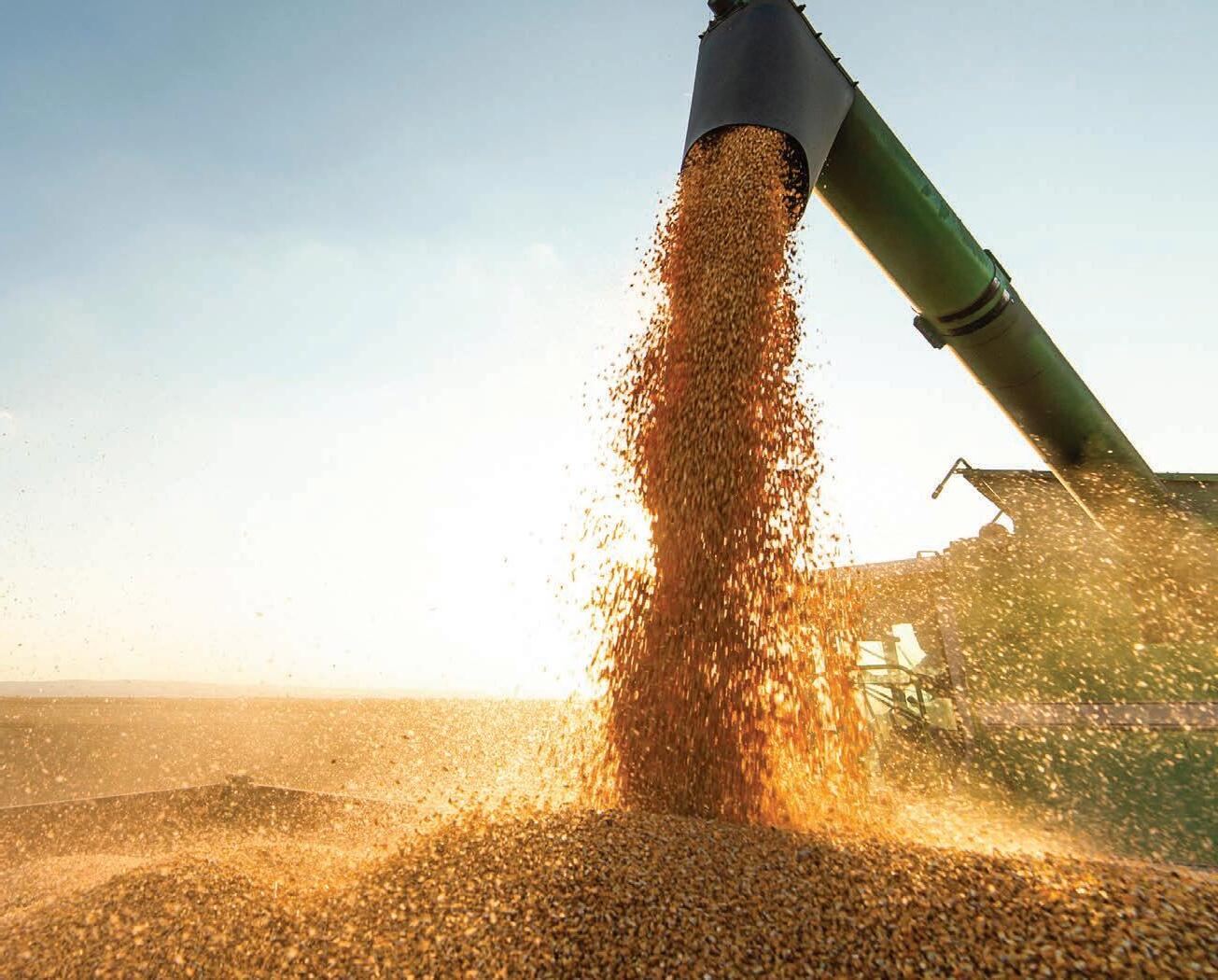
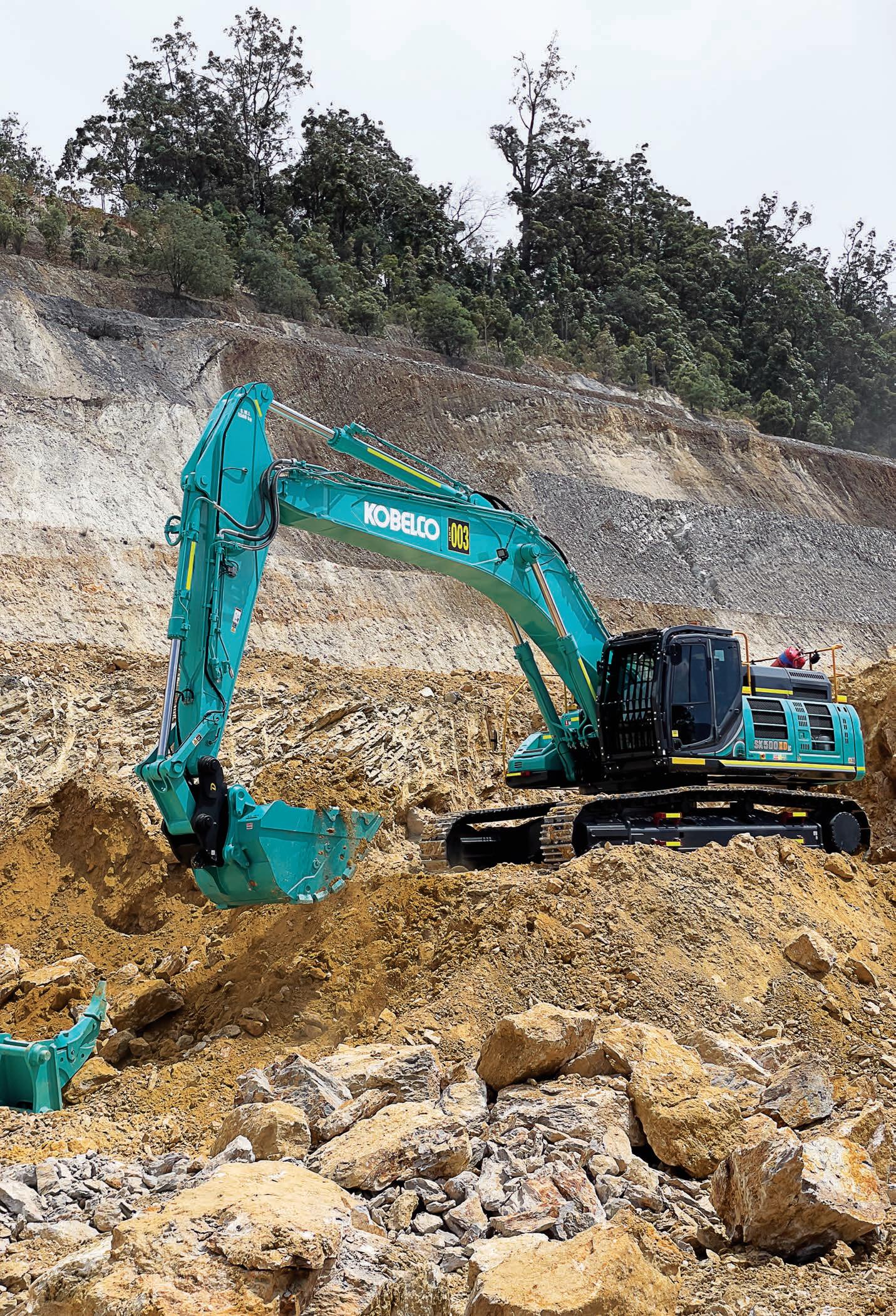
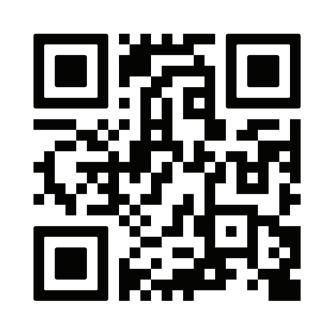
Komatsu’s Smart Quarry Site is an innovative fleet management solution designed to empower site and project management personnel with unparalleled production visualisation for quarry and major civil construction sites. With a simple glance, you gain access to real-time animated insights into every aspect of your production machines, as well as the material they are handling, extracting, shifting, or placing.
Kinder
Quarry
How
echnology without complexity
Deere delivers dozers
Platform for productivity
Tech in Tennessee
Bonfiglioli’s gearbox growth 30 The nuts and bolts of Virsbolt
A sustainable journey
Quarry
Talking resources in PNG
Super belt splicing solutions
35 years and counting
Taming quarry water
Tech for rain, hail or shine
Confidence in accessories
Quarry
An unfortunate fact about the nature of machinery is that breakdowns are inevitable. If you run a machine for long enough, eventually something will stop working. The more moving parts there are, the more potential things that could go wrong.
On a quarry site, there are several machines that rely on critical components, each with the potential to fail. When this happens, then it can quickly cascade.
For example, a bearing could come loose in a roller, which could damage surrounding components or itself, which could then damage a conveyor belt – leading to costly repairs and unplanned downtimes.
To avoid these calamities, quarries follow maintenance routines. If routine maintenance is not performed, it becomes more likely that small things won’t be caught before they become big things, costing the operations thousands (if not millions) of dollars.
Most businesses offer after sales support, to ensure their customers can rely on the equipment even if something goes wrong. Some have now embraced the Internet
of Things, incorporating sensors into equipment to help monitor the performance of a system in real time.
Access to this data allows sites to make more informed decisions and can highlight when something has gone wrong. In many cases, digital monitoring can spot potential problems well in advance of manual maintenance, giving the operators more time to respond in scheduled downtime.
Others are even beginning to embrace machine learning and cloud-based computing to help predict when something will go wrong before it even happens.
However you handle it, maintenance is a key part of keeping quarries profitable. New technology is helping find ways of removing risks and speeding up the process so that machinery can get back to earning a profit.
Next month, Quarry will shine the spotlight on screening, feeders, and road transport. If you would like to see your business covered, please get in touch.
William Arnott EditorPublished by:
379 Docklands Drive
Melbourne VIC 3008
T: 03 9690 8766
www.primecreativemedia.com.au
Chief Executive Officer
John Murphy
john.murphy@primecreative.com.au
Managing Editor
Paul Hayes paul.hayes@primecreative.com.au
Editor
William Arnott william.arnott@primecreative.com.au
Journalist
Adam Daunt adam.daunt@primecreative.com.au
Business Development Manager
Les Ilyefalvy les.ilyefalvy@primecreative.com.au
Client Success Co-ordinator
Janine Clements janine.clements@primecreative.com.au
Art Director
Michelle Weston
Subscriptions
T: 03 9690 8766
subscriptions@primecreative.com.au
The Publisher reserves the right to alter or omit any article or advertisement submitted and requires indemnity from the advertisers and contributors against damages or liabilities that may arise from material published. © Copyright – No part of this publication may be reproduced, stored in a retrieval system or transmitted in any means electronic, mechanical, photocopying, recording or otherwise without the permission of the publisher.
MOBISCREEN EVO
HIGH FLEXIBILITY AND FIRST CLASS SCREENING RESULTS. The MOBISCREEN MSC EVO screening plants are characterised by high application versatility, excellent transport characteristics and fast set-up times. Precise results with a very wide variety of feed materials and low consumption are guaranteed – where flexibility meets precision. The efficient MSC EVOs thus impress with top performance values across the board.
www.kleemann.info
The IQA has a long and proud history of connecting and supporting the extractive industry. In fact, it’s part of our vision to see communities thrive thanks to the industry.
Part of that support is shining the spotlight on the remarkable achievements and contributions that are shaping the future of our industry.
The 2024 IQA Awards are a fantastic opportunity to honour and celebrate the outstanding individuals and organisations that contribute significantly to the quarrying industry across various categories.
This year’s award categories include:
• Alec Northover Award (sponsored by AIQEF)
• Gold Hard Hat Site Safety Award (sponsored by IQA)
• Gold Environment Award (sponsored by Groundwork Plus)
• Excellence in Innovation and Community Engagement (sponsored by Eltirus)
• Quarry Manager of the Year <10 FTE Quarry Manager of the Year >10 FTE
• Quarry Operator of the Year
• IQA Conference Exhibitor of the Year (sponsored by IQA)
• President’s Medal (sponsored by IQA) Nominations are open and welcome for both IQA members and non-
members. The closing date for all award nominations is 7th August 2024. If you know an outstanding individual or organisation making waves in quarrying, I encourage you to nominate them to honour their invaluable impact.
The President’s Medal award is exclusive to IQA members and recognises a member who has given outstanding and ongoing service to the extractive industry and demonstrates leadership and the advancement of the industry as a whole. The winner will have supported the IQA through involvement in areas such as branch, sub-branch, committee, Board and Council membership over a period of time.
of
Educating and connecting people engaged with the extractive and associated industries.
www.quarry.com.au
The IQA’s Strategic Plan 2023 to 2026 embodies the following vision, values and strategic priorities:
Vision:
The IQA Conference Exhibitor of the Year award will be judged from all exhibitors during the IQA conference in October 2024. All exhibitors are automatically entered, and a separate nomination form is not required.
The 2024 IQA Award winners will be finalised in August/September, with winners announced during the 2024 IQA National Conference in Adelaide 15-17 October 2024. I hope to see you all there.
Duncan Harris President Institute of Quarrying AustraliaTHE 2024 IQA AWARDS ARE A FANTASTIC OPPORTUNITY TO HONOUR AND CELEBRATE THE OUTSTANDING INDIVIDUALS AND ORGANISATIONS THAT CONTRIBUTE SIGNIFICANTLY TO THE QUARRYING INDUSTRY ACROSS VARIOUS CATEGORIES.
Thriving communities supported by a sustainable industry
Operational Priorities:
• Deepen industry participation
• Sustainable revenue streams
• Highly capable team
• Technological innovation
• Effective engagement
• Great governance
Strategic Priorities:
• Support industry participants with compliance and regulation
• Build a diverse and skilled industry workforce
• Foster strong industry connectivity
IQA Contacts:
Phone: 02 9484 0577
Email: admin@quarry.com.au
Deputy President
Michael Close
Company Secretary David Cowie
For all education, member and branch enquires please email: admin@quarry.com.au.
“AN ONGOING LIME OPERATIONS REVIEW HAS IDENTIFIED A NUMBER OF OPPORTUNITIES FOR COCKBURN CEMENT.”
MARK IRWIN
taking steps to ensure we are aligned with the needs of our customers,”
AdBri chief executive Mark Irwin said.
“An ongoing lime operations review has identified a number of opportunities for Cockburn Cement.
“This includes the potential to adopt a hybrid supply model, which may involve a mix of locally manufactured products and imported lime, enabling us to deliver additional product grades to the marketplace.”
