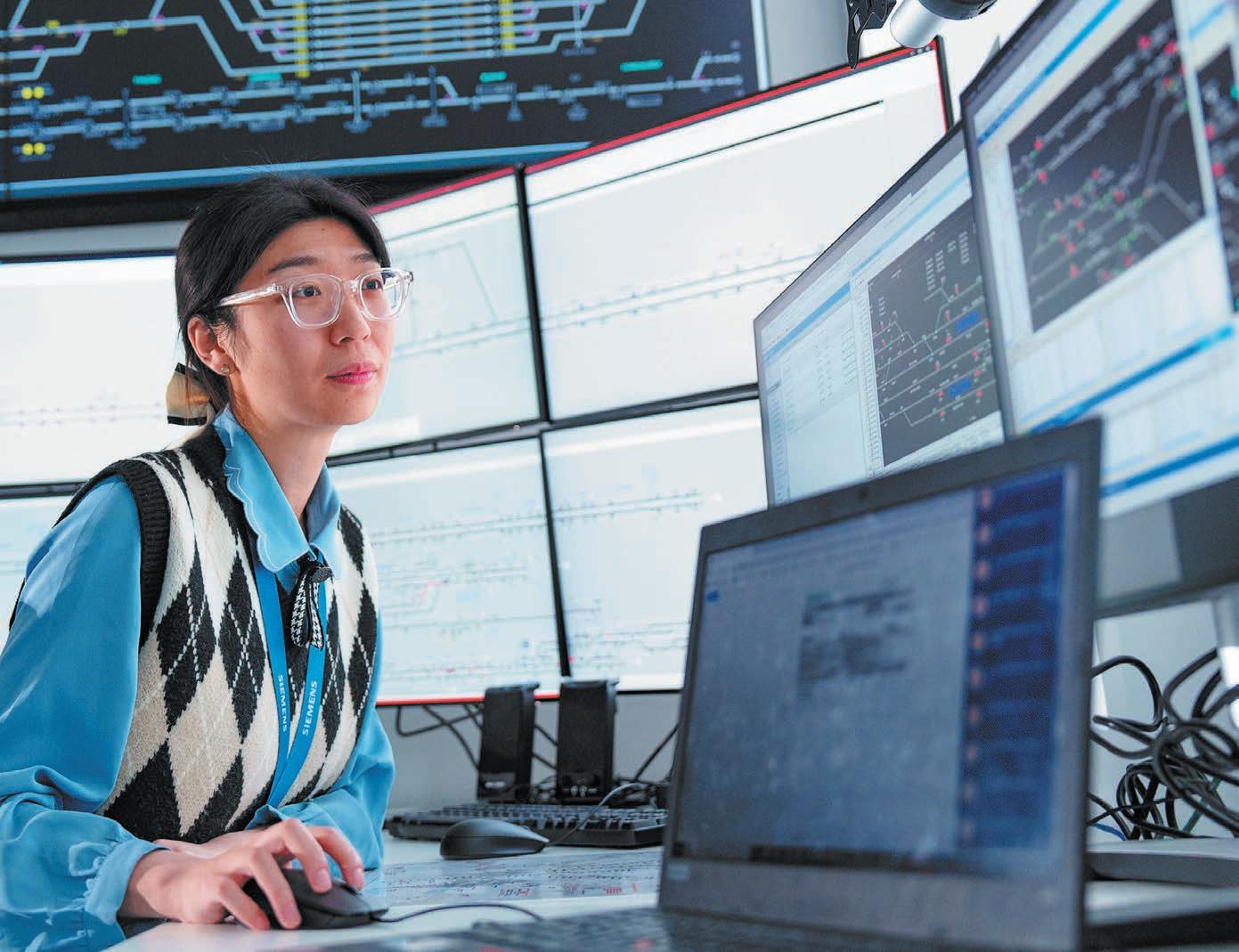
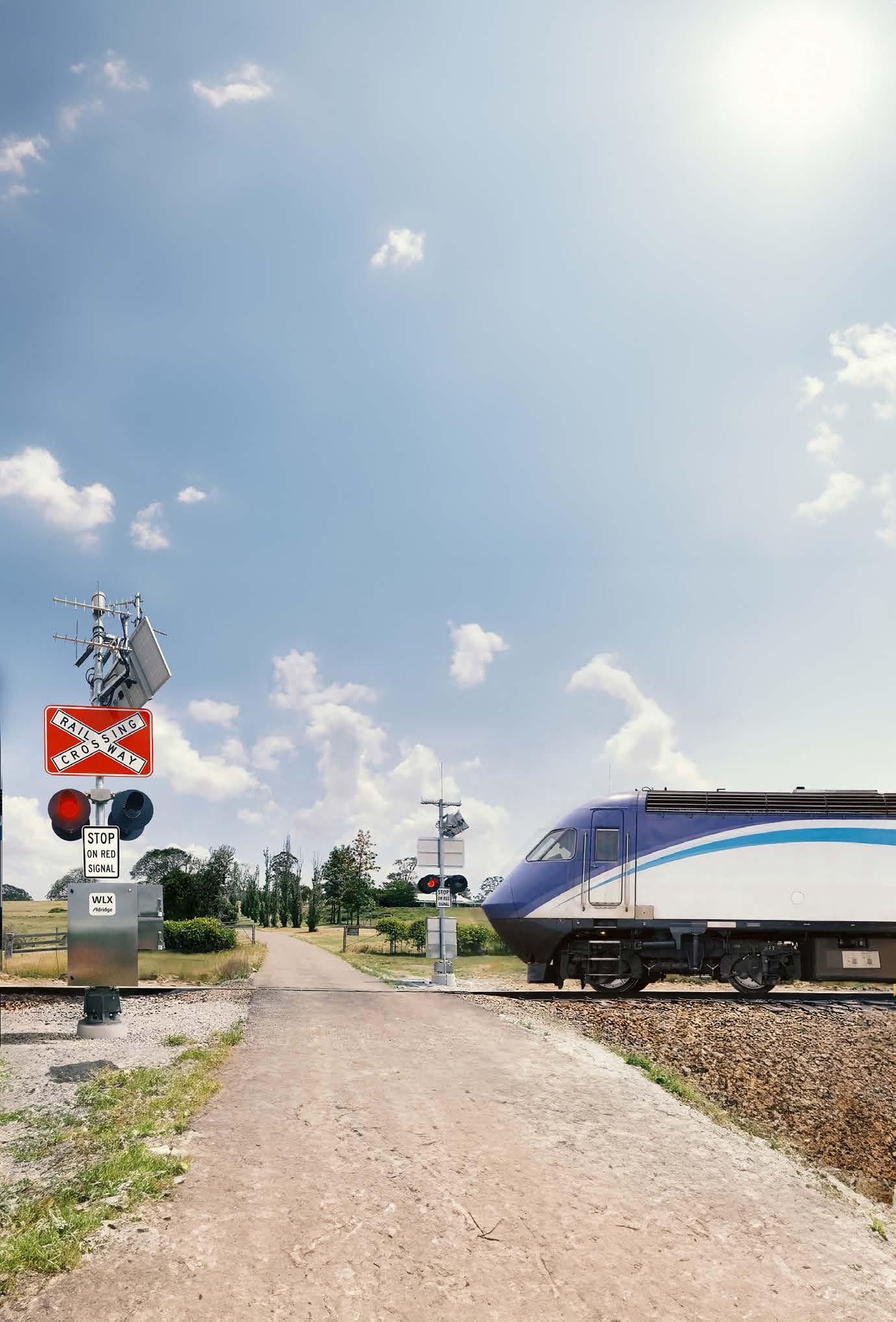
How Aldridge’s cost-effective technology improves rail crossing safety. PAGE 14.
Improving interoperability thanks to signalling PAGE 23
UK knowhow for Australian trains PAGE 30
TFNSW update PAGE 42
We’re the leading provider of end-to-end rail and transport solutions in Australia and New Zealand. From designing and constructing transport networks to operating them, we’re transforming the way people travel and providing better connections across the country.
Every day, more than one million passengers journey are taken on our networks. Our longstanding experience in mass transport means we know how to put together the right solution - from start to finish. Focused on the future of transport, we innovate today for the best outcomes tomorrow. From digital engineering to digital asset management, to targeting zeroemission transport modes; we’re in it for the long haul.
Published by:
379 Docklands Drive
Dockalnds, VIC 3008
T: 03 9690 8766
www.primecreativemedia.com.au
Publisher John Murphy
E: john.murphy@primecreative.com.au
Chief Operating Officer
Christine Clancy
E: christine.clancy@primecreative.com.au
Managing Editor
Mike Wheeler
E: mike.wheeler@primecreative.com.au
Editor Josh Farrell
E: joshua.farrell@primecreative.com.au
Business Development Manager
Alex Cowdery
M: 0422 657 148
E: alex.cowdery@primecreative.com.au
Client Success Manager
Salma Kennedy
E: salma.kennedy@primecreative.com.au
Design Production Manager
Michelle Weston
E: michelle.weston@primecreative.com.au
Art Director
Blake Storey
E: blake.storey@primecreative.com.au
Design Caterina Zappia
Subscriptions subscriptions@primecreative.com.au
www.RailExpress.com.au
The Publisher reserves the right to alter or omit any article or advertisement submitted and requires indemnity from the advertisers and contributors against damages or liabilities that may arise from material published.
© Copyright – No part of this publication may be reproduced, stored in a retrieval system or transmitted in any means electronic, mechanical, photocopying, recording or otherwise without the permission of the Publisher.
Josh Farrell Editor - Rail Express
me a great chance to meet with industry and discuss the pressing issues that rail is facing in Australia.
In my role as editor, I am taking the time, where possible, to catch various rail networks to better understand the experience of those who work in the rail network every day. I am a regular user of the Metro network in Melbourne for my daily commute to work and have traversed many of the lines, giving me a great insight into the network and an understanding of the good work it does.
Recently I travelled to Geelong for an AFL match and caught the V/Line train. Having grown up in the regional town I have a lot of experience on the train so it was good to travel on the network once again.
The train departed Southern Cross at 4:25 and arrived at Geelong station at 5:30, making great time from the city. The line was first opened in 1856 running between Lara and Melbourne and was one of the first country networks in the state.
From 2015 V/Line services to Geelong and Warrnambool began using the new Regional Rail Link tracks to avoid suburban services that use the original route that went via Newport.
While this new rail line is further as the crow flies, it allows the V/Line trains to avoid the sometimes-congested suburban network in and around Werribee, ensuring the train can remain on schedule. The train itself was comfortable, spacious and with the onboard bathroom, has great amenities.
Regional networks like these are so critical to assisting governments in helping to ease the strains on capital cities by creating a strong connection between employment opportunities in major cities, and more costeffective living situations in regional hubs. While it is critical we continue to support
our growing city networks, we cannot let the regional networks fall by the wayside. Recent work on the Geelong line has shown strong commitment to updating the network but this must continue in all states.
I implore government, private enterprise and those working in the industry to continue championing for regional networks Australia wide and their continued improvement, whether that be level crossing removals or the implementation of fast rail.
It has once again been enjoyable collating this month’s magazine with a strong focus on cybersecurity and signalling. These critical areas work hand in hand, as developing the rail network and its infrastructure will be pivotal to improving efficiency on the networks.
This month we got the opportunity to sit down with Mick Spiers from Siemens Mobility to learn more about the benefits of European Train Control Systems level 2 and what it can mean for improving Australia’s rail network.
We also spoke with the team from KeTech who are making a concerted effort to improve Australia’s passenger information systems and is calling upon all of its experience from the UK to bring to the local market. We spoke with Michael Dixon and Paul Warren to better understand what the company can do to improve Australia’s rail network.
At the PWI NSW executive breakfast, Transport for New South Wales secretary Josh Murray gave an update on the organisation and what is in store for it in the near future and what industry can expect.
This month also includes regular comments from the ARA, RTAA and the PWI.
Happy reading!
joshua.farrell@primecreative.com.au
All across the world, cities are expanding. People need better connections to access new places, MTR makes it happen in Hong Kong, Melbourne, Sydney, the United Kingdom, Sweden, as well as in the Mainland of China and Macao.
Inland Rail has ticked off a major construction milestone in Victoria, completing foundation pile drilling at the Seymour-Avenel Road site marking the end of the important pile drilling process across the first four Victorian Inland Rail construction sites.
Fifty-six piles have been drilled and filled with concrete and will form the foundation of the new Seymour-Avenel Road bridge. Each pile is approximately 15 metres
deep and a metre-wide and will support the substructure of the bridge, including the pile cap, blade walls and bridge beams.
Inland Rail Program Delivery Director of B2A, Ed Walker, celebrated the milestone.
“The completion of the underground foundation work marks an important milestone in the delivery of the first four tranche 1 sites,” he said.
“Barnawartha North and Glenrowan sites are almost finished, and Wangaratta and
Seymour-Avenel Road are progressing well.”
Once the material is excavated, a steel cage is inserted and roughly 15 cubic metres of concrete is poured.
A 130-tonne piling rig completed the drilling of the 56 piles at Seymour-Avenel Road in three weeks.
McConnell Dowell Seymour-Avenel Road Area Manager, Kelvin Kumangai, explained the significance of the milestone.
