Designing a pump station for varied discharge head
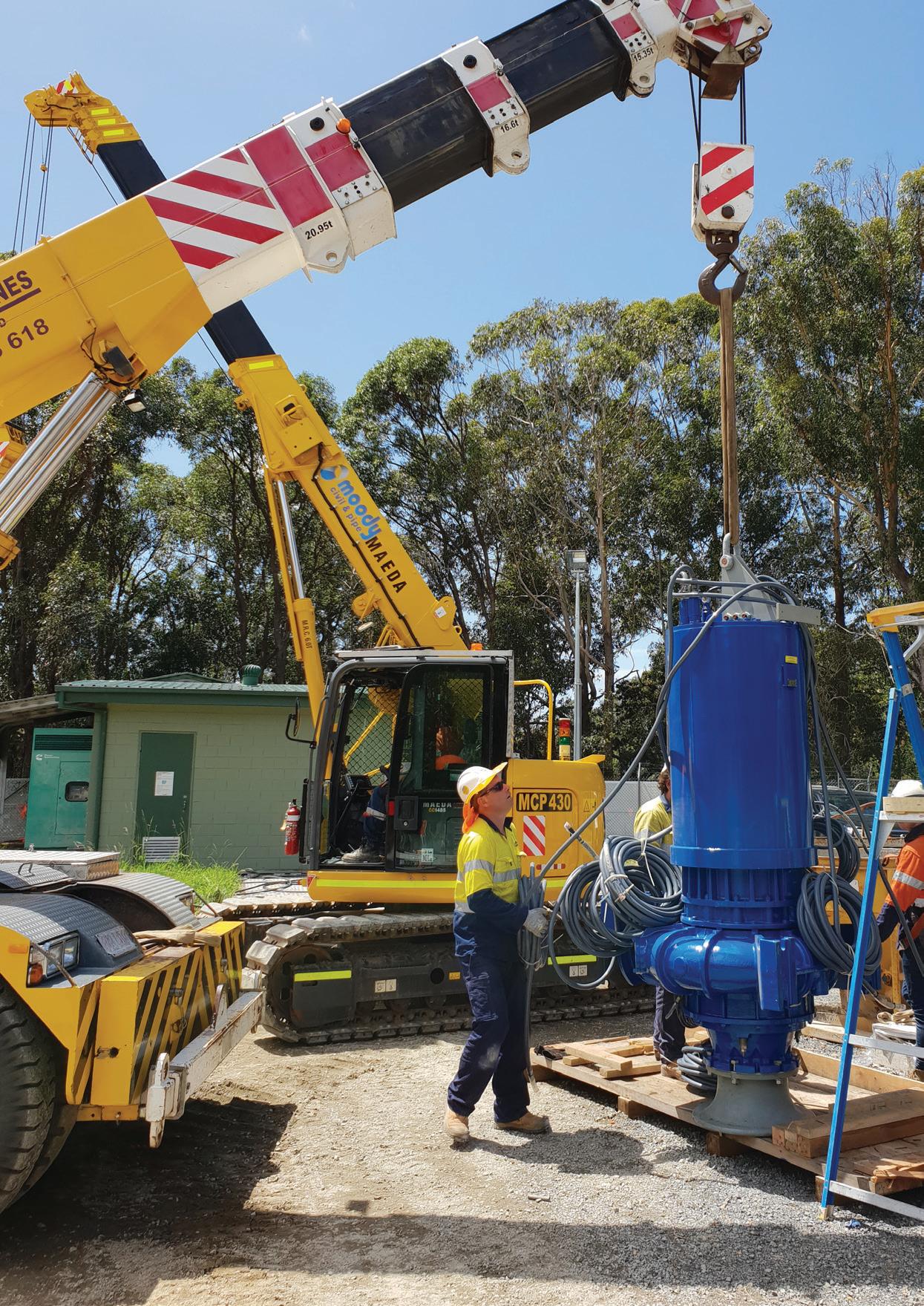
Accelerating mine dewatering at a nickel mine
System troubleshooting:
Can you identify the problem?
Designing a pump station for varied discharge head
Accelerating mine dewatering at a nickel mine
System troubleshooting:
Can you identify the problem?
The key to successful, hassle free sump pumping is to eliminate priming issues.
Which is exactly how our ‘V’ Series Vertical shaft column pump works. Unlike a surface mounted unit, the ‘V’ Series is always primed as it’s submerged in the liquid, avoiding the need and expense of a suction line or foot valve and the NPSH restrictions associated with surface mounted pumps.
Its space saving design minimizes or eliminates floor space required for installation with the motor out of the liquid for easy maintenance and monitoring.
With the ability to pump water, suspended solids or semi viscous products and be used in high temperature applications and explosive atmospheres, the ‘V’ Series is also very versatile.
Save time, money and space up top, with an ASM ‘V’ Series pump down below. For more information contact ASM Pumps on (03) 9793 7577 or visit asmpumps.com.au
Pump Industry Australia Incorporated PO Box 55, Stuarts Point NSW 2441 Australia Ph/Fax: (02) 6569 0160 pumpsaustralia@bigpond.com
PIA Executive Council 2019
John Inkster – President Brown Brothers Engineers
James Blannin – Vice President Stevco Pumps & Seals
Kevin Wilson – Treasurer/Secretary Executive Officer
Alan Rowan – Councillor Executive Officer – Publications and Training, Life Member
Ken Kugler Executive Officer – Standards, Life Member
David Alexander – Councillor KSB Australia
Andrew Black – Councillor Envirotech Water Solutions
Mike Bauer – Councillor DynaPumps
Jim Athanas – Councillor Xylem Water Solutions
Hem Prakash – Councillor Davey Water Products
Anant Yuvarajah – Councillor ASC Water Tanks
Hello all and welcome to the Winter edition of Pump Industry magazine. A lot has happened since the last edition. First and foremost the Coalition being returned to government with a majority—how the polls got it so wrong! It certainly strengthens the argument that the only poll that counts is the one on election day. Maybe now we just might see some continuity in government over the next three years; that would be good.
In the Calendar of Events it has been a quiet YTD with a Technical Meeting having been held in Melbourne in March and an Installation & Commissioning Course having been held in Brisbane in May at KSB’s premises in Bundamba. It was intended to have a Technical Meeting in May in Brisbane as well, but this was postponed until we had a speaker confirmed; we have approached Irrigation Australia (IAL) to do a presentation tentatively for Wednesday 10 July. Technical Meetings are planned for Adelaide in July, Perth in August and Sydney in October.
Another important event we are working on is in assisting the Fire Protection Association Australia (FPAA) to run two half-day Fire Pump Seminars in July: one in Melbourne and one in Sydney. Ken Kugler is working alongside Brett Dundules, Senior Technical Officer at FPAA on this. The Seminar will be titled, ‘AS2941 – Fire Pumpset Selection, Installation, Commissioning and Servicing’. We presently have four speakers from the fire industry confirmed.
Expanding on this collaboration, PIA and FPAA are working towards having closer ties; the reason for this to be frank is that when it comes to the fire industry, FPAA has “more legislative teeth” than PIA. I think its fair to say that FPAA would be equally concerned as PIA members about the poor quality of some fire pump builds and installations that we see from time to time. This is not a quick fix, but in speaking with FPAA recently I was told that “FPAA is happy to work with PIA to develop a program that could be used to better inform the industry about best practice”.
Integral to this as outlined in my last editorial are the shortcomings in the selfregulation and certification processes in the building industry, and ensuring every fire pumpset complies with the technical requirements of AS2941 to ensure absolute reliability. Hopefully the FPAA seminars will herald the start of such collaboration. It’s in our interests that it does.
Tragically, as a stark reminder to all of us who are Directors of companies, the importance of ensuring the products we sell comply with the Electrical Safety Act 2002 was laid bare when the Director of an online company was fined $1.2 million and ordered to pay court costs after a water pump he sold was held responsible for the death of a woman in QLD after being found to be electrically defective. Of real concern
is the fact the owner of the business had little knowledge of Australian electrical safety requirements. Needless to say, this will most likely spark greater interest and direct action from Electrical Safety Boards whose role is to lead and enable all aspects of electrical safety across all sectors of the community including electrical workers/ contractors and electrical equipment manufacturers/suppliers.
Further to my note above regarding IAL, Dave Alexander and I had a meeting in March with Bryan Ward and Geoff Harvey of IAL, the peak body representing the irrigation industry. The purpose of the meeting was to see how PIA and IAL could work more closely together and, more particularly, how PIA could tap into the greater resources that IAL have and to learn from them how we can deliver a better package to our members; we already have a Memorandum of Understanding with IAL but we need to leverage this more. A visit to their website shows the depth and breadth of their capabilities and competency-based training that goes towards a qualification/certification. It is hoped we can learn more from them at the upcoming Technical Meeting in Brisbane to be held at their premises in Murarrie.
Following up on the Opal Towers saga at Olympic Park in Sydney, the NSW Government has said it will “shake up the way high rise residential towers are regulated to rebuild trust in the industry after the Opal Tower debacle”. NSW will have a new high rise watchdog and a registration scheme for engineers and builders under an overhaul of construction activity after “significant and concerning” problems were identified with the construction industry.
As you know or may not know, PIA has links with the Hydraulic Institute (HI) and PIA members are entitled to a 25 per cent reduction on their webinars; their last webinar was on 25 June and our Secretary, Kevin Wilson, will be posting more information on our website shortly, so please keep a lookout. To give you an idea, HI do 2, 3 and 4 part series and the topics coming up, including Assessing Pumping Systems to Optimise Operation, Slurry Pumps and Advanced Dynamics of Pumping Machinery, are all available to you at a discounted price being a PIA Member.
On other matters of interest, we have had nine new Members join PIA since the New Year and I extend a hearty welcome to them all; also my thanks to those Councillors who have been actively recruiting new members. Please keep up the good work.
To all PIA members, I wish you all the best over the coming months and if you have any ideas or thoughts to improve our organisation please make yourself heard; we need and welcome your input.
John Inkster PresidentRexnord Elastomeric Couplings have been an industry benchmark for over 40 years.
Ideal for the Pump Industry — Rexnord® Elastomeric Omega®, and Wrapflex Couplings are non-lubricated, material flexing couplings. These products have excellent vibration dampening capability and high misalignment capacity, providing extended life to connected equipment, making them ideal for the demanding pump industry.
Reduce Maintenance Costs and Downtime — Designed for quick replacement, Rexnord elastomeric elements can be installed without moving the driving or driven equipment from their mounted locations or removing the hubs.
Designed for Specific Applications — Each of the elastomer coupling designs feature attributes that meet unique customer needs. The Wrapflex Coupling incorporates a patented hub design to reduce operating thrusts on seals and bearings and the Omega Coupling is available in the HSU model designed specifically for hot and humid applications.
Contact Rexnord today to see which coupling is right for your application. sales.australia@rexnord.com or Tel 02 4677 6000
ABN: 36 426 734 954
204/23–25 Gipps St
Collingwood VIC 3066
P: (03) 9988 4950
F: (03) 8456 6720
monkeymedia.com.au
info@monkeymedia.com.au pumpindustry.com.au magazine@pumpindustry.com.au
Editor: Lauren Cella
Assistant Editor: Siobhan Day
Journalist: Eliza Booth
Business Development Managers: Alastair Bryers, Rima Munafo
Senior Designer : Alejandro Molano
An importer and online seller of pumps has been fined $1.2 million for failing to meet obligations under electrical safety laws, following the 2016 death of a woman who was electrocuted by a submersible pump in the backyard well of a Townsville home.
Zoran Kacavenda, sole director of online business the Pump Factory, pleaded guilty as an individual and as a business to breaches of the Electrical Safety Act 2002 which caused the woman’s death.
The Townsville Magistrates court heard that in March 2016 the Pump Factory purchased hundreds of submersible water pumps from a Chinese manufacturer before selling them online into Australia under its own name and as Kasa Pumps and Kasa Factory.
The court heard that Kacavenda and the Pump Factory failed to ensure the devices were electrically safe and met the relevant Australian Standard before doing so.
Victoria Thomson, head of Queensland’s Electrical Safety Office, which led the investigation into the death, said the ruling was a stark
reminder for importers to ensure their products are safe before importing or offering them for sale in Australia.
“Anyone who imports electrical goods for sale in Australia must ensure they meet Australian standards and are tested to be electrically safe,” Ms Thomson said.
“The consequences of failing to meet this requirement are extremely serious—and in this instance, tragic.
“This is also a strong warning for consumers shopping online for electrical products. Make sure your seller is contactable, then make a point of asking
them if their product meets Australian safety standards before you buy.
“Consumers have a right to be electrically safe when they buy electrical products, despite the enormous growth in online stores.
“Be very wary if you cannot verify the company’s business details. You cannot think too much about safety when you’re buying online.”
Ms Thomson said tested and compliant products would have the RCM mark on them, giving assurance that they meet Australian standards.
The ESO’s investigation found the pumps were substandard quality and poorly designed, allowing internal wires to tangle, rip out of their connections and come into contact with the metal body of the pump. Of equal concern, the investigation also found the home had no electrical safety switch installed on the circuit the pump was plugged into, which could have prevented the tragic death.
“Despite your best efforts to buy wisely, there’s still no way of knowing what work has been done on your home before you moved into it—or if any of your appliances are going to become electrically unsafe,” Ms Thomson said.
“The most effective way to protect against this risk is to have safety switches installed on all circuits in your home. Put simply, safety switches save lives.”
A research group at Saarland University in Germany has developed motorless pumps and self-regulating valves—using ultrathin electroactive silicone film—offering a lot more than just the typical ‘open/close’ or ‘on/off’ functionality of traditional pumps.
The researchers are able to control the film electrically and can make it execute precise vibrations or pulses on demand, while also monitoring its exact position or shape. This responsiveness makes it possible to continuously vary the flow rate through a valve, or continuously regulate the performance of a pump.
Another feature of these film-based devices is that they can indicate if they have become blocked by a foreign body. As the researchers can shape the films to fit into almost any casing, the films can be used in a broad range of practical applications.
The failure of small valves or pumps in a large industrial plant can cause major problems for maintenance and repair teams as it can take quite some time to locate the faulty component. This can be all the more problematic if the fault took time to be observable as the longer it takes to find a fault, the greater the potential damage to the plant. For example, if a foreign body becomes trapped in a valve and the valve doesn’t close properly as a result, it can take time before operators are aware of the malfunction.
Thankfully, this situation does not arise with the novel pumps and valves that have been developed by Professor Stefan Seelecke and his research team.
“Our devices are able to communicate their status and their activity in real time. For instance, the valve can tell us not only whether it is open or closed, but exactly how far open it is. If it can’t close because of the presence of a foreign body, it can also communicate this fact to us,” explained Professor Seelecke.
The valves and pumps created by the Saarbrücken research group are made from a thin silicone film that is printed on both sides with an electrically conducting material. Scientists refer to these materials as dielectric elastomers.
“If we apply a voltage to the film, it generates an electrostatic attractive force that compresses the film, causing it to expand out sideways,” said Steffen Hau, a PhD engineer working in Seelecke’s team.
By altering the applied electric field in a controlled manner, the engineers can make the film undergo high-frequency vibrations or continuously variable flexing motions. Effectively, the film can adopt almost any required position or orientation.
“These properties mean that the film can be used to design novel drive systems,” explained Mr Hau.
Using intelligent algorithms to control the movement of the film, the researchers at Saarland University and at the Center for Mechatronics and Automation Technology (ZeMA) in Saarbrücken are developing selfregulating valves and motorless pumps.
“We don’t need any separate moving parts for our pumps. Because the pumps can run without a rotating motor, they are flat, compact and very energy efficient,” said Mr Hau.
“We can control the volume flow rate in these pumps using the amplitude of the applied voltage rather than the frequency, which is what is normally used.”
This enables very quiet pumps to be built.
“As the film itself can act as a poition sensor, so too can a component made from it,” said Philipp Linnebach, a doctoral research student who is studying the new film-based drive systems.
When the film distorts, an electrical capacitance value can be precisely assigned to any particular position of the film.
“If we measure a change in capacitance, we know exactly by how much the film has distorted,” explained Mr Linnebach.
This allows specific motion sequences to be calculated precisely and programmed in a control unit. The film-based valve can therefore be used to deliver exactly the required amount of compressed air or liquid. The film itself is essentially a flat structure.
“We have now developed the technology to a point where we can produce films of the required shape. So we can now adapt the films to meet the needs of specific applications,” said Mr Hau.
The technology is cost-effective to manufacture and the components are very lightweight. They also consume very little energy and are more than a hundred times more energy efficient than conventional components.
Compared to a conventional solenoid valve, the film-based valve consumes up to 400 times less energy.
• BUTT-wELD ENDS
• FULLy LUGGED
• DOUBLE FLANGED
• SUITABLE FOR - LIQUIDS, GASES & STEAM
• TEMPERATURE RANGE -60°C TO +427°C
• ISO STANDARD ACTUATOR MOUNTING
SHORT FACTORY LEAD TIMES
South East Water has reached a new milestone with the installation and commissioning of one of its largest pressure sewer installations to date.
Installed at a greenfield industrial site in Dandenong South, the pressure sewer includes a truck wash, workshop and large office facilities. South East Water expects the truck wash on its own to generate around seven kilolitres of trade waste every day, but the sewer system is built to handle it.
The system is made up of a primary vessel of 15kl, complete with a three phase duplex pump package, and an adjoining 10kl of emergency storage capacity, resulting in a total effective capacity of 25kl. The Programmable Logic Controller (PLC) operates the system which enables constant monitoring and management by the Sewer Operations team.
Despite significant timeline and logistics challenges, the project was executed by the South East Water pressure sewer team, from the planning and designing to installation.
Working within the constraints of the property’s available space, and considering the massive sewer storage requirements, the team developed the most cost-effective and environmentally sensitive solution for this industrial area.
The business will now have a safe and reliable system, managed and maintained by South East Water, to dispose of wastewater.
