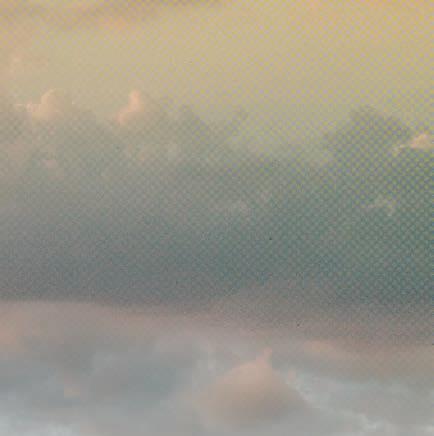
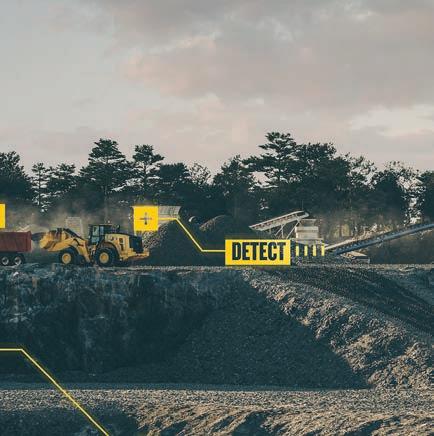
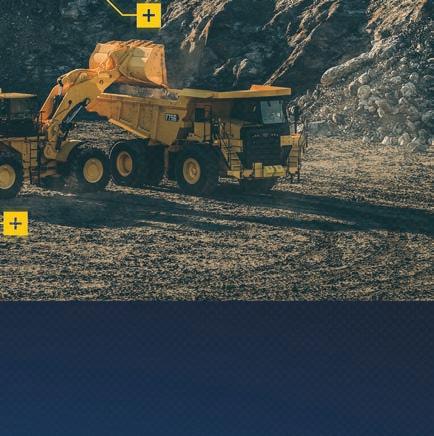
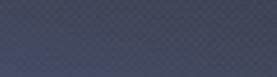
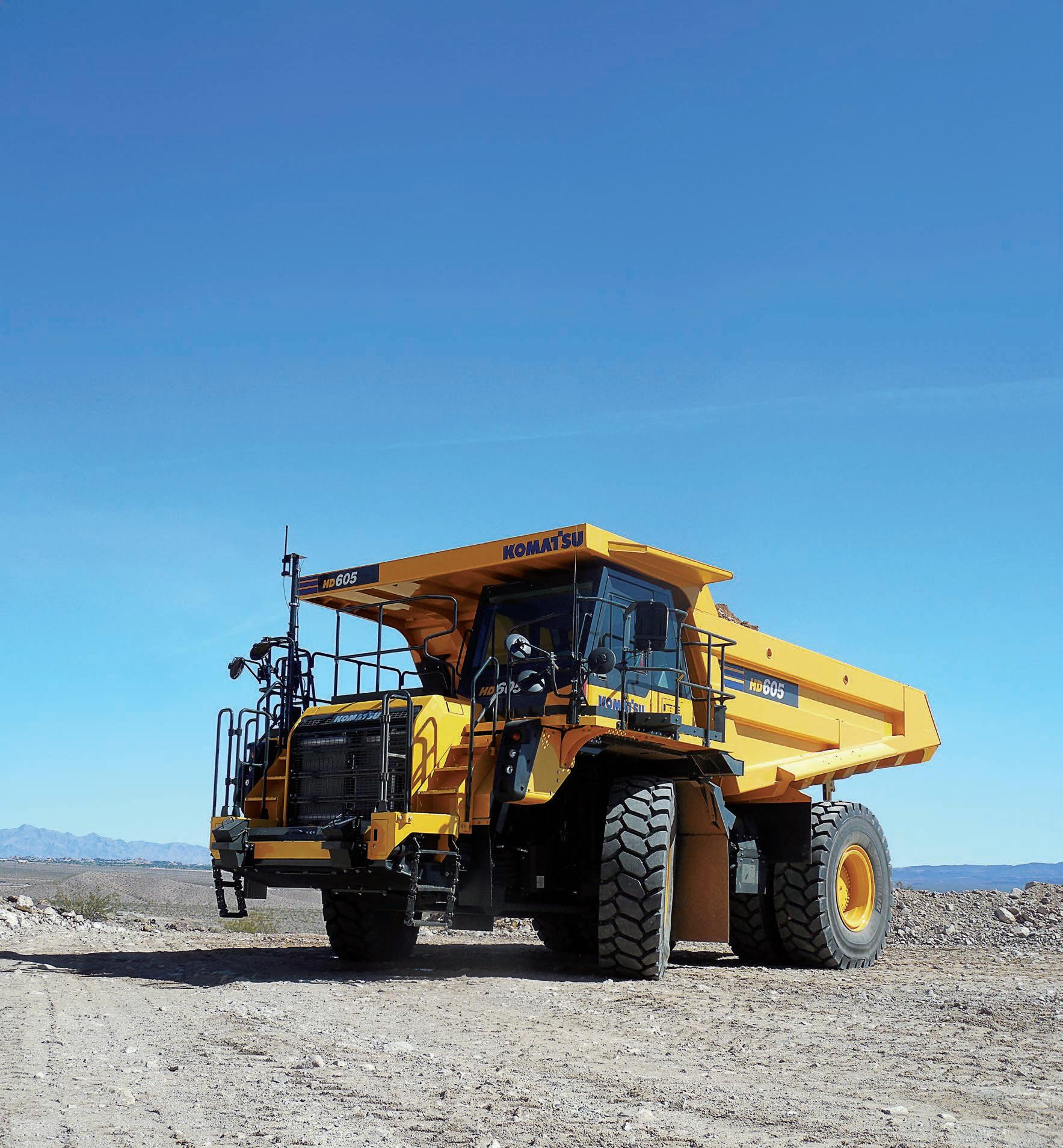
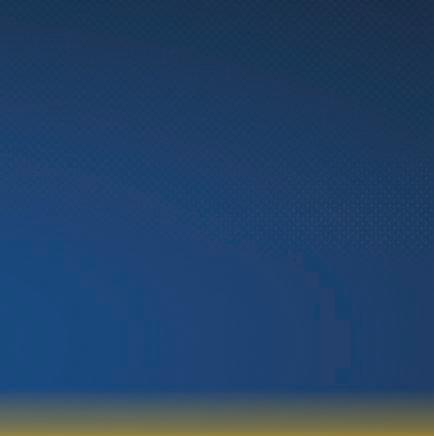
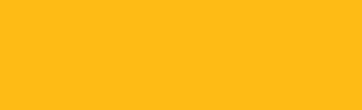
Shortages of quality natural sand are creating headaches. Kayasand believes quarries can provide the solution.
DRUM UP SUPPORT
Tricon Equipment is supplying its customers with heavy-duty screening equipment.
since they launched Brooklyn
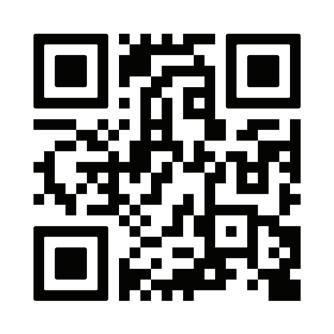
Shortages of quality natural sand are creating headaches. Kayasand believes quarries can provide the solution.
DRUM UP SUPPORT
Tricon Equipment is supplying its customers with heavy-duty screening equipment.
since they launched Brooklyn
Komatsu’s Smart Quarry Site is an innovative fleet management solution designed to empower site and project management personnel with unparalleled production visualisation for quarry and major civil construction sites. With a simple glance, you gain access to real-time animated insights into every aspect of your production machines, as well as the material they are handling, extracting, shifting, or placing.
Sustainability – it’s a word you’ve no doubt heard a million times at this point, and for good reason.
Governments around the world have pledged to reduce their carbon emissions by 2050, a herculean task that relies on industry support.
The impacts of this have flown through the extractive industries, especially as incentives are pushing quarries to adopt environmentally friendly methods.
However, sustainability goes a lot further than just looking after the environment. A sustainable industry is one that continues to flourish well into the future.
As conditions change, the industry needs to be able to adapt and change with them.
Quarrying is currently undergoing a digital transformation, which is helping to reduce costs and improve productivity.
There are still many challenges that digital technology alone cannot solve, such as the nationwide skills shortage.
The Institute of Quarrying Australia (IQA) 2024 conference in Adelaide attempts to tackle these important topics.
The conference focuses on the future, recognising innovation as a key strategy to keep the industry moving forward to create growth opportunities.
It also aims to highlight examples the resources industry can learn from that could create opportunities for industry growth, employment, training, and overall development.
Attendees at the conference can gain valuable insights into evolving customer requirements, meet key decision makers and industry professionals, and showcase their organisation’s products and services.
In addition, there will be a combination of field trips and site visits, and a three-day program that explores the latest developments within the industry.
Quarry, as the official magazine of the IQA, will be on the ground at the show, shining the spotlight on what the industry has to offer. We look forward to learning more about the latest innovations.
William Arnott Editor
A SUSTAINABLE INDUSTRY IS ONE THAT CONTINUES TO FLOURISH WELL INTO THE FUTURE. AS CONDITIONS CHANGE, THE INDUSTRY NEEDS TO BE ABLE TO ADAPT AND CHANGE WITH THEM.
Published by:
379 Docklands Drive
Melbourne VIC 3008
T: 03 9690 8766
www.primecreativemedia.com.au
Chief Executive Officer
John Murphy
john.murphy@primecreative.com.au
Managing Editor
Paul Hayes paul.hayes@primecreative.com.au
Editor
William Arnott william.arnott@primecreative.com.au
Journalist
Adam Daunt adam.daunt@primecreative.com.au
Business Development Manager
Les Ilyefalvy les.ilyefalvy@primecreative.com.au
Client Success Co-ordinator
Janine Clements janine.clements@primecreative.com.au
Art Director
Michelle Weston
Subscriptions
T: 03 9690 8766
subscriptions@primecreative.com.au
The Publisher reserves the right to alter or omit any article or advertisement submitted and requires indemnity from the advertisers and contributors against damages or liabilities that may arise from material published. © Copyright – No part of this publication may be reproduced, stored in a retrieval system or transmitted in any means electronic, mechanical, photocopying, recording or otherwise without the permission of the publisher.
THE MOBICAT MC 110 EVO2 AND MOBICONE MCO 90 EVO2
TEAM PLAYERS THAT WORK TOGETHER INTELLIGENTLY AND STRENGTHEN EACH OTHER. In linked plant combinations, the MOBICAT MC 110 EVO2 jaw crusher and the MOBICONE MCO 90 EVO2 cone crusher really flex their muscles. SPECTIVE makes both plants easy and intuitive to operate. Also, an advanced drive concept ensures greater effi ciency with lower consumption. Maximum throughput is achieved thanks to the material fl ow concept coordinated via line coupling across both crushing stages. Go for the perfect team!
www.kleemann.info
Safety is an important and integral part of the IQA’s mission. The IQA held two more safety and health conferences with the 10th NSW Quarries Health & Safety Conference, held at the Western Sydney Conference Centre.
There are always a range of topics across these conferences with updates from regulators and speakers on the importance of safety and health in the workplace. More recently these topics have extended to not only includes physical safety but an emphasis on psychosocial safety in the workplace. At the NSW conference, we had two sessions on managing psychosocial risks at work with information-sharing from UNSW academic dean Carlo Caponecchia and practical applications by Charlotte Kelly and Paul Slough from Hanson. Keynote speaker Steve Simpson discussed unwritten ground rules and change management, an interactive and interesting perspective on different workplaces, their cultures and ways to help change culture for the better.
In north Queensland, Chris Wilson, quarry manager at Wolffdene, a Hanson Quarry, gave a presentation on redesigning site movements, acceptable controls and verification techniques. The attendance at these conferences continues to grow.
The feedback from attendees was positive and we thank our sponsors and exhibitors for attending and supporting these major events on the calendar.
Our AGMs have commenced and will continue through until the IQA Board AGM in October. All IQA members appreciate the work that committees do throughout the year and the time committed to bringing together networking events, site tours and education which benefits the quarrying sector. To date a small number of committees have elected
their 2024–25 chairs and committee members.
Special mention should go to Craig ‘Shine’ Summerfield. Shine has held the role of Chair of the Southern NSW Region Sub-Branch for just two years, he has been a Fellow and a member of the Institute since 2008. His commitment to the IQA’s vision of education and connection has resulted in significant membership growth, offering facilities for faceto-face education, and support for branch networking events, including site tours. His enthusiasm is further reflected in his work, which led to the boards and members’ support for renaming the sub-branch from the Illawarra sub-branch to the Southern Region sub-Branch, a name more representative of the regional membership landscape. Although Shine has stepped down from his role as Chair of the Southern NSW Region subbranch this year, he will continue to be a member of the IQA. We have welcomed Michael Holz, FIQ and quarry manager of Benedict Industries, as his successor.
and
Another special mention must go to Tinus Nagel who has stepped down as the Chair of the WA branch after four years but has agreed to remain on the committee into 2024–25. Tinus was instrumental in sponsors in Western Australia, securing a number of partnerships last year. Tinus is always in attendance at meetings, encouraging of young members and Women in Quarrying. He has been a positive role model enabling a young member to step up and take the reigns under his leadership. The IQA welcomes Johan Barnard into the position of Chair for 2024–25.
Duncan Harris President Institute of
Quarrying Australia
ALL IQA MEMBERS APPRECIATE THE WORK THAT COMMITTEES DO THROUGHOUT THE YEAR AND THE TIME COMMITTED TO BRINGING TOGETHER NETWORKING EVENTS, SITE TOURS AND EDUCATION THAT BENEFITS THE QUARRYING SECTOR.
The IQA’s Strategic Plan 2023 to 2026 embodies the following vision, values and strategic priorities:
Vision:
Thriving communities supported by a sustainable industry
Operational Priorities:
• Deepen industry participation
• Sustainable revenue streams
• Highly capable team
• Technological innovation
• Effective engagement
• Great governance
Strategic Priorities:
• Support industry participants with compliance and regulation
• Build a diverse and skilled industry workforce
• Foster strong industry connectivity
IQA Contacts:
Phone: 02 9484 0577
Email: admin@quarry.com.au
Chief Executive Officer
Jane Schmitt
Deputy President
Michael Close
Company Secretary
David Cowie
For all education, member and branch enquires please email: admin@quarry.com.au.
Eltirus Exploration, Geological Modelling, and Resource Assessment services.
We work with quarry operators to explore, model, and assess your resource, increasing certainty of operation and reducing risk. Our experienced geological team help identify gaps in understanding, create exploration programs, and manage the program for you. Whether it be field mapping or blast hole, RC, aircore or diamond drilling, we not only help you explore and assess your deposit, but also ensure outputs are accessible through the use of world-class geological modelling software that provides you with interactive models that truly make a difference on the ground and in the field.
Metso has confirmed its acquisition of Jindex in an agreement that expands its offering in slurry handling capabilities.
Jindex is an Australian-based company that specialises in valves and process flow control. The acquisition will add to Metso’s existing slurry handling portfolio including slurry handling and hydrocyclones, including equipment, parts, after-
market and lifecycle services and digital services. The equipment offering includes slurry pumps, pipes, hoses, valves and hydrocyclones.
“This acquisition is yet another important step in the development of Metso’s Pumps business line offering to bring us closer to being our customers’ lifecycle partner of choice,” Metso’s head of pumps Tiago Oliveira said.
