
24 minute read
NO PROBLEM WITH THE HAUL ROAD CURVE A curved rail running conveyor may provide an alternative to load and haul vehicles
from Quarry May 2020
by Prime Group
NO PROBLEM WITH THE CURVE: RAIL RUNNING CONVEYOR SOLUTIONS
Larger quarries are increasingly looking for economical solutions to transporting aggregates from the face to the crushing circuit. A proposed curved rail running conveyor may yet provide an alternative to conventional transport by dump trucks and off-road vehicles.
Innovative operators in the quarrying business are constantly adapting to overcome the lean operating margins and environmental constraints at their sites. Now a new conveying technology from thyssenkrupp and the University of Newcastle relieves familiar challenges faced by larger quarry operations, including: • Costly truck haulage from the face to the plant, especially where there is substantial elevation change. • Concerns about diesel and dust emissions. • Fugitive dust from conveyor transfer points. • Mine layouts that are awkward or unfeasible for conventional trough conveyors.
This new belt conveying technology allows a conveyor to run in a single flight from pit to plant along the curve of the haul road, hairpins excepted. For many pit layouts where the haul road curve radii can be configured to about 100m or greater, mines will be able to run haul trucks adjacent to the conveying corridor, allowing for the flexibility of truck haulage alongside the extremely low cost per tonne of belt conveying.
The payback time for replacing the truck haulage by the curved conveyor can be less than a year in some cases, according to estimates by thyssenkrupp. Those estimates include the operating cost of feeding the conveyor from a mobile primary crusher sizing down to perhaps minus 200mm.
RAIL RUNNING CONVEYOR
This new type of curved conveyor is a “pipe conveyor” version of the “Rail Running Conveyor” (or RRC) technology now being commercialised in Australia under an exclusive agreement between thyssenkrupp and the University of Newcastle. The product is part of a new “platform technology” that combines the efficiency of rail transport with the continuous nature of belt conveying, and
A concept image of the thyssenkrupp/University of Newcastle Rail Running Conveyor.
promises a “revolution” in overland, steep angle and pipe conveying, according to Luke Bennett, the national sales manager for strategic accounts at thyssenkrupp Industrial Solutions Australia.
The pipe conveyor version of the system is now ready to be deployed in a pilot installation at a quarry, ideally carrying the full output from a large tracked jaw crusher for a distance of up to one kilometre or through an elevation change of 50m to 100m. For this technology, testing and analysis point to: • Capital expenditure (CAPEX) being about the same as a conventional trough conveyor of similar length, lift and tonnage, and less than half of that for a conventional pipe conveyor in the same duty. • Power consumption being about 40 per cent lower than a conventional pipe conveyor, even though most of the power requirement for the example above is needed for lifting the rock. • Lower maintenance costs, because the transport mode eliminates almost all of the maintenance effort associated with the idlers, belt tracking and carry-back.
For some mine layouts, a planner might be considering costly trough conveyors on an elevated structure, such as that visible in the Google Earth image of a haulage route in a large limestone quarry (Figure 1). Due to the Rail Running Conveyor’s ability to negotiate very tight curves, the material could be carried by either trough or pipe RRC versions along the haul road, on a path indicated by the blue line. Even though the length of the RRC is greater than the direct, elevated route, the CAPEX cost per metre as well as the much lower maintenance intensity makes the curved RRC the lowest cost choice by far.
The RRC technology has been carefully developed over nearly a decade by TUNRA Bulk Solids at the University of Newcastle, and is covered by a number of international patents. Contemporaneously, thyssenkrupp’s heavy duty conveyor group created designs based on similar principles, and now the University of Newcastle and thyssenkrupp are collaborating to bring this product family to the industrial minerals industry.
To put this technology in context, it is
worth remembering that conventional belt conveyors are constrained by well known inherent limitations, including: • Intermediate transfer points, with their high maintenance requirements, which are often unavoidable because of limited horizontal and vertical curvability. Rail running pipe conveyors can curve much more tightly than conventional pipe conveyors, allowing transfer points to be eliminated in many cases. • Idler rolls that are subject to multiple modes of failure all along the length of the conveyor. The failing idlers must be detected and replaced wherever they happen to be. Conventional pipe conveyors typically have more than twice as many idler rolls as a trough conveyor, increasing the idler-related maintenance demands. • Energy loss that is caused by the belt/ idler interaction which consumes as much as 50 per cent of the power, even in plantscale pipe conveyors. • Belt speed that is limited by several factors related to the fixed idlers, which drives up belt width and strength requirements.
“The Rail Running Conveyor system overcomes these limitations, allowing breakthrough performance improvements in each of these areas,” Martin Lurie, thyssenkrupp’s product lifecycle manager for rail running conveyors, said.
BENEFITS OF CARTAGE
Operators of large quarries are intimately familiar with the two core technologies that make up RRCs, namely belt conveyors and rail haulage. In RRCs, conventional fixed idlers carry a standard belt in the usual configuration near the head and tail of the conveyor, and the belt itself still carries all the tension. But between the head and tail, the belt rests securely in the cradles of slim, wheeled carts rolling on light rails.
In the trough version of a RRC, the loading point is exactly the same as in a conventional trough conveyor. The loaded belt travels a short distance from the load point by rolling on conventional idlers. Then the wheeled carts glide upwards on their rails to take over the load from the fixed idlers. Similarly - for the pipe belt version - the loading point and pipe formation is the same as a conventional pipe conveyor. For a short distance, the pipe belt moves through conventional pipe conveyor idler panels. Then the carts move up to take over from the fixed idlers. To keep
Figure 1. A Google Earth image of a haul road in a large limestone quarry. Material could be carried by either trough or pipe RRC versions along the haul road, on a path indicated by the blue line.

the belt closed in its pipe form, the cradle of each cart has a circular bottom, and every two metres there is a fixed idler that presses down on the belt edge to keep the pipe closed, mounted in a frame above the carts.
Before reaching the head or tail, the cart train turns around independently of the belt, and a light wire rope keeps the carts moving through the turnaround. Automated inspection devices continuously monitor the condition of wheels and bearings at these turnaround locations, where deteriorating bearings or wheels can easily be exchanged. As with conventional rail systems, derailment is a possibility, but carts can be designed to be both resistant to and tolerant of derailments. Low cost automated derailment detection will allow the conveyor to be stopped should a derailment occur.