As the biggest pressure sewer installation, it came with its own risks onsite which needed to be proactively and reactively managed, so a lot of planning was required in advance.
South East Water’s Pressure Sewer Connections Manager, Chris Smolka, said he was really proud of the team and contractors for their hard work and commitment in ensuring they implemented this project smoothly and efficiently.
“The project was run to a very tight deadline and on top of that, this installation was on a scale not regularly encountered.
“Our employees and contractors went above and beyond to ensure a safe and effective delivery of this system. This was a testament to their care and dedication to achieving a positive outcome for the customer,” said Chris.
Kelair stock a wide range of high quality pump brands. Find the Brand you’re looking for.
From mining to pharmaceutical, Kelair has an extensive range for applications across all industries.
Whether you need Positive Displacement Pumps or Centrifugal Pumps, we’ve got one that will hit the target.
The Federal Government has announced $100 million of funding for the Tasmanian Tranche 3 Pipeline to Prosperity project, adding to the state’s thriving agricultural sector.
Water is liquid gold and irrigation is transforming Tasmanian agriculture, creating jobs and expanding farm production to meet the growing demand for Tasmania’s premium produce.
Pipeline to Prosperity will be the third tranche of irrigation schemes developed in Tasmania by State and Federal Governments in partnership with farmers. The Tasmanian Government has already committed $70 million to Tranche 3 of Pipeline to Prosperity.
The Federal Government commitment will enable Tasmanian Irrigation to proceed with five irrigation projects, whilst the planning for other proposed schemes continues.
Access to this irrigation water will enable farmers to consider new high-value enterprises such as wine grapes, dairy, cropping, horticulture, value add existing enterprises and livestock finishing.
Irrigation development is a key plank of the Tasmanian Government’s AgriFood Plan and to meet Tasmanian Irrigation’s target to grow the farm gate value of Tasmania’s agricultural sector to $10 billion per annum by 2050.
When fully implemented, Pipeline to Prosperity will deliver ten proposed irrigation schemes which will provide an additional 78,000 ML of water, creating thousands of jobs and returning an estimated $114 million each year to the agriculture sector, and the Tasmanian economy more broadly.
The contract for the construction of the 60km Atlas Gas Pipeline has been awarded, with the first gas expected to flow before the end of 2019.
For transferring, dosing and metering
● Ideal for heavy-duty applications
● 3-5 times longer hose lifetime
● Advanced rolling design
● Pump up to 80 % solids
● Save up to 40 % energy
●
●
Jemena announced it has appointed Spiecapag Australia to construct the pipeline—forming part of Jemena’s $140 million project in southwest Queensland.
Jemena’s Atlas Gas Pipeline Project Director, Mark Turner, said Spiecapag was selected following a competitive tender process in quarter one of 2019.
“Spiecapag has a proven record in constructing complex pipelines in regional Queensland, and brings to the table an exceptional understanding of the local terrain and environment,” said Mr Turner.
“Spiecapag’s performance as Jemena’s Queensland construction partner on the $800 million Northern Gas Pipeline in 2018 means we have
every confidence that they are the right team to help us deliver this project on time and on budget.”
Mr Turner said Spiecapag joined Jemena at a series of information sessions in early May 2019 in Roma, Miles and Wandoan where it outlined business and other opportunities associated with the construction of the Atlas Gas Pipeline.
“In its entirety, we expect the construction of the Atlas Gas Pipeline Project will create between 150 to 200 jobs.”
Jemena was awarded the right to build, own and operate the Atlas Gas Pipeline Project by Senex Energy in 2018.
The Atlas acreage is the first of 13 acreages awarded by the Queensland Government, with all gas from the project earmarked for the domestic market.
The Atlas Gas Pipeline will span 60km from Senex Energy’s Atlas acreage, south-west of Wandoan, to Jemena’s Darling Downs Pipeline, near Yuleba.
The project also includes a compressor station, currently under construction by Valmec, approximately 20km from Wandoan.
Once completed by the end of 2019, the Atlas Gas Pipeline will have the capacity to transport 40 terajoules of gas per day.
Remote monitoring of weather and system operation
Intelligent adaptive control system to eliminate spray drift
No clogging in high TDS waters and suitable for any pH water
Enquiries: gjc@gjc.com.au
10 Peekarra Street, Regency Park, SA 5010
Phone: 08 8118 6450 www.gjc.com.au
The latest two contracts for the installation of the final 18km of the $225 million Haughton Pipeline in Townsville have been awarded, with 200 jobs and an additional $30 million to be injected into the local economy as the next stage of construction begins.
Minister for Communities, Disability Services and Seniors and Member for Mundingburra, Coralee O’Rourke, said, “BMD has a long-standing history in Townsville and will construct the final leg of the 36.5km pipeline while using local businesses and creating local jobs.
“This next stage of the project means hundreds of jobs.”
Member for Townsville, Scott Stewart, said with the community still recovering from an unprecedented flooding event, the jobs and economic investment that flow from the next two stages of the pipeline provided a much-needed boost for the economy.
“Being on site, it is great to see this vital piece of infrastructure coming together—one that will secure a reliable water supply for the region for decades to come,’’ Mr Stewart said.
More than 400 workers are now on the project.
Water and Waste Committee Chair, Cr Russ Cook, said the package of works included the installation of 18km of pipeline, and construction of one river crossing at the Haughton River and creek crossing at Major’s Creek South.
“The work will be delivered in sequence with civil works and land acquisitions along the pipeline easement and is expected to begin within weeks,” Cr Cook said.
Group Executive Director – Operations, BMD Group, Scott Power, said BMD was looking forward to successfully delivering another key project for the Townsville region.
“BMD has been delivering key infrastructure in North Queensland for 25 years and as a local company we are proud to be contributing to an important project such as the Haughton Pipeline Duplication,” Mr Power said.
“As a company dedicated to collaborative contracting and local input, we are focusing on the creation of local jobs during construction and are looking at spending in excess of $30 million with local businesses.”
Townsville Mayor, Cr Jenny Hill, said the contract would ensure the project remained on schedule for completion in March 2020.
“Townsville’s long-term water security is well on the way to being delivered,” Cr Hill said.
“The water pipeline is the most critical infrastructure project in the city in decades.
“This package of works alone will deliver 200 direct and indirect jobs, and because of the major focus on local suppliers, $30 million will be spent with 90 local businesses right here in Townsville.
“That is a huge economic injection into the city.”
The Coomera River in Queensland is undergoing a multi-million dollar works program, with dredging works commencing following the completion of a sediment management facility.
State Minister for Transport and Main Roads, Mark Bailey, said the Gold Coast Waterways Authority’s (GCWA) Coomera Dredged Sediment Management Facility and Coomera River dredging program is a $10.3 million dollar investment in the marine industry’s future.
“The Marine Precinct supports two and a half thousand jobs and is one of the key boat building and servicing centres on Australia’s east coast. It adds to the 199,000 jobs created under the Palaszczuk Government since 2015,” Mr Bailey said.
“The completion of the sediment management facility allows the waterways authority to dredge navigational channels on the Coomera River between Sanctuary Cove and the Marine Precinct for the first time.
The EHEDG certified BCFH range of progressive cavity pumps handles thin to highly viscous products, including those containing soft solids with a low shear action and minimal pulsation which enables accurate flow control. BCFH pumps fulfill the stringent demands of cleanliness in the food, beverage, chemical, pharmaceutical and cosmetic industries.
EHEDG Type EL Class I and 3-A Sanitary Standards certified
Enhanced internal design ensures residue free cleaning with CIP/SIP
Equipment requires less cleaning time compared to other CIP solutions
Easy maintenance due to detachable rotor connection and split suction casing
“This will support growth of existing businesses and attract new investment.
“There are already plans by existing businesses to double the number of jobs and create new berthing, storage and maintenance facilities in the precinct.”
GCWA CEO, Hal Morris, said up until now, the authority had not been able to dredge the upper Coomera River because there was no way to deal with the silt found in that part of the river in an economical and environmentally friendly way.
“The material being dredged is too fine and silty to use for beach nourishment or offshore disposal.
“The alternative would’ve been to transport it to somewhere like Brisbane which would’ve been prohibitively expensive.
“Having a facility like this is a game changer for the Gold Coast Marine Industry Precinct, marina operators, waterways users, residents and the Gold Coast economy.
“There’ll be easier access and deeper water, keeping the river safe and navigable for all types of boats, including superyachts up to 60m in length, to come into the precinct.
“Dredging will also improve water flow for flood mitigation,” Mr Morris said.
The Coomera Dredged Sediment Management Facility is the first of its kind on the Gold Coast.
The facility contains a six-hectare settling pond and a twohectare area where the sediment will be dried out before being available for reuse as topsoil or non-structural fill.
The facility will not only take material dredged under the GCWA’s dredging program but also enables the environmentally sound disposal of river and canal sediment for the City of Gold Coast, businesses in the marine precinct and managers of residential areas like Hope Island and Sanctuary Cove.
GCWA engaged South East Queensland firm Synergy Resource Management to design, construct, operate and maintain the facility following a competitive tender process.
Synergy Resource Management CEO, Andrew Reardon, said 26 direct and indirect jobs were created as a result of the project.
“We’re proud to deliver a local option for processing dredged sediment that’s unsuitable for normal disposal options such as beach or foreshore nourishment.
“Now that the facility is complete, we’re focusing on dredging the Coomera River on behalf of GCWA.
“We recognise the river’s importance to the Gold Coast economy which is why we’ve engaged two contractors to dredge the upper and lower reaches at the same time,” Mr Reardon said.
The City of Gold Coast contributed over $1 million to the dredging of the Coomera River.
Mayor, Tom Tate, said, “This is all about jobs—jobs for the marine industry today, and jobs for our future generation.
“The dredging will open up the precinct for super yachts to arrive for servicing and reprovisioning. Some of these vessel owners spend millions in refurbishment costs alone.
“Those funds flow into our local economy, through employment and supply chains.
“I applaud the Queensland Government for pushing the green light on this important project.’’
Dredging of the river between Sanctuary Cove and the Marine Precinct should be completed in September 2019.
The winner of the 2019 Massachusetts Institute of Technology’s (MIT) $100,000 Entrepreneurship Competition has been awarded to a startup that is helping oil well owners remotely monitor and control the pumping of their wells, increasing production while reducing equipment failures and cutting methane emissions.
Acoustic Wells, a team that includes two MIT postdoctoral scholars, was awarded the grand prize after eight finalist teams pitched their projects to judges and hundreds of attendees at the university’s Kresge Auditorium.
The majority of North America’s 1.4 million oil and gas wells are run by independent owners operating batches of hundreds or thousands of aging wells. Working with thin profit margins and older equipment, the owners rely on small teams of workers to manually
inspect each well in a yearlong, labourintensive, daily process.
When setting up their pumping equipment, each owner must strike a balance. If they set up the wells to pump too slowly, they risk leaving oil in the ground and losing much-needed revenue. If they pump too fast, they risk breaking their equipment and causing pollution.
“The result [of pumping too fast] is similar to when you’re drinking with a straw from a cup and there’s nothing left, so you hear that bubble sound,” said Acoustic Wells founder and CEO, Sebastien Mannai.
“The same thing happens with oil wells, but on a much bigger scale.”
In the case of oil wells, those bubbles are pockets of methane that enter the pump and cause it to fail, unleashing unnecessary greenhouse gases in the process.
To address this problem, Acoustic Wells is developing an IoT device based on a novel sensor and an online cloud solution to help well owners control their equipment using real-time pumping data.
Mr Mannai, a postdoc in the Department of Aeronautics and Astronautics, compared the device’s sensor to a stethoscope. It works
via a sensor similar to a microphone connected to the wellhead at the surface.
The sensor records the sound of the pump and a field computer processes the data on the edge before sending the results to a cloud-based system for real-time analysis. Owners can view the processed data on a dashboard and remotely send orders to the well to change its pump settings, simplifying the inspection and control processes.
The company has already conducted field tests with an early version of its solution on 30 wells across Oklahoma, Texas and Louisiana. In those tests, the solution was able to detect key issues and the wells were adjusted to increase their efficiency and reduce their emissions.
The team also includes Charles-Henri Clerget, a postdoctoral associate in the Department of Mathematics who is also affiliated with the Earth Resources Laboratory (ERL), and Louis Creteur, the IoT and cloud architect of the company Leanbox.
Overall, it is believed the solution could save independent well owners US$6 billion annually while preventing the methane equivalent of 240 million tonnes of carbon dioxide.
Coliban Water will invest more than $15 million on water and wastewater upgrades in the Echuca region over the next four years, including a new water pump station and network booster pumps.
Coliban Water Chairperson, Lucy Roffey, announced the funding commitment, which will be spent on a range of projects to meet the growing needs of residential, commercial and industrial customers in the region.
“The highlight of this funding will be a $9 million upgrade to Echuca’s Water Treatment Plant to improve capacity, storage and disinfection,” Ms Roffey said.
“The project will increase the town’s security of supply and ability to meet growing demands through the construction of two additional 3.3 megalitre treated water storage tanks. Combined, this is the equivalent volume of 2.6 olympic-size swimming pools.
“It will also see construction of a new treated water pump station and a UV disinfection system at the plant,” Ms Roffey said.
Approximately $3.7 million of the funding will be spent on new water storage tanks for Echuca West on Wilkinson Drive and network booster pumps.
Site works are expected to start in early 2020 and be completed in 2022.
“This project will help us address the significant growth that has occurred in Echuca West and ensure that we can continue to supply adequate water pressure to these households. The
extra pumps will help to accommodate this growth and provide additional security of supply for our customers.”
In regards to wastewater improvements, new sewer odour mitigation systems will be installed at Anstruther Street and Terricks Road at existing sewer pump stations in those locations.
The remainder of the funding will be spent on a number of smaller projects which include valve replacements at the Echuca Water Treatment Plant which will occur prior to the plant’s upgrade project, pump refurbishment for the transfer of Echuca’s raw water, annual water main renewals, planned maintenance works on the Echuca Water Tower and the replacement of sewer pumps at two locations.
“The replacement of these sewer pumps is part of an ongoing renewals program to help ensure future reliability and efficiency for our customers,” Ms Roffey said.
Pump Industry Australia publishes two handbooks, the Australian Pump Technical Handbook and the Australian Pipe Friction Handbook, which are designed as reference manuals for people who work in the industry or are associated with the pump industry such as manufacturers, distributors, educators, designers, operators and users. These handbooks complement each other and both are easy to follow and can be readily understood with a basic knowledge of physics. Updated editions of these handbooks will soon be released.
The Pump Technical Handbook has been produced and designed for the Australian pump industry. The handbook is for those interested in learning about pumping and acquiring the technical knowledge of pumps and their operation including the overall pump system in which the pump works.
The handbook covers a wide range of topics beginning with the definitions that are used when working with pumps. It is then followed by details of the classification of both centrifugal and positive displacement pumps.
The next chapters comprehensively cover the characteristics, selection and application of centrifugal pumps, positive displacement and slurry pumps.
The efficient operation of pump systems is covered in a chapter which details how you can make sure a pump system operates efficiently throughout its working life. It also includes a discussion on the calculation of the lifecycle costs for a pump system.
What are pumps made of? This chapter discusses the metallic and non-metallic materials that pumps are constructed from and provides basic pump material selection data for applications other than water. A table of Australian, European and American material standards is included.
Pipe systems are covered including how to calculate system head. This is done in conjunction with the PIA Pipe Friction Handbook
Good intake design is critical to the correct and efficient operation of a pump system. This is extensively covered together with how to construct a wide variety of intakes. The common problems to be avoided with intakes is discussed.
How are pumps tested, to what standard and to what tolerances are pumps tested? What data can you expect from a pump test? All this and more is covered in the pump test chapter.
The next two chapters cover installation, commissioning, operation and maintenance, and troubleshooting. These chapters discuss how pumps should be looked after once they are shipped from the manufacturer and delivered to the end user together with how to troubleshoot problems.
Finally, there are comprehensive sections with conversion tables and pumping formulae.
This brief description of what is in the Pump Technical Handbook illustrates how comprehensive and useful it is.
The Pipe Friction Handbook is a handbook which complements PIA’s Pump Technical Handbook. The book teaches the user how to calculate pipe friction losses in a wide range of pipe types and sizes up to, in some cases, 1800mm. The handbook includes easyto-understand instructions on how friction losses are calculated for straight pipe and a wide range of pipe fittings.
The first section if the handbook covers pipe friction losses in the most commonly used pipes in Australia. With the exception of commercial steel pipe which is to ASTM B36:10M standard, all the other pipes and tubes are to an Australian standard. The following are the piped types covered by the friction tables:
• Commercial steel pipe
• Large fabricated pipe
• Medium and heavy duty galvanised steel pipe
• Uncoated and cement lined ductile cast iron pipe
• Copper tube
• Brass tube
• Stainless steel tube
• Series 1 and 2 PVC pipe
• Polyethylene pipe
• Rural polyethylene pipe
• Aluminium irrigation tube
• Elastomeric rubber hose
• Concrete pipe
In addition to the above tables there is a table for the friction loss of viscous liquids in commercial steel pipe and a chart for the calculation of friction loss in layflat hose.
The second section of this handbook covers friction loss factors for valves and fittings, and how to calculate friction loss in pump systems. The following tables are included that will be useful to the pump engineer:
• Value of gravity at selected Australian sites
• Physical properties of water
• Pressure, boiling point of water at various altitudes
• Suction lift reduction with temperature
• Viscosity equivalents at constant temperature
• Viscosity of liquids
• Specific gravity and temperature relationship for various liquids
• Density and specific gravity for various liquids
• Flow through orifices and nozzles
• Approximating discharge from pipes
• Irrigation table
• Discharge from syphon lines
• Pressure surges and waterhammer
• Acceleration head—reciprocating pumps
• Conversion equivalents
• Power transmission— Recommended flow rates and pressures for hydraulic hose
This handbook covers all the reader needs to calculate friction losses in a pumps system.
