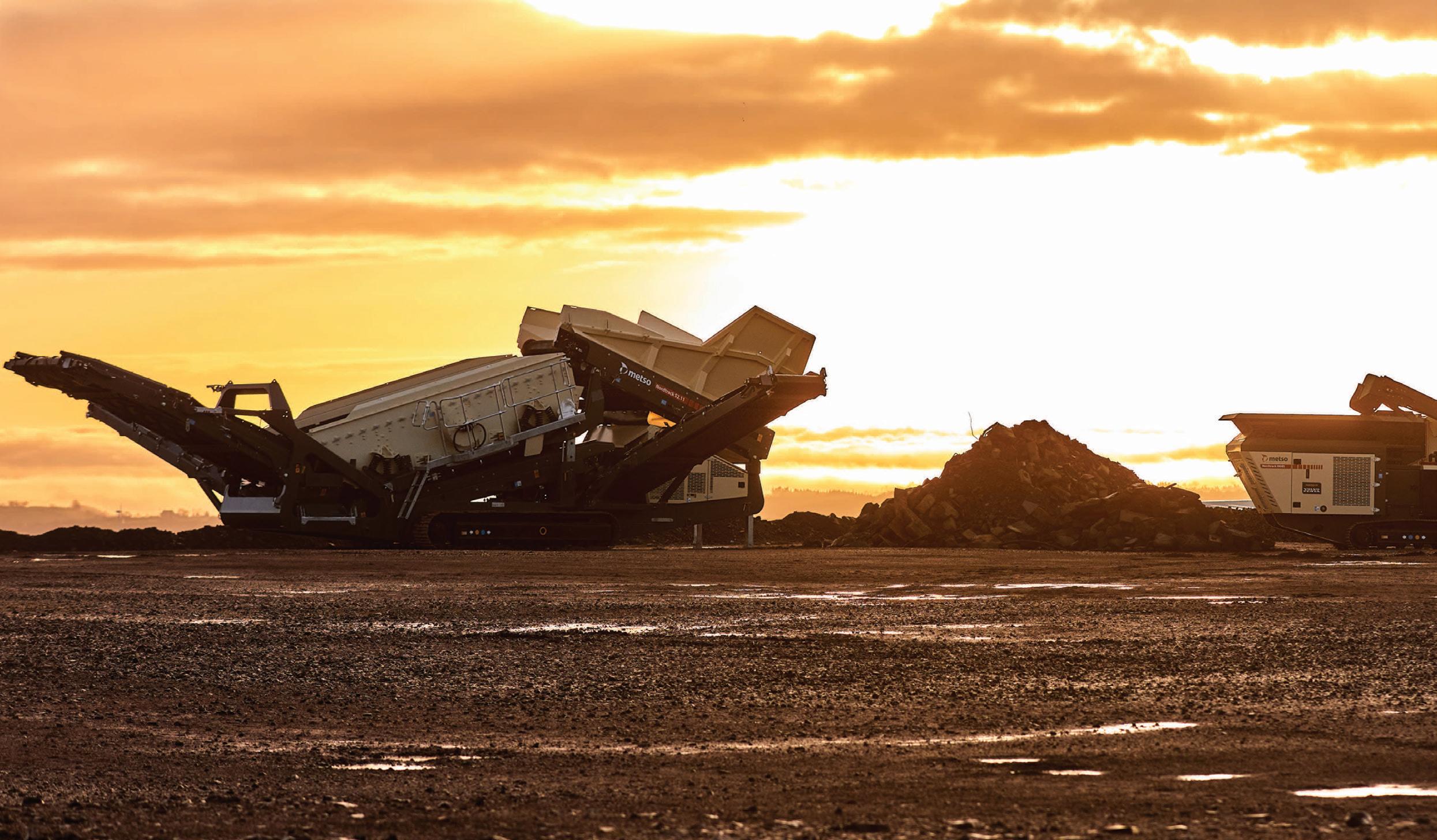
46 minute read
MOBILE SOLUTION FOR QUARRIES, CONTRACTORS OEM launches suite of mobile crushers and screens to the Australian market
from Quarry May 2020
by Prime Group
OF MOBILE SOLUTIONS FOR SMALL QUARRIES, CONTRACTORS OEM LAUNCHES PORTFOLIO
Multinational crushing and screening manufacturer Metso has been renowned for many years for its innovations in mobile crushing and screening solutions. Now, in conjunction with its local distributor, it is launching a new suite of mobile solutions to the Australian market.
Metso has expanded its mobile crushing and screening solutions offering with an extensive new portfolio of equipment. The new Metso Nordtrack range consists of 19 machines designed to meet the requirements of aggregates producers and contractors to the construction industry. With standard configurations and a global sales and support network, Nordtrack machines are suitable for contractors and quarries that need to meet tight project timelines and guarantee capacity quickly.
Metso’s Australian vice president of aggregates Shaun Fanning says the Nordtrack range has been purpose-designed for asphalt recycling, concrete demolition, aggregate production and for screening of organic materials such as topsoil. “While we have traditionally had a strong performance in hard rock applications, the Nordtrack range caters for a wider scope of work,” Fanning explained. “It is ideal for companies and contractors who need the right combination of productivity, availability and dependability at an affordable price point.”
The new range consists of 19 mobile units,
J127 mobile jaw crusher


I908S mobile HSI crusher
TECHNICAL SPECIFICATIONS - J127 MOBILE JAW CRUSHER VS I908S MOBILE HSI CRUSHER
Crushing unit J127 jaw crusher I908S HSI crusher Feed Opening 1270mm x 735mm 860mm x 650mm
Engine
Weight
Transport width Transport height
Transport length Included in basic configuration Tier 3 LRC: Cat C9 261kW Stage IIIB: Cat C9.3 CSE 275kW Tier 4F/Stage V: Cat C9.3B 261kW 56.5 tonnes
3000mm 3600mm
15,500mm Remote controller for the tracks, water spraying system with pump, aluminum dust cover on main conveyor, working lights, crusher deflector plate, side conveyor Volvo D8 188kW
27.5 tonnes
2600mm 3000mm
14,100mm Remote controller for tracks, water spraying system with pump, working lights, crusher automation

