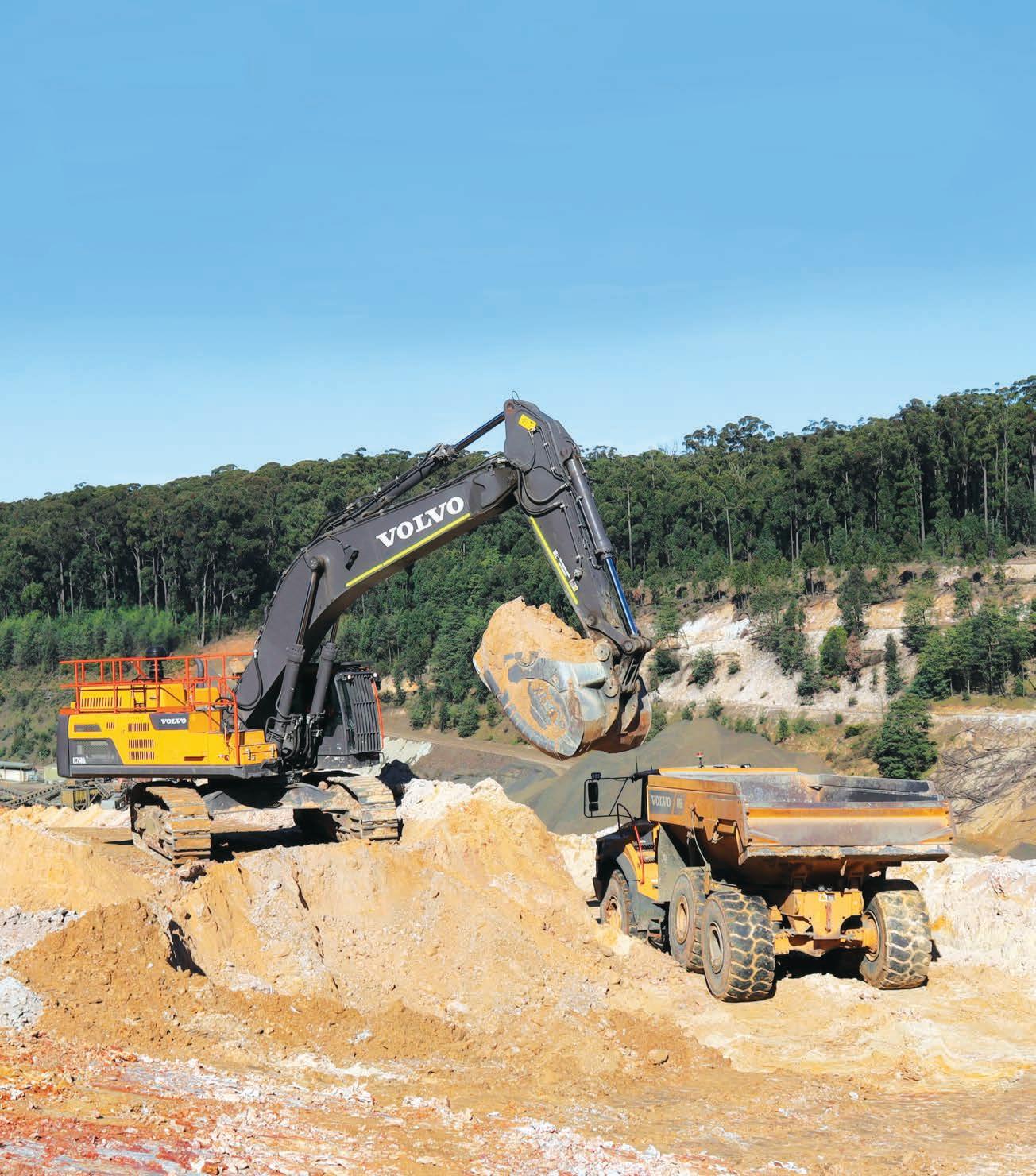
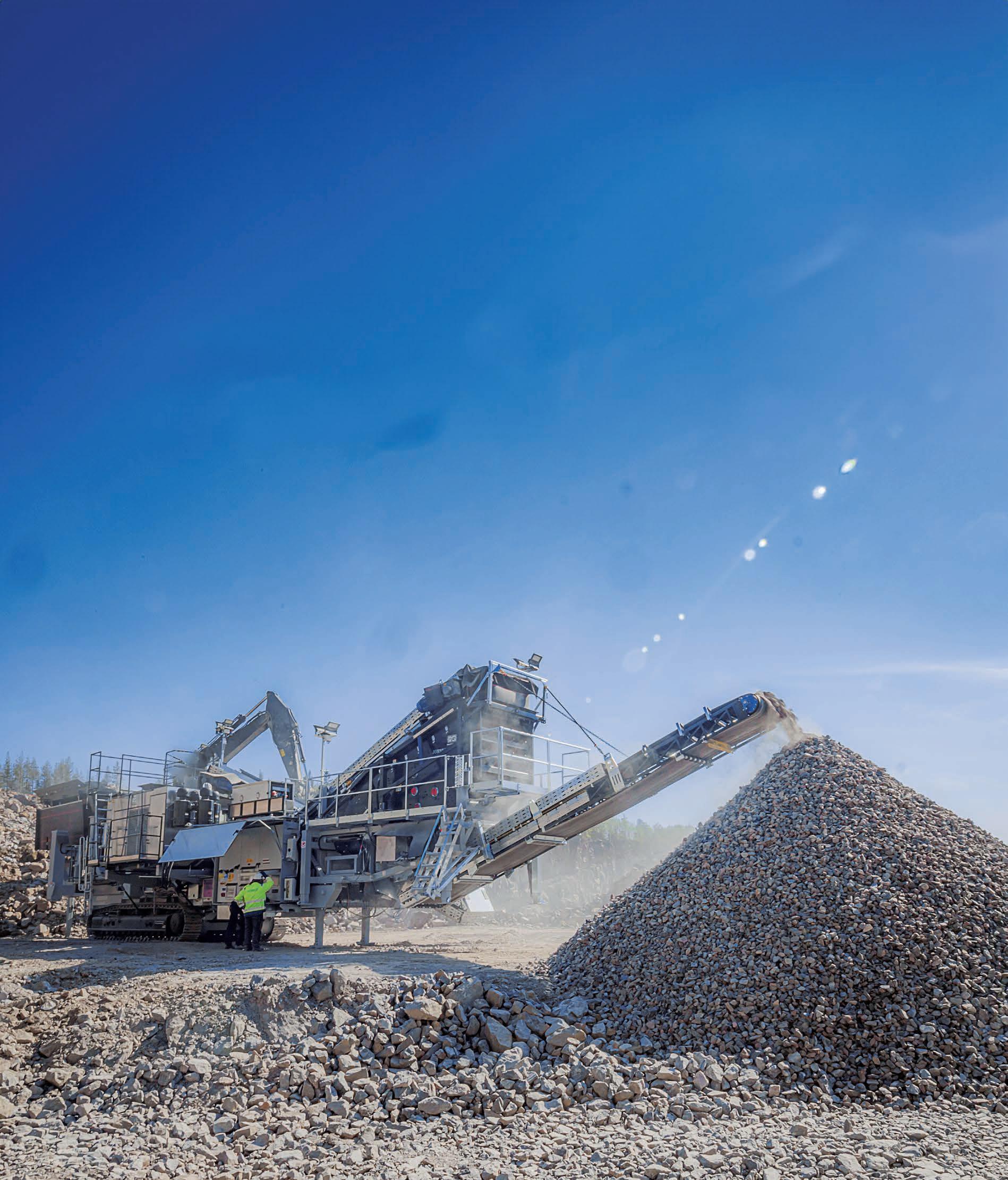
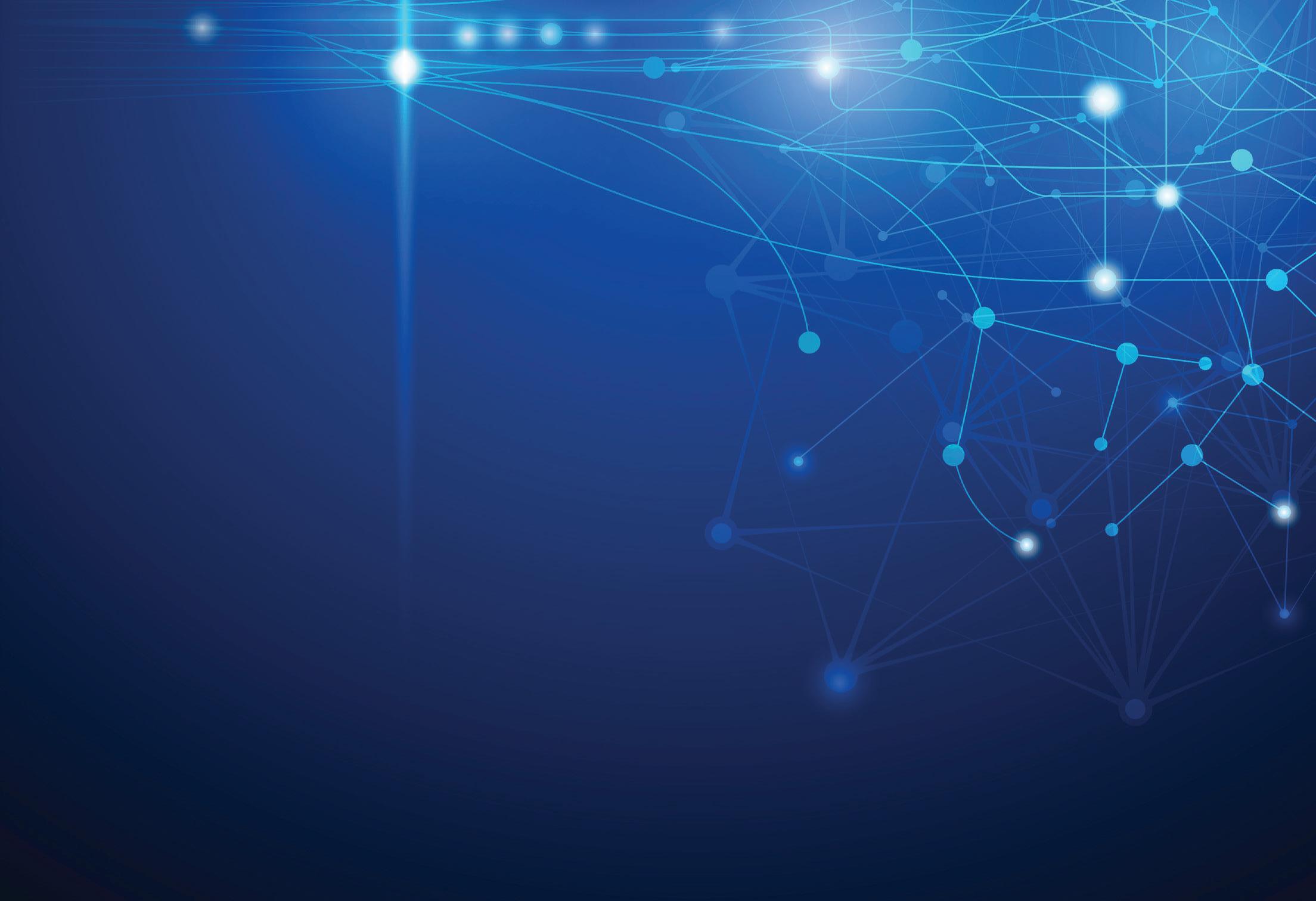

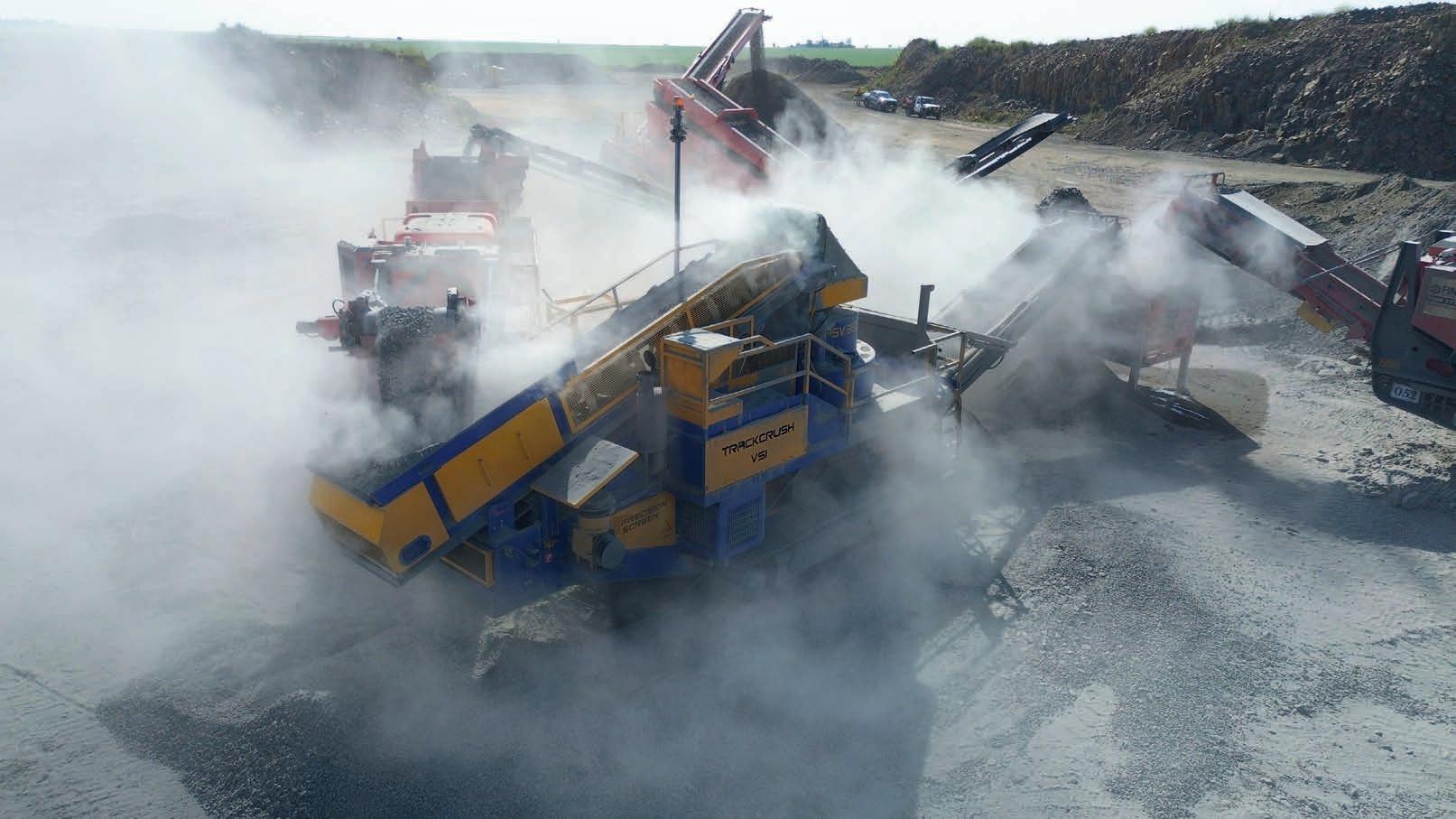
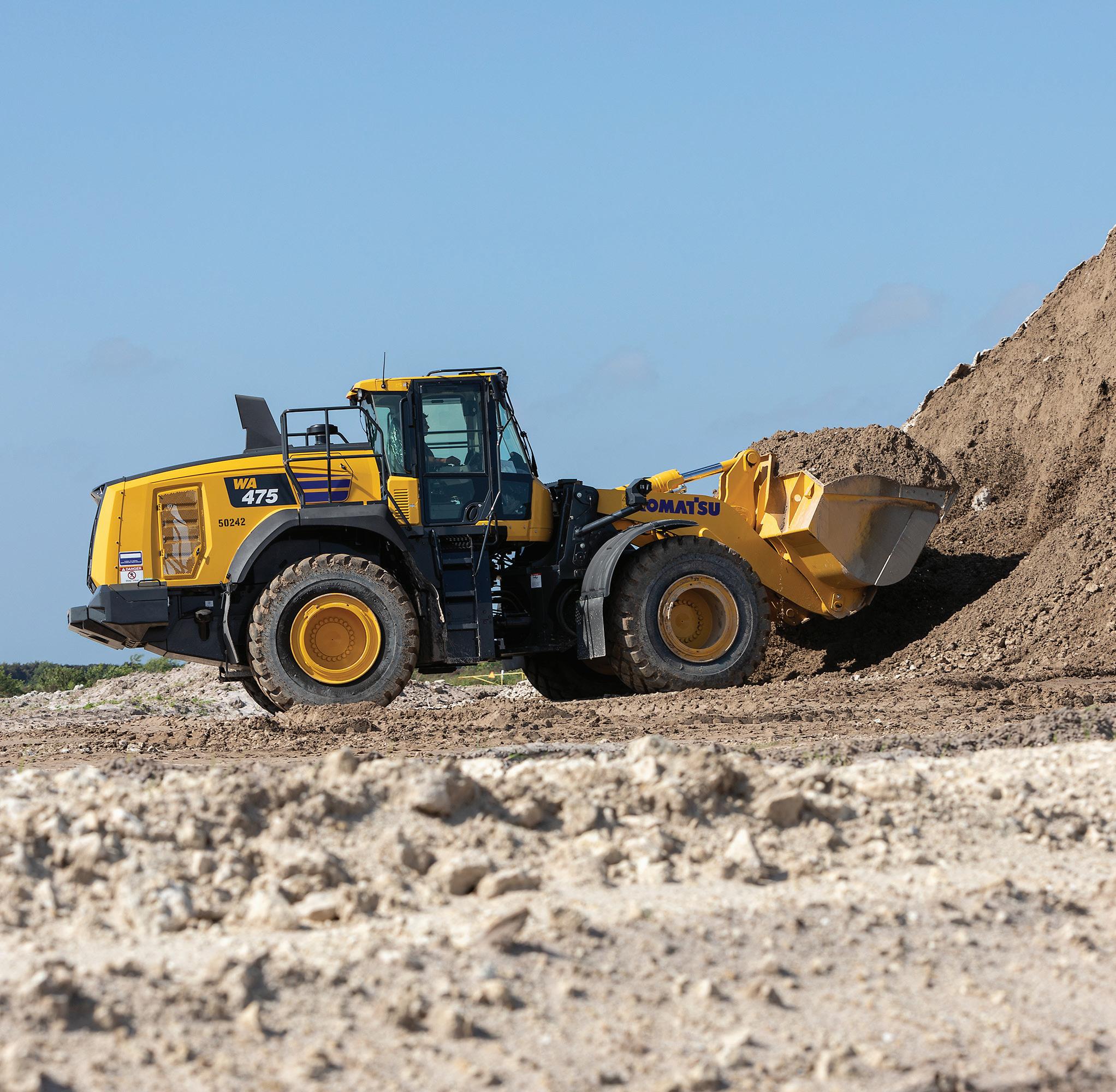
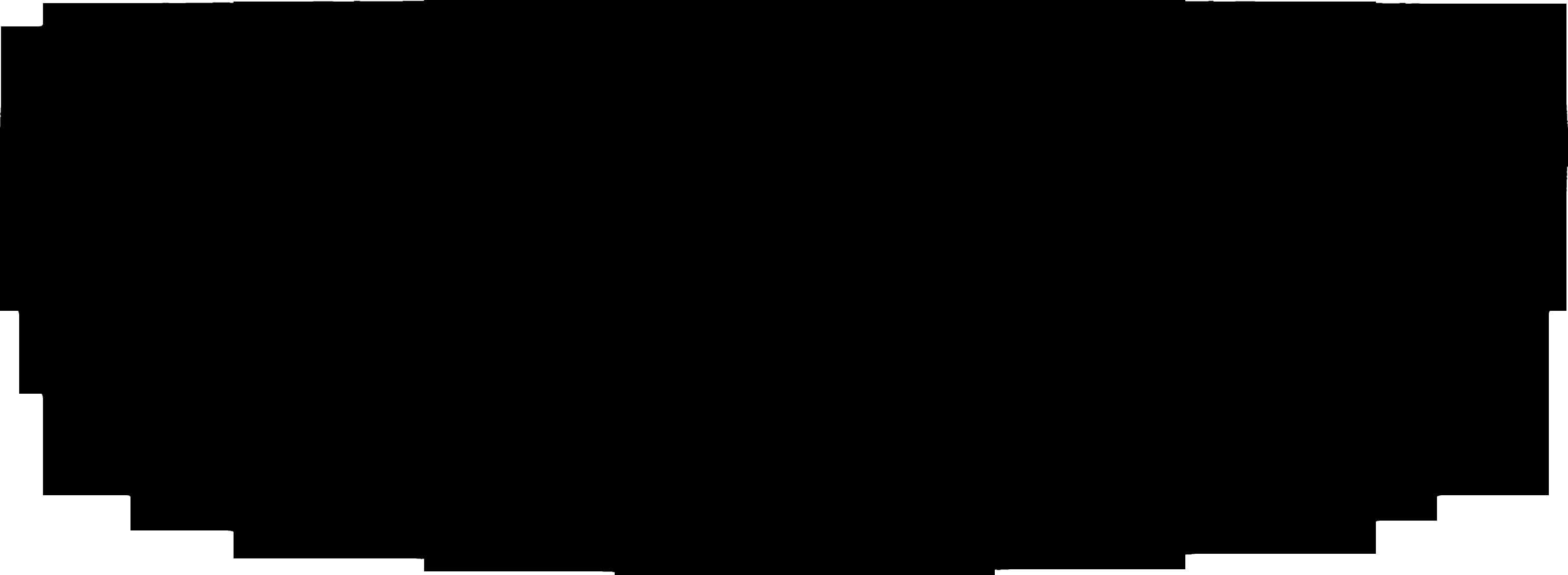

Albury
Komatsu
A
Steve Franklin writes about what he learned at AggNexus and what digital transformation looks like in practice.
Dedicated support
Quarry learns more about Wirtgen Group’s new dedicated aftersales team and how they support customers.
Iconic crushing
The Lippmann 1200j heavy duty mobile crusher’s ease of maintenance is providing quarries with peace of mind.
32 Central expansion
Learn why Lincom Group has recently expanded its presence with a new branch in South Australia.
34 Jewel in the crown
Precisionscreen discusses how its Trackcrush PV350 VSI Crusher has become a success story.
36 Rock solid partner
ARC Laboratory Services is using a collaborative approach to become the trusted partner of Australian quarries.
38 Upgraded impact
Terex Washing Systems’ equipment is helping Barro Group reach its production goals in Victoria.
40 Continued expansion
Astec has expanded its partnership with equipment dealer Mineral Processing Solutions.
On the outside, quarrying looks deceptively simple –it’s digging up big rocks and turning them into little rocks.
This isn’t the whole story though. Modern construction projects, including roads, runways, buildings, and more require highly specific materials – which in turn require very intelligent business practises. The technology used to crush and screen this product has also grown smarter, more efficient, and more effective to keep up with an evergrowing need to produce more.
Crushers are at the heart of many operations, handling extremely demanding tasks all day, every day. They need to be designed to withstand these rigours and bounce back if something does go wrong, or the entire site could halt.
On top of that, managing quarries has become more complex, as every ounce of productivity is needed to remain competitive. A shortage of skills, urban encroachment, uncertain economy, and changing legislation means modern quarries need to be
operating as efficiently as possible.
Some have begun to adopt digital technologies to better manage truck movements, maintenance, production processes, and more.