“This is an important milestone for the Seymour Avenel Road Bridge, and the Inland Rail project as it is the last site on Tranche 1 to complete piling works.
“The focus now shifts to building the bridge structure out of the ground, at a new raised height to provide clearance for double-stacked trains.”
Inland Rail is a nation building project that will transform how goods are moved around Australia, first connecting Beveridge to Parkes, NSW, by 2027 before later connecting from Narromine, New South Wales, to Ebenezer, Queensland.
In Victoria, work will take place at 12 sites between Beveridge and Albury, to enable double-stacked freight trains to pass safely and ensure everyday products can be delivered faster and more reliably around Australia.
Early designs have been released for two more level crossing removals in Melbourne’s west, to make Melton boom gate-free by 2026.
New road bridges will be built over the rail line at Ferris Road in Melton and Hopkins Road in Truganina, creating smoother and safer journeys for drivers while minimising disruption during construction.
In response to community feedback, the road bridges will feature new walking and cycling paths, funded as part of the Victorian Government’s Growth Areas Infrastructure Contribution, creating more ways for locals to get around.
A $229 million contract has been awarded to an alliance comprising of Fulton Hogan, Metro Trains Melbourne and the Level Crossing Removal Project to build the Ferris Road and Hopkins Road bridges.
These early designs follow the artist’s impressions released earlier this year for new rail bridges that will take trains over Coburns and Exford Roads in Melton, as well as a new Melton Station, which will cater for one of the
fastest-growing communities in Australia.
Minister for Transport Infrastructure Danny Pearson announced the designs.
“The release of the latest designs is an exciting step towards getting rid of these Melton level crossings once and for all,” he said.
“We’re building a new Melton Station, getting rid of four dangerous and congested level crossings and making Melton boom gate free by 2026, improving safety and busting congestion for locals in the west.”
unclog roads for more than 73,000 vehicles travelling these roads each day. Drivers currently face up to 28 minutes of boom gate down time in the morning peak. Major construction on all four level crossings and the new Melton Station is scheduled to begin later this year, with the new station open and all four sets of boom gates gone for good in 2026 –two years ahead of schedule.
The Melton level crossing removals will also pave the way for the introduction of larger nine-car VLocity trains as part of the increasing
Zaxis-7
Create your vision
Intensive work to rebuild the foundations of the busiest section of the Western Line in Auckland, New Zealand, allowing more reliable trains and helping prepare the network for City Rail Link, is substantially complete.
KiwiRail completed the majority of Stage 3a of the Rail Network Rebuild during an extended weekend of work, allowing trains to return to 10-minute frequencies at peak as planned. The work was carried out at more than 30 different sites between Newmarket and New Lynn.
Final upgrades at a small number of sites were finished and essential track work, including de-stressing rails, is being completed.
KiwiRail chief infrastructure officer Andre Lovatt said completion of this stage of the rail rebuild is another important step on the path to building a network that can support faster, more frequent and reliable
trains for passengers and greater capacity for freight trains.
“We know this work has been disruptive for both passengers and our rail network neighbours, so we would like to thank them for their understanding as this vital work was carried out,” he said.
“To ensure the rail network is ready for City Rail Link a huge amount of new and upgraded infrastructure is required. Over three to four years KiwiRail is carrying out what would usually be 10 years of work – so there will be disruption on the way to unlocking the significant improvements City Rail Link will bring passengers.
“More than half of the Rail Network Rebuild is now complete. The sections of the Southern and Eastern lines that have been rebuilt have seen improved reliability and train speeds –they are the best performing on the Auckland rail network.
“Although there will continue to be rail closures and changes to services as other upgrades continue, Western Line passengers can expect to see some reliability improvements in the coming months as final track work is completed.”
The Rail Network Rebuild team is now upgrading drainage in the Papakura area, part of Stage 3b between Puhinui and Papakura. The next major stage of work, Stage 4 between Papakura and Pukekohe began in May and continue until midJanuary 2025.
The Papakura to Pukekohe section of Auckland’s network has been closed since September 2022, for the project to extend the overhead electricity from Papakura to Pukekohe. It was expected to open by the end of 2024 and now will now remain closed for a short while longer until after the summer block of line – reopening in January 2025.
The boom gates at Keon Parade in Reservoir have been removed.
In the early hours of the morning, crews reopened Keon Parade after 14 days of aroundthe-clock works.
The new rail bridges will improve the journeys for more than 18,000 vehicles travelling through this level crossing each weekday, where the boom gates were down for more than 41 minutes during the morning peak.
Removing the level crossing also improves safety for pedestrians who walk through the area to access education, work and leisure activities. Removing 77 level crossings has saved more than 50 hours of boom gate down time daily during the morning peak.
Designed with safety and convenience in mind, the new Keon Park Station precinct will provide easier access to the station, new local
connections for the community, and access to shops and public transport.
The integrated transport hub will give passengers improved connections between train, bus and taxi services with new bus stops, secure Parkiteer bike storage and a pick-up and drop-off zone all within the precinct.
Works around the station precinct will
reinstating more than 160 car spaces and planting 44,500 shrubs and grasses and 220 trees around the station.
In the lead up to the station opening, a shuttle bus will run between Ruthven and Thomastown to connect Keon Park passengers with trains.
Sydney has a new train station for the first time in five years, as Waterloo Metro becomes the first to cross the construction finish line for the City and Southwest Metro project, which is set to welcome passengers this year.
Nearly 19,000 passengers are expected to use the state-of-the-art Waterloo Station each day when it opens.
Waterloo Station is the first of six new stations on the City Metro line to be complete, and the remaining five are following close behind.
When City Metro services begin in coming months, Waterloo will provide fast, safe and reliable journeys to Central in two minutes, Barangaroo in eight minutes and to Victoria Cross in North Sydney in 11 minutes.
NSW Premier Chris Minns said this is an important milestone for Sydney Metro.
“This is a good example of what happens when we link the provision of housing and public transport. Everybody wins,” he said.
“More homes close to our train stations means we’ll have better connected communities.
“This is a great example of revitalising an inner-city community and incorporating housing and public transport.”
There are further steps before the official opening of the Sydney Metro City and Southwest later this year. These include approval from the Office of the National Rail
Safety Regulator, the handover of the line and all stations to the operator, and a period of full trial running. These milestones are all on schedule.
Minister for Transport Jo Haylen said the government is taking a huge step towards opening the next stage of Metro.
This will see tens of thousands of people using these new stations and enjoying faster connections.
“This mega station will be a game-changer for Waterloo, Redfern and Alexandria and significantly reduce traffic on our inner-city roads, while alleviating pressure at nearby Redfern and Green Square stations,” she said.
“It took more than 5,000 people five million work hours – more than four years – to complete the new station, including the excavation of 330,000 tonnes of material.
“This is a striking station with a design that honours Aboriginal heritage and pays homage to Waterloo’s history.
“Its 170-metre-long platforms will receive a lightning-fast train every four minutes in the peak.”
The Waterloo Renewal Project is a major redevelopment that will transform the estate into a modern, sustainable and vibrant community with a mix of social, affordable and private housing, as well as retail, community facilities and public open spaces.
The Waterloo Metro Quarter development
above the new Sydney Metro station will include 220 social, affordable and private residential homes. It will also feature student accommodation, retail outlets and commercial space across four buildings, along with public open space and a car park.
The Waterloo Metro Quarter development will provide apartments near transport infrastructure, giving people a place to call home where they can move around the city easier, according to Haylen.
contact@anchoram consulting.com.au
contact@certifer.eu
Parramatta Light Rail Stage 2 has received final project planning approval after the Federal Minister for Environment and Water endorsed the Western Sydney mega project.
The Federal approval covers the full project, which will connect Stage 1 and the Parramatta CBD to Sydney Olympic Park via Camellia, Rydalmere, Ermington, Melrose Park and Wentworth Point.
The first phase of delivery is the construction of a new 320-metre public and active transport bridge over Parramatta River between Wentworth Point and Melrose Park.
State planning approval was granted in February 2024 and came after the NSW Government allocated an additional $200 million in the 2023-24 NSW Budget to expedite the project’s planning processes.
The bridge will provide a much-needed active and public transport link to connect the growing communities north and south of the river, unlocking the Greater Parramatta
bridge works is currently underway, with the contract for enabling works expected to be awarded later this year. Major construction
The planning and design phase is being further developed through consultation with the community and stakeholders.
Construction is complete on Parkville Station. The new station will provide easy rail access to Victoria’s health and education precinct when it opens to passengers in 2025.
Parkville Station is the second of five new state-of-the-art stations to be finished as part of the Metro Tunnel.
The station will transform travel for thousands of medical staff, patients, families, students, teachers and researchers who travel to the area every day.
The station includes entrances directly outside the Royal Melbourne Hospital, Peter
MacCallum Cancer Centre and The University of Melbourne. It also has a 44-metre-long pedestrian underpass beneath Royal Parade to make crossing the road easier and safer.
Parkville Station features a 54-metre-long steel and glass canopy filling the concourse with natural light.
Over the past six years, hundreds of workers have built the station and the four station entrances, and installed 16 escalators, seven lifts and Victorian-first platform screen doors. Premier Jacinta Allan celebrated the milestone.
“We are two down and three to go on the Metro Tunnel stations – and we’re another step closer to transforming Melbourne forever,” she said.
A new level-access tram stop on Royal Parade opened last year. This will allow people to easily switch between trams and trains when the Metro Tunnel opens in 2025.
The station’s landmark artwork Vernal Glade, by internationally acclaimed Melbourne artist Patricia Piccinini, was recently installed inside the main entrance.
Minister for Transport Infrastructure, Danny Pearson, went on to further celebrate the milestone.
“This year’s Budget investment will get the Metro Tunnel ready for kick-off – delivering the staff, station infrastructure and customer information on the ground to support day one and beyond,” he said.
Test trains have run around 18,500km so far as part of the Metro Tunnel testing program. Over the coming months, the project team will test Parkville Station systems to make sure everything works together. This includes passenger information displays, platform screen doors and ventilation.
Work is continuing on the three remaining underground stations – State Library, Town Hall and Anzac. Construction on Arden Station finished earlier this year.
Training, consultancy, insight.
The Rail Safety and Standards Board is the independent safety, standards and research body for Great Britain’s rail network. We’ve powered safer, smarter rail for more than 20 years – and now rail organisations around the world can benefit from this experience and insight. To see how we could help your organisation, download your guide to our international services.
Get your guide at rssb.co.uk/international
Rail manufacturing specialist Aldridge is aiming to improve safety around level crossings with its ITS Wireless Level Crossing Controller.
Level crossing safety is front of mind for the rail sector. The industry came together in March for a level crossing roundtable to create a cohesive direction for the sector to improve safety around level crossings, particularly in regional areas.
Rail specialist Aldridge, through its Intelligent Transport Systems division (ITS), is aiming to be at the forefront of this.
Aldridge can trace its roots back to 1989 where it began as a series of companies called the Aldridge Group. They then acquired a company that had tooling with the ability to manufacture railway signals, thus beginning the company’s foray into the rail space.
The company prides itself on never compromising on quality to ensure safety.
With 25 years’ experience in producing railway crossing components and manufacturing signalling equipment, the company uses best practice to get maximum value out of every project dollar.
This experience has laid the foundation for Aldridge to develop a new product to improve safety for level crossings.
The Aldridge-ITS Wireless Level Crossing (WLX) Controller has been designed in Australia by Aldridge-ITS to provide a low cost, low maintenance, stand-alone solar and batterypowered active level crossing solution.
The WLX utilises wireless communications and axle counter-based train detection
to control type-approved RX5 warning devices and includes data logging and alarm management (local and remote) along with live remote monitoring.
The controller has been designed from the ground up with a design criteria of lower cost, lower power consumption and integration resulting in a reliable and secure level crossing system.
In Australia, the majority of level crossings are in remote regions with low population density and little or no surrounding infrastructure.
Installation of traditional level crossing protection systems is expensive where buried cable routes are necessary. In addition, the lack of infrastructure and a reliable power supply
together; we have designed every component and manufactured it locally allowing us to have complete control of the manufacturing and the IP.
“For example, the wheel flange sensor was designed and built to meet Safety Integrity Level 4 (SIL4).
“It includes lightning and surge protection and it’s permanently active, allowing it to monitor all complex rail traffic movements.
“Because we designed it to be maintenancefree, requiring no adjustments during the normal course of operation, we then tested its integrity by fitting it to a 20-metre test track at our Lidcombe factory.
“It has now completed 2.5-million-wheel detection cycles.”
In another example of Aldridge’s “Ground Up” approach, the WLX controller utilises the latest micro controller technology (ISO 26262 ASIL D) with a Texas Instrument chipset designed for IEC 61508 SIL 3 Safety-Critical Applications.
“The micro controller provides advanced integrated safety features and is companioned
“The integration of this micro controller technology into the WLX controller has significantly reduced the cost of the system while maintaining functional safety.
“Then we needed to work out how to get the signal from the sensor without using cables, so we designed our own radio system.
The WLX radio system is also a bespoke, proprietary radio system specifically designed for this application.
“It’s a 900Mhz ISM, Broad Digital Spread Spectrum with 20-channel Frequency Hopping, Forward Error Correction (FEC), AES128 security encryption and dual antenna diversity.”