The company said it expects demand for the balance of its products to “remain strong” and in line with the past financial year. This is supported by pricing and cost-to-fuel margin expansion in the 2024 financial year.
Irwin said the company would look at this model moving forward.
AdBri has revealed a new arrangement with Alcoa for its quick lime supply agreement to reflect the ‘changing demand’ in the market.
Cockburn Cement Limited will supply Alcoa on revised terms until the end of April 2024.
This arrangement differs from the previous agreement, which ran until October 2024.
AdBri has told its shareholders it expects lower lime volumes from 2024 and beyond.
The company confirmed in its public statement that it is reviewing its lime operations to match the “evolving lime outlook” and the “changing demand profile” of customers.
“The Western Australian lime market is important to Adbri, and we are
“We will investigate the feasibility of this model within the footprint of our Munster facility, utilising existing infrastructure such as silo and storage facilities, while continuing to leverage the site’s valuable rail access,” Irwin said.
Recently, AdBri has been working with major aggregate producer CRH and Barro Group on a potential takeover. •
The Victorian Earth Resources regulator is urging quarries to ensure their operations are compliant with regulations for commercial activities.
In recent times, the Victorian Earth Resources regulator has issued notices to quarries across the state to remind them of compliance measures.
“Most operators in the resources sector across the state are working hard, meeting all their obligations and performing to a high standard,” Resources Victoria chief executive Matt Vincent said.
“The Earth Resources Regulator is focussed on those falling short of this benchmark to ensure their poor practices don’t put the environment, infrastructure and communities at risk.”
Earlier this month Inspectors found a gravel quarry operator in eastern Victoria had extracted material outside their approved area. The Earth Resources Regulator issued a stop work notice to cease unapproved activities and submit a plan for the rehabilitation of the area.
In western Victoria a sand quarry operator was found to have failed to conduct an adequate review of their tailings dam, where waste is stored.
Compliance with set conditions for tailings and waste storage is critical to ensure that structures function as designed and do not pose an unacceptable risk to the surrounding area.
The Earth Resources Regulator has also issued a remedial notice requiring the operator of a hard rock quarry in northern Victoria to cease extraction that is placing long-term stability of the site at risk.
Work will now be required to reinstate the approved angle of the pit slope, which is critical to safety.
Resolution of all these issues found by the regulator will mean operators incurring extra expense and delay, which the regulator said could have been avoided with higher levels of diligence and compliance with their approved plans.
“Operators across Victoria’s resources sector must do the right thing and comply
with regulations to be entrusted to develop and extract the state’s minerals and quarry materials,” Vincent said.
“Industry will see us continue to promote our increased use of notices to formalise our requirements when we find risks not being managed appropriately or authority holders not complying with their Work Plans, a strong and active regulator reflects well on the broader resources sector.” •
John Deere has been lauded as one of the world’s most ethical companies following the release of Ethisphere’s latest data.
Ethisphere marked 2024 by releasing its 18th annual Most Ethical Companies list which features 136 companies, including John Deere, spanning 20 countries.
“We’re absolutely thrilled to be recognised as one of the world’s most ethical companies once again. It’s a reflection of our deep-rooted commitment to operating with integrity, which drives everything we do globally,” John Deere chief people officer Felecia Pryor said.
“This recognition really speaks to our strong ethical culture as propelled forward by our employees and stakeholders.”
John Deere employs a series of strategies across its business to underline its commitment to ethical business practices. These include John Deere’s Leap Ambitions which focus on delivering economic value and sustainability for customers and stakeholders.
Ethisphere began the World’s Most Ethical Companies’ initiative in 2007 with John Deere named on the list 17 times since its inception.
“THIS RECOGNITION REALLY SPEAKS TO OUR STRONG ETHICAL CULTURE AS PROPELLED FORWARD BY OUR EMPLOYEES AND STAKEHOLDERS.”
FELECIA PRYOR
Ethisphere assesses companies based on a complex questionnaire which covers five categories and 243 multiple choice and text questions.
The method, which Ethisphere calls the Ethics Quotient, assesses companies against areas of governance, culture of ethics, third party management, ethics, and compliance as well as environmental and social impact.
Ethisphere says the framework enables them to calculate the assessment in an objective and consistent way.
The companies that demonstrate the strongest application across all of the methodologies are awarded a designation on the World’s Most Ethical Companies list.
“Every day, businesses must earn and keep the trust of stakeholders, from employees and investors, to regulators, and others,” Ethisphere chief strategy officer and executive chair Erica Salmon Byrne said.
“By leading with business integrity—and investing in strong governance, an ethical culture, corporate citizenship, and compliance—organisations not only build trust, but also outperform.” •
Komatsu Australia has signed up for a million-dollar pilot program to utilise sustainable aviation fuel to reduce the emissions related to Komatsu’s air express shipments in Australia in 2024.
The new initiative is part of Komatsu’s ambitious commitment to slash its carbon footprint by 50 per cent by 2050.
Komatsu Australia has recently signed up for the GoGreen Plus program run by logistics partner DHL Express. Komatsu has committed to invest one million dollars in GoGreen Plus, a new service of DHL that allows Komatsu to reduce (‘inset’) the carbon emissions associated with their international shipments through the use of Sustainable Aviation Fuel (SAF). The impact of the investment will be announced at the end of the year.
With GoGreen Plus, Komatsu will use sustainable aviation fuel produced from waste oils to provide greenhouse gas (GHG) emission reductions of up to 80 per cent over its lifecycle compared with the conventional jet fuel it replaces.
“GoGreen Plus is one of the most effective ways companies can choose to reduce their carbon emissions for their international shipments as they have the opportunity to invest in SAF,”
Phil Corcoran, DHL Express Australia and Papua New Guinea managing director, said.
“GoGreen Plus allows companies like Komatsu to track their progress toward their sustainability goals, backed by science-based, verified and certified reporting on their carbon reduction insets.”
“GOGREEN PLUS ALLOWS COMPANIES LIKE KOMATSU TO TRACK THEIR PROGRESS TOWARD THEIR SUSTAINABILITY GOALS, BACKED BY SCIENCEBASED, VERIFIED AND CERTIFIED REPORTING ON THEIR CARBON REDUCTION INSETS.”
PHIL CORCORAN
Komatsu Australia general manager, safety and sustainability, Henrietta Jukes, says the trial is just one of many programs the company has signed up for to reduce its GHG emissions at every possible point.
“We are very excited to be one of the first customers to purchase SAF, but it’s important to note that by undertaking this trial we are not shifting focus from what we were already doing, but expanding our focus,” Jukes said.
“We have 27 major sustainability projects that we are working on right now and we will be considering all of them in terms of how well they help us to support our customers to achieve emissions reductions, so we can decide where to make future investments. Logistics and transportation is one important area where we can make a difference. Others include the work we are doing to make our machines more efficient, through telemetry that lets customers monitor machine movements and fuel loads and make instant changes.
“We are doing some extremely detailed modelling right now to thoroughly understand the emissions impacts of machine models in specific applications, across both construction and mining. This will give us really valuable and important insights to relay back to our customers.”•
Bio-bitumen is being used as part of a trial in New South Wales to create a more environmentally friendly road network.
Bio-bitumen, known as ECO5, uses repurposed material including recycled crushed glass, asphalt and crumbed rubber from end-of-life tyres to create a lower carbon output asphalt.
NSW Transport is currently monitoring the road material as part of a trial with Colas.
If the Raymond Terrace trial is successful, the department could adopt the ECO5 as part of its wider road network.
“This trial is an important milestone in moving towards using more sustainable and environmentally friendly materials as part of our daily road practices,” Port Stephens MP Kate Washington said.
“The asphalt company Colas developed the ECO5 product, and the asphalt produced for this trial came from their Tomago plant in Port Stephens. The product was developed through a combination of local and international research and development. It’s great to see Port Stephens is laying the foundations for a greener future and better local roads.”
Transport for NSW senior manager maintenance Stuart Baverstock said the trial could lead to a wider, positive impact for the state.
“Transport for NSW wanted to see what sort of environmentally beneficial asphalt products were out in the market and what we could utilise on our roads as a better environmental product,” he said.
“Transport for NSW uses a huge amount of asphalt. It is a very carbon-rich product, so if we can reduce that even in small amounts then we will get huge savings.”•
Sometimes you want the latest tech. Sometimes you just want the essentials done exceptionally well. That’s why we offer distinct levels of innovation, comfort, and performance so you can get done faster, more efficiently, and on budget.
The MOBICAT MC 110 EVO2 has been designed to overcome evolving challenges in different applications.
To submit new product and equipment releases, email: les.ilyefalvy@primecreative.com.au
For the past 100 years, Kleemann GmbH has been designing, evolving and manufacturing machines for the mining, quarrying and recycling industries. High levels of performance and innovative features, simple handling and maximum safety for the operator – this is what Kleemann crushing and screening plants stand for.
As a powerful mobile jaw crusher the MOBICAT MC 110 EVO2 has been designed to overcome evolving challenges in different applications. With its ingenious machine design and flexibility on configuration, an optimised through put can be guaranteed for natural stone and recycling applications.
With the increasing demands that are placed on modern crushing plants, their complexity also increases. At the same time, the technology must be safe and as simple as possible to master – and without long training sessions. This is precisely the strength of the SPECTIVE operating concept. The MOBICAT MC 110 EVO2 can be operated simply and intuitively with the various SPECTIVE components. Along with the touch panel, the holistic operating concept includes a SPECTIVE INTUITIVE OPERATING CONCEPT for a better result – guaranteed. large and small radio remote control, and the SPECTIVE CONNECT digital solution.
The MOBICAT MC 110 EVO2 also features the innovative D-DRIVE “diesel-direct-electric” drive concept and excels with its dynamic performance combined with low fuel consumption. The MC 110 EVO2 stands out with its holistic drive concept with an efficient diesel-direct drive whereby the crusher is driven directly via a fluid coupling from the diesel engine. The power and load-dependent fan ensures a low-noise and even more economical operation. Via a power splitter gear box, the generator is driven direct by a cardinal shaft, The drive system pumps are activated via a clutch coupling and can therefore draw on the full power of the diesel engine. All other hydraulic pumps for auxiliary and set up functions and for the cooler drive are also driven via the gearbox.
With a focus on cost-effectiveness, intuitive operation, and an eye on sustainability the MOBICAT MC 110 EVO2 Jaw Crusher is ideally equipped to combat these challenges successfully.
For more information visit wirtgen-group.com
Quarry finds out why major limestone producer Graymont purchased two Kobelco SK500XD excavators.
Lime and limestone are among some of the oldest and most vital materials used by humans. The materials were the literal building blocks for ancient pyramids, temples, and roads.
Nowadays, lime is used in road stabilisation, asphalt, water treatment, steel making and metalliferous processing. Limestone is utilised as a mineral filler in stockfeed, for cropping and pasture improvement and flue gas desulphurisation, among many other applications.
Canadian-owned company Graymont is a world leader producing lime and limestone solutions critical for a decarbonised world. Graymont’s Australian operations are located on the east coast and Tasmania. This network is supported by its operations in New Zealand, Malaysia and the Philippines. Graymont also has a significant presence in the North American lime and limestone market.
While limestone is not particularly abrasive, Graymont wanted to update and upgrade its excavators. Damian Power, site manager at Graymont’s Attunga plant, told Quarry this
is why the company purchased two Kobelco SK500XD diggers.
“We were in the market for a good, reliable machine that was well supported by the dealer,” he said.
“The SK500XD ticked all the boxes – it is ergonomic, has low noise output and is economical to run.”
Kobelco designed the SK500XD for extreme durability. It is engineered to operate in the harshest conditions worldwide, making it ideally suited for a variety of applications in Australia, such as quarry excavation.
Weighing in at 52,200 kg, the SK500XD is the heaviest machine in its class. It is purpose-built with a robust machine body and substantial additional reinforcements to all key areas of stress and wear across the boom, arm, underbody, and undercarriage.
It features a specially adapted heavyduty boom and arm set to handle harsh quarrying conditions. It comes with factoryfitted, triple-plated, hardened steel applied to all key structural sections, including the boom-to-arm connection, the boom centre, and the end of the arm—providing a
high level of durability and longevity to the attachment structures.
A specially designed full-length rock guard is installed on the inside of the dipper arm, on top of additional steel plating. A quadruple track guide frame allows it to operate reliably in harsh and rocky conditions, while reinforced heavy-duty 600mm triple grouser shoes make easy work of rough terrain.
Kobelco has also worked to improve the durability of the track links. The idler frame has received substantial double reinforcement plating inside and out, preventing premature wear of this key structure.
Power said one of the key benefits of the machine was its fuel efficiency.
“It has one of the lowest fuel burns of all the diggers we looked at,” he said.
“That adds up. It means we’re spending less on fuel, and we’re emitting less carbon, which is becoming even more important.”
Fuel efficiency is a key part of the SK500XD’s design. It delivers an average fuel consumption under 30 L/hr in typical Australian heavy digging conditions.
Part of this is due to a new boom-to-arm regeneration system, which more efficiently controls hydraulic fluid flow and delivers a significant reduction of in-line resistance and pressure loss. As the need for fluid to be forced from the pump is reduced, the engine and hydraulic workload will be less, which means higher fuel savings.
Three work modes allow the operator to select the best mode for the job at hand –heavy-duty and standard work options, and an ECO-mode that automatically optimises digging efficiency, delivering a 13 per cent decrease in fuel consumption.
Power said the machine came highly recommended by others in the local industry.
“We did our homework and looked at the excavators that were available. A major Tamworth business had given them a go and were happy with them,” he said.
“Gato Sales and Repairs, one of the dealers that supplied the machines, were great to
notifying the operator if filter performance is compromised, ensuring reduced downtime while maximising the machine’s value.
The addition of a new hydraulically driven cooling package with independently driven fans for the hydraulic cooler, engine radiator and intercooler, not only improves fuel economy but also reduces engine noise while providing optimal oil temperature control—for increased reliability and performance in demanding high ambient temperature environments.
However, the highlight of the machines for Power is its ergonomic factor.
“The cabin is spacious and feels comfortable to sit in for extended periods of time. It’s got a large front window and a lot of noise dampening inside,” he said.
“It’s also got a heated and air-cushioned suspension seat, protecting the operator from vibration, with climate control to keep you cool on hot days.”
Also inside the cabin is a colour LCD multidisplay screen, that shows all the important information, including fuel consumption and maintenance intervals, as well as an integrated rear-view camera.
Power said the Kobelco excavators, which have been used across the quarry, have been fantastic.
“They’re reliable machines. We’re very happy with them and looking forward to continue seeing these great results.”•
Quarry spoke to McBride Sands about how embracing Aptella’s technology helped boost their operations near Bundaberg.
