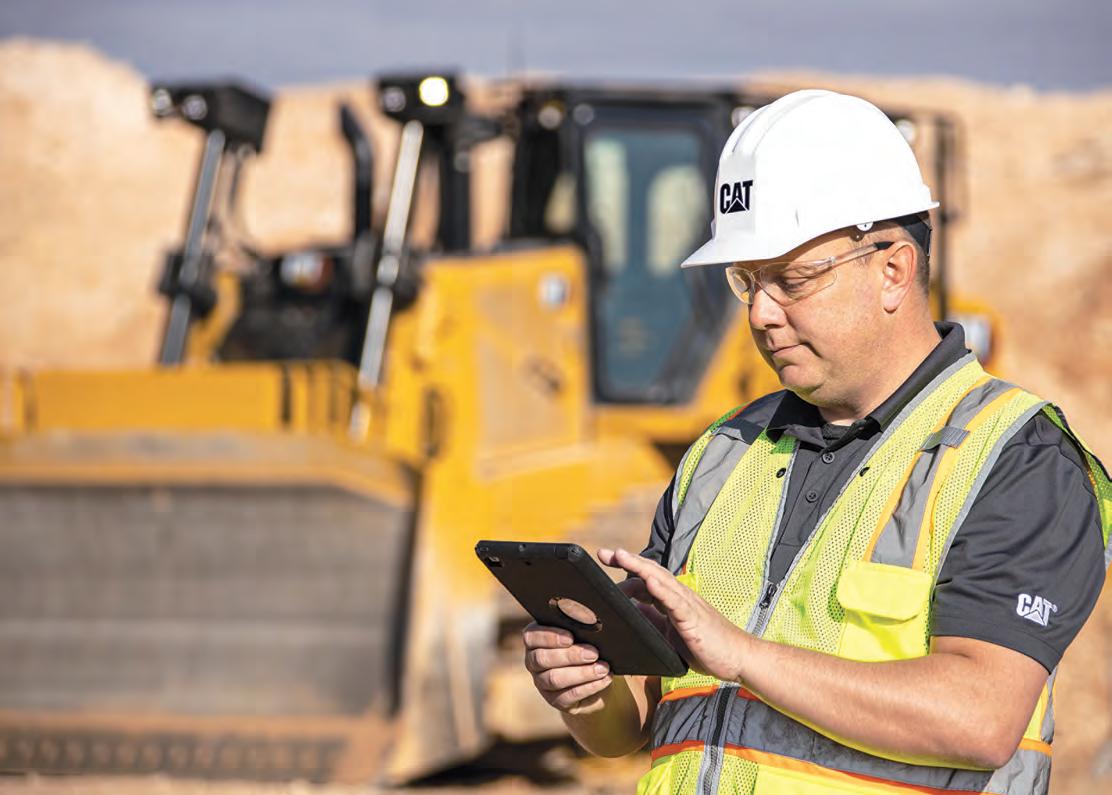
15 minute read
CLOUD-BASED PROGRAM OFFERS MORE PRODUCTIVITY
from Quarry December 2021
by Prime Group
CLOUD-BASED PROGRAM
OFFERS MORE PRODUCTIVITY ON-SITE
An earthmoving OEM’s telematics and machine data system has made its mark on the global quarrying landscape, and is being increasingly taken up in Australia. Caterpillar’s Kit Kyarsgaard tells Quarry all about Cat Productivity.
No matter the profession, work is about achieving results – and improvements. Even if a task is satisfactorily completed, there is scope to review and determine how it can be bettered. A holistic view of an organisation will encompass multiple tasks, some which may be related or integrate. How effectively do these tasks affect the organisation’s productivity? And what can be done to improve their functionality and outcomes to wholly benefit it?
Kit Kyarsgaard has spent the best part of 21 years with global earthmoving original equipment manufacturer (OEM) Caterpillar – and has pondered some of these questions more specifically for quarrying operations in a variety of roles.
Indeed, more than two decades with the same company has enabled him to better understand the needs and wants of aggregate businesses the world over. When Kyarsgaard started his career for Caterpillar in Peoria, Illinois, USA in 2000, little did he know he was embarking on a journey that would see him work in marketing and sales representative roles for Caterpillar’s northwest region (Alaska, Idaho, Washington, Montana and Oregon) and Texas and Louisiana in the rebuilding period after the devastating impact of Hurricane Katrina.
