kWh and $13,200 per annum with an outlay of $22,100.
Centrifugal pump and VSDs provide energy saving opportunity for horticulture grower
A horticulture grower5 has replaced a 30kW centrifugal pump with a new efficient model and a variable speed drive, as well as adding VSDs to an 11kW submersible bore pump and a 22kW centrifugal bore pump. The grower is expected to reduce power consumption from 56kWh/tonne to 49kWh per tonne saving 42,000kWh and $21,600 per year as well as 34 tonnes of carbon emissions.
The pumping requirements vary because the pump supplies water to a number of different irrigation blocks with different irrigation systems including drippers and booms. The bore level varies as well, with levels currently very low. On some blocks, the pressure is higher than required so it is managed by the grower by throttling with a valve at the discharge side of the pump. This significantly increases the friction losses, and therefore the amount of energy consumed per megalitre of water. The auditor has based the recommended pump on the most uphill position of the irrigation system and recommended
a variable speed drive so the pump speed can be reduced to provide the correct pressure to the lower blocks.
and time savings realised for Brisbane
A Brisbane nursery6 reported consistent product and time savings as two of the best outcomes of reducing the size of an irrigation pump as part of a group of efficiency projects which included hot water and lighting efficiency. The pump was reduced from 7.5kW to a variable speed 5.5kW, giving the nursery consistent water and pressure over different sized blocks. The nursery invested $12,000 to save $12,000 per year, reducing its power consumption from 130,000kWh to 73,000kWh per year, bringing them under the threshold for a large user and reducing carbon emissions by 28 tonnes.
Solar PV helps to reduce pumping costs
140 solar systems were recommended in the energy audits ranging in size from 5kW to 100kW, with 30kW the most common size; it is the largest inverter size that can connect to the electricity distribution network as a microembedded generator in Queensland. With some of their power provided by solar systems, farms have been able to reduce the consumption of grid energy for pumping and also adjust their irrigation strategy to irrigate during the day using solar power rather than in the evenings on lower tariffs.
VSDs reduce power consumption on Gatton horticulture farm
A Gatton horticulture farm7 is on track to reduce power consumption by 42 per cent by adding variable speed drives to nine submersible bore pumps under 7.5kW to allow for variable aquifer levels; and replacing two 7.5kW pumps with 5.5kW models with variable speed drives. The audit also recommended installing a soil moisture monitoring system to help manage irrigation scheduling as well as a 15kW solar PV system which are yet to be implemented. The average payback on all of the recommended projects is three years and the annual energy savings are estimated at 141,000kWh per year, reducing power consumption from 30kWh/tonne to 17kWh/ tonne and reducing carbon emissions by 114 tonnes per year.
Looking to the future of energy savings
Queensland Farmers’ Federation is working with industry partners on a number of other exciting energy transition projects including microgrids in agriculture and digital agriculture.
See the agricultural energy efficiency case studies at https://www.qff.org.au/newsroom/case-studies/ and subscribe to the QFF bi-monthly energy e-news https://rgc.us6.list-manage.com/subscribe?u=be9cc2409cc55bcb17498482a&id=531de30e19.
Please contact the team at energysavers@qff.org.au.
The Energy Savers Plus Extension Program is delivered by the Queensland Farmers Federation with support and funding from the Queensland Department of Energy and Public Works.
1. https://www.qff.org.au/newsroom/case-studies/mondure-irrigation-farm/
2. https://www.qff.org.au/newsroom/case-studies/gatton-fruit-farm/
3. https://www.qff.org.au/newsroom/case-studies/mareeba-irrigation-farm-2/
4. https://www.qff.org.au/newsroom/case-studies/mackay-sugar-cane-farm/
5. https://www.qff.org.au/newsroom/case-studies/laidley-horticulture-farm/ 6. https://www.qff.org.au/newsroom/case-studies/aspley-nursery/ 7. https://www.qff.org.au/newsroom/case-studies/gatton-horticulture-farm/
Inspired by recent events, I hope to clear up the continual confusion around net positive suction head (NPSH), specifically as it pertains to self-priming pumps on a lift application.
*Note this article was originally created using the measurement standard of United States Customary Units (USC) of feet and has been converted to metres for this forum, therefore some rounding differences may occur.