Family-run Queensland quarry company
McBride Sands has adopted tradeapproved scales and iWeigh office software to streamline administration.
Owners Dean and Melissa McBride said simplicity has meant technology helped rather than hindered their operations.
“Using the Loadmaster system keeps our trucks moving more efficiently,” Dean told Quarry.
“Because the system is weighing during the load, there’s no delay, so as soon as the truck is full, they can get going.”
Based near Bundaberg, McBride Sands specialises in high-quality sand for concrete and asphalt plants, landscaping businesses, blockworks, and construction companies, with options for delivered or ex-pit collection, as well as screened and unscreened products.
For many years, McBride Sands has used Topcon Loadmaster trade-approved loader scales serviced and supported by Australian distributor Aptella (formerly Position Partners).
Installed on two Hitachi wheel loaders, Loadmaster is a simple, user-friendly on-board weighing system that accurately measures the weight of every load.
Customers and materials can be saved in the system to record loads for each job.
With a digital record of the weight and type of materials for each customer, McBride
Sands has saved time and improved the accuracy of information compared with paper-based records.
The company has now installed a printer box that enables drivers to pull up alongside the printer and tear off its docket without having to park and go into the office.
“It may seem like a small thing but removing the need for our drivers to stop and start to get paperwork really helps to keep everything moving,” Dean said.
Operators have reported being happy with the system due to its straightforward to use.
Dean said using the loader scale technology gives him peace of mind for his trucks on the road.
“You know the trucks aren’t going to be overloaded, so you’re minimising risk when travelling. If we get pulled up and inspected, or worst case, one of our trucks was involved in an accident, we know we’re covered,” he said.
“We don’t use all the bells and whistles that it’s capable of; for us, it’s about keeping it simple and getting the fundamentals right.”
From a business perspective, Loadmaster also helps to ensure that every load is optimised without being under- or over-loaded.
“If you were loading a 27.5 tonne load by eye, you might be under or over by half a tonne, which means you’d either have to tip off or you’d be running light,” Dean said.
“With the Loadmaster system, if you need 27.5, you know you’ll be accurate every time, maximising your loads.”
McBride Sands gets the scales calibrated regularly to ensure they are working accurately. The company also uses a weighbridge periodically to compare weights and check for any discrepancies.
“The service we get from the Aptella team is spot on. We always get calibration certificates, which are required by all the concrete companies and are tracked by them over time,” Dean said.
“Our customers have always been happy, and we’ve never had a problem in all the years we’ve been using the technology.”
Melissa McBride runs the company’s administrative work and invoicing. She told Quarry she is excited to extend the benefits of the Loadmaster technology through to invoicing by integrating iWeigh software.
Originally designed to integrate weighbridge data with accounting software, iWeigh is now compatible with Loadmaster solutions thanks to the company’s collaboration with Aptella.
For Melissa, finding a straightforward software solution that would suit her workflow and the business’s requirements was crucial.
“I was aware of systems designed for larger quarries, but they would be overkill for what we need and too complex to implement,” she said.
Having researched options with other similar-sized businesses, Melissa came across iWeigh and hoped that it could provide the perfect setup if it could be integrated with the loader scales.
“We’ve had a longstanding business relationship with Chris from Aptella, so I reached out to see what was possible and
now we’re ready to start implementing it,” Melissa said.
Once set up, data recorded by the Loadmaster loader scales will feed directly into iWeigh’s platform via the Internet. From there, it will automatically convert into MYOB, the accounting software used by McBride Sands.
The new setup will give Melissa access to the data almost instantly, eliminating the need to visit the office or the printer box for a hard copy.
“I’m really excited about the potential for this solution; it will be so much more current and streamlined than our current setup, which has more manual invoicing,” she said.
“I will be able to process invoices quickly, and it will make things easier for our customers, too, because I can email documents straight away. There’s no delay, and it doesn’t matter if a driver loses a docket, as I have a digital copy.”
Melissa expects a few teething issues as the new solution is rolled out, but she feels confident about the level of support she’ll receive from Aptella and iWeigh.
“I think we’ve found the right fit for our business that won’t overwhelm our team with complex technology that would be overkill for our needs,” she said.
“Like the loader scales, we just need a simple solution that improves our efficiency.”
John Deere has introduced updated models of its dozers with increased power and new designs.
Bulldozers are a workhorse on any quarry site, but they can be overlooked.
Kat Roberts, John Deere product manager for dozers and crawler loaders, believes they can separate an okay operation from a great one.
“I think that the average person should care about dozers in general, and these large dozers in particular, because anything around us that needs development, you need a dozer to move the land to shape it and sculpt it,” she told Quarry
This is why John Deere has bolstered its portfolio with two new bulldozer versions, which will be introduced later this year.
The company has introduced the 950 P-Tier and the 1050 P-Tier, which are updated models of the 950K and 1050K, with increased power and new designs.
“These are big dozers, and they can push a lot,” Roberts said.
“The 1050 P-Tier has enough drawbar pull that it can push 29 F-150s, which when you think about the F-150s, that is a big truck, and 29 of those is pretty outstanding.”
The 1050 P-Tier dozer has a JD14 (13.6L) engine, which is a revamped version replacing the 13.5L on the 1050K dozer.
The increased power improves the durability and reduces fuel consumption on the 1050 P-Tier.
The JD14 engine uses a single canister in the after-treatment system to meet emission regulations without the need for a diesel particulate filter.
The new 1050 P-Tier features a redesigned hood, front-end design, and increased engine power. Both new models have been updated with safety features, including standard LEDs, to improve operator’s visibility and safety.
The cold-weather hydraulic lines have been built to keep the dozers operating all year, especially in the colder seasons. These hoses, which replace the standard option, are rated for lower temperatures, ensuring smooth hydraulic function in the depths of winter.
“The 950 P-Tier and 1050 P-Tier dozer models were updated with the customer in mind, helping them increase efficiency, visibility, and gradeability in even the most demanding conditions,” John Deere construction and forestry marketing manager Matt Costello said.
John Deere has added the Operator Presence System as an advanced safety measure. The system registers an operator in the control seat with the seat belt fastened before the parking brake can be released for operation. The dozers also integrate the park brake switch into the system status monitor, eliminating the traditional park lock levers to improve the safety mechanism.
“John Deere is dedicated to providing its customers with large dozer options that fit the needs of every job site, and the new P-Tier machines offer the durability and reliability our customers demand from machines of this size class,” Costello said.
The operator will benefit from the heated and ventilated seat option, which is airsuspended with adjustments to suit every operator’s unique ergonomics.
The cab has new ergonomic controls, including a neutral counter rotation and an integrated forward-neutral reverse switch to ensure operators can comfortably work for extended periods.
John Deere has adjusted the tag link and blade design to bring the blade 25.4 centimetres closer to the frame. It may seem like a minor adjustment, but repositioning the 427-centimetre blade, the redesigned hood, and the larger front window gives the operator more visibility when the blade is in operation. The changes will enable a clearer view of the blade corners from the cabin, which is critical in precision and grading work.
Roberts said the John Deere team had worked hard to design a machine to suit the current needs of operators.
“Every time I come to the factory, it hits me like it’s the first time; it gives me goosebumps,” she said.
“There’s thousands of parts, hundreds of people really when you think about the design to the manufacturing to the assembly of it. It is amazing to think about all those things coming together at the right time to make this product.”
Roberts said the customer had been at the forefront of the design process for John Deere’s new entries into the P-Tier range.
“My job really fits in with our John Deere strategy of smarter, safer, and more sustainable construction in a real way,” she said.
“The products that I work with directly impact our customers in those three ways, which is neat to see.
“It feels surreal, almost like a pinch me moment, when you think about a John Deere dozer, I get to be part of that story and that journey.” •
For more information, visit deere.com.au
Komatsu rebranded its fleet management platform iSite into Smart Quarry Site. Quarry looks at how the platform has been helping customers.
There was a time when a site manager measured their quarry’s fleet performance using old-fashioned pen and paper.
However, quarries are increasingly focused on compliance, with higher productivity requirements and many moving parts.
Komatsu’s Smart Quarry Site brings site and fleet management into the digital era and away from the eye of the beholder.
Smart Quarry Site (SQS), formerly iSite, was rebranded late last year, but as Komatsu technology consultant Mark Boyes told Quarry, its impact remains significant.
“We wanted to make it more targeted towards the quarrying sector, and the reception itself has been quite good,” he said.
“For existing Smart Quarry Site customers,
allows operators and site managers to see immediately what is happening around the site.
The platform delivers real-time insights into key areas that underpin a quarry’s performance so managers can make informed decisions. Komatsu designed the platform to analyse site management, optimise production, monitor machine health, enable proactive management, and deliver enhanced safety around the worksite.
The Smart Quarry Site platform provides these insights on a dashboard using animated visualisations and can track the performance of any brand’s trucks, loaders, excavators, graders, or dozers.
Boyes told Quarry that the Smart Quarry Platform was a modern approach to quarry management for site managers, supervisors,
they may have been making decisions based on gut feel rather than analytical data,” he said.
“Some people may have found it challenging previously to decide what to do with this information, but Smart Quarry Site can take that data and turn it into something easily accessible and user-friendly.”
Using the platform, managers and supervisors can track key performance indicators across the entire quarry fleet.
The Smart Quarry Site can be set up to provide updates on payload, fuel consumption, and a machine’s uptime, enabling leaders to assess a quarry’s efficiency and productivity quickly.
The platform benefits machine operators. Each driver can access the system via their log-in to see site information immediately. The operator cabin screen displays real-time information about the machine’s current payload, material type, and destination.
This can be shared between operators to make use of cycle times across the site. Operators can also register customised or general pre-start checks on the Smart Quarry Site. These are stored on the platform and accessible when required.
Boyes said Komatsu had worked with the quarry to transition from old-school methods to the SQS platform, they had found benefits.
burn with an additive, for example. They know
additive using data analytics,” Boyes said.
“Other customers haven’t had an effective way to manage the utilisation of their plant, but we can track the utilisation on their cycle and measure working time versus idling time to give them that picture.
“It can be either very basic, or we can get very specific depending on what the customer needs.”
Komatsu staff visit the quarry site before deploying the SQS program to identify the key areas the program should address.
The Komatsu Training Academy then teaches operators, managers, and supervisors how to use the Smart Quarry Site.
“We hone down, target, and then eliminate the pain points depending on what the customer needs and then help them move into the digital form,” he said.
“When you invest in SQS, you get the backing of a full training program that explains how the program works and how to best use it for your business.”
Boyes said most customers achieved their primary savings through payload management using data from the Smart Quarry Site.
However, the platform can help quarries achieve auxiliary savings.
According to Komatsu, these savings include the smaller factors that are still key to a quarry’s day-to-day operations. Boyes uses the example of recording pre-starts on a paper copy.
The quarry could save not only the cost of paper but also printing costs and the need for a room to store it.
“When you factor in all those costs when you go to a digital solution, there are a lot of auxiliary savings you can get,” Boyes said.
While Smart Quarry Site might be the new name for Komatsu’s fleet and site management service, the OEM-agnostic tool
provides real-time benefits to quarries.
“We’ve kept hearing from customers that this has improved their visibility,” Boyes said.
“They had perceived visibility by having an experienced supervisor watch from the top of a quarry with his knowledge, but this tool gives them complete visibility.
“With Smart Quarry Site, they have access to analytical data, but they’re getting it in such a way that it is easy to use.”• For more information, visit komatsu.com.au
Steve Franklin, founder of Eltirus, attended the AGG1 Academy & Expo in Nashville, Tennessee. He reports what he found at a key event for the North American aggregates industry.
Co-hosted with the World of Asphalt, the AGG1 Aggregates Academy & Expo witnessed a recordbreaking attendance.
More than 15,800 industry professionals participated in the three-day event, marking a significant 38 per cent increase from the previous record of 11,400 attendees in 2022. This surge in attendance underscores the event’s growing importance and influence within the aggregates and asphalt industries.
The show not only set new records in attendance but also expanded its reach in terms of educational sessions and exhibitors, offering more than 120 educational sessions and featured over 400 exhibitors across 18,000 square meters of place with attendees from all over the world, including as far as Australia, New Zealand, the UK, and Europe to engage with the latest innovations, technology, and education in the field.
The exhibitor area was well represented by equipment manufacturers and equipment.
In terms of aggregate equipment suppliers, all the companies that you would expect to be there were – Caterpillar, Epiroc, Develon, HD Hyundai, John Deer, Komatsu, Liebherr, Sandvik, Volvo, and more.
On the technology side, I saw Carlson, Inform, Loadrite, Price Bee, Topcon (to name but a few).
I also ran into a range of people from companies that I know who were not exhibiting, but nevertheless there catching up with customers and prospects.
I was much disappointed to see very little in terms of this type of technology. The only notable machine was a small electric wheel loader. The big news in the North American market in terms of autonomous operation is of course the Luck Stone Caterpillar trial at their Bull Run quarry, however I didn’t hear any discussion of this at the show.
Monitoring of environmental performance can be a pretty time-consuming affair when done manually. I have often thought there should be an easier way of doing things and I saw just that at AGG1.
Sauls Seismic provides a fully managed service that provides, installs, and manages IoT sensors that measure ground vibration, rainfall, water flow and water level, pH, dissolved oxygen, turbidity, conductivity, weather and dust deposition.
I have never seen a company that has all the environmental sensors that a site might need, installs, and maintains them and provides access to the data in a consistent format through a public API. Is there such a service in Australia – if so, please let me know.
Using drones for stockpile management is a big step up from manual measurement in terms of accuracy.
However, I am sure that you will also know that the approach can result in variable outcomes at time.
All it takes is someone to start changing densities, mis-pick the material type, alter the elevation of a stockpile base or boundary for
you to see big swings in tonnages. In short, it is a good approach, but not an infallible one. Enter Stockpile Reports (SR). Famous for their app that allows you to measure a stockpile using your iPhone (and more recently using the new Apple Vision Pro
VR goggles), they also offer an enterprise inventory management service. So, what do I mean by inventory management service and how is this different to the way that we are used to measuring stockpiles with say Propeller or DroneDeploy?
Stockpile Reports is the only automated, controlled, and scalable third-party solution for managing bulk materials inventory that provides third-party verification and stockpile measurement accuracy scoring. Whether the imagery is captured with planes, drones,
phones, or installed cameras, their patented technology ensures precision with reports that auto-correct obstructions, provide an objective surface score, and measure confidence in toe and base calculations.
The thing that really makes it stand out is the fact that your stockpile volumes are verified, and SR stand behind the numbers.
They also provide API access to the data and sensors that can provide real time analysis of stockpile volumes using fixed cameras that help identify potential stockouts. It is amazing technology.