He spent time as a Cat system applications analyst in Houston, Texas which he said helped him develop a solid understanding of Caterpillar’s customers, eg “Understanding how they use our products, helping them to justify the right fleet or right systems approach, how to move equipment more efficiently, drive and show them value, and understand from our customers how they make money. What do they do with our products to drive and increase their bottom lines?”
From 2011, Kyarsgaard was the regional products application specialist for excavators, based in Singapore, where he covered South East Asia, India and Australia. “That was an awesome experience, I learned a lot about the different regions and territories,” he told Quarry. “In the Asia-Pacific region, operations are powered by the costs per hour or costs per tonne, and in Australia the cost of the job justifies the efficiencies. It was interesting to learn about the life cycle value and performance of customers, to understand their thoughts.”
Kyarsgaard was subsequently elevated to the position of global products applications specialist for medium-sized excavators from the Cat 320 up to the 335, bringing voice of customer (VOC) perspectives into the engineering team to develop the next generation excavator.
After nearly a decade in Singapore, Kyarsgaard returned to Peoria to commence his current role as global product marketing consultant for Cat Productivity. He described the role as “taking all the advantages of the technology that we have on our latest products, and thinking about how we can make it useful for our customers, increase their bottom lines and decrease the inefficiencies on the job site to help them make more profits”.
WHAT IS CAT PRODUCTIVITY? Cat Productivity is a cloud-based program that captures quarries’ GPS and telematics data about detailed production measurements and job site data via Cat Product Link devices fitted to Caterpillar or mixed fleet machines. Figures from a given site are transmitted via digital phone connection to the cloud and they can be downloaded in the form of payload and cycle segmentation data by quarry producers for analysis and customer insights.
“Imagine you have a quarry,” Kyarsgaard said. “You want to know how many loads are being produced, which loader filled which
truck, how many tonnes went into that truck, how long that truck went from point A to point B, and how many dumps happened that day. Traditionally, those counts are manually done by the operators, and you get those sheets and they have to be tallied at the end of the day or the end of the week. Customers are saying: ‘Please give me that data ahead of time, I need to get this data before the end of the week because I need to know if I have to work this weekend to meet my production goals’. So it’s about understanding what is being produced that day in 30 to 60 minutes, and knowing exactly what is being produced now.”
Kyarsgaard explained that with the collection and collation of telematics and machine data, quarrying producers can create customer insights that help them better plan the job site. “As a quarry aided by customer insights, I know how many loads I did per day, how many tonnes of material I produced per day. I can compare how long the cycle times are from this week to last week. I can see where my inefficiencies are, so I can see my loaded stop or my empty stop events occur. If I’ve just had my truck loaded and suddenly I’m stopping in one spot all the time because of a single lane bridge or a traffic jam or a stop sign, how much is that costing me each time? What if I widen that bridge at $50,000? If I’m sitting there waiting at the bridge or stop sign for five minutes at a time, I can really see the costs very quickly.”
Cat Productivity provides producers with a summary dashboard that has three major tabs: production, utilisation and cost. The production tab tracks by site or individual asset the load count, the payload, segments and estimated volumes. For load counts, it is possible to report full data on actual fleet production or individual assets. The payload tool can supply data on hourly fleet performance and identify opportunities for increased productivity on-site, eg optimised management of shift changes, refuelling processes and breaks. The segments tool tracks cycle segments, load times, fill levels, and loader positioning to promote site efficiency.
“The Cat Product Link devices on the machines gives us the basic machine information. With the latest Cat products you get more advanced data which can include all the payload and cycle segmentation data,” Kyarsgaard said. “We can measure payload on the wheel loader or truck, and we can get that cycle by cycle payload off the machines into Cat Productivity to help the customer have an in-depth view of what’s happening in the quarry.”
The utilisation dashboard can compare working versus idle hours and fuel burn. “Now you can start to see all your stop/start events occurring, and idle times,” Kyarsgaard elaborated. “If your idle time is three to six, six to nine, or nine or more minutes, you can see where all these events are occurring. Now you can ask: ‘Why are these guys stopping in certain places or at certain times? Why is this stop occurring? What can I do to increase productivity? It’s about understanding how much time is being used. You know where these idle events are occurring.
“A lot of customers are focused on idling over five minutes or more. The utilisation dashboard tells me specifically what machine is idling, at what time and for how long, so we can solve some of these problems and reduce inefficiency on the job site.”
