pumpindustry
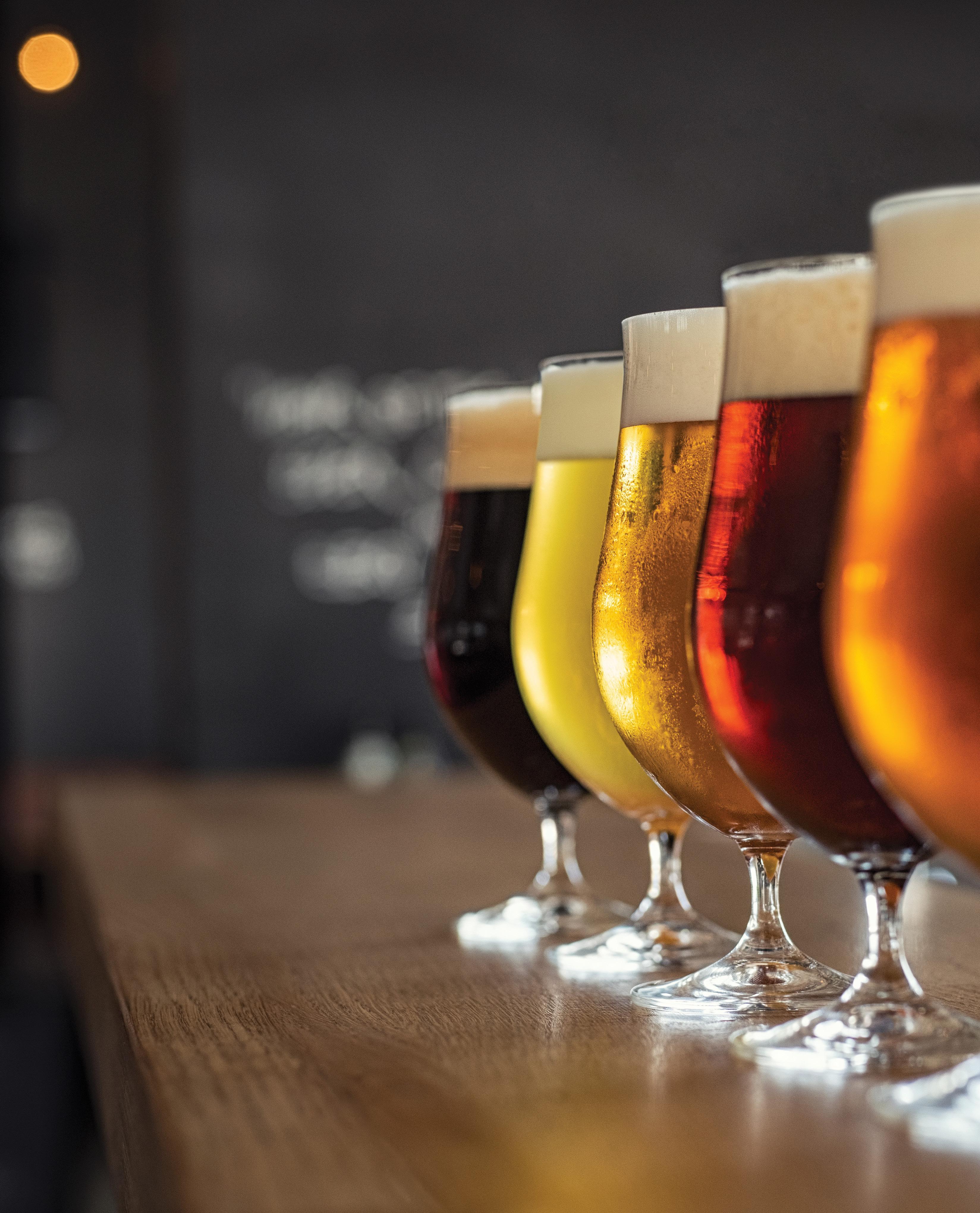
Maximising slurry pump efficiency
SA Water gets smart about pump asset maintenance
Maximising slurry pump efficiency
SA Water gets smart about pump asset maintenance
Hello all and welcome to the Autumn Edition of Pump Industry Magazine, the official voice of Pump Industry Australia. It’s some 16 months into the pandemic now and at the time of writing Melbourne was coming out of a 14 day lockdown, the number of days in lockdown now totalling 200, which demonstrates yet again there is still a lot to learn about this virus and these scenarios will continue to play out for some time to come. Globally, the death toll has now surpassed 3.5 million.
This year we note that three of our colleagues have passed away. In April, we noted with sadness the death of Bob Neale from COVID whilst he was working for Southern Cross in PNG. Bob had a long and successful career in the pump industry; he had management roles with Flowserve, Southern Cross and BCIP.
it was hard-covered in red, dated 1993 and the foreword was written by Anthony Grage who was President of the APMA at the time. It tells the story that the Australian Pump Manufacturers Association was formed in 1964, off the back of a trade export mission to South Africa attended by a group of pump manufacturers. The benefits of the mission extended beyond its immediate findings, and the companies involved and other companies voted for the formation of a viable body of pumping interests which could speak with authority for the industry.
Pump Industry Australia Incorporated C/-340, Stuarts Point Road
Yarrahapinni NSW 2441 Australia Ph/Fax: (02) 6569 0160 pumpsaustralia@bigpond.com www.pumps.org.au
PIA Executive Council 2020
John Inkster – President Brown Brothers Engineers
James Blannin – Vice President Stevco Pumps & Seals
Kevin Wilson – Treasurer/Secretary Executive Officer
Alan Rowan – Councillor Executive Officer – Publications and Training, Life Member
Ken Kugler Executive Officer – Standards, Life Member
Geoff Harvey – Councillor Irrigation Australia Limited
Anant Yuvarajah – Councillor ASC Water Tanks
Joel Neideck – Councillor TDA Pumps
Matt Arnett – Councillor Ebara Pumps Australia
Michael Woolley – Councillor Tsurumi Australia
Steve Bosnar – Councillor Pioneer Pumps
Billie Tan – Councillor Regent Pumps
It is also with sadness that we advise the recent passing of one of our initial Life Members Bill Aitken. You can read more about Bob and Bill’s careers and contributions to the industry on page 16.
Many of you might also know of Brian Pritchard who passed away in March after an illness. Brian owned B Line pumps, an industrial pump company in Sydney.
On behalf of the membership of the PIA, we express our sincere condolences to all their families and close friends.
During these unpredictable times, PIA is still committed to holding events for the benefit of Members. In March we successfully held another Pumps and Systems Training Course in Melbourne. This was our second, and to date we have had 21 people attend; we propose to hold another in the coming months. Strong interest was shown in the Course at the Perth meeting.
On 22 April, PIA held an evening in Perth sponsored by Tsurumi Australia. Our thanks to Michael Woolley and his team for putting on an excellent meeting attended by some 30 people. Michael raised the bar somewhat by having a raffle on the night for a bottle of whiskey – won by Troy Drysdale of Cummins South Pacific.
On Wednesday 21 July, it is planned to have a breakfast session sponsored by DAB Pumps Oceania, so please pencil that date in your diaries as an opportunity to meet with colleagues and to learn more about DAB.
And now for a little bit of history. When I was in Sydney recently, I found an old edition of the Pipe Friction Handbook;
On 10 March 1977, the Association was incorporated in Victoria. The administration of APMA activities was carried out by a National Council consisting of eight Members. APMA played an important role in representing the pump industry in government enquiries. In 1987, APMA prepared a major submission to an IAC Inquiry into mining, construction and agricultural equipment.
In the early 2000s, the Association changed its name to Pump Industry Australia to better meet the needs of the industry, which had greatly changed from representing manufacturers to that of importers and wholesalers, reflecting the changing nature of manufacturing as a whole in Australia. That said, there is still a degree of manufacturing taking place and local assembly.
I also found a 1980 edition of the Australian Pump Technical Handbook, this was a soft cover in red, as was the custom at the time, and was issued with the compliments of Ajax Pumps, a Member of McPhersons Group Ltd, with the foreword written by the Minister for Productivity, Parliament House, Canberra. The opening sentence was ‘The Australian pump industry is a vital supplier to any water user requiring a system for the movement of fluids’ –how little has changed!!
In closing, I can advise that I have had my first jab of AstraZeneca and suffered no ill effects, and encourage you all to do the same. We know the virus has a long way to run and we know the vaccinations significantly decrease the likelihood of catching the virus with an efficacy of around 63 per cent.
Best Regards
John Inkster PresidentABN: 36 426 734 954
C/- The Commons, Office 1, 36-38 Gipps St, Collingwood VIC 3066
P: (03) 9988 4950
F: (03) 8456 6720
monkeymedia.com.au info@monkeymedia.com.au pumpindustry.com.au magazine@pumpindustry.com.au
Editor: Lauren Cella
Contributing Editor: Michelle Goldsmith
Marketing Assistant: Stephanie Di Paola
Business Development Manager: Rima Munafo
Design Manager: Alejandro Molano
Designers: Jacqueline Buckmaster, Danielle Harris
Publisher: Chris Bland
Managing Editor: Laura Harvey
ISSN: 2201-0270
Kempsey CBD was able to quickly get back in operation following flood conditions in March, thanks to Fire and Rescue, the RFS and a ‘super pump’.
Fire and Rescue pumped out the centre of town. Various pumps were used to attempt to clear the floodwater from Belgrave Street, with no great success, so the Fire and Rescue team employed the use of the super pump: the Bulk Water Transfer System ‘Hytrans’.
The Hytrans moved roughly 6,000L of water a minute and was crewed by two specialists assisted by the local FRNSW crew, 345 Kempsey. There is only one pump of this capacity in NSW and it was brought in by Fire and Rescue and used
on Belgrave Street, with near instant, incredible impact.
When the pump was turned off in the centre of Kempsey at 3pm on Saturday
27 March, it was estimated that the total amount of water removed was ten million litres.
The HYTRANS was then moved about 1km up the road to pump out a section of water in another area of Kempsey. There they had to run 500m of 150mm hose to send the water back to the Macleay River. Another large amount of water was removed from Kempsey, almost another ten million litres.
Fire and Rescue was also busy in the outer areas. Two Rapid Damage Assessment teams were assigned to the problem areas of Stuarts Point and Maria River Road. Another crew went to Frederickton.
Central Highlands Regional Council has employed a helicopter to hoist an almost 50-year-old structure and pumps from the Blackwater Water Treatment Plant site.
As a part of the raw water pipework and pump station upgrades taking place at the Blackwater Water Treatment Plant, due to the complexity of the lift, local contractor HeliCentral was engaged to fly in to replace the pumps from within the raw water dam.
Acting General Manager Infrastructure and Utilities, Jason Hoolihan, said the project will optimise many aspects of the raw water plant process.
“Our process for providing drinking water to Blackwater will be more efficient and cost-effective going forward,” Mr Hoolihan said.
“The project also includes replacement of the raw water switchboard and pump station building structure.”
The EHEDG certified BCFH range of progressive cavity pumps handles thin to highly viscous products, including those containing soft solids with a low shear action and minimal pulsation which enables accurate flow control. BCFH pumps fulfill the stringent demands of cleanliness in the food, beverage, chemical, pharmaceutical and cosmetic industries.
EHEDG Type EL Class I and 3-A Sanitary Standards certified
Enhanced internal design ensures residue free cleaning with CIP/SIP
Equipment requires less cleaning time compared to other CIP solutions
Easy maintenance due to detachable rotor connection and split suction casing
The Federal Government has handed down its 2021-22 Budget, with funding allocated for agriculture, and water and energy infrastructure.
The 2021-22 Budget delivers substantial new investment to drive the competitiveness, growth and resilience of the Australian agriculture industry, with $850 million in funding to support the industry to reach its goal of $100 billion by 2030.
The Federal Government’s focus remains on delivering targeted measures for Australia’s farmers, fishers and foresters in the Agriculture 2030 2021-22 Budget package.
Resources
The Federal Government said it will invest in a global strategy to highlight the quality, strength and reliability of Australia as a supplier of crucial resources and energy to the world while supporting companies to diversify and develop new markets.
Supporting junior explorers is expected to help the industry make the next big discoveries. The resources sector employs more than 260,000 people, with many of these jobs in regional Australia. More than a million Australians rely on the sector indirectly.
The 2021-22 Budget includes:
• $100 million in fiscal balance terms to extend the Junior Minerals Exploration Incentive for four years from 1 July 2021, to encourage exploration and development of new deposits and to ensure a strong investment pipeline for development across regional Australia
• New funding to implement the Government’s Strategic Basin Plans, including $15.7 million to support Gas Field Trials in the North Bowen and Galilee Basins, and $2.2 million for the Northern Land Council to help provide better services to Traditional Owners in the Beetaloo Basin
The Government is investing $189.6 million over five years for the Next Five Year Plan for Northern Australia, with a focus on job creation, stronger digital connectivity, and support for businesses to scale up and diversify.
Our North, Our Future: 2021-2026 represents the next phase of the 20-year framework set out in the 2015 White Paper on Developing Northern Australia, to build on the economic potential of the north and to create jobs and opportunities to help attract people to live and do business in the north.
Measures include:
• $9.3 million over five years to pilot the targeted Regions of Growth (ROG) program in four locations: Beetaloo Basin to Darwin; Broome to Kununurra to Darwin; Cairns to Gladstone; and Mount Isa to Townsville. The program will target investment to the strengths of each region and help identify future geographical areas of economic potential
• $111.9 million over five years for a Northern Australia Development Program. The program will support northern
Australian businesses to scale up and diversify by providing co-investment funding to businesses for activities including infrastructure, assets, feasibility studies and business planning
Our North, Our Future: 2021-2026 builds on the Federal Government’s plans to drive job creation and industry growth, supporting national recovery efforts from the impacts of the COVID-19 pandemic.
In the water portfolio, Minister for Resources, Water and Northern Australia, Keith Pitt, said Budget measures are centred on three key areas to set Australia up for the future:
• Providing practical support to farmers who experienced drought to improve their on-farm water infrastructure in partnership with states
• Reforming water markets to ensure water users could have confidence in their integrity and operation
• Improving Murray-Darling Basin modelling to build the confidence of governments, water users and communities in planning for an uncertain future
“We have extended the On-farm Emergency Water Infrastructure Rebate Scheme for 12 months until June 2022, to ensure drought-affected farmers can access the $50 million in rebate funding secured through the 2020-21 Budget,” Mr Pitt said.
“We will form an expert panel to progress important reforms to Murray-Darling Basin water markets in ways that support water users while improving market efficiency, information and governance.
“Reforming our water markets will need strong collaboration between governments, as well as with communities.
“And we’re committed to developing a state-of-the-art modelling capability for the whole Basin to ensure farmers, communities and governments can make decisions confident in the data they rely on.
“These measures are on top of the $270 million MurrayDarling Communities Investment Package announced last year to put communities and jobs at the heart of Basin Plan implementation. In 2021-22, $130 million of that is committed to support our communities.
“We have also closed the Water Efficiency Program and ruled out water buybacks, diverting over $1.3 billion to focus on offfarm efficiency projects.
“Off-farm water recovery means we can actually progress our river health targets and, unlike on-farm programs, we do not reduce water availability in the consumptive pool.”
The 2021-22 Budget invests up to a further $258 million, including up to $160 million through the National Water Grid Connections pathway, from the $3.5 billion National Water Grid Fund towards the construction of new and augmented water infrastructure projects, building a more resilient and secure Australia.
The Government’s ongoing investment in water infrastructure builds on the eight construction projects already completed since the establishment of the National Water Grid Authority in late 2019 and brings the total number of construction projects in the investment pipeline to 30. The new and augmented construction projects being funded in partnership with states include:
• Eurobodalla Southern Storage (New South Wales) – $51.2 million
• Werribee Irrigation District Modernisation (Victoria) – $11 million
• Recycled Water on the Bellarine (Victoria) – $5.5 million
• Warwick Recycled Water for Agriculture – Recycled Water Treatment Upgrade (Queensland) – $0.5 million
• An additional $7.5 million for Rookwood Weir to deliver water security in North Queensland by raising the weir wall a further 700mm to deliver an additional 10,000 megalitres. This brings total Australian Government investment in the project to $183.6 million.