This edition of Quarry highlights the companies that have innovated in this key part of the quarrying industry. It includes interviews and articles that dive deep into the latest crushing and screening technology, highlighting original equipment manufacturers.
It also includes editorials that look towards the future of quarrying, detailing some of the new innovations that are helping grow the industry.
Additionally, the magazine looks at how the Institute of Quarrying Australia (IQA) is supporting members across the country, especially young members.
The next edition will take a look at sand – including the equipment and organisations working to produce it. If you would like to get involved, please get in touch.
William Arnott Editor
Published by:
379 Docklands Drive
Melbourne VIC 3008
T: 03 9690 8766
www.primecreativemedia.com.au
Chief Executive Officer
John Murphy john.murphy@primecreative.com.au
Managing Editor
Paul Hayes paul.hayes@primecreative.com.au
Editor
William Arnott william.arnott@primecreative.com.au
Assistant Editor
Adam Daunt adam.daunt@primecreative.com.au
Business Development Manager Les Ilyefalvy les.ilyefalvy@primecreative.com.au
Client Success Co-ordinator
Janine Clements janine.clements@primecreative.com.au
Art Director
Michelle Weston
Subscriptions
T: 03 9690 8766
subscriptions@primecreative.com.au
The Publisher reserves the right to alter or omit any article or advertisement submitted and requires indemnity from the advertisers and contributors against damages or liabilities that may arise from material published. © Copyright – No part of this publication may be reproduced, stored in a retrieval system or transmitted in any means electronic, mechanical, photocopying, recording or otherwise without the permission of the publisher.
IMPRESSIVE FROM A TO Z. Thanks to its robust design and extensive range of screen linings, the MSS 802 EVO can easily adapt to changing locations and new operating conditions – making it ideal for a wide variety of applications. The coarse screening plant features an intuitive system control that reduces the risk of operating error. And all relevant functions can be operated from a safe distance for increased work safety. The MOBISCREEN MSS 802 EVO –the heavy-duty, versatile solution in natural stone and recycling.
www.kleemann.info
It is with great enthusiasm that I step into the role of 29th President of the IQA.
