Upgrading and expanding Melbourne’s wastewater infrastructure
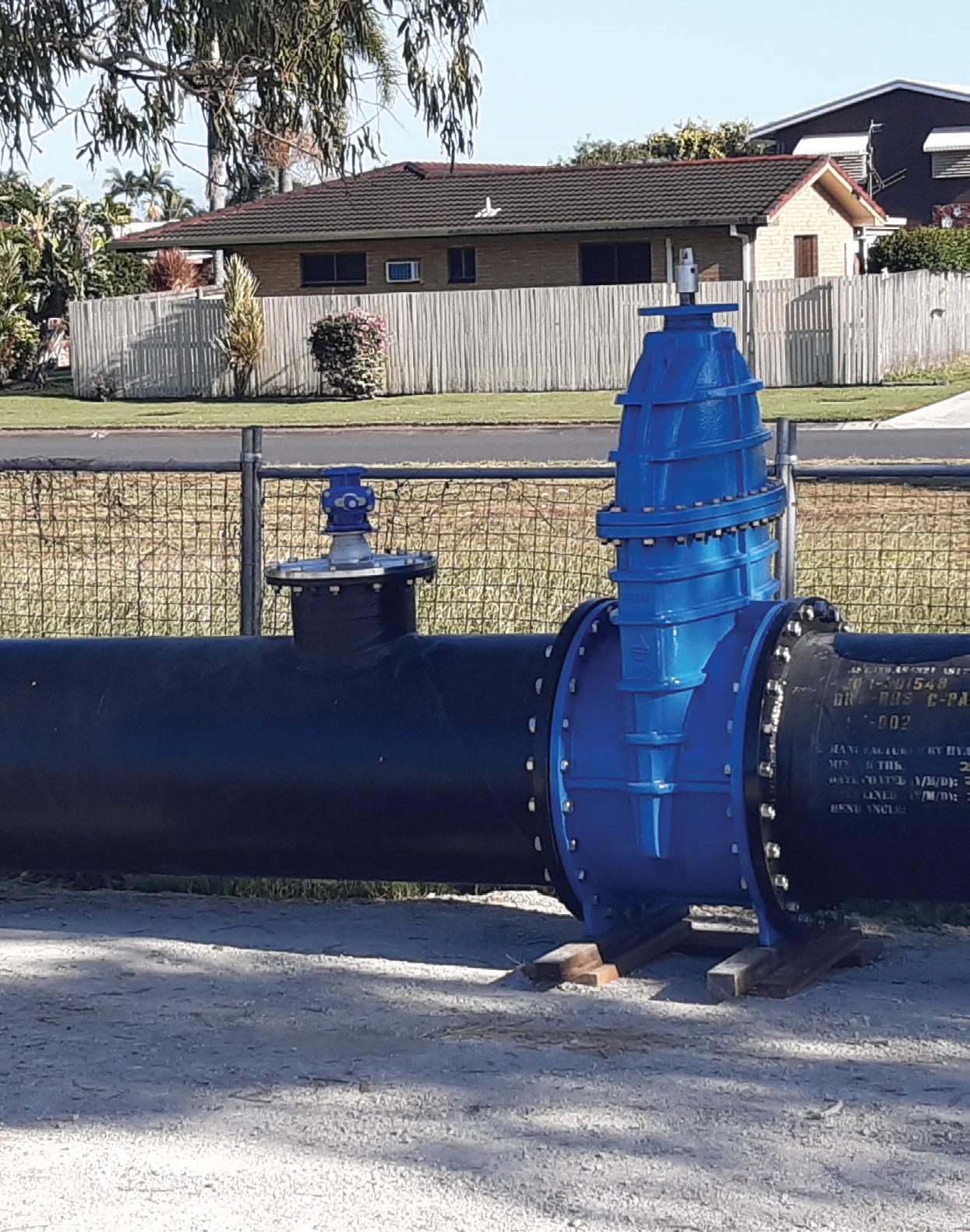
New isolation and air valves FOR MACKAY
State of the Industry 2023: WHAT’S IN STORE?
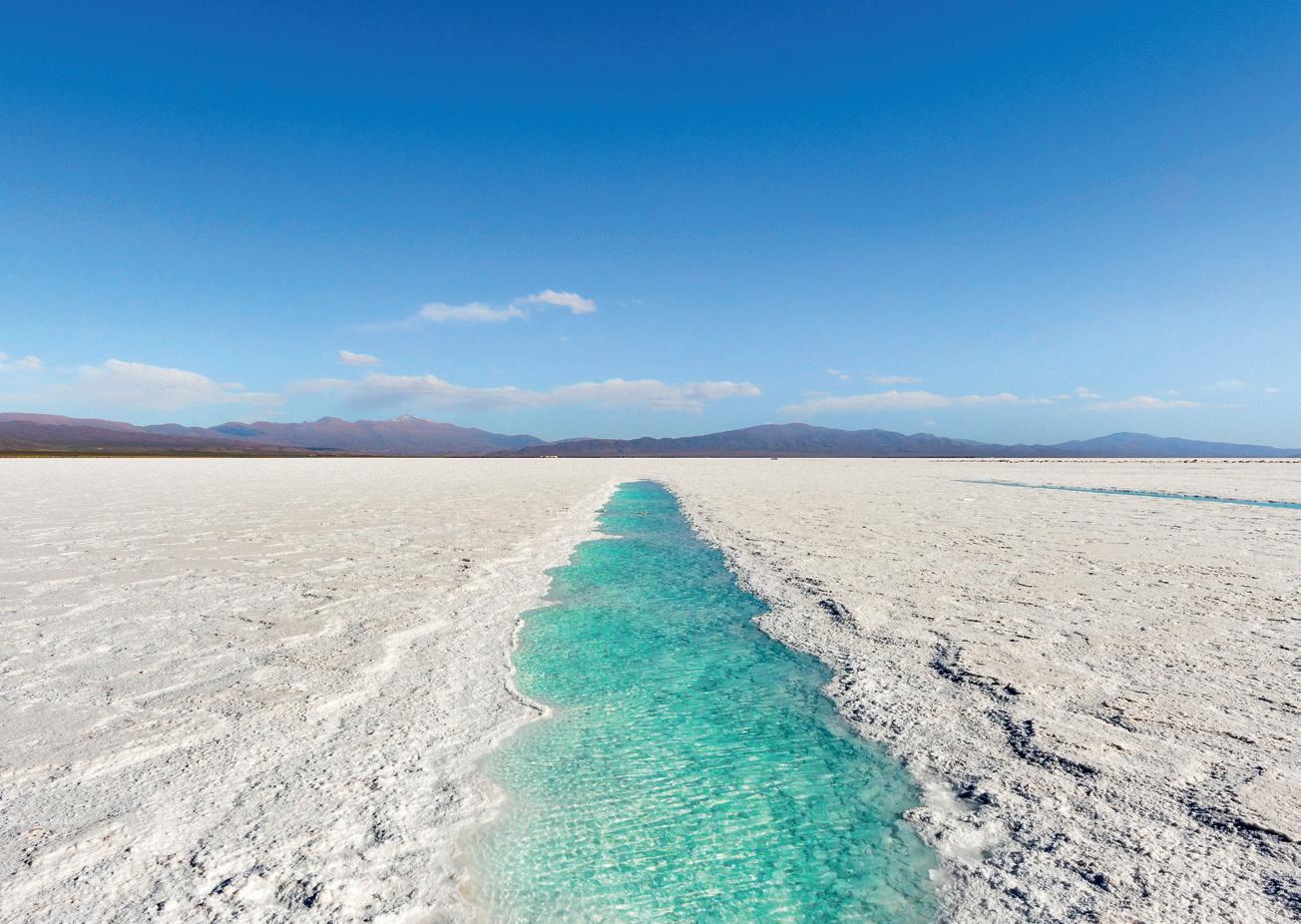

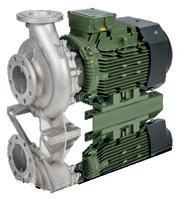

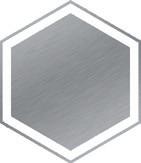

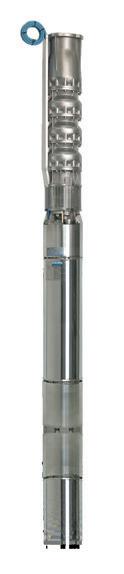

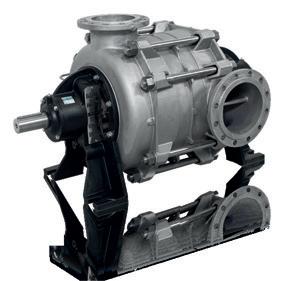
Upgrading and expanding Melbourne’s wastewater infrastructure
New isolation and air valves FOR MACKAY
State of the Industry 2023: WHAT’S IN STORE?
Polymaster’s unique Enclosed IBC Bund solves many of the problems associated with IBC storage and chemical/fluid decanting in a weather resistant, purpose-built enclosure.
Æ Full weather protection – stops rain entering the enclosure
Æ Easy forklift loading with wide forklift access from both side and back
Æ 250ltr day tank
Æ Lockable cabinet to keep system secure
Æ Venting by two sides
Æ Viewing windows incorporated into the doors
Æ 110% bund capacity complies with AS3780
Æ Sight tube and low-level alarm available
Æ Chemical resistant – high grade polyethylene construction
Hello all and welcome to the Summer Edition of Pump Industry Magazine. I notice temperatures starting to climb already, now just waiting for the humidity to arrive here in Brisbane.
As we draw to the end of another year, we all ponder on what 2023 might look like for our Industry. We are a very diversified group which includes mining, oil and gas, energy, chemicals, municipal, water and wastewater treatment, industrial, irrigation, horticulture, fire protection, and building services to name just a few ranging from large multimillion dollar projects right down to small household pumps.
Currently we continue to see pent up demand for our services and products across all sectors bolstered by government infrastructure and private investment spending. In talking to colleagues at our recent AGM, it seems the order books continue to fill with work extending well into 2023 which augurs well for the industry.
that allows a person in Queensland to exclusively service, repair and maintain pumps without a Plumbers Licence.
PIA has petitioned the Department of Energy and Public Works to review this anomaly, asking for a special dispensation for PIA Members. We understand the issue was tabled at the Services Trade Council (STC) meeting on 30 November.
The STC was established under the PD Act 2018 to provide a voice for the service trades and to protect the public’s health and safety and the environment. The STC promotes and enhances the QBCC’s licensing of plumbing and drainage tradespeople.
We await the outcome of the STC meeting, which hopefully will provide a way forward; how this might manifest itself remains to be seen. PIA would like to see some form of concession, regulatory change or maybe the creation of a new Pump Service Licence based on experience, competency, knowledge of pump systems, best practice etc.
Pump Industry Australia Incorporated C/-340, Stuarts Point Road Yarrahapinni NSW 2441 Australia Ph/Fax: (02) 6569 0160 pumpsaustralia@bigpond.com www.pumps.org.au
PIA Executive Council 2023
John Inkster – President Brown Brothers Engineers
James Blannin – Vice President De.mem – Stevco
Kevin Wilson – Treasury/Secretary Executive Officer
Alan Rowan – Councillor Executive Officer – Publications and Training, Life Member
Ken Kugler Executive Officer – Standards, Life Member
Steve Bosnar – Councillor Franklin Electric/Pioneer Pumps
Geoff Harvey – Councillor Irrigation Australia
Joel Neideck – Councillor TDA Pumps
Jamie Oliver – Councillor Grundfos Pumps
Mat Arnett – Councillor Ebara Pumps
Michael Wooley – Councillor Tsurumi Pumps
Billie Tan – Councillor Regent Pumps
Is this the "calm before the storm" before the northern hemisphere "headwinds" come our way? Maybe, but my belief is that our industry is well positioned to “weather the storm” such is the continuing need and demand for our resources both in agriculture and mining.
In mining we can expect to see large offshore investment in the search for alternative supplies of rare earths. Australia is the world's fourth largest producer of rare earths, holding 3.4 per cent of the world's resources.
So in spite of growing inflation and higher interest rates, and while we expect economic growth to slow below trend in the second half of the year, the strength of the labour market with a low unemployment rate we may only experience a soft recession. Let’s hope this is the case.
At our AGM on 14 November, your PIA Council was reelected to serve another year. We are privileged to serve the pump industry community and will continue to work for you as best we can.
There were 66 attendees at the AGM including those who attended via Zoom courtesy of Monkey Media.
The dinner afterwards was well attended with over 80 Members and colleagues enjoying the splendid facilities and views on offer at the Commonwealth Golf Club in Oakleigh. It was a cold windy day but there were a few hardy individuals out there defying the Melbourne weather.
A topic that received significant discussion at the AGM was the ongoing dialogue with the Queensland Department of Energy and Public Works where under the PD Act 2018 there is no Class of Licence or Restricted Licence
The findings of the STC are of extreme importance to all of you because if left unaddressed it could have a significant bearing on business with very high fines potentially being applicable. That said the dialogue to date has been constructive and it is hoped we will have an opportunity to discuss the matter further in the New Year.
Also of interest to Members but not raised at the AGM is the mystery around the Regulatory Compliance Mark (RCM) regarding the electrical classification of submersible pumps whereby they will move from a Level 1 low risk device to a Level 3 device. The RCM is a trademark owned by the electrical operator that represents compliance with the Electrical Equipment Safety Scheme (EESS). For electrical safety, in scope electrical equipment cannot be sold unless the item is marked with the RCM in compliance with AS/NZS 4417.1 and 2.
PIA is seeking further clarification with the EESS regarding the matter and its application
And just a reminder to you all that the Pipe Friction Handbook has been updated and that the 6th Edition of the Pump Technical Handbook was released in September with 40 per cent more content; a must have on your desk or library.
I take this opportunity to welcome back our Councillors, Secretary/ Treasurer, Executive Officers and Monkey Media as our Marketing and Communications Partner.
Thank you for your continued support of Pump Industry Australia.
Wishing you all a safe and happy Xmas and New Year and a prosperous 2023.
John Inkster – PresidentScan to subscribe to Pump Industry Magazine’s weekly newsletter – delivered to your inbox every Thursday afternoon.
ABN: 36 426 734 954
C/- The Commons, 36–38 Gipps St, Collingwood VIC 3066 P: (03) 9988 4950 monkeymedia�com�au info@monkeymedia�com�au pumpindustry com au magazine@pumpindustry com au
Managing Editor: Lauren Cella
Assistant Editors: Rebecca Todesco, Stephanie Nestor
Journalist: John Thompson
National Media and Events Executives: Rima Munafo, Brett Thompson, Christine Circosta
Design Manager: Alejandro Molano
Senior Designer: Luke Martin
Designers: Ozlem Munur, Danielle Harris
Marketing Manager: Radhika Sud
Marketing Associate: Andie James
Digital Marketing Assistants: James Holgate, Jackson Barnes, Natalie Ta
Publisher: Chris Bland
GM Growth and Strategy: Laura Harvey
ISSN: 2201-0270
This document has been produced to international environmental management standard ISO14001 by a certified green printing company.
This magazine is published by Monkey Media in cooperation with the Pump Industry Australia Inc. (PIA). The views contained herein are not necessarily the views of either the publisher or the PIA. Neither the publisher nor the PIA takes responsibility for any claims made by advertisers. All communication should be directed to the publisher.
The publisher welcomes contributions to the magazine. All contributions must comply with the publisher’s editorial policy which follows. By providing content to the publisher, you authorise the publisher to reproduce that content either in its original form, or edited, or combined with other content in any of its publications and in any format at the publisher's discretion.
Acontract for the construction and operation of an advanced wastewater recycling facility, to be built in Western Sydney, has been awarded by Sydney Water.
Sydney Water awarded the contract for the Upper South Creek Advanced Water Recycling Plant (AWRC) to a consortium of John Holland, TRILITY, GHD and Jacobs
Operating at full capacity, the facility will treat around 70ML of wastewater each day and produce high-quality treated water for sustainable use in homes and businesses across Western Sydney, and biosolid products for use in agriculture.
Sydney Water Managing Director, Roch Cheroux, said the plant is an important piece of infrastructure for the region and will leave a positive legacy for the communities of Sydney.
“AWRC will produce high-quality water suitable for a wide range of non-drinking uses for homes, businesses, industrial sites, agriculture and for the watering of public open spaces,” Mr Cheroux said.
The world-class facility will be located between Kemps and South Creek and service the Aerotropolis and Western Parkland City.
John Holland will be responsible for the design and construction. GHD and Jacobs will provide engineering and design services, while TRILITY will provide operations and maintenance advice as the project is delivered.
In a joint venture with John Holland, TRILITY will be responsible for the operations and maintenance of the facility for up to ten years once completed.
John Holland’s General Manager of Water and Optimisation, Margaret Riley, said she’s thrilled to continue a long-term
left) TRILITY
Francois
collaboration with Sydney Water alongside partners TRILITY, GHD and Jacobs.
“It’s exciting to launch a project with such industry leading circular economy ambitions and Sydney Water is to be congratulated on its vision,” Ms Riley said.
TRILITY’s Managing Director, Francois Gouws, echoed the sentiments of its joint venture partner.
“It’s a real privilege to be working in collaboration with Sydney Water and alongside our partners John Holland, GHD, and Jacobs on such an exciting project, and one with motivations to drive innovation and a circular economy,” said Mr Gouws.
The Upper South Creek Advanced Water Recycling plant is due to be operational in 2026.
Kelair Pumps Building & Fire Division is one of the most technically-competent suppliers in Australia. We can provide a complete range of fire sprinkler pumpsets for all applications, fully compliant to technical specificiations.
- Purpose built to individual requirements
- Compact, pre-fabricated, complete packaged solutions
- Fully tested to AS2941/ISO9906 and pre-commissioned
- Turnkey installation saves time and labour costs
- Simple to mobilise and transport
- Routine maintenance packages also available
We know the importance of choosing the right equipment to match your process. With our extensive range of pumps, first class customer service and ongoing comprehensive support, Kelair Pumps are second to none when it comes to your pumping requirements.
The New South Wales Resources Regulator issued a safety alert after a maintenance contractor had to swim to shore when a pontoon pump overturned and sank his boat.
The contractor was working at Ravensworth coal handling processing plant (CHPP) in the New South Wales Hunter Valley when tasked with servicing a pump on a pontoon on 17 August 2022.
The worker used a boat to access the pontoon.
The pontoon and pump configuration had a dry weight of about 15.7t and a wet weight (fuel/water in pump line) of about 17t. The pontoon had a cube container filled with water on one side as a ballast control.
While carrying out the service, the worker identified that a pulley on the primer pump (vacuum) was faulty.
He had taken off his floatation device to carry out his work, as it was not required by the mine operator.
The primer pump was removed while draining the water line and put into the boat.
The subsequent change in the centre of gravity of the whole unit caused the pontoon to overbalance and overturn.
Within minutes, the worker noticed the pontoon tilt and jumped in the water to swim 30m to the bank, without a floatation device. The pontoon then overturned and dragged the boat under the water with it.
Fortunately, the worker was not injured.
Initial investigations by the mine operator identified:
1. The site standard for working on or near water was not complied with
• Verify awareness of the roles and responsibilities for maintaining compliance to their site’s standards for working on or near water
• Review the use of work authorisation standards
• Review safe work systems for this type of task considering:
» The requirement for wearing flotation devices on pontoons
2. The work authorisation for pump maintenance did not identify any additional controls associated with a body of water
3. No operational risk assessment was in place that identified the flotation characteristics of the pontoon and pump
The New South Wales Resources Regulators recommends that mine operators should:
» The requirement for a spotter while undertaking maintenance activities on water
» Emergency response capability around water
» The suitability of boats for transporting workers and equipment
• Consider building a jetty for longterm access to pumps on dams
The Sunshine Coast utilised a technique never-beforeseen in the area to help replenish Maroochydore Beach, importing sand from Moreton Bay and placing it in the water, about 300m off the beach.
