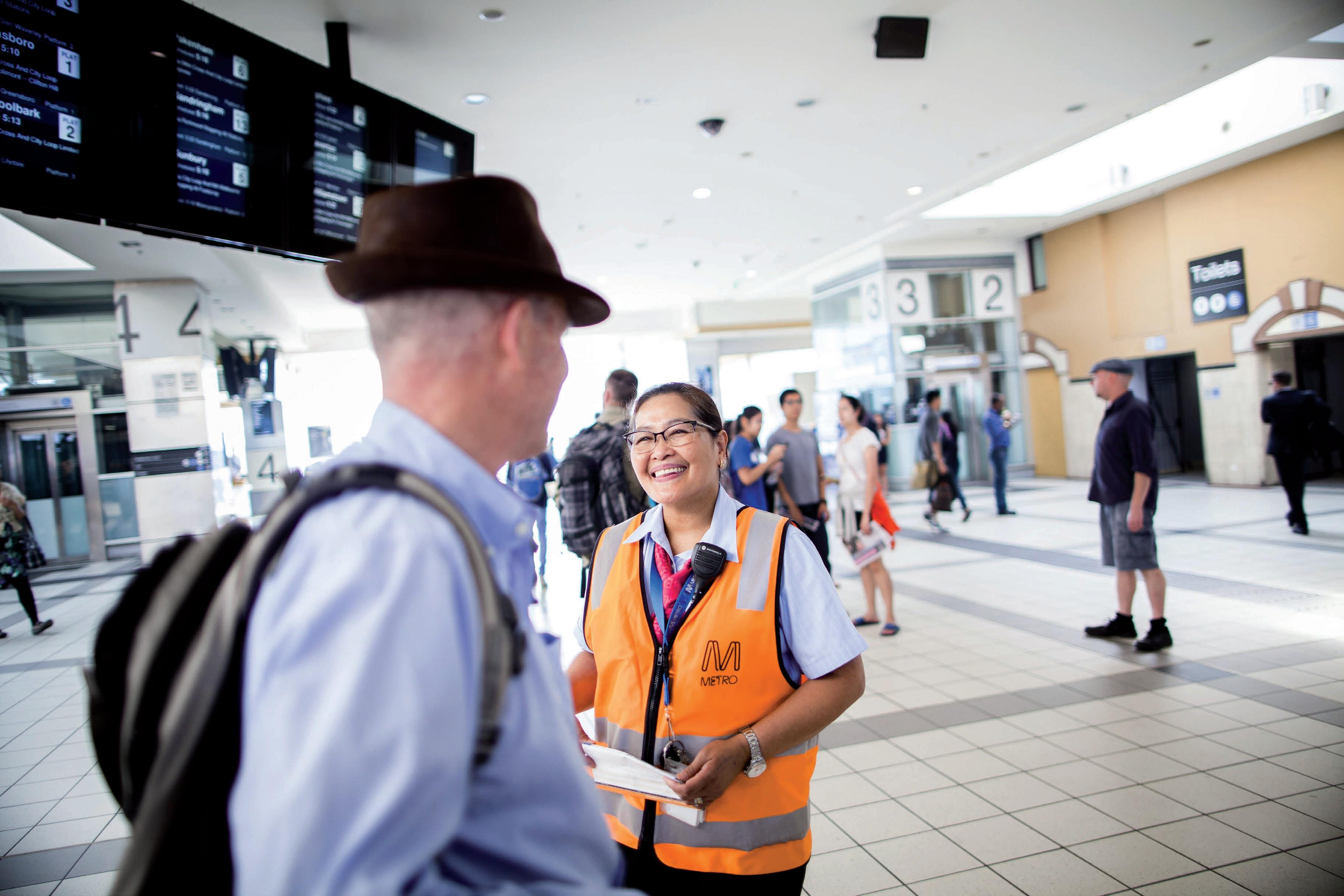
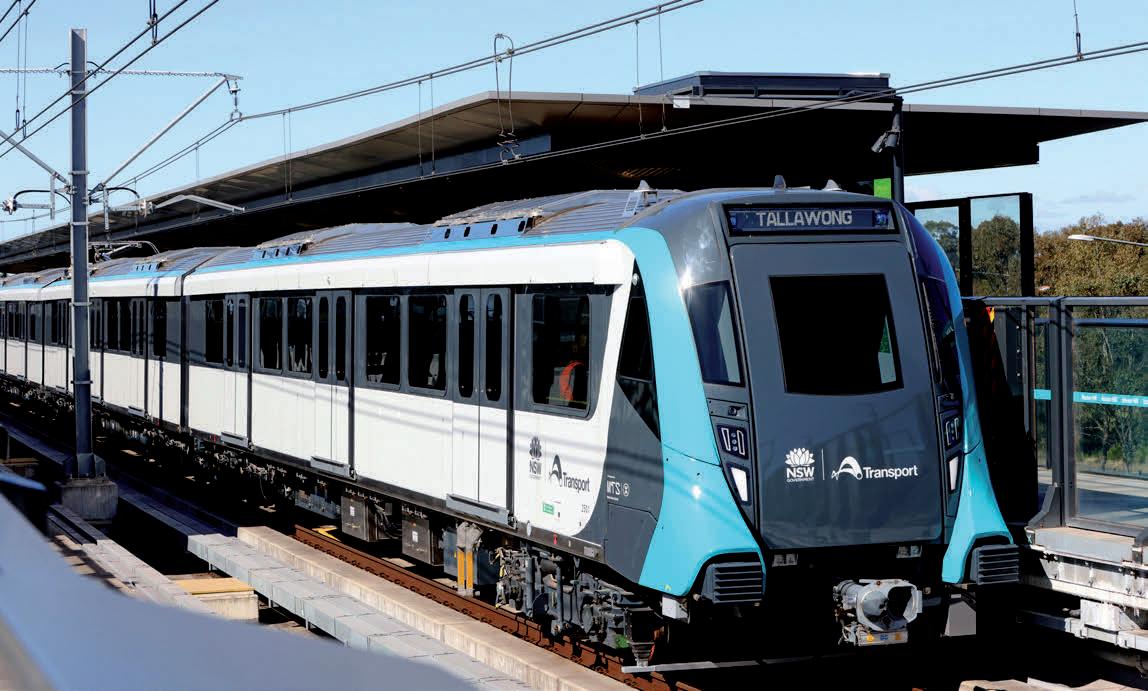
KiwiRail has been using some interesting techniques to help make tunnel works more efficient in one of the country’s longest tunnels. PAGE 13
Published by:
379 Docklands Drive
Dockalnds, VIC 3008
T: 03 9690 8766
www.primecreativemedia.com.au
Publisher John Murphy
E: john.murphy@primecreative.com.au
Chief Operating Officer
Christine Clancy
E: christine.clancy@primecreative.com.au
Managing Editor
Lisa Korycki
E: lisa.korycki@primecreative.com.au
Editor
Josh Farrell
E: joshua.farrell@primecreative.com.au
Business Development Manager
Alex Cowdery
M: 0422 657 148
E: alex.cowdery@primecreative.com.au
Client Success Manager
Salma Kennedy
E: salma.kennedy@primecreative.com.au
Design Production Manager
Michelle Weston
E: michelle.weston@primecreative.com.au
Art Director
Blake Storey
E: blake.storey@primecreative.com.au
Design Daniel Truong
Subscriptions subscriptions@primecreative.com.au
www.RailExpress.com.au
The Publisher reserves the right to alter or omit any article or advertisement submitted and requires indemnity from the advertisers and contributors against damages or liabilities that may arise from material published.
© Copyright – No part of this publication may be reproduced, stored in a retrieval system or transmitted in any means electronic, mechanical, photocopying, recording or otherwise without the permission of the Publisher.
Josh Farrell Editor - Rail Express
Welcome to the August edition of Rail Express
industry, and Rail Express. The early work for this year’s rail directory is underway.
The team is making some exciting adjustments to this year’s directory to make it more accessible for the industry and simpler to use. Keep your eyes open for emails prompting you to update your company’s information over the coming months.
This recent period has had some exciting announcements and milestones reached across the country. We have seen some progress on the Metro tunnel for Melbourne, with a 2025 start date looking more and more likely.
Sydney Metro has committed to a start date this month and I am excited to see the first passengers using the game-changing network for the city.
In what many might view as a far smaller, but in no way less significant, project, trains are closer to returning to Port Adelaide with Port Dock line testing underway.
The focus on building infrastructure has been important for the sector but it is expected that spending will begin to slow down in the coming years. It will be critical the industry turns it attention to ensuring networks run as efficiently as possible.
Getting more vehicles off the road is a critical step in Australia’s battle to lower emissions. I have had a number of interesting conversations over recent months regarding this focus and it’s obvious there needs to be a multifaceted and multi-disciplined approach.
Greater use of automation in signalling will be critical to shortening the gaps between passenger trains. It will also allow passenger trains and freight trains to operate in closer proximity.
Modern technology can give drivers a greater insight into the exact position of other trains on the network. It can even
prompt a driver as to what speed they can drop to instead of completely stopping the train to keep the network running smoothly.
Maintenance operators are getting smarter in how they work on track and play a critical role in improving efficiency. We are seeing more technology to monitor the track condition which, in turn, is reducing the instances of full network shutdowns.
If industry stakeholders continue to work together and support one other, as a nation we can improve our networks to truly capitalise on the government’s spending on rail.
The Rail Express team has collated interesting stories this month with a focus on condition monitoring and tunnelling.
Our cover story delves into some fascinating work by KiwiRail on a tunnel originally built in the 1950s and the remediation work they have been doing in confined spaces.
The team at Brimble explained the work it’s doing to improve asset monitoring, allowing its maintenance machines to remain on track longer and better predict upcoming faults.
Key Source Rail brings the French range of GEISMAR track monitoring equipment to Australia and the team believes it will be an asset across the country.
And we learnt more about the GS1’s project i-Trace and how it has been helping rail supplier Cold Forge better track and trace its components throughout the sector.
This month also includes regular comments from the ARA and the PWI.
Happy reading!
joshua.farrell@primecreative.com.au
The first test train has successfully travelled along the new Port Dock spur line in a major milestone for the $51 million project to return rail services to the heart of Port Adelaide.
The test train was part of works to test the line and the signalling system, as the project gears up to open in late August.
During the testing, the train was driven from Woodville Station and along the Outer Harbor line, then into Port Dock Railway Station.
Minister for Infrastructure and Transport Tom Koutsantonis said testing of the rail signalling system is a vital part of the project to return trains along the re-established line to Port Dock Railway Station.
“It’s genuinely exciting to see a train again travelling into the Port down the one-kilometre spur line, and it is of course a significant milestone as we move closer to the project being completed,” he said.
“Once open in late August, the new Port Dock Railway Station and bus interchange will provide a dedicated rail and bus service for the many people who live and work in the heart of
The High Speed Rail Authority (HSRA) is on track to deliver the first key milestone for Australia’s first high speed rail line, with tenders awarded for the Sydney to Newcastle Business Case.
Advisers will support HSRA to plan and develop the East Coast High Speed Rail Network, connecting Sydney, Central Coast and Newcastle.
A competitive open tender process sought industry experts with extensive experience in planning and delivering major infrastructure projects like high-speed rail.
Industry was also encouraged to form suitable consortia, where necessary, and comply with all requirements set out by the Commonwealth Approach to Market Terms.
The eight work packages have been awarded to the applicants in the table attached. These advisers will bring a wealth of knowledge and experience to the program.
With 14.9 million passengers annually, Sydney to Newcastle is the busiest intercity rail line in Australia.
The business case will determine important elements of the network, including proposed corridor alignment, station locations, fleet, cost estimate and construction timeframes.
It will be an opportunity to benchmark best practice and explore lessons learnt from high-
Port Adelaide, as well as visitors to the area.”
Once complete, the one-kilometre spur line will connect the new Port Dock station, plaza and bus interchange at Baker Street to the existing Outer Harbor rail line. It will also provide improved access for pedestrians and cyclists.
The test train was driven by experienced train driver Brett Watson, who has been driving trains on the Adelaide Metro network for almost 14 years.
“It is great to see the Port Dock Railway Line Project moving closer to completion, and I’m proud to have been chosen to drive the
Trains are expected to be running on the spur line by late August.
“The testing of the signalling system is a vital part of the project, to make sure everything is working as it should or to identify any issues that might need to be rectified.
“It was a successful test, and I can’t wait to have the opportunity to regularly drive trains to Port Dock Railway Station once regular services commence.”
The Port Dock Railway Line Project is funded by the South Australian Government and is supporting 100 full-time equivalent jobs during construction.
Project Control Services (Costs, Schedule and Risks)
Economics, Funding and Financing, Demand Modelling and Economic Development Strategy
Commercial, Delivery Strategy and Industry Engagement
Transport, Land Use and Property
Technical Advisory, Environment and Sustainability, Community and Stakeholder Engagement
and Arcadis High Speed Rail Network Operations Planning
and Engagement
and
speed rail networks across the globe.
The Federal Government has committed $500 million for the planning and corridor protection of the Sydney to Newcastle section, and established the HSRA to conduct the work independently.