I extend my sincere gratitude to Duncan Harris and the outgoing board members for their dedicated leadership and the solid foundation they have laid for our organisation.
My journey in the quarrying industry spans over two decades, during which I’ve held various senior positions across different facets of the extractive sector. This diverse experience has prepared me well for the challenges and opportunities that lie ahead.
The IQA continues to be a cornerstone of our industry, and I’m committed to furthering its mission.
Our recent 2024 National Conference in Adelaide, attended by over 600 delegates, showcased the vibrancy and unity of our sector.
We are actively advancing several key initiatives:
Launching an IQA Ambassador Programme to bolster our support for new and existing members.
Developing a public education campaign on the vital role quarries play in building communities.
Further developing the IQA Education Hub, a comprehensive platform for professional development.
We have conducted an IQA Membership survey to ensure we
effectively meet our members’ needs whilst refining our membership offerings and services.
We will share the outcomes in the next edition of Quarry
These efforts align closely with our Strategic Plan 2023-2026, focusing on industry compliance, workforce diversity, and strengthening connections within our community.
The IQA’s rich history of fostering professional growth and industry connections remains at the heart of our mission.
Our Branch and Sub-Branch network continues to be vital in this regard, offering invaluable opportunities for involvement and knowledge sharing.
As we move forward, guided by our vision of “Thriving communities supported by a sustainable industry,” I encourage all members to actively engage with the IQA.
Your participation is vital to our collective success.
I look forward to working alongside each of you as we navigate the future of our industry and contribute to Australia’s growth and development.
Michael Close President Institute of
Quarrying Australia
THE IQA’S RICH HISTORY OF FOSTERING PROFESSIONAL GROWTH AND INDUSTRY CONNECTIONS REMAINS AT THE HEART OF OUR MISSION.
and
www.quarry.com.au
The IQA’s Strategic Plan 2023 to 2026 embodies the following vision, values and strategic priorities:
Vision:
Thriving communities supported by a sustainable industry
Operational Priorities:
• Deepen industry participation
• Sustainable revenue streams
• Highly capable team
• Technological innovation
• Effective engagement
• Great governance
Strategic Priorities:
• Support industry participants with compliance and regulation
• Build a diverse and skilled industry workforce
• Foster strong industry connectivity
IQA Contacts:
Phone: 02 9484 0577
Email: admin@quarry.com.au
Chief Executive Officer
Jane Schmitt
President
Michael Close
Company Secretary
David Cowie
For all education, member and branch enquires please email: admin@quarry.com.au.
“UNDER ALBERT’S LEADERSHIP CRH HAS DELIVERED SUPERIOR GROWTH AND PERFORMANCE WITH CONSISTENTLY IMPROVING PROFITABILITY, CASH GENERATION AND RETURNS.”
RICHIE BOUCHER
and has more than 30 years of industry experience.
Boucher said Mintern possessed many qualities which will make him a strong performer in his new role.
“The Board has a significant focus on succession planning throughout CRH. With the support of independent advisors, we have followed best practice, including a review of external candidates, and we have carefully monitored the development plans for potential internal candidates,” he said.
“Over recent years we have closely observed Jim’s character, qualities and abilities, as well as his significant influence on the evolution of CRH.
CRH has revealed its next chief executive officer after Albert Manifold announced his decision to retire at the end of the year.
Manifold will retire as CRH’s chief executive officer after serving in the role since January 2014. He has held various roles within the company since he first joined in 1998. Manifold will remain an advisor to CRH for another 12 months after he relinquishes the top job on December 31.
“It has been a privilege to lead CRH. I am profoundly grateful to my colleagues within the business and on the board for their commitment and support over the years as the entire team has strengthened and grown our company, positioning CRH for a bright future ahead,” Manifold said.
Richie Boucher, chairman of CRH, added: “CRH has made enormous
progress thanks to Albert’s clear vision and his leadership of a talented, hard-working team. CRH is a very focused, high performing group and is recognised by its customers as the industry’s leading provider of innovative building materials solutions.
“Under Albert’s leadership CRH has delivered superior growth and performance with consistently improving profitability, cash generation and returns.”
The company has announced Jim Mintern will take over as chief executive officer of CRH following Manifold’s departure at the end of the year.
Mintern currently serves as the chief financial officer of CRH and has been a director on its board since June 2021. He has worked for CRH for 22 years in various roles
Hanson Australia and the Resources Victoria regulator have worked together to restore areas of a Northern Victorian quarry in a “win-win” for all stakeholders.
Hanson Australia has restored areas of the sand and gravel quarry and made a $136,000 donation to Landcare Victoria to support its environmental work.
After entering an enforceable agreement with Resources Victoria’s Earth Resources Regulator in 2023, the company is on track to complete the work by the end of the year. While undertaking the restoration work, Hanson has also rehabilitated several other
areas of the quarry as part of progressive rehabilitation practices, which the regulator encourages.
“In a win-win for the environment, we’re pleased to see that Hanson has restored damaged areas, rehabilitated additional areas of the quarry and made a sizable donation to Landcare Australia, so they can continue their important work,” Chris Webb, executive director for regulatory operations at Resources Victoria, said.
According to the regulator, an audit in 2021 identified more than 20 issues at the quarry across several areas that breached
“We are very pleased to have a successor of such calibre and are confident that Jim is best positioned to lead the CRH team, building the future of the company for the benefit of our investors, customers, colleagues and communities.”
Mintern said it is an incredible honour for me to be appointed the next CEO at such an exciting time for CRH.
“CRH has an impressive legacy of continuous growth and financial performance by providing value enhancing solutions for its customers,” he said.
“I look forward to working alongside our highly talented team as we build on this foundation and continue to successfully grow the business while delivering exceptional returns for our shareholders.” •
the operations set out in the site’s work plan.
According to the regulator, quarries wanting to implement new processes in additional areas within the quarry or impact the waste material’s disposal must submit a work plan variation. The regulator will assess the variation.
“We regulate to ensure risks to environment, community, infrastructure and cultural heritage are considered and appropriately addressed before work starts and observed once work begins,” Webb said. •
The New Zealand Infrastructure Commission, Te Waihanga has revealed the identity of its new chief executive officer.
Geoff Cooper will take over the top job after Ross Copland announced his intention to step down earlier this year.
Copland led the commission for four years after joining in September 2020.
Cooper, who previously served as general manager of strategy, has been the acting chief executive since June 2024 while the board searched for Copland’s replacement.
“It has been a privilege to lead the Commission through its formative years as we have studied, listened, summarised and built consensus on the big infrastructure issues and opportunities for our country,” Copland said at the time.
“It feels like the right time to pass the baton as we reach the end of the financial year and shift gears from a focus on developing a robust infrastructure strategy for New Zealand into supporting the execution of our strategic recommendations and commencing work on the National Infrastructure Plan.”
“IT’S A HUGE PRIVILEGE TO LEAD THE TEAM IN BUILDING ON THE WORK WE’VE DONE, ADVISING GOVERNMENT AND SETTING THE DIRECTION FOR A BETTER INFRASTRUCTURE SYSTEM.”
GEOFF COOPER
Cooper has experience in several industries, including stints at the United Nations, the European Bank for Reconstruction and Development, and the United States Federal Reserve.
He is a former chief economist for both PwC and Auckland Council, where he worked on infrastructure, housing, regulation and financial policy.
Dr Alan Bollard, chair of the Te Waihanga Board, said Cooper has the expertise and knowledge to help Te Waihanga build on its success, and drive its work to improve NZ’s infrastructure.
“Geoff has already led some major pieces of work at Te Waihanga. As general manager, he led the National Infrastructure Pipeline and the development of New Zealand’s first Infrastructure Strategy, which pinpointed both the challenges our
infrastructure system faces as well as solutions,” he said.
“Geoff also has a significant profile as an economist and infrastructure expert, with a talent for communicating important issues in a way that resonates.
“These are vital skills as Te Waihanga now works to develop a National Infrastructure Plan to help build consensus on our long-term infrastructure priorities.”
Cooper added: “I’ve been at Te Waihanga since 2020 and know firsthand how important a part it plays in helping New Zealanders get the infrastructure they need.
“It’s a huge privilege to lead the team in building on the work we’ve done, advising government and setting the direction for a better infrastructure system.•
To submit new product and equipment releases, email: les.ilyefalvy@primecreative.com.au
mounted crushers and screens are now stocked at 888CSE, for the aggregate, mining, and recycling industries. 888CSE has partnered with Lippmann to bring a new line of mobile crushers and screeners to WA, NT and SA. Starting with the L1300j-E, this 125te track mounted jaw plant is one of the largest mobile crushers in the market offering professional operators the highest production and performance efficiency in mining and large quarry operations.
Capable of processing over 1000tph in certain mining applications, this electric powered jaw crusher features a CAT genset to provide self-contained onboard power. The L1300j-E can also be plugged into a mains power supply for the lowest cost of operation. Alternatively, the plant can run off a single larger genset, which can be used to power a complete Lippmann crushing circuit, for the most fuel efficient and cost saving operation. Additional “dual power” diesel/ electric Lippmann machines include 300c and 400c cone crushers with 300/400HP hydraulic adjust cone, Lippmann 1200j-E, 75te class jaw crusher capable of processing up to 600tph, an L620R heavy duty scalper screen with apron feeder, and an L622-3 triple deck sizing screen with class leading 22ft x 6ft triple deck side tension screening system.
For more information, visit 888cse.com.au
The Volvo EC950E is built to withstand the rigours of demanding applications. It features a heavy-duty boom and arm and a strong frame structure with additional protection provided by a built-in, heavy-duty plate shielding the machine’s underside. Volvo Construction Equipment offers a heavy-duty bucket with wear-resistant steel plates for quarrying and mining, ensuring longevity and sustained uptime.
A wide range of wear parts, including teeth, adapters, segments, side cutters, and shrouds, are available to protect the complete bucket and further enhance its durability.
Equipped with a 450kW Volvo engine, the excavator delivers unparalleled digging force, making it exceptionally effective against hard and heavy materials. Its wide track gauge, long track length, retractable undercarriage, and optimised counterweight, ensure it maintains its balance even in the most challenging environments.
As Volvo’s largest crawler excavator, the EC950E boasts a high bucket capacity that significantly enhances on-site production. This allows for more tonnes per hour and increases overall profitability and productivity.
The excavator also offers flexibility and versatility through its range of attachments and work modes that are tailored to meet the demands of various jobs. The attachment management system allows operators to pre-set hydraulic flow and pressure from the comfort of the cab.
In addition, the integrated work mode feature permits operators to select the best mode for the task at hand, ranging from idle to power max, which enhances the machine’s efficiency and adaptability to different working conditions.
This combination of customisable settings and powerful performance tools ensures that the EC950E can easily tackle the toughest demands.
For more information, visit cjd.com.au
"A
Albury Quarries specialises in Crushing and cleanup operations for councils often around Tamworth and Northwest New South Wales. As a new business, its initial challenge was to find a reliable, efficient, and cost-effective Crushing solution.
The Keestrack R6H from Screenmasters Australia (SMA), known for its enhanced horsepower from its predecessor the R6, offers increased production capabilities and enables the quarry to efficiently produce 20mm or 40mm road base materials. Combined with exceptional support from SMA, Albury Quarries has seen remarkable business growth. Initially renting the R6 for 12 months, the reliability and performance of the machine led them to purchase a brand new unit.
You too can count on SMA
Tutt Bryant has enjoyed a monumental year, from winning global awards to introducing new products to the Australian market.
Tutt Bryant Equipment, a key crushing and screening equipment dealer in Australia, has enjoyed a significant year in the industry.
The company’s achievements were underscored earlier this year when prominent industry figures and equipment dealers gathered in Finland for Metso’s Lokolaunch.
The Australian-based dealer was
EC Lokotrack range was a “significant step” for both the OEM and the Australianbased dealer.
“It is very significant; it is a significant step change for the company,” he said.
“[Metso] has always been at the forefront, but this is a big step for them; it has been three years in the making.
“A company like that doesn’t sink the
high-quality aggregates.
Doran tipped a bright future for the new Lokotrack EC range in the Australian market.
“I think once we start getting them installed and people see the value and how efficient and competitive it makes them, I think the adoption rate will go up dramatically,” he said.
“Having electric crushers and conveyors running on-site means there are fewer things to maintain and more time to crush.
“It means you’ll be able to put out more tonnes per day, which contractors particularly need to aim for.”
Tutt Bryant Group has grown substantially since its establishment in 1938. The company employs around 500 people across nearly 30 locations.
Tutt Bryant Equipment is the group’s dedicated equipment and aftersales support
and low operating costs of its equipment.
When Jonsson sought a dealer to partner with in the Australian market, Tutt Bryant’s reputation for handling high-capacity crushers from international brands stood out.