The project – which was expected to commence in November – deployed a method called nearshore nourishment, which involves a dredge that will collect sand from the Spitfire Channel and transport it to Maroochydore Beach for release, potentially using two techniques.
One technique may include dropping the sand from the bottom of the barge and the other will spray the sand in a rainbow shape into the water, with the results of both methods then being compared.
It was hoped that waves, currents and tides would then deposit the sand onto the beaches providing an additional buffer against future storms and coastal erosion.
Strict safety measures were in place on the beach and in the water during the trial for the public’s protection, and visitors to the area were asked to follow council and lifeguard instructions.
Sunshine Coast Council’s Environment Portfolio Councillor, Peter Cox, said the Coastal Hazard Adaptation Strategy guided Council’s work to manage the region’s beaches from the risk of future coastal erosion.
“A lot of work has gone on behind the scenes over several years to inform the long-term management of our coastline,” Mr Cox said.
“We are using coastal data captured through wave buoys, beach surveys, hydrographic surveys, ecological monitoring, and wind data to shape the project.
“This is in addition to studies that have shown there is a limited supply of sand on the Sunshine Coast.”
Mr Cox said Maroochydore Beach had been subject to significant erosion events over the years and adding new sand from outside the region – such as the Spitfire Channel in Moreton Bay – could help nourish the area and protect it from further erosion.
“The trial will supplement the existing sand renourishment program that involves collecting sand from the Maroochy River and pumping it onto the beach,” Mr Cox said.
“The trial will provide critical evidence to support our understanding of how this technique works here on the Sunshine Coast.”
Mr Cox said although this technique had not been used on the Sunshine Coast, it was a well-established method and had proven to be successful for other government bodies on the Australian east coast, including the Gold Coast.
“We expect the trial will show that additional sand placed in the nearshore area, close to the sand bar, will naturally migrate to the shoreline over time,” Mr Cox said.
“This will confirm the effectiveness of this well-established methodology to enable us to use it in the future if we need to.”
Sunshine Coast Council has established a technical advisory group to act on behalf of the community and contribute to the project, with members including Sunshine Coast Council officers and councillors, Queensland Government representatives, Surf Lifesaving Queensland, Queensland Police Service and expert engineering consultants.
All necessary environmental approvals are being progressed for the trial to be conducted.
For answers to frequently asked questions about the trial, please visit Council’s website and search for ”Maroochydore nearshore beach nourishment trial”.
A$400,000 investment by the Western Australian Government will support the construction of three community desalination units, built to test new desalination technologies for improved climate resilience and sustainability in community water supplies.
A brackish water desalination unit will be installed in Katanning during summer 2022-23, as part of a network of demonstration sites to examine how the technology can help overcome seasonal variability, reduce reliance on scheme water and support community development.
The Katanning unit will supply 30kL per day of fresh water to augment services for three local parks, as well as other town infrastructure.
This summer a 100kL/day desalination unit will be installed at Merredin to service farm and town water needs, while a new 10kL/day salty groundwater system at Dumbleyung will service farm and town water supplies, as well as underpin repairs to the town’s swimming pool.
A further 30kL/day brackish water off-grid reverse osmosis unit will be installed at the Wongutha Christian
Aboriginal Parent-Directed School at Esperance, as part of a collaboration with the Australian Government’s National Water Grid Authority.
Western Australia’s former Minister for Water, Dave Kelly, said long-term statistics indicated an urgent need for diversified water sources.
“This important work, supported by Water Corporation, will help to serve not only these first three communities but others in the future, as the technology is better understood and adopted throughout the state,” Mr Kelly said.
The project received funding from the state’s WaterSmart Farms initiative, and is led by the Department of Primary Industries and Regional Development in partnership with Water Corporation.
Western Australian Minister for Agriculture and Food, Alannah MacTiernan, said the trial project would further support primary producers’ growing interest in desalination technologies.
“This initiative is assisting our farmers and communities to build resilience in dry years by undertaking scientific research on how best to apply this technology to tap into benefits for rural businesses and the regions,” Ms MacTiernan said.
“While recent rainfall in the agricultural region has been favourable, now is the time to invest in how to future-proof farming operations and regional communities so they are set up and well-resourced to manage the dry years.
“The greater use of groundwater can also help lower the water table and reduce salinity.”
Lowara’s Smart Pump range is all about the right combination of motor, variable speed drive and pump. For top efficiency, ensuring reliable performance, maximum savings and a rapid return on investmentyou need the Lowara Smart Pump range.
Contact us to find your smart pumping solution. Featuring an integrated intelligent pumping system with an electronically driven, permanent magnet motor and an embedded electronic drive, these simply smart pumps will greatly enhance system performance and maximize flexibility.
Following 18 months of work, a team of engineers from the University of New South Wales (UNSW Sydney) has successfully converted a diesel engine to run as a hydrogen-diesel hybrid engine, meaning existing diesel engines can run using 90 per cent hydrogen as fuel.
Led by Professor Shawn Kook, the team from the School of Mechanical and Manufacturing Engineering developed the Hydrogen-Diesel Direct Injection Dual-Fuel System, reducing CO2 emissions by more than 85 per cent in the process.
Green hydrogen, which is produced using clean renewable energy sources such as wind and solar, is much more environmentally friendly than diesel.
The researchers said that any diesel engine used in trucks and power equipment in the transportation, agriculture and mining industries could
ultimately be retrofitted to the new hybrid system in just a couple of months.
The UNSW Sydney team’s solution to the problem maintains the original diesel injection into the engine, but adds a hydrogen fuel injection directly into the cylinder.
The collaborative research, completed with Dr Shaun Chan and Professor Evatt Hawkes, found that specifically timed hydrogen direct
injection controls the mixture condition inside the cylinder of the engine, which resolves the problem of harmful nitrogen oxide emissions that have been a major hurdle for commercialisation of hydrogen engines.
“If you just put hydrogen into the engine and let it all mix together you will get a lot of nitrogen oxide (NOx) emissions, which is a significant cause of air pollution and acid rain,” Mr Kook said.
“But we have shown in our system if you make it stratified – that is in some areas there is more hydrogen and in others there is less hydrogen – then we can reduce the NOx emissions below that of a purely diesel engine.”
Importantly, the new HydrogenDiesel Direct Injection Dual-Fuel System does not require extremely high purity hydrogen which must be used in alternative hydrogen fuel cell systems and is more expensive to produce.
Member Custom Editions Available
Complete review & update
• Three new chapters – Installation, Commissioning and Operations
• Completely rewritten Slurry Pumping and Energy Efficiency chapters
• 80 additional pages
Compared to existing diesel engines, an efficiency improvement of more than 26 per cent has been shown in the diesel-hydrogen hybrid, achieved by independent control of hydrogen direct injection timing, as well as diesel injection timing, enabling full control of combustion modes –premixed or mixing-controlled hydrogen combustion.
The research team hopes to be able to commercialise the new system in the next 12 to 24 months and is keen to consult with prospective investors.
They say the most immediate potential use for the new technology is in industrial locations where permanent hydrogen fuel supply lines are already in place.
That includes mining sites, where studies have shown that about 30 per cent of greenhouse-gas emissions are caused by the use of diesel engines in such items as mining vehicles and power generators.
“At mining sites, where hydrogen is piped in, we can convert the existing diesel engines that are used to generate power,” Mr Kook said.
“In terms of applications where the hydrogen fuel would need to be
stored and moved around, for example in a truck engine that currently runs purely on diesel, then we would also need to implement a hydrogen storage system to be integrated into our injection system.
“This new technology significantly reduces CO2 emissions from existing diesel engines, so it could play a big
Running an optimised and sustainable mining and mineral processing operation has never been so important with pressures on water availability, rising costs and environmental regulations becoming stricter.
Water conservation is vital in countries such as Australia, the driest inhabited continent in the world, and good water management reduces disruption to mining operations as well as damage to the environment.
Using reliable and efficient peristaltic pump technology from Watson-Marlow Fluid Technology Solutions (WMFTS) for mining procedures can produce water savings of 71% in comparison with typical centrifugal pumps.
Bredel hose pumps from WMFTS can be considered water-saving devices in their capabilities, such as being able to handle undiluted tailings and thickener underflow with up to 80% solids. Since Bredel hose
pumps do not have seals, it eliminates the requirement of water for flushing, to treat process wastewater and provide pump service water.
A reduction in water usage also delivers associated benefits through lower chemical usage and energy required for the treatment of process wastewater. Pumps must be capable of high operating pressures and flow rates to ensure a smooth liquid passage and deny the opportunity for the product to settle. Bredel hose pumps are self-priming to 9 metres, can run dry safely and can meter accurately to ±1%.Reducing water usage is better for the environment too, as less storage is needed for tailings and the number of basins can be minimised.
The wear-free performance of clog-free peristaltic pumps also means the need for routine maintenance and spare parts is reduced greatly.
part in making our carbon footprint much smaller, especially in Australia with all our mining, agriculture and other heavy industries where diesel engines are widely used.”
The Australian market for dieselonly power generators is currently estimated to be worth around $765 million.
A paper published in the International Journal of Hydrogen Energy by Mr Kook’s team shows that using their patented hydrogen injection system reduces CO2 emissions to just 90g/ kWh – 85.9 per cent below the amount produced by the dieselpowered engine.
“Being able to retrofit diesel engines that are already out there is much quicker than waiting for the development of completely new fuel cell systems that might not be commercially available at a larger scale for at least a decade,” Mr Kook said.
“With the problem of carbon emissions and climate change, we need some more immediate solutions to deal with the issue of these many diesel engines currently in use.”
Bredel hose pumps have a corrosionresistant enclosure which suits arduous mining environments
MORE INFORMATION
For more information on how peristaltic pump technology can deliver significant water savings for mining and water treatment companies, go here: wmfts.com/en/mining/
Find out more today
+61 2 8787 1400 Fluid Technology Solutions
Following two years of virtual events, Pump Industry Australia (PIA) Members were once again able to meet face to face at the 19th annual AGM, held at the Commonwealth Golf Club in Melbourne. The first in-person AGM since 2019 boasted a great turnout, with a sizable crowd gathering to hear how the industry had fared over the last 12 months and to see what was in store for the coming year.
For those unable to attend, the event was run virtually as well, with attendees from all over the country – and even one from New Zealand –able to tune in, access presentations and engage.
PIA President, John Inkster, started by welcoming everyone to the event and encouraging attendees to reflect on the difficult and turbulent times many families and businesses had faced over the past few years.
Despite being once again able to conduct an in-person AGM, Mr Inkster mused that the pump industry – and indeed the world – had not seen the last of COVID-19, with variants and sub variants continuing to wreak havoc on supply chains, and a looming, eminent fourth wave of the virus expected for Australia.
Mr Inskter said that although many had thought 2023 would be different, it was shaping up to be a year not too different to 2022, referencing the ‘new
normal’ that individuals and businesses would have to adjust to.
Despite COVID-19’s ongoing presence, it wasn’t all doom and gloom; throughout the industry people had been experiencing pent up demand for products and had full order books.
An abundance of public restructuring spending and private investment meant the industry was having no problems getting cash flow in – a trend Mr Inkster predicts will continue until the fourth quarter of 2023.
However, Mr Inskter warned that this cash influx may be the calm before the storm, and that despite some headwinds coming for the pump industry in 2023, Australia was in a strong position to weather the storm well.
Since 2021’s AGM, the PIA has been continuing to engage with the industry, including holding the Energy and
Efficiency of Pipelines Training online in November 2021.
The Pump Performance and Monitoring Training was also held online in March 2022 and boasted a great turnout.
In September 2022, ABB presented the Flow Meter Seminar, which was hosted by Brown Brothers Engineers in Keysborough, where attendees were given the option of attending in person or via Zoom.
On the topic of Council’s submission to the Services Trades Council (STC) regarding its request for suitably qualified Members to undertake repairs and service under the PD Act 2018, the PIA said it continues to liaise with associated parties throughout the year.
Further dialogue between the PIA and Acting Manager of Building Policy at the Department of Energy and Public Works, Elanor Ketter, was scheduled for 30 November 2022, with the PIA hoping to reach a resolution.
The PIA has been continuing its involvement with three committees on Australian standards, including with the longest running committee, the Fire Pump Committee.
AS2941 - Fixed fire protection installations - Pumpset systems
Although the committee is currently inactive, the PIA thinks it’s time this system was updated, with the current one from 2013. PIA is currently assisting Fire Protection Association Australia to write a Proposal to Standards to have the standard analysed and revised, and hopes something will come of this in 2023.
AS5414 - Bushfire water sprays system
A document was released, containing specifications for residential bushfire pumps, to which the PIA suggested it be included in the Fixed Fire Pump standard but as it stands, it is just in abeyance.
ISO 9906:2012 Rotodynamic pumpshydraulic performance acceptance tests grade one, two and three
In 2018, this was adopted as an Australian standard. There is currently a ballot as to whether the original standard should be amended, confirmed or withdrawn. It is the PIA’s intention to vote to Review and Amend.
ISO 2858:1975 End suction centrifugal pumps (rated 16 bar) - designation, nominal duty point and dimensions
The PIA was asked to vote on this standard again and, as some of these pumps are still manufactured in Australia, the PIA voted to confirm.
ISO 9905:1994 Technical specifications for centrifugal pumps class one
The PIA voted to abstain.
ISO 9908:1993 Technical specifications for centrifugal pumps class 111
As with above, PIA voted to abstain as it appears there is little interest in these standards overseas.
EL-058 Energy Efficiency for Swimming Pool pumps Committee
Draft AS 5352 Swimming Pool and Spa Heat pump systems
Despite highlighting that they were not in fact heat pump people and instead worked with hydraulic water pumps, the PIA was asked to stay part of the committee. The PIA made numerous comments to have the standard improved, with expected publication before the end of 2022.
AS 5102.1:2019 Performance of household electrical appliancesSwimming pool pump-units, Part 1: Measurement of energy consumption and performance
Amendments are being made as there were some errors with complicated calculations or formulae that need to be corrected. Expected publication was late 2022, if not early 2023.
Changes from the Federal Government came in the form of new regulations that replace the Voluntary Energy Rating Label program that applied to pool pumps until now.
From 1 October 2022, manufacturers, suppliers and importers of a pool pump will need to declare the minimum energy performance efficiency of in-scope pool pumps sold in Australia in accordance with the Greenhouse and Energy Minimum Standards (Swimming Pool pump-units) Determination 2021.
Additionally, the revised National Construction Code 2022 will be adopted as of May 2023, in which lead free plumbing equipment or parts in contact with drinking water is no longer acceptable. Also, air conditioning pumps
and circulators must comply with MEPs requirements.
There’s a proposal by the Australian Buildings Codes Board to Standards Australia to make a modification to the plumbing code. The proposal says that the design and installation of pumps is not covered sufficiently by the AS/NZ 3500 series, suggesting that the current provisions in the AS/NZ 3500 may be insufficient.
The proposed scope is to add a deemed-to-satisfy solution for the design of plumbing systems relating to pumps in the plumbing code.
PIA Executive Officer – Standards and Life Member Ken Kugler thinks the PIA should get heavily involved in this as there will be lots of benefits for many in the industry.
The Pump Technical Handbook has undergone major upgrades over the last two years, with chapters carefully reviewed and improved to ensure they’re relevant, up to date and easy to read. These upgrades have resulted in a content increase of almost 40 per cent.
Differences in publishing the handbooks means that PIA members now have the ability to customise either or both of the Pipe Friction Handbook and the Pump Technical Handbook, featuring their companies’ colours and logos on the cover. Members were encouraged to get in touch with the Council via email if they wanted to take advantage of the fantastic opportunity.
The PIA intends to keep up its industry engagement and continue its commitment to providing valuable training and learning opportunities for members and the industry as a whole.
Re-elected PIA President, John Inkster, said the PIA needs to grow, but that it needs to also make sure it has relevance and improves its presence.
Due to the ongoing effects of COVID-19, the 2022 PIA Council did not formulate a concrete plan for 2023, instead deciding that the 2023 Council could prepare one as the world returns to pre-COVID normal.
Mr Inskter said that although the last few years were difficult on account of not being able to do much, the coming year would present an opportunity to do more and promote the industry.
The 2022 AGM concluded with a dinner, where members were able to reconnect and once again engage face to face with each other, after two years of seeing each other through screens.
Pump Industry Australia is pleased to announce the publication of the sixth edition of the Australian Pump Technical Handbook, which is now available via its website, www.pumps.org.au.
For the past two years, the Pump Technical Handbook has undergone a major upgrade in which all chapters have been carefully reviewed and upgraded to ensure they are fully up to date and readily understood for all those reading the book – all resulting in a nearly 40 per cent increase in content�
In addition to the review, two new chapters were created based on splitting of the current Installation, Commissioning, Operation and Maintenance chapter to become three chapters as follows:
• Chapter 16 – Pump Installation
• Chapter 17 – Pump Commissioning
• Chapter 18 – Operation and Maintenance
The first two of these chapters have been upgraded and expanded to include the latest pump installation requirements, along with a complete run down of the commissioning process including the evaluation of that process The Operation and Maintenance chapter has also been expanded to cover Pump Safety, as well as the inclusion of sections detailing routine and preventative maintenance
While all chapters were fully reviewed, updated and simplified for easy reading, the following chapters underwent a more detailed upgrade:
• Chapter 5 – Selection of Centrifugal Pumps: The section on specific speed which was in Chapter 3 has been relocated here and an extra section on suction specific speed has been added
• Chapter 9 – Application and Selection of Slurry Pumps: The chapter has been completely rewritten with a more detailed logical emphasis on the process of selecting and applying a slurry pump for a specific slurry, including an example of the selection calculation
• Chapter 10 – Efficient Operation of Pump Systems: With the continuing emphasis on the need for more efficient pumping systems, this chapter has been reviewed and upgraded to take into account the latest advances in this field
• Chapter 11 – Pump Materials: In light of the major rewrite to slurry pump chapter, a section on slurry pump materials has been added to this chapter along with a full review of the standards relating to pump materials
• Chapter 13 – Intake Design: The section on the calculation of optimum sump volumes has been updated because the original was not clear and required clarification
• Chapter 15 – Pump Testing: Since the publication of the fifth edition of the Pump Technical Handbook, in 2018 the Australian Standard on pump testing was updated resulting in the need to update this chapter due to, among other things, changes in the test tolerances
• Chapter 22 – Pumping Formulae: The revamp of the slurry pump chapter with its own sample calculation is such that the sample slurry calculation shown in previous editions in this chapter is no longer required and has been deleted Due to the change in how we publish our handbooks, we are able to offer PIA members the opportunity to customise either or both the Pipe Friction Handbook and the Pump Technical Handbook with covers in their companies’ colours and logos� We would provide you the detailed sizing for you to design the cover copy as well as some small restrictions we will need you to comply with
The above is a short summary of the changes in the latest edition of the Pump Technical Handbook which we believe greatly improves the handbook as far as its technical content and readability is concerned We commend this latest edition to you
The sixth edition of the Australian Pump Technical Handbook, as well as the Pipe Friction Handbook, are available at www.pumps.org.au/publications.
