
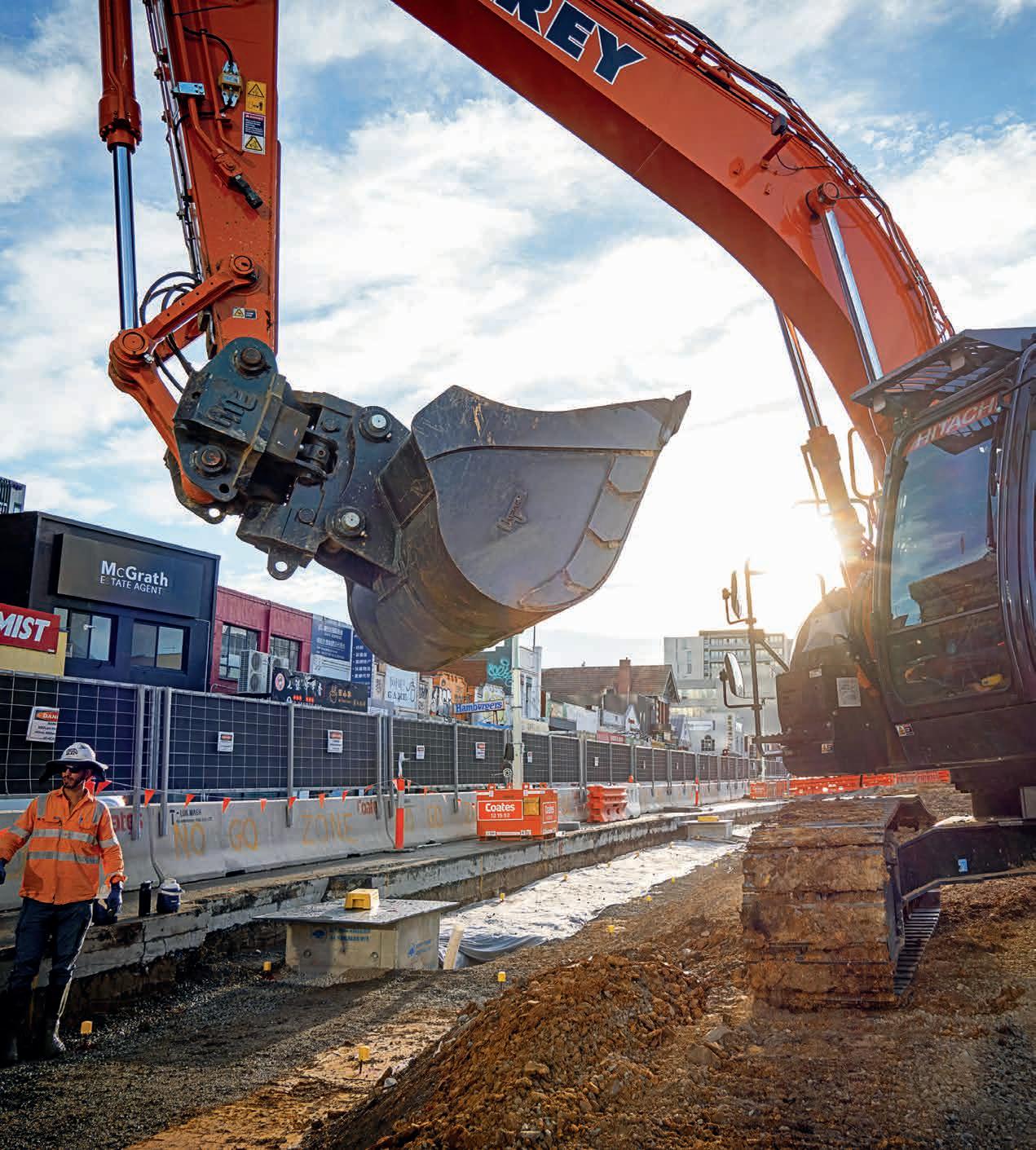
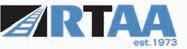

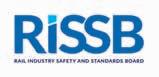


100% SYSTEM AVAILABILITY
100% SYSTEM AVAILABILITY
At Siemens Mobility, we value our local manufacturing facilities and engineering teams for their innovative and sustainable ways of working, as they are the key to revitalizing old and new rail technology that will #transformtheeveryday and change the way we travel globally.
379 Docklands Drive
Dockalnds, VIC 3008
T: 03 9690 8766
www.primecreativemedia.com.au
Publisher John Murphy
E: john.murphy@primecreative.com.au
Chief Operating O cer
Christine Clancy
E: christine.clancy@primecreative.com.au
Managing Editor
Mike Wheeler
E: mike.wheeler@primecreative.com.au
Editor Joshua Farrell
E: joshua.farrell@primecreative.com.au
Business Development Manager
Alex Cowdery
M: 0422 657 148
E: alex.cowdery@primecreative.com.au
Client Success Manager
Salma Kennedy
E: salma.kennedy@primecreative.com.au
Design Production Manager
Michelle Weston
E: michelle.weston@primecreative.com.au
Art Director
Blake Storey
E: blake.storey@primecreative.com.au
Design Caterina Zappia
Subscriptions subscriptions@primecreative.com.au
www.RailExpress.com.au
The Publisher reserves the right to alter or omit any article or advertisement submitted and requires indemnity from the advertisers and contributors against damages or liabilities that may arise from material published.
© Copyright – No part of this publication may be reproduced, stored in a retrieval system or transmitted in any means electronic, mechanical, photocopying, recording or otherwise without the permission of the Publisher.
Known as the Beveridge to Albury –Tranche 2 section, John Holland will start site investigations and progress design work. This will be at Benalla, Euroa, Wandong, Hume Freeway, Tallarook, Seymour, and three sites in Broadford on the existing North-East rail line to allow for the safe passage of doublestacked freight trains.
Activities will include geotechnical investigations, ground water monitoring and additional surveys, as well as development of key management plans.
Inland Rail’s appointment of a construction partner for the remaining Victorian sites is on schedule for mid-2024, with construction commencing in early-2025 and project completion in 2027.
Inland Rail Program Delivery Director for the section, Ed Walker, said the works at the remaining eight sites in Victoria were an important step forward for Australia’s largest infrastructure project.
“Inland Rail is getting on with delivering the project,” Walker said.
“We’ve selected John Holland based on their experience delivering major civil and rail projects including Inland Rail Narrabri to
The Victorian Government has removed Melbourne’s 75th level crossing, with tra c returning to Bedford Road in Ringwood while trains start running in the new rail trench more than a year ahead of schedule.
Premier Jacinta Allan announced the milestone as new data shows that, on top of easing congestion across Melbourne’s suburbs, level crossing removals have made the roads safer – preventing more than 100 crashes and near misses every year.
“We’re getting rid of these dangerous and congested level crossings that frustrate thousands of drivers every day,” she said.
Metro Trains data indicates the number of train and vehicle collisions and near misses across the metropolitan network has fallen by almost three-quarters, from an average of 21 incidents a month in 2017 to just five incidents a month in 2023 as a result of the Level Crossing Removal Project.
Removing the crossings has also slashed commutes – saving close to 50 hours of boom gate down time during the morning peak each
North Star Phase 1 last year, and the Northeast Rail Line Upgrade (NERL) in 2021. They are also responsible for delivering Melbourne’s Metro Tunnel Project and Sydney Metro.
“Over the coming weeks local communities will see the John Holland team on Tranche 2 sites carrying out early works for new bridges, track lowers and station modifications.
“Inland Rail will look for every opportunity to involve local people and businesses in the project, to maximise the economic and social benefits for communities along the route.”
John Holland Executive General Manager, Steve Butcher, said this was an exciting project that would transform how goods were
moved around Australia.
“We know that expanding the nation’s rail freight network creates safer and less congested roads and minimises carbon emissions,” Butcher said.
“Projects like these also create jobs and allows us to work with local businesses, leaving a positive legacy for regional communities.
“This builds on our proud and longstanding partnership with ARTC to deliver transformative rail projects across the country, allowing us to leverage our skills and experience in providing end-to-end rail solutions.”
day and allowing additional train services without more congestion.
The state government has also delivered 47 new and upgraded stations, created the equivalent of 31 MCGs of open space for communities to enjoy, and built 58 kilometres of walking and cycling paths across the city.
The Project has averaged one crossing removal almost every six weeks since the first set of boom gates were removed at Burke Road in Glen Iris in 2016.
More than 91 million hours have been worked across the congestion-busting program, making it one of Victoria’s biggest employers supporting almost 6,000 jobs.
More than 13,500 vehicles used the busy Bedford Road crossing every day, experiencing frustrating delays when the boom gates were down for 23 minutes in the morning peak –including families and school buses dropping students at Ringwood Secondary College, which sits next door to the crossing.
With the level crossing gone, the Belgrave Line is now boom-gate free from the city to
Ferntree Gully. The Lilydale Line will be the first rail line to be boom-gate free later this year when level crossings at Dublin Road in Ringwood East, Coolstore Road in Croydon, and Cave Hill Road in Lilydale go a year ahead of schedule.
Boom gates at Brunt Road in Beaconsfield, Keon Parade in Reservoir, Warrigal and Parkers roads in Parkdale, plus three level crossings in Pakenham, are all set to go this year – with the Pakenham Line extended two kilometres and two new stations being built.
We’re the leading provider of end-to-end rail and transport solutions in Australia and New Zealand. From designing and constructing transport networks to operating them, we’re transforming the way people travel and providing better connections across the country.
Every day, more than one million passengers journey are taken on our networks. Our longstanding experience in mass transport means we know how to put together the right solution - from start to finish. Focused on the future of transport, we innovate today for the best outcomes tomorrow. From digital engineering to digital asset management, to targeting zeroemission transport modes; we’re in it for the long haul.
Consistent, accurate information across all channels.
A ‘single source of truth’ for everyone.
A new heavy rail connection is tracking towards construction on the Sunshine Coast, which will make a trip to Brisbane 45 minutes faster than a car.
The Queensland Government is committing an initial $2.75 billion to deliver Stage 1 of the Direct Sunshine Coast Rail Line project, which includes protection of the updated rail alignment to Maroochydore.
The first stage will see a 19-kilometre dual track built from Beerwah to Caloundra, the longest spur line in the southeast passenger network.
Staged delivery will see the line ultimately run to Birtinya and Maroochydore. This will deliver faster rail to the Sunshine Coast, with trains able to reach speeds of 140km per hour on some sections of the track.
Premier Steven Miles explained the connection will unlock thousands of homes in the Sunshine Coast region.
“Without the rail line, that development would bring an unmanageable level of congestion to the local road network, making this connection essential for new housing to be brought forward,” he said.
“Through to Cross River Rail, we are removing the bottleneck in Brisbane’s CBD and creating opportunities to provide better rail services to some of Southeast Queensland’s fastest growing regions.
“With better, more connected rail options available we hope commuters will leave the car at home, reducing congestion and lowering transport emissions on the path to net zero.”
The Beerwah to Caloundra stage could be operational in time for the Brisbane Olympics in 2032, subject to a matched funding agreement from the Federal Government.
The Sunshine Coast is one of the fastest growing regions in the state and is forecast to be home to 600,000 people by 2046.
Modelling shows most of the population growth will be concentrated along the first stage of the rail line, around Caloundra South (Aura).
Member for Caloundra, Jason Hunt, explained what the line will mean for the region.
“Expanding the Southeast Queensland rail network with this direct line will benefit Queenslanders well into the future,” he said.
“This rail line will connect people on the Sunshine Coast to Moreton Bay and Brisbane for work, medical appointments, sporting and cultural events.
“We are committed to maintaining the liveability of the Sunshine Coast region. Direct Sunshine Coast Rail will help to support sustainable growth that ensures that we spend less time in tra c, and more time doing the things that we love.”
Stage 1 of the Direct Sunshine Coast Rail Line will be an enabler for new housing, including supply for 50,000 people at Caloundra South and up to 100,000 people at Beerwah East.
It’s expected the initial stage of the project will accelerate the delivery of more than 3,000 a ordable and diverse homes already
planned within the region.
The funding envelope for Stage 1 is expected to be between $5.5 billion and $7 billion, with final costs to be confirmed at the completion of the procurement phase.
A ‘funding envelope’ is an approach taken on other similar projects around the world, allowing costs to be finalised when contracts are executed.
