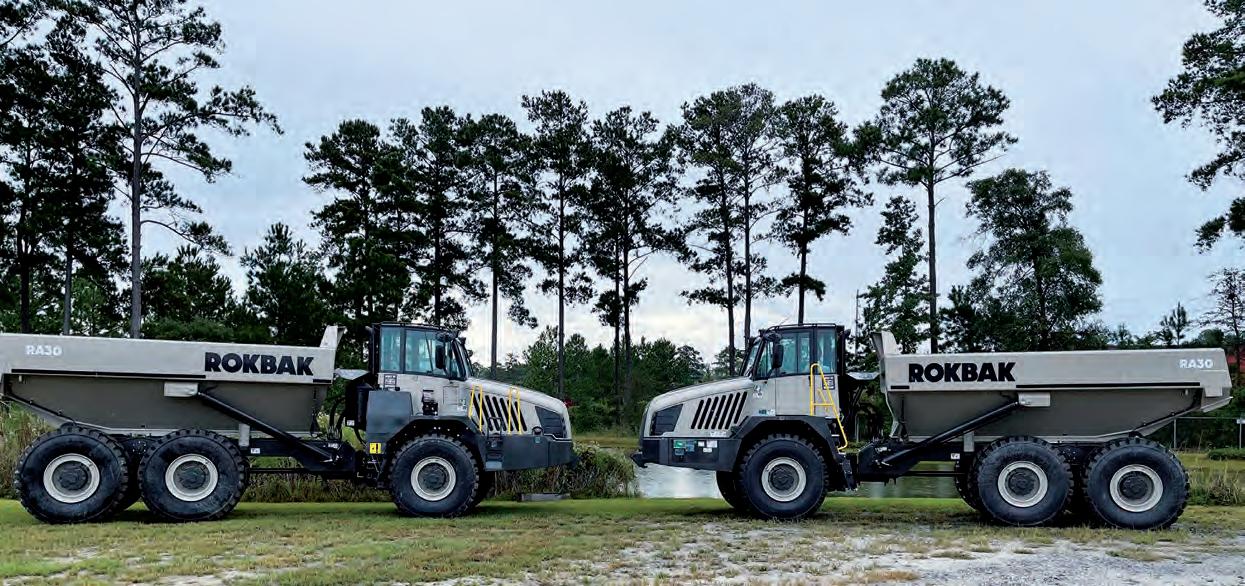
25 minute read
DEALER MAKES HISTORY WITH ARTIC HAULER SALE
from Quarry December 2021
by Prime Group
US construction firm Linco was the first in the world to purchase the new Rokbak RA30 articulated haulers.
US CONSTRUCTION FIRM MAKES HISTORY WITH HAULER PURCHASE
US-based equipment dealer Easton Sales and Rentals and its client Linco Construction have registered a notable moment in construction equipment history, with the sale of the first ever Rokbak articulated haulers globally.
The Rokbak brand launched on 1 September, 2021 as part of the Volvo Group, with its RA30 and RA40 articulated haulers built at the company factory in Motherwell, Scotland.
Easton Sales and Rentals has sold a package of two RA30 models sold to Linco Construction, a family-owned and operated company founded in Houston, Texas in 1992. Linco Construction has already put the Rokbak machines to work, helping with earthworks, underground utilities, and clearing work.
Although the Rokbak brand is new, Easton Sales and Rentals is a long-term partner of the company in its previous incarnation and was the 2020 Dealer of the Year. Jeff Udelson, the managing principal of Easton Sales and Rentals, was delighted to take delivery of the first Rokbak units.
“It’s a great honour for our company to get the first Rokbak articulated hauler and there was real excitement around the dealership when it arrived,” he said. “Rokbak has only been in existence a short time, but it’s built on the legacy of a company with a long history,” he said. “What’s most impressive about the new Rokbak brand is how clear it is to see what it stands for – hard work, performance, reliability, sustainability. It’s also backed by the Volvo Group so there’s no doubt about the quality or performance.
“It looks fantastic but a great exterior is just a small part of what makes these machines such excellent haulers,” Udelson continued. “They are unstoppable on site, and can power through anything a project throws at them. So you get unbeatable performance and durability but with a fuel-efficient design which means better ROI on the job.”
Steve Brown, the president of Linco Construction, said the design and performance of the Rokbak machines was a perfect match for his company.
“Our business is built on delivering quality work that is competitively priced and performed by experts, so these new Rokbak machines are ideal tools to help us do that,” Brown said. “They’ve only been at work for a few weeks, but we can already see they are workhorses. We have built relationships with our clients on our commitment, hard work and quality, and when we look at the Rokbak haulers, we see those same values shining through.”