HSRA will work closely with state, territory and local governments, industry and peak groups, community and First
Nations stakeholders on business case development.
The first major milestone will be progressing with onsite studies such as geotechnical investigations to test ground condition. This will help inform high-speed rail corridor alignment and station locations.
The business case is expected to be presented by the end of 2024.
With the largest rail machine fleet in Australia, Brimble can deliver any track renewal or maintenance project in any gauge anywhere nationwide, from the Pilbara to our home in the Hunter Valley.
Experience the Brimble difference with our custom technology, experienced team and dedication to the future of rail.
Victorian town Mordialloc will be boom gate free by 2026. Updated designs have been released for the project to remove three bayside level crossings and build a new premium station.
A new elevated premium station will be built in the heart of Mordialloc and will feature modern facilities, all-abilities access, improved lighting, public spaces and landscaping. Entrances at both ends will make accessing the station easier and more convenient.
The existing Mordialloc Station building, as well as the historic water tower, will take pride of place in the new station precinct with extensive planting of trees, plants and shrubs in the area.
Removing the level crossings at McDonald Street, Mordialloc and Station Street,
Aspendale, and building two new rail bridges, is designed to deliver more reliable journeys for locals, with the boom gates currently down for a third of the morning peak.
The project will deliver local street improvements, including upgrading the roundabout where McDonald Street meets Nepean Highway, adding a new slip lane to allow traffic to merge seamlessly. South of Mordialloc Creek, a new roundabout will keep traffic moving between Station Street and Pine Crescent, providing smooth access to a new link road that will connect Station Street to Nepean Highway.
A level crossing-free McDonald Street and these improvements to local streets will allow for the closure of the Bear Street level crossing, helping create a vibrant station precinct with safe access for pedestrians and cyclists.
Feedback from the community has informed the updated designs, including helping shape a station precinct that celebrates the local character with native planting, colours, and materials to reflect Mordialloc’s close connection to the beach and bayside identity.
An Australian-first trial to adopt a system of nationally standardised approvals for products to be used in rail and road projects is underway, and could save taxpayers tens of millions of dollars annually.
Under the agreement reached between the New South Wales and Victorian governments, any new product used in rail or road infrastructure projects must meet minimum regulatory, technical and safety standards to obtain type approval.
Currently there is significant inconsistency in approval processes across Australian jurisdictions. Road and rail construction industry bodies and product suppliers are calling for change to complex and timeconsuming approvals.
Australasian Railway Association research suggests inefficient processes cost the rail industry alone up to $40 million per year.
Transport for NSW and Victoria’s
Department of Transport and Planning have signed a Memorandum of Understanding and started trialling a nationally harmonised process for product type approval, covering a range of road and rail infrastructure products, such as signalling and electrical equipment, and civil products.
Transport for NSW Secretary Josh Murray said he is excited that New South Wales and Victoria are together working to innovate the rail and road infrastructure industries in a way that will promote technological disruption and cost savings in the tens of millions of dollars.
“Faster and more smoother approvals will assist us as we engage industry to help the government in New South Wales procure more locally made products to stimulate domestic manufacturing,” he said.
“Standardising processes across state jurisdictions could be a game changer. There are significant implications for thousands of items associated with train control systems, active level crossings, electrical substations, track, bridges, traffic lights, road pavements, drainage and pipes.
“In New South Wales alone the existing catalogues of type approved products stretches to 3,000 items listed across 40 different registers.”
Victoria Department of Transport and
Planning Secretary Paul Younis said working with other states to provide greater consistency in standards is a win-win in delivering important road and rail projects with quality and tested components while reducing costs.
“This trial will help test the benefits and effectiveness of this approach and delivers on our joint commitment to the National Rail Action Plan and delivering nationally harmonised outcomes for public transport,” he said. “We are co-operating closely with industry to support jobs and local content and this trial will help manufacturers comply with the relevant standards in both states.”
The Chief Transport Engineers of the two states are also collaborating with 49 members across Australia and New Zealand representing organisations including:
• Australasian Railway Association
• ARTC Austroads
• Crane Industry Council of Australia
• Kiwi Rail
• National Transport Commission
• National Transport Research Organisation
• Queensland Rail
• RISSB
• Transport and Main Roads
• Queensland
• Transport Certification Australia
be run by a
Transport operators Transdev and John Holland have formed a consortium to run Melbourne’s world-famous tram network for the next nine years. The partnership will improve reliability, deliver passengers more consistent real-time information and better customer service.
Minister for Public and Active Transport Gabrielle Williams announced the Yarra Journey Makers consortia signed a $6.8 billion contract to operate the world’s largest tram network, which manages 500 trams, 1,600 tram stops, 24 routes and more than 250 kilometres of double track.
Commencing on 1 December 2024, Transdev and John Holland will operate under the Yarra Trams brand and progressively
deliver improvements to services and customer experience.
Transdev brings a wealth of experience, operating large-scale networks across 19 locations around the world, including France and Spain, while John Holland operates light rail across Australia and is part of the consortium that run Melbourne’s metropolitan train network – Transdev John Holland also operate Region 9 buses in Sydney.
Minister for Public and Active
Transport Gabrielle Williams celebrated the announcement.
“Melbourne is home to the largest tram network in the world and this new contract will make sure our trams continue to move Victorians around safely, quickly and easily,” she said.
“We look forward to working with Transdev John Holland as we continue to modernise and improve the passenger experience on our iconic tram network.”
The new contract has a focus on performance, with strict benchmarks and more monitoring points across day and night services – holding the operator to account to deliver reliable services, while making sure the right tram is used for the right trip.
The mediator for the Melbourne Airport Rail Link has handed down his report for the project, making a number of recommendations to get it back on track.
Mediator Neil Scales reported that the project remains viable and necessary, and has support from the Australian and Victorian governments, Melbourne Airport operator APAM, and the public. He also reported that it is possible to find a solution to the location of the station at Melbourne Airport.
The report made three main recommendations, including that the Commonwealth and Victorian Government proceed with “no regrets” work at Sunshine Station to transform it into a major transport hub and capitalise on the early works already completed for the Melbourne Airport Rail Link.
The Commonwealth will commence discussions with the Victorian Government on
the proposal to upgrade capacity at Sunshine Station, with funding to be formally considered once costs and scope are finalised.
The report recommended that refreshed modelling work be undertaken on the timeline for capacity of Tullamarine Freeway. Minister for Infrastructure, Transport, Regional Development and Local Government, Catherine King, has instructed her department to scope this work.
The mediation process was undertaken to determine if a resolution is possible between the Victorian Government and the operator of Melbourne Airport as to the location of the station.
The report recommended against further Commonwealth and state consideration of an underground option at this time. Should APAM wish to progress with the option of an underground station, it recommended that
The agreement will also roll out more accessible Next Generation Trams which will replace the longer serving high floor fleets – further modernising Melbourne’s transport network before the Metro Tunnel opens to passengers in 2025.
During the contract term, new technology will be rolled out to provide passengers more consistent information in real time, including possible alternative transport options during disruptions and tailored updates for blind and low vision passengers in large text and text to speech.
There will also be more training for frontline staff to better support passengers with particular needs and customers who are culturally and linguistically diverse.
In a first for any Victorian public transport franchise, there will be board gender parity from day one. Transdev John Holland will also set targets to increase employment opportunities for women, Victorian First Peoples, long-term unemployed, young people and people living with a disability.
Melbourne’s tram network transports more than 147 million passenger trips each year – complementing the city’s sophisticated integrated road and rail network.
they produce a suitable and comprehensive business case, so that key stakeholders can examine the proposal in detail.
The government has shared the report with both parties, and the department has offered to provide further briefings on the report’s findings.
King encouraged the parties to consider the report recommendations and to work constructively together to determine next steps to progress the project.
Lycopodium is trusted by private and public transport operators across the nation. We provide routine safety critical independent track inspections and assessments of rail infrastructure and annual detailed inspections and asset condition reports, including:
Long term asset management plans and preventive maintenance plans
Fit for purpose inspections and maintenance to suit your specific operational requirements
Trusted to manage upgrades and maintenance, whilst remaining independent
We manage your safety and compliance leaving you to do what you do best
Lycopodium operates and maintains a purpose-built maintenance management system (MMS) which provides a high level of transparency to our clients with regard to the risk management required under safety legislation.
Asset owners can access real-time information about their assets, including a full list of assets with corresponding inspection and maintenance records, current and historical defects, as well as the maintenance schedule for each asset.
Contact us to arrange a live demonstration of the LycoMMS.
We operate with the simple goal that your assets be fit for purpose with no surprises at minimal cost
KiwiRail has been working closely with its partners to minimise disruptions as it improves the network with some interesting technology.
On an island where one fifth of the land is mountains, tunnels are a common occurrence for New Zealand’s north island rail network – the country has close to 150 tunnels and ensuring they are kept up to standard is no easy task.
KiwiRail has been implementing some exciting and innovative practices to replace all the drainage and track inside one of the county’s longest tunnels, the Remutaka Tunnel in Wairarapa, just outside of Wellington.
The 8.8-kilometre tunnel was opened to traffic on 3 November 1955. It was the longest tunnel in New Zealand, superseding the Otira Tunnel in the South Island until the completion of the 9.03-kilometre Kaimai Tunnel, near Tauranga, in 1978. Remutaka remains the longest tunnel in New Zealand with scheduled passenger trains.
KiwiRail and Greater Wellington Regional Council (GWRC) are working together to build
a better, more efficient and sustainable rail network for Wellingtonians and are working with Metlink to help deliver the project.
KiwiRail is in the middle of an $870 million upgrade of the Wellington metro network and Wairarapa Line, to improve service reliability and enable more frequent trains. The upgrade includes:
• installing modern new power systems for the overhead lines and signals.
• essential maintenance including, renewing track (including in tunnels), and refurbishing bridges.
• building additional track, passing loops and platforms so more trains can run.
• making level crossings safer.
The Remutaka Tunnel comes under the maintenance and renewal works the organisations are undertaking.
In 2018 the New Zealand Government made a large investment in maintenance
on Wellington’s rail infrastructure, such as replacing worn-out track and structures, redoing drainage systems and stabilising slopes.
These works include:
• replacing all track on the Wairarapa Line (including inside tunnels and over bridges) in addition to drainage and vegetation work stabilisation on the Kāpiti Line, as well as upgrading drainage in Tawa tunnels and renewing sleepers within the Paekākāriki tunnels.
• replacing track inside seven tunnels along the Johnsonville Line.
• renewing tracks and track connections at Wellington Railway Station.
A big part of the project is renewing the track inside the Remutaka Tunnel. KiwiRail renewed the drainage during the last Christmas network shutdown. The teams have started on the track renewal on weekends and public
KiwiRail is taking the time to steadily improve the country’s network.
KiwiRail have introduced a new purposebuilt conveyor system to efficiently remove large quantities of old ballast from inside the Remutaka Tunnel.
Project manager David Sauvageon said the special equipment consists of two conveyors with a custom-designed hopper that can be loaded directly with an excavator inside the tunnel and transported outside using standard rail wagons.
“At almost nine kilometres long, the tunnel’s single track and confined space makes it a challenging place to work,” he said. “The conveyor is a game changer in the way it
exhaust fumes, cramped spaces, limited access and darkness are challenging for the team working in the tunnels.
To help the team, KiwiRail has made use of gaming technology to build a ‘tunnel simulator’ that mimics the tunnel environment.
“This initiative gets workers actively involved in critical health and safety planning and is used extensively by the team managing the Remutaka Tunnel renewal,” Sauvageon said.
“The tunnel simulator is providing crucial ‘real life’ experience of how things will be in there when work is underway. It allows the team to transform a 2D handwritten health
other environments, and we are looking to incorporate it into KiwiRail’s tunnel training curriculum.”
The Wairarapa Line is a critical cog in KiwiRail’s network, moving both passengers and freight. To minimise the impact on each, work will be completed on weekends and public holidays. The decision was made by KiwiRail and GWRC to have one long period of work as opposed to intermittent shutdowns over several years.
More than 13 million rail passenger journeys were taken in 2016 by the 500,000 people who live in the Wairarapa region.
This reflects the rail network’s integral role in Wellington region’s overall transport system. Improvements to the rail network accrue benefits to the wider transport system.
The project commenced construction activities in 2023, and successfully delivered the track renewal through the 572 metre Maoribank Tunnel (tunnel one).
This work provided an opportunity to test and refine the methodology for undertaking the same task through the 8,779-metre Remutaka Tunnel (tunnel two).
In addition to this work, the team completed enabling works including the construction of a new drainage system through the full extent of the Remutaka Tunnel and a spoil laydown site.
In its budget for the coming year, the Queensland Government has made
Queensland’s Big Build program is set to continue the state’s commitment to improving the rail sector.
The Queensland Government has handed down its budget for 2024-25 with a focus on getting more people on public transport and funding projects.
Deputy Premier Cameron Dick announced the $107 billion Big Build program, which will deliver a range of projects, as part of this year’s budget.
