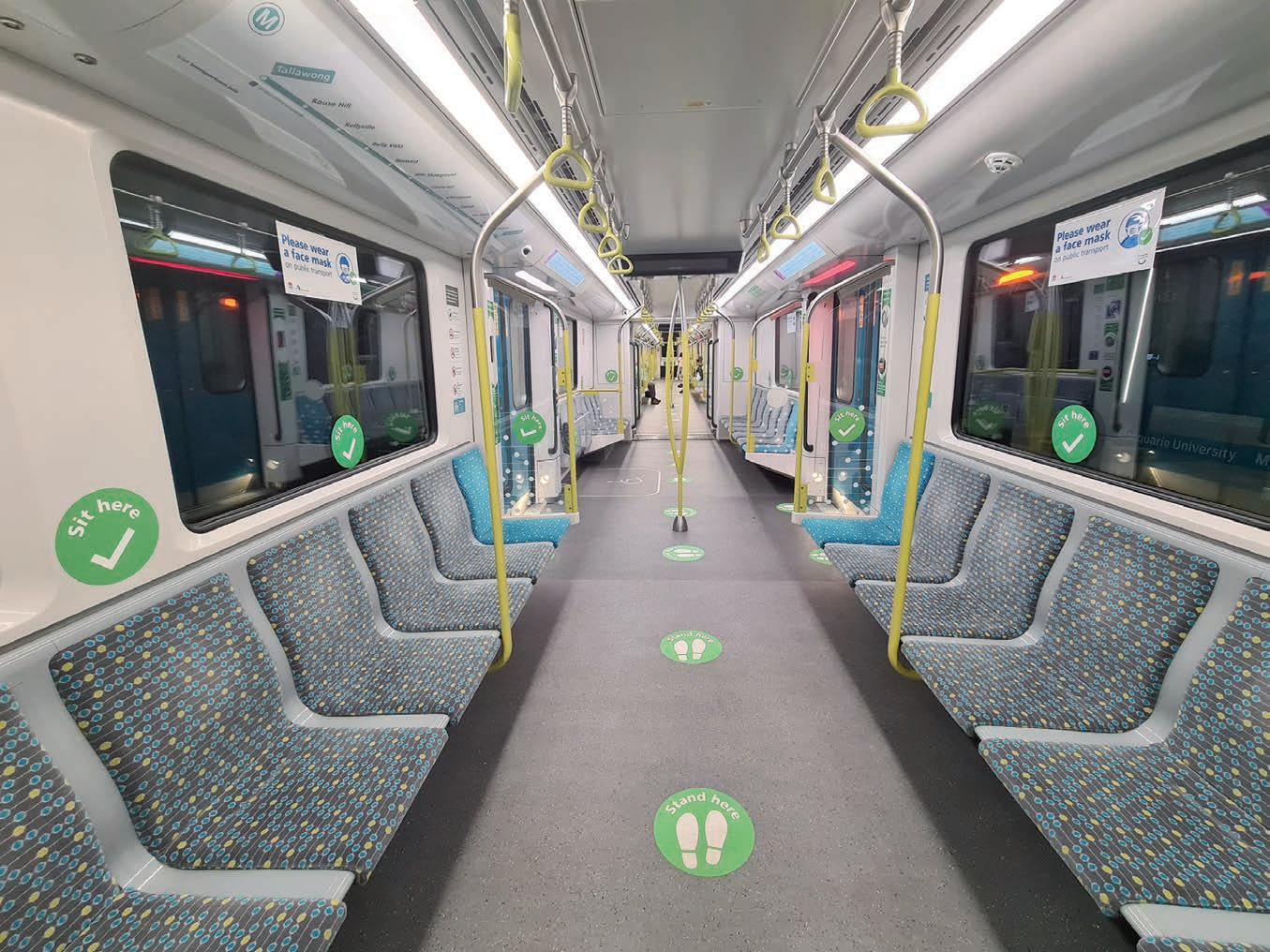
13 minute read
Passenger comfort and care
by Prime Group
Passenger Care and Comfort
The right room temperature inside the vehicle goes a long way to creating a feeling of well-being.