Gas infrastructure and emissions reduction
In total, more than $1.8 billion has been allocated in the 2021-22 Budget for the energy sector, with $58.6 million of that going towards the gas sector.
As well as a suite of electricity funding, the Budget initiatives to drive Australia’s gas-fired recovery include:
• Up to $38.7 million to support critical gas infrastructure projects to alleviate the forecast gas supply shortfalls
• $5.6 million to further strengthen the Federal Government’s gas system planning framework through delivery of the National Gas Infrastructure Plan
• $6.2 million to design, consult and implement reforms to accelerate the development of the Wallumbilla Gas Supply Hub
• $4.6 million to develop initiatives that empower gas reliant businesses to negotiate competitive outcomes in their gas supply agreements
• $3.5 million to design and implement a framework to facilitate Commonwealth support for medium to long-term gas infrastructure to secure Australia’s future gas supply
The Budget also sets out measures to further strengthen Australia’s long-term fuel security, building on the Government’s investment in the 2020-21 Budget, including:
• A refinery production payment to help maintain Australia’s refining capability
• Support to assist the refiners to conduct infrastructure upgrades, subject to consultation with industry
• $50.7 million to establish a new fuel security framework, including for the implementation and monitoring of the minimum stockholding obligation and the production payment, ensuring industry complies
• New initiatives in the Budget will support investment in new and emerging low-emissions technologies prioritised under the Government’s Technology Investment Roadmap, collaborate internationally on achieving technology breakthroughs, lower energy costs and create more than 6,000 jobs.
In total, $1.2 billion has been allocated to establish Australia at the forefront of low emissions technology innovation and commercialisation.
The response to the Budget from the energy industry has been mixed.
APPEA Chief Executive, Andrew McConville, said support for gas-related strategic basins is a big tick, as is the announcement for new hydrogen and carbon storage initiatives to help lower emissions.
“Increased funding for gas infrastructure of $173.6 million in the Northern Territory on top of the $58.6 million will mean more supply for the domestic market and that will help keep prices competitive,” Mr McConville said.
Clean Energy Council Chief Executive, Kane Thornton, said the Budget was a missed opportunity for the Federal Government to embrace Australia’s renewable energy sector and follow the lead of international, state and territory counterparts to use the clean energy transition to drive job creation and economic recovery.
“If this truly is the infrastructure budget, Infrastructure Australia has identified that there is a need for major transmission upgrades to supply network access to renewable energy zones as a high priority, particularly in light of retiring thermal generation,” Mr Thornton said.
“The lack of transmission investment is now one of the most critical challenges facing Australia’s energy industry.
“It’s disappointing that in a ‘nation-building’ infrastructure budget, upgrades that will enable the access and security of clean, low-cost power have not been prioritised.”
The most compact and integrated booster set on the market. Connect 1, 2, 3 or 4 Esybox MAX units.
Easy to maintain
Connect and control from anywhere with DConnect.
Quick On-Site Assembly.
Leaps ahead in terms of energy efficiency with the DAB inverter, brand new permanent magnet motor and new hydraulics.
The Federal Government has committed $3.5 million in the 2021/2022 Federal Budget to the Barossa New Water project in South Australia, improving access to water infrastructure and partnering with the state to breathe new life to the Barossa and Eden Valley wine region.
Estimates show additional water to the Barossa and Eden Valley could generate $292 million for the state’s economy, through securing existing vineyards, additional plantings and by creating 1,000 jobs.
Minister for Primary Industries and Regional Development, David Basham, said it was pleasing to see the Federal Government supporting such an important project – building on the State Government’s $1.5 million commitment to date.
“Barossa New Water aims to deliver safe, reliable, recycled water from the Bolivar Wastewater Treatment Plant to meet industry demand in the Barossa Valley and Eden Valley,” said Mr Basham.
“Securing funding from the Commonwealth is an important milestone for Barossa New Water and we will continue to work closely with key stakeholders as we push ahead with this project.
“The detailed business case will explore demand for water, economic viability, and supply and delivery of new, secure, climate-independent water infrastructure for the region.
“This project could be a gamechanger for the region’s wine industry to drive economic growth and support thousands of jobs.
“Earlier this year, achieving a new water supply for the Barossa Valley region was identified as a Priority Initiative by Infrastructure Australia.
“It is one of a number of projects regarded by the State Government as being potentially transformative for South Australia – supporting regional growth and jobs.
“This project supports our Growth State Plan to create additional jobs and boost the economy by building the infrastructure that matters in regional areas, supporting both agriculture and tourism.”
Member for Schubert, Stephan Knoll, said having improved access to a secure water supply is a key concern for his local community.
“We know that the Barossa is one of South Australia’s premier wine regions, producing some of the highest value wine grapes in Australia, with an average
value of $2,278/tonne in 2020, but a key constraint to agricultural productivity and growth in the region is the lack of secure water,” Mr Knoll said.
“There are 2,700 people employed in the wine and grape sector in the Barossa and the region accounts for nearly ten per cent of national wine sector jobs.
“Delivering a long-term water security solution will significantly boost productivity for the region’s agriculture sector – and importantly create local jobs.”
Layne Bowler vertical turbine and submersible pumps have a proven record under the most demanding and toughest of conditions.
• Flows to 7,500 L/Sec
• Heads to 500 m
• Power to 1000+ kW
• Temperatures to 150°C
• Bowls Diameter up to 45 inch
Applications
• Irrigation
• Water supply
• Process water
• Geothermal
• Cooling towers
• Fire protection
• Marine
• Water treatment
• Dewatering
• Flows to 140 L/Sec
• Heads to 200 m
• Power to 110 kW
• Bowls Diameter in sizes 6”, 7”, 8” and 10” Applications
• Irrigation
• Deep well water supply
• Inline booster
• Service water
• Dewatering
Brown Brothers Engineers have innovative solutions whatever your application. Contact us today about your requirements.
Construction is set to commence on the $777 million Kidston Stage 2 pumped hydro energy storage (PHES) project – following Genex Power reaching financial close on it – with pumps now being mobilised to site for initial dewatering works.
The project will be the first pumped hydro plant to be built in Australia since 1984, and the first to be used specifically to support the integration of variable renewable energy generation from solar and wind.
Located at the former Kidston Gold Mine at the Kidston Clean Energy Hub in North Queensland, the facility will produce approximately 250MW/2,000MWh of baseload power, equivalent to eight hours of energy storage.
The Australian Renewable Energy Agency (ARENA) will provide $47 million in funding towards the project. ARENA also already provided funding for feasibility and development totalling $9 million for this current pumped hydro stage, as well as initially providing $8.9 million towards Genex’s 50MW Kidston Solar Project in 2016.
The Queensland Government will invest $147 million to connect Genex’s Kidston Pumped Storage Hydro Project to Queensland households and businesses, and the project is set to create 900 construction jobs.
The project is also supported with $610 million in concessional debt finance from the Northern Australia Infrastructure Facility (NAIF).
Genex has now finalised its capital raising process to allow the project to reach financial close. EnergyAustralia is to be the project offtake partner for up to 30 years. A joint venture of John Holland and McConnell Dowell is the EPC contractor.
Two existing mining pits at the former gold mine will be utilised as the upper and lower reservoirs for the PHES to minimise construction time and costs.
Rock material sampling and testing for concrete production has been completed, and pumps are being mobilised to site to commence the initial dewatering of the Eldridge pit.
During peak power demand periods, water will be released from the upper to the lower reservoir, passing through reversible turbines.
During off-peak periods and when the sun is abundant, water will be pumped back from the lower reservoir to the upper reservoir using electricity imported from the National Electricity Market (NEM).
A 187km transmission line, supported by the Queensland Government and Genex, will be required to connect the Kidston Clean Energy Hub to the NEM.
ARENA CEO, Darren Miller, welcomed the announcement and thanked everyone involved in achieving this significant milestone.
“On behalf of ARENA, I’d like to congratulate Genex on reaching financial close on a project that has been many years in the making,” Mr Miller said.
”The Kidston PHES project will supply dispatchable, renewable energy to the grid when and where it is needed and provide a blueprint for how we store excess solar and wind energy at scale.
“Projects like this play a significant role in progressing Australia’s energy transition.
“Storage solutions such as pumped hydro and large-scale batteries are a key part in providing backup power and grid stability as highlighted in the Australian Government’s first Low Emissions Technology Statement.”
ARENA has previously supported 16 PHES projects with over $28 million including the feasibility studies for Snowy 2.0 and Tasmania’s Battery of the Nation.
Queensland Treasurer and Minister for Investment, Cameron Dick, said Genex achieving financial close confirmed the status of Queensland’s nation-leading renewable energy credentials.
“As part of our Economic Recovery Strategy to grow the renewable energy sector and the jobs that come with it, the Palaszczuk Government has played a crucial role in getting the Kidston Pumped Storage Hydro Project over the line,” Mr Dick said.
“This decision will further secure our strong renewables future in North Queensland and will unlock hundreds of renewables jobs.”
Minister for Energy, Renewables and Hydrogen, Mick de Brenni, said the 250MW project will help secure the future of North Queensland’s energy system with a reliable supply of dispatchable power.
“As Queensland charges towards its renewable energy target, storage projects like Kidston will enable the continued investment in otherwise intermittent renewables,” Mr de Brenni said.
“Our $147 million commitment will support publicly-owned Powerlink to build a 186km transmission line from Kidston to Mount Fox near Ingham, creating 400 jobs.
“Construction of the pumped hydro project will create a further 500 jobs, powering North Queensland’s economic recovery.”
The Kidston Clean Energy Hub will integrate large-scale solar and pumped storage hydro using an abandoned gold mine 270km north-west of Townsville.
Water pumped into its reservoir will store approximately 2000MWh worth of dispatchable electricity that can be delivered back to the electricity market when needed.
Genex CEO, James Harding, said the announcement marks an important step in the rollout of large-scale energy storage capability in the NEM.
“Financial close for the Kidston Pumped Storage Hydro Project is a monumental achievement and one Genex has been working towards for over five years,” Mr Harding said.
“Site preparation activities are now well progressed as we prepare for full-scale construction activities over the next few months.
“I would sincerely like to thank the Queensland Government for the significant funding support and continued commitment to the Kidston project.”
The Kidston Pumped Storage Hydro Project and its associated transmission infrastructure is expected to be completed and fed into the NEM by early 2025.
Brown Brothers Engineers Australia, part of the AxFlow Group, has announced its acquisition of INCA Control, a manufacturer of control panels for pumps in agricultural, industrial and commercial settings. With the acquisition of INCA Control, Brown Brothers Engineers will become a full-service provider for water boosting pressure systems in Australia.
INCA Control is a family-owned business with an operational history surpassing 50 years. Located in Glendenning, Sydney, the company is involved in the pumping field, supplying control systems for water sump drainage, water pressure systems including VSD (Variable Speed Drives), water booster or transfer systems and fire pump controls to AS 2941 for both diesel and electric pumps. All these highly customised systems incorporate level, pressure and all associated control measuring devices.
“INCA Control has been a reliable supplier to Kelair Pumps and Brown Brothers Engineers in both New Zealand and Australia for several years. They are very well respected in the market for their technical competence and high-quality products,” said John Inkster, Managing Director of Brown Brothers Engineers Group.
“Control panels constitute a critical part of a pump installation. Having them in our portfolio will enable us to grow the aftermarket offering for the many pump installations that we service today.”
Mark Griffith, owner and CEO of INCA Control, is equally as enthusiastic about the acquisition commenting.
“We at INCA Control are excited about the next chapter in our history. We are proud to become a part of the AxFlow, Brown Brothers Engineers Group and we look forward to working with and supporting the Group and our current customer base as we grow moving forward,” Mr Griffith said.
The City of Townsville has achieved a number of recent milestones on the second stage of its Haughton Pipeline project.
Townsville Mayor, Jenny Hill, said Council had a team managing the project, which was being funded by the Queensland Government.
Ms Hill said Council had also engaged a number of specialist external consultants to undertake front-end engineering and design principles addressing pipe alignment, materials and pump station requirements.
“Detailed capital and operational costs continue to be validated against independent cost estimates prior to making a recommendation to Council,” Ms Hill said.
“Private and commercial landowners have been consulted on the options for the pipe alignment and three landowner access agreements have already been agreed.
“The project team has also engaged with the traditional custodians of the land along the proposed pipe alignment options and entered into a Cultural Heritage Management Agreement.
“After a series of information sessions and tender briefings in Townsville and
Ayr during 2020, five local construction contractors have been appointed to participate in an interactive tender process to assist with project design and costings.
“Suppliers and manufacturers of long lead materials and equipment have also been engaged to participate in the tender process for pipes, pumps and fittings supplies.”
Member for Townsville, Scott Stewart, said providing funding for water security for the city was essential.
“The State Government has invested more than $400 million in stages one and two of the Haughton Pipeline because we know it will set Townsville
up for the future,” Mr Stewart said.
“I’m excited about the opportunities that are out there for Townsville’s economy moving forward and that’s what this government is focused on.”
Ms Hill said stage one of the Haughton Pipeline project had provided a tremendous boost to the local economy, with around 95 per cent of the construction work delivered by locallybased contractors.
“We want to repeat that with stage two. That’s why Council will package the works into smaller parcels of work to give local businesses the opportunity to tender for it,” Ms Hill said.
Respected pump professional Bob Neale passed away from COVID-19 in Papua New Guinea on 28 March 2021.
Bob was a well-known and respected figure in the industry, having started his career in 1971 as a Water Advisor for the Queensland Water Resources Commission. He then went on to work as General Manager Sales and Services at Flowserve Pump Division for over 21 years; Managing Director HydroFlo Solutions, and Director of H20 Epiphany – trading as Thinkwater Newcastle – for over 11 years; and most recently as Business Development and Trading Manager at Southern Cross Pumps since February 2019.
He was well-liked and respected by all those he came across in the industry as a mentor, friend and colleague.
Long-time pump professional and one of the first Life Members of the PIA, Bill Aitken has passed away.
Bill started his career at Harland through IEL/Indeng for over 25 years. He was a key member of the Engineering team, working on both large custom-engineered capital projects and standard pump ranges with David McLiesh and David Macpherson.
He was renowned for his creative and practical approach, often sketching design concepts on the floor and the walls for the benefit of the drafting team. Some of the bigger projects he was a part of include Arthurs Lake pumping station, Ord River verticals, and Muja Power Station cooling water pumps.
In the early 80s, moved to Ingersoll Rand as Chief Engineer of the pump division in Dandenong. He later moved to GAAM where he worked with Ken Willcock and designed fire pumps for the CFA and the MFB.
Bill was instrumental in the team that created the first edition of the APMA Pump Tech Handbook
Bill will be long remembered by many of the PIA Members from the initial APMA days.
On 22 April, for the first time in over a year, PIA held a Meeting in Perth at Tsurumi Australia, with around 30 pump professionals in attendance.
Attendees heard from PIA President, John Inkster, and Tsurumi Australia Managing Director, Michael Woolley, before hearing a presentation about Tsurumi Australia and taking a factory tour.
The successful meeting finished off with attendees enjoying drinks and paella.
Engineered to deliver industry leading durability and performance, even for the most severe applications and environments.
Energy efficient air operated diaphragm pumps with the capability to pump abrasive and viscous liquids make these pumps great for many industries : - General industry
We know the importance of choosing the right equipment to match your process. With our extensive range of pumps, first class customer service and ongoing comprehensive support, Kelair Pumps are second to none when it comes to your pumping requirements.
The W22 Magnet Drive System composes premium and ultra premium efficiency motors with permanent magnets driven by frequency inverters. Perfect for applications where speed variation, precise control at low speeds, low noise levels and compact design are critical.