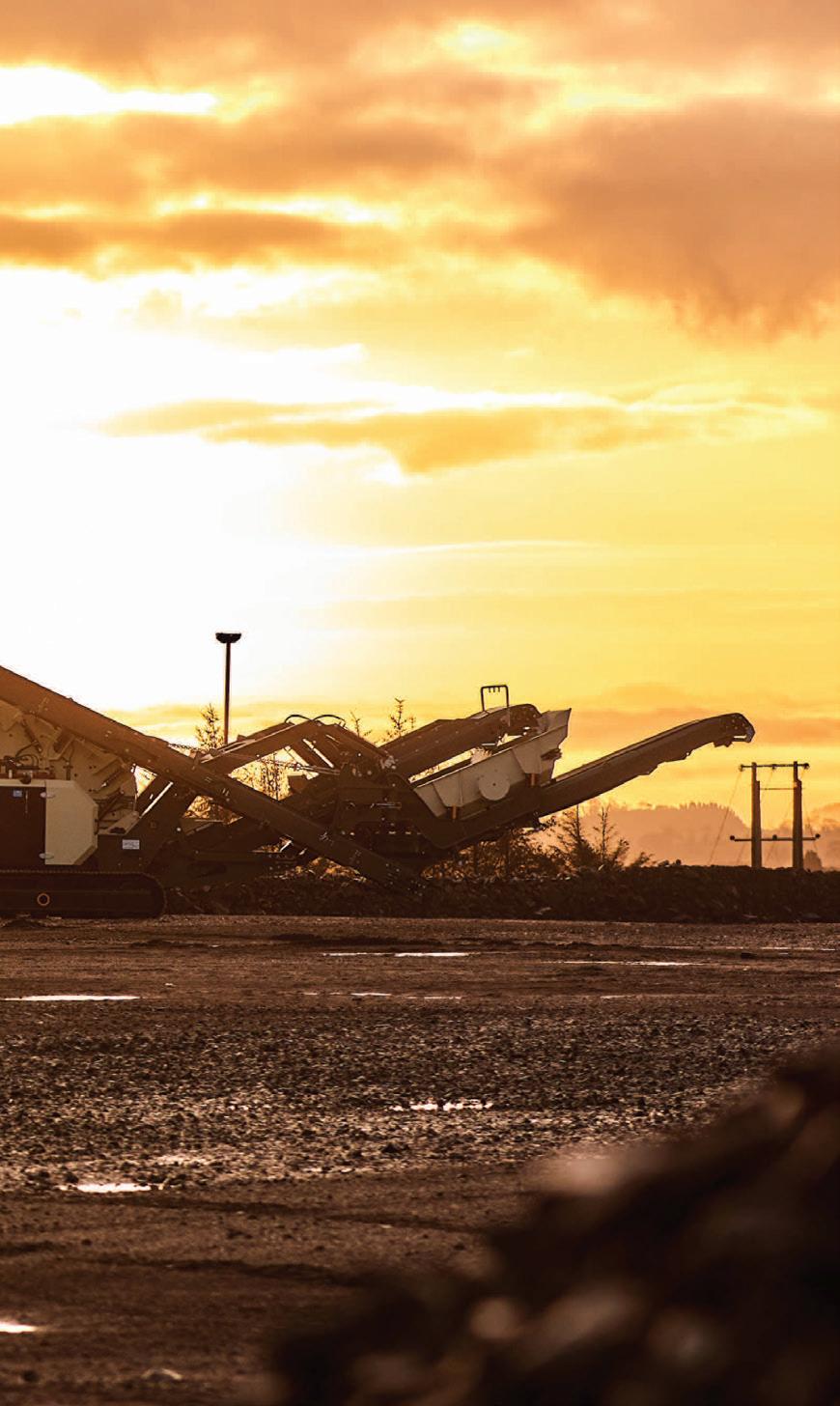
including jaw crushers, impact crushers, screens and conveyors. According to Fanning, Australian customers are fully supported by Metso’s Australian distributor Tutt Bryant Equipment, whose representatives are trained on the capabilities of each machine and have direct access to Metso’s global technical support network.
“It is vital that our customers are fully supported throughout their ownership journey. The team at Tutt Bryant are well equipped to support Nordtrack, backed by the knowledge and expertise of Metso’s global product and service design centres,” he said.
Business development manager for Tutt Bryant Equipment Paul Doran said Nordtrack adds new capabilities to Metso’s mobile equipment offering. “The new range fills a few product gaps and provides additional options for our customers,” he said. “This, along with their price point and simple operation will appeal to a large proportion of Aussie end users. We look forward to seeing these robustly constructed and reliable machines helping our customers both in Australia and offshore.”
Doran said some of the key additions include: • The J127 mobile jaw crusher, which is built to deliver high productivity after deployment in the field. The wide crusher feed opening and the two-stage feeder enable high throughput in both quarrying and recycling operations. • The I908S mobile horizontal shaft impact (HSI) crusher, which provides superior performance in a very compact size. Equipped with a HSI crushing unit, a hanging screen module with easy to use attachment system, and a 180-degree radial conveyor, the I908S is flexible enough for most types of jobs. • The S2.11 mobile scalping screen, which is designed to process large volumes of feed material with precision. It has the flexibility to screen a wide variety of feed materials in different recycling, demolition and aggregate applications. • The S4.12 mobile screen, which is equipped with three decks for effective high volume screening. The standard remote controller can be upgraded with additional functionality, enabling operators to control the feeder parameters at a safe distance from the machine.
The mobile Nordtrack range is now available to the Australian market through Tutt Bryant Equipment. •
Source: Metso
S2.11 mobile scalping screen

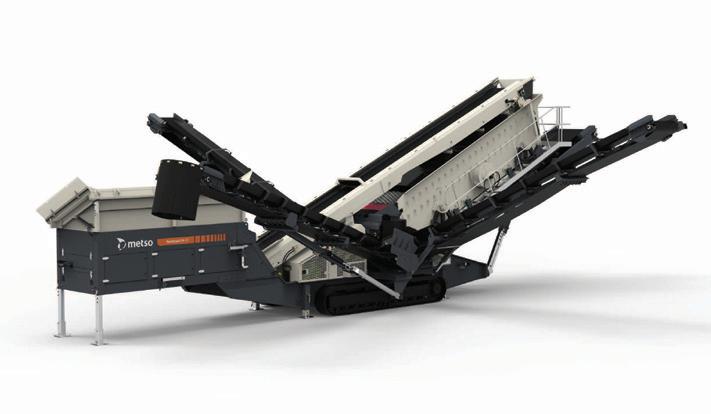
S4.12 mobile screen
TECHNICAL SPECIFICATIONS - S2.11 MOBILE SCALPING SCREEN VS S4.12 MOBILE SCREEN
Screening unit S2.11 scalper S4.12 screen Decks 2 3 Screen size 6100mm x 1800mm top deck, 5500mm x 1800mm bottom deck 6710mm x 1830mm top deck, 6710mm x 1830mm middle deck, 6100mm x 1830mm bottom deck Feed hopper 11.5m³ 10m³
Engine
Weight
Transport width Transport height Transport length Included in standard configuration
Options
Tier 3 LRC: Cat C7.1 165kW Stage IIIB: Cat C7.1 CSE 209kW Tier 4F/Stage V: Cat C7.1 165kW 37 tonnes
3000mm 3600mm 17,000mm
Remote controller for tracks, working lights
Apron feeder, two-way split, kit for side conveyors on same side, water spraying system with pump, extra remote controller for feeder functions, bi-power system to drive hydraulic circuit Tier 3 LRC: Cat C7.1 165kW Stage IIIB: Cat C7.1 CSE 209kW Tier 4F/Stage V: Cat C7.1 165kW 42.4 tonnes
3700mm 3600mm 19,600mm
Tipping grid, three-way platform, hydraulic lifting conveyor raising, hydraulic fines conveyor lowering, remote controller for tracks, working lights, hydraulic PTO Water spraying system with pump, extra remote controller for feeder functions, two-deck vibrating grid

Over the past four years, Komatsu New Zealand’s product support and technical teams have been working with customers and suppliers to ensure Komatsu wheel loaders achieve high accuracy and consistent results when fitted with third party load scales.
As a result of an ongoing program of research, testing and many hours of trials, Komatsu wheel loaders fitted with these third party scales are now consistently achieving levels of accuracy that are significantly better than other brands of loader.
Following this program, Komatsu loaders are consistently achieving 0.5 per cent accuracy or better.
Due to NZ regulations covering road trucks, sites that do not have a certified weighbridge should have their wheel loaders equipped with “legal for trade” load scales, which require annual calibration to maintain their certification. Generally they are required to achieve load accuracies of one per cent (or better in some cases).
The program was led by Komatsu NZ’s product support manager Brent Hepple, who had several requests to ensure Komatsu loaders could achieve exceptionally accurate readings with load scales. The concern was the company could lose sales in significant numbers to quarries and mineral processing operations if it wasn’t achievable.
“Inaccurate or inconsistent load scale results are particularly critical in operations where there is no weighbridge, so the weight of material in each bucket load must be spot on,” Hepple said. “If your operation is relying on a loader fitted with scales to ensure your trucks are not overloaded, then each bucket load weight is critical.
“We have customers who want their trucks loaded to exactly 30 tonnes to optimise their haulage operations. But if their trucks are even slightly overloaded, they’ll get a ticket.”
IQT High-strength BMRC brass material Type of bushing materials Comparison of resistance to seizure Surface pressure. MPa 100 90 80 70 60 50 40 30 20 10 0