Premier Steven Miles said the investment will bring a generational change, creating more jobs, better communities, and stronger regions.
“Almost 70 per cent of this work is happening in regional areas representing the biggest investment in regional job creation in the state’s history – supporting around 50,000 jobs outside of Greater Brisbane,” he said.
“As the economy slows, this level of investment and job creation is critical to Queensland’s future success and economic prosperity.”
The 2024-25 capital investment includes $18.57 billion for projects outside the Greater Brisbane region, supporting about 50,000 jobs.
Minister for Transport and Main Roads Bart Mellish said the Big Build is a massive commitment to Queenslanders to build the
infrastructure for the growing state.
“Investing in our roads, including the Bruce Highway, in our rail revolution for South East Queensland, and improved public transport across the state, means that Queenslanders will be able to get where they need to go, safely and reliably,” he said.
The Direct Sunshine Coast Rail was front and centre in the budget, with the government committing to the largest spur line ever delivered in South East Queensland.
Staged delivery will see the line ultimately run to Birtinya and Maroochydore. This will deliver faster rail to the Sunshine Coast, with trains able to reach speeds of 140 kilometres per hour on some sections of the track.
Joint funding of $5.5 billion by the State and Federal government has been committed for the line between Beerwah and Marrochydore.
The first stage will be a 19 kilometre dual track from Beerwah to Caloundra, the longest spur line in the south-east passenger network.
Construction of Stage 3 of the Gold Coast Light Rail, from Broadbeach South to Burleigh Heads, will connect to the existing Gold Coast Light Rail, providing eight additional stations, at an estimated total cost of $1.219 billion
jointly funded by the Federal Government and Gold Coast City Council.
Key features of Stage 3:
• 6.7 kilometre extension from Broadbeach South to Burleigh Heads
• dual track in the centre of the Gold Coast Highway
• eight stations
• retain two traffic lanes either side of light rail tracks
• five additional trams
• a journey time of about 16 to 17 minutes from Broadbeach South station to Burleigh Heads
A $5.75 billion commitment, between the state and Federal Government, is allocated for the Logan and Gold Coast Faster Rail upgrade between Kuraby to Beenleigh.
There is a plan to increase the number of tracks between Kuraby and Beenleigh from two to four, with modernised rail systems, station upgrades and level crossing removals along the 20-kilometre corridor.
Lowering public transport fares to a flat fare of 50 cents across the state’s public transport network for six months from 5 August 2024 and saving Queensland public transport customers $150 million in 2024–25 was also announced in the budget.
In handing down its 2024-25 budget the New South Wales Government has made a commitment to further improving the state’s networks.
The 2024-25 New South Wales Government is investing $22.09 billion to build and improve transport services.
being provisioned for construction of the Parramatta Light Rail Stage 2, to accelerate the delivery of betterconnected communities.
This will connect the growing communities along the 12-kilometre alignment between Ermington, Melrose Park, Parramatta and Olympic Park, and includes;
• 14 new stops between Camellia and Carter Street, Olympic Park
• dedicated 8.5-kilometre active transport corridor
• new river crossings.
Construction will be phased, with initial work to begin later in 2024 on a new 320-metre public and active transport bridge over Parramatta River, between Melrose Park and Wentworth Point.
Stage 1 of the Parramatta Light Rail project is currently in testing and is on track to service tens of thousands of commuters in the coming months.
The iconic New South Wales-made Tangara
A $447 million commitment will keep the current Tangara fleet on the tracks for about 12 more years to ensure passengers have safe and reliable services while the new fleet is built.
The state’s 55 Tangaras make up a quarter of the Sydney Trains fleet. They are the highest contributor to maintenance faults on the rail network and will continue to face reliability issues as they age.
Without life extension works, an estimated five Tangaras per year are at risk of breaking down and being pulled from service, greatly impacting commuters.
“New South Wales workers are great at building trains and under this government we will build trains here again. It’s going to take time, but we’re determined to do it,” said Premier Chris Minns.
“This is a modest investment now that will eventually unlock a huge boost to New South Wales jobs and industry well into the future.”
million to the continued reliability, resilience, and future of the rail network across the state.
Funding focuses on the key areas of procurement, safety and the workforce, this includes:
• a new digital train radio system
• the Illawarra Rail Resilience Plan.
The government has allocated $5.5 billion to the Sydney Metro-Western Sydney Airport project delivering six new stations to service the future Western Sydney International Airport and the Western Sydney Aerotropolis.
Australia’s biggest transport project, Sydney Metro West will receive $13.4 billion to support more housing and double the rail capacity between Parramatta and Sydney Central Business District.
This is part of the New South Wales Government’s plan to ensure infrastructure is built alongside housing to produce better and well-serviced communities.
The South Australian Government has committed funding to a range of rail and road projects to further grow the state’s infrastructure.
The South Australian Government has committed $10.8 million over five years to start operations of the Port Dock railway line.
The new line will provide a 30-minute service on weekdays and weekends, and bus connectivity to the new Port Dock bus and rail interchange.
The project will re-establish the spur line and construct a new train station and bus interchange. The one-kilometre spur line will link Port Adelaide’s commercial centre and residential precinct to the Adelaide Central Business District. It will provide rail services for those who already call the area home and the many more set to live, work and visit Port Adelaide. It will also serve as an important destination station for the Port’s tourist attractions.
The government has also committed funding to expand the reach of the state’s rail network to the north and the south.
Over three years, $10 million will go toward planning for transport network improvements to support Adelaide’s northern growth areas.
A further $10 million over two years will be set aside for planning for outer metropolitan and regional passenger rail service extensions.
The government has already secured a 60-metre-wide corridor of land from Quinliven Road to Aldinga Beach Road for the extension of that line.
In Adelaide’s north, the study will look at where the Gawler line could be extended to the Barossa, using the existing rail corridor.
Decarbonisation is a major focus for the rail fleet in South Australia. The government
has committed $2 million to deliver planning studies to identify solutions to support a transition to a zero-emissions public transport rail fleet.
Adelaide’s Metro fleet is currently electrified along three lines – Seaford, Flinders and Gawler – with the rest of the train lines operated by diesel locomotives.
In 2021 it was announced that 45 of the state’s 70 diesel rail cars would be upgraded with hybrid energy storage and recovery systems, as part of a $10 million 2021-22 State Budget initiative. It is aimed at reducing the fleet’s fuel consumption, noise, vibration and diesel emissions.
After the successful testing period of its first hybrid-diesel train, Adelaide Metro is now in the process of converting to a fleet of 50 hybrid diesel trains. These trains are already running on the Outer Harbor, Grange, and Belair lines and are recognisable by their distinctive bright green colour.
Each railcar is fitted with an energy storage and recovery system that recovers excess energy when the train brakes and stores it in a battery for later use.
The stored energy will also be used to supply power for lighting and air-conditioning at the Adelaide Railway Station train platform, reducing noise, emissions, and air pollution.
The Metro Trains Melbourne consortium is valuing the biosites that exist around its rail corridors and is taking a proactive role in supporting the success of these areas.
The land next to Metro’s hundreds of kilometres of train tracks is teeming with life, ranging from the smallest of insects to significant plants and animals.
Some of the endangered species that call Metro’s biosites home include the Southern Brown Bandicoot, Golden Sun Moth, Growling Grass Frog, Spiny Rice-flower, Tall Leek-orchid, Button Wrinklewort and Matted Flax-lily.
Metro Trains’ Biodiversity Manager Ben Roberts touched on the importance of caring for these sites.
“Metro is custodian of these significant pockets of biodiversity across our network,” Roberts said. “By protecting and managing
home to many rare and threatened flora, fauna, and plant communities.
Metro Trains Melbourne chairman and MTR Australia Chief Executive Officer Raymond Yuen praised the work being done.
“We are incredibly proud of our Biodiversity team, whose knowledge and expertise are paving the way for other organisations around Australia,” he said.
Metro Trains Chief Executive Officer Raymond O’Flaherty is responsible for running Melbourne’s expansive city network, but understands the importance of caring for the areas around the track. He said sustainability is a big focus for Metro.
“Our Biodiversity team is helping to protect threatened plants and wildlife across metropolitan Melbourne, with our biosites reporting a 314 per cent increase in the abundance of threatened plant species since 2018,” O’Flaherty said..
Metro undertakes up to 10 ecological burns every autumn to help restore and protect these biosites and their inhabitants from threats such as invasive species. These types of burns help maintain a balance of plant diversity and animal habitat and provide an opportunity to control invasive weeds.
Ecological burns occur in Metro’s grassland and grassy woodland biosites on the Sunbury,
“We are incredibly proud of our Biodiversity team, whose knowledge and expertise are paving the way for other organisations around Australia.”
Raymond Yuen, Metro Trains Melbourne chairman and MTR Australia CEO
Craigieburn, Pakenham and Stony Point lines using the best practice program of mosaic burning. Metro conducts most of its burns on the Sunbury line, where some of the best remaining native grasslands occur.
Mosaic burns are planned low-intensity fires that vary in scale within a broader landscape to create patches (a mosaic) of burnt and unburnt areas that change over time.
This pattern provides a refuge area for animals during the burns and to ensure they have somewhere to live until new plants grow.
The Metro burning program’s primary objective is improving or maintaining the ecological condition of the grassland and grassy woodland biosites.
The program also has the added advantage of efficiently managing grass fire risk within the rail reserve.
“Ecological burns help to maintain a balance of plant diversity and animal habitat as well as providing an opportunity to control threats such as invasive weeds,” said Roberts.
“They are essential to improving and maintaining the condition of grassland and grassy woodland ecosystems.”
He said that as Melbourne increasingly urbanises and spreads into new biodiverse areas, these programs will become even more critical for Metro.
“Many of the Metro biosites are located in the outer parts of the Metro network,” Roberts said.
“These sites were typically interfaced with rural or semi-rural properties. However, most of these areas have been developed into residential or industrial estates, particularly since the Metro franchise commenced operating in 2017.
“The increased rate of urbanisation on the outskirts of Melbourne has put pressure on some of the last remaining areas of biodiversity within these outer growth areas. The continuation of the ecological burning program is essential for maintaining the condition of these significant biodiversity areas within the Metro network.”
Preparing a robust Biodiversity Management Plan at the commencement of the program has been a key reason for the biosite program’s success. The management plan sets out
information on the baseline condition of each of the biosites and outlines clear targets and objectives for each site so that performance can be measured at a site and program level.
Roberts explained that at the start of the Metro Franchise, the organisation worked with experienced ecologists to develop a Biodiversity Management Plan.
“That plan sought to provide expert and detailed guidance for the ongoing management and monitoring of the biosites across the Metro network,” he said. “We continue to prepare site-based management plans as new biosites are identified and established.”
Roberts believes having several expert ecological restoration contractors on hand is vital for developing and delivering the biosite management program.
“We also participate in several threatened species recovery groups for which the Metro rail corridors provide important habitat,” he said. “We’ve built strong relationships with research ecologists from the University of Melbourne
and La Trobe University. They provide ongoing technical support and advice. One strength is their collective knowledge around native grassland management and restoration.”
This research includes a recent two-year partnership with the University of Melbourne. The project will test the effectiveness of native grassland direct seeding methods to restore native grasslands in an operating rail environment.
The ecological burns and recovery groups form just part of Metro’s efforts to improve biodiversity around train lines and stations within its network. Metro has seen a significant increase in the number of biosites it manages, from 30 to 49.
“Metro has recently engaged an expert urban and transport ecologist to undertake a biodiversity connectivity opportunity study,” Roberts said. “The goal is to identify priority locations where small interventions could be implemented to improve biodiversity connectivity across the greater Melbourne landscape.”
It is well noted the essential function that rural and urban rail networks fulfil in facilitating biodiversity connectivity across the landscape. It is also accepted that transport networks can act as a barrier to biodiversity movement.
Roberts said Metro is interested in understanding priority actions that could be taken to maintain or improve biodiversity movement across the landscape in which it operates.
RATP Dev is leaning on its long international experience and innovative mindset to ensure its networks operate safely.
Everyone deserves the right to move around with peace of mind. It’s a philosophy at the core of RATP Dev, one of the world’s leading public transport operators.
Running and maintaining tens of thousands of kilometres of metro, bus, tram, and rail lines around the globe, the company puts security and safety first, aiming to prevent accidents and incidents and reduce their consequences, improving its solutions through innovation and lessons learned over decades in the industry.
Safety takes precedence over all other considerations, said RATP Dev Australia general manager Denis Masure.
As RATP Dev prepares for the Sydney Metro-Western Sydney Airport line’s launch, it maintains its commitment to upholding the highest security and safety standards.
Masure highlighted successful strategies it can draw from, including a comprehensive 360-degree security reinforcement plan aimed at instilling confidence in passengers and reducing any feeling of vulnerability.
“We break down security into three pillars of focus to protect passengers across our networks – prevention, protection and intervention,” he said.
“We first seek to reassure passengers to reduce feelings of insecurity through several means. One way is to roll out multifaceted awareness campaigns to educate the general public on the right behaviour to adopt when an incident occurs using posters, local press and digital communications,” he said.
