pumpindustry
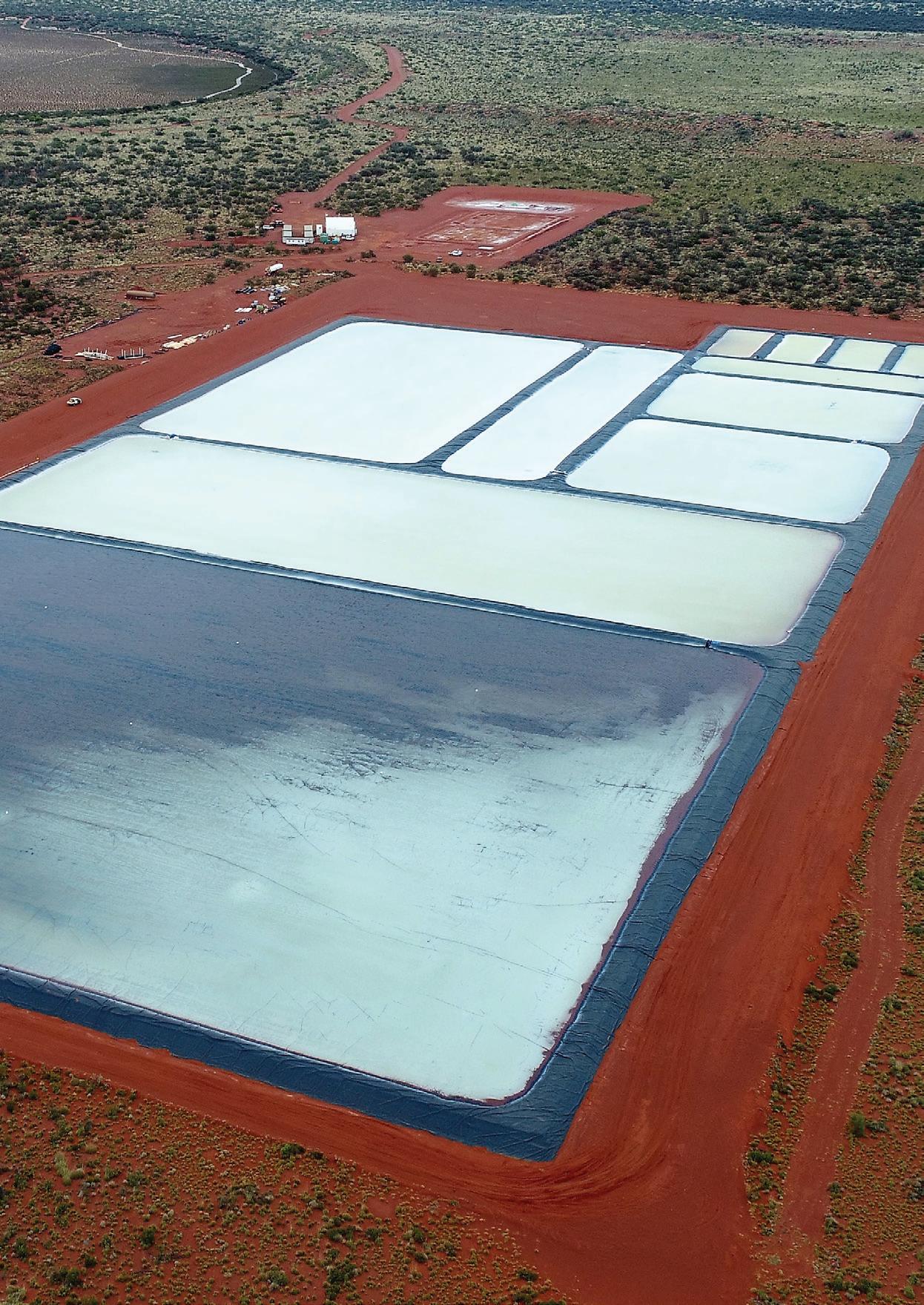
Thank you to all our
18 months
Pump Industry Australia Incorporated PO Box 55, Stuarts Point NSW 2441 Australia
Ph/Fax: (02) 6569 0160 pumpsaustralia@bigpond.com
PIA Executive Council 2018
Dave Alexander – President KSB Australia
John Inkster – Vice President Brown Brothers Engineers
Kevin Wilson – Treasurer/Secretary Executive Officer
Keith Sanders – Councillor Executive Officer - Marketing & Statistics Life Member
Alan Rowan – Councillor Executive Officer - Publications & Training Life Member
Ken Kugler Executive Officer –Standards Life Member
Jim Athanas – Councillor Xylem
Mike Bauer – Councillor Dynapumps
Andrew Black – Councillor Envirotech Water
Malcolm Eyre – Councillor Franklin Electric
Ashley White – Councillor Davey Products
The PIA has had a productive couple of months and are pleased to see several new members join our ranks in recent weeks. Welcome aboard.
The PIA committee have produced a new flyer to outline the features of PIA membership which is shared on our website. Please spread the word to encourage new members. It is one of our principal objectives for 2018 to increase the number and diversity of members to get the broadest possible input into initiatives that will benefit everyone.
The PIA were proud to present another seminar at Bruce County Conference Centre in May on Pump energy efficiency and reliability in operation. Our thanks to Albert Dessi for making a presentation on the Industrial Equipment Upgrade program under development by the government. This continues the work PIA has been doing with several government authorities in the past 12 months. Further seminars are planned for later this year in Brisbane and Sydney, and we invite you to participate.
Alan Rowan organised another Installation & Commissioning course in Brisbane which was well attended. These courses are based on best industry practice and we encourage all members to send their Installation Supervisors to complete this program. The next course will be in Melbourne on 14 August. Look out for the flyer for more information.
As members will know, PIA recently concluded a reciprocal agreement with Irrigation Australia. This allows both organisations to cooperate on issues of common interest and we hope to develop this relationship further over time.
The recent Irrigation Australia Expo in Sydney attracted a number of pump companies and proved to be a valuable platform for introducing new products to this important market segment. In my day job as Managing Director of KSB Australia, I was very interested to attend since irrigation is a competitive market in Australia. Many players are well established, and we were keen to get our new products in front of the experts in irrigation. Irrigation Australia did a great job and we thank them for their support.
Let me say a big thank you to Ron Astall, who recently advised us that he would be resigning as Councillor with work and travel commitments in his role with United Pumps taking the lead. We hope Ron will still find time to attend PIA functions and add some humour to meetings and events that are organised in future, as well as continuing to provide his valuable insight.
Jim Athanas of Xylem will also be joining the Council to round out the PIA representatives voted in at the last AGM. Be in touch if you have any requests or inspiration for our team and your PIA.
Here’s to pumping,
Dave Alexander President – PIAThe ASM C Series sump pump is built tough for reliable uninterrupted operation in the most demanding conditions.
What makes the ‘C’ Series so robust is what it doesn’t have; a submerged motor, bearings or mechanical seals, the primary causes of failure in conventional sump pumps. The heavy duty shaft and bearing assembly is above the mounting plate, clear of the sump environment. This feature allows the pump to run dry indefinitely without damage, pump extreme temperature liquids and have a high tolerance to abrasive fluids.
Additional to these benefits is the fact that the pump is always
primed and ready to work. The C Series is available with material and design options for clean liquids, solids handling, chemicals and extreme temperatures.
This is the pump you need when you want peace of mind. For more information contact ASM Pumps on (03) 9793 7577 or visit asmpumps.com.au
Cover image highlights the mining feature in this issue, showing the potash ponds in Western Australia.
3,583
Published by Monkey Media Enterprises
ABN: 36 426 734 954 PO Box 1763
Preston South VIC 3072
P: (03) 9988 4950
F: (03) 8456 6720
monkeymedia.com.au
info@monkeymedia.com.au
pumpindustry.com.au
magazine@pumpindustry.com.au
Publisher: Chris Bland
Editor: Lauren Cella
Senior Associate Editor: Jessica Dickers
Journalists: Elisa Iannunzio, Kirsty Hutton, Lauren Butler
Marketing Associate: Sam Penny
Business Development Manager:
Rima Munafo
Marketing Consultants: Helena Brace, Stephanie Shaw
Production and Customer Service:
Titian Bartlau
Senior Designer: Alejandro Molano
Designer: Jacqui Abela
ISSN: 2201-0270
This magazine is published by Monkey Media in cooperation with the Pump Industry Australia Inc. (PIA). The views contained herein are not necessarily the views of either the publisher or the PIA. Neither the publisher nor the PIA takes responsibility for any claims made by advertisers. All communication should be directed to the publisher.
The publisher welcomes contributions to the magazine. All contributions must comply with the publisher’s editorial policy which follows. By providing content to the publisher, you authorise the publisher to reproduce that content either in its original form, or edited, or combined with other content in any of its publications and in any format at the publisher's discretion.
new DryWet sewage pumps set to change the market
The Senate Economic References Committee has conducted a public hearing on the future of Australia’s new submarine fleet, with the use of pump jets questioned.
Australia’s next generation of submarines will be built under the Federal Government’s Future Submarine Program, with French company DCNS designing 12 Future Submarines.
A pump jet propulsion system has been proposed as a key feature of the Shortfin Barracuda submarine, however the inquiry revealed discrepancies between expert opinion and the project team’s design.
Aidan Morrison, a physicist who compiled a report for the inquiry, noted that the pump jet is not efficient at the speeds that a conventional submarine operates in.
“Pump jets have a far lower efficiency than propellers at a low speed of travel in contrast to high speeds, where jets tend to become more efficient,” Mr Morrison said.
“The crossover does not lie near or anywhere under the probable transit speed of eight to 10 knots of a diesel-electric submarine. One world-renowned expert I discussed the matter with said it was impossible that a pump jet could be designed to be more efficient than a well-designed propeller under 18 knots.”
He claimed that no other conventional submarines used this type of system.
“There are none in service at all. I’m aware of a prototype or demonstrator that was built once on a Russian submarine, a Kilo class submarine. I’ve seen a photo of that, but as far as I can tell it was never put into much active service.”
Mr Morrison also contested claims made by French company Naval Group that pump jets meant that the Shortfin Barracuda would be able to move more quietly.
“The pump jet is only quieter when compared with an obsolete propeller. This could actually be the statement that was intended to be made, in which case it is perfectly consistent with the research that I have done and put before you today,” Mr Morrison said.
While pump jet propulsion systems are generally used in nuclear submarines, they are generally not used in conventional submarines.
Anew water treatment plant –consisting of two containerised facilities as well as several new tanks – has been craned in to place at Bronte Park in Tasmania’s Central Highlands region.
It is one of 12 new treatment plants installed by TasWater around the state to meet its commitment to end all public health alerts by the end of August 2018.
The plant has been manufactured in a factory in Launceston by TasWater contractor TRILITY and its subsidiary Hydramet. In total, eight similar modular plants have been built – the Bronte Park treatment plant is the last to roll off the production line.
It was transported by road to site and lifted into place by crane. Once installation is complete, the treatment plant will complete the integrated water supply system.
Bronte Park’s water supply was originally installed by the Hydro Electric Commission in the 1940’s with much of it replaced by a private developer from the 1960’s. TasWater took over Bronte Park’s water supply in 2016.
The water will continue to be sourced from Hydro Tasmania’s Bronte Canal which is fed from Pine Tier Lagoon. Following treatment the drinking water will be stored in both the existing and two new reservoirs before being piped to the existing reticulation network.
Now the treatment plant modules are in place, the piping, mechanical and electrical connections will be completed ahead of a stringent testing program overseen by the Department of Health and Human Services.
It is only after this that Bronte Park’s current Boil Water Alert can be lifted. TasWater is on track to meet this commitment by the end of August 2018.
The New South Wales Government has announced the expansion of Hunter Water’s sewerage network, allowing over 400 businesses and residences in Wyee to be connected, with capacity for hundreds more to be connected in the future.
Minister for Energy and Utilities, Don Harwin, said the State Government recognised the growth potential of Wyee.
“We have long acknowledged Wyee has great potential and we’re committed to helping it meet that potential by investing in the expansion of this scheme.
“Expanding the scheme now makes economic sense, ensuring the right infrastructure is delivered to provide capacity for new homes in Western Lake Macquarie, increasing the overall investment to more than $36 million.
“I’m pleased to report that Hunter Water has made significant progress in the design and environmental assessments for the new sewer system, with construction work expected to start by mid next year.
“Even with the expansion plans, the project remains on track to be delivered for connection by December 2020,” said Mr Harwin.
Member for Lake Macquarie, Greg Piper, welcomed the expansion.
“I’m delighted the NSW Government has decided to expand this important project. In addition to the 400 homes and businesses, which will be directly connected now, the system will be built for the future needs of Wyee with the capacity to service 2750 new homes.
“I genuinely believe this project lays the groundwork for a very bright future for the Wyee township.
“The residents have waited a long time for these changes and I have no doubt they are eager to see the works completed.”
AGL has announced the progression of its proposed gas import project at Crib Point in Victoria. Two agreements have been signed, the first enabling berth upgrades at the Port of Hasting as well as a leasing agreement that would be required should the AGL project go ahead.
The second, with APA Group, is for the Crib Point to Pakenham pipeline to transport imported gas to homes and businesses.
The project itself remains subject to approvals, community consultation and a final investment decision by AGL.
AGL project spokesman Kelly Parkinson said, “Although we have been consulting with community members and governments since 2017, some community members are still understandably concerned about the project and the impact it might have.
“We’re carrying out feasibility into using the Crib Point Jetty because this has been identified as the best site to minimise local impact.”
AGL Managing Director and CEO, Andy Vesey, said, “The Crib Point LNG Import Jetty project has significant potential to provide AGL with the ability to deliver a new flexible source of gas supply to the southern states of Australia. This will deliver liquidity, increasing competition to put downward pressure on wholesale prices and provide much needed capacity and long-term security of supply.
“As highlighted in the Australian Energy Market Operator (AEMO)’s Victorian Gas Planning Report released in March 2018, without additional gas supply there is a potential shortfall in the market from 2022 and a potential shortfall in meeting peak Victorian winter daily demand in 2021. Our proposed project is uniquely placed to address this challenge.
Mr Parkinson said he is aware of concerns over the environmental impact of the project.
“We are very aware that Western Port is an environmentally sensitive area and many areas within it are covered by the RAMSAR international convention on the protection of wetlands,” Mr Parkinson said.
“There is already an existing jetty that currently functions for petrol importation.
“It has an existing deep water berth that does not require deep dredging and importantly it’s a relatively short distance from the Victorian gas network.”
Selecting another location would require the construction of a new jetty and significant excavation of the bay floor.
Kelair
SANDPIPER Air Operated Double Diaphragm Pumps
• Capacity: To 59 m³/hr
• Pressure: To 8.6 bar
• Temperature: To 150°C
• Viscosities: To 25,000 cps
Applications
Chemical Processing, Mining, Paints, Food Processing, Industrial Maintenance, Electronics, Construction, Utilities
PULSAFEEDER Metering Pumps
• Capacity: To 52m³/hr
• Pressure: To 383 bar
• Temperature: To 260°C
• Viscosities: To 25,000 cps
Applications
Water and Wastewater Treatment, Chemical Processing, Hydrocarbon Processing, Food Processing
ALBIN Peristaltic / Hose Pumps
• Capacity: To 155m³/hr
• Pressure: To 15 bar
• Temperature: To 50°C
• Viscosities: To 100,000 cps
Applications
Mining, Thickener Underflow, Pulp and Paper, Filter Press, Brewery, Water Treatment, Quarry, Grout, Concrete, Waste Liquids
LOWARA Single & Multistage Centrifugal Pumps
• Capacity: To 187m³/hr
• Pressure: To 15 bar
• Temperature: To 150°C
• Viscosities: To 500,000 cps
Applications
Pressure Boosting, Industrial Washing, Water Supply, Water Conditioning, Demineralised Water, Glycol, Boiler Feed, Multi-pump, Pressure Sprinkler Systems
Visit kelairpumps.com.au for more information on our extensive range today.