The ride’s as important as the journey
As more commuters return to rail, it’s important for industry to recognise the importance of the passenger experience.
Even though increasing numbers of business and leisure travellers making a welcome return to rail, the key to retaining them as customers lies in guaranteeing trips that match their expectations.
From the initial ticket purchase in the station to the rail car, the industry needs to offer experiences that make passengers eager to return again and again.
Whether it’s running on time, or addressing physical comfort requirements such as stringent cab hygiene, better seat material, having more room to move or using optimal ventilation, the industry has unprecedented opportunities to comprehensively monitor the comfort of its passengers’ experience and make improvements where necessary.
PASSENGER PRIORITIES
A recent UK report on what passengers want when they travel on trains reveals priorities that are common to Australia.
The research, undertaken by the independent watchdog for transport users in the UK, Transport Focus, involved asking 14,300 passengers across the country to rank a series of 30 possible improvements to their rail service, in order of priority.
The survey found the top priority for improvement was punctuality, with commuters wanting a reliable railway that delivered on the promise of the timetable day in and day out.
Improving value for money came a close second and while passengers did not realistically expect prices to drop, they did expect the basic promises of the industry to be met in return for their fares.
Passenger comfort was also important, with many prioritising the need to get a seat on the train. While the industry is enjoying a resurgence in current times, it has struggled to provide the extra capacity to meet this demand.
As Transport Focus chief executive Anthony Smith outlines, more and more services have run on increasingly congested infrastructure, often with a knock-on hit to reliability and punctuality. These basics – being reliably on time and getting a seat – also contribute to passengers’ perceptions of value for money.
So when delays or even disruptive industrial action occur, it is understandable that passenger dissatisfaction escalates.
• Priorities by journey purpose
Smith said reliability, punctuality and value for money were key improvement areas for all groups regardless of journey purpose.
“But while the ranking order of priorities is similar, there are differences in the priorities between commuters, business and leisure passengers,” he said.
“Commuters are more concerned about the core timetabled service, including with frequency of trains, disruption due to engineering works and journey times. While still not a high priority, commuters also place greater importance on making it easier to claim compensation for delays.
“They also place great emphasis on a robust, consistent, reliable delivery of the basic service.
“For business and leisure passengers, there is more of an emphasis on the quality of the journey. Business travellers are more concerned about staying connected while travelling, with greater emphasis on free Wi-Fi and a better mobile phone signal on the train.
“Leisure passengers are more concerned about getting a seat on the train and that toilets on trains are clean and well maintained.”
• Priorities by age
While the key priorities remain the same, analysis by age factors revealed some interesting differences.
“As may be expected, older passengers are more concerned with getting a seat on the train and with clean, well-maintained toilets on long journeys,” Smith said.
“Passengers aged 16–25 are much more concerned about journey times and environmental impact than older passengers.”
• Priorities for passengers with disabilities
There were also notable differences in priorities for improvement between passengers with a disability and those without.
“For passengers with a disability, toilet facilities, step-free access, improved security and availability of staff to help are more important,” Smith said.
“However, it is also important not to underplay the importance of the ‘core product’
– passengers with disabilities still placed reliability and punctuality, in addition to their fares offering better value for money, as their top priorities.”
• Passenger expectation at stations
It was clear that train performance and the experience on the train tended to feature more prominently in the overall list of priorities for improvement than station issues.
“However, there is still value in identifying passengers’ views to help inform station improvements,” Smith said.
“Having completed the main priorities exercise, passengers were presented with a separate, more detailed list of station facilities and asked to select which they felt needed to be improved at the station where they start their most frequent journey.”
The station facilities included in the list comprised platform facilities (such as seating, toilets, shelter), information (departure boards, public address system, help points), general station amenities (refreshment outlets, shops, cash points), ticketing and step-free access.
The research again showed a quite pragmatic approach from passengers. The emphasis was on improving basic station amenities: toilets, seating and shelter.