“For instance, we hold talks in schools. In Paris, we taught school children how to travel on the city’s transport network and in September 2023, launched the very first public transport licence for young passengers aged nine to 13 to ensure they were prepared for public transport use.”
In Florence, Italy, RATP Dev raised awareness of violence against women with the ‘Stop and Think’ campaign.
As part of International Day for the Elimination of Violence against Women, RATP
Dev’s subsidiary launched the second series of the ‘Not a Single Story’ video project in partnership with Florence-based association Nosotras Onlus.
Another tool the organisation has also been developing hand-in-hand with local communities and stakeholders is undertaking exploratory walks to identify any sources that could cause passengers to feel unsafe and has organised trials to reduce such feelings.
“In Paris this meant walking on particular train lines to gather passenger feedback on the measures implemented to combat feelings of being unsafe,” Masure said.
“We also gathered volunteers to give feedback on a set itinerary and share the level of comfort they felt for each. Itineraries were assessed according to the overall atmosphere of the station; how easy it is to navigate and how facilities are installed and used.”
The teams at RATP Dev continuously strive for innovative, meaningful solutions, leading them to test new ideas, such as installing
mirrors and new light arrangements in stations that mimic the sky.
RATP Dev also understands protection is the second essential element of keeping networks safe for those who use them. For this purpose, the company has been working with communities to develop and implement on-demand stops on bus routes and co-walking solutions to enhance passenger safety.
“The on-demand services were rolled out in Paris during evening and night services,” Masure said. “This allows buses to stop between designated stops, at a place which may be closer to a passenger’s residence, minimising walking in the dark.”
The organisation has also implemented joint programs between security, inspection and law enforcement teams. For example, canine units are used to detect explosives and process unattended objects and bags in several stations. Mobile security teams across the network are deployed to respond and intervene quickly where needed. This led to the creation of the Groupement de Protection et de Sécurité des Réseaux - Network protection and security unit (GPSR), whose purpose is to protect, dissuade, assist, and respond as needed. It is part of a regional management policy and was first implemented in Paris then rolled out in other big cities. About 1000 employees are qualified to intervene at all times, after a rigorous 15 week training program.
The organisation has been gathering feedback to better understand what areas of a station feel unsafe.
RATP Dev has turned all this accumulated experience and knowledge into innovative tools, to improve its reaction when faced with unexpected events.
“Our long experience in welcoming large numbers of visitors for big-scale events proves invaluable in ensuring events run smoothly
our teams on the field, from big events to daily commutes.”
RATP Dev identified the importance of intervening effectively in the event of an incident and has implemented facilities that allow victims or witnesses to call for help using call terminals installed at stations and on all trains. A mobile app has also been created for simple reporting, along with an emergency hotline.
In Paris, passengers can also use an alert number by phone or SMS to report delinquent behaviour or a situation that presents a security risk.
Masure said 5,000 call terminals, including 3000 on the metro and RER commuter rail networks, were set up resulting in 11,000
“Safety is an absolute prerequisite in every decision and action taken as part of RATP Dev’s activities,” he said.
This was evident in London where RATP Dev implemented the Mobileye solution to better alert drivers of imminent collisions.
The Mobileye system uses smart cameras to alert drivers of impending collisions with pedestrians and cyclists in vehicle blind spots. The bus driver receives visual and sound alerts in real time in the case of imminent collision with a pedestrian, cyclist or vehicle; when the distance is too close to the vehicle in front; when speeding, or the bus is deviating from the traffic lane.
RATP Dev London has been testing this solution on a bus line since August 2020.
The result was a 37 per cent reduction in the number of faults compared to the year before and a 35 per cent reduction in the total number of incidents for the same period.
“Similar success was seen on Hong Kong’s 120-year-old tramway network,” Masure said.
“The network carries over 200,000 passengers per day on 165 double decker tramcars. RATP Dev has been committed to diligently improve the tram’s braking systems, and created a control centre to regulate traffic. Signalling modifications were made to ensure the trams direction changes were clear to the traffic around them.
“There was an increase in radar speed gun checks on the network, coupled with a system to reduce over-speeding which included driver alerts and archiving of overruns for the management team to consult.
“As a result, the number of speeding violations decreased by 352 in a year for the network.”
AI can help the rail industry to be more flexible, efficient and automate the railway. For Siemens, they have been using AI for over a decade to support their customers.
While Artificial Intelligence (AI) seems like an emerging technology, especially with the emergence of ChatGPT, global technology company Siemens has been using AI across its technology solutions for more than a decade to help analyse the complex ecosystems they operate in.
Dr Claus Bahlmann, head of research and development for Artificial Intelligence, and principal expert for AI and computer vision in Siemens Mobility, explained that it is all about getting smarter and automating as much as possible.
“With automation – powered by AI – we can increase flexibility to deal with varying peak travel times, reduce the downtime caused by maintenance and staffing issues, and even carry out upgrades without affecting rail operation so much. All of this benefits the passengers,” he said. “There’s a limit to how much new railway infrastructure we can build, and investment is also limited, which is why we need to take this digital approach. The technology is there to increase capacity while making rail travel more reliable, more comfortable, and more inclusive.”
AI can also make maintenance more effective and efficient.
“Technicians in the field have traditionally relied on a service log and manual, but now
they can point a tablet at the area of concern and AI will identify what part they are looking at,” Bahlmann said.
“AI will then provide all the contextual information they need: the manual, the circuit diagrams, or a catalogue of spare parts.”
Inspection is another area where AI is being deployed into Siemens’ products.
Bahlmann said sensors are mounted on the infrastructure where it is possible to inspect the rollingstock, because vehicles are scheduled to pass that location, and sensor data of the rollingstock can be collected and inspected.
When sensors are mounted on the vehicles, they will acquire sensor data from the infrastructure and the AI will recognise specific areas that need inspection or maintenance.
“For example, we can inspect the condition of rail tracks from images captured by cameras mounted on trains and looking into the track
Gonzalo Martinez Delgado, head of customer service for Australia and New Zealand at Siemens Mobility, recalled how AI helped a Swiss rail operator who wanted to improve its network availability and minimise impacts
“Delayed minutes of trains caused frustration to the end customers, the passengers, and impacted the network operation,” Martinez Delgado said. “It was realised that much of the
the aim was to reduce that delay to improve the operation and customer satisfaction, and at the same time, save money for the operator.
“We saw the opportunities of using AI that could predict some of these failures to avoid delays.”
Martinez Delgado said the customer defined the targets and Key Performance Indicators (KPI’s) to measure the success of the initiative at the beginning of this joint cooperative journey.
The project started in 2019 and through the following four years, both parties worked together expanding the AI capabilities based on customer needs, starting with a pilot project, followed by a proof of operations phase and finally incorporating the AI tools into the daily maintenance process of the customer, with the aim of helping the customer to achieve 100 per cent system availability.
The use of AI technology on the Swiss network meant it could not only track the condition of infrastructure but could also anticipate potential faults and alert the maintenance team, improving efficiency.
“The team then know in advance where a failure might occur and how critical the situation is, to properly plan in advance when
best to go to site, the tools needed, etc,”
Martinez Delgado said. “I use the example of how much easier it is to go to the supermarket with the shopping list for your groceries than blindly walking around for your shopping wondering what you need at home.”
It is not just about having the tool of AI itself, but knowing how best to provide the inputs, implement the tools, and analyse the data that makes it beneficial.
Martinez Delgado said it’s important to understand the problem the customer is trying to solve and how the end user consumes the data.
He spoke about the importance of the three integrated core elements of the golden triangle, people, processes, and products that need to be addressed together when implementing innovation to drive productivity and efficiency successfully.
“AI is not enough on its own, at the end of the day, the person still needs to be there,” he said.
“AI will not replace people. We can have the most wonderful tool but if the people don’t believe in it and don’t want to use it, then it is pointless.
“The technology is simply a tool, and we still need the person to go out and decide whether the work is needed and then carry out the work.”
Martinez Delgado emphasised the importance of listening to each customer and understanding their specific needs to find the right solution.
He described it as a journey of collaboration between the Siemens team and customers.
“I don’t think AI is a plug and play system, it needs a lot of adaptation to meet customers’ needs,” he said.
“What we are doing is listening to problems they may be having and systematically bringing in ideas to fix those issues.
“We are introducing this technology across all our new projects as well as legacy systems. All these projects, both new and legacy, give us an opportunity to learn and improve the digital platform Railigent X, where all the different use cases are implemented in reusable apps.”
Martinez Delgado said one of the difficulties with this new predictive maintenance technology system is that it is difficult to prove that it is working.
He uses the term “prediction paradox” to describe the fact that it is difficult to prove that you have a valid tool to predict failures in a running system, because once implemented, the failures will be avoided and then obviously
Siemens believes the golden triangle needs to be addressed when implementing innovation.
you cannot prove a failure would have indeed occurred. In other words, how can you measure something that does not happen?
The term highlights the difficulty in validating the success of a prediction tool when its effectiveness prevents the very events it aims to predict.
At the beginning of the project the system was monitored by the technicians, but no special interventions were made beyond the prescriptive preventive maintenance tasks. The aim was to confirm the correlation in between AI failure warnings and actual failures.
“It was an opportunity for us to confirm the system was working and give a clear indication of its effectiveness compared to the KPIs defined by the customer,” Martinez Delgado said.
“Once the customer trusted the technology the next step was to make it available to the end users in the way they need it. We learnt that the technicians were not necessarily interested in how the AI tool was doing the predictions but more in the specific action required. They expected a simple input and not a sophisticated engineering tool. This is where the relevance of the people and process implementation is crucial. And the other key factor was the low number of false positives because otherwise the technicians would have discarded the tool. They did not want to be alerted unnecessarily.
“Initially this was a challenge, but as we had more and more data come through, we found ways to prove the success of our system and the benefits to the customer.”
Martinez Delgado said that as more data came in, the team could graph the number of operational faults compared to the number of predictions, which resulted in an interesting correlation – as the number of predictions went up, the number of operational faults in the network would decrease, whereas when predictions
went down the number of faults would climb.
“For both parties, this was the best indication that the system was effective and working,” he said.
Siemens Mobility is already using AI as part of its service offering for projects in Australia, and Martinez Delgado believes the country is well positioned to capitalise on the technology across its varying networks.
“At the end of the day it doesn’t matter how different the networks are, every train has bogies, wheels, doors and we can use the data coming from the different diagnosis systems to harness AI and support our customers,” he said.
“Often the problem is the same, it is simply the details of the problem that can be different.”
Martinez Delgado said that the basis of Siemens’ AI systems remains the same but will be customised across networks. Once the system is fine-tuned to a network’s specific needs it is set up for success.
He said that from the recent record levels of investment into rail projects across Australia, it is important to ensure rail operators are maximising the effectiveness and availability of their networks.
“Budgets are reducing, and governments cannot be spending billions on new trains. They need to ensure they are extending the life of the network and the trains running on them,” he said.
“AI ensures greater efficiency in maintenance teams as well. We work with a freight customer to help monitor and assess their critical wayside infrastructure in real time. This saves manual inspection and reporting, where previously it was taking days for an issue to be investigated.
“AI will make all of our networks more efficient and productive.”
DT Infrastructure is maintaining the trackside infrastructure for the state-of-the-art High Capacity Metro Trains (HCMT) Pakenham East Depot, working closely with a range of stakeholders to keep 70 HCMTs moving.
Melbourne’s High Capacity Metro Trains (HCMT) have been an exciting addition to the city’s rail network. Supporting the operation of the 70 strong fleet is the Pakenham East Depot (PED).
The HCMT PED is one of the largest state-of-the-art stabling yards in Victoria. Its dense concentration of trackside assets includes more than 21 kilometres of linear track, 28 overhead structures spread across 13 overhead sections, 46 turnouts and point machines, six derailers, 53 signals, seven train stops, 140 axle counters, three train gates and six signal Relocatable Equipment Buildings (REBs).
It contains the vital signalling equipment required to manage the safe operation of the trains, such as an integrated test facility that is currently being used to prove the latest high tech CBTC signalling equipment for the Metro Tunnel Project.
DTI is responsible for the reactive and scheduled maintenance of all rail systems components within the depot, including signalling, track and overhead wiring assets. It also provides 24/7 on-call service for any rail systems faults, performing reactive works and planning future corrections.
Rail Express spoke with David Khoo, Program Manager at DTI to learn more about the company’s approach to innovative asset management.
“Maintenance of components within a complex rail system are scheduled based on tailored Technical Maintenance Plans (TMP’s) developed by our in-house subject matter experts, which can mean a mixture of monthly, quarterly, half-yearly, yearly and ad-hoc basis,” Khoo said.
“DTI acts as the engineering authority for the trackside infrastructure, providing support, assurance and acceptance services
for third party rail systems works within the depot facilities.
“We are responsible for ensuring all scheduled maintenance activities occur in a timely manner and are of the standard required to ensure reliability of the overall network.”
Khoo said the team conducts disciplined maintenance informed by the TMPs and supported by the use of comprehensive datasets to identify variations in patterns or anomalies requiring specific attention.