Finally, Aldridge recognised the need for a management system that allows it to monitor the performance of any WLX Installation both locally and remotely.
The system integrates a range of safety features to support users and ensure the system is operating at an optimal level of safety.
“The WLX can provide email alerts on any system faults and warning messages, back to base monitoring and a web server for remote monitoring, generating system reports with multiple sites managed from the server,” Aldridge said.
The Aldridge-ITS WLX is Australian designed with all components manufacturedlocally.
The company has also begun exporting globally. It is 51 per cent Aboriginal owned, managed and controlled and Aldridge was awarded the 2023 Australian Indigenous
for integrated video camera surveillance and anti-pole climbing security to ensure the equipment is not vandalised.
“To further minimise the risk of any disruption, we utilise forward and reverse facing warning lights at the level crossings so that if one unit goes down, then there is a second unit on the other side to
hand the challenges of maintaining 100 per centreliability.
“The server can manage maintenance records and integrate with existing control room monitoring equipment. It provides vehicle and train analytics, monitoring of
“We understand that much of these systems are operating in harsh and remote areas of the country so we ensured we designed a system that could stand up to those challenges,” Aldridge said.
Aldridge’s system eliminates expensive installation and maintenance and can be delivered for a quarter of the price, with uncompromising safety, performance and reliability and is already operating at multiple sites in Australia.
WLX is scalable for multiple track operations and it’s even possible to include type-approved gates. WLX can be installed and commissioned in 5-7 days whereas existing systems can take six to eight weeks to be up and running.
“The system can be installed much faster than existing automated systems with only four poles to be installed,” Aldridge said.
“As a matter of fact, you can install one system a day. After all it is simply four poles in the ground.
“We are beginning to get a lot of interest from overseas now and so we are gearing up to really roll it out.
“We make it in Sydney, and we ship from our factory fully tested. We are excited to really grow this product in Australia.”
The Federal Government released its 2024/25 budget in May and Rail Express took the time to unpack what it means for the industry.
The Federal Government has said it is committed to investing in the infrastructure Australia needs by providing $9.5 billion over the forward estimates, and $16.5 billion over 10 years, for projects that improve productivity, liveability, and sustainability.
It will also maintain focus on ensuring the deliverability of the more than $120 billion, ten-year infrastructure investment pipeline.
As part of the Government’s investment in new projects, $158 million is being committed to deliver critical planning for nationally significant projects under the Major Projects Business Case Fund.
It has committed $78.8 million over three years for the High Speed Rail Authority to undertake the development of a business case for the Sydney to Newcastle high-speed rail corridor.
The Federal Budget has a focus on Australia’s national network to help get more freight moved by rail.
This includes $540 million to improve the reliability of the Australian Rail Track Corporation’s (ARTC) interstate freight rail network, with $150 million to upgrade the Maroona to Portland Line in Victoria.
This brings the investment up to $1 billion, which is an addition of the ARTC’s own commitment of $500 million via the corporation’s Network Investment Program, which was developed in collaboration with industry and shareholders.
Each day, numerous interstate and regional passenger rail services also operate across the breadth of the ARTC network. These entities will benefit directly from this
years to one in 100 years between Tarcoola to Crystal Brook in South Australia, Tarcoola to Kalgoorlie in West Australia and between Albury and Sydney in New South Wales;
• $100 million for the replacement of 47kg rail with 60kg rail to reduce risk of broken rails and support larger trains between Tarcoola and Kalgoorlie in Western Australia;
• $150 million for track rehabilitation and operational upgrades between Albury and Sydney; and
• $150 million for the upgrade of the Maroona to Portland Line in Victoria.
Importantly, this funding builds on the Australian Government’s continued commitment to Inland Rail, and complementary terminal infrastructure that will ensure the rail network can respond to the challenges of the freight task increase and climate change in the future.
ARTC CEO and Managing Director, Wayne Johnson, said these investments are underpinned by ARTC’s Network Investment Program, which has been developed with customer and industry insights and input.
“The freight and logistics task in Australia is rapidly growing and rail is central to supporting the national objective,” he said.
“The objective is to transport large volumes of goods and commodities efficiently to market to help increase economic productivity and growth with a reduced emissions footprint.
“Targeted and strategic investments along key sections of ARTC’s 8500-kilometre network will have a measurable impact on the ability of the national supply
“The commitment by the Australian Government, coupled with ARTC’s investment, will deliver outcomes that will improve the networks resilience, reliability, and therefore overall operational performance.”
These funding commitments build on the $150 million already invested in resilience activities by ARTC over the past two years, to upgrade the existing national network.
Since 2021, the ARTC network and its freight and passenger customers have experienced disruptions because of extreme weather events leading to flooding and damage to railway infrastructure.
CEO of the Australasian Railway Association (ARA) Caroline Wilkie said the ARA is pleased to see investment in several new and existing projects in the Federal Budget.
“The Australian Government’s decision to invest $540 million in upgrading critical sections of the 8500-kilometre national rail network will help ensure the safe, reliable and efficient delivery of large volumes of containerised products and bulk commodities like grain, minerals, and steel across the country,” she said.
“This announcement recognises the critical role rail plays in supporting a strong national supply chain and the great economic and environmental benefits of having a more reliable and resilient network and getting more freight onto rail.”
NSW will receive $20.8 billion over 10 years in infrastructure funding for road and rail.
This will enhance public transport
funding for planning to extend the rail line from the Aerotropolis to Macarthur. It will also see $1.9 billion for Western Sydney Road and rail infrastructure.
Queensland has $21.6 billion over 10 years coming from the Federal Government, which will include $1.15 billion for the direct Sunshine Coast Rail line.
The there is the $39.4 million that has also been committed for the relocation of the Loganlea Station to ensure better connectivity for the growing hubs south of Brisbane.
Loganlea train station is an important transport hub that helps the surrounding community connect to Southeast Queensland.
The Australian and Queensland governments are planning to relocate and upgrade Loganlea train station, to make sure it can accommodate future growth in the region and deliver the most benefits to the community.
The Loganlea train station relocation project will deliver:
• improved access to the train station with ramps, stairs and lifts from Valencia Street and Armstrong Road;
• better connectivity to local facilities and across the rail line;
• a new train station building to include real-time display screens, new wayfinding signage and hearing loops;
• improved safety by increasing visibility to the train station concourse and platforms and providing additional lighting and CCTV;
• raised platforms and flush kerbing to allow level access to trains;
• better active transport and a secure bicycle enclosure;
• platform widening and tactile ground surface indicators on platforms;
• provision for fare gates to the platforms that can only be accessed by customers; and
• provision for future track and platform expansion, enabling the delivery of the Logan and Gold Coast Faster Rail project. These investments to increase accessibility, capacity and reliability of transport networks also help prepare for the 2032 Olympic and Paralympic Games.
Tasmania will receive $2.2 billion over 10 years in infrastructure funding. Victoria will receive $19.2 billion over 10 years in infrastructure funding. South Australia will receive $9.7 billion over 10 years in infrastructure funding.
The Federal Government has committed $8.9 billion over 10 years to Western Australia with $1.4 billion for METRONET, including a new project and funding for existing projects.
There will be $300 million worth of funding going to METRONET to deliver a capacity signalling program in Western Australia.
The government has also committed $33.5 million towards planning works to support the development of Westport. The Westport project is the linchpin for future trade growth in Western Australia. It includes planning a new port and the connected road, rail and logistics operations required to move container trade from Fremantle to Kwinana.
The Commonwealth’s commitment to the Westport project will progress planning that is critical to facilitate construction of Westport, which will include freight rail duplication and level crossing removal.
The Government’s $33.5 million investment will match the state’s contribution, taking the total investment for this planning phase to $67 million.
The ACT will receive $808.6 million over 10 years with $50 million for the planning of Stage 2B of the Canberra Light Rail set aside.
This work will design the extension of the current light rail line from Commonwealth Park to Woden, so that Canberra’s southern suburbs can experience the benefits of improved public transport currently enjoyed by those in the north.
The ACT will also benefit from $100 million of investment in a new national Active Transport Fund.
This fund will upgrade and deliver new bicycle and walking paths to support zero emissions travel, provide a safer environment for cyclists and pedestrians, and promote
“Light rail has been a transformative project for the ACT and soon Canberrans on the southside will be able to reap its benefits,” said Minister for Finance and Senator for the ACT, Katy Gallagher.
The draft Environmental Impact Statement (EIS) is currently being developed by Major Projects Canberra for the construction of Light Rail Stage 2B. This is the important next step forward in progressing the project towards construction.
Minister for Infrastructure, Transport, Regional Development and Local Government, Catherine King, spoke about the announcement.
“We’re delivering the infrastructure that improves safety while better connecting people with opportunities and their families,” she said.
“We want to ensure that Australia is well placed to compete in the new, net zero economy, to revitalise regions and support communities in cities, suburbs and regions.”
ACT Minister for Transport Chris Steel elaborated on what the funding means.
“We welcome this significant investment from the Commonwealth and their support for the design and approvals for the southside extension of Canberra’s masstransit light rail line,” he said.
“Canberra’s population is expected to increase from around 460,000 today, to more than 780,000 people by 2060. Both the Australian Government and the ACT Government are investing now to deliver an integrated public transport network fit for our growing city.
“I encourage people living along the future line and public transport users to get involved by having their say on the design of the transport corridor. This feedback will be used to inform the draft EIS and ongoing design of the project.”
In its Budget for 2024/25, the WA government has made a strong commitment to delivering the METRONET program and improving freight movement.
Over the next four years a total of $11.8 billion has been allocated for new rail and transport infrastructure projects across Western Australia, part of the WA Government’s overall $42.4 billion investment in new infrastructure across the State.
The 2024-25 State Budget provides $4.8 billion over the next four years to deliver the METRONET program, supported by $2.9 billion in funding from the Federal Government.
This includes an additional $254 million in State Government investment for the METRONET infrastructure program.
The Yanchep Rail Extension is set to commence operations in July, the historic Morley-Ellenbrook Line is on track to be completed by the end of 2024, and a further three major rail projects are expected to be delivered in 2025 (the Victoria Park-Canning Level Crossing Removal, Byford Rail Extension and Thornlie-Cockburn Link).
Premier Roger Cook said the WA government is investing in transport infrastructure to set up the state for decades to come.
“Through METRONET, we’re transforming Perth’s suburbs, slashing congestion and creating jobs in the community,” he said.
“Right across WA we’re investing in our road network, including billions of dollars for major regional road projects and upgrades, improving road safety and cutting travel times for regional Western Australians.”
Completion of these five major METRONET rail projects will see the delivery of:
• 17 new train stations.
• 61.5 kilometres of new tracks.
• 5.5 kilometres of new elevated rail.
• Six hectares of new public open space.
• The first east-west connecting rail between the Mandurah and Armadale Lines.
Transport Minister Rita Saffioti said the Government is focused on ensuring it delivers a better transport system for WA, with investment across regional Western Australia and in Perth over the next four years.
“The strong investment in this State Budget will see a significant number of projects delivered over the next 12 to 18 months,” she said.
“Not only will these projects connect thousands of people to our rail network for the first time, but they will also help families with cost of living pressures by providing better access to our two-zone fare cap scheme, which allows a person to travel anywhere on our public transport network for no more than about five dollars.”
The METRONET program has also seen the removal of 15 level crossings around Perth.
Transport is also a key feature of the Government’s cost of living package, with $125 million being allocated in the State Budget for a range of initiatives including:
• $21 million for school students to access free public transport;
• $20 million for free public transport for all SmartRider holders during the January 2024 Summer period and on Sundays; and
• $20.3 million to increase the Regional
Pensioner Travel Card by $100 (from $575 to $675), to further assist eligible pensioners in the regions with the cost of fuel and/or taxi travel.
The Government has also committed $116 million for the Westport project, including for early marine, civil and road works to transition container trade from Fremantle to Kwinana, unlocking future trade opportunities and economic capacity.
Westport is a long-term planning program to move container trade from Fremantle to Kwinana. Westport’s investigating, planning and delivering a future port in Kwinana with integrated road and rail transport networks.
The Government is delivering $373 million in investment in the states port facilities, including delivery of the Dampier Bulk Handling Facility, plus upgrades to maintain capacity and resilience of infrastructure.
The Victorian Government has placed a focus on opening the metro tunnel and continuing level crossing removals in the 2024/25 state budget.
The Victorian Government has released the 2024/25 State Budget in which it has made a commitment to continuing the pipeline of infrastructure projects.
The major focus for the next year will be the opening of the Metro Tunnel. It will be the biggest and most transformational public transport project since the City Loop opened more than 40 years ago.
This year’s Budget provides $233 million for activities to get the state ready for the opening on day one.
Recruiting and training drivers, timetabling, completing final testing, preparing customer information and education, and training a dedicated customer service team is where the funding will be targeted.
The State Government is committed to remove 110 dangerous and congested level crossings by 2030. Since its last Budget, the Government has removed eight more level crossings, bringing the total to 77 – a year ahead of schedule.
This Budget invests $752 million to switch on the Big Build project, funding the operation of the expanded network and new stations. It also funds additional network improvements, including:
• $214 million to maintain the Digital Train Radio System and plan for future upgrades.