A comparison of the resistance to seizure in bushing materials.
Another important customer sector reliant on highly accurate scale results is the lime industry.
“Lime blends have to have very precise mixes to meet their customer specifications,” Hepple explained. “If there’s too much of a lower quality mix, customers aren’t getting what they’ve paid for. If there’s too much of the premium product, the producers are losing money.”
Hepple, along with Ron Chilton, Komatsu NZ’s technical support representative for the South Island, spent a lot of time working with customers to try to solve these issues, and also to figure out why they seemed to be unique to Komatsu loaders, and didn’t as a rule happen with other brands.
Hepple and Chilton – whom Hepple credits as having done the bulk of the work with customers and suppliers – also worked closely with Loadrite and RDS, the two leading load scale suppliers in NZ.
As it turned out, there were two areas to focus on, and each interacted with the other to prevent Komatsu achieving the highly accurate, consistent results required.
“Fairly early on, we identified that friction in the loader bucket bushing was part of the issue,” Hepple said. “Over a number of years, we tried a number of different low friction bushings. They gave us some encouraging results, but they still weren’t giving us the accuracy we needed.
“Then we stumbled on something in a Komatsu excavator parts book that referred to a BMRC bush, which is a special sintered aluminium/copper bush fitted to some models of Komatsu excavators so they could raise greasing intervals to more than 500 hours. We tried some of these, and found the accuracy was significantly improved.
“Loader scales work on hydraulic pressure to calculate load weights, and the slightest increase in friction in the bushings meant more pressure in the hydraulic system, which in turn meant the scales gave an incorrect reading.”
Hepple and his team brought in some sets of BMRC bushes from Komatsu Japan, and trialled them on some loaders in a couple of operations. While these addressed some of the issues, the consistency required still wasn’t there, so Hepple and the team did some more research.
“We started looking at the Closed-Centre Load Sensing System or CLSS hydraulic system that’s been used on just about all Komatsu construction machines since the late 1990s,” Hepple said. “It’s pretty much unique to Komatsu, and something no other manufacturers use, certainly not on loaders. Most hydraulics on other earthmoving brands are open-centre systems.
“Our CLSS gives us significant advantages in precision and control. It’s faster, and more reliable and robust, plus it also contributes to Komatsu machines’ reputation for excellent fuel efficiency,” he added.
“So we started adjusting the loader hydraulic circuits on these loaders that we’d
fitted with the new bushes, using data logging to measure and calibrate the hydraulic systems’ wave pattern. These wave patterns are used by the load scales to calculate bucketload weights. We found we were able to adjust our Komatsu CLSS hydraulic systems to get the wave patterns in precisely the right spot.
“By doing this, we were able to get to accuracies of 0.5 per cent consistently with Komatsu loaders – which is even better than the scale manufacturers can guarantee,” Hepple said. “So the solution turned out to be the combination of these ultra-low friction bushes and the calibration of our hydraulic systems.
“As with all loaders fitted with load scales that are used for sales and truck loading work, our hydraulic systems do need regular calibration and checking to maintain accuracy,” he added. “But we are now finding as a result of our research that Komatsu machines as they get older actually get even more accurate in measuring bucket load weights, as things wear a bit and there’s a touch less friction.”
As a result of this program, all Komatsu loaders in the WA380 to WA480 size range sold in New Zealand and Australia are now fitted with BMRC ultra-low friction bushes as a standard fitment.
“We also think that Komatsu will be very well positioned into the future, as aftermarket load scales are getting more and more accurate, with increased levels of sensitivity,” Hepple said. “Now that we know exactly how to set up and calibrate our loaders to get the best possible results, we believe we have a significant advantage over other suppliers.”
Hepple also acknowledged the assistance provided by load scale suppliers Loadrite, which started in NZ and still carries out the bulk of its research and manufacturing in the country, and RDS.
“Loadrite has the larger market share in NZ, while I believe RDS is more prevalent in Australia,” he said. “We were having these issues with both brands, and both were
The BMRC special sintered aluminium/copper bush was previously fitted to some Komatsu excavators to raise greasing intervals to more than 500 hours.
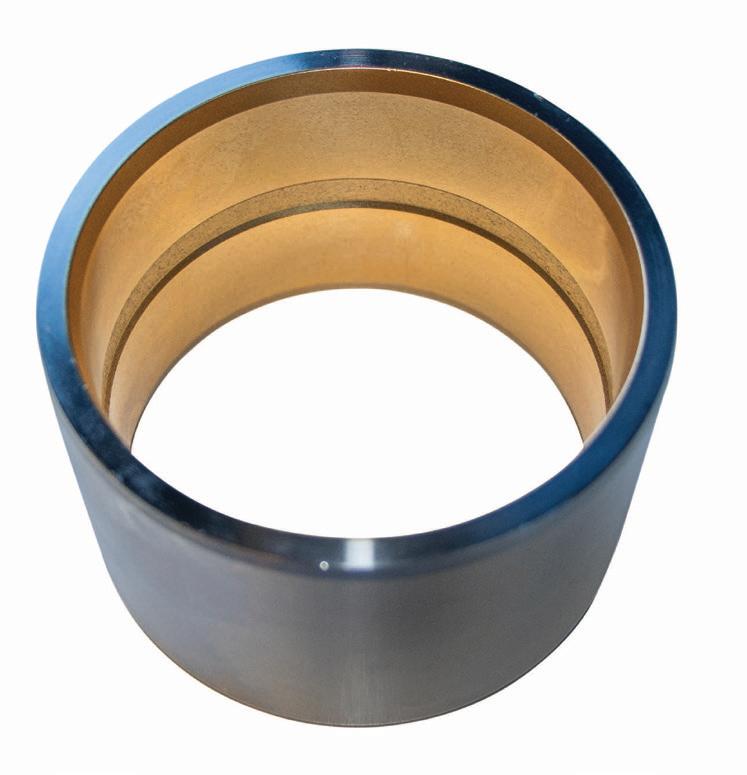
very helpful in assisting us to resolve them. Thanks to our Komatsu NZ team, along with engineering support from Komatsu Australia and Japan, plus the input from load scale suppliers and customers, we have solved this issue.
“We’ve had this solution since the start of 2019, and it’s proven itself in that time. We’re now highly confident in our ability to supply loaders that consistently deliver load scale accuracies that significantly exceed industry requirements.” •
Source: Komatsu Australia
PLANT . EQUIPMENT . PARTS . SERVICE & SUPPORT



ASTEC AUSTRALIA PAVING SOLUTIONS
EQUIPMENT TO BUILD AND RESTORE THE WORLD’S INFRASTRUCTURE
SENSOR TECHNOLOGY STEERS QUARRIES AWAY FROM COLLISION COURSE

With vehicle drivers needing to be constantly on the lookout on-site, ifm’s smart sensor technology is offering a higher level of visibility that allows them to be better aware of their surroundings. ifm’s latest generation of 3D smart sensors detects three-dimensional objects to provide a high level of awareness and collision avoidance. The O3M 3D smart sensor determines the distance between the sensor and nearest surface point through to the use of what the company refers to as the “time of flight (ToF) phase shift principle, an ifm patent”.
Syed Ahmad, ifm’s senior technical field support engineer for mobile control systems, told Quarry3D sensors provide quarry vehicles with a vital advantage over their one- or twodimensional counterparts.
“Other sensors which are available in the market are usually one-dimensional or twodimensional,” Ahmad said. “The unique quality of this sensor is that it gives you the information about the object in a 3D plane. That makes it unique because you can see the whole XYZ coordinates of a particular object within the region of interest or field of view.”
The O3M sensor provides distance monitoring with 64 regions of interest, removing the issue of vehicle blind spots. ifm tested the sensor in quarries before it was released to the industry, allowing the company to implement solutions to machines on both flat and inclined surfaces. One of the areas that testing examined was visibility in dust levels. Ahmad said ifm’s sensors found a way to tackle this.
“We implemented some of the techniques through integrating some additional sensors which can tell us whether the machine is on a flat surface or an inclined surface,” he said. “That enabled us to program the logic of what
ifm’s 3D smart sensor has the ability to detect objects in vehicle blind spots.
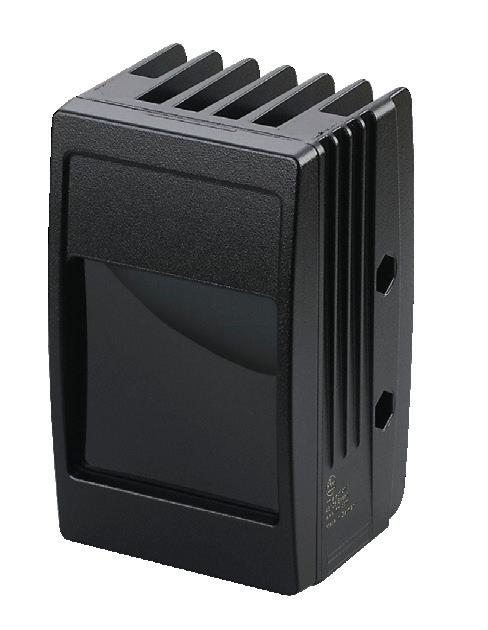