End users now have more choice than ever when it comes to selecting a pump brand, from local to international manufacturers, and can shop around for the cheapest prices both in stores and online. However, one important consideration that should be taken into account when selecting a brand is the level of customer service provided, from advice and proposal, through to after sales support.
Having a high level of customer service is important for both the application requirements and the lifecycle of the equipment. Not only will this ensure that you are getting the right equipment for your needs and it runs efficiently, but any problems or changes to pumping requirements in the future will be handled quickly, effectively and with minimal hassle.
There are a lot of factors that need to be taken into account when selecting a pump, and talking to an experienced technical service manager is key to getting the right pump for your application.
Malcolm Eyre, Managing Director at Franklin Electric, said there are a number of considerations that need to be taken into account when selecting a pump, from size, to power and water source.
“Getting the right pump for your application is imperative to keeping costs down.
“If an over or undersized pump is selected, the end user will find their power usage and costs higher than necessary. The pump is also more likely to require maintenance more often and have a shorter lifespan.”
Power and water source also need to be carefully considered.
“Diesel has traditionally been used by those in remote locations where there is no access to the electricity grid.
“Another option that has been gaining popularity is solar. This is a great option for those looking to improve their bottom line over the long term. Solar pumps can also be integrated with diesel or electricity to create a hybrid energy source for when there is limited sun exposure.”
The water source the pump will be drawing from will also impact on the type of pump that is required.
If groundwater is the main source, a submersible or vertical turbine pump will need to be used; however, if drawing from a deep aquifer, a special deep well pump may be required to lift the water and pressurise it.
“Being able to speak to a knowledgeable technical service manager is important to ensure you’re getting the right pump for your requirements. The distributor or manufacturer will be able to determine the size of the pump that will best meet your requirements, the type of pump based on the water source, and advise if solar is a good option for you.”
Another area where customer service should be valued is access to troubleshooting and maintenance from the manufacturer.
“At some point pumps will experience problems or need maintenance, and having easy access to a pump engineer is needed to get the pump working optimally again. If any problems need troubleshooting, the manufacturer is best placed to evaluate the pump and find the solution.
“However, this level of customer service from manufacturers can be hard to find. International brands may not have a base in Australia, so there may not be anyone who can come out to check on the pump in person.
“Manufacturers are the best option, but depending on where they have offices, they may not offer in-person services if you are located too far away and they don’t have regional technical teams.
“Selecting a manufacturer with a presence across the country or regional technical managers that are able to travel will ensure any problems that do arise can be fixed quickly.”
Malcolm said that Franklin Electric prides itself on providing a high level of customer service to its clients, and the team will go out of its way to ensure clients have the right pump and that it keeps on running.
“We have a team of highly experienced technical service managers, covering both metro and regional locations, so no matter where you’re located, someone can come out and speak to you in person or troubleshoot onsite.
“We take local service seriously and can help you find the right pump for your needs—no matter the size, energy source or water source—to ensure you get the most efficient and cost-effective solution. Or if you think your current pump is wrong for you, we can assess it and give advice about the best course of action.
“Our team is always ready to go out of their way to give you the best service and fix any problems that may occur to our pumps over the course of their lifecycle.”
Franklin Electric uses the experience gained over 75 years to offer industry-leading technical service, robust training programs, and unwavering support and communication.
Leading the industry in service standards
Maximum resistance and extreme reliability for the MAC6, MAC8 and MAC10 submersible motors.
Innovating to discover increasingly efficient solutions for water management is a fundamental part of Caprari's core business. Thanks to its internal research and development division and production capabilities, the Modena-based industrial group is able to offer highly efficient and reliable products.
Each new solution is designed to meet a specific market demand in the most effective and technologically advanced way.
With this objective in mind, Caprari internally develops exclusive patents aimed at improving the performance of its products.
Starting from the design stage, the company pays the utmost attention to all the measures that can improve the life of the product and has patented several devices like Defender®, Easy Check, Sand-Out system, Smart-Fix system, ConnectoFlex, HT coupling and HT-High thrust bearing that protect the pump and extend the product lifecycle, reducing its environmental impact and overall costs for the end user.
The MAC series submersible motors have significantly increased performance thanks to the innovative HT-High thrust bearing, patented exclusively by Caprari (Caprari International Patent), with margins of tolerance that make the device extremely reliable in all conditions of use.
Today, the HT-High thrust bearing is present in MAC6 submersible motors, as well as in the MAC8 and MAC10 larger-sized motors, both in cast iron and stainless steel versions.
This special patent allows obtaining a more durable product and improved axial load resistance.
Its performance provides the motor with a structural oversizing with respect to the actual thrust that the wet end generates, even during operation transients.
To achieve this result, the cage, supports and skids have been completely redesigned on new concepts.
With the same dimensions, the HT thrust bearing withstands at least three times the load of a traditional Mitchell bearing.
Thanks to its exclusive and diversified know-how, Caprari provides complete solutions for every major water requirement, including collection from deep wells, wastewater and drain water lifting, water supply and distribution for residential, industrial and agricultural purposes and various water treatment applications. Innovation and reliability of exclusive products, and services dedicated to the customer; these are the strategic assets that have always distinguished Caprari.
Alerts, advanced analysis, and automated reporting help to improve maintenance strategies and critical asset decision-making.
Overview
A power plant in Southeast Australia had recently experienced chronic high vibration amplitudes on a critical multistage boiler feed water pump. Given the criticality of the pump and the risks associated with catastrophic pump failure, the power plant contacted Hydro Australia for support. In collaboration with Hydro, Inc.’s wireless condition monitoring team, Hydro Australia was able to provide the power plant with a significantly improved IIoT-based monitoring system. This would assist the plant by closely monitoring the status of its asset, making the best possible decisions for equipment maintenance, and ensuring equipment availability (Figure 1).
Background
For pumps that are critical to plant operation, the difference in availability and in the frequency of emergent situations can be significantly impacted by the plant’s reliability program and the engineering practices employed to ensure uninterrupted operation.
In this situation, the power plant experienced chronic and severe vibration amplitudes on a critical multistage barrel pump (BB5) in boiler feed water service. The pump with high vibrations present was one of three installed pumps in the specific power unit within the plant. The chronic vibration issues previously resulted in significant downtime of the asset in addition to delayed critical maintenance and preventative maintenance (PdM) operations on the two sister units. This created a significant risk of lost production if one of the sister pumps experienced a catastrophic failure.
This asset serves a fundamental role in the process of producing power. As a result of the pump’s role in the plant, the asset is considered “critical” and the risk associated with the severity of the vibration amplitudes was deemed unacceptable by the plant. The plant’s reliability team required immediate corrective action.
Hydro Australia, in collaboration with Hydro, Inc.'s wireless condition monitoring team, was able to showcase its commitment to reducing out-of-pocket cost by increasing equipment reliability, achieved through the use of predictive maintenance (PdM), advanced engineering analysis and wireless vibration monitoring services.
Hydro Australia quickly deployed two experienced Pump Improvement Engineers (PIEs) to the power plant in order to evaluate all possible troubleshooting options and to further assess the hydraulic and mechanical conditions of the asset. The PIEs were also able to assist the plant in developing a more permanent solution that would prevent an imminent failure of the pump.
The plant had previously installed permanent vibration monitoring hardware onto the pump bearing housings. However, due to a lack of available funding, the plant was only able to install single axis accelerometers in the vertical plane of each bearing housing. This left both the horizontal and axial
directions on each bearing housing without any means of continuously monitoring their condition. In addition, the other components in the drive train such as the fluid drive coupling, motor and booster pump were not monitored.
While the two installed sensors did provide data and some indication of the pump’s condition, only being able to analyse in the same direction meant that there was a lack of available historical data; this made analysis difficult, if not ineffective. As a result, the plant reliability team often relied on routebased data collection to accurately assess the pump and drive train condition. The data from the route-based collection was what informed maintenance decisions to prevent and predict equipment failure.
Hydro Australia, a global aftermarket pump service provider known for its extensive engineering knowledge, in collaboration with Hydro Reliability Services, quickly identified the benefit that wireless vibration monitoring would offer plant engineering and operations.
Hydro Australia’s PIEs recommended a path forward that would allow the plant to closely monitor its critical asset by utilising the low-cost wireless sensors and Industrial-Internetof-Things (IIoT) solution provided by Hydro Reliability Services, a Hydro, Inc. company. Working in partnership with the plant condition monitoring team, the PIEs installed a total of nine SDOF (Single Degree of Freedom) wireless vibration sensors on the pump and drive (Figure 2).
With the sensors installed, the data collection gateway was positioned near the machine train asset. The gateway collected data from the installed sensors and provided a means to send the data to a cloud-based server via a cellular connection (alternatively plant Wi-Fi or LAN connection could have been utilised by the gateway). The collected data is then accessible from any internet connected computer, tablet or smartphone provided the correct credentials are entered. This
allows the plant reliability team and Hydro Australia's team to monitor the asset in real time.
A set of specific alarm bands or vibration alarm thresholds were then identified for the specific pump. Should the amplitude at any one of the nine locations exceed the alarm settings, the system would immediately notify both plant engineers and Hydro Australia's engineers (Figure 3).
The wireless sensors were programmed to collect and trend vibration data (including FFT spectrums, Time Waveforms and Cross Channel Phase) every ten minutes. By applying the wireless vibration monitoring technology, the plant and its reliability team were able to monitor the pumps vibration behaviour 24 hours a day, seven days a week—offering a significant improvement from the route-based model used previously. The ability to closely monitor the boiler feed pump assisted the customer in maintenance decision-making, including decisions regarding the other two neglected sister pumps in the unit.
With the advent of low-cost IIoT solutions, wireless sensors play an essential role in predictive maintenance improvements. This has allowed plant operators and reliability engineers to economically replace old approaches to condition-based maintenance. Unlike route-based data strategies, wireless condition monitoring offers the following improvements to the plant in order to improve maintenance decisions and mitigate emergent issues:
• Real-time data
• High frequency data collection
• Increased resources available for data analysis (analytical tools)
• Customisable alerts and alarms
Wireless condition monitoring offers support to today's demands on equipment life's extendibility and higher mean time between repair (MTBR). Vibration analysis has proven to be an effective tool for detecting problems early on, thereby reducing the potential for more serious problems to escalate. As the work is collected wirelessly, it reduces the amount of labour and the possibility of error.
By monitoring the health of industrial equipment, plants and utilities can optimise their process management and create timely and efficient maintenance—all of which are critical to maintaining efficiency and reliability of a pump system and production.
Ebara Corporation (Japan) has recently released its new global range of EN733 standard end suction centrifugal pumps.
Utilising the most advanced hydraulic computer design software available, Ebara engineers in Japan have been able to improve and increase the pump efficiencies of the new GS range above most other available pumps of similar design and standard on the global market.
As a major manufacturer of industrial pumps to JIS and API610 standards, Ebara Corporation has embarked on a globalisation of its range of pumps for the world market. This includes the introduction of a range of industrial pumps to European EN733 standards and a new range of vertical multistage pumps.
The new Ebara GS range of EN733 standard pumps are manufactured in component form at Ebara Corporation Japan owned and managed factories in the Asia Pacific region with final assembly of market range models undertaken by skilled tradesmen at Ebara Pumps Australia’s Melbourne facility.
The new GS series are 16 bar rated pumps, with a close coupled version (GSD) offered as well. The GSD is now available in Australia.
Ebara Corporation was founded in Japan in 1912 as a manufacturer of pumps. Today, as a group, it consists of more than 70 companies in six continents with a workforce of more
11,000 people and with company owned and Japanese managed factories in eight countries covering four continents.
The huge scale of production and distribution is matched by a constant commitment to research, development and design of new products and the modern technologies for manufacturing them. Ebara products have gained a worldwide reputation for their technology and quality.
Contact your local Ebara dealer or Ebara Pumps Australia for more information.
Two of the more popular models that are stocked in Australia are both solids handling pumps. For more details contact us at Ebara Pumps Australia or visit our website.
Stamped stainless steel pumps with open impeller
Maximum 19mm passage size
50mm discharge
1.1 to 1.5kW - 1 phase
1.1 to 3.0kW - 3 phase
Cast iron submersible pumps with semi vortex impeller
32 to 56mm passage size
(Depending on model)
50 and 80mm discharge
0.4 to 0.75kW - 1 phase
0.75 to 3.7kW - 3 phase
Manual or automatic
Combining over 100 years of experience with the latest computer aided design, EBARA has developed the new GS series of pumps that offer world leading performance and efficiencies.
Pumps to EN733 dimensions
16 Bar rated. PN16 flanges (24 Bar hydrostatic test pressure)
High efficiencies. MEI ³0.6 (Minimum Efficiency Index)
Mechanical seals to EN12756
Protectors to ISO13852
O’ Ring seal for casing
Cast iron components ED painted (Electro deposition painting)
Available soon
The new Lowara Smart Pump range is designed to “plug and play” and is all about the right combination of motor, variable speed drive and pump — featuring an integrated, intelligent pumping system with an electronically driven, permanent magnet motor.
With an embedded electronic drive dubbed the “e-SM”, the Smart Pump range already meets the 2020 performance standards expected to be implemented by the EU, with its “ultra-premium” IE5 motor and a power drive system of IES2 (highest efficiency class). This equates to up to a 50 per cent savings in operating cost when compared to a similar standard non-VSD pump.
The new series is also easy to install and commission in both new and retrofit applications, and is flexible, precise and more compact than ever. With a reduced footprint of up to 14 per cent the Smart Pump range is better suited to small spaces, and has the capacity to handle extreme environmental temperatures from as low as -20°C and up to +50°C.
The new Lowara Smart Pump range is all about the right combination of motor, variable speed drive and pump.
Featuring an integrated intelligent pumping system with an electronically driven, permanent magnet motor and an embedded electronic drive, these simply smart pumps will greatly enhance system performance and maximize flexibility.
- 14% smaller in size
- Already meets EU 2020 directives today
- Harmonic and electromagnetic filters built in
- Intuitive interface and integrated control panel
- Low operating costs
- Plug & Play for easy install and retrofit
- Reduced mechanical stress and wear
- Available in horizontal or vertical multistage pumps
Call us today to see how Lowara ’s new simply smart pumps can assist with your water requirements.
1300 4
The e-SM drive can operate up to three pumps at once with no need for an external control panel. It also features state-ofthe-art technology to optimise performance, communicate with other building systems, reduce energy usage and dramatically decrease operational costs.
Product features
• 14 per cent smaller in size
• Already meets 2020 directives today
• Built-in Harmonic Filters
• Built-in Electromagnetic Filters
• Intuitive interface and integrated control panel
• Low operating costs
• Easy to install
• Reduced mechanical stress and wear
Specifications
• Voltage: 208 to 240V
• Power: up to 1.5kW
• Multi-pump capability: up to three units
• Power supply: single phase 50/60 Hz
• Comms: BACnet and Modbus standard in single pumps
• IES2 package with IE5 motors
• Enclosure rate: IP55
• Ambient temperature: -20°C/+50°C full power
• EMC: C1-category compliant with EN 61800-3 for residential environment
• Harmonics: compliant with IEC/EN 61000-3-2
Materials
• 304 stainless steel casing
• 304 stainless steel impellers
• 304 stainless steel diffusers
• Sic/Sic mechanical seal
Market sectors
• Residential
• Light industrial
• Commercial
• Irrigation
Applications
• Water supply systems
• Water treatment plants
• Irrigation systems
• Booster systems
Models
• e-HME – horizontal multistage
• e-SVE – vertical multistage
Improvements in 3G and 4G mobile network coverage, advancements in battery technology, low power electronics and cloud services have enabled the development of a new generation of devices that can be used to remotely monitor, control and log data from pumps and associated infrastructure.
ETM, one of Sweden’s leading manufacturers of Industrial IoT cellular edge solutions, has released two products that exploit these new technologies, with the new family of cellular remote monitoring, alarming and logging solutions for analog and digital signals:
• DeltaBlack optimised for industrial environments. DIN rail mount, wide DC operating voltage and flexible I/O configuration
• DeltaBlue designed for outdoor remote deployment. Battery-powered, IP66 enclosure, GPS, vibration/ movement detection and flexible I/O configuration
ETM ensured that simplicity and cost effectiveness were two key criteria in designing its new range. Recognising that deploying cellular or mobile network devices have often been a frustrating exercise for engineers having to deal with procurement, IT departments and having to select antenna, power supplies etc., these units come bundled with active Telstra
SIM cards and are preconfigured for specific inputs such as temperature, current and vibration.
DeltaBlack and DeltaBlue connect to ETM’s IoT Cloud Dashboard (EWO) for real-time and historical data display. In addition, pre-set customised alarms can be simultaneously sent to multiple recipients as simple user-friendly SMS text messages direct from the device.
For more information about DeltaBlack and DeltaBlue call (02) 9956 7377 www.etmpacific.com.
In 1919 things were a little different. The First World War had just ended and an unassuming businessman called Milton P. Levy from Dallas, Texas, started the National Disinfectant Company, offering only a handful of products. It didn’t seem like much at the time.
The work wasn’t glamorous. People didn’t think too hard about the soap their doctors used or how their water was treated, but it soon became clear that Milton was a pioneer in this new industry.
It turned out that Milton’s dedication to providing both quality products and service to his customers paid off. The company invested in research and development, and before long it produced almost all its own products.
When Milton died in 1946, his three sons took over the business, and they had a vision—to become a leader in the specialty maintenance market. That might not sound too exciting to most, but to the Levy brothers it was. “We love it,” they said, and so, it seems, did plenty of others.
Across the US, customers began regarding the NCH sales reps as maintenance experts, relaying their knowledge and expertise.
By the 50s and 60s offices started opening across the US, and then around the world. Now the company wasn’t just selling disinfectant, it was cleaning and conserving water, conserving energy, increasing safety, and decreasing waste. It was starting to change the world.
