
6 minute read
Andrew Engineering embracing digital with depot fit outs
from REX Dec 2019
by Prime Group
The new era of rail depots
Andrew Engineering’s Chris Parish tells Rail Express how the trend towards digital integration has impacted the fit out of rail depots.
“We can go right from the design and engineering through to manufacture or procurement, depending on whether or not we’re providing a third-party product such as a wheel lathes, or our own product such as a BES, turntables, lift platforms, these sorts ofproducts. “Along with the procurement comes the project management, the commercial management, the delivery, installation, conditioning and the full sign off, then at the end of it all the through life support. So, you have an organisation that can effectively take a project from the ideas phase through to full completion and through life support on the other side.” In the passenger rail sector, Andrew Engineering has worked on a number of projects, one such being on the New Generation Rolling Stock maintenance facility for Bombardier Transportation at Wulkuraka, Queensland. In partnership with Laing O’Rourke, Andrew Engineering worked onsite to deliver, install and F OUNDED IN 1951 AS A SMALL tooling company, Andrew Engineering has come to offer the design, manufacture and supply of special purpose machinery for a wide range of industries. In the late 1990s, the company shifted from being 85 per cent dedicated to supplying the automotive industry and became a major supplier to the rail industry.
“Around 2007, 2008 we had our first major rail project which was the bogie exchange system at the Auburn maintenance centre,” engineering director Chris Parish tells Rail Express. “We completely regeared the business away from what was effectively a special purpose equipment supplier to the automotive industry to being a major supplier to the rail industry, as far as rolling stock maintenance equipment solutions go. So, in the last 10 years we’ve seen a 100 per cent, complete U-turn in the way we do business.”
Andrew Engineering was contracted to design, build and install a solution to remove and replace all 16 bogies of an eight-car Electric Multiple Unit (EMU) at the Downer Rail operated train depot for the maintenance of Millennium and Waratah trains. Andrew Engineering was asked to replace the 16 bogies without the EMU moving and within a 12- hour cycle.
In response, the company designed, built, delivered and installed a first of its kind bogie exchange system (BES) consisting of 6 self-propelled bogie drop machines, 72 automated removable rails, 6 pairs of 12T vehicle jacks, 6 pairs of bogie jacks, 36 bogie drop stations and 3 bogie turntables. The new BES exceeded the facility’s cycle time requirements. The company has, however, created railway products for decades, upgrading machines and equipment, in-house manufacture and OEM supply and delivering breakdown and on-call support, and so they have significant experience in the sector and are well acquainted with the Australian Standards of railway production.
As an engineering firm, they have also developed prototype parts, such as automated assembly systems, etc. “We can develop bespoke technology or provide off-the-shelf solutions,” Parish said.
What’s different about the business now, according to Parish, is that they are a one stop shop.
“We provide a turnkey solution from depot fit-out through to life support, and we offer a full suite of products in order to maintain the vehicles effectively. We’re effectively a one stop shop to cover that particular area, whether it be in passenger rail or the freight area, we can efficiently provide a full solution and hand over the reins to the customer and say there you go – there’s your working facility. Andrew Engineering provide a turnkey solution, from depot fit-out through to life support.
commission depot management systems and specialist rolling stock maintenance equipment and machinery for the NGRS Maintenance Workshop in Wulkuraka, Andrew Engineering was awarded by Laing O’Rourke as a quality supplier of rail asset maintenance equipment for its “meticulous eye for detail and expert knowledge within rail engineering”. The purpose-built Wulkuraka facility was designed to maintain the 75 new trains purchased under the Queensland Government’s wider NGRS project for 30 years. Within the freight sector, Andrew Engineering has worked on key projects such as the FMG Thomas Rail Yard in Port Hedland, Western Australia. In partnership with Niles-Simmons-Hegenschedit Group, Andrew Engineering delivered a full turnkey project of the fully automated ore car and wheel and axle repair shop. The greenfield project was delivered from concept to fully operational within 22 months. Andrew Engineering worked onsite to deliver, install and manage all of the wheel shop machinery and remain the primary service and maintenance provider for this facility. According to Parish, “Andrew Engineering has a highly skilled team of engineers and technicians to provide comprehensive support for rail depot equipment with custom designed rail wheels, turntables and automated handling systems also in our repertoire.”