It’s expected that Stage 1 of project will support 2,200 good jobs in the region.
Fast facts:
• The Direct Sunshine Coast Rail Line is a proposed 37.8km rail extension between Beerwah and Maroochydore to increase public transport opportunities and improve connectivity to Moreton Bay, Brisbane and beyond.
• The detailed business case has determined an optimal realignment of the corridor between Beerwah and Maroochydore, which enables rail speeds of up 160km/h. The current trains can and do travel 140km/h, their maximum speed.
• The realignment aims to minimise environmental impact and reduce curves in the line to allow for faster train speeds. The new corridor will be protected in 2024.
• More than 80 per cent of community feedback received during community consultation in 2023 were supportive of Direct Sunshine Coast Rail, helping inform the business case.
The WA Government’s METRONET program has reached another milestone with the New Bayswater Station – one of the biggest outside of the CBD – now complete.
The METRONET New Bayswater Station will become the meeting point for three separate train lines – it is already servicing the Midland and Airport Lines, with METRONET MorleyEllenbrook Line trains on track to commence services later this year.
The elevated four-platform station also includes a new bus interchange, car park, bike parking and 10 new retail spaces around the base of the station.
An expression of interest is progressing for the 10 new retail spaces, with the first businesses expected to be occupied later this year.
The project has been complex, delivering an elevated station in a constrained space, while also connecting three separate train lines into one.
Works on the new station commenced in late 2020 and included a number of significant moments, such as the demolition of the iconic Bayswater Bridge.
The demolition of the bridge garnered huge community attention, with plans in place for a public art installation utilising a section of the old bridge.
Transport Minister Rita Sa oti said
that right across Perth they are seeing communities being transformed and better connected.
“The Bayswater town centre is completely unrecognisable to what it was before, with an elevated four-platform station replacing what was e ectively a shed at the old station,” she said.
“We are now in the process of undertaking landscaping and installation of public art pieces, and one of those pieces will include a segment of the old bridge.
“I know the past couple of years have been
very challenging for local businesses and residents and I want to say a big thank you for everyone’s patience.”
The southern half of the station was completed and opened in October last year, while works have been continued on the northern half of the station over the past six months.
With major works wrapping up, attention has turned to landscaping around the station with more than 170 trees being planted, as well as around 16,000 plants and shrubs in 4300 square metres of new garden beds.
The O ce of the National Rail Safety Regulator (ONRSR) has welcomed the Western Australian Parliament’s decision to approve the full application of Rail Safety National Law (RSNL).
While Western Australia formally adopted the national legislation in 2015, until now it was implemented using what is known as “Mirror Legislation” – e ectively locking down a 2015 localised version of the national act.
ONRSR Chief Executive and National Rail Safety Regulator, Dr. Natalie Pelham, said the decision to bring WA into line with all other states and territories would remove any inconsistencies and ensure that rail operators in the west benefited from a range of amendments made to the RSNL since 2015.
The new law will not come into e ect until the second half of 2024, and the ONRSR will use the time to conduct an engagement program with all WA-based rail
transport operators and rail safety workers and their representatives.
“This is about making sure that railways in Western Australia are as safe as they can be and that ONRSR is as e cient and e ective as possible in regulating safety across Australia,” Pelham said.
“For the most part, and certainly for the time being, it will be business as usual, but this decision does give clarity and certainty, with operators and rail safety workers having the same requirements in WA as everywhere else in the country, ultimately reducing the complexity of regulation and costs.”
A series of information sessions, to be conducted by rail safety o cers and senior sta from ONRSR’s Perth o ce, will be held to ensure operators and rail safety workers understand the application of the national law in Western Australia.
“We will work closely with all our stakeholders in Western Australia over the
coming months to explain exactly how this change will be managed and what it means for them,” Pelham said.
Pacific National has announced a 10-year contract extension with logistics company Linfox to provide national linehaul rail freight services.
Pacific National CEO, Paul Scurrah, said the renewed contract cements the longstanding partnership between the two companies and will ensure Linfox can continue to provide world-class end-to-end freight delivery solutions for its customers.
“As Australia’s largest private rail freight operator, Pacific National has deep unrivalled experience and capacity in hauling freight on rail and we are honoured to be able to continue to deliver what matters for Linfox,” Scurrah said.
Linfox Australia and New Zealand CEO, Mark Mazurek, said the ongoing partnership with Pacific National ensures they can continue to deliver on their purpose of creating a safe, secure, e cient, sustainable future.
“Pacific National’s network, ability to scale freight services and investment pipeline will ensure Linfox remains on track to meet our future growth and sustainability
aspirations,” Mazurek said
“Rail-based intermodal freight systems o er three times greater fuel e ciency than road transport, leading to significant reductions in greenhouse gas emissions.
“Linfox and Pacific National have enjoyed a
The Victorian Government’s investment in the states regional rail-freight network means the state’s $4.4 billion grain industry can shift more grain by rail freight for both domestic and export markets.
Grain volumes moved by rail in Victoria increased by 95 per cent between July and December 2023 compared to the same period in 2022 and by 57 per cent between July 2023 to March 2024 compared to the previous year.
This has resulted in an extra 500,000 tonnes of grain transported across the state by rail – with one standard 3,000-tonne grain train carrying about $1.2 million worth of produce being the equivalent of removing 70 B-Double trucks from regional roads.
GrainCorp COO Klaus Pamminger spoke about the relationship between the organisation and the government.
“GrainCorp is working closely with the Victorian Government and industry stakeholders to improve rail infrastructure in Victoria, to facilitate quicker and more
e cient movement of grain from our sites to end users in domestic and export markets,” he said.
The investment in the regional freight network has allowed heavier trains to discharge at Geelong Port through increasing axle-load capability at key grain handling sites as well as through recommissioning the Gheringhap loop near Geelong.
V/Line has already delivered axleload capability upgrades across Piangil, Woorinen, Tocumwal, Murchison East, Elmore, Mitiamo, Charlton, and Wycheproof, with more upgrades in the pipeline.
GrainCorp has since invested in rail improvements at several of its up-country sites in Victoria, to handle larger and more modern wagons, including extending railway sidings at some terminals in partnership with V/Line to accommodate longer, heavier trains.
Further confidence in the rail network was demonstrated by operator Southern
longstanding relationship that has stood the test of time, and worked together e ectively through the challenges of COVID-19 restrictions and network weather impacts to continue to deliver and move essential freight for Australian communities.”
Shorthaul Railroad’s recent purchase of 22 new broad-gauge grain wagons – the first order for new broad-gauge grain wagons in 16 years.
In October 2022, V/Line, bulk grain handling companies, and rail freight operator Pacific National, formed the Grain Rail Improvement Plan Working Group –formalising their commitment to optimise the rail freight network.
The intermodal Fairfield Freight Hub was opened at an event attended by Transport
Minister Simeon Brown, Ashburton Mayor Neil Brown and senior managers from the Wareing Group and KiwiRail, in Ashburton, New Zealand.
KiwiRail Chief Executive, Peter Reidy, said the hub is great news for KiwiRail and the Ashburton area.
“Mid Canterbury is a base for moving significant container volumes to South Island ports and around New Zealand, whether it’s grain, seed, horticultural produce or meat,” he said.
“However, our existing container terminal in central Ashburton was too small to meet today’s freight demand.
“Working with the Wareing Group to move operations to Fairfield, and with support from the Ashburton District Council and central Government, we will increase the amount of local freight carried by rail from 6,000 containers to 20,000 containers a year.
“That’s half a million tonnes of freight o the region’s roads – the equivalent of 40,000 truck movements – which helps manage road maintenance costs.
“Intermodal hubs like the Fairfield Freight Hub make use of both road and rail transport – enabling trucks to complete the first and last mile of collection and delivery, and for rail to do the heavy longer-distance movements. It highlights how road and rail can work e ciently together, which delivers wider
benefits for the community.”
Brown said the hub had a number of benefits for Mid Canterbury.
“Significantly reducing shunting in the centre of town means locals aren’t stuck at level crossings anymore while wagons are connected or disconnected.”
Wareing Group director, Mark Wareing, said the Fairfield Freight Hub will streamline freight volumes in and out of Mid-Canterbury and at the same time reduce the impact of trucks on road.
“It’s setting the region up for a lower carbon
future and the location near the Northpark Industrial Park is ideally located to take advantage of this new hub,” he said.
“Helping exporters and freight partners move more freight by rail makes sense both from a business and sustainability perspective and will help stabilise the supply chain issues our clients and their customers are facing.”
The Fairfield Freight Hub development cost $14 million. It included some funding from the Ashburton District Council and Government.
Rail operations to and from the hub started on 8 April.
Work is underway to assemble the rail bridge needed to remove the Fyans Street level crossing in Geelong later this year.
Key sections of the bridge that will replace the congested Fyans Street level crossing and roundabout in South Geelong have been delivered to site in recent weeks, ready for assembly.
Work to assemble the three bridge spans is underway onsite at the Fyans Street construction compound, before the full bridge structure is moved into place later this year.
The central span of the bridge will be made from four steel girders totalling 400 tonnes, which were manufactured and delivered from Haywards in Launceston.
The steel girders and 27 cross girders travelled more than 700 kilometres by ship to the Port of Melbourne then by truck to site, where the concrete deck and maintenance walkways will be installed.
A further two bridge spans made up of precast concrete “Super T” beams that will sit either end of the steel girder bridge were
also delivered, with eight 70-tonne, 1.5-metre high, 25-metre-long beams manufactured at
Rail Express toured two Suburban Rail Loop sites to gain a greater understanding about the work being done and what it means for local communities.
Suburban Rail Loop (SRL) will deliver 90 kilometres of rail line linking every major train service from the Frankston Line to the Werribee Line in Melbourne.
The SRL project is broken into four sections, which include SRL East, North, Airport and West. The North section will connect to the Melbourne Airport and the Airport section will connect to the west.
Melbourne Airport is ranked as the 50th busiest airport in the world but is among only six of those 50 to not have an airport link.
SRL East is now under construction and the Rail Express team was given access to the sites at Box Hill and Burwood to learn more about the project and speak to some of the team putting the project together.
SRL is designed to future-proof Melbourne for growth. The areas around the new stations will have diverse housing options, local services and jobs closer to where people want to live.
Three transport super hubs at Clayton, Broadmeadows and Sunshine will connect regional services, so passengers outside Melbourne won’t have to travel through the CBD to get to employment, hospitals and
universities located in the suburbs.
Construction of SRL East from Cheltenham to Box Hill is underway following the release of the SRL Business and Investment Case and planning approvals, leading on from a detailed Environment E ects Statement.
SRL East will slash travel times, connect people to the network from the Gippsland corridor and create up to 8000 direct jobs during its construction.
Construction is forging ahead across the
project. More than 1,200 people are already working across all sites, and expressions of interest are now open for the two contracts to build the six new underground stations.
Construction started in June 2022 and trains will be running on the East section by 2035.
As an integrated transport and planning project, Suburban Rail Loop will deliver both more public transport and more homes in the right places – with a long-term vision
revealed for 70,000 more homes above and around the six SRL East precincts.
Lissa van Camp is the Executive General Manager, Land Planning Environment and Sustainability at the project. She explained what the project means for the communities and Melbourne more broadly.
“We are going to grow from 6 million people to about 9 million people living in Melbourne by 2050 and Victoria itself will have over 11 million,” van Camp said.
“That is a lot of growth to get ready for and we know it can only happen in a planned and coordinated way.
“We began in 2019 with a reference design, which highlighted the way in which the project can proceed. What we are proposing is a rail line that links all of the major lines between Frankston and Werribee and that will in turn transform Melbourne into a city of multiple centres.”
Van Camp explained that this project will alleviate the need for residents to go into the city and then back out on a di erent line to get to di erent suburbs. SRL East will provide easier access to universities.
Monash University and Deakin University will have train stations nearby to support sta and students. Van Camp explained that the SRL will provide equity of jobs not previously seen.
“A person may not have taken a job in Box Hill previously because the commute would
have taken them away from their families,” she said.
“SRL will cut tra c o the road for commuters going to other areas as well. We are expecting 70,000 trips every day on Suburban Rail Loop East, with 40 per cent shifting from their cars”.
Van Camp said Suburban Rail Loop is based on the core values outlined in the reference design of productivity, connectivity and liveability – ensuring Melbourne remains one of the world’s most liveable cities for generations to come.