object or what obstacles to pick depending on what surface we’re on.” ifm’s sensors can detect reflective objects from up to 30 metres away by using technology that prevents sunlight from distorting the sensor. In dusty environments, such as a quarry, the O3M sensor can detect objects with reflective material, such as an operator’s high-vis vest by picking up on the amplitude of reflections in the environment. According to Ahmad, this provides another way for the sensor to detect objects through dust.
“Also, the sensor has a functionality which can tell you if the lens is dirty, so it gives you the information – say, for example, the lens is 70 per cent dirty now, so the operators can go and clean it,” Ahmad said.
With no moving components, the sensor is extremely robust compared to products such as laser sensors. The sensor is also backed by a five-year warranty for added peace of mind.
The O3M sensor also features a collision avoidance system that will activate an alarm if an object is too close or in a blind spot. “It basically triggers an audible alarm,” Ahmad said. “Of course, you can have a visual indication of what’s happening at the back while you are reversing and it can give you an output when there is an obstacle within the field of view, so it is enhanced safety for the machines,” Ahmad said. ifm’s O3M sensor also avoids motion blur that can occur with traditional line scanners. This is achieved by the sensor detecting objects three-dimensionally with the one camera – similar to augmented reality technology. With this technology, the 3D smart camera system produces customer-specific symbols, warning messages, text and drawings of complex geometric shapes in the environment.
Its active suppression of background illumination also allows it to work in direct sunlight. The sensor is also easy to set up with ifm’s user-friendly Vision Assistant software. The Vision Assistant software allows the user to check settings during operation and record the data from the sensor directly from a Windows computer.
According to Ahmad, the sensor eliminates the need for an extra worker to be a spotter on site. “Commonly used applications are on the front end load in a quarry,” he said. “We have got a couple of successful applications where the customers want to eliminate the possibility of having a spotter.”
With an innovative R&D team in Germany, ifm continue to push the boundaries of sensor technology through on-site testing and applications. •
MEASUREMENT TECH INTEGRAL TO OPTIMISING CRUSHING CIRCUIT
Crushers require a lot of energy to produce a finished product. In addition to the actual comminution, processes such as pre-washing, cleaning, sorting, etc must be considered. Thanks to Italian OEM Ma-estro’s systems, energy consumption per tonne of product can be significantly reduced.
The key to these energy savings lies in intelligent automation of the entire production chain and real time data management. Maestro’s systems virtually dismantle the entire crushing process, from the quarry to the end product, and assess many individual parameters in the respective processes from very different angles. On average, 15 per cent of the total energy consumption can be saved in this way.
It is not only energy costs that are the focus of optimisation. The real challenge for the operator of a quarry is to deliver an end product with uniform quality.
Quality and reproduction depends to a large extent on the load placed on the crushers. The harder the material, the greater the stress on crushers and mills. Wet material can also become a problem for conveyors, hydrocyclones and screens. Moreover, the properties of the raw materials, such as mass, density or hardness, can change. This places different demands on plant components.
Manual intervention in the process is usually difficult. The aim of continuous monitoring of the individual process steps is therefore to reduce the load on the respective machine components – depending on the current situation in the crusher. Ma-estro’s system automatically controls the entire process by connecting all the machines in the system. The sensors installed in the critical areas make it possible to constantly adjust the load in the system’s individual parts. For example, loading is controlled, material flow is adjusted or clogging scenarios are avoided. This protects the equipment, saves energy and also leads to higher product quality.
In Ma-estro’s world, sensor technology plays a major role. For about a year, measurement technology from Vega has been involved in the monitoring and optimisation of the crushers. A total of 50 instruments are being used for this, including the VEGASON 61, 62 and 63, the VEGAPULS 69 and the VEGABAR 82. Most of
Vega radar technology (top left) has been successfully employed to measure material in OEM Ma-estro’s crushers.

them are level sensors. Vega radar technology is being used to measure material in crushers and mills but it also warns of screen clogging and measures the level of water used for washing the material. Other examples are the Vega sensors located at the opening of the press to control the level in the machine, on the conveyor belts to measure the load and in the storage containers to measure the quantity of the end product.
Ma-estro had previously used sensors from other manufacturers for these tasks. However, these had to be integrated at great expense into the existing automation systems. Dust, residual material and moisture cause a lot of interfering reflections. It was a set of circumstances that caused considerable problems for the previously used sensors and led to inaccurate measurement.
Up to the time of the devices’ implementation, Ma-estro knew very about Vega or its products. Nevertheless, sensors were installed for testing and from the very beginning of the project Ma-estro became convinced of the technology. The sensors have since found their permanent place in the crushing systems. The measurement engineering team was especially impressed by the simple configuration of the instruments. Thanks to the plics concept – ie the standardised user interface independent of measuring principle – the Ma-estro team didn’t have to re-familiarise themselves with the different sensor types over and over again.
The VEGAPULS 69 in particular delivered extremely reliable and accurate measured values – an important prerequisite for starting an optimisation of the crushing process. The level sensor operates with 80 GHz and has an antenna diameter of about 75mm. The 80 GHz beam thus bypasses anything that could otherwise get in the way, such as internal fixtures or build-up on the vessel wall. Furthermore, it easily penetrates even dense clouds of dust. This makes measurement more reliable, especially in the harsh environments found around crushers.
There was yet another feature that greatly delighted the Italian company – the option to use wireless communication via Bluetooth. This is particularly useful for hard to reach areas, harsh industrial environments and ex-hazardous zones. Vega sensors can be configured and parameterised from a safe distance with a smartphone or tablet. Fast and easy to use displays and diagnostic functions are also available. Vega technology thus fits perfectly into Ma-estro’s optimisation environment. •

RIGHT ON OUR DOORSTEP TOUGHNESS MEETS WORKABILITY –
Australia’s only manufacturer of high tensile and abrasion-resistant quenched and tempered steel plate says it owes its success to the benefits of local knowledge, imbued with a successful combination of resilience and formability.
With its heritage firmly grounded in the mining and manufacturing sectors, Bisalloy Steel provides its highly sought after products to a range of markets, including defence, energy, mineral processing, structural engineering, and transport.
Given the battering that plant and equipment takes at the hands of earth, rocks and so forth, wear resistance is a key measure when comparing the quality of steel plate products in this sector.
Due to their excellent wear resistant properties, Bisalloy Wear grades have been used to make dump truck bodies, mining and earthmoving buckets, tipper bodies, and liner plates for chutes and hoppers.
In addition to wear resistance, other factors like weldability and formability are also important when comparing wear grade steel plate. The wear resistance of steel is primarily determined by the amount of carbon and alloys it contains.
High carbon and alloy contents can enhance wear resistance but at the same time the carbon equivalent of the steel will increase.
As it requires a high pre-heating temperature during thermal cutting and welding, steel with a high carbon equivalent also tends to be difficult to work with. Therefore, in the absence of the right R&D efforts, wear resistance comes at the cost of less workability.
The important thing to note here is this trade-off – between wear resistance and workability – is not necessarily directly proportionate. Through careful development, it is possible to manufacture products that achieve both characteristics. This is precisely what Bisalloy has done.
Through its exacting research and testing efforts, the company has struck the right balance between durability and workability and is able to deliver the extractive industry with the wear grade steel plate products it needs.
Within the extractive sector, the company’s Bisalloy Wear steel plates have found use in a broad range of products including demolition and ground engaging tools, earthmoving buckets, dragline buckets, wear plates, chutes, dump truck bodies, storage bins and hoppers.
Bisalloy Wear steel plates are specifically designed, hot-rolled and heat-treated to handle these demanding applications. The four core products in the range have been developed to maximise properties such as wear resistance, while also meeting the challenging workability and weldability requirements demanded by miners.
Bisalloy Wear 400 steel has proven itself to be a highly versatile, through hardened, abrasion-resistant steel plate with the ability to withstand high impact and medium level abrasion applications.
Bisalloy Wear 450 – the “all rounder” of the range – offers the optimum combination of hardness, impact resistance and formability for wear applications. Combining well balanced toughness with excellent formability and weldability, Wear 450 is suitable for heavy industrial tasks like dragline excavation and is also commonly used to manufacture dump truck bodies.
One of Bisalloy Steels’ first ever products – Bisalloy Wear 500 – has been continually manufactured in Australia for more than 35 years. Through a very high hardness and abrasion-resistant steel plate, it is readily weldable and formable, and therefore suitable for use in a range of applications.
At the other end of the scale, in terms of its introduction to the market, the final product in the range – Bisalloy Wear 600 – was developed just seven years ago. With a nominal Brinell hardness of 600 HBW, it is extremely wear-resistant and recommended for liners in chutes and hoppers that need to carry high hardness rocks and minerals.
The success of these products has been made possible by Bisalloy’s close collaboration with leaders in science, technology and steel manufacture on intensive research programs, and it involves knowledge of – and experience in – Australian industry.
By forming partnerships with local businesses, Bisalloy can develop a deep understanding of their needs and customise value-added products and services to ensure their success.
The demands of high strength and high hardness steels and their subsequently stringent process routes have made it possible for Bisalloy to compete successfully in this highly specialised market. Further, as the company is local, and has all its resources in Australia, it can offer levels of development support that overseas competitors cannot easily match.
Bisalloy’s collaborative approach and proximity to its Australian clients puts it in a solid position to handle engineering problems as they arise. Combined with an understanding of local conditions and Australian business culture, this is a benefit that overseas competitors cannot replicate.
There is no substitute for resources on the ground, being on-hand (or at least close by) to deal with problems as they arise, and the creativity that well functioning business relationships engender.
Over the years Bisalloy’s proximity, along with its demonstrated commitment to the Australian extractive sector, has made it possible for the company to achieve important incremental product improvements and meet its customers’ performance requirements. •
BOOM SYSTEM OFFERS MORE PRODUCTIVITY
If your quarrying business is seeking a pedestal boom system – for a new crushing plant installation or replacing an older boom system – it is important to consider: • Rock hardness and size, the expected duty cycle (number of rocks per hour) and physical size of chute or crusher. • The type of applications, eg fixed crushing installation, grizzly or mobile crushing. • If it meets horizontal and vertical reach and breaker size requirements. • Control systems, such as advanced safety processors, remote operation options and readiness to spare parts access.
Montabert’s boom systems, developed in conjunction with global pedestal boom manufacturer Tramac, consist of robust designs that include a low profile base incorporating a shaped plate steel that provides a strong foundation to fit any platform mounting requirement. Heavy-duty cylinders with high strength steel, welded construction and aligned bushing ensure a long product life.
For safe operating practices, technology is essential in pedestal boom systems and is achieved through utilisation of line of site remote control, collision avoidance systems, automation, and teleremote operation.
Montabert has long been involved in breaker innovation, including its patented variable speed technology. This knowhow, along with the breaker’s lower input power requirement and energy recovery and regulation system, results in better percussion efficiency and greater hydraulic effectiveness. Overall, higher output power results in greater productivity in fractured and semi-fractured rock. •
Source: Komatsu Mining/Joy Global