“The technical maintenance plans and facilities manuals we create govern how we maintain the assets and we review them periodically to ensure they are up to date and fit-for-purpose,” he said.
The documentation is critical in the early stages of maintenance work as it
ensures every team member is aware of the processes and the expectations of all stakeholders.
Khoo said DTI also uses a range of technologies to manage, plan and streamline asset management and maintenance.
“We adopt a data-driven decision-making process and employ a technology platform to manage the end-to-end maintenance process and plan the work that needs to be done.
“The platform that we use stores all maintenance records in the system and issues workflow requests. This way we have visibility of all maintenance that has been undertaken and what work needs to be completed in the future.”
A triage system based on the maintenance data gathered and analysed is used to rank the criticality of works required. This starts at P1 for critical issues and then moves to P3 for lower priorities. Items can move along this system, giving our team a clear idea of where we need to step in to stop an issue becoming critical.
“DTI tracks the maintenance work through dashboard reporting. The goal for us is to have visibility of asset performance, and to maintain the asset at a high enough standard to ensure high availability of the system.”
While DTI works to ensure no major disruptions occur, they can be inevitable, and it’s imperative that the impact is minimised as much as possible.
“We have a team on-call that responds and addresses those issues in a timely manner if they occur. By having a team ready to react and respond quickly, it means that any faults can be rectified without delay.”
The arrival of the new HCMT trains marked a significant shift in Melbourne’s train network and the experience of an organisation like DTI can play a huge part in setting networks like it up for success.
“A robust engineering change management process is established to ensure that the testing, introduction and acceptance of new software and equipment introduced by the CBTC system is managed in a methodological way. We are able to manage the testing process by documenting the changes well.”
The implementation of newer and higher performance trains is being seen in more Australian cities and is resulting in a huge step forward in the capability and capacity of train networks.
With so many interdependencies in these complex networks, careful collaboration between all stakeholders is required to ensure their successful operation.
“As the maintainer of the trackside infrastructure that connects all systems, our approach is to work in collaboration with depot operations, rolling stock and CBTC system suppliers, commissioning teams, engineers and technical personnel, to conduct acceptance on the system,” Khoo said.
“In the case of PED, there has been fantastic collaboration between the Rail Network Alliance (the CBTC system supplier), MTM (the operator) and Downer (the asset owner), along with the Department of Transport and Planning.”
He explained that the maintenance projects DTI undertake also include
responsibility for third party acceptance and assurance of new technology in depot facilities. As a result, the organisation’s in-house expert teams have established a process to ensure the process gateways are carefully managed from the project’s early stages. This, Khoo said, allows DTI to ensure it can track the engineering changes as required.
“It is critical that our team manages the expectations of all stakeholders” he said.
“It has been important for us to have open communication to ensure maintenance and acceptance activities are completed in an efficient and collaborative way.
“We strive to achieve a win-win solution for our partners. Ensuring these new state-of-the-art passenger trains are available to meet the demands of growing Melbourne.”
Brimble continues to innovate the rail maintenance sector and bring strong asset management to the fore of its operations.
machines already upgraded to include asset monitoring technology, Brimble has created a clearer picture of its machines for the maintenance team.
Rail Express spoke with Michael Curby, general manager of Engineering, supervisor Mark Tuxford, and engineer Kaiden Ritchie to learn more about what the company is doing to improve its assets and minimise downtime.
“Growing our asset monitoring ability was an internal push from the Brimble team,” Curby said.
“By doing this, it allows us to simplify our machines, making training and use far easier.”
The Brimble fleet is being updated to include more condition monitoring capabilities. While new machines have much of this technology built in, Brimble has also been adding the new technology
“We can monitor the machines ourselves and change components when needed but in a perfect world we want to be changing out components before failure,” Curby explained.
“In the past, often a component would be changed out every six months because historically it failed every seven months –based off a procedure written 50 years ago. But in reality, that component can last three years. This is where the asset monitoring technology will be a game changer for us.”
The asset monitoring technology can track engine hours, how far the machines travelled and even how often the windscreen wipers were used. Brimble has also incorporated sensors that can give an indication of how many times the brakes were applied.
“A machine can work for a 12-hour shift but the clamps for example, might only be closed for three of those hours, this is the kind of information that is so critical for us,”
smallest teams available to us.”
Curby said the challenges for Brimble as it grows will be maintaining its everexpanding fleet and minimising downtime and breakdowns across that fleet.
“In the past you would need a highly skilled or qualified tradesperson to diagnose a problem,” Curby said. “Now you can see the problem on the screen in front of you and lean on our experts that we have working with us, even if the machine is hundreds of kilometres away.
“Those experts can look at it and remember when they had the same problem back in the past and suggest fixes to the team member operating that machine.”
“Our technology upgrade gives us the ability to pre-empt any issues and gives our technicians a greater understanding of the machine before it even arrives back in the shop. This, coupled with our other monitoring systems, gives us great insights on the machines as they are working.”
The Human to Machine Interface (HMI) technology moves away from the historically complex and inconsistent technology used in track resurfacing, in many cases leaving behind antiquated control panels made up of countless dials, switches, lights, and alarms.
Brimble HMI utilises user-friendly touchscreen monitors and a network of highdefinition video cameras, making it simpler for operators to oversee, operate, and optimise rail resurfacing machinery.
Tuxford referenced one of Brimble’s machines working in the Pilbara as an example of the importance of strong asset monitoring.
“We couldn’t get any more remote than out there, and if a machine breaks down, we will be in trouble,” he said.
“But we can have a team member log onto the computer and talk to the team members who are on site and having the problem. They may have seen this issue before and have a fix to get them back on track.
“This kind of insight gives us the best opportunity to keep machines operating to their maximum capability.”
Curby and Tuxford said machines are often working during narrow shutdown periods, so it remains critical to pre-empt any potential issues before they become a problem on site.
we will often have a replacement part on hand to get our machines back and working as quickly as possible.”
For Brimble, setting up the teams for success revolves around strong processes for every time they use a machine.
Each time an operator gets into a machine after it has been sitting idle for any period of time, they have a checklist to go through to ensure the machine is up to standard.
Tuxford describes it as a last line of defence to any potential issues that may
other’s strengths.
“All three of us have different experiences and we utilise that to best support our machines,” he said.
Curby said that Brimble is committed to using technology in new and forwardthinking ways to ensure success.
Over the next five to 10 years, the company will continue to compile data and how it records that data to grow the dashboards for each machine and track its general wear and tear over its life.
Loram is using its RailPro system to improve condition monitoring and rail grinding offerings to the rail industry.
more about how the
monitors rail condition.
Keogh has spent 13 years in the rail industry after completing university and joining Aurizon’s graduate program. He spent time working across a range of sectors for the organisation but says his time in the data science team was an insightful experience as a young engineer.
“Everyone is recording so much information, so it was insightful to see how that information was interpreted,” he said. “It was great to gain an awareness of how to interpret data and what
The track performance team straddles multiple realms in the organisation. In the day-to-day operations, it influences the machines to ensure they are maximising the effectiveness of each one.
“We are always exploring and fine-tuning the ways the machines operate out on the track,” Keogh said. “We spend a lot of time evaluating just what the machines can do and how we can best utilise that to benefit the customers.”
ascertain high volume of profile measurements and other rail parameters that they can feed into pipelines for feedback on trends for the rail and to generate reports and recommendations for themselves and the customer.
“When the industry started high production, mechanised grinding in the 1980s they pretty much got it right straight away; the goal was to restore profile and remove corrugations and it did just that,” Keogh said.
“In the past 15 to 20 years we have seen the growth of technology in this space as a means of improving the offerings of rail grinding leading to incremental improvements across the industry. Nowadays, preventative profile management are the norm.
“What you can buy off the shelf is great but the technology we are developing at Loram has really unlocked the capabilities of rail grinding.”
Loram has progressed its rail grinding equipment to be productive and reliable. The majority of the grinding can be done in a single pass at high speeds with Loram’s larger machines. The single pass means it has to be right with how it applies the power of the machine.
Keogh said to get this right and a highlight of Loram’s improved technology is its RailPro system. The system relies on an intelligence base of specialised grinding knowledge accumulated through decades of experience in rail grinding and track maintenance.
By combining this knowledge and experience with accurate, real time, rail
“We spend a lot of time evaluating just what the machines can do and how we can best utilise that to benefit the customers.”
Nick Keogh, Senior Track Performance Engineer at Loram
condition and asset data, useful information is produced that supports micro and macro level planning of a grind program.
The system has been designed for use with light axle load metros through to large heavy haul railroads in mind and can be customised to meet customers’ specific needs.
“RailPro is your one-stop-shop for rail grinding management, including modules for data collection, rail inspection, grind performance monitoring, analysis and reporting,” Keogh said. “It makes the cyclical processes of a grind program more manageable.
“The inspection module uses intelligent, knowledge-based, predictive algorithms to analyse the rail condition and determine the grind passes, patterns, and speeds that will remove the optimal amount of metal while delivering precise profile control.”
The rail profile and rail surface condition information required by the grind planning algorithms is acquired by a number of methods but typically on large heavy haul networks with a Rail Inspection Vehicle (RIV).
Loram’s RIV is equipped with state-of the-art hardware and software including an optical Rail Profile Measurement System (RPMS), Rail Surface Monitoring System (RSMS), and Loram’s RailPro Inspection software enabling the railroad to perform timely, automatic pre-grind rail inspections.
This automated inspection allows for more accuracy, consistency, and repeatability, which ultimately leads to cost savings through maximising the life of the rail.
“The concept of RailPro really came out of the notion of how a maintenance worker knows where to put the stones. How do they know how much metal needs to be removed?”
Keogh said. “This is where the technology is an asset as it gives the worker much clearer insights into the work that needs to be done.”
Keogh said that the RailPro system has a high level of maturity which sets it apart. The system can emulate what a human would do, quickly identifying the needs of the rail. He said it takes the guesswork out of rail grinding.
“In the past, people had to make the decision to grind rail on the fly and quickly,” he said.
“Whereas with the RailPro it simply lays out for the team exactly where they need to go to improve the condition of the rail.”
He said the RailPro system signalled a fundamental change in the way Loram maintains track from the operators on the machines through to the engineers.
From pre-inspections through to post grinds and quality auditing, it has given the organisation greater clarity in the work needed. Keogh emphasised the importance of the company’s rail experts and machine operators to ensure success, stating their insights are still a critical part of the work.
“They have this fundamental knowledge of hyper specific areas of rail that they can enhance with our RailPro system. They can share their own knowledge with the client and then support that with the data collected by RailPro.
“It’s the conduit in which the human interacts with the rail. At its core it executes the same work every time and that consistency is what makes it beneficial.”
Keogh said that the rail grinding provided by Loram is always predictive in nature, it’s how the RailPro works with the team that ensures its success.
“As an industry we have really grown from reactive grinding to preventive grinding,” he said.
“Our system is giving that clearer picture to identify potential issues and then determines how best to apply the grinder long before those issues develop to faults and cause premature rail replacement or even shuts down the track.”
When Loram discovers issues and defects it is recorded in its database, giving clear records to customers. That information can be collated and passed on whenever desired.
Keogh noted the data can provide interesting information around the source of a defect.
As an example, a client may be getting wheel burns on a specific part of the track, and they can pass that information back on to close the loop.
“We have seen changes in driver methodology based on this feedback,” Keogh said. “It comes back to the ethos that Loram always wants what is best for the rail.
“Whatever the source of the problem is not something caused by the rail, we want to find ways to help our clients improve their rail networks.”
How Loram reports information and works completed varies for each customer. Often the team will report monthly for simple checks and Loram will go through line by line to make note of any problems identified.
“We will then deep dive those problems to make recommendations on the work that can be done,” Keogh said.
“The initial communication is generally relayed during planned monthly meetings and when the contractual reporting is fulfilled we can put our engineering hats on and dive into the nitty gritty.
“Once we have worked with the clients project managers we as engineers can have some fun with it and work our way through the data to better understand their network and propose ideas for optimising.”
Aptella is helping to improve safety on rail networks, bringing the globally successful Senceive technology to Australia.
Wireless monitoring technology is growing in prevalence in the construction sector globally. It is utilised to measure movement during construction and ongoing maintenance work on rail track, rail bridges, embankments and tunnels.
This technology enables engineers, project managers and other stakeholders to capture near real-time data and be notified instantly if movement occurs outside of tolerance parameters.
The safety and efficiency gains of these wireless platforms such as Senceive, distributed locally in Australia, New Zealand and Indonesia by Aptella, are significant.
When compared with traditional monitoring methods that utilise optical total stations, wireless solutions offer greater flexibility and options to scale to even the largest of projects.
The small nodes and sensors can be mounted to any surface and have a 10 to 15-year battery life, making them ideal for large projects and hazardous or inaccessible landscapes as they require less maintenance than traditional methods.
Senceive solutions combine three key elements. Sensor nodes placed on or nearby
areas to be monitored for movement; a solarpowered cellular communication gateway to collate data from the nodes and transmit to cloud-based servers; and lastly an online portal for customers to manage and analyse the data.