Volvo Penta. Robust, fuel efficient industrial diesel engines that keep running even in the toughest conditions. Easy to install, operate and maintain. A powerful partnership you can trust all the way from the drawing board throughout the operational life of your engine. Competitively priced complete power-pack units ready for delivery Australia wide with a local support team on hand 24/7. To find your nearest dealer visit www.volvopenta.com
Ebara Pumps' new GSD close coupled EN733 motor pump has been selected as one of the primary water pumps for the new billion-dollar Festival Plaza upgrade in the heart of the Adelaide Arts and Culture precinct. The Ebara GSD range of ED coated pumps will be used on chlorinated water for the Festival Plazas new water feature.
The Festival Plaza Water Feature is one of the many new highlights and attractions that have been incorporated in this new development of public realm that connects Adelaide CBD and the riverbank
The specialist contractor who supplied the pumps and water treatment equipment for the new water feature – Total Water Resources chose the Ebara GSD pump due to its quality, proven hydraulic design and competitive pricing
The GS/GSD pumps come as standard with a high-quality electro deposition corrosion resistant coating to the ferrous static components, both internal and external making them ideally suited to treated fresh water environments
The GS/GSD range is the Ebara Corporation (Japan) new global range of EN733 water pumps and utilising the most advanced hydraulic computer software available, Ebara Engineers in Japan have been able to improve and increase the pump efficiencies of the new GS/GSD range above most other available pumps of similar design and standard on the global market The majority of the GS/GSD pump range are MEI>0 7 efficiency index with the balance MEI>0.6, an indication of the high-quality design and manufacture by Ebara
The Ebara GSD range of close coupled motor pumps and the GS range of bare shaft EN733 end suction pumps are both manufactured in component form at Ebara Corporation (Japan) owned and managed factories in South East Asia
After being assembled from these components by skilled tradesmen at the Ebara Pumps Australia facility in Melbourne, the pumps are then hydrostatically tested and inspected to our Japanese parent’s strict QA policies and procedures
The Ebara GS/GSD range of EN733 pumps are a true 16 bar working pressure with a high grade SiC/Carbon/EPDM
Burgmann mechanical seal fitted as standard. Galvanised steel baseplates that have been fully engineered by Ebara Japan engineers are also available as an optional extra for the GSD motor pumps�
In addition to the GS/GSD range of pumps Ebara Pumps has also recently introduced the GSO range of semi open impeller ISO 2858/5199 process pumps which are also available in 304,316L and Duplex stainless steel The GSO range of pumps have been designed by Ebara Japan with a unique reverse open impeller reducing axial thrust and creating a low seal/stuffing box pressure. The pumps can be fitted with a vast range of single/double mechanical seal options and piping plans They are also available with the option of oil lubricated bearings and ANSI drilled flanges.
Ebara Corporation was founded in Japan in 1912 as a manufacturer of industrial pumps Today, as a group it consists of more than 70 companies in six continents with a workforce of more than 12,000 and with company-owned and Japanese-managed factories covering nine countries and four continents.
The huge scale of production and distribution is matched by a constant commitment to research, development and design of new products and the modern technologies for the manufacturing of them Ebara products have gained a worldwide reputation for their technology and quality
Combining over 100 years of experience with the latest computer aided design, EBARA has developed the new GS series of pumps that offer world leading performance and efficiencies.
Pumps to EN733 dimensions
16 Bar rated. PN16 flanges (24 Bar hydrostatic test pressure)
High efficiencies. MEI ³0.6 (Minimum Efficiency Index)
Mechanical seals to EN12756
Protectors to ISO13852
O’ Ring seal for casing
Cast iron components ED painted (Electro deposition painting)
The WEG W60 line motors present an excellent power density with an enhanced and robust design.
The use of modern computer programs and mathematical tools for numerical simulations and analyses optimised each component and their respective interactions.
This line is capable of speed variation and operation with frequency inverters and soft starters. The concept allows adjustments that guarantee high performance in environments with the most varied temperature ranges and comply with the most stringent criteria for efficiency, reliability and safety.
The flexibility in electrical and mechanical designs made it suitable for applications with low inrush current and high efficiency. In addition, it resulted in a reduced motor weight that will reduce base construction and installation costs.
You can install the best pumps in the world, but without good mechanical seals, those pumps won’t last long. Mechanical pump seals prevent fluid leaks, keep contaminants out, and can help save on energy costs by creating less friction on the shaft. Here, we reveal our top five secrets to selecting a good seal, to help ensure pump longevity.
1. Supply – Go local
The global mechanical seals market size is projected to reach US$4.77 billion by 2026, with the highest market growth expected in Asia-Pacific. Australian supplier, Mechanical Seal Engineering, has had to open a new location in Western Australia to support this growth, with the established business offering a large range of pump-specific, component and cartridge seals, as well as refurbishment and repair services and technical advice.
Some of the world’s best seal solutions are indeed right here on your doorstep!
Avoid the current global supply chain and freight delay issues by sourcing your high-quality, cost-effective seals locally.
An initial pressure test, combined with stringent quality control checks, should be undertaken on every seal before you receive them, prior to pump installation. You may otherwise find yourself wasting precious time uninstalling and disassembling your pump to remove a faulty seal. Repairing pumps as soon as faults are suspected is also critical. Quick action is vital to operations, and to the associated cost.
To guarantee high-quality, effective pump performance from the start, ensure your seal supplier has the proper pressure testing facilities and a proven commitment to quality control. In addition, find a trusted supplier who will support you across the whole pump seal’s lifecycle – offering much more than just the product. And check waitlists for repairs – sometimes an issue can’t afford to wait.
If you’re looking to optimise your operating conditions, seek authentic technical advice on material selection, stuffing box piping plans, design problems, etc.
Remember – anyone can pose as an expert and ultimately rip you off! Do your research on those offering advice. Approach an established mechanical pump seal provider and ask questions to help ensure the advice they’re giving is solid, and theirs to give.
A supplier who offers up free knowledge and education is one who is comfortable in demonstrating their understanding and capabilities. Check supplier websites to see if they offer useful tutorials, blogs, case studies, and if they’re authentic in their approach.
There are several possible causes of pump seal failure –improper installation, excess pressure, lack of fluids. You may be tempted to self diagnose the cause, but to ensure best practice and minimise cost, it’s recommended you appoint an expert to analyse the issue and determine how to best rectify it.
Did you know you can request a seal failure report from your seal supplier? Such reports can help improve the productivity and long-term reliability of your seals, minimising potential breakdowns and downtime, and maximising operational efficiency. If your supplier isn’t willing to share failure reports, ask yourself what it is they may be hiding.
5. Customer service – About the people
Customer service can make or break a business. Your pump supplier should know your business as well as their own, and should genuinely want your business to succeed as much as you do.
Select a supplier who can provide a genuine end-to-end service – one who also installs, tests, manages, refurbishes, repairs, converts, reports, advises, understands. A partner in pump seals. Someone you can trust to help keep your pumps operating at their best across their lifecycle.
An Australian-owned business based in SA and WA, Mechanical Seal Engineering is dedicated to providing the best seal services across Australia. We deliver holistic pump seal services to a wide range of industries, keeping it all about our customers – the people. Contact us today for a non-obligatory chat to find out more about the local, reliable seal solutions available to you: 0448 440 612 | sales@mechsealengineering.com.au.
With its EP series and VY series, Vogelsang GmbH & Co. KG from Essen (Oldenburg), Germany, is launching two new pump series that meet the high demands of industrial use. The rotary lobe pumps are made of a flow-optimised one-piece housing and are therefore particularly efficient. They reliably convey thin-bodied as well as highly viscous, pure and solids-containing media at temperatures of up to 200°C. The pumps are ATEX and TA-Luft compliant and thus suited for use in highly demanding areas such as the oil, gas and chemical industries.
TThe high-pressure performance and temperature limit of 200°C along with its seal versatility make the EP series suitable for applications for which companies previously used screw, gear and progressing cavity pumps. These include the oil and gas sector, tank farms, the petrochemical industry, and the production of paints and varnishes, paper, glue and sugar.
Vogelsang has additionally equipped its EP series with an AirGap for increased operational reliability. This gap atmospherically separates the gearbox and the pump chamber, ensuring that in the event of a leak, liquid will drain out rather than entering the gearbox.
hanks to increased efficiency and added seal versatility, Vogelsang is able to open up new areas of application for its proven pump technology. As the inventor of the elastomer-coated rotary lobe pump in 1970, Vogelsang has been for decades one of the world's leading companies in the field of pumps.
EP series: rotary lobe pumps with up to 18 bar pressure
The EP series is designed for extreme conditions and permanently high pressures. Its high-performance gearbox allows for a constant pressure output of up to 18 bar, making it unique on the market today. The pumps of the EP series consist of a one-piece housing made from either cast iron or stainless steel. Helical gears in the gearbox ensure smooth performance and reduce noise emissions. Pulsationfree transferring reduces wear on the adjacent pipeline to a minimum.
The performance spectrum of the VY series ranges from 1m³/h to 120m³/h at a maximum pressure of 10 bar.
VY series: a highly efficient all-rounder
VY series rotary lobe pumps are based on Vogelsang's proven VX series. The versatility of the VY series makes it suitable for use in the chemical industry, as well as in the paper sector. The performance spectrum ranges from 1m³/h to 120m³/h at a maximum pressure of 10 bar. Integrated sensors provide all important information about
Exploded view EP series: The helical high-performance gearbox allows pressures of up to 18 bar.
the pump's operating status. The VY series is also available with axial and radial wear protection for media with abrasive components.
Seal versatility for increased flexibility
A variety of different sealing systems can be used in the housing of the new pump series depending on the industryspecific standard and requirement. In addition to the Vogelsang QualityCartridge, further special mechanical seals are available for the EP and VY series. Vogelsang worked with leading manufacturers to develop the CoXCartridge and offer the right solution for a variety of applications; from use in oil and sugar production, to conveying hot, chemically demanding media or latex paints. The seal's robust design also makes it suited for high-pressure use. The new pump series can also be equipped with mechanical seals according to API 682 if required.
Service-friendly assembly and cleaning
For increased ease of service, both pump series feature a quick connection. Thanks to this, pipelines can be connected to pumps in a matter of minutes. The Quick-Service cover allows access to all internal components. Furthermore, when designing the EP and VY series pumps, the engineers placed significant importance on easy cleaning. The pumps can be rinsed and disinfected according to the CIP (Cleaning in Place) and SIP (Sterilisation in Place) cleaning procedures. The housing design also reduces dead space to a minimum, thus preventing liquids from accumulating in gaps or uneven surfaces.
In everything we do, we never lose sight of what is more important to our customers: to work economically with a technology that is modern, innovative and reliable.
In everything we do, we never lose sight of what is more important to our customers: to work economically with a technology that is modern, innovative and reliable.
As the inventor of the elastomer-coated rotary lobe pump and innovation driver in the field of pumping, grinding and disintegration technology, Vogelsang has been one of the world’s leading mechanical engineering companies for decades. With progressive concepts and sophisticated technology, such as the RotaCut macerator or the wastewater twinshaft grinder XRipper, we work daily on efficient solutions for the individual applications of our customers.
As the inventor of the elastomer-coated rotary lobe pump and innovation driver in the field of pumping, grinding and disintegration technology, Vogelsang has been one of the world’s leading mechanical engineering companies for decades. With progressive concepts and sophisticated technology, such as the RotaCut macerator or the wastewater twinshaft grinder XRipper, we work daily on efficient solutions for the individual applications of our customers.
We use our extensive know-how, the continuous further development of our technical solutions and our many years of experience in the field of environmental technology to support our customers as a competent partner. Among other things, with powerful and service-friendly technology. You can rely on competent and personal advice and reliable service.
We use our extensive know-how, the continuous further development of our technical solutions and our many years of experience in the field of environmental technology to support our customers as a competent partner. Among other things, with powerful and service-friendly technology. You can rely on competent and personal advice and reliable service.
VOGELSANG – LEADING IN TECHNOLOGY
VOGELSANG – LEADING
Unit 2/7 Dunn Road | Smeaton Grange NSW 2567 | Australia
Unit 2/7 Dunn Road | Smeaton Grange NSW 2567 | Australia
Phone: +61 2 4647 8511 | E-mail: sales.au@vogelsang.info vogelsang.info
Phone: +61 2 4647 8511 | E-mail: sales.au@vogelsang.info vogelsang.info
Commencing back in 1962 in Dandenong, Victoria, close-by its present site, Franklin Electric began importing and distributing 4” submersible products. Soon after, local manufacturing commenced with specialised imported parts to offer the Australian water industry Franklin’s world-leading 4” submersible motors.
Over the decades, Franklin Electric motor products were designed and evolved to provide the industry with the highest quality 4”, 6”, 8”, 10” and 12” submersible motor products available.
Quality, reliability and performance
The main benefit that the Australian industry has come to rely on from Franklin is its quality, reliability and performance. Franklin demonstrates these every day to its customers through its Five Key Factors for Success: quality, availability, service, innovation and cost.
Franklin submersible motor products became Australia’s leading submersible motor and indeed the world’s most installed submersible electric motors.
Franklin had been partnering with pump manufacturers for decades and had developed a deep understanding of the market. When the industry started to consolidate around the world in the late 1990s and early 2000s, Franklin had some serious decisions to make.
In 2004, Franklin Electric announced the purchase of JBD (the former Jacuzzi industrial range), and that it was entering the pumping industry by launching Franklin Pumping Systems, now known as FPS. Starting from a very low share, FPS is now leading the US market.
As the pumping industry is global, similar issues applied in Australia. In late 2007, Franklin Electric Australia, after three years of evaluating the market, entered the main water pump industry by launching and distributing its FPS range of submersible pumps and above ground pumps, motors, drives and controls direct to its own Australian dealer network.
In 2005, Franklin Electric purchased a 35 per cent stake of Pioneer Pump Inc, situated in Canby, Portland, Oregon. Pioneer manufactures a large range of centrifugal pumps and automatic self-priming pumps, as well as solids handling selfpriming pumps.
Outside of the US, Pioneer Pump has factories for fabrication, and assembly and warehousing facilities operational in South Africa, England and Australia.
In 2011, Franklin Electric agreed to purchase the remaining 65 per cent of Pioneer. In 2020, Franklin Electric decided to consolidate its water business group globally under one Franklin Electric company.
Today, Franklin Electric Australia and Pioneer Pump Holdings Australia are one company, Franklin Electric Australia New Zealand Pty Ltd, with two facilities operating: the warehouse and assembly facility in Dandenong South, Victoria; and the fabrication assembly and test facility in Sunshine West, Victoria, which includes a logistic warehouse in Ravenhall, Victoria.
Along with the consolidation of the businesses comes the staff and the years of pump experience, the company has hundreds of years of experience to assist every person who needs help with a pump or application.
Today, the range of products have expanded to:
• A full range of surface mount pumps, ISO, split case, multistage, small and large centrifugal motor pumps, progressive cavity (MONO TYPE) and self-priming ranges, small volume low head, to extreme high volumes (2500 LPS) and discharge heads exceeding 300m
• Solar pumps and pumping equipment
• A huge range of belowground pumps: submersible turbine, line shaft, bore hole and dewatering
Truly one of the largest and most comprehensive ranges of pumping and associated products supplied by a single company globally.
“Moving Water Moving Forward”
United Pumps designs and manufactures pumps, our extensive Melbourne testing facility is utilized for product development, new pump test and customer pump testing. 2.5Mw capacity with NPSHr capability.
United have made a commitment to API610 pump manufacture in Australia. With decades of experience, we can provide you with the finest engineered equipment and support
Our extensive range of process and water pumps are available in materials to suit your application. With all design and manufacture carried out in Australia we can offer a true Sovereign solution.
Proven track record in municipal water applications over a wide range of the highest quality pumping equipment. Horizontal Split Case, Vertical Turbine, End Suction and Sewage.
They say good things come in tens: ten fingers, ten toes, ten drummers drumming and ten years of Pump Industry Magazine’s State of the Industry report. With the report hitting its double digit birthday, it’s important to reflect on not only the year that was and the year that will be, but the past few years that have gotten the industry to where it is today.
After its enormous global impact over the past few years, 2022 saw the COVID-19 outlook looking up, with the third and fourth vaccine shot made available to the public, the absence of lockdowns, and the long-awaited reopening of Australia’s international border to vaccinated tourists.
In spite of this, Australia and the industry continued to feel the aftershocks of COVID-19, with new variants emerging that delayed international travel’s return, and continuing strict lockdowns in China impacting the global supply chain.
Climate change has been making itself known over the past few years, and none more so than 2022, when climate change was thrust into the global spotlight for the devastating effects it was having around the world.
Over the last 12 months, Australia registered its hottest ever temperature on record, Sydney had its wettest start to the year since records began, and Australia’s south east coast was lashed by the third La Nina weather event in as many years, with flooding affecting farming and bore pump sectors for businesses.
The trend of positive thinking for the year ahead that has emerged over the past few years continued in the latest State of the Industry survey, with many in the pump industry seemingly standing on firmer ground and looking towards 2023 slightly more confident and cautiously optimistic than previous years.
The overarching take away from the latest State of the Industry report is that the events of the last 12 months have not dampened industry spirits, with an overwhelming number of respondents seeing 2023 as brimming with opportunity, and the perfect chance to grow businesses and make headway on projects that have been delayed by COVID-19 over the past few years.
an increase in respondents who are uncertain about the year ahead, rising from last year’s 0.88 per cent.
Concurrent with the increase in positivity for 2023, is the percentage of respondents who have reported a negative outlook for the year ahead, which has also increased, growing from 0.88 per cent last year to the most recent figure of 6.25 per cent.
Despite this increase in negative outlook, the current percentage is still lower than it was during the throes of COVID-19 in 2020 and 2021.
Although there appears to be plenty of factors that could contribute to the overwhelmingly positive outlook for 2023, some of the things that may have contributed to the increase in negative outlooks for the year ahead is the ongoing effects of climate change, the fluctuations of the Australian dollar, inflation, and the uncertainty and effects borne from the Ukraine-Russia war.
Evaluating company performance for 2022
As is visible in Figure 1, a record-breaking majority of respondents reported possessing a positive outlook for their company in 2023 – 87.5 per cent to be exact – a slight increase from the 84.07 per cent of the previous year and a noteworthy jump from the 2021 and 2020 surveys, which indicated 69.56 and 68.25 per cent respectively.
This overwhelming majority could be attributed to the belief that the worst was over in terms of the pandemic.
On equal footing, at 3.13 per cent, is the percentage of respondents who noted either a neutral outlook for the year ahead and those who indicated that they were uncertain.
The figure for respondents with a neutral outlook is down significantly from last year – perhaps due in part to individuals feeling confident and secure enough to adopt a stronger opinion on 2023 and what it holds. This comes contrary to
The performance of their company over the past year likely heavily influenced whether respondents indicated expectations for company performance when looking towards the next year.
Although 2022 was plagued by the Ukraine-Russia war, unprecedented weather events and the ongoing effects of COVID-19, only 6.25 per cent of survey respondents (Figure 2) indicated that the performance of their company had fallen short of expectations for the year.
This number is in line with the decreasing trend of company performance falling short of expectations, down from 14.16 per cent in 2021 and 2020’s 42.75 per cent.
Although some companies have learned to adapt to the new COVID-19 ‘normal’, there are still respondents who are yet to fully experience the light at the end of the pandemic tunnel, especially in locations affected by La Nina.