Locally Engineered & Supported
End-suction or Horizontal Split case
Optimum Efficiencies
High pressure, up to 40bar
Conforms to API standards
Complies with ISO 2858, ISO 5199 & EN 733
Townsville City Council has awarded the contract to build a new sewage pump station in Cranbrook, Queensland. NQ Excavations has been awarded the contract to construct the $1.5 million sewage pumping station, including a sewage rising main and gravity sewer, and installing a new sewage pump.
Townsville Water and Waste Committee chairman, Paul Jacob, said the new pump station upgrade will improve capacity of the sewerage network in the Cranbrook area and prevent overflow occurring during heavy rain events.
“Providing high-quality infrastructure throughout our suburbs is a key priority for Council,” Mr Jacob said.
“This pump station will be built to the highest standards and is designed to be as unobtrusive as possible.”
The pump station will be installed at McConachy Park, after an extensive community consultation was undertaken.
Mr Jacob said the chosen site was the best option out of five areas examined.
“We have spoken with residents in the area and we have selected a site after reviewing all other potential locations,” Mr Jacob said.
“The final site location of this project was chosen as it is located near existing services, significantly more cost effective and accessible for Council and contractors to complete this important project.”
www.masterflow.net.au
~ over ~ 30YEARS
The Image Flat Water Treatment Plant on the Sunshine Coast hinterland is celebrating five decades of operation, having produced 365 billion litres of water for the community. Seqwater held a small ceremony at the facility to celebrate those who have worked at the plant.
The plant, which was officially opened in 1968, formed part of Maroochy Shire’s first reticulated town water scheme, until individual householders became responsible for their own water supply through rainwater tanks.
Image Flat is the main treatment facility in the Maroochy River area. It draws water from Poona Dam, Wappa Dam or the South Maroochy River which is supplemented by water from Cooloolabin Dam.
Treated water from the Image Flat Water Treatment Plant supplies numerous suburbs, including Nambour, Yandina, Eumundi and coastal urban developments north of the Maroochy River.
Also in attendance was Nambour grandmother Muriel Harrison-Peters, whose late husband Jack Harrison worked as the first Water Officer for Maroochy Shire Council from 1957 to 1984.
Ms Harrison-Peters, 88, said she was among those in attendance when the Image Flat Water Treatment Plant was officially opened in 1968 by then Maroochy Shire Council Chairman David Low.
Among those to attend the celebratory ceremony was 91-year-old Martin Schultz, who was the first Water Treatment Plant Operator to work at the Image Flat plant and worked there for more than 20 years.
“Being back inside the plant again brings back a lot of memories. It sure doesn’t feel like 50 years since it was opened,” Mr Schultz said.
“There’s been a lot of technological advancement in water treatment since I worked here which was interesting to see.
“Machines and software systems
have replaced a lot of the tasks that would previously have needed to be done by hand.”
Pressure: up to 8 bar
Downtime: drastically reduced
Maintenance: simple and quick
Energy use: significantly reduced
“I remember we all went on a tour of the plant when it was opened with council members and engineers, including Jack Mulholland who was crucial to the installation of numerous Sunshine Coast dams,” Mrs Harrison-Peters said.
“With his job, my husband would have to travel to different pump stations a few times a day to control the water supply to different tanks.”
Seqwater Acting Chief Executive Officer, Dan Spiller, said anniversaries were opportunities to look back and take stock of the past as well as plan for the future.
“It can be easy to take a safe, secure water supply for granted, but water is essential for all aspects of life, and we’re very proud of the role we play in a healthy and prosperous South East Queensland,” Mr Spiller said.
“The history of South East Queensland’s water supply is a fascinating and often dramatic story as engineers and planners work to adapt to a rapidly growing population in an ever-changing climate.
“These challenges continue as Seqwater plans for a sustainable water future that meets the needs of all South East Queenslanders.”
Productivity and efficiency: significantly
Rotor and stator life:
Life cycle costs:
Standards Australia has approved the development of a national standard that defines the criteria for material suitable for toilet flushing, along with appropriate labelling requirements.
The Water Services Association of Australia (WSAA) and the urban water industry in Australia and New Zealand have been concerned about the contribution of wet wipes products to pipe blockages and, in turn, disruption to customer services, extra costs and impacts on the environment.
“An Australian Standard would provide manufacturers with clear specifications to design products compatible with the sewerage network,” WSAA Executive Director, Adam Lovell, said.
WSAA and its members started developing the standard in May 2018 and it is anticipated that the standard will take between 12 to 24 months to complete.
Separately, the International Water Sector Flushability Group (IWFSG) published its flushability specification in June 2018, outlining the preferred requirements for flushability as developed by water industry representatives from the US, Canada, Japan, Spain, Israel, New Zealand and Australia.
The documents are in the form of three publically available specifications or PAS documents.
“This is an international issue for water utilities around the globe and while there is no standard at present, customers need clearer labelling to ensure these products do not contribute to blockages in urban wastewater systems,” Mr Lovell said.
You’ve probably heard about the innovation and progress LaserBond is achieving in surface engineering technology. We apply new surfaces to worn parts so they work literally better than new. And brand new parts can also be treated so they last a lot longer. Customers enjoy longer wear life, fewer shutdowns for component replacement, and better workplace health and safety control. Our laser-applied coatings typically at least double the life of a part.
The new ‘laser cell’ in our SA engineering facility will have the highest-power laser beam used for laser cladding in the Southern Hemisphere. We already operate the three most powerful lasers in this industry in Australia. These are supported by many other processes and technologies, such as HP HVOF, all supported by our own well-equipped metallographic laboratory and state-of-the-art workshops. If you’re looking for the best surface engineering available, look no further.
With the world of pumps continuously evolving at both an Australian and global level, the challenge is to keep all stakeholders aware of these activities, so that the latest technologies, pump standards and legislation being contemplated can be successfully introduced. To address this challenge, Pump Industry Australia (PIA) hosted the one-day Energy Efficiency and Savings in Pumping Systems seminar on the 15 May at the Bruce County Hotel in Mt Waverley, Melbourne.
The seminar provided attendees with the opportunity to hear from key stakeholders, including government representatives, pump user groups, and leading national equipment suppliers and manufacturers about the latest developments on the impacts of
pumping systems on energy and the environment, energy efficiency policies and planned legislation, and technical and commercial advances made in the application and penetration of energyefficient pumping systems.
Keith Sanders, PIA Executive Officer Marketing and Statistics, opened the seminar and introduced the day’s keynote speaker, Albert Dessi, Assistant Director at the Department of Energy and Environment.
Mr Dessi’s keynote presentation ‘Industrial equipment upgrades program under the Emissions Reduction Fund’ set out the eligibility criteria for energy efficiency upgrades in pumping systems.
The Emissions Reduction Fund (ERF) provides incentives for Australian businesses, farmers, land holders and
others to adopt new practices and technologies to reduce greenhouse gas emissions by giving people an opportunity to earn money while reducing emissions.
Under the ERF a new Industrial Equipment Upgrades method has been put forward to provide incentives for energy efficiency projects involving replacing or upgrading common industrial and related equipment such as pumps, boilers, compressed air systems, refrigeration and industrial cooling systems.
“The way the fund works is you register for the fund using an approved method, then you bid into an auction and the government pays you for your credits once you have realised them, so you measure and verifiy that you have obtained emission reductions, and then
Members of the pump industry gathered in Melbourne in May to discuss the latest in government energy policies and planned legislation, as well as advances in the application and penetration of energy-efficient pumping systems.
you are paid once you report those credits,” Mr Dessi said.
“In order to use the Emissions Reduction Fund, you need to use an approved method of calculation, you need to have a project registered, and then you need to obtain the savings in energy efficiency to prove this and verify and measure that they’ve occurred.
“Credits run for seven years, but depending on how you do the measurements under this method the credits will tend to be discounted in later years.”
In order to apply for the fund, the government requires approved
methods to be used to determine and verify that emission reduction has occurred.
“The method establishes the calculations you have to do to determine those emissions and they establish reporting requirements so that we can verify that the savings are genuine, and that they can be measured and verified,” Mr Dessi said.
One of the aims of the fund is to provide incentives for projects that would not normally have gone ahead in order to encourage emission reductions additional to what would happen in the ordinary course of business as usual.
“It calculates emission reductions by measuring your energy consumption for
a representative measurement period before you undertake a project and after you’ve made the energy efficiency improvements, and in that way we can ensure that the measurements are comparable and that you have actually achieved the intended results.”
Strict energy boundary and professional measurement and verification oversight are also in place.
“To make sure emission reductions are additional to what would normally happen, we first off require that the project be recommended through an energy audit or through another energy efficient assessment by a suitable professional. This cuts out equipment suppliers that are selling equipment just because they want to sell equipment, where there isn’t a good energy efficiency reason to replace that equipment,” Mr Dessi said.
Mr Dessi also mentioned that there is ongoing work by the Equipment Energy Efficiency program which is looking into minimum energy efficiency standards for pumps.
To learn more about the ERF, visit www.environment.gov.au/ climate-change/government/ emissions-reduction-fund.
Setting the Standards
Standards were a key focus of the seminar with several papers presented on proposed and newly implemented standard changes, as well as approaches to standards overseas.
Ken Kugler, PIA Executive OfficerStandards, talked about the new pump test code AS/ISO 9906:2018.
As a member of the Standards Australia ME-030 sub-committee, Mr Kugler provided attendees with an update on the changes to the standard.
“AS 2417 is now withdrawn and considered obsolete, and was replaced by AS/ISO 9906:2018 in February this year,” Mr Kugler said.
“Previously, acceptance grades [from AS 2417:2001] were levels 1 or 2 with
tolerance values based on specific flow and/or pressure ranges – regardless of industry or pump type.
"The new guidelines recognise that different pumps and/or industries have differing needs and established a multitude of default acceptance grades based on the application and rated power of the pump.”
For more information about changes to AS/ISO 9906:2018 see page 18.
Keith Sanders’ presentation ‘Energy auditing and certification: ISO 14414’ reviewed energy saving approaches in the UK and US, and the need for a uniform approach to auditing and certification in Australia.
“Legislation on energy consumption in Europe and in the US is more advanced than it is in Australia; they already have more standards and more procedures, and these are harmonised to ensure auditing follows consistent guidelines. The standards are already in operation, and Europump, BPMA and Hydraulic Institute offer courses for auditing of pumping equipment and certification,” Mr Sanders said.
“While there is no industry standard for commissioning of pumping equipment to determine base operating data in Australia, the PIA has developed a program to train specialists to conduct commissioning and energy evaluations.
“ISO 14414:2015 is also being considered at this time and may be recommended to Standards Australia for adoption.”
PIA also welcomed back Brett Dundules, Senior Technical Officer at the Fire Protection Association of Australia (FPAA), who has presented at a number of PIA events .
Mr Dundules’ presentation ‘The mechanics approach to the NCC by FPAA’ explored the changes in the mechanics approach to the National Construction Code (NCC). He presented the proposed changes for sprinkler systems in buildings less than 25m, how the code addresses primary and secondary referenced documents, and how these changes would impact pumpsets.
Pumpset standards for fire installations were further explored by Bala Thuraisingam from the FPAA and Ken Kugler in their presentation ‘Fire pumps and conformance to AS 2941’.
The presentation looked at what is specified in the standard, why it is needed and who is responsible for ensuring compliance.
Mr Thuraisingam and Mr Kugler also presented a number of case studies to illustrate where compliance has or has not been met.
Insights from the industry
Attendees also had the opportunity to hear from specialists, and leading national equipment suppliers and manufacturers about the technical and commercial advances made in the application and penetration of energy-efficient pumping systems in Australia and overseas.
Naren Gangaiah, Project Engineering Manager - KSB Australia delivered his presentation ‘European Extended Product Approach (ErP and EEI explained)’ which provided a manufacturer’s view on European legislation and product availability.
Warwick Stannus, Group Engineering Manager at A.G. Coombs, talked about efforts to establish guidelines and standard templates for a range of pump installations in his presentation ‘HVAC Pump Installations - An integrated approach to pump selection, installation and maintainability’.
Mr Stannus said he has seen a lot of different approaches to installation and commissioning leading to inconsistency between installations, which is a problem, especially if it’s happening within a business.
James Chalmers, Global Water Industry Manager – ABB (UK), discussed effective water utility management techniques, focusing on managing leakage, optimising pump performance and energy efficiency.
According to Mr Chalmers, business intelligence and performance metrics play a large role in the efficient
use of water and meeting the utility’s challenges, which relies on the use of digital technology to optimise operations. In particular, he discussed the use of different technologies for early detection of faults in the system in order to reduce costs, as well as customer complaints.
Malcolm Robertson, Robertson Technology, explored strategies for performance assessment and improvement using the thermodynamic method of measuring pumping performance on-site.
From Davey Water Products, Andrew Rathjen’s presentation ‘Remote data capture for power savings in Industry and Irrigation’ looked at the management of data to achieve improved pump performance.
To ensure the Australian pump industry remains up to date with the latest PIA news, changes in standards and training, the PIA runs a number of seminars, technical meetings and training courses throughout the year in various states. For more information or to see when the next event is on, visit https://pumps.asn.au/.
Pump
Industry Australia (PIA)
has continued to liaise
with industry organisations and government departments
to promote cooperation
between industries,
and improve standards. Here, we look at the most recent changes to standards relating to pumping systems that you need to know.
In late February, AS/ISO 9906:2018 Rotodynamic pumps - Hydraulic performance acceptance tests - Grades 1, 2 and 3 was officially published and is now in effect. As a result, AS2417:2001 Rotodynamic pumps - Hydraulic performance acceptance tests - Grades 1 and 2 has been superseded.
In November 2015, Standards Australia advised that AS 2417:2001 was considered an aged standard and could be subject to withdrawal.
ISO 9906:2012 had previously been adopted in Europe and member countries with an equivalent British Standard introduced the same year and other countries following suit soon after. Therefore, the AS 2417:2001 standard was out of sync with the rest of the world by five years. Additionally, the US had published ANSI/HI 14.6:2011 Rotodynamic pumps for hydraulic performance acceptance tests. This standard is “harmonized” with ISO 9906:2012 and the outcome from testing in either standard is identical.
Due to this, the PIA Council decided to initiate the procedure required for the direct adoption of ISO 9906:2012 in Australia as the direction globally is toward one worldwide standard for pump performance testing.
AS/ISO 9906:2018 specifies hydraulic performance tests for customers’ acceptance and specifies the requirements at test facilities. The tests can be applied to pumps of any size, and any pumped liquids that behave as clean, cold water. It only applies to the bare pump itself without any fittings, electric motors or any other associated equipment.
When evaluating and making pump selections, it forms part of the guidelines intended to ascertain the performance of the pump and to compare this with the manufacturer’s guarantee.