Today, NCH distributes to more than 50 countries, with over 8500 employees across six continents, and an extensive and varied product line. We’ve cleaned millions of gallons of water, saved gigawatts of power and kept thousands of kilos of toxic chemicals out of the environment.
Yet to this day, millions of people that benefit from the work we do have never even heard of NCH.
That’s ok with us, we’re not in it for the glory. Just like Milton P Levy when he founded the company 100 years ago, we want to make the world a better place.
Within a highly comprehensive range, FPT Industrial offers a series of engines specifically designed for Industrial Power Unit (IPU) applications. Highly durable components such as industrial clutches, radiators, control panels, and pressure and temperature senders ensure that FPT engines provide maximum reliability and durability, as well as greatly reduce running costs with outstanding ease of access for maintenance and servicing.
These characteristics make the engines ideal for horizontal pump installations, deep well pump installations, centre line pivot systems, defrost machines, transfer pump applications and de-flooding systems (where water is transferred to channels).
FPT Industrial’s IPU lineup comprises of the families of the F5, NEF and Cursor series, ranging from 3.2 litres to 12.9 litres and with power output from 75hp to 510hp. The engines meet all customers’ needs and are easily customised with a broad range of
options, suitable for multiple working scenarios and complying with the most stringent emissions legislations.
With over 150 years of experience and expertise, FPT offers superior technology and outstanding advantages through all its products. The industrial power units (IPUs) incorporate either electronic or mechanical injection systems that enable them to be optimised for superior performance and extremely favourable fuel consumption.
The NEF engines in particular have proven their reliability with more than 1.7 million units produced since 2001. In the medium power range, this series ensures robust performance, durability, reliability and easy maintenance on both its models: the N45 and N67.
The N45 engine is a four-cylinder inline unit with a displacement of 4.5 litres that delivers maximum power of 126hp. It is an easily-installed power solution compliant with Tier 3/Stage III regulations and with extended oil service intervals to reduce downtime and improve productivity. The other NEF model is a six-cylinder inline engine with a displacement of 6.7 litres and a power output of 175hp. It is by far best-in-class for oil change intervals, which are up to 600 hours.
FPT Industrial Power Units are designed for reliable operations in all working conditions, with excellent fuel efficiency and best in class uptime.
A pumping installation for a local ski field in the South Island of New Zealand had a tight deadline and harsh environment to work with in order to successfully supply water for the field’s snow making facility. The solution for installer Think Water Leeston all came down to its choice of hose and fittings.
Think Water wanted to avoid rigid pipes that can be affected by the high iron-bacteria levels, which can cause clogging and unpleasant odours. They also required a product that would not rust over time.
The limited space in the bore and need for a cost-effective and speedy installation left them with limited options.
Think Water chose Crusader Hose’s Flexibore based on its previous successful experience using the product. Flexibore 250 series bore water hose is a flexible riser used for groundwater pumping. The depth of the installation was 105m using 6” (152mm) Crusader Hose Flexibore 250 series hose and fittings.
Grant Collier, Owner of Think Water Leeston, NZ, said, “We have learnt over the few years since we have been using Flexibore that it far out performs any alternatives in all facets.”
Mr Collier said that they chose Flexibore for this particular project due to the ease and speed of installation, which was particularly important as they only had a limited time to get the pump into the bore.
The cost of the Flexibore was also an important factor, with Think Water needing to stick to the project’s budget. Mr Collier said Crusader Hose Flexibore 250 series was the obvious and preferred choice.
“The other option of steel pipe and flanging was prohibitive, and there was limited space in the bore so standard flanges wouldn’t fit.”
Flexibore also had the advantage of not being affected by the high iron-bacteria levels which Think Water sometimes encounters with other products especially steel risers.
“We know from past experience there won’t be any ironbacteria building up on the hose thus optimising the pumping efficiency to deliver the required flowrate,” Mr Collier said.
Think Water was impressed by Crusader Hose’s customer service, especially when solving the issue of quick product delivery.
“It is just great as they hold good stocks of all products making it very convenient for us resellers/installers.
“The team at Crusader have been great with all of our questions or queries. They have the product knowledge and will respond very quickly.”
Think Water was also reassured by the fact that Flexibore is manufactured to Australian standards, which are recognised and highly regarded by New Zealand customers.
“It is a quality product manufactured in Australia to Australian quality standards,” Mr Collier said.
“Our customer has been very pleased since the installation was completed and commissioned.”
Crusader Hose Flexibore® flexible risers for bore water pumping and dewatering, and Waterlord irrigation layflat hose is distributed and sold in New Zealand by Water Supply Products, NZ.
The introduction of our new SSW900, low voltage soft starter series continues to build on our broad motor starter range offered in Australia.
Torque control through the starting, processing and stopping functions remains the core to any good plant operation(s), and the product features and functionality of all WEG variable speed drives (VSD) and soft starters are designed to deliver just that.
A risk of any product diversity is complexity in programming with the subsequent difficulties for those providing general support services, but we have that covered.
Every VSD and soft starter from WEG is designed and manufactured in-house, and comes with a common and universal approach to parameters, setup and complex programming functions.
Low and high voltage soft starters covering outputs from 2.2 to 5740kW, ultimately shares the same manual. Similarly our VSD range covers drives from smallest single phase units up to state of the art 11kV systems, which share a majority of parameters and logic.
Maximising the investment in the training of operators and technicians is made profoundly easier by this strategic approach to product design.
Speed in commissioning and during the fine tuning of processes underpins an overall lower cost to the customer, and having a consistent platform across all our motor controllers makes this a reality.
The new SSW900 low voltage soft starter is the latest addition to our range. While keeping with the consistent approach, the SSW900 comes with additional functionality and contemporary features and will be taking over from the SSW06 series, which has been a product of choice for over 12 years.
This product fits seamlessly into our portfolio, with no disruption to our customers, distributors or service network, bringing functionality and practicality to the idea of "thinking globally, acting locally".
Volvo Penta. Robust, fuel efficient industrial diesel engines that keep running even in the toughest conditions. Easy to install, operate and maintain. A powerful partnership you can trust all the way from the drawing board throughout the operational life of your engine. Competitively priced complete power-pack units ready for delivery Australia wide with a local support team on hand 24/7. To find your nearest dealer visit www.volvopenta.com
TECO Electric and Machinery is a market leader, well-known for producing high-quality motors. Unsatisfied with producing only motors, TECO committed to the manufacture of motor drives over 20 years ago. In 2016, the company launched the TECO MV510 range of medium and high voltage drives that showcases its manufacturing prowess.
Founded in 1956 for motor production, TECO Electric & Machinery Co has evolved into a major business group spanning heavy electric equipment, home appliances, information technology, communications, key electronic components and parts, infrastructural engineering, financial investment, dining, and services, with its business scope covering over 100 cities in more than 80 countries in the five major continents.
In the future, in addition to continuing profound cultivation of its core businesses, TECO will develop in the direction of businesses with high added value, such as smart products and systematic solutions and dedicate to the expansion of hi-tech businesses, with the objective of "energy conservation, emissions reduction, intelligence and automation," in order to build up a macroperspective and high-quality world-class brand.
TECO drives and motors are used in a variety of applications including industrial automation, industrial machinery, air conditioning systems, mining, oil and gas, energy-saving projects, pipelines and wastewater treatment.
Its MV510 range of drives is in compliance with global specifications for energy efficiency and environmental protection. The comprehensive portfolio ranges from 200–8000kW, boasts power-unit connection overlappedwave technology, and is capable of lowering damage to the insulated stress of a motors copper wire dv/dt and providing timely monitoring of operational status.
Options of IP31 and IP42 grade protections are available, plus RS485 interface, various communications formats—such as Modbus, Profibus, Devicenet and Ethernet—and passage of CE and IEC certifications.
The power supply input and output of MV510 general medium voltage drive meet the most stringent IEEE 519-1992 and GB/T145491993 standards, so there is no need for an independent input filter, saving customers the
cost for harmonic elimination.
Because of the high power factor of the system, the compensation device for power factor is not needed, thus the reactive input and the input capacity are reduced, and the cost for capacity increasing the power network is minimised.
Compared with other high voltage and high power MVDs, the MV510 has a number of significant advantages. Firstly, there is no need for extra output filtering devices or direct driving of the general high voltage synchronous or asynchronous motor, and the temperature of the motor will not increase. There is also no need for motor derating operation, and no dv/dt damage will occur to the motor and cable insulation.
Due to the modular design of the power cell, it is quite simple to replace it and moreover, only a few spare parts are necessary. The power cells are universal and can be used in drives of the same current rating, regardless of voltage class.
Other functions and features include:
• Protection of overload and overcurrent
• Protection of open phase and grounding
• Protection of overvoltage
• Overheat protection
• Current limited function
• Interlock protection of control power supply
• Two sets of control power for redundancy power cell bypass function (optional)
• Cabinet door opening alarm function
• Lock-phase function
• Synchronising switch function between variable frequency and work frequency
• Soft start of motors, no impact to mechanical equipment and network
• IoT (Internet of Things)
With units already being sold, the TECO MV510 range of drives is making a significant contribution to the motor and drive market.
We provide collaborative, quality design and development services ranging from concept to high volume manufacturing. As a leading wholesale plumbing business, we carry various brands and use innovative technologies such as 3D printing to bring concepts to life. In addition, our team of engineers can ensure products hold current industry specific standards and licenses.
So, if you have a great idea for a product, we’re here to help. We can assist you from inspiration to reality with collaborative design, engineering and manufacturing resources. Beyond that we can distribute your product nationwide and present it to significant players in the Australian plumbing industry.
At Austworld, we may be one of Australia’s largest suppliers and manufacturers of quality plumbing and drainage solutions, but when it comes down to it we’re a family that’s here to help you achieve the best for your family.
For many years the development in technology and design of taper grid couplings has been stuck in the 1970s and 80s, with leading manufactures of grid couplings being copied by cheap, inferior product from questionable manufacturers.
Traditionally when grid coupling teeth have worn out, you have to replace the complete hub assembly.
Drive Systems and CMD Winflex now offer customers something new in the development of grid couplings.
Drive Systems is the Australian and New Zealand distributor of CMD Winflex couplings manufactured 100 per cent in France. CMD Winflex has developed its replaceable tooth ring design hubs for both its larger sizes of the DG horizontal aluminium cover and T Series vertical steel cover couplings.
On larger size taper grid couplings, it becomes an expensive process to replace the complete hub assembly. Especially when most of the time there is nothing wrong with the hub section of the couplings, just worn teeth.
Winflex Tooth Ring Hubs—Winflex DG and T Series Taper Grid Couplings sizes
Tooth ring hub design in the DH series starts at size 15DG (1150T10) and in the T series vertical steel cover from size 28T.
CMD Winflex Tooth Ring Hubs allow users to just replace the tooth component of the hubs. A great bonus when there is absolutely nothing wrong with the existing bore and keyway.
• 40 per cent of the price of a complete hub assembly
• 85 per cent lighter than complete standard hubs
• Less weight allowing easier and safer handling
• Faster change over time reducing downtime
• Cost reduction of critical spares
CMD WINFLEX COUPLING APP
Download our new mobile app “CMD Couplings” on App Store or Google Play. Use our coupling selection tool which helps you to find the type of coupling required for your application! Just enter the service factor, the absorbed power and the operating speed. CAD files of your coupling can be downloaded for your convenience.
For more details on the CMD Winflex coupling range, contact Dean Hansen at Drive Systems on +61 (0) 3 9796 4800 or www.drivesystems.com.au.
The role of plant management is to operate both efficiently and safely. Just as blood is pumped around our body through a network of arteries and veins, the lifeblood of most industrial processes is usually pumped through a vast network of pipes and valves.
With pumps providing the required head and flow, valves are then used to relieve pressure (safety valves), mix and direct flow (control valves), and isolate one section of pipework from another (isolation valves of various designs, for example ball, gate and butterfly valves).
Where absolute isolation is necessary for either process or safety considerations then the selection of the correct valve becomes critical.
For almost 50 years the triple offset valve has been continuously developed to fill this space. Known as triple offset because the axis controlling rotation and seating are displaced from their traditional position, these valves offer some unique benefits to many industry applications.
The greatest of these advantages is the low torque required for sealing and the high integrity level of the seal.
Unlike a traditional butterfly valve which relies on greater force to achieve better sealing, the triple offset design allows the disc to move to its final sealing position with extremely low torque, then the high-level sealing is achieved by way of a laminated disc face closing onto a stellited seat.
The ARI ZETRIX triple offset valve guarantees a permanent, tight seal conforming to leakage rate A according to DIN EN 12266-1. In addition, the ZETRIX valve has been tested and approved as fire safe, according to German clean air regulations (TA-Luft), SIL and ATEX. The wide operating temperature range of -60 °C to +427°C allows the ZETRIX valve to operate in most liquid, gas and steam applications.
In the UK, the ZETRIX valve is increasingly being installed in a double block and bleed arrangement to meet the stringent demands of British HSE Guidance 253. In many piping installations the overall length of this configuration is actually shorter than the existing isolation valve and thus can easily be installed with minimal piping modifications.
With end connections available in butt weld, fully lugged and double flanged—and overall design in conformance with most international standards (EN 12516, ASME B16.34, API 609)—the ZETRIX triple offset valve is the natural choice for many traditional (and harsh) industrial applications.
Where an emergency shutdown function is demanded, ARI engineers have the expertise to design the required actuator mechanism. For one such recent application ARI achieved a 0.6 second close time on a DN600 (24”) ZETRIX valve. This performance provides reassurance of complete safety, with a quality valve designed to rapidly stop the flow of a hazardous fluid or gas upon the detection of a potentially dangerous event.
With the available size range being constantly increased— currently double flanged DN80 to DN1200, lugged DN80 to DN600, and butt weld ends DN80 to DN600—the ARI ZETRIX triple offset valves, in cast and stainless steel, are being installed for liquid, gases and steam applications in:
• Oil and gas processing
• Refineries
• Petrochemical plants
• Solar thermal power stations
• Power plants
• District heating (Europe)
• Pulp and paper production
• Steelworks
• Sugar processing
• Industrial and plant manufacturing in general
Spanning six years and five major projects, Unitywater’s $30 million upgrade of the greater Caloundra area’s sewerage network culminated late last year as construction of a new 10m diameter and 10m deep sewage pump station at Duck Holes Creek was completed. With the only pump able to meet the varied discharge head requirements of the pump station manufactured in Europe and a long procurement time expected, preplanning was vital to ensure the equipment arrived at the right time for the contractor to install without delay.
With the population in the Caloundra area continuing to grow, the area’s sewerage network needed to be upgraded to meet the expanding needs of the community.
Unitywater Acting Executive Manager Sustainable Infrastructure Solutions, Amanda Creevey, said, “The purpose of the upgrade was to improve the capacity and efficiency of the sewerage network and manage sewage flows to cater for the growing communities of Caloundra, Pelican Waters, Little Mountain, Golden Beach and Bellvista.
“We also had to consider the new Caloundra South (Aura) development and ensure we had the infrastructure in place to service the early stages of the development.
“As well as the new pump station, we upgraded 2.5km of sewerage pipeline with a new 900mm diameter pipe. Construction was completed using two horizontal directional drills, with one being the longest horizontal directional drill of its kind in Australia.
“Constructing the pipeline in this way minimised the impact on the environment and community.
“The new pump station allows us to better manage flows in extreme wet weather events and minimises any overflows into the Pumicestone Passage.”
Designing and constructing the pump station
“We were able to take parts off-line while construction works took place, while still having an operational pump station.
During the design stages of the project, four options for the Duck Holes Creek Pump Station were considered, with the final design chosen as it allowed Unitywater to maximise the life of its assets by re-using the existing 10m-deep wet well that had been constructed in the 1990s.
“One of the challenges with this project was managing sewage flows, as the construction was carried out in stages,” Ms Creevey said.
“Another challenge was considering the logistics of the upgrade, particularly the size and weight of the three new pumps, which each weigh three tonnes. We had to keep this in mind for future access and maintenance.”
Pump selection and procurement
Ms Creevey said pre-planning was very important during the procurement stage, as Unitywater knew which pumps were needed when the project was designed. However, the
pumps had a particularly long procurement time as they were manufactured in Europe.
“In order to reduce the procurement time for our contractor during the construction phase, we purchased the pumps early and transferred them to our contractor when the project began. This allowed us to reduce any unnecessary delays,” Ms Creevey said.
“In this scenario, the chosen pump was the only one that met our requirements for this project. This pump station delivers into a common rising main that extends approximately 9.4km to the sewage treatment plant.
“This rising main also receives inflows from five other pump stations, therefore discharging head varies depending on flows from other contributing pump stations. It was critical that these pumps were able to operate safely for the full range of contributing flows from these pump stations.
“The new pumps were tested to ISO 9906 Grade 1B, which is the European equivalent to the specified Australian Standard. The pumps were manufactured and tested in Europe.”
Ms Creevey said maintenance and repair schedules are vital for all of Unitywater’s assets to ensure they operate efficiently and meet their expected service life.
“The pump station is on our annual maintenance program, and each pump is inspected and serviced twice per year.”
As part of Unitywater’s Reconciliation Action Plan, the Duck Holes Creek Pump Station was given a bright and contemporary facelift through a highly creative and collaborative community artwork process involving local Aboriginal emerging artists. The initiative formalised the utility’s commitment to provide opportunities for Aboriginal and Torres Strait Islander people and celebrate their culture in the areas it operates.
“Local artist Bianca Beetson was commissioned to work together with members of the Kabi Kabi community to design and paint the artwork,” Ms Creevey said.
“This site has significant cultural heritage as it was one of the last functioning Aboriginal camps on the Sunshine Coast, and was still operating in the early to mid-1900s.
“The design reflects the ancient and sacred connection of Indigenous people to the Duck Holes Creek area and the Sunshine Coast region more broadly.