One respondent said “weather and COVID held up projects” when providing a reason for company performance falling short, with another respondent noting “too many suppliers, not enough customers and low pricing” as the cause for their company not meeting expectations.
The remaining number of respondents were split 50/50 – with 46.88 per cent apiece saying their company’s performance over the last year either met or exceeded expectations.
Those that indicated that their company met expectations listed “strong sales figures around the country”, “company ownership changes, some personnel changes, refocusing on core business opportunities” and “new development happened successfully” as some of the reasons expectations were met.
Multiple respondents have attributed their company meeting expectations to thorough preparation, with one respondent saying “previous excellent pre-planning and preparedness for material and components supply chain issues” was a key factor, and another saying their company “planned for positive growth and achieved it”.
Although the most recent figure of businesses who met expectations has reduced from 2021’s 57.52 per cent and 32.61 percent in 2020, this may not be a bad thing and instead may be due to the significant increase in businesses who exceeded their performance expectation, growing from 28.32 per cent in 2021 (Figure 2).
This can likely be attributed to the continued utilisation of COVID strategies and coping mechanisms, with companies now well-adjusted and accustomed to operating in a postpandemic world, learning to adapt and accommodate for supply chain disturbances, filling gaps in the market, and turning their focus to increasing their company name within Australia.
Several respondents indicated that a backlog from previous COVID delays has caused their company performance to exceed expectations, with one respondent noting “COVID delayed many projects and tender decisions” but “over the past six to eight months [we] have experienced a progressive improvement”.
Another respondent said, “Our order book has grown significantly – this is partially due to the delays in shipping resulting in delays in building and supplying pushing us back in the first quarter 22.”
Additionally, multiple respondents simply said “more sales” was the area that pushed companies to exceed expectations, with one respondent pinpointing that “demand has exploded” and another saying “strong project sales” had a huge impact.
Another respondent noted that for some companies to exceed expectations, it was as easy as returning to the basics; in other words “great product, great customer service, good delivery times, growing brand awareness in Australia”.
The outlook for the pump industry in 2023
Unsurprisingly, respondents’ feelings about whether or not 2023 would be a good year was influenced by their company’s performance over the past year, among other things.
Although the State of the Industry respondents had shown an overwhelming sense of positivity in regards to company outlook for 2023, there was less positivity towards the future of the pump industry as a whole in 2023, with only 62.5 per cent adopting a positive mindset for the year ahead (Figure 3).
This is a minute decrease from 2021’s 62.83 per cent, but still higher than the percentages of years 2020, 2019 and 2018.
The percentage of people with a negative attitude towards the pump industry’s 2023 grew from 0.88 per cent in 2021 to the current recent figure of 3.13 per cent.
Despite the increase in those with a negative outlook, the percentage is still lower than it was during the years of strict COVID lockdowns. This could be indicative of new issues companies have begun facing instead of the knock on effects of COVID-19, including inflation, the unprecedented natural disasters, and the Ukraine-Russia war.
The percentage of respondents with a neutral outlook towards the pump industry in 2023 is 31.25 per cent – the highest it’s been since 2020. On the other hand, the percentage of people with an uncertain outlook for 2023 sits at 3.13 per cent, a significant decrease from 2021’s 19.47 per cent and the lowest figure of the last four years.
This indicates that a great deal of the uncertainty that companies faced due to the pandemic has vanished, with companies instead gauging the future based on 2022 performances and other factors to draw their own conclusions about what may come in the year ahead.
In order to determine how key verticals are expected to perform in the year ahead, it is essential to analyse and understand sector performance throughout the last year.
Survey respondents were asked to provide details about the volume of work experienced over key verticals – including mining, water and wastewater, and irrigation – over the last 12 months.
These results were then compared alongside the responses gathered from last year’s State of the Industry.
It’s important to keep in mind that at the time industry sector predictions were made for 2022, optimism for COVID-19 recovery was buoyed by the rollout of vaccines, the approval of a booster vaccine for COVID-19, as well as the planned announcement that fully vaccinated Australian citizens and permanent residents would be able to leave Australia without needing an outwards travel exemption.
With all of this influential progress, survey respondents expected that performance in all industry sectors would grow, with the largest increases expected for water and wastewater, mining, and irrigation – all of which were slated to increase or increase significantly.
As depicted in Figure 4, except for plastics and rubber, all of the performance figures reported for 2022 fell short of expectations.
Water and wastewater was the highest performing sector over the last 12 months according to respondents, a result that is in line with survey respondents’ predictions.
Other front-runners included mining – also predicted by respondents – and food and beverage, a surprising result when compared to respondents’ expectations and especially when compared to 2021 performance, which saw food and beverage performance decrease.
The worst performing sectors were pulp and paper, plastics and rubber, chemicals and pharmaceuticals, and power generation, with pulp and paper once again prevailing as the worst performing sector, in line with the performance results of 2021.
However, unlike 2021, which saw performance decrease in three industry sectors, 2022 industry sector performance only decreased for pulp and paper – although overall performance for this sector was better in 2022 than 2021.
At Brown Brothers Engineers we have the most comprehensive range of quality pumps and innovative pumping solutions. We are the distributor for some of the world’s leading brands including:
Layne Bowler vertical turbine pumps have a proven record under the most demanding and toughest of conditions.
• Flows to 2,300 L/Sec
• Heads to 350 m
• Power to 1000+ kW
• Temperatures to 150°C
• Bowls Diameter up to 45 inch
When high head and high flows are required look no further than this
• Flows to 5000m³/h
• Head to 220m
• Pumps that exceed EN733 (DIN 24255 standard)
Call us today to see how we can deliver your pumping solution.
Figure 5: How growth across sectors tracked in 2022 compared to recent years, and expectations for 2023.
In Figure 5, the trends of sector performance can be seen over the last few years, with expected performance for 2023 also included.
Continuing on the theme of optimism, respondents expect growth across all sectors for 2023, with water and wastewater once again the predicted front-runner. Other sectors where respondents expect performance growth are irrigation, mining, oil and gas, and – despite not performing as well as expected in 2022 – food and beverage.
Figure 6: Most sectors are expected to perform better in 2023 than they did in 2022.
Sector growth predictions for the year ahead
Due to the diversity of sectors and businesses within the pump industry and across respondents’ businesses, trends and events across the industry affected businesses differently.
Survey respondents were asked to indicate trends, positive or negative, that had impacted their business over the last 12 months, as well as their expected impact over the year ahead.
Many highlighted the investment in new infrastructure as a positive trend, as well as new projects and the uptake of new technologies. Respondents indicated that growth in certain sectors directly relating to businesses – including food and beverage, and water and wastewater – as a positive trend affecting business.
Despite there being some businesses that noted COVID-19 had a positive impact to their business, the overwhelming majority of respondents noted it had a negative impact throughout 2022.
As can be seen in Figure 7, as predicted in the 2022 State of the Industry report, supply chain, freight and pricing issues did linger in 2022, as well as new issues and negative trends arising from global events.
Factors respondents expect to have a negative impact on the industry in 2023 include the value of the Australian dollar, interest rates, commodities prices, and the Ukraine-Russia war and the resulting increase in energy prices.
Closer to home, unsurprisingly, many pinpointed unprecedented weather patterns, including La Nina weather events and the resulting floods as having a significant negative impact on business, which respondents expect to continue into 2023.
Additionally, results indicated that the labour and skill shortage and “lack of qualified human resources” was also having a negative effect on businesses.
Among factors that most respondents expected to have a positive impact were new technologies and innovations, agricultural industry, the performance of the mining industry, and the major projects approved and/or underway.
Russia-Ukraine war continuing to place pressure on LNG prices.
Buyers in Europe are scrambling for uncontracted LNG cargoes to supplement loss following Russia’s interruption of gas flow to Europe, which in turn could result in Asian customers having to compete for available LNG.
Australia’s LNG earnings rely quite heavily on whether or not Russia restores European gas flows – if the LNG flow continues to be reduced, Australia’s earnings will rise.
The La Nina weather systems have battered Australia’s south east coast, producing higher than average rainfall and resulting in extreme flooding in certain areas, with Southern Queensland and northern New South Wales at one point each receiving more than a year’s worth of rainfall in a week.
The effects of the Ukraine-Russia war were felt throughout the world over the course of 2022.
Countries around the world are placing new sanctions on Russia, and the European Union has agreed to a plan to block two thirds of Russia’s oil, resulting in soaring energy prices –for both oil and gas.
Shockwaves were also felt by the global freight logistics system, with rising energy prices resulting in an increase in shipping costs and supply chain delays worldwide.
Global iron ore markets continue to experience fallout from Russia’s invasion of Ukraine, and with Ukraine’s typical supply chains disrupted or blocked by Russian forces, iron ore exports have taken a nosedive in recent months.
As one of the top five exporters of LNG in the world, Australia’s LNG export earnings have risen throughout the year and are expected to continue to rise as a result of the
Many communities and councils around Australia have turned to the pump industry, seeking assistance to mitigate the effects of the floods and as a way to prepare and safeguard against future weather events.
The New South Wales Government committed $145 million in funding for the repair and upgrade of critical water and sewerage infrastructure – including pump stations – damaged by floods across the Northern Rivers area. The works are set to make permanent repairs to damaged infrastructure as well as upgrade to future-proof the critical infrastructure.
Survey respondents indicated that investment in new infrastructure was a positive trend helping businesses thrive during 2022. This infrastructure investment is set to continue into the new year, especially following the 2022-23 Federal Budget, which is set to deliver more than $2 billion to water security and infrastructure projects.
IIoT is opening new doorways for the pump industry as pump operators look to improve the sustainability and efficiency of their systems.
Investment in water security and infrastructure to futureproof water accessibility in the face of population growth and climate change include the following:
• $600 million towards the Paradise Dam Improvement project in Queensland
• $107.5 million towards the Cairns Water Security – Stage 1 project in Queensland
• $3.5 million towards the Mount Morgan Water Supply project in Queensland
• $12.5 million towards groundwater improvement and water efficiency in the lower Burdekin, Queensland
• $11.5 million towards strategic planning for improving water security in Queensland
• $8.0 million in additional funding towards Big Rocks Weir in Queensland
• $100.0 million towards the Pipeline to Prosperity Tranche 3 projects in Tasmania
• $300.6 million towards the Darwin Region Water Supply –Stage 1 in the Northern Territory
• $7.1 million towards the Adelaide River Science project in the Northern Territory
• $23.0 million towards the Nyngan to Cobar Pipeline – Stage 1 in New South Wales
On a state and territory level, New South Wales committed to the biggest spend, pledging a $1.1 billion investment into the state’s water resources to ensure sustainable and secure water in the changing climate. Projects funded include maintaining assets within the Hunter Valley Flood Mitigation Scheme to help minimise flood risk; improving critical water supply infrastructure for the towns of Wilcannia and Cobar; and for its Off-Farm Efficiency Program.
Queensland followed up with a commitment of $510 million for water infrastructure and planning projects to improve water security for the state’s communities and provide economic growth and job opportunities. Projects that received funding include the Toowoomba to Warwick Pipeline; Stage One of the Cairns Water Security program; construction of a drinking water pipeline from Gracemere to Mt Morgan; and the development of Flinders Shire Council’s Hughenden Water Bank project.
Victoria pledged $112 million to manage water sustainably into the future – maintaining green spaces, supporting farmers, and securing the drinking water supply.
The critical skills and labour shortage
Despite Australia's international borders reopening to welcome visa holders, respondents have flagged the labour and skills shortage as something that has negatively impacted the industry.
In October 2022, the National Skills Commission released its 2022 Skills Priority List (SPL), which provides an indepth look at occupations in shortage and the future demand for occupations in Australia.
The SPL looked at occupations in shortage during 2022 but not 2021, occupations in shortage for both 2022 and 2021, and occupations in shortage during 2021 but no longer in shortage in 2022.
Among the occupations in shortage in 2022 that were not in shortage in 2021 are mechanical engineering draftspersons and technicians, and electronics engineers.
Occupations in shortage across both 2021 and 2022 include electrical engineers, mechanical engineers, and airconditioning and mechanical services plumbers.
Notably, the SPL highlighted shortages within the Technicians and Trades Workers occupation groups, with almost half (47 per cent) of all occupations within this group experiencing a shortage in 2022.
According to State of the Industry responses, it seems that respondents across different organisations in the pump industry were feeling the effects of the occupation shortages.
Respondents said the labour shortage and having to compete with the mining industry boom had created a “bidding war”, significantly increasing labour rates and inflating salaries.
Respondents leaned towards two solutions to combat labour shortage impacts for 2023: attracting more people into the industry domestically and increasing skilled worker immigration caps.
One respondent said the pump industry should “start apprenticeships for [the] industry to coax young people into it” and not charge huge learning prices, all of which needs to be implemented at a government level.
As noted by another respondent, the government should focus on campaigns to “encourage people into trades instead of university”, allowing domestic workers to “train up quickly”.
However, this highlighted a separate problem; the lack of trade recognition in the pump industry.
According to one respondent, “if a trade recognition was available in pumping (ie trade, like a plumber) it may attract more younger people into our industry”.
In an effort to combat this skills shortage at a domestic level, the 2022-23 Federal Budget committed $550 million to fee-free TAFE and an additional 20,000 university places, from the $1 billion National Skills Agreement, jointly funded by state and territory governments.
Additionally, the Federal Government is also delivering 180,000 fee-free TAFE and vocational education places, with extra support for participation of women and other disadvantaged groups.
Queensland is taking action to address this skills shortage, with a new, independent board, fuelled by a $16.5 million Queensland Government investment over three years, forming and having its first meeting.
The Board of Manufacturing Skills Queensland (MSQ) seeks to provide manufacturers across the state with essential support to access the skilled workers the industry needs to continue its impressive growth.
Queensland Minister for Training and Skills Development, Dianne Farmer, said the State Government is committed to driving Queensland’s manufacturing industry to new heights.
“Manufacturing delivers $20 billion a year to the state’s economy, and we are determined to help the industry thrive by providing evidence-based advice and local insights on the broad range of manufacturing needs across Queensland.”
Ms Farmer said MSQ directs future skills strategies by tracking and analysing manufacturing supply chains and industry needs and trends, by combining engagement with industry and training providers and research to develop annual training plans and recognised skills pathways.
According to Ms Farmer, a workforce with skills tailored to industry needs is essential to future growth.
“Manufacturing Skills Queensland will review training for workers and small and medium businesses to help them build skills and capability,” Ms Farmer said.
The other way respondents noted to combat the lack of skilled workers was through outsourcing skilled labour from overseas.
One respondent said “the government must allow for a significant increase in immigration”, with another saying that to stop the skills shortage holding the industry back, the “government should ease migrant restrictions further for skilled workers”.
While the permanent migration cap increase that was announced at the Federal Government’s Jobs and Skills Summit September 2022, from 160,000 to 195,000, is a step in the right direction, more of a focus on “skilled immigration programs” is crucial to keep the industry thriving in 2023.
The final months of 2022 have seen international border relaxations around the world and there is an expectation the relaxations may result in an influx of visa holders to Australia.
A positive outlook for the agricultural industry
Although torrential downpours and floods have caused devastation across the country, the increased rainfall may just be what the agricultural sector needs, providing critical rainfall to help crops and farms thrive after years of drought.
On the topic of the future of the agricultural industry in 2023, more respondents expect it to have a positive effect on the pump industry than a negative effect.
This could be due to a variety of reasons, including farmers needing pump equipment to mitigate the effects of flooding and extreme rainfall.
As with other sectors that could impact the pump industry, the agricultural industry is set to benefit from significant funding allocations announced in the 2022-23 Federal Budget. These include $500 million to the agriculture sector through the National Reconstruction Fund, $1.1 billion to increase connectivity in regional and rural Australia, and $111.3 million through targeted grants to stimulate regional manufacturing, including funding to expand food manufacturing capability and capacity across Australia.
Despite this, the latest results from the Rabobank Rural Confidence survey has shown that for the first time since December 2019, rural confidence around Australia has moved into negative territory. Even keeping in mind the high rainfall and fantastic commodity prices of the last two years, a large number of farmers believe conditions are set to worsen over the coming year, rather than improve.
This could be attributed to concern that commodity prices will fall, the rising cost of farm inputs – like fuel, fertiliser, energy and building materials – and the amplified risk of foot and mouth disease.
Rabobank Australia CEO, Peter Knoblanche, while the Australian farm sector faced several uncertainties over the coming months, levels of farm sector investment were still encouraging, albeit down on last quarter, demonstrating a longer-term optimism in agriculture.
“The latest survey revealed 25 per cent of farmers nationally were looking to further increase investment in their farm businesses (although this was down from 40 per cent at the start of 2022). A further 60 per cent also plan to maintain current levels of investment, which is a positive sign”, Mr Knoblanche said.
The survey findings over 2022 pointed to a growing trend of farmers investing in new technology – planned by 44 per cent of those increasing investment in their farm business this quarter. A total of 71 per cent of those increasing the spend on their business said on-farm infrastructure was a priority, followed by new plant and equipment purchases.
And almost one quarter of those farmers nationally looking to increase investment are planning to expand their
enterprises through property purchase (a similar level to last quarter).
Although Australia’s farming and agricultural sector appears to be in a healthy financial state, there are several challenging factors tainting the previously positive outlook. Only time will tell what effect these factors will have on the pump industry in 2023.
Despite the significant investment in the mining industry and critical minerals, respondents remain divided on whether or not they expect another mining boom to occur in the future.
The 2022 Federal Budget announced a commitment of more than $150 million towards critical minerals projects, to be informed by the forthcoming National Critical Minerals Strategy.
This commitment includes an initial four-year spend of $50.5 million towards the new Australian Critical Minerals Research and Development Hub, alongside a three year commitment to the $50 million Critical Minerals Development Program, building on a recent $50 million investment in six critical minerals projects.
Mechanical engineers are included in the occupations experiencing shortages throughout 2022.
One survey respondent flagged a potential climb in “the exotic mining sector for battery production e.g. lithium” as a key sector which will see growth in 2023.
This prediction is not too left-of-field, with Australia the world’s largest lithium producer, and latest figures forecast the value of lithium exports are due to increase more than tenfold over two years, from $1.1 billion in 2020-21 to almost $14 billion in 2022-23, with continued growth over future years.
Additionally, a projection by the International Energy Agency showed a potential growth of at least 30 times to 2040 of mineral demand for use in electric vehicles and battery storage.
Around the country, state and territory governments are also throwing their weight behind growth in critical minerals.
In Queensland, recent amendments were made to legislation, with the Coal Mining Safety and Health and Other Legislation Amendment Bill now allowing for the deferment of rents for specific critical minerals projects, which includes some in the prominent Northwest Minerals Province.
It’s expected that rent deferrals such as this will attract new investment in critical minerals and fasttrack projects.
Additionally, a discussion paper released by Queensland Resources Minister, Scott Stewart, suggested speeding up project approvals as a way to change how exploration for critical minerals is run.
This is on top of $79.6 million in funding allocated in the state budget to help grow and diversify the resources industry, an additional $40 million for new economy minerals to support good jobs and encourage economic opportunities for Gladstone; and $68.5 million to drive key actions from the newly released Queensland Resources Industry Development Plan and boost the state’s resources industry.
Other states are following suit, with New South Wales announcing a $1.6 billion package to set the state up as a major investment destination for critical minerals mining and advanced manufacturing; more than $17 million allocated in the Victorian budget to mining and exploration; and funding from the South Australian Government for to digitise and automate exploration and mining related approvals, and facilitate the delivery of sustainable water to the Gawler Craton.