All of the technical studies were peer reviewed to ensure accuracy and this is what helped decide the locations for SRL East. The team then moved onto consultation with a range of stakeholders.
The SRL team is making a concerted e ort to consult with local communities throughout the planning, design and delivery of the project.
The latest phase of community consultation is about how the future of the neighbourhoods around the new underground SRL stations and how they evolve in the decades ahead.
‘Key directions’ are now open for community feedback, which outline how SRL precincts can host more jobs, housing and services over time – and o er more choices
for the next generation who want to live closer to their family and work.
“We want to hear as much as we possibly can – working with communities and councils to understand what the areas around the stations should look like.”
This latest round of consultation follows the release of a Discussion Paper in August 2023, followed by Draft Precinct Visions for each of the six SRL East neighbourhoods in December, outlining opportunities for more housing choice, increased economic activity and open spaces for the areas around the new underground SRL stations.
The interactive online survey was visited more than 33,000 times and the Draft Visions were downloaded more than 6800 times, with more than 3400 responses received.
A key component of the consultation process has been working closely with local organisations and institutes in each area, including education stakeholders like Deakin University and the Box Hill Institute. The station is also across the road from a high school in Burwood.
“We can help shape Burwood into a worldclass education precinct and Box Hill into a world-class retail area,” van Camp said.
“A major part of this is about making sure there are logical and easy access points for people to move around.”
Another component for this project is cultural vibrancy and van Camp said this is
particularly important in the Box Hill precinct.
“A thing we spoke about is the vibrancy because I feel it every time I come here,” she said.
“It is about enhancing that and using it to drive the project forward. We want to understand what communities love about this area and bring that to life at the new Box Hill station.
“We then also need to plan for sustainable outcomes including future buildings and creating open green spaces.”
Van Camp said the project is working closely with businesses while construction occurs and incentivising to help keep people coming to the areas. The project will aim to minimise the impacts of construction for local residents and businesses in these communities. Over a recent long weekend, the project shut down to ensure the area maintained its vibrancy and residents could have peaceful surrounds during their time o .
Christian D’Agnolo is the Package Director, Stations, Rail and Infrastructure Delivery on the project and has been part of SRL since day one. He explained that the network had the benefit of being a standalone rail network.
This freedom allows the venture to be purpose-built to suit specific needs of Victoria into the future, including modern high-tech trains that can travel at speed and provide a turn-up-and-go service.
“We have conducted extensive market sounding, and we have strong market participants,” D’Agnolo said.
The six stations in SRL East are split into two station packages according to D’Agnolo.
“We are putting together the station architecture kit of parts,” he said.
“It is always important that we have common elements amongst all of our stations. We are looking to get consistency so the touchpoint for users is considered and thought out.
“This approach has been well received by market and will be helpful when we engage with the ultimate operator.”
D’Agnolo explained that SRL East is looking at future precinct integration and consistently understanding what intermodal benefits and connectivity can be achieved.
“The success of the project will really be centred on how we manage and minimise impacts of construction on residents, businesses and local organisations during the delivery,” he said.
“That is an ongoing task and a key focus for the team, and we are working in that space with some key processes and
encouraging collaboration and engagement with the community.”
SRL will be building a new temporary electricity substation near the site in Burwood to support the power needed for the tunnel boring machines. Once tunnelling works are complete the facility will be reconfigured to provide a permanent power supply to operate the stations and the train line.
Adam Mellino is the Senior Delivery Manager for the Burwood station and explained what the important components of this site are.
“SRL is bringing options to people who may not have previously had them – whether that’s educational opportunities, job opportunities, housing opportunities,” he said.
“People who may not have chosen Deakin or Monash Universities due to inaccessibility, for example.”
Mellino explained that a component of the Burwood site is the pedestrian overpass that crosses over the Burwood Highway connecting the station to Deakin University and the high school.
“We explored the options of an overpass and underpass but from a safety perspective, and through our consultation with community and stakeholders, an overpass was the best solution,” he said.
“We have a bus interchange adjacent to the station and the new tram stop as well so we have some excellent connections with other transport for users.”
The new station’s 94m long platform will sit around 18m below ground, with lifts and escalators connecting passengers to SRL’s ‘turn-up-and-go’ train services.
A new tram stop outside the station on Burwood Highway, near Deakin University, will make interchanges quick and easy, providing a new rail connection for local workers, students and residents.
The project is also looking at improving the Gardiners Creek waterway along with the green areas around it.
“What we found with consultation with the community was there were opportunities to improve the water, trees and trails so the naturalisation project associated with SRL will improve this,” Mellino said.
“We will have separated walking and cycling tracks that will connect to existing infrastructure.”
The station will have a range of bicycle parking to encourage users to ride to the station and utilise them once the naturalisation is completed.
Mellino said that each SRL station will have unique aspects that reflect the local areas, but also common elements to make the train journeys simple for passengers.
“You will have those common elements at the platform and concourse level, but individual features outside of that. This
station will have a large skylight to let in plenty of natural light for example,” he said.
“We will consider meeting places and di erent paths people will be taking when designing the station and its surrounds.”
Similarly to the Burwood station, Box Hill Station will have a large skylight to provide natural light onto the platforms, but it will then have a range of design elements unique to the Box Hill area.
The challenge with the Box Hill site is the narrow construction zone in a relatively built-up area, and minimising disruptions to the community. The tram terminus for the 109 service has been shifted further west along Whitehorse Road to accommodate the construction site and keep tram services running during construction.
The Box Hill station will be well connected with a pedestrian promenade linking it to Box Hill Gardens and an enhanced open space.
It will have tra c-free connections to buses and the moved tram terminus. It will have a pickup and drop o area, taxi bays and more than 500 bicycle parking spaces.
The station will be located in the heart of Box Hill with two station entrances at Market Street and another north of Whitehorse Road.
The 94m-long platform will sit 23m below ground, with lifts and escalators connecting passengers to SRL.
Anthony Baldi is the Senior Project Manager at Box Hill and explained the site in greater detail.
“Our station intends to operate with up to 15,000 people per day and we expect one third of those passengers to interchange with the metro network,” he said.
“Coming up to the surface level we have the ancillary buildings that will house our critical station infrastructure. It will store the tunnel ventilation system.
“At surface level we will also have this rolling linear reserve path running between Whitehorse Road, from Lesley Street down to Nelson Road. That is about 800 metres of public space, which will create a new plaza area.”
It has been imperative for the team at Box Hill to minimise disruption as much as possible. Contractor Laing O’Rourke is building a temporary bridging structure to allow Whitehorse Road to remain open to tra c during construction.
“We needed to have a solution so we did not impact road users, and this bridging structure ensured we could have continuous tra c while we were working,” Baldi said.
It is expected that employment in Box Hill will double to 48,500 jobs as a result of SRL.
“We are looking to make this into a real cultural hub and pedestrian friendly once completed,” he said.
“This area is a real asset to the community of Box Hill and we will look to build upon that.”
RATP Dev has leveraged detailed surveys across its international networks to better understand local expectations.
RATP Dev is placing a focus on customer experience across its international networks thanks to customer surveys to better understand passengers’ needs, leading the way in public transport by o ering personalised solutions.
RATP Dev, a subsidiary of RATP Group, operates and maintains networks in over 100 operations across 15 countries. They ensure the transportation of close to 840 million passengers a year. RATP Group runs Paris’ multimodal network one of the densest in the world and is the launching o point for the trial of many new passenger initiatives.
At RATP Dev, the passenger experience comes first. The company has created a range of core principles it aims to abide by when running its networks.
These include:
• Adapt user experiences to each local context;
• continuous improvement for constant improvement of customer satisfaction;
• an extensive services availability that takes into account mobility as a whole and being there for everyone;
• digital and human combinations to enrich the range of user services.
To uncover irritating elements and tailor the actions and initiatives that will help make a customer’s journey more enjoyable, RATP Dev utilises customer surveys.
The results from the surveys have seen a range of projects rolled out across RATP Dev’s networks to improve passenger satisfaction and the network appeal.
Denis Masure is the general manager Australia New Zealand for RATP Dev. He explained how important these surveys are
and their impact the decision making of the organisation.
“RATP Dev is present worldwide, and we pride ourselves in tailoring our solutions and customer experience solutions to the local context and specifics,” he said.
“We prefer to avoid duplicating o -theshelf solutions, and surveys help us identify the specific needs of passengers on each network to bring them the best solution.”
Customer surveys are part of the continuous improvement principle adopted by RATP Dev to set the highest standards of passenger experience in its networks. “These surveys support RATP Dev’s day-to-day initiatives such as the Welcome Program, which is our passenger-centric customer experience
programme adaptable to each type of network,” he said. “It aims to understand our customers better and improve passenger experience.”
One method included in the Welcome Program is the Voice of the Customer workshop.
“This pragmatic, hands-on method, with its action follow-up plan, is used to analyse customer feedback from surveys and comments left online by passengers,” Masure said.
“To ensure a holistic approach to customer experience, we make sure to have all the roles within the network represented, from the frontline sta such as drivers, and executive directors, and have them work together to identify customer pain points, come up with solutions and set up an ambitious and realistic action plan.”
These actions and results are shared with the rest of RATP Group’s networks forming the Welcome Program community, collecting best practices and setting the standard higher for passenger experience. This knowledge sharing within the community cultivates RATP Dev’s expertise on customer experience.
This strategy has proven successful many times, especially in Cairo. RATP Dev has taken over the operations of the metro Line 3 since 2021, and in two years of operations, managed to increase customer satisfaction from 75 per cent to 90 per cent. Several actions that were proven in other networks of the RATP Group
were implemented, including the overhaul of passenger information with a simpler, more legible metro line map and network plan; and the installation of artwork by local artists celebrating the Egyptian history in stations.
This cultural initiative has been implemented in other networks, such as in Tuscany, Italy, where buses are turned into art exhibition spaces for local artists to display their works.
To increase the passenger satisfaction rate, another initiative developed by RATP Dev was the implementation of video games for its metro customers in Cairo line 3 (available through QR Codes), to get passengers entertained and make their journey a fun time. These QR codes are placed inside metro trains and give access to the dashboard of RATP Dev games. The aim is to associate the company’s logo with a source of fun and happiness in the passenger’s subconscious.
With 120 years of experience operating the Paris metro and knowledge sharing from its international networks, RATP Group aims to bring the best solutions to Australian customers, while ensuring they are fit to their specific needs.
RATP Group’s decades of experience led
to the development of a unique expertise in station design, with a special focus on universal accessibility. This includes signage that can be easily understood by all passengers, especially passengers with special needs – with physical or cognitive disabilities.
To ensure a customer-centric design, RATP worked with associations for the diversely abled during the full overhaul of the Châtelet-Les Halles station (Paris central railway station), to clarify the orientation signs and make the station accessible to all. The results saw improvements for all passengers and a renovation of the interior spaces of interconnection areas for accessibility.
This experience was used in Sydney, where RATP Dev organised several workshops with architecture firm Hassell, for the Sydney Metro – Western Sydney Airport project. The purpose was to ensure the design of the stations would be customer-centric and incorporate previous learnings: three options for the interior design were presented to a panel of passengers and advice was provided by them on what they believe would be the best station design.
RATP Group has also accumulated years of experience in handling international customers utilising airport links and o ering them the latest innovations to make their journey easy and seamless.
Since 2020, Orlyval shuttles between Paris and Orly International Airport have been equipped with communicating windows made up of LCD screens that o er adapted information in real time, which includes flight schedules, interconnections, RSS feeds and international news.
As Paris is hosting the 2024 Olympic and Paralympic Games, RATP has successfully trialled new solutions to ensure international passengers and sport fans travelling on its network would benefit from the same high-quality quality of service, and even improve it. On the fully automated Line 14, which south extension to Paris Orly International Airport will open in June, an AI-driven crowding solution is being tested to provide passengers with crowding information.
RATP Dev surveyed Sydney residents around potential barriers to public transport use and what they are looking for in the new Sydney Metro Western Sydney Airport network.
Out of a panel of 500 respondents in Sydney, 54 per cent of them perceived
public transport to have better environmental impacts than a smaller 33 per cent who perceived electric cars as having a greater impact.