I think we can all agree that keeping quarry production and sales teams can sometimes get out of sync, with less than desirable outcomes.
Plant Demand aims to help alleviate this problem by putting in place a system that helps to keep everyone on the same page by helping to improve stock level visibility and reduce potential stock-outs. Increasingly common in North America, I think it has the opportunity to help businesses in our region too.
Whether you deliver ready-mix concrete, cement, aggregates, asphalt, or any other building materials, effective transport
planning can mean the make a big difference to the bottom line. Inform, a German company provides a remarkable AI based system that claims to increase truck fleet performance up to 30 per cent by calculating an optimised delivery schedule and fleet configuration for the next day based on service levels.
I am sure that to anyone who runs a fleet of trucks, 30 per cent improvement sounds like a big number. With this in mind, I was looking to talk to people at the show who had experience of Inform and could validate the sort of improvement that they are promoting.
One former managing director of a European aggregates operation who had experience of the system confirmed that they had indeed seen improvements on the order of 25-30 per cent in fleet productivity through the use of Inform and that its approach to fleet sizing or redistribution, truck right-sizing, fleet size/mix, haulage contracts made a profound difference to how they ran their fleet.
Price Bee was very kind in allowing us to co-show with them at AGG1. I was amazed by the interest their product generated at the show, with many, many people stopping by to see their integrated quoting and pricing system for aggregates, concrete and asphalt.
Having seen the system from its inception many years ago, it was very interesting to get a deep dive into the software and how it can help providers. Even more so was to see the progress they have made into the North American market with a number of bigname customers.
If you haven’t seen Price Bee, it provides a fast, effective way to quote aggregates, concrete and asphalt (if you are using Excel for quotes, you must see this), but it also integrates pricing optimisation into the quote to ensure that different customers are charged the right pricing tiers and works to help you maximise price across the board.
Last but not least, great to see a home-grown technology solution at the show – Komatsu’s Smart Quarry Site system which was well represented and created a lot of interest.
Probably the most noticeable trend at AGG1 this year was the focus on digital transformation. The vast majority of producers I spoke to have an accelerated interest in this area and were working on projects to change how they did business. •
If you would like to know more, you can contact the author at steve.franklin@eltirus.com
In addition to XCMG Lubricants, as an Authorised Shell Lubricants Reseller we offer a comprehensive range of Shell Lubricants and will assist in selecting the right lubricants for your equipment needs.
SShheellll LLuubbrriiccaannttss AAuutthhoorriisseedd RReesseelllleerrWhen mobility and toughness matter, count on the Lippmann 300c and 400c. These mobile cone crusher plants were specifically designed to take on the most abrasive and toughest materials in aggregates and mining — all with mobile capabilities. Heavy duty cone crushers with an innovative material flow that maximizes capacity and throughput while delivering a consistently high quality product.
E: sales@triconequipment.com.au www.triconequipment.com.au
Effective and efficient.
The MDS M515 Heavy Duty Trommel excels at crafting rip rap and reclaiming rocks entangled with clay and other adhesive materials. Comes complete with fold out stockpiling conveyors and has four hydraulic jacking legs to raise the machine to increase stockpile capacities and lower for transportation. See triconequipment.com.au or call 1300 859 885
Superior’s Telestacker® Conveyor is a material handler’s most effective weapon against costly stockpile segregation. Its variable height, length, and axle positions allow for layered stockpile construction, which is key to achieving partially and fully desegregated piles. The design has been carefully fine-tuned for hard work and dependability in numerous applications.
Call Tricon on 1300 859 885 or see triconequipment.com.au
Italian company Bonfiglioli is providing quarries with simple, sustainable and reliable gearboxes.
It’s no surprise to learn the Australian quarrying industry is in the middle of a skills shortage. According to Jobs and Skills Australia, the country has a national shortage of key professions across the entire resources sector.
Part of this is due to an increasingly challenging and competitive labour market.
The Organisation for Economic Co-operation and Development found in 2022 that labour markets had globally tightened across all countries and sectors.
Martin Broglia, managing director at Bonfiglioli Australia, told Quarry the shortage of labour is prompting organisations to improve their equipment maintenance and plant performance.
“Customers are increasingly seeking out standardised, modular solutions that are easily customised, installed and maintained, and which offer a long service life,” he said.
What helps set the company’s gearboxes apart is their unique design offering.
The company can provide a hybrid helical bevel and planetary gearboxes as a combination unit.
Suitable for any heavy-duty applications that requires slow, controlled movements, the combination unit can provide the best of both worlds while having a significantly reduced weight, lead time and cost. This provides an economical and lightweight solution, providing the same power output as two separate devices.
Another part of the company’s focus on simple designs is ensuring they are longlasting with low maintenance requirements. This not only helps to keep the total cost of ownership down, but it also reduces the amount of time required on intensive servicing and repairs.
Broglia said Bonfiglioli’s collaboration with
“For example, our solutions for mining applications are designed to be extremely resilient, ensuring high performance in harsh environments where extreme temperatures, sandstorms, humidity and salty air are commonplace,” he said.
branches, distributors, and service companies,
customers, ensuring they achieve optimal productivity, uptime and profitability,” he said.
Sustainability is also important to the company, which has adopted a new mindset at the highest level. The industrial headquarters in Italy – called EVO – meets the latest in energy efficiency standards. Last year, it was awarded ISO 50001:2018 certification for its energy management system.
The company has also designed its headquarters be a nearly zero energy building. It features geothermal heat pumps and radiant ceilings to save energy, as well as a green garden to promotes natural ventilation of the building. To make the best use of natural light, the roof of the building is slanted to enlarge the north-facing side of the building, while the roof and south-facing façade are cladded in a customised, pleated aluminium mesh inspired by Bonfiglioli gears.
Broglia said the company continues to develop new products with a special focus on energy efficiency, recovery, as well as lower
fuel consumption and emissions reduction.
“In the wind turbine industry – a sector that’s crucial to the renewable energy industry - we are a global leader, with market share of over 30 per cent,” he said.
“The gearbox systems we deliver to local industries offer exceptional power and torque, compactness, are easily customised and robust. With low maintenance requirements, these offer a low cost of ownership. We also offer a wide range of gearbox customisation options and accessories, to meet a diverse range of application requirements.”
Bonfiglioli’s gearboxes have proven to be popular throughout the quarrying sector, with the company’s HD solutions in high demand.
This high demand has led to local investment into the company’s local manufacturing capabilities. Bonfiglioli opened a new warehouse in Melbourne last year as part of its aim to decentralise its operations in Australia. The new facility spans
1800 square metres and generates 40 kW of solar power. It is currently producing several gearbox ranges, with plans to expand further.
The company’s Sydney assembly plant had, until recently, processed several gearboxes each week. Broglia said the company plans to expand its Sydney facility with a new HD assembly machine from the group’s headquarters in Italy, allowing it to almost double production.
“Our New Zealand branch is also planning a relocation to larger facilities, which will facilitate greater stock holding, faster delivery, etc. This is in response to market growth in the region,” he said.
“We plan to grow our market share locally, through the consistent supply of top-quality products, coupled with expertise, extensive local stock holding, as well as prompt service and support. The expansion of the Sydney and New Zealand facilities will facilitate this.” •
SSAB expandable bolts have a new name but the same quality. Quarry learns how the resources industry around the world has put them to good use.
Heavy industries rely on quality equipment, not only to keep the job done, but also to keep workers safe.
SSAB developed its Virsbolt, previously known as the ERB, to ensure workers in these industries can reinforce the rock roof, especially when mining or drilling into rocks.
Cimertex executive director Álvaro Bastos told Quarry he saw the quality of the product to be “unmatched” on the market.
“Our SSAB Virsbolt bolts are by far the market leaders because of quality and logistics,” he said.
“When our customers source the bolts, they also expect a high level of local service, and we have a structure to provide that.
“The support from SSAB is world-class, from quality and traceability to sales management.”
The Virsbolt’s fundamental feature is speed.
SSAB designed the bolt to be installed and expanded as soon as the hole is drilled and water from a high-pressure pump is applied.
When the rock is expanded, it squeezes against the rock and is secured. It may seem small, but this easy install-and-expansion process saves operators from waiting for grout or resin to set or working with dangerous chemicals.
The process is conducted in four stages. The operator drills the necessary hole and the bolt is inserted before the pressure pump is attached to expand the pipe. Finally, the pressure pump is removed, and the bolt is secured in the rock.
The bolt forms a mechanical interlock between the borehole wall and the bolt over the full bolt length. When the SSAB Virsbolt is inflated, it also contracts in the bolt length, effectively tensioning the bolt’s face plate against the rock surface.
The rock bolts are designed to accommodate large rock movements and maintain their high load-bearing capacity.
SSAB Virsbolt is suitable for both manual and mechanised installation.
The Virsbolt, made from pure steel, does not impact the natural environment
negatively and is not disrupted by drill vibrations.
The Neves-Corvo underground copper-zinc mine in Portugal, operated by Somincor, has used Virsbolts for years. The mine processes around 2.6 million tonnes per year, which means its products need to withstand high drilling loads.
The company has employed the use of SSAB’s Virsbolt across its mining operations due to its installation process, which
requirements,” Somincor, head of rock mechanics Rodolfo Machado, told Quarry.
“The fact that the industry is moving in a sustainable direction also speaks strongly for this technology.”
In the Neves-Corvo underground mine, the SSAB Virsbolt serves as key support in the production phases. The Virsbolts work in challenging terrain containing sulphide.
our safety standards and the fact that we do not feel the necessity of change because operational and performance issues prove that this support has been fulfilling our operational
The Virsbolt can handle arduous conditions because SSAB manufactures the bolts with high-quality Nordic steel and an extensive testing regime. This ensures the Virsbolt can handle the rigours of heavy industries, including quarrying and mining.
The bolts are guaranteed to a minimum breaking load and undergo eddy current nondestructive testing, as well as inflation and flattening tests, before being sold.
Dragon Mining, which operates the Jokisivu gold mine in Finland, attests to its structural quality. The company has used the Virsbolt at depths of 645m for rock roof support.
“We prefer inflatable bolts instead of splitset bolts due to split set’s availability issues in the Nordic region,” Jokisivu mine manager Timo Ridaskoski said.
“It’s also easier to run one bolting system rather than two. We can get the bolts directly from SSAB in Sweden, which secures our supply of bolts.” •
For more information, visit ssab.com
for Aust ralia, Papua N ew Guine a and South East Asia
The New IMS-BP1200-48TB Track Blender, with four five-meter-long feed hoppers holding 12m3 each with separate feed hopper conveyors with attached belt scales and fully automate with a PLC control and recording system that can be operated with an iPad from a loader or site office. Powered by a Cat C7 Generator that can be connected to mains power, driving Nord Electric motors with variable speed and feed hooper stop/start sensors with remote. The genset can also drive a 24-meter radial conveyor. The BP1200-48TB can produce up to 1000 tonnes per hour.
IMS have added the new BP1200-48TB track electric twin power blender to its impressive collection of blenders and pugmills, the new BP1200-48TB has four separate feed hopper each five meters long holding 12m3 each. All feed hopper conveyors are fitted with belt scales and controlled by a PLC control and recording system that can be operated from an iPad or phone from its own Wi-Fi system from a loader or site office. A Cat C7 Generator powers the Nord electric motors all fitted with invertors offering variable speed to each feed hopper conveyor. The generator can be connected to mains power and could power an extra 24-meter radial stacker increasing the stockpile capacity.
A new IMS-PM1200-20TB Track Pugmill with twin 10m3 feed hoppers has just commissioned to Braeside Quarry on the New England Highway Warrick in Qld, the options the PM1200-20TB offered Braeside improved product management with the twin feed hoppers blending fines into roadbase to make spec or having two different products available ready for moisture control and CTB. The PLC control and recording system can be operated from an iPad in a loader managing all aspects of the operation including loading trucks and multiple trailers stopping when the required weight has been reached for each unit and recording the ID number of each load.
The BP1200-48TB can also work in conjunction with the IMS modular electric pugmill on skids producing up to 500 TPH of water or powder blended material and stockpiled with an IMS 24-meter radial conveyor with auto radial return.
IMS – PM1200-20TB Track Pugmill with two separate five-meter-long feed hoppers holding 10m3 each which can be extended to 12m3, the feed hoppers have the option of fitting vibrating hydraulic tipping grids. Both feed hoppers have front of hopper adjustable flow gates, variable speed, and belt scales with the option of being fully automated. There is the option of adding two powder hoppers and two liquids.
Kinder Australia is helping quarries keep dust down while protecting material from the elements with its K-AllShelter Capotex covers.
Quarries can be a harsh and unrelating place for conveyors and the material they move.
Being exposed to the Australian elements can invite disaster. Rain adds more complications to the mix, as adding water to quarried material can quickly alter the consistency and lead to screen blinding, clogging, chute hangups and blockage. Heat and humidity can interfere with material quality and flow, while the sun’s harsh ultraviolet rays can shorten the belt life.
Strong winds can blow material off the belt, and in some cases, even flip the belting entirely. This also has the added problem of creating dust emissions.
Peter Laskey, a Kinder Australia field application specialist, told Quarry that dust prevention is becoming even more important in the sector.
“We are seeing quarries around the country looking to minimise dust as much as they can,” he said.
“Regulations are strict and it’s important to ensure the safety of the nearby workforce.”
Baffles were previously used, but this solution was not enough to combat excessive dust emissions during normal production.
Laskey said the K-AllShelter Capotex conveyor cover was the proven, cost-effective dust suppression solution.
“The K-Shelter Capotex conveyor cover was chosen for its lightweight, high strength and easy to install features. The covers feature a dust-tight seal that prevents dust from escaping and causing problems on site.
“Future conveyor maintenance is made simple and hassle free due to the conveyor
covers being hinged on both sides and due to the Caposafe Service Prop. The prop holds the cover and lets the maintenance team get access easily.”
K-AllShelter conveyor belt covers are manufactured using a wide range of optional materials and engineered as a waterproof, durable barrier. They can be custom made to suit all belt widths and models.
They help to provide durable protection from extreme environmental elements and help to control moisture levels of conveyed materials. Covering the conveyor is also beneficial to operators, improving safety by covering the moving parts.
One Victorian Quarry reached out to Kinder Australia to rectify its onsite dust issues. The site had recently improved one of its transfer points to deal with dust that had been building up.
However, following the transfer point upgrade, dust was being redirected to a different point of the conveyor system. Two vertical shaft impactors were frequently creating excessive dust emissions, particularly around the front of the transfer site, during the start up and production phase.
K-ALLSHELTER
• Cost effective
• Self-supporting (no support structure required)
• Accessible from both sides of the conveyor
• No sharp edges
• Build-in inspection points available
• Site specific wind load report available to confirm compliance to Australian Standard
Laskey said the dust emissions were eliminated following the installation of the covers, as the dust would settle onto the belt instead of becoming airborne.