Boral’s newest cement facility has become fully operational in a major boost to the Victorian economy.
The Geelong facility has the capacity to grind 1.3 million tonnes annually, including granulated blast furnace slag and clinker.
“Our state-of-the-art cement facility in Geelong is now up and running,” the company said. “We’re excited about the positive impact this facility will have on sustainability and the local community.”
The company will use slag, a by-product of steel manufacturing, to help reduce
“JINDEX HAS EXTENSIVE EXPERTISE AND STRONG CAPABILITIES IN VALVE TECHNOLOGY AND CONTROL EQUIPMENT, AS WELL AS IN MANY TYPES OF SLURRY VALVE PROJECTS, AND THUS THEIR PRODUCTS COMPLEMENT OUR OFFERING WELL.”
TIAGO OLIVEIRA
Flow and isolation control play a vital role in ensuring smooth slurry handling to maximize the productivity and efficiency of minerals processing plants. In the past, we have collaborated with Jindex on many customer projects and are now glad to welcome the Jindex experts to the Metso team.
“Jindex has extensive expertise and strong capabilities in valve technology and control equipment, as well as in many types of slurry valve projects, and thus their products complement our offering well.”
Jindex is a privately owned technology company established in 1995. The company is based in Sydney, Australia, and has 25 employees. Jindex serves the mining and minerals processing sector with approximately 50 per cent of sales in Australia.
“This is a great development and an exciting next step. The Jindex product offering and our technical expertise in valves are an excellent addition to Metso’s Pumps business and will enable Metso to provide more extensive flow control solutions to the mining industry,” Jindex managing director Stephen Fowler said.
“We look forward to contributing our unique knowledge and experience as part of the Metso team, and providing enhanced outcomes to all our collective customers.” •
landfill waste and substitute cement in concrete products.
The new facility is located near Lascelles Wharf and features a covered conveyor system to reduce local truck traffic.
Clinker and slag are unloaded from ships and delivered to the site via covered belt conveyors situated on Lascelles Wharf. Following processing, the final cement product is transported to the Victorian market via enclosed tanker trucks.
Boral invested heavily to bring the Walchs Road, North Shore location to life. It began construction in 2018. •
Delta Rent operates one of the largest earthmoving equipment rental fleets of more than 450 high performance machines in Australia.
We understand that production is key for quarry owners and operators. In particular, the importance of high optimisation rates for the heavy plant and machines required to process raw materials and meet demand.
24/7 service Australia wide
Our late model, low hour and meticulously maintained fleet – combined with expert 24/7 advice and analysis from an experienced and professional sales team – ensures our clients maximise production output without compromising quality, safety or environmental performance standards. Expert advice and analysisPurpose built fleets tailored
55-ton payload
Move more material in less time
6x6 traction
Unstoppable in tough terrain
Haul Assist
Optimise your hauls with real-time data
Spacious cab
Comfortable and ergonomic design
Robust design
Built for the toughest quarry conditions
Fast cycle times
Get more done in less time
Sometimes, quarry operators need an extra machine to get a job done without the risk of a full-scale financial investment.
A rental hire can help quarries add the missing piece to their fleet without that risk.
Delta Rent operates one of Australia’s largest earthmoving equipment rental fleets, featuring more than 450 high-performance machines.
The company can provide quarry operators with complete fleet packages comprised of newgeneration, low-hour machines with an extensive range of attachments to suit their project specifications. Nothing in Delta’s fleet is over 6000 hours to ensure operators receive the latest and best equipment.
Delta Rent has some of the latest industry machines available for hire, including the HD785 and HD605 Komatsu rigid haul trucks, Hitachi and Komatsu excavators from 60t to 125t, and Hitachi Komatsu and Volvo excavators from 30t to 60t. Delta also has Hitachi excavators from 8t to 30t for smaller-scale jobs.
In line with an industry continuously embracing technology, Delta Rent’s fleet has full GPS tracking and telematics reporting supported by the OEM.
Delta Rent, committed to fast service, offers all customers round-the-clock support and transport and logistics support to relieve the pressure of organising machinery on-site.
For more information, visit deltarent.com.au
To submit new product and equipment releases, email: les.ilyefalvy@primecreative.com.au
For the past 100 years, Kleemann GmbH has been designing, evolving, and manufacturing machines for the mining, quarrying, and recycling industries.
As a powerful mobile cone crusher, the Mobicone MCO 90 EVO2 has been designed to overcome evolving challenges in different applications. An optimised throughput can be guaranteed for natural stone, recycled asphalt or river pebble applications, thanks to the machine’s design and flexibility. With the increasing demands that are placed on modern crushing plants, their complexity also increases. At the same time, the technology must be safe and as simple as possible to master – and without long training sessions.
This is the strength of the spective operating concept. The Mobicone MCO 90 EVO2 can be operated simply and intuitively with the various Spective components. Along with the touch panel, the holistic operating concept includes a Spective intuitive operating concept for a better result.
The Mobicone MCO 90 EVO2 also features the innovative D-Drive “dieseldirect-electric” drive concept and excels with its dynamic performance combined with low fuel consumption. The MCO 90 EVO2 stands out with its holistic drive concept with an efficient diesel-direct drive whereby the crusher is driven directly via a fluid coupling from the diesel engine.
The power and load-dependent fan ensures a low-noise and even more economical operation. The generator is driven direct by a cardinal shaft and the drive system pumps are activated via a clutch coupling, which can draw on the
full power of the diesel engine. All other hydraulic pumps are for auxiliary and set up functions and for the cooler drive are also driven via the gearbox.
The MCO 90 EVO2 can come in two configurations with either a large single deck 16’x5’ (4.87x1.52m) or a large double deck 16’x5’ (4.87x1.52m) post screen box and recirculating conveyor and mid fine product belt, creating a closed loop operation with the benefit of having two classified products on the ground or opt for it without the post screen box option making it an open circuit crusher.
For more information, visit wirtgen-group.com
As sustainability becomes increasingly important, Smart Quarry Site can help quarries reach their targets.
As requirements for ESG reporting become more stringent for many Australian businesses, including quarries, it’s important that OEMs continue to support their customers with data and insights that not only drive their business forward but also help them meet and track any sustainability metrics.
Komatsu Australia is strongly committed to environmental best practices and continuously focuses on reducing its environmental impacts and carbon footprint while supporting customers on the net-zero journey through research and development efforts, product support, and expert advice.
Aaron Marsh, national product and solution manager from Komatsu Australia, said it’s important the company meets the challenge of sustainability across all its sectors.
“Quarries are continuously working to extract aggregates, so machines need to be productive and efficient to meet production targets. But quarry fleets now also need to be
monitored to manage emissions, with some fleets not having the technology in place to support this or to see where they need to make improvements,” he told Quarry
“This is where systems like Komatsu’s Smart Quarry Site (SQS) can support fleet operators. It’s our innovative fleet management solution that focuses on five essential areas: site management, production optimisation, machine health monitoring, proactive maintenance and enhanced safety for quarry operations.
“It was designed to give a real-time overview of an entire quarry fleet, and caters to not only Komatsu equipment, but a wide range of other equipment types and various machine makes, making it the ideal choice for managing mixed fleets efficiently.”
SQS allows users to manage and review site carbon emission trends in approximately realtime. Marsh said the data aggregation from the site visualisation dashboards provides
information to site operators, managers, and executives on several measures.
“These include total accumulated fuel, footprint tonnes of CO2, average CO2 per hour, average CO2 per tonne and calls out CO2 by machine utilisation in working and idle hours, really focusing on the effective utilisation of quarry fleets. We also measure the emission trends and load and haul circuits by trucks to understand the emission impact of a particular circuit or material,”
reporting in the dashboard a quarry site can make changes to optimise fleet, pit, load and haul and focus on effective utilisation of the fleet especially around litre per tonne.
“This can lead to immense savings in fuel efficiency. In one of our customers sites, we have seen a measurable saving of 8.6 per cent on litres per tonne, which is equivalent to 81,000 litres of fuel and a CO2 saving of 217 tonnes over 12 months of operation.”
It’s vital for a quarry owner and manager to track material moved, as quarries have multiple benches and at time move multiple materials.
“Productive throughput to the crusher and ROM is critical, and SQS reports all of this in almost real time to the site allowing site managers to create targets or tonnes per hour KPIs, and act on them immediately,” Marsh said.
“Tracking where material is picked up and where it has been dropped off is also critical, and many of our customers are also running material hoppers and tracking there stockpile movements through SQS, giving them another level of data to track and understand their productivity.”
Marsh said that tracking effective utilisation is key and not all utilisation is the same.
“Simply increasing utilisation alone is not effective, unproductive cycles, inefficient operations and double handling all require more machine hours and higher fuel burn that can contribute to your emission trends and carbon footprint,” he said.
“Managing bottlenecks and stoppages is a thing of the past now thanks to SQS. To be able to see the fleet activity in almost real time allows the site manager to understand bottlenecks, activities and delays, with SQS
automating 95 per cent of this reporting and providing the visualisation to the user as if the quarry manager is standing right in the pit with the machines.
“At one of our SQS customer sites, the quarry management team, through this visualisation, decreased idle time on the load and haul trucks by ight per cent and the face loader increased utilisation by seven per cent, a significant effective utilisation increase.”
Komatsu’s expert team visits each quarry site before they start using Smart Quarry Site, to make sure the technology is set up to reach the right targets and troubleshoot any issues the users have.
“When you partner with Komatsu, you don’t just get the product, but a full-service solution backed by our team,” Marsh said.
“Newer quarry models, like our HD605-10, now come with SQS as standard, meaning quarry site managers and operators will have the technology they need to make smart, informed decisions at their fingertips.
“We want to make sure we are fully supporting our customers with solutions and insights right across their quarry site – whether that be metrics for ESG reporting, understanding their productivity levels or maximising their fleets to be more efficient and profitable.”
Komatsu is a platinum partner of the IQA 2024 National Conference in Adelaide from October 15–17. The Komatsu team at the conference will be able to discuss the benefits of the Smart Quarry Site and how it can benefit your quarry. •
For more information, visit komatsu.com.au
Precisionscreen has adapted its range to suit the growing need for mobile quarrying equipment.
Given the Australian geography, precoating equipment needs can vary from state to state and from the major aggregate players to the small, independent contractors.
However, precoating can be expensive, so it is imperative to do it as efficiently and effectively as possible.
Precisionscreen’s 3000 and 6500 Precoater models have been proven popular in South Australia, Western Australia, and the Northern Territory. Due to the nature of their work, more job sites in these regions need mobile equipment, whereas eastern states like New South Wales have a greater demand for quarrybased precoating.
Since the Brisbane-based manufacturer bought the two models to market, the industry needs in those regions have been in demand.
Jonny McMurtry, Precisionscreen’s chief operating officer, estimates the Brisbanebased company has sent eight to ten mobile Precoaters to South Australia, the Northern Territory, and Western Australia in the past 12 months.
“It’s been a consistent demand; it usually comes in waves, but it has been a consistent demand for those styles of machines and that type of precoating application,” he said.
“Those states west of New South Wales and Queensland focus more on mobile precoating. I think the distance between centres and capitals is probably one of the main reasons they do.
“The fact they can couple it up and conduct precoating by the side of the road or quarrybased precoating – whichever they need –makes it a particularly sought-after machine.”
Operators can use the Precoater 3000 and 6500 models for job-site-specific applications while maintaining quick and effective delivery.
The Precoater 3000 has an eight-by-fourfoot screen box, a 3000-litre tank, and a tail conveyor that can discharge over four metres. It has 12 individually controlled precoat spray nozzles across three bars attached to the tumbler chute. The 3000 model can deliver a consistent throughput of more than 120 tonnes per hour.
For those needing a greater capacity, the 6500 model offers a bigger build. The larger
model is equipped with a 6500-litre tank, a ten-by-five-twin-deck screen box, and a discharge point of more than four metres. It comes with more precoater nozzles (14), which deliver a greater throughput rate of more than 150 tonnes per hour.
Both models use PLC electronic panels and machine controls to make them easier for operators to control. Precisionscreen partnered with electronic hardware supplier IFM to upgrade the previous hydraulic controls. Operators can start and stop material flow remotely using these controls, and the equipped CAT engines have a shutdown function to ensure operator safety.
As an Australian-based manufacturer, Precisionscreen can modify the Precoaters to suit the customer’s requirements from its Wacol headquarters, including adding extra filters or modified spraying systems.
The the 3000 and 6500 Precoaters have earned plenty of repeat customers.
“Over the past four to five years, it has probably been a 50-50 split where we’ve had customers adding onto their fleet or replacing existing machines.
“But the last eight to ten machine sales over the past year or so, 50 per cent have probably been new companies where it’s been their first machine, and they’re entering this market.
“[The 3000 and 6500] cover both bases. If customers have bigger demands, they can lean towards the 6500, whereas the 3000 can still cover many applications and customer requirements , including high volume daily production, where needed.”
In addition to the 3000 and 6500 Precoaters, Precisionscreen’s Scorpion Precoater is an adaptation of the company’s Scorpion Reclaimer Screening Plant with an added precoating conveyor.
It is equipped with an eight-by-four-foot two-deck screen box, an onboard precoat chute, and an independent feeder belt with variable speed. The Scorpion Precoater’s specially designed chute allows material to be sufficiently tumbled and turned while the precoat nozzles coat the material quickly and efficiently.
“It’s a cost-effective way for quarry-based precoating to occur. It has all the same elements as our road-towable machines, the same Australian-designed screen boxes and all the fabricated framing, but it is a semimobile application,” McMurtry said.
“It achieves an adequate tumble and coating on your aggregate with the precoat liquid, but
it caters more to the companies coming to the quarries to collect the material.”
As the quarrying industry shifts and costs catch up with operators at all levels, some are looking at ways to adapt operations to be more cost-efficient.
Alongside this trend, Precisionscreen has noticed an increased demand for precoat attachment kits. These packages transform standard conveyors into precoater conveyors thanks to the hydraulically-driven precoat pump. It pumps the material to the tumbler chute, which can hang off most conveyors in the industry, where the material is coated quickly and efficiently.
McMurtry said the company can adapt the precoat kits to suit most conveyors with information from the customer.
“All of a sudden, you’ve got a quarrybased precoating conveyor from a preexisting conveyor that you might have already on site,” he said.
The company supports customers across Australia in achieving the most from their Precoater machines. Through a combination of its internal staff and state-based contractors, Precisionscreen has a network of experts to help quarry companies and contractors.
Precisionscreen will attend the IQA 2024 National Conference in Adelaide from October 15–17. •
For more information, visit precisionscreen.com.au.
Tecweigh’s latest conveyor belt scales are designed for weighing in all conditions in the quarry industry.
In an industry that needs tailored solutions and quick turnarounds, Tecweigh’s Australian advantage has shone through for the customers in the quarry sector.
The Australian manufacturer has been producing a range of conveyor belt scales, weigh belt feeders and volumetric feeders for two decades from its Melbourne headquarters.
Being an Australian-made brand ensures Tecweigh’s custom-engineered products can perform dynamic measuring in the harshest of conditions.
Barry Gamble, Tecweigh’s business development manager, said being a local manufacturer has allowed the company to keep costs down and ensure continued supply.
“We do all our manufacturing in Carrum Downs, Melbourne, which gives us a fast response time,” he said.
“We can normally deliver what the client needs within seven to 10 days.”
Dynamic measuring is a key component in the quarrying industry which helps relay accurate throughput information.
Without accurate information about how much material is being conveyed, monitoring, storage management and feed metering become incredibly difficult.
