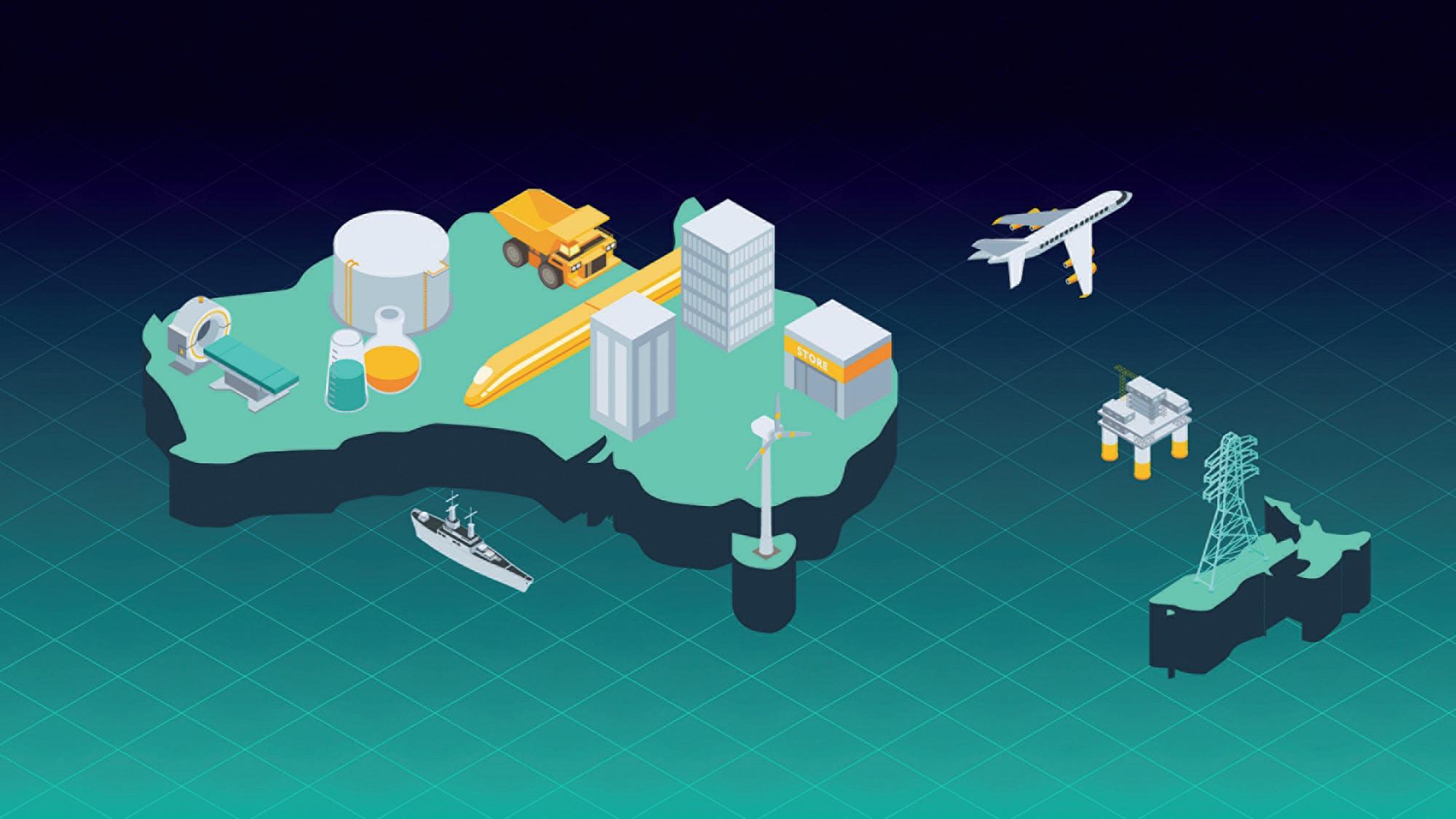
17 minute read
Siemens: 150 years in Australia
by Prime Group
150 Years of Siemens
Transforming the everyday for 150 years
Celebrating its 150th year of operations in Australia in 2022, transport solutions provider Siemens Mobility remains firmly committed to the country’s economic and technological growth.