Yes, I have written numerous articles on NPSH, and I predict there will be many more after this one. There are two areas I wish to address in this column. First, we will look at why the tedious and elusive game of obtaining adequate NPSH can look like a game of whack-a-mole, trying to skirt the laws of physics. Secondly, some insight into the negative effects of a prolonged system “priming time” and why you do not want a pump suction line that is too big or too long.
The column will focus on NPSH available (NPSHa). Before we proceed, it is important to review and understand the equation/formula for the calculation of NPSHa in a suction lift situation. As I tell my students, “The formula is your friend”.
For simplicity, we will examine systems that are open to atmospheric pressure and assume the liquid is water. The
simple definition for a system in a lift condition is that the upper level (surface) of the liquid to be pumped is at a level below the centreline of the pump impeller.
If you are uncomfortable working the formula or are confused on how to determine and fill in the factors for your specific situation, I suggest you review my previous articles on this subject, especially July and August of 2018.1
Equation 1
NPSHa = habs – h vpa – hstatic – hfriction
Where:
habs = Absolute pressure head = A h vpa = Vapor pressure head = V
hstatic = Static suction lift = S hfriction = Friction head = F
For simplicity, I have renamed the four factors in Equation 1 as A, V, S and F (see Equation 1 for a definition of the assigned terms). The simplified formula can now be expressed in Equation 2 as:
NPSHa = A - V - S - F
Note that A is always positive and will normally be less than ten metres and the other three factors are all negative terms. Notice that if the three negative factors add up to be any number even close to ten metres, you will have no NPSHa.
As a paradigm shift, let’s turn things around a little from how we typically conduct the calculation. Normally we determine the four factors in the equation and calculate to find the value of NPSHa. Typically, in the field, we already know the NPSH required (NPSHr) for the pump. Further, we would also determine how much additional head we require/desire above the NPSHr for a reasonable NPSH safety margin.
Next, I suggest that we take the NPSHr value from the pump, add the desired NPSH margin and set that total on one side of the equation as equal to the four unknowns on the other side of the equation/formula.
For example, if the pump required three metres of NPSH and we wanted a 1.5-metre margin, then the NPSHr needs
to be at least 4.5 metres rather than three metres. We will designate this new factor as NPSH desired or NPSHd. NPSHd in this example is the sum of NPSHr (three metres) and the margin (1.5 metres) for the 4.5 metres of NPSH desired.
The previous formula would now look like this in Equation 3: NPSHd = A - V - S - F
Perhaps A - V - S - F ≥ 4.5 metres may be the better way to think of the equation because 4.5 metres is the desired minimum and more is acceptable. The absolute sum of the four factors (A, V, S, F) in the equation must total 4.5 metres or higher for the pump application to work correctly (satisfy the equation).
Next, we will examine each of the four factors one at a time to examine possible outcomes.
The A term is based on absolute pressure exerted by the atmosphere. We already stated that the system was open to atmosphere, but we didn’t state the site elevation above sea level.
For ease of working the problem, assume we are close to sea level and round down the normal sea level value of 10.33 metres (absolute) to ten metres. I like to be conservative in these calculations, so this is the reason why I rounded down.
The three remaining terms (V, S, F) are all negative and their sum total will be subtracted from the A term (ten metres), we can also reason that the sum of the three remaining terms must be ≤ 5.5 metres or the pump will not work properly. Assume the absolute total of the three terms is X and solve for X.
Equation 4
(10- X = 4.5) solve for X yields
10 – 4.5 = 5.5
From this step, you can surmise that the total (absolute) values of V, S and F must be less than 5.5 metres.
For the next step in the example, we will establish the negative static head (the lift) as 2.5 metres. Note that this term is an actual measurement, not a calculation. Consequently, the S term in our simplified Equation 5 now has a value of 2.5 metres. If S is 2.5 metres, then the sum of friction F and vapor pressure V total must be less than three metres.
Equation 5
5.5 = V + S + F
S was measured at 2.5 metres, so:
5.5 = V + 2.5 + F therefore: 3 = V + F
We need to view this as 3 ≥ V + F, where we are expressing the terms in their absolute values and not the negative terms from the formula. You can look at this mathematically, but I think it is more important to look at it as you have limits on how much friction and vapor pressure can be present. If the value is exceeded, the pump will not operate properly or at all.
