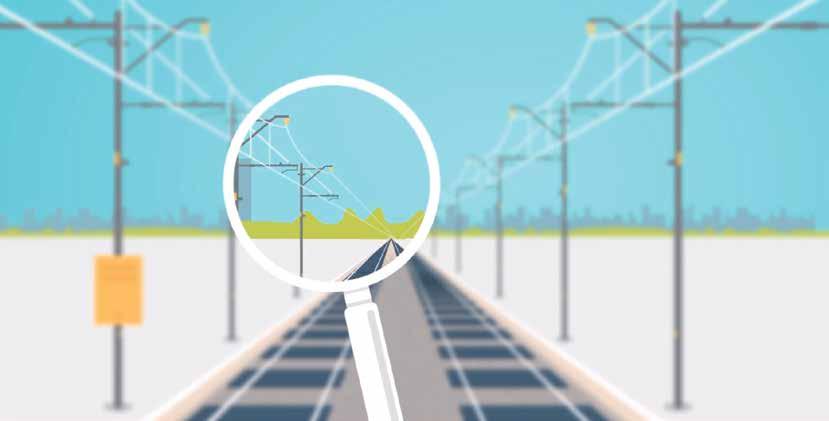
6 minute read
ART focused on pantographs, overheads
from REX Sep 2019
by Prime Group
Catenary and pantograph monitoring catching snags before they bite
Australian Rail Technology tells Rail Express about a pair of solutions helping reduce operators’ overheads by protecting their overhead.
BELOW: The Pantograph Condition Monitoring System.
WHEN A PANTOGRAPH atop an electric train, tram or locomotive snags overhead wiring, a large amount of damage can result to both the fixed infrastructure and the train itself. A train travelling at line speed can tear down a significant length of overhead wiring, costing the operator in many ways.
“Tear downs of overhead wiring are a major issue to transport operators,” Australian Rail Technology (ART) National Sales Manager Darren Will says. “They can create a dangerous situation for

people inside and outside the rollingstock, greatly disrupt the operation of the network. and require emergency call out of repair resources. Additionally, there can be operational penalties as well as the cost of employing buses to ferry passengers around the impacted part of the network.”
ART provides a range of rollingstock, engineering, infrastructure and condition monitoring products and services. Among them are a pair of solutions to reduce tear downs.
Pantograph monitoring The Pantograph Condition Monitoring System (PCMS) is installed above the railway to automatically scan the condition of pantographs as they pass underneath. The process occurs without any contact between the system and the rollingstock itself: as the vehicle passes through the scan location, the system assesses wear on the pantograph head, and scans for any chips or damaged areas.
The system can measure carbon thickness, carbon damage (e.g. missing carbon, edge chips, abnormal wear and cracks), pantograph head yaw angle, missing horns, horn alignment, uplift force and train speed, with real time analysis reported back to the asset owner. Exception reports can then be viewed in client software, and also sent
via email. By regularly monitoring the condition of pantographs throughout its fleet, an operator can perform predictive maintenance of that equipment, saving it from unexpected downtime, and potentially preventing a heavily worn or damaged pantograph from damaging overhead infrastructure.
The PCMS is supplied and installed in Australia by ART, in partnership with Dutch technology group, ImageHouse.
Will says ART has worked with operators who have reported a return on investment (ROI) timeframe of just three to six months for the system. “The obvious saving is in the form of faster and accurate identification of damage or excessive wear to the carbon strips on the pantograph head. This allows the carbon to be worn to condemning limits accurately to gain maximum useable life out of the carbon,” he says.
“Additionally, it removes the need for manual inspection of the pantograph, which is typically done in the maintenance yard or workshop by accessing the roof or using an elevated gantry. This can require isolation of the traction power, working at heights permits, and more factors that have an impact on overall productivity. Intervals between traditional inspections can also vary based on the time available.” ART says the PCMS can operate with train speeds of up to 180km/h in all weather conditions, and can be installed on the main line, meaning there is no need for a custom shed or slow zone.
Collision detection While automated inspection of pantographs can go a long way to reducing tear down incidents on an electrified railway, another of ART’s solutions aims to cut down on another key culprit: faults in the overhead infrastructure itself.
When a pantograph shows up damaged, two key questions must be answered. First: how did the damage occur? Second, and more important: where did it occur?
The Pantograph Collision Detection System (PCDS) – developed in Australia by ART – is mounted on top of rollingstock, and is designed to continuously monitor the interface between the overhead catenary and the pantograph, providing real time warnings for unusual contacts or strikes. When the system’s high-performance 3-axis linear accelerometer detects an unusual impact, it reports GPS details and other relevant data to the asset manager. This information is further supported by a camera which monitors the overhead in real time, and captures and transmits video footage of the area immediately before and after the collision.
From there, the asset manager could trigger a work crew to attend the exact site to perform repairs, and potentially have other rollingstock avoid the area until work is complete.
Without the location information provided by the PCDS, pantograph damage can appear with with no indication of where it has occurred. Loose or defective catenary can damage a pantograph without causing a major incident – knowing where the incident has occurred can save serious man hours, and prevent a tear down before it occurs.
PCDS is powered by two in-built solar panels, with high-performance batteries, meaning it doesn’t need to be connected to the rollingstock’s systems in any way.
Data is collected and delivered to the cloud, allowing the user to receive direct alarms and access data via a web dashboard. The system can also deliver an API for integration of that data into a third party management platform. System data contained and reported by the device includes vehicle ID, speed, location, time and date, status and impact levels. Adjustable parameters to help fine-tune the device include impact thresholds, sleep/wake parameters, and Admin and Status User phone numbers.
“Over time, any trend or increase in the severity or quantity of detected impacts are displayed and allow the asset owners to identify an impending issue on the overhead network,” Will explains.
“Similarly, the detection of a severe impact and communication of it to the network operations group, allows them to determine if services should be stopped until the fault can be rectified, thereby removing the potential of a teardown and associated penalty of this happening.”
Next steps Will says ART has chosen to employ a flexible architecture for the PCDS, and to provide for independent data collection and transmission, in order to facilitate a wide range of current and future applications in addition to just collision detection. “Our key technologies in the predictive maintenance and condition monitoring space are focused on the interfaces between electric or passenger rollingstock and the infrastructure and environment in which they operate,” Will says. In the future, PCDS could be enhanced with capabilities like recording of climatic conditions, odometer validation, live vehicle/asset location tracking, and monitoring and reporting of other onboard systems.
In addition, it could record overhead line stagger, pantograph height, arcing and current draw. In regional areas, the system is also suitable for monitoring other fixed assets, like switch points and signalling systems, monitoring the track for seismic shifts, and monitoring the condition of additional trackside infrastructure like power and compressed air lines.
Will says ART’s strong partnerships with overseas suppliers, and a demonstrated ability to develop custom condition monitoring systems in-house, will drive future condition monitoring innovations and enhancements.
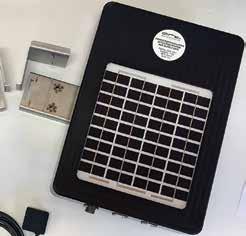
ABOVE: The Pantograph Collision Detection System is solar-powered.