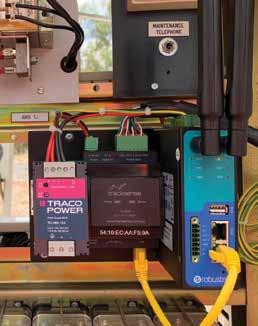
5 minute read
MRD enhancing condition monitoring range
from REX Dec 2019
by Prime Group
Smarter all the time: Local firm enhancing remote condition monitoring technologies
As the rail industry trends towards more efficient operating practices, MRD Rail Technologies managing director, Rob Gersbach, sees no limit to the application of predictive asset maintenance technology throughout the rail corridor.
IN THE FUTURE, WE BELIEVE ALL major rail assets will be remotely monitored by condition monitoring systems,” MRD managing director Rob Gersbach tells Rail Express. “These will be either built in by the manufacturers (smart) or implemented by third party integrations such as TrackSense. MRD are also working with points machine manufacturers to include TrackSense in their products.”
TrackSense is MRD’s predictive asset condition monitoring system. Relying on Australian-manufactured plug and play loggers designed to be robust, compact and affordable, TrackSense’s primary goal is to give meaning to data to allow the customer to make data driven maintenance decisions. MRD has 30 years’ experience designing and manufacturing electronic equipment for the rail industry. Three years ago, it launched TrackSense to capitalise on this with a push into the growing space of predictive maintenance and condition monitoring. Now, Gersbach explains, MRD is moving to ensure it can help customers apply predictive “
asset condition monitoring to improve each of its core maintenance tasks. “We see all trackside location cabinets (LOCs) being transformed into ‘Smart LOCs’ containing remote condition monitoring systems capable of monitoring all assets within the LOC using one Remote Condition Monitoring (RCM) Logger,” he said. “Price has been a major barrier to achieving this in the past but this has rapidly changed due to competition and technology such as cloud hosting. MRD has adopted this technology and is at the forefront of the movement towards affordable open platform RCM solutions.”
Gersbach says one of the key benefits of TrackSense for his customers is that it is open protocol. “Open protocol solutions will become the standard in RCM solutions as this gives the customer security, independence and the flexibility to shop around for the most competitive hosting solution and analytics package of their choice,” he said. “It also allows for easy integration with the customer’s Asset Maintenance System.” This preference towards open protocol is also being driven by specialisation of analytics platforms from major computing vendors.
“We are also seeing the emergence of
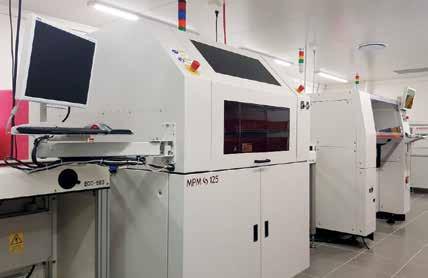
Through the TrackSense system all assets within the LOC can be monitored remotely using one Remote Condition Monitoring Logger.
TrackSense loggers are manufactured in Australia.
sophisticated big data analytics packages by vendors such as IBM, Microsoft, and Amazon to name a few,” Gersbach explained. “TrackSense provides API integration with these systems as standard which allows the customer to tap into the power of these systems including advanced machine learning and AI systems as they emerge.”
Since it was launched three years ago, TrackSense has grown to now collect data and measure various parameters of condition in thousands of railway assets across Australia and in international markets. Product manager Yvie Hough says through a continued focus on listening to and communicating with customers, the TrackSense team hopes to refine its state-of-the-art approach, and help new and existing customers best take advantage of what it has to offer. “The MRD team has been working closely with our customers to refine and improve our solution to provide a robust, easy to install system that is user friendly and provides valuable information to users,” Hough said.
Despite operational savings being a core benefit of condition monitoring and predictive maintenance systems, one major obstacle MRD has seen operators struggle to overcome is simply the cost of installing and maintaining a condition monitoring system, and the inflexibility of many common solutions available in the market. “Some vendors charge exorbitant amounts for hardware and lock customers into fixed contracts,” Gersbach said. “The obvious downside to this is that should you decide to break ties with the vendor or they go out of business, you’re basically left with an expensive paperweight.” Taking a different approach, the MRD loggers used in the TrackSense solution are not bound to that system. “Yes, we offer a local or cloud server option for accessing the data, but this is optional as our loggers are capable of stand-alone operation,” Gersbach explained. “Our loggers log, process and alarm directly from the device without the need for external servers or software. “This gives the customer total ownership and control of their hardware and data.”
MRD has recently expanded monitoring capabilities of TrackSense through the addition of new sensors and communication protocols for its range of loggers. “This sets our customers up for future expansion,” Gersbach said. “They can start off monitoring points machines, then expand to monitoring track circuits, batteries, boom gates, earth leakage and more just by adding additional sensors.” Another recent addition to the TrackSense offering is a mobile App, which literally puts key data in the operator’s hands, providing a convenient way to view asset performance both on and off site.