Before we address the vapor pressure, I want to skip ahead to the friction factor F. The total friction head was calculated at 1.11 metres, but to be conservative and to also allow for “aging” of the system, we will round off to 1.2 metres of friction head. Now we have a value of 1.2 metres to assign to the F term in the equation. From this, we can calculate that we now have 1.8 metres of possible margin before we calculate the value of the vapor pressure term (Equation 6).
Equation 6
3 = V + 1.2, or V = 1.8, and again we should think of this as V ≤ 1.8
Vapor pressure in the US-C system is normally expressed in pounds per square inch absolute (psia), consequently you will need to convert to head ([psi X 2.31] ÷ [specific gravity] = head of vapor pressure absolute). In the SI system, vapor pressure may be expressed in pascals or kilopascals (kPa) or even sometimes in Torr or mmHg. Regardless, you will need to convert to metres of head (absolute) to work the factor in this equation.
The V term (vapor pressure) seems to be an almost insignificant factor for liquid temperatures near ambient, which can be misleading and lure you into the false sense that it is not important. For a more detailed explanation of vapor pressure, please refer to my detailed column in the April 2018 issue of Pumps and Systems magazine.
Realise that as the liquid temperature increases, so does the vapor pressure (V) and it does so at an exponential rate. At around 20°C (68°F), the value of V would only be 0.237 metres (0.78 feet) absolute, but at 32.2°C (90°F) it would increase to 0.494 metres (1.62 feet) absolute and at 71°C (160°F), it would be 3.42 metres (11.21 feet) absolute, and at 93.3°C (200°F) it would be 8.43 metres (27.65 feet) absolute. Hint: this is the main reason you will not see a self-primer on applications with a static lift at liquid temperatures over 62°C. You do not need to calculate the value of vapor pressure, you simply look it up in a handy-dandy trusted chart. I like to use the Cameron Hydraulic Data book
For our example, let’s assume the water is 25°C and so the corresponding V will be 0.3232 metres absolute, which I will round off to 0.32 metres absolute.
With this value of 0.32 metres for the vapor pressure, we can finalise/satisfy our equation (Equation 7).
Equation 7
V ≤ 1.8? Yes, 0.32 is less than 1.8
We can surmise that this application will work, and we even have an extra margin of approximately 1.5 metres.
In the previous example, the water was near ambient temperature and the pump was close to the sump (suction source) with a properly sized suction pipe. I recently witnessed performance issues with two separate installations where the pumps were placed a long distance from the sump, and in one instance the suction pipe was several sizes bigger than it needed to be.
The larger pipe size reduces the friction factor but significantly increases the air volume to be removed. Both factors (pipe length and diameter) increase the air volume and require the pump to “work” harder and spend more time in the air removal process.
During the priming process, the water in the priming cavity/ chamber is being recirculated and churned by the impeller. This shearing action adds heat and increases the liquid temperature rather quickly. It is difficult to accurately calculate how fast the liquid temperature will rise for your installation as there are many factors involved but note that the amount of power (kW) and speed are two major factors. Be aware that 3,000 rotations per minute (rpm) units will heat the liquid about eight to ten times faster than 1,500 rpm units.
It is not uncommon for the liquid in the chamber on the higher-speed pumps to heat up at the rate of 20 to 25 degrees Celsius a minute. Some of that heat will be dissipated to ambient, but my point is that the liquid does heat rather quickly and that changes the vapor pressure. As the temperature and vapor pressure increase, the risk/probability of flashing the liquid in the priming chamber also increases. Additionally, the liquid surrounding the mechanical seal will also heat up and flash to vapor (not all mechanical seals are subjected to this seal chamber situation, and it depends on the manufacturer, model and design).
In any open system with a self-priming pump lift application, vapor pressure, friction and static lift are not your friends. You do not have an infinite amount of available positive energy to combat them. Your only friend is absolute pressure. Design the system to have short priming times by placing the pump near the source and size the suction pipe properly.
1. Equation 1 is valid for a suction lift condition. If the system was in a flooded condition, the static head term would be positive.
2. Only consider the suction side of the system in a NPSHa calculation.
3. All the factors in the formula must be expressed as absolute values.
4. All factors need to be consistent. That is, they should either all be in US customary units of feet or units of metres for (SI) metric calculations.
5. Since we are dealing with a static head that is negative, it is designated as a “lift” situation.
6. Calculate the system NPSHa for the worst-case lift/ scenario. What is the lowest liquid level that will be experienced?