Global technology company Siemens owes its formation to the genius of its founder, Werner von Siemens.
The German electrical engineer and industrialist laid the foundation for today’s Siemens AG (Siemens Aktiengesellschaft in full) in 1847, with his design for the pointer telegraph. The 30-year-old inventor hit upon an idea for substantially improving the electric telegraph developed by Charles Wheatstone and William Fothergill Cooke.
Together with precision mechanic Johann Georg Halske, he established the telegraph construction company TelegraphenBauanstalt von Siemens & Halske to manufacture his new device.
In 1848, the young company won a contract to build Europe’s first long-distance telegraph line. Extending largely underground from Berlin to Frankfurt, the roughly 670 kilometre link went into operation in February 1849.
In 1868, having formed the company Siemens & Halske with brothers Carl Wilhelm and Carl Heinrich, he embarked on a capital-intensive project that was both technologically and logistically demanding: the construction of a telegraph link between Europe and India.
Building of the line, which was commissioned by the Indo-European Telegraph Company, began on Russian territory and took place in three phases stretching from the Prussian-Russian border to Tehran.
After only two years of construction, it put the “Indoline” into operation in April, 1870. Instead of 30 days, it now took only 28 minutes to transmit messages from London to Calcutta – a sensation at the time.
The successful implementation of this major project earned Siemens & Halske international acclaim and marked a high point in the company’s business activities. von Siemens is also renowned for discovering the dynamo-electric principle, and constructed the dynamo machine, the forerunner of modern, large-scale electric generators, in 1866. Recognising the economic significance of his invention, his company quickly took out patents to ensure his right to commercialise it.
After roughly 10 years of development and testing, the dynamo was ready for series production in 1875. Its launch marked the start of a new era in the history of electrical engineering. The ability to generate and distribute large amounts of electrical energy at low cost gave a major boost to the economy.
In 1879, von Siemens presented the first electric railway, powered by electricity supplied via the rails. This was a significant breakthrough, as previously, engineers and designers had been trying to adapt electric motors for transportation. von Siemens immediately recognised railways’ potential for mass transportation, and two years later, in 1881, the company produced – at its own expense – the world’s first tramway, which went into operation in Berlin.
The self-propelled cars had a size and features similar to their horse-drawn predecessors, with electric power provided by a DC dynamo machine of the kind normally used to generate power for lighting systems. The wheels served as the power pickups, because the current ran through the rails.
This first tramway was a milestone in transportation technology, and began the triumphant development of electric railways – whether trams, subways or high-speed intercity rail.
From these humble yet impressive beginnings, the Siemens name has grown to be a global trademark, with the company now a giant shaping the mobility and technological evolution of countries across the world, including, of course, the Pacific region.
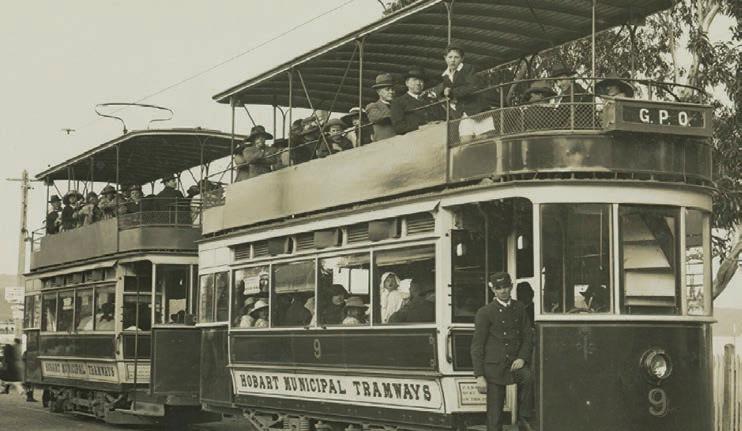
SIEMENS IN AUSTRALIA
Not content with working across Europe and Asia, the Siemens group extended its telegraphy expertise into Australia in 1872, marking the entry point of the company’s work in the country.
The company’s first task was supplying 36,000 porcelain insulators for an overland telegraph line between Adelaide and Darwin.