“The artwork is spectacular and has really helped brighten up our new pump station.”
A chance meeting in the car park at the 2018 WIOA (Tamworth) conference between David Cashen (WIOA Operator of the Year and Supervisor of the Bathurst Water Treatment Plant) and Phil Rothheudt, the NSW Regional Manager for Hydro Innovations (H-I) led David to the H-I display stand featuring a Ragazzini peristaltic pump.
Hydro Innovations is an Australianowned pump engineering company and is the exclusive Australian distributor for the world recognised Gorman-Rupp pump range, Edur Pumps from Germany, J S Proputec Lamella Pumps from Denmark, Venturi Aerators from the US, as well as the Ragazzini peristaltic pump range from Italy.
David’s plant had two peristaltic pumps transferring carbon slurry for use in the plant’s treatment process. The slurry is quite abrasive, so hoses needed replacing once or twice per year. This in itself was okay, but the hose changes were exceedingly messy because the pump casing needed to be filled with lubricating fluid—because of the “shoe on hose” design. In the event of a hose failure, a mixture of carbon slurry and lubricating oil resulted in a mammoth mess to clean up, inside and outside of the pump.
Hose replacements and the consequential cleanup of carbon mixed with lubricating oil could take days, and David also had the cost of the—not inexpensive—lubrication fluid to replace each time, on top of hose costs.
Once David had been shown the features and benefits of the Ragazzini peristaltic pump over his existing ones, he was convinced he had found the answer to his messy hose changing issues.
The Ragazzini peristaltic pump features a number of enhancements over other brands which make them highly reliable, easy to service and maintain, with features including:
• A “roller on bearings” design which eliminates the need for lubricating oil, reduces friction on hose (rollers instead of “shoes”) resulting in extended hose life
• An automatic retractable roller system for easy maintenance, hose change over and to take pressure off hoses during pump rest periods
• A leak detector to automatically stop the pump when a hose fails and send an alarm, which minimises product loss
• No (hose) lubricating oil in pump chamber; no mess to clean up or potential contamination of pumped product or surrounding area in the event of a hose failure, greatly simplifying hose change outs
• Choice of seven different hoses—the right hose for the right product
• Duties from 1L/hour up to 180,000L/hour, operating pressures up to 15 bar
Two Ragazzini model MSO pumps were subsequently supplied and one fitted immediately to see if it performed to expectations and to the promises made.
The one pump has now been operating since July 2018 (running continuously for up to 18–20 hours per day in the hotter periods). At a recent inspection in April 2019, there had been no hose failure or need to change out the original hose.
David Cashen’s expectations have been more than realised with not only a clean and reliable system to pump the carbon slurry, but a hose life that is up to nine months and still going.
The initial outlay has also been vindicated by the cost savings in down time and clean up time, reliability, reduced hose replacement and all
Specialising in custom design, manufacture, repair and service of centrifugal pumps for over 30 years
• Complete range of API 610 (ISO13709)
• Hydraulic and mechanical design
• Custom engineering, retro-fit, redesign
• Performance testing
• Service and repair
www.unitedpumps.com.au
T: +61 3 9464 9500 31 Western Avenue, Sunshine Victoria 3020, Australia
E: unitedpumps@unitedpumps.com.au
Why would anyone want to fill a perfectly good electric motor with oil? If you were to ask the manufacturer’s of oil filled submersible pump motors this question, they will give a number of good reasons. On the other hand, the manufacturer’s of air filled units will provide just as many good reasons why one should not!
This short article will explore this question in depth and investigate the pros and cons of each design. I will also try to expose any myths that each group of advocates may have inflicted upon the other. Although we may not decide upon a single clear choice for all applications, we should gain a better understanding of the capabilities of each.
Let us start with a short review of non-submersible motors and then compare their characteristics to those of submersible motors. I will also use these comparisons as we debate the pros and cons of each design.
The vast majority of electric motors are not filled with oil. A couple of notable exceptions include sealed refrigeration units and certain hydraulic systems that use oil for bearing lubrication and cooling. These oil filled applications are analogous to water filled circulating and submersible turbine pump motors that also use water for bearing lubrication and cooling. The rest, however, have nothing but air within the motor housing. They may use oil as a bearing lubricant, as is the case with vertical hollow shaft motors, but that oil is isolated from the stator housing.
The two most common enclosures found in NEMA frame motor construction are the open drip proof (ODP) and totally enclosed fan cooled (TEFC) designs. The ODP motor is open to atmosphere and uses an internal fan to force outside air through the motor housing. Because outside air is always moving through the motor housing, cooling is simple and efficient. There are times, however, when contaminants within the air can damage the motor windings and the ODP enclosure is not the best choice.
The TEFC enclosure is closed to atmosphere and relies on an external fan to force air around the outside of the motor housing. Cooling is not as efficient as the ODP enclosure and often one finds that the motor service factor is reduced when these enclosures are employed. A variant of the TEFC enclosure is known as totally enclosed non ventilated (TENV). These enclosures are normally used in direct drive fan applications and rely on the air moved by the driven machine
for their cooling. In non-fan applications, they may be fitted with a water jacket (heat exchanger) for cooling.
The submersible sewage pump motor also uses a TENV enclosure that has been modified in such a way as to prohibit water from entering the motor housing. Instead of a fan, the surrounding water is used to transfer heat from the motor housing. In unsubmerged applications, a water jacket may also be employed.
So far so good. We now know that the submersible sewage pump motor is just an underwater version of its TENV cousin. With this in mind, let the arguments begin. Figure 1 is a cross section of a typical submersible sewage pump. Although designs vary by manufacturer, each have a motor housing and rotor that are close coupled to a non-clog pump end. Higher end pumps will incorporate a dual shaft seals with an oil filled chamber between. Some manufacturers will install a seal leak sensor in this chamber to detect outer seal leakage before water has the opportunity to enter the motor housing. Some will also use a multiple sealing arrangement at the cord entry that includes epoxy potting of the individual motor leads. This step eliminates the “wicking” of water into the motor housing if the cord insulation is damaged. Sealing is a very important topic and probably has a greater impact on pump life than the motor fill. But our discussion here centres around why some manufacturers fill these motor housings with oil while others do not.
Unfortunately the stated pluses and minuses of oil and air filled motors are not always objective. If you check the literature, you probably will not find an objective comparison by a knowledgeable, independent author. Most of our own prejudices are influenced by the manufacturers themselves. And, why should we blame them? After all, their objective is to sell their own products, not those of their competitors. Let's see if we can remedy this situation by taking an unbiased look at each point of contention and either sustain it or cast it aside. And, by the way, I will let you make the final judgment.
Table 1 (page 50) lists some of the common pros and cons that are tossed about by the competing manufacturers. You will notice that the pros of one are, more often than not, the cons of the other.
The efficiency of a three phase induction motor is dependent upon the quality of its materials, how well they are assembled, and the design of the rotor/ stator assembly. If we were to look at the published efficiencies of three phase, horizontal T-Frame motors produced by various mainstream manufacturers, we would find that they vary by no more than a few tenths of a per cent. Also, we would find that larger motors are more efficient than smaller ones. Typical efficiencies for T-Frame motors range from about 84–90 per cent for motors under 10HP and increase to 96 per cent as horsepower approaches 200. Single phase motors are much less efficient and tend to lag three phase units by seven to 15 per cent.
Submersible sewage pump motors are similar in design to T-Frame motors but tend to utilise a more elongated stator in order to reduce the motor’s overall diameter. This design trade off results in a lower maximum efficiency when compared with a T-Frame motor of the same horsepower and speed. This efficiency reduction is especially evident in submersible turbine pump motors where their diameter must be greatly reduced in order to allow installation in a narrow well casing.
Oil filled motors are often accused of being less efficient because of a purported increase in the clearance between the stator and rotor. This increase, which is presumably required to accommodate the oil, is said to reduce the stator’s ability to induce a charge on the rotor. Although this may be the case in some models, all of the oil filled motors, with which I am familiar, utilise the same rotor/stator clearance as air filled
models. What does reduce an oil filled motor’s efficiency is the energy loss due to oil circulation within the stator housing. As a rule of thumb, this circulation requirement reduces efficiency by about 1.5 per cent when compared to an air filled motor.
Although 1.5 per cent may sound significant, we have to remember that motor efficiency is not our only concern. Pump efficiency is an equally important factor and, typically, pumps are not nearly as efficient as motors. In fact the efficiency of the total machine (pump and motor), known as wire to water efficiency, is the product of the two individual efficiencies. For example, when a pump with a hydraulic efficiency of 70 per cent is connected to a motor that is 90 per cent efficient, the efficiency of the entire machine is only 63 per cent. If motor efficiency is reduced to 88.5 per cent the total efficiency drops just one per cent to 62 per cent—so efficiency does not appear to be a major issue.
In an ODP motor, heat transfer is accomplished through conduction. Although some conduction occurs via direct contact of the stator laminations with the stator housing, the majority is due to air flowing around and through the stator. Normally we think of convection as the heat transfer agent when a fluid such as air is involved but, if that fluid is flowing, the physics changes and the result, although complex, is a combination of both conduction and convection.
In a TENV motor, the spinning rotor causes air movement within the stator housing and both conduction and convection are involved. In this case, most of the conduction occurs through stator/housing contact, but some is also due to moving air contacting the motor housing. The major difference, as compared to the ODP motor, is that there
Air filled motors
Oil filled motors
Pros Cons
• Higher motor efficiency
• Better bearing lubrication
• Longer life
• Easier maintenance
• Better heat transfer
• Better bearing lubrication Longer life
• Permanent lubrication
is a finite amount of air within the motor and therefore, its ability to transfer heat to the housing is limited 1. Once heat is transferred to the motor housing, it is removed by forced air or a water jacket.
Air filled submersible pump motors cool themselves in exactly the same way as the TENV motor. They do have a distinct advantage in that water is in direct contact with the motor housing and conducts heat more rapidly than does the air provided by a fan or even an external water jacket. But, if it is operating unsubmerged that advantage disappears.
The oil filled motor also cools itself primarily through stator/ housing conduction, however, it does have an additional advantage. The circulating oil with its greater heat capacity and thermal conductivity transfers more heat, more quickly to the motor housing than does air 2. For this reason, oil filled motors tend to operate at somewhat lower temperatures than do air filled models. Oil filled motors also reduce the possibility of winding hot spots by providing a more even heat distribution. This is a particular advantage when Class B winding insulation is employed. For example, even a small increase in operating temperature from 100ºC to 110ºC reduces the projected life of Class B insulation from 140,000 to 80,000 hours 3. With Class H insulation, this advantage is less significant at operating temperatures below 120ºC.
Another factor that affects operating temperature is the stator mounting method. If the stator is pressed into the motor housing, the metal to metal surface area contact becomes greater when compared to a non-pressed (bolted) stator. The result is better conductive heat transfer, and this is the reason non-submersible T-Frame motors utilise pressed in stators. But, there is also a significant advantage to the bolted stator—it is easier to remove and replace, and therefore reduces the cost of maintenance. When a submersible motor is filled with oil, the conductive differences between the two stator installation methods becomes moot because the oil’s greater thermal conductivity increases the heat transfer between the stator and the housing.
Both oil and air filled motors can operate in an unsubmerged environment. Although oil filled motors transfer heat more rapidly to the motor housing than do air filled models, how long either can operate depends more upon the mass of the motor than it does with the fill fluid. After all, one could easily design a TENV motor of almost any horsepower that can cool itself without outside intervention if the size of the motor and its cost were not a concern. For example, if one were to construct a 2HP submersible motor on a 10HP frame, it could run unsubmerged indefinitely. Its sheer mass and surface area would provide the necessary cooling. Unfortunately, one does not often have
• Poor heat transfer
• More frequent maintenance
• Lower efficiency
• Environmental hazard
• More difficult to maintain
that luxury when designing a submersible sewage pump. Therefore, supplemental cooling is usually required. In some instances, diversion of a portion of the pumpage so that it flows over the motor body is sufficient. In other cases, a cooling jacket and an external liquid source is required.
Depending upon the application, a motor’s bearings must support both axial (back and forth) and radial (sideways) forces. For example, when a T-Frame motor is flex coupled to a base mounted centrifugal pump, the motor’s bearings will see radial forces generated by the spinning rotor and the torque generated by the pump. They experience very little, if any, axial loading. That same motor in a belt drive application would undergo an additional radial force generated by the tension on the belt.
In the case of close coupled pump motors, where the impeller is attached directly to the motor shaft, these same radial forces exist but are joined by axial forces. The axial forces are either backward or forward loads that are generated by the pump and its application environment. Vertical close coupled pumps, like the submersible sewage pump, see an additional axial force in the form of the hanging weight of the rotor/impeller assembly.
Roller and ball bearings belong to a somewhat misnamed family known as antifriction bearings. These bearings reduce friction and wear by utilising a thin film of oil or grease to separate the balls or rollers from their inner and outer races. The sole purpose of this lubricating film is to reduce metal to metal contact. Theoretically, this film could be only a single molecule thick and still meet its objective.
Although there are ongoing debates over which form of lubrication, oil or grease, provides superior protection, it appears that both perform equally well in most applications. Under conditions of extremely high heat, grease is preferred, while oil is the choice in unusually high thrust applications. Since the submersible sewage pump motor typically sees neither of these extremes, either should suffice.
The air filled motor’s bearings are usually grease lubricated. An exception is the high thrust vertical hollow shaft motor where the lower bearing resides in an oil chamber. Smaller air filled motors usually incorporate sealed bearings. This type of bearing is greased for life, where life is defined as a certain number of hours under certain conditions. Medium and larger motors use regreasable bearings. Oil filled motors, on the other hand, rely upon their dielectric oil for lubrication. As long as the proper grade of lubricant is used and the manufacturer’s instructions are followed, both lubrication methods will perform satisfactorily.
One precaution, however, is advised. Over greasing of the bearings of air filled motors, especially those with external grease fittings, must be avoided. Grease can damage the stator winding insulation and create hot spots by limiting heat transfer.
Most of the normal maintenance a submersible sewage pump receives tends to be the same regardless of its fluid fill.
Replacement of the power cord, control cords, impeller, wear ring and seals are very similar regardless of the design. One area that can differ is relubrication. The oil filled motor does not require relubrication as long as an inspection of the oil verifies that it is has not been contaminated by water or degraded by excessive heating. The air filled motor does require regreasing, but if it is fitted with external grease fittings, this can usually be accomplished during normal maintenance inspections. If external fittings are not supplied, the motor must be disassembled for regreasing.
Although bearings are more reliable than ever and Class H insulation is prolonging stator life, there will come a time when a motor must be disassembled. With the oil filled motor, an extra step is required. The oil must be drained and disposed of properly. If it was not damaged by excessive heat (motor overload etc) it can be filtered and reused in seal chambers or other white oil applications. Once the oil is removed, stator, rotor and bearing replacement proceed in the same manner as air filled motors.
Pressed in stators, whether they reside in air or oil filled motors, require that the stator housing be heated for removal and replacement. For this reason, manufacturers of pressed stator motors offer replacement stators preinstalled in the stator housing. Although the stator can be rewound, the cost is often a wash. For this reason they are often replaced. Bolted stators are less costly to rewind due to the reduced labor required for removal and reinstallation.
Finally, one of the concerns that is sometimes raised about oil filled motors is the potential for the oil to enter the environment. Although modern dielectric oils do not contain environmentally hazardous chemicals and are not considered hazardous waste by the EPA, they are not readily biodegradable. Therefore, it is important to minimise the introduction of any lubricant into our wastewater systems.
Catastrophic failures involving loss of oil from oil filled, double sealed pumps are rare in monitored pump stations. Because of the very different operating environments of the inner and outer seals, it is statistically improbable that the inner seal will fail before the outer one. The vast majority of the oil resides within the stator housing. The amount that resides in the seal chamber
is small and, in the event of an outer seal failure, a seal leak probe located in the seal chamber detects the presence of water and produces an alarm condition. This allows replacement of the outer seal long before the possibility of an inner seal failure.
Most air filled motors also utilise a leak probe in the seal chamber to detect an outer seal failure. Some, however, locate the probe in the motor chamber—a design that can compromise the stator windings if both the outer and inner seals fail.
Well, there you have it—a comparison of the pros and cons and, in a format I believe to be reasonably accurate and unbiased. There are, without question, several differences, but are these differences really advantages or disadvantages? Below is a summary of each:
1. There is a small difference in air and oil filled motor efficiency but it has little effect on the overall efficiency of the system.
2. The oil filled motor does run cooler and distributes heat more evenly, but class H insulation may make heat transfer less important at temperatures under 120ºC. In bolted stator designs, oil also increases conductive heat transfer.
3. Oil filled motors may also have an advantage in unsubmerged applications where a water jacket is not used, but it disappears when one is installed.
4. Bearing lubrication does not seem to be an issue if the manufacturer’s instructions are followed, but care must be exercised when regreasing air filled motors via external grease fittings. Oil filled motors usually do not require relubrication.
5. Although oil must be drained from an oil filled motor prior to its disassembly, most of the normal maintenance procedures are similar for both designs. One disadvantage is found in air filled motors without external grease fittings. They must be disassembled for regreasing.
6. Although dielectric oil is not a hazardous material, it is not readily biodegradable and should not be introduced into the environment. Dual seals with an internal leak sensor located in the seal chamber will prevent oil leakage from the motor housing.
Wastewater treatment is an integral part of the sustainable development of modern cities. According to international water association (2017), only 20 per cent of all wastewater is treated globally. Meanwhile, this figure is projected to increase substantially by 2030 as part of the sustainable development goals, UN-Water 2017 theme. Additionally, factors including population growth, water shortage and stricter environmental regulations demand a considerable increase in the capacity as well as the efficiency of current wastewater treatment plants (Munro-Smith 2018).
Alarge portion of the total energy consumption in wastewater treatment plants is used for pumping wastewater and sewage within the treatment processes (Longo, d’Antoni et al. 2016).