7. Remember that the critical submergence must also be calculated. Pump performance can easily be diminished by air entrainment.
8. The head due to vapor pressure is a direct function of the liquid temperature and is always a negative term.
9. The head due to friction is always a negative term.
10. The head from absolute pressure is, in essence, the atmospheric/barometric pressure and must be corrected for the site elevation above sea level.
11. The absolute pressure (head) can theoretically be as low as zero, but it cannot be a negative term. Since we are working with an open system in a lift condition, it is unlikely that the absolute pressure would ever be less than 3.6 metres.
The original version of this article appeared in Pumps & Systems magazine. Visit pumpsandsystems.com for more of Jim Elsey’s columns.
Jim Elsey is a mechanical engineer with more than 50 years of design and operating experience, primarily focused on rotating equipment reliability in most industrial applications and markets worldwide. Elsey is GM of Summit Pumps and an active member of the American Society of Mechanical Engineers, the American Society of Metals, the National Association of Corrosion Engineers and the Naval Submarine League. Elsey is also the principal of MaDDog Pump Consultants LLC. He may be reached at Jim@SummitPump.Com.
The PIA’s Australian Pump Technical Handbook is a cornerstone text for the Australian pump industry and, in our opinion, a must have for anyone who deals with pumps on a regular basis. In this ongoing series, we feature abridged chapters from the classic book to showcase the various areas covered and to reacquaint readers with the technical aspects of pumps. In this issue, we continue exploring energy efficiency in pumping systems, focusing on drives and controls.
There are several major classes of driver that are commonly used in pump applications:
• Electric motors
• Internal combustion engines
• Steam turbines
• Compressed air
• Hydraulic motors
Electric motors
Electric motors are probably the most economical and common driver for pumps, and it is generally not complicated to select a motor as a driver.
To select the most energy efficient electric motor, the following should to be considered:
• The motor should not be oversized – electric motors meeting International Standards come in specific ratings (i.e. 1.1kW, 2.2kW, 3kW, etc). Normally a motor would be selected in a standard-size up from the maximum kW absorbed by the pump, for example, for 13.4kW absorbed, a 15kW motor would be selected. However, if the pump kW absorbed is less than five per cent below a standard motor size, the next size up should be selected
• The motor efficiency from several manufacturers should be checked in order to maximise the motor efficiency relative to the capital cost. This is particularly important for larger motors where a one per cent efficiency improvement can reduce the lifecycle cost of the pumpset by an amount that could make a cheaper but less efficient motor look expensive
• The motor should be MEPS Hi Efficiency certified Electric motors come in all shapes and sizes, and can be categorised into two main types:
• Standard motors
• Special motors
Standard motors are available as DC motors in low power sizes and AC induction motors. In Australia, the most common type of standard motor found in pumps are AC induction motors.
AC induction motors
Some fundamental points that should be considered when applying a squirrel cage induction motor to a pumping applications, include:
• Rating voltage – the motor winding should be chosen to suit the power supply available
• Standard voltages – these include 240V, 415V, 690V, 1,000V, 3.3kV, 6.6kV, 11kV and 33kV. It should be remembered that the higher the voltage, the lower the current for the same power rating
• Rated speed – the motor windings should be configured to suit the rotational speed of the motor. Standard speeds include: 2-pole (nominally 3,000rpm); 4-pole (nominally 1,500rpm); 6-pole (nominall 1,000rpm); and 8-pole (nominally 750rpm). Pump performance curves are often based on these speeds
• Rated torque – it should be established how much torque an application needs, and a motor with a rated power that suits the starting and running requirements of the pump should be selected. This is particularly important for many positive displacement pump applications, but less so generally for rotodynamic pumps which don’t have high starting torque requirements
Most pump applications simply need the pump to start and stop as required to meet the demand from the user. There are a variety of commercially available motor starting methods, which are summarised in Table 1.
Table 1.
The preferred starting method would be determined by the conditions of service for the pump and local restrictions on
starting currents for electric driven machines. The different options for starting devices should be reviewed carefully to ensure the most appropriate one is selected.
