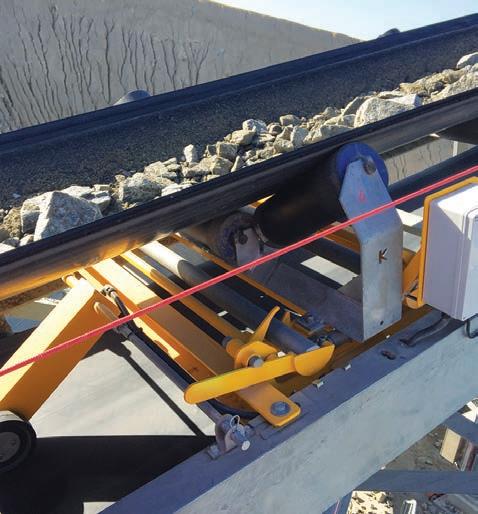
44 minute read
WEIGHING SYSTEMS AIM TO ELIMINATE ‘BAD BATCHES’
from Quarry February 2022
by Prime Group
AUSTRALIAN MADE CONVEYOR WEIGHING SYSTEMS AIM TO ELIMINATE ‘BAD BATCHES’
With COVID-19 continuing to bite, it’s challenging enough for quarries’ loads and deliveries to comply with regulations and recipe requirements for construction. A Melbourne-based manufacturer of weighing solutions is providing accuracy and reassurance through its products.
The belt scale is utilised midway through the conveying process after the feed is first delivered to the belt.
Conveyor systems are an integral part of industrial mass production, enabling multiple items to be dispensed in the supply chain. The key for many organisations is running them seamlessly and efficiently.
While they may be contending with crushed rock rather than manufactured goods, quarries are reliant on good working conveyor systems and must comply with prescribed loads in their end products. This has been ratcheted up in recent years with the introduction of Chain of Responsibility/gross vehicle mass obligations across Australian jurisdictions. Indeed, quarries can be held accountable for incorrect weights on a tipper truck, even if that truck is not part of its own fleet and being managed by a third party. Further, accurate readings are important for quarries that need to provide the right grades and formulae for cement production and road construction materials, as dictated by roads and transport authorities around the country, eg VicRoads, NSW RMS, TMR, etc. Therefore, accurate readings on throughput are essential not only to a quarry’s productivity but its reputation for reliability and quality end products.
Conveyor belt scales and weigh belt feeders play an important role in minimising the risks for quarries of producing “bad batches” of end product. As Barry Gamble, the business development manager for Tecweigh, an Australian manufacturer of custom-engineered weighing solutions, told Quarry, the two devices are essentially one and the same – except one is designed for existing conveyor infrastructure while the other is custom-designed by Tecweigh.
“The customer has his own infrastructure running,” Gamble said of the conveyor belt scales. “Each scale has plus minus three idlers which are shimmed level with the scale to ensure a smooth transition of the product over the weighing area. The centre idler is removed and remounted on the belt scale on a spreader bar connecting the two load cells and this becomes the weigh idler. We combine that weight information with belt speed data from the speed sensor which shows us the tonnes per hour.
“If you’re installing a weigh belt feeder, that’s when we provide both the conveyor infrastructure and drive mechanism.”
BELT SCALES The belt scale is best utilised midway in the conveyor, away from any extraneous forces where the product is first delivered to the belt. “We let the product settle down after it has been dispensed, ” Gamble said. “It’s what we call ‘shimmed and levelled’, this allows us to achieve the stated accuracy.
“Whether used in conjunction with a screen, crusher, portable stacker, pugmill or truck, the result with the throughput is the same. We can tell you how many tonnes per hour passes across the belt scale.. However, it’s possible to have separate belt scales sorting product sizes, eg 5mm coming across one scale, 7mm across another, and 10mm across a third. That’s useful if a customer like VicRoads requires a recipe for an aggregate mixture of 5mm, 10mm or 15mm.”
Tecweigh’s signature belt product is the WY15 single idler scale which has an accuracy of +/-0.5 per cent, enabling the end user to determine instantaneous and total product flow in tonnes per hour or other selectable units. For more precise accuracy, they can also opt for the WY25 dual idler at +/-0.25%.
The WY15 and WY25 are built primarily from powder-coated mild steel but there is also an option for stainless steel in harsh environments. Their other key features include self-storing calibration weights, user-friendly electronic processors, built-in relays for remote counting, belt slip detection and rate alarm tripping sensors, and 4-20mA scaling calculators for remote rate display.
WEIGH BELT FEEDERS Gamble said weigh belt feeders are suitable in blending aggregate products to a customer’s formula, in cement production or truck filling. In particular, the weigh belt feeder is shorter and more flexible than the traditional conveyor and therefore it can be adapted to suit purposes such as truck filling. For example, weigh belt feeders can be fitted to a range of silos at the end of the conveying process to facilitate easier and more efficient filling of trucks en route to the weighbridge.
“You could have a silo of 5mm product, a silo of 10mm, and a silo of 15mm, and then you can dispense a certain amount of each one as per the quarry customer’s requirements,” Gamble explained.
“The benefit of the truck filling is it guarantees
one trip to the weighbridge. Normally, people will fill up a truck, the truck goes to the weighbridge, there’s not enough or too much material aboard, and the truck has to make another pass. With our products, we can fill to within a plus/minus percentage and the truck can go on its way.”
Tecweigh’s weigh belt feeders are customdesigned. The belt widths vary from 900mm to 1600mm and belt lengths from three to 10 metres. For what the industry calls “the live load”, there are two load cells per weigh belt feeder, and depending on the throughput, the load cells can range from 30 kilograms to 300kg Each.
Gamble added the average quarry would incorporate weigh belt feeders of about 3.2m in length. “The longest weigh belt feeder we’ve manufactured is about 10m,” he said. “It depends on what the customer requires to fill their battery limits and the delivery speed required. So going back to the silo application, if you’re just storing aggregate, you would want to fill trucks as quickly as possible and stop when you get to the right figure. However, if you’re overseeing the recipe blending application, you would want to control the blend as accurately as possible.”
The weigh belt feeders also use stainless steel, hermetically sealed IP66 load cells and utilise self-storing calibration weights.
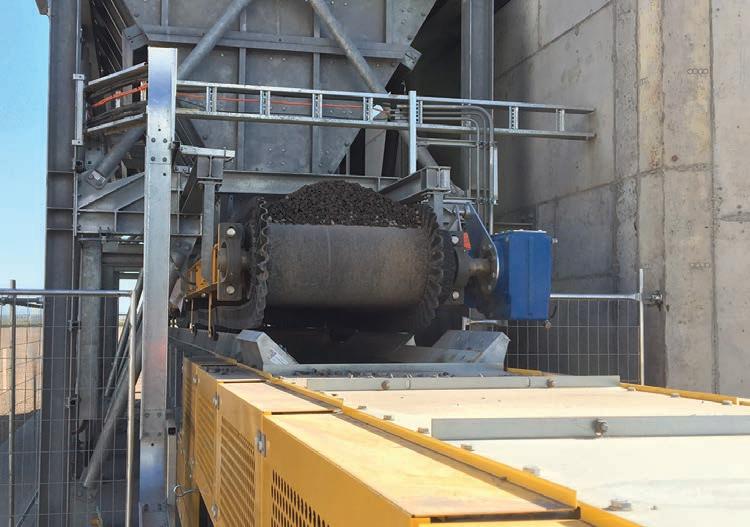
CUSTOMISED PROCESSORS Tecweigh’s conveyor belt scales and weigh belt feeders are driven by WP20 weight processors which can be equipped with an Ethernet
Weigh belt feeders are suitable in blending aggregate products to a customer’s formula, in cement production or truck filling.
input/output (I/O) to allow a plant’s personal computer (PC)/programmable logic controller (PLC) to interrogate all parameters of the scale in real time. The WP20 may also draw on the accuracy of a trade-approved weighbridge to optimise the calibration in the processor.