Although the energy usage of the sludge transportation systems is critically important, wastewater pumping systems are not commonly operating in their best efficiency points. By improving the pumping systems, better energy efficiency for wastewater treatment processes can be achieved. Several reasons underlie the inefficient operation of sewage sludge pumping systems.
1. Typical variation of sludge rheology
Composition of sludge is subjected to seasonal change as such in rain season there is more water in the influent of a wastewater treatment plant or hot summer the sludge microorganisms are more active, and the biological treatments are more efficient (Mahmoud, Zeeman et al. 2004, Water Environment 2008).
So far, no research has shown the variation of sludge flow properties due to the season changes or process changes. Because of that, pumping systems were designed based on significant assumptions of the sludge flow properties to accommodate such variations.
To address this issue, we have determined the rheological variation of three types of sludge over one-year of measurements in a wastewater treatment plant in Melbourne, VIC using Herschel-Bulkley model. Figure 1 shows the relative variability of sludge rheology as well as its composition. It shows the extent of variability concerning the mean of data.
Among the Herschel-Buckley parameters, variation in k impacts more than others on the variation of pressure drop in the pipeline. k shows 34 per cent relative variation in digested sludge, 54 per cent in primary sludge and 61 per cent in thickened waste activated sludge. While, τH shows 20 per cent relative variation in digested sludge, 40 per cent in primary sludge and 40 per cent thickened waste activated sludge.
Also, our studies (Farno, Baudez et al. 2015, Hii, Farno et al. 2019) suggested a possibility of predicting rheology from the variation of organic matter. In this method, a variation of solubilised organic matter in respect to the original soluble organic matter before thermal treatment was shown directly proportional to the variation of rheological parameters of sludge with respect to their values before the treatment. We also showed that the percentages of sludge solubilisation and its solubilisation kinetic rate were not influenced by sludge concentration.
The design of wastewater pumping systems requires a reliable means of calculating pressure drop at various flow rates. But due to the complex behaviour of sludge (i.e. flow behaviour) which typically requires a few rheological parameters rather than a single ‘viscosity’ (Malkin, Masalova et al. 2004, Slatter 2004), pressure drop calculations are not accurate.
To obtain the rheological data, one needs to fit the sludge flow curve with a rheological model (Mulbarger, Copas et al. 1981, Carthew, Goehring et al. 1983, Eshtiaghi, Markis et al. 2013). Three models mostly used for sludge are Bingham Plastic, Herschel-Bulkley and modified Herschel-Bulkley:
Where τ [Pa] is shear stress, γ= -dv/dr [s-1] is shear rate, v [m/s] is velocity along the flow direction (e.g., along a pipeline), r [m] is flow cross section distance (e.g. radial distant from pipe centre), and τB [Pa], τH [Pa], k [Pa.sn], n [-] and α [Pa.s] are fitting parameters of the models.
As the parameters increase in the model, the model becomes non-linear, while the predictions are more accurate, the fitting procedure and the pressure drop calculations become more complicated.
2.1.
Common fitting software dealt with non-linear models (e.g. Herschel-Bulkley and modified Herschel-Bulkley) just like a minimisation problem defined with an objective function to be minimised at a value. As such, the operator can choose between different objective functions, algorithms as well as model equations which impact on the results (Dochain and Vanrolleghem 2001).
In contrast, for Bingham-Plastic model, there is an analytical solution derived by differentiating the objective function concerning the model parameters. It is worth noting that, some minimisation methods linearised the non-linear models to reduce the complexity of parameters estimation which leads to biased results.
Generally, in a curve fitting, the measured variables are assumed independent holding an identical normal distribution at each measured point. But this is not always the case. For sludge, we showed that the residual error of flow curve fitting where Herschel-Bulkley and Bingham models are used is not normally distributed and increases with shear rate. To make fitting better for this system, one solution is to give weighting to residual errors but to avoid subjective judgments; one can use robust algorithms. In a robust fitting, outlier data do not impact on the estimation of model parameters (MathWorks 2016).
Another approach is to cut the data posing large residual errors at the high shear rate where pumping system is not operated. In fact, no perfect algorithm exists for estimating nonlinear model parameters. Through residual analysis on a broad set of sludge flow curve data, the best scenario for sludge parameter estimation has been identified in Table 1 (Farno, Coventry et al. 2018).
DS Robust least-squared Herschel-Bulkley shear rate 10 – 400 s-1
PS Robust least-squared Bingham-Plastic angular velocity 10 – 300 rad.s-1
TWAS Robust least-squared Herschel-Bulkley shear rate 10 – 200 s-1
Table 1: Regression scenarios with the best performance for each sludge sample.
Herschel-Bulkley model best-fitted sludge flow curve data between 10-300 s-1 with a robust fitting method while modified Herschel-Bulkley best-fitted sludge flow curve data between
0.1-1000 s-1 with either robust or conventional fitting method. Bingham Plastic model only shows acceptable performance for primary sludge.
Nevertheless, there are no unique results for non-linear parameter estimation (Dochain and Vanrolleghem 2001). Each parameter is determined with a confidence region (commonly 95 per cent confidence is selected) in which true model parameter exists. As a result, the calculation of pressure drops using the fitting parameters within the confidence region results in a range of pressure drops and not a unique value.
To investigate the impact of variation of rheological parameters on pressure drop calculation, critical pressure drops (transition point from laminar to turbulent) was calculated by integrating Eq.1 to 3 in respect to a pipe radius (Eq.4) and using Re3 friction model.
Eq.4 has an analytical solution for α equals to zero, but the numerical approach is required for n and α ≠ 0.
Figure 2 presents the probability distribution of critical pressure drop calculation in a typical sludge pipeline (300m length and 100 mm diameter) when the model parameters vary in the 95 per cent confidence region.
By comparing the variation of the pressure drop because of variation of fitting parameters, it was shown that among the studied models, the Herschel-Bulkley model performed best (least standard deviation); it fits a reasonably good range of shear rates whereas it does not induce uncertainty over pressure drop calculations.
Whereas, modified Herschel-Bulkley fits better but produced massive uncertainty over the pressure drop calculation. Also, Bingham-Plastic model was shown unable to fit most sludge flow curve in addition to the wide variation in calculated pressure drop.
We also performed a sensitivity analysis to compare the impact of variation of each parameter on pressure drop calculation which showed for all models, k has the highest sensitivity (Table 2).
Table 2: Sensitivity analysis of pressure drop calculation (With permission from Water Research for this table published in Farno et al. 2018).
We have developed a gadget software for the industry to design and optimise pipeline systems. We adopted Re3 friction loss model which was successfully used in mineral industries to develop this new platform for sewage sludge.
Although a rule of thumb was adequate for calculating pressure drop, and the laminar-turbulent transition point in a dilute sludge pipeline, for sludge at high concentration which exhibits significant visco-plastic property, a precise calculation based on Re3 friction loss model requires. This adoption is based on the similarities between the rheological behaviour of thickened sludge and thickened mineral slurries.
The gadget was also made capable of fitting the three models to raw flow curve data by implementing the best regression methods mentioned above. It can predict pressure drop of a number of pipes at different diameters to estimate total pressure drop and provide the system curve for each pipe (Figure 3).
By utilising this gadget, engineers are not only able to use our specialised regression method to obtain rheological properties, but they can also visualise the laminar-turbulent transition point. So by this way, they can optimise the system to prevent laminar settling as well as inefficient heat transfer in
Figure 3: Design gadget for sludge pipeline.
heat exchangers which happens in laminar flow. Another interesting feature of this platform is that it can predict the rheology of three types of sludge (anaerobic digested sludge, waste activated sludge and primary sludge) from its solid concertation and organic matter content using a fully trained model by experimental data.
Figure 2: Probability distribution of calculated critical pressure drop using three models, (a) Bingham Plastic (b) Herschel-Bulkley (c) modified Herschel-Bulkley, in a typical sludge pipeline (two per cent digested sludge in a pipeline composed of 300m length and 100mm diameter). With permission from Water Research for this figure published in Farno et al. 2018.
Any enquiry regarding this new platform can be directed to A./Prof. Nicky Eshtiaghi at RMIT University (nicky.eshtiaghi@rmit.edu.au).
Acknowledgement: The authors would like to acknowledge the financial support of Melbourne Water and South East Water in partnership with Water Research Australia for this study.
'International Water Association, 2017, Wastewater Report: The reuse opportunity'
Carthew, G, Goehring, C and Van Teylingen, J 1983, ‘Development of dynamic head loss criteria for raw sludge pumping’, Journal (Water Pollution Control Federation 55(5), pp. 472-483
Dochain, D and Vanrolleghem, P A 2001, Dynamical Modelling & Estimation in Wastewater Treatment Processes, IWA publishing
Dodge, D and Metzner, A 1959, ‘Turbulent flow of non-Newtonian systems’, AIChE Journal, 5(2), pp. 189-204
Eshtiaghi, N, Markis, F, Yap, S D, Baudez, J C and Slatter, P 2013, ‘Rheological characterisation of municipal sludge: A review’, Water Research 47(15), pp. 5493-5510
Farno, E, Baudez, J C, Parthasarathy, R and Eshtiaghi, N 2015, ‘Impact of temperature and duration of thermal treatment on different concentrations of anaerobic digested sludge: Kinetic similarity of organic matter solubilisation and sludge rheology’, Chemical Engineering Journal, 273(0), pp. 534-542
Farno, E, Coventry, K, Slatter, P and Eshtiaghi, N 2018, ‘Role of regression analysis and variation of rheological data in calculation of pressure drop for sludge pipelines’, Water Research, 137, PP. 1-8
Hii, K, Farno, E, Baroutian, S, Parthasarathy, R and Eshtiaghi, N 2019, ‘Rheological characterization of thermal hydrolysed waste activated sludge’, Water Research, 156, PP. 445-455
Longo, S, d’Antoni, B M, Bongards, M, Chaparro, A, Cronrath, A, Fatone, F, Lema, J M, Mauricio-Iglesias, M, Soares, A and Hospido, A 2016, ‘Monitoring and diagnosis of energy consumption in wastewater treatment plants. A state of the art and proposals for improvement’, Applied Energy, 179, pp. 1251-1268
Mahmoud, N, Zeeman, G, Gijzen, H and Lettinga, G 2004, ‘Anaerobic stabilisation and conversion of biopolymers in primary sludge—effect of temperature and sludge retention time’, Water Research, 38(4), pp. 983-991
Malkin, A, Masalova, I, Pavlovski, D and Slatter, P 2004, ‘Is the choice of flow curve fitting equation crucial for the estimation of pumping characteristics?’, Applied Rheology, 14(2), pp. 89-95
MathWorks, T 2016, ‘Matlab Documentation’, Disponıvel em
Metzner, A and Reed, J 1955, ‘Flow of non-newtonian fluids—correlation of the laminar, transition, and turbulent-flow regions’, Aiche journal, 1(4), pp. 434-440
Mulbarger, M C, Copas, S R, Kordic, J R and Cash, F M 1981, ‘Pipeline friction losses for wastewater sludges’, Journal (Water Pollution Control Federation), pp. 1303-1313
Munro-Smith, H 2018, IBISWorld Industry Report D2921 Waste Treatment and Disposal Services in Australia
Slatter, P 2004, ‘The hydraulic transportation of thickened sludges’, Water SA, 30(5), pp. 66-68
Slatter, P 2008, ‘Pipe flow of highly concentrated sludge’, Journal of Environmental Science and Health. Part A, Toxic/Hazardous Substances & Environmental Engineering, 43(13), pp. 1516-1520
Slatter, P T 1995, ‘Transitional and turbulent flow of non-Newtonian slurries in pipes’, PhD thesis, University of Cape Town
'Water Environment Federation, 2007. Operation of Municipal Wastewater Treatment Plants: Manual of Practice 11, Chapter 6: Pumping of Wastewater and Sludge, Sixth Edition, McGraw-Hill Education.'
In the previous issue of Pump Industry magazine, Heinz P. Bloch and Tom Grove looked at the use of mechanical seals in the mining industry, focusing on the water saving aspects of sealing systems engineered to save both water and maintenance money. In this article, they continue the discussion, looking at mechanical seals design and selection in the potash industry.
Seal performance in slurry services is largely influenced by two parameters: the design of the seal chamber and maintaining proper control of the fluid film. The conventional option is an open throat seal chamber shown in Figure 1.
However, this design can have problems with erosion at the seal gland, caused by the velocity of the slurry around the seal face. The remedy is to use flow modifiers (ridges) machined or cast into the inside diameter of the seal chamber. In addition, the back vanes on the impeller are usually filled in, if a seal is used, to prevent dry running.
The second option (not shown) is to mount a mechanical seal into a stuffing box that had originally been designed for braided packing. Suppose the design intent was to use ½” cross section packing—for standard packing boxes this means there is about 1/8” clearance around the
seal rotary. As heat is generated by the seal, the process fluid dewaters and compacts around the rotating seal. As this occurs, the packing box eventually becomes clogged and the seal parts wear; fluid film is lost, which shortens life and ultimately leads to failure.
Figure 2 shows the third option, which is used in the applications described in part one of this article. Note the large cavity around the seal. The slurry velocity is interrupted by the closed frame plate between the impeller and the seal chamber. The seal mounts to a seal back plate, machined so that standard off-the-shelf seals can be used.
Seal selection differs with the severity of the slurry. The ANSI Hydraulic Institute Rotodynamic (Centrifugal) Slurry Pump Standard, 12.1–12.6-2005 specification for centrifugal pumps classifies slurries based on a Miller Number, which is
actually a value tied to abrasive wear on standard reference materials. Factors such as particle hardness, size and shape as well as corrosiveness can affect the Miller Number.
Slurries are ranked in four possible classes (Table 1):
• Class 1 = Light
• Class 2 = Medium
• Class 3 = Heavy
• Class 4 = Very Heavy
The class ranking for slurries is linked to the slurry specific gravity, concentration by volume (as a percentage) and average d50 particle size (in microns). At least one major seal manufacturer uses this guide to select the best seal for the application; this manufacturer accommodates the stipulations found in the ANSI Hydraulic Institute Rotodynamic (Centrifugal) Slurry Pump Standard, 12.1–12.6-2005 by using the following table:
the system must be sized and configured to remove the heat generated by the seal faces. Water management systems are pre-engineered to satisfy all requirements.
Piping plans for double mechanical seals fall under API Plan 52, Plan 53-(A,B,C) or Plan 54. Plan 53 (Figure 3) has a seal pot mounted above the pump and a fixed volume of liquid, the tank is charged with nitrogen to set a higher differential pressure between the pot and the box (Plan 52 has a lower differential pressure). If the inboard seal leaks (e.g. cavitation), the nitrogen forces the fixed volume of liquid into the pump and the seal runs dry if the tank barrier fluid is not immediately replenished.
Explaining the seal types used in slurry services
CDSA is the designation for a prominent manufacturer’s cartridge-mounted double mechanical seal. The seal operates in either rotational direction; it is built on a modular face component platform. The seal’s rotary is loaded by individual Alloy C276 springs, all of which are out of the process fluid. Inboard and outboard stationaries are interchangeable, monolithic and available in silicon carbide or tungsten carbide. CDSA can be mounted in horizontal or vertical orientation. Glands are available for standard bore and ANSI-Plus stuffing boxes. Smaller frame pumps using 5/16” cross section packing can be retrofitted with a CDSA without modification to the pump.
Another seal type is designated CDPH—essentially a cartridge-mounted heavy-duty double mechanical seal. It too allows operation with clockwise as well as counterclockwise rotation—its wetted components have large crosssections. In a CDPH, the rotating assembly consists of a 316L stainless steel holder; inserted into this holder is a press-fitted rotary face, available in carbon, tungsten carbide or silicon carbide. The inboard rotary is again loaded by individual Alloy C276 springs and all springs are out of the process media. The inboard rotary is designed with reverse face balance in order to withstand process system upsets. Inboard and outboard stationaries are interchangeable, monolithic and available in silicon carbide and tungsten carbide. In most designs, the area below the stationary seal faces is enlarged for maximum cooling and circulation.
With the decision on the seal type and an optimised seal chamber, the discussion reverts back to how to control the barrier fluid pressure and the general quality of the barrier fluid, outlined earlier in the previous article.
The control of the fluid film is a function of the piping plans and control systems used to ensure the barrier fluid is always at a higher pressure. Moreover,
Plan 54 (Figure 4) is a pressurised water-to-drain arrangement (or water is circulated by an external pump back to a holding tank), where the pressure is provided by an external seal water pump. The problem with a water-to-drain setup is that it is difficult to control the consistent flow and pressurisation of barrier fluid to a bank of pumps from a common pump header.
The representations in Figure 5 illustrate the problem. Three pumps are connected to a common header, the pump on the right is starved because an operator taps into the seal water to wash-down the area and directs water to an alternate flow/ use. When the pump on the right fails, it cross contaminates the other pumps if the line returns to a central holding tank. In addition, the water flowing through the seal is like a garden hose. If there is no resistance to the outlet pipe, the water has flow
and no pressure. This means the slurry ends up serving as the fluid film (in the inset) since the pressure across the slurry is higher than the differential pressure from water header to open drain. Slurry does not serve us well as a fluid film.
One widely used packaged solution combines two API Piping Plans: Plan 53-A and Plan 54. The advantageous water management system in Figure 6 isolates the application so that the fluid film in Figure 7 is controlled. Like Plan 53-A, the water management tank (Figure 8) is mounted above the seal application — the system pressure is controlled by a regulator on the top of the tank. Unlike traditional Plan 53-A systems, water is connected directly to the tank from a water header, which is similar to Plan 54.