Most perceived public transport benefits in Sydney are related to better city living with 67 per cent of respondents saying it o ers everyone the possibility to move around (for an average 65 per cent in 12 territories worldwide). Furthermore, 66 per cent said it contributed to improving the quality of life, five points above the average percentage, placing the Sydney population among those with a positive perception of public transport and, therefore anticipating high standards aligned with this perception.
“Residents will be looking for a service that is reliable, comfortable, e cient, with access to clear and accurate information and a personalised approach to customer across Sydney Trains and Sydney Metro,” Masure said.
“As we want to attract new customers and support sustainable urban development with new, denser precincts around the delivered stations, we know how critical the customer satisfaction will be.
“A good integration with other transport
modes is a crucial element people will be looking for.”
Being a part of the Sydney MetroWestern Sydney Airport project from the design phase is giving RATP Group the added possibility to understand and tackle barriers to public transport use.
“RATP Dev runs and maintains 23 subway lines, 13.700 bus, 22 tramway lines, and urban or intercity rail lines around the globe,” Masure said.
“To do so e ciently, our first duty is to have flawless engineering to ensure optimum availability and timeliness, which are the prime needs of passengers. And RATP Dev has unrivalled expertise in this field. But putting the traveller at the centre, as we do, goes beyond that, with relevant, legible and accurate information for passengers.
With high standards of comfort, not only in terms of cleanliness, but also in everything that contributes to the travel experience, such as train and station temperature, lighting, etc. It’s by intervening at all these levels, thanks to our user understanding programs, that our teams mobilise to guarantee a passenger experience of the highest standards.”
In the quest for sustainable rail travel, the debate rages on between two contenders, hydrogen vs. battery-powered trains. Siemens Mobility is exploring why both deserve a spotlight.
When it comes to the core technology, both hydrogen and battery-driven trains share a foundation – an electric drive train powered by controlled motors. Batteries are integral for swift acceleration and crucial energy recuperation during braking. Hydrogen trains incorporate an additional element – a fuel cell sustained by high-pressure hydrogen tanks, ensuring continuous battery recharge.
In Australia, the transport sector ranks as the third-largest contributor to greenhouse gas emissions, accounting for 21 per cent of the nation’s total emissions. Furthermore, transport emissions have experienced the highest growth rate compared to other sectors. Notably, Australia’s per capita transport emissions exceed the OECD average by 45 per cent.
It is important that the move to net-zero is a transition, but there is a caveat in that it can’t be achieved with the flick of a switch that solves all the issues the country is facing. Long-term investment is required from across
the energy, transport, and infrastructure sectors to support the journey to net-zero.
This will require commitment, alignment, coordination and communication between governments, infrastructure managers and train operators. But the results of this work will mean positive benefits for stakeholders and passengers, and this helps bring the transportation sector closer to the goal of decarbonisation and Australia’s goal of netzero by 2050.
As Albrecht Neumann, CEO for Rolling Stock at Siemens Mobility explains, hydrogenpowered trains are a leap forward in innovation.
“With an impressive range of up to 1200 km and a swift 15-minute refuelling time, trains like the Mireo Plus H are formidable contenders,” he said.
“The only by-product of a hydrogen fuel cell is water, underlining the environmental integrity of this technology.”
Hydrogen can be produced through electrolysis, tapping into green energy sources like wind or solar power. This leads to a carbon-neutral operation, making a direct contribution to emissions reduction.
The Australian government has announced $2 billion for the Hydrogen Headstart initiative for green hydrogen projects to be built in Australia, and to cover the commercial gap between the cost of hydrogen production from renewables and the current market price. This can support the revolutionising of Australia’s rail sector to create a cleaner, more e cient rail network.
However, the journey towards hydrogenpowered trains isn’t without challenges. Building refuelling stations, hydrogen production, and distribution all require substantial investment.
Also, the current cost per kilometre (km) for
hydrogen fuel is approximately three times that of battery-powered alternatives. It’s this balance between benefits and challenges that guides the Siemens Mobility approach to portfolio decisions.
Looking ahead, hydrogen could establish itself as a viable alternative to diesel locomotives, particularly in regions like Australia and the USA.
Already, legislation in California mandates deposits of up to USD $1 million (depending on emissions value) for diesel operators into a trust account, creating a financial incentive to explore environmentally friendly technologies. Operators have the discretion to utilise the funds to promote environmentally friendly technologies. Substantial sums accrue in these accounts, while the introduction of new diesel locomotives into service is prohibited. This transition aligns with Siemens Mobility’s vision for a sustainable future in rail transport.
Battery-powered trains are a cost-e ective solution for shorter ranges, especially on routes with electrified tracks. They align seamlessly with the imperative for a greener future, especially when paired with electricity from renewable sources.
Yet, it’s crucial to acknowledge the technology’s limitations. As of now, batterypowered trains face challenges related to their range per charge.
After approximately 120 km, these trains
require a minimum one-hour recharge. The environmental impact of battery production is another factor demanding attention and further emphasises the importance of holistic sustainability assessments, urging the industry to explore more eco-friendly battery manufacturing techniques.
In the choice between hydrogen and battery propulsion, it’s clear that both technologies have their place. Battery technology o ers simplicity, while hydrogen provides higher ranges.
These technologies don’t compete; they complement each other seamlessly, ensuring
a versatile and sustainable future for rail travel. This dual approach allows Siemens Mobility to cater to diverse operational needs, from short-haul routes to long-distance journeys, and tackle varying environmental challenges head-on.
Embracing both hydrogen and battery propulsion technologies is not just an option, it’s a strategic imperative for shaping the future of rail transport.
The rail industry knows this isn’t something it can solve overnight, and it is a longer term transition to support Australia’s net-zero targets. As much as Siemens Mobility want to support customers to reach net-zero it understands there is a financial consideration that needs to be acknowledged in the journey.
DT Infrastructure’s home-grown technology solution for asset management has been rolled out on the Waurn Ponds to Warrnambool line in Victoria and now they are looking to bring it to the rest of Australia.
DT Infrastructure is climbing the ranks of the Australian rail sector, leading the way in rail asset management solutions. With a team of more than 250 rail systems specialists, the constructor is working on some of the most complex rail and infrastructure projects in the country.
Underpinning this capability in rail is the company’s whole-of-life asset management strategy, which includes a suite of interconnected technology solutions that sit within its patented TrackDNA platform.
The key to the success of this technology and the increased e ciency of signalling infrastructure is the continuous collection and monitoring of data from the client’s rail assets.
It provides insights into usage patterns, allowing for informed decision-making regarding asset optimisation, renewal or replacement.
With further analytics, customers can demonstrate compliance to asset management frameworks, monitor asset depreciation (remaining life) and ultimately, enhance overall operational e ectiveness and longevity.
By e ectively harnessing this data, DT Infrastructure can e ectively identify potential issues and ine ciencies for clients as soon as possible, allowing for proactive maintenance to minimise the risk of costly interruptions to rail operations.
TrackDNA helps infrastructure owners to aggregate fragmented rail systems technology and assets into a single, unified platform that allows for a diagnostic approach to improving rail asset performance.
The system is technology agnostic, using standard market interfaces that can connect with all third-party systems. The digitisation of rail systems assets enables rail operators and asset owners to better understand the condition of their assets, gain insights on the performance of their assets, and make decisions to optimise their performance.
Wije Nallathamby is the Operations Manager for DT Infrastructure’s Rail Systems Engineering group, and he spoke with Rail Express to explain the system.
“We first launched TrackDNA on the 200-kilometre Warrnambool line,” he said.
“It was originally commissioned in May of 2022, and it will be next commissioned in August of 2024. The platform can collect so much data but we don’t collate it all just for the sake of it. We worked closely with our customers and end users to understand what data was important to them.
“Our client now has two years of data and has seen improved performance, demonstrating the benefits of using TrackDNA. This has helped us expand the use of the platform even further.”
Work on the Geelong and Warrnambool Line Upgrade being delivered by DT Infrastructure utilised two key pieces of technology within the TrackDNA platform: The TrackDNAInControl train control system, which monitors rail tra c along the corridor, and the TrackDNA-InSupport maintenance support system that collects data from trackside assets and feeds back to the end user V/Line to improve the performance of operations.
Trackside assets monitored on this project included:
• InControl train control system.
• Alstom’s signalling interlocking systems
• Object controllers.
• Siemens axle counter systems.
• Level crossings.
• Siemens network switches and routers, power supply, UPS and generators.
• Voestalpine point condition monitoring.
• Equipment temperature sensors.
• Rail temperature sensors.
• Vital servers and gateway platforms.
• Alarm management.
Nallathamby explained that a lot of other comparable technology available utilises AI to aggregate the data, which can become expensive as the volume of data grows.
“We don’t want to put the whole system into data paralysis, so we capture only what we need and provide the information that will make a di erence back to the client,” he said.
“A lot of organisations will come in and provide all the data, which becomes nearly impossible to discern.
“We supply the data that is needed to allow simple visualisations that are tailored for the end user.”
Nallathamby explained that DT Infrastructure’s claim to fame is that its technology is agnostic. In other words, it uses common language interfaces to connect assets and the system can be picked up and utilised across a variety of networks.
“This means our system can talk to any other system type,” he said.
“Our technology is highly customisable and highly adaptable, which allows us to capture what the customer needs, in a way that’s meaningful to them.
“For our customers it’s all about the whole of life of the asset and whether they want
to extend the life of that asset or reduce the maintenance schedule – that is where TrackDNA comes in.
“A lot of private rail in Australia can utilise predictive maintenance as they don’t have the same safety regulations as passenger networks.”
The engineering team always had the desire to make this system customisable for the Australian market, where rail operations across states are often completely di erent. So instead of clients needing to source a specific or tailored system from Europe, our system can be picked up from its current use in Victoria and placed into any network in Australia.
“We want to take our clients on the journey with us as we expand the use of this technology. We are starting on a smaller scale and taking incremental steps. We’re confident that in the coming years, our approach will become prevalent in the market.
“Rail in Australia is heavily regulated so we are committed to proving this can work by slowly implementing it and proving its e ectiveness to regulators.”
Nallathamby explained that rail networks across Australia often have di erent requirements, which is why DT Infrastructure and its technology is suited to Australia’s national market.
“For us it is about ensuring we have perfected our core competencies, which we
then scale them to meet the needs of our partners,” he said.
“We faced some challenges and solved some complex problems. For example, on the Warrnambool line where the length of track involved meant, we had to roll out the program in stages to ensure we were communicating e ectively with the existing systems.
“We wanted to make a commitment to innovate on that project and show the benefits of homegrown technology. We can say that while this success was born out of Victoria – it is just as well suited to the rest of Australia.”
Nallathamby explained that one key
asset for the company is that it is a national organisation that has experience across numerous networks.
“Our intellectual property sits at the national level so it can be passed down to individual networks,” he said.
“So we are perfectly placed really. A technology that can be tailored for the network it’s required on and national business with knowledge of the di erent rail networks across the country and the things that make them unique. It means we will always be able to build the right solution.”
“It’s the combination of both that sets us up as a key partner for Australian networks.”
After nearly a decade in business, Brimble is looking to share its methodology for mutual success.
Brimble has expanded rapidly from its humble beginnings in 2017. Now in its eighth year, the business wants to share more of its methodology with the industry, encouraging clients to include the organisation early in the process when it comes to rail maintenance and construction planning.
Rail Express spoke with Steven Johnson, general manager of operations East, at Brimble to understand the company’s overall goal of supporting the rail industry.
“The general background is that construction organisations come at these challenges from their own perspective,” he said.
“They are working out how they want to develop a delivery methodology, and they may be looking through a narrow lens.
“We can be incorporated quite late in a project, which has some challenges. We don’t want to just be there when something has gone wrong. We can be of greater benefit when we are engaged early.”
Johnson explained that with Brimble’s range
of machines, there is a possibility to improve the methodology and make users aware of di erent equipment solutions available and even sometimes better equipment than what has been used in the past.
“Rather than just being engaged to give them a machine, we want to be engaged to actually provide a solution,” he said.
“We are not competing with these organisations tendering for major projects, we are machine-focussed and want people to utilise that skillset.”
Brimble organises its fleet into three core o erings for the rail sector: the Ultimate Series, the Pro Series, and the Utility Series.
Johnson explained that Brimble takes on the pressure of upgrading and modifying its fleet to meet the needs of the ever-growing rail industry.