For high risk, remote or hard to access areas, there is also an option to integrate cameras with the monitoring platform to give users eyes on the scene when movement is detected.
With an instant visual of the scenario, in addition to movement data, the platform helps stakeholders differentiate between a false alarm or something more serious and respond appropriately and efficiently.
The value of wireless monitoring was demonstrated in the United Kingdom at Barnehurst on Network Rail’s Bexleyheath line in 2019. Around 200 Senceive triaxial tilt sensors and seven cellular cameras were installed on the slope above the track.
In the early hours of Monday 11th February some of the nodes detected slow and gradual ground movement. The system, now known as InfraGuard, automatically requested
further data samples from nearby nodes to see if the initial small movements were widespread. It also ‘told’ the gateway to stay open to transmit data and minimise any lag in decision making.
These smart characteristics combined to provide a picture of the situation at any point in time. With alerts and alarms from sensors and images from the cameras being automatically sent to the route engineers as trigger points were breached, it provided an early indication of the potential for failure.
The embankment collapsed a few hours later, it left a tree and debris on the track, but everyone was ready, and the line was closed to traffic. Repairs were completed and the line was re-opened a week later.
In New Zealand, Senceive technology was deployed on the North Island Main Truck Route to monitor 160 kilometres of track and three existing rail overbridges.
The setup included 82 tilt sensors installed on the rail tracks and a further 10 fitted to monitor the three overbridges.
All 82 track sensors were installed by a team of three surveyors in about five hours,
significantly faster than the time it would have taken to install total stations and optical targets to the rail.
Three-quarters of the monitored section of track was fitted with timber sleepers, many of which were degraded and needed spot replacements during nightshifts as the project progressed.
An advantage of the Senceive sensors was that they could be quickly detached from the old sleeper and reinstalled onto the replacement in time for rail services to resume during the day.
Track corrugation on the remaining quarter of the monitored track, where Senceive nodes were fitted to concrete sleepers, required technical assistance from the Aptella team to find a solution.
The corrugation caused the nodes to detect irrelevant movement and vibration, so a scale factor was calculated to dampen the x-axis values that were being reported and achieve accurate tilt measurements.
Upon completion of the monitoring project, the nodes were unclipped from their mounts and available for redeployment on the next project.
New York City (NYC) was severely affected by Hurricane Sandy in 2012. Considered the
In New York the system was perfect as it allowed for quick installation and less infrastructure to support it.
Works were planned to replace ageing pier fenders, with monitoring required to ensure stability during the
bridge, precluding traditional survey methods
assurance and control, proposed an alternative approach using Senceive wireless monitoring technology.
Site access and installation was challenging, with track outages not possible, and only short access windows available in between trains. The discreet monitoring system from Senceive, including sensors and two data communication gateways, were quickly installed within available access windows, without having to deal with bulky equipment and external power systems.
A total of 56 tilt sensors were installed every 20 feet along the track to measure changes in twist and cross-level displacements. A further 10 triaxial tilt sensors and 20 optical displacement sensors were installed on five of the piers to measure pier rotation and displacement.
The two cellular gateways with internal batteries and small 20-watt solar panels were installed on opposite ends of the bridge for continuous data collection.
The use of Senceive’s wireless monitoring technology helped the construction team keep the bridge open throughout the upgrade work by providing insight into the structural stability of the tracks and piers.
It helped engineers and other stakeholders proceed with confidence that they will be immediately alerted of any concerning movements. With long-life batteries and very low power consumption, this type of system can be re-used on further projects.
over 15 years with GEISMAR track monitoring and recording equipment.
GEISMAR specialise in the development of measurement and verification equipment for railways. For almost a century, teams from GEISMAR have been developing technology to improve rail transport.
Key Source Rail has embraced the development of track geometry measurement as it plays a crucial role in improving the safety, efficiency, and reliability of railway networks.
Rail Express spoke with Key Source Rail Chief Executive Officer David Gallagher to better understand what the company is offering Australia and the intricacies of track monitoring.
“Over the years, technological advances and an increasing emphasis on accuracy have transformed the methods used to measure track geometry,” Gallagher said.
“GEISMAR are continually developing their technology in a state-of-the-art laboratory where they are consistently coming up with better methods for recording track measurements.
“These developments set Australia up well to benefit from the work being done by GEISMAR around the globe and we are excited to bring this technology to the local market.
is segmented into three categories: track geometry, rail geometry, and gauge and structure.
Track geometry involves measurement criteria linking both rail tracks. Aspects measured are track gauge, elevation, cross level, versine, switch, twist, horizontal versine and horizontal alignment.
“Key Source Rail offers several pieces of equipment for measuring these various metrics,” Gallagher said.
These include the RCFF track and level measurement gauge; the RCA track and turnout gauge; the Garnet-DL digital track and switch gauge; the Amber manual track recording unit; the Amber-T track geometry and versine
track and switch geometry digital measuring and recording trolley; and the Emerald towed track recording unit.”
Rail geometry includes measurement criteria where users can measure each rail independently. This includes measurement and recording of rail straightness, rail inclination, rail corrugation measurement and vertical versine.
Key Source Rail has three pieces of equipment for this purpose. They comprise the Opal Mini laser alignment system, the Rectirail DL2 portable electronic straightness measurer and the JET rail inclination gauge.
Gauge and structure measurement relates to metrics surrounding the track including
The Key Source Rail team often travel to France to ensure its skills are up to standard.
Over the past few decades, GPSs have been integrated into Key Source Rail’s track geometry measurement instruments. This has further improved accuracy and efficiency by providing real-time location data.
This is particularly true of the GEISMAR Emerald measurement trolley, which can record track geometry over long distances while being towed at speeds of up to 20 kilometres per hour.
“This saves a great deal of time in collecting and analysing data,” Gallagher said.
“The Emerald can be easily towed through switches and crossings making it ideal for the great distances we have in Australia.”
The other machines that utilise GPS technology are the Amber, the Amber-T and the Topaz.
“The Amber is a robust and lightweight recording trolley that displays and stores accurate measurements. The system can be set up on a smart phone, which is connected to a Bluetooth system enabling efficient data management and ease of use,” Gallagher said.
“This machine accurately measures gauge, cross-level, twist, distance and speed travelled.”
GEISMAR has developed an enhancement to the Amber, which is the Amber-T.
“The Amber-T provides real-time measuring and displaying of all track geometry parameters similarly to the regular Amber, on a smartphone,” Gallagher said.
“Once stored, the data can be processed later on a desktop computer. This machine maintains conformity to the local track standards measuring gauge, cross-level, twist, horizontal and vertical alignment, distance and curve radius.”
The Topaz is a light and portable track geometry trolley that can be easily folded for carrying to site and is quick and easy to set up.
“The Topaz enables the collection and display of gauge, cross-level, twist, horizontal
using bluetooth technology.”
These advances make it possible for network operators to identify risks at an early stage, improving safety and reducing maintenance costs.
The Mephisto and the Opal Mini are two pieces of measuring equipment that utilise laser technology.
“Laser-based technologies have become valuable assets in rail measurement, enabling more detailed and accurate assessments of rail and track conditions,” Gallagher said.
“The Mephisto laser survey recorder is a magnificent piece of measuring equipment. It has an on-screen digital display for all its measurements.”
The unit records several key track structure measurements including position of track (fixed point and low point), track structure gauge, infringements to track structure gauge, position of reception areas (platform edges and walls), bridges curvature, overhead line position, and the distance between two sets of tracks.
Meanwhile, the Opal Mini is a compact laser measurer that is lightweight and able to be set up in a matter of seconds.
It is composed of one laser source and a
The systems are simple to use and are lightweight.
laser target with a maximum of 30 metres in between placed on the same rail.
“This is a dynamic device that is particularly useful to assist hand tamping operations to ensure level track,” Gallagher said.
“The Rectirail-DL2 portable electronic straightness measurer. This provides an easy and reliable way to measure and record rail head straightness and is principally used across welded rail and corrugated rail.
“The machine is non-contact and takes one sample every 10mm using 100 sensors over a one-metre base.
“To support all of our products Key Source Rail offers preventative and corrective maintenance services as well as our equipment calibration service in Perth and Newcastle and the GEISMAR laboratory.”
All of these machines are supplied to Key Source Rail by GEISMAR and the two organisations have formed a strong relationship.
Gallagher went on to explain how the relationship benefits the Australian rail industry.
“We get the benefit of picking up what everyone is doing in our local industry,” he said.
“We like to think that we are at the cutting edge of new development in the field, and we communicate with GEISMAR to ensure we remain there.”
The Key Source Rail team go once a year to France to collaborate with GEISMAR and get the opportunity to take any issues the team may have and take suggestions to them.
“We have our technicians in Australia who are qualified to calibrate these machines, they travel to France to be qualified to operate and calibrate them correctly,” he said. “It ensures they are experts in this technology to support
The Australasian Rail Directory is a comprehensive, all encompassing rail services directory, available both online and as a traditional hardcopy publication.
The Rail Directory is an industry driven project to provide a complete listing of all businesses involved in the Australasian, Oceanic and Asian rail industries.
This year’s rail directory will be revamped to become even simpler to use. Listings will be sorted into categories allowing users to easily find businesses working in each area of the rail industry.
With over 1000 listings from areas as manufacturing, signalling and maintenance, make your listing standout with a frame advertisement.
To ensure you are in prime position in this year’s rail directory contact Alex Cowdery today.
Free Listing
To ensure that the Australasian Rail Directory is comprehensive, we offer all businesses who operate or trade in the region one free listing in the directory.
Premium Category
Listing Available
From $600 (+gst)
Double page, full page, half page and quarter page advertisement space also available.
To discuss the advertising opportunities available, please contact: Alex Cowdery on 0422 657 148 or email: alex.cowdery@primecreative.com.au
Anne Modderno from Swietelsky Rail Australia took home the Excellence in Transport Award at the Women in Industry Awards held in June.
The Women in Industry Awards aim to recognise the women in Australia who are delivering excellence across industry sectors, making active contributions to break down barriers to equity and inclusion, and showing future generations what is possible.
Anne Modderno, managing director of Swietelsky Rail Australia (SRA), won the Excellence in Transport award at the 2024 event held in Sydney.
Sponsored by Kenter Logistics, the award is for an individual who has gone above and beyond to improve and positively impact the Australian transport industry.
Modderno said she was honoured to be nominated alongside other fantastic women and was shocked to win.
“With the amazing women nominated in my category, I had no expectations to win. They’re all breaking down barriers in their own businesses in so many different ways,” Modderno said.
“They are all huge inspirations, and I was so proud to be named as a finalist with them.”
Modderno was nominated alongside Alice Reis from Arup, Jenny Fellows from Fellows Bulk Haulage, Monica Dryden from Mott Macdonald, Orlane Mortimer from Wollongong Crane Trucks and Shani Davies from Metro Trains Melbourne.
increasing female participation across all industries.
“We need awards like this. We need to get comfortable talking about what we achieve because if we can’t project it, if we can’t show it, then no one else will see it. No one else will want to be it,” she said.
“As parents, family members and friends raising the next generation, we can actively share stories and experiences about all the opportunities we know exist now but didn’t know were possible when we were growing up or studying at school.
“[We need to be] Intentionally not ‘gender badging’ roles, careers or industries in our stories, because there really aren’t any ‘girls’ jobs’ or ‘boys’ jobs’ – there are just jobs. The earlier our daughters, nieces and granddaughters hear about what types of jobs and careers are out there for them, the less likely they are to be intimidated by an industry or doubt themselves in any way. Instead, they will be more likely to have the confidence to achieve anything. Future generations will know no limit.”
Modderno attributed her win to her ongoing commitment to organisational
Strategy, and new strategic direction.
During more than 15 years in the transport industry, across rail and civil construction sectors, Modderno has successfully led teams to manage and deliver large-scale maintenance and capital projects.
She continues to be an advocate for inclusivity and diversity within the transport sector. As the first female managing director at any Swietelsky International subsidiary, Modderno wants to pave the way for women in transport, and actively finds ways to increase their participation.
“I am so proud of the strides we’re making towards improving diversity and inclusion within the transport industry, but there’s more work to do,” she said.
“I hope this award shows the women in my team, and other women in transport and all other industries, that you can be the change you want to see.”
Women in Industry Awards were presented across a number of fields including transport, engineering and manufacturing, mining, construction and energy. Awards were also presented for safety advocacy, mentoring and business development.
MRD Rail’s tracksense is helping to improve condition monitoring across Australia’s rail industry.
Technology continues to advance at a rapid pace, the railway industry is no exception.
Remote Condition Monitoring (RCM) has revolutionised rail operations, enhancing efficiency and safety. The landscape of RCM continues to evolve, and MRD Rail Technologies is at the forefront of this transformation with its TrackSense Autonomous RCM system.
Since its introduction, TrackSense has set itself apart by offering a fully autonomous system that operates independently of external servers and network connections. This autonomy is a game changer, providing rail operators with several advantages.
Data breaches have become a common concern in today’s digital landscape. TrackSense addresses this issue by ensuring that all data is stored locally, reducing the risk of external threats.