• $133 million to support the regional rail network, including operating newly delivered train stabling yards, stations and VLocity trains, and upgrading the 150-year-old historic rail tunnel between Geelong and South Geelong.
• $104 million for works to keep rail freight moving across Victoria, including encouraging operators to take up rail, reducing trucks on local roads.
• $30 million for better bus travel and continuation of ferry services. This includes improved links to new bus interchanges being built at Croydon, Pakenham and Greensborough Stations.
• $21 million for public and active transport
upgrades, including construction of shared bike and pedestrian paths in Altona, Epping and South Morang and safety and accessibility upgrades at Essendon train station.
In the Budget the government acknowledged the challenges of historically low unemployment, high inflation and the continued impact of COVID-19.
In its statement, it also said it is taking this year’s budget as a chance to recalibrate. The International Monetary Fund, in its recent report on Australia, said now is the time for governments to implement infrastructure projects at a more measured pace, given supply constraints.
The Airport rail link will be delayed by four years as the state and federal governments work together to better understand the needs of the rail link. The airport remains firm in its desire for an underground station.
The Upfield Train line level crossing removal has also been delayed until at least 2030.
Siemens Mobility is bringing its international expertise to the signalling sector of Australia’s rail industry to improve the whole network.
Siemens Mobility is a pioneer of the European Train Control System (ETCS) across the world.
Mick Spiers, Siemens Mobility’s chief operating officer for railway infrastructure in Australia and New Zealand, to learn more about how the company’s signalling technology can improve interoperability across Australia.
Spiers spoke about the infrastructure challenges Australia is currently facing with an escalation in costs and the need to increase services to help move people quicker to their destination. With the rail network in Australia using four different gauges and 29 different signalling systems, spread over great distances, the country needs to ensure its networks run efficiently, safely, and reliably for a positive customer experience.
The nation’s challenge is not unique and is faced by many countries around the world, especially in Europe and the United States.
“Our network in Australia exists similarly to how it does in Europe where each of our states is basically a separate country from the other,” Spiers said.
Europe has adopted ETCS technology and
first company to implement ETCS Level 1 in Adelaide.
Spiers said that while it can be difficult to switch from tried-and-tested methods to the new ETCS Level 2 system, rail operators can be assured that the efforts to improve and progress this technology will have lasting benefits for the network.
“The key to improving the connectivity between rail and other forms of transport will be data, and ETCS is data-rich, providing the insights and scope to enhance and connect mobility services,” Spiers said.
“If someone is more than 800 metres from a station, it gets more tempting to get behind the wheel rather than utilise the rail network.
cannot compete against the heavy lifting of rail, network connects everyone to where they work and live. We need integrated mobility.”
The ETCS Level 2 system also offers the opportunity to increase network capacity. As Australia has been investing billions on infrastructure, the evolution of ETCS Level 2 will enable more capacity and efficiency from that infrastructure and investment.
“ETCS improves service reliability and capacity. People get to move around their cities without delays; without disruptions; and with full confidence of a reliable and safe service,” Spiers said.
Spiers explained the ETCS Level 2 system in greater detail and how it works to improve the transport network.
“The ETCS system allows the European rail network to be better connected and more interoperable,” he said. “And through
the evolution to ETCS Level 2, we have also increased the safety and efficiency through continuous supervision, improved capacity and punctuality to increase reliability of train services.
“The implementation of ETCS Level 2 in projects such as Finland will see a reduction in costs due to less trackside equipment, which also means fewer disruptions.”
The Australian government has established rail interoperability as a priority to maximise investments in rail by taking advantage of digital technologies to create an integrated national rail system.
Spiers explained Australia can feel like multiple countries with different operating systems and working requirements.
ETCS Level 2 allows the rail network to become standardised. This standardisation allows greater connectivity between all stakeholders working on the networks.
Spiers explained that the main difference between ETCS Level 1 and ETCS Level 2 is the transition from limited supervision to continuous supervision.
With this change, the implementation of Level 2 is a necessary improvement that Australia’s rail network needs to align with interoperability targets.
“By implementing ETCS Level 2, you are standardising the network,” Spiers said.
“You can have multiple vendors working across the same region and network. Each state has different requirements, and that creates challenges. However, ETCS standardises the network without overhauling infrastructure.”
Spiers explained that another benefit of the ETCS Level 2 system is realised as
an improvement in through traffic on rail corridors. The system can enhance corridors to accommodate for more trains, which would generate greater passenger rail use as well as better co-existence with freight.
“ETCS is something that doesn’t just impact urban rail but freight rail as well. It has benefits for operators in both spaces,” he said.
“You look at most networks in Australia, you have different rolling stock already using the passenger network, and then you have freight operators that want to come through the same rail lines,” he said.
“To do that optimally, instead of providing a window in which freight operators can pass through a network, if they are all using ETCS Level 2, the traffic can be managed more efficiently.”
ETCS Level 2 can reduce the headway between trains, minimising disruptions freight trains can have on the passenger networks.
Spiers said many networks across Australia already have examples of multi-vendor networks working together.
“We can see that these collaborations work locally, but we have also seen the success of the ETCS Level 2 systems internationally, which shows that this collaboration can continue,” he said.
“Switzerland is a perfect example. Its rail system has nearly every signalling vendor on its network. The system can smoothly handover signals and data between each vendor. The success and innovation of this approach is what drives our determination to bring the learnings from international experiences like this to our local network.”
In 2023, Siemens Mobility signed a Memorandum of Cooperation aimed at enhancing rail interoperability throughout
Australia and addressing long-standing legacy issues in the rail industry. The National Transport Commission has coordinated these signings between rail industry manufacturers, operators and Federal and State Transport Ministers to make rail more interoperable across Australia.
Technology like the ETCS level 2 will be instrumental in meeting these requirements.
Spiers explained that the continuous supervision of ETCS Level 2 has clear benefits, which can improve safety on the rail network.
“As opposed to existing systems where all you know is that the train is somewhere in the block, ETCS Level 2 can give you a clearer picture of where exactly the train is,” he said.
He explained that the system is now designed to augment the drivers’ skills and help them do their jobs – not replace them.
The ETCS Level 2 system gives the driver greater capability around optimal speed control and a clearer picture of their movement authority.
“With technologies such as DAS, you can determine the optimal speed of train rather than having a movement authority of 80kph and then the train having to stop,” Spiers said.
“But the system isn’t just improving safety by giving the driver greater visibility, it also has the capability to apply the emergency brake if the train has passed its movement authority.
“For example, if the driver is in an area with a temporary speed restriction and has missed it, the system can automatically reduce the trains speed.”
Spiers also explained that this system can help reduce the wear and tear on rolling stock.
“ETCS can reduce instances of complete stopping and reduce the speed instead,” he said.
“You will see a longer lifespan on rolling stock if there is less strain placed on the system.”
“Another benefit of ETCS Level 2, will be an opportunity for a single competency framework, as everyone is trained on the same technology.”
The existing rail competency framework is exceptionally complex and simplification is greatly needed.
Siemens Mobility’s success with these systems across Europe has set them up well to roll out the same system across Australia. Spiers said the rollout of the ETCS system is a stepby-step process. And as the states and rail operators continue to unite to achieve greater interoperability, the ETCS system can be the service that helps this succeed locally.
“The way we like to do these projects is
to bring in experts and knowledge from our global counterparts,” Spiers said.
“We welcome overseas delegations to work closely with our team, which creates a handson learning experience for our local teams.”
Siemens Mobility will upgrade the first section of Finland’s rail network under the Finnish government’s “Digirail project”, which involves renewing the country’s train control system.
The contract was recently awarded and includes installing the ETCS Level 2 and the Hybrid Train Detection for the first time in Finland on the 191-kilometre stretch between Lielahti and Rauma-Pori.
Spiers explained that the key for Australia is that the handover between the systems is seamless.
“You do not have to do it all in one go, and make sweeping changes. It is a change that you can implement gradually,” he said.
“This means that a network that is currently operating conventional signalling or ETCS Level 1 can progressively upgrade to Level 2 over time.
“Trains operating through this section will seamlessly switch their operating principles as required.
“It is time for Australia to continue its investment in ETCS Level 2 as an interoperable standard and to maximise the capacity of our rail infrastructure.”
Hitachi Construction Machinery Australia has reaffirmed its commitment to supporting the rail sector in Australia with a strong range of equipment on offer.
Hitachi Construction Machinery Australia (HCA) is reaffirming its commitment to the rail sector with the belief much of its offerings are well suited to the industry. The company was founded in 1910 by electrical engineer Namihei Odaira and has since grown to more than 320,000 employees working globally in a number of sectors.
Rail Express spoke with Nitin Khanna, who is the general manager at HCA to learn more about the company’s commitment to rail in Australia.
“We wanted to be present in this segment for the customers that we already have working in this space,” he said.
“We do have a product line that can create a difference to our customers. We have a lot of exciting products coming out of Japan that are well suited to rail.”
These machines include Hitachi’s wheeled excavators and mini excavators, both suitable for narrow rail corridors.
The ZAXIS wheeled excavators have been designed to offer versatility and can be used with a number of attachments. They have seen the lifting capacity increased by seven per cent. A new power boost function increases the digging force by 6 per cent for up to eight seconds when needed.
The front speed of the new models has been enhanced by the HIOS III boom recirculation system – pressurised oil is circulated in the boom cylinder when lowering the boom, allowing pressurised oil from the pump to be used efficiently to increase the speed of the arm.
Khanna explained that while the new developments are exciting, Hitachi has a strong focus on maintaining its reliability and safety standards.
“We have an integrated engineering team in Australia, which works on the design aspects and requirements for the Australian market,” he said.
“We have seamless communication with Japan to make sure that all compliance around safety and reliability is being met. A lot of OEMs will just manufacture a machine and send it down here, that is not what we do.
“It is actually the other way around. We do the groundwork and research and then communicate that with Japan. The machines are then tested in Japan and then further tested here to stand up to our local needs.”
Hitachi has placed an emphasis on improving its electric offerings. It recently provided a ZE85 electric excavator to Anric Group. The machine is 100 per cent electric and is well suited to the Australian market.
“Our electric machines align well with the government’s net zero commitment by 2050,” Khanna said.
“It’s an important sector and we need to
keep up with the needs of the industry and that includes bringing the electric range to Australia for a solution here and now that allows us to make the right steps forward.”
Khanna explained that the feedback on the machines has been good.
“The machines are quiet and energy efficient,” he said.
“You have quick charging in 30 minutes and a run time of five and a half hours when running on three batteries, or you have the option to upgrade to a four-battery pack.
“This machine is one of the most tested products before launching and was heavily tested in Japan. Anric Group has had nothing but positive feedback around these machines.”
Khanna said that many of the machines have the benefit of quiet operations. Rail corridors where the machines work can often be in residential areas, so removing the instances of a dull diesel engine operating can be beneficial.
While much of the electric infrastructure is catching up, Khanna detailed that the industry still has a while to go but it will go on the journey with its partners.
“I think moving forward you will see more and more electric machines coming onto construction sites, so it is important we provide that support,” he said.
“That is why every OEM including Hitachi is at the forefront of research and development and delivering a product for the future.
“The infrastructure around this is still lacking a little but you will see it improve more and more on site, and more electric machines will be used.”
The main feature of the two- and 13-tonne excavators is the combined use of battery power and a commercial electricity supply while maintaining the same workload as engine-powered models. Long operating hours are achieved by this use of battery power in conjunction with a commercial power supply. Additionally, the two-tonne class prototype has the same outside dimensions as an engine-powered mini excavator of the same class and can work efficiently in confined spaces due to its short rear-end swing design.
The ZE85, a compact and agile 8.5-tonne electric excavator, is built on the foundation of the highly efficient Hitachi ZX85USB-5. With a 40kW output, the ZE85 meets the same performance standards as its diesel-powered counterpart, but with zero emissions. In contrast to machines powered by combustion engines, the electric powertrain demands no maintenance, minimising downtime.
“We do have a product line that can create a difference to our customers. We have a lot of exciting products coming out of Japan that are well suited to rail.”
Nitin Khanna, general manager
Hitachi has an established national support network for its users. With almost 30 branches across the country, the company is well set up to support Australia’s rail market.
“We have our local engineering team but also our sales reps across the country,” Khanna said.
“We don’t sell our machines through dealers, we have our own representatives who work with our customers directly. They work with them day in, day out and understand their needs.
“We have a huge amount of infrastructure
built around providing aftersales support to our customers. This includes a 24/7 hotline for our customers to call.”
Khanna explained that the organisation has committed resources, infrastructure and stock around its aftersales support locally.
“For our customers we have decades of experience in Australia and that knowledge and know-how around supporting the local industry,” he said.
“That knowledge has been built on over decades and is something that we rely heavily on when supporting our existing customers.”
MTR corporation has worked closely with Sydney Metro to help deliver the exciting new project for the city.
The next component in the delivery of Australia’s biggest public transport project is edging closer to completion, and the MTR corporation has been a critical cog in the process.
On completion, Sydney Metro will include a network of four metro lines, 46 stations and 113 kilometres of new metro rail.
MTR Australia is currently completing the Testing and Commissioning program for the city section of the Sydney Metro City & Southwest project, ahead of the line opening later this year. The city section covers the construction and operation of the Sydney Metro rail line from Chatswood (where the current Metro North West Line finishes) through to Sydenham.