Variable frequency drive (VFD) motor control
For motors with a speed control facility, the methods for selecting the required speed can range from fully manual to fully automated. Many VFD systems utilise PLC controllers to achieve a particular control philosophy. Common control philosophies include:
• Constant pressure (for booster systems, etc)
• Constant level (for sumps, etc)
• Surge minimisation
Typical VFD control systems have been developed to accept signals for a variety of condition monitoring devices:
• From a pressure signal which allows a VFD to maintain a set system delivery pressure irrespective of what the system flow demand is, for example, irrigation systems where the pressure requirement is constant but flow varies depending on the size of the area being irrigated
• From a level sensor which allows a VFD to maintain a set level in a tank or sump irrespective of how the flow varies to or from the tank or sump, for example, a sewage sump with variable in-flow
• From a flow meter to allow a VFD to alter the pump speed up or down to maintain a set system flow, for example, in a process situation where a steady flow must be maintained for process purposes
• From a temperature sensor allowing a VFD to maintain a set system temperature by varying the flow up or down, for example, in a heating system where flow is increased as the temperature falls below setting, and decreased as it rises above setting
Using a VFD can also help maximise pumping system efficiency, particularly when the system demands a variety of duty points. However, there are some important considerations:
• Any VFD has its own internal losses, which should be taken into account
• Electric motors must be suitable for projected VFD waveforms and not overheat at low rotational speeds due to poor fan performances
• Special electrical installations methods should be adopted, i.e. screened cable
• Equipment may have a reduced operational life due to unexpected factors
When used correctly, VFDs can save a considerable amount of power. However, there are circumstances where VFDs are inappropriate, effectively turning them into an expensive soft starter which spends the majority of its life running at full speed.
• They should not be used as a safety net for poor system design
• A proper cost versus benefit analysis should be conducted to justify the additional investment
Internal combustion engines are normally used to drive pumps in situations where there is no electric power available or as a standby option (black start) where electric power failure cannot be tolerated.
One of the advantages of using an engine to drive a pump is that it can run over a range of speeds often by manual or remote adjustment, therefore allowing the pump to run at the speed that optimises its efficiency for a particular duty. This
minimises the engine size, however, it needs to be balanced with the engine’s fuel consumption.
When selecting an engine with the best combined efficiency, it should be remembered that engines have ratings which are based on whether it runs continuously – 24 hours a day – or intermittently – eight hours a day maximum. At its continuous rating, an engine’s power is limited to a lower amount than when rated intermittently. This means that a pumpset that is operated intermittently can possibly use a smaller engine than one that must run continuously.
Once it has been established whether a continuous or intermittent engine is required, an engine can be selected for the rating for the power required to run the pump. However, the selected engine should not be oversized. Once the engine power and speed have been selected, it is recommended that several engine makes are considered to determine the most fuel efficient engine for the application.
While these considerations should allow the selection of the most energy efficient engine to drive the selected pump, however, it should be noted that engine maintenance is generally higher than for the same size electric motor.
Steam turbines are often used in plants where steam is generated as part of the main process. The are commonly found in power station, process plants and refineries (petrochemical, sugar, etc), and provide a high speed of rotation either for direct drive or through a reduction gearbox, making it relatively economical to operate the pumps energywise, which would probably not be the case if one generated steam to power the pumps alone.
If steam is available at an economic cost, it can be an energy efficient option provided that all the ancillary costs are properly taken into account.
As a driver, compressed air is used most commonly to operate air operated diaphragm pumps and sump pumps in the construction and mining industries.
While compressed air is appropriate in certain circumstances, it is an expensive and generally inefficient way to power pumps because, as well as the energy used to drive the pump, energy has to be expended to compress the air. In addition to high energy consumption, the nature of compressors, air motors, etc. generally require a higher than normal maintenance.
For energy conscious pump users, compressed air should only be used when no other practical alternative is available.
As a drive method, hydraulic equipment can be used in two ways:
• Hydraulic cylinders on single mechanical diaphragm pumps
• Using hydraulic motors to drive pumps (mainly submersible pumps)
Both methods can be used to drive other types of centrifugal and positive displacement pumps.
The type of drive requires a hydraulic power unit to provide oil flow and pressure, this means that they have similar inefficiencies to a compressed air system. Hydraulic motors and rams generally require higher maintenance than electric drives.
For pump users that are energy conscious, they should try to avoid using hydraulics to drive a pump, however, this type of drive does have benefits in specialised applications.
Further information and detailed diagrams, equations and schematics can be found in the Australian Pump Technical Handbook, available from the PIA website. In the next edition of Pump Industry, we continue to explore energy efficiency in pumping systems, looking at lifecycle costs.