“The customer was very happy – they saw how well it contained dust and decided to continue it to the head pulley. Once they saw how effective it was, they decided to go for the whole length of the conveyor,” he said.
“This is a classic example of how Kinder Australia works to find the right solution for a site. Our team looked at one part of the system, got that right, then moved to another. It’s not about isolating the symptom – we want to rectify the problem itself.
“We’re a solutions-based company with a large engineering base. Kinder is always working on new ways of solving problems that work best for each site.” • For more information, visit kinder.com.au
BULK2024 plans to highlight the mining industry. Quarry learns how the resources sector can benefit.
As Australia grows, its demand for minerals grows too. The country’s metals are needed to create vital infrastructure, manufacturing, and for export. Changes to technology are also having a major impact on mining and mining methods.
The Minerals Council of Australia claims that by 2030, to meet the world’s demand for storage alone will require 50 new lithium mines, 60 new nickel mines and 17 new cobalt mines.
The council also expects mining investment is expected to increase by US$100 billion annually from current levels to produce the mineral commodities required for the world to achieve net-zero emissions by 2050.
It’s an important time for the industry, bringing about new challenges and lessons to be learned.
For this reason, the resources industry will play a major role at the upcoming Australian Bulk Handling Expo (BULK2024).
Located at the Melbourne Exhibition and Convention Centre, the event aims to help spread industrial knowledge, showcase the latest technologies and innovations, and provide an opportunity to network with likeminded peers.
BULK2024 show director Lauren Chartres said that while the event will bring all producers of bulk commodities together, there will be a special focus on how other sectors can learn from the resources industry.
“There is so much happening in the mining industry, and the scale of the technology that is used creates engineering challenges and solutions that could help other industries,” she said.
“The quarrying sector, in particular, shares a lot of technologies and types of equipment with the mining industry.
“Tapping into that wealth of knowledge and expertise can help businesses find an edge.”
BULK2024 is aimed at bulk commodity producers who are looking to run their businesses more efficiently and keep one step ahead of the competition.
To ensure they can do that, the latest in equipment will be on display, including conveyors, silos, motors and drives, belt scrapers, container tipplers, dust control systems, and weighing or level measuring products.
“The mining industry is also embracing innovative new technology. Industry 4.0, automation, and artificial intelligence have
the potential to radically change the way businesses operate,” Chartres said.
Attendees will have the chance to connect with industry leaders and innovators on the show floor and at various networking opportunities at the show.
It will also offer the opportunity to meet with new clients, learn about new markets and connect with customers you might never have met elsewhere.
The expo will be held in conjunction with one of Australia’s biggest transport, logistics and supply chain events, MEGATRANS2020.
The two events will be hosted over 30,000 square metres at the Melbourne Convention and Exhibition Centre, with one ticket entry for access to both exhibitions.
“We’re inviting everyone to be a part of this game-changing expo – from hands-on decision makers in the bulk handling industry to CEOs, COOs, regulatory bodies, and government at all levels,” Chartres said.
“We’ve seen how impactful bringing the industry together was at BULK2022 and are excited to see the industry continue to grow.” •
BULK2024 will take place at the Melbourne Convention and Exhibition Centre from 18 – 19 September, 2024.
The 2024 IQA Awards will be presented in the following categories:
Alec Northover Award
Gold Hard Hat Site Safety Award
Gold Environment Award
Excellence in Innovation and Community Engagement
Quarry Manager of the Year <10 FTE
Quarry Manager of the Year >10 FTE
Quarry Operator of the Year
IQA Conference Exhibitor of the Year
President’s Medal
Sponsored by AIQEF
Sponsored by IQA
Sponsored by Groundwork Plus
Sponsored by Elitrus
Sponsor to be announced
Sponsor to be announced
Sponsor to be announced
Sponsor to be announced
Sponsor to be announced
CJD Equipment recently sold Hutchison Quarries three Volvo machines. Quarry finds out how the new equipment has benefited the business.
Hutchison Quarries was established in July 2004 as a local business by the Hutchison Family. Initially catering to the needs of the Warwick Shire Council and select private contractors, the quarry steadily expanded its operations over the years. Today, it is a crucial supplier for significant corporations involved in landscaping, road construction, concrete production, and building projects.
Hutchison Quarries became part of the COLAS Australia Group in 2022. This union integrates the quarry into a more extensive network and has propelled it to prominence in the Darling Downs region.
Evan Boone, the COLAS’s Group Manager for Quarries and Aggregate Supply, oversees the Hutchison Quarries business, as well playing a pivotal role as the representative for the Asia Pacific region within COLAS Group’s global operations. Within Asia Pacific, the group operates quarries in Queensland,
Victoria, and Tasmania, alongside additional operations in New Caledonia and Korea. With approximately 470 quarries worldwide, COLAS Group is a premier entity in constructing and maintaining transport infrastructure globally.
“Hutchison Quarries has a strong DNA of quality and performance. It’s a DNA of how it’s run and how the Hutchison families expected the place to run,” Boone said.
“We’re trying to maintain that and only add good things, not take away things.”
Hutchison Quarries has recently purchased two Volvo A45G articulated haulers and a Volvo L260H wheel loader from CJD Equipment.
“Our decision to opt for Volvo machinery was a straightforward one,” Boone said.
“As part of the COLAS group, there’s a preference for sourcing equipment collectively,
and Volvo has consistently been their supplier of choice.”
“While we have the flexibility to choose other suppliers. What drew us to Volvo was primarily the exceptional operator comfort and impressive fuel efficiency.”
“Fuel efficiency is a paramount consideration for us. Volvo has built a strong reputation for reliability and durability, which translates into equipment that not only endures but also holds its value well over time.”
“And considering that our operators spend extended hours in these machines, providing a comfortable working environment is essential for retaining top talent. Investing in Volvo machinery aligns with our commitment to fostering a productive and satisfying workplace.”
Boone and the Hutchison Quarries team have spent a lot of time on equipment replacement and midlife rebuilds, ensuring optimal efficiency for their quarry operations.
The recent addition of this new machinery marks a significant step in upgrading its fleet, guaranteeing the presence of reliable, safe, comfortable, and highly efficient machinery.
“The versatility of the new L260H, being in a quarry means it will do everything a bit, including tasks such as loading road trucks, stockpile management, and facilitating the loading of our pug mill for road base production and pre-coated material preparation,” Boone said.
Hutchison Quarries’ commitment to operator training underscores its dedication to safety and efficiency. Partnering with CJD Equipment for training sessions facilitated by knowledgeable CJD staff like Product Demonstrator Sheridan O’Reilly demonstrates Hutchison Quarries’ proactive approach to maximising equipment performance and ensuring workforce competency.
“Our Hutchison Quarries staff did some operator training with CJD Equipment in January,” Boone said. “CJD Equipment staff member Sheridan, he’s an enthusiastic guy; he’s great.”
“The training has been quite good, and the fact that we can also ask Sheridan to come in and do some efficiency training and some other things more than just the basic ‘this is how you operate it’ and there you go, I think, is actually probably better than I’ve seen anyone else do it.”
In an era of environmental consciousness, sustainability is no longer an option—it’s a necessity. Hutchison Quarries, as part of the broader COLAS Group, recognises this and has embarked on a journey towards a more sustainable future. At the heart of this endeavour lies the ambitious 30 by 30 initiative, a commitment shared across the COLAS Group, including its regional entities such as COLAS Australia Group, under which Hutchison Quarries operates. This initiative, which originated at the international level, sets forth a collective target to reduce fuel consumption and emissions by 30 per cent by 2030, leveraging 2019 carbon emission figures as the baseline. It represents a concerted effort undertaken by the entire COLAS network, encompassing diverse approaches tailored to the specific challenges and opportunities within each operational domain.
The reality is that we have very limited ways to change fuel efficiency,” Boone said. “But the biggest way we initially can change it is to
buy fuel-efficient equipment and make sure we train our operators to use that equipment in a way that is fuel-efficient.”
“We’ve obviously just got our new L260H wheel loader earlier this year. So certainly, movements in that direction are going to be very important, and I think we’ll see more of that in the future.
“By replacing two older loaders with the Volvo L260H, we’ve downsized our fleet from four to three, opting for a slightly larger
model. I’m particularly impressed by the size of the bucket on the L260H, as it reduces the number of passes needed to load a truck, making the loading cycle quicker. It certainly helps with the quarry’s efficiency.”
Looking ahead, Hutchison Quarries remains poised for growth and innovation. Boone said COLAS will continue efforts to lead the industry towards a more sustainable future. •
For more information, visit cjd.com.au
Superior Industries explains how performing regular maintenance can support a quarry’s operations.
There is a saying that the catalogue might sell the first product, but support sells the ones after.
This is why Superior Industries invests in workers like sales engineer Joe Gibson to help provide maintenance training.
For Gibson, it is as much about product support as it is about supporting the next generation of operators.
“What we’re seeing around the world is a changeover in the labour force, so we have a lot of older people retiring out of the labour force and a lot of newer young people transitioning into it,” he said.
“And with that, a lot of the technical information, things like how to train a belt and set-up cleaners isn’t being transferred well at the end-user level.
“We’ve been setting up training seminars and I’ll talk to them about belt cleaning, setting up a load point, things like that or go out into the field and talk next to their equipment.
“At Superior, we’re working to fill in those knowledge gaps at different locations.”
After starting as an engineer, Gibson has worked in and around the industry for 30
years. He has seen many approaches to maintenance, and has found a clear standout at Superior.
“I think that Superior really stands above everyone else on that aspect,” he said.
“We have all kinds of educational material, charts and graphs, and videos available to anyone to do their own in-house training as they see fit.”
Superior Industries sales engineers can offer customers a wide range of support for their machine maintenance needs.
The company trains its staff and customers to conduct conveyor site surveys to optimise their machines. One of the biggest mistakes Gibson sees is operators setting up their belt tracking incorrectly.
Some operators tend to steer the belt with the tail pulley instead of the idlers, which can damage the belt, the pulley, and the bearings.
“They don’t often realise they are doing it the wrong way until you explain why it should be done the way it should be done,” he said.
“Screw take-ups are designed to put tension in the belt, not steer the belt.
“They can tend to think it is the easiest and best way but in fact they’re doing more damage to their system in the long run,” Gibson said.
Customers can see rolling components and the downstream effects of issues in their setup by performing a site survey and inspecting their machinery, like a conveyor set-up.
Superior Industries recommends using a site survey to assess any concerns across the three main areas of a conveyor: the tail and load zone, main flight, and discharge chute.
Conveyor maintenance is key to optimising the conveyor set-up.
“A big part of what I try to impress on them is to find the root cause of the problem,” Gibson said.
“Whether that is belt damage, carryback, spillage, or refuge material … if it is belt damage, only a certain number of things can contact the belt and damage it.”
“The conveyor is a very big piece of equipment, and all the parts affect one another. It is best to go out and look for the problem … it is about trying to cure the disease rather than treat the symptom.”
It is important to check the tail and load zone for signs of dust liberation, spillage, and carryback. This zone also contains key conveyor parts, including the tail pulley and bearings and the skirting.
Surveying this area also enables customers to check the loading conditions, load support, dust containment, and the belt tracking and condition of the conveyor. The main flight encompasses the idlers, main structure, midstream pulley, and the mid-drive.
Inspecting the discharge area enables customers to monitor the head pulley and drive unit containing the gearbox and motor.
They can also monitor the discharge chute, snub pulley, and structure for any impact damage.
Gibson said Superior Industries can advise customers about what to do based on what they see in their site surveys.
“Look for the end result of the problem and then trace that back to what the possible causes could be,” Gibson said.
Gibson said any operator, from newcomers to industry veterans, could benefit from investing in maintenance.
“Sometimes you need a quick fix to get through to the end of the shift, but it is always good to have a plan in place to fix the root cause of the problem when they have time to do it.” •
For more information, visit superior-ind.com
Our innovative mining portfolio - developed over more than 60 years, in collaboration with leading industry partners includes solutions for conveying, bulk materials handling, crushing, grinding, slurry processes and more
www.bonfiglioli.com/australia/en www.bonfiglioli.com/new-zealand/en
From new mines to critical minerals, the Papua New Guinea resources sector is thriving with potential.
The 2024 PNG Industrial and Mining Resources Exhibition and Conference (PNG Expo) will be the premier event for industry professionals to discuss the latest developments in the Pacific nation.
Quarry takes a look at the top talking points.
With its vast reserves of copper, cobalt, nickel and mineral sands, PNG is well-placed to help provide the critical minerals necessary for the world’s transition to net-zero.
Mayur Resources has been working to get its lime and mineral sands project up and running to help strengthen supply.
The company’s Central Lime Project is located along Papua New Guinea the coast near Port Moresby and was recently bolstered by a $9.4 million funding commitment.
“This capital injection is a vote of confidence in our ability to deliver high-value, sustainable projects,” Mayur managing director Paul Mulder said.
“It enables us to continue progressing the early development works at our Central Lime Project, setting a solid foundation for the commencement of construction.”
Mayur is aiming for the Central Lime Project to become Asia-Pacific’s first carbon-neutral cement and lime producer.
It’s this sort of innovative planning that will
be on show at the PNG Expo in Port Moresby from July 3–4.
“PNG Expo will be the platform to engage and drive transformative changes towards a sustainable future,” show director Lauren Chartres said.
“Our mission is to equip the industry with the right tools.”
The name Ok Tedi Mining (OTML) often goes hand-in-hand with education, training and apprenticeship opportunities in Papua New Guinea.
The first three months of 2024 have seen OTML deliver over $121,000 in scholarships to university students, welcome 22 new apprentices, and pledge to donate vehicles and an analytical chemistry laboratory facility at PNG University of Technology.
The scholarshipshave seen 10 third-year university students supported with full tuition and boarding for the year, as well as a book allowance and stipend, travel assistance, industrial training and an automatic offer into the two-year graduate development program upon completion of studies.
“The program aims to assist university undergraduate students with school fees and other associated costs while ensuring OTML maintains an industry-institution relationship with respective universities that provide
graduates into its training programs and workforce,” OTML said.
Elsewhere in the resources sector, Kumul Petroleum’s training entity Kumul Petroleum Academy is building a new facility to expand its coaching and employment capabilities.
“We are passionate about investing in programs and projects that will upskill and develop our young Papua New Guineans so that they are ready for the projects that are coming online now,” Kumul Petroleum managing director Wapu Sonk said.
The Kumul Petroleum Academy is expected to open within two years and will have the capacity to train 350–400 trainees.
The restart of the Porgera gold mine has been in the news a lot recently, and for good reason.