The W22 Magnet enables a reduction of up to 55 per cent in energy consumption when used in bag filter applications.
Induction Motor IE4
Output: 30kW
Speed: 3000 rpm
Frame: 200L
Mass: 265kg
Volume: 7dm3
W22 Magnet Motor IE4
Output: 30kW
Speed: 3000 rpm
Frame: 132M/L
Mass: 76kg
Volume: 24dm3
W22 Magnet IE5
• Output: 3 to 315kW
• Frame: 132S to 315S/M
• Speed: 3000, 1500 and 1000 rpm
• Voltage: 400 V
• Degree of protection: IP55
• Bearing seal:
• V´ring (frames 132S to 200L)
• WSeal (from frame 225S/M and above
• Insulation: F (ΔT 80K)
• Service factor: 1.0
• Thermal protection: PTC
• Insulated NDE bearing hub and AEGIS shaft grounding (from frames 225S/M and above)
• Mounting: B3T
• TEFC (IC 411) per IEC 60034-6
• Possibility of operation in overspeed
• Optional characteristics on request
Voltage supply: 380 to 480V
• Power: up to 1141 A (500kW)
• Sensorless vector control: it allows the CFW11 to control the speed motor from zero up to its rated speed
• Remote Operating Interface (HMI) with backlight, soft keys, graphic display and real-time clock
• Inductors incorporated on the DC Link to improve harmonic mitigation
• Communication protocol and accessories: Profibus, DeviceNet, CANopen, Ethernet / IP, Modbus-RTU and Profinet
• IP55 available as optional item up to 211A (110kW)
• Adaptable to all kinds of load
• USB port
• FLASH memory
Ebara Corporation (Japan) has recently released its new global range of EN733 standard end suction centrifugal pumps.
Utilising the most advanced hydraulic computer design software available, Ebara engineers in Japan have been able to improve and increase the pump efficiencies of the new GS range above most other available pumps of similar design and standard on the global market.
As a major manufacturer of industrial pumps to JIS and API610 standards, Ebara Corporation has embarked on a globalisation of its range of pumps for the world market. This includes the introduction of a range of industrial pumps to European EN733 standards and a new range of vertical multistage pumps.
The new Ebara GS range of EN733 standard pumps are manufactured in component form at Ebara Corporation Japan owned and managed factories in the Asia Pacific region with final assembly of market range models undertaken by skilled tradesmen at Ebara Pumps Australia’s Melbourne facility.
The new GS series are 16 bar rated pumps, with a close coupled version (GSD) offered as well. Both the GS bareshaft pump and GSD are now available in Australia.
About Ebara Corporation
Ebara Corporation was founded in Japan in 1912 as a manufacturer of pumps. Today, as a group, it consists of more than 70 companies in six
continents with a workforce of more 11,000 people and with company owned and Japanese managed factories in eight countries covering four continents.
The huge scale of production and distribution is matched by a constant commitment to research, development and design of new products and the modern technologies for manufacturing them. Ebara products have gained a worldwide reputation for their technology and quality.
Contact your local Ebara dealer or Ebara Pumps Australia for more information.
Ebara continues to expand the range of products they stock and supply in Australia with two recent additions. For more details contact us at Ebara Pumps Australia or visit our website.
Very economically priced cast iron end suction motor pumps to EN733. They are based on the well proven 3M using the same extended shaft motor and stainless steel impeller, but with a cast iron casing.
A range of robust submersible grinder pumps with a high torque motor & powerful grinding mechanism. Another quality product in the well regarded and proven D’ series of Ebara submersible sewage & wastewater pumps.
with powerful grinding mech
Combining over 100 years of experience with the latest computer aided design, EBARA has developed the new GS series of pumps that offer world leading performance and efficiencies.
Pumps to EN733 dimensions
16 Bar rated. PN16 flanges (24 Bar hydrostatic test pressure)
High efficiencies. MEI ³0.6 (Minimum Efficiency Index)
Mechanical seals to EN12756
Protectors to ISO13852
O’ Ring seal for casing
Cast iron components ED painted (Electro deposition painting)
Caprari’s K+ Energy range is now being expanded, including models for both small and medium flow rates.
Caprari K+ Energy electric pump for wastewater management offers truly revolutionary features. This is thanks to its exclusive and internationally patented DryWet System: a truly unique cooling system that allows one electric pump model to be used for both submersed installations and applications in dry chambers, guaranteeing excellent reliability even when liquid levels inside the tank are unknown.
Advantages offered by the K+ Energy range include:
• Excellent energy savings: IE3 efficiency class motors guarantee premium efficiency to cut costs
• Versatility: the DryWet system means the K+ Energy range can be used for any type of application, thus allowing for considerable stock reduction
• Maximum ease of maintenance and handling: usability is greatly enhanced thanks to the standard plug (which allows the electric pump to be removed without having to disconnect the cables from the panel), the large micro-cast stainless steel handle, and the new system for disassembling the pump side mechanical seals
• Reliability and operational safety: the conductivity probe in the oil chamber (also in the Atex version), the temperature probes, and the double mechanical seal are all design solutions aimed at guaranteeing total protection for the electrical components. Moreover, the Caprari non-stop system ensures continuity of wet end operation even under the most severe operating conditions.
Browse the new website www.kenergy.caprari.com/en to find out all the features of the K+ ENERGY model.
Split seals are an innovative sealing solution for environments where it may be difficult to install or replace conventional mechanical seals, such as hard to access equipment. They are also ideal for minimising costly downtime for assets critical to production by overcoming the assembly and disassembly difficulties associated with rotating equipment. Several semi and fully split mechanical seals have been designed by various manufacturers, however, with so many options available on the market how do you know what is really the best choice for your application?
While many designs may achieve the goal of reducing the amount of time required to change out a mechanical seal, they have introduced other issues.
These inherent design problems can be attributed to a few factors:
• Some component-style split seal designs have several loose parts which must be handled with extreme care
• Installation may require precise measurements or the use of various shims or special tooling to accurately align and set the mechanical seal assembly on the rotating shaft
• Some seals utilise an internal clamping method, limiting the torsional and axial holding power to positively locate the seal on the equipment
Another potential concern arises when the shaft position must be adjusted after the seal has been set. In certain designs, the set screws lock the rotary seal ring assembly to the shaft and cannot be reached after the two stationary gland assemblies have been bolted together. This means total disassembly of the seal once it has been installed, leaving the end user responsible for verifying that a complicated seal with precision lapped faces is correctly reassembled on the pump.
Flexaseal solution
Flexaseal addresses these disadvantages and limitations with the Style 85 two-piece split cartridge mechanical seal assembly.
The Style 85 split seal consists of only two unitised, selfcontained assemblies which fit together over a shaft to form a self-setting and self-aligning cartridge seal design. This fully split cartridge mechanical seal design eliminates the handling of a lot of loose, delicate, precision manufactured components and allows for a very simple, easy and time-saving installation with no measurements or guesswork. The critical primary sealing faces are held together and safely contained within the two split gland and sleeve assemblies, well protected from any mishandling, dirt or contaminants.
• The easiest installation of any split seal in the world: simply attach the two cartridge halves over the shaft and mount to the pump like any other cartridge seal
• The first split cartridge mechanical seal in the world in which just two pieces are handled: the lapped faces are secured safely in cartridge halves and cannot be cocked or chipped
• Only split cartridge mechanical seal in which the impeller can be adjusted without removing the seal: simply reinstall setting clips, release set screws and adjust impeller position then retighten set screws and remove the clips
• Only split cartridge mechanical seal that is fully assembled, and pressure tested at the factory: sealing integrity is confirmed before being sent to the field, thereby ensuring a high success rate for each installation
• No measurements, no shims, no special tools, and no glue: cartridge setting clips assures proper axial and radial alignment to make installation even easier
The design of the Style 85 is like no other on the market. While most split mechanical seals are mounted outside the stuffing box and are designed to function like an outside seal, the Style 85 was engineered as a true, fully split cartridge mechanical seal. It is a hydraulically balanced, stationary multi-spring design that is primarily mounted outside the stuffing box.
These features allow the centrifugal force to keep the solids away from the seal faces while maintaining the ability to handle higher speeds, internal pressures and misalignment. No need to worry about solids, as the springs are protected and out of the product to eliminate clogging. The static shaft sleeve “o” ring is positioned outside of the stuffing box to assure a good sealing surface, even on worn packing sleeves.
The Flexaseal Style 85 Split Cartridge Mechanical Seal… Fast, Simple and Reliable!
The Intermediate Bulk Container (IBC) is the number one container for storing and shipping chemicals worldwide. IBCs are regarded as an economical way to transport thousands of litres of chemicals to all corners of the globe. They are compact and take up no more than the footprint of a standard shipping pallet.
Despite some obvious benefits, there is a downside to this versatile container. Regulatory bodies also target IBCs because they can be mishandled, resulting in spills that can contaminate the surrounding ground, including waterways. They can also be a cause of workplace injuries through skin and eye contact when emptying the chemicals.
Organisations such as Victoria's EPA have developed and implemented liquid storage and handling guidelines to address specific issues around IBCs. These guidelines set out clear instructions on how to correctly store and handle these chemical containers for everyone's safety.
Up until now, there has been a limited range of free-standing, all-weather units that can encase an IBC and at the same time provide safe and clean dispensing options.
Designed to address the challenges of IBCs
The introduction of the Polymaster Enclosed IBC Bund addresses all concerns around the IBC.
Complete weather protection stops rain from entering the storage unit as the IBC is contained within an enclosed bund.
In the event of an IBC rupture, the unit would contain the entire contents within itself, preventing any chemical entering stormwater or the surrounding area as the design exceeds AS3780-2008: The storage and handling of corrosive substances bunding requirements of 110 per cent.
Operators have free and easy access via outward swing doors. Each door has clear viewing panels so that an operator can see inside without putting themselves at risk in the event of a spill. The unique door design acts as a splash guard, ensuring no chemicals can exit the unit.
The wide-opening doors allow an IBC to be easily forklifted into position from either side or rear. Extra clearance on all sides of the opening is advantageous to outside storage where forklifts may be operating on uneven ground.
The Enclosed IBC Bund includes a built-in vent to expel gases and a 250L day tank for continuous dosing if incorporated into an in-line process.
The day tank has safe, quick connect/
operator. A mounted audible and visual low-level alarm can be viewed through viewing panels.
The front cabinet can either accommodate a fully customised dosing system or an off-the-shelf dispensing kit suggested by Polymaster that suits chemicals.
For further information on the Enclosed IBC Bund, contact the Engineered Solutions team at Polymaster on 1800 062 064.
Polymaster’s unique Enclosed IBC Bund solves many of the problems associated with IBC storage and chemical/fluid decanting in a weather resistant, purpose-built enclosure.
Æ Full weather protection – stops rain entering the enclosure
Æ Easy forklift loading with wide forklift access from both side and back
Æ 250ltr day tank
Æ Lockable cabinet to keep system secure
Æ Venting by two sides
Æ Viewing windows incorporated into the doors
Æ 110% bund capacity complies with AS3780
Æ Sight tube and low-level alarm available
Æ Chemical resistant – high grade polyethylene construction
Mechanical seal design and manufacturing company
SPE has launched several innovative sealing products for industrial equipment applications. The nuclear, petrochemical, pharmaceutical, mining and wastewater industries in over 40 countries use SPE's products. The company's Chief Operating Officer, Yi-Chieh Huang, is a significant driver behind this success.
Huang holds an MIT Sloan MBA degree and has over 14 years of experience in the machinery manufacturing and sealing technology equipment fields. Huang combines mechanical engineering expertise and business acumen to champion sealing systems’ product development and technology commercialisation of sealing systems for energy industry applications. Furthermore, Huang has been admitted by several prominent international professional organisations such as the American Petroleum Institute, American Fluid Sealing Association, Taiwan Nuclear Grade Industry Association, Society of Manufacturing Engineers, American Society of Mechanical Engineers, and API-682 standards committee in industrial specification development. Developing technologies to meet end user needs
During her career, Huang has invented over 30 patented technologies covering over 20 advanced seal designs with comprehensive technology commercialisation. Huang developed high-performance seal products offering excellent reliability and significantly longer mechanical seal mean time between failure (MBTF) for equipment. Huang championed efforts resulting in more than US$3.5 million annual cost savings by improving equipment MTBF. Further, Huang's team implemented sealing technology upgrades for a chemical plant in China. The facility reduced maintenance costs by $3.6
million within three years, allowing the end user to achieve 40K+ tons of chemical compound production annually.
Huang's R&D team designed the APD-series products for API682 applications for hazardous, flammable and toxic processes requiring a grander scale of a mechanical seal's reliability for improving pump operating life with lower emissions and reduced end user lifecycle sealing costs. They work in various critical operating conditions with a wide temperature range of -40oF to 500oF and pressures up to 570 psi.
For lower rotating equipment electrical consumption, Huang developed CARFB, the first complete cartridge seal design with multi-segment tandem rings. CAR-FB seals are for industrial blower applications operating in temperatures up to 720oF to avoid dry running, prevent toxic gas leakage, and reduce power consumption by over ten per cent. Moreover, Huang's team lowered nitrogen consumption by upgrading a next-generation non-contacting seal with a unique spiral pattern.
For wastewater treatment, Huang's team launched the CL99SS series seals with over 35 per cent part interchangeability for five to 35 per cent of suspended particle-containing slurries, including sulfur dioxide leakage reduction and plant spare parts inventory by about 50 per cent when over 70 per cent of the pumps have the CL seal line of products installed. The CL series products handle short periods of dry running and eliminate the need for a complicated piping system, reducing water consumption. Also, CL
series seals can align shaft misalignment for up to +/-0.5mm and extend MTBF by at least 50 per cent.
In response to new government ecological policies, Huang's team reduced equipment Volatile Organic Compound (VOC) emissions below 500 ppm on average and less than 50 ppm in specific sealing technology. Typically, dual seal buffer pressure is at least 40 psi higher than the process, requiring an external resource and increasing energy consumption. Huang's LD series invention requires under 30 psi because of its automatic balancing structure with high sealing performance. This technology greatly improves the sealing heat exchange rate. It has a 15 per cent higher recirculation efficiency than the average dual cartridge seal, increasing the pump's operating reliability by at least 20 per cent, saving about 25 per cent maintenance time.
In summary, Huang contributed many extraordinary dynamic fluid sealing sector innovations, making industrial environments better.
"I am enthusiastic about providing a technical solution for various market segments according to market demands. We demonstrated SPE's technical strength by innovating and leading industrial sealing trends and thereby improving industrial environments. Our clients' needs always inspire us to create meaningful innovation," Huang said.
Trust your motor and pump protection to the experts. Littelfuse protection relays stand up to the harshest conditions and safeguard the most critical parts of your operation. Our field application experts will help you update your protection to extend the life of your equipment, mitigate arc-flash hazards, and reduce the risk of electric shock.
relays@fuseco.com.au
www.fuseco.com.au
Accounting for around 98 per cent of Australia's Economic Demonstrated Resources (EDR) of iron ore (about 28 billion tonnes) and as the largest supplier to the global seaborne iron ore trade, the iron ore mines in the Pilbara region of Western Australia are a leading powerhouse for the Australian economy. These mines are at the forefront of best practice for efficiency and safety, and – along with other Australian mines as a whole – are highly rated across the world for their skilled processing and ore extraction techniques. Crusader Hose, an innovative Australian manufacturer, has produced a world-first flexible rising main for ultra-deep bores – Flexibore® 400 – to help support Australia’s mining industry remain world-class.
Crusader Hose, a Melbourne-based company with over 35 years in manufacturing layflat hose, has a strong connection with the mining, pump and drilling industries, having built relationships with players in these sectors over many years through industry networks, site visits and trade shows. As a result, Francois Steverlynck, the Managing Director for 30 years, understands the importance of water extraction in mining operations.