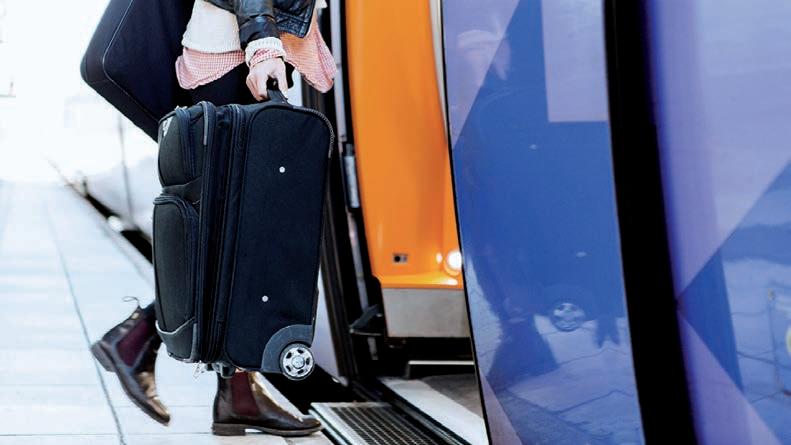
THE COMFORT FACTOR
The development of new high-speed trains has promoted an evolution in coach interior design, aimed at making railway transportation more attractive. New requirements have been set, namely high levels of comfort and safety.
Historically, the importance of comfort was first highlighted in the 1970s, when academic researchers Osborne and Clark from the University of Swansea began to establish systems that measured passenger comfort, and tried to obtain assessment results using questionnaires and surveys. Their research focused on how best to obtain quantitative assessment data from a survey, leading them to study the best methodologies for assessing passenger comfort in two areas.
The first area concerned aspects of the transportation system itself, such as ride, carriage and organisational comfort. The second area related to behavioural aspects.
Their studies offered them a new understanding of passenger comfort, a definition of the concept of comfort, and insights into its relationship with passengers’ other travel experiences and complementary factors that influence comfort, such as temperature, ventilation, illumination, photic stimulation, pressure changes, travel length and task impairment.
For the Knorr-Bremse Group, based in Munich, comfort has always been key, as it carries out its mission to make mobility on railways safe, sustainable and environmentally friendly.
A number of highly innovative systems and solutions from the group are already helping to make train travel quieter, easier and more comfortable.
The company points out that passengers often give little thought to the surface beneath their feet when boarding: that little step that folds, slides or swivels out helps them to enter the train quickly, effortlessly and safely, particularly by bridging the gap between platform and train.
Knorr-Bremse has introduced folding steps, for example, which are controlled by the door drive, so no separate drive or control components are required. Sliding steps cleverly vanish beneath the vehicle.
Swivel steps, employing kinematic solutions, often come into use when extension paths need to be precisely defined.
Public transport operators in Germany are coming under increasing pressure to install such systems across their networks, with legislation stating that accessibility of public transport must be in place from 2022.
Meanwhile, Knorr-Bremse in the USA is currently supplying systems for light rail vehicles that use hydraulic leveling systems to raise and lower the boarding height to match the platform, making it much easier for passengers to get on and off. The existing hydraulic braking system is designed with the ability to supply the additional leveling cylinders installed in the bogie area along with the standard steel springs.
Then there are sliding door systems. By improving the sound insulation of both exterior and pocket sliding doors, the company significantly reduces the noise level in the compartment (and thus for the passengers).
Whereas conventional seals only close at the side edges of the doors, these systems have a mechanism that lifts the door leaf before closing – so the upper and lower edges are sealed too.
Besides enhanced noise insulation, this means less cold air is forced into the vehicle, especially at high speeds.
The bottom line for passengers is that they can travel in comfort at a constant temperature, stretch their legs or read the paper without feeling a cold draft and getting a stiff neck. Meanwhile, the train crew can control the compartment temperature with efficient ventilation and air-conditioning (HVAC) systems that use less energy.