The Porgera mine, owned by Barrick Gold, is located in the Enga Province of Papua New Guinea, about 600km north-west of the capital of Port Moresby.
The Papua New Guinea Government backed the restart throughout 2023 and the mine was able to pour first gold in February 2024, with Prime Minister James Marape on hand to witness the milestone.
“Today marks a significant moment where we are witnessing New Porgera Limited’s first gold pour and stamping of the first gold bar,” Marape said at the time.
“This first gold pour is the outcome of the [Papua New Guinea] Government, New Porgera Limited, Enga Provincial
Government, and mine-affected communities working together. This is teamwork.”
Enga landowners, the Enga Provincial
Government and the state will receive a combined equity share of 51 per cent from Porgera. A three per cent royalty has also been included for landowners, a step up from the previous five per cent.
In the energy sector, the PNG LNG project is ramping up, with Santos selling its five per cent stake to Kumul Petroleum.
The $US19 billion liquified natural gas project is an integrated development that includes gas production and processing facilities that extend from the Hela, Southern Highlands, Western and Gulf provinces to Port Moresby in Central Province.
As Papua New Guinea’s national oil and gas company, Kumul is already an existing partner in the PNG LNG project.
These key projects, and much more, will be among the top discussion points at the 2024 PNG Expo, the safest and strongest place to network, share ideas and learn more about what companies are doing in these spaces. •
Book your ticket today through the PNG Expo website.
MLT Group has devised the Super-Screw for heavy-duty conveyor rubber belt splicing and joining to address a common pain point for customers.
Three French coal mine engineers came together in 1945 and decided there was no “optimal way” to repair conveyor belts available to them.
They began creating quick-join solutions to solve the issue.
More than 75 years later, in this seminal moment in the company’s history, MLT Group has created the market’s only SuperScrew splice join to provide operators with optimal solutions.
MLT’s Super-Screw is designed for conveyor belt specifications and setup with cleaners and scrapers installed along conveyors.
This permanent solution is available in various specifications to suit most conveyor belts in quarry and mining applications.
in very high abrasion-resistant with premium hard-wearing polyurethane material, in stainless steel for metal detectors or corrosive environments, in FRAS to ISO 340 & ISO 284 standards, in heat resistant/retardant up to 200˚Celsius and for low temperature down to -30˚Celsius.
The MLT Super-Screw steel screws and inserts are of high tensile with great mechanical resistance and are the ideal choice for quarries and cement plants.
MLT has designed and manufactured the Super-Screw to use high tensile screws and inserts to make it easier to install when compared with competitor products.
“Our solution is a permanent solution, some people may think it is a temporary solution, but it is not, because of the Super-
“The high tensile screws and inserts themselves are specially designed; this has now been used for more than 30 years around the world and more than 15 years in Australia.”
On the New South Wales Central Coast, a coal-powered power station suffered from repeated emergency belt breakdowns on its feeder conveyors.
When the company approached MLT Group, it was clear that any worthwhile solution needed to be a permanent type, easy to install, quick, and without requiring additional templates or special toolings for on-site installation.
The MLT Super-Screw proved to be the ideal solution to get conveyor belts up and running again.
nickel mines as well as quarries. When conveyor belts break or are damaged, an effective, seamless solution is required.
This is why MLT’s Super-Screw are turning into popular options for site, maintenance managers, plant operators, and belt splicers across Australia.
The MLT Super-Screw allows belt splicers to repair and join belts, which only require cordless skivers and drill drivers to do the complete installation.
“The traditional way of joining conveyor rubber belts is by hot weld using a vulcanising press or cold join using glues and chemicals,” he said.
This process lets the rubber or fabric melt or bond into each other.
“Usually, that takes the whole day or more and requires a crew of six or eight people. “For a solution like the Super-Screw, you only need two to three people, and this can be done in a couple of hours with the conveyor belt up and running in no time.”
The company, which began in France more than 75 years ago, created its Super-Screw solution over three decades ago.
“We find that when customers are previously unaware of our products,
they become quite pleased with the time they save and the effectiveness and durability of the splice joins after installing our Super-Screw,” Oudomvilay said.
MLT opened its Australian subsidiary in 2008 before it became MLT Asia Pacific seven years later under the complete control of the MLT Group France.
Customers receive high-level support and technical advice. All MLT products are manufactured in France and come with certificates of authenticity to prove their quality.
Oudomvilay said customers can work with MLT Asia Pacific to create tailored solutions for their Australian applications and conditions.
“Once they use them, we hear positive things about the timesaving, effectiveness, and durability of the products,” he said.
“When you lack personnel, lack time for maintenance downtime, and are faced with production deadlines, this is one of the options you can consider as opposed to conventional methods. This is a quick and permanent solution.”
For more information, contact sales@mltlacing.com or call 02 9605 6555
•
•
OPS celebrated its 35th anniversary earlier this year. Quarry looks back at the successful partnership between the dealer and Astec Industries.
OPS was the toast of the town earlier this year when the brand notched up 35 years of business and counting in Bibra Lake, Western Australia.
The company, which began as a small parts distributor, has worked across the mining, screening, crushing, blockmaking, washing, construction and earthmoving industries since 1989.
A key part of the company’s success has been its partnership with Astec Industries, the international equipment manufacturer.
OPS became a Telestack Mobile Bulk Materials Handling dealer for Astec in 2014 and currently supports this product range Australia-wide.
“We’re happy with the performance and growth of OPS over the years, and that record has led to us giving them more areas, more products and more responsibility,” Astec business line manager for material solutions, Adam Gordon, told Quarry
“Through the partnership, both businesses have grown well. We’re strong individually but we’re stronger working together.
OPS hosted clients and partners at a
become one of Australia’s largest minerals processing and handling solutions providers.
Attendees ventured from many parts of the world to participate in the celebration and see the latest innovations and technology from OPS’s portfolio of original equipment manufacturers (OEMs).
The festivities also included comprehensive training seminars from the Astec team, including four sessions available to the general public and attendees across the two days.
Astec began in the United States in 1972, when Dr. Don Brock and four friends started a business that would use creative solutions to support the local construction industry.
What began as a small idea in Tennessee has become one of the largest OEMs of its kind. Since its founding more than five decades ago, Astec has acquired, grown, and developed 16 different business units.
Three years ago, Astec decided to bring all these units under the company banner as part of a global rebranding called OneAstec.
It saw previously subsidiary brands like JCI, KPI, BTI, Telsmith, Roadtec, Carlson, Osborn,
While the global presence was restructured, the company has always maintained a local hub in each region. Astec Australia also took over its dealer network as part of the change.
“It’s about giving customers greater access to innovative, high-quality equipment,” Astec Australia general manager David Smale told Quarry at the time.
“Ultimately, our goal is to design and build state-of-the-art equipment which makes it possible for our partners to supply their customers with industry-leading equipment producing great results and profitability.”
In the years since Astec Australia took over the dealer network, its OPS partnership, has grown.
“Under the centralised model, anything that happens within the region goes through the hub, as we call it,” Gordon said.
“The hub looks after all our dealers and representatives.
“OPS supplies Astec’s materials handling, rock breaking and fixed crushing and screening products for the majority of the Australian market. Then we have TURNCO as our dealer in New Zealand, and we sell Astec products directly in the Pacific Islands.
“As we’re establishing more dealers in some other parts of the Pacific Islands, they’ll come under our banner as well.”
The partnership with OPS is set to be bolstered further by the expansion of Astec’s manufacturing facility in Northern Ireland.
Initially, Astec commissioned a $5 million expansion of the Omagh site in 2022 before ordering a further increase to keep up with demand from its global customers.
The most recent extension, which opened In February, will increase Astec’s production capacity and enable greater global distribution through dealers like OPS.
Astec’s decision to increase capacity in Omagh frees up space in the company’s other manufacturing facilities around the world.
Demand for Astec equipment has been so strong, a second expansion was required.
“We built the original new factory, and 18 months later, we doubled its size, and 14 months after that, we doubled its total size again,” Gordon said.
Gordon said Astec was delighted to celebrate the 35th anniversary of OPS.
“We are proud to be associated with OPS. We work well together, and we’re looking forward to a great future and continued growth.”•
For more information, visit astecindustries.com
Quarry learns how Pinnacle Hire is helping the industry with
Water – while it’s essential for dust suppression and processing, if uncontrolled, it can grind productivity to a halt.
Pinnacle Hire offers a comprehensive suite of rental solutions to tackle any dewatering or dredging challenge a quarry could face. Recently, the company delivered advanced dewatering for a client in the Northern Territory.
Pinnacle Hire kept the customer’s quarry on schedule and productive by renting out highvolume 6” dewatering pumps, the SPP Q150 model, to ensure efficient pit dewatering.
The SPP Q150 offers a range of features ideal for quarry environments.
The rugged pump is built to last, housed on a two-wheel road trailer for easy transport and features a fully enclosed design for noise reduction and security. It can handle tough jobs, passing solids up to 65mm in diameter and 80mm long.
Double mechanical seals allow the pump to run dry and ensure extended life, while efficient “Smartprime”
technology optimises performance and saves on fuel.
Pinnacle Hire’s portfolio includes diesel and electric centrifugal pumps in sizes ranging from 4” to 12”, ideal for various applications.
If a quarry needs to handle tough, abrasive materials, Pinnacle Hire can provide its vortex solids handling pumps, which are built for the harshest mining environments.
The company’s high-head dewatering and transfer pumps provide extra muscle for those hard-to-reach areas or high-pressure dewatering needs.
Pinnacle Hire goes beyond just pumps. It offers complete bore packages for efficient water extraction from depths exceeding 200m.
Its pump and standpipe solutions (available in 4” to 12” configurations) ensure effective water distribution throughout a quarry. To keep things running smoothly, Pinnacle Hire provides full-service support, including installation and remote telemetry monitoring –ensuring the dewatering system is operating optimally.
For businesses looking to delve into the world of hydro mining, Pinnacle Hire offers more than equipment—it can also offer expertise.
The company’s team can provide customised hydro-mining packages, including setup and operational guidance, to ensure quarries get the most out of this efficient extraction method.
Pinnacle Hire’s remote-controlled dredge is a game-changer for those battling thick sediment or needing to move large volumes of material underwater.
Available in three models with varying capacities (120-700 m³/h), heads (16-72m), and solids handling capabilities (35-90 mm), this adaptable solution tackles everything from general-purpose dredging to highcapacity and high-head tasks.
Pinnacle Hire’s extensive rental inventory, expert support, and proven track record make it an ideal partner for keeping a quarry flowing smoothly. •
For more information, visit pinnaclehire.com.au
Hardox® 500 Tuf is a new wear-resistant steel from SSAB. It combines the hardness of Hardox® 500 with the toughness of Hardox® 450. The high wear resistance of Hardox® 500 Tuf makes it possible to increase the load capacity by using a thinner plate and still have the same outstanding service life. Or stay with the same thickness and increase service life by 30% or more, depending on the abrasive material.
Hardox® 500 Tuf is also tough enough to perform as a structural steel, allowing for a stronger and lighter mining body with less supporting structures. Hardox® 500 Tuf takes the load instead.
Get the full story of Hardox® 500 Tuf at www.hardox.com
Contact SSAB Brisbane. Melbourne. Perth G1, 28 Balacalva Street Woolloongabba, QLD 4102
Email: australia@ssab.com www.hardox.com
Explore the world of Hardox® wear plateEuropean manufacturer Hazemag believes many Australian quarries could benefit from installing a roller screen.
Traditionally, the roller screen has been the domain of limestone producers due to its ability to handle sticky and difficult material.
However, a new generation of roller screens is being developed to help quarries with more than just a sticky situation, especially if they want extra versatility.
“We’re seeing a lot of inquiries at the moment for the roller screen because in the rainy season and winter time, quarries can get flooded with water, and the material can get quite sticky, so they need something that can be used in the dry and wet season,” Hazemag and allmineral managing director of Australia Teddy Craies told Quarry
It is a familiar story for Craies and project and service engineer Jaco Botha when they visit quarries, especially around the Victorian and eastern coast markets.
When winter strikes and the seasonal conditions worsen, their productivity drops as their equipment struggles to handle the change.
The Hazemag Roller Screen can help quarry operators handle different weather conditions, raw material consistencies and specification requirements.
The Hazemag Roller Screen has a separation surface area featuring disc-fitted rollers. The polygonal-shaped rollers help transport, circulate, and loosen material for the downstream equipment. Fines pass the gaps between the rollers while coarse material is conveyed from the screen to the screen overflow.
Compared to a vibrating screen, the Roller Screen from Hazemag is non-vibrating, which is helpful in specific operations like limestone, clay stone, natural stone, and gypsum.
Hazemag has heard from customers that their roller screens have become an effective pre-screening tool.
“We’ve heard from a few Australian quarries when they’ve approached us about the roller screen, the main reason is their crushers and chutes are getting clogged up during winter,” Craies said.
“The roller screen, in installations across South East Asia and PNG helps the crusher do the job and helps operations in terms of variance in materials and the season and optimised energy utilisation.
“It helps the crusher perform better.”
The Hazemag new generation of roller screens, with gap setting adjusted for product size primary 70mm to 120mm and secondary 20mm to 70mm, is available to the quarrying industry.
This enables operators to adapt to changing requirements and suit material specifications easily. It can handle difficult material, which means less wear and reduced energy consumption for downstream equipment.
“You can put it in front of your primary crusher because it can handle quite a big lump size compared to a conventional vibrating screen,” Jaco Botha said.
“Putting it in front of the primary crusher enables you to get away with a smaller crusher because you’re dealing with smaller sizes.”
Hazemag’s Roller Screen can benefit other machines with a quarry’s downstream set-up.
“This helps the crusher do what it is meant to do and crush the bigger material, not crush things that don’t need to be crushed,” Craies said.
“When you compare it to a vibrating screen, they can’t handle the lump sizes and volume (like a roller screen).
“The roller screen helps pre-screen material which optimises the crusher’s lifespan and the production and energy consumption as well.”
In a traditional vibrating screen, which has two oscillating screens, these types of materials can adhere and bake onto the screen. This enhances wear and the need for maintenance.
The Hazemag Roller Screen has none of this movement, and each roll is equipped with scraper elements to ensure an enhanced clean.
“Each roller has a scraper which helps to scrape and move and then breakdown the separated materials to help get them moving forward,” Craies said.
Hazemag has designed its roller screen with a modular design, available in modules of four or six shafts. The roller screen’s modular nature enables customers to place extra steps between the individual modules.
All Hazemag’s shafts are solid core but can be altered to fit the customer’s application.
For example, the welded three-bow disc design is better suited to heavy-duty applications, while the form-locked join design is more versatile.