“Mines are extending and digging deeper, and are, therefore, reliant on water transfer systems which can handle the greater pressures at these deeper depths,” Francois said.
Manufacturing the highest pressure layflat hose in the world
A recent breakthrough by the Research and Development Team has been the development of ultra-high-pressure hose for the extraction of bore water.
Several years in the making, this breakthrough was made possible by a series of upgrades along the manufacturing chain.
Apart from loom modifications, the polyester fibre used in weaving the textile reinforcement is of a higher calibre than what is used in lower-pressure Flexibore® products; the tenacity of these higher-calibre fibres is unparalleled.
The $1 million investment in a new extruder system has brought world-class quality to this very important process. As a result, the Flexibore® 400 series hose is the highest pressure layflat hose in the world for groundwater pumping, boasting a burst pressure of 100 bar or 1000m. Groundwater now can be safely pumped from 400m below.
Committed to supporting mining operations
Crusader Hose is committed to supporting mining and the Australian economy by investing in technology to design and manufacture world-class hose systems for both vertical and horizontal dewatering.
“Flexible rising mains such as Flexibore®, have been the system of choice for many Australian mines for in-pit bores due to the simplicity with which the submersible pumps can be retrieved and installed,” said Francois.
The typical installation method uses a roller, crane or mechanised spool, as the riser pipe is one continuous length. In the most recent installation, after the 380m of hose was laid out and power cables were attached, the 160kW pump was lifted by a crane then lowered 15-25m at a time by repositioning the lifting clamps along the hose. This system has proved to be less time-consuming and arduous than using steel or fibreglass pipe.
“The Flexibore® 400 is a pioneering achievement in the history of our company, which we believe is a world first,” said Francois.
“This Australian development will hopefully be keenly adopted by more mining companies, to enable them to keep at the forefront of productivity and profitability.”
In mining and ore processing operations, slurry pumps provide a vital means of effectively transporting slurry over any distance. Their running costs also contribute a significant component of total operating costs, and any failure of this key piece of equipment can bring a mining project grinding to a halt. Therefore, improvements in the sustained efficiency and reliability of slurry pumps can result in substantial bottom-line benefits to mining operators.
Despite their importance, the highly demanding nature of the application and the complex set of factors affecting slurry pump performance in mining operations mean that it is still relatively common to find pumps being operated inefficiently, or in ways that reduce equipment lifespan, resulting in lower overall efficiency and higher costs for the project. Maximising slurry pump efficiency requires the correct specification and selection of pumps, and ensuring that they are optimally operated to deliver sustained efficiency and reliability over the longer term.
Slurry pumps are required to transport large volumes of slurry, composed of target minerals and overburden suspended in a carrier fluid, to mineral extraction process plants for separation. Therefore, they must be able to handle the abrasive solids in the slurry and, in some cases, corrosive fluids.
Due to the nature of the material being pumped and the distances involved, slurry pumps are usually large and consume significant amounts of power. This is an extremely demanding application, and slurry pumps often operate 24/7, meaning that in severe conditions the wear life of wetted components can be only two to three months. Any failure or inefficiency in slurry pumping can have significant repercussions for the entire plant and project, impacting the overall profitability of mining operations.
Optimising the efficiency of slurry pumps over their entire service life requires:
• Specifying and selecting the right pump and other equipment for the application
• Ensuring the pump is operating at its best efficiency point (BEP) flow rate
• Regular monitoring and maintenance to prevent unplanned outages and declining performance
Choosing the right pump
To deliver maximum slurry pumping efficiency, the performance characteristics of the pump or pumps employed must be well matched to the unique requirements of the particular application on a project. If wrongly specified, even a pump that appears to be operating with a high efficiency can quickly become worn down and damaged. This can result in failure or other problems, like higher power consumption and shorter pipeline equipment life, that will negate the initial efficiency and, ultimately, incur higher costs over time.
The majority of slurry pump issues are caused by a mismatch between the pump’s performance characteristics and the application requirements, either from the initial specification or due to circumstances changing since that specification.
Two main types of pumps are regularly used for transporting slurries: centrifugal pumps and positive displacement pumps. Centrifugal pumps are usually employed
for flow rates from a few litres to thousands of litres per second, and can handle solid particle sizes from microscopic to large rocks up to 300mm. However, they generally can’t develop pressures higher than 7MPa even when they are arranged in series. Their casings can be unlined or lined with internal replaceable liners, composed of materials appropriate to the features of the slurry. The wearing parts are mostly impellers, volutes and side liners.
Positive displacement pumps are often employed for pumping through very long pipelines, because of their ability to generate high pressures, which are well in excess of multistage centrifugal pumps. Their design flow rate range is limited from 50 to 1000 litres per second, due mainly to their large physical sizes, both at low and high flows. They are best suited to transporting slurries with high concentrations of fine particles with a maximum size of about 6mm. The maximum particle size is dictated by the poppet valves, which can jam in semiopen position by large particles. Poppet valves are high wear components that need to be replaced frequently.
An array of different factors come into play when it comes to choosing the best pump for the job. These include the pump’s BEP, the characteristics of the slurry to be pumped, the distance the slurry must travel, and more.
Some of the most important parameters of slurries to consider when selecting a pump include:
• The particle size, shape (angular, round, long and stringy) and hardness
• Corrosiveness
• Chemical compatibility with elastomers
• Solids concentration
• Likelihood of running dry Hydraulic considerations and BEP match
A number of factors should be taken into account in order to select a centrifugal pump that matches the system and application’s hydraulic requirements. These include the system’s design, the required flow rate, the system resistance, and system curve.
System design – Oversizing or undersizing the pump for the application can result in the pump operating outside the range of its BEP or its allowable operating range. This can cause problems such as circulation issues, vibration, cavitation and loud operation.
Flow rate – The flow rate achieved in a pumping system is the result of the head created by the pump.
System resistance – The system resistance head is the head necessary to overcome the static head and the friction head in the pipeline. The duty point of the pump is the flow at which the head created by the pump is equal to the system resistance head.
Duty point (rated flow at differential head) – The key to successful pump selection is to accurately specify the required duty point.
The pump’s BEP flow rate is the optimum flow rate for the slurry to travel through the system at a particular impeller speed.
Net positive suction head available
Net positive suction head (NPSH) is the total absolute head at the pump suction minus the vapour head of the pumped fluid. To prevent cavitation, and the resulting damage, the system net positive suction head available (NPSHA) must be greater than the pump net positive suction head required (NPSHR), preferably with an appropriate safety margin.
Determining the required flow rate, total dynamic head to be generated by the pump, and the suction lift or NPSHA, enables the selection of a pump with a performance curve that satisfies these requirements.
The performance curves provided by pump manufacturers indicate pump efficiency, power use, and the suction lift or NPSH required for the pump’s flow range. The speed (rpm) and input power (kW) required can then be determined by plotting the required flow, total head and suction lift on the performance curves. However, determining the requirements for slurry pumping applications is complicated by the variable individual characteristics of a slurry. The manufacturers’ performance curves are generally based on the process fluid being clear, cold water. Therefore, pumping a comparatively heavier or lighter fluid will require comparatively more or less power, and this must be taken into account in pump selection.
Other possible features of slurry pumps that could influence final pump selection include:
• Leveling (on/off control devices)
• Self-priming
• Thermal overload protection
• Non-clog
• Plug-in
• Reversible
• Dry-running capabilities
• Ease of maintenance
In reality, final selection is often a trade-off between high capital and low maintenance costs, or low capital and high maintenance costs. Therefore, the total cost of ownership over the pump’s service life and the duration of mining operations should be taken into account and balanced.
Once an appropriate pump is selected for a mining slurry application its sustained efficient operation requires that it remain in good condition. Among the key factors that impact upon pump wear is the flow at which the pump is actually operating in relation to its BEP flow rate.
Even a large, robustly-built pump running at a slow speed can experience gouging and wear that reduces the lifespan of its components, subsequently reducing efficiency and increasing its lifetime ownership costs.
A pump operating at a high flow rate relative to its BEP often results in increased pipe friction losses, reduced efficiency, increased power, noise and vibration, high radial loads on bearings, and cavitation due to lack of NPSH available.
Meanwhile, when pumps operate at low flow rates relative to BEP, sedimentation and sanding can occur in pipes, causing blockages. Other problems that may occur include recirculation, increased noise and vibration, increased radial loads on bearings due to unbalanced volute pressures, reduced seal, bearing and impeller life, low flow cavitation, and temperature rise due to dissipated energy created by low efficiency.
Ideally, slurry pumps would be operated at 100 per cent of BEP flow, resulting in maximum efficiency and minimum wear. However, in reality this is not always possible. Nevertheless, ensuring pumps run as close as possible to BEP will improve their performance and service life, maximising efficiency and profitability.
In some cases, although a pump may be correctly specified prior to installation, changes in circumstances that result in changes to flow, such as slurry composition, can require it to operate further away from its BEP flow. Over time, even small changes can result in significant losses of efficiency and increases to wear.
As a result, to achieve optimised slurry pumping efficiency, it is important to undertake regular inspection and maintenance, and to evaluate how any changes to conditions that occur may affect the application requirements, duty point and pump BEP.
Optimising slurry pumps to maximise profitability
Slurry pumps are critical to mining and extraction operations, moving the extracted minerals and associated material to and throughout processing facilities. This demanding application can result in significant wear to pumps, which are required to be powerful and robustly built, and often require significant amounts of power. As a result, the pumps themselves and the power to run them contribute significantly to the overall costs of a mining operation, and improving slurry pumping efficiency can significantly increase profitability for operators within the industry. Maximising efficiency involves determining the requirements of a given slurry pumping application and choosing the right pump for the job (with a BEP well matched to the duty flow rates), operating it as close to its BEP as possible to increase efficiency and equipment lifespan, and undertaking smart monitoring and maintenance to sustain this efficiency over the longer term. By following these steps, operators can increase the likelihood that their slurry pumps will be performing efficiently and reliably for a long time to come, maximising return on investment, and keeping mining operations running smoothly and profitably.
SAER, an Italian pump and motor manufacturer with over 70 years of experience and knowledge in the pumping industry, offers a wide range of products available in several different materials and configurations. Its products are suited for mining applications where reliable and robust pumping equipment is a mandatory requirement. The launch of its new supermining motor builds on its product range, providing an efficient solution engineered specially for the mining industry.
The new 4" supermining motor
SAER’s new range of 4” submersible motors designed for the mining industry – the supermining CLXV95 – addresses users’ needs, offering performance, efficiency and reliability in harsh environments. Using its experience gathered in the field, and combining it with engineers' knowledge and problem-solving skills for application-specific issues, SAER’s supermining motor is designed to be durable, portable and heavy duty in order to cope with the tough conditions and demanding environment of mining applications.
The SAER CLXV95 supermining motor, made in Italy, has a number of features to help it overcome common issues for equipment on mining sites, including:
• Reinforced structure to withstand stress
• Special cable for aggressive environments
• Thicker components
• External support in stainless steel AISI316
• Duplex shaft
• Rubber parts manufactured from FPM
• Triple seal system on the rotor shaft
• Diaphragm membrane for pressure balancing
• Oversized bearings
Built to last
Coming from SAER's knowledge in borehole pumps, its brand new VS series – high efficiency submersible borehole pumps available in sizes from 6" to 14" – is now a reality.
Designed and manufactured in Italy, the VS series is already available in various material configurations including cast iron, full stainless steel AISI316 and full Superduplex.
The new VS series features:
• Efficiency values up to 84 per cent
• Flow range from 10m3/h up to 670m3/h
• Head range from 10m up to 390m
• Motor power from 4kW up to 300kW
Thanks to precision casting of parts, long lasting performance is assured and provides an ideal solution in mining applications such as underground dewatering, dust suppression and raw water supply.
The importance of looking for the right material is indeed sometimes underestimated; cheaper materials could lead to problems such as greater costs for maintenance or replacement, while selecting a well-built, reliable pump will have lower lifecycle costs. In order to have an efficient pumping system, it is important to select the most appropriate pump for the specific application and operating conditions, so SAER’s team can help customers step by step through the product selection process to ensure it meets their specific needs.
Further to its well-known ranges of precision cast products in cast iron, AISI 316 and bronze, SAER now offers them in super duplex, featuring a flow range up to 5,000m³/h and head range up to 60 bars. These products have one of the best delivery times on the market, thanks to their production in Italy.
SAER’s NCB-NCBK end suction pumps series, SKD series split casing pumps, submersible pumps and motors, as well as its TM range of high pressure pumps are available in several configurations and able to withstand the toughest environments.
Laboratory tests can be performed, as well as third parties certifications when needed.
It is now possible to request NCB-NCBK series end suction pumps, as well as TM series multistage pumps, with bearings support in stainless steel AISI316.
Climate change, population growth, and water scarcity are creating new challenges, and desalination is becoming an important alternative to traditional freshwater resources.
A $130 million molybdenum (moly) processing plant is being constructed at Newcrest Mining’s Cadia mine in New South Wales. The plant will extract moly from the mine’s copper concentrate stream to produce a 50 per cent moly concentrate in dry powder form, with an anticipated production of 4.1 million pounds a year. Construction began in February 2020, with commissioning starting in March 2021 and first commercial production expected in the September quarter. Here, we take a look at how the processing plant operates and the equipment used.
Moly is a silvery white metal used to enhance strength, prevent corrosion and reduce brittleness in steels and superalloys, as well as for lubricants, fertilisers and pigments. While it is sometimes mined as a primary product, it is most commonly recovered as a by-product or co-product of copper or tungsten mining.
Moly processing at Cadia
Newcrest will produce moly by extracting it from the copper concentrate stream prior to it being pumped back to Blayney.
Moly project manager, Malcolm McPhan, said, “We’re literally tapping into the pipeline that runs to Balyney.
“We divert copper concentrate from the pipeline on its way to Blayney to the moly plant where we extract the moly via floatation process, then we pump it back into that pipeline and send it on its merry way to Blayney.”
The small floatation plant is made of a series of floatation cells, thickeners, a grinding mill, dryer, scrubber, bagging plant and instrumentation to control it all. The level of control and automation provided is world-class to optimise recoveries and concentrate grades. At nameplate capacity, it is expected it will generate an additional revenue stream of about $45 million per annum.
The plant was designed using the latest intelligent 3D modelling software which provided insights throughout the design process and was expected to offer substantial benefits over conventional packages during construction and commissioning.
The project was expected to employ 140 people during construction and about 15 full-time roles when operational.
Copper and moly are often found together as sulfides, which in solution will
float or sink with the right combination of chemicals and gas bubbles (froth flotation). The sulfide ores are separated from gangue (waste) material, then from each other, by froth flotation.
This separation and concentration of copper and moly is called the coppermoly flotation circuit, and is made up of a number of steps. Various equipment is used throughout this process, depending on project needs and circuit design, but can include sludge pump skid, underflow pump skid, sand pump, diaphragm pump, rotary vacuum filter, flotation cell, SAG mill, ball mill, cyclone and spiral screen.
Grinding mills separate the ore from the gangue material, such as silica and organics, and reduce it to an optimal size for flotation. In this step a rod or ball mill is used and arranged with special non-sliming features
like a peripheral discharge or large diameter discharge trunnion opening to prevent choking and provide greater grinding flexibility. Any particles that are oversized will be caught by fine screens and transported back to the mill for regrinding, this can be done via a bucket elevator, sand pump or spitzkasten.
Once particles are fine enough, water mixes in to form slurry to help in the transportation and separation of the solids.
The flotation stage consists of multiple steps, usually running through rougher flotation cells, then cleaner column cells, and often scavenger cells which work together to give a high total yield of the bulk ore.
The regrind circuit usually consists of a closed-circuit steel head ball mill with a flotation cell and spiral classifier. The flotation cell helps remove the freed mineral coming from the mill.
The unit cell discharge is then transported to a heavy-duty spiral classifier which separates it into the fine flotation feed and the coarse regrind product.