GETTING INSPIRED
Siemens Mobility is among the many rail transport providers which have made passenger comfort a priority, as exemplified in its latest version of its lauded cutting edge electric multiple unit (EMU) train, the Inspiro, which is designed specifically for metros (mass rapid transit systems).
As Siemens Mobility Country CEO for Australia and New Zealand, Raphaelle Guerineau, told Rail Express last year, the mass transit vehicles cater to the needs of customers, from train width to sitting capacity and other comfort factors, while being manufactured to meet firm sustainability targets.
“Mass transit providers in cities and metropolitan areas in the 21st century face tremendous challenges,” she said. “Passenger volume, post-COVID concerns as well as the need for sustainable transport solutions are growing. Our response has been to use cutting-edge technologies that fully meet the needs of operators and passengers
Little steps that fold, slide or swivel out help passengers enter the train quickly, effortlessly and safely.
Passenger Care and Comfort
while also protecting the environment. We are leaders in this.
“Public transportation must ensure that passengers are transported in a safe and comfortable environment.
“Commuters today expect to travel in a friendly and connected environment.
“We have the highest level of customisation to meet all our customer requirements. When we design systems, we look at the length, the width, the number of doors and all the equipment’s insights, for example.” The comfort characteristics start from the outside, with large entrance doors welcoming passengers into the Inpiro.
Inside, a thoughtfully designed interior with wide passageways impart a generous feeling of space.
The innovative ambient lighting system, with its carefully placed groups of lights, creates a pleasant atmosphere; while instead of the usual grab poles and hand rails, Inspiro offers innovative and distinctive supports in the form of a stylised branched tree, allowing several passengers to hold on while maintaining a comfortable distance from others.
Some of the passengers supports in the Inspiro also feature large displays that provide information at convenient places throughout the car. Known as “virtual conductors,” they can also be used for other purposes, such as advertisement or entertainment.
Additional displays can be installed on the side walls.
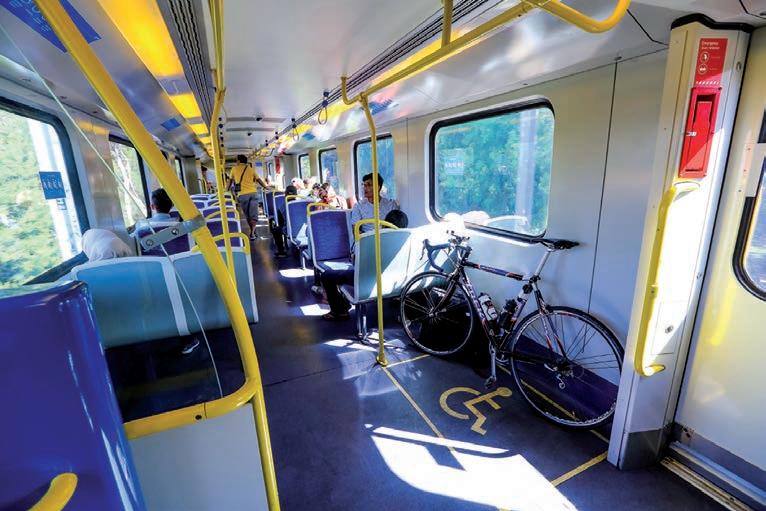
GOOD VIBRATIONS
In a joint paper for the Foundation for Science and Technology, PhD students Patrícia Filipa Pinheiro da Silva and Joaquim Mendes pointed out that the evaluation of ride comfort is vital to understand and assess the quality and experience of a passenger on a train journey.
“The passenger level of comfort is a combination of physical and psychological factors,” they said.
“Therefore, the ride comfort can be affected by parameters such as vibration, temperature, acoustic noise, humidity, smell, visual stimuli and design layout.
“Vibration is considered as the main parameter to affect the users’ comfort, as once it is caused by the train motion the passengers are subject to it throughout the trip due to the contact with the seat, backrest and the floor.
“Due to the influence of vibration, the ride comfort evaluation methods are based on the passenger’s exposure to it.