“The WP20 is designed to be customised to the individual application, in terms of belt speed,” Gamble said. “It can interface with whatever the quarry has – an analogue or digital output.
“In its basic form, the unit has two interfaces, one which gives tonnes per hour, which is instantaneous, and the other which is tonnes per hour accumulative, since the last time you zeroed the processor. Then you have various analogue and digital outputs, and the data can be transferred to a personal computer. We also offer the option of a third party application which can transfer the data to a mobile phone.”
Gamble added that if producers want to know more about throughputs, their PC or PLC can question the scale in real time, and that information can be used to change the speed of the belt, either slowing or lifting the speed on the conveyor belt or the belt weigh feeder.
“In terms of saving time or costs, if there’s a reduction in throughput for a particular reason, we can pick that up early,” he said. “If you have a slippage of the conveyor belt itself – or the belt stops – we can detect that immediately and inform the user. There is a speed wheel on the conveyor and we can send an output to advise that it has stopped or is going slow. That’s a secondary benefit; the main one is knowing what is going across the top.”
AUSTRALIAN MADE With supply chains tightening domestically and globally due to the COVID-19 pandemic, a reassuring fact about Tecweigh is it is an Australian Made-certified company, with all its products manufactured at its Carrum Downs factory, in outer suburban Melbourne. In addition to its Australian Made credentials, Tecweigh can also provide a certificate from the Victorian Chamber of Commerce that shows its powdered steel and stainless steel scales have been manufactured locally. Gamble said there would not be a major quarry producer around Australia that doesn’t use Tecweigh’s conveyor weighing products on its sites and the business caters to medium- and small-sized quarries alike. Tecweigh is also exporting its Australian-made steel products to China, Indonesia, the Philippines and other parts of South East Asia.
Gamble also predicted that as the extractive industries wrestle with the dual challenges of skilled labour and automation, so the need to improve product information and real time data will increase. To that end, Tecweigh is working on next generation iterations of its weighing solutions, promising some more reassurance for quarries in a period of uncertainty. •
Belt weigh feeders can be fitted to a range of silos in the conveying process to facilitate easier, more efficient filling of trucks en route to the weighbridge. For more information about Tecweigh and its conveyor weighing solutions, visit tecweigh.com.au

SEALING THE DEAL WITH
GAME-CHANGING CONVEYOR SKIRT
A specialist in conveyor belt skirting and transfer point technology has taken its expertise to the world stage with a revolutionary package of products.
Kinder Australia had previously kept to its corner and made a name for itself in what it knew best: bulk handling solid materials for Australia’s heavy process industries.
Since 1985, the family-owned operation has displayed a can-do attitude to deliver Australian ore, quarried products, grain, sugar, salt and coal from A to B.
But when Kinder operations manager Charles Pratt came across German company ScrapeTec and was acquainted with a product called the AirScrape, things took a slightly new direction.
Pratt has worked with Kinder since 2004 and watched conveyor technology evolve in many ways over that time, but across his tenure, he’s seen nothing more game-changing than the AirScrape.
As operations manager, Pratt oversees the sales, engineering and warehousing departments at Kinder which often involves the research and procurement of new business relationships and products.
“During COVID, the interesting part about my role has been looking after the sales side of the international market,” Pratt told Quarry.
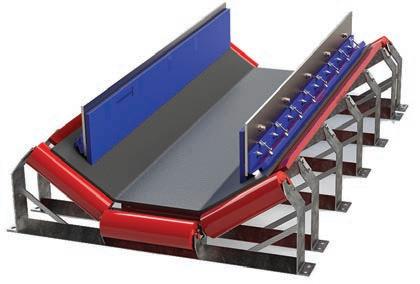
The AirScrape conveyor skirt design creates a contactless air seal to ensure dust is kept inside the conveyor section, while minimising material spillage.
“So, because I couldn’t travel, I’ve been searching the globe online for specific products to complement our range and I became aware of this AirScrape product.”
AirScrape is a non-contact, dustless, material containment skirting and sealing system designed to hover 1mm from the surface of the conveyor belt.
The design creates a contactless air seal to ensure dust is kept inside the conveyor section, while also minimising material spillage.
Pratt said such a design baffled some of the most experienced in the bulk handling industries.
“It’s a bit like walking into a car dealership and the salesman shows you a car without any wheels,” Pratt said.
“For decades, conveyor transfer points have relied on a rubber or polyurethane soft skirting system to make contact with the conveyor, whereas this AirScrape product is radical because it doesn’t.
“This creates its own challenges because when you first introduce it to people, they struggle to get their head around it and that was my reaction at first too. I thought, ‘this is amazing if it works but how can it?’”
Not only has Kinder adopted the AirScrape and begun distributing it throughout Australia, it has also secured a reciprocal trading agreement with ScrapeTec.
This agreement saw Kinder work with ScrapeTec to further improve the performance of AirScrape in response to customer feedback.
“The AirScrape works best with a consistent 1mm air gap underneath it and to do that, customers will need an impact bed or one of our K-Sure belt support products,” Pratt said.
“When we received the base product from ScrapeTec, they didn’t have that adequate belt support so Kinder turned around and supplied it to them.”
“This has expanded our global network by connecting us with their distributors and we’ve gained some customers we wouldn’t otherwise have throughout the world.”
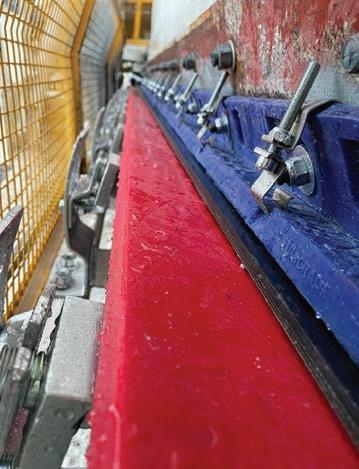
The AirScrape is a non-contact, dustless, material containment skirting and sealing system designed to hover 1mm from the surface of the conveyor belt.
The combination of ScrapeTec and Kinder has resulted in four complementary products which all work best when installed together – the AirScrape, TailScrape, K-Containment Seal and the K-Sure Belt Support System.
To understand and assess an operation’s need for these products, Kinder has field application specialists and engineers who can travel to site and make recommendations.
“You never find yourself just proposing the one product in the range, there’s usually a few products that a customer will benefit most from,” Pratt said.
And once installed, the results bear repeating.
“It should theoretically last for the life of the conveyor because there’s no contact with the belt and it’s only containing dust,” Pratt said.
“This presents cost savings in not having to perform maintenance on the skirting, and not having to order it, deliver it or stock it.
“There are so many costs that are reduced throughout the supply chain when you don’t have to replace something anymore. It’s not just the cost of the product, it’s all the other bits and pieces.”
Even Pratt, the Kinder veteran, said he had never seen anything like the AirScrape and may not again for some time.
“This is the most radically different thing I’ve seen in my time. We’ve been producing some pretty creative products at Kinder but this one is a game-changer,” he concluded. •
For more information about the AirScrape and other Kinder products, visit kinder.com.au
REDEFINING
UNDERGROUND WATER MANAGEMENT
Through their new PC pump station, Xylem and Seepex have built a compact unit perfect for fixed and mobile mine dewatering applications underground.
It is Xylem’s mission to solve the world’s most challenging water issues, no matter the situation or environment.
Through its many brands and partnerships, Xylem has cracked the most difficult codes to ensure water is safely, sustainably and efficiently managed across industries.
Xylem has been at the forefront of evolving water management and its next advancement has it diving deeper into underground mines with a new compact pump station fit for the narrowest spaces.
The company’s partnership with leading pump technology specialist Seepex has seen the two create a progressive cavity pump (PCP) and hopper package designed for use in mobile and fixed mine dewatering applications.