Previously, AS 2417:2001 consisted of two acceptance levels: Grade 1 and Grade 2. Both grades had bilateral tolerances for rated head or rated flow and allowed a negative
tolerance on efficiency. As an annex to the standard, it had Annex A which provided a minimum tolerance which general purpose pumps were to meet unless otherwise specified.
The new standard contains three levels of acceptance criteria for pump performance test results, with each grade broken down into further subgrades with differing tolerance bands for pump acceptance levels.
• Grades 1B, 1E and 1U with tighter tolerance (old AS2417 Grade 1)
• Grades 2B and 2U with broader tolerance (old AS2417 Grade 2)
• Grade 3B with even broader tolerance (old AS2417 Annex A)
Compared with the previous test standard, in general the level of acceptable tolerance value increases from Grade 1 to Grade 3 and can either be unilateral (one sided, designated by U) or bilateral (two sided, designated by B). Tests to U grades do not have an allowable negative tolerance for flow and head.
ISO pump standards are reviewed by the appropriate committee every three to five years and PIA is in the process of submitting a proposal to Standards Australia to have international participation. This would allow PIA to have direct input to the responsible ISO committee in Europe. It is expected that this will be finalised in the next couple of months.
Discussions with Fire Protection Association of Australia (FPAA) are ongoing regarding the adoption of a checklist to accompany AS2941 Fixed fire protection installations – pumpset systems.
In the meantime, an abridged version can be found on the PIA website for use by members who want to adopt a uniform approach for the verification of compliance to the requirements of AS2941
Reliable, powerful, robust.
For several decades, AUMA actuators have proved their reliability in automating sluice gates, butterfly valves and gates in weirs, fish ladders, locks, and hydropower plants.
AUMA’s comprehensive portfolio covers torques ranging from 10 Nm to 675,000 Nm offering homogeneous automation schemes throughout the plant: from simple OPEN-CLOSE applications to level control using an integral PID controller.
Jacmor Engineering is an authorised supplier of world-leading Thordon Self Lubricating Pump Bearings. Utilising proprietary polymers, Thordon high-performance bearing solutions have the capability to run dry, deliver high reliability and long wear life, particularly in tough abrasive operating conditions. This high level of product performance results in decreased lifecycle costs and increased mean time between failures for Thordon’s customers.
Jacmor Engineering regularly supplies fully finished bearings to leading pump companies, mining, sewage treatment plants, power generation, marine, offshore, pulp and paper, irrigation and other Industries across Australia. We also offer drinking water and FOOD grade bearings. Based out of Melbourne – Australia, Jacmor Engineering provides full technical and installation support. We carry a huge inventory and bearings can be dispatched overnight from our state of the art machining facility. To date, bearings to suit shaft diameters ranging from 25mm–1500mm have been supplied to valued clients across Australia. Thordon Bearings is the proven, cost-effective, environmentally-friendly, solution for rigorous and demanding journal bearing applications. For specific applications, feel free to contact Josh Sayed at Jacmor Engineering via email on joshs@jacmor. com.au or on 0447 546 142.
Imagine if Coke didn’t have Pepsi. If there was no PC vs Mac. If GM never came close to Ford. That’s pretty much what it’s like with Warman pumps. We have been the top of the industry for decades. We’re the only people we have to beat. And we don’t make it easy for ourselves.
Here’s to 80 years of being the best and another 80 years of being even better. It’s always been Warman, and it always will be.
To find out more visit www.alwayswarman.weir
www.minerals.weir
Ebara Pumps Europe is expanding its range of EVMS (Shurricane) vertical multistage pumps, with models of 32, 45, 64 and 90 m3/hr capacities.
Following the success of the smaller EVMS vertical multistage pump—and its unique “Shurricane” impeller design which greatly reduces axial thrust—Ebara Corporation Japan and its Italian factory have invested in research and development, and tooling to expand the design and concept for larger capacity vertical multistage pump (VMS) models.
The EVMS model VMS pump—with its Shurricane impeller design—greatly reduces axial thrust and allows the use of standard electric motors without any modifications or additional bearings up to and including 30kW. Motor bearing life is greatly increased and the overall cost is reduced as larger thrust bearings don’t need to be fitted to the motor and no additional thrust bearings need to be fitted to the pump.
Other features include a minimum efficiency index (MEI) of >0.7 and a cartridge type mechanical seal utilising standard EN 12756 mechanical seal
components. All models over 5.5kW are fitted with a spacer coupling, allowing the easy removal of the cartridge seal and if needed the standard EN 12756 mechanical seal can be sourced from your local seal supplier, as well as your local Ebara dealer or sales office.
The new larger EVMS model pumps are available in a variety of materials including CI/304SS, all 304SS and all 316SS materials, plus hard faced and standard mechanical seals (balanced and unbalanced). Other features include smart plug solutions with separate air vent plug, and water filling and sensor plug.
Ebara continues to expand the range of products they stock and supply in Australia with two recent additions. For more details contact us at Ebara Pumps Australia or visit our website.
Very economically priced cast iron end suction motor pumps to EN733. They are based on the well proven 3M using the same extended shaft motor and stainless steel impeller, but with a cast iron casing.
A range of robust submersible grinder pumps with a high torque motor & powerful grinding mechanism. Another quality product in the well regarded and proven D’ series of Ebara submersible sewage & wastewater pumps.
with powerful grinding mechanism
In mid-March, a bush fire tore through Cobrico in Victoria’s south-west, igniting the peat bog underneath. This left behind toxic levels of carbon monoxide and caused the temporary relocation of 20 per cent of residents. With no decent rainfall expected, a four kilometre layflat hose was laid to create a temporary pipeline to pump water to the site and extinguish the threat.
The recent fire that tore through Cobrico, burned over 15,000 hectares of land in a peat bog. Firefighters worked day and night using fire trucks, helicopters and bulldozers to try to contain it. However, peat fires are extremely difficult to manage as they require a significant amount of water running continuously to extinguish them.
Peat is created over time in wetlands through the build-up of partially decayed vegetation such as leaves, grass and root systems. Once ignited, it is a challenge to extinguish and can burn for months or years. It burns similarly to briquettes, emitting significant smoke as it does.
This smoke can reduce air quality, and contains fine particles, water vapour and gases including carbon monoxide and nitrogen oxides. It may also contain sulphur compounds which are odorous.
If left to burn, the Cobrico peat fire could have spread through the vegetable matter up to 10m below the surface and damaged prime farming land.
Since the traditional method of using fire trucks and the expenses of helicopter water bombing were not having the desired effect, the decision was made by the local authorities to flood the area using large volumes of water. After careful consideration of the pipeline options available to bring in this water, flexible layflat hose was decided upon as the most efficient and economical option. 200mm diameter layflat was rapidly connected to a valve in the Major Ottway Pipeline, four kilometres away, and this brought water to the peat fire in just 48 hours.
State Emergency Management Commissioner, Craig Lapsley, said that with no decent rainfall on the horizon, an above-ground temporary pipeline was deemed the only feasible way to get a constant and significant amount of water onto the peat fires in a short time.
“One of those is to put above-ground piping to bring [water] from a major reticulation main; it’s quite extensive but necessary without rain,” Mr Lapsley said.
The temporary pipeline was assembled using Crusader Hoses’ flexible layflat hose which was supplied on reels of 200m plus some shorts. This was easily and efficiently transported to the site in only three truckloads, due to its compactness, and the full four kilometres of hose was unrolled and in-situ within one and a half days. The water was soon flowing through at 50 litres per second at 10 bar pressure and this rapidly contained the fire behind an inactive edge.
The segmented hose pumps water 24 hours a day alongside roadsides and across paddocks until it reaches two dams dug at the edge of the peat fire at Lake Cobrico. There are irrigation pumps going from the dams into sprinklers which directly attacks the fire. The water is also being used to flood a trench which is acting as a fire break.
The construction of the pipeline took just 48 hours—one expert said such a feat would ordinarily take weeks—and is understood to be the first time such a method has been used to fight a peat fire in Victoria.
Francois Steverlynck, Managing Director of the Australianmade Crusader Hose, said, “We have been in the development and manufacturing of high-quality flexible layflat hose systems for over 33 years and we are happy that the benefits of this method were proven in extinguishing the Cobrico peat fire.”
Once the layflat hose and pump was installed, roads were reopened without obstacles as the hose had been placed in culverts at crossings and ran alongside. The layflat hose was deployed with minimal environmental impact and a soft footprint.
Residents were permitted to return with health risks significantly reduced.
The layflat hose will next be retrieved by rolling it up on reels or pallets. It will then be ready to move water again at whatever site it is needed at.
Founded in 1968 in Montecchio, Italy, Lowara is recognised as a world leader in stainless steel manufacturing for turbine, centrifugal and submersible pumps for use in the building services, residential, public utilities, agriculture, aquaculture and mining industries. In June, Lowara celebrated its 50th anniversary, with distributors and dealers coming together in Sydney to mark the occasion.
Lowara celebrated the occasion with a Sydney Harbour cruise, with 110 dealers and customers enjoying a great night and a spectacular view of the Vivid Sydney festival illuminations.
Lowara pumps are distributed in New Zealand, and Australia in QLD, NSW, VIC and TAS by Brown Brothers Engineers, in SA and NT by WBS Pumps, and in WA by Advanced Pump Technologies.
It’s success in Australia and New Zealand is built upon the passion of its distributors and dealer network, and the quality of the materials used for manufacture.
John Inkster, CEO at Brown Brothers Engineers Australia, was among those to attend the celebration in Sydney.
“Brown Brothers Engineers congratulates Lowara on celebrating 50 years of manufacturing, growing from a small business in Montecchio, Maggiore, to a world renowned global pump company. Quite an achievement in the space of 50 years,” Mr Inkster said.
“Brown Brothers has been a distributor for 28 of those 50 years starting in New Zealand in 1990 and in Sydney, Australia, in 1994.
“Being a Lowara distributor for such a long time very much defines who we are; it has been a rewarding journey and enabled Brown Brothers to make ‘the jump’ across the Tasman where we are now the sole distributor on the eastern seaboard with sales offices, warehousing and workshop facilities in Brisbane, Sydney and Melbourne.”
An evolving product range
Lowara continues to grow as a manufacturer, making its mark on the pump market with the introduction of new and improved models to meet the demands of end users.
“For me one of the most significant achievements by Lowara was the introduction of the Hydrovar in the mid-90s and now up to version Gen5—dubbed ‘giving a pump a brain’— which is a truly remarkable example of technology at work reducing energy costs across all sectors, from households to large industrial end users,” Mr Inkster said.
“The next generation of smart pumps is about to be released here in Australia and NZ with the Lowara Smart Pump range which incorporates a permanent magnet motor that meets IE5 standard, providing efficiencies well above a standard IE3 asynchronous motor.
“We had an e-HM model on display at the Irrigation conference in Sydney and it attracted a lot of interest.”
1968–1977
• LOWARA Spa was established in 1968 by the Ghiotto brothers
• Production started with the iconic PM16 pump, followed by the A - AZ - F - JET - DN series, Lowara SMC circulators, the 4” submersible pump and the Hydrosphere tank 1978–1987
• Earlier pump models were joined by the CV - JET inox - ROBBY - MB, and 4”, 5” and 6” submersible series
• LOWARA Spa was acquired by Goulds Pump in 1985 1988–1997
• Goulds Pump was acquired by ITT Industries in 1997
• With the introduction of stamped stainless technology, stainless steel took centre stage and new pump ranges were developed, including CE/CA - DOC
- DOMO - HM - BG - HF 1998–2007
• Stainless steel features are included in all LOWARA products, both new and old 2008 - 2018
• ITT Industries created a spin-off company, Xylem, which is active in the water movement sector through many brands, including Lowara
• Due to a new production layout some of the series produced, such as SV - LNE - LNT - NSC - HM - HVL - XL, reach maximum reliability and competitiveness levels
Today, Lowara is a leader in providing long-term economical solutions for pumping and circulating clean or dirty water.
Lowara pumps, drives and packaged solutions, such as pressure booster sets and wastewater lifting stations, are all developed with low lifecycle cost in mind, ensuring robust, efficient products that are easy to install and service, and have a long service life.
Full range of Watermarked fittings and valves to suit your every requirement
Extensive range of precision valves, already installed around the country in many commercial, agricultural and industrial projects around the country. The range includes the likes of dual approved ball valves, gate valves, gas isolation valves, non-return valves. dual check valves and more.
Made tough to endure the harsh demands of the Australian environment, the range includes everything from T Head Tapware, compression and screwed brassware.
An extension of our Logi valves into civil and other projects, these valves are designed to respond to the incredible demands of an ever changing lanscape, and includes our brass poly connector range.
Corrosive liquids on mining and construction sites are a fact of life. Pumps used for metalliferous mines are susceptible to breakdowns simply because the material of construction is not compatible with the required mid-range PH liquids. Tsurumi’s new 316 cast stainless steel high head pumps have been designed for such applications and challenges.
Australian Pump Industries is working with Tsurumi to develop a range of big electro submersible pumps designed to deal with these issues. The pumps are available in 316 stainless steel are now in a range of up to 110 kW with heads as high as 200m.
Called the Tsurumi LH series, the new pump claimed by API to change the way mines, quarries, industrial applications and even infrastructure projects think about moving inconvenient water fast.
Aussie Pumps’ Tsurumi Product Manager, Neil Bennett, said, “Tsurumi’s LH series will deliver flows of up to 6,500 lpm.
“They are loaded with features that Tsurumi has integrated as standard to maintain the highest levels of reliability.”
The big pumps, with their high flows and high head combination are designed in the unique ‘slimline’ that enables the pump to be used in bores and wells. For example, even the 110kW pump has a diameter of only 606mm.
Additionally, the pump incorporates a centred discharge flange that ensures the pump is ideally balanced for lifting in its installed position. Discharge ports are up to 200mm (8”) and are flanged.
The pumps achieve their high performance by using two 316 stainless steel impellers. Pumps over 55kW are fitted with electro type leakage sensors and protection anodes where required.
Tsurumi’s anti-wicking cable entry prevents water getting into the motor if the power lead is damaged or the end submerged. Their unique double dual silicone carbide mechanical seal system is an added feature, and seals are incorporated in an oil chamber fitted with a patented ‘oil lifter’ that provides forced lubrication into the mechanical seals thus ensuring they always stay ‘wet’.
The extension of seal life and the anti-wicking cable entry point eliminates 90 per cent of the reasons of failure in submersible motors, dramatically extending the pump’s life and ultimately its reliability on-site.
“Tsurumi’s commitment to Australian Pump and the Australian market is tremendous,” Mr Bennett said.
“The establishment of the pump banks in Singapore and Japan mean fast delivery even if Australian Pump’s huge warehouse in Sydney doesn’t have product for immediate shipment.”
For many years, the octavis diagnostic amplifiers have been a mainstay in ifm efectors’ condition monitoring suite, and have been continuously upgraded to include more features with every generation of firmware and software.
Traditionally, the amplifiers took four MEMS accelerometers with two speed inputs into a FFT and a H-FFT environment so that raw signals could be pre-processed to offer protection from bearing faults and unbalance conditions, and to meet ISO standards.
It also had a small (by its current standards) history function where its diagnostic outputs could be monitored internally.
Like most technology, nothing stays the same, and the octavis VSE amplifiers are no exception. They have been upgraded over time to meet different needs, with recent upgrades catering for an increased demand for more information and better protection.