This 15.5km section of the rail line is almost entirely comprises underground rail tunnels – including beneath Sydney Harbour. New metro stations have been built at Crows Nest, Victoria Cross, Barangaroo, Martin Place, Gadigal and Waterloo, and new underground platforms at Central, with an above-ground metro platform at Sydenham.
MTR corporation partnered with Sydney Metro to deliver the 23 new trains, CBTC, communications and Platform Screen Doors (PSD) systems for the project, as well as
“Sydney Metro is a gamechanger for Sydney and we have brought a lot of international experience to help ensure its success.”
Wai Lau, deputy project director
Rail Express spoke with Wai Lau, a deputy project director at MTR, to better understand the work undertaken and how the MTR team is getting ready for the opening.
“I have a been a part of the Sydney Metro City & Southwest project pretty much since day one,” Lau said.
“I arrived from Hong Kong to work on stage one design and the augmentation and tender, back in 2017. We developed the specifications between all of the different contractors, and our key role was on systems integration.
“Sydney Metro is a gamechanger for Sydney and we have brought a lot of international experience to help ensure its success.”
EXPERIENCE HELPED DELIVER PROJECT
For the Sydney Metro project, the challenge
proved invaluable for Sydney Metro.
“We have been designing, building, operating and handing over railway systems in Hong Kong and other parts of the world,” Lau said.
“The Sydney Metro systems were different, and our role was slightly different. Our role was integrating with other contractors and working closely with those building the stations. We were all pieces of the puzzle.
“As the integrator, we have to stitch together all of the station contracts, and that is where our expertise has been important.”
Lau explained the work they have done on this system is similar to what was done in Hong Kong.
When MTR corporation came onboard, back in 2017, it brought a number of team members across from Hong Kong to assist
the team was going to grow exponentially, and we were able to bring local talent into the team.
“This was a great opportunity for our international team to come together with the local teams and share expertise, to create a local workforce with the knowledge we have gained overseas.”
Flash forward to today and Lau said much of the team working on the project is local, ably supported by the team from Hong Kong.
“We can still lean on those experts overseas, when need be, but we have all of the knowledge here now,” he said. “We have become self-sufficient.”
The key for MTR throughout the project was program management, which helped ensure the project ran smoothly. It was a delicate process for MTR, as it worked in and around station contractors as they built the stations.
“As they were constructing, we would go in as the systems contractor to deliver the systems required,” Lau said.
“The complex stations took time to construct and so we knew it was important for us to be dynamic in the work we were doing and when we could do it. We had challenges around COVID, so timelines were constantly adjusting to deal with the unique challenges. That was where MTR’s experience became important. We knew where we could fit into the processes and deliver what we needed, when it was needed.”
The next section of the Sydney Metro project
will see automated trains running through the city for the first time.
The degree of automation is indicated by the Grade of Automation (GoA), up to GoA4, in which the train is automatically controlled, without any staff on board.
On most systems with lower grades of automation up to GoA2, there is a driver present to mitigate risks associated with failures or emergencies.
Lau explained that the process of getting this fully automated system online has been one of the highlights of the project.
“Getting the testing underway to get the next section running had posed some unique challenges but it is exciting to get these trains on track,” he said.
“Other GoA4 lines are often brought online on existing tracks but the challenge with this system is, we need to test the track
with an automated train.
“Normally testing is easier when you have a driver, so we had to find a new way to do it, but the team have done well to find a system that works.”
Updating the existing communications and signalling system used for operations on the North West Line to incorporate the City & Southwest Line, was another unique experience for the MTR team.
“We needed to integrate the Northwest software and make it one with the new system,” Lau said.
“We had to cut the existing software in with the new software, which was very significant. It was imperative to make sure the two systems worked together seamlessly, so we spent a lot of time delivering on that.
“All of this has been achievable thanks to the support from Sydney Metro.”
KeTech is making a commitment to bringing its technology to Australia to improve the passenger experience.
KeTech has been changing the game for the UK’s passenger rail network. It is improving real-time journey information systems in stations, on trains and in the driver’s cab and has identified Australia as an area for growth.
Rail Express spoke with Mike Dixon who is the company’s technical director and Paul Warren who is the sales director, to learn more about KeTech’s technology and its goals for improving passenger experience through smarter information systems in Australia.
“We have a great customer base in the UK, which we will continue to develop. However, our systems have been developed to be internationally portable and as such, we are now ready to address other markets,” Warren said.
“Australia has a very similar rail network to the UK with similar information gaps where we are confident that our technology can be deployed to significantly improve passenger experience, while providing train operators with much greater control over the flow of information.
“We are seen as a mission critical data provider. We work closely with a range of train
operating companies, asset owners and train builders throughout the UK to better integrate and improve their systems.”
Dixon explained that KeTech is on the cutting edge of new technology, giving it the ability to adapt its systems for any project.
“The unique feature of KeTech is that while we are a leading-edge software business, we also specialise in electronic design, including for rail vehicles, and also have inhouse systems design capability for network wide projects,” he said.
These skills and experience enable KeTech to create tailored systems with its latest cloud-hosted software. These can be deployed in ‘greenfield’ projects, and importantly as it has proven many times in the UK, can be overlaid into well-established legacy systems, repurposing existing equipment while providing up-to-the-second accurate information. This presents huge cost efficiencies while transforming passenger experience. Warren said that the decision to expand into Australia was carefully considered
and researched by the team.
“Last year when we were in Australia attending meetings, we took some time to journey on the trains to better understand how it was for passengers and where potential gaps were,” he said.
“It was obvious to us that our technology had the capability to enhance the local networks and remove the reliance on manual PA announcements and create more timely, accurate and consistent messaging for users.
“When you are a tourist in a new city and you don’t know the routes, it can be very challenging, and it can create a lot of anxiety around missing the stop. Our systems can simplify it for everyone travelling by train.”
Dixon explained that current information systems on stations and trains are not connected, posing numerous challenges. For example, on-train information systems are based around the doors opening and telling the system which station is next on the route. However, if changes need to be made, like opening a door for a second time, or if
“We are seen as a mission critical data provider. We work closely with a range of train operating companies, asset owners and train builders throughout the UK to better integrate and improve their systems.”
Mike Dixon, technical director
the calling pattern changes, it can throw off the messaging system making the onboard messaging out of sync with the journey and hence unusable.
“Historically in the UK, the information systems between stations were not even connected together,” Dixon said.
“What KeTech has done for the network is not only integrate the stations and control centres, we have also been able to fully integrate train-borne information systems to the same system – this has been carried out with legacy and new trains.
“The end game is for a customer to walk into a station and get on a train and to see and hear the same consistent information, providing a seamless experience across the railway and that includes the use of apps.”
Warren went on to detail that the system is more dynamic than existing software and can keep up with potential delays.
“Without this capability and when there’s disruption, the operators are kind of dead in the water. What they tend to do is they’ll focus on stations, because the stations tend to be easier to communicate with unlike moving assets, such as trains” he said.
“What we are doing with our system is connecting to that moving asset and allowing customers who are both on trains and at stations to get the same information.
“Our system gives the details people want and need for normal service and is far more dynamic when it comes to delays and disruption.”
Dixon explained that the centralised system can be rolled out relatively simply and easily as it is cloud hosted.
“It can run anywhere, and we can monitor from our head office,” he said.
“The reason we’ve been able to carry out that level of integration is because we deal with local signal information, with local timetables and other real-time data feeds.
“We process it using our proprietary algorithms and we distribute packets of information where they are most relevant.
“We don’t send out huge swathes of data, we send targeted data to targeted devices.
That means that we only send information that is relevant.”
Cloud hosting technology was the obvious choice for KeTech as it is remotely accessible, even with different time zones. It is also simple to use and maintain.
Warren explained that it is not just the farreaching technology that will ensure success for KeTech in Australia, it is the ability to integrate into legacy equipment, allowing an upgrade of technology without a major change to infrastructure.
Dixon said Australia is a burgeoning market with a lot of legacy systems with very little integration so there is a lot of scope for
and we can also work with legacy systems,” he said.
“We understand the old because we have delivered technology into the rail industry for decades, and we are still loving and nurturing equipment on London Underground today and keeping it alive with updates long after others are issuing obsolescence notices.
“We have got that mix of new technology and knowledge of legacy systems enabling us to economically enhance an operator’s information systems without having to rip out usable older infrastructure – making it more sustainable too.
“After all, displays are displays and PA is a PA, there is no point replacing usable equipment when they can be repurposed – it is the quality of the information presented on these devices that adds the real value.”
Dixon explained that KeTech has had the opportunity to work with numerous operators in the UK to improve its systems and has cultivated experience delivering tailored solutions.
“We not only engage the management
use this system and so we have had great success conducting workshop sessions to better understand what the users need from our systems.
“What we tend to get is members of the teams adding their own ideas to solve their operational challenges.
“This is perfect for us; it gives us the opportunity to learn, improve and enhance what we can offer to other customers, too. It can be something really simple like giving the ability to show if toilets or lifts etc, are locked out of use. All of this is about improving the travel experience for those using public transport.”
Dixon and Warren both agree that because the Australian rail system has its roots in the UK, with similar standards and working practices, it will assist KeTech to bring its experience to the local market.
“When it comes to supporting our systems, the core is cloud hosted, so can be supported remotely by us, allowing monitoring and reporting of the state of the system including all interfaces.” Dixon said.
“We already have our 24/7 support service and thus it is simple for us to incorporate any further systems as we roll them out across
Australia. We have already got local partners here that we can lean on for the support of the low-level system elements and we are keen to partner with more people here.
“KeTech is committed to operating in the Australian market, supporting customers both locally and remotely.
“We also have the benefit of being in a
different time zone so when it comes to updating systems we can conduct updates that fit a schedule around the Australian rail networks.
“We are so excited to bring this technology to Australia and we believe it is ideally suited to improving passenger and operator experience.”
The contract for the Sydenham to Bankstown upgrade was recently awarded to a joint venture between John Holland and Laing O’Rourke with work set to get underway on transforming the rail line.
A joint venture between John Holland and Laing O’Rourke has meant the companies have secured a second Sydney Metro contract along the Sydenham to Bankstown corridor, which will upgrade the Bankstown Station precinct.
The Southwest Metro Conversion and Station Works package also includes upgrades to nine other Metro stations, as well as the final conversion works for 13 kilometres of the almost 130-year-old T3 Bankstown Line to metro standards.
John Holland’s executive general manager – rail and transport, Steve Butcher, said this latest package supports the future of public transport in Sydney.
“This builds on the incredible work of our joint venture project team to modernise and futureproof the rail line between Sydenham and Bankstown,” Butcher said.
Laing O’Rourke’s acting managing director, Mark Dimmock, said it was an exciting opportunity to bring world-class metro services to communities in Sydney’s Inner West and Southwest.
“We’re proud to continue our longstanding partnership with Sydney Metro delivering complex rail projects – with our teams working tirelessly to improve the rail network over the last six years.
“This sets up an exciting future for public transport.”
The works to be delivered along the 13-kilometre alignment from Marrickville to Bankstown include:
• Significant upgrades at Bankstown – construction of a new metro station; modifying and building new infrastructure and systems to allow for continued Sydney Trains operations at Bankstown Station when metro services commence; and precinct work for a new cross corridor plaza between The Appian Way and Restwell Street.
• Completion works to convert nine stations to metro standards including the installation of wayfinding and upgrades to station buildings and structures.
• Completion of overhead wiring and final track alignment work.
Upgrade works are continuing on the T3 Bankstown Line with crews working around the clock during a recent 12-day school holiday closure to deliver the first mechanical gap fillers external site at Marrickville, Dulwich Hill, Hurlstone Park, Canterbury and Campsie stations – 89 of the total 170 mechanical gap fillers were installed.
Works were also undertaken to construct the new metro platforms at Bankstown, having installed the structural steel and precast panels, and completing a concrete pour crucial to the platform’s overall structure.
The project leverages the combined and multi-disciplinary rail expertise of John Holland and Laing O’Rourke, which has played a key role in the delivery of rail improvements between Sydenham and Bankstown since 2018, including the Sydenham Station and Junction works.
LSM Technologies’ newest innovation looks set to revolutionise safety, incident prevention and efficiency around rail level crossings. Rail Express sat down with the company’s founder and CEO to learn more about what is a transformative device.
Over the course of close to two decades, LSM Technologies has become a highly sought after provider of technologies concerning workplace OH&S, productivity and minimising down time.
Peter Woodford is the engineering director, CEO and founder, with experience in the mining, earthmoving, construction, manufacturing, heavy road transport and now rail sectors.
With his specialised engineering expertise and thorough industry knowledge, he’s set out to design devices that can make a lasting impact within industry workplaces.
Woodford is previously quoted as saying, “I have learnt a lot in my life so far – but then I find that there is so much more still to learn and therefore so much more to share”.
It’s this belief that has led to one of his latest innovations, a device that could create a national unity towards increasing the safety of both road and rail called LSM TrainSense.
WHAT IS
LSM Technologies’ TrainSense Rail Level Crossing Collision Awareness/Avoidance
System aims to directly address a well-known issue. That is the alarming trends around level crossing vehicular collision incidents.