If there is a loss of barrier fluid, the water source from the Plan 54 connection automatically recharges the system. A flow indicator on top of the tank indicates water is entering the system. Water quality is controlled by using an in-line filter prior to the regulator. The filter can be replaced online, although filter replacement is infrequent because the filter is not exposed to continuous flow of water. With a higher differential pressure in
7: The slurry makes contact with the inboard portion of a double (dual) mechanical seal. However, with the correct differential pressure between a clean barrier fluid (blue), only the clean fluid is found in the seal gap.
the tank, the inboard seal face seals clean water and does so even during process upsets.
An experienced water systems manufacturer recommends a 25 litre (6.5 gallon) tank for many of the more common slurry pumps in a potash processing facility. Although somewhat smaller tanks are available, a typical heat generation graph (Figure 9) shows the benefits obtained with a larger tank. Heat is dissipated over a greater surface area. This means the seal faces are sealing cooler water and heat is more efficiently dumped if the flow to the water header is interrupted or there is a process upset where the seal is operating dry on the process side.
In 2009, an abnormally cold winter at one of the various potash processing plants caused the water management systems to freeze. Despite this freeze incident, the mechanical seals continued to perform. Since this occurrence, the plant decided to retrofit the patented Freeze-Fuse™ option (Figure 10) on its many water management systems.
During normal production runs, even when the weather is below freezing, the mechanical seal produces heat at faces. As the density of the barrier fluid changes in the seal, it rises back to the tank and circulates back to the seal from the bottom of the tank. This produces enough heat to prevent freezing.
If the plant is idle and the pumps are shut-down, the water is subject to freezing. To prevent this, the Freeze Fuse™ is
fitted with a temperature sensor and bypass valve on the return line from the seal. This device will open at approximately 1.5ºC (34ºF), dumping water to drain from the tank and then closing again to allow circulation at 3.8ºC (39ºF).
Look for mechanical seals and suitable auxiliaries from experienced vendors. Strive to assign extra credit to providers that can point to successful partnerships with leading slurry pump manufacturers. And as you perhaps consider different slurry pump suppliers, be certain to coordinate and/or compare procurement standards, regardless of who supplies your pumps.
Heinz P. Bloch’s professional career commenced in 1962 and included long-term assignments as Exxcon Chemical’s Regional Machinery Specialist for the US. He has authored or co-written close to 700 publications, among them 20 comprehensive books on practical machinery management, failure analysis, failure avoidance, compressors, steam turbines, pumps, oil mist lubrication and practical lubrication for industry. He is an ASME Life Fellow and was awarded lifetime registration as a Professional Engineer in New Jersey.
Tom Grove has spent his career as an executive in the sealing technology industry. He is CEO for AESSEAL, Rockford, TN; reach him at tom.grove@aesseal.com.
With energy efficiency and lifecycle costs key concerns for end users, it is more important than ever to purchase a high-quality pump from an experienced manufacturer that meets the exact specifications of an application. Selecting a manufacturer who focuses on innovation, quality and exceptional customer service ensures the best pump for your application will be supplied and that it will be built to last, resulting in long-term cost savings.
Pioneer Pump has over 140 years of combined experience in the pump industry. Its founding principle to make pumps better ensures customers get extreme performance while using less energy, giving them the best lifetime value.
Since opening its operations in Australia in 2013, Pioneer Pump has established itself as a main player in the industry, with a focus on quality products, innovation and exceptional value and customer service.
Customers can rest assured that the team at Pioneer Pump will help them select and supply a pump that matches the needs of their unique application and that it will perform its duty as expected.
There are many considerations when selecting a pump and how closely it meets your unique operational specifications will determine its energy efficiency and lifecycle costs. Working with a manufacturer with experienced engineers on staff ensures you will be recommended the best solution.
Pioneer Pump prides itself on its extensive knowledge, experience and innovation; whether it’s sales, building, repairing, testing or supplying pumps. It has the know-how to ensure customers’ needs are met.
The sales team is on hand to provide friendly, knowledgeable service solutions, while its design engineers
specialise in designing and supplying products that meet customers’ specific requirements, ensuring best energy efficiency and low lifecycle costs can be realised.
From the time Pioneer Pump sits down with you to determine the best pump for your application until it delivers a pumpset that exactly meets those needs, the company infuses quality and innovation into every step.
The design engineers have the latest engineering software for the design and supply of General Assembly and Certified drawings in various types of pump builds. This gives the company the flexibility to manufacture products that its customers want and need.
Pioneer Pump products use an innovative impeller design, which moves more pumpage, more efficiently, size-for-size. The stainless steel air separation valve allows for quick priming with no product carryover and are designed for easy maintenance.
Pioneer Pump aims to stay ahead of the pack by constantly pursuing new ways to improve pump hydraulics, efficiency, reliability and performance.
quality and meeting standards
With manufacturing, assembly, testing and painting capabilities in its Australian factory, Pioneer Pump provides high-quality products that meet Australian Standards for safety and manufacturing.
The factory features four dedicated fabrication bays with a further two part utilisation fabrication bays, as well as experienced and qualified boilermaker welders on site. With an assembly area that takes up a large portion of the factory, every package is built from the ground up, from electric drive packages to diesel pumpsets, skids, trailers, tanks and manifolding.
Pioneer Pump is committed to ensuring that every unit it produces operates and performs to expectations and is the highest quality available. All diesel pumpsets are tested in its 50,000 litre test rig prior to dispatch to all customers.
Pioneer Pump aims for all customers to have a positive experience, from start to finish. Its customer service staff are courteous and friendly, ensuring a smooth and enjoyable interaction for the customer.
The Pioneer Pump Australia operation is also highly committed to servicing its customers in the region, so it carries over 200 pump ends in stock for approximately 60 different models and pumps are ready for quick build ups or dispatch as wet ends.
If you value quality products, leading market experience and innovation, exceptional customer service and a tailored, efficient experience, Pioneer Pump is on hand to assist with all your pump needs.
Learn more at dewateringsolutions.weir
There’s nothing worse than an unknown variable and there’s nothing more variable than water. Floods, torrential downpours, moving water from A to B – it can very quickly get out of control. That’s why the Weir Minerals team works tirelessly with sites to design tailored dewatering solutions. We use our expertise in both process and products to maximise efficiency and help you take control of your water. Copyright © 2019, Weir Minerals Australia Limited. All rights reserved.
www.minerals.weir
Located 30km north of Leinster in Western Australia, Western Areas’ $299 million Odysseus Project—part of the company’s Cosmos Nickel Complex—is expected to produce 130,000 tonnes of nickel concentrate and have a ten-year life. In January, stage one of an early works program was completed, including the construction of two new water management ponds (WMPs), an associated dewatering program and rehabilitation of existing decline infrastructure.
The Odysseus Project sits on a granted mining lease that is part of the high grade Cosmos Nickel Complex, and lies in the heart of the prolific Leinster-Wiluna nickel camp, home to many high-quality deposits such as Mt Keith, Cliffs, Perseverance, Rocky’s Reward, Honeymoon Well, Venus and Yakabindie.
Odysseus was identified in 2010 and is the most recent discovery in a string of successes at Cosmos. From 2000–2012, over 127,000 tonnes of nickel concentrate was produced.
The Odysseus Project will involve mining of the ore reserve via an extension of the existing Cosmos decline and processing via the existing plant and infrastructure, both of which will be upgraded.
The project will incorporate some of the latest technology, to further enhance safety, operational efficiency and reduce costs, including a stateof-the-art mine control room that will be the real-time operational centre, monitoring and controlling ventilation, refrigeration, pumping, paste filling and mobile fleet activity. The system will monitor personnel and equipment location, providing real-time feedback to the Ventilation on Demand (VOD) system to optimise power draw and ensuring chilled air is directed to the appropriate areas.
Western Areas Managing Director, Dan Lougher, said, “Odysseus will utilise a shaft hoisting system, which is justified based on a ten-year operating life and throughput averaging around 900,000 tonnes per annum. Western Areas has already secured an option over a high-quality, second-hand, shaft hoisting asset from South Africa that is ideally suited to Odysseus and has been
Cosmos open pit at the beginning of January 2018. Image from Western Areas.
costed into the DFS. The shaft hoisting operation will utilise a top-down mining approach, rather than the bottomup method assumed in the PFS, and accordingly has generated substantial savings in ore transportation costs, as well as a reduction in mine development CapEx.”
The early works program
Western Areas acquired the Cosmos Nickel Complex through a deal with Glencore in 2015, however, as the dewatering pumping system was deactivated in 2013, the groundwater inflows had flooded the underground mine workings and partially filled the Cosmos pit.
In order for mining operations to commence, in April last year a $32 million early works program begun and involves three major work programs over an 18-month period.
Stage one
Stage one of the early works program began in 2018 and was completed in January, with a focus on the rehabilitation of existing water management ponds (WMPs) and dewatering activities.
Dewatering of the main Cosmos pit commenced at 50L/s at the start of 2018 and was accelerated to 120L/s as the new water management ponds (WMPs) came online.
By the end of last December, over one million cubic metres of water had been pumped into surface water management ponds, reducing the water level by 37m.
Following the success of dropping the open pit water levels, a Schlumberger submersible pump was installed and commissioned in the southern vent in early January, adding 100L/s of additional pump capacity from a depth of 500m below the surface. This raised the total dewatering capacity to 220L/s.
The in-pit diesel pump was removed in late February having dewatered 90 per cent of the in-pit water and was expected to be replaced by an electrical pump station in early June.
Other progress during this stage included electrical reticulation, shaft headgear installation and upgrades for the 520-room camp site (the Cosmos village) to meet the needs of staff during initial works.
Stage two of the early works program began in January, and involves the construction of two new evaporation ponds and dewatering of the decline by Barimco for six months.
By the end of March, 2033m of decline had been rehabilitated to a depth of 236 vertical metres from surface. Primary ventilation has also been reestablished with the commissioning of a 55kW exhaust fan.
Following the expected completion of decline rehabilitation in June, a new pump station will be installed to assist ongoing dewatering.
The final stage will focus on infrastructure to support the rehabilitation of the decline from the portal to 500m underground. This stage will involve the pump station to be recommissioned and new pumping infrastructure to be
installed for the life of the mine. The design capacity of the ongoing normal operational pumping infrastructure for Odysseus will be 100L/s, which will be sufficient to manage estimated inflows of around 25–50L/s.
Once all three stages of early works are complete, Odysseus will be development ready based on the prefeasibility study schedule.
With first nickel concentrate scheduled for 2022, Odysseus will be one of the few nickel sulphide mines coming online just as forecast demand for Class 1 nickel is expected to substantially increase in the electric vehicle sector.
“The demand for Class 1 nickel sulphides in the battery and electric vehicle market is forecast to grow substantially over coming years,” Mr Lougher said.
“Odysseus is an important growth asset for Western Areas and should be one of the few new global nickel sulphide operations scheduled to come online as the forecast uplift in nickel demand for electric vehicles impacts the market in the 2022 timeframe.”
Some day all motors will be this efficient. But why wait?
The idea is beautifully simple. Combine conventional stator technology and a magnet-free rotor design, take a top-of-the-line industrial drive and software, and optimize the whole package for variable speed pump and fan applications. What you get is the performance of a permanent magnet motor at IE4 efficiency and the simplicity and ease of service of a regular induction motor. Stop waiting and take a closer look on www.abbaustralia.com.au
ABB Australia Pty Limited Contact Centre: 1800 222 435
Located in the Denison Trough area of Queensland’s Bowen Basin, Comet Ridge’s Mahalo gas project is considered to be in one of the largest undeveloped gas resources on the Australian east coast with and estimated 172PJs of 2P gas reserves. In March, Comet Ridge undertook initial production testing on last of three new wells, with initial results showing scope for increased pumping speed.
While early exploration in the region focused on conventional resources in Permian sandstone reservoirs, the Mahalo JV Project Area is now prospective for both coal seam gas (CSG) and coal extraction. Over 20 wells have been drilled in the Mahalo JV Project Area, with a majority of these drilled after 2004 when Comet Ridge acquired its interest and CSG exploration began. In mid-2017, Comet Ridge entered an agreement with Santos to assume responsibility to manage the field subsurface work in respect of the Mahalo 2017 Joint Venture Exploration Work Program and Budget until December 2018, which included the following works:
• Initial stimulation (underreaming) of the four Mira vertical pilot wells to improve water and gas offtake rates, and the potential of drilling a horizontal well in the pilot area to establish consistent production performance with the Mahalo pilot
• Drilling of a single step-out corehole to confirm reserves (Humboldt 1)
• Drilling of a horizontal well at Mira (Mira 6) which intercepts Mira 2
Underreaming work began in August 2017 and involved pulling out tubing and pumps from the wells, underreaming the coals in Mira 3, 4 and 5, and then re-running tubing and pumps. Mira 2 was also set up as the intercept well for the Mira 6 horizontal well.
The Mira 6 horizontal well was designed to intersect the thickest of the four seams at Mira (Castor seam) and run for approximately 500m in seam prior to intersecting Mira 2 after which around 450m was drilled in the same seam. On completion of drilling, the pump and tubing was reinstalled in Mira 2.
At first Mira 6/2 was brought online with low pump speeds which was gradually increased over time. With initial production rates encouraging, by March 2018 production had passed 1TJ/d and by June 2018 production had reached 1.4TJ/d.
In February 2018, Comet Ridge entered a second agreement with Santos to operate and manage the Mahalo 2018 Joint Venture Exploration Work Program and Budget on behalf of Santos.
With the successful exploration and appraisal program in 2017, Comet Ridge began planning and preparing for a five-well exploration and appraisal drilling program that started in 2018.
In January this year, the fifth and final well for the program was successfully completed after a three-month long drilling campaign that began in October 2018.
The new wells comprise of:
• Memooloo 2: Drilled to a total depth of 300m
• Struan 3/2: The Struan 2 vertical intercept well was successfully drilled to a total depth of 510m with the Struan 3 dual lateral well drilled to a total length of 822m
• Sirius Road 2/1: The Sirius Road 1 vertical intercept well was drilled to a total depth of 506m with Sirius Road 2 lateral well drilled to a total length of 1990m
Once drilling was completed on each of these wells, tubing and pumps were re-run and then put online for production testing.
Each of the production test wells were brought online at very low pump speeds, resulting in initial water rates of approximately ten to 12 bwpd (barrels of water per day) for each well.
Pump speeds have been progressively and slowly increased on the wells over the past couple of months. This has been to ensure bottomhole pressures are brought down slowly to avoid mechanical damage to the natural fracture system in the coal reservoirs.
As of March, Memooloo 2, the first well online, was producing 36 bwpd; Struan 3/2, the second well to be started, was producing 25 bwpd; and Sirius Road 2/1 was producing 20 bwpd.
When production tested, water rates for all wells (these and others) in the Mahalo Block had been consistently low, notwithstanding the significant gas rate of 1.4 MMcfd that was achieved in 2017 on the Mira 6/2 combination in the Mira pilot scheme.
Comet Ridge Managing Director, Tor McCaul, said these early production testing results are still preliminary but pleasing.
There is significant scope to increase pump speeds in these wells, with only about a quarter of the bottomhole pressure in each of the wells drawn down so far.
Core data was also taken from the three vertical wells (Memooloo 2, Struan 2 and Sirius Road 1) for gas content and isotherm analysis. Gas content laboratory analysis has now been completed on the Memooloo 2 and Struan 2 vertical wells and was ongoing on the Sirius Road 1 well in early June. Preliminary results for gas contents on the first two wells are in line with expectations, with Memooloo 2 results being particularly pleasing where one of the key objectives was to demonstrate developable gas content in the north of the block at a shallow depth.
Centrifuges are commonly used in the food and beverage industry for beer, wine, milk, water and juice. Internally the centrifuge has many layers of plates (or discs) stacked closely together so the speed of the liquid changes where different products are driven out of solution into solids and liquids. As an example, milk is heavier than cream, so the cream is driven by centrifugal force to the surface of the milk. The cream in turn flows off into a channel which leads to a collection vessel. The milk is forced out to the periphery of the drum and is collected in another channel into a separate vessel.
One is commonly called a basket centrifuge, normally a vertical machine used for smaller continuous processes, and the other is called a separator which is normally horizontally mounted and used for larger flow rates. Other uses for centrifuges are in sewage, wastewater, tallow, pathology, grinding machining coolant, oil industry to remove solids from the drilling fluid and the list goes on.
Centrifuges work at a relatively high speed and can have issues with imbalance and overall vibration. Pumps operate at rotational speeds between 1000 and 3000 rpm but frequently reach in excess of 6000 rpm.
All it takes is for the centrifuge to be out by 500g and the centrifugal forces will create up to 500kg of imbalance which can be extremely destructive. The more imbalance, the worse the final
result and damage. Initially it could just be damage to bearings and fatigue to the machine and pipework in particular. In the worst case, it could be a total and catastrophic failure of the machine.
An important factor that is often overlooked is the impact to production. If a machine is off-line, production is lost. If a machine completely destroyed, there could be no product produced for weeks while awaiting repair or replacement.
ifm has been involved with vibration analysis for almost 20 years with sensing technology to determine the level of machine wear and imbalance. In the simplest form, a single sensor is mounted on the centrifuge to detect the imbalance to give a warning to the operator or automatically turn the machine off if a critical imbalance is detected.
I first started in the industry selling air operated positive displacement pumps in 2004 for Oliver Spray Equipment. I had worked in manufacturing of oils and then adhesives before applying for an internal role at Oliver Spray Equipment, it was then that the Manager offered me the role in external sales.
Since then I have worked for Transmark FCX—which was bought out by Cooper Fluid Systems—then Pumpline which changed to Airblast. I have worked on some great and memorable projects during my time in the industry, but personally the most memorable moment in my career to date was when I made the move from Branch Manager to Part Owner in STEVCO Seals & Pumps Victoria.
One of the things I really enjoy about working in this industry is the variety of pump applications, whether its for wastewater, freshwater, food processing, plural component mixing for potting or adhesive applications.
I also enjoy the general industry—it is amazing the different solutions that people use for transferring fluids.