The very low losses in the RRC systems arise from the highly efficient wheel-on-rail interface. For context, rolling resistance in a haul truck is typically in the two to three per cent range. The measured rolling resistance for RRCs of about 0.4 per cent of the moving weight is comparable to that of light rail transport. This low level of rolling resistance contrasts to the best in class trough conveyors which are typically designed to handle rolling resistances about three times higher – at perhaps 1.2 per cent of the moving weight (DIN f of 0.012) – or to more typical trough conveyors designed to overcome rolling resistances five times higher – at about two (2.0) per cent of the moving weight. Conventional pipe conveyors have still much higher losses than conventional trough conveyors, with those conventional pipe conveyors operating in very cold conditions designed for rolling resistances of perhaps 4.5 per cent, or 10 times higher than a RRC.
An added feature of RRCs is that frictional losses don’t increase in cold operating conditions. This new low resistance paradigm translates directly into substantial CAPEX and operational expenditure (OPEX) savings. The CAPEX savings are due mainly to cost reductions for belt, drives and erection. For example, elevated gantries do not require walkways for idler maintenance, which allows enormous reductions in structural weight. The OPEX benefits come from lower power consumption, smaller maintenance crews, and lower costs from idler monitoring and replacement. thyssenkrupp’s offices around the world have recently begun exploring suitable trial installations for the trough overland version of the RRC, with notable interest from major Australian mining companies. Now, Australian innovation and tax incentives may be available to industrial minerals and aggregates companies that partner with thyssenkrupp to build a pilot-scale system for demonstrating the pipe version of the RRC technology. •
ABOUT THE AUTHORS Martin S Lurie is the product lifecycle manager for rail running conveyors for thyssenkrupp Industrial Solutions (USA). Luke Bennett is the national sales manager for strategic accounts at thyssenkrupp Industrial Solutions (Australia). Prof Craig A Wheeler is based in the School of Engineering (Mechanical Engineering) at the University of Newcastle, New South Wales.
DOES LONG DISTANCE CONVEYING EQUATE TO LONG-TERM SAVINGS BENEFITS?
Conveyors have long been touted as an alternative to earthmoving vehicles for the cartage of aggregates on-site, particularly over long distances. However, what really are the pros and cons of long distance conveyors – in terms of finance, safety and the environment – and is bigger necessarily better?
The landscape of the world continues to change in many different facets in the aggregate and mining industries. Aggregate reserves are becoming rare commodities in many areas, transportation issues are priorities because of rising costs and residents’ concerns, and industry requirements for specialised products are all factors in the discussion surrounding this transformation. These factors continue to drive the need for change in the way that aggregates are transported, not only from the source of the aggregate and/or the production area but also from the production site to the area of further processing or end use.
The decision to move product from the aggregate reserve to the crusher or to the area of stockpiling by truck or by conveyor is made because of a number of inputs that are analysed: • Cost benefit. • Product quality. • Topography. • Environmental issues.
Improvements in conveyor mobility, function, design, and flexibility, as well as escalating costs for operating haul trucks show the decision to use conveyors much more cost-effective.
COST BENEFIT
The main benefits of using conveyors instead of haul trucks are as follows: • Decreased operating expense. • Limited inflationary effect. • Improved product quality. • Continuous flow. • Environmental friendliness. • The flexibility of design for conveyor systems.
Conveyors are beneficial not only in overland applications of short, medium, or longer length, but also in radial stacking or telescoping stockpiling applications where
An example of a 60m-long overland conveyor.
trucks have been traditionally used.
The maintenance costs of conveyors are considered less as more downtime is required to keep trucks and loaders running efficiently. In addition, most conveyor replacement parts are available locally. Conveyor systems are also less labourintensive as trucks or loaders require one or sometimes two operators. Conveyors can also operate at maximum efficiency every hour of operation. This can decrease workforce and training requirements (see Table 1.)
While the big advantage of the haul truck continues to be its flexibility, even bigger disadvantages are increased fuel prices, increased labour costs to operate, maintenance costs, and the shortage of parts such as tyres, with lead times of more than six months being reported (see Figure 1 on page 24).
Overland conveyors offer cost-effective

material transport and a wide spectrum of capacities that can vary from a trickle of material all the way up to 30,000 tonnes per hour. Furthermore, with a lifespan of more than 20 years, the benefits of their high capacity and low cost operation are realised long after the initial truck fleet is retired.
As an example, a Texas-based mining operation has reported that its three kilometre-long conveyor has eliminated more than 140,000 truck trips and more than 917,000 vehicle kilometres on an annual basis. Added to the fuel savings, this operation is significantly reducing costs associated with labour, workers’ compensation costs, safety training, emissions, maintenance, and engine depreciation.
The above costs, and cycle time considerations when truck hauling in urban traffic congestion, were also factors in an Atlanta Airport project where an eight
kilometre-long overland conveyor was chosen as the method to transport 30.5 million cubic metres of fill material from several nearby quarries to the construction site of a fifth runway. This overland conveyor also allowed the proper blending of crushed rock and overburden material in desired percentages as it was fed onto the belt.
A limited inflationary effect is achieved because rising fuel and energy prices have little effect on the operating costs of conveyors, and are not sensitive to fuel shortages. Electricity costs are fairly stable compared to diesel prices and conveyors can be run at off-peak energy times.
Improved product quality is seen because conveyors eliminate multiple handlings of material, which prevents compaction and contamination typically caused by trucks and/ or loaders. Telescoping conveyors eliminate segregation and material degradation.
Continuous flow is another advantage realised because conveyors are not affected by weather and can be fully automated and
TABLE 1. OPERATING COSTS
Equipment Model Equipment cost*
Telestacker conveyor TSFD150 $200,000 Articulated truck 35 tonnes $455,000 Mine truck 50 tonnes $540,000 *All dollar denominations in $USD. Operating cost per hour (labour, maintenance, fuel)*
$25.08
$120.00
$81.00 Annual cost*
$62,700
$142,500
$202,500 Cost per tonne*
$0.08
$1.10
$0.84
operated at the touch of a button.