“The risk appetite is just not there for these organisations,” he said.
“A lot of companies are intimidated by the idea of upgrading and modifying equipment to suit a project., but this is our core business.”
Johnson went on to explain that what separates Brimble is its willingness to take a machine, or a machine with a slightly di erent functionality, and modify it to suit the needs of the project.
“It is quite a di erent way of approaching things,” he said.
“Other maintenance companies are more focussed on their own programs of work whereas we are more focussed on our machines.
“We aren’t in the manufacturing game, but we do focus on updating our assets to suit the needs of projects and the ever-changing needs of the industry.
“Modification of a machine is not a concern to us. When somebody has a piece of equipment or an asset, that’s ageing, or it’s got a slightly di erent functionality, we’re quite happy to assist them with a new methodology for their
piece of equipment and/or their approach for net-zero.”
Brimble is taking the time to invest in machinery and tweaking it to ideally suit the Australian market instead of bringing in new machinery that may not be purpose-built for Australia’s railways.
THE RIGHT MACHINE AT THE RIGHT TIME
Johnson went on to detail how long lead times on machines when purchasing them brand new, can restrict the success of a tender.
“A lot of these companies cannot compete on these mega projects as they simply don’t have the equipment in their stables,” he said.
“Whereas if we are brought in during the early stages of a tender writing process, we can provide a unique perspective and o er up machinery they have not thought of.”
Brimble is positioning itself to package up solutions for its partners.
The companies that can take on projects like Inland Rail have the funds to take on new machines for these projects, but it is not that simple.
“The cycle of winning a project and getting the work underway is about 12 months, but the lead time for a new machine can be anywhere from 24 to 36 months,” Johnson said.
“We take that risk on owning that asset, so these construction companies don’t have to.”
Johnson has spent time on the other side of the fence, selling many of the machines Brimble has to contractors. This has given a unique understanding of the barriers many see, and he has helped to position Brimble to meet this gap.
“It is not surprising that many companies do not want to make that massive investment
in new machines. What we can o er is an ability to harness what we have to ensure the success of the project,” he said.
Johnson provided an example of why bringing in Brimble to the fray early can make them an asset to the success of a tendering process.
“We have brought machinery on board that will allow organisations to move materials in and out by rail as opposed to doing it through trucks and similar machines,” he said.
“For one example, we can employ our extensive fleet of MFS wagons to deliver materials directly to on-site locations where they are required. Additionally, we can extract a substantial amount of material
from sites, particularly during upgrades of a brownfield project.”
By doing this Johnson said it reduced the instances of having to heavily adjust rail corridors to allow access for trucks and other ancillary machinery.
“A tender can be so much more successful if you can guarantee you will take vehicles o the road,” he said.
Instead of taking weeks to stockpile materials brought in by trucks, by bringing it all in utilising the rail network, companies can reduce the time needed.
“It makes sense to use the rail corridor for what it is designed to do,” Johnson said.
“There are significant potential benefits to this, but it requires a totally di erent way of thinking and the willingness to go on the journey with us.
“You might not be able to eliminate all the trucks from the road, but if you can reduce it significantly, that’s a win for everyone involved.”
Johnson explained that 50 or 60 years ago as trucks and machinery were less advanced, the use of the rail corridor for the movement of materials was commonplace.
“Over time the cheapness and availability of transport and excavators has seen the move to utilising them as opposed to rail corridors,” he said.
“We now have di erent constraints like access to sites at specific times of day and environmental concerns.
“This is why bringing Brimble into the conversations early can revolutionise a construction company’s o ering in a tender and give them the edge to win over competitors.”
Dr Natalie Pelham from ONRSR had the opportunity to speak at the beginning of the RISSB safety conference around the role of the regulator in a changing environment.
Dr Natalie Pelham from the O ce of the National Rail Safety Regulator (ONRSR) is optimistic about the independent body corporates role in the rail landscape when she spoke at the Rail Industry Safety and Standards Board (RISSB) safety conference in early May.
Pelham gave the ONRSR’s perspective of the topic of co-regulation and what it might mean for improving safety across Australia’s network. She has more than 25 years’ experience in the public sector working for Transport for NSW, the O ce of Transport Safety Investigations and now with ONRSR.
“When I first heard about the conference I wondered if there was much to talk about,” Pelham said when commenting on the topic of co-regulation.
“But since joining ONRSR and talking with a range of people both within the organisation and external to it, I realised that while on the surface it might sound like a well understood concept, researchers have lacked a clear operational definition of what co-regulation is.”
The safety law itself makes no mention of co-regulation but cites principles like shared responsibility, accountability and integrated risk management.
According to Pelham the government does not prescribe how the railway should operate. It sets up performance requirements that are qualified through the application of risk management. This provides operators the flexibility to establish standards, rules and operational methods to manage the risks.
Over the past decade ONRSR has worked diligently to deliver on its functions. A key one has been working with rail operators, safety workers and others involved in rail operations, to improve safety at a national level.
“Industry has enjoyed the flexibility to operate and innovate without a big stick regulator snapping at its heels, waving the rulebook,” Pelham said.
“We don’t tell operators what to do in the identification and treatment of safety risks even though that is in our remit. We do provide information that may assist operators.
“We have worked well together. The recent development of the National Rail Safety Strategy is a case in point.”
Pelham went on to ask the question on whether the national regulator was working as e ectively as needed. She recalled that when ONRSR was being established that it was seen as the silver bullet to fix the problems in the industry.
“It was supposed to unlock the barriers to full interoperable networks and harmonised systems and to see the Australian rail landscape mimic the European one,” she said.
“The reality is that much more needs to be done by rail infrastructure managers, rail operators, and indeed governments, particularly in relation to the need for greater alignment of investment strategies to achieve interoperability.
“Perhaps there needs to be acceptance that the current environment is no longer serving as well, and there needs to be stronger involvement of the government and the regulator.”
Moving forward, Pelham sees the role of the regulator as providing greater leadership and working with the rail industry and governments to identify and address important safety issues.
“Integral to that is the opportunity for ONRSR to be involved in discussions nationally to progress key issues such as interoperability, infrastructure and technology investment, along with identifying opportunities to facilitate safety improvements, especially where there are productivity benefits to be gained,” she said.
“We are pleased to be working with the National Transport Commission (NTC), RISSB and others in trying to achieve those goals.
“We continue to look into each and every occurrence reported to us with a view to taking the necessary action, whether it be to provide information to influence change, and to assess compliance and enforce the law as necessary for the optimal safety outcome.”
Through the National Rail Action Plan, the NTC bring together network owners, investors, builders, and educators to:
• deliver a more interoperable national rail system that operates seamlessly;
• reduce the number of di erent parts and systems by creating common standards and ways of working; and
• create more nationally recognised credentials for rail workers so they can work anywhere, not just on the network they trained on.
The National Rail Action Plan has three components that include interoperability. This is especially for new technology such as digital train control, according to Pelham.
“No one wants to see a break of tape gauge response to the introduction of these technologies and indeed other technology,” she said.
“We will lose the potential safety improvements and productivity benefit if there isn’t national coordination. It’s also focusing on where best to harmonise operating standards and approaches to achieve further safety and productivity benefits.”
Headway is being made to develop a model that is not only going to look at an ongoing role for brands but is designed to deliver the safety improvements and the productivity benefits more generally.
“We really welcome the work of the NTC and their leadership in this area,” she said.
“At its heart are stronger definitions of what an interoperable network might entail, and where it is. We need to go further and create certainty, but do we need to go further in creating certainty in the interest of driving safety improvement, general improvements, and productivity benefits?”
The ONRSR know that industry has long identified the lack of harmonised standards as a hindrance to growth and e ciency. While work has either been completed or is underway to inform and develop harmonised standards, the sector does not yet have a full suite in place.
“By taking a more serious look at areas that might need to be mandated, some of these performance outcomes to deliver truly national approaches, along with greater government involvement, investment decisions to drive interoperability and harmonisation can occur,” Pelham said.
“In this context, ONRSR can continue to play a part in encouraging the adoption of new technologies and innovations. For example, as a regulator, I want to see and support things like the testing and uptake of alternative fuels, like ammonia, batteries, hydrogen, or the introduction of automation and similar technologies.
“Of course, as a safety regulator, we are going to want to see the safety case that supports the introduction of those things. The rail safety law should not be seen as an impediment to these sorts of changes.”
Pelham noted the introduction over the past decade of driverless trains in both the
freight and passenger sectors are prime examples of where ONRSR has worked well with the industry to support the introduction of new technologies.
“We will want to understand how proponents will manage the associated change, including contingencies if the developing technology fails, so there isn’t an over reliance on new systems to manage risk to safety during implementation,” she said.
“We will ask questions to ensure that operators understand the di erent systems that impact on each other and for evidence of how they will be e ectively integrated into existing operations.”
Pelham asked the question of how far the industry can push the role of the regulator. She said the work being done by the NTC on the National Rail Safety Law is important and is
being supported by ONRSR.
“After 10 years, it’s worth having a look at whether or not ONRSR allows us to actually deliver the law in a most e cient and e ective way. Does it meet the needs of the industry and the community?
“It could also be an opportunity for ONRSR to embrace new roles and responsibilities that might arise from the National Rail Action Plan, or changes that may be needed.
“A good example is the work has been done already on rolling stock type approvals. The regulator could take a more active role of working at national processes to deliver a single approach to rolling stock type approvals.
“I look forward to that continuing discussion and debate, particularly around a potential evolving role for ONRSR.”
MTR Corporation have been improving train-to-train communication technology, leading the way on the Hong Kong Disneyland Line.
MTR Corporation’s Disneyland line was opened in 2005 and has been providing a reliable railway service for the local community and tourists travelling to and from the Hong Kong Disneyland resort ever since.
The organisation recently announced it would be bringing trains with advanced battery-driven functions into service on the line, as well as deploying advanced train-totrain communication technology for the first time in Hong Kong.
As a part of MTR’s continual improvements, it recently announced it would be implementing an asset renewal plan for the Disneyland Resort Line. This will include purchasing three new four-car trains equipped with advanced battery-driven systems.
The trains currently in use have adopted fully automatic operations (FAO) but have begun to approach the end of their lifespan.
MTR Corporation will procure new trains from CRRC, which can trace its manufacturing roots back to 1900 where it started as Sifang Locomotive Works.
Sifang Locomotive Works manufactured China’s first steam train wholly made in China in 1952 and has expanded a lot since that time.
The first Chinese trains that could travel at 200 km/h, 300 km/h and 380 km/h were manufactured by CRRC and the first “Fuxing” EMU, and the first intercity EMU, were built by the organisation.
All of these developments have positioned
CRRC as a leader in train technology both in China and globally.
The new trains will be the first to be custom built for the Disneyland line providing flexibility in the design process.
Both the exterior and interior of the trains, and decorations on the line, feature Disney themes. The current trains have bronze statues of Disney characters, and all windows are shaped in the style of Mickey Mouse’s head.
MTR Corporation plans to work closely with Disney to enhance the passenger experience for those attending the resort.
The new signalling system will be supplied by Tra c Control Technology, replacing the existing FAO communications-based train
control technology that is commonly used in the industry, with the advanced “train-to-train” communication technology.
To enable the expansion of automated metros over the past decade, TCT’s focus on standardisation has delivered:
• interoperability between suppliers and systems;
• faster project delivery (giving greater certainty at reduced cost); and
• reduced integration risks.
MTR is aiming to invest in the improvements of its rail lines across Hong Kong and beyond and not simply the Hong Kong Disneyland line.
Dr Tony Lee is the operations and innovation director of the company, and he explained the company’s direction.
“We look forward to applying new technologies including artificial intelligence in this comprehensive asset renewal project to create more favourable conditions for future railway facilities, operations and maintenance, and passenger experience,” he said.
“As the replacement of trains and the signalling system are both complex works, we will implement the projects prudently and gradually.
“ We will carry out the relevant testing,
safety verification and inspections in a stringent and orderly manner.
“Various tests and fine-tuning in accordance with international standards will also be conducted and the new trains and signalling system will be put into service upon the approval from relevant government departments.”
MTR Corporation will be making a number of investments on its rail systems. Between 2023 and 2027 it will invest more than
$12.9 billion AUD in railway asset renewal and maintenance.