The standard rougher tailings can then go to the scavenger cells which pull out the last trace of mineral. The product is then subjected to two or three stages of cleaner flotation to produce a final flotation concentrate.
At this stage, a high rate thickener dewaters most of the coppermoly concentrate before further separation occurs.
The moly flotation circuit has similar groups of flotation cells with chemicals to float the moly concentrate and settle out the copper concentrate. Here, the less dense ore rises in the froth to be collected, while the gangue sinks to be discarded. Flotation separates the metallic minerals from the gangue this way and separates molybdenite from copper sulphide.
High rate thickeners are then used to thicken each of the copper and moly concentrates, and a vacuum drum (or other) filter dewaters the concentrates further before refining or storing until sale.
The gangue (waste) from the rougher and scavenger cells flows to a tailings thickener to recover water for the process. Filters dewater these tailings further, or they are stored in a tailings pond.
• Self-lubricating
• Non-galling
• Survives run dry episodes
• Corrosion resistant
• Dimensionally stable
• Won’t swell
• Improves efficiencies
• -400˚F to 1000˚F (-240˚C to 535˚C)
Kalium Lakes’ Beyondie Sulphate of Potash (SOP) project in Western Australia has reached a number of major milestones in recent months, with construction work of major infrastructure completed or entering the commissioning stage, and reaching nameplate capacity at its brine extraction and supply infrastructure. Here, we take a look at these milestones and some of the equipment being used throughout the project.
Since 2019, more than 93,000 tonnes of contained SOP has been pumped from the bore field and trenches into the primary evaporation ponds. Nameplate flow rates were reached in October following the completion of brine extraction and supply infrastructure, including brine production bores and pump stations.
Brine is supplied from two resource locations – Ten Mile and Sunshine –and each of the brine extraction areas includes a series of production bores to extract brine from the paleochannel and sandstone aquifer resources located between 10m and 140m below ground level. Actual flow rates achieved from commissioning and test pumping matched modelling for the bore field within each of the extraction areas.
Two trench pump stations are installed at each of the resource lakes to extract brine from the shallow brine resources contained within the lakes. The pumps have a combined flow rate in excess of the planned 100L/sec, with average grades to date of 12,470mg/L potassium against the mine plan of 8,970mg/L.
Power station commissioning complete
In March, the first major commissioning activity for the project was completed, with gas being
introduced all the way to the delivery station near the SOP processing facility. From the high pressure gas delivery station, gas will be supplied through low pressure pipelines to the power station, boiler and other process equipment. This milestone was followed by full commissioning and completion of performance testing for the project’s 7.5MW gas power station in May. Following on-site performance testing, the three 2.5MW gas engines and the associated equipment were fully operational, and all operating licences and permits are in place.
Rudolph van Niekerk, CEO at Kalium Lakes, said, “The power station for the Beyondie SOP project has now been commissioned and is ready to provide power for the process plant commissioning...This milestone, combined with harvesting activities that are in full swing and an operations team that is ready for production, represents a major step forward and significantly de-risks the project in meeting its first production targets.”
Engineering and design work for the SOP purification plant was completed by April and all key process equipment supplied by Ebtec delivered to site including flotation cells, agitators, cyclones, conveyor packages, centrifuges, pumps, cooling crystalliser package, feeder, hammer mill, tanks, thickeners, piping and instrumentation. The standard grade SOP plant entered
the final stages of construction in May, with the focus moving to piping, electrical and instrumentation works.
Erection of the granular SOP plant also began and is on schedule to be completed when the first standard grade SOP is ready for granulation.
There are only a handful of similar brine based SOP mines operating across the world and as a result access to specific equipment design, supply, construction and the necessary operating expertise is limited. Kalium Lakes formed a partnership with German engineering and equipment supply consortium Ebtec, which has completed similar services for a successful SOP plant in Austria, ensuring it is uniquely positioned in the Australian SOP development space.
Work is also underway to increase production beyond 100ktpa and Kalium
Lakes has identified the potential to increase throughput up to 120ktpa through several short-term, low capital intensity improvements.
“We are pleased to announce that a ‘debottlenecking’ style review of the plant design for the Beyondie SOP project confirms that an annual steady-state production rate of at least 100ktpa is achievable. Additionally, the current evaporation ponds’ performance indicates that this production rate can be achieved by mid-2022,” Mr van Niekerk said.
“The company is also confident that a production increase to 120ktpa can be achieved without the need for substantial plant modifications and is currently examining pathways to deliver this outcome.
“Every key milestone de-risks the project for completion on budget and on schedule.
“Methodically and deliberately we are working through this project’s construction phase, making sure everything is aligned for successful commissioning and commencement of production in the third quarter of the 2021 calendar year.”
Irrigated agriculture contributes more than 50 per cent of the value of Tasmania’s agricultural production from eight per cent of the land, with the State Government aiming to further grow the farm gate value of the agricultural sector to $10 billion by 2050 through investment in irrigation infrastructure. The Pipeline to Prosperity program is the third tranche of irrigation schemes being delivered by Tasmanian Irrigation consisting of ten proposed projects – eight new schemes and two scheme augmentations. Here, we take a look at the projects, what infrastructure they are proposing and at what stage of development they’re at.
The Pipeline to Prosperity program is looking to deliver ten irrigation projects in the agricultural areas of Tasmania, delivering up to 78,000ML of irrigation water at an estimated capital cost of $496 million. Phase one includes four new schemes: Don, Fingal, Northern Midlands and Tamar, and one project to augment the existing SassafrasWesley Vale scheme. Phase two includes consideration of new schemes in the Detention, Flowerdale, Harcus and Southern Midlands areas, as well as augmentation to the South East Irrigation Scheme.
Collectively, the ten potential schemes of the Pipeline to Prosperity program comprise:
• 78,000ML
• 479km pipelines
• Seven dams
• 23 pump stations
• Four power stations
Tranche three builds on Tasmanian Irrigation’s successful delivery of tranche one (ten schemes across 2010-2015) and tranche two (five schemes over 2016-2019).
It is jointly funded by the Federal Government, Tasmanian Government and Tasmanian farmers.
Pipeline to Prosperity is expected to create:
• $114 million per annum net present value at the farm gate
• A total of $783 million in economic benefit over the life of the project
• A farm gate benefit to cost ratio of 2.4
• 2,600 full-time jobs
• $150 million on-farm private investment
Don Irrigation Scheme
The Don Irrigation Scheme is the most progressed scheme in tranche three, with the business case now approved.
The preferred option is for a 4,750ML/p.a. irrigation scheme in the state’s north-west, providing high reliability water to the area from West Kentish and north to Don Heads, which is famous for its cropping and dairy enterprises. The Forth River Catchment is regarded as the best water source in the area and provides the 95 per cent reliability required for Tasmanian Irrigation schemes.
The scheme has a capital cost of $29.02 million and the design includes two pump stations (one on Lake Barrington and one downstream of Paloona Dam at Forthside) which will pump to balance tanks with distribution to irrigators via a 67km distribution pipeline. The peak flow rate is 41.7ML/day for a 180-day summer irrigation season, with a winter delivery option available in the future if demand is adequate.
Water sales closed in June 2020 and 3,225ML worth of contracts have been issued.
The scheme is now in the approvals phase after the preferred option was launched in March 2020 and the tender for design support was expected to be awarded in midMarch 221 to prepare the design to be ready to put out the construction tender. Efforts in early 2020 have been focused on gaining all required approvals to commence construction. The approval process involves the finalisation of ecological and heritage surveys, geotechnical investigations and local government approval. Once these tasks are complete tenders will be issued for construction.
Construction is expected to commence in the first half of 2021, with scheme water available to irrigators for the 2022/23 irrigation season.
The DEIS proposed for the Waratah-Wynyard Council region is part of the Future Irrigation Project which will inform the development of the Pipeline to Prosperity suite of schemes proposed by Tasmanian Irrigation.
The Waratah-Wynyard Council region has a small number of land holdings that provide a range of agriculture products that support dairying, including pasture and cereal crops for stock.
The proposed design for the scheme assumes a minimum 3,000ML of water sales and includes approximately 12-15km of distribution pipeline and a pump station with a 0.4km rising main from the Detention River pumping winter flows to a dam to be constructed on the Alarm River. This design will provide flexibility to supply irrigators through either a piped supply or riparian release into the Detention River or Wilsons Creek. The concept scheme incorporates an uplift in costs to reflect current pricing and to allow for additional pump stations and pipelines to be installed.
To date there has been insufficient demand expressed to develop a detailed engineering concept design report with the proposed scheme assuming the minimum water sales to proceed. Furthermore, a preliminary water assessment suggests that there may be insufficient water available to support delivery of 3,000 ML in accordance with Tasmanian
Irrigation’s irrigator service charter. Further water monitoring will take place to confirm this.
The Fingal Irrigation Scheme is proposed for the area along the South Esk River, downstream of Fingal. As one of the state’s drier areas, agriculture is focused primarily on fodder crops, potatoes, seed and poppy production. A major impediment to the expansion of irrigation is the limited availability of water and lack of security supply during the summer months.
The current preferred design option for the scheme is a 12,600ML riparian delivery, South Esk only scheme to allow for future demand and potential augmentation of the scheme to include piped sections (such as St Marys and Royal George) in the future if there is sufficient demand and water availability.
The scheme has a capital cost of $53.6 million and includes a 14,000ML dam located about 12km north of Fingal, a pump station on the South Esk River and 2.3km of dual supply pipeline. It will have a 150-day irrigation season nominally from November through to March annually with water being able to be taken over a 120-day delivery period within this. It is possible that the delivery period can be decreased in order to allow increased flexibility as the scheme progresses through the detailed design phase.
The preferred option was presented for public consultation in September 2020, and development is progressing with flora and fauna and transmission loss assessments taking place in addition to the initial geotechnical investigations conducted in late 2020. Flood modelling and heritage assessments were expected to be conducted in the first half of 2021.
Works for the concept dam design and preliminary geotechnical investigations were conducted in late 2020, with no major issues at the proposed site being found. These works have provided guidance as to the next steps of work required. Additional investigations are underway to confirm quantities of specific construction materials, and will provide greater clarity around the constructability of the dam with the field work portion scheduled to commence in April 2021.
The transmission loss assessment for the South Esk River was completed in early 2021. The aim of having an adaptive model that allows for varying losses dependent on time of year, release volume, base flow and distance from the offtake point will be achieved through a simplified model which is currently being worked through. The model will likely have set loss rates on a per kilometer basis within each management zone of the river, allowing for simplified seasonal variation.
Relevant surveys will be conducted on the pipeline, pump station and any borrow pit areas once better understood in addition to potential gauging weir site investigations which will monitor flows upstream of the proposed pump station site.
The Flowerdale Irrigation Scheme is proposed for the Waratah-Wynyard Council region and is part of the Future Irrigation Project. The region proposed for the Flowerdale scheme has a moderate number of land holdings that provide a range of agricultural products that support dairying, as well as a number of boutique agricultural services including nurseries and flower farms.
The proposed design includes a pump station with a 0.3km rising main from the Flowerdale River which will pump winter flows to a 4,000ML dam to be constructed on a tributary of the river, and approximately 25km of distribution pipelines. The design has been developed to allow for further development in the region and is sized at 3,000ML/season.
Demand for 1,865 ML/season was indicated from initial Expressions of Interest (EOI) sought in March 2018.
The current scheme design indicates an upfront irrigator capital contribution in excess of $2,200/ML and operational charges varying from $195-$295/ML. There is a concern that the scheme costs may impact the viability of the scheme, however, given the extent of uncertainty about the project in its current formative stage, it is considered that additional investigation and design still be pursued.
The Harcus Irrigation Scheme is proposed for the Circular Head Council region and is part of the Future Irrigation Project. The region has a small number of large land holdings that provide a range of agricultural products to enable and support dairying.
The proposed design includes a pump station with a 5.6km rising main from the Welcome River which will pump winter flows to a 9,000ML dam to be constructed at Jims Plains, and approximately 28.4km of distribution pipelines.
The Northern Midlands Irrigation Scheme is proposed for the lower Isis Valley and Macquarie River region to provide additional high reliability water for cropping and will be underpinned by large Hydro Tasmania storages in the state’s central highlands.
The project capital cost is $73.29 million and the proposed design includes three pump stations, two balance tanks, approximately 30 property outlets and 99.7km of HDPE pipe to deliver 76ML/day. The main line is proposed to be constructed from Poatina to short of Ross, and connecting branch lines east of Campbell Town, Powranna, Conara and the Lower Isis Valley. The scheme will utilise outflows from the Poatina Power Station during the summer months, providing water during the 180-day summer period from October to March.
Construction is expected to begin in 2022 with water available in early 2024 and the scheme fully operational by summer 2024-25.
SWISA will expand the existing Sassafras Wesley-Vale Irrigation Scheme (SWIS) which was developed by Tasmanian Irrigation and commenced operations in the 2011-12 irrigation season. SWIS is committed to supplying 5,660ML to 99 irrigators over a 150-day irrigation season from November to March. In a survey conducted in 2019, 28 existing and 33 new irrigators expressed interest in an additional 5,785ML. To meet this interest, the proposed SWISA will allow the SWIS to meet the contracted plus requested total water demand of 11,445ML at 76.3ML/day.
The capital cost for the project is $57.5 million and condition assessment have been completed on the now 50-year-old ex-Wesley Vale Paper Mill assets, which include the Great Bend pump station and reservoir, and the Wesley Vale rising main and main pipeline, to determine what assets are degraded and need repairs or replacements.
Following assessments, the SWISA project has been split into two distinct interrelated projects: one to rectify and, where necessary, replace the degraded assets, and the other to expand the scheme to meet the demand for new water.
The preferred design option is expected to be approved by August 2021, with water sales to follow soon after.
Construction is expected to begin in July 2022 and the first full irrigation season is anticipated to begin in November 2024.
The SEIP is part of the Future Irrigation Project and is proposed for the region that is currently serviced by three existing schemes: South East 1 – services by riparian delivery into the Coal River from Craigbourne Dam; South East 2 –
takes water from TasWater potable supply or riparian release from Craigbourne Dam into the Coal River and pumping from Richmond into Daisy Banks Dam; and South East 3 – supplied exclusively from TasWater potable supply with an offtake located near Granton.
The existing schemes lack the capacity to cater for the continued growth and increasing demand in the region, prompting concerns about future availability and cost of water from TasWater, and concerns around water quality from the Coal River.
The Coal River Valley has a large number of smaller land holdings that generally provide a range of high value agricultural products, typically viticulture, fresh fruit and vegetables etc..
SEIP is investigating options for increasing irrigation water availability in the existing area including new raw water supplies and the potential expansion of the existing irrigation districts into the Derwent and Jordan River Valleys.
The project also includes a 7.5km pipeline from the Tea Tree Road Pump Station along Middle Tea Tree Road into Daisy Banks Dam to allow for the interconnection of South East 2 with South East 3.
An expression of interest process for additional irrigation demand for the SEIP concluded in March 2020 and around 300 expressions of interest were received, totalling approximately 33,500ML of water (20,400ML of summer irrigation water, 6,100ML of winter irrigation water and 7,000ML of resume water).
Concept designs have been developed to service a majority of expression of interest for raw water. Preliminary costings indicate a standalone scheme for the Gretna area may be the best option to deliver around 7,000ML. The design for the main South East area is progressing, with the preferred water source appearing to be the lower River Derwent catchment upstream of New Norfolk and a new trunk main extending east to Forcett. It also includes connections to the existing South East 2 and 3 schemes, and possibly new pipelines in the South East 1 area. Up to 200km of pipelines will potentially be installed.
Engineering assessments are underway and the preferred design option is expected to be released for public comment in July with water sales following in December.
The SMIS is part of the Future Irrigation Project and will be situated across the Central Highlands and Southern Midlands Council regions. These regions have a significant number of land holdings providing a range of agricultural products
including livestock, broadacre cropping, wool, dairy, fruit and wine grapes.