Some notable upgrades include:
• Faster processor
• Ability to take any accelerometer (of any IEPE rating or MEMS style) as inputs
• History memory has been upgraded to take 660,000 readings — this normally equates to around two years of on board data for every channel and diagnosis programmed at around a 30 minute interval
• Full time waveform diagnostics are now available and can be converted to a full spectral view at the click of a button. Waveform samples can be taken at 20, 50 or 100KHz samples depending on resolution requirements
• VSE15x models now have a Fieldbus Interface. This feature is model dependent for Ethernet IP, Profinet, and Modbus TCP, with Ethercat and Powerlink options available soon. While only some models have OPC UA ability, all models have OPC DA ability to talk directly to SCADA systems
• All models have the ability to take 4-20mA devices into six channels, so now the unit can be a monitor and controller for any system such as a pump controller or a compressor
• Flow, pressure, temperature, level and vibration can be monitored from
one unit, and trending and switching each point can be done without the use of a PLC
• New diagnosis objects, in addition to unbalance and bearing wear alarms, have been created making it simple to create:
» Acceleration RMS in the time domain
» Displacement RMS in the time domain
» Acceleration peak in the time domain
» A RMS in the frequency domain
» V RMS in the frequency domain
» D RMS in the frequency domain
» Specific frequency alarms in G/ mm/sec or mm
» Time waveform
• History
• Alarm display
• Spectral views
With all of these features, the system is flexible and cost effective.
As usual, all of these new features from functional VES004 programming and diagnostic software are free to download after registering on the ifm website.
The octavis diagnostic amplifiers can also be used in conjunction with the new SmartObserver Software suite.
SmartObserver is a Real-Time Maintenance system that can be implemented to expand the octavis system and assist operators to get a very good handle on asset status.
SmartObserver monitors all amplifier points continuously by reading information that has been programmed into the octavis processor. This data sent by an agent in VSE amplifier is then used to create a dashboard of the exact condition of the plant. Alarms can also be emailed or sent by SMS to any staff that need to know the machines status. There is also a cloud based version available.
With the population of Melbourne’s Northern Growth Area expected to rapidly increase in the coming decades, Yarra Valley Water was faced with the task of needing to install major water, recycled water and sewerage infrastructure to meet the increasing demand. To deliver services in the coming years, a $400 million program of works is being completed, including the construction of the Craigieburn Sewage Transfer Hub (CSTH)—an innovative facility designed to expand with the community.
The Northern Growth Area runs from Craigieburn up the Hume Highway to the Wallan area and covers roughly 20km. By 2040, the area is planned to accommodate an additional 128,000 properties and around 300,000 new residents.
At the time of the planning, there was no existing major sewerage infrastructure between Craigieburn and Wallan where most of the population growth will occur.
This presented a challenge, as the predicted growth could not occur without the construction of new infrastructure including sewage tunnels, water transfer mains, storage tanks, and new and upgraded treatment plants.
Yarra Valley Water is undertaking a $400 million program of works over the next five years to build this much needed infrastructure, which will be largely supported by the CSTH.
Once completed in late 2018, the CSTH will be the largest mid-system sewage storage facility in Australia, with the facility able to expand as development in the area continues.
It will send waste from the Amaroo Main Sewer downstream to the Western Treatment Plant, storing flows when required, allowing Yarra Valley Water to make the best use of the existing infrastructure that it has to service growth.
The facility will ensure large quantities of sewage flows associated with wet weather can be captured and managed without expensive upgrades to the downstream sewer network, reducing the risk of sewage spills.
By creating flexible infrastructure which can grow along with the community and keep up, it provides an innovative, cost-effective alternative to building a large sewer in the area at a much higher cost.
A sewage transfer facility of this scale is an unusual approach to sewage management, and traditionally Yarra Valley Water would have installed a large sewer tunnel — similar to the Amaroo Main Sewer—to transfer flows from the area at Craigieburn to the nearest downstream sewer with sufficient capacity — most likely sending it down to Melbourne Water’s main trunk sewer, the Northern Intercepting Sewer. Following an innovative planning and design process, it was decided that the CSTH would be built to locally store and distribute flows, and designed to grow as needed to match development. This approach has resulted in a saving of over $100 million through this alternative solution.
Sewage generated in the growth area will flow into the site of the existing Craigieburn Sewage Treatment Plant via the Amaroo Main Sewer, which is currently reaching the final stage of construction, and the existing Aitken Creek Branch Sewer. The existing sewerage network does not currently have the capacity to accept peak sewer flows from the area.
As a result, the CSTH is required to store flows temporarily when there is insufficient capacity in the downstream network, reducing the risk of sewage spills. The sewage will then be transferred to the Western Treatment Plant for treatment.
The CSTH is a unique sewerage flow storage and distribution facility consisting of two 16 Megalitre (ML) storage tanks making it the biggest in Australia, with plans for future on-site storage of over 200ML across 14 tanks. There will also be a built-in inlet drop structure to help regulate wet weather flows to the storages, and an emergency relief structure.
To manage the flows there will be three sewer pump stations with a total capacity of approximately 1000L/s, with provision to be upgraded to around 2000L/s if needed.
Andrew Cosham, Divisional Manager Major Projects, said
the facility will receive daily dry weather flows which will then be pumped offsite into the existing network.
“During a wet weather event when the incoming flows from the new area are greater than the capacity of the downstream network, the flows in excess of the downstream capacity will be temporarily stored at the facility and fed back into the system when capacity becomes available.”
Andrew said extensive research was undertaken in the design stage of the project on the pump and impeller options available.
“This helped to develop specific functional requirements and a list of preferred pumps. The contractor then undertook the procurement process as part of the construction phase of the project.”
Due to the high load of rags that are being encountered in newer developments, Yarra Valley Water said the key factors when selecting pumps for the CSTH were the pumps ability to handle solids—either by passing or chopping them. Other important factors that were a priority when considering pumps were energy efficiency, cost, replacement availability and lead times.
“Energy efficiency is always important in selecting pumps, however, it was not the primary selection criteria. Due to the highly varied operating points (300L/s at 2m head or 14m head) for the wet weather pumps, high efficiency was always going to be hard to achieve with a limited pump selection,” Andrew said.
“As the pumps have all been type tested, the on-site testing will be limited to checking that the design setpoints can be achieved. There will be a trial period to refine the pump cut in and out points, as well as the control programming.”
The project has pumps of varying sizes and functions:
• The main dry weather transfer pumps are Sulzer XFP 205J-CB2 PE 900/4 pumps with contrablock impellers
• The main wet weather pumps are Sulzer XFP 305M-CB2, PE 750/6 pumps with contrablock plus impeller
• Mono progressive cavity pumps were chosen for sludge transfer
• Three JWC Environmental Muffin Monster macerators were chosen to reduce ragging of the dry weather pumps
The Craigieburn Sewage Transfer Hub includes the following key elements:
• Excavation of approximately 120,000m3 of rock
• Stabilisation of cut batters and retaining wall construction
• Concrete works including manhole, sewage pumping facility, emergency relief structure and tank foundations slabs
• Site roadworks and drainage
• Sewage macerator, pumps and associated pipework valves and fittings
• Two 16ML circular storage tanks with sealed roof
• Air treatment facility
• Site electrical works
• Assorted site steelwork
The CSTH is an example of the type of innovation required to service growing cities where traditional infrastructure approaches are high cost and face significant technical challenges.
The process adopted has ultimately provided a significant direct saving to the community, maximised the use of existing infrastructure, and delivered a facility that is low risk and simple to operate and maintain, whilst still satisfying all involved stakeholders and providing an equivalent level of service to customers.
By implementing this unique strategy, Yarra Valley Water has been able to provide the community with an innovative lower cost sewerage network compared to what would have been implemented if traditional planning, servicing and design philosophies were adopted.
CPB contractors are the principal construction contractors, with Jacobs initially involved for three years from the creation of functional design through to detailed design. The project is in its final stages, with installation, testing and commissioning of equipment taking place before it is completed in mid-2018.
At Brown Brothers Engineers we have expanded our capabilities with two more quality pump manufacturers. In addition to the current world leading brands we can now offer the following range:
Layne Bowler
vertical turbine pumps have a proven record under the most demanding and toughest of conditions.
WELCOME TO THE BIG END OF TOWN.
When high head and high flows are required look no further than this quality Italian made range.
• Flows to 5000m³/h
• Head to 220m
• Pumps that exceed EN733 (DIN 24255 standard)
NCBK
In a previous issue, we reviewed the drawdown analysis portion of my pump and motor field test spreadsheet. The calculations performed by that section of the spreadsheet provided us the flow and total dynamic head produced by the pump during testing. In this issue, we will review the motor testing section.
Motor testing is important for two reasons.
First, it provides us with the information necessary to calculate horsepower at the test point. Horsepower allows for calculation of pump efficiency at the test point. We can then compare the tested head, flow, horsepower and hydraulic efficiency with those shown on the manufacturers
pump curve. Pump efficiency also allows us to monitor the cost per thousand gallons pumped each time we perform a test.
Second, motor testing provides operational data that can be used to identify unhealthy conditions that can lead to premature failure. Motor temperature, loading and the actual supply voltage are important components.
Another factor that has a major influence on submersible pump reliability is unbalanced phase voltage and current. A small voltage unbalance will give rise to a current unbalance that is six to ten times greater. Unbalanced currents increase the stator operating temperature which reduces insulation life. Phase unbalance is one of the largest causes of premature motor failure in the US.
Figure 1 is the motor test portion of the ‘Submersible Wastewater Pump and Motor Testing’ spreadsheet. As with the pump test portion, the gray cells are entered data and the yellow ones are the calculated results. The equations on the right show how certain results were calculated. The
information required includes phase voltage and current, motor nameplate efficiency and power factor (PF) and the power cost per kilowatt hour (kWh). Voltage and current are measured with a high-quality voltmeter and clamp on ammeter. The spreadsheet instructions detail the optional use of kW and PF meters.
The phase voltage and current should be measured at the beginning of the pump down cycle in order to provide an accurate horsepower calculation. They should also be measured on the motor side of the contactor. Contactor corrosion cannot be detected when voltage is measured on the line side. Before or after the pump down test, measure the phase voltage on the line side with the pump off. If any phase voltage unbalance occurs with the pump off, the supply side can be identified as the source of the unbalance. As seen in Figure 1, the calculated voltage unbalance was 1.1 per cent with the motor off. I have other articles which cover effect of voltage variation and phase unbalance in detail.
The average voltage and current are used to compute the motor horsepower at the test point. The test point horsepower and hydraulic horsepower (assumes 100 per cent pump efficiency) are used to compute the actual pump efficiency at the test point. The cost per thousand gallons pumped is calculated using the equation shown at the bottom right in Figure 1.
It is important to test submersible pumps and motors annually. Changes in system conditions can have a large impact on the pump operating point. This can result in a reduced life for several components including seals, wear rings and bearings. Off BEP operation will also increase the cost per thousand gallons pumped. Unbalanced phase voltage can occur at any time. Just because they were balanced a year ago doesn’t necessarily mean they will still be balanced this year. My Field Test spreadsheet is available on the ‘Pump Evaluation, Selection & Testing Tools’ page at PumpEd101.com.
Joe Evans has been in the pumps industry since 1986 and is passionate about the sharing of knowledge within the industry. To read more of his insights into the world of pumping,
With work health and safety (WHS) practices under increased scrutiny, there is a safer way to pump wastewater, according to engineered pump solutions provider Hydro Innovations. It has made available a white paper on ways to improve or even eliminate some of the dangers associated with working on or around wastewater pumps.
Firstly, Hydro Innovations maintains that using its Gorman-Rupp self-priming centrifugal pumps eliminates the dangers of “working over heights” and “working over water” usually associated with pumping wastewater with submersible pumps. Because the pumps are located “high and dry” above the wet well, operators do not have to be exposed to the dangers of open wet well pits when monitoring, inspection or maintenance is necessary. A correctly engineered solution will also eliminate the need for working in confined spaces.
Also, because maintenance can occur while the pump is still connected to the pipe system, and no cranes or lifting devices are needed, the dangers
of working with heavy swinging weights and cranes is eliminated.
When pump clearances need to be adjusted, Gorman-Rupp “V Series” pumps allow operators to make
adjustments externally, without removing the pump from service and without having to come in contact with the pumped fluid. To adjust submersible pump clearances, operators need to open wet well lids, use a lifting device and “manhandle” pumps that are covered in the pumped fluid, which could be corrosive, contain “sharps” or be full of bacteria.
The Gorman-Rupp Ultra V Series pump has been built with operator safety as a high priority. These pumps feature pressure relief valves, “burst disc” flap valves that can uniquely be replaced without opening the pump, and the safest “fill port cover” of any self-priming pump on the market. These features and others, separate Gorman-Rupp as the leader in self-priming pump technology.
For the complete white paper on wastewater pump operator safety, go to www.pump-stations.com.au or call Hydro Innovations on 02 9898 1800.
An $8.1 million upgrade of the Gunnedah Wastewater Treatment Plant in Gunnedah, New South Wales was completed in May, securing the town’s sewage treatment works until 2038.
The project was jointly funded, with the New South Wales Government providing $1.98 million through the Restart NSW Resources for Regions Program, and Gunnedah Shire Council allocating the remaining funds from its own budget for the works.
Member for Tamworth, Kevin Anderson, said, “The $1.98 million contribution by the NSW Government to the Gunnedah Wastewater Treatment Plant is an investment in the future of Gunnedah.
“The plant has not been upgraded since 1968 and was in need of improvement to enable additional treatment volume to support a strong and growing Gunnedah.
“This upgrade is about meeting residential and business
needs on the horizon as Gunnedah continues to expand to meet growth in both the mining and agricultural sectors.”
The project was in the planning for a number of years, with work beginning in 2017.
The Gunnedah Sewage Treatment Plant (STP) uses a trickling filter and maturation pond to treat sewage. Under normal operating conditions, all of the treated effluent from the works is transferred to the North Gunnible Cotton Farm where it is used for irrigation under a reuse agreement.
While the old plant met the water quality requirements specified by the EPA it needed to be upgraded to improve reliability and increase treatment capacity. The upgrade aimed
to extend the working life of the existing treatment assets until 2038; provide additional hydraulic capacity to service population growth and a planned expansion of the sewerage network to service an industrial estate; and improve workplace safety at the site.
Michael Ludlow, Project Manager Water Services at Gunnedah Shire Council, said Council considered both rebuilding and upgrading in the initial planning stages.
“Council looked at all options before the decision was made to upgrade. The main factors that led to this decision were being able to keep the plant operational during construction; the cost of a new plant was over $30 million compared to the cost of the upgrade at $8 million; the trickle filter process is a cost effective way of treating effluent; nutrients left in the water from the trickle filter process are good for Councils effluent reuse program to North Gunnible Cotton Farm; and Council was able to fund the project with a $1.9 million grant from the NSW State Government.”
Introducing modern processes and equipment
Various works were completed as part of the upgrade, including:
• Decommissioning the existing inlet works, lift pump station, belowground sludge digesters and digester building, and sludge drying beds
• Constructing new facilities including a septage reception facility, an inlet lift pump station, an inlet works facility with screening and grit removal, an above-ground anaerobic digester, a sludge transfer pump station, a biosolids dewatering facility and a new switchroom
• Refurbishing existing assets units including the stage one Imhoff, primary tanks and trickle filters; the stage two primary tank and trickle filter; the humus tanks; and the maturation ponds
• Site works including a new amenities building; roads; stairs and access ways and hand rails across the site; a new service water system; site services; and landscaping
Heavy duty ISO2858, End Suction Pump Design
Proven reliability in Australia’s harshest conditions over the last 20 Years.