Another factor contributing to a potential mining boom is the global move to diversify the supply chain. The global supply
chain of certain critical minerals has always been heavily reliant on a select few countries.
For a long time China has held a position of dominance across critical minerals supply chains, but there is growing concern that dependence on China for these minerals may create energy security risks. Additionally, tensions between countries and COVID-19 disruptions have led nations to build their own critical minerals supply chains.
In July 2022, Australia participated in The Global Supply Chain Resilience Forum, working to build supply chain resilience.
The forum was also attended by members from countries including the UK, Singapore, Indonesia, Japan, India, Canada, Mexico, Brazil, France, Germany, Italy, Netherlands, Spain and the Democratic Republic of Congo.
A new partnership between Australia and Japan will see the development of a supply chain for critical minerals. The Critical Minerals Partnership will boost opportunities for information sharing and collaboration, including research, investment and commercial arrangements between Japan and Australian projects, as well as building a secure critical minerals supply chain between Australia and Japan.
Opportunities for the pump industry going forward
Pumps and storage
As the world – and Australia – turns to a greener, environmentally-friendlier way of living, generating energy and storing energy, pumped hydro is the word on everyone’s lips and, as the name suggests, pumps play an essential role.
Throughout 2022 the Federal Government and state and territory governments have continued to investigate the feasibility of pumped hydro storage around the country.
The New South Wales Government pledged $97.5 million to accelerate pumped hydro projects that could fastrack the state to reach its goal of building at least 2GW of new long duration storage by 2030.
Additionally, the Queensland Government has committed to developing the world’s largest pumped hydro scheme, in its $62 billion Queensland Energy and Jobs Plan, in a bid to help secure the diverse energy system and clean energy storage essential to the state’s future.
These kinds of large-scale projects are set to unlock new potential for the pump industry.
Flood-proofing against an unknown future
Flood-affected areas and regions throughout Australia have turned to the pump industry for help in their time of need, utilising pump services to mitigate the effects of La Nina and frequent flooding over the past 12 months.
This kind of reactive asset management – although crucial – is only half of the equation. Councils and cities across the country are adopting a more proactive approach and looking to flood-proof assets and build resilience to natural disasters and the impact of climate change.
Among these is Tweed Shire Council which is looking to build a new pump station in flood-affected Murwillumbah, to help ensure the community is better prepared for and protected from potential flooding.
This kind of proactive natural disaster preparation could prove beneficial for the pump industry in 2023 as supply for pumps increases, and in turn leads to an increase in future maintenance and repairs.
Technology spurring efficiency
Cutting edge IIoT is expected to continue to change the realms of possibility for the pump industry, specifically motordriven, peristaltic and solenoid pump applications involved in processes, from swimming pools to wastewater and cooling water treatment.
Pump operators looking to improve the sustainability and efficiency of their systems are increasingly turning to
costs on, among other things, printing and distribution of the revised manuals.
IoT systems also provide unparalleled insight into the equipment operation, consistently receiving data from pump sensors that are constantly monitoring and collecting data on things like vibration, chemical consumption and cycle status.
This constant monitoring also proves to be exceptionally valuable as IoT technology allows the performance and status of specific pump components such as bearings, couplings and belts to be assessed, meaning operators receive advanced warnings if equipment is faulty or needs to be replaced.
New IoT systems allow users to receive smartphone notifications if defects are detected or if faults occur, in turn improving the efficiency of equipment repair, maintenance and upgrade planning and mitigating inconvenient and expensive downtime. This also helps to drive aftermarket sales for suppliers.
Looking ahead to the next
While COVID-19 recovery continues, the past 12 months dished out a range of curveballs and global events, none of which were possible to plan for. Despite this, pump industry individuals refuse to be deterred from looking ahead with a positive, confident and optimistic outlook.
As the State of the Industry celebrates its first decade, there’s one thing that the last year – and in fact the last few years have shown and that is that it’s impossible to anticipate
MAIRS Technology uses traditional technologies and innovative engineered solutions to service a range of industries and customers to help manage their environmental needs and systems, whilst meeting environmental and health safe regulations, and health of nearby communities.
Our capabilities:
• Project Management Services
• Engineering Service Support
• Equipment Spares Supply
• Construction services and supervision
• Sub-contract management
• Commissioning and training
• Asset inspections and reports
• Asset maintenance and management planning
• Optimisation and system improvements
03 9028 8080 sales@mairstech.com www.mairstech.com
Angus Flexible Pipelines Australia offers a range of customengineered equipment to suit particular flood situation applications. Our flexible pipelines are designed for ease of use when deploying, retrieving, transporting and storing in difficult environmental conditions.
Flexible pipelines
Today, flooding appears to be an ever-increasing factor in large parts of the world. The resultant impact can be devastating on life and property, and having the ability to quickly, and effectively move large volumes of water in response to such a disaster is becoming more and more essential.
Angus Flexible Pipelines Australia has a Flood Relief package that is a fully-integrated system capable of pumping large volumes of water over considerable distances – away from infrastructure and residential areas. Utilising a single line of Angus 12” Super Aquaduct system, it can pump up to 19,000 litres of water over a distance of 8km.
A typical system comprises several pieces of equipment including satellite and booster pumping systems, hose deployment and retrieval systems, XLD layflat hose technologies, and accessories.
Collecting heads and manifolds
Collecting heads
Custom collecting heads can be used to flow feedwater from multiple inlets to a larger single source outlet – typically 250/300mm – to optimise flow over long distances and minimise pressure losses, especially when using Angus Super Aquaduct hose.
Manifolds
Custom spider manifolds can be used to control water flow and distribution, allowing connectivity to smaller diameter hose lines – typically using Angus Armourline hoses via gated valves with storz or instantaneous connections. Inlets can be 200, 250 300mm – either storz, twin star or victaulic connections for use with Angus Super Aquaduct hose.
Unvalved large wye manifold/dividing breechings to direct water flow from a single source to smaller sources – typically from 1 x 300mm to 2 x 200mm – ideal for use with Angus Super Aquaduct hoses when transporting water over distance. Connections can be storz, twin star, victaulic or other multiple configurations.
“Mo-Man” Wheeled Hose Hydrant Trailer for rapid easy deployment with six gated valves – either storz or any other connections, to direct, control water flow and distribution. Throughput either 250 or 300mm connections with valved options.
Hose deployment and retrieval equipment
Angus Flexible Pipelines Australia supplies single or quadruple hose reelers for easy deployment and retrieval of large diameter hose such as Angus Super Aquaduct. Each reel will house 600m of 300mm hose. For a smooth easy efficient use, this can be trailer or skid mounted with hydraulic control system for smooth easy efficient use.
System connections
Typically used to connect the systems normal pipe-to-pipe connections, pipe-to-hydrant connections, pipe-to-pump connections or pipe-to-water supply connections.
Stock availability
The great news is that we have available stock for immediate delivery across Australia of our range of flexible pipelines for flood risk – Super Aquaduct; irrigationFlowmaster; and mine dewatering – Wellmaster.
More information is available by contacting us
Contact: +617 3256 7624
Email: sales.australia@angusfire.com Or Visit: https://angusflexiblepipelines.com.au
Yarra Valley Water covers a vast area stretching from Wallan in the north of Melbourne to Warburton in the east. The network includes more than 10,000km of sewer mains, nine sewage treatment plants and more than 100 sewage pumping stations. Investment in rapidly developing areas such as Melbourne’s Northern Growth Corridor is critical to ensure the system can cater for population growth and meet demand for essential water and sewerage services.
Bespoke pumps to improve services and support growth: Doreen to Diamond Creek Sewerage Project
Yarra Valley Water invested $332 million in water and sewerage infrastructure in 2021-22 to improve services and support growth. Major works completed in this period include the Doreen to Diamond Creek Sewerage Project to service the Mernda, Doreen and Diamond Creek areas. Delivery partners Jaydo and MFJ constructed the $34 million project over two years. It involved building a 10km section of sewer pipe and 17 new sewer maintenance holes under public parkland and road reserves.
Major Projects Manager, Ash Hamer, said the project also included construction of a new high flow pump station which can pump a massive 420 litres every second – the equivalent of three full bathtubs a second.
“It’s one of our biggest sewer pump stations and the pressure main is the largest in our network,” Mr Hamer said.
“The most important factor in the selection of the pumps for this project was their capacity to process high volumes quickly. They had to deal with approximately 90m head and operate in a duty/assist combination to maintain 420L/s –meaning very bespoke pumps were required.
“When we went to tender for the pumps, there were very few suppliers with options that could do the job. To protect the environment from spills, the pumps were selected on the maximum possible intake the downstream sewer could accommodate. Variable Speed Drives operate between 5060Hz. A single pump had to be able to operate (standard dry weather flow rates) at 200-260L/s. The 250kW pumps are 2m tall and weigh about two tonnes.”
Trenchless drilling technology was used in construction to reduce excavation, protect vegetation, and minimise disruption. Special care was taken to avoid disruption to areas of cultural sensitivity.
Project design partners Jacobs salvaged almost 400 artefacts during construction and worked in partnership with Yarra Valley Water and the Wurundjeri Woi Wurrung Cultural Heritage Corporation to sensitively repatriate them at the completion of the project.
“Our approach to this project is a great example of our commitment to care for customers, the community and the environment while providing vital sewerage infrastructure where it’s needed,” Mr Hamer said.
New dosing stations and improved sewage treatment: Craigieburn to Epping Sewage Transfer Project
Other projects currently in construction include the $13 million Craigieburn to Epping Sewage Transfer Project to upgrade the sewerage network in Craigieburn, Wollert and Epping. This includes building new dosing stations at Yarra Valley Water’s Craigieburn and Aurora hubs to reduce odour and pipe corrosion, and is currently scheduled for completion in early 2023 with our delivery partner MFJ.
“As part of the project we’ve improved our Aurora and Craigieburn sewage treatment and transfer facilities to increase the sewerage system’s capacity to receive more sewage,” Mr Hamer said.
“This work will ensure the reliability of the sewerage system, improve network efficiency, and reduce the likelihood of sewage spilling into the environment during heavy rain. It will allow more flexibility in our network to accommodate for growth in the northern suburbs and enable us to produce more recycled water.”
In addition to new wastewater projects to support rapidly developing suburbs, Yarra Valley Water also has an extensive Community Sewerage Program to enable customers in older outer areas to connect to the sewerage system. This means they can get rid of their septic tank systems which can pose a risk to human health and the environment. There are about 10,000 properties on the program, to be serviced over the next 10-15 years.
Work was recently completed to expand the sewerage system to the town of Monbulk, about 40km east of Melbourne, in the Dandenong Ranges.
Community Sewerage Program Acting Manager, Lizzie Scott, said the organisation worked closely with the Shire of Yarra Ranges to develop a new pressurised sewer network for the area.
“We have a regulatory obligation to identify and prioritise provision of sewerage systems to properties at high risk of not being able to contain their wastewater within their property boundary,” Ms Scott said.
“The project in Monbulk involved installing over 22km of reticulation pressure sewer to service approximately 900 properties. The new network complements an existing gravity sewer system that services some of the local properties and businesses within the main township.”
The Monbulk Sewage Pumping Station was built to collect sewage from both the existing gravity sewerage network and the new pressurised sewerage network and transfer it via a network of pumps and pipework for treatment away from the local area. Flows from the pressure reticulation system and existing gravity reticulation system are collected and transferred to the Kallista network, via the new station and a 2km transfer main.
Ms Scott said that by working closely with designers Iota and Jacobs the pipework alignment was designed to avoid environmentally significant areas. Delivery partners Melbourne Pipelines, Interflow and Jaydo installed pipework using non-invasive drilling techniques to minimise environmental impacts during construction.
COVID-19 created some challenges for the project team, with extensive lead times for the pumps. Jaydo and Yarra Valley Water worked closely in the early stages of the project to finalise pump selections and ensure orders were placed at least six months in advance.
Ms Scott said the above ground pumps also had to meet stringent noise requirements, due to their proximity to residents and park users. Custom-made acoustic enclosures were needed to minimise noise.
“With the unique design of this pump station, both below and above ground, we required two different types of pumps – submersible centrifugal for the below ground pump station and progressive cavity pumps for above ground,” she said.
The two submersible pumps in the underground gravity storage tank pump the sewage 10m up into the above ground tank at 21L/s. The pumps operate one at a time to give resilience to the system, with a third pump available onsite if one requires maintenance or repair.
As the pumping station is at the bottom of a steep hill, the pumps in the above ground pumping station need to pump sewage at 21L/s up to 80m above the pumping station to a site over 2km away.
Both types of pumps are capable of handling solids up to 15mm in size, making them perfect for sewer applications.
Ms Scott said the installation of the precast below ground pump station was quite challenging as the local water table from the adjacent creek was approximately 2m below ground level, and the pump station extended to 7m depth.
This meant there was a significant amount of groundwater, that due to environmental considerations, could not be discharged locally. The preliminary work on the groundwater chemistry also indicated the groundwater had a high level of mineral salts. That meant that not only could it not be discharged locally, the sewage would need to be treated before it could be discharged into the sewerage system.
To tackle this issue, a storage tank and mobile water treatment plant were brought onsite to collect and treat the water before trucking it away to discharge into the sewerage system in a neighbouring town. Trucks were on standby to empty the onsite storage. The amount of groundwater that
needed to be removed from the site was limited by minimising the construction time by using a precast concrete tank.
Ms Scott said the new system would make managing sewage easier and more convenient for Monbulk residents.
“Customers now have the option to flush and let us take care of their wastewater. This is a great outcome for the community, local businesses and the environment,” Ms Scott said.
To encourage residents to learn more about the benefits and connect to the new system, Yarra Valley Water opened a shop in Monbulk staffed one day a week by the Community Sewerage Program team. Customers can pop in to talk to staff and learn more about the pressure sewer system and the connection process.
Ms Scott said the Monbulk project would also make a huge difference to local amenity.
“There are many leaking septic tanks in the area that could be affecting local waterways,” she said. “The new system will help to prevent sewage run-off and improve Monbulk’s beautiful environment.”
Apart from the environmental benefits, connecting to the sewerage system also gives residents greater flexibility for home improvement and extension options, freeing up land previously used for wastewater treatment.
Ms Scott said the Community Sewerage Program also contributes to Yarra Valley Water’s purpose to support the health and wellbeing of customers and create a brighter future for communities and the natural environment.
Yarra Valley Water is now continuing construction work to extend the sewerage network in the Dandenong Ranges to the neighbouring towns of Kallista, The Patch and Sherbrooke. This will involve constructing a further 70km of reticulation pipes and several booster pump stations.
Construction in Sassafras is expected to begin in 2023, and Olinda is currently in design.
Yarra Valley Water engaged with Monbulk residents to learn more about the benefits and connect to the new system.
Works are underway on a significant project to improve a southern Townsville suburb’s sewerage system. The Wulguru Pump Station project contract was awarded to Townsvillebased company Civil Plus Constructions to carry out the $7 million project to construct a new sewerage pump station, with the works addressing the suburb’s sewer service capacity issues.
Townsville Water and Waste Committee chairperson, Russ Cook, said the upgrades were not glamorous but were necessary.
“The sewer system was unable to cope with the increased capacity for the Wulguru community, particularly in the southern and western parts of the area,” Cr Cook said.
“The Wulguru Sewer Upgrade Project has been split into two components; and contractor Newlands Civil Construction was awarded component one to construct a gravity sewer and rising main.
“Construction of the sewerage pump station is set to be finished in early 2023 and is the final bit of infrastructure needed to ensure the sewerage system can meet the current and future demands of the Wulguru community.
“The overarching project started in 2019, following careful budgeting by Council to achieve the best outcome for Wulguru.”
The Wulguru Pump Station is the final step needed to finalise the Wulguru Sewer Upgrade project, which will ensure the wastewater system in the area will continue to cater for continued population growth.
Catering for population growth
Cr Cook said this significant investment into the city’s southern suburbs demonstrated Council’s commitment to securing water and wastewater capabilities for locals for years to come.
“By the time stage three of this project is complete, close to $54 million will have been invested, enhancing our wastewater network in our southern suburbs,” Cr Cook said.
“This is an impressive investment and demonstrates Council’s commitment to ensuring our wastewater network can continue to meet the needs of the community.
“Townsville is looking at a population surge during the next 50 years, which is why we’re putting critical infrastructure in place now to plan for our future.”
Cr Cook said Council had a strong focus on water supply as the city’s population continued to grow.
“Townsville is one of the most arid regions in Australia, which is why water supply and management continue to be one of the biggest areas of strategic investment,” Mr Cook said.
“Townsville’s population is growing rapidly, and we are attracting significant interest from industry to build and operate out of our region.
“Water supply is critical for supporting both of those things which is why we are investing to ensure we have the best infrastructure in place to keep pace with the increased demand.”
Council employing locals
Townsville Mayor, Jenny Hill, said more than 220 jobs had been generated during the three stages of the project.
“Projects like this are essential for generating local jobs in Townsville. Stage one of this project supported 100 jobs, as did stage two, while stage three has provided employment opportunities for between 20 to 30 workers,” she said.
“Procurement is an effective way for Council to support Townsvillebased businesses.
“We have also launched a tendering system called VendorPanel which gives businesses a platform to submit tenders and quotes for upcoming projects, respond to queries and provide updates to registered suppliers.
“As a signee of the Small Business Friendly Council charter, Council is committed to continuing its support of local businesses, with a goal of reaching 90 per cent procurement spend with local businesses in the next five years.”
Cr Hill said stage three of the Southern Suburbs Rising Main project included a $20 million investment from Council.
“Stages one and two of the project have included more than 13km of pipeline laid to cater for anticipated population growth in Townsville over the next 30 years,” Cr Hill said.
“During stages one and two, Council constructed the pipeline from the Yolanda Drive pump station in Annandale to the Cleveland Bay Purification Plant.
“This project supports the area’s anticipated population growth and supports Townsville University Hospital, Lavarack Barracks and James Cook University.
“Townsville is one of Australia’s fastest-growing cities and investing in infrastructure like this is vital to meeting the needs of a growing community.”
Cr Hill said Council exercised strong financial management throughout the year with a focus on capital works like roads, footpaths, water infrastructure and wastewater assets.
“As a council, we’re looking beyond the next 12 months and are laying
down the foundations for our city to take advantage of emerging energy industries, future-proofing our community’s employment opportunities,” she said.
“As part of this, we set aside more than $18 million in the 2021/22 budget to develop the city’s hydrogen strategy, reduce waste going to landfill, and build resilience through our natural environment.
“In its 2021-2026 Corporate Plan, Council committed to bolstering Townsville as a sustainable destination that embraces and participates in recreational activities, which is why it’s essential that we do our part to protect
our land and the 180km of coastline that connects Townsville to the Great Barrier Reef.”
During this financial year Council will invest a record $214.9 million into critical water infrastructure projects across the city as part of its strategic focus on water security for the city’s growing population.
The investment includes projects like the pipeline duplication project between Ross River Dam and the Douglas Water Treatment Plan, Haughton Pipeline Project Stage 2 and upgrading of the underground water network across the city.
For more information on the Southern Suburbs Rising Main and Wulguru Sewer Upgrade projects, visit the Southern Suburbs Rising Main Project page on Council’s website, www.townsville.qld.gov.au/building-planning-and-projects/council-projects/southern-suburbs-rising-main-project.