The concept design is based on 30,000ML for a 180day summer irrigation season and includes a low lift pump station sourcing water from Hydro Tasmania’s upper Derwent catchment supplying the Bothwell region with a lift pump station near Shiners Hill to Jericho and Kempton. There is also potential to supply the Hollow Tree, Elderslie and Broadmarsh areas with additional branch lines. It also provides an interconnection with the existing Southern Highlands Irrigation Scheme and the potential for connections to the South East Irrigation schemes.
Based on expressions of interest sought in March 2018, there is demand for 31,500ML during the summer season. As over 200km of pipeline would be required to service this demand, multiple pipeline routes are being investigated.
The Tamar Irrigation Scheme is proposed to service the area east and west of the Tamar River, from Lake Trevallyn to Westwood, Beaconsfield, and from Hillwood, Lilydale, Pipers River and Pipers Brook. Agricultural production in this region includes a range of high quality products such as pasture and cereal crops for stock through to fruit and wine production from orchards and vineyards, as well as boutique agricultural services including nurseries and flower farms.
The preferred design option has a capital cost of $146.2 million for a 12,000ML piped delivery through approximately 240km of pipe based on a 180-day irrigation system with water source from Lake Trevallyn. The design proposes East Tamar irrigators will be supplied via booster pumps for those east of East Arms Road, with a second smaller booster pump planned near Second River Road; West Tamar irrigators will be supplied under gravity pressure from a balance tank; and irrigators on Pipers River to be supplied by riparian deliveries north of Karoola.
Constructability assessments were undertaken in early 2021 and construction is expected to start in September 2022.
Tenders for tranche three works are posted on Tasmanian Irrigation’s website at www.tasmanianirrigation.com.au/contractors-notices
Lowara has an extensive range of pumps and pressure systems suitable for commercial buildings, homes, general industries, agriculture and irrigation.
Call us today to see how we can deliver your pumping solution.
Reliable, high performance, quality materials, and the widespread Lowara support network make these pumps an ideal selection for your water supply requirements.
Ph: 1300 4 BBENG www.brownbros.com.au
In April 2020, Arrow Energy sanctioned the first phase of the $10 billion Surat Gas Project (SGP), a world-scale coal seam gas (CSG) project aimed at commercialising the majority of the company’s gas reserves in the Surat Basin in Southern Queensland, approximately five trillion cubic feet (TCF). The project is expected to run for 27 years, and will include up to 2,500 new wells and create about 1,000 jobs across its lifetime. With the first phase of the project now underway, there are a number of opportunities for manufactures and suppliers of pumping and associated equipment to take hold of.
Arrow Energy has operated in the Surat Basin for more than 15 years. The sanction decision follows the final investment decision (FID) for phase one of the SGP from its shareholders, PetroChina and Shell.
Arrow Energy CEO, Cecile Wake, said, “The decisions by PetroChina, Shell and Arrow demonstrate commitment to and confidence in Queensland and the Australian market at a time of global economic turmoil from COVID-19 and against the backdrop of sustained low oil prices.
“This significant investment comes at a critical time and will cement Arrow’s position as a major producer of natural gas on the east coast.
“The Surat Gas Project is the first large-scale CSG project in Australia to be underpinned by a significant infrastructure collaboration and gas sales agreement, together with a suite of supporting agreements, which have been put in place between Arrow and the Shell-operated QGC joint venture.
“This agreement enables the use of capacity in QGC’s existing gas and water processing, treatment and transportation infrastructure, reducing the impacts on
landholders, communities and the environment and ensuring that more gas can be economically developed.”
Phase one works were scheduled to begin in the second half of 2020 with a focus on an expansion between Arrow Energy’s current operational areas at Daandine and Tipton, with expansion to take place later to the north and south of Daandine, down to Tipton. Initial works will bring around 300TJ/ day of gas to the market.
The first phase will see more than 600 wells drilled and the construction of inlet processing facilities (IPFs) at Shell-QGC operated David and Harry Field Compression Stations. The IPFs will enable the company to supply gas from its operational fields under the gas sales agreement, with the David IPF to be the first delivery point online from late 2021.
Arrow Energy will continue to use its existing gas compression facilities at Daandine and Tipton, with upgrades to the Tipton Central Gas Processing Facility to take place.
The company will use its existing water treatment facilities, which will be improved through upgrades to the Tipton and
Daandine Water Treatment Plants, including a connection to existing Shell-QGC operated water facilities at David, Broadwater and Glendower Ponds. Water will be sent to the Shell-QGC operated Kenya Water Treatment facility and two new brine storage ponds will be constructed at the facility to support coal seam water treatment for a Beneficial Use Network. The Beneficial Use Network is expected to be in place by 2023 to return a portion of treated water to users with Condamine Alluvium allocations in order to offset any potential impact from drawdown on the Condamine Alluvium and to maximise beneficial use of its treated CSG water. Additional treated water will be beneficially used via the existing SunWater Chinchilla scheme.
In November, Valmec was awarded the first phase of the project, initially to deliver critical water treatment facilities, valued at $16 million, and involves procurement, construction and commissioning works at the Daandine facility.
“An initial 200 construction jobs will be created during phase one, with an anticipated further 800 construction and operating roles over the life of the Surat Gas Project,” Ms Wake said.
“The decision to sanction phase one of the Surat Gas Project and commence construction...is good for Queensland. It will mean more jobs, more opportunities for local companies and other economic benefits for regional Queensland, which has been home to Arrow for more than 20 years.”
Peak construction is anticipated for 2021-2025.
Works beyond phase one
Planning for subsequent phases continues and Arrow Energy will seek shareholder investment for these phases once engineering definition is complete. Ultimately, up to 2,500 wells are planned across all phases, to bring a peak of 700TJ/day of gas to market from tenure areas north of Wandoan to south of Cecil Plain
Subsequent phases in the future plans include:
• An additional 1,900 wells and associated gathering to expand across Arrow Energy’s Surat tenure areas
• Construction of two new field compression stations at Lynwood, south of Arrow Energy’s Tipton development and Girrahween, near Miles
• Construction of two additional Inlet Processing Facilities (IPFs) at Shell-QGC operated Jammat and McNulty Field Compression Stations
Wells and gathering nearby the new compression stations will be constructed to feed into the new infrastructure. Arrow Energy also plans to step out into new development areas to construct wells and gathering south of Wandoan, and south and east of Cecil Plains.
Reducing site footprint with innovative drilling technique
Traditionally, CSG wells are drilled straight down to create a vertical well. Where conditions allow ‘deviated’ wells –wells that are drilled at angles away from vertical – can be drilled instead.
In the Surat Basin, the seams are thin and discontinuous, so the wells need to target multiple, smaller seams. This is why Arrow Energy is using deviated wells from multi-wells pads in the Basin where possible, allowing the company to cluster the wellheads in groups on single well pads to reduce the impact on farmland and farming operations, while still reaching the same area of coal seam from a single surface point that would otherwise require multiple vertical wells with their own well pads.
Where geology allows, Arrow Energy has committed to multi-well pads and deviated wells on Intensively Farmed Land (IFL). Multi-well pads are preferred where the lowest
coal targets are deeper than 400m with surface spacing for deviated wells is up to 2.5km on average. This benefits landholders by reducing the overall footprint by 25 to 50 per cent compared to traditional vertical well field design.
The deviated section of a well can extend at an angle of 7082 degrees to horizontal distance of up to 800m from the well pad, enabling the company to target a greater amount of coal without impacting the agricultural land directly above, while minimising its infrastructure footprint. Outside of IFL areas, or where coals are shallower (less than 400m), vertical wells are used with surface spacing from 800m to 1.5km (or greater).
There are five major steps in construction of wells and associated gathering infrastructure:
• Site survey and construction or upgrading of access tracks as required
• Construction of well pads
• Well drilling
• Installation of well pad infrastructure, including well head skid and generators or power connection
• Completion of the well, including installation of downhole pumping apparatus
• Connection of the well to Arrows water and gas networks with underground collection pipes, referred to as the gathering system
• Well commissioning
The site survey involves a small team in a light vehicle surveying the well pad location and other necessary infrastructure, such as access roads and pipeline routes. The establishment of access tracks to the site, if not already existing, may also be required. This work can take between two and five days to complete.
After the survey is complete, the well pad site is cleared and levelled. Where required, fauna spotters/handlers inspect the site prior to these works commencing to rescue or relocate any birds or animals.
The pad area that is cleared and levelled will be much larger than the final size of the constructed well pad to accommodate the drilling and completions works, and will be rehabilitated once the works are completed. In general, an area of 100mx100m is cleared for a single well pad, while a multi-well pad that can accommodate up to eight wells can require an area of up to 100mx200m. Depending on the size of the pad, construction can take up to eight days to complete.
Drilling activities may occur on a 24-hour basis and can take up to seven days to complete. The process involves a drill rig, and both heavy and light vehicles delivering parts and personnel to site.
Once the drill rig is mobilised to site, an initial surface hole is drilled to a planned depth, a steel casing is inserted into the surface hole and cemented in place. The cement is pumped down through the steel casing, out the open end at the bottom of the hole and back up the outside of the casing to the top to ensure any gaps are filled between the steel casing and the surrounding rock.
Deviated drilling tools are then used to drill on a designated path to reach the coal. Once the production hole has reached its final depth, a specifically tailored casing is installed. Expanding (swelling) packers are used around the outside of the casing to isolate the coal seams from other aquifers or rock formations, and cement is pumped around the outside of
the production casing to ensure the isolation. Testing is then undertaken on all casings to ensure well integrity and the well is “suspended” (made inoperable to prevent gas production) until it can be “completed” (made ready to operate) through the installation of a downhole submersible pump, and commissioned (started up).
Completion and commissioning
At this stage, surface infrastructure is installed on the well pad, including:
• A well head
• A metering skid to manage and measure gas flow
• Gas-driven generator or reticulated power equipment for a submersible pump
• A control cabinet and communications aerial to enable remote monitoring
To complete a well, a completion/workover rig and about nine workers will arrive at the well pad. The crew will take four to seven days to drill out the internal cementing tools and install an electric submersible pump into the well. The pumps reduce water pressure in the coal seam to allow the gas to flow.
Once this has been completed, the well sites are ready to be connected to the water and gas networks and commissioned for operation.
Site rehabilitation
The well pad construction site will then be reduced to the final operating size and the excess area will be rehabilitated. Typically, a single-well pad may have a fenced area about 20mx30m, while the multi-well pad size will vary depending on the number of wells and site layout.
The remaining disturbed area will then be rehabilitated in accordance with the landholder requirements, and can be used by the landholder for regular agricultural purposes.
The rehabilitated area may be required from time-to-time for well maintenance activities.
Gas and water gathering pipeline construction
Before constructing pipelines, surveying and pegging of the pipeline route and construction areas, known as a “right-of-
way” (RoW), need to take place. The route will be planned with the property owners, and designed to minimise impacts to the day-to-day use of the property and future land use.
Once the RoW is pegged, the area is cleared, with vegetation and topsoil stockpiled separately, for use during rehabilitation after works are completed. Erosion and sediment controls are implemented and gypsum is spread on top of the exposed sub soil. The pipeline route is then excavated by a trenching machine. The depth of the trench is dependent on land use, however there will be a minimum of 750mm of cover over the pipe.
The gathering pipeline will then be laid out along the route, before being welded together to create a “string” and lowered into the trench and backfilled. At this stage, aboveground safety infrastructure, such as high point vents and low point drains, is installed as required.
After backfilling and compaction of the trench, the RoW is rehabilitated including grading the ground and reinstating original formations and natural contours. The grading/profiling is followed by evenly spreading the preserved topsoil across the RoW using a grader.
The buried pipeline is then pressure tested to ensure strength and to test for leaks.
The final step is to seed vegetation on the RoW which is done in consultation with the landholder.
The frequency of maintenance of the wells will vary, but Arrow Energy has averaged it to once every two to three years.
Where there are up to eight wells on a multi-well pad, the frequency will be higher than for vertical well pads, with two to eight maintenance events per year, on average. For a four well pad, it is expected to undertake one to four maintenance events per year.
Routine inspections and maintenance of the well pads will also need to be undertaken, which could range from weekly to quarterly, depending on the individual well. Typically for these wells, Arrow Energy expects fortnightly inspections for maintenance and safety checks.
There are a number of opportunities for Australian manufacturers and suppliers to get involved in the project, including for the provision of electric submersible pumps and choke valves. All procurement and supply opportunities are advertised on the Industry Capability Network (ICN) Gateway. To view current work package listings or register your interest in future contracting opportunities, visit www.arrowenergy.com.au/suppliers-contractors/supplier-portal.
ITT Blakers providing the most widely recognized and respected brands in the global pump industry, ITT Blakers is a one-stop shop for highly engineered critical components and customized technology solutions that achieve significantly improved results. We supply and recondition all brands of pumps and rotating equipment, restoring them to original specification. No need to source different product specialists depending on the equipment needing repair.
One call takes care of your service headaches.
Trusted to deliver mining solutions like this for more than 40 years, ITT Blakers have been supplying various types of horizontal and vertical pumps to the mining and mineral processing industry throughout Australia.
• Lifetime, Reliable Performance Confidence.
• Optimized, Trusted OEM TCO Maintenance.
• Enabled by Accurate Remote Monitoring and Conditioning.
• Proven by Extensive Track Record.
• 100% Australian, Responsive Expert Local Support.
The Goulds Model XHD is the result of 100 years of slurry pumping experience. The XHD incorporates the latest technology including CFD analysis to provide the next generation in severe-duty slurry pumping. Extensive “Voice of the Customer” input was utilized to ensure our customers’ most important needs were met. This includes high efficiency with extended wear life, along with maximum reliability and ease of maintenance. The XHD is designed to keep your process running.
Ebsray® V Series Sliding Vane Pumps have been designed and precision built for efficient transfer of a variety of liquids over a wide range of viscosities with lubricating or nonlubricating characteristics. Built for versatility, V series sliding vane pumps feature numerous mounting options, including up to eight different porting and drive configurations. V Series sliding vanes are widely used in fuel transfer applications in the mining industry and offer a very reliable option in a tough mining environment. ITT Blakers have been representing EBSRAY range of products for over 40+ years.
Seepex N range Product group N pumps are the model for the design of all SEEPEX progressive cavity pumps. They are used in all industries and convey thin to highly viscous liquids with or without solids. They are available with various rotor / stator geometries (conventional, 6L, Tricam and Equal Wall). These benefits and others ensure the pump’s economical operation.Product group N pumps form the basis of the modular concept that supports all SEEPEX progressive cavity pumps, this makes the offering very service friendly and ideal for tough mining applications. ITT Blakers have been representing Seepex range of products in Australia for over 30+ years.
To safely, efficiently and economically transport natural gas long distances, it is converted to liquified natural gas (LNG), which reduces it to around 1/600th of its original volume. Keeping LNG in its liquid form requires cryogenic conditions of at least -162ºC to be maintained throughout the transportation process. The pumps that transport LNG, such as those that move it into, around, and out of the storage tanks on LNG tankers, must therefore operate at cryogenic temperatures. Due to the significant safety and economic consequences should equipment fail or leak LNG, the pumps used must be highly reliable, durable and constructed of compatible materials.
For LNG applications, specialised submerged motordriven cryogenic pumps are used. Some of the benefits of submerged operation include that, as a cryogenic fluid, LNG is an excellent electrical insulator, and the motor is completely isolated from oxygen in the atmosphere, eliminating the risk of fire or explosion. This design also removes the need for rotating seals, which can be problematic and introduce a potential point of failure.
Submerged LNG pumps are constructed as a single unit, with the pump mounted on the same shaft as the motor, to be submerged in the LNG. Some of the cryogenic LNG fluid moves through the gap between the pump’s rotor and stator to cool the motor.
There are three main types used – fixed, vessel-mounted and retractable – with various adaptations available to suit the needs of a specific project and application.