The TrainSense concept is a safety mitigation device that would be best described as a small puck in terms of its visual appearance.
While its appearance may be understated, this small device has the potential to transform level crossing safety.
Level crossing safety is an issue that has been a subject of discussion for years and while there have been developments from a policy and equipment standpoint, traditional technologies leave much to be desired Woodford explained.
“It’s an issue that costs the sector hundreds of millions of dollars,” he said. “This isn’t just an Australian issue. In the US, Canada and Europe it’s also a big deal.”
A key catalyst for many of these incidents is what Woodford labels as ‘human behavioural issues’.
“There’s plenty of articles out there that talk about road users breaching passive warning signs, taking potluck, ignoring active
alerts or going through the boom gates,” Woodford said.
“In the Rail Level Crossing, Rail Bridge Impact discussion paper I released, there’s a big focus on how we could overcome, or work around, human behaviour and error. That’s where TrainSense comes in.”
TrainSense aims to reduce the impacts of human behaviour and error that may lead to road and rail vehicle interactions, such as complacency, situation awareness and distractions.
The concept is that inside TrainSense is a database of all mapped railway level crossing GPS co-ordinates. Once the users vehicle is moving, the device is dynamically comparing real-time GPS data, between the location of the vehicle and the coordinates of nearby level crossings.
If the user approaches a level crossing, TrainSense will provide an audible and visual warning to the driver inside the vehicle cabin.
This happens in real time and the user doesn’t need to pre-route or update coordinates during their journey. As such the TrainSense is a relatively cheaper, simpler
and more accurate tool that can compliment conventional warning devices.
It’s also customisable, with options around the frequency and distance at which alerts are provided to the driver. The device is simple to attach and can be installed on the corner of the windscreen.
TrainSense is also compatible with automated technologies to increase its effectiveness in high-risk situations. The device can be programmed to decelerate and apply the brake to mitigate an interaction if the driver ignores multiple device warnings. This feature encompasses the potential to apply Automatic Emergency Braking with compatible vehicles if required so as to bring them to a stop at a level crossing.
All this and more is provided at no extra cost, as well as no subscription or telematics related charges.
As Woodford explained, industry support is already there, but further support is needed to ensure that public can reap the rewards of such a beneficial system.
“TrainSense merits have already been supported by Heavy Vehicle Industry Australia, as well as TrackSafe.
“It’s a low-cost solution that’s all about providing mitigation and a strategy to overcome human error and behaviour and to mitigate collisions. It’s a new technology, it meets all the criteria of the 2024National Rail Level Crossing Strategic Plan and eventually I’d hope to see it become a standard feature such as Automatic Emergency Braking is today with the ADR97/00 and ADR108/00.”
LSM TrainSense is also compatible for use with LSM BridgeSense, another patent-pending device from the minds of LSM Technologies. As the name suggests, BridgeSense utilises similar technology to that of TrainSense to help reduce the frequency and chance of bridge and structure
In order for the transport network to fully benefit, Woodford envisages a reality where all road vehicles are equipped at manufacture with devices such as TrainSense and BridgeSense, reducing the chances of level crossing and bridge impact incidents.
To achieve this, Woodford is seeking more support from both the public and private sectors to drive growth around what could be a transformative device.
“I’m optimistic that we’re going to save lives, that we’re going to save the taxpayer and industry a lot of money in repairs, while also reducing inconvenience and costs connected to traffic congestion,” Woodford said.
“The LSM TrainSense and BridgeSense
The UK’s Rail Safety and Standards Board is bringing its skillset to Australia to support the development of the industry.
The Rail Safety and Standards Board (RSSB) was established in 2003 in the United Kingdom. This was based on key recommendations from Lord Cullen’s public inquiry into the Ladbroke Grove rail accident in which improvements to the framework around safety were recommended.
The Southall and Ladbroke Grove train crashes, in September 1997 and October 1999 respectively, led to the deaths of 38 people as well as 100s of injuries, which in turn led to three separate public inquiry reports: one for each crash and a report on Automatic Train Protection.
The inquiries took a fundamental look at the generic issues surrounding safety in the British Railway Industry. A principal conclusion focused on the improvement of safety management and specifically safety culture.
The inquiry stated that “achievement of
an improved safety culture on the railways is at the core of the whole programme of change initiated by Lord Cullen’s Inquiries ... if an organisation has the right culture in place, it will find the right people and the right technology to deliver safe and effective performance.…the need for a positive safety culture is the most fundamental thought before the inquiry”.
The reports resulted in 295 recommendations, setting “a necessary and challenging criteria to change the state of the railways”.
A section of the recommendations fell under the title ‘Culture, Safety Leadership and Health and Safety Management’, which presented 25 recommendations relating to the internal structures of companies, safety culture, and the management of health and safety.
The recommendations were aimed at
securing improvements in the following areas:
• safety auditing processes;
• fault repor ting and maintenance;
• risk assessment;
• application of a railway safety case regime; and
• safety leadership and communication in companies.
Since 2003, RSSB has been helping its members keep the UK moving with safer, smarter rail. Its core purpose is to support industry, so that it can achieve better results.
It offers services and resources that capture and share standards and best practice, with rail organisations and other industries in Britain and abroad.
RSSB’s remit is bigger than standards. It promotes industry safety, research and
development, monitors and reports on safety performance, and provide guidance and good practice.
It has developed the common standards that allow the UK’s diverse network to function as a single system. It leads cross-industry strategies, like Leading Health and Safety on Britain’s Railways, the Rail Standards Strategy and the Sustainable Rail Blueprint. There are also cross-industry working groups and committees on subjects from mental wellbeing to driver advisory systems.
The organisation’s research has allowed existing and new vehicles to operate at different speeds on the same track, optimising journey times and maximising route capacity. The revised standards for AC electrification have the potential to save AUD$1.05 billion if all the 13,000 single-track kilometres in the Traction Decarbonisation Network Strategy are electrified. This is mainly by reducing costs in the design, construction, and maintenance of infrastructure.
the investigation process and techniques for derailment, delivered in 2021/22.
international organisations greater access and flexibility.
RSSB’s insights and analysis have helped put rail at the cutting edge of health and wellbeing practice in the country. It has started a programme to gather consistent sustainabilityrelated data from across the industry, and its rule book ensures industry knowledge is reliably applied on the front line.
RSSB is enabling more radical changes too. It is enhancing its data science abilities with new datasets, like weather data, to help model how the changing climate will affect rail’s fixed assets. RSSB has access to more data than any other rail organisation, and is working with academia to lay the groundwork for bluesky innovations.
RSSB is looking to bring its experience and knowledge to the Asia Pacific. The organisation receives its greatest number of global enquiries from Asia. It also recognised the connection between the region and the UK’s rail network, making the sharing of knowledge and ideas simpler.
Every day its specialists work to solve the safety challenges faced by rail operators, infrastructure partners and suppliers. Its expertise is hands-on, current and cuttingedge, covering a variety of topics from risk management and operational safety to human factors and system thinking.
Some of the projects the organisation has worked on in the APAC region include:
• PTA Western Australia: Ballast Depth and Sleeper Spacing Review, delivered in 2021/22.
• MTR Hong Kong: Training on derailment and wheel-rail interface, delivered in 2021/22.
• MTR Hong Kong: Training on understanding
• MTR Hong Kong: Benchmarking consultancy support, delivered 2021-2023.
• NTC Australia: Consultancy support on rail interoperability, current project.
RSSB makes its experts available on a project-to-project basis, to help organisations answer technical questions that are critical to its success.
RSSB advise on reducing system risk and supporting safe and effective operations, improving operational safety by helping design, and co-ordinate railway operations safely and efficiently.
The company helps guide an organisation in the best practice of taking safe, defensible decisions by providing toolkits, insights and resources built on two decades of safety research and analysis. It also provides knowledge, tools and techniques to optimise human performance in the workplace, as well as resources and guidance on helping people manage fatigue and remain alert.
Then there are its mental health support with tools, training and resources to help manage and prevent mental ill-health.
It can work with companies on effective approaches to understanding and working with complex rail systems.
All of these consulting tools ensure RSSB provides the required information for its partners to ensure success.
RSSB training is tailored to the specific needs of organisations with an interest in rail. The courses are created and delivered by some of the world’s leading rail experts. Most have been adapted for remote delivery, offering
The courses are designed and delivered by leaders in their field and updated regularly to reflect the everchanging environment of the rail sector. RSSB’s courses blend practical application with academic theory. This enables delegates to gain knowledge and learn skills they can apply immediately at work and make a positive impact on businesses.
The Accident Investigation Training course is informed by RIS-3119-TOM, the Rail Industry Standard (RIS) for Accident and Incident Investigation. This RIS sets out the requirements to fulfil legal obligations for investigations involving more than one duty holder. This is so system improvements necessary to prevent or reduce the likelihood of recurrence, or mitigate the consequences, are identified and implemented.
The Mental Wellbeing for Line Managers training course was developed through rail industry research on effective mental health training for line managers. It has been designed by rail industry clinical psychologists and covers psychosocial risk factors experienced by the workforce, grounded in rail specific content.
RSSB’s G-FORCE model supports rail personnel to make rational decisions when under pressure or when they are faced with unfamiliar or unusual situations. It works by taking the user through a rational decisionmaking framework, helping them come to a logical decision. RSSB uses past real-life examples of incidents across the rail network to discuss with delegates and discuss outcomes that would fit the G-FORCE model.
It has experts not just from the rail industry, but those with experience in related industries such as aviation, transport, oil and gas to name a few, bringing a wider perspective to delegates and facilitating cross-sharing.
Anchoram and Certifer Solutions are bringing each organisation’s expertise to assist Australia in improving cybersecurity on the rail network.
Technology is present in every part of our lives, and the railway sector is no different. The efficiency and quality of service provided by rail operations have improved with the integration of digital systems.
The safe operation of new technology presents its own set of challenges given that the railway network may be vulnerable to cyber threats that could disrupt services and jeopardise safety.
Sophisticated control systems are essential to modern railways for scheduling, train control, and signalling. Due to their frequent connections – either direct or indirect – to the internet and other networks, these systems are open to cyberattacks. If such an attack is successful, it could result in data breaches, unauthorised access to control systems, disruptions to train services, and serious harm.
As the railway industry continues to evolve, the collaboration between technology experts, regulators, and rail operators will be essential in developing resilient systems that can withstand the challenges of the digital age.
Anchoram and Certifer Solutions see four pillars where assessment and gap analysis can prove valuable, both during projects and during the operations and maintenance phase. This includes governance, standards compliance, independent assurance and risk management – all of which have an impact on safety if not performed with due diligence.
When looking for subject matter expertise
Anchoram and Certifer Solutions can provide an integrated approach to the assessment of cyber risk, safety assessment and independent certification that will provide railway operators with a proactive approach to ensure the safety and reliability of their rail operations.
Started in 2019, Anchoram provides professional services and experience that are well-tailored to critical infrastructure.
Headquartered in Canberra, with people spread across all major locations in Australia and a growing presence in India, Singapore, and New Zealand, the company is rapidly expanding.
Australia based Certifer Solutions is part of the French Certifer Group founded over 25 years ago. A rail industry focus is its strength, ensuring its services areat the cutting edge of innovation and in-depth, constantly updated knowledge of regulatory frameworks.
The Rail Safety National Law, which imposes obligations on all parties involved in the Australian railway sector, is a framework laid out to support the safe operations of the rail industry.
A safety management system outlining the methods for managing and controlling safety risk is a requirement for all Rail Transport Operators (RTOs) as a safety control measure.
The law acknowledges the need to record security risks and put safeguards in place against dangers like sabotage.
Many nations and organisations have created standards and guidelines to reduce these risks because they understand the importance of rail cyber security.
For example, RTOs can manage cyber
security risks using the framework provided by the Australian Standard AS 7770:2018 – Rail Cyber Security. This standard and industry guidelines describe what is needed to have a strong cyber security posture within the rail industry.
More recently, TS 50701 provides guidance on how to implement an IEC 62443-based compliant design to railway systems and ties in with Reliability, Availability, Maintainability and Safety (RAMS).
These generic processes ensure cyber risks are thought of with more traditional rail operational risks and are due to become the dedicated International Electrotechnical Commission (IEC) Standard 63462 in 2025.
The IEC has created IEC 63452 in response to the digital revolution in the rail industry. This standard is at the forefront of efforts to strengthen cybersecurity within railway networks, reflecting the growing significance of safeguarding our rail infrastructure from cyber threats. The standard was also created as a result of the combined efforts of the IEC Technical Committee 9/PT 63452, which consists of more than a 100 industry professionals, including prominent figures from rail companies and the suppliers.
The standard is designed to address the unique cybersecurity requirements that emerge from the increasing interconnection of railway operations.
The primary goal of IEC 63452 is to offer a robust, understandable, and useful set of guidelines that will strengthen the security of rail system components, such as infrastructure, control systems, and trains.
with a comprehensive cybersecurity strategy,
it aims to expand upon the foundation of current cybersecurity protocols.
Crafted with a worldwide scope, IEC 63452 is intended to resonate with various international regulations and operational standards. This global perspective is crucial for a standard that will be used in many different countries and with different regulatory frameworks.