“The discomfort of the passengers will increase with the increasing time of exposure to vibration and its level. The condition of the railway vehicles and the track conditions such as railway profile, rail irregularities or curvature will influence the passenger’s perception of comfort.”
As these parameters were not the same in all, it was difficult to establish a universal standard for ride comfort of railway vehicles, they added.
Passengers with disabilities value cab spaces, yet still place reliability and punctuality as their top needs.
COPING WITH COVID
COVID has had undeniable impact on passengers’ travel patterns and priorities – not least when it comes to personal safety, space on the train and cleanliness.
According to Edina Hadzovic, systems safety engineer with rail consultants Systematiq, a large source of this concern is through maintaining social distancing on board a carriage.
“Practising social distancing outdoors has been a shift Australians have responded to well, however, maintaining a healthy distance within a constrained space poses additional challenges which at times may be out of a person’s control,” she said.
“However, despite these challenges, key rail operators around the nation have continued to find alternate ways to improve the safety standards on trains to aid in the comfort of passengers.”
As an example, Hadzovic cited the High Capacity Metro Trains (HCMT) used by Metro Trains Melbourne, a project which Systematiq is involved with.
“The increased capacity on the HCMT will provide additional capability to practice social distancing on trains as we progress into a COVID-normal environment. Further, the HCMT will also automatically estimate the passenger load, which will have the ability to be accessed remotely,” she said.
However, with an existing fleet where the luxury of additional capacity or enhanced ICT systems may not be available, rail transport operations have turned to rapid digital innovation to tackle the environmental, social and health effects of the pandemic.
Today, systems rely on recorded digital measurements in addition to surveys, and enable a broader quantifiable data set that can show baselines figures, changes and trends.
All aspects of bogie dynamics can nowadays be measured, from the quality of the track to the movement of the car body – as well as noise, vibration and harshness measurements, which indicate the reality of the journey. Within the carriage, factors such as air temperature, humidity, internal noise volumes and general ride quality can be accurately measured.
Of interest, New South Wales Transport has invested in an upgrade to the Opal Travel app, which now provides passengers with updates of the expected levels of crowding during their normal departure times.
Instead of utilising a digital on-board passenger counting system, authorities measure the weight of train carriages and then gauge the additional weight of each passenger to calculate how close to capacity a section is.
“It is additional investments like these which will help promote passenger safety and comfort, and continue to keep Australia’s public transport system in a healthy financial status,” Hadzovic said.
“As we address the increasing demand and Government priority for large infrastructure projects, Australia’s rail network is effectively building a culture whereby compliance with relevant standards is merely the benchmark for safety, performance and overall quality.
“The HCMT and Sydney Rail are exemplar demonstrations of how rail transport operators are prioritising the provision of an enhanced customer experience through rapid innovation to address environmental and socia challenges.”