The RA30 articulated hauler from Rokbak is suitable for construction sites, infrastructure developments and quarries. The 28-tonne unit offers a heaped capacity of 17.5m3 and is powered by a Scania DC9 engine, which develops gross power of 276kW and a maximum torque of 1880Nm. Its fuel-efficient engine is emissions-compliant and meets the requirements of the latest North American legislation with T4F.
The hauler’s EP320 transmission comes with eight forward and four reverse gears, with a top speed of 55km per hour, high overall gear ratio spread, equal ratio steps between gears and optimised gear shifting with partial load shifts. This adds up to lower fuel consumption, smoother gear shifting, better operator comfort and faster cycle times. Increased productivity and uptime, plus lower cost per tonne, are further boosted by the long-life transmission fluid, which increases the time needed between oil changes from 1000 to 4000 hours.
In addition to the two Rokbak RA30 units it has already received, Easton Sales and Rentals has a further three on their way to Texas. Two have been sold to JMC Equipment LLC, another Houston-based company, while the third will join the inventory fleet at Easton Sales and Rentals.
At its locations across Texas, Easton Sales and Rentals provides earthmoving equipment for hauling, trench digging, loading, grading and excavating to contractors in the construction and road building sectors. The relationship between Easton Sales and Rentals and Rokbak dates back more than two decades.
“We are absolutely thrilled with the enthusiasm our long-standing dealer partners in North America have shown for the new brand and are looking forward to working closely with them over the coming months and years as we establish Rokbak as the industry benchmark for performance, power and reliability,” Daniel Meara, the regional sales manager for Rokbak in North America, said. •
In Australia, the distributor of the Rokbak product will be Porter Construction Equipment. Visit porterce.com.au For more information about the RA30 and the Rokbak products, visit rokbak.com
WHAT DOES CHRONIC
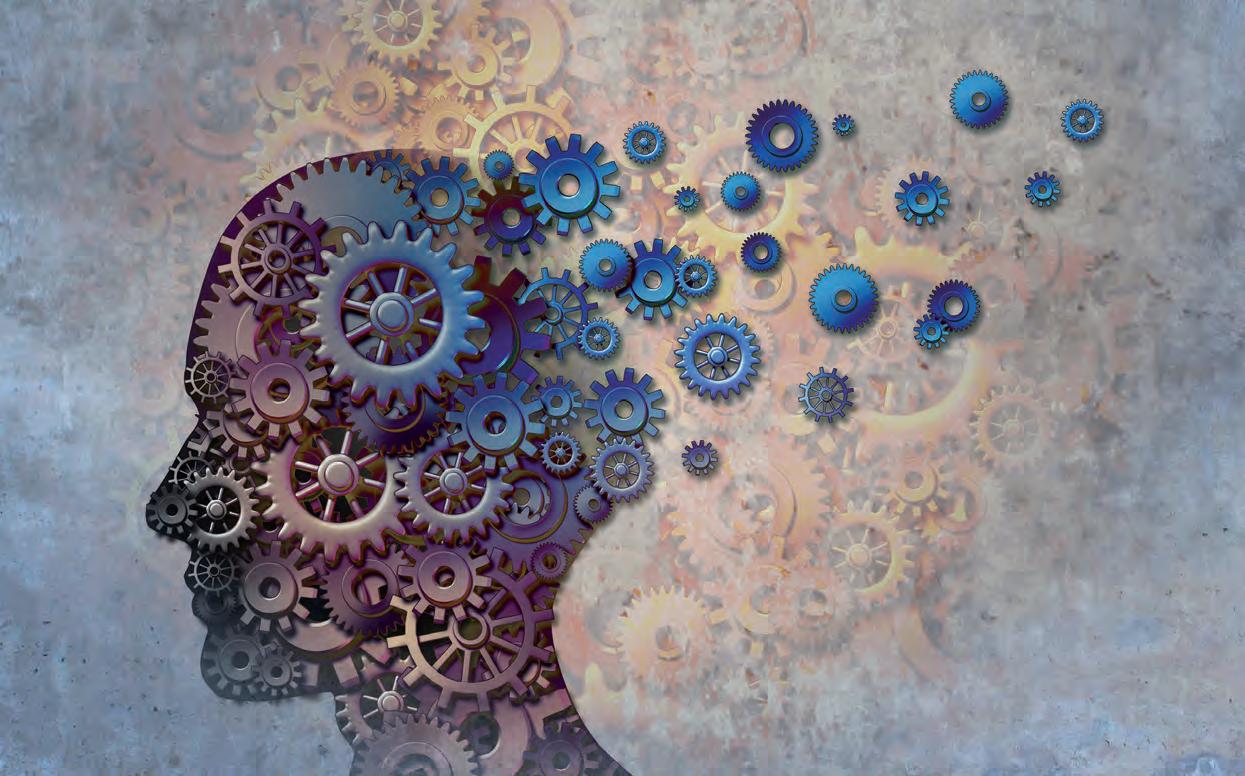
UNEASE LOOK LIKE IN PRACTICE?
Accidents don’t just happen when things are going badly; they often happen when things appear to be going well. Jodi Goodall, of Brady Heywood, explains the concept of chronic unease in high hazard industries like quarrying, and how it can be applied in practice.
Following a serious accident in his workshop, where one of his most experienced maintenance team members had both of his legs crushed, the workshop manager confided to me that it felt “out of the blue”. His workshop had an excellent safety reputation.
The event occurred during a crane lift of a large steel pipe. The pipe dislodged, knocked a nearby team member to the floor and rolled onto his legs. He would never walk again.
Afterwards, when the investigation was complete, what frustrated the workshop manager most was that he already knew most of these issues. Similar incidents had happened, but with no bad outcome … They had a PO in the system to get the right lifting equipment ... He himself, had observed that as they got busier there were too many jobs going on with too little space … The end of month bonus did encourage the team to take shortcuts to complete the jobs on time … The list went on.
Investigations are helpful for bringing out vital learnings from incidents. But in my experience investigations also cause good business leaders anguish over actions not taken in hindsight – not to mention the devastating impacts of the incidents themselves. So rather than waiting for people in our group to suffer before we take stock and act, we can instead understand the techniques that best-in-class businesses use to prevent serious accidents altogether.
There are organisations out there that manage to maintain near-accident-free performance over many decades, despite operating in high hazard and complex environments. They are called High Reliability Organisations (HROs). One of the five characteristics that helps them to achieve this feat is called chronic unease, or a preoccupation with failure.
CHRONIC UNEASE How long has it been since a major accident or failure in your business? Long periods of success can result in us taking our eye off the ball – we might even start celebrating our success. What we know about major accidents is that when organisations are in this mindset, they are often drifting towards failure. Accidents don’t just happen when
things are going badly; they often happen when things appear to be going well.
Chronic unease is a strategy to combat this. It’s a psychological state where individuals at all levels of an organisation feel a sense of constant discomfort and healthy scepticism about how risks are being managed. This leads them to relentlessly hunt for warning signs of potential failure. Then the trick is to make those warning signs more vivid, and act on them to prevent those failures occurring.
In September this year, I delivered a webinar discussing chronic unease and how it can be applied in practice. There was a lot of interest in the topic; a lot of people are keen to incorporate chronic unease in their organisations.
A common misconception is that chronic unease is just about combatting complacency at the frontline. But exhibiting chronic unease isn’t the responsibility of one group. And in practice, chronic unease is only able to flourish in organisations in the long run when environmental factors are structured to support its presence.
There are four areas that are essential for an organisation to work on to create chronic unease and sustain it (see Figure 1): 1. A questioning attitude. 2. Psychological safety. 3. Risk competence. 4. Systems to detect and capture warning signs.
1. ADOPTING A QUESTIONING ATTITUDE A questioning attitude is a curiosity about the signs in front of you and a commitment to looking deeper. It helps you explore risks, uncover warning signs, and understand what those warning signs might mean. It provides a clearer picture of what your organisation’s real performance is and where the real issues are. You should question your assumptions, any unintended outcomes (positive or negative) and anomalies. Ask questions like: • Do we understand why we got that result? • What could be the worst outcome? • How could that control fail? • What is our backup plan if it does?
2. CREATING PSYCHOLOGICAL SAFETY Psychological safety is a cultural environment where people feel like they will not be personally judged or punished for speaking up about warning signs or issues – especially by their seniors in the organisation. Psychological safety is important if you want to make sure you have a chance of receiving the benefit of everyone’s observations. You don’t want anything left unsaid, such as: • People’s own mistakes and errors. • Near misses. • Things that look strange or different.
Ever heard the phrase “that’s career limiting”? If your people feel they could be personally judged or punished for reporting incidents, making mistakes, or challenging decisions or directions they perceive as unsafe (especially to more senior people),
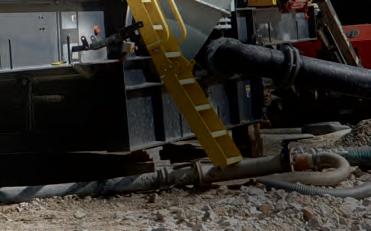
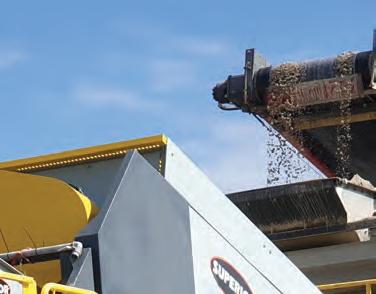
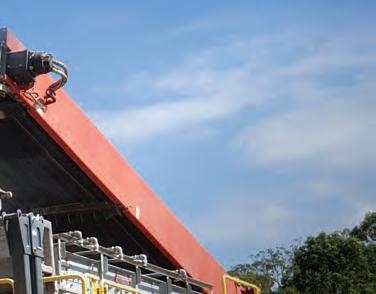
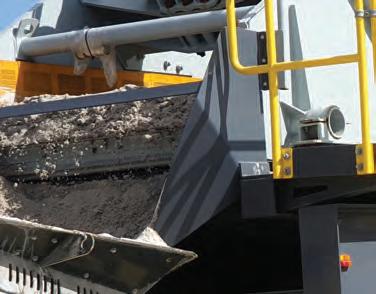
PORTABLE AGGREDRY® WASH PLANT
–in stock, ex NSW
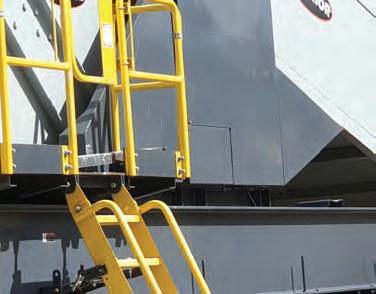
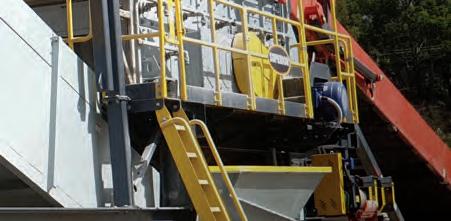

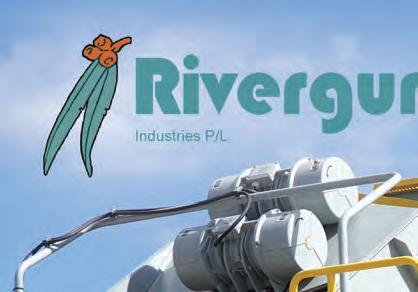
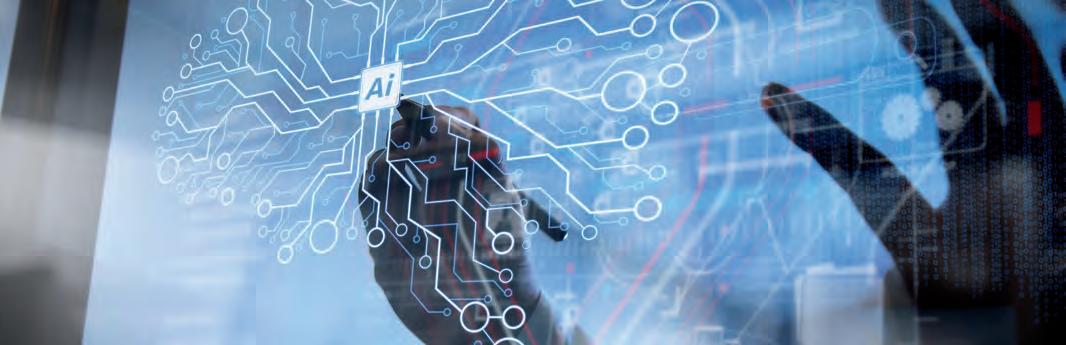
they may choose not to raise issues – and rarely is it obvious if people are holding back.
Psychological safety is cultivated when leaders reward and recognise those who speak up, even if it turns out to be nothing, or even incorrect. Punitive approaches often discourage speaking up.
3. IMPROVING RISK COMPETENCE Everyone from the board to the frontline needs to have a clear understanding of the hazards and how they are managed – in other words, a high level of risk competence. If we can’t visualise what could go wrong, or if we don’t have a clear picture of what our hazards look like when they’re being well controlled, then it’s easy to assume that things are going well.
I’m not talking about classroom training in risk management. Risk competence is improved by a combination of technical knowledge and experience, gathered from a wide range of sources.
The more risk competence your organisation possesses, the more understanding there will be about any weaknesses in how the risks are controlled, and the more easily that warning signs can be noticed.
4. CAPTURING WARNING SIGNS Our systems for detecting and capturing warning signs may include: • Systems to monitor physical risk such as strata, dust or gas monitoring systems. • Reliability systems such as maintenance and inspection systems. • Reporting systems for your people to tell you when unexpected things happen.
These systems should support the process of capturing, analysing and taking action on our warning signs. Even if we collect a lot of data, if the data isn’t turned into meaningful information or doesn’t reach the right people, it can’t inform our decision-making.
CREATING CHRONIC UNEASE Practical ways to create chronic unease include: • Storytelling. Storytelling is hands down one of the best ways to create chronic unease. People are more likely to retain
information if they hear it as part of a story. Also, as big failures don’t happen very often, storytelling is the best way to recreate an experience for people that they can learn from and relate the details to their own situation. You can use stories or findings from your industry or other industries, use your own stories, or invite your technical experts to share theirs. • Technical experts taking a teaching role. Invite your experts (internal and external) to share their technical knowledge about a particular aspect of a risk or a control. You could have regular 15-minute presentations from these people instead of a toolbox talk. • Exploring your data. Take time in groups to explore your data (maintenance, incident, quality, production) with fresh eyes. Get “fidelity” on the numbers by reading incident descriptions and asking experts. For example, start with your hazard reports. Get a deep understanding of the types of reports you are getting.
For example, are they all related to one type of hazard? Are there blind spots elsewhere? Do all the reports come from one team? • Leaders spending time in the field. Field time is all about learning for everyone involved. Listen to those doing the work about what makes it successful and what makes it challenging. Take an expert or a set of fresh eyes with you (not a pack of people). • Using LEAN continuous improvement techniques to explore successful work. For example, “learning teams” and
Kaizen approaches. Leaders can use the knowledge discovered through these techniques to increase learning. • Using bowtie diagrams as shared risk knowledge. Organisations need a clear picture of their major hazards and something to anchor conversations to.
Bowties enable everyone to speak the same language and to have a common
Risk competence is improved by a combination of technical knowledge and experience, gathered from a wide range of sources.
understanding of hazards and controls – from the board room, to the planning team, to front-line workers.
FINAL THOUGHTS There are many factors working against us practicing chronic unease. That is why telling people to “report more”, “notice more”, “care more” or to “have more chronic ease” doesn’t work. Without the right organisational environment, chronic unease cannot survive the long haul.
Leaders must address the organisational factors that suppress chronic unease, and build practical influences into their organisation to encourage its continued presence at all levels. Organisations must ensure they are set up to incentivise wanted behaviours through their actions as well as their words.
The way we message, measure and reward within our organisations, the level of our understanding of hazards and controls, and the systems we put in place to capture information all have a profound effect on whether warning signs can rise to the surface, receive attention, and be acted upon.
Chronic unease takes effort to build into your organisation so that it sticks and becomes chronic. It’s worth it. In the end it’s all about finding multiple ways to amplify your warning signs and make them more vivid, so you can act on them before they lead to failure. •
Jodi Goodall is Head of Organisational Reliability at Brady Heywood, Brisbane, Queensland. Brady Heywood has also developed the Queensland mining and quarrying podcast series “Rethinking Safety” as part of the Brady Review. This podcast contains interviews with key industry leaders, the regulator and unions about key challenges faced by the industry. Visit bradyheywood.com.au/podcasts Sean Brady and Jodi Goodall’s thoughts about serious accidents, mine safety and High Reliability Organisations can also be found at bradyheywood.com.au/insights Check out the recording of the webinar “What does chronic unease look like in practice?” on the Brady Heywood YouTube channel, where Jodi digs deeper into practices for risk competence and systems that capture warning signs.
IQA NEWS
The Institute of Quarrying
Australia
IQA ACKNOWLEDGES ITS SPONSORS, SUPPORTERS AHEAD OF NEWCASTLE
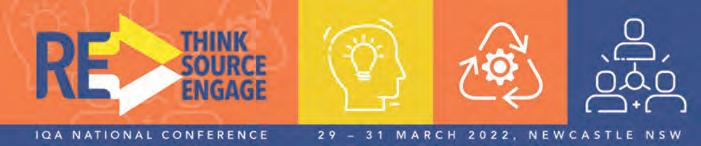
As 2021 draws to a close the IQA keenly acknowledges the support of event partners for the IQA National Conference. At the IQA, we have been overwhelmed by the ongoing support of our industry partners that have stuck with us through a change of date and have joined us on the journey to March 2022.
For many years, the IQA has been supported by three Platinum Partners who are on board with us again for the 63rd IQA National Conference in March 2022.
Caterpillar For more than 90 years, Caterpillar Inc has been making sustainable progress possible and driving positive change on every continent. Customers turn to Caterpillar to help them develop infrastructure, energy and natural resource assets. With 2018 sales and revenues of nearly $55 billion, Caterpillar is a leading manufacturer of construction and mining equipment, diesel and natural gas engines, industrial gas turbines and dieselelectric locomotives. The company principally operates through its three primary segments - construction industries, resource industries and energy and transportation - and also provides financing and related services through its financial products segment.
As a platinum sponsor, Caterpillar will be exhibiting at the conference and host the Caterpillar Gala Dinner on 31 March, 2022.
Hitachi Hitachi Construction Machinery Australia (HCA) is a subsidiary of Hitachi Construction Machinery Co Ltd (Japan) and part of the global and diversified Hitachi Ltd group. HCA is the exclusive distributor of Hitachi and Bell products in Australia. It is committed to delivering machinery sales and support to Australian customers across the mining, construction, quarrying, forestry, materials handling and recycling industries through a wholly owned national branch network.
Hitachi will join us as an exhibitor and host the Welcome Reception on the first night in Newcastle, 29 March, 2022.
Komatsu Technology and innovation is built into Komatsu’s DNA. Whether it is ICT-based machine management, autonomous haulage mining trucks or fuel-efficient hybrid excavators, Komatsu has been at the forefront of innovation and is recognised globally as a technology leader in all sectors of the earthmoving industry. Komatsu’s commitment to innovation is ongoing, as demonstrated through its SmartConstruction concept and the next generation of Komatsu machines which increase productivity, reduce costs and eliminate rework.
Komatsu will host the Komatsu Conference Dinner at Newcastle Racecourse on Wednesday 30 March, 2022 as well as exhibiting at the conference.
OTHER SUPPORTERS The IQA National Conference has also been fortunate to receive support from both Destination NSW and the City of Newcastle. As the host city sponsor, the City of Newcastle will warmly welcome our delegates, sponsors and exhibitors to the city over the three days. Situated on the east coast of NSW, Newcastle is surrounded by golden sand beaches, a breathtaking coastline and a beautiful working harbour. The cafes, restaurants and bars, unique architecture and rich history stretch from the city to the suburbs. For further information on things to do in Newcastle or extending your stay pre- or post-conference, view visitnewcastle.com.au
The IQA Partner Day is a conference tradition and we thank Orica for its continued support of this important program. Partners at the conference in March 2022 will be treated to a unique itinerary featuring some of Newcastle’s key highlights, a chance to explore their creative side and a tour of an integral support service for the Hunter Region.
The companies supporting other aspects of the conference – including the conference master of ceremonies, the site visit, shuttle bus, conference app, IQA Awards, coffee cart, conference satchel, hydration station and inaugural after party – are Wirtgen Australia, RTV Training, Lincom Group, Liebherr Australia, Hetherington Environmental, WesTrac, Cement and Aggregate Consulting and Access Environmental Systems.
Our sponsors will be joined by more than 50 exhibitors showcasing the latest in equipment and services available to the extractive and associated industries. We thank all event partners that have supported IQA2021 and look forward to a fantastic conference in Newcastle in March 2022.
To register or for further information visit iqa. eventsair/conference For now, best wishes from Newcastle for a safe and happy Christmas.•
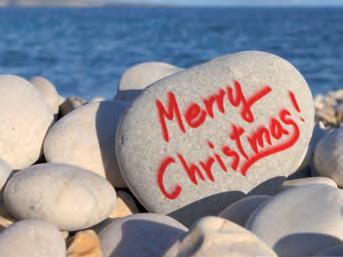
IQA NEWS
The Institute of Quarrying
Australia
IQA AND THE INDUSTRY
To help promote our engagement with industry, the IQA has developed an industry supporter badge. It is being released to industry so businesses that support the IQA can promote the Institute. In addition, all current IQA members will receive a digital membership badge. The badge denotes each member’s grade. The electronic badge can be used on email signatures, LinkedIn, Facebook and more.
GET INVOLVED IN THE IQA
Quarry Content Advisor – contract role The Quarry Magazine Content Advisor will support the technical accuracy of articles in Quarry (print and electronic) and provide advice to help with factually correct technical information. The contractor will collaborate with the editor of Quarry, the IQA CEO and the magazine’s editorial panel to identify relevant news stories and support editorial content. For more information, download the EOI form from the IQA website: quarry.com.au (> Extractive Industry > Our Partners). Membership Review Committee nomination The IQA is seeking an EOI for up to five representatives from industry, branches and sub-branches, and suppliers to join the Membership Review Committee (MRC). The MRC’s role is to: i) Determine applications for member status, where applicants do not have a formal or exempting qualification. ii) Determine member applications referred to it by the Committee Chair or National Office staff. iii) Determine member applications referred by applicants that are unhappy with decisions of the Committee Chair or National Office staff. iv) Review and provide recommendations to the Board via the IQA CEO on all Fellowship nominations. v) Review and provide recommendations to the Board on all Honorary Fellowship nominations. vi) Review and provide advice to the CEO on all membership matters. vii) Review and provide advice to the CEO on strategies to sustain and grow membership. viii) Refer matters of Committee composition, membership guideline amendments, membership grades and annual membership fees to the Board via the CEO.
For more information, download the EOI form from the IQA website: quarry.com.au (>Membership Review Committee). IQA AWARDS
Given the challenges of the past 12 months there has been a slow uptake for the 2021 IQA Awards. As a result: • The IQA Board has extended the nomination closing date to 18 January, 2022. • Non-IQA members can now apply for the 2022 award cycle in all categories (excluding the President’s Medal). • The Exhibitor of the Year will be judged from the conference exhibitors at the national conference on 29 and 30 March, 2022.
The IQA Awards are an opportunity for members to nominate their peers and showcase talented industry people and innovative ideas.
Hanson Bass Point Quarry manager Steve Butcher (2018 Quarry Manager of the Year) has told Quarry the awards are “a really good avenue to let the industry know what your operations are doing and share those ideas as best practice”. He added submitting an application “helps you put perspective on your own career” and what you would like to do next.
Malcolm Sawers, a maintenance supervisor at Hanson’s Kulnura Quarry, collected the 2017 Excellence in Innovation Award for devising, with colleague Michael Bennic, a device called KAMMP that dispenses paint whenever tramp metal is detected on the conveyor belt. The belt automatically stops and workers will follow the paint marks to find and remove the pieces of stray metal, reducing downtime in the crushing and screening circuit dramatically.
Sawers told Quarry that “sitting in the IQA conference and hearing your name being called out in front of a lot of your peers was very exciting. It was great to be recognised, and hearing all the feedback from a lot of colleagues and other people in the business”.
Andrew Hauser, Barro Group Seymour Quarry manager, was the recipient of the 2019 Alex Northover Award for best portfolio submitted to a RTO by an IQA member who has completed a qualification in surface extraction operations. He said he never set out to win an award but it “was good to see that the hard work was acknowledged. The Award is a great recognition of your knowledge, the hard work and learning capabilities”.
Further, the learnings that Hauser took from his studies were successfully implemented at Seymour Quarries. Barro’s Victorian quarry operations manager Craig Banthorpe wrote as part of Hauser’s Alec Northover nomination that “Andrew has been able to put into practice in the workplace many of the competencies introduced” and the ‘Manage People Performance’ module had provided “the tools he required to manage the people at and connected to the site”.
Further information about the IQA Awards can be found on the IQA website: quarry.com.au
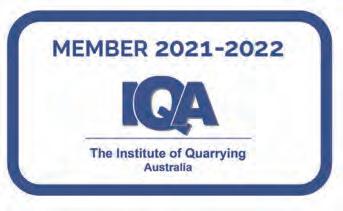
An example of the digital IQA Membership Badge.
BRANCH NEWS
The following online education events were held in October. Learning from Disasters The mandatory New South Wales course was delivered virtually to a sold out audience. It is mandatory for all quarry managers at Tier 1 and Tier 2 quarries to undertake the course. The IQA is an Approved Training Provider: No. 0004206. Quarry Roads & Onsite Vehicles Safety This popular webinar was delivered to a full complement of 25 attendees. A second webinar was run on 25 November. Quarry Products Technical Training The IQA delivered a successful Quarry Products Technical Training online workshop on 21 October. The course was run at capacity with participants representing a cross-section of the industry. Facilitator Tony Ferrazza ensured the group left the course with relevant key outcomes seen via the positive feedback received from some of the delegates.
“Just wanted to express my thanks to Tony and the IQA for the excellent course. It was very enjoyable and I got a lot from it. Could you please pass my thanks to Tony for presenting as well? He did a great job!” – Jason, Senior Geologist
“Great course yesterday, really got a lot out of it, please pass on my thank you to Tony!” – David, Key Account Manager
NSW NORTHERN REGION AGM
The NSW Northern Region sub-branch (NR) met virtually on 27 October for its AGM. The meeting saw a newly-formed committee enthusiastic
IQA NEWS
The Institute of Quarrying
Australia
GOODBYE TO 2021: A YEAR OF
CHALLENGES, RESILIENCE AND CHANGE
I simply can’t believe I am writing for the December edition of Quarry. Where has the year gone? 2021 was a year full of challenges and constant change that required resilience.
At the time of writing this article there is a level of optimism that international and state borders will open. I wrote last month that the uptake of the vaccine was a key part of many states’ and territories’ roadmaps to easing restrictions and how many businesses were responding to encourage vaccination in various ways.
The focus must remain on vaccination for the foreseeable future to help save lives, protect jobs and keep the economy moving. As our borders open the need to encourage vaccination remains critical. The message will soon need to include getting booster shots for those who are fully vaccinated.
So, to the year that was. The IQA faced change and challenges head on. Overall, we had a solid year and maintained engagement and services to members. This was due to the support and commitment of branch committees, Women in Quarrying and Young Member Network co-ordinators, our sponsors and partners and tireless work by the team. Thank you for all that you did in the past 12 months.
In January this year, we were still busy implementing processes to manage in a virtual world and were juggling the planning of events in many states still facing lockdowns. Branch committees responded and ensured they stayed connected with the industry through virtual meetings, then face to face events.
This positivity saw branch events resume in all states in 2021 with great success. A highlight for me was hearing the Honorable Julie Bishop speak at the Diversity and Inclusion conference in Perth on the importance of diversity and share some insights from her amazing career. Building on the work of the Women in Quarrying network and moving into a broader dialogue of diversity will be a focus of the Institute in 2022 and beyond.
The ability for the IQA to pivot, adapt and respond to change was due to our loyal supporter network. Our sponsors gave their time generously to participate in branch committees, support education programs, speak at events and contribute financially. I want to thank all supporters for your generosity and flexibility in what was a challenging year. Your support was a key part of the IQA’s overall stability and recovery as we managed during 2021.
The next 12 months and beyond will see the IQA deliver on its strategic plan. I am especially excited about the market research we are undertaking to identify new ways to add value, serve the industry and deliver training. Several new education programs are being prepared for release and we will look to strengthen our engagement with the younger generation.
The IQA team juggled a lot of change and still delivered. Thanks to Ned Worboys, Lisa Stromborg, Donna Turner, Belinda Virgo, Emily Logan, Teresa Everett, Rod Lester and Marie Cunningham. Your flexibility, dedication and willingness to find a solution made all the difference in 2021.
I wish everyone a wonderful holiday season and a safe and prosperous 2022.
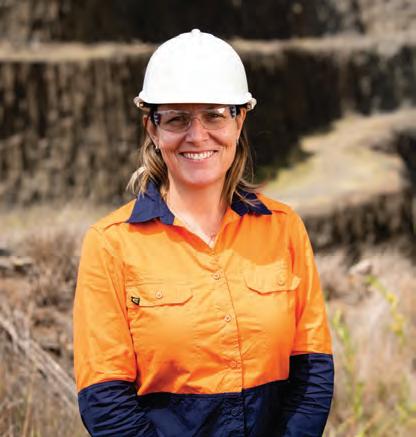
about revitalising the branch after a challenging two years. The committee welcomes new chair Chris Brown MIQ, supported by outgoing chair Jason Williams, who has returned as deputy chair for 2021-22. Thomas Sherd MIQ returns to the role of secretary/treasurer. Bradley Brown AIQ and Matt Kelly MIQ join the revitalised executive team as committee members.
The NR committee also met in late November to discuss plans for the delivery of professional development and networking events across Northern NSW in 2022.
“I am looking forward to working with the branch committee in planning worthy events in the north,” Brown said. “Exploring how we as a committee can best service the existing member network while expanding the reach to future members in our industry is very exciting.”
NORTHERN QUEENSLAND NEWS
Mackay Golf Day The Mackay Golf Club hosted its first IQA Golf Day on 8 October. Fifty-nine players took to the course for nine holes. The day concluded with a post-game presentation and networking.
A big thanks to the IQA’s Mackay team and all participants for making the day a success, including the following sponsors: • Tenkate. • Astec Industries. • EXEL Drilling. • Australian Mining & Quarry Supplies. • A2B Crushing & Screening. • D&M Electrical.
KYLIE FAHEY Chief Executive Officer Institute of Quarrying Australia
CENTRAL QUEENSLAND SUB-BRANCH NEWS
The Central Queensland sub-branch held a networking dinner to a capacity room of 40 people. A presentation was delivered by Gavin Hill, the project manager of the Rockhampton Ring Road Project from Queensland’s Transport & Main Roads. Attendees also heard from the event sponsor Kerryanne Tawhai, the director of DTE Training & Safety Skills.