Cameron Pate, Xylem’s product and marketing manager for Australia and New Zealand, said the pump station was built with the confines of an underground mine in mind.
“It’s a lower, more narrow space underground so the design of the pump station is built around being compact and mobile and easy to install and move around,” Pate said. “We also made these units safer for underground by not having ladders go up to the top of the tank.”
Some underground pump stations can be two to three metres tall, requiring workers to scale ladders in slippery conditions. The compact design makes it easier and safer to complete the daily inspections and servicing.
“Part of the daily inspection is for someone to physically climb up to the top of the tank and hose out all of the sediment that builds up in the bottom of the tank, so we’ve tried to engineer a solution to minimise the height in which people have to climb,” Pate says.
Himanth Prathap, Xylem’s business development manage for mining, metals and industrial, said the quality of the PC pump station resulted from the unique expertise Xylem and Seepex have brought to the partnership.
“Seepex has been making PCPs for a
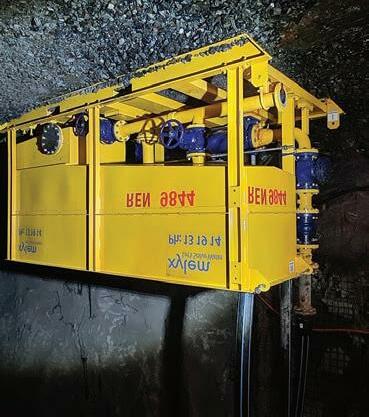
The pump station is built for the confines of an underground mine.
long time now,” he said.
“This particular model was specifically developed for mining and there was a fair bit of work that had been done by Seepex themselves to understand what the typical challenges are with PCPs.
“It was based on that feedback from customers that they came up with this particular design and when we came into the picture with the Seepex partnership, we were able to build on those features to come up with an improved pump station design.”
Developing a unique and innovative product can be one of the biggest challenges in manufacturing and having competitive awareness is critical to gaining an edge.
Constructed to be more ergonomic and user-friendly than the competition, Pate said the PCP station also excels when it comes to maintenance or rebuilds.
This is made possible with Seepex’s “Maintain-In-Place” (MIP) technology, which greatly improves the pump’s repairability, whereby the rotor-stator cartridge can be replaced in-situ without disconnecting the pipework.
Seepex’s NSM70-12V pump (an attachment to the PCP station) is significantly lighter than competitor models, while even wall stator technology allows the one pump model to cover a range of duty points that would otherwise require multiple competitor models.
The capability of the pump station isn’t just the perception of Xylem and Seepex either, verification is also coming from the field.
A well known underground mining operation in Kalgoorlie took on the pump station as part of a three-month trial in August. The company was so happy with the product compared to their current units that it has signed a long-term contract with no designated end date.
“We have had a few units go out to site now and the feedback so far has been, these pump stations are really compact and really easy to manage – these are the words from the customers themselves,” Prathap said.
“The fact that it’s compact really makes a big difference because real estate is limited in the underground mining space so every time there is an opportunity to have a compact and more manageable asset underground, the end users would prefer that over the larger alternative.”
With its new PCP station gaining traction, Xylem continues to evolve the concept and possibility of water management in mining through its end-to-end focus.
“We’ve managed to build a product portfolio that offers solutions at every stage of managing water – whether it be how water is sourced, then moved, tested, treated and then discharged back to where it was sourced from,” Prathap said.
“And given how much of an emphasis there is today around how water is being managed on mine sites, the PCP station is just another valued-added solution that we’ve been able to bring to the customer, to complement all of the existing solutions that we have around water management.” •
For more information about Xylem’s PCP and hopper package and other products, visit xylem.com/au
DEPENDABLE OILS KEEP
QUARRIES RUNNING SMOOTHLY
When searching for the best in engine and hydraulic oils for heavy-duty quarrying machinery, the goal is reduced service intervals and improved efficiency and emissions. Luckily, the Mobil Delvac range satisfies both.
After ExxonMobil and Ampol entered a marketing alliance in late 2020, Ampol took the reins on the manufacture and distribution of Mobil* lubricants in 2021, with cornerstone products like Mobil Delvac continuing to improve.
The Delvac* range of diesel engine oils was first developed in 1925, but Ampol technical solutions specialist Abdulla Nasser told Quarry that the range and quality of current day Mobil Delvac is worlds away from its origins.
“There is an excellent range of engine oils depending on what a customer’s emissions requirements are,” Nasser said, “but we usually recommend the Mobil Delvac Modern 15W-40 range of engine oils.”
This high-performance product range is the result of Mobil’s recognition that the mining and quarrying sectors need the best in efficiency and reliability.
Whether machines are running hot and heavy, or regulations call for strict emissions reductions – or both – Mobil Delvac Modern 15W-40 is a common calling card for the Ampol team.
“The best of the Mobil Delvac Modern 15W-40 range is the Full Protection option, which supports emissions standards and longer service intervals are achieved,” Nasser said.
“This product gives you extended drain intervals, and with our recent transition to Mobil lubricants, we’ll be looking being able to increase drain intervals by another 25 to 50 per cent.”
In a sector like quarrying, where time is money, the lengthening of service intervals can be a game-changer for operations of all shapes and sizes.
What makes high performance oils attractive to machinery and equipment operators, besides spacing out the service intervals, is the potential to improve the reliability and efficiency of their equipment.
“If they somehow overextend on their service intervals, they still have enough of a buffer from this range,” Nasser said.
“If they’re supposed to change the oil out at 500 hours and they get around to it at 550 hours, they can still be confident that it won’t have much effect on the performance of the equipment.”
In hydraulic oils, Ampol continues to be a leader in the market with the Mobil range.
One example Nasser highlighted was the DTE 10 Excel Series hydraulic oil, designed to meet the needs of modern, high pressure, industrial and mobile equipment.
“Ampol are looking to show the quarrying and mining sector more about DTE 10 Excel because it’s a real stand-out product and we know the true benefit it can have to them,” Nasser said.
“It runs cleaner, and it lasts longer, even in hotter temperatures.
“The beauty of it is that it doesn’t break down through the machine’s pumps which could potentially decrease efficiencies for the machine overall.”
An added benefit of DTE 10 is its longevity over varying temperatures compared to similar oils in the market.
“Usually, hydraulic oils left in the sump too long can form a varnish and it thickens and becomes sticky which can build up and cause wear in various components,” Nasser explained.
“Whereas the DTE10 Excel series oils don’t tend to do that and in fact have been shown in the field to have a cleaning effect as well.”
Ampol customers include household names across the quarrying and construction sector, right down to the little operators who require just as much attention to their lubricant needs.
To cater to all kinds, Nasser said a lot of time is put into understanding unique customer requirements.
“The Ampol Technical and Product Solutions team (or TaPS) has a great understanding of
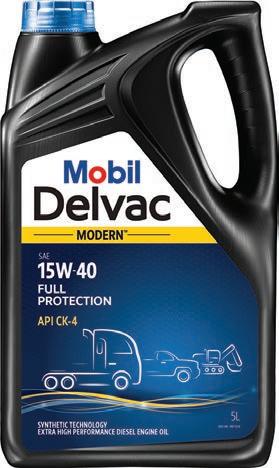
Mobil Delvac Full Protection is highly recommended for quarrying applications.
Mobil products and how high-performance engine and hydraulic oils can benefit a machine as well as a customer’s operations,” he said.
“We look at the specific applications for the customer and their required service intervals. We ask questions around what efficiency they want and how much uptime they’re targeting.”
And if for any reason the final product doesn’t seem up to scratch, which Nasser admitted would come as a shock, one can be sure that the next generation of Mobil Delvac oils or Mobil hydraulic oils will be another step in the right direction.
“The results of equipment performance and used oil analysis which Ampol and its customers are seeing in the DTE Excel fluids shows that this is most likely the best hydraulic oil in the Australian market today,” Nasser concluded.