“It is a good fit for us and a good fit for them because we have bought in some big gear over the years and know how to look after the customer and the equipment,” Doran said.
“You won’t get a better cost per tonne if you are using mains power, which these machines provide. With it being high capacity, we see it being a really good fit for those bigger quarry operators, contractors and miners.”
Jonsson’s expansive range of crushing equipment means it will likely have the solution for a high-capacity quarrying operation in Australia. From jaw and cone crushers to boutique equipment, its main crushing products range from 80-tonne to
“design genius,” which is showcased on its L130 jaw crusher.
“Transportability is another feature that makes Jonsson plants suitable for the Australian market,” he said.
“The L130 jaw crusher weighs about 110 tonnes, which usually requires physical disassembly and reassembly using cranes on site. Jonsson’s innovative chassis design allows the heavy component of the machine to split into smaller or hydraulically-propelled components for transport.
“These are arguably the most efficient crushers in the world, particularly for the serious operators at the big end of town.
Having extended our partnership with Metso, we plan to continue our great performance in serving customers with this innovative range, with an eye on operational sustainability.” •
For more information, visit tuttbryant.com.au
Albury Quarries has become a contract-crushing success through its partnership with Screenmasters Australia (SMA).
When David and Andrea Dunstan returned to the crushing industry after a 20-year break, one of their most important choices was the equipment. Their business, Albury Quarries, specialised in crushing and clean-up operations for councils around the Tamworth and Northwest region of New South Wales. As a smaller operation, they were looking for one machine to get the business underway in the competitive world of contract crushing.
David understood what worked and what was needed from his 20-years’ experience at ReadyMix Concrete. He knew the crushing equipment needed to be reliable, efficient, and cost-effective.
For small operations like Albury Quarries, downtime is a key concern, and weather conditions, including wet weather, can significantly impact crushing production.
Screenmasters Australia (SMA) provided the ideal solution with the Keestrack R6h Impact Crusher.
Ciaran Lagan, national sales manager at SMA, met with David and Andrea to understand their requirements and ensure they received the best machine tailored to their needs.
SMA has an extensive inventory of machines and is the authorised dealer for some of the world’s most well-known crushing and screening equipment manufacturers. Its inventory of crushers and screeners means the team can tailor a solution for clients.
This is then supported by the SMA team across Australia, from their strategic locations in Sydney, Melbourne, Central West NSW, and the Gold Coast.
At Lagan’s suggestion, they began by renting a Keestrack R6 Impact Crusher to test its performance on their site, but it did not take long for Albury Quarries to invest in a brand new R6h unit.
As David said, they were immediately taken with the R6h’s ability to handle everything from large rocks to wetter, stickier materials and achieve high-tonnage rates.
“The decision to invest in an R6h was not only influenced by previous problems with other crushers, but also the machine’s capacity, reliability, and efficient operation in wet weather conditions,” he said.
“A huge reason for our success is SMA and its Keestrack Crusher.”
The Keestrack R6h has a 3.1m double-deck pre-screen with a belt underneath instead of a chute. It is powered by a 757hp Volvo engine and 6.5-tonne rotor drive, which produces high levels of inertia and torque and delivers highcapacity crushing. The Keestrack R6h has 120hp more than its predecessor model and greater production capabilities.
Maintenance is kept to a minimum with key features, including sealed bearings on all conveyors and steel hydraulic lines instead of hydraulic hosing for better cooling and fewer leaks.
With the features of the Keestrack R6h, Albury Quarries has been able to produce 20mm to 40mm roadbase materials while meeting high-tonnage requirements.
The Keestrack R6h Impact Crusher has a 16 x 5 double deck after screen and swivelling return conveyor. This allows end users to create up to two products in a closed circuit or up to three in an open circuit.
Thanks to the partnership with SMA and the performance of its Keestrack R6h Impact Crusher, Albury Quarries is thriving in the world of contract crushing. • For more information, visit screenmasters.com.au
Steve Franklin, founder of Eltirus, attended AggNexus 2024. He writes about what he learned and what digital transformation looks like in practice.
Over two days in September, some ninety attendees met at the Joe C Thompson Conference Centre at the University of Texas in Austin for the first AggNexus Digital Innovation conference.
The idea was to bring together the leading construction material technologists with industry decision makers who were serious about changing their businesses. While the group may sound small, the horsepower in the room was remarkable, with decision makers from most of the major players in the North American market (I have never seen so many senior people in one room) in attendance.
The format was unique. Participation was by invitation. Each of the technologists had five minutes to explain what problem their business solves and the value of it. Producers • Buying or creating your software
Enable is an operational reporting software product from Eltirus.
technologists. This wasn’t some “prove to me that digital transformation is relevant to my business”, it was “show me how”.
The reach for digital solutions to solve problems is very strong in North America with the sheer breadth of what some companies are working on being quite remarkable.
The short story is this – while my generation was happy to do things with paper and spreadsheets, the generations following are not. They see it as old, inefficient and slow –
We have certainly seen innovation across the industry – the popularisation of drone survey for stockpile management is a good example, but there is so much opportunity for effective data capture and analysis, digitisation and management of quarry sales, maintenance, planning, optimisation of fixed plant and logistics, hence the decision to bring people together for AggNexus.
Attendees ranged from the large multinationals to the regional players (noting of
course that many of these are in the tentwenty million tonne per annum range).
In general, the sort of questions they were trying to solve were something like:
How do I identify opportunities in the market or targets for expansion?
Burgex are a mining consulting company based in Utah that have built a software product called Mineralocity.
In essence, a geographic information system tool that covers continental USA, it shows who all the producers are, their estimated (or known) production, the estimated demand in the areas they service and the geology of the regions in which they operate.
Mineralocity is the ultimate tool for anyone in North America trying to understand gaps in the market, opportunities for organic expansion or targets for mergers and acquisitions.
Unfortunately there is no equivalent in the Australian or New Zealand market at this time.
How can I ensure that my operational processes are being carried out?
Hailing from Sweden, Checkproof provides a user-friendly, all-in-one platform primarily for the construction materials industry.
The platform digitises maintenance and health, safety, environment and quality management, with tasks including, quality and maintenance routines, defects, deviation, and incident reporting.
CheckProof’s client base spans across several segments from within the construction materials industry, ranging from asphalt, cement, aggregates, concrete, and OEM among others.
How can I reduce the cost of materials in my concrete?
Concrete.ai, based in California, harnesses the power of artificial intelligence to optimise concrete production and quality. Its advanced algorithms and data analytics tools help producers enhance mix designs, reduce costs, and achieve sustainable, highperformance concrete solutions.
How do I ensure I don’t run out of rock?
Eltirus, based in Brisbane is a global consulting company that works to help the construction materials, cement and industrial minerals industries better understand what’s
Concrete.ai, based in California, harnesses the power of artificial intelligence to optimise concrete production and quality.
in the ground, how to extract it sustainably and how to ensure compliance to plan and statutory requirements.
Application of digital transformation tools to quarry resource management can save tens of millions of dollars and the potential embarrassment of putting a quarry in the wrong place, being tripped over by unpredictable geology or simply not being able to work out how to schedule extraction.
How do I make sure I am meeting targets? Enable is an operational reporting software product from Eltirus.
The best way to hit targets is to know what they are, and then track performance through the month against them. Eltirus Enable was written with just this in mind – collect the data (as automatically as possible) and then present it in a way enables the players to see the score and what they are playing for without having to hop backwards and forwards through multiple systems and spreadsheets.
How do I make it easy for my customers to order from me?
GoBuild360 are based in South Africa. It provides an enterprise resource planningintegrated e-commerce solutions tailored for the construction industry. Its platform offers robust customer portals and delivery
apps, enabling seamless order management, real-time tracking, and efficient payment processing, enhancing overall sales and operational efficiency.
What can I do to optimise my deliveries to maximise truck utilisation?
INFORM is a pioneer of AI-powered operational excellence in aggregates and ready-mix logistics. Its transport planning and execution software allows dispatchers and planners to move more payloads with fewer trucks each day, resulting in savings such as a cut in logistics unit costs by up to 20 per cent, an increase in loads/truck/day by up to 37 per cent and a reduction in truck fleet size by up to 30 per cent.
How can I ensure I am getting the best price?
PriceBee is the leading pricing and quoting tool for construction materials. Integrating with common weighbridge/allocation systems and point of sale systems, it allows salespeople to quickly quote its clients and ensure that the price is right.
How do I know for sure that my inventory is correct?
Based out of Seattle, Stockpile Reports is the brainchild of David Boardman. It focuses exclusively on stockpile
measurement, validation and certification of quantity.
Stockpile Reports is unique in offering solutions that can use fixed cameras (say at a concrete plant), drones or an innovative iPhone app that now in use in over one hundred and five countries since release last October. This app allows you to measure a stockpile using any late model Apple iPhone. The latter is a great tool for anyone who just needs to get a quick quantity check and is especially useful to anyone in the contract crushing game. Stockpile Reports also certifies stockpile quantities, a truly unique service. In essence, they have a process and QA approach to the measurement of stockpiles that they will stand behind and can be used for corporate accounting purposes.
Do I know what is going out the gate and to who?
TAC Insight delivers cloud-based logistics and operational solutions for the construction materials industry. Its flagship product, FastWeigh, streamlines ticketing, dispatching, and reporting, providing real-time visibility and control over material movements and transactions. •
For more information. contact steve.franklin@eltirus.com.
for Aust ralia, Papua N ew Guine a and South East Asia
IMS have added the new BP1200-48TB track electric twin power blender to its impressive collection of blenders and pugmills, the new BP1200-48TB has four separate feed hopper each five meters long holding 12m3 each. All feed hopper conveyors are fitted with belt scales and controlled by a PLC control and recording system that can be operated from an iPad or phone from its own Wi-Fi system from a loader or
Quarry learns more about Wirtgen Group’s new dedicated aftersales team and how they are working to improve support.
The Wirtgen Group manufactures specialist equipment that requires specialist care.
Quarries are a harsh environment for machinery, and keeping equipment up and running is key to production.
That’s why Wirtgen has committed to supporting its customers through a dedicated Australian aftersales team.
John Richardson, parts manager for
The Australian aftersales team is made up of three specialists: Daniel Hughes, Shaun Howe, and David Lefroy. Hughes is responsible for providing aftersales support in Victoria, South Australia, and Tasmania. He has been with Wirtgen Australia since 2007 and has a wealth of knowledge. His expertise spans the entire Wirtgen Group product lineup, allowing him
to the team. He is familiar with the local market and equipment which enables him to provide insightful recommendations and support that is tailored to the specific needs of each customer.
Richardson said Howe’s dedication to building strong relationships is evident in his consistent engagement and follow-up, ensuring that clients feel supported every step of the way.
“Whether it’s troubleshooting a technical issue or providing training on new equipment, Shaun is always ready to assist,” he said.
“Even though he’s only been in the role for less than a month, and has spent two weeks in Germany learning, there has already been great feedback.”
Lefroy has been with Wirtgen Australia since 2012 and specialises in the company’s Kleemann portfolio. He works closely with customers across Australia and New Zealand to provide solutions specific to their Kleemann mobile crushing needs.
His application knowledge allows him to understand the diverse needs of clients in the crushing and screening sector, ensuring that they receive aftersales support that aligns perfectly with their operational goals.
Richardson said Hughes, Howe and Lefroy exemplify Wirtgen Group’s commitment to customer satisfaction and operational excellence.
“Their combined expertise and dedication to supporting our clients ensure that Wirtgen Group remains a trusted partner in the road and minerals industries,” he said.
“With this exceptional team at your side, you can be confident that you have the right support to drive your success and staying true to our company values.” •
For more information, visit wirtgen-group.com
Lokotrack® ST4.10™ Aggregate Screen
The Lokotrack® ST4.10™ is designed for efficient screening of crushed rock, sand, and gravel. It’s the ideal choice for producing quality aggregates for concrete and asphalt, road base, building foundations, and railway ballast. You can rely on its durable build, reliable performance, and simple operation to meet all your aggregate production needs.
For more information on the extensive range of Metso mobile plants, email us today at metso@tuttbryant.com.au!
Find out how US-based Dodge Industrial offers solutions for quarry customers instead of just products.
Dodge Industrial produces high-quality mechanical power transmission equipment – but the company is more than just a supplier.
Halden Engela, division manager at Dodge Industrial Australia, said the company is focused on being a solutions provider.
“We believe in using our products to address problems,” he told Quarry. “We’re not just there to be another supplier.”
“Our products are developed with the customer in mind, trying to address particular problems – be it shaft attachment, incorrect bearing setups, bearing lifespan, and more.”
Dodge has extensive experience solving customer problems. Wallace Dodge founded the company in 1878 to produce wagon jacks and split wood pulleys. Since then, the company has grown significantly, expanding into the Australian market around 30 years ago through a distribution network.