This localised data storage ensures that critical information remains secure and in the hands of the operators, providing peace of mind and reliability.
The reliance on Cloud services introduces the risk of internet disruptions and server crashes. TrackSense, however, operates independently, ensuring continuous and uninterrupted monitoring. This reliability is crucial for maintaining safe and efficient rail operations, as it eliminates the vulnerabilities associated with external network dependencies.
TrackSense’s compatibility with thousands of industry-standard Modbus and 4-20mA sensors means that it can monitor virtually any asset.
From points machines and batteries to power supplies and environmental factors, TrackSense offers simple customisation. Operators can tailor the system to their specific needs, optimising their monitoring capabilities and improving overall efficiency.
One of the primary benefits of TrackSense is the elimination of ongoing subscription fees.
Unlike Cloud-based RCM solutions, TrackSense requires only a one-time investment, offering substantial long-term savings. This financial independence allows rail
operators to allocate resources more efficiently and avoid the recurring costs associated with Cloud services.
MRD Rail Technologies has not rested on its laurels. Since the last edition, TrackSense has seen significant advancements, including the addition of an insulation monitoring card and the development of a measurement card specifically for monitoring track circuits. These enhancements further expand TrackSense’s capabilities, allowing for more comprehensive monitoring and ensuring the highest levels of safety and reliability.
As the rail technology landscape continues to evolve, MRD Rail Technologies remains
committed to innovation and excellence. The TrackSense system embodies this commitment, providing rail operators with the tools they need to maintain and improve their networks. By offering a fully autonomous, customisable, and reliable RCM solution, TrackSense is setting a new standard in the industry.
Rob Gersbach is the managing director at MRD Rail Technologies and said the TrackSense stands out as a beacon of innovation.
“With its unique combination of autonomy, security, and versatility, it is no wonder that TrackSense is quickly becoming the preferred choice for rail operators worldwide,” he said.
“As MRD Rail Technologies continues to push the boundaries of what’s possible, the future of railway condition monitoring looks brighter than ever.”
RA I L EXP R E S S is compulsory reading and a vital tool for all people working in and around the
Rail Express is Australia’s authoritative business to business rail publication.
Combining the resources of our respected journalism team Rail Express provides extensive, comprehensive and balanced coverage of breaking news and trends in key areas like infrastructure, investment , government policy, regulatory issues and technical innovation.
Published both in print and digitally every month, Rail Express is active par ticipation of the main railway associations in Australia and the broad suppor t of the rail industry.
The only way to ensure you get every copy of Rail Express is to subscribe today Visit railexpress.com.au/subscribe.
Lycopodium has strong asset management experience across multiple sectors and is working closely with a range of rail operators.
Lycopodium’s asset management specialists operate across a host of sectors, including utilities, mining, manufacturing, rail and government infrastructure.
It applies best-in-class asset management and maintenance processes and principles to manage costs, risk and performance from concept planning to asset creation, operations and maintenance, right through to removal or renewal.
Smith said Lycopodium’s proactive asset management planning ethos is rooted in the development and delivery phases of a project. It’s an integrated approach that enables the organisation to identify potential management and maintenance issues and create plans that streamline ongoing maintenance, minimising
information and roll it out across the network.
“Additionally, the asset owner can effectively model different strategies, either CAPEX (capital expenditure) or OPEX (operating expenditure) focused, and understand how this looks from an asset condition and fiscal sense across the whole life cycle.
“This allows asset owners to make informed decisions around balancing the resources needed for the assets and to maximise the efficiency and effectiveness of asset management.”
Lycopodium has been operating its asset management division for 13 years and has been consistently improving its offerings.
“Into our life cycle cost model, we have incorporated maintenance effectiveness and an asset degradation component,” Smith said. “We can take the work history and identify particular
to track assets to understand its existing condition. Smith said that recording data from pre- and post-works allows the organisation to track activity and better understand the effectiveness of maintenance practices, the current life cycle position of the asset and when works are needed.
Ballast, he said, is a prime example of an area where data can be used to track its effectiveness.
“As ballast ages, we can track when certain maintenance activities stop being effective and establish when intervention is required and a new layer of ballast should be added,” Smith said.
Smith said Lycopodium’s preference is always to use real data available from the network it is working on because each network is unique with its own characteristics.
“We typically utilise real data to determine what works well rather than turning to academic papers specific to a network or location for our knowledge,” he said.
“Where this data may be missing or there are gaps, our team takes the principles that we know work across rail networks in Australia and bring that knowledge to our work.”
Smith and his team will then determine exactly what the client is looking for from their asset management. Some operators are looking for a fit-for-purpose solution, others may be wanting to improve track condition to step up performance.
Smith said it is about understanding what clients are looking for in terms of improvement and identifying a range of solutions to meet that need.
Lycopodium has worked across diverse train lines ranging from lower tonnage to higher tonnage lines. It has also worked with small clients, for which rail is not the main focus, and major organisations for which rail is a critical component of the work they do. This cross-section of clients has given the company experience and knowledge of diverse networks and an understanding of the importance of clear communication.
“It is a combination of looking at track performance, the client’s requirements around reliability and speed and then tailoring the maintenance response to that,” Smith said. “It is all about finding the right balance for each line, everyone wants something a little
bit different, so it is important to manage those expectations.
“With smaller clients where rail is not their core business, we are extremely transparent with what work we are doing so they have clear visibility across all the work that is required. We deliver this in a clear concise way, aligned to core asset management strategies that is easy to understand, with a recommendation on the suggested approach to meet their needs” he said.
“Larger network owners typically have more resources and more in depth understanding of rail specific asset management, so we tailor our response to provide options and scenarios to enable them to make an informed maintenance decision.”
Lycopodium’s life cycle cost model allows it to provide insights into where a network owner can optimise their network. Operators have the freedom to explore and simulate potential upgrades or configuration changes available to them and understand what downstream maintenance and resourcing requirements look like.
“Most large clients have got a wealth of information on their assets, as they are often retrieving data in real time across their network” Smith said.
“We can use data in our analysis in different ways and different scales to provide solutions that fit our client’s needs. An example is we can use actual asset data to inform assessments for upgrade solutions to help understand project benefits clearer.
“A key area of opportunity I see in the rail industry is predictive maintenance. As network operators aim to be less reactive to issues and operate more efficiently and safer.”
Smith said generally assets are managed to an intervention limit but as information becomes more readily available, there is an opportunity to move more into the predictive maintenance space.
“The amount of information being captured
degrading and the user can be a lot more informed about how an asset is performing. We can embrace ideas and practices from other industries such as machine learning to improve how we manage assets.”
Smith outlined how Lycopodium’s bottom-up life cycle cost model allows the identification of outlier variables which may be leading to additional cost or time associated with maintenance activities.
“Often we will identify issues on a network, for example locations where it is inherently difficult to get in and do the required maintenance that is required due to the location or configuration of the area,” he said.
“The bottom-up cost model allows us to better inform the customer and show exactly where the inefficiencies are occurring on the network and allow us to investigate any potential fixes and amendments that can be made to improve efficiency.
‘It allows the asset owner to quickly identify issues and where they can gain the most bang for their buck in maintenance.”
Recently, Australia’s rail networks have faced unprecedented climate events that have caused multiple critical lines to be shut down for repair works. Smith said it is critical that asset management strategies for the nation’s assets consider and build in resilience to these unpredictable events to prepare networks for these challenges.
“It is a complex problem and something that needs to be considered in the whole of asset life cycle,” he said.
“We need to consider the changing climate and the need to build in resilience considering the need to have reliable freight links from a design perspective through to the operations and maintenance phases. The whole life cycle of the network must be considered.”
Smith also noted the importance of technology in the future of rail and using it for asset management.
“There is an opportunity to progress so that asset management philosophies are more of a predictive state and having real time information and predictions to the point where we constantly have an instant picture of where the asset is, how it’s acting, how it’s reacting, and most importantly, predict where issues are likely before they arise,” he said.
“With the ongoing evolution and continued introduction of new of technologies and the information that’s already been gathered, I think it’s an exciting place with a lot of opportunity for the industry as a whole.”
GS1’s project i-Trace has been a game-changing addition to supplier Cold Forge and its ability to track and trace components.
GS1 Australia is a provider of standards and solutions for over 25 industry sectors. It introduced barcoding to Australia in 1979 and today enables more than 22,000 member companies, of all sizes, to become more efficient by implementing the GS1 system.
Project i-TRACE is an industry approach that uses GS1 standards to identify and track assets, parts, and components in the supply chain through the adoption of digitisation in rail operations.
Engineered rail products supplier Cold Forge has been using project i-Trace to better track and trace its assets. The company is focused on delivering competitive, reduced cost-of-ownership product solutions for the maintenance of rail permanent way including track, sleepers, fastenings and other trackrelated components.
Maintenance is a major expenditure item for all rail networks. Cold Forge managing director Andrew Carroll said the cost of permanent way maintenance is particularly highlighted on both mainline and noneconomic rail lines that are the subject of either contractual or statutory obligations.
Cold Forge was started in 1958 as a fastener manufacturer in Sydney and was a Tier 1 supplier for companies such as GM, Holden and Ford. It continues to service select customers in this space where needed.
The company developed a range of rail fasteners in 2008 which drove the business into the rail sector, including export markets in the United States. It is a Progress Rail reseller and resells a number of Progress Rail products in Australia, as well as being the exclusive distributor for British Steel rail and steel sleeper products in Australia and the Australian representative for Calenberg ballast mats. Cold Forge still operates from Sydney and supplies nationally.
Cold Forge’s journey with Project i-TRACE began in the mid 2010s with Queensland Rail’s first Project i-TRACE information session in Brisbane. This led to deeper discussions directly with the i-TRACE team at GS1 about how these standards would integrate into Cold Forge’s everyday operations, as well as the benefits that were possible.
“Once these discussions began, the GS1 team encouraged us to join their digital communication lists, which included monthly user groups as well as regular newsletters that outline project updates, initiatives, and stories of all the other organisations utilising GS1 standards to such great effect,” he said.
“This, along with the regular communication from GS1 Australia, showed us how easy it would be to begin the integration of Project i-TRACE.
“A primary driver of our decision to adopt Project i-Trace is one of our key business targets which is to issue zero credit notes. We believe that most credit notes are an indication of an error in the order entry, and or shipping process. Therefore increasing accuracy and removing uncertainty reduces these time-consuming errors.”
A credit note (also known as credit memo) is issued to indicate a return of funds in the event of an invoice error, incorrect or damaged products, purchase cancellation or otherwise specified circumstance.
“Once we took the first step, it was easy to see how wide-ranging the benefits of i-TRACE
could be, from streamlining all our internal processes, and allowing us to communicate more efficiently with our customers and in time, external suppliers,” Carroll said.
“While we have always had product traceability, with Project i-TRACE, we are able to track the journey of our products from manufacture to delivery with pinpoint accuracy.
“This level of detail is essential for ensuring our quality control level is as high as possible, we are meeting delivery targets, and of course, exceeding our customers’ expectations.”
Carroll said that another key consideration in the decision to adopt GS1’s i-Trace was the choice of business software. The organisation chose SAP BusinessOne as it aligned with both its business needs and the requirements of i-Trace relatively seamlessly.
When implementing the new system, Cold Forge used a good, better, best staged implementation.
In stage one – the good stage – Cold Forge gave the customer what they needed with i-Trace labelling remaining 100 per cent under Cold Forge control.
In the second stage, Cold Forge worked with its supply chain to label as required using its templates.
In the third and final stage – the best stage –the supply chain generated required labelling from its purchase orders with no further support requirements.
“As we continue our implementation journey, i-TRACE, and our use of GS1 standards, will be hugely beneficial to our collaboration with external suppliers,” Carroll said. “With it, we can ensure consistency in the identification
of products and assets across the supply chain. The standardised approach to barcoding and serialisation facilitates seamless data exchange, improving the accuracy and efficiency of transactions.
“Our external stakeholders can easily align with the system, reducing the complexity of integration and communication.”
Carroll said that this leads to more streamlined operations and enables realtime visibility and inventory management. The enhanced traceability also supports the company’s compliance and regulatory requirements. If any fault is discovered, Cold Forge can quickly identify which parts are affected.
“The accuracy and reliability of information reduces errors and associated costs, leading to cost savings for both suppliers and Cold Forge,” Carroll said.
“By fostering a transparent and responsive supply network, Project i-TRACE ultimately enhances partners experience through better product availability and timely delivery, strengthening the competitive edge of us and our partners.”
Carroll said efficiency gains through the manufacturing process had been achieved through better data capture and a reduction in administrative work, allowing staff more time in value-adding activities.
The organisation expects to see more improvements as the system is further implemented including greater cost savings and a leaner and more responsive supply chain.
“We see great value in the wider industry
system. i-TRACE creates a more cohesive network, where every component, from the smallest bolt to the largest locomotive, can be tracked effortlessly across different systems and organisations.”
He said that as the rail industry is subject to stringent regulatory standards, adopting i-Trace simplifies compliance by providing a clear audit trail. This not only enhances safety but also builds public and regulatory trust in rail operations.