Modern technology is essential in pedestal boom systems to enable safe operating practices.
ALLMINERAL New Machines, Parts & Services MARIO AMARANTI m.amaranti@allmineral.com.au +61 448051682





HAZEMAG New Machines TEDDY CRAIES teddy.craies@hazemag.de +61 448893402
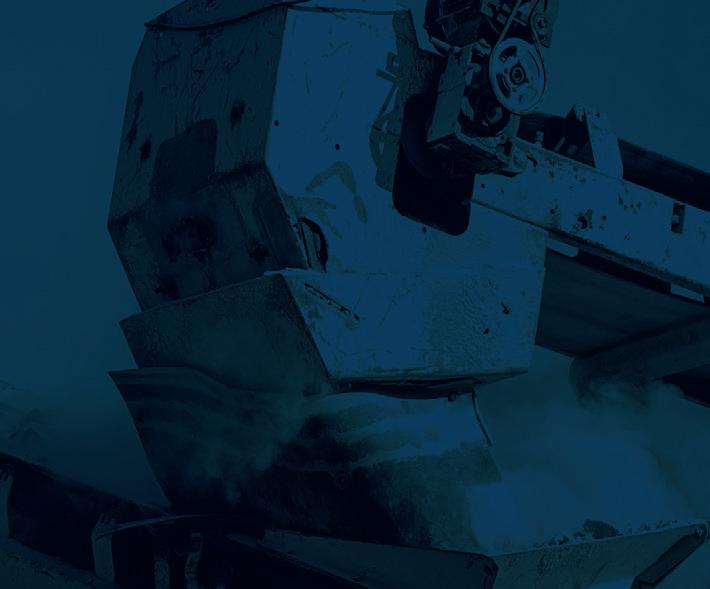
HAZEMAG Parts & Services JUSTIN FAITHFULL Justin.faithfull@hazemag.de +61 429537243
HAZEMAG & ALLMINERAL HAVE COMBINED THEIR OPERATIONS IN AUSTRALIA AND ESTABLISHED “HAZEMAG ALLMINERAL AUSTRALIA PTY LTD”
allmineral is a world-renowned specialist in the preparation of gravel, sand, coal and ore with their OEM product and services “allair®, allflux®, allgauss®, alljig® and allflot®” with several installations in Australia. Highest quality, longevity of the products, service, consulting, customer service and the satisfaction of the customers is the top priority for allmineral.
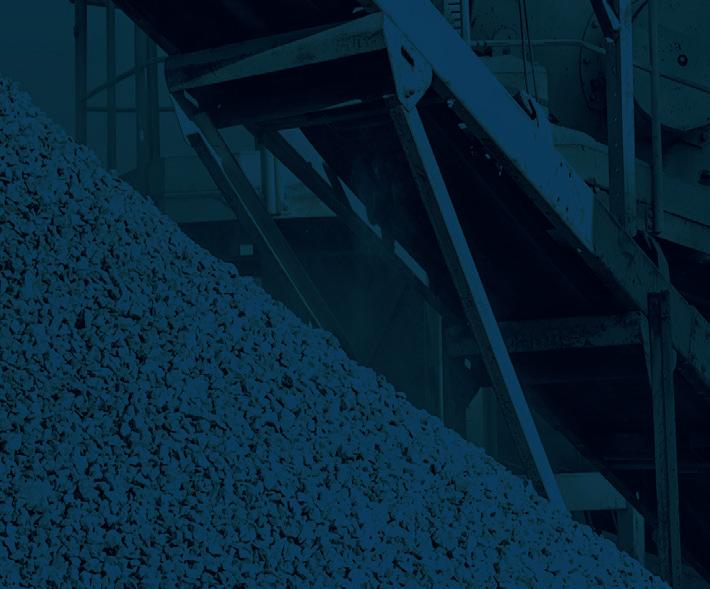




HAZEMAG is a global Minerals Processing leader with trusted technology and services spanning over 175 years with broad beneficiation experience in Engineering and Equipment Optimization across the entire processing chain with durability, capacity and efficiency in our products and services offering OEM products as such as “Impact Crusher, Sizers, Roller Crushers, Hammer Mills, Roller Screens, Apron Feeders, Feeder Breakers, Chain Feeders and Mobile Plants.
Engineered and manufactured in Germany, with machine installations in Australia operating for over 50 years in the quarry, mineral and recycling industries.
CORONAVIRUS PROTECTION: TIPS FOR AGGREGATES PRODUCERS
Coronavirus has undoubtedly taken industries globally by surprise. However, as Kevin Garcia explains, well prepared teams in the aggregates industry, equipped with the right tools and precautions, can still succeed in this challenging, health-conscious environment.
Aggregate producers and contractors are facing unprecedented challenges, as is every other industry to a greater or lesser degree. But how we deal with adversity and find workable solutions will dictate a positive outcome in the future. Whereas we may have looked to the flexibility of our teams to help us through, we now have a range of new workflows enabled by technology to help us cope. Now is a great time to learn more about the options available and talk with technology partners about your unique challenges, your goals and how technology can work for you.
Managers can help restore calm, mitigate spread and equip staff with tools to look after themselves and others. After any immediate isolation or quarantine strategies, how can smart aggregates operations protect staff and customers, and reduce costs from their operations to weather the pandemic?
TAKE A BREATH
Every day, the news media confronts us with updates of the spread. It can seem overwhelming for managers and teams alike. Take a breath, pause and think through your response. As more time passes, we can understand the situation better, and a better understanding leads to more predictable outcomes.
Wait to make decisions on reducing your workforce. It was tough to find skilled operators before, and you often can’t just hire someone with no experience, especially if you expect a rebound. Before taking drastic measures of reducing staff, consider how to cut costs caused by waste and improve efficiency.
TAKE PREVENTATIVE MEASURES
Embed good hygiene practices into your toolbox talks and walk-around inspections. The toolbox talk is a good time to discuss health and safety with your crew, including reminder advice to practise good hygiene, including
Using third party on-board scales on your mobile plant and equipment can collect productivity data that can be easily shared with teams for better decision-making.