In Australia, the company targets bulk material handling industries in heavy, hardworking environments such as quarrying, grain handling and mining.
Engela said the company’s range of products was designed for these industries.
“In the US, we are industry leaders in those segments, and we cater our product profile locally to suit those markets,” he said.
“In terms of our full range, our scope is narrow, but it’s geared towards these markets, both in the product itself and the depth of support for those markets.”
Dodge maintains patented designs for many of its products, including unique shaft attachment methods for its gearboxes.
Both its belt-driven Torque-Arm II (TAII) and Motorised Torque-Arm (MTA) have a twintapered bushing system that addresses one of the biggest issues its customers faced.
Most shaft-mounted gearboxes are attached to the driven shaft with a straight bore mounting system, which is not easily removed.
The twin-tapered bushing system allows
conveyor drum pulley, which is stocked and supported locally, and the Raptor elastomeric split-tire coupling that comes with a fiveyear warranty.
Engela said Dodge’s solutions-centric approach is also seen in its ISN mounted spherical roller bearings.
ISN mounted bearings are a dropin replacement for SN style bearings, engineered with a patented tapered adapter for easier, faster installation and removal without damaging the shaft. Unlike SN bearings, each ISN bearing arrives completely assembled and pre-lubricated to be shaft-ready out of the box.
“ISN bearings were developed to address issues where customers had an incorrect bearing set up and addressing the life of a bearing,” he said.
“Some of these challenges boil down to lubrication, set up, sealing of the unit, so when
and environment which can be very abrasive for these kinds of products.”
Dodge also offers a Trident triple-lip “combination seal,” which is a labyrinth and contact seal that extends the life of its
bearings. The rubber used for this was specifically designed and has been incorporated into several other key products.
This method of finding improvements, incorporating them across product lines and enhancing the customer experience is how Dodge positions itself as a partner for quarries instead of just being a supplier.
“Dodge has been on the forefront of many technological developments,” Engela said.
“We have developed advanced Industrial Internet of Things (IIoT) compatible sensors to monitor the performance of our equipment, and to obtain data that gives users the ability to conduct condition monitoring.
“That allows us to support our customers, preventing failures by providing real-time information for preventative maintenance.”
• Large Gape.
• High Production.
• Low Operating Costs.
• Proven design with a long history of trouble free operation in tough mining and quarrying applications.
• Frame fabricated from low carbon steel, reinforced with ribs throughout. All mounting surfaces are fully machined for accurate alignment of critical components.
• Heavy duty self-aligning double row roller bearings throughout, sealed against the ingress of dust and dirt.
In 2021, the company established itself in Australia with the introduction of Dodge Industrial Australia.
It has representation across Victoria, Queensland, NSW, WA, and SA and a hub in Melbourne, which houses a wide range of inventory and provides technical support.
Engela said the company still believes strongly in the distribution model and has been looking at distribution partners to ensure its specialised team can support the wide footprint of its customer base.
“We support our Australian customers through our technical ability, our resources, and our depth of stock,” he said.
“All of our team members have visited the factory for training on our product lines, so we have the resources to provide support.
“We can also offer our clients online and face-to-face training, or tailor packages to support them and their staff.” •
For more information, visit dodgeindustrial.com
Innovative designs focusing on power, efficiency, and operator comfort.
Eco-friendly operations with smart connectivity for optimal fleet management.
When mobility and toughness matter, count on the Lippmann 300c and 400c. These mobile cone crusher plants were specifically designed to take on the most abrasive and toughest materials in aggregates and mining — all with mobile capabilities. Heavy duty cone crushers with an innovative material flow that maximizes capacity and throughput while delivering a consistently high quality product.
• MC400 High Speed Cone Crusher
• CAT C18 Engine
• Direct Drive
• 250mm Feed Opening
T: 1300 859 885
E: sales@triconequipment.com.au www.triconequipment.com.au
Effective and efficient.
The MDS M515 Heavy Duty Trommel excels at crafting rip rap and reclaiming rocks entangled with clay and other adhesive materials. Comes complete with fold out stockpiling conveyors and has four hydraulic jacking legs to raise the machine to increase stockpile capacities and lower for transportation. See triconequipment.com.au or call 1300 859 885
Superior’s Telestacker® Conveyor is a material handler’s most effective weapon against costly stockpile segregation. Its variable height, length, and axle positions allow for layered stockpile construction, which is key to achieving partially and fully desegregated piles. The design has been carefully fine-tuned for hard work and dependability in numerous applications. Call Tricon on 1300 859 885 or see triconequipment.com.au
Komatsu Australia’s partnership with Endeavour Foundation is helping people with disabilities and the environment.
Komatsu Australia has renewed its partnership with disability service organisation Endeavour Foundation, which will provide more employment opportunities for people with disabilities.
The partnership between the two organisations provides employment opportunities for people within Komatsu’s Oil Wear Analysis (KOWA) area. Employees help clean recycled plastic canisters, used as part of KOWA, so they can be re-used up to six times.
The partnership was established in 2021, but the renewal extends the agreement by another three years.
Russell Hodson, Komatsu Australia’s executive general manager for supply chain, said the company was excited to continue the partnership with the Endeavour Foundation.
“We’ve been able to not only offer meaningful employment to a number of people, but with more than 30 per cent of Komatsu’s plastic packaging waste generated through our KOWA bottles this program and partnership also means we can significantly reduce the volume of plastic packaging waste that we are sending to landfill,” he said.
“As a large, global company, we are always looking at ways we can use our presence to bring about some good in the world.
“This partnership is just one of the ways we are focusing on our ESG principles - it helps Komatsu reduce their environmental footprint, while also providing some meaningful employment to people with disabilities - and has proved to be such an important part of our overall supply chain in the KOWA division.”
Endeavour Foundation is an independent organisation that supports people with disabilities through independent living or other forms of accommodation, community initiatives and employment opportunities.
According to Hodson, since 2021, the initiative has helped 450,000 KOWA bottles be recycled and prevented 12,000kg of waste going to landfill.
Shannon Foley, executive general manager for work at Endeavour Foundation, said being employed was a key goal for many people with disabilities.
“Meaningful employment is valuable to everyone, and we’re proud to play our part by helping to create roles for people with disability,” Foley said.
“We’re looking forward to continuing to work together with Komatsu on this valuable initiative and seeing what other future opportunities we can create.”
Back in 2021, Komatsu Australia introduced more sustainable packaging for its plastic bottles and packaging, which customers receive as part of the KOWA samples.
The company made the change so the yellow outer plastic bottles used for collecting the KOWA oil samples would be 100 per cent recycled plastics. The sample registration card and delivery boxes were also switched to be made from 100 per cent recycled paper and cardboard.
The move initially accounted for around 100,000 sample kits used by Komatsu Australia’s customers on the East Coast.
According to the company, customers in that region accounted for 60 per cent of the oil samples collected from Australia, New Zealand, and New Caledonia each year. By the company’s measure, the sustainable initiative accounts for 10 tonnes less of packaging materials going to landfills annually.
According to Komatsu Australia, this is part of how it has taken steps to ensure it meets its corporate social responsibility principles.
“This sourcing strategy for our oil sample bottles allows us to contribute to our strategic goal of zero harm by significantly reducing the environmental impact of our current method of procuring and managing KOWA bottles,” Hodson said.
The change to lighter packaging allowed for smaller-dimension packing, which meant more kits could be stacked on the pallet, reducing transport costs and logistics for Komatsu Australia’s customers across the country.
“Komatsu’s KOWA oil sampling services are critical to our customers and our business,” Hodson said.
“This new sourcing strategy allows us to reduce landfill and carbon emissions, without compromising quality or security of supply –and at no extra cost to customers. Initiatives such as our recycled, reusable KOWA bottles are another step on this journey.”•
For more information, visit komatsu.com.au.
• Ideal for processing overburden, riprap/armour rock, limestone mixed with fines, clay and sticky materials
• High capacity, handling up to 500 tons per hour and up to 800mm sized rocks
• Hydraulically adjustable chassis riser for greater stockpile capacity and ease of access
• A tracked machine that’s perfect for moving from site to site
A new report has flagged possible shortfalls in material supply in the United Kingdom and the potential impacts on the region’s infrastructure projects.
Concerns have been raised over the medium-term future of the supply of construction materials in the United Kingdom.
The Mineral Products Association (MPA) has published its Annual Mineral Planning Survey, which showcases the “declining levels” of planning permissions granted to extract permitted material reserves. The MPA says this decline will impact the future sand, gravel, or crushed rock supply, including limestone and granite.
The association’s primary concern is the material consumption rate, primarily for construction, outpacing the approval rate of new consents for quarrying. According to the survey, for every 100 tonnes of sand and gravel used in Great Britain, 61 tonnes of new permissions were granted on average between 2014 and 2023.
The reported gap widens when the material in focus shifts to hard rock over the same period. According to the MPA, for every 100 tonnes of hard rock used, only 33 tonnes of new hard rock material received planning consent.
The current state of play sees Britain as almost self-sufficient in its material supply.
The data from the survey illustrates that the region is currently able to meet its requirement of around 250 million tonnes a year, with recycled materials and materials from secondary sources accounting for 30 per cent.
However, the evident gap between usage and planning consents has underlined the MPA’s concerns about the region’s medium-term future of material supply, especially for construction.
“MPA’s members are working hard to produce and deliver the essential mineral products needed to deliver the government’s ambitions,” Aurelie Delannoy, director of economic affairs at MPA, said.
“But unless there are significant reforms to streamline mineral planning and permitting, along with a change in the investment environment, these mineral reserves will not be fully replaced.
“That will not only impact the mineral products industry but also the UK construction industry and the wider economy.”
The shortfall is more evident in certain parts of England, primarily due to the country’s geology. The East Midlands and South West of England, which contain several ‘super quarries’, have traditionally been strong suppliers of construction materials. However, according to the new report, shortfalls are possible in these traditional strongholds.
Over the 2014-2023 period, the South West of England, the biggest sand and gravel producer, used a volume of materials close to three times higher than the newly consented sand and gravel reserves. This sentiment was shared across two-thirds of reported geographic data sets.
The East Midlands, the largest hard rockproducing region, saw material sales around 18 times higher than the volume of new permitted consents.
The MPA noted that the average time to determine these planning applications is just over 22 months for sand and gravel, while crushed rock takes over 36 months. This period measures the “commencement of pre-application discussions to the permission being issued.”
However, the report estimated the development cycle was “significantly longer.”
This time period encompassed the time from application preparation through to operation.
According to the MPA’s data, this timeframe, from site exploration to active and operational, can take from five to 15 years.
“Given the continued demands required to support the delivery of the nationally significant infrastructure programme, housing and commercial developments, this situation needs to be urgently addressed by government,” the survey noted.
Mark Russell, executive director at MPA, added: “Our survey shows the availability of essential minerals is fast approaching a cliffedge. If the long-term trend of diminishing reserves from local domestic sources continues, it is inevitable that the tensions involved in maintaining future supply will be exacerbated.
“In turn, this will result in increased costs to supply, but also increased energy consumption and emissions, as materials will have to be transported over ever-growing distances to fulfil demand.
“An increasing number of planning applications appear to be being refused against local authority planning officer recommendations. Consequently, the mineral products industry is increasingly having to plan by appeal, as was the situation in the 1990s.
“Nothing gets built without minerals, and that’s why we’re asking the government to include mineral planning as an integral part of the proposed planning reforms.”
In the background of the concerns raised by the MPA are the new plans to bolster housing and overhaul the UK planning system announced by Rachel Reeves.
Reeves, installed as chancellor of the exchequer earlier this year, laid out a series of reforms to increase house building and infrastructure projects. The government’s fundamental promise is to build 1.5 million homes over the next five years.
They have also outlined plans to end the “de-facto ban” for on-shore wind projects and add 300 additional planning officers across the country.
“I am taking immediate action to fix Britain’s economic foundations,” Reeves said.
“By growing our economy, we can rebuild Britain and make every part of the country better off.”
Angela Rayner, deputy prime minister, added: “The Chancellor and I will work in lockstep to kickstart the economy, unleashing housebuilding and powering local growth.
“We will unblock the bottlenecks and drive forward a transformational package to build the homes people need.”
Reeves has won admirers from the aggregates industry in the UK for her early work in the role.
“We wholeheartedly welcome the government’s announcement to ‘get Britain building again.’ The ambition and clarity it brings are crucial in these times. As a leading sustainable building materials supplier within the UK, we are fully on board with this initiative and ready to support key areas such as housebuilding, infrastructure and onshore wind,” Lee Sleight, chief executive officer at Aggregate Industries, said.
Industry advocates have linked the low rate of home building and infrastructure projects to a low rate of construction material sales.
According to the MPA, 2024 will remain challenging for the industry, with a recovery anticipated in 2025, according to its outlook.