The Most Reliable Heavy Duty Helical Rotor Positive Displacement Pumps for Critical Wastewater Applications
Key Applications
Key Applications
Primary, Secondary & Tertiary Clarification Process I Sludge Thickening Process I Digestion Process I Dewatering and Sludge Incineration Process
The Malabar Biomethane Injection Project is an Australian-first biogas-to-grid trial; converting wastewater into renewable biomethane and blending it with Sydney’s existing gas networks. Not only will the five-year pilot will put gas directly into the supply network, it will also help industries across New South Wales meet their net zero emissions targets. Here, we look at the $16 million project, and breakdown the equipment and technology powering the process.
Partnering with Jemena, and with support from the Australian Renewable Energy Agency (ARENA), the project will generate zero-carbon emissions and highquality biomethane gas from the wastewater treatment process and inject it into the gas grid for heating, cooking and hot water. Biomethane production began in 2022, and it is expected to enhance New South Wales’ energy resilience and contribute to the establishment of a sustainable green gas market in Australia.
The Malabar Biomethane project is expected to offset 5,000t of carbon, and up to 11,000t if fully scaled. From 2022, approximately 95,000GJ of biomethane is expected to be generated each year through the Malabar project, enough to meet the gas demand of 6,300 homes.
What is biomethane?
Biomethane is produced from biological waste via a process called anaerobic digestion – similar to composting but instead conducted in an oxygen-free environment – this creates biogas, which is then purified in a process that removes excess materials including carbon dioxide, hydrogen sulphide and water. The resulting product is a low-cost net zero alternative to carbon-intensive natural gas and can be used to supplement Australia’s existing gas distribution network.
Anaerobic digestion occurs in wastewater treatment plants to break down waste products, producing methane that can be captured and refined into a sustainable and green bioenergy source. Many wastewater treatment plants use this process to provide an alternative power source. However, upgrading these existing systems for biomethane production could offer broader solutions in everyday applications.
The Malabar Biomethane Injection Project
Jemena constructed the Malabar Biomethane Injection Project, which was installed at Sydney Water’s Malabar Wastewater Treatment Plant, with Zinfra engaged for project management, engineering, procurement and construction. Previously, the biogas from the wastewater treatment plant was used to power cogeneration engines that produce electricity to reduce the overall energy of the plant, with some excess biogas being flared.
In the future, at least 95,000GJ will go to the new biomethane production, with the rest used for onsite operational use. The Malabar Biomethane Injection Project will redirect raw biogas into a biogas upgrader system and convert it into biomethane – turning waste into clean, green energy.
The biogas upgrading system is easily integrated into a biogas plant, providing a refined and efficient method of gas cleaning that can recover up to 99.5 per cent of methane.
The biomethane is refined to Australian standards before ultimately ending up in the gas grid as a green gas alternative.
Complementing the existing biogas electricity generators, this project will enhance Malabar Wastewater Treatment Facility’s performance as a clean and renewable bioenergy producer, creating more energy than is needed to run the entire facility.
Zinfra engaged Brisbane-based company Eneraque to deliver the upgrader package, who in turn contracted Dutch biomethane specialist Bright Biomethane to provide the major equipment. The electrical components of the equipment were converted to meet Australian standards.
The Australian-first biomethane upgrader was sized for 1100Nm3/hr of biogas to the inlet prior to separating the CO2 and CH4 with a patented three-stage membrane system.
How does biogas upgrading work?
Biogas upgrading is the process to remove impurities and moisture from raw biogas to transform it into high-quality biomethane that meets the stringent gas specification requirements stipulated by the grid infrastructure provider. This purified gas is then blended into the gas grid network.
Membrane separation – the process being used at Malabar –is one technology available to produce renewable natural gas. It consists of a number of stages and equipment.
Pretreatment – After biogas has been produced by the anaerobic digesters it enters the upgrading plant where it is cooled and dehumidified, before Volatile Organic Compounds (VOCs) and Hydrogen Sulfide (H2S) are removed through the use of activated carbon filters. During this stage, the extracted heat can be reused for other purposes.
Compression – The pre-treated biogas is then compressed to the required pressure for the final upgrading process.
Upgrading process and control – The upgrading process usually consists of a two or three stage membrane system, whereby CO2 and biomethane are separated into concentrated gas streams for final processing. Biomethane is then purified to meet network quality standards and CO2 is reprocessed for maximum biomethane recovery. Depending on the application, CO2 can be recovered for industrial users.
Biogas can be both compressed into the front of the membrane system to roughly 200psi and pulled out the back end with a vacuum pump to enhance performance.
Injection/blending – Once the biogas has passed through the membrane system, THT is injected to give it the characteristic gas smell to allow it to be safely and easily detected. Different technologies are available for this step, with absorption and pump systems traditionally used, but new technologies that incorporate solenoid valve injection can also be used.
It is then blended with natural gas within the gas network.
For the Malabar project, once the biomethane has been processed it will be injected into Jemena’s existing gas distribution network, specifically its Eastern Gas Pipeline between Victoria and New South Wales.
The product will be transferred from the Malabar facility to Jemena’s compressor stations, which pressurise the biomethane to be consistent with national and local standards.
The main function of these stations is to propel the medium forwards by boosting pressure and keeping natural gas moving through the network. Compressor stations are usually centrifugal compressors powered by turbines, electric motors or reciprocating compressors.
Natural gas compressor systems contain monitoring and backup measures to ensure safety and reliability. Heat is generated when gas is compressed, with every 100psi increase in pressure creating a seven to eight degree increase in natural gas temperature.
As a result compressor stations need to have safety measures in place to cool the gas to a manageable temperature before the gas is sent out into the pipeline again.
The project will supply biomethane to these stations, where it will be blended into the natural gas network for distribution to commercial and residential customers.
Before the biogas enters the biogas upgrading system, the waste that will become biogas goes through anaerobic digestion, a process through which bacteria break down organic matter – such as animal manure, wastewater biosolids, and food wastes – in the absence of oxygen.
Anaerobic digestion is driven by positive displacement pumps such as progressive cavity or peristaltic, which enables the movement of raw waste materials – including agricultural, food, and municipal waste – from large hoppers through to the primary anaerobic digesters.
Positive displacement pumps excel in transferring fluids with higher viscosity, such as waste materials, a role unsuited to centrifugal pumps as they are less efficient in maintaining flow rates for thicker fluids.
In biogas production, a grinder can be integrated into some progressive cavity systems to break down biomass into a slurry mixture for more efficient transportation and processing.
The slurried biomass is then transferred to the anaerobic digester silo, consisting of layered rubber membranes that expand and contract to accommodate the resulting biogas product.
Other pumps can be used for various applications in anaerobic digestion including:
• Submersible centrifugal pumps for general flow duties in sumps and chambers, site surface water drainage, slurry pumping, etc
• Chemical dosing pumps where precisely times flow is required for the dosing of a liquid
• Chopper pumps
• Slurry pumps
• Screw pumps
• Lobe pumps
The Malabar Wastewater Treatment Plant currently hosts extensive anaerobic digestion facilities for the production of biogas, which is used for power generation and water heating, with excess materials combusted via onsite waste gas burners.
Building business in biogas
Jemena’s General Manager Renewable Gas, Peter Harcus, said biomethane has the potential to play a huge role in meeting Australia’s net zero emissions targets.
“This project will start to allow Sydney households to keep using gas, while also reducing their carbon footprint,” Mr Harcus said.
“For our commercial and industrial customers – whose manufacturing processes are difficult to decarbonise – this project will help enable them to maintain their operations, keep people in jobs, and help to decarbonise their supply chain.”
According to ARENA’s Bioenergy Roadmap, by 2030 the bioenergy sector will not only enhance Australia’s fuel security but also contribute to around $10 billion in GDP per annum, create 26,200 new jobs, reduce emissions by about nine per cent and divert an extra six per cent of waste from landfill.
The Malabar Wastewater Treatment Plant will be the first participant in the five-year pilot, which seeks to establish the groundwork for a green gas certification scheme.
Delivered as a partnership between Jemena, GreenPower and Energy Networks Australia, the project will provide customers with a way to purchase verified and accredited zero emission gas.
The gas certification scheme was announced following ARENA’s $16 million investment in the Malabar project.
Jemena's Executive General Manager, Shaun Reardon, said such a scheme could improve investments in renewable gas alternatives, including biomethane and hydrogen.
“We are driving the call for a national certification scheme because our customers have told us they want certainty in their ability to purchase verified and accredited zero emission gas just as is currently the case for renewable electricity,” Mr Reardon said.
“This is an important first step towards a Renewable Gas Target, which Jemena is calling for to achieve net zero emissions in Australia by 2050.”
Though biomethane production is by now well underway at Malabar, much remains to be seen in whether such processes can be reliably and sustainably implemented at-scale. But no matter the result, the Malabar project and resulting certification scheme will be instrumental in shaping the future of Australian gas supply.
Non-degradable materials entering sewer networks has become an ever increasing problem. Many of these issues can be largely attributed to wet wipes –which do not readily disintegrate when flushed down the toilet – but also other materials such as feminine hygiene products and substances like fat, oil and grease (FOG). Together these materials and substances act as knitting agents with other items that make their way into the sewerage system that don’t deteriorate, or don’t deteriorate quickly. When this happens, they form rag balls which can then form into fatbergs if not removed from the system.
Rag balls and fatbergs are a concern to wastewater utilities as not are they expensive and time consuming to remove, but they clog pipelines, as well as block pumps and cause excessing wear to the pump equipment, which can lead to system failures.
The risk of this increases during storm events as old sewerage infrastructure is vulnerable to chokepoints forming as stormwater enters the system. When this happens any non-flushable materials and substances, rag balls and the beginnings
Fatbergs and sewer blockages are problems faced by wastewater utilities around Australia, and globally. Not only are they time consuming and costly to remove, but they can also clog pipelines, and block and damage pump equipment. Here, we look at how incorporating digitalisation into deragging technology is a key weapon to predict, prevent and eradicate issues from occurring.
of fatbergs can get flushed into the pumps. Not only can this cause pump failure when they’re most needed or equipment damage, there is also an environmental risk if the sewerage system overflows and the associated costly cleanup.
The problem is that by the time utilities are aware a fatberg has formed, often a severe blockage has already occurred.
Waging war against fatbergs: what utilities have done to prevent them
In 2022, Standards Australia announced a world-first labelling standard to define what shouldn’t be flushed down the toilet, in an effort to prevent unflushable products clogging up sewers. The final Australian and New Zealand standard sets out the criteria for determining if certain products are suitable to be flushed, and provides requirements to manufacturers for correct and informative labelling for consumers.
Furthermore, wastewater utilities have tried a number of other methods to prevent rag balls and fatbergs from occurring including through community engagement campaigns to teach people
what can and can’t be put down the drain or flushed.
They have also taken steps to upgrade the sewerage system to cope with non-flushable materials and substances such as by installing chopper, macerator or grinder pumps or variable frequency drives (VFDs). However, these are not without problems. While chopper, macerator and grinder pumps can help reduce the frequency of operator intervention, they can still jam and require service, and issues can occur when they are midslice at the time the level control system shuts the pump off. They also do not have the torque to restart and finish the cut without intervention. The problem faced with traditional VFD-controlled systems is that they are designed to allow the pump to operate in reverse on startup or when they reach a high current set point. By the time it reaches this point, it is often too late to reverse the pump as a fatberg has already formed, and doing so will only throw the fatberg back into the well to cause a blockage later.
The installation of dual-shaft grinders is another cost-effective solution to upgrading sewerage infrastructure
that utilities have implemented. This has had some success in keeping the introduction of materials that don’t disintegrate as the low speed and high torque design of grinders allows them to shred tougher solids. The use of grinders has provided a lower cost alternative to upgrading older wastewater lift stations as pump upgrades aimed at dealing with wipes and other materials can be costly due to new electrical requirements, hydraulic considerations and potentially lower efficiency. The other disadvantage of pump upgrades is that some pumps may not be able to handle larger tougher materials or larger rag balls – both of which high torque grinders can shred.
However, grinder selection is important as conventional grinders can exacerbate the problem due to them shredding products into longer strips that are able to reweave with FOG and other materials and substances. There are now some newer grinders available
that use cutters that cross-shred materials so that they are small enough to be pumpable.
Upgrading outdated technologies at the headwords is another solution that utilities have tried. Older bar or rake style screens are not suitable for removing wipes even though they are often required to remove large debris. Newer fine screens using 6mm or less hole sizes are now available and are able to capture wipes as they have been designed with two directional screening panels which can capture smaller materials.
While these steps help, they cannot be relied upon to solve the challenge, and as such using intelligent monitoring solutions with deragging technology is important to achieve proactive pump care and predictability.
Deragging technology
One way to prevent blockages and equipment damage is to use digital
monitoring technology – such as those that measure the pump’s raw power signature and understand its torque profile – that can help monitor and protect the pump in real time. One such technology is able to identify when solids catch on the impeller, prompting it to slow down before stopping and reversing flow to loosening it before more solids can accumulate and become too large to be processed. This allows any solids to pass through the system and be captured by screens.
Furthermore, software with complex algorithms is available that has variable settings and is designed to understand pump behaviour and detect any inconsistencies from potential blockages. It can control the pump when needed, which means each reversal, or clean cycle, is started before the buildup of damaging solids rather than reversing the pump arbitrarily or waiting for a high current setpoint to be reached.
One of the major benefits of deragging technology is that it keeps any solids intact. While shredders and macerators have their place in some applications and can prevent pumps from clogging, they can negatively impact the composition of wastewater and lead to pollution. This is because shredders and macerators can cause a high volume of microparticles in the wastewater, which pass through screens at the treatment facility and then aggregate in the aeration basins downstream. At this stage blockages can occur as the process equipment used is not designed to deal with largediameter aggregates. Microparticles also pose a problem for clean water systems, with health and environmental risks associated with them. Therefore, it is advantageous to keep wet wipes, rags and other material intact. This is the benefit of deragging technology as it keeps materials whole so they can pass through the system and get caught by treatment works screens, ensuring they are safely collected and reducing microparticle concerns.
Other benefits of this technology keeping a pump running clean include:
• Reduced lift and cleaning – saving labour time and costs, and allowing more time to be spent on other maintenance
• Improved safety – safety risks to personnel are reduced as the system handles less sewage, and there is less exposure to potentially dangerous materials
• Fewer blockages – reduced risk of overspill
• Preventative maintenance –detection of issues such as bearing or seal wear are detected earlier so the operator can plan maintenance before failure occurs
• Reduced overall runtime – reduces energy costs and improves asset life
This technology is starting to become more common with a number of pump manufacturers offering pumps with this feature included, as well as some control system companies offering it as a separate controller that can be installed on new and existing pump control panels.
Deragging technology is continuing to evolve and improve, and there are opportunities for it to improve operations beyond dealing with materials in sewerage systems as pump manufacturers incorporate more smart technology into their designs.
For example, health and safety improvements are being made, with deragging technology that is designed to automatically monitor and keep the pump clean. This removes the need for manual labour to lift the pump and clean it. Other integrated features can include odour control, which prevents water stagnation and odour buildup by instructing the pump to periodically run during low activity.
Smart technology also enhances data collection, which can help utilities better measure results, monitor equipment efficiency, adjust settings and predict maintenance timing. Utilities can also get ahead of weather events and catch problems if they have the ability to track conditions in the well and adapt to them, reducing the risk of spillage.
Therefore, deragging and real-time data monitoring will be a key tool to have constant visibility of the pump.
Undertaking the largest repair project for the city, Mackay Regional Council navigated heavy rainfall to find a long-term solution for one of its essential sewage rising mains. But finding such a solution required equipment specifically designed to withstand damage and heavy rainfall, including custom-built pipework along with a gate valve and VS4 air valves.
Mackay Regional Council conducted repairs on a section of damaged sewage rising main in June 2022. The southern main is a critical pipeline for the Queensland city, with over 18 million litres of sewage being transported every day through the city to the Mackay South Water Recycling Facility, and servicing 27,000 connected customers.
The 914mm mild steel cement-lined rising main stretched 11km long, with an isolation valve at Sydney Street pump station and another at the Mackay South Water Recycling Facility. The repairs involved replacing 18m of pipe with a custom-made section and installing new isolation valve and air valves.
The southern rising main repairs became some of the largest undertakings by Mackay Regional Council. Despite facing challenges, the work proved to be a learning experience for the council to better understand how to set up a resilient wastewater network.
The repairs had to be undertaken after a community member informed Council about a leak adjacent to Paradise Street. Following investigations, it was determined that the main’s high point was 4m from the air valve offtake point, meaning decade’s worth of corrosive gas cavitation had caused the release of raw sewage and Council took immediate action to stop the leak with a repair clamp.
Mackay Regional Council Water and Waste Services Chief Operating Officer, Stuart Boyd, said the team had to find a long-term solution to avoid more leaks in the future along this essential pipeline, but any work would inevitably require releasing raw sewage.
“A 20m section of the main was to be replaced with custombuilt pipework, including new fixtures. But how to safely and responsibly isolate or bypass the main without an uncontrolled release of raw sewage?” Mr Boyd said.
“In under 12 hours, we had to drain and redistribute 995,000L of raw sewage from four scour points to adjacent catchments, and remove and replace it with the new custombuilt pipework section and valves.
“While planning to manage this critical risk, Mackay Water and Waste Services (WWS) assessed isolation methodologies to establish an agreed permanent repair method for isolation to allow for repair.”
The draining involved turning off 88 sewerage pump stations in Mackay, which meant an overuse of water in the area could have inundated the pump stations and caused harmful discharges to the local environment.
“Corporate risks were considered and evaluated with a costeffective way of managing all the design, flow management, asset isolation and construction in-house. Being a regional council, we wanted to provide the best solution to our ratepayers while considering the environmental, safety, and financial risks,” Mr Boyd said.
Preventing further leaks in the future along the pipeline meant finding the right equipment that could withstand both everyday demands and high wastewater flow during storm events.
Mackay Regional Council decided to use a custom-built pipework that could suit precise dimensions and be coated for extra protection, in addition to installing a 900mm gate valve. While the custom pipework was procured from a third party supplier, the gate valve was sourced using a threequote method.
“As part of the 20m custom-built pipework section, we took the opportunity to install a 900mm mechanical gate valve. The pipework was epoxy-coated 540° internally and for extra protection, we decided to coat the inside and outside of the 900mm valve,” Mr Boyd said.
On top of the custom pipework and gate valve, Mackay WWS procured two new VS4 air valves which ideally suited for the pipeline. Following the works, the valves were kept as a council store-stocked item.
“The design of these air valves is perfect to use on sewage-rising mains. The valves are accessible and sit within a rectangular concrete pit with a lockable aluminium lid,” Mr Boyd said.
However, before repairs could begin, works were postponed from the original start date in May to June because of unprecedented wet weather, which caused a significant increase in wastewater flowing through the city.
“Sewage infiltration after the rain event saw higher flows that were not manageable. Any inundation could cause harmful discharges to our environment – something we want to avoid at all costs,” Mr Boyd said.
“The rain had soddened the ground at the construction site, which meant heavy vehicles could not access it. We had to redistribute and redo the radio ads, all while maintaining the community’s interest.”
These repairs proved to be one of the largest undertakings for Mackay WWS thanks to the challenges posed by heavy rainfall.
“We had 55 crew members working across five locations on the night of the shutdown. Communication was maintained through the use of mobile phones and two-way radios.”
With repairs unable to take place, Mackay Regional Council had to work with the community to reassure them works would go ahead and would require residents to cut down on water use to prevent inundation of the pump stations.
“Humour was used for the ‘if it’s yellow, let it mellow’ campaign. The use of memes helped engage our community to get our message across to minimise water usage across the catchment on the night of the shutdown and construction.”