Various MTR lines have been replacing the trains and signalling systems over the past few years due to the development of local railway networks and the life cycle of railway assets.
MTR Corporation has formulated forward-looking railway asset renewal programmes to ensure the systems are fit for future operational needs and, to “keep cities moving”.
RAIL EXPRESS is compulsory reading and a vital tool for all people working in and around the rail sector.
Rail Express is Australia’s authoritative business to business rail publication.
Combining the resources of our respected journalism team and our unparalleled industry contacts and affiliations, Rail Express provides extensive, comprehensive and balanced coverage of breaking news and trends in key areas like infrastructure, investment, government policy, regulatory issues and technical innovation.
Published both in print and digitally every month, Rail Express is the only publication to have both the official endorsement and active participation of the main railway associations in Australia and the broad support of the rail industry.
The only way to ensure you get every copy of Rail Express is to subscribe today. Visit railexpress.com.au/subscribe.
KeTech is looking to close the gap at the intersection of impairments and inaccessible rail environments with universally designed real-time information.
Although the UK and Australia are at opposite ends of the globe, when it comes to the rail networks, they are not all that dissimilar.
Since 1997, the UK has navigated the environment of a part government and part privately owned rail environment. Around the same time, Australia’s railway was privatised, too.
The main barrier faced by both was the challenge of the implementation of innovation. A high degree of fragmentation in the industry caused siloed data and duplication of systems that don’t work cohesively across various networks.
This had a negative impact on both passenger experience and operational e ciency in both countries.
KeTech has more than 25 years of experience in the UK rail industry and has been working with train manufacturers and operators since the late 1990s to provide real-time, intelligent passenger journey information. It is trying to eliminate di erent versions of the same data and provide a ‘single source of the truth’ that
passengers and operations sta can rely on.
KeTech has implemented several innovative cloud-hosted systems across the UK, such as passenger information systems, customer information systems, connected driver advisory
systems and remote condition monitoring systems. These systems integrate with existing technology and data feeds in the environment, connecting them and improving system interoperability.
KeTech’s systems were created with universal design principles in mind to meet the needs of users with a variety of characteristics.
Its systems are non-discriminatory, helping to improve accessibility across the network through removing the barrier to information. KeTech’s systems provide realtime, accessible, transparent, accurate, and consistent information to enable passengers with or without disabilities a dignified mobility experience.
Removing this barrier allows passengers to feel acknowledged and valued through providing them with the information they need to accurately make sense of their travel journey.
For example, KeTech’s real-time systems consider that people with disabilities may require more time throughout each stage of their journey. Providing live, clear, and reliable information visually and audibly both at the station and on the train about features such as lift status, locations of accessible toilets and correct departure and connections along with platform information, positively impacts journeys for people with disabilities.
According to the Australian Bureau of Statistics, in 2023 there are 4.4 million Australians living with a disability, representing nearly 20 per cent of the population.
Research consistently shows that people with disabilities experience a greater quality of life and better wellbeing when they can interact with the community around them, whether to work, socialise, or access amenities.
Therefore, an accessible public transport system is crucial to enabling people with disabilities. Yet, despite the importance of this accessibility, people with disabilities in Australia report that what is provided is inadequate.
An impediment to achieving accessibility and inclusion for Australians with a disability begins
at the intersection between impairments and environments that lack accessible facilities.
Australia is making progress towards step-free stations, tactile paving, and other accessible infrastructure but it is timeconsuming and costly.
KeTech has delivered systems to create an inclusive railway through the provision of clear, consistent, real-time information that will not only help people with impairments travel seamlessly but the wider public, too.
The organisation believes the right data, presented in the right way, can be a powerful tool, and if used correctly, can fill these gaps that still exist in Australia.
KeTech created cloud-hosted systems that can integrate with a variety of data feeds and translate data into rich information.
The systems can also be scaled easily and are secure and resilient.
Unplanned rail disruptions are sometimes unavoidable. However, a Melbourne research paper found that it’s not the disruption that passengers find most frustrating – it’s the authority’s response to it, and more specifically, the lack of communication with passengers.
A survey shows that ‘being informed when a delay has occurred, when services are likely to resume, alternate route options and being kept up to date throughout the disruption’ all score highly on the importance scale for passengers, but scores low on the real performance rank.
For passengers without disabilities, a lack of real-time information during disruption can be frustrating, but for passengers travelling with disabilities it can make them feel undignified, anxious and vulnerable.
KeTech’s systems can change this, providing the latest updates to each specific rail journey within 30 seconds of it becoming available. This is via integrating with the wayside and multiple other data feeds to provide operators
and passenger with a holistic view of the rail environment.
KeTech’s systems improve the value of feeds already available such as seat reservation, passenger load and coach lettering.
The intelligent system processes this data and presents it through the correct channel at the correct time, providing contextual information for passengers in real-time, including Auslan sign language and hearing loops.
There is $155 billion to be spent on rail projects in Australia over the next 15 years with a clear focus on innovation and technology according to the Australasian Railway Association.
The fact that Australia is behind when it comes to implementing innovative technology could be used to its advantage for first adopters.
For example, the UK first implemented on train real-time journey information in 2015, a system supplied by KeTech; the train operator, First Hull Trains was seen as innovative and proactive in responding to passenger needs when they implemented this technology.
KeTech’s PIS provides a consistent stream of real-time information between the wayside and the train, keeping passengers informed about their journey, onward journey or connections, and any disruptions.
As with many innovations, the rail market approached the idea of real-time information with some scepticism until seeing success stories from operators such as First Hull Trains.
Soon after, multiple UK train operators adopted KeTech’s real-time PIS. The Australian rail industry has the benefit of now seeing not one, but several successful implementations of innovative technology such as this and the challenges it solves and how it could help overcome similar barriers for Australia.
John Holland has been working across a number of projects in Australia including Canberra Light Rail and Sydney Metro.
Dating back 75 years, John Holland has a history of transforming communities across Australia and New Zealand as a infrastructure, building, rail and transport business.
It’s long-standing experience in rail goes back more than 50 years. This includes Melbourne’s City Loop in 1978, to the construction, intergration and future maintenance of the nine-kilometre twin tunnels and five underground stations and systems for the Melbourne Metro Tunnel Project today.
From designing, constructing, testing and commissioning to operating and maintaining transport networks – John Holland is involved in all parts of the rail asset lifecycle.
The rail and transport business is focus on transforming the way people travel and providing better connections across Australia and New Zealand. Expertise in all parts of the rail lifecycle ensures the best solutions for its customers and communities at every stage.
John Holland’s in-house skills, knowledge, and resources, including owning and operating specialist machinery and equipment, allow it
to deliver key rail, operations and maintenance services, and provide certainty and consistency of delivery across a range of disciplines, such as:
• track and civil;
• overhead wiring;
• power and electrical;
• signalling and communications;
• interface design management, and testing and commissioning; and
• rail safety, assurance and accreditation.
John Holland rail and transport executive general manager, Steve Butcher, spoke to Rail Express about the company’s expertise in rail and transport operations.
“What drew me to John Holland more than six years ago, was the end-to-end capability of the rail and transport business – we do everything from drawing a line on paper in the design phase, right through to putting people on trains, trams and buses in our operations and maintenance businesses,” he said.
“Our whole-of-life mindset that means we’re not just designing and delivering for today; we’re thinking about the future.
“We have more than 1300 people working directly in our rail and transport business across Australia and New Zealand.
“On top of that, there’s a further 9,000 people working in our trains, tram and bus operations around the country which we operate with joint venture partners, connecting hundreds of thousands of people to their destinations every day.”
The group operates and maintains some of Australia’s largest public transport networks, providing reliable, and customer-focused public transport services.
“As an accredited operator, our transport services include the design, development, and implementation of customer experience strategies, network control and timetabling, rail safety accreditation with regulatory agencies, along with asset management, maintenance, fleet, and depot strategies,” Butcher said.
John Holland specialises in the systems and processes that lead to the safe and successful design, construction and operation of heavy rail, light rail, bus, and other transport solutions.
This includes design management, design standards and waivers, and reliability, availability, and maintainability engineering.
“We carry out systems engineering, validation, verification, and safety assurance.
John Holland is part of the Canberra Metro consortium, which designed and constructed the Canberra Metro light rail network that opened in 2019. This included the systems engineering delivery and integration to bring the network online.
“We now proudly operate and maintain the network as part of Canberra Metro Operations (CMET) for an initial 20 year period,” Butcher said.
“In April, CMET celebrated five years of successful operations of the light rail network – a 12km line with 14 light rail stops that connects Gungahlin with the city.
“Since starting operations in April 2019, 16.5 million passenger trips have been made and over 4.5 million kilometres travelled on the network.
“While doing this, the team has delivered outstanding service for customers, with 99.98 per cent of services running on time,” he said.
A recent study showed that 43 per cent of passengers on light rail have never previously used the bus network.
Last year it was announced that the Canberra Metro consortium will deliver and operate the Stage 2A extension of Canberra’s light rail system, which will connect the city to Commonwealth Park.
The project will see three new stops built at Edinburgh Avenue, City South and
Commonwealth Avenue, extending the network by 1.7 kilometres – providing a greater connection between the city and the lake.
Light rail to Commonwealth Park will be delivered wire-free to supporting requirements for a future connection through the Parliamentary Triangle. In a Canberra first, the light rail corridor to Commonwealth Park will include sections of green track where the light rail line sits within a bed of specially selected grass or plants instead of concrete.
“Back in 2022 we were awarded the contract to deliver the Light Rail Vehicle Procurement, Retrofit and Depot Expansion (LPRDE) Modification to the CMET Operations and Maintenance contract,” Butcher said. “It’s an exciting time for light rail in Canberra.”
The team have been delivering this project for the CMET network in preparation for the Stage 2A extension of light rail to Commonwealth Park including:
• procurement of five new light rail vehicles;
• retrofitting of existing 14 light rail vehicles with onboard batteries;
• maintenance of new Light rail vehicles and battery systems; and
• expansion of the existing CMET Depot to allow for the increased fleet size.
After delivering the design and construction for operations, trains and systems for Sydney Metro Northwest – with its construction partners – John Holland now operates the nation’s first driverless metro as part of the Metro Trains Sydney consortium.
The new-generation metro trains are
designed to make customer journeys easy – from level access and platforms, to multi-purpose areas for prams, luggage and bicycles, and real-time travel information.
“John Holland is now part of the joint venture that manages the operations and maintenance, Metro Trains Sydney, across 13 stations from Tallawong to Chatswood in Sydney’s north and northwest,” Butcher said.
“Services operate every four minutes in the peak in each direction. Each month the team is delivering millions of passenger trips, with customer satisfaction is consistently above 98 per cent.
“We have continued to be involved on the city extension including building the new tunnel under Sydney Harbour and excavating the station boxes, then where the tunnel emerges, we delivered all of the complex junction remodelling at Sydenham Station with the conversion from the existing Sydney Trains network through to Bankstown.
“Along the route we are building the integrated station development at Waterloo. And as part of the Joint Venture operator, Metro Trains Sydney, we have been integral to the overall operational readiness and working with all of the teams getting the infrastructure ready to expand the operational railway.”
“The team is also working on the testing and commissioning programs for Sydney Metro City and SouthWest.”
“Looking at our footprint across the country, I’m proud of our how we’re keeping Australia moving – people, communities and the economy, and how we continue to grow and look at new opportunities.”
In his first public speech as chief executive o cer of Inland Rail, Nick Miller has told the Australasian Railway Association Rail Freight Conference that Inland Rail is on track to deliver strong progress in 2024 despite challenges.
Inland Rail is a 1,600-kilometre freight rail line, now under construction. It will connect Melbourne and Brisbane via regional Victoria, New South Wales and Queensland.
Having completed successful possession works on the Beveridge to Albury project in Victoria, and the Stockinbingal to Parkes section in New South Wales, Inland Rail CEO Nick Miller told Australasian Railway Association Rail Freight Conference delegates that Inland Rail was making strong progress towards to completing the Beveridge to Parkes sections by 2027.
Miller said Inland Rail environmental approvals in New South Wales were also progressing well, with the New South Wales government in the final stages of the
approvals process for the Albury to Illabo and Illabo to Stockinbingal sections in southern New South Wales. This comes on top of the Australian Government approving the Narromine to Narrabri section in February.