The cost dashboard enables producers to track working time costs, idle time costs and costs per tonne. Kyarsgaard said this dashboard has really excited quarrying producers because they have been keen to know exactly how costly each cycle or idle event can be. “All of a sudden, if I have a machine or an operator that is fully burdened at $200, and is idle for 30 minutes, it’s $100
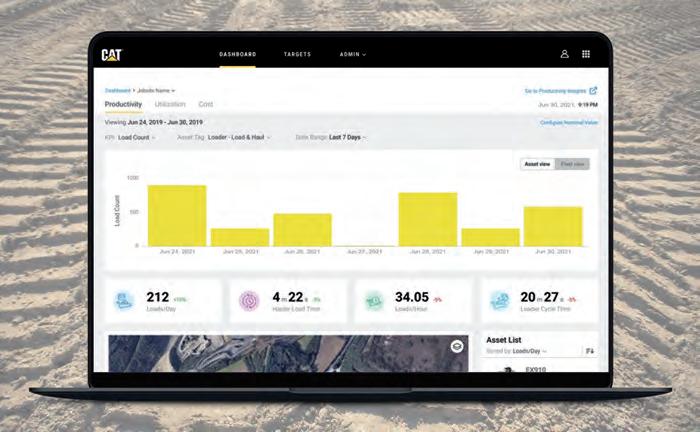
A fleet view of load count on the productivity dashboard.
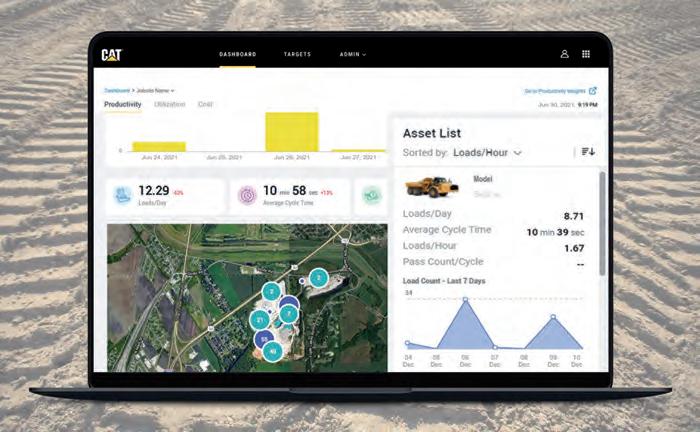
in wasted operating expense, not to mention burning three or four gallons [11 to 15 litres] of fuel at $8,” he said. “That’s $108 wasted in 30 minutes of idle time.”
The production tab can also go deeper with productivity insights, enabling the viewer to analyse at the cycle and asset levels the sources of inefficiencies. The production dashboard is also split into three subsegments, including production, utilisation and asset summary. This enables producers to track individual cycle times by machine and monitor the asset movement over a 24hour period with a playback view.
For quarrying businesses running multiple sites, there is the capacity to create job sites to reflect each individual quarry. “It gives you figures to make comparisons and compile it into one job site,” Kyarsgaard said. “You can have as many job sites as you like out there to compare. When you start with Cat Productivity, we have job site score cards which specifically examine the high level key performance indicators (KPI), and the customer can change and adapt them to what he thinks the KPI should be, and he can quickly look across all those job sites to compare, see where something is versus the target, and make suggestions from there”.
Cat Productivity is configured to work on numerous devices: desktop/laptop, mobile phone and mobile tablet. “We optimise it for mobile so that customers can be in the field with the fleet to know exactly what’s going on, how much material one needs, even off-site for quick meetings,” Kyarsgaard said. “When you’re on vacation, you can even quickly look at your quarry to see how it’s performing. Is it producing enough? You can make a quick call to your supervisor or superintendent to know exactly what’s going on. It’s designed for the owner right down to the site manager and the fleet manager to know how much material is being produced.”
NEW VS OLD Kyarsgaard said Cat Productivity is designed for all quarries depending on the customers’ needs. “It’s dependent on the customer, what they want and need, and what problems they’re trying to solve,” he explained. “We get our data within 30 to 60 minutes and that’s what we’re striving for, to make sure customers can have the reaction time in that duration.”
He said it was also possible to customise the program to fit a quarry’s needs. “You can gather summary dashboards, you can put in different fleets, and you can do competitive fleets, older fleets, new fleets. The beauty of this tool is you can customise it while getting all the same data. If you have a newer machine you can extract a lot more, in-depth fidelity of data versus the basic, competitive or older machine. You can still get the data off older machines but it just won’t be as in-depth.