The pump industry relies on expertise from a large and varied range of specialists, from experts in particular pump types to those with an intimate understanding of pump reliability; and from researchers who delve into the particulars of pump curves to experts in pump efficiency. To draw upon the wealth of expert knowledge the Australian pump industry has to offer, Pump Industry has established a panel of experts to answer all your pumping questions.
This edition of Ask an Expert will look at a particular challenge all maintenanceintense progressive cavity pump applications face on a regular basis; how can quick, easy and cost-efficient maintenance solutions reduce downtimes to a minimum?
All pump applications that require a stable process and minimal downtimes rely on efficient maintenance of pumping equipment. The larger the pumps are, the more difficult maintenance becomes. Thanks to creative engineers, some easy-maintenance solutions can significantly reduce downtimes and save costs.
Progressive cavity pump maintenance: a blessing and a curse
The optimal duty point of a pump is of utmost importance for the performance of the plant’s operating process. Rotor, stator and mechanical seal can face tremendous forces within the pump. Abrasive or corrosive mediums constantly abrade the surfaces and therefore impact on pump performance. Thus, maintenance is a regularly due process that
unfortunately leads to downtime of either part, or the whole of a plant. Additionally, the task requires allocation of trained staff, the right spare parts, perhaps some special tools, plus dismantling of pipework and sometimes moving the pump out of place. This means maintenance always consumes human and financial resources as well as valuable time. The absence of proper and regular maintenance can lead to catastrophic failures and long downtimes, whereas a thoroughly maintained pump assures smooth plant operation. Simplified maintenance by way of MIP (Maintain-in-Place) pumps has been a feature for some progressive cavity pump manufacturers for more than ten years, but designs have generally been limited to smaller sizes with some limitations on flow rates and pressures.
The individual components of large PC pumps often weigh several hundred kilos. From the piping to the pressure branch, stator and suction casing, at times mechanics must dismantle virtually the entire pump for maintenance. Occasionally, transporting the pumps to a workshop is necessary. The maintenance can therefore extend over several days, meaning high costs and an enormous amount of work for the plant operator.
The good news is that it is now possible to change the rotor, stator and mechanical seal without removing the suction casing or pressure branch from the pipeline or dismantling one of the joints. This means no removal of pipework or installation of heavy lifting and transportation equipment. Only a few progressive cavity pumps manufacturers offer a Maintainin-Place solution, even less offer this feature for large PC pumps. The best solutions enable a quick access to the rotor and drive joint, which can save up to 80 per cent maintenance time. This paves the way for preventive maintenance. Regular, easy and quick inspection of drive side components results in increased uptime and lowers the lifecycle costs of the
pump. This is especially important in critical applications that require high operational safety and performance as well as absolute reliability such as wastewater management or
Peter Vila, Managing Director of SEEPEX Australia, is a progressive cavity pump expert. He has been involved with pumps for over 40 years. Peter spent the first five years repairing pumps and the following 35 years in technical sales, 20 of which have been with SEEPEX progressive cavity pumps. For more information on progressive cavity pumps, please contact SEEPEX Australia on (02) 4355 4500 or at info.au@seepex.com
Pump applications may involve handling liquid and gas mixtures either as part of the process or as a result of unwanted application conditions or upsets. Although symptoms may be similar to cavitation, the process is a little different.
Cavitation is the formation and subsequent collapse of vapour bubbles that are formed when pressure within the pump drops below the vapour pressure of the pumped product. As pressure increases within the pump, the vapour bubbles recondense (implode) resulting in shock waves that cause damage to pump components.
The pumping of entrained gas is different in that the gas is non-condensable. Centrifugal action tends to cause a separation between the liquid and gas due to differences in density. This centrifugal action moves the liquid to the outside and concentrates the gas in the eye of the impeller. This restricts the flow area for the liquid causing significant pressure drop and hence cavitation even though NPSH calculations will indicate that cavitation should not occur.
The proper selection of a centrifugal pump for liquid and gas (two-phase) mixtures is highly dependent on the amount of gas and the characteristics of the liquid. The presence of entrained gases will reduce the hydraulic performance of centrifugal pumps and can potentially cause loss of prime. Standard centrifugal pump designs can be used for entrained gases up to four per cent by volume.