frequent hand washing, covering your mouth with an arm during coughs and avoiding touching your face.
Regular maintenance of the machine is well understood, so leverage the walkaround inspection as a time to also disinfect the cab, especially when multiple operators share a machine.
LISTEN TO FEARS, CONCERNS
There is plenty of misinformation and confusion about the pandemic, so listen carefully to concerns to help identify staff anxiety. Laying out a strategy for how your team will respond to the pandemic is a good start but proving to your team you are supporting them with new tools is even better.
BE FLEXIBLE
Emergency protocols within affected communities, such as government-mandated containment areas and mandatory sheltering in place, could trigger a variety of challenges. When public transportation shuts down or schools close, many employees find it difficult or impossible to show up for work. An employer who can maintain a flexible approach to production is more likely to retain staff. Consider how production targets are more important than hours at work. Can your operation use technology tools to allow operators to move between machines and still be productive?
Even your customers may ask for more flexibility in materials delivery. This may mean increasing your stockpiles to be ready for changes in demand. Make sure you equip your sales team with an accurate understanding of your product on the ground with real time stockpile management. Measurement tools like Loadrite loader scales and belt scales, for example, give you real time information about the amount of materials going into or taken out of the stockpile, and loader scales can also help ensure that every truck is loaded correctly.
ISOLATION AT SITE
“Like many countries, Australia has been tasked with the difficult prospect of keeping core industry running, stipulating that quarries serve as a critical part of the construction industry,” said Dan Berry, the general manager of Loadrite dealership SmartTech Australia,
which has offices across the country.
For sites where operators are working but exercising safe social distancing, technology can reduce the need for customer truck drivers to engage directly with loader operators, as job information can be transmitted directly from the scale house to the loader operator’s in-cab screen.
REDUCED PAPER HANDLING
Many operators will be isolated by the cab, and beyond regular cleaning of surfaces, technology can help to isolate them further. Electronic ticketing technology, for example, can email the loading ticket to the truck driver’s mobile phone or the office, just as a paper ticket does. By replacing the physical handover of a loading ticket, it reduces the need for proximity of any objects that may have the virus.
New load and haul monitoring systems have also replaced haul truck tally sheets. In fact, some newer systems require no haul truck operator interaction to track cycles, with remote reporting for anyone off-site.
“We have been working with key industry leaders to help drive change in the move to paperless docket solutions on jobsites and within the subcontractor ecosystems,” Berry said. “We feel this pandemic will be the catalyst for driving e-docket solutions into acknowledged market best practice to help prevent increased site risks of transmission via the removal of paper-based document hand-off hundreds of times per day to multiple sites.”
KEEPING SKELETON CREWS SAFE
Loading trucks, feeding hoppers, moving stockpiles and the co-ordination and supervision of these tasks need to be done on-site. Some technology solutions not only monitor production but also track staff and machine movement. Through mobile smart devices, the on-site team leader can tell the team is working and safe.
STAYING IN TOUCH FROM HOME
Many employers have asked staff who are able to work from home to stay away for the time being but that doesn’t mean they can’t keep track of that shift’s production. The new Trimble Insight, for example, is a real time, mobile-friendly dashboard of each machine as it feeds the processing plant, during crushing, and as material is loaded onto customer trucks. The dashboard keeps track of start time, delays and each machine’s productivity.
Just because staff have been asked to work at home doesn’t mean they can’t keep track of a shift’s production.
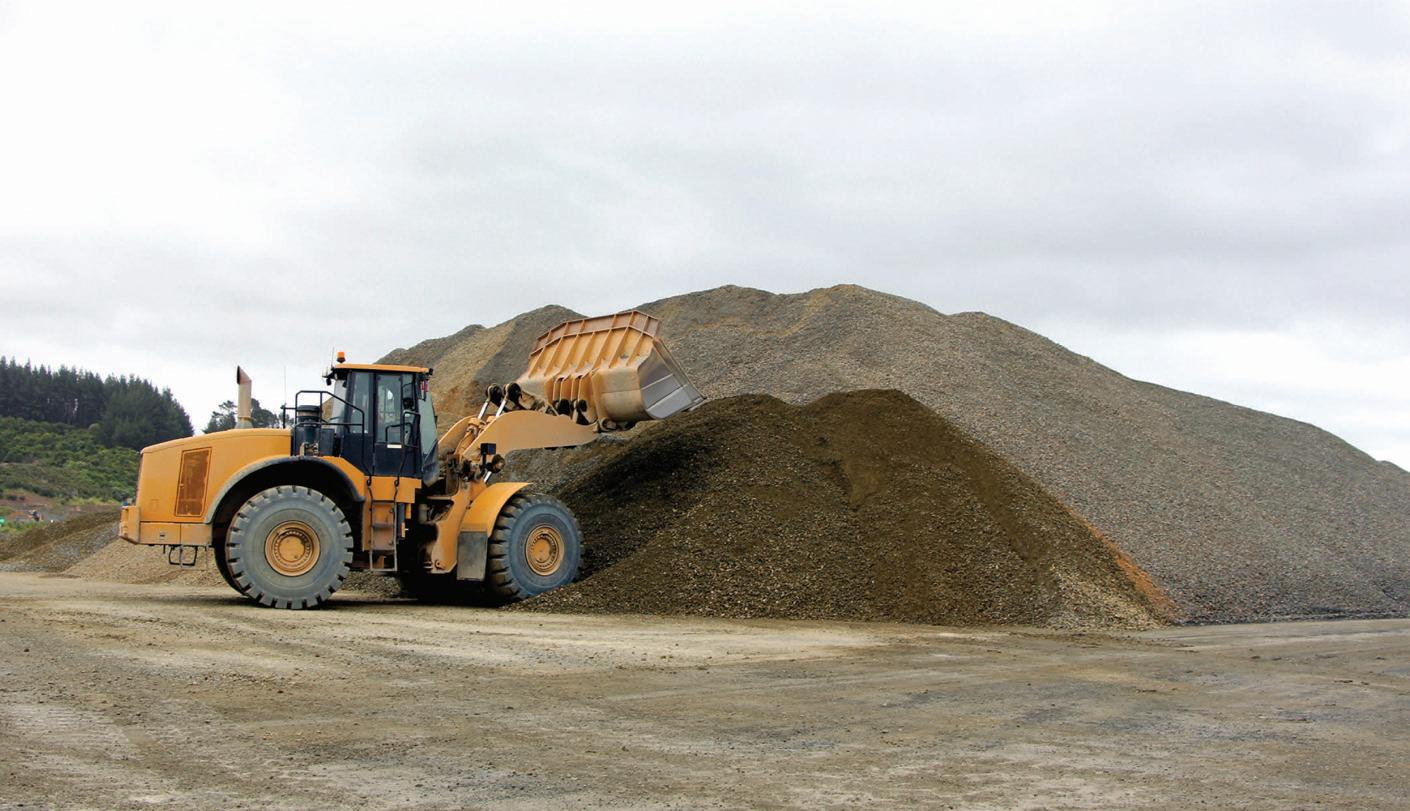
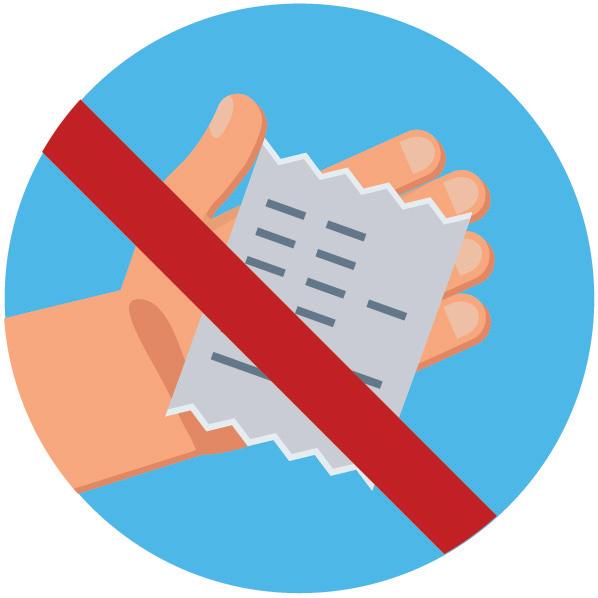

Electronic ticketing technology can now be sent to a truck driver’s mobile phone or the office, replacing a physical paper ticket.
The toolbox talk is a good time to remind workers to practise good hygiene.
REDUCE WASTE
It seems likely that the construction sector will contract in the near-term future, so look for process improvement opportunities to reduce costs. Are there any pinch points or delays that can be solved?
GET MORE FROM YOUR MACHINE ASSETS
In 2019, the lead times for mobile machines extended out by months and forced operators to look at a mixed fleet with different makes and models. However, this can make it difficult to collect all your production data in a single place. Using third party on-board scales on your loaders, excavators, haul trucks and conveyors collects productivity data that can be easily shared with teams for better decision-making.
A LONG GAME
The Australian economy may go into a recession, but generally construction activity lags the overall economy.
This means that many contractors can expect more difficult circumstances next year.
By playing a long game, managers can endure the short-term and be ready for what 2021 will bring.
Producers that are sufficiently prepared can prosper even during difficult economic times. •
Kevin Garcia is the general manager of civil specialty solutions for Trimble’s Civil Engineering and Construction Division, which includes Trimble’s solutions for the aggregates industry.
WHAT DO YOU DO WHEN THE WORLD COMES TO A GRINDING HALT?
In just a matter of months, the world has been literally transformed – thanks to a biological disruptor that has virtually brought whole industries and societies to a crawl at exactly the same time. John McGuire contemplates what businesses will need to do to right their course in these unsettling times – and to prepare for a future beyond COVID-19.
Four years ago, I started a blog – called Just Imagine 1 – with a single goal: to give people inspiration to think differently about the future.
Since that time, people have written about an amazing array of topics covering leadership, diversity, disruption and sustainability, to name but a few. Each time, the content, topic and position has been rather controversial and future-orientated – both provocateur and challenging the status quo to shake things up and make people look twice.
Yet four years ago – or even four weeks ago – no one could ever have seriously contemplated the scenario we are seeing right now unfold before our eyes. I wouldn’t have been taken seriously had I written a blog that started with “Just imagine the world coming to a grinding halt for six months”!
But here we are!
So, what do we do when the almost implausible becomes the new reality? What do you do when a disruptor – in this case biological rather than digital – rewrites the business plan for almost every organisation on the planet?
DEFENDING YOUR HORIZONS
True disruptors are rarely your current competitors. They come from below or places you are not expecting. Mehrdad Baghai, co-author of The Alchemy of Growth 2 , recommended that organisations need to work across three horizons simultaneously in order to achieve sustainable growth and defend against disruption.
Horizon 1 was your current business as usual. Horizon 2 was new products and services, and Horizon 3 was the space for experimenting and seeding options for the future. This strategy has received much recognition in the business world. However, most organisations fail to implement it effectively. Most companies are too busy in
Pieter Bruegel’s The Triumph of Death (1562) portrayed the social upheaval after plague in medieval Europe. Human labour became a premium, giving rise to today’s work style.