The South Australian Government would ultimately take on project management and commercial risk for the ambitious project, under the leadership of Postmaster General and Superintendent of Telegraphs, Charles Todd. Todd’s party was reliant upon camels and drivers to transport materials across the dry interior, as had been pioneered by the Indoline breakthrough. With the overland sections of the line joined, it was Todd himself who on August 22, 1872 would tap out the first message using a portable relay set at a remote camp. Nine months behind schedule, the 2700-kilometre Overland Telegraph Line and its 11 repeater stations cost the then princely sum of £479,175 — more than AU$104 million in today’s money. Today, the Adelaide to Darwin Overland Line is recognised as one of the great engineering achievements of 19th century Australia, and is credited with opening up telegraph communication from Australia to the world.
In 1879, the first railway interlocking machine was used in NSW, made by signalling manufacturers McKenzie, Holland & Westinghouse, which Siemens was to later acquire.
Typical of the multi-levered mechanical devices used in NSW railway signal boxes and on station platforms from the 1880s, it comprises a collection of levers for operating railway points and signals brought together in one machine. It was designed so that it prevented conflicting signal functions being set up simultaneously which might cause an accident. Before this, points were worked independently of each other, often by pointsmen in cabins stationed along the line. This machine was exhibited at the Sydney International Exhibition from 1879 to 1880. At the time, Britain led the world in the design and manufacture of safe railway working apparatus. The patent for the first interlocking machine was taken out in England by John Saxby in 1856 and by the 1870s thousands were in use in Britain but not in NSW.
It was both the display of this McKenzie & Holland machine in Sydney, together with the 1878 train collision at Emu Plains west of Sydney the year before, that prompted the NSW railway commissioners to introduce interlocking machines on NSW railways in 1881.
This interlocking machine is significant because it was the forerunner of all interlocking machines used in NSW.
In 1893, Siemens was contracted to build an electric tram service in Hobart, which became the first successful electric tramway system in the southern hemisphere.
It had several unique features: it was the only Australian system to use double deck trams as standard vehicles; it was the first street tramway on a rail gauge of three feet six inches in Australia and survived to be the last; its use of bow current collectors throughout its life was unique in Australia; and in 1949 it became the first tramway system in the world to use automatic conversion of AC to DC power supply.
The line was also at first operated by Siemens itself, before the Hobart Electric Tramway Company Ltd took over, until the Hobart City Council assumed ownership in 1913.
The trams were attractive single deck vehicles with enclosed saloons and open sections, painted maroon and yellow, outlined in gold. The fleet grew to 29 vehicles, the last three being large double bogie trams which were very popular. Most of the original fourteen trams lasted the life of the system.
In 1910, power signalling arrived in Sydney, with the commissioning of the Sydney Station Box. This installation was electro-pneumatic and controlled from a miniature lever frame supplied by McKenzie, Holland & Westinghouse. Over the next few years, the company would be involved in signal box installations at several other sites.
In 1930, there was another milestone when Siemens made its first point machine. The company has become a leader in this field, with several upgrades to units made in ensuing years, enabling points to be switched reliably, allowing for increased train throughput and a high level of operational safety. It also considerably improves the dynamic operating characteristics and prolongs the life of the track body.
Another impressive breakthrough came in 1936, when Siemens was contracted to lay the submarine telephone cable between Victoria and Tasmania, a world record distance at the time.
In the 60s, the company made its presence felt at the State Electricity Commission of Victoria’s railway system in the Yallourn/ Morwell area.
Siemens provided about 40 electric locomotives to transport coal from the open cut Yallourn mine to both the power station and the briquette factory at Morwell. The tracks ran around the various levels of the site on unballasted sleepers with the posts for the overhead wire attached to extended sleepers.
In other fields, Siemens was also leading the way, with its technologies used in projects such as the Parkes radio telescope, the Snowy Hydro Scheme, and provision of colour TV transmitters and componentry.
Siemens’ electrified tramway network in Hobart, the first in the southern hemisphere. Image: Jim Davidson Australian postcard collection, 1880-1980, National Library of Australia.

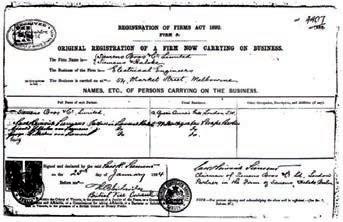
The overland telegraph line being built between Adelaide and Darwin. The formal registration of Siemens and Bros in Australia in 1894.