“Obviously our latest machines give us the best data,” Kyarsgaard continued. “When we move onto older Cat or mixed fleet machines, that’s when we can hook them up, gather all the hours and the locations and the fuel data and tie that into the system so we can use and analyse the data as well. We’re focused on the job site – we’re not focused on the individual machines, and that’s really how a customer looks at this data. They want to see how the whole job site works. It means we have to make sure all competitive wheel loaders, trucks or back-up loaders are connected to show a true picture of what’s happening on the job site.”
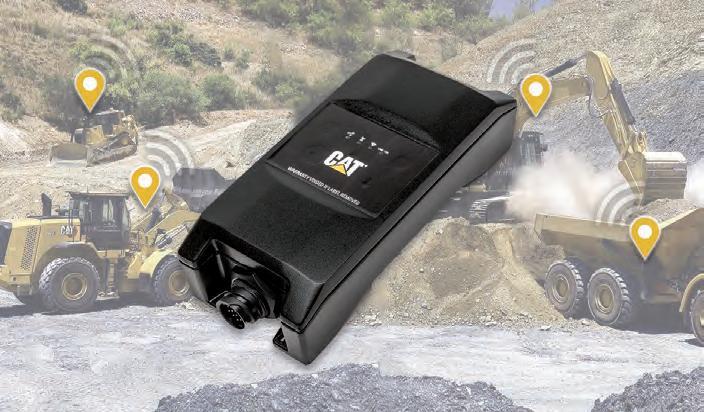
The Cat Product Link can be fitted to most new and old Cat vehicles, as well as competitor products.
ECONOMY, ACCESSIBILITY Kyarsgaard said the affordability of Cat Productivity for quarry businesses varies from country to country and dealer to dealer. “If you fitted the machine and set it up, a reasonable subscription fee is charged per asset per month to get the data, and using the analytics and the logic in Cat Productivity,” he said. “Some dealers will offer some additional services, depending on their capability and the number of job sites.”
Cat Productivity is available worldwide and is offered with Caterpillar products in Australia via distributors WesTrac (New South Wales, ACT and Western Australia), William Adams (Victoria and Tasmania), Hastings Deering (Queensland and the Northern Territory), and Cavpower (South Australia). Aggregates producers can also contact Caterpillar of Australia directly with inquiries.
Kyarsgaard said the feedback from customers about Cat Productivity inside and outside Australia has been positive and the program has increased its global subscription base in the past 12 months by almost 50 per cent. Indeed, he expects continuing subscription growth once Caterpillar releases an expansion to the program in 2022.
“Our customers are saying they need to add more and multiple job sites, so we’re getting the expansion out next year,” he said. “It’s encouraging that customers are believing in the data, making changes from the data, making sure their bottom lines are improving and they can start pinpointing exactly where their problems are and making improvements in their job sites to maximise production. Right now, everyone in quarrying is seeking to maximise everything they can and they’re seeing these low hanging fruits with Cat Productivity.”
Quarry asked Kyarsgaard what advice he had for quarries interested in implementing a cloud-based system for the first time. “You need to start measuring different things, understand what you can measure, and start analysing where those inefficiencies are in your quarry to optimise and improve them,” he said. “That doesn’t just relate to Caterpillar’s systems, it also applies to other OEM programs.
“If you don’t measure your job site, you’ll never know. You need to review and understand your quarry site to get really good data and start measuring where you’re at, to understand your inefficiencies, and where you can optimise improvements. That’s a number one thing for a quarry: How do we maximise what we have today? We’re not going to go out and buy all new equipment, it’s really how we maximise our job site. There are a lot of inefficiencies on the job site where we can do a few things to significantly improve that bottom line and profit. Once you start measuring it, you can implement plans to solve problems for the future.” •
For more information about Cat Productivity, visit cat.com/en_AU/products/new/technology/ productivity/productivity/103285.html
RIMEX MAKES ITS MARK IN TYRE MONITORING
RIMEX has evolved from a wheel manufacturer in Canada in the 1970s into a leading global supplier of the offthe-road (OTR) tyre pressure monitoring and maintenance system TyreSense.
With a history servicing all sectors of the extractive industry, RIMEX has recently made big in-roads in supplying tyres and rims to the quarry market and is well prepared to increase its servicing of Australia’s quarrying and contractor environment.
The continual development of TyreSense has kept RIMEX at the forefront of this quickly emerging market tool and the web-based software ensures live up to date data to maximise tyre productivity and efficiency.