Aside from initial capital cost, operating expenses are the next major measured costs in aggregate operations. Initial comparative areas show that conveyor systems have high capacity and a low cost of operation; while depending on distance, the capital cost of a conveyor system can be higher than a haul truck. However, no matter what the distance, the cost of operating a conveyor will be less. Long range costs show that conveyors have limited inflationary effect and a long life span of at least 20 years.
TOPOGRAPHY, DESIGN EFFICIENCIES
Current conveyor technology can take on inclines up to 35 degrees while truck efficiency is compromised in any inclined application. There are also immovable issues such as the lay of the land. Haul trucks are not designed to tackle grades much above six per cent. It is clear that more and more operations are limiting truck transport to the area between the working face and the pit crusher. That means haul trucks are suitable mainly for level applications and truck efficiency is compromised in any inclined application.
4HEBENEFITSOF4UFFLEX
s ,ONGERLIFEOVERWIRESCREENSUPTOX
s %ASIESTSCREENTOREPLACEINENDTENSION MOBILESCREENSLIGHTERCOMPACTAND EASIERTOPLACEINTOPOSITION
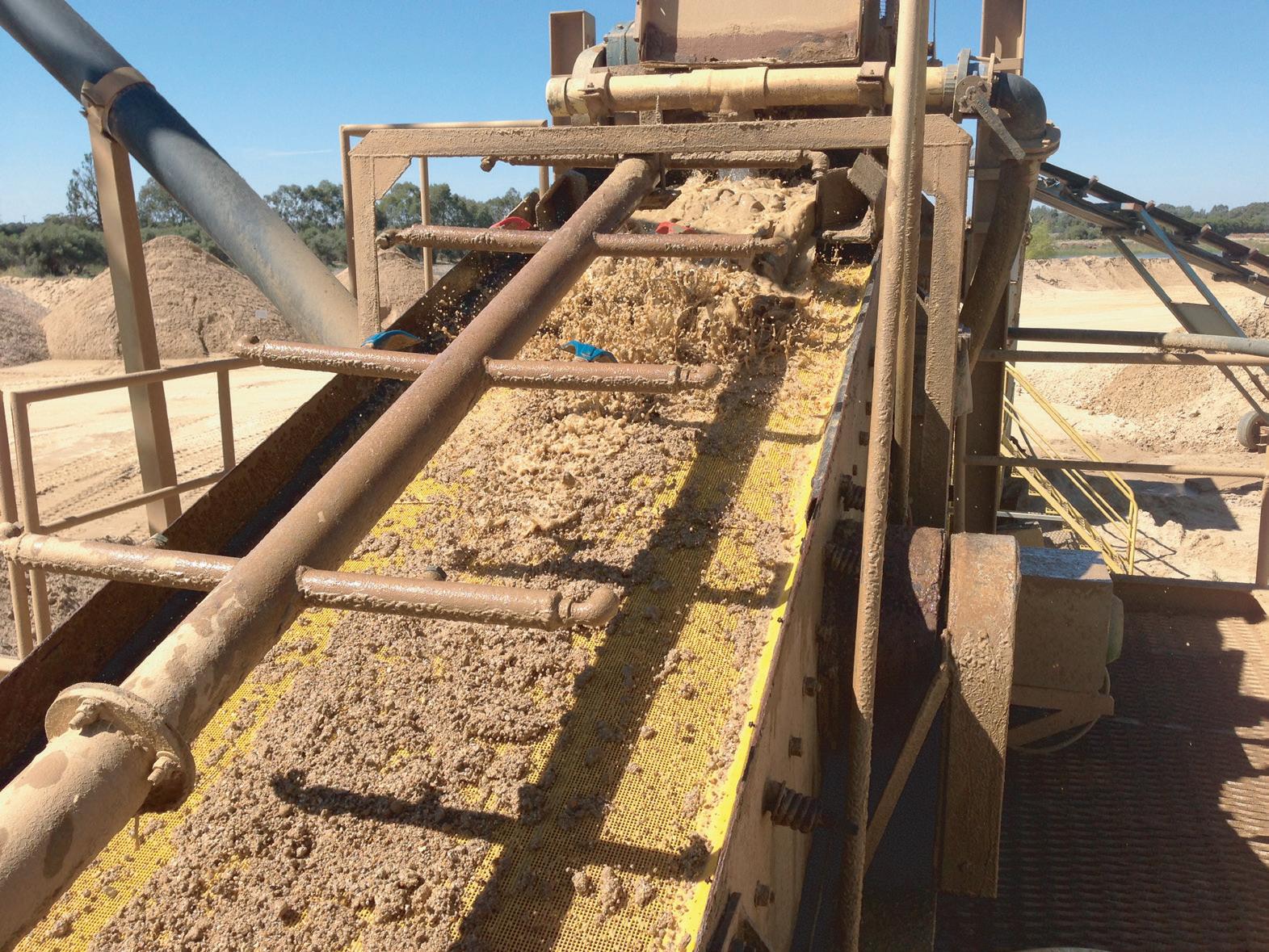
#ONTACTA,OCKERREPRESENTATIVEFOR PRICINGANDADVICETODAY
Figure 1. The cost comparison per tonne of a haul truck versus a conveyor.

Overland conveyors offer cost-effective material transport and a wide spectrum of capacities.