This is what sets Andrew Engineering apart from its competitors, that they are a one stop shop in the full sense. “We have a strong engineering focus, so we’re not just a reseller or an agent, we have a full understanding of the engineering aspects of the products and projects that we do, and we have the full project management and commercial management capability, so it doesn’t require third party to engage in that process, and we have in house capability on the technical side. We have a large number of tradespeople that work alongside with engineers and project managers all within the same organisation. “We have a 3500 sqm facility where we can
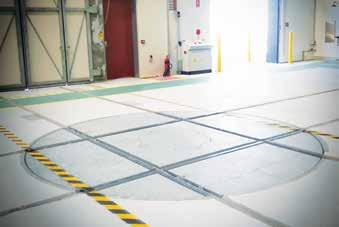
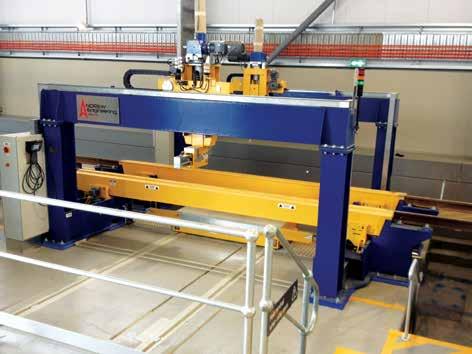
actually provide local solutions even with imported products, so for instance at the moment, in the construction industry we’re manufacturing building maintenance units at the moment for an overseas company who are actually behind in one of their projects and they’ve asked us to do a major fabrication here in our facility.”
Since entering the rail space, Andrew Engineering says it has seen the entire industry change and become much leaner. “The drive for asset utilisation has been a big shift. Whereas before they would simply just buy a huge amount of stock of spares, and hold them as contingency spares, today they are a lot leaner. The emphasis now is on minimising capital investment and and maximising the output from assets. So the expectation of high quality performance of maintenance equipment is a lot higher these days. “Another big thing for us is the rise in the desire for electronic depot protection systems, which we offer in partnership with Zonegreen, which takes people away from the conventional, mechanical locks and padlocks and more into the digital sphere. On a safety side, that’s been a big aspect.”
Having experienced and adapted to these changes in the industry, Andrew Engineering is confident in tackling the integration of equipment into the digitisation of asset management.
“Automatic tagging or RFID tagging, communication with asset information systems, we’re advancing into the idea of having all of the equipment digitally connected with real time information regarding performance and how that effects maintability and availability of assets, whether by allowing remote access, remote d iagnostics, and automatic data collection and transfer.”
The Australian firm says it’s looking forward to seeing what the future will bring to the space.
Andrew Engineering is a one stop shop.
The company sees the rise in the desire for electronic depot protection systems.
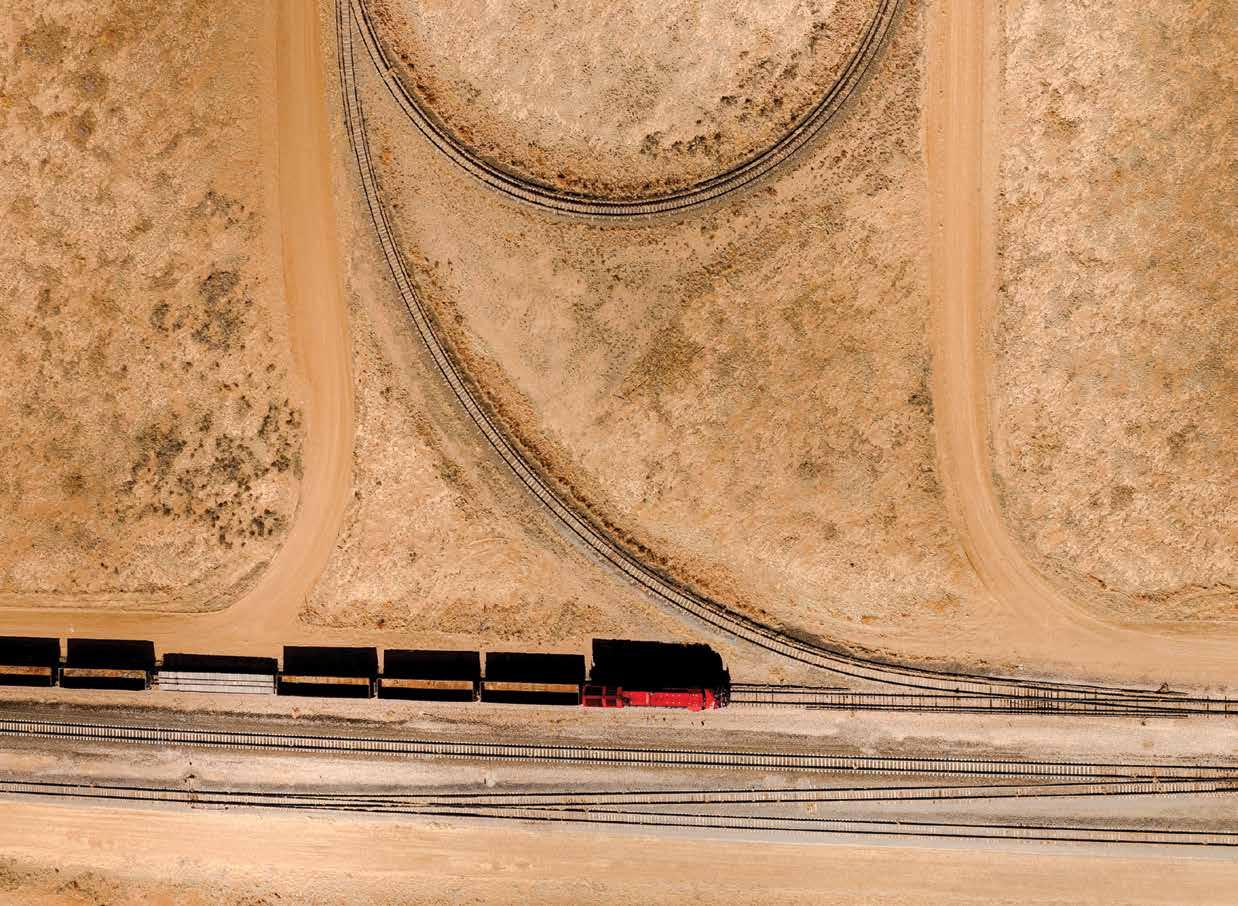
Want a no-delay railway?