“Inland Rail is one of the biggest infrastructure projects ever undertaken by the Australian Government. It is a critical part of the transport supply chain and the economic development of Australia and is needed to keep pace with the freight demands of our growing population,” he said.
“Like all major projects, Inland Rail has had its share of setbacks and challenges, and I dare say there are more to come in the years ahead. However, let’s make one thing clear, Inland Rail is not a ‘stalled project’. We
are making strong progress on the ground, two sections have already been completed in New South Wales, work is well underway on a third, and we should receive two more major environmental approvals in the coming months.
“More importantly, we are also delivering significant benefits for regional communities. Last month we saw the first GrainCorp train travel on the upgraded Narrabri to North Star line, picking up canola at Croppa Creek and taking it all the way down to the Port of Newcastle for global export.
“This is what Inland Rail is all about, opening up new opportunities for our critical primary producers in rural and regional Australia, allowing them to get their products
to domestic and international markets quickly and cost e ectively.”
In Queensland, Miller told the conference that Inland Rail was hopeful of finalising the Environmental Impact Statement for the Border to Gowrie section with the Queensland co-ordinator general in the coming months.
With construction moving ahead in New South Wales and Victoria, Miller said the project was already delivering direct benefits to rural and regional communities during
construction. He noted that more than $420 million has been spent with in excess of 530 local businesses on the alignment, with some $42 million spent with nearly 30 First Nations businesses.
At the same conference, Australasian Railway Association CEO Caroline Wilkie talked about the importance of getting more freight moved by rail.
“The critical role that rail plays in delivering large volumes of goods across vast
distances has never been more keenly felt, with the urgent need for a focus on network resilience underscored by the pandemic and multiple flood and bushfire events that have caused disruptions over recent years,” Wilkie said.
“There is an urgent need for rail to increase its share of Australia’s significant and growing national freight task to meet future demand.
“Our freight task will continue to grow, and road and shipping alone will not be enough – we need a resilient, reliable, and e cient national rail freight network to support the economy and community.
“There is also a huge environmental imperative to move more freight from road to rail. It will be critical to reducing our transport emissions and making sure we meet Australia’s net zero target by 2050.”
Australia’s total domestic freight task is projected to grow by 26 per cent between 2020 and 2050.
Despite this, only two per cent of freight is hauled by trains between Sydney and Melbourne – the busiest freight corridor by volume in the country – and less than five per cent of freight is currently moved by rail between Sydney and Brisbane.
Even the critical Melbourne-Brisbane transport corridor has a rail mode share of less than 30 per cent.
This year the industry celebrated the 10th year of Rail R U OK? Day, a day on the rail calendar to show support for those struggling with their mental health.
Thursday, 18 April 2024 marked the 10th anniversary of Rail R U OK?, an initiative dedicated to building a supportive workplace culture where colleagues look out for each other every day of the year.
Rail was the first sector to have its own dedicated R U OK? Day and this year, the TrackSAFE Foundation and R U OK? called on the rail industry to bring their teams together for a workplace event, focusing on this year’s theme, ‘R U OK? I’m Here to Hear.’ And no surprises, the rail industry responded.
The day saw hundreds of organisations and more than 120,000 rail workers coming together, connecting and sharing experiences of when support has helped during tough times. Events on the day also helped build confidence to have a conversation and the value of making space to really listen.
Research shows the initiative successfully motivates individuals to support their colleagues. A 2021 survey found 70 per cent of those who were aware of Rail R U OK? had checked in with someone.
when colleagues showed genuine concern as he navigated a tough time.
“When I returned to work after my mother passed away, nearly a dozen people noticed I wasn’t myself and checked in with me,”
for me to say outwardly that I wasn’t OK.” Hardman’s personal challenges and his understanding of the struggles that come with being a rail worker have made him passionate about creating supportive work
happens when you embody the simple steps of R U OK? as a business. One by one, people feel more comfortable checking in with others, and eventually, it becomes the norm,” Hardman explained.
“Because of that, employees who are struggling seek help earlier, lives are transformed, and sometimes saved.”
Katherine Newton, CEO R U OK?, said that over the past decade, the day has evolved from a national day of industry-wide action into a year-round movement that fosters a culture of compassion and understanding among colleagues.
“To those who have championed this conversation movement, thank you. You are pivotal in breaking down stigma and encouraging authentic and open conversations,” she said.
Jules Robinson has worked with Metro Trains Melbourne for 12 years and was involved in the first Rail R U OK? Day in 2015.
“I’ve noticed a huge company-wide shift since we launched Rail R U OK?, and it consistently resonates with our sta each year,” Robinson said.
“Building an R U OK? culture is about recognising that we are all human, we all go through tough times, and we need to hold space for people to talk and learn to really listen.
“Rail R U OK? isn’t about training everyone to become a counsellor, it’s about acknowledging that life isn’t always easy
and making work a safe place to talk.”
Rail R U OK? has grown to become more than just a day, it’s now a movement that aims to empower rail workers to identify the signs that someone might not be OK and o er guidance on how to listen and also how to help.
If you would like to become more involved, contact Hope Steele at TrackSAFE, hsteele@tracksafefoundation.com.au
Resources: visit tracksafe.org.au for free resources to help you have an R U OK? conversation and keep the conversation going throughout the year.
Support: If you or someone you know
needs some extra support, you can find contact information for national support and services at ruok.org.au/findhelp.
For support at any time of day or night, Lifeline Australia provides free and confidential crisis support. Call 13 11 14, text 0477 13 11 14 or chat online at: lifeline.org.au.
13YARN is a free 24/7 service o ering crisis support for Aboriginal & Torres Strait Islander people. Call 13YARN (13 92 76).
MensLine Australia is a free 24/7 service o ering support for Australian men. Call 1300 78 99 78 or chat online at: mensline.org.au.
Canberra’s Light Rail project has been an exciting addition to the city. Rail Express looked into the project, its history and the upcoming Stage 2B.
Canberra’s light rail project is beginning to take shape and with Stage 1 complete and up and running in 2019, Stage 2 is set to get underway soon.
The idea for Canberra’s Light Rail has been in the works since 1911, when Walter Burley Gri n, who designed the city originally, intended for the nation’s capital to be serviced by trams.
The plan did not eventuate, and the city was serviced by buses from 1926 until 2019 when the first light rail began running.
This new light rail is designed to future proof the city and take more vehicles o the road. Light rail provides an opportunity to link Canberra’s buses, park-and-ride facilities, cycling networks and pedestrian paths to the activity centres that feed the network.
The network is a 12-kilometre line that links the northern town centre of Gungahlin to the city centre and has 14 stops. Services commenced on 20 April 2019. The 14th stop at Sandford Street in Mitchell commenced operation in September 2021.
In July 2019, the ACT Transport minister, Chris Steel, announced that Stage 2 would be divided into two parts, 2A to stop before Lake Burley Gri n at Commonwealth Park and 2B to continue across the lake to Woden. The line will be 11 kilometres long, with 12 new stops along the route.
The Federal Government, through the National Capital Authority (NCA), granted works approval in 2023 to extend the network.
The National Capital Authority has a key role in planning the future of the city. It has three core responsibilities, which are planning the capital, promoting the capital, and maintaining and enhancing the capital. The NCA considered a variety of di erent criteria, such as the quality of the public realm, community amenity, environment, heritage, and landscape values when approving Stage 2A of the project.
Work on Stage 2A is planned to commence in late 2024.
Construction and testing is expected to take approximately three years, with services commencing from January 2028.
The 2A project is funded by the Australian Government and the Australian Capital Territory (ACT) Government.
Canberra Metro was awarded the $577 million contract following a single select procurement process, generating revenue of approximately $227.5m for CPB Contractors and UGL.
The project will see three new stops built at Edinburgh Avenue, City South and Commonwealth Avenue, extending the network by 1.7 kilometres – providing a greater connection between the city and the lake.
The Stage 2A “catenary-free”, or wireless extension, will be delivered under Canberra Metro’s existing public private partnership (PPP) with the ACT Government.
Stage 2 also includes:
• construction of five new light rail vehicles;
• retrofitting 14 vehicles with onboard batteries; and
• building an expanded depot at Mitchell (expected completion early 2024).
Enabling road works for Stage 2 also include the $60 million Raising London
Circuit project, which involves a series of works to raise the southern portion of London Circuit by six metres to form an at-grade intersection with Commonwealth Avenue (expected completion late 2024).
It was estimated in 2020 that Stage 2 of the project will cost $1.9 billion. The network is projected to move 39,000 passengers a day as Canberra’s population grows to over half a million people.
Light Rail Stage 2B Commonwealth Park to Woden will extend the network to complete a north-south public transport link from Gungahlin, through the City Centre and on to Woden. Stage 2B will deliver at least nine new stops between Commonwealth Park and Woden.
Light rail vehicles will cross Lake Burley Gri n via a new bridge constructed between the existing Commonwealth Avenue bridges, travel through the National Triangle, and along Adelaide Avenue and Yarra Glen.
The ACT Government’s preferred alignment is to take light rail past Parliament House via State Circle. However, alternative stop options in the National Triangle and Barton are also being studied to ensure the project can be flexible and responsive as planning work progresses.
Di erent alignment and stop options deliver di erent opportunities in accessing employment and cultural institutions, place enhancement and urban renewal. Similarly, they each present di erent challenges in approvals processes, technical considerations, design, and construction.
Consultation with the community and stakeholders on Stage 2B has been
Construction on Stage 2A is set to get underway this year.
ongoing since 2017, with more community consultation planned in 2024 as environmental approvals progress.
Views captured through community engagement will be used to inform the Environmental Impact Statement and draft Concept Design.
The Australasian Railway Association (ARA) has thrown its support behind stage 2B of the project. It said the project will be a catalyst for continued urban renewal, delivering economic, social and environmental benefits to the local community.
The ARA CEO Caroline Wilkie said claims that the Light Rail Stage 2B is not cost e ective simply do not take into consideration the long-term economic benefits light rail delivers beyond providing
an e cient public transport solution.
“Light rail projects in Australia and across the globe have consistently shown to dramatically transform communities, driving urban renewal and growth along its corridor, supporting better housing and job opportunities,” she said.
“As with heavy and metro rail, investment in light rail infrastructure provides certainty to the community and local businesses, encouraging land development and increasing property values.
“For example, the first stage of the Canberra light rail project facilitated hundreds of millions of dollars in private investment and completely transformed the gateway corridor into the nation’s capital. This level of revitalisation simply does not happen without the investment certainty that light rail infrastructure provides.”
The National Rail Skills hub is working with industry and educators to grow a diverse rail workforce by showcasing the diverse jobs available in the industry.
IN PROFILE: RUW PALAPATHWALA
Transport Planner, Aurecon
Ruw Palapathwala is a transport planner at Aurecon, a design, engineering and advisory company.
Palapathwala said that working in the rail industry is not just something he does to pay the bills.
“I think of it as a vocation; it’s something I do to make a better world,” he said.
“Rail is exciting. It a ects communities. Particularly when you look at the construction and design of cities. It is transport infrastructure, and rail in
particular, which provides the veins and arteries.
“By expanding rail networks and creating great interchanges, you help people get where they need to go to access jobs, education and participate in life.
“By providing a way to travel distances in a cost-e ective way, rail helps break transport poverty creating social equity and opportunity for people.”
Palapathwala explained that rail is something that people get passionate about, everyone has an opinion.
“I graduated from Swinburne University in
Melbourne with a Bachelor of Engineering and a Bachelor of Business,” he said.
“While I was studying, I worked at a small transport consultancy as part of an entry-based learning program o ered to engineering students. This gave me realworld, industry experience.
“Six months after graduating I got a job at Aurecon. It was a role I chose carefully.”
Palapathwala said that before deciding where he wanted his career to go, he developed a network in the engineering sector.
“I spoke to many di erent people about
the opportunities and what was best suited to my experience and what I wanted out of life,” he said.
“At Aurecon I work on the rail team as a transport planner, modeller and project manager. Most of the work is on larger projects.
“My role is not a traditional rail job. I help Aurecon to understand how a new rail line will fit with, and impact, the wider transport network and surrounding land.”
Palapathwala explained that his role is to work out how many people will take the train, where they’re travelling to and from and what other modes of transport they use on their trip.
“We try to understand what level of service will provide the best outcome for passengers today and into the future,” he said.