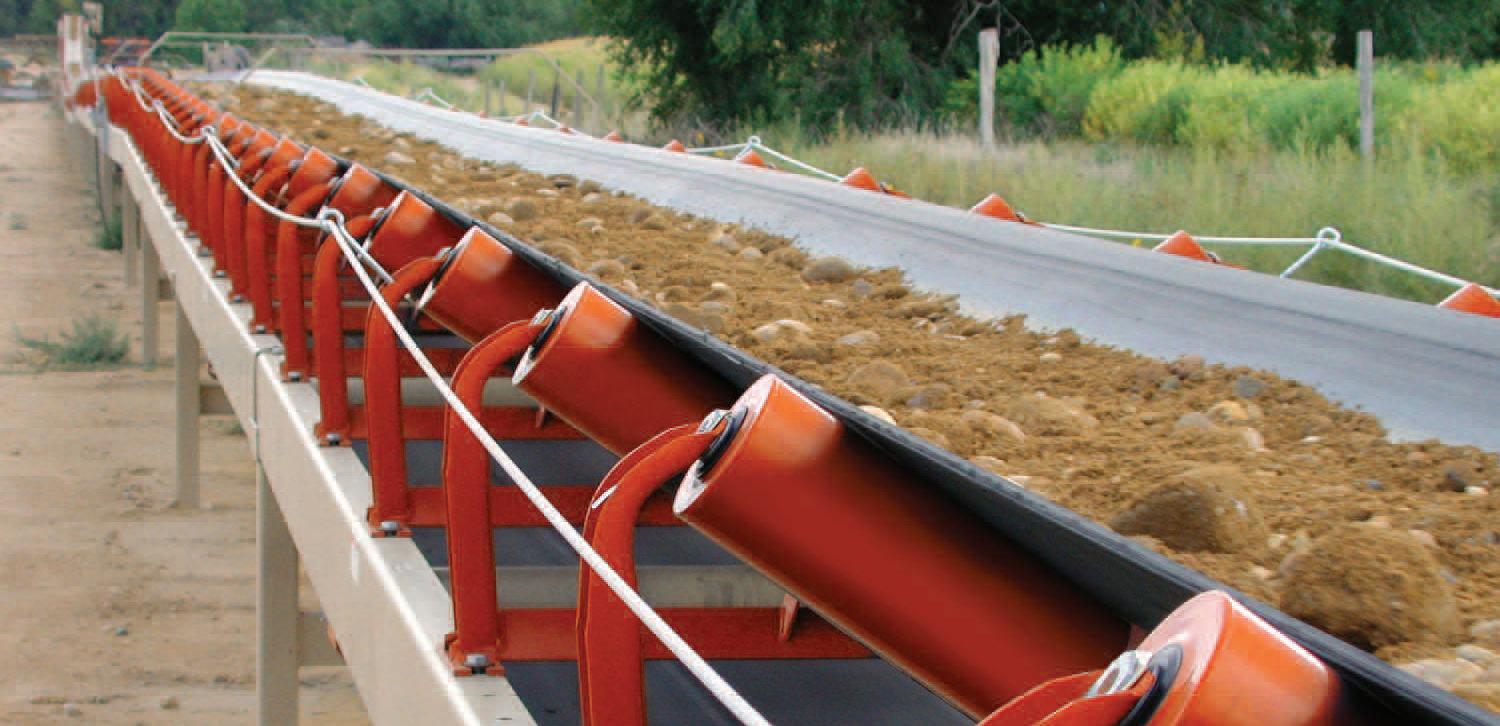
However, bigger isn’t necessarily better. A common misconception is that oversized equipment lasts longer and requires less maintenance. Conveyors should be sized according to the expected load yet allow for a small capacity increase. For example, going with a 90cm belt when you only need a 76cm belt will ultimately result in additional belt and idler rolling resistance, and less energy efficiency.
Also, overland conveyors do not need to be eight kilometres long over rugged, mountainous terrain to be considered as a legitimate option. Overland conveyor lengths as short as 150 metres have been shown to have significant cost reductions over haul trucks. Payback of a system from 300m to 900m has been shown to be as short as 88 days to 182 days.
Electric motors consume 64 per cent of the electricity produced in the United States, according to a northeast utilities provider whose report cites the example of a 75kW AC induction motor that costs approximately $USD5000, yet will use as much as $USD35,000 worth of electricity over its lifetime.
With that said, it is clear that small improvements in efficiency can generate notable energy savings. As such, today’s conveyor manufacturers normally install new premium efficiency motors on each unit they build. Since these motors perform most efficiently near their designed power rating, it is recommended to run at between 75 per cent and near 100 per cent of full load rating. If you’re running at 50 per cent of capacity or lower, the efficiency of the motor drops dramatically. Motor size should be matched to the wattage requirements of the load.
Again, some producers will oversize a motor, thinking that it will require less maintenance. However, the energy savings realised from a properly sized motor will outperform any maintenance savings derived from a larger model.
Monitoring and minimising rolling resistance requires paying close attention to the quality of your belt and idlers. Manufacturers are now designing belts with special covers that help to counter rolling resistance. Idlers may look similar but they vary in performance. Speak to your conveyor manufacturer for a recommendation about the right bearing and seal type for your application. Proper idler spacing is also important. Again, consult with your conveyor manufacturer for idler spacing and rolling resistance formulas.
Systems must be designed and operated relative to the maximum material lump size. This is particularly applicable to material conveyed from the primary crusher. As the lump size increases, the potential capacity for a given belt width decreases. Some producers may skimp on belt width while running at higher speeds or capacities. While they may size their belt according to lump size, they may be running at a capacity that is not suitable to that lump size.
A basic rule of thumb dictates that you should never run at an excess of 80 per cent of volumetric capacity. Plus, when you’re running material that is at maximum lump size, it is best to remain under 80 per cent volumetric capacity to maintain standard edge distance and safe operation.
SAFETY, MAINTENANCE, ENVIRONMENT
Obviously safe conveyor maintenance does not allow for crawling under the unit to get to the other side. A ground line or overland conveyor must be designed with crossover points (for pedestrians and/or vehicles) at convenient intervals, so that producers can safely, easily and efficiently complete maintenance tasks on both sides of the system.
However, beyond costs per tonne, there are other key drivers in an emerging overland conveying trend.
Consider the ever-tightening environmental regulations. Individual mobile haulage units emit and stir pollution along the entire transfer path. As production sites expand and encroach upon suburban development, concerns arise over dust, noise and traffic. As such, quarry owners are often involved in decade-long negotiations over leasing and permits.
For instance, when faced with government and community opposition, a California-based aggregate operation proposed the use of overland conveyors over scrapers and trucks. It was armed with an environmental impact statement issued by the US Bureau of Land Management. It reported that the use of overland conveyors over haul trucks would reduce estimated PM-10 emissions (ie particulate matter larger than 10 microns) by mobile haulage from 95kg per day to as little as 2.3kg per day. In addition, community concerns could be eased by the fact that an overland conveyor would offer quiet material transport, and when designed properly, could blend in with the environment.
DESIGN QUESTIONS
A long distance conveying system needs to be based in reality, and according to specific site parameters. The following questions should be considered during the purchasing process: • What is the lay of the land? • What is the percentage of incline? • Will you need to cross roads or streams? • What is the best way to route the conveyor? • What is your power availability? • What are your power requirements?