To ensure its products are reliable in Australia’s often-harsh conditions and provide accurate information, Tecweigh uses stainless steel, hermetically sealed IP68 load cells designed to provide accuracies of ± 0.5 or ± 0.25 per cent for its weigh belt feeders and conveyer belt scales.
The weigh idler system has been designed to be easy to calibrate to provide consistent accuracy.
Its weigh belt feeders can also be manufactured to specific lengths and widths, using powder-coated mild steel or stainless steel, depending on the application.
“Custom designs are our standard. Whether it is chemicals, crushed stone, sand, coal, or materials that are low density, sticky, or abrasive, we specialise in building the equipment needed to accurately weigh it,”
Gamble said.
“Our products are also designed for heavy-duty work and have been proven over time to be accurate in some of the world’s harshest environments.”
With more than 100 years of industry experience collectively among its employees, the company is continuing to look for new innovations.
The fact it is based in Australia means Tecweigh can also offer local after-sales support. The company maintains a significant stock inventory for its conveyor belt scales, volumetric feeders, and weigh belt feeders. It also offers field service support and spare parts supply.
From humble beginnings, Tecweigh has built its bespoke business to provide weighing-in-motion solutions for industries nationally and internationally.
The company has built a long-lasting relationship with its own local suppliers and aims to further grow in the industry. •
For more information, visit tecweigh.com.au
At 40 tons and over 30 feet long, safety comes first. By combining cameras, radar, and machine learning, obstacle intelligence gives operators eyes in the back of their head. To protect your crew, and other investments, like never before.
Returning for the fourth time, John Deere’s annual Technician of the Year Awards are set to recognise unsung heroes.
When Caleb Dover visited the Ulverstone Show in Tasmania as a young child, it set him on an award- winning career path.
For Dover, the day spent exploring the historic equipment in Ulverstone ignited a passion for restoring machinery, a journey that continues to this day, filled with pride and a sense of accomplishment.
He kept that passion as a young apprentice with Midland Tractors in Latrobe in Tasmania’s North West, where Dover was crowned John Deere’s inaugural Australian and New Zealand Parts Apprentice of the Year in 2021.
“At the time, when I was an apprentice, it felt like the pinnacle of my career,” he said.
“I care deeply about my customers, the John Deere brand, and making sure I always do my job to the absolute best of my ability, so winning the award and getting recognised for the care and effort I put in felt like a vindication of all that work.
“To this day, it still means a lot to me, and I look back on it as one of my proudest moments.”
Three years after that success, Dover has advanced his career and relocated to Western Australia, where he helps those in the Wheatbelt region as the parts manager for AFGRI Equipment in Wongan Hills.
While he may have moved to the other side of the country, his approach to the role is based on the same fundamentals that earned him award recognition three years ago. As he leads a team of four in the parts department, Dover has invested in professional development through John Deere University to expand his skill set.
“I’ve always focused on finding new solutions for customers, and this role allows me to do that,” Dover said.
“I enjoy having some younger people to mentor and encourage them to give that high level of customer service.
“My journey shows how you can end up in a management role in a completely different part of the country than you started because of the strong John Deere network.”
Caleb’s career journey and accomplishments are one of the many success stories that have emerged since John Deere launched its Technician of the Year Awards.
The awards recognise an Australian and New Zealand winner across several categories. The Service Apprentice and Parts Apprentice of the Year awards will be chosen from a combined pool of applicants from both countries.
In their fourth iteration, the awards will see finalists tested at John Deere’s Australian headquarters in early September before
the award night is held at a gala dinner on September 5 in Brisbane.
“This year, contestants will complete additional technical testing before they can move to the in-person testing at our Crestmead head office, and they must also hit specific training targets,” John Deere Australia and New Zealand director of aftermarket and customer support Emma Ford said.
“We want to ensure our technicians are best equipped to meet the needs of our customers and John Deere’s ever-expanding portfolio of equipment.
“Continuous investment in building capabilities is key to what sets a John Deere technician apart, so it’s important our awards program assesses both the technicians’ technical skills and their commitment to ongoing training.”
Nominations have increased by 30 per cent compared to 2023, with more than 130 technicians being submitted across the eight award categories.
“We’re incredibly proud to highlight the invaluable service they provide and the role they play in helping industries and communities thrive,” Ford said.
Dover encouraged technicians to nominate for the event due to its positive impact on his career to date.
“Winning the award helped build trust, respect, and a better relationship with our customers, and it helped people understand that the service we offered was among the best in the country. We had the certificate to prove it,” he said. •
For more information, visit deere.com.au
The Next Generation Diesel-Electric Mobile Jaw Crusher
The Lokotrack LT400J is a robust hybrid mobile jaw crusher ideal for primary crushing of hard rock and producing recycled aggregates. Its new diesel-electric power system and improved usability ensure maximum uptime, while its modular design allows for easy upgrades to meet evolving market needs.
For more information on the extensive range of Metso mobile plants, email us today at metso@tuttbryant.com.au!
Caterpillar’s VisionLink Productivity platform aims to ramp up quarry production by eliminating inefficiencies.
As a quarry manager or owner, it may seem overwhelming to oversee everything that happens on the site. They prioritise increasing material output and monitoring machinery to improve productivity and prevent downtime. However, the limited workforce means the challenges lie in managing these tasks effectively throughout the workday.
Caterpillar has created a solution to address these concerns and give quarry workers an accurate picture of what happens across their site.
VisionLink Productivity is a cloud-based platform that enables workers to see critical business insights, spot inefficiencies, and turn accurate information into ways to improve production and safety.
While workers can gather a wealth of data on the machine’s health, production levels, fuel burn, and idle time, VisionLink Productivity consolidates it all. It can be scaled across multiple quarry sites.
For businesses with multiple quarry sites, which run bigger operations with multiple fleets and job sites, seeing how an individual machine performs against the rest of the organisation is imperative to making informed decisions.
Using the VisionLink Productivity platform, managers can drill down into the data while getting a high-level overview of the operation.
“It allows your people to get a high-level overview of your operation and drill down to find the detailed information that you need to make the right business decisions,” a Caterpillar spokesperson said.
“VisionLink Productivity gives the decision maker an accurate picture of their operation and providing them with opportunities to implement change and make improvements to machine utilisation and operational efficiency.”
Quarry operations involve a lot of work, including extraction, processing, and transporting the material. Managers need to understand how long specific functions take, including empty and load times, site travel times, and dig and wait times, which are fundamental to getting the most production out of the quarry.
Caterpillar’s cloud-based platform tracks all of these measures and enables managers to spot inefficiencies, failures and bottlenecks on site from which they can produce better processes.
In one example, if a manager could track machine movement and see how long each machine spent in each part of the cycle, they could slow down machines in the return phase. This would reduce excessive wait times and needless fuel consumption.
“Being able to include your operators in this review, with powerful visuals including maps and graphs, allows you to work together to identify inefficiencies and find solutions,” a Caterpillar spokesperson said.
“Discussions like these – based on hard data – strengthen partnerships with operators. It facilitates objective,
Eltirus founder Steve Franklin looks at the past, present and future of digital transformation in Australian quarries.
In 2016, Eltirus collaborated with Fulton Hogan at the Stonemaster quarry near Brisbane as one of the early adopters of digital transformation.
Since that time, many of what were then novel ideas have become commonplace across the industry.
We thought it was time to revisit where things were, how we see things now and what the future might look like.
Site surveys were generally conducted once a year by aerial survey. The aerial survey companies determined site extraction volumes for royalty calculation purposes and not much else. Drone survey was in its infancy and regarded as little more than a novelty.
While geological drilling was conducted, there was very little done with the data. At best, cross sections were created in printed in paper reports and there was generally no way to correlate these to the field.
Most design work was conducted in either AutoCAD or Geovia Surpac. Getting accurate survey data to design with was incredible difficult – I remember spending a week manually editing the contours from a site flyover to try and create a surface to design to.
If software was used, it was generally to create concept designs or final pit shells (often without ramps).
Drone survey has tended to become ubiquitous. Companies are either employing drones themselves or getting contractors to fly their sites for them.
The focus tends to be towards drone survey for stockpile measurement, with a lesser number of sites flying “whole of site” on a regular basis. Where whole of site flights are conducted, they are generally not flown using a “terrain following” method, resulting in reduced accuracy where there are significant differences in elevation between the top and bottom of the quarry.
While drone technology is commonplace on many sites, we find that the results can be quite variable. While a whole of site survey can “look ok”, the reality is often very different, particularly if the site uses Ground Control Points (GCPs) to provide accuracy rather than high accuracy systems such as post-processing kinematic and real-time kinematic (RTK).
By way of example, if the site relies on GCPs for accuracy, it often only needs one or two of them to be moved or lost to destroy the accuracy in that area, resulting in warping that you won’t see unless you do a crosssection comparison or other quality check.
Most quarry companies do not have their own technical teams with many relying on a range of small consulting groups and independent contractors to perform these functions for them. This is often further
broken down at state and even site level such that there is not a consistent approach to data management. In many cases, consulting groups and contractors will have a more comprehensive set of data than the client. This is risky.
We have seen instances where an independent contractor has performed all of the geological or engineering work for a client over many years, only to get sick or go out of business and with it, went much of the client’s data.
Even worse is the fact that because work is conducted by multiple or independent parties, there is often a lack of consistency in conventions such as file naming or data structures. Not only does this increase the likelihood of errors and data loss it results in a level of risk that is unacceptable.
Where companies are creating their own technical teams, they are also facing the need to update their software. Advanced geological software such as Leapfrog Geo is a quantum leap when compared to past systems. Instead of manually having to add data and reinterpret models, new software allows for automatic addition and re-creation of models, saving hundreds of hours of work. Likewise, mining software programs such as Deswik.Suite can manage and manipulate massive point clouds, create and manipulate solids and automatically create quarry designs based on geotechnical and operational parameters.
These new generation software packages open up the opportunity to provide new insights, get work done faster and make it accessible to other stakeholders.
It is now possible to provide site users with complex extraction and geological models through web browsers that give new levels of access and insight and that facilitate collaborate between technical and field users and allow people in the field to provide real time feedback about what they are encountering to help ensure that technical staff are continually updated on developments and can update the models to increase both their accuracy and relevance.
Given the free AusCORS network widely available across the country, we see this ultimately displacing paid RTK services and sites relying on GCPs.
We also expect to see a rise in “drone in a box” technology as the issues around flying beyond line of site are resolved.
The key thing we see as important is providing better, more consistent access to data for decision making.
Whether you choose to work with external partners or build your own technical team, putting in place the workflows, approvals, data structures, file naming and colouring conventions is vital. We see these systems being setup in such a way as to provide secure access to all relevant stakeholders who need access to it – internal or external.
The types of data that we expect to see centralised:
• All geological drill hole and sampling data with relevant test results attached and accessible by the relevant geological modelling systems.
• Geological modelling systems that contain all the different geological models for each site and the different versions and interpretations of these.
• Optimised pit designs and stages for each site.
• Detailed designs for each site and the related survey files for consumption by 3D machine guidance, drill rig hole navigation systems, autonomous equipment
In all instances we would also expect to see systems that logged who added/changed and edited data to ensure that there is a clear chain of responsibility of action.
MDM is a good example) will also include approvals workflows and the attachment of all relevant unstructured documents to them. These systems already exist in the mining industry and could be re-purposed for the construction materials industry.
While there is a lot of discussion about AI and its potential impact on the industry, we see it following hand in glove with work carried out to sort out data management first.
For example, we have a knowledge base of some five hundred articles detailing how we do our work. This is probably our greatest asset and we spend a considerable effort on creating and maintaining it. The opportunity to access this knowledge through an AI engine which can also potentially look at how we have done similar jobs and studies in the past will be game changing.
Likewise, where it could look at geological data in one quarry and consider similarities or problem-solving approaches from other sites might result in substanital gains.
Note that the key thing is bringing the data together and in a consistent fashion, if the true value of it is to be realised.
One of the greatest advances that will occur is around resource optimisation to maximise net present value (NPV). Tools such as Deswik.GO can consider the pit shape and extraction sequence as determined by cost and revenue, geological and geotechnical data, mining rules and capital requirements, bringing a substantial difference to pit design
and scheduling – in fact, it’s a quantum leap and deserves considerable attention at COO, CFO and board level
The ability to be able to clearly determine the amount of material needs to be stripped and when can improve resource NPV by 2040 per cent. It also provides accurate stage shells for effective scheduling (the absence of which is a primary barrier to this activity) and help ensure that critical supply contracts can be met and reserves better understood.
As we gain access to more and more data systems, whether they be machine telematics systems, weighbridge, environmental and
Operational data reporting systems like Eltirus Enable help to bring together all the different types of data into a cohesive whole and provide an “executive summary”. This is invaluable not only for providing that overview of critical forward-looking metrics, but also to provide a clean, comprehensive and collated data set that can then be effectively utilised by machine learning and AI tools.
Autonomous operation is all around us and has been for many years. While there is much discussion about whether you could trust to drive a manned vehicle in an area where autonomous haulers are in operation, we forget the fact that every time we fly in a commercial airliner, the vast majority of the flying is done by the aircraft itself – including landing. By way of example, auto-land technology has been around since 1968, and I can’t remember anyone expressing any concern about this before getting on a plane. Likewise, we see driverless trains and an increasing number of machines on quarries that provide a level of autonomous service. These comments are in no way to ignore or play down potential safety concerns, but more to say that we have solved similar, difficult autonomy problems before and with an extremely high level of safety and can likely solve this one too.
Innovation is the future. There are exciting developments in hand and on the way – make the most of them.•
For more information, visit eltirus.com
Meet the XD Series of heavy excavators – designed to tackle the toughest challenges. From Australia’s best-selling heavy excavator brand, the SK380XD and SK500XD represent the pinnacle of Kobelco’s legendary reliability, fuel efficiency and productivity.
Featuring a rugged machine body, and reinforced boom, arm and undercarriage to conquer the most punishing of worksites around the world, these machines deliver the lowest total cost of ownership in class.
XD Series. Built for power. Built for reliability. Built to last.
Shortages of quality natural sand are creating headaches for the concrete industry, but Kayasand believes quarries can provide the solution.
Sand remains a key component of concrete – but keeping up with demand is increasingly difficult.
In 2022, the United Nations Environment Programme (UNEP) called the global sand extraction rate “unsustainable”. The group urged for sand to be considered a “strategic resource” given its importance to construction and the environment.
“If we can get a grip on how to manage the most extracted solid material in the world, we can avert a crisis and move toward a circular economy,” Pascal Peduzzi, director of GRIDGeneva at UNEP, said at the time.
Not all sand is created equally, and the amount of sand required compared with the
Frank Grech, Kayasand’s national sales manager, told Quarry that there is another proven way.
“I have been in the industry for a long time,” he said. “When natural sand was readily available, there was no reason not to use it.”
“But now it’s getting much harder to access while demand is getting higher and higher. There’s also been a lot of publicity about the scarcity of quality natural sand, which is bringing it front of mind for people.”
Kayasand’s solution to the growing demand for quality concrete sand is its V7 engineered sand plants.
The specialist crusher and air screen technology was originally developed by
In fact, in a recent concrete trial with a normal Auckland mix design, sand engineered from Greywacke-based crusher dust was used to replace 100 per cent natural sand. The resulting concrete proved to be 24 per cent stronger and used 10 per cent less cement.
Grech said the final product is a concrete technologist’s dream.
“You don’t need to blend the product – it comes straight out, ready to go,” he said.