“Investment uncertainty is hurting our sector and the broader construction supply chain. The latest cancellation of the Stonehenge tunnel and Arundel bypass schemes, following the previous cancellation of the northern leg of HS2, further erodes business confidence,” Delannoy said.
“Likewise, new government reviews on transport and the hospital building programme add to this uncertainty, turning any attempt at forecasting and business planning into parody.
“This worsens the already weak outlook for the industry.
“The Chancellor must urgently address these issues by providing clear policies to reduce uncertainty and spur growth in line with the government’s ambitions.
“This includes improving delivery on critical infrastructure investment and upgrades and ensuring that the planning system supports the domestic supply of minerals and mineral products, which is essential for the wider construction and economic recovery.”
The MPA’s quarterly report showed a “modest overall improvement” for construction aggregates and asphalt in the second quarter. Asphalt volumes (5.3 per cent increase) and crushed rock sales (up by 4 per cent) led the way. However, readymixed concrete sales (down by 1.1 per cent) and sand and gravel sales (down 10 per cent) were notable declines linked to the lack of housing and infrastructure work.
With the homebuilding targets in mind, members of the sector have called on support from the chancellor and government to support material supply in line with the homebuilding objectives.
Certain members, including Aggregates Industries, have suggested recycled materials could play a more significant role with the proper support.
“The construction industry must responsibly embrace the Chancellor’s national mission for growth but can only achieve this by building in a wholly sustainable way … by decreasing the carbon footprint of building materials and going circular,” Sleight said.
“This goes far beyond just minimising waste. Effectively, we need to build new cities from the ‘urban quarry’ of our old stock, thereby conserving the precious resources of our island nation.”
Learn why Lincom Group has recently expanded its presence with a new branch in South Australia.
Clint Hart understands what quarry managers are going through. He has spent the last eight years managing them.
But a few months ago, a new opportunity came knocking. The Lincom Group, a specialist company that supplies the quarry industry with crushing equipment, conveyors, and more, was looking to expand its presence in South Australia and the Northern Territory.
“The interesting thing about the quarrying industry, is that every cubic metre of dirt is different,” Hart told Quarry. “There’s no onesize-fits-all solution.”
“I saw the role as a great opportunity for me. I’ve been involved with quarrying for about 16 years, and I have an understanding about what quarries need when it comes to equipment, personnel, parts, and reliability.”
The new branch, located in Wingfield, Adelaide, is part of Lincom’s strategy of strengthening its relationships with customers throughout the region. The facility was selected for its strategic location, that provides easy access to major highways.
The warehouse is stocked with a comprehensive range of original equipment manufacturer (OEM) parts as well as quality spare parts sourced locally.
The company’s CEO, Stephen Watterson, said throughout Lincom’s history, it has been a priority to expand its reach across all major Australian cities, with a sharp focus on delivering exactly what customers need, when they need it most.
“Our Adelaide branch embodies this philosophy perfectly,” he said. “Our success is built on a foundation of exceptional customer service and the simple yet powerful idea that being closer to our customers is paramount.”
Previously, Lincom supported its SA and NT customers from its Victorian and Queensland branches. Spare parts were shipped out from the main branch in Brisbane, or from Ballarat.
With the establishment of the new warehouse, spare parts are stored significantly closer to customers.
Hart said there have already been situations where he has been able to take parts out of the warehouse and deliver it to site personally in a matter of hours instead of days.
“Downtime in the quarry industry is quite expensive – one cog can derail the rest of the outfit,” he said.
“If equipment isn’t running, that means the plant isn’t producing. If an operation is producing around 1000 tonnes of material a day for example, then goes down for three days, that’s a fair bit of missed production and material at a cost.”
“Having replacement parts available quickly is vital. Our parts team can work out what our clients require and how quickly they can get it to them.”
For the NT, this is even more important. Many quarries in the territory are quite remote when compared with the east coast, so they need equipment that can be relied on.
Lincom’s expansion has freed up more resources within the company to cover the
Hart and the Lincom team have made visiting NT quarries a priority.
“These give us an understanding about our current customer base and what it could look like in future,” he said.
“We’re in discussions about who we can be working with up there to store parts even closer to customers. Moving forward, we want to supply them more frequently to what they’ve previously experienced.
“In places like Katherine, trucks will go straight though to Darwin, get unloaded, then head back down. We want to know what people have on their sites, what the most common parts they need, and support the market.”
One unique support offering that Lincom has available is a technical institute that opened in April at its Narangba facility in Queensland. Here, clients can get up close and personal with Lincom equipment and undertake
This training is part of the group’s belief that to use equipment properly requires more than just a basic understanding.
This is why the company has designed programs from beginners to professionals to provide a thorough understanding of the equipment’s fundamental systems, coupled with practical tips and techniques for maintenance.
Hart said customers in SA and NT have and will be invited to make use of the facility.
“It’s been an eye-opener for some of the customers I’ve caught up with,” he said.
“Our customers can now visit the training centre, work through different diagnostic and problem-solving exercises with our equipment and improve their skills.”
“While it’s only been open for a few months at this stage, it’s been really popular. As a previous quarry manager myself, it’s a strong step – Lincom is one of the first in the industry to do something like this.”
Hart said the industry response to the new branch has been heartwarming, with customers excited to see the investment.
In particular, he’s proud of how much the company as a whole has focused on providing support for its customers.
“I can see Lincom having more of a major impact on the market. Customer support is their top priority,” he said,
“I’ve seen what it’s like when you’re trying to run a quarry without that support and am glad that caring for customers is just as important for Lincom Group as it is for me.” •
ISN mounted spherical roller bearings are the drop-in replacement solution to traditional SN-dimensioned products and feature a patented tapered adapter for easier, faster installation and removal without damaging the shaft—streamlining maintenance to save you valuable time and money.
Scan to learn more or visit dodgeindustrial.com
Precisionscreen discusses how its Australian-made Trackcrush PV350 VSI Crusher has positively impacted the quarrying industry.
Crushing equipment is a competitive market within the Australian quarrying industry.
Many manufacturers stake their claim on the quality of their crushing equipment when it comes to these flagship machines, and the same is true for Precisionscreen.
The Brisbane-based company takes great pride in the fact that its equipment is made in Australia at its Wacol headquarters. Yet, for all its equipment, from pugmills to stockpilers and more, one piece of machinery is the “jewel in the crown.”
Precisionscreen’s innovatively designed and Australian-made Trackcrush PV350 VSI Crusher has proven to be the key to success for Australian contractors.
“We’re pretty bloody proud of it, to be honest,” Jonny McMurtry, chief operating officer at Precisionscreen, told Quarry.
According to Precisionscreen, the Trackcrush PV350 VSI Crusher is still considered the largest tracked vertical shaft impact (VSI) crusher produced worldwide and is the only tracked VSI crusher manufactured in Australia.
Precisonscreen has produced the Trackcrush PV350 VSI Crusher or similar versions for more than 20 years after director Harold Kerr first recognised a need for this type of machine in the Australian market.
Precisionscreen began building versions of the tracked-mounted mobile units for Fulton Hogan and Boral in conjunction with Metso and Sandvik.
This process saw Precisionscreen essentially track-mount crushers from both original equipment manufacturers before they went out into the field and became operational.
Eventually, the Brisbane-based company took the process a step further. It developed its own crushing chamber and direct hydraulic drive, which resulted in the Trackcrush PV350 VSI Crusher, which has served contractors for two decades.
The company equipped the Trackcrush PV350 VSI Crusher to withstand the harsh conditions of the Australian quarrying sector. This meant getting the fundamentals right, like including triple-sealed bearings and extra oil coolers to keep the crusher operating in the most demanding conditions in the industry.
“That was essential to optimise the production of the machine,” McMurtry said.
“We know there is a need out there for high-tonnage, high-volume and high-powered machines, and we manufacture to suit that. We recognise Australian conditions and design and manufacture the machines to suit.”
The major difference operators may notice about the Trackcrush PV350 VSI Crusher is its 350-kilowatt direct hydraulic drive on the crusher chamber. This enables the Trackcrush PV350 VSI Crusher to deliver high-capacity production of up to 350tph, depending on the material density and set-up.
The lined spinning rotor can accelerate the material before it is impacted by the crushing chamber, which delivers a highly energised force onto the material. Combining these two factors enables operators to use the Trackcrush PV350 VSI Crusher to shape aggregate, which is often critical to creating construction materials like roadbase.
Other VSI crushers, including ones imported from overseas OEMs, can often be belt and pulley-driven. Other equipment options in this space can focus more on hybrid models, which may not always suit Australian operators’ specialised requirements.
McMurtry explained to Quarry that the direct hydraulic drive has key advantages compared to other approaches.
“For VSI crushers, a lot of them are belt and pulley driven, which is quite inefficient as there is a lot of slippage, and it is quite an inefficient way for driving these crusher chambers,” he said.
“The benefit of our direct hydraulic crusher drive is it is able to deliver quite a high [amount of] power … it can be sped up or slowed down to suit the operator based on the volumes going through or the shape that they need or the volume of fines that they need.
“The adaptability and the variability as part of the Trackcrush PV350 VSI Crusher as standard makes the other units pale in comparison.”
Since it was introduced over twenty years ago, more than 20 units have entered the Australian quarrying industry.
The Trackcrush PV350 VSI Crusher is popular with contractors and businesses based on Australia’s East Coast, but other units are in Darwin and South Australia.
One of the original Trackcrush PV350 VSI Crushers has stood the test of time and remains in operation today, a testament to the longevity provided by Precisionscreen’s quality manufacturing processes.
Due to the high-velocity speed of the rotor in the Trackcrush PV350 VSI Crusher, contractors have plenty of options. Many have used it to create a premium product for road-related material, but others have used it to work on 7mm-14mm chips, 20mm aggregates and for generating dust or fines.
“It is all about that superior cubicle shape that all the quarrying manufacturers are chasing for their road aggregates. It helps knock off the jagged edges of the stone and gives a real cubic shape,” McMurtry said.
“That high-velocity speed from the rotor can obviously pick up and throw the material quite aggressively … the greatest application is the shaping for the road base aggregates.”
McMurtry said the family-owned and operated company took immense pride and satisfaction in designing and manufacturing the Trackcrush PV350 VSI Crusher for the Australian market.
“We’re obviously proud of all the machines we manufacture but this really would be the jewel in our crown,” McMurtry said. •
For more information, visit precisionscreen.com.au.
ARC Laboratory Services is using a collaborative approach to become the trusted partner of Australian quarries.
Relationships can often make or break businesses in the quarrying and aggregates sector. This was especially so for ARC Laboratory Services.
Laboratories can help ensure quarries produce the highest-quality construction material, but some sites see them as a hurdle they need to clear.
Matt van Herk, managing director at ARC Laboratory Services, saw a need to bring a collaborative approach for laboratory analysis and quality control around construction materials testing in the quarrying and aggregate sector.
ARC Laboratory Services is designed to be a trusted advisor throughout the quarry’s lifecycle, from formation to site rehabilitation.
While van Herk has started other geotechnical businesses in Western Geotechnical & Laboratory Services and Pilbara Geotechnical & Laboratory Services, ARC Laboratory Services is dedicated to the quarrying and aggregates sector.
With a sole focus on aggregate, rock and concrete services, the company provides specialised services to quarrying operators in a ‘one-stop-shop’ approach.
“I’ve been fortunate enough to have good exposure to reputable clients in regard to specialised testing services and effective collaborations with other laboratories in regards to best practice,” van Herk told Quarry
“The ARC Laboratory team has been precisely put together to provide our clients with the greatest expertise and knowledge in concrete and aggregate testing, rock testing, and petrographic analysis. They’re able to utilise the equipment to achieve the best outcomes for the clients in those services.”
Beau Griffiths, laboratory operations manager at ARC Laboratory Services, and Rahul Pillai, senior petrologist, are two key figures in the team of seven who work with the quarrying clients across their testing.
“They’re the two pillars of our business. Beau has really good leadership qualities
and has really brought into the culture of the business, and Rahul is an expert analyst, and everything he puts out is top quality,” van Herk said.
ARC Laboratory Services is a Western Australian-based business accredited by the National Association of Testing Authorities (NATA).
The accreditation ensures that the company meets stringent standards across the range of services it provides to the construction materials sector within Australia.
ARC Laboratory Services has one of the largest scopes for NATA-accredited services in the industry. This means customers can trust that ARC’s work will help them meet the required regulations and standards for their materials to be usable and insurable for any project, including major infrastructure projects, commercial construction, and more. According to van Herk, the major shift for quarries and laboratory services has been the need to meet changing regulations and standards driven by insurance and legislation.
“The insurance requirements around some of these projects and the indemnity have changed, and the testing space has grown significantly in the past five to ten years,”he said.
“Previously, quarries may have been able to use a test result from two years ago, now that needs to be from 12 months ago, or six months ago in some cases. This is to ensure the quality control is 100 per cent there.