Answering these questions will provide a clearer picture of what type of conveyor system will not only work for you but will make your operation safer for personnel, environmentally friendlier and more economical. •
Source: Superior Industries

Conveyors are also beneficial for radial stacking or telescoping stockpiling applications where trucks have been traditionally used.
Since 1989 Red Star has been devoted to wire cloth and screen media production in China, and is renowned for its high durability, precision and impactresistant products, which have been widely implemented by clients across US, Europe, Australia and the MiddleEast. As of 2016, Ying Hui and Red Star have set up a joint venture warehouse in Melbourne, in order to provide the quickest response time to meet all the demands of our Australian customers.
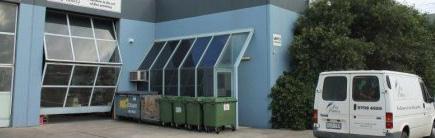
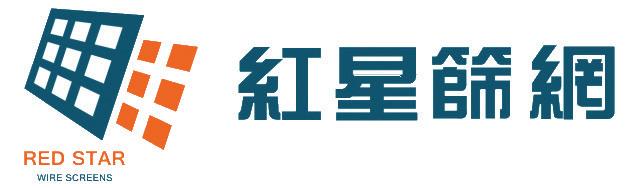
Visit our mobile-friendly website to check stock and order efficiently. We help your business run faster.
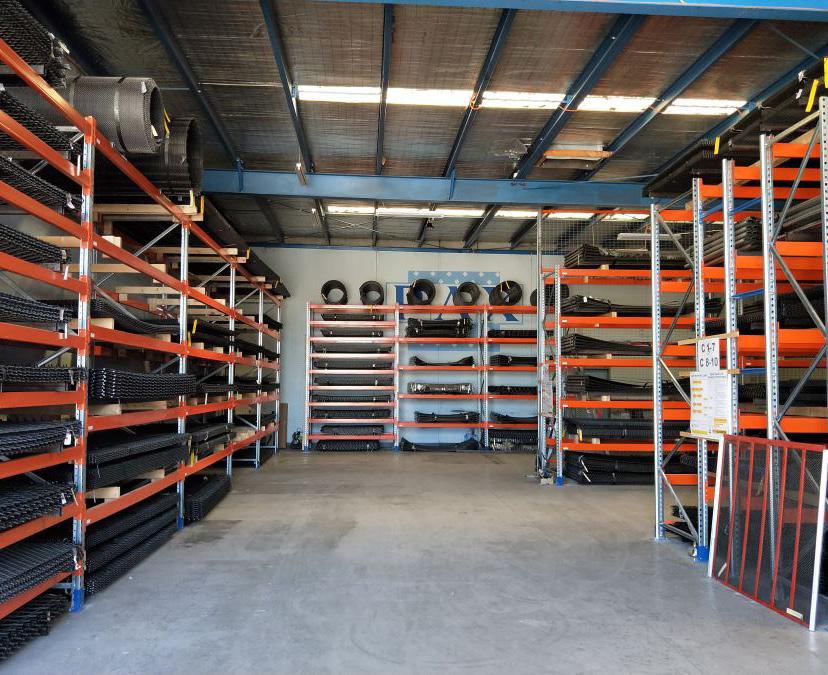
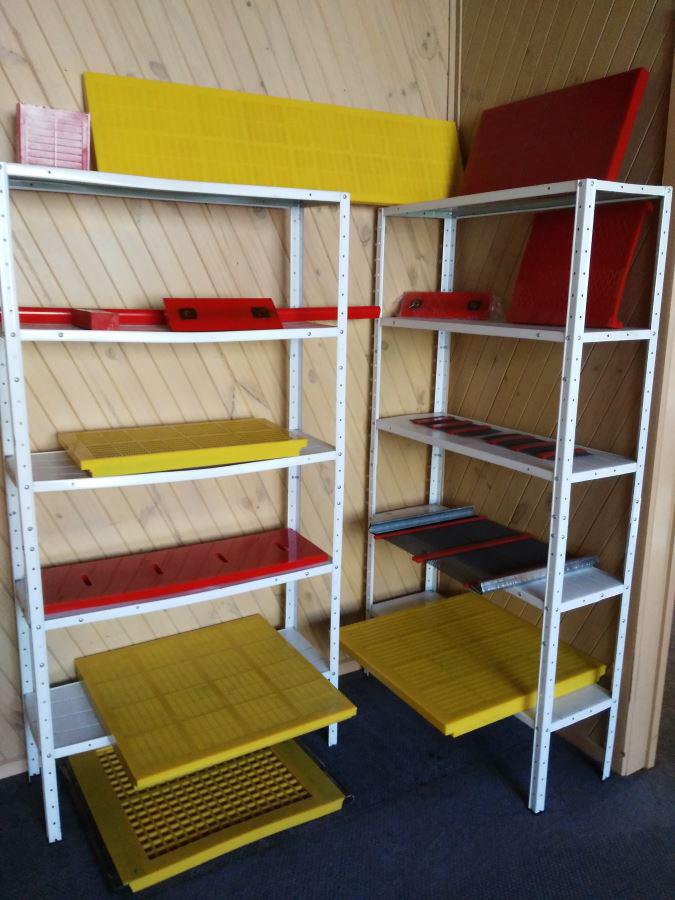

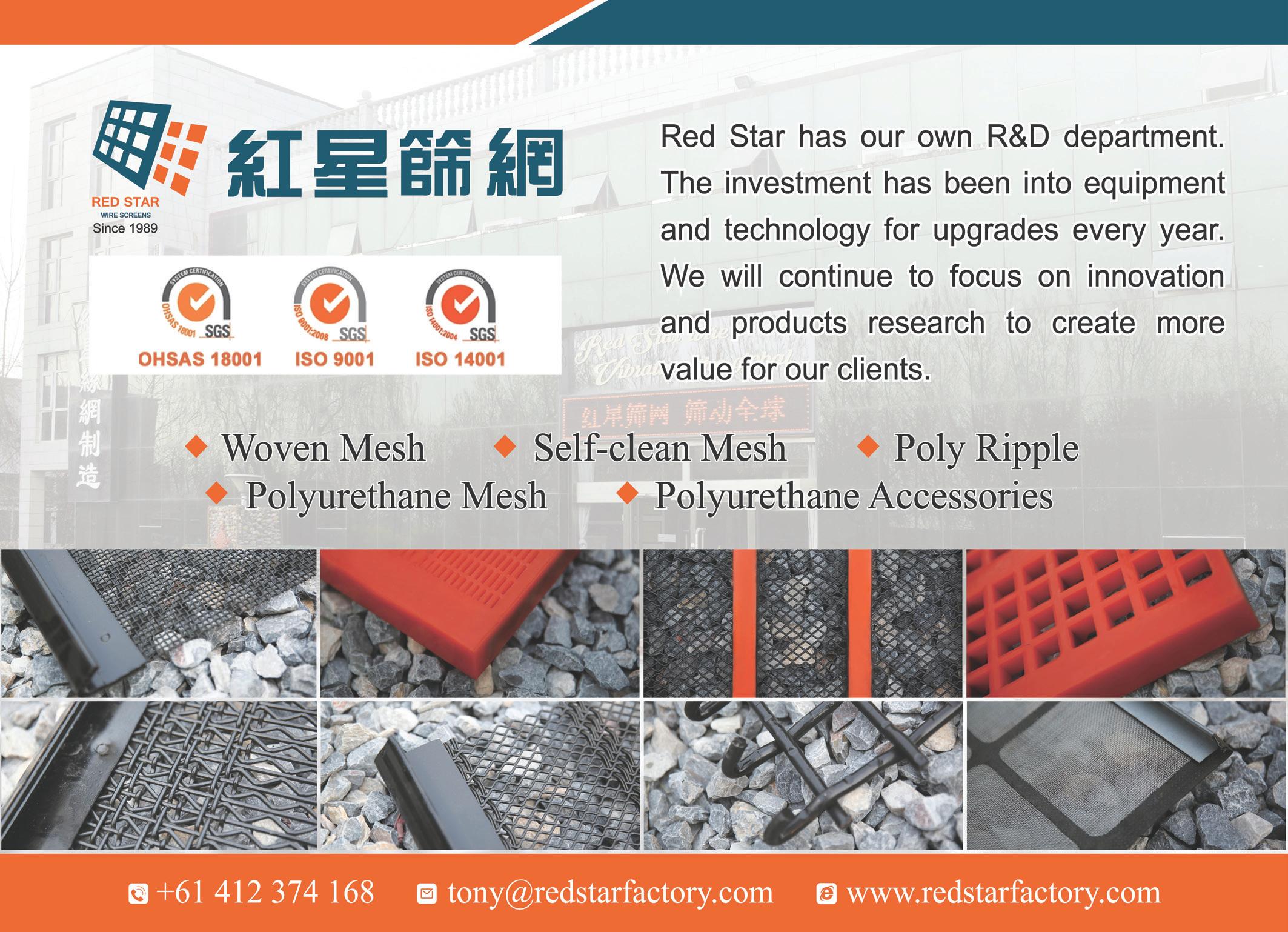
ONLINE SHOP: hhjv.myshopify.com
RADIAL STACKER PROMISES MASTERY OF PEAK EFFICIENCY
A US-based aggregates producer continues to reach new heights with the development of its recycled asphalt products – thanks to its acquisition of a radial stockpiling conveyor.
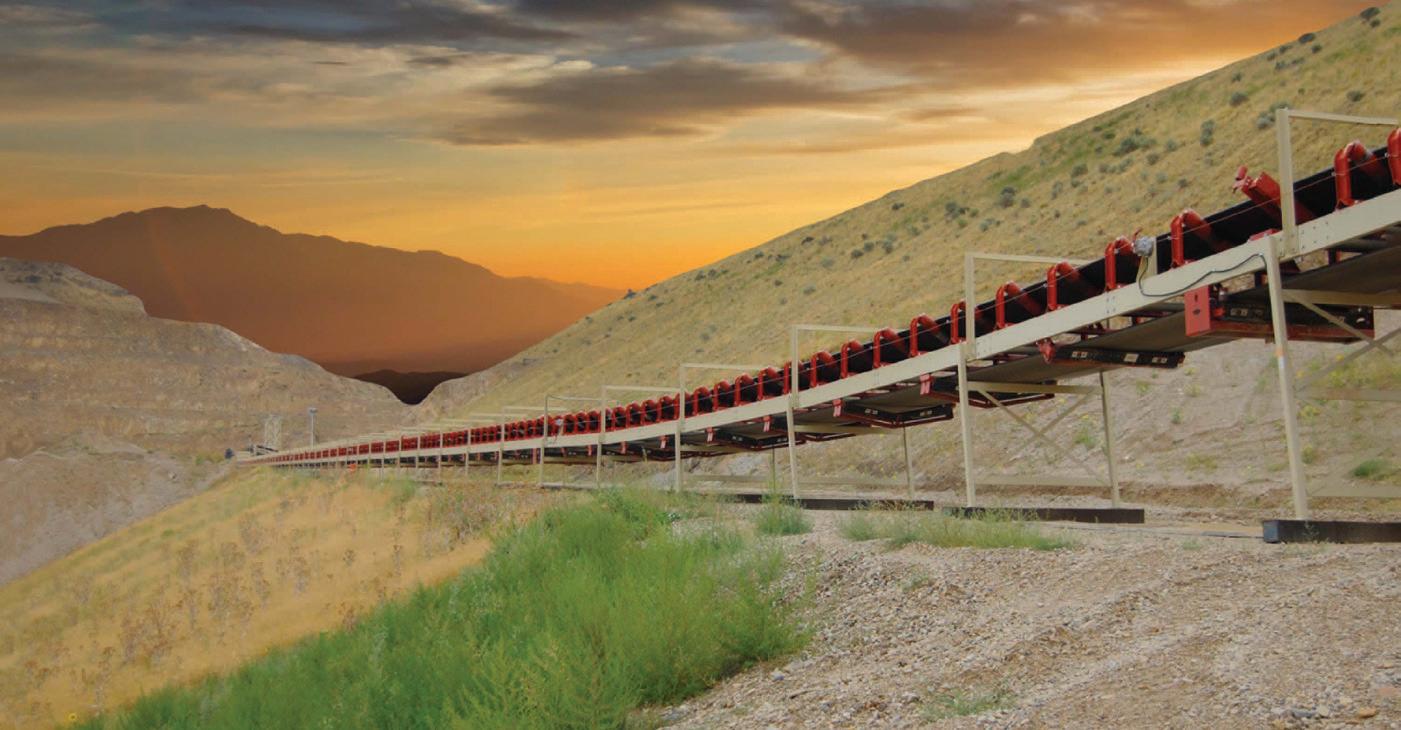
Achieving peak efficiency levels is an everyday feat of engineering and teamwork at the Geneva Rock Products Point-of-the-Mountain site in Utah, in the USA.