“That’s because we precisely control the shape and size of the sand particles, the levels of contaminants and consistency of the final product. Not only does engineered sand make the concrete mix stronger, but it also needs less cement to do it
Kayasand’s process can be meticulously controlled to meet certain specifications, if required. This also helps to improve the pumpability and finish of the final concrete mix.
In 2023, the company received a $3.5 million investment from New Zealand Green
The company has invited major aggregate suppliers to test out the plant to see if the
crushing technology could provide the right solution. One Australian supplier sent 40 tonnes of aggregate to the plant in New Zealand as a high volume trial.
Grech said Kayasand plans to expand across Australia and New Zealand.
“People are realising the full potential of what’s on offer, and that quarries play an important part in meeting the growing demand for concrete sand,” he said.
“The industry has been using concrete for a very long time. It allows builders to create versatile and durable structures – it’s even being used in 3D printing and precast construction.
“We want to help the industry innovate and believe quarries are part of the solution to meet the growing demand for concrete sand. We have the plant and equipment to help. Our technology is proven and it’s already out there in the market being used.” •
For more information, visit kayasand.com
Komatsu is known for its machinery but also makes reclaim feeders for the quarrying industry.
Reclaim feeders are proven technology used to process and transfer material off-site.
Reclaim feeders are suited for continuous haulage. Their adjustable flow gates enable materials to transition from loading to discharge, and operators use variable-speed drives to manage the material flow to a downstream area such as transportation.
Komatsu has designed its reclaim feeders to be ideally suited to the quarrying
sector, with a range of features and an advanced control system.
Quarry owners are constantly looking to reduce maintenance, material waste, and energy costs while maintaining productivity to a maximum level. As a result, Komatsu’s critical aim is to balance costs against productivity.
According to the company, its reclaim feeders have an average in-service life of more than 20 years. Komatsu has used steel
components in a simple and effective design to maximise the durability and reliability of the reclaim feeder.
The Stamler RF-5 reclaim feeder can accept pre-engineered bolt-on/plugin options and upgrades to maximise performance. It also features modern safety features for on-site operation to keep operators safe, including emergency stops, covers, guards and screens. These minimise the operator’s contact with moving parts during operation and maintain a high level of safety.
When Komatsu designed the Stamler RF-5 reclaim feeder, it kept this front of mind and ensured its advanced control system, the Komatsu LINCS II package, could provide the data to achieve this goal.
Operators can use the LINCS II interactive touchscreen display to access real-time information, including power consumption, component condition, conveyor speed, and
service intervals. The data is displayed in a customisable dashboard and graphs that can be tailored to the quarry’s goals.
Operators and quarry managers can use this information to adjust performance to suit the applications and conditions. They can use remote access to control the machine and check machine health through the onsite network using a tablet or smartphone.
As operators and quarry contractors look to more versatile machinery, mobility has become a key feature of many machines. Komatsu’s reclaim feeders are no different. They are designed to be transported from site to site and handle a variety of applications,
ranging from aggregates to limestone and sticky materials.
Komatsu’s versatile machines are suited to Australian quarries, offering reliability and flexibility. With Komatsu’s focus on minimising the total cost of ownership, quarries can now purchase efficient material handling equipment they can truly rely on.
Komatsu will participate in the IQA 2024 National Conference in Adelaide this October, providing a platform for customers to explore its range of reclaim feeder in more detail. •
For more information, visit komatsu.com/en-au
When mobility and toughness matter, count on the Lippmann 300c and 400c. These mobile cone crusher plants were specifically designed to take on the most abrasive and toughest materials in aggregates and mining — all with mobile capabilities. Heavy duty cone crushers with an innovative material flow that maximizes capacity and throughput while delivering a consistently high quality product.
• MC400 High Speed Cone Crusher
• CAT C18 Engine
• Direct Drive
• 250mm Feed Opening
T: 1300 859 885
E: sales@triconequipment.com.au www.triconequipment.com.au
Effective and efficient.
The MDS M515 Heavy Duty Trommel excels at crafting rip rap and reclaiming rocks entangled with clay and other adhesive materials. Comes complete with fold out stockpiling conveyors and has four hydraulic jacking legs to raise the machine to increase stockpile capacities and lower for transportation. See triconequipment.com.au or call 1300 859 885
Superior’s Telestacker® Conveyor is a material handler’s most effective weapon against costly stockpile segregation. Its variable height, length, and axle positions allow for layered stockpile construction, which is key to achieving partially and fully desegregated piles. The design has been carefully fine-tuned for hard work and dependability in numerous applications. Call Tricon on 1300 859 885 or see triconequipment.com.au
Quarry sat down with Andrew Rankin, quarry manager at Boral Wollert, to see how the XMOR bucket is performing after one year.
After more than 12 months with the unique excavator bucket, Boral Wollert quarry manager Andrew Rankin was clear on the performance of the XMOR Bucket from ONTRAC Group.
“I had some doubts initially, as with anything you trial, but it’s been really good,” he said.
“And it’s been on some of the hardest rock as well. While it’s been on some of the softer stuff when it’s been on overburden, some of the rock we’ve been dealing with and the conditions, it’s been dealing with a lot of oversize; it hasn’t been all good digging.”
Boral’s Wollert Quarry is located about 30 kilometres from Melbourne CBD. Its materials supply some of Victoria’s biggest projects, including the North East Link.
In the 2023 August edition of Quarry, Boral confirmed a 45 per cent increase in bucket capacity in cubic metres since switching to the XMOR Bucket.
“I can tell you that it is using less fuel, the operators feel more comfortable with that bucket on it than a standard bucket digging, it’s more productive – we’ve done the numbers on that and they still stand up. And it’s probably more productive, like I said, in overburden or bulk density material,” Rankin said
While the quarry has seen benefits from the XMOR in its hard rock activities, it has found significant advantages from the bucket when it removed overburden.
“When you’re bulk digging overburden, that’s when you notice the major benefits … that’s due to the density of the product. With the hard rock, we’re still getting more capacity [compared to] a standard bucket, but stuff like sand, clays, all those materials, that’s where you get the full bang for buck out of the weight of the bucket,” Rankin said.
Rankin said that shots can vary from brickette size to larger sizes on site at Wollert and confirmed that a good blast allows them to maximise the XMOR Bucket’s performance up to 40 per cent increase in tonnes per hour output as an isolated loading tool.
“The feedback from operators is still good. They haven’t got the drag through the rock, which is harder on operator and machine [because] with the XMOR Bucket on, you haven’t got the surface contact area on the bucket that you’re scraping over when you’re digging shot rock, so it’s definitely smoother,” he said.
“As soon as you put a traditional bucket on it or they get on another machine, they comment that the machine is working harder and it’s harder on them. If you look at ergonomics in a machine, some of those are all around an operator and how he feels in it, so that’s a win in itself.”
The XMOR Bucket’s unique inverted tub and heel segment design enables it to have a greater capacity than a standard bucket whilst also reducing downtime.
Rankin said that the XMOR Bucket when compared to a traditional bucket, does not shy away from anything that a standard bucket would do. “I would say it’s better, it’s just the repair I was concerned about over the long term, but it’s passing that test.”
“To be fair, I expected that we’d get repair work on that design and probably on the keel, that always seemed to me the place that we’d have issues, and it has, but nothing major.”
“There’s no wash, hardly any there, which that’s one of the benefits of that buckets as well, and usually you need 12 months to identify that”
Rankin has been happy that the bucket’s unique design has enabled it to maintain its increased capacity. Other buckets can require the addition of another skin, which reduces capacity and increases the bucket’s weight.
“Generally, repair work on a standard bucket is building a skin in, or you do something, and you reduce volume again and add more weight to it. So, it would be comparable or maybe a touch better in the overall,” he said.
This is due to the high-quality Hardox 500 Tuf and Strenx Performance steel, which delivers high performance while ensuring a lower weight and flexibility compared to
standard buckets on the market.
“I had a manager say to me, ‘Oh, it looks flimsy’ I said, ‘Yes, it’s not though, it’s around that design that the strength comes from’. If you just look at it, it does look light, but it’s proved itself, definitely here.”
“Again, the whole bucket, if you can buy in in parts, that’s great. We haven’t had to do a side or a floor in it yet, which is great, but we’ve had some minor repair work done in that area, which isn’t unusual.”
As an Australian-owned and operated company, ONTRAC Group is the exclusive manufacturer and distributor of XMOR Buckets in the country and has the capability to provide full support in its facility.
The XMOR bucket’s benefits are still holding true since Quarry last spoke to Rankin 12 months ago.
“It’s been really good. We’ve had no problems getting parts for it or anything like that, and that can be an issue when you try
something new, and that was something I thought about initially,” he said.
“But there’s been no problems with that.”
After seeing how well the bucket performs, Rankin has recommended the product to other quarry managers.
“Other Boral sites have called me and managers from New South Wales, and I have recommended it. Especially the sites with the lower abrasion rates and the like,”
Rankin said.
Rankin said he had no regrets about the purchase of the XMOR Bucket which had helped Boral Wollert’s operations.
“Cheaper is not always the best, I’ve always been a big believer in let’s measure apples with apples,” he said.
ONTRAC Group will be at the IQA 2024 National Conference in Adelaide from October 15–17. The company will have team members at its stall to discuss what the XMOR Bucket could achieve on a site. •
For more information, visit ontracgroup.com.au
Quarry learns how Kobelco’s biggest production-class digger is helping quarries improve their productivity.
Designing quarrying equipment to be tough is an important part of the job. After all, if machinery breaks down, production stops.
But the team at Kobelco knew its largestever production-class excavator needed to be more than just tough. It needed to survive the worst a quarry could throw at it.
Mark Johnson, Kobelco Australia’s general manager of product and distribution, told Quarry that the SK850LC-10 is designed for the harshest conditions.
“Kobelco manufactures excavators for markets around the world,” he said. “That means we needed to design the machine to handle some of the most extreme conditions out there.”
The SK850LC-10 soon proved it could handle the harshest climates around the world and was well suited for work sites across Australia. Kobelco saw great potential for the excavator in quarry applications.
“Quarries generally have an asset lifecycle in mind when they purchase equipment and want to know that the product they buy will remain productive and efficient for that entire life cycle,” Johnson said.
The SK850LC-10 features a 12.9L turbocharged and intercooled 380kW engine, which delivers impressive power to tackle heavy-duty applications. Powerful bucket breakout force and arm tearout forces let operators deliver fast digging cycle times and outstanding productivity.
The massive machine can climb stockpiles with ease, thanks to its class-leading 653kN of drawbar pulling force. Three heavy-duty track guides are also installed on each crawler side frame to further increase undercarriage durability.
But what Johnson said surprised quarry customers the most about the excavators was its fuel efficiency.
“The SK850LC delivers an impressive average fuel consumption of under 50L per hour—substantially boosting operating profit in a production environment,” he said.
“Compared to similar machines of this size, that’s potentially a saving of 20L of fuel an hour. When you consider these excavators will be working long days, week on week, that’s potentially saving customers hundreds of thousands of dollars a year just on fuel costs.”
An enhanced hydraulic system design minimises hydraulic pressure resistance to reduce energy loss. The SK850LC also features Kobelco’s latest cooling system – a hydraulically-driven twin fan engine cooling system.
This hydraulic version also prevents over-cooling by use of integrated sensors to reduce the speed of the twin-fan unit, helping to improve fuel economy and reduce noise. A variable-geometry turbocharger contributes to lower fuel consumption, and a new selective catalytic reduction system decreases NOx emissions by 80 per cent to provide low operation emissions.
The operator can also choose from three modes: H-mode, S-mode and ECO-mode— allowing for minimum fuel consumption while optimising digging efficiency.
From the comfort of the cabin, the operator can also pre-set multiple attachment settings. The SK850LC comes factory equipped with bidirectional primary auxiliary hydraulics, along with proportional hand-controlled tilt/rotate piping and quick hitch piping as standard.
Johnson said the SK850LC features best-inclass lifting and digging performance.
“With the 8.25m and 3.6m heavy-duty boom and arm, the SK850LC has an operating capacity exceeding 10.6 tonnes at a reach of 11.6m.
“The SK850LC is also available in a mass excavation specification, with a shorter boom and arm as well as an optional heavier 3000kg counterweight—for applications which call for maximum bucket capacity and digging productivity.
“The larger machine lets quarries move more material and uses less fuel, improving the bottom line drastically.”
Comfort is another key part of productivity. Operators who dread getting into the cabin are likely to perform worse, which is why Kobelco prioritises ergonomics.
Because there can be a lot of vibration on a quarry site, the SK850LC features an air suspension seat. Combined with a 25 per cent reduction in lever control force, operators face less fatigue during long hours
of operation, while added climate control outlets and a spacious cab interior provide a comfortable work environment.
The high level of pressurisation in the large, sealed cab keeps out dust and ensures a quiet environment for the operator. A standard 12V port and AUX jack are provided, while the standard Bluetooth-integrated stereo system allows the operator to stream audio.
The operator-friendly colour multi-display LCD screen uses easily recognisable graphics for quick navigation of important information, including fuel consumption and maintenance intervals. An intuitive one-touch attachment mode switch lets the operator confirm the proper configuration at a glance.
A falling object protective structure top guard along with a front window guard and swing flashers come standard for enhanced jobsite safety. In addition to the rear-view camera, an optional right-side camera can be fitted, for easy safety checks around the machine.
Johnson said maintenance is made easy to ensure the machines can get back to work as quickly as possible.
“The new and improved hydraulic fluid filter in the SK850LC is regarded as the best in the industry, with a new cover that prevents contamination even when changing filters,” he said.
“Pressure sensors at the inlet and outlet of the hydraulic oil filter monitor pressure differences to assess filtration performance,
triggering a warning on the cab display screen if the filter needs to be replaced.”
A standard onboard grease gun on a retractable reel makes greasing the SK850LC a fast and convenient task. Kobelco has also installed a standard onboard refuelling pump to make the process faster and safer.
To further improve machine uptime the SK850LC is equipped with Kobelco’s K-Assist system. This remote diagnostic and troubleshooting system allows local dealers to provide advanced support for the machine without a technician being present.
The system monitors key system operational data, which can provide real-time and historical monitoring of the engine and hydraulic systems. The system enables a
Kobelco dealer to perform diagnostic testing and upload machine software, significantly reducing potential machine downtime.
“Our dealers are second to none,” Johnson said. “We have a large footprint throughout Australia, with a presence in every state and territory,” he said.
“They have factory-trained technicians and access to our national parts division, with more than $20 million worth of spare parts available.
“Last year, Kobelco was the top heavy excavator supplier in Australia – it was an enormous achievement and we are striving to continue this growth.” •
For more information, visit kobelco.com.au
At Kinder, we understand productivity.
Our engineers are experts in innovation with the ability to design bespoke solutions and provide products to suit all conveyor applications.
Selected to increase your efficiency and reduce downtimeIf it’s above, around or below the belt, we have the answer.
Unlock your productivity potential. Visit kinder.com.au
From its beginnings in the Victorian goldfields to its international presence today, Orica’s journey has been driven by innovation and excellence.
Jones, Scott, and Company began selling explosives in the Victorian goldfields in 1874. While the gold rush is long past, their small company, now called Orica, is one of the world’s leading mining and infrastructure resources companies.
When it comes to legacy, Orica’s impact can be seen in spades. From innovating across the quarrying and heavy industries through to the build of Australia’s first skyscraper, and the world’s first lead-free detonator, Orica has a rich and impactful legacy.
Sanjeev Gandhi, managing director and chief executive officer for Orica, said the 150th anniversary was a “significant occasion” for the company.