The roller screen drive system and disc arrangement are selected based on the customer’s application. The chain-link system is where one geared motor drives several shafts, and the individual drive system is where each shaft is driven by a geared drive.
“We can customise it to the customer’s requirements to their needs and application,” Craies said.
“We use all the information, including what the customer is trying to achieve and what their current set-up and footprint are, and we will do some testings to find the best solution for them.”
Hazemag’s updated HAZconnect system enables site managers and operators to access data on all Hazemag machines including the Roller Screen.
The digital maintenance platform enables operators to perform preventative maintenance using detailed data insights from the dashboard on HAZconnect.
“It brings information about the machine to the operator, and they can adjust the settings and gives them control,” Craies said.
“This kind of preventative and digital maintenance lets them reduce downtime.”•
For more information, visit hazemag.com
Quarry learns how Toolkwip Pumps’ accessories catalogue is helping sites find the right tool for the job.
The Toolkwip Pumps team knows its market. The Victorian-based company has been operating for more than two decades in the industry, providing pumps for quarries.
Edward Taylor, a sales specialist at the company, said this experience is vital.
“We go out and visit sites to make sure we supply the right gear,” he told Quarry
“We know what’s worked best in the past and keep certain parts and products in stock.
“If a quarry wants a particular pump, we’ll ask them what it’s for. More often than not, we can tell if it’s the correct pump to use.
“We don’t want to just sell a pump. We want to make sure quarries get the best solution possible.”
Toolkwip supplies accessories tailored for pumps, filtration equipment and flow meters as part of its offering. These include hoses, valves, clamps, electrical pressure
“It’s a quick reference guide for all of our products, all a customer needs to do is ring us and we can tell them if it’s in stock,” he said.
The company can supply hoses, valves, clamps, electrical pressure transducers, and more.
“It saves a lot of hassle. Toolkwip is a onestop shop, so quarries don’t need to call up a dozen different suppliers to get the parts they need.
“All of the accessories are competitively priced, and if a quarry is looking to purchase in bulk we can work with them to find the best price.”
Time is money in the quarrying industry, which is why Toolkwip offers next or sameday delivery for anything ‘off the shelf’.
In a situation where there is an urgent breakdown, Toolkwip has a service team that can handle installations, repairs, and upgrades.
The company encourages its customers to undergo preventative maintenance and will set up reminders to ensure the equipment is
and manpower, we can tackle almost any job,
over the past several years.
The Brisbane branch is stocked with leading brands of pumps, valves, hoses, fittings, and accessories to service Queensland’s civil, quarry and mining sectors. It also features a fully equipped workshop for routine pump maintenance and repairs.
Taylor said the company plans to continue growing across Australia, supporting quarries with fast, reliable service.
“We’re also planning to improve the catalogue so it can serve as a living document,” he said.
“As we expand our offering, it will get regular updates, providing an even more indepth look at what we offer.” •
For more information, visit toolkwippumps.com.au
Boasting a 500-hour* drain interval that’s twice the industry norm, John Deere Plus-50TM II has been engineered to leave conventional oils in the dust. Made with cutting-edge technology and specifically formulated for use in John Deere machinery, expect fewer oil changes and a boost to your bottom line. Double the life. Half the hassle. Not all oils are created equal.
QR
Xuzhou Construction Machinery Group Co (XCMG) has partnered with Shell to launch a new range of lubricants.
Chinese multinational heavy machinery company (XCMG) has entered into a global partnership with Shell Lubricants.
This move aims to leverage the lubrication expertise of Shell with the cutting-edge technology of XCMG to provide advanced XCMG-branded lubricant solutions that optimise equipment performance, reduce downtime, and enhance operational efficiency.
“Locally, XCMG Australia is excited by the prospect of teaming up with the exclusive Shell Lubricants Macro-Distributor in Australia, Viva Energy, to bring XCMG branded Lubricants to our XCMG customers,” XCMG national parts and warehouse manager, mining equipment Australia Gary Koglin said.
“The launch of XCMG Tailored Lubricants will provide XCMG’s customers with confidence in their lubricant supply and performance.”
“Since the establishment of XCMG Excavator Division in 1999, Shell has been co-operating with XCMG in the field of lubrication,” Viva Energy lubricants sales and marketing manager Renee Reilly said.
“In recent years, with the accelerated pace of XCMG’s equipment business, Shell and
XCMG have strengthened their partnership, jointly launching lubricants tailored for XCMG to bring the best out of XCMG equipment.”
“Lubricant is an indispensable part of the operation of construction machinery,” Silvana Farrugia, Viva Energy technical specialist, said.
“The XCMG tailored lubricants developed by Shell will bring even better protection to XCMG’s equipment with world-class product standards and quality assurance.”
Lubricants are used to reduce friction, wear, and corrosion, and can also remove dirt and deposits inside the machinery, providing protection for industrial equipment, and improving the operating efficiency and life of the equipment.
“Contaminated fluids are known to cause up to 75 per cent of repair costs and equipment downtime, including 65 per cent – 75 per cent of bearing failures1. Routine fluid analysis combined with high-quality lubricants developed with Shell Lubricant technology can better protect construction machinery resulting in less downtime,” Farrugia said.
Shell has five research and development centres around the world and more than
300 scientists and engineers engaged in the research and development of lubricants and greases. The company continuously invests into research and development and makes breakthroughs in innovation.
It aims to always put customers at the centre of its efforts to provide high-quality products, which have won the praise and trust of its customers around the world.
“Shell Lubricants has been named the world’s leading supplier of finished lubricants for the 17th consecutive year by Kline & Company,” Reilly said.
Koglin encourages workshop and equipment owners to get in touch with XCMG Australia.
“By stocking genuine XCMG Lubricants, users can be sure that they will have the right oil for their equipment,” he said.•
For more information, contact Gary Koglin directly on 03 9796 3075 or 0423 528 314 or contact Viva Energy Technical Helpdesk, on 1300 134 205.
Quarry finds out how Motion Australia is living out its promise to provide Australian industrial businesses with ‘more choices, more solutions’.
“If it moves, we can add value to it,” Ryan Kendrigan, executive general manager of engineering services at Motion Australia said. “Each business within the Motion family comes with its own specialty. What’s advantageous is that with all of these businesses and their specialties consolidated, our customers have an incomparable breadth of offer.”
The Motion family includes longestablished businesses BSC and CBC –which have traditionally supplied bearing and power transmission products to industry – as well as businesses that specialise in fluid power such as AIP, Hardy Spicer and Powell, and the hydraulic engineering business, CRAM. Under each of these businesses is a vast inventory of branded products – totalling over 600,000 individual items –which is supported by a network of over 1600 employees, 180 branches, 30 repair and service facilities and eight dedicated distribution centres.
“Over the past few decades Motion has shifted its focus from being a supplier of componentry to being a full solutions provider,” Kendrigan said. “We came to the decision through our relationships with customers, and learning what their needs are. To truly service our customers and give them tailored solutions, we felt we needed to add more value across the product portfolio.”
While some legacy customers may still not be familiar with the ‘Motion’ name, the businesses and brands within the business are well-regarded. Stephen Forbes, executive general manager of fluid power solutions at Motion Australia, said Motion’s approach is still fundamentally a family-business – which is essential to the company’s evolution.
“For most of our history, we’ve operated as a group of family-owned companies and this heritage is reflected in the approach we take today, which is relationship focussed,” Forbes said.
“And our customers are looking to us to make it easier for them. They trust us, the
brands that we supply, and the expertise we have to now provide full-service solutions.”
Motion’s businesses can be grouped into three key areas – industrial solutions, fluid power and engineering services. As executive general manager for industrial
of the company’s core businesses has only had positive implications for customers.
“We’ve worked with many of our bearing and power transmission suppliers for decades and have built on a wealth of expertise both in partnership with suppliers and in our own
businesses with a holistic offering – that incorporates everything from traditional rotating componentry to hydraulics, hoses and fittings to bespoke engineering services, and training, – is hugely beneficial.”
When Ryan Kendrigan began his career with Motion it was with the bearing company, BSC. He has since been part of an evolution that has seen the engineering division grow from being one or two people in each business arm, to some 350 specialised engineers.
“We started out as a bearing company that provided engineering support for traditional rotating equipment,” he said. “Now we can look at anything that’s operating in rotary motion, linear motion or hydraulic motion and provide a turnkey solution that will maximise the efficiency and output of that equipment.”
Kendrigan provides an example of a solution that was delivered to a steel manufacturer to illustrate how the consolidation of the company and its collective of skilled engineers can benefit customers.
“The customer needed a custom-built acid tank and one of the key constraints was the space in their facility was very tight. We came up with a solution where we half-built it in our workshop, then we dropped through the roof, coming through a whole bunch of different pipework at the sides, slotted it in position, and then built the top part of the tank once it was in-situ,” he said. “Once upon a time this would have required six or seven different companies to make that happen. Instead, we created the process, and saw the solution executed from concept to delivery – ensuring it was working effectively afterwards.”
Having such a broad range of expertise means that the Motion engineering team can
come up with a process for a challenging situation like the one Kendrigan has described.
“It’s being able to offer that turnkey solution. We can design a concept, manufacture a concept, install it, maintain it. It’s a fullservice offering.”
Importantly, the journey is ongoing.
Kendrigan said that while engineering services comprises 14 per cent of Motion’s current revenue, he projects that this will climb to about 30 per cent within the next decade.
“We’re constantly looking at how we can better support our customers in Australia, and actively expanding our offering and capability,” he said. “I’m certainly proud and fortunate to work with a host of best-in-class engineers that amaze me every day with their skills, particularly when we get into the automation and motion control side of things.”
Brad Hudson, Motion’s national quarry business development manager, recently showcased this dedication to support.
A quarry in Western Australia had broken down and needed a specific part. However, Hudson was on the other side of the country in Melbourne at the time.
There was one particular part the quarry needed to get things moving again. The problem? There was a national shortage of that particular bearing.
All hope was not yet lost. Earlier that week, Hudson has visited a local quarry that had that exact part as a spare. He called them up and asked if they could take it off them. By Saturday afternoon, the bearing was on a plane heading towards the site. By Monday morning, the site had started production.
as much as possible to ensure they can
provide a low cost material for major construction projects around the country,” Hudson said.
“There’s demand for quarries to deliver cost effective outputs. Profitability becomes a major challenge. Quarries are looking for a trusted partner they can rely on to keep costs low.”
What does the future hold for Motion?
According to Kendrigan, it’s about continued growth for the benefit of the customers.
“There are hundreds of thousands of customers that deal with Motion, but only a fraction of those have engaged with engineering services – I see this expanding, and am looking forward to providing more value to people over time.”
Forbes said there’s plenty of room for the Motion business to grow both in its geographical coverage and range of solutions.
“We’re always looking for opportunities to extend our capabilities to cover any gaps in our offering,” he said. “We’re also very conscious of exploring emerging technologies such as renewable energy. Plus, we’re looking to invest further into our e-commerce capability to better enable customers to access the whole Motion offering.”
This ties into Motion’s broader commitment to streamlining the customer experience.
“We’re working very hard on integrating our business operations so that it’s completely seamless for customers. We have a strong desire to offer our customers the sort of experience that best suits their needs. This is the plan we have in Motion, and we’re steadfast in our commitment to delivering on it.”•
Auckland is running out of sand. With a looming sand shortage, Quarry looks at how New Zealand is confronting the issue.
The sands of time are slipping away from Auckland and the North Island, and New Zealand needs solutions to cover material shortfalls.
According to the Aggregate and Quarry Association (AQA) of New Zealand, Auckland ran out of sand for construction briefly before Christmas.
This led to concrete manufacturers being unable to deliver to customers and building delays.
For AQA chief executive Wayne Scott, the sand shortage is a familiar tale. In March last year, he wrote to the New Zealand Government to warn about the pending shortfall.
“This will impact across transport, infrastructure, economic development, housing and much more. We know this is not of the Government’s making, but interim solutions are desperately needed,” Scott said.
“The quarry industry has done all it can to issue the warnings and meet the shortfall but it’s beyond us to resolve.”
Traditionally, sand extraction from rivers and beaches in New Zealand has been used as a flood mitigation technique, which in turn created a supply of sand for construction.
Local councils’ regular sand extraction created affordable sand, but as demand for the material has increased within the market,
the price has expanded.
Other issues have also been key to the shortage. Growing environmental concerns and pressure from activist groups about river and land based extraction are some aspects, while the AQA has highlighted delayed resource consents and the new National Policy Statements on Highly Productive Land and Indigenous Biodiversity as factors faced within the quarrying sector. According to AQA, one third of current consents are being impacted by these Policy Statements.
“Unless there is urgent action to allow resource consents to proceed and resolve issues relating to extraction off the coast near Mangawhai, construction projects across the upper North Island will suffer delays waiting for sand and concrete,” Scott said.
In the past, the Auckland City Council have rejected McCallum Bros’ resource consent application to extract two million cubic metres of sand over 35 years. The company was one of Auckland’s leading sand suppliers and indicated after the rejection in 2022 that it would impact the construction industry.
“Without this sand, the construction market could be hit with a major supply shock, seriously impacting housing, transport and other infrastructure developments,” McCallum Bros managing director Callum McCallum told RNZ.
“Sustainable extraction at Pakiri is the best solution not only because of the quality of the sand but also due to its ability to be delivered into the centre of Auckland in bulk by shipping. Up to half of the city’s construction sand requirements come from Pakiri.”
The company is currently waiting on an appeal to the Environment Court.
The shortfall in New Zealand follows several global bodies warning about a sand crisis.
The United Nations Environment Programme (UNEP) called the global sand extraction rate “unsustainable” after its findings in a 2022 report. The report estimated that 50 billion tonnes of sand is used per year globally.
The United Nations group urged that sand be considered a “strategic resource” given its importance to construction and the environment. The report also considered an
international standard on sand extraction among ten strategic recommendations.
“If we can get a grip on how to manage the most extracted solid material in the world, we can avert a crisis and move toward a circular economy,” Pascal Peduzzi, director of GRIDGeneva at UNEP, said at the time.
McCallum Bros commissioned a 2019 report prepared by Greg Akehurst as part of its resource consent hearing. The report stated that the construction boom in New Zealand would require “significant” amounts of sand.
The report stated, “The majority of this investment requires significant volumes of concrete and, therefore, significant volumes of sand.”
“Sand is a low-value, high-transport-cost item that needs to be sourced close to final use; sources in the south should be used by southern developments, while developments in the centre and north should be supplied by the northern sand.”
A report from Sapere Research Group showed that obtaining resource consent had increased in cost by 70 per cent and that the timeline had nearly doubled by 2021.
“The results of this study are quite concerning,” New Zealand Infrastructure Commission, Te Waihanga chief executive Ross Copland said at the time.