Widely supported by over 75 Xylem service personnel, across fifteen service locations nationwide, as well as throughout our national distribution network.
For more information, call us at 13 19 14 or visit www.xylem.com/au
www.xylem.com/au
• An electrical upgrade including a new Form 3B main switchboard/MCC; local control panels and operator stations for all equipment; cabling; site lighting; lightning protection; site security and smoke detection system; and new PLC, SCADA and telemetry system.
Council’s Manager Water Services, Kevin Sheridan, said some of the equipment replaced was nearly 80 years old and the upgrade has allowed new technology to be introduced to improve the plant’s efficiency.
“The dewatering building has allowed the plant to enter the world of modern technology. It has the ability to dry treat sludge to 28 per cent dry solids, where most other technology sits at around 18 per cent. It also replaces the old drying beds which were really labour intensive and unsightly. We are really pleased with the outcome,” Mr Sheridan said.
Mr Ludlow said Council procured a number of items for the project. These included:
• Inlet works from VOR environmental, including a reception chamber, inlet screening, grit chamber and splitter chamber
• Sludge mixing equipment from Aquatec Moxon
• Sludge dewatering unit from Ishigaki - this is a screw press that is producing 25-27 per cent dry solids
• Amenities building from Austam Homes
• Fully automated ClearSCADA Telemetry system for monitoring and control from Alliance Automation
“The upgrade was on the inlet structure, new digester, dewatering building, sludge pump station, feed averaging tank and new amenities building the rest of the plant was all reused,” Mr Ludlow said.
“There was no added treatment process added to the upgrade, and all effluent that passes through the new inlet works is treated through the existing sedimentation tanks, trickle filters, humus tanks and maturation ponds.”
Mr Ludlow said the Inlet Lift Pump Station has three submersible N-series pumps installed in a duty/assist/standby configuration.
“The pumps are fitted with variable speed drives (VSDs) to assist in the balancing of flows presented to the inlet works and process streams. At full speed, lift pumps transfer 3ADWF to the inlet works with two pumps running. There are also Roto mono pumps and a Vogelsang grinder pump for sludge transfer,” Mr Ludlow said.
“Reliability, service, durability and adaptability were all important considerations for the pumping equipment.
“Energy efficiency is particularly important, so Councils design consultants added VSD’s to the inlet pumps for this very purpose of power savings and flow control.”
Mr Ludlow said there were a number of challenges that needed to be overcome including keeping the plant running during construction and maintaining water quality.
“We needed to keep the existing plant working while the upgrade was constructed with cut overs and parts of the plant needing to be isolated for periods of time. Having an experienced contractor and involving operational staff with decisions about cut overs and plant isolation was the key to overcoming this,” Mr Ludlow said.
“Keeping Councils EPA water quality requirement while under construction with all the disruptions to the plant was also a challenge. Key to overcoming this was regular monitoring of water quality and experienced operational staff that were able to adapt and overcome obstacles that arose on a daily basis while still keeping within Councils EPA Licence conditions.”
Gunnedah Shire Mayor, Jamie Chaffey, commended those that worked on the project to ensure it was delivered on time and on budget.
“Gongues Construction was contracted for the works and has put in a fantastic effort ensuring this project has come in under budget and on time. I would also like to commend Council staff for their forward-thinking and initiative shown throughout this project,” Mr Chaffey said.
“Gunnedah is in a unique position as one of few rural towns in NSW still experiencing growth and it is important we strive to see our infrastructure match this expected growth.”
The project is now in the running for the Institute of Public Works Engineering Australasia (IPWEA) Engineering Excellence Awards which will be held in the Hunter Valley later this year.
As part of the IPWEA’S State Conference, the awards recognise excellence in Local Government and Public Works Projects, as well as individual teams.
The Gunnedah Wastewater Treatment Plant upgrade is nominated in Category 3 – Innovation in Water Supply and Wastewater, which requires nominated projects to demonstrate innovations in water supply and/or wastewater, reflect efficiencies and demonstrate cost savings.
Acting Director of Infrastructure Services and IPWEA member, Daniel Noble, said, “To receive this nomination is the icing on the cake and a sweet reward for the hard work of the project managers, in particular Manager of Water Services, Kevin Sheridan, who has been the driving force behind this project since its inception.”
Caprari has launched an innovative new product with an exclusive patent, that is set to be a turning point in wastewater pump design. The new K + Energy range of pumps take reliability and efficiency to a new level, and captures Caprari’s core business to find new efficient solutions for water management.
Thanks to its dedicated research and development division, Caprari—headquartered in Modena, Italy—is able to offer its customers products with high efficiency and distinctive performance. Each new pump is designed be efficient and technologically advanced, ensuring they meet market demands.
To meet the needs of end users who are increasingly concerned about energy savings and operational costs, as well as to anticipate changes to the European Union’s Ecodesign Directive, Caprari has released a new pump range which has unique and revolutionary features for dealing with wastewater—the K + Energy range.
The new K + Energy range of pumps is designed with IE3 Premium Efficiency motors, as defined in EC Regulation 640/2009 specific for surface motors, to ensure optimum efficiency. The careful selection of the best performing materials and cooler motors ensure total reliability of operation, even in critical applications.
The brand new K + Energy range represents a turning point due to its innovative and unique "DryWet" system which keeps the pump cool.
The "DryWet" cooling system is simple and reliable, can be easily activated, and is standard for the full
range. Customers are able to use a single model for both submerged applications and in dry chambers.
In addition, the "DryWet" system has two important advantages: it does not require additional maintenance and does not absorb energy, allowing the pump to perform at its best. The K+Energy range is also available in an explosion-proof version with ATEX and IECEx (North America explosion protection directive) certifications.
Another interesting feature is the conductivity probe in the oil chamber— also available in the ATEX version (patent pending)—which is unique to the K + Energy range.
If the first seal is damaged, an alarm signal is immediately sent to the panel so that repairs can be carried out before the pumped liquid passes the barrier created by the second seal. This ensures the electric motor is always protected.
The connector—supplied as standard on all K+Energy models—allows the pump to be disconnected without having to remove the cables from the panel, before transporting and reconnecting them. This significantly reduces intervention time and guarantees the safety of operations.
The large precision cast stainless steel handle is robust, ensuring easy handling of the pump and allowing operators to easily recover it when submerged.
There are numerous features of the new DryWet pump to ensure reliability over time and operational performance, including:
• Configuration
» Anti-sedimentation system on the suction side
» Fibre-cutting system on the back impeller to protect the mechanical seal
» Blades on the back have the dual advantage of cleaning the area for seal protection, as well as compensating for axial thrust to protect the bearings
» It has amongst the widest passages for real anti-clogging
• Double mechanical seal
» Independent and non-proprietary mechanical seals (no cartridge system)
» Less oil is required to ensure low environmental impact and ease of disposal
» Disassembly of mechanical seals has been improved so they can be replaced on the pump side, leaving the motor safe
• The gasket is between pump and coupling foot to ensure perfect sealing between components with no head loss over time
Caprari, with its new K + Energy range and exclusive "Dry Wet" system, presents itself as the leading company in advanced solutions for water management and meeting customers needs.
Designing the future with highly appreciated and advanced solutions for Industrial Applications
Pumps and electric pumps able to raise primary process water and waste water.
ENERGY | METAL INDUSTRY | PAPER INDUSTRY | FOOD & BEVERAGE
www.caprari.com |
Every year, the Water Industry Operators Association of Australia (WIOA) presents the Operator of the Year award to an outstanding operator, recognising excellent performance, initiative and all round attention to detail. In April, the NSW Operator of the Year was awarded to David Cashen, Bulk Water Supply Supervisor at Bathurst Regional Council.
Mr Cashen has been a supervisor at Bathurst Water Filtration Plant for nearly a decade and has worked with the Council for 23 years. He is a fully trained Water Filtration Plant operator and motor mechanic who ‘lives and breathes’ Water Filtration.
During his time working at the Water Filtration Plant, Mr Cashen has been involved in everything from coordinating multimillion dollar upgrades, to conducting tours for school groups. His idea to add water injection to the flocculation chamber channel has allowed for greater mixing and improved its settling ability in sedimentation but also stops sludge accumulation in the channel from turning anaerobic and reducing water quality.
Mr Cashen said his current role as Bulk Water Supply Supervisor for the Council is a challenging and changing role.
“As technology and processes improve you have to be able to adapt to new methods but also be able to understand and direct my staff to be the best they can be while still maintaining quality, and also very importantly value for our ratepayers money,” he said.
“My expertise does not only relate to running and managing the Water Filtration Plant but is far more diverse when you add in both supply dams, pump stations and approximately 34 reservoirs spread out over the Bathurst area.
“Part of my day-to-day tasks involve liaising with local contractors, businesses, sales reps on new products and equipment, and of course answering the public's questions relating to water quality.”
The Bathurst Water Filtration Plant
The Water Filtration Plant is designed to treat raw water to remove undesirable material, and make it fit and safe for drinking.
The raw water is lifted into the plant by four 11m-long pumps which are installed on a platform beside the river. The water is delivered into a pit chamber where chemicals are added and the mixture agitated by a propeller-type ‘Flash Mixer’ before it is distributed into one of three flocculation tanks. From here, the water moves to the sedimentation tanks where any large particles settle to the bottom under gravity.
A sludge rake is used to collect the settled particles, or sludge, and pushes it towards hoppers at one end. It is then released into the sludge lagoons where it dries and is removed.
Once the heavier floc has settled, the water passes through sand filters to collect smaller particles. The filtered water then drops into underground concrete water tanks, where it is pH corrected, treated with Chlorine and Fluoride.
The water is then pumped from the underground tanks into the town’s water supply system. To supplement the use of pumps, water is held in reservoirs located at high points in the system where it is then fed out to maintain pressure in the system when the pumps are not in use.
The plant has a complex control and monitoring system, allowing the equipment to be operated automatically or manually from a central control area, and a telemetry system complements the original electrical control system.
Mr Cashen said his job requires him to complete various tasks on a day-to-day basis to ensure the plant equipment is maintained and working efficiently to ensure the water produced meets Australian Drinking Water Standards.
“A typical work day involves facts and figures, from checking what has been consumed over the previous 24 hours, to quality testing on the day. Paperwork is also a big job because there is so much to check, repair and/or replace, and all this needs to be documented, ordered and of course paid for,” Mr Cashen said.
“Chemicals that we need to treat the river water to the Australian Drinking Water Guidelines (ADWG) 2011 and to comply with Council’s own CCP's (Critical Control Points ) for quality fit for consumption need to be maintained and stock rotated. Maintenance is also a major part of our day-to-day activities to keep things running smoothly.”
Mr Cashen said there have been a number of recent innovations that the plant has adopted, and it is import that frequent training occurs to ensure everyone is aware of and knows how to use new technology and methods.
“Recent innovations that we have adopted are WiFi for internal data communications, optic fibre which allows for previously off system treatment units to be placed onto the network, allowing all operators to remotely monitor and adjust parameters.
“Online monitoring equipment which will automatically adjust chemicals based on certain quality parameters. On system (alarm/shut off) with adjustable set points, system processes with graphing availability and microwave link capabilities.
“One of the challenges with new technology is keeping up-to-date with current training and new innovations within the testing and monitoring fields. We overcome these by always upgrading our skills and having good networking programs using RISK EDGE, WIOA,TAFE NSW, Office of Water, DPI, EPA and also liaising with other Council operators around the region.”
Despite the challenges that new innovations and technology brings, Mr Cashen said this was also one of the reasons he enjoys working as a water operator.
“I find it enjoyable that every day is different, from upgrading and designing new ways and methods, to researching new technologies. Providing good quality water to the public and having great pride in what we do makes the job.”
Historically, Australia has had few known resources of potash, but ongoing exploration has led to some deposits discovered in Western Australia, South Australia and Victoria. Kalium Lakes is one of the exploration companies leading the race to become the first domestic sulphate of potash (SOP) producer in Australia, and is currently undertaking a Bankable Feasibility Study on its Beyondie Sulphate Of Potash Project (BSOPP) in Western Australia.
Potash is the common name for various salts that contain potassium minerals in water-soluble form. While not as glamorous as other mining commodities, it is becoming increasingly sought after because it is an important component of many fertilisers as it is a source of potassium which helps raise yields and disease resistance for plants. With the global population expected to grow to 9.6 billion by 2050 and the amount of arable land per capita declining, the global demand for fertiliser will also grow due to the need to improve agricultural yields and productivity.
There are four main forms of potash: potassium chloride (KCl or MOP), potassium sulphate (K2SO4 or SOP), potassium nitrate (KNO3), and sulphate of potash magnesia (SOPM). SOP in particular is sought after for fertilisers due to its minimal chloride content and lower salinity index than other forms of potash, both of which can be harmful to plants, and diminish quality and crop yield. There has been a surge in SOP demand with the market growing from 3.5Mtpa in 2009 to 7Mtpa in 2016, and it now attracts a price premium over MOP of between 40 to 100 per cent.
SOP is not a naturally occurring mineral and primary production requires extracting potassium and sulphate ions from naturally occurring complex ores or brines via evaporation and/or chemical methods. SOP can be produced from either: salt lake brine processing; potassium chloride and sulphate salts reaction; or the Mannheim process.
processing
Processing of natural brines is a relatively low-cost option, but is limited because of the small number of salt lakes in the world that contain both potassium and sulphate. There are brine operations in Utah (Great Salt Lake Minerals Corporation, owned by Compass Minerals International), Chile (Salar de Atacama, owned by SQM) and China (with the largest producer being SDIC Xinjiang Luobupo Potash). As lakes with sufficient brine mineral levels are rare, this method only accounts for 15-20 per cent of global supply.
Potassium chloride and sulphate salts reaction
Potassium chloride can be reacted with various sulphate salts to form a double salt that can be decomposed to yield potassium sulphate. The most common raw material employed for this purpose is sodium sulphate. Sodium sulphate, either in the form of mirabilite (also known as Glauber's Salt) or sulphate brine, is treated with brine saturated with MOP to produce glaserite.
The glaserite is separated and treated with fresh MOP brine, decomposing into potassium sulphate and sodium chloride. There are only a few operations in the world with K+S Kali and Rusal being the key producers utilising this method.
The most common method of producing potassium sulphate is the Mannheim process, which is the reaction of potassium chloride with sulphuric acid at high temperatures. The raw materials are poured into the centre of a muffle furnace heated to above 600ºC. Potassium sulphate is produced, along with hydrochloric acid, in a two-step reaction via potassium bisulphate. There are a number of operations in the world with Tessenderlo Group and Chinese privates being the key producers utilising this method. This method for creating SOP accounts for 50 per cent to 60 per cent of global supply. The Mannheim process is also the most expensive of the processing techniques due to the high input costs associated with purchasing MOP and sulphuric acid.
The BSOPP covers an area of around 2,400km2 in Western Australia’s Beyondie, 10 Mile and Sunshine Lakes area, and Kalium Lakes intends to develop a sub-surface brine deposit to produce approximately 150 kilotonne per annum of SOP product and by-products through evaporation and processing operations.
The project includes the development of evaporation and crystalliser ponds, installation of production bores, trenches, pumps, pipelines, purification facility, access road upgrades, natural gas pipeline, and expansion of accommodation village, buildings, and services and utilities (including water, power and waste disposal).