For more information about the Mobil DTE10 Excel series, visit ampol.com.au/fuels-andoils/lubricants/business/industry-solutions/ agriculture/hydraulic-oil •
*MobilTM and Mobil DelvacTM are trademarks of Exxon Mobil Corporation and used under licence by Ampol Australia Petroleum Pty Ltd.
VISION, VALUES KEY TO
THE SUCCESS OF LONG-TIME INDUSTRY SUPPLIER
As part of the commentary in the past year about the characteristics of effective leadership, industry stalwart Neil Kinder charts the journey of his company Kinder Australia from its modest origins in a two-bedroom house in metropolitan Melbourne to a SME success story, both within Australia and around the world.
In 2021, the Institute of Quarrying Australia (IQA) invited me to present a monthly article, based on one of the seven core characteristics of effective leadership (see Figure 1).
Rather than write all seven scenarios myself, I invited numerous people from diverse demographics and industries to make contributions.
This additional chapter on vision and values comes from Neil Kinder, a long-time, well-known and respected supplier to the quarrying and extractive industries.
In my books Emerging Leaders and Effective Leaders, I have provided a relatively simple definition of visions and values as follows:
Visionary leaders appreciate that, while values make a contribution, vision is futurefocused and about developing clarity and purpose around their goals.
As part of Effective Leaders, I’ve also discussed in depth the four values – or attributes – that underpin the foundation of trust and the effectiveness of leadership (see Figure 1): 1. Respect: Diversity/Gender Equality and
Inclusion/Culture. 2. Courage: Internal and External. 3. Integrity: Accountability and
Transparency/Authenticity. 4. Agility: Alignment and Agility – Emotional,
Management and Leadership.
Mike Cameron, Yours Strategically
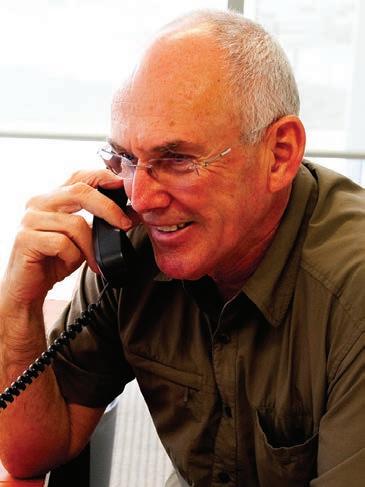
NEIL KINDER: VISION AND VALUES 1985 was a pivotal time with the birth of iconic technology including the Microsoft Windows operating system, Portable CD Discman and Nintendo Entertainment System. It was a time of big hair, shoulder pads and acid wash jeans. In our two- bedroom house in Prahran, Victoria, it was also the time my wife, Christine and I began our business, then called NC Kinder & Co Pty Ltd.
Kinder’s original focus was to supply conveyor and vibrating screen components, to keep aligned with my foundations in the field. When I left school, I began as a sales trainee for heavy lifting earth-moving machinery with a company used by the quarry, mining and timber industries. I later moved towards large helical gear reducers for the mining industry, among other related conveyor products. It gave me the confidence to begin this journey of starting our own business, myself – together with Christine – with the motivation to succeed.
With no computers and high-tech databases to record inventory, and no mobile phones to quickly get in touch, I had to carry a pager to be reached by Christine whilst on my Australia-wide business trips. As soon as they were available, I was quick to obtain an early phone in my car, which I deemed imperative for the business’s evolution. Early business was based on mobile coverage at the time, during the rapid progression of 1990’s e-technology. As the mobile phone network expanded, so too did the business, reaching the rest of Victoria and eventually covering Australiawide.
We were early users of both mobile phones and the internet, and I have always been a big believer in keeping up with technology; enabling us to market our products and services and reach both current and prospective customers

Figure 1. The seven characteristics of effective leadership, supplemented by the four attributes of trust. Neil Kinder, CEO of Kinder Australia.
effectively. We began our customer database from day one, and originally we contacted them using letters and brochures in the post, but this has evolved to informative email campaigns and the maintenance of a thoroughly maintained CRM system (Customer Relationship Management).
Staying organised and efficient is key to keeping on top of an ever-growing and ever- changing customer base and product inventory. Naturally as our business progressed, we acquired a variety of software to assist us and provide different functions. However, the issue with this was that these programs did not “talk to each other” and we found ourselves overwhelmed by information and double- handling. I considered it a huge milestone to move everything to one platform in 2011. Shifting all our data to SAP Business One felt unknown and unfamiliar, and we had to let go of quite a number of our crutches. It is very fortunate that we found a Logistics and IT Manager, who I discovered in an unconventional way. When we were moving our inventory to the new SAP system, we engaged a number of temporary staff to assist us with counting and data entry. Ian was one of those temps, and while chatting to him I discovered his remarkable background in computer engineering. I asked him if he could assist further with more of the complexities in the migration. He was willing to share his knowledge, come on board with us as a full time employee, and in time manage our IT and logistics department. Getting to know your staff and really understand and utilise their talents is so important – you never know what people are capable of until you listen and learn.
The addition of the internet presented a new-found digital horizon for us and allowed the business to go global, bringing markets closer together. I still find it amazing that you can buy something today from the other side of the world and have it arrive in the next week. It is simple to set up a virtual meeting and chat to anyone globally. Kinder can service the South-East Asian market with a multi- language website on top of our extensive Australian website and in 2021 we were able to employ two international staff members who are local to their territories of Indonesia and South Africa. Without adapting to technology this would not have been possible. It absolutely feels like the world is more connected now.
People are not too concerned about where something comes from now. Instead, they are more interested in who they are buying from. The important questions are: Are they a trustworthy organisation? Will their products be reliable? What sort of global name have they got? We use these questions to keep ourselves grounded.
Trustworthiness and reliability are at the core of what we do.
The addition of Charles Pratt to Kinder in 2004 as a fresh-faced engineer, with a mechanical engineering and management background, provided an enormous benefit to the company in propelling it forward and gaining new ideas. An energetic and
Customer training sessions need to be educational and worthwhile, not sales-driven.
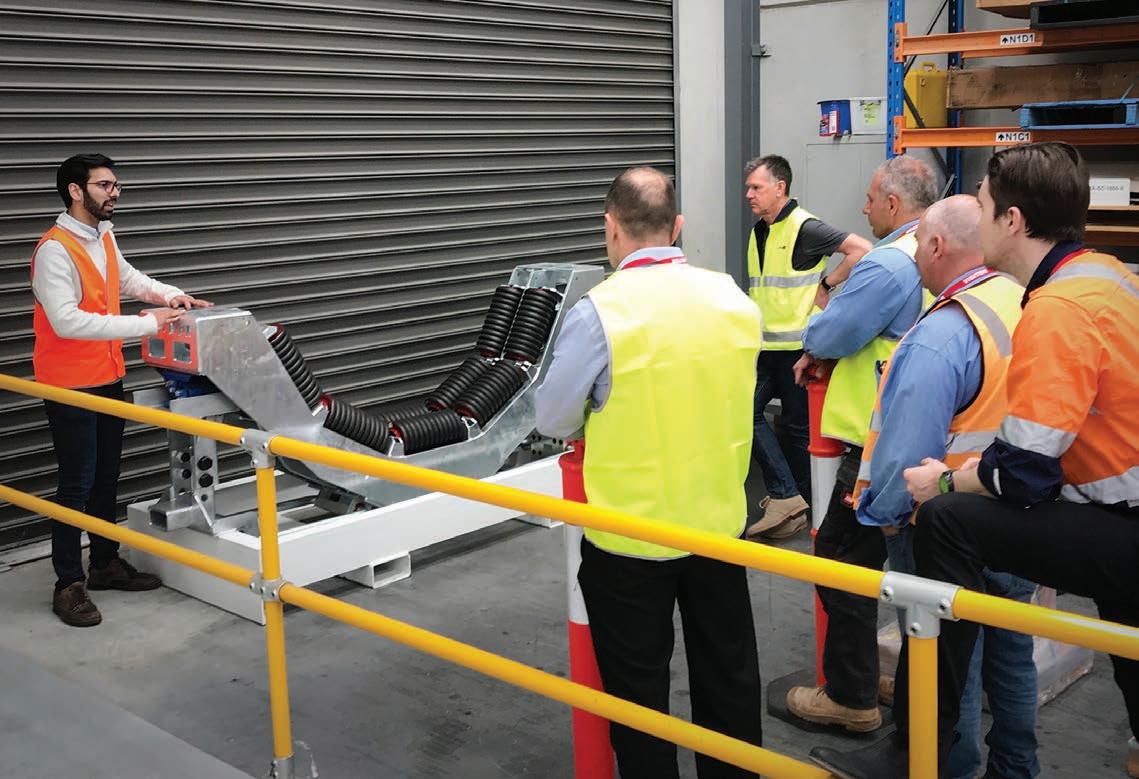
driven operations manager and shareholder, Charles encouraged the importance of inclusiveness and upskilling.