“Orica’s legacy is built on the trust our customers and partners place in us, and the
operators, business specialists, and onsite crew to support customers in mining, quarrying, construction tunnelling, and many other sectors.
worked for Orica for 29 years. In his current role, he serves as the territory manager for Orica’s metals team.
as the Australian branch of the British-based Imperial Chemical Industries (ICI) following mergers with Nobel Explosives and then ICI. As a trainee MMU operator in ICI Quarry Services in 1995, Whackett was part of a team that had seven employees at Beenleigh. Now, the Beenleigh site has 50 staff, while Whackett looks after the operations of Orica’s Queensland and Tasmanian plants as well as its commercial contracts in those states.
within the company, he believes two things have turned it into an international success.
did those years go? I have always enjoyed working for Orica and I think that is why the time has flown past. I regret that I did not start earlier with them sometimes.”
1984 to 1987, and Michael Deeley are credited with influencing the company’s culture. They ensured employees were heard by executives, including initiating town hall meetings.
the company, Hampson credits the focus on employees with making the company more “customer-orientated,” as ICI Australia took great care of its customers.
Australia. ICI Plc sold 62.4 per cent of it in 1997 and then the following year sold its global explosive business to Australia. In 1998, ICI Australia was listed on the Australian Securities Exchange (ASX) as Orica.
These two moves created the foundations for Orica, which many people would recognise today as an international presence in mining, quarrying and many other sectors.
improve the efficiency of their drill and blast operations while reducing overall costs. It allows quarry operators to design blasts according to performance objectives and presents drill and blast insights for continuous blast optimisation.
According to Whackett, the company’s embrace of technology in its innovations has been a key to its current success.
“I think ANE-based bulk explosives and electronics have been the two big important innovations. ANE bulk explosives make loading blasts with wet holes a lot easier and quicker and produce more consistent results, rather than using ANFO (Ammonium Nitrate Fuel Oil) and packaged products, like we used to back in the day,” he said.
“Blast pattern expansion combined with using ANE, mean lesser drilling and lower costs. The timely accuracy with electronics makes it easier to comply with Environmental restraints which means we can do larger blasts at these quarries to reduce the cost for the customer.” 4D technology takes bulk explosives to a whole new level and has revolutionised how customers blast compared to conventional solutions. The 4D bulk system allows for a tailored application of explosive energy, adjusting to the specific geology of each hole. This customisation reduces bulk explosives consumption, optimises fragmentation, and supports compliance and licence to operate in environmentally sensitive areas.
Since becoming Orica almost 30 years ago, the company has grown to serve more than 100 countries worldwide and has a market capitalisation of $9 billion.
It is focused on working with its customers and stakeholders to help transition
to net-zero operations through the advancement of technology.
“I think Orica will keep growing, helped by all the digital offerings we have now and the innovation of wireless blasting with WebGen,” Whackett said.
Broomhead said the Orica’s milestone was a “testament” to the company’s values.
“As we celebrate 150 years, we look back at a story of resilience, innovation,
and the unwavering commitment of our people,” he said. “Orica’s 150th milestone is a testament to the company’s strength, adaptability, and ability to thrive in a constantly evolving business landscape.” Orica will be attending the IQA 2024 National Conference in Adelaide from October 15–17.
For more information, visit orica.com
• Throughput rates up to 2,500 t/h
• Used extensively in the cement, aggregate and recycling industries.
• Capable of handling material up to 3m³
• High reduction ratio.
• Designed for economic processing of soft, medium-hard or hard rock.
• Modular system
• Feed sizes up to 450mm
• Reliable production up 700 t/h
• Designed for economic tertiary crushing of hard rock.
• Modular system
• Feed sizes up to 150mm
• Reliable production up to 160 t/h
• Production of crushed stone fines and high-quality stone chippings.
Find out what innovative features Volvo’s range of articulated dump trucks use to improve safety and productivity.
In the high-stakes world of heavy-hauling and opencast mines, the performance and reliability of an articulated dump truck (ADT) can spell the difference between success and failure.
Recognising this, Volvo has designed its range of ADTs to meet the rigorous demands of off-road terrains while maximising haulers’ stability and payload capacity.
Volvo’s ADTs offer some of the highest payload capacities in their class. Its range of models from the A25G to the A60H provides diverse options tailored to meet specific operational needs, ensuring optimal performance across various applications.
Part of this performance is due to the trucks’ articulated design, which allows for better weight distribution across the axles. This enables the truck to carry more without sacrificing stability or manoeuvrability.
They also feature a robust chassis design, with a strong, durable frame that can handle heavier loads without compromising structural integrity. The body itself is optimised to maximise volume, while onboard weighing system technology ensures optimal loading for each cycle.
Volvo articulated dump trucks feature a robust drivetrain specifically engineered for heavy hauling. This includes a high-
performance, low-emission Volvo diesel engine with electronically controlled fuel injection, ensuring low emissions and high performance. The drivetrain components are meticulously matched and designed for hauler applications, optimising power, and efficiency throughout the work cycle.
The trucks contains several innovative features, including:
• A dynamic drive system that adjusts gear shifting strategy based on payload and slope gradient, automatically selecting the best gear for maximum efficiency.
• The Volvo engine brake system controls downhill speed without overusing the brakes, improving brake life, and enhancing safety.
• Adaptive suspension that automatically adjusts to payload and ground conditions, improving stability and comfort.
• No -slip, no-wear differential locks that can be fully engaged when necessary, ensuring excellent grip in all conditions.
• High ground clearance, allowing the truck to navigate rough terrain more easily.
Volvo’s ADTs are equipped with features that enhance the operator’s safety and
ensure the well-being of pedestrians and other site users.
For example, Volvo allows operators to set safe dumping parameters based on the truck’s side inclination, preventing potential tip-overs during dumping operations.
Cabs are designed to meet roll over protection structure and falling object protective structure standards.
An intelligent speed adaptation system displays speed limits for the specific vehicle combination, helping operators maintain safe speeds.
The safety features are the result of more than 50 years of accident research and analysis. Integrating these advanced safety systems underscores Volvo’s commitment to achieving zero accidents.
Volvo ADTs are engineered to excel in the most challenging off-road conditions, ensuring high performance and reliability across diverse terrains.
These trucks can easily navigate steep inclines, uneven surfaces, muddy conditions, and loose terrain, maintaining high productivity and stability where conventional rigid dump trucks often struggle.•
For more information, visit cjd.com.au
Liebherr’s wide range of machinery enables it to meet all the challenges a quarry can face while delivering productivity and efficiency.
Liebherr has designed a range of modern, economical, and efficient machinery by balancing the quarry industry’s power requirements with technological advancements.
The company’s ability to produce innovative designs and major componentry in-house has led to the creation of crawler excavators, wheel loaders, articulated dump trucks and dozers.
Quarry looks at the key machines within the Liebherr machinery portfolio that make a difference to the quarry industry.
Liebherr’s L 550 XPower – L 586 XPower wheel loaders are ideal for high capacity handling.
Liebherr-XPower is a complete, innovative machine concept that sets new standards in terms of fuel efficiency, power, robustness and comfort. The power-split travel drive combines the hydrostatic drive, which is optimal for short loading cycles, with the mechanical drive, the advantages of which come to the fore when driving long distances and also driving uphill.
The XPower range is designed to achieve machine efficiency and productivity across all terrains and distances. Fundamental to this is the Liebherr-XPower driveline and Liebherr-Power-Efficiency. According to Liebherr’s data, the combination of these two features results in up to 30 per cent less fuel consumption. At maximum handling capacity this reduces a quarry’s operating costs and improves their productivity and profits.
The modern ergonomic cab design provides the operator with maximum comfort enabling him to concentrate on accurate operation for whole working period, which once again means more safety and productivity. The Liebherr control lever, which is built into the operator’s seat as standard, allows precise and sensitive control of the machine.
The TA 230 is one of the latest articulated dump trucks from Liebherr. This powerful all-terrain machine is specially designed for efficient use in the quarrying industry and for overburden transport. It was subjected to Liebherr’s rigorous testing, including test trials, to ensure the componentry and parts met the company’s high standards.
without blind-spot-inducing pillars and the short, sloping engine bonnet, the machine operator always has an optimum view of the machine’s driving, working and articulation areas from the operator’s cab. A rear camera is integrated into the touch display, providing a clear view of the area behind the vehicle.
The model features a powerful drivetrain, reliable traction control, and solid axle suspension, which allows it to handle any terrain. The machine can remove up to 28 tonnes of material per loading operation with a maximum dump box capacity of 18.1 m³. Under the bonnet, a 6-cylinder construction machinery engine with 12 litres displacement and 265 kW / 360 hp capably does its job. The machine has a top speed of up to 57 km/h in forward travel and up to 16 km/h in reverse. Since the machine will be largely exposed to abrasive materials in punishing quarry applications, Liebherr offers optional equipment to minimise wear and tear and extend the vehicle’s service life.
The six-cylinder Liebherr construction engine is emissions Tier 4 Final, while meeting modern specifications, the Liebherr D956 engine achieves power and efficiency.
Operator wellbeing is front of mind for Liebherr, which is why the TA 230 is equipped with spacious cab, various storage areas, clearly and intuitively arranged control elements, as well as staggered steps and a generous driver’s door. Liebherr shock absorbers on the front axle and the viscoelastic suspension on the cab also optimally absorb the vibrations that occur in tough quarry operations, thereby increasing driving comfort. The soundproofed operator’s cab reduces the interior noise level to just 72 dB(A).
More importantly, the lighting and visibility concept of the TA 230 ensures optimum visibility and safety – both for the machine operator and for anyone working nearby. Thanks to the excellent all-round glazing
The travel path and working area are illuminated by LED low beam headlights with integrated high beam and extra powerful LED headlights on the front of the cab. This innovative lighting concept creates optimal conditions for working in the dark. At the same time, it ensures that the machine is always clearly visible to everyone else on the construction site. The lighting at the rear of the body and another light package on the mud guards ensure optimum illumination of the manoeuvring areas at night.
Liebherr offers numerous, modern driver assistance systems that support the machine operator and thus increase productivity and safety. For example, the innovative weighing device, which is installed as standard, records the loaded weight in real time. During the loading process, the current payload is shown on the display in the operator’s cab, and all collected data is displayed in LiDAT, Liebherr’s data transmission and location system.
With the weighing device, optimal loading of the machine can always be ensured, its productivity measured and at the same time overloading of the machine components can be prevented. In addition, the speed maintenance assistant, also fitted as standard, limits the truck’s maximum travel speed. Activated via a button on the retarder lever, the system monitors the current speed when the accelerator is pressed and automatically adjusts it to the set value. When driving downhill, the vehicle decelerates automatically using the engine brake and retarder. The standard Hill Start
Assist intelligently regulates the starting torque and thus eliminates the risk of rolling backwards on slopes.
In an industry that deals with harsh and heavy rock, using a dozer with high penetration and force can be a gamechanger. The PR 756, PR 766 and PR 776 are the headline dozers from Liebherr to meet the industry’s requirements.
Designed for a range of applications, from powerful ripping excavation to shifting heavy material, Liebherr’s dozers balance performance and economy.
The PR 756, PR 766, and PR 776 have operating weights of 40, 50, and 70 tonnes and a hydrostatic drive designed to deliver
the engine force required to get material loose and moving without slippage.
The dozers use Liebherr’s latest diesel engine technology. The engine’s low speed ensures fuel savings and a longer uptime even in the harshest working environments. The hydrostatically driven cooling fan and separate hydraulic oil cooler help provide reliable engine cooling and reduce needless fuel consumption wasted in extended warmup and cooling situations.
The cabin is integrated with a roll-over protection system and falling object protective structure protection to maximise worker safety while operating in the quarry. Its spacious design provides the operator with an all-around view of the work site, which provides peace of mind during the work day.
Liebherr designs its excavators based on one key principle: to maximise power while improving the efficiency of individual parts, ensuring optimum serviceability and minimum downtimes for machines. For Liebherr, protection of the environment is one of its guiding principles for a long time. Environmentally-configured power regulation of the hydraulic system and engine performance optimises the fuel efficiency of the machine to match the quarrying application. The automatic idling system reduces engine speed when the machine is stationary, and if less power is required, “eco mode” can be selected on the control panel to reduce the engine load, further improving the fuel efficiency and reducing CO₂ emissions.
Liebherr’s reputation for providing robust and reliable components is fundamental to the company’s fulfilment of this principle. The stick and bucket cylinders, which provide a higher breakout and digging force, are reinforced with internal protection, which results in a longer service life.
Liebherr excavators can be serviced from one side, with easy access to the key service points, ensuring more time is spent in the quarry than on maintenance. •
For more information, visit liebherr.com.au
Pinnacle Hire’s range of dewatering, pumping and water treatment solutions are helping businesses across Australia tackle key pain points.
In Western Australia, a mining operation faced a significant headache with its expansive on-site sedimentation pond.
The mining company wanted to manage the sedimentation safely, but it did not know where to begin. The project would be no small feat. The sedimentation pond measured 126 metres by 126 metres, with an average depth of three metres, and a slurry volume of approximately 29,392m³.
After exploring its options, the WA-based mining company engaged Pinnacle Hire to design and install a solution that would not only manage the sedimentation but minimise any operational disruptions.
Established in 2021, Pinnacle Hire has supported quarry, mining and civil construction clients manage their water. Since its establishment, the company has successfully delivered more than 2032 projects across five states in the past two years. With this range of project experience to draw upon, Pinnacle Hire highlighted three key issues the WA-based operation faced.
The site’s sedimentation pond had an inconsistent depth across it, which made sediment removal difficult. The pond’s expansive size further complicated the matter, creating a safety risk for on-site personnel and a challenge to keeping the site operational while the sediment was removed.
The Pinnacle Hire team knew the equipment would have to be flexible and adaptable to match the variable pond depth while also being able to be operated remotely to increase safety and maintain the site’s operations.
A pontoon system, which was able to be remote controlled, and equipped with a highcapacity slurry pump from Pinnacle Hire was able to achieve all of these requirements.
The pontoon system’s capacity was 450m³/h, which was significantly higher than conventional methods, which managed
a third of that capacity at 150m³/h. This reduced the project’s duration and avoided the need to shut down the mining site.
This system worked with the resources the mining company already had on-site and lowered the project cost significantly despite using high-capacity equipment.
Using the remote control, operators could safely operate the slurry pump from the shore without the need to enter the water. By eliminating the need to work on or around the pontoon, Pinnacle Hire was also able to keep the site operational while the sediment management was ongoing.
Pinnacle Hire managing director Jeremy Sailsbury said the project was a testament to
the company’s expert team and their skills.
“We’ve carefully selected staff who are experienced and dedicated, but also know the value of teamwork,” he said.
“We’ve also invested in a formidable new fleet of pumps and treatment equipment that is the envy of the industry. This has enabled us to grow from just a single location based in Victoria, to 10 locations in five states in just the last 24 months.
“No matter where you are around Australia, you can find a Pinnacle Hire specialist to help plan and deliver your next pumping or watering treatment project.” •
For more information, visit pinnaclehire.com.au
Tricon Equipment is supplying its customers with heavy-duty screening equipment that can withstand some of the harshest applications.
Sticky clays can pose a serious problem for crushing operations. If not removed, it can clog a crusher’s screens, cause unnecessary wear, and lead to expensive downtime.
To avoid these headaches, quarries often use trommels to separate materials into different streams.
These machines need to be tough to withstand the heavy-duty nature of quarrying. Cailean Woods, sales manager for Victoria and NSW at Tricon Equipment, told Quarry how the company’s flagship product can deliver.