Despite the delays, responding to heavy rainfall and planning the works around the community helped to gain insights for when Council has to undertake repairs on other mains in the future.
Mr Boyd said the shutdown offered a chance for Mackay WWS to better understand the water network and what would be required during further works.
“The capture of newfound data and knowledge was obtained on the night through shutting down and ponding within the sewerage network and draining and pumping down of the main,” Mr Boyd said.
In terms of future works, Mackay Regional Council intends to improve permanent draining infrastructure, install inline 900mm gate valves at strategic locations, and upgrade air valves along the network.
Mr Boyd said the newfound knowledge from this project of works gave WWS an opportunity to learn from challenges that would not normally affect works, which would greatly benefit upcoming works if the city is once again hit with unprecedented rainfall.
“The size and complexity of this project and having an operational and planning team undertake and complete this work while conducting business as usual is a testament to the committed effort of the project team.”
Sense and Process
With this solution the following issues can be detected:
■ Ragging
■ Blockage by foreign objects
■ Faulty or damaged bearings
■ Faulty or damaged seals
■ Wear issues and rub issues
■ Imbalance
■ Cavitation
■ Looseness
■ Unusually high signatures in grinders and macerators
Submersible pumps do the essential – but dirty work – of transporting sewage to treatment plants. Prone to blockages, ragging, and general wear and tear, pumps need to be monitored to avoid events such as overflow and environmental contamination of public and residential areas.
Optionally, the system can also monitor:
■ Excess Current
■ Sewage Level and Control
■ Flow and Temperature
Direct Comms to PLC via front end dedicated ports is also available for:
■ Ethernet Ip
■ Modbus TCP/IP
■ Ethercat
■ Profinet
Australia’s thermal power capacity is progressively retiring, with almost two thirds of the country’s coal-fired generation capacity expected to retire by 2040. This is propelling a move away from aging, emissions-heavy energy production towards greener energy production that utilises Australia’s natural environmental resources, including hydro power. Here, we look at some of the major hydro power projects underway or being investigated in Australia that could provide tender opportunities in the future.
It is becoming increasingly likely that this retirement goal might happen sooner than originally expected, following AGL’s surprise announcement earlier this year that it intends to shut down all coal-fired generation by the end of fiscal year 2035, reducing the company’s annual greenhouse gas emissions from 40 million tonnes to net zero.
Adding to this is the Western Australian Government’s announcement that all state-owned coal power stations will be closed by 2030.
Further driving this move is the passing of the nation’s first climate change legislation in a decade, cementing Australia’s commitment to cutting emissions by at least 43 per cent by 2030 (compared with 2005), reaching net zero emissions by 2050.
According to the 2021 Australian Energy Statistics, in 2019 renewable energy already delivered an average of
21 per cent of Australia’s electricity, and significantly more at certain times and in certain states.
Australia’s bounty of high-quality wind and solar resources is now widely acknowledged and greatly exceeds the amount required to meet domestic electricity demand.
However, full dependence on these kinds of intermittent energy sources may give rise to grid instability and uncertainty on days it is cloudy or still.
Energy storage of the future
Energy storage is proving itself to be an increasingly important part of the electricity system, granting peace of mind that energy will always be available, even at times when the sun and wind are not.
As output from intermittent energy sources like solar and wind power increases, so too does the need to introduce power when wind and solar PV output fails to meet demand, and store
excess when wind and solar PV output exceeds demand.
Pumped hydro acts like a giant battery for the electricity system, using surplus renewable energy to pump water up a hill to an upper dam when it is sunny and windy, and releasing the water back down the hill towards a smaller dam through giant turbines that create electricity when it is still and dark.
An energy storage system, such as pumped hydro, provides flexible, on-demand power while reusing the water in a closed loop, maximising the efficiency of renewables by using surplus solar and wind power to pump the water to the higher dam for future use.
The utilisation of pumped hydro means that dispatchable power can be added into the market to balance electricity supply and demand. Pumped hydro projects, including Battery of the Nation and Snowy 2.0, can help
deliver a more reliable energy system to Australians, reducing the risk of blackouts and electricity price volatility.
The Australian Government, recognising the significant potential that pumped hydro has to offer, is making targeted investments which will deliver additional electricity generation and energy storage to the National Electricity Market (NEM), with New South Wales playing host to the majority of them.
Australia’s investment in pumped hydro
Australia has more than 100 operating hydroelectric power stations – both large and small – with the most well-known the Snowy Mountains Hydro-Electric Scheme.
In 2020 construction kicked off on the Snowy 2.0 project will link two existing dams in the Snowy region – Tantangara and Talbingo – with 27km of tunnels. Once complete, Snowy 2.0 will provide 2000MW of capacity and 350,000MWh of pumped hydro energy storage.
The Snowy 2.0 project is forecast to be able to power approximately three million homes over a week upon completion.
Not only will the project generate more power and lower electricity prices, it is also slated to generate around 4,000
direct jobs in the Snowy Mountains region throughout the project’s life, with thousands more in supply chain and service roles.
New South Wales powering ahead
New South Wales has an ambitious target to build at least 2GW of new long duration storage by 2030, and the State Government has committed $97.5 million to accelerate pumped hydro projects that could meet that target.
This includes funding for private projects as well as funding to undertake site investigations for pumped hydro potential on existing WaterNSW dams.
The New South Wales Government has awarded $45 million in funding to five pumped hydro projects, which will deliver a combined capacity of almost 1.75GW of energy storage to the state.
New South Wales Treasurer and Minister for Energy, Matt Kean, said the state’s Pumped Hydro Recoverable Grants Program will assist pumped hydro developers to cover upfront costs and lower investment barriers for the private sector.
“Funding agreements are already in place with five applicants who have received a total of $44.8 million to support pre-investment activities, establish project feasibility and develop a strategic business case,” Mr Kean said. Lake Lynell pumped hydro project EnergyAustralia is currently investigating a pumped hydro project on Wiradjuri Country at Lake Lyell near Lithgow. This project intends to use Lake Lyell as a lower reservoir with a new upper reservoir to be built on the southern side of the nearby Mt Walker.
EnergyAustralia estimates that this site could accommodate a facility capable of producing up to 335MW of electricity with around eight hours of storage, a sufficient amount to power 150,000 households during peak periods.
The proposed facility would use existing infrastructure, water, transmission lines and Energy Australiaowned land.
“New South Wales has the most ambitious renewable energy policy in the nation, which is needed to replace aging coal-fired power stations and build a clean energy future for the state,” Mr Kean said.
In December 2021, the New South Wales Government formally declared the New England region around Armidale a Renewable Energy Zone (REZ) – the equivalent of modern-
day power stations, combining new renewable energy infrastructure, energy storage and high-voltage transmission infrastructure.
The New England region has been acknowledged as having some of the best natural gas resources in the country, including some of the best potential sites for pumped hydro development in the state.
This REZ is expected to deliver new network capacity to host up to 8GW of new generation, and it is on the eastern side of this REZ that the Oven Mountain project – declared Critical State Significant Infrastructure (CSSI) in October 2020 – is located.
The project will deliver local economic and community benefits, and it is anticipated that it will complement other local renewable energy sources, such as solar and wind, and will play a crucial role in ensuring the stability of the future network.
Construction is slated to span over four years, and will create as many as 1,000 jobs encompassing a broad range of skills and activities.
Upon completion, around 30 to 50 operational jobs will also be necessary to support the project over its 50-plus year lifespan.
Some of the works needed to bring this project to fruition include improved road access and the installation of high grade communications. Improved road access will provide ready access to the site as well as ensuring local road safety. Additionally, the roads and reservoirs have the potential to improve emergency services access and fire management in the region.
As part of the high grade communications required for the ongoing operations of the Oven Mountain facility, new fibre optic infrastructure will be installed, delivered as part of the proposed electricity transmission work and facilitating improvements to local mobile telecommunications.
The Central West Pumped Hydro Project – located between Bathurst and Lithgow, within 2.5 hours of Sydney – is in the early stages of project assessment and development.
When completed, the project will generate enough sufficient energy to power over 153,000 homes, creating some 200 jobs during construction and 30 jobs on an ongoing basis.
The project is set to deliver other benefits to the community, including upgrades to local infrastructure and
roads, and improvements to local telecommunications infrastructure which will improve coverage in the local area.
The proposed 250MW Muswellbrook Pumped Hydro Project in the Hunter region has been awarded $9.45 million funding under the Pumped Hydro Recoverable Grants Program and is set to provide eight hours of storage when completed.
The Muswellbrook Project will test an innovative approach, whereby a preexisting mine void from Idemitsu’s Muswellbrook Coal mine will be utilised as the lower reservoir.
The grant funding will be used to complete a detailed design of the project, connection studies, contractor engagement and a targeted geotechnical due diligence program.
AGL and Idemitsu Australia Resources (IAR) announced a joint venture (JV) for the project –Muswellbrook Pumped Hydro Pty Ltd – and signed an agreement with Energy Corporation of NSW (EnergyCo), which will secure funding to expand on feasibility work already undertaken for the proposed project.
The JV will also undertake thorough Traditional Owner and community consultation to prepare the project for an investment decision.
AGL Chief Operating Officer, Markus Brokhof, welcomed the support of the New South Wales Government and said he was pleased to see the project progressing to the next stage.
“We’re announcing another step forward in planning for what could be a significant energy asset for the people of Australia and the Upper Hunter community,” Mr Brokhof said.
“As we transition to more renewable energy sources, pumped hydro provides a reliable on-demand generation source and acceleration of our development studies will help us understand how the project could be delivered.
“AGL has 2.9GW of wind, battery, pumped hydro and other low carbon and firming projects in active planning and development, and we will continue to look to invest in projects like Muswellbrook Pumped Hydro.”
A preliminary engineering study began in 2019 to determine whether the project is technically feasible, provide cost estimates for both construction and operation, and assess the required planning and approval processes.
Tasmania’s Battery of the Nation
Battery of the Nation is a Hydro Tasmania initiative to broaden Tasmania’s renewable electricity generation capacity to supply mainland Australia, including hydropower system improvements and new pumped hydro opportunities.
Through the Bilateral Energy and Emissions Reduction Agreement the Federal Government has provided $65 million to the upgrade of the Tarraleah hydropower scheme, which is a key component of Battery of the Nation.
Additionally, in October 2022, the Federal Government announced the availability of up to $1 billion of lowcost loans from Rewiring the Nation to eligible Tasmanian Battery of the Nation projects.
The Marinus Link is the proposed second interconnector that will utilise Tasmania’s extensive renewable energy resources to provide an additional 1500MW of capacity between Tasmania and mainland Australia.
When constructed, Marinus Link will provide the NEM with over 500MW of dispatchable generation, which is currently unavailable due to limited BassLink capacity. This would result in the powering of up to 500,000 homes and help mitigate the impact of variable wind and solar generation, unplanned outages and extreme weather events.
The link will also unlock additional renewable energy investment in Tasmania by expanding Tasmania’s hydro capacity through Battery of the Nation. Estimates show that Marinus Link will contribute savings of up to 70 million tonnes of CO² equivalent by 2050.
During its construction it is expected that Marinus Link will create up to 2,800 direct and indirect jobs, delivering up to $3.65 billion of economic stimulus to north-western Tasmania and regional Victoria.
The Federal and Tasmanian Governments signed the Bilateral Energy and Emissions Reduction Agreement in October 2020, in which the governments agreed to support the design and approvals phase of the Marinus Link project.
On 3 April 2022, the Australian Government announced it will invest a further $75 million, on top of the previous $56 million to the Tasmanian Government, to support the Marinus Link project through the next stages of planning, design and approvals.
Additionally, the Australian Government announced in October 2022 that it would provide access
to low cost finance from Rewiring the Nation for Marinus Link and the associated North West Transmission Developments.
Western Australian investment and feasibility tests
Alongside the Western Australian Government’s decision to close all state-owned coal power stations by 2030, came the announcement of an estimated $3.8 billion set to be invested into the South West Interconnected System (SWIS).
This investment commitment comes as the state’s electricity system is increasingly challenged by the overwhelming uptake of rooftop solar. These pressures have forced Synergy and Water Corporation to offload excess power generated during the day at a loss, and add additional maintenance and generation costs, which are ultimately borne by taxpayers.
Synergy is currently undertaking analysis to determine the feasibility of a pumped hydro project forming part of its storage needs, and also investigating the feasibility of using hydrogen to power its existing gas generation assets.
By phasing out coal-fired power, Synergy’s carbon emissions will be reduced by 80 per cent by 2030, including a 40 per cent emissions
reduction on the SWIS, compared to 2020-21 levels.
It is expected that additional industry demand for renewable energy will result in even greater emissions reductions on the SWIS.
The Australian Energy Market Operator has identified that Queensland will need significant energy storage as part of a diverse future energy system, with clean energy storage, including
Borumba Dam was selected as the first site for a detailed design and cost analysis. The State Government has also announced Pioneer-Burdekin as the second site for detailed analytical studies.
Both sites were selected after a statewide assessment of potential pumped hydro locations through the Queensland Hydro Study. Various engineering, geological, hydrological, environmental and social studies are currently under way at both sites.
pumped hydro, crucial to secure Queensland’s energy system in the long term.
As such, the State Government has committed to developing the world’s largest pumped hydro scheme, in its $62 billion Queensland Energy and Jobs Plan, which will see the construction of a new dam in the Pioneer Valley near Mackay, capable of supplying half of Queensland’s energy needs with clean, reliable and affordable renewable energy.
To develop and deliver the largescale pumped hydro assets that will be the cornerstone of the state’s energy system, the Queensland Government established a publicly-owned entity, Queensland Hydro.
Furthermore, to meet Queensland’s future energy demand, the State Government is also investigating pumped hydro as a technology to store energy over days, weeks or months.
A key element of the landmark Queensland Energy and Jobs Plan includes progressing the development of the largest pumped hydro energy storage project in the world – the Pioneer-Burdekin project.
Queensland will need a portfolio of large-scale, long-duration pumped hydro options to support additional renewable generation development (i.e. wind and solar) and deliver lowcost and reliable renewable electricity for Queensland.
Due to the long lead times for pumped hydro projects, extra sites need initial investigation to ensure Queensland has sufficient large-scale energy storage capacity in development.
Together, the Borumba Dam and Pioneer-Burdekin projects could have a combined generation capacity of up to 7GW.
The Pioneer-Burdekin project will be constructed well clear of protected areas, and also offers significant supply chain and economic opportunities for the greater Mackay region.
Queensland Hydro intends to conduct further studies, with a detailed assessment for the Pioneer-Burdekin project to be delivered to the State Government in 2024.
This assessment is slated to include consultation with Traditional Owners and the community, hydrological modelling and assessment of environmental and social impacts, as well as commercial and financial modelling.
Queensland Hydro will also continue to conduct investigations of other largescale, long-duration pumped hydro sites in the unlikely event the PioneerBurdekin project is unable to proceed.
Realising the potential of pumped hydro in Australia will have a number of benefits, including increasing the security and reliability of the grid.
As with most energy projects, pumped hydro projects have a tendency to be located away from urban areas, injecting investment and job opportunities into regional communities that may still be feeling the effects of COVID-19.
There is significant overlap between the types of the skilled workers needed for pumped hydro projects and those required for civil construction, including mining and road/rail tunnelling projects.
As well as having a lower environmental impact, pumped hydro will result in lower electricity prices and is a highly cost-effective solution for energy storage.
Researchers at Australian National University identified more than 22,000 potential pumped hydro locations across the country – approximately 1,000 times the storage capacity needed to transition to an 100 per cent renewable electricity system which meets 100 per cent of domestic electricity demand.
If Australia’s pumped hydro potential is properly embraced, it will allow Australia to emerge as a clean energy superpower, enabling a reliable, greener electricity supply system that distributes power at globally competitive prices.
Pumped hydro offers Australia an opportunity to utilise the fundamental and unique features of the country’s topography as a competitive advantage that will continue to serve the nation for generations to come.
In a trial that aims to boost shellfish aquaculture in Western Australia, the Department of Primary Industries and Regional Development (DPIRD) installed one of Australia’s first large-scale Floating Upweller Systems (FLUPSY) at Albany’s Oyster Harbour. Utilising a pump to push seawater through mesh pots allowing the seed to feed on phytoplankton, FLUPSY offers a sustainable and efficient nursery environment which allows for high stocking densities of oysters. Pump Industry spoke to Scott Bennett, Aquaculture Systems Co-ordinator at DPIRD, to find out more about the trial and the pump used to help grow oysters.
A FLUPSY is a mechanical system designed for the culture of seed stock during the nursery stage of commercial bivalve production. They are mobile and cheaper than more traditional land-based methods and are often used for oyster culture in the US, mainly in homemade structures made from timber and plastic drums.
“Traditional upweller systems are housed in a building very close to a seawater source, requiring considerable equipment, infrastructure and coastal land, making them both capital and energy expensive,” Mr Bennett said.
“Such systems pump water up through an array of ‘pots’ held within a large flat tank that are screened on the bottom to hold the spat. Some land-based systems pump seawater from ocean intakes which provides the algae that the spat feed on. Other systems require the algae to be cultured in a laboratory and added to the seawater. Upwellers thus provide feed to the spat as well as have their excrement removed with the upwelling water current.
“A FLUPSY is an alternative way to upwell oyster spat where all infrastructure can be installed on a floating pontoon in protected waterways, utilising the water and feed naturally occurring in the area.
“It is a more affordable and sustainable form of shellfish nursery culture, taking advantage of the natural environmental conditions.”
The DPIRD FLUPSY was designed to hold 30 square pots with the capacity to hold up to 250,000 oyster spat in each. These pots have a screen attached to the base to prevent the oysters from falling through but allowing water to upwell past.
“In the centre of the FLUPSY there is a long gutter which has 30 pipes attached to it and a large shroud on the base at one end where a pump is installed to constantly push water out of the gutter,” Mr Bennett said.
“The gutter would sit so all 30 pipes were just below the water surface. Each of the 30 square pots have a hole on the side which would slide tightly over the gutter pipes, locking them in place. As water is pushed out of the gutter by the pump, new water would be drawn in up through the pots, into the pipe and into the gutter to be pushed out of the gutter by the pump.
"This pot and gutter system was installed with a floating pontoon around it, allowing it to be walked around for servicing and supporting all the FLUPSY components.”
“Greg saw potential in the system for use in Western Australia and sought funding from the Minister of Fisheries to design and build a FLUPSY for testing with a local species of oyster.”
The FLUPSY was designed, constructed, and supplied in 2021/22 by DPIRD to Harvest Road Oceans (HRO) for commercial trial undertaken at its farm site at Emu Point, Albany and was supported by DPIRD’s aquaculture research and development team, with rock oyster spat (Saccostrea glomerata) supplied by the Albany Shellfish Hatchery.
The WA-based FLUPSY design and development was led by one of the shellfish R&D teams.
The trial was supported by $125,000 through the WA Recovery Plan and saw one of the first large-scale FLUPSYs in Australia installed, with a production capacity estimated at 5-10 million 5mm rock oyster seed per year.”
Mr Bennett said there were a number of considerations that needed to be taken into account during the design and development phase as the only component that was available off the shelf was the pump.
“The pontoon and other components all required custom fabrication so significant time was spent designing the system so each fabricator could be provided with accurate specifications. Local West Australian fabricators were used to build all the components. This ensured easy communication and the ability for site visits to check on progress and measurements throughout the build,” Mr Bennett said.