Charles has been an exceptional collaborator to work with in the management of the company. He is a keen problem solver, not only for the company but for our customers. Charles digs deep and gives his best to find issues that even the customer may not see. He is diligent and diplomatic, striving for the best outcome and most practical solution.
I discussed previously the importance of getting to know your employees’ passions and skills in order to utilise their talents. Charles is especially a big believer that people can be taught if they have the desire to learn. It all comes down to personality and getting the right person for the right job. We have a great mix of introverts and extroverts, and each has their advantages. Some people excel in building relationships with customers, giving presentations and networking at events. Some people prefer to quietly do the number crunching. Both
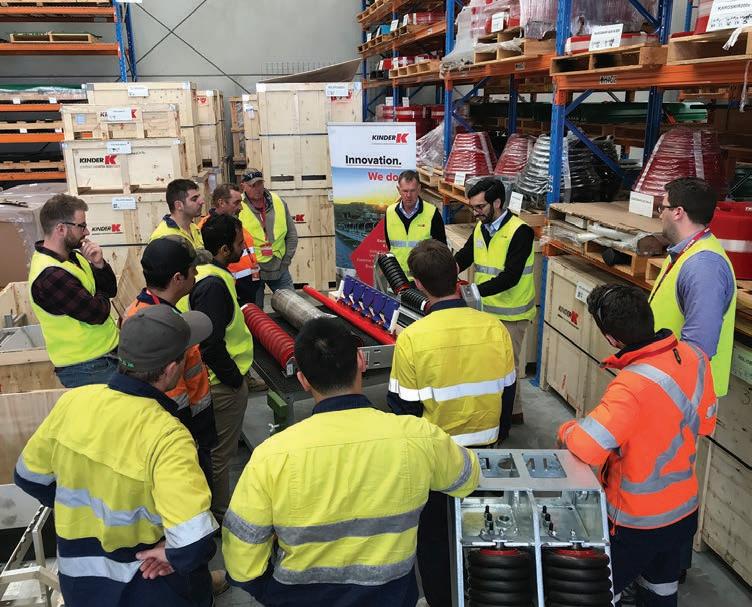
Before the COVID-19 pandemic, Kinder regularly hosted face to face workshops at its head office and warehouse, with as many as 50 attendees at any one time. Many of these workshops have been successfully adapted as webinars.
load up on productity
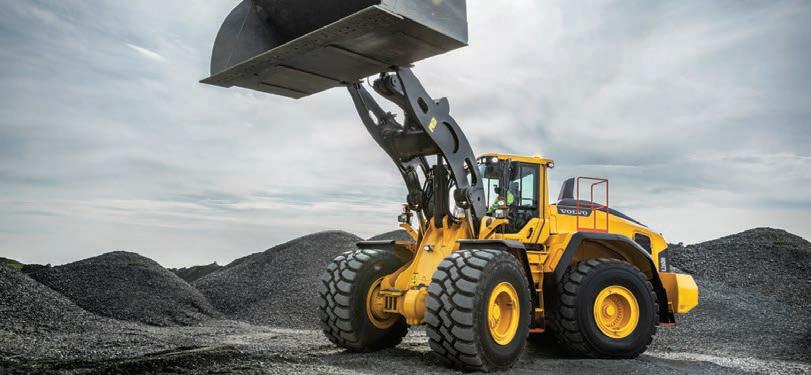
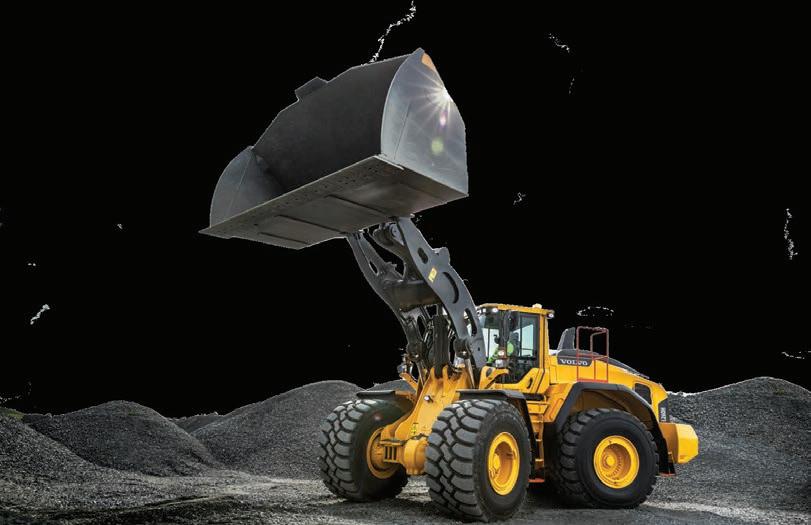
MEET THE TEAM:
L110H
18,560kg / 191 kW L120H
19,640kg / 203 kW L150H
24,090kg / 220 kW L180H
27,060kg / 245 kW Volvo wheel loaders are the ultimate all-rounders. Offering the high quality performance and a whole host of features that gives you all the versatility and stability to handle any workload. The Volvo H Series wheel loaders have been refined to not only deliver greater fuel efficiency but optimise productivity while ensuring operator comfort.
Images are for illustration purposes only.
L220H
31,190kg / 273 kW L260H
33,240kg / 309 kW
are equally important for a team to work. Everybody has their own personality and you simply work with that whilst gently encouraging to upskill and grow.
Kinder have always held their family business values at the core. Christine and I have continued to oversee the business and encourage growth and innovation. Our son Sean is a field mechanical engineer who enjoys building relationships with key customers, and our daughter Tracey plays a key role in the marketing team. Both Tracey and Sean were hired for their qualifications and professional merit; Sean possessing a Bachelor of Mechanical Engineering and Business, and Tracey having six years of marketing experience prior to working with us. Christine and I also found it to be important that they do not report directly to us.
Being a good leader is about showing respect. People have to feel that they are growing and not simply another number. Of course, a business is there to be viable, but without happy staff the company will simply not flourish. Staff celebrating both professional and personal milestones is a win-win in my opinion – whether it be publishing a white-paper or purchasing a first home.
Being happy and healthy, both mentally and physically, is also important for myself and Christine to both be effective and dynamic leaders. Each morning I begin my day with running the local trails, and this gives me the clarity and energy to start my day properly.
Surrounding ourselves with the right people has been paramount to the business’ success. It has been our mission to engage with the right specialists and engineers who have the ability to provide the expertise that our customers require. Our early home-grown business of two, has developed over the years to become a reputable engineering company, with a solid team of mechanical, aeronautical, electrical and chemical engineers who possess proficiency with conveyor engineering and design. We have a team who really are specialists when handling complex problems with excellent precision, execution and creativity. It all adds to our reputation.