“The NATA accreditation is essentially our assurance to the client that we are following rigorous internal processes and procedures which ensure our results are 100 per cent correct.
“While it can be frustrating to see the amount of conformance work required to be completed, it does give assurance to the quarry and end-user that the material is completely fit for use and that all standards and specifications have been met.”
ARC Laboratory Services offers a wide range of aggregate, concrete, rock, and geology services, including petrographic analysis, from its lab, which is open seven days a week.
The company’s ability to conduct petrographic services internally means customers can receive expert analysis on potential quarry material for construction quickly to help mitigate any risks and get it to market.
“It is a forensic examination of the rock that allows us to make interpretations around
Beau Griffiths and Rahul Pillai are experts in their fields.
potentially what the quarry can make from the rock in regard to products,” van Herk said.
“It is your step one in understanding the risks and limitations around the rock. It is the first thing we encourage customers to get done because from there, we can outline the risks or standards available to certify the products for usage.”
Another example of its specialised services to the sector is the assessment of AlkaliSilica in aggregate for concrete providers. Alkali-Silica Reactivity (ASR) is determinantal
to concrete, effectively known as “concrete cancer”. ASR can cause expansion and cracking within the material and cause loss of strength and structural problems.
According to van Herk, ARC Laboratory Services is well-equipped to handle specialised testing requirements.
“ASR is something we can quickly identify in the petrographic analysis and then work with the client on accelerated mortar bar testing,” he said.
“For products such as sealing aggregates, we run the Polished Aggregate Friction Value Test internally and there is only a handful of laboratories that have the capability to run this test.”
For quarries, having geotechnical results quickly can help them make decisions about operations, including purchasing machinery and applying for licences.
With ARC Laboratory Services’ team of industry experts, van Herk wants laboratories to be a lifecycle partner for quarries.
“We’re trying to build lasting partnerships with organisations and quarries to give them the trust to put their product out to market and stand by it 100 per cent,” he said.
“As a valuable partner in the lifecycle of the quarry operation, we assist our customers to ensure testing standards are met. We want to provide quarries confidence through our quality and efficiency.” •
For more information, visit arctesting.com.au
Terex Washing Systems’ equipment is helping Barro Group reach its production goals in Victoria.
Barro Group is one of the recognisable names in the Australian quarrying sector. Its distinctive green and red logo can be seen around the country, and the independent construction materials producer’s products are used in everything from infrastructure projects to residential construction and more.
Adam Wilkinson, quarry manager at Barro Group’s Wodonga Quarries, spoke to Quarry about the company’s partnership with Terex Washing Systems through its Wodonga Quarries operation.
The Wodonga site focuses on producing concrete aggregates and sand, which supports Barro Group’s distribution of premixed concrete and other construction materials. The site also serves construction projects around Wodonga, including road projects, buildings, housing, and subdivisions.
The Terex partnership with Barro Group began during COVID-19, when the two organisations worked together to install a new integrated crushing, screening, and washing modular plant to replace the ageing plant. At the time, both Terex and Barro Group described the Terex Jaques/Terex Washing Systems processing plant as a “one-stop shop” for the quarry’s needs.
The original circuit consists of an AggreSand 206 modular wash plant –comprising a primary three-deck, 6m x 1.8m rinsing screen with an integrated sand plant, self-regulating sump tank, twin cyclones, 4.3m x 1.8m dewatering screen, and radial sand stockpilers – backed by a modular MC1150 cone crusher with integrated surge bin and pan feeder, and another 6m x 1.8m part-rinsing, aggregate sizing screen. A Terex-designed MCC and electrical control system control all of the equipment.
The MC1150 modular plant comprises a 14-tonne TC1150 roller-bearing cone crusher with a nominal head diameter of 1150mm. It can accommodate fine, medium-fine, and extra-fine manganese profiles and is powered by a 220kW motor.
Years later, the Barro Group wanted to enhance its sand production rates at the Edwards Road site, which sparked another collaboration with Terex Jaques and Terex Washing Systems.
“We approached them about putting the second dewatering screen in for our manufactured sand, which allowed us to increase our sand production. It was sort of an option in the original proposals. It was already thrown out there when Terex did the
original plans, so we knew it was an option if we wanted to do it.
“[The original] plant was up and running, and we thought it was time to add to it and get some increased production out of it.”
Terex Washing Systems helped install the FM120, which provided Barro Group with the production and processing capability it was after. The FM120 is a sand processing unit designed to be cost— and energy-efficient. It can recover one or two grades of sand with an output of 80-120 tonnes per hour and works in conjunction with the other equipment from Terex Washing Systems. According to the company, its dedicated high-frequency dewatering screen can reduce residual water in the final product by 10 to 15 per cent.
It has a collection tank, centrifugal slurry pumps, hydrocyclones, and a dewatering screen on a single chassis. The FM120’s cyclones use centrifugal force to remove clay, silt, and slimes from the sand product and bring it up to specification.
“Within the first month, we knew it was going to do well, and we had noticed the increase in production, and we’re not losing as many fines in our waste water,” Wilkinson said.
“It is a nice, compact set-up, and it uses the same parts, cyclones, and pumps as our current plant, so it gives us interchangeability with parts. Having the interchangeability was a big bonus.”
One of the main benefits of the new system is enhanced water management.
“It has helped with our water management a fair bit. Especially because you’re not transferring material around, we’ve cut our water usage down and increased production by a fair bit,” Wilkinson said.
“It also allowed us to dedicate the original dewatering screen completely to sand, and it has led to about a 30 per cent increase in production, which is what we wanted.”
For a partnership that began during the COVID-19 pandemic, Terex Washing Systems’ equipment has helped Barro Group’s Wodonga Quarries increase its production.
Through smart planning and clever design, Terex Washing Systems has been able to seamlessly add onto the Wodonga system
to help Wodonga Quarries and Barro Group achieve their production goals.
“We looked at other suppliers but stuck with Terex because they supplied the original plant and we wanted consistency,” Wilkinson said
“To have your original request met and then have options in the future if you wanted to upgrade is definitely a plus and probably a big reason why we went with Terex originally.” •
For more information, visit terex.com/washing
Our engineers are experts in innovation with the ability to design bespoke solutions and provide products to suit all conveyor applications.
Selected to increase your efficiency and reduce downtimeIf it’s above, around or below the belt, we have the answer.
Unlock your productivity potential. Visit kinder.com.au
Astec has announced its expanded partnership with equipment dealer Mineral Processing Solutions (MPS), part of the OPS Group.
Astec Australia and Mineral Processing Solutions (MPS) have signed an expanded dealer agreement for the construction materials sector to support Astec’s Australian customers.
The new dealer agreement includes the construction materials product lines in Queensland, Victoria and Tasmania. This means that MPS, part of the OPS Group, will supply Astec Material Solutions with fixed and modular plant, equipment, parts and services throughout Australia.
Under the terms of the new agreement, MPS will distribute all Astec fixed and modular crushing, fixed screening and washing equipment and systems, as well as material handling (Telestack) and Breaker Technology (BTI) products to all states and territories.
David Smale, regional managing director for Astec Industries, said expanding the partnership with MPS was easy given their long-standing history.
“We have the same values. It’s like when you’re looking for a business partner and you’re looking to grow; it is so much easier when you have the same values,” he told Quarry.
“They hold the customer front of mind with their relationships and look after the customer long-term, and there is a lot of alignment there.”
This follows the two companies’ announcement earlier this year that MPS would take over Astec’s fixed plant equipment distribution in New South Wales, with further states to follow in the coming years.
Those plans have been brought forward, and Smale credited the work of Adam Gordon, business line manager for material solutions at Astec Industries, and Shane Czerkasow, managing director at OPS Group, for growing the partnership.
“Shane is very operational, he’s in front of the customer all the time, and he’s
driving us to perform better as well, which is nice,” Smale said.
“Adam deserves a special mention as well … I put him in charge when we took over the dealership with MPS; that was his baby. I am looking forward to this expansion and seeing how Adam makes it hum because he’s a big part of it.”
The expanded agreement effectively creates a “one-stop shop” for Astec’s fixed crushing and screening equipment, material handling (Telestack), and breaker technology through MPS. While little will change for existing customers, they can now use the Australian-based dealer to access the complete range of Astec’s fixed plant screening and crushing throughout Australia. Through the new agreement, Astec’s customers will have a clear point of contact for equipment, parts, and services. However, the expanded partnership is set to benefit customers in Queensland, Victoria, and Tasmania greatly.
OPS Group celebrated 35 years of operation earlier this year. MPS maintains depots across Australia’s East Coast in Goodna (Queensland), Rutherford (New South Wales) and Laverton (Victoria), which are well-stocked for parts. It also possesses an experienced sales and service team with extensive industry knowledge in all states and territories.
“We choose the dealer who will have a better impact on our customers. If we can’t find a dealer who improves what we’re doing for our customers, then what’s the point?”
Smale said.
“So, through MPS, we will be able to get a lot closer to our customers, particularly in those regions where we don’t have the resources to do so. We are aligned in our values in how we service the customer.
“The third consideration is that we felt we could have a stronger business, with more volume in the business and service the customer better with MPS.”
With the expanded partnership underway, Smale said he was excited to see what the future would bring for MPS and Astec and their Australian customers.
technologies and manufacturing capability – has made MPS the perfect partner to MPS, part of OPS Group, has been a long-standing Astec dealer.
deliver outstanding products and service. I’m delighted to be making this announcement and look forward to the positive impact this collaboration will have on our customers working alongside MPS. Such synergy will
continue to strengthen our market presence but also set highest standard for service in building the infrastructure of Australia.” •
For more information, visit astecindustries.com.
Hazemag’s range of hammer mills are helping operators achieve the right product size across several applications.
With its wide variety of adjustable tools; grinding path to grinding wall heating, the Hazemag Hammer Mill is a versatile machine for all seasons.
The machine has been a long-standing part of Hazemag’s offering, with its primary uptake being in the cement, fertiliser and limestone industries as well as in other industries, including coal mining.
Teddy Craies, Hazemag allmineral’s managing director for Australia, said the hammer mill is helpful for many materials, including coal, shale, gypsum, glass, limestone, phosphate, potash, dolomite, lignite and clay.
Now, Hazemag envisages its hammer mill range having a big future in two of Australia’s key markets.
“The coal market and the quarry market, as well as those markets which are looking for finer products. It is used in some power plants and steel industries for secondary and tertiary crushing for various different materials, it works quite well for fine crushing,” Craies said.
“The thing with the hammer mill is the reliability and the product size. It gives you a very defined product size and product distribution, which is easy to access for maintenance and adjustments.”
In addition to its usage in traditional industries, the Hazemag Hammer Mill is expected to play a larger role in recycled materials in the future.
“With recycling materials coming up more and more, and the need to be more environmentally friendly and have a better environmental footprint … these machines will play a bigger part,” Craies said.
Hazemag has continuously innovated its hammer mills to ensure they remain up-todate with modern technology to meet the needs of traditional and emerging industries.
Hazemag produces two types of hammer mills, with the main variance being the single rotor (Hazemag Unirotor) or the double rotor (Hazemag Novorotor). While both types can be used for fine grinding construction materials, the rotors provide subtle differences for the operator.
The HNM model from Hazemag has a double rotor, while the HUV and HUM models have single rotors. The double rotor in the HNM model provides operators with a machine with a higher capacity capable of processing more feed material at once.
A vital component of the Hazemag Hammer Mill is the disc-type rotor, to which the hammers are mounted. The hammers are free-swinging and able to swing 360 degrees. The steel disc design rotor is hard-faced for maximum life. The rotor is shaft-mounted and fitted with self-aligning roller bearings.
The dual-rotor HNM model has been used primarily for fine crushing or mill drying of materials, including gypsum, glass, limestone and clays. The dual rotors are non-reversible but can produce a better product fineness due to its two-stage reduction.
“With the dual rotor, the capacity is one thing, but you can also feed it laterally, which gives you dual-stage crushing. While your capacity will be a bit lower, you will gain dual stages and
your reduction in size will be quite large if you go that way,” Hazemag and allmineral’s project and service engineer Jaco Botha said.
The single-rotor can be run in reverse, optimising the wear parts’ usage within the machine. Operators can also run the single-rotor models continuously or at variable speeds. This is because Hazemag has designed the HUM and HUV models’ mill housing with a symmetrical structure, enabling the rotor’s direction to be reversed.
“With the single-rotor models, you can reverse the rotors which helps provide the best life to the [hammer mills’] parts and wear parts,” Craies said.
“For any crusher, you want to protect the heart of it (the rotor with shaft and bearings), and you can get the maximum life out of the crusher and the hammer, with the hammers being able to rotate in both directions.”
The grinding paths can be equipped with an oil heating system. The system helps heat the impact walls, improving the material flow when
the hammer mill is processing. This is useful when working with wet and sticky materials that contain moisture and tend to cake.