“The FLUPSY needed to be able to fit into a 10m x 4m boat pen, be lightweight, strong, and built-in sections so it could be easily transportable. The pontoon was designed so it could be split into six smaller sections and the gutter could be split into three sections allowing the entire system to be transported on a flatbed truck.
“Buoyancy had to be perfect, so the system did not float too high too or low in the water. Flotation pods could be moved around the pontoon, added, or removed as required. As the project commenced and more weight was added to the FLUPSY, extra floatation was easily installed.”
The operational implications and spat performance in the FLUPSY were the two main factors being considered in the early trial, with the data gathered giving a starting point for the determination of more focused and detailed work to determine more accurate and definitive operational parameters for the FLUPSY.
Trialling the technology at the Albany Oyster Harbour
Mr Bennett said the FLUPSY concept was first raised at an oyster workshop in Broome in February 2019.
“Jonathan Bilton, a well-known shellfish hatchery operator, mentioned FLUPSYs to Greg Jenkins, the Director of Aquaculture Research and Development for DPIRD, “Mr Bennett said.
The pump keeping the water current moving
The FLUPSY required a pump that could reliably operate 24/7 in a harsh saltwater environment where the possibility of entanglement with seaweed was high. There was little need for the delivery of high head but there was the need for a high flow rate.
“The aim was to draw 20lpm through each pot containing oysters, the more water we could move the more food that could be drawn through the oyster through the upwelling process,” Mr Bennett said.
“A variable speed pump would also be of advantage as this would allow the adjustment of water flow depending on the number of oyster spat being cultured in the FLUPSY.
“There are FLUPSY systems in the USA operating on a de-icing pump which moves a significant amount of water to prevent ice from forming in saltwater marinas. A company
called Bearon Aquatics in the USA had a vari-speed axial flow pump which suited the requirement for our FLUPSY. The pump can push a huge amount of water which allows a large volume of water to be drawn through each of the FLUPSY’s pots containing oyster spat. This would ensure they received the most amount of feed and clean water possible, resulting in optimal growth and condition.
“The DPIRD FLUPSY is currently powered from 240v shore power; however, if required the pump used could operate on a photovoltaic power system.”
The pump’s specifications for the Bearon Aquatics
P1000 vari-speed Ice Eater are:
• Power – 240v, 750W, 3.2A at 100 per cent operation
• Maximum flow rate – 36lbs of Thrust at 5,200Lpm /312,000Lph
• Weight – 20kg
• Size – 200mm diameter x 350mm high
Observations of the day-to-day operational performance of the pump
Stocking capacity is in part a function of water flow through the upwellers. The pump evacuated the gutter and gravity drove the flow of water through the upwellers. Increasing the pump speed caused the buoyant gutter to raise the FLUPSY out of the water and stop the flow. The pump speed needed to be balanced against the weight to maintain a consistent flow of water through the upwellers.
Resetting the pump speed and checking valve settings were completed each day. A maximum water flow of ten to 15L per minute was recorded through each pot. With 16 of the 30 upwellers in operation, the pump was set at 60 per cent. With 30 upwellers in operation the pump can be set at 100 per cent.
pump.
the Ice Eater pump and other equipment
Mr Bennett said the Ice Eater pump has proven to be very low maintenance.
“There are two sacrificial anodes installed on the pump. One is on the pump’s housing, the second is on the shaft. Both have been checked for deterioration monthly and have been replaced every six months, which is a quick and easy process. The propeller is also replaceable however it has not required replacement after ten months of operation,” Mr Bennett said.
“General cleaning on the FLUPSY can be carried out with the system in the water using a broom and hose to remove fouling and unwanted growth. The pots are lifted onto the pontoon and the oysters are sprayed with a hose to wash out any faeces. Divers check the pump’s anodes for corrosion and can clean the underside of the gutter to remove any excess fouling.
“Every six months all the 30 pots containing oysters can be removed from the FLUPSY and the entire system can be removed from the water using a large boat trailer. This allows a thorough check of the system for damage or wear and the removal of heavier fouling such as barnacles in hard-toreach places.”
Corrosion was an issue on other components of the FLUPSY – the bolts, nuts and washers mounting the screens onto the upwellers and the protective metal screen on the bottom of the upwellers all showed signs of corrosion. This impacted the nylon mesh that supported the oysters and could lead to a breach of the screens.
Mr Bennett said the trial FLUPSY has performed very well, and excellent results were seen in the oysters cultured in the system during the initial trial.
The final report on the trial – which Harvest Road Oceans funded and provided resources – found the compact size of the floating sea-based nursery allowed for high stocking densities of oysters that could be held in it, providing a major benefit compared to traditional systems.
Observations were made during the trial that will help improve their design and operations in Western Australia and it also provided a baseline for further and more detailed work.
One observation was the safety risk posed to workers during manual handling, specifically lifting of the upwellers from the water onto the deck of the FLUPSY which involved lifting the upwellers from floor level and raising them out of the water at approximately 200mm away from the worker’s centre of gravity up to waist height then twisting to move the pot onto the deck.
The upwellers weigh 13kg dry plus several kilograms of oysters and the weight of the water that is retained – this can reach a total of approximately 40kg.
“The pots, once full of oysters, became heavy and a hazard to lift safely so a lightweight gantry was designed and installed on the pontoon. The gantry is tracked so I can roll up and down the pontoon, allowing the pots to be quickly and safely lifted for cleaning, saving significant time and eliminating the manual handling hazard,” Mr Bennett said.
Another observation during the trial was that the FLUPSY was quite sensitive to weight distribution. Keeping the FLUPSY low in the water is important to maintain water flow through the upwellers, however, this leads to a situation where the FLUPSY sinks during cleaning when the upwellers are out of the water and up on the walkway.
“The pontoon at times sank a bit low in the water when there were extra personnel onboard for servicing so the spacing of the floatation under the pontoon was adjusted to improve its stability.
"A second pontoon has since been constructed which allows the flotation pods to be installed on a different angle, giving it more stability without affecting the overall buoyancy of the pontoon,” Mr Bennett said.
Other recommendations for potential modification noted included:
• Offset the upweller pipes so that flow from one is not directed into another
• Make the upweller flange internal instead of external to allow for easier handling of the upwellers and prevent them catching between the rail and the gutter
• Add a lock box to the FLUPSY for storage of tools, lubricants etc.
• Reduce the height and weight of the upwellers
• Change the wing nuts, that secure the upwellers, to a quick release clip to prevent them rattling loose
• Build a jinker to transport the FLUPSY and allow for easy launch and retrieve
The work undertaken in this trial is preliminary and provides a baseline for further and more detailed work. More work is required to improve the mechanical aspects of the FLUPSY, such as floatation, buoyancy, and stability; improved access
and egress; determine the suitability for other locations with different environmental conditions; and investigate options for operation of the FLUPSY remotely from mains power.
Further trials are required to better define bivalve performance in the FLUPSY, such as carrying capacity and growth performance of oyster spat in various environmental conditions; refine stocking density and response of various sizes to density and the relationship between flow rate and density.
The future of FLUPSY is Western Australia
DPIRD has plans to install a second FLUPSY system in protected waters of the Perth metropolitan coastline to trial its suitability for Saucer Scallop culture. This system will require further design and fabrication and is expected to commence mid-2023.
Welling & Crossley can now supply a range of self-priming & mixed-flow China Pumps.
Ranging from 100ml (4”x 4”) to 300ml (12”x 12”). (larger sizes to come).
Mixed-flow pumps feature:
• Table D flanges
• Oil bath / Mechanical seals
• Stainless steel shaft
Can be base mounted with our Lister/Kirloskar diesel engines.
The PIA’s Australian Pump Technical Handbook is a cornerstone text for the Australian pump industry and, in our opinion, a must have for anyone who deals with pumps on a regular basis. In this ongoing series, we feature abridged chapters from the classic book to showcase the various areas covered and to reacquaint readers with the technical aspects of pumps. In this issue we continue looking at selecting pump materials, taking a deep dive into plastic and non-metallic pumps, and preferred materials.
Plastic, in particular more recently developed thermoplastics and thermosets, are attractive to pump manufacturers due to their qualities, including:
• Lightweight
• Relatively strong
• Inexpensively fabricated
• Excellent corrosion resistance
• Appearance
There are a number of engineered thermoplastics that are commonly used in commercial pump manufacturing in Australia.
Nylon
Nylon is one of the most, if not the most, extensively used thermoplastic and is commonly used to manufacture impellers, housings, venturis, etc. Nylon, nylon 11 and nylon 23 – natural or glass filled – provide high impact strength and toughness, making them attractive in pump manufacturing.
Acetals are attractive due to their excellent wear resistance, their ability to operate at reasonable high temperatures, and good chemical resistance. They are often used in the manufacture of poppets, bushes, jets, etc..
Thermoplastic polyesters (PBTs)
Natural or glass-filled PBTs are used to manufacture components such as diffusers, impellers, pressure tanks, pump housings, etc. due to their high heat deflection.
Polycarbonate
Polycarbonate is extensively used by pump manufactures as it offers high impact resistance and good dimensional stability. It is commonly used to manufacture impellers, casings, etc..
Polycarbonate is normally used as a glass-filled material, however, natural clarity is sometimes a required property.
Polysulfone
Polysulfone is typically used where severe temperatures or stress conditions are present as it has a very high heat temperature deflection and excellent chemical resistance. It is normally used as a glass-filled material for impellers, housings, etc..
Modified polyphenylene oxide (Noryl)
Noryl is commonly used as a glass-filled material to provide mouldings with good dimensional stability and a hard, scratch resistant surface. It has a high enough tensile strength that allows it to be used for casings, injector housings, etc..
Polyphenylene sulphide (PPS)
PPS is a dimensionally stable material with excellent electrical, high temperature and solvent resistance. It is used for pump components which are intended for operation in more severe conditions.
Thermosets
Thermoset construction uses continuous strand fibreglass reinforcement for optimal strength and corrosion resistance. Typical thermosets include vinyl ester resin, cross linked unsaturated polymer resin (epoxy), and unsaturated polyester.
It is often referred to as fibreglass reinforced plastic (FRP) and is used for all wetted parts of a non-metallic pump.
The preferred manufacturing process for thermosets is resin transfer moulding as it allows for long-strand fibreglass mat to be cut into specific shapes and sizes, with controlled placement of more glass in high stress areas to ensure structural integrity under high pressure.
FRP has excellent corrosion resistance, with different resins and catalysts available to cover a wide range of corrosive fluids.
The PIA, in association with the Australian pump industry, has compiled a list of cast and wrought alloys, which can be found in full in the Australian Pump Technical Handbook
When compiling the list, consideration was given to user requirements, service performance and availability. It is possible to select an alloy from the list to meet a majority of pumping applications and to obtain the necessary material without great difficulty. When possible, materials should be selected from the list unless specific application requirements indicate otherwise.
Any decision to use alloys other than those listed should be carefully considered and discussed with the pump manufacturer.
The Australian Pump Technical Handbook does not intend to provide a list of materials suitable for use with the multitude of liquids that can be pumped. However, if this information is required, a comprehensive table indicating materials commonly used to pump various liquids can be found in the American Hydraulic Institute Standards for Centrifugal, Rotary and Reciprocating Pumps.
Further information and detailed diagrams, equations and schematics can be found in the Australian Pump Technical Handbook, available from the PIA website. The Handbook has recently undergone an update, with the new 6th edition available now. In the next edition of Pump Industry, we continue to explore pipe systems. Polycarbonate.
The pump industry relies on expertise from a large and varied range of specialists, from experts in particular pump types to those with an intimate understanding of pump reliability; and from researchers who delve into the particulars of pump curves to experts in pump efficiency. To draw upon the wealth of expert knowledge the Australian pump industry has to offer, Pump Industry has established a panel of experts to answer all your pumping questions.
This edition of Ask an Expert will look at customised progressive cavity pumps for your wastewater and sludge treatment application.
Q: Can progressive cavity (PC) pumps handle sludge with variable dry solids content?
A: Yes, they can efficiently handle a wide variety of sludge applications with differing dry solids content due to their stable flow rates, minimal pulsation, excellent suction lift and high self-priming capabilities. They also accurately meter flocculants to aid thickening and integrate easily with control systems to maximise productivity.
PC pump manufacturers focus on offering solutions that not only operate effectively but also save you costs in the long run.
• Energy efficient: lower energy requirements
• Easy maintenance: quick and easy access to the drive side and rotor side components of the pump without dismantling the pipework
• Extended pump life: high-quality parts, predictive maintenance and pump monitoring options along with reduced wear on components
• Flexibility: installation and pump design customised to your application
Q: One of the industry’s major concerns today is reducing energy costs. Do PC pumps offer any special solutions?
A: PC pumps already reduce operating costs because of their efficient operation, but on top of that, several PC pump manufacturers have designed pumps specifically focused on energy-efficient performance. These newer technologies mean reduced maintenance time, extended service life and significantly reduced lifecycle costs.
One example of modern PC technology – in this case the SEEPEX SCT pump.
Q: Can PC pumps be incorporated into existing pumping systems?
A: Yes, they can work within various customer systems or be supplied as a complete solution directly from the manufacturer. There are many diverse connection options: control systems, higher-level automation systems, digital monitoring and analytic systems or with macerating, dosing and/or chopping pumps (2-in-1 system).
A state-of-the-art PC pump system with automated stator adjustment – in this case showing SEEPEX SCT AutoAdjust pump.
Q: Can PC pumps transport dewatered sludge over long distances?
A: Transporting dewatered sludge over long distances poses great challenges for WWTPs, as the high viscosity and abrasiveness of the medium results in a considerable pressure loss in the conveying line. Accordingly, expending a large amount of energy to overcome this and the high-pressure load increases wear, resulting in high maintenance costs.
A PC pump manufacturer has developed an innovative combination of PC sewage pumping and compressed air conveying resulting in a low-pressure level in the conveying pipeline. This solution extends service life and reduces investment and operating costs.
Combination of PC pump and pneumatic conveying system –in this case SEEPEX Smart Air Injection.
From primary and thickened sludge transfer to chemical dosing, progressive cavity pumps provide the best pumping solution designed specifically for your application.
Peter Vila, Managing Director of SEEPEX Australia, is a progressive cavity pump expert. He has been involved with pumps for over 40 years. Peter spent the first five years repairing pumps and the following 35 years in technical sales, 20 of which have been with SEEPEX progressive cavity pumps.
For more information on progressive cavity pumps, please contact SEEPEX Australia on (02) 4355 4500 or at info.au@seepex.com
Smart Conveying Technology (SCT) provides quick maintenance, significantly reduced life cycle costs and the shortest downtime. Smart Seal Housing, the newest innovation for SCT pumps, removes the need to dismantle the suction or discharge pipework for inspection and replacement of the mechanical seal.
y Adjustable stator restores pump efficiency
y Reduced maintenance time by up to 85%
y Increased energy savings compared to conventional progressive cavity pumps
y Easy retrofit onto your existing SEEPEX pumps
y Up to 200% longer stator life
y Rapid removal and reassembly of mechanical seal
When it comes to pump selection, there are so many different pumps on the market and finding the correct solution can be tough.
An air operated double-diaphragm (AODD) pump is widely regarded as a safe, reliable and versatile performer, requiring minimal maintenance and able to handle a vast array of fluids in the harshest of environments. This makes it an immensely popular choice across a myriad of applications as they offer unique benefits that set them apart from other pump technologies.
These advantages include:
An AODD pump does not require electricity to run. This means it is safe to operate the pump in explosive or hazardous environments where an electrical supply would pose a risk. This feature also aids portability with the array of base mounting options allowing the pump to be easily transported from site to site.
Being completely sealed also allows the pump to be fully submerged in liquid without affecting operational performance so long as the pump’s materials are compatible with the surrounding fluid and the exhaust from the pump is piped away to be above the fluid line.
The simple design of an AODD pump is a key point of difference when compared with other pumps. It offers significant benefits, none more so than its ability to pump a wide array of materials.
They do not require the use of expensive mechanical seals to operate and their simplistic design and construction with no rotating parts makes them easy to assemble, dismantle, clean and repair.
AODD pumps are capable of running dry without damage. This makes AODD pumps very useful in applications where the fluid being pumped may suddenly run out.
Since an AODD pump does not require connection to a fixed electrical power source to operate, they can easily be moved from location to location if required.
Well known for its versatility, an AODD pump is capable of safely handling an extensive range of fluids including solid-laden liquids as well as
abrasive and viscous fluids, without sustaining damage to the pump.
As with most pumps, selecting the right design elements depends on the pump's intended purpose. AODD pumps are available in a wide range of materials including metals and plastics, meaning they are capable of pumping even the most abrasive fluids.
Just as pump size is determined by the desired flow rate and pressure conditions, the flow rate for an AODD pump is easily managed by controlling the supply of air to the pump or by throttling a valve at the pump discharge if one has been fitted.
It goes without saying that no single pump can be a perfect fit for all applications, however, an AODD pump can cover a wide range of applications and materials and is often preferred because of the many advantages they present.
With a vast array of pumping designs and solutions available, ensuring you have the right pump for the right application involves a thorough set of considerations. If in doubt, consult your pump supplier.
In B2B, the sales cycle is long. You’ll always have people at different stages of the buying cycle, so your marketing needs to be always on.
Decision makers in the pump industry gain information from a wide range of sources. The team at Pump Industry are able to provide a complete range of marketing solutions:
● Brand building
● Educating the market
● Generating leads
● Creating engaging content
● Managing your social media and SEO
● Setting up marketing funnels
We also have a team of editors, designers and marketing experts who specialise in the pump sector and can help make the most of your campaign.
Scan this code to learn how we can help you ensure your marketing is always on.
www.pumpindustry.com.au
The MaxiSave Rains/Mains Valve is a fully automatic mechanical rainwater/mains water changeover device designed for pressure pump supply systems for harvesting rainwater for the toilet, laundry and household applications with automatic mains backup.
Suitable for these pump series:
Submersible Pressure Pump with built in pressure controller, suitable for household water supply and irrigation.
Install Options:
Horizontal, self-priming jet pumps, ideal for pumping clear water and other non- aggressive liquids.
Horizontal, self-priming jet pumps, ideal for pumping clear water and other non-aggressive liquids. Made in Italy.
MHR20: 20mm
MHR25: 25mm Ideal for higher flow
Horizontal Multistage Pumps suitable for higher pressure applications, ideal for residential, commercial, and industrial applications.
MaxiSAVE 20mm Rain / Mains Changeover Valve Top of Tank Assembly with Cover. Hole size required - 290mm.
Submersible water pumps (sometimes called “submergible pumps”) can be operated while completely submerged underwater. Mechanical seals are used to keep any water from entering the pump motor and short circuiting it. Submersible pumps have many useful applications, but the typical use is to pump water from a certain source, such as a water well, to a different desired destination.
A true dry-prime pump, our self-priming system eliminates the need for water to prime the pump and is engineered to prevent product carryover. The Pioneer Prime hydraulic design maximizes lift capability and offers both quick initial priming and continuous, unattended reprime under auto stop/start conditions.
Vertical multistage pump booster and pressure system, designed in various combinations to suit, whether it be Industrial, Building Services, Commercial, HVAC, Domestic or irrigation applications. Ranging from a singular pump system through to a complex 8 piece design.
Standard sizes available from 4”-12” (100 to 300 mm) sizes, engineered packages available up to 18” (457 mm). Vacuum-assisted pump configurations. Our team of experts designed Pioneer pump packages with select diesel engine models that deliver maximum performance when paired with the right Pioneer pump end