I have had many people I have sought advice from during my career in the industry. The first mentor I had was Tony Warby at Oliver Spray Equipment. He taught me a lot about myself on a personal level, as well as being a mentor on large projects teaching me how to pull together a successful proposal to completing a project. I am glad to say that I still keep in contact with him.
Other than Tony, I have worked with a number of other memorable pump personalities during my time in the industry, such as Peter King, who would be better known in the industrial spray game, but his knowledge and ability to recall part numbers off the top of his head is impressive.
I have also worked with John Lynch who was well known in Automotive/APV circles.
I became Vice President of PIA this year, after I was approached by John Inkster to support him in his role as President. I have a lot of respect for John and was humbled that he would invite me to take up this role.
I would like the PIA to be better known as the industry representative among pump distributors in the near future.
James Blannin began his career as an apprentice screen printer before finding his way into the pump industry in sales. Since then he has gone on to become Part Owner at Stevco Pumps & Seals’ Victoria branch and is currently Vice President of Pump Industry Australia (PIA). Here, James talks about his career to date, where the industry is heading and the important role the PIA plays in the industry.
As the only association dedicated to pumps, I think it is important for people in the industry to have a body that can provide information, training, consultation to government and peak bodies as well as provide networking opportunities for all.
One of the developments that has happened since I started in the industry that comes to mind is the mandatory star rating that will be enforced soon on smaller pool pumps.
Although it does not affect my business directly I believe the move towards energy efficiency will eventually affect us all in the industry.
I think one of the greatest challenges currently facing the pump industry is the access to information, and this will continue to play a big part in the future. It can be difficult to purchase or sell the best solutions if you are unaware of what current technology exists, hence the importance of a body like the PIA.
While a career in the pump industry is not going to make you rich, it is a rewarding industry if you persevere.
You will meet a lot of interesting and inspiring characters, and hear a lot of stories, but like any other career, you need to work hard.
My best advice for those starting out is to find a mentor who will spend the time to work through problems and applications and will help guide you in finding the best solution.
You don’t need to do it all yourself.
This year I have coached a junior basketball team, as well as playing in a senior’s team. I have also spent the last year coordinating the local Auskick centre, and having a go at Super Rules Football.
I also enjoy camping and getting out on the motorbike.
At Brown Brothers Engineers we have expanded our capabilities with two more quality pump manufacturers. In addition to the current world leading brands we can now offer the following range:
VERTICAL TURBINE PUMPS
Layne Bowler vertical turbine pumps have a proven record under the most demanding and toughest of conditions.
• Flows to 2,300 L/Sec
• Heads to 350 m
• Power to 1000+ kW
• Temperatures to 150°C
• Bowls Diameter up to 45 inch
WELCOME TO THE BIG END OF TOWN.
When high head and high flows are required look no further than this quality Italian made range.
• Flows to 5000m³/h
• Head to 220m
• Pumps that exceed EN733 (DIN 24255 standard)
Call us today to see how we can deliver your pumping solution.
System troubleshooting can be a difficult process for even the most experienced professionals and securing the necessary data to support your conclusions can be even more challenging. Before you can get started, you will need to know how your system was designed, how it is supposed to operate, and where on the curve your pumps are operating at, among other factors. In this article, we will walk you through a system that is operating correctly, two problem scenarios that we encountered with this system, and throughout this article we will also explain some common pitfalls and tips on how to avoid them.
When it comes to gathering data on a system, building services are among the hardest. This is because most of the piping system may be hidden behind equipment or built into the physical structure, such as the walls and ceiling, and instrumentation is often few and far between. For example, one of our engineers recently visited a mechanical room where over half of the pressure gauges on the pumps were either broken or outside of their rated range.
In a situation such as this, it is important to never speculate on how well they were calibrated, and when comparing these systems, you may have to get a little creative.
Don’t get discouraged, and you should not attempt to take exact measurements in this instance but can still receive general data. For instance, if the pressure gauge only goes to 80 psi, but the needle is slightly past the 80, do not attempt to calculate the pressure because you have passed the
instruments range, and any readings will be unreliable. What you will know however, is that there is a fault somewhere in the system that is causing it to operate outside of its design parameters.
As all components of a piping system are interconnected, a problem with one component will impact the hydraulic performance of the entire system. Because of this, we must be able to understand the symptoms the system is showing, and then focus in on the root cause of the problem. Before we can do this however, we need to know what is “NORMAL”? If the system has been operational for some time, then the systems operator should have a decent understanding of what normal is for their system.
However, it is always helpful, whether you have worked with the pumping system before or are new to it, to build a flow model to give you a better understanding of what is going on
and what “normal” should be. For this example, we’ll say that the pressure, flow, level and valve position readings in Figure 1 are the normal steady state operating conditions for this particular system.
Normal operation:
• The supply tank is open to atmosphere and its level maintained at 10ft
• The supply pump has a suction pressure of 15 psig and a discharge pressure of 80.5 psig
• The heat exchanger has an inlet pressure of 67 psig and an outlet pressure of 57 psig, for a total differential pressure of 10 psid at 1000 gpm
• The flow control valve is 85 per cent open with 1000 gpm flowing through it
• The product tank is pressurised to 25 psig and has a level of 15ft
After being placed into operation, the system began to
experience a variety of issues. One operational note is that the flow rate from the product tank is reduced to maintain the tank level, which limits the flow rate for the entire system. While this is an issue, it is not the main system problem.
Take a minute, and compare Figure 1 with Figure 2, and see if you can identify what is causing the system issue in Figure 2.
A good first step is to look at how everything compares to the normal system operation. Here is a quick summary of how the operation differs.
• Supply tank level: OK
• Pump suction pressure: OK
• Pump discharge pressure: Higher than normal
• Pump dP: Higher than normal
• HX inlet pressure: Higher than normal
• HX outlet pressure: Lower than normal
• HX dP: Higher than normal
• FCV: Open farther than normal
• System flow rate: Less than normal
• Product tank level and pressure: OK
What’s abnormal and what could cause it?
It would be understandable to look at the pump first, as the discharge pressure is higher and the differential pressure is higher, which indicates that the pump is producing more head, but this is expected because the pump is running farther back on the pump curve at the lower flow rate. The heat exchanger inlet pressure is also slightly higher, but this is due to the higher pump discharge pressure.
The total pressure drop across the heat exchanger is 18 psi at 940 gpm, when under normal operating conditions it should be 10 psi an even higher flow rate. This would indicate that the heat exchanger has been plugged up, and thanks to this flow model we have solved the mystery of this systems main problem.
Now to move on to a new system. The system is Figure 3 was built with a system expansion in mind, but they ran into issues during implementation. A trial run was done to determine the maximum flow rate possible, and even with the flow control valve at 100 per cent open, the maximum flow rate was limited to just over 1000 gpm.
Compare the system in Figure 3 with the system in Figure 1 and see if you can determine the root cause of this system’s problem.
Look again at how all our devices compare to normal:
• Supply tank level: OK
• Pump suction pressure: OK
• Pump discharge pressure: Lower than normal
• Pump dP: Lower than normal
• HX inlet pressure: Lower than normal
• HX outlet pressure: Lower than normal
• HX dP: OK
• FCV: Open farther than normal
• System flow rate: Normal
• Product tank level and pressure: OK
Were you able to determine what is abnormal and what could be causing it? The flow control valve is open farther to maintain the same flow rate, and this could be due to the lower inlet pressure. The system pressures downstream of the pump are lower than normal, and so is the differential pressure across the pump. This indicates that it is producing less head for the same flow rate of 1000 gpm, so that it is operating below its pump curve. This shows that there is a pump problem, which could be caused by a damaged impeller, worn wear rings or a clearance issue.
In any system there are as many potential problems as there are components, and as you increase the number of branches, loops and/or multiple malfunctions, it can become increasingly more challenging to discover the root cause of your problem. Having a good model or digital twin of your own system can be an invaluable tool to let you make changes and see how the system interacts with itself. Regardless of the complexity of your system, we hope these two examples have given you some insights into the troubleshooting process and given you a few new tools for your troubleshooting tool box.
Don’t risk being non-compliant with the new Queensland Building & Construction Commission regulations. Manufactured to Zetco’s high standards in Italy, our extensive range of WaterMarked valves passes rigorous design and testing processes to ensure that every valve is of premium quality. Ask for Zetco WaterMarked valves at major plumbing retailers. Zetco Valves. Best range. Best quality. Best brand.
The pump industry relies on expertise from a large and varied range of specialists, from experts in particular pump types to those with an intimate understanding of pump reliability; and from researchers who delve into the particulars of pump curves to experts in pump efficiency. To draw upon the wealth of expert knowledge the Australian pump industry has to offer, Pump Industry has established a panel of experts to answer all your pumping questions.
This edition of Ask an Expert will look at open hopper progressive cavity pumps versus conveyors or tote bins.
Q: How can using progressive cavity (PC) pumps with an open hopper instead of conveyors or tote bins enhance the work environment and reduce costs?
A: PC open hopper pumps are adept at transporting media with or without entrained solids and with little to no flowability. The combination of auger feed screw and hopper positively feed viscous products to the conveying elements, ensuring optimum product handling. They are successfully utilised in various industries but stand out in the following applications.
Traditionally, fruit waste from juicing machines and other food waste products have been transported to external collection points via conveyor systems. Another method was to remove food waste using tote bins. When production increased then the number of tote bins increased, along with the labour needed to remove them, and this, in addition to essential cleaning before reintroduction to a high risk area, increased disposal costs. These systems are now proving to be redundant as a more cost effective and cleaner solution is available: an open hopper progressive cavity pump.
Once the pump is installed, food waste goes straight from the production machinery into the pump without being handled. The PC pump then rapidly removes the waste to a collection point in a hygienic, enclosed pumping system that is simple to disassemble, inspect and service in place without removing the piping.
• Enclosed system improves hygiene and reduces odours
• Automated system reduces labour costs
• Space saving compared to conveyor systems
• No manual handling, no spills
• Improved health and safety
• Major cost savings
• Enhanced working environment
In order to further reduce waste volume such as skins, peels, animal frames etc, the pumps can also be outfitted with internal rotating knives or other macerating options. For further automation in high care areas, the pumps can be supplied with a control panel, variable speed drive and level controls.
Environmental engineering applications
When it comes to health and safety, sludge waste transfer is even more problematic than food waste. A conveyor system can mean contamination of the factory floor and a health risk for operatives, unpleasant odours from being open to the environment and contamination of the new product with the old.
An automated, enclosed piping system along with an open hopper PC pump can eliminate these risks. PC pumps can be further coupled with grinding or macerating options to dewater and compact waste, thereby reducing its volume and associated costs.
PC pump manufacturers also offer intelligent combination solutions which can include dense-phase conveying with PC pump technology to transfer sludge long distances in enclosed pipelines while improving the energy efficiency of the system as a whole.
Peter Vila, Managing Director of SEEPEX Australia, is a progressive cavity pump expert. He has been involved with pumps for over 35 years. Peter spent the first five years repairing pumps and the following 30 years in technical sales, 15 of which have been with SEEPEX progressive cavity pumps.
For more information on progressive cavity pumps, please contact SEEPEX Australia on (02) 4355 4500 or at info.au@seepex.com
You know irrigation, we know diesel engines
Irrigation equipment works hard, so it needs a hard-working engine. Meet Hatz Diesel’s compact and all new H-50 Series.
• Up to 90 kg lighter than other engines in the power range
• Long engine life and premium components
• 500-hour maintenance interval
• 18.4 kW to 64 kW*
• Unsurpassed fuel efficiency
*(intermittent loading / ISO 3046-1)
900 CREATING POWER SOLUTIONS.
The PIA’s Australian Pump Technical Handbook is a cornerstone text for the Australian pump industry and, in our opinion, a must have for anyone who deals with pumps on a regular basis. In this ongoing series, we feature abridged chapters from the classic book to showcase the various areas covered and to reacquaint readers with the technical aspects of pumps. In this issue, we continue to look at selecting and applying different types of slurry pumps.
Slurry head correction
A derating of pump total head is usually necessary because of the presence of solids in the slurry. Suction losses within the pump increase as the density of the slurry increases. Additionally, slip occurs between the transporting fluid and the solid particles as the slurry passes through the pump impeller, which produces an energy loss.
Due to the variability of slurries, pump manufacturers provide curves showing performance when pumping clear water. To select the appropriate pump and motor configuration using the manufacturer’s performance curve, the total head for slurry should be expressed in terms of equivalent water head.
Formulae have been developed for calculating correction factors for head and efficiency based on solids particle size and slurry specific gravity. These correction factors are applied to transform the required slurry head (or efficiency) into equivalent water values.
The slurry viscosity further affects the pump total head and hydraulic efficiency. Viscosity effects should be considered when calculating the equivalent water duty for slurry service.
The pump absorbed power derived for water is multiplied by the slurry specific gravity to calculate the power required to pump the slurry.
Pump speed reduction
The impeller materials used for slurry pumps (hard iron or elastomer lined) generally mean it is not feasible to reduce the impeller diameter to match the required duty point so that a pump can be run at the motor synchronous speed.
Slurry pumps generally run at slow speeds and it often becomes necessary to reduce the pump speed to below nominal motor speed based on the number of poles in the motor. This is commonly achieved through a wedge belt drive for transmitted power up to 350kW, or through a gearbox.
Variable speed drives are common in mining applications to handle variations in process flow. However, consideration of starting torque requirements and other factors need to be considered when selecting the driver.
Horizontal pump installation
The mounting and installation of horizontal slurry pumps are generally subject to a number of considerations, including floor space, overhead space for lifting and the likelihood of flooding from spills. Pumps in critical services are often paired in duty/standby mode so that maintenance can be carried out on one pump while the other is running.
Large pumps with high-energy motors — and perhaps with speed reduction gearboxes — would generally be mounted with the shaft axes in the same horizontal plane for ease of maintenance access.
A pump with a belt drive may have the motor mounted beside it if there is sufficient floor space. However, if floor space is limited or there is a risk of flooding, the motor can be mounted above it either directly overhead (also known as “C drive”) or to its rear (reverse overhead mounting or “Z drive”).
Vertical cantilever shaft sump pumps should be selected so that the suction inlet is close to the sump floor. If shaft length is limited by the required running speed and power to be transmitted, a suction pipe (generally two metres long) may be fitted to the suction branch to ensure the sump can be emptied.
Positive displacement pumps are often more suitable than centrifugal slurry pumps when one or more of the following conditions or requirements apply:
• Low flow rate
• High head
• Improved efficiency is desired
• Dilution water is either expensive to provide, remove and/or dispose of
• High solids concentration
• High viscosity
• Flow control required
Many manufacturers have developed special versions of their positive displacement pumps for slurry services. As the nature of slurry and operating conditions are variable, it is not possible to provide concise selection procedures, so it is imperative to discuss your specific application with pump suppliers who have experience in pumping similar slurries.
Some of the important parameters of slurries to consider when selecting a pump include:
• Particle size, shape (angular, round, long and stringy) and hardness
• Corrosiveness
• Chemical compatibility with elastomers
• Solids concentration
• Likelihood of running dry
Previous experience with pumping similar slurries in your own plant or industry can provide an invaluable guide to share with potential suppliers.
Pump speed is generally reduced for slurry applications, however, care needs to be taken so that speeds are not so low that solids are able to settle in either the pump or piping.
Final selection can often be a tradeoff between high capital and low maintenance costs, or low capital and high maintenance costs.
A wide range of positive displacement pumps can be considered for these applications, including:
• Progressive cavity
• Rotary lobe
• Peristaltic
• Air operated diaphragm (AOD)
Most suppliers can offer specialised designs and materials, and reduced operating speeds to extend the life of the pump depending on the abrasiveness of the slurry.
Capital cost is likely to be low or moderate.
When the application exceeds the capabilities of the above pump types, it is often necessary to consider specialised mechanical or hydraulically driven piston, plunger, diaphragm and hose pumps. For abrasive slurries, these pumps use a variety of features to minimise abrasive wear, including:
• Continuous flushing of pistons and plunger seals with clean water or compatible flushing liquid
• Extended frames so that no part of the cylinder or plunger that is in contact with the slurry, contacts the sealing surfaces
• Combinations of hard surfaces and resilient surfaces
• Slow speeds and long strokes
• Slurry values with combinations of hard and resilient surfaces
• Design features to allow easy replacement of wear parts with minimum downtime
The capital cost of these pumps is likely to be very high.
Typical applications of various types of positive displacement pumps in mining and some industrial slurry applications can be seen in Table 1.
Most centrifugal and rotary pumps have steady state flow characteristics. Under normal conditions there is very little change in the velocity of the fluid pumped. That is not the case with reciprocating metering pumps, which cause the fluid to experience peak velocities and accelerations in both the suction and discharge lines. With these pumps, the fluid is initially at rest (0° of piston cam rotation), and fluid velocity and acceleration are both zero.
The fluid is accelerated during the discharge cycle through peak velocity at 90° of piston cam rotation. Similarly, the suction cycle begins at rest (180° piston cam rotation) and the fluid is accelerated through peak velocity at 270° rotation. The inertial force required to initiate flow for both pumping cycles is of major significance. Because of these unique flow conditions, common to all reciprocating metering pumps, special consideration is required of all factors that will affect pump performance.
When all variables are considered and basic hydraulic principles are followed, the installation and operation of a Reciprocating Metering Pump will be successful.
Checklist of difficult conditions:
1. Piping with excessive fittings, valves, bends
2. Suction lift or low suction head
3. Undersized piping on either suction or discharge
4. Dissolved gases in product pumped; unusually high vapor pressure
5. Pumping near the required net positive suction head (NPSHR)
6. Product specific gravity unusually high
7. High product viscosity
8. Long suction or discharge lines
9. Pumping downhill—suction pressure higher than discharge pressure
10. Pumping at unusually high or low temperatures
11. Solids content or slurry (pipe size important to minimise settling)
12. Outdoor installation in cold climate
13. Changing elevations in suction or discharge lines (air traps cause problems)