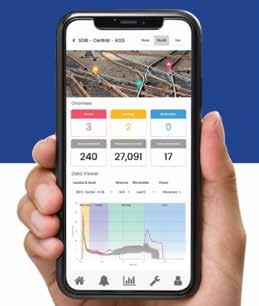
Auto-tuning One misconception Gersbach says he always aims to address is that a condition monitoring solution will provide maximum results from day one. “When implementing a condition monitoring solution it’s important to understand it’s not a set and forget solution. It requires operator training, tuning and data input from the user,” he said. To address this, MRD has developed tried and tested workflows to help operators get started with condition monitoring. The TrackSense team will also work with the customer to refine that workflow to their individual needs. “Our auto-tuning feature will get you up and running fast and our teach feature will keep the system performing optimally,” Gersbach added.
“We use shape recognition to identify anomalies, and KPIs are extracted from logged parameters and used to gauge an assets health and identify trends. All positive alerts and alarms are sent to the system’s fault library and fed back into the system to improve the systems performance. This library is also available for reference and training purposes.”
Critical to this is the use of machine learning to refine how data is analysed.
“The primary output of any condition monitoring system is data. Performing complex analysis of data collected from hundreds or thousands of sensors is a tedious and time-consuming activity, beyond the capabilities of human operators.”
By putting machine learning to work, Gersbach says TrackSense can help operators maximise the value of predictive maintenance while keeping costs down. MRD designs and builds hardware, and develops its software and applications locally in Australia. Along with TrackSense, the company also provides EarthSense, a solution for detecting earth leakage; and RelaySense, a solution to test the condition ofrelays.
A new App for mobile devices will put TrackSense data in the operator’s hands.
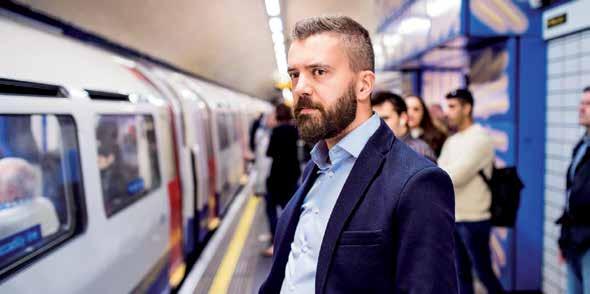
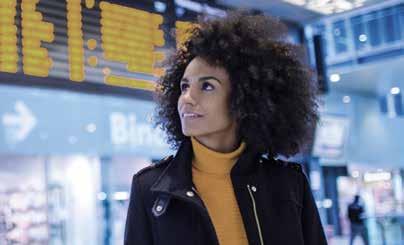
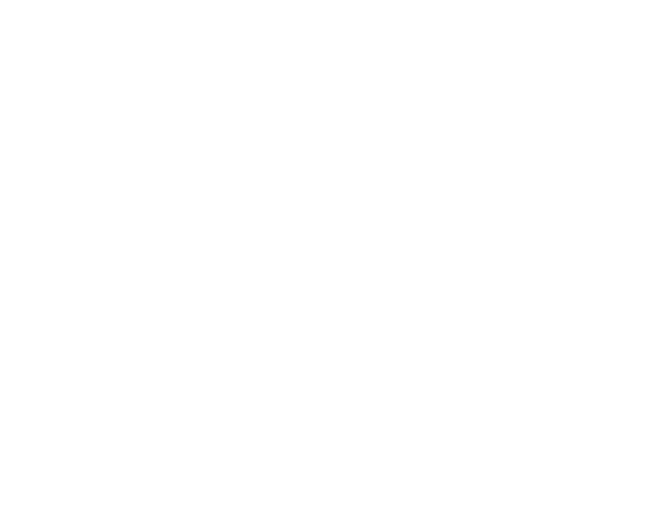
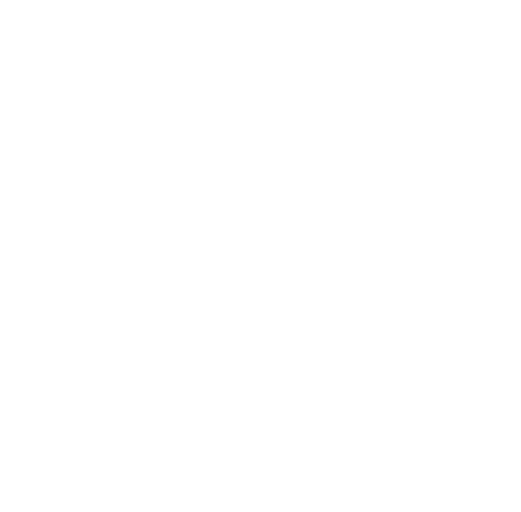