Horizon 1 (H1) to dedicate the necessary time and effort to Horizons 2 and 3 (H2 and H3). What this does is leave organisations vulnerable to disruption and, for many, this is where we are seeing them now.
What COVID-19 has unwittingly done is reduced the H1 revenue stream of many businesses around the world, in a matter of weeks, in some cases, to zero. It is proving to be the ultimate disruptor. New business models will need to be written and quickly. The imperative of finding new sources of revenue from your current underutilised assets will come to the fore.
Businesses have a choice now. The natural reaction – either in busy times or times of crisis – is to focus on H1 only and ignore H2 and H3. Yet history shows that life changes significantly after a major event. Do you hunker down, and hope that when things are over, you’ll still be able to put up an “open for business” sign? The trap in this thinking is that your customers’ behaviours are likely to have changed. They might not want your products or services in the way you had previously delivered them.
RISK OF BEING RISK AVERSE
The obvious reaction for many will be anxiety and, what follows from that, fear. In the face of these emotions, we inherently seek security and safety. We become risk averse.
When we become risk averse we don’t try new things and don’t experiment. If this occurs at an organisational level, and many organisations become risk averse, then we quickly end up all looking the same. This is a world of lack of differentiation and a sure path to commoditisation.
Success after COVID-19 will require a
new way of thinking about your assets and customers and it will need a design mindset. Your innovation will need to be the sharpest it has ever been to make it through to the other side and grow stronger as a result.
Understanding how customer behaviours are going to change will be crucial for future success.
How can you innovate and use assets differently? For example, hotels are now being used as isolation spots. What IT infrastructure do you have that could be used to augment the National Broadband Network? What pain points are your customers experiencing right now from social isolation and what insight can you gain to design a better product/service? I’ve seen nimble gym owners pivot and rent out their equipment – perhaps this model will be continued even when they reopen.
Almost every industry will be impacted as this is disruption on a scale we’ve never seen before. Previously disruption was thought about on an industry by industry basis, but we haven’t considered the same disruptor disrupting everything at the exact same time.
WHAT’S THE ALTERNATIVE?
Over the months ahead, we are all likely to get a crash course in the very foundations of economic theory. We will need to think deeply about how customer behaviour will change in the way they consume our products and services.
By now, I’m sure you’ve seen the memes circulating about how Shakespeare wrote King Lear and Isaac Newton invented calculus during quarantine for the plague. The Great Plague has been christened as giving birth to modern society 3 , resulting in the creation of hospitals, guns and
Interconnected human ingenuity is the key to overcoming not just the epidemiological but the sociological, industrial and technological challenges of COVID-19.

modern homes. As labour became more precious, tools that made work easier were invented. Clocks and hourglasses came into existence to track the time people spent working, and the first eyeglasses were introduced to increase productivity.
Boston smallpox resulted in the first independent newspaper in the US. The SARS epidemic in China is largely credited with the penetration of e-commerce in China, and it is expected a post-COVID China will be a cashless society.
For the next few months, Just Imagine will focus on thinking differently about assets, customers, human behaviour and business models, giving oxygen to the innovations and inventions that could potentially emerge from COVID-19. We will use our imagination to think of the world after coronavirus, and what this could mean for businesses and infrastructure.

And perhaps when we “just imagine” alternative possibilities in the future, they might not be such a far stretch from our actual reality. •
John McGuire is the global chief design officer at Aurecon.
REFERENCES & FURTHER READING: 1. Aurecon launches Just Imagine – a future focused blog. https://www.aurecongroup. com/about/latest-news/2016/march/aureconlaunches-just-imagine-future-focused-blog 2. Baghai M, Coley S, White D. The alchemy of growth: Practical insights for building the enduring enterprise. Basic Books, 2000. ISBN10: 0738203092; ISBN-13: 978-0738203096. 3. Mehta K. Why coronavirus will stimulate innovation. Forbes, 9 March, 2020. https:// www.forbes.com/sites/kmehta/2020/03/09/ why-coronavirus-will-stimulateinnovation/#4a4e75b82283
IQA NEWS
The Institute of Quarrying Australia
TRAINING, SUPPORT MATERIAL FOR MEMBERS, QUARRIES IN COVID-19 RESTRICTION PERIOD
The impacts of COVID-19 have meant people right across our industry and our communities have had to make many adjustments and difficult decisions, including realigning how our teams work and realignment of our businesses. I want to thank our branches, committees, sponsors, administrators and staff for their co-operation and hard work to help the industry and the IQA adjust.
It is vital that the quarrying industry can continue operations during COVID-19 restrictions. This is only possible if the industry continues to provide a safe environment for its workers and stakeholders by implementing the correct safety practices pertaining to COVID-19. The IQA will continue to release training and support material to help the industry during this time.
A detailed COVID-19 Health and Safety Management Plan Assessment Tool has been developed. The tool can be used to guide on-site assessment and will support the requirements in various states for COVID-19 management plans.
The IQA has also developed and now released a suite of resources to educate the industry about respirable crystalline silica (RCS). This includes a workshop that will cover, in depth, the recent changes to the Work Exposure Standard (WES) for RCS from 0.1mg/m 3 to 0.05mg/m 3 . The workshop will specifically focus on topics such as health effects, the WES and the adjustment for longer shifts, risk assessment, controls, reporting, communication and training, and principal health hazard plans.
Post-COVID-19 restrictions, face to face workshops will be scheduled accordingly. Until then, a three-phase release is occurring – fact sheets, webinars and workshops to educate on RCS best practice guidelines, product exposure, and employee health and safety.
Fact sheets and advice about RCS and COVID-19 can be found under the “Education” tab at quarry.com.au
During the COVID-19 restrictions the IQA has been engaged in its strategic planning process. In a time that has required unprecedented actions, this process has provided a refreshing opportunity to look towards the future. As we look at our industry and its contribution to the economy, employment, innovation and the community we can be encouraged
FROM THE CEO
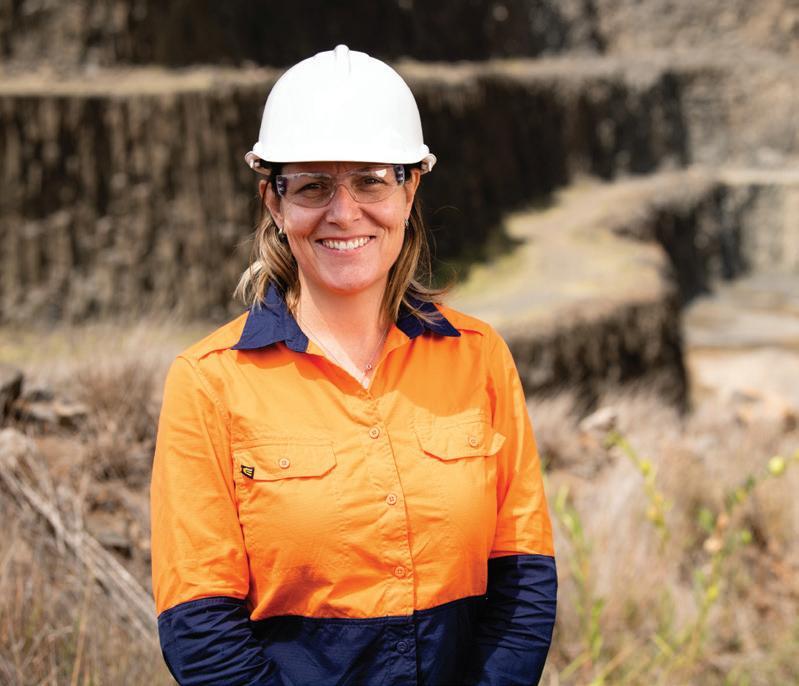
by the opportunity that is ahead.
The IQA is continuing to develop education content to ensure members have access to information via the website and online. We have successfully moved content online and managed a range of activities virtually.
Please visit the IQA website – quarry.com.au – for new courses and what’s available. We are busy planning the year ahead and are always seeking input on what is needed.
If you have any training needs, please email education@quarry.com.au
KYLIE FAHEY CEO Institute of Quarrying Australia
FREE RESOURCES TO SUPPORT MEMBERS DURING COVID-19
We are living in a time like no other. The impacts of COVID-19 have meant people right across our industry and our communities have had to make many adjustments and difficult decisions, including re-aligning how our teams work and realignment of our businesses. It is vital that the quarrying industry continues to operate during COVID-19 restrictions. This is only possible if the industry continues to provide a safe environment for workers and stakeholders by implementing the correct safety practices pertaining to COVID-19.
The IQA will continue to release training and support material to help the industry during this time. A detailed COVID-19 Health and Safety Management Plan Assessment Tool has been developed and can be used to guide on-site assessment to support the requirements in various states for COVID-19 management plans.
Here’s what else we’ve been working on!
We have created a range of resources to help you operate effectively, efficiently and with compliance. We want you to view, print and distribute these Fact Sheets to promote best practice in your workplace.
COVID-19 FACT SHEETS • COVID-19 Stimulus Package for Business
Owners Fact Sheet • How to clean your heavy vehicle cabin to reduce the spread of COVID-19 • Workplace Safety Compliance COVID-19 • Video Conferencing Fact Sheet • Working From Home Fact Sheet
RCS FACT SHEETS
• RCS Cabin Integrity Fact Sheet • RCS Hygiene and Housekeeping Fact Sheet • RCS Protective Equipment Fact Sheet • RCS Silicosis Fact Sheet • RCS - What is it? Fact Sheet
GENERAL FACT SHEETS • Anxiety Management Strategies Fact Sheet
We are excited to deliver industry-leading and innovative online content in the coming weeks – keep an eye on the IQA website – quarry.com.au – for more details. The IQA staff remain contactable via phone and email (see contact details on page 6).
14-16 APRIL 2021 MELBOURNE
AWARDS