“The Terex MDS trommels are in a league of their own for processing materials such as blasted rock, rip-rap, gabion stone, overburden, and pre-crushing applications,” he said.
“What sets them apart is the heavy-duty rotating drum mechanism. This lets the machines handle the demanding task of sorting and cleaning sizable rocks, at a rate of up to 800 tonnes per hour.”
One of the key features of MDS trommel screens is their ability to remove elements like dirt and clay deposits from rocks, especially limestone, leaving them prepared for the crushing process.
The heavy-duty rotating drum offers a different cleaning mechanism. The material tumbles and scrubs against each other and drum walls, giving a much cleaner output product. They’re also effective in cleaning
clay-bound rock and rocks mixed with other sticky materials.
The feed mechanism also allows the trommels to handle larger feeds, meaning the equipment can handle large rocks for sea defence and rip-rap.
Tricon Equipment is an Australian-based importer and reseller of mobile crushing, screening, recycling and conveying equipment. The company works closely with its international partners like Terex MDS and local quarries to find the best tool for the job.
Woods said Tricon will visit sites to find out exactly what they are looking to achieve, and to learn more about the process.
“We advise them on the best configuration of equipment,” he said. “We will go out and see what their feed product is and advise them on what configuration would work best for their application so we can deliver on what they want to achieve.”
“We also have a heavy emphasis on health and safety, which is an important factor for a lot of quarries, so we ensure all our equipment is delivered fully mine spec’d.”
The MDS trommels can screen rocks as large as 800mm in size and can separate materials into more than just fines and oversize. The range’s drum cleaners are also designed to keep the drum openings clear, even in the harshest conditions, to ensure year-round screening. They also feature a swing-out engine bay, which makes maintenance much more accessible.
Woods said customer feedback on the MDS trommels has been very good.
“We’ve heard from our customers that they’ve tried other options, but the MDS trommels are the ones that produce the cleanest product they’ve ever had,” he said. Because the range is user friendly, general maintenance is relatively simple and the units are heavy-duty which helps minimise downtime, as a result consistent production increases which helps quarries meet their targets.
Tricon has been involved in the quarrying industry for more than 20 years and has a well-established and loyal customer base.
Woods said the company’s equipment is proven to work in the tough quarry applications.
“With our dedicated service team, we can support customers with advice and technical support. They are experts with years of experience handling the MDS trommels. •
Metso’s range of screeners from the FS Series range provides an effective solution to an overlooked part of the quarry.
Efficient and cost-effective screening of aggregates is often the forgotten part of many quarry operations. Many times, the focus is on the reduction of material when considering the production of products for sale. Unless the crushed rock can be correctly sorted at a high and efficient rate there is no value to be had in the sales yard. Metso understands that a quarry is a holistic process from material selection, blasting, crushing screening and storage of finished products. As a result, it has always considered how the materials are sorted and either presented to the next crushing stage or sent to the final product.
This is where highly efficient vibration technology comes into play, which is why Metso is introducing the FS Series range of low-profile horizontal screens to the Australian market. The FS Series lowprofile horizontal screens are part of the wider range of Metso vibrating technology offerings, which includes the inclined CVB Series, multi-slope TS Series and selfsynchronising horizontal ES Series.
More importantly, the FS Series offers the improved design, efficiency, and ease of maintenance of Nordberg MV modular mechanisms. Designed as a grease-filled, easy-to-change-out bearing and vibration unit, Metso has eliminated the messy and costly oil gearboxes of decades past.
Metso’s number one priority is personnel health and well-being. Eliminating risk is the best solution to preventing injury, which is the key factor in the design of all Metso equipment. The FS Series is no different. Risk reduction through safer operation and maintenance is now possible with the MV mechanism, being a one-piece modular construction that reduces risk without the multiple-parts replacement and repairs. Further, the mechanism end cap is lightweight aluminium design, removable by hand for easy maintenance tasks and functional design changes.
Aggregate separation involves high forces and stresses. To ensure the longevity of assets, care must be taken during the design, manufacture and operation of vibration equipment.
Screens not only have to be rugged enough to function and last in the harsh quarry environment but handle long term stresses. The FS Screen is designed with Finite Element Analysis, which ensures a balance between strength and performance. Each FS Screen is factory tested to ensure the highest quality and customer-specific vibrating characteristics.
The FS Series is a weld-free side plate screen using huck bolt construction, with bolted reinforcement plates and stiffeners. Removal of welds is key to a long life, given the high G-forces and the material load required to be transported along the decks in a manner to maximise separation; huck bolting provides such durability.
To provide the throw and forces needed for separation, the Metso FS design combines the revolutionary feature of the Modular Vibrator (MV) with an extra heavy screen body. MV Mechanism true cartridge vibrator system design that drastically increases uptime.
Four bearings per shaft line provide a longer bearing life, allowing for larger load capacities while lowering operating costs. The bearings are in the centreline of the side plate for equal loading and reliability.
Individual bearing systems eliminate lubrication cross-contamination. No refill or draining is required; only a simple lowfrequency greasing schedule is needed.
High G-force and liner motion design ensure the low-profile horizontal FS Series are the best separation solution both as a scalping unit or finishing screen. The primary twodeck model has heavy-duty deck frames for the most arduous applications and can be fitted with top-deck punch plates as required. All models come with one of the easiest stroke adjustments in the industry via the MV Mechanisms. The lightweight aluminium end cap is easily removed by hand for a quick stroke adjustment, for to fit any application.
The low-profile design of the FS Series is an important consideration in today’s world where providing value is critical. With a low installation height savings are made in the design of new stations on conveyor length and overlay plant height. Access to the top deck is also easier and safer as is brownfields replacement of other less efficient and costly horizontal screens. The FS Series replicates the same envelope and footprint as the older style units, making upgrading a simple task. Metso and its Australian distribution and service partners can offer a safer, more efficient, and cost-effective solution with the FS Series vibrating screens. •
For more information, visit metso.com
A WA-based business is helping quarries hit tight targets and stringent quality demands.
B&F Consolidated Group (BFCG) doesn’t purely focus on just volumes. What sets it apart is its focus on high-end materials with stringent quality requirements.
The company, which started in 2017, provides quarries with ongoing baseload contract crushing support and when a project exceeds the site’s installed capacity.
Johan Barnard, operations director at BFCG, said the company can produce pavement materials as well as aggregates for the aviation industry, marine, civil engineering projects, rip-rap, and more.
“We’ve never missed a spec,” Barnard told Quarry. “We’re meticulous in our planning and layouts, and always come in under budget and ahead of schedule.”
“We manage projects from the drill bit to the weighbridge, using bespoke blast designs, bespoke blending, bespoke crushing, and batching.
“This gives us exceptional quality management as a result.”
BFCG’s customers are predominantly in the quarrying and gold mining industry, specifically the construction material side of things. Whenever a quarry needs additional crushing support or expertise in providing a certain specification, BFCG can provide its fleet of equipment.
During the campaign, BFCG will work closely with the quarry to better understand the quality criteria and processing dynamics at the site to provide a highly productive operation at the lowest cost.
Through meticulous scheduling and planning, the company can find the optimal number of resources a site needs.
In situations where the market will pay a premium for a product, maximising the yield at a steady pace minimises operating costs.
Barnard said BFCG’s fleet of equipment is fit for purpose and includes custom-built plants when necessary.
“Most of the equipment is bought for the capability of the individual machine, designed to provide the specific task we need it for,” he said.
Supporting this equipment is a suite of software. BFCG has the technology to manage drill and blast, load and haul, processing, and internal testing. In particular, the company has invested heavily in its monitoring capabilities to ensure it can provide the right specifications.
“Testing is dependent on the product, because no two products will look or handle the same,” Barnard said.
“We take the product spec and develop the methodology to suit the final specification.
Our team is highly experienced and knows what works.
“For example, we provided runway products that needed to be high strength, durable and conform to strict criteria. We were able to succeed where others hadn’t, thanks to our ability to manage the quality functions of the materials.
“It required us to be selective in the mining and processing operations, along with strict quality management applied on the backend.”
BFCG plans to continue growing its operations, serving small-scale private operators and large quarrying conglomerates.
The company is looking to develop further opportunities in the Western Australian market, with a goal of becoming the contractor of choice for local industry.
“Getting to that goal is based on the relationships we form,” Barnard said. “That means delivering what you say you will, when you say you will. It means being flexible and meeting the demands of clients to resolve challenges together.
“BFCG has the experience to help our clients bring long-term sustainability to their operations instead of short-term gains. From pit planning, short haul arrangements, and more, we can set them up for decades of productivity.” •
For more information, visit bfcg.com.au
Upgraded 800i crushers with new ACS-c 5
Even the best can always get better. Upgraded 800i crushers with new ACS-c 5 are our smartest, safest and most productive yet – designed around the needs of the people who work with them to raise the bar of what a crusher can be. Combining simple yet robust mechanical design with powerful user-friendly automation, 800i crushers are true workhorses that improve your ability to process more material, more accurately and more sustainably. Discover the upgraded 800i crusher series with new ACS-c 5 today, and see what’s possible when a crusher is designed with you in mind.
Jonsson has become a well-recognised name in the Nordic region for its range of high-capacity crushers, and now it is set to test them down under.
When Jonsson was looking for its dealer, it wanted a company that had dealt with the bigger quarries, equipment, and projects.
Luckily, the Swedish-based original equipment manufacturer found Tutt Bryant Equipment. The Australian dealer was recognised earlier this year at Metso’s Lokolaunch event in Finland as the highest selling Lokotrack distributor worldwide.
“[Jonsson] is really for the big end of town for the big, professional crushing contractors, quarry operators and mines,” Doran said.
“Our name came up because of our experience with large Lokotrack distribution.
“It is a good fit for us and a good fit for them because we have bought in some big gear over the years and know how to look after the customer and the equipment.”
Jonsson introduced its first crusher in 1984. Six years ago, the company became part of Metso, which fuelled an expansion of its factory to supply more quarries with high-capacity crushers with minimised operating costs.
Now, Tutt Bryant Equipment, the exclusive Jonsson distributor in Australia, is bringing the robustly designed crushers to help Australian quarries cope with highcapacity crushing.
The Jonsson range includes jaw and cone crushers as well as boutique equipment, including the double crusher, which has a jaw crusher, cone crusher, and screen all on the same chassis. Its primary crushing range goes from 80-tonne to 200-tonne models, while it also has around five cone-crushing
models and a wide range of screening options. Its L160 tracked jaw crusher is one of the largest available on the market but is also mobile.
“The experienced operators would understand that this is a whole of life exercise. They know that it is going to cost them a little more upfront, but it is going to last them 15-plus years, around 30,000-plus hours and low-energy use of those hours,” Doran said
“The machine is going to pay for itself pretty quickly despite being a bigger capital investment.”
Jonsson understands that quarry operators, depending on the application, are searching for transportable machines to take with them from site to site. Because of this, the manufacturer has designed all of its equipment to be towable.
“It allows you to have that high-capacity equipment, but you don’t need six trucks and two weeks to assemble the plant. You could assemble one of these machines and be crushing in a day,” Doran said.
“Some of the expert contractors can do it in four hours like a full assembly and then be crushing straight away.”
Jonsson has rigorously tested its electrical components to work in the harsh conditions. The Jonsson Monitoring System (JMS) provides access to a range of digital services.
The JMS can upload a signal from the crusher via a modem to a database that tracks all its activities. The database information is showcased in a graphical dashboard, with reports and analysis on
everything from day-to-day operations to preventive maintenance.
All the belts on the crushers are equipped with a scale which the JMS can display data on. This enables operators to monitor the product coming off each belt and track the yield and performance to ensure optimal productivity.
“The control system and the monitoring system that is available on this machinery is world-class,” Doran said.
“It offers an amazing amount of detail. It is great information for a smart operator to be able to apply and make their operation more efficient and more profitable.”
All of Jonsson’s crushing equipment use diesel-electric drives, as opposed to the conventional diesel-hydraulic drives, which lowers fuel costs. The machines are equipped with an engine and generator on board and can function off mains power.
If a quarry has mains power access available, the Jonsson crusher can be fully operational at full capacity while running at the cheapest cost possible compared to diesel.
“You won’t get a better cost per tonne if you are using mains power, which these machines provide,” Doran said. “With it being high capacity, we see it being a really good fit for those bigger quarry operators and contractors and mines,” he said.
Tutt Bryant Equipment will attend the IQA 2024 National Conference in Adelaide from October 15–17.•
For more information, visit tuttbryant.com.au
When it comes to producing quarry products, the size and consistency of the blasted rock makes all the difference. Get it right, and you can increase your digging, throughput and recovery rates.
At Orica we use our technology and innovation to find solutions to the blasting challenges you face every day. We can work toward pre agreed targets to deliver a reliable and consistently fragmented rock to the level you expect in every bucket load.
To learn more about how we can support your operation, scan the QR code or contact your local Orica representative.
Visit us at the IQA Conference, 15 - 17 October, Adelaide.
Hazemag’s range of sizers can deliver in all conditions to keep production running.
Quarrying can be challenging during the winter as operators deal with arduous conditions.
Having the right equipment to deal with wet conditions can ensure quarries maintain uptime. Teddy Craies, Hazemag allmineral’s managing director for Australia, said the company’s sizers have proven itself in these operations, including markets like Indonesia.
“It works well because in the rain seasons, you have a lot of clay, and when you have a lot of clay, and it’s wet, it is difficult for many crushers to perform efficiently like an impact crusher and others because, with that type of material, it gets clogged easily,” he said.
“This (sizer) is meant for sticky material; it has the scrapers, and it works by working through that wet, sticky material.
“Even here in Australia during the winter, quarries can deal with a lot of wet and sticky material, but that is where the sizer works well.”
The sizers use two toothed rolls, which run towards each other, producing continuous pressure on the material while maintaining a smooth operation. The crushing rolls turn at low speed but with high torque as the material gets deeply immersed between the rolls and punctuated with force.
Each section has its own scraper to remove sticky material, reducing maintenance time and ensuring more crushing time.
Their design makes them ideal for applications dealing with sticky materials such as clay, where fines need to be limited, or on sites where height is a concern due to their low profile.
Hazemag’s sizers have become quite popular in Indonesia, where operators use them in coal mining and limestone applications. Here, the Hazemag sizers shine as a primary or secondary crusher on soft to medium-hard materials.
“It works well and is low-profile, so it can get to areas where you can’t use a jaw crusher. It fits in quite well when you have an issue with space,” Craies said.
“The operating cost is low; it is very energy efficient. We have options where the customer can have different kinds of teeth made for different applications.
Hazemag understands quarries prioritise uptime where possible, so its sizer has been developed to function with minimal maintenance. It is equipped with the standard Hazemag motor, an off-the-shelf option enabling the company to provide replacements quickly.
The old method of sizer maintenance saw operators working with copper hammers to remove the teeth, which was labour-intensive and time-consuming. The Hazemag sizer’s teeth can be removed easily through its hydraulic system. Hazemag estimates the whole process can be done in a 12-hour shift, compared to the week-long process of some sizers.
All of the Hazemag sizer rolls can be fixed in position to allow safe maintenance practices to be carried out. The track roll lifting device makes the roll retraction into the maintenance position easy and gives operators access to the sizer and its internal parts.
For applications where tramp metal is a concern, Hazemag has simplified the process of removing foreign material.
The drive system has a motor with a fluid coupling gear designed to disconnect when foreign metal is detected. The disconnect stops the motor on the rollers and prevents damage to the machine.
“Each supplier is different with their sizers. You have to take the crusher out (of production) and hammer all the segments out, and that can take days,” Craies said.