“To see annual consent costs escalating by half a billion dollars since 2014 is evidence of the ‘arms race’ of experts we have seen unfolding - with council planners
demanding that infrastructure providers pay for as many expert reports, peer reviews and independent studies as they deem necessary.
“Worst of all, the system disproportionately penalises smaller communities and projects.”
Part of the solution to overcome the sand shortfall is manufactured sand, which is undergoing significant development in New Zealand.
The country has been carefully watching across the Tasman to see Australia’s efforts with manufactured sand. Initial theories seem to be that manufactured sand has good qualities for concrete but can be dearer than natural sand due to the production process.
“We could see an upward shift in the price of sand, which is the experience in countries that have increased the percentage of manufactured sand they use” Scott said.
“I don’t think there’s a big grasp on that … when governments and local authorities talk about infrastructure, they talk in big numbers, in billions of dollars. I think everyone is numb to the impact of cost increases across the supply chain.
“They seem to be numb to the impacts of localised supply; the price of aggregate sand doubles when you cart it 30 kilometres, so you don’t have to be too far away for it to have a huge impact.”
New Zealand’s aggregate producers in the North Island have responded with initial investments in manufactured sand
equipment. While manufactured sand is produced in small quantities already, Kaipara Limited introduced its manufactured sand plant in April, which is understood to be the first at-scale operation of its kind in the country.
While manufactured sand is more commonly used in overseas markets like China and Japan, Kaipara Ltd. has invested around $12 million in its manufactured sand plant, according to reports. The company aims to produce up to 300,000 tonnes of sand per annum.
Scott said he believes governments and local authorities need to have serious conversations about the role of quarrying going forward.
It is a view shared by others around the sector, including Copland, who has previously expressed a similar view about the need to take a long-term view of projects and resources.
“There are a lot of things that no one wants to talk about, and one of them is the aggregate story. We want houses and development, but where is the stuff going to come from to do it?” Scott said.
“If you don’t want it in your backyard, where are you going to get it from, and what is it going to cost? Let’s have those conversations with the public.
“Here in New Zealand and, having lived in Australia, we don’t tend to have those adult conversations with the public … but if they see the impact of carting materials in, maybe they might see the value of having a quarry nearby.” •
At Kinder, we understand productivity.
Our engineers are experts in innovation with the ability to design bespoke solutions and provide products to suit all conveyor applications.
Selected to increase your efficiency and reduce downtimeIf it’s above, around or below the belt, we have the answer.
Unlock your productivity potential. Visit kinder.com.au
Diesel could be the next frontier for heavy industries in the push towards decarbonisation. Quarry learns how the fuel is being made renewable.
Advocacy groups from the renewable sector and heavy industries are eager to see renewable diesel advanced in Australia, and soon.
There has been a concerted push in the renewable diesel sector over the past year with calls being amplified after the Renewable Energy Conference was held in Canberra.
“Australia’s economy is reliant on liquid fuels, and our heavy industries, aviation, marine, agriculture, and mining, need affordable and immediate decarbonisation options,” Bioenergy Australia chief executive officer Shahana McKenzie said.
“Touting electrification as the only solution is naïve and delaying a robust discussion about how we achieve decarbonisation of these hard-to-abate sectors.
“We must give businesses in these critical sectors the unimpeded ability to reduce their emissions and not simply leave them to their own devices, or their own demise.
“Renewable fuel is their answer. We just need to provide it, affordably and at scale.”
The Australian Constructors Association has joined the chorus of calls to develop better renewable fuel infrastructure in Australia.
The association has publicly expressed that electrification is a preferred method, but technology constraints render it a long-term option for construction and heavy industries.
“We need to rapidly adopt low carbon liquid fuels to bridge the gap until electric options mature and the best transition fuel for the construction industry is renewable diesel,”
ACA chief executive Jon Davies said.
“Renewable diesel enables necessary emission reductions in the short term without modifications to existing machinery.
“The problem is, there is currently no domestic renewable diesel production in Australia – this reflects a policy vacuum that lags other countries significantly.”
Renewable diesel has already gained traction in overseas markets overtaking biodiesel in the process. Countries like the United States and Germany, have embraced new fuel standards, tax treatments, waste levies and grants to turbocharge the uptake of renewable diesel.
Renewable diesel and biodiesel are made from similar feedstocks, such as vegetable
According to a study from the University of Illinois and the US Department of Agriculture, biodiesel has traditionally outpaced renewable diesel. However, greater production facilities for renewable diesel have supported its recent growth.
American-based firm Aemetis is set to open its renewable fuel plant in Riverbank, California, later this year.
According to the company, the plant has secured $7 billion in purchase contracts for renewable fuels it will make at the site, which is a repurposed army ammunition plant. This is made up of $3.8 billion in sustainable aviation contracts and $3.2 billion in renewable diesel supply contracts.
When the plant opens, the company estimates it will produce up to 90 million gallons per year of sustainable aviation fuel and renewable diesel.
“Thank you to Aemetis for being the type of company that you are and for doing such a great job at the Riverbank site which has already created new local jobs in the green economy,” Riverbank City Council member Darlene Barber-Martinez said.
Closer to Australian shores, Ampol and Hanson joined forces for a two-month trial of renewable diesel last year. As part of the trial, Hanson used a blend of 20 per cent renewable diesel and 80 per cent ultra-low sulphur diesel in addition to Ampol additives in some of its machines. It comes after Ampol partnered with
heavy industries, including quarrying.
According to the Department of Climate Change, Energy, the Environment and Water (DCCEEW) data, 40 per cent of diesel used in Australia is for non-transport reasons like heavy construction.
Due to the lifespan of heavy machinery and associated costs, replacing a diesel fleet would “not be viable” for the industry.
The department said in a paper last year that “Unlike biodiesel, renewable diesel has the potential to be used in many existing heavy-duty diesel engines.”
“A low-carbon substitute for mineral diesel is vital to assist hard-to-abate sectors in efforts to decarbonise until other options are viable.”
Renewable diesel can be supplied in Australia if it meets the Fuel Quality Standards Act 2000; however, neat renewable diesel doesn’t meet the minimum density specification of the diesel specification in the act.
This creates a situation in which suppliers must apply for approvals to legally sell a high percentage of renewable diesel.
The DCCEEW is considering altering the fuel standard to accommodate renewable diesel. This would enable suppliers to sell renewable diesel without needing to apply. The department recently closed its public submissions process for the fuel standard.
According to its position paper released last year, the DCCEEW proposes to use
“paraffinic” would give the fuel standard greater scope to include other fuels like synthetic diesel in the future rather than just renewable diesel.
According to the department, preliminary discussions with industry groups have supported the creation of a standalone fuel standard to encompass paraffinic fuels. This move would provide “more market differentiation” and “mirror” the European framework.
The recent report from BioEnergy Australia, prepared by Deloitte, concluded that if government support were not provided to renewable fuels, Australia’s heavy industries, including quarrying and mining, would need to maintain their reliance on fossil fuels.
“Every day we fall further behind in the race for renewable fuels. We are being beaten to the punch on what looms as an incredible economic and environmental opportunity,” McKenzie said.
“Many other nations are embracing fuel carbon intensity standards, concessional loans, tax treatments, waste levies and grants, but we are yet to see a strategic approach to the decarbonisation of liquid fuel reliant sectors in recent policy announcements.
“The market is looking for a strong regulatory signal from Australian governments; the necessary green light for investors, producers and refiners.” •
The IQA Central Queensland sub-branch embarked on an enriching site tour of Graymont quarry, offering attendees an insightful glimpse into the site’s operations. Following the tour, members convened for networking refreshments at the Railway Hotel Motel in Calliope, which allowed for valuable connections and discussions among peers.
The convenience of group transportation by bus ensured a seamless and enjoyable experience for all participants throughout the day. We are immensely grateful to Finlay Screening and Crushing for its sponsorship of the day, which played a pivotal role in making this event possible, and we extend our sincere appreciation to Simon Havis and the team at Graymont’s Calliope site for hosting an educational tour.
The North Queensland branch dinner meeting was held on Thursday March 21 in Townsville.
BRI Ferrier’s Moira Carter was the first guest presenter, delving deeply into the intricacies of creditor management. Attendees were treated to an insightful exploration of topics such as the assessment of creditors’ financial
situations, the establishment of credit limits, and identifying key indicators of companies facing financial challenges.
Moira’s presentation fostered engaging discussions during the Q&A session, providing valuable understandings.
The evening’s second guest presenter, TMR Director Mike Pickering, provided an overview of TMR’s plant mixed stabilised mix design registration system and its associated requirements.
We extend our gratitude to all attendees, including members, non-members, guests and associates.
The Queensland branch embarked on a visit to the Caterpillar office in Brisbane for a collaborative technical event focused on operational optimisation.
Participants gained invaluable insights into various aspects including leveraging productivity solutions, achieving wins for customers’ sites through enhanced productivity, and Caterpillar’s methodologies for optimising cost per tonne and idle time.
We extend our heartfelt gratitude to Jason Barnwell and Jenny Krasny from Caterpillar for their role in facilitating such an informative and engaging session. Their expertise and dedication to knowledge-sharing have enriched the learning experience.
Members and guests had the unique opportunity to tour the $2.2 billion Coffs Harbour Bypass Project and connect with senior project management.
Attendees had the opportunity to witness first-hand the challenges the site has with muddy conditions as a result of the previous days of heavy rainfall that resulted in the site tour being restricted to the Bruxner Park area of the roadworks. Thank you to the Coffs Harbour Bypass team for hosting the site tour with ad-hoc changes due to muddy conditions and to the attendees for their understanding of fact the tour had to be restricted and shortened.
The site tour was followed with a networking dinner at the Coffs Harbour Surf Club, which brought together a fantastic crowd of 64 members and guests.
Special presenter Dan Hazeldene, Coffs Harbour Bypass Project senior supervisor, further discussed the complexity, challenges and opportunities of the project.
NSW branch premium sponsor Sitech provided a great overview of the solutions it can provide to challenges in the extractive industry. Sitech technical product specialist Nick Pryke was on hand to deliver the presentation.
Thanks to Westrac and to Komatsu. Our appreciation also extends to the Northern NSW Region sub-branch committee and the IQA for pulling together such great events and to members, associates and all who were able to join us on the day. See you all in Port Macquarie in June.
Members of the Southern NSW sub-branch recently gathered for a networking dinner at the Warilla Bowls and Recreation Club.
The evening featured a presentation from Lincom Group product manager Alan Dunbar, who captivated the audience as he unveiled Lincom’s array of dewatering options. In discussed solid–liquid separation, Alan explained the intricate details of the process, including pre-treatment, solid concentration, solid separation through to post-treatment. Discussion also delved into the technical area of particle size and shape, and that old nemesis, clay. Alan also discussed a unit called a decanter centrifuge (a Broadbent unit distributed by Lincom Group), as well as centrifuge configurations including solid bowl, parallel screen bowl, and divergent screen bowl.
To finish off, attendees looked over a filter press, and walked everyone through press plate types.
A huge thank you to Lincom Group for its premium sponsorship and continued support.
The autumn technical breakfast, William Adams in Clayton on March 14, kicked off with a breakfast. Registrants then enjoyed a presentation by Jevan Davenport from William Adams about their eCommerce capabilities.
The guest presenter was Chris Barrett, Caterpillar Australia global construction and infrastructure ANZ technology application specialist. He discussed the comparison between certified and uncertified on-board payload weighing scales, focusing on their legality for trade purposes.
The event concluded with a tour of the William Adams facility.
We thank all members, non-members, guests and associates for attending. •
Scotland, home of the Loch Ness Monster, doesn’t lack quirky tales, but its Barnton Quarry may top the unsighted monster with its James Bond-esque history.
Located in Edinburgh, Barnton Quarry was home to the country’s biggest nuclear bunker, which, according to a BBC report, would have housed Queen Elizabeth II if she had been in Scotland during a nuclear attack.
The nuclear bunker was built around the time of the Cold War as the world contemplated nuclear warfare between the United States and the Soviet Union.
The bunker is 100 feet beneath Corstorphine Hill in Barnton Quarry, which makes it the place to be if you were ever in Edinburgh during a 1940s nuclear attack.
The facility was once the central operations centre in Scotland as part of the British Government’s ROTOR program.
ROTOR was Britain’s response to the potential threat of long-range nuclear Soviet Union attacks.
It served as an advanced radar monitoring network and required a three-level extension built deep underground with reinforced concrete walls.
After the extension, it was marked as a Regional Seat of Government in Scotland. Some reports suggest that around 1960, the site would have become a central emergency government hub for the Scottish government if the country had detached from London in the event of a nuclear attack. Its existence was a government secret until the 1963 Spies for Peace campaign. The campaign, which revealed the location of the bunker and other Regional Seat of Government in mass-produced pamphlets, made Banton a central part of the protests against nuclear war in Scotland at the time.
Mike Lessner, one of the campaign activists, detailed his experiences with The Times in finding out about the RSGs.
“We were on a high because we knew we had hit the jackpot. At the same time I remember being very frightened,” he told The Times.
“I was terrified because the bunker meant the government was quite
uninhibited about the destruction of the civilian population if it felt that was what had to be done.
“Some of the others probably won’t thank me for going public. But this is something I want to do for me.”
In modern times, plans to turn the bunker into a museum to showcase the quarry site’s unique history have emerged after James Mitchell, a local businessman, bought the site from a property group.
“They couldn’t do anything with it because they weren’t given planning permission for flats, so I asked if I could buy it,” Mitchell told the BBC.
“They said they were in a board meeting and would call me back.
“I was in my car, and by the time I was driving over the Forth Road Bridge I had bought it.”
Mitchell, who runs Scotland’s Secret Nuclear Bunker in Fife, wants to showcase RAF and Cold War history at the Barnton site.
Volunteers have slowly transformed the site after it was ravaged by fires in the 1990s.
“The vandalism that preceded Scotcrown’s acquisition of this unique slice of Edinburgh’s more recent history is well on the way to
being rectified,” plans submitted to the City of Edinburgh Council read.
“Scotcrown’s aspirations for the site has always been the restoration of the bunker into an authentic, historically accurate representation of the functioning bunker.
“To this end, it has been a gradual labour of love for many years now, with the growing involvement of enthusiasts and the local community. It is fully envisaged that this relationship and involvement will continue and continue to prosper and develop into the future.”
In 2021, after a campaign from the Barnton Quarry Restoration Project, the site received category A status, reserved for buildings of special architectural or historical interest.
“Working with community groups and listening to their ambitions to protect and engage with their local historic environment is a priority for HES,” deputy head of designations at Historic Environment
Scotland (HES) Phil Robertson said.
“As one of only four purpose-built radar system headquarters of its type in the UK, the Barnton building is a very rare survival from the Cold War.”•