For gas entrainment values above four per cent, specifically modified impellers can be used effectively. Pump performance corrections are required in all cases with gas content from around two per cent. Gas concentrations above ten per cent can be handled, however pumps designed with specific gas handling characteristics are required e.g. vortex impeller pumps, side channel pumps and regenerative turbine pumps.
Most centrifugal pumps can handle low concentrations of entrained gas although continued gas accumulation may cause the pump to vapour lock and lose prime. Figure 1 below shows performance variation as gas concentrations vary from zero per cent to ten per cent. At concentrations up to two per cent, the impact is relatively insignificant. Impact on performance is still reasonably acceptable up to four per cent.
1: Head and power vs capacity zero to ten per cent air by volume for normal running clearance.
As the percentage of gas increases further, the performance begins to quickly deteriorate until the pump becomes unstable and loses prime. Increasing the running clearances between the impeller and pump casing (.004 to .008mm) allows for additional leakage and this may assist in preventing loss of prime at the higher gas concentrations. Much testing has been done by various manufacturers, however the many variables impacting on the effect of gas entrainment does not allow for presenting specific selection information.
Volvo Penta. Robust, fuel efficient industrial diesel engines that keep running even in the toughest conditions. Easy to install, operate and maintain. A powerful partnership you can trust all the way from the drawing board throughout the operational life of your engine. Competitively priced complete power-pack units ready for delivery Australia wide with a local support team on hand 24/7. To find your nearest dealer visit www.volvopenta.com
A leading Australian water utility required improved process efficiency and drastic cuts in their increasing annual maintenance costs. The ITT Blakers pump engineering team rose to the challenge, providing upgraded, fit for purpose drop-in replacements.
Trusted to deliver water solutions like this for more than 40 years, ITT Blakers have been supplying horizontal and vertical pumps to municipal water facilities, distribution networks, water treatment and flood control stations throughout Australia.
• Lifetime, Reliable Performance Confidence.
• Optimized, Trusted OEM TCO Maintenance.
• Enabled by Accurate Remote Monitoring and Conditioning.
• Proven by Extensive Track Record.
• 100% Australian, Responsive Expert Local Support.
As a global major OEM, ITT Goulds Pumps, with its 170 years chemical processing heritage, provides a broad range of sealed and sealless chemical pumps to “polish” water treatment plant effluent making it safe for drinking.
ITT Blakers provides a complete range of aftermarket services reducing equipment total cost of ownership via reliability improvement, along with parts, upgrades, repairs, inventory services, life cycle design, monitoring and control.
The i-ALERT Ai Machine Monitoring System provides customers with a low cost, integrated package, flexible predictive maintenance program for any level of operation, scalable to customers’ monitoring requirements.
SENSORS
Monitor tri-axial vibration, temperature, run-time hours and pressure
MOBILE APP
Monitor your machine right from your phone with the free mobile app
GATEWAY
Add remote monitoring capabilities by leveraging remote data collection
DIAGNOSTICS
Built in intelligence automatically detects and diagnoses machine issues
Ai PLATFORM
Monitor all of your i-ALERT sensors and machines from a simple web app
DRIVEN SKIDS & TRAILERS
HWR SERIES
VORTEX SERIES
WET PRIME SERIES
VERTICAL TURBINES
SUBMERSIBLE MOTORS
END SUCTION CENTRIFUGAL
DRIVES & PROTECTION
CLEANWATER CENTRIFUGAL
VR SERIES
A comprehensive range of Auto Prime diesel packaged options for fixed and portable installations.
Wear-resistant pumps manufactured with high-chrome white iron to maximize resistance against destructive abrasives and maintain peak performance in light slurry applications.
A unique pumping solution that eliminates costly and disruptive downtime by passing through the most challenging solids using a recessed impeller.
Self-priming pumps designed for reliable solids and clear liquids handling. Continues to reprime automatically after initial priming.
Submersible turbine pumps available in custom configurations to meet demanding application requirements.
Our submersible motors are tough, built to last and come in a variety of construction options.
Close-coupled, electric motor driven pumps available in singleor three-phase standard voltages to fit your site requirements.
Equip a Franklin drive to protect, monitor, and meet the different needs and demands of each application with the same pump.
Centrifugal pumps that feature heavy-duty ductile iron volutes, designed to handle tough applications with high efficiency.
Vertical multi-stage pumps are available in high- and low-speed models for superior durability, efficiency, and performance in a wide variety of applications.