“And as well as the cost of time to do that, there is a safety factor. With our crusher, you can do it in situ. It is quick, and we give you all the tools as well.
“And it saves the cost of having another crusher on standby as well because you’re able to do this change in one shift, so downtime is reduced, and the safety is really good.”
According to the company, the lowprofile nature of Hazemag’s sizer can suit crushing systems where height restrictions are a concern.
Hazemag has spent the past five decades innovating its sizer to be among the best in the quarrying market. The company has invested heavily in testing the product with customers to track its performance with clay materials to ensure it will perform when quarries need it most.
“We look at the customer’s specified cubicle product, and we can then use the right tools and the right settings to achieve that for the right result,” Craies said.
“If they need it for different applications, for example, roadbuilding, or their customer who receives the product has specific needs, we’re making sure the sizer produces the right product.
“With our sizer, you get a troublefree operation.” •
For more information, visit hazemag.com
Proficiency Testing Australia has successfully completed the first large-scale proficiency study on 14mm Steel Furnace Slag Aggregate, which is the 33rd round of the aggregate proficiency testing program. The study aims to introduce sustainable and manufactured material alternatives to its programs.
Proficiency testing is a means of determining the performance of individual laboratories for specific tests or measurements and provides an external audit of their quality control procedures. A standard proficiency testing program compares the measuring results of different laboratories on identical samples.
Proficiency Testing Australia (PTA), one of Australia’s largest proficiency testing providers, services the construction materials industry by offering proficiency testing programs for aggregate, soils, concrete, rocks, cement, asphalt, and bitumen.
PTA recently announced the completion of its 33rd Aggregates Proficiency Testing Program. The program is accredited by International Accreditation New Zealand and was organised in collaboration with Australian Steel Mill Services (ASMS) for sample supply and Luke Murphy of Colas NSW for sample preparation, pretesting and technical assistance.
The program’s aim was to assess the laboratories’ abilities to competently perform the prescribed analyses on a 14mm steel furnace slag aggregate sample. It was the first proficiency testing program organised by PTA that did not use a natural quarry aggregate.
Overall, 87 laboratories participated in the program, demonstrating an interest among construction materials testing laboratories in testing alternative materials. The laboratories were provided with 17kg of 14mm steel furnace slag aggregate.
The program was designed to cover the following methods:
• AS 1141.4 Bulk Density
• AS 1141.6.1 Particle Density and Water Absorption of Aggregate
• AS 1141.11.1 Particle Size Distribution
• AS 1141.12 Material Finer than 75 µm
• AS 1141.14 Particle Shape by Proportional Caliper (2:1 Ratio)
• AS 1141.15 Flakiness Index
Prior to sample distribution, 10 samples were randomly selected and analysed for
homogeneity, which was established for the prescribed tests.
PTA used a robust statistical approach to assess the laboratories’ testing performance which has provided understanding as to how steel furnace slag (SFS) aggregate performs under proficiency testing conditions in comparison to natural quarry aggregate.
Table A provides a comparison of the coefficient of variation (CV) between previous rounds and the most recent round in which 14 mm natural quarry aggregate was tested.
It is evident that steel furnace slag exhibits a larger variability of results than natural quarry aggregate, characterised by higher robust CVs for Particle Density and Water Absorption, Particle Size Distribution, Material Finer than 75 µm, Particle Shape and Flakiness Index. Steel furnace slag is subject to a number of conditions that can affect its physical properties and, in turn, the results’ variability, including the production process, raw material chemical composition, and the rate at which it is cooled. In comparison, natural quarry
Table A - Comparison of Previous Round CV’s. Note: N/A = “Not Applicable”
aggregate sourced from a single geological deposit is more likely to have a relatively uniform composition.
While asphalt laboratories may test SFS aggregate on a regular basis and are familiar with the material, there are many laboratories that have not tested it prior to PTA’s program which may have attributed to the higher variability observed. Despite its variability, steel furnace slag exhibits many physical and mechanical properties that are appropriate for its application in the asphalt industry, making it a versatile and financially viable alternative to natural quarry aggregate.
Australian Steel Mill Services follows the Basic Oxygen Steelmaking process, which utilises the molten iron from a blast furnace with the addition of scrap steel and fluxes (burnt lime or dolomite), which promote fluidity and enable impurities to be removed
in the form of slag. These fluxes are fed into a vessel, and a lance injects oxygen, enabling a reaction between constituents to produce steel and steel slag.
The steel is tapped from the vessel into a steel ladle, and the steel slag is poured into a slag pot. The slag pot is then handled by specialised equipment, and the slag is poured into pits for cooling. The steel slag is then removed from the pits and processed by ASMS into asphalt aggregates, road bases, fill materials and filter materials. The products produced are known as Steel Furnace Slag, and their ASMS product codes commence with ‘SFS”.
The application of steel furnace slag aggregates in road construction offers several notable benefits, particularly under the Transport for NSW Heavy Duty Asphalt specification in NSW. Its high density and angularity make it an excellent alternative to natural quarry aggregate for creating
durable and stable asphalt pavements. These properties enhance the strength and loadbearing capacity of the pavement, making it ideal for heavy-duty applications. SFS also has a high Polished Aggregate Friction Value, which can improve the resistance of the asphalt-wearing surface, increasing safety for road users. Using this by-product in road construction aids in conserving natural aggregate resources and minimises environmental impact. The Colas NSW Tomago asphalt plant has incorporated steel furnace slag into its asphalt mixes for many years, to produce high-quality asphalt that meets stringent performance specifications. Using steel slag aggregate in heavy-duty asphalt under local specifications can deliver benefits to NSW’s road infrastructure.
For more information, visit pta.asn.au
Acknowledgments: This article was authored by Christian Foia from Proficiency Testing Australia, Luke Murphy from Colas NSW, and Mark Micallef from Australian Steel Mill Services.
Toolkwip Pumps is providing Australian quarries with exceptionally quiet dewatering solutions.
Quarries are an excellent vessel for water. Like natural lakes, they allow rainwater to pool over time.
This has the side effect of making life very difficult for the quarry operators, who need a dry quarry floor before they can continue extracting materials.
Brenton Mauger, a sales representative at Toolkwip Pumps, said this leads to unwanted downtime.
“Water is a key part of the quarrying process, whether it’s moving it or removing it,” he said.
“Quarries need high-quality pumps they can rely on to maximise the amount of work they can do.
“If a pump fails and needs to be repaired or replaced, that can make an already stressful situation much worse.”
Toolkwip Pumps is the distributor of Selwood pumps, a high-quality, compact drainage pump ideal for quarry applications.
Designed and manufactured in the United Kingdom, Selwood has established a reputation for being user-friendly and low maintenance.
Selwood provides dewatering solutions across the civil construction, pipeline, sewer bypass, mining, and quarry sectors.
In Australia, the Selwood D75 super compact drainage pump has proven popular, thanks to
D75 Selprime D Pumps centrifugal pumps have been designed for high-volume fluid transfer, with an ability to manage flows of up to 59 cubic metres per hour. The D pumps feature emission-compliant engines and are easy to operate and maintain. Manufactured to a robust engineering standard, the D pumps have been designed to take on the most challenging tasks to remove water of varying conditions, right up to those with fine or larger solids and screened sewage.
The design incorporates a water-tolerant diaphragm air pump that emits zero oil vapour, making it an environmentally friendly solution. In addition, the pump design uses a mechanical seal immersed in an oil bath, allowing it to run dry for extended periods.
The pumps can be made with stainless steel interiors that are durable and highly resistant to corrosion and abrasion. Some pumps can be heat-treated to make them more robust, which are suitable for tough environments such as mines or quarries.
Selwood’s D75 pumps are also exceptionally quiet, which Mauger said is a major selling point for quarries that are looking to minimise noise on site.
The ‘Super Silent’ units are ranked the quietest pumps on the market, based on the EU directive 2000/14/EC. Selwood canopies are engineered to a high technical standard, complete with silencers, protective enclosures, and incorporate sound attenuation on diesel and electric motors.
“One of our customers was surprised by just how quiet it was and asked us to install a light so he could tell when it was running,” Mauger said.
Most of the pumps that Toolkwip provide are adapted to fit individual applications.
“It could be a ceramic coating in the pump, or a telemetry system for remote control,” Mauger said.
“We can include pressure reading devices, flow meters and switches, monitor bearing temperature, the sky’s the limit.”
Toolkwip is committed to reducing its environmental impact by supplying the most efficient equipment possible. All Selwood Eco5 pumps are fully bunded for safety and can run on hydrotreated vegetable oil fuel.
A cloud-based information management telemetry system has fully programmable software and can measure a multitude of pump and engine conditions, including engine speed, fuel status, and engine temperature.
Mauger said one of the key benefits of the D75 pumps is the ease of maintenance.
“They’re very easy to maintain – it doesn’t require any fancy tools, you can service them with a basic tool kit,” he said.
“They’re so well built that all you need is a bit of preventative maintenance.”
Toolkwip Pumps is the authorised distributor of the complete range of Selwood Pumps in Victoria, New South Wales, Queensland, South Australia, and Tasmania.
The company maintains a full inventory of pumps and parts, as well as providing fullservice support which includes an in-house rebuild capability.
Mauger said the company maintains a full range of service technicians for onsite and in-workshop repairs.
“We have service technicians across the east coast and workshops in Queensland and Victoria,” he said.
“We test everything in our workshop before it gets sent out to site and work with our customers to make sure they have the right tool for the job.
“The Selwood pumps are some of the very best on offer. They’re hand assembled to a very high standard and always outperform.”
Toolkwip’s staff will be in attendance at the IQA National Conference and will have the Selwood equipment available for guests to get up close and personal with.
Guests are encouraged to visit the company and learn more about how the pumps can improve a quarry. •
For more information, visit toolkwippumps.com.au
The RazerTail Truck Unloader helps quarries streamline their material handling processes without a sting in the tail.
Valuable time is lost when the material isn’t moved quickly enough from the truck to the stockpile.
But why waste time when most quarries don’t have a second to waste?
Superior Industries asked the same question when they developed the RazerTail Truck Unloader, which provides quarries with a direct way to transfer material from the truck to the target.
“In our original home region, in the Midwest of America, a lot of contractors will stockpile material after bringing it into a site. Historically, they’d truck it in and use a dozer to push it into a pile,” Superior Industries vice-president of marketing Mary Erholtz told Quarry.
“That dozer consumes a lot of fuel, requires an operator or two, and contaminates the integrity of the material,” Erholtz said.
The RazerTail Truck Unloader’s ability to transfer from trucks to stackers, barges, ship loaders, or rail cars has made it popular across many industries working
with bulk materials. Most importantly, with no additional handling steps, owners and operators maintain the integrity of their material as it moves from truck to target.
In as little as two minutes, a truck operator can dump material into the hopper of the RazerTail Truck Unloader, which transfers it to a stockpile conveyor enroute to the target. This process is significantly streamlined compared to needing the intervention of a dozer to move the material from the.
The RazerTail Truck Unloader features self-cleaning, hydraulically controlled ramps and can automatically dump any left-over material from the truck into the hopper. The easy cleaning solution ensures more material makes it into the target and reduces the maintenance required to keep the RazerTail Truck Unloader in operation.
Superior Industries has equipped the RazerTail Truck Unloader with onboard, hydraulicly-operated truck ramps, eliminating the need for operators to support the
machine with earth ramps. The height of the discharge conveyor is adjustable with different conveyor lengths available so operators can match the required height of the stockpile conveyor. Operators can hydraulically adjust the head pulley height which will enable them to hit any transfer target on the site.
The discharge conveyor also folds into a transport position, tightening up the length of the mobile package for compact road travel. This hydraulic power folds features an inverted cylinder that houses the valuable cylinder rods and prevents them from being damaged or collecting debris during operation.
The RazerTail Truck Unloader has a wrap drive configuration which helps maintain a consistent tension on the belt. The combination of pulleys work in sync to generate a strong tension when the belt is operational. This results in less material being spilled during transfer and more material getting to the target.
Erholtz said Superior Industries has regularly updated the RazerTail Truck Unloader with new innovations to make it easier to use and more robust.
“It looks tremendously different [compared to its first version]. Originally it was a channelframed conveyor but now it is a very stout and robust truss-framed design,” she said.
As more contractors need equipment that can move from project to project, the ability to easily transport machinery on the road has become valuable to the modern operator.
“It is a very mobile system that they can move in and out as they need for different material.”
Carver Companies, which loads material along the Hudson River in New York, uses the RazerTail Truck Unloader to feed its TeleStacker Conveyor which loads barges. The haul trucks dump 50 to 70-tonnes of material at a time into the RazerTail Truck Unloader which seamlessly transfers the material without the need for it to ever touch the ground.
Pete Farinelli, who serves as the terminal foreman, explained the RazerTail Truck Unloader had streamlined the company’s loading process.
“[With the old set-up] it worked out, but it wasn’t loading efficiently or fast enough,” he said.
“Now we’ve incorporated two of them [with] the RazerTail Truck Unloader loading into our hopper which loads the Superior TeleStacker Conveyor. We handle a lot of road trucks and it is easier to road trucks through the RazerTail Truck Unloader than it is through our hopper.”
Erholtz said the RazerTail Truck Unloader would be a valuable addition to a quarry’s arsenal.
“We’ve added dual lanes, so you can unload two trucks at a time versus just one single truck. Additionally, we started with the 72 (1830mm) but also added a 48 (1220mm) which is less wide, more compact onsite, and can still handle the unload capacity needed.”
Superior Industries designed the equipment in a low-profile package that can be easily shifted, set up, and operational within minutes. The hydraulic power folds help the machine fold up into an easy, transportable piece of equipment.
“It is highly portable because a lot of times within a week these contractors are onto the next job,” Erholtz said. “Often, they’ll come in, unload however many tonnes the job requires, and move onto the next job.
“Being able to go from job to job or site to site due to its portability and being able to build a stockpile quickly and cleanly has been a real advantage,” she said.
ToThink Equipment is supplying vital screens and overcoming
Protection of wet application sand and gravel screens goes above and beyond that of a typical aggregate screen with surface coatings such as rubber lining, galvanising and polyurethane screen media.
This is due to the abrasive nature of the material and, often, mineralised water used in the washing process.
Neilsens Brendale had a requirement to replace one of its vibrating screens that had reached the end of its service life.
The corrosive environment had shortened the projected life of the screen, especially compared to a screen in a dry application.
Darren Toth, director of ToThink Equipment, was approached to find a solution.
“ToThink Equipment was approached on a recommendation to the client as a reliable equipment supplier to provide a replacement machine,” he told Quarry.
“The site needed a new vibrating screen that could handle between 220 to 240 tonnes per hour of infeed material.”
ToThink made slight changes to their existing 16 by 6-foot screen design to match the specifications of the client. Client requested options included: increased clearance between each deck, a modular polyurethane screen media system on the
bottom deck, rubber lined deck frames and cross-tube in addition to galvanising of major structural components. Design changes and assembly of the screen were carried out at ToThink’s workshop in Knoxfield, Victoria.
“They’re rapt with it – they like the look and finish of the screen and
they are pleased with its heavy-duty performance,” Toth said.
“I’ve vibration tested thousands of screens at this point, and it’s one of the most consistently running screens I’ve ever seen.”
Over the past eight years, ToThink has transitioned from an organisation focused on optimising existing machines to being a local supplier of screens and feeders built to their own designs. ToThink prides itself in having a broad range of screens and feeders for almost any application. Its range includes incline screens, linear motion screens, horizontal screens, dewatering screens, and vibrating grizzly screens.