150 Years of Siemens
But the rail sector was where Siemens kept on making a name for itself. In 1968, the New South Wales Government Railways installed 96 Siemens audio frequency track circuits on the newly electrified Liverpool to Glenlee line.
Between 1979 and 1991, Siemens delivered the microprocessor controls for the motors of every Melbourne tram put into service.
In 1990 Siemens installed the first Westrace Interlocking unit in Australia: an arrangement of signal apparatus that prevents conflicting movements through an arrangement of tracks such as junctions or crossings.
In 1992, it received the contract to supply Sydney CityRail with a train radio network.
And in 1999, Australia made global Siemens history when the rail energy saver, Metromiser, was installed in Adelaide - the first in the world market. The system was designed to support drivers and planning staff for light-rail, suburban and metro systems.
In short, drivers received an on-board advice that enabled them to reach the stations in time with respect to maximum coasting.
It used a timetable optimiser, an off-board based software program checking the energy efficiency of timetables. Using basic data (acceleration, rolling behaviour of the train, topology, passenger flows, etc), it draws up a new energy-optimised timetable fitting in with the existing running schedule of the railway network.
The other component was an on-board unit which converts the data into driving recommendations such as: “make full use of permitted speed”, “coast” or “brake”. The OBU has learning capacity: the specific rolling qualities of the individual vehicle (which may differ even within one vehicle class) are recorded and used for the calculation of further recommendations.
At the turn of the century, Siemens’ presence in the industry continued to grow in strength. Melbourne’s National Express Group awarded Siemens the supply and maintenance contract for 62 new trains and 59 new trams.
It also completed the signalling works for the Alice Springs-Darwin Railway - the longest Australian rail construction undertaken in over 100 years.
In 2005, it was involved with the overhead electrification project for the Perth to Mandurah line, and in 2007, it received a $9 million contract to install the railway signalling for the newly-electrified Craigieburn Rail line in Victoria.
Siemens proved its leadership in the sustainability field in 2008, when it delivered the first electric locomotives in Australia.
Freight transport company Pacific National placed an initial order of 23 units, with the first delivered in February 2009. In July 2010, the order was increased to 32. By 2012, Pacific National had ordered a further 10 locomotives, bringing the fleet of Siemens Class 7100s to 42, and a total of 163 locomotives in Queensland.
Siemens also provided the train-borne distributed control system (TCMS) for the Regional Rail Link (RRL) in Victoria, one of the most significant and complex infrastructure projects in the state’s history, and the largest public transport development in Australia during its construction.
The $4.8 billion project, jointly funded by the Australian and Victorian governments, took approximately six years from commencement in 2009 to completion in 2015.
RRL has removed major bottlenecks in Melbourne’s rail network, expanded the regional network and created significant extra capacity for metropolitan and regional services. It has delivered 90 kilometres of new rail track, including dedicated regional tracks from the suburbs of West Werribee Junction to Deer Park and along the existing rail corridor from Sunshine to Southern Cross Station in Melbourne’s CBD.
Another coup came in 2013, when Siemens was contracted to South Australia’s first electrified passenger train network. The project delivered the electric traction power infrastructure as part of the government’s Rail Revitalisation project.
It comprised the detailed design, procurement, construction, testing, commissioning and warranty for a complete 25kV traction power system, including a SCADA system that monitors and controls the equipment. The additional use of Siemens SVC PLUS technology in the substation increased power quality, reducing the risk of power failures, and improving the stability of the system.
Meanwhile, a couple of other landmarks were achieved.
In May 2013, Siemens formally took over Invensys Rail, recognised as a designer, manufacturer and integrator of railway equipment, including automation, signalling and controls.
And in a first for the Australian market, Siemens was awarded the AustralianMade registered trademark, a significant accomplishment as the company is the only trackside railway company with AustralianMade recognition, with the signalling and rail detection products manufactured in Australia.
As Siemens Mobility CEO Raphaelle Guerineau points out, Australian-made technology makes it easy for rail operators to know that the equipment they are using meets Australian standards and is produced specifically with Australian conditions in mind.