“Rail is such a colourful industry to be in. Rail infrastructure developments engage people at all levels of society, from top o cers in government to residents in surrounding communities. I work with people from multiple disciplines, architects, town planners, geotechnical engineers, civil mechanical electrical engineers, environmental scientists. It’s incredibly diverse.”
Palapathwala said that what he finds most satisfying is what you can achieve.
“Rail stations leave a lasting impact on communities,” he said.
“They become a meeting point, a landmark in a lot of instances. They can be the identity piece of the city. I love being a part of that.”
IN PROFILE: CHELSEA WINSKILL
Acting Senior Regulatory Data Analyst, O ce of the National Rail Safety Regulator Chelsea Winskill has a background in data analytics and has brought this skillset to the O ce of the National Rail Safety Regulator (ONRSR).
“I never would have thought that I’d find rail interesting but it’s fascinating,” she said.
“There is so much happening in the sector, you’re always learning. I’m part of the risk and analysis team at ONRSR.
“I work with some highly intelligent people who have specific domain knowledge, whether that’s tracks or rolling stock, and who enjoy sharing that knowledge.”
Winskill said that there is a lot of collaboration both within the team and across teams at the ONRSR.
“This makes for a great working environment. Whenever there’s a challenge or issue, you’re never short of people who
are keen to help you solve it,” she said.
“It’s also a very diverse environment in culture, gender, age.
“Usually, analytics can be male dominated, but our team has a very even pool of talent. This reflects the fact we’re trying to get the very best skills possible.
Winskill explained that the team is mostly aged under 40, but older workers across the rail sector are really valued.
“This ensures knowledge isn’t lost. People respect and value knowledge and experience. It’s what you bring to the table that counts – nothing else matters.
“Most of my work is on report automation. This involves designing and modelling data and reports in a way that people can use and access reports for themselves, on demand.
“In terms of analytics, some of the work
the rail industry is doing is at a really high level.”
Winskill said that the skills and experience she has gained, she could go and work anywhere.
“I’ve been at ONRSR for five years now and have grown to love working in rail and with a team of analysts. We are like minded and I really feel valued in what I do.
“I would encourage anyone who naturally finds maths or statistics interesting, who can identify with being a critical thinker, and who enjoys applying their knowledge in practical ways, to give data analytics a go.
“Industries like rail are fantastic environments to practice analytics because they are, by nature, technical environments which rely on accuracy, data and expertise for safety, e ciency and quality outcomes.”
The Australasian Railway Association held its annual rail freight conference in Sydney in April, bringing the industry together to discuss important issues.
The ARA is dedicated to championing regulatory and operational reforms that enhance the efficiency of Australia’s rail freight sector. The recent ARA Rail Freight Conference provided an opportunity for industry, freight customers and government to come together to discuss ways to improve the resilience, productivity and sustainability of the sector.
The Conference, held at Rydges World Square in Sydney in April, attracted 240 people including local and international industry leaders and government representatives for two days of insightful, frank and forward-looking discussions on the future of rail freight.
The presentations took a deep dive on critical topics such as public and private collaboration, sustainability, interoperability and harmonisation, building resilience, workforce shortages and technology.
There was a star-studded speaker including Dr. Kerry Schott AO, chairIndependent Advisory Panel on NSW Freight Reform Policy Program; Mark Mazurek, chief executive officer, Linfox; Wayne Johnson, CEO and managing director, Australian Rail Track Corporation (ARTC); Nick Miller, CEO of Inland Rail; and Natalie Pelham, National Rail Safety Regulator and chief executive, Office of the National Rail Safety Regulator.
Overseas speakers included Milind Nirmal, executive director – Asia Pacific, DB Engineering & Consulting GmbH, who shared his insights on the benefits of shared infrastructure for freight and high-speed rail in Europe; and Matt Soule, CEO and Co-founder of Los Angeles-based Parallel
Systems, who talked about the company’s autonomous, battery-electric freight wagons and their local partnership with Arc Infrastructure.
Everyone agreed that industry and government needed to step up efforts to build a more resilient, reliable and productive rail freight industry that was fit for the future and better equipped to deliver services that are competitive with road. And there is no time to waste.
National Transport Commission Chair, Carolyn Walsh, summed up the task ahead.
“We have a unique window of opportunity for national rail reform with full alignment of industry, government and policy makers. But the window will close quickly,” she said.
As Nirmal pointed out in his presentation, interoperability and harmonisation measures must be the industry’s immediate focus because it is a long journey and 20 years after having begun, Europe is still progressing.
“I will send a message here to Australia –it is that you’ve got to do something now... otherwise 50 years from now we will be having the same conversation,” he said.
He described Germany’s “Strong Rail” strategy as having delivered “incredible” improvements in network performance and pointed out that the Northern European country – with its 25 passenger operators
and over 400 freight operators – has the most open network in Europe.
Systemic interoperability and harmonisation challenges are key to addressing market share and productivity, and the work occurring through the National Rail Action Plan provides a once in-ageneration opportunity to transform the rail industry. The ARA will be embracing this opportunity by advocating for practical implementation mechanisms and pathways to ensure these reforms become a reality and move our industry forward in a meaningful way
We have also expanded our Interoperability Working Group to ensure we can continue to proactively represent industry on interoperability work being progressed at the national level, driven by the National Transport Commission.
Schott, who conducted the Inland Rail review, provided a frank opening address on the challenges that lay ahead for the freight industry that must be overcome.
Schott said the NSW freight reform program panel has been asked to deliver a comprehensive strategic reform agenda and action plan to optimise freight transport in NSW and she encouraged industry to respond to the discussion paper.
Among her main points were the need to
do a better job of reserving industrial land and making use of it, seeking opportunities to better coordinate operational settings across NSW networks, addressing workforce challenges, and maintaining decarbonisation as a priority.
Hon. Jenny Aitchison MP, NSW Minister for Regional Transport and Roads, opened day two of the conference and expressed her commitment to achieving interoperability and growing the mode share of rail.
Minister Aitchison stressed the need for increased productivity through a collaborative approach between industry and government to support a strong, sustainable industry.
“We can’t truck our way out of the freight task, we have to be prepared to invest in the rail freight network,” she said.
Aurizon Managing Director and Chief Executive O cer. Andrew Harding. discussed the company’s role in managing more than 5,000km of track and operating bulk and general freight services across the country. He said rail had untapped opportunities in emerging markets and emphasised the importance of rail to realising national decarbonisation targets. Harding also stressed the need for improving level crossing safety and shared a compelling video of near misses on the network ahead of releasing a campaign aimed at improving safety in coming months.
Pacific National’s chief strategy and sustainability o cer, Saskia Groen-in’t-Woud, in her presentation on the industry’s outlook, brought her rich international experience in freight, shipping and rail to the Australian context both in terms of operational optimisation and decarbonisation.
Miller provided an update on this nationbuilding project and detailed the economic benefits it is delivering for local communities and in particular indigenous businesses, with more than $420 million spent with local entities.
The conference was timely, coinciding with the reopening of the crucial Trans-Australia line after a prolonged closure due to flooding, which had a significant impact in WA, with rows of empty supermarket shelves featuring in the news for weeks.
This latest disruption again illustrated the critical role that rail plays in delivering large volumes of goods across vast distances and the impact felt every time there is a flood or bushfire that stops rail in its tracks.
Improving the resilience and reliability of ageing rail infrastructure remains a priority for the ARA this year, particularly for key rail freight routes that form a critical part of our national supply chains.
A joint submission by the ARA and Freight on Rail Group (FORG) to the Commonwealth Government’s review of the National Freight and Supply Chain Strategy outlines several examples of freight outages, costing the economy hundreds of millions of dollars in 2022 alone. Some of the examples highlighted include flooding in regional NSW in March 2022, which led to a total of 200 days of track outages, with 26 return services impacted each week, costing the economy $35 million. Washouts on the east-west rail line in regional South Australia cost the economy $320 million, resulting in product shortages and empty supermarket shelves.
Upgrading the interstate rail network would not only improve climate resilience, but also improve overall network performance and provide greater capacity for longer, heavier trains – driving down freight costs and therefore contributing to an easing of the cost of living. The ARA progressed a joint project on rail freight resilience last year, partnering with FORG, ARTC, Arc Infrastructure and Aurizon. Industry has since done considerable work to advance detailed thinking on network resilience, with ARTC having invested in detailed hydrological
modelling to underpin network investment planning with a focus on climate resilience.
The ARA will continue to advocate for additional Commonwealth funding support to strengthen the resilience and reliability of our critical national rail freight infrastructure.
I am very pleased the ARA has been asked to contribute to two crucial freight reviews in NSW and Victoria, including membership of the NSW Freight Transport Advisory Council and Freight Victoria’s Industry Stakeholder Reference Group.
This will ensure our industry continues to have a strong voice at the table on rail freight.
Australia’s domestic freight task is projected to grow by 26 per cent between 2020 and 2050. Despite this, two per cent of freight is hauled by trains between Sydney and Melbourne – the busiest freight corridor by volume in the country – and less than five per cent of freight is currently moved by rail between Sydney and Brisbane. Even the critical Melbourne-Brisbane transport corridor has a rail mode share of less than 30 per cent.
The ARA’s general manager of Freight and Heavy Haul, Georgia Nicholls, gave an update at the Conference on the Future of Freight report, which we launched in partnership with the Freight on Rail Group late last year.
This research was supported by the Department of Infrastructure, Transport, Regional Development, Communications and the Arts and provides a platform for industry and government to work together to increase the use of rail freight. The report highlights the need to increase rail’s share of Australia’s growing freight task – otherwise, even with the addition of the game-changing Inland Rail, we will not meet future demand.
There is also a environmental imperative to move more freight from road to rail. It will be critical to reducing our transport emissions and making sure we meet Australia’s net zero target by 2050.
Rail freight generates 16 times less carbon emissions per tonne kilometre than road transport.
The ARA’s research also shows that a 10 per cent mode shift away from road to rail between major capital cities in Australia would reduce the social costs created through emissions, crashes and accidents and health costs by more than $700 million per year.
The ARA is encouraged by the enthusiasm for change felt at the conference and looks forward to seeing the plans talked about and the vision of a thriving rail freight sector become a reality.
President, PWI NSW
SYSTEM AVAILABILITY
As we approach a monumental milestone in the history of the Permanent Way Institution (PWI), it’s time to shine a spotlight on an event that promises to be a cornerstone for reflection, innovation, and forward-thinking in the rail industry.
This year marks the 50th anniversary of the PWI, and with it comes our muchanticipated PWI Convention, scheduled for the 24th and 25th of October 2024. As professionals dedicated to advancing rail infrastructure, we invite you to join us in celebrating half a century of railway excellence.
is more than just a social gathering; it is a celebration of the legacy and camaraderie that have been the backbone of the PWI for five decades. It’s an opportunity to reconnect with old colleagues and forge new industry connections.
see a timeline marked by significant breakthroughs and milestones that have shaped our profession and society through enhanced mobility and economic growth.
The PWI has been at the forefront of these transformations, advocating for excellence and education in rail infrastructure. As we celebrate this golden jubilee, we also look forward to the future—anticipating the next advancements that will continue to revolutionise our industry.
The convention starts with a series of technical presentations that underscore the strides we’ve made and the future we envisage for rail technology. These sessions, led by pioneers and experts in the field, are designed to showcase cutting-
The second day of the convention will open with panels comprising of experts who have been instrumental in steering the course of our industry. These discussions are set to cover a range of topics, from safety and sustainability to technological integration and policy innovation. Following the panels, the floor will be given over to industry presentations that reflect the ongoing work and future projects that continue to push the boundaries of what is possible in rail infrastructure.
At Siemens Mobility, we value our local manufacturing facilities and engineering teams for their innovative and sustainable ways of working, as they are the key to revitalizing old and new rail technology that will #transformtheeveryday and change the way we travel globally.
WITH A NETWORKING EVENT PAR EXCELLENCE
No PWI Convention would be complete without its renowned networking event.
Mark your calendars for October 24th and 25th, and be part of this historic event in the rail industry. Whether you’re a seasoned professional or new to the field, the PWI Convention o ers a unique opportunity to connect with leading minds, engage with transformative ideas, and celebrate a remarkable legacy.
We look forward to welcoming you to an event that promises to be as memorable as the journey that has brought us here. Here’s to 50 years of the PWI and many more to come!