For applications where a LNG pump is used in a piping system, it is mounted in its own suction vessel. The suction vessel takes the loads of the piping system and other structural elements, reducing the forces affecting the pump itself. This design eliminates the need for alignment, as the pump bolts to the headplate of the suction vessel. Additionally, the vessel and liquid dampen the noise from the pump, and the pump can remain in the liquid, ready to operate whenever needed.
A retractable in-tank pump design allows the pump to be removed from the storage tank for maintenance while the tank itself continues to operate. These pumps are arranged in vertical pump columns, with a foot valve at the bottom, which prevents LNG from entering the column when the pump is removed. The pump can be raised or lowered to open or close the foot valve without removing the headplate at the top of the column. The operators purge the column with nitrogen, and it can be safely removed at the top of the column. The only penetration from the pump to the outside atmosphere is the electrical leads to the motor.
In the oil and gas industry, specialised pumps play a range of critical roles throughout the process of converting gas into LNG, storing it, and loading and unloading LNG tankers. Pumps that handle LNG are specialised and specified for the unique requirements of these applications, which require operation under cryogenic conditions, submersion of the pump unit, very high reliability and more. In this article, we take a closer look at some of the key requirements and considerations for LNG pumps.
Cryogenic LNG pumps incorporate unique features to meet the requirements of their specialised application. Some of the important requirements and considerations for pumping LNG include:
• Basic type – fixed, retractable, or vessel-mounted
• Construction materials
• Cooldown and warmup considerations
• Hydraulic considerations (e.g. operation at low NPSH)
• Handling considerations for pump size and weight
• Thrust equalising
• Bearing configuration
• Junction box assembly and electrical penetrations
• Vibration monitoring
• Adequate testing at the cryogenic temperatures and the power levels expected in service
Fixed, retractable, or vessel-mounted LNG pumps
As previously discussed, there are three basic types of submerged motor-driven LNG pumps. The exact configuration suited to an application depends on factors such as whether the pump potentially needs to be able to be removed from its tank for maintenance while the tank is still full of LNG, whether it is attached to a piping system, space considerations, and more.
Due to the contact between the submerged pump and the LNG, and the cryogenic application temperatures, LNG pumps (and associated equipment like valves) must be made of suitable materials for these conditions. The materials must adhere to applicable regulatory and industry standards to ensure safety.
Housings and rotating elements, such as impellers and inducers, are often fabricated from cast aluminium alloys, such as ASTM A356-T6, providing excellent thermal conductivity, stability and ductility at low temperatures, with a light weight (an important consideration for handling and on ships).
Austenitic stainless steel and wrought aluminium are also sometimes used for casings and other fixtures.
Impellers are hard-coat anodised to provide erosion resistance. Shafts are frequently made from appropriate grades of stainless steel, chosen for ductility and strength at cryogenic temperatures, as well as electrical properties, as the motor rotor is installed directly on the shaft shared by the pump and motor. Bronze is often used for wear rings and bushings, due to its thermal characteristics in the required temperatures. Other bushings options include graphite and sintered bronze materials.
The bearings that support the rotor assembly are typically made of 440C steel (a martensitic high carbon 400
series stainless steel), providing corrosion resistance and temperature stability. The electric pump motor and rotor are usually made from silicon steel laminated plates. The strength, light weight, and heat-transfer properties of this material are well suited to cryogenic applications.
Cooldown and warmup considerations
Before LNG can be taken on, the LNG tanks, lines and pumps must be pre-cooled to prevent stress on their materials from overly rapid cooling, or LNG converting to gas form. Likewise, LNG tank warmup is an important part of the process for removing gas prior to dry docking or when tanks must be prepared for inspection. The cooldown and start-up, as well as warmup, processes of the application should be considered in pump specification.
Hydraulic considerations
Like all pumps, to fulfill its duty, an LNG pump must be well-matched to the hydraulic requirements of the application. These include the required flow rates, suction pressure, and NPSH available. For in-tank applications, NPSHr (net positive suction head required) determines the usable and non-usable volume of an LNG tank. The non-usable volume is that which remains in the tank due to the NPSHr limitations of the pump. Below the non-usable volume height, the pump will experience cavitation damage. If the pump is required to operate at low NPSH, high-performance inducers and high-efficiency impellers are often required.
Handling considerations for pump size and weight
Pump size and weight have significant implications for ease of installation and maintenance, and pumps contribute to the total load on LNG tankers.
Thrust-equalising
Thrust-equalising mechanisms balance thrust across the entire operating flow range, removing axial bearing loads. The system, which can be located either upstream or downstream of the motor, keeps the motor at discharge pressure, preventing vapour from forming in the motor housing.
Bearing configuration
Due to the poor lubricating qualities of cryogenic fluids, LNG pumps use specialised durable rolling-element bearings that can tolerate thrust in either direction and handle load
reversals. Pumps associated with variable frequency drives (VFDs) may have ceramic ball bearings to prevent arcing due to eddy currents.
Electricity is connected to the submerged pumps through specialised junction boxes. As a penetration point between the LNG within the tank and the external atmosphere, the junction box and the electrical feed-through assemblies must be composed of appropriate materials and the design should incorporate various redundancies to prevent gas leakage to ensure safety.
Vibration monitoring
Vibration monitoring systems alert operators to potential cavitation and operation outside set parameters, which could indicate the presence of vapour, meaning LNG is converting to natural gas.
Testing cryogenic LNG pumps
As a result of the unique design of LNG pumps and the operating temperatures required, they cannot be tested using water, and must be tested with LNG to verify performance as close to the conditions of actual use as possible. Testing with LNG close to design conditions verifies:
• Motor performance and starting ability in cryogenic liquid
• Mechanical alignment
• Pump performance characteristics using the cold boiling liquid, vital for NPSH testing
• No internal leakage due to deformation or differential shrinkage when the components are stressed at actual operating conditions
The unique requirements and safety-critical nature of LNG pumping applications mean that the pumps used must be specifically designed for the job and meet extremely high standards of durability and reliability. As a result, a wide range of considerations go into specifying submerged motor-driven cryogenic LNG pumps for a project, ensuring that they can operate effectively in the extreme conditions required. As the means of moving LNG between processing, storage and transport facilities, these pumps are instrumental to enabling LNG projects, allowing product to be transported safely and economically to markets.
AUSTRALIA AS-NZS4020-2005 APPROVED
UK WRAS APPROVAL to BS6920
USA NSF61 LISTED
GERMANY KTW-DVGW APPROVED POLAND PZH APPROVED
Smart maintenance technologies are enabling SA Water to adopt a proactive and predictive approach to asset management.
New technological capabilities are enabling SA Water to save time and money by increasing pump reliability and availability as well as pump performance and lifespan, reducing maintenance times through improved root cause analysis and repetitive preventative maintenance work orders, and optimising maintenance and capital investment.
SA Water’s specialist business unit Water Engineering Technologies is leading the way in the development and provision of smart maintenance capabilities to organisations that own and operate rotating assets.
Organisations that rely on rotating assets to deliver safe, reliable, sustainable, and cost-effective water and wastewater services to their customers must invest in maintenance.
To achieve the lowest lifecycle costs for assets and to minimise forced outages and breakdowns, maintenance is a key component of risk management, asset management and business strategy.
This involves identifying assets that present a high risk to the delivery of services, and the use of risk management strategies to reduce disruptive or negative outcomes.
Asset risk calculations are based on two components: likelihood and consequence of failure.
While the results of asset failure can be relatively constant over time, the probability of failure is not – as assets age and deteriorate, the likelihood of failure can increase. There is a strong relationship between the condition of an asset, its likelihood of failure, its risk rating, and the reliability of the provided service.
Once the level of risk associated with the asset is known, it can either be accepted, or reduced through an operational and/or capital intervention.
The critical question for asset owners or managers is ‘what is the best way to assess the risk that an asset will fail and determine the most appropriate intervention solution –to repair, rehabilitate, or replace?’
Asset management covers a broad spectrum of practice across the water and wastewater services industry, ranging from the basic reactive ‘run to failure’ approach, through to preventative maintenance regimes and the use of innovative predictive maintenance methods and strategies.
Water Engineering Technologies Senior Manager Maintenance, Nima Gorjian, says you can’t rely on intuition and guesswork based on visual inspections and fixed time-based maintenance to keep assets safe, reliable and profitable or provide the best use of asset management budgets.
“Simply refurbishing or replacing components at fixed time intervals, based on the rationale that this will reduce incidence of breakdowns can be flawed,” Nima says.
“In most cases, scheduled preventative maintenance is based on original equipment manufacturers’ recommendations, best guesses or a mixture of both, with limited evidence of root causes of actual or potential failures identified.
“Not surprisingly, these maintenance approaches lead to repeated failures, spiralling costs and short-term planning. And, with a lack of good evidence that these approaches achieve positive business returns in plant or financial performance, pressure to reduce maintenance budgets increases.”
“For these reasons, we can now better understand how and why rotating assets wear out, how they behave, why they fail, and the ways in which they respond to various operating conditions and environments,” he says.
“Our planned programs at SA Water adopt a reliabilitycentred maintenance approach across the life of the pump asset. This sees asset life realised, lifecycle costings optimised, and level of service maintained.”
To achieve this, Nima says the asset’s physical condition is used to predict the end-of-life replacement, or total failure of the asset, rather than the day-to-day failures that will be rectified through regular corrective or breakdown maintenance.
“Reliability and CBM keeps a watch on asset condition parameters, such as vibration, temperature and pressure, so that early signs of asset deterioration, diagnosis of asset degradation or significant changes in asset health can be readily identified.”
In general, vibration analysis techniques are applied in the condition monitoring of rotating equipment such as pumps and motors.
“Our advanced condition-based maintenance processes and technologies enable early signs of asset degradation to be identified to inform accurate risk assessments, providing critical information to identify the appropriate timing for interventions to bring assets back to an appropriate standard.”
The use of advanced asset monitoring capabilities –portable vibration, temperature and pressure sensing analysers – negates the limited value of visual/audible inspections of assets.
Nima says that in contrast to past practices, maintenance management today is a technologically advanced practice, drawing on an array of sophisticated techniques and technologies to determine an asset’s condition.
“Our reliability and conditioning monitoring team use portable analysers to ‘listen’ and analyse an asset’s condition – much like a doctor uses a stethoscope, blood test or thermometer to check a person’s inner workings,” Nima says.
“With portable analysers, we monitor the condition of rotating assets by capturing data that is processed and
analysed using an advanced machine health monitoring program to determine the condition of the asset to diagnose and fix faults.”
Water Engineering Technologies’ use of portable and online sensors to collect new data is combined with existing data, such as event history, and reliability engineering techniques, data analytics and Artificial Intelligence (AI) algorithms to predict asset faults the repair or replacement needs of key assets and avoid maintaining unnecessary redundancy.
By installing smart technologies on critical rotating assets and analysing real time sensor data, owners and operators of pump stations can avoid ‘catastrophic’ failures. By being proactive and predictive with asset maintenance and replacement you can reduce repetitive preventative maintenance work and optimise maintenance investments.
Late last year, Water Engineering Technologies installed online vibration and temperature sensors at one of SA Water’s Swan Reach water pump stations, as part of a smart maintenance program proof of concept.
The aim was to test how well real time data flowed from smart sensors to SA Water’s state-wide, industry-leading monitoring system and machine health software and AI platform to proactively predict potential faults and avoid failures.
Overseen by Water Engineering Technologies' reliability and condition monitoring team, best practice artificial intelligence modelling was developed using real time and historical data to build intelligence and diagnose rotating asset fault patterns.
In April 2020, the AI solution alerted the team to a potential issue at the pump station.
Data Analytic Engineer Kaushik Sesha Dollaiah notified subject matter expert and Lead Condition Monitoring Engineer, Stephen Moore who investigated and confirmed there was a problem with the pump and worked to rectify the issue.
"Previously, we would routinely check the pump every three months using a portable analyser. Without the use of smart technology, the issue would have gone undetected until this time." Stephen says.
Manager Reliability Integrity and Condition Monitoring, Harvey Pantow, added, “By predicting the fault early, we avoided any potential catastrophic failures and further degradation of the asset, as well as impacts to water services for the outer-metropolitan Adelaide area from an unplanned shutdown which typically would incur more costs.”
Water Engineering Technologies' performance and conditionbased maintenance program enables SA Water to maximise asset lifecycle and reduce operational costs, through the application of data-driven innovative reliability techniques.
In the near future, Water Engineering Technologies will look to roll out smart online sensors across SA Water’s regional critical pump sets providing predictive maintenance analysis and continued monitoring. Moving to this approach provides the continued reliable operation of this critical infrastructure, reducing the need for unplanned maintenance and enabling improved safe work practices.
Combined with the optimisation of work management planning and effective work delivery, this will see Water Engineering Technologies work smarter, improve the quality of their maintenance services and free up their people to work on capital projects, achieving continued reliable water and wastewater services for South Australians.
Volvo Penta. Robust, fuel efficient industrial diesel engines that keep running even in the toughest conditions. Easy to install, operate and maintain. A powerful partnership you can trust all the way from the drawing board throughout the operational life of your engine. Competitively priced complete power-pack units ready for delivery Australia wide with a local support team on hand 24/7. To find your nearest dealer visit www.volvopenta.com
Over the past decade, microbreweries have become an increasingly expanding section of the Australian beer market, with over 500 brands worth more than $807 million a year in 2020 – a value that is estimated to be rising by five to ten per cent each year. IBIS World forecasts that rising consumer demand for innovative new beer varieties and flavours, and low barriers to entry will see enterprise numbers increase as new entrants try to capitalise on strong consumer demand. The growing appetite for craft beers also represents an opportunity for pump equipment suppliers and manufacturers, as pumps, valves and pipes play an important role in the brewing process. Here, we look at the brewing process and the equipment that is used throughout the process.
The beer brewing process
1. Malting
Malting is the first step in the beer production process. The fresh barley is soaked in water and germinated in germinating boxes. In this phase, the enzymes (amylase), which are needed for starch separation, are formed. The germinating process is then interrupted at the optimal stage by the drying (kilning) and the green malt is dried at 80°C. The malt sugar will later serve to feed the yeast cultures that form the alcohol.
2. Milling
The second step is milling. The finished malt is milled so that it dissolves better in water. Malt mills produce various grades of crushed malt: husks, groats, meal, semolina and powder (from coarsest to finest).
3. Mashing
The milled malt is then mixed with water in the mash tun where the starch in the grist dissolves and sugar, protein and tannin are released. This mashing process produces the malt extract.
4. Lautering
The mash is filtered in the lauter tun. In this step, the husks sink and the wort is separated from the solid substances (spent grains). While the wort is further used in the brewing process, the spent grains are usually used as cattle fodder.
5. Wort boiling
The wort is transferred to a brewing pan or wort kettle and brought to the boil to ensure sterility. Hops are added at various times during the boiling process to impart hop bitterness, flavour and aroma – these are determined by the type and amount of hops used with more hops creating a more bitter tasting beer. As the water evaporates, the wort becomes concentrated to the original wort, the malt enzymes are deactivated, and tannin and protein elements are separated out to form the trub.
6. Wort clarification
The wort is then sent to the whirlpool to be clarified or drawn off. The whirlpool rotates, forcing the hop particles that have not dissolved and protein – the trub – to form a cone in the middle of the container, with the clear wort tapped off at the side. The clear wort is cooled to a temperature of between 10-20°C in the wort cooler.
7. Fermentation
The cooled wort is pumped into a fermentation tank where special brewing yeast is added. The yeast converts the malt sugar into alcohol and carbon dioxide. Once the malt sugar has fermented, the yeast sinks and is collected. Depending on the type of yeast and the wort preparation used, a top- or bottom-fermented beer is produced.
8. Storage
The young beer is then transferred to maturation tanks where it is stored at 1-2°C from anywhere between three weeks to three months. When the sugars have almost completely dissolved, a secondary fermentation takes place where the remaining yeast particles and proteintannin sink to the bottom. The beer becomes clear and acquires its characteristic colour.