The project, which is located close to key infrastructure, is already well progressed and has completed a Pre-Feasibility Study (PFS) involving detailed technical reports, test pumping of brine, environmental, heritage surveys and economic analysis; and a Bankable Feasibility study is currently underway.
Kalium Lakes is undertaking a pilot project using trenches and bores to capture brine from beneath the surface and pump it to lined evaporation ponds. The liquid is then dried by the sun, leaving behind a solid mixed-potassium salt which is sent to a German purification plant that produces the final SOP product.
The pilot evaporation pond trials begun construction in June 2017 with first brine entering the system in August 2017. These pilot ponds have been run continuously and form the basis of pond design for the Bankable Feasibility Study (BFS).
Since August last year, more than 164 million litres of brine has been pumped from a bore and/or trench, with 83 million litres pumped into the trial ponds where it has evaporated prior to reaching the salting point.
At this point brine is gravity fed to the next series of ponds where the sodium salts crystallise out of solution. The brine is again gravity fed to the series of ponds where potassium salts begin crystallising out of solution. Finally, a residual magnesium bittern remains, representing only one to two per cent of the original brine volume pumped into the concentrator pond. This residual brine has been the subject of magnesium product investigations and pilot trials. Importantly, all the ponds are tiered so that the brine can flow via gravity, without the need for pumping between ponds.
The response of the water levels to brine abstraction has been monitored in a number of monitoring bores throughout the filling and operations of the trial evaporation ponds.
During the filling of the ponds flow rates ranged from 10 litres per second (L/s) to 20 L/s, associated with approximately 17m of aquifer drawdown in the deep confined aquifer between August and October 2017.
Between October 2017 and April 2018, abstraction continued intermittently in response to water levels in the ponds, pumping rates ranged from six to 12 L/s with deep confined aquifer drawdown steady at approximately six metres during March and April 2018 in relation to constant pumping at 6.5 L/s.
Kalium Lakes Managing Director, Brett Hazelden, said, “These Large Scale Pilot Evaporation Ponds cover around five MCGs in total size and have proved invaluable in testing every facet of a fully operational potash evaporation pond process.
“It has enabled Kalium Lakes to assess pump and pipe requirements from bores and trenches, determine pond design parameters to achieve a fully gravity fed system, observe brine evaporation behaviour, and measure salt crystallisation and growth, test harvesting techniques and identify maintenance requirements.”
Kalium Lakes procured Franklin 8” 22.30 kW bore pumps for the trial bores, with flexibility a key consideration during the testing phase to allow trials on the evaporation ponds, as well as monitoring and testing the aquifer.
“With the two pilot bores currently operating, we performed many trials to determine the actual pumping dynamics and pressure losses within our trial system. With this data, when we up-scale to full production, a more fit for purpose solution can be installed,” Mr Hazelden said.
“As we have a total brine flow rate of over 300 L/s within summer in a network over 50km long, an overly conservative design will add significant capital cost to the project. Our trial equipment has allowed a more narrowly defined design to be completed to reduce the upfront costs to the project.”
With the procurement of pumps for the final production bores underway, energy efficiency has become an important consideration for equipment, as well as material selection to reduce maintenance and repair costs.
“Energy is a special consideration for the full production bores as the project is drawing from over 30 bores over an 80km2 area. Operating cost will become a major driver of this project. The procurement of the full production bores is currently ongoing and the pumping efficiencies will be adjudicated for each vendor within the tender process,” Mr Hazelden said.
“As we are dealing with brine, materials selection is critical to ensure our production targets are met and corrosion can be managed with pump maintenance and replacement. As we have a large number of bores, dependent on the time of year, there is redundancy within our system. During winter months, bores can be taken offline for servicing where required.”
A Bankable Feasibility Study of the project is currently underway with the results of the pilot pond trial being used to inform design parametres. In May, the sonic monitoring bore installation and air-core geological programs were successfully completed.
The program has involved drilling 142 aircore exploration holes on transects totalling 7,794m of drilling. This has closed the drill spacing to between 265m and 422m at the 10 Mile and Sunshine deposits respectively, and confirmed the geological extent of the target geology and brine mineralisation. A sonic drilling rig has followed up the aircore drilling to twin 10 key aircore holes, in order to obtain cores for laboratory testing, and install monitoring bores for a total of 710m of drilling.
Downhole geophysics (spectral gamma, conductivity and Borehole Magnetic Resonance (BMR)) has been completed on all monitoring bores to measure lithological changes and in-situ aquifer properties and will be calibrated to laboratory testing of core plugs to assist with resource estimation.
Notably, the BMR tool has been able to provide insight into aquifer properties on a resolution across the palaeovalley sequence and bedrock lithologies not previously observed from test pumping, drilling or laboratory testing. The results indicate that in-situ specific yields of the basal sand and silcrete aquifer zones may be between eight and 25 per cent, however these zones are significantly thicker than previously considered, the sandy lenses of the lower clay sequences have higher specific yields which were previously categorised as lacustrine clays, which will now be incorporated into to the deep aquifer resource.
The drilling and geophysical surveys have also identified additional resources within the weathered zones of the sandstone and vesicular basalts encountered within the stage one area. These zones will now be brought into the brine resource envelope.
An additional production bore has been installed within the weathered sandstone aquifer at Lake Sunshine and is currently undergoing long-term test pumping.
More than 10,000 tonnes of salts have been produced so far, including 3,160 tonnes of mixed potassium salts that can be processed to generate approximately 520 tonnes of SOP.
The project’s pre-feasibility study suggests BSOPP will generate $1 billion in free cash flow over a 20-plus year mine life.
“The program has continued to confirm the Pre-Feasibility Study Resource model within our initial stage one Mining Lease Areas,” Mr Hazelden said.
“We envisage these results will enable an upgrade of the deposit to include a future Measured Resource and Proved Reserve, which in turn will support the Bankable Feasibility Study and project financing.”
The current assumed stage one Area has a mine life of 23 years at 75ktpa SOP, when utilising the existing Probable Reserve. If the project were to be expanded to ramp up to a rate of 150Ktpa, the stage one production from Beyondie, 10 Mile and Sunshine would comprise 45km of trenches with eight pumping stations and 30-40 bores.
Beyondie resource testing snapshot (as of April)
• 232 aircore/diamond/ sonic drill holes to collect geological and brine samples
• 12 large 200–250mm diameter cased test bores
• 13,948m drilled
• 13 mini aquifer tests
• 11 constant rate tests
• 11 weeks of bore test pumping
• 32 weeks of trial pond pumping
• >175 million litres of brine pumped from aquifers
• First Australian brine project to report reserves signed off by expert external to the company
Motors: Pumps:
4”–12” 0.37kW to 400kW
Flows rates to 1000 m3/hr
Heads up to 400m
It’s been 80 years since Charles Warman invented the iconic Warman® slurry pump, a pump that revolutionised the mining industry and continues to push the boundaries of pump performance. In May, Weir Minerals held an event in Kalgoorlie, WA, to honour Warman® pumps’ history and provide an insight into some of the future innovations planned.
Ricardo Garib, Divisional President of Weir Minerals, said, “Warman is one of our leading brands. It has truly shaped the mining industry over the past 80 years and is a product we are all very proud of. The Warman pump, invented to solve high wear issues in slurry pumping, created a thriving industrial business that is now the cornerstone of Weir Minerals with over 8000 people, and over 150 manufacturing and service centres across the globe.”
Always inventing
Charles Warman invented the Warman® slurry pump in Kalgoorlie in 1938. It was a hard wearing slurry pump that used replaceable liners and impeller—something that had never been done before—to reduce total ownership costs, be safer to handle, and extend wear life in many abrasive slurry applications.
It was quickly adopted throughout the goldfields in WA and by the 1950s, as customer demand rose, Charles Warman expanded his business by opening offices in Sydney and Perth.
During the 1960s the rapid growth of the business continued with manufacturing and sales outlets
established around the world. The Warman® Series ‘A’ pump was accepted and became world leader in its field.
Innovations continued throughout the decades, with the development of interchangeable metal and rubber wearing components and pumps designed for a number of tough applications including Flue Gas Desulphurisation.
Always innovating
The Weir Group PLC acquired the Warman® pump in 1999. A number of technological advancements followed the acquisition, including the development of a revolutionary new impeller and inlet design for pumping mineral froths and high density viscous
slurries, and the development of a pump with axial and rotationally adjustable throatbush to even out wear.
Today the Warman® pump has an unparalleled worldwide reputation in slurry pumping, commanding a leading share of the global mining market. There are few mining sites in the world where Warman® slurry pumps cannot be found.
Technology is increasing at an incredible pace, and as technology progresses and society demands new materials, the Warman® pump is primed and ready to provide them.
Weir Minerals has developed its own IoT platform Synertrex™, which can be fitted to a Warman® pump to monitor its performance and determine how efficiently it's operating.
Following the anniversary event, Weir Minerals has embarked on a six month celebration, sharing the history of Warman®, commemorating the experts behind the brand, revealing key innovations and presenting case studies from around the world. To find out more, visit www.alwayswarman.weir
• Size & weight reductions of up to 50%
• Lower electricity consumption costs
• Same mounting possibilities as (B3, B5 etc) as standardized IEC range
• Full flexibility regarding motor speed
• Customisation
• Material Handling
• Treadmills
• HVAC/R
• Liquid Pumps
• Fans and Ventilation
• Cooling Compressors
• Air Technology
• Blowers
• Renewable Energy
• Coolers
• Air Compressors & Vacuum Pumps
• TENV (totally enclosed non-ventilated)
• TEFC (totally enclosed fan cooled)
• EFFI, EFF2 & Premium Efficiency
• 63 frame to 160 frame
• 304 or 316 stainless steel
• Longevity & versatility
• Minimum maintenance
• NEMA & cURus
Rising groundwater levels in Bendigo’s historic mines has been causing odour problems and impacting on water quality. To combat the problem, the Department of Environment, Land, Water and Planning (DELWP) in partnership with Coliban Water, implemented a transitional solution to pump the groundwater from the mine voids to a treatment plant. With construction of the transnational solution now complete, DELWP is searching for a permanent solution for managing the groundwater.
Naturally occurring groundwater in the historical mines beneath Bendigo, north west of Melbourne, was originally suppressed through pumping during mine activities, however it has been recovering to natural levels since mining activity ceased in 2011. It started to become a problem in early 2015 when it began causing odours, impacting local water quality and resulting in small surface discharges. It also had the potential to impact local infrastructure.
The groundwater contains elevated levels of hydrogen sulphide gas (rotten egg gas)—which was causing the odour— as well as salinity, arsenic and other heavy metals.
A transitional solution
Late last year, construction of a $27.4 million state-ofthe-art groundwater management system was completed, providing a transitional solution to the problem and will operate for four years until a permanent solution can be implemented.
The project was funded by the Victorian Government and included refurbishment of a treatment plant at New Moon, north of Eaglehawk, building two pipelines from New Moon to Coliban Water’s Bendigo Water Reclamation Plant in Epsom, and creating a new brine storage lagoon at the plant.
Pumps transfer groundwater from the mines to the New Moon Groundwater Treatment Plant, where it is treated to remove arsenic, salt, heavy metals and hydrogen sulphide. The treated water is then sent to the Bendigo Water Reclamation Plant in Epsom via a pipeline where, if possible, it is reused or returned to the environment. The salty water
from the treatment process is piped via a second pipeline to the Bendigo Water Reclamation Plant to a brine storage and evaporation lagoon.
The submersible pumps being used to move groundwater from the Central Deborah Mine—consisting of a 95kw pump motor and 20 pump stages in the wet end—were chosen as they met the requirements of pumping groundwater, which was a head pressure in excess of 260m and maximum volume of two ML per day, per pump. Other considerations were lead time, as well as the ease of acquiring spare pumps and parts, the cost, and the reliability of the pump units. Having two provided redundancy and allowed pumping at higher than normal rates when required.
Since being installed, the pumps have pumped 1.5 to two ML per day from minus 40mAHD to surface 220mAHD. Water extraction from the Central Deborah Gold Mine is owned and managed by Bendigo Heritage Trust which also manages groundwater pumping at the Londonderry Shaft on the Garden Gulley Reef.
Groundwater extraction also occurs at the New Moon Mine Shaft on the Garden Gully Reef at an average rate of two ML per day or 730 ML per year. This pump is owned by GBM Global.
Construction was completed in September 2017 and the system will operate until June 2021.
Lendlease designed and constructed the groundwater treatment plant, Veolia Water Network constructed the pipelines, and Ward Bros from Rochester constructed the brine storage lagoon.
Member for Bendigo West, Maree Edwards, said, “This community-led solution not only gives assurances for the future but importantly safeguards our ever-popular Central Deborah Gold Mine, as well as our local waterways from rising groundwater.”
With the transitional solution now complete, DELWP—on behalf of the Bendigo community—is now working on a longterm solution to the town’s rising groundwater that will last 25-30 years.
The permanent solution needs to identify ongoing funding and governance options, as well as incorporating the management of groundwater from historic mines other than Central Deborah. Through the Innovation for a Permanent Solution process, the Bendigo Groundwater Project aims to gather concepts about how Bendigo might best manage groundwater in the mine voids, consistent with community and stakeholder expectations. It is expected that the investment to date in research, design, planning and the infrastructure used in the interim solution will be used to inform the long-term solution.
Consultation on a permanent solution began in late 2017, with industry, academia, community organisations and the public invited to submit their ideas for sustainable, long-term treatment and funding options. Submissions closed in late February 2018.
One idea put forward is turning the gold mine into a pumped hydro site. Such a solution would not only help manage groundwater levels in the mine voids, but would also deliver peak energy generation capacity to put downward pressure on power bills.
Mines cover a number of requirements needed for pumped hydro storage, including a large area with elevation differences, low environmental impact, grid connection proximity and a water source. For this reason, a number of mine sites around Australia are being considered for pumped hydro facilities, including Kidston Gold Mine in QLD, Iron Duchess Mine in SA, and Muswellbrook Coal Mine in NSW, among others.
Rock stability at mine sites is one of the main concerns around developing them into pumped hydro facilities, however preliminary work at Bendigo suggests that the hard nature of the rock and the construction techniques used when mining will make it suitable.
The concept for the Bendigo site includes a generation capacity of 30MW and a storage capacity of six hours of energy (180MWh) with a round trip efficiency of around 70 per cent. The Garden Gully reef mine voids would be used as an upper storage volume, while the Swan Decline would be used as a lower storage volume. These two voids would be linked by a 1.5m diameter shaft, allowing water to follow between them, and valving to isolate flow.
At the bottom of the shaft, a new structure would be excavated off the decline where the turbines would be kept, with another structure 150m below this to house the pumps. The lower structure would be linked to the top structure by a wide shaft for personnel and crane access.
The system would be connected to the 66kV sub transmission network in Bendigo and would link into a new substation on the site of the Eve Street vent shaft where the power cable would be installed.
This submission as well as others are currently being reviewed and evaluated by reference groups, who will make recommendations as to which options should be investigated further.
The Cooper Basin spanning across north-east South Australia and south-west Queensland is one of Australia’s most mature onshore oil and gas production regions, and has the potential to help ease the looming Eastern Australian gas shortfall. Oil and gas exploration company Strike Energy is currently targeting the gas potential of a series of very thick coals in the southern part of the basin, and has recently completed one of the most technically advanced coal seam gas (CSG) wells ever drilled.