Some rail operators may have regulatory obligations as part of the Security of Critical Infrastructure Act of 2018.
This includes the requirement to adopt, maintain and comply with a written critical infrastructure risk management program (CIRMP) that encompasses all hazards, of which cyber risks are one facet.
This program should identify, and as far as is reasonably practicable, take steps to minimise or eliminate the ‘material risks’ that could have a ‘relevant impact’ on the rail asset. This is even though a broad definition shows that there is a depth of assessment to cover all aspects of a modern rail operation including rollingstock, signalling, power control, tunnel ventilation, track and any other area of modern transport networks.
The structured management of cyber security
the delivery phases of a project and onwards to the operations and maintenance phase.
With the complexity of digital systems increasing, it is essential that the processes adopted for assuring safety are appropriately scrutinised for effectiveness.
For major railway projects in Australia, ONRSR recommends the use of Independent Safety Assessment (ISA) to review and challenge safety risk management and outcomes.
An effective ISA requires an understanding of both safety management processes and principles, coupled with technical knowledge of the engineering domains and disciplines to provide pragmatic and valuable support to a complex railway project.
Augmenting ISA, independent verification that a project has delivered its design, installation and testing in accordance with its original requirements can provide an RTO with assurance that a project is delivering against the specified standards. Such standards can often be part of the RTO’s safety management system, providing the engineering controls that manage safety risk.
Independent verification provides assurance to an RTO that a project has delivered against the contracted specification and implemented the specified risk controls. For some projects, verification activity can result in certification of the project works.
Advanced technologies are improving the safety and productivity of Australia’s railways, but they’re also increasing networks’ vulnerability to cyber-attacks. The NTC is working with industry to grow the skills needed to keep rail systems safe.
The Internet of Things and artificial intelligence’s ability to collect, share and analyse data is helping to streamline rail operations, allowing operators to make better decisions and maximise the benefits of 21st century technologies.
While this high-level connectivity brings benefits, it puts organisations at greater risk of hackers, malware and data theft.
Rail operators, infrastructure managers and organisations across the rail supply chain have made cybersecurity a priority as they introduce digital technologies to improve operations.
Demand for cybersecurity skills is expected to grow faster than the supply of workers as the digitisation of the sector increases at pace.
The National Transport Commission (NTC), through its National Rail Action Plan (NRAP), is working with industry and the education sector to address this skills gap.
NTC Executive Leader, Facilitated Reform, Sandra McKay said cybersecurity will be a key element of NRAP’s future rail skills framework.
“The framework is part of our commitment to ensuring rail has the skills to build, run and maintain $155 billion of investment scheduled over the next 10 to 15 years to expand and modernise Australia’s rail networks,” she said.
“Early consultation in the framework’s development shows that cybersecurity is one of the most in-demand skills areas across all elements of rail.
“There is a global shortage of four million cybersecurity workers, so we’re not going to be able to buy in this talent. We need to grow
“We’re committed to investing in our people, to ensure they are equipped to meet the future needs of our customers and our organisation”
Philippa Johnston, Queensland Rail Pillar Lead
approach to building Australia’s cyber abilities. This starts with identifying skills that are common to multiple networks.
“We are focused on creating a pool of workers experienced and trained in cybersecurity whose skills are recognised across Australia, allowing them to move more easily between jurisdictions and projects to meet demand,” McKay said.
Common skills identified during the initial research and consultation process include:
• an understanding of cybersecurity principles;
• knowledge of encryption techniques to secure data transmissions;
• expertise in securing network systems;
• familiarity with IT security and data privacy laws and regulations, to ensure technology is implemented according to the Rail Industry Safety and Standards Board’s (RISSB) standard and guidelines and relevant privacy laws;
• the ability to respond effectively to cybersecurity breaches and to detect unauthorised intrusions or hacking
the secure use of digital train control technology.
The need for rail-specific training in basic cybersafe practices is also growing as more rail workers use network-connected computers in their day-to-day tasks.
The Future Digital Skills in Rail report developed for the NTC by Deloitte suggests that cybersecurity will form a critical element across all digital competencies in the future.
In the meantime, the NTC’s Digital Rail Champions pilot program is helping to identify the specific digital competencies that rail needs. The program offers courses across five streams of learning, including cybersecurity. It includes free courseware and access to trainers.
Learnings from the pilot will be used to develop foundation level training that is recognised nationally.
Queensland Rail is one of the program’s early adopters, as part of its efforts to enhance training and upskilling to prepare its workforce for the future. Queensland Rail Pillar Lead, Build the Future Workforce, Philippa Johnston explained in greater detail.
“We’re committed to investing in our people, to ensure they are equipped to meet the future needs of our customers and our organisation,” Johnston said.
“This includes a focus on important areas such as digital security, and continuously educating our people about their role in building cyber resilience, at work and at home.
“Through opportunities like this pilot, we aim to empower our people to be ready for the jobs of the future, as we work towards becoming a digital railway.”
For more information about NRAP’s future skills program visit the National Rail Skills Hub.
RAIL EXPRESS is compulsory reading and a vital tool for all people working in and around the rail sector.
Rail Express is Australia’s authoritative business to business rail publication.
Combining the resources of our respected journalism team and our unparalleled industry contacts and affiliations, Rail Express provides extensive, comprehensive and balanced coverage of breaking news and trends in key areas like infrastructure, investment, government policy, regulatory issues and technical innovation.
Published both in print and digitally every month, Rail Express is the only publication to have both the official endorsement and active participation of the main railway associations in Australia and the broad support of the rail industry.
The only way to ensure you get every copy of Rail Express is to subscribe today. Visit railexpress.com.au/subscribe.
Transport for New South Wales secretary Josh Murray spoke at the PWI executive breakfast, giving an update on the organisation.
In the first year of his role as Secretary for Transport for New South Wales, Josh Murray spoke at the PWI executive breakfast, discussing the future of transport in the state and what the focus for the organisation will be moving forward.
Murray has a long history in and around the rail sector, working in government assisting with policies impacting transport and even working on some of the early business cases for the Sydney Metro project.
He began his speech by celebrating those who work on Sydney’s transport network and all the success it has seen recently. He went on to explain what the period since joining has been like.
“I rejoined the transport portfolio, at a very busy time,” he said.
“A change of government, new priorities, at least five or six independent reviews into capital programmes and the way we deliver services for the people of New South Wales.
“Our purpose remains very familiar to you. It is to deliver a safe, reliable and modern transport network.”
Murray explained that meeting the needs of the community is what drives those who work in rail but said that the industry can’t do it alone.
“I did see that changes were required,” he said.
“Not just as a new boss who has to come in and redraw an old chart but to embark on a transformative agenda that reshapes the
of schedule,” he said.
“Further work commences now on recommendations relating to the broad areas of training, maintenance, and operation, in particular how we double down on the efforts and the capability across Sydney trains to
“The Sydney trains effort will now focus alongside how we ensure we bring back that passenger service and reliability as quickly as possible. Over the next four years, we will continue to deliver vital public transport services, alongside roads and exciting projects
Murray touched on projects like Sydney’s light rail as an important example of how Transport for NSW can create more accessibility, reliability and modern connectivity and choice in travel.
The new projects are a short walk to stations for people who have previously had no access
“Transport does have to recognise we don’t just dance to the beat of our own drum,” he said. “Sometimes when you’ve got the biggest capital budget in town, you can convince yourself of that. But we are the constant in everyone else’s success across government.
across multiple projects. We know that safe and secure pipeline is critical to providing industry with the certainty that enables you to build up investments in resources, skills and capabilities.”
The organisation is in the early stages of investigating the application of the 50 per cent target for its future rollingstock contracts. Replacing the Tangara trains is the next priority and will result in renewing a quarter of its fleet.
of that.
“We are proud to be halfway there on our sustainability target of net zero emissions from operations and fleet by 2035. Our electrified rail networks are powered by 100 per cent renewable energy.”
Murray said these numbers are important symbols of change and as so much federal funding goes through the transport network, they must set the agenda and the standards for the economy.
government dollars is spent on transport. We’ve traditionally invested in two things, which is growing the network and making it run faster. Now we need to be more engaged in those government priorities and housing in particular, and unlocking those new communities will set up the Sydney of the future.”
Murray explained that Transport for NSW is seeing more targeted infrastructure spending from the Federal Government.
“There is a lot of debate currently about whether the Federal Government are going to be a strategic partner or a silent investor,” he said.
“The states and the Commonwealth do need to reset their relationship around this. We want to make sure that Canberra really understands what we can do for the national economy, and that they understand their role in helping us along the way.”
Murray expects to see more opportunities for local manufacturing as this becomes a focus for Transport for NSW.
“New South Wales has one of the largest rail manufacturing pipelines in the country,” he said.
“But everyone is coming to the market over the next few years, we need to be coordinated. We need to really do this alongside your capabilities and where you can help us grow the local economy.
“We have set a 50 per cent local content target for future rollingstock contracts, and we are committed to increasing the waiting
“Building that capability and expertise now will give us a long-term pipeline in New South Wales to deliver first-grade rollingstock,” he said.
“We need your advice on how we bring the market towards those opportunities over the long term and how we work with our interstate colleagues.”
Murray said that the focus for Transport for NSW will also be to get more freight moved by rail in the state. He touched on the reforms being led by Dr Kerry Schott and how the state can optimise that.
“The New South Wales and Australian Governments are working together to support the delivery of the final business case for the Western Sydney freight line,” he said.
“We also joined ARTC and Inland Rail to discuss strategic opportunities between our multiple organisations.
“I’d like to say that with new leadership teams across the three bodies, we do feel that great gains can be made working more closely together between New South Wales and those vital public projects.”
Murray rounded out his speech by touching on the sustainability targets and the work being done around this.
“We look to the role that we can play,” he said.
“The transport sector makes up 24 per cent of New South Wales’ greenhouse gas emissions
“Thirty per cent of public transport commuters say they’ll pay more for a carbonfree service, and another 30 per cent would prioritise public transport if they could be assured that it was sustainable,” he said.
“A key outcome for us this year is to encourage more people back to public transport, building this back to patronage, pre COVID and beyond. Sustainability must be a core consideration throughout all of the work we do together, but I’m also committed to the sustainability of our very industry, the businesses, the supply chain, the people and training.”
Gender diversity will remain at the forefront of Transport for NSW’s work in the coming years.
“I’m privileged at Transport for NSW to work alongside a senior leadership team that includes many talented women,” Murray said.
“Fifty per cent of my direct reports are women, which is important to the culture that we wish to set and work with. I acknowledge it’s far from representative across the broader organisation.
“And we’re currently working with the Federal Government and other states to build on the culture standard that many of the construction industry leads have been piloting.
“I think it’s time those trials moved on, from test cases on road and rail across the various states. And we look to embed something in all of our contracts where we can progress, better culture on all of our projects, not just for women in construction and infrastructure, but changes that will benefit us all.”
The ARA is continuing to grow and develop the Rail Industry Worker Program to support the industry’s tracking of worker competency.
The Australasian Railway Association’s (ARA) Rail Industry Worker Program (RIW), the national competency and safety management system for Australian rail workers, has been enhancing rail industry safety culture for more than a decade. The RIW Card is now used by 100,000 rail workers and almost 6000 companies and has been adopted by all major Australian network operators.
The RIW program brings together a worker’s competencies, education and health assessments into a single electronic record. Each worker receives a smart card linked to their profile which can be used to verify their qualifications to perform roles on a rail network. The RIW system also helps
Law (RSNL) and other regulations.
The ARA established RIW in 2013 on behalf of the Australian rail industry to fill a significant gap in managing worker competency, harmonising job roles and understanding workforce capabilities across the country. Governed by representatives from accredited rail network operators, infrastructure owners and principal contractors, RIW continues to evolve under the stewardship of the ARA.
RIW SUPPORTS A STRONG SAFETY
The RIW system puts the safety of workers and rail users at the forefront of every shift. It assists network operators ensure work is undertaken by suitably trained and experienced workers.
An analysis conducted by Herbert Smith Freehills in 2023 reviewed how the RIW system assists rail transport operators, including rolling stock operators and rail infrastructure managers and contractors to manage their obligations.
Herbert Smith Freehills concluded that the RIW program is “a powerful tool for ensuring compliance with those key elements of an
the RSNL, and the principles required for compliance with the general duties under WHS law.”
Given the scale of construction currently underway in the rail industry, with a $155 billion pipeline of infrastructure projects across the country, the RIW system is increasingly critical in ensuring safety and efficiency on job sites. Real-time verification of competence and fatigue management has been central to worker safety and the ability of the RIW system to suspend and block workers who do not produce negative drug and alcohol tests has also reduced the potential for safety incidents.
Beyond being an important tool for safety, compliance and competency management, RIW’s ability to provide a system-wide single credentials program provides additional benefits for industry and workers.
A key focus for the ARA is supporting a growing, sustainable rail workforce that promotes skills development. ARA research has showed that our 165,000-strong Australian rail workforce is battling with a “retirement cliff” and a 70,000 skills gap, mostly in operational and project roles, including engineers, train drivers and controllers and IT specialists.
The ARA’s The Rail Workforce – An Analytical Overview published in December 2023 also found that about 35 per cent of the Australian rail workforce would retire by 2035, with almost a third of train drivers currently aged over 55.