9. Filtration
During the filtration stage, any substances still remaining after fermentation and secondary fermentation, such as yeast particles, hop resin and protein are removed and the beer gets its final clear colour.
10. Filling
The last stage in the brewing process is the filling. The beer is put into bottles or cans, or into kegs for distribution.
From large breweries to microbreweries and home brewers, various pumps are used at multiple steps throughout the brewing process. Due to the important role pumps play in the brewing process, pump selection needs careful attention and the equipment needs to be well-maintained to sustain performance and operation.
The production process can be roughly divided into hot and cold applications, with each of these having different requirements.
Hot applications include filtering, cooking and cooling work, and cleaning in place.
Cold applications include fermentation/propagation, cooling down and bearing, filtering, filling, and bottle fermentation.
It is crucial that the pumps are able to handle difficult fluids such as yeast, mash and wort which are abrasive and viscous in nature. These need gentle handling and require a pump that provides moderate pumping action. Furthermore, pumps that are moving the product need to be made from hygienic materials to comply with food regulations.
There are three main types of pumps recommended for brewing applications – centrifugal, peristaltic and diaphragm –depending on what it will be used for.
Typical applications for a centrifugal pump are:
• Hot liquor transfer
• Hot wort transfer
• CUP pumping and scavenging
• Tank to tank transfer
• Tank cleaning
Typical applications for a peristaltic or diaphragm pump are:
• Mash recirculation
• Liquid sugar transfer
• Mash-in-wort
• Yeast slurry transfer
• Bottling, casking and canning
• Syrup transfer
Centrifugal pumps are the most commonly used pump in the beer brewing process as they are able to handle high enough temperatures to be able to transfer hot wort or recirculate the mash. They are also ideal for transfer and filling applications in bottling, casking and canning. Hygienic, food grade versions of this type of pump should be selected to ensure it remains sanitary and the product moving through it is able to be consumed by people.
The main benefits of using a centrifugal pump is that there is minimal upkeep and therefore a lower maintenance cost; they can be fitted with a heat jacket; and they are compact with a simple design and few parts.
However, these pumps must be kept below the liquid level being pumped and if a self-priming version is not selected, they need to be primed before starting as the motor can be burned out if run dry.
Peristaltic pumps have a simple but effective design where the liquid passes through a flexible tube or hose which is compressed to move the liquid. The advantage of this is that the tube or hose is the only part of the pump that comes in contact with the wort, which reduces the risk of contamination and makes cleaning easier. They are also typically self-priming so dry running is not generally a problem.
The main benefits of peristaltic pump include:
• Available in different sizes with a range of flow rates
• Can handle fragile fluids with little wear
• The tube or hose can be easily replaced
• Able to pass solids in the material being pumped
• Seal-less design eliminates leaks, contamination and wear problems
• Reversible operation allows pumping in both directions
• Low maintenance requirements
However, these pumps tend to be more expensive than centrifugal or diaphragm pumps.
Diaphragm pumps are designed to allow the liquid to move in and out of a diaphragm by alternatively increasing and reducing pressure in the pump housing. These pumps are great for transferring lower temperature liquids, such as moving cooled wort into the fermenters or for pumping beer between fermenters or into kegs for carbonation. For higher temperature applications such as recirculating wort or transferring hot wort through a chiller, specially-designed high temperature models will need to be purchased.
Selecting a sanitary model is also important as standard diaphragm pumps can be difficult to clean. They often come with features such as lubricant-free air distribution system, maintenance-free ball check valve system, easy and complete visual inspection of wetted pumps, and support cleaning and sterilization in place (CIP or SIP), making them ideal for food and beverage applications.
Breweries also have a vast system of pipes, and various valves required to regulate the flow of fluid through the system.
Pipes are an integral part of a brewery as it supports all the steps in the brewing processes, transporting not only the ingredients and fluid at every stage but also gases and liquids for cleaning, sanitation, wort cooling, etc..
Different sized pipes are needed to handle the range of volume being moved, and knowing piping size and capacity is crucial, as well as a knowledge of fluid dynamics.
Each pipe size requires a certain amount of length to contain the fluid, for example a half inch pipe requires just over 459m of pipe to contain one barrel of fluid while a 12 inch pipe requires only 1.5m of pipe to contain the same amount of liquid. This knowledge is important considering all the different uses for pipes in this application and the amount of space needed to accommodate each stage of the process.
Fluid dynamics on the other hand, determines what happens to the liquid or gas and its molecules when travelling through the pipes at different velocities. There are two types of flow that need to be considered:
• Laminar flow – where the fluid moves through the pipe at a velocity that leaves the molecules’ travel undisturbed in the direction of the flow. This flow type ensures fluid travels smoothly and molecules move in a parallel direction. When velocity increases, a change occurs, resulting in varying direction of the molecule flow
• Turbulent flow – when molecules become scattered and flow chaotically
Both flow types can be used in the brewing process, with different steps requiring different flow types. Pipe diameter also has a role to play in determining the flow type. There are a number of valves types that can found throughout the piping system in a brewery, including:
• Cock valve – this valve is a plug with a hole that can be turned to restrict or stop flow. Some come with a handle that can be turned 90 degrees, from fully open to fully closed
• Diaphragm valve – this valve has a soft diaphragm that pushes against a bell-shaped feature by a mechanical screw, allowing the gas or liquid flow to be controlled within its total variability. Flow pressure tolerance is fairly tight
• Butterfly valve – most commonly used in breweries due to its compact design, and wide pressure and flow tolerances. This valve has a metal disc that rotates within the valve body and closes against a rubber seal. It’s easy to clean due to its flow-through design
• Manifold valve – common in large breweries where systems are hard piped, and in release matrixes. It is a more complex valve that can be installed vertically or crossed with horizontal piping. This type of valve tends to be more costly than other options
Submersible pumps do the essential – but dirty work – of transporting sewage to treatment plants. Prone to blockages, ragging, and general wear and tear, pumps need to be monitored to avoid events such as overflow and environmental contamination of public and residential areas.
Smartobserver can detect the following:
n Ragging
n Blockage by foreign objects
n Faulty or damaged bearings & seals
Optionally, the system can also monitor:
n Excess Current
n Sewage Level and Control
n Flow and Temperature
In the previous article in this series on successful pump project management, Keith Sanders looked at pump system design and equipment selection – the first of three pillars that will help upcoming projects not only be successful, but also help to contribute to better outcomes for other important objectives such as climate change, water resources and energy conservations. In this article, he takes a deep dive into the second pillar: energy audits.
As the pressure to conserve energy in industrial plants increases, the need for routine energy audits will increase, especially if financial incentives or penalties are introduced by the Australian Government in an effort to meet carbon emissions targets moving forward.
From our discussion on the ‘systems approach’ in Part 2 of this series of articles, it is evident that pumping facilities can be operating sub-optimally from an energy perspective, despite appearing to operate satisfactorily. This can also give rise to higher service and maintenance costs. For this reason, energy management programs have been developed based on ISO 50001 – Energy Management standard, which are already being adopted in Europe. However, this adds upfront costs to the project. Resources in equipment and personnel need to be available for systems to be assessed on a consistent basis. As a result, thorough assessment at commissioning is not always conducted and benchmarks for future assessment are not recorded.
ISO 14414 – an international standard for pump system energy assessment audits – was introduced, which Standards Australia recently approved the direct adoption. AS/ISO 14414-2020 is now part of the drive to align with the European approach to energy management. The goal has been to ensure that pumps and motor driven systems are audited to a recognised and uniform set of procedures.
In Europe, mandated audits are being introduced by the Energy Efficiency Directive across all member countries to ensure that pump systems achieve the energy reducing focus they deserve. However, it is important that AS/ISO 14414 is used when carrying out a pump system energy audit and that the energy auditor is suitably trained to carry out this task. Accreditation of a pump system auditor is generally carried out on a national basis and it is anticipated that Australia will need to follow this pathway in the years ahead.
The objective of a pumping system energy assessment is to determine the current energy consumption of an existing system and identify ways to improve system efficiency.
These requirements consist of:
• Organising and conducting an assessment
• Analysing the data from the assessment
• Reporting and documenting the assessment findings
AS/ISO 14414 Energy Assessment
This standard provides a standardised framework for conducting audits of pumping systems that should create a uniform approach to energy assessment. These assessments should involve a careful analysis of system design, equipment operation, energy use and performance data. The audit should be sufficiently comprehensive to identify major energy efficiency opportunities that may exist, with the report used to document and prioritise energy improvement options that might be implemented. Appropriate action plans can then be developed.
of standards for energy management.
Look out for Part 4 of this article in the Spring edition of Pump Industry, looking at the third and final pillar for successful project management.
The pump industry relies on expertise from a large and varied range of specialists, from experts in particular pump types to those with an intimate understanding of pump reliability; and from researchers who delve into the particulars of pump curves to experts in pump efficiency. To draw upon the wealth of expert knowledge the Australian pump industry has to offer, Pump Industry has established a panel of experts to answer all your pumping questions.
This edition of Ask an Expert will look at the challenging demands of the food and beverage industry and how they can be met.
High-quality food and beverage production always requires absolute hygiene and safety. In the face of global competition, companies have to meet increasingly strict requirements to comply with international standards and to meet the high demands of critical consumers asking for innovative, high-quality products. This requires pumps that ensure absolute cleanliness and gentle handling in all processes. Furthermore, easy maintenance is just as important as high operational safety and reliability.
Q. What makes processing food and beverages so challenging?
A: Mother Nature offers a huge variety of products, which end up in processed and unprocessed form on our plates. As manifold as these products are, so are the media to be conveyed. They range from temperature and shear sensitive media such as milk and dairy to highly viscous products such as dough. They might contain solids whose structure is to be preserved (strawberries in yoghurt
for instance), need to be precisely metered (e.g. tomato sauce on pizza) or could easily oxidise which could happen to fruits. And in the end, food waste needs to be cut and further processed as animal food which is common for peels, seeds, stalks and stems.
Q. Which pumps are used in food and beverage production?
A: Traditionally, many food and beverage producers rely on centrifugal pumps for primary production or choose tote bins, flumes and air vacuum systems for removing food waste. However, the better choice would be progressive cavity pumps. They comply with the strictest hygiene regulations, combine gentle product handling, exact dosing
and easy handling of temperature, and shear sensitive products with and without soft solids. Their closed conveying systems prevent products from oxidation, and integrated cutting knives easily chop food waste for further processing. Some producers also offer easy maintenance solutions to prevent long downtimes.
Q. Are there any requirements to be met or certificates needed to supply pumps for the food industry?
A: Certificates that confirm absolute hygiene are very important to convince customers and meet the standards of global authorities. In fact, there are two very important certificates to
comply with: the American 3A-Sanitary Standard set up by the Food and Drug Administration (FDA) in the US, and European Hygienic Design Guidelines (EHEDG). In fact, only one progressive cavity manufacturer has managed to achieve the highest EHEDG Type EL Class I certificate for this style of the pump. Its residue-free cleaning was confirmed by the EHEDG in-place cleanability test.
Benefits of EHEDG Type EL Class I awarded pump at a glance
• Meets highest standards
Awarded EHEDG Type EL Class I certificate and certified according to 3-A Sanitary Standard, FDAapproved components
• Low pulsation
Minimal pulsation and low shear enable gentle handling of sensitive products – even with integrated soft solids
BCFH pump with EHEDG certificate.
• Hygienic design
CFD-optimised inlet geometry, joint-free flexrod and possibility for Clean in Place, Sterilisation in Place
• Easy to maintain Split suction casing for easy and quick maintenance without disassembly of the suction pipe –easy detachment of the flexrod from the rotor and drive shaft
• Process-optimised Low cleaning effort as well as reduced downtime of the production plant due to quick and easy maintenance
Peter Vila, Managing Director of SEEPEX Australia, is a progressive cavity pump expert. He has been involved with pumps for over 40 years. Peter spent the first five years repairing pumps and the following 35 years in technical sales, 20 of which have been with SEEPEX progressive cavity pumps.
For more information on progressive cavity pumps, please contact SEEPEX Australia on (02) 4355 4500 or at info.au@seepex.com
Petrol
As a pump user, you will be confronted with the decision as to whether your application requires a dynamic or positive displacement pump. There are two general types:
1. Rotodynamic (which the main subclassification is centrifugal)
2. Positive displacement
Rotodynamic
Rotodynamic pumps are rotary machines in which energy is continuously imparted to the pumped liquid by a rotating impeller, propeller or rotor.
Positive displacement
Positive displacement pumps are rotary or reciprocating machines in which energy is periodically added by application of force to movable boundaries of enclosed fluid containing volumes, resulting in a direct increase in pressure. Which to use?
In general, the basic conclusion/rule is that:
• Centrifugal pumps are for pumping clean, low viscosity liquids
• Positive displacement pumps are best for slurries and high viscosity liquids
As with all general rules there are important exceptions – in fact there are times when you can use a centrifugal pump on high viscosity and when you can employ a positive displacement pump for clean, cold, low viscosity liquids. If in doubt, consult your pump supplier.
Rotodynamic
Positive displacement
Combining our experience in publishing, live events, digital marketing and video production, Monkey Media has the capability to deliver a range of online events for your organisation.
03 9988 4950
Specialising in the energy, infrastructure and utility sectors, we combine our expert knowledge in these fields with our behind-the-scenes knowhow to help you deliver your events in a range of online formats.
We work closely with our partners to understand why and how you want to connect with your audience online, and can recommend the right solution to help you cut through and achieve the high levels of audience engagement and participation you’re looking for.
Some of the online events we can help you deliver include:
Webinars
Virtual conferences
Awards nights
Round tables
Online learning
Hybrid virtual/live events for a complete online event solution
www.monkeymedia.com.au/services/custom-virtual-events/
DRIVEN SKIDS & TRAILERS
HWR SERIES
VORTEX SERIES
WET PRIME SERIES
VERTICAL TURBINES
SUBMERSIBLE MOTORS
END SUCTION CENTRIFUGAL
DRIVES & PROTECTION
CLEANWATER CENTRIFUGAL
VR SERIES
A comprehensive range of Auto Prime diesel packaged options for fixed and portable installations.
Wear-resistant pumps manufactured with high-chrome white iron to maximize resistance against destructive abrasives and maintain peak performance in light slurry applications.
A unique pumping solution that eliminates costly and disruptive downtime by passing through the most challenging solids using a recessed impeller.
Self-priming pumps designed for reliable solids and clear liquids handling. Continues to reprime automatically after initial priming.
Submersible turbine pumps available in custom configurations to meet demanding application requirements.
Our submersible motors are tough, built to last and come in a variety of construction options.
Close-coupled, electric motor driven pumps available in singleor three-phase standard voltages to fit your site requirements.
Equip a Franklin drive to protect, monitor, and meet the different needs and demands of each application with the same pump.
Centrifugal pumps that feature heavy-duty ductile iron volutes, designed to handle tough applications with high efficiency.
Vertical multi-stage pumps are available in high- and low-speed models for superior durability, efficiency, and performance in a wide variety of applications.
At Inoxpa, our focus is on ensuring the quality and suitability of our products (mixing skids, CIP skids, product recovery systems, pasteurizers, manifolds, process automation, pumps, agitators, blenders, mixers, valves and fittings) for each industry.
Stainless steel, sanitary centrifugal, rotary lobe and progressive cavity pumps, hygenic agitators and mixers for:
Dairy
Food and beverage
Chemical
Cosmetic
Pharmaceutical
At Hammelmann Australia, our primary focus is on delivering customer-specific solutions for pumping high pressure liquids and gases in diverse applications and industries:
Offshore platforms
HPUs
FPSOs
Mining and minerals
Chemical Petrochemical
Ship cleaning
Construction
Our positive displacement high pressure process pumps are used for a variety of industrial uses:
Chemical injection
Sea water reinjection
Flowline services
Dosing