Charles and I have always encouraged our engineers to go outside their comfort zone to further their own credibility. Whether it be writing a white-paper with their name and qualifications on it, being interviewed for their professional opinions in an industry magazine, performing a technical presentation, and/or joining engineering groups such as the IQA, the CMPA and Engineers Australia. They need to know that they have our support and endorsement as professionals.
Since many of Kinder’s products are designed and sourced to problemsolve difficult conveyor issues, a deep understanding of a customer’s industry is crucial for staying abreast of challenges that they may be facing.
We determined that training workshops could be a useful thing for us to provide, and in return we could learn the sorts of issues that may be faced by our attendees when they are on site. It is no good blindly releasing products if they would not be useful, effective and appropriate for our customers. Before the COVID-19 pandemic, it was simpler for us to host face to face workshops and we had close to fifty attendees, from a variety of our customers, visit our head office. Throughout 2020 we were able to pivot these to become webinars, and this allowed for our customers to continue to touch base with us and learn how to get the most from our Kinder-K products directly from their interstate site and home offices.
It is crucial that these are worthwhile training sessions for customers and not “just another sales session” – educational content is key. As our Marketing Manager, Christine believes that we want our customers to walk away from the workshops knowing that if there is a problem, all they need to do is to reach out and contact us for help. We are the company with the knowledge. Whether or not we have the product, it is the engineering we can provide.
When learning about their industry, one needs to understand the main issues that are being faced by the customers. What problems are they wanting to solve? This enables the correct focus on the right products. An example of this is dust and noise. Time and time again, these issues are raised by our field specialists who travel on site; therefore, it makes the most sense to align our products accordingly. It is even more crucial to follow this path where legal ramifications might arise, such as dust at a site that can lead to silicosis and other airborne diseases. This is an OH&S nightmare for companies. Therefore, it is likely that they will invest in equipment that will minimise dust.
In recognition of the environmental and global warming challenges, which will undoubtably face our industry, we will continue to source and manage our business to this end – using safe practices, in an attempt to minimse our impact on the environment, while continuing to support the growth of infrastructure.
Solving the right problems and taking controlled steps towards goals is the best measure to ensure a viable business. We are conservative in the way we operate, and we do not try to take on jobs that are bigger than we are capable of managing. We do not want to operate a business where if we have one little problem, the whole thing implodes. If you do not have a vision to survive – which comes from deep in your soul – then even with all the best plans in the world, it is not going to work!
Thirty five years later after the humble beginnings of our simple business, Christine and I, together with Charles, continue to keep our finger on the pulse of Kinder
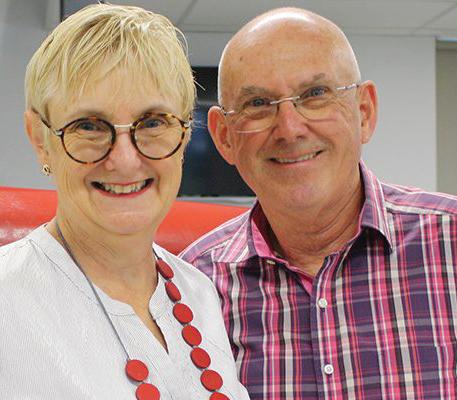
An early NC Kinder advertisement.
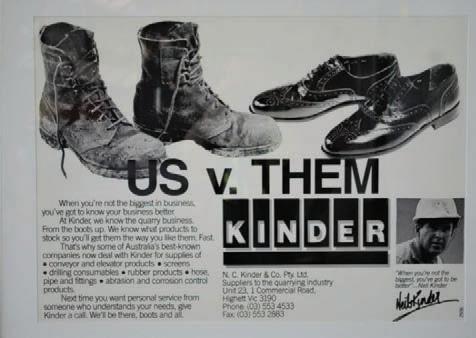
Photo by Will Arnott.
Neil and Christine Kinder have been invaluable members of the extractive and bulk handling industries for more than 35 years.
Australia Pty Ltd. Together with a skilled and trained team, we have moved premises several times to accommodate the growth of product range and storage, as well as an increase in staff and their needs. We have travelled the world to display at and attend international trade shows and events, as well as collaborate and build relationships with global suppliers and partners. It is all about surrounding yourself with the right people, utilising the skills they already have, or show potential to have, while offering encouragement and support for both our employees and customers, and a keen eye for problem-solving in the industry.
What it is not about is putting yourself up on a pedestal. You need to harness the skills and energy around you to build a knowledgeable and effective team.
Neil Kinder is the chief executive officer of Kinder Australia, in Braeside, Victoria. For more information about Kinder Australia, visit kinder.com.au
EFFECTIVE LEADERS – AVAILABLE NOW
Neil Kinder’s chapter and other chapters on effective leadership published in Quarry in the past year form part of a new book – Effective Leaders: Four attributes that underpin the core characteristics Of Effective Leadership, written and edited by Mike Cameron.
Built on a strong foundation of trust, and guided by leaders who continuously hone their skills, results and performance are achieved through an engaged and empowered workplace.
These leaders understand the importance of four attributes (values) that underpin the seven core characteristics of effective leadership: Respect, Courage, Integrity and Agility.
The book is available to order via the Strategically Yours website: strategically.com.au Effective Leaders continues the journey identified within The Emerging Leader by offering numerous narratives, from active and experienced leaders, based on the seven core characteristics of effective leadership. While highlighting the importance of buildingTrust, Mike Cameron encourages the reader to lead with their own blend of the four key attributes: Respect, Courage, Integrity and Agility. There are chapters, containing storiesand anecdotes about these important values, from some of the best writers and contributors in their field, that will inspire readers and persuadethem to indulge in theselifelessons.
Martin Toomey Business owner of Transport Equipment Australia and Chair of ARTSA Institute
2021 HIRE FLEET OVERVIEW
MAJOR OEM RELATIONSHIPS
Delta Rent enjoys long standing relationships with all heavy machinery OEMs and operates Australia’s largest privately owned fleet of specialist construction plant and equipment.
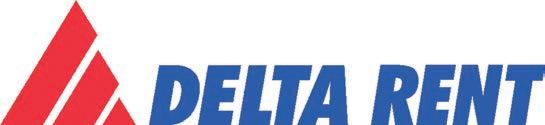
RIGID REAR DUMP TRUCKS
+ HD785 Komatsu Rigid Haul Trucks + 773 Series Rigid Caterpillar Haul Trucks + HD605 Komatsu 60t Rigid Haul Trucks
EXCAVATORS
+ Hitachi & Komatsu 60t - 125t + Hitachi, Komatsu & Volvo 30t - 60t + Hitachi 8t - 30t
WHEEL LOADERS
+ Hitachi, Komatsu & CAT Loaders ZW150 (up to) WA600
SITE & ROAD WATER TRUCKS
+ Bell & CAT Rigid & Articulated 24,000L - 40,000L + Fuso Road Registered 13,000L
ARTICULATED REAR DUMP TRUCKS
+ Bell 30t | 40t | 45t Dump Trucks + Bell & Volvo 50t Dump Trucks
DOZERS
+ CAT & Komatsu D6-D11 Dozers
GRADERS
+ John Deere & CAT Graders 14-16m
COMPACTORS + CAT 815 & 825
IQA NEWS
The Institute of Quarrying
Australia
FEDERAL RESOURCES MINISTER TO OPEN IQA2022 IN NEWCASTLE
The Institute is looking forward to next month when we – the IQA, our members and our industry at large – finally have the chance to get together at the 63rd National IQA Conference in Newcastle, from 29 to 31 March, 2022. The conference represents a fantastic engagement platform for all sectors of the extractive and associated industries that have not convened face to face for two years.
There are so many reasons to attend IQA2022 but we have outlined just a few below. If you are still deciding whether to join us, this information should convince you!
QUALITY PROGRAM
The program for this year’s conference is a standout. Under the theme of ReThink, ReSource, ReEngage, the stage is set for some fantastic speakers who will share their knowledge and expertise with our delegates.