The facility has long been lauded for its commitment to sustainability, energy savings, and safety – which is well illustrated by a unique energy-generating downhill overland conveyor system that was commissioned more than five years ago. This much-touted material handling system (which according to the company paid for itself in under three years) transfers up to 2725 tonnes of material per hour from a mountain of upper-ledge rock to ground-level processing operations – while generating enough electricity to power the entire facility.
As to the latter, most people would say that Geneva Rock has indeed reached its peak performance. However, the company continues to climb higher and higher with ongoing improvements to each circuit and system, and to every transfer point, belt, pulley, idler, and more. For Geneva Rock, truly mastering peak efficiency is all in the material handling details.
DESEGREGATED RECYCLE STOCKPILING
One of the facility’s most recent upgrades was revamping material handling methods in its asphalt recycling operations. When specifications for the use of recycled asphalt became far more stringent in Utah, the operation needed to avoid segregation not only in the materials but also in the oil content of the recycled asphalt.
“When the rules of the game change, we need to change with them,” said Geneva Rock Aggregates’ production manager Ed Clayson, an industry veteran with more than 45 years of service.
Geneva Rock’s energy-saving overland conveyor system transfers up to 2725 tonnes of material per hour from a mountain of upper-ledge rock to ground-level processing operations.
Clayson said his company consulted with Superior Industries, a long-time, singlesource provider of aggregate processing equipment and material handling systems and components. “Superior Industries had designed and manufactured our downhill overland conveyor, which has performed flawlessly since we put it into operation,” he said.
Superior recommended the use of a 914mm x 46m TeleStacker conveyor, a telescoping radial stacking conveyor which eliminates material segregation by stockpiling materials in windrows to ensure that the stockpiled material meets specifications.
“There is quite a variance in the oil content between the chunk asphalt and the milled asphalt that’s hauled into our facility for recycling,” Clayson said. He explained that prior to the use of the new TeleStacker conveyor, the business had used a standard radial stacker to stockpile the recycled asphalt. Attempts were then made to blend the material with the use of a dozer – and even with additional materials handling, there was too much discrepancy in the specs.
“The TeleStacker has eliminated these costly issues as we introduce the material back into our HMA plant,” Clayson said. “We’re getting more uniform gradations in our pile and have not had any specification issues to date. Due to the way the unit is programmed, we get a much better blend of material, and the product is the same on one end of the pile as it is on the other.”
LATEST DESIGN ADVANCEMENTS
Superior Industries designed and manufactured the very first telescopic radial stacker in 1997, and over the years, feedback from the field has led to numerous innovations in its design.
“The latest design advancements to the TeleStacker conveyor make it the best value for money,” Clayson said. He adds that his team particularly likes the new FD Auto Level technology, which automatically maintains a level head pulley while in radial travel mode – an important factor since an uneven conveyor structure is one of the leading causes of belt mistracking on radial telescopic conveyors.
“In the location where we’re stockpiling, it’s not like we can build a concrete pad or runway to keep it perfectly level, so the auto-levelling feature is a really big deal that ensures the integrity of the belt and structure,” Clayson said.
Equally important, he said, is the addition of a material flow sensor (the SonicScout material sensor) which causes the telescopic conveyor to stop radial travel should there be a stoppage in feed material.
“With recycling, there is often some contamination in the material that may stop material flow,” Clayson explained. “If there is no feed material hitting the conveyor, the sensor causes the conveyor to stop its travel,
preventing the potential of gaps in the stockpile.”
Clayson also said the unit’s PilePro automation program is user-friendly, easy to operate, and easy to troubleshoot via one call to Superior’s in-house automation team. The zoning technique of the program allows Geneva Rock to build a higher volume stockpile on a limited footprint.
“We need to stockpile as much as we can in our designated area,” he said. “During the [northern hemisphere] winter, we’ll build a 27,215-tonne stockpile that will feed the asphalt plant all summer long.”
HIGH QUALITY COMPONENTS
A big advantage in working with Superior, Clayson said, is the fact it is one of very few manufacturers to design and build both the conveyor systems and the components.
“I have been around conveyors and components throughout my entire career and I am a firm believer that Superior offers the best components,” Clayson said. “We maintain a
Superior Industries’ fixed radial stacking conveyor at Geneva Rock eliminates material segregation by stockpiling materials in windrows to meet material specifications.

large inventory of their pulleys and idlers, and over the years, they have delivered significant cost per tonne savings due to increased wear life and belt protection.”
One of the standouts of the component line, he stressed, is the Chevron pulley, a V-shaped wing pulley that extends belt and pulley life by preventing rocks and debris from becoming trapped between the pulley’s wings. Compared to a conventional wing pulley, the V-shaped pulley deflects material far more effectively, while providing smooth operation with less vibration, less belt wear, less of an impact and load on the bearings, and less noise.
Superior is also providing custom idlers for Geneva Rock in a few locations. “We have two existing overland conveyors built by other conveyor manufacturers, and the components on them do not offer the quality we require,” Clayson said. “To eliminate the potential of costly downtime and belt damage, we are changing out the idlers on those conveyors with the custom components provided by Superior.
“When we need a solution, we don’t just buy the equipment, but we also buy the service and support that goes with it,” Clayson said. “We’re very lucky to have the highest caliber of support from both Superior Industries and its local dealer, Kimball Equipment Company. I’ve learned over time that you can’t do this by yourself. Having the right solutions and the right support makes us successful.”