NOW OPEN BULKHANDLINGAWARDS.COM.AU

MHD Supply Chain Solutions
PROUDLY SPONSORED BY

GEOLOGY TALK
VISITING PARLIAMENT’S OLDEST MEMBER
Members of the public viewed the Capital Hill unconformity in a rare tour on 14 and 15 March this year. Image courtesy of www.australias.guide
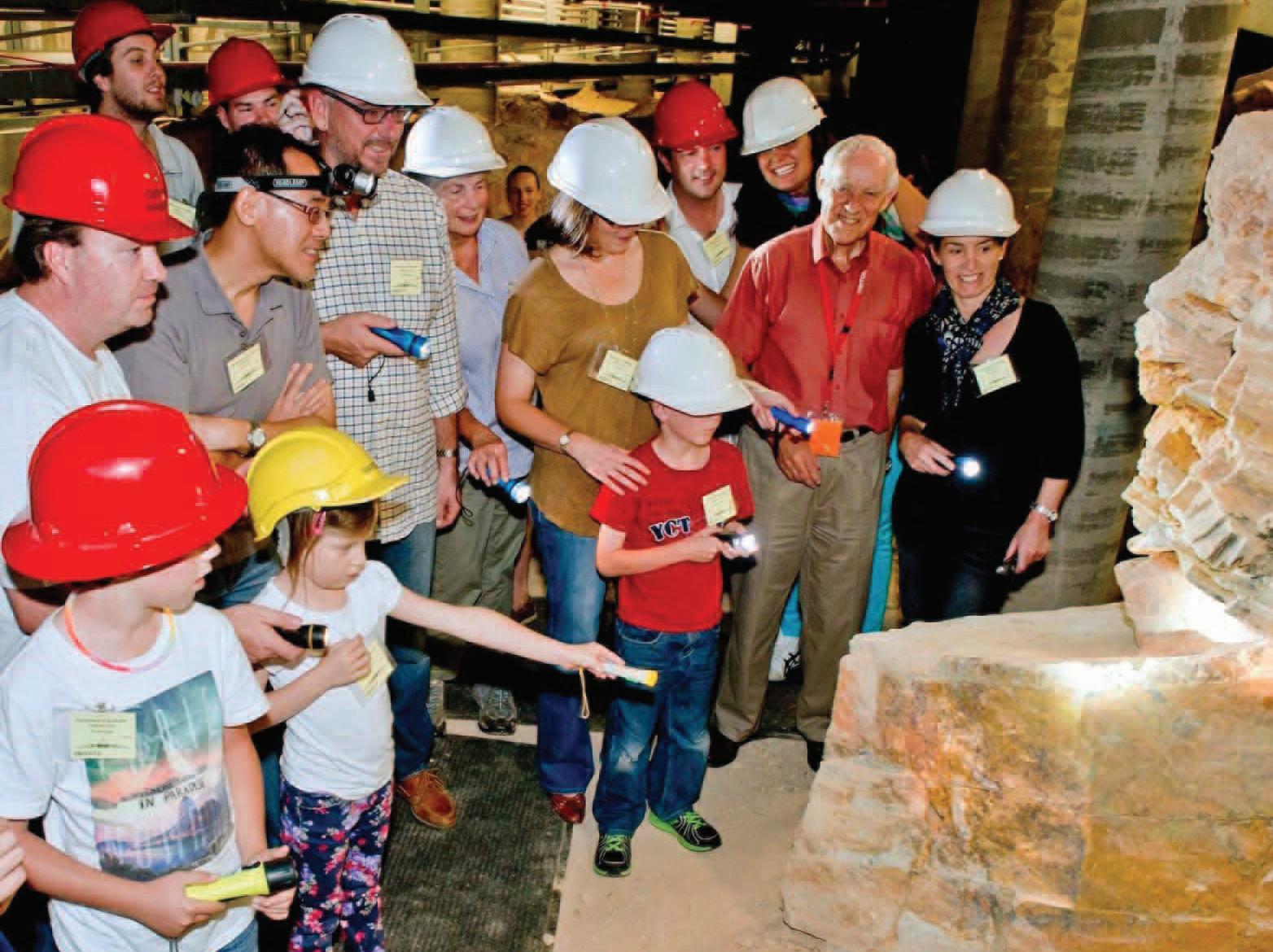
Parliament House is one of Canberra’s most renowned landmarks but it is far from its oldest. A 430 million-year-old rock formation dwelling in the basement provides a glimpse into Canberra’s ancient history. Nickolas Zakharia reports.
Rather than living under one, the national parliament has been living on top of a 430 million-year-old rock for decades.
Located in Parliament House’s basement, the rock hides clues about some of the earliest life in Canberra. Referred to as the Capital Hill unconformity, the formation shows the connection of two rock masses that existed 10 million years apart.
A special tour of the formation took place in March this year and is only conducted once a year. Next year’s tickets are yet to go on sale.
Hosted by geologist and author Wolf Mayer, the tours provide a glimpse into the past as he explains what the rock formations mean and how its younger and older rocks can unpack Canberra’s ancient history.
“This is a useful and an extremely important remnant that is now housed in the basement of Parliament House,” Mayer told Region Media. “It is probably the only parliament house in the world with an unconformity in its basement.
“We can tell how the Canberra region looked some 430 million years ago when Australia was still connected to Antarctica. We can read the rocks, layer by layer, and piece together a history that shows how Canberra was at that time.”
The rocks are made from sandstone, with mudstone scattered between, suggesting that Canberra was once at least two kilometres underwater. In basic terms, an unconformity is two rocks from different periods of time that are fused together. It shows a missing gap of time where no sediments were preserved in a region.
Geologists are now able to use the unconformity to find clues about Canberra’s distant past.
The unconformity, which was left by Parliament House’s builders, was concreted over until 1995 when Mayer was alerted to rocks being under the building.
“The unconformity that we see shows the
The Capital Hill unconformity is believed to hide clues about the earliest life in Australia’s capital.

tectonic plates moving and shifting, so it’s very important to us,” Mayer said. “It is significant that it incorporates a piece of ancient history which has been preserved. Having parliament directly above it is a continuation of our current history, albeit there is a big gap in it all. It’s ancient history versus modern history, and they now sit one on top of the other.”
However, what happened remains unclear, with about 10 million years of geological record missing due to the formation. “It’s just been wiped, it’s gone,” Mayer said in another interview with The Canberra Times.
With rocks found above an unconformity being younger than the rocks below, Mayer believes this will help geologists find clues about the 10 million-year-old time gap.
“In a sense you might think of an unconformity as a negative feature as it erases so much of the geological history,” Mayer said. “In fact it does the opposite. Some of the features below and above, we can actually use to reconstruct what happened in that gap.
“In that sense, an unconformity is a very positive thing to have. It’s a very important feature to help us understand the very ancient history of the Canberra region.” •
GEN



Your business is our business, which is why we’re proud to present our new generation X.e industrial gear unit. Tailored exactly to operational application and environment, SEW-EURODRIVE has your interests at the forefront with this considered unit offering maximum efficiency, increased safety and a long service life – welcome the new generation.

Premium efficiency Higher operational safety Robust performance Extended service life and longer maintenance intervals Adaptable to specific applications