The Honourable Keith Pitt MP, the Federal Minister for Resources, Water and Northern Australia, will officially open the conference program. A former electrical fitter mechanic and an electrical engineer for Bundaberg Sugar, Pitt established the Australian Training and Safety Alliance in 2002. He has represented the seat of Hinkler in the Federal Parliament since 2013.
The 2022-23 Federal Budget is expected to coincide with the opening of the conference, so the Minister will likely expand on the initiatives and incentives that form the core of the Federal Government’s re-election pitch. These could include increases to the instant asset write-off for new plant and equipment and the Job Trainer fund which in 2021-22 contributed $1 billion to the training and upskilling of job seekers and young people.
Futurist Michael McQueen will deliver an insightful keynote on ReThinking the Future. McQueen is a multi-award-winning speaker, trend forecaster and bestselling author of nine books. He is looking forward to being a part of IQA2022 and will play an important role in setting the scene for the conference.
Victoria Sherwood from Boral will discuss innovation in recycling and waste management and thought leader Rachael Robertson will discuss great leadership.
Sherwood has spent her career successfully optimising business performance and overseeing large scale transformational change within engineering and manufacturing-based companies across a multitude of industries globally, including mining, construction materials, building products and infrastructure.
Robertson is the best-selling author of the book Leading on the Edge - Extraordinary stories from the most extreme workplace on the planet. This relates her experiences as an Antarctic expedition leader of a 120-strong team for a year in one of the world’s most “most extreme, hostile environments”. She facilitates a 12-part, online workshop in Extreme Leadership, covering areas such as self-reflection, inspiration, regret, language, socialisation, generational differences, respect, difficult conversations, mental health, and crisis leadership.
Leaders from Boral, Adbri, Hanson and Holcim will take centre stage for an inaugural panel discussion. This is the first time representatives from all the major aggregates and cement producers in Australia will convene for a session at an IQA conference.
NETWORKING
More than 50 exhibitors will showcase the latest in equipment and services available to the extractive and associated industries. IQA2022 provides the perfect opportunity to reconnect with key representatives and update product knowledge.
In addition to the conference sessions, the IQA National Conference provides three great opportunities to network with industry colleagues and suppliers: the Hitachi Welcome Reception, the Komatsu Conference Dinner and the Caterpillar Gala Dinner. These events will enable delegates, sponsors and exhibitors to assemble on a social level. The IQA thanks its Platinum Partners for their support of the IQA2022 social program. Additional tickets are available to each event, providing a great opportunity to reward local team members or invite additional staff who are unable to attend the conference in full.
ENJOY THE HOST CITY
Newcastle is surrounded by golden, sandy beaches, a breathtaking coastline and a beautiful working harbour. For more information on things to do in Newcastle or extending your stay pre- or post-conference, see visitnewcastle.com.au
SUPPORT YOUR INDUSTRY ASSOCIATION
The IQA has a long, proud history of connecting and supporting the networking and professional development and careers of those in the extractive and associated industries. This role is largely delivered through the connectivity and support provided by the IQA’s branches and subbranches. The IQA has a branch in every state or territory, and several sub-branches in New South Wales, Queensland and Victoria. The IQA National Conference provides the opportunity to bring members and nonmembers from across Australia together to share ideas and innovation across the quarrying and associated industries.
To register for IQA2022 or for more information, visit iqa.eventsair/conference
GET INVOLVED IN THE IQA
Quarry Magazine Content Advisor – contract role The Quarry Magazine Content Advisor is responsible for supporting the technical accuracy of articles in Quarry magazine (print and electronic) and for providing advice on factually correct technical information. The contractor will collaborate with the editor of Quarry, the IQA CEO and the magazine’s editorial panel to identify relevant news stories and support editorial content.. For more information, download the EOI form from the IQA website: quarry.com.au (> About Quarrying > Our Partners).
Membership Review Committee nomination The IQA is seeking an EOI for up to five representatives from industry, branches and sub-branches, and suppliers to join the Membership Review Committee (MRC). The MRC’s role will be to: i) Determine applications for member status, where applicants do not have a formal or
IQA NEWS
The Institute of Quarrying
Australia
exempting qualification. ii) Determine applications for membership that are referred to it by the National Office staff or Chair of the Committee. iii) Determine applications for membership that are referred to it by applicants that are not happy with the decision of the National Office staff or Chair of the Committee. iv) Review and provide recommendations to the Board via the Chief Executive Officer on all nominations for Fellowship. v) Review and provide recommendations to the Board via the CEO on all nominations for Honorary Fellowship. vi) Review and provide advice to the CEO on all membership matters. vii) Review and provide advice to the CEO on strategies to sustain and grow membership. viii) Refer matters of Committee composition, membership guideline amendments, membership grades and annual membership fees to the Board via the CEO.
For more information, download the EOI form from the IQA website: quarry.com. au (Membership >Membership Review Committee). •
IQA NEW MEMBERS
GRADE NAME
ASSOC Nerida Worboys
ASSOC Troy Newman
MIQ Wayne Evans
MIQ Billy Lewis
MIQ Kurt Bridges
TMIQ Andrew Wade
TMIQ Nicholas Vrontas
TMIQ Graham Spice
TMIQ Brad Trindall BRANCH
NQLD
NQLD
NSW
NSW
NSW
NSW
NSW
NSW
NSW ASSOC Emily Tremelling
TMIQ Dean Little NSW
NSW
MIQ Thomas Walter NSW
TMIQ Simon Taylor
ASSOC Gabriel Maiug
MIQ Lee Wilson NSW
NSW
QLD
MIQ Andrew Jones QLD
TMIQ Keelan McNulty QLD
TMIQ Matthew Ferguson QLD MIQ Andrew Smith QLD
TMIQ Andrew Britton SA
MIQ Mathew Renton SA TMIQ Wayne Barker
MIQ Peter Baker SA
SA
ASSOC Daniel Nanthathammiko VIC
TMIQ Sherwin Ng
TMIQ Paul Harris VIC
VIC
ASSOC Cathy Moon VIC
MIQ Craig Tanner VIC
MIQ Cameron McIntosh VIC
MIQ Matt Murnane VIC
TMIQ Jason Trindall VIC
TMIQ Teresa Parkinson VIC

GEOLOGY TALK
CLAY RESOURCE KEY TO COW POLLUTION
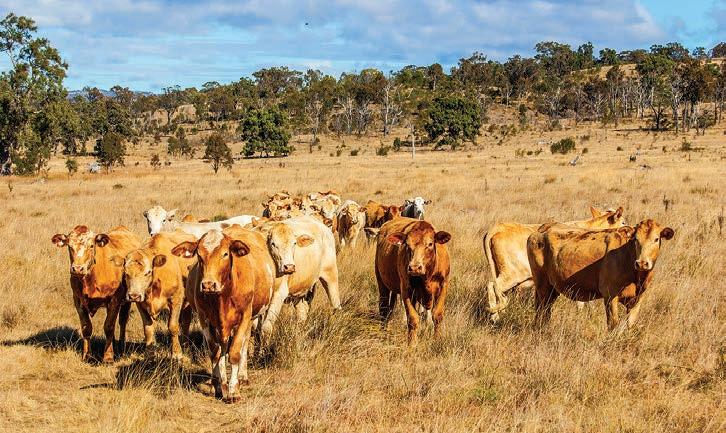
A high grade halloysite may be adapted into a low cost feed supplement to be added to the diet of beef or dairy cattle to reduce the methane in their stomachs. Examples of macro mineral quartz stone containing halloysite.
A natural clay mineral has been identified as a potential fix for a major carbon emitter, reducing pollution while providing a new end use for this quarried material.