“Manufacturing and servicing of the technology here in Australia retains local skills and knowledge. Siemens sees a future where Australian-Made is the global mark of quality and innovation,” she said.
Indeed, the company has more than 100 patents and patent applications in Australia and New Zealand, with over 4250 products locally designed and assembled in Australia. It also has achieved more than 650 rail equipment type approvals. The spend on research and development is on average $4 million.
In 2021, Siemens Mobility was awarded two contracts worth around $190 million by the
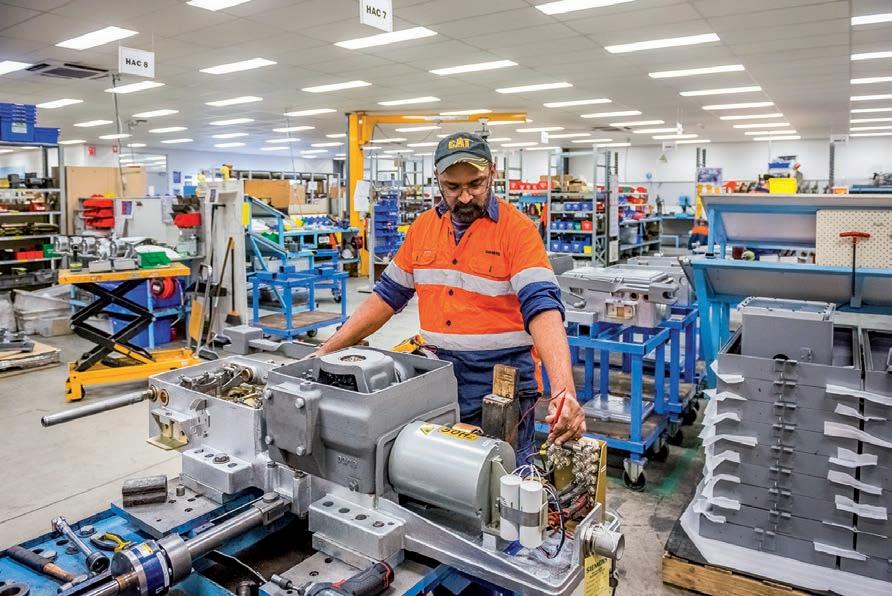
Siemens is the only trackside railway company with Australian-made recognition.
New South Wales Government to significantly upgrade the rail network in metropolitan Sydney.
Aiming to improve the overall efficiency and capacity of the rail network, the total contract consists of two key packages, including the introduction of a new Traffic Management System (TMS) along with the upgrading of Sydney Trains’ network conventional signalling to a digital ETCS-L2 train control system.
This work is part of the NSW Government’s broader Digital Systems Program, a ‘once in a generation change’ to replace legacy signalling and train control technologies with modern, internationally proven, intelligent systems. The systems are due to be available for operation in 2023.
The TMS will be integrated with the new European Train Control System (ETCS) Level 2 technology, which is today’s leading technology running on some of the best and most efficient rail networks worldwide.
The Digital Systems Program upgrades will enable more frequent and reliable services and increase capacity to allow 24 trains to operate during peak hours and up to 30 trains per hour for recovery from disruptions.
The other key project element will include implementation of Automatic Train Operation (ATO) that assists drivers by providing more frequent, reliable, and consistent train journeys. Train drivers will remain in control but will be assisted in improving operations and reducing journey times, which subsequently benefits passengers.
Siemens Mobility also developed the Train Control System for the entire Melbourne metropolitan rail network, ensuring commuters arrive at their destination every day of the year; and, in Queensland, engineered software to monitor noise from cooling blower fans to significantly reduce noise in residential and ecological areas, with the product installed on about 110 locomotives.
In 2017, the company expanded its portfolio in the field of predictive maintenance by digitalisation through its acquisition of the MRX Technologies Group, founded and headquartered in Perth., and which offers services in Australia and the UK for manufacturers and operators of rail systems including the mining sector.
Demand for the Siemens expertise in Australia continues to run strong, with other examples of projects including the Gawler electrification scheme in South Australia, e-inspection overhauls for BMA Rail as well as the powering of stage 2 of Gold Coast Light Rail in 2017, the award of the Sydney traffic management system contract in 2020, and the implementation of Project iTRACE, the standardised barcoding system that collates data on assets and materials used across the rail industry.