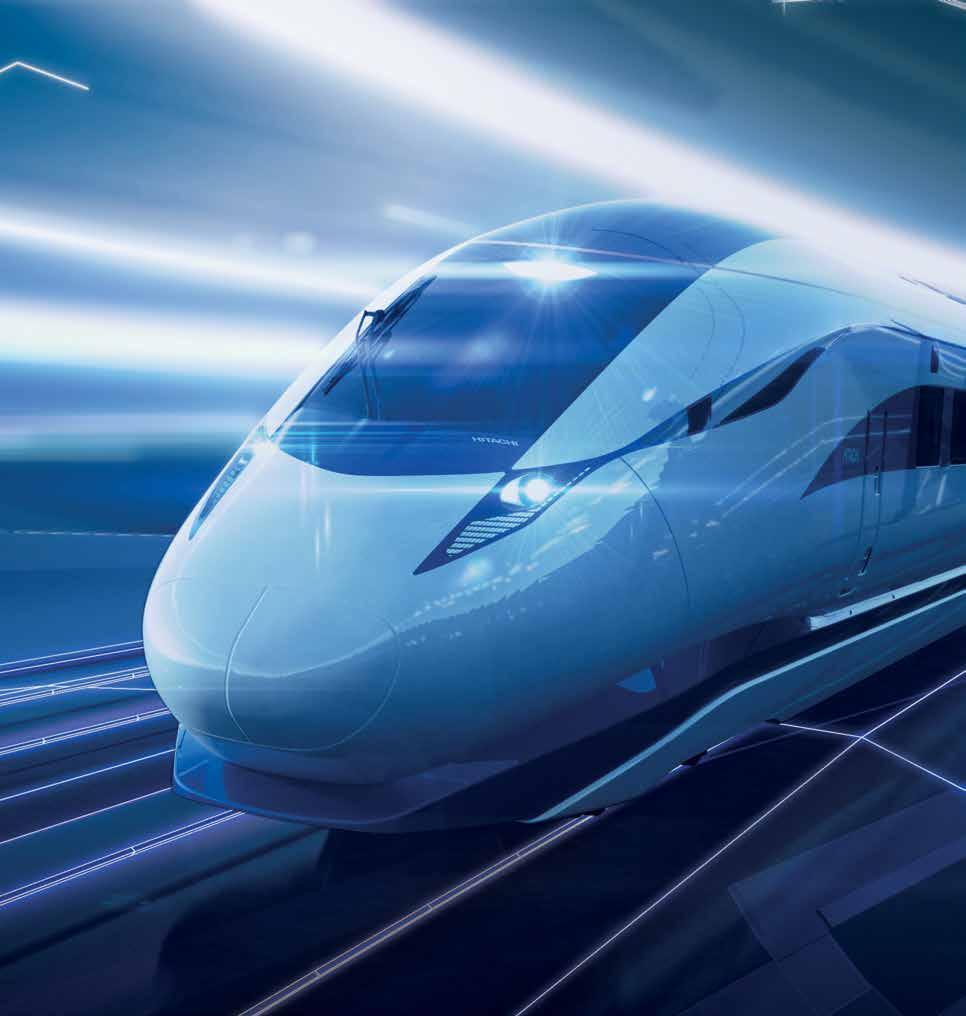
Design the network with dessan
Introducing dessan, the only specialist design software created exclusively for rail, allowing rail signallers to experiment, plan and test entire networks using an interface that is simple, intuitive and accurate.