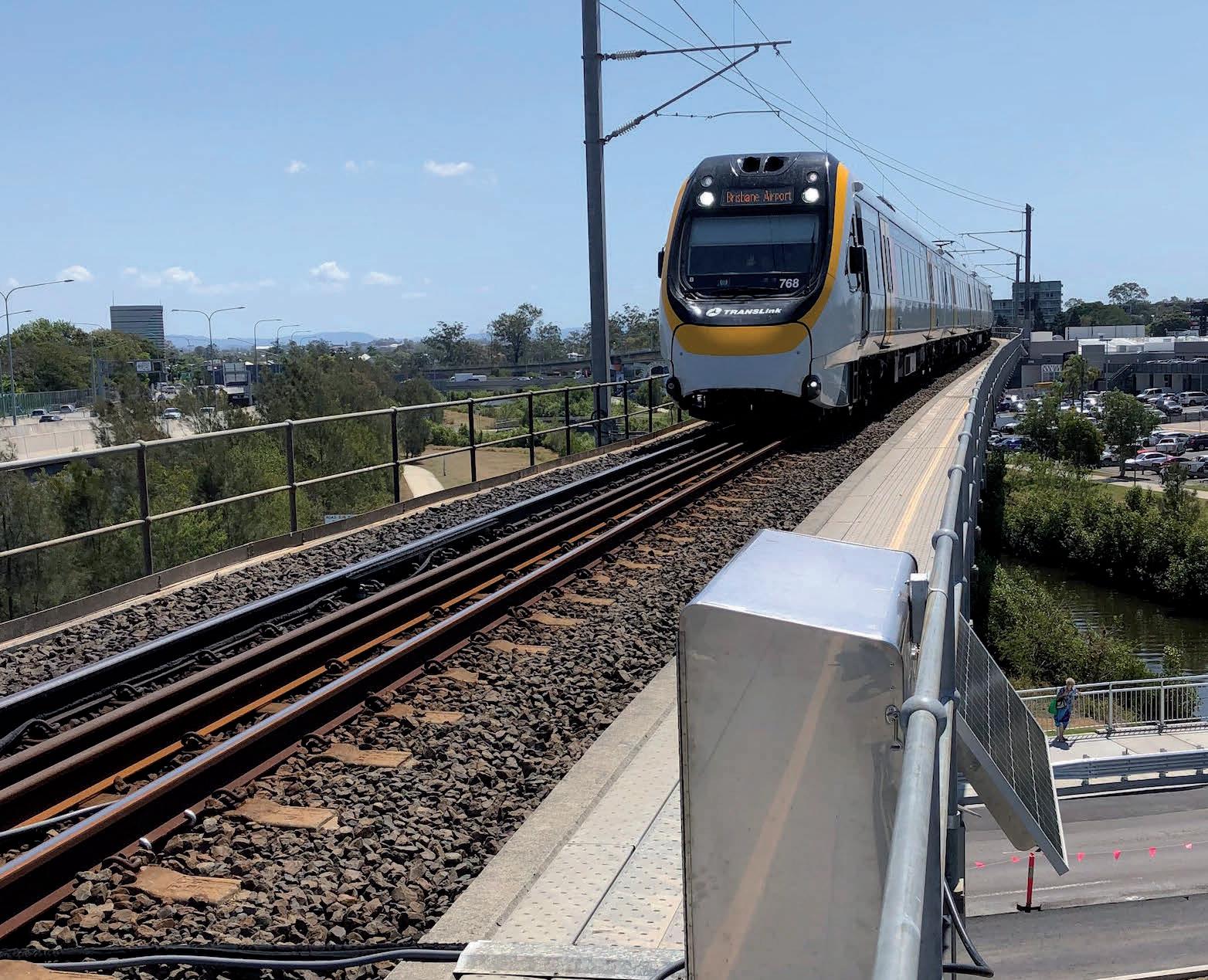
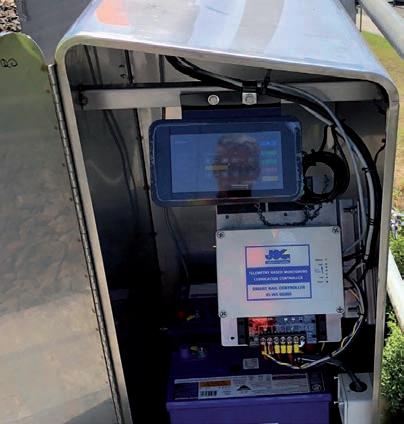
Increase your operating time while lowering your energy consumption With Lincoln Lubrication
Thousands of trains around the world operate more reliably and efficiently because of SKF and Lincoln automatic lubrication systems. By delivering precise amounts of lubricant directly to the wheel/rail interface, automatic lubrication systems provide significant benefits in terms of wear, energy and noise reduction. SKF EasyRail on-board systems for wheel Wayside lubrication systems effectively apply a consistent and controlled volume of lubricant to the rail. The systems hold that grease or friction modifier in place, allowing the wheels to grab and carry it around the track curve. The product range includes solutions for gauge face, top-of-rail and restraining rail.