Typically, CSG is trapped in coal formations between 400-1000m underground, however, at a depth of over 2000m, Jaws-1 is the deepest horizontal/ vertical intercept to have been achieved in the history of Australian drilling operations, and the first CSG well of its scale to be drilled outside of the US.
The seven inch vertical well was completed in April at a depth of 2880m with an 800m horizontal section that will intercept a second
vertical producing well and will target the placement of seven stimulation stages.
The well will test the application of advanced drilling and stimulation technologies on the gas-charged 35m thick Vu Upper coal seam and their effects on the productivity of the reservoir.
The groundbreaking project is located within the Klebb appraisal area and has been sited in order to leverage the existing dewatering that has been achieved to date,
and holds the potential to unlock an onshore gas resource up to 11Tcf. It is being drilled by oilfield services company Halliburton in collaboration with drilling contractor Ensign.
Strike Energy Managing Director, Stuart Nicholls, said, “The timing of this groundbreaking well is critical to Australia’s energy security and may indeed be one of the highest impact well results in the East Coast gas landscape in 2018.”
Linear and fracture stimulation sleeves have been installed at a total depth of 2873m. The packers have been set in the wellbore and Strike Energy has been able to position these to allow for the full seven stage stimulation program to be achieved. Completion of this activity significantly de-risks the project, and operations will now progress to hydraulic stimulation before final completion and installation of artificial lift pumps.
Fracture stimulation, or fraccing, involves stimulating tiny fractures in a rock layer in order to increase the flow of gas, oil or other substances. To create the cracks in the target rock reservoir fluid is pumped down the well at high pressure to produce cracks in the target rock reservoir.
The Jaws-1 project is utilising the Indirect Vertical Fracture Completion (IVFC) technique to fracture stimulate the Vu Upper coal from below the seam. This technique is quickly becoming the preferred method in the US shale gas industry as it utilises gravity assisted drainage of the reservoir and can offer better fracture initiation due to the mechanical properties of the formation.
The interburden displays such properties and it is believed this alternate design will enable completion of the drilling operations without compromising the original well objectives.
The pumping equipment used in CSG exploration and production play a key role in the success of a project. Strike Energy is using a combination of existing and new pumping equipment for the Jaws-1 project. The design and procurement of services and equipment was undertaken in partnership with Halliburton with the electric submersible and beam pumps purchased as part of a competitive tender due to high value, while other pumps were procured using a variety of methods both as standalone purchases or as part of packaged skids.
Mr Nicholls said a key factor in the selection process was robustness and reliability.
“The downhole pumps were selected to suit the wide ranging operating envelope for both initial
and later life reservoir management. A key focus on these pumps was robust and reliable operation due to the high cost of workover rigs required to change out any damaged equipment downhole. High temperature, pressure and flow rates were also key considerations.
“These pumps have undergone rigorous factory acceptance and on-site pre-commissioning testing. As the electric submersible pumps are run into the wellbore they are tested at regular intervals.
“The surface pumps chosen to suit service and application—mostly utility service—and were factory tested by the vendors prior to shipment."
A number of pumps are being used for the Jaws-1 project, including:
• Electric submersible pumps and beam pumps (with sucker rod) for dewatering of reservoir at 2000m depth
• Pneumatic diaphragm pumps for bulk water transfer at surface
• Centrifugal pumps for load out and transfer of bulk water
• Various positive displacement pumps for chemical dosing
The Jaws-1 project is using electric submersible pump systems for artificial lift to increase pressure within the reservoir and encourage gas to the surface.
“The high flow rates, gas handling and need for extensive data feed made electric submersible pumps the only practical choice for the new Jaws-1 project wells,” Mr Nicholls said.
This system is installed at the bottom of the tubing string and is comprised of a centrifugal pump below the coal seam which is connected to a long electron motor. The pump is connected to an aboveground electricity source via an electric cable. The system creates artificial lift by spinning the impellers on the pump shaft while pressure is put on the trapped gas to force it to the surface, and facilitating gas and water separation in the well.
The two new electric submersible pumps will be installed at the Jaws-1 project wells during July this year.
As part of preparations for the project, Strike Energy also undertook a workover of the existing Klebb-4 well near the project site including the removal of the existing electronic submersible pump completion equipment and setting of a bridge plug to provide a wellbore suitable for the microseismic survey during the fracture stimulation of the Jaws-1 horizontal well.
The electric submersible pump cable was tested successfully upon retrieval and was confirmed to be compatible with the new electric submersible pump which will be deployed on the Jaws-1 vertical well, saving $50,000. The chemical injection line and various surface equipment were also confirmed to be suitable for reuse.
The electric submersible pump itself was returned to Adelaide for diagnostics and inspection to capture additional learnings for the future dewatering operations at Jaws-1. The pump will then be re-built to provide an on-site contingency for the Jaws-1 wells or for future use in Jaws-2.
The Klebb-4 well is currently suspended and any future plans are yet to be confirmed.
Throughout the project, Strike Energy has also taken into account lessons learnt from a previous campaign which saw five wells drilled that were able to flare gas for an extended period of time. However, the campaign was not without its challenges. It was found that the vertical well design was too narrow at five inches and the pumping technology used was insufficient to produce adequate commercial outcomes.
Learning from this campaign, a number of changes were implemented for Jaws-1 to make it more commercially viable, including better pumping technology and making the well wider, taking it up to seven inches, as well as including a 800m horizontal section that can be hydraulically fractured.
“Lessons learnt from the previous electric submersible pump installation include reducing the number of possible failure points and increasing the size of the wellbore to improve the cooling of the motor,” Mr Nicholls said.
“Previous experience with jet pumping has also demonstrated that the reservoir does not respond well to the aggressive nature and start-stop operation.”
Jaws-1 is the precursor to having the final data and information
required to book a reserve, which will then trigger the beginning of the development phase of the Southern Cooper Basin Gas Project.
In June, Strike Energy announced it had successfully completed the seven stage fracture stimulation program of the Jaws-1 well, including the successful deployment of five of the first indirect vertical fractures ever executed in Australia.
All seven stages were fully completed placing targeted proppant quantities, with stages six and seven each placed over 150,000lbs per stage. All fractures had excellent fracture height growth through the Vu Upper and penetrated extensively in a perpendicular direction to the wellbore path.
Strike Energy is now conducting clean-out operations with coiled tubing on-site before commencing flowback which will be followed by running the electric submersible pump completion and connection of surface equipment.
“Following commissioning of the wells, a period of dewatering will be required prior to gas flows being delivered to flare. Once the gas flows are sufficient to provide commerciality of the resource a development program will be undertaken to drill additional wells and establish a longterm path to market via existing gas infrastructure adjacent to the permit,” Mr Nicholls said.
The Jaws-1 project is expected to come online in early to mid-July, with first gas delivered in 2019.
A 53-hectare greenfield site in Maroochydore on Queensland’s Sunshine Coast is being transformed into a Central Business District for the 21st century, with smart technology being employed to create a clean, green, dynamic city. In an Australian first, the development will include a high-tech, automated vacuum waste collection system to collect and transport waste.
Replacing traditional wheelie bins, the system will transport waste from commercial buildings and apartments at up to 70kmh through a 6.5km system of underground vacuum pipes located beneath the city centre to a central waste collection station. The system will collect three waste streams including general, organic and recyclable waste.
Sunshine Coast Mayor, Mark Jamieson, said the waste system would be installed in stages over the coming decade and would make the 53-hectare Maroochydore City Centre one of the cleanest and greenest cities in the country.
“I’m very proud the Sunshine Coast is leading the charge in Australia with this innovative waste collection solution, and I’m sure other cities and major urban projects will soon be following in our footsteps,” Mr Jamison said.
“The rubbish revolution means that city workers and residents will never have to walk past rows of wheelie bins or be woken early by noisy garbage trucks in the Maroochydore City Centre.
“Common aspects of waste collection such as odours and vermin will be avoided, and the costs of daily street cleaning will be reduced.
“As well as making our city heart more attractive, this technology has a track record of increasing recycling rates, so our natural environment will benefit too.
“The waste system will cost $21 million, which will be fully recovered from occupants of the CBD over the life of the system.”
Envac, which invented underground automated waste collection in the 1960s, will handle the waste of over 2,000 apartments, retail outlets and commercial spaces in Maroochydore, with each building including at least three waste inlets for organic, recyclable and general waste.
Public areas will also have their own waste inlets, enabling the new city streets, parks and plazas to be effectively serviced by the new technology and avoiding overflowing bins.
Users discard their waste as usual in Envac’s self-emptying waste inlets—which look the same as other bins—with the waste stored in a sealed compartment below ground until the vacuum pump is activated at the central waste facility, usually twice each day.
The vacuum system will then consecutively collect each type of waste, sucking the waste through a system of underground pipes to the central facility, where it will be stored in sealed compactors for collection by council’s contractor.
“New urban developments in Stockholm, Seoul, Barcelona, London, Singapore and Beijing have all utilised the Swedishdesigned Envac waste collection system—but no Australian city has done so—until now,” Mr Jamison said.
Installation of the automated waste system is underway with the first shipment of pipes for Stage 1A of the project arriving in February last year and construction commencing in June 2017.
Construction of the pipe network for Stage 1A is progressing and is on track to be complete in September.
A development application for the waste collection station was submitted late last year and is currently under consideration by the Department of State Development, Manufacturing, Infrastructure and Planning.
The proposed site for the collection station is behind the Carnaby Street office buildings, and will house all central plant and equipment required to operate the system, as well as containers for storage and offsite transport of the three waste streams.
It is designed to process up to 13.8 tonnes of combined general, organic and recycling waste per day at full capacity, and will be capable of automatic and remote operation.
In the Sunshine Coast Council’s CEO’s Quarterly Progress Report Quarter 3, 2017/2018, it is reported that construction
of the collection station is scheduled for completion in February 2019.
Council’s Waste Management Branch is responsible for the design, construction and ongoing operation and maintenance of the system.
Sunshine Coast Council Deputy Mayor, Tim Dwyer, said “It’s exciting to see an innovative, nation-first project like this taking shape on the Sunshine Coast.
“Workers and residents in the new CBD will never have to walk past rows of wheelie bins or be woken early by noisy garbage trucks.
“This system will also benefit our environment and help make the Sunshine Coast Australia’s most sustainable region by increasing recycling rates, as has occurred in systems installed overseas.”
Smart technology for smart cities
CEO for SunCentral Maroochydore the company established to oversee the design of the new city centre—John Knaggs, said, "Automated underground waste collection is just one of the ways in which the new Maroochydore CBD will be one of the smartest cities in Australia.
“Envac’s technology can be installed because we are building on an undeveloped, greenfield site within an existing urban area – and that has many other benefits.
“For instance, we are also building a high-speed fibre optic network into the city’s very foundations, which will enable us to provide ‘smart’ signage, free WiFi hotspots, real-time transport information, movement sensors and smart lighting."
“Our city centre will be an exciting place to live, work and visit while setting a new standard for urban design in Australia.”
John Knaggs, CEO SunCentral Maroochydore
The need for water and wastewater capacity is continually growing on a global scale, and with rising energy costs and a greater emphasis on being green, the users and designers of pumping systems in this industry are realising the need for more efficient designs and practices. It is estimated that water/wastewater facilities account for 35 per cent of typical municipal energy budget (1). With pumping systems being responsible for much of this power consumption, design optimisation can result in significant energy savings.
In fact, a considerable number of users, suppliers and designers in all industries, as well as government agencies and industry consortiums, are developing and implementing strategies to improve the energy efficiency of industrial equipment.
In most cases, the potential savings are significant. With a 10 per cent increase in the energy efficiency of US drinking water and wastewater systems the nation would collectively save approximately $400 million and five billion kWh annually (1). According to the US EPA, “Incorporating energy efficiency practices into their water and wastewater plants, municipalities and utilities can save 15 to 30 per cent, saving thousands of dollars with payback periods of only a few months to a few years” (2).
With the number of pumping stations found throughout water distribution and wastewater collection systems, there are many opportunities for improving energy efficiency. However, with the seemingly endless variety of design options, finding the optimal solution can be daunting. Fortunately, for the modern engineer, fluid piping software provides the necessary analysis to design an efficient pumping system or evaluate current installations for potential improvements.
Fluid piping software packages typically allow the user to evaluate a system under different design and operating conditions, as well as determine operating costs for various pump models and configurations. Some even allow the user to perform a complete lifecycle cost analysis. This considers capital, operating, and maintenance costs in order to assess the true cost of the system. Fluid piping software is a powerful tool with which the user can evaluate pumping system designs and determine the most efficient and cost-effective approach with relative ease.
The following is a list of typical fluid piping software features:
• Accurately model any pumping system with as much design detail as necessary
• Evaluate the model under various design conditions (e.g. pipe size, system configuration)
• Evaluate the model under various operating conditions (e.g. tank level, pump operation)
• Evaluate different pumping configurations (e.g. single or multiple configurations, variable speed drives)
• Select a pump from manufacturers' electronic catalogs to immediately determine how it will operate in a system
• Compare different pumps from various manufacturers
• Calculate and compare the operating cost of the various designs for any duration
Though fluid piping software has been in existence for over 35 years, it has only recently received considerable attention. This software allows engineers to conduct the type of rigorous design evaluations that they have not previously been able to perform. In the past, we have often relied on standard designs for new pumping system installations. For example, typical design practice for lift stations has involved specifying a duplex pumping arrangement in which each pump is sized for peak capacity. The units alternate operation to ensure even wear and the duplex configuration allows one pump to be taken offline for maintenance. This basic design has not changed much in the past 50 years, and for good reason, it works and provides redundancy to avoid major failures (3). Clearly, the inherent design is sound, but with the proper software solution, we can look at ways of improving the system which will lead to greater energy efficiency and lower maintenance and operating costs.
Let's consider a case where we have an existing lift station and would like to look at ways to optimise the design for improved energy efficiency. The current system includes a wet well lift station with two 40hp submersibles pumping into a 5000ft, eight-inch force main. There is an elevation gain of about 55ft from the discharge of the submersibles to the inlet of the gravity sewer. Figure 1 shows a schematic of the lift station model created with Engineered Software's PIPE-FLO Professional. The daily capacity of the system is approximately 320,000 gallons and the pumps are sized for a peak design flow rate of 800gpm at 101ft of head. Currently, the average pump operation is about 6.7 hours per day. Assuming a power cost of $.10 per kWh, the annual energy usage and cost to operate the lift station is 56,931kWh and $5693, respectively.
By modelling the lift station in PIPE-FLO with all necessary design information and operating conditions, we can quickly identify where the inefficiencies lie. At the peak design flow rate of 800gpm, there is an excessive head loss of 57ft through the force main, which can essentially be thought of as wasted energy that has been put into the pump. From Figure 2 we can see that the head loss in the force main can be drastically reduced by lowering the flow rate, a result of the characteristic second order relationship between head loss and flow rate in a pipe. Considering the pump only needs to be capable of delivering the peak flow rate a few times throughout the day, by operating the lift station at a reduced flow rate we can significantly lessen energy usage and operating cost.
To accomplish this, some lift station designers are employing the use of a jockey pump, which is typically less than 10 hp and is included in addition to the traditional duplex pump configuration. The main duty pumps are run only a few times a day during peak hours while the jockey runs most of the day to pump the off-peak inflow to the lift station (3).