THE NEXT 150 YEARS
Today, Siemens technology can be found supporting many industries and critical projects around the world, from resource-efficient factories, to smarter buildings and cleaner and more comfortable transportation.
Siemens Mobility, with an emphasis on digitalisation, is enabling mobility operators worldwide to make trains and infrastructure intelligent, increase value sustainably over the entire lifecycle, enhance the passenger experience and guarantee availability.
Siemens also actively supports local industry, governments and stakeholders to understand and prepare for key economic and societal changes such as the fourth industrial revolution (Industry 4.0), the transition to “intelligent infrastructure” and a “sustainable energy” future.
A strong supporter of ESG principles, Siemens prioritises the mental wellbeing of its employees, with 15 trained mental health and first aid officers on board.
The diverse management team comprises 43 per cent female executives , and the culturally diverse workforce includes employees from over 30 different nationalities.
In fact, Siemens enables 31,000 jobs in Australia and its operations are linked to a GDP contribution of approximately $4.3 billion.
The company employs approximately 2000 people across all the Siemens entities in Australia and New Zealand, including all capital states.
In addition, Siemens Mobility’s rail business has two manufacturing sites in Melbourne and Perth and a service centre in Mackay, as well as people working directly on customer sites including remote regions. It recently supported the local Mackay community during the initial period of COVID, to source and donate essential supplies to allow organisations to remain open.
“We’re increasingly focusing on the future of transport globally, and are also committed to helping industrial companies become more productive, efficient, flexible, and therefore more competitive,” Guerineau said.
The Siemens mission is clear: by constantly reflecting in the present the guidelines, values, principles and core ideas that have provided orientation to the company throughout its history, and by infusing them with life, it makes an important contribution toward the company’s identity – both for Siemens employees and for the societies in which it operates as a business.
Siemens technologies are a part of the fabric of Australia, and have played a role in transforming the everyday for millions of people in this country.
Its relevance in Australia has always been and will continue to be via the application of the latest technologies to help address current challenges facing the nation.
For 150 years Siemens has been supporting the building blocks of the nation. And through technology with purpose and passionate people, the company is motivated to continue to be an integral part of Australia’s future for the next 150.
Siemens is a staunch supporter of Australian manufacturing, with local research, design and innovation facilities in Perth and Melbourne.
D o n ’ t m i s s a n i s s u e , s u b s c r i b e t o d a y.

railexpress.com.au/subscribe
ISSUE 4 | MAY 2022
WWW.RAILEXPRESS.COM.AU
Next generation rail crossing safety system
A game-changing rail active level crossing protection system is set to improve safety in rural and remote areas. - PAGE 34
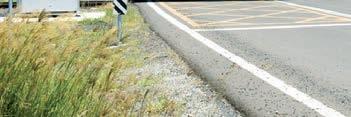
Siemens: transforming the everyday for 150 years
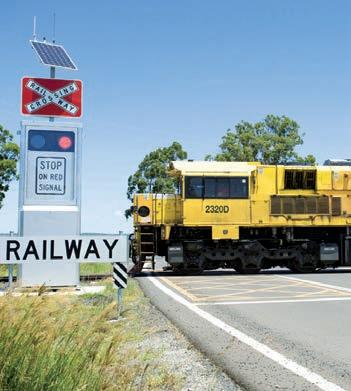
PAGE 26
SUPPORTED BY:
Turning graduates into engineering professionals
PAGE 31
Lubrication partnership keeps trains moving
PAGE 36
RAIL EXPRESS is compulsory reading and a vital tool for all people working in and around the rail sector.
Rail Express is Australia’s authoritative business to business rail publication.
Combining the resources of our respected journalism team and our unparalleled industry contacts and affiliations, Rail Express provides extensive, comprehensive and balanced coverage of breaking news and trends in key areas like infrastructure, investment, government policy, regulatory issues and technical innovation.
Published both in print and digitally every month, Rail Express is the only publication to have both the official endorsement and active participation of the main railway associations in Australia and the broad support of the rail industry.