In addition to local assembly and design, the company also provides spare parts and technical backup for its customers.
Toth said the company’s aim is to provide the best value possible.
Toth will also be attending the 2024 IQA National Conference to connect with key decision makers in the industry. Attendees will be able to speak to Toth and his team about the company’s growth and can learn more about ToThink’s capacity to design and deliver quarrying equipment.
“I’m also interested in learning more about the South Australian market and looking forward to seeing people face to face at the conference,” he said. •
For more information, visit tothink.com.au
Aptella is now offering intelligent anti-collision technology designed to increase safety for quarrying operations without reliance on tags or identifiers.
Automation and positioning specialist Aptella has signed a distribution agreement with TORSA to supply and support innovative collision avoidance technology designed specifically for quarrying industries throughout Australia, New Zealand and Southeast Asia.
The innovative system promises to elevate safety protocols to unprecedented levels, mitigating risks associated with vehicle collisions and enhancing overall site efficiency.
“Prioritising safety is the lead value at Aptella and of equal importance to any customer that works with heavy machinery,” Aptella chief executive officer Martin Nix told Quarry.
“As we continue to seek the best innovation from around the world, we are excited to bring this advanced solution from Torsa to our local customers. This system ultimately guarantees a level of safety we’ve never seen before on work sites, and that’s something we always want to be a part of.”
The new system is able to analyse interactions between vehicles and people with centimetre-level precision due to the implementation of different technologies and its predictive algorithm which improves the safety of workers during loading and approaching operations. By detecting potential objects and collisions in advance, the technology is able to prevent accidents before they occur, protecting the vehicle operator at all times by proactively and predictively assessing and alerting potential risks.
The high-precision anti-collision system works by centralising data on a single platform in order to provide relevant information to the different areas of the quarry operation. In this way, it is intended to bridge the gap between the operational personnel in the field and the “decision makers” in the quarry operation to help them make informed decisions.
“This development will ultimately save lives because it enhances safety for all workers across almost all domains and enables people to quite simply avoid accidents on job sites. This system is the only one on the market that detects obstacles without the need for them to be metallic or have an identifier.
“Thanks to LIDAR technology, the system is capable of detecting rocks, quarrying fronts, berms or any obstacle that may be considered a risk.”
One of the standout features of TORSA’s new technology is its adaptability to diverse operational environments. Whether navigating rugged terrain or managing complex site layouts, the system offers customisable alerts and adaptive responses tailored to specific conditions. This versatility not only enhances safety but also optimises operational workflows, contributing to increased productivity and savings for the quarry industry.
TORSA has collaborated with peak industry bodies to remain at the forefront of regulation and safety standards, including the International Council on Mining and Metals (ICMM) and its Innovation for Cleaner Safer Vehicles (ICSV) program. The ICSV program brings together 27 of the world’s leading mining companies and machine and technology manufacturers to accelerate heavy machinery development in a non-
advancing industry wide safety initiatives.
The collision avoidance system is certified to levels seven, eight and nine, enabling full intervention control of a machine if required. TORSA’s solution is configurable to each site and customer’s requirements and suitable for all asset types, including draglines, dozers, haul trucks, and light vehicles.
“At TORSA, we believe in creating systems that can be used for all assets, on all sites, which is why we engaged at the Earth Moving Equipment Safety Round Table (EMESRT) and with the ICMM,” Santana said.
“With the ability to work across all makes, models and types of machinery, Aptella was a natural choice as our distribution partner in the region.
“Our team looks forward to working together to enable advanced safety for Aptella’s customers.”
With locations throughout all states and territories of Australia, Southeast Asia and New Zealand, Aptella supports the quarrying and mining, civil construction, building, and geospatial industries with inventive technology solutions. Aptella is majorityowned by global business investment and development firm, Mitsui & Co. Under the distribution agreement with TORSA, Aptella will offer full sales, deployment, training and technical support to customers.
“TORSA’s collision avoidance system complements our safety portfolio and range of machine guidance and fleet management solutions for the quarrying sector,” Aptella’s executive manager of mining, Andrew Granger, said.
“With a large network of technical and application specialists, we offer customers full support from a local team.”
Granger said the proximity detection systems (PDS) and collision avoidance systems (CAS) market is predicted to grow exponentially in the next decade.
“Recent studies and articles show PDS technologies will be where quarries will focus efforts and investments in the coming years,” he said.
“At Aptella, we’re committed to being at the very forefront of these developments and we’re thrilled to be able to confidently say we can keep you and your workers safe on your job site by offering this state of the art safety solution to our customers.”
As Australia continues to uphold its reputation for excellence in quarrying, TORSA’s Collision Avoidance Technology represents a significant step towards achieving improved levels of safety.
By embracing this modern solution, quarrying operators can confidently navigate the challenges of their environments while safeguarding the wellbeing of their workforce. This new technology stands as a testament to the ongoing evolution of safety
practices in the Australian quarrying sector.
As adoption grows, the future promises not only safer work environments but also greater operational efficiency and sustainability across the quarrying sectors. Aptella is dedicated to finding innovative solutions and deploying them for the safety of its customers.
Aptella will attend the IQA 2024 National Conference in Adelaide from October 15–17.•
For more information, visit aptella.com.
Michelle Knott and Scott Blake have been on an incredible rise since they launched Brooklyn Quarry two years ago.
“Irang them up and said, ‘Hi, I want to start a quarry … how do I do it?’”
When Michelle Knott and her partner Scott Blake decided to go all in on their hard rock quarrying operation, Brooklyn Quarry, they never imagined how successful it could be.
Located in the New England region on Walcha Road, Brooklyn Quarry is a family operation that employs family and local contractors from the community.
Scott had a civil construction and earthmoving background, and Michelle had a business management background in other sectors, but neither had a quarrying background.
But despite the lack of quarrying experience, the opportunity to lease the land from Scott’s uncle proved too good to turn down.
“We don’t come from a quarry background, but we combined our forces in a sense to work together on this.
“It was just a case of right place, right time, right conversations, right combination of skillsets and sheer determination.”
But, as many in the quarrying sector would know all too well, starting a quarry is no overnight achievement.
Michelle and Scott laboured through approvals, community consultation, paperwork, administration, and planning meetings for nearly three years to get their business off the ground.
Given Michelle and Scott were utterly new to the industry, they started at square one. The pair spoke to the Institute of Quarrying Australia, conducted hours of research, and trawled Google for information and
then relocated the family from Coffs Harbour to the area once the business was operational.
However, their hard work and in-depth research paid off when Brooklyn Quarry received the green light to start producing material as a commercially registered hard rock quarry.
“We always used those moments to learn more because you only know what you know,” Michelle said.
“There’s been so many rollercoasters like getting an EPA licence, community consultation, marketing and advertising, and all these things you have to do to have a viable business.
“And keeping it a viable business as well because it is not just your job on the line, it is your whole livelihood on the line.
“I thrive in that environment of working for yourself, setting goals and benchmarks to meet and going for it.
“Scott and I are very persistent. We’ve been here for almost two years now, and the business has been open and running for two and a half years.”
The company uses its hard rock basalt to make a wide range of specifications across New England and surrounding areas. It specialises in roadbase and aggregate but also makes landscaping and decorative rock, focusing on providing a premium product.
Initially, the company was focused on opportunities related to the renewable energy projects proposed in the New England region. Along the way, it has also found other opportunities, like supplying rock to a winery in the Hunter Valley that is tailored to the exact specifications of the vineyard.
When Quarry sat down with Michelle to discuss the story behind the family operations, she received national recognition as a finalist in the Women In Industry Awards 2024.
On a regular afternoon, Michelle was kicking the soccer ball around with her kids when her phone buzzed with the email confirming her as a finalist—the confirmation and realisation of her achievement left her in tears.
Partner Scott nominated Michelle for the Business Development award. The pair flew to
me, let alone a finalist,” Michelle said. “I remember reaching out to all the other women who were nominated in the category to congratulate them because it just didn’t seem real.
“It was so humbling but then exciting to be recognised for all the work that I’ve done for our business to get it where it is.
“It really was an incredible night, to be honest, especially looking around the room and seeing all the women who were there for different awards and their speeches. It was really moving and motivating.”
Beyond the award recognition, Michelle hopes her nomination empowers her three daughters in their future ambitions.
Sydney for the significant industry night, where they mixed with people from various industries.
On the night, Michelle found herself flicking through the booklet to see their humble operation named alongside some
of the biggest companies in Australia and internationally.
“You never think you’ll get to that stage when it’s an Australia-wide award. I would’ve been just chuffed that Scott nominated
“I do hope it pivots people’s thoughts a little bit that a girl or woman, anybody, can join any profession that they want,” she said.
“They shouldn’t feel like it is a man’s world that they can’t work in.” •
For more information, visit brooklynquarry.com.au
Manufacturer of conveyer belt scales (weightometers) and weigh belt feeders all manufactured in australia
Mild Steel Powder Coated for Quarry and Mine installations and Stainless Steel construction for Harshest Environments. Throughput up to 1,000 TPH For Belt Widths between 450mm and 2,000 mm accuracies of +-0.5% for a single idler and +-0.25% for a dual idler
The event was a great success, offering attendees valuable insights from the tour and presentation.
Victorian sub-branch site tour and networking dinner
The IQA Victorian sub-branch networking dinner and presentation took place on Thursday July 18, featuring a site tour and a networking dinner with a presentation.
The event commenced with a tour of LS Precast, a locally owned and operated business specialising in high-quality precast elements
for major infrastructure projects across the country. The tour included a walkthrough of operational sheds showcasing static moulds and carousels in action, as well as a visit to the pre-stressing shed, demonstrating the entire process of creating precast segments from drawings to completion.
Following the tour, attendees reconvened at EllaGoose for a networking dinner, which featured a guest presentation by Ben Wright,
NQLD
manager of earth resources and silica at WorkSafe Victoria. Ben’s presentation provided valuable insights into the quarry sector, reviewing the past 12 months, and offering an outlook for the industry in 202425. The event was a great success, offering attendees valuable insights from the tour and presentation, along with ample networking opportunities among members, non-members, and associates.
Chain of responsibility online workshop
1912:00pm – 3:30pm Online
Stefan Hajkowicz uncovers global megatrends and looks at the future of quarrying at the IQA 2024 National Conference.
Excitement is evident for Stefan Hajkowicz, the chief research consultant in science and technology at CSIRO, to present his keynote speech at the IQA 2024 National Conference.
Hajkowicz’s keynote promises to be a highlight of the IQA 2024 National Conference. It will offer valuable insights and actionable strategies for navigating the quarrying industry’s future.
Don’t miss this opportunity to hear from one of the leading experts in strategic foresight and global megatrends.
Quarry had the pleasure of sitting down with Hajkowicz to get a glimpse of what attendees can expect from his talk on “The Economic and International Environment: Global Megatrends.” His insights promise to be both enlightening and essential for anyone in the quarrying industry.
Can you tell us a bit about your background and your role at CSIRO?
I’ve been with CSIRO for quite some time—25 years this September. My PhD focused on decision-making and economics, comparing rational and intuitive approaches. I’ve always worked at the interface between science, technology, policy, and strategy. Our aim at CSIRO is to understand how the world around science and technology is changing and to help industries, including quarrying, make better decisions.
What inspired you to focus on megatrends and their impact on the economy and international environment?
I realised that fine-tuning models and data was helpful, but the big gains came from understanding what decisions we needed to make in the first place. Strategic foresight allows us to systematically explore the future, helping us see things coming and make early, smarter decisions. It’s about comprehending what’s coming, handling uncertainty, and translating that into actions that yield better outcomes.
Could you share a teaser of what attendees can expect from your keynote presentation?
I’ll introduce the concept and rationale behind strategic foresight work, and
use efficiency, and innovations relevant to the quarrying sector.
What are some of the key global megatrends you believe will significantly impact the quarry industry in the coming years?
Resource use efficiency, recycling, energy technologies, and AI are all highly relevant to the quarrying sector. We’ll cover health and wellbeing, geopolitical shifts, digital disruption, and the rise of AI. These trends will impact supply chains, productivity, safety, and business models in the quarrying industry.
What do you see as the biggest opportunities for growth and innovation in the quarry industry over the next decade?
Recycling quarry waste and understanding demand growth for infrastructure materials are crucial. AI will be a major disruptor, offering new market opportunities and improved forecasting. I’ll delve into how AI is being used in quarrying, from safety applications to predictive maintenance and energy consumption optimisation.
Don’t underestimate the impact of AI on your business. It presents significant opportunities for accessing new markets and enhancing operations. I’ll cover various AI pilot projects in quarrying, from autonomous loading systems to environmental protection and intelligent traffic management.
transformation of its famed but once-abandoned central station.
Michigan Central Station had sat abandoned, unloved and unwanted in Detroit since 1988.
The landmark building, originally designed by architects Warren & Wetmore and Reed & Stem, had 4000 daily passengers at its peak. The firms had also designed New York’s Grand Central station, but the two transport hubs shared vastly different fates.
Grand Central is still in operation today, while Michigan Central Station was closed in 1988.
“Michigan Central means a great deal to us all. In many ways, this building tells the story of our city. This station was our Ellis Island – a place where dreamers in search of new jobs and new opportunities first set foot in Detroit,” Ford Motor Company executive chairman Bill Ford said.
“But once the last train pulled out, it became a place where hope left.”
As the Michigan Station sat in a dilapidated state, Detroit fell alongside it. The Motor City had lost its swagger. From 1950 to 2010, Detroit’s population shrank by 61 per cent and dropped from being the fourth-largest city in the United States to the 27th.
plan to turn the abandoned train station into a “technology and cultural hub” with three other buildings, the scale of the project was extensive.
The US$740 million ($1.1 billion) project involved four buildings across the 30-acre precinct, which housed ,000 workers and focused on autonomous and electric vehicles as well as modern transportation solutions. It took six years, 3100 tradespeople, and around 1.7 million hours for Ford to rebuild the fallen symbol into a revitalised Michigan Central Station.
John Goodrow Sr, a stone carver from midMichigan, spent more than 400 hours carving the 11,500-pound replica of the station’s capital stone from a 21,000-pound limestone block. The replica will be used to create three 3D replicas for other capital stones in the station with 10 original capital stones restored for the project.
It started in September 2020 and was completed in late October, as Goodrow Sr considered it the largest capital stone he had completed in his 37-year career.
The limestone was sourced from Dark Hollow Quarry in Indiana. The site closed in 1988, but began its life supplying stone to the original build of Michigan Central’s capital stone in 1913.
“To come back to the same quarry where the first limestone was sourced from allows us not only an exact match in colour and texture, but to maintain a strong connection to its storied past,” Ford construction manager for the project Richard Bardelli said.
The return of the limestone to restore the Michigan Central façade also extended a family legacy, as Jim Hillenburg followed in his grandfather’s footsteps.
The elder Hillenburg worked at the Dark Hollow Quarry originally when Michigan Central required limestone before grandson Jim helped find the stone to use in the restoration. Jim Hillenburg’s father also worked at the quarry, meaning the family has a three-generation quarrying history.
“I’m proud that my grandfather and I both played a role in building Michigan Central Station, I’m picking up where he left off,” Hillenburg said.
Michigan Central Station reopened earlier this year with a massive concert including Eminem, Diana Ross, Big Sean and Jack White.
Detroit governor Gretchen Whitmer said the project had become a key part of the city’s path to a better future.
“Michigan Central Station is a living symbol of Detroit’s resurgence,” she said. “The evidence is undeniable; Detroit is on the move.” •