Using hydraulic simulation software, it was determined that a flow rate of about 160gpm for the jockey pump would be sufficient for off-peak operation and would reduce the head loss in the force main from 57ft to 3ft, as shown in Figure 2. The jockey pump will run for about 18.3 hours per day at the design flow rate and the duty pump will run about three hours per day. A 3hp jockey pump was selected from within the software by digitally searching a manufacturer's catalog for pumps that satisfied the design specifications of the lift station model.
Looking at the system resistance curve plotted against the pump curve in Figure 3, we can see that the pump will be operating just to the left of its BEP. Certainly, a pump with higher overall efficiency that intersected the system resistance curve closer to the pump's BEP could have been found, but for the example, only a single manufacturer's catalog was utilised. Regardless, the chosen pump is operating at an efficiency of 72.3 per cent and the flow rate falls within 88 per cent of the BEP flow, which should help to ensure prolonged life.
After assessing the performance characteristics of the jockey pump, its operation in the lift station model was evaluated. The only concern encountered with using the jockey pump was a potential accumulation of solids in the force main, due to the lower flow rate. The velocity through the force main at 160gpm is about 1ft/sec, less than the minimum recommended 2ft/sec for solids removal. However, the operation of the duty pump during peak hours should be sufficient to prevent clogging.
An operating cost analysis performed in the software showed that the new design would consume 43,621kWh per year with an annual cost of $4362. It is clear from the analysis that the use of a jockey pump will significantly reduce the energy usage of the lift station. Table 1 shows a comparison of the two designs, which indicates an annual cost saving of $1331 and energy savings of 13,310kWh.
Despite the long daily runtime of the jockey pump, its low power consumption results in an overall more efficient system. The 3hp jockey pump should not require a significant investment and the payback period would likely justify the expense. Additionally, the reduced daily run time of the duty pumps will help to increase their lifetime and reduce their maintenance costs. Since the duty pumps represent much greater capital and maintenance costs compared to the jockey pump, this design benefits from not only operating cost savings, but also should yield a significantly reduced lifecycle cost for the lift station.
The example illustrates how fluid piping software can be used to quickly evaluate the efficiency of any pumping system. In less than an hour, I was able to model the lift station, determine the energy usage, evaluate and select a pump for the new design, and compare the energy usage and operating cost of both designs. However, where the benefit of software really becomes evident is when we compound our analysis
by evaluating all design options and elements. If we were designing a new pump station, we might have considered a triplex pump arrangement or the use of variable frequency drives to achieve operation at lower flow rates during off peak hours. Combine the different designs with the myriad of pump models available from a variety of manufacturers and the thought of performing the necessary calculations by hand or spreadsheet methods seems, if not impossible, considerably time consuming and error prone.
Fluid piping software enables us to easily model the different designs, quickly select the appropriate pumps from digital catalogs, and compare the energy use and operating costs of all the design scenarios. Along with the overall ease of use, the software also provides graphs, reports and other presentation materials to aid the project. Whether designing wastewater lift stations, booster stations in water distribution networks, treatment facilities, or any other piping systems, the accuracy and flexibility of fluid piping software will certainly facilitate the design of a highly energy efficient and cost-effective system.
1. Energy Efficiency in Water and Wastewater Facilities, EPA, 2013
2. https://www.epa.gov/sustainable-water-infrastructure/ energy-efficiency-water-utilities
3. Municipal Wastewater Pump Station Design Problems and Solutions, Jeff Chapin, 2006.
4. Piping System Fundamentals: The Complete Guide to Gaining a Clear Picture of Your Piping System, Ray T. Hardee, ESI Press, 2008.
The pump industry relies on expertise from a large and varied range of specialists, from experts in particular pump types to those with an intimate understanding of pump reliability; and from researchers who delve into the particulars of pump curves to experts in pump efficiency. To draw upon the wealth of expert knowledge the Australian pump industry has to offer, Pump Industry has established a panel of experts to answer all your pumping questions.
This edition of Ask an expert will look at progressive cavity pumps in the mining industry.
Progressive cavity (PC) pump experts are often asked if these pumps are suitable for the mining industry. Actually, PC pumps are very common on mine sites throughout Australia. For these pumps, this particular market sector would be on par with water and wastewater as one of Australia’s most popular. To list in detail the various applications would take up this entire magazine issue, so instead I have summarised the typical applications and key benefits of this pump design.
Overview of types of mining where progressive cavity pumps are used in Australia
• Bauxite (also refined alumina)
• Coal
• Copper
• Gold
• Iron ore
• Mineral sands
• Nickel
• Shale oil
• Tin
• Uranium
• Vanadium
• Zinc
Also used by countless suppliers of mining equipment and chemicals for:
• Decanters and centrifuges
• Tunnel drilling equipment
• Flocculants
• Chemical dosing
• Liquid explosives
Common applications for PC pumps in mining
• Transfer of mineral slurries
• Void back-filling applications
• Dosing of explosives
• Thickener underflow applications
• Centrifuge filling
• Chemical dosing
• Water treatment
• Cake transfer
• Leachate treatment
• Gland water supply
• Sludge feed to dewatering machines
Typical transfer liquids include polymers, sludge, slurries, grout, various chemicals, and clean and dirty water.
This is one of the most common areas where progressive cavity pumps can be seen, usually installed on a transportable skid with collection tanks for incoming water and generally incorporating some kind of solids separation to partially clean the muddy, high sediment mine water. The range of progressive cavity pumps used for these applications have a long length due to the pressure generation required for pumping to the surface from several hundred meters underground.
There are currently several companies who specialise specifically within this application sector and occasionally there can be new design developments which may give significant benefits to the users of this product range. Keeping oneself abreast of these developments can certainly pay significant dividends to mine operators. More detailed information on specific design developments can be requested via the contact details at the end of this article.
Mine dewatering unit outfitted with progressive cavity pumps
• Self-priming
• Minimal pulsation
• Valveless operation and flow control
• Reversible for backflushing
• Flow proportional to speed
• No day-to-day maintenance required
• Versatile: can be installed horizontally or vertically and in virtually any position
• Minimal flow rate variation even with changing pressures
• Handle multiphase products (liquid and gas)
Peter Vila, Managing Director of SEEPEX Australia, is a progressive cavity pump expert. He has been involved with pumps for over 35 years. Peter spent the first five years repairing pumps and the following 30 years in technical sales, 15 of which have been with SEEPEX progressive cavity pumps.
For more information on progressive cavity pumps, please contact SEEPEX Australia on (02) 4355 4500 or at info.au@seepex.com Specialising
and
over 30 years
• Complete range of API 610 (ISO13709)
• Hydraulic and mechanical design
• Custom engineering, retro-fit, redesign
• Performance testing
• Service and repair
The PIA’s Australian Pump Technical Handbook is a cornerstone text for the Australian pump industry and, in our opinion, a must have for anyone who deals with pumps on a regular basis. In this ongoing series, we feature abridged chapters from the classic book to showcase the various areas covered and to reacquaint readers with the technical aspects of pumps. In this issue, we go into detail regarding selecting and applying different types of slurry pumps.
Australia’s very active mining and mineral processing industry has led to the local manufacturing and importation of a wide range of slurry handling pumps.
In mining operations, slurry pumps are used to transport the target minerals and overburden to plants which use a system of wet separation. After crushing and screening, the mineral is usually milled before being transported for further separation. This process requires a large volume of slurry to be transported across often long distances. Once this process is complete, the tailings are usually disposed of via piping systems to the tailings dumping site. Special designs are also available for handling froth in the separation process.
Slurry pumps can also be used in a number of other applications, including the manufacture of fertilisers, transportation of coal, mining using dredges, land reclamation and flue gas desulphurisation in thermal power stations.
Slurry pump selection is a complex process and requires close cooperation between the pump manufacturer and the end user as the medium to be pumped and the pump operating conditions are extremely important to the correct pump selection.
This article will outline the basic principles involved in selecting the right pump for the job, and will look predominantly at centrifugal slurry pumps.
Centrifugal slurry pumps are typically used in mineral extraction process plants, and are designed to handle abrasive solids mixed with a carrier fluid.
The basic characteristics of a slurry pump are:
• Wide impeller passages capable of passing large solids
• Materials of construction of wetted parts are capable of resisting abrasive wear and provided with a wear allowance above that required to meet the normal operating pressure
• Shaft and bearings are of robust design and capable of withstanding shock loads
• Easy replacement of wearing parts in the field
Slurry pumps often operate 24/7, and in severe conditions the wear life of wetted components can be up to two to three months.
Since excessive wear would be generated on the inter-stage passages of a multi-stage slurry pump, they are invariably single-stage equipment.
Both horizontal and vertical shaft configurations are available, with transmission of process slurries around a plant usually handled by horizontal pumps, while vertical pumps are used in sumps and generally have a cantilevered shaft so that all bearings are located above fluid level.
The service class is largely dependent on the nature of the slurry being pumped. A service class chart can be used to get an indication of the expected wear rate of the major wetted components.
The chart is based on aqueous slurries of silica-based solids (Specific Gravity = 2.65), and can be used to provide guidance for mineral slurries if the SG for the slurry is used to determine the severity of service for a slurry pump. For non-silica materials, the equivalent SG can be found by applying an abrasivity correction factor to the slurry SG and to the d50 particle size, which is the screen that 50 per cent of particticles would pass through.
Slurries are often very abrasive and may contain large solid particles. This makes wear life and the ability to pass these large solids key considerations in pump design and application.
Wear can be controlled by proper pump selection based on the application details provided by the user, and is related to the velocity between the pumped slurry and the pump. For pumps in more severe services to have a satisfactory life, liquid velocities should be reduced.
Table 1 provides recommended service limitations for different service classes that, when coupled with proper design and selection, can result in acceptable wear rates.
In Class 4 service, high rotational speed of the impeller may lead to high wear in the impeller front sealing area and on the suction liner adjacent to it. Some designs allow for the clearance between the impeller face and suction liner to be adjusted to compensate for any wear that occurs so that the desired hydraulic performance can be maintained over time.
Experience has shown that the impeller rotational speed should be kept as low as possible for pumps handling abrasive fluids. Wear will vary approximately as the cube of the speed and with particle concentration.
Rubber-lined pumps are limited to lower impeller peripheral speeds because pressure fluctuations from the passing impeller vanes may cause internal heating due
to the deformation hysteresis of the rubber. Increasing pressure fluctuations would eventually lead to degradation of the rubber polymer structure.
When operating conditions or other considerations require longer component life, the peripheral speeds should be lowered, noting that wear life would be approximately doubled by a 20 per cent drop in pump rotational speed.
Even the largest, most robust pump running at slow speed may still experience gouging and wear. Where the pump is running compared to its design best efficiency point (BEP) is important. Acceptable gouge-free wear depends, among other factors, on the actual percentage of BEP flow rates experienced during operation, with 100 per cent BEP being the optimum.
Further information and detailed diagrams, equations and schematics can be found in the Australian Pump Technical Handbook, available from the PIA website. In the next edition of Pump Industry, we continue our explorations into the selection and application of slurry pumps.
There are a number of instruments which are essential to maintaining a close check on the performance and condition of a pump. A compound pressure gauge should be connected to the suction of the pump and a pressure gauge should be connected to its discharge at the pressure taps which may be provided in the suction and discharge flanges. The gauges should be mounted in a convenient location so that they can be easily observed.
In addition, it is advisable to provide a flow metering device. Depending upon the importance of the installation, indicating meters may be supplemented by recording attachments.
Whenever pumps incorporate various leak-off arrangements, such as a balancing device or pressure-reducing labyrinths, a check should be maintained on the quantity of these leakoffs by measuring orifices and differential gauges installed in the leak-off lines.
Pumps operating in important or complex services, or operating completely unattended by remote control, may have additional instrumentation such as speed indicators, vibration monitors, and bearing or casing temperature indicators.
Waste Expo Australia will return to Melbourne Convention and Exhibition Centre on 3 – 4 October 2018. This year’s show will be strengthened by the addition of Wastewater Expo Australia which alongside Waste Expo Australia and All Energy Australia forms the most comprehensive event for the waste, recycling, wastewater treatment, clean energy and energy efficiency industries in Australia. These three premium events will showcase over 300 suppliers, attract over 8,000 visitors and feature 10 concurrent conferences that are free to attend over the two days.
Waste Expo Australia offers a number of unique opportunities for attendees, including an exhibition, networking events, live demonstrations and the highly acclaimed Waste Summit Conference. Waste Summit is Australia’s largest free-to-attend waste management conference that will focus on four key themes including landfill and transfer stations, waste-to-energy, resource recovery and collections. These themes will address policy, legislation, circular economy and solid waste management, and will be where the industry tackles its most pressing issues.
Mark Smith, Executive Officer Victorian Waste Management Association, said that few industry sectors experience the momentum of change that is currently being experienced in the waste industry.
“The challenge of National Sword, consumer behaviour, politics, pollution and environmental protection, technology changes and increasing media scrutiny has put a spotlight on the waste and resource recovery sector like never before,” said Mr Smith.
“Waste Expo Australia is coming at the perfect time for us to come together to discuss the challenges and opportunities our essential service is dealing with now and into the future.”
In direct response to the development and growth of Australia’s wastewater sector, Wastewater Expo Australia will showcase the opportunities in technology that will drive cost effective strategies and create new revenue streams through wastewater to energy development.
Wastewater Expo Australia will feature a comprehensive free-to-attend conference and exhibition that will confront the challenges and opportunities in wastewater treatment through technology, strategy and compliance.
The Wastewater Summit Conference will focus on three key themes – growth, costs and compliance – and will be where the industry converges to source new technology and gain insights from industry leading experts.
Among the key sessions on the Wastewater Summit program is a case study presentation led by South East Water. This session titled “Internet of Sewers using IoT to improve efficiency and safety of wastewater assets” will share learnings on how they leveraged machine-to-machine technology to transmit real-time technology to control wastewater flows and identify faults in the network. This stands among 12 other sessions that will feature practical and innovative technology targeted at reducing operational costs and increasing efficiency.
Wastewater Summit will also feature speakers from ARENA, Unitywater, Goulburn Valley Water, Sustainability Victoria, EPA, Melbourne Water, South East Water, Coliban Water, DELWP, Victoria University and many more who will be addressing the key topics facing the sector. The program will provide unparalleled opportunity to all attendees to remain abreast of the key developments in a dynamic and ever changing industry.
These events, presented by Reed Exhibitions Australia, are free-to-attend and open to all industry stakeholders looking for products, services and solutions for the waste and wastewater sectors.
Volvo Penta. Robust, fuel efficient industrial diesel engines that keep running even in the toughest conditions. Easy to install, operate and maintain. A powerful partnership you can trust all the way from the drawing board throughout the operational life of your engine. Competitively priced complete power-pack units ready for delivery Australia wide with a local support team on hand 24/7. To find your nearest dealer visit www.volvopenta.com
2018
7 September 2018
SUMMER 2019
the 2019 Industry Capability Guide
30 November 2018
2019
WINTER 2019
TBC
For superior flow and suction lift capabilities consider the Pioneer Prime series. Our pumps deliver extreme flows with high head capability, combined with the UltraPrime™ priming system are capable of rapid 50 CFM unattended priming and run-dry operation. Our patented PosiValve valve prevents leakage and product carry over. Pumps are available in a variety of different metallurgies.
Leading-edge hydraulic engineering makes our centrifugal pumps the highest performing pumps on the market. Our pumps provide better flow, higher head, greater efficiency, and unparelleled service designed to meet your unique challenges.
www.pioneerpump.com