Data integrity is critically important to safeguard the value of workforce data. Recognising this, the RIW program introduced a direct upload function for Registered Training Organisations. The function simplifies the process of adding competencies to worker profiles. The feature complements the similar direct upload function for Authorised Health Professionals.
In combination, these measures improve data integrity, speed up job role certification and further enhance worker safety and compliance.
The detailed workforce model also facilitates the harmonisation of skill requirements for job roles common across rail networks and sites. Skills harmonisation unlocks workforce mobility, and the digital RIW cards support that portability.
The ARA has brought industry subject matter experts together to create nationally consistent, standardised job roles. These National Job Roles establish the competencies and health obligations required to complete specific jobs on any
and signalling, which are areas of critical demand across our industry. A suite of civil construction roles has also been defined. These full workforce roles facilitate the use of RIW on rail sites that commence as civil construction projects. This means even greater portability of skills and mobility for our workforce.
In addition, the ARA released a new National Assessment Framework. The framework helps employers ready their workforce to meet the requirements of the National Job Roles.
The adoption of National Job Roles prevents unnecessary re-certification of worker competencies wherever identical work will be performed. Employers can mobilise staff working over many sites and network jurisdictions and it gives them the
workers can move between different job sites, swipe their RIW card and, with an appropriate briefing, begin work immediately.
The benefits of National Job Roles are not lost on State and Federal governments either. Governments have increased their focus on skills harmonisation and recognition across employment, training, and education portfolios.
As our industry continues to grow and develop, so does the RIW program.
In 2024, the ARA is working on behalf of industry with the National Transport Commission (NTC) on the review of Rail Safety National Law (RSNL). Our participation in the review helps the ARA ensure RIW remains fit-for-purpose and compliant with any changes to RSNL and is part of our program of work to improve safety, interoperability and harmonisation.
The ARA continues to improve functionality and develop new features in response to the needs of participants. We also consult with industry to further harmonise competency and health requirements to establish National Job Roles.
The program’s commitment to data integrity and collaboration with regulatory bodies like the NTC underscores our industry’s dedication to maintaining the highest standards of safety and compliance.
The ARA is also looking at RIW’s success
example of a collaborative industry initiative driving positive change and fostering a safer,
The RTAA Field Day was opportunity to come together and get hands on experience with new technology.
The Rail Track Association of Australia (RTAA) held its Field Day back in early May. Held at Chullora Rail Precinct and supported by Sydney Trains, the day was an opportunity for industry to come together and share new technologies, revolutionary ideas and learn from experts.
RTAA president Jonathan Barnes said the day was a success for those in attendance regardless of the sometimes inclement weather.
“We definitely learnt from our past experiences and you can see that in the way we met the very poor weather,” Barnes said.
“General feedback from exhibitors and those in attendance was positive. Speaking with people from places like Sydney Trains they said the demonstrations like the flashbutt welding were extremely beneficial.
“It gives them a different appreciation for what the technology actually does. It affords them a better understanding of how the technology could be useful in their networks. These are conversations that can’t always be had in an office or a regular convention centre, so days like this make it possible.”
Barnes said events like the Field Days still maintain an important part in the industry and is excited to continue growing the day
“Given the nature of our industry, it is prohibitively difficult to show people the work that we do and field days like this gives us an opportunity to show people the work we do.”
Jonathan Barnes, RTAA president
in the years to come.
“I think when you look to the future, we have an important role to play in workforce development,” he said.
“Given the nature of our industry, it is prohibitively difficult to show people the work that we do and field days like this gives us an opportunity to show people the work we do.
“Even the back-office staff get the opportunity to attend events like this, which can enhance their understanding of the work that gets done on site. I absolutely believe there is a need for an event like this.”
The Field Day had a number of welding demonstrations for those in attendance. It saw companies such as Key Source
Rail explaining new technology. These demonstrations were a great insight for those attending.
The event also had the opportunity to raise money for Beyond Blue and its support of mental health work.
Artist Luke Penrith painted a traditional artwork that will be raffled off on the RTAA website to raise money for the charity.
Barnes went on to detail what was in store for the next 12 months for the RTAA.
“Our focus for the rest of the year will be smaller technical events,” he said.
“We are working now with our members to try and build up that program.”
Barnes said the organisation is still working on its events after the challenges it faced throughout the pandemic.
Jonathan Barnes is grateful for all the support the organisation received that ensured this years field day was once again a success.
And we have a wrap on this year’s Field Day, and what an event it was! The weather was once again challenging but with lessons learned from last time and some periods of blue skies we didn’t let it dampen the event, and with visitors from across the country it was one of our most successful events to date. Occasions like this are a massive labour, which only can only succeed,with the efforts of individuals and the support of our members and industry. Special thanks go to our event partner and host Sydney Trains and Transport for NSW, who made the event possible, and to those in Sydney Trains who went above and beyond –Arjun Pokharel, Nikkita Cullum Andrew Lagos, Rick Vidler and Dennis Lo.
I would also like to once again thank our event sponsors Brimble Rail, Pandrol Australia and Kennards Hire. Your generous support allows us to host the event and keep it free and accessible to all.
and gratitude to all those that supported the organising committee and event, and in particular I recognise Paul Bertino of Saint Gobain Australia and Brett Harvey of Kennards Hire.
The Field Day is a unique event in our industry calendar. The chance to see and experience the equipment and tools in their native environment is immensely valuable. At its simplest it is an opportunity to showcase the tools and equipment that makes our jobs easier. But behind this is an opportunity to communicate and collaborate. Many of the conversations I had over the event were with those in the support services “behind the scenes” of the boots on the ground.
For these people, the field day is a chance to understand the scale of the machines, the weight of the tools and the realities of walking on ballast. These experiences are invaluable for the individuals but also helps them better understand and support their teams by understanding of what they are talking about.
This also presents another opportunity to extend that communication and collaboration beyond those currently in our industry. We have been attempting this in a limited way for the past few years, but there exists here an opportunity to expand this to be a
apprentices, but is open to all. We could also take this a step further and extend the invitation and encourage everyone to bring a rail outsider along with them, be it a partner, a friend or a child to extend this sharing and awareness to those that support us in our roles.
I recognise that while this will positively impact numbers of attendees it is unlikely to drive business leads. So this is a concept we will explore over the next 18 months as we develop for the 2026 event, and I welcome feedback and interest from industry. Is this something that you would like to see, and participate in? And is it something you would be interested in supporting?.
And the final word on the Field Day is the amazing artwork created by our friend Luke Penrith. This traditional style painting was contributed to by many of the attendees and represents the links between us and the combing together to share and learn. It is our great wish now to leverage this piece to raise money for Beyond Blue in support of their mental health works. We will be running a raffle draw so please go to our website where you can find how to purchase tickets.
For now the team is focused on the rest of the year as we develop our event calendar and prepare to support AusRail at the Gold
Simple mistakes are often to blame for incidents at Australian level crossings but stopping them is a complex problem as Dr Natalie Pelham explains.
It’s the statistic I’ve heard most since I took on the role of Australia’s National Rail Safety Regulator in November last year – Australia is home to more than 23,000 level crossings.
Think about this for a moment – there are more places across our country where trains interface with cars, trucks, cyclists and pedestrians than there are churches, McDonalds restaurants and petrol stations combined.
Generally speaking, even with that mind boggling number, the safety record at Australian level crossings is, by world standards, quite good. Nationwide, there were 38 level crossing collisions in 2022-2023 between trains and either trucks, cars, cyclists or pedestrians resulting in five fatalities and six serious injuries.
Of course, like our counterparts in road safety, we covet a zero-harm reality and are working extremely hard to get there.
The not insignificant efforts of various state governments through multi-milliondollar level crossing removal programs and commitments to no new level crossings is helping. However, it’s neither feasible nor commercially practical to imagine an Australian transport network without them.
They’re a vital valve in the arteries of a network spanning the length and breadth of the country that serve many and varied interests – and herein lies the truly wicked problem.
The National Level Crossing Safety Roundtable in Brisbane was attended by more than 60 different stakeholders representing the road and rail industries, regulators, academics and researchers.
It came in the wake of an incident on New Year’s Eve 2023, where two train drivers were killed when their freight train collided with a truck at a level crossing near Broken Hill.
The incident prompted Pacific National Chief Executive, Paul Scurrah, to call for a national summit on the issue of level crossing safety.
The roundtable was a productive and collaborative forum and while it’s early days, I’m confident that the outcomes will drive tangible safety results. But this will only happen if that abundance of interested parties play the roles required of each of them, in good faith, to manage and address safety at level crossings.
I was energised and enthused to be part of some intelligent and sophisticated discussion that focussed on the complexity of the problems and solutions, and with the dust now settling, stakeholders from across the rail and road industries have to stay the course.
We can’t take the easy way out by bowing to age old, overly simplistic and populist viewpoints that promote single solutions
such as in-vehicle alarms for cars and trucks, improved road and rail signage or strobe lighting on freight trains as silver bullets.
The reality is safety at level crossings is a shared responsibility which requires significant, ongoing coordination to identify and solve the problems.
We know we need to address the continued over representation of heavy vehicles in level crossing incidents. The reality is that despite accounting for only two per cent of vehicles on Australian roads, trucks account for 20 per cent of the accidents at level crossings.
And we know better train illumination is part of the solution. Research conducted by the Monash Institute of Railway Technology tells us so. However, while it found the addition of beacon lighting and the conversion of train lighting from halogen to LED was effective to a point, it is only under specific atmospheric conditions and operational circumstances that these solutions address some risks at level crossings.
It is also important to remember that most accidents occur during the day. While higher
profile and convenient arguments for some, these are just part of the problem and only small contributors to the solution.
At the conclusion of the National Level Crossing Safety Roundtable, ten actions were identified as integral to delivering short-, medium- and long-term level crossing safety benefits in addition to actions under the National Level Crossing Strategy.
They were assigned to multiple agencies and cover topics such as driver education, camera technology, a code of practice for train visibility, better use of telematics and data, a review of the road and rail manager agreements and a renewed investigation into penalties for drivers who disobey road rules at level crossings.
This list of solutions is by no means exhaustive, nor is it a simple fix – and that’s the point. It will require a concerted, collaborative effort by all of us with a stake in safety, which, let’s face it is all of us. It’s time for the self-interest, to give way to the public interest and for all of us to accept our share of the responsibility.
PWI NSW has had a busy period of events but has a lot of exciting engagements coming in the near future.
The Permanent Way Institution (PWI) of New South Wales had the pleasure of hosting another successful Executive Breakfast on the 9th of May 2024 at the prestigious Fullerton Hotel in Sydney. This event is a hallmark of our commitment to fostering industry dialogue and collaboration.
Our keynote speaker, Josh Murray, Secretary of Transport for New South Wales, delivered a compelling address, highlighting the strategic initiatives and future directions of the state’s transport infrastructure. His insights set a robust foundation for the following panel discussion, which featured esteemed industry experts: Juliette Economo from Laing O’Rourke, Rob Munro from Sydney Trains, and Rebecca Want from GHD, who served as the panel chair.
The panel delved into critical rail sector issues, including sustainable practices, technological advancements, and policy frameworks. The discussions were enlightening and engaging, underscoring the importance of collaborative efforts in addressing our industry’s challenges and opportunities.
We thank all attendees, including VIPs and our corporate members, for their invaluable support. Your participation continues to drive the success of our events and the overall mission of the PWI.
The PWI’s recent country meeting in Newcastle was another highlight, demonstrating our
commitment to engaging with regional stakeholders and promoting knowledge sharing across the state.
The afternoon featured presentations by two notable industry figures: Steven Johnson of Brimble, and Michael Turnbull of the Australian Rail Track Corporation. Their discussions focused on tamping and its effectiveness, sparking meaningful dialogue among attendees. The insights shared enhanced our understanding of this critical maintenance practice and highlighted innovative approaches and technologies shaping the future of rail infrastructure.
We sincerely appreciate all participants, particularly GHD, for their sponsorship and support. Events like these are vital in fostering a collaborative and informed industry community.
As we continue our knowledge dissemination and industry engagement journey, we are excited to announce our next Lunch n Learn session, scheduled for 17 July 2024. This session will focus on switch grinding technology, a critical rail maintenance and
expertise and insights into switch grinding technology promise to provide attendees with a comprehensive understanding of the latest advancements and best practices in this field.
We encourage all members and industry professionals to mark their calendars for this insightful session. To register, visit our website.
As we look forward to the remainder of 2024, we are excited about our upcoming annual conference, which holds special significance this year. It promises to be a premier event for industry professionals and marks the 50th year of the PWI.
This milestone is a testament to the enduring commitment and contributions of our members, partners, and the broader rail community. The conference will feature high-profile speakers, panel discussions, and networking opportunities designed to celebrate our rich history while looking ahead to the future of rail infrastructure and technology. Make sure to put a placeholder in your calendar for the 24th and 25th of October.
The PWI remains steadfast in its mission to promote excellence, knowledge sharing, and collaboration within the rail industry. We thank
MAXIMISED NETWORK CAPACITY
At Siemens Mobility, we are pursuing technologies and solutions for more sustainable, comfortable, and cost-effective rail transport to shape the future of mobility and #transformtheeveryday for a better tomorrow.