“The wider adoption of i-TRACE in the rail industry promises to elevate safety, efficiency, and reliability, which are the cornerstones of successful rail operations,” Carroll said.
“It’s a strategic move that aligns with the
STRAIL is seeking to improve safety in tunnels for maintenance teams and emergency egresses with its rubberised track crossings.
Phoenix has been managing Kraiburg STRAIL’s rubberised crossing systems for level crossings across Australia and New Zealand for almost 35 years, now it’s expanding to support the region’s growing tunnel industry.
The organisation is working closely with KiwiRail on the City Rail Link project to ensure emergency egresses are as safe as possible.
Director and civil engineer Andrew Roseman said that tunnels have parallel walkways that can be accessed by maintenance workers or passengers in the instance of an emergency.
“In set locations along the tunnel, our rubber crossings are placed to allow users to safely cross the track,” he said.
“It is pretty simple; it stops people tripping over the track in what is often an emergency situation.”
Roseman said the company’s experience across level crossings in Australia and New Zealand means it is better prepared to support these exciting new projects – level crossings installed across Australia in the early 2000s are still in operation today.
“I think the organisations we work with are confident with our offering based on the work we have done previously,” he said.
“Our products have been tested to European standards and our track crossing systems have been rolled out across a number of tunnels around the world.”
Trains are a critical transport option for people with disabilities. However, when evacuating a train a wheelchair user will be
unable to get over the tracks. That’s where STRAIL’s level crossing systems come into play. The track crossing system is designed to make access within tunnels as safe as possible.
Phoenix works with designers to understand where it’s best placed.
“The rail is also a tripping hazard for people trying to get out in an emergency or for workers. Installing this system makes it safer,” Roseman said.
“The rubber used in the STRAIL system is anti-slip, making it safer for those who walk across and use it,” he said.
STRAIL is developed in Germany and is customisable to suit the needs of individual networks. It’s been installed across multiple gauges and even on tracks with dual gauge or gauntlet track.
“Even if the tunnel has different widths throughout, we can find a rubber solution that can fit that specific part of the network,” Roseman said.
The STRAIL level crossing system is made of recycled rubber core and is encased in a fire-retardant material to allow it to withstand high heat and the lowest smoke emission standards, adding to its safety credentials for tunnel applications.
Roseman said the products have tested to European industry standards for fire classification, as well as ASTM (formerly known as American Society for Testing and Materials).
While the STRAIL level crossing system allows tunnels to be safer for those exiting or in an emergency, it can also be used to enhance hi-rail access for maintenance teams and emergency vehicles.
“We have been progressively installing hi-rail pads across Melbourne’s network and are beginning to roll it out in other states as well,” Roseman said. “Now the network has safe and controlled access points to get on and off the track with minimal need for costly traffic management.”
The pads are simple to remove to allow maintenance works to be completed on the rail. They can be pulled out to allow tamping machines and track inspections along the network.
Aside from the safety aspect, the system is also a win for sustainability, Roseman said.
“When asphalt is used it has to be removed and then more asphalt installed after track maintenance work is completed,” he said.
“An operator may hold back its maintenance in these areas so it does not have to remove the asphalt, whereas the rubber pads can be taken out easily and
reinstalled quickly, also minimising shutdown time for a network.”
STRAIL has also developed noise walls along tunnels. These noise walls are used to minimise sound pollution in the tunnel to make the journey more pleasurable for passengers.
“It not only makes the noise more bearable for passengers, it minimises noise and vibrations making its way into the ground around the tunnel which can potentially damage infrastructure and buildings nearby.”
Phoenix has worked closely with KiwiRail and Auckland CRL to help deliver this project. Roseman said that the company worked closely with engineers to provide solutions for the track crossings.
“What these tunnels needed was quite unique and we hadn’t provided rubber crossings for something like this before,”
he said. “We worked with the engineers to find a way to deliver a system that would work for its specific needs. The engineers saw the work we had done on other tunnels and appreciated the experience we had would be beneficial in setting up this system.”
Roseman said these relationships were beneficial as a level of trust had already been established.
“We provide technical assistance on site as well, particularly with these bespoke installations. This, I believe, is the benefit of the work that we do.
“We are engineers first, so we have the technical expertise in construction to help deliver these massive infrastructure projects.”
Roseman said the team at Phoenix has an appreciation for the challenges Australia’s rail industry faces. The many gauges operating across the country and different operating systems can create headaches but the organisation has worked to manage these complexities.
“Some of the tracks are over 100 years old and with different sleeper profiles it can introduce huge amounts of variability,” he said.
“This is where our experience as engineers and working across a range of networks becomes invaluable. Coupled with the international experience STRAIL provides from its base in Germany supplying rubberised level crossings since 1976, we have that maturity and understanding required.
“We have worked across the country, including from the Pilbara, putting our rubberised crossings in some of the harshest environments and they have stood up to those challenges.
“We can really say we continue to be leaders in this space, working from heavy haul through to tunnels and everything in between.
The Australasian Railway Association is set to a release a report into the industry’s approach to decarbonisation and what work is needed to hit net-zero targets.
Caroline Wilkie, Chief Executive Officer, Australasian Railway Association
New research by the Australasian Railway Association (ARA) has confirmed that the rail industry is at a critical juncture in its efforts to decarbonise its operations.
In the next eight to 13 years, about half of the nation’s diesel-powered rollingstock will need to be replaced, with the next generation of locomotives to have a lifespan well beyond 2050.
While the industry has progressed a range of trials in new technologies to replace diesel-powered trains, low and zero emissions rollingstock are not yet commercially available in Australia.
The ARA’s Rollingstock Decarbonisation Critical Path, released in July, found that a shared, national strategy developed in partnership by governments and industry is urgently needed to confirm the policy, regulatory, skills and infrastructure settings required to support this transition.
Without this, uncertainty around the ability to introduce new technologies to the Australian network will act as a handbrake on research and innovation and constrain the industry’s ability to address hard to abate sections of its operations.
In the short term, greater use of rail can deliver substantial emissions reductions in the transport sector.
Rail generates significantly less emissions than other transport modes and is the most energy efficient form of transport for moving people and goods.
On our passenger networks, greater use of active and public transport not only reduces emissions, but improves health and safety, busts congestion and reduces air pollution. Cities and communities planned with
public transport at its heart are generally more sustainable, because they reduce the distances we travel and promote healthy options such as walking and cycling.
Meanwhile, a number of governments have targets to move more freight on rail in recognition of the significant carbon savings that can be delivered by rail.
As the nation’s freight task continues to grow, moving more freight on rail is becoming increasingly important to supporting a sustainable and resilient freight network.
Greater use of rail will therefore be a crucial part of the transport sector’s decarbonisation, particularly as we approach 2030 emissions reduction targets.
While the immediate emissions benefits the industry offers is clear, rail will also need to decarbonise to meet the needs of a net zero future.
scope 1 and 2 emissions are generated by traction energy used to power locomotives.
About 30 per cent of this is related to passenger operations and is primarily generated by electricity. While renewable energy sources for electrified rail networks will need to be confirmed, this transition is already in progress and the pathway to decarbonised operations is relatively clear.
The remaining 70 per cent is related to rail freight, where most freight operations are powered by diesel on sections of the national network that are not easily electrified.
Emissions from these operations will be more difficult to abate, because they require new, low or zero emissions technologies to be adopted.
At the moment, those technology solutions are not yet clear.
The ARA’s research identified a phased transition will be required between now
retrofitting existing rollingstock or purchasing new models – a significant investment for industry.
Early planning now will be essential to prove new technology pathways and ensure other considerations such as changing regulations and building new skills and supply chain capability to support these technologies have been fully considered.
Urgent action is therefore needed to create the certainty required to unlock the significant investment in low and zero emissions technologies that is approaching.
A number of research and pilot projects are underway to test new technologies. Several resources companies are trialling battery electric locomotives in the Pilbara region of Western Australia, as is Aurizon on the east coast.
Fortescue is exploring ammonia powered locomotives in the west as well.
While this progress on battery-electric trials is promising, Australia has not seen the same degree of focus on hydrogen – in stark contrast to the overseas experience.
More research and innovation will be required, and stronger collaboration and information sharing will be essential to speed the industry’s progress.
The ARA is supporting collaboration across the industry, with its Heavy Haul Decarbonisation Working Group and Rollingstock Decarbonisation Working Group both providing avenues for information
work on together.
The research also explored funding models to support further research and collaboration.
The ARA welcomed the recent announcement of the Australian Renewable Energy Agency (ARENA) funding for battery electric tender demonstration project led by Aurizon.
Our research confirmed that ARENA provided an ideal funding stream for new and novel technologies to prove concepts that could support the industry’s decarbonisation.
Additional financing through bodies such as the Clean Energy Finance Corporation and National Reconstruction Fund could provide opportunities to assist industry in building scale once technologies had been proven.
Beyond this, more research is likely to be required at a systems level to support the integration of new technologies on the national network. Research bodies such as the recently created Australian Rail, Research and Innovation Network (AusRRIN) may be well placed to have a role in this work.
A key issue identified by the research was the need for energy certainty for the rail industry.
An interim solution of biofuels and renewable diesel will require greater access to these resources, at the same time the demand for renewable fuels is rising across many industries.
Similarly, the hydrogen industry is still developing, and would need to be in abundant supply and available in key
the national rail network.
The ARA has highlighted the importance of planning for the transport sector’s energy needs in its submission to the Federal Government’s electricity and energy sector plan consultation.
But there are opportunities here too.
Aligned energy and transport sector planning could benefit regions, where rail networks are already well developed and provide an opportunity for the co-location of renewable energy infrastructure.
This highlights the importance of coordinated planning across sectors as Australia continues to work towards net zero.
The ARA has recommended that the development of a national strategy for rollingstock decarbonisation be considered as an action in the transport and infrastructure net zero roadmap and action plan, providing an opportunity for collaboration between federal and state governments, as well as industry.
We are also exploring opportunities to better define the skills needed to support a decarbonised rail industry. This includes through new research being delivered by Infrastructure Net Zero, of which the ARA is a founding member.
The pathway to decarbonising rollingstock is long term, but there are strong opportunities for early gains in the years ahead. The ARA is committed to supporting these efforts.
The Permanent Way Institution has been working closely with the NSW Government and is showing its appreciation for rail’s major partner, state and federal government.
As we reflect on the rail industry’s achievements and contributions, it is essential to recognise the vital role that government support has played in advancing transportation infrastructure in New South Wales.
The Permanent Way Institution (PWI) of New South Wales, with its long history dating back to 1974, is a testament to our industry’s dedication and expertise. Today, we take this opportunity to extend our deepest gratitude to the NSW Government for its unwavering support and investment in our rail systems.
The PWI NSW has been at the forefront of promoting excellence and innovation in railway design, construction, and maintenance. With a robust membership base comprising more than 500 individual members and more than 80 active corporate members, our institution thrives on knowledge sharing and professional development.
Our annual conventions, technical meetings, and awards celebrate our members’ ingenuity and hard work, fostering a spirit of collaboration and continuous improvement within the rail sector.
The NSW Government’s commitment to enhancing our transportation infrastructure has been instrumental in the rail industry’s growth and modernisation. Since 2016, significant budget allocations have fuelled numerous projects to improve safety, efficiency, and connectivity across the state.
Investments in major rail projects such as the Sydney Metro, the Parramatta Light Rail, and the Regional Rail Project have not only transformed the commuting experience but also created thousands of jobs, contributing to the economic prosperity of New South Wales.
These projects exemplify the government’s strategic vision for a sustainable and futureready transportation network.
The impact of government support extends beyond infrastructure development. It has facilitated the adoption of cutting-edge technologies and practices, ensuring that our rail systems remain at the forefront of global standards. The emphasis on sustainability and innovation aligns perfectly with the goals of PWI NSW, which continuously strives to push the boundaries of what is possible in railway engineering.
At the heart of the rail industry is a community of passionate, intelligent individuals dedicated to their craft. The PWI NSW proudly represents such a vibrant and diverse group of professionals. From engineers and project managers to site supervisors and maintenance teams, our members bring knowledge and experience to every project.
One of the most significant growth areas within the rail industry has been the increased inclusion of women. The PWI NSW is committed to promoting gender diversity, recognising that a diverse workforce drives innovation and excellence. While the government does not directly sponsor PWI activities, it fosters and promotes initiatives encouraging women to pursue careers in rail, from engineering to project management. Programs to support women in rail have created a more inclusive environment where women are both participants and leaders. By providing mentorship, training, and development opportunities, we are breaking down barriers and ensuring women have a strong presence in the industry.
The rail industry’s future lies in the hands of our young professionals. The PWI NSW strongly emphasises supporting under35s, understanding that they bring fresh perspectives and new ideas. Government initiatives focusing on youth engagement and development are vital in cultivating the next generation of rail leaders.
All across the world, cities are expanding. People need better connections to access new places, MTR makes it happen in Hong Kong, Melbourne, Sydney, the United Kingdom, Sweden, as well as in the Mainland of China and Macao.