It works by pumping heat-conducting oil through the system, located behind the grinding path, to stop material caking and impacting material flow.
“The oil heating system helps with higher moisture applications,” Craies said.
“The grinding wall heating system helps to keep a stable process and also protects investment as well. Just having those heating walls and the grinding plate protects the whole crusher because it creates a better operating process.”
Hazemag can equip its hammer mills with different features depending on the application, including a direct drive, to help tailor the machine to the customer.
The direct drive benefits the customer by creating less slippage, less machine weight, and fewer maintenance requirements. It also requires less investment. The grinding path, which is casted, can be easily exchanged for maintenance.
“By doing these things, you’re getting a better life out of the machine. It adds to the safety factor as well,” Craies said.
With three hammer mill models in its portfolio, Hazemag can find the machine that best suits the operator’s application.
Hazemag maintains a comprehensive database of customers using Hazemag machinery in different global applications.
This list provides Hazemag with a range of reference points that it can use to help find the best machine for a customer’s application based on past success stories.
The company will find the best fit for specific applications between its Australian team, led by Craies and Botha, and its team of German engineers. The Australian team can also conduct on-site testing, and the
company can do material testing in Germany to select the suitable machine.
“Our hammer mills are versatile and from our experience, you get a good life out of it and the required product size, getting the required product distribution size consistently,” Craies said. •
For more information, visit hazemag.com
Rammer Boom Systems can help quarries minimise downtime, protect their crushers, and safely deal with oversized material.
Wimproving efficiency are important for any operation, it is of the critcal importance that everyone goes home safely at the end of the day.
For crushing operations, remote solutions that can safely address blockages and oversized material within the crushing set-up have become a “must-have” investment. Solutions like the Rammer Boom System are among these options for Australian quarries.
oversized material via remote control, which can occasionally occur and cause the material to feed to the bridge.
Jeff Jackson, sales manager and director at Total Rockbreaking Solutions in Western Australia, said the Rammer Boom System offered several benefits for quarries.
“Quarry managers love them,” he said.
“They might go a few years without one, but once they’ve got it, they say, ‘How did we survive without having it?’.
“It is a proven design, and it is fit for purpose. The Rammer Boom System is strong, reliable, and made of good- quality materials.
“It saves them time, it saves them money, and it is a lot safer, and the end result is there is more product that they can sell.”
The Rammer Boom System saves operators from undertaking a more laborious approach to removing oversized material from their crusher. In the past, operators may have needed to rely on overhead cranes or a more DIY method, which require hours to remove oversized material.
The Rammer Boom System can be located towards the side of the crusher, which allows the rockbreaker to be positioned over the crusher and access any blockages.
The operator controls the hydraulic hammer to break or move the rock so the crusher can continue to crush unimpeded.
The Rammer Boom Package comprises the hydraulic boom system, hydraulic power pack, and control system, and it is paired with the rockbreaker.
Rammer has produced the Boom System for more than 40 years for crushing circuits in Australia and overseas. The company manufactures 28 models ranging from onetonne to 18-tonne heavy-duty models, which can be matched to the quarry’s application. The reaches can range from one metre to 17 metres to suit any set-up from stationary crushing plants to mobile crushers.
“Most quarries today go for a radio remote control, which allows them to stand out of harm’s way but still see what’s is going on,” Jackson said.
“The remote control enables the operator to use the system safely and effectively. For the cost of it, you wouldn’t have it any other way.”
The Australian Rammer Dealer network is available to help quarries understand the right boom system and rockbreaker for their application.
Rammer maintains a presence in each Australian state with Walkers Hammers (Victoria, South Australia, and Tasmania), Groundtec (NSW), QLD Rock Breakers (Queensland, Northern Territory, and
Papua New Guinea), and Total Rockbreaking Solutions (Western Australia) as part of its distribution network.
Customers also receive exclusive access to resources, such as operational training, manuals and videos, for all Rammer products.
Rammer is also part of the Sandvik Group’s Rock Processing Solutions business, which can provide further support to Australian customers when required.
“The Australian Rammer dealers are specialists; they know their products, what they can do and how to identify a customer’s needs, which is a benefit,” Jackson said.
“Then you’ve got Sandvik, which owns Rammer, and we purchase the equipment off of; they’re worldwide, so the support is good.”
A Rammer-authorised dealer, like the Australian network, is qualified to complete a complete turn-key solution. This includes the rockbreaker, boom system, power pack and full electrification of the system to be operational and tailored to the quarry’s specific needs.
“We can do a turnkey installation as well, where they come to us and explain what they need, and we can do the whole thing,” Jackson said.
“We can provide the whole turnkey operation, supply everything to them, and they just have to turn it on and start using it.”•
For more information, visit attachmentspecialists.com. au/rammer or rammer.com
Several industry figures from the Australian quarrying sector have revealed what makes their chosen field so rewarding.
The Australian quarrying sector is living proof of the six degrees of separation theory.
Many of the workforce have been in the sector for a long time, so the chances are often high that you and the people you meet will have a mutual quarrying acquaintance.
With this in mind, networking and ongoing education are paramount to forging a successful career in this field. They are also fundamental reasons to join the Institute of Quarrying Australia (IQA).
The IQA’s latest campaign uncovers why members are part of the IQA and the wider quarrying industry and how their membership benefits them.
Clayton Hill, technical director for resources and operations at Groundwork and former IQA president, said the IQA opened many employment opportunities.
There is a whole lot of things that the Institute provides which, as a young member, is just such a great thing to be involved in.”
As part of the broader Institute of Quarrying network—including the United Kingdom, New Zealand, South Africa, Malaysia, and Hong Kong —the IQA provides ongoing training and education for the industry’s diverse workforce.
Designed for everyone in the quarrying industry, from entry-level operators to management, the training ensures all workers are updated with the latest occupational health and safety practices, legislation, and standards. It also showcases how the industry can promote environmental and social responsibility through responsible environmental management of quarry sites.
The IQA provides a wide range of training types for every individual in the
Jason Egan has been around the quarrying industry for more than three decades. The industry stalwart has served in multiple roles in that time and believed the IQA was an essential part of his ongoing learning.
“The education that the IQA provides is quite detailed, really important, and up to date,” he said.
“I think the sharing of knowledge and experience is critical, and you don’t do that if you don’t blend and mix with others, and the IQA offers that.”
Cathy Young, an IQA member of 13 years, shared the sentiment and believed the training had helped her throughout her career. Young has been part of the Groundwork Plus team for more than a decade and currently serves as its data systems manager after starting as an office administrator.
“I really enjoyed the training provided by the IQA; I find it very beneficial and very focused on the industry,” she said.
“Being a member of the IQA certainly created exposure for me to people in the industry.”
Alongside its extensive work in educating
The major event presented an opportunity for the industry to come together and catch up through site tours, gala dinners, and educational keynote speeches over three days.
Tegan Smith has been an IQA member for 15 years and said networking has played a role in her successful career. Smith has played a significant role in the sector as the national women in quarrying coordinator
relationships,” she said. “The people in our industry are usually in our industry for a long time. Those relationships are so important. Our industry is full of good saltof-the-earth people who want to share their knowledge, and I’ve had the benefit of that over my career.”
Chris Wilson, quarry manager at Hanson Australia, said IQA events led him to develop a strong professional network in the industry.
Michael Higgins is Boral’s quarry support manager for metropolitan Queensland. He has been an IQA member for 12 years and recommends joining the Institute for newcomers to the industry.
“It is a great way to start your career in quarrying,” he said.
“It obviously helps you; it is very aligned with what we need to know in our industry, and
North Queensland branch annual golf day
On September 13, 2024, the North Queensland branch hosted the 26th Annual Golf Day at Rowes Bay Golf Club in Townsville. It was a fantastic day filled with sunshine, allowing industry peers to connect and enjoy a fun-filled 18 holes of golf.
With 22 registered teams of four, the event fostered great camaraderie among
attendees and created opportunities for valuable networking.
A big thank you to all the participants who joined us, making the day such a success.
We’d also like to extend our gratitude to our generous sponsors:
• Drinks cart sponsors: RLA Finance and Orica.
• Catering sponsors: Komatsu and Unyte. Hole Sponsors: Unyte, TSP Group, BQC
Quarries, Taro Software, Finlay Screening & Crushing, CAMM Quarries & Concrete, Impact Drill & Blast, Komatsu, Markwell Group, Smarttech Aus, Dodge, SLR Consulting, Brown & Hurley, Aptella, Hastings Deering, and Nordev.
• Novelty Competition Sponsors: Britrac, Smarttech Aus, Lincom, ETS Geo Pty Ltd, Ausdraulics, AON, and Gallivanter Travel.
A special shoutout to Greg Rains for his hard work in organising such a memorable event for the North Queesnsland Branch. We appreciate all your efforts.
On Thursday evening, 29 August 2024, the Queensland branch and Central Queensland sub-branch gathered at the Broncos Club, Red Hill, for a delightful evening of dining, networking, and the formalisation of the 2024/2025 AGM committee for the upcoming financial year.
During the event, attendees had the opportunity to hear about the recent overseas adventures of the young member network in the UK.
We extend our gratitude to our guest presenters—Keelan McNulty, Ryan Grech, Dean Smith, Siri Schlebaum, and Lachlan Mills—for sharing their insights and key takeaways from the various quarry site tours.
A special thanks to EEA Group for sponsoring the event, and to Anita and Grant for introducing our audience to the latest product offerings.
On Thursday evening, 5 September 2024, the Queensland branch hosted its second Women in Quarrying (WIQ) fireside chat at the Jindalee Hotel. The event provided a fantastic opportunity for industry peers to come together over refreshments and engage in meaningful discussions.
In line with September’s diversity month, attendees participated in a lively conversation centered on fostering greater diversity within their workplaces and the quarrying industry.
The session, led by Jenny Krasny and guest speaker Jason Johnson, allowed participants to connect and network on all things WIQ.
A big thank you to our WIQ Sponsor, Orana Drill & Blast, for supporting this wonderful event.
The IQA Victorian sub-branch networking dinner and AGM took place on Thursday 19th September 2024 at The Criterion Hotel in Sale.
The evening began with a brief AGM. The chair provided a summary of the year’s activities, sponsorship, and membership, followed by the election of the new Victorian sub-branch committee for FY25. Laura Bennie was appointed as the new chair, replacing outgoing chair, Adrian Bourke.
Barry Strong, deputy chief inspector (east) at Earth Resources Regulator (ERR), provided a short overview of ERR’s compliance priorities for the extractive industry for 2024-25.
Attendees were then joined by Warren Davies, also known as ‘the unbreakable farmer’. Warren is one of Australia’s leading rural mental health speakers and advocates. His presentation centred on resilience, persistence, determination, leadership, and wellbeing, highlighting their moral relevance to all ages and communities.
The event was a great success, featuring engaging presentations and opportunities for networking among members, non-members, and associates. •
Rover prototypes have been tested to their limits in a UK quarry before being sent to Mars.
AUK quarry has provided the backdrop of a significant milestone for a future Mars-bound rover.
Airbus and European Space Agency (ESA) engineers tested a four-wheeled rover and a six-wheeled rover, named Codi and Charlie, respectively, at a UK quarry. This year, the testing took place at a quarry near Leighton Buzzard in south England.
The team of engineers tested the rover prototypes across a range of challenges, including dodging boulders, driving long distances, and fetching sample tubes without human involvement.
“Quarry tests are an important step in the development process. They offer a unique and dynamic landscape that cannot be replicated in our Mars Yard test facility at Airbus in the UK,” Airbus Space posted about the testing.
According to ESA, the quarry’s terrain, and quarries in general, can resemble Mars, which the rovers will eventually encounter and is hard to replicate in an indoor facility.
“The reddish terrain, although not fully representative of Mars in terms of soil composition, had plenty of slopes and rocks of different sizes, similar to what a rover might encounter on the martian surface,” ESA posted.
“The quarry gave engineers the flexibility to present the robot with several challenges at varying speeds such as adding obstacles between way points, or altering the sequence of commands to see which course of action the rover decided to take.”
Engineers from both companies were tracking the rovers in a control room as they took on the obstacles set out for them. They also tested special tyres on Codi which were made from mesh with a memory shape alloy and upgraded 3D software.
Codi, the four-wheeled rover, was equipped with a robotic arm to retrieve samples which it successfully demonstrated. It also managed to traverse the quarry and park within an accuracy of 10 centimetres.
Airbus Space said this was a “world first” test of this capability.
Charlie, the six-wheeled rover, also trialled a sensor know as LiDAR which is designed to
allow rovers to move without using cameras in a dark environment.
Going forward, ESA has said it will continue to fund research using the rovers focused on developing knowledge and capabilities.
“Testing technologies creates competence and generates confidence towards success. The trials prepare the teams for the challenges to come and make them ready for future missions,” ESA posted. •