TyreSense was pioneered by RIMEX in 2001 in Vancouver. RIMEX general manager Karl Krajewski told Quarry the Australian market took advantage of a then new product.
“We’ve found that Australian mines and quarries are always looking for that next advantage, whereas our branches in other countries have only seen a small take-up,” Krajewski said. “So, I think Australia can give itself a pat on the back for that. It always seems that we lead here in Australia and eventually our overseas counterparts realise how well it’s working for us.”
TyreSense began as an in-cabin tool for operators to monitor their tyre pressures, built on the idea of reduced downtime and improved safety. As technology developed and remote monitoring started trending throughout the heavy industries, TyreSense grew into a more useful tool.
“It fast evolved into having sensors inside the tyres for both pressure and temperature which can now be sent via ethernet and cellular network back to supervisors, senior management, or even head office anywhere in the world,” Krajewski said.
“It’s turned into a whole fleet management system to understand speeds, location, direction, and can download data from the machine to become fully integrated with existing fleet management systems.”
Once an issue is observed using the TyreSense suite, RIMEX also specialises in the next step to return to production, mending the tyre or rims.
To cater to the growth of effective tyre management systems, RIMEX bought a tyre-fitting company in Mackay, Queensland, called Complete Tyre Services.
Krajewski said it was a stringent process to find the most reliable business in tyre handling for off-the-road tyres.
“I visited some tyre manufactures in China in late 2019 and the facilities were impeccable as there’s a lot of synergies there with other well-known tyre manufacturers,” he said. “Over the past 18 to 24 months this business has been performing really well in the quarrying and contractor environment – working with 35-inch and below tyre sizes and providing our key service of fitting, testing and servicing tyres.”
Just as RIMEX forged a path into the tyre monitoring systems space, it also had the foresight to establish seven purpose-built rim certification facilities across Australia – the first of which was built in 2008. These mine- and quarry-heavy locations include Queensland’s Mount Isa, Blackwater and Mackay, Musselbrook in New South Wales, Adelaide, Perth and Newman in Western Australia.
“The facilities will provide the full wheel recertification process in-house, plus RIMEX supplies all products required for the whole tyre fitting process including tyres, wheels, valves, gauges, and tooling,” Krajewski said.
RIMEX’s Australian footprint combines with its expertise for an average turnaround time of about 10 days for the complete refurbishment process. This is aided by a new online portal which allows customers to track the process from start to finish while storing all customer information for use at any time.
Krajewski said it’s why RIMEX leads the way in tyre maintenance and monitoring. “We’re the only ones who do this, so we’ve evolved and professionalised things.”
Of course, as small to medium-size quarry businesses look to improve their total cost of ownership, one could be forgiven for any apprehension towards the outsourcing of maintenance duties.
However, Krajewski said if you want to ensure the safety and productivity of your fleet and you were going to send your wheels anywhere, it would be RIMEX.
“I think some people can always be fearful of sending equipment off to get inspected and tested,” he said. “But we are the biggest and best because we’re not sitting here trying to find reasons to spend money on it.
“We’re just trying to make things as safe as possible. We measure our pass rate and about 90 per cent of rims that come through don’t have anything done to it – you blast test, paint and out it goes again with that assurance that downtime will be avoided.”•
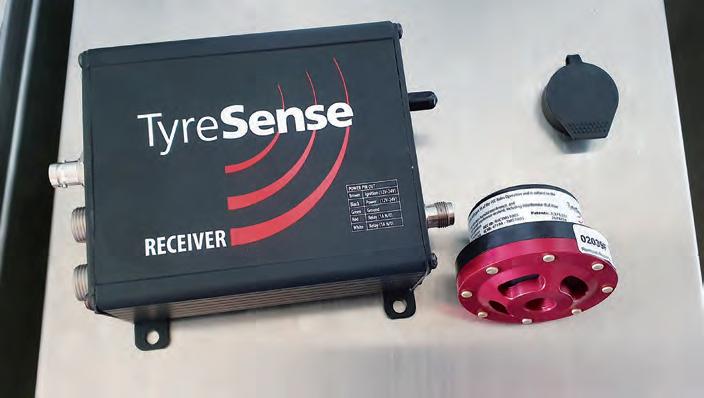
TyreSense has become one of the world’s leading tyre pressure monitoring systems.
To learn more about RIMEX’s TyreSense technology and services, visit rimex.com.au