Methane from cattle has long been recognised as a major source of greenhouse gas globally. So, the Cooperative Research Centre for Contamination Assessment and Remediation of the Environment (CRC CARE) and miner Latin Resources have partnered to make change.1
Latin Resources owns the Noombenberry halloysite-kaolin project in Western Australia and the team at CRC CARE has chosen the Cloud Nine deposit at Noombenberry as a prime source for this important resource.2
CRC CARE researchers have developed a way for high grade halloysite to be adapted into a low cost feed supplement to be added to the diet of beef or dairy cattle to reduce the methane in their stomachs.
“If we can find a way to reduce methane output from grazing animals like cattle, sheep and goats, we can limit a major source of global pollution that worries governments and climate policymakers – as well as farmers – everywhere,” said CRC CARE managing director professor Ravi Naidu.
Halloysite deposits have developed naturally over millions of years in arid environments like Australia and must be extracted from the clay in which it forms.
“If we succeed, it will mean that farmers everywhere do not have to cull their herds to meet climate targets, but can continue to produce quality beef and dairy to help feed the world,” Naidu said.
“This is vital for two key food industries, together worth $2 trillion and employing over 12 million people globally. Australia alone has 45,000 cattle enterprises.”
A secondary use was identified for the halloysite, which forms in nanotubes, where the material could be placed inside a cattle shed to trap and absorb the methane. The methane trapped in the halloysite could then be burned as a fuel to heat the shed, operate the farm or produce fertiliser.
“Cutting back on methane emissions is one of the most effective things we can do to reduce near-term global warming and keep to 1.5°C,” European Commission President Ursula von der Leyen said at the United Nations’ Climate Conference (COP26) in Glasgow, Scotland.3
Naidu said Australia had a responsibility to take advantage of its natural resources in innovative and helpful ways such as this.
“Australia is richly endowed with large, diverse clay resources, which include deposits of world class size and purity,” Naidu said. “These resources are largely underutilised due to poor market transformation, high transport costs and limited industry knowledge of clay properties, process methods and markets.”
Latin Resources managing director Chris Gale agreed the company was committed to using its resources to create a better world.
“As a resources company with a strong focus on environmental, social and governance processes, we are excited by the potential of this research project,” Gale said.
“There are few resources projects globally that have the potential to be world-changing and, while it’s early days, we believe we have partnered with the right team to deliver.” •
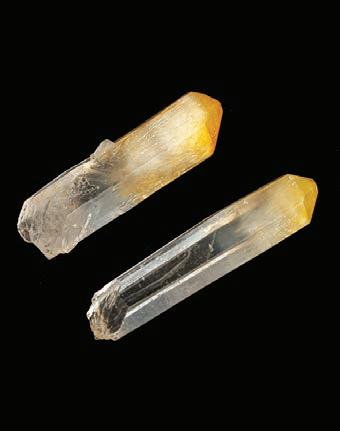
REFERENCES & FURTHER READING 1 CRC Care. Australians to help solve global methane threat. 9 December, 2021. crccare.com/news/australians-to-help-solveglobal-methane-threat 2 Latin Resources. Cloud Nine halloysite - Research and development project to reduce methane emissions. 18 November, 2021. asx.com.au/asxpdf/20211118/ pdf/4533jkksvddrqh.pdf 3 Politico. At COP26, more than 100 countries commit to reducing methane emissions. 2 November, 2021. politico.eu/article/cop26-100-countriesreducing-methane-emissions/
We are a global team unified by a common purpose: creating advanced, sustainable technology solutions to the world’s water challenges across more than 150 countries. Developing new technologies that will improve the way water is used, conserved, and re-used in the future is central to our work. Our products and services move, treat, analyse, monitor and return water to the environment and in public utility, industrial, residential and commercial building services settings. Sustainability is at the core of everything we do, and we aim to ensure our footprints leave a positive impact on the environment and the wider community as we strive to build a healthier and more water-secure world. Our commitment to water quality is Xylem’s foremost priority at both an organisational and global scale, with our corporate social responsibility program Watermark aiming to provide education and equitable access to safe water and sanitation to support healthy lives and help build resilient communities around the world.
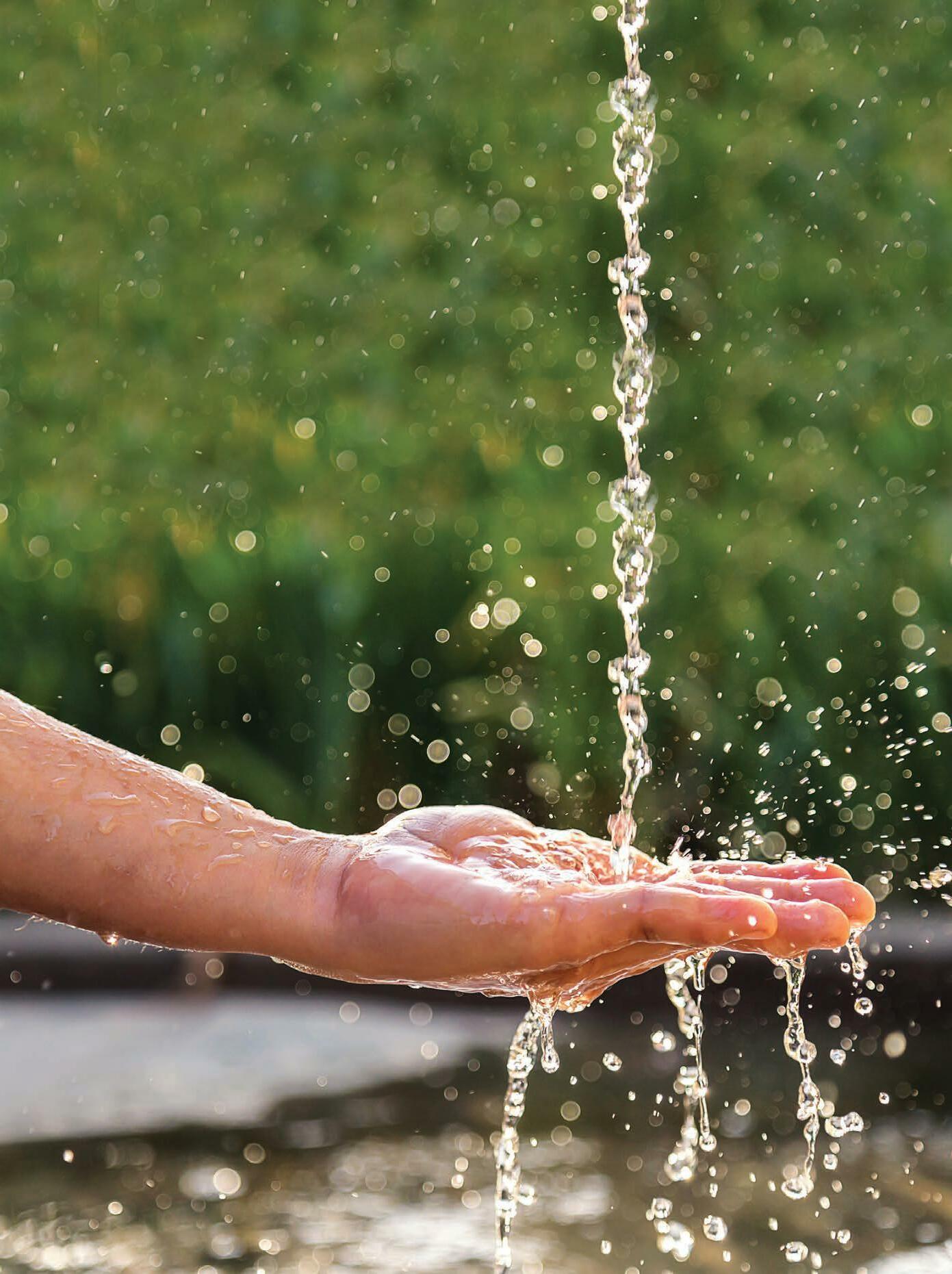