In Australia, the national distributor of Superior Industries plant and equipment is 888 Crushing & Screening Equipment. •
Source: Superior Industries
Loaded by: Product: Dump Location: Hex 1 Shot Rock Primary Crusher
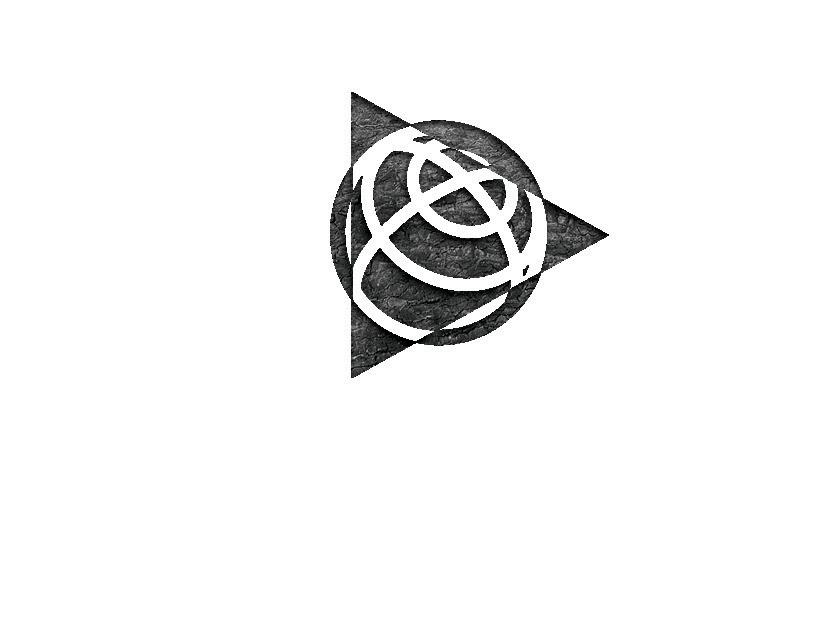
Product: TPH: Total tons: 1/4" Chip 253 2075
Product: Last loaded time: Idle time: Washed stone 12:01:07 pm 1:50:11
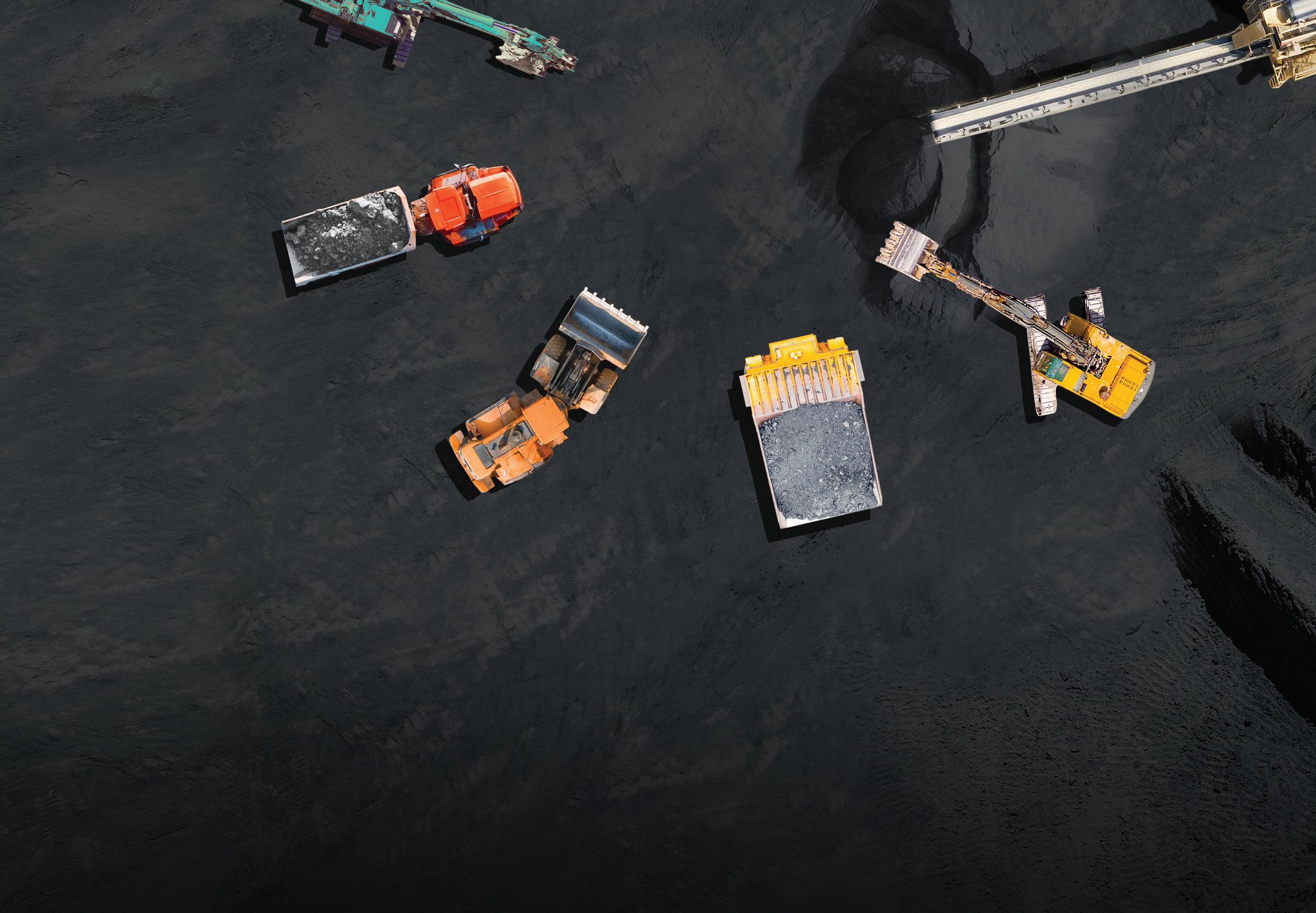
GET YOUR MIXED FLEET TALKING
Loads: Tons: Payload: Cut: Loads: Cycle time: 19 3,965 t 33.7 t 610.70 Yd 3 24 29.5 seconds
Trimble LOADRITE scales enable your mixed fleet to centralize payload and productivity data. Trimble turns that data into real insights that you need to make the right decisions, at the right time, and act with confidence.
OPTIMIZE LOAD/HAUL MONITOR PRODUCTION TRACK INVENTORY DRIVE